Раствор для арболитовых блоков: Кладочный раствор для арболитовых блоков
Кладка арболитовых блоков своими руками без мостиков холода, технология
Арболит — легкий бетон с органическим заполнителем древесной щепой (не опилками или стружкой). Материал не перегружает фундамент, хорошо сохраняет тепло, пригоден для жилых и производственных зданий высотой до трех этажей. Он выпускается в виде панелей, плит, стеновых и перегородочных блоков. Построить дом из своими руками сравнительно несложно даже при отсутствии опыта за счет удобного размера и небольшого веса.
Оглавление:
- Нюансы проведения работ
- Виды растворов
- Инструкция по монтажу своими силами
Правила кладки блоков из арболита
Идеальную геометрию, предполагающую отклонения от стандартных размеров до 1 мм, имеют лишь изделия, изготовленные на крупных предприятиях, использующих специальное оборудование, они стоят сравнительно дорого. Чаще для частного строительства покупают камни, произведенные ручным методом. Они дешевле, но отклонения по размерам могут достигать 3 мм.
Чтобы избежать мостиков холода в стенах, можно выполнить швы по технологии терморазрыв. Для этого перед нанесением раствора на ряд камней размещают рейку шириной 4-5 см или ленту — джутовую или из вспененного пенопропилена. Затем наносят по обеим сторонам от ленты или рейки полосы кладочной смеси. Между полосками остается пустое пространство, которое после монтажа следующего ряда заполняется воздухом. Рейку, завершив наносить массу, убирают, ленту можно оставить. Терморазрыв нужен для швов толщиной от 8 мм. Если камни имеют минимальные отклонения по размерам от стандарта, то смесь или клей распределяют тонким слоем (до 5 мм). Дополнительные меры утепления швов не нужны.
Приготовление кладочного раствора
Выбор подходящей разновидности делают на основании качества геометрии блоков. Если нужны швы от 8 мм, то необходимо свести к минимуму потери тепла через них. Поэтому в их состав добавляют различные утепляющие компоненты.
Для стен из арболитоблоков используют следующие виды:
1. Цементно-песчаный. Можно приготовить самостоятельно или купить готовую сухую смесь. Оптимальные пропорции — на 1 часть цемента 3 ч песка. Этот вариант допустим лишь для камней с идеальной геометрией. Широкие швы неизбежно становятся мостиками холода.
2. Перлитовый. Относится к теплым, отличается намного лучшим показателем по предотвращению потерь тепла. Можно купить готовые смеси перлитового песка с цементом, но дешевле делать их своими силами. Для приготовления понадобятся 1 часть цемента, 2 ч обычного песка и 3 части ч из вспученного перлита. Готовить массу лучше в бетономешалке: сначала засыпают перлит, затем вливают воду. Перлит сразу вбирает в себя всю влагу (приобретает вид сухого порошка), при смешивании с цементом и песком начинает ее отдавать, поэтому нельзя добавлять воду до всыпания остальных компонентов.
3. Кладочная теплая масса с микрощепой. Для ее приготовления используют готовую пескоцементную смесь марки не ниже М-200 и обработанную мелкую щепу. По сути получается монолитная арболитовая стена. Микрощепу можно купить у производителей блоков. Расход: 1 мешок (180 л) на 2 м3 раствора. В отличие от перлитовой не дает усадку. Рецепт: 1 часть цемента, 1 ч песка, 2 ч микрощепы, пластификатор — профессиональный или простое жидкое мыло.
4. Цементно-песчаный с опилками (опилкобетон). Рецепт: 1 ведро цемента, 2 ведра песка, 2 ведра опилок, раствор из 150 г хлористого кальция, 15-20 г жидкого мыла.
5. Клеевые сухие смеси (клеи монтажные). Допустимая толщина слоя для них — 2-5 мм. Готовые массы пригодны для склеивания камней, имеющих отклонения по размерам до 1 мм.
6. Пенополиуретановый клей-пена для изделий из ячеистых бетонов с отклонениями по высоте до 1 мм. Некоторые марки такого средства пригодны только для внутренних стен и перегородок. Расход 1 баллон 850 мл на 10 м2.
При выборе учитывают, что арболит почти не впитывает влагу, содержащуюся в воздухе, но вытягивает ее при монтаже из раствора, поэтому блоки перед установкой нужно обильно смачивать. При использовании клея такой проблемы нет.
Пошаговая инструкция по кладке первого ряда
- Разметить по схеме места расположения дверных проемов и стыков между внешними и внутренними стенами. Для этой цели применять арболитовые камни (без раствора).
- Приготовить массу. Наносить ее на торец, контактирующий со следующим изделием, и верхнюю поверхность.
- На каждом стыке стен установить по два блока под прямым углом по отношению друг к другу. Для первого ряда выбирают камни с минимальными отклонениями по размерам. Между углами натянуть шнуры.
- Уровнем проверить положение элементов.
- Выложить по схеме первый ряд. Арболит режут болгаркой или дисковой пилой, уровнем проверяют точность.
- Продолжают монтаж последующих рядов не ранее, чем через сутки после завершения первого.
Если необходимо ускорить процесс, то в раствор добавляют затвердители.
Руководство по укладке остальных рядов блочных стен
- Все последующие ряды начинают размещать с углов.
- Кладку арболита ведут, как кирпичную, в шахматном порядке — вертикальные швы между блоками разных рядов не должны совпадать, смещение делают на полкамня.
- Через каждые два ряда смесь в швах разравнивают по поверхности камней.
- В каждом третьем-пятом ряду поверх раствора настилают армирующую сетку.
- За день выкладывают не более трех рядов.
- Для усиления делают армопояс. Это монолитная железобетонная полоса, на которую опираются плиты перекрытий и стропильная система. Монтируют из специальных U-образных блоков с выемкой. В желоб помещают арматуру и заливают бетон.
- Перемычки над проемами усиливают готовыми железобетонными или металлическими балками. С каждой стороны перемычка должна опираться на стену минимум на 20 см.
Ошибки могут быть связаны с неверным выбором толщины шва и клея, результат — мостики холода.
Кладка блоков зимой
Особенности монтажа при низкой температуре воздуха на улице:
- Резку камней производят заранее, внутри помещения, чтобы не тратить время на эту работу на улице.
- Раствор разводят теплой водой, в отапливаемом помещении. Порции замешивают такими, чтобы смесь не успевала замерзать.
- Укладку блоков делают секциями. Выкладывают сразу до 7 коротких рядов. Тогда смесь успевает схватиться до замерзания под весом уложенных камней.
- В цементно-перлитовый состав допустимо добавлять противоморозные присадки.
Кладка арболитовых блоков
Как правильно армировать и делать перевязки?
Кладка арболитовых блоков не имеет значительных отличий к примеру с кладкой обычного газоблока, но, как и в любом деле присутствуют свои особенности и хитрости. В первую очередь стоит отметить, что арболит – это самый прочный строительный материал, среди всех представителей ячеистых бетонов из органического наполнителя. С отличными показателями плотности и теплопроводности.
Структура арболитового блока, заключается в плотном сцеплении щепы, цемента и минерализатора. Ввиду хаотичного расположения щепы, блок становиться ячеистым, то есть имеет небольшие поры, которые позволяют, не только отказаться от утепления, но увеличить сцепление с арболитовыми блоками, расположенными в кладочном ряду. Так как кладочный раствор довольно глубоко проникает внутрь пор снизу, и сверху кладочных рядов. Как следствие швы в стене получаются очень прочными. А благодаря не большой массе и лёгкости монтажа, c кладкой арболитовых блоков, может справиться один человек.
