Π‘ΠΏΠΎΡΠΎΠ±Ρ Π·ΠΈΠΌΠ½Π΅Π³ΠΎ Π±Π΅ΡΠΎΠ½ΠΈΡΠΎΠ²Π°Π½ΠΈΡ: ΠΠ΅ΡΠΎΠ½ΠΈΡΠΎΠ²Π°Π½ΠΈΠ΅ Π·ΠΈΠΌΠΎΠΉ: ΡΠΏΠΎΡΠΎΠ±Ρ, ΠΎΡΠΎΠ±Π΅Π½Π½ΠΎΡΡΠΈ, Π½Π΅ΠΎΠ±Ρ ΠΎΠ΄ΠΈΠΌΡΠ΅ ΠΌΠ΅ΡΠΎΠΏΡΠΈΡΡΠΈΡ
ΠΠΈΠΌΠ½Π΅Π΅ Π±Π΅ΡΠΎΠ½ΠΈΡΠΎΠ²Π°Π½ΠΈΠ΅
ΠΠΈΠΌΠ½Π΅Π΅ Π±Π΅ΡΠΎΠ½ΠΈΡΠΎΠ²Π°Π½ΠΈΠ΅: Π°ΠΊΡΡΠ°Π»ΡΠ½ΠΎΡΡΡ ΠΏΡΠΎΠ±Π»Π΅ΠΌΡ
ΠΠ΅ΠΎΠ³ΡΠ°ΡΠΈΡΠ΅ΡΠΊΠΎΠ΅ ΠΏΠΎΠ»ΠΎΠΆΠ΅Π½ΠΈΠ΅ Π½Π°ΡΠ΅ΠΉ ΡΡΡΠ°Π½Ρ ΠΈ ΠΎΡΠΎΠ±Π΅Π½Π½ΠΎΡΡΠΈ Π΅Ρ ΠΎΡΠ΄Π΅Π»ΡΠ½ΡΡ
ΠΊΠ»ΠΈΠΌΠ°ΡΠΈΡΠ΅ΡΠΊΠΈΡ
Π·ΠΎΠ½ ΡΠΏΠΎΡΠΎΠ±Π½Ρ Π²Π½ΠΎΡΠΈΡΡ ΡΠ²ΠΎΠΈ ΠΊΠΎΡΡΠ΅ΠΊΡΠΈΠ²Ρ Π² ΡΡΠ΅ΡΡ ΡΡΡΠΎΠΈΡΠ΅Π»ΡΡΡΠ²Π° Π² Ρ
ΠΎΠ»ΠΎΠ΄Π½ΡΠΉ ΠΏΠ΅ΡΠΈΠΎΠ΄ Π³ΠΎΠ΄Π°. ΠΡΡΠ΅ΡΡΠ²Π΅Π½Π½ΠΎ ΠΏΡΠ΅Π΄ΠΏΠΎΠ»ΠΎΠΆΠΈΡΡ, ΡΡΠΎ Π·Π°ΡΡΠ°ΡΡ Π½Π° ΡΡΡΠΎΠΈΡΠ΅Π»ΡΡΡΠ²ΠΎ Π² Π·ΠΈΠΌΠ½Π΅Π΅ Π²ΡΠ΅ΠΌΡ Π³ΠΎΠ΄Π°, Π½Π΅ΡΠΊΠΎΠ»ΡΠΊΠΎ Π²ΡΡΠ΅, Π½Π΅ΠΆΠ΅Π»ΠΈ Π² Π»Π΅ΡΠ½ΠΈΠΉ ΠΏΠ΅ΡΠΈΠΎΠ΄ ΠΈΠ»ΠΈ Π² ΠΌΠ΅ΠΆΡΠ΅Π·ΠΎΠ½ΡΠ΅, Π° ΠΏΡΠΎΠ²Π΅Π΄Π΅Π½ΠΈΠ΅ ΡΠ°Π±ΠΎΡ ΡΠ²ΡΠ·Π°Π½ΠΎ Ρ ΡΠ°Π·Π»ΠΈΡΠ½ΠΎΠ³ΠΎ ΡΠΎΠ΄Π° ΠΏΡΠΎΠ±Π»Π΅ΠΌΠ°ΠΌΠΈ ΠΈ ΡΠ»ΠΎΠΆΠ½ΠΎΡΡΡΠΌΠΈ. ΠΠ΄Π½ΠΈΠΌ ΠΈΠ· Π²Π°ΠΆΠ½ΡΡ
ΡΡΠ°ΠΏΠΎΠ² ΡΡΡΠΎΠΈΡΠ΅Π»ΡΠ½ΡΡ
ΡΠ°Π±ΠΎΡ ΡΠ²Π»ΡΠ΅ΡΡΡ ΠΈ Π·ΠΈΠΌΠ½Π΅Π΅ Π±Π΅ΡΠΎΠ½ΠΈΡΠΎΠ²Π°Π½ΠΈΠ΅, ΠΊΠΎΡΠΎΡΠΎΠ΅ ΠΈΠΌΠ΅Π΅Ρ ΡΠ²ΠΎΠΈ ΠΎΡΠΎΠ±Π΅Π½Π½ΠΎΡΡΠΈ ΠΈ ΠΎΡΡΡΠ΅ΡΡΠ²Π»ΡΠ΅ΡΡΡ Ρ ΠΈΡΠΏΠΎΠ»ΡΠ·ΠΎΠ²Π°Π½ΠΈΠ΅ΠΌ ΡΠΎΠ²ΡΠ΅ΠΌΠ΅Π½Π½ΡΡ
ΠΌΠ΅ΡΠΎΠ΄ΠΎΠ².
Π‘ΡΠΎΠΈΡ ΠΏΠΎΠ½ΠΈΠΌΠ°ΡΡ, ΡΡΠΎ ΡΠ°Π·Π²ΠΈΡΠΈΠ΅ ΡΡΡΠΎΠΈΡΠ΅Π»ΡΠ½ΡΡ
ΡΠ΅Ρ
Π½ΠΎΠ»ΠΎΠ³ΠΈΠΉ Π½Π΅ ΡΡΠΎΠΈΡ Π½Π° ΠΌΠ΅ΡΡΠ΅: ΠΏΠΎΡΠ²Π»ΡΡΡΡΡ Π½ΠΎΠ²ΡΠ΅ ΡΠΏΠΎΡΠΎΠ±Ρ Π±Π΅ΡΠΎΠ½ΠΈΡΠΎΠ²Π°Π½ΠΈΡ, ΠΈΡΠΏΠΎΠ»ΡΠ·ΡΡΡΡΡ ΠΈΠ½Π½ΠΎΠ²Π°ΡΠΈΠΎΠ½Π½ΡΠ΅ ΠΌΠ°ΡΠ΅ΡΠΈΠ°Π»Ρ, ΡΠΏΠΎΡΠΎΠ±Π½ΡΠ΅ Π²ΠΎΡΠΏΡΠ΅ΠΏΡΡΡΡΠ²ΠΎΠ²Π°ΡΡ ΠΈΠ·ΠΌΠ΅Π½Π΅Π½ΠΈΡ ΡΠΎΡΡΠ°Π²Π° ΠΈΠ»ΠΈ ΡΠΊΡΠΏΠ»ΡΠ°ΡΠ°ΡΠΈΠΎΠ½Π½ΡΡ
Ρ
Π°ΡΠ°ΠΊΡΠ΅ΡΠΈΡΡΠΈΠΊ Π·Π°ΡΠ²Π΅ΡΠ΄Π΅Π²ΡΠ΅Π³ΠΎ ΡΠ°ΡΡΠ²ΠΎΡΠ°. ΠΠ°ΡΡΠΎΡΡΠ΅Π΅ Π²ΡΠ΅ΠΌΡ ΡΠ°ΠΊΠΎΠ²ΠΎ, ΡΡΠΎ ΡΠ΅Π³ΠΎΠ΄Π½Ρ Π½Π°ΡΠΈΡ
ΡΠΎΠΎΡΠ΅ΡΠ΅ΡΡΠ²Π΅Π½Π½ΠΈΠΊΠΎΠ² ΠΏΡΠ°ΠΊΡΠΈΡΠ΅ΡΠΊΠΈ Π½Π΅Π»ΡΠ·Ρ Π·Π°ΡΡΠ°ΡΡ Π²ΡΠ°ΡΠΏΠ»ΠΎΡ
, ΠΏΠΎΡΡΠ°Π²ΠΈΠ² ΠΏΠ΅ΡΠ΅Π΄ Π½ΠΈΠΌΠΈ Π·Π°Π΄Π°ΡΡ ΡΡΡΠΎΠΈΡΠ΅Π»ΡΡΡΠ²Π° ΠΈ, Π² ΡΠ°ΡΡΠ½ΠΎΡΡΠΈ, Π·ΠΈΠΌΠ½Π΅Π³ΠΎ Π±Π΅ΡΠΎΠ½ΠΈΡΠΎΠ²Π°Π½ΠΈΡ.
Π Π²ΡΠ΅ ΠΆΠ΅ ΡΡΠΎΠΈΡ ΠΎΡΠΌΠ΅ΡΠΈΡΡ, ΡΡΠΎ Π±Π΅ΡΠΎΠ½ΠΈΡΠΎΠ²Π°Π½ΠΈΠ΅ ΠΏΡΠΈ ΠΎΡΡΠΈΡΠ°ΡΠ΅Π»ΡΠ½ΡΡ ΡΠ΅ΠΌΠΏΠ΅ΡΠ°ΡΡΡΠ°Ρ β ΡΡΠΎ Π³ΠΎΠ»ΠΎΠ²Π½Π°Ρ Π±ΠΎΠ»Ρ ΠΌΠ½ΠΎΠ³ΠΈΡ ΡΠ°Π±ΠΎΡΠΈΡ ΠΈ ΡΡΠΊΠΎΠ²ΠΎΠ΄ΠΈΡΠ΅Π»Π΅ΠΉ ΡΡΡΠΎΠΈΡΠ΅Π»ΡΠ½ΡΡ ΠΎΡΠ³Π°Π½ΠΈΠ·Π°ΡΠΈΠΉ. Π§ΡΠΎΠ±Ρ ΡΡΠΎΡ ΠΏΡΠΎΡΠ΅ΡΡ Π±ΡΠ» ΠΎΠΏΡΠ°Π²Π΄Π°Π½Π½ΡΠΌ Π½Π° 100%, Π½Π΅ΠΎΠ±Ρ ΠΎΠ΄ΠΈΠΌΠΎ ΠΎΠ±Π΅ΡΠΏΠ΅ΡΠΈΡΡ Π½Π°ΠΈΠ±ΠΎΠ»Π΅Π΅ ΡΠ°ΡΠΈΠΎΠ½Π°Π»ΡΠ½ΡΠΉ ΠΌΠ΅ΡΠΎΠ΄ Π·ΠΈΠΌΠ½Π΅Π³ΠΎ Π±Π΅ΡΠΎΠ½ΠΈΡΠΎΠ²Π°Π½ΠΈΡ, ΠΎΡΡΡΠ΅ΡΡΠ²ΠΈΡΡ ΠΊΠΎΠ½ΡΡΠΎΠ»Ρ Π·Π° ΡΠ΅Ρ Π½ΠΈΡΠ΅ΡΠΊΠΈΠΌΠΈ Ρ Π°ΡΠ°ΠΊΡΠ΅ΡΠΈΡΡΠΈΠΊΠ°ΠΌΠΈ ΡΠ°ΡΡΠ²ΠΎΡΠ°, Π° ΡΠ°ΠΊΠΆΠ΅ ΡΠΎΠ·Π΄Π°ΡΡ Π½Π°ΠΈΠ±ΠΎΠ»Π΅Π΅ Π±Π»Π°Π³ΠΎΠΏΡΠΈΡΡΠ½ΡΠ΅ Π΄Π»Ρ ΠΎΡΡΡΠ΅ΡΡΠ²Π»Π΅Π½ΠΈΡ ΡΠ°Π±ΠΎΡ ΠΏΠΎ Π·ΠΈΠΌΠ½Π΅ΠΌΡ Π±Π΅ΡΠΎΠ½ΠΈΡΠΎΠ²Π°Π½ΠΈΡ ΡΡΠ»ΠΎΠ²ΠΈΡ ΠΈ ΠΏΡΠΈ ΡΡΠΎΠΌ ΠΏΡΠΈΠΎΠ±ΡΠ΅ΡΠ°ΡΡ Π±Π΅ΡΠΎΠ½ ΡΠΎΠ»ΡΠΊΠΎ Π½Π° ΠΏΡΠΎΠΈΠ·Π²ΠΎΠ΄ΡΡΠ²Π΅, ΠΊΠΎΡΠΎΡΠΎΠ΅ ΡΠΏΠ΅ΡΠΈΠ°Π»ΠΈΠ·ΠΈΡΡΠ΅ΡΡΡ Π½Π° ΠΈΠ·Π³ΠΎΡΠΎΠ²Π»Π΅Π½ΠΈΠΈ ΡΠ°ΡΡΠ²ΠΎΡΠ°, ΠΏΡΠΈΠ³ΠΎΠ΄Π½ΠΎΠ³ΠΎ Π΄Π»Ρ Π±Π΅ΡΠΎΠ½ΠΈΡΠΎΠ²Π°Π½ΠΈΡ Π·ΠΈΠΌΠΎΠΉ. ΠΠ±Π΅ΡΠΏΠ΅ΡΠ΅Π½ΠΈΠ΅ ΠΊΠΎΠΌΠΏΠ»Π΅ΠΊΡΠ½ΠΎΠ³ΠΎ ΠΏΠΎΠ΄Ρ ΠΎΠ΄Π° β ΠΌΠ΅ΡΠ°, ΠΊΠΎΡΠΎΡΠΎΠΉ Π½Π΅ ΡΡΠΎΠΈΡ ΠΏΡΠ΅Π½Π΅Π±ΡΠ΅Π³Π°ΡΡ ΠΏΡΠΈ ΡΡΡΠΎΠΈΡΠ΅Π»ΡΡΡΠ²Π΅ Π·Π΄Π°Π½ΠΈΠΉ ΠΈ ΡΠΎΠΎΡΡΠΆΠ΅Π½ΠΈΠΉ Π² Π·ΠΈΠΌΠ½Π΅Π΅ Π²ΡΠ΅ΠΌΡ Π³ΠΎΠ΄Π°.
ΠΠ± ΠΎΡΠΎΠ±Π΅Π½Π½ΠΎΡΡΡΡ Π·ΠΈΠΌΠ½Π΅Π³ΠΎ Π±Π΅ΡΠΎΠ½ΠΈΡΠΎΠ²Π°Π½ΠΈΡ
ΠΠ΅ΡΠΎΠ½ΠΈΡΠΎΠ²Π°Π½ΠΈΠ΅ Π² Π·ΠΈΠΌΠ½Π΅Π΅ Π²ΡΠ΅ΠΌΡ ΡΠΎΠΏΡΡΠΆΠ΅Π½ΠΎ Ρ ΠΎΠΏΡΠ΅Π΄Π΅Π»Π΅Π½Π½ΡΠΌΠΈ ΠΎΡΠΎΠ±Π΅Π½Π½ΠΎΡΡΡΠΌΠΈ. Π‘ΡΠΎΠΈΡ ΠΏΠΎΠ½ΠΈΠΌΠ°ΡΡ, ΡΡΠΎ ΡΠΊΠΎΡΠΎΡΡΡ Π·Π°ΡΠ²Π΅ΡΠ΄Π΅Π½ΠΈΡ Π±Π΅ΡΠΎΠ½Π° ΠΏΡΠΈ ΠΎΡΡΠΈΡΠ°ΡΠ΅Π»ΡΠ½ΡΡ
ΡΠ΅ΠΌΠΏΠ΅ΡΠ°ΡΡΡΠ°Ρ
Π·Π½Π°ΡΠΈΡΠ΅Π»ΡΠ½ΠΎ ΡΠ½ΠΈΠΆΠ°Π΅ΡΡΡ, ΠΏΠΎΡΡΠΎΠΌΡ ΠΏΠ΅ΡΠ΅Π΄ ΡΠ°Π·Π²Π΅Π΄Π΅Π½ΠΈΠ΅ΠΌ Π΄ΠΎΠ±Π°Π²ΠΊΠΈ ΠΈ Π²ΠΎΠ΄Ρ Π΄Π»Ρ Π±ΡΠ΄ΡΡΠ΅Π³ΠΎ ΡΠ°ΡΡΠ²ΠΎΡΠ° Π½Π΅ΠΎΠ±Ρ
ΠΎΠ΄ΠΈΠΌΠΎ ΠΏΠΎΠ΄ΠΎΠ³ΡΠ΅Π²Π°ΡΡ. Π’Π΅ΠΌΠΏΠ΅ΡΠ°ΡΡΡΠ° Π²ΠΎΠ΄Ρ ΠΈ ΠΊΠΎΠΌΠΏΠΎΠ½Π΅Π½ΡΠΎΠ² Π±Π΅ΡΠΎΠ½Π° Π² ΠΌΠΎΠΌΠ΅Π½Ρ Π·Π°Π³ΡΡΠ·ΠΊΠΈ Π² Π±Π΅ΡΠΎΠ½ΠΎΠΌΠ΅ΡΠ°Π»ΠΊΡ Π΄ΠΎΠ»ΠΆΠ½Π° Π±ΡΡΡ ΡΠ°ΠΊΠΎΠΉ, ΡΡΠΎΠ±Ρ ΠΎΠ±Π΅ΡΠΏΠ΅ΡΠΈΡΡ ΠΏΠΎΠ»ΡΡΠ΅Π½ΠΈΠ΅ Π·Π°Π΄Π°Π½Π½ΠΎΠ³ΠΎ ΡΠ΅ΠΌΠΏΠ΅ΡΠ°ΡΡΡΠ½ΠΎΠ³ΠΎ ΡΠ΅ΠΆΠΈΠΌΠ° ΠΏΡΠΈ Π²ΡΡ
ΠΎΠ΄Π΅ ΠΏΠΎΠ»ΡΡΠ΅Π½Π½ΠΎΠ³ΠΎ ΡΠ°ΡΡΠ²ΠΎΡΠ° ΠΈΠ· Π±Π΅ΡΠΎΠ½ΠΎΠΌΠ΅ΡΠ°Π»ΠΊΠΈ.
ΠΡΠΈΠ½ΠΈΠΌΠ°ΠΉΡΠ΅ Π² ΡΠ°ΡΡΠ΅Ρ ΠΈ ΡΠΎΡ ΡΠ°ΠΊΡ, ΡΡΠΎ Π½ΠΎΡΠΌΠ°Π»ΡΠ½ΠΎΠΉ Π΄Π»Ρ Π·Π°ΡΠ²Π΅ΡΠ΄Π΅Π½ΠΈΡ Π±Π΅ΡΠΎΠ½Π° ΡΠ΅ΠΌΠΏΠ΅ΡΠ°ΡΡΡΠΎΠΉ ΡΡΠΈΡΠ°ΡΡΡΡ ΠΏΠΎΠΊΠ°Π·Π°ΡΠ΅Π»ΠΈ Π² +15 +20 Π³ΡΠ°Π΄ΡΡΠΎΠ² ΠΏΠΎ Π¦Π΅Π»ΡΡΠΈΡ. ΠΡΠ»ΠΈ ΡΠ΅ΠΌΠΏΠ΅ΡΠ°ΡΡΡΠ° ΡΠ½ΠΈΠΆΠ΅Π½Π°, ΠΎΡΠ²Π΅ΡΠ΄Π΅Π½ΠΈΠ΅ ΡΠ°ΡΡΠ²ΠΎΡΠ° Π·Π°ΠΌΠ΅Π΄Π»ΡΠ΅ΡΡΡ, Π° ΠΏΡΠΈ Π½ΡΠ»Π΅ Π³ΡΠ°Π΄ΡΡΠΎΠ² ΠΏΠΎ Π¦Π΅Π»ΡΡΠΈΡ ΠΈ Π²ΠΎΠ²ΡΠ΅ ΠΏΡΠ΅ΠΊΡΠ°ΡΠ°Π΅ΡΡΡ. ΠΡΠΏΡΠ°Π²ΠΈΡΡ ΡΠΈΡΡΠ°ΡΠΈΡ ΠΌΠΎΠ³ΡΡ ΡΠΏΠ΅ΡΠΈΠ°Π»ΡΠ½ΡΠ΅ ΠΏΡΠΎΡΠΈΠ²ΠΎΠΌΠΎΡΠΎΠ·Π½ΡΠ΅ Π΄ΠΎΠ±Π°Π²ΠΊΠΈ Π² Π±Π΅ΡΠΎΠ½, ΠΊΠΎΡΠΎΡΡΠ΅ ΠΏΠΎΠ·Π²ΠΎΠ»ΡΡΡ ΠΈΡΠΏΠΎΠ»ΡΠ·ΠΎΠ²Π°ΡΡ ΡΠ°ΡΡΠ²ΠΎΡ Π΄Π°ΠΆΠ΅ ΠΏΡΠΈ ΠΎΡΡΠΈΡΠ°ΡΠ΅Π»ΡΠ½ΡΡ ΡΠ΅ΠΌΠΏΠ΅ΡΠ°ΡΡΡΠ°Ρ .
Π‘Π°ΠΌΠΎΠ΅ ΠΏΡΠΈΡΡΠ°Π»ΡΠ½ΠΎΠ΅ Π²Π½ΠΈΠΌΠ°Π½ΠΈΠ΅ ΡΡΠΎΠΈΡ ΡΠ΄Π΅Π»ΡΡΡ ΠΈ ΠΊΠ°ΡΠ΅ΡΡΠ²Ρ Π±Π΅ΡΠΎΠ½Π°. ΠΡΠ±ΠΎΡ Π½Π΅ΠΎΠ±Ρ ΠΎΠ΄ΠΈΠΌΠΎ Π΄Π΅Π»Π°ΡΡ Π² ΠΏΠΎΠ»ΡΠ·Ρ ΠΊΠΎΠΌΠΏΠ°Π½ΠΈΠΉ-ΠΏΡΠΎΠΈΠ·Π²ΠΎΠ΄ΠΈΡΠ΅Π»Π΅ΠΉ, ΠΊΠΎΡΠΎΡΡΠ΅ Π΄ΠΎΡΡΠ°ΡΠΎΡΠ½ΠΎ Π΄ΠΎΠ»Π³ΠΎ ΡΠ°Π±ΠΎΡΠ°ΡΡ Π½Π° ΡΡΠ½ΠΊΠ΅ ΠΈ ΠΈΠΌΠ΅ΡΡ ΠΎΠΏΡΡ ΠΏΡΠΎΠΈΠ·Π²ΠΎΠ΄ΡΡΠ²Π° ΡΠ°ΡΡΠ²ΠΎΡΠΎΠ², ΠΏΡΠΈΠΌΠ΅Π½Π΅Π½ΠΈΠ΅ ΠΊΠΎΡΠΎΡΡΡ Π±ΡΠ΄Π΅Ρ ΠΎΠ±ΡΡΠ»ΠΎΠ²Π»Π΅Π½ΠΎ Π² Ρ ΠΎΠ»ΠΎΠ΄Π½ΠΎΠ΅ Π²ΡΠ΅ΠΌΡ Π³ΠΎΠ΄Π°.
ΠΠ΅ΠΎΠ±Ρ
ΠΎΠ΄ΠΈΠΌΠΎ ΡΠ°ΠΊΠΆΠ΅ ΠΎΠ±Π΅ΡΠΏΠ΅ΡΠΈΠ²Π°ΡΡ ΠΏΡΠΎΠ΄ΠΎΠ»ΠΆΠΈΡΠ΅Π»ΡΠ½ΠΎΡΡΡ ΡΠΌΠ΅ΡΠΈΠ²Π°Π½ΠΈΡ Π±Π΅ΡΠΎΠ½Π½ΡΡ
ΡΠ°ΡΡΠ²ΠΎΡΠΎΠ². ΠΠ΅ΡΠΎΠ½ΠΈΡΠΎΠ²Π°Π½ΠΈΠ΅ Π² Π·ΠΈΠΌΠ½ΠΈΡ
ΡΡΠ»ΠΎΠ²ΠΈΡΡ
Π΄ΠΎΠ»ΠΆΠ½ΠΎ Π·Π°Π½ΠΈΠΌΠ°ΡΡ Π½Π° 25% Π±ΠΎΠ»ΡΡΠ΅ Π²ΡΠ΅ΠΌΠ΅Π½ΠΈ, ΡΠ΅ΠΌ Π»Π΅ΡΠΎΠΌ.
ΠΠ»Ρ ΠΈΠ·Π³ΠΎΡΠΎΠ²Π»Π΅Π½ΠΈΡ ΡΠ°ΡΡΠ²ΠΎΡΠ° Π½Π΅ΠΎΠ±Ρ ΠΎΠ΄ΠΈΠΌΠΎ ΠΈΡΠΏΠΎΠ»ΡΠ·ΠΎΠ²Π°ΡΡ ΡΠΎΠ»ΡΠΊΠΎ ΠΊΠ°ΡΠ΅ΡΡΠ²Π΅Π½Π½ΡΠ΅ ΠΊΠΎΠΌΠΏΠΎΠ½Π΅Π½ΡΡ. ΠΠ°ΠΆΠ½ΠΎ, ΡΡΠΎΠ±Ρ Π² Π·ΠΈΠΌΠ½Π΅Π΅ Π²ΡΠ΅ΠΌΡ Π³ΠΎΠ΄Π° ΠΊΠΎΠΌΠΏΠΎΠ½Π΅Π½ΡΠ°ΠΌΠΈ ΡΠ°ΡΡΠ²ΠΎΡΠ° ΡΡΠ°Π½ΠΎΠ²ΠΈΠ»ΠΈΡΡ Π»ΠΈΠ±ΠΎ ΡΠΈΡΡΠΎ ΡΠ΅ΠΌΠ΅Π½ΡΠ½ΡΠ΅ ΡΠΌΠ΅ΡΠΈ, Π»ΠΈΠ±ΠΎ ΡΠΌΠ΅ΡΠΈ Ρ ΠΈΡΠΏΠΎΠ»ΡΠ·ΠΎΠ²Π°Π½ΠΈΠ΅ΠΌ ΡΠ΅ΠΌΠ΅Π½ΡΠ° ΠΈ Π½Π΅Π±ΠΎΠ»ΡΡΠΈΠΌ ΠΊΠΎΠ»ΠΈΡΠ΅ΡΡΠ²ΠΎΠΌ ΠΈΠ·Π²Π΅ΡΡΠΈ: ΡΠΈΡΡΠΎ ΠΈΠ·Π²Π΅ΡΡΠΊΠΎΠ²ΡΠ΅ ΡΠ°ΡΡΠ²ΠΎΡΡ, ΠΈΡΠΏΠΎΠ»ΡΠ·ΡΠ΅ΠΌΡΠ΅ Π² Π»Π΅ΡΠ½Π΅Π΅ Π²ΡΠ΅ΠΌΡ ΠΈ Π² ΠΌΠ΅ΠΆΡΠ΅Π·ΠΎΠ½ΡΠ΅, Π΄Π»Ρ Π·ΠΈΠΌΠ½Π΅Π³ΠΎ Π±Π΅ΡΠΎΠ½ΠΈΡΠΎΠ²Π°Π½ΠΈΡ Π°Π±ΡΠΎΠ»ΡΡΠ½ΠΎ Π½Π΅ ΠΏΡΠΈΠ³ΠΎΠ΄Π½Ρ.
Π‘ΠΏΠΎΡΠΎΠ±Ρ Π·ΠΈΠΌΠ½Π΅Π³ΠΎ Π±Π΅ΡΠΎΠ½ΠΈΡΠΎΠ²Π°Π½ΠΈΡ
ΠΠ»Ρ ΡΠΎΠ³ΠΎ ΡΡΠΎΠ±Ρ ΠΎΠ±Π΅ΡΠΏΠ΅ΡΠΈΡΡ Π²ΡΡΠΎΠΊΠΎΠΊΠ°ΡΠ΅ΡΡΠ²Π΅Π½Π½ΠΎΠ΅ Π±Π΅ΡΠΎΠ½ΠΈΡΠΎΠ²Π°Π½ΠΈΠ΅ ΠΏΡΠΈ ΠΎΡΡΠΈΡΠ°ΡΠ΅Π»ΡΠ½ΡΡ
ΡΠ΅ΠΌΠΏΠ΅ΡΠ°ΡΡΡΠ°Ρ
, Π½Π΅ΠΎΠ±Ρ
ΠΎΠ΄ΠΈΠΌΠΎ ΡΠΎΠ±Π»ΡΠ΄Π°ΡΡ ΠΎΠΏΡΠ΅Π΄Π΅Π»Π΅Π½Π½ΡΠΉ ΡΠ΅ΠΏΠ»ΠΎΠ²ΠΎΠΉ ΡΠ΅ΠΆΠΈΠΌ, ΠΊΠΎΡΠΎΡΡΠΉ ΠΌΠΎΠΆΠ΅Ρ Π±ΡΡΡ ΡΠΎΠ·Π΄Π°Π½ Ρ ΠΈΡΠΏΠΎΠ»ΡΠ·ΠΎΠ²Π°Π½ΠΈΠ΅ΠΌ Π½Π΅ΠΊΠΎΡΠΎΡΡΡ
ΠΌΠ΅ΡΠΎΠ΄ΠΎΠ².
ΠΠ΄ΠΈΠ½ ΠΈΠ· Π½ΠΈΡ
β ΠΌΠ΅ΡΠΎΠ΄ ΡΠ΅ΡΠΌΠΎΡΠ°. Π‘ΡΡΠ½ΠΎΡΡΡ ΡΡΠΎΠ³ΠΎ ΡΠΏΠΎΡΠΎΠ±Π° Π·ΠΈΠΌΠ½Π΅Π³ΠΎ Π±Π΅ΡΠΎΠ½ΠΈΡΠΎΠ²Π°Π½ΠΈΡ Π·Π°ΠΊΠ»ΡΡΠ°Π΅ΡΡΡ Π² ΡΠΎΠΌ, ΡΡΠΎΠ±Ρ Π±Π΅ΡΠΎΠ½, Π·Π°ΡΡΡΠ²Π°Ρ ΠΏΡΠΈ Π½ΡΠ»Π΅ Π³ΡΠ°Π΄ΡΡΠΎΠ² ΠΈ Π½ΠΈΠΆΠ΅, ΡΠΌΠΎΠ³ Π½Π°Π±ΡΠ°ΡΡ Π½Π΅ΠΎΠ±Ρ
ΠΎΠ΄ΠΈΠΌΡΠ΅ ΠΏΠΎΠΊΠ°Π·Π°ΡΠ΅Π»ΠΈ ΠΏΡΠΎΡΠ½ΠΎΡΡΠΈ. Π£ΡΠΈΡΡΠ²Π°Ρ ΡΡΠΎ, Π½Π΅ΠΎΠ±Ρ
ΠΎΠ΄ΠΈΠΌΠΎ Π½Π°Π·Π½Π°ΡΠΈΡΡ ΡΠΎΠ»ΡΠΈΠ½Ρ ΠΈ Π²ΠΈΠ΄ ΡΡΠ΅ΠΏΠ»ΠΈΡΠ΅Π»Ρ. ΠΠ»Ρ ΡΡΠΎΠ³ΠΎ ΡΠ΅ΠΏΠ»Π°Ρ Π±Π΅ΡΠΎΠ½Π½Π°Ρ ΡΠΌΠ΅ΡΡ ΡΠΊΠ»Π°Π΄ΡΠ²Π°Π΅ΡΡΡ Π² ΡΡΠ΅ΠΏΠ»Π΅Π½Π½ΡΡ ΠΎΠΏΠ°Π»ΡΠ±ΠΊΡ, Π° ΠΎΡΠΊΡΡΡΡΠ΅ ΠΏΠΎΠ²Π΅ΡΡ
Π½ΠΎΡΡΠΈ Π½Π°ΠΊΡΡΠ²Π°ΡΡ.
ΠΡΡ ΠΎΠ΄ΠΈΠ½ ΡΠΏΠΎΡΠΎΠ± Π±Π΅ΡΠΎΠ½ΠΈΡΠΎΠ²Π°Π½ΠΈΡ ΠΏΡΠΈ ΠΎΡΡΠΈΡΠ°ΡΠ΅Π»ΡΠ½ΡΡ ΡΠ΅ΠΌΠΏΠ΅ΡΠ°ΡΡΡΠ°Ρ β ΡΡΠΎ ΡΠ»Π΅ΠΊΡΡΠΎΠΏΡΠΎΠ³ΡΠ΅Π² Π±Π΅ΡΠΎΠ½Π°. Π Π°Π·ΠΎΠ³ΡΠ΅Π² ΡΠΌΠ΅ΡΠΈ ΡΠΏΠ΅ΡΠΈΠ°Π»ΠΈΡΡΡ ΠΌΠΎΠ³ΡΡ ΠΎΡΡΡΠ΅ΡΡΠ²Π»ΡΡΡ Π½Π΅ΠΏΠΎΡΡΠ΅Π΄ΡΡΠ²Π΅Π½Π½ΠΎ Π½Π° ΡΡΡΠΎΠΈΡΠ΅Π»ΡΠ½ΠΎΠΉ ΠΏΠ»ΠΎΡΠ°Π΄ΠΊΠ΅ Ρ ΠΈΡΠΏΠΎΠ»ΡΠ·ΠΎΠ²Π°Π½ΠΈΠ΅ΠΌ ΡΠ»Π΅ΠΊΡΡΠΎΠ΄ΠΎΠ², ΠΊΠΎΡΠΎΡΡΠ΅ ΠΏΠΎΠ³ΡΡΠΆΠ°ΡΡΡΡ Π² ΡΠ°ΡΡΠ²ΠΎΡ. ΠΡΠΈ ΠΏΡΠΈΠΌΠ΅Π½Π΅Π½ΠΈΠΈ ΡΡΠΎΠ³ΠΎ ΠΌΠ΅ΡΠΎΠ΄Π° ΡΡΠΎΠΈΡ ΡΡΠΈΡΡΠ²Π°ΡΡ, ΡΡΠΎ Π±Π΅ΡΠΎΠ½ ΠΏΠΎΠ΄ Π΄Π΅ΠΉΡΡΠ²ΠΈΠ΅ΠΌ ΡΠ°Π·ΠΎΠ³ΡΠ΅Π²Π° ΠΌΠΎΠΆΠ΅Ρ ΡΠ΅ΡΡΡΡ ΡΠ²ΠΎΡ ΠΏΠΎΠ΄Π²ΠΈΠΆΠ½ΠΎΡΡΡ. Π§ΡΠΎΠ±Ρ ΡΠΎΡ ΡΠ°Π½ΠΈΡΡ ΡΠ²ΠΎΠΉΡΡΠ²Π° ΡΠ°ΡΡΠ²ΠΎΡΠ°, ΡΡΠΎΠΈΡ Π²Π²ΠΎΠ΄ΠΈΡΡ Π² Π΅Π³ΠΎ ΡΠΎΡΡΠ°Π² ΠΏΠ»Π°ΡΡΠΈΡΠΈΠΊΠ°ΡΠΎΡΡ.
Π Π°Π·ΠΎΠ³ΡΠ΅Π² Π±Π΅ΡΠΎΠ½Π½ΠΎΠ³ΠΎ ΡΠ°ΡΡΠ²ΠΎΡΠ° ΠΌΠΎΠ³ΡΡ ΠΏΡΠΎΠ²ΠΎΠ΄ΠΈΡΡ Π² Π±Π°Π΄ΡΡΡ
, Π³Π΄Π΅ Π±Π΅ΡΠΎΠ½ Π³ΠΎΡΠΎΠ²ΠΈΡΡΡ. ΠΠ°Π΄ΡΠΈ Π΄ΠΎΠΏΠΎΠ»Π½ΠΈΡΠ΅Π»ΡΠ½ΠΎ ΠΎΡΠ½Π°ΡΠ°ΡΡΡΡ ΡΠ»Π΅ΠΊΡΡΠΎΠ΄Π°ΠΌΠΈ, Π° ΡΠ°ΠΊΠΆΠ΅ ΡΠ΅ΡΠΌΠΎΠΌΠ΅ΡΡΠ°ΠΌΠΈ, ΡΡΠΎΠ±Ρ ΠΊΠΎΠ½ΡΡΠΎΠ»ΠΈΡΠΎΠ²Π°ΡΡ ΡΠ΅ΠΌΠΏΠ΅ΡΠ°ΡΡΡΡ ΠΏΡΠΎΠ³ΡΠ΅Π²Π°. ΠΡΠΎΠΌΠ΅ ΡΠΎΠ³ΠΎ, ΡΠ»Π΅ΠΊΡΡΠΎΠΏΡΠΎΠ³ΡΠ΅Π² Π±Π΅ΡΠΎΠ½Π° ΠΌΠΎΠΆΠ΅Ρ ΠΎΡΡΡΠ΅ΡΡΠ²Π»ΡΡΡΡΡ Π½Π΅ΠΏΠΎΡΡΠ΅Π΄ΡΡΠ²Π΅Π½Π½ΠΎ Π² ΠΊΡΠ·ΠΎΠ²Π΅ Π°Π²ΡΠΎΡΠ°ΠΌΠΎΡΠ²Π°Π»Π°, Π΄Π»Ρ ΡΠ΅Π³ΠΎ ΡΡΠ΄Π° ΠΏΠΎΠ³ΡΡΠΆΠ°ΡΡ ΠΏΠ°ΠΊΠ΅Ρ ΡΠ»Π΅ΠΊΡΡΠΎΠ΄ΠΎΠ², ΠΈΠ»ΠΈ Π² Π°Π²ΡΠΎΠ±Π΅ΡΠΎΠ½ΠΎΠΌΠ΅ΡΠ°Π»ΠΊΠ°Ρ
, Π³Π΄Π΅ Π² ΡΠ°ΡΠ°Ρ
ΡΠΆΠ΅ ΠΌΠΎΠ³ΡΡ Π±ΡΡΡ ΡΡΡΠ°Π½ΠΎΠ²Π»Π΅Π½Ρ ΡΡΠ΅ΡΠΆΠ½ΠΈ-ΡΠ»Π΅ΠΊΡΡΠΎΠ΄Ρ, ΠΏΠΎ ΠΊΠΎΡΠΎΡΡΠΌ ΠΏΡΠΎΠ²ΠΎΠ΄ΠΈΡΡΡ ΡΠ»Π΅ΠΊΡΡΠΈΡΠ΅ΡΠΊΠΈΠΉ ΡΠΎΠΊ.
ΠΠ»Π΅ΠΊΡΡΠΎΠΏΡΠΎΠ³ΡΠ΅Π² ΡΠΌΠ΅ΡΠΈ ΡΠ°ΠΊΠΆΠ΅ ΠΌΠΎΠΆΠ΅Ρ ΠΎΡΡΡΠ΅ΡΡΠ²Π»ΡΡΡΡΡ Π² ΡΠΏΠ΅ΡΠΈΠ°Π»ΡΠ½ΡΡ ΠΊΠΎΠ½ΡΡΡΡΠΊΡΠΈΡΡ . ΠΡΠΎΡ ΡΠΏΠΎΡΠΎΠ± Π±Π΅ΡΠΎΠ½ΠΈΡΠΎΠ²Π°Π½ΠΈΡ ΠΎΡΠ½ΠΎΠ²Π°Π½ Π½Π° ΠΈΡΠΏΠΎΠ»ΡΠ·ΠΎΠ²Π°Π½ΠΈΠΈ Π²ΡΠ΄Π΅Π»ΡΠ΅ΠΌΠΎΠΉ ΡΠ΅ΠΏΠ»ΠΎΡΡ ΠΏΡΠΈ ΠΏΡΠΎΡ ΠΎΠΆΠ΄Π΅Π½ΠΈΠΈ ΡΠ΅ΡΠ΅Π· ΡΠ°ΡΡΠ²ΠΎΡ ΡΠ»Π΅ΠΊΡΡΠΈΡΠ΅ΡΠΊΠΎΠ³ΠΎ ΡΠΎΠΊΠ°. Π Π·Π°Π²ΠΈΡΠΈΠΌΠΎΡΡΠΈ ΠΎΡ ΡΠ°ΡΠΏΠΎΠ»ΠΎΠΆΠ΅Π½ΠΈΡ ΡΠ»Π΅ΠΊΡΡΠΎΠ΄Π½ΡΡ ΡΡΠ΅ΡΠΆΠ½Π΅ΠΉ ΠΏΠΎΠ΄ΠΎΠ³ΡΠ΅Π² Π±ΡΠ²Π°Π΅Ρ ΡΠΊΠ²ΠΎΠ·Π½ΡΠΌ (ΠΊΠΎΠ³Π΄Π° ΡΠ»Π΅ΠΊΡΡΠΎΠ΄Ρ ΡΠ°ΡΠΏΠΎΠ»Π°Π³Π°ΡΡΡΡ ΠΏΠΎ Π²ΡΠ΅ΠΌΡ ΡΠ΅ΡΠ΅Π½ΠΈΡ) ΠΈΠ»ΠΈ ΠΏΠ΅ΡΠΈΡΠ΅ΡΠΈΠΉΠ½ΡΠΌ (ΡΡΠ΅ΡΠΆΠ½ΠΈ ΡΠ°Π·ΠΌΠ΅ΡΠ°ΡΡΡΡ ΠΏΠΎ Π½Π°ΡΡΠΆΠ½ΠΎΠΉ ΠΏΠΎΠ²Π΅ΡΡ Π½ΠΎΡΡΠΈ). ΠΡΠΏΠΎΠ»ΡΠ·ΡΡ ΡΡΠΎΡ ΠΌΠ΅ΡΠΎΠ΄, Π½Π΅ΠΎΠ±Ρ ΠΎΠ΄ΠΈΠΌΠΎ ΠΏΡΠ΅Π΄ΡΠΏΡΠ΅Π΄ΠΈΡΡ ΠΎΡΠ»ΠΎΠΆΠ΅Π½ΠΈΠ΅ ΡΠΎΠ»Π΅ΠΉ, Π΄Π»Ρ ΡΠ΅Π³ΠΎ ΠΏΡΠΈΠΌΠ΅Π½ΡΠ΅ΡΡΡ ΠΏΠ΅ΡΠ΅ΠΌΠ΅Π½Π½ΡΠΉ ΡΠΎΠΊ. ΠΡΠ»ΠΈ ΠΏΡΠ΅Π΄ΠΏΠΎΠ»Π°Π³Π°Π΅ΡΡΡ Π±Π΅ΡΠΎΠ½ΠΈΡΠΎΠ²Π°Π½ΠΈΠ΅ Π΄Π»ΠΈΠ½Π½ΠΎΠΌΠ΅ΡΠ½ΡΡ ΠΊΠΎΠ½ΡΡΡΡΠΊΡΠΈΠΉ, Π΄Π»Ρ ΡΠ»Π΅ΠΊΡΡΠΎΠΏΡΠΎΠ³ΡΠ΅Π²Π° Π±Π΅ΡΠΎΠ½Π° ΠΈΡΠΏΠΎΠ»ΡΠ·ΡΡΡΡΡ ΡΡΡΡΠ½Π½ΡΠ΅ ΡΠ»Π΅ΠΊΡΡΠΎΠ΄Ρ, ΠΈΠ·Π³ΠΎΡΠΎΠ²Π»ΡΡΡΠΈΠ΅ΡΡ ΠΏΡΠ΅ΠΈΠΌΡΡΠ΅ΡΡΠ²Π΅Π½Π½ΠΎ ΠΈΠ· Π³Π»Π°Π΄ΠΊΠΎΠΉ Π°ΡΠΌΠ°ΡΡΡΡ ΡΠΎΠ»ΡΠΈΠ½ΠΎΠΉ 4-6 ΠΌΠΈΠ»Π»ΠΈΠΌΠ΅ΡΡΠΎΠ².
ΠΠ΅ΡΠΎΠ½ΠΈΡΠΎΠ²Π°Π½ΠΈΠ΅ Π² ΡΠ΅ΡΠΌΠΎΠ°ΠΊΡΠΈΠ²Π½ΠΎΠΉ ΠΎΠΏΠ°Π»ΡΠ±ΠΊΠ΅ β Π΅ΡΡ ΠΎΠ΄ΠΈΠ½ ΡΡΡΠ΅ΠΊΡΠΈΠ²Π½ΡΠΉ ΡΠΏΠΎΡΠΎΠ± Π·ΠΈΠΌΠ½Π΅Π³ΠΎ Π±Π΅ΡΠΎΠ½ΠΈΡΠΎΠ²Π°Π½ΠΈΡ. Π’Π΅ΡΠΌΠΎΠ°ΠΊΡΠΈΠ²Π½ΠΎΠΉ ΠΎΠΏΠ°Π»ΡΠ±ΠΊΠΎΠΉ Π² Π΄Π°Π½Π½ΠΎΠΌ ΡΠ»ΡΡΠ°Π΅ ΡΡΠΎΠΈΡ Π½Π°Π·Π²Π°ΡΡ ΡΠΏΠ΅ΡΠΈΠ°Π»ΡΠ½ΡΠ΅ ΠΌΠ½ΠΎΠ³ΠΎΡΠ»ΠΎΠΉΠ½ΡΠ΅ ΡΠΈΡΡ, ΠΊΠΎΡΠΎΡΡΠ΅ ΠΈΠ·Π³ΠΎΡΠΎΠ²Π»ΡΡΡΡΡ ΡΠΎ ΡΠΏΠ΅ΡΠΈΠ°Π»ΡΠ½ΡΠΌΠΈ Π½Π°Π³ΡΠ΅Π²Π°ΡΠ΅Π»ΡΠ½ΡΠΌΠΈ ΡΠ»Π΅ΠΌΠ΅Π½ΡΠ°ΠΌΠΈ. Π’Π΅ΠΏΠ»ΠΎΡΠ° Π΄Π»Ρ ΠΏΠΎΠ΄ΠΎΠ³ΡΠ΅Π²Π° Π±Π΅ΡΠΎΠ½Π° ΠΏΠ΅ΡΠ΅Π΄Π°Π΅ΡΡΡ ΡΠ΅ΡΠ΅Π· ΠΏΠ°Π»ΡΠ±Ρ ΡΠ°ΠΊΠΎΠ³ΠΎ ΡΠΈΡΠ° Π²Π΅ΡΡ
Π½Π΅ΠΌΡ ΡΠ»ΠΎΡ ΠΈΠ·Π³ΠΎΡΠΎΠ²Π»ΡΠ΅ΠΌΠΎΠΉ ΠΊΠΎΠ½ΡΡΡΡΠΊΡΠΈΠΈ, Π° Π·Π°ΡΠ΅ΠΌ ΠΏΠΎΡΡΠ΅ΠΏΠ΅Π½Π½ΠΎ ΡΠ°ΡΠΏΡΠΎΡΡΡΠ°Π½ΡΠ΅ΡΡΡ ΠΈ Π½Π° Π²ΡΡ ΠΊΠΎΠ½ΡΡΡΡΠΊΡΠΈΡ.
ΠΡΡΠ³ΠΈΠΌ ΡΠΎΠ²ΡΠ΅ΠΌΠ΅Π½Π½ΡΠΌ ΠΌΠ΅ΡΠΎΠ΄ΠΎΠΌ ΡΡΠΎΠΈΡ ΡΡΠΈΡΠ°ΡΡ ΠΈ ΠΎΠ±ΠΎΠ³ΡΠ΅Π² Π±Π΅ΡΠΎΠ½Π° ΠΈΠ½ΡΡΠ°ΠΊΡΠ°ΡΠ½ΡΠΌΠΈ Π»ΡΡΠ°ΠΌΠΈ, ΠΈΡΡΠΎΡΠ½ΠΈΠΊΠΎΠΌ ΠΊΠΎΡΠΎΡΡΡ ΠΌΠΎΠ³ΡΡ Π²ΡΡΡΡΠΏΠ°ΡΡ Π’ΠΠΡ ΡΠ°Π·Π»ΠΈΡΠ½ΠΎΠΉ ΠΌΠΎΡΠ½ΠΎΡΡΠΈ ΠΈ ΡΠ°Π±ΠΎΡΠ΅Π³ΠΎ Π½Π°ΠΏΡΡΠΆΠ΅Π½ΠΈΡ. Π§ΡΠΎΠ±Ρ ΡΠΎΠ·Π΄Π°ΡΡ Π½Π°ΠΏΡΠ°Π²Π»Π΅Π½Π½ΡΠΉ ΠΏΠΎΡΠΎΠΊ, Π΄ΠΎΠΏΠΎΠ»Π½ΠΈΡΠ΅Π»ΡΠ½ΠΎ ΠΈΡΠΏΠΎΠ»ΡΠ·ΡΡΡ ΠΎΡΡΠ°ΠΆΠ°ΡΠ΅Π»ΠΈ ΠΏΠ°ΡΠ°Π±ΠΎΠ»ΠΈΡΠ΅ΡΠΊΠΎΠ³ΠΎ, ΡΡΠ΅ΡΠΈΡΠ΅ΡΠΊΠΎΠ³ΠΎ ΠΈ ΡΡΠ°ΠΏΠ΅ΡΠΈΠΈΠ΄Π°Π»ΡΠ½ΠΎΠ³ΠΎ ΡΠΈΠΏΠΎΠ². ΠΠ±ΠΎΠ³ΡΠ΅Π² Π² Π΄Π°Π½Π½ΠΎΠΌ ΡΠ»ΡΡΠ°Π΅ ΠΌΠΎΠΆΠ΅Ρ ΠΎΡΡΡΠ΅ΡΡΠ²Π»ΡΡΡΡΡ Ρ Π΄Π²ΡΡ ΡΡΠΎΡΠΎΠ½, Π΄Π»Ρ ΡΠ΅Π³ΠΎ ΠΈΡΠΏΠΎΠ»ΡΠ·ΡΡΡ ΠΎΡΡΠ°ΠΆΠ°ΡΠ΅Π»ΠΈ ΠΊΠΎΡΠΎΠ±ΡΠ°ΡΠΎΠ³ΠΎ ΡΠΈΠΏΠ°; Π²ΠΎΠ·ΠΌΠΎΠΆΠ΅Π½ ΡΠ°ΠΊΠΆΠ΅ ΠΎΠ΄Π½ΠΎΡΡΠΎΡΠΎΠ½Π½ΠΈΠΉ ΠΎΠ±ΠΎΠ³ΡΠ΅Π² Ρ ΠΈΡΠΏΠΎΠ»ΡΠ·ΠΎΠ²Π°Π½ΠΈΠ΅ΠΌ ΠΈΠ·Π»ΡΡΠ°ΡΠ΅Π»Π΅ΠΉ ΡΡΠ΅ΡΠΈΡΠ΅ΡΠΊΠΎΠ³ΠΎ ΡΠΈΠΏΠ°.
ΠΠΈΠΌΠ½Π΅Π΅ Π±Π΅ΡΠΎΠ½ΠΈΡΠΎΠ²Π°Π½ΠΈΠ΅: ΠΊΠΎΠ½ΡΡΠΎΠ»Ρ ΡΠ΅Ρ Π½ΠΈΡΠ΅ΡΠΊΠΈΡ Ρ Π°ΡΠ°ΠΊΡΠ΅ΡΠΈΡΡΠΈΠΊ ΠΌΠ°ΡΠ΅ΡΠΈΠ°Π»Π°
ΠΠ»Ρ ΡΠΎΠ³ΠΎ ΡΡΠΎΠ±Ρ Π·ΠΈΠΌΠ½Π΅Π΅ Π±Π΅ΡΠΎΠ½ΠΈΡΠΎΠ²Π°Π½ΠΈΠ΅ Π² Ρ
ΠΎΠ»ΠΎΠ΄Π½ΡΡ
ΡΡΠ»ΠΎΠ²ΠΈΡΡ
ΠΎΡΠ»ΠΈΡΠ°Π»ΠΎΡΡ ΡΡΡΠ΅ΠΊΡΠΈΠ²Π½ΠΎΡΡΡΡ, Π½Π΅ΠΎΠ±Ρ
ΠΎΠ΄ΠΈΠΌΠΎ ΠΎΠ±Π΅ΡΠΏΠ΅ΡΠΈΡΡ ΠΏΠΎΡΡΠΎΡΠ½Π½ΠΎΠ΅ ΠΎΡΡΡΠ΅ΡΡΠ²Π»Π΅Π½ΠΈΠ΅ ΠΊΠΎΠ½ΡΡΠΎΠ»Ρ Π·Π° Ρ
Π°ΡΠ°ΠΊΡΠ΅ΡΠΈΡΡΠΈΠΊΠ°ΠΌΠΈ ΠΏΡΠΎΡΠ½ΠΎΡΡΠΈ ΡΠ°ΡΡΠ²ΠΎΡΠ°, Π° ΡΠ°ΠΊΠΆΠ΅ Π·Π° ΡΠ΅ΠΌΠΏΠ΅ΡΠ°ΡΡΡΠΎΠΉ, Π² ΠΊΠΎΡΠΎΡΠΎΠΉ ΠΏΡΠΎΠΈΡΡ
ΠΎΠ΄ΠΈΡ ΠΎΡΠ²Π΅ΡΠ΄Π΅Π½ΠΈΠ΅ Π±Π΅ΡΠΎΠ½Π°.
Π’Π°ΠΊΠΆΠ΅ Π½ΡΠΆΠ½ΠΎ ΠΎΠ±Π΅ΡΠΏΠ΅ΡΠΈΡΡ ΡΠΎΠ±Π»ΡΠ΄Π΅Π½ΠΈΠ΅ Π²ΡΠ΅Ρ ΡΡΠ΅Π±ΠΎΠ²Π°Π½ΠΈΠΉ ΠΈ Π½ΠΎΡΠΌ ΠΏΡΠΈ Π·ΠΈΠΌΠ½Π΅ΠΌ Π±Π΅ΡΠΎΠ½ΠΈΡΠΎΠ²Π°Π½ΠΈΠΈ ΠΈ ΠΈΡΠΊΠ»ΡΡΠΈΡΡ ΠΎΡΠΊΠ»ΠΎΠ½Π΅Π½ΠΈΠ΅ ΡΠ΅ΠΆΠΈΠΌΠΎΠ² Π²ΡΠ΄Π΅ΡΠΆΠΈΠ²Π°Π½ΠΈΡ Π±Π΅ΡΠΎΠ½Π° ΠΎΡ ΠΏΡΠΈΠ½ΡΡΡΡ ΡΡΠ°Π½Π΄Π°ΡΡΠΎΠ². ΠΠ°ΠΆΠ½ΠΎ ΠΈ ΡΠΎ, ΡΡΠΎΠ±Ρ ΠΊΠ²Π°Π»ΠΈΡΠΈΡΠΈΡΠΎΠ²Π°Π½Π½ΡΠΉ ΡΠΏΠ΅ΡΠΈΠ°Π»ΠΈΡΡ ΠΏΡΠΈΠΌΠ΅Π½ΡΠ» ΡΠ²ΠΎΠΉ ΠΎΠΏΡΡ ΠΈ Π·Π½Π°Π½ΠΈΡ Π΄Π»Ρ ΠΏΠΎΠΈΡΠΊΠ° Π²Π΅ΡΠ½ΡΡ ΡΠ΅ΡΠ΅Π½ΠΈΠΉ Π΄Π°ΠΆΠ΅ ΠΏΡΠΈ Π½Π΅Π³Π°ΡΠΈΠ²Π½ΠΎ ΡΠΊΠ»Π°Π΄ΡΠ²Π°ΡΡΠ΅ΠΉΡΡ ΡΠΈΡΡΠ°ΡΠΈΠΈ.
ΠΡΠ½ΠΎΠ²Π½ΠΎΠΉ Π²ΠΈΠ΄ ΠΊΠΎΠ½ΡΡΠΎΠ»Ρ Π·Π° ΠΎΡΠ²Π΅ΡΠ΄Π΅Π½ΠΈΠ΅ΠΌ Π±Π΅ΡΠΎΠ½Π° — ΠΈΠ·ΠΌΠ΅ΡΠ΅Π½ΠΈΠ΅ ΡΠ΅ΠΌΠΏΠ΅ΡΠ°ΡΡΡ Π² ΡΠ°Π·Π»ΠΈΡΠ½ΡΡ ΡΠΎΡΠΊΠ°Ρ ΠΊΠΎΠ½ΡΡΡΡΠΊΡΠΈΠΈ. ΠΠ»Ρ ΡΡΠ°Π²Π½Π΅Π½ΠΈΡ ΠΈ ΠΎΠ±Π΅ΡΠΏΠ΅ΡΠ΅Π½ΠΈΡ ΠΊΠ°ΡΠ΅ΡΡΠ²Π΅Π½Π½ΠΎΠ³ΠΎ Π±Π΅ΡΠΎΠ½ΠΈΡΠΎΠ²Π°Π½ΠΈΡ Π·ΠΈΠΌΠΎΠΉ ΠΈΡΠΏΠΎΠ»ΡΠ·ΡΡΡΡΡ Π½Π΅ ΡΠΎΠ»ΡΠΊΠΎ ΠΎΠΏΡΡ ΠΈ Π·Π½Π°Π½ΠΈΡ ΠΏΡΠΎΡΠ΅ΡΡΠΈΠΎΠ½Π°Π»ΠΎΠ², Π½ΠΎ ΡΠ°ΠΊΠΆΠ΅ ΡΠ°Π±Π»ΠΈΡΡ ΠΈ Π³ΡΠ°ΡΠΈΠΊΠΈ, ΠΊΠΎΡΠΎΡΡΠ΅ ΠΎΠ±Π΅ΡΠΏΠ΅ΡΠΈΠ²Π°ΡΡ ΡΠΎΡΠ½ΠΎΡΡΡ ΡΠ°ΡΡΠ΅ΡΠΎΠ² ΠΈ ΠΏΠΎΠ²ΡΡΠ°ΡΡ ΠΏΡΠΎΠ³Π½ΠΎΠ· ΠΏΠΎΠ²Π΅Π΄Π΅Π½ΠΈΡ Π±Π΅ΡΠΎΠ½Π½ΠΎΠ³ΠΎ ΡΠ°ΡΡΠ²ΠΎΡΠ° ΠΏΡΠΈ ΠΎΡΡΠΈΡΠ°ΡΠ΅Π»ΡΠ½ΡΡ ΡΠ΅ΠΌΠΏΠ΅ΡΠ°ΡΡΡΠ°Ρ .
ΠΠ°ΠΆΠ½ΠΎ ΠΎΠ±Π΅ΡΠΏΠ΅ΡΠΈΠ²Π°ΡΡ ΠΎΠΏΡΠ΅Π΄Π΅Π»Π΅Π½Π½ΡΡ Π°Π²ΡΠΎΠΌΠ°ΡΠΈΠ·Π°ΡΠΈΡ Π·ΠΈΠΌΠ½Π΅Π³ΠΎ Π±Π΅ΡΠΎΠ½ΠΈΡΠΎΠ²Π°Π½ΠΈΡ Π½Π° ΡΡΠ°Π΄ΠΈΠΈ ΠΊΠΎΠ½ΡΡΠΎΠ»Ρ Π·Π° ΡΠ΅ΠΌΠΏΠ΅ΡΠ°ΡΡΡΠ½ΡΠΌ ΡΠ΅ΠΆΠΈΠΌΠΎΠΌ ΠΈ ΠΏΡΠΎΡΠ½ΠΎΡΡΡΡ ΠΊΠΎΠ½ΡΡΡΡΠΊΡΠΈΠΈ, ΡΡΠΎ Π²ΠΎΠ·ΠΌΠΎΠΆΠ½ΠΎ Π·Π° ΡΡΠ΅Ρ ΠΈΡΠΏΠΎΠ»ΡΠ·ΠΎΠ²Π°Π½ΠΈΡ ΡΠΏΠ΅ΡΠΈΠ°Π»ΡΠ½ΡΡ
ΠΏΡΠΎΠ³ΡΠ°ΠΌΠΌ ΠΈ ΠΏΡΠΈΠ±ΠΎΡΠΎΠ².
ΠΠ°ΠΊ ΠΈΠ·Π±Π΅ΠΆΠ°ΡΡ ΠΎΡΠΈΠ±ΠΎΠΊ Π² Π·ΠΈΠΌΠ½Π΅ΠΌ Π±Π΅ΡΠΎΠ½ΠΈΡΠΎΠ²Π°Π½ΠΈΠΈ?
ΠΡΠ»ΠΈ Π²Ρ Ρ
ΠΎΡΠΈΡΠ΅ Π² Π±Π΅ΡΠΎΠ½ΠΈΡΠΎΠ²Π°Π½ΠΈΠΈ Π² Π·ΠΈΠΌΠ½ΠΈΡ
ΡΡΠ»ΠΎΠ²ΠΈΡΡ
ΠΈΠ·Π±Π΅ΠΆΠ°ΡΡ ΠΎΡΠΈΠ±ΠΎΠΊ, ΡΠ°ΠΊΠΈΡ
, ΠΊΠ°ΠΊ:
— ΡΠ²Π΅Π»ΠΈΡΠ΅Π½ΠΈΠ΅ Π²ΡΠ΅ΠΌΠ΅Π½ΠΈ, Π½Π΅ΠΎΠ±Ρ
ΠΎΠ΄ΠΈΠΌΠΎΠ³ΠΎ Π΄Π»Ρ ΠΎΡΠ΄Π΅Π»ΠΊΠΈ ΠΏΠΎΠ²Π΅ΡΡ
Π½ΠΎΡΡΠΈ Π±Π΅ΡΠΎΠ½Π°;
— ΡΠ»Π°Π±Π°Ρ ΠΏΡΠ»ΡΡΠ°Ρ ΠΏΠΎΠ²Π΅ΡΡ Π½ΠΎΡΡΡ;
— ΠΎΠ±ΡΠ°Π·ΠΎΠ²Π°Π½ΠΈΠ΅ ΡΡΠ΅ΡΠΈΠ½,
Π²Π°ΠΌ Π½Π΅ΠΎΠ±Ρ ΠΎΠ΄ΠΈΠΌΠΎ ΠΏΡΠΈΠ΄Π΅ΡΠΆΠΈΠ²Π°ΡΡΡΡ ΡΠ»Π΅Π΄ΡΡΡΠΈΡ ΡΠ΅ΠΊΠΎΠΌΠ΅Π½Π΄Π°ΡΠΈΠΉ Π² ΠΏΡΠΎΡΠ΅ΡΡΠ΅ ΠΏΡΠΈΠ³ΠΎΡΠΎΠ²Π»Π΅Π½ΠΈΡ ΠΈ ΠΈΡΠΏΠΎΠ»ΡΠ·ΠΎΠ²Π°Π½ΠΈΡ Π±Π΅ΡΠΎΠ½Π½ΠΎΠ³ΠΎ ΡΠ°ΡΡΠ²ΠΎΡΠ°.
1. Π’Π΅ΠΌΠΏΠ΅ΡΠ°ΡΡΡΠ° Π±Π΅ΡΠΎΠ½Π½ΠΎΠΉ ΡΠΌΠ΅ΡΠΈ Π΄ΠΎΠ»ΠΆΠ½Π° ΡΠΎΡΡΠ°Π²Π»ΡΡΡ Π½Π΅ Π±ΠΎΠ»Π΅Π΅ ΡΡΠΈΠ½Π°Π΄ΡΠ°ΡΠΈ Π³ΡΠ°Π΄ΡΡΠΎΠ² ΡΠ΅ΠΏΠ»Π° ΠΏΡΠΈ ΡΠΎΠ»ΡΠΈΠ½Π΅ ΠΊΠΎΠ½ΡΡΡΡΠΊΡΠΈΠΈ Π΄ΠΎ 30 ΡΠ°Π½ΡΠΈΠΌΠ΅ΡΡΠΎΠ². ΠΡΠ»ΠΈ ΡΠ΅ΠΌΠΏΠ΅ΡΠ°ΡΡΡΠ° Π±ΡΠ΄Π΅Ρ Π²ΡΡΠ΅, ΡΡΠΎ ΠΏΠΎΡΡΠ΅Π±ΡΠ΅Ρ Π±ΠΎΠ»ΡΡΠ΅Π³ΠΎ ΠΊΠΎΠ»ΠΈΡΠ΅ΡΡΠ²Π° Π²ΠΎΠ΄Ρ, ΡΡΠΎ Π² Π΄Π°Π»ΡΠ½Π΅ΠΉΡΠ΅ΠΌ ΠΏΡΠΈΠ²Π΅Π΄Π΅Ρ ΠΊ ΠΎΠ±ΡΠ°Π·ΠΎΠ²Π°Π½ΠΈΡ ΡΡΠ΅ΡΠΈΠ½ Π² ΠΊΠΎΠ½ΡΡΡΡΠΊΡΠΈΠΈ;
2. ΠΠ΅ Π΄ΠΎΠΏΡΡΠΊΠ°ΠΉΡΠ΅ ΡΡΠ΅Π·ΠΌΠ΅ΡΠ½ΠΎΠ³ΠΎ ΡΠ²Π΅Π»ΠΈΡΠ΅Π½ΠΈΡ Π²ΡΠ΅ΠΌΠ΅Π½ΠΈ ΠΈ Π·Π°ΠΌΠ΅Π΄Π»Π΅Π½ΠΈΡ Π½Π°Π±ΠΎΡΠ° ΠΏΡΠΎΡΠ½ΠΎΡΡΠΈ Π±Π΅ΡΠΎΠ½Π½ΠΎΠ³ΠΎ ΡΠ°ΡΡΠ²ΠΎΡΠ°, ΠΏΠΎΡΠΊΠΎΠ»ΡΠΊΡ ΡΡΠΎ ΠΏΡΠΈΠ²Π΅Π΄Π΅Ρ ΠΊ Π·Π°Π΄Π΅ΡΠΆΠΊΠ°ΠΌ ΠΌΠ½ΠΎΠ³ΠΈΡ ΡΡΡΠΎΠΈΡΠ΅Π»ΡΠ½ΡΡ ΠΎΠΏΠ΅ΡΠ°ΡΠΈΠΉ. ΠΠ»Ρ ΡΠ΅ΡΠ΅Π½ΠΈΡ ΡΡΠΎΠΉ ΠΏΡΠΎΠ±Π»Π΅ΠΌΡ ΠΈΡΠΏΠΎΠ»ΡΠ·ΡΠΉΡΠ΅ ΠΏΡΠΎΡΠΈΠ²ΠΎΠΌΠΎΡΠΎΠ·Π½ΡΠ΅ Π΄ΠΎΠ±Π°Π²ΠΊΠΈ Π² Π±Π΅ΡΠΎΠ½, ΠΊΠΎΡΠΎΡΡΠ΅ ΡΡΠΊΠΎΡΡΡΡ Π²ΡΠ΅ΠΌΡ Π·Π°ΡΡΡΠ²Π°Π½ΠΈΡ. ΠΠΌΠ΅ΠΉΡΠ΅ Π² Π²ΠΈΠ΄Ρ, ΡΡΠΎ Π²Ρ Π΄ΠΎΠ»ΠΆΠ½Ρ ΠΈΡΠΊΠ»ΡΡΠΈΡΡ ΠΏΡΠΈΠΌΠ΅Π½Π΅Π½ΠΈΠ΅ ΡΠ΅Ρ Π΄ΠΎΠ±Π°Π²ΠΎΠΊ, ΠΊΠΎΡΠΎΡΡΠ΅ Π² ΡΠ²ΠΎΠ΅ΠΌ ΡΠΎΡΡΠ°Π²Π΅ ΠΈΠΌΠ΅ΡΡ Ρ Π»ΠΎΡΠΈΠ΄Ρ, ΠΏΡΠΈΠ²ΠΎΠ΄ΡΡΠΈΠ΅ Π² Π΄Π°Π»ΡΠ½Π΅ΠΉΡΠ΅ΠΌ ΠΊ ΠΊΠΎΡΡΠΎΠ·ΠΈΠΈ Π°ΡΠΌΠ°ΡΡΡΡ, ΠΊ ΠΎΠ±Π΅ΡΡΠ²Π΅ΡΠΈΠ²Π°Π½ΠΈΡ ΡΡΠ°ΡΡΠΊΠΎΠ² ΠΊΠΎΠ½ΡΡΡΡΠΊΡΠΈΠΈ, ΠΊ ΡΠ½ΠΈΠΆΠ΅Π½ΠΈΡ ΠΌΠ΅Ρ ΠΏΠΎ Π·Π°ΡΠΈΡΠ΅ Π±Π΅ΡΠΎΠ½Π°.
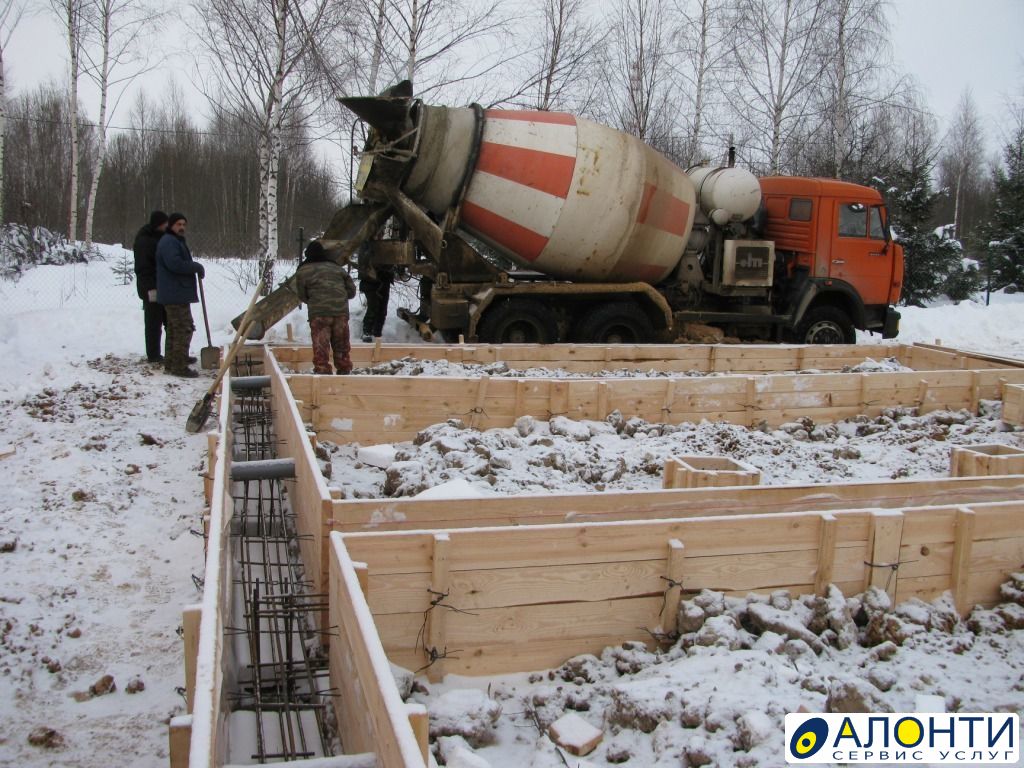
3. Π£Π΄Π΅Π»ΡΠΉΡΠ΅ Π²Π½ΠΈΠΌΠ°Π½ΠΈΠ΅ ΠΏΠΎΠ΄Π³ΠΎΡΠΎΠ²ΠΊΠ΅ ΠΏΠΎΠ²Π΅ΡΡ Π½ΠΎΡΡΠΈ, ΠΊΠΎΡΠΎΡΠ°Ρ Π±ΡΠ΄Π΅Ρ ΠΏΠΎΠ΄Π²Π΅ΡΠ³Π°ΡΡΡΡ Π·ΠΈΠΌΠ½Π΅ΠΌΡ Π±Π΅ΡΠΎΠ½ΠΈΡΠΎΠ²Π°Π½ΠΈΡ. ΠΠ΅ΠΎΠ±Ρ ΠΎΠ΄ΠΈΠΌΠΎ ΠΎΠ±Π΅ΡΠΏΠ΅ΡΠΈΡΡ ΡΠ²ΠΎΠ΅Π²ΡΠ΅ΠΌΠ΅Π½Π½ΠΎΠ΅ ΡΠ΄Π°Π»Π΅Π½ΠΈΠ΅ Ρ ΠΏΠΎΠ²Π΅ΡΡ Π½ΠΎΡΡΠΈ Π»ΡΠ΄Π°, ΡΠ½Π΅Π³Π°. ΠΠ»Ρ ΡΠ°Π·ΠΌΠΎΡΠ°ΠΆΠΈΠ²Π°Π½ΠΈΡ Π½Π΅ ΠΈΡΠΏΠΎΠ»ΡΠ·ΡΠΉΡΠ΅ Ρ Π»ΠΎΡΠΈΠ΄Ρ ΠΊΠ°Π»ΡΡΠΈΡ, ΠΏΠΎΡΠΊΠΎΠ»ΡΠΊΡ Π² Π΄Π°Π»ΡΠ½Π΅ΠΉΡΠ΅ΠΌ ΡΡΠΎ ΠΎΡΡΠΈΡΠ°ΡΠ΅Π»ΡΠ½ΠΎ ΠΌΠΎΠΆΠ΅Ρ ΡΠΊΠ°Π·Π°ΡΡΡΡ Π½Π° ΠΏΡΠΎΡΠ½ΠΎΡΡΠΈ Π±Π΅ΡΠΎΠ½Π° ΠΈ ΠΈΠ½ΡΡ Π΅Π³ΠΎ ΡΠΊΡΠΏΠ»ΡΠ°ΡΠ°ΡΠΈΠΎΠ½Π½ΡΡ Ρ Π°ΡΠ°ΠΊΡΠ΅ΡΠΈΡΡΠΈΠΊΠ°Ρ . Π‘Π»Π΅Π΄ΠΈΡΠ΅ ΡΠ°ΠΊΠΆΠ΅ Π·Π°ΡΠ΅ΠΌ, ΡΡΠΎΠ±Ρ ΡΠ΅ΠΌΠΏΠ΅ΡΠ°ΡΡΡΠ° Π²ΡΠ΅Ρ ΠΏΠΎΠ²Π΅ΡΡ Π½ΠΎΡΡΠ΅ΠΉ, Π½Π° ΠΊΠΎΡΠΎΡΡΠ΅ Π±ΡΠ΄Π΅Ρ ΡΠΊΠ»Π°Π΄ΡΠ²Π°ΡΡΡΡ Π±Π΅ΡΠΎΠ½Π½ΡΠΉ ΡΠ°ΡΡΠ²ΠΎΡ, Π±ΡΠ»Π° Π²ΡΡΠ΅ ΡΠΎΡΠΊΠΈ Π·Π°ΠΌΠ΅ΡΠ·Π°Π½ΠΈΡ.
4. ΠΡΠ΄Π΅ΡΠΆΠΈΠ²Π°ΠΉΡΠ΅ ΠΏΡΠΎΠΌΠ΅ΠΆΡΡΠΎΠΊ Π²ΡΠ΅ΠΌΠ΅Π½ΠΈ ΠΎΡ ΠΏΡΠΎΠΈΠ·Π²ΠΎΠ΄ΡΡΠ²Π° ΡΠΌΠ΅ΡΠΈ Π΄ΠΎ ΡΠΊΠ»Π°Π΄ΠΊΠΈ Π΅Ρ Π½Π° ΠΎΡΠ½ΠΎΠ²Π°Π½ΠΈΠ΅ β ΠΎΠ½ Π΄ΠΎΠ»ΠΆΠ΅Π½ Π±ΡΡΡ ΠΌΠΈΠ½ΠΈΠΌΠ°Π»ΡΠ½ΡΠΌ, ΡΡΠΎΠ±Ρ ΡΠ²Π΅ΡΡΠΈ ΠΊ ΠΌΠΈΠ½ΠΈΠΌΡΠΌΡ ΠΏΠ°Π΄Π΅Π½ΠΈΠ΅ ΡΠ΅ΠΌΠΏΠ΅ΡΠ°ΡΡΡΡ ΠΏΡΠΈΠ³ΠΎΡΠΎΠ²Π»Π΅Π½Π½ΠΎΠΉ ΡΠΌΠ΅ΡΠΈ.
5. ΠΠΎΡΠ»Π΅ ΡΠΊΠ»Π°Π΄ΠΊΠΈ ΡΠ°ΡΡΠ²ΠΎΡΠ° Π½Π΅ΠΎΠ±Ρ ΠΎΠ΄ΠΈΠΌΠΎ ΠΎΠ±Π΅ΡΠΏΠ΅ΡΠΈΡΡ Π·Π°ΡΠΈΡΡ ΠΏΠΎΠ²Π΅ΡΡ Π½ΠΎΡΡΠΈ, ΠΊΠΎΡΠΎΡΠ°Ρ Π±ΡΠ΄Π΅Ρ ΠΏΡΠ΅Π΄ΡΠΏΡΠ΅ΠΆΠ΄Π°ΡΡ ΠΎΡ Π·Π°ΠΌΠ΅ΡΠ·Π°Π½ΠΈΡ ΠΈ ΠΎΡ ΡΡΠ΅Π·ΠΌΠ΅ΡΠ½ΠΎ Π±ΡΡΡΡΠΎΠ³ΠΎ Π²ΡΡΡΡ Π°Π½ΠΈΡ. ΠΠ»Ρ ΡΡΠΎΠ³ΠΎ Π²Ρ ΠΌΠΎΠΆΠ΅ΡΠ΅ ΠΈΡΠΏΠΎΠ»ΡΠ·ΠΎΠ²Π°ΡΡ ΠΏΠΎΠ»ΠΈΡΡΠΈΠ»Π΅Π½ΠΎΠ²ΡΡ ΠΏΠ»Π΅Π½ΠΊΡ ΠΈΠ»ΠΈ ΡΠΏΠ΅ΡΠΈΠ°Π»ΡΠ½ΡΡ ΠΎΠ±ΡΠ°Π±ΠΎΡΠΊΡ ΠΆΠΈΠ΄ΠΊΠΈΠΌ ΡΠΈΠ»Π΅ΡΠΎΠΌ.
ΠΠΎΠ΄Π²Π΅Π΄Π΅ΠΌ ΠΈΡΠΎΠ³ΠΈ
ΠΡΠ»ΠΈ Π²Ρ Ρ
ΠΎΡΠΈΡΠ΅ Π±ΡΡΡ ΡΠ²Π΅ΡΠ΅Π½Π½ΡΠΌ Π² ΡΠΎΠΌ, ΡΡΠΎ Π² Π·ΠΈΠΌΠ½Π΅ΠΌ Π±Π΅ΡΠΎΠ½ΠΈΡΠΎΠ²Π°Π½ΠΈΠΈ ΠΈΡΠΏΠΎΠ»ΡΠ·ΡΠ΅ΡΠ΅ ΡΠΎΠ»ΡΠΊΠΎ ΠΊΠ°ΡΠ΅ΡΡΠ²Π΅Π½Π½ΡΠΉ ΡΠ°ΡΡΠ²ΠΎΡ, Π΅ΡΠ»ΠΈ Ρ Π²Π°Ρ Π΅ΡΡΡ ΠΏΠΎΡΡΠ΅Π±Π½ΠΎΡΡΡ Π² Π·Π°ΠΊΠ°Π·Π΅ Π±ΠΎΠ»ΡΡΠΈΡ
ΠΎΠ±ΡΠ΅ΠΌΠΎΠ² ΡΠ°ΡΡΠ²ΠΎΡΠ° Π² Π·ΠΈΠΌΠ½Π΅Π΅ Π²ΡΠ΅ΠΌΡ Π³ΠΎΠ΄Π°, Π·Π½Π°ΠΉΡΠ΅: ΠΌΠ°ΡΠ΅ΡΠΈΠ°Π» Π½Π΅ΠΎΠ±Ρ
ΠΎΠ΄ΠΈΠΌΠΎ ΠΏΡΠΈΠΎΠ±ΡΠ΅ΡΠ°ΡΡ ΡΠΎΠ»ΡΠΊΠΎ Ρ Π±Π΅ΡΠΎΠ½Π½ΠΎΠ³ΠΎ Π·Π°Π²ΠΎΠ΄Π°.
ΠΡΠ°ΠΊΡΠΈΠΊΠ° ΠΏΠΎΠΊΠ°Π·ΡΠ²Π°Π΅Ρ: Ρ ΡΠ΅Ρ ΡΡΡΠΎΠΈΡΠ΅Π»ΡΠ½ΡΡ ΠΎΡΠ³Π°Π½ΠΈΠ·Π°ΡΠΈΠΉ, ΡΡΠΊΠΎΠ²ΠΎΠ΄ΠΈΡΠ΅Π»ΠΈ ΠΊΠΎΡΠΎΡΡΡ ΠΎΡΠ΄Π°ΡΡ ΠΏΡΠ΅Π΄ΠΏΠΎΡΡΠ΅Π½ΠΈΠ΅ Π±Π΅ΡΠΎΠ½Ρ, ΠΈΠ·Π³ΠΎΡΠΎΠ²Π»Π΅Π½Π½ΠΎΠΌΡ Π½Π° Π·Π°Π²ΠΎΠ΄Π΅, ΡΠ΅ΠΉ ΠΎΠΏΡΡ ΠΏΡΠΎΠΈΠ·Π²ΠΎΠ΄ΡΡΠ²Π° ΠΈ ΡΠ΅Ρ Π½ΠΎΠ»ΠΎΠ³ΠΈΠΈ ΠΈΠ·Π³ΠΎΡΠΎΠ²Π»Π΅Π½ΠΈΡ ΠΌΠ°ΡΠ΅ΡΠΈΠ°Π»Π° Π½Π΅ Π²ΡΠ·ΡΠ²Π°ΡΡ Π½Π°ΡΠ΅ΠΊΠ°Π½ΠΈΡ, Π½Π΅ Π²ΠΎΠ·Π½ΠΈΠΊΠ°Π΅Ρ ΠΏΡΠΎΠ±Π»Π΅ΠΌ Ρ ΠΏΡΠΎΡΠ΅ΡΡΠΎΠΌ Π·ΠΈΠΌΠ½Π΅Π³ΠΎ Π±Π΅ΡΠΎΠ½ΠΈΡΠΎΠ²Π°Π½ΠΈΡ, ΠΊΠ°ΠΊΠΎΠΉ Π±Ρ Π½ΠΈΠ·ΠΊΠΎΠΉ Π½ΠΈ Π±ΡΠ»Π° ΡΠ΅ΠΌΠΏΠ΅ΡΠ°ΡΡΡΠ°. ΠΠ±ΡΠ°ΡΠ°ΠΉΡΠ΅ΡΡ Π·Π° ΠΏΠΎΠΌΠΎΡΡΡ ΡΠΎΠ»ΡΠΊΠΎ Π² ΡΠ΅ ΠΎΡΠ³Π°Π½ΠΈΠ·Π°ΡΠΈΠΈ, Π³Π΄Π΅ Π²Π°ΠΌ ΠΏΡΠ΅Π΄Π»Π°Π³Π°ΡΡ Π½Π΅ ΠΏΡΠΎΡΡΠΎ ΠΏΡΠΈΠΎΠ±ΡΠ΅ΡΡΠΈ ΡΠ°ΡΡΠ²ΠΎΡ, ΠΏΠΎΠ΄Ρ ΠΎΠ΄ΡΡΠΈΠΉ Π΄Π»Ρ Π±Π΅ΡΠΎΠ½ΠΈΡΠΎΠ²Π°Π½ΠΈΡ ΠΏΡΠΈ ΠΎΡΡΠΈΡΠ°ΡΠ΅Π»ΡΠ½ΡΡ ΡΠ΅ΠΌΠΏΠ΅ΡΠ°ΡΡΡΠ°Ρ , Π½ΠΎ ΠΈ ΠΎΠ±Π΅ΡΠΏΠ΅ΡΠΈΠ²Π°ΡΡ ΡΠ²ΠΎΠ΅Π²ΡΠ΅ΠΌΠ΅Π½Π½ΡΡ Π΄ΠΎΡΡΠ°Π²ΠΊΡ ΠΌΠ°ΡΠ΅ΡΠΈΠ°Π»Π° Π² ΡΠΏΠ΅ΡΠΈΠ°Π»ΡΠ½ΡΡ Π°Π²ΡΠΎΠ±Π΅ΡΠΎΠ½ΠΎΠΌΠ΅ΡΠ°Π»ΠΊΠ°Ρ , ΠΊΠΎΡΠΎΡΡΠ΅ ΠΏΠΎΠ΄Π΄Π΅ΡΠΆΠΈΠ²Π°ΡΡ Π²ΡΡΠΎΠΊΡΡ ΡΠ΅ΠΌΠΏΠ΅ΡΠ°ΡΡΡΡ Π±Π΅ΡΠΎΠ½Π° ΠΈ ΠΏΡΠ΅Π΄ΡΠΏΡΠ΅ΠΆΠ΄Π°ΡΡ Π΅Π³ΠΎ ΡΠ°Π½Π΅Π΅ ΠΎΡΠ²Π΅ΡΠ΄Π΅Π½ΠΈΠ΅.
