Технология производство газоблоков: Производство газобетонных блоков своими руками, оборудование, формы, технология и видео
Технология производства газобетона
Газобетонные блоки, как и пенобетонные изделия, являются одной из разновидностей ячеистых бетонов. Пористая структура придает этому материалу хорошие тепло и шумоизоляционные свойства, малый вес при больших размерах и достаточную прочность, что качественно выделяет его среди остальных стеновых материалов, широко использующихся при строительстве перегородок, гаража, дачи и др. Кроме этого, сама технология производства газобетона довольно проста, при этом она не требует больших затрат, а цена готового продукта приятно удивляет.
Содержание
- Виды изготовления
- Сырьевые компоненты
- Оборудование
- Основные этапы
- Вывод
Виды изготовления
Существует 2 разновидности технологии производства газобетонных блоков, а именно: автоклавного твердения и естественной выдержки. В первом случае используют специальные камеры – автоклавы, снабженные регулятором давления и температуры. Газобетон, получаемый таким способом более качественный и прочный, нежели тот, который был высушен в естественных условиях, но зато вторая технология приемлема для тех, кто хочет изготовить блоки в домашних условиях, хоть он получится не настолько надежный как хотелось бы, но он все равно будет пригоден для строительства малоэтажных частных домов.
Сырьевые компоненты
Для изготовления газобетонных блоков по любой технологии понадобятся следующие его составляющие:
Вода
Для блоков пригодна любая питьевая и техническая чистая вода, однако она должна отвечать всем требованиям ГОСТ 23732-79. Вода с температурой 45, качественно увеличит скорость твердения, прочность и производительность линии изготовления. Подогрев воды поможет снизить количество применяемого цемента, за счет искусственной стимуляции его активности.
Песок
Подойдет любой речной или карьерный, главное, чтобы в нем содержалось минимальное количество глинистых и илистых частиц, а максимальная крупность зерен не превышала 2 мм.
Портландцемент
Предпочтительно вяжущее марок М 400 и М 500, лучший цемент тот, который по всем критериям удовлетворяет требования ГОСТ 10178-85.
Газообразователь
В его качестве используется алюминиевая пудра марок ПАП-1 или ПАП-2.
Оборудование
Технологическая линия изготовления газоблоков подразумевает наличие специального оборудования, которое приобретается в комплексе у производителя. Как правило, такой комплекс представляет собой автоматизированный мини–завод, который имеет довольно компактные размеры. Некоторые производители, бонусом к приобретаемому оборудованию предоставляют услуги временного технолога, который обучит вас, настроит производственную линию и подберет оптимальный состав газобетонной смеси.
Основные этапы
Конкретный алгоритм производства зависит от специфики приобретенного оборудования, но в общем он подразумевает 3-этапное производство газоблоков:
- Первым делом происходит точная дозировка компонентов и их перемешивание, в среднем этот цикл длится не более 10 минут.
- После чего, приготовленную бетонную массу, посредством специального оборудования, выгружают в заранее смазанные формы ровно до половины. Далее, в течении 4-часов смесь «растет» и заполняет весь объем форм, еще через 2 часа излишки смеси убираются.
- И третий, завершающий этап – распалубка изделий после 16-часовой выдержки и складирование их на поддоны для дальнейшего набора отпускной прочности, которая происходит в течение 2 или 3 суток, после чего изделия отправляются на склад. Марочной прочности газобетонные блоки достигают на 28 сутки.
Вывод
Чтобы получить на выходе хороший газобетон, нужно приобрести надежное оборудование и качественное сырье. Также обязательно следование всем правилам технологии, и только три эти составляющие в совокупности помогут не только окупить вложения, но и принести хорошую прибыль.
Удачной стройки!
Технология производства газобетона
Автоклавный газобетон производится на крупных заводах и на стройплощадку попадает в виде готовых блоков. Изготовление этого материала на малом производстве или изготовление газобетона автоклавного своими руками — невозможны. Процесс производства ячеистого бетона напоминает выпекание хлеба: в смесителе замешивается вода, цемент, молотый кварцевый песок, тщательно размельченная известь и гипс (не на всех производствах), добавляется газообразователь. В теплой влажной камере смесь поднимается.