Какой кладочный раствор использовать в кладке из арболитовых блоков?
ЦПС или цементно-песчаная смесь один из самых распространённых и не дорогих вариантов. Швы при высыхании приобретают каменную структуру, что предаёт стене большую прочность, но теплопотери на них значительно увеличиваются. Вследствие чего вероятность появления мостиков холода при кладке цементо песчаной смесью значительно выше. Поэтому такой раствор вполне пригоден в случае постройки сельхоз помещений, гаражей и саун. Что касается рецептуры, то тут все, как и в обычной кладке:
- Одна часть цемента марки 400 на две части просеянного песка;
- Либо одна часть цемента марки 500 на три части просеянного песка.
Воду следует добавлять в уже перемешанный сухой состав. Количество воды обычно равно объёмы цемента. Готовый кладочный раствор должен принять сметано образную массу.
Клей для ячеистых бетонов – менее распространённый вариант для кладки арболитовых блоков. Связано это с банальной и не всегда оправданной экономией. Клей для блоков значительно превосходит ЦПС не только удобством в работе, но и прочностными характеристиками. Так как при его изготовлении используется более мелкая фракция песка, марочный цемент и пластификаторы, которые позволяют смеси оставаться подвижной довольно длительное время.
Для средней полосы и юга России, подойдет стандартный арболитовый блок толщиной 300мм. Для северных широт лучше заострить внимание на так называемом «северном блоке» его толщина 400мм.
Некоторые предпочитают кладку арболитовых блоков «на ребро», то есть когда ширина стены составляет 200мм. Такой подход к строительству значительно экономит блоки, но он уместен при постройке не жилых помещений, таких как бани, гаражи, сараи. Среди наших клиентов попадались и те, кто при кладке в пол блока, обкладывал наружную стену клинкерным кирпичом. В таком случае возникает масса проблем не только с перевязкой кирпича к арболитовой стене, но и с мауэрлатом, хотя в итоге толщина несущих стен варьируется в пределах 300-320мм. Но, пожалуй, самое главное – это целесообразность покупки арболитового блока.
Первый ряд кладки арболитовых блоков.
Первый ряд кладки – это самый ответственный момент, потому как именно он задаёт дальнейший уровень всей постройке. Основание должно быть предварительно защищено от влаги, причём не имеет значения из чего изготовлено основание – цокольная лента или фундамент. Гидроизоляцией для кладки первого слоя арболитовых блоков послужит слой рубероида. Так же стоит обратить внимание на цоколь будущей постройки, потому как он позволит снизить водопоглощение у блоков.
Далее необходимо разложить первый ряд арболитовых блоков во всю длину будущей стены. Это необходимо для того чтобы определить точное количество целых блоков и количество блоков которые необходимо подрезать. К слову сказать, арболитовые блоки лучше всего пилятся обычной бензопилой.
Строительной кельмой или мастерком наносим и выравниваем первый слой кладочного раствора, толщина которого не превышает 5-6мм. Стоит отметить, что арболит – пористый материал, часть раствора попадёт в полости между щепками на блоке и толщина кладочного шва будет немного меньше, около 2-3мм. Далее при помощи строительного уровня и угольника выравниваем блок во всех плоскостях. Данная процедура повторяется по всем углам здания.
Затем, между блоками натягивается шнур, который значительно упростит арболитовую кладку. Далее промазываем кладочным раствором тычковую сторону углового блока и подгоняем его под уровень, стыкуемого блока и натянутого шнура. Таким же образом выкладываются и последующие арболитовые блоки. По истечению 5-6 часов после того как раствор схватился, на верх первого ряда желательно проложить армирующую сетку. Последующие 2-4 рядя армировать не обязательно. Для выравнивания вертикальной плоскости, необходимо пользоваться строительным отвесом.
Нужно ли армировать стены, из арболитовых блоков?
Ввиду не однозначного понимания сути вопроса давайте разберёмся, что Вы подразумеваете под армированием стены.
Если речь идёт об укреплении стены арматурой, то в этом нет необходимости, так как арболитовые блоки обладают прекрасной адгезией.
В случае с армированием кладочного ряда, то лучше всего с этой задачей справиться специальная сетка, которая продаётся в любом строительном магазине. Прокладывается она, через каждые 3-5 рядов.
Если же под армированием мы подразумеваем сетку, которая крепиться на готовую стену, с дальнейшим оштукатуриванием, то в этом нет необходимости. Так как, арболитовые блоки пористые, и благодаря этому свойству обеспечивают отличное прилипание штукатурного раствора. Стоит отметить, что это возможно, лишь в том случае, если на блоках нет следов отработки. Так как некоторые производители в целях экономии смазывают формы не эмульсолом, а отработанным маслом.
Не меньшего внимания заслуживает армо пояс. Армо поясом называют кладочный ряд по всему периметру здания. Внутрь армо пояса укладывается арматура, которая в дальнейшем заливается бетонным раствором. Первостепенная задача армопояса – это распределение нагрузки от цокольного, межэтажного или чердачного перекрытия. Армо пояс необходим для установки мауэрлата, для крепления стропильной системы и в случае если здание больше одного этажа.
Установка армо пояса.
Самый распространённый способ заключается в установке опалубки, внутри которой уложены хлысты арматуры. Далее внутрь заливается цементный раствор. Такой способ очень трудоёмкий, так как необходимо установить опалубку, сколоченную из досок, а после её демонтажа выравнивать армо пояс вровень со стеной. Кроме того такой армо пояс необходимо утеплять.
Менее трудоёмкий способ заключается в установке армо блока, или U-образного арболитового блока. Арболитовые блоки укладываются так же как обычные блоки, только у них есть продольное отверстие, внутрь которого укладывается арматура и заливается цементный раствор. Таким образом, монтаж армо пояса занимает меньше сил и времени.
Как класть арболитовые блоки на плиту перекрытия?
Дом, построенный из арболитовых блоков, способен выдержать не только деревянные перекрытия, но и бетонные. Безусловно, для более подробного расчёта необходима консультация специалиста, так как каждый проект индивидуален. Любой инженер примет в расчёт вес постройки, несущую способность почвы, и вес мебели которая будет на этажах здания. Так что Вам следует заранее всё хорошенько обдумать.
Если Вы планируете массивную трёх этажную конструкцию, на втором этаже которого будет бытовая техника или другие тяжёлые предметы, то следует рассмотреть вариант с бетонным перекрытием. Арболитовые блоки укладываются, так же как и вначале первого этажа, только на плиту перекрытия второго.
Если Вы планируете эксплуатировать второй этаж без серьёзных нагрузок, то можно обойтись и деревянным перекрытием. Стоит отметить, что балки или лаги, в местах, где они опираются на меж этажный армо пояс должны быть хорошо изолированы, как правило это рубероид либо аналогичный гидроизоляционный материал. Это необходимо, для того чтобы конденсат который образуется при температурных перепадах не попадал внутрь арболитовых блоков.
Кладочный ряд без мостиков холода.
Для того, чтобы снизить к минимуму теплопотери образующиеся в кладочном шве, необходимо учесть несколько правил.
- В первую очередь стоит обратить внимание на геометрию арболитового блока, допустимое отклонение не должно превышать 5мм. Такими пропорциями может обладать арболитовый блок, изготовленный строго по ГОСТу и только методом вибропрессования в металлической форме, а не на так называемой несушке.
- Толщина кладочных швов не более 3мм. Опять же соблюдение такой толщины возможно только на качественном арболитовом блоке, изготовленным по ГОСТу.
