Состав цемента и его производство: состав, химическая формула и производство
Производство цемента и состав цементного клинкера
Состав цементного клинкера который получается от производства цементного камня по новой технологии. Способы схем процесса производства цемента из клинкера.
В статье
Производство цемента из клинкера
Романцемент — получают путем обжига известняков, содержащих глинистых не менее 25% при температуре 1000-1200 градусов по Цельсию. Применение: производство бетонов низких марок, стеновые панели, блоки.
Портландцемент — после обжига известняков, мергелей и глинистых примесей получают цементный клинкер. Клинкер смешивают с добавками (ракушечник, доменный шлак).
Способы производства портландцемента
1. Мокрый — компоненты измельчают и смешивают в присутствии воды, полученную суспензию (шлам) обжигают.
2. Сухой — все тоже самое, только в сухом состоянии.
Минералогический состав цементного клинкера
Трехкальциевый силикат (алит) является активным минералом. Быстро твердеет и набирает прочность, сопровождается значительным тепловыделением.
Двухкальциевый силикат (белит) в начальный период твердеет медленно.
Трехкальциевый алюминат — низкая стойкость против серно-кислых соединений.
Четырехкальциевый алюмоферрит твердеет медленнее алита, но быстрее белита. Прочность ниже алита.
Применение портландцемента
Приготовление растворов невысоких марок для кладочных и штукатурных работ, бетонные изделия.
Виды портландцемента
Глиноземистый — быстро твердеет. Получают путем обжига известняков и бокситов (богаты глиноземом). Процесс твердения сопровождается большим тепловыделением.
Свойства: сульфатостойкий, водонепроницаемый, жаростойкий, в 3-4 раза дороже портландцемента.
Применение: срочные ремонтные работы, аварийные работы, бетонные работы в зимних условиях, производство жаростойких бетонов.
Водонепроницаемый расширяющийся портландцемент получают путем тщательного измельчения глиноземистого цемента, гипса и гидроалюминатов кальция. При взаимодействии двух последних происходит образование гидросульфатоалюминатов кальция. Твердение сопровождается увеличением объема.
Применение: создание гидроизоляционных покрытий, заделка стыков и трещин железобетонных конструкций.
Быстротвердеющий портландцемент характеризуется быстрым нарастанием прочности.
Конечно, скорость твердения не сравнить с гипсом. Но самая быстрая из всех видов цемента.
Применение: возведение монолитных сооружений, приготовление высокопрочных бетонов.
Шлакопортландцемент жаро-, водо- и сульфатостойкий. Процесс твердения медленный.
Применение: изготовление железобетонных конструкций для работы в горячих цехах, гидротехнические сооружения.
Пуццолановый портландцемент твердеет медленно, требует систематического увлажнения.
Свойства: водостойкий, сульфатостойкий, не морозостойкий.
Применение: бетонные и ж/б конструкции.
Пластифицированный позволяет снизить водопотребление бетонных смесей и расход цемента на 5-8%.
Применение: дорожные бетоны, аэродромное и гидротехническое строительство.
Гидрофобный по своим свойствам похож на пластифицированный. Применение тоже.
Белый и цветной портландцемент
Белый изготавливают из сырья в котором мало окрашивающих оксидов (чистый известняк). Цветной — в которых много (охра, железный сурик).
Применение: облицовочные плитки, фактурный слой стеновых панелей, искусственный мрамор.
Сульфатостойкий портландцемент изготавливают из клинкера с другими примесями не более 7%.
Производство цемента
Цемент — это один из самых востребованных строительных материалов на рынке. Однако, производство готового цемента является затратным как по капитальным вложениям, так и по использованию энергии. Заводы по его производству обычно расположены вблизи мест добычи основного сырьевого компонента, каковым является известняк. Сам цемент используется в строительстве, как в чистом виде, так и в качестве основы для изготовления незаменимых материалов (бетона и железобетона).