Вы можете более подробно прочитать про производство газобетон в статье с фотографиями с ведущего предприятия России перейи по ссылке .
Содержание
Благодаря автоклавированию, непосредственно после его окончания газобетон имеет соответствующую прочность, долговечность и морозостойкость. Автоклавирование исключает возможность усадки, а также обеспечивает долговечность газобетона.
Газобетон хорошо подлежит обработке простейшими инструментами: пилится, сверлится, строгается. В него легко забиваются гвозди, скобы. Со временем газобетон становится твёрже. Дома из газобетона сегодня очень популярны в России. К тому же, проекты домов из газобетона и цена на него, доступны всем.
Автоклавная обработка газобетона производится не только для того, чтобы ускорить процесс твердения смеси. Основной смысл состоит в том, что в автоклаве при температуре +180 °С и давлении до 14 бар в газобетоне образуется новый минерал — доберморит. Благодаря этому повышается прочность материала и, что особенно важно, в несколько раз уменьшается усадка. За счет своих характеристик автоклавный бетон имеет гораздо больше способов применения. Он может использоваться, например, в армированных конструкциях — перемычках, панелях, и др. Ячеистый бетон автоклавного твердения имеет пониженную трещиностойкость и морозостойкость. Автоклавная обработка позволяет в более короткие сроки получать изделия с достаточно высокой прочностью при пониженном расходе вяжущего. У автоклавной обработки имеются и недостатки: дорогостоящее оборудование, специфика его эксплуатации, требующая высококвалифицированного обслуживающего персонала, высокая металлоемкость автоклавов, низкий коэффициент использования внутреннего объема автоклава. Мелкосерийное производство при автоклавном способе оказывается экономически невыгодным.
Основными компонентами этого материала являются цемент, кварцевый песок (либо зола унос), газообразователи, также возможно добавление гипса и извести. В качестве специализированных газообразователей используются алюминиевые пасты и пудры. Сырьё смешивается с водой заливается в форму и происходит реакция воды и газообразователя, приводящая к выделению водорода, который и образует поры, смесь поднимается как тесто. После набора пластической прочности, массив разрезается на блоки, плиты и панели. Ипользование высокотехнологичного резательного оборудования позволяет разрезать полученный массив с высокой точностью на блоки и плиты.
После этого изделия подвергаются закалке паром в автоклаве, где они приобретают необходимую жёсткость, либо высушиваются в условиях электроподогрева.
Процесс газообразования происходит вследствие химической реакции между гидратом окиси кальция и алюминием; выделяющийся при этом водород вызывает вспучивание раствора, который, затвердевая, сохраняет пористую структуру.
При определении состава газобетона необходимо обеспечить заданную объемную массу и его наибольшую прочность при минимальных расходах порообразователя и вяжущего вещества. При этом структура газобетона должна характеризоваться равномерно распределенными мелкими порами правильной шаровидной формы.
Объемная масса газобетона и его пористость зависят главным образом от расхода порообразователя и степени использования его порообразующей способности. Некоторое влияние на них оказывают температура смеси и количество воды, принятое для затворения смеси, т.е. водотвердое отношение В/Т. Увеличение В/Т повышает текучесть смеси, а следовательно улучшает условия образования пористой структуры, если обеспечивается достаточная пластичная прочность смеси к концу процесса газообразования.
Прочность газобетона зависит также от характера его пористости, размеров и структуры пор и прочности межпоровых оболочек. С увеличением В/Т до оптимального значения, обеспечивающего наилучшие условия формирования структуры смеси, прочность газобетона повышается. Прочность оболочек, в свою очередь, зависит от оптимального соотношения основного вяжущего и кремнеземистого компонента, В/Т, а также условий тепловлажностной обработки. Из этого следует, что применение смесей с минимальным значением В/Т при условии образования высококачественной структуры (например виброспучиванием) позволяет получить газобетон более высокой прочности.