- Не желательно использование других строительных материалов в арболитовой кладке. Связано это с тем, что арболит отличается высокой паропроницаемостью, и как следствие вода в нём не остаётся. В таких случаях используют разнообразные минеральные ваты, и ни в коем случае пеноплекс, пенопласт и тому подобные материалы.
Дверные и оконные проёмы в арболитовой кладке.
Как правило, все проёмы в доме заранее запланированы, но случается так, что в процессе возведения дома, хозяин решил установить дополнительный оконный или дверной проём. Еще одной отличительной особенностью арболитовых блоков является лёгкость обработки. Арболит очень тяжело сломать, но легко распилить обычной бензопилой. Лучше всего с этой задачей справиться цепь с победитовой напайкой.
После того как проём был выпилен, арболитовые блоки, на местах где был произведён срез необходимо обработать био защитной пропиткой, которой пропитывают древесину от паразитов, плесени и грибка.
Ввиду того что арболитовые блоки практически не дают усадки, нет необходимости в установке обсадной рамы или как её называют – закладная. Для усиления можно воспользоваться U-образным блоком.
Строительство дома из арболитовых блоков в зимний период.
Наверное, ни для кого не секрет, что строится зимой гораздо выгоднее, так как строительный сезон начинается с середины марта. Спрос на строительные материалы растёт, как следствие растёт и цена на них. Не говоря уже о стоимости на услуги рабочих и техники. Для того, что бы немного сэкономить на стройке следует учесть ряд следующих факторов.
- Необходимо заранее приготовить доборные блоки, для того чтобы не заниматься их подгонкой на морозе.
- Сухие строительные смеси, такие как клей или цементный кладочный раствор необходимо размешивать в тёплой воде, небольшими порциями. Так как от замёрзшего раствора толку будет мало.
- Кладку необходимо производить не рядами, а секциями по пять-семь рядов. Потому как раствор под весом арболитовых блоков успел схватиться, а не замёрзнуть.
- При кладке арболитовых блоков в зимнее время нельзя мешкать, так как попросту кладочный раствор не должен замёрзнуть. Особенно это стоит учитывать при выравнивании кладочной секции.
- Арболитовые блоки уложенные на поддоны следует укрыть. Так как вода, попавшая на блок потом смешается с кладочным раствором, что значительно увеличит время схватывания на швах. Стоит отметить, что арболитовые блоки не боятся мороза, посему утеплять из нет необходимости.
- Что касается противоморозных строительных присадок то тут все, так же как и других строительных блоков.
Всё зависит от Вашего опыта и финансовых возможностей.
Самые распространённые ошибки в кладке стен из арболитовых блоков.
Главная и самая распространённая ошибка – это его утепление паронепроницаемыми утеплителями, такими как пенопласт и тому подобными утеплителями. Арболитовые блоки не нуждаются в утеплении! Так как они прекрасно сохраняют тепло зимой и прохладу летом.
Не меньшего внимания заслуживает кладочный шов. Он не должен быть очень широким. Для того чтобы снизить тепло потери лучше использовать клей для ячеистых бетонов.
К остальным ошибкам можно отнести приобретение арболитового блока у гаражных производителей. Чтобы потом не жалеть о потраченных деньгах попросите у производителя сертификат качества или съездите на производство.
системы и методы выполнения работ
Строительство из арболитовых блоковПроцесс работ и кладка арболитовых блоков, это не сложный строительный процесс. Особенно, если знать характеристики и свойства самого арболита.
Из чего изготавливаются арболитовые блоки
На данный момент применение материала в строительстве стало встречаться довольно часто. Обусловлено это тем, что материал имеет высокие технические показатели и свой определенный состав.
Состоит арболит:
- Из сульфатного цемента.
- Портландцемента.
- Связывающих веществ.
- Стружки, опилок и так далее.
- Целлюлозного сырья.
- Минеральных ферментов.
- Химических добавок.
- Жидкости.
- Все материалы прошли испытания на прочность и надежность.
- Используют их в определенном количестве.
- Изготавливается арболит только на специальных заводах.
- Но, есть возможность при помощи оборудования сделать его в домашних условиях.
- Для этого понадобятся все выше перечисленные ингредиенты и инструкция.
Технологические особенности и свойства материала
Особенности материала и характеристикиУже давно был установлен тот факт, что арболитовые блоки являются самым оптимальным решением для строительства жилого дома. Цена на этот строительный материал доступная, что дает возможность использовать его и для других целей.
Рассмотрим подробнее почему?
- Арболитовые блоки имеют крупную пористую структуру.
- Благодаря чему есть возможность поддерживать в помещении постоянный температурный режим.
- Влажность воздуха в строении также находится на одном и том же показателе (при правильной эксплуатации здания).
- По своим свойствам и характеристикам арболитовые блоки немного похожи на свойства древесины.
Свойства арболитовых блоков:
- Этот материал является экологически чистым, так как не содержит синтетических веществ и элементов.
Изготавливается он только из чистого сырья.
- Арболит не подвергается воздействию огня. Этим обеспечивается безопасность строения в случае пожара.
- Блоки имеют нестандартные размеры, которые очень помогают выстроить дом быстро и просто.
- Они имеют меньшую массу, чем кирпич. Таким образом, не создается нагрузка на фундамент дома.
- Несмотря на свой небольшой вес, блоки выдерживают значительные нагрузки и способны нести на себе любой вид крыши (на деревянном или металлическом каркасе).
- Арболит довольно просто подвергается разрезанию.
- Благодаря своей структуре и составу блоки дышат, и тем самым обеспечивается благоприятный микроклимат в помещении.
- Материал имеет высокий показатель теплопроводности, что позволяет обойтись без дополнительного утепления.
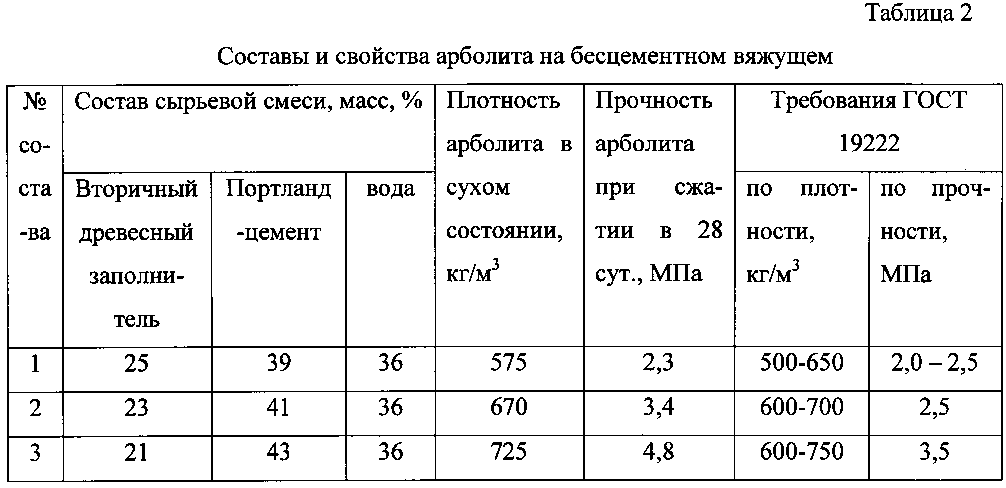
- Самым главным свойством арболита является то, что структура и состав его не способен подвергаться воздействию гниения, чего нельзя сказать о древесине.
- Материал свободно переносит любые климатические и погодные явления. Его структура от такого воздействия не изменяется на протяжении длительного времени эксплуатации.