Производство цемента начинается с добычи клинкера. Затем клинкер измельчают и получают вещество в виде порошка, в которое добавляют гипсовый компонент и другое. Расходы на добычу клинкера — большая доля затрат в себестоимости цемента. В итоге такая статья затрат, как добыча сырья, составляет долю в себестоимости готового продукта равную 70%.
Метод, с помощью которого осуществляют добычу и разработку залежей известняка называется «сносом». Используя этот метод, часть горной породы «сносят», освобождая путь к известняку желто-зеленого цвета. Глубина залегания известняка обычно составляет 10 м, толщина пласта равна 70 см. До принятой глубины породу желто-зеленого цвета можно встретить еще примерно четыре раза. На следующем этапе добытый известняк с помощью ленты для транспортировки отправляется на измельчение. Здесь известняковая порода должна приобрести размер кусков не более 10 см в диаметре. Измельченный до таких размеров известняковый компонент транспортируется на сушку и повторное перемалывание, где к нему добавляются другие составляющие. Затем известняковая смесь обжигается. Так происходит процесс получения клинкера.
Следующая стадия заключается в обработке клинкера. В первую очередь, клинкер дробят. Одновременно проходит процесс подсушки минеральных компонентов и дробление гипсового камня. Затем все компоненты смешивают и еще раз подвергают перемалыванию.
Поскольку сырье имеет порой разные технические и физические характеристики, то в промышленности существует три метода производства готового продукта. Так, при производстве цемента применяется три способа изготовления готовой смеси: мокрый, сухой и комбинированный.
Цементная смесь, произведенная мокрым способом, сделана на основе карбоната (мела), силикатов (глины) и добавок, содержащих железо. К последним относятся конвертерный шлам, огарки пирита и железистый продукт. При этом глина должна содержать влагу не более 20%, а мел не более 29%. Все компоненты смеси проходят измельчение в воде, в итоге получается суспензия, влажность которой составляет 30-50%. Суспензия, а вернее шлам, поступает в специальные печи, где проходит обжиг. Печь для обжига имеет весьма внушительные размеры: ее высота составляет 7 м, а длина — 200 м. В процессе обжига из шлама происходит выделение углекислот. На выходе из печи после обжига получается клинкер, который имеет вид шариков. Эти шарики измельчают и получают готовую цементную смесь.
При сухом способе производства происходит сушка всех сырьевых составляющих цемента, и только затем перемалывание. Таким образом, смесь имеет вид порошка.
При комбинированном способе осуществляется частичное использование двух предыдущих. Таким образом, комбинированный способ производства подразделяется на два вида. При первом из них смесь сырьевых компонентов готовят по мокрому способу, и только затем влажность смеси снижают с помощью специальных фильтров, она не должна превышать 16-18%. Потом эту массу отправляют на обжиг. При втором виде для получения смеси используется способ сухого получения первоначальной смеси, а затем в нее добавляют воду. Так получают гранулы, размер которых составляет не более 10-15 мм. Затем эти гранулы отправляют в печь для обжига.
Из чего делают строительный цемент на заводе
Цемент –незаменимый материал, без которого нельзя представить ни один строительный объект. Уникальность материала неоспорима, ведь так или иначе он участвует практически во всех строительных этапах. Современные комбинаты используют три базовых метода изготовления цемента, которые зависят от метода подготовки сырьевого материала к обжигу: мокрая технология, сухая и полумокрая (комбинированная). Как устроить производственную базу, зависит от возможностей каждой компании: технологических, технико-экономических.
Технология изготовления портландцемента делится на три ключевые стадии:
Механическая — отвечает за добычу, подготовку и переработку сырья, цель которой получить необходимую смесь для последующей термической обработки путём обжига. К таким операциям относятся измельчение, перемешивание и корректировка.
Стадия термической обработки отвечает за обжиг сырья в высокотемпературных печах, целью которой станет получение клинкера – базовой составляющей цемента.
Стадия помола и смешивания компонентов для получения сухой смеси, состоящей из нескольких компонентов: клинкера, гипсовых вяжущих веществ и активных минеральных добавок, которые будут влиять на тип цемента.
