Щепа с цементом блоки: Арболитовые блоки — недостатки, технические характеристики, размеры, состав
Щепа для арболита
Арболит – современный высокотехнологичный строительный материал, который изготавливают на основе древесной щепы и цемента. Блоки арболит обладают высокой степенью теплоизоляции, относятся к легким бетонам, подходят для малоэтажного строительства. Для того чтобы изготовить качественный конструкционный арболит необходимо взять правильные компоненты и смешать в нужной пропорции.
Информация о строительных стеновых арболитовых блоках от производителя на странице Производство арболита
До 90% арболитового блока составляет щепа, остальное приходится на цемент высшей марки и химические добавки, которые нужны, чтобы улучшить качество материала, ускорить процесс твердения и прочность арболита.
Выбор и подготовка щепы — важный этап производственного процесса по изготовлению арболита, поэтому так важно чтобы щепа для арболита соответствовала параметрам, указанным в ГОСТе.
Предлагаем высокорентабельное оборудование для изготовления арболитовых блоков Оборудование для производства арболита
Конструкционно-теплоизоляционный арболит – легкий бетон на цементном вяжущем и органических заполнителях растительного происхождения, предназначенный для несущих и ограждающих конструкций зданий и сооружений, к которым предъявляют требования технической безопасности и энергоэффективности.
Материал для изготовления щепы для арболита
Щепу для арболита изготавливают из древесины, причем это могут быть древесные отходы лесозаготовительных предприятий (ветки, сучья, вершины деревьев), отходы лесопильных и деревообрабатывающих производств (горбыль, оппилы, отходы оцилиндровки), переработка вторичных отходов древесины (б/у паллеты, лом деревянных конструкций, деревянная мебель). Щепа может быть результатом работы деревообрабатывающих станков или ее можно изготовить с помощью специальных рубительных и щеподробительных машин.
Лучше всего для производства арболита подходит древесина хвойных пород – сосна, ель, пихта. Если брать древесину лиственных пород, то подойдут такие деревья, как береза, осина, дуб, тополь. Но в этом случае придется потратить больше химических добавок для подготовки щепы. Не рекомендуется использовать щепу бука и лиственницы. Также не следует использовать для изготовления щепу из свежесрубленной древесины. Лучше, если дерево вылежит 3-4 месяца.
В качестве органических заполнителей растительного происхождения должны применяться: измельченная древесина из отходов лесозаготовок, лесопиления и деревообработки хвойных (ель, сосна, пихта) и лиственных (береза, осина, тополь) пород, костра конопли и льна, измельченные стебли хлопчатника и рисовой соломы.
Размер и структура щепы для арболита
В ГОСТе указаны размеры щепы для арболита, но производители предпочитают практическим путем подбирать оптимальный размер и форму щепок, главное чтобы он не превышал заявленные размеры. Считается, что качественный арболит можно получить, если выбрать щепу игольчатого типа. Это объясняется анизотропными свойствами древесины, которые включают в себя упругость, теплопроводность, звукопоглощение материала.
Щепа игольчатой формы располагается хаотично и по-разному деформируется при воздействии влаги, что повышает анизотропность готовых блоков арболита. В связи с этим, не стоит использовать стандартную технологическую или топливную щепу, которая имеет прямоугольную или квадратную форму. Щепа для арболита должна иметь гладкую поверхность без ворсистости, что также важно для хорошего сцепления с цементным вяжущим и повышения прочности готового материала.
Измельченная древесина – древесные частицы различной формы и величины, получаемые в результате механической переработки. К измельченной древесине относятся: щепа, древесная дробленка, стружка. Щепа – измельченная древесина установленных размеров, получаемая в результате измельчения древесного сырья рубильными машинами и специальными устройствами.
Щепорезы для арболита
Чтобы получить щепу для арболита правильной игльчатой формы используют специальные щепорезы для арболита, которые представляют собой молотковые дробилки. В некоторых случаях можно совмещать роторные рубительные машины, которые подходят для первичного измельчения крупнокусоквых древесных отходов, а потом доизмельчать щепу в барабанных и молотковых щеподробилках.
Щеподробилки для древесных отходов снабжены специальными калибровочными сетками, что позволяет в процессе работы получать щепу заданной фракции. Также для производства арболита отлично подходит щепа, полученная посредством шредеров для древесины. С помощью шредера удается за один прием получить необходимую игольчатую структуру щепы. Единственная проблема в том, что шредеры для дерева стоят значительно дороже, чем щепорубительные машины и щепорезы для арболита.
Подготовка щепы для арболита
Щепа для арболита не должна содержать плесени, грибка, трухи и гнили. Процент коры, листьев и хвои не должен превышать указанные в ГОСТе нормы. Перед тем, как начать подготовку щепы для арболита ее просеивают с помощью вибросита, чтобы избавиться от пылевой составляющей и опилок.