- Арболит не боится морозов. Ему не страшны температурные изменения. Даже если дом на протяжении длительного времени не отапливается, то в нем за небольшой промежуток времени можно создать оптимальную температуру, так как сразу в помещении будет прогреваться воздух, а не стены.
Виды и марки арболитовых блоков
Марки арболитовых блоковНа данный момент в строительстве используется два вида арболитовых блоков:
- Теплоизоляционные.
- Конструкционные.
Все они разделяются на марки и подвиды:
- Прочность арболита зависит от его марки.
- Самыми прочными и надежными считаются арболитовые блоки марки 50.
- Все блоки марок менее 50 могут также использоваться для строительства, только нужно правильно рассчитывать нагрузки на материал.
- Есть еще марки: 5-10-15-25-35.
- Из аналогичных марок изготавливаются не блоки, а плиты из арболита.
- Их спектр применения заключается в утеплении и изоляции наружных стен строения.
Второй размер материала подойдет больше для строительства межкомнатных перегородок.
Выполнение кладки арболитовых блоков
Кладка арболитовых блоковАрболитовые блоки кладутся довольно быстро и просто, все работы можно произвести самостоятельно.
Рассмотрим процесс работы:
- Кладка из арболитовых блоков проста благодаря размерам материала.
- Внутри каждого блока имеет терморазрыв, который и обеспечивает теплоизоляцию строения.
- Кладка каждого блока выполняется: в 0,5 блока или в 1 блок.
Благодаря тому, что кладка выполняется аналогично кладке кирпича, то выполняется она своими руками:
- Если в процессе кладки заполнять терморазрыв бетонным раствором, то прочность стены из арболитовых блоков увеличивается.
- Есть различные технологии кладки арболитовых блоков: с заполнением терморазрыва и без.

По своей технологии кладки и возведения стен строения из арболитовых блоков схожи с саманными кирпичами. Они имеют практически такие размеры и аналогичные свойства в применении.
Для того чтобы сделать кладку арболитовых блоков понадобится:
- Залить основание строения, которое бы соответствовало его размерам и весу кровельной конструкции.
- Затем изготавливается бетонный раствор, в который для большей прочности вмешиваются специальные добавки.
- Сам раствор изготавливается из портландцемента, очищенного песка и воды.
- Основанием для кладки арболитовых блоков может быть: монолитный, свайный, столбчатый фундаменты.
- Такие типы основания являются самыми оптимальными для строения.
- Если строение одноэтажное, то достаточно использовать кладку в 0,5 блока.
- Если же строение двух- или трехэтажное, то лучше применить кладку в 1 блок.
Из инструментов для кладки понадобится:
- Строительный уровень.
- Отвес.
- Мастерки.
- Емкость для более удобного использования раствора.
- Болгарка со специальными насадками для разрезания материала.
- Арматурная сетка небольшого размера, которая может прокладываться между блоками для более прочного их скрепления.
Сама кладка выполняется при помощи бетонного раствора и весь процесс похож на кладку кирпича.
Выполнять кладку нужно начиная с углов строения. Таким образом, несущие угловые конструкции будут более прочные, и состоять из цельного материала.Кладка выполняется постепенно:
- Изначально раствор накладывается на основание и на него ставятся при помощи строительного уровня блоки.
- Они надежно закрепляются.
- Толщина бетонного раствора не должна превышать 15-20 мм.
- Далее кладутся блоки по сторонам. Сверху накладываться сразу нельзя, так как плоскость стены под весом арболитовых блоков нарушится.
Отделка арболитовых блоков, как наружная, так и внутренняя, выполняется с применением современных облицовочных материалов, но тут стоит учесть вентиляционный зазор в работах, так как материал дышит. На видео можно просмотреть процесс работ, связанных с кладкой материала.
Делаем арболитовые блоки своими руками.

Арболит – это строительные блоки на основе цемента и древесной щепки. Он обладает хорошими характеристиками, которые существенно лучше, чем у опилкобетона. В статье речь пойдет о том, в каких сферах применяются арболитовые блоки, об их достоинствах и недостатках, а также о технологии изготовления.
Содержание:
- Что такое арболитовые блоки
- Преимущества и недостатки арболитовых блоков
- Виды арболитовых блоков
- Технология производства арболитовых блоков
- Производители арболитовых блоков
- Инструмент для арболитовых блоков
- Подготовка щепы для изготовления арболитовых блоков
- Раствор для арболитовых блоков и заливка в формы
- Советы для изготовления арболитовых блоков
Что такое арболитовые блоки
Бетон – это универсальный строительный материал. Его свойства напрямую зависят от наполнителя. Работать с ним легко, благодаря жидкой консистенции. Он заливается в опалубку или специальную форму и приобретает нужные размеры и проектную прочность. Арболит также изготавливается из бетона, но из-за опилок в составе имеет ряд отличий от привычных составов.
- В основе арболитовых блоков лежит древесная щепка. К ее размеру и количеству применяются строгие требования – эти два параметра влияют на качество материала и его марку. Кроме этого, есть производства арболита, которые используют стебли хлопчатника, рисовую солому или кору.
- Вяжущим компонентом выступает цемент марки не ниже М300. Его марка влияет на прочность готового изделия и, следовательно, на его маркировку.
- Для улучшения соединения компонентов смеси, в нее добавляют специальные добавки, обеспечивающие быстрое затвердение и т.д. В большинстве случаев это жидкое стекло, хлористые соли калия или алюминия.
- Изначально древесная щепка и цемент плохо сочетаются, чтобы доиться качественных и равномерных по прочности блоков требуется правильно поставить производство с четким технологическим процессом.
Во время которого важную роль играет продолжительное и тщательное перемешивание всех составляющих.
- Щепка, отбираемая для изготовления должна проходить жесткий контроль. Лучше всего подходят сосна, ель или бук. Немаловажен и характер древесины – поздняя или ранняя заготовка. Размер щепки не должен превышать 10 мм в ширину и 25 мм в длину. Соблюдая эти условия, материал получится с высокой паропроницаемостью, но прочный.
- Для достижения лучших теплоизоляционных показателей. Смесь делается из щепы, вяжущего (цемент с добавками) и воды в пропорции 1:1:1,5. Если нужен более прочный блок для стены с высокой несущей нагрузкой, то пропорции вяжущего соответственно меняются
Арболитовые блоки видео
Преимущества и недостатки арболитовых блоков
Самое главное – это высокие энергоэффективные показатели при строительстве внешних стен дома и невысокая стоимость материала. Но из-за невысокой прочности, допустим только для строительства малоэтажных домов.
Достоинства арболита
- По теплоизоляционным качествам он опережает обычный бетон или кирпич. Его теплопроводность составляет всего 0,08 Вт/(м*С).
- Он обладает лучшими качествами древесины, но в отличие от нее, является пожаробезопасным. Арболит трудновоспламеняемый материал, который во время пожара образует мало дыма.
- При нагревании дома и последующем отключении системы отопления, тепло в помещении будет сохраняться еще долгое время даже при отрицательной температуре снаружи.
- По своим паропроницаемым характеристикам он уступает только древесине. Поэтому внутри помещения будет всегда хороший микроклимат, даже при высокой влажности. Вот почему этот материал выбирают для строительства сауны или бани.
- Несмотря на невысокую прочность (допускается строительство зданий из арболитовых блоков не выше 3 этажей), он хорошо противостоит нагрузкам на растяжении.
Что особенно важно при сезонном пучении грунта, когда дом начинает «ходить». Это свойства материала убережет строение от появления трещин.