Для изготовления газобетона применяют портландцемент марок 300, 400, 500, удовлетворяющий требованиям ГОСТ 970-61, 31108-2016. Производство газобетона предъявляет специальные требования к портландцементу в отношении щелочности цементного теста – рН теста не должна быть ниже 12. Щелочность цемента определяется количеством свободной СаО и суммой Na2О и K2О. По данным работы газобетонных заводов, содержание щелочей (Nа2О, К20) в 1 л раствора цемента не должно быть менее 75 мг. В случае недостаточной щелочности раствора в газобетонную массу следует дополнительно вводить известь или щелочь в виде каустической соды (NаОН).
При применении в качестве основного вяжущего извести особое внимание уделяют значительному количеству активных окиси кальция (СаО) и магния (МgО). Общая активность извести не должна быть менее 75%, количество МgО — не более 1,5%. В производстве можно применять известь. Известь должна быть равномерно обожженной.
Введение извести как добавки к цементу сокращает расход цемента и одновременно увеличивает щелочность раствора, обеспечивая энергичное протекание реакции газообразования:
3 Са(ОН)2 + 2 Аl + 6 Н2О 3 СаО·Аl2О3·6Н2О + 3 Н2
В качестве кремнеземистого компонента в производстве газобетона применяют речной или горный кварцевый песок, золу-унос тепловых электростанций, маршалит и другие материалы. Кварцевый песок для изготовления газобетона и газосиликата должен быть чистым, без примесей глины и органических веществ, с содержанием SiO2 не менее 80%. Присутствие глины замедляет твердение газобетона и уменьшает его прочность. Органические примеси вредно сказываются на протекании реакции газовыделения; вспучивание газобетона при наличии органических примесей ухудшается. Зола-унос может применяться в производстве газозолобетона при содержании SiО2 более 55%. Зола-унос должна иметь незначительное количество сернистых соединений, несгоревших частиц угля и карбонатов кальция.
Важнейшей технологической особенностью получения высококачественных газобетонных изделий максимальной пористости и достаточной прочности является создание оптимальных условий для двух одновременно протекающих процессов газовыделения и газоудержания. Необходимо обеспечить соответствие между скоростью реакции газовыделения и скоростью нарастания структурной вязкости цементного теста или раствора. При этом выделение газа должно как можно полнее закончиться к началу схватывания системы цемент — вода. Протекание процесса газообразования определяется большим количеством различных факторов. Наибольшее влияние на скорость этого процесса оказывают вид, количество и свойства газообразователя, щелочность и температура среды и т. д.
Способы производства Изготовление газобетона осуществляется мокрым или сухим способом. Экономически более целесообразным является мокрый способ, при котором помол кремнеземистого компонента или его смеси с известью производится в присутствии воды с получением шлама. При сухом способе помол и смешение компонентов осуществляются в шаровых мельницах в сухом виде. Песок размалывают в шаровых мельницах. Для осуществления мокрого помола в мельницу вводят подогретую воду. При применении в производстве извести, последнюю вводят в мельницу для совместного помола с песком. Из мельницы шлам пропускают через сито для отделения от крупных включений. Далее шлам собирают в сборнике и с помощью мембранного насоса или путем передавливания сжатым воздухом подают в шламовый бассейн или шламовый силос. Для предотвращения разделения шлама, т. е. осаждения частиц песка, шлам в бассейнах и силосах подвергают непрерывному перемешиванию. Одновременно производят барботаж шлама.
Дозировка шлама, подогрев и предварительное смешение осуществляются в ванне-дозаторе. Для подогрева шлама до 40-45° применяют острый пар. Дозировка цемента – весовая. Газообразователь взвешивают и подают в бачок с клееканифольной эмульсией, снабженный пропеллерной мешалкой.
