Сырье производства цемента: Из чего делают цемент: состав, марки
РИФЕЙ | Сырье для производства цемента и минеральные добавки
Компания ООО «ПЛАСТ-РИФЕЙ» предлагает глинистое сырье для производства белого цемента. Минеральный состав каолина-сырца: 51% каолинита, 45% кварцевого песка, 4% Калиевые полевые шпаты и слюды, химический состав каолина-Сырца приведен в таблице.Таблица 1. Химический состав Каолина-Сырца
Оксид | содержание, % |
Al2O3 | 20±2 |
SiO2 | 70±2 |
K2O |
1,1±0,3 |
Na2O | 0,1±0,02 |
MgO | 0,18±0,03 |
CaO | 0,15±0,03 |
Fe2O3 | 0,4±0,2 |
TiO2 |
0,3±0,2 |
Cr2O3 | отсутствует |
MnO | отсутствует |
Также ПЛАСТ-РИФЕЙ предлагает Каолин (белую глину), как минеральный наполнитель высокой чистоты, обладающий вяжущими свойствами.

Растворная смесь из каолина и цемента имеет высокую пластичность, удобообрабатываемость, предотвращает расслоение раствора, в процессе твердения раствора каолин удерживает воду, необходимую для гидратации цемента.
- водоудерживающую способность;
- Пластичность и удобоукладываемость;
- Прочность на сжатие и изгиб;
- Водонепроницаесость;
- Морозостойкость.
Россия, Челябинская обл., г. Пласт, Магнитогорский тракт, 1
Тел.: 8 800 333 0498, +7 351 602 2945, +7 351 242 0398
www.kaolinzhl.ru
Использование опубликованных на сайте материалов допускается только с упоминанием источника (журнал «Цемент и его применение») и активной гиперссылкой на цитируемый материал.
что это такое, бетон и сваи из цинк сульфатного строительного материала, состав клинкера для цемента
Бытует мнение, что железобетонные изделия являются самыми прочными и долговечными. Однако подобная формулировка является заблуждением. При несоответствующих условиях эксплуатации конструкции из бетона также подвержены серьезным деформациям и повреждениям. На них оказывают негативное воздействие сильные морозы, оседание слоев почвы, кислородное окисление, атмосферные осадки и влияние различных химических веществ.
Лучшим вариантом для строительства считается сульфатостойкий цемент. Наибольшую популярность данный строительный материал получил в тех регионах, где погодные условия оставляют желать лучшего. Это касается территорий, для которых характерными особенностями являются резкие перепады температур и большое количество выпадающих осадков.
Что это такое?
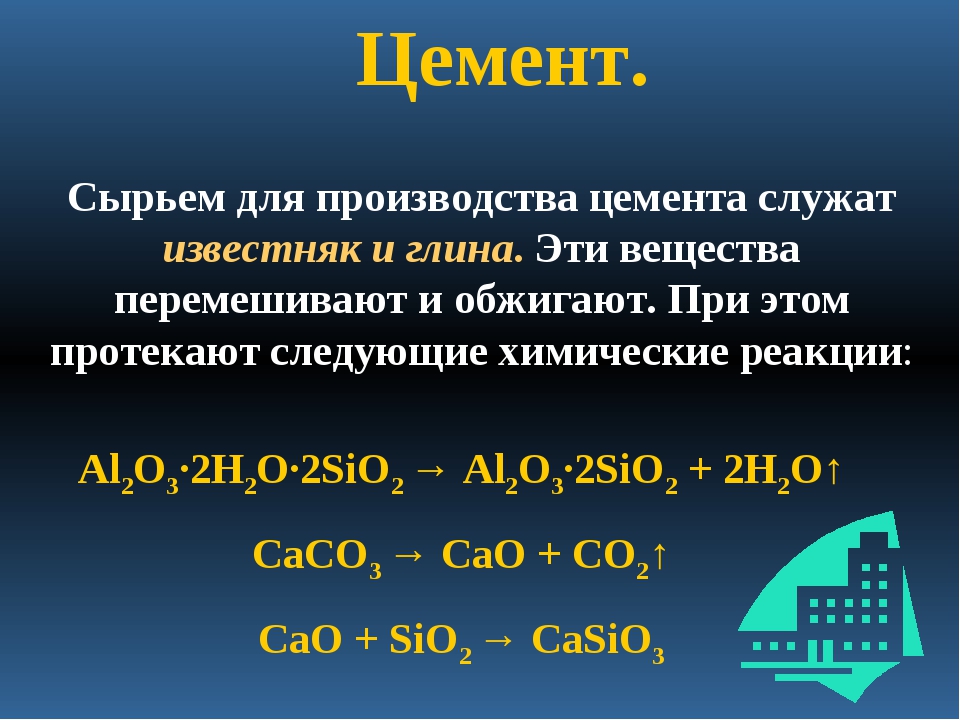
Сульфатостойкий цемент достаточно медленно застывает, но в затвердевшем состоянии имеет очень высокую плотность. Последний фактор является его основным достоинством среди других строительных материалов.
Виды
По своему составу сульфатостойкий цемент разделяется на следующие разновидности:
- пуццолановый портландцемент;
- сульфатостойкий шлакопортландцемент;
- сульфатостойкий портландцемент;
- сульфатостойкий портландцемент с добавлением минеральных веществ.
Теперь рассмотрим вкратце каждый из этих строительных материалов:
- Пуццолановый портландцемент содержит смесь из гранулированного доменного шлака и пуццоланов. Под последними подразумеваются продукты вулканического происхождения в виде пепла, туфа и пемзы. Пуццоланы являются активными минеральными добавками при изготовлении портландцемента. Этот строительный материал сравнительно плохо переносит режим попеременного увлажнения и высыхания, а также оттаивания и резкого замораживания.
- Сульфатостойкий шлакопортландцемент изготавливается путем смешивания клинкера с доменным шлаком в гранулированном виде (примерно 50-60%) и незначительным количеством гипса. Шлак, который используют для производства, должен содержать ограниченное количество оксида алюминия (приблизительно до 10-12%). Сульфатостойкому шлакопортландцементу присваиваются марки М300 и М400.
Он относительно устойчив по отношению к воздействию сульфатов, однако плохо переносит сильные морозы.
- Сульфатостойкий портландцемент имеет марку М400. Он склонен к медленному затвердеванию и низкому тепловыделению. Является универсальным и выдерживает любые виды температурных режимов и влажности.
- В сульфатостойкий цемент с минералами добавляется около 15-20% от общей цементной смеси доменного шлака в гранулах или 5-10% минеральных веществ. Этот вид стройматериала выпускается с марками М400 и М500. Сульфатостойкий цемент с минеральными добавками отлично подходит для сооружения различных конструкций, имеет повышенную морозостойкость и устойчивость к сильной влажности и засухе.
Применение
Портландцемент используется для создания сульфатостойкого бетона, а также следующих конструкций:
- сульфатостойкие сваи;
- железобетонные сооружения;
- мостовые опоры;
- гидротехнические постройки.
Отдельное внимание следует уделить сульфатостойким сваям, чтобы понять, что это такое.
Сваи – это изделия, представляющие собой большие стержни, которые производятся из портландцемента. Их основное применение – укрепление конструкций и создание прочной опоры при возведении фундамента.
Качество данных изделий всецело влияет на долговечность и безопасность построек. Сваи закапывают глубоко в почву. Они устойчивы к влаге, осадкам, грунтовым водам и химическим элементам, находящимся в покровах почвы. Чаще всего служат для сооружения крупногабаритных мостов, гидротехнических станций и дамб.
Сульфатостойкий бетон можно сделать даже из обычного цемента, если в раствор включить минеральные добавки.
Состав клинкера
Клинкер является промежуточным изделием при производстве портландцемента. Впервые о нем услышали в 1817 году, когда французский инженер Луи Вика изобрел цементный клинкер. Данное полезное открытие помогло впоследствии в 1840 году создать искусственный цемент (портландцемент).
В состав сульфатостойкого цемента входят компоненты дробленого клинкера, состоящего из минералов. При производстве материала в обязательном порядке учитываются точные дозировки всех необходимых компонентов. Как правило, готовая продукция содержит 5% алюмината и 50% силиката. Данное соотношение обусловлено тем, что в самих слоях почвы и выпадающих атмосферных осадках уже имеется достаточно много сульфатных соединений.
При вступлении в реакцию с алюминатом начинается разрушение сульфатов и, как следствие, деформация самого сооружения.
По этой причине в исходном сырье для производства портландцемента должно присутствовать лишь небольшое количество алюминатной фазы.
На основной состав клинкера большое влияние оказывает не только исходное сырье, но и условия изготовления. Когда сырье обжигают, то примеси в нем размещаются хаотично. Данный фактор создает переменчивую структуру клинкерных фаз. Под последними принято подразумевать базовые минералы: алит и белит.
- Алит представляет собой важный минерал, имеющий большое значение в составе клинкера. Он быстро затвердевает и имеет высокую прочность. Алит проявляет большую активность в соединении с водой.
- Белит по своей реакции менее активен в отличие от алита. Также его тепловыделение меньше в два раза чем у главного минерала клинкера – алита. Белит медленно застывает и за счет этого обеспечивает высокую прочность материала.