- Морозостойкость в зависимости от марки изделия может быть в пределах F25 – F50, Но если зимой чередуются влажность и отрицательная температура, срок годности арболита значительно снижается.
- Этот недорогой материал легко подгонять под нужные размеры, в нем достаточно прочно держится закрепленные предметы. Он станет лучшим вариантом для небольших хозяйственных построек или гаражей.
- Небольшой вес блоков позволяет экономить на фундаменте, так как на последний не будет оказываться высоких нагрузок.
Недостатки арболита
- Невысокая прочность ставит использование арболитовых блоков в узкие рамки. Разрешено только малоэтажное строительство, межкомнатные перегородки или в качестве дополнительной теплоизоляции.
- Долговечность материала зависит от его качества. Помимо специализирующихся крупных заводов, сегодня по стране очень много частных маленьких фирм, которые изготавливают блоки и продают их по более низким ценам.
Но, к несчастью, качество их продукции зачастую остается низким из-за желания максимально удешевить товар и сделать его привлекательным для покупателя.
- Изготовленный по ГОСТу материал имеет стоимость, практически равную пенобетону. Это связано с тем, что при его изготовлении не обойтись без человеческого труда.
- Из-за погрешностей в размерах блоков, во время кладки швы получаются неравномерными. Да и сам материал не отличается красивым внешним видом, поэтому требуется финишная декоративная облицовка фасадов дома.
Виды арболитовых блоков
Всего производят 2 основных вида:
- Конструкционный. Отличается наивысшей плотностью – 500-800 кг/куб.м. В нем пропорционально больше содержание цемента по отношению к щепе. По характеристикам он пригоден для кладки несущих стен и опор. Для большей прочности допускается его армирование стержнями или сеткой.
- Теплоизоляционный. Плотность в пределах 500 кг/куб.м. Предназначается для строительства межкомнатных перегородок, на которые не оказывается нагрузки и в качестве теплоизоляционного слоя.
Арболит может иметь 2 формы:
- В виде блоков. Это уже готовый к использованию материал определенных размеров. Но из-за особенностей материала и его изготовления в размерах могут быть существенные погрешности. Хотя они регламентированы ГОСТом, на деле чаще нестыковки превышают эти параметры. Это надо учитывать еще на стадии проектирования и подсчета требуемого количества материалов. Блоки имеют большой размер, поэтому темпы строительства высокие.
- Монолитный. Его изготавливают непосредственно перед использованием прямо на строительной площадке. После замеса сразу же используют полностью. Такой способ подойдет для создания тонкого теплоизоляционного слоя (когда арболит заливается в несъемную опалубку из пеноплэкса или пенопласта). После заливки придется остановить на работы на время схватывания состава. Это не менее 7 дней.
Технические характеристики арболитовых блоков
- Хоть в арболите и присутствует древесина на равне с бетоном, все же этот класс материала относится именно к строительному камню.
Поэтому его маркируют и дают класс прочности именно как любому другому изделию из бетона.
По форме арболитовые блоки могут быть:
- с U-образным углублением. Удобны для дверных или оконных поемов с перемычками;
- стеновые блоки могут быть крупными, средними или узкими;
- плоты. Но они обязательно имеют слой прочного и плотного бетона, так как характеристики арболита не могут отвечать необходимым, в данном случае, требованиям. Допустимая длина по ГОСТу не превышает 480 см.
Технология производства арболитовых блоков
Сам технологический процесс довольно прост, поэтому для небольших построек, например сарая или курятника, арболитовые блоки моно сделать своими руками. Но из-за медленного отвердения состава, изготовление займет очень много времени, особенно если форм для заливки немного. Особенно при условии, что арболит будет набирать необходимую прочность только при температуре от 12 градусов и выше. Конечно, можно добавить специальные химические компоненты, которые сделают возможным работы и при более низких температурах, но это приведет к удорожанию материала.
Этапы технологического процесса
- Получение деревянных щепок. Для этого подойдут отходы от деревообработки, которые имеются в большом количестве на любой лесопилке. Подходят практически все сорта древесины, кроме лиственницы и тополя. Нельзя забывать и про строгие ограничения в размере, которые являются основополагающими качества арболита. Поэтому изготовители изготавливают щепу самостоятельно при помощи различных дробилок (шредера, молотковой, дисковой или роторно-ножевой).
- Пропорции. Если профессионалы используют специализированные дозаторы, то при самостоятельном изготовлении придется руководствоваться весом или объемом.
- Соединение компонентов. Вначале соединяют щепку и цемент. Сделать это вручную лопатой не получится, допускается только длительный замес в бетономешалке.
- Заливка формы. Готовая смесь по желобу подается в специальные формы из металла или дерева.
- Трамбовка. Это очень ответственный этап, который нельзя упускать. Здесь используется ручной труд, так как сначала смесь надо проколоть, чтобы удалить пузырьки воздуха. Далее утрамбовка производится на вибростоле.
Совет: из-за плохой адгезии цемента с щепой, утрамбовка должна продолжаться не более 20 мин, иначе бетон начнет отделяться от щепы и утрамбовываться на дне.
- Отвердение. Происходит на проветриваемых складах, где нет прямых солнечных лучей. Формы снимаются через сутки. Дальнейшая транспортировка возможна через 2-3 недели.
Производители арболитовых блоков
В каждом городе есть не одно производство арболитовых блоков. Но чаще всего их производят в кустарных условиях и продают через объявления на местных ресурсах. Если поблизости нет крупного завода, то лучше обратиться в компании, которые занимаются строительством арболитовых домов. Как правило, у них всегда есть свое производство, на котором соблюдаются все технологии.
- Наиболее крупное предприятие в России, занимающееся арболитовыми блоками – «ЭкоДрев Продукт». Они поставляют свою продукцию на крупные рынки строительных материалов. В среднем стоимость конструкционного материала составляет 5500 – 6000 руб/м3, а теплоизоляционного 4500 руб/м3.
- Более низкие цены у производителя «Арболит Трейд» — 5300 руб/м3 с доставкой. Они производят не только полнотелый, но и пустотелый кирпич.
- Вологодский завод арболита также предлагает свою продукцию в большинстве регионов. Цена конструкционного блока от 4100 руб/м3.
Покупая большие объемы напрямую от изготовителя, всегда можно договориться о дополнительной скидке.
Инструмент для арболитовых блоков
Специального оборудования для арболитовых блоков не потребуется, достаточно подготовить стандартные инструменты:
- бетономешалка;
- большой металлический поддон;
- форма для заливки арболита;
- разделитель.
Он нужен, если в одной форме планируется залить несколько более маленьких блоков или сделать пустоты;
- большое сито с вибрацией;
- вибростол или молоток;
- вилы, лопата и ведро;
- мастерок.
Чертежи арболитовых блоков
Подготовка щепы для изготовления арболитовых блоков
Делается это двумя методами.
Выдержка на открытом воздухе
- Вначале на любой пилораме приобретается большой объем стружки или щепки подходящей породы древесины. Как правило, ее всегда отдают бесплатно, понадобится только оплатить доставку.
- Если такой возможности нет или материал там низкого качества, тогда при помощи рубильной машины (которую можно взять в аренду) материал подготавливается самостоятельно из пиломатериала.
- Перед использованием, щепу выдерживают на открытом воздухе 2-2,5 мес. За это время опил очищается от присутствующей в нем сахарозы, которая отрицательно влияет на качество готовых блоков (может начаться брожение).
На протяжении этого времени несколько раз щепу тормошат и обрабатывают оксидом кальция, переворачивают. Желается это для того, чтобы воздух попал и в нижний слой. Это предотвратит загнивание материала.