Смешивание компонентов Окончательное интенсивное смешение всех компонентов газобетонной массы происходит в передвижной самоходной пропеллерной газобетономешалке. Материалы в газобетономешалку загружают в определенной последовательности. Сначала заливают песчаный шлам, затем немолотый песок (в случае необходимости) и в последнюю очередь – цемент. После этого в течение 2-3 мин перемешивают всю массу. Введение алюминиевой суспензии определяет начало перемешивания газобетонной массы. Одновременно с этим газобетономешалка начинает передвигаться. Перемешивание газобетонной массы должно продолжаться 2-3 мин. Тщательное перемешивание массы обеспечивает однородность смеси и равномерность вспучивания. Излишняя продолжительность перемешивания вредна, так как возможно начало интенсивного газообразования в газобетономешалке. При этом теряется часть выделившегося газа и три заливке в формы газобетонная масса не даст нужного вспучивания. Разливают массу в формы через отверстия в нижней части мешалки при помощи гибких резинотканевых рукавов. Формы до заливки газобетона смазывают минеральным маслом или специальными эмульсиями для предотвращения сцепления газобетона с металлом форм.
Газобетонную массу заливают с учетом вспучивания на 2/3 или 3/4 высоты формы.
После заливки газобетонной массы начинается вспучивание. процесс вспучивания продолжается 30-40 мин. После вспучивания происходит схватывание и твердение газобетона. Для ускорения схватывания и твердения газобетона, а также для ускорения процесса газовыделения в цехе по производству газобетонных тонных изделий температура воздуха должна поддерживаться не ниже +25°. Формы, в которых вспучивается и твердеет газобетон, нельзя передвигать, подвергать сотрясениям и ударам, так как вспученная, но не затвердевшая масса может при этом осесть. При вспучивании газобетонная масса образует так называемую горбушку, которую после затвердевания срезают ручными или механическими ножами. Затем застывшую массу разрезают на изделия нужного размера, формы устанавливают на автоклавные вагонетки в 2-3 яруса по высоте и загоняют в автоклав для ускоренного твердения.
На сайте Вы можете найти информацию: видео о газобетоне, возведение стен, стоимость газобетона, производители газобетона, что лучше — газобетон или пенобетон, отзывы, а также купить газобетон.
Центр данных по альтернативным видам топлива: Производство возобновляемого природного газа
Этот грузовик для перевозки молока заправляется на заправочной станции, работающей на возобновляемом природном газе. Фото из ampCNG
Возобновляемый природный газ (RNG) — это газ трубопроводного качества, который полностью взаимозаменяем с обычным природным газом и, таким образом, может использоваться в транспортных средствах, работающих на природном газе. RNG — это, по сути, биогаз (газообразный продукт разложения органического вещества), обработанный до стандартов чистоты. Как и обычный природный газ, RNG может использоваться в качестве транспортного топлива в виде сжатого природного газа (CNG) или сжиженного природного газа (LNG). RNG квалифицируется как усовершенствованное биотопливо в соответствии со стандартом возобновляемого топлива.
Биометан, который является еще одним термином для этого очищенного топлива трубопроводного качества, относится к биогазу, который также был очищен и подготовлен для удаления или уменьшения содержания неметановых элементов. Биогаз производится из различных источников биомассы с помощью биохимического процесса, такого как анаэробное сбраживание, или с помощью термохимических средств, таких как газификация. При незначительной очистке биогаз можно использовать для выработки электроэнергии и тепла, а также вместо традиционного природного газа для выработки комбинированного электричества и тепла для электростанций, а не для транспортных средств.
Для использования в качестве топлива для транспортных средств биогаз должен быть обработан до более высокого стандарта чистоты. Этот процесс называется кондиционированием или модернизацией и включает удаление воды, двуокиси углерода, сероводорода и других микроэлементов. Полученный RNG, или биометан, имеет более высокое содержание метана, чем сырой биогаз, что делает его сравнимым с обычным природным газом и, таким образом, подходящим источником энергии в приложениях, где требуется газ трубопроводного качества, например, в транспортных средствах.
Полный список проектов по модернизации газа для закачки в трубопроводы или использования в качестве автомобильного топлива см. в Базе данных по возобновляемому природному газу, разработанной и поддерживаемой Аргоннской национальной лабораторией.