ΠΡΠ½ΠΎΠ²Ρ Π·ΠΈΠΌΠ½Π΅Π³ΠΎ Π±Π΅ΡΠΎΠ½ΠΈΡΠΎΠ²Π°Π½ΠΈΡ
ΠΠ΅ΡΠΎΠ½Π½ΡΠ΅ ΡΠ°Π±ΠΎΡΡ ΠΏΡΠΈ ΡΡΠ΅Π΄Π½Π΅ΡΡΡΠΎΡΠ½ΠΎΠΉ ΡΠ΅ΠΌΠΏΠ΅ΡΠ°ΡΡΡΠ΅ Π½Π°ΡΡΠΆΠ½ΠΎΠ³ΠΎ Π²ΠΎΠ·Π΄ΡΡ Π° Π½ΠΈΠΆΠ΅ 5Β°Π‘ ΠΈ ΠΌΠΈΠ½ΠΈΠΌΠ°Π»ΡΠ½ΠΎΠΉ ΡΡΡΠΎΡΠ½ΠΎΠΉ ΡΠ΅ΠΌΠΏΠ΅ΡΠ°ΡΡΡΠ΅ Π½ΠΈΠΆΠ΅ 0Β°Π‘ Π²ΡΠΏΠΎΠ»Π½ΡΡΡ ΠΏΠΎ ΡΠΏΠ΅ΡΠΈΠ°Π»ΡΠ½ΡΠΌ ΠΏΡΠ°ΒΠ²ΠΈΠ»Π°ΠΌ, ΡΡΡΠ°Π½ΠΎΠ²Π»Π΅Π½Π½ΡΠΌ Π΄Π»Ρ ΡΠ°Π±ΠΎΡ Π² Π·ΠΈΠΌΠ½ΠΈΡ ΡΡΠ»ΠΎΠ²ΠΈΡΡ (Π‘ΠΠΈΠ III-15-76).
Π Π·ΠΈΠΌΠ½ΠΈΡ
ΡΡΠ»ΠΎΠ²ΠΈΡΡ
ΠΎΡΠ½ΠΎΠ²Π½ΠΎΠΉ Π·Π°Π΄Π°ΡΠ΅ΠΉ ΡΠ²Π»ΡΠ΅ΡΡΡ Π½Π΅ Π΄ΠΎΠΏΡΡΡΠΈΡΡ ΠΏΡΠ΅ΠΆΠ΄Π΅Π²ΡΠ΅ΠΌΠ΅Π½Π½ΠΎΠ³ΠΎ Π·Π°ΠΌΠ΅ΡΠ·Π°Π½ΠΈΡ ΡΠ»ΠΎΠΆΠ΅Π½Π½ΠΎΠ³ΠΎ Π±Π΅ΒΡΠΎΠ½Π°. ΠΠ΅ΠΎΠ±Ρ
ΠΎΠ΄ΠΈΠΌΠΎ, ΡΡΠΎΠ±Ρ Π±Π΅ΡΠΎΠ½ ΡΠΎΡ
ΡΠ°Π½ΡΠ» ΠΏΡΠΈ ΡΠΊΠ»Π°Π΄ΠΊΠ΅ ΠΈ Π²ΡΠ΄Π΅ΡΠΆΠΈΠ²Π°Π½ΠΈΠΈ ΠΏΠΎΠ»ΠΎΠΆΠΈΡΠ΅Π»ΡΠ½ΡΡ ΡΠ΅ΠΌΠΏΠ΅ΡΠ°ΡΡΡΡ (Π²ΡΡΠ΅ 0Β°) 4 Π΄ΠΎ ΡΠ΅Ρ
ΠΏΠΎΡ, ΠΏΠΎΠΊΠ° Π΅Π³ΠΎ ΠΏΡΠΎΡΠ½ΠΎΡΡΡ Π½Π΅ Π΄ΠΎΡΡΠΈΠ³Π½Π΅Ρ ΠΎΠΏΡΠ΅Π΄Π΅Π»Π΅Π½ΒΠ½ΠΎΠ³ΠΎ Π·Π½Π°ΡΠ΅Π½ΠΈΡ, Π½Π°Π·ΡΠ²Π°Π΅ΠΌΠΎΠ³ΠΎ Β«ΠΊΡΠΈΡΠΈΡΠ΅ΡΠΊΠΎΠΉΒ» ΠΏΡΠΎΡΠ½ΠΎΡΡΡΡ.
ΠΠ»Ρ ΠΊΠΎΠ½ΡΡΡΡΠΊΡΠΈΠΉ, ΠΏΠΎΠ΄Π²Π΅ΡΠ³Π°ΡΡΠΈΡ ΡΡ ΡΡΠ°Π·Ρ ΠΏΠΎΡΠ»Π΅ Π²ΡΒΠ΄Π΅ΡΠΆΠΈΠ²Π°Π½ΠΈΡ ΠΏΠΎΠΏΠ΅ΡΠ΅ΠΌΠ΅Π½Π½ΠΎΠΌΡ Π·Π°ΠΌΠΎΡΠ°ΠΆΠΈΠ²Π°Π½ΠΈΡ ΠΈ ΠΎΡΡΠ°ΠΈΠ²Π°ΒΠ½ΠΈΡ, ΠΊΡΠΈΡΠΈΡΠ΅ΡΠΊΠ°Ρ ΠΏΡΠΎΡΠ½ΠΎΡΡΡ Π±Π΅ΡΠΎΠ½Π° Π½Π΅Π·Π°Π²ΠΈΡΠΈΠΌΠΎ ΠΎΡ Π΅Π³ΠΎ ΠΊΠ»Π°ΡΡΠ° Π΄ΠΎΠ»ΠΆΠ½Π° Π±ΡΡΡ Π½Π΅ ΠΌΠ΅Π½Π΅Π΅ 70%. Π° Π² ΠΏΡΠ΅Π΄Π½Π°ΠΏΡΡΠΆΠ΅Π½Π½ΡΡ ΠΊΠΎΠ½ΡΡΡΡΠΊΡΠΈΡΡ β Π½Π΅ ΠΌΠ΅Π½Π΅Π΅ 80% ΠΏΡΠΎΠ΅ΠΊΡΠ½ΠΎΠΉ ΠΏΡΠΎΡΒΠ½ΠΎΡΡΠΈ.
ΠΠ»Ρ ΠΊΠΎΠ½ΡΡΡΡΠΊΡΠΈΠΉ, ΠΏΠΎΠ΄Π²Π΅ΡΠ³Π°ΡΡΠΈΡ ΡΡ ΡΡΠ°Π·Ρ ΠΏΠΎ ΠΎΠΊΠΎΠ½ΡΠ°ΒΠ½ΠΈΠΈ Π²ΡΠ΄Π΅ΡΠΆΠΈΠ²Π°Π½ΠΈΡ Π΄Π΅ΠΉΡΡΠ²ΠΈΡ ΡΠ°ΡΡΠ΅ΡΠ½ΠΎΠ³ΠΎ Π΄Π°Π²Π»Π΅Π½ΠΈΡ Π²ΠΎΠ΄Ρ (ΡΠ΅Π·Π΅ΡΠ²ΡΠ°ΡΠΎΠ², ΠΏΠΎΠ΄ΠΏΠΎΡΠ½ΡΡ ΡΡΠ΅Π½), Π° ΡΠ°ΠΊΠΆΠ΅ ΠΊΠΎΠ½ΡΡΡΡΠΊΡΠΈΠΉ, ΠΊ ΠΊΠΎΡΠΎΡΡΠΌ ΠΏΡΠ΅Π΄ΡΡΠ²Π»ΡΡΡ ΡΠΏΠ΅ΡΠΈΠ°Π»ΡΠ½ΡΠ΅ ΡΡΠ΅Π±ΠΎΠ²Π°Π½ΠΈΡ ΠΏΠΎ ΠΌΠΎΡΠΎΠ·ΠΎΡΡΠΎΠΉΠΊΠΎΡΡΠΈ ΠΈ Π²ΠΎΠ΄ΠΎΠ½Π΅ΠΏΡΠΎΠ½ΠΈΡΠ°Π΅ΠΌΠΎΡΡΠΈ, ΠΊΡΠΈΡΠΈΡΠ΅ΡΠΊΠ°Ρ ΠΏΡΠΎΡΠ½ΠΎΡΡΡ Π΄ΠΎΠ»ΠΆΠ½Π° Π±ΡΡΡ Π½Π΅ Π½ΠΈΠΆΠ΅ 100% ΠΏΡΠΎΠ΅ΠΊΡΠ½ΠΎΠΉ ΠΏΡΠΎΡΒΠ½ΠΎΡΡΠΈ.
ΠΠ»Ρ ΠΌΠ°ΡΡΠΈΠ²Π½ΡΡ ΡΠΎΠΎΡΡΠΆΠ΅Π½ΠΈΠΉ ΡΠΏΠ΅ΡΠΈΠ°Π»ΡΠ½ΠΎΠ³ΠΎ Π½Π°Π·Π½Π°ΡΠ΅ΒΠ½ΠΈΡ (ΠΏΠ»ΠΎΡΠΈΠ½, ΠΎΠΏΠΎΡ, ΠΌΠΎΡΡΠΎΠ² ΠΈ Π΄Ρ.) ΡΡΠ»ΠΎΠ²ΠΈΡ ΠΈ ΡΡΠΎΠΊΠΈ Π΄ΠΎΠΏΡΒΡΡΠΈΠΌΠΎΠ³ΠΎ Π·Π°ΠΌΠ΅ΡΠ·Π°Π½ΠΈΡ Π±Π΅ΡΠΎΠ½Π° ΡΡΡΠ°Π½Π°Π²Π»ΠΈΠ²Π°ΡΡ Π² ΠΏΡΠΎΠ΅ΠΊΡΠ΅.
ΠΠ΅ΡΠ΅ΡΠΈΡΠ»Π΅Π½Π½ΡΠ΅ Π²ΡΡΠ΅ ΡΡΠ΅Π±ΠΎΠ²Π°Π½ΠΈΡ Π²ΡΠ·Π²Π°Π½Ρ ΡΠ΅ΠΌ, ΡΡΠΎ Π±Π΅ΡΠΎΠ½ ΠΏΡΠΈ ΠΎΡΡΠΈΡΠ°ΡΠ΅Π»ΡΠ½ΠΎΠΉ ΡΠ΅ΠΌΠΏΠ΅ΡΠ°ΡΡΡΠ΅ (Π½ΠΈΠΆΠ΅ 0Β°Π‘) Π½Π΅ ΡΠ²Π΅ΡΠ΄Π΅Π΅Ρ, ΡΠ°ΠΊ ΠΊΠ°ΠΊ Π²ΠΎΠ΄Π° Π² Π½Π΅ΠΌ ΠΏΡΠ΅Π²ΡΠ°ΡΠ°Π΅ΡΡΡ Π² Π»Π΅Π΄ ΠΈ ΡΠΈΒΠ·ΠΈΠΊΠΎ-Ρ
ΠΈΠΌΠΈΡΠ΅ΡΠΊΠΈΠ΅ ΠΏΡΠΎΡΠ΅ΡΡΡ Π²Π·Π°ΠΈΠΌΠΎΠ΄Π΅ΠΉΡΡΠ²ΠΈΡ ΠΌΠ΅ΠΆΠ΄Ρ ΡΠ΅ΒΠΌΠ΅Π½ΡΠΎΠΌ ΠΈ Π²ΠΎΠ΄ΠΎΠΉ Π·Π°ΡΠ²ΠΎΡΠ΅Π½ΠΈΡ ΠΏΡΠ°ΠΊΡΠΈΡΠ΅ΡΠΊΠΈ ΠΏΡΠ΅ΠΊΡΠ°ΡΠ°ΡΡΡΡ. ΠΠ΄Π½Π°ΠΊΠΎ, ΠΊΠΎΠ³Π΄Π° Π·Π°ΠΌΠ΅ΡΠ·ΡΠΈΠΉ Π±Π΅ΡΠΎΠ½ ΠΎΡΡΠ°Π΅Ρ, ΠΏΡΠΎΡΠ΅ΡΡΡ ΡΠ²Π΅ΡΒΠ΄Π΅Π½ΠΈΡ Π²ΠΎΠ·ΠΎΠ±Π½ΠΎΠ²Π»ΡΡΡΡΡ, ΠΈ, Π΅ΡΠ»ΠΈ Π·Π°ΠΌΠ΅ΡΠ·Π°Π½ΠΈΠ΅ ΠΏΡΠΎΠΈΠ·ΠΎΡΠ»ΠΎ Π½Π΅ ΡΠ°Π½Π΅Π΅ Π΄ΠΎΡΡΠΈΠΆΠ΅Π½ΠΈΡ ΠΈΠΌ ΠΊΡΠΈΡΠΈΡΠ΅ΡΠΊΠΎΠΉ ΠΏΡΠΎΡΠ½ΠΎΡΡΠΈ, ΡΠΎ Π±Π΅ΒΡΠΎΠ½ Π²ΠΏΠΎΡΠ»Π΅Π΄ΡΡΠ²ΠΈΠΈ ΠΏΡΠΈΠΎΠ±ΡΠ΅ΡΠ΅Ρ Π·Π°Π΄Π°Π½Π½ΡΡ (ΠΏΡΠΎΠ΅ΠΊΡΠ½ΡΡ) ΠΏΡΠΎΡΠ½ΠΎΡΡΡ. ΠΡΠ»ΠΈ ΠΆΠ΅ Π΄Π°ΡΡ Π±Π΅ΡΠΎΠ½Ρ Π·Π°ΠΌΠ΅ΡΠ·Π½ΡΡΡ.ΡΠ°Π½ΡΡΠ΅, ΡΠΎ ΠΏΡΠΎΠΈΠ·ΠΎΠΉΠ΄Π΅Ρ ΡΠ°ΡΡΠΈΡΠ½ΠΎ Π±Π΅Π·Π²ΠΎΠ·Π²ΡΠ°ΡΠ½Π°Ρ ΠΏΠΎΡΠ΅ΡΡ ΠΏΡΠΎΡΠ½ΠΎΡΡΠΈ (Π³Π»Π°Π²Π½ΡΠΌ ΠΎΠ±ΡΠ°Π·ΠΎΠΌ ΠΈΠ·-Π·Π° Π½Π°ΡΡΡΠ΅Π½ΠΈΡ ΡΡΠ΅ΠΏΠ»Π΅Π½ΠΈΡ ΠΌΠ΅ΠΆΠ΄Ρ ΠΊΡΡΠΏΠ½ΡΠΌ Π·Π°ΠΏΠΎΠ»Π½ΠΈΡΠ΅Π»Π΅ΠΌ ΠΈ ΡΠ΅ΠΌΠ΅Π½ΡΠ½ΡΠΌ ΡΠ°ΡΡΠ²ΠΎΡΠΎΠΌ). ΠΠΎΡΠ΅ΡΡ ΠΏΡΠΎΡΠ½ΠΎΡΡΠΈ Π±ΡΠ΄Π΅Ρ ΡΠ΅ΠΌ Π±ΠΎΠ»ΡΡΠ΅, ΡΠ΅ΠΌ ΠΌΠΎΠ»ΠΎΠΆΠ΅ Π±ΡΠ» Π±Π΅ΡΠΎΠ½ ΠΊ ΠΌΠΎΠΌΠ΅Π½ΡΡ Π·Π°ΠΌΠ΅ΡΠ·Π°Π½ΠΈΡ (ΡΠ°ΠΊ, Π½Π°ΠΏΡΠΈΠΌΠ΅Ρ, Π±Π΅ΡΠΎΠ½ Π½Π° ΠΏΠΎΡΡΒΠ»Π°Π½Π΄ΡΠ΅ΠΌΠ΅Π½ΡΠ΅, Π΄ΠΎΡΡΠΈΠ³Π°ΡΡΠΈΠΉ ΠΏΡΠΎΡΠ½ΠΎΡΡΠΈ Π½Π° 28-ΠΉ Π΄Π΅Π½Ρ ΠΈ Π·Π°ΠΌΠΎΡΠΎΠΆΠ΅Π½Π½ΡΠΉ ΡΠ΅ΡΠ΅Π· ΡΡΡΠΊΠΈ, ΠΏΠΎΡΠ»Π΅ ΡΠΊΠ»Π°Π΄ΠΊΠΈ, Π±Π΅Π·Π²ΠΎΠ·Π²ΡΠ°ΡΒΠ½ΠΎ ΡΠ΅ΡΡΠ΅Ρ Π΄ΠΎ ΠΏΠΎΠ»ΠΎΠ²ΠΈΠ½Ρ ΡΠ²ΠΎΠ΅ΠΉ ΠΏΡΠΎΡΠ½ΠΎΡΡΠΈ). ΠΠ΅ΡΠΎΠ½, Π·Π°ΠΌΠΎΒΡΠΎΠΆΠ΅Π½Π½ΡΠΉ ΠΏΡΠΈ Π΄ΠΎΡΡΠΈΠΆΠ΅Π½ΠΈΠΈ ΠΈΠΌ ΡΠΊΠ°Π·Π°Π½Π½ΡΡ
Π²ΡΡΠ΅ Π·Π½Π°ΡΠ΅ΒΠ½ΠΈΠΉ ΠΊΡΠΈΡΠΈΡΠ΅ΡΠΊΠΎΠΉ ΠΏΡΠΎΡΠ½ΠΎΡΡΠΈ, Π½Π΅ΠΎΠ±Ρ
ΠΎΠ΄ΠΈΠΌΠΎ Π²ΡΠ΄Π΅ΡΠΆΠΈΠ²Π°ΡΡ ΠΏΠΎΡΠ»Π΅ ΠΎΡΡΠ°ΠΈΠ²Π°Π½ΠΈΡ Π² ΡΡΠ»ΠΎΠ²ΠΈΡΡ
, ΠΎΠ±Π΅ΡΠΏΠ΅ΡΠΈΠ²Π°ΡΡΠΈΡ
ΠΏΠΎΠ»ΡΡΠ΅ΒΠ½ΠΈΠ΅ ΠΈΠΌ ΠΏΡΠΎΠ΅ΠΊΡΠ½ΠΎΠΉ ΠΏΡΠΎΡΠ½ΠΎΡΡΠΈ Π΄ΠΎ ΠΌΠΎΠΌΠ΅Π½ΡΠ° Π·Π°Π³ΡΡΠΆΠ΅Π½ΠΈΡ ΠΊΠΎΠ½ΡΡΡΡΠΊΡΠΈΠΈ ΠΏΡΠΎΠ΅ΠΊΡΠ½ΠΎΠΉ Π½Π°Π³ΡΡΠ·ΠΊΠΎΠΉ.
Π ΠΌΠΎΠΌΠ΅Π½ΡΡ ΡΠ½ΡΡΠΈΡ Π½Π΅ΡΡΡΠ΅ΠΉ ΠΎΠΏΠ°Π»ΡΠ±ΠΊΠΈ Π±Π΅ΡΠΎΠ½Π½ΡΡ
ΠΈ ΠΆΠ΅Π»Π΅Π·ΠΎΠ±Π΅ΡΠΎΠ½Π½ΡΡ
ΠΊΠΎΠ½ΡΡΡΡΠΊΡΠΈΠΉ ΡΡΠ΅Π±ΡΠ΅ΡΡΡ, ΡΡΠΎΠ±Ρ ΠΏΡΠΎΡΒΠ½ΠΎΡΡΡ Π±Π΅ΡΠΎΠ½Π° ΡΠΎΡΡΠ°Π²Π»ΡΠ»Π° 50. ..100% ΠΏΡΠΎΠ΅ΠΊΡΠ½ΠΎΠΉ. Π’Π°ΠΊΠΈΠ΅ ΠΊΠΎΠ½ΡΡΡΡΠΊΡΠΈΠΈ ΠΏΠΎΡΠ»Π΅ ΡΠ°ΡΠΏΠ°Π»ΡΠ±Π»ΠΈΠ²Π°Π½ΠΈΡ ΠΌΠΎΠ³ΡΡ Π±ΡΡΡ Π²ΠΎ ΠΌΠ½ΠΎΒΠ³ΠΈΡ
ΡΠ»ΡΡΠ°ΡΡ
Π±Π΅Π· Π²ΡΠ΅Π΄Π° Π΄Π»Ρ Π½ΠΈΡ
ΠΏΠΎΠ΄Π²Π΅ΡΠ³Π½ΡΡΡ Π΄Π΅ΠΉΡΡΠ²ΠΈΡ Π½ΠΈΠ·ΠΊΠΈΡ
ΡΠ΅ΠΌΠΏΠ΅ΡΠ°ΡΡΡ, Π½ΠΎ Π² ΠΊΠ°ΠΆΠ΄ΠΎΠΌ ΠΊΠΎΠ½ΠΊΡΠ΅ΡΠ½ΠΎΠΌ ΡΠ»ΡΡΠ°Π΅ Π½Π΅ΒΠΎΠ±Ρ
ΠΎΠ΄ΠΈΠΌΠΎ Π²ΡΠ΅ ΠΆΠ΅ ΡΠΎΠΏΠΎΡΡΠ°Π²ΠΈΡΡ ΡΠ°ΡΠΏΠ°Π»ΡΠ±ΠΎΡΠΏΡΡ ΠΈ ΠΊΡΠΈΡΠΈΡΠ΅ΒΡΠΊΡΡ ΠΏΡΠΎΡΠ½ΠΎΡΡΡ. Π ΡΠ΅Ρ
ΡΠ»ΡΡΠ°ΡΡ
, ΠΊΠΎΠ³Π΄Π° ΠΈΠ· ΡΡΠ»ΠΎΠ²ΠΈΠΉ ΠΌΠ½ΠΎΠ³ΠΎΒΠΊΡΠ°ΡΠ½ΠΎΠΉ ΠΎΠ±ΠΎΡΠ°ΡΠΈΠ²Π°Π΅ΠΌΠΎΡΡΠΈ ΠΎΠΏΠ°Π»ΡΠ±ΠΊΠΈ ΠΏΠΎΡΠ»Π΅Π΄Π½ΡΡ (Π½Π°ΠΏΡΠΈΒΠΌΠ΅Ρ, Π±ΠΎΠΊΠΎΠ²ΡΠ΅ ΡΠΈΡΡ ΠΎΠΏΠ°Π»ΡΠ±ΠΊΠΈ ΡΡΠ½Π΄Π°ΠΌΠ΅Π½ΡΠΎΠ², ΠΏΠΎΠ΄ΠΊΠΎΠ»Π΅Π½Π½ΠΈΠΊΠΎΠ², ΡΡΠ΅Π½ ΠΈ Ρ. ΠΏ.) ΡΠ½ΠΈΠΌΠ°ΡΡ ΡΠ°Π½ΡΡΠ΅ Π΄ΠΎΡΡΠΈΠΆΠ΅Π½ΠΈΡ Π±Π΅ΡΠΎΠ½ΠΎΠΌ ΠΊΡΠΈΡΠΈΡΠ΅ΡΠΊΠΎΠΉ ΠΏΡΠΎΡΠ½ΠΎΡΡΠΈ, ΡΠ°ΡΠΏΠ°Π»ΡΠ±Π»Π΅Π½Π½ΡΠ΅ ΠΏΠΎΠ²Π΅ΡΡ
Π½ΠΎΡΡΠΈ ΡΠ»Π΅Π΄ΡΠ΅Ρ Π²ΡΠ΅ΠΌΠ΅Π½Π½ΠΎ ΡΠΊΡΡΠ²Π°ΡΡ.
ΠΡΠΎ ΠΆΠ΅ ΠΏΡΠΈΡ ΠΎΠ΄ΠΈΡΡΡ Π΄Π΅Π»Π°ΡΡ ΠΈ Π² ΡΠ΅Ρ ΡΠ»ΡΡΠ°ΡΡ , ΠΊΠΎΠ³Π΄Π° ΡΠ°Π·Π½ΠΎΡΡΡ ΡΠ΅ΠΌΠΏΠ΅ΡΠ°ΡΡΡ ΠΏΠΎΠ²Π΅ΡΡ Π½ΠΎΡΡΠΈ Π±Π΅ΡΠΎΠ½Π° ΠΈ Π½Π°ΡΡΠΆΠ½ΠΎΠ³ΠΎ Π²ΠΎΠ·Π΄ΡΡ Π° ΠΏΡΠ΅Π²ΡΡΠ°Π΅Ρ ΡΠ»Π΅Π΄ΡΡΡΠΈΠ΅ Π·Π½Π°ΡΠ΅Π½ΠΈΡ: 20Π‘ β Π΄Π»Ρ ΠΊΠΎΠ½ΡΡΡΡΠΊΡΠΈΠΉ Ρ ΠΌΠΎΠ΄ΡΠ»Π΅ΠΌ ΠΏΠΎΠ²Π΅ΡΡ Π½ΠΎΡΡΠΈΒ ΠΎΡ 2 Π΄ΠΎ 5. Π‘ β Π΄Π»Ρ ΠΊΠΎΠ½ΡΡΡΡΠΊΡΠΈΠΉ Ρ ΠΌΠΎΠ΄ΡΠ»Π΅ΠΌ ΠΏΠΎΠ²Π΅ΡΡ Π½ΠΎΡΡΠΈ 5 ΠΈ Π²ΡΡΠ΅. ΠΠ½Π°ΡΠ΅ ΠΏΡΠΈ Π±ΡΡΡΡΠΎΠΌ ΠΎΡ Π»Π°ΠΆΠ΄Π΅Π½ΠΈΠΈ Π½Π° ΠΏΠΎΠ²Π΅ΡΡ Π½ΠΎΡΡΠΈ 6Ρ Π³ΠΎΠ½Π° ΠΎΠ±ΡΠ°Π·ΡΡΡΡΡ ΡΠ΅ΠΌΠΏΠ΅ΡΠ°ΡΡΡΠ½ΡΠ΅ ΡΡΠ΅ΡΠΈΠ½Ρ.
Π Π°ΡΠΏΠ°Π»ΡΠ±Π»ΠΈΠ²Π°Π½ΠΈΠ΅ ΠΊΠΎΠ½ΡΡΡΡΠΊΡΠΈΠΉ Π²ΡΠΏΠΎΠ»Π½ΡΡΡ ΠΏΡΠΈ ΠΏΠΎΒΠ»ΠΎΠΆΠΈΡΠ΅Π»ΡΠ½ΠΎΠΉ ΡΠ΅ΠΌΠΏΠ΅ΡΠ°ΡΡΡΠ΅ Π±Π΅ΡΠΎΠ½Π°; Π½ΠΈ Π² ΠΊΠΎΠ΅ΠΌ ΡΠ»ΡΡΠ°Π΅ Π½Π΅Π»ΡΠ·Ρ Π΄ΠΎΠΏΡΡΠΊΠ°ΡΡ ΠΏΡΠΈΠΌΠ΅ΡΠ·Π°Π½ΠΈΡ ΠΎΠΏΠ°Π»ΡΠ±ΠΊΠΈ ΠΊ Π±Π΅ΡΠΎΠ½Ρ.
ΠΠ»Ρ ΡΠ²Π΅ΡΠ΄Π΅Π½ΠΈΡ Π² Π·ΠΈΠΌΠ½ΠΈΡ
ΡΡΠ»ΠΎΠ²ΠΈΡΡ
Π±Π΅ΡΠΎΠ½Π°, ΠΏΡΠΈΠ³ΠΎΡΠΎΠ²ΒΠ»Π΅Π½Π½ΠΎΠ³ΠΎ Π½Π° ΠΎΠ±ΡΡΠ½ΠΎΠΉ Π²ΠΎΠ΄Π΅ (Π±Π΅Π· Π²Π²Π΅Π΄Π΅Π½ΠΈΡ Π² Π½Π΅Π΅ Ρ
ΠΈΠΌΠΈΡΠ΅ΒΡΠΊΠΈΡ
Π΄ΠΎΠ±Π°Π²ΠΎΠΊ ΡΠΎΠ»Π΅ΠΉ, ΠΏΠΎΠ½ΠΈΠΆΠ°ΡΡΠΈΡ
ΡΠΎΡΠΊΡ Π·Π°ΠΌΠ΅ΡΠ·Π°Π½ΠΈΡ ΠΎΠ±ΒΡΠ°Π·ΡΡΡΠ΅Π³ΠΎΡΡ ΠΏΡΠΈ ΡΡΠΎΠΌ ΡΠΎΠ»Π΅Π²ΠΎΠ³ΠΎ ΡΠ°ΡΡΠ²ΠΎΡΠ°), Π½Π΅ΠΎΠ±Ρ
ΠΎΠ΄ΠΈΠΌΠΎ ΠΏΡΠ΅ΠΆΠ΄Π΅ Π²ΡΠ΅Π³ΠΎ, ΡΡΠΎΠ±Ρ ΡΠΌΠ΅ΡΡ Π±ΡΠ»Π° ΡΠ»ΠΎΠΆΠ΅Π½Π° Π² ΠΎΠΏΠ°Π»ΡΠ±ΠΊΡ ΡΠ΅ΠΏΠ»ΠΎΠΉ ΠΈ Π²ΡΠ΅ Π΅Π΅ ΡΠΎΡΡΠ°Π²Π½ΡΠ΅ ΡΠ°ΡΡΠΈ ΠΈΠΌΠ΅Π»ΠΈ ΠΏΠΎΠ»ΠΎΠΆΠΈΡΠ΅Π»ΡΠ½ΡΡ ΡΠ΅ΠΌΠΏΠ΅ΡΠ°ΡΡΡΡ. ΠΠ΅Π»ΡΠ·Ρ, Π½Π°ΠΏΡΠΈΠΌΠ΅Ρ, ΡΠΊΠ»Π°Π΄ΡΠ²Π°ΡΡ Π² ΠΎΠΏΠ°Π»ΡΠ±ΠΊΡ Π±Π΅ΡΠΎΠ½Π½ΡΡ ΡΠΌΠ΅ΡΡ, ΠΏΡΠΈΠ³ΠΎΡΠΎΠ²Π»Π΅Π½Π½ΡΡ Π½Π° ΠΌΠ΅ΡΠ·Π»ΠΎΠΌ ΠΏΠ΅ΡΠΊΠ΅ ΠΈ ΡΠ΅Π±Π½Π΅. ΠΡΠΈ ΠΎΠ±ΠΎΠ³ΡΠ΅Π²Π΅ ΡΠ°ΠΊΠΎΠΉ ΡΠΌΠ΅ΡΠΈ ΠΏΠΎΡΠ»Π΅ ΡΠΊΠ»Π°Π΄ΠΊΠΈ ΡΠΎΠ΄Π΅ΡΒΠΆΠ°ΡΠ°ΡΡΡ Π² ΠΌΠ΅ΡΠ·Π»ΠΎΠΌ ΡΠΎΡΡΠΎΡΠ½ΠΈΠΈ Π² ΠΏΠ΅ΡΠΊΠ΅ ΠΈ ΡΠ΅Π±Π½Π΅ Π²Π»Π°Π³Π° ΠΎΡΡΠ°Π΅Ρ ΠΈ Π·Π°ΠΉΠΌΠ΅Ρ ΠΌΠ΅Π½ΡΡΠΈΠΉ ΠΎΠ±ΡΠ΅ΠΌ (ΠΈΠ·Π²Π΅ΡΡΠ½ΠΎ, ΡΡΠΎ Π²ΠΎΠ΄Π° ΠΏΡΠΈ Π·Π°ΠΌΠ΅ΡΠ·Π°Π½ΠΈΠΈ ΡΠ²Π΅Π»ΠΈΡΠΈΠ²Π°Π΅ΡΡΡ ΠΈ, Π½Π°ΠΎΠ±ΠΎΡΠΎΡ, Π»Π΅Π΄ ΠΏΡΠΈ ΠΎΡΒΡΠ°ΠΈΠ²Π°Π½ΠΈΠΈ ΡΠΌΠ΅Π½ΡΡΠ°Π΅ΡΡΡ Π² ΠΎΠ±ΡΠ΅ΠΌΠ΅ ΠΏΡΠΈΠΌΠ΅ΡΠ½ΠΎ Π½Π° 10%) 13 ΡΠ΅Π·ΡΠ»ΡΡΠ°ΡΠ΅ ΡΡΠΎΠ³ΠΎ ΠΏΠΎΠ»ΡΡΠ°Π΅ΡΡΡ ΡΡΡ
Π»ΡΠΉ, ΠΏΠΎΡΠΈΡΡΡΠΉ, Π° ΡΠ»Π΅ΒΠ΄ΠΎΠ²Π°ΡΠ΅Π»ΡΠ½ΠΎ, ΠΈ ΠΌΠ°Π»ΠΎΠΏΡΠΎΡΠ½ΡΠΉ Π±Π΅ΡΠΎΠ½.
ΠΠΎΡΡΠΎΠΌΡ Π² Π·ΠΈΠΌΠ½Π΅Π΅ Π²ΡΠ΅ΠΌΡ Π±Π΅ΡΠΎΠ½Π½ΡΡ ΡΠΌΠ΅ΡΡ ΠΏΡΠΈΠ³ΠΎΡΠΎΠ²Π»ΡΒΡΡ Π½Π° ΠΏΠΎΠ΄ΠΎΠ³ΡΠ΅ΡΠΎΠΉ Π²ΠΎΠ΄Π΅; Π·Π°ΠΏΠΎΠ»Π½ΠΈΡΠ΅Π»ΠΈ (ΠΏΠ΅ΡΠΎΠΊ, ΡΠ΅Π±Π΅Π½Ρ) ΡΠ°ΠΊΠΆΠ΅ Π½Π°Π³ΡΠ΅Π²Π°ΡΡ ΠΈΠ»ΠΈ ΠΎΡΡΠ°ΠΈΠ²Π°ΡΡ Π΄ΠΎ ΠΏΠΎΠ»ΠΎΠΆΠΈΡΠ΅Π»ΡΠ½ΠΎΠΉ ΡΠ΅ΠΌΒΠΏΠ΅ΡΠ°ΡΡΡΡ. ΠΡΠΊΠ»ΡΡΠ΅Π½ΠΈΠ΅ ΠΌΠΎΠΆΠ΅Ρ Π±ΡΡΡ Π΄ΠΎΠΏΡΡΠ΅Π½ΠΎ Π΄Π»Ρ ΡΡΡ
ΠΎΠ³ΠΎ ΡΠ΅Π±Π½Ρ ΠΈΠ»ΠΈ Π³ΡΠ°Π²ΠΈΡ, Π½Π΅ ΡΠΎΠ΄Π΅ΡΠΆΠ°ΡΠ΅Π³ΠΎ Π½Π°Π»Π΅Π΄ΠΈ Π½Π° Π·Π΅ΡΠ½Π°Ρ
Π½Π΅ ΡΠΌΠ΅ΡΠ·ΡΠΈΡ
ΡΡ ΠΊΠΎΠΌΡΠ΅Π² (Π²Π»Π°ΠΆΠ½ΠΎΡΡΡ Π½Π΅ Π²ΡΡΠ΅ 1… 1,5 %). Π’Π°ΠΊΠΎΠΉ Π·Π°ΠΏΠΎΠ»Π½ΠΈΡΠ΅Π»Ρ ΠΌΠΎΠΆΠ½ΠΎ Π·Π°Π³ΡΡΠΆΠ°ΡΡ Π² ΡΠΌΠ΅ΡΠΈΡΠ΅Π»Ρ Π½Π΅ΠΎΡΠΎΠ³ΡΠ΅ΡΡΠΌ ΠΏΡΠΈ ΡΡΠ»ΠΎΠ²ΠΈΠΈ, ΡΡΠΎ ΠΏΠΎ Π²ΡΡ
ΠΎΠ΄Π΅ ΠΈΠ· ΡΠΌΠ΅ΡΠΈΡΠ΅Π»Ρ Π±Π΅ΡΠΎΠ½ΒΠ½Π°Ρ ΡΠΌΠ΅ΡΡ Π±ΡΠ΄Π΅Ρ ΠΈΠΌΠ΅ΡΡ Π·Π°Π΄Π°Π½Π½ΡΡ ΠΏΠΎΠ»ΠΎΠΆΠΈΡΠ΅Π»ΡΠ½ΡΡ ΡΠ΅ΠΌΠΏΠ΅ΒΡΠ°ΡΡΡΡ. Π¦Π΅ΠΌΠ΅Π½Ρ Π½Π΅ ΠΏΠΎΠ΄ΠΎΠ³ΡΠ΅Π²Π°ΡΡ, ΡΠ°ΠΊ ΠΊΠ°ΠΊ ΠΏΡΠΈ ΠΏΠ΅ΡΠ΅ΠΌΠ΅ΡΠΈΒΠ²Π°Π½ΠΈΠΈ Ρ Π²ΠΎΠ΄ΠΎΠΉ ΠΈ Π·Π°ΠΏΠΎΠ»Π½ΠΈΡΠ΅Π»ΡΠΌΠΈ ΠΎΠ½ Π±ΡΡΡΡΠΎ ΠΏΡΠΈΠ½ΠΈΠΌΠ°Π΅Ρ ΠΏΠΎΠ»ΠΎΠΆΠΈΡΠ΅Π»ΡΠ½ΡΡ ΡΠ΅ΠΌΠΏΠ΅ΡΠ°ΡΡΡΡ.
ΠΠ΅ΡΠ΅Π²ΠΎΠ·ΠΊΡ ΠΈ ΡΠΊΠ»Π°Π΄ΠΊΡ Π±Π΅ΡΠΎΠ½Π½ΠΎΠΉ ΡΠΌΠ΅ΡΠΈ ΠΎΡΡΡΠ΅ΡΡΠ²Π»ΡΡΡ Π±ΡΡΡΡΠΎ, ΡΡΠΎΠ±Ρ Π΅Π΅ ΡΠ΅ΠΌΠΏΠ΅ΡΠ°ΡΡΡΠ° Π² ΠΎΠΏΠ°Π»ΡΠ±ΠΊΠ΅ Π±ΡΠ»Π° ΠΏΠΎΠ»ΠΎΒΠΆΠΈΡΠ΅Π»ΡΠ½ΠΎΠΉ.
ΠΡΠΊΡΡΡΡΠ²Π΅Π½Π½Π°Ρ ΡΠ΅ΠΏΠ»ΠΎΠ²Π»Π°ΠΆΠ½ΠΎΡΡΠ½Π°Ρ ΡΡΠ΅Π΄Π° Π΄Π»Ρ ΡΠ²Π΅ΡΠ΄Π΅ΒΠ½ΠΈΡ Π±Π΅ΡΠΎΠ½Π½ΠΎΠΉ ΡΠΌΠ΅ΡΠΈ, ΠΏΡΠΈΠ³ΠΎΡΠΎΠ²Π»Π΅Π½Π½ΠΎΠΉ ΠΈΠ· ΠΏΠΎΠ΄ΠΎΠ³ΡΠ΅ΡΡΡ ΠΌΠ°ΒΡΠ΅ΡΠΈΠ°Π»ΠΎΠ² ΠΈ ΡΠ»ΠΎΠΆΠ΅Π½Π½ΠΎΠΉ ΡΠ΅ΠΏΠ»ΠΎΠΉ Π² ΠΎΠΏΠ°Π»ΡΠ±ΠΊΡ, ΠΌΠΎΠΆΠ΅Ρ Π±ΡΡΡ ΡΠΎΠ·Π΄Π°Π½Π° ΠΊΠ°ΠΊ Π±Π΅Π· Π΅Π΅ ΠΎΠ±ΠΎΠ³ΡΠ΅Π²Π° ΠΏΠΎΡΠ»Π΅ ΡΠΊΠ»Π°Π΄ΠΊΠΈ (ΠΌΠ΅ΡΠΎΠ΄ ΡΠ΅ΡΠΌΠΎΡΠ°), ΡΠ°ΠΊ ΠΈ Ρ ΠΈΡΠΊΡΡΡΡΠ²Π΅Π½Π½ΡΠΌ ΠΏΡΠΎΠ³ΡΠ΅Π²ΠΎΠΌ ΡΠΌΠ΅ΡΠΈ ΠΈΠ»ΠΈ ΠΎΠΊΡΡΒΠΆΠ°ΡΡΠ΅ΠΉ Π΅Π΅ ΡΡΠ΅Π΄Ρ (ΡΠ»Π΅ΠΊΡΡΠΎΠΏΡΠΎΠ³ΡΠ΅Π², ΠΏΠ°ΡΠΎΠΏΡΠΎΠ³ΡΠ΅Π² ΠΈ Π΄Ρ.).
ΠΠ΅ΡΠΎΠ΄ ΡΠ΅ΡΠΌΠΎΡΠ° ΠΏΡΠΈΠΌΠ΅Π½ΡΡΡ Π΄Π»Ρ ΠΌΠ°ΡΡΠΈΠ²Π½ΡΡ ΠΊΠΎΠ½ΡΡΡΡΠΊΒΡΠΈΠΉ, Π½Π°ΠΏΡΠΈΠΌΠ΅Ρ Π±ΠΎΠ»ΡΡΠΈΡ ΡΡΠ½Π΄Π°ΠΌΠ΅Π½ΡΠΎΠ², ΡΠΎΠ»ΡΡΡΡ ΠΏΠ»ΠΈΡ, ΠΈ Π»ΠΈΡΡ ΠΎΡΡΠ°ΡΡΠΈ β ΠΏΡΠΈ Π½Π΅Π±ΠΎΠ»ΡΡΠΈΡ ΠΌΠΎΡΠΎΠ·Π°Ρ β Π΄Π»Ρ ΠΊΠ°ΡΠΊΠ°ΡΒΠ½ΡΡ ΠΊΠΎΠ½ΡΡΡΡΠΊΡΠΈΠΉ (Π±Π°Π»ΠΎΠΊ, ΠΊΠΎΠ»ΠΎΠ½Π½) Ρ Π±ΠΎΠ»ΡΡΠΈΠΌΠΈ ΠΏΠΎΠΏΠ΅ΡΠ΅ΡΒΠ½ΡΠΌΠΈ ΡΠ°Π·ΠΌΠ΅ΡΠ°ΠΌΠΈ.
ΠΡΠΎΡ ΡΠΏΠΎΡΠΎΠ± ΠΎΡΠ½ΠΎΠ²Π°Π½ Π½Π° ΡΠΎΠΌ, ΡΡΠΎ ΡΠΌΠ΅ΡΡ, ΡΠ»ΠΎΠΆΠ΅Π½Π½Π°Ρ Π² ΠΏΠΎΠ΄ΠΎΠ³ΡΠ΅ΡΠΎΠΌ ΡΠΎΡΡΠΎΡΠ½ΠΈΠΈ Π² ΡΡΠ΅ΠΏΠ»Π΅Π½Π½ΡΡ ΠΎΠΏΠ°Π»ΡΠ±ΠΊΡ ΠΈ Ρ
ΠΎΡΠΎΡΠΎ ΡΠΊΡΡΡΠ°Ρ ΠΎΡ ΠΌΠΎΡΠΎΠ·Π°, ΠΎΡΡΡΠ²Π°Π΅Ρ Π½Π°ΡΡΠΎΠ»ΡΠΊΠΎ ΠΌΠ΅Π΄Π»Π΅Π½Π½ΠΎ, ΡΡΠΎ ΠΊ ΠΌΠΎΠΌΠ΅Π½ΡΡ Π·Π°ΠΌΠ΅ΡΠ·Π°Π½ΠΈΡ Π±Π΅ΡΠΎΠ½ ΡΡΠΏΠ΅Π²Π°Π΅Ρ Π½Π°Π±ΡΠ°ΡΡ Π½Π΅ΠΎΠ±Ρ
ΠΎΒΠ΄ΠΈΠΌΡΡ ΠΏΡΠΎΡΠ½ΠΎΡΡΡ. ΠΠ΅Π΄Π»Π΅Π½Π½ΠΎΠ΅ ΠΎΡΡΡΠ²Π°Π½ΠΈΠ΅ ΠΌΠ°ΡΡΠΈΠ²Π° (ΠΏΠΎ ΡΡΠ°Π²Π½Π΅Π½ΠΈΡ Ρ ΡΠΎΠ½ΠΊΠΈΠΌΠΈ ΠΊΠΎΠ½ΡΡΡΡΠΊΡΠΈΡΠΌΠΈ, Π½Π°Ρ
ΠΎΠ΄ΡΡΠΈΠΌΠΈΡΡ Π² ΡΠ΅Ρ
ΠΆΠ΅ ΡΡΠ»ΠΎΠ²ΠΈΡΡ
) ΠΎΠ±ΡΡΡΠ½ΡΠ΅ΡΡΡ ΡΠ΅ΠΌ, ΡΡΠΎ Π΅Π³ΠΎ ΠΏΠΎΠ²Π΅ΡΡ
Π½ΠΎΡΡΡ, ΡΠ΅ΡΠ΅Π· ΠΊΠΎΡΠΎΡΡΡ ΡΠ΅ΠΏΠ»ΠΎ ΡΡ
ΠΎΠ΄ΠΈΡ Π² ΠΎΠΊΡΡΠΆΠ°ΡΡΠ΅Π΅ ΠΏΡΠΎΡΡΡΠ°Π½ΡΡΒΠ²ΠΎ, ΠΌΠ°Π»Π° ΠΏΠΎ ΡΡΠ°Π²Π½Π΅Π½ΠΈΡ Ρ Π΅Π³ΠΎ ΠΎΠ±ΡΠ΅ΠΌΠΎΠΌ. Π ΡΠΎΠΌΡ ΠΆΠ΅ ΠΎΡΡΡΒΠ²Π°Π½ΠΈΠ΅ ΠΌΠ°ΡΡΠΈΠ²Π° Π·Π°ΠΌΠ΅Π΄Π»ΡΠ΅ΡΡΡ Π΅ΡΠ΅ ΡΠ΅ΠΌ, ΡΡΠΎ ΡΠ΅ΠΌΠ΅Π½Ρ ΠΏΡΠΈ ΡΠ²Π΅ΡΠ΄Π΅Π½ΠΈΠΈ Π²ΡΠ΄Π΅Π»ΡΠ΅Ρ ΡΠ΅ΠΏΠ»ΠΎ (ΠΏΡΠΎΠΈΡΡ
ΠΎΠ΄ΠΈΡ ΡΠ°ΠΊ Π½Π°Π·ΡΠ²Π°Π΅ΠΌΠ°Ρ ΡΠΊΠ·ΠΎΡΠ΅ΡΠΌΠΈΡΠ΅ΡΠΊΠ°Ρ ΡΠ΅Π°ΠΊΡΠΈΡ). Π ΠΎΡΠ΅Π½Ρ Π±ΠΎΠ»ΡΡΠΈΡ
ΠΌΠ°ΡΡΠΈΠ²Π°Ρ
ΡΡΠΎ ΠΏΡΠΈΠ²ΠΎΠ΄ΠΈΡ Π΄Π°ΠΆΠ΅ ΠΊ Π΄Π»ΠΈΡΠ΅Π»ΡΠ½ΠΎΠΌΡ ΠΏΠΎΠ²ΡΡΠ΅Π½ΠΈΡ ΡΠ΅ΠΌΠΏΠ΅ΡΠ°ΒΡΡΡΡ Π² Π±Π΅ΡΠΎΠ½Π΅ (Π΄ΠΎ 30…40Β°Π‘).
Π’ΠΎΠ½ΠΊΠΈΠ΅ ΠΊΠΎΠ½ΡΡΡΡΠΊΡΠΈΠΈ ΠΎΡΡΡΠ²Π°ΡΡ ΠΎΡΠ΅Π½Ρ Π±ΡΡΡΡΠΎ, ΠΏΠΎΡΡΠΎΠΌΡ ΠΏΡΠΈΠ±Π΅Π³Π°ΡΡ ΠΊ ΠΈΡ ΠΈΡΠΊΡΡΡΡΠ²Π΅Π½Π½ΠΎΠΌΡ ΠΏΡΠΎΠ³ΡΠ΅Π²Ρ (ΡΠ»Π΅ΠΊΡΡΠΈΡΠ΅ΡΠΊΠΈΠΌ ΡΠΎΠΊΠΎΠΌ, ΠΏΠ°ΡΠΎΠΌ, ΡΠ΅ΠΏΠ»ΡΠΌ Π²ΠΎΠ·Π΄ΡΡ ΠΎΠΌ). ΠΡΠΈ ΡΡΠΎΠΌ Π² ΡΠ΅Π»ΡΡ ΡΠΊΠΎΒΠ½ΠΎΠΌΠΈΠΈ ΡΠ΅ΠΏΠ»Π°, ΡΠ»Π΅ΠΊΡΡΠΎΡΠ½Π΅ΡΠ³ΠΈΠΈ ΠΈ ΠΏΠ°ΡΠ° ΡΠΎΡΠ΅ΡΠ°ΡΡ ΠΌΠ΅ΡΠΎΠ΄ ΡΠ΅ΡΒΠΌΠΎΡΠ° Ρ ΠΈΡΠΊΡΡΡΡΠ²Π΅Π½Π½ΡΠΌ ΠΏΡΠΎΠ³ΡΠ΅Π²ΠΎΠΌ Π±Π΅ΡΠΎΠ½Π½ΠΎΠΉ ΡΠΌΠ΅ΡΠΈ ΠΈΠ»ΠΈ Π±Π΅ΡΠΎΠ½Π°.
ΠΠ°ΠΈΠ±ΠΎΠ»Π΅Π΅ ΡΠΊΠΎΠ½ΠΎΠΌΠΈΡΠ½ΡΠΌ ΠΈ ΡΠ΄ΠΎΠ±Π½ΡΠΌ Π² ΠΏΡΠΎΠΈΠ·Π²ΠΎΠ΄ΡΡΠ²Π΅Π½ΒΠ½ΠΎΠΌ ΠΎΡΠ½ΠΎΡΠ΅Π½ΠΈΠΈ ΠΏΠΎΠΊΠ°Π·Π°Π» ΡΠ΅Π±Ρ ΡΠΏΠΎΡΠΎΠ± ΠΏΡΠ΅Π΄Π²Π°ΡΠΈΡΠ΅Π»ΡΠ½ΠΎΠ³ΠΎ ΡΠ»Π΅ΠΊΡΡΠΎΠΏΡΠΎΠ³ΡΠ΅Π²Π° Π±Π΅ΡΠΎΠ½Π½ΠΎΠΉ ΡΠΌΠ΅ΡΠΈ ΠΏΠ΅ΡΠ΅Π΄ Π΅Π΅ ΡΠΊΠ»Π°Π΄ΠΊΠΎΠΉ. ΠΡΒΠΏΠΎΠ»ΡΠ·ΠΎΠ²Π°Π½ΠΈΠ΅ ΡΡΠΎΠ³ΠΎ ΡΠΏΠΎΡΠΎΠ±Π° ΠΏΠΎΠ·Π²ΠΎΠ»ΡΠ΅Ρ Π·Π½Π°ΡΠΈΡΠ΅Π»ΡΠ½ΠΎ ΡΠ°ΡΡΠΈΒΡΠΈΡΡ ΠΎΠ±Π»Π°ΡΡΡ ΠΏΡΠΈΠΌΠ΅Π½Π΅Π½ΠΈΡ ΠΌΠ΅ΡΠΎΠ΄Π° Β«ΡΠ΅ΡΠΌΠΎΡΠ°Β», ΠΎΡΠΎΠ±Π΅Π½Π½ΠΎ ΠΏΡΠΈ Π½Π΅Π±ΠΎΠ»ΡΡΠΈΡ ΠΌΠΎΡΠΎΠ·Π°Ρ .
ΠΠ»Ρ ΠΏΡΠΎΠ³ΡΠ΅Π²Π° Π±Π΅ΡΠΎΠ½Π° ΡΡΠ½Π΄Π°ΠΌΠ΅Π½ΡΠΎΠ², ΡΠ°ΡΠΏΠΎΠ»ΠΎΠΆΠ΅Π½Π½ΡΡ
Π² ΠΎΡΠ΄Π΅Π»ΡΠ½ΡΡ
ΠΊΠΎΡΠ»ΠΎΠ²Π°Π½Π°Ρ
ΠΈ ΠΈΠΌΠ΅ΡΡΠΈΡ
ΠΏΠΎΠ΄ΠΎΡΠ²Ρ Π·Π½Π°ΡΠΈΡΠ΅Π»ΡΠ½ΠΎ Π½ΠΈΠΆΠ΅ ΡΡΠΎΠ²Π½Ρ ΠΏΡΠΎΠΌΠ΅ΡΠ·Π°Π½ΠΈΡ Π³ΡΡΠ½ΡΠ°, ΠΎΡΠ΅Π½Ρ ΡΠ΄ΠΎΠ±Π½ΠΎ ΡΠΎΡΠ΅ΡΠ°ΡΡ ΠΌΠ΅ΡΠΎΠ΄ ΡΠ΅ΡΠΌΠΎΡΠ° Ρ Π²ΡΠ΄Π΅ΡΠΆΠΈΠ²Π°Π½ΠΈΠ΅ΠΌ Π² ΡΠ΅ΠΏΠ»ΡΠΊΠ΅. ΠΡΠ»ΠΈ ΠΊΠΎΡΠ»ΠΎΒΠ²Π°Π½Ρ Ρ
ΠΎΡΠΎΡΠΎ Π·Π°ΠΊΡΡΡΡ ΡΠ²Π΅ΡΡ
Ρ Ρ Π·Π°Ρ
Π²Π°ΡΠΎΠΌ Π±ΡΠΎΠ²ΠΎΠΊ ΡΠ°ΠΊ, ΡΡΠΎ- βΠ±Ρ Π² Π½ΠΈΡ
Π½Π΅ ΠΏΠΎΠΏΠ°Π΄Π°Π» Ρ
ΠΎΠ»ΠΎΠ΄Π½ΡΠΉ Π²ΠΎΠ·Π΄ΡΡ
, ΡΠΎ Π² Π·Π°ΠΊΡΡΡΠΎΠΌ ΠΏΡΠΎΡΡΡΠ°Π½ΡΡΠ²Π΅ Π·Π° ΡΡΠ΅Ρ ΠΎΡΠ΄Π°ΡΠΈ ΡΠ΅ΠΏΠ»Π° ΡΠ°Π»ΡΠΌ Π³ΡΡΠ½ΡΠΎΠΌ ΠΏΠΎΒΡΡΠ΅ΠΏΠ΅Π½Π½ΠΎ ΡΡΡΠ°Π½Π°Π²Π»ΠΈΠ²Π°Π΅ΡΡΡ Π½Π΅Π±ΠΎΠ»ΡΡΠ°Ρ ΠΏΠΎΠ»ΠΎΠΆΠΈΡΠ΅Π»ΡΠ½Π°Ρ ΡΠ΅ΠΌΠΏΠ΅ΡΠ°ΡΡΡΠ° (1 Β°Π‘), ΠΎΠ±ΡΡΠ»ΠΎΠ²Π»ΠΈΠ²Π°ΡΡΠ°Ρ ΡΠ²Π΅ΡΠ΄Π΅Π½ΠΈΠ΅ Π±Π΅ΡΠΎΠ½Π°.
Β
Π’Π΅Ρ Π½ΠΎΠ»ΠΎΠ³ΠΈΡ Π±Π΅ΡΠΎΠ½Π½ΡΡ ΡΠ°Π±ΠΎΡ Π² Π·ΠΈΠΌΠ½ΠΈΡ ΡΡΠ»ΠΎΠ²ΠΈΡΡ
Π€ΠΈΠ·ΠΈΡΠ΅ΡΠΊΠΈΠ΅ ΠΏΡΠΎΡΠ΅ΡΡΡ ΠΈ ΠΎΠΏΡΠ΅Π΄Π΅Π»ΡΡΡΠΈΠ΅ ΠΏΠΎΠ»ΠΎΠΆΠ΅Π½ΠΈΡ
ΠΠΎΠ½ΡΡΠΈΠ΅ Β«Π·ΠΈΠΌΠ½ΠΈΠ΅ ΡΡΠ»ΠΎΠ²ΠΈΡΒ» Π² ΡΠ΅Ρ Π½ΠΎΠ»ΠΎΠ³ΠΈΠΈ ΠΌΠΎΠ½ΠΎΠ»ΠΈΡΠ½ΠΎΠ³ΠΎ Π±Π΅ΡΠΎΠ½Π° ΠΈ ΠΆΠ΅Π»Π΅Π·ΠΎΠ±Π΅ΡΠΎΠ½Π° Π½Π΅ΡΠΊΠΎΠ»ΡΠΊΠΎ ΠΎΡΠ»ΠΈΡΠ°Π΅ΡΡΡ ΠΎΡ ΠΎΠ±ΡΠ΅ΠΏΡΠΈΠ½ΡΡΠΎΠ³ΠΎ — ΠΊΠ°Π»Π΅Π½Π΄Π°ΡΠ½ΠΎΠ³ΠΎ. ΠΠΈΠΌΠ½ΠΈΠ΅ ΡΡΠ»ΠΎΠ²ΠΈΡ Π½Π°ΡΠΈΠ½Π°ΡΡΡΡ, ΠΊΠΎΠ³Π΄Π° ΡΡΠ΅Π΄Π½Π΅ΡΡΡΠΎΡΠ½Π°Ρ ΡΠ΅ΠΌΠΏΠ΅ΡΠ°ΡΡΡΠ° Π½Π°ΡΡΠΆΠ½ΠΎΠ³ΠΎ Π²ΠΎΠ·Π΄ΡΡ Π° ΡΠ½ΠΈΠΆΠ°Π΅ΡΡΡ Π΄ΠΎ +5Β°Π‘, Π° Π² ΡΠ΅ΡΠ΅Π½ΠΈΠ΅ ΡΡΡΠΎΠΊ ΠΈΠΌΠ΅Π΅Ρ ΠΌΠ΅ΡΡΠΎ ΠΏΠ°Π΄Π΅Π½ΠΈΠ΅ ΡΠ΅ΠΌΠΏΠ΅ΡΠ°ΡΡΡΡ Π½ΠΈΠΆΠ΅ 0Β°Π‘.
ΠΡΠΈ ΠΎΡΡΠΈΡΠ°ΡΠ΅Π»ΡΠ½ΡΡ
ΡΠ΅ΠΌΠΏΠ΅ΡΠ°ΡΡΡΠ°Ρ
Π½Π΅ ΠΏΡΠΎΡΠ΅Π°Π³ΠΈΡΠΎΠ²Π°Π²ΡΠ°Ρ Ρ ΡΠ΅ΠΌΠ΅Π½ΡΠΎΠΌ Π²ΠΎΠ΄Π° ΠΏΠ΅ΡΠ΅Ρ
ΠΎΠ΄ΠΈΡ Π² Π»Π΅Π΄ ΠΈ Π½Π΅ Π²ΡΡΡΠΏΠ°Π΅Ρ Π² Ρ
ΠΈΠΌΠΈΡΠ΅ΡΠΊΠΎΠ΅ ΡΠΎΠ΅Π΄ΠΈΠ½Π΅Π½ΠΈΠ΅ Ρ ΡΠ΅ΠΌΠ΅Π½ΡΠΎΠΌ. Π ΡΠ΅Π·ΡΠ»ΡΡΠ°ΡΠ΅ ΡΡΠΎΠ³ΠΎ ΠΏΡΠ΅ΠΊΡΠ°ΡΠ°Π΅ΡΡΡ ΡΠ΅Π°ΠΊΡΠΈΡ Π³ΠΈΠ΄ΡΠ°ΡΠ°ΡΠΈΠΈ ΠΈ, ΡΠ»Π΅Π΄ΠΎΠ²Π°ΡΠ΅Π»ΡΠ½ΠΎ, Π±Π΅ΡΠΎΠ½ Π½Π΅ ΡΠ²Π΅ΡΠ΄Π΅Π΅Ρ. ΠΠ΄Π½ΠΎΠ²ΡΠ΅ΠΌΠ΅Π½Π½ΠΎ Π² Π±Π΅ΡΠΎΠ½Π΅ ΡΠ°Π·Π²ΠΈΠ²Π°ΡΡΡΡ Π·Π½Π°ΡΠΈΡΠ΅Π»ΡΠ½ΡΠ΅ ΡΠΈΠ»Ρ Π²Π½ΡΡΡΠ΅Π½Π½Π΅Π³ΠΎ Π΄Π°Π²Π»Π΅Π½ΠΈΡ, Π²ΡΠ·Π²Π°Π½Π½ΡΠ΅ ΡΠ²Π΅Π»ΠΈΡΠ΅Π½ΠΈΠ΅ΠΌ (ΠΏΡΠΈΠΌΠ΅ΡΠ½ΠΎ Π½Π° 9%) ΠΎΠ±ΡΠ΅ΠΌΠ° Π²ΠΎΠ΄Ρ ΠΏΡΠΈ ΠΏΠ΅ΡΠ΅Ρ
ΠΎΠ΄Π΅ Π΅Π΅ Π² Π»Π΅Π΄. ΠΡΠΈ ΡΠ°Π½Π½Π΅ΠΌ Π·Π°ΠΌΠΎΡΠ°ΠΆΠΈΠ²Π°Π½ΠΈΠΈ Π±Π΅ΡΠΎΠ½Π° Π΅Π³ΠΎ Π½Π΅ΠΎΠΊΡΠ΅ΠΏΡΠ°Ρ ΡΡΡΡΠΊΡΡΡΠ° Π½Π΅ ΠΌΠΎΠΆΠ΅Ρ ΠΏΡΠΎΡΠΈΠ²ΠΎΡΡΠΎΡΡΡ ΡΡΠΈΠΌ ΡΠΈΠ»Π°ΠΌ ΠΈ Π½Π°ΡΡΡΠ°Π΅ΡΡΡ. ΠΡΠΈ ΠΏΠΎΡΠ»Π΅Π΄ΡΡΡΠ΅ΠΌ ΠΎΡΡΠ°ΠΈΠ²Π°Π½ΠΈΠΈ Π·Π°ΠΌΠ΅ΡΠ·ΡΠ°Ρ Π²ΠΎΠ΄Π° Π²Π½ΠΎΠ²Ρ ΠΏΡΠ΅Π²ΡΠ°ΡΠ°Π΅ΡΡΡ Π² ΠΆΠΈΠ΄ΠΊΠΎΡΡΡ ΠΈ ΠΏΡΠΎΡΠ΅ΡΡ Π³ΠΈΠ΄ΡΠ°ΡΠ°ΡΠΈΠΈ ΡΠ΅ΠΌΠ΅Π½ΡΠ° Π²ΠΎΠ·ΠΎΠ±Π½ΠΎΠ²Π»ΡΠ΅ΡΡΡ, ΠΎΠ΄Π½Π°ΠΊΠΎ ΡΠ°Π·ΡΡΡΠ΅Π½Π½ΡΠ΅ ΡΡΡΡΠΊΡΡΡΠ½ΡΠ΅ ΡΠ²ΡΠ·ΠΈ Π² Π±Π΅ΡΠΎΠ½Π΅ ΠΏΠΎΠ»Π½ΠΎΡΡΡΡ Π½Π΅ Π²ΠΎΡΡΡΠ°Π½Π°Π²Π»ΠΈΠ²Π°ΡΡΡΡ.
ΠΠ°ΠΌΠΎΡΠ°ΠΆΠΈΠ²Π°Π½ΠΈΠ΅ ΡΠ²Π΅ΠΆΠ΅ΡΠ»ΠΎΠΆΠ΅Π½Π½ΠΎΠ³ΠΎ Π±Π΅ΡΠΎΠ½Π° ΡΠΎΠΏΡΠΎΠ²ΠΎΠΆΠ΄Π°Π΅ΡΡΡ ΡΠ°ΠΊΠΆΠ΅ ΠΎΠ±ΡΠ°Π·ΠΎΠ²Π°Π½ΠΈΠ΅ΠΌ Π²ΠΎΠΊΡΡΠ³ Π°ΡΠΌΠ°ΡΡΡΡ ΠΈ Π·Π΅ΡΠ΅Π½ Π·Π°ΠΏΠΎΠ»Π½ΠΈΡΠ΅Π»Ρ Π»Π΅Π΄ΡΠ½ΡΡ ΠΏΠ»Π΅Π½ΠΎΠΊ, ΠΊΠΎΡΠΎΡΡΠ΅ Π±Π»Π°Π³ΠΎΠ΄Π°ΡΡ ΠΏΡΠΈΡΠΎΠΊΡ Π²ΠΎΠ΄Ρ ΠΈΠ· ΠΌΠ΅Π½Π΅Π΅ ΠΎΡ Π»Π°ΠΆΠ΄Π΅Π½Π½ΡΡ Π·ΠΎΠ½ Π±Π΅ΡΠΎΠ½Π° ΡΠ²Π΅Π»ΠΈΡΠΈΠ²Π°ΡΡΡΡ Π² ΠΎΠ±ΡΠ΅ΠΌΠ΅ ΠΈ ΠΎΡΠΆΠΈΠΌΠ°ΡΡ ΡΠ΅ΠΌΠ΅Π½ΡΠ½ΠΎΠ΅ ΡΠ΅ΡΡΠΎ ΠΎΡ Π°ΡΠΌΠ°ΡΡΡΡ ΠΈ Π·Π°ΠΏΠΎΠ»Π½ΠΈΡΠ΅Π»Ρ.
ΠΡΠ΅ ΡΡΠΈ ΠΏΡΠΎΡΠ΅ΡΡΡ Π·Π½Π°ΡΠΈΡΠ΅Π»ΡΠ½ΠΎ ΡΠ½ΠΈΠΆΠ°ΡΡ ΠΏΡΠΎΡΠ½ΠΎΡΡΡ Π±Π΅ΡΠΎΠ½Π° ΠΈ Π΅Π³ΠΎ ΡΡΠ΅ΠΏΠ»Π΅Π½ΠΈΠ΅ Ρ Π°ΡΠΌΠ°ΡΡΡΠΎΠΉ, Π° ΡΠ°ΠΊΠΆΠ΅ ΡΠΌΠ΅Π½ΡΡΠ°Π΅Ρ Π΅Π³ΠΎ ΠΏΠ»ΠΎΡΠ½ΠΎΡΡΡ, ΡΡΠΎΠΉΠΊΠΎΡΡΡ ΠΈ Π΄ΠΎΠ»Π³ΠΎΠ²Π΅ΡΠ½ΠΎΡΡΡ.
ΠΡΠ»ΠΈ Π±Π΅ΡΠΎΠ½ Π΄ΠΎ Π·Π°ΠΌΠ΅ΡΠ·Π°Π½ΠΈΡ ΠΏΡΠΈΠΎΠ±ΡΠ΅ΡΠ°Π΅Ρ ΠΎΠΏΡΠ΅Π΄Π΅Π»Π΅Π½Π½ΡΡ Π½Π°ΡΠ°Π»ΡΠ½ΡΡ ΠΏΡΠΎΡΠ½ΠΎΡΡΡ, ΡΠΎ Π²ΡΠ΅ ΡΠΏΠΎΠΌΡΠ½ΡΡΡΠ΅ Π²ΡΡΠ΅ ΠΏΡΠΎΡΠ΅ΡΡΡ Π½Π΅ ΠΎΠΊΠ°Π·ΡΠ²Π°ΡΡ Π½Π° Π½Π΅Π³ΠΎ Π½Π΅Π±Π»Π°Π³ΠΎΠΏΡΠΈΡΡΠ½ΠΎΠ³ΠΎ Π²ΠΎΠ·Π΄Π΅ΠΉΡΡΠ²ΠΈΡ. ΠΠΈΠ½ΠΈΠΌΠ°Π»ΡΠ½ΡΡ ΠΏΡΠΎΡΠ½ΠΎΡΡΡ, ΠΏΡΠΈ ΠΊΠΎΡΠΎΡΠΎΠΉ Π·Π°ΠΌΠΎΡΠ°ΠΆΠΈΠ²Π°Π½ΠΈΠ΅ Π΄Π»Ρ Π±Π΅ΡΠΎΠ½Π° Π½Π΅ ΠΎΠΏΠ°ΡΠ½ΠΎ, Π½Π°Π·ΡΠ²Π°ΡΡ ΠΊΡΠΈΡΠΈΡΠ΅ΡΠΊΠΎΠΉ.
ΠΠ΅Π»ΠΈΡΠΈΠ½Π° Π½ΠΎΡΠΌΠΈΡΡΠ΅ΠΌΠΎΠΉ ΠΊΡΠΈΡΠΈΡΠ΅ΡΠΊΠΎΠΉ ΠΏΡΠΎΡΠ½ΠΎΡΡΠΈ Π·Π°Π²ΠΈΡΠΈΡ ΠΎΡ ΠΊΠ»Π°ΡΡΠ° Π±Π΅ΡΠΎΠ½Π°, Π²ΠΈΠ΄Π° ΠΈ ΡΡΠ»ΠΎΠ²ΠΈΠΉ ΡΠΊΡΠΏΠ»ΡΠ°ΡΠ°ΡΠΈΠΈ ΠΊΠΎΠ½ΡΡΡΡΠΊΡΠΈΠΈ ΠΈ ΡΠΎΡΡΠ°Π²Π»ΡΠ΅Ρ: Π΄Π»Ρ Π±Π΅ΡΠΎΠ½Π½ΡΡ
ΠΈ ΠΆΠ΅Π»Π΅Π·ΠΎΠ±Π΅ΡΠΎΠ½Π½ΡΡ
ΠΊΠΎΠ½ΡΡΡΡΠΊΡΠΈΠΉ Ρ Π½Π΅Π½Π°ΠΏΡΡΠ³Π°Π΅ΠΌΠΎΠΉ Π°ΡΠΌΠ°ΡΡΡΠΎΠΉ — 50% ΠΏΡΠΎΠ΅ΠΊΡΠ½ΠΎΠΉ ΠΏΡΠΎΡΠ½ΠΎΡΡΠΈ Π΄Π»Ρ Π7,5. ..Π10, 40% Π΄Π»Ρ Π12,5… Π25 ΠΈ 30% Π΄Π»Ρ Π 30 ΠΈ Π²ΡΡΠ΅, Π΄Π»Ρ ΠΊΠΎΠ½ΡΡΡΡΠΊΡΠΈΠΉ Ρ ΠΏΡΠ΅Π΄Π²Π°ΡΠΈΡΠ΅Π»ΡΠ½ΠΎ Π½Π°ΠΏΡΡΠ³Π°Π΅ΠΌΠΎΠΉ Π°ΡΠΌΠ°ΡΡΡΠΎΠΉ — 80% ΠΏΡΠΎΠ΅ΠΊΡΠ½ΠΎΠΉ ΠΏΡΠΎΡΠ½ΠΎΡΡΠΈ, Π΄Π»Ρ ΠΊΠΎΠ½ΡΡΡΡΠΊΡΠΈΠΉ, ΠΏΠΎΠ΄Π²Π΅ΡΠ³Π°ΡΡΠΈΡ
ΡΡ ΠΏΠΎΠΏΠ΅ΡΠ΅ΠΌΠ΅Π½Π½ΠΎΠΌΡ Π·Π°ΠΌΠΎΡΠ°ΠΆΠΈΠ²Π°Π½ΠΈΡ ΠΈ ΠΎΡΡΠ°ΠΈΠ²Π°Π½ΠΈΡ ΠΈΠ»ΠΈ ΡΠ°ΡΠΏΠΎΠ»ΠΎΠΆΠ΅Π½Π½ΡΡ
Π² Π·ΠΎΠ½Π΅ ΡΠ΅Π·ΠΎΠ½Π½ΠΎΠ³ΠΎ ΠΎΡΡΠ°ΠΈΠ²Π°Π½ΠΈΡ Π²Π΅Ρ-Π½ΠΎΠΌΠ΅ΡΠ·Π»ΡΡ
Π³ΡΡΠ½ΡΠΎΠ² — 70% ΠΏΡΠΎΠ΅ΠΊΡΠ½ΠΎΠΉ ΠΏΡΠΎΡΠ½ΠΎΡΡΠΈ, Π΄Π»Ρ ΠΊΠΎΠ½ΡΡΡΡΠΊΡΠΈΠΉ, Π½Π°Π³ΡΡΠΆΠ°Π΅ΠΌΡΡ
ΡΠ°ΡΡΠ΅ΡΠ½ΠΎΠΉ Π½Π°Π³ΡΡΠ·ΠΊΠΎΠΉ — 100% ΠΏΡΠΎΠ΅ΠΊΡΠ½ΠΎΠΉ ΠΏΡΠΎΡΠ½ΠΎΡΡΠΈ.
ΠΡΠΎΠ΄ΠΎΠ»ΠΆΠΈΡΠ΅Π»ΡΠ½ΠΎΡΡΡ ΡΠ²Π΅ΡΠ΄Π΅Π½ΠΈΡ Π±Π΅ΡΠΎΠ½Π° ΠΈ Π΅Π³ΠΎ ΠΊΠΎΠ½Π΅ΡΠ½ΡΠ΅ ΡΠ²ΠΎΠΉΡΡΠ²Π° Π² Π·Π½Π°ΡΠΈΡΠ΅Π»ΡΠ½ΠΎΠΉ ΡΡΠ΅ΠΏΠ΅Π½ΠΈ Π·Π°Π²ΠΈΡΡΡ ΠΎΡ ΡΠ΅ΠΌΠΏΠ΅ΡΠ°ΡΡΡΠ½ΡΡ ΡΡΠ»ΠΎΠ²ΠΈΠΉ, Π² ΠΊΠΎΡΠΎΡΡΡ Π²ΡΠ΄Π΅ΡΠΆΠΈΠ²Π°ΡΡ Π±Π΅ΡΠΎΠ½. ΠΠΎ ΠΌΠ΅ΡΠ΅ ΠΏΠΎΠ²ΡΡΠ΅Π½ΠΈΡ ΡΠ΅ΠΌΠΏΠ΅ΡΠ°ΡΡΡΡΡΠ²Π΅Π»ΠΈΡΠΈΠ²Π°Π΅ΡΡΡ Π°ΠΊΡΠΈΠ²Π½ΠΎΡΡΡ Π²ΠΎΠ΄Ρ, ΡΠΎΠ΄Π΅ΡΠΆΠ°ΡΠ΅ΠΉΡΡ Π² Π±Π΅ΡΠΎΠ½Π½ΠΎΠΉ ΡΠΌΠ΅ΡΠΈ, ΡΡΠΊΠΎΡΡΠ΅ΡΡΡ ΠΏΡΠΎΡΠ΅ΡΡ Π΅Π΅ Π²Π·Π°ΠΈΠΌΠΎΠ΄Π΅ΠΉΡΡΠ²ΠΈΡ Ρ ΠΌΠΈΠ½Π΅ΡΠ°Π»Π°ΠΌΠΈ ΡΠ΅ΠΌΠ΅Π½ΡΠ½ΠΎΠ³ΠΎ ΠΊΠ»ΠΈΠ½ΠΊΠ΅ΡΠ°, ΠΈΠ½ΡΠ΅Π½ΡΠΈΡΠΈΡΠΈΡΡΡΡΡΡ ΠΏΡΠΎΡΠ΅ΡΡΡ ΡΠΎΡΠΌΠΈΡΠΎΠ²Π°Π½ΠΈΡ ΠΊΠΎΠ°Π³ΡΠ»ΡΡΠΈΠΎΠ½Π½ΠΎΠΉ ΠΈ ΠΊΡΠΈΡΡΠ°Π»Π»ΠΈΡΠ΅ΡΠΊΠΎΠΉ ΡΡΡΡΠΊΡΡΡΡ Π±Π΅ΡΠΎΠ½Π°. ΠΡΠΈ ΡΠ½ΠΈΠΆΠ΅Π½ΠΈΠΈ ΡΠ΅ΠΌΠΏΠ΅ΡΠ°ΡΡΡΡ, Π½Π°ΠΎΠ±ΠΎΡΠΎΡ, Π²ΡΠ΅ ΡΡΠΈ ΠΏΡΠΎΡΠ΅ΡΡΡ Π·Π°ΡΠΎΡΠΌΠ°ΠΆΠΈΠ²Π°ΡΡΡΡ ΠΈ ΡΠ²Π΅ΡΠ΄Π΅Π½ΠΈΠ΅ Π±Π΅ΡΠΎΠ½Π° Π·Π°ΠΌΠ΅Π΄Π»ΡΠ΅ΡΡΡ.
ΠΠΎΡΡΠΎΠΌΡ ΠΏΡΠΈ Π±Π΅ΡΠΎΠ½ΠΈΡΠΎΠ²Π°Π½ΠΈΠΈ Π² Π·ΠΈΠΌΠ½ΠΈΡ
ΡΡΠ»ΠΎΠ²ΠΈΡΡ
Π½Π΅ΠΎΠ±Ρ
ΠΎΠ΄ΠΈΠΌΠΎ ΡΠΎΠ·Π΄Π°ΡΡ ΠΈ ΠΏΠΎΠ΄Π΄Π΅ΡΠΆΠΈΠ²Π°ΡΡ ΡΠ°ΠΊΠΈΠ΅ ΡΠ΅ΠΌΠΏΠ΅ΡΠ°ΡΡΡΠ½ΠΎ-Π²Π»Π°ΠΆΠ½ΠΎΡΡΠ½ΡΠ΅ ΡΡΠ»ΠΎΠ²ΠΈΡ, ΠΏΡΠΈ ΠΊΠΎΡΠΎΡΡΡ
Π±Π΅ΡΠΎΠ½ ΡΠ²Π΅ΡΠ΄Π΅Π΅Ρ Π΄ΠΎ ΠΏΡΠΈΠΎΠ±ΡΠ΅ΡΠ΅Π½ΠΈΡ ΠΈΠ»ΠΈ ΠΊΡΠΈΡΠΈΡΠ΅ΡΠΊΠΎΠΉ, ΠΈΠ»ΠΈ Π·Π°Π΄Π°Π½Π½ΠΎΠΉ ΠΏΡΠΎΡΠ½ΠΎΡΡΠΈ Π² ΠΌΠΈΠ½ΠΈΠΌΠ°Π»ΡΠ½ΡΠ΅ ΡΡΠΎΠΊΠΈ Ρ Π½Π°ΠΈΠΌΠ΅Π½ΡΡΠΈΠΌΠΈ ΡΡΡΠ΄ΠΎΠ²ΡΠΌΠΈ Π·Π°ΡΡΠ°ΡΠ°ΠΌΠΈ. ΠΠ»Ρ ΡΡΠΎΠ³ΠΎ ΠΏΡΠΈΠΌΠ΅Π½ΡΡΡ ΡΠΏΠ΅ΡΠΈΠ°Π»ΡΠ½ΡΠ΅ ΡΠΏΠΎΡΠΎΠ±Ρ ΠΏΡΠΈΠ³ΠΎΡΠΎΠ²Π»Π΅Π½ΠΈΡ, ΠΏΠΎΠ΄Π°ΡΠΈ, ΡΠΊΠ»Π°Π΄ΠΊΠΈ ΠΈ Π²ΡΠ΄Π΅ΡΠΆΠΈΠ²Π°Π½ΠΈΡ Π±Π΅ΡΠΎΠ½Π°.
ΠΡΠΈ ΠΏΡΠΈΠ³ΠΎΡΠΎΠ²Π»Π΅Π½ΠΈΠΈ Π±Π΅ΡΠΎΠ½Π½ΠΎΠΉ ΡΠΌΠ΅ΡΠΈ Π² Π·ΠΈΠΌΠ½ΠΈΡ ΡΡΠ»ΠΎΠ²ΠΈΡΡ Π΅Π΅ ΡΠ΅ΠΌΠΏΠ΅ΡΠ°ΡΡΡΡ ΠΏΠΎΠ²ΡΡΠ°ΡΡ Π΄ΠΎ 35…40Π‘ ΠΏΡΡΠ΅ΠΌ ΠΏΠΎΠ΄ΠΎΠ³ΡΠ΅Π²Π° Π·Π°ΠΏΠΎΠ»Π½ΠΈΡΠ΅Π»Π΅ΠΉ ΠΈ Π²ΠΎΠ΄Ρ. ΠΠ°ΠΏΠΎΠ»Π½ΠΈΡΠ΅Π»ΠΈ ΠΏΠΎΠ΄ΠΎΠ³ΡΠ΅Π²Π°ΡΡ Π΄ΠΎ 60Π‘ ΠΏΠ°ΡΠΎΠ²ΡΠΌΠΈ ΡΠ΅Π³ΠΈΡΡΡΠ°ΠΌΠΈ, Π²ΠΎ Π²ΡΠ°ΡΠ°ΡΡΠΈΡ ΡΡ Π±Π°ΡΠ°Π±Π°Π½Π°Ρ , Π² ΡΡΡΠ°Π½ΠΎΠ²ΠΊΠ°Ρ Ρ ΠΏΡΠΎΠ΄ΡΠ²ΠΊΠΎΠΉ Π΄ΡΠΌΠΎΠ²ΡΡ Π³Π°Π·ΠΎΠ² ΡΠ΅ΡΠ΅Π· ΡΠ»ΠΎΠΉ Π·Π°ΠΏΠΎΠ»Π½ΠΈΡΠ΅Π»Ρ, Π³ΠΎΡΡΡΠ΅ΠΉ Π²ΠΎΠ΄ΠΎΠΉ. ΠΠΎΠ΄Ρ ΠΏΠΎΠ΄ΠΎΠ³ΡΠ΅Π²Π°ΡΡ Π² Π±ΠΎΠΉΠ»Π΅ΡΠ°Ρ ΠΈΠ»ΠΈ Π²ΠΎΠ΄ΠΎΠ³ΡΠ΅ΠΉΠ½ΡΡ ΠΊΠΎΡΠ»Π°Ρ Π΄ΠΎ 90Π‘. ΠΠΎΠ΄ΠΎΠ³ΡΠ΅Π² ΡΠ΅ΠΌΠ΅Π½ΡΠ° Π·Π°ΠΏΡΠ΅ΡΠ°Π΅ΡΡΡ.