На следующем этапе готовую щепу засыпают в специальный контейнер и заливают раствором химикатов. Это может быть гашеная известь, хлорид кальция, жидкое стекло или другая добавка.
Содержание водорастворимых редуцирующих веществ (сахаров) не должно быть более 2 %. Насыпная плотность опилко-стружечной смеси в высушенном до постоянной массы состоянии должна быть в пределах от 100 до 140 кг/м3. Содержание очесов и пакли должно быть не более 5 % массы сухого заполнителя.
Химические добавки экологически безопасны, они нужны, чтобы нейтрализовать сахара в древесине, что поможет повысить ее адгезивные свойства и обеспечит лучшее сцепление с вяжущим компонентом на основе цемента. Обычно в растворе химикатов щепа должна вылежаться трое суток, после чего ее необходимо просушить. Для улучшения свойств готового арболита также щепу можно обработать специальными антисептическими составами. Если нет желания использовать химикаты, то щепу для арболита можно оставить вылежаться на открытом воздухе в защищенном от влаги месте в течение трех месяцев. Таким способом можно нейтрализовать сахара в древесине и сделать ее пригодной для производства арболита.
Дома из арболитовых блоков. Арболитовый-Блок.рф
Специализированный рынок для строительства полнится разнообразными материалами для возведения сооружений. Благодаря широкому ассортименту проблема выбора решается, но если кирпич – всем понятное сырье для строительства, то есть разные категории строительных материалов, о каких мало кому известно. Арболит, цена на который вполне приемлема, – это сегодня для многих новый материал, хотя на самом деле просто хорошо позабытый.Структура материала
Арболитовые блоки относятся к категории легкого бетона, у них уже получилось отвоевать себе место под солнцем в сфере строительства.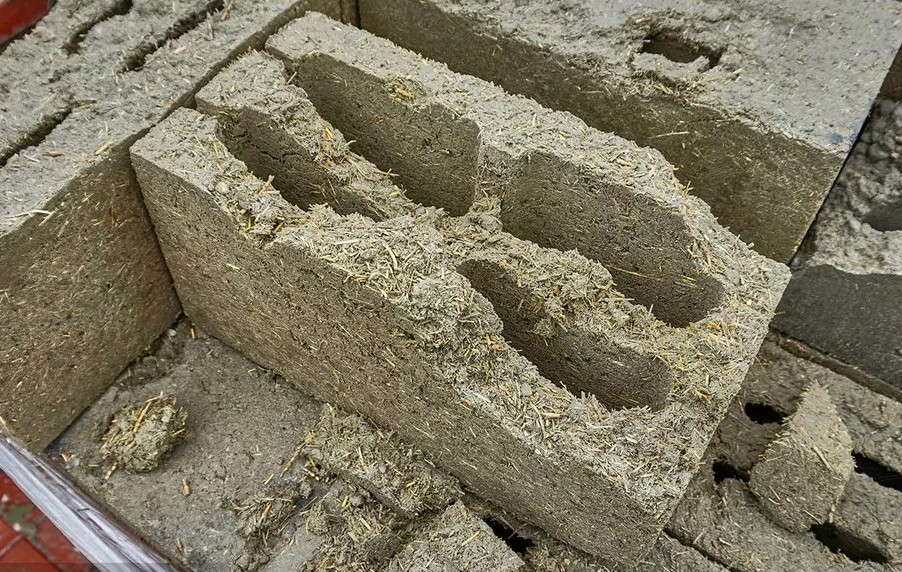
- Древесная щепа. Она представляет собой тщательно измельченные опилки хвои, стебли хлопчатника, льна или же конопляные, тоже мелко измельченные. Такие органические компоненты занимают большую часть объема, а именно 80-90%. У этого наполнителя есть определенная форма и параметры.
- Цементный раствор. Вяжущий минеральный состав. Для большей прочности задействуется цемент марки М400-М500.
- Различные минерализирующие добавки. Они нейтрализуют действие сахара, что есть в древесине. Оказывают непосредственное влияние на прочность материала. Соединение с цементным раствором проходит лучше.
- Подготовительный. Щепка подлежит измельчению, вымачиванию и обработке специальным химическим составом. Если щепка заблаговременно выдержана на свежем воздухе в течение от 4 месяцев до полугода, то никакие дополнения не понадобятся, сахар уничтожится сам.
- Этап формовки. Требуемое, точно отмеренное число щепы и цементного раствора замешивается и формируется в определенные блоки.
- Этап сушки. На вибропрессе блоки из арболита подлежат уплотнению, они приобретают завершающую плотность, что соответствует государственным стандартам.
