Срубка оголовков свай технология: технологическая карта для отбойного молотка
что такое и технология устройства
Фундамент свайного типаОголовки свай служат опорой для цокольной конструкции обвязки свайного фундамента возводимого строения. После завершения процесса ввинчивания свайные полости заполняют бетонной смесью. Верхушки свай срезают специальным оборудованием до проектного уровня. Для создания единой опорной горизонтальной конструкции свайного фундамента, на которую будут опираться стены будущего строения, необходимо на верхнем окончании винтовой сваи крепить оголовок. Оголовки могут иметь разные очертания. Самая простая форма этого конструктивного элемента выполнена из металлического листа с приваренными к нему насадными кольцами с ребрами жесткости.
Назначение оголовков
Оголовком винтовой сваи называется переходная металлическая деталь сопряжения верхнего торца свайной конструкции, изготовленная из элементов фундаментной балки или ростверков. Ростверк, металлический или железобетонный, монтируется в строго горизонтальном положении.
Размер оголовка выбирают в зависимости от диаметра сваи и веса опорной конструкции, которая будет непосредственно опираться на фундаментную балку. При этом его внутренний диаметр должен немного превышать наружный диаметр сваи. Это необходимо для свободного и глубокого надевания. При значительных осевых нагрузках на ростверк или фундаментную балку применяют усиленные оголовки.
Чтобы сделать усиленный вариант такой переходной детали, необходимо к конструкции оголовка приварить 4 стальные «косынки» с антикоррозийным покрытием.
Виды и формы
Размеры и контур поперечного сечения оголовка, как правило, совпадает с размерами сваи и может иметь различную форму: круглую, квадратную, тавровую и прямоугольную. Соединение его со сваей или фундаментной балкой может быть П-образным или Т-образным:
- Т-образный оголовок.
Такой вид изделия чаще всего применяется в строительстве из-за его универсальности. Монтаж Т-образного оголовка производится методом сварки или при помощи болтов, которые фиксируются к верхней части сваи. На верхнюю полочку оголовка устанавливается и закрепляется фундаментная балка или плитный ростверк.
- На П-образных изделиях монтируются только балки фундамента. При этом толщина П-образной скобы должна обязательно совпадать с толщиной балки.
Чтобы сделать правильный выбор оголовка, желательно посоветоваться со специалистами–строителями, которые помогут подобрать нужное и качественное изделие.
Разъемное соединение на болтах способно выдерживать меньшие нагрузки, чем в случае применения сварки, однако позволяет многократно применять опоры и переносить объект на новое место без повреждения конструкции. Именно поэтому их используют при возведении малоэтажных зданий и вспомогательных объектов.
Типы оголовков по методу крепления
Оголовки для винтовых свай по способу крепления подразделяют на:
- Съемные используются при ручном монтаже опорной конструкции.
Также их рекомендуют выбирать при устройстве свайных фундаментов на тяжелых грунтах. При вкручивании сваи только до уровня промерзания грунта ее верхнюю часть обрезают и надевают съемный оголовок. Конструкция съемной переходной детали, как правило, выполнена в виде стакана с приваренной квадратной пластиной, на которой расположены треугольные металлические пластины. Съемные изделия бывают следующих размеров: 150 мм х 150 мм, 200 мм х 200 мм. Оголовки для угловых свай имеют большее сечение, например, 150 мм х 300 мм или 200 мм х 400 мм.
- Если при ввинчивании свай используется ямобур, то в этом случае применяют оголовки приваренного типа. Полость сваи с таким типом наголовника защищена от попадания воды и меньше контактирует с атмосферным кислородом, что значительно увеличивает срок службы свайного фундамента. Размеры круглых оголовков приваренного типа могут иметь диаметр 150, 200 и 250 мм.
Монтаж методом срубки
После установки свай в грунт, необходимо хвостовые части привести к единому горизонтальному уровню для устройства горизонтальной обвязки. Такую процедуру можно выполнить методом срубки или обрезки ненужного участка сваи. Для этого строительным уровнем (лазерным или гидроуровнем) отмечают проектную отметку и последовательно передают ее на каждую сваю.
Если изделие изготовлено из железобетона, то можно срубить лишнюю часть сваи отбойным молотком. Такой вариант считается самым дешевым, правда, не всегда эффективным. Часто для этих целей используют более дорогое оборудование – гидравлические ножницы, которые дают четкую линию реза и увеличивают производительность труда. В этом случае срубка будет происходить значительно быстрее.
На срубку голов свай с применением гидравлических ножниц уходит значительно меньше времени, примерно 5–10 минут. Такая высокая производительность достигается за счет особого устройства гидроножниц: кольцевая насадка устанавливается по отмеченному уровню на верхнюю часть сваи. Благодаря этому его режущая кромка легко отделяет арматурный каркас от бетонной оболочки идеально ровно.
Смонтированная сваяСрубка оголовков свай проводится вертикальными движениями, не трогая при этом каркас из арматуры.
Метод срезки
Методика резки свай считается универсальной. Ее разрешается применять к деревянным, железобетонным и металлическим изделиям. Для осуществления процесса резки достаточно выбрать подходящую насадку.
Срез может осуществляться вручную или при помощи станочного устройства для работы. Обычно для этих целей используют режущие инструменты, например, ленточную, дисковую пилу или болгарку. Методика срезки идентична для каждого инструмента и состоит из следующих видов работ:
- Для начала при помощи маркера необходимо отметить линию среза.
- После этого при помощи выбранного электрического инструмента по намеченной линии проделывают борозду для калибровки. Двигать инструмент рекомендуется по прямой к центральной части изделия или по кольцу. Для того чтобы обезопасить этот процесс необходимо периодически обрабатывать инструмент охлаждающей жидкостью.
Установка методом сварки
Фундамент свайного типа считается окончательно смонтированным в том случае, если на каждой свае будет зафиксирован определенный вид оголовка.
- Монтируемый оголовок для винтовой сваи устанавливают горизонтально.
- На следующем этапе производят контактную сварку по трем или четырем точках.
- После этого производят сварку по всей длине окружности сваи. При этом необходимо оставлять зазор около 1-2 см. Это необходимо для того чтобы обеспечивать вентиляцию и не допустить образование конденсата.
- На завершающем этапе производят очистку сварного шва при помощи молотка.
Далее сваю с оголовком покрывают грунтующим составом и окрашивают.
Ознакомиться с процессом монтажа оголовков свайного фундамента можно на видео:
Оголовки считаются основным элементом в конструкции фундамента свайного типа. В сочетании с надежным креплением этой промежуточной детали с прочной опорой конструкция фундамента обеспечивает восприятие нагрузки строения и равномерную ее передачу грунту, поэтому к установке оголовка нельзя относиться, как к второстепенному процессу. При монтаже этого конструктивного элемента рекомендуется на каждом этапе устраивать промежуточную проверку правильности установки.
Срубка оголовков свай 👉 технологический процесс
По завершении ввода свайных опор в толщу грунта, стройплощадка напоминает частоколы разной высоты, выступающие из поверхности земли. Верхняя часть оголовков свайных элементов обрубается.
Необходимость сруба оголовков
Есть несколько видов свайных конструкций, отличающихся назначением. У них свои особенности, положительные, отрицательные стороны. Виды фундамента свайного типа:
- забивной. Введение свайных элементов в грунт выполняется физической силой. Вспомогательный инструмент — механические и ручные молоты-копры. В промышленных масштабах прибегают к вибрационным механизмам и оборудованию, своим весом вдавливающим опору в полость земли;
- буронабивной. Предварительно выполняется бурение скважины нужной глубины и сечения. Ее размеры зависят от габаритов сваи. В отверстии создается армирующий каркас. Выполняется заливка бетонного раствора;
- винтовой — труба, один край которой выполняется заостренным.
Вокруг него предусматривается спиралевидный лепесток. Методика введения винтовой конструкции — вращение опоры вокруг своей оси. Применяется сваекрут. Свайный элемент, углубляясь в полость земли, работает как штопор, вкручивающийся в пробку.
Глубина введения фундаментной опоры, ее высота над уровнем земли регламентируются проектом капительного строения. Эти значения полностью зависят от глубины залегания грунтовых водных прослоек и точки промерзания почвы. Учитывается масса будущего строения и климатические особенности местности, на которой предполагается строительство.
Свайные конструкции — опоры для верхней обвязки фундамента или ростверка. Последние передают нагрузку от здания. Оголовки должны находиться на одном уровне.
Достижение ровности и одинаковой высоты выступающих опор над уровнем земли — нереальная задача. Разница по высоте свай может равняться десяткам сантиметров. Строители прибегают к срезке опорных элементов до одного уровня.
Методика рубки свайных конструкций
Применяют несколько методик рубки верхней части опоры фундамента. Выбор зависит от:
- стройматериала сваи;
- габаритов свайного сооружения;
- количества свай;
- доступа к техническому оборудованию.