ΠΡΠΈ ΠΏΡΠΈΠ³ΠΎΡΠΎΠ²Π»Π΅Π½ΠΈΠΈ ΠΏΠΎΠ΄ΠΎΠ³ΡΠ΅ΡΠΎΠΉ Π±Π΅ΡΠΎΠ½Π½ΠΎΠΉ ΡΠΌΠ΅ΡΠΈ ΠΏΡΠΈΠΌΠ΅Π½ΡΡΡ ΠΈΠ½ΠΎΠΉ ΠΏΠΎΡΡΠ΄ΠΎΠΊ Π·Π°Π³ΡΡΠ·ΠΊΠΈ ΡΠΎΡΡΠ°Π²Π»ΡΡΡΠΈΡ
Π² Π±Π΅ΡΠΎΠ½ΠΎΡΠΌΠ΅ΡΠΈΡΠ΅Π»Ρ. Π Π»Π΅ΡΠ½ΠΈΡ
ΡΡΠ»ΠΎΠ²ΠΈΡΡ
Π² Π±Π°ΡΠ°Π±Π°Π½ ΡΠΌΠ΅ΡΠΈΡΠ΅Π»Ρ, ΠΏΡΠ΅Π΄Π²Π°ΡΠΈΡΠ΅Π»ΡΠ½ΠΎ Π·Π°ΠΏΠΎΠ»Π½Π΅Π½Π½ΠΎΠ³ΠΎ Π²ΠΎΠ΄ΠΎΠΉ, Π²ΡΠ΅ ΡΡΡ
ΠΈΠ΅ ΠΊΠΎΠΌΠΏΠΎΠ½Π΅Π½ΡΡ Π·Π°Π³ΡΡΠΆΠ°ΡΡ ΠΎΠ΄Π½ΠΎΠ²ΡΠ΅ΠΌΠ΅Π½Π½ΠΎ. ΠΠΈΠΌΠΎΠΉ Π²ΠΎ ΠΈΠ·Π±Π΅ΠΆΠ°Π½ΠΈΠ΅ Β«Π·Π°Π²Π°ΡΠΈΠ²Π°Π½ΠΈΡΒ» ΡΠ΅ΠΌΠ΅Π½ΡΠ° Π² Π±Π°ΡΠ°Π±Π°Π½ ΡΠΌΠ΅ΡΠΈΡΠ΅Π»Ρ Π²Π½Π°ΡΠ°Π»Π΅ Π·Π°Π»ΠΈΠ²Π°ΡΡ Π²ΠΎΠ΄Ρ ΠΈ Π·Π°Π³ΡΡΠΆΠ°ΡΡ ΠΊΡΡΠΏΠ½ΡΠΉ Π·Π°ΠΏΠΎΠ»Π½ΠΈΡΠ΅Π»Ρ, Π° Π·Π°ΡΠ΅ΠΌ ΠΏΠΎΡΠ»Π΅ Π½Π΅ΡΠΊΠΎΠ»ΡΠΊΠΈΡ
ΠΎΠ±ΠΎΡΠΎΡΠΎΠ² Π±Π°ΡΠ°Π±Π°Π½Π° — ΠΏΠ΅ΡΠΎΠΊ ΠΈ ΡΠ΅ΠΌΠ΅Π½Ρ. ΠΠ±ΡΡΡ ΠΏΡΠΎΠ΄ΠΎΠ»ΠΆΠΈΡΠ΅Π»ΡΠ½ΠΎΡΡΡ ΠΏΠ΅ΡΠ΅ΠΌΠ΅ΡΠΈΠ²Π°Π½ΠΈΡ Π² Π·ΠΈΠΌΠ½ΠΈΡ
ΡΡΠ»ΠΎΠ²ΠΈΡΡ
ΡΠ²Π΅Π»ΠΈΡΠΈΠ²Π°ΡΡ Π² 1,2… 1,5 ΡΠ°Π·Π°. ΠΠ΅ΡΠΎΠ½Π½ΡΡ ΡΠΌΠ΅ΡΡ ΡΡΠ°Π½ΡΠΏΠΎΡΡΠΈΡΡΡΡ Π² Π·Π°ΠΊΡΡΡΠΎΠΉ ΡΡΠ΅ΠΏΠ»Π΅Π½Π½ΠΎΠΉ ΠΈ ΠΏΡΠΎΠ³ΡΠ΅ΡΠΎΠΉ ΠΏΠ΅ΡΠ΅Π΄ Π½Π°ΡΠ°Π»ΠΎΠΌ ΡΠ°Π±ΠΎΡΡ ΡΠ°ΡΠ΅ (Π±Π°Π΄ΡΠΈ, ΠΊΡΠ·ΠΎΠ²Π° ΠΌΠ°ΡΠΈΠ½). ΠΠ²ΡΠΎΠΌΠ°ΡΠΈΠ½ΡΠΈΠΌΠ΅ΡΡ Π΄Π²ΠΎΠΉΠ½ΠΎΠ΅ Π΄Π½ΠΈΡΠ΅, Π² ΠΏΠΎΠ»ΠΎΡΡΡ ΠΊΠΎΡΠΎΡΠΎΠ³ΠΎ ΠΏΠΎΡΡΡΠΏΠ°ΡΡ ΠΎΡΡΠ°Π±ΠΎΡΠ°Π½Π½ΡΠ΅ Π³Π°Π·Ρ ΠΌΠΎΡΠΎΡΠ°, ΡΡΠΎ ΠΏΡΠ΅Π΄ΠΎΡΠ²ΡΠ°ΡΠ°Π΅Ρ ΡΠ΅ΠΏΠ»ΠΎΠΏΠΎΡΠ΅ΡΠΈ. ΠΠ΅ΡΠΎΠ½Π½ΡΡ ΡΠΌΠ΅ΡΡ ΡΠ»Π΅Π΄ΡΠ΅Ρ ΡΡΠ°Π½ΡΠΏΠΎΡΡΠΈΡΠΎΠ²Π°ΡΡ ΠΎΡ ΠΌΠ΅ΡΡΠ° ΠΏΡΠΈΠ³ΠΎΡΠΎΠ²Π»Π΅Π½ΠΈΡ Π΄ΠΎ ΠΌΠ΅ΡΡΠ° ΡΠΊΠ»Π°Π΄ΠΊΠΈ ΠΏΠΎ Π²ΠΎΠ·ΠΌΠΎΠΆΠ½ΠΎΡΡΠΈ Π±ΡΡΡΡΠ΅Π΅ ΠΈ Π±Π΅Π· ΠΏΠ΅ΡΠ΅Π³ΡΡΠ·ΠΎΠΊ. ΠΠ΅ΡΡΠ° ΠΏΠΎΠ³ΡΡΠ·ΠΊΠΈ ΠΈ Π²ΡΠ³ΡΡΠ·ΠΊΠΈ Π΄ΠΎΠ»ΠΆΠ½Ρ Π±ΡΡΡ Π·Π°ΡΠΈΡΠ΅Π½Ρ ΠΎΡ Π²Π΅ΡΡΠ°, Π° ΡΡΠ΅Π΄ΡΡΠ²Π° ΠΏΠΎΠ΄Π°ΡΠΈ Π±Π΅ΡΠΎΠ½Π½ΠΎΠΉ ΡΠΌΠ΅ΡΠΈ Π² ΠΊΠΎΠ½ΡΡΡΡΠΊΡΠΈΠΈ (Ρ
ΠΎΠ±ΠΎΡΡ, Π²ΠΈΠ±ΡΠΎΡ
ΠΎΠ±ΠΎΡΡ ΠΈ Π΄Ρ.) ΡΡΠ΅ΠΏΠ»Π΅Π½Ρ.
Π‘ΠΎΡΡΠΎΡΠ½ΠΈΠ΅ ΠΎΡΠ½ΠΎΠ²Π°Π½ΠΈΡ, Π½Π° ΠΊΠΎΡΠΎΡΠΎΠΌ ΡΠΊΠ»Π°Π΄ΡΠ²Π°ΡΡ Π±Π΅ΡΠΎΠ½Π½ΡΡ ΡΠΌΠ΅ΡΡ, Π° ΡΠ°ΠΊΠΆΠ΅ ΡΠΏΠΎΡΠΎΠ± ΡΠΊΠ»Π°Π΄ΠΊΠΈ Π΄ΠΎΠ»ΠΆΠ½Ρ ΠΈΡΠΊΠ»ΡΡΠ°ΡΡ Π²ΠΎΠ·ΠΌΠΎΠΆΠ½ΠΎΡΡΡ Π΅Π΅ Π·Π°ΠΌΠ΅ΡΠ·Π°Π½ΠΈΡ Π² ΡΡΡΠΊΠ΅ Ρ ΠΎΡΠ½ΠΎΠ²Π°Π½ΠΈΠ΅ΠΌ ΠΈ Π΄Π΅ΡΠΎΡΠΌΠ°ΡΠΈΠΈ ΠΎΡΠ½ΠΎΠ²Π°Π½ΠΈΡ ΠΏΡΠΈ ΡΠΊΠ»Π°Π΄ΠΊΠ΅ Π±Π΅ΡΠΎΠ½Π° Π½Π° ΠΏΡΡΠΈΠ½ΠΈΡΡΡΠ΅ ΡΡΠ½ΡΡ. ΠΠ»Ρ ΡΡΠΎΠ³ΠΎ ΠΎΡΠ½ΠΎΠ²Π°Π½ΠΈΠ΅ ΠΎΡΠΎΠ³ΡΠ΅Π²Π°ΡΡ Π΄ΠΎ ΠΏΠΎΠ»ΠΎΠΆΠΈΡΠ΅Π»ΡΠ½ΡΡ ΡΠ΅ΠΌΠΏΠ΅ΡΠ°ΡΡΡ ΠΈ ΠΏΡΠ΅Π΄ΠΎΡ ΡΠ°Π½ΡΡΡ ΠΎΡ Π·Π°ΠΌΠ΅ΡΠ·Π°Π½ΠΈΡ Π΄ΠΎ ΠΏΡΠΈΠΎΠ±ΡΠ΅ΡΠ΅Π½ΠΈΡ Π²Π½ΠΎΠ²Ρ ΡΠ»ΠΎΠΆΠ΅Π½Π½ΡΠΌ Π±Π΅ΡΠΎΠ½ΠΎΠΌ ΡΡΠ΅Π±ΡΠ΅ΠΌΠΎΠΉ ΠΏΡΠΎΡΠ½ΠΎΡΡΠΈ.
ΠΠΏΠ°Π»ΡΠ±ΠΊΡ ΠΈ Π°ΡΠΌΠ°ΡΡΡΡ Π΄ΠΎ Π±Π΅ΡΠΎΠ½ΠΈΡΠΎΠ²Π°Π½ΠΈΡ ΠΎΡΠΈΡΠ°ΡΡ ΠΎΡ ΡΠ½Π΅Π³Π° ΠΈ Π½Π°Π»Π΅Π΄ΠΈ, Π°ΡΠΌΠ°ΡΡΡΡ Π΄ΠΈΠ°ΠΌΠ΅ΡΡΠΎΠΌ Π±ΠΎΠ»Π΅Π΅ 25 ΠΌΠΌ, Π° ΡΠ°ΠΊΠΆΠ΅ Π°ΡΠΌΠ°ΡΡΡΡ ΠΈΠ· ΠΆΠ΅ΡΡΠΊΠΈΡ
ΠΏΡΠΎΠΊΠ°ΡΠ½ΡΡ
ΠΏΡΠΎΡΠΈΠ»Π΅ΠΉ ΠΈ ΠΊΡΡΠΏΠ½ΡΠ΅ ΠΌΠ΅ΡΠ°Π»Π»ΠΈΡΠ΅ΡΠΊΠΈΠ΅ Π·Π°ΠΊΠ»Π°Π΄Π½ΡΠ΅ Π΄Π΅ΡΠ°Π»ΠΈ ΠΏΡΠΈ ΡΠ΅ΠΌΠΏΠ΅ΡΠ°ΡΡΡΠ΅ Π½ΠΈΠΆΠ΅ — 10Β°Π‘ ΠΎΡΠΎΠ³ΡΠ΅Π²Π°ΡΡ Π΄ΠΎ ΠΏΠΎΠ»ΠΎΠΆΠΈΡΠ΅Π»ΡΠ½ΠΎΠΉ ΡΠ΅ΠΌΠΏΠ΅ΡΠ°ΡΡΡΡ.
ΠΠ΅ΡΠΎΠ½ΠΈΡΠΎΠ²Π°Π½ΠΈΠ΅ ΡΠ»Π΅Π΄ΡΠ΅Ρ Π²Π΅ΡΡΠΈ Π½Π΅ΠΏΡΠ΅ΡΡΠ²Π½ΠΎ ΠΈ Π²ΡΡΠΎΠΊΠΈΠΌΠΈ ΡΠ΅ΠΌΠΏΠ°ΠΌΠΈ, ΠΏΡΠΈ ΡΡΠΎΠΌ ΡΠ°Π½Π΅Π΅ ΡΠ»ΠΎΠΆΠ΅Π½Π½ΡΠΉ ΡΠ»ΠΎΠΉ Π±Π΅ΡΠΎΠ½Π° Π΄ΠΎΠ»ΠΆΠ΅Π½ Π±ΡΡΡ ΠΏΠ΅ΡΠ΅ΠΊΡΡΡ Π΄ΠΎ ΡΠΎΠ³ΠΎ, ΠΊΠ°ΠΊ Π² Π½Π΅ΠΌ ΡΠ΅ΠΌΠΏΠ΅ΡΠ°ΡΡΡΠ° Π±ΡΠ΄Π΅Ρ Π½ΠΈΠΆΠ΅ ΠΏΡΠ΅Π΄ΡΡΠΌΠΎΡΡΠ΅Π½Π½ΠΎΠΉ.
Π‘ΡΡΠΎΠΈΡΠ΅Π»ΡΠ½ΠΎΠ΅ ΠΏΡΠΎΠΈΠ·Π²ΠΎΠ΄ΡΡΠ²ΠΎ ΡΠ°ΡΠΏΠΎΠ»Π°Π³Π°Π΅Ρ ΠΎΠ±ΡΠΈΡΠ½ΡΠΌ Π°ΡΡΠ΅Π½Π°Π»ΠΎΠΌ ΡΡΡΠ΅ΠΊΡΠΈΠ²Π½ΡΡ ΠΈ ΡΠΊΠΎΠ½ΠΎΠΌΠΈΡΠ½ΡΡ ΠΌΠ΅ΡΠΎΠ΄ΠΎΠ² Π²ΡΠ΄Π΅ΡΠΆΠΈΠ²Π°Π½ΠΈΡ Π±Π΅ΡΠΎΠ½Π° Π² Π·ΠΈΠΌΠ½ΠΈΡ ΡΡΠ»ΠΎΠ²ΠΈΡΡ , ΠΏΠΎΠ·Π²ΠΎΠ»ΡΡΡΠΈΡ ΠΎΠ±Π΅ΡΠΏΠ΅ΡΠΈΡΡ Π²ΡΡΠΎΠΊΠΎΠ΅ ΠΊΠ°ΡΠ΅ΡΡΠ²ΠΎ ΠΊΠΎΠ½ΡΡΡΡΠΊΡΠΈΠΉ. ΠΡΠΈ ΠΌΠ΅ΡΠΎΠ΄Ρ ΠΌΠΎΠΆΠ½ΠΎ ΡΠ°Π·Π΄Π΅Π»ΠΈΡΡ Π½Π° ΡΡΠΈ Π³ΡΡΠΏΠΏΡ: ΠΌΠ΅ΡΠΎΠ΄, ΠΏΡΠ΅Π΄ΡΡΠΌΠ°ΡΡΠΈΠ²Π°ΡΡΠΈΠΉ ΠΈΡΠΏΠΎΠ»ΡΠ·ΠΎΠ²Π°Π½ΠΈΠ΅ Π½Π°ΡΠ°Π»ΡΠ½ΠΎΠ³ΠΎ ΡΠ΅ΠΏΠ»ΠΎΡΠΎΠ΄Π΅ΡΠΆΠ°Π½ΠΈΡ, Π²Π½Π΅ΡΠ΅Π½Π½ΠΎΠ³ΠΎ Π² Π±Π΅ΡΠΎΠ½Π½ΡΡ ΡΠΌΠ΅ΡΡ ΠΏΡΠΈ Π΅Π΅ ΠΏΡΠΈΠ³ΠΎΡΠΎΠ²Π»Π΅Π½ΠΈΠΈ ΠΈΠ»ΠΈ ΠΏΠ΅ΡΠ΅Π΄ ΡΠΊΠ»Π°Π΄ΠΊΠΎΠΉ Π² ΠΊΠΎΠ½ΡΡΡΡΠΊΡΠΈΡ, ΠΈ ΡΠ΅ΠΏΠ»ΠΎΠ²ΡΠ΄Π΅Π»Π΅Π½ΠΈΠ΅ ΡΠ΅ΠΌΠ΅Π½ΡΠ°, ΡΠΎΠΏΡΠΎΠ²ΠΎΠΆΠ΄Π°ΡΡΠ΅Π΅ ΡΠ²Π΅ΡΠ΄Π΅Π½ΠΈΠ΅ Π±Π΅ΡΠΎΠ½Π° — ΡΠ°ΠΊ Π½Π°Π·ΡΠ²Π°Π΅ΠΌΡΠΉ ΠΌΠ΅ΡΠΎΠ΄ Β«ΡΠ΅ΡΠΌΠΎΡΠ°Β», ΠΌΠ΅ΡΠΎΠ΄Ρ, ΠΎΡΠ½ΠΎΠ²Π°Π½Π½ΡΠ΅ Π½Π° ΠΈΡΠΊΡΡΡΡΠ²Π΅Π½Π½ΠΎΠΌ ΠΏΡΠΎΠ³ΡΠ΅Π²Π΅ Π±Π΅ΡΠΎΠ½Π°, ΡΠ»ΠΎΠΆΠ΅Π½Π½ΠΎΠ³ΠΎ Π² ΠΊΠΎΠ½ΡΡΡΡΠΊΡΠΈΡ — ΡΠ»Π΅ΠΊΡΡΠΎΠΏΡΠΎΠ³ΡΠ΅Π², ΠΊΠΎΠ½ΡΠ°ΠΊΡΠ½ΡΠΉ, ΠΈΠ½Π΄ΡΠΊΡΠΈΠΎΠ½Π½ΡΠΉ ΠΈ ΠΈΠ½ΡΡΠ°ΠΊΡΠ°ΡΠ½ΡΠΉ Π½Π°Π³ΡΠ΅Π², ΠΊΠΎΠ½Π²Π΅ΠΊΡΠΈΠ²Π½ΡΠΉ ΠΎΠ±ΠΎΠ³ΡΠ΅Π², ΠΌΠ΅ΡΠΎΠ΄Ρ, ΠΈΡΠΏΠΎΠ»ΡΠ·ΡΡΡΠΈΠ΅ ΡΡΡΠ΅ΠΊΡ ΠΏΠΎΠ½ΠΈΠΆΠ΅Π½ΠΈΡ ΡΠ²ΡΠ΅ΠΊΡΠΈΡΠ΅ΡΠΊΠΎΠΉ ΡΠΎΡΠΊΠΈ Π²ΠΎΠ΄Ρ Π² Π±Π΅ΡΠΎΠ½Π΅ Ρ ΠΏΠΎΠΌΠΎΡΡΡ ΡΠΏΠ΅ΡΠΈΠ°Π»ΡΠ½ΡΡ ΠΏΡΠΎΡΠΈΠ²ΠΎΠΌΠΎΡΠΎΠ·Π½ΡΡ Ρ ΠΈΠΌΠΈΡΠ΅ΡΠΊΠΈΡ Π΄ΠΎΠ±Π°Π²ΠΎΠΊ.
Π£ΠΊΠ°Π·Π°Π½Π½ΡΠ΅ ΠΌΠ΅ΡΠΎΠ΄Ρ ΠΌΠΎΠΆΠ½ΠΎ ΠΊΠΎΠΌΠ±ΠΈΠ½ΠΈΡΠΎΠ²Π°ΡΡ. ΠΡΠ±ΠΎΡ ΡΠΎΠ³ΠΎ ΠΈΠ»ΠΈ ΠΈΠ½ΠΎΠ³ΠΎ ΠΌΠ΅ΡΠΎΠ΄Π° Π·Π°Π²ΠΈΡΠΈΡ ΠΎΡ Π²ΠΈΠ΄Π° ΠΈ ΠΌΠ°ΡΡΠΈΠ²Π½ΠΎΡΡΠΈ ΠΊΠΎΠ½ΡΡΡΡΠΊΡΠΈΠΈ, Π²ΠΈΠ΄Π°, ΡΠΎΡΡΠ°Π²Π° ΠΈ ΡΡΠ΅Π±ΡΠ΅ΠΌΠΎΠΉ ΠΏΡΠΎΡΠ½ΠΎΡΡΠΈ Π±Π΅ΡΠΎΠ½Π°, ΠΌΠ΅ΡΠ΅ΠΎΡΠΎΠ»ΠΎΠ³ΠΈΡΠ΅ΡΠΊΠΈΡ
ΡΡΠ»ΠΎΠ²ΠΈΠΉ ΠΏΡΠΎΠΈΠ·Π²ΠΎΠ΄ΡΡΠ²Π° ΡΠ°Π±ΠΎΡ, ΡΠ½Π΅ΡΠ³Π΅ΡΠΈΡΠ΅ΡΠΊΠΎΠΉ ΠΎΡΠ½Π°ΡΠ΅Π½Π½ΠΎΡΡΠΈ ΡΡΡΠΎΠΈΡΠ΅Π»ΡΠ½ΠΎΠΉ ΠΏΠ»ΠΎΡΠ°Π΄ΠΊΠΈ ΠΈ Ρ. Π΄.
ΠΠ΅ΡΠΎΠ΄ Β«ΡΠ΅ΡΠΌΠΎΡΠ°Β»
Π’Π΅Ρ Π½ΠΎΠ»ΠΎΠ³ΠΈΡΠ΅ΡΠΊΠ°Ρ ΡΡΡΠ½ΠΎΡΡΡ ΠΌΠ΅ΡΠΎΠ΄Π° Β«ΡΠ΅ΡΠΌΠΎΡΠ°Β» Π·Π°ΠΊΠ»ΡΡΠ°Π΅ΡΡΡ Π² ΡΠΎΠΌ, ΡΡΠΎ ΠΈΠΌΠ΅ΡΡΠ°Ρ ΠΏΠΎΠ»ΠΎΠΆΠΈΡΠ΅Π»ΡΠ½ΡΡ ΡΠ΅ΠΌΠΏΠ΅ΡΠ°ΡΡΡΡ (ΠΎΠ±ΡΡΠ½ΠΎ Π² ΠΏΡΠ΅Π΄Π΅Π»Π°Ρ 15… 30Β°Π‘) Π±Π΅ΡΠΎΠ½Π½Π°Ρ ΡΠΌΠ΅ΡΡ ΡΠΊΠ»Π°Π΄ΡΠ²Π°Π΅ΡΡΡ Π² ΡΡΠ΅ΠΏΠ»Π΅Π½Π½ΡΡ ΠΎΠΏΠ°Π»ΡΠ±ΠΊΡ. Π ΡΠ΅Π·ΡΠ»ΡΡΠ°ΡΠ΅ ΡΡΠΎΠ³ΠΎ Π±Π΅ΡΠΎΠ½ ΠΊΠΎΠ½ΡΡΡΡΠΊΡΠΈΠΈ Π½Π°Π±ΠΈΡΠ°Π΅Ρ Π·Π°Π΄Π°Π½Π½ΡΡ ΠΏΡΠΎΡΠ½ΠΎΡΡΡ Π·Π° ΡΡΠ΅Ρ Π½Π°ΡΠ°Π»ΡΠ½ΠΎΠ³ΠΎ ΡΠ΅ΠΏΠ»ΠΎΡΠΎΠ΄Π΅ΡΠΆΠ°Π½ΠΈΡ ΠΈ ΡΠΊΠ·ΠΎΡΠ΅ΡΠΌΠΈΡΠ΅ΡΠΊΠΎΠ³ΠΎ ΡΠ΅ΠΏΠ»ΠΎΠ²ΡΠ΄Π΅Π»Π΅Π½ΠΈΡ ΡΠ΅ΠΌΠ΅Π½ΡΠ° Π·Π° Π²ΡΠ΅ΠΌΡ ΠΎΡΡΡΠ²Π°Π½ΠΈΡ Π΄ΠΎ 0Β°Π‘.
Π ΠΏΡΠΎΡΠ΅ΡΡΠ΅ ΡΠ²Π΅ΡΠ΄Π΅Π½ΠΈΠΉ Π±Π΅ΡΠΎΠ½Π° Π²ΡΠ΄Π΅Π»ΡΠ΅ΡΡΡ ΡΠΊΠ·ΠΎΡΠ΅ΡΠΌΠΈΡΠ΅ΡΠΊΠ°Ρ ΡΠ΅ΠΏΠ»ΠΎΡΠ°, ΠΊΠΎΠ»ΠΈΡΠ΅ΡΡΠ²Π΅Π½Π½ΠΎ Π·Π°Π²ΠΈΡΡΡΠ°Ρ ΠΎΡ Π²ΠΈΠ΄Π° ΠΏΡΠΈΠΌΠ΅Π½ΡΠ΅ΠΌΠΎΠ³ΠΎ ΡΠ΅ΠΌΠ΅Π½ΡΠ° ΠΈ ΡΠ΅ΠΌΠΏΠ΅ΡΠ°ΡΡΡΡ Π²ΡΠ΄Π΅ΡΠΆΠΈΠ²Π°Π½ΠΈΡ.
ΠΠ°ΠΈΠ±ΠΎΠ»ΡΡΠΈΠΌ ΡΠΊΠ·ΠΎΡΠ΅ΡΠΌΠΈΡΠ΅ΡΠΊΠΈΠΌ ΡΠ΅ΠΏΠ»ΠΎΠ²ΡΠ΄Π΅Π»Π΅Π½ΠΈΠ΅ΠΌ ΠΎΠ±Π»Π°Π΄Π°ΡΡ Π²ΡΡΠΎΠΊΠΎΠΌΠ°ΡΠΎΡΠ½ΡΠ΅ ΠΈ Π±ΡΡΡΡΠΎΡΠ²Π΅ΡΠ΄Π΅ΡΡΠΈΠ΅ ΠΏΠΎΡΡΠ»Π°Π½Π΄ΡΠ΅ΠΌΠ΅Π½ΡΡ. ΠΠΊΠ·ΠΎΡΠ΅ΡΠΌΠΈΡ Π±Π΅ΡΠΎΠ½Π° ΠΎΠ±Π΅ΡΠΏΠ΅ΡΠΈΠ²Π°Π΅Ρ ΡΡΡΠ΅ΡΡΠ²Π΅Π½Π½ΡΠΉ Π²ΠΊΠ»Π°Π΄ Π² ΡΠ΅ΠΏΠ»ΠΎΡΠΎΠ΄Π΅ΡΠΆΠ°Π½ΠΈΠ΅ ΠΊΠΎΠ½ΡΡΡΡΠΊΡΠΈΠΈ, Π²ΡΠ΄Π΅ΡΠΆΠΈΠ²Π°Π΅ΠΌΠΎΠΉ ΠΌΠ΅ΡΠΎΠ΄ΠΎΠΌ Β«ΡΠ΅ΡΠΌΠΎΡΠ°Β».
ΠΠΎΡΡΠΎΠΌΡ ΠΏΡΠΈ ΠΏΡΠΈΠΌΠ΅Π½Π΅Π½ΠΈΠΈ ΠΌΠ΅ΡΠΎΠ΄Π° Β«ΡΠ΅ΡΠΌΠΎΡΠ°Β» ΡΠ΅ΠΊΠΎΠΌΠ΅Π½Π΄ΡΠ΅ΡΡΡ ΠΏΡΠΈΠΌΠ΅Π½ΡΡΡ Π±Π΅ΡΠΎΠ½Π½ΡΡ ΡΠΌΠ΅ΡΡ Π½Π° Π²ΡΡΠΎΠΊΠΎΡΠΊΠ·ΠΎΡΠ΅ΡΠΌΠΈΡΠ½ΡΡ ΠΏΠΎΡΡΠ»Π°Π½Π΄ΡΠΊΠΈΡ ΠΈ Π±ΡΡΡΡΠΎΡΠ²Π΅ΡΠ΄Π΅ΡΡΠΈΡ ΡΠ΅ΠΌΠ΅Π½ΡΠ°Ρ , ΡΠΊΠ»Π°Π΄ΡΠ²Π°ΡΡ Ρ ΠΏΠΎΠ²ΡΡΠ΅Π½Π½ΠΎΠΉ Π½Π°ΡΠ°Π»ΡΠ½ΠΎΠΉ ΡΠ΅ΠΌΠΏΠ΅ΡΠ°ΡΡΡΠΎΠΉ ΠΈ ΡΡΠ°ΡΠ΅Π»ΡΠ½ΠΎ ΡΡΠ΅ΠΏΠ»ΡΡΡ.
ΠΠ΅ΡΠΎΠ½ΠΈΡΠΎΠ²Π°Π½ΠΈΠ΅ ΠΌΠ΅ΡΠΎΠ΄ΠΎΠΌ Β«Π’Π΅ΡΠΌΠΎΡ Ρ Π΄ΠΎΠ±Π°Π²ΠΊΠ°ΠΌΠΈ-ΡΡΠΊΠΎΡΠΈΡΠ΅Π»ΡΠΌΠΈΒ»
ΠΠ΅ΠΊΠΎΡΠΎΡΡΠ΅ Ρ
ΠΈΠΌΠΈΡΠ΅ΡΠΊΠΈΠ΅ Π²Π΅ΡΠ΅ΡΡΠ²Π° (Ρ
Π»ΠΎΡΠΈΡΡΡΠΉ ΠΊΠ°Π»ΡΡΠΈΠΉ Π‘Π°Π‘l, ΡΠ³Π»Π΅ΠΊΠΈΡΠ»ΡΠΉ ΠΊΠ°Π»ΠΈΠΉ — ΠΏΠΎΡΠ°Ρ Π2Π‘Π3, Π½ΠΈΡΡΠ°Ρ Π½Π°ΡΡΠΈΡ NaNO3 ΠΈ Π΄Ρ. ), Π²Π²Π΅Π΄Π΅Π½Π½ΡΠ΅ Π² Π±Π΅ΡΠΎΠ½ Π²Π½Π΅Π·Π½Π°ΡΠΈΡΠ΅Π»ΡΠ½ΡΡ
ΠΊΠΎΠ»ΠΈΡΠ΅ΡΡΠ²Π°Ρ
(Π΄ΠΎ 2% ΠΎΡ ΠΌΠ°ΡΡΡ ΡΠ΅ΠΌΠ΅Π½ΡΠ°), ΠΎΠΊΠ°Π·ΡΠ²Π°ΡΡ ΡΠ»Π΅Π΄Ρ ΡΡΠ΅Π΅ Π΄Π΅ΠΉΡΡΠ²ΠΈΠ΅ Π½Π° ΠΏΡΠΎΡΠ΅ΡΡ ΡΠ²Π΅ΡΠ΄Π΅Π½ΠΈΡ: ΡΡΠΈ Π΄ΠΎΠ±Π°Π²ΠΊΠΈ ΡΡΠΊΠΎΡΡΡΡ ΠΏΡΠΎΡΠ΅ΡΡ ΡΠ²Π΅ΡΠ΄Π΅Π½ΠΈΡ Π² Π½Π°ΡΠ°Π»ΡΠ½ΡΠΉ ΠΏΠ΅ΡΠΈΠΎΠ΄ Π²ΡΠ΄Π΅ΡΠΆΠΈΠ²Π°Π½ΠΈΡ Π±Π΅ΡΠΎΠ½Π°. Π’Π°ΠΊ, Π±Π΅ΡΠΎΠ½ Ρ Π΄ΠΎΠ±Π°Π²ΠΊΠΎΠΉ 2%-Π½ΠΎΠ³ΠΎ Ρ
Π»ΠΎΡΠΈΡΡΠΎΠ³ΠΎ ΠΊΠ°Π»ΡΡΠΈΡ ΠΎΡ ΠΌΠ°ΡΡΡ ΡΠ΅ΠΌΠ΅Π½ΡΠ° ΡΠΆΠ΅ Π½Π° ΡΡΠ΅ΡΠΈΠΉ Π΄Π΅Π½Ρ Π΄ΠΎΡΡΠΈΠ³Π°Π΅Ρ ΠΏΡΠΎΡΠ½ΠΎΡΡΠΈ, Π² 1,6 ΡΠ°Π·Π° Π±ΠΎΠ»ΡΡΠ΅ΠΉ, ΡΠ΅ΠΌ Π±Π΅ΡΠΎΠ½ ΡΠΎΠ³ΠΎ ΠΆΠ΅ ΡΠΎΡΡΠ°Π²Π°, Π½ΠΎ Π±Π΅Π· Π΄ΠΎΠ±Π°Π²ΠΊΠΈ. ΠΠ²Π΅Π΄Π΅Π½ΠΈΠ΅ Π² Π±Π΅ΡΠΎΠ½ Π΄ΠΎΠ±Π°Π²ΠΎΠΊ-ΡΡΠΊΠΎΡΠΈΡΠ΅Π»Π΅ΠΉ, ΡΠ²Π»ΡΡΡΠΈΡ
ΡΡ ΠΎΠ΄Π½ΠΎΠ²ΡΠ΅ΠΌΠ΅Π½Π½ΠΎ ΠΈ ΠΏΡΠΎΡΠΈΠ²ΠΎΠΌΠΎΡΠΎΠ·Π½ΡΠΌΠΈ Π΄ΠΎΠ±Π°Π²ΠΊΠ°ΠΌΠΈ, Π² ΡΠΊΠ°Π·Π°Π½Π½ΡΡ
ΠΊΠΎΠ»ΠΈΡΠ΅ΡΡΠ²Π°Ρ
ΠΏΠΎΠ½ΠΈΠΆΠ°Π΅Ρ ΡΠ΅ΠΌΠΏΠ΅ΡΠ°ΡΡΡΡ Π·Π°ΠΌΠ΅ΡΠ·Π°Π½ΠΈΡ Π΄ΠΎ -3Β°Π‘, ΡΠ²Π΅Π»ΠΈΡΠΈΠ²Π°Ρ ΡΠ΅ΠΌ ΡΠ°ΠΌΡΠΌ ΠΏΡΠΎΠ΄ΠΎΠ»ΠΆΠΈΡΠ΅Π»ΡΠ½ΠΎΡΡΡ ΠΎΡΡΡΠ²Π°Π½ΠΈΡ Π±Π΅ΡΠΎΠ½Π°, ΡΡΠΎ ΡΠ°ΠΊΠΆΠ΅ ΡΠΏΠΎΡΠΎΠ±ΡΡΠ²ΡΠ΅Ρ ΠΏΡΠΈΠΎΠ±ΡΠ΅ΡΠ΅Π½ΠΈΡ Π±Π΅ΡΠΎΠ½ΠΎΠΌ Π±ΠΎΠ»ΡΡΠ΅ΠΉ ΠΏΡΠΎΡΠ½ΠΎΡΡΠΈ.
ΠΠ΅ΡΠΎΠ½Ρ Ρ Π΄ΠΎΠ±Π°Π²ΠΊΠ°ΠΌΠΈ-ΡΡΠΊΠΎΡΠΈΡΠ΅Π»ΡΠΌΠΈ Π³ΠΎΡΠΎΠ²ΡΡ Π½Π° ΠΏΠΎΠ΄ΠΎΠ³ΡΠ΅ΡΡΡ
Π·Π°ΠΏΠΎΠ»Π½ΠΈΡΠ΅Π»ΡΡ
ΠΈ Π³ΠΎΡΡΡΠ΅ΠΉ Π²ΠΎΠ΄Π΅. ΠΡΠΈ ΡΡΠΎΠΌ ΡΠ΅ΠΌΠΏΠ΅ΡΠ°ΡΡΡΠ° Π±Π΅ΡΠΎΠ½Π½ΠΎΠΉ ΡΠΌΠ΅ΡΠΈ Π½Π° Π²ΡΡ
ΠΎΠ΄Π΅ ΠΈΠ· ΡΠΌΠ΅ΡΠΈΡΠ΅Π»Ρ ΠΊΠΎΠ»Π΅Π±Π»Π΅ΡΡΡ Π² ΠΏΡΠ΅Π΄Π΅Π»Π°Ρ
25…35Β°Π‘, ΡΠ½ΠΈΠΆΠ°ΡΡΡ ΠΊ ΠΌΠΎΠΌΠ΅Π½ΡΡ ΡΠΊΠ»Π°Π΄ΠΊΠΈ Π΄ΠΎ 20Β°Π‘. Π’Π°ΠΊΠΈΠ΅ Π±Π΅ΡΠΎΠ½Ρ ΠΏΡΠΈΠΌΠ΅Π½ΡΡΡ ΠΏΡΠΈ ΡΠ΅ΠΌΠΏΠ΅ΡΠ°ΡΡΡΠ΅ Π½Π°ΡΡΠΆΠ½ΠΎΠ³ΠΎ Π²ΠΎΠ·Π΄ΡΡ
Π° -15… -20Β°Π‘. Π£ΠΊΠ»Π°Π΄ΡΠ²Π°ΡΡ ΠΈΡ
Π² ΡΡΠ΅ΠΏΠ»Π΅Π½Π½ΡΡ ΠΎΠΏΠ°Π»ΡΠ±ΠΊΡ ΠΈ Π·Π°ΠΊΡΡΠ²Π°ΡΡ ΡΠ»ΠΎΠ΅ΠΌ ΡΠ΅ΠΏΠ»ΠΎΠΈΠ·ΠΎΠ»ΡΡΠΈΠΈ. Π’Π²Π΅ΡΠ΄Π΅Π½ΠΈΠ΅ Π±Π΅ΡΠΎΠ½Π° ΠΏΡΠΎΠΈΡΡ
ΠΎΠ΄ΠΈΡ Π² ΡΠ΅Π·ΡΠ»ΡΡΠ°ΡΠ΅ ΡΠ΅ΡΠΌΠΎΡΠ½ΠΎΠ³ΠΎ Π²ΡΠ΄Π΅ΡΠΆΠΈΠ²Π°Π½ΠΈΡ Π² ΡΠΎΡΠ΅ΡΠ°Π½ΠΈΠΈ Ρ ΠΏΠΎΠ»ΠΎΠΆΠΈΡΠ΅Π»ΡΠ½ΡΠΌ Π²ΠΎΠ·Π΄Π΅ΠΉΡΡΠ²ΠΈΠ΅ΠΌ Ρ
ΠΈΠΌΠΈΡΠ΅ΡΠΊΠΈΡ
Π΄ΠΎΠ±Π°Π²ΠΎΠΊ. ΠΡΠΎΡ ΡΠΏΠΎΡΠΎΠ± ΡΠ²Π»ΡΠ΅ΡΡΡ ΠΏΡΠΎΡΡΡΠΌ ΠΈ Π΄ΠΎΡΡΠ°ΡΠΎΡΠ½ΠΎ ΡΠΊΠΎΠ½ΠΎΠΌΠΈΡΠ½ΡΠΌ, ΠΏΠΎΠ·Π²ΠΎΠ»ΡΠ΅Ρ ΠΏΡΠΈΠΌΠ΅Π½ΡΡΡ ΠΌΠ΅ΡΠΎΠ΄ Β«ΡΠ΅ΡΠΌΠΎΡΠ°Β» Π΄Π»Ρ ΠΊΠΎΠ½ΡΡΡΡΠΊΡΠΈΠΉ Ρ ΠΠΏ
ΠΠ΅ΡΠΎΠ½ΠΈΡΠΎΠ²Π°Π½ΠΈΠ΅ Β«ΠΠΎΡΡΡΠΈΠΉ ΡΠ΅ΡΠΌΠΎΡΒ»
ΠΠ°ΠΊΠ»ΡΡΠ°Π΅ΡΡΡ Π² ΠΊΡΠ°ΡΠΊΠΎΠ²ΡΠ΅ΠΌΠ΅Π½Π½ΠΎΠΌ ΡΠ°Π·ΠΎΠ³ΡΠ΅Π²Π΅ Π±Π΅ΡΠΎΠ½Π½ΠΎΠΉ ΡΠΌΠ΅ΡΠΈ Π΄ΠΎ ΡΠ΅ΠΌΠΏΠ΅ΡΠ°ΡΡΡΡ 60… 80Β°Π‘, ΡΠΏΠ»ΠΎΡΠ½Π΅Π½ΠΈΠΈ Π΅Π΅ Π² Π³ΠΎΡΡΡΠ΅ΠΌ ΡΠΎΡΡΠΎΡΠ½ΠΈΠΈ ΠΈ ΡΠ΅ΡΠΌΠΎΡΠ½ΠΎΠΌ Π²ΡΠ΄Π΅ΡΠΆΠΈΠ²Π°Π½ΠΈΠΈ ΠΈΠ»ΠΈ Ρ Π΄ΠΎΠΏΠΎΠ»Π½ΠΈΡΠ΅Π»ΡΠ½ΡΠΌ ΠΎΠ±ΠΎΠ³ΡΠ΅Π²ΠΎΠΌ.
Π ΡΡΠ»ΠΎΠ²ΠΈΡΡ ΡΡΡΠΎΠΈΡΠ΅Π»ΡΠ½ΠΎΠΉ ΠΏΠ»ΠΎΡΠ°Π΄ΠΊΠΈ ΡΠ°Π·ΠΎΠ³ΡΠ΅Π² Π±Π΅ΡΠΎΠ½Π½ΠΎΠΉ ΡΠΌΠ΅ΡΠΈ ΠΎΡΡΡΠ΅ΡΡΠ²Π»ΡΡΡ, ΠΊΠ°ΠΊ ΠΏΡΠ°Π²ΠΈΠ»ΠΎ, ΡΠ»Π΅ΠΊΡΡΠΈΡΠ΅ΡΠΊΠΈΠΌ ΡΠΎΠΊΠΎΠΌ. ΠΠ»Ρ ΡΡΠΎΠ³ΠΎ ΠΏΠΎΡΡΠΈΡ Π±Π΅ΡΠΎΠ½Π½ΠΎΠΉ ΡΠΌΠ΅ΡΠΈ Ρ ΠΏΠΎΠΌΠΎΡΡΡ ΡΠ»Π΅ΠΊΡΡΠΎΠ΄ΠΎΠ² Π²ΠΊΠ»ΡΡΠ°ΡΡ Π² ΡΠ»Π΅ΠΊΡΡΠΈΡΠ΅ΡΠΊΡΡ ΡΠ΅ΠΏΡ ΠΏΠ΅ΡΠ΅ΠΌΠ΅Π½Π½ΠΎΠ³ΠΎ ΡΠΎΠΊΠ° Π² ΠΊΠ°ΡΠ΅ΡΡΠ²Π΅ ΡΠΎΠΏΡΠΎΡΠΈΠ²Π»Π΅Π½ΠΈΡ.
Π’Π°ΠΊΠΈΠΌ ΠΎΠ±ΡΠ°Π·ΠΎΠΌ, ΠΊΠ°ΠΊ Π²ΡΠ΄Π΅Π»ΡΠ΅ΠΌΠ°Ρ ΠΌΠΎΡΠ½ΠΎΡΡΡ, ΡΠ°ΠΊ ΠΈ ΠΊΠΎΠ»ΠΈΡΠ΅ΡΡΠ²ΠΎ Π²ΡΠ΄Π΅Π»ΡΠ΅ΠΌΠΎΠΉ Π·Π° ΠΏΡΠΎΠΌΠ΅ΠΆΡΡΠΎΠΊ Π²ΡΠ΅ΠΌΠ΅Π½ΠΈ ΡΠ΅ΠΏΠ»ΠΎΡΡ Π·Π°Π²ΠΈΡΡΡ ΠΎΡ ΠΏΠΎΠ΄Π²ΠΎΠ΄ΠΈΠΌΠΎΠ³ΠΎ ΠΊ ΡΠ»Π΅ΠΊΡΡΠΎΠ΄Π°ΠΌ Π½Π°ΠΏΡΡΠΆΠ΅Π½ΠΈΡ (ΠΏΡΡΠΌΠ°Ρ ΠΏΡΠΎΠΏΠΎΡΡΠΈΠΎΠ½Π°Π»ΡΠ½ΠΎΡΡΡ) ΠΈ ΠΎΠΌΠΈΡΠ΅ΡΠΊΠΎΠ³ΠΎΡΠΎΠΏΡΠΎΡΠΈΠ²Π»Π΅Π½ΠΈΡ ΠΏΡΠΎΡΠ΅Π²Π°Π΅ΠΌΠΎΠΉ Π±Π΅ΡΠΎΠ½Π½ΠΎΠΉ ΡΠΌΠ΅ΡΠΈ (ΠΎΠ±ΡΠ°ΡΠ½Π°Ρ ΠΏΡΠΎΠΏΠΎΡΡΠΈΠΎΠ½Π°Π»ΡΠ½ΠΎΡΡΡ).
Π ΡΠ²ΠΎΡ ΠΎΡΠ΅ΡΠ΅Π΄Ρ, ΠΎΠΌΠΈΡΠ΅ΡΠΊΠΎΠ΅ ΡΠΎΠΏΡΠΎΡΠΈΠ²Π»Π΅Π½ΠΈΠ΅ ΡΠ²Π»ΡΠ΅ΡΡΡ ΡΡΠ½ΠΊΡΠΈΠ΅ΠΉ Π³Π΅ΠΎΠΌΠ΅ΡΡΠΈΡΠ΅ΡΠΊΠΈΡ
ΠΏΠ°ΡΠ°ΠΌΠ΅ΡΡΠΎΠ² ΠΏΠ»ΠΎΡΠΊΠΈΡ
ΡΠ»Π΅ΠΊΡΡΠΎΠ΄ΠΎΠ², ΡΠ°ΡΡΡΠΎΡΠ½ΠΈΡ ΠΌΠ΅ΠΆΠ΄Ρ ΡΠ»Π΅ΠΊΡΡΠΎΠ΄Π°ΠΌΠΈ ΠΈ ΡΠ΄Π΅Π»ΡΠ½ΠΎΠ³ΠΎ ΠΎΠΌΠΈΡΠ΅ΡΠΊΠΎΠ³ΠΎ ΡΠΎΠΏΡΠΎΡΠΈΠ²Π»Π΅Π½ΠΈΡ Π±Π΅ΡΠΎΠ½Π½ΠΎΠΉ ΡΠΌΠ΅ΡΠΈ.
ΠΠ»Π΅ΠΊΡΡΠΎΡΠ°Π·ΠΎΡΠ΅Π² Π±Π΅ΡΠΎΠ½Π½ΠΎΠΉ ΡΠΌΠ΅ΡΠΈ ΠΎΡΡΡΠ΅ΡΡΠ²Π»ΡΡΡ ΠΏΡΠΈ Π½Π°ΠΏΡΡΠΆΠ΅Π½ΠΈΠΈ ΡΠΎΠΊΠ° 380 ΠΈ ΡΠ΅ΠΆΠ΅ 220 Π. ΠΠ»Ρ ΠΎΡΠ³Π°Π½ΠΈΠ·Π°ΡΠΈΠΈ ΡΠ»Π΅ΠΊΡΡΠΎΡΠ°Π·ΠΎΡΠ΅Π²Π° Π½Π° ΡΡΡΠΎΠΈΡΠ΅Π»ΡΠ½ΠΎΠΉ ΠΏΠ»ΠΎΡΠ°Π΄ΠΊΠ΅ ΠΎΠ±ΠΎΡΡΠ΄ΡΡΡ ΠΏΠΎΡΡ Ρ ΡΡΠ°Π½ΡΡΠΎΡΠΌΠ°ΡΠΎΡΠΎΠΌ (Π½Π°ΠΏΡΡΠΆΠ΅Π½ΠΈΠ΅ Π½Π° Π½ΠΈΠ·ΠΊΠΎΠΉ ΡΡΠΎΡΠΎΠ½Π΅ 380 ΠΈΠ»ΠΈ 220 Π), ΠΏΡΠ»ΡΡΠΎΠΌ ΡΠΏΡΠ°Π²Π»Π΅Π½ΠΈΡ ΠΈ ΡΠ°ΡΠΏΡΠ΅Π΄Π΅Π»ΠΈΡΠ΅Π»ΡΠ½ΡΠΌ ΡΠΈΡΠΎΠΌ.
ΠΠ»Π΅ΠΊΡΡΠΎΡΠ°Π·ΠΎΠ³ΡΠ΅Π² Π±Π΅ΡΠΎΠ½Π½ΠΎΠΉ ΡΠΌΠ΅ΡΠΈ ΠΎΡΡΡΠ΅ΡΡΠ²Π»ΡΡΡ Π² ΠΎΡΠ½ΠΎΠ²Π½ΠΎΠΌ Π² Π±Π°Π΄ΡΡΡ ΠΈΠ»ΠΈ Π² ΠΊΡΠ·ΠΎΠ²Π°Ρ Π°Π²ΡΠΎΡΠ°ΠΌΠΎΡΠ²Π°Π»ΠΎΠ².
Π ΠΏΠ΅ΡΠ²ΠΎΠΌ ΡΠ»ΡΡΠ°Π΅ ΠΏΡΠΈΠ³ΠΎΡΠΎΠ²Π»Π΅Π½Π½ΡΡ ΡΠΌΠ΅ΡΡ (Π½Π° Π±Π΅ΡΠΎΠ½Π½ΠΎΠΌ Π·Π°Π²ΠΎΠ΄Π΅), ΠΈΠΌΠ΅ΡΡΡΡ ΡΠ΅ΠΌΠΏΠ΅ΡΠ°ΡΡΡΡ 5…15Β°Π‘, Π΄ΠΎΡΡΠ°Π²Π»ΡΡΡ Π°Π²ΡΠΎΡΠ°ΠΌΠΎΡΠ²Π°Π»Π°ΠΌΠΈ Π½Π° ΡΡΡΠΎΠΈΡΠ΅Π»ΡΠ½ΡΡ ΠΏΠ»ΠΎΡΠ°Π΄ΠΊΡ, Π²ΡΠ³ΡΡΠΆΠ°ΡΡ Π² ΡΠ»Π΅ΠΊΡΡΠΎΠ±Π°Π΄ΡΠΈ, ΡΠ°Π·ΠΎΠ³ΡΠ΅Π²Π°ΡΡ Π΄ΠΎ 70… 80Β°Π‘ ΠΈ ΡΠΊΠ»Π°Π΄ΡΠ²Π°ΡΡ Π² ΠΊΠΎΠ½ΡΡΡΡΠΊΡΠΈΡ. Π§Π°ΡΠ΅ Π²ΡΠ΅Π³ΠΎ ΠΏΡΠΈΠΌΠ΅Π½ΡΡΡ ΠΎΠ±ΡΡΠ½ΡΠ΅ Π±Π°Π΄ΡΠΈ (ΡΡΡΠ΅Π»ΡΠΊΠΈ) Ρ ΡΡΠ΅ΠΌΡ ΡΠ»Π΅ΠΊΡΡΠΎΠ΄Π°ΠΌΠΈ ΠΈΠ· ΡΡΠ°Π»ΠΈ ΡΠΎΠ»ΡΠΈΠ½ΠΎΠΉ 5 ΠΌΠΌ, ΠΊ ΠΊΠΎΡΠΎΡΡΠΌ Ρ ΠΏΠΎΠΌΠΎΡΡΡ ΠΊΠ°Π±Π΅Π»ΡΠ½ΡΡ ΡΠ°Π·ΡΠ΅ΠΌΠΎΠ² ΠΏΠΎΠ΄ΠΊΠ»ΡΡΠ°ΡΡ ΠΏΡΠΎΠ²ΠΎΠ΄Π° (ΠΈΠ»ΠΈ ΠΆΠΈΠ»Ρ ΠΊΠ°Π±Π΅Π»Π΅ΠΉ) ΠΏΠΈΡΠ°ΡΡΠ΅ΠΉ ΡΠ΅ΡΠΈ. ΠΠ»Ρ ΡΠ°Π²Π½ΠΎΠΌΠ΅ΡΠ½ΠΎΠ³ΠΎ ΡΠ°ΡΠΏΡΠ΅Π΄Π΅Π»Π΅Π½ΠΈΡ Π±Π΅ΡΠΎΠ½Π½ΠΎΠΉ ΡΠΌΠ΅ΡΠΈ ΠΌΠ΅ΠΆΠ΄Ρ ΡΠ»Π΅ΠΊΡΡΠΎΠ΄Π°ΠΌΠΈ ΠΏΡΠΈ Π·Π°Π³ΡΡΠ·ΠΊΠ΅ Π±Π°Π΄ΡΠΈ ΠΈ Π»ΡΡΡΠ΅ΠΉ Π²ΡΠ³ΡΡΠ·ΠΊΠ΅ ΡΠ°Π·ΠΎΠ³ΡΠ΅ΡΠΎΠΉ ΡΠΌΠ΅ΡΠΈ Π² ΠΊΠΎΠ½ΡΡΡΡΠΊΡΠΈΡ Π½Π° ΠΊΠΎΡΠΏΡΡΠ΅ Π±Π°Π΄ΡΠΈ ΡΡΡΠ°Π½ΠΎΠ²Π»Π΅Π½ Π²ΠΈΠ±ΡΠ°ΡΠΎΡ.
ΠΠΎ Π²ΡΠΎΡΠΎΠΌ ΡΠ»ΡΡΠ°Π΅ ΠΏΡΠΈΠ³ΠΎΡΠΎΠ²Π»Π΅Π½Π½ΡΡ Π½Π° Π±Π΅ΡΠΎΠ½Π½ΠΎΠΌ Π·Π°Π²ΠΎΠ΄Π΅ ΡΠΌΠ΅ΡΡ Π΄ΠΎΡΡΠ°Π²Π»ΡΡΡ Π½Π° ΡΡΡΠΎΠΈΡΠ΅Π»ΡΠ½ΡΡ ΠΏΠ»ΠΎΡΠ°Π΄ΠΊΡ Π² ΠΊΡΠ·ΠΎΠ²Π΅ Π°Π²ΡΠΎΡΠ°ΠΌΠΎΡΠ²Π°Π»Π°. ΠΠ²ΡΠΎΡΠ°ΠΌΠΎΡΠ²Π°Π» Π²ΡΠ΅Π·ΠΆΠ°Π΅Ρ Π½Π° ΠΏΠΎΡΡ ΡΠ°Π·ΠΎΠ³ΡΠ΅Π²Π° ΠΈ ΠΎΡΡΠ°Π½Π°Π²Π»ΠΈΠ²Π°Π΅ΡΡΡ ΠΏΠΎΠ΄ ΡΠ°ΠΌΠΎΠΉ Ρ ΡΠ»Π΅ΠΊΡΡΠΎΠ΄Π°ΠΌΠΈ. ΠΡΠΈ ΡΠ°Π±ΠΎΡΠ°ΡΡΠ΅ΠΌ Π²ΠΈΠ±ΡΠ°ΡΠΎΡΠ΅ ΡΠ»Π΅ΠΊΡΡΠΎΠ΄Ρ ΠΎΠΏΡΡΠΊΠ°ΡΡ Π² Π±Π΅ΡΠΎΠ½Π½ΡΡ ΡΠΌΠ΅ΡΡ ΠΈ ΠΏΠΎΠ΄Π°ΡΡ Π½Π°ΠΏΡΡΠΆΠ΅Π½ΠΈΠ΅. Π Π°Π·ΠΎΠ³ΡΠ΅Π² Π²Π΅Π΄ΡΡ Π² ΡΠ΅ΡΠ΅Π½ΠΈΠ΅ 10… 15 ΠΌΠΈΠ½ Π΄ΠΎ ΡΠ΅ΠΌΠΏΠ΅ΡΠ°ΡΡΡΡ ΡΠΌΠ΅ΡΠΈ Π½Π° Π±ΡΡΡΡΠΎΡΠ²Π΅ΡΠ΄Π΅ΡΡΠΈΡ
ΠΏΠΎΡΡΠ»Π°Π½Π΄ΡΠ΅ΠΌΠ΅Π½ΡΠ°Ρ
60Β°Π‘, Π½Π° ΠΏΠΎΡΡΠ»Π°Π½Π΄ΡΠ΅ΠΌΠ΅Π½ΡΠ°Ρ
70Β°Π‘, Π½Π° ΡΠ»Π°ΠΊΠΎΠΏΠΎΡΡΠ»Π°Π½Π΄ΡΠ΅ΠΌΠ΅Π½ΡΠ°Ρ
80Β°Π‘.
ΠΠ»Ρ ΡΠ°Π·ΠΎΠ³ΡΠ΅Π²Π° ΡΠΌΠ΅ΡΠΈ Π΄ΠΎ ΡΡΠΎΠ»Ρ Π²ΡΡΠΎΠΊΠΈΡ ΡΠ΅ΠΌΠΏΠ΅ΡΠ°ΡΡΡ Π·Π° ΠΊΠΎΡΠΎΡΠΊΠΈΠΉ ΠΏΡΠΎΠΌΠ΅ΠΆΡΡΠΎΠΊ Π²ΡΠ΅ΠΌΠ΅Π½ΠΈ ΡΡΠ΅Π±ΡΡΡΡΡ Π±ΠΎΠ»ΡΡΠΈΠ΅ ΡΠ»Π΅ΠΊΡΡΠΈΡΠ΅ΡΠΊΠΈΠ΅ ΠΌΠΎΡΠ½ΠΎΡΡΠΈ. Π’Π°ΠΊ, Π΄Π»Ρ ΡΠ°Π·ΠΎΠ³ΡΠ΅Π²Π° 1 ΠΌ ΡΠΌΠ΅ΡΠΈ Π΄ΠΎ 60Β°Π‘ Π·Π° 15 ΠΌΠΈΠ½ ΡΡΠ΅Π±ΡΠ΅ΡΡΡ 240 ΠΊΠΡ, Π° Π·Π° 10 ΠΌΠΈΠ½ — 360 ΠΊΠΡ ΡΡΡΠ°Π½ΠΎΠ²Π»Π΅Π½Π½ΠΎΠΉ ΠΌΠΎΡΠ½ΠΎΡΡΠΈ.
ΠΡΠΊΡΡΡΡΠ²Π΅Π½Π½ΡΠΉ ΠΏΡΠΎΠ³ΡΠ΅Π² ΠΈ Π½Π°Π³ΡΠ΅Π² Π±Π΅ΡΠΎΠ½Π°
Π‘ΡΡΠ½ΠΎΡΡΡ ΠΌΠ΅ΡΠΎΠ΄Π° ΠΈΡΠΊΡΡΡΡΠ²Π΅Π½Π½ΠΎΠ³ΠΎ ΠΏΡΠΎΠ³ΡΠ΅Π²Π° ΠΈ Π½Π°Π³ΡΠ΅Π²Π° Π·Π°ΠΊΠ»ΡΡΠ°Π΅ΡΡΡ Π² ΠΏΠΎΠ²ΡΡΠ΅Π½ΠΈΠΈ ΡΠ΅ΠΌΠΏΠ΅ΡΠ°ΡΡΡΡ ΡΠ»ΠΎΠΆΠ΅Π½Π½ΠΎΠ³ΠΎ Π±Π΅ΡΠΎΠ½Π° Π΄ΠΎ ΠΌΠ°ΠΊΡΠΈΠΌΠ°Π»ΡΠ½ΠΎ Π΄ΠΎΠΏΡΡΡΠΈΠΌΠΎΠΉ ΠΈ ΠΏΠΎΠ΄Π΄Π΅ΡΠΆΠ°Π½ΠΈΠΈ Π΅Π΅ Π² ΡΠ΅ΡΠ΅Π½ΠΈΠ΅ Π²ΡΠ΅ΠΌΠ΅Π½ΠΈ, Π·Π° ΠΊΠΎΡΠΎΡΠΎΠ΅ Π±Π΅ΡΠΎΠ½ Π½Π°Π±ΠΈΡΠ°Π΅Ρ ΠΊΡΠΈΡΠΈΡΠ΅ΡΠΊΡΡ ΠΈΠ»ΠΈ Π·Π°Π΄Π°Π½Π½ΡΡ ΠΏΡΠΎΡΠ½ΠΎΡΡΡ.
ΠΡΠΊΡΡΡΡΠ²Π΅Π½Π½ΡΠΉ ΠΏΡΠΎΠ³ΡΠ΅Π² ΠΈ Π½Π°Π³ΡΠ΅Π² Π±Π΅ΡΠΎΠ½Π° ΠΏΡΠΈΠΌΠ΅Π½ΡΡΡ ΠΏΡΠΈ Π±Π΅ΡΠΎΠ½ΠΈΡΠΎΠ²Π°Π½ΠΈΠΈ ΠΊΠΎΠ½ΡΡΡΡΠΊΡΠΈΠΉ Ρ ΠΠΏ > 10, Π° ΡΠ°ΠΊΠΆΠ΅ ΠΈ Π±ΠΎΠ»Π΅Π΅ ΠΌΠ°ΡΡΠΈΠ²Π½ΡΡ
, Π΅ΡΠ»ΠΈ Π² ΠΏΠΎΡΠ»Π΅Π΄Π½ΠΈΡ
Π½Π΅Π²ΠΎΠ·ΠΌΠΎΠΆΠ½ΠΎ ΠΏΠΎΠ»ΡΡΠΈΡΡ Π² ΡΡΡΠ°Π½ΠΎΠ²Π»Π΅Π½Π½ΡΠ΅ ΡΡΠΎΠΊΠΈ Π·Π°Π΄Π°Π½Π½ΡΡ ΠΏΡΠΎΡΠ½ΠΎΡΡΡ ΠΏΡΠΈ Π²ΡΠ΄Π΅ΡΠΆΠΈΠ²Π°Π½ΠΈΠΈ ΡΠΎΠ»ΡΠΊΠΎ ΡΠΏΠΎΡΠΎΠ±ΠΎΠΌ ΡΠ΅ΡΠΌΠΎΡΠ°.
Π€ΠΈΠ·ΠΈΡΠ΅ΡΠΊΠ°Ρ ΡΡΡΠ½ΠΎΡΡΡ ΡΠ»Π΅ΠΊΡΡΠΎΠΏΡΠΎΠ³ΡΠ΅Π²Π° (ΡΠ»Π΅ΠΊΡΡΠΎΠ΄Π½ΠΎΠ³ΠΎ ΠΏΡΠΎΠ³ΡΠ΅Π²Π°) ΠΈΠ΄Π΅Π½ΡΠΈΡΠ½Π° ΡΠ°ΡΡΠΌΠΎΡΡΠ΅Π½Π½ΠΎΠΌΡ Π²ΡΡΠ΅ ΡΠΏΠΎΡΠΎΠ±Ρ ΡΠ»Π΅ΠΊΡΡΠΎΡΠ°Π·ΠΎΠ³ΡΠ΅Π²Π° Π±Π΅ΡΠΎΠ½Π½ΠΎΠΉ ΡΠΌΠ΅ΡΠΈ, Ρ. Π΅. ΠΈΡΠΏΠΎΠ»ΡΠ·ΡΠ΅ΡΡΡ ΡΠ΅ΠΏΠ»ΠΎΡΠ°, Π²ΡΠ΄Π΅Π»ΡΠ΅ΠΌΠ°Ρ Π² ΡΠ»ΠΎΠΆΠ΅Π½Π½ΠΎΠΌ Π±Π΅ΡΠΎΠ½Π΅ ΠΏΡΠΈ ΠΏΡΠΎΠΏΡΡΠΊΠ΅ ΡΠ΅ΡΠ΅Π· Π½Π΅Π³ΠΎ ΡΠ»Π΅ΠΊΡΡΠΈΡΠ΅ΡΠΊΠΎΠ³ΠΎ ΡΠΎΠΊΠ°.
ΠΠ±ΡΠ°Π·ΡΡΡΠ°ΡΡΡ ΡΠ΅ΠΏΠ»ΠΎΡΠ° ΡΠ°ΡΡ ΠΎΠ΄ΡΠ΅ΡΡΡ Π½Π° Π½Π°Π³ΡΠ΅Π² Π±Π΅ΡΠΎΠ½Π° ΠΈ ΠΎΠΏΠ°Π»ΡΠ±ΠΊΠΈ Π΄ΠΎ Π·Π°Π΄Π°Π½Π½ΠΎΠΉ ΡΠ΅ΠΌΠΏΠ΅ΡΠ°ΡΡΡΡ ΠΈ Π²ΠΎΠ·ΠΌΠ΅ΡΠ΅Π½ΠΈΠ΅ ΡΠ΅ΠΏΠ»ΠΎΠΏΠΎΡΠ΅ΡΡ Π² ΠΎΠΊΡΡΠΆΠ°ΡΡΡΡ ΡΡΠ΅Π΄Ρ, ΠΏΡΠΎΠΈΡΡ ΠΎΠ΄ΡΡΠΈΡ Π² ΠΏΡΠΎΡΠ΅ΡΡΠ΅ Π²ΡΠ΄Π΅ΡΠΆΠΈΠ²Π°Π½ΠΈΡ. Π’Π΅ΠΌΠΏΠ΅ΡΠ°ΡΡΡΠ° Π±Π΅ΡΠΎΠ½Π° ΠΏΡΠΈ ΡΠ»Π΅ΠΊΡΡΠΎΠΏΡΠΎΠ³ΡΠ΅Π²Π΅ ΠΎΠΏΡΠ΅Π΄Π΅Π»ΡΠ΅ΡΡΡ Π²Π΅Π»ΠΈΡΠΈΠ½ΠΎΠΉ Π²ΡΡΠ΅Π»ΡΠ΅ΠΌΠΎΠΉ Π² Π±Π΅ΡΠΎΠ½Π΅ ΡΠ»Π΅ΠΊΡΡΠΈΡΠ΅ΡΠΊΠΎΠΉ ΠΌΠΎΡΠ½ΠΎΡΡΠΈ, ΠΊΠΎΡΠΎΡΠ°Ρ Π΄ΠΎΠ»ΠΆΠ½Π° Π½Π°Π·Π½Π°ΡΠ°ΡΡΡΡ Π² Π·Π°Π²ΠΈΡΠΈΠΌΠΎΡΡΠΈ ΠΎΡ Π²ΡΠ±ΡΠ°Π½Π½ΠΎΠ³ΠΎ ΡΠ΅ΠΆΠΈΠΌΠ° ΡΠ΅ΡΠΌΠΎΠΎΠ±ΡΠ°Π±ΠΎΡΠΊΠΈ ΠΈ Π²Π΅Π»ΠΈΡΠΈΠ½Ρ ΡΠ΅ΠΏΠ»ΠΎΠΏΠΎΡΠ΅ΡΡ, ΠΈΠΌΠ΅ΡΡΠΈΡ ΠΌΠ΅ΡΡΠΎ ΠΏΡΠΈ ΡΠ»Π΅ΠΊΡΡΠΎΠΏΡΠΎΠ³ΡΠ΅Π²Π΅ Π½Π° ΠΌΠΎΡΠΎΠ·Π΅.
ΠΠ»Ρ ΠΏΠΎΠ΄Π²Π΅Π΄Π΅Π½ΠΈΡ ΡΠ»Π΅ΠΊΡΡΠΈΡΠ΅ΡΠΊΠΎΠΉ ΡΠ½Π΅ΡΠ³ΠΈΠΈ ΠΊ Π±Π΅ΡΠΎΠ½Ρ ΠΈΡΠΏΠΎΠ»ΡΠ·ΡΡΡ ΡΠ°Π·Π»ΠΈΡΠ½ΡΠ΅ ΡΠ»Π΅ΠΊΡΡΠΎΠ΄Ρ: ΠΏΠ»Π°ΡΡΠΈΠ½ΡΠ°ΡΡΠ΅, ΠΏΠΎΠ»ΠΎΡΠΎΠ²ΡΠ΅, ΡΡΠ΅ΡΠΆΠ½Π΅Π²ΡΠ΅ ΠΈ ΡΡΡΡΠ½Π½ΡΠ΅.
Π ΠΊΠΎΠ½ΡΡΡΡΠΊΡΠΈΡΠΌ ΡΠ»Π΅ΠΊΡΡΠΎΠ΄ΠΎΠ² ΠΈ ΡΡ
Π΅ΠΌΠ°ΠΌ ΠΈΡ
ΡΠ°Π·ΠΌΠ΅ΡΠ΅Π½ΠΈΡ ΠΏΡΠ΅Π΄ΡΡΠ²Π»ΡΡΡΡΡ ΡΠ»Π΅Π΄ΡΡΡΠΈΠ΅ ΠΎΡΠ½ΠΎΠ²Π½ΡΠ΅ ΡΡΠ΅Π±ΠΎΠ²Π°Π½ΠΈΡ: ΠΌΠΎΡΠ½ΠΎΡΡΡ, Π²ΡΠ΄Π΅Π»ΡΠ΅ΠΌΠ°Ρ Π² Π±Π΅ΡΠΎΠ½Π΅ ΠΏΡΠΈ ΡΠ»Π΅ΠΊΡΡΠΎΠΏΡΠΎΠ³ΡΠ΅Π²Π΅, Π΄ΠΎΠ»ΠΆΠ½Π° ΡΠΎΠΎΡΠ²Π΅ΡΡΡΠ²ΠΎΠ²Π°ΡΡ ΠΌΠΎΡΠ½ΠΎΡΡΠΈ, ΡΡΠ΅Π±ΡΠ΅ΠΌΠΎΠΉ ΠΏΠΎ ΡΠ΅ΠΏΠ»ΠΎΠ²ΠΎΠΌΡ ΡΠ°ΡΡΠ΅ΡΡ, ΡΠ»Π΅ΠΊΡΡΠΈΡΠ΅ΡΠΊΠΎΠ΅ ΠΈ, ΡΠ»Π΅Π΄ΠΎΠ²Π°ΡΠ΅Π»ΡΠ½ΠΎ, ΡΠ΅ΠΌΠΏΠ΅ΡΠ°ΡΡΡΠ½ΠΎΠ΅ ΠΏΠΎΠ»Ρ Π΄ΠΎΠ»ΠΆΠ½Ρ Π±ΡΡΡ ΠΏΠΎ Π²ΠΎΠ·ΠΌΠΎΠΆΠ½ΠΎΡΡΠΈ ΡΠ°Π²Π½ΠΎΠΌΠ΅ΡΠ½ΡΠΌΠΈ, ΡΠ»Π΅ΠΊΡΡΠΎΠ΄Ρ ΡΠ»Π΅Π΄ΡΠ΅Ρ ΡΠ°ΡΠΏΠΎΠ»Π°Π³Π°ΡΡ ΠΏΠΎ Π²ΠΎΠ·ΠΌΠΎΠΆΠ½ΠΎΡΡΠΈ ΡΠ½Π°ΡΡΠΆΠΈ ΠΏΡΠΎΠ³ΡΠ΅Π²Π°Π΅ΠΌΠΎΠΉ ΠΊΠΎΠ½ΡΡΡΡΠΊΡΠΈΠΈ Π΄Π»Ρ ΠΎΠ±Π΅ΡΠΏΠ΅ΡΠ΅Π½ΠΈΡ ΠΌΠΈΠ½ΠΈΠΌΠ°Π»ΡΠ½ΠΎΠ³ΠΎ ΡΠ°ΡΡ
ΠΎΠ΄Π° ΠΌΠ΅ΡΠ°Π»Π»Π°, ΡΡΡΠ°Π½ΠΎΠ²ΠΊΡ ΡΠ»Π΅ΠΊΡΡΠΎΠ΄ΠΎΠ² ΠΈ ΠΏΡΠΈΡΠΎΠ΅Π΄ΠΈΠ½Π΅Π½ΠΈΠ΅ ΠΊ Π½ΠΈΠΌ ΠΏΡΠΎΠ²ΠΎΠ΄ΠΎΠ² Π½Π΅ΠΎΠ±Ρ
ΠΎΠ΄ΠΈΠΌΠΎ ΠΏΡΠΎΠΈΠ·Π²ΠΎΠ΄ΠΈΡΡ Π΄ΠΎ Π½Π°ΡΠ°Π»Π° ΡΠΊΠ»Π°Π΄ΠΊΠΈ Π±Π΅ΡΠΎΠ½Π½ΠΎΠΉ ΡΠΌΠ΅ΡΠΈ (ΠΏΡΠΈ ΠΈΡΠΏΠΎΠ»ΡΠ·ΠΎΠ²Π°Π½ΠΈΠΈ Π½Π°ΡΡΠΆΠ½ΡΡ
ΡΠ»Π΅ΠΊΡΡΠΎΠ΄ΠΎΠ²).
Π Π½Π°ΠΈΠ±ΠΎΠ»ΡΡΠ΅ΠΉ ΡΡΠ΅ΠΏΠ΅Π½ΠΈ ΡΠ΄ΠΎΠ²Π»Π΅ΡΠ²ΠΎΡΡΡΡ ΠΈΠ·Π»ΠΎΠΆΠ΅Π½Π½ΡΠΌ ΡΡΠ΅Π±ΠΎΠ²Π°Π½ΠΈΡΠΌ ΠΏΠ»Π°ΡΡΠΈΠ½ΡΠ°ΡΡΠ΅ ΡΠ»Π΅ΠΊΡΡΠΎΠ΄Ρ.
ΠΠ»Π°ΡΡΠΈΠ½ΡΠ°ΡΡΠ΅ ΡΠ»Π΅ΠΊΡΡΠΎΠ΄Ρ ΠΏΡΠΈΠ½Π°Π΄Π»Π΅ΠΆΠ°Ρ ΠΊ ΡΠ°Π·ΡΡΠ΄Ρ ΠΏΠΎΠ²Π΅ΡΡ Π½ΠΎΡΡΠ½ΡΡ ΠΈ ΠΏΡΠ΅Π΄ΡΡΠ°Π²Π»ΡΡΡ ΡΠΎΠ±ΠΎΠΉ ΠΏΠ»Π°ΡΡΠΈΠ½Ρ ΠΈΠ· ΠΊΡΠΎΠ²Π΅Π»ΡΠ½ΠΎΠ³ΠΎ ΠΆΠ΅Π»Π΅Π·Π° ΠΈΠ»ΠΈ ΡΡΠ°Π»ΠΈ, Π½Π°ΡΠΈΠ²Π°Π΅ΠΌΡΠ΅ Π½Π° Π²Π½ΡΡΡΠ΅Π½Π½ΡΡ, ΠΏΡΠΈΠΌΡΠΊΠ°ΡΡΡΡ ΠΊ Π±Π΅ΡΠΎΠ½Ρ ΠΏΠΎΠ²Π΅ΡΡ Π½ΠΎΡΡΡ ΠΎΠΏΠ°Π»ΡΠ±ΠΊΠΈ ΠΈ ΠΏΠΎΠ΄ΠΊΠ»ΡΡΠ°Π΅ΠΌΡΠ΅ ΠΊ ΡΠ°Π·Π½ΠΎΠΈΠΌΠ΅Π½Π½ΡΠΌ ΡΠ°Π·Π°ΠΌ ΠΏΠΈΡΠ°ΡΡΠ΅ΠΉ ΡΠ΅ΡΠΈ. Π ΡΠ΅Π·ΡΠ»ΡΡΠ°ΡΠ΅ ΡΠΎΠΊΠΎΠΎΠ±ΠΌΠ΅Π½Π° ΠΌΠ΅ΠΆΠ΄Ρ ΠΏΡΠΎΡΠΈΠ²ΠΎΠ»Π΅ΠΆΠ°ΡΠΈΠΌΠΈ ΡΠ»Π΅ΠΊΡΡΠΎΠ΄Π°ΠΌΠΈ Π²Π΅ΡΡ ΠΎΠ±ΡΠ΅ΠΌ ΠΊΠΎΠ½ΡΡΡΡΠΊΡΠΈΠΈ Π½Π°Π³ΡΠ΅Π²Π°Π΅ΡΡΡ. Π‘ ΠΏΠΎΠΌΠΎΡΡΡ ΠΏΠ»Π°ΡΡΠΈΡΠ½Π°ΡΡΡ ΡΠ»Π΅ΠΊΡΡΠΎΠ΄ΠΎΠ² ΠΏΡΠΎΠ³ΡΠ΅Π²Π°ΡΡ ΡΠ»Π°Π±ΠΎΠ°ΡΠΌΠΈΡΠΎΠ²Π°Π½Π½ΡΠ΅ ΠΊΠΎΠ½ΡΡΡΡΠΊΡΠΈΠΈ ΠΏΡΠ°Π²ΠΈΠ»ΡΠ½ΠΎΠΉ ΡΠΎΡΠΌΡ Π½Π΅Π±ΠΎΠ»ΡΡΠΈΡ ΡΠ°Π·ΠΌΠ΅ΡΠΎΠ² (ΠΊΠΎΠ»ΠΎΠ½Π½Ρ, Π±Π°Π»ΠΊΠΈ, ΡΡΠ΅Π½Ρ ΠΈ Π΄Ρ.).
ΠΠΎΠ»ΠΎΡΠΎΠ²ΡΠ΅ ΡΠ»Π΅ΠΊΡΡΠΎΠ΄Ρ ΠΈΠ·Π³ΠΎΡΠΎΠ²Π»ΡΡΡ ΠΈΠ· ΡΡΠ°Π»ΡΠ½ΡΡ ΠΏΠΎΠ»ΠΎΡ ΡΠΈΡΠΈΠ½ΠΎΠΉ 20…50 ΠΌΠΌ ΠΈ ΡΠ°ΠΊ ΠΆΠ΅, ΠΊΠ°ΠΊ ΠΏΠ»Π°ΡΡΠΈΠ½ΡΠ°ΡΡΠ΅ ΡΠ»Π΅ΠΊΡΡΠΎΠ΄Ρ, Π½Π°ΡΠΈΠ²Π°ΡΡ Π½Π° Π²Π½ΡΡΡΠ΅Π½Π½ΡΡ ΠΏΠΎΠ²Π΅ΡΡ Π½ΠΎΡΡΡ ΠΎΠΏΠ°Π»ΡΠ±ΠΊΠΈ.
Π’ΠΎΠΊΠΎΠΎΠ±ΠΌΠ΅Π½ Π·Π°Π²ΠΈΡΠΈΡ ΠΎΡ ΡΡ
Π΅ΠΌΡ ΠΏΡΠΈΡΠΎΠ΅Π΄ΠΈΠ½Π΅Π½ΠΈΡ ΠΏΠΎΠ»ΠΎΡΠΎΠ²ΡΡ
ΡΠ»Π΅ΠΊΡΡΠΎΠ΄ΠΎΠ² ΠΊ ΡΠ°Π·Π°ΠΌ ΠΏΠΈΡΠ°ΡΡΠ΅ΠΉ ΡΠ΅ΡΠΈ. ΠΡΠΈ ΠΏΡΠΈΡΠΎΠ΅Π΄ΠΈΠ½Π΅Π½ΠΈΠΈ ΠΏΡΠΎΡΠΈΠ²ΠΎΠ»Π΅ΠΆΠ° ΡΠΈΡ
ΡΠ»Π΅ΠΊΡΡΠΎΠ΄ΠΎΠ² ΠΊ ΡΠ°Π·Π½ΠΎΠΈΠΌΠ΅Π½Π½ΡΠΌ ΡΠ°Π·Π°ΠΌ ΠΏΠΈΡΠ°ΡΡΠ΅ΠΉ ΡΠ΅ΡΠΈ ΡΠΎΠΊΠΎΠΎΠ±ΠΌΠ΅Π½ ΠΏΡΠΎΠΈΡΡ
ΠΎΠ΄ΠΈΡ ΠΌΠ΅ΠΆΠ΄Ρ ΠΏΡΠΎΡΠΈΠ²ΠΎΠΏΠΎΠ»ΠΎΠΆΠ½ΡΠΌΠΈ Π³ΡΠ°Π½ΡΠΌΠΈ ΠΊΠΎΠ½ΡΡΡΡΠΊΡΠΈΠΈ ΠΈ Π² ΡΠ΅ΠΏΠ»ΠΎΠ²ΡΠ΄Π΅Π»Π΅Π½ΠΈΠ΅ Π²ΠΎΠ²Π»Π΅ΠΊΠ°Π΅ΡΡΡ Π²ΡΡ ΠΌΠ°ΡΡΠ° Π±Π΅ΡΠΎΠ½Π°. ΠΡΠΈ ΠΏΡΠΈΡΠΎΠ΅Π΄ΠΈΠ½Π΅Π½ΠΈΠΈ ΠΊ ΡΠ°Π·Π½ΠΎΠΈΠΌΠ΅Π½Π½ΡΠΌ ΡΠ°Π·Π°ΠΌ ΡΠΎΡΠ΅Π΄Π½ΠΈΡ
ΡΠ»Π΅ΠΊΡΡΠΎΠ΄ΠΎΠ² ΡΠΎΠΊΠΎΠΎΠ±ΠΌΠ΅Π½ ΠΏΡΠΎΠΈΡΡ
ΠΎΠ΄ΠΈΡ ΠΌΠ΅ΠΆΠ΄Ρ Π½ΠΈΠΌΠΈ. ΠΡΠΈ ΡΡΠΎΠΌ 90% Π²ΡΠ΅ΠΉ ΠΏΠΎΠ΄Π²ΠΎΠ΄ΠΈΠΌΠΎΠΉ ΡΠ½Π΅ΡΠ³ΠΈΠΈ ΡΠ°ΡΡΠ΅ΠΈΠ²Π°Π΅ΡΡΡ Π² ΠΏΠ΅ΡΠΈΡΠ΅ΡΠΈΠΉΠ½ΡΡ
ΡΠ»ΠΎΡΡ
ΡΠΎΠ»ΡΠΈΠ½ΠΎΠΉ, ΡΠ°Π²Π½ΠΎΠΉ ΠΏΠΎΠ»ΠΎΠ²ΠΈΠ½Π΅ ΡΠ°ΡΡΡΠΎΡΠ½ΠΈΡ ΠΌΠ΅ΠΆΠ΄Ρ ΡΠ»Π΅ΠΊΡΡΠΎΠ΄Π°ΠΌΠΈ. Π ΡΠ΅Π·ΡΠ»ΡΡΠ°ΡΠ΅ ΠΏΠ΅ΡΠΈΡΠ΅ΡΠΈΠΉΠ½ΡΠ΅ ΡΠ»ΠΎΠΈ Π½Π°Π³ΡΠ΅Π²Π°ΡΡΡΡ Π·Π° ΡΡΠ΅Ρ Π΄ΠΆΠΎΡΠ»Π΅Π²ΠΎΠΉ ΡΠ΅ΠΏΠ»ΠΎΡΡ. Π¦Π΅Π½ΡΡΠ°Π»ΡΠ½ΡΠ΅ ΠΆΠ΅ ΡΠ»ΠΎΠΈ (ΡΠ°ΠΊ Π½Π°Π·ΡΠ²Π°Π΅ΠΌΠΎΠ΅ Β«ΡΠ΄ΡΠΎΒ» Π±Π΅ΡΠΎΠ½Π°) ΡΠ²Π΅ΡΠ΄Π΅ΡΡ Π·Π° ΡΡΠ΅Ρ Π½Π°ΡΠ°Π»ΡΠ½ΠΎΠ³ΠΎ ΡΠ΅ΠΏΠ»ΠΎΡΠΎΠ΄Π΅ΡΠΆΠ°Π½ΠΈΡ, ΡΠΊΠ·ΠΎΡΠ΅ΡΠΌΠΈΠΈ ΡΠ΅ΠΌΠ΅Π½ΡΠ° ΠΈ ΡΠ°ΡΡΠΈΡΠ½ΠΎ Π·Π° ΡΡΠ΅Ρ ΠΏΡΠΈΡΠΎΠΊΠ° ΡΠ΅ΠΏΠ»ΠΎΡΡ ΠΎΡ Π½Π°Π³ΡΠ΅Π²Π°Π΅ΠΌΡΡ
ΠΏΠ΅ΡΠΈΡΠ΅ΡΠΈΠΉΠ½ΡΡ
ΡΠ»ΠΎΠ΅Π². ΠΠ΅ΡΠ²ΡΡ ΡΡ
Π΅ΠΌΡ ΠΏΡΠΈΠΌΠ΅Π½ΡΡΡ Π΄Π»Ρ ΠΏΡΠΎΠ³ΡΠ΅Π²Π° ΡΠ»Π°Π±ΠΎΠ°ΡΠΌΠΈΡΠΎΠ²Π°Π½Π½ΡΡ
ΠΊΠΎΠ½ΡΡΡΡΠΊΡΠΈΠΉ ΡΠΎΠ»ΡΠΈΠ½ΠΎΠΉ Π½Π΅ Π±ΠΎΠ»Π΅Π΅ 50 ΡΠΌ. ΠΠ΅ΡΠΈΡΠ΅ΡΠΈΠΉΠ½ΡΠΉ ΡΠ»Π΅ΠΊΡΡΠΎΠΏΡΠΎΠ³ΡΠ΅Π² ΠΏΡΠΈΠΌΠ΅Π½ΡΡΡ Π΄Π»Ρ ΠΊΠΎΠ½ΡΡΡΡΠΊΡΠΈΠΉ Π»ΡΠ±ΠΎΠΉ ΠΌΠ°ΡΡΠΈΠ²Π½ΠΎΡΡΠΈ.
ΠΠΎΠ»ΠΎΡΠΎΠ²ΡΠ΅ ΡΠ»Π΅ΠΊΡΡΠΎΠ΄Ρ ΡΡΡΠ°Π½Π°Π²Π»ΠΈΠ²Π°ΡΡ ΠΏΠΎ ΠΎΠ΄Π½Ρ ΡΡΠΎΡΠΎΠ½Ρ ΠΊΠΎΠ½ΡΡΡΡΠΊ ΡΠΈΠΈ. ΠΡΠΈ ΡΡΠΎΠΌ ΠΊ ΡΠ°Π·Π½ΠΎΠΈΠΌΠ΅Π½Π½ΡΠΌ ΡΠ°Π·Π°ΠΌ ΠΏΠΈΡΠ°ΡΡΠ΅ΠΉ ΡΠ΅ΡΠΈ ΠΏΡΠΈΡΠΎΠ΅Π΄ΠΈΠ½ΡΡΡ ΡΠΎΡΠ΅Π΄Π½ΠΈΠ΅ ΡΠ»Π΅ΠΊΡΡΠΎΠ΄Ρ. Π ΡΠ΅Π·ΡΠ»ΡΡΠ°ΡΠ΅ ΡΠ΅Π°Π»ΠΈΠ·ΡΠ΅ΡΡΡ ΠΏΠ΅ΡΠΈΡΠ΅ΡΠΈΠΉΠ½ΡΠΉ ΡΠ»Π΅ΠΊΡΡΠΎΠΏΡΠΎΠ³ΡΠ΅Π².
ΠΠ΄Π½ΠΎΡΡΠΎΡΠΎΠ½Π½Π΅Π΅ ΡΠ°Π·ΠΌΠ΅ΡΠ΅Π½ΠΈΠ΅ ΠΏΠΎΠ»ΠΎΡΠΎΠ²ΡΡ ΡΠ»Π΅ΠΊΡΡΠΎΠ΄ΠΎΠ² ΠΏΡΠΈΠΌΠ΅Π½ΡΡΡ ΠΏΡΠΈ ΡΠ»Π΅ΠΊΡΡΠΎΠΏΡΠΎΠ³ΡΠ΅Π²Π΅ ΠΏΠ»ΠΈΡ, ΡΡΠ΅Π½, ΠΏΠΎΠ»ΠΎΠ² ΠΈ Π΄ΡΡΠ³ΠΈΡ ΠΊΠΎΠ½ΡΡΡΡΠΊΡΠΈΠΉ ΡΠΎΠ»ΡΠΈΠ½ΠΎΠΉ Π½Π΅ Π±ΠΎΠ»Π΅Π΅ 20 ΡΠΌ.
ΠΡΠΈ ΡΠ»ΠΎΠΆΠ½ΠΎΠΉ ΠΊΠΎΠ½ΡΠΈΠ³ΡΡΠ°ΡΠΈΠΈ Π±Π΅ΡΠΎΠ½ΠΈΡΡΠ΅ΠΌΡΡ
ΠΊΠΎΠ½ΡΡΡΡΠΊΡΠΈΠΉ ΠΏΡΠΈ ΠΌΠ΅Π½ΡΡΡ ΡΡΠ΅ΡΠΆΠ½Π΅Π²ΡΠ΅ ΡΠ»Π΅ΠΊΡΡΠΎΠ΄Ρ — Π°ΡΠΌΠ°ΡΡΡΠ½ΡΠ΅ ΠΏΡΡΡΠΊΠΈ Π΄ΠΈΠ°ΠΌΠ΅ΡΡΠΎΠΌ 6. .. 12 ΠΌΠΌ, ΡΡΡΠ°Π½Π°Π²Π»ΠΈΠ²Π°Π΅ΠΌΡΠ΅ Π² ΡΠ΅Π»ΠΎ Π±Π΅ΡΠΎΠ½Π°.