Категории арболитовых блоков
Из арболита изготавливаются не только блоки, но и панели и плиты. Если говорить о государственном стандарте, то конструкциям из арболита не требуется дополнительное утепление. Все конструкции различаются по плотности (какой процент содержания наполнителя). Поэтому классификация выглядит следующим образом:- Конструкционные. Используются для возведения наружных несущих конструкций.
- Теплоизоляционные. Они используются для внутренних несущих конструкций.
- широкие;
- средние;
- узкие;
- соединительные.
Технические особенности
Арболитовые блоки (цена за штуку вполне приемлема) используются в различных климатических зонах: сооружения из арболита возведены не только в умеренных широтах, но и в Антарктиде. Все это возможно благодаря следующим характеристикам:- Маленькая масса. Плотность арболитовых блоков для внешнего строительства составляет 500-850 метров кубических на килограмм. Для внутреннего – до 500.
- Небольшая теплопроводность. Хорошо сохраняет тепло.
- Экологичность. Арболит полностью безопасен для здоровья человека. В этом материале не заводятся микроорганизмы или грибок. Не подвержен гниению.
- Устойчивость к огню. Материал может выдерживать открытый огонь, температура которого больше 1000 градусов до 1,5 часов, затем начинает тлеть.
- Отличная звукоизоляция и проходимость пара. Блоки имеют такую структуру, что они хорошо поглощают звуки извне и поддерживают естественное вентилирование и регулируют состояние влажности, благодаря чему в помещении создается комфортный благоприятный микроклимат.
Теги: Дом из арболита , Дома из арболита под ключ , Изготовление арболита , Продажа арболитовых блоков , Производство блоков из арболита , Стеновые блоки из арболита , Строительство дома из арболита , Строительство дома из арболита под ключ
Blocks Blossom From Waste Wood
КОГДА Джеймс Бэнкрофт показывает посетителям привлекательный новый сарай и студию, которую он построил за своим домом в сельском округе Камберленд, штат Нью-Джерси, он любит говорить им, что это «самая красивая куча древесных отходов, которую вы когда-либо видели». пила.» Он также надеется, что это предвестник большого количества высококачественного недорогого жилья по всей стране.
Это потому, что студия была построена из древесно-фибробетонных блоков, настолько простых в использовании, что люди, не имеющие строительных навыков, могут легко возвести основную конструкцию. На самом деле, цель некоммерческой организации Community Innovations, которую он основал, состоит в том, чтобы вовлечь неквалифицированную городскую молодежь в строительство недорогого жилья именно там, где оно больше всего необходимо. Поскольку древесные отходы могут легко стать основным компонентом блоков, система может одновременно решить проблему удаления твердых отходов.
Принято считать, что древесные волокна и бетон плохо смешиваются, потому что содержащиеся в древесине сахара, дубильные вещества и масла препятствуют ее правильному сцеплению с бетоном. Кроме того, частицы древесины разлагаются при длительном воздействии влаги.
Но несколько десятилетий назад швейцарские и австрийские ученые разработали процесс, при котором частицы древесины покрываются минерализующим слоем, благодаря чему они легко сцепляются с цементом, песком и камнем. Древесина в Европе дороже, чем в Северной Америке, и это подтолкнуло к развитию. «Это было слишком дорого, чтобы просто выбросить или сжечь», — объясняет Хансруди Вальтер из Faswall Concrete Systems в Огасте, штат Джорджия, которая привезла систему в Соединенные Штаты.
Система, слегка адаптированная к более высокому содержанию сахара в некоторых американских деревьях, использует природные минералы, добываемые в США, для обработки древесины. «Здесь не используются агрессивные химические вещества», — настаивает г-н Уолтер, утверждая, что «процесс действительно очень прост, если вы знаете, как это сделать».
То, что и продукт, и процесс являются «экологически приемлемыми», радует г-на Бэнкрофта, который возглавляет отдел общественных инноваций в Бриджтоне, штат Нью-Джерси. Но в основном его привлекает древесно-волокнистый бетон, потому что он «очень прост в использовании». Помимо легкого веса (менее половины веса обычного бетона), его можно «распиливать, прибивать гвоздями или привинчивать, как любой кусок дерева», — говорит он.
Забери его сарай и студию. В первый день два человека без опыта каменной кладки «всего за два часа возвели четырехфутовую фундаментную стену по периметру».
В то время как на заводе Faswall Concrete Systems в Виндзоре, Южная Каролина, производятся различные строительные изделия из древесно-волокнистого бетона, Бэнкрофт использовал базовые блоки длиной 36 дюймов, высотой 12 дюймов и глубиной 9 дюймов.
Переплетенные блоки весом всего 39 фунтов были уложены в сухом виде на высоту четыре фута, а затем в полые центры был залит жидкий бетон, чтобы соединить конструкцию в сплошную стену. Другим вариантом может быть нанесение тонкого слоя поверхностного клея на каждую сторону стены, что в то же время защитит стену от атмосферных воздействий.
