Чертежи мини станка для производства шлакоблоков своими руками: Чертежи станка для изготовления шлакоблоков своими руками
Изготовление станка и бетонных блоков своими руками, самодельные строительные станки и стеновые бетонные блоки
Изготовление станка и бетонных блоков своими руками, самодельные строительные станки и стеновые бетонные блоки.
Состав бетона для шлакоблоков своими руками.
Подойдет в качестве наполнителя: шлак, зола, отходы горения угля, отсев щебня (камня, гранита), отходы кирпича, гравий, песок, опилки (после обработки), керамзит, перлит, песчано-гравийная смесь, граншлак, зала, щебень, опилки, гипс, кирпичный бой и т.д.
Раствор для шлакоблоков: шлак угольный:песок крупный (керамзитовый):гравий 5-15 мм, цемент М500, вода (7:2:2:1,5:1,5-3). Важно следить за количеством воды, чтобы блоки не растеклись при снятии. Раствор должен при падении на землю рассыпаться, но в кулаке должен соединяться.
Процесс производства самодельных бетонных блоков.
Кладем в форму с горкой раствора, включаем вибратор на 3-5 с, раствор осаживается. Если раствора мало – доложить, затем вставить прижим и опять включить вибратор. Когда прижим «сядет» на ограничители – формовка завершена. Осталось включить вибратор на 5-10 с и снять форму. Важно! Форму нужно снимать при работающем вибраторе, то есть окончание съема должно происходить уже на «излете». Сохнуть блоки должны 5-7 дней (а вообще полное затвердевание шлакоблоков (или вибробетонных камней) происходит в течении месяца при температуре не менее 20 град и соблюдением условия высокой влажности.
Производительность станка при двух работниках 40-70 штук/час (от засыпки до съема формы 45 сек.
Добавление пластификатора.
Для пластичности блоков можно добавить пластификатор (5 грамм на блок — прочность, водонепроницаемость и морозостойкость, меньше трещин) при вибролитье, можно и при вибропрессовании, но нужно добавлять слишком много для эффекта, а это дорого.
Чтобы шлакоблоки были прочными, нужно учитывать.
Качество песка – нужен крупный.
Шлак идеален доменный.
Цемент – качественный М400.
Оборудование – чтобы лучше прессовало, нужно добиться вибропрессования.
Время приготовления и хранение.
Снимать с ленты можно через сутки. Полное высыхание через пару месяцев. Через день блоки уже можно носить — не ломаются, класть через неделю.
При использовании пластификатора готовые блоки можно убирать с площадки и складировать уже через 6-8 часов. Без УПД – через двое суток. Хранить готовые шлакобетонные блоки нужно в пирамидальных штабелях по 100 штук с небольшим (2-3 см) промежутком между блоками – чтобы досыхали «боковушки.
На первых порах бетон можно готовить вручную. В последствии эффективнее и легче – на электрической бетономешалке объемом 0,2-0,5 куб. м.
Производственная площадка – помещение с ровным полом, хорошей вентиляцией/отоплением или ровная площадка на улице под навесом.
Шлакоблоки – строительные блоки, полученные вибропрессованием раствора бетона в специальной форме. Размер стандартного блока 390мм х 190мм х 188мм с тремя отверстиями.
Преимущества шлакоблоков.
низкая себестоимость.
высокая скорость постройки из шлакоблоков.
хорошая звукоизоляция.
хорошая теплоизоляция.
можно изготавливать и для себя, и на продажу.
Отрицательные мнения по изготовления блоков из бетона своими руками.
Станок выгоден лишь при наличии дешевого или «халявного» сырья или же при огромных объемах работ.
Пустотный блок, изготовленный где угодно, дороже, участка стены такого же размера, сделанного методом съемной или несъемной опалубки, тем более вы тратите свое время и силы. Поэтому, в основном, продажа этих станков – это всего лишь возможность заработать на других.
Пример расходов и стоимости изготовления самодельных блоков.
На производство одного шлакоблока уходит 0,011 куб.м раствора, в пропорции 1:7 (цемент:граншлак), т.е. 1 мешок цемента = 36 блоков.
Постановлениями Правительства РФ от 13.08.97 № 1013, Госстандарта РФ № 86 от 08.10.2001 г. и Госстроя РФ № 128 от 24.12.2001 г. в перечень продукции, требующей обязательной сертификации не входят строительные бетонные блоки с различными наполнителями (шлак, керамзит, опил и т. п.), а так же виброформовочное оборудование для их производства.
Изготовление формы своими руками для литья бетонных блоков.
Форма для самостоятельного изготовления шлакобетонных блоков представляет собой ящик из 3-мм металла без дна с ручками. Чтобы лицевая часть блоков была более ровной, их нужно сушить на резиновой ленте, смоченной раствором какого-нибудь моющего средства.
Чертеж вибростанка, чтобы изготовить форму своими руками.
Пояснения к чертежу.
1 развертка матрицы. 2,3,4 заготовки поддона. 5,6,7 обрамление матрицы снизу (уголок 25х25). 8 планка крепления пустотников. 9 пустотник. 10 верхняя заглушка пустотника. 11 нижняя заглушка пустотника.
Еще некоторые чертежи станков для самодельных шлакобетонных блоков.
Фотографии станка по типу «Мечта застройщика» для изготовления шлакоблоков своими руками.
Особенности конструкции.
Двигатель смонтирован на корпусе, вибрация происходит за счет дисбаланса грузов.
Цилиндры имеют конусность 2-3 мм, чтобы легче было снимать форму.
Процесс изготовления станка.
Болгаркой раскроить лист 2.5 мм.
На местах сгибов надрезать изнутри на треть диском 2 мм, чтобы лист не потрескался.
Изготовление матрицы – проверить все углы (сначала всю конструкцию лучше сделать на прихватах, а затем только намертво швами по 5 см.
Наварить уголок по низу матрицы (для амортизатора.
Наварить поддон под раствор.
