Состав цемент: состав, химическая формула и производство
Особенности производства, свойства и области применения белого цемента
Опубликовано 10 сентября 2019, вторник
Белый цемент от LafargeHolcim – это больше, чем просто строительный материал. Его универсальность, непревзойденный внешний вид и высокие эксплуатационные качества обеспечивают ему особое место среди других строительных материалов – это символ симбиоза эстетики и функциональности.
По своему вещественному составу белый цемент не содержит каких-либо минеральных добавок, он состоит только из клинкера и гипса. Белый цемент имеет марку прочности 500 (его прочность при сжатии в возрасте 28 суток достаточно высока и составляет 55-60 МПа), а по степени белизны он относится к первому сорту (его коэффициент отражения света составляет 83-85%). Благодаря высокой белизне и возможности окрашивания бетона цветными пигментами белый цемент предоставляет безграничные возможности для яркой и долговечной отделки улиц, фасадов и помещений.
Отличительной особенностью белого цемента является его высокая теплота гидратации (тепловыделение) на начальных этапах твердения, поэтому он обладает быстрой кинетикой набора прочности.
Важными характеристиками белого цемента, к которым потребители предъявляют требования, являются водопотребность, время потери подвижности, сроки схватывания. Преимуществом белого цемента LafargeHolcim является повышенная эффективность его работы в сочетании с суперпластификаторами, которые входят в состав практически любой бетонной или растворной смеси. Пластифицирующие добавки позволяют снизить водоцементное отношение и получить бетоны и строительные растворы с плотной структурой, обладающие низкой проницаемостью. Кроме того, бетонные смеси и строительные растворы на белом цементе обладают лучшей подвижностью, чем бетонные смеси и растворы на общестроительном сером цементе.
Области применения и конечные продукты на основе белого цемента
Области применения белого цемента аналогичны общестроительному серому цементу – это:
- готовые бетонные смеси и растворы
- сборные железобетонные элементы
- мелкоштучные бетонные изделия
- строительные смеси
Однако применение белого цемента позволяет получить широкий спектр форм, цветов и фактур, создавая яркий визуальный эффект, и обеспечив при этом заданную прочность, водонепроницаемость, морозостойкость, атмосферную и коррозионную стойкость конечных продуктов на его основе.
Для изготовления и укладки декоративной бетонной смеси на основе белого цемента необходимо строго контролировать стабильность качества и точность дозирования всех сырьевых компонентов, поддерживать чистоту технологического оборудования и автотранспорта для доставки свежеприготовленной бетонной смеси на объект строительства. Особого контроля требует подготовка опалубки, технология укладки готовой бетонной смеси и уход за твердеющим бетоном. Несмотря на то, что применение товарного бетона на основе белого цемента требует дополнительных затрат, он незаменим для достижения яркой архитектурной выразительности, что неоднократно подтверждено европейской и российской строительной практикой.
В отличие от товарного архитектурного бетона на основе белого цемента, элементы заводского изготовления все чаще пополняют продуктовый портфель заводов сборного железобетона. Белый цемент обеспечивает прекрасные реологические свойства свежеприготовленной бетонной смеси, что позволяет использовать фактурную оснастку для выразительного дизайна фасадных элементов.
Мелкоштучные бетонные изделия заводского изготовления на основе белого цемента представлены в широком ассортименте – это плиты «терраццо» и искусственный камень для устройства полов, отделки фасадов и помещений, тротуарная плитка и стеновые блоки. При производстве мелкоштучных бетонных изделий применяется различное технологическое оборудование. Изготовление плит «терраццо» предусматривает вибровакуумирование с последующей шлифовкой и полировкой поверхности изделий, что в сочетании с окраской цементной матрицы в яркие цвета и возможностью подбора фракционного состава декоративных заполнителей позволяет имитировать натуральный гранит различной цветовой гаммы.
Отличительной особенностью искусственного камня является тонкая имитация цвета и фактуры различных горных пород, что достигается при помощи укладки литой мелкозерныстой бетонной смеси в текстурированные пластиковые формы.
Производство сухих строительных смесей является одним из самых больших сегментов потребления белого цемента. Он широко применяется в производстве декоративных штукатурок для наружных и внутренних работ, шпатлевок для финишного выравнивания стен и потолков помещений с повышенной влажностью, плиточных клеев для укладки полупрозрачной плитки, белого мрамора, мозаики, а также затирок для швов и наливных полов.
