Технология производства блоков газосиликатных: Технология производства газосиликатных блоков своими руками: оборудование и материалы
Технология производства и срок службы газосиликатных блоков
Когда обычный рядовой житель большого города решает построить дом на своем участке и принимается за изучение вопросов, связанных с выбором строительных материалов, разновидностей фундамента, утепления стен и прочих немало важных нюансов – голова его идет кругом от всех тонкостей строительства, о которых новоиспеченный владелец будущего дома ни разу до этого и не задумывался. Не будучи профессионалом или, как минимум, не обратившись за помощью к профессионалу, сложно будет определиться с проектом дома, стройматериалом для его возведения, да и вообще лучшим местом на участке, предназначенном для строительства. Поэтому не стоит переоценивать свои возможности, считая, что все можно сделать самому, своими руками и при этом не хуже, чем любой другой строитель. Не стоит экономить на знаниях и опыте специалистов в своем деле, которые помогут воплотить в жизнь все Вами задуманное, при этом сделают это профессионально, качественно и довольно быстро. И тогда довольны будут все: и Вы, что теперь у Вас есть дом Вашей мечты, в котором с удовольствием хочется проводить как можно больше времени, и строительная фирма, за помощью к которой Вы обратились, будет удовлетворена своими результатами. Конечно, в интернете, да и во многих других источниках можно найти много полезной информации, различных статей о строительстве и многое другое. Но этого не достаточно для начала самостоятельного строительства, к примеру, дома. Можно принять к сведению полезные советы по выбору строительных материалов или перенять опыт других строителей, которые зачастую делятся своими успехами на специализированных форумах. Но это только малая часть того, что вообще надо знать для того, чтобы что-то построить. Итак, в этой статье рассмотрим положительные качества такого строительного материала как газосиликатный блок. Начнем с того, что
Такой материал, как газосиликатные блоки, можно отнести к очень эффективным стройматериалам. Изначально технология производства газосиликатных блоков была открыта в Швеции, а затем, благодаря удачному сочетанию хороших качеств, газосиликатные блоки стали производить по всему миру. Процесс производства блоков уже давно поставлен на конвейер и человеческий фактор тут исключен. Благодаря своим уникальным качествах и техническим характеристикам газосиликатный блок можно считать идеальным материалом для возведения различных построек.