ΠΠ°ΠΈΠ±ΠΎΠ»Π΅Π΅ ΡΠ΅Π»Π΅ΡΠΎΠΎΠ±ΡΠ°Π·Π½ΠΎ ΠΈΡΠΏΠΎΠ»ΡΠ·ΠΎΠ²Π°ΡΡ ΡΡΠ΅ΡΠΆΠ½Π΅Π²ΡΠ΅ ΡΠ»Π΅ΠΊΡΡΠΎΠ΄Ρ Ρ Π²ΠΈΠ΄Π΅ ΠΏΠ»ΠΎΡΠΊΠΈΡ ΡΠ»Π΅ΠΊΡΡΠΎΠ΄Π½ΡΡ Π³ΡΡΠΏΠΏ. Π ΡΡΠΎΠΌ ΡΠ»ΡΡΠ°Π΅ ΠΎΠ±Π΅ΡΠΏΠ΅ΡΠΈΠ²Π°Π΅ΡΡΡ Π±ΠΎΠ»Π΅Π΅ ΡΠ°Π²Π½ΠΎΠΌΠ΅ΡΠ½ΠΎΠ΅ ΡΠ΅ΠΌΠΏΠ΅ΡΠ°ΡΡΡΠ½ΠΎΠ΅ ΠΏΠΎΠ»Π΅ Π² Π±Π΅ΡΠΎΠ½Π΅.
ΠΡΠΈ ΡΠ»Π΅ΠΊΡΡΠΎΠΏΡΠΎΠ³ΡΠ΅Π²Π΅ Π±Π΅ΡΠΎΠ½Π½ΡΡ ΡΠ»Π΅ΠΌΠ΅Π½ΡΠΎΠ² ΠΌΠ°Π»ΠΎΠ³ΠΎ ΡΠ΅ΡΠ΅Π½ΠΈΡ ΠΈ Π·Π½Π°ΡΠΈΡΠ΅Π»ΡΠ½ΠΎΠΉ ΠΏΡΠΎΡΡΠΆΠ΅Π½Π½ΠΎΡΡΠΈ (Π½Π°ΠΏΡΠΈΠΌΠ΅Ρ, Π±Π΅ΡΠΎΠ½Π½ΡΡ ΡΡΡΠΊΠΎΠ² ΡΠΈΡΠΈΠ½ΠΎΠΉ Π΄ΠΎ 3… 4 ΡΠΌ) ΠΏΡΠΈΠΌΠ΅Π½ΡΡΡ ΠΎΠ΄ΠΈΠ½ΠΎΡΠ½ΡΠ΅ ΡΡΠ΅ΡΠΆΠ½Π΅Π²ΡΠ΅ ΡΠ»Π΅ΠΊΡΡΠΎΠ΄Ρ.
ΠΡΠΈ Π±Π΅ΡΠΎΠ½ΠΈΡΠΎΠ²Π°Π½ΠΈΠΈ Π³ΠΎΡΠΈΠ·ΠΎΠ½ΡΠ°Π»ΡΠ½ΠΎ ΡΠ°ΡΠΏΠΎΠ»ΠΎΠΆΠ΅Π½Π½ΡΡ Π±Π΅ΡΠΎΠ½Π½ΡΡ ΠΈΠ»ΠΈ ΠΈΠΌΠ΅ΡΡΠΈΡ Π±ΠΎΠ»ΡΡΠΎΠΉ Π·Π°ΡΠΈΡΠ½ΡΠΉ ΡΠ»ΠΎΠΉ ΠΆΠ΅Π»Π΅Π·ΠΎΠ±Π΅ΡΠΎΠ½Π½ΡΡ ΠΊΠΎΠ½ΡΡΡΡΠΊΡΠΈΠΉ ΠΈΡΠΏΠΎΠ»ΡΠ·ΡΡΡ ΠΏΠ»Π°Π²Π°ΡΡΠΈΠ΅ ΡΠ»Π΅ΠΊΡΡΠΎΠ΄Ρ — Π°ΡΠΌΠ°ΡΡΡΠ½ΡΠ΅ ΡΡΠ΅ΡΠΆΠ½ΠΈ 6… 12 ΠΌΠΌ, Π²ΡΠ°ΠΏΠ»ΠΈΠ²Π°Π΅ΠΌΡΠ΅ Π² ΠΏΠΎΠ²Π΅ΡΡ Π½ΠΎΡΡΡ.
Π‘ΡΡΡΠ½Π½ΡΠ΅ ΡΠ»Π΅ΠΊΡΡΠΎΠ΄Ρ ΠΏΡΠΈΠΌΠ΅Π½ΡΡΡ Π΄Π»Ρ ΠΏΡΠΎΠ³ΡΠ΅Π²Π° ΠΊΠΎΠ½ΡΡΡΡΠΊΡΠΈΠΉ, Π΄Π»ΠΈΠ½Π° ΠΊΠΎΡΠΎΡΡΡ
Π²ΠΎ ΠΌΠ½ΠΎΠ³ΠΎ ΡΠ°Π· Π±ΠΎΠ»ΡΡΠ΅ ΡΠ°Π·ΠΌΠ΅ΡΠΎΠ² ΠΈΡ
ΠΏΠΎΠΏΠ΅ΡΠ΅ΡΠ½ΠΎΠ³ΠΎ ΡΠ΅ΡΠ΅Π½ΠΈΡ (ΠΊΠΎΠ»ΠΎΠ½Π½Ρ, Π±Π°Π»ΠΊΠΈ, ΠΏΡΠΎΠ³ΠΎΠ½Ρ ΠΈ Ρ. ΠΏ.). Π‘ΡΡΡΠ½Π½ΡΠ΅ ΡΠ»Π΅ΠΊΡΡΠΎΠ΄Ρ ΡΡΡΠ°Π½Π°Π²Π»ΠΈΠ²Π°ΡΡ ΠΏΠΎ ΡΠ΅Π½ΡΡΡ ΠΊΠΎΠ½ΡΡΡΡΠΊΡΠΈΠΈ ΠΈ ΠΏΠΎΠ΄ΠΊΠ»ΡΡΠ°ΡΡ ΠΊ ΠΎΠ΄Π½ΠΎΠΉ ΡΠ°Π·Π΅, Π° ΠΌΠ΅ΡΠ°Π»Π»ΠΈΡΠ΅ΡΠΊΡΡ ΠΎΠΏΠ°Π»ΡΠ±ΠΊΡ (ΠΈΠ»ΠΈ Π΄Π΅ΡΠ΅Π²ΡΠ½Π½ΡΡ Ρ ΠΎΠ±ΡΠΈΠ²ΠΊΠΎΠΉ ΠΏΠ°Π»ΡΠ±Ρ ΠΊΡΠΎΠ²Π΅Π»ΡΠ½ΠΎΠΉ ΡΡΠ°Π»ΡΡ) — ΠΊ Π΄ΡΡΠ³ΠΎΠΉ. Π ΠΎΡΠ΄Π΅Π»ΡΠ½ΡΡ
ΡΠ»ΡΡΠ°ΡΡ
Π² ΠΊΠ°ΡΠ΅ΡΡΠ²Π΅ Π΄ΡΡΠ³ΠΎΠ³ΠΎ ΡΠ»Π΅ΠΊΡΡΠΎΠ΄Π° ΠΌΠΎΠΆΠ΅Ρ Π±ΡΡΡ ΠΈΡΠΏΠΎΠ»ΡΠ·ΠΎΠ²Π°Π½Π° ΡΠ°Π±ΠΎΡΠ°Ρ Π°ΡΠΌΠ°ΡΡΡΠ°.
ΠΠΎΠ»ΠΈΡΠ΅ΡΡΠ²ΠΎ ΡΠ½Π΅ΡΠ³ΠΈΠΈ, Π²ΡΠ΄Π΅Π»ΡΠ΅ΠΌΠΎΠΉ Π² Π±Π΅ΡΠΎΠ½Π΅ Π² Π΅Π΄ΠΈΠ½ΠΈΡΡ Π²ΡΠ΅ΠΌΠ΅Π½ΠΈ, Π° ΡΠ»Π΅Π΄ΠΎΠ²Π°ΡΠ΅Π»ΡΠ½ΠΎ, ΠΈ ΡΠ΅ΠΌΠΏΠ΅ΡΠ°ΡΡΡΠ½ΡΠΉ ΡΠ΅ΠΆΠΈΠΌ ΡΠ»Π΅ΠΊΡΡΠΎΠΏΡΠΎΠ³ΡΠ΅Π²Π° Π·Π°Π²ΠΈΡΡΡ ΠΎΡ Π²ΠΈΠ΄Π° ΠΈ ΡΠ°Π·ΠΌΠ΅ΡΠΎΠ² ΡΠ»Π΅ΠΊΡΡΠΎΠ΄ΠΎΠ², ΡΡ Π΅ΠΌΡ ΠΈΡ ΡΠ°Π·ΠΌΠ΅ΡΠ΅Π½ΠΈΡ Π² ΠΊΠΎΠ½ΡΡΡΡΠΊΡΠΈΠΈ, ΡΠ°ΡΡΡΠΎΡΠ½ΠΈΠΉ ΠΌΠ΅ΠΆΠ΄Ρ Π½ΠΈΠΌΠΈ ΠΈ ΡΡ Π΅ΠΌΡ ΠΏΠΎΠ΄ΠΊΠ»ΡΡΠ΅Π½ΠΈΡ ΠΊ ΠΏΠΈΡΠ°ΡΡΠ΅ΠΉ ΡΠ΅ΡΠΈ. ΠΡΠΈ ΡΡΠΎΠΌ ΠΏΠ°ΡΠ°ΠΌΠ΅ΡΡΠΎΠΌ, Π΄ΠΎΠΏΡΡΠΊΠ°ΡΡΠΈΠΌ ΠΏΡΠΎΠΈΠ·Π²ΠΎΠ»ΡΠ½ΠΎΠ΅ Π²Π°ΡΡΠΈΡΠΎΠ²Π°Π½ΠΈΠ΅, ΡΠ°ΡΠ΅ Π²ΡΠ΅Π³ΠΎ ΡΠ²Π»ΡΠ΅ΡΡΡ ΠΏΠΎΠ΄Π²ΠΎΠ΄ΠΈΠΌΠΎΠ΅ Π½Π°ΠΏΡΡΠΆΠ΅Π½ΠΈΠ΅. ΠΡΠ΄Π΅Π»ΡΠ΅ΠΌΠ°Ρ ΡΠ»Π΅ΠΊΡΡΠΈΡΠ΅ΡΠΊΠ°Ρ ΠΌΠΎΡΠ½ΠΎΡΡΡ Π² Π·Π°Π²ΠΈΡΠΈΠΌΠΎΡΡΠΈ ΠΎΡ ΠΏΠ΅ΡΠ΅ΡΠΈΡΠ»Π΅Π½Π½ΡΡ Π²ΡΡΠ΅ ΠΏΠ°ΡΠ°ΠΌΠ΅ΡΡΠΎΠ² ΡΠ°ΡΡΡΠΈΡΡΠ²Π°Π΅ΡΡΡ ΠΏΠΎ ΡΠΎΡΠΌΡΠ»Π°ΠΌ.
Π’ΠΎΠΊ Π½Π° ΡΠ»Π΅ΠΊΡΡΠΎΠ΄Ρ ΠΎΡ ΠΈΡΡΠΎΡΠ½ΠΈΠΊΠ° ΠΏΠΈΡΠ°Π½ΠΈΡ ΠΏΠΎΠ΄Π°Π΅ΡΡΡ ΡΠ΅ΡΠ΅Π· ΡΡΠ°Π½ΡΡΠΎΡΠΌΠ°ΡΠΎΡΡ ΠΈ ΡΠ°ΡΠΏΡΠ΅Π΄Π΅Π»ΠΈΡΠ΅Π»ΡΠ½ΡΠ΅ ΡΡΡΡΠΎΠΉΡΡΠ²Π°.
Π ΠΊΠ°ΡΠ΅ΡΡΠ²Π΅ ΠΌΠ°Π³ΠΈΡΡΡΠ°Π»ΡΠ½ΡΡ ΠΈ ΠΊΠΎΠΌΠΌΡΡΠ°ΡΠΈΠΎΠ½Π½ΡΡ ΠΏΡΠΎΠ²ΠΎΠ΄ΠΎΠ² ΠΏΡΠΈΠΌΠ΅Π½ΡΡΡ ΠΈΠ·ΠΎΠ»ΠΈΡΠΎΠ²Π°Π½Π½ΡΠ΅ ΠΏΡΠΎΠ²ΠΎΠ΄Π° Ρ ΠΌΠ΅Π΄Π½ΠΎΠΉ ΠΈΠ»ΠΈ Π°Π»ΡΠΌΠΈΠ½ΠΈΠ΅Π²ΠΎΠΉ ΠΆΠΈΠ»ΠΎΠΉ, ΡΠ΅ΡΠ΅Π½ΠΈΠ΅ ΠΊΠΎΡΠΎΡΡΡ ΠΏΠΎΠ΄Π±ΠΈΡΠ°ΡΡ ΠΈΠ· ΡΡΠ»ΠΎΠ²ΠΈΡ ΠΏΡΠΎΠΏΡΡΠΊΠ° ΡΠ΅ΡΠ΅Π· Π½ΠΈΡ ΡΠ°ΡΡΠ΅ΡΠ½ΠΎΠΉ ΡΠΈΠ»Ρ ΡΠΎΠΊΠ°.
ΠΠ΅ΡΠ΅Π΄ Π²ΠΊΠ»ΡΡΠ΅Π½ΠΈΠ΅ΠΌ Π½Π°ΠΏΡΡΠΆΠ΅Π½ΠΈΡ ΠΏΡΠΎΠ²Π΅ΡΡΡΡ ΠΏΡΠ°Π²ΠΈΠ»ΡΠ½ΠΎΡΡΡ ΡΡΡΠ°Π½ΠΎΠ²ΠΊΠΈ ΡΠ»Π΅ΠΊΡΡΠΎΠ΄ΠΎΠ², ΠΊΠ°ΡΠ΅ΡΡΠ²ΠΎ ΠΊΠΎΠ½ΡΠ°ΠΊΡΠΎΠ² Π½Π° ΡΠ»Π΅ΠΊΡΡΠΎΠ΄Π°Ρ ΠΈ ΠΎΡΡΡΡΡΡΠ²ΠΈΠ΅ ΠΈΡ Π·Π°ΠΌΡΠΊΠ°Π½ΠΈΡ Π½Π° Π°ΡΠΌΠ°ΡΡΡΡ.
ΠΠ»Π΅ΠΊΡΡΠΎΠΏΡΠΎΠ³ΡΠ΅Π² Π²Π΅Π΄ΡΡ Π½Π° ΠΏΠΎΠ½ΠΈΠΆΠ΅Π½Π½ΡΡ
Π½Π°ΠΏΡΡΠΆΠ΅Π½ΠΈΡΡ
Π² ΠΏΡΠ΅Π΄Π΅Π»Π°Ρ
50… 127 Π. ΠΡΡΠ΅Π΄Π½Π΅Π½Π½ΠΎ ΡΠ΄Π΅Π»ΡΠ½ΡΠΉ ΡΠ°ΡΡ
ΠΎΠ΄ ΡΠ»Π΅ΠΊΡΡΠΎΡΠ½Π΅ΡΠ³ΠΈΠΈ ΡΠΎΡΡΠ°Π²Π»ΡΠ΅Ρ 60… 80 ΠΊΠΡ/Ρ Π½Π° 1 ΠΌ3 ΠΆΠ΅Π»Π΅Π·ΠΎΠ±Π΅ΡΠΎΠ½Π°.
ΠΠΎΠ½ΡΠ°ΠΊΡΠ½ΡΠΉ (ΠΊΠΎΠ½Π΄ΡΠΊΡΠΈΠ²Π½ΡΠΉ) Π½Π°Π³ΡΠ΅Π². ΠΡΠΈ Π΄Π°Π½Π½ΠΎΠΌ ΠΌΠ΅ΡΠΎΠ΄Π΅ ΠΈΡΠΏΠΎΠ»ΡΠ·ΡΠ΅ΡΡΡ ΡΠ΅ΠΏΠ»ΠΎΡΠ°, Π²ΡΠ΄Π΅Π»ΡΠ΅ΠΌΠ°Ρ Π² ΠΏΡΠΎΠ²ΠΎΠ΄Π½ΠΈΠΊΠ΅ ΠΏΡΠΈ ΠΏΡΠΎΡ ΠΎΠΆΠ΄Π΅Π½ΠΈΠΈ ΠΏΠΎ Π½Π΅ΠΌΡ ΡΠ»Π΅ΠΊΡΡΠΈΡΠ΅ΡΠΊΠΎΠ³ΠΎ ΡΠΎΠΊΠ°. ΠΠ°ΡΠ΅ΠΌ ΡΡΠ° ΡΠ΅ΠΏΠ»ΠΎΡΠ° ΠΏΠ΅ΡΠ΅Π΄Π°Π΅ΡΡΡ ΠΊΠΎΠ½ΡΠ°ΠΊΡΠ½ΡΠΌ ΠΏΡΡΠ΅ΠΌ ΠΏΠΎΠ²Π΅ΡΡ Π½ΠΎΡΡΡΠΌ ΠΊΠΎΠ½ΡΡΡΡΠΊΡΠΈΠΈ. ΠΠ΅ΡΠ΅Π΄Π°ΡΠ° ΡΠ΅ΠΏΠ»ΠΎΡΡ Π² ΡΠ°ΠΌΠΎΠΌ Π±Π΅ΡΠΎΠ½Π΅ ΠΊΠΎΠ½ΡΡΡΡΠΊΡΠΈΠΈ ΠΏΡΠΎΠΈΡΡ ΠΎΠ΄ΠΈΡ ΠΏΡΡΠ΅ΠΌ ΡΠ΅ΠΏΠ»ΠΎΠΏΡΠΎΠ²ΠΎΠ΄Π½ΠΎΡΡΠΈ. ΠΠ»Ρ ΠΊΠΎΠ½ΡΠ°ΠΊΡΠ½ΠΎΠ³ΠΎ Π½Π°Π³ΡΠ΅Π²Π° Π±Π΅ΡΠΎΠ½Π° ΠΏΡΠ΅ΠΈΠΌΡΡΠ΅ΡΡΠ²Π΅Π½Π½ΠΎ ΠΏΡΠΈΠΌΠ΅Π½ΡΡΡ ΡΠ΅ΡΠΌΠΎΠ°ΠΊΡΠΈΠ²Π½ΡΠ΅ (Π³ΡΠ΅ΡΡΠΈΠ΅) ΠΎΠΏΠ°Π»ΡΠ±ΠΊΠΈ ΠΈ ΡΠ΅ΡΠΌΠΎΠ°ΠΊΡΠΈΠ²Π½ΡΠ΅ Π³ΠΈΠ±ΠΊΠΈΠ΅ ΠΏΠΎΠΊΡΡΡΠΈΡ (Π’ΠΠΠ).
ΠΡΠ΅ΡΡΠ°Ρ ΠΎΠΏΠ°Π»ΡΠ±ΠΊΠ° ΠΈΠΌΠ΅Π΅Ρ ΠΏΠ°Π»ΡΠ±Ρ ΠΈΠ· ΠΌΠ΅ΡΠ°Π»Π»ΠΈΡΠ΅ΡΠΊΠΎΠ³ΠΎ Π»ΠΈΡΡΠ° ΠΈΠ»ΠΈ Π²ΠΎΠ΄ΠΎΡΡΠΎΠΉΠΊΠΎΠΉ ΡΠ°Π½Π΅ΡΡ, Ρ ΡΡΠ»ΡΠ½ΠΎΠΉ ΡΡΠΎΡΠΎΠ½Ρ ΠΊΠΎΡΠΎΡΠΎΠΉ ΡΠ°ΡΠΏΠΎΠ»ΠΎΠΆΠ΅Π½Ρ ΡΠ»Π΅ΠΊΡΡΠΈΡΠ΅ΡΠΊΠΈΠ΅ Π½Π°Π³ΡΠ΅Π²Π°ΡΠ΅Π»ΡΠ½ΡΠ΅ ΡΠ»Π΅ΠΌΠ΅Π½ΡΡ. Π ΡΠΎΠ²ΡΠ΅ΠΌΠ΅Π½Π½ΡΡ
ΠΎΠΏΠ°Π»ΡΠ±ΠΊΠ°Ρ
Π² ΠΊΠ°ΡΠ΅ΡΡΠ²Π΅ Π½Π°Π³ΡΠ΅Π²Π°ΡΠ΅Π»Π΅ΠΉ ΠΏΡΠΈΠΌΠ΅Π½ΡΡΡ Π³ΡΠ΅ΡΡΠΈΠ΅ ΠΏΡΠΎΠ²ΠΎΠ΄Π° ΠΈ ΠΊΠ°Π±Π΅Π»ΠΈ, ΡΠ΅ΡΡΠ°ΡΡΠ΅ Π½Π°Π³ΡΠ΅Π²Π°ΡΠ΅Π»ΠΈ, ΡΠ³Π»Π΅ΡΠΎΠ΄Π½ΡΠ΅ Π»Π΅Π½ΡΠΎΡΠ½ΡΠ΅ Π½Π°Π³ΡΠ΅Π²Π°ΡΠ΅Π»ΠΈ, ΡΠΎΠΊΠΎΠΏΡΠΎΠ²ΠΎΠ΄ΡΡΠΈΠ΅ ΠΏΠΎΠΊΡΡΡΠΈΡ ΠΈ Π΄Ρ. ΠΠ°ΠΈΠ±ΠΎΠ»Π΅Π΅ ΡΡΡΠ΅ΠΊΡΠΈΠ²Π½ΠΎ ΠΏΡΠΈΠΌΠ΅Π½Π΅Π½ΠΈΠ΅ ΠΊΠ°Π±Π΅Π»Π΅ΠΉ, ΠΊΠΎΡΠΎΡΡΠ΅ ΡΠΎΡΡΠΎΡΡ ΠΈΠ· ΠΊΠΎΠ½ΡΡΠ°Π½ΡΠ°Π½ΠΎΠ²ΠΎΠΉ ΠΏΡΠΎΠ²ΠΎΠ»ΠΎΠΊΠΈ Π΄ΠΈΠ°ΠΌΠ΅ΡΡΠΎΠΌ 0,7… 0,8 ΠΌΠΌ, ΠΏΠΎΠΌΠ΅ΡΠ΅Π½Π½ΠΎΠΉ Π² ΡΠ΅ΡΠΌΠΎΡΡΠΎΠΉΠΊΡΡ ΠΈΠ·ΠΎΠ»ΡΡΠΈΡ. ΠΠΎΠ²Π΅ΡΡ
Π½ΠΎΡΡΡ ΠΈΠ·ΠΎΠ»ΡΡΠΈΠΈ Π·Π°ΡΠΈΡΠ΅Π½Π° ΠΎΡ ΠΌΠ΅Ρ
Π°Π½ΠΈΡΠ΅ΡΠΊΠΈΡ
ΠΏΠΎΠ²ΡΠ΅ΠΆΠ΄Π΅Π½ΠΈΠΉ ΠΌΠ΅ΡΠ°Π»Π»ΠΈΡΠ΅ΡΠΊΠΈΠΌ Π·Π°ΡΠΈΡΠ½ΡΠΌ ΡΡΠ»ΠΊΠΎΠΌ. ΠΠ»Ρ ΠΎΠ±Π΅ΡΠΏΠ΅ΡΠ΅Π½ΠΈΡ ΡΠ°Π²Π½ΠΎΠΌΠ΅ΡΠ½ΠΎΠ³ΠΎ ΡΠ΅ΠΏΠ»ΠΎΠ²ΠΎΠ³ΠΎ ΠΏΠΎΡΠΎΠΊΠ° ΠΊΠ°Π±Π΅Π»Ρ ΡΠ°Π·ΠΌΠ΅ΡΠ°ΡΡ Π½Π° ΡΠ°ΡΡΡΠΎΡΠ½ΠΈΠΈ 10… 15 ΡΠΌ Π²Π΅ΡΠ²Ρ ΠΎΡ Π²Π΅ΡΠ²ΠΈ.
Π‘Π΅ΡΡΠ°ΡΡΠ΅ Π½Π°Π³ΡΠ΅Π²Π°ΡΠ΅Π»ΠΈ (ΠΏΠΎΠ»ΠΎΡΠ° ΡΠ΅ΡΠΊΠΈ ΠΈΠ· ΠΌΠ΅ΡΠ°Π»Π»Π°) ΠΈΠ·ΠΎΠ»ΠΈΡΡΡΡ ΠΎΡ ΠΏΠ°Π»ΡΠ±Ρ ΠΏΡΠΎΠΊΠ»Π°Π΄ΠΊΠΎΠΉ Π°ΡΠ±Π΅ΡΡΠΎΠ²ΠΎΠ³ΠΎ Π»ΠΈΡΡΠ°, Π° Ρ ΡΡΠ»ΡΠ½ΠΎΠΉ ΡΡΠΎΡΠΎΠ½Ρ ΠΎΠΏΠ°Π»ΡΠ±ΠΎΡΠ½ΠΎΠ³ΠΎ ΡΠΈΡΠ° — ΡΠ°ΠΊΠΆΠ΅ Π°ΡΠ±Π΅ΡΡΠΎΠ²ΡΠΌ Π»ΠΈΡΡΠΎΠΌ ΠΈ ΠΏΠΎΠΊΡΡΠ²Π°ΡΡ ΡΠ΅ΠΏΠ»ΠΎΠΈΠ·ΠΎΠ»ΡΡΠΈΠ΅ΠΉ. ΠΠ»Ρ ΡΠΎΠ·Π΄Π°Π½ΠΈΡ ΡΠ»Π΅ΠΊΡΡΠΈΡΠ΅ΡΠΊΠΎΠΉ ΡΠ΅ΠΏΠΈ ΠΎΡΠ΄Π΅Π»ΡΠ½ΡΠ΅ ΠΏΠΎΠ»ΠΎΡΡ ΡΠ΅ΡΡΠ°ΡΠΎΠ³ΠΎ Π½Π°Π³ΡΠ΅Π²Π°ΡΠ΅Π»Ρ ΡΠΎΠ΅Π΄ΠΈΠ½ΡΡΡ ΠΌΠ΅ΠΆΠ΄Ρ ΡΠΎΠ±ΠΎΠΉ ΡΠ°Π·Π²ΠΎΠ΄ΡΡΠΈΠΌΠΈ ΡΠΈΠ½Π°ΠΌΠΈ.
Π£Π³Π»Π΅ΡΠΎΠ΄Π½ΡΠ΅ Π»Π΅Π½ΡΠΎΡΠ½ΡΠ΅ Π½Π°Π³ΡΠ΅Π²Π°ΡΠ΅Π»ΠΈ Π½Π°ΠΊΠ»Π΅ΠΈΠ²Π°ΡΡ ΡΠΏΠ΅ΡΠΈΠ°Π»ΡΠ½ΡΠΌΠΈ ΠΊΠ»Π΅ΡΠΌΠΈ Π½Π° ΠΏΠ°Π»ΡΠ±Ρ ΡΠΈΡΠ°. ΠΠ»Ρ ΠΎΠ±Π΅ΡΠΏΠ΅ΡΠ΅Π½ΠΈΡ ΠΏΡΠΎΡΠ½ΠΎΠ³ΠΎ ΠΊΠΎΠ½ΡΠ°ΠΊΡΠ° Ρ ΠΊΠΎΠΌΠΌΡΡΠΈΡΡΡΡΠΈΠΌΠΈ ΠΏΡΠΎΠ²ΠΎΠ΄Π°ΠΌΠΈ ΠΊΠΎΠ½ΡΡ Π»Π΅Π½Ρ ΠΏΠΎΠ΄Π²Π΅ΡΠ³Π°ΡΡ ΠΌΠ΅Π΄Π½Π΅Π½ΠΈΡ.
Π Π³ΡΠ΅ΡΡΡΡ ΠΎΠΏΠ°Π»ΡΠ±ΠΊΡ ΠΌΠΎΠΆΠ΅Ρ Π±ΡΡΡ ΠΏΠ΅ΡΠ΅ΠΎΠ±ΠΎΡΡΠ΄ΠΎΠ²Π°Π½Π° Π»ΡΠ±Π°Ρ ΠΈΠ½Π²Π΅Π½ΡΠ°ΡΠ½Π°Ρ Ρ ΠΏΠ°Π»ΡΠ±ΠΎΠΉ ΠΈΠ· ΡΡΠ°Π»ΠΈ ΠΈΠ»ΠΈ ΡΠ°Π½Π΅ΡΡ. Π Π·Π°Π²ΠΈΡΠΈΠΌΠΎΡΡΠΈ ΠΎΡ ΠΊΠΎΠ½ΠΊΡΠ΅ΡΠ½ΡΡ
ΡΡΠ»ΠΎΠ²ΠΈΠΉ (ΡΠ΅ΠΌΠΏΠ° Π½Π°Π³ΡΠ΅Π²Π°, ΡΠ΅ΠΌΠΏΠ΅ΡΠ°ΡΡΡΡ ΠΎΠΊΡΡΠΆΠ°ΡΡΠ΅ΠΉ ΡΡΠ΅Π΄Ρ, ΠΌΠΎΡΠ½ΠΎΡΡΠΈ ΡΠ΅ΠΏΠ»ΠΎΠ²ΠΎΠΉ Π·Π°ΡΠΈΡΡ ΡΡΠ»ΡΠ½ΠΎΠΉ ΡΠ°ΡΡΠΈ ΠΎΠΏΠ°Π»ΡΠ±ΠΊΠΈ) ΠΏΠΎΡΡΠ΅Π±Π½Π°Ρ ΡΠ΄Π΅Π»ΡΠ½Π°Ρ ΠΌΠΎΡΠ½ΠΎΡΡΡ ΠΌΠΎΠΆΠ΅Ρ ΠΊΠΎΠ»Π΅Π±Π°ΡΡΡΡ ΠΎΡ 0,5 Π΄ΠΎ 2 ΠΊΠ Π/ΠΌ2. ΠΡΠ΅ΡΡΡΡ ΠΎΠΏΠ°Π»ΡΠ±ΠΊΡ ΠΏΡΠΈΠΌΠ΅Π½ΡΡΡ ΠΏΡΠΈ Π²ΠΎΠ·Π²Π΅Π΄Π΅Π½ΠΈΠΈ ΡΠΎΠ½ΠΊΠΎΡΡΠ΅Π½Π½ΡΡ
ΠΈ ΡΡΠ΅Π΄Π½Π΅ΠΌΠ°ΡΡΠΈΠ²Π½ΡΡ
ΠΊΠΎΠ½ΡΡΡΡΠΊΡΠΈΠΉ, Π° ΡΠ°ΠΊΠΆΠ΅ ΠΏΡΠΈ Π·Π°ΠΌΠΎΠ½ΠΎΠ»ΠΈΡΠΈΠ²Π°Π½ΠΈΠΈ ΡΠ·Π»ΠΎΠ² ΡΠ±ΠΎΡΠ½ΡΡ
ΠΆΠ΅Π»Π΅Π·ΠΎΠ±Π΅ΡΠΎΠ½Π½ΡΡ
ΡΠ»Π΅ΠΌΠ΅Π½ΡΠΎΠ².
Π’Π΅ΡΠΌΠΎΠ°ΠΊΡΠΈΠ²Π½ΠΎΠ΅ ΠΏΠΎΠΊΡΡΡΠΈΠ΅ (Π’Π ΠΠ) — Π»Π΅Π³ΠΊΠΎΠ΅, Π³ΠΈΠ±ΠΊΠΎΠ΅ ΡΡΡΡΠΎΠΉΡΡΠ²ΠΎ Ρ ΡΠ³Π»Π΅ΡΠΎΠ΄Π½ΡΠΌΠΈ Π»Π΅Π½ΡΠΎΡΠ½ΡΠΌΠΈ Π½Π°Π³ΡΠ΅Π²Π°ΡΠ΅Π»ΡΠΌΠΈ ΠΈΠ»ΠΈ Π³ΡΠ΅ΡΡΠΈΠΌΠΈ ΠΏΡΠΎΠ²ΠΎΠ΄Π°ΠΌΠΈ, ΠΎΠ±Π΅ΡΠΏΠ΅ΡΠΈΠ²Π°ΡΡΠΈΠ΅ Π½Π°Π³ΡΠ΅Π² Π΄ΠΎ 50Β°Π‘. ΠΡΠ½ΠΎΠ²ΠΎΠΉ ΠΏΠΎΠΊΡΡΡΠΈΡ ΡΠ²Π»ΡΠ΅ΡΡΡ ΡΡΠ΅ΠΊΠ»ΠΎΡ ΠΎΠ»ΡΡ, ΠΊ ΠΊΠΎΡΠΎΡΠΎΠΌΡ ΠΊΡΠ΅ΠΏΡΡ Π½Π°Π³ΡΠ΅Π²Π°ΡΠ΅Π»ΠΈ. ΠΠ»Ρ ΡΠ΅ΠΏΠ»ΠΎΠΈΠ·ΠΎΠ»ΡΡΠΈΠΈ ΠΏΡΠΈΠΌΠ΅Π½ΡΡΡ ΡΡΠ°ΠΏΠ΅Π»ΡΠ½ΠΎΠ΅ ΡΡΠ΅ΠΊΠ»ΠΎΠ²ΠΎΠ»ΠΎΠΊΠ½ΠΎ Ρ ΡΠΊΡΠ°Π½ΠΈΡΠΎΠ²Π°Π½ΠΈΠ΅ΠΌ ΡΠ»ΠΎΠ΅ΠΌ ΠΈΠ· ΡΠΎΠ»ΡΠ³ΠΈ. Π ΠΊΠ°ΡΠ΅ΡΡΠ²Π΅ Π³ΠΈΠ΄ΡΠΎΠΈΠ·ΠΎΠ»ΡΡΠΈΠΈ ΠΈΡΠΏΠΎΠ»ΡΠ·ΡΡΡ ΠΏΡΠΎΡΠ΅Π·ΠΈΠ½Π΅Π½Π½ΡΡ ΡΠΊΠ°Π½Ρ.
ΠΠΈΠ±ΠΊΠΎΠ΅ ΠΏΠΎΠΊΡΡΡΠΈΠ΅ ΠΌΠΎΠΆΠ½ΠΎ ΠΈΠ·Π³ΠΎΡΠΎΠ²Π»ΡΡΡ ΡΠ°Π·Π»ΠΈΡΠ½ΠΎΠ³ΠΎ ΡΠ°Π·ΠΌΠ΅ΡΠ°. ΠΠ»Ρ ΠΊΡΠ΅ΠΏΠ»Π΅Π½ΠΈΡ ΠΎΡΠ΄Π΅Π»ΡΠ½ΡΡ ΠΏΠΎΠΊΡΡΡΠΈΠΉ ΠΌΠ΅ΠΆΠ΄Ρ ΡΠΎΠ±ΠΎΠΉ ΠΏΡΠ΅Π΄ΡΡΠΌΠΎΡΡΠ΅Π½Ρ ΠΎΡΠ²Π΅ΡΡΡΠΈΡ Π΄Π»Ρ ΠΏΡΠΎΠΏΡΡΠΊΠ° ΡΠ΅ΡΡΠΌΡ ΠΈΠ»ΠΈ Π·Π°ΠΆΠΈΠΌΠΎΠ². ΠΠΎΠΊΡΡΡΠΈΠ΅ ΠΌΠΎΠΆΠ½ΠΎ ΡΠ°ΡΠΏΠΎΠ»Π°Π³Π°ΡΡ Π½Π° Π²Π΅ΡΡΠΈΠΊΠ°Π»ΡΠ½ΡΡ , Π³ΠΎΡΠΈΠ·ΠΎΠ½ΡΠ°Π»ΡΠ½ΡΡ ΠΈ Π½Π°ΠΊΠ»ΠΎΠ½Π½ΡΡ ΠΏΠΎΠ²Π΅ΡΡ Π½ΠΎΡΡΡΡ ΠΊΠΎΠ½ΡΡΡΡΠΊΡΠΈΠΉ. ΠΠΎ ΠΎΠΊΠΎΠ½ΡΠ°Π½ΠΈΠΈ ΡΠ°Π±ΠΎΡΡ Ρ ΠΏΠΎΠΊΡΡΡΠΈΠ΅ΠΌ Π½Π° ΠΎΠ΄Π½ΠΎΠΌ ΠΌΠ΅ΡΡΠ΅ Π΅Π³ΠΎ ΡΠ½ΠΈΠΌΠ°ΡΡ, ΠΎΡΠΈΡΠ°ΡΡ ΠΈ Π΄Π»Ρ ΡΠ΄ΠΎΠ±ΡΡΠ²Π° ΡΡΠ°Π½ΡΠΏΠΎΡΡΠΈΡΠΎΠ²ΠΊΠΈ ΡΠ²ΠΎΡΠ°ΡΠΈΠ²Π°ΡΡ Π² ΡΡΠ»ΠΎΠ½. ΠΠ°ΠΈΠ±ΠΎΠ»Π΅Π΅ ΡΡΡΠ΅ΠΊΡΠΈΠ²Π½ΠΎ ΠΏΡΠΈΠΌΠ΅Π½ΡΡΡ Π’Π ΠΠ ΠΏΡΠΈ Π²ΠΎΠ·Π²Π΅Π΄Π΅Π½ΠΈΠΈΠΏΠ»ΠΈΡ ΠΏΠ΅ΡΠ΅ΠΊΡΡΡΠΈΠΉ ΠΈ ΠΏΠΎΠΊΡΡΡΠΈΠΉ, ΡΡΡΡΠΎΠΉΡΡΠ²Π΅ ΠΏΠΎΠ΄Π³ΠΎΡΠΎΠ²ΠΎΠΊ ΠΏΠΎΠ΄ ΠΏΠΎΠ»Ρ ΠΈ Π΄Ρ. Π’Π ΠΠ ΠΈΠ·Π³ΠΎΡΠΎΠ²Π»ΡΡΡ Ρ ΡΠ΄Π΅Π»ΡΠ½ΠΎΠΉ ΡΠ»Π΅ΠΊΡΡΠΈΡΠ΅ΡΠΊΠΎΠΉ ΠΌΠΎΡΠ½ΠΎΡΡΡΡ 0,25… 1 ΠΊΠ-Π/ΠΌ2.
ΠΡΠΈ ΠΈΠ½ΡΠ°ΠΊΡΠ°ΡΠ½ΠΎΠΌ Π½Π°Π³ΡΠ΅Π²Π΅ ΠΈΡΠΏΠΎΠ»ΡΠ·ΡΡΡ ΡΠΏΠΎΡΠΎΠ±Π½ΠΎΡΡΡ ΠΈΠ½ΡΡΠ°ΠΊΡΠ°ΡΠ½ΡΡ
Π»ΡΡΠ΅ΠΉ ΠΏΠΎΠ³Π»ΠΎΡΠ°ΡΡΡΡ ΡΠ΅Π»ΠΎΠΌ ΠΈ ΡΡΠ°Π½ΡΡΠΎΡΠΌΠΈΡΠΎΠ²Π°ΡΡΡΡ Π² ΡΠ΅ΠΏΠ»ΠΎΠ²ΡΡ ΡΠ½Π΅ΡΠ³ΠΈΡ, ΡΡΠΎ ΠΏΠΎΠ²ΡΡΠ°Π΅Ρ ΡΠ΅ΠΏΠ»ΠΎΡΠΎΠ΄Π΅ΡΠΆΠ°Π½ΠΈΠ΅ ΡΡΠΎΠ³ΠΎ ΡΠ΅Π»Π°.
ΠΠ΅Π½Π΅ΡΠΈΡΡΡΡ ΠΈΠ½ΡΡΠ°ΠΊΡΠ°ΡΠ½ΠΎΠ΅ ΠΈΠ·Π»ΡΡΠ΅Π½ΠΈΠ΅ ΠΏΡΡΠ΅ΠΌ Π½Π°Π³ΡΠ΅Π²Π° ΡΠ²Π΅ΡΠ΄ΡΡ ΡΠ΅Π». Π ΠΏΡΠΎΠΌΡΡΠ»Π΅Π½Π½ΠΎΡΡΠΈ Π΄Π»Ρ ΡΡΠΈΡ ΡΠ΅Π»Π΅ΠΉ ΠΏΡΠΈΠΌΠ΅Π½ΡΡΡ ΠΈΠ½ΡΡΠ°ΠΊΡΠ°ΡΠ½ΡΠ΅ Π»ΡΡΠΈ Ρ Π΄Π»ΠΈΠ½ΠΎΠΉ Π²ΠΎΠ»Π½Ρ 0,76… 6 ΠΌΠΊΠΌ, ΠΏΡΠΈ ΡΡΠΎΠΌ ΠΌΠ°ΠΊΡΠΈΠΌΠ°Π»ΡΠ½ΡΠΌ ΠΏΠΎΡΠΎΠΊΠΎΠΌ Π²ΠΎΠ»Π½ Π΄Π°Π½Π½ΠΎΠ³ΠΎ ΡΠΏΠ΅ΠΊΡΡΠ° ΠΎΠ±Π»Π°Π΄Π°ΡΡ ΡΠ΅Π»Π° Ρ ΡΠ΅ΠΌΠΏΠ΅ΡΠ°ΡΡΡΠΎΠΉ ΠΈΠ·Π»ΡΡΠ°ΡΡΠ΅ΠΉ ΠΏΠΎΠ²Π΅ΡΡ Π½ΠΎΡΡΠΈ 300…2200Β°Π‘.
Π’Π΅ΠΏΠ»ΠΎΡΠ° ΠΎΡ ΠΈΡΡΠΎΡΠ½ΠΈΠΊΠ° ΠΈΠ½ΡΡΠ°ΠΊΡΠ°ΡΠ½ΡΡ Π»ΡΡΠ΅ΠΉ ΠΊ Π½Π°Π³ΡΠ΅Π²Π°Π΅ΠΌΠΎΠΌΡ ΡΠ΅Π»Ρ ΠΏΠ΅ΡΠ΅Π΄Π°Π΅ΡΡΡ ΠΌΠ³Π½ΠΎΠ²Π΅Π½Π½ΠΎ, Π±Π΅Π· ΡΡΠ°ΡΡΠΈΡ ΠΊΠ°ΠΊΠΎΠ³ΠΎ-Π»ΠΈΠ±ΠΎ ΠΏΠ΅ΡΠ΅Π½ΠΎΡΡΠΈΠΊΠ° ΡΠ΅ΠΏΠ»ΠΎΡΡ. ΠΠΎΠ³Π»ΠΎΡΠ°ΡΡΡ ΠΏΠΎΠ²Π΅ΡΡ Π½ΠΎΡΡΡΠΌΠΈ ΠΎΠ±Π»ΡΡΠ΅Π½ΠΈΡ, ΠΈΠ½ΡΡΠ°ΠΊΡΠ°ΡΠ½ΡΠ΅ Π»ΡΡΠΈ ΠΏΡΠ΅Π²ΡΠ°ΡΠ°ΡΡΡΡ Π² ΡΠ΅ΠΏΠ»ΠΎΠ²ΡΡ ΡΠ½Π΅ΡΠ³ΠΈΡ. ΠΡ Π½Π°Π³ΡΠ΅ΡΡΡ ΡΠ°ΠΊΠΈΠΌ ΠΎΠ±ΡΠ°Π·ΠΎΠΌ ΠΏΠΎΠ²Π΅ΡΡ Π½ΠΎΡΡΠ½ΡΡ ΡΠ»ΠΎΠ΅Π² ΡΠ΅Π»ΠΎ ΠΏΡΠΎΠ³ΡΠ΅Π²Π°Π΅ΡΡΡ Π·Π° ΡΡΠ΅Ρ ΡΠΎΠ±ΡΡΠ²Π΅Π½Π½ΠΎΠΉ ΡΠ΅ΠΏΠ»ΠΎΠΏΡΠΎΠ²ΠΎΠ΄Π½ΠΎΡΡΠΈ.
ΠΠ»Ρ Π±Π΅ΡΠΎΠ½Π½ΡΡ ΡΠ°Π±ΠΎΡ Π² ΠΊΠ°ΡΠ΅ΡΡΠ²Π΅ Π³Π΅Π½Π΅ΡΠ°ΡΠΎΡΠΎΠ² ΠΈΠ½ΡΡΠ°ΠΊΡΠ°ΡΠ½ΠΎΠ³ΠΎ ΠΈΠ·Π»ΡΡΠ΅Π½ΠΈΡ ΠΏΡΠΈΠΌΠ΅Π½ΡΡΡ ΡΡΡΠ±ΡΠ°ΡΡΠ΅ ΠΌΠ΅ΡΠ°Π»Π»ΠΈΡΠ΅ΡΠΊΠΈΠ΅ ΠΈ ΠΊΠ²Π°ΡΡΠ΅Π²ΡΠ΅ ΠΈΠ·Π»ΡΡΠ°ΡΠ΅Π»ΠΈ. ΠΠ»Ρ ΡΠΎΠ·Π΄Π°Π½ΠΈΡ Π½Π°ΠΏΡΠ°Π²Π»Π΅Π½Π½ΠΎΠ³ΠΎ Π»ΡΡΠΈΡΡΠΎΠ³ΠΎ ΠΏΠΎΡΠΎΠΊΠ° ΠΈΠ·Π»ΡΡΠ°ΡΠ΅Π»ΠΈ Π·Π°ΠΊΠ»ΡΡΠ°ΡΡ Π² ΠΏΠ»ΠΎΡΠΊΠΈΠ΅ ΠΈΠ»ΠΈ ΠΏΠ°ΡΠ°Π±ΠΎΠ»ΠΈΡΠ΅ΡΠΊΠΈΠ΅ ΡΠ΅ΡΠ»Π΅ΠΊΡΠΎΡΡ (ΠΎΠ±ΡΡΠ½ΠΎ ΠΈΠ· Π°Π»ΡΠΌΠΈΠ½ΠΈΡ).
ΠΠ½ΡΡΠ°ΠΊΡΠ°ΡΠ½ΡΠΉ Π½Π°Π³ΡΠ΅Π² ΠΏΡΠΈΠΌΠ΅Π½ΡΡΡ ΠΏΡΠΈ ΡΠ»Π΅Π΄ΡΡΡΠΈΡ
ΡΠ΅Ρ
Π½ΠΎΠ»ΠΎΠ³ΠΈΡΠ΅ΡΠΊΠΈΡ
ΠΏΡΠΎΡΠ΅ΡΡΠ°Ρ
: ΠΎΡΠΎΠ³ΡΠ΅Π²Π΅ Π°ΡΠΌΠ°ΡΡΡΡ, ΠΏΡΠΎΠΌΠΎΡΠΎΠΆΠ΅Π½Π½ΡΡ
ΠΎΡΠ½ΠΎΠ²Π°Π½ΠΈΠΉ ΠΈ Π±Π΅ΡΠΎΠ½Π½ΡΡ
ΠΏΠΎΠ²Π΅ΡΡ
Π½ΠΎΡΡΠ΅ΠΉ, ΡΠ΅ΠΏΠ»ΠΎΠ²ΠΎΠΉ Π·Π°ΡΠΈΡΠ΅ ΡΠΊΠ»Π°Π΄ΡΠ²Π°Π΅ΠΌΠΎΠ³ΠΎ Π±Π΅ΡΠΎΠ½Π°, ΡΡΠΊΠΎΡΠ΅Π½ΠΈΠΈ ΡΠ²Π΅ΡΠ΄Π΅Π½ΠΈΡ Π±Π΅ΡΠΎΠ½Π° ΠΏΡΠΈ ΡΡΡΡΠΎΠΉΡΡΠ²Π΅ ΠΌΠ΅ΠΆΠ΄ΡΡΡΠ°ΠΆΠ½ΡΡ
ΠΏΠ΅ΡΠ΅ΠΊΡΡΡΠΈΠΉ, Π²ΠΎΠ·Π²Π΅Π΄Π΅Π½ΠΈΠΈ ΡΡΠ΅Π½ ΠΈ Π΄ΡΡΠ³ΠΈΡ
ΡΠ»Π΅ΠΌΠ΅Π½ΡΠΎΠ² Π² Π΄Π΅ΡΠ΅Π²ΡΠ½Π½ΠΎΠΉ, ΠΌΠ΅ΡΠ°Π»Π»ΠΈΡΠ΅ΡΠΊΠΎΠΉ ΠΈΠ»ΠΈ ΠΊΠΎΠ½ΡΡΡΡΠΊΡΠΈΠ²Π½ΠΎΠΉ ΠΎΠΏΠ°Π»ΡΠ±ΠΊΠ΅, Π²ΡΡΠΎΡΠ½ΡΡ
ΡΠΎΠΎΡΡΠΆΠ΅Π½ΠΈΠΉ Π² ΡΠΊΠΎΠ»ΡΠ·ΡΡΠ΅ΠΉ ΠΎΠΏΠ°Π»ΡΠ±ΠΊΠ΅ (ΡΠ»Π΅Π²Π°ΡΠΎΡΡ, ΡΠΈΠ»ΠΎΡΡ ΠΈ Ρ. ΠΏ.).
ΠΠ»Π΅ΠΊΡΡΠΎΡΠ½Π΅ΡΠ³ΠΈΡ Π΄Π»Ρ ΠΈΠ½ΡΡΠ°ΠΊΡΠ°ΡΠ½ΡΡ ΡΡΡΠ°Π½ΠΎΠ²ΠΎΠΊ ΠΏΠΎΡΡΡΠΏΠ°Π΅Ρ ΠΎΠ±ΡΡΠ½ΠΎ ΠΎΡ ΡΡΠ°Π½ΡΡΠΎΡΠΌΠ°ΡΠΎΡΠ½ΠΎΠΉ ΠΏΠΎΠ΄Ρ
ΠΠ΅ΡΠΎΠ½ΠΈΡΠΎΠ²Π°Π½ΠΈΠ΅ Π½Π° ΡΠ°ΡΡΠ½ΠΎΠΌ ΡΡΠ°ΡΡΠΊΠ΅ Π·ΠΈΠΌΠΎΠΉ. ΠΡΠΎΠ³ΡΠ΅Π² Π±Π΅ΡΠΎΠ½Π° β ΠΎΡΠ½ΠΎΠ²Π½ΡΠ΅ ΡΠΏΠΎΡΠΎΠ±Ρ. Π‘ΠΏΠΎΡΠΎΠ± ΡΠ΅ΡΠΌΠΎΡΠ°
ΠΡΠΎΠ³ΡΠ΅Π² Π±Π΅ΡΠΎΠ½Π° Π½Π΅ΠΎΠ±Ρ ΠΎΠ΄ΠΈΠΌ Π΄Π»Ρ ΠΏΡΠ΅Π΄ΠΎΡΠ²ΡΠ°ΡΠ΅Π½ΠΈΡ ΠΊΡΠΈΡΡΠ°Π»Π»ΠΈΠ·Π°ΡΠΈΠΈ Π²ΠΎΠ΄Ρ. ΠΡΠΈΡΠΈΠ½ ΡΠ΅Π»ΡΠΉ ΡΡΠ΄, Π½Π΅ΠΊΠΎΡΠΎΡΡΠ΅ ΠΈΠ· Π½ΠΈΡ :
- Π¦Π΅ΠΌΠ΅Π½ΡΠ½ΠΎΠ΅ Π²ΡΠΆΡΡΠ΅Π΅ Π² ΡΠ΅Π°ΠΊΡΠΈΡ ΡΠΎ Π»ΡΠ΄ΠΎΠΌ Π½Π΅ Π²ΡΡΡΠΏΠΈΡ ΠΈ ΡΠ΅ΠΌΠ΅Π½ΡΠ½ΡΠΉ ΠΊΠ°ΠΌΠ΅Π½Ρ Π½Π΅ ΠΎΠ±ΡΠ°Π·ΡΠ΅ΡΡΡ, ΠΈ ΡΠ΅Π·ΡΠ»ΡΡΠ°Ρ Π½Π΅ΠΎΠ±ΡΠ°ΡΠΈΠΌ — ΠΏΠΎΡΠ»Π΅ ΠΎΡΡΠ°ΠΈΠ²Π°Π½ΠΈΡ Π²ΠΌΠ΅ΡΡΠΎ Π±Π΅ΡΠΎΠ½Π½ΠΎΠΉ ΠΊΠΎΠ½ΡΡΡΡΠΊΡΠΈΠΈ ΠΏΠΎΠ»ΡΡΠΈΡΡΡ Π½Π΅ΠΏΡΠΎΡΠ½ΡΠΉ ΠΊΠΎΠ½Π³Π»ΠΎΠΌΠ΅ΡΠ°Ρ ΠΈΠ· Π·Π°ΠΏΠΎΠ»Π½ΠΈΡΠ΅Π»Π΅ΠΉ ΠΈ Π½Π΅ΠΏΡΠΎΡΠ΅Π°Π³ΠΈΡΠΎΠ²Π°Π²ΡΠ΅Π³ΠΎ ΡΠ΅ΠΌΠ΅Π½ΡΠ°.
- Π ΡΠ»ΡΡΠ°Π΅, ΠΊΠΎΠ³Π΄Π° Π±Π΅ΡΠΎΠ½Π½Π°Ρ ΡΠΌΠ΅ΡΡ Π±ΡΠ΄Π΅Ρ ΠΎΡΡΡΠ²Π°ΡΡ ΠΌΠ΅Π΄Π»Π΅Π½Π½Π΅Π΅ ΠΈ Π³ΠΈΠ΄ΡΠ°ΡΠ°ΡΠΈΡ Π½Π°ΡΠ½Π΅ΡΡΡ, Π½ΠΎ Π²ΠΎΠ΄Π° ΠΊΡΠΈΡΡΠ°Π»Π»ΠΈΠ·ΡΠ΅ΡΡΡ Π΄ΠΎ ΠΎΠ±ΡΠ°Π·ΠΎΠ²Π°Π½ΠΈΡ ΡΡΡΡΠΊΡΡΡΡ Π±Π΅ΡΠΎΠ½Π° Π΄ΠΎΡΡΠ°ΡΠΎΡΠ½ΠΎΠΉ ΠΏΡΠΎΡΠ½ΠΎΡΡΠΈ: ΡΡΠ° ΡΡΡΡΠΊΡΡΡΠ° Π±ΡΠ΄Π΅Ρ ΡΠ°Π·ΡΡΡΠ΅Π½Π° Π²ΠΎΠ΄ΠΎΠΉ, ΠΊΠΎΡΠΎΡΠ°Ρ ΠΏΡΠΈ Π·Π°ΠΌΠ΅ΡΠ·Π°Π½ΠΈΠΈ ΡΠ²Π΅Π»ΠΈΡΠΈΠ²Π°Π΅ΡΡΡ Π² ΠΎΠ±ΡΠ΅ΠΌΠ΅ Π½Π° 9%. ΠΠΎΡΠ»Π΅ ΠΎΡΡΠ°ΠΈΠ²Π°Π½ΠΈΡ Π²ΠΎΠ·ΠΌΠΎΠΆΠ½ΠΎ Π΄Π°Π»ΡΠ½Π΅ΠΉΡΠ΅Π΅ ΡΡ Π²Π°ΡΡΠ²Π°Π½ΠΈΠ΅ ΠΈ ΡΠ°ΡΡΠΈΡΠ½ΡΠΉ Π½Π°Π±ΠΎΡ ΠΌΠ°ΡΠΎΡΠ½ΠΎΠΉ ΠΏΡΠΎΡΠ½ΠΎΡΡΠΈ, Π² ΡΡΠ΄Π΅ ΡΠ»ΡΡΠ°Π΅Π² Π½Π΅Π΄ΠΎΡΡΠ°ΡΠΎΡΠ½ΡΠΉ.
- ΠΡΠΈ ΡΠ΅ΠΌΠΏΠ΅ΡΠ°ΡΡΡΠ΅ Π±Π΅ΡΠΎΠ½Π½ΠΎΠΉ ΡΠΌΠ΅ΡΠΈ ΠΎΠΊΠΎΠ»ΠΎ Π½ΠΎΠ»Ρ ΡΡ Π²Π°ΡΡΠ²Π°Π½ΠΈΠ΅ ΠΏΡΠ°ΠΊΡΠΈΡΠ΅ΡΠΊΠΈ ΠΏΡΠ΅ΠΊΡΠ°ΡΠ°Π΅ΡΡΡ. ΠΡΠΈ ΠΏΠΎΠ²ΡΡΠ΅Π½ΠΈΠΈ ΡΠ΅ΠΌΠΏΠ΅ΡΠ°ΡΡΡΡ ΡΠ΅Π°ΠΊΡΠΈΡ Π½Π°ΡΠΈΠ½Π°Π΅ΡΡΡ Π·Π°Π½ΠΎΠ²ΠΎ, Π½ΠΎ Π² ΠΌΠ°ΡΡΠ΅ Π±Π΅ΡΠΎΠ½Π° Π±ΡΠ΄ΡΡ ΠΏΡΡΡΠΎΡΡ, Π½Π°Π±ΠΎΡ ΠΏΡΠΎΡΠ½ΠΎΡΡΠΈ Π±ΡΠ΄Π΅Ρ ΠΏΡΠΎΡ ΠΎΠ΄ΠΈΡΡ ΠΌΠ΅Π΄Π»Π΅Π½Π½ΠΎ ΠΈ, Π½Π°ΠΈΠ±ΠΎΠ»Π΅Π΅ Π²Π΅ΡΠΎΡΡΠ½ΠΎ, Π½Π΅ Π΄ΠΎΡΡΠΈΠ³Π½Π΅Ρ Π½Π΅ΠΎΠ±Ρ ΠΎΠ΄ΠΈΠΌΡΡ ΠΏΠΎ ΠΏΡΠΎΠ΅ΠΊΡΡ ΠΏΠΎΠΊΠ°Π·Π°ΡΠ΅Π»Π΅ΠΉ.
- ΠΡΠΈ ΠΊΠΎΠ»Π΅Π±Π°Π½ΠΈΡΡ ΡΡΡΠΎΡΠ½ΡΡ ΡΠ΅ΠΌΠΏΠ΅ΡΠ°ΡΡΡ Π² ΠΏΠ΅ΡΠ²ΡΠ΅ ΡΡΠΎΠ΅ ΡΡΡΠΎΠΊ ΠΏΠΎΡΠ»Π΅ Π·Π°Π»ΠΈΠ²ΠΊΠΈ, Π΄Π°ΠΆΠ΅ ΠΏΡΠΈ Π±Π΅ΡΠΎΠ½ΠΈΡΠΎΠ²Π°Π½ΠΈΠΈ Π² ΡΠ΅ΠΏΠ»ΡΡ ΠΏΠΎΠ³ΠΎΠ΄Ρ β Π½Π°Π±ΠΎΡ ΠΏΡΠΎΡΠ½ΠΎΡΡΠΈ Π±ΡΠ΄Π΅Ρ Π·Π°ΠΌΠ΅Π΄Π»Π΅Π½ ΠΈ ΠΊ 28-ΡΡΡΠΎΡΠ½ΠΎΠΌΡ Π²ΠΎΠ·ΡΠ°ΡΡΡ ΠΏΡΠΎΡΠ½ΠΎΡΡΡ ΠΊΠΎΠ½ΡΡΡΡΠΊΡΠΈΠΈ Π²ΡΠ΅ Π΅ΡΠ΅ Π½Π΅Π΄ΠΎΡΡΠ°ΡΠΎΡΠ½Π°, ΡΡΠΎΠ±Ρ Π΅Π΅ Π½Π°Π³ΡΡΠΆΠ°ΡΡ (Π½Π°ΡΠΈΠ½Π°ΡΡ ΠΊΠ»Π°Π΄ΠΊΡ ΡΡΠ΅Π½, ΡΠ°Π±ΠΎΡΡ Π½Π° ΠΏΠ΅ΡΠ΅ΠΊΡΡΡΠΈΠΈ Ρ.ΠΏ.).
ΠΠ΅ΡΠΎΠ½ΠΈΡΡΠ΅ΠΌΠΎΠΉ ΠΊΠΎΠ½ΡΡΡΡΠΊΡΠΈΠΈ Π΄Π»Ρ Π½Π°Π±ΠΎΡΠ° ΠΏΡΠΎΡΠ½ΠΎΡΡΠΈ Π½Π΅ΠΎΠ±Ρ ΠΎΠ΄ΠΈΠΌΡ ΡΡΠ»ΠΎΠ²ΠΈΡ: ΡΠ΅ΠΌΠΏΠ΅ΡΠ°ΡΡΡΠ° +20-25β°Π‘ ΠΈ Π²Π»Π°ΠΆΠ½ΠΎΡΡΡ Π² ΡΠ΅ΡΠ΅Π½ΠΈΠΈ 28 ΡΡΡΠΎΠΊ. ΠΡΠΎΠ±Π΅Π½Π½ΠΎ Π²Π°ΠΆΠ½ΠΎ ΡΠΎΠ·Π΄Π°ΡΡ ΡΡΠΈ ΡΡΠ»ΠΎΠ²ΠΈΡ Π² ΠΏΠ΅ΡΠ²ΡΠ΅ ΡΡΠΎΠ΅ ΡΡΡΠΎΠΊ ΡΠ²Π΅ΡΠ΄Π΅Π½ΠΈΡ Π±Π΅ΡΠΎΠ½Π°. ΠΠΎΡΠ»Π΅ ΡΠ΅ΠΌΠΈ ΡΡΡΠΎΠΊ ΡΠ²Π΅ΡΠ΄Π΅Π½ΠΈΡ Π² Π½ΠΎΡΠΌΠ°Π»ΡΠ½ΡΡ ΡΡΠ»ΠΎΠ²ΠΈΡΡ ΡΠ°ΡΠ°Π»ΡΠ½ΡΠΌ Π΄Π»Ρ Π±Π΅ΡΠΎΠ½Π° ΠΌΠΎΠΆΠ΅Ρ ΡΡΠ°ΡΡ ΡΠΎΠ»ΡΠΊΠΎ ΠΏΠΎΠ»Π½ΠΎΠ΅ ΠΏΡΠΎΠΌΠΎΡΠ°ΠΆΠΈΠ²Π°Π½ΠΈΠ΅. Π‘Π½ΠΈΠΆΠ΅Π½ΠΈΠ΅ ΡΠ΅ΠΌΠΏΠ΅ΡΠ°ΡΡΡΡ Π΄Π°ΠΆΠ΅ Π΄ΠΎ Π½ΠΎΠ»Ρ Π³ΡΠ°Π΄ΡΡΠΎΠ², ΠΎΡΠΎΠ±Π΅Π½Π½ΠΎ ΠΊΡΠ°ΡΠΊΠΎΠ²ΡΠ΅ΠΌΠ΅Π½Π½ΠΎΠ΅, ΠΏΡΠΈΠ²Π΅Π΄Π΅Ρ Π»ΠΈΡΡ ΠΊ ΡΠ½ΠΈΠΆΠ΅Π½ΠΈΡ ΠΈΡΠΎΠ³ΠΎΠ²ΠΎΠΉ ΠΏΡΠΎΡΠ½ΠΎΡΡΠΈ. Π ΡΠ°ΡΡΠ΅ΡΠ΅ Π½Π° Π²ΠΎΠ·ΠΌΠΎΠΆΠ½ΠΎΡΡΡ ΡΠ°ΠΊΠΎΠ³ΠΎ ΡΠΎΡΡ-ΠΌΠ°ΠΆΠΎΡΠ° Π·ΠΈΠΌΠΎΠΉ ΠΏΡΠΈΠ½ΠΈΠΌΠ°ΡΡ ΠΌΠ°ΡΠΊΡ Π±Π΅ΡΠΎΠ½Π° Π½Π° Π΄Π²Π΅-ΡΡΠΈ ΠΏΠΎΠ·ΠΈΡΠΈΠΈ Π²ΡΡΠ΅. ΠΠΎ ΠΏΠΎΠ»ΡΡΠΈΡΡ Π½Π°Π΄Π΅ΠΆΠ½ΡΡ Π±Π΅ΡΠΎΠ½Π½ΡΡ ΠΊΠΎΠ½ΡΡΡΡΠΊΡΠΈΡ ΠΏΡΠΎΠ΅ΠΊΡΠ½ΠΎΠΉ ΠΏΡΠΎΡΠ½ΠΎΡΡΠΈ Π²ΠΎΠ·ΠΌΠΎΠΆΠ½ΠΎ ΡΠΎΠ»ΡΠΊΠΎ ΠΎΠ΄Π½ΠΈΠΌ ΡΠΏΠΎΡΠΎΠ±ΠΎΠΌ β ΡΠΎΠ·Π΄Π°ΡΡ ΠΎΠΏΡΠΈΠΌΠ°Π»ΡΠ½ΡΠ΅ ΡΡΠ»ΠΎΠ²ΠΈΡ Π΄Π»Ρ ΡΠ²Π΅ΡΠ΄Π΅Π½ΠΈΡ Π² ΡΠ΅ΡΠ΅Π½ΠΈΠΈ 28 ΡΡΡΠΎΠΊ, ΠΈ Π·ΠΈΠΌΠΎΠΉ Π² ΡΠ°ΠΉΠΎΠ½Π°Ρ Ρ Ρ ΠΎΠ»ΠΎΠ΄Π½ΡΠΌ ΠΊΠ»ΠΈΠΌΠ°ΡΠΎΠΌ Π±Π΅Π· ΠΏΡΠΈΠΌΠ΅Π½Π΅Π½ΠΈΡ ΠΈΡΠΊΡΡΡΡΠ²Π΅Π½Π½ΠΎΠ³ΠΎ ΠΏΡΠΎΠ³ΡΠ΅Π²Π° Π±Π΅ΡΠΎΠ½Π° ΡΠ°ΠΊΠΎΠΉ Π²ΠΎΠ·ΠΌΠΎΠΆΠ½ΠΎΡΡΠΈ Π½Π΅Ρ.
ΠΡΠ½ΠΎΠ²Π½ΡΠ΅ ΠΌΠ΅ΡΠΎΠ΄Ρ ΠΏΡΠΎΠ³ΡΠ΅Π²Π°, ΠΏΡΠΈΠΌΠ΅Π½ΡΠ΅ΠΌΡΠ΅ Π² ΠΈΠ½Π΄ΠΈΠ²ΠΈΠ΄ΡΠ°Π»ΡΠ½ΠΎΠΌ ΡΡΡΠΎΠΈΡΠ΅Π»ΡΡΡΠ²Π΅:
- Π’Π΅ΡΠΌΠΎΡ β ΠΏΡΠΈΠΌΠ΅Π½Π΅Π½ΠΈΠ΅ ΡΡΠ΅ΠΏΠ»Π΅Π½Π½ΡΡ ΠΈ/ΠΈΠ»ΠΈ Π³ΡΠ΅ΡΡΠΈΡ ΠΎΠΏΠ°Π»ΡΠ±ΠΎΠΊ, ΡΠ΅ΠΏΠ»ΠΎΠΈΠ·ΠΎΠ»ΡΡΠΈΡ ΠΏΠΎΠ²Π΅ΡΡ Π½ΠΎΡΡΠ΅ΠΉ Π±Π΅ΡΠΎΠ½Π°
- Π’Π΅ΡΠΌΠΎΡ Ρ Π°Π½ΡΠΈΠΌΠΎΡΠΎΠ·Π½ΡΠΌΠΈ Π΄ΠΎΠ±Π°Π²ΠΊΠ°ΠΌΠΈ ΠΈ/ΠΈΠ»ΠΈ ΠΌΠΎΠ΄ΠΈΡΠΈΠΊΠ°ΡΠΎΡΠ°ΠΌΠΈ-ΡΡΠΊΠΎΡΠΈΡΠ΅Π»ΡΠΌΠΈ ΡΠ²Π΅ΡΠ΄Π΅Π½ΠΈΡ
- ΠΠ°ΠΌΠ΅Ρ Π±Π΅ΡΠΎΠ½Π° Π½Π° Π³ΠΎΡΡΡΠ΅ΠΉ Π²ΠΎΠ΄Π΅ ΠΈ ΠΏΡΠΎΠ³ΡΠ΅ΡΡΡ ΠΌΠ΅Π»ΠΊΠΎΠΌ ΠΈ ΠΊΡΡΠΏΠ½ΠΎΠΌ Π·Π°ΠΏΠΎΠ»Π½ΠΈΡΠ΅Π»ΡΡ
- ΠΠ±ΠΎΠ³ΡΠ΅Π² Π²ΠΎΠ·Π΄ΡΡ Π° Π²ΠΎΠΊΡΡΠ³ Π·Π°Π±Π΅ΡΠΎΠ½ΠΈΡΠΎΠ²Π°Π½Π½ΠΎΠΉ ΠΊΠΎΠ½ΡΡΡΡΠΊΡΠΈΠΈ ΡΠ΅ΠΏΠ»ΠΎΠ²ΡΠΌΠΈ ΠΏΡΡΠΊΠ°ΠΌΠΈ, ΠΊΠ°Π»ΠΎΡΠΈΡΠ΅ΡΠ°ΠΌΠΈ ΠΈ Ρ.Π΄. Ρ ΡΡΡΡΠΎΠΉΡΡΠ²ΠΎΠΌ Π²Π΅ΡΡΠΎΠ·Π°ΡΠΈΡΡ β ΠΏΠ°Π»Π°ΡΠΊΠΈ, ΡΠ°ΡΡΠ°, ΡΡΡΠΎΠΈΡΠ΅Π»ΡΠ½ΠΎΠ³ΠΎ ΠΏΠΎΠ»ΠΎΠ³Π°
- ΠΠ±ΠΎΠ³ΡΠ΅Π² ΠΈΠ½ΡΡΠ°ΠΊΡΠ°ΡΠ½ΡΠΉ. ΠΡΠ²Π΅ΡΠ°Π΅ΡΡΡ ΠΈ Π½Π°Π³ΡΠ΅Π²Π°Π΅ΡΡΡ Π½Π΅ ΠΎΠΊΡΡΠΆΠ°ΡΡΠΈΠΉ Π²ΠΎΠ·Π΄ΡΡ , Π° Π±Π΅ΡΠΎΠ½Π½ΡΠ΅ ΠΏΠΎΠ²Π΅ΡΡ Π½ΠΎΡΡΠΈ, ΡΡΡΠ΄Π½ΠΎΠ΄ΠΎΡΡΡΠΏΠ½ΡΠ΅ ΡΡΡΠΊΠΈ ΠΈ Π·Π°ΠΊΠ»Π°Π΄Π½ΡΠ΅ ΠΌΠ΅ΡΠ°Π»Π»ΠΈΡΠ΅ΡΠΊΠΈΠ΅ Π΄Π΅ΡΠ°Π»ΠΈ, ΠΈΠ½ΠΎΠ³Π΄Π° Π°ΡΠΌΠΎΠΊΠ°ΡΠΊΠ°Ρ — ΠΊΠ°ΠΊ ΠΏΡΠΈ ΡΠΎΠ»Π½Π΅ΡΠ½ΠΎΠΌ ΠΎΠ±ΠΎΠ³ΡΠ΅Π²Π΅
- ΠΠ»Π΅ΠΊΡΡΠΎΠΏΡΠΎΠ³ΡΠ΅Π² ΡΠ»Π΅ΠΊΡΡΠΎΠ΄Π½ΡΠΉ β Π½Π°Π³ΡΠ΅Π²ΠΎΠΌ Π°ΡΠΌΠ°ΡΡΡΠ½ΠΎΠ³ΠΎ ΠΊΠ°ΡΠΊΠ°ΡΠ° ΠΊΠΎΠ½ΡΡΡΡΠΊΡΠΈΠΈ, Π½Π°Π³ΡΠ΅Π²ΠΎΠΌ ΡΠ»Π΅ΠΊΡΡΠΎΠ΄ΠΎΠ² ΡΠ°Π·Π»ΠΈΡΠ½ΡΡ ΡΠΎΡΠΌ ΠΈ ΡΠΈΠΏΠΎΠ², ΡΡΡΠ°Π½ΠΎΠ²Π»Π΅Π½Π½ΡΡ Π² Π±Π΅ΡΠΎΠ½ ΠΈ Π½Π° Π΅Π³ΠΎ ΠΏΠΎΠ²Π΅ΡΡ Π½ΠΎΡΡΡΡ . ΠΡΠΎΠΏΡΡΠΊΠ°Ρ ΡΠ»Π΅ΠΊΡΡΠΈΡΠ΅ΡΠΊΠΈΠΉ ΡΠΎΠΊ ΡΠ΅ΡΠ΅Π· ΡΠ»Π΅ΠΊΡΡΠΎΠ΄Ρ ΠΈΠ»ΠΈ Π°ΡΠΌΠΎΠΊΠ°ΡΠΊΠ°Ρ, Π΄ΠΎΠ±ΠΈΠ²Π°ΡΡΡΡ ΠΏΡΠΎΠ³ΡΠ΅Π²Π° Π±Π΅ΡΠΎΠ½Π° ΠΏΠΎ Π²ΡΠ΅ΠΌΡ ΠΎΠ±ΡΠ΅ΠΌΡ
- ΠΠ»Π΅ΠΊΡΡΠΎΠΏΡΠΎΠ³ΡΠ΅Π² Π½Π°Π³ΡΠ΅Π²Π°ΡΠ΅Π»ΡΠ½ΡΠΌΠΈ ΠΏΡΠΎΠ²ΠΎΠ΄Π°ΠΌΠΈ β ΡΠ°ΠΊ ΠΆΠ΅, ΠΊΠ°ΠΊ ΠΈ ΡΠ»Π΅ΠΊΡΡΠΎΠ΄Π½ΡΠΉ, ΡΡΠ΅Π±ΡΠ΅Ρ ΡΠ°ΡΡΠ΅ΡΠ° Π΄Π»Ρ ΠΎΠΏΡΠ΅Π΄Π΅Π»Π΅Π½ΠΈΡ Π½Π΅ΠΎΠ±Ρ ΠΎΠ΄ΠΈΠΌΠΎΠ³ΠΎ ΠΌΠ΅ΡΡΠ°ΠΆΠ° ΠΏΡΠΎΠ²ΠΎΠ΄Π° ΠΈ ΠΎΠΏΡΠΈΠΌΠ°Π»ΡΠ½ΠΎΠΉ ΡΡ Π΅ΠΌΡ Π΅Π³ΠΎ ΡΠΊΠ»Π°Π΄ΠΊΠΈ Π² ΡΠ΅Π»ΠΎ Π±Π΅ΡΠΎΠ½Π½ΠΎΠΉ ΠΊΠΎΠ½ΡΡΡΡΠΊΡΠΈΠΈ
- ΠΠ»Π΅ΠΊΡΡΠΎΠΏΡΠΎΠ³ΡΠ΅Π² ΠΈΠ½Π΄ΡΠΊΡΠΈΠΎΠ½Π½ΡΠΉ β ΠΈΡΠΏΠΎΠ»ΡΠ·ΡΠ΅ΡΡΡ Π²ΡΠ΄Π΅Π»Π΅Π½ΠΈΠ΅ ΡΠ΅ΠΏΠ»Π° Π²Π½ΡΡΡΠΈ ΡΠ»Π΅ΠΊΡΡΠΎΠΌΠ°Π³Π½ΠΈΡΠ½ΠΎΠ³ΠΎ ΠΊΠΎΠ½ΡΡΡΠ°. ΠΠΈΡ ΡΠ΅Π²ΡΠ΅ ΡΠΎΠΊΠΈ ΡΠ°Π·ΠΎΠ³ΡΠ΅Π²Π°ΡΡ Π°ΡΠΌΠ°ΡΡΡΡ ΠΈ Π·Π°ΠΊΠ»Π°Π΄Π½ΡΠ΅ Π΄Π΅ΡΠ°Π»ΠΈ Π² ΠΊΠΎΠ½ΡΡΡΡΠΊΡΠΈΠΈ, Π° Π±Π΅ΡΠΎΠ½ ΠΏΠΎΠ»ΡΡΠ°Π΅Ρ ΡΠ΅ΠΏΠ»ΠΎ ΠΎΡ Π°ΡΠΌΠΎΠΊΠ°ΡΠΊΠ°ΡΠ°. ΠΠ΅ΡΠΎΠ΄ Π΄Π»Ρ ΠΊΠΎΠ»ΠΎΠ½Π½, ΡΡΠΎΠ΅ΠΊ ΠΈ ΠΏΠΎΠ΄ΠΎΠ±Π½ΡΡ ΡΠ»Π΅ΠΌΠ΅Π½ΡΠΎΠ², Ρ ΠΊΠΎΡΠΎΡΡΡ Π΄Π»ΠΈΠ½Π° ΠΏΡΠ΅Π²ΡΡΠ°Π΅Ρ ΡΠ°Π·ΠΌΠ΅Ρ ΡΠ΅ΡΠ΅Π½ΠΈΡ. ΠΠΌΠ΅Π΅Ρ ΡΠΌΡΡΠ» ΡΠΎΠ»ΡΠΊΠΎ Π΄Π»Ρ ΠΊΠΎΠ½ΡΡΡΡΠΊΡΠΈΠΉ Ρ Π³ΡΡΡΡΠΌ Π°ΡΠΌΠΈΡΠΎΠ²Π°Π½ΠΈΠ΅ΠΌ (ΠΊΠΎΡΡΡΠΈΡΠΈΠ΅Π½Ρ Π°ΡΠΌΠΈΡΠΎΠ²Π°Π½ΠΈΡ Π±ΠΎΠ»ΡΡΠ΅ 0,5)
ΠΠ²Π΅Π΄Π΅Π½ΠΈΠ΅ Π² Π±Π΅ΡΠΎΠ½ ΠΏΡΠΎΡΠΈΠ²ΠΎΠΌΠΎΡΠΎΠ·Π½ΡΡ Π΄ΠΎΠ±Π°Π²ΠΎΠΊ ΠΈ ΡΡΠΊΠΎΡΠΈΡΠ΅Π»Π΅ΠΉ/Π·Π°ΠΌΠ΅Π΄Π»ΠΈΡΠ΅Π»Π΅ΠΉ ΡΠ²Π΅ΡΠ΄Π΅Π½ΠΈΡ Π½Π΅ ΡΠ²Π»ΡΠ΅ΡΡΡ ΡΠΏΠΎΡΠΎΠ±ΠΎΠΌ Π·ΠΈΠΌΠ½Π΅Π³ΠΎ Π±Π΅ΡΠΎΠ½ΠΈΡΠΎΠ²Π°Π½ΠΈΡ, ΠΏΠΎΡΠΊΠΎΠ»ΡΠΊΡ Π½ΠΈ ΠΎΠ΄Π½Π° Ρ ΠΈΠΌΠΈΡΠ΅ΡΠΊΠ°Ρ Π΄ΠΎΠ±Π°Π²ΠΊΠ° Π½Π΅ ΡΠΏΠ°ΡΠ΅Ρ Π±Π΅ΡΠΎΠ½ ΠΎΡ ΠΏΡΠΎΠΌΠΎΡΠ°ΠΆΠΈΠ²Π°Π½ΠΈΡ Π² ΡΡΠ»ΠΎΠ²ΠΈΡΡ Π·ΠΈΠΌΡ Π² ΡΠ°ΠΉΠΎΠ½Π°Ρ ΡΡΠ΅Π΄Π½Π΅ΠΉ ΠΏΠΎΠ»ΠΎΡΡ. ΠΡΠΎΡΠΈΠ²ΠΎΠΌΠΎΡΠΎΠ·Π½ΡΠ΅ Π΄ΠΎΠ±Π°Π²ΠΊΠΈ ΠΏΡΠΈΠΌΠ΅Π½ΡΡΡ Π·ΠΈΠΌΠΎΠΉ Π½ΡΠΆΠ½ΠΎ ΠΎΠ±ΡΠ·Π°ΡΠ΅Π»ΡΠ½ΠΎ β ΠΎΡ Π±ΡΠ΄ΠΆΠ΅ΡΠ½ΠΎΠ³ΠΎ Β«ΠΏΠΎΠ΄ΡΠ°Π»ΠΈΠ²Π°Π½ΠΈΡΒ» ΠΎΠ±ΡΡΠ½ΡΠΌ Ρ Π»ΠΎΡΠΈΠ΄ΠΎΠΌ Π½Π°ΡΡΠΈΡ ΠΈΠ»ΠΈ ΠΏΠΎΡΠ°ΡΠ΅ΠΌ, ΠΈΠ»ΠΈ Π½ΠΈΡΡΠΈΡΠΎΠΌ Π½Π°ΡΡΠΈΡ, Π΄ΠΎ ΠΊΠΎΠΌΠΏΠ»Π΅ΠΊΡΠ½ΡΡ Π΄ΠΎΡΠΎΠ³ΠΈΡ ΠΌΠΎΠ΄ΠΈΡΠΈΠΊΠ°ΡΠΎΡΠΎΠ², ΡΠΏΠΎΡΠΎΠ±Π½ΡΡ ΠΎΠΏΡΠΈΠΌΠΈΠ·ΠΈΡΠΎΠ²Π°ΡΡ ΡΠ΅ΠΎΠ»ΠΎΠ³ΠΈΡ ΡΠΌΠ΅ΡΠΈ Π΄Π°ΠΆΠ΅ ΠΏΡΠΈ Π½Π΅Π±Π»Π°Π³ΠΎΠΏΡΠΈΡΡΠ½ΡΡ ΡΡΠ»ΠΎΠ²ΠΈΡΡ . Β«Π‘ΠΎΠ»ΠΈΡΡΒ» ΡΠ»Π΅Π΄ΡΠ΅Ρ Π² ΠΌΠ΅ΡΡ, ΠΏΠΎΡΠΊΠΎΠ»ΡΠΊΡ Π½Π΅ΠΊΠΎΡΠΎΡΡΠ΅ ΡΠΎΠ»ΠΈ ΡΠΏΠΎΡΠΎΠ±ΡΡΠ²ΡΡΡ ΠΊΠΎΡΡΠΎΠ·ΠΈΠΈ Π°ΡΠΌΠ°ΡΡΡΡ ΠΈ Π½Π° Π±ΡΠ΄ΡΡΡΡ ΠΏΡΠΎΡΠ½ΠΎΡΡΡ Π±Π΅ΡΠΎΠ½Π° Π²Π»ΠΈΡΡΡ Π½Π΅Π³Π°ΡΠΈΠ²Π½ΠΎ. Π‘ΠΎΠ²ΡΠ΅ΠΌΠ΅Π½Π½ΡΠ΅ Π΄ΠΎΠ±Π°Π²ΠΊΠΈ Π² Π±Π΅ΡΠΎΠ½ ΠΈΠΌΠ΅ΡΡ ΠΊΠΎΠΌΠΏΠ»Π΅ΠΊΡΠ½ΡΠΉ ΡΠΎΡΡΠ°Π²: Π²ΠΌΠ΅ΡΡΠ΅ Ρ Π²Π΅ΡΠ΅ΡΡΠ²Π°ΠΌΠΈ, ΠΏΠΎΠ½ΠΈΠΆΠ°ΡΡΠΈΠΌΠΈ ΡΠΎΡΠΊΡ Π·Π°ΠΌΠ΅ΡΠ·Π°Π½ΠΈΡ Π²ΠΎΠ΄Ρ ΠΈ ΡΡΠΊΠΎΡΠΈΡΠ΅Π»ΡΠΌΠΈ ΡΠ²Π΅ΡΠ΄Π΅Π½ΠΈΡ, Π² ΠΌΠΎΠ΄ΠΈΡΠΈΠΊΠ°ΡΠΎΡΡ Π²Ρ ΠΎΠ΄ΡΡ ΠΏΡΠΈΡΠ°Π΄ΠΊΠΈ Π΄Π»Ρ ΡΠ²Π΅Π»ΠΈΡΠ΅Π½ΠΈΡ ΠΏΡΠΎΡΠ½ΠΎΡΡΠΈ ΠΈ ΠΌΠΎΡΠΎΠ·ΠΎΡΡΠΎΠΉΠΊΠΎΡΡΠΈ Π±Π΅ΡΠΎΠ½Π°, ΠΏΠ»Π°ΡΡΠΈΡΠΈΠΊΠ°ΡΠΎΡΡ ΠΈ Π²ΠΎΠ·Π΄ΡΡ ΠΎΠ²ΠΎΠ²Π»Π΅ΠΊΠ°ΡΡΠΈΠ΅ Π΄ΠΎΠ±Π°Π²ΠΊΠΈ. ΠΡΠΈΠΌΠ΅Π½ΡΡΡ Π΄ΠΎΠ±Π°Π²ΠΊΠΈ Π² Π±Π΅ΡΠΎΠ½ ΡΡΡΠΎΠ³ΠΎ ΠΏΠΎ ΠΈΠ½ΡΡΡΡΠΊΡΠΈΠΈ, Π° Π²ΡΠ±ΠΎΡ ΠΈΡ Π΄ΠΎΡΡΠ°ΡΠΎΡΠ½ΠΎ ΡΠ»ΠΎΠΆΠ΅Π½ ΠΈ Π·Π°Π²ΠΈΡΠΈΡ ΠΎΡ Π²ΠΈΠ΄Π° ΠΈ ΠΊΠ»Π°ΡΡΠ° Π±Π΅ΡΠΎΠ½Π°, Π²ΠΈΠ΄Π°, ΡΠ°Π·ΠΌΠ΅ΡΠΎΠ² ΠΈ Π½Π°Π³ΡΡΠ·ΠΎΠΊ Π½Π° ΠΊΠΎΠ½ΡΡΡΡΠΊΡΠΈΡ, ΡΡΠ»ΠΎΠ²ΠΈΠΉ ΡΠ°Π±ΠΎΡΡ ΠΊΠΎΠ½ΡΡΡΡΠΊΡΠΈΠΈ ΠΈ Π΄Ρ.