Срубить оголовки можно вручную, или применяя механизированные средства. Первый вариант предполагает использование ручного инструмента: отбойного молотка, болгарки. Во втором случае, используется тяжеловесная строительная техника. Срезка оголовков выполняется без применения физической силы человека. Механизированный способ выполняется двумя типами оснащения: режущими фрезами и гидравлическим механизированным оборудованием.
Техпроцесс выравнивания оголовков свай выполняется по строительным нормам. Приступать к рубке голов разрешено только после заглубления всех свайных опор по проекту. Выполняется создание технологической карты. Маркируют линии среза.
Маркировать можно точными инструментами — лазерным уровнем или нивелиром. Точка отсчета — репер. Он наносится на самую низкую опору. От него маркируются следующие сваи.
Запрещается выполнять маркировку от нулевого уровня грунта. Появляется риск расхождения по высоте из-за неровности поверхности земли.
Ручная методика
Потребуются следующие инструменты:
- отбойный молоток. Рекомендуется при выравнивании монолитных или сборных железобетонных свай;
- гидравлические ножницы. Срезают выступающие остатки металлических прутков. Позволяют укоротить опоры из металлических трубопроводов небольшого сечения, бетонных оголовков;
- угловая шлифовальная машинка для выравнивания бетонных и металлических типов свай. Зависит от вида отрезного круга.
Если сравнивать ручной и механизированный метод, в первом случае, сводятся к минимуму траты. Это хорошая возможность сэкономить хозяину с ограниченным бюджетом на строительство. Для масштабного строительства вариант непригоден. Работы будут длиться вечно.
Контроль качестваСрезка металлических свай
Выполнять обрезку свайных изделий из металлических трубопроводов можно собственными силами. Винтовые сваи оснащаются винтом в нижней части. Введение сооружения в грунт выполняется на глубину до 2 м.
Срезание верхних частей опоры производится по следующей технологии:
- На угловой свае выполняется белым цветом разметка линии среза. Выполнить ровную линию по круглой трубе легко. Берется ровная бумажная полоса. Обволакивается свая. Обводится маркирующая линия.
- Срез выполняется болгаркой. Разрезают линию по окружности, глубиной 1 мм.
- По намеченной метке срезается оголовок.
- Маркировка и вычисление общего уровня среза проводится лазерным уровнем. Его можно заменить нивелиром. Метки делают на каждой свайной опоре. Работы проводятся аналогично.
Сруб бетонной опоры
Сооружение тяжеловесных многоэтажных зданий требует обустройства железобетонных свайных изделий. Выполняются заливные сваи — цилиндрический каркас, внутри которого произведено армирование металлическими прутками. Потом, полость заливается бетонным раствором до заданного уровня. Забивные подвергаются срезу.
Выравнивать железобетонный тип свай сложнее, чем стандартные стальные аналоги. Требуется сохранение стержневой арматуры. Она выступает над поверхностью опоры и будет использоваться для создания деревянного ростверка. Решить задачу можно пневматическим отбойным молотом.
Срезка сваи отбойным молотом пневматического исполненияТехпроцесс выполняется в несколько этапов:
- По аналогии со срезом металлического свайного элемента, производится маркировка опор. На каждом без исключения изделии выполняется разметка с помощью лазерного уровня. Проверяется ровность нанесенных меток. Может использоваться маркер или лист бумаги высокой плотности.
- По линии маркировки выполняется канавка с небольшим углублением в 20 мм.
- В указанном уровне отбойным молотком делаются движения, влекущие откалывание кусков железобетонного сооружения. Работа продолжается, пока не уберется нужный шар бетона.
- Если не предполагается обустройство ростверка, нужно болгаркой срезать выступающие части армирующего каркаса.
Минусы такой методики выравнивания — высокая шумность технологического процесса, образуется много пыли. Соседствующим жильцам это точно не понравится. Рабочие должны быть в спецодежде. Применяются средства защиты органов слуха, зрения, дыхания.
Если опор много, лучше обратиться к мастеру. Здесь требуется оборудование, опыт работы.
Техника безопасности
Технология выравнивания свайных элементов отличается травмоопасностью. Рекомендуется все работы выполнять в по требованиям охраны труда:
- допуск получают подготовленные работники, имеющие образование или прошедшие курсы. Они должны при себе иметь удостоверение на право пользования пневматическим инструментом или гидравлическим оборудованием;
- посторонние находиться на территории стройплощадки не должны. Это строго запрещается. Определение опасной зоны выполняется с учетом размера сбиваемой части опоры и 5 м вокруг нее;
- выполнять рубку верхушек рядом расположенных свай запрещено.
Образуется много осколков. Они разлетаются. Могут навредить стоящему рядом человеку;
- рабочие должны применять средства защиты. Быть в спецодежде и спецобуви;
- сбивать верхнюю часть свайной конструкции с лестницы запрещается;
- пневматический тип инструментов должен соответствовать требованиям. Он должен находиться в полной исправности. Обеспечивается надежность, безопасность подключения к воздуховодам. Места стыковки соединений проверяются на герметичность. Шланги должны лежать ровно. Не допускается перегиб. Нужно исключить их пересечение с электрическими коммуникациями;
- не разрешается работа с болгаркой или отбойным молотком на лестнице. Появляется высокий риск травмы при падении, вплоть до смертельного исхода;
- если предполагается срез массивного опорного сооружения, верхняя часть конструкции фиксируется стропами крана или лебедкой. Это не даст крупному фрагменту упасть на работника. Механизмом аккуратно снимают, переставляют бетонный сруб на место.
Механизированный способ
Механизированный способ рубки свай применяется для масштабного строительства. Строительные механизмы и оборудование ускоряют работу. Если брать оборудование в аренду, обойдется дорого. Но купить его может позволить себе не каждая строительная компания. Это дорогое удовольствие.
Механическая срезка выполняется сваерезами:
- фрезы пыльного метода исполнения. Воздействие на сооружение выполняется гидравлическим приводом. Обеспечивается ровная и красивая линия среза. Не требуются реконструкционные мероприятия по доводке поверхности к оптимальным параметрам;
- резка с открытым пламенем. Обеспечивается растрескивание и разрушение бетонного монолита;
- ударного действия зарядом пороха. Используют для рубки железобетонных опор.
Резка гидроцилиндрами требует привлечения экскаватора и подъемного крана. Благодаря стреле, корпус механизма срезки сваи устанавливается и фиксируется в нужном положении. Сила давления масла действует на рабочие органы. Часто, это заостренные высокопрочные стальные стержни. Они внедряются в тело опорного элемента и переламывают его. Верхушка опоры откалывается. Не появляется много бетонных осколков и фрагментов.
В процессе выбора нужного оборудования для выравнивания фундаментных опор, нужно оценить объем работ. Учитывать, из какого материала выполнены конструкции. Узнать больше информации об особенностях технологического процесса. Ознакомиться с условиями. Только это позволит реализовать рубку верхушек свай быстро, качественно, с минимальными тратами.
Вконтакте
Google+
Средняя оценка оценок более 0 Поделиться ссылкойОпишем технологию срубки оголовков свай — ЗАО «СИ» Тел.: 84992359878 89055749848 zaosi@zaosi.
com
Опишем технологию срубки оголовков свай
Насадка для срубки оголовков свай, навешивается к стреле экскаватора/крана. Родная гидросистема крана/экскаватора является источником питания оборудования для срубки свай. Очень часто насадку подключают к рукавам высокого давления за место ковша. Гидравлические цилиндры насадки для срубки свай обладают режущими зубьями, которые за счет гидравлического воздействия и ходу штока, осуществляют вдавливание, разлом и распушение бетона, из которого состоит свая. Цилиндры сжимаются на полный ход, саму насадку поднимают вверх, разрушенный бетон от оголовка сваи убирается со сваи и сбрасывается (за счет разжимания цилиндров и зубьев) в необходимую точку в радиусе действия стрелы экскаватора, выпуски арматуры не повреждаются (это позволяет использовать их в дальнейшем). При типовом использовании насадки на стандартных объектах строительства эффективность оборудования составляет – более 250 срубленных свай за одну 10-ти ч. рабоч. смену. В случае буронабивных свай (БНС) эта цифра составляет от 30 шт. (на количество влияет диаметр и высота оголовка сваи).
Хотим отметить простоту эксплуатации, практически полное отсутствие шума. Высокая производительность. Значительно более качественный результат по сравнению с отбойными молотками. Приемлемая цена является важным фактором при принятии результирующего решения в направлении применения высокотехнологичных методов срубки свай.
ЗАО «СИ» по праву можно назвать инновационной производственной организацией, являющейся одной из первых компаний, кто стал внедрять использование безударной технологии срубки оголовков свай на территории Российской Федерации и странах СНГ. Сегодня нас можно назвать лидерами в этой сфере, имеем большой опыт работ в этом направлении, имеем мощную производственную и инженерную базу. Работы по срубке оголовков свай абсолютно любой сложности могут быть произведены на оборудовании нашего производства.
Мы провели большое количество работ по срубке свай, и поэтому, мы можем смело убедить заказчиков в обоснованности выбора в пользу оборудования нашей компании.