Наша компания предлагает на Ваш выбор газосиликатные блоки разной плотности отечественного и импортного производства для использования в различных целях. У нас широкий диапазон типоразмеров по доступным ценам!
Возврат к списку
Производство газосиликатных блоков.
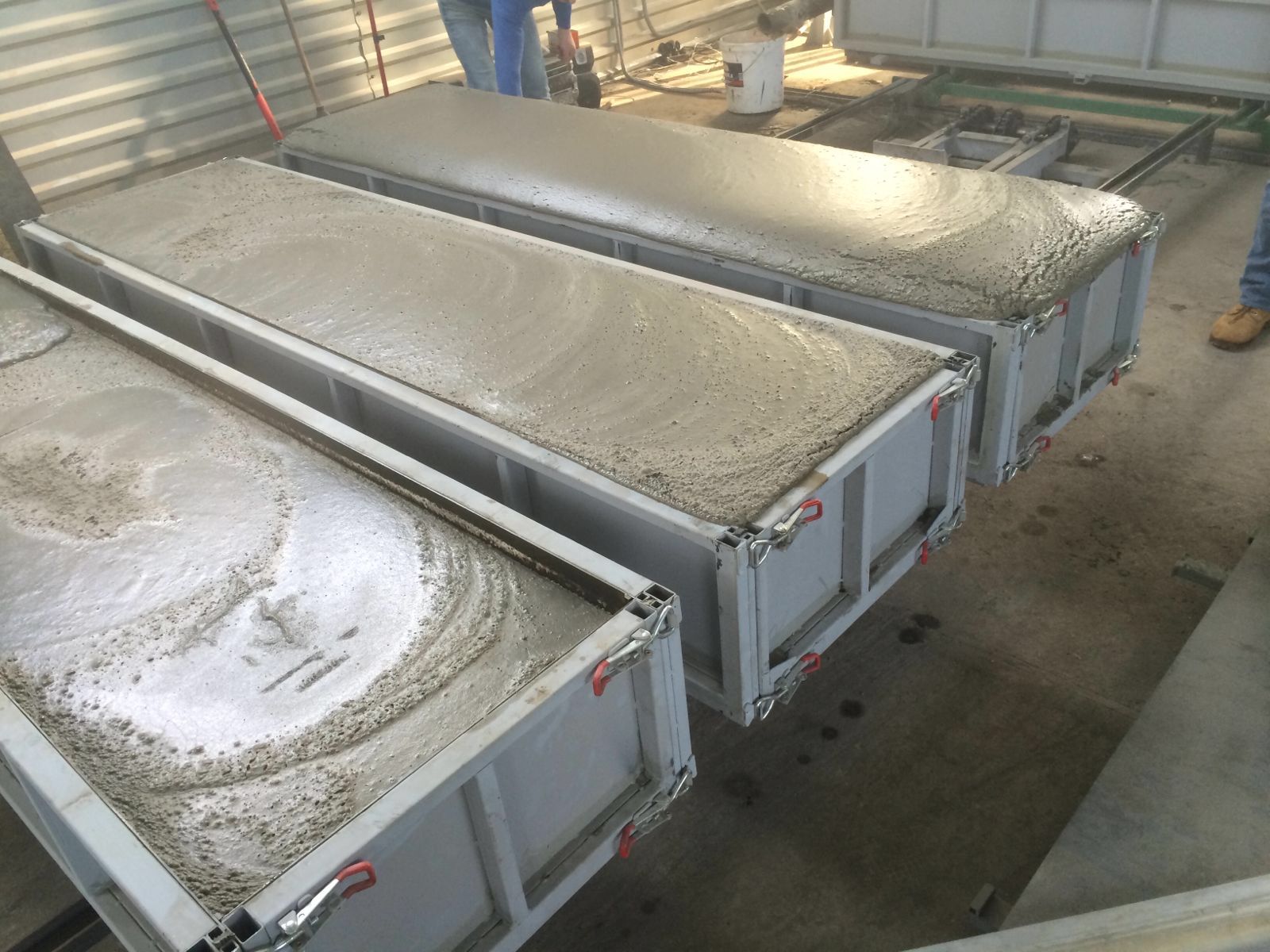
11 Окт 21
- Опубликовал: ЧП Газосиликатстрой
Изготовлением газосиликатных блоков занялись в начале минувшего века в Скандинавии. Материал был изобретен весьма давно, однако его использование началось сравнительно недавно. Технология производства газосиликатных блоков практически не изменилась с тех пор, поскольку формула производства данного материала подарила этому миру по-настоящему универсальный материал, который не потерял своей актуальности на протяжении всей истории своего существования.
Главные моменты производства газосиликатных блоков
Для производства газосиликатных блоков используют исключительно натуральные материалы, такие как: известь, песок, цемент и вода. Из ранее перечисленных материалов замешивают субстанцию, в которую в процессе замешивания, добавляется алюминиевая пудра. За счет пудры которая образуется газ, вспенивается данная масса. Благодаря этому и получается необходимая, универсальная структура.
Газосиликатные блоги производятся посредствам станков и машин. Являясь при этом полностью автоматизированным, в процесс производства можно вносить определенные настройки, которые будут изготавливать материал под заданную плотность. За счет такого типа производства, блоки на выходе получаются недорогими.
Оборудование и системы производства
Изготовление газосиликатных блоков является практически полностью машинным и включает в себя использование различных машин и систем.
Системы производства газосиликатных блоков
- Дробящая система – состоит из элеватора, мельницы, сушилки и весов;
- Заливающая система – представляет собой заливающий смеситель;
- Система нарезки – представляет собой раму, оснащенную ножами, переворачивающими получившуюся субстанцию;
- Система жарки – в нее входят котел и обжигающая печь;
- Упаковочный процесс – в нее входит кран и гидравлическая колодка.