Обработка известняком
- Известняк смешивают с водой до получения 1,5% раствора. Для этого потребуется очень большая емкость. В полученный раствор засыпают щепку из расчета 200 л/1м3 щепы. Перемешивают 2 раза в день на протяжении 4 дней.
- Потом просеивают через крупное сито, чтобы отделить крупный мусор и оставляют просыхать.
Раствор для арболитовых блоков и заливка в формы
- Примерные пропорции для арболитовых блоков выглядят так: 25-30 кг цемента М400/25-30 кг щепы/1 кг жидкого стекла/35-40 л воды.
- Для замеса нужна электрическая бетономешалка. Вначале заливают нужный объем воды, добавляют жидкое стекло и начинают перемешивать в течение нескольких минут, для качественного смешивания.
- Затем засыпается щепа и перемешивается.
Она должна вся намокнуть, чтобы не оставалось сухих участков.
- Далее идет очереди цемента. Если засыпать сразу весь объем, неизбежно образуются комки. Поэтому засыпать надо постепенно в работающую бетономешалку.
- Не останавливая работы бетономешалки, добавляется весь цемент, пока он не образует со щепой однородной массы. Это возможно только в том случае, если щепа вся равномерно намокла.
- Готовую арболитовую смесь раскладывают в разъемные формы или опалубку. Если есть вибростол, то процесс очень упрощается. После заполнения форм только остается дождаться результата и извлечь готовые блоки.
- При самостоятельном изготовлении арболитовых блоков кустарным методом, чаще всего используется ручной труд при уплотнении. Для этого нужно подготовить трамбовалку в виде листа металла по размеру формы с ручкой.
- Форма представляет собой ящик из металла или досок без дна. Устанавливают его на абсолютно ровную поверхность, наливают слой смеси и утрамбовывают. Количество слоев зависит от высоты формы.
Чем их больше, тем более качественный и прочный получится блок. В среднем заливают примерно 5 слоев. Для удаления лишнего воздуха, смесь после каждой заливки протыкают вилами или металлическим прутом.
- Для наивысшей плотности, трамбовать нужно так, чтобы наименьше проявлялась распрессовка. Лучше всего поочередно чередовать сильные и более слабые нажимы.
- По окончанию излишки раствора счищаются мастерком.
- Наилучшей прочности добиваются посредством вибростола. В этом случае трамбовать вручную не надо. После заливки смеси в форму ее прижимают грузом и включают вибрацию на 15-20 мин.
- Дальше происходит момент сушки. Если прочность арболитового раствора высокая, форму допускается снимать сразу с сырых блоков и отправлять их на досушку. Но при более жидкой консистенции делать это нельзя. Так как блок потеряет свою геометрию.
- Технологический процесс подразумевает просушку блоков в течение 2 суток при температуре 60°C. Но в домашних условиях их сушат просто на улице в течение 2-3 недель, предварительно накрыв пленкой.
Производство арболитовых блоков видео
Советы для изготовления арболитовых блоков
- Готовую щепу можно купить у небольших производителей арболитовых блоков.
- Для более легкого извлечения блока из формы, ее внутреннюю часть отделывают гладким материалом, например, линолеумом.
- Для набора прочности блоки должны проходить гидратацию. Первые 10 дней они должны сохнуть под пленкой при температуре 13-15 °C.
- Если арболитовые блоки нужны только для утепления несущих стен, то технологический процесс можно незначительно упростить.
- Можно изготовить сразу отделочные блоки. Для этого на сырой блок прямо в форме наносят шпателем слой шпаклевки и разравнивают.
Арболитовые блоки своими руками: технология, пропорции, состав (+видео)
Благодаря современным экономичным материалам, постройка своего дома уже не кажется несбыточной мечтой. Арболит считают одним из самых выгодных и надежных вариантов. Арболитовые блоки сочетают в себе лучшие характеристики камня и дерева. Их реально сделать своими руками в домашних условиях без помощи профессиональных мастеров.
Свойства арболитовых блоков
Арболит – это легкий бетон с крупными порами. Технология производства предусматривает, что в его состав входит органический целлюлозный заполнитель (рисовая солома, древесная дробленка, сечка тростника), минеральное вяжущее вещество (цемент М500), вода и химдобавки – пластификаторы, ингибиторы коррозии стали, парообразователи. Блоки используют во время строительства жилых, промышленных зданий для покрытия, перекрытия, создания пространственных конструкций, несущей основы.
Этот материал стойкий к механическим повреждениям, имеет хорошую паропроницаемость – 0,11 мг/м·ч·Па. Он позволяет сделать расход материалов, раствора намного меньше. Дом из арболита своими руками будет прочным, легким, дешевым, защищенным от гниения. Важно, что при повышенной нагрузке изделия не трескаются, а сжимаются.
Совет прораба: замена кирпичной кладки арболитом позволит снизить массу здания в 7-8 раз.
В зависимости от плотности, арболитовые блоки изготавливаются как теплоизоляционный (класс В0,35; В0,75, В1), конструкционно-теплоизоляционный (класс В1,5; В2; В2,5) и конструкционный материал (В3,5).
Преимущества арболитовых блоков
- Высокий уровень теплоизоляции (теплопроводность – 0, 07 – 0, 17 Вт/мК), огнестойкости (не поддерживает горение в течение 0,75-1,5 часа), морозостойкости.
- Быстрая кладка и хорошая плотность до 600 кг/м3.
- Экологичность (на 80-90% состоит из древесной щепы).
- Низкая гигроскопичность (плохо впитывает влагу).
- Отсутствие необходимости в дополнительном утеплении.
- Нет лишней нагрузки на фундамент, так как снижается масса здания, низкий уровень усадки (0,4-0,5).
- Состав изделий обеспечивает хорошую сцепляемость с отделочными материалами.
- Изделия отлично поддаются моделированию (резка, фиксация крепежей).
Совет прораба: себестоимость 1 м² стены жилого дома из арболита обойдется в несколько раз дешевле, чем при использовании других материалов с похожими техническими характеристиками.
Технология создания арболитовых блоков своими руками
Сделать арболитовые блоки своими руками в домашних условиях вполне реально. Но нужно учитывать, что их технические характеристики могут отличаться от тех, которые будут у заводской продукции согласно ГОСТу19222-84, СН 549-82.
Первый этап производства блоков – это изготовление деревянных опилок, щеп. Оптимальные размеры:
- длина 30-60 мм;
- ширина 2-10 мм;
- толщина до 10 мм.
Для нейтрализации сахара в древесине в заводских условиях используют сернокислый алюминий, а в нашем случае опилки высушивают на солнце не меньше 40-80 дней. Для ускорения процесса их спрыскивают 1,5% раствором хлористого кальция с расчетом 200 л раствора на один куб щепы.
Затем, для того чтобы очистить от мусора, заготовку пропускают через сито. Ее нужно замочить в смеси воды и жидкого стекла (как вариант: смешать портландцементом и пластификатором). Альтернативный способ – замочить стружку в гашеной извести (5:10%) на 3 часа. После того как стечет жидкость, ее можно использовать для замеса. Изготовление состава происходит в бетономешалке в пропорции 1:2:6 (цемент, песок, опилки). Сначала соединяют опилки с водой, потом добавляют жидкое стекло и цемент. Масса должна быть пластичной и однородной.
Для того чтобы у блоков была правильная геометрическая форма, смесь заливают в металлические формы (20 см*20 см*50, 30 см*20 см*50 см), смазанные петромином, оббитые линолеумом или обтянутые пленкой и смазанные жидким мылом. Мастера советуют выкладывать массу поэтапно, каждый раз, хорошо трамбуя слой.