Осноовным промежуточным веществом, участвующим в создании цементного клинкера, является трехкальциевый алюминат. Содержание этого вещества в стандартном замесе сульфатостойкого цемента составляет всего 5-10%. Избыточное количество данного материала может спровоцировать, как уже было отмечено выше, сульфатную коррозию. Этот процесс чреват негативными последствиями в виде разрушения структуры бетона и кристаллизации солей на стенках материалов.
Что касается последнего разрушительного воздействия, то кристаллизация оставляет свой след в виде заметного расширения цементного камня в объеме. Иногда влияние сульфатов приводит к формированию гипса, который также способствует значительному расширению камня и постепенному разрушению построек.
Вредное влияние сульфатов на железобетонные конструкции отмечается при поочередном высушивании и увлажнении почвы и самого сооружения. В качестве примера можно привести постоянно изменяющийся уровень воды в реке. Железобетонные сваи, изготовленные из сульфатостойкого цемента, в ходе этого воздействия влаги подвергаются медленному разъеданию структуры материала и изнашиванию конструкций вплоть до полного разрушения.
Выбирая цемент для работы, следует внимательно изучить его основной состав. Важно учитывать, что для каждого конкретного вида почвы нужен особый вид цемента.
Как сделать?
Получение сульфатостойкого цемента возможно двумя методами:
- изготавливают цементный раствор со специальными добавками из минеральных веществ;
- применение особой цинк-сульфатной цементно-песчаной смеси, изготовленной промышленным способом, которая отличается долговечностью и гарантирует защиту сооружения во время всего периода эксплуатации.
При изготовлении растворов следует придерживаться точных соотношений компонентов.
В том случае, если минеральные добавки в несколько раз превышают стандартную норму, прочность раствора значительно снижается, соответственно увеличивается и хрупкость строений, из-за чего происходит их разрушение. Раствор сульфатостойкого цемента обязательно должен соответствовать основным нормам государственных стандартов.
Использование портландцемента является дорогостоящей процедурой, поэтому применяют его не так часто, как простой аналог. Однако сульфатостойкий цемент просто несравним по своим характеристикам с обычным бетонным раствором.
Ведь долговечность портландцемента в несколько раз выше аналогичного показателя обычных материалов. Следует отметить, что его главные отличительные свойства полностью оправдывают высокую стоимость.
Сульфатостойкий цемент надежно защищает здания и постройки от влияния влаги и морозов, повышает износостойкость конструкций. Он также может значительно улучшить качество простого бетонного раствора, в результате чего такой строительный материал прослужит дольше обычного заявленного срока.
О том, как правильнозамешивать цементный раствор, смотрите в видео ниже.
Что такое цементный клинкер: применение и методы производства
При возведении высотных зданий и небольших домов используется цементный клинкер. Твердый раствор увеличивает срок службы покрытий, подходит для облицовки печей и искусственных водоемов. Клинкерной плиткой, вместо натурального камня, украшают фасады, применяют как керамогранит при отделке интерьера, а также для реставрации пенобетонных и деревянных поверхностей. Строительный материал выдерживает избыточную влажность и обладает высокими теплоизоляционными свойствами.
Что такое цементный клинкер
В ходе обжигания смеси, состоящей из известняка и нескольких разновидностей глины, при высокой температуре получается вязкий гранулированный полуфабрикат, называемый клинкером. Для производства цемента в вещество добавляют гипс или сульфат кальция и другие минеральные компоненты, которые измельчают в порошок.
Впервые процесс спекания строительного сырья, добываемого из недр земли, путем нагревания его до 1450°, был описан в 19 веке инженером из Франции, создавшим полуфабрикат и цемент. Луи Вика использовал полученный промежуточный продукт при возведении подвесного моста, чтобы доказать его качество.
Каким методом получают цементный клинкер
Для создания материала, не уступающего по прочности натуральному камню, голландские строители стали обжигать специальную глину при высокой температуре. Сейчас при производстве цементного клинкера используют сырье, в составе которого содержатся двух-трехкальциевые силикаты или алюминаты. Смесь нагревают в печах до плавления или спекания. На свойства клинкера влияют несколько факторов:
- характеристики используемых добавок и присадок;
- состав сырья;
- метод охлаждения и помола;
- технология нагрева.
При мокром способе обжига применяется много различных компонентов, среди которых триполифосфат, сода, торфяная вытяжка, жидкое стекло. Из шлама выделяются углекислоты, а клинкер приобретает форму шарика.
При сухом методе минеральные вещества высыхают в печи, а потом измельчаются в порошок. При комбинированном варианте смесь производят с помощью мокрого метода, затем влажность уменьшают до 16% путем фильтрования, после сырье обжигают. Если применяется сухой способ, то смесь соединяют с водой. А образовавшиеся гранулы высыпают в печь для дальнейшего спекания. Почти 67% в них приходится на оксид калия, 4% — алюминия. Около 22% составляет диоксид кремния, до 6% в составе гранул — добавки и присадки.
В клинкере, из которого производится цемент, количество минеральных искусственных компонентов достигает 70%.
Четыре главные фазы клинкера
Для возведения многоэтажных зданий требуется материал высокого качества. На свойства и характеристики цемента влияет объем и состав смесей, применяемых в процессе обжига. В клинкере обязательно должны присутствовать 4 компонента в определенных пропорциях.
Алит
В составе основного продукта, используемого для производства цемента, содержится силикат, представляющий собой смесь диоксида кремния и тройного объема оксида кальция. В клинкере его количество составляет не менее 52%. В кристаллической решетке алита вкраплены ионы:
- железа;
- алюминия;
- магния.
Силикат быстро вступает в реакцию с водой. Такое свойство минерала обеспечивает прочность клинкера на всех этапах нагревания и обжига.
Белит
В полуфабрикате цемента от 14% до 31% приходится на фазу, представляющую смесь диоксида кремния и двойного объема оксида кальция. Вещество не вступает в реакцию с водой, но спустя год приобретает такую же прочность, как и алит. В кристаллической решетке белита выявляют ионы разных металлов.
Алюминатная фаза
В гранулах цементного клинкера содержится силикат, в котором оксид алюминия смешан с тройным объемом оксида кальция. На эту фазу в продукте приходится не менее 4%, но и не более 11.В кристаллической решетке в небольшом количестве наблюдаются вкрапления ионов микроэлементов:
- железа;
- кремния;
- калия;
- натрия.
При взаимодействии с водой вещество быстро схватывается. Для предупреждения нежелательной реакции в смесь добавляют гипс.
Алюмоферритная фаза
В промежуточном продукте цемента обязательно присутствует еще один компонент, объем которого составляет 5% — 15%. Четырехкальциевый алюмоферрит может менять состав в зависимости от концентрации оксида железа и алюминия. Дополнительные компоненты и примеси, содержащиеся в продукте, на его прочность влияния не оказывают. Скорость взаимодействия фазы с водой уменьшают или увеличивают, используя разные соединения.
Характеристика минералов цементного клинкера
Трехкальциевый силикат обуславливает свойства материала, включая скорость затвердевания. Вещество выделяет тепло и обладает высокой прочностью. Добавки, содержащиеся в фазе алита, влияют на его характеристики, изменяют структуру.
Двухкальциевый силикат (C2S) медленно затвердевает, почти не выделяет тепло, но постепенно приобретает высокую прочность. Техническим свойствам портландцемент обязан белиту и алиту, поскольку концентрация этих твердых растворов в клинкере превышает 70%. Объем между кристаллами силикатов заполнен различными веществами, не влияющими на свойства материала.
В процессе обжига трехкальциевый алюминат очень быстро затвердевает и выделяет большой объем тепла, но при этом получается не очень прочным. Присутствие значительного количества минерала в клинкере провоцирует появление коррозии, в портландцементе содержание вещества не превышает 5%.
Целит обладает высокой скоростью взаимодействия с молекулами воды, однако раствор алюмофферита кальция не влияет на процесс затвердевания материала.
Содержание основных минералов в клинкере:
Наименование | Количество, % |
Целит | 10—20 |
Трехкальциевый алюминат | 4—12 |
Белит | 20—30 |
Алит | 45—60 |
Щелочные оксиды попадают в сырье, используемое при производстве цемента, с полевым шпатом или глиной. Большая часть примесей при обжиге испаряется, а остальные включаются в состав других соединений. Количество щелочей в клинкере стараются уменьшить до 1%, поскольку они препятствуют затвердеванию раствора.
Окись кальция появляется при неполном обжиге, вследствие нарушения соотношения между основными компонентами сырья. Вещество присоединяет молекулы воды, увеличивает объем твердой фазы, что приводит к растрескиванию и потере пластичности клинкера.
Чтобы снизить содержание окиси кальция, гранулы перед измельчением месяц держат на складе.
Для производства клинкера в карьерах добывают сланцы и глинистые породы, в которых содержатся соединения алюминия, железа, а также известняки. Сырьевые смеси обжигают до спекания.
Полученный промежуточный продукт измельчают, добавляют гипс и производят портландцемент, из которого изготавливают прочный бетон, плитку для облицовки, искусственный камень.