Совокупная система производства газосиликатных блоков управляется за счет схем, при помощи которых можно изменять параметры производства.
Последовательность производства газосиликатных блоков
Последовательность изготовления газосиликатных блоков разделяется на несколько этапов:
- Приготовление материала – измельченный песок смешивается с водой до тех пор, пока не превратится в шлам;
- Изготовление смеси – в замешиваемый шлам постепенно добавляется цемент и также в конце добавляют алюминиевую пудру;
- Формовка – получившеюся смесь заливают в формы, где она остывает, образуя внутри пористость и необходимую структуру;
- Резка – с помощью ножей, остывшая масса извлекается из формы, после чего нарезается струнами, а отходы от нарезки подвергаются вторичной обработке;
- Обработка – блоки на сутки оставляют в печи при температуре в 180 градусов, за счет чего они доводятся до необходимого уровня прочности;
- Упаковка – Блоки вынимаются краном, немного остывают, затем проходят стадию упаковки на ленте и подготовке к продаже.
Команда под руководством профессора Калифорнийского университета в Лос-Анджелесе выиграла NRG COSIA Carbon XPRIZE в размере 7,5 млн долларов
Группа инженеров Калифорнийского университета в Лос-Анджелесе стала первой университетской командой, получившей главный приз в глобальном конкурсе NRG COSIA Carbon XPRIZE. Благодаря уменьшению углеродного следа бетона изобретение команды может в конечном итоге стать важным шагом в глобальной борьбе с изменением климата.
Команда CarbonBuilt Калифорнийского университета в Лос-Анджелесе под руководством Гаурава Сента, профессора гражданской и экологической инженерии Инженерной школы Самуэли Калифорнийского университета в Лос-Анджелесе, выиграла 7,5 миллиона долларов на конкурсе технологий, связанных с выработкой электроэнергии на угле.
Технология-победитель — это первый в своем роде экологически чистый подход к сбору выбросов углекислого газа непосредственно с электростанций и других промышленных объектов — выбросов, которые в противном случае попали бы в атмосферу — и превращению их в новый тип бетон, изобретенный командой. По мере затвердевания и набора прочности специально разработанный бетон постоянно поглощает и улавливает парниковые газы.
Благодаря обширным исследованиям в Калифорнийском университете в Лос-Анджелесе и испытаниям в Интегрированном испытательном центре, объекте за пределами Джиллета, штат Вайоминг, исследователи продемонстрировали, что их процесс снижает углеродный след бетона более чем на 50%, при этом производя бетон, который является таким же прочным и долговечным. как традиционный материал.
В каждом бетонном блоке CarbonBuilt содержится около трех четвертей фунта углекислого газа — значительное количество, учитывая, что к 2027 году ежегодно будет производиться около 1 триллиона бетонных блоков. и группа штатных ученых, постдокторантов и докторантов начала исследования, которые привели к награде в 2014 году. Carbon Management и занимает должность преподавателя в инженерном отделе материаловедения и инженерии Калифорнийского университета в Лос-Анджелесе. «Как инженер-строитель в третьем поколении я был очарован той ролью, которую строительство сыграло в решении социальных проблем. Потратить последнее десятилетие на разработку решения для уменьшения углеродного следа бетона с феноменальной командой и выиграть NRG COSIA Carbon XPRIZE, занимаясь тем, чем я увлечен, — это сбывшаяся мечта».
В сентябре 2015 года при поддержке NRG Energy и Канадского альянса по разработке месторождений нефтеносных песков был запущен конкурс NRG COSIA Carbon XPRIZE с бюджетом 20 миллионов долларов США для поиска способов эффективного использования выбросов углекислого газа. Некоммерческая организация XPRIZE Foundation поставила перед глобальным сообществом специалистов по решению проблем задачу разработать технологии превращения углекислого газа из выбросов электростанций, работающих на угле и природном газе, в ценные продукты. Канадская команда CarbonCure выиграла другой этап конкурса — производство электроэнергии на основе природного газа.