Сухие смеси на основе белого цемента очень технологичны, легко наносятся и выравниваются, создавая при этом тонкие текстуры. Пластичность, связность и однородность смесей на основе белого цемента, позволяет выполнять отделочные работы любой сложности как внутри, так и снаружи помещений. А высокая прочность и стойкость затвердевшего раствора к попеременному замораживанию и оттаиванию гарантирует его долговечность даже в условиях интенсивных атмосферных воздействий.
Технологические особенности производства белого цемента
Для производства белого цемента используют наиболее чистые разновидности карбонатного и глинистого сырья с минимальным количеством окрашивающих примесей. Известняк (СаСО3) должен содержать не более 0,15% оксида железа (Fe2O3) и до 0,03% оксида марганца (MnO). Глинистым компонентом служит белая глина (каолин). Для повышения силикатного модуля применяют белый кварцевый песок. Содержание Fe2O3 в глинистом и кремнеземистом компонентах суммарно не должно превышать 1%, а оксида титана (TiO2) – 0,8%.
На заводе LafargeHolcim в Коломне производство белого цемента осуществляется по мокрому способу, который предусматривает обжиг сырьевого шлама с влажностью около 40%. Сырьевые компоненты – известняк, каолин и кварцевый песок тонко измельчают в сырьевой мельнице с добавлением воды, на выходе из которой получают сырьевой шлам. В процессе приготовления сырьевого шлама необходимо полностью исключить его загрязнение присадками металлического железа, которые могут увеличить содержание Fe2О3 в шламе и отрицательно повлиять на коэффициент отражения света (белизну) цемента. По этой причине для внутренней оснастки сырьевых мельниц используют бронефутеровку и мелющие тела, изготовленные из износостойкой высоколегированной стали.
Сырьевой шлам заданного химического состава подают на обжиг во вращающуюся печь диаметром 3,6 м и длинной 127 м, на выходе из которой получают белый клинкер. В качестве топлива для обжига белого клинкера используют природный газ, который, в отличие от угля или жидкого топлива, не содержит загрязняющих примесей. Образование клинкерных минералов в тугоплавкой сырьевой смеси, содержащей минимальное количество Fe2О3, происходит при температуре около 1700°С, тогда как для обычного серого клинкера она составляет 1450°С.
С целью повышения белизны клинкер обжигают в бескислородной газовой среде для восстановления Fe2O3, что понижает красящую способность соединений железа и способствует повышению коэффициента отражения света (белизны) клинкера. На выходе из вращающейся печи клинкер резко охлаждают водой до 300°С. За счет этого образуется мелкокристаллическая структура клинкерных минералов, обладающих более высоким коэффициентом отражения света и большей гидравлической активностью, т.е. способностью взаимодействовать с водой и набирать высокую прочность при твердении.
Измельчение белого клинкера осуществляют в шаровой мельнице с добавкой белого гипса, который служит регулятором сроков схватывания цементного теста. Цементная мельница работает в замкнутом цикле с сепаратором, который отделяет тонкомолотые частицы цемента, а грубую фракцию возвращает в обратно в мельницу на домол. Для уменьшения агрегации (слипания) частиц белого цемента и достижения высокой тонкости помола в мельницу вводят интенсификатор помола – поверхностно-активное вещество на основе триэтаноламина в количестве до 0,05%. Удельная поверхность белого цемента находится в пределах 4500-5000 см2/г, что значительно превышает тонкость помола рядового серого цемента, которая составляет около 3500 см2/г. Применение мельницы с сепаратором позволяет производить белый цемент с полидисперсным гранулометрическим составом, что обеспечивает наиболее полное протекание процессов гидратации цемента и быструю кинетику набора прочности цементного камня.
Контроль показателей качества при производстве белого цемента осуществляется на всех технологических переделах – от разработки карьера и контроля химического состава сырьевых компонентов до замола цемента в силос и его отгрузки конечному потребителю. Каждая произведенная партия белого цемента проходит обязательные приемо-сдаточные испытания в заводской лаборатории с выдачей документа о качестве. При этом соответствие показателей белого цемента требованиям ГОСТ 965-89 к цементу марки ПЦБ 1-500-Д0 ежегодно подтверждается в независимой аккредитованной лаборатории с выдачей обязательного сертификата соответствия.
Читать далее
19.06.2023Чем уникален тонкодисперсный тампонажный портландцемент компании ЦЕМЕНТУМ для нефтегазовых скважин?