Обварить матрицу снизу и сверху.
Наварить уголки для крепления вибратора.
Чтобы пустотники были конусными, конец трубы нужно заузить на 2-3 мм, можно больше.
На станок для одной формы подойдет любой асинхронный движок от 120 Вт.
Двигатель: мощность 180 Вт, трехфазный, подключен по схеме питания от одной фазы.
Видео, помогающие понять процесс изготовления блоков своими руками.
Статьи и обсуждения.
Продажа вибростанков, чтобы сделать блоки самому.
Стильная постройка из самодельных блоков.
Упорство и настойчивость помогли разрешить проблему реконструкции дома.
Все началось с того, что наши соседи по просили меня реконструировать кухню их дома, выстроенного 40 лет назад. Они вырастили в этом доме двенадцать детей, которые разъехались кто куда. Но на праздники взрослые дети со своими семьями приезжают к родителям и старая кухня не в состоянии вместить всех. Вот для таких праздничных застолий и потребовалось помещение более значительных размеров. Когда решение о расширении кухни было принято, за дело взялись архитектор и инженер.
Поиски материала.
В самом начале работы владельцы дома сказали нам, что им безразлично, какой реконструкции будет подвергнуто здание, но в любом случае они хотят, чтобы были сохранены его первоначальный архитектурный стиль и материалы, из которых дом построен. Перед нами встала любопытная проблема, поскольку весь дом был возведён из стеновых блоков небольшого размера, происхождения которых мы не знали.
После бесед с многочленными подрядчиками, специализирующимся в области кладки, и местными поставщиками нам стало ясно, что обеспечить соответствие нового материала тому, из которого был построен дом, будет задачей не из легких. Блоки представляли собой строительный материал, по размерам походивший на кирпич, но сделанный на основе песка и цемента и имеющий характерную поверхность с «оспинами» крошечных пустот. В настоящее же время эти блоки в строительстве не применяют.
Мы предполагали, что когда начнем разбирать старую кухню, сохраним как можно больше старых блоков. Но при попытке отделить один блок от другого непрочная наружная часть разламывалась, оставляя неповреждённой твердую бетонную сердцевину. Кроме того, такие блоки (даже если бы мы смогли сохранить их) нельзя было считать приемлемым материалом, поскольку пристройка должна была удовлетворять более строгим современным требованиям сейсмостойкости.
В конце концов мы приняли решение возводить каркас пристройки из дерева, а в качестве наружной отделки использовать блоки. Такое решение сокращало наши потребности в блоках, но проблему всё-таки не решало.
В разговоре с нынешними владельцами дома удалось выяснить, что прежние хозяева по-прежнему живут где-то неподалеку. Мы позвонили им и выяснили, что блоки, из которых построен дом, в своё время привезли из г. Фресно. Это была наша самая большая удача на тот момент: мы очень надеялись найти там завод, который и по сей день изготавливает нужные нам блоки. За тем мы узнали, что во Фресно налажено весьма крупное производство песка, гравия и цемента и что множество небольших компаний выпускают на этой основе разнообразные стройматериалы. Однако ни одна из этих компаний не изготавливает блоки наподобие тех, что мы хотели бы приобрести. Быть может, завод, который производил нужные нам блоки, больше не существовал? Или же старые хозяева просто ошибались? Требовалось во всем разобраться на месте.
Живописные руины.
До Фресно было четыре часа езды, поэтому, когда мы добрались до места, там было уже жарко и пыльно. Большинство складов стройматериалов, к тому же, оказалось закрыто по случаю выходных, а на единственном складе, который в этот день работал, нам ничего не смогли предложить. Экспедиция судя по всему должна была закончиться неудачей. На дворе стало темнеть, и мы к тому же изрядно утомились. Но когда на обратном пути домой в небольшом городке мы подъехали к газозаправочной станции, мы просто не поверили своим глазам — прямо возле станции мы увидели мотель, выстроенный из материала, который мы разыскивали. Тщательный осмотр здания подтвердил первое впечатление — материал, из которого оно было построено, оказался абсолютно идентичным нашим блокам, вплоть до отделочных элементов, использованных в оконных проемах. Осмотревшись вокруг, мы заметили ещё четыре здания, выстроенные из таких же блоков.
Расспросив нескольких человек, мы выяснили, что когда-то в этих местах существовало небольшое предприятие по производству блоков, но оно дотла сгорело, и никто точно не знал, где оно тогда располагалось. Нам посоветовали проехать по дороге в карьер, который здесь до сих пор функционировал, и поискать там сторожа.
Мы спустились в карьер и поняли, что сегодняшний день был прожит не зря — встретившийся по пути большой ангар, маленький магазин, флигель и два полуразрушенных дома были сложены когда-то из «наших» блоков. Кроме того, обойдя вокруг магазин, мы обнаружили аккуратно сложенные в штабель блоки для наружных подоконников точно такого типа, которые нам требовались. Их насчитывалось, вероятно, штук 50, и они были превосходной формы и подходящего цвета, который, быть может, лишь слегка выцвел.
Здесь видимо некогда стоял завод: плиты фундамента сгоревшего здания были по-прежнему на месте, как и какое-то ржавое оборудование, идентифицировать которое было невозможно. Однако, кроме подоконных блоков, здесь не нашлось ничего такого, что мы могли бы использовать. Но возле руин стоял прицеп, в котором жил сторож.
Сюжет запутывается.
Сторож рассказал нам, что материал, который здесь добывали, называется пемзой. По его представлениям её красноватый цвет получается благодаря железу, содержащемуся в верхних слоях карьера. Глубже в карьере цвет материала блекнет и переходит от красного оттенка к рыжевато-коричневому, а затем к серому и белому. Белый материал в наиболее глубокой части карьера напоминает тальковую пудру и называется пуццоланом. Строительные компании используют его в качестве добавок при производстве бетона. Это всё, что наш собеседник смог нам сообщить. Однако он дал нам номер телефона своего босса — хозяина карьера.