Раствор после помещения в форму встряхивают для устранения воздуха. Сэкономит время и улучшит результат в домашних условиях использование специального станка для производства арболитовых блоков. Одну сторону блока можно декорировать: залить сверху цементным раствором, зафиксировать фрагменты плитки, создать рельеф. Через сутки изделия можно вынимать из формы. Потом блоки должны сушиться несколько недель при температуре не менее 15° (это важное условие). Если поверхность будет иметь изъяны, ее дополнительно шлифуют. При необходимости проводится армирование. Цены на арболитовые блоки колеблются от 50 до 200 р. за штуку.
Форма для арболитовых блоков
Арболит – это один из лучших стеновых материалов для строительства малоэтажных зданий, возведения высотных строений каркасной конструкции. Рецепт его состава не очень сложен, и при соблюдении технологии процесса, нужных пропорций, изделия получатся прочными и надежными, даже если они сделаны своими руками.
Видео
youtube.com/embed/Q-PLQ4Y4SYk» frameborder=»0″ allowfullscreen=»allowfullscreen»/>
производство и кладка своими руками. Как построить дом из арболитовых блоков быстро и качественно Как выкладывать стену из арболита
Что такое арболитовые блоки
Массовое изготовление арболитовых блоков началось еще в середине 20-го века. Тогда этот материал стал пользоваться необычайным спросом. Арболит и все производимые из него строительные материалы прошли полностью все стадии испытания.
Примечание. После испытаний, проведенных учеными, установилось, что такой материал считается самым оптимальным для возведения жилого дома.
Представляет собой смесь из:
- Портладнцемента.
- Сульфатного цемента.
- Отходов лесоперерабатывающей промышленности (стружка, опилки и прочиее).
- Связывающий элементов.
- Минеральных ферментов.
- Органического целлюлозного сырья.
- Химических добавок.
- Воды.
Процесс изготовления такого материала довольно сложный и требует особых познаний. Но, это не мешает простому человеку изготовить его своими руками. Такой вариант также возможен.
Технические характеристики и свойства арболитовых блоков
По своей структуре в составе арболитового блока находится около 90% древесных материалов. Этот процент дает возможность считать сам материал экологически чистым, который не наносит вреда человеческому здоровью и окружающей среде. Особенности материала:
- Арболитовые блоки имеют отличную звуко- и теплоизоляцию. По последнему показателю они превосходят кирпич в несколько раз. Благодаря свойствам такого материала есть возможность внутри помещения создавать благоприятный микроклимат и постоянно поддерживать одну и ту же температуру.
Важно! Стоит учесть, что если строение возведено из кирпича или любого другого строительного материала, то при обогревании конструкции первоначально станут прогреваться ее стены и только потом внутренний воздух.
С применением арболитовых блоков изначально в помещении прогревается воздух и только потом сам материал.
- Прочность арболита обусловлена его структурой и составом сырья. Так как состоит он из довольно большого количество и разнообразия цементных растворов и связывающих веществ, то плотность структуры будет довольно высокой, что и придает надежность материалу.
- Арболитовые блоки не способны реагировать на влажные погодные или климатические условия (внешний климат или внутренний микроклимат). Даже если дом на протяжении длительного периода времени не отапливается, то сырость в нем не будет присутствовать. Они не впитывают влагу и при этом не деформируются.
- Материал спокойно переносит воздействия прямого источника огня. Обусловлено это тем, что в его составе есть цемент и химические добавки, которые не только повышают прочность, но и защищают материал от различного рода воздействий.
- Основным преимуществом арболита является его устойчивость гниение.
В нем никогда не заведутся различные насекомые или грызуны. Он является морозостойким материалом, который способен выдерживать очень низкие температурные колебания. Также он не реагирует на высокие температуры. Структура его остается неизменной на протяжении всего срока эксплуатации.
- По сравнению с кирпичом, цена на арболитовые блоки довольно низкая. Они имеют различные размеры, которые в отличии от других материалов на несколько порядков больше.
Совет. При выборе для строительства дома арболитовых блоков есть возможность сэкономить на самом материале, так как его размеры нестандартные.
Разновидности арболитовых блоков
Основными параметрами материала являются:
- 50х25х15 см.
- 30х20х50 см.
- 51х18.8х30 см.
Подробнее:
- Каждый для себя выбирает оптимальный вариант. Как советуют профессионалы, блоки размером 30х20х50 см предназначаются для возведения несущих стен конструкции. Они очень прочные и способны выдерживать довольно большие нагрузки.
- Для межкомнатных и других внутренних перегородок применяется арболит, который имеет размеры 20х20х30 см. Он менее прочный, и обладает такими же характеристиками и свойствами.
Совет. Чтобы повысить качества и свойства материала будет обязательным сделать внутренние и наружные отделочные работы.
- Для этого на данный момент есть огромное количество материалов, которые могут быть по техническим показателям аналогичны самим арболитовым блокам.
Совет. Лучше выбирать именно такие материалы, так как арболитовые блоки дышат, если использовать очень герметичные материалы, то есть допустимость появления влаги под отделкой.
- Срок эксплуатации арболитовых блоков практические не имеет никаких ограничений, особенно, если все работы по их укладке и отделке выполняются правильно и качественно.
Арболитовые блоки имеет две разновидности:
- Конструкционный арболит.
- Теплоизоляционный.
Марки:
- Есть несколько марок арболитовых блоков, которые имеют разную плотность структуры и от этого зависит их прочность:5, 10, 15, 25, 35, 50. Самыми прочными и устойчивыми к любым воздействия считают арболитовые блоки марки 50.
Очень часто из арболита изготавливаются не только блоки, но и плиты. Они используются для утепления и изоляции строения,но их поверхность также требует отделки, так как они не имеют привлекательного внешнего вида.
Особенности материала
Арболит относится к композитным стройматериалам. Когда-то он уже пользовался достаточно большим спросом в жилом строительстве. На его основе было построено немало домов, в том числе и в качестве эксперимента в Заполярье. Затем материал был незаслуженно забыт и только сейчас вновь стал востребованным.
Он представляет собой легкий бетон с наполнителем в виде древесной щепы хвойных и твердолиственных пород. В нем присутствует также некоторое количество вполне мирных добавок и присадок, улучшающих эксплуатационные качества материала, но не влияющих на его экологичность.
Блочный арболит
Выпускается арболит в основном в виде блоков, облегчающих процесс строительства домов, но может производиться и для заливки опалубки. Бывают такие разновидности этого материала, как:
- конструкционный;
- теплоизоляционный.
Применяются арболитовые блоки преимущественно для малоэтажного строительства. Используется материал для постройки зданий самого различного хозяйственного назначения.
Внимание! Есть у данного материала и некоторые ограничения в применении – это помещения с повышенной влажностью, а также те, в которых существует возможность присутствия агрессивных газов.
Из-за высокого содержания древесины в составе и безопасности используемых добавок данный материал характеризуется довольно высокими экологическими качествами. Они вполне сравнимы с характеристиками натуральной древесины. Обладает арболит и другими весомыми преимуществами, практически не имея при этом каких-либо значительных недостатков.
Как выполняется кладка арболитовых блоков
Технологии кладки арболитовых блоков могут быть разными. Есть кладка в 0,5 блока или в 1 блок. Большее количество блоков, как правило, не используется, так как материал обладает большими размерами. Итак:
- Толщина стен дома, который выстроен из арболитовых блоков может достигать 50 см.