Первая стадия. Добыча и подготовка сырьевой смеси.
Основные компоненты портландцемента — это натуральное сырье: глина, известняк, мел. Из экономических соображений производственные узлы по возможности устанавливают недалеко от карьеров добычи этих материалов. Наряду с поставками из карьеров нередко приходится дополнительно обеспечивать производство сырьевыми компонентами от партнёров, чтобы гарантировать требуемое качество сырья по химическому составу. Так же дополнительные закупки проводят для обеспечения производства недостающими материалами, такими как гипс, зола, пирит, боксит и так далее.
Составляющие цемента можно разделить на 4 группы оксидов, каждая из которых по составу является соединением химического элемента с кислородом:
- оксид кальция (СаО), в эту группу входят глинисто-карбонатные горные породы, такие как известняк, мел или мергель;
- оксид кремния (Si₂O3), к ней относятся мелкозернистые осадочные горные породы, например, песок, глина, шлак, сланцы;
- оксид алюминия(Al₂O3) – бокситы;
- оксид железа(Fe₂O3) – железная руда.
Первая вторая. Сырьевая смесь и ее подготовка
Месторождения природного известняка разрабатывают открытым способом. Применяемый технологический метод зависит от оснащения карьера и типа известняковой породы. Для добычи горных пород используют взрывной, экскаваторный, комбайновый способы. Там же, в карьере на производственных узлах измельчают известняк, используя стационарные дробильные установки. Далее по ленточному конвейеру, протяжённость которого доходит до 7 км, материал доставляют до производственной площадки, где его укладывают штабелями в разных направлениях. На этапе дробления необходимо провести анализ твёрдой породы, для этого над конвейерным транспортёром устанавливают анализатор РФА. Установка определяет химический состав известняка для последующей корректировки.
Современные производственные площадки оснащены специальными дозаторами, чтобы с точностью вымерять весовое соотношение всех компонентов.
На устаревших цементных заводах процесс не настолько технологичный, что в результате приводит к повышению издержек. На таких заводах карьерный материал доставляют до производственных площадок на автомобильном или железнодорожном транспорте. Что в целом ухудшает экономические показатели производственного процесса. Вместо ленточных конвейеров применяют грейферные краны. Трудозатраты и время на производственный цикл увеличиваются, повышая себестоимость.
На этапе подготовки сырьё проходит еще одну стадию — помол. В зависимости от оснащённости производственной линии, используется технология сухого, мокрого или полумокрого помола. В первом случае технологическая линия оснащена мощными мельницами. Нижняя часть оборудования измельчает известняк, в верхней части происходит сепарирование на фракции. Грубую фракцию оставляют для вторичного измельчения, мелкую отправляют на следующую производственную стадию. В процессе помола сырьевая мука просушивается до состояния влажности — 0,5%.
До термической обработки сырьевую смесь хранят в специальных складах сыпучих материалов, где для усреднения концентрации сыпучих компонентов через люки аэрации подаётся сжатый воздух.
Для метода мокрого и комбинированного помола сырьевую смесь подготавливают в виде шлама, увлажняя его до 40%. Сырьевую муку перемалывают в мельницах, работающих по принципу самоизмельчения, типа гидрофол. Погруженный в барабанный отсек печи, шлам разрушается под действием вращательных движений посредством ударов друг о друга. Таким образом происходит одновременное дробление и помол известняка. Состав сырьевой смеси доводят до нужной формулы в специальных бассейнах. При такой технологии производства, как и при сухом методе, шлам усредняют путём воздействия сжатого воздуха, только делают это в шламовом бассейне. Полумокрый метод отличается от мокрого тем, что перед обжигом смесь пропускают через пресс-фильтр для её обезвоживания.
Чтобы получить клинкер высокого качества, используют первосортное сырьё, которое в дальнейшем определит качество цемента. При анализе сырьевой муки исследуют следующие модульные показатели:
Силикатный модуль – отношение грамм-молекул оксида кремния к числу грамм-молекул оксидов алюминия и железа. Чем выше силикатный модуль, тем хуже способность к обжигу у сырьевой смеси. Оптимальное соотношение измеряется в процентах и варьируется в пределах 2.2-2.8.