19.06.2023Передовое решение DOROMIX помогло стабилизировать слабый грунт при строительстве автомобильной дороги М-12
07.06.2023Вклад строительных материалов со сниженным воздействием на окружающую среду в критерии «зеленой» таксономии
06.04.2023Мосты на века. Применение сверхпрочного фибробетона в российском мостостроении
01.11.2022В российском мостостроении впервые применили сверхпрочный фибробетон
Rapid Set Cement ALL / Рапид Цементол состав для ремонта бетонных конструкций мешок 25 кг
Описание продукта
При смешивании с водой продукт CEMENT ALL производит удобообрабатываемый, высококачественный ремонтный раствор, который
идеально подходит в тех случаях, когда необходимо обеспечить быстрое увеличение прочности, увеличить срок службы и понизить
усадку. Наносите CEMENT ALL слоем толщиной с лезвие до 6 дюймов. Прочен во влажной среде. СХВАТЫВАЕТСЯ ЧЕРЕЗ 15 МИНУТ И
ГОТОВ К ВОЗОБНОВЛЕНИЮ ДВИЖЕНИЯ ТРАНСПОРТА ЧЕРЕЗ 1 ЧАС. Из одного 55-фунтового мешка Rapid Set®Cement ALL™ получают
приблизительно 0,5 кубического фута раствора.
Применение
CEMENT ALL представляет собой универсальный продукт, который может быть использован для общего ремонта бетонных конструкций, крепление (кровли) штыревой крепью и анкерования, промышленной заливки, опалубки, проектов строительства аэропорта и для ремонта шоссейных дорог.
Состав
Rapid Set®Cement ALL™ представляет собой смесь высококачественную смесь Rapid Set®Cement ALL™ и специального песка. CEMENT ALL не содержит металлов и хлоридов. Rapid Set®Cement ALL™ внешне похожа на ремонтные материалы на основе портладцемента и может использоваться аналогичным образом.
Цвет: светло-серый
Окончательный цвет Cement ALL может меняться в зависимости от способа применения и условий окружающей среды.
Ограничения:
Не предназначен для применения на глубине свыше 4 дюймов, на большей глубине используйте Rapid Set® Concrete Mix или Rapid Set® Mortar Mix. При нанесении в качестве слоя износа следует провести испытание, по крайней мере, на одном участке, чтобы определить пригодны ли материалы и процедуры их нанесения.
Технические характеристики
Характеристика | Значение |
Время схватывания ASTM C-191(мод.) при 70°F | |
Начальное схватывания | через 15 минут |
Окончательное схватывания | через 35 минут |
Прочность на сжатие ASTM C-109 мод. Нарастание прочности | |
1-час | 3000 — фунтов на кв. дюйм |
3-часа | 5000 — фунтов на кв.![]() |
1-день | 6000 — фунтов на кв. дюйм |
7-дней | 7000 — фунтов на кв. дюйм |
28-дней | 9000 — фунтов на кв. дюйм |
Скалывания под углом: ASTM C-882 мод. | |
1-день | 1400 — фунтов на кв. дюйм |
28-дней | 2600 — фунтов на кв. дюйм * = после завершения схватывания |
Использование цементной смеси
Подготовка поверхности
При проведении ремонта прилегающие поверхности должны быть чистыми, бездефектными и свободными от любых материалов,
которые могут препятствовать скреплению, таких, как масло, асфальт, отвердители, кислоты, грязь и мусор. Придайте шероховатость
поверхностям и удалите все дефектные материалы. Непосредственно перед нанесение раствора ремонтируемая поверхность должна
быть тщательно смочена неотстоявшейся воды.
Смешивание
Рекомендуется использовать смесители с механическим приводом, такие, как, растворосмеситель или вращаемый смеситель. Перед
смешиванием постарайтесь сделать так, чтобы весь персонал, выполняющий работу, и оборудование находились на своем месте.
Используйте чистую питьевую воду. Rapid Set®Cement ALL™ можно смешивать с 3,5 до 5,5 литров воды на 55-фунтовый мешок.
Используйте меньше воды для достижения более высокой прочности. НЕ превышайте количество воды более чем на 5,5 литров воды
на мешок. Для повышения текучести и обрабатываемости используйте пластификатор Rapid Set®FLOW CONTROL®, поставляемый
Concrete Pharmacy®. Залейте необходимое количество воды в смеситель. В то время как смеситель работает, добавьте Rapid Set®Cement
ALL™. Смешивайте с минимальной затратой времени необходимой для достижения однородной консистенции без комков (обычно от 1
до 3 минут). НЕ проводите повторное перемешивание.