Было уже поздно, и нам пришлось вернуться домой. Однако мы уже знали, каким должен стать наш следующий шаг. Мы решили изготовить блоки своими силами.
Добыча сырья.
В понедельник утром я позвонил владельцу карьера. Ему ничего не было известно о заводе, однако он предположил, что мы сможем найти достаточно сырья для своих блоков в его карьере. И с удовольствием пригласил нас туда.
На следующий день вместе с архитектором мы снова отправились во Фресно. Теперь — на большом самосвале, прихватив штаты и кирки. Площадь карьера составляла больше двух квадратных километров, а глубина — около 30 м. И пока мы обходили вокруг карьера в поисках нужного нам материала, все покрылись пылью и потом. Борта карьера были тверды как камень, но при растирании материал превращался в пылевидный порошок. После тщательного поиска мы нашли место, где цвет пемзы был почти таким, какой нам требовался. Именно здесь мы и решили приступить к делу. Но взглянув на наши кирки и лопаты, хозяин карьера засмеялся. «-Вам придётся слишком долго потеть, если вы собираетесь копать вручную, — заявил он. — Я знаю более эффективный способ». С этими словами он нас покинул и через несколько минут вернулся на небольшом экскаваторе.
После того как загрузка была завершена, мы накинули на наш драгоценный материал брезент, а поверх брезента положили сорок самых лучших подоконных блоков, выбранных из штабеля, который накануне обнаружили.
Изготовление блоков и кладка.
Теперь у нас было сырьё для производства блоков. Но вот технологию этого производства мы не знали. И принялись экспериментировать. Смесь, рецепт которой опытным путём был, в конце концов, найден, состояла из воды, песка, цемента, красителя и измельченного минерала, добытого нами в карьере.
Для приготовления бетона мы использовали ручную бетономешалку и крутили её для приготовления одного замеса минимум десять минут. Несмотря на то, что минерал был очень близок по цвету старым блокам нашего дома, цвет смеси изменялся по мере добавления в неё других составляющих, необходимых для придания прочности и нужной текстуры.
В конце концов, мы решили и эту проблему методом проб и ошибок. Изготовили большую серию образцов, указав на каждом точный тип и количество использованного красителя и других составляющих, прежде чем нашли подходящее соотношение частей смеси. Новые блоки после изготовления сушили до приобретения ими окончательного цвета целую неделю.
Первые сделанные нами формы, которые были изготовлены из тонколистового металла, мы отвергли. Дело в том, что даже при использовании большего количества дизельного топлива в качестве смазки бетон прилипал к этим формам, и поверхности блоков получались шероховатыми и не устраивали нас.
Решение, которое мы нашли, сказалось достаточно простым. Были изготовлены деревянные рамы, разделённые таким образом, чтобы в них можно было отливать одновременно пять блоков (это предельное количество, с которым один человек мог легко справиться). Для закруглённых углов, которые нам требовались на элементах отделки, мы добавили к формам вставки из тонколистового металла.
Когда приступили к отливке блоков, то старались точно придерживаться соотношения частей смеси, чтобы свести к минимуму отличия (в первую очередь по цвету) между блоками в разных партиях. Что же касается обеспечения соответствия текстуре первоначальных блоков, то необходимые неровности получили, отказавшись от чересчур тщательной трамбовки бетонной смеси при заполнении форм и чистки их при выгрузке готовых блоков.
Формы с бетонной смесью на первые 24 часа укутали плёнкой, чтобы сохранить поверхность более влажной дня равномерного схватывания бетона. На вторые сутки блоки вынули из рамы и аккуратно уложили в штабель, а через неделю их уже трудно было разбить молотком. Для реконструкции кухни нам потребовалось 600 блоков. Однако мы решили для уверенности изготовить несколько больше, чем было нужно. За день мы делали примерно 75 блоков, и уже скоро задний двор был заполнен штабелями новеньких изделий, дозревающих под нежарким солнцем поздней осени.
Затратив массу времени и усилий на изготовление блоков, мы захотели найти каменщика, который бы обращался с этими творениями наших рук как со слитками золота, упакованными в пластиковую взрывчатку. Как оказалось, владельцы дома знали каменщика с хорошей репутацией. И уже вскоре мы смогли со всё возрастающим доверием наблюдать, как он их укладывал. Соответствие старой кладке было полным.
Сейчас ни по материалу, ни по цветовой гамме наружные стены кухни-пристройки ничем не отличаются от остальных частей дома. И ничто не говорит о том, сколько труда всё это потребовало.
Были ли эти усилия оправданы? Кто знает. Однако владельцы дома получили то, чего они желали, мы же удовлетворились тем, что сумели решить проблему, которая казалась неразрешимой.
Изготовление шлакоблоков в домашних условиях.
Изготовление шлакоблоков в домашних условиях.