Π’Π΅ΡΠΌΠΎΡ
Π’Π΅ΠΏΠ»ΠΎΠΈΠ·ΠΎΠ»ΡΡΠΈΡ ΠΊΠΎΠ½ΡΡΡΡΠΊΡΠΈΠΈ Ρ ΡΠ΅Π»ΡΡ ΠΏΡΠ΅Π΄ΠΎΡΠ²ΡΠ°ΡΠΈΡΡ ΠΏΠΎΡΠ΅ΡΠΈ Π²Π½ΡΡΡΠ΅Π½Π½Π΅Π³ΠΎ ΡΠ΅ΠΏΠ»Π° ΡΠ΅ΡΠ΅Π· ΠΏΠΎΠ²Π΅ΡΡ Π½ΠΎΡΡΠΈ, ΡΠΎΠΏΡΠΈΠΊΠ°ΡΠ°ΡΡΠΈΠ΅ΡΡ Ρ Ρ ΠΎΠ»ΠΎΠ΄Π½ΡΠΌ Π²ΠΎΠ·Π΄ΡΡ ΠΎΠΌ ΠΈ ΠΎΠΏΠ°Π»ΡΠ±ΠΊΠΎΠΉ; ΠΈΡΠΏΠΎΠ»ΡΠ·ΠΎΠ²Π°Π½ΠΈΠ΅ Π²Π½ΡΡΡΠ΅Π½Π½Π΅Π³ΠΎ ΡΠ΅ΠΏΠ»Π° Π±Π΅ΡΠΎΠ½Π° ΠΈ ΡΠΊΠ·ΠΎΡΠ΅ΡΠΌΠΈΠΈ Π³ΠΈΠ΄ΡΠ°ΡΠ°ΡΠΈΠΈ. Π‘ΠΏΠΎΡΠΎΠ± ΡΠ΅ΡΠΌΠΎΡΠ° ΠΎΡΠΎΠ±Π΅Π½Π½ΠΎ ΡΡΡΠ΅ΠΊΡΠΈΠ²Π΅Π½ Π΄Π»Ρ ΠΌΠ°ΡΡΠΈΠ²Π½ΡΡ ΠΊΠΎΠ½ΡΡΡΡΠΊΡΠΈΠΉ Ρ ΠΌΠΎΠ΄ΡΠ»Π΅ΠΌ ΠΏΠΎΠ²Π΅ΡΡ Π½ΠΎΡΡΠΈ Π΄ΠΎ 4-6 (ΠΎΡΠ½ΠΎΡΠ΅Π½ΠΈΠ΅ ΠΏΠΎΠ²Π΅ΡΡ Π½ΠΎΡΡΠΈ, ΡΠ΅ΡΠ΅Π· ΠΊΠΎΡΠΎΡΡΡ Π±Π΅ΡΠΎΠ½ ΠΎΡΠ΄Π°Π΅Ρ ΡΠ΅ΠΏΠ»ΠΎ, ΠΊ ΠΎΠ±ΡΠ΅ΠΌΡ ΠΎΠ±ΡΠ΅ΠΌΡ ΡΠ»Π΅ΠΌΠ΅Π½ΡΠ°).
Π§ΡΠΎΠ±Ρ ΡΠΎΠ·Π΄Π°ΡΡ ΡΠ΅ΡΠΌΠΎΡ Π΄Π»Ρ Π±Π΅ΡΠΎΠ½Π°, Π½Π΅Π΄ΠΎΡΡΠ°ΡΠΎΡΠ½ΠΎ ΠΏΡΠΈΠΊΡΡΡΡ Π΅Π³ΠΎ ΡΠ²Π΅ΡΡ Ρ Π² ΠΎΠΏΠ°Π»ΡΠ±ΠΊΠ΅ ΡΠ΅ΠΏΠ»ΠΎΠΈΠ·ΠΎΠ»ΡΡΠΈΠΎΠ½Π½ΡΠΌ ΠΌΠ°ΡΠ΅ΡΠΈΠ°Π»ΠΎΠΌ. ΠΡΠΎΡ Π²Π°ΡΠΈΠ°Π½Ρ β Π½Π΅ Π΄Π»Ρ ΠΌΠΎΡΠΎΠ·ΠΎΠ², Π° Π΄Π»Ρ ΡΠΎΠ·Π΄Π°Π½ΠΈΡ Π±Π΅ΡΠΎΠ½Ρ Π½ΠΎΡΠΌΠ°Π»ΡΠ½ΡΡ ΡΡΠ»ΠΎΠ²ΠΈΠΉ ΠΏΡΠΈ ΠΏΠΎΠ³ΠΎΠ΄Π΅ Ρ ΡΠ΅Π·ΠΊΠΈΠΌΠΈ ΠΊΠΎΠ»Π΅Π±Π°Π½ΠΈΡΠΌΠΈ Π΄Π½Π΅Π²Π½ΡΡ ΠΈ Π½ΠΎΡΠ½ΡΡ ΡΠ΅ΠΌΠΏΠ΅ΡΠ°ΡΡΡ, ΠΆΠ°ΡΠ΅ ΠΎΡ +30β°Π‘, Ρ ΠΎΠ»ΠΎΠ΄Π½ΠΎΠΌ Π²Π΅ΡΡΠ΅ ΠΈΠ»ΠΈ ΠΏΡΠΎΡΡΠΎ Π½Π΅ΡΡΠ°Π±ΠΈΠ»ΡΠ½ΠΎΠΉ ΠΎΡΠ΅Π½Π½Π΅ΠΉ ΠΈ Π²Π΅ΡΠ΅Π½Π½Π΅ΠΉ ΠΏΠΎΠ³ΠΎΠ΄Π΅. ΠΠΎΠ½ΡΡΡΡΠΊΡΠΈΡ ΡΠΊΡΡΠ²Π°ΡΡ ΠΏΠΎΠ»ΠΎΠ³Π°ΠΌΠΈ, ΡΡΠ΅ΠΏΠ»ΡΡΡΠΈΠΌ ΡΡΠ»ΠΎΠ½Π½ΡΠΌ ΠΈΠ»ΠΈ Π·Π°ΡΡΠΏΠ½ΡΠΌ ΠΌΠ°ΡΠ΅ΡΠΈΠ°Π»ΠΎΠΌ β ΠΎΠΏΠΈΠ»ΠΊΠ°ΠΌΠΈ, ΡΠ»Π°ΠΊΠΎΠΌ. Π¦Π΅Π»Ρ β ΡΠ³Π»Π°Π΄ΠΈΡΡ ΠΊΠΎΠ»Π΅Π±Π°Π½ΠΈΡ ΡΠ΅ΠΌΠΏΠ΅ΡΠ°ΡΡΡ Π² ΠΏΡΠ΅Π΄Π΅Π»Π°Ρ +10-30β°Π‘.
ΠΠ΅ΡΠΎΠ΄ ΡΠ΅ΡΠΌΠΎΡΠ° ΡΠΎΡΡΠΎΠΈΡ Π² Π²ΡΠ΄Π΅ΡΠΆΠΊΠ΅ ΠΊΠΎΠ½ΡΡΡΡΠΊΡΠΈΠΈ Π² ΠΎΠΏΡΠΈΠΌΠ°Π»ΡΠ½ΠΎΠΌ ΡΠ΅ΠΏΠ»Π΅ Π΄ΠΎ Π΄ΠΎΡΡΠΈΠΆΠ΅Π½ΠΈΡ Π½ΡΠΆΠ½ΠΎΠΉ ΠΏΠΎ ΠΏΡΠΎΠ΅ΠΊΡΡ ΠΏΡΠΎΡΠ½ΠΎΡΡΠΈ, Π²ΠΏΠ»ΠΎΡΡ Π΄ΠΎ ΡΠ°ΡΠΏΠ°Π»ΡΠ±ΠΊΠΈ. ΠΠ»Ρ ΡΡΠΎΠ³ΠΎ ΠΏΡΠΈΠΌΠ΅Π½ΡΡΡ ΡΡΠ΅ΠΏΠ»ΠΈΡΠ΅Π»ΠΈ ΠΈ Π³ΡΠ΅ΡΡΠΈΠ΅ ΠΎΠΏΠ°Π»ΡΠ±ΠΊΠΈ. ΠΡΠ΅ΡΡΡΡ, ΠΈΠ»ΠΈ ΡΠ΅ΡΠΌΠΎΠ°ΠΊΡΠΈΠ²Π½ΡΡ ΠΎΠΏΠ°Π»ΡΠ±ΠΊΡ ΠΏΡΠΈΠΌΠ΅Π½ΡΡΡ ΠΏΡΠΈ Π±Π΅ΡΠΎΠ½ΠΈΡΠΎΠ²Π°Π½ΠΈΠΈ ΡΡΠ½Π΄Π°ΠΌΠ΅Π½ΡΠΎΠ² Π»Π΅Π½ΡΠΎΡΠ½ΡΡ ΠΈ ΠΏΠ»ΠΈΡΠ½ΡΡ , ΠΏΠ΅ΡΠ΅ΠΊΡΡΡΠΈΠΉ, ΡΡΠ΅Π½. ΠΡΡΠ΅ΠΊΡΠΈΠ²Π½Ρ Π³ΡΠ΅ΡΡΠΈΠ΅ ΠΎΠΏΠ°Π»ΡΠ±ΠΊΠΈ ΠΏΡΠΈ ΠΌΠΎΡΠΎΠ·Π°Ρ Π½Π΅ ΡΠΈΠ»ΡΠ½Π΅Π΅ -25β°Π‘, ΠΏΡΠΈΡΠ΅ΠΌ Π±Π΅Π· ΠΎΡ Π»Π°ΠΆΠ΄Π΅Π½ΠΈΡ, Π° ΠΏΡΠΈ Π½Π΅ΠΏΡΠ΅ΡΡΠ²Π½ΠΎΠΌ Π±Π΅ΡΠΎΠ½ΠΈΡΠΎΠ²Π°Π½ΠΈΠΈ, Π±ΡΡΡΡΠΎΠΉ ΡΠΊΠ»Π°Π΄ΠΊΠ΅ ΠΈ ΡΠΏΠ»ΠΎΡΠ½Π΅Π½ΠΈΠΈ Π±Π΅ΡΠΎΠ½Π½ΠΎΠΉ ΡΠΌΠ΅ΡΠΈ. ΠΠΏΠ°Π»ΡΠ±ΠΊΠ° ΠΌΠΎΠΆΠ΅Ρ Π±ΡΡΡ ΠΊΠ°ΠΊ Π½Π΅ΡΡΠ΅ΠΌΠ½ΠΎΠΉ, ΡΠ°ΠΊ ΠΈ ΠΎΠ±ΡΡΠ½ΠΎΠΉ ΠΌΠ΅Π»ΠΊΠΎΡΠΈΡΠΎΠ²ΠΎΠΉ, ΠΈΠ½ΠΎΠ³Π΄Π° ΠΎΡΠ³Π°Π½ΠΈΠ·ΡΡΡ ΠΏΡΠΎΠ³ΡΠ΅Π² ΠΈ ΠΊΡΡΠΏΠ½ΡΡ ΠΎΠΏΠ°Π»ΡΠ±ΠΎΡΠ½ΡΡ ΡΠΈΡΠΎΠ². Π ΠΊΠ°ΡΠ΅ΡΡΠ²Π΅ Π½Π°Π³ΡΠ΅Π²Π°ΡΠ΅Π»ΡΠ½ΡΡ ΡΠ»Π΅ΠΌΠ΅Π½ΡΠΎΠ² ΠΏΡΠΈΠΌΠ΅Π½ΡΡΡ ΡΡΠ°Π»ΡΠ½ΡΡ ΡΠ΅ΡΠΊΡ, ΠΏΡΠΎΠ²ΠΎΠ΄Π° ΠΈ ΠΊΠ°Π±Π΅Π»ΠΈ, ΡΠ°Π·Π»ΠΈΡΠ½ΡΠ΅ ΠΈΡ ΠΊΠΎΠΌΠ±ΠΈΠ½Π°ΡΠΈΠΈ.
ΠΠ΅ΡΠ΅Π΄ ΡΠ΅ΠΌ ΠΊΠ°ΠΊ Π½Π°ΡΠ°ΡΡ ΡΠΊΠ»Π°Π΄ΠΊΡ Π±Π΅ΡΠΎΠ½Π°, ΠΏΡΠΎΠ³ΡΠ΅Π²Π°ΡΡ ΠΎΠΏΠ°Π»ΡΠ±ΠΊΡ ΠΈ ΠΎΡΠ½ΠΎΠ²Π°Π½ΠΈΠ΅ Π΄ΠΎ +20β°Π‘. ΠΡΠΈ Π·Π°Π»ΠΈΠ²ΠΊΠ΅ ΠΈ ΡΠΏΠ»ΠΎΡΠ½Π΅Π½ΠΈΠΈ Π½Π°Π³ΡΠ΅Π² ΡΡΠΈΠ»ΠΈΠ²Π°ΡΡ Π΄ΠΎ +30-55β°Π‘. ΠΡΠΆΠ½ΠΎ ΡΡΠΈΡΡΠ²Π°ΡΡ ΡΠ΅ΠΌΠΏΠ΅ΡΠ°ΡΡΡΡ ΡΠΊΠ»Π°Π΄ΡΠ²Π°Π΅ΠΌΠΎΠΉ ΡΠΌΠ΅ΡΠΈ, ΠΏΠΎΡΠΊΠΎΠ»ΡΠΊΡ Π±Π΅ΡΠΎΠ½, ΠΈΠΌΠ΅ΡΡΠΈΠΉ ΡΠ΅ΠΌΠΏΠ΅ΡΠ°ΡΡΡΡ ΠΎΡ +40β°Π‘, Π±ΡΡΡΡΠΎ ΡΡ Π²Π°ΡΡΠ²Π°Π΅ΡΡΡ ΠΈ ΠΈΠΌΠ΅Π΅Ρ ΠΌΠ΅Π½ΡΡΡΡ ΠΏΠΎΠ΄Π²ΠΈΠΆΠ½ΠΎΡΡΡ. Π£ΠΊΠ»Π°Π΄ΡΠ²Π°ΡΡ ΡΠ΅ΠΏΠ»ΡΠΉ Π±Π΅ΡΠΎΠ½ ΡΠ»Π΅Π΄ΡΠ΅Ρ Π±ΡΡΡΡΠΎ. Π£ΡΠ΅ΠΏΠ»ΠΈΡΠ΅Π»ΠΈ ΠΌΠΎΠΆΠ½ΠΎ ΠΏΡΠΈΠΌΠ΅Π½ΡΡΡ ΡΠ°ΠΌΡΠ΅ ΡΠ°Π·Π½ΡΠ΅, ΠΏΠΎ ΠΌΠ΅ΡΡΡ β Π΄Π΅ΡΠ΅Π²ΡΠ½Π½ΡΠ΅ Π΄ΠΎΡΠΊΠΈ, ΠΏΡΠΎΠ»ΠΎΠΆΠ΅Π½Π½ΡΠ΅ ΡΠΎΠ»Π΅ΠΌ ΠΈΠ»ΠΈ ΡΡΠ±Π΅ΡΠΎΠΈΠ΄ΠΎΠΌ, ΡΠ°Π½Π΅ΡΠ½ΡΠ΅ Π»ΠΈΡΡΡ Ρ ΠΏΡΠΎΠΊΠ»Π°Π΄ΠΊΠΎΠΉ ΠΏΠ΅Π½ΠΎΠΏΠ»Π°ΡΡΠΎΠΌ, ΡΠΎΠ»ΡΡΡΠΉ Π³ΠΎΡΡΠΎΠΊΠ°ΡΡΠΎΠ½, Π²Π°ΡΡ ΠΈ ΡΠ»Π°ΠΊΠΎΠ²Π°ΡΡ, Π·Π°ΡΡΠΏΠΊΡ ΡΡΡΡΠΆΠΊΠΎΠΉ ΠΈΠ»ΠΈ Π΄ΡΠ΅Π²Π΅ΡΠ½ΡΠΌΠΈ ΠΎΠΏΠΈΠ»ΠΊΠ°ΠΌΠΈ. ΠΠΎ Π±ΠΎΠ»Π΅Π΅ ΡΡΡΠ΅ΠΊΡΠΈΠ²Π½Ρ Π½Π΅ ΠΏΡΠΎΠ΄ΡΠ²Π°Π΅ΠΌΡΠ΅ ΠΌΡΠ³ΠΊΠΈΠ΅ ΡΡΠ΅ΠΏΠ»ΠΈΡΠ΅Π»ΠΈ Ρ Π²ΠΎΠ΄ΠΎΠΎΡΡΠ°Π»ΠΊΠΈΠ²Π°ΡΡΠΈΠΌΠΈ ΠΏΠΎΠΊΡΡΡΠΈΡΠΌΠΈ. ΠΡΠΎΠ±ΠΎΠ΅ Π²Π½ΠΈΠΌΠ°Π½ΠΈΠ΅ ΠΏΡΠΈ ΠΈΠ·ΠΎΠ»ΡΡΠΈΠΈ ΡΠ΄Π΅Π»ΡΡΡ ΠΊΠΎΠ½ΡΡΡΡΠΊΡΠΈΡΠΌ ΠΏΠ΅ΡΠ΅ΠΌΠ΅Π½Π½ΠΎΠ³ΠΎ ΡΠ΅ΡΠ΅Π½ΠΈΡ, ΡΠΎΠ½ΠΊΠΈΠΌ ΡΠ»Π΅ΠΌΠ΅Π½ΡΠ°ΠΌ, ΡΠ³Π»Π°ΠΌ ΠΈ Π΄ΡΡΠ³ΠΈΠΌ Π±ΡΡΡΡΠΎ ΠΎΡΡΡΠ²Π°ΡΡΠΈΠΌ ΡΠ°ΡΡΡΠΌ β ΠΈΡ ΡΡΠ΅ΠΏΠ»ΡΡΡ Π² ΠΏΠ΅ΡΠ²ΡΡ ΠΎΡΠ΅ΡΠ΅Π΄Ρ. ΠΠΎ ΡΠΈΡΡΠ°ΡΠΈΠΈ β ΠΈΠ½ΠΎΠ³Π΄Π° Π²ΡΡΡΡΠΏΠ°ΡΡΠΈΠ΅ ΡΠ»Π΅ΠΌΠ΅Π½ΡΡ ΠΈ ΡΡΡΠΊΠΈ ΠΏΠ΅ΡΠ΅Π΄ ΡΠ΅ΠΏΠ»ΠΎΠΈΠ·ΠΎΠ»ΡΡΠΈΠ΅ΠΉ Π΄ΠΎΠΏΠΎΠ»Π½ΠΈΡΠ΅Π»ΡΠ½ΠΎ Π±ΡΡΡΡΠΎ ΠΏΡΠΎΠ³ΡΠ΅Π²Π°ΡΡ ΠΈΠ½ΡΡΠ°ΠΊΡΠ°ΡΠ½ΡΠΌ ΠΌΠ΅ΡΠΎΠ΄ΠΎΠΌ, Π½Π°ΠΏΡΠΈΠΌΠ΅Ρ Π³Π°Π·ΠΎΠ²ΠΎΠΉ Π³ΠΎΡΠ΅Π»ΠΊΠΎΠΉ.
Π‘ΠΏΠΎΡΠΎΠ± Π²ΡΠ΄Π΅ΡΠΆΠΈΠ²Π°Π½ΠΈΡ Π±Π΅ΡΠΎΠ½Π° ΡΠ΅ΡΠΌΠΎΡΠΎΠΌ ΠΏΡΠΎΡΡ ΠΈ Π΄ΠΎΡΡΠ°ΡΠΎΡΠ½ΠΎ ΡΠΊΠΎΠ½ΠΎΠΌΠΈΡΠ΅Π½, ΠΈ Π² ΠΏΠΎΠ»Π½ΠΎΠΉ ΠΌΠ΅ΡΠ΅ ΠΏΠΎΠ·Π²ΠΎΠ»ΡΠ΅Ρ ΠΈΡΠΏΠΎΠ»ΡΠ·ΠΎΠ²Π°ΡΡ Π½Π΅ΠΌΠ°Π»ΠΎΠ΅ Π²Π½ΡΡΡΠ΅Π½Π½Π΅Π΅ ΡΠ΅ΠΏΠ»ΠΎ Π±Π΅ΡΠΎΠ½Π° — ΡΠΊΠ·ΠΎΡΠ΅ΡΠΌΠΈΡ ΡΠ΅Π°ΠΊΡΠΈΠΈ Π³ΠΈΠ΄ΡΠ°ΡΠ°ΡΠΈΠΈ. ΠΠΎΠ»ΡΡΠ΅ Π²ΡΠ΅Π³ΠΎ ΠΏΠΎΠ΄Ρ ΠΎΠ΄ΠΈΡ ΡΠ΅ΡΠΌΠΎΡ Π΄Π»Ρ ΠΊΠΎΠ½ΡΡΡΡΠΊΡΠΈΠΉ Ρ ΠΌΠΎΠ΄ΡΠ»Π΅ΠΌ ΠΏΠΎΠ²Π΅ΡΡ Π½ΠΎΡΡΠΈ Π΄ΠΎ 8, ΠΏΡΠΈ ΡΡΠ»ΠΎΠ²ΠΈΠΈ ΠΈΠ·Π³ΠΎΡΠΎΠ²Π»Π΅Π½ΠΈΡ Π±Π΅ΡΠΎΠ½Π½ΡΡ ΡΠΌΠ΅ΡΠ΅ΠΉ Π½Π° ΠΏΠΎΡΡΠ»Π°Π½ΡΠ΅ΠΌΠ΅Π½ΡΠ°Ρ ΡΡΠ΅Π΄Π½Π΅ΠΉ Π°ΠΊΡΠΈΠ²Π½ΠΎΡΡΠΈ. ΠΡΡΠΎΠΊΠΎΠ°ΠΊΡΠΈΠ²Π½ΡΠΉ Π±ΡΡΡΡΠΎΡΠ²Π΅ΡΠ΄Π΅ΡΡΠΈΠΉ ΡΠ΅ΠΌΠ΅Π½Ρ ΠΈΠ»ΠΈ Π²Π²Π΅Π΄Π΅Π½ΠΈΠ΅ Π² Π±Π΅ΡΠΎΠ½Π½ΡΡ ΡΠΌΠ΅ΡΡ ΠΌΠΎΠ΄ΠΈΡΠΈΠΊΠ°ΡΠΎΡΠΎΠ²-ΡΡΠΊΠΎΡΠΈΡΠ΅Π»Π΅ΠΉ ΡΠ²Π΅ΡΠ΄Π΅Π½ΠΈΡ Π΄Π°ΡΡ Π²ΠΎΠ·ΠΌΠΎΠΆΠ½ΠΎΡΡΡ ΡΡΡΠ΅ΠΊΡΠΈΠ²Π½ΠΎ Π²ΡΠ΄Π΅ΡΠΆΠΈΠ²Π°ΡΡ ΡΠ΅ΡΠΌΠΎΡΠΎΠΌ ΠΊΠΎΠ½ΡΡΡΡΠΊΡΠΈΠΈ, ΠΈΠΌΠ΅ΡΡΠΈΠ΅ ΠΌΠΎΠ΄ΡΠ»Ρ ΠΏΠΎΠ²Π΅ΡΡ Π½ΠΎΡΡΠΈ ΠΎΡ 10 ΠΈ Π²ΡΡΠ΅, ΠΌΠ°ΠΊΡΠΈΠΌΡΠΌ Π΄ΠΎ 15.
Π‘ΡΡΠΎΠ³ΠΎ Π³ΠΎΠ²ΠΎΡΡ, Π΄Π»Ρ ΠΏΡΠ°Π²ΠΈΠ»ΡΠ½ΠΎΠ³ΠΎ ΠΈ ΡΠΊΠΎΠ½ΠΎΠΌΠΈΡΠ½ΠΎΠ³ΠΎ ΡΠ΅ΡΠΌΠΎΡΠ° Π½ΡΠΆΠ΅Π½ ΡΠ΅ΠΏΠ»ΠΎΡΠ΅Ρ Π½ΠΈΡΠ΅ΡΠΊΠΈΠΉ ΡΠ°ΡΡΠ΅Ρ ΠΏΠΎ ΠΊΠ°ΠΆΠ΄ΠΎΠΉ ΠΊΠΎΠ½ΡΡΡΡΠΊΡΠΈΠΈ. ΠΠ° ΡΠ°ΡΡΠ½ΠΎΠΉ ΡΡΡΠΎΠΉΠΊΠ΅ Π² ΠΎΡΠ½ΠΎΠ²Π½ΠΎΠΌ ΠΏΡΠΈΡ ΠΎΠ΄ΠΈΡΡΡ ΠΏΡΠΈΠΌΠ΅Π½ΡΡΡ ΠΏΡΠΎΠ³ΡΠ΅Π² Β«Ρ Π·Π°ΠΏΠ°ΡΠΎΠΌΒ».
ΠΡΠ΅ΡΡΠΈΠ΅ ΠΎΠΏΠ°Π»ΡΠ±ΠΊΠΈ ΠΌΠΎΠΆΠ½ΠΎ ΠΊΠΎΠΌΠ±ΠΈΠ½ΠΈΡΠΎΠ²Π°ΡΡ Ρ ΡΠ»Π΅ΠΊΡΡΠΎΠ΄Π½ΡΠΌ ΠΏΡΠΎΠ³ΡΠ΅Π²ΠΎΠΌ Π±Π΅ΡΠΎΠ½Π° ΠΈ ΠΏΡΠΎΠ³ΡΠ΅Π²ΠΎΠΌ Π½Π°Π³ΡΠ΅Π²Π°ΡΠ΅Π»ΡΠ½ΡΠΌΠΈ ΠΏΡΠΎΠ²ΠΎΠ΄Π°ΠΌΠΈ. Π Π±Π΅ΡΠΎΠ½ Π΄ΠΎΠ±Π°Π²Π»ΡΡΡ Π°Π½ΡΠΈΠΌΠΎΡΠΎΠ·Π½ΡΠ΅ Π΄ΠΎΠ±Π°Π²ΠΊΠΈ ΠΈ ΠΌΠΎΠ΄ΠΈΡΠΈΠΊΠ°ΡΠΎΡΡ Π΄Π»Ρ ΡΡΠΊΠΎΡΠ΅Π½ΠΈΡ Π½Π°Π±ΠΎΡΠ° ΠΏΡΠΎΡΠ½ΠΎΡΡΠΈ. ΠΠ΅ΡΠΎΠ½Π½ΡΡ ΡΠΌΠ΅ΡΡ, ΠΊΠΎΡΠΎΡΡΡ Π³ΠΎΡΠΎΠ²ΡΡ Π½Π° ΡΡΠ°ΡΡΠΊΠ΅ Π² Π±Π΅ΡΠΎΠ½ΠΎΠΌΠ΅ΡΠ°Π»ΠΊΠ΅, Π²ΠΎΠ·ΠΌΠΎΠΆΠ½ΠΎ Π·Π°ΠΌΠ΅ΡΠΈΠ²Π°ΡΡ Π½Π° Π³ΠΎΡΡΡΠ΅ΠΉ Π²ΠΎΠ΄Π΅ β Π΄ΠΎ +90β°Π‘ ΠΈ ΠΏΡΠΎΠ³ΡΠ΅ΡΡΡ Π΄ΠΎ +50-70β°Π‘ Π·Π°ΠΏΠΎΠ»Π½ΠΈΡΠ΅Π»ΡΡ . ΠΠ°ΠΊΠΈΠ΅ ΠΌΠ΅ΡΡ ΠΊΠΎΠΌΠ±ΠΈΠ½ΠΈΡΠΎΠ²Π°ΡΡ β ΡΠ΅ΡΠ°Π΅ΡΡΡ ΠΈΠ½Π΄ΠΈΠ²ΠΈΠ΄ΡΠ°Π»ΡΠ½ΠΎ ΠΈ Π·Π°Π²ΠΈΡΠΈΡ ΠΎΡ ΡΠΏΠ΅ΡΠΈΡΠΈΠΊΠΈ ΠΌΠ΅ΡΡΠ½ΡΡ ΡΡΠ»ΠΎΠ²ΠΈΠΉ, ΠΎΡ Π²ΠΎΠ·ΠΌΠΎΠΆΠ½ΠΎΡΡΠ΅ΠΉ ΡΡΡΠΎΠΉΠΊΠΈ ΠΈ ΠΊΠΎΠ½Π΅ΡΠ½ΠΎ, ΠΎΡ Π±Π΅ΡΠΎΠ½Π° β Π΅Π³ΠΎ Π²ΠΈΠ΄Π°, ΠΊΠ»Π°ΡΡΠ°, ΡΡΠ»ΠΎΠ²ΠΈΠΉ ΡΠ°Π±ΠΎΡΡ Π±ΡΠ΄ΡΡΠ΅ΠΉ Π±Π΅ΡΠΎΠ½Π½ΠΎΠΉ ΠΊΠΎΠ½ΡΡΡΡΠΊΡΠΈΠΈ.
ΠΠ½ΡΡΠ°ΠΊΡΠ°ΡΠ½ΡΠΉ ΠΎΠ±ΠΎΠ³ΡΠ΅Π²
ΠΠ½ΡΡΠ°ΠΊΡΠ°ΡΠ½ΡΠ΅, ΠΈΠ»ΠΈ ΡΠ΅ΠΏΠ»ΠΎΠ²ΡΠ΅ Π»ΡΡΠΈ, Π½Π°Π³ΡΠ΅Π²Π°ΡΡ Π±Π΅ΡΠΎΠ½Π½ΡΡ ΠΊΠΎΠ½ΡΡΡΡΠΊΡΠΈΡ ΠΌΡΠ³ΠΊΠΎ ΠΈ ΠΌΠ΅Π΄Π»Π΅Π½Π½ΠΎ, ΠΏΡΠ΅Π³ΡΠ°Π΄ΠΎΠΉ Π΄Π»Ρ Π½ΠΈΡ ΡΠ²Π»ΡΡΡΡΡ ΡΠΎΠ»ΡΠΊΠΎ ΠΌΠ΅ΡΠ°Π»Π»ΠΈΡΠ΅ΡΠΊΠΈΠ΅ Π΄Π΅ΡΠ°Π»ΠΈ. ΠΠ° Π±ΠΎΠ»ΡΡΠΈΡ ΡΡΡΠΎΠΉΠΊΠ°Ρ ΠΏΡΠΈΠΌΠ΅Π½ΡΡΡ ΡΡΠΈΠ»Π΅Π½Π½ΡΠ΅ ΡΠ΅ΡΠΌΠΎΠΌΠ°ΡΡ, ΠΈΠ½ΡΡΠ°ΠΊΡΠ°ΡΠ½ΡΠ΅ ΠΏΡΠΎΠΌΡΡΠ»Π΅Π½Π½ΡΠ΅ ΡΡΡΠ°Π½ΠΎΠ²ΠΊΠΈ. Π ΡΡΠ»ΠΎΠ²ΠΈΡΡ ΡΠ°ΡΡΠ½ΠΎΠΉ ΡΡΡΠΎΠΉΠΊΠΈ ΠΏΡΠΈΠΌΠ΅Π½ΠΈΡΡ ΡΠ΅ΡΠΌΠΎΠΌΠ°ΡΡ Π΄Π»Ρ Π±Π΅ΡΠΎΠ½ΠΈΡΠΎΠ²Π°Π½ΠΈΡ ΡΡΠ½Π΄Π°ΠΌΠ΅Π½ΡΠ½ΠΎΠΉ ΠΏΠ»ΠΈΡΡ Π΄ΠΎΡΠΎΠ³ΠΎ, Π½ΠΎ ΡΠ΅Ρ Π½ΠΈΡΠ΅ΡΠΊΠΈ ΠΎΠΏΡΠ°Π²Π΄Π°Π½ΠΎ β Π΄Π»Ρ ΠΏΡΠΎΠ³ΡΠ΅Π²Π° Π±ΠΎΠ»ΡΡΠΎΠΉ ΡΠΎΠ²Π½ΠΎΠΉ Π³ΠΎΡΠΈΠ·ΠΎΠ½ΡΠ°Π»ΡΠ½ΠΎΠΉ ΠΏΠΎΠ²Π΅ΡΡ Π½ΠΎΡΡΠΈ ΡΠ΅ΡΠΌΠΎΠΌΠ°ΡΡ ΡΡΡΠ΅ΠΊΡΠΈΠ²Π½Ρ Π΄Π°ΠΆΠ΅ Π±ΠΎΠ»Π΅Π΅, ΡΠ΅ΠΌ ΡΠ»Π΅ΠΊΡΡΠΎΠ΄Ρ.
Β«ΠΠ°ΠΌΠΎΡΠΎΠΆΠ΅Π½Π½ΡΠΉΒ» Π°ΡΠΌΠΎΠΊΠ°ΡΠΊΠ°Ρ, ΡΡΡΠ°Π½ΠΎΠ²Π»Π΅Π½Π½ΡΠΉ Π² ΠΎΠΏΠ°Π»ΡΠ±ΠΊΡ, Π° ΡΠ°ΠΊΠΆΠ΅ ΠΌΠ΅ΡΠ°Π»Π»ΠΈΡΠ΅ΡΠΊΠΈΠ΅ Π·Π°ΠΊΠ»Π°Π΄Π½ΡΠ΅ Π΄Π΅ΡΠ°Π»ΠΈ, ΡΠ°Π»ΡΠ½ΠΈΠΊΠΈ ΠΈ Ρ.ΠΏ., ΠΏΠ΅ΡΠ΅Π΄ Π±Π΅ΡΠΎΠ½ΠΈΡΠΎΠ²Π°Π½ΠΈΠ΅ΠΌ ΠΏΡΠΎΠ³ΡΠ΅Π²Π°ΡΡ Π½Π° ΡΠ°ΡΡΠ½ΠΎΠΉ ΡΡΡΠΎΠΉΠΊΠ΅ ΡΠ°ΡΠ΅ Π²ΡΠ΅Π³ΠΎ Π³Π°Π·ΠΎΠ²ΡΠΌΠΈ Π³ΠΎΡΠ΅Π»ΠΊΠ°ΠΌΠΈ. Π’Π΅ΠΏΠ»ΠΎΠ²ΡΠΌΠΈ Π»ΡΡΠ°ΠΌΠΈ ΠΎΡ Π³Π°Π·ΠΎΠ²ΠΎΠΉ Π³ΠΎΡΠ΅Π»ΠΊΠΈ ΠΌΠΎΠΆΠ½ΠΎ ΠΏΡΠΎΠ³ΡΠ΅ΡΡ ΡΡΡΠΊΠΈ ΠΈ ΡΡΠ°ΡΡΠΊΠΈ ΠΊΠΎΠ½ΡΡΡΡΠΊΡΠΈΠΈ, ΡΡΡΠ΄Π½ΠΎΠ΄ΠΎΡΡΡΠΏΠ½ΡΠ΅ Π΄Π»Ρ ΡΠ΅ΠΏΠ»ΠΎΠΈΠ·ΠΎΠ»ΡΡΠΈΠΈ. ΠΠΠ Ρ Π³ΠΎΡΠ΅Π»ΠΎΠΊ Π²ΡΡΠΎΠΊΠΈΠΉ β ΠΎΡ 90%, ΠΈ ΠΏΡΠΈΠΌΠ΅Π½ΡΡΡ Π΄Π°Π½Π½ΡΠΉ ΠΌΠ΅ΡΠΎΠ΄ ΠΏΡΠΎΠ³ΡΠ΅Π²Π° Π±Π΅ΡΠΎΠ½Π° Π½Π° ΡΠ°ΡΡΠ½ΡΡ ΡΡΡΠΎΠΉΠΊΠ°Ρ Π΄ΠΎΠ²ΠΎΠ»ΡΠ½ΠΎ ΡΠ°ΡΡΠΎ.
Π’Π΅ΠΏΠ»ΠΎΠ²ΠΎΠΉ ΠΎΠ±ΠΎΠ³ΡΠ΅Π² Ρ ΡΠΊΡΡΡΠΈΠ΅ΠΌ
ΠΠΎΠ²ΠΎΠ»ΡΠ½ΠΎ ΠΏΡΠΎΡΡΠ°Ρ ΠΈ ΡΡΡΠ΅ΠΊΡΠΈΠ²Π½Π°Ρ, Π½ΠΎ Π½Π΅ΡΠΊΠΎΠ½ΠΎΠΌΠΈΡΠ½Π°Ρ ΡΠ΅Ρ Π½ΠΎΠ»ΠΎΠ³ΠΈΡ. Π£ΡΡΡΠ°ΠΈΠ²Π°Π΅ΡΡΡ ΡΠΊΡΡΡΠΈΠ΅ β Π² Π²ΠΈΠ΄Π΅ Π½Π΅ ΠΏΡΠΎΠ΄ΡΠ²Π°Π΅ΠΌΠΎΠ³ΠΎ ΡΠ°ΡΡΠ°, ΠΏΠ°Π»Π°ΡΠΊΠΈ, ΠΏΠΎΠ»ΠΎΠ³Π° ΠΈΠ»ΠΈ Π»ΡΠ±ΠΎΠ³ΠΎ ΡΠ΄ΠΎΠ±Π½ΠΎΠ³ΠΎ ΠΊΡΠΏΠΎΠ»Π°, ΠΈ ΡΡΡΠ°Π½Π°Π²Π»ΠΈΠ²Π°Π΅ΡΡΡ ΡΠ΅ΠΏΠ»ΠΎΠ²Π°Ρ ΠΏΡΡΠΊΠ°. ΠΠ΅Π»ΠΎ ΡΡΡΠ΄ΠΎΠ΅ΠΌΠΊΠΎΠ΅ ΠΈ ΡΠ»Π΅Π΄ΠΈΡΡ Π½ΡΠΆΠ½ΠΎ ΠΏΠΎΡΡΠΎΡΠ½Π½ΠΎ — ΡΡΠΎΡ ΡΠΏΠΎΡΠΎΠ± ΡΡΠΈΡΠ°ΡΡ Β«Π΄Π΅Π΄ΠΎΠ²ΡΠΊΠΈΠΌΒ», Π½ΠΎ Π΄Π»Ρ ΠΎΠ±ΠΎΠ³ΡΠ΅Π²Π° Π±Π΅ΡΠΎΠ½Π° Π½Π° Π½Π΅Π±ΠΎΠ»ΡΡΠΈΡ ΡΡΡΠΎΠΉΠΊΠ°Ρ ΡΡΠΏΠ΅ΡΠ½ΠΎ ΠΏΡΠΈΠΌΠ΅Π½ΡΡΡ ΠΈ Π² Π½Π°ΡΠ΅ΠΉ ΡΠΎΠ²ΡΠ΅ΠΌΠ΅Π½Π½ΠΎΡΡΠΈ. Π₯ΠΎΡΠΎΡΠΈΠΉ ΠΏΠ»ΡΡ ΡΡΠΎΠΉ Β«ΠΌΠ΅ΡΠΎΠ΄ΠΈΠΊΠΈΒ» ΡΠΎΡ, ΡΡΠΎ ΠΌΠΎΠΆΠ½ΠΎ Π³ΡΠ΅ΡΡ Π±Π΅Π· ΡΠ»Π΅ΠΊΡΡΠΎΡΠ½Π΅ΡΠ³ΠΈΠΈ — Π°Π²ΡΠΎΠ½ΠΎΠΌΠ½ΠΎΠΉ ΡΠ΅ΠΏΠ»ΠΎΠ²ΠΎΠΉ ΠΏΡΡΠΊΠΎΠΉ, ΡΠ°ΡΠ΅ Π²ΡΠ΅Π³ΠΎ Π΄ΠΈΠ·Π΅Π»ΡΠ½ΠΎΠΉ. ΠΡΠ»ΠΈ ΡΠ΅ΡΡ 220Π Π½Π΅Π΄ΠΎΡΡΡΠΏΠ½Π°, ΡΠΎ Π΄Π°Π½Π½ΡΠΉ Π²Π°ΡΠΈΠ°Π½Ρ ΠΌΠΎΠΆΠ΅Ρ ΡΡΠ°ΡΡ Π±Π΅ΡΠΏΡΠΎΠΈΠ³ΡΡΡΠ½ΡΠΌ.
ΠΠ°ΠΊΠΈΠΌ Π±Ρ ΡΠΏΠΎΡΠΎΠ±ΠΎΠΌ Π½Π΅ ΠΎΠ±Π΅ΡΠΏΠ΅ΡΠΈΠ²Π°Π»ΠΎΡΡ Π±Π΅ΡΠΎΠ½Ρ ΡΠ΅ΠΏΠ»ΠΎ Π² Π·ΠΈΠΌΠ½ΠΈΠ΅ ΠΌΠΎΡΠΎΠ·Ρ, ΠΎΠ΄Π½ΠΎ ΠΈΠ· Π³Π»Π°Π²Π½ΡΡ ΡΡΠ»ΠΎΠ²ΠΈΠΉ ΡΡΠΏΠ΅Ρ Π° β ΠΏΠΎΡΡΠΎΡΠ½Π½ΡΠΉ ΠΊΠΎΠ½ΡΡΠΎΠ»Ρ. Π’Π΅ΠΌΠΏΠ΅ΡΠ°ΡΡΡΠ° Π±Π΅ΡΠΎΠ½Π° Π΄ΠΎΠ»ΠΆΠ½Π° Π±ΡΡΡ Π²ΡΠ΅Π³Π΄Π° ΠΏΠ»ΡΡΠΎΠ²Π°Ρ, ΠΎΠΏΡΠΈΠΌΠ°Π»ΡΠ½ΠΎ +20-25β°Π‘, Π½ΠΎ Π½ΠΈ Π² ΠΊΠΎΠ΅ΠΌ ΡΠ»ΡΡΠ°Π΅ Π½Π΅ Π²ΡΡΠ΅, ΡΠ΅ΠΌ +45-50β°Π‘. Π‘Π»ΠΈΡΠΊΠΎΠΌ Π²ΡΡΠΎΠΊΠΈΠ΅ ΡΠ΅ΠΌΠΏΠ΅ΡΠ°ΡΡΡΡ Π½Π΅ ΠΌΠ΅Π½Π΅Π΅ ΠΎΠΏΠ°ΡΠ½Ρ Π΄Π»Ρ Π±Π΅ΡΠΎΠ½Π°, ΡΠ΅ΠΌ ΠΌΠΎΡΠΎΠ·. ΠΠΎΠ»Π΅Π±Π°Π½ΠΈΡ ΡΠ΅ΠΌΠΏΠ΅ΡΠ°ΡΡΡ Π±Π΅ΡΠΎΠ½Π° Π½Π° ΡΠ°ΡΡΠ½ΠΎΠΉ ΡΡΡΠΎΠΉΠΊΠ΅ Π΅ΡΡΡ Π²ΡΠ΅Π³Π΄Π°, ΠΈ Π½Π°Π³ΡΠ΅Π² Π±Π΅ΡΠΎΠ½Π° ΠΏΡΠΎΠΈΡΡ ΠΎΠ΄ΠΈΡ Ρ ΡΠ°Π·Π½ΠΎΠΉ ΡΠΊΠΎΡΠΎΡΡΡΡ, ΡΠ°ΠΊ ΠΆΠ΅, ΠΊΠ°ΠΊ ΠΈ Π΅Π³ΠΎ ΠΎΡΡΡΠ²Π°Π½ΠΈΠ΅. ΠΡΠ΅Π΄Π΅Π» ΡΡΠΎΠΉ ΡΠΊΠΎΡΠΎΡΡΠΈ β 10 Π³ΡΠ°Π΄ΡΡΠΎΠ² Π·Π° ΠΎΠ΄ΠΈΠ½ ΡΠ°Ρ, ΠΈ ΡΡΠΎ ΡΠΎΠΆΠ΅ Π½Π΅ΠΎΠ±Ρ ΠΎΠ΄ΠΈΠΌΠΎ ΠΎΡΡΠ»Π΅ΠΆΠΈΠ²Π°ΡΡ, ΡΡΠΎΠ±Ρ ΠΏΠΎΠ»ΡΡΠΈΡΡ ΠΊΠΎΠ½ΡΡΡΡΠΊΡΠΈΡ ΠΏΡΠΎΠ΅ΠΊΡΠ½ΠΎΠΉ ΠΏΡΠΎΡΠ½ΠΎΡΡΠΈ.
ΠΠ΅ΡΠΎΠ΄Ρ Π±Π΅ΡΠΎΠ½ΠΈΡΠΎΠ²Π°Π½ΠΈΡ Π² Ρ ΠΎΠ»ΠΎΠ΄Π½ΡΡ ΠΏΠΎΠ³ΠΎΠ΄Ρ | GCP Applied Technologies
Π‘ΡΡΠΎΠΈΡΠ΅Π»ΡΡΡΠ²ΠΎ Π² Π·ΠΈΠΌΠ½Π΅Π΅ Π²ΡΠ΅ΠΌΡ ΡΡΠ΅Π±ΡΠ΅Ρ ΠΎΡΠΎΠ±ΠΎΠ³ΠΎ Π²Π½ΠΈΠΌΠ°Π½ΠΈΡ, ΠΎΡΠΎΠ±Π΅Π½Π½ΠΎ ΠΊΠΎΠ³Π΄Π° ΡΠ΅ΡΡ ΠΈΠ΄Π΅Ρ ΠΎ Π·Π°Π»ΠΈΠ²ΠΊΠ΅ Π±Π΅ΡΠΎΠ½Π° Π² Ρ ΠΎΠ»ΠΎΠ΄Π½ΡΡ ΠΏΠΎΠ³ΠΎΠ΄Ρ. ΠΡΠ°ΠΉΠ½Π΅ Π²Π°ΠΆΠ½ΠΎ, ΡΡΠΎΠ±Ρ Π±Π΅ΡΠΎΠ½ Π±ΡΠ» Π·Π°ΡΠΈΡΠ΅Π½ ΠΎΡ Π·Π°ΠΌΠ΅ΡΠ·Π°Π½ΠΈΡ Π΄ΠΎ ΡΠ΅Ρ ΠΏΠΎΡ, ΠΏΠΎΠΊΠ° ΠΎΠ½ Π½Π΅ Π΄ΠΎΡΡΠΈΠ³Π½Π΅Ρ ΠΏΡΠΎΡΠ½ΠΎΡΡΠΈ Π½Π° ΡΠΆΠ°ΡΠΈΠ΅ Π½Π΅ ΠΌΠ΅Π½Π΅Π΅ 500 ΡΡΠ½ΡΠΎΠ² Π½Π° ΠΊΠ²Π°Π΄ΡΠ°ΡΠ½ΡΠΉ Π΄ΡΠΉΠΌ (3,5 ΠΠΠ°), ΡΡΠΎ ΡΠΎΡΡΠ°Π²Π»ΡΠ΅Ρ ΠΎΠΊΠΎΠ»ΠΎ Π΄Π²ΡΡ Π΄Π½Π΅ΠΉ Π΄Π»Ρ Π±ΠΎΠ»ΡΡΠΈΠ½ΡΡΠ²Π° Π±Π΅ΡΠΎΠ½ΠΎΠ², ΠΏΠΎΠ΄Π΄Π΅ΡΠΆΠΈΠ²Π°Π΅ΠΌΡΡ ΠΏΡΠΈ ΡΠ΅ΠΌΠΏΠ΅ΡΠ°ΡΡΡΠ΅ 50 Β° F (10 Β° C). Π ΠΏΡΠΎΡΠΈΠ²Π½ΠΎΠΌ ΡΠ»ΡΡΠ°Π΅ ΡΡΠΎ Π·Π°ΠΌΠ΅Π΄Π»ΠΈΡ Π½Π°Π±ΠΎΡ ΠΏΡΠΎΡΠ½ΠΎΡΡΠΈ Π±Π΅ΡΠΎΠ½Π°.
Π ΡΡΠ°ΡΡΡΡ, Π΅ΡΡΡ Π½Π΅ΡΠΊΠΎΠ»ΡΠΊΠΎ ΠΎΡΠ½ΠΎΠ²Π½ΡΡ ΡΠ°Π³ΠΎΠ², ΠΊΠΎΡΠΎΡΡΠ΅ Π²Ρ ΠΌΠΎΠΆΠ΅ΡΠ΅ ΠΏΡΠ΅Π΄ΠΏΡΠΈΠ½ΡΡΡ, ΡΡΠΎΠ±Ρ Π·Π°ΡΠΈΡΠΈΡΡ Π±Π΅ΡΠΎΠ½.ΠΠ΅ΡΠΎΠ½, ΠΊΠΎΡΠΎΡΡΠΉ Π΄ΠΎΠ»ΠΆΠ½ΡΠΌ ΠΎΠ±ΡΠ°Π·ΠΎΠΌ Π·Π°ΡΠΈΡΠ΅Π½, Π΄ΠΎΡΡΠΈΠ³Π½Π΅Ρ ΡΠ²ΠΎΠ΅ΠΉ ΠΏΠΎΡΠ΅Π½ΡΠΈΠ°Π»ΡΠ½ΠΎΠΉ ΠΏΡΠΎΡΠ½ΠΎΡΡΠΈ ΠΈ ΡΠΎΡ ΡΠ°Π½ΠΈΡ ΡΡΡ ΠΏΡΠΎΡΠ½ΠΎΡΡΡ, Π½Π΅ΡΠΌΠΎΡΡΡ Π½Π° ΠΏΠΎΡΠ»Π΅Π΄ΡΡΡΠ΅Π΅ Π²ΠΎΠ·Π΄Π΅ΠΉΡΡΠ²ΠΈΠ΅ Ρ ΠΎΠ»ΠΎΠ΄Π°.
- Π‘Π»Π΅Π΄ΠΈΡΠ΅ Π·Π° ΡΠ΅ΠΌΠΏΠ΅ΡΠ°ΡΡΡΠΎΠΉ. ΠΡΠΈ ΠΏΠΎΠ½ΠΈΠΆΠ΅Π½ΠΈΠΈ ΡΠ΅ΠΌΠΏΠ΅ΡΠ°ΡΡΡΡ ΡΠΌΠ΅Π½ΡΡΠ°Π΅ΡΡΡ ΠΈ ΡΠΊΠΎΡΠΎΡΡΡ Π³ΠΈΠ΄ΡΠ°ΡΠ°ΡΠΈΠΈ ΡΠ΅ΠΌΠ΅Π½ΡΠ°, ΡΡΠΎ Π·Π°ΠΌΠ΅Π΄Π»ΡΠ΅Ρ ΡΠΊΠΎΡΠΎΡΡΡ Π½Π°Π±ΠΎΡΠ° ΠΏΡΠΎΡΠ½ΠΎΡΡΠΈ Π±Π΅ΡΠΎΠ½Π°. ΠΠΎΠ³Π΄Π° ΠΎΠΏΡΠ΅Π΄Π΅Π»Π΅Π½Π½Π°Ρ ΠΏΡΠΎΡΠ½ΠΎΡΡΡ Π±Π΅ΡΠΎΠ½Π° Π΄ΠΎΠ»ΠΆΠ½Π° Π±ΡΡΡ Π΄ΠΎΡΡΠΈΠ³Π½ΡΡΠ° ΠΏΠΎ ΠΎΠΏΡΠ΅Π΄Π΅Π»Π΅Π½Π½ΠΎΠΌΡ Π³ΡΠ°ΡΠΈΠΊΡ, ΡΠ»Π΅Π΄ΡΠ΅Ρ ΡΠΎΠ±Π»ΡΠ΄Π°ΡΡ ΡΠ΅ΠΌΠΏΠ΅ΡΠ°ΡΡΡΡ ΡΠΊΠ»Π°Π΄ΠΊΠΈ ΠΈ ΠΎΡΠ²Π΅ΡΠΆΠ΄Π΅Π½ΠΈΡ Π±Π΅ΡΠΎΠ½Π° Π² ΡΠΎΠΎΡΠ²Π΅ΡΡΡΠ²ΠΈΠΈ Ρ ACI 306- Π ΡΠΊΠΎΠ²ΠΎΠ΄ΡΡΠ²ΠΎ ΠΏΠΎ Π±Π΅ΡΠΎΠ½ΠΈΡΠΎΠ²Π°Π½ΠΈΡ Π² Ρ
ΠΎΠ»ΠΎΠ΄Π½ΡΡ ΠΏΠΎΠ³ΠΎΠ΄Ρ.
- ΠΠΎΠ΄Π³ΠΎΡΠΎΠ²ΠΈΡΡ ΡΠ°ΠΉΡ. Π£Π΄Π°Π»ΠΈΡΠ΅ ΡΠ½Π΅Π³ ΠΈΠ»ΠΈ Π»Π΅Π΄ Ρ Π±Π΅ΡΠΎΠ½Π½ΡΡ
ΠΎΠΏΠ°Π»ΡΠ±ΠΎΠΊ ΠΈΠ»ΠΈ ΠΎΡΠ½ΠΎΠ²Π°Π½ΠΈΡ ΠΈ ΡΠ±Π΅Π΄ΠΈΡΠ΅ΡΡ, ΡΡΠΎ Π²ΡΠ΅ ΠΏΠΎΠ²Π΅ΡΡ
Π½ΠΎΡΡΠΈ, ΠΊΠΎΡΠΎΡΡΠ΅ Π±ΡΠ΄ΡΡ ΠΊΠΎΠ½ΡΠ°ΠΊΡΠΈΡΠΎΠ²Π°ΡΡ ΡΠΎ ΡΠ²Π΅ΠΆΠΈΠΌ Π±Π΅ΡΠΎΠ½ΠΎΠΌ, ΠΈΠΌΠ΅ΡΡ ΡΠ΅ΠΌΠΏΠ΅ΡΠ°ΡΡΡΡ, ΠΊΠΎΡΠΎΡΠ°Ρ Π½Π΅ ΠΌΠΎΠΆΠ΅Ρ Π²ΡΠ·Π²Π°ΡΡ ΠΏΡΠ΅ΠΆΠ΄Π΅Π²ΡΠ΅ΠΌΠ΅Π½Π½ΠΎΠ΅ Π·Π°ΠΌΠ΅ΡΠ·Π°Π½ΠΈΠ΅ ΠΈΠ»ΠΈ ΡΠ΅ΡΡΠ΅Π·Π½ΠΎ Π·Π°ΠΌΠ΅Π΄Π»ΠΈΡΡ ΡΡ
Π²Π°ΡΡΠ²Π°Π½ΠΈΠ΅ Π±Π΅ΡΠΎΠ½Π°.
- Π Π°ΡΡΠΌΠΎΡΡΠΈΡΠ΅ Π²ΠΎΠ·ΠΌΠΎΠΆΠ½ΠΎΡΡΡ ΠΈΡΠΏΠΎΠ»ΡΠ·ΠΎΠ²Π°Π½ΠΈΡ Π³ΠΈΠ΄ΡΠ°Π²Π»ΠΈΡΠ΅ΡΠΊΠΈΡ
ΡΠΈΡΡΠ΅ΠΌ. Π Π½Π΅ΠΊΠΎΡΠΎΡΡΡ
ΡΠ»ΡΡΠ°ΡΡ
Π²Ρ ΠΌΠΎΠΆΠ΅ΡΠ΅ Π²ΡΠ±ΡΠ°ΡΡ ΠΎΠ±ΠΎΠ³ΡΠ΅Π² ΠΏΠΎΠΌΠ΅ΡΠ΅Π½ΠΈΡ, ΠΏΡΠΎΠΏΡΡΡΠΈΠ² ΡΠ΅ΠΏΠ»ΡΡ Π²ΠΎΠ΄Ρ ΠΈ Π³Π»ΠΈΠΊΠΎΠ»Ρ ΡΠ΅ΡΠ΅Π· ΡΠΈΡΡΠ΅ΠΌΡ ΡΡΡΠ±ΠΎΠΏΡΠΎΠ²ΠΎΠ΄ΠΎΠ². ΠΡΠΎ ΠΌΠΎΠΆΠ΅Ρ ΠΎΡΡΠ°ΡΡΡ ΠΈ Π½Π°Π³ΡΠ΅ΡΡ ΡΡΠ°ΡΡΠΊΠΈ Π·Π΅ΠΌΠ»ΡΠ½ΠΎΠ³ΠΎ ΠΏΠΎΠ»ΠΎΡΠ½Π° ΠΏΠ΅ΡΠ΅Π΄ ΡΠΊΠ»Π°Π΄ΠΊΠΎΠΉ ΠΈ ΠΎΠ±Π΅ΡΠΏΠ΅ΡΠΈΡΡ ΡΠ΅ΠΏΠ»ΠΎ ΠΏΡΠΈ Π·Π°ΡΠ²Π΅ΡΠ΄Π΅Π²Π°Π½ΠΈΠΈ Π±Π΅ΡΠΎΠ½Π°.
- ΠΡΠΏΠΎΠ»ΡΠ·ΡΠΉΡΠ΅ ΠΊΠΎΡΠΏΡΡΠ°. ΠΡΠ΅ΠΌΠ΅Π½Π½ΡΠ΅ ΠΎΠ³ΡΠ°ΠΆΠ΄Π΅Π½ΠΈΡ Π²ΠΎΠΊΡΡΠ³ ΡΠ°Π±ΠΎΡΠ΅ΠΉ Π·ΠΎΠ½Ρ ΠΌΠΎΠΆΠ½ΠΎ ΠΈΡΠΏΠΎΠ»ΡΠ·ΠΎΠ²Π°ΡΡ Π΄Π»Ρ Π·Π°ΡΠΈΡΡ ΠΎΡ Π½Π΅ΠΏΠΎΠ³ΠΎΠ΄Ρ. ΠΠΎ Π²ΡΠ΅ΠΌΡ ΡΠΊΠ»Π°Π΄ΠΊΠΈ ΠΈ ΠΎΡΠ²Π΅ΡΠΆΠ΄Π΅Π½ΠΈΡ Π±Π΅ΡΠΎΠ½Π° ΠΏΠ΅ΡΠ΅Π΄ ΡΠΊΠ»Π°Π΄ΠΊΠΎΠΉ Π±Π΅ΡΠΎΠ½Π° Π½Π΅ΠΎΠ±Ρ
ΠΎΠ΄ΠΈΠΌΠΎ Π½Π°Π³ΡΠ΅ΡΡ ΠΎΠ³ΡΠ°ΠΆΠ΄Π΅Π½ΠΈΡ Π΄Π»Ρ Π·Π°ΡΠΈΡΡ ΠΎΡ ΡΡΠ΅Π·ΠΌΠ΅ΡΠ½ΠΎΠ³ΠΎ Ρ
ΠΎΠ»ΠΎΠ΄Π°. Π£Π±Π΅Π΄ΠΈΡΠ΅ΡΡ, ΡΡΠΎ ΠΎΠ±ΠΎΠ³ΡΠ΅Π²Π°ΡΠ΅Π»Ρ Π½Π΅ Π΄ΡΠ΅Ρ ΠΏΡΡΠΌΠΎ Π½Π° Π±Π΅ΡΠΎΠ½, ΡΠ°ΠΊ ΠΊΠ°ΠΊ ΡΡΠΎ ΠΌΠΎΠΆΠ΅Ρ Π²ΡΠ·Π²Π°ΡΡ ΠΏΠ΅ΡΠ΅Π³ΡΠ΅Π² ΠΈΠ»ΠΈ Π²ΡΡΡΡ
Π°Π½ΠΈΠ΅. ΠΡΠΎΠΌΠ΅ ΡΠΎΠ³ΠΎ, ΡΠ±Π΅Π΄ΠΈΡΠ΅ΡΡ, ΡΡΠΎ Π²ΠΎΠ·Π΄ΡΡ
ΠΈΠ· ΠΎΠ±ΠΎΠ³ΡΠ΅Π²Π°ΡΠ΅Π»Ρ Π²ΡΡ
ΠΎΠ΄ΠΈΡ Π½Π°ΡΡΠΆΡ, ΡΡΠΎΠ±Ρ Π·Π°ΡΠΈΡΠΈΡΡ ΡΠ°Π±ΠΎΡΠΈΡ
ΠΎΡ ΡΠ³Π°ΡΠ½ΠΎΠ³ΠΎ Π³Π°Π·Π° ΠΈ ΠΏΠ°ΡΠΎΠ², Π° ΡΠ°ΠΊΠΆΠ΅ Π·Π°ΡΠΈΡΠΈΡΡ Π±Π΅ΡΠΎΠ½ ΠΎΡ ΠΊΠ°ΡΠ±ΠΎΠ½ΠΈΠ·Π°ΡΠΈΠΈ.
- Π£Π»ΠΎΠΆΠΈΡΠ΅ Π±Π΅ΡΠΎΠ½ Π½Π° Π±ΠΎΠ»Π΅Π΅ Π½ΠΈΠ·ΠΊΡΡ, ΡΠ΅ΠΌ ΠΎΠ±ΡΡΠ½ΠΎ, ΠΏΡΠΎΡΠ°Π΄ΠΊΡ. ΠΡΠΎ ΡΠ²Π΅Π΄Π΅Ρ ΠΊ ΠΌΠΈΠ½ΠΈΠΌΡΠΌΡ ΠΊΡΠΎΠ²ΠΎΡΠ΅ΡΠ΅Π½ΠΈΠ΅ ΠΈ Π·Π°Π΄Π΅ΡΠΆΠΊΠΈ ΡΡΡΠ°Π½ΠΎΠ²ΠΊΠΈ. ΠΠ°ΡΠΈΡΠ° ΠΈ ΠΎΡΠ²Π΅ΡΠΆΠ΄Π΅Π½ΠΈΠ΅ Π΄ΠΎΠ»ΠΆΠ½Ρ Π½Π°ΡΠΈΠ½Π°ΡΡΡΡ ΡΡΠ°Π·Ρ ΠΏΠΎΡΠ»Π΅ ΡΠΊΠ»Π°Π΄ΠΊΠΈ Π±Π΅ΡΠΎΠ½Π°.
- ΠΠΎΠΊΡΠΎΠΉΡΠ΅ Π±Π΅ΡΠΎΠ½. ΠΡΠ»ΠΈ Π²Ρ Π½Π΅ ΠΈΡΠΏΠΎΠ»ΡΠ·ΡΠ΅ΡΠ΅ ΠΎΠ±ΠΎΠ³ΡΠ΅Π²Π°Π΅ΠΌΡΠΉ ΠΊΠΎΡΠΏΡΡ, Π²Ρ ΠΌΠΎΠΆΠ΅ΡΠ΅ ΠΈΡΠΏΠΎΠ»ΡΠ·ΠΎΠ²Π°ΡΡ ΠΈΠ·ΠΎΠ»ΠΈΡΠΎΠ²Π°Π½Π½ΡΠ΅ ΠΎΠ΄Π΅ΡΠ»Π° ΠΈΠ»ΠΈ ΠΌΠ°ΡΡ, ΠΈΠ·ΠΎΠ»ΠΈΡΠΎΠ²Π°Π½Π½ΡΠ΅ ΠΏΠ°Π½Π΅Π»ΠΈ ΠΈΠ· ΠΏΠΎΠ»ΠΈΡΡΠΈΡΠΎΠ»Π° ΠΈΠ»ΠΈ ΡΠΎΠ»ΠΎΠΌΡ, ΠΏΠΎΠΊΡΡΡΡΠ΅ ΠΏΠ»Π°ΡΡΠΈΠΊΠΎΠ²ΡΠΌΠΈ Π»ΠΈΡΡΠ°ΠΌΠΈ, ΡΡΠΎΠ±Ρ Π·Π°ΡΠΈΡΠΈΡΡ Π±Π΅ΡΠΎΠ½ Π²ΠΎ Π²ΡΠ΅ΠΌΡ ΠΎΡΠ²Π΅ΡΠΆΠ΄Π΅Π½ΠΈΡ. ΠΡΠΈ ΠΌΠ΅ΡΠΎΠ΄Ρ ΠΎΡΠ½ΠΎΠ²Π°Π½Ρ Π½Π° ΡΠ΅ΠΏΠ»Π΅ Π³ΠΈΠ΄ΡΠ°ΡΠ°ΡΠΈΠΈ ΡΠ΅ΠΌΠ΅Π½ΡΠ° Π΄Π»Ρ ΠΏΠΎΠ΄Π΄Π΅ΡΠΆΠ°Π½ΠΈΡ ΡΠΎΠΎΡΠ²Π΅ΡΡΡΠ²ΡΡΡΠ΅ΠΉ ΡΠ΅ΠΌΠΏΠ΅ΡΠ°ΡΡΡΡ.
- ΠΠ·Π±Π΅Π³Π°ΠΉΡΠ΅ ΡΠ΅Π·ΠΊΠΈΡ ΠΏΠ΅ΡΠ΅ΠΏΠ°Π΄ΠΎΠ² ΡΠ΅ΠΌΠΏΠ΅ΡΠ°ΡΡΡΡ. ΠΡΠΈ ΡΠ½ΡΡΠΈΠΈ Π·Π°ΡΠΈΡΡ Π±ΡΠ΄ΡΡΠ΅ ΠΎΡΡΠΎΡΠΎΠΆΠ½Ρ, ΡΡΠΎΠ±Ρ Π½Π΅ ΠΏΠΎΠ΄Π²Π΅ΡΠ³Π½ΡΡΡ Π±Π΅ΡΠΎΠ½ ΡΠ΅ΡΠΌΠΈΡΠ΅ΡΠΊΠΎΠΌΡ ΡΠ΄Π°ΡΡ ΠΈΠ·-Π·Π° ΡΠ»ΠΈΡΠΊΠΎΠΌ ΡΠΈΠ»ΡΠ½ΠΎΠ³ΠΎ ΠΏΠ°Π΄Π΅Π½ΠΈΡ ΡΠ΅ΠΌΠΏΠ΅ΡΠ°ΡΡΡΡ Π² ΡΠ΅ΡΠ΅Π½ΠΈΠ΅ ΠΏΠ΅ΡΠ²ΡΡ 24 ΡΠ°ΡΠΎΠ² ΠΏΠΎΡΠ»Π΅ ΠΎΠΊΠΎΠ½ΡΠ°Π½ΠΈΡ ΠΏΠ΅ΡΠΈΠΎΠ΄Π° Π·Π°ΡΠΈΡΡ. Π‘ΠΌ. Π’Π°Π±Π»ΠΈΡΡ 5.1 ACI 306 Π΄Π»Ρ ΠΏΠΎΠ»ΡΡΠ΅Π½ΠΈΡ ΠΈΠ½ΡΠΎΡΠΌΠ°ΡΠΈΠΈ ΠΎ ΠΌΠ°ΠΊΡΠΈΠΌΠ°Π»ΡΠ½ΠΎΠΌ ΠΏΠ°Π΄Π΅Π½ΠΈΠΈ ΡΠ΅ΠΌΠΏΠ΅ΡΠ°ΡΡΡΡ ΡΠ΅ΡΠ΅Π· 24 ΡΠ°ΡΠ° ΠΏΠΎΡΠ»Π΅ ΡΠ½ΡΡΠΈΡ Π·Π°ΡΠΈΡΡ.
ΠΠΎΠ΄ΡΠΎΠ±Π½Π΅Π΅ ΠΎ CONCERA β’ Π΄Π»Ρ Π±Π΅ΡΠΎΠ½Π° Ρ ΡΠ΅Π³ΡΠ»ΠΈΡΡΠ΅ΠΌΡΠΌ ΠΏΠΎΡΠΎΠΊΠΎΠΌ
ΠΡΠΏΠΎΠ»ΡΠ·ΠΎΠ²Π°Π½ΠΈΠ΅ Π΄ΠΎΠ±Π°Π²ΠΎΠΊ, ΡΠ½ΠΈΠΆΠ°ΡΡΠΈΡ ΡΡΠΎΠ²Π΅Π½Ρ Π²ΠΎΠ΄Ρ, ΡΠ°ΠΊΠΈΡ ΠΊΠ°ΠΊ Π΄ΠΎΠ±Π°Π²ΠΊΠΈ CONCERA β’ Π΄Π»Ρ Π±Π΅ΡΠΎΠ½Π° Ρ ΡΠ΅Π³ΡΠ»ΠΈΡΡΠ΅ΠΌΡΠΌ ΠΏΠΎΡΠΎΠΊΠΎΠΌ, ΠΌΠΎΠΆΠ΅Ρ ΡΠΌΠ΅Π½ΡΡΠΈΡΡ ΡΠ°ΡΡΡΠ΅ΡΠΊΠΈΠ²Π°Π½ΠΈΠ΅ ΠΈΠ·-Π·Π° Π±ΠΎΠ»Π΅Π΅ Π½ΠΈΠ·ΠΊΠΎΠ³ΠΎ ΡΠΎΠΎΡΠ½ΠΎΡΠ΅Π½ΠΈΡ Π²ΠΎΠ΄Π° / ΡΠ΅ΠΌΠ΅Π½Ρ ΠΈ ΠΎΠ±Π΅ΡΠΏΠ΅ΡΠΈΡΡ Π΄ΠΎΠΏΠΎΠ»Π½ΠΈΡΠ΅Π»ΡΠ½ΡΠ΅ ΠΏΡΠ΅ΠΈΠΌΡΡΠ΅ΡΡΠ²Π°, ΡΠ°ΠΊΠΈΠ΅ ΠΊΠ°ΠΊ ΡΠ°Π·ΠΌΠ΅ΡΠ΅Π½ΠΈΠ΅ Ρ ΠΌΠΈΠ½ΠΈΠΌΠ°Π»ΡΠ½ΠΎΠΉ Π²ΠΈΠ±ΡΠ°ΡΠΈΠ΅ΠΉ.
ΠΠ»Ρ ΠΏΠΎΠ»ΡΡΠ΅Π½ΠΈΡ Π΄ΠΎΠΏΠΎΠ»Π½ΠΈΡΠ΅Π»ΡΠ½ΠΎΠΉ ΠΈΠ½ΡΠΎΡΠΌΠ°ΡΠΈΠΈ ΠΎ ΡΠΊΠ»Π°Π΄ΠΊΠ΅ Π±Π΅ΡΠΎΠ½Π° Π·ΠΈΠΌΠΎΠΉ ΠΎΠ±ΡΠ°ΡΠΈΡΠ΅ΡΡ ΠΊ Π΄ΠΎΠΊΡΠΌΠ΅Π½ΡΠ°ΠΌ CIP27 Β«ΠΠ΅ΡΠΎΠ½ΠΈΡΠΎΠ²Π°Π½ΠΈΠ΅ Π΄Π»Ρ Ρ ΠΎΠ»ΠΎΠ΄Π½ΠΎΠΉ ΠΏΠΎΠ³ΠΎΠ΄ΡΒ» ΠΠ°ΡΠΈΠΎΠ½Π°Π»ΡΠ½ΠΎΠΉ Π°ΡΡΠΎΡΠΈΠ°ΡΠΈΠΈ ΠΏΡΠΎΠΈΠ·Π²ΠΎΠ΄ΠΈΡΠ΅Π»Π΅ΠΉ Π³ΠΎΡΠΎΠ²ΡΡ Π±Π΅ΡΠΎΠ½Π½ΡΡ ΡΠΌΠ΅ΡΠ΅ΠΉ, Β«Π’Π΅ΡΠΌΠΈΡΠ΅ΡΠΊΠΎΠ΅ ΡΠ°ΡΡΡΠ΅ΡΠΊΠΈΠ²Π°Π½ΠΈΠ΅ Π±Π΅ΡΠΎΠ½Π°Β» CIP 42 ΠΈ Β«Π ΡΠΊΠΎΠ²ΠΎΠ΄ΡΡΠ²ΠΎ ΠΏΠΎ Π±Π΅ΡΠΎΠ½ΠΈΡΠΎΠ²Π°Π½ΠΈΡ Π² Ρ ΠΎΠ»ΠΎΠ΄Π½ΡΡ ΡΡΠ»ΠΎΠ²ΠΈΡΡ Β» ΠΠΌΠ΅ΡΠΈΠΊΠ°Π½ΡΠΊΠΎΠ³ΠΎ ΠΈΠ½ΡΡΠΈΡΡΡΠ° Π±Π΅ΡΠΎΠ½Π°.
Π‘ΡΡ ΠΈΡ ΠΏΠΎΠ»ΠΈΠΌΠ΅ΡΠΎΠ² ΠΏΠΎ ΡΡΠ°Π²Π½Π΅Π½ΠΈΡ Ρ Π²Π»Π°ΠΆΠ½ΡΠΌΠΈ ΠΏΠΎΠ»ΠΈΠΌΠ΅ΡΠ°ΠΌΠΈ Π΄Π»Ρ GFRC: ΠΏΠΎΠ΄ΡΠΎΠ±Π½ΡΠΉ Π°Π½Π°Π»ΠΈΠ· ΠΈ ΡΠ΅ΠΊΠΎΠΌΠ΅Π½Π΄Π°ΡΠΈΡ
ΠΠ ΠΠΠΠ§ΠΠΠΠ. ΠΡΠ° ΡΡΠ°ΡΡΡ Π±ΡΠ»Π° ΠΈΠ·ΠΌΠ΅Π½Π΅Π½Π° ΠΏΠΎ ΡΡΠ°Π²Π½Π΅Π½ΠΈΡ Ρ ΠΏΠ΅ΡΠ²ΠΎΠ½Π°ΡΠ°Π»ΡΠ½ΠΎ ΠΎΠΏΡΠ±Π»ΠΈΠΊΠΎΠ²Π°Π½Π½ΠΎΠΉ Π²Π΅ΡΡΠΈΠ΅ΠΉ. ΠΡΠΎΠΈΠ·Π²ΠΎΠ΄ΠΈΡΠ΅Π»Ρ ΠΎΠ΄Π½ΠΎΠ³ΠΎ ΠΈΠ· ΡΠ°ΡΡΠΌΠΎΡΡΠ΅Π½Π½ΡΡ ΠΏΡΠΎΠ΄ΡΠΊΡΠΎΠ² ΠΎΠ±ΡΠ°ΡΠΈΠ»ΡΡ Ρ ΡΠ³ΡΠΎΠ·Π°ΠΌΠΈ ΡΡΠ΄Π΅Π±Π½ΠΎΠ³ΠΎ ΠΈΡΠΊΠ° ΠΊΠ°ΠΊ Π² CCI, ΡΠ°ΠΊ ΠΈ Π² ΠΎΡΠ½ΠΎΡΠ΅Π½ΠΈΠΈ Π΄ΡΡΠ³ΠΎΠ³ΠΎ ΠΏΡΠΎΠΈΠ·Π²ΠΎΠ΄ΠΈΡΠ΅Π»Ρ, ΡΠΏΠΎΠΌΡΠ½ΡΡΠΎΠ³ΠΎ Π² ΡΡΠΎΠΌ ΠΎΡΡΠ΅ΡΠ΅.Π₯ΠΎΡΡ ΠΌΡ ΠΏΠΎΠ΄Π΄Π΅ΡΠΆΠΈΠ²Π°Π΅ΠΌ ΡΠ΅Π·ΡΠ»ΡΡΠ°ΡΡ Π½Π°ΡΠΈΡ ΠΈΡΠΏΡΡΠ°Π½ΠΈΠΉ ΠΈ ΡΠ²Π΅ΡΠ΄ΠΎ Π²Π΅ΡΠΈΠΌ, ΡΡΠΎ ΡΡΠ°Π²Π½ΠΈΡΠ΅Π»ΡΠ½ΡΠ΅ ΠΈΡΡΠ»Π΅Π΄ΠΎΠ²Π°Π½ΠΈΡ, ΠΏΠΎΠ΄ΠΎΠ±Π½ΡΠ΅ ΡΡΠΎΠΌΡ, ΡΠ²Π»ΡΡΡΡΡ ΠΏΠΎΠ»Π΅Π·Π½ΠΎΠΉ ΠΈ Π²Π°ΠΆΠ½ΠΎΠΉ ΡΡΠ»ΡΠ³ΠΎΠΉ Π΄Π»Ρ Π²ΡΠ΅ΠΉ ΠΈΠ½Π΄ΡΡΡΡΠΈΠΈ Π±Π΅ΡΠΎΠ½Π½ΡΡ ΡΡΠΎΠ»Π΅ΡΠ½ΠΈΡ ΠΈ ΠΌΠΎΠ³ΡΡ ΡΠΎΠ»ΡΠΊΠΎ ΡΠΏΠΎΡΠΎΠ±ΡΡΠ²ΠΎΠ²Π°ΡΡ ΡΡΠΏΠ΅Ρ Ρ ΠΊΠ°ΠΆΠ΄ΠΎΠ³ΠΎ, ΠΌΡ ΠΏΡΠ΅Π΄ΠΏΠΎΡΠ»ΠΈ Π±Ρ ΠΏΡΠΎΠ²ΠΎΠ΄ΠΈΡΡ Π±ΠΎΠ»ΡΡΠ΅ Π²ΡΠ΅ΠΌΠ΅Π½ΠΈ, ΠΏΡΠΎΠ²ΠΎΠ΄Ρ Π΄ΠΎΠΏΠΎΠ»Π½ΠΈΡΠ΅Π»ΡΠ½ΡΠ΅ ΠΈΡΡΠ»Π΅Π΄ΠΎΠ²Π°Π½ΠΈΡ, Π° Π½Π΅ Π±ΠΎΡΠΎΡΡΡΡ ΡΡΠ΄Π΅Π±Π½Π°Ρ ΡΡΠΆΠ±Π°. ΠΡΠΎΠΌΠ΅ ΡΠΎΠ³ΠΎ, ΠΎΠ±ΡΠ°ΡΠΈΡΠ΅ Π²Π½ΠΈΠΌΠ°Π½ΠΈΠ΅, ΡΡΠΎ Π½ΠΈ ΠΎΠ΄ΠΈΠ½ ΠΈΠ· ΠΏΡΠΎΠΈΠ·Π²ΠΎΠ΄ΠΈΡΠ΅Π»Π΅ΠΉ Π½Π΅ Π·Π½Π°Π», ΡΡΠΎ ΡΡΠΎ ΠΈΡΡΠ»Π΅Π΄ΠΎΠ²Π°Π½ΠΈΠ΅ ΠΏΡΠΎΠ²ΠΎΠ΄ΠΈΡΡΡ, ΠΈ ΡΡΠΎ CCI ΠΏΠΎΡΡΠ°ΡΠΈΠ»Π° Π½Π° ΡΡΠΎ Π½Π΅ΡΠΊΠΎΠ»ΡΠΊΠΎ ΠΌΠ΅ΡΡΡΠ΅Π² ΠΈ ΡΡΡΡΡΠΈ Π΄ΠΎΠ»Π»Π°ΡΠΎΠ². ΠΡ Π³Π»ΡΠ±ΠΎΠΊΠΎ ΠΈΠ·Π²ΠΈΠ½ΡΠ΅ΠΌΡΡ ΠΏΠ΅ΡΠ΅Π΄ ΡΠ΅ΠΌΠΈ, ΠΊΠΎΠΌΡ ΠΎΡΠΊΠ°Π·ΡΠ²Π°ΡΡ Π² Π΄ΠΎΡΡΡΠΏΠ΅ ΠΊ Π°ΠΊΡΡΠ°Π»ΡΠ½ΠΎΠΉ, ΠΏΠΎΠ»Π΅Π·Π½ΠΎΠΉ ΠΈ ΠΏΡΠ°Π²Π΄ΠΈΠ²ΠΎΠΉ ΠΈΠ½ΡΠΎΡΠΌΠ°ΡΠΈΠΈ, Π½Π°Π΄ ΠΊΠΎΡΠΎΡΠΎΠΉ ΠΌΡ ΡΠ°ΠΊ ΠΌΠ½ΠΎΠ³ΠΎ ΡΠ°Π±ΠΎΡΠ°Π»ΠΈ.
GFRC — ΡΡΠΎ ΡΠ·ΠΊΠΎΡΠΏΠ΅ΡΠΈΠ°Π»ΠΈΠ·ΠΈΡΠΎΠ²Π°Π½Π½Π°Ρ ΡΠΎΡΠΌΠ° Π±Π΅ΡΠΎΠ½Π°, ΡΠ°Π·ΡΠ°Π±ΠΎΡΠ°Π½Π½Π°Ρ ΠΈ ΠΎΠΏΡΠΈΠΌΠΈΠ·ΠΈΡΠΎΠ²Π°Π½Π½Π°Ρ Π΄Π»Ρ ΠΈΠ·Π³ΠΎΡΠΎΠ²Π»Π΅Π½ΠΈΡ Π±ΠΎΠ»ΡΡΠΈΡ , ΡΠΎΠ½ΠΊΠΈΡ ΠΏΠ°Π½Π΅Π»Π΅ΠΉ ΠΈ Π»Π΅Π³ΠΊΠΈΡ ΡΡΠ΅Ρ ΠΌΠ΅ΡΠ½ΡΡ ΠΎΠ±ΡΠ΅ΠΊΡΠΎΠ². ΠΠ»ΡΡΠ΅Π²ΡΠΌ ΡΠ²ΠΎΠΉΡΡΠ²ΠΎΠΌ GFRC, ΠΊΠΎΡΠΎΡΠΎΠ΅ Π΄Π΅Π»Π°Π΅Ρ ΡΡΠΎ Π²ΠΎΠ·ΠΌΠΎΠΆΠ½ΡΠΌ, ΡΠ²Π»ΡΠ΅ΡΡΡ Π΅Π³ΠΎ Π²ΡΡΠΎΠΊΠ°Ρ ΠΏΡΠΎΡΠ½ΠΎΡΡΡ Π½Π° ΠΈΠ·Π³ΠΈΠ± (ΠΈΠ·Π³ΠΈΠ±). Π ΠΎΡΠ»ΠΈΡΠΈΠ΅ ΠΎΡ ΠΎΠ±ΡΡΠ½ΠΎΠ³ΠΎ Π°ΡΠΌΠΈΡΠΎΠ²Π°Π½Π½ΠΎΠ³ΠΎ Π±Π΅ΡΠΎΠ½Π°, Π³Π΄Π΅ Π²Π°ΠΆΠ½Π° ΠΏΡΠΎΡΠ½ΠΎΡΡΡ Π½Π° ΡΠΆΠ°ΡΠΈΠ΅, ΡΠ΅ΡΠ°ΡΡΠ΅Π΅ Π·Π½Π°ΡΠ΅Π½ΠΈΠ΅ ΠΈΠΌΠ΅Π΅Ρ ΠΏΡΠΎΡΠ½ΠΎΡΡΡ Π½Π° ΠΈΠ·Π³ΠΈΠ± GFRC. ΠΠ΅ΡΠΎΠ½ ΡΠΎ ΡΠ²Π΅ΡΡ Π²ΡΡΠΎΠΊΠΎΠΉ ΠΏΡΠΎΡΠ½ΠΎΡΡΡΡ Π½Π° ΡΠΆΠ°ΡΠΈΠ΅ Π½Π΅ ΡΠΎΠ»ΡΠΊΠΎ Π½Π΅ ΠΈΠΌΠ΅Π΅Ρ Π·Π½Π°ΡΠ΅Π½ΠΈΡ, ΠΎΠ½ Ρ ΠΎΡΠΎΡΠΎ ΠΈΠ·Π²Π΅ΡΡΠ΅Π½ ΡΠ²ΠΎΠ΅ΠΉ Ρ ΡΡΠΏΠΊΠΎΡΡΡΡ, ΡΡΠΎ ΡΠ²Π»ΡΠ΅ΡΡΡ Ρ Π°ΡΠ°ΠΊΡΠ΅ΡΠΈΡΡΠΈΠΊΠΎΠΉ, ΠΏΡΠΎΡΠΈΠ²ΠΎΠΏΠΎΠ»ΠΎΠΆΠ½ΠΎΠΉ ΡΠΎΠΌΡ, ΡΡΠΎ Π΄Π΅Π»Π°Π΅Ρ Π²ΡΡΠΎΠΊΠΎΠΊΠ°ΡΠ΅ΡΡΠ²Π΅Π½Π½ΡΠΉ GFRC.