Биогаз со свалок
Свалки – это специальные места для захоронения отходов, собранных с жилых, промышленных и коммерческих предприятий. По данным Агентства по охране окружающей среды США (EPA), свалки являются третьим по величине источником выбросов метана, связанных с деятельностью человека, в Соединенных Штатах. Биогаз со свалок также называют свалочным газом (СГ), так как процесс сбраживания происходит в земле, а не в анаэробном метантенке. По данным EPA, по состоянию на сентябрь 2021 года в США действовало 548 проектов по переработке биогаза. Однако в большинстве этих проектов для производства электроэнергии используется биогаз, а не транспортные средства, работающие на природном газе.
Узнайте об этих проектах по транспортировке альтернативного топлива на свалочном газе:
- Свалка Альтамонт компании Waste Management недалеко от Ливермора, Калифорния
- Свалка округа Сент-Лэндри в Вашингтоне, штат Луизиана
- Совместные заводы по борьбе с загрязнением воды в округе Лос-Анджелес, Калифорния
Биогаз в животноводстве
Системы регенерации биогаза в животноводстве могут использоваться для производства RNG. Навоз животных собирается и доставляется в анаэробный реактор для стабилизации и оптимизации производства метана. Полученный биогаз можно перерабатывать в ГСЧ и использовать для заправки транспортных средств, работающих на природном газе, или для производства электроэнергии.
По состоянию на август 2017 года на коммерческих животноводческих фермах в США работало около 250 систем анаэробного сбраживания. Большинство этих объектов используют биогаз для производства электроэнергии. Несколько ферм используют биогаз для производства топлива для транспорта, в том числе Hilarides Dairy в Калифорнии и Fair Oaks Farms в Индиане. База данных AgSTAR Агентства по охране окружающей среды предоставляет дополнительную информацию об использовании таких систем в Соединенных Штатах.
Биогаз при очистке сточных вод
Биогаз можно получить путем сбраживания твердых частиц, удаляемых в процессе очистки сточных вод. По оценкам EPA, этот биогазовый потенциал составляет около 1 кубического фута метанового газа на 100 галлонов сточных вод. Согласно исследованию, опубликованному Национальной ассоциацией агентств чистой воды, Фондом исследований водной среды и Федерацией водной среды, энергия, вырабатываемая на очистных сооружениях США (СОСВ), потенциально может удовлетворить 12% национального спроса на электроэнергию. Это также может стимулировать производство ГСЧ для использования в транспортных средствах.
В Соединенных Штатах насчитывается более 16 000 очистных сооружений, но только около 1 300 имеют анаэробные метантенки, а 860 из них имеют оборудование для использования биогаза на месте. Станция очистки сточных вод Джейнсвилля в Висконсине является примером установки, использующей биогаз для производства RNG для использования в транспортных средствах.
Другие источники биогаза
Другие источники биогаза включают органические отходы промышленных, институциональных и коммерческих предприятий, таких как производство продуктов питания и оптовые торговцы, супермаркеты, рестораны, больницы и учебные заведения. Узнайте о биореакторе в городе Перрис, штат Калифорния, который производит достаточно ГСЧ, чтобы заправлять их парк из 9 машин.00 автомобилей.
Биогаз также может быть получен из лигноцеллюлозного материала (например, растительных остатков, древесной биомассы и специальных энергетических культур) посредством термохимической конверсии, совместного сбраживания и сухой ферментации. Эти технологии находятся в стадии разработки в Европе, с ограниченным применением в Соединенных Штатах.
Block Energy и Baker Hughes внедрят энергоэффективные технологии для добычи нефти и газа в Грузии компания Бейкер Хьюз. Меморандум о взаимопонимании предусматривает несколько наград за передовые нефтегазовые технологии в рамках программы многоскважинного бурения, ориентированной на добычу. Первоначальный проект предусматривает бурение горизонтальной скважины с извлекаемым объемом, который оценивается в 2,1 млн баррелей нефтяного эквивалента (млн бнэ) на целевом участке скважины WR-BA в Западном Рустави.