И так кто серьезно решил заняться изготовлением стеновых блоков я дам практические рекомендации из ходя из собственного опыта изготовления шлакоблоков своими руками.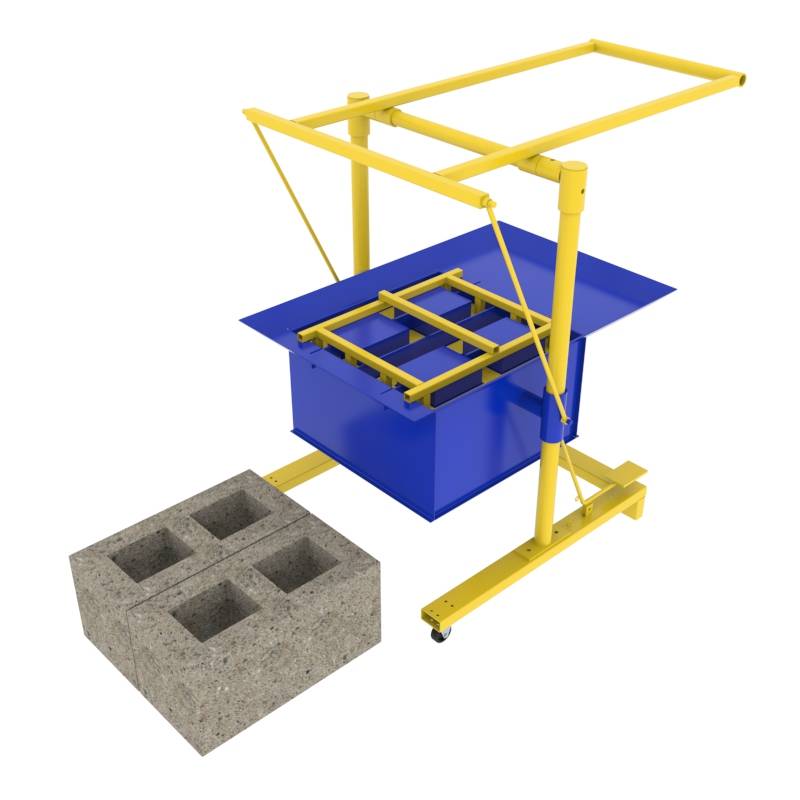
Кто внимательно прочтет сможет не только освоить процесс производства, а даже создать с нуля свой бизнес с целью реализации блоков застройщикам.
Первым делом нужно определится какую форму Вы будете использовать на вашем оборудовании. Чем больше пусто-образователи тем экономичней становится производить сам шлакоблок. Вот на примере посмотрите на рисунок:
И так самая выгодная форма шлакоблока это с двумя большими квадратами. Наполнителя нужно лишь 60% процентов по сравнению с другими формами для станков.Второе это выбор станка для изготовления стеновых шлакоблоков. Есть два типа станков: стационарный и мобильно-передвижной «несушка».
Я даже молчу за высокую цену на оборудование такого типа.
Для изготовления шлакоблоков в домашних условиях подойдет небольшой вибростанок «несушка» с формой от одного до двух блоков производимых за один цикл.
1. Доступная цена.
2. Небольшой вес.
3. Малая физическая нагрузка на оператора.
Под итожу выше сказанное мной о мини производстве шлакоблока:
— Для производства шлакоблоков в домашних условиях первым делом нужен вибростанок типа «несушка» и форма с двумя большими квадратами.
Идем дальше, допустим что Вы приобрели по моим советам свой первый станок для мини производства блоков. Теперь нужно приготовить полусухую смесь для изготовления шлакоблока. Если Вы оптимист это хорошо но готовить смесь вручную я не рекомендую. В состав смеси входит очень малое количество воды и Вы физически не сможете перемешать до полусухого состояния.

Все разобрались с оборудованием теперь перейдем к технологическому процессу. Подробное описание изготовления читайте в другой статье:
- Технологии производства шлакоблока.
Следующее Главная страница
Подписаться на: Комментарии к сообщению (Atom)
Машина для производства бетонных блоков— BESS
На рисунке ниже показан образец машины для производства бетонных блоков. Прежде чем обсуждать машину, во-первых, нам нужно знать, что такое машина для производства бетонных блоков.
Машина для производства бетонных блоков — это машина, которая использует давление и вибрацию для формования бетонных изделий в специальных формах. Возможно, вам будет интересно узнать, какую продукцию она производит. Ниже приведен список наиболее важных продуктов, которые может производить эта машина:
- Полые блоки различной формы
- Сплошные блоки разных размеров
- Тумбы разных форм и размеров
- Брусчатка разной толщины
- Блоки Asmolen для крыш (блок потолочный пустотелый)
- Водосточные желоба
- Газонные камни
Почему пустотелые блоки так популярны?
Благодаря высокой прочности и легкому весу. Высокая прочность обусловлена давлением, используемым машиной для производства бетонных блоков в процессе производства пустотелых цементных блоков. Это позволяет иметь многоэтажные здания с меньшим весом. Меньший вес делает ваши фундаменты дешевле, а общий вес здания значительно уменьшается.
Формы бетонных изделий также не подвержены воздействию высоких температур, а это означает, что если ваше здание загорится, основная конструкция не рухнет.
Размер машины определяется количеством стандартных пустотелых бетонных блоков, производимых каждым прессом.
Ширина стандартного пустотелого блока 20 см, длина 40 см, высота 20 см.
Скорость машины для производства пустотелых блоков связана с гидравлической системой машины. Насос, клапаны и уровень автоматизации машины являются факторами скорости машины. Обычно это должно быть от 100 до 120 нажатий в час.
Прежде всего, не путайтесь, когда машина для производства бетонных блоков называется машиной для производства кирпича. Это потому, что эта машина также производит полнотелые кирпичи и блоки, а также обычные бетонные блоки. Производительность машины обычно определяется как общая производительность машины за 8 часов. Наши самые маленькие машины обычно производят 4000 штук пустотелых блоков за восьмичасовую смену, а машина называется PRS 400.0003 Существует всего 3 уровня автоматизации для полуавтоматической системы производства бетонных блоков
- : для управления всей установкой требуется около 7 человек, поддоны перевозятся на ручных тележках, и для всего оборудования требуется не менее 2500 м² земли.
и зона хранения.
- автоматическая система: для управления всей установкой требуется около 5 человек, поддоны доставляются в зону отверждения вилочными погрузчиками, а для всего оборудования и зоны хранения требуется не менее 1500 м² земли.
- полностью автоматическая система: в этой системе нет необходимости в операторе машины, поэтому для установки требуется всего 3 человека. Эта система подходит для районов с высокими трудозатратами и дорогими землями.
В автоматической системе соотношение бетонного раствора, используемого в машине для производства бетонных блоков, всегда будет одинаковым, поскольку это выполняется автоматической машиной. В результате качество бетонных изделий всегда будет оставаться неизменным. Это очень важно для производителей, потому что покупатель всегда будет доволен одинаковым качеством.