При эксплуатации специализированного инновационного оборудования для обрубки, срезки и срубки оголовков свай – вы получаете единственный метод, при котором все работы будут произведены в срок, без задержек, согласно всем оговоренным срокам по заданию обеих сторон (заказчик-исполнитель).
На рынке имеется ряд аналогов насадки для обрубки свай фирмы «СИ», но можно с уверенностью сказать, что наше оборудование выделяется своими эксплуатационными качествами, технической надежностью, правильной инженерной конструкцией, простотой использования и технического обслуживания, высококачественным сервисом и гарантией, адекватной ценой.
© 2015 — 2017, wpadmincheg963. Все права защищены.
Вырубка свай: способы и практические рекомендации
- Монтаж фундамента
- Выбор типа
- Из блоков
- Ленточный
- Плитный
- Свайный
- Столбчатый
- Устройство
- Армирование
- Гидроизоляция
- После установки
- Ремонт
- Смеси и материалы
- Устройство
- Устройство опалубки
- Утепление
- Цоколь
- Какой выбрать
- Отделка
- Устройство
- Сваи
- Виды
- Инструмент
- Работы
- Устройство
- Расчет
Поиск
Фундаменты от А до Я.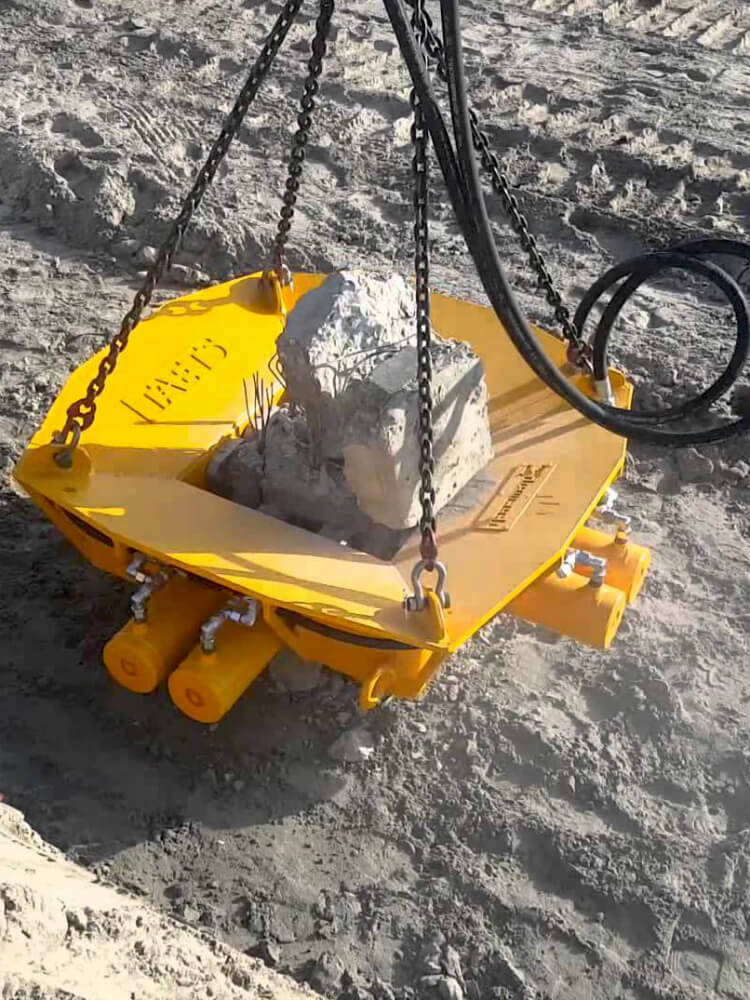
- Монтаж фундамента
- ВсеВыбор типаИз блоковЛенточныйПлитныйСвайныйСтолбчатый
Фундамент под металлообрабатывающий станок
Устройство фундамента из блоков ФБС
Заливка фундамента под дом
Характеристики ленточного фундамента
- ВсеВыбор типаИз блоковЛенточныйПлитныйСвайныйСтолбчатый
- Устройство
Оголовок для винтовой сваи: функции и методы срубки
- Монтаж фундамента
- Выбор типа
- Из блоков
- Ленточный
- Плитный
- Свайный
- Столбчатый
- Устройство
- Армирование
- Гидроизоляция
- После установки
- Ремонт
- Смеси и материалы
- Устройство
- Устройство опалубки
- Утепление
- Цоколь
- Какой выбрать
- Отделка
- Устройство
- Сваи
- Виды
- Инструмент
- Работы
- Устройство
- Расчет
Поиск
Фундаменты от А до Я.
- Монтаж фундамента
- ВсеВыбор типаИз блоковЛенточныйПлитныйСвайныйСтолбчатый
Фундамент под металлообрабатывающий станок
Устройство фундамента из блоков ФБС
Заливка фундамента под дом
Характеристики ленточного фундамента
- ВсеВыбор типаИз блоковЛенточныйПлитныйСвайныйСтолбчатый
- Устройство
Срубка оголовков свай технология
Срубка оголовков свай, оборудование и технология
Современное строительство сложно представить без применения свай. Чаще всего используются железобетонные сваи с арматурным каркасом. С какой бы точностью они не были забиты или установлены всегда необходимо производить срубку оголовков свай.
Обрубаем сваи своими руками
В зависимости от материала опор срубка оголовков свай может производиться с помощью различных инструментов и выполняться как специализированными строительными бригадами, так и самими владельцами земельного участка. О профессиональных способах выполнения данного вида работ расскажем ниже. Сначала разберем, как можно выполнить срубку свай доступными инструментами без необходимой квалификации работников.
На сколько сложен процесс срубки оголовков свай?
При строительстве зданий в качестве опоры фундамента используют сваи. Чтобы завести их под плиту нам придется распустить арматуру. Для этого можно использовать отбойные молотки, а лучше — современное технологичное оборудование.
Технология срубки свай, оголовков
После того, как все сваи для фундамента забиты в грунт, из земли остается торчать неравномерный по высоте частокол. Понятное дело, что возвести хоть какое-то мало-мальски устойчивое сооружение на нем не получится. Поэтому необходимо срубить сваи – привести их к единой высоте, обозначенной проектными расчетами.
Для чего осуществляется срезка голов свай
Необходимость возникает из-за неоднородности грунта на участке возведения фундамента. Сваи погружают в почву до получения заданного «отказа». Если требуемое значение сопротивления при полном проникновении не получают, то используют еще одну до тех пор, пока необходимый параметр не будет достигнут. Иногда «отказ» наступает раньше погружения на нужную глубину.
И в первом и во втором случае на поверхности грунта остаются выступающие оголовки повышенной длины, поэтому для продолжения работы требуется срубить до требуемого уровня.
Режущая головка DiaLine — Абразивная гидроабразивная режущая головка
- Логин
- Поиск
- 1-866-566-7099
- Дом
- Товары
- Обзор
- Насосы-усилители гидроабразивной резки
- Головки для гидроабразивной резки
- Обзор
- Dialine
- Обзор
- течь
- омакс
- кмт
- край струи
- Режущая головка Dialine в сборе
- A2
- вода
- Регулятор абразива Hypertherm II
- Горшки для абразивной гидроабразивной резки
- Гидроабразивный кирпич
- Система обратного осмоса
- Запасные части
- Обзор
- Для AccuStream
- Обзор
- Детали насоса
- Детали спускного клапана
- Отверстия и сопла
- Обзор
- Рубиновые и алмазные отверстия
- Ультра отверстия
- Насадки
- Сборки DiaLine
- Обзор
- Сборки DiaLine
- Отверстия DiaLine
- Форсунки DiaLine
- Запасные части DiaLine
- Подключения DiaLine
- DiaLine Защита
- Режущая головка A2
- Обзор
- Комплектная режущая головка A2
- Режущие головки A2
- Отверстия A2
- Только вода
- Обзор
- Режущая головка только для воды
- Отверстия только для воды
- Клапан включения / выключения
- Обзор
- Узлы двухпозиционного клапана
- Детали клапана включения / выключения
- Адаптеры включения / выключения
- Клапан включения / выключения UltraValve
- Включение / выключение монтажного оборудования
- Разное.
Товары
- Для BFT
- Обзор
- Детали насоса
- Для потока
- Обзор
- Отверстия
- Обзор
- Рубиновые отверстия
- Алмазные отверстия
- Ультра отверстия
- Насадки
- Обзор
- Насадки
- Форсунки с установочным кольцом Performance
- Режущие головки
- Обзор
- Компоненты режущей головки 60k
- Компоненты режущей головки 94k
- Детали насоса
- Обзор
- Части насоса 60k
- 60k Полные усилители
- 94k детали насоса
- Клапан включения / выключения
- Обзор
- Узлы двухпозиционного клапана
- Детали клапана 94k
- Детали клапана Insta 1
- Детали клапана Insta 2
- Детали мини-клапана
- Детали клапана h30
- Вертлюги
- Фильтры
- Разное.