ΠΠ±ΡΡΠ½ΠΎ GFRC Π΄ΠΎΠ»ΠΆΠ΅Π½ ΠΎΡΡΠ°Π²Π°ΡΡΡΡ Π²Π»Π°ΠΆΠ½ΡΠΌ Π²Π½ΡΡΡΠΈ Π½Π΅ ΠΌΠ΅Π½Π΅Π΅ 7 Π΄Π½Π΅ΠΉ Π΄Π»Ρ Π΄ΠΎΡΡΠΈΠΆΠ΅Π½ΠΈΡ Π½Π΅ΠΎΠ±Ρ ΠΎΠ΄ΠΈΠΌΠΎΠΉ ΠΏΡΠΎΡΠ½ΠΎΡΡΠΈ. ΠΡΠ΅ΠΆΠ΄Π΅Π²ΡΠ΅ΠΌΠ΅Π½Π½ΠΎΠ΅ Π²ΡΡΡΡ Π°Π½ΠΈΠ΅ Π·Π°ΠΌΠ΅Π΄Π»ΠΈΡ ΠΈΠ»ΠΈ ΠΎΡΡΠ°Π½ΠΎΠ²ΠΈΡ ΠΎΡΠ²Π΅ΡΠΆΠ΄Π΅Π½ΠΈΠ΅, Π² ΡΠ΅Π·ΡΠ»ΡΡΠ°ΡΠ΅ ΡΠ΅Π³ΠΎ Π±Π΅ΡΠΎΠ½ ΡΡΠ°Π½Π΅Ρ ΠΌΡΠ³ΠΊΠΈΠΌ, ΠΏΠΎΡΠΈΡΡΡΠΌ ΠΈ Π½Π΅ΠΏΡΠΎΡΠ½ΡΠΌ. ΠΠ΄Π΅ΠΊΠ²Π°ΡΠ½ΠΎΠ΅ ΠΎΡΠ²Π΅ΡΠΆΠ΄Π΅Π½ΠΈΠ΅ ΠΌΠΎΠΆΠ΅Ρ Π±ΡΡΡ Π΄ΠΎΡΡΠΈΠ³Π½ΡΡΠΎ Ρ ΠΏΠΎΠΌΠΎΡΡΡ ΡΡΠ°Π΄ΠΈΡΠΈΠΎΠ½Π½ΠΎΠ³ΠΎ Π²Π»Π°ΠΆΠ½ΠΎΠ³ΠΎ ΠΎΡΠ²Π΅ΡΠΆΠ΄Π΅Π½ΠΈΡ, ΠΊΠΎΠ³Π΄Π° Π±Π΅ΡΠΎΠ½ Π²ΡΠ΄Π΅ΡΠΆΠΈΠ²Π°Π΅ΡΡΡ Π²ΠΎ 100% Π²Π»Π°ΠΆΠ½ΠΎΠΉ ΡΡΠ΅Π΄Π΅ Π² ΡΠ΅ΡΠ΅Π½ΠΈΠ΅ 7 Π΄Π½Π΅ΠΉ ΠΏΠΎΠ΄ΡΡΠ΄. ΠΠ»Ρ Π±ΠΎΠ»ΡΡΠΈΠ½ΡΡΠ²Π° ΠΏΡΠΈΠΌΠ΅Π½Π΅Π½ΠΈΠΉ ΡΡΠΎ Π½Π΅ΠΏΡΠ°ΠΊΡΠΈΡΠ½ΠΎ, ΠΏΠΎΡΡΠΎΠΌΡ Π²ΠΌΠ΅ΡΡΠΎ ΠΎΡΠ²Π΅ΡΠΆΠ΄Π°ΡΡΠ΅ΠΉ Π΄ΠΎΠ±Π°Π²ΠΊΠΈ ΠΈΡΠΏΠΎΠ»ΡΠ·ΡΠ΅ΡΡΡ ΠΏΠΎΠ»ΠΈΠΌΠ΅Ρ.
ΠΠ΅ΡΠ²ΠΈΡΠ½Π°Ρ ΠΈ ΠΊΡΠ°ΠΉΠ½Π΅ Π²Π°ΠΆΠ½Π°Ρ ΡΠ΅Π»Ρ ΠΏΠΎΠ»ΠΈΠΌΠ΅ΡΠ½ΠΎΠΉ Π΄ΠΎΠ±Π°Π²ΠΊΠΈ Π΄Π»Ρ ΠΎΡΠ²Π΅ΡΠΆΠ΄Π΅Π½ΠΈΡ — ΠΏΠΎΠ΄Π΄Π΅ΡΠΆΠΈΠ²Π°ΡΡ ΡΡΠΎΠ²Π΅Π½Ρ Π²Π½ΡΡΡΠ΅Π½Π½Π΅ΠΉ Π²Π»Π°ΠΆΠ½ΠΎΡΡΠΈ Π±Π΅ΡΠΎΠ½Π°, ΡΡΠΎΠ±Ρ ΠΏΠΎΡΡΠ»Π°Π½Π΄ΡΠ΅ΠΌΠ΅Π½ΡΠ½Π°Ρ ΠΏΠ°ΡΡΠ° GFRC ΠΏΡΠΎΠ΄ΠΎΠ»ΠΆΠ°Π»Π° Π³ΠΈΠ΄ΡΠ°ΡΠΈΡΠΎΠ²Π°ΡΡ (ΠΎΡΠ²Π΅ΡΠΆΠ΄Π°ΡΡΡΡ), Π΄Π°ΠΆΠ΅ ΠΊΠΎΠ³Π΄Π° ΠΈΠ·Π΄Π΅Π»ΠΈΠ΅ Π½Π°Ρ ΠΎΠ΄ΠΈΡΡΡ Π½Π° ΠΎΡΠΊΡΡΡΠΎΠΌ Π²ΠΎΠ·Π΄ΡΡ Π΅.ΠΠΎΠ»ΠΈΠΌΠ΅Ρ Π΄Π΅Π»Π°Π΅Ρ ΡΡΠΎ, ΠΏΠΎ ΡΡΡΠ΅ΡΡΠ²Ρ ΠΎΠ±ΡΠ°Π·ΡΡ Π²Π½ΡΡΡΠ΅Π½Π½ΡΡ ΠΎΡΠ²Π΅ΡΠΆΠ΄Π°ΡΡΡΡ ΠΌΠ΅ΠΌΠ±ΡΠ°Π½Ρ, Π·Π°ΠΌΠ΅Π΄Π»ΡΡ ΠΏΠΎΡΠ΅ΡΡ Π²Π»Π°Π³ΠΈ.
ΠΠ°ΠΊ ΠΈ Π΄Π»Ρ Π»ΡΠ±ΠΎΠ³ΠΎ Π΄ΡΡΠ³ΠΎΠ³ΠΎ Π±Π΅ΡΠΎΠ½Π°, ΠΎΡΠ²Π΅ΡΠΆΠ΄Π΅Π½ΠΈΠ΅ ΠΈΠΌΠ΅Π΅Ρ ΠΆΠΈΠ·Π½Π΅Π½Π½ΠΎ Π²Π°ΠΆΠ½ΠΎΠ΅ Π·Π½Π°ΡΠ΅Π½ΠΈΠ΅ Π΄Π»Ρ Π΄ΠΎΡΡΠΈΠΆΠ΅Π½ΠΈΡ ΠΆΠ΅Π»Π°Π΅ΠΌΡΡ ΡΠΈΠ·ΠΈΡΠ΅ΡΠΊΠΈΡ ΡΠ²ΠΎΠΉΡΡΠ². ΠΡΠΎΡΠ½ΠΎΡΡΡ Π½Π° ΠΈΠ·Π³ΠΈΠ± (ΠΈ ΡΠΆΠ°ΡΠΈΠ΅), ΠΆΠ΅ΡΡΠΊΠΎΡΡΡ, ΠΏΠΎΡΠΈΡΡΠΎΡΡΡ ΠΈ ΠΌΠ΅Ρ Π°Π½ΠΈΡΠ΅ΡΠΊΠ°Ρ Π²ΡΠ·ΠΊΠΎΡΡΡ Π·Π°Π²ΠΈΡΡΡ ΠΎΡ ΡΠΎΠ³ΠΎ, ΠΎΡΡΠ°Π΅ΡΡΡ Π»ΠΈ ΡΠ΅ΠΌΠ΅Π½ΡΠ½Π°Ρ ΠΏΠ°ΡΡΠ° Π²Π»Π°ΠΆΠ½ΠΎΠΉ, ΠΏΠΎΡΡΠΎΠΌΡ ΠΎΠ½Π° ΠΌΠΎΠΆΠ΅Ρ ΠΏΡΠΎΠ΄ΠΎΠ»ΠΆΠ°ΡΡ Π³ΠΈΠ΄ΡΠ°ΡΠΈΡΠΎΠ²Π°ΡΡ. ΠΡ Π½Π°Π·ΡΠ²Π°Π΅ΠΌ ΡΡΠΎ ΠΎΡΠ²Π΅ΡΠΆΠ΄Π΅Π½ΠΈΠ΅ΠΌ, ΠΈ ΡΠ΅ΠΌ Π΄ΠΎΠ»ΡΡΠ΅ Π±Π΅ΡΠΎΠ½ Π·Π°ΡΡΡΠ²Π°Π΅Ρ, ΡΠ΅ΠΌ Π»ΡΡΡΠ΅ ΠΎΠ½ ΡΡΠ°Π½ΠΎΠ²ΠΈΡΡΡ.
Π Π‘Π¨Π ΠΠ½ΡΡΠΈΡΡΡ ΡΠ±ΠΎΡΠ½ΠΎΠ³ΠΎ ΠΈ ΠΏΡΠ΅Π΄Π²Π°ΡΠΈΡΠ΅Π»ΡΠ½ΠΎ Π½Π°ΠΏΡΡΠΆΠ΅Π½Π½ΠΎΠ³ΠΎ Π±Π΅ΡΠΎΠ½Π° (PCI) ΠΈΠΌΠ΅Π΅Ρ ΡΡΠΊΠΎΠ²ΠΎΠ΄ΡΡΠΈΠ΅ ΠΏΡΠΈΠ½ΡΠΈΠΏΡ ΠΈ ΡΠΏΠ΅ΡΠΈΡΠΈΠΊΠ°ΡΠΈΠΈ Π΄Π»Ρ Π΄ΠΎΠ±Π°Π²ΠΎΠΊ Π΄Π»Ρ ΠΏΠΎΠ»ΠΈΠΌΠ΅ΡΠΈΠ·Π°ΡΠΈΠΈ.Π ΡΠΊΠΎΠ²ΠΎΠ΄ΡΡΠ²ΠΎ PCI ΠΏΠΎ ΠΊΠΎΠ½ΡΡΠΎΠ»Ρ ΠΊΠ°ΡΠ΅ΡΡΠ²Π° Π΄Π»Ρ Π·Π°Π²ΠΎΠ΄ΠΎΠ² ΠΈ ΠΏΡΠΎΠΈΠ·Π²ΠΎΠ΄ΡΡΠ²Π° ΠΈΠ·Π΄Π΅Π»ΠΈΠΉ ΠΈΠ· Π±Π΅ΡΠΎΠ½Π°, Π°ΡΠΌΠΈΡΠΎΠ²Π°Π½Π½ΠΎΠ³ΠΎ ΡΡΠ΅ΠΊΠ»ΠΎΠ²ΠΎΠ»ΠΎΠΊΠ½ΠΎΠΌ, 2-Π΅ ΠΈΠ·Π΄Π°Π½ΠΈΠ΅ MNL 130-09, ΠΏΡΠΈΠ»ΠΎΠΆΠ΅Π½ΠΈΠ΅ G: Β«Π’Π΅Ρ Π½ΠΈΡΠ΅ΡΠΊΠΈΠ΅ ΡΡΠ»ΠΎΠ²ΠΈΡ Π½Π° Π΄ΠΎΠ±Π°Π²ΠΊΠΈ Π΄Π»Ρ ΠΏΠΎΠ»ΠΈΠΌΠ΅ΡΠΈΠ·Π°ΡΠΈΠΈΒ», ΡΠΎΠ΄Π΅ΡΠΆΠΈΡ ΡΡΠ΅Π±ΠΎΠ²Π°Π½ΠΈΡ ΠΊ ΡΠ²ΠΎΠΉΡΡΠ²Π°ΠΌ ΠΈ Ρ Π°ΡΠ°ΠΊΡΠ΅ΡΠΈΡΡΠΈΠΊΠ°ΠΌ Π΄ΠΎΠ±Π°Π²ΠΎΠΊ Π΄Π»Ρ ΠΏΠΎΠ»ΠΈΠΌΠ΅ΡΠΈΠ·Π°ΡΠΈΠΈ. ΠΡΠΈ ΡΡΠ΅Π±ΠΎΠ²Π°Π½ΠΈΡ ΠΏΡΠΈΠ·Π²Π°Π½Ρ ΠΎΠ±Π΅ΡΠΏΠ΅ΡΠΈΡΡ ΠΊΠ°ΡΠ΅ΡΡΠ²ΠΎ ΠΏΡΠΎΠ΄ΡΠΊΡΠΈΠΈ GFRC ΠΈ Π³Π°ΡΠ°Π½ΡΠΈΡΠΎΠ²Π°ΡΡ, ΡΡΠΎ ΠΎΡΠ²Π΅ΡΠΆΠ΄Π°ΡΡΠΈΠ΅ ΠΊΠΎΠΌΠΏΠ°ΡΠ½Π΄Ρ ΠΏΡΠΎΠ²Π΅ΡΠ΅Π½Ρ Π½Π΅Π·Π°Π²ΠΈΡΠΈΠΌΠΎΠΉ Π»Π°Π±ΠΎΡΠ°ΡΠΎΡΠΈΠ΅ΠΉ, ΡΡΠΎΠ±Ρ ΠΏΡΠΎΠ΄Π΅ΠΌΠΎΠ½ΡΡΡΠΈΡΠΎΠ²Π°ΡΡ, ΡΡΠΎ:
- Π Π΅ΠΊΠΎΠΌΠ΅Π½Π΄ΡΠ΅ΠΌΠΎΠ΅ ΠΊΠΎΠ»ΠΈΡΠ΅ΡΡΠ²ΠΎ ΠΏΠΎΠ»ΠΈΠΌΠ΅ΡΠ½ΠΎΠΉ Π΄ΠΎΠ±Π°Π²ΠΊΠΈ Π΄Π»Ρ ΠΎΡΠ²Π΅ΡΠΆΠ΄Π΅Π½ΠΈΡ Π² ΡΠΌΠ΅ΡΠΈ GFRC Π±Π΅Π· ΠΎΡΠ²Π΅ΡΠΆΠ΄Π΅Π½ΠΈΡ Π²ΠΎ Π²Π»Π°ΠΆΠ½ΠΎΠΌ ΡΠΎΡΡΠΎΡΠ½ΠΈΠΈ ΡΠ°Π²Π½ΡΠ΅ΡΡΡ ΡΠ²ΠΎΠΉΡΡΠ²Π°ΠΌ ΠΈΠ·Π³ΠΈΠ±Π° GFRC, ΠΎΡΠ²Π΅ΡΠΆΠ΄Π΅Π½Π½ΠΎΠ³ΠΎ Π² ΡΠ΅ΡΠ΅Π½ΠΈΠ΅ 7 Π΄Π½Π΅ΠΉ Π²ΠΎ Π²Π»Π°ΠΆΠ½ΠΎΠΌ ΡΠΎΡΡΠΎΡΠ½ΠΈΠΈ, ΠΊΠΎΠ³Π΄Π° ΠΎΠ±Π° ΠΈΡΠΏΡΡΠ°Π½ΠΈΡ ΠΏΡΠΎΡ ΠΎΠ΄ΡΡ ΡΠ΅ΡΠ΅Π· 28 Π΄Π½Π΅ΠΉ.
- ΠΠΎΠ»Π³ΠΎΠ²Π΅ΡΠ½ΠΎΡΡΡ ΠΌΠΎΠ΄ΠΈΡΠΈΡΠΈΡΠΎΠ²Π°Π½Π½ΠΎΠ³ΠΎ ΠΊΠΎΠΌΠΏΠΎΠ·ΠΈΡΠ° Ρ Π΄ΠΎΠ±Π°Π²Π»Π΅Π½ΠΈΠ΅ΠΌ ΠΏΠΎΠ»ΠΈΠΌΠ΅ΡΠΎΠ², ΠΎΡΠ²Π΅ΡΠΆΠ΄Π΅Π½Π½ΠΎΠ³ΠΎ ΡΡΡ ΠΈΠΌ ΡΠΏΠΎΡΠΎΠ±ΠΎΠΌ, ΠΏΠΎΠ΄ΡΠ²Π΅ΡΠΆΠ΄Π΅Π½Π½Π°Ρ ΠΈΡΠΏΡΡΠ°Π½ΠΈΡΠΌΠΈ Π½Π° ΡΡΠ°ΡΠ΅Π½ΠΈΠ΅, ΡΠ°Π²Π½Π° ΠΈΠ»ΠΈ ΠΏΡΠ΅Π²ΡΡΠ°Π΅Ρ Π΄ΠΎΠ»Π³ΠΎΠ²Π΅ΡΠ½ΠΎΡΡΡ GFRC, ΠΎΡΠ²Π΅ΡΠΆΠ΄Π΅Π½Π½ΠΎΠ³ΠΎ Π² ΡΠ΅ΡΠ΅Π½ΠΈΠ΅ 7 Π΄Π½Π΅ΠΉ Π²ΠΎ Π²Π»Π°ΠΆΠ½ΠΎΠΌ ΡΠΎΡΡΠΎΡΠ½ΠΈΠΈ.
- Π£Π΄Π΅Π»ΡΠ½ΡΠΉ Π²Π΅Ρ (ΠΏΠ»ΠΎΡΠ½ΠΎΡΡΡ) ΡΠΌΠ΅ΡΠΈ, Π²ΠΊΠ»ΡΡΠ°ΡΡΠ΅ΠΉ ΠΏΠΎΠ»ΠΈΠΌΠ΅ΡΠ½ΡΡ ΠΎΡΠ²Π΅ΡΠΆΠ΄Π°ΡΡΡΡ Π΄ΠΎΠ±Π°Π²ΠΊΡ, ΠΏΡΠ΅Π²ΡΡΠ°Π΅Ρ 120 ΡΡΠ½ΡΠΎΠ² Π½Π° ΡΡΡ (1930 ΠΊΠ³ / ΠΌ3).
- ΠΠΎΠ»ΠΈΠΌΠ΅Ρ ΠΏΡΠΎΡΠ²Π»ΡΠ΅Ρ Π΄ΠΎΠ»Π³ΠΎΠ²Π΅ΡΠ½ΠΎΡΡΡ, ΡΡΡΠΎΠΉΡΠΈΠ²ΠΎΡΡΡ ΠΊ ΡΠ»ΡΡΡΠ°ΡΠΈΠΎΠ»Π΅ΡΠΎΠ²ΠΎΠΌΡ ΠΈΠ·Π»ΡΡΠ΅Π½ΠΈΡ, ΡΡΠΎΠΉΠΊΠΎΡΡΡ ΠΊ ΠΎΠΊΠΈΡΠ»Π΅Π½ΠΈΡ ΠΈ ΡΡΠ°Π±ΠΈΠ»ΡΠ½ΠΎΡΡΡ Π² ΡΠ΅Π»ΠΎΡΠ½ΠΎΠΉ ΡΡΠ΅Π΄Π΅.
ΠΠΎ ΡΡΡΠΈ, ΡΡΠΈ ΡΡΠ΅Π±ΠΎΠ²Π°Π½ΠΈΡ Π³Π°ΡΠ°Π½ΡΠΈΡΡΡΡ, ΡΡΠΎ ΠΏΠΎΠ»ΠΈΠΌΠ΅Ρ ΠΏΠΎΠ΄Π²Π΅ΡΠ³Π½Π΅ΡΡΡ Π½Π΅Π·Π°Π²ΠΈΡΠΈΠΌΠΎΠΌΡ ΡΠ΅ΡΡΠΈΡΠΎΠ²Π°Π½ΠΈΡ, ΠΊΠΎΡΠΎΡΠΎΠ΅ Π΄ΠΎΠΊΠ°Π·ΡΠ²Π°Π΅Ρ, ΡΡΠΎ ΠΎΠ½ ΡΠ²Π»ΡΠ΅ΡΡΡ ΠΏΡΠΈΠ΅ΠΌΠ»Π΅ΠΌΠΎΠΉ Π·Π°ΠΌΠ΅Π½ΠΎΠΉ 7-Π΄Π½Π΅Π²Π½ΠΎΠ³ΠΎ Π²Π»Π°ΠΆΠ½ΠΎΠ³ΠΎ ΠΎΡΠ²Π΅ΡΠΆΠ΄Π΅Π½ΠΈΡ.
ΠΠ΅ΠΊΠΎΡΠΎΡΡΠ΅ ΠΊΠ»ΡΡΠ΅Π²ΡΠ΅ ΡΡΠ΅Π±ΠΎΠ²Π°Π½ΠΈΡ ΠΊ ΡΠ²ΠΎΠΉΡΡΠ²Π°ΠΌ, ΠΏΡΠ΅Π΄ΡΡΠΌΠΎΡΡΠ΅Π½Π½ΡΠ΅ ΡΠΏΠ΅ΡΠΈΡΠΈΠΊΠ°ΡΠΈΠ΅ΠΉ PCI:
- ΠΠΎΠ΄Π½Π°Ρ Π΄ΠΈΡΠΏΠ΅ΡΡΠΈΡ ΡΠ΅ΡΠΌΠΎΠΏΠ»Π°ΡΡΠΈΡΠ½ΠΎΠ³ΠΎ ΡΠΎΠΏΠΎΠ»ΠΈΠΌΠ΅ΡΠ° (ΠΆΠΈΠ΄ΠΊΠΈΠΉ ΠΏΠΎΠ»ΠΈΠΌΠ΅Ρ Π½Π° Π²ΠΎΠ΄Π½ΠΎΠΉ ΠΎΡΠ½ΠΎΠ²Π΅)
- Π½Π° Π°ΠΊΡΠΈΠ»ΠΎΠ²ΠΎΠΉ ΠΎΡΠ½ΠΎΠ²Π΅
- ΠΡ 45% Π΄ΠΎ 55% ΡΠ²Π΅ΡΠ΄ΡΡ Π²Π΅ΡΠ΅ΡΡΠ² ΠΏΠΎ Π²Π΅ΡΡ
Π’ΡΠ΅Π±ΠΎΠ²Π°Π½ΠΈΡ ΠΊ Ρ Π°ΡΠ°ΠΊΡΠ΅ΡΠΈΡΡΠΈΠΊΠ°ΠΌ ΠΈ Ρ Π°ΡΠ°ΠΊΡΠ΅ΡΠΈΡΡΠΈΠΊΠ°ΠΌ PCI ΠΎΡΠ΅Π½Ρ ΠΏΠΎΡ ΠΎΠΆΠΈ ΠΈΠ»ΠΈ Π°Π½Π°Π»ΠΎΠ³ΠΈΡΠ½Ρ ΡΡΠ΅Π±ΠΎΠ²Π°Π½ΠΈΡΠΌ, ΡΠΊΠ°Π·Π°Π½Π½ΡΠΌ Π² Π‘ΠΏΠ΅ΡΠΈΡΠΈΠΊΠ°ΡΠΈΠΈ ΠΠ΅ΠΆΠ΄ΡΠ½Π°ΡΠΎΠ΄Π½ΠΎΠΉ Π°ΡΡΠΎΡΠΈΠ°ΡΠΈΠΈ ΠΏΠΎ Π°ΡΠΌΠΈΡΠΎΠ²Π°Π½Π½ΠΎΠΌΡ ΡΡΠ΅ΠΊΠ»ΠΎΠ²ΠΎΠ»ΠΎΠΊΠ½ΠΎΠΌ (GRCA), 4-Π΅ ΠΈΠ·Π΄Π°Π½ΠΈΠ΅, ΡΠ°Π±Π»ΠΈΡΠ° 2.
ΠΡΡΠ΅ΠΊΡΠΈΠ²Π½ΠΎΡΡΡ ΠΏΠΎΠ»ΠΈΠΌΠ΅ΡΠ½ΠΎΠΉ Π΄ΠΎΠ±Π°Π²ΠΊΠΈ Π΄Π»Ρ ΠΎΡΠ²Π΅ΡΠΆΠ΄Π΅Π½ΠΈΡ (Π΄Π°Π»Π΅Π΅ ΠΈΠΌΠ΅Π½ΡΠ΅ΠΌΠΎΠΉ ΠΏΡΠΎΡΡΠΎ Β«ΠΏΠΎΠ»ΠΈΠΌΠ΅ΡΒ») ΠΏΡΠΈ ΡΠΎΡ ΡΠ°Π½Π΅Π½ΠΈΠΈ Π²Π½ΡΡΡΠ΅Π½Π½Π΅Π³ΠΎ ΡΡΠΎΠ²Π½Ρ Π²Π»Π°ΠΆΠ½ΠΎΡΡΠΈ Π±Π΅ΡΠΎΠ½Π° ΠΎΡΠ΅Π½Ρ Π²Π°ΠΆΠ½Π° Π½Π° Π½Π°ΡΠ°Π»ΡΠ½ΠΎΠΌ ΡΡΠ°ΠΏΠ΅ ΡΠΊΡΠΏΠ»ΡΠ°ΡΠ°ΡΠΈΠΈ GFRC, ΠΏΠΎΡΠΎΠΌΡ ΡΡΠΎ, Π΅ΡΠ»ΠΈ ΠΎΠ½Π° Π½Π΅ ΠΎΡΡΠ°Π½Π΅ΡΡΡ Π΄ΠΎΡΡΠ°ΡΠΎΡΠ½ΠΎ Π²Π»Π°ΠΆΠ½ΠΎΠΉ, Π±Π΅ΡΠΎΠ½ Π±ΡΠ΄Π΅Ρ ΡΠ»Π°Π±ΡΠΌ, ΡΡΠΎ ΠΏΠΎΠΊΠ°ΠΆΠ΅Ρ ΡΠ°ΡΡΡΠ΅ΡΠΊΠΈΠ²Π°Π½ΠΈΠ΅ ΠΈ ΡΠ°ΡΡΡΠ΅ΡΠΊΠΈΠ²Π°Π½ΠΈΠ΅, ΠΈ ΠΎΠ½ Π±ΡΠ΄Π΅Ρ Π±ΠΎΠ»Π΅Π΅ ΠΏΠΎΡΠΈΡΡΡΠΌ.ΠΡΠΎΠΌΠ΅ ΡΠΎΠ³ΠΎ, Π±ΡΠ»ΠΎ ΠΏΠΎΠΊΠ°Π·Π°Π½ΠΎ, ΡΡΠΎ ΠΊΠΎΠΌΠΌΠ΅ΡΡΠ΅ΡΠΊΠΈΠ΅ ΠΏΠΎΠ»ΠΈΠΌΠ΅ΡΡ GFRC ΠΏΡΠ΅Π΄ΠΎΡΠ²ΡΠ°ΡΠ°ΡΡ Π²ΡΠ΅Π΄Π½ΡΠ΅ ΡΡΡΠ΅ΠΊΡΡ ΡΡΠ°ΡΠ΅Π½ΠΈΡ Π² GFRC Π²Π½Π΅ ΠΏΠΎΠΌΠ΅ΡΠ΅Π½ΠΈΠΉ. ΠΠ΅Π· ΠΏΠΎΠ»ΠΈΠΌΠ΅ΡΠ° GFRC ΠΈΠΌΠ΅Π΅Ρ ΡΠ΅Π½Π΄Π΅Π½ΡΠΈΡ ΡΡΠ°Π½ΠΎΠ²ΠΈΡΡΡΡ Π±ΠΎΠ»Π΅Π΅ Ρ ΡΡΠΏΠΊΠΈΠΌ ΠΈ ΡΠ»Π°Π±ΡΠΌ ΡΠΎ Π²ΡΠ΅ΠΌΠ΅Π½Π΅ΠΌ, ΠΈ ΠΎΠ±ΡΠΈΡΠ½ΡΠ΅ ΠΈΡΠΏΡΡΠ°Π½ΠΈΡ (ΡΡΠΊΠΎΡΠ΅Π½Π½ΠΎΠ΅ ΡΡΠ°ΡΠ΅Π½ΠΈΠ΅ ΠΈ ΡΡΠ°ΡΠ΅Π½ΠΈΠ΅ Π² ΡΠ΅Π°Π»ΡΠ½ΠΎΠΌ Π²ΡΠ΅ΠΌΠ΅Π½ΠΈ Π² ΡΠ΅ΡΠ΅Π½ΠΈΠ΅ ΠΌΠ½ΠΎΠ³ΠΈΡ Π»Π΅Ρ) ΠΏΠΎΠΊΠ°Π·Π°Π»ΠΈ ΠΏΡΠ΅ΠΈΠΌΡΡΠ΅ΡΡΠ²Π° ΠΏΠΎΠ»ΠΈΠΌΠ΅ΡΠ° Π² GFRC. ΠΠ΅ΠΊΠΎΡΠΎΡΡΠ΅ ΠΈΠ· ΠΎΡΠ½ΠΎΠ²Π½ΡΡ ΠΏΡΠΈΠΌΠ΅Π½Π΅Π½ΠΈΠΉ GFRC Π² ΠΊΠΎΠΌΠΌΠ΅ΡΡΠ΅ΡΠΊΠΎΠΌ ΠΌΠΈΡΠ΅ — ΡΡΠΎ Π±ΠΎΠ»ΡΡΠΈΠ΅ Π½Π°ΡΡΠΆΠ½ΡΠ΅ ΡΡΡΠΎΠΈΡΠ΅Π»ΡΠ½ΡΠ΅ ΠΏΠ°Π½Π΅Π»ΠΈ, Π³Π΄Π΅ Π΄Π»ΠΈΡΠ΅Π»ΡΠ½Π°Ρ ΠΏΡΠΎΡΠ½ΠΎΡΡΡ ΠΈ Π΄ΠΎΠ»Π³ΠΎΠ²Π΅ΡΠ½ΠΎΡΡΡ ΠΆΠΈΠ·Π½Π΅Π½Π½ΠΎ Π²Π°ΠΆΠ½Ρ Π΄Π»Ρ ΠΎΠ±Π΅ΡΠΏΠ΅ΡΠ΅Π½ΠΈΡ Π΄ΠΎΠ»Π³ΠΎΠ²Π΅ΡΠ½ΠΎΡΡΠΈ ΠΏΡΠΎΠ΄ΡΠΊΡΠ° ΠΈ Π±Π΅Π·ΠΎΠΏΠ°ΡΠ½ΠΎΡΡΠΈ Π½Π°ΡΠ΅Π»Π΅Π½ΠΈΡ.
ΠΠ²Π° ΠΏΠΎΠ»ΠΈΠΌΠ΅ΡΠ° GFRC, ΡΠΈΡΠΎΠΊΠΎ ΠΈΡΠΏΠΎΠ»ΡΠ·ΡΠ΅ΠΌΡΠ΅ Π² ΠΊΠΎΠΌΠΌΠ΅ΡΡΠ΅ΡΠΊΠΎΠΉ ΠΏΡΠΎΠΌΡΡΠ»Π΅Π½Π½ΠΎΡΡΠΈ GFRC Π² Π‘Π΅Π²Π΅ΡΠ½ΠΎΠΉ ΠΠΌΠ΅ΡΠΈΠΊΠ΅, — ΡΡΠΎ Forton VF-774 ΠΈ Polyplex.ΠΡΠΈ Π΄Π²Π° ΠΏΠΎΠ»ΠΈΠΌΠ΅ΡΠ° ΡΠΎΠΎΡΠ²Π΅ΡΡΡΠ²ΡΡΡ ΡΡΠ°Π½Π΄Π°ΡΡΡ PCI.
ΠΠ° ΠΏΠΎΡΠ»Π΅Π΄Π½ΠΈΠ΅ Π½Π΅ΡΠΊΠΎΠ»ΡΠΊΠΎ Π»Π΅Ρ ΠΈΡΠΏΠΎΠ»ΡΠ·ΠΎΠ²Π°Π½ΠΈΠ΅ GFRC Π² ΠΌΠ΅Π»ΠΊΠΎΠΌΠ°ΡΡΡΠ°Π±Π½ΠΎΠΌ Π°ΡΡ ΠΈΡΠ΅ΠΊΡΡΡΠ½ΠΎΠΌ Π±Π΅ΡΠΎΠ½Π΅ (Π½Π°ΠΏΡΠΈΠΌΠ΅Ρ, Π±Π΅ΡΠΎΠ½Π½ΡΡ ΡΡΠΎΠ»Π΅ΡΠ½ΠΈΡΠ°Ρ , ΠΌΠ΅Π±Π΅Π»ΠΈ ΠΈ Ρ. Π.) Π‘ΡΠ°Π»ΠΎ ΠΏΠΎΠΏΡΠ»ΡΡΠ½ΡΠΌ, ΠΏΡΠ΅ΠΆΠ΄Π΅ Π²ΡΠ΅Π³ΠΎ ΠΈΠ·-Π·Π° Π΅Π³ΠΎ ΡΠ½ΠΈΠ²Π΅ΡΡΠ°Π»ΡΠ½ΠΎΡΡΠΈ, ΠΏΡΠΎΡΠ½ΠΎΡΡΠΈ, Π΄ΠΎΠ»Π³ΠΎΠ²Π΅ΡΠ½ΠΎΡΡΠΈ ΠΈ ΠΎΡΠ½ΠΎΡΠΈΡΠ΅Π»ΡΠ½ΠΎΠΉ ΠΏΡΠΎΡΡΠΎΡΡ ΠΈΠ·Π³ΠΎΡΠΎΠ²Π»Π΅Π½ΠΈΡ. ΠΡΠΎΡΡΠΎΡΠ° ΡΠΎΡΠΌΠΎΠ²Π°Π½ΠΈΡ, Π²ΠΎΠ·ΠΌΠΎΠΆΠ½ΠΎΡΡΡ ΠΎΡΠ½ΠΎΡΠΈΡΠ΅Π»ΡΠ½ΠΎ Π»Π΅Π³ΠΊΠΎΠ³ΠΎ ΡΠΎΠ·Π΄Π°Π½ΠΈΡ ΡΠ»ΠΎΠΆΠ½ΡΡ ΡΡΠ΅Ρ ΠΌΠ΅ΡΠ½ΡΡ ΠΈΠ·Π΄Π΅Π»ΠΈΠΉ ΠΈ Π·Π½Π°ΡΠΈΡΠ΅Π»ΡΠ½ΠΎΠ΅ ΡΠ½ΠΈΠΆΠ΅Π½ΠΈΠ΅ ΠΎΠ±ΡΠ΅Π³ΠΎ Π²Π΅ΡΠ° ΡΠ΄Π΅Π»Π°Π»ΠΈ GFRC ΠΌΠ°ΡΠ΅ΡΠΈΠ°Π»ΠΎΠΌ, ΠΊΠΎΡΠΎΡΡΠΉ Π²ΡΠ±ΠΈΡΠ°ΡΡ ΠΌΠ½ΠΎΠ³ΠΈΠ΅ ΠΌΠ°ΡΡΠ΅ΡΠ°.
ΠΠ΄ΠΈΠ½ ΠΈΠ· ΠΊΠ»ΡΡΠ΅ΠΉ ΠΊ ΡΡΠΏΠ΅ΡΠ½ΠΎΠΌΡ ΠΈΡΠΏΠΎΠ»ΡΠ·ΠΎΠ²Π°Π½ΠΈΡ GFRC — ΡΡΠΎ ΠΈΡΠΏΠΎΠ»ΡΠ·ΠΎΠ²Π°Π½ΠΈΠ΅ ΠΏΡΠ°Π²ΠΈΠ»ΡΠ½ΡΡ ΠΈΠ½Π³ΡΠ΅Π΄ΠΈΠ΅Π½ΡΠΎΠ² ΠΈ ΠΏΠΎΠ½ΠΈΠΌΠ°Π½ΠΈΠ΅ ΠΈΡ ΡΠ΅Π»ΠΈ ΠΈ ΡΡΠ½ΠΊΡΠΈΠΈ. ΠΠΎΠ»ΠΈΠΌΠ΅Ρ ΠΈΠ³ΡΠ°Π΅Ρ Π²Π°ΠΆΠ½ΡΡ ΡΠΎΠ»Ρ Π² Π΄ΠΎΡΡΠΈΠΆΠ΅Π½ΠΈΠΈ ΠΏΡΠΎΡΠ½ΠΎΡΡΠΈ ΠΈ Π΄ΠΎΠ»Π³ΠΎΠ²Π΅ΡΠ½ΠΎΡΡΠΈ, ΠΎΠΆΠΈΠ΄Π°Π΅ΠΌΡΡ ΠΎΡ GFRC. ΠΡΠΏΠΎΠ»ΡΠ·ΠΎΠ²Π°Π½ΠΈΠ΅ Π½Π΅ΠΏΡΠ°Π²ΠΈΠ»ΡΠ½ΠΎΠ³ΠΎ ΠΏΠΎΠ»ΠΈΠΌΠ΅ΡΠ° ΠΈΠ»ΠΈ Π½Π΅ΠΏΡΠ°Π²ΠΈΠ»ΡΠ½ΠΎΠ³ΠΎ ΠΈΡΠΏΠΎΠ»ΡΠ·ΠΎΠ²Π°Π½ΠΈΡ ΠΏΠΎΠ»ΠΈΠΌΠ΅ΡΠ° ΠΌΠΎΠΆΠ΅Ρ ΠΏΡΠΈΠ²Π΅ΡΡΠΈ ΠΊ ΡΠΎΠΌΡ, ΡΡΠΎ Π±Π΅ΡΠΎΠ½ Π±ΡΠ΄Π΅Ρ ΠΏΠ»ΠΎΡ ΠΎΠ³ΠΎ ΠΊΠ°ΡΠ΅ΡΡΠ²Π°, ΠΊΠΎΡΠΎΡΡΠΉ Π±ΡΠ΄Π΅Ρ ΡΠ»Π°Π±ΡΠΌ ΠΈΠ»ΠΈ ΠΏΠΎΠΊΠ°ΠΆΠ΅Ρ ΡΡΠ΅ΡΠΈΠ½Ρ ΠΈΠ»ΠΈ ΡΠΊΡΡΡΠΈΠ²Π°Π½ΠΈΠ΅.
Π Π΄ΠΎΠΏΠΎΠ»Π½Π΅Π½ΠΈΠ΅ ΠΊ ΡΡΠ°ΡΠ΅Π»ΡΠ½ΠΎ ΠΏΠΎΠ΄ΠΎΠ±ΡΠ°Π½Π½ΠΎΠΌΡ Ρ ΠΈΠΌΠΈΡΠ΅ΡΠΊΠΎΠΌΡ ΡΠΎΡΡΠ°Π²Ρ, ΡΠ°Π·ΡΠ°Π±ΠΎΡΠ°Π½Π½ΠΎΠΌΡ Π΄Π»Ρ ΠΎΠ±Π»Π΅Π³ΡΠ΅Π½ΠΈΡ ΠΎΡΠ²Π΅ΡΠΆΠ΄Π΅Π½ΠΈΡ ΠΈ ΡΠΎΡ ΡΠ°Π½Π΅Π½ΠΈΡ Π΄ΠΎΠ»Π³ΠΎΠ²ΡΠ΅ΠΌΠ΅Π½Π½ΠΎΠΉ ΠΏΡΠΎΡΠ½ΠΎΡΡΠΈ Π½Π° ΠΈΠ·Π³ΠΈΠ±, ΠΏΠΎΠ»ΠΈΠΌΠ΅ΡΡ GFRC ΡΠ°ΠΊΠΆΠ΅ ΡΠΎΠ΄Π΅ΡΠΆΠ°Ρ ΠΏΠ΅Π½ΠΎΠ³Π°ΡΠΈΡΠ΅Π»ΠΈ ΠΈ ΠΏΡΠΈΡΠ°Π΄ΠΊΡ, ΡΠΌΠ΅Π½ΡΡΠ°ΡΡΡΡ ΡΡΠ°Π΄ΠΊΡ.ΠΡΠΈ Π΄ΠΎΠ±Π°Π²ΠΊΠΈ ΡΠ»ΡΡΡΠ°ΡΡ ΠΏΡΠΎΡΠ½ΠΎΡΡΡ ΠΌΠ°ΡΠ΅ΡΠΈΠ°Π»Π° Π·Π° ΡΡΠ΅Ρ ΡΠΌΠ΅Π½ΡΡΠ΅Π½ΠΈΡ ΠΊΠΎΠ»ΠΈΡΠ΅ΡΡΠ²Π° Π·Π°Ρ Π²Π°ΡΠ΅Π½Π½ΠΎΠ³ΠΎ Π²ΠΎΠ·Π΄ΡΡ Π° ΠΈ ΡΡΡΡΠ°Π½Π΅Π½ΠΈΡ ΠΌΠΈΠΊΡΠΎΡΡΠ΅ΡΠΈΠ½, ΠΎΠ±ΡΠ°Π·ΠΎΠ²Π°Π²ΡΠΈΡ ΡΡ ΠΏΡΠΈ ΡΡΡΠΊΠ΅. ΠΡΠΎ, Π° ΡΠ°ΠΊΠΆΠ΅ ΠΎΡΠΎΠ±ΡΠΉ Ρ ΠΈΠΌΠΈΡΠ΅ΡΠΊΠΈΠΉ ΡΠΎΡΡΠ°Π² ΡΠ°ΠΌΠΎΠ³ΠΎ ΠΏΠΎΠ»ΠΈΠΌΠ΅ΡΠ° — Π²ΠΎΡ ΡΡΠΎ ΠΎΡΠ»ΠΈΡΠ°Π΅Ρ ΠΏΠΎΠ»ΠΈΠΌΠ΅ΡΡ GFRC ΠΎΡ Π±Π΅ΡΡΠΈΡΠ»Π΅Π½Π½ΡΡ Β«ΠΏΠΎΠ»ΠΈΠΌΠ΅ΡΠΎΠ²Β», ΠΈΡΠΏΠΎΠ»ΡΠ·ΡΠ΅ΠΌΡΡ Π² Π±Π΅ΡΠΎΠ½Π½ΠΎΠΉ ΠΏΡΠΎΠΌΡΡΠ»Π΅Π½Π½ΠΎΡΡΠΈ. ΠΠ²ΡΠΌΡ ΡΠ°ΡΠΏΡΠΎΡΡΡΠ°Π½Π΅Π½Π½ΡΠΌΠΈ ΠΏΡΠΈΠΌΠ΅Π½Π΅Π½ΠΈΡΠΌΠΈ Π΄ΡΡΠ³ΠΈΡ Π²ΠΈΠ΄ΠΎΠ² ΠΏΠΎΠ»ΠΈΠΌΠ΅ΡΠΎΠ² ΡΠ²Π»ΡΡΡΡΡ ΠΏΠΎΠ²Π΅ΡΡ Π½ΠΎΡΡΠ½ΠΎ-ΡΠ²ΡΠ·ΡΠ²Π°ΡΡΠΈΠ΅ Π°Π³Π΅Π½ΡΡ ΠΈ ΠΏΠΎΠ»ΠΈΠΌΠ΅ΡΡ, ΠΈΡΠΏΠΎΠ»ΡΠ·ΡΠ΅ΠΌΡΠ΅ Π² ΠΏΠΎΠΊΡΡΡΠΈΡΡ ΠΈ ΠΌΠΈΠΊΡΠΎΠ²ΠΎΠ»Π½Π°Ρ . ΠΠΎΠ½ΠΊΡΠ΅ΡΠ½ΡΠ΅ ΠΎΠ±ΡΠ°Π·ΠΎΠ²Π°Π½ΠΈΡ ΡΡΠΈΡ ΠΏΠΎΠ»ΠΈΠΌΠ΅ΡΠΎΠ² Π±Π»Π°Π³ΠΎΠΏΡΠΈΡΡΡΡΠ²ΡΡΡ ΠΏΠΎΠ²Π΅ΡΡ Π½ΠΎΡΡΠ½ΠΎΠΉ Π°Π΄Π³Π΅Π·ΠΈΠΈ ΠΏΠΎ ΡΡΠ°Π²Π½Π΅Π½ΠΈΡ Ρ Π΄ΡΡΠ³ΠΈΠΌΠΈ Ρ Π°ΡΠ°ΠΊΡΠ΅ΡΠΈΡΡΠΈΠΊΠ°ΠΌΠΈ, ΠΈ ΠΈΠΌΠ΅Π½Π½ΠΎ ΡΡΠΈ ΡΠ°Π·Π»ΠΈΡΠΈΡ Π² ΡΠΎΡΡΠ°Π²Π°Ρ Π΄Π΅Π»Π°ΡΡ ΠΈΡ Π½Π΅ΠΏΡΠΈΠ³ΠΎΠ΄Π½ΡΠΌΠΈ Π΄Π»Ρ GFRC.Π’ΠΎ, ΡΡΠΎ ΡΡΠΎ ΠΆΠΈΠ΄ΠΊΠΎΡΡΡ ΠΌΠΎΠ»ΠΎΡΠ½ΠΎ-Π±Π΅Π»ΠΎΠ³ΠΎ ΡΠ²Π΅ΡΠ° (ΠΈΠ»ΠΈ Π±Π΅Π»ΡΠΉ ΠΏΠΎΡΠΎΡΠΎΠΊ), Π½Π΅ ΠΎΠ·Π½Π°ΡΠ°Π΅Ρ, ΡΡΠΎ Π΅Π΅ ΠΌΠΎΠΆΠ½ΠΎ ΠΈΡΠΏΠΎΠ»ΡΠ·ΠΎΠ²Π°ΡΡ Π² GFRC.
Π ΠΏΠΎΡΠ»Π΅Π΄Π½Π΅Π΅ Π²ΡΠ΅ΠΌΡ ΡΡΡ ΠΈΠ΅ ΠΏΠΎΡΠΎΡΠΊΠΎΠΎΠ±ΡΠ°Π·Π½ΡΠ΅ ΠΏΠΎΠ»ΠΈΠΌΠ΅ΡΡ (ΠΏΠΎ ΡΡΠ°Π²Π½Π΅Π½ΠΈΡ Ρ ΠΆΠΈΠ΄ΠΊΠΈΠΌΠΈ ΠΏΠΎΠ»ΠΈΠΌΠ΅ΡΠ°ΠΌΠΈ) ΡΡΠ°Π»ΠΈ ΠΏΠΎΠΏΡΠ»ΡΡΠ½ΡΠΌΠΈ Π² Π½Π°ΡΠ΅ΠΉ ΠΎΡΡΠ°ΡΠ»ΠΈ, Π·Π°ΡΠ²Π»ΡΡ ΠΎ ΡΠ°Π²Π½ΠΎΠΉ ΡΡΡΠ΅ΠΊΡΠΈΠ²Π½ΠΎΡΡΠΈ, ΠΏΡΠΎΡΡΠΎΡΠ΅ ΠΈΡΠΏΠΎΠ»ΡΠ·ΠΎΠ²Π°Π½ΠΈΡ ΠΈ ΡΠΊΠΎΠ½ΠΎΠΌΠΈΠΈ ΡΡΠ΅Π΄ΡΡΠ² Π·Π° ΡΡΠ΅Ρ ΠΎΡΡΡΡΡΡΠ²ΠΈΡ Π½Π΅ΠΎΠ±Ρ ΠΎΠ΄ΠΈΠΌΠΎΡΡΠΈ ΠΎΡΠ³ΡΡΠΆΠ°ΡΡ ΡΡΠΆΠ΅Π»ΡΠ΅ ΠΆΠΈΠ΄ΠΊΠΎΡΡΠΈ Π½Π° Π²ΠΎΠ΄Π½ΠΎΠΉ ΠΎΡΠ½ΠΎΠ²Π΅.
Π Π°Π²Π½Π°Ρ ΡΡΡΠ΅ΠΊΡΠΈΠ²Π½ΠΎΡΡΡ ΠΈ ΡΠΊΠΎΠ½ΠΎΠΌΠΈΡ ΡΡΠ΅Π΄ΡΡΠ² ΡΠ°ΡΡΠΌΠ°ΡΡΠΈΠ²Π°ΡΡΡΡ Π΄Π°Π»Π΅Π΅ Π² ΡΡΠΎΠΉ ΡΡΠ°ΡΡΠ΅. Π§ΡΠΎΠ±Ρ ΡΠ΅ΡΠΈΡΡ ΠΏΡΠΎΠ±Π»Π΅ΠΌΡ ΠΏΡΠΎΡΡΠΎΡΡ ΠΈΡΠΏΠΎΠ»ΡΠ·ΠΎΠ²Π°Π½ΠΈΡ, ΠΎΠ±ΡΠ°ΡΠΈΡΠ΅ Π²Π½ΠΈΠΌΠ°Π½ΠΈΠ΅ Π½Π° ΡΠ»Π΅Π΄ΡΡΡΠ΅Π΅.
ΠΠΎΠ·ΠΈΡΠΎΠ²Π°Π½ΠΈΠ΅ ΠΆΠΈΠ΄ΠΊΠΎΠ³ΠΎ ΠΏΠΎΠ»ΠΈΠΌΠ΅ΡΠ° ΡΡΠ΅Π±ΡΠ΅Ρ Π·Π½Π°Π½ΠΈΡ ΡΠΎΠ΄Π΅ΡΠΆΠ°Π½ΠΈΡ ΡΠ²Π΅ΡΠ΄ΡΡ Π²Π΅ΡΠ΅ΡΡΠ² ΠΏΠΎΠ»ΠΈΠΌΠ΅ΡΠ° Π² ΠΆΠΈΠ΄ΠΊΠΎΠΌ ΠΏΠΎΠ»ΠΈΠΌΠ΅ΡΠ΅ Π² ΠΌΠ°ΡΡΠ΅, Π° ΡΠ°ΠΊΠΆΠ΅ ΡΠΌΠ΅Π½ΠΈΡ ΡΠ°ΡΡΡΠΈΡΡΠ²Π°ΡΡ, ΡΠΊΠΎΠ»ΡΠΊΠΎ Π²ΠΎΠ΄Ρ Π² ΠΏΠΎΠ»ΠΈΠΌΠ΅ΡΠ΅ ΡΡΠΈΡΠ°Π΅ΡΡΡ Π²ΠΎΠ΄ΠΎΠΉ ΠΏΠ°ΡΡΠΈΠΈ.ΠΠ°ΠΏΡΠΈΠΌΠ΅Ρ, Forton VF-774 ΠΏΡΠ΅Π΄ΡΡΠ°Π²Π»ΡΠ΅Ρ ΡΠΎΠ±ΠΎΠΉ ΠΆΠΈΠ΄ΠΊΡΡ ΠΏΠΎΠ»ΠΈΠΌΠ΅ΡΠ½ΡΡ Π΄ΠΎΠ±Π°Π²ΠΊΡ Π΄Π»Ρ ΠΎΡΠ²Π΅ΡΠΆΠ΄Π΅Π½ΠΈΡ ΠΈ ΡΠΎΠ΄Π΅ΡΠΆΠΈΡ 51% ΡΠ²Π΅ΡΠ΄ΡΡ Π²Π΅ΡΠ΅ΡΡΠ², ΡΠΎ Π΅ΡΡΡ 49% Π²ΠΎΠ΄Ρ.
Π‘ΡΡ ΠΈΠ΅ ΠΏΠΎΠ»ΠΈΠΌΠ΅ΡΡ ΡΠΎΡΡΠΎΡΡ Π½Π° 100% ΠΈΠ· ΡΠ²Π΅ΡΠ΄ΡΡ Π²Π΅ΡΠ΅ΡΡΠ², ΠΏΠΎΡΡΠΎΠΌΡ ΡΠ°ΡΡΠ΅ΡΡ ΠΎΠ±ΡΠ΅ΠΌΠ½ΠΎΠΉ Π²ΠΎΠ΄Ρ ΠΏΡΠΎΡΠ΅.
Π§ΡΠΎΠ±Ρ ΠΈΠ·Π±Π°Π²ΠΈΡΡΡΡ ΠΎΡ ΠΌΠ°ΡΠ΅ΠΌΠ°ΡΠΈΡΠ΅ΡΠΊΠΈΡ Π²ΡΡΠΈΡΠ»Π΅Π½ΠΈΠΉ ΠΈ ΡΠΏΡΠΎΡΡΠΈΡΡ ΠΈΡΠΏΠΎΠ»ΡΠ·ΠΎΠ²Π°Π½ΠΈΠ΅ ΠΆΠΈΠ΄ΠΊΠΈΡ ΠΏΠΎΠ»ΠΈΠΌΠ΅ΡΠΎΠ², ΠΊΠ°Π»ΡΠΊΡΠ»ΡΡΠΎΡ ΡΠΌΠ΅ΡΠΈ GFRC ΠΎΡ CCI Π°Π²ΡΠΎΠΌΠ°ΡΠΈΡΠ΅ΡΠΊΠΈ ΡΠ΅Π³ΡΠ»ΠΈΡΡΠ΅Ρ ΠΊΠΎΠ»ΠΈΡΠ΅ΡΡΠ²ΠΎ Π²ΠΎΠ΄Ρ Π² ΠΏΠ°ΡΡΠΈΠΈ Π΄Π»Ρ Π»ΡΠ±ΠΎΠ³ΠΎ ΠΆΠΈΠ΄ΠΊΠΎΠ³ΠΎ ΠΏΠΎΠ»ΠΈΠΌΠ΅ΡΠ°, ΡΡΡΡΠ°Π½ΡΡ Π»ΡΠ±ΡΠ΅ ΠΏΡΠ΅Π΄ΠΏΠΎΠ»Π°Π³Π°Π΅ΠΌΡΠ΅ ΡΠ»ΠΎΠΆΠ½ΠΎΡΡΠΈ ΠΏΡΠΈ Π΄ΠΎΠ·ΠΈΡΠΎΠ²Π°Π½ΠΈΠΈ ΠΆΠΈΠ΄ΠΊΠΎΡΡΠ΅ΠΉ. Π’Π΅ΠΏΠ΅ΡΡ ΠΌΡ ΡΠ°ΠΊΠΆΠ΅ ΠΏΡΠ΅Π΄Π»Π°Π³Π°Π΅ΠΌ ΠΊΠ°Π»ΡΠΊΡΠ»ΡΡΠΎΡ, ΠΊΠΎΡΠΎΡΡΠΉ ΡΠ°ΠΊΠΆΠ΅ ΠΌΠΎΠΆΠ΅Ρ ΠΎΠ±ΡΠ°Π±Π°ΡΡΠ²Π°ΡΡ ΠΈΡΠΏΠΎΠ»ΡΠ·ΠΎΠ²Π°Π½ΠΈΠ΅ ΡΡΡ ΠΈΡ ΠΏΠΎΠ»ΠΈΠΌΠ΅ΡΠΎΠ² Ρ ΡΠ°ΠΊΠΎΠΉ ΠΆΠ΅ ΡΠΎΡΠ½ΠΎΡΡΡΡ ΠΈ Π»Π΅Π³ΠΊΠΎΡΡΡΡ.
CCI ΠΏΡΠΎΠ²Π΅Π»Π° ΠΎΠ±ΡΠΈΡΠ½ΠΎΠ΅ ΠΈ ΠΏΠΎΠ΄ΡΠΎΠ±Π½ΠΎΠ΅ ΡΠ΅ΡΡΠΈΡΠΎΠ²Π°Π½ΠΈΠ΅ ΡΡΠ΅Π±ΠΎΠ²Π°Π½ΠΈΡ PCI β 1: ΡΠ΅ΠΊΠΎΠΌΠ΅Π½Π΄ΡΠ΅ΠΌΠΎΠ΅ ΠΊΠΎΠ»ΠΈΡΠ΅ΡΡΠ²ΠΎ ΠΏΠΎΠ»ΠΈΠΌΠ΅ΡΠ½ΠΎΠΉ Π΄ΠΎΠ±Π°Π²ΠΊΠΈ Π΄Π»Ρ ΠΎΡΠ²Π΅ΡΠΆΠ΄Π΅Π½ΠΈΡ Π² ΡΠΌΠ΅ΡΠΈ GFRC Π±Π΅Π· ΠΎΡΠ²Π΅ΡΠΆΠ΄Π΅Π½ΠΈΡ Π²ΠΎ Π²Π»Π°ΠΆΠ½ΠΎΠΌ ΡΠΎΡΡΠΎΡΠ½ΠΈΠΈ ΡΠΎΠΎΡΠ²Π΅ΡΡΡΠ²ΡΠ΅Ρ ΡΠ²ΠΎΠΉΡΡΠ²Π°ΠΌ ΠΈΠ·Π³ΠΈΠ±Π° GFRC, ΠΎΡΠ²Π΅ΡΠΆΠ΄Π΅Π½Π½ΠΎΠ³ΠΎ Π² ΡΠ΅ΡΠ΅Π½ΠΈΠ΅ 7 Π΄Π½Π΅ΠΉ Π²ΠΎ Π²Π»Π°ΠΆΠ½ΠΎΠΌ ΡΠΎΡΡΠΎΡΠ½ΠΈΠΈ, ΠΊΠΎΠ³Π΄Π° ΠΎΠ±Π° ΠΈΡΠΏΡΡΠ°Π½ΠΈΡ ΠΏΡΠΎΡ ΠΎΠ΄ΡΡ ΡΠ΅ΡΠ΅Π· 28 Π΄Π½Π΅ΠΉ. ΠΡ ΡΠ°ΠΊΠΆΠ΅ ΠΏΡΠΎΠ²Π΅ΡΠΈΠ»ΠΈ ΡΡΠ΅Π±ΠΎΠ²Π°Π½ΠΈΠ΅ β3. ΠΡ Π½Π΅ ΡΠ΅ΡΡΠΈΡΠΎΠ²Π°Π»ΠΈ ΡΡΠ΅Π±ΠΎΠ²Π°Π½ΠΈΡ β2 ΠΈΠ»ΠΈ β4, ΠΈ, Π½Π°ΡΠΊΠΎΠ»ΡΠΊΠΎ Π½Π°ΠΌ ΠΈΠ·Π²Π΅ΡΡΠ½ΠΎ, Π½ΠΈ ΠΎΠ΄Π½Π° Π½Π΅Π·Π°Π²ΠΈΡΠΈΠΌΠ°Ρ Π»Π°Π±ΠΎΡΠ°ΡΠΎΡΠΈΡ Π½Π΅ ΠΏΡΠΎΠ²Π΅Π»Π° ΡΠ΅ΡΡΠΈΡΠΎΠ²Π°Π½ΠΈΠ΅ ΡΡΠΈΡ ΡΡΠ΅Π±ΠΎΠ²Π°Π½ΠΈΠΉ.
CCI ΠΏΡΠΎΡΠ΅ΡΡΠΈΡΠΎΠ²Π°Π» ΡΡΠΈ ΠΏΠΎΠ»ΠΈΠΌΠ΅ΡΠ½ΡΠ΅ ΡΠΈΡΡΠ΅ΠΌΡ: ΠΎΠ΄Π½Ρ ΠΆΠΈΠ΄ΠΊΡΡ ΠΈ Π΄Π²Π΅ ΡΡΡ ΠΈΠ΅.
- ΠΠΈΠ΄ΠΊΠΈΠΉ ΠΏΠΎΠ»ΠΈΠΌΠ΅Ρ: Forton VF-774
- Π‘ΡΡ ΠΎΠΉ ΠΏΠΎΠ»ΠΈΠΌΠ΅Ρ β1: CENSOREDβs GFRC Admix
- Π‘ΡΡ ΠΎΠΉ ΠΏΠΎΠ»ΠΈΠΌΠ΅Ρ β2: ΠΠΎΠ±Π°Π²ΠΊΠ° GFRC Π΄Π»Ρ Π±Π΅ΡΠΎΠ½Π½ΡΡ ΠΈΠ·Π΄Π΅Π»ΠΈΠΉ ΠΠ°Π΄Π΄ΠΈ Π ΠΎΡΠ΄ΡΠ° (BRCP) (ΠΈ ΡΠΌΠ΅ΡΡ BRCP GFRC Blended Mix)
Π€ΠΎΡΡΠΎΠ½ ΠΠ€-774
Forton VF-774 — ΠΆΠΈΠ΄ΠΊΠ°Ρ ΠΏΠΎΠ»ΠΈΠΌΠ΅ΡΠ½Π°Ρ ΠΎΡΠ²Π΅ΡΠΆΠ΄Π°ΡΡΠ°Ρ Π΄ΠΎΠ±Π°Π²ΠΊΠ°.ΠΡΠΎ ΠΏΡΠΎΠΌΡΡΠ»Π΅Π½Π½ΡΠΉ ΡΡΠ°Π½Π΄Π°ΡΡ Ρ ΠΌΠ½ΠΎΠ³ΠΎΠ»Π΅ΡΠ½Π΅ΠΉ ΠΈΡΡΠΎΡΠΈΠ΅ΠΉ ΠΈΡΠΏΠΎΠ»ΡΠ·ΠΎΠ²Π°Π½ΠΈΡ Π² ΠΊΠΎΠΌΠΌΠ΅ΡΡΠ΅ΡΠΊΠΎΠΉ ΠΈΠ½Π΄ΡΡΡΡΠΈΠΈ GFRC, ΠΏΠΎΠ»Π½ΠΎΡΡΡΡ ΡΠΎΠΎΡΠ²Π΅ΡΡΡΠ²ΡΡΡΠΈΠΉ ΡΡΠ΅Π±ΠΎΠ²Π°Π½ΠΈΡΠΌ PCI MNL 130-09, ΠΡΠΈΠ»ΠΎΠΆΠ΅Π½ΠΈΠ΅ G. Π€ΠΎΡΡΠΎΠ½ ΠΈΠΌΠ΅Π΅Ρ ΡΠΎΠ΄Π΅ΡΠΆΠ°Π½ΠΈΠ΅ ΡΠ²Π΅ΡΠ΄ΡΡ ΡΠ°ΡΡΠΈΡ 51% ΠΈ ΠΈΡΠΏΠΎΠ»ΡΠ·ΠΎΠ²Π°Π»ΡΡ ΠΏΡΠΈ Π΄ΠΎΠ·ΠΈΡΠΎΠ²ΠΊΠ΅ 5% ΠΈ 6% ΡΠ²Π΅ΡΠ΄ΡΡ Π²Π΅ΡΠ΅ΡΡΠ² ΠΏΠΎΠ»ΠΈΠΌΠ΅ΡΠ°.
Π ΡΠ΅ΡΡΠΎΠ²ΡΡ ΠΎΠ±ΡΠ°Π·ΡΠ°Ρ , ΠΈΠ·Π³ΠΎΡΠΎΠ²Π»Π΅Π½Π½ΡΡ Ρ ΠΈΡΠΏΠΎΠ»ΡΠ·ΠΎΠ²Π°Π½ΠΈΠ΅ΠΌ Π€ΠΎΡΡΠΎΠ½Π°, ΡΠ°ΠΊΠΆΠ΅ ΠΈΡΠΏΠΎΠ»ΡΠ·ΠΎΠ²Π°Π»ΠΈΡΡ Π΄Π²Π° ΡΠ°Π·Π½ΡΡ ΠΏΡΡΡΠΎΠ»Π°Π½Π°, ΠΊΠΎΡΠΎΡΡΠ΅ ΠΈΡΠΏΠΎΠ»ΡΠ·ΠΎΠ²Π°Π»ΠΈΡΡ Π² ΠΊΠ°ΡΠ΅ΡΡΠ²Π΅ ΡΠ°ΡΡΠΈΡΠ½ΠΎΠΉ Π·Π°ΠΌΠ΅Π½Ρ ΡΠ΅ΠΌΠ΅Π½ΡΠ°: Π² Π½Π΅ΠΊΠΎΡΠΎΡΡΡ ΠΎΠ±ΡΠ°Π·ΡΠ°Ρ ΠΈΡΠΏΠΎΠ»ΡΠ·ΠΎΠ²Π°Π»ΡΡ VCAS ΠΏΡΠΈ 20% Π·Π°ΠΌΠ΅ΡΠ°ΡΡΠ΅ΠΉ Π΄ΠΎΠ·Π΅, Π° Π² Π΄ΡΡΠ³ΠΈΡ ΠΈΡΠΏΠΎΠ»ΡΠ·ΠΎΠ²Π°Π»ΡΡ Π±Π΅Π»ΡΠΉ Π΄ΡΠΌ ΠΊΡΠ΅ΠΌΠ½Π΅Π·Π΅ΠΌΠ° ΠΏΡΠΈ 10% Π·Π°ΠΌΠ΅ΡΠ°ΡΡΠ΅ΠΉ Π΄ΠΎΠ·Π΅.
Π‘ΡΡ ΠΈΠ΅ ΠΏΠΎΠ»ΠΈΠΌΠ΅ΡΡ
ΠΠ²Π΅ ΡΠΈΡΡΠ΅ΠΌΡ ΡΡΡ ΠΈΡ ΠΏΠΎΠ»ΠΈΠΌΠ΅ΡΠΎΠ² ΡΠ°Π·Π»ΠΈΡΠ°ΡΡΡΡ ΠΏΠΎ ΡΠΎΡΡΠ°Π²Ρ.ΠΠ±Π° Π·Π°ΡΠ²Π»ΡΡΡ, ΡΡΠΎ ΡΠΎΠ΄Π΅ΡΠΆΠ°Ρ ΡΡΡ ΡΡ ΠΏΠΎΠ»ΠΈΠΌΠ΅ΡΠ½ΡΡ ΠΎΡΠ²Π΅ΡΠΆΠ΄Π°ΡΡΡΡ Π΄ΠΎΠ±Π°Π²ΠΊΡ, ΡΠΌΠ΅ΡΠ°Π½Π½ΡΡ Ρ Π΄ΡΡΠ³ΠΈΠΌΠΈ Π΄ΠΎΠ±Π°Π²ΠΊΠ°ΠΌΠΈ, ΡΠ°ΠΊΠΈΠΌΠΈ ΠΊΠ°ΠΊ ΠΏΠ΅Π½ΠΎΠ³Π°ΡΠΈΡΠ΅Π»Ρ, Π΄ΠΎΠ±Π°Π²ΠΊΠ° Π΄Π»Ρ ΡΠΌΠ΅Π½ΡΡΠ΅Π½ΠΈΡ ΡΡΠ°Π΄ΠΊΠΈ ΠΈ ΡΠΌΠ°ΡΠΈΠ²Π°ΡΡΠΈΠ΅ Π°Π³Π΅Π½ΡΡ, Π° ΡΠ°ΠΊΠΆΠ΅ Π΄ΡΡΠ³ΠΈΠ΅ ΡΠΏΠ΅ΡΠΈΠ°Π»ΠΈΠ·ΠΈΡΠΎΠ²Π°Π½Π½ΡΠ΅ Π΄ΠΎΠ±Π°Π²ΠΊΠΈ, ΡΠ½ΠΈΠΊΠ°Π»ΡΠ½ΡΠ΅ Π΄Π»Ρ ΠΊΠ°ΠΆΠ΄ΠΎΠΉ ΠΊΠΎΠΌΠΏΠ°Π½ΠΈΠΈ.
ΠΡΠΈΠΌΠ΅ΡΡ CENSORED Π½Π΅ Π²ΠΊΠ»ΡΡΠ°Π΅Ρ ΠΏΡΡΡΠΎΠ»Π°Π½ ΠΊΠ°ΠΊ ΡΠ°ΡΡΡ ΡΠ²ΠΎΠ΅ΠΉ ΡΠ΅ΡΠ΅ΠΏΡΡΡΡ, ΠΏΠΎΡΡΠΎΠΌΡ Π΄ΠΈΠ·Π°ΠΉΠ½ ΡΠΌΠ΅ΡΠΈ GFRC CENSORED ΡΡΠ΅Π±ΡΠ΅Ρ ΠΎΡΠ΄Π΅Π»ΡΠ½ΠΎΠ³ΠΎ ΠΏΡΡΡΠΎΠ»Π°Π½Π°. ΠΠΎΠΌΠΈΠΌΠΎ Π±Π΅Π»ΠΎΠ³ΠΎ ΠΌΠΈΠΊΡΠΎΠΊΡΠ΅ΠΌΠ½Π΅Π·Π΅ΠΌΠ°, VCAS ΡΠ°ΠΊΠΆΠ΅ ΡΠ΅ΡΡΠΈΡΠΎΠ²Π°Π»ΡΡ Ρ Π΄ΠΎΠ±Π°Π²ΠΊΠΎΠΉ CENSORED .Π ΠΎΡΠ»ΠΈΡΠΈΠ΅ ΠΎΡ ΡΡΠΎΠ³ΠΎ, BRCP GFRC Admixture Π²ΠΊΠ»ΡΡΠ°Π΅Ρ ΠΏΡΡΡΠΎΠ»Π°Π½, ΠΏΡΠ΅Π΄Π²Π°ΡΠΈΡΠ΅Π»ΡΠ½ΠΎ Π΄ΠΎΠ±Π°Π²Π»Π΅Π½Π½ΡΠΉ ΠΊ ΡΠΌΠ΅ΡΠΈ.ΠΠΎΠ±Π°Π²ΠΊΠ° CENSORED Π΄ΠΎΠ±Π°Π²Π»ΡΠ»Π°ΡΡ Π² ΠΊΠΎΠ»ΠΈΡΠ΅ΡΡΠ²Π΅ 3% ΠΏΠΎ Π²Π΅ΡΡ ΠΎΡ ΡΡΡ ΠΎΠ³ΠΎ Π²ΡΠΆΡΡΠ΅Π³ΠΎ ΠΌΠ°ΡΠ΅ΡΠΈΠ°Π»Π°, Π° Π΄ΠΎΠ±Π°Π²ΠΊΠ° BRCP GFRC Π΄ΠΎΠ±Π°Π²Π»ΡΠ»Π°ΡΡ Π² ΠΊΠΎΠ»ΠΈΡΠ΅ΡΡΠ²Π΅ 14,63%. ΠΠ±ΡΠ°ΡΠΈΡΠ΅ Π²Π½ΠΈΠΌΠ°Π½ΠΈΠ΅, ΡΡΠΎ Π΄ΠΎΠ·Π° BRCP Π±ΡΠ»Π° Π½Π°ΠΌΠ½ΠΎΠ³ΠΎ Π²ΡΡΠ΅, ΠΏΠΎΡΠΎΠΌΡ ΡΡΠΎ ΠΎΠ½Π° Π²ΠΊΠ»ΡΡΠ°Π΅Ρ Π±ΠΎΠ»ΡΡΠ΅ ΠΈΠ½Π³ΡΠ΅Π΄ΠΈΠ΅Π½ΡΠΎΠ², Π² ΡΠΎΠΌ ΡΠΈΡΠ»Π΅ ΠΏΡΡΡΠΎΠ»Π°Π½ ΠΈΠ· Π΄ΡΠΌΠ° Π±Π΅Π»ΠΎΠ³ΠΎ ΠΊΡΠ΅ΠΌΠ½Π΅Π·Π΅ΠΌΠ°.
ΠΠΎ Π²ΡΠ΅Ρ ΡΠ΅ΡΠ΅ΠΏΡΡΡΠ°Ρ ΡΠΌΠ΅ΡΠ΅ΠΉ ΠΈΡΠΏΠΎΠ»ΡΠ·ΠΎΠ²Π°Π»ΡΡ Π±Π΅Π»ΡΠΉ ΠΏΠΎΡΡΠ»Π°Π½Π΄ΡΠ΅ΠΌΠ΅Π½Ρ Federal White Type 1, ΠΏΠ΅ΡΠΎΠΊ Π΄Π»Ρ ΠΏΠ΅ΡΠΊΠΎΡΡΡΡΠΉΠ½ΠΎΠΉ ΠΎΠ±ΡΠ°Π±ΠΎΡΠΊΠΈ ΠΊΡΠ΅ΠΌΠ½Π΅Π·Π΅ΠΌΠΎΠΌ β 30 ΠΈ ΡΡΠ΅ΠΊΠ»ΠΎΠ²ΠΎΠ»ΠΎΠΊΠ½ΠΎ GFRC ΡΠΎΠ»ΡΠΈΠ½ΠΎΠΉ 19 ΠΌΠΌ, ΠΈ Π²ΡΠ΅ ΡΠ΅ΡΠ΅ΠΏΡΡΡΡ ΡΠΌΠ΅ΡΠ΅ΠΉ GFRC ΡΠΎΠΎΡΠ²Π΅ΡΡΡΠ²ΠΎΠ²Π°Π»ΠΈ ΡΠ΅ΠΊΠΎΠΌΠ΅Π½Π΄ΠΎΠ²Π°Π½Π½ΡΠΌ ΠΏΡΠΎΠΈΠ·Π²ΠΎΠ΄ΠΈΡΠ΅Π»Π΅ΠΌ ΠΏΡΠΎΠΏΠΎΡΡΠΈΡΠΌ ΠΈ Π΄ΠΎΠ·ΠΈΡΠΎΠ²ΠΊΠ΅.
ΠΠ°Π·ΠΎΠ²ΡΠ΅ ΠΊΠΎΠ½ΡΡΡΡΠΊΡΠΈΠΈ ΡΠΌΠ΅ΡΠΈ Π΄Π»Ρ ΡΡΠ΅Ρ ΡΠ°Π·Π»ΠΈΡΠ½ΡΡ ΠΏΠΎΠ»ΠΈΠΌΠ΅ΡΠ½ΡΡ ΡΠΈΡΡΠ΅ΠΌ Π±ΡΠ»ΠΈ:
Π€ΠΎΡΡΠΎΠ½ / VCAS
- 1 ΡΠ°ΡΡΡ ΠΏΠ΅ΡΠΊΠ°, 1 ΡΠ°ΡΡΡ ΡΠ΅ΠΌΠ΅Π½ΡΠ° (ΠΏΠΎΡΡΠ»Π°Π½Π΄ΡΠ΅ΠΌΠ΅Π½Ρ + ΠΏΡΡΡΠΎΠ»Π°Π½ VCAS)
- 20% VCAS Π΄ΠΎΠ·ΠΈΡΠΎΠ²Π°Π½ΠΎ Π² ΠΊΠ°ΡΠ΅ΡΡΠ²Π΅ ΡΠ°ΡΡΠΈΡΠ½ΠΎΠΉ Π·Π°ΠΌΠ΅Π½Ρ ΡΠ΅ΠΌΠ΅Π½ΡΠ°
- 5% (ΠΈ 6%) Π€ΠΎΡΡΠΎΠ½ ΠΠ€-774
- ΠΡ / C (Π²ΠΎΠ΄Π° Π² ΡΠ΅ΠΌΠ΅Π½Ρ) 0.32
- 3% ΠΠΎΠ·Π° ΡΡΠ΅ΠΊΠ»ΠΎΠ²ΠΎΠ»ΠΎΠΊΠ½Π° 19 ΠΌΠΌ
Π€ΠΎΡΡΠΎΠ½ / Π±Π΅Π»ΡΠΉ ΠΊΡΠ΅ΠΌΠ½Π΅Π·Π΅ΠΌ
- 1 ΡΠ°ΡΡΡ ΠΏΠ΅ΡΠΊΠ°, 1 ΡΠ°ΡΡΡ Π²ΡΠΆΡΡΠ΅Π³ΠΎ (ΠΏΠΎΡΡΠ»Π°Π½Π΄ΡΠ΅ΠΌΠ΅Π½Ρ + Π±Π΅Π»ΡΠΉ Π΄ΡΠΌΡΠ°ΡΡΠΉ ΠΏΡΡΡΠΎΠ»Π°Π½)
- 10% Π±Π΅Π»ΡΠΉ Π΄ΡΠΌΠΎΠΊ ΠΊΡΠ΅ΠΌΠ½Π΅Π·Π΅ΠΌΠ°, Π΄ΠΎΠ·ΠΈΡΡΠ΅ΠΌΡΠΉ Π² ΠΊΠ°ΡΠ΅ΡΡΠ²Π΅ ΡΠ°ΡΡΠΈΡΠ½ΠΎΠΉ Π·Π°ΠΌΠ΅Π½Ρ ΡΠ΅ΠΌΠ΅Π½ΡΠ°
- 5% (ΠΈ 6%) Π€ΠΎΡΡΠΎΠ½ ΠΠ€-774
- W / C (Π²ΠΎΠ΄Π° Π² ΡΠ΅ΠΌΠ΅Π½Ρ) 0,30
- 3% ΠΠΎΠ·Π° ΡΡΠ΅ΠΊΠ»ΠΎΠ²ΠΎΠ»ΠΎΠΊΠ½Π° 19 ΠΌΠΌ
Buddy Rhodes Concrete Products GFRC ΠΠΎΠ±Π°Π²ΠΊΠ° 0,84: 1
- 0,886 ΡΠ°ΡΡΠΈ ΠΏΠ΅ΡΠΊΠ°, 1 ΡΠ°ΡΡΡ ΠΏΠΎΡΡΠ»Π°Π½Π΄ΡΠ΅ΠΌΠ΅Π½ΡΠ° (Π² ΡΠ΅Π·ΡΠ»ΡΡΠ°ΡΠ΅ ΠΏΠΎΠ»ΡΡΠ°Π΅ΡΡΡ 0.ΠΡΠ½ΠΎΡΠ΅Π½ΠΈΠ΅ ΠΏΠ΅ΡΠΊΠ° ΠΊΠΎ Π²ΡΠ΅ΠΌΡ Π²ΡΠΆΡΡΠ΅ΠΌΡ ΡΠΎΡΡΠ°Π²Ρ 84: 1 ΠΈΠ·-Π·Π° Π²ΡΠΆΡΡΠ΅Π³ΠΎ ΡΠΎΠ΄Π΅ΡΠΆΠ°Π½ΠΈΡ Π΄ΠΎΠ±Π°Π²ΠΊΠΈ GFRC)
- 14,63% BRCP GFRC ΠΡΠΈΠΌΠ΅ΡΡ
- ΠΡ / C (Π²ΠΎΠ΄Π° Π² ΡΠ΅ΠΌΠ΅Π½Ρ) 0,32
- 3% ΠΠΎΠ·Π° ΡΡΠ΅ΠΊΠ»ΠΎΠ²ΠΎΠ»ΠΎΠΊΠ½Π° 19 ΠΌΠΌ
Buddy Rhodes Concrete Products GFRC ΠΠΎΠ±Π°Π²ΠΊΠ° 1: 1
- 1 ΡΠ°ΡΡΡ ΠΏΠ΅ΡΠΊΠ°, 1 ΡΠ°ΡΡΡ ΠΏΠΎΡΡΠ»Π°Π½Π΄ΡΠ΅ΠΌΠ΅Π½ΡΠ°
- 14,63% BRCP GFRC ΠΡΠΈΠΌΠ΅ΡΡ
- ΠΡ / C (Π²ΠΎΠ΄Π° Π² ΡΠ΅ΠΌΠ΅Π½Ρ) 0,32
- 3% ΠΠΎΠ·Π° ΡΡΠ΅ΠΊΠ»ΠΎΠ²ΠΎΠ»ΠΎΠΊΠ½Π° 19 ΠΌΠΌ
CENSORED / Π±Π΅Π»ΡΠΉ ΠΊΡΠ΅ΠΌΠ½Π΅Π·Π΅ΠΌ
- 1 ΡΠ°ΡΡΡ ΠΏΠ΅ΡΠΊΠ°, 1 ΡΠ°ΡΡΡ Π²ΡΠΆΡΡΠ΅Π³ΠΎ (ΠΏΠΎΡΡΠ»Π°Π½Π΄ΡΠ΅ΠΌΠ΅Π½Ρ + Π±Π΅Π»ΡΠΉ Π΄ΡΠΌΡΠ°ΡΡΠΉ ΠΏΡΡΡΠΎΠ»Π°Π½)
- 10% Π±Π΅Π»ΡΠΉ Π΄ΡΠΌΠΎΠΊ ΠΊΡΠ΅ΠΌΠ½Π΅Π·Π΅ΠΌΠ°, Π΄ΠΎΠ·ΠΈΡΡΠ΅ΠΌΡΠΉ Π² ΠΊΠ°ΡΠ΅ΡΡΠ²Π΅ ΡΠ°ΡΡΠΈΡΠ½ΠΎΠΉ Π·Π°ΠΌΠ΅Π½Ρ ΡΠ΅ΠΌΠ΅Π½ΡΠ°
- 3% Π¦ΠΠΠΠ£Π Π GFRC Admix
- ΠΡ / C (Π²ΠΎΠ΄Π° Π² ΡΠ΅ΠΌΠ΅Π½Ρ) 0.30
- 3% ΠΠΎΠ·Π° ΡΡΠ΅ΠΊΠ»ΠΎΠ²ΠΎΠ»ΠΎΠΊΠ½Π° 19 ΠΌΠΌ
Π‘ Π¦ΠΠΠΠ£Π ΠΠ / VCAS
- 1 ΡΠ°ΡΡΡ ΠΏΠ΅ΡΠΊΠ°, 1 ΡΠ°ΡΡΡ ΡΠ΅ΠΌΠ΅Π½ΡΠ° (ΠΏΠΎΡΡΠ»Π°Π½Π΄ΡΠ΅ΠΌΠ΅Π½Ρ + ΠΏΡΡΡΠΎΠ»Π°Π½ VCAS)
- 20% VCAS Π΄ΠΎΠ·ΠΈΡΠΎΠ²Π°Π½ΠΎ Π² ΠΊΠ°ΡΠ΅ΡΡΠ²Π΅ ΡΠ°ΡΡΠΈΡΠ½ΠΎΠΉ Π·Π°ΠΌΠ΅Π½Ρ ΡΠ΅ΠΌΠ΅Π½ΡΠ°
- 3% Π¦ΠΠΠΠ£Π Π GFRC Admix
- ΠΡ / C (Π²ΠΎΠ΄Π° Π² ΡΠ΅ΠΌΠ΅Π½Ρ) 0,32
- 3% ΠΠΎΠ·Π° ΡΡΠ΅ΠΊΠ»ΠΎΠ²ΠΎΠ»ΠΎΠΊΠ½Π° 19 ΠΌΠΌ
ΠΠΎΠ΄Π³ΠΎΡΠΎΠ²ΠΊΠ° ΠΏΡΠΎΠ±
ΠΡΠ΅ ΠΎΠ±ΡΠ°Π·ΡΡ (Π·Π° ΠΈΡΠΊΠ»ΡΡΠ΅Π½ΠΈΠ΅ΠΌ ΡΠ΅ΡΠΈΠΈ ΠΈΡΠΏΡΡΠ°Π½ΠΈΠΉ SCC) Π±ΡΠ»ΠΈ ΠΎΡΠ»ΠΈΡΡ Π² Π΄Π²Π° ΡΠ»ΠΎΡ, ΠΊΠ°ΠΆΠ΄ΡΠΉ ΡΠ»ΠΎΠΉ Π±ΡΠ» ΡΡΠ°ΡΠ΅Π»ΡΠ½ΠΎ ΡΠΏΠ»ΠΎΡΠ½Π΅Π½ Π²Π°Π»ΠΈΠΊΠΎΠΌ Π΄Π»Ρ ΡΠ΄Π°Π»Π΅Π½ΠΈΡ ΠΏΡΠ·ΡΡΡΠΊΠΎΠ².
ΠΠ±ΡΠ°Π·ΡΡSCC Π±ΡΠ»ΠΈ ΠΎΠ±ΡΠ°Π±ΠΎΡΠ°Π½Ρ ΠΆΠΈΠ΄ΠΊΠΎΡΡΡΡ, Π²ΡΠ»ΠΈΡΡ Π² ΡΠΎΡΠΌΡ ΠΎΠ΄Π½ΠΈΠΌ ΡΠ»ΠΎΠ΅ΠΌ ΠΈ ΠΎΡΡΠΎΡΠΎΠΆΠ½ΠΎ Π²ΡΡΡΡΡ ΠΈΠ²Π°Π»ΠΈ Π΄Π»Ρ Π²ΡΡΠ°Π²Π½ΠΈΠ²Π°Π½ΠΈΡ ΡΠΌΠ΅ΡΠΈ. ΠΡΠ»ΠΈ ΠΏΡΠΈΠ½ΡΡΡ ΠΌΠ΅ΡΡ, ΡΡΠΎΠ±Ρ ΡΠ²Π΅ΡΡΠΈ ΠΊ ΠΌΠΈΠ½ΠΈΠΌΡΠΌΡ Π½Π°ΡΡΡΠ΅Π½ΠΈΠ΅ ΠΈΠ»ΠΈ ΠΌΠ°Π½ΠΈΠΏΡΠ»ΡΡΠΈΠΈ ΡΠΎ ΡΠΌΠ΅ΡΡΡ.
ΠΠ°Π½Π΅Π»ΠΈ Π΄Π»Ρ ΠΈΡΠΏΡΡΠ°Π½ΠΈΠΉ ΠΎΡΠ»ΠΈΠ²ΠΎΠΊ.