Если вы живете в стране с высокой стоимостью рабочей силы, вы можете предпочесть роботов, потому что в долгосрочной перспективе общая стоимость будет ниже, но общая стоимость машины будет выше.
Это зависит от вашего целевого продукта и рынка. Существуют различные типы добавок, которые вы можете добавить в свой раствор, каждый из которых имеет свои плюсы и минусы. Вам могут понадобиться более легкие блоки, для этого вам нужно добавить какую-то добавку, но если вам нужно производить звукоизоляционные блоки, есть другие добавки. Обратите внимание, что это повлияет на конечную стоимость вашего продукта, поскольку некоторые добавки стоят дорого. Основным материалом, который вам нужен для машины для производства бетонных блоков, является песок, цемент, вода и цветные пигменты, если вы хотите производить цветные блоки для мощения.
Для заполнения полостей между частицами раствора необходима вибрация. Если вибратор неисправен или недостаточно мощный, качество продукции будет низким.
Если есть вода нормального качества, она сослужит вам службу, но учтите, что вода не должна быть слишком соленой. Если вода соленая, при сушке на поверхности продуктов остаются белые полосы. Это также повлияет на долговечность блоков, потому что цемент не скрепит все части вместе, если будет слишком много соли.
Высококачественные миксеры оснащены мощным электродвигателем с установленной на них подходящей системой безопасности для предотвращения возгорания двигателя. Механически он также должен быть прочным, потому что он должен хорошо функционировать при длительном использовании. Кроме того, внутри смесителя должен быть дополнительный лист изнашиваемой пластины, установленный с помощью болтов и гаек. Это особенно важно для длительного использования машины для производства бетонных блоков. Когда внутренние пластины изношены, их можно заменить, а корпус смесителя останется целым.
Bess Concrete Block Machines
В настоящее время Bess производит различные типы машин с различной производительностью и уровнем автоматизации. Все стационарные и мобильные машины Bess могут производить высококачественные бетонные изделия. В соответствии с вашими потребностями и вашим бюджетом Bess может разработать и изготовить лучшую машину для вашего бизнеса. Ниже вы можете увидеть некоторые преимущества машин Bess, которые производит компания Bess.
♦ Для уровня автоматизации вашей машины для производства бетонных блоков Bess предлагает полуавтоматические, автоматические и полностью автоматические типы.
♦ Вы можете приобрести машину с одним или двумя бункерами.
Преимущество двухбункерной машины для производства бетонных блоков по сравнению с однобункерной машиной заключается в том, что на двухбункерной машине можно производить двухслойные брусчатые блоки.
Благодаря этому преимуществу вы можете производить верхний слой бетонной брусчатки разного качества и разных цветов. Эти машины называются машинами для укладки тротуарной плитки.
Машины с одним бункером называются машинами с полыми блоками.
♦ Элементы из общего списка можно добавлять или удалять в зависимости от вашего сайта и состояния вашего бизнеса.
♦ Два различных варианта машины:
1. Полная установка: Вы можете купить машину для производства бетонных блоков со всем оборудованием, необходимым для полной установки. Это для клиентов, которым нужны более высокие производственные мощности в их компании с меньшим количеством сотрудников.
2. Мини-завод: в этот вариант входит блок-машина и необходимое для бизнеса оборудование. Это подходит для начинающих и стран, в которых стоимость рабочей силы ниже.
♦ Перед монтажом и вводом в эксплуатацию компания Bess предоставляет технические чертежи для вашего предприятия.
♦ Bess использует высококачественные детали для машины, что означает, что вы можете использовать их в течение длительного времени без какой-либо деформации или проблем. Машины разработаны на основе евростандартов.
♦ Техническая команда Bess приедет на ваш завод для установки и обучит ваших операторов. Таким образом, ваши операторы узнают, как управлять машиной для производства бетонных блоков. Эти услуги абсолютно бесплатны.
Процесс производства бетонных блоков
Он состоит из процесса взвешивания, смешивания, формования, отверждения и упаковки.
Сначала песок и гравий взвешиваются и доставляются в смеситель в нужном соотношении. Затем добавляют воду и цемент в необходимом количестве.
Порошкообразный портландцемент хранится в цементных силосах и доставляется цементными шнеками в специальный бункер, называемый цементным бункером, а затем добавляется в смеситель.
Вода также добавляется с помощью цифровых счетчиков. Затем миксер начинает перемешивать раствор до его гомогенизации. После этого он подается в бункер бетоноблока. Из бункера он подается в растворную тележку, которая затем заполняет формы раствором.
Вибрация уплотняет раствор, находящийся в формах, после чего верхняя форма начинает прижимать раствор к нижней форме с помощью гидравлического давления, формируя пустотелые блоки. Это самая важная работа машины.
Это действие выполняется на поверхности поддонов, после чего обе формы машины для производства бетонных блоков поднимаются с помощью гидравлического привода, и поддон выдвигается из машины.
Затем бетонные блоки доставляются в участок твердения и после просушки перемещаются на европоддоны, упаковываются и готовятся к транспортировке.
Вы также можете посетить канал Bess на YouTube для получения дополнительных видео.
Машина для производства бетонных блоков Цена Цена машины для производства бетонных блоков зависит от оборудования, которое вы выберете в комплекте с машиной. Другими факторами являются уровни автоматизации, количество пресс-форм и количество поддонов, заказанных вместе с машиной. Есть отдельная статья, в которой подробно рассматривается этот вопрос. пожалуйста, проверьте прайс-листы машины для производства бетонных блоков для продажи.
Заключение
Лучше немного потратиться на станок для производства бетонных блоков для повышения качества, чем дальнейшие неисправности, которые часто останавливают ваше производство. Если машина для изготовления блоков не предназначена для длительного использования, у вас будут серьезные проблемы. Потому что через некоторое время большая часть деталей сломается. Некоторые машины даже не подлежат ремонту, и они предназначены для замены, а не для ремонта. Так что нужно внимательно относиться к тому, что покупаешь.