Глиноземный (алюминатный) модуль – соотношение грамм-молекул двух оксидов — алюминия и железа, для контроля состояния жидкой фазы клинкера на этапе обжига, также говорит о взаимосвязи минералов в материале, нормальный показатель 1.5-2.5%.
Говоря о влиянии модулей друг на друга, можно отметить, что если показатель алюминатного модуля высокий, а силикатного, наоборот, низкий, то цемент будет слишком быстро схватываться. Добавление гипса корректирует сроки твердения.
Коэффициент насыщения кремнезема известью (КН) – показывает неполноту насыщения кремнезёма оксидом кальция в процессе образования клинкера. Нормативный показатель находится в интервале от 0.92 до 1 %.
Коэффициент однородности сырьевой смеси – говорит о химическом составе и его стабильности. Для производства сухим способом показатель должен быть не больше 14, применение мокрого или комбинированного способов должно обеспечивать показатель не больше 10 %.
Третья стадия. Обжиг
Обжиг смеси и получение клинкера — самая важная стадия производственных процессов.
Эксплуатационные свойства цемента напрямую зависят от качества клинкера, температуры и времени обжигания. Дело в том, что в естественных условиях основные компоненты сырьевой смеси не вступают в химическую реакцию друг с другом, но процесс взаимодействия между глиной, известняком и другими компонентами запускается при нагревании.
Чаще всего промышленные предприятия оснащены печными агрегатами вращающегося типа. Основные составляющие агрегата – это печь, холодильник, топочные устройства, вентиляторы, дымососы, пылеулавливатели. Вращающиеся печи делятся на два типа – для сухого и мокрого способов производства.
Вращающийся барабан сварен из стальных обечаек, зона обжига барабанной печи облицована внутри огнеупорной футеровкой, за счет чего снижается температура воздействия на металлические сварные кольца. Барабан печи расположен под небольшим уклоном и совершает вращательные движения вокруг продольной оси с частотой от 0,5 до 4 оборотов в минуту, с учётом производительности агрегата.
Если сухой метод производства цемента сравнивать с мокрым, то он считается более технологичным, современным и экономичным. Печное оборудование потребляют энергии на 30-40% меньше за счет того, что отсутствует одна из рабочих фаз — необходимость в испарении влаги клинкера.
Печную установку можно поделить на температурные зоны с разной функциональностью:
В зоне сушки поддерживается температура до 200°С, здесь из шлама испаряется излишняя влага.
В зоне подогрева, где температура варьируется в пределах 200 — 650°С происходит процесс дегидратации, в результате чего глинистый компонент обезвоживается, выгорают органические примеси.
В зоне декарбонизации поддерживается температурный режим от 650 до 1000°С. Здесь из вещества удаляется углерод путём разложения карбонатов кальция и магния, которые под воздействием температур переходят в оксиды этих химических элементов — СаО и МgO.
В зоне спекания клинкера при диапазоне температур 1300-1450°С активируется движение молекул в сырьевых компонентах и в веществе формируются минералы, которые влияют на конечные эксплуатационные свойства цемента. Повышение температуры обжига повышает интенсивность всех физико-химических процессов, которые претерпевают компоненты клинкера.
- Клинкерные минералы, образовавшиеся при обжиге, определяют свойства будущего портландцемента и оказывают следующее влияние:
- Алит или трехкальциевый силикат (С₃S) – основной минерал портландцемента отвечает за ускоренный набор начальной и марочной прочности;
- Белит или двухкальциевый силиката (С₂S) – отвечает за медленный набор прочности, в течение длительных сроков затвердевания;
- трехкальциевый алюминат (С₃А) – наиболее активный минерал, не обладает высокой прочностью, но в значительной степени влияет на ускорение набора начальной прочности;
- четырехкальциевый алюмоферрит (С₄АF) – отличается умеренной скоростью твердения и средним тепловыделением, его влияние на физико-химические свойства портландцемента не столь значительны, но минерал определяет цвет цемента. Чем выше содержание, тем интенсивнее цвет.