Заявка Калифорнийского университета в Лос-Анджелесе была одной из 47 заявок от 38 команд из семи стран. CarbonBuilt, ранее известная как CO 2 Concrete, была названа одним из 10 финалистов в октябре 2017 года.
Сант сказал, что оригинальное вдохновение для победившей технологии пришло из неожиданного источника: морских ракушек.
«Морские ракушки сделаны из карбоната кальция, который является естественным связующим веществом», — сказал он. «Нас очень вдохновила идея о том, как скрепляются ракушки. И именно так мы действительно приступили к превращению углекислого газа в бетон».
Эксперты из академических и промышленных кругов, заявившие, что это невозможно, бросили вызов, Сант и его команда потратили следующие семь лет на миссию, чтобы доказать их неправоту.
Инженерная школа Самуэли Калифорнийского университета в Лос-Анджелесе
Бетонные блоки CarbonBuilt, сходящие с производственной линии. Каждый бетонный блок CarbonBuilt хранит около трех четвертей фунта углекислого газа.
Во-первых, исследователи Калифорнийского университета в Лос-Анджелесе разработали новую формулу цемента, который является связующим веществом в бетоне. Они использовали гашеную известь или портландит, который может быстро поглощать углекислый газ, чтобы заменить традиционный цемент на основе силиката кальция, известный как обычный портландцемент. Затем команда создала метод, при котором углекислый газ, взятый непосредственно из дымовых газов, быстро поглощается портландитом по мере затвердевания бетона.
Помимо поглощения углекислого газа бетоном, процесс Reversa от CarbonBuilt снижает количество обычного портландцемента, необходимого для производства бетона, на 60-90%. Процесс происходит и при обычных температурах и давлениях. В результате бетон CarbonBuilt имеет гораздо меньший углеродный след, чем обычный бетон. Это может иметь большое значение для сокращения выбросов парниковых газов в мире, поскольку производство традиционного цемента, используемого в бетоне, является причиной почти 9% мировых выбросов углекислого газа.
Еще одним неоспоримым преимуществом новой технологии является ее экономичность. В отличие от других технологий снижения выбросов углерода, которые требуют дорогостоящей установки для улавливания выбросов углекислого газа или их очистки, процесс CarbonBuilt позволяет напрямую использовать углекислый газ в дымовых газах электростанций и промышленных предприятий и преобразовывать его в источнике без этих дополнительных шагов.
«Это преобразующий момент, озарение для Калифорнийского университета в Лос-Анджелесе, а также для науки и техники», — сказал Джаяти Мурти, декан Рональда и Валери Шугар из Калифорнийского университета в Лос-Анджелесе. «Благодаря исключительному упорству и решимости Гаурав и его команда смогли превратить исследовательский проект в инновационную технологию, которая может решить реальную социальную проблему и привести к позитивным изменениям в мире».
Чтобы выйти в финал, исследователи Калифорнийского университета в Лос-Анджелесе продемонстрировали, что их технология может потреблять 135 кг (около 297 фунтов) углекислого газа за 24 часа. В 2017 году команда должна была соответствовать определенным техническим требованиям, подлежащим проверке независимой фирмой. Затем эти результаты были оценены экспертным жюри из академических и промышленных кругов, которые оценили количество углекислого газа, преобразованного в бетон CarbonBuilt, а также инженерную, экологическую и экономическую ценность строительного материала.
Финальный раунд конкурса, первоначально запланированный на февраль 2020 года, был отложен из-за пандемии COVID-19. В июне 2020 года команда Калифорнийского университета в Лос-Анджелесе направилась в Интегрированный испытательный центр, чтобы продемонстрировать свою систему в промышленном масштабе. Демонстрация длилась четыре месяца, и было произведено почти 150 метрических тонн (более 330 000 фунтов) бетонных блоков CarbonBuilt. Некоторые бетонные блоки были переданы в дар племени восточных шошонов для жилищного строительства в резервации Винд-Ривер в Форт-Вашаки, штат Вайоминг.