Каждый раз, когда ваша машина выходит из строя, вы теряете производительность, а затраты, которые вы платите за обслуживание, и стоимость, которую вы платите за потерю производительности, будут намного больше, чем деньги, которые вы платите при покупке вашей машины. Чтобы лучше понять это, вы можете прочитать нашу статью о бизнес-плане производства бетонных блоков или связаться с нашим английским отделом.
Институт Земли Ауровиля
Блок сжатой стабилизированной земли
Первые попытки изготовления спрессованных земляных блоков были предприняты в начале 19 века в Европе. Архитектор Франсуа Куантро изготовил небольшие блоки из утрамбованной земли и использовал ручные трамбовки, чтобы спрессовать влажную почву в небольшую деревянную форму, удерживаемую ногами. Первым стальным ручным прессом, выпущенным в мире в 1950-х годах, был Cinvaram. Это стало результатом исследовательской программы для социального жилья в Колумбии, направленной на улучшение формованного вручную и высушенного на солнце кирпича (саман). Такой пресс мог получить обычные по форме и размеру блоки, более плотные, прочные и водостойкие, чем обычный саман. Грунт, сырой или стабилизированный, для спрессованного земляного блока слегка увлажняют, заливают в стальной пресс (со стабилизатором или без него) и затем прессуют либо ручным, либо моторизованным прессом. CEB может быть сжат во множество различных форм и размеров. Например, пресс Auram 3000 предлагает 18 типов пресс-форм для производства около 70 различных блоков. Блоки из спрессованного грунта могут быть стабилизированы или нет. Но в большинстве случаев их стабилизируют цементом или известью. Поэтому сегодня мы предпочитаем называть их сжатыми стабилизированными земляными блоками (CSEB). Стабилизация грунта позволила людям строить более высокие здания с более тонкими стенами, которые обладают гораздо большей прочностью на сжатие и водостойкостью. | Первые попытки спрессованных земляных блоков в 1803 г. Cinvaram, первый пресс для прессованных земляных блоков |
Блоки из спрессованного стабилизированного грунта прессом Auram 3000
УСТОЙЧИВОСТЬ И ЭКОЛОГИЧЕСКАЯ ЧИСТОСТЬ CSEB
| |
НАЧАЛЬНАЯ ПОТРЕБЛЕННАЯ ЭНЕРГИЯ НА МЕС. | |
CSEB = 572,6 МДж/м 3 Обожженный кирпич (CFB) = 6 122,5 МДж/м 3 | CSEB = 51,5 кг / м 3 Обожженный кирпич (CFB) = 642,9 кг / м 3 |
Примечание: Данные по Ауровилю и Пондишери, Индия, 2005 г.
Не каждый грунт подходит для земляных работ и CSEB в частности. Но при наличии определенных знаний и опыта многие почвы можно использовать для производства CSEB. Верхний слой почвы и органические почвы использовать нельзя. Определение свойств почвы имеет важное значение для производства продукции хорошего качества. Небольшой чувствительный анализ можно выполнить после короткого обучения. Стабилизация цементом будет лучше для песчаных грунтов. Для глинистых почв лучше подойдет стабилизация известью.
ХОРОШАЯ ГРУНТА ДЛЯ БЛОКОВ СЖАТОГО СТАБИЛИЗИРОВАННОГО ЗЕМЛЯ
Выбор стабилизатора будет зависеть от качества почвы и требований проекта. Цемент предпочтительнее для песчаных грунтов и для быстрого достижения более высокой прочности. Известь скорее подойдет для очень глинистой почвы, но ей потребуется больше времени для затвердевания и образования прочных блоков.
Грунт для стабилизации цемента: скорее песчаный, чем глинистый | Гравий = 15 % | Песок = 50 % | class=»bordure»>Ил = 15 % | Глина = 20 % |
Почва для стабилизации извести: она более глинистая, чем песчаная | Гравий = 15% | Песок = 30% | Ил = 20% | Глина = 35% |
Средняя доля стабилизатора довольно низкая:
Минимум | Среднее | Максимум | |
Цементная стабилизация | 3 % | 5 % | Технический максимум отсутствует |
стабилизация известью | 2 % | 6 % | 10 % |

ЭНЕРГОЭФФЕКТИВНОСТЬ
Начальная воплощенная энергия (МДж/м 3 материалов) | Углерод выбросы (кг CO2/м 3 материалов) |
CSEB потребляют в 11 раз меньше энергии, чем обожженный кирпич: CSEB, произведенный на месте с 5 % цемента = 548,32 МДж/м 3 Обожженный кирпич = 6 122,54 МДж/м 3 | CSEB загрязняет окружающую среду в 13 раз меньше, чем обычный обожженный кирпич: CSEB производится на месте с 5 % цемента = 49,37 кг CO 2 /м 3 9028 1 обожженных кирпичей = 642,87 кг CO 2 /м 3 |
ЭКОНОМИЧНОСТЬ
CSEB в большинстве случаев дешевле обожженного кирпича и бетонных блоков. В Ауровиле готовый м 3 кладка CSEB всегда дешевле, чем обожженный кирпич: на 15–20% меньше, чем обожженный кирпич (апрель 2009 г.). См. Сравнение строительных материалов в Ауровиле . Распределение стоимости 5 % CSEB, произведенного в Ауровиле с помощью пресса AURAM 3000, выглядит следующим образом (июль 2012 г.):
Трудозатраты (просеивание почвы и изготовление блоков): ~45 % | 902 79Цемент: ~25 % | Оборудование: ~3 % |
Конечно, это разделение будет сильно различаться в зависимости от местных условий, но в целом стоимость рабочей силы (которая включает в себя копание почвы, ее подготовку и изготовление блоков) и стоимость цемента являются самыми высокими. Поэтому при снижении производительности стоимость блока пропорционально возрастет в разы. В целом для снижения себестоимости блока следует оптимизировать производительность труда рабочих и уменьшить количество цемента, если не требуется 5% цемента. Далее, стоимость оборудования не так высока и поэтому не стоит пытаться удешевить замок, покупая дешевые качественные станки, которые прослужат недолго и не дадут крепких замков.