Для создания других видов строительного материала клинкер соединяют с ракушечником и шлаком или смешивают с добавками.
Чтобы получить глиноземистый цемент, обжигают смесь бокситов и известняков. Состав не пропускает влагу, устойчив к высоким температурам, подходит для производства жаропрочного бетона, а также используется при аварийных работах.
При нагревании известняков до 1 тыс.° получают романцемент, который применяется для создания панелей и блоков, но обладает меньшей прочностью.
Вы знали, как производится цементный клинкер до этого?
Популярное
Состав белого цемента
Сайт строителя
Основными компонентами входящими в состав сырьевой смеси для получения белого цемента являются известняковые породы (известняк, мел, мергель, мрамор), а также глины н песок. В сырье должно содержаться минимальное количество красящих окислов: железа, марганца, титана, хрома и др. Окиси железа в клинкере для получения белого портландцемента должно быть не больше 0,45%.
Требования к составу смеси для получения белого цемента
В соответствии с этим были разработаны требования к карбонатному сырью для белого портландцемента. По данным исследований, окислов железа должно быть не более 0,15 — 0,25, а марганца — не более 0,15%. В нашей стране имеются месторождения маложелезистого карбонатного сырья, пригодного для производства белого портландцемента.Все прочие требования, предъявляемые к карбонатным породам при производстве белого портландцемента, сводятся к следующему. В них не должно быть неравномерно распределенных грубых кварцевых зерен, вредных примесей сернокислых соединений, магнийсодержащих включений и щелочей.
В состав любого цемента входят два компонента: известь и глинозем.
Они составляют 75 — 80 % состава самого клинкера.
Компоненты сырьевой смеси для получения белого цемента
В качестве глинистого компонента при получении белого портландцемента используются главным образом первичные каолины, а также шликеры, получаемые в результате обогащения каолина. Шликер представляет собой смесь мельчайших кварцевых зерен с частичками слюды и некоторым количеством каолинита.Содержание окислов железа в каолинах не должно превышать 1%. Не рекомендуется применять каолины с включениями крупных зерен песка, так как они осаждаются в болтушках и вызывают неудобства как при транспортировке, так и при подготовке сырьевой смеси заданного химического состава. НИИ Цементов была изучена возможность замены таких каолинов. С этой целью были исследованы огнеупорные глины Латненского и Часов-Ярского месторождений. Химические составы этих глин приводятся в табл. 3. Эти глины были с успехом применены на Щуровском цементном заводе вместо каолинов в их отходов, что свидетельствует о целесообразности такой замены. Для повышения силикатного модуля сырьевой смеси при производстве белого портландцемента используют кварцевые пески с малым содержанием окислов железа.
Для выпуска белого цемента необходимо сырье очень высокого качества. Сырьевые материалы должны иметь невысокое содержание красящих примесей (оксида железа, оксида марганца). А такого сырья, в нашей стране мало.
Наряду с природными сырьевыми материалами для получения белого портландцемента можно применять и искусственные — отходы других производств. Так, в качестве известнякового компонента может быть использован белый шлам, являющийся отходом алюминиевого производства и представляющий собой тонкий порошок белого цвета с коэффициентом отражения не менее 75%.
Из чего делают белый цемент- клинкер
- диатомит
- минеральные добавки
Дополнительные компоненты цементной смеси
Библиотека строителя
Здесь приведены материалы цементной сырьевой смеси, содержание которых в цементе ограничивается нормами или опытными данными.
Оксид магния.
Оксид магния. Оксид магния в количестве около 2% по массе находится в связанном состоянии в основных клинкерных фазах и, кроме того, содержится в клинкере в виде свободного MgO (периклаз). Перпклаз с водой образует Mg(ОН)2: Mg0+H2O=Mg(0H)2, однако эта реакция протекает очень медленно, когда остальные реакции твердения уже завершены. Поскольку Mg(OH)2 занимает больший объем, чем MgO, то возникает опасность разрушения цементного камня и появления усадочных трещин (магниевая усадка).
В основном MgO содержится в известняке в виде доломита (CaC03•MgC03). Иногда большое количество MgO содержится также в доменных шлаках. При использовании таких шлаков вместо глины в составе цементной сырьевой смеси необходимо следить за тем, чтобы содержание MgO в клинкере оставалось в допустимых пределах (см. пример 2.5 и табл. 2.5)
Щелочи.
Щелочи. Щелочи вносятся с обрабатываемым сырьем — глиной и мергелями, где K2O и Na2O содержатся в мелкозернистом полевом шпате, включениях слюды и глинистом минерале иллите; небольшая часть щелочей образуется из угольной золы при сжигании твердого топлива. В Средней Европе в составе глин содержится значительно больше K2O, чем Na2O, а в других районах мира, например в США, в глинах содержится большее количество K2O.
При обжиге цемента во вращающихся печах часть щелочей улетучивается в зоне спекания и возникает возможность щелочкой циркуляции.
Некоторые заполнители для бетона, применяющиеся, например, в ряде районов США и Европы, содержат компоненты, чувствительные к щелочам, например опал (водосодержащий кремнезем), которые вступают в реакцию со щелочами цемента, что при определенных неблагоприятных условиях может привести к неравномерному изменению объема (щелочному вспучиванию).
На основе опытных данных для предотвращения щелочного вспучивания в рассматриваемом случае рекомендуют применять цемент с низким содержанием щелочей, при котором общее количество щелочей в пересчете на Na2O(Na2O+0,659K2O, % по массе) не превышает 0,6% по массе. С учетом практики в ряде стран введено ограничение содержания щелочей, равное 0,6% по массе в пересчете на Na20, однако это ограничение распространяется только на портландцемент.
Было установлено, что для шлакопортландцементов можно увеличить предельное содержание щелочей, и поэтому для цементов с низкой эффективной щелочностью (цемент NA) при количестве шлака до 50% допускается предельное содержание щелочей, равное 0,9%, а при количестве шлака до 65%—2,0% по массе.
В тех случаях, когда требуется цемент NA, а щелочность клинкера, полученного из имеющегося в наличии сырья, превышает допустимые пределы, необходимо удалить часть летучих щелочей путем частичного отвода (байпаса) печных газов перед их поступлением в теплообменник.
Сера.
Сера. Сера встречается в основном в виде сернистых соединений (пирит и марказит FeS2) почти во всех типах цементной сырьевой смеси. При обследовании более 90 месторождений известняка в Германии установлено, что максимальное содержание серы (сульфатные и сульфидные соединения) равно 0,16%, а при обследовании 67 месторождений глины оно составляет в среднем 0,22%. Сернистость топлива меняется в значительных пределах — от нуля для природного газа до 3,5% для тяжелого мазута. Уголь Рурского бассейна в среднем содержит 1,1% серы. При обследовании 21 цементной печи с предварительным подогревом сырья установлено, что с сырьевой смесью вносится от 0,5 до 11 г S03 на 1 кг клинкера, а с топливом — при использовании жидкого топлива с очень высоким содержанием серы максимум 6 г S03 на 1 кг клинкера.
При горении и газообразовании в зоне спекания печи сера, содержащаяся в топливе и сырьевой смеси, превращается в газообразный продукт SO2, который, вступая во взаимодействие с летучими щелочами печных газов и кислородом, образует парообразный сульфат щелочного металла, конденсирующийся на обжигаемом материале в более холодных зонах печи и подогревателе. Весь сульфат щелочного металла, за исключением небольшой части, остающейся в летучей пыли, возвращается с обжигаемым материалом в зону спекания и вследствие летучести серы разносится по клинкеру.
Если количество S02 недостаточно для связывания всей щелочи, то возникает циркуляция летучих карбонатов или хлоридов щелочных металлов. Углекислые соли щелочных металлов, не вошедшие в клинкерные фазы, могут снова испариться в зоне спекания.
При избытке S02 еще в подогревателе начинается его соединение с СаС03 и образование CaSO4, который возвращается в зону спекания. В зоне спекания снова происходит разложение CaSO4, что приводит к росту содержания S02 в циркулирующих печных газах. Однако часть неразложившегося CaSO4 попадает в клинкер.
Наличие в сырьевой смеси избыточного количества щелочей по сравнению с количеством, нейтрализуемым при взаимодействии с серой, имеет преимущество, связанное с возможностью применения топлива с высоким содержанием серы без выпуска из печи в атмосферу отработанных газов с заметным содержанием SO2. Сульфат щелочного металла, связанный в клинкере, оказывает благоприятное влияние на начальную прочность цемента.
В противоположность этому повышенное содержание серы может привести к возрастанию количества SO2 в отходящих газах, к засорению подогревателей сырьевой смеси и образованию колец привара во вращающихся печах.
Цемент требует добавления минимального количества сульфата кальция — чаще всего в форме молотого гипса — для регулирования сроков схватывания; с другой стороны, максимально допустимое суммарное содержание SO3, которое должно предотвратить сульфатное вспучивание цемента, регламентировано соответствующими нормами и составляет от 2,5 до 4%. В определенных условиях при минимальных нормативных значениях S03 отсутствует возможность глубокой сульфатизации щелочей.
Книга Вальтера Дуды «Цемент».
Из чего делается цемент состав?