Вместе с полезными минералами при нагревании в клинкере образуются нежелательные компоненты, в основном оксиды: магния, калия, натрия. Побочные продукты попадают в клинкер и в результате сгорания топлива, допустимое количество неблагоприятных веществ может отразиться на свойствах цемента и экологической атмосфере на предприятии, поэтому содержание таких элементов нормируется и контролируется.
Далее клинкерную массу охлаждают в холодильном отделении до 100°С. После охлаждения клинкер поступает в крытые хранилища для сыпучих веществ, ожидая дальнейшей переработки.
Четвертая стадия. Помол клинкера и добавок
Заключительная рабочая стадия получения готового цемента — размол клинкера совместно с добавками или по отдельности с последующим смешиванием. Процесс полностью механический, его проводят в мельничных установках закрытого или открытого типа. От помола сырьевых компонентов на стадии подготовки, этот процесс отличается тем, что клинкер значительно твёрже, к тому же конечная фракция цементного зерна должна иметь заданные критерии по составу и размеру.
Принцип работы помольного агрегата сводится к следующему:
- Клинкерный материал, обогащённый добавками транспортируется по ленте конвейера из силосов в мельницу.
- После помола материал высыпается в разгрузочную цапфу, затем поступает на элеватор. Цементную муку просеивают через сито с размером ячейки 0,08 мм, по процентному остатку определяют тонкость помола, остаток непросеянного цемента должен быть не более 15%.
- Элеватор переносит перемолотый клинкер в сепаратор центробежной силы, где разделяется на муку и крупу по размеру фракций. Тонкий помол считается готовым продуктом, крупу отправляют на вторичный помол в мельницу.
- Двухкамерные пневматические насосы переносят готовый цемент по трубопроводу на склад сыпучих материалов. Камеры работают попеременно. Если в правую поступает цемент, то из левой сжатым воздухом выталкивается пылевоздушная смесь.
Для улучшения аэрации цементной муки в части усечённого конуса установлены пористые перегородки, через которые подается сжатый воздух. Камеры оснащены манометрами, что позволяет контролировать давление сжатого воздуха.
На современных технологических линиях помол осуществляют методом замкнутого цикла, что позволяет добиться высокого качества портландцемента со стабильными физико-химическими свойствами. При использовании такой схемы после сепаратора выходит цементная мука с заданными характеристиками. Это положительно влияет на энергосберегающий ресурс промышленного производства. Высокотехнологичные помольные агрегаты с автоматическим управлением оснащены контрольными измерителями.
Размолоспособность клинкера зависит не только от способа обжига, но и от состава клинкерных минералов. Клинкер, полученный в шахтной печи, имеет более пористую структуру и легче перемалывается. Коэффициент размолоспособности у такого клинкера 1,25. Коэффициент у клинкера, полученного во вращающейся печи равен 1.
Некоторые производственные линии c мельницами открытого цикла не используют в схеме сепаратор. На таких линиях цемент отправляется в хранилище сразу после мельничного агрегата. Качество такого цемента ниже.
До отгрузки потребителю готовый цемент хранится на силосных складах. Конструктивно современные силосы устроены в виде обратного усечённого конуса из железобетона или металла.
Анализ применяемых технологий позволяет сделать вывод, что наиболее технологичным и современным считается сухой метод. Именно такие технологии использует LafargeHolcim на своих цементных заводах. Помимо получения продукции с высокими эксплуатационными характеристиками и физико-химическими свойствам, данный метод позволяет значительно снизить расходы потребляемого топлива, сократить не менее 40 % объема газовых выбросов печной переработки, сократить потребление пресной воды и при этом с 1 м³ печи получить большее количество клинкера.
Состав цемента | Функции
Двумя основными компонентами цемента являются глинистый и известняковый .