ΠΡΠ»ΠΈ ΠΎΡΠ»ΠΈΡΡ Π΄Π²Π΅ ΠΈΡΠΏΡΡΠ°ΡΠ΅Π»ΡΠ½ΡΠ΅ ΠΏΠ°Π½Π΅Π»ΠΈ Π΄Π»Ρ ΠΊΠ°ΠΆΠ΄ΠΎΠ³ΠΎ ΠΊΠ°Π½Π΄ΠΈΠ΄Π°ΡΠ° Π½Π° ΡΠΌΠ΅ΡΠ°Π½Π½ΡΠΉ Π΄ΠΈΠ·Π°ΠΉΠ½ (ΡΠ°ΠΊ Π½Π°Π·ΡΠ²Π°Π΅ΠΌΠ°Ρ ΡΠ΅ΡΠΈΡ ΠΈΡΠΏΡΡΠ°Π½ΠΈΠΉ). ΠΠ±ΡΠ°Π·ΡΡ Π±ΡΠ»ΠΈ ΠΎΡΠ»ΠΈΡΡ, ΠΎΡΠ²Π΅ΡΠΆΠ΄Π΅Π½Ρ ΠΏΠΎΠ΄ ΠΏΠ»Π°ΡΡΠΈΠΊΠΎΠΌ Π² ΡΠ΅ΡΠ΅Π½ΠΈΠ΅ Π½ΠΎΡΠΈ, Π° Π½Π° ΡΠ»Π΅Π΄ΡΡΡΠΈΠΉ Π΄Π΅Π½Ρ ΠΈΠ·Π²Π»Π΅ΡΠ΅Π½Ρ ΠΈΠ· ΡΠΎΡΠΌΡ. ΠΠ°ΡΠ΅ΠΌ ΠΈΠ·Π²Π»Π΅ΡΠ΅Π½Π½ΡΠΌ ΠΎΠ±ΡΠ°Π·ΡΠ°ΠΌ Π΄Π°Π²Π°Π»ΠΈ Π²ΠΎΠ·ΠΌΠΎΠΆΠ½ΠΎΡΡΡ ΠΎΡΠ²Π΅ΡΠΆΠ΄Π°ΡΡΡΡ Π½Π° Π²ΠΎΠ·Π΄ΡΡ Π΅ Π½Π° ΡΡΠ΅Π»Π»Π°ΠΆΠ°Ρ , ΠΊΠΎΡΠΎΡΡΠ΅ ΠΎΠ±Π΅ΡΠΏΠ΅ΡΠΈΠ²Π°Π»ΠΈ ΡΠ²ΠΎΠ±ΠΎΠ΄Π½ΡΡ ΡΠΈΡΠΊΡΠ»ΡΡΠΈΡ Π²ΠΎΠ·Π΄ΡΡ Π° Π²ΠΎΠΊΡΡΠ³ Π²ΡΠ΅Ρ ΡΡΠΎΡΠΎΠ½ ΠΊΠ°ΠΆΠ΄ΠΎΠ³ΠΎ ΠΎΠ±ΡΠ°Π·ΡΠ°.ΠΠ΅ΡΠ΅Π΄ 28-Π΄Π½Π΅Π²Π½ΡΠΌ ΠΈΡΠΏΡΡΠ°Π½ΠΈΠ΅ΠΌ ΠΎΠ±ΡΠ°Π·ΡΡ ΡΠΏΠ»ΡΡΠΈΠ²Π°Π»ΠΈ ΡΠ»ΠΈΡΠΎΠ²Π°Π½ΠΈΠ΅ΠΌ, ΡΠ°Π·ΡΠ΅Π·Π°Π»ΠΈ Π½Π° ΠΊΡΠΏΠΎΠ½Ρ ΡΡΠ°Π½Π΄Π°ΡΡΠ½ΠΎΠ³ΠΎ ΡΠ°Π·ΠΌΠ΅ΡΠ° ΠΈ Π²ΡΠΌΠ°ΡΠΈΠ²Π°Π»ΠΈ Π² Π²ΠΎΠ΄Π΅ Π½Π° 24 ΡΠ°ΡΠ° Π² ΡΠΎΠΎΡΠ²Π΅ΡΡΡΠ²ΠΈΠΈ Ρ ΠΏΡΠ°ΠΊΡΠΈΠΊΠΎΠΉ ΠΈΡΠΏΡΡΠ°Π½ΠΈΠΉ ASTM C-947.
ΠΡΡΠ΅Π·Π°Π½ΠΈΠ΅ ΠΎΠ±ΡΠ°Π·ΡΠΎΠ² ΠΈΠ· ΠΈΡΠΏΡΡΠ°ΡΠ΅Π»ΡΠ½ΠΎΠΉ ΠΏΠ°Π½Π΅Π»ΠΈ.
Π§ΡΠΎΠ±Ρ ΠΈΡΡΠ»Π΅Π΄ΠΎΠ²Π°ΡΡ ΠΏΡΠΎΡΠ½ΠΎΡΡΡ ΠΈ ΡΡΡΠ΅ΠΊΡΠΈΠ²Π½ΠΎΡΡΡ Π΄Π²ΡΡ ΡΡΡ ΠΈΡ ΠΈ ΠΎΠ΄Π½ΠΎΠΉ ΠΆΠΈΠ΄ΠΊΠΎΠΉ ΠΏΠΎΠ»ΠΈΠΌΠ΅ΡΠ½ΠΎΠΉ ΡΠΈΡΡΠ΅ΠΌΡ GFRC, ΠΠ½ΡΡΠΈΡΡΡ Π±Π΅ΡΠΎΠ½Π½ΡΡ ΡΡΠΎΠ»Π΅ΡΠ½ΠΈΡ ΠΏΡΠΎΠ²Π΅Π» ΠΎΠ±ΡΠΈΡΠ½ΡΠΉ ΡΡΠ΄ ΠΈΡΠΏΡΡΠ°Π½ΠΈΠΉ Π½Π° ΠΈΠ·Π³ΠΈΠ±, ΡΡΠΎΠ±Ρ ΠΎΠΏΡΠ΅Π΄Π΅Π»ΠΈΡΡ, ΡΡΠ½ΠΊΡΠΈΠΎΠ½ΠΈΡΡΡΡ Π»ΠΈ Π΄Π²Π° ΡΡΡ ΠΈΡ ΠΏΠΎΠ»ΠΈΠΌΠ΅ΡΠ° ΠΊΠ°ΠΊ ΠΏΠΎΠ»ΠΈΠΌΠ΅ΡΠ½ΡΠ΅ ΠΎΡΠ²Π΅ΡΠΆΠ΄Π°ΡΡΠΈΠ΅ Π΄ΠΎΠ±Π°Π²ΠΊΠΈ.ΠΡΠΎΠΌΠ΅ ΡΠΎΠ³ΠΎ, Π² ΠΊΠ°ΡΠ΅ΡΡΠ²Π΅ ΠΊΠΎΠ½ΡΡΠΎΠ»Ρ Π±ΡΠ»ΠΈ ΠΏΡΠΎΠ²Π΅Π΄Π΅Π½Ρ ΠΈΡΠΏΡΡΠ°Π½ΠΈΡ Π½Π° ΠΈΠ·Π³ΠΈΠ± GFRC, ΡΠΎΠ΄Π΅ΡΠΆΠ°ΡΠ΅Π³ΠΎ Forton VF-774. ΠΠΎΠΌΠΏΠ°Π½ΠΈΡ CCI ΠΏΡΠΎΠ²Π΅Π»Π° Π±ΠΎΠ»Π΅Π΅ 200 ΠΈΡΠΏΡΡΠ°Π½ΠΈΠΉ Π½Π° ΠΈΠ·Π³ΠΈΠ± Π² ΡΠΎΠΎΡΠ²Π΅ΡΡΡΠ²ΠΈΠΈ Ρ ΡΠ΅ΠΊΠΎΠΌΠ΅Π½Π΄Π°ΡΠΈΡΠΌΠΈ ASTM C-947 Β«Π‘ΡΠ°Π½Π΄Π°ΡΡΠ½ΡΠΉ ΠΌΠ΅ΡΠΎΠ΄ ΠΈΡΠΏΡΡΠ°Π½ΠΈΠΉ ΡΠ²ΠΎΠΉΡΡΠ² Π½Π° ΠΈΠ·Π³ΠΈΠ± ΡΠΎΠ½ΠΊΠΈΡ ΡΡΠ΅ΠΊΠ»ΠΎΠ²ΠΎΠ»ΠΎΠΊΠΎΠ½Π½ΡΡ Π±Π΅ΡΠΎΠ½ΠΎΠ²Β», ΠΈΡΠΏΠΎΠ»ΡΠ·ΡΡ Π½Π°ΡΡ ΡΠΎΠ±ΡΡΠ²Π΅Π½Π½ΡΡ ΠΌΠ°ΡΠΈΠ½Ρ Π΄Π»Ρ ΠΈΡΠΏΡΡΠ°Π½ΠΈΠΉ Π½Π° ΠΈΠ·Π³ΠΈΠ±.
ΠΡΠΏΡΡΠ°ΡΠ΅Π»ΡΠ½Π°Ρ ΠΌΠ°ΡΠΈΠ½Π° Π½Π° ΠΈΠ·Π³ΠΈΠ±
ΠΊΠΎΠΌΠΏΠ°Π½ΠΈΠΈ CCIΠΠ»Ρ ΠΏΠΎΠ΄ΡΠ²Π΅ΡΠΆΠ΄Π΅Π½ΠΈΡ ΡΠ΅ΡΡΠΈΡΠΎΠ²Π°Π½ΠΈΡ, ΠΏΡΠΎΠ²Π΅Π΄Π΅Π½Π½ΠΎΠ³ΠΎ Π² CCI, ΠΎΡΠΎΠ±ΡΠ°Π½Π½ΡΠ΅ ΠΈΠ΄Π΅Π½ΡΠΈΡΠ½ΡΠ΅ ΠΎΠ±ΡΠ°Π·ΡΡ Π±ΡΠ»ΠΈ ΠΎΡΠΏΡΠ°Π²Π»Π΅Π½Ρ Π² Π½Π΅Π·Π°Π²ΠΈΡΠΈΠΌΡΡ ΠΈΡΠΏΡΡΠ°ΡΠ΅Π»ΡΠ½ΡΡ Π»Π°Π±ΠΎΡΠ°ΡΠΎΡΠΈΡ Π² ΠΠΊΠ»Π΅Π½Π΄Π΅, ΠΠ°Π»ΠΈΡΠΎΡΠ½ΠΈΡ. ΠΡΠΈ ΠΎΡΠΎΠ±ΡΠ°Π½Π½ΡΠ΅ ΠΎΠ±ΡΠ°Π·ΡΡ Π±ΡΠ»ΠΈ ΠΎΡΠ»ΠΈΡΡ ΠΈΠ· ΠΎΠ΄Π½ΠΎΠΉ ΠΏΠ°ΡΡΠΈΠΈ Π±Π΅ΡΠΎΠ½Π° Π² ΠΎΠ΄ΠΈΠ½ ΠΈ ΡΠΎΡ ΠΆΠ΅ Π΄Π΅Π½Ρ ΠΎΠ΄Π½ΠΈΠΌ ΠΈ ΡΠ΅ΠΌ ΠΆΠ΅ ΡΠ΅Π»ΠΎΠ²Π΅ΠΊΠΎΠΌ, ΠΈ ΠΈΡΠΏΡΡΠ°Π½ΠΈΡ Π½Π° ΠΈΠ·Π³ΠΈΠ± Π±ΡΠ»ΠΈ Π²ΡΠΏΠΎΠ»Π½Π΅Π½Ρ Π² ΡΠΎΡ ΠΆΠ΅ Π΄Π΅Π½Ρ.Π Π΅Π·ΡΠ»ΡΡΠ°ΡΡ ΠΈΡΠΏΡΡΠ°Π½ΠΈΠΉ Π½Π° ΠΈΠ·Π³ΠΈΠ± 18 ΠΎΠ±ΡΠ°Π·ΡΠΎΠ², ΠΈΡΠΏΡΡΠ°Π½Π½ΡΡ Π² ΡΡΠ°ΡΠ°Ρ Π‘Π΅Π²Π΅ΡΠ½Π°Ρ ΠΠ°ΡΠΎΠ»ΠΈΠ½Π° ΠΈ ΠΠ°Π»ΠΈΡΠΎΡΠ½ΠΈΡ, Π±ΡΠ»ΠΈ ΡΡΠ°ΡΠΈΡΡΠΈΡΠ΅ΡΠΊΠΈ ΠΈΠ΄Π΅Π½ΡΠΈΡΠ½ΡΠΌΠΈ, ΡΡΠΎ ΠΏΠΎΠ΄ΡΠ²Π΅ΡΠΆΠ΄Π°Π΅Ρ ΡΠΎΡΠ½ΠΎΡΡΡ ΠΈ Π΄ΠΎΡΡΠΎΠ²Π΅ΡΠ½ΠΎΡΡΡ ΡΠ΅Π·ΡΠ»ΡΡΠ°ΡΠΎΠ² Π²Π½ΡΡΡΠ΅Π½Π½ΠΈΡ ΠΈΡΠΏΡΡΠ°Π½ΠΈΠΉ Π² CCI.
ΠΡΠ»ΠΈ ΠΏΡΠΎΠ²Π΅Π΄Π΅Π½Ρ ΠΈΡΠΏΡΡΠ°Π½ΠΈΡ Π½Π° ΡΠ΅ΡΡΡΠ΅Ρ ΡΠΎΡΠ΅ΡΠ½ΡΠΉ ΠΈΠ·Π³ΠΈΠ± Ρ ΠΈΠ·ΠΌΠ΅ΡΠ΅Π½ΠΈΠ΅ΠΌ ΠΏΠΈΠΊΠΎΠ²ΠΎΠΉ Π½Π°Π³ΡΡΠ·ΠΊΠΈ ΠΏΡΠΈ ΡΠ°Π·ΡΡΠ²Π΅, Π² ΡΠ΅Π·ΡΠ»ΡΡΠ°ΡΠ΅ ΡΠ΅Π³ΠΎ Π±ΡΠ»ΠΈ ΠΏΠΎΠ»ΡΡΠ΅Π½Ρ Π΄Π°Π½Π½ΡΠ΅ ΠΎ ΠΌΠΎΠ΄ΡΠ»Π΅ ΡΠ°Π·ΡΡΠ²Π° (MOR), ΠΊΠΎΡΠΎΡΡΠ΅ ΠΏΡΠ΅Π΄ΡΡΠ°Π²Π»ΡΡΡ ΡΠΎΠ±ΠΎΠΉ ΠΏΠΈΠΊΠΎΠ²ΡΡ ΠΏΡΠΎΡΠ½ΠΎΡΡΡ ΠΌΠ°ΡΠ΅ΡΠΈΠ°Π»Π° Π½Π° ΠΈΠ·Π³ΠΈΠ±, ΠΈΠ·ΠΌΠ΅ΡΠ΅Π½Π½ΡΡ ΠΏΡΠΈ ΡΠ°Π·ΡΡΡΠ΅Π½ΠΈΠΈ ΠΎΠ±ΡΠ°Π·ΡΠ°.
ΠΠ±ΡΠ°Π·Π΅ΡGFRC ΠΏΡΠΈ 4-ΡΠΎΡΠ΅ΡΠ½ΠΎΠΌ ΠΈΠ·Π³ΠΈΠ±Π΅. ΠΡΠΈΠΌΠ΅ΡΠ°Π½ΠΈΠ΅: ΠΏΡΠΈΠ»ΠΎΠΆΠ΅Π½Π½Π°Ρ Π½Π°Π³ΡΡΠ·ΠΊΠ° Π² 4 ΡΠ°Π·Π° Π±ΠΎΠ»ΡΡΠ΅, ΡΠ΅ΠΌ ΡΠΈΡΡΠΎΠ²ΠΎΠ΅ ΡΡΠΈΡΡΠ²Π°Π½ΠΈΠ΅.
Π‘ΡΠ΅Π΄Π½ΠΈΠ΅ Π΄Π°Π½Π½ΡΠ΅ MOR Π΄Π»Ρ ΡΡΠ΅Ρ ΡΠΈΡΡΠ΅ΠΌ ΠΏΠΎΠ»ΠΈΠΌΠ΅ΡΠ½ΡΡ Π΄ΠΎΠ±Π°Π²ΠΎΠΊ Π΄Π»Ρ ΠΎΡΠ²Π΅ΡΠΆΠ΄Π΅Π½ΠΈΡ ΠΏΠΎΠΊΠ°Π·Π°Π½Ρ Π½ΠΈΠΆΠ΅ Π²ΠΌΠ΅ΡΡΠ΅ Ρ Π΄Π°Π½Π½ΡΠΌΠΈ Π΄Π»Ρ Π°Π½Π°Π»ΠΎΠ³ΠΈΡΠ½ΡΡ GFRC, ΠΈΠ·Π³ΠΎΡΠΎΠ²Π»Π΅Π½Π½ΡΡ Π±Π΅Π· ΠΊΠ°ΠΊΠΈΡ -Π»ΠΈΠ±ΠΎ Π΄ΠΎΠ±Π°Π²ΠΎΠΊ Π΄Π»Ρ ΠΎΡΠ²Π΅ΡΠΆΠ΄Π΅Π½ΠΈΡ ΠΈ ΠΎΡΠ²Π΅ΡΠΆΠ΄Π΅Π½Π½ΡΡ Π²ΠΎ Π²Π»Π°ΠΆΠ½ΠΎΠΉ ΡΡΠ΅Π΄Π΅ Π² ΡΠ΅ΡΠ΅Π½ΠΈΠ΅ 7 Π΄Π½Π΅ΠΉ Π½Π΅ΠΏΡΠ΅ΡΡΠ²Π½ΠΎ ΠΏΠ΅ΡΠ΅Π΄ ΠΎΡΠ²Π΅ΡΠΆΠ΄Π΅Π½ΠΈΠ΅ΠΌ Π½Π° Π²ΠΎΠ·Π΄ΡΡ Π΅. ΠΡΠ΅ Π΄Π°Π½Π½ΡΠ΅ ΠΏΡΠ΅Π΄ΡΡΠ°Π²Π»Π΅Π½Ρ Π·Π° 28 Π΄Π½Π΅ΠΉ.
ΠΠ°ΠΆΠ΄Π°Ρ ΡΠ²Π΅ΡΠ½Π°Ρ ΠΏΠΎΠ»ΠΎΡΠ° Π² ΠΏΡΠΈΠ²Π΅Π΄Π΅Π½Π½ΠΎΠΉ Π²ΡΡΠ΅ ΡΠ°Π±Π»ΠΈΡΠ΅ ΠΏΡΠ΅Π΄ΡΡΠ°Π²Π»ΡΠ΅Ρ ΡΡΠ΅Π΄Π½Π΅Π΅ Π·Π½Π°ΡΠ΅Π½ΠΈΠ΅ MOR Π΄Π»Ρ ΠΊΠΎΠ½ΠΊΡΠ΅ΡΠ½ΠΎΠΉ ΡΠ΅ΡΠΈΠΈ ΠΈΡΠΏΡΡΠ°Π½ΠΈΠΉ, ΠΈ ΠΊΠ°ΠΆΠ΄Π°Ρ ΡΠ΅ΡΠΈΡ ΠΈΡΠΏΡΡΠ°Π½ΠΈΠΉ ΡΠΎΡΡΠΎΡΠ»Π° ΠΈΠ· Π΄ΠΎ 12 ΠΎΡΠ΄Π΅Π»ΡΠ½ΡΡ ΠΎΠ±ΡΠ°Π·ΡΠΎΠ² Π΄Π»Ρ ΠΈΡΠΏΡΡΠ°Π½ΠΈΠΉ Π½Π° ΠΈΠ·Π³ΠΈΠ±, ΠΎΡΠ»ΠΈΡΡΡ ΠΈΠ· ΠΎΠ΄Π½ΠΎΠΉ ΠΏΠ°ΡΡΠΈΠΈ Π±Π΅ΡΠΎΠ½Π°.ΠΠ° Π΄ΠΈΠ°Π³ΡΠ°ΠΌΠΌΠ΅ ΠΏΡΠ΅Π΄ΡΡΠ°Π²Π»Π΅Π½Ρ ΡΠ΅Π·ΡΠ»ΡΡΠ°ΡΡ Π±ΠΎΠ»Π΅Π΅ 200 ΠΎΡΠ΄Π΅Π»ΡΠ½ΡΡ ΠΈΡΠΏΡΡΠ°Π½ΠΈΠΉ Π½Π° ΠΈΠ·Π³ΠΈΠ±.
ΠΠ°ΡΠΈΠ°ΡΠΈΠΈ MOR Π΄Π»Ρ ΠΊΠ°ΠΆΠ΄ΠΎΠΉ ΡΠ΅ΡΠΈΠΈ ΠΈΡΠΏΡΡΠ°Π½ΠΈΠΉ ΠΏΠΎΠΊΠ°Π·Π°Π½Ρ ΠΏΠΎΠ»ΠΎΡΠ°ΠΌΠΈ ΠΎΡΠΈΠ±ΠΎΠΊ, ΠΊΠΎΡΠΎΡΡΠ΅ ΠΏΠΎΠΊΠ°Π·ΡΠ²Π°ΡΡ ΠΎΠ΄Π½ΠΎ ΡΡΠ°Π½Π΄Π°ΡΡΠ½ΠΎΠ΅ ΠΎΡΠΊΠ»ΠΎΠ½Π΅Π½ΠΈΠ΅ Π²Π°ΡΠΈΠ°ΡΠΈΠΈ. ΠΠΎΠ»Π΅Π΅ ΠΊΡΡΠΏΠ½ΡΠ΅ ΠΏΠΎΠ»ΠΎΡΡ ΠΏΠΎΠ³ΡΠ΅ΡΠ½ΠΎΡΡΠ΅ΠΉ ΠΏΡΠ΅Π΄ΡΡΠ°Π²Π»ΡΡΡ Π±ΠΎΠ»ΡΡΠ΅Π΅ ΠΈΠ·ΠΌΠ΅Π½Π΅Π½ΠΈΠ΅ MOR Π² ΡΠ΅ΡΠΈΠΈ ΡΠ΅ΡΡΠΎΠ².
ΠΠ΅ΡΠ΅Π΄ΠΊΠΎ ΠΌΠΎΠΆΠ½ΠΎ Π±ΡΠ»ΠΎ ΡΠ²ΠΈΠ΄Π΅ΡΡ Π·Π½Π°ΡΠ΅Π½ΠΈΡ MOR, ΠΎΡΠ»ΠΈΡΠ°ΡΡΠΈΠ΅ΡΡ Π½Π° Π½Π΅ΡΠΊΠΎΠ»ΡΠΊΠΎ ΡΠΎΡΠ΅Π½ ΡΡΠ½ΡΠΎΠ² Π½Π° ΠΊΠ²Π°Π΄ΡΠ°ΡΠ½ΡΠΉ Π΄ΡΠΉΠΌ Π΄Π»Ρ ΡΠΎΡΠ΅Π΄Π½ΠΈΡ ΠΎΠ±ΡΠ°Π·ΡΠΎΠ², Π²ΡΡΠ΅Π·Π°Π½Π½ΡΡ ΠΈΠ· ΠΎΠ΄Π½ΠΎΠΉ ΠΈ ΡΠΎΠΉ ΠΆΠ΅ ΠΈΡΠΏΡΡΠ°ΡΠ΅Π»ΡΠ½ΠΎΠΉ ΠΏΠ°Π½Π΅Π»ΠΈ GFRC. ΠΠΎΡΠ»Π΅ ΡΡΠ°ΡΠ΅Π»ΡΠ½ΠΎΠ³ΠΎ Π°Π½Π°Π»ΠΈΠ·Π° ΠΌΡ ΠΎΠΏΡΠ΅Π΄Π΅Π»ΠΈΠ»ΠΈ, ΡΡΠΎ Π²Π΅Π»ΠΈΡΠΈΠ½Π° ΠΈ ΠΈΠ·ΠΌΠ΅Π½Π΅Π½ΠΈΠ΅ ΠΏΡΠΎΡΠ½ΠΎΡΡΠΈ Π² ΠΎΡΠ½ΠΎΠ²Π½ΠΎΠΌ ΡΠ²ΡΠ·Π°Π½Ρ Ρ Π½Π°Π»ΠΈΡΠΈΠ΅ΠΌ ΠΈ ΡΠ°ΡΠΏΡΠ΅Π΄Π΅Π»Π΅Π½ΠΈΠ΅ΠΌ Π·Π°Ρ Π²Π°ΡΠ΅Π½Π½ΡΡ ΠΏΡΠ·ΡΡΡΠΊΠΎΠ² Π²ΠΎΠ·Π΄ΡΡ Π° Π² ΠΌΠ°ΡΡΠΈΡΠ΅ GFRC ΠΈ ΡΠ°ΡΡΠΈΡΠ½ΠΎ Ρ Π½Π΅ΠΎΠ΄Π½ΠΎΡΠΎΠ΄Π½ΠΎΠΉ ΠΎΡΠΈΠ΅Π½ΡΠ°ΡΠΈΠ΅ΠΉ ΠΈ ΡΠ°ΡΠΏΡΠ΅Π΄Π΅Π»Π΅Π½ΠΈΠ΅ΠΌ ΡΡΠ΅ΠΊΠ»ΠΎΠ²ΠΎΠ»ΠΎΠΊΠΎΠ½ Π² ΠΎΠ±ΡΠ°Π·ΡΠ°Ρ .ΠΠΎΠ»ΡΡΠ΅ Π·Π°Ρ Π²Π°ΡΠ΅Π½Π½ΠΎΠ³ΠΎ Π²ΠΎΠ·Π΄ΡΡ Π° ΠΏΡΠΈΠ²Π΅Π»ΠΎ ΠΊ ΡΠ½ΠΈΠΆΠ΅Π½ΠΈΡ ΠΏΡΠΎΡΠ½ΠΎΡΡΠΈ. ΠΡΠΎ Π΄ΠΎΠ±Π°Π²Π»ΡΠ΅Ρ Π΄ΠΎΠ²Π΅ΡΠΈΡ ΠΊ ΠΌΠ½Π΅Π½ΠΈΡ, ΡΡΠΎ Π±ΠΎΠ»Π΅Π΅ ΠΏΠ»ΠΎΡΠ½ΡΠΉ GFRC Π»ΡΡΡΠ΅ GFRC. ΠΡΠΎ ΡΠΎΠ³Π»Π°ΡΡΠ΅ΡΡΡ Ρ ΡΡΠ΅Π±ΠΎΠ²Π°Π½ΠΈΠ΅ΠΌ β 3 ΡΡΠ°Π½Π΄Π°ΡΡΠ° PCI ΠΎΡΠ½ΠΎΡΠΈΡΠ΅Π»ΡΠ½ΠΎ ΡΠ΄Π΅Π»ΡΠ½ΠΎΠ³ΠΎ Π²Π΅ΡΠ° (Ρ. Π. ΠΠ»ΠΎΡΠ½ΠΎΡΡΠΈ) Π±ΠΎΠ»Π΅Π΅ 120 ΡΡΠ½ΡΠΎΠ² Π½Π° ΠΊΡΠ±ΠΈΡΠ΅ΡΠΊΠΈΠΉ ΡΡΡ.
Π Π°Π·Π»ΠΈΡΠΈΡ Π² ΠΊΠΎΠ»ΠΈΡΠ΅ΡΡΠ²Π΅ Π·Π°Ρ Π²Π°ΡΠ΅Π½Π½ΠΎΠ³ΠΎ Π²ΠΎΠ·Π΄ΡΡ Π° Π² ΡΠΎΡΠ΅Π΄Π½ΠΈΡ ΠΎΠ±ΡΠ°Π·ΡΠ°Ρ , Π²ΡΡΠ΅Π·Π°Π½Π½ΡΡ ΠΈΠ· ΠΎΠ΄Π½ΠΎΠΉ ΠΈΡΠΏΡΡΠ°ΡΠ΅Π»ΡΠ½ΠΎΠΉ ΠΏΠ°Π½Π΅Π»ΠΈ.
ΠΠ°ΠΆΠ΄Π°Ρ ΡΠ΅ΡΠΈΡ ΠΈΡΠΏΡΡΠ°Π½ΠΈΠΉ ΠΏΠΎΠΌΠ΅ΡΠ΅Π½Π° ΡΠΎΠΊΡΠ°ΡΠ΅Π½Π½ΡΠΌ ΠΊΠΎΠ΄ΠΎΠΌ, ΠΊΠΎΡΠΎΡΡΠΉ ΡΠ°ΡΠΊΡΡΠ²Π°Π΅Ρ Π΄Π΅ΡΠ°Π»ΠΈ ΠΊΠΎΠ½ΠΊΡΠ΅ΡΠ½ΠΎΠΉ ΠΏΡΠΎΡΠ΅ΡΡΠΈΡΠΎΠ²Π°Π½Π½ΠΎΠΉ ΠΊΠΎΠ½ΡΡΡΡΠΊΡΠΈΠΈ ΡΠΌΠ΅ΡΠΈ.ΠΠ°ΠΏΡΠΈΠΌΠ΅Ρ, ΠΏΠ΅ΡΠ²Π°Ρ ΠΊΡΠ°ΡΠ½Π°Ρ ΠΏΠΎΠ»ΠΎΡΠ° ΠΎΡΠΈΠ±ΠΊΠΈ ΠΏΠΎΠΌΠ΅ΡΠ΅Π½Π° Β«D1 3T, 10SF, 2,55% 19, 0,30Β».
- Β«D1Β» ΠΎΠ·Π½Π°ΡΠ°Π΅Ρ ΡΠ΅ΡΡ D, ΡΠ΅ΡΠ²Π΅ΡΡΡΡ ΡΠ΅ΡΠΈΡ ΡΠ΅ΡΡΠΎΠ², Π° 1 ΠΎΡΠ½ΠΎΡΠΈΡΡΡ ΠΊ ΠΏΠ΅ΡΠ²ΠΎΠΉ ΠΈΠ· Π΄Π²ΡΡ ΠΎΡΠ»ΠΈΡΡΡ ΠΈΡΠΏΡΡΠ°ΡΠ΅Π»ΡΠ½ΡΡ ΠΏΠ°Π½Π΅Π»Π΅ΠΉ. (Π¦ΠΈΡΡΠ° 7 Π²ΠΌΠ΅ΡΡΠΎ 1 ΠΎΡΠ½ΠΎΡΠΈΡΡΡ ΠΊΠΎ Π²ΡΠΎΡΠΎΠΉ ΠΏΠ°Π½Π΅Π»ΠΈ, ΠΏΠΎΡΠΊΠΎΠ»ΡΠΊΡ ΠΊΠ°ΠΆΠ΄Π°Ρ ΠΏΠ°Π½Π΅Π»Ρ ΠΈΠΌΠ΅Π»Π° 6 ΠΎΠ±ΡΠ°Π·ΡΠΎΠ² Π΄Π»Ρ ΠΈΡΠΏΡΡΠ°Π½ΠΈΠΉ Π½Π° ΠΈΠ·Π³ΠΈΠ±, Π²ΡΡΠ΅Π·Π°Π½Π½ΡΡ ΠΈΠ· Π½Π΅Π΅).
- ΠΠ°Π»Π΅Π΅ ΡΠ»Π΅Π΄ΡΠ΅Ρ ΠΏΠΎΠ»ΠΈΠΌΠ΅ΡΠ½Π°Ρ ΠΎΡΠ²Π΅ΡΠΆΠ΄Π°ΡΡΠ°Ρ Π΄ΠΎΠ±Π°Π²ΠΊΠ° ΠΈ Π΅Π΅ Π΄ΠΎΠ·Π°.
- Π ΡΡΠΎΠΌ ΠΏΡΠΈΠΌΠ΅ΡΠ΅ Β«3CΒ» ΠΎΡΠ½ΠΎΡΠΈΡΡΡ ΠΊ 3% Π΄ΠΎΠ·Π΅ CENSORED’s GFRC Admix.
- Forton ΠΏΠΎΠΌΠ΅ΡΠ΅Π½ Π±ΡΠΊΠ²ΠΎΠΉ Β«FΒ», Π° ΡΠΈΡΡΠ° 5 ΠΈΠ»ΠΈ 6 ΠΎΡΠ½ΠΎΡΠΈΡΡΡ ΠΊ Π΄ΠΎΠ·Π΅ 5 ΠΈΠ»ΠΈ 6%.
- BR ΠΎΠ·Π½Π°ΡΠ°Π΅Ρ Π΄ΠΎΠ±Π°Π²ΠΊΡ GFRC Π΄Π»Ρ Π±Π΅ΡΠΎΠ½Π½ΡΡ ΠΈΠ·Π΄Π΅Π»ΠΈΠΉ Buddy Rhodes; 3BR — ΡΡΠΎ Π΄ΠΎΠ·Π° 3%, Π° 3+ ΠΎΡΠ½ΠΎΡΠΈΡΡΡ ΠΊ Π΄ΠΎΠ·Π΅ Π½Π΅ΠΌΠ½ΠΎΠ³ΠΎ Π²ΡΡΠ΅ 3%.
- Π ΠΎΠ΄Π½ΠΎΠΌ ΠΈΠ· ΠΈΡΠΏΡΡΠ°Π½ΠΈΠΉ ΠΈΡΠΏΠΎΠ»ΡΠ·ΠΎΠ²Π°Π»Π°ΡΡ ΡΠΌΠ΅ΡΡ BRCP Blended GFRC, ΠΊΠΎΡΠΎΡΠ°Ρ Π²ΠΊΠ»ΡΡΠ°Π»Π° ΠΏΠ΅ΡΠΎΠΊ ΠΈ ΡΠ΅ΠΌΠ΅Π½Ρ Π²ΠΌΠ΅ΡΡΠ΅ Ρ Π΄ΠΎΠ±Π°Π²ΠΊΠΎΠΉ Π² ββΠ΅Π΄ΠΈΠ½ΡΡ ΡΠΌΠ΅ΡΡ Π² ΠΌΠ΅ΡΠΊΠ°Ρ . ΠΡΠΎΡ ΡΠ΅ΡΡ Π½Π°Π·ΡΠ²Π°Π΅ΡΡΡ Β«BR Blended MixΒ».
- ΠΠΎΠ½ΡΡΡΡΠΊΡΠΈΡ ΡΠΌΠ΅ΡΠΈ BRCP GFRC ΡΡΠ΅Π±ΡΠ΅Ρ ΠΎΡΠ½ΠΎΡΠ΅Π½ΠΈΡ ΠΏΠ΅ΡΠΊΠ° ΠΊ ΡΠ΅ΠΌΠ΅Π½ΡΡ ΠΎΠΊΠΎΠ»ΠΎ 0,84: 1, ΡΠΎΠ³Π΄Π° ΠΊΠ°ΠΊ Π΄Π»Ρ Π²ΡΠ΅Ρ Π΄ΡΡΠ³ΠΈΡ ΡΠΌΠ΅ΡΠ΅ΠΉ, Π½Π΅ ΠΎΡΠ½ΠΎΡΡΡΠΈΡ ΡΡ ΠΊ BRCP, ΠΈΡΠΏΠΎΠ»ΡΠ·ΡΠ΅ΡΡΡ ΡΠΎΠΎΡΠ½ΠΎΡΠ΅Π½ΠΈΠ΅ 1: 1. ΠΠ»Ρ ΠΏΡΡΠΌΠΎΠ³ΠΎ ΡΡΠ°Π²Π½Π΅Π½ΠΈΡ ΠΎΠ΄Π½Π° ΡΠ΅ΡΠΈΡ ΠΈΡΠΏΡΡΠ°Π½ΠΈΠΉ BRCP Π±ΡΠ»Π° ΠΈΡΠΏΡΡΠ°Π½Π° ΠΏΡΠΈ ΡΠΎΠΎΡΠ½ΠΎΡΠ΅Π½ΠΈΠΈ ΠΏΠ΅ΡΠΎΠΊ: ΡΠ΅ΠΌΠ΅Π½Ρ 1: 1.ΠΡΡΡΠ΄Π° ΠΈ ΠΎΠ±ΠΎΠ·Π½Π°ΡΠ΅Π½ΠΈΡ Β«3BR Admix 0.84: 1Β» ΠΈ Β«3BR Admix 1: 1Β». ΠΡΠΏΠΎΠ»ΡΠ·ΠΎΠ²Π°Π»Π°ΡΡ 3% Π΄ΠΎΠ·Π° Admix Ρ ΡΠ°Π·Π»ΠΈΡΠ½ΡΠΌ ΡΠΎΠΎΡΠ½ΠΎΡΠ΅Π½ΠΈΠ΅ΠΌ ΠΏΠ΅ΡΠΊΠ° ΠΈ ΡΠ΅ΠΌΠ΅Π½ΡΠ°.
- Β«0PΒ» ΠΎΠ·Π½Π°ΡΠ°Π΅Ρ, ΡΡΠΎ Π΄ΠΎΠ±Π°Π²ΠΊΠ° Π΄Π»Ρ ΠΎΡΠ²Π΅ΡΠΆΠ΄Π΅Π½ΠΈΡ ΠΏΠΎΠ»ΠΈΠΌΠ΅ΡΠ° (0%) Π½Π΅ ΠΈΡΠΏΠΎΠ»ΡΠ·ΠΎΠ²Π°Π»Π°ΡΡ.
- ΠΠ°Π»Π΅Π΅ ΠΈΠ΄ΡΡ ΠΏΡΡΡΠΎΠ»Π°Π½ ΠΈ Π΄ΠΎΠ·Π°, ΠΏΠΎΡΡΠΎΠΌΡ Β«10SFΒ» ΠΎΠ·Π½Π°ΡΠ°Π΅Ρ, ΡΡΠΎ ΠΈΡΠΏΠΎΠ»ΡΠ·ΠΎΠ²Π°Π»ΡΡ Π±Π΅Π»ΡΠΉ Π΄ΡΠΌ ΠΊΡΠ΅ΠΌΠ½Π΅Π·Π΅ΠΌΠ° Π² 10% Π·Π°ΠΌΠ΅ΡΠ°ΡΡΠ΅ΠΉ Π΄ΠΎΠ·ΠΈΡΠΎΠ²ΠΊΠ΅. Β«20VΒ» ΠΎΠ·Π½Π°ΡΠ°Π΅Ρ Π΄ΠΎΠ·Ρ 20% VCAS.
- ΠΠ°Π»Π΅Π΅ ΡΠΊΠ°Π·Π°Π½Ρ ΠΎΠ±ΡΠ΅ΠΌΠ½Π°Ρ Π΄ΠΎΠ»Ρ ΠΈ ΡΠ°Π·ΠΌΠ΅Ρ Π²ΠΎΠ»ΠΎΠΊΠ½Π°, ΠΊΠΎΡΠΎΡΡΠ΅ ΠΏΡΠ΅Π΄ΡΡΠ°Π²Π»ΡΡΡ ΡΠΎΠ±ΠΎΠΉ ΡΡΠ΅ΠΊΠ»ΠΎΠ²ΠΎΠ»ΠΎΠΊΠ½ΠΎ AR Π΄Π»ΠΈΠ½ΠΎΠΉ 19 ΠΌΠΌ. ΠΠ±ΡΠ΅ΠΌΠ½Π°Ρ Π΄ΠΎΠ»Ρ Π²ΠΎΠ»ΠΎΠΊΠ½Π° ΠΎΠΏΡΠ΅Π΄Π΅Π»ΡΠ΅ΡΡΡ ΠΊΠ°ΠΊ Π²Π΅Ρ Π²ΠΎΠ»ΠΎΠΊΠΎΠ½, Π΄Π΅Π»Π΅Π½Π½ΡΠΉ Π½Π° ΠΎΠ±ΡΠΈΠΉ Π²Π΅Ρ Π±Π΅ΡΠΎΠ½Π°, Π²ΠΊΠ»ΡΡΠ°Ρ Π²Π΅Ρ Π²ΠΎΠ»ΠΎΠΊΠΎΠ½ ΠΏΠ»ΡΡ Π²ΡΠ΅ ΠΎΡΡΠ°Π»ΡΠ½ΡΠ΅ ΠΈΠ½Π³ΡΠ΅Π΄ΠΈΠ΅Π½ΡΡ ΡΠΌΠ΅ΡΠΈ, Π²Π»Π°ΠΆΠ½ΡΠ΅ ΠΈ ΡΡΡ ΠΈΠ΅.Π’Π°ΠΊΠΈΠΌ ΠΎΠ±ΡΠ°Π·ΠΎΠΌ, Β«3% 19Β» ΠΎΠ·Π½Π°ΡΠ°Π΅Ρ, ΡΡΠΎ ΠΈΡΠΏΠΎΠ»ΡΠ·ΠΎΠ²Π°Π»Π°ΡΡ 3% -Π½Π°Ρ ΠΎΠ±ΡΠ΅ΠΌΠ½Π°Ρ Π΄ΠΎΠ»Ρ 19-ΠΌΠΈΠ»Π»ΠΈΠΌΠ΅ΡΡΠΎΠ²ΡΡ Π²ΠΎΠ»ΠΎΠΊΠΎΠ½.
- ΠΠΊΠΎΠ½ΡΠ°ΡΠ΅Π»ΡΠ½ΠΎΠ΅ ΡΠΈΡΠ»ΠΎ — ΠΎΡΠ½ΠΎΡΠ΅Π½ΠΈΠ΅ Π²ΠΎΠ΄Ρ ΠΊ Π²ΡΠΆΡΡΠ΅ΠΌΡ. Π’Π°ΠΊΠΈΠΌ ΠΎΠ±ΡΠ°Π·ΠΎΠΌ, Β«0,30Β» ΠΎΠ·Π½Π°ΡΠ°Π΅Ρ, ΡΡΠΎ ΡΠΎΠΎΡΠ½ΠΎΡΠ΅Π½ΠΈΠ΅ Π² / Ρ ΡΠΌΠ΅ΡΠΈ ΡΠΎΡΡΠ°Π²Π»ΡΠ΅Ρ 0,30. ΠΠ±ΡΠ°ΡΠΈΡΠ΅ Π²Π½ΠΈΠΌΠ°Π½ΠΈΠ΅, ΡΡΠΎ Π²ΡΠ΅ ΡΠΎΠΎΡΠ½ΠΎΡΠ΅Π½ΠΈΡ Π²ΠΎΠ΄ / ΡΠ΅ΠΌΠ΅Π½Ρ Π±ΡΠ»ΠΈ Π² ΠΏΡΠ΅Π΄Π΅Π»Π°Ρ ΠΎΡ 0,30 Π΄ΠΎ 0,32, ΡΡΠΎ ΡΠΎΠΎΡΠ²Π΅ΡΡΡΠ²ΠΎΠ²Π°Π»ΠΎ Ρ ΠΎΡΠΎΡΠ΅ΠΉ ΠΏΡΠ°ΠΊΡΠΈΠΊΠ΅ Π±Π΅ΡΠΎΠ½ΠΈΡΠΎΠ²Π°Π½ΠΈΡ ΠΈ ΠΈΡΠΊΠ»ΡΡΠΈΠ»ΠΎ ΠΏΠ»ΠΎΡ ΠΎΠ΅ ΡΠΎΠΎΡΠ½ΠΎΡΠ΅Π½ΠΈΠ΅ Π²ΠΎΠ΄ / ΡΠ΅ΠΌΠ΅Π½Ρ, ΡΠ°ΠΊΠΎΠ΅ ΠΊΠ°ΠΊ 0,40, ΠΊΠ°ΠΊ ΡΠΌΠ΅ΡΠΈΠ²Π°ΡΡΠΈΠΉ ΡΠ°ΠΊΡΠΎΡ.
- ΠΡΠΎΠΌΠ΅ ΡΠΎΠ³ΠΎ, Π½Π΅ΠΊΠΎΡΠΎΡΡΠ΅ ΡΠ΅ΡΡΡ ΠΈΠΌΠ΅ΡΡ Π² ΠΊΠΎΠ½ΡΠ΅ ΠΎΠ±ΠΎΠ·Π½Π°ΡΠ΅Π½ΠΈΠ΅ Β«SCCΒ», ΡΡΠΎ ΠΎΠ·Π½Π°ΡΠ°Π΅Ρ, ΡΡΠΎ ΠΎΠ½ΠΈ Π±ΡΠ»ΠΈ ΠΎΡΠ»ΠΈΡΡ Ρ ΠΈΡΠΏΠΎΠ»ΡΠ·ΠΎΠ²Π°Π½ΠΈΠ΅ΠΌ ΠΌΠ΅ΡΠΎΠ΄Π° Β«ΡΠ°ΠΌΠΎΡΠΏΠ»ΠΎΡΠ½ΡΡΡΠ΅Π³ΠΎΡΡ Π±Π΅ΡΠΎΠ½Π°Β».
ΠΡΠ²ΠΎΠ΄Ρ ΠΏΠΎ ΡΠ΅Π·ΡΠ»ΡΡΠ°ΡΠ°ΠΌ ΠΈΡΠΏΡΡΠ°Π½ΠΈΠΉ Π½Π° ΠΈΠ·Π³ΠΈΠ±
ΠΠ°ΠΊ Π²ΠΈΠ΄Π½ΠΎ ΠΈΠ· Π΄ΠΈΠ°Π³ΡΠ°ΠΌΠΌΡ Π²ΡΡΠ΅, Π²ΡΠ΅ ΡΡΠΈ ΠΏΠΎΠ»ΠΈΠΌΠ΅ΡΠ½ΡΠ΅ Π΄ΠΎΠ±Π°Π²ΠΊΠΈ Π΄Π»Ρ ΠΎΡΠ²Π΅ΡΠΆΠ΄Π΅Π½ΠΈΡ ΡΠΌΠΎΠ³Π»ΠΈ Π΄ΠΎΡΡΠΈΡΡ ΡΡΠ΅Π΄Π½Π΅ΠΉ ΡΠΊΠ²ΠΈΠ²Π°Π»Π΅Π½ΡΠ½ΠΎΠΉ 28-Π΄Π½Π΅Π²Π½ΠΎΠΉ ΠΏΡΠΎΡΠ½ΠΎΡΡΠΈ Π½Π° ΠΈΠ·Π³ΠΈΠ± GFRC, ΠΎΡΠ²Π΅ΡΠΆΠ΄Π΅Π½Π½ΠΎΠ³ΠΎ Π²ΠΎ Π²Π»Π°ΠΆΠ½ΠΎΠΌ ΡΠΎΡΡΠΎΡΠ½ΠΈΠΈ Π² ΡΠ΅ΡΠ΅Π½ΠΈΠ΅ 7 Π΄Π½Π΅ΠΉ: ΡΡΠ΅Π΄Π½ΡΡ ΡΡΡΠ΅ΠΊΡΠΈΠ²Π½ΠΎΡΡΡ Π΄Π»Ρ ΠΊΠ°ΠΆΠ΄ΠΎΠ³ΠΎ ΠΈΠ· 3 ΠΏΠΎΠ»ΠΈΠΌΠ΅ΡΠΎΠ², ΠΎΡΠ²Π΅ΡΠΆΠ΄Π΅Π½Π½ΡΡ ΡΡΡ ΠΈΠΌ ΡΠΏΠΎΡΠΎΠ±ΠΎΠΌ, Π±ΡΠ»Π° ΠΏΡΠΈΠΌΠ΅ΡΠ½ΠΎ ΡΠΊΠ²ΠΈΠ²Π°Π»Π΅Π½ΡΠ½Π° Ρ Π°ΡΠ°ΠΊΡΠ΅ΡΠΈΡΡΠΈΠΊΠ°ΠΌ ΠΏΠΎΠ»ΠΈΠΌΠ΅Ρ Π½Π΅ ΠΏΠΎΠ΄Π²Π΅ΡΠ³Π°Π»ΡΡ Π²Π»Π°ΠΆΠ½ΠΎΠΌΡ ΠΎΡΠ²Π΅ΡΠΆΠ΄Π΅Π½ΠΈΡ Π² ΡΠ΅ΡΠ΅Π½ΠΈΠ΅ 7 Π΄Π½Π΅ΠΉ (ΠΏΠΎΠΊΠ°Π·Π°Π½ΠΎ ΡΠ΅ΡΠΎΠΉ ΠΏΠΎΠ»ΠΎΡΠΎΠΉ).
ΠΠ΅ΠΊΠΎΡΠΎΡΡΠ΅ ΠΏΠ°ΡΠ°ΠΌΠ΅ΡΡΡ ΡΠΌΠ΅ΡΠΈ (SCC ΠΈΠ»ΠΈ Π΄ΡΡΠ³ΠΎΠΉ ΠΏΡΡΡΠΎΠ»Π°Π½, Π½Π°ΠΏΡΠΈΠΌΠ΅Ρ) ΠΏΠΎΠΊΠ°Π·Π°Π»ΠΈ ΠΈΠ½Π΄ΠΈΠ²ΠΈΠ΄ΡΠ°Π»ΡΠ½ΡΡ ΠΏΡΠΎΡΠ½ΠΎΡΡΡ Π½ΠΈΠΆΠ΅ ΠΈΠ»ΠΈ Π²ΡΡΠ΅ ΡΡΠ΅Π΄Π½Π΅ΠΉ ΠΏΡΠΎΡΠ½ΠΎΡΡΠΈ ΠΏΡΠΈ Π²Π»Π°ΠΆΠ½ΠΎΠΌ ΠΎΡΠ²Π΅ΡΠΆΠ΄Π΅Π½ΠΈΠΈ Π·Π° 7 Π΄Π½Π΅ΠΉ, Π½ΠΎ ΠΊΠ°ΠΆΠ΄Π°Ρ ΠΏΠΎΠ»ΠΈΠΌΠ΅ΡΠ½Π°Ρ ΠΎΡΠ²Π΅ΡΠΆΠ΄Π°ΡΡΠ°Ρ Π΄ΠΎΠ±Π°Π²ΠΊΠ° Π±ΡΠ»Π° ΡΠΏΠΎΡΠΎΠ±Π½Π° Π΄ΠΎΡΡΠΈΡΡ ΡΠ°ΠΊΠΎΠΉ ΠΏΡΠΎΡΠ½ΠΎΡΡΠΈ Π² Π½Π΅ΠΊΠΎΡΠΎΡΡΡ ΡΠ΅ΡΠΈΡΡ ΠΈΡΠΏΡΡΠ°Π½ΠΈΠΉ.
ΠΠΈΠΊΠ°ΠΊΠ°Ρ ΠΊΠΎΠ½ΠΊΡΠ΅ΡΠ½Π°Ρ ΠΏΠΎΠ»ΠΈΠΌΠ΅ΡΠ½Π°Ρ Π΄ΠΎΠ±Π°Π²ΠΊΠ° Π΄Π»Ρ ΠΎΡΠ²Π΅ΡΠΆΠ΄Π΅Π½ΠΈΡ Π½Π΅ Π±ΡΠ»Π° Π·Π½Π°ΡΠΈΡΠ΅Π»ΡΠ½ΠΎ Π»ΡΡΡΠ΅ ΠΈΠ»ΠΈ Ρ ΡΠΆΠ΅ Ρ ΡΠΎΡΠΊΠΈ Π·ΡΠ΅Π½ΠΈΡ ΡΠΏΠΎΡΠΎΠ±Π½ΠΎΡΡΠΈ Π΄ΠΎΡΡΠΈΠ³Π°ΡΡ Π΄ΠΎΡΡΠ°ΡΠΎΡΠ½ΠΎ Π²ΡΡΠΎΠΊΠΈΡ Π·Π½Π°ΡΠ΅Π½ΠΈΠΉ ΠΏΡΠΎΡΠ½ΠΎΡΡΠΈ Π½Π° ΠΈΠ·Π³ΠΈΠ±. ΠΡΠ΅ ΠΏΠΎΠΊΠ°Π·Π°Π»ΠΈ Π·Π°ΠΌΠ΅ΡΠ½ΡΠ΅ ΡΠ°Π·Π»ΠΈΡΠΈΡ Π² ΠΏΡΠΎΡΠ½ΠΎΡΡΠΈ, Π½Π΅ΡΠΌΠΎΡΡΡ Π½Π° ΡΠΎ, ΡΡΠΎ ΠΎΠ½ΠΈ Π±ΡΠ»ΠΈ ΠΎΡΠ»ΠΈΡΡ ΠΈ ΡΠΏΠ»ΠΎΡΠ½Π΅Π½Ρ ΠΊΠ°ΠΊ ΠΌΠΎΠΆΠ½ΠΎ Π±ΠΎΠ»Π΅Π΅ ΠΈΠ΄Π΅Π½ΡΠΈΡΠ½ΠΎ.
ΠΠΎΠ±Π°Π²ΠΊΠΈ Π΄Π»Ρ ΠΎΡΠ²Π΅ΡΠΆΠ΄Π΅Π½ΠΈΡ ΠΏΠΎΠ»ΠΈΠΌΠ΅ΡΠΎΠ² Π½Π΅Π΄Π΅ΡΠ΅Π²Ρ, Π½Π° ΠΈΡ Π΄ΠΎΠ»Ρ ΠΏΡΠΈΡ ΠΎΠ΄ΠΈΡΡΡ ΠΎΠΊΠΎΠ»ΠΎ 1/3 (ΠΈΠ»ΠΈ Π±ΠΎΠ»Π΅Π΅) ΡΡΠΎΠΈΠΌΠΎΡΡΠΈ ΠΌΠ°ΡΠ΅ΡΠΈΠ°Π»Π° GFRC. Π’ΠΈΠΏΠΈΡΠ½Π°Ρ ΠΏΡΠΈΡΠΈΠ½Π° ΠΈΡΠΏΠΎΠ»ΡΠ·ΠΎΠ²Π°Π½ΠΈΡ ΡΡΡ ΠΈΡ ΠΏΠΎΠ»ΠΈΠΌΠ΅ΡΠΎΠ² — ΡΡΠΎ ΡΠΊΠΎΠ½ΠΎΠΌΠΈΡ ΡΡΠ΅Π΄ΡΡΠ² ΠΈΠ·-Π·Π° ΠΎΡΡΡΡΡΡΠ²ΠΈΡ Π΄ΠΎΡΡΠ°Π²ΠΊΠΈ Π²ΠΎΠ΄Ρ.
Π§ΡΠΎΠ±Ρ ΠΎΡΠ΅Π½ΠΈΡΡ ΡΠ°ΠΊΡΠΈΡΠ΅ΡΠΊΡΡ ΡΡΠΎΠΈΠΌΠΎΡΡΡ ΠΈΠ·Π³ΠΎΡΠΎΠ²Π»Π΅Π½ΠΈΡ GFRC Ρ ΠΈΡΠΏΠΎΠ»ΡΠ·ΠΎΠ²Π°Π½ΠΈΠ΅ΠΌ ΠΊΠ°ΠΆΠ΄ΠΎΠ³ΠΎ ΠΈΠ· ΡΡΠ΅Ρ ΡΠ°Π·Π»ΠΈΡΠ½ΡΡ ΠΏΠΎΠ»ΠΈΠΌΠ΅ΡΠΎΠ², Π½Π΅ΠΎΠ±Ρ ΠΎΠ΄ΠΈΠΌΠΎ ΡΠΌΠΎΡΡΠ΅ΡΡ Π½Π° ΠΎΠ±ΡΡΡ ΡΡΠΎΠΈΠΌΠΎΡΡΡ ΠΏΡΠΎΠΈΠ·Π²ΠΎΠ΄ΡΡΠ²Π° ΠΈΠ·Π²Π΅ΡΡΠ½ΠΎΠ³ΠΎ ΠΊΠΎΠ»ΠΈΡΠ΅ΡΡΠ²Π° GFRC, Π° Π½Π΅ Π½Π° ΡΡΠΎΠΈΠΌΠΎΡΡΡ ΠΏΠΎΠ»ΡΡΠ΅Π½ΠΈΡ ΡΠΎΠ»ΡΠΊΠΎ ΡΡΠΏΡΡΠ΅ΠΉ ΠΏΠΎΠ»ΠΈΠΌΠ΅ΡΠ½ΠΎΠΉ Π΄ΠΎΠ±Π°Π²ΠΊΠΈ Π΄Π»Ρ ΠΎΡΠ²Π΅ΡΠΆΠ΄Π΅Π½ΠΈΡ. ΠΡΠΎ ΡΠ²ΡΠ·Π°Π½ΠΎ Ρ ΡΠ΅ΠΌ, ΡΡΠΎ ΠΊΠ°ΠΆΠ΄Π°Ρ ΠΈΠ· ΡΡΠ΅Ρ ΠΏΠΎΠ»ΠΈΠΌΠ΅ΡΠ½ΡΡ ΡΠΈΡΡΠ΅ΠΌ ΠΈΡΠΏΠΎΠ»ΡΠ·ΡΠ΅Ρ ΡΠΎΡΠΌΡΠ»Ρ ΡΠΌΠ΅ΡΠΈ, ΠΊΠΎΡΠΎΡΡΠ΅ ΠΎΠΏΡΠ΅Π΄Π΅Π»ΡΡΡ ΡΠ°Π·Π»ΠΈΡΠ½ΡΠ΅ ΡΠ΅ΠΊΠΎΠΌΠ΅Π½Π΄ΡΠ΅ΠΌΡΠ΅ Π΄ΠΎΠ·Ρ, ΠΎΡΠ½ΠΎΡΠ΅Π½ΠΈΡ Π²ΠΎΠ΄Ρ ΠΊ Π²ΡΠΆΡΡΠ΅ΠΌΡ, Π΄ΠΎΠ·Ρ ΠΏΡΡΡΠΎΠ»Π°Π½ΠΎΠ² ΠΈ ΠΏΡΡΡΠΎΠ»Π°Π½ΠΎΠ², Π° ΡΠ°ΠΊΠΆΠ΅ ΠΎΡΠ½ΠΎΡΠ΅Π½ΠΈΡ ΠΏΠ΅ΡΠΊΠ° ΠΊ Π²ΡΠΆΡΡΠΈΠΌ.
ΠΠ°ΠΊ ΡΠΏΠΎΠΌΠΈΠ½Π°Π»ΠΎΡΡ ΡΠ°Π½Π΅Π΅, ΠΎΡΠ½ΠΎΠ²Π½Π°Ρ ΡΠ΅Π»Ρ ΠΏΠΎΠ»ΠΈΠΌΠ΅ΡΠ½ΠΎΠΉ Π΄ΠΎΠ±Π°Π²ΠΊΠΈ Π΄Π»Ρ ΠΎΡΠ²Π΅ΡΠΆΠ΄Π΅Π½ΠΈΡ — ΠΏΠΎΠ΄Π΄Π΅ΡΠΆΠΈΠ²Π°ΡΡ ΡΡΠΎΠ²Π½ΠΈ Π²Π½ΡΡΡΠ΅Π½Π½Π΅ΠΉ Π²Π»Π°ΠΆΠ½ΠΎΡΡΠΈ GFRC, ΡΡΠΎΠ±Ρ Π±Π΅ΡΠΎΠ½ ΠΌΠΎΠ³ Π΄ΠΎΠ»ΠΆΠ½ΡΠΌ ΠΎΠ±ΡΠ°Π·ΠΎΠΌ Π·Π°ΡΠ²Π΅ΡΠ΄Π΅ΡΡ ΠΈ Π΄ΠΎΡΡΠΈΠ³Π½ΡΡΡ ΠΆΠ΅Π»Π°Π΅ΠΌΠΎΠΉ ΠΏΡΠΎΡΠ½ΠΎΡΡΠΈ Π½Π° ΠΈΠ·Π³ΠΈΠ±. ΠΠ±ΡΠΈΡΠ½ΡΠ΅ ΠΈΡΠΏΡΡΠ°Π½ΠΈΡ Π½Π° ΠΈΠ·Π³ΠΈΠ± ΠΏΠΎΠΊΠ°Π·Π°Π»ΠΈ, ΡΡΠΎ ΠΈ Forton, ΠΈ ΡΠΌΠ΅ΡΡ Buddy Rhodes GFRC Admixture, ΠΈ Π΄ΠΎΠ±Π°Π²ΠΊΠ° CENSORED ΡΠ°Π±ΠΎΡΠ°ΡΡ, ΠΊΠ°ΠΊ ΠΎΠΆΠΈΠ΄Π°Π»ΠΎΡΡ, Ρ ΡΠΎΡΠΊΠΈ Π·ΡΠ΅Π½ΠΈΡ ΡΡΠ΅Π±ΠΎΠ²Π°Π½ΠΈΡ β 1 PCI, Ρ ΠΎΡΡ ΠΎΠ½ΠΈ ΡΠ°ΠΊΠΆΠ΅ ΡΠΎΠΎΡΠ²Π΅ΡΡΡΠ²ΡΡΡ ΡΡΠ΅Π±ΠΎΠ²Π°Π½ΠΈΡ PCI β 3 ΠΏΠΎ ΠΏΠ»ΠΎΡΠ½ΠΎΡΡΠΈ.
ΠΠ±ΡΠ°ΡΠΈΡΠ΅ Π²Π½ΠΈΠΌΠ°Π½ΠΈΠ΅, ΡΡΠΎ Π½Π΅ΠΏΡΠ΅ΡΡΠ²Π½ΠΎΠ΅ Π²Π»Π°ΠΆΠ½ΠΎΠ΅ ΠΎΡΠ²Π΅ΡΠΆΠ΄Π΅Π½ΠΈΠ΅ Π² ΡΠ΅ΡΠ΅Π½ΠΈΠ΅ 7 Π΄Π½Π΅ΠΉ Π±Π΅Π· ΠΏΠΎΠ»ΠΈΠΌΠ΅ΡΠ° ΠΎΠ±Π΅ΡΠΏΠ΅ΡΠΈΠ²Π°Π΅Ρ ΡΠ°ΠΊΡΡ ββΠΆΠ΅ Π½Π΅ΠΎΠ±Ρ ΠΎΠ΄ΠΈΠΌΡΡ ΠΏΡΠΎΡΠ½ΠΎΡΡΡ Π½Π° ΠΈΠ·Π³ΠΈΠ±.ΠΠ°ΠΈΠ±ΠΎΠ»ΡΡΠ°Ρ ΡΠΊΠΎΠ½ΠΎΠΌΠΈΡ ΡΡΠ΅Π΄ΡΡΠ² Π±ΡΠ΄Π΅Ρ Π΄ΠΎΡΡΠΈΠ³Π½ΡΡΠ° ΠΏΡΠΎΡΡΠΎ Π·Π° ΡΡΠ΅Ρ ΠΎΡΠΊΠ°Π·Π° ΠΎΡ ΠΏΠΎΠ»ΠΈΠΌΠ΅ΡΠ°. ΠΠ΄Π½Π°ΠΊΠΎ Π²Π»Π°ΠΆΠ½ΠΎΠ΅ ΠΎΡΠ²Π΅ΡΠΆΠ΄Π΅Π½ΠΈΠ΅ Π² ΡΠ΅ΡΠ΅Π½ΠΈΠ΅ 7 Π΄Π½Π΅ΠΉ Π½Π΅ΡΠ΅Π°Π»ΡΠ½ΠΎ Π΄Π»Ρ Π±ΠΎΠ»ΡΡΠΈΠ½ΡΡΠ²Π° ΡΠ²ΠΎΡΡΠ΅ΡΠΊΠΈΡ ΠΌΠ°ΡΡΠ΅ΡΠΎΠ² ΠΏΠΎ Π±Π΅ΡΠΎΠ½Ρ, ΠΎΡΡΡΠ΄Π° ΠΈ Π½Π΅ΠΎΠ±Ρ ΠΎΠ΄ΠΈΠΌΠΎΡΡΡ Π² ΠΏΠΎΠ»ΠΈΠΌΠ΅ΡΠ΅.
ΠΠΎΡΡΠ°Π²ΠΊΠ° ΠΌΠΎΠΆΠ΅Ρ ΡΠΈΠ»ΡΠ½ΠΎ ΠΏΠΎΠ²Π»ΠΈΡΡΡ Π½Π° ΡΡΠΎΠΈΠΌΠΎΡΡΡ ΠΈΠ½Π³ΡΠ΅Π΄ΠΈΠ΅Π½ΡΠΎΠ² ΠΈ, ΡΡΠΎ Π±ΠΎΠ»Π΅Π΅ Π²Π°ΠΆΠ½ΠΎ, Π½Π° ΡΠ°ΠΊΡΠΈΡΠ΅ΡΠΊΡΡ ΡΡΠΎΠΈΠΌΠΎΡΡΡ ΠΏΡΠΎΠΈΠ·Π²ΠΎΠ΄ΡΡΠ²Π° GFRC. ΠΠ»ΠΈΡΠ½ΠΈΠ΅ Π΄ΠΎΡΡΠ°Π²ΠΊΠΈ Π½Π° ΡΡΠΎΠΈΠΌΠΎΡΡΡ ΠΌΠΎΠΆΠ΅Ρ Π±ΡΡΡ Π²ΡΡΠ²Π»Π΅Π½ΠΎ ΡΠΎΠ»ΡΠΊΠΎ ΠΏΡΠΈ ΡΡΠ΅ΡΠ΅ ΡΠ°ΠΊΡΠΈΡΠ΅ΡΠΊΠΈΡ Π½ΠΎΡΠΌ ΠΈΡΠΏΠΎΠ»ΡΠ·ΠΎΠ²Π°Π½ΠΈΡ ΠΌΠ°ΡΠ΅ΡΠΈΠ°Π»ΠΎΠ² ΠΏΡΠΈ ΡΠΎΠ·Π΄Π°Π½ΠΈΠΈ GFRC. ΠΡΠΎΡΡΠΎΠ΅ ΡΡΠ°Π²Π½Π΅Π½ΠΈΠ΅ ΡΡΠΎΠΈΠΌΠΎΡΡΠΈ Π΄ΠΎΡΡΠ°Π²ΠΊΠΈ Π²Π΅Π΄ΡΠ° ΠΎΠ΄Π½ΠΎΠ³ΠΎ ΠΌΠ°ΡΠ΅ΡΠΈΠ°Π»Π° Ρ ΡΡΠΌΠΊΠΎΠΉ Π΄ΡΡΠ³ΠΎΠ³ΠΎ ΠΌΠ°ΡΠ΅ΡΠΈΠ°Π»Π° Π½ΠΈΡΠ΅Π³ΠΎ Π½Π΅ Π³ΠΎΠ²ΠΎΡΠΈΡ ΠΎ Π²Π°ΡΠΈΡ ΡΠ°ΠΊΡΠΈΡΠ΅ΡΠΊΠΈΡ ΡΠ°ΡΡ ΠΎΠ΄Π°Ρ .ΠΠ½Π°Π»ΠΎΠ³ΠΈΡΠ½ΡΠΌ ΠΎΠ±ΡΠ°Π·ΠΎΠΌ, ΠΏΡΠΎΡΡΠΎΠ΅ ΡΡΠ°Π²Π½Π΅Π½ΠΈΠ΅ ΠΎΠΏΡΠΎΠ²ΡΡ ΡΠ΅Π½ ΠΎΠ΄Π½ΠΎΠ³ΠΎ ΠΈΠ½Π³ΡΠ΅Π΄ΠΈΠ΅Π½ΡΠ° Ρ Π΄ΡΡΠ³ΠΈΠΌ Π΄Π°Π΅Ρ ΠΈΡΠΊΠ°ΠΆΠ΅Π½Π½ΠΎΠ΅ ΠΏΡΠ΅Π΄ΡΡΠ°Π²Π»Π΅Π½ΠΈΠ΅ ΠΎ ΡΠΎΠΌ, Π½Π°ΡΠΊΠΎΠ»ΡΠΊΠΎ Π΄ΠΎΡΠΎΠ³ΠΎ (ΠΈΠ»ΠΈ Π½Π΅Π΄ΠΎΡΠΎΠ³ΠΎ) ΡΡΠΎΠΈΡ ΠΏΠΎΠΊΡΠΏΠ°ΡΡ ΠΈ ΠΈΡΠΏΠΎΠ»ΡΠ·ΠΎΠ²Π°ΡΡ ΠΎΠ΄ΠΈΠ½ ΠΈΠ½Π³ΡΠ΅Π΄ΠΈΠ΅Π½Ρ ΠΏΠΎ ΡΡΠ°Π²Π½Π΅Π½ΠΈΡ Ρ Π΄ΡΡΠ³ΠΈΠΌ.
Π§ΡΠΎΠ±Ρ Π²ΡΡΠ²ΠΈΡΡ ΡΠ°ΠΊΡΠΈΡΠ΅ΡΠΊΠΈΠ΅ Π·Π°ΡΡΠ°ΡΡ, ΡΠ²ΡΠ·Π°Π½Π½ΡΠ΅ Ρ ΠΏΠΎΠΊΡΠΏΠΊΠΎΠΉ, Π΄ΠΎΡΡΠ°Π²ΠΊΠΎΠΉ ΠΈ ΠΈΡΠΏΠΎΠ»ΡΠ·ΠΎΠ²Π°Π½ΠΈΠ΅ΠΌ ΡΠ°Π·Π»ΠΈΡΠ½ΡΡ ΡΠΈΡΡΠ΅ΠΌ ΠΏΠΎΠ»ΠΈΠΌΠ΅ΡΠΎΠ² ΠΈ ΠΏΡΡΡΠΎΠ»Π°Π½ΠΎΠ², Π±ΡΠ»ΠΈ Π²ΡΠ±ΡΠ°Π½Ρ ΡΠΈΠΏΠΈΡΠ½ΡΠ΅ ΠΊΠΎΠ»ΠΈΡΠ΅ΡΡΠ²Π° Π΄Π»Ρ ΠΊΠ°ΠΆΠ΄ΠΎΠ³ΠΎ ΠΈΠ½Π³ΡΠ΅Π΄ΠΈΠ΅Π½ΡΠ°, ΠΊΠΎΡΠΎΡΡΠ΅ Π±ΡΠ΄ΡΡ ΠΈΡΠΏΠΎΠ»ΡΠ·ΠΎΠ²Π°ΡΡΡΡ Π΄Π»Ρ ΠΏΠΎΠ΄Π΄Π΅ΡΠΆΠΊΠΈ GFRC Ρ ΠΈΡΠΏΠΎΠ»ΡΠ·ΠΎΠ²Π°Π½ΠΈΠ΅ΠΌ ΡΡΠΈΡ ΠΈΠ½Π³ΡΠ΅Π΄ΠΈΠ΅Π½ΡΠΎΠ².
ΠΠ°Π»ΡΠΊΡΠ»ΡΡΠΎΡ ΡΠΌΠ΅ΡΠΈ CCI GFRC ΠΈΡΠΏΠΎΠ»ΡΠ·ΠΎΠ²Π°Π»ΡΡ Π΄Π»Ρ ΡΠ°ΡΡΠ΅ΡΠ° ΠΊΠΎΠ»ΠΈΡΠ΅ΡΡΠ²Π° ΠΊΠ°ΠΆΠ΄ΠΎΠ³ΠΎ ΠΈΠ½Π³ΡΠ΅Π΄ΠΈΠ΅Π½ΡΠ° ΠΈ Π΅Π³ΠΎ ΠΈΠ½Π΄ΠΈΠ²ΠΈΠ΄ΡΠ°Π»ΡΠ½ΠΎΠΉ ΡΡΠΎΠΈΠΌΠΎΡΡΠΈ (Ρ Π΄ΠΎΡΡΠ°Π²ΠΊΠΎΠΉ ΠΈ Π±Π΅Π· Π½Π΅Π΅), Π½Π΅ΠΎΠ±Ρ ΠΎΠ΄ΠΈΠΌΠΎΠΉ Π΄Π»Ρ ΠΏΡΠΎΠΈΠ·Π²ΠΎΠ΄ΡΡΠ²Π° 100 ΠΊΠ²Π°Π΄ΡΠ°ΡΠ½ΡΡ ΡΡΡΠΎΠ² ΒΎ βΠ²ΠΊΠ»Π°Π΄ΡΡΠ° ΠΈΠ· GFRC.ΠΡΠ΅Π΄ΠΏΠΎΠ»ΠΎΠΆΠ΅Π½ΠΈΡ Π±ΡΠ»ΠΈ:
- ΠΠ΅ΡΠΎΠΊ ΠΈ Π±Π΅Π»ΡΠΉ ΡΠ΅ΠΌΠ΅Π½Ρ, ΠΈΡΠΏΠΎΠ»ΡΠ·ΡΠ΅ΠΌΡΠ΅ Π² ΠΊΠ°ΠΆΠ΄ΠΎΠΉ ΠΈΠ· ΡΠΌΠ΅ΡΠ΅ΠΉ, Π±ΡΠ»ΠΈ ΠΌΠ΅ΡΡΠ½ΠΎΠ³ΠΎ ΠΏΡΠΎΠΈΠ·Π²ΠΎΠ΄ΡΡΠ²Π° ΠΈ ΠΎΡΠ½ΠΎΠ²Π°Π½Ρ Π½Π° ΡΠ΅Π°Π»ΡΠ½ΡΡ ΡΠ΅Π½Π°Ρ Π½Π° Π±Π΅Π»ΡΠΉ ΡΠ΅ΠΌΠ΅Π½Ρ Federal ΠΈ ΠΊΠ²Π°ΡΡΠ΅Π²ΡΠΉ ΠΏΠ΅ΡΠΎΠΊ β 30 Π² ΠΌΠ΅ΡΠΊΠ°Ρ , Π΄ΠΎΡΡΡΠΏΠ½ΡΠ΅ Π½Π° ΠΌΠ΅ΡΡΠ½ΠΎΠΌ ΡΡΠ½ΠΊΠ΅ Π² Π ΠΎΠ»ΠΈ, Π‘Π΅Π²Π΅ΡΠ½Π°Ρ ΠΠ°ΡΠΎΠ»ΠΈΠ½Π°. Π‘ΡΠ΅ΠΊΠ»ΠΎΠ²ΠΎΠ»ΠΎΠΊΠ½ΠΎ
- AR, ΡΠ°ΠΊΠΎΠ΅ ΠΊΠ°ΠΊ ΠΏΠΎΠ»ΠΈΠΌΠ΅Ρ ΠΈ ΠΏΡΡΡΠΎΠ»Π°Π½Ρ, ΡΠ°ΡΡΠΎ Π½Π΅ΠΎΠ±Ρ ΠΎΠ΄ΠΈΠΌΠΎ ΠΎΡΠ³ΡΡΠΆΠ°ΡΡ, ΠΈ ΠΈΡ Π½Π΅ Π²ΡΠ΅Π³Π΄Π° ΠΌΠΎΠΆΠ½ΠΎ Π½Π°ΠΉΡΠΈ Π½Π° ΠΌΠ΅ΡΡΠ΅.
- ΠΠΎΠ»ΠΎΠΊΠ½Π° ΠΎΠ±ΡΡΠ½ΠΎ Π·Π°ΠΊΡΠΏΠ°ΡΡΡΡ ΠΈ ΠΎΡΠΏΡΠ°Π²Π»ΡΡΡΡΡ ΠΈΠ· ΡΠΎΠ³ΠΎ ΠΆΠ΅ ΠΈΡΡΠΎΡΠ½ΠΈΠΊΠ°, ΡΡΠΎ ΠΈ ΠΏΠΎΠ»ΠΈΠΌΠ΅Ρ ΠΈ ΠΏΡΡΡΠΎΠ»Π°Π½. ΠΠ°ΡΡΠ°ΡΡ Π½Π° ΠΌΠ°ΡΠ΅ΡΠΈΠ°Π»Ρ ΠΈ ΡΡΠ°Π½ΡΠΏΠΎΡΡΠΈΡΠΎΠ²ΠΊΡ Π²ΠΎΠ»ΠΎΠΊΠΎΠ½ Π±ΡΠ»ΠΈ Π²ΠΊΠ»ΡΡΠ΅Π½Ρ Π² ΡΠ°ΡΡΠ΅ΡΡ, Π½ΠΎ Π½Π΅ ΡΠΊΠ°Π·Π°Π½Ρ, Π½ΠΈΠΆΠ΅ ΠΏΠΎΠΊΠ°Π·Π°Π½Ρ ΡΠΎΠ»ΡΠΊΠΎ ΡΠ°Π·Π»ΠΈΡΠΈΡ Π² ΡΡΠΎΠΈΠΌΠΎΡΡΠΈ ΠΏΠΎΠ»ΠΈΠΌΠ΅ΡΠΎΠ² ΠΈ ΠΏΡΡΡΠΎΠ»Π°Π½ΠΎΠ², ΠΏΠΎΡΠΊΠΎΠ»ΡΠΊΡ Π² ΠΎΠ±Π΅ΠΈΡ ΡΠΌΠ΅ΡΡΡ ΠΈΡΠΏΠΎΠ»ΡΠ·ΠΎΠ²Π°Π»ΠΈΡΡ ΠΎΠ΄Π½ΠΈ ΠΈ ΡΠ΅ ΠΆΠ΅ Π²ΠΎΠ»ΠΎΠΊΠ½Π°.
United Parcel Service (UPS), ΠΎΡΠ΅Π½Ρ ΡΠ°ΡΠΏΡΠΎΡΡΡΠ°Π½Π΅Π½Π½ΡΠΉ ΠΌΠ΅ΡΠΎΠ΄ Π΄ΠΎΡΡΠ°Π²ΠΊΠΈ, Π΄Π΅Π»ΠΈΡ Π½ΠΈΠΆΠ½ΠΈΠ΅ 48 ΡΡΠ°ΡΠΎΠ² Π‘Π¨Π Π½Π° Π½Π΅ΡΠΊΠΎΠ»ΡΠΊΠΎ Π·ΠΎΠ½ Π΄ΠΎΡΡΠ°Π²ΠΊΠΈ. ΠΠΎΠ½Π° 2 ΠΏΡΠ΅Π΄ΡΡΠ°Π²Π»ΡΠ΅Ρ ΡΠΎΠ±ΠΎΠΉ ΠΊΠΎΡΠΎΡΠΊΠΎΠ΅ ΡΠ°ΡΡΡΠΎΡΠ½ΠΈΠ΅ Π΄ΠΎΡΡΠ°Π²ΠΊΠΈ, ΠΊΠΎΠ³Π΄Π° Π°Π΄ΡΠ΅Ρ Π΄ΠΎΡΡΠ°Π²ΠΊΠΈ Π½Π°Ρ ΠΎΠ΄ΠΈΡΡΡ Π½Π΅Π΄Π°Π»Π΅ΠΊΠΎ ΠΎΡ ΠΎΡΠΏΡΠ°Π²ΠΈΡΠ΅Π»Ρ. ΠΠΎΠ½Π° 8 ΠΏΡΠ΅Π΄ΡΡΠ°Π²Π»ΡΠ΅Ρ ΡΠΎΠ±ΠΎΠΉ ΡΠ°ΠΌΠΎΠ΅ Π΄Π°Π»ΡΠ½Π΅Π΅ ΡΠ°ΡΡΡΠΎΡΠ½ΠΈΠ΅ ΠΌΠ΅ΠΆΠ΄Ρ ΠΎΡΠΏΡΠ°Π²ΠΈΡΠ΅Π»Π΅ΠΌ ΠΈ Π°Π΄ΡΠ΅ΡΠΎΠΌ Π΄ΠΎΡΡΠ°Π²ΠΊΠΈ, ΡΡΠΎ ΡΠΊΠ²ΠΈΠ²Π°Π»Π΅Π½ΡΠ½ΠΎ Π΄ΠΎΡΡΠ°Π²ΠΊΠ΅ ΠΏΠΎ ΡΡΡΠ°Π½Π΅. Π ΡΠ°ΡΡΠ΅ΡΠ°Ρ ΠΈΡΠΏΠΎΠ»ΡΠ·ΠΎΠ²Π°Π»ΠΈΡΡ ΡΠ΅ΠΊΡΡΠΈΠ΅ (ΠΏΠΎ ΡΠΎΡΡΠΎΡΠ½ΠΈΡ Π½Π° 3/2015) ΡΠ°ΡΠΈΡΡ Π½Π° Π½Π°Π·Π΅ΠΌΠ½ΡΡ Π΄ΠΎΡΡΠ°Π²ΠΊΡ UPS Π² 48 ΡΡΠ°ΡΠ°Ρ Π‘Π¨Π.
Π ΡΠ»Π΅Π΄ΡΡΡΠ΅ΠΉ ΡΠ°Π±Π»ΠΈΡΠ΅ ΠΏΠΎΠΊΠ°Π·Π°Π½Ρ ΡΠ΅ΠΊΡΡΠΈΠ΅ ΡΠΎΠ·Π½ΠΈΡΠ½ΡΠ΅ ΠΎΠ½Π»Π°ΠΉΠ½-ΡΠ΅Π½Ρ Π½Π° ΡΡΠΏΡΡΠΈΠ΅ ΠΌΠ°ΡΠ΅ΡΠΈΠ°Π»Ρ, ΠΊΠΎΠΌΠ±ΠΈΠ½ΠΈΡΠΎΠ²Π°Π½Π½ΡΠ΅ ΡΠ΅Π½Ρ Π½Π° ΠΊΠ°ΠΆΠ΄ΡΠΉ ΠΌΠ°ΡΠ΅ΡΠΈΠ°Π», Π²ΠΊΠ»ΡΡΠ°Ρ Π΄ΠΎΡΡΠ°Π²ΠΊΡ, ΠΈ ΡΠΈΡΡΡΡ ΡΡΠΎΠΈΠΌΠΎΡΡΡ ($ / ΠΊΠ²Π°Π΄ΡΠ°ΡΠ½ΡΠΉ ΡΡΡ) Π΄Π»Ρ ΠΈΠ·Π³ΠΎΡΠΎΠ²Π»Π΅Π½ΠΈΡ ΒΎ βΡΠΏΠΎΠ½ΡΠΎΡΠ° GFRC Ρ ΠΈΡΠΏΠΎΠ»ΡΠ·ΠΎΠ²Π°Π½ΠΈΠ΅ΠΌ ΡΡΠΈΡ ΠΌΠ°ΡΠ΅ΡΠΈΠ°Π»ΠΎΠ².Π‘ΠΊΠΈΠ΄ΠΊΠΈ Π½Π° ΠΎΠΏΠ»Π°ΡΡ ΡΡΡΠ΄Π°, Π½Π°Π»ΠΎΠ³ΠΈ ΠΈ ΡΠ»Π΅Π½ΡΡΠ²ΠΎ Π½Π΅ Π²ΠΊΠ»ΡΡΠ΅Π½Ρ.
ΠΠ΅ΡΠΌΠΎΡΡΡ Π½Π° ΡΠΎ, ΡΡΠΎ ΠΎΠ±ΡΠ΅ΠΌΠ½ΡΠ΅ Π·Π°ΡΡΠ°ΡΡ Π½Π° ΠΌΠ°ΡΠ΅ΡΠΈΠ°Π»Ρ ΠΈ ΡΡΠ°Π½ΡΠΏΠΎΡΡΠΈΡΠΎΠ²ΠΊΡ Π΄Π»Ρ ΠΊΠ°ΠΆΠ΄ΠΎΠΉ ΠΏΠΎΠ»ΠΈΠΌΠ΅ΡΠ½ΠΎΠΉ ΡΠΈΡΡΠ΅ΠΌΡ ΡΠ°Π·Π»ΠΈΡΠ°ΡΡΡΡ, Π²Π΅Π»ΠΈΡΠΈΠ½Π° Π·Π°ΡΡΠ°Ρ Π½Π° ΠΈΠ·Π³ΠΎΡΠΎΠ²Π»Π΅Π½ΠΈΠ΅ GFRC Ρ ΠΈΡΠΏΠΎΠ»ΡΠ·ΠΎΠ²Π°Π½ΠΈΠ΅ΠΌ Π»ΡΠ±ΠΎΠΉ ΠΈΠ· ΡΡΠ΅Ρ ΠΏΠΎΠ»ΠΈΠΌΠ΅ΡΠ½ΡΡ ΡΠΈΡΡΠ΅ΠΌ Π΄ΠΎΠ²ΠΎΠ»ΡΠ½ΠΎ Π½ΠΈΠ·ΠΊΠ° ΠΏΠΎ ΡΡΠ°Π²Π½Π΅Π½ΠΈΡ Ρ ΡΠΎΠ·Π½ΠΈΡΠ½ΠΎΠΉ ΡΠ΅Π½ΠΎΠΉ ΠΏΡΠΎΠ΄ΡΠΊΡΠΎΠ², ΡΠ΄Π΅Π»Π°Π½Π½ΡΡ ΠΈΠ· GFRC. ΠΡΠΈ ΡΡΠΎΠΌ ΡΠ°Π·Π½ΠΈΡΠ° Π² ΡΡΠΎΠΈΠΌΠΎΡΡΠΈ Π»ΡΠ±ΠΎΠΉ ΠΈΠ· ΡΡΠ΅Ρ ΠΏΠΎΠ»ΠΈΠΌΠ΅ΡΠ½ΡΡ ΡΠΈΡΡΠ΅ΠΌ Π½Π΅Π²Π΅Π»ΠΈΠΊΠ° ΠΈ ΠΎΡΠ½ΠΎΡΠΈΡΠ΅Π»ΡΠ½ΠΎ Π½Π΅Π·Π½Π°ΡΠΈΡΠ΅Π»ΡΠ½Π°: Π½Π°ΠΈΠ±ΠΎΠ»ΡΡΠ°Ρ ΡΠ°Π·Π½ΠΈΡΠ° Π² ΡΡΠΎΠΈΠΌΠΎΡΡΠΈ ΡΠΎΡΡΠ°Π²Π»ΡΠ΅Ρ ΠΌΠ΅Π½Π΅Π΅ 0,75 Π΄ΠΎΠ»Π»Π°ΡΠ° Π·Π° ΠΊΠ²Π°Π΄ΡΠ°ΡΠ½ΡΠΉ ΡΡΡ.ΠΡΠ΅Π½Ρ Π»Π΅Π³ΠΊΠΎ ΠΏΠΎΠ΄Π½ΡΡΡ ΡΠ΅Π½Ρ Π½Π° Π²Π°ΡΠΈ ΡΠ²ΠΎΡΠ΅Π½ΠΈΡ ΠΈΠ· GFRC ΠΊΠ°ΠΊ ΠΌΠΈΠ½ΠΈΠΌΡΠΌ Π½Π° 0,75 Π΄ΠΎΠ»Π»Π°ΡΠ° Π·Π° ΠΊΠ²Π°Π΄ΡΠ°ΡΠ½ΡΠΉ ΡΡΡ, ΡΡΠΎΠ±Ρ Π²ΠΎΠ·ΠΌΠ΅ΡΡΠΈΡΡ Π»ΡΠ±ΡΠ΅ Π·Π°ΡΡΠ°ΡΡ Π½Π° ΠΌΠ°ΡΠ΅ΡΠΈΠ°Π»Ρ (ΠΈ Π΄ΠΎΡΡΠ°Π²ΠΊΡ)!