Запчасти
- Для Jet Edge
- Обзор
- Отверстия и сопла
- Детали насоса
- Обзор
- Детали насоса 7/8 »
- Детали насоса 1 »
- Детали клапана включения / выключения
- Для КМТ
- Обзор
- Отверстия и сопла
- Детали насоса KMT
- Обзор
- Детали насоса KMT SL4
- Детали насоса KMT SL5
- КМТ SL5 (75 / 100S)
- Детали клапана включения / выключения
- Обзор
- Детали клапана включения / выключения 60k
- Детали клапана включения / выключения 100k
- Компоненты режущей головки
- Для OMAX
- Обзор
- Отверстия и сопла
- Компоненты режущей головки
- Детали клапана включения / выключения
- Детали насоса
- Обзор
- Детали насоса
- Детали насоса E-Max
- Трубки и фитинги
- Обзор
- Трубки высокого давления
- Катушки высокого давления
- Детали высокого давления
- Для WSI
- Обзор
- Детали клапана включения / выключения
- Детали насоса
- Трубки и фитинги высокого давления
- Обзор
- 100 тыс.
Трубок и фитингов
- 60к НКТ
- инструменты
- Детали инструмента для нарезания конусов и резьб
- Манометр высокого давления
- Вертлюги HP
- Фильтры высокого давления
- Ошейники и сальники
- Вилки
- Прямые муфты
- Муфты редуктора
- Адаптеры
- Тройники
- Локти
- Кресты
- Двухходовые прямые клапаны
- Двухходовые угловые клапаны
- Встроенный WYE
- Соски
- Катушки
- Поддержка
- Обзор
- Обслуживание клиентов
- Техническое обслуживание
- Гидроабразивное обучение
- Литература по продукту
- Руководства и загрузки
- Обзор
- для AccuStream
- для Flow
- для Jet Edge
- для КМТ
- для OMAX
- Загрузки
- Наша компания
- Обзор
- Технологии
- Новости
- Обзор
- Архив
- Обзор
- Новый насос-усилитель AccuStream AS-60150
- Новый насос-усилитель AccuStream AS-60150
- Видео новой штаб-квартиры
- Accustream перемещает офисы в новую просторную штаб-квартиру
- Торговые выставки
- Дистрибьюторам
- Связаться с нами
- Логин
- Продукты Головки гидроабразивной резки Режущая головка в сборе
- Dialine
Головки для абразивной резки в сборе
Скачать Литература по продукту Скачать Руководство для покупателей Посмотреть видео о продуктеИнтернет-магазин
Руководство по покупке
Загрузить руководство для покупателейВыбор процесса резки трубы
Изготовители труб используют различные методы — пиление, токарную резку, вращательную резку, резку с опорой на ножницы, резку с двумя ножами и лазерную резку — для резки труб из мельничных длин на более короткие части для использования в окончательном производстве. Ни один метод не является оптимальным для резки широкого спектра трубчатых материалов и трубных профилей, производимых в этой отрасли.
Кроме того, стремительный рост продукции, связанной с трубами, потребовал от производителей увеличения производства и автоматизации операций по резке.
Какой тип оборудования для резки труб использовать для операции, зависит от требований к трубам:
- Какая производительность требуется?
- Какое конечное состояние требуется для вырезанной детали?
- Как поставляется исходный материал — произвольной длины или рулонов?
- Трубы производятся собственными силами или поставляются сторонним производителем?
- Будет ли трубчатая деталь изготовлена полностью собственными силами или будет отправлена другому производителю для отделки?
Распиловка
Распиловка — один из самых универсальных и широко применяемых методов резки труб.Каждый вид пиления уникален, но, как правило, пиление подходит для мелкосерийного производства.
Рисунок 1 Холодная пила с одной головкой обычно режет по одной трубе за раз; однако он может сразу разрезать пучок труб малого диаметра. |
Самым важным моментом при пилении является установка правильного лезвия на трубу, которую нужно разрезать. Во всех случаях пиления необходимое количество зубьев на полотне зависит от количества зубцов, которые контактируют с трубой на максимальной дуге реза.Слишком мало зубьев, контактирующих с трубой, ограничивает производительность и вызывает вибрацию. Из-за того, что слишком много зубьев контактирует с трубкой, стружка забиваются в зубах, что может привести к поломке зубов или лезвия.
Используются два типа пильных станков — пила для холодной резки и ленточная пила.
В принципе, холодная пилка аналогична токарно-фрезерной обработке. Металл удаляется резкой положительными граблями. Базовая конструкция полотна для холодной резки — это обычная форма зуба, но также используются и другие.На толстостенных трубах используются специальные фаски для разрушения стружки. Зона резания охлаждается, чтобы свести к минимуму размягчение зуба пилы, смазывая ее растворимыми масляными эмульсиями или синтетическим маслом.
непосредственно в зоне резания. Системы затопления могут использоваться для подачи большого количества охлаждающей жидкости, необходимой для толстостенных конструкций.
Процесс холодной распиловки адаптирован к множеству машин с разной производительностью. Холодная пила с одной головкой режет по одной трубе за раз, хотя она может разрезать сразу пучок труб малого диаметра (см. , рисунок 1, ).Многопильные станки могут иметь до 12 режущих головок и разрезать трубы на несколько частей (см. , рисунок 2, ).
Преимущества холодного пиления:
- Холодное пиление с одной головкой относительно недорого.
- Многоголовочные пилы обладают высокой производительностью.
- Режет квадратные и прямоугольные формы, а также круглые.
- Режет как толстостенные, так и легкостенные материалы.
- Режет материалы от мягкой до нержавеющей стали.
- Специальные односторонние пилы для резки под углом и под углом.
- Состояние режущей кромки хорошее, когда лезвия острые — минимальные заусенцы и искажения.
- Сразу режет пучок труб малого диаметра. Некоторые пилы для холодной резки могут отрезать две трубы с наружным диаметром 1,25 дюйма за раз.
Рисунок 2 Многоголовочные станки для холодной резки могут иметь до 12 пильных голов и могут разрезать трубы на несколько частей. |
Недостатки холодного пиления:
- Поскольку все потери на пропиле превращаются в стружку, во время упаковки или вторичных операций могут возникнуть царапины и другие проблемы.
- Может потребоваться очистка трубки.
- На многоголовочных пилах бывает трудно соблюдать допуск по длине.
- На многоголовочных пилах время переналадки длины детали и пильных полотен может быть большим в зависимости от количества используемых пильных голов.
- Необходимость частой переточки лезвий при резке определенных материалов может снизить производительность.
- Когда лезвия затупляются, на обрезанном конце появляется большой висячий заусенец.
- Может деформировать очень тонкостенные трубки.
Ленточная пила подходит для резки целых пучков труб на более короткие отрезки. Он может разрезать большой пучок (до 40 на 40 дюймов) больших массивных квадратных и прямоугольных труб на секции. Ни один другой метод не может сделать это так эффективно.Однако трубы имеют тенденцию смещаться во время резки пучков, что приводит к некруглому сечению. Круглые трубы могут вращаться во время цикла резки, поэтому
может потребоваться прихватить один конец пучка, чтобы трубы не смещались и не вращались. Это может занять много времени и расточительно.
Ленточная пила имеет ограниченное применение при разрезании одной трубы, хотя некоторые специальные одноголовочные пилы могут разрезать отдельные трубы под углом. Он наиболее подходит для резки диаметром более 5 дюймов.OD и толстостенные секции.
Преимущества ленточной пилы:
- Режет весь пучок трубок.
- Выполняет резку под углом и под углом на специальных одноголовочных пилах.
Недостатки ленточной пилы:
- Прихваточная сварка одного конца пучка может потребоваться для предотвращения смещения и вращения трубок.
Токарно-режущий
Рисунок 3 Этот токарно-режущий станок вращает вращающуюся режущую головку вокруг неподвижной трубы.Он может разрезать деталь, а затем выполнять на ней внутреннюю и внешнюю фаску. ![]() |
Для резки труб адаптированы два типа токарной резки. Стандартный токарный станок используется уже много десятилетий. Трубка подается через зажимной механизм патронного типа, трубка вращается, и режущие инструменты (вставки), установленные на механизмах скольжения, разделяют трубку.
Поскольку труба вращается, ее длина не может превышать 20 футов. Такое ограничение длины может снизить производительность.
Другой тип токарного станка (токарный станок) вращает вращающуюся режущую головку вокруг неподвижной трубы (см. Рисунок 3 ).На вращающуюся головку можно установить до четырех режущих инструментов. Этот тип станка может разрезать деталь и выполнять на ней внутреннюю и внешнюю фаску. Дополнительные адаптеры позволяют снимать внутренние и внешние фаски на задней стороне каждой детали.
Токарная резка предназначена только для круглых труб. Как правило, он используется для резки высокопрочных труб с толстыми стенками для таких компонентов, как вкладыши подшипников (сталь 52100) и корпуса подушек безопасности, а также из экзотических материалов, таких как титан и сплавы INCOLOY®, для таких компонентов, как автомобильные оси.
Преимущества токарной резки:
- Режет все типы материалов — низкоуглеродистые и нержавеющие стали; алюминий; медь; бронза; и высокопрочные низколегированные (HSLA) стали.