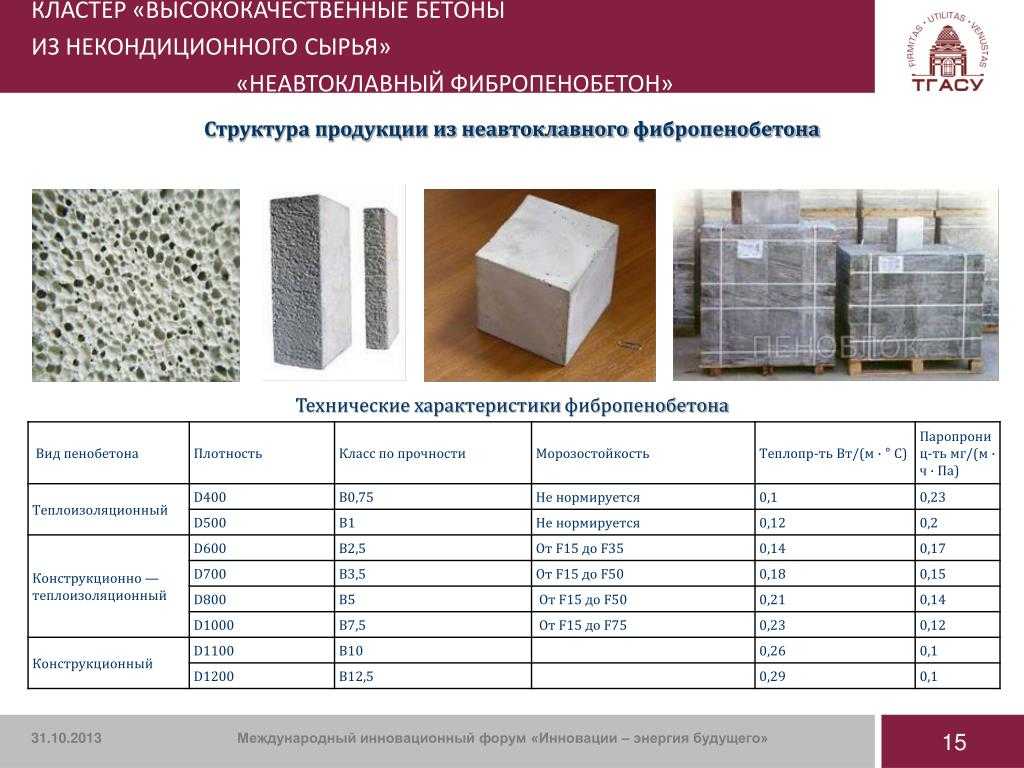
Сотрудничество Block Energy с Baker Hughes будет способствовать текущему и будущему развитию всего ее портфолио. Услуги, предоставляемые Baker Hughes , включают буровые растворы, цементирование, буровые долота, наклонно-направленное бурение с использованием передовых технологий роторных управляемых систем и услуги каротажа во время бурения премиум-класса.
«Я рад сообщить нашим заинтересованным сторонам об этом соглашении с одной из ведущих мировых компаний в области энергетических технологий», — прокомментировал главный исполнительный директор Block Energy Пол Хейвуд. «Я с нетерпением жду начала бурения нашей первой скважины с использованием нашей недавно приобретенной 3-D сейсморазведки и самых современных услуг наклонно-направленного бурения и гарантии качества скважин, предоставляемых Baker Hughes. Дополнительный технический и операционный опыт, никогда ранее не использовавшийся в Грузии, обеспечивает качественное изменение наших технических возможностей и позволит команде лучше раскрыть значительный потенциал нашей базы активов.
Первоначальный проект, первая новая горизонтальная скважина Блока на месторождении WR-BA, включает в себя передовую вращательную управляемую технологию, которая значительно повысит эффективность бурения, безопасность и точность размещения скважины. Замеры каротажа во время бурения также будут проводиться для определения характеристик резервуара и оптимизации добычи.
Baker Hughes также предоставит ряд эффективных услуг по внутрискважинным работам и повышению производительности, чтобы повысить текущие темпы добычи и повысить эффективность. Это будет достигнуто за счет применения усовершенствованных механических и химических технологий при плановых ГТМ Компании, включая ГТМ на скважине WR-16aZ.