Цемент – широко распространенный материал, который применяют при любых видах работ, связанных с ремонтом, реставрацией, строительством. Цементная основа – вяжущие компоненты неорганического происхождения. Из цемента производятся бетонные, кладочные, штукатурные растворы, железобетонные изделия, используемые при строительстве промышленных объектов и частных построек.
Особенностью порошкообразной цементной массы, смешанной с водой, является способность постепенно твердеть, превращаясь в каменный массив. Процесс приобретения эксплуатационной прочности происходит как в воздушной среде, так и в воде. Главное условие твердения – избыточная влажность.
Все сталкивались с цементом, однако мало кто знает, из чего делают этот универсальный строительный материал, как его производят. Его основа – клинкер, специальные минеральные добавки и гипс. Рассмотрим подробно, как делают цемент, какое сырье для этого используется.
По-прежнему клинкер – это основной компонент, входящий в состав цемента
Сырьевые материалы
Производство цемента осуществляется на специальных заводах, расположенных близко к местам добычи исходного сырья для его изготовления. Главным исходным сырьем для цементного производства являются следующие естественные породы:
- ископаемые карбонатного типа. Это ценное природное сырье, отличающееся особенностями кристаллической структуры, физическими характеристиками. Материал может иметь кристаллическую или аморфную структуру, определяющую эффективность его взаимодействия при обжиге с другими компонентами;
- глинистые материалы, горные породы осадочного характера. Они имеют минеральную основу, становятся пластичными, объемно увеличиваются при избыточном увлажнении. Сырье характеризуется вязкостью, применяется при сухом методе производства.
Карбонатные породы
Остановимся на карбонатных породах, характерными представителями которых являются:
- Мел, являющийся горной породой осадочного характера, которая легко перетирается, относится к разновидностям мажущего известняка. Он популярен при изготовлении цемента.
- Мергель или мергелистый известняк – ископаемые осадочного типа, которые добываются в рыхлом или твердом состоянии, отличаются удельным весом, концентрацией влаги. Содержат примеси глины, что позволяет относить их к переходному сырью, имеющему много общего с известняковыми породами и ископаемыми на основе глины.
В состав входят активные минеральные добавки (15%) в соответствии со стандартами производства
Глинистое сырье
К глинистым породам относятся:
- глина, содержащая минеральные включения, разбухающие при добавлении воды;
- суглинки, являющиеся разновидностью глины, с повышенной концентрацией песчаной фракции и пылеобразных частиц;
- сланцы на глинистой основе, относящиеся к горным породам с повышенной прочностью, которые при измельчении расслаиваются на пластинчатые частицы. Сырье характеризуется стабильным гранулометрическим составом, низкой концентрацией влаги.
- лесс, представляющий рыхлую горную, непластичную породу, отличающуюся пористостью, мелкозернистостью. Содержит включения силиката, кварца.
Возможно применение отходов промышленного производства, других видов природных материалов и шлаков.
Корректирующие добавки
Цементный состав делают из минерального сырья с применением специальных пластификаторов, добавляемых при производстве.
Если увеличить количество добавок до 20%, то свойства цемента будут несколько изменены
Технология предусматривает использование добавок на базе ископаемых, содержащих:
Введение корректирующих добавок, с помощью которых делают цемент и улучшают его характеристики, предусмотрено технологией. Пластификаторы позволяют улучшить следующие свойства цементного состава:
- стойкость к воздействию коррозионных процессов;
- устойчивость к воздействию перепадов температуры, глубоким циклам замораживания;
- прочностные характеристики;
- продолжительность твердения;
- подвижность цементного раствора, его эластичность;
- степень проницаемости водой.
Состав
Задумывались ли вы, из чего сделан цемент? Его состав обусловлен особенностями сырья и конкретной маркой продукции. Так, пользующийся широкой популярностью портландцемент имеет следующий состав:
- Кремниевый диоксид (кремниевая кислота или кварц) – 25 %.
- Известь – 60 %.
- Алюминий (глинозем) – 5 %.
- Оксиды железа и гипс – 10 %.
Сегодня производится множество видов цемента
Процентное соотношение ингредиентов может изменяться, согласно особенностям технологии и марки цементной продукции. Отдельные виды цементов, в частности шлакопортландцемент, включают в свой состав шлак, представляющий уголь, полученный в результате обжига клинкера.
Независимо от рецептуры, основные ингредиенты при изготовлении цементного состава – глина и известняк. Концентрация известняка трехкратно превышает содержание глины, что обеспечивает необходимое качество клинкера для производства цементной продукции.
Основными компонентами, из которых производят цемент, являются:
- клинкер, определяющий прочностные характеристики, получаемый при обжиге исходного сырья (известняка, глины). Клинкер является основой конечной продукции, используется в гранулированном виде диаметром 10-60 мм. Клинкер термообрабатывается при температуре порядка полторы тысячи градусов Цельсия. Он плавится с образованием массы с высоким содержанием кальциевого диоксида и кремнезема, которые определяют эксплуатационные характеристики цементных составов. Гранулы дробятся до пылеобразного состояния с последующим обжигом;
- гипс, процентное содержание которого определяет период твердения. Базовая рецептура предусматривает использование до 6% чистого порошкообразного гипса или гипсового камня, содержащего примеси;
- специальные добавки, вводимые для усиления имеющихся свойств или придания составу специальных характеристик, расширяющих сферу применения.
Очень часто цемент применяют в строительстве для создания бетона и армированных конструкций
Процесс изготовления
Производство цемента осуществляется поэтапно, предусматривает следующее технологические операции:
- Предварительное смешивание ингредиентов для изготовления клинкера, который делают из известняка, вводимого в количестве 75%, и из глины, доля которой составляет 25%.
- Высокотемпературный обжиг, после которого образуется клинкер. Он – результат процесса соединения глины и извести под воздействием повышенной до 1450 градусов Цельсия температуры.
- Измельчение, осуществляемое с помощью шаровых мельниц. Они представляют горизонтально расположенные барабаны с находящимися внутри стальными шарами, обеспечивающими измельчение клинкера до порошкообразного состояния. С уменьшением фракции помола возрастают эксплуатационные характеристики и марка цементного состава.
Этапы производства
Особенности производства предусматривают изготовление цемента различными методами, что сказывается на особенностях применяемого сырья. Это обусловлено расположением цементного производства, спецификой применяемого оборудования, спросом на определённые марки продукции.
Все варианты технологий отличаются только особенностями подготовки исходного сырья, которые осуществляются:
- мокрым путем. Мокрая технология предусматривает использование вместо извести мела, смешивание которого с необходимыми ингредиентами происходит одновременно с измельчением в горизонтальном барабане с обязательным добавлением воды. При этом образуется шихта с концентрацией влаги 30-50%. Шихтовый материал обжигается в печи, превращаясь в шарообразный клинкер, который затем измельчается;
- сухим методом. Сухая технология характеризуется уменьшенной себестоимостью производства цемента, сокращением технологического цикла. Это связано с объединением технологических операций, позволяющих одновременно осуществлять помол и сушку компонентов в шаровой мельнице под воздействием поступающих горячих газов. Полученная шихта имеет порошкообразную консистенцию;
- комбинированным способом. Комбинированный вариант объединяет особенности мокрого и сухого способа производства, но на разных предприятиях имеет определенные отличия. Один из вариантов обеспечивает возможность получение полусухого состава с влажностью до 18%, произведенного путем высушивания шихты, полученной по мокрой технологии. Второй метод предусматривает подготовку сухой смеси с последующим ею увлажнением до 14%, гранулированием, заключительным отжигом.
Заключение
Материал статьи предоставляет информацию о том, как делают цемент, какое сырье применяют, какие технологические особенности используют в процессе производства. Имеется множество технологических нюансов, которыми в совершенстве владеют специалисты, занимающиеся изготовление цемента.
Как и из чего делают цемент: состав, технология и этапы производства
Цемент является основным строительным материалом, без него не обходится практически ни одна стройка. Для изготовления цементной смеси необходимы специальные материалы, которые перемалываются и смешиваются по определенной технологии.
Из чего делают цемент: основное сырье
Основным сырьем при цементном производстве являются породы из глины и карбоната, а также другие материалы, имеющие естественное происхождение, и отходы производств, такие как шлаки.
Породы карбонатного происхождения включают известняк, мел, мергель и доломиты.
Физические свойства этих пород сильно влияют на качество произведенного цемента. Породы, имеющие кристаллическую структуру, хуже вступают во взаимодействие с остальными компонентами во время обжига, если сравнивать с породами, у которых аморфная структура. Свойства этих пород следующие:
- Мел — это мягкая порода осадочного типа, которая представляет из себя известняк с мажущей способностью. Мел можно без труда измельчить. Этот материал — важный компонент при создании цементной смеси.
- Мергель — порода осадочного происхождения, находящаяся между известью и глиной по своим свойствам. Бывает как в твердом, так и рыхлом состоянии. Плотность и влажность этой породы различаются зависимо от того, какой процентный состав глины в нее входит.