- Режет диаметр от 0,375 до 8,00 дюймов и толщину стенки от 0,020 до 0,500 дюйма.
- Может производить готовые прецизионные детали за одну операцию.
- Имеется ЧПУ.
- Инструмент с твердосплавными вставками для быстрой переналадки.
- В процессе резки используется охлаждающая жидкость с сухим или мелкодисперсным туманом, поэтому для охлаждающей жидкости не требуется система фильтрации.
Недостатки токарной резки:
- Полностью автоматизированные системы относительно дороги.
- Время цикла относительно невелико.
- Профили, которые можно разрезать, ограничиваются круглой трубой.
- Длина трубы должна быть короткой при использовании стандартного метода резки на токарном станке.
- На детали необходимо снять фаску, чтобы избежать искажения идентификатора.
- Пластины режущего инструмента образуют значительное количество стружки.
Ротационная резка
Рисунок 4 Трубка удерживается на опорных роликах, в то время как режущее лезвие (колесо) вращается, врезаясь в трубку. |
Вращающаяся резка труб используется в промышленности более 50 лет. Первоначально он использовался в производстве алюминиевых труб для резки труб для кондиционирования воздуха. По мере развития технологии ее использование распространилось на все типы материалов и продуктов.
Ротационная резка трубы включает отрезание круглой трубы с помощью режущего лезвия, которое вращается вокруг диаметра трубы (см. Рисунок 4 ). Трубка удерживается на опорных роликах, в то время как вращающееся режущее лезвие (колесо) вращается, врезаясь в трубку.
Поскольку этим методом не образуется пропилов или сколов, потери материала отсутствуют. Вместо этого материал трубки перемещается — толкается к поверхности каждой стороны режущего лезвия. Вот почему на обрезанном конце трубки получается небольшой угол.Часть материала проталкивается к внутреннему диаметру трубки и небольшая часть к внешнему диаметру, создавая небольшую выпуклость на обрезанном конце трубки.
Этот метод подходит для резки прямых участков от 20 до 25 футов. НКТ, или для разрезания бухты трубок, которые можно разматывать и выпрямлять в процессе резки.
Основными применениями роторного метода являются производство алюминиевых автомобильных линий кондиционирования воздуха, стальных автомобильных трубопроводов перекачки жидкости, медных компонентов систем отопления, вентиляции и кондиционирования воздуха и, в некоторой степени, общих компонентов из углеродистой стали.
Традиционный ротационный отрезной станок имеет тенденцию искажать внутренний диаметр трубы. Были разработаны усовершенствования технологии, чтобы попытаться улучшить качество резки и уменьшить искажение ID.
Преимущества ротационной резки:
- Отсутствие потерь материала между резками.
- Без значительного заусенца.
- Нет пропила и сколов.
- Может использоваться со второстепенными операциями, такими как обработка канавок и снятие фаски.
- Позволяет достичь высокой производительности при обработке коротких деталей.
- Для резки мягких материалов, таких как алюминий и медь.
- Режет рулонный материал или отрезки прямой длины.
Недостатки роторной резки:
- Может вызывать усталость металла на обрезанных концах, что может быть вредным для вторичных операций.
- Профили, которые можно разрезать, ограничиваются круглой трубой.
- Концы трубок не имеют прямоугольной формы. Возникает небольшая фаска по внешнему диаметру, а также внутренний заусенец и деформация.
- Срок службы инструмента сокращается при резке твердых материалов.
Резка с опорой на ножницы
Рисунок 5 Материал режется между неподвижной секцией инструментов и подвижной секцией инструментов, подобно режущему действию ножниц. ![]() |
Метод резки с опорой на сдвиг был разработан в США более 50 лет назад. Станок для резки с опорой на ножницы оборудован двумя секциями инструментов — стационарной и подвижной.Каждая инструментальная секция содержит внутренний пуансон и внешний штамп. Стационарная секция инструментов поддерживает внутреннюю полость НКТ с помощью внутреннего штампа и поддерживает внешнюю часть с помощью плотно прилегающая внешняя матрица (см. Рисунок 5 ).
Последовательность резки начинается, когда трубная заготовка фрезерной длины загружается на станок через внешние матрицы обеих секций инструмента и через оба внутренних пуансона. Толкатель продвигает трубку к регулируемому упору пальца, расположенный позади подвижной инструментальной оснастки.Стопорный палец регулируется по длине реза. Когда трубка попадает в стопорный механизм или заданную длину, срезание
цикл начинается. Материал режется между неподвижной секцией инструментов и подвижной секцией инструментов, подобно режущему действию ножниц.
На некотором оборудовании подвижная секция сначала перемещается по вертикали, а затем по горизонтали. В других случаях подвижная часть выполняет эллиптическую петлю для завершения разреза.
В конце цикла резки подвижная часть возвращается в фиксированное положение, концентричное с неподвижной частью, и следующая труба, которую нужно разрезать, продвигается вперед.Это выталкивает отрезанный сегмент, и процесс повторяется.
Поддерживаемые преимущества резки ножницами:
- Отсутствие потерь материала между резками.
- Качественный пропил, без заусенцев.
- Режет все типы материалов.
- Высокая скорость цикла обработки деталей короче 24 дюймов
- Требуется длительный срок службы инструмента до переточки.
- Режет квадратные и прямоугольные формы, а также круглые.
- Для резки толстостенных и толстостенных труб.
Поддерживаемые недостатки резки ножницами:
- Трубы тонкой длины должны быть очень прямыми.
- Трубы тонкой длины должны иметь минимальный внутренний заусенец сварного шва.
- Качество резки зависит от точной подгонки внутреннего и внешнего диаметра.
Ножницы для резки с двумя лезвиями
Ножницы для резки НКТ используются более 75 лет. Режущие ножницы с двумя лезвиями пришли на смену технологии резки с одним лезвием. Двойное лезвие было разработано для устранения ямок, которые обычно образуются на конце трубы во время резки с одним лезвием.
При использовании этого метода трубка удерживается в зажимных штампах. Горизонтальное лезвие выполняет начальную зачистку части стенки трубы, так что вертикальное лезвие встречает меньшее сопротивление и пробивает стенку трубы без углублений (см. Вводную фотографию ).
Наиболее подходит для углеродистых сталей и легированных сталей, включая ферритные нержавеющие стали.
Для каждого диаметра трубы требуется собственный набор зажимных матриц. Зажимные матрицы закалены и отшлифованы с точными допусками. Они относительно недороги и могут быть переточены для использования до 3 миллионов резов. Четыре секции зажимной матрицы собраны в две секции, что позволяет им открываться и закрываться для подачи и зажима трубки и обеспечивать зазор для горизонтального и вертикального
лезвия.
Во время процесса резки горизонтальное лезвие удаляет только небольшое количество материала, но это необходимо для создания зоны с надрезами для входа вертикального лезвия. Первоначальное проникновение вертикального лезвия направляет пулю внутрь трубы.Эта пуля складывается под лезвием и проталкивается через дно трубы.
В зависимости от толщины и диаметра стенки на торце могут быть заусенцы и острые края.
Преимущества резки с двумя ножами:
- Режет квадратные и прямоугольные формы, а также круглые.
- Для резки труб из прямых отрезков или из бухт.
- Может быть интегрирован со второстепенными операциями.
- Крой квадратный, без искажений.
- Допуски на общую длину 0,010 дюйма достижимы.
- Имеет быстросменный инструмент.
- Может быть интегрирован с загрузчиками пакетов для резки больших объемов.
- Возможна производительность до 7000 резов в час.
Недостатки резки ножницами с двумя ножами:
- Диапазон материалов, которые он может резать, ограничен диаметром от 0,125 до 6,50 дюйма. и толщиной стенки от 0,020 до 0,250 дюйма
- При каждой резке происходит потеря материала.
- Нельзя резать аустенитную нержавеющую сталь, экзотические сплавы, мягкую медь или алюминий.
- На некоторых размерах есть заусенцы и острые кромки.
Лазерная резка
Рисунок 6 Материал режется между неподвижной секцией инструментов и подвижной секцией инструментов, подобно режущему действию ножниц. |
Первые рабочие лазеры были разработаны в 1960 году.К 1969 году промышленные лазеры применялись для различных операций сварки и резки. В технологии лазерной резки используется источник питания, который генерирует луч электромагнитного (ЭМ) излучения. Луч имеет определенную длину волны, и эти длины волн однородны, параллельны и синфазны друг с другом (см. , рисунок 6, ).
Две наиболее широко используемые лазерные системы — это двуокись углерода (CO 2 ) и неодим, взвешенный в кристалле иттриевого алюминиевого граната (Nd: YAG).
Лазеры чаще всего используются для резки сложных деталей труб, которые требуют нескольких последовательных процедур, таких как сверление, штамповка, фрезерование, распиловка и удаление заусенцев. Лазерная резка позволяет полностью обработать деталь за одну операцию на одном станке с использованием одного инструмента. Можно исключить последовательные вторичные операции. Лазерная резка — неэффективный метод производства одного типа профиль, например только квадратные трубы.
Кроме того, лазерная резка хорошо подходит для производства по требованию и мелкосерийного производства, а также когда требуется множество модификаций.