Нанесение
Rapid Set®Cement ALL™ можно наносить обычным образом. Перед нанесение убедитесь, что весь персонал, выполняющий работу и оборудование готовы. Быстро нанесите, уплотняйте и разравнивайте шаблоном для того, чтобы обеспечить максимальное время окончания. НЕ ждите, пока вода выступит на поверхности бетона, примените отделочную аппретуру как можно скорее. Rapid Set®Cement ALL™ можно наносить шпателем, разравнивать валком или щеткой. НЕ наносите раствор на плоскую поверхность слоями, заполняйте на всю глубину сразу, постепенно смещаясь по горизонтали. НЕ наносите раствор на замороженные поверхности. Используйте метод уплотнения, чтобы устранить воздушные пузыри. Для увеличения времени нанесения используйте замедлитель схватывания Rapid Set®SET CONTROL®.
Созревание
Проводите созревание Rapid Set®Cement ALL™ водой во всех случаях. Начните созревание, как только поверхность потеряла свой сырой
блеск. Сохраняйте наружные поверхности мокрыми в течение минимум 1 часа. При замедлении схватывания, из-за низких температур
или использования замедлителя, может потребоваться больше времени для отверждения. Целью отверждения водой состоит в том,
чтобы сохранить поверхность постоянно мокрой, пока продукт не станет достаточно прочным.
Температура
Высокая температура окружающей среды и температура материалов приведет к сокращению срока годности Cement ALL. Чтобы
снизить воздействие высокой температуры, храните материал в прохладном месте и используйте охлажденную воду для затворения
раствора. При температурах ниже 70ºF (21ºC) снижается скорость нарастания прочности, поэтому Cement ALL не следует наносить на
поверхность, имеющую температуру менее 7,2 ºC, или при окружающей температуре ниже 7,2 ºC.
Обыкновенный портландцемент — составные части, свойства, типы и применение
🕑 Время чтения: 1 минута
Обыкновенный портландцемент — один из наиболее широко используемых типов цемента.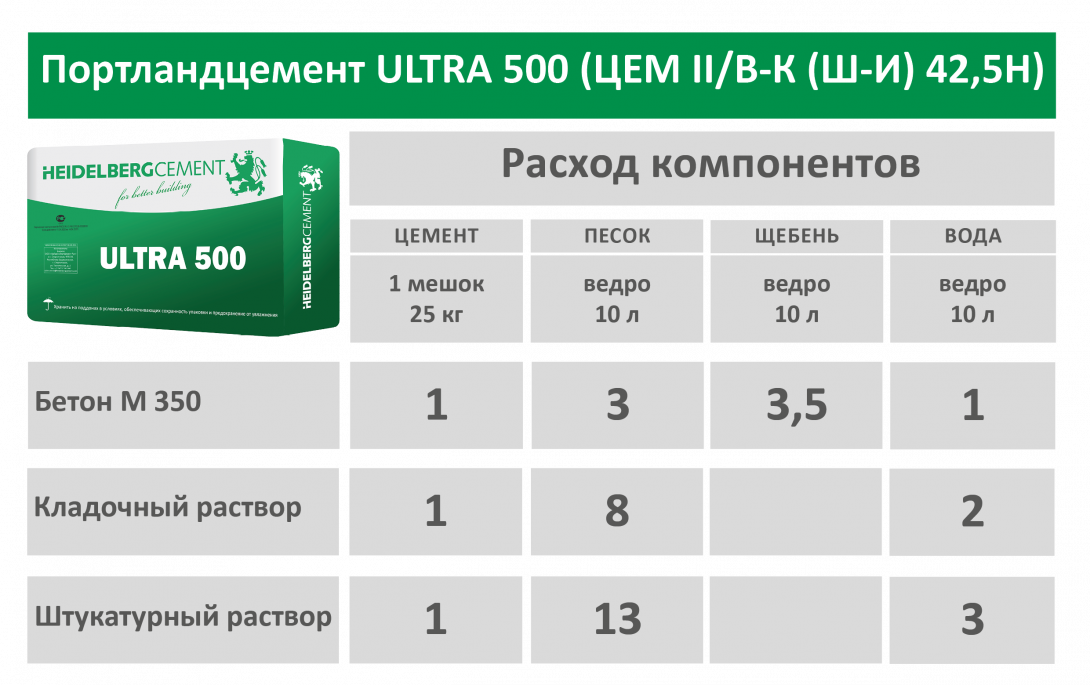
В комплекте: 9 шт.0003
- Компоненты обычного портландцемента
- Основные химические компоненты портландцемента:
- Состав и содержание соединений в портландцементе:
- Свойства обычного портландцемента
- Производство цемента OPC
- 1. Измельчение и измельчение сырья
- 2. Смешивание или смешивание
- 3. Нагрев
- 4. Измельчение
- Типы обычного портландцемента
- 1. AS согласно ASTM 150 (американские стандарты)
- 2. Согласно норме EN 197 (европейская норма)
- 3. Согласно CSA A3000-08 (канадские стандарты)
- Использование обычного портландцемента
- Преимущества обычного портландцемента
- Недостатки обычного портландцемента
- Глинистые или силикаты глинозема в виде глин и сланцев.