- Глины являются породами осадочного типа, которые включают минералы с различными свойствами, при смачивании они становятся пластичными и набухают. Если изготавливать цемент с помощью сухого метода, пластифицирующая способность глины дает возможность гранулировать муку и создавать брикеты. Суглинок — это обыкновенная глина, в которую попали частицы пыли и песка.
- Глинистый сланец — порода с высокой плотностью и твердостью. Пластинки, из которых состоит эта порода, имеют небольшую толщину. По сравнению с глиной сланцы не такие влагоемкие и имеют более стабильный состав.
- Лесс состоит из мельчайших частиц минералов, таких как кварц, полевой шпат, имеет высокую рыхлость, пористость и невысокую пластичность. Между суглинком и лессом по свойствам находится лессовидный суглинок.
Корректирующие добавки
Процесс изготовления цемента предполагает применение различных добавок, в зависимости от типа необходимого на выходе итогового продукта. Чаще они делаются на основе ископаемых, содержащих следующие компоненты: глинозем, диоксид кремния, флюорит, глину и апатиты.
С помощью корректирующих добавок, ввод которых в состав цемента осуществляется по определенной технологии, улучшают характеристики этого строительного материала. Например, с применением пластификаторов цементный состав начинает обладать такими свойствами:
- Становится более стойким к отрицательному воздействию коррозии.
- Более высокое сопротивлением к изменениям температуры и долгому замораживанию.
- Улучшается прочность бетона.
- Увеличивается время затвердевания.
- Увеличивается подвижность и эластичность цементного раствора.
- Уменьшается степень водопроницаемости.
Добавки, содержащие железо, глинозем и кремнезем — добавляют в цементную смесь, чтобы скорректировать величины модулей этих минералов. В качестве добавки, содержащей железо, обычно выступают пиритные огарки с промышленных предприятий, производящих серную кислоту. Также в этом качестве используют, но чуть реже, колошниковую пыль, получаемую из домн.
Глиноземистая добавка включает в себя глины с малым содержанием железа, бокситы, иногда каолин.
Специальные добавки применяются для получения различных видов цемента. С помощью добавок производятся нижеследующие:В качестве кремнеземистой добавки в цемент выступают пески из кварца, опоки, трепелы. Чтобы понизить влажность шлама применяют концентраты сульфитно-дрожжевой бражки.
- Гидрофобный. Противодействует высокой влажности. Благодаря этому цементу готовый бетон имеет хорошую сопротивляемость низким температурам и минимальную проницаемость для влаги.
- Белый цемент. Применяют в качестве сырья, из которого производят разные сухие смеси, в дальнейшем используемые при финишной отделке.
- Расширяющийся. При применении этого вида готовый бетон начинает увеличиваться в объеме, что нехарактерно для других видов этого строительного материала (обычно бетон сжимается).
- Пуццолановый. Этот строительный материал обладает низким тепловыделением, поэтому применяется при строительстве крупных объектов. При этом заметно снижается вероятность того, что произойдет неравномерная осадка здания.
- Цветной. Применяют для производства изделий, которые в дальнейшем не потребуют обработки. При изготовлении цветного цемента обычно добавляют белый клинкер или красители.
- Глиноземистый. Прочность уложенного бетона, который замешан на таком цементе, уже через сутки достигает 50%. Часто применяется на бетонных заводах в зимнее время благодаря большому количеству выделяемого тепла.
Как делают цемент на производстве
При производстве цемента имеется определенная технология, которая предусматривает проведение следующих операций:
- Все ингредиенты предварительно подвергаются смешиванию для изготовления клинкера, состоящего из известняка и глины. Доля этих материалов в общей массе клинкера составляет соответственно 75 и 25%.
- Затем производят обжиг при высокой температуре, собственно благодаря этому и образуется клинкер. Это происходит при взаимодействии глины и извести, находящихся под воздействием высокой температуры, достигающей 1450 о С.
- Затем производят измельчение в шаровых мельницах. Такие мельницы представляют собой специальные барабаны с металлическими шарами внутри. Барабаны имеют горизонтальное расположение и позволяют измельчить клинкер в порошок. Чем меньше фракция измельченного материала, тем качественнее получится цемент и марка строительного материала будет выше.
При производстве цемента используются различные методы, что обусловлено расположением цементного завода, применяемым оборудованием, а также спросом на определенные марки продукции.
Технологии производства имеют отличие только по способам подготовки компонентов для изготовления цемента. Они осуществляются следующими способами:
- Мокрый. Такая технология предполагает применение мела вместо извести, который при соединении с остальными ингредиентами одновременно измельчается в шаровой мельнице с непременным добавлением воды. В результате образуется шихта, в которой концентрация влаги достигает 40-50%. Далее получившийся продукт проходит обжиг в печи и превращается в клинкер в виде шара, а впоследствии подвергается измельчению.
- Сухой. Эта технология позволяет уменьшить затраты на изготовление цемента и добиться сокращения времени цикла производства. Такое удешевление и ускорение процесса связано с тем, что одновременно происходит перемалывание и сушка компонентов цемента в мельнице под воздействием нагретых до высокой температуры газов. В конечном итоге получается шихта в виде порошка.
- Комбинированный. Этот вариант соединяет в себе мокрый и сухой методы, но у этого способа есть свои отличия. Один из вариантов предполагает итоговое получение полусухого состава, имеющего влажностью до 18%, который производится с помощью сушки шихты, полученной по технологии мокрого производства. Другая методика основана на подготовке сухой смеси, которую впоследствии увлажняют до 14%, гранулируют, и в заключение отжигают полученную смесь.
Полученный цемент требуется хранить в местах с пониженной влажностью. Иначе при длительном хранении связующие свойства строительного материала ухудшаться и качество произведенного из него бетона не будет соответствовать заявленным характеристикам.
Как делают цемент: технология производства и состав смеси
Цемент входит в число основных строительных материалов. Он используется при создании связующих строительных растворов, цемент используют при изготовлении бетонных и железобетонных изделий. От качества данного материала зависит, насколько прочное и долговечное будет здание, или железобетонная конструкция.
История цемента началась в Англии, где в 1824 году был зарегистрирован патент на его изобретение. В то время для изготовления цемента использовалась известковая пыль, смешанная с глиной. Полученная смесь подвергалась воздействию высокой температуры, при которой она спекалась.
Обожжённый полуфабрикат цемента называется клинкер. Цементом он становится после перемалывания клинкера до порошкообразного состояния.
В строительстве используется основное свойство цемента – при смешивании с водой он постепенно твердеет, а затем превращается в прочный камень. Характерную для готового изделия прочность материал может приобрести даже в воздушной среде, если присутствует избыточная влажность.
Сырьё для производства цемента, из чего он делается, технология изготовления
Сегодня процесс изготовления цемента изменился. Изготовляют его несколькими способами, да и компоненты, входящие в его состав, тоже отличаются от использовавшихся две сотни лет назад.
Чтобы было понятно, из чего делают цемент и как происходит его производство, необходимо знать, какие виды сырья используют сегодня производители этого важного строительного материала.
Так как сырьём для производства цемента гост31108 2003, гост 30515 2013 служат естественные породы, то и предприятия, занимающиеся его изготовления, чаще всего размещают поблизости от мест добычи этих пород.
Все ископаемые, из которых делается цемент, делятся на два вида:
- Карбонатные ископаемые, отличающиеся характеристиками и особенностью структуры. Именно структура породы обеспечивает эффективное её взаимодействие с остальными ингредиентами состава продукта.
- Глинистые и горные породы, имеющие осадочное происхождение. Имея минеральную основу, при увлажнении они приобретают пластичность и увеличиваются в объёме. Так как для данного вида сырья характерна вязкость, то их можно использовать, производя цемент сухим способом.
Теперь следует назвать конкретно, какие ископаемые относятся к каждому из видов сырья, используемых при производстве цемента.
К карбонатным породам относят следующие виды природного сырья:
- мел, представляющий разновидность известняка. Обладает способностью легко измельчаться;
- мергелистый известняк, в природе встречается как в рыхлом, так и в твёрдом состоянии. В породе могут содержаться примеси глины, поэтому данный вид известняка считается сырьём переходным, обладающим свойствами, характерными и для известняков, и для глины;
- известняки – ракушечники, не имеющие включений кремния. Порода имеет пористую, легко разрушающуюся при сжатии структуру;
- доломитовые породы и другие ископаемые осадочного происхождения. Они содержат карбонаты, придающие породе ценные свойства.
Глинистые породы включают следующие виды ископаемых:
- глина с минеральными включениями, набухающими при контакте с водой;
- суглинки, содержащие повышенную концентрацию частиц песка;
- сланцы, имеющие глинистую основу. Данное сырьё относят к горным породам, повышенной прочности. При механическом воздействии разделяется на пластинчатые пластины. Характеризуется стабильным составом и низким содержанием влаги;
- лесс, пористая порода, с включениями частиц кварца и силиката.
Кроме данных видов сырья, что изготавливать цементную смесь на заводе используют некоторые виды производственных отходов. Для улучшения качества в его состав добавляют добавки, предусмотренные технологическим процессом: глинозём и кремнезём, плавиковый шпат и апатиты.
Применение песка просто необходимо при проведении самых разных ремонтных и строительных работ. Тут все о применении карьерного песка.