ΠΡΠ΅ΠΈΠΌΡΡΠ΅ΡΡΠ²Π° ΡΡΡ ΠΎΠ³ΠΎ ΠΏΠΎΠ»ΠΈΠΌΠ΅ΡΠ°
- ΠΠ΅Ρ ΠΏΡΠΎΠ±Π»Π΅ΠΌ Ρ ΡΡΠ°Π½ΡΠΏΠΎΡΡΠΈΡΠΎΠ²ΠΊΠΎΠΉ ΠΈ Ρ ΡΠ°Π½Π΅Π½ΠΈΠ΅ΠΌ Π² Ρ ΠΎΠ»ΠΎΠ΄Π½ΡΡ ΠΏΠΎΠ³ΠΎΠ΄Ρ.
ΠΠΈΠ΄ΠΊΠΈΠΉ ΠΏΠΎΠ»ΠΈΠΌΠ΅Ρ ΠΌΠΎΠΆΠ΅Ρ Π·Π°ΠΌΠ΅ΡΠ·Π½ΡΡΡ. ΠΠΎΠ·ΠΌΠΎΠΆΠ½ΠΎ ΠΎΡΡΠ°ΠΈΠ²Π°Π½ΠΈΠ΅, ΠΈ Π΅Π³ΠΎ ΠΌΠΎΠΆΠ½ΠΎ Π±ΡΠ΄Π΅Ρ ΠΈΡΠΏΠΎΠ»ΡΠ·ΠΎΠ²Π°ΡΡ ΠΏΠΎΡΠ»Π΅ ΠΎΠ΄Π½ΠΎΠ³ΠΎ Π·Π°ΠΌΠΎΡΠ°ΠΆΠΈΠ²Π°Π½ΠΈΡ, Π½ΠΎ ΡΠ»Π΅Π΄ΡΠ΅Ρ ΠΏΡΠΈΠ½ΡΡΡ ΠΌΠ΅ΡΡ ΠΏΡΠ΅Π΄ΠΎΡΡΠΎΡΠΎΠΆΠ½ΠΎΡΡΠΈ, Π²ΠΊΠ»ΡΡΠ°Ρ Π΄ΠΎΡΡΠ°Π²ΠΊΡ Π±Π΅Π· Π·Π°ΠΌΠΎΡΠ°ΠΆΠΈΠ²Π°Π½ΠΈΡ, ΠΊΠΎΡΠΎΡΠ°Ρ ΡΠ²Π΅Π»ΠΈΡΠΈΠ²Π°Π΅Ρ ΡΡΠΎΠΈΠΌΠΎΡΡΡ.
- ΠΠ΅Π½ΡΡΠ΅ ΠΌΠ΅ΡΡΠ° Π΄Π»Ρ ΠΎΡΠΈΠ±ΠΎΠΊ Π² ΡΠ°ΡΡΠ΅ΡΠ°Ρ ΡΠΌΠ΅ΡΠΈ
Π‘ΡΡ ΠΎΠΉ ΠΏΠΎΠ»ΠΈΠΌΠ΅Ρ ΡΠΎΡΡΠΎΠΈΡ ΠΈΠ· 100% ΡΠ²Π΅ΡΠ΄ΡΡ Π²Π΅ΡΠ΅ΡΡΠ².ΠΠΈΠ΄ΠΊΠΈΠΉ ΠΏΠΎΠ»ΠΈΠΌΠ΅Ρ ΡΠΎΡΡΠΎΠΈΡ ΠΈΠ· 45% — 55% ΡΠ²Π΅ΡΠ΄ΡΡ Π²Π΅ΡΠ΅ΡΡΠ², ΠΈ ΡΠ°ΡΡΡ Π΅Π³ΠΎ Π²Π΅ΡΠ° ΡΠ»Π΅Π΄ΡΠ΅Ρ ΡΠ°ΡΡΡΠΈΡΡΠ²Π°ΡΡ ΠΊΠ°ΠΊ Π²ΠΎΠ΄Ρ Π΄Π»Ρ ΡΠΌΠ΅ΡΠΈΠ²Π°Π½ΠΈΡ. ΠΠΎΡΡΠΎΠΌΡ ΡΡΡΠ½ΡΠ΅ ΡΠ°ΡΡΠ΅ΡΡ ΡΠΌΠ΅ΡΠΈ Π±ΠΎΠ»Π΅Π΅ ΡΠ»ΠΎΠΆΠ½Ρ. ΠΠ΄Π½Π°ΠΊΠΎ ΠΎΠ±ΡΠ°ΡΠΈΡΠ΅ Π²Π½ΠΈΠΌΠ°Π½ΠΈΠ΅, ΡΡΠΎ ΠΊΠ°Π»ΡΠΊΡΠ»ΡΡΠΎΡ ΡΠΌΠ΅ΡΠΈ CCI GFRC ΠΈΡΠΊΠ»ΡΡΠ°Π΅Ρ ΡΡΡΠ½ΡΠ΅ Π²ΡΡΠΈΡΠ»Π΅Π½ΠΈΡ.
- ΠΠ΅Π½ΡΡΠ΅ Π²ΡΠ΅ΠΌΠ΅Π½ΠΈ Π½Π° Π²Π·Π²Π΅ΡΠΈΠ²Π°Π½ΠΈΠ΅ ΠΈΠ½Π³ΡΠ΅Π΄ΠΈΠ΅Π½ΡΠΎΠ².
ΠΠΎΡΠΊΠΎΠ»ΡΠΊΡ ΠΈΡΠΏΡΡΠ°Π½Π½ΡΠ΅ ΡΡΡ ΠΈΠ΅ ΠΏΠΎΠ»ΠΈΠΌΠ΅ΡΡ Π²ΠΊΠ»ΡΡΠ°ΡΡ ΠΏΠ΅Π½ΠΎΠ³Π°ΡΠΈΡΠ΅Π»Ρ ΠΈ Π΄ΠΎΠ±Π°Π²ΠΊΡ, ΡΠΌΠ΅Π½ΡΡΠ°ΡΡΡΡ ΡΡΠ°Π΄ΠΊΡ (SRA), ΡΡΡΠ΅ΡΡΠ²ΡΠ΅Ρ Π²ΠΎΠ·ΠΌΠΎΠΆΠ½ΠΎΡΡΡ ΡΡΠ°ΡΠΈΡΡ ΠΌΠ΅Π½ΡΡΠ΅ Π²ΡΠ΅ΠΌΠ΅Π½ΠΈ Π½Π° Π²Π·Π²Π΅ΡΠΈΠ²Π°Π½ΠΈΠ΅ ΠΈΠ½Π³ΡΠ΅Π΄ΠΈΠ΅Π½ΡΠΎΠ² ΠΏΡΠΈ ΠΈΡΠΏΠΎΠ»ΡΠ·ΠΎΠ²Π°Π½ΠΈΠΈ ΠΏΠ΅Π½ΠΎΠ³Π°ΡΠΈΡΠ΅Π»Ρ ΠΈ SRA.
ΠΠ΅ΠΉΡΡΠ²ΠΈΡΠ΅Π»ΡΠ½ΠΎ, ΠΏΠ΅Π½ΠΎΠ³Π°ΡΠΈΡΠ΅Π»Ρ ΡΠ²Π»ΡΠ΅ΡΡΡ Π²Π°ΠΆΠ½ΡΠΌ Π΄ΠΎΠΏΠΎΠ»Π½Π΅Π½ΠΈΠ΅ΠΌ ΠΊ GFRC, ΠΏΠΎΡΠΎΠΌΡ ΡΡΠΎ, ΠΊΠ°ΠΊ ΠΏΠΎΠΊΠ°Π·ΡΠ²Π°ΡΡ ΡΠΎΡΠΎΠ³ΡΠ°ΡΠΈΠΈ Π²ΡΡΠ΅, Π²Π°ΡΠΈΠ°ΡΠΈΠΈ ΠΊΠΎΠ»ΠΈΡΠ΅ΡΡΠ²Π° Π·Π°Ρ Π²Π°ΡΠ΅Π½Π½ΠΎΠ³ΠΎ Π²ΠΎΠ·Π΄ΡΡ Π° Π² ΡΠΎΡΠ΅Π΄Π½ΠΈΡ ΠΎΠ±ΡΠ°Π·ΡΠ°Ρ , Π²ΡΡΠ΅Π·Π°Π½Π½ΡΡ ΠΈΠ· ΠΎΠ΄Π½ΠΎΠΉ ΠΈ ΡΠΎΠΉ ΠΆΠ΅ ΠΈΡΠΏΡΡΠ°ΡΠ΅Π»ΡΠ½ΠΎΠΉ ΠΏΠ°Π½Π΅Π»ΠΈ, Π·Π½Π°ΡΠΈΡΠ΅Π»ΡΠ½ΠΎ Π²Π»ΠΈΡΡΡ Π½Π° ΠΏΡΠΎΡΠ½ΠΎΡΡΡ Π½Π° ΠΈΠ·Π³ΠΈΠ±.ΠΠ΅Π½ΡΡΠ΅ Π·Π°Ρ Π²Π°ΡΠ΅Π½Π½ΠΎΠ³ΠΎ Π²ΠΎΠ·Π΄ΡΡ Π° ΠΏΡΠΈΠ²ΠΎΠ΄ΠΈΠ»ΠΎ ΠΊ Π±ΠΎΠ»ΡΡΠ΅ΠΉ ΠΏΡΠΎΡΠ½ΠΎΡΡΠΈ.
ΠΠΎΡΠΊΠΎΠ»ΡΠΊΡ Buddy Rhodes GFRC Admix ΡΠΎΠ΄Π΅ΡΠΆΠΈΡ ΠΏΡΡΡΠΎΠ»Π°Π½, ΠΎΠ½ ΠΈΡΠΊΠ»ΡΡΠ°Π΅Ρ Π½Π΅ΠΎΠ±Ρ ΠΎΠ΄ΠΈΠΌΠΎΡΡΡ Π²Π·Π²Π΅ΡΠΈΠ²Π°Π½ΠΈΡ Π΅ΡΠ΅ ΠΎΠ΄Π½ΠΎΠ³ΠΎ ΠΈΠ½Π³ΡΠ΅Π΄ΠΈΠ΅Π½ΡΠ°.
ΠΠΎΡΠΊΠΎΠ»ΡΠΊΡ Π·Π°ΡΡΠ°ΡΡ Π½Π° ΡΠ°Π±ΠΎΡΡΡ ΡΠΈΠ»Ρ Π΄Π»Ρ ΡΠΎΠ·Π΄Π°Π½ΠΈΡ Ρ ΡΠ΄ΠΎΠΆΠ΅ΡΡΠ²Π΅Π½Π½ΡΡ ΠΈΠ·Π΄Π΅Π»ΠΈΠΉ ΠΈΠ· GFRC-Π±Π΅ΡΠΎΠ½Π° Π·Π½Π°ΡΠΈΡΠ΅Π»ΡΠ½ΠΎ ΠΏΡΠ΅Π²ΡΡΠ°ΡΡ Π·Π°ΡΡΠ°ΡΡ Π½Π° ΠΌΠ°ΡΠ΅ΡΠΈΠ°Π»Ρ, ΡΠΊΠΎΠ½ΠΎΠΌΠΈΡ Π²ΡΠ΅ΠΌΠ΅Π½ΠΈ Π·Π° ΡΡΠ΅Ρ Π²Π·Π²Π΅ΡΠΈΠ²Π°Π½ΠΈΡ ΠΌΠ΅Π½ΡΡΠ΅Π³ΠΎ ΠΊΠΎΠ»ΠΈΡΠ΅ΡΡΠ²Π° ΠΈΠ½Π³ΡΠ΅Π΄ΠΈΠ΅Π½ΡΠΎΠ² ΡΠ²Π»ΡΠ΅ΡΡΡ Π²Π°ΠΆΠ½ΡΠΌ ΡΠ°ΠΊΡΠΎΡΠΎΠΌ ΠΏΡΠΈ ΠΏΡΠΈΠ½ΡΡΠΈΠΈ ΡΠ΅ΡΠ΅Π½ΠΈΡ ΠΎ ΡΠΎΠΌ, ΠΊΠ°ΠΊΠΎΠΉ ΡΡΡ ΠΎΠΉ ΠΏΠΎΠ»ΠΈΠΌΠ΅Ρ ΡΠ΅ΠΊΠΎΠΌΠ΅Π½Π΄ΠΎΠ²Π°ΡΡ.
ΠΠ΅Π΄ΠΎΡΡΠ°ΡΠΊΠΈ ΡΡΡ ΠΎΠ³ΠΎ ΠΏΠΎΠ»ΠΈΠΌΠ΅ΡΠ°
- ΠΠ΅ ΡΠ΅ΡΡΠΈΡΠΈΡΠΈΡΠΎΠ²Π°Π½ΠΎ Π½Π΅Π·Π°Π²ΠΈΡΠΈΠΌΡΠΌΠΈ ΠΎΡΠ³Π°Π½ΠΈΠ·Π°ΡΠΈΡΠΌΠΈ Π½Π° ΡΠΎΠΎΡΠ²Π΅ΡΡΡΠ²ΠΈΠ΅ ΡΡΠ°Π½Π΄Π°ΡΡΠ°ΠΌ PCI ΠΈ Π½Π΅ ΠΏΠΎΠ΄ΡΠ²Π΅ΡΠΆΠ΄Π΅Π½ΠΎ Π΄Π΅ΡΡΡΠΈΠ»Π΅ΡΠΈΡΠΌΠΈ ΠΈΡΠΏΠΎΠ»ΡΠ·ΠΎΠ²Π°Π½ΠΈΡ Π² ΡΠΊΡΡΡΠ΅ΠΌΠ°Π»ΡΠ½ΡΡ ΡΠΈΡΡΠ°ΡΠΈΡΡ
ΠΠ°ΠΈΠ±ΠΎΠ»Π΅Π΅ Π²Π°ΠΆΠ½ΡΠΌ Π½Π΅Π΄ΠΎΡΡΠ°ΡΠΊΠΎΠΌ ΡΠ²Π»ΡΠ΅ΡΡΡ ΡΠΎ, ΡΡΠΎ Π½ΠΈ ΠΎΠ΄ΠΈΠ½ ΡΡΡ ΠΎΠΉ ΠΏΠΎΠ»ΠΈΠΌΠ΅Ρ Π½Π΅ Π±ΡΠ» ΡΡΠ°ΡΠ΅Π»ΡΠ½ΠΎ ΠΏΡΠΎΡΠ΅ΡΡΠΈΡΠΎΠ²Π°Π½ Π½Π΅Π·Π°Π²ΠΈΡΠΈΠΌΠΎΠΉ Π»Π°Π±ΠΎΡΠ°ΡΠΎΡΠΈΠ΅ΠΉ Π½Π° ΡΠΎΠΎΡΠ²Π΅ΡΡΡΠ²ΠΈΠ΅ Π²ΡΠ΅ΠΌ ΡΠ΅ΡΡΡΠ΅ΠΌ ΡΡΠ΅Π±ΠΎΠ²Π°Π½ΠΈΡΠΌ PCI.ΠΡΡΠΏΠ½ΠΎΠΌΠ°ΡΡΡΠ°Π±Π½Π°Ρ ΠΊΠΎΠΌΠΌΠ΅ΡΡΠ΅ΡΠΊΠ°Ρ ΠΏΡΠΎΠΌΡΡΠ»Π΅Π½Π½ΠΎΡΡΡ GFRC, ΠΊΠΎΡΠΎΡΠ°Ρ ΠΏΡΠΎΠΈΠ·Π²ΠΎΠ΄ΠΈΡ ΡΡΡΠΎΠΈΡΠ΅Π»ΡΠ½ΡΠ΅ ΠΏΠ°Π½Π΅Π»ΠΈ ΠΈ Π΄ΡΡΠ³ΠΈΠ΅ ΠΏΡΠΎΠ΄ΡΠΊΡΡ, ΡΡΠ΅Π±ΡΡΡΠΈΠ΅ ΠΎΠ±ΡΠ΅ΡΡΠ²Π΅Π½Π½ΠΎΠΉ Π±Π΅Π·ΠΎΠΏΠ°ΡΠ½ΠΎΡΡΠΈ, Π½Π΅ ΠΈΡΠΏΠΎΠ»ΡΠ·ΡΠ΅Ρ ΡΡΡ ΠΈΠ΅ ΠΏΠΎΠ»ΠΈΠΌΠ΅ΡΡ. ΠΠΎΠ»ΡΡΠΈΠ½ΡΡΠ²ΠΎ ΠΊΠΎΠΌΠΌΠ΅ΡΡΠ΅ΡΠΊΠΈΡ Π·Π°Π²ΠΎΠ΄ΠΎΠ² GFRC ΡΠ΅ΡΡΠΈΡΠΈΡΠΈΡΠΎΠ²Π°Π½Ρ PCI, ΠΈ ΡΠ°ΡΡΠΎ ΡΠΏΠ΅ΡΠΈΡΠΈΠΊΠ°ΡΠΈΠΈ Π΄Π»Ρ ΠΊΡΡΠΏΠ½ΡΡ ΠΏΡΠΎΠ΅ΠΊΡΠΎΠ², Π½Π° ΠΊΠΎΡΠΎΡΡΠ΅ ΠΎΠ½ΠΈ ΠΏΡΠ΅ΡΠ΅Π½Π΄ΡΡΡ, ΡΡΠ΅Π±ΡΡΡ ΡΠ΅ΡΡΠΈΡΠΈΠΊΠ°ΡΠΈΠΈ PCI.
Π Π½Π°ΡΠ΅ΠΉ Π³ΠΎΡΠ°Π·Π΄ΠΎ Π±ΠΎΠ»Π΅Π΅ ΠΌΠ΅Π»ΠΊΠΎΠΉ ΠΎΡΡΠ°ΡΠ»ΠΈ, ΠΏΡΠΎΠΈΠ·Π²ΠΎΠ΄ΡΡΠ΅ΠΉ Ρ ΡΠ΄ΠΎΠΆΠ΅ΡΡΠ²Π΅Π½Π½ΡΠ΅ ΠΈΠ·Π΄Π΅Π»ΠΈΡ, ΠΏΡΠΎΠΈΠ·Π²ΠΎΠ΄ΠΈΡΠ΅Π»ΡΠ½ΠΎΡΡΡ Π½Π°ΡΠ΅Π³ΠΎ Π±Π΅ΡΠΎΠ½Π° ΠΎΠ±ΡΡΠ½ΠΎ Π½Π΅ ΡΠ²Π»ΡΠ΅ΡΡΡ ΠΆΠΈΠ·Π½Π΅Π½Π½ΠΎΠΉ ΡΠΈΡΡΠ°ΡΠΈΠ΅ΠΉ. ΠΠ΄Π½Π°ΠΊΠΎ Π±Π΅Π· ΠΏΠΎΠ»Π½ΠΎΠ³ΠΎ ΠΏΠΎΠ½ΠΈΠΌΠ°Π½ΠΈΡ ΠΏΡΠΎΠ΄ΡΠΊΡΠ°, ΠΊΠΎΡΠΎΡΡΠΉ Π²Ρ ΠΈΡΠΏΠΎΠ»ΡΠ·ΡΠ΅ΡΠ΅, Π²Ρ ΠΌΠΎΠΆΠ΅ΡΠ΅ ΠΈΡΠΏΠΎΠ»ΡΠ·ΠΎΠ²Π°ΡΡ ΠΏΡΠΎΠ΄ΡΠΊΡ Ρ ΡΡΠΏΠ΅Ρ ΠΎΠΌ Π² ΡΠ΅ΡΠ΅Π½ΠΈΠ΅ ΠΌΠ½ΠΎΠ³ΠΈΡ Π»Π΅Ρ, Π° Π·Π°ΡΠ΅ΠΌ, ΠΊΠΎΠ³Π΄Π° Π²Ρ ΡΠ°Π·Π΄Π²ΠΈΠ³Π°Π΅ΡΠ΅ Π³ΡΠ°Π½ΠΈΡΡ ΠΈ ΠΏΡΠΎΠΈΡΡ ΠΎΠ΄ΠΈΡ ΡΠ±ΠΎΠΉ, Π²Ρ Π½Π΅ Π·Π½Π°Π΅ΡΠ΅, ΠΏΠΎΡΠ΅ΠΌΡ.ΠΡΠΎΠΌΠ΅ ΡΠΎΠ³ΠΎ, Π΅ΡΠ»ΠΈ Π²Ρ ΡΡΠ°ΡΡΠ²ΡΠ΅ΡΠ΅ Π² ΠΏΡΠΎΠ΅ΠΊΡΠ΅, ΠΊΠΎΡΠΎΡΡΠΉ Π²ΠΊΠ»ΡΡΠ°Π΅Ρ Π² ΡΠ΅Π±Ρ ΡΡΡΠΎΠΈΡΠ΅Π»ΡΠ½ΡΠ΅ ΠΏΠ°Π½Π΅Π»ΠΈ ΠΈΠ»ΠΈ ΠΊΠ°ΠΊΠΎΠΉ-Π»ΠΈΠ±ΠΎ Π΄ΡΡΠ³ΠΎΠΉ ΡΠ»Π΅ΠΌΠ΅Π½Ρ, ΠΊΠΎΡΠΎΡΡΠΉ ΠΏΠΎΡΠ΅Π½ΡΠΈΠ°Π»ΡΠ½ΠΎ ΠΌΠΎΠΆΠ΅Ρ Π±ΡΡΡ ΠΏΡΠΎΠ±Π»Π΅ΠΌΠΎΠΉ ΠΎΡΠ²Π΅ΡΡΡΠ²Π΅Π½Π½ΠΎΡΡΠΈ Π·Π° ΠΊΠ°ΡΠ΅ΡΡΠ²ΠΎ ΠΏΡΠΎΠ΄ΡΠΊΡΠΈΠΈ, Π²ΠΎΠ·Π½ΠΈΠΊΠ°Π΅Ρ ΠΏΡΠΎΠ±Π»Π΅ΠΌΠ°, ΠΈ ΠΎΠ±Π½Π°ΡΡΠΆΠΈΠ²Π°Π΅ΡΡΡ, ΡΡΠΎ Π²Ρ ΠΈΡΠΏΠΎΠ»ΡΠ·ΡΠ΅ΡΠ΅ ΠΌΠ΅ΡΠΎΠ΄Ρ ΠΈ ΠΈΠ½Π³ΡΠ΅Π΄ΠΈΠ΅Π½ΡΡ, ΠΊΠΎΡΠΎΡΡΠ΅ Π½Π΅ ΡΠΎΠΎΡΠ²Π΅ΡΡΡΠ²ΡΡΡ ΡΡΠ°Π½Π΄Π°ΡΡΠ°ΠΌ PCI, ΡΡΠΎ ΠΌΠΎΠΆΠ΅Ρ ΠΈΠΌΠ΅ΡΡ ΡΠ΅ΡΡΠ΅Π·Π½ΡΠ΅ ΡΡΠΈΠ΄ΠΈΡΠ΅ΡΠΊΠΈΠ΅ ΠΏΠΎΡΠ»Π΅Π΄ΡΡΠ²ΠΈΡ.
ΠΠ°ΡΠ΅ ΡΠ΅ΠΌΠ΅ΡΠ»Π΅Π½Π½ΠΎΠ΅ ΠΏΡΠΎΠΈΠ·Π²ΠΎΠ΄ΡΡΠ²ΠΎ ΠΎΡΠ½ΠΎΠ²Π°Π½ΠΎ Π½Π° ΡΡΠ°Π΄ΠΈΡΠΈΡΡ Π΄ΠΎΠΌΠ°ΡΠ½Π΅Π³ΠΎ ΠΏΠΈΠ²ΠΎΠ²Π°ΡΠ΅Π½ΠΈΡ, Π³Π΄Π΅ ΠΏΡΠ΅ΠΎΠ±Π»Π°Π΄Π°ΡΡ ΠΏΠΎΡΡΠΎΡΠ½Π½ΡΠ΅ ΠΈΠ·ΠΌΠ΅Π½Π΅Π½ΠΈΡ ΠΈ ΠΎΡΠ΅Π²ΠΈΠ΄Π½ΡΠ΅ ΠΈΠ½Π½ΠΎΠ²Π°ΡΠΈΠΈ. Π’Π΅ΠΌ Π½Π΅ ΠΌΠ΅Π½Π΅Π΅, Π½ΠΎΠ²ΡΠ΅ ΠΈΠ½Π³ΡΠ΅Π΄ΠΈΠ΅Π½ΡΡ, ΠΈΠΌΠ΅ΡΡΠΈΠ΅ ΡΠ΅ΡΠ°ΡΡΠ΅Π΅ Π·Π½Π°ΡΠ΅Π½ΠΈΠ΅ Π΄Π»Ρ ΠΊΡΠ°ΡΠΊΠΎΡΡΠΎΡΠ½ΠΎΠΉ ΠΈ Π΄ΠΎΠ»Π³ΠΎΡΡΠΎΡΠ½ΠΎΠΉ ΡΡΡΠ΅ΠΊΡΠΈΠ²Π½ΠΎΡΡΠΈ ΡΠ°ΠΌΠΎΠ³ΠΎ ΠΌΠ°ΡΠ΅ΡΠΈΠ°Π»Π°, Π½Π° ΠΊΠΎΡΠΎΡΠΎΠΌ ΠΌΡ ΡΡΡΠΎΠΈΠΌ ΡΠ²ΠΎΠΉ Π±ΠΈΠ·Π½Π΅Ρ ΠΈ ΡΠ΅ΠΏΡΡΠ°ΡΠΈΡ, Π΄ΠΎΠ»ΠΆΠ½Ρ Π²ΡΠ±ΠΈΡΠ°ΡΡΡΡ ΠΈ ΠΈΡΠΏΠΎΠ»ΡΠ·ΠΎΠ²Π°ΡΡΡΡ ΡΠΎΠ»ΡΠΊΠΎ ΠΏΠΎΡΠ»Π΅ ΠΎΡΠ΅Π½Ρ ΡΡΠ°ΡΠ΅Π»ΡΠ½ΠΎΠ³ΠΎ ΡΠ°ΡΡΠΌΠΎΡΡΠ΅Π½ΠΈΡ ΠΈ ΠΏΠΎ ΡΡΠ½ΡΠΌ, ΠΊΠΎΠΌΠΌΠ΅ΡΡΠ΅ΡΠΊΠΈΠΌ ΠΏΡΠΈΡΠΈΠ½Π°ΠΌ.
CCI ΠΏΡΠΈΠ΄Π΅ΡΠΆΠΈΠ²Π°Π΅ΡΡΡ ΠΊΠΎΠ½ΡΠ΅ΡΠ²Π°ΡΠΈΠ²Π½ΠΎΠ³ΠΎ ΠΏΠΎΠ΄Ρ ΠΎΠ΄Π°, ΠΏΡΠ΅Π΄ΠΏΠΎΡΠΈΡΠ°Ρ ΠΈΡΠΏΠΎΠ»ΡΠ·ΠΎΠ²Π°ΡΡ ΠΏΡΠΎΠ²Π΅ΡΠ΅Π½Π½ΡΠ΅ Π²ΡΠ΅ΠΌΠ΅Π½Π΅ΠΌ ΠΏΡΠΎΠ΄ΡΠΊΡΡ ΠΈ ΠΌΠ΅ΡΠΎΠ΄Ρ, Π΅ΡΠ»ΠΈ ΡΠΎΠ»ΡΠΊΠΎ ΡΠ²Π½Π°Ρ ΠΏΡΠΎΠ±Π»Π΅ΠΌΠ° Ρ ΡΡΡΠ΅ΡΡΠ²ΡΡΡΠΈΠΌΠΈ ΠΏΡΠΎΠ΄ΡΠΊΡΠ°ΠΌΠΈ ΠΈΠ»ΠΈ ΠΌΠ΅ΡΠΎΠ΄Π°ΠΌΠΈ Π½Π΅ ΡΡΠ΅Π±ΡΠ΅Ρ ΡΠ΅ΡΠ΅Π½ΠΈΡ. ΠΠ΄ΠΈΠ½ΡΡΠ²Π΅Π½Π½Π°Ρ ΡΠ΅ΡΡΠ΅Π·Π½Π°Ρ ΠΏΡΠΎΠ±Π»Π΅ΠΌΠ° Π²Π»Π°ΠΆΠ½ΠΎΠ³ΠΎ ΠΏΠΎΠ»ΠΈΠΌΠ΅ΡΠ° — ΡΡΠΎ Π²ΠΎΠ·ΠΌΠΎΠΆΠ½ΠΎΡΡΡ Π΅Π³ΠΎ Π·Π°ΠΌΠ΅ΡΠ·Π°Π½ΠΈΡ. ΠΡΠΎ Π΄Π΅ΠΉΡΡΠ²ΠΈΡΠ΅Π»ΡΠ½ΠΎ ΠΏΡΠ΅Π΄ΡΡΠ°Π²Π»ΡΠ΅Ρ ΡΠΎΠ±ΠΎΠΉ ΡΠ΅Π°Π»ΡΠ½ΡΡ Π±ΠΈΠ·Π½Π΅Ρ-ΠΏΡΠΎΠ±Π»Π΅ΠΌΡ Π΄Π»Ρ ΡΠ΅Ρ , ΠΊΡΠΎ ΠΆΠΈΠ²Π΅Ρ Π² Π±ΠΎΠ»Π΅Π΅ Ρ ΠΎΠ»ΠΎΠ΄Π½ΠΎΠΌ ΠΊΠ»ΠΈΠΌΠ°ΡΠ΅, ΠΈ ΠΊΠΎΡΠΎΡΡΠΌ ΠΏΡΠΈΡ ΠΎΠ΄ΠΈΡΡΡ ΠΏΠ»Π°ΡΠΈΡΡ Π·Π½Π°ΡΠΈΡΠ΅Π»ΡΠ½ΡΡ Π΄ΠΎΠΏΠΎΠ»Π½ΠΈΡΠ΅Π»ΡΠ½ΡΡ ΠΏΠ»Π°ΡΡ Π·Π° Π΄ΠΎΡΡΠ°Π²ΠΊΡ Π±Π΅Π· Π·Π°ΠΌΠΎΡΠ°ΠΆΠΈΠ²Π°Π½ΠΈΡ, Π° ΠΏΡΠΈ ΡΡΠΎΠΌ Π²ΡΠ΅ Π΅ΡΠ΅ ΠΎΡΡΠ°Π΅ΡΡΡ Π²ΠΎΠ·ΠΌΠΎΠΆΠ½ΠΎΡΡΡ Π·Π°ΠΌΠΎΡΠ°ΠΆΠΈΠ²Π°Π½ΠΈΡ.
ΠΠ΄Π½Π°ΠΊΠΎ ΡΡΡ ΠΏΡΠΎΠ±Π»Π΅ΠΌΡ Ρ ΡΡΠ°Π½ΡΠΏΠΎΡΡΠΈΡΠΎΠ²ΠΊΠΎΠΉ ΠΌΠΎΠΆΠ½ΠΎ ΡΠ΅ΡΠΈΡΡ, ΠΏΡΠΎΡΡΠΎ ΡΠΏΠ»Π°Π½ΠΈΡΠΎΠ²Π°Π² Π·Π°ΡΠ°Π½Π΅Π΅ ΠΈ ΡΠ΄Π΅Π»Π°Π² Π·Π°ΠΏΠ°ΡΡ Π΄ΠΎ Π·ΠΈΠΌΡ.ΠΠ΅ΠΊΠΎΡΠΎΡΡΠ΅ ΠΎΡ ΠΎΡΠ½ΠΈΠΊΠΈ Π½Π° ΡΡΠ»Π΅Π½Π΅ΠΉ ΡΠ°ΠΊΠΆΠ΅ Π΄ΠΎΠ»ΠΆΠ½Ρ ΠΎΡΠΏΡΠ°Π²Π»ΡΡΡ Π² Π·ΠΈΠΌΠ½ΠΈΠ΅ ΠΌΠ΅ΡΡΡΡ Π±Π΅Π· Π·Π°ΠΌΠΎΡΠΎΠ·ΠΊΠΈ. Π ΡΠΎΠΌΡ ΠΆΠ΅, ΠΊΠ°ΠΊ ΠΏΠΎΠΊΠ°Π·Π°Π½ΠΎ Π² ΡΡΠΎΠΉ ΡΡΠ°ΡΡΠ΅, ΠΎΡΠ½ΠΎΠ²Π½ΠΎΠΉ ΠΏΡΠΈΡΠΈΠ½ΠΎΠΉ ΠΏΠΎΠ²ΡΡΠ΅Π½ΠΈΡ ΠΌΠ°ΡΠ΅ΡΠΈΠ°Π»ΡΠ½ΡΡ Π·Π°ΡΡΠ°Ρ ΡΠ²Π»ΡΠ΅ΡΡΡ Π½Π΅ ΠΏΠ»Π°Π½ΠΈΡΠΎΠ²Π°Π½ΠΈΠ΅ Π·Π°ΡΠ°Π½Π΅Π΅. Π‘ΡΠΎΠΊ Π³ΠΎΠ΄Π½ΠΎΡΡΠΈ Π€ΠΎΡΡΠΎΠ½Π° ΡΠΎΡΡΠ°Π²Π»ΡΠ΅Ρ ΠΎΠΊΠΎΠ»ΠΎ Π³ΠΎΠ΄Π°. ΠΠ°ΠΏΠ°ΡΠΈΡΠ΅ΡΡ ΠΏΠ΅ΡΠ΅Π΄ Π·ΠΈΠΌΠΎΠΉ ΠΈ Ρ ΡΠ°Π½ΠΈΡΠ΅ Π² ΠΏΠΎΠΌΠ΅ΡΠ΅Π½ΠΈΠΈ Ρ ΠΊΠΎΠ½ΡΡΠΎΠ»ΠΈΡΡΠ΅ΠΌΡΠΌ ΠΊΠ»ΠΈΠΌΠ°ΡΠΎΠΌ.
ΠΡ ΡΠ΅ΠΊΠΎΠΌΠ΅Π½Π΄ΡΠ΅ΠΌ ΠΏΡΠΈΠ΄Π΅ΡΠΆΠΈΠ²Π°ΡΡΡΡ Π²Π»Π°ΠΆΠ½ΡΡ ΠΏΠΎΠ»ΠΈΠΌΠ΅ΡΠΎΠ², Π΅ΡΠ»ΠΈ Π²Ρ Π½Π΅ ΠΆΠΈΠ²Π΅ΡΠ΅ Π² Ρ ΠΎΠ»ΠΎΠ΄Π½ΠΎΠΌ ΠΊΠ»ΠΈΠΌΠ°ΡΠ΅ ΠΈ Π½Π΅ Ρ ΠΎΡΠΈΡΠ΅ ΡΡΠΊΠΎΠ½ΠΎΠΌΠΈΡΡ Π²ΡΠ΅ΠΌΡ, Π²Π·Π²Π΅ΡΠΈΠ²Π°Ρ ΠΌΠ΅Π½ΡΡΠ΅ ΠΈΠ½Π³ΡΠ΅Π΄ΠΈΠ΅Π½ΡΠΎΠ². Π ΡΡΠΎΠΌ ΡΠ»ΡΡΠ°Π΅ ΠΌΡ ΡΠ΅ΠΊΠΎΠΌΠ΅Π½Π΄ΡΠ΅ΠΌ Π΄ΠΎΠ±Π°Π²ΠΊΡ Buddy Rhodes GFRC Admixture, Π½Π΅ΡΠΌΠΎΡΡΡ Π½Π° Π΅Π΅ Π½Π΅ΠΌΠ½ΠΎΠ³ΠΎ Π±ΠΎΠ»Π΅Π΅ Π²ΡΡΠΎΠΊΡΡ ΡΡΠΎΠΈΠΌΠΎΡΡΡ, ΠΏΠΎΡΠΎΠΌΡ ΡΡΠΎ ΡΡΠΎ ΠΎΠ΄Π½ΠΎΠΊΠΎΠΌΠΏΠΎΠ½Π΅Π½ΡΠ½Π°Ρ ΡΠΈΡΡΠ΅ΠΌΠ°, ΠΏΠΎΠ΄Π΄Π΅ΡΠΆΠΈΠ²Π°Π΅ΠΌΠ°Ρ ΡΠΈΠ»ΠΎΠΉ ΠΈ ΡΠ΅ΠΏΡΡΠ°ΡΠΈΠ΅ΠΉ ΠΊΠΎΠΌΠΏΠ°Π½ΠΈΠΈ Buddy Rhodes Concrete Products (BRCP).ΠΠ±ΡΠ°ΡΠΈΡΠ΅ Π²Π½ΠΈΠΌΠ°Π½ΠΈΠ΅, ΡΡΠΎ ΠΈΡΠΏΡΡΠ°Π½ΠΈΡ ΠΈ Π°Π½Π°Π»ΠΈΠ· Π±ΡΠ»ΠΈ Π·Π°Π²Π΅ΡΡΠ΅Π½Ρ Π΄ΠΎ ΡΠΎΠ³ΠΎ, ΠΊΠ°ΠΊ ΠΌΡ Π½Π°ΡΠ°Π»ΠΈ ΠΏΡΠΎΠ΄Π°Π²Π°ΡΡ Π±Π΅ΡΠΎΠ½Π½ΡΠ΅ ΠΈΠ·Π΄Π΅Π»ΠΈΡ Buddy Rhodes. (ΠΠ±ΡΠ°ΡΠΈΡΠ΅ Π²Π½ΠΈΠΌΠ°Π½ΠΈΠ΅, ΡΡΠΎ ΠΌΡ ΡΠ΄Π΅Π»Π°Π»ΠΈ ΡΡΡ ΡΠ΅ΠΊΠΎΠΌΠ΅Π½Π΄Π°ΡΠΈΡ Π΄ΠΎ ΡΠΎΠ³ΠΎ, ΠΊΠ°ΠΊ Π΄ΡΡΠ³ΠΎΠΉ ΠΏΡΠΎΠΈΠ·Π²ΠΎΠ΄ΠΈΡΠ΅Π»Ρ ΡΠ³ΡΠΎΠΆΠ°Π» ΡΡΠ΄Π΅Π±Π½ΡΠΌ ΠΈΡΠΊΠΎΠΌ.)
CCI Π²ΡΠ΅Π³Π΄Π° ΡΡΠΈΠ»Π° Π³ΠΎΡΠΎΠ²ΠΈΡΡ ΡΠΌΠ΅ΡΠΈ Ρ Π½ΡΠ»Ρ, ΠΈ ΡΡΠΎ ΠΏΠ΅ΡΠ²ΡΠΉ ΡΠ°Π·, ΠΊΠΎΠ³Π΄Π° ΠΌΡ ΡΠ΅ΠΊΠΎΠΌΠ΅Π½Π΄ΠΎΠ²Π°Π»ΠΈ ΠΊΠ°ΠΊΠΎΠΉ-Π»ΠΈΠ±ΠΎ Π²ΠΈΠ΄ Π³ΠΎΡΠΎΠ²ΡΡ ΡΠΌΠ΅ΡΠ΅ΠΉ. ΠΡ Π½ΠΈΠΊΠΎΠ³Π΄Π° Π½Π΅ ΡΡΠ²Π΅ΡΠΆΠ΄Π°Π»ΠΈ, ΡΡΠΎ ΡΠΌΠ΅ΡΠΈ Π² ΠΌΠ΅ΡΠΊΠ°Ρ ΠΈΠ»ΠΈ Π³ΠΎΡΠΎΠ²ΡΠ΅ ΡΠΌΠ΅ΡΠΈ — ΡΡΠΎ ΠΏΠ»ΠΎΡ ΠΎ, ΠΏΡΠΎΡΡΠΎ ΠΎΠ±ΡΡΠ΅Π½ΠΈΠ΅ Ρ Π½ΡΠ»Ρ Π΄Π°Π΅Ρ Π²Π°ΠΆΠ½ΠΎΠ΅ ΡΡΠ½Π΄Π°ΠΌΠ΅Π½ΡΠ°Π»ΡΠ½ΠΎΠ΅ ΠΏΠΎΠ½ΠΈΠΌΠ°Π½ΠΈΠ΅ Π±Π΅ΡΠΎΠ½Π°, Π½Π΅ΠΎΠ±Ρ ΠΎΠ΄ΠΈΠΌΠΎΠ΅ Π΄Π»Ρ Π΄ΠΎΡΡΠΈΠΆΠ΅Π½ΠΈΡ ΡΡΠΏΠ΅Ρ Π° Ρ Π»ΡΠ±ΠΎΠΉ ΠΈΡΠΏΠΎΠ»ΡΠ·ΡΠ΅ΠΌΠΎΠΉ ΡΠΌΠ΅ΡΡΡ.ΠΡΠΎ ΡΠ°ΠΊΠΆΠ΅ Π΄Π°Π΅Ρ Π²Π°ΠΌ ΡΠ²ΠΎΠ±ΠΎΠ΄Ρ Π²ΡΠ±ΡΠ°ΡΡ Π»ΡΠ±ΠΎΠΉ ΠΌΠΈΠΊΡ, ΠΊΠΎΡΠΎΡΡΠΉ Π²Ρ Ρ ΠΎΡΠΈΡΠ΅, ΠΈΡΡ ΠΎΠ΄Ρ ΠΈΠ· Π²Π°ΡΠΈΡ Π»ΠΈΡΠ½ΡΡ ΠΏΡΠ΅Π΄ΠΏΠΎΡΡΠ΅Π½ΠΈΠΉ ΠΈ ΠΏΠΎΡΡΠ΅Π±Π½ΠΎΡΡΠ΅ΠΉ Π² ΡΠ΄ΠΎΠ±ΡΡΠ²Π΅, ΡΡΠΎΠΈΠΌΠΎΡΡΠΈ ΠΈ ΡΡΡΠ΅ΡΠΈΠΊΠ΅. BRCP ΡΠ°ΠΊΠΆΠ΅ ΠΏΡΠ΅Π΄Π»Π°Π³Π°Π΅Ρ Π³ΠΎΡΠΎΠ²ΡΠ΅ Π²Π°ΡΠΈΠ°Π½ΡΡ ΡΡΡΡΡ ΠΈΠ½Π³ΡΠ΅Π΄ΠΈΠ΅Π½ΡΠΎΠ², Π° ΡΠ°ΠΊΠΆΠ΅ ΠΌΠ½ΠΎΠΆΠ΅ΡΡΠ²ΠΎ ΡΠΌΠ΅ΡΠ΅ΠΉ Π΄Π»Ρ ΡΠ΄ΠΎΠ²Π»Π΅ΡΠ²ΠΎΡΠ΅Π½ΠΈΡ ΡΠ°Π·Π»ΠΈΡΠ½ΡΡ ΠΏΠΎΡΡΠ΅Π±Π½ΠΎΡΡΠ΅ΠΉ. ΠΠ΅ΡΠΌΠΎΡΡΡ Π½Π° ΡΠΎ, ΡΡΠΎ Ρ Π½Π°Ρ ΡΠ°Π·Π½ΡΠ΅ ΠΌΠ΅ΡΠΎΠ΄Ρ ΠΈ Ρ Π°ΡΠ°ΠΊΡΠ΅ΡΡ, ΠΈ CCI, ΠΈ BRCP Π½Π°ΡΠ΅Π»Π΅Π½Ρ Π½Π° ΡΠ°Π·Π²ΠΈΡΠΈΠ΅ Π½Π°ΡΠ΅ΠΉ ΠΎΡΡΠ°ΡΠ»ΠΈ Π½Π° ΠΏΠ»Π°ΡΡΠΎΡΠΌΠ΅ ΠΊΠ°ΡΠ΅ΡΡΠ²Π° ΠΈ ΡΠ΅Π»ΠΎΡΡΠ½ΠΎΡΡΠΈ. (ΠΡ ΡΠ½ΠΎΠ²Π° ΡΠΊΠ°Π·Π°Π»ΠΈ ΡΡΠΎ Π΄ΠΎ ΡΠΎΠ³ΠΎ, ΠΊΠ°ΠΊ Π΄ΡΡΠ³ΠΎΠΉ ΠΏΡΠΎΠΈΠ·Π²ΠΎΠ΄ΠΈΡΠ΅Π»Ρ ΡΠ³ΡΠΎΠΆΠ°Π» ΡΡΠ΄Π΅Π±Π½ΡΠΌ ΠΈΡΠΊΠΎΠΌ.)
ΠΡΠΈΠΌΠ΅ΡΠ°Π½ΠΈΠ΅. Π‘ΠΌ. Π’Π°ΠΊΠΆΠ΅ ΡΡΡ Π΄ΠΎΠΏΠΎΠ»Π½ΠΈΡΠ΅Π»ΡΠ½ΡΡ ΡΡΠ°ΡΡΡ Ρ Π±ΠΎΠ»Π΅Π΅ ΠΏΠΎΠ΄ΡΠΎΠ±Π½ΠΎΠΉ ΠΈΠ½ΡΠΎΡΠΌΠ°ΡΠΈΠ΅ΠΉ ΠΎ ΠΏΡΠΎΡΠ΅Π΄ΡΡΠ΅ ΡΠ΅ΡΡΠΈΡΠΎΠ²Π°Π½ΠΈΡ.
6 Π‘ΠΠΠ‘ΠΠΠΠ ΠΠ’ΠΠΠ ΠΠΠΠΠΠ― ΠΠΠ’ΠΠΠ
Π‘ΡΡΠ΅ΡΡΠ²ΡΡΡ ΡΠ°Π·Π»ΠΈΡΠ½ΡΠ΅ ΠΌΠ΅ΡΠΎΠ΄Ρ Π»Π΅ΡΠ΅Π½ΠΈΡ. ΠΡΠΈΠ½ΡΡΠΈΠ΅ ΡΠΎΠ³ΠΎ ΠΈΠ»ΠΈ ΠΈΠ½ΠΎΠ³ΠΎ ΠΌΠ΅ΡΠΎΠ΄Π° Π·Π°Π²ΠΈΡΠΈΡ ΠΎΡ Ρ Π°ΡΠ°ΠΊΡΠ΅ΡΠ° ΡΠ°Π±ΠΎΡΡ ΠΈ ΠΊΠ»ΠΈΠΌΠ°ΡΠΈΡΠ΅ΡΠΊΠΈΡ ΡΡΠ»ΠΎΠ²ΠΈΠΉ. ΠΠ±ΡΡΠ½ΠΎ ΠΈΡΠΏΠΎΠ»ΡΠ·ΡΡΡΡΡ ΡΠ»Π΅Π΄ΡΡΡΠΈΠ΅ ΠΌΠ΅ΡΠΎΠ΄Ρ ΠΎΡΠ²Π΅ΡΠΆΠ΄Π΅Π½ΠΈΡ Π±Π΅ΡΠΎΠ½Π°.
ΠΡΠ²Π΅ΡΠΆΠ΄Π΅Π½ΠΈΠ΅ Π±Π΅ΡΠΎΠ½Π°- ΠΠ°ΡΠ΅Π½Π΅Π½ΠΈΠ΅ Π±Π΅ΡΠΎΠ½Π½ΡΡ ΡΠ°Π±ΠΎΡ
- ΠΠΎΠΊΡΡΡΠΈΠ΅ Π±Π΅ΡΠΎΠ½Π½ΡΡ ΠΏΠΎΠ²Π΅ΡΡ Π½ΠΎΡΡΠ΅ΠΉ ΠΌΠ΅ΡΠΊΠ°ΠΌΠΈ ΠΈΠ· Π³Π΅ΡΡΠΈΠ°Π½Π° ΠΈΠ»ΠΈ ΡΠΎΠ³ΠΎΠΆΠΊΠΈ
- ΠΠ±ΡΡΠ·Π³ΠΈΠ²Π°Π½ΠΈΠ΅ Π²ΠΎΠ΄ΠΎΠΉ
- ΠΠ΅ΡΠΎΠ΄ ΠΏΠΎΠ½Π΄ΠΈΠ½Π³Π°
- ΠΠ΅ΠΌΠ±ΡΠ°Π½Π½ΠΎΠ΅ ΠΎΡΠ²Π΅ΡΠΆΠ΄Π΅Π½ΠΈΠ΅
- ΠΡΠ²Π΅ΡΠΆΠ΄Π΅Π½ΠΈΠ΅ ΠΏΠ°ΡΠΎΠΌ
1.ΠΠ°ΡΠ΅Π½Π΅Π½ΠΈΠ΅ Π±Π΅ΡΠΎΠ½Π½ΡΡ ΡΠ°Π±ΠΎΡ
ΠΠ°Π΄Π°ΡΠ° Π·Π°ΡΠ΅Π½Π΅Π½ΠΈΡ Π±Π΅ΡΠΎΠ½Π½ΡΡ ΡΠ°Π±ΠΎΡ — ΠΏΡΠ΅Π΄ΠΎΡΠ²ΡΠ°ΡΠΈΡΡ ΠΈΡΠΏΠ°ΡΠ΅Π½ΠΈΠ΅ Π²ΠΎΠ΄Ρ Ρ ΠΏΠΎΠ²Π΅ΡΡ Π½ΠΎΡΡΠΈ Π΅ΡΠ΅ Π΄ΠΎ ΡΡ Π²Π°ΡΡΠ²Π°Π½ΠΈΡ. ΠΡΠΎ ΠΏΡΠΈΠ½ΡΡΠΎ Π² ΠΎΡΠ½ΠΎΠ²Π½ΠΎΠΌ Π² ΡΠ»ΡΡΠ°Π΅ Π±ΠΎΠ»ΡΡΠΈΡ Π±Π΅ΡΠΎΠ½Π½ΡΡ ΠΏΠΎΠ²Π΅ΡΡ Π½ΠΎΡΡΠ΅ΠΉ, ΡΠ°ΠΊΠΈΡ ΠΊΠ°ΠΊ Π΄ΠΎΡΠΎΠΆΠ½ΡΠ΅ ΠΏΠ»ΠΈΡΡ. ΠΡΠΎ Π²Π°ΠΆΠ½ΠΎ Π² ΡΡΡ ΡΡ ΠΏΠΎΠ³ΠΎΠ΄Ρ Π΄Π»Ρ Π·Π°ΡΠΈΡΡ Π±Π΅ΡΠΎΠ½Π° ΠΎΡ ΠΆΠ°ΡΡ, ΠΏΡΡΠΌΡΡ ΡΠΎΠ»Π½Π΅ΡΠ½ΡΡ Π»ΡΡΠ΅ΠΉ ΠΈ Π²Π΅ΡΡΠ°. ΠΠ½ ΡΠ°ΠΊΠΆΠ΅ Π·Π°ΡΠΈΡΠ°Π΅Ρ ΠΏΠΎΠ²Π΅ΡΡ Π½ΠΎΡΡΡ ΠΎΡ Π΄ΠΎΠΆΠ΄Ρ. Π Ρ ΠΎΠ»ΠΎΠ΄Π½ΡΡ ΠΏΠΎΠ³ΠΎΠ΄Ρ Π·Π°ΡΠ΅Π½Π΅Π½ΠΈΠ΅ ΠΏΠΎΠΌΠΎΠ³Π°Π΅Ρ ΡΠΎΡ ΡΠ°Π½ΠΈΡΡ ΡΠ΅ΠΏΠ»ΠΎ Π³ΠΈΠ΄ΡΠ°ΡΠ°ΡΠΈΠΈ ΡΠ΅ΠΌΠ΅Π½ΡΠ°, ΡΠ΅ΠΌ ΡΠ°ΠΌΡΠΌ ΠΏΡΠ΅Π΄ΠΎΡΠ²ΡΠ°ΡΠ°Ρ Π·Π°ΠΌΠ΅ΡΠ·Π°Π½ΠΈΠ΅ Π±Π΅ΡΠΎΠ½Π° Π² ΡΡΠ»ΠΎΠ²ΠΈΡΡ ΡΠΌΠ΅ΡΠ΅Π½Π½ΠΎΠ³ΠΎ ΠΌΠΎΡΠΎΠ·Π°.ΠΠ°ΡΠ΅Π½Π΅Π½ΠΈΠ΅ Π΄ΠΎΡΡΠΈΠ³Π°Π΅ΡΡΡ Π·Π° ΡΡΠ΅Ρ Π½Π°ΡΡΠ½ΡΡΠΎΠ³ΠΎ Π½Π° ΡΠ°ΠΌΡ Ρ ΠΎΠ»ΡΡΠ°. ΠΡΠΎΡ ΠΌΠ΅ΡΠΎΠ΄ ΠΈΠΌΠ΅Π΅Ρ ΠΎΠ³ΡΠ°Π½ΠΈΡΠ΅Π½Π½ΠΎΠ΅ ΠΏΡΠΈΠΌΠ΅Π½Π΅Π½ΠΈΠ΅.
2. ΠΠΎΠΊΡΡΡΠΈΠ΅ Π±Π΅ΡΠΎΠ½Π½ΡΡ ΠΏΠΎΠ²Π΅ΡΡ Π½ΠΎΡΡΠ΅ΠΉ ΠΌΠ΅ΡΠΊΠ°ΠΌΠΈ Hessian ΠΈΠ»ΠΈ Gunny
ΠΡΠΎ ΡΠΈΡΠΎΠΊΠΎ ΠΈΡΠΏΠΎΠ»ΡΠ·ΡΠ΅ΠΌΡΠΉ ΠΌΠ΅ΡΠΎΠ΄ ΠΎΡΠ²Π΅ΡΠΆΠ΄Π΅Π½ΠΈΡ, ΠΎΡΠΎΠ±Π΅Π½Π½ΠΎ Π΄Π»Ρ ΠΊΠΎΠ½ΡΡΡΡΠΊΡΠΈΠΎΠ½Π½ΠΎΠ³ΠΎ Π±Π΅ΡΠΎΠ½Π°. Π’Π°ΠΊΠΈΠΌ ΠΎΠ±ΡΠ°Π·ΠΎΠΌ, ΠΎΠ±Π½Π°ΠΆΠ΅Π½Π½Π°Ρ ΠΏΠΎΠ²Π΅ΡΡ Π½ΠΎΡΡΡ Π±Π΅ΡΠΎΠ½Π° Π½Π΅ Π²ΡΡΡΡ Π°Π΅Ρ, Π΅ΡΠ»ΠΈ Π½Π°ΠΊΡΡΡΡ Π΅Π΅ Π³Π΅ΡΡΠΈΠ°Π½ΠΎΠΌ, Π±ΡΠ΅Π·Π΅Π½ΡΠΎΠΌ ΠΈΠ»ΠΈ ΠΏΡΡΡΡΠΌΠΈ ΠΌΠ΅ΡΠΊΠ°ΠΌΠΈ Π΄Π»Ρ ΡΠ΅ΠΌΠ΅Π½ΡΠ°. ΠΠΎΠΊΡΡΡΠΈΠ΅ Π½Π° Π²Π΅ΡΡΠΈΠΊΠ°Π»ΡΠ½ΡΡ ΠΈ Π½Π°ΠΊΠ»ΠΎΠ½Π½ΡΡ ΠΏΠΎΠ²Π΅ΡΡ Π½ΠΎΡΡΡΡ Π΄ΠΎΠ»ΠΆΠ½ΠΎ Π±ΡΡΡ Π½Π°Π΄Π΅ΠΆΠ½ΠΎ Π·Π°ΠΊΡΠ΅ΠΏΠ»Π΅Π½ΠΎ. ΠΡ ΠΏΠ΅ΡΠΈΠΎΠ΄ΠΈΡΠ΅ΡΠΊΠΈ ΡΠΌΠ°ΡΠΈΠ²Π°ΡΡ.ΠΠ½ΡΠ΅ΡΠ²Π°Π» ΡΠΌΠ°ΡΠΈΠ²Π°Π½ΠΈΡ Π±ΡΠ΄Π΅Ρ Π·Π°Π²ΠΈΡΠ΅ΡΡ ΠΎΡ ΡΠΊΠΎΡΠΎΡΡΠΈ ΠΈΡΠΏΠ°ΡΠ΅Π½ΠΈΡ Π²ΠΎΠ΄Ρ. Π‘Π»Π΅Π΄ΡΠ΅Ρ ΡΠ»Π΅Π΄ΠΈΡΡ Π·Π° ΡΠ΅ΠΌ, ΡΡΠΎΠ±Ρ ΠΏΠΎΠ²Π΅ΡΡ Π½ΠΎΡΡΡ Π±Π΅ΡΠΎΠ½Π° Π½Π΅ Π²ΡΡΡΡ Π°Π»Π° Π΄Π°ΠΆΠ΅ Π² ΡΠ΅ΡΠ΅Π½ΠΈΠ΅ ΠΊΠΎΡΠΎΡΠΊΠΎΠ³ΠΎ Π²ΡΠ΅ΠΌΠ΅Π½ΠΈ Π² ΠΏΠ΅ΡΠΈΠΎΠ΄ ΠΎΡΠ²Π΅ΡΠΆΠ΄Π΅Π½ΠΈΡ. ΠΠΎ Π½ΠΎΡΠ°ΠΌ ΠΈ Π² ΠΏΡΠ°Π·Π΄Π½ΠΈΡΠ½ΡΠ΅ Π΄Π½ΠΈ Π½Π΅ΠΎΠ±Ρ ΠΎΠ΄ΠΈΠΌΠΎ ΡΠΎΠ±Π»ΡΠ΄Π°ΡΡ ΠΎΡΠΎΠ±ΡΠ΅ ΠΌΠ΅ΡΡ ΠΏΠΎ ΡΠΎΡ ΡΠ°Π½Π΅Π½ΠΈΡ ΠΏΠΎΠ²Π΅ΡΡ Π½ΠΎΡΡΠΈ Π²Π»Π°ΠΆΠ½ΠΎΠΉ.
3. ΠΡΠΎΡΠ΅Π½ΠΈΠ΅ Π²ΠΎΠ΄ΠΎΠΉ
ΠΠ΅ΠΏΡΠ΅ΡΡΠ²Π½ΠΎΠ΅ ΠΏΠΎΠ»ΠΈΠ²Π°Π½ΠΈΠ΅ Π²ΠΎΠ΄ΠΎΠΉ Π±Π΅ΡΠΎΠ½Π½ΠΎΠΉ ΠΏΠΎΠ²Π΅ΡΡ Π½ΠΎΡΡΠΈ ΠΎΠ±Π΅ΡΠΏΠ΅ΡΠΈΠ²Π°Π΅Ρ ΡΡΡΠ΅ΠΊΡΠΈΠ²Π½ΠΎΠ΅ ΠΎΡΠ²Π΅ΡΠΆΠ΄Π΅Π½ΠΈΠ΅. Π ΠΎΡΠ½ΠΎΠ²Π½ΠΎΠΌ ΠΎΠ½ ΠΈΡΠΏΠΎΠ»ΡΠ·ΡΠ΅ΡΡΡ Π΄Π»Ρ ΠΏΠΎΠ»ΠΈΠΌΠ΅ΡΠΈΠ·Π°ΡΠΈΠΈ ΠΏΠ»ΠΈΡ ΠΏΠ΅ΡΠ΅ΠΊΡΡΡΠΈΡ. ΠΠ΅ΡΠ΅Π΄ Π½Π°ΡΠ°Π»ΠΎΠΌ ΠΎΡΠΎΡΠ΅Π½ΠΈΡ Π±Π΅ΡΠΎΠ½Ρ Π½Π΅ΠΎΠ±Ρ ΠΎΠ΄ΠΈΠΌΠΎ Π΄Π°ΡΡ Π΅ΠΌΡ Π΄ΠΎΡΡΠ°ΡΠΎΡΠ½ΠΎ Π·Π°ΡΡΡΡΡ.Π‘ΠΏΡΠ΅ΠΉ ΠΌΠΎΠΆΠ½ΠΎ ΠΏΠΎΠ»ΡΡΠΈΡΡ ΠΈΠ· ΠΏΠ΅ΡΡΠΎΡΠΈΡΠΎΠ²Π°Π½Π½ΠΎΠ³ΠΎ ΠΏΠ»Π°ΡΡΠΈΠΊΠΎΠ²ΠΎΠ³ΠΎ ΡΡΠΈΠΊΠ°. ΠΠ° Π½Π΅Π±ΠΎΠ»ΡΡΠΈΡ ΡΠ°Π±ΠΎΡΠ°Ρ ΡΠ°Π·Π±ΡΡΠ·Π³ΠΈΠ²Π°Π½ΠΈΠ΅ Π²ΠΎΠ΄Ρ ΠΌΠΎΠΆΠ½ΠΎ ΠΏΡΠΎΠΈΠ·Π²ΠΎΠ΄ΠΈΡΡ Π²ΡΡΡΠ½ΡΡ. ΠΠ΅ΡΡΠΈΠΊΠ°Π»ΡΠ½ΡΠ΅ ΠΈ Π½Π°ΠΊΠ»ΠΎΠ½Π½ΡΠ΅ ΠΏΠΎΠ²Π΅ΡΡ Π½ΠΎΡΡΠΈ ΠΌΠΎΠΆΠ½ΠΎ ΠΏΠΎΠ΄Π΄Π΅ΡΠΆΠΈΠ²Π°ΡΡ ΠΏΠΎΡΡΠΎΡΠ½Π½ΠΎ Π²Π»Π°ΠΆΠ½ΡΠΌΠΈ, ΡΠ°Π·Π±ΡΡΠ·Π³ΠΈΠ²Π°Ρ Π²ΠΎΠ΄Ρ Π½Π° Π²Π΅ΡΡ Π½ΠΈΠ΅ ΠΏΠΎΠ²Π΅ΡΡ Π½ΠΎΡΡΠΈ ΠΈ ΠΏΠΎΠ·Π²ΠΎΠ»ΡΡ Π΅ΠΉ ΡΡΠ΅ΠΊΠ°ΡΡ ΠΌΠ΅ΠΆΠ΄Ρ ΡΠΎΡΠΌΠ°ΠΌΠΈ ΠΈ Π±Π΅ΡΠΎΠ½ΠΎΠΌ. ΠΠ»Ρ ΡΡΠΎΠ³ΠΎ ΠΌΠ΅ΡΠΎΠ΄Π° ΠΎΡΠ²Π΅ΡΠΆΠ΄Π΅Π½ΠΈΡ ΠΏΠΎΡΡΠ΅Π±Π½ΠΎΡΡΡ Π² Π²ΠΎΠ΄Π΅ Π²ΡΡΠ΅.
4. ΠΠ΅ΡΠΎΠ΄ Ponding
ΠΡΠΎ Π»ΡΡΡΠΈΠΉ ΠΌΠ΅ΡΠΎΠ΄ Π»Π΅ΡΠ΅Π½ΠΈΡ. ΠΠΎΠ΄Ρ ΠΎΠ΄ΠΈΡ Π΄Π»Ρ ΠΏΠΎΠ»ΠΈΠΌΠ΅ΡΠΈΠ·Π°ΡΠΈΠΈ Π³ΠΎΡΠΈΠ·ΠΎΠ½ΡΠ°Π»ΡΠ½ΡΡ ΠΏΠΎΠ²Π΅ΡΡ Π½ΠΎΡΡΠ΅ΠΉ, ΡΠ°ΠΊΠΈΡ ΠΊΠ°ΠΊ ΠΏΠΎΠ»Ρ, ΠΏΠ»ΠΈΡΡ ΠΊΡΡΡΠΈ, Π΄ΠΎΡΠΎΠΆΠ½ΡΠ΅ ΠΏΠΎΠΊΡΡΡΠΈΡ ΠΈ ΠΏΠΎΠΊΡΡΡΠΈΡ Π°ΡΡΠΎΠ΄ΡΠΎΠΌΠΎΠ².ΠΠΎΡΠΈΠ·ΠΎΠ½ΡΠ°Π»ΡΠ½ΡΠ΅ Π²Π΅ΡΡ Π½ΠΈΠ΅ ΠΏΠΎΠ²Π΅ΡΡ Π½ΠΎΡΡΠΈ Π±Π°Π»ΠΎΠΊ ΡΠ°ΠΊΠΆΠ΅ ΠΌΠΎΠ³ΡΡ Π±ΡΡΡ ΠΏΠ΅ΡΠ΅ΠΊΡΡΡΡ. ΠΠΎΡΠ»Π΅ ΡΠΊΠ»Π°Π΄ΠΊΠΈ Π±Π΅ΡΠΎΠ½Π° Π΅Π³ΠΎ ΠΎΡΠΊΡΡΡΠ°Ρ ΠΏΠΎΠ²Π΅ΡΡ Π½ΠΎΡΡΡ ΡΠ½Π°ΡΠ°Π»Π° ΠΏΠΎΠΊΡΡΠ²Π°Π΅ΡΡΡ Π²Π»Π°ΠΆΠ½ΠΎΠΉ ΡΠΊΠ°Π½ΡΡ ΠΈΠ»ΠΈ Ρ ΠΎΠ»ΡΡΠΎΠΌ. Π§Π΅ΡΠ΅Π· 24 ΡΠ°ΡΠ° ΡΡΠΈ ΠΏΠΎΠΊΡΡΡΠΈΡ ΡΠ½ΠΈΠΌΠ°ΡΡ ΠΈ Π²Π΄ΠΎΠ»Ρ ΡΡΠΎΡΡΠ°ΡΠΎΠ² ΡΡΡΠΎΡΡ Π½Π΅Π±ΠΎΠ»ΡΡΠΈΠ΅ ΠΏΡΡΠ΄Ρ ΠΈΠ· Π³Π»ΠΈΠ½Ρ ΠΈΠ»ΠΈ ΠΏΠ΅ΡΠΊΠ°. Π’Π°ΠΊΠΈΠΌ ΠΎΠ±ΡΠ°Π·ΠΎΠΌ, ΠΎΠ±Π»Π°ΡΡΡ Π΄Π΅Π»ΠΈΡΡΡ Π½Π° Π½Π΅ΡΠΊΠΎΠ»ΡΠΊΠΎ ΠΏΡΡΠΌΠΎΡΠ³ΠΎΠ»ΡΠ½ΠΈΠΊΠΎΠ². ΠΠΎΠ΄Π° Π·Π°Π»ΠΈΠ²Π°Π΅ΡΡΡ ΠΌΠ΅ΠΆΠ΄Ρ ΠΏΡΡΠ΄Π°ΠΌΠΈ. ΠΠ°ΠΏΠΎΠ»Π½Π΅Π½ΠΈΠ΅ Π²ΠΎΠ΄ΠΎΠ΅ΠΌΠΎΠ² Π²ΠΎΠ΄ΠΎΠΉ ΠΏΡΠΎΠΈΠ·Π²ΠΎΠ΄ΠΈΡΡΡ Π΄Π²Π° ΠΈΠ»ΠΈ ΡΡΠΈ ΡΠ°Π·Π° Π² Π΄Π΅Π½Ρ, Π² Π·Π°Π²ΠΈΡΠΈΠΌΠΎΡΡΠΈ ΠΎΡ Π°ΡΠΌΠΎΡΡΠ΅ΡΠ½ΡΡ ΡΡΠ»ΠΎΠ²ΠΈΠΉ. Π₯ΠΎΡΡ ΡΡΠΎΡ ΠΌΠ΅ΡΠΎΠ΄ ΠΎΡΠ΅Π½Ρ ΡΡΡΠ΅ΠΊΡΠΈΠ²Π΅Π½, ΠΏΠΎΡΡΠ΅Π±Π½ΠΎΡΡΡ Π² Π²ΠΎΠ΄Π΅ ΠΎΡΠ΅Π½Ρ Π²ΡΡΠΎΠΊΠ°.ΠΡΡΠ΄Ρ Π»Π΅Π³ΠΊΠΎ ΡΠ°Π·Π±ΠΈΠ²Π°ΡΡΡΡ, ΠΈ Π²ΠΎΠ΄Π° Π²ΡΡΠ΅ΠΊΠ°Π΅Ρ. ΠΠΎΡΠ»Π΅ Π·Π°ΡΠ²Π΅ΡΠ΄Π΅Π²Π°Π½ΠΈΡ Π³Π»ΠΈΠ½Ρ ΡΡΡΠ΄Π½ΠΎ ΠΎΡΠΈΡΡΠΈΡΡ.
5. ΠΠ΅ΠΌΠ±ΡΠ°Π½Π½ΠΎΠ΅ ΠΎΡΠ²Π΅ΡΠΆΠ΄Π΅Π½ΠΈΠ΅
ΠΠΏΠΈΡΠ°Π½Π½ΡΠΉ Π²ΡΡΠ΅ ΠΌΠ΅ΡΠΎΠ΄ ΠΎΡΠ²Π΅ΡΠΆΠ΄Π΅Π½ΠΈΡ ΠΎΡΠ½ΠΎΡΠΈΡΡΡ ΠΊ ΠΊΠ°ΡΠ΅Π³ΠΎΡΠΈΠΈ Π²Π»Π°ΠΆΠ½ΠΎΠ³ΠΎ ΠΎΡΠ²Π΅ΡΠΆΠ΄Π΅Π½ΠΈΡ. ΠΡΡΠ³ΠΎΠΉ ΠΌΠ΅ΡΠΎΠ΄ ΠΎΡΠ²Π΅ΡΠΆΠ΄Π΅Π½ΠΈΡ — ΠΏΠΎΠΊΡΡΡΠΈΠ΅ ΡΠΌΠΎΡΠ΅Π½Π½ΠΎΠΉ Π±Π΅ΡΠΎΠ½Π½ΠΎΠΉ ΠΏΠΎΠ²Π΅ΡΡ Π½ΠΎΡΡΠΈ ΡΠ»ΠΎΠ΅ΠΌ Π²ΠΎΠ΄ΠΎΠ½Π΅ΠΏΡΠΎΠ½ΠΈΡΠ°Π΅ΠΌΠΎΠ³ΠΎ ΠΌΠ°ΡΠ΅ΡΠΈΠ°Π»Π°, ΠΊΠΎΡΠΎΡΡΠΉ ΡΠ΄Π΅ΡΠΆΠΈΠ²Π°Π΅ΡΡΡ Π² ΠΊΠΎΠ½ΡΠ°ΠΊΡΠ΅ Ρ Π±Π΅ΡΠΎΠ½Π½ΠΎΠΉ ΠΏΠΎΠ²Π΅ΡΡ Π½ΠΎΡΡΡΡ Π² ΡΠ΅ΡΠ΅Π½ΠΈΠ΅ ΡΠ΅ΠΌΠΈ Π΄Π½Π΅ΠΉ. ΠΡΠΎΡ ΠΌΠ΅ΡΠΎΠ΄ ΠΎΡΠ²Π΅ΡΠΆΠ΄Π΅Π½ΠΈΡ Π½Π°Π·ΡΠ²Π°Π΅ΡΡΡ ΠΌΠ΅ΠΌΠ±ΡΠ°Π½Π½ΡΠΌ ΠΎΡΠ²Π΅ΡΠΆΠ΄Π΅Π½ΠΈΠ΅ΠΌ. ΠΠ΅ΠΌΠ±ΡΠ°Π½Π° ΠΏΡΠ΅Π΄ΠΎΡΠ²ΡΠ°ΡΠΈΡ ΠΈΡΠΏΠ°ΡΠ΅Π½ΠΈΠ΅ Π²ΠΎΠ΄Ρ ΠΈΠ· Π±Π΅ΡΠΎΠ½Π°.ΠΠ΅ΠΌΠ±ΡΠ°Π½Π° ΠΌΠΎΠΆΠ΅Ρ Π±ΡΡΡ ΠΊΠ°ΠΊ Π² ΡΠ²Π΅ΡΠ΄ΠΎΠΉ, ΡΠ°ΠΊ ΠΈ Π² ΠΆΠΈΠ΄ΠΊΠΎΠΉ ΡΠΎΡΠΌΠ΅. ΠΠ½ΠΈ ΡΠ°ΠΊΠΆΠ΅ ΠΈΠ·Π²Π΅ΡΡΠ½Ρ ΠΊΠ°ΠΊ Π³Π΅ΡΠΌΠ΅ΡΠΈΠΊΠΈ. ΠΠΈΡΡΠΌΠ½Π°Ρ Π²ΠΎΠ΄ΠΎΠ½Π΅ΠΏΡΠΎΠ½ΠΈΡΠ°Π΅ΠΌΠ°Ρ Π±ΡΠΌΠ°Π³Π°, Π²ΠΎΡΠΊΠΎΠ²ΡΠ΅ ΡΠΌΡΠ»ΡΡΠΈΠΈ, Π±ΠΈΡΡΠΌΠ½ΡΠ΅ ΡΠΌΡΠ»ΡΡΠΈΠΈ ΠΈ ΠΏΠ»Π°ΡΡΠΌΠ°ΡΡΠΎΠ²ΡΠ΅ ΠΏΠ»Π΅Π½ΠΊΠΈ ΡΠ²Π»ΡΡΡΡΡ Π½Π°ΠΈΠ±ΠΎΠ»Π΅Π΅ ΡΠ°ΡΠΏΡΠΎΡΡΡΠ°Π½Π΅Π½Π½ΡΠΌΠΈ ΡΠΈΠΏΠ°ΠΌΠΈ ΠΈΡΠΏΠΎΠ»ΡΠ·ΡΠ΅ΠΌΡΡ ΠΌΠ΅ΠΌΠ±ΡΠ°Π½.
ΠΠ°ΠΆΠ΄ΡΠΉ ΡΠ°Π·, ΠΊΠΎΠ³Π΄Π° Π±ΠΈΡΡΠΌ Π½Π°Π½ΠΎΡΠΈΡΡΡ Π½Π° ΠΏΠΎΠ²Π΅ΡΡ Π½ΠΎΡΡΡ Π΄Π»Ρ ΠΎΡΠ²Π΅ΡΠΆΠ΄Π΅Π½ΠΈΡ, ΡΡΠΎ ΡΠ»Π΅Π΄ΡΠ΅Ρ Π΄Π΅Π»Π°ΡΡ ΡΠΎΠ»ΡΠΊΠΎ ΡΠ΅ΡΠ΅Π· 24 ΡΠ°ΡΠ° ΠΎΡΠ²Π΅ΡΠΆΠ΄Π΅Π½ΠΈΡ Ρ ΠΏΠΎΠΌΠΎΡΡΡ ΠΌΠ΅ΡΠΊΠΎΠ²-ΠΌΠ΅ΡΠΊΠΎΠ². ΠΠΎΠ²Π΅ΡΡ Π½ΠΎΡΡΠΈ Π΄Π°ΡΡ Π²ΡΡΠΎΡ Π½ΡΡΡ, ΡΡΠΎΠ±Ρ ΡΡΡ Π»Π°Ρ Π²ΠΎΠ΄Π° Π½Π΅ Π±ΡΠ»Π° Π²ΠΈΠ΄Π½Π°, Π° Π·Π°ΡΠ΅ΠΌ ΠΆΠΈΠ΄ΠΊΠΈΠΉ Π°ΡΡΠ°Π»ΡΡ ΡΠ°Π·Π±ΡΡΠ·Π³ΠΈΠ²Π°Π΅ΡΡΡ ΠΏΠΎ Π²ΡΠ΅ΠΉ ΠΏΠΎΠ²Π΅ΡΡ Π½ΠΎΡΡΠΈ. Π’Π°ΠΊΠΈΠΌ ΠΎΠ±ΡΠ°Π·ΠΎΠΌ ΡΠΎΡ ΡΠ°Π½ΡΠ΅ΡΡΡ Π²Π»Π°Π³Π° Π² Π±Π΅ΡΠΎΠ½Π΅.ΠΠ»Ρ Π»Π΅ΡΠ΅Π½ΠΈΡ ΡΡΠΎΠ³ΠΎ Π²ΠΏΠΎΠ»Π½Π΅ Π΄ΠΎΡΡΠ°ΡΠΎΡΠ½ΠΎ.
ΠΡΠΎΡ ΠΌΠ΅ΡΠΎΠ΄ ΠΎΡΠ²Π΅ΡΠΆΠ΄Π΅Π½ΠΈΡ Π½Π΅ ΡΡΠ΅Π±ΡΠ΅Ρ ΠΏΠΎΡΡΠΎΡΠ½Π½ΠΎΠ³ΠΎ Π½Π°Π±Π»ΡΠ΄Π΅Π½ΠΈΡ. ΠΠ³ΠΎ Ρ ΡΡΠΏΠ΅Ρ ΠΎΠΌ ΠΏΡΠΈΠΌΠ΅Π½ΡΡΡ Π² ΠΌΠ΅ΡΡΠ°Ρ , Π³Π΄Π΅ Π½Π΅Ρ Π²ΠΎΠ΄Ρ Π² Π΄ΠΎΡΡΠ°ΡΠΎΡΠ½ΠΎΠΌ ΠΊΠΎΠ»ΠΈΡΠ΅ΡΡΠ²Π΅ Π΄Π»Ρ Π²Π»Π°ΠΆΠ½ΠΎΠ³ΠΎ ΠΎΡΠ²Π΅ΡΠΆΠ΄Π΅Π½ΠΈΡ. ΠΡΠΎΡ ΠΌΠ΅ΡΠΎΠ΄ ΠΎΡΠ²Π΅ΡΠΆΠ΄Π΅Π½ΠΈΡ Π½Π΅ΡΡΡΠ΅ΠΊΡΠΈΠ²Π΅Π½ ΠΏΠΎ ΡΡΠ°Π²Π½Π΅Π½ΠΈΡ Ρ Π²Π»Π°ΠΆΠ½ΡΠΌ ΠΎΡΠ²Π΅ΡΠΆΠ΄Π΅Π½ΠΈΠ΅ΠΌ ΠΈΠ·-Π·Π° ΠΌΠ΅Π½ΡΡΠ΅ΠΉ ΡΡΠ΅ΠΏΠ΅Π½ΠΈ Π³ΠΈΠ΄ΡΠ°ΡΠ°ΡΠΈΠΈ. ΠΡΠΎΠΌΠ΅ ΡΠΎΠ³ΠΎ, ΠΏΡΠΎΡΠ½ΠΎΡΡΡ Π±Π΅ΡΠΎΠ½Π°, ΠΎΡΠ²Π΅ΡΠΆΠ΄Π΅Π½Π½ΠΎΠ³ΠΎ Π»ΡΠ±ΠΎΠΉ ΠΌΠ΅ΠΌΠ±ΡΠ°Π½ΠΎΠΉ, ΠΌΠ΅Π½ΡΡΠ΅, ΡΠ΅ΠΌ ΠΏΡΠΎΡΠ½ΠΎΡΡΡ Π±Π΅ΡΠΎΠ½Π° Ρ Π²Π»Π°ΠΆΠ½ΡΠΌ ΠΎΡΠ²Π΅ΡΠΆΠ΄Π΅Π½ΠΈΠ΅ΠΌ. ΠΠΎΠ³Π΄Π° ΠΌΠ΅ΠΌΠ±ΡΠ°Π½Π° ΠΏΠΎΠ²ΡΠ΅ΠΆΠ΄Π΅Π½Π°, ΠΎΡΠ²Π΅ΡΠΆΠ΄Π΅Π½ΠΈΠ΅ ΡΠΈΠ»ΡΠ½ΠΎ ΡΡ ΡΠ΄ΡΠ°Π΅ΡΡΡ.
6. ΠΡΠ²Π΅ΡΠΆΠ΄Π΅Π½ΠΈΠ΅ ΠΏΠ°ΡΠΎΠΌ
ΠΠ½ΠΎΠ³Π΄Π° ΠΏΡΠΈΠΌΠ΅Π½ΡΠ΅ΡΡΡ ΠΎΡΠ²Π΅ΡΠΆΠ΄Π΅Π½ΠΈΠ΅ ΠΏΠ°ΡΠΎΠΌ ΠΈ ΠΎΡΠ²Π΅ΡΠΆΠ΄Π΅Π½ΠΈΠ΅ Π² Π³ΠΎΡΡΡΠ΅ΠΉ Π²ΠΎΠ΄Π΅.ΠΡΠΈ ΠΈΡΠΏΠΎΠ»ΡΠ·ΠΎΠ²Π°Π½ΠΈΠΈ ΡΡΠΈΡ ΠΌΠ΅ΡΠΎΠ΄ΠΎΠ² ΠΎΡΠ²Π΅ΡΠΆΠ΄Π΅Π½ΠΈΡ ΠΏΡΠΎΡΠ½ΠΎΡΡΡ Π±Π΅ΡΠΎΠ½Π° ΡΠ²Π΅Π»ΠΈΡΠΈΠ²Π°Π΅ΡΡΡ ΠΎΡΠ΅Π½Ρ Π±ΡΡΡΡΠΎ.
ΠΡΠΈ ΠΌΠ΅ΡΠΎΠ΄Ρ Π»ΡΡΡΠ΅ Π²ΡΠ΅Π³ΠΎ ΠΏΠΎΠ΄Ρ ΠΎΠ΄ΡΡ Π΄Π»Ρ ΡΠ±ΠΎΡΠ½ΡΡ Π±Π΅ΡΠΎΠ½Π½ΡΡ ΡΠ°Π±ΠΎΡ. ΠΡΠΈ ΠΎΡΠ²Π΅ΡΠΆΠ΄Π΅Π½ΠΈΠΈ ΠΏΠ°ΡΠΎΠΌ ΡΠ΅ΠΌΠΏΠ΅ΡΠ°ΡΡΡΠ° ΠΏΠ°ΡΠ° Π΄ΠΎΠ»ΠΆΠ½Π° Π±ΡΡΡ ΠΎΠ³ΡΠ°Π½ΠΈΡΠ΅Π½Π° ΠΌΠ°ΠΊΡΠΈΠΌΡΠΌΠΎΠΌ 75 0 Β° C, ΡΠ°ΠΊ ΠΊΠ°ΠΊ ΠΏΡΠΈ ΠΎΡΡΡΡΡΡΠ²ΠΈΠΈ Π½Π°Π΄Π»Π΅ΠΆΠ°ΡΠ΅ΠΉ Π²Π»Π°ΠΆΠ½ΠΎΡΡΠΈ (ΠΎΠΊΠΎΠ»ΠΎ 90%) Π±Π΅ΡΠΎΠ½ ΠΌΠΎΠΆΠ΅Ρ Π²ΡΡΠΎΡ Π½ΡΡΡ ΡΠ»ΠΈΡΠΊΠΎΠΌ Π±ΡΡΡΡΠΎ. Π ΡΠ»ΡΡΠ°Π΅ ΠΎΡΠ²Π΅ΡΠΆΠ΄Π΅Π½ΠΈΡ Π² Π³ΠΎΡΡΡΠ΅ΠΉ Π²ΠΎΠ΄Π΅ ΡΠ΅ΠΌΠΏΠ΅ΡΠ°ΡΡΡΠ° ΠΌΠΎΠΆΠ΅Ρ Π±ΡΡΡ ΠΏΠΎΠ²ΡΡΠ΅Π½Π° Π΄ΠΎ Π»ΡΠ±ΠΎΠ³ΠΎ ΠΏΡΠ΅Π΄Π΅Π»Π°, ay 100 0 C.
ΠΡΠΈ ΡΡΠΎΠΉ ΡΠ΅ΠΌΠΏΠ΅ΡΠ°ΡΡΡΠ΅ ΡΠ°Π·Π²ΠΈΡΠΈΠ΅ ΠΏΡΠΎΡΠ½ΠΎΡΡΠΈ ΡΠΎΡΡΠ°Π²Π»ΡΠ΅Ρ ΠΎΠΊΠΎΠ»ΠΎ 70% ΠΎΡ 28-Π΄Π½Π΅Π²Π½ΠΎΠΉ ΠΏΡΠΎΡΠ½ΠΎΡΡΠΈ ΡΠ΅ΡΠ΅Π· 4β5 ΡΠ°ΡΠΎΠ².Π ΠΎΠ±ΠΎΠΈΡ ΡΠ»ΡΡΠ°ΡΡ ΡΠ»Π΅Π΄ΡΠ΅Ρ ΠΏΠΎΠ»Π½ΠΎΡΡΡΡ ΠΊΠΎΠ½ΡΡΠΎΠ»ΠΈΡΠΎΠ²Π°ΡΡ ΡΠ΅ΠΌΠΏΠ΅ΡΠ°ΡΡΡΡ, ΡΡΠΎΠ±Ρ ΠΈΠ·Π±Π΅ΠΆΠ°ΡΡ Π½Π΅ΠΎΠ΄Π½ΠΎΡΠΎΠ΄Π½ΠΎΡΡΠΈ.