Преимущества лазерной резки:
- Может использоваться практически для всех форм труб.
- Подходит для сложных деталей.
- Подходит для мелкосерийного производства.
- Некоторые второстепенные операции можно исключить.
- Качество резки хорошее.
Недостатки лазерной резки:
- Большинство систем относительно дороги по сравнению с другими методами резки. • Серьезное внимание следует уделять всему производственному процессу, включая затраты на техническое обслуживание и эксплуатацию, а также потенциальную экономию за счет сокращения затрат на рабочую силу, погрузочно-разгрузочные работы и вторичных операций, чтобы обеспечить приемлемую окупаемость инвестиций (ROI).
- Неэффективный метод изготовления одного профиля или простой операции.
Достижения в технологии резки
Лезвия. Постоянное развитие технологии пильных полотен расширяет область применения пилы. Многие пилы, ножницы и вращающиеся полотна изготавливаются из высокопрочных сталей. Некоторые из них имеют покрытие, чтобы продлить срок службы лезвия, сохранить твердость и противостоять размягчению от тепла, выделяемого во время процесса пиления. В некоторых случаях лезвия имеют твердосплавные наконечники для улучшения производительность.
Автоматика. Сегодняшние высокие производственные требования и потребность в деталях более высокого качества привели к тенденции к большей автоматизации. Возможно, больше не будет рентабельно вырезать детали на одном станке и вручную передавать их на вспомогательную операцию. Автоматизированное погрузочно-разгрузочное оборудование обрабатывает трубы на высоких скоростях, автоматически загружает трубы для резки или вторичных операций, и укладывает трубки в бункеры или связки.
Сервоприводы. Новые машины для резки с опорой на ножницы загружают трубы в отрезную машину с серводвигателем в узле захвата.
Интеграция. Встроенная автоматизация была разработана для интеграции отрезных станков со второстепенными операциями, такими как удаление заусенцев с помощью проволочной щетки и чистовая обработка концов. Благодаря интегрированным системам возможна скорость производства более 5000 готовых трубчатых деталей в час.
Алек Баниш — вице-президент по продажам и маркетингу, Haven Mfg. Corp., 370 Sterling Industrial Park, Brunswick, GA 31525-3938, 912-265-7536, факс 912-264-9001, [email protected], www.havencut.com.
Руководство для инженера по гидроабразивной резке> ENGINEERING.com
Детали, вырезанные с использованием абразивной гидроабразивной резки. (Изображения любезно предоставлены Jet Edge, Omax и Flow International.)
Вы не приблизитесь к духу инженерии, чем когда-то начинали гидроабразивную резку.«Я начал много лет назад, примерно в 71 году», — сказал доктор Джон Олсен, один из основоположников технологии гидроабразивной резки и в настоящее время вице-президент по производству Omax Abrasive Waterjets. «Я читал об экспериментах, проведенных в Англии и моем друге по резке горных пород, и подумал, что было бы весело попробовать построить насос и что-нибудь отрезать.Это было что-то вроде закулисной операции; это было в моем гараже и в его гараже ».
Доктор Джон Олсен держит водомет с наклонной головкой и двумя линейными приводами. (Изображение любезно предоставлено Omax.)
Это может походить на многие истории, которые вы слышите о стартапах в Кремниевой долине сегодня, но связь между гидроабразивной обработкой и вычислительными технологиями более глубокая, как объяснил д-р Олсен:«Как ни странно, одним из самых больших изменений, сделавших абразивные струи практичными, стало появление ПК.Струя — не очень жесткий инструмент — он изгибается повсюду, сужается и все такое. Чтобы изготавливать прецизионные детали, вам понадобится немало вычислительных мощностей, чтобы предсказать, какой будет форма струи, чтобы вы могли ее компенсировать. В то время нам сказали: «Никто и никогда не возьмёт ПК в заводском цеху. Разве это не смешно сегодня?
Основы Waterjet
Чистая и абразивная водоструйная очистка
Абразивная водоструйная насадка. (Изображение любезно предоставлено Omax.)
В самом широком смысле термин «гидроабразивная резка» охватывает любой режущий инструмент, в котором используется струя воды под высоким давлением.Более конкретно, гидроабразивы можно разделить на подкатегории чистых и абразивных материалов.Термин «чистая гидроабразивная резка» относится к режущим инструментам, в которых используется только вода, в то время как термин «абразивная гидроабразивная струя» или иногда просто «абразивная струя» относится, как вы могли догадаться, к гидроабразивным инструментам, в которых для ускорения процесса резки используется абразив.
Pure waterjet используется для резки более мягких материалов, включая прокладки, пену, продукты питания, бумагу, пластик и ковер.
Абразивная гидроабразивная резка используется для резки более твердых материалов, таких как металл, керамика, камень, дерево и стекло.
АбразивыWaterjet обычно изготавливаются из граната с размером зерна от 50 до 220 меш, хотя 80 является наиболее распространенным. Многие гидроабразивные машины могут переключаться с чистой гидроабразивной резки на абразивную гидроабразивную резку, что делает их универсальными.
Материалы для гидроабразивной резки
Универсальность — одна из главных сильных сторон гидроабразивной технологии. Чтобы проиллюстрировать огромное количество материалов, которые можно разрезать с помощью гидроабразивной резки, Чип Бернхэм, вице-президент по глобальному маркетингу Flow International Corporation, представил список материалов в порядке скорости резки, от самой медленной до самой быстрой, для любой заданной постоянной толщины материала. :
Примерный список материалов, которые можно резать с помощью абразивной гидроабразивной резки, в порядке скорости резания от самой низкой до самой высокой.
Этот список ни в коем случае не является исчерпывающим, и на самом деле легче перечислить то, что не поддается гидроабразивной резке.«Есть только несколько вещей, которые мне не удалось сократить за свою карьеру», — сказал Бернхэм.
«Одно из них — закаленное стекло — хотя некоторые люди до сих пор это делают, закаленное стекло необходимо снова запечатать, потому что в нем есть напряжения, и когда вы режете его водяной струей, вы снимаете напряжение. Я вырезал красивые вещи из закаленного стекла и изумлял стеклодувов в первые годы водоструйной резки, чтобы вернуться в лабораторию на следующий день и найти миллион частей, потому что они разбились за ночь.”
Скотт Виртанен, региональный менеджер по продажам Jet Edge, также подчеркнул универсальность гидроабразивной резки: «Гидроабразивная резка будет практически одинаково работать практически с любым материалом. Таким образом, универсальность гидроабразивной резки как по материалам, так и по толщине не имеет себе равных ».
Давление гидроабразивной резки
Если вы хоть немного пообщались с инженерами по гидроабразивной резке, вы, вероятно, знакомы с давней темой споров: насколько сильно давление?
Один из способов понять, какое огромное давление возникает при гидроабразивной резке, — это сравнить его с другими источниками воды с точки зрения максимальных фунтов на квадратный дюйм (psi).
Логарифмическая шкала для сравнения четырех источников воды с точки зрения верхних пределов давления.
Как видно из этого графика, давление может иметь огромное значение — например, между мытьем рук и их отрезанием. Но колебания давления в гидроабразивной струе намного меньше, обычно 60 000–90 000 фунтов на квадратный дюйм.
Некоторые инженеры утверждают, что более высокое давление является ключом к более быстрой резке, в то время как другие утверждают, что действительно имеет значение эффективность двигателя.
Чтобы встряхнуть обе стороны, давайте на минутку рассмотрим их аргументы.
90,000psi против 60,000psi
Сторонники 90k отмечают, что увеличение давления гидроабразивного насоса с 60 000 фунтов на квадратный дюйм до 90 000 фунтов на квадратный дюйм увеличивает скорость потока, что, по их мнению, увеличивает скорость резания на 50 процентов или более, в зависимости от применения.
A Flow Mach 4c Dynamic XD для гидроабразивной резки углеродного волокна. (Изображение любезно предоставлено Flow International.)
Они также утверждают, что резка под давлением 90 000 фунтов на квадратный дюйм снижает расход абразива, поскольку каждая частица граната передает больше энергии.Наконец, предполагается, что более высокое рабочее давление при прошивке и резке уменьшает расслоение композитных материалов.«Скорость резки напрямую зависит от мощности сопла», — сказал Бернхэм. «Итак, потребляемая мощность в лошадиных силах зависит от количества воды, выходящей из отверстия, и давления. Небольшое отверстие с низким давлением потребляет очень мало энергии и медленно режет. Напротив, отверстие большего размера с высоким давлением потребляет много энергии и быстрее режет. Количество воды и давление требуют лошадиных сил.”
Виртанен соглашается, заявляя, что если бы вы использовали ту же комбинацию сопла и отверстия, такое же количество абразива и тот же объем воды, 90 000 фунтов на квадратный дюйм все равно будут превосходить 60000 фунтов на квадратный дюйм каждый раз.