При проведении отделочных работ на кухне, в ванной или в любом другом помещении необходимо знать время высыхания плиточного клея. Здесь можно узнать, сколько сохнет плиточный клей.
В настоящее время декоративная штукатурка по праву является самым популярным и прогрессивным методом отделки. Перейдя по ссылке ознакомитесь с самостоятельным ее приготовлением.
Все добавки, называемые пластификаторами, также природного происхождения. Они влияют в лучшую сторону на следующие качества цемента:
- увеличивают стойкость к изменениям температуры;
- усиливают прочность;
- подвижность и эластичность продукта;
- уменьшает проникновение воды в готовое изделие.
В зависимости от свойств, добавленных в состав цемента пластификаторов, его раствор будет застывать быстрее, или же медленнее.
Состав, из которого производят цемент
Часть людей работающих в сфере строительства не знают, из чего делается цемент.
Состав цемента может быть различным в зависимости от марки и предназначения.
Однако вне зависимости от вида цемента, то есть рецепта, использованного при его производстве, основой для него служат два компонента – известняк с добавлением глины.
Количество известняка в три раза превышает количество глины. Такие пропорции необходимы для получения качественного клинкера, являющегося полуфабрикатом для производства цемента.
Теперь можно назвать основные компоненты состава, чтобы каждому было ясно, из чего делают цемент:
- клинкер, основа конечной продукции, определяющая её характеристики прочности. Используется в виде гранул диаметром до 60 мм. Его термообработка выполняется при температуре, доходящей до 1500°. При плавлении клинкера образуется масса, для которой характерно высокое содержание кремнезёма и кальциевого диоксида;
- данные компоненты влияют на эксплуатационные характеристики конечного продукта. Перед обжигом гранулы клинкера измельчаются до пылеобразного состояния;
- гипс, определяющий скорость затвердевания цемента. В базовых рецептах предусмотрено добавление в состав чистого гипса до 6 % от общего количества компонентов;
- специальные добавки (пластификаторы, морозостойкие присадки, жидкое мыло и т.д.), усиливающие свойства, уже имеющиеся у продукции, или же придающие ей специальные характеристики, способные расширить область применения цемента.
Производство – как изготавливают цемент, процесс получения на заводе
Изготовление материала выполняется в определённом порядке, поэтапно. В технологии его производства предусмотрены следующие операции:
- Ингредиенты, предназначенные для изготовления клинкера, предварительно смешиваются. Обязательно необходимо точное соблюдение пропорций состава – 25 % глины и 75% известняка.
- Полученный состав обжигается при высокой температуре. При высокотемпературном обжиге глина и известь соединяются, образуя клинкер.
- Готовый продукт измельчается шаровыми мельницами, состоящими из барабанов, расположенных в горизонтальном положении, внутри которых размещены стальные шары. Помещённый в них клинкер размельчается до состояния порошка.
- Чем мельче полученные фракции цемента, тем лучшие эксплуатационные характеристики он будет иметь.
Существует несколько методов изготовления данного строительного материала. Их выбор обусловлен многими факторами, основными из которых является специфика имеющегося на предприятии оборудования и спрос на определённые марки цемента.
Разработанные технологии имеют отличие в способах подготовки сырья, используемого при производстве состава. Порядок его изготовления остаётся прежним.
Цементные заводы: сырье
Материалы, используемые в цементной промышленности в Великобритании и Ирландии
Практически любой минерал может быть использован в цементной сырой смеси при условии, что основной состав смеси будет давать желаемые силикаты кальция и флюсы (см. Клинкер), и при условии, что некоторые вредные компоненты сведены к минимуму. Вообще говоря, минералы с высоким содержанием кальция (обычно карбонат) смешаны с минералами с низким содержанием кальция, содержащими кремний , алюминий и железо .Далее следует список материалов, которые использовались при производстве цемента в Великобритании и Ирландии, в порядке их геологического возраста. В дополнение к этому, на протяжении всей истории отрасли в качестве компонентов смеси использовался ряд промышленных отходов. Процесс объединения этих материалов в окончательную смесь rawmix обсуждается в разделе «Подготовка сырья».
Традиционное название | Период | Возраст Ma | CaCO 3 содержание |
---|---|---|---|
Намыв | Голоцен | 0-0.01 | 0-5% |
Боулдер-глина | Плейстоцен | 0,01-1,6 | 5-40% |
Мергель Хэмстед | Олигоцен | 28-34 | 20-40% |
Известняк Бембридж | Олигоцен | 34-36 | 75-85% |
Лондонская глина | Эоцен | 48-55 | 2-10% |
Верхний мел | Меловой | 70- 90 | 92-99% |
Средний мел | Меловой период | 90-94 | 85-98% |
Серый мел | Меловой период | 94-97 | 80-92% |
Мел, мергель | Меловой период | 97-100 | 50-75% |
Голт-глина | Меловой период | 100-112 | 20-40% |
Киммериджская глина | 900 30 Юрский период151-156 | 2-10% | |
Коралловая глина | Юрский период | 156-160 | 2-10% |
Корнбраш известняк | Юрский период | 165 | 85-95 % |
Великий оолитовый известняк | Юрский | 166-168 | 70-90% |
Великий оолитовый глина | Юрский период | 166-168 | 5-45% |
Нижний оолитовый известняк | Юрский | 168-176 | 85-95% |
Голубой лиас Известняк | Юрский период | 190-200 | 70-85% |
Голубой лиас сланец / глина | Юрский период | 190 -200 | 30-50% |
Ретический известняк | Триас | 200-205 | 85-95% |
Сланец St Bees | Пермь | 9003 0 252-2605-15% | |
Ангидрит | Пермь | 251-271 | CaSO 4 |
Уголь Меры Сланцы | Карбон | 300-315 | 2-10% |
Угольные меры Известняк | Карбон | 300-315 | 60-80% |
Каменноугольный известняк | Карбон | 330-355 | 70-99% |
Карбон Сланец | Карбон | 318-355 | 5-15% |
Девонский известняк | Девон | 385-398 | 75-95% |
Лудловский известняк | Силурийский период | 423-426 | 75-98 % |
Венлок Известняк | Силурийский период | 427-428 | 75-98% |
Верхнесилурийские сланцы | Силурия n | 419-430 | 1-5% |
Изменение производственной мощности (тонны клинкера в год) в зависимости от вида сырья
Моделирование и оптимизация процесса смешивания цементного сырья
В этой статье основное внимание уделяется моделированию и решению проблемы оптимизации соотношения ингредиентов в процессе смешивания цементного сырья.Общая нелинейная изменяющаяся во времени модель (G-NLTV) создана для процесса смешивания цементного сырья с учетом химического состава, колебаний потока сырья и различных ограничений ремесла и производства. Представлены различные целевые функции для получения оптимального соотношения ингредиентов при различных производственных требованиях. Задача оптимизации соотношения ингредиентов преобразуется в задачу оптимизации с одной или несколькими задачами с дискретным временем и нелинейными ограничениями. Представлена структура метода внутренних точек сетки для решения задачи оптимизации скользящих нелинейных ограничений.На основе платформы MATLAB-GUI разработано соответствующее программное обеспечение для определения соотношения ингредиентов для получения оптимального соотношения ингредиентов. Наконец, представлены несколько численных примеров для изучения и решения задач оптимизации соотношения ингредиентов.
1. Введение
Цемент — широко используемый строительный материал в мире. Производство цемента будет проходить через несколько процедур, включая процесс смешивания и обжига сырья, процесс измельчения цементного клинкера и процесс упаковки.Цементное сырье и цементный клинкер в основном содержат четыре оксида: оксид кальция или известь (CaO), диоксид кремния (SiO 2 ), оксид алюминия (Al 2 O 3 ) и оксид железа (Fe 2 O 3). ). Качество цементного клинкера оценивается по указанным выше четырем оксидам. Следовательно, соотношение ингредиентов цементного сырья значительно повлияет на качество и свойства цементного клинкера. Оптимальное соотношение ингредиентов улучшит и стабилизирует качество цемента и ремесло производства. Поэтому цементное сырье должно быть разумно перемешано.Следовательно, получение оптимального соотношения ингредиентов является серьезной проблемой.
Во многих публикациях изучаются различные цементные процессы в производстве цемента. В [4], при различных коэффициентах заполнения шарового заряда, размерах шаров и времени пребывания, шаровая мельница непрерывного действия изучается для оптимизации процесса измельчения цементного сырья. В [5] представлена структура адаптивного управления процессом смешивания сырья, а также обсуждается соответствующая оптимальная структура управления. В [6, 7] представлены стратегии управления процессом смешивания цементного сырья методами наименьших квадратов, методами нейронных сетей и методами адаптивного нейронно-нечеткого вывода.В [8–10] обсуждались проблемы идентификации модели и расширенного управления с учетом возмущения вариаций химического состава, а для расчета оптимального соотношения подачи сырья используется контроллер с прогнозированием модели. В [11] предложен изменяющийся во времени фильтр Калмана для рекурсивной оценки оксидного состава цементного сырья с помощью рентгеновского анализа. В [12] предлагается нечеткий контроллер T-S для улучшения характеристик в реальном времени в процессе смешивания. В [13] питатель, шаровая мельница и бункер гомогенизации рассматриваются как единая система, входные и выходные данные используются для анализа процесса смешивания.В [1, 14, 15] нечеткая нейронная сеть с методами оптимизации роя частиц (FNN-PSO) и искусственная нейронная сеть (ИНС) применяются для установления и оптимизации процесса смешивания цементного сырья. В [2, 16–24] алгебраические методы, методы наименьших квадратов, методы нейронных сетей, методы линейных программ и эмпирические методы используются для расчета или получения оптимальных соотношений ингредиентов в процессе смешивания цементного сырья. В [3, 25–28] в процесс купажирования вводится новое оригинальное сырье и инструменты.В [29–33] обсуждаются проблемы производства цемента.