Средства от премии NRG COSIA Carbon XPRIZE пойдут на поддержку инновационных исследований и разработки технологий по снижению выбросов углерода в UCLA Engineering. CarbonBuilt, частная компания, основанная Сэнтом, получила права, связанные с патентным портфелем проекта, принадлежащим Калифорнийскому университету в Лос-Анджелесе, для коммерциализации технологии.
UCLA Samueli School of Engineering
Гаурав Сант: «Потратить последнее десятилетие на разработку решения для уменьшения углеродного следа бетона с феноменальной командой и выиграть NRG COSIA Carbon XPRIZE, занимаясь тем, чем я увлечен. это сбывшаяся мечта».
Прежде чем выиграть главный приз, команда собрала 10 миллионов долларов на разработку технологии CarbonBuilt. В дополнение к награде в размере 500 000 долларов США от XPRIZE Foundation в 2018 году за выход в финал Сант в 2019 году получил грант в размере 1,8 миллиона долларов от Министерства энергетики. (Дополнительные испытания для завершения гранта Министерства энергетики США недавно завершились в Национальном центре улавливания углерода в Уилсонвилле, штат Алабама.) Семейный фонд Энтони и Жанны Притцкер выделил 1,5 миллиона долларов в 2017 году9.0003
Многие преподаватели Калифорнийского университета в Лос-Анджелесе внесли свой вклад в успех команды, в том числе Данте Симонетти, доцент кафедры химической и биомолекулярной инженерии; Дж. Р. ДеШазо, профессор государственной политики, гражданского и экологического строительства и директор Центра инноваций Лускина Калифорнийского университета в Лос-Анджелесе; Лоран Пилон, профессор машиностроения, аэрокосмической техники и биоинженерии; Ричард Канер, выдающийся профессор химии и биохимии, материаловедения и инженерии; и Матье Боши, адъюнкт-профессор гражданской и экологической инженерии.
Дополнительные члены команды включают нынешних и бывших ученых инженерного проекта Калифорнийского университета в Лос-Анджелесе Дейла Прентиса, Габриэля Фальзоне, Имана Мехдипура и Бу Ванга; Хюкмин Квеон, бывший докторант Калифорнийского университета в Лос-Анджелесе; Чжэньхуа Вэй, бывший докторант в области гражданского и экологического строительства; Камли Тран, исполнительный директор Института управления выбросами углерода; и опытные отраслевые консультанты, включая Эдварда Мюллера, Стивена Рааба и генерального директора CarbonBuilt Рахула Шендура.
Возможность сделать каждый блок на счету – Masonry Magazine
Скотт Биггар и Челси Код-МакНил
Достижения в области технологий самовоспроизводятся — проведение исследований и разработок неизбежно приводит к открытиям, которые продвигают инновации вперед. CarbonCure Technologies не новичок в этом цикле. Технология компании началась, когда их генеральный директор Роберт Нивен начал исследовать химическую реакцию между углекислым газом (CO2), цементом и водой, одновременно получая степень магистра в Университете Макгилла в Монреале, Канада.
Позже это исследование стало основой для разработки CarbonCure в течение следующих восьми лет и превратилось в жизнеспособное решение для производителей бетона по переработке отходов CO2 в их бетонные смеси.
Рис. 1 — Химия, связанная с добавлением CO2 в бетонную смесь. (Любезно предоставлено CarbonCure Technologies)Углекислый газ, известный как парниковый газ и фактор изменения климата, быстро становится главной темой для строительной отрасли. Архитекторы и застройщики десятилетиями совершенствовали строительные системы и методы, чтобы уменьшить выбросы CO2, связанные с их зданиями. Тем не менее, этот подход затрагивает только один конец дымовой трубы, и разрабатываются новые технологии, позволяющие использовать CO2 для производства новых строительных материалов.
В основе технологии CarbonCure лежит химическая реакция, называемая минерализацией. Реакция происходит при впрыскивании CO2 в процессе производства бетонных кладочных блоков (БКМ). Газ CO2 вступает в реакцию с ионами кальция, находящимися в цементе, и подвергается обратной реакции прокаливания (рис.