Состав обычного цемента и ингредиентов следующий:
Ингредиенты | Нормальный диапазон в % | Типовой состав н % | |
1)Лайм (Cao) | 60-70% | 62 | |
2)Двуокись кремния (SiO2) | 17-25% | 22 | |
3) Глинозем (Al2O3) | 3-8% | 5 | |
4) Оксид железа (Fe2O3) | 0,5 – 6% | 3 | |
5) Магнезия (MgO) | 0,1–4% | 2 | |
6) Триоксид серы (SO3) | 1-3% | 1 | |
7) Сода или поташ | 0,5 – 1,3% | 1 | |
8) Сульфат кальция (CaSo4) | 3 – 5% | 4 | |
Всего | 100 |
Для лучшего понимания посмотрите видео:
youtube.com/embed/Cn2806nVBmU?feature=player_embedded» frameborder=»0″ allowfullscreen=»allowfullscreen» data-thumbnail-src=»https://i.ytimg.com/vi/Cn2806nVBmU/0.jpg»/>
Читайте также : Вопрос интервью Процесс производства цемента Наиболее повторяющаяся и имп. гидратация цемента
Функции ингредиентов цемента и средний состав цемента:
1. Известь:
Является основным компонентом цемента и составляет около двух третей цемента.
- Придает цементу прочность и прочность.
- Известь в избыточном количестве делает цемент неустойчивым и вызывает его распад.
- Если извести мало, смесь будет неподходящей, что однажды приведет к низкой прочности , так как этот цемент быстро схватывается.
- Отсутствие извести снижает прочность цемента.
- Его доля составляет 60-70%
2.
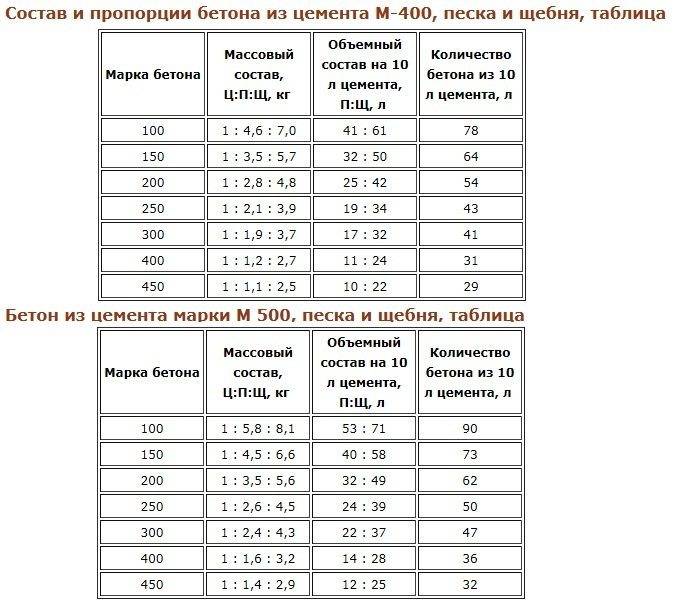
- Является важным компонентом цемента и придает прочность цементу за счет образования двухкальциевых и трехкальциевых силикатов.
- Избыток диоксида кремния придает цементу большую прочность, но в то же время продлевает время его схватывания.
- Его процентное содержание составляет от 17 до 25 %
3. Глинозем:
- Придает цементу свойство быстрого схватывания.
- Действует как флюс и снижает температуру спекания.
- Избыток глинозема снижает прочность цемента.
- Его состав в цементе составляет от 3 до 8%
4. Оксид железа:
- Придает цвет, твердость и прочность цементу.
- Также способствует плавлению сырья при производстве цемента.
- Его содержание в цементе составляет от 0,5 до 6%
5. Оксид магния:
- Придает цементу твердость и цвет , если присутствует в небольших количествах.
- Избыток оксида магния делает цемент некачественным .
6. Триоксид серы:
- Придает цементу звук, если присутствует в очень небольшие количества .
- Если его использовать в избытке, он вызывает расширение цемента, что делает его непригодным для использования, а также избыток трехокиси серы увеличивает время схватывания .
7. Щелочи (сода и калий):
- Они используются в виде соды и калия .