«Однако, — добавил он, — эта область может быть немного затемнена, если вы начнете смотреть на две режущие головки, использующие один насос. Например, насос-усилитель на 60 000 фунтов на квадратный дюйм при мощности 100 лошадиных сил будет производить два галлона в минуту. Насос мощностью 100 лошадиных сил при давлении 90 000 фунтов на квадратный дюйм выдает примерно 1.4 или 1,5 галлона в минуту. Таким образом, способность приводить в действие двойные режущие головки в этот момент ограничена для насоса 90 000 фунтов на квадратный дюйм из-за того, на что он способен ».
Гидроабразивная установка Mach 4c с двумя головками. (Изображение любезно предоставлено Flow International.)
Виртанен продолжил: «При 1,4 или 1,5 галлона в минуту с насосом мощностью 90 000 фунтов на квадратный дюйм и мощностью 100 лошадиных сил вы можете работать при максимальном давлении через отверстия 0,011 дюйма. Насос мощностью 100 лошадиных сил и 60 000 фунтов на квадратный дюйм может работать через отверстия 0,015 дюйма. Таким образом, из-за этой разницы, обусловленной пропускной способностью каждого из насосов, вы можете резать с одинаковой скоростью с двумя головками.”
В ответ на эти утверждения сторонники 60k указывают, что если вы увеличиваете давление, вам необходимо уменьшить размер сопла. Это основано на том факте, что мощность пропорциональна давлению, умноженному на объемный расход, как показано в формуле:
Мощность = кПВ
Сторонники 90k могут ответить, что сопло с более высоким давлением и меньшим объемом будет резать быстрее, потому что оно имеет более высокую удельную мощность (то есть такое же количество мощности на меньшей площади), но сторонники 60k отрицают, что это верно за пределами применения чистой гидроабразивной резки. .
«Одна из серьезных проблем заключается в том, что если вы хотите прокачать 90 000, то вы застряли с усилителем, а насосная система усилителя настолько неэффективна, что вы действительно получаете большую мощность резки при более низком давлении с насосом с прямым приводом, — сказал Олсен. «Таким образом, эффективность превосходит давление».
Это поднимает важное различие в гидроабразивной технологии и другую спорную тему: усилители и насосы с прямым приводом.
Водоструйные насосы: усилитель против прямого привода
Схема насоса гидроусилителя.(Изображение любезно предоставлено Jet Edge.)
В водоструйных насосах есть два основных типа насосов: с прямым приводом и с усилителем. Насосы с прямым приводом используют коленчатый вал для перемещения плунжеров, которые создают давление воды, тогда как в усилителях используются гидроцилиндры.У каждого типа есть преимущества и недостатки, как объяснил Виртанен:
«Насосы с прямым приводом по своей сути имеют более простую конструкцию, но требуют значительно большего обслуживания, чем насос с усилителем. Поскольку они более просты в конструкции, они менее дороги для первоначальных вложений, но в долгосрочной перспективе насосы-интенсификаторы имеют значительно более низкую стоимость владения.”
Схема насоса с прямым приводом. (Изображение любезно предоставлено Jet Edge.)
Следовательно, если первоначальные вложения являются вашей основной задачей, тогда вам подойдет насос с прямым приводом. С другой стороны, если вы стремитесь к минимальным затратам на техническое обслуживание, лучше использовать насос-усилитель. Это иллюстрирует один из основных принципов производства: все сводится к вашему конкретному применению.Стоимость гидроабразивной резки
Как и в случае с любой производственной технологией, существует несколько способов расчета стоимости гидроабразивной резки.Однако некоторые дают более точную оценку, чем другие. Например, попытка подсчитать затраты в долларах за час машинного времени проблематична, потому что гидроабразивы могут быть сконфигурированы с одной или несколькими режущими головками, что влияет на время резки.
Толстые детали из пеноматериала, вырезанные с помощью гидроабразивной машины Flow Mach 4c Dynamic XD. (Изображение любезно предоставлено Flow International.)
Типичный ценовой диапазон для гидроабразивной машины с одной режущей головкой составляет приблизительно 100-135 долларов США в час, хотя дорогие детали могут работать до 2000 долларов США в час в зависимости от типа материала и толщины, а также геометрии детали.Эти же три фактора затрудняют расчет стоимости гидроабразивной резки в долларах на квадратный дюйм разрезаемого материала, поскольку все они способствуют увеличению времени резки.Наилучший подход к расчету затрат на гидроабразивную резку — в долларах за деталь. Однако есть большой список факторов, которые используются в таких расчетах, в том числе:
- Время, необходимое для программирования траектории инструмента
- Риск поломки хрупким материалом
- Сколько раз нужно проткнуть материал
- Стоимость расходных материалов
- Время установки, разгрузки и обслуживания
- Количество для заказа
Распространенные заблуждения о гидроабразивной резке
Режущая головка на обрабатывающем центре MAXIEM 1515 JetMachining.(Изображение любезно предоставлено Omax.)
«Когда они начинались, они были своего рода орудием последней надежды», — объяснил д-р Олсен. «Струя не была очень жестким и точным режущим инструментом, поэтому первые абразивные струи, скажем, в 80-х годах, использовались, если у вас не было абсолютно другого способа резать материал. Затем вы возьмете абразивную струю и ожидаете получить очень неточный рез, почти как при кислородно-ацетиленовом горении. Поскольку гидроабразивная резка началась с этого приложения, потребовалась долгая борьба за то, чтобы принять их в качестве точной техники обработки.”Еще одно распространенное заблуждение о гидроабразивных станках связано с их способностью резать более толстые материалы, как объяснил Бернхэм: «Люди говорят, что вода и абразив не могут резать толстые [секции], но мы можем прорезать толщину более одного фута практически в любом обычном материале. Нам придется резать медленнее, но он может резать толстые «.
Толстая стальная шестерня для резки с гидроабразивом. (Изображение любезно предоставлено JetEdge.)
«У меня есть люди, которые экономят недели на резке за счет черновой обработки материала толщиной 24 дюйма», — добавил Бернем.«Они черново обрабатывают его, а затем помещают на мельницу и, черновая обработка, экономят недели времени на измельчение, но это не обычное дело — большинство резки в наши дни составляет три дюйма или меньше»Конечно, тот факт, что черновая обработка с помощью гидроабразивной резки позволяет сэкономить время, не означает, что это особенно быстрый метод резки по сравнению с плазменной или лазерной резкой.
«Многие клиенты ожидают, что они будут резать на той же скорости, что и лазер или плазма», — заметил Виртанен. «Гидроабразивная резка определенно медленнее, поэтому нельзя упускать из виду важность двух режущих головок или трех из четырех режущих головок.”
Это приводит нас к неизбежным сравнениям между гидроабразивной резкой и другими технологиями резки, включая лазерную, плазменную и плазменную резку. Несмотря на то, что каждый метод резки имеет свои преимущества и недостатки, гидроабразивной резке часто не уделяется должного внимания, несмотря на ее преимущества.
«Сейчас это начинает меняться, — сказал доктор Олсен, — но, по крайней мере, десять лет я бы сказал, что так было. Но он начинает меняться, потому что стал популярным и теперь используется в качестве первой операции практически для всего, что человек хотел бы сделать.Многие магазины используют водоструйную очистку таким образом ».
Так каковы преимущества гидроабразивной резки?
Преимущества гидроабразивной резки
Waterjet имеет два основных преимущества по сравнению с другими методами резки: универсальность и простота.
Его универсальность иллюстрируется огромным разнообразием материалов и толщин, которые можно разрезать с помощью гидроабразивной резки, но его простоту лучше всего можно проиллюстрировать, сравнив гидроабразивную резку с лазерной, плазменной и газовой резкой.
Waterjet vs.Лазер
Лазерная резка.
При лазерной резке сфокусированный луч света используется для плавления, сжигания или испарения разрезаемого материала. Лазер может быть статическим, когда материал движется под ним, или он может двигаться по материалу, который остается на месте. В последнем случае требуется дополнительная оптика для компенсации изменений расстояния от излучающего конца лазера.Хотя лазерная резка часто рассматривается как дополнение к гидроабразивной резке, и многие магазины используют обе технологии, последняя имеет некоторые явные преимущества перед первой.
«По сравнению с лазером, например, когда вы смотрите на титан, нержавеющую сталь или алюминий, есть ограниченные возможности по толщине. Я думаю, что максимальная толщина в целом составляет от полутора до полутора дюймов », — сказал Виртанен.
«Мы прорезали материал толщиной восемь или девять дюймов. Когда вы смотрите на возможности лазера, обычно понимаете, что есть трудности с обработкой отражающих материалов, таких как алюминий или любые желтые металлы, такие как бронза или медь », — добавил он.
Другими словами, материалы и толщина материалов, которые трудно или невозможно разрезать с помощью лазера, обычно не представляют особых трудностей для гидроабразивной резки. Эта способность резать толстые материалы — одна из причин, по которой гидроабразивная резка является популярным выбором для черновой обработки деталей, а обработка поверхности — другой.
«Самое прекрасное в черновой обработке с помощью гидроабразивной резки на мельнице — это то, что это чистая поверхность, прошедшая процесс эрозии», — сказал Бернхэм. «Если вы попытаетесь выполнить черновую резку с помощью плазмы или лазера, а затем закончите ее на фрезере, вы удаляете механически упрочненный и термоупрочненный материал.”