- Известняк или карбонат кальция в виде известняка, мела и мергеля, представляющий собой смесь глины и карбоната кальция.
Известь (CaO) | от 60 до 67% |
Кремнезем (SiO2) | от 17 до 25% |
Глинозем (Al2O3) | от 3 до 8% |
Оксид железа (Fe2O3) | от 0,5 до 6 % |
Магнезия (MgO) | от 0,1 до 4 % |
Триоксид серы (SO3) | от 1 до 3% |
Сода и/или калий (Na2O+K2O) | от 0,5 до 1,3% |
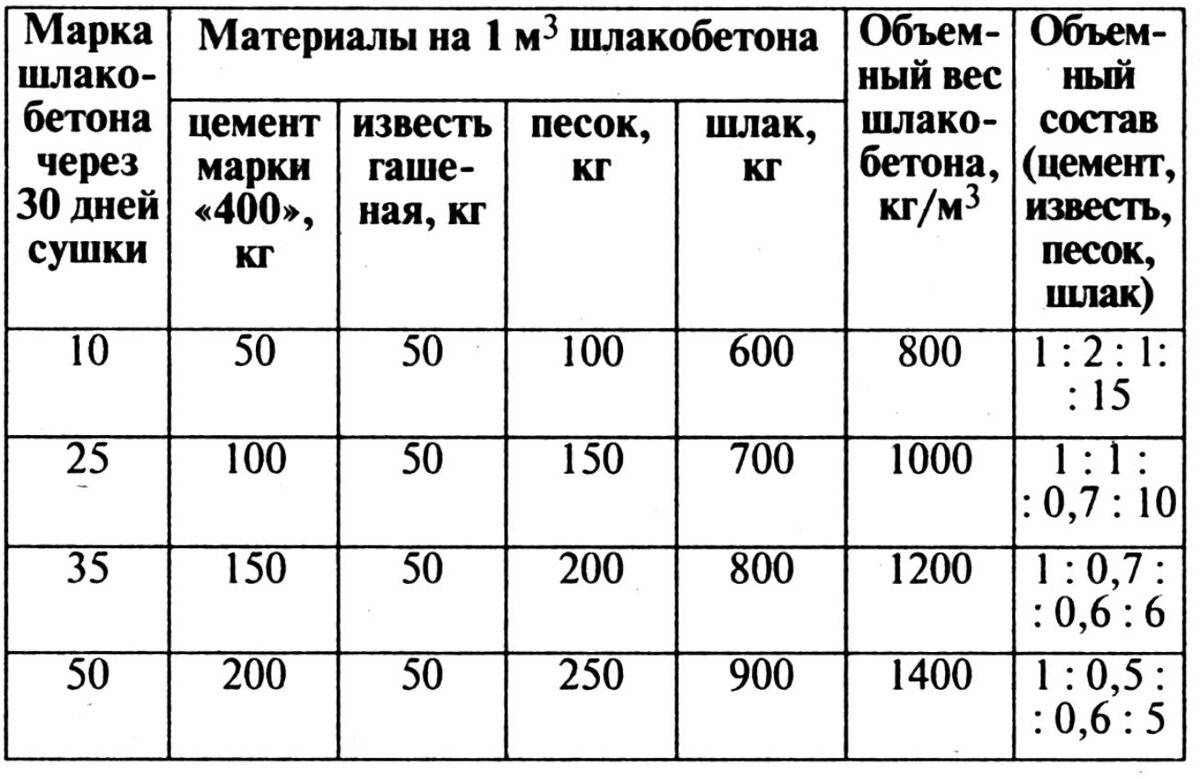
Соединение | Сокращенное обозначение |
Трехкальциевый силикат (3CaO.SiO2) | К3С |
Двухкальциевый силикат (2CaO.SiO2) | К2С |
Трехкальциевый алюминат (3CaO.Al2O3) | К3А |
Тетракальциевый алюмоферрит (4CaO.Al2O3.Fe2O3) | C4AF |
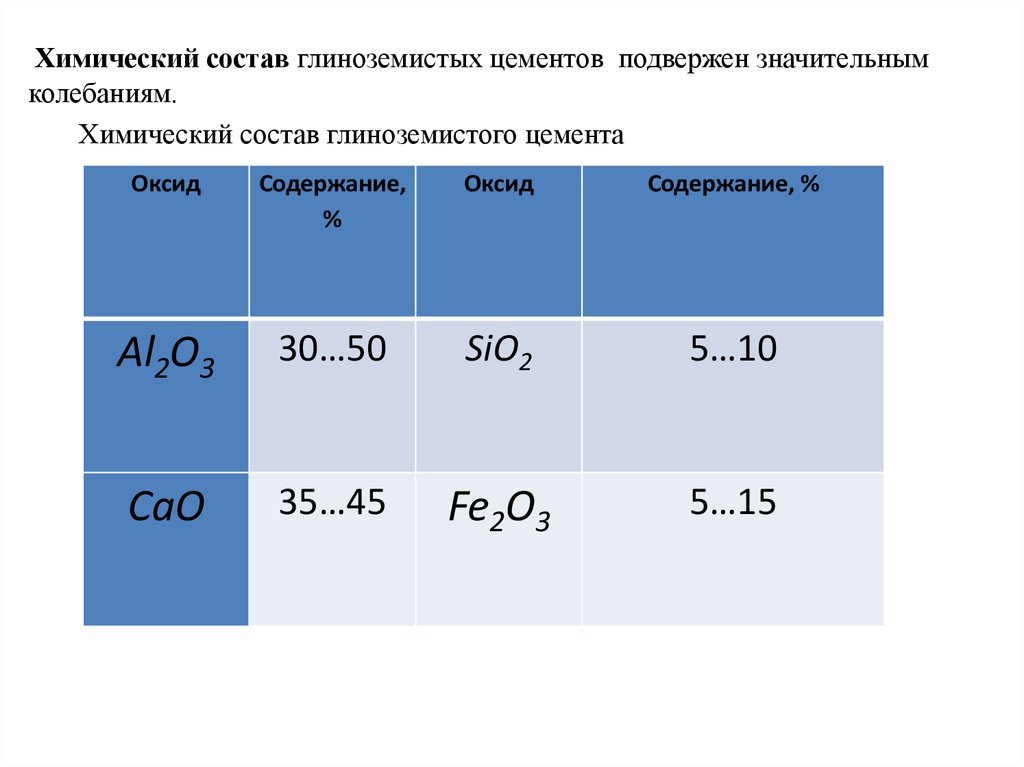
Портландцемент | Обычный | Быстротвердеющий | Низкотемпературный |
(а) Состав: Проценты | |||
Известь | 63,1 | 64,5 | 60 |
Силикагель | 20,6 | 20,7 | 22,5 |
Глинозем | 6,3 | 5,2 | 5,2 |
Оксид железа | 3,6 | 2,9 | 4,6 |
(б) Соединение: Процент | |||
К3С | 40 | 50 | 25 |
К2С | 30 | 21 | 35 |
С3А | 11 | 9 | 6 |
С3А | 12 | 9 | 14 |
Значения Удельный вес 3,12 Нормальная консистенция 29% Время начальной настройки 65мин Время окончательного схватывания 275 мин Тонкость 330 кг/м 2 Прочность 2,5 мм Производство цемента OPC В основном производство цемента OPC включает 5 этапов: Насыпная плотность 830-1650 кг/м 3

- Сухой процесс
- Мокрый процесс
- Полумокрый процесс
Рис. 1: Технологическая схема производства цемента OPC.
2. Смешивание или смешивание На этом этапе измельченное сырье (известняк) смешивается или смешивается с глиной в желаемой пропорции (известняк: 75%, глина: 25%) и хорошо перемешивается с помощью сжатого воздуха для получения однородной смеси. При сухом способе эти смеси хранятся в силосах; шламоемкости используются в мокром процессе. Полученный материал известен как суспензия, содержащая 35-40% воды. 3. Отопление Это основной важный шаг в производстве цемента OPC, продукт, полученный в результате смешивания, подается в печь с помощью ленточных конвейеров.