CMU, изготовленный по технологии CarbonCure, который поставляется на объект, имеет точно такие же физические свойства и внешний вид, как и традиционный CMU. Разница в том, что CarbonCure CMU поглощает CO2 и удерживает его внутри, откуда он больше не может высвобождаться. Поскольку газ был преобразован в карбонат кальция, он больше не способствует изменению климата.
Дизайнеров и архитекторов постоянно просят расставлять приоритеты в отношении свойств материалов, чтобы оставаться функционально верными мотивам своих клиентов. При рассмотрении вопроса об использовании CMU в проекте многие свойства материалов складываются в пользу материалов: долговечность, прочность, огнестойкость и тепловая масса. Все эти свойства материалов способствуют устойчивости здания, и с появлением LEED v4 вводятся новые меры для поощрения материалов, которые могут противостоять климатическим воздействиям.
Несмотря на материальные преимущества каменной кладки, в КМУ есть один ингредиент, который имеет большой углеродный след: цемент. Строительная отрасль уже много лет знает о выбросах CO2 при производстве цемента и подталкивает производителей к поиску решений для уменьшения этого следа.
В то время как некоторые считают CO2 из бетона проблемой, CarbonCure видит в этом возможность адаптивного повторного использования. Каждый блок — это возможность сохранить небольшое количество углерода, шанс уменьшить часть выбросов цементной промышленности и вернуть его обратно в бетон.
Brampton Brick, производитель каменной кладки, работающий на юге Онтарио, был одним из первых, кто внедрил технологию CarbonCure в Северной Америке, впервые установив партнерские отношения с компанией в 2013 году. В сентябре 2015 года Brampton принял решение установить технологию еще на двух своих заводов, ссылаясь на желание начать производство всей своей продукции с использованием вторичного CO2.
«Все, что мы производим сегодня, содержит CO2», — сказал Дейв Картер, генеральный директор Brampton Brick. Он указывает на стандарты зеленого строительства, такие как LEED, как на драйверы этой тенденции.
(любезно предоставлено CarbonCure Technologies)
Использование CMU в качестве резервуара для хранения углерода не сильно увеличило общие затраты Brampton Brick и не изменило их методы производства. Но Картер не рекламирует блоки своей компании с впрыском CO2 как волшебную палочку для бетонной промышленности.
«Это всего лишь часть головоломки», — сказал он, указав также на растущее использование альтернативных видов топлива и материалов в цементной и бетонной промышленности.
Добавление CarbonCure в состав смеси не влияет на вес CMU, цвет или требования ASTM. С 2013 года CarbonCure установила свою технологию на 22 заводах в США и Канаде.
Разработчики и архитекторы в США начинают узнавать о перспективах хранения углерода в бетонных блоках. Kimco Realty, крупнейший в Северной Америке владелец и оператор торговых центров под открытым небом, недавно построила первый проект в Орегоне с использованием блока CarbonCure. Блок был изготовлен и поставлен Mutual Materials, недавним партнером CarbonCure.
Рис. 3 — Строящаяся торговая точка Kimco. (Предоставлено Кимко Риэлти) |
Рис. 4 — CarbonCure CMU предоставлен Mutual Materials. (Предоставлено Кимко Риэлти) |
«Добавление CarbonCure в наш проект Sunset Mall прошло довольно гладко, — сказал Тим Хаманн, директор по строительству Kimco Realty.
В новом торговом центре разместятся два ресторана и розничный магазин, а строительством будет заниматься компания Lanphere Construction and Development.
«У нашего генерального подрядчика и каменщиков не было проблем с блоком», — сказал Хаманн. «Проект уложен так же, как и обычная кладка. Переработка CO2 в этом проекте была как раз тем, что соответствовало целям устойчивого развития Kimco».
Интеграция технологии CarbonCure в блочный завод также очень проста. После того, как производитель наладил поставку промышленного CO2 из местных источников, инженеры CarbonCure устанавливают свое оборудование и работают с группой контроля качества завода, чтобы интегрировать CO2 в свои бетонные смеси.