- Они должны присутствовать в небольших количествах.
- Щелочи в избытке количества вызовут высолы .
- Средний состав составляет около 1%
8.
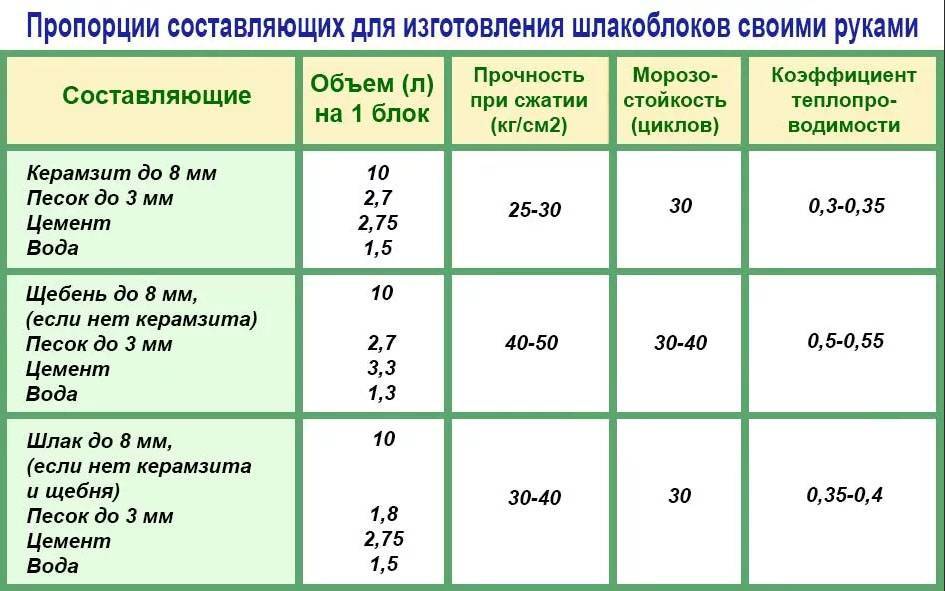
- Составляет около 3% цемента и добавляется в виде гипса в процессе помола клинкера
- Является замедлителем схватывания, так как увеличивает время начального схватывания цемента.
- Если гипс не добавлен, цемент затвердеет в момент добавления воды, не давая времени для смешивания и укладки.
Вредные ингредиенты цемента:
Следующие два ингредиента влияют на качество цемента:
1. Оксиды щелочных металлов.
2. Оксид магния.
Если количество оксидов щелочных металлов превышает 1% . это приводит к разрушению бетона, изготовленного из этого цемента. Если содержание 9Оксид магния 0009 превышает 5% , он вызывает трещины после затвердевания раствора или бетона.
Пропорции ингредиентов цемента, их функции и ограничения
🕑 Время чтения: 1 минута
Обычный портландцемент содержит различные ингредиенты в различных пропорциях.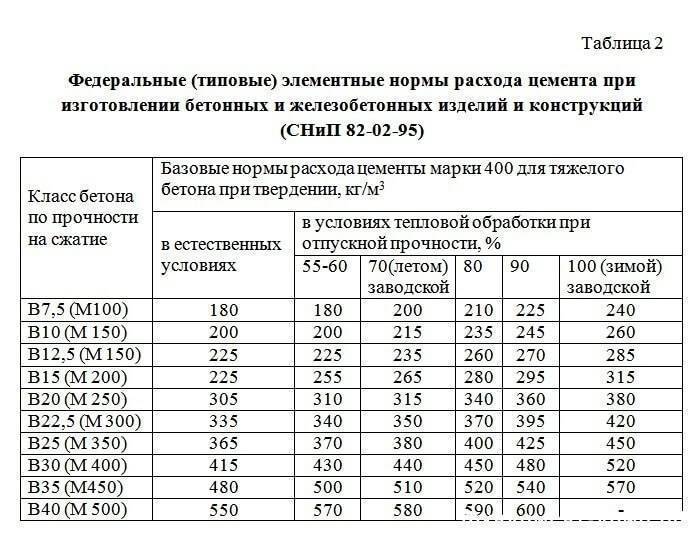
Состав:
- Доля компонентов цемента
- Функции и ограничения компонентов цемента
- 1. Известь (CaO)
- 2. Кремнезем (SiO2) 9015 4 3. Глинозем (Al2O3)
- 4. Оксид железа (Fe2O3)
- 5. Магнезия (MgO)
- 6. Сульфат кальция (CaSO4)
- 7. Сера (SO3)
- 8. Щелочи
- Известь (CaO)
- Силикагель (SiO 2 )
- Глинозем (Al 2 O 3 )
- Железо (Fe 2 O 3 )
- Магнезия (MgO)
- Сульфат кальция (CaSO 4 )
- Сера (SO 3 )
- Щелочи
Рис. 1: Доля цементных ингредиентов
Рис. 2: Известь в порошке