Бэнкрофт отделал стены своей студии виниловым сайдингом, но «самый дешевый способ придать законченный вид — нанести штукатурку», — говорит он.
Поскольку блоки в основном состоят из древесного волокна с небольшим количеством мелкого песка и цемента для обеспечения сцепления, блоки имеют высокую пористость. На самом деле блоки примерно на 40 процентов состоят из воздуха, что дает им теплоизоляционную способность R11. Другими словами, они очень медленно проводят тепло из дома (или в него в жаркие летние дни). Это улучшается до R19, когда полые центры заполнены залитым бетоном с его высокой теплоемкостью.
Таким образом, «эти дома дешево обогревать и охлаждать», — говорит Бэнкрофт, и расходы на страхование будут относительно низкими, потому что «стены, построенные из этих блоков, имеют четырехчасовую огнестойкость». Другими словами, постоянно горящему огню потребуется четыре часа, прежде чем он сможет прожечь стену. Бетонные блоки не поддерживают горение сами по себе. Еще один плюс в том, что стены делают здания «удивительно тихими и умиротворяющими», — говорит Бэнкрофт. Фактически, одно из первых применений этой технологии в Соединенных Штатах было в качестве звуковых барьеров и барьеров на дорогах.
Испытания в нескольких тропических странах, включая Шри-Ланку, Конго и Марокко, показали, что блоки не боятся термитов и очень устойчивы к гниению.
В настоящее время древесно-волокнистые блоки производятся только в одном месте. Но идея состоит в том, чтобы лицензировать эту технологию любым заинтересованным сторонам, хотя предприятия, уже вовлеченные в производство сборного железобетона, будут в лучшем положении, чтобы воспользоваться преимуществами этой технологии.
В то время как блоки, панели и другие формы могут быть изготовлены из девственной древесины и при этом оставаться конкурентоспособными, Уолтер надеется, что древесные отходы станут основным источником сырья, как и в Европе. По его словам, деревянные поддоны, часто сделанные из дуба, были бы особенно хорошим источником волокна для промышленности. Он также отмечает, что «побочные отходы бумажной промышленности могли бы обеспечить нас всем необходимым древесным волокном».
Бэнкрофт узнал о строительных блоках из древесного волокна, когда посетил высотный проект в Канаде, построенный коммерческим подрядчиком. Очарованный возможностями, Бэнкрофт построил сарай-студию на своем заднем дворе, чтобы проверить систему на себе и, в частности, посмотреть, можно ли ее построить с помощью неподготовленного труда.
Проект подтвердил, что эту строительную систему можно легко использовать для строительства прочного и надежного жилья в районах с низким доходом. Теперь он надеется, что корпорации или фонды поддержат демонстрационные проекты в разных уголках страны.
Для получения дополнительной информации пишите:
Faswal, Box 189,
Windsor, SC 29856
Телефон: (803) 642-9346
Древесная щепа, пеллеты для гриля и пеллеты для копчения в Ace Аппаратное обеспечение
Выбрать 2 или более продуктов для бок о бок по сравнению с функциями comparrishson.compare
Выберите 2 или более продуктов для бок о бок по сравнению с функциями. параллельное сравнение функций.Сравнить
Выберите 2 или более продуктов для прямого сравнения характеристик. 003
Выберите 2 или более продуктов для параллельного сравнения характеристик.
Сравните
Выберите 2 или более продуктов для параллельного сравнения характеристик. Сравните
Выберите 2 или более продуктов для параллельного сравнения характеристик. Сравните
Выберите 2 или более продуктов для параллельного сравнения характеристик. Сравните
- 90 002 Выберите 2 или более продуктов для параллельного сравнения функций. Сравните
Выберите 2 или более продуктов для параллельного сравнения функций. Сравните
Выберите 2 или более продуктов для параллельного сравнения функций сравнение.Сравнить
Выберите 2 или более продуктов для сравнения характеристик. 003
Выберите 2 или более продуктов для параллельного сравнения функций.
Сравните
Выберите 2 или более продуктов для параллельного сравнения функций. Сравните
Выберите 2 или более продуктов для параллельного сравнения характеристик. Сравните
Выберите 2 или более продуктов для параллельного сравнения характеристик. Сравните
- 90 048
Выберите 2 или более продукты для параллельного сравнения функций. Сравните
Выберите 2 или более продуктов для параллельного сравнения функций. Сравните
Выберите 2 или более продуктов для параллельного сравнения сравнение функций.Сравнить
Выберите 2 или более продуктов для прямого сравнения характеристик. 003
Выберите 2 или более продуктов для параллельного сравнения характеристик.