Это раскрывает одно из самых больших преимуществ гидроабразивной резки — отсутствие зон термического влияния (HAZ). Это проблема лазерной резки и другой конкурирующей технологии производства: плазменной резки.
Гидравлическая струя против плазмы
Плазменная резка.
Плазменная резка работает с электропроводящими материалами с использованием ускоренного потока газа, который превращается в плазму с помощью электрической дуги. Плазма плавит материал, двигаясь достаточно быстро, чтобы выдувать расплавленный металл из зоны резки.Хотя плазменная резка обычно быстрее, чем гидроабразивная, она страдает, когда дело касается чистовой обработки поверхности.
«Плазма может превзойти гидроабразивную резку по скорости, но качество резки намного хуже», — сказал Виртанен. «Что касается качества кромок, допусков и дополнительных операций, которые требуются для плазменной резки, вы не увидите тех, которые используются для гидроабразивной резки».
ЗТВ делает вторичные операции плазменной (и лазерной) резки еще более проблематичными, так как ЗТВ может упрочнить поверхности и сделать их более хрупкими.Это, в свою очередь, затрудняет выполнение второстепенных операций, таких как нарезание резьбы или снятие фаски.
Еще одно преимущество гидроабразивной резки перед плазменной, в частности, заключается в способности резать материалы, которые нелегко плавятся, например гранит, или материалы, разрушающиеся при плавлении, например ламинат.
Гидроабразивная резка против газовой резки
Газовая резка.
Газовая резка, которая используется только для чугуна и стали, включает нагрев металлов до высоких температур с последующим введением кислорода для плавления металла для резки.Нагретый металл реагирует с кислородом и образует оксид железа, температура плавления которого ниже, чем у самого металла.Еще раз, основное преимущество гидроабразивной резки перед этой конкурирующей технологией резки — это ее способность резать не только железо и сталь. В отличие от газовой резки, при которой образуются зоны термического влияния, гидроабразивная резка не вызывает значительного нагрева разрезаемого материала. Несмотря на то, что во время прошивки он может нагреваться до 120 ° F (49 ° C), во время резки материал нагревается только на несколько градусов.
Гидроабразивная резка также более точна, чем газовая резка, и первая оставляет почти пескоструйную обработку, которая значительно более гладкая, чем шероховатые края, полученные при газовой резке. Меньший пропил, получаемый с помощью гидроабразивной резки, является еще одним преимуществом, особенно при резке дорогих материалов.
Будущее гидроабразивной резки
Несмотря на универсальность и простоту, гидроабразивная резка остается относительно нишевой технологией резки. У такого положения вещей множество причин, но Бернхэм особо выделил одну:
«Какая резка из твердых материалов наиболее распространена? Это низкоуглеродистая сталь, которую можно резать все: плазменная резка, лазер, пуансоны, фрезы, фрезерные станки, пилы; резать низкоуглеродистую сталь может каждый.Переходя к листу, все еще многие процессы могут разрезать низкоуглеродистую сталь в листе. По сути, по мере того, как вы уходите от супер-распространенных материалов к более экзотическим материалам и получаете более толстые, примерно до 30 см, вы попадаете в царство, где сияет гидроабразивная струя ».
Металлические шестерни, нарезанные гидроабразивом. (Изображение любезно предоставлено Flow International.)
Это говорит о том, что по мере того, как производители переходят на более экзотические материалы, спрос на гидроабразивную обработку будет расти. Итак, если вы хотите заняться гидроабразивной резкой, с чего начать?«Самое важное — это сделать тестовые разрезы, чтобы убедиться, что он делает то, что вы думаете», — сказал доктор- посоветовал Олсен. «Вы хотите знать, насколько точной получилась деталь. Подходит ли покрытие для моего применения? Как долго это займет?
«Эти вещи лучше всего известны, когда на самом деле изготавливаются детали, которые указывают на то, какие детали вы собираетесь изготавливать. Есть много вещей, на которые стоит обратить внимание. Например, если вы делаете что-то из углеродного волокна и хотите его разрезать, вам нужно посмотреть и узнать о расслоении при пирсинге и найти способ его минимизировать », — заключил он.
Для получения дополнительной информации о гидроабразивной резке посетите сайт WaterJets.org или посетите веб-сайты Flow International, Jet Edge и OMAX.
Следуйте за Иэном Райтом на Twitter.
Создайте свой собственный опрос отзывов пользователейОценка методов резки | Оценка методов снятия морских сооружений
2
Оценка техники резания
Для того чтобы любая техника резки была эффективной, она должна быть безопасной, надежной, воспроизводимой, гибкой и адаптируемой к полевым условиям, экологически чувствительной и экономичной.Методы резки, описанные в этой главе, либо доступны в промышленности, либо находятся в стадии разработки для использования при подводной резке свай, проводов и других компонентов платформы.
Методы резки можно разделить на две общие категории: взрывные и невзрывоопасные. В настоящее время используемые взрывные резаки представляют собой объемные заряды, сконфигурированные объемные заряды и другие режущие заряды, такие как линейно кумулятивные заряды. Заряды для гидроразрыва и режущая лента, такая как контактная и рефракционная лента, могут найти применение в будущем.Доступные методы невзрывной резки включают механические резаки с вращающимися лезвиями с гидравлическим приводом; абразивные резаки с использованием песка или шлака с водяными насосами большого объема и низкого давления; абразивные фрезы с использованием водяных насосов малого объема под высоким давлением с впрыскиванием граната в сопло; и водолазные режут с помощью кислородно-дуговой горелки. Потенциальные методы невзрывной резки могут включать гидравлические ножницы, алмазные канатные пилы, химические резаки, лазерные резаки, пиротехнику (металлический порошок), химикаты и криогенную технику.Ни один из методов невзрывной резки не был разработан для коммерческого использования, хотя некоторые из них были продемонстрированы в контролируемых условиях.
МЕТОДЫ ВЗРЫВОРЕЗКИ
В Таблице 2-1 перечислены три метода взрывной резки, которые доступны в настоящее время, а некоторые могут быть доступны в будущем.
ТАБЛИЦА 2-1 Методы взрывной резки
Настоящее время | Будущее |
Объемные заряды ВВ (C-4, Comp B) | Режущие заряды (лента взрывчатого вещества) |
Настроенные объемные заряды (кольцевые заряды, фокусирующие заряды) | Заряды гидроразрыва (контактная гипсовая лента; ударопреломляющая лента) |
Режущие заряды (линейно-кумулятивные заряды со сборными контейнерами) | Заряды взрывчатого вещества прочие (сфокусированные ударной волной, радиальные полые заряды) |
Существующие методы взрывной резки
Заряды массовых взрывчатых веществ
Чаще всего используется метод резки свай и проводов с использованием насыпных взрывчатых веществ.Литые и формованные взрывчатые вещества, такие как C-4 и Comp B, имеют высокую скорость при детонации и разрушающую способность (бризанс), которая на 15–30 процентов выше, чем TNT (Herbst, 1986). Компоненты B и C-4 не так опасны в обращении, как другие взрывчатые вещества, и могут быть отформованы в полевых условиях до требуемых размеров и формы. После более чем четверти века использования и сотен тысяч рабочих часов не было зарегистрировано серьезных травм в результате обращения или использования взрывчатых веществ в больших объемах при перемещении платформы.
При установке платформы сваи свариваются в трубчатые секции. Цилиндрические стальные направляющие (называемые направляющими для опор) обычно привариваются к внутренней части нижней части каждой секции сваи для облегчения стыковки с предыдущей секцией. Следовательно, внутренний диаметр на направляющей для зазубрин (выше и ниже сварного шва) меньше внутреннего диаметра сваи. Это важное соображение при использовании большинства других методов резки, но это лишь незначительное неудобство при размещении насыпных зарядов, размер которых может быть достаточным для разделения кучи, и их не нужно извлекать.Объемные заряды могут иметь форму, соответствующую размерам сваи или колодца, которые отличаются от строительных чертежей. Например, если самая маленькая обсадная колонна в скважине имеет диаметр 7 дюймов вместо 9,5 дюймов, как ожидалось, объемные взрывчатые вещества могут быть преобразованы в меньший контейнер с небольшой задержкой или без нее. Насыпные взрывчатые вещества также могут быть размещены в обычных сваях и колодцах без использования водолазов.
Насыпные заряды опускаются в подготовленные сваи и колодцы и взрываются практически одновременно (с 0.9-секундная задержка) группами по восемь или меньше человек. Все сваи и колодцы можно разрубить в течение часа или двух; это включает время, необходимое для загрузки взрывчатых веществ в конструкцию и проведения воздушного поиска черепах и морских млекопитающих (наблюдатели Национальной службы морского рыболовства [NMFS] проводят визуальный поиск в течение как минимум 48 часов до взрыва). Когда используются объемные взрывчатые вещества, колодцы и сваи обычно опускаются на несколько дюймов, что является явным признаком того, что они полностью прорваны.