При этом не уделяется много внимания моделированию и получению оптимального соотношения ингредиентов в процессе смешивания. В данной статье анализируется задача оптимизации соотношения ингредиентов для процесса смешивания цементного сырья в различных условиях. Модель G-NLTV создана для процесса смешивания цементного сырья. Задачу оптимизации соотношения ингредиентов можно эквивалентно преобразовать в задачи выпуклой формы. Для решения задачи оптимизации соотношения ингредиентов предлагается структура метода внутренней точки сетки.Программное обеспечение разработано для решения проблемы оптимизации соотношения ингредиентов через MATLAB-GUI. Этот документ организован следующим образом: процесс смешивания сырья и критические параметры цементного ремесла представлены в разделе 2; Модель G-NLTV процесса смешивания сырья при различных обстоятельствах установлена в Разделе 3; структура метода внутренней точки сетки и программное обеспечение для ингредиентов цемента представлены в Разделе 4; числовые примеры в процессе смешивания представлены в разделе 5; содержание статьи завершено в разделе 6.
2. Процесс смешивания сырья и критические параметры изготовления цемента
Процесс производства цемента можно условно разделить на три этапа. На первом этапе производится цементное сырье, которое включает процесс смешивания сырья и процесс измельчения. Второй этап и третий этап предназначены для сжигания сырья и измельчения цементного клинкера соответственно. Процесс смешивания цементного сырья является важным звеном, потому что процесс смешивания влияет на качество цементного клинкера и критические параметры цементного производства, таким образом, процесс смешивания в конечном итоге влияет на качество цемента.На рисунке 1 показан процесс смешивания цементного сырья и система его контроля. Исходные материалы для цемента — это обычно известняк, стальной шлак, сланец, песчаник, глина и другие материалы. Исходные цементные материалы должны быть смешаны в разумных пропорциях, а затем оригинальные цементные материалы транспортируются в шаровую мельницу, которая измельчает исходные цементные материалы до определенных размеров. Классификатор выбирает подходящий размер исходного цементного материала, который транспортируется в цементную печь для сжигания.
Качество цементного сырья и цементного клинкера оценивается по коэффициенту насыщения цементной извести (LSF), силикатному соотношению (SR) и соотношению оксидов алюминия (AOR). LSF, SR и AOR напрямую определяются известью, кремнеземом, глиноземом и оксидом железа, которые содержатся в цементном сырье. LSF, SR и AOR являются критическими параметрами цементных судов, поэтому соотношение ингредиентов определяет критические параметры цементных судов. Аналогичным образом, критические параметры цементного ремесла также используются для оценки процесса смешивания.При производстве цемента LSF, SR и AOR должны контролироваться или стабилизироваться в разумных пределах. Критические параметры цементного корабля не стабилизированы, поэтому он не может производить цемент высокого качества. Рентгеновский анализатор на Рисунке 1 используется для анализа химического состава исходного цементного материала или сырья, затем рентгеновский анализатор может получать обратную связь LSF, SR и AOR за фиксированное время отбора проб. На LSF, SR и AOR могут влиять многие неопределенные факторы, такие как колебания состава и поток подачи материала.В таблице 1 представлен химический состав исходных цементных материалов. Химический состав — это функция, изменяющаяся во времени. Символы,, и представляют химический состав исходного цементного материала-. В таблице 1 R 2 O представляет собой общий химический состав оксида натрия (Na 2 O) и калия (K 2 O).
|
АЛЬТЕРНАТИВНЫЙ ИСТОЧНИК СЫРЬЯ ДЛЯ ПРОИЗВОДСТВА ЦЕМЕНТА
Просмотры сообщений: 101
АЛЬТЕРНАТИВНЫЕ ИСТОЧНИКИ СЫРЬЯ ДЛЯ ПРОИЗВОДСТВА ЦЕМЕНТА
РЕФЕРАТ
Общеизвестно, что цемент производится из известняка, мрамора / глины и гипса по следующим трем основным процессам: влажное полусухое процесс.
Стоимость эксплуатации известняка: основное сырье составляет около 50% стоимости производства, что приводит к высокой стоимости цемента. Следовательно, становится крайне необходимо снизить стоимость цемента, исследуя альтернативный источник сырья для производства цемента и, следовательно, этот проект.
Из литературы, зола рисовой шелухи, день Укпо и день Нсу содержат основные минеральные компоненты, которые есть в известняке. Обжигание рисовой шелухи составляло 500 0 ° C, 600 0 ° C, 700 0 ° C и 800 0 ° C.Наилучшая зола была получена при температуре 700 0 с. Вышеупомянутые материалы также были проанализированы для определения их минеральных составляющих. Результат показал, что рисовая шелуха содержит мало алюминия (Al 2 0 3 ) и не содержит извести (C a 0). Чтобы восполнить эти минеральные компоненты, Upo day, который богат алюминатом, был смешан с известью (C a 0) — побочным продуктом газового завода, и три минерала были смешаны с использованием метода коэффициента насыщения известью.Использовалось соотношение смеси 70% извести, 20% ПГА и 10% глинозема (Укпо день). Смесь перемешивали сухим способом и обжигали в печи при температуре 1200 0 ° C. Полученная масса, известная как динкер, была измельчена с 5% гипса. Полученный цемент дал общую прочность 2 Н / м 2 .
ОПРЕДЕЛЕНИЕ УСЛОВИЙ
OPC — Обычный портландцемент
LSF — Коэффициент насыщения известью
Известь негашеная — оксид кальция C a 0
Сырьевая мука — Вторичное сырье, которое подается в печь для сжигания
Сырьевая мельница — трубчатое оборудование, в котором происходит измельчение сырья
.
ASTM — Американское общество испытаний материалов.
Гидравлический модуль — Отношение извести (C a 0) к оксидам кремнезема, оксида алюминия и железа
.
Клинкер — промежуточное сырье и продукт из печи.
C 3 S — Силикат трикальция
C 2 S — Силикат дикальция
C 3 A — Алюминат трикальция
C 4 AF — Тетракальций алюмоферит
ЗАГРУЗИТЬ МАТЕРИАЛ ПРОЕКТА 9 АЛЬТЕРНАТИВНЫЕ ИСТОЧНИКИ СЫРЬЯ ДЛЯ ПРОИЗВОДСТВА ЦЕМЕНТА
Связанные
SeRaMCo: Вторичное сырье для сборных железобетонных изделий
Краткое описание проекта
Строительный сектор является наиболее ресурсоемким промышленным сектором в ЕС .Он использует около 50% доступного первичного сырья, тем самым истощая природные ресурсы, ухудшая окружающую среду и создавая высокие затраты для бизнес-операторов.
Хотя существует потенциальных возможностей использования вторичного сырья из отходов строительства и сноса (CDW) , это далеко не стало основным направлением в Европе . В настоящее время в этом секторе используется только 4% переработанных отходов строительства и сноса (CDW), хотя CDW представляет собой крупнейший поток отходов в ЕС, составляя 1/3 всех европейских отходов.
На этом фоне ситуация не ужасающая для всей Европы. Некоторые страны Северо-Западной Европы (NWE) , а именно Германия, Франция, Бельгия и Нидерланды лидируют в переработке CDW . В зависимости от страны эти ставки варьируются от 70 до 95%.
Тем не менее, несмотря на то, что уровень переработки отходов в СЗЭ впечатляет, бизнес-операторы строительного сектора все еще сталкиваются с проблемами при размещении своих переработанных продуктов на рынке .В первую очередь это связано с тем, что до сих пор нет ниши на рынке бетонных изделий из вторичного сырья. Отсутствие нишевого рынка сопровождается отсутствием четкой законодательной базы в некоторых штатах СЗЕ и невозможностью сделать точную оценку затрат, отражающую как социальные, так и экономические издержки производства.
Чтобы максимально использовать доступные ресурсы, SeRaMCo стремится заменить первичное сырье на высококачественные материалы, переработанные из CDW , e.грамм. бетон, кирпич, плитка и керамика (CBTC), в производстве цемента и бетонных изделий для использования на Северо-Западе. Для достижения этой цели в рамках проекта будут:
анализировать и улучшать сортировку CDW, как предварительное условие для успешной переработки;
разрабатывает и испытывает новые бетонные смеси и технологии для производства сборных железобетонных изделий (СЗЖ), изготовленных из переработанных ЖБТ;
создает рыночную нишу для CPP, что дает экономические преимущества производителям CPP и создает новые рабочие места в строительном секторе.