ОСНОВНЫЕ ДАННЫЕ О CSEB
СВОЙСТВА | СИМВОЛ | БЛОК | КЛАСС A | КЛАСС B | КЛАСС C |
Прочность на сжатие при раздавливании в сухом состоянии (при 28 днях, +10% через 1 год)0227 | 4–5 | 3–4 | |||
Прочность на сжатие во влажном состоянии (спустя 28 дней, после 24 часов погружения) | σ Cw | МПа | 3–4 | 9040 4 2 – 31,5 – 2 | |
Прочность на раздавливание при растяжении, в сухом состоянии (на сердцевине через 28 дней) | τ | МПа | 0,5–1 | 0,5 — 1 | 0,5 — 1 |
Прочность на раздавливание при изгибе, сухая (28 дней) | σ Bd | МПа | 0,5–1 | 0,4–0,8 9 0227 | 0,3 — 0,6 |
Прочность на сдвиг при раздавливании, сухая (28 дней) | τ | МПа | 0,4–0,6 | 0,3–0,5 | 0,2 — 0,3 |
Общее водопоглощение | — | % массы | 8 — 10 | 10 — 12 | 12 – 15 |
Кажущаяся объемная плотность | γ | кг/м 3 0227 17:00 — 18:00 | | ||
Коэффициент Пуассона | µ | — | 0,15 — 0,35 | ||
Модуль Юнга | E | МПа | 700 — 1000 | ||
Коэффициент теплового расширения | — | мм/мºC | 0,010-0,015 | ||
Набухание после насыщения (погружение на 24 часа) | — | мм/м | 0,5 — 1 | ||
Усадка (из-за естественной воздушной сушки) | — | мм/м | 0,2 — 1 | ||
Проницаемость | мм/сек | 1,10 -5 | |||
Удельная теплоемкость | C | кДж/кг | 0,65–0,85 | ||
Коэффициент электропроводности | λ | Вт/мºC | 0,81 – 0,93 | ||
Коэффициент демпфирования | м | % | 5 — 10 | ||
Время запаздывания (для стены толщиной 40 см) | d | ч | 10 — 12 | ||
Коэффициент звукопоглощения (для стены толщиной 40 см при частоте 500 Гц) | — | дБ | 50 | ||
Огнестойкость * | — | — | Хорошо | ||
Воспламеняемость * | — | — | Бедные | ||
Воплощенная энергия (для 5% цемента, стабилизированного и произведенного ручным прессом) | — | МДж/м 3 | 572,58 ** | ||
Выбросы углерода (CO 2 /м 3 сырье) | — | CO 2 /м 3 9 0208 | 49.![]() |
Примечания
— 1 МПа = 10,197 кг/см 2 = 145 PSI
– Эти значения могут быть получены при 5 % стабилизации цемента и давлении сжатия от 2 до 4 МПа.
– Прочность блоков зависит от качества почвы, типа и количества стабилизатора, качества изготовления и отверждения.
– Эти значения получены через 6 недель (4 недели на отверждение и 2 недели на сушку).
– Эти значения получены через 6 недель (4 недели на отверждение и 2 недели на сушку).
– Классы A, B и C определяются прочностью блоков на сжатие во влажном состоянии.
– Другие значения, указанные в таблице выше, являются ориентировочными и дают представление об ожидаемых характеристиках.
– Эти значения получены в лабораториях признанными органами. Они дают представление о том, что можно разумно ожидать от продукта, изготовленного в соответствии с современным уровнем техники.
– Источники: «Земляное строительство, всеобъемлющее руководство» – CRATerre, Hugo Houben и Hubert Guillaud
Исследования Ауровильского института Земли (прочность на сжатие в сухом и влажном состоянии, прочность на раздавливание при изгибе, водопоглощение, воплощенная энергия и выбросы углерода)
* Насколько нам известно, до сих пор не проводилось никаких научных испытаний на огнестойкость.
** Для сравнения: уездный обожженный кирпич (6122,54 МДж/м 3 ), железобетон 1:1,5:3 (4913,56 МДж/м 3 ) и монолитные бетонные блоки (1156,00 МДж/м 3 )
• Местный материал В идеале производство производится на самой площадке или на близлежащей территории . Таким образом, это сэкономит транспорт, топливо, время и деньги. • Биоразлагаемый материал Но давайте представим себе обрушившееся здание, а на нем растут джунгли: биохимические вещества, содержащиеся в гумусе верхнего слоя почвы, через 10 или 20 лет разрушат почвоцементную смесь… И КСЭБ вернется к нашей Матери-Земле! • Ограничение вырубки лесов • Управление ресурсами | • Энергоэффективность и экологичность Требуя совсем немного стабилизатора, расход энергии на м 3 может быть от 5 до 15 раз меньше, чем на м 3 обожженного кирпича. Выбросы загрязняющих веществ также будут в 2,4-7,8 раза меньше, чем у обожженного кирпича. • Экономическая эффективность • Адаптированный материал • Передаваемая технология • Возможность создания рабочих мест | • Возможность рынка риалы, оборудование и т. д.) окончательная цена будет варьироваться, но в большинстве случаев это будет дешевле, чем обожженный кирпич. • Сокращение импорта • Гибкие производственные масштабы • Социальное признание |
• Требуется правильная идентификация почвы или отсутствие почвы. • Неосознавание необходимости управлять ресурсами. ![]() • Незнание основ производства и использования. • Широкие пролеты, высокие и длинные здания трудно построить. | • Низкие технические характеристики по сравнению с бетоном. • Неподготовленные команды, производящие продукцию низкого качества. • Чрезмерная стабилизация из-за страха или невежества, подразумевающая возмутительные действия | • Недостаточная стабилизация, приводящая к низкому качеству продукции. • Некачественное или неадаптированное производственное оборудование. • Низкое общественное признание из-за противоположных примеров (неквалифицированных людей или плохой почвы и оборудования). |
Разработка CSEB предлагает в настоящее время широкий ассортимент продукции различных размеров и форм.