2. Кремнезем (SiO 2 ) Кремнезем или диоксид кремния является вторым по величине ингредиентом цемента, составляющим от 17 до 25%. Кремнезем можно получить из песка, глинистой породы и т. д. Достаточное количество кремнезема способствует образованию двухкальциевых и трехкальциевых силикатов, придающих прочность цементу.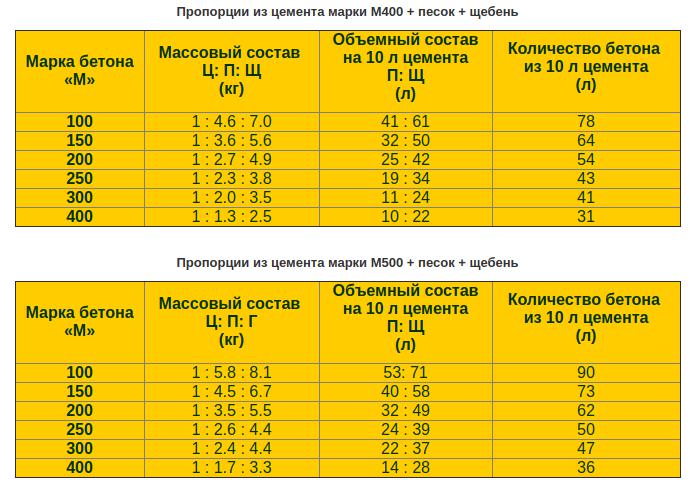
Рис. 3: Микрокремнезем
3. Глинозем (Al 2 O 3 ) Глинозем в цементе присутствует в виде оксида алюминия. Содержание глинозема в цементе должно быть от 3 до 8%. Его получают из бокситов, алюмосодержащих глин и т. д. Глинозем придает цементу свойство быстрого схватывания. Как правило, для получения требуемого качества цемента требуется высокая температура. Но глинозем при добавлении к цементным ингредиентам ведет себя как флюс и снижает температуру спекания, что в конечном итоге ослабляет цемент. Так, для поддержания высокой температуры глинозем не следует использовать в избыточном количестве.Рис. 4: Глинозем
4. Оксид железа (Fe 2 O 3 ) Количество оксида железа в цементе колеблется от 0,5 до 6%. Его можно получить из летучей золы, железной руды, железного лома и т.
Рис. 5: Пигмент на основе оксида железа
5. Магнезия (MgO) Цемент содержит магнезию или оксид магния в диапазоне от 0,1 до 3%. Магнезия в цементе в небольших количествах придает твердость и цвет цементу. Если его больше 3%, цемент становится непрочным, а также снижается его прочность.Рис. 6: Оксид магния
6. Сульфат кальция (CaSO 4 ) Сульфат кальция присутствует в цементе в виде гипса. Встречается вместе с известняком. Он колеблется от 1 до 3%. Функция сульфата кальция в цементе заключается в увеличении времени начального схватывания цемента.Рис. 7: Гипсовый порошок
7.Сера (SO 3 ) Содержание серы или трехокиси серы в цементе составляет от 1 до 3%.