Ожидаемые объемы производства SeRaMCo — это цемент и CPP из до 100% переработанных заполнителей , сравнимых с традиционными продуктами как по стоимости, так и по качеству, и готовых к коммерциализации в СЗЕ.
Перед развертыванием в Северо-Западном Востоке и Европе в целом SeRaMCo протестирует свои конечные продукты в 3 пилотных регионах, а именно в городе Сераинг (Бельгия), городе Саарлуис (Германия) и регионе Мозель (Франция). После фазы тестирования будут внедрены ранее разработанные бизнес-модели, поддерживающие цепочку поставок в новой рыночной нише и создающие экосистему с заинтересованными сторонами, действующими в этой области.
Белый цемент — сырьевые и производственные компании
- Бизнес-планы
- Рекламное агентство
- BPO
- Консультации
- Управление событиями
- Финансовые услуги
- Ресторан
- Туристическое агентство
- Формат
- Индийских компаний
- Автомобильные компании
- Ведущие авиационные компании
- Транснациональные компании
- Лучшие банковские компании
- Лучшие компании Индии
- Страхование
- Сельское хозяйство
- Автомобиль
- Общий
- Здоровье
- Страховые полисы
- Страхование жизни
- Медицинский
- Крупнейшие страховые компании
- Путешествия
- Руководители бизнеса
- Ананд Махиндра
- Анил Амбани
- Азим Премжи
- Дхирубхай Амбани
- Лакшми Нараян Миттал
- Мукеш Амбани
- Рахул Баджадж
- Финансы
- Кредитные карты
- Рефинансирование
- Топ-10 финансовых компаний
- Top Auto Finance
- Top Asset Management
- Финансовый глоссарий
- Банки Индии
- Аллахабад Банк
- Axis Bank
- Банк HDFC
- ICICI Банк
- Мудра Банк
- Национальный банк Пенджаба
- SBI
- Резервный банк Индии
- Лучшие бренды в Индии
- Косметика
- Сумка
- Сумки
- Наушники
- Ноутбук
- Красное вино
- Ром
- Пиво
- Шоколад
- Туфли
- Часы
- Водка
- B-школ
- Бизнес-школа Amity
- ИММ дистанционное обучение
- IIPM Дели
- Интернет-школа бизнеса
- С.Институт П. Джайна
- Лучшие школы B в Индии
- XLRI
доля Сырье | Статья о сырье по The Free Dictionary
материал, на который были затрачены трудозатраты и который будет подлежать дальнейшей обработке. В процессе производства сырье составляет материальную базу готовой продукции или полуфабрикатов.Вся стоимость сырья включается в стоимость единицы, принимающей товарную форму. Сырье имеет много общего с основными материалами в том, что касается экономической значимости и их роли в производственном процессе.
Все сырье классифицируется по происхождению как промышленное или сельскохозяйственное. Промышленное сырье, в свою очередь, подразделяется на минеральное и техногенное, причем доля последнего постоянно растет. Сырье минерального происхождения также сгруппировано по использованию.Некоторые из них используются в качестве источников энергии (нефть, природный газ, уголь, горючие сланцы, уран) или при производстве строительных материалов (цемент, керамические материалы), другие находят применение в металлургии (руды черных, цветных, редких и благородных металлов). , технология (алмазы, графит, слюда) и горно-химическая технология (агрономические руды, барит, флюорит, сера). Искусственное сырье включает синтетические смолы и пластмассы, синтетический каучук, заменители кожи и синтетические моющие средства. Сельскохозяйственное сырье, а также сырье лесной и рыбной промышленности подразделяется на сырье растительного (зерновые и технические культуры, древесина, дикие растения, лекарственные растения) и животного происхождения (мясо, рыба, молоко, шкуры, шкуры, шерсть. ) происхождение.В некоторых отраслях промышленности различают первичное (руды в металлургии, целлюлозу в бумажной промышленности) и вторичное (металлолом, макулатура) сырье. Разумное использование вторичного сырья может принести экономию общественного труда. Комплексная переработка первичного сырья — важный источник расширения сырьевой базы и повышения экономической эффективности промышленности. Повышение качества сырья — необходимое условие повышения технико-экономических показателей работы промышленных предприятий.
СПИСОК ЛИТЕРАТУРЫ
Marx, K. Kapital , vol. 1. Маркс К. и Энгельс Ф., Соч , 2 изд., Т. 23. С. 189–90.
Экономика социалистической промышленности , 5 изд. Под редакцией Л. И. Итина. М., 1974. А.И. И МШЕНЕЦКИЙ
Сырье играет важную роль в мировой экономике и международных экономических отношениях. В силу природных факторов распределение минерального и другого природного сырья в мире очень неравномерно.Страна получает сырье, необходимое для ее экономики, и продает сырье в основном через внешнеэкономические связи. Характер этих связей определяется социально-экономическим укладом стран-участниц. Экономические связи между социалистическими странами, в том числе договоренности о поставках сырья, развиваются планомерно, характеризуются взаимной договоренностью и экономически обоснованными, стабильными ценами.
В капиталистических экономиках покупка и продажа сырья подвергаются постоянным сбоям, что составляет сырьевую проблему мировой капиталистической экономики.Проявления проблемы — нестабильность спроса и предложения, неконтролируемое чередование периодов избытка и дефицита сырья на рынках с соответствующими резкими изменениями мировых цен и противоречия между различными группами капиталистов-монополистов, а также между экономически развитыми и слаборазвитыми странами. Сырьевая проблема особенно остро стоит в развитых капиталистических странах, которые испытывают острую нехватку различных видов сырья.В то же время проблема сырья имеет значение для развивающихся стран, богатых сырьем и выступающих в качестве поставщиков, что влечет за собой высокую степень зависимости от капризов капиталистических рынков.
После Второй мировой войны капиталистическая экономика пережила несколько периодов нехватки сырья и роста цен. Периоды, которые обычно совпадали с периодами роста делового цикла, приходились на начало и середину 1950-х, середину 1960-х и первую половину 1970-х годов.Ввиду исключительной остроты проблемы последний период получил название сырьевого кризиса. Мировые цены на сырье выросли в период 1970-74 годов почти в пять раз, а цены на промышленные товары — вдвое; В сочетании с другими факторами это увеличение вызвало серьезные потрясения в капиталистической экономике. В течение этих лет рыночные факторы взаимодействовали с давними тенденциями к кризису капитализма как социально-экономической системы, включая дальнейшую интернационализацию производительных сил и растущую взаимозависимость национальных экономик, кризис традиционных отношений господства и подчинения между капиталистическими центрами и окраинами, хронические колебания валютных курсов и ухудшение качества окружающей среды из-за иррационального, часто хищнического отношения капиталистических монополий к использованию природных ресурсов.
В 1950-х и 1960-х годах, несмотря на рыночные колебания, наблюдалась четкая тенденция к снижению цен на капиталистических рынках сырья, особенно в отношении цен на промышленные товары. Этот спад отразил не только положительные результаты развития производительных сил на фоне научно-технической революции, но и отрицательные последствия политики монополий, которые в конечном итоге ограничили поток капиталовложений в добывающие отрасли.
ЗАГРУЗИТЬ МАТЕРИАЛ ПРОЕКТА 9 АЛЬТЕРНАТИВНЫЕ ИСТОЧНИКИ СЫРЬЯ ДЛЯ ПРОИЗВОДСТВА ЦЕМЕНТА
Связанные
анализировать и улучшать сортировку CDW, как предварительное условие для успешной переработки;
разрабатывает и испытывает новые бетонные смеси и технологии для производства сборных железобетонных изделий (СЗЖ), изготовленных из переработанных ЖБТ;
создает рыночную нишу для CPP, что дает экономические преимущества производителям CPP и создает новые рабочие места в строительном секторе.
- Рекламное агентство
- BPO
- Консультации
- Управление событиями
- Финансовые услуги
- Ресторан
- Туристическое агентство
- Формат
- Автомобильные компании
- Ведущие авиационные компании
- Транснациональные компании
- Лучшие банковские компании
- Лучшие компании Индии
- Сельское хозяйство
- Автомобиль
- Общий
- Здоровье
- Страховые полисы
- Страхование жизни
- Медицинский
- Крупнейшие страховые компании
- Путешествия
- Ананд Махиндра
- Анил Амбани
- Азим Премжи
- Дхирубхай Амбани
- Лакшми Нараян Миттал
- Мукеш Амбани
- Рахул Баджадж
- Кредитные карты
- Рефинансирование
- Топ-10 финансовых компаний
- Top Auto Finance
- Top Asset Management
- Финансовый глоссарий
- Аллахабад Банк
- Axis Bank
- Банк HDFC
- ICICI Банк
- Мудра Банк
- Национальный банк Пенджаба
- SBI
- Резервный банк Индии
- Косметика
- Сумка
- Сумки
- Наушники
- Ноутбук
- Красное вино
- Ром
- Пиво
- Шоколад
- Туфли
- Часы
- Водка
- Бизнес-школа Amity
- ИММ дистанционное обучение
- IIPM Дели
- Интернет-школа бизнеса
- С.Институт П. Джайна
- Лучшие школы B в Индии
- XLRI