Чтобы выбрать наиболее подходящий продукт для своих нужд, следует обратить особое внимание на следующие факторы:
Модуль блока | • Это размер блока плюс толщина раствора.![]() • Выберите предпочтительно простой модуль в десятичной системе, чтобы не тратить время на расчеты конструкции. • Выберите также модуль с самым тонким растворным швом. |
Возможность различной толщины стенки | • В зависимости от модуля блока, какая толщина стенки может быть достигнута при легком скреплении? • По толщине можно определить, может ли блок быть несущим или нет. |
Площадь блока | • Чем она больше, тем слабее будет блок. • Для большой площади требуется большая энергия уплотнения: Ручной пресс мощностью 15 тонн не сможет должным образом сжать более 600 см². |
Гладкие, полые или Блокирующие блоки…? | • Каждый из них имеет различные возможности: — Плоские укладываются на толстый раствор (от 1 до 1,5 см) — Плоские укладываются на тонкий раствор (от 0,5 до 1 см) — Взаимоблокирующиеся блоки требуют тонкого раствора (0,5 см), очень специальных деталей и предназначены для сейсмостойкости. ![]() |
Возможности форм | • Возможна ли форма для изготовления полноразмерных форм, 3/4 половины блока. • Чтобы сделать правильное соединение, необходимо использовать эти 3 размера, чтобы добиться хорошего качества без поломок. |
ТИПОВАЯ ОРГАНИЗАЦИЯ БЛОКИРОВКИ
Шесть этапов производства
Существует 6 этапов производства CSEB.
Следующие данные приведены для пресса Auram Press 3000, который может производить 1000 блоков 240 в день:
Подготовка (копание + просеивание) Измерение Смешивание (сухое + влажное) Прессование Первоначальное отверждение и первая укладка Окончательное отверждение и штабелирование Всего № | 2–4 человека 1 человек 2 человека 3 человека 1 человек 2 человека 11–13 человек 9022 7 |
Количество людей для копания и просеивания зависит от типа почвы.
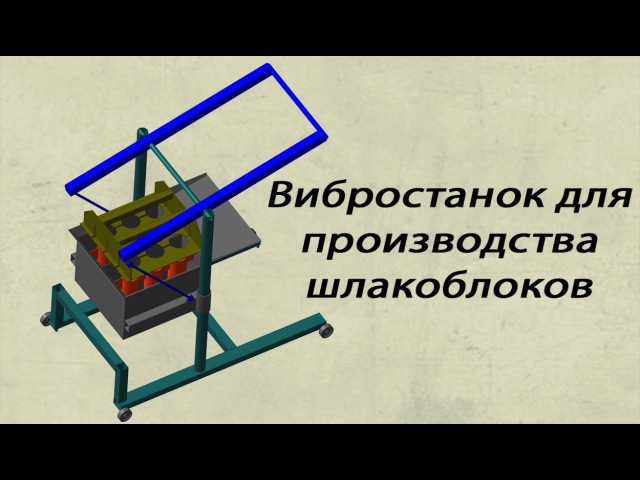
Количество людей для окончательного отверждения и укладки зависит от расстояния транспортировки.
Ключевые слова для организации блокпоста
• Сократить расстояние транспортировки. • Оптимизируйте соотношение производительность/количество рабочих, чтобы добиться максимальной эффективности. • Обустроить блочный двор как можно ближе к площадке. • Расположите кладовую как можно ближе к блочному двору. • Обустройте место окончательного складирования как можно ближе к блочному двору. • Предпочтительнее иметь линейную организацию, но может подойти и кольцевая. |
Типовая линейная организация Типовая планировка блочного двора для пресса Auram 3000
ОПТИМИЗАЦИЯ СООТНОШЕНИЯ ИНВЕСТИЦИИ / ПРОИЗВОДИТЕЛЬНОСТЬ / КАЧЕСТВО
• Легкое ручное оборудование имеет преимущество в дешевизне, но недостаток в низкой долговечности, низкой производительности и не очень хорошо сжатых блоках.

• Тяжелое ручное оборудование представляет собой более интересное соотношение, с большей производительностью, большей долговечностью и большей прочностью для последующего увеличения затрат.
• Моторизованное оборудование переходит в другую категорию затрат: оно будет производить блоки лучшего качества с большей производительностью, но дороже.
Таким образом, тяжелые ручные прессы в большинстве случаев являются лучшим выбором с точки зрения оптимизации соотношения инвестиции/производительность/качество. Мобильные подразделения всегда сильно отстают. Индустриализация не приспособлена к производству CSEB. Полуиндустриализация — лучший вариант: она дает преимущество в том, что она более гибкая и легко адаптируется к местным условиям. Это повышает качество без значительного увеличения стоимости блока. Под полуиндустриализацией здесь следует понимать централизованное производство, но скорее с ручными прессами, чем с моторизованными.
РАЗНООБРАЗИЕ И ВЫБОР ОБОРУДОВАНИЯ Было предпринято много попыток использовать бетонное оборудование для производства CSEB.
Дешевый ручной пресс, а потому легкий и привлекательный по цене, не будет таким долговечным. Преимущество моторизованного пресса состоит в высокой производительности при более высоком и стабильном качестве. Но он потребует энергии и более сложного обслуживания, а его стоимость не будет идти ни в какое сравнение с ручным прессом. Кроме пресса, не следует забывать и все остальное необходимое оборудование: сито, может быть дробилка, тачки, может быть миксер, устройства контроля качества, все мелкие инструменты, листы ПВХ и т.д.
Таким образом, в развивающейся стране, где доступно много рабочей силы, ручные и тяжелые прессы лучше приспособлены, чем моторизованные, поскольку они будут нанимать больше людей и будут производить качественные материалы по более низкой цене.