- Тип I Портландцемент известен как цемент общего назначения.
Обычно предполагается, если не указан другой тип.
- Тип II обеспечивает умеренную устойчивость к сульфатам и выделяет меньше тепла во время гидратации.
- Тип III имеет относительно высокую начальную прочность. Этот цемент похож на тип I, но имеет более мелкий помол.
- Тип IV Портландцемент широко известен своей низкой теплотой гидратации.
- Тип V используется там, где важна устойчивость к сульфатам. Этот цемент имеет очень низкий (C 3 A) состав, что объясняет его высокую стойкость к сульфатам.
- CEM I Содержит портландцемент и до 5 % второстепенных дополнительных компонентов.
- CEM II Портландцемент и до 35% других отдельных компонентов
- СЕМ III Портландцемент и повышенное содержание доменного шлака
- CEM IV Портландцемент и до 55 % пуццолановых компонентов
- CEM V Портландцемент, доменный шлак или зольная пыль и пуццолан

- GU, GUL > Цемент общего назначения
- MS > Цемент средней сульфатостойкости
- MH, MHL > Среднетемпературный цемент
- HE, HEL > Цемент с высокой начальной прочностью
- LH, LHL > Низкотемпературный цемент
- HS > Высокая стойкость к сульфатам; обычно развивает силу медленнее, чем другие типы.
- Он используется в общестроительных целях, где не требуются особые свойства, например, железобетонные здания, мосты, тротуары, а также там, где грунтовые условия являются нормальными.
- Используется для большинства бетонных блоков
- Обладает высокой устойчивостью к растрескиванию и усадке, но менее устойчив к химическим воздействиям.
- Первоначальное время настройки OPC меньше, чем PPC, поэтому рекомендуется в проектах, в которых реквизит нужно удалить раньше.
- Период отверждения OPC меньше, чем у PPC, и стоимость отверждения снижается. Следовательно, рекомендуется, когда стоимость отверждения непомерно высока. Недостатки
- Его нельзя использовать для массового бетонирования, так как он имеет большую теплоту гидратации по сравнению с ППК.
- Прочность бетона, изготовленного с использованием OPC, меньше, чем у бетона, изготовленного с использованием PPC.
- Он производит сравнительно менее связный бетон, чем PPC, поэтому перекачка бетона становится немного затруднительной.
- OPC имеет более низкую крупность, следовательно, более высокую проницаемость и, как следствие, более низкую износостойкость.
- OPC дороже, чем PPC.
Состав и классификация цемента — PetroWiki
Почти все буровые цементы изготавливаются из портландцемента — прокаленной (обожженной) смеси известняка и глины. Раствор портландцемента в воде используется в скважинах, потому что его легко перекачивать и он быстро затвердевает даже под водой. Он называется портландцементом, потому что его изобретатель Джозеф Аспдин считал, что затвердевший цемент напоминает камень, добытый на острове Портленд у берегов Англии.
Содержание
- 1 Дозирование материалов
- 2 Классификация цемента
- 3 классификации API
- 3.1 Класс А
- 3.2 Класс В
- 3.3 Класс С
- 3.4 Класс G
- 3.5 Класс Н
- 4 Свойства цемента, указанные в спецификациях API
- 5 Каталожные номера
- 6 См. также
- 7 примечательных статей в OnePetro
- 8 Внешние ссылки
- 9 Категория
Дозирование материалов
Портландцементы легко модифицируются в зависимости от используемого сырья и процесса их объединения.
Дозирование сырья основано на серии одновременных расчетов, учитывающих химический состав сырья и тип производимого цемента: Американское общество по испытаниям и материалам (ASTM), тип I, II, III , или белый цемент V, или класс Американского института нефти (API) A, C, G или H. [1] [2]
Классификация цемента
Основным сырьем, используемым для производства портландцемента, являются известняк (карбонат кальция) и глина или сланец. Часто добавляют железо и глинозем, если они еще не присутствуют в достаточном количестве в глине или сланце. Эти материалы смешивают друг с другом, влажным или сухим, и подают во вращающуюся печь, которая плавит известняковую суспензию при температуре от 2600 до 3000°F в материал, называемый цементным клинкером. После охлаждения клинкер измельчают и смешивают с небольшим количеством гипса, чтобы контролировать время схватывания готового цемента.
Когда эти клинкеры гидратируются водой в процессе схватывания, они образуют четыре основные кристаллические фазы, как показано в Таблица 1 и Таблица 2 . [3]
Портландцементы обычно производятся в соответствии с определенными химическими и физическими стандартами, которые зависят от их применения. В некоторых случаях для получения оптимальных композиций необходимо добавлять дополнительные или корректирующие компоненты. Примеры таких добавок:
- Песок
- Кремнистые суглинки
- Пуццолан
- Диатомовая земля (DE)
- Железный колчедан
- Глинозем
В расчетах также учитываются глинистые или кремнистые материалы, которые могут присутствовать в больших количествах в некоторых известняках, а также зола, образующаяся при сжигании угля в печи. Незначительные примеси в сырье также должны быть приняты во внимание, так как они могут оказывать значительное влияние на характеристики цемента.
В США есть несколько агентств, которые изучают и пишут спецификации для производства портландцемента. Из этих групп наиболее известными в нефтяной промышленности являются ASTM, которая имеет дело с цементами для строительства и использования в строительстве, и API, которая пишет спецификации для цементов, используемых только в скважинах.
Спецификация ASTM. C150 [1] предусматривает восемь типов портландцемента: Типы I, IA, II, IIA, III, IIIA, IV и V, где «А» обозначает воздухововлекающий цемент. Эти цементы предназначены для удовлетворения различных потребностей строительной отрасли. Цементы, используемые в скважинах, подвергаются воздействию условий, не встречающихся в строительстве, таких как широкий диапазон температур и давлений. По этим причинам были разработаны различные спецификации, которые охватываются спецификациями API. В настоящее время API предоставляет спецификации, охватывающие восемь классов тампонажных цементов, обозначенных как классы от A до H. Наиболее широко используются классы API G и H.
Цементы для нефтяных скважин также доступны в классах умеренной сульфатостойкости (MSR) или высокой сульфатостойкости (HSR). Сульфатостойкие марки используются для предотвращения разрушения затвердевшего цемента в скважине, вызванного воздействием сульфатов пластовыми водами.
Классификация API
Нефтяная промышленность закупает цемент, произведенный преимущественно в соответствии с классификацией API, опубликованной в API Spec. 10А. [4] Далее определяются различные классы цементов API для использования при забойных температурах и давлениях.
Класс A
- Этот продукт предназначен для использования, когда не требуются особые свойства.
- Доступен только в обычном классе O (аналогично ASTM Spec. C150, Type I). [1]
Класс B
- Этот продукт предназначен для использования в условиях, требующих умеренной или высокой устойчивости к сульфатам.
- Доступны марки MSR и HSR (аналогично ASTM Spec. C150, тип II). [1]
Класс С
- Этот продукт предназначен для использования в условиях, когда требуется высокая начальная прочность.
- Доступен в обычном, O, MSR и HSR классах (аналогично ASTM Spec. C150, Type III). [1]
Класс G
- Никакие добавки, кроме сульфата кальция или воды, или и того, и другого, не должны перемалываться или смешиваться с клинкером во время производства скважинного цемента класса G.
- Этот продукт предназначен для использования в качестве основного скважинного цемента.
Доступны марки MSR и HSR.
Класс H
- Никакие добавки, кроме сульфата кальция или воды, или того и другого, не должны перемалываться или смешиваться с клинкером во время производства скважинного цемента класса H.
- Этот продукт предназначен для использования в качестве основного скважинного цемента. Доступны марки MSR и HSR.
Свойства цемента, указанные в спецификациях API
Химические свойства и физические требования приведены в Таблицах 3 и Таблице 4 соответственно. [3] Типичные физические требования к различным классам цемента по API приведены в таблице 5 . [3]
Хотя эти свойства описывают цементы для целей спецификации, цементы для нефтяных скважин должны иметь другие свойства и характеристики, чтобы обеспечить их необходимые функции в скважине. (API RP10B содержит стандарты для процедур испытаний и специального оборудования, используемого для испытаний тампонажных цементов, и включает:
- Приготовление суспензии
- Плотность навоза
- Испытания на прочность при сжатии и неразрушающие акустические испытания
- Испытания на время загустевания
- Статические испытания на водоотдачу
- Эксплуатационные испытания свободной жидкости
- Испытания на проницаемость
- Реологические свойства и прочность геля
- Расчеты перепада давления и режима течения для шламов в трубах и кольцевых пространствах
- Процедуры испытаний в Арктике (вечной мерзлоте)
- Испытание на стабильность шлама
- Совместимость скважинных флюидов.