- Практически, как саманные стены, которые по своим свойствам аналогичны арболитовым.
- Для выполнения работ самостоятельно понадобится бетономешалка, которая замешивает раствор бетона довольно быстро и качественно.
Также потребуется:
- Раствор бетона.
- Мастерок для использования раствора.
- Строительный уровень для ровной кладки арболитовых блоков.
- Емкость для удобного использования раствора.
Совет. У такого строения, как из арболитовых блоков должно быть хорошее основание. Как таковую усадку оно давать не будет, но могут действовать на дом перемещения грунта или его деформация под воздействием климатических или погодных условий.
Как правило, под строение из арболита используется монолитный фундамент или столбчатый. Все зависит от этажности строения. Изначально приготавливается бетонный раствор, для этого понадобится:
- Вода.
- Песок.
- Цемент.
Проведения работ:
- Песка понадобится 3 ведра на 1 ведро цемента. Вода добавляет при перемешивании и оценке структуры средства. Консистенция раствор бетона должна быть не слишком густой.
Совет. Чтобы увеличить прочность раствора и время его высыхания, необходимо добавлять в него специальные средства.
- Берется первый арболитовый блок и укладывается в углу будущего строения. Накладывается раствор на подготовленную поверхность основного фундамента, на сам материал класть его не нужно. При помощи строительного уровня выставляется блок и только после этого плотно прижимается. Излишки раствор убираются мастерком.
- Следующий блок кладется рядом. Но тут стоит учесть, что раствор наносится не только на поверхность фундамента, но и на боковую сторону блока, которая будет соприкасаться с первым.
Расстояние между ними должно быть равномерным и для этого используются специальные приспособления. Опытные строители работы такого типа выполняют на глаз, так как знают все тонкости.
Совет. Выкладываются арболитовые блоки несколькими рядами. По внешнему виду кладка должна напоминать «шахматку».
- Обусловлено это тем, что материал должен быть между собой перевязан и надежно скреплен. Два-три ряда в день по всему периметру будущего строения будет достаточно. Сохнет раствор в течении суток, если в него не добавляются затвердители. На следующий день уже начинается кладка последующих рядов.
Совет. Чтобы использовать затвердители правильно, на их упаковке есть инструкция. Согласно ей и выполняются все действия по их добавлению в раствор.
Кладка из арболитовых блоков выполняется довольно быстро и просто. Стоит изначально проконсультироваться со специалистами в этой области, которые подскажут, как правильно выполнять работы. На видео показан такой процесс от начала и до его завершения.
Советы и рекомендации
Чтобы обеспечить долговечность и надежность постройки, необходимо соблюдать следующие правила:
- Необходимо сделать качественную и прочную гидроизоляцию, так как арболит сильно гигроскопичен.
- Обязательно обустроить цоколь, высотой 50-60 см.
- Кровлю нужно вынести за пределы стены на 30-50 см.
- Производить отделку следует сразу после строительства.
- Для одноэтажных домов допустимо использование блоков меньшей плотности, в ином случае — потребуется большая плотность, так как конструктивные элементы не выдержат веса постройки.
- Важно увлажнять блок перед укладкой, иначе они вытянут всю воду из раствора.
- Если в доме имеется мансарда, то утепляется потолок и крыша.
- В процессе работы используется классический цементный раствор или специальная смесь.
- Если в работе используется металл, то его следует защитить от коррозии, так как арболит негативно на него воздействует.
Арболит — это качественный и долговечный материал, который часто используется в строительстве. Однако монтаж блоков имеет некоторые нюансы, которые нужно соблюдать, чтобы получить надежный и красивый дом.
Чем отделать арболитовые блоки снаружи
Чтобы обезопасить строительный материал от губительных воздействий погодных или климатических условий, должна быть выполнена качественная отделка. Самыми оптимальными материалами для облицовки арболитового дома будут:
- Штукатурка.
- Кирпич.
- Декоративный или природный камень.
Рассмотрим подробнее:
- Этот выбор обусловлен тем, что технические характеристики такого типа отделки аналогичны арболитовым блокам.
- Все эти материалы дышат и создают в помещении благоприятный микроклимат. Также они имеют широкий ассортимент оформления, и создать с ними интересный дизайн всего строения будет очень легко.
Совет. В процессе отделки лучше всего сделать изоляцию дома и утепление.
Для этого используются аналогичные материалы:
- Пенопласт.
- Экструдированный пенополистирол.
- Пенополиуретан.
Эти материалы легкие и не создадут дополнительной нагрузки на дом.
Совет. Обязательный будет сделать вентиляционный зазор в строении, который позволит выводить влагу.
Как правило, его размер составляет не менее 10 см. И под саму отделку стоит изначально предусмотреть основание. Его можно будет в процессе строительства подлить, но лучше сделать общий фундамент и для отделки, и для несущих конструкций.
Арболитовый блок производится из бетона (в качестве вяжущего) с органическими наполнителями и рядом добавок, которые предотвращают гниение наполнителя, обеспечивают затвердевание связующего и сцепление с щепой и другими материалами.
Себестоимость арболитовых блоков относительно невысока:
- порядка 2500…3000 р/м3, если брать только материалы для кустарного производства;
- если подход профессиональный, то с учетом вложений в оборудование и его нормальной амортизацией, себестоимость может быть и меньше.
Вы меньше в итоге тратите электричества, можете закупать сырье оптом (его стоимость реально на 20…25% меньше, чем отпускная цена в рознице). Средняя цена реализации готового продукта на февраль 2020 г. составляла порядка 4000 руб/м3 (цена указана примерно, так как реально цены отличаются в зависимости от качества и сырья).
Свойства арболита
Преимущества и недостатки
В процессе проектирования дома из деревобетона следует всесторонне изучить свойства и характеристики арболита. Основными преимуществами этого материала являются:
- Хорошие показатели теплоизоляционных свойств. Присутствие в составе материала опилок древесины способствует повышению этого показателя. Теплая штукатурка, применяемая в современном строительстве, производится по аналогичному принципу.
- Прочностные характеристики находятся на уровне показателей, которыми обладает шлакоблок, ракушняк или газобетон.
- Срок эксплуатации не отличается от традиционных материалов при условии правильного выполнения технологических операций в ходе производства и соблюдения правил укладки и отделки.
- Относительно небольшая масса арболитовых блоков существенно облегчает ведение работ с ними.
- Производство материала достаточно простое и не сопряжено со значительными материальными затратами. Найти материалы для изготовления арболита своими силами не составляет труда, при этом можно обойтись без использования специального оборудования.
Арболитовые блоки
При всех положительных качествах арболита, материал не лишен ряда недостатков:
- Присутствие в составе арболита значительного количества древесных опилок обуславливает подверженность его воздействию влаги, что может привести к разрушению материала. Для того, чтобы защитить материал от разрушения, применяется оштукатуривание поверхности блоков, которое, кроме того, придает им дополнительную прочность. Ситуация в данном случае подобна с той, когда при строительстве применяется ракушняк. Он также при отсутствии штукатурки хрупок и выкрашивается под влиянием внешних факторов. Нанесение штукатурки придает материалу высокую прочность.
- Для мелких грызунов арболит может служить и жильем, и пищей. Чтобы ликвидировать эту проблему, создается цоколь из бетона с толщиной не менее 500 мм и высотой порядка полуметра. Прекратить атаки грызунов можно путем закладки сетки-рабицы под слой штукатурки.
Классификация блоков арболита
Материал подразделяется в зависимости от следующих признаков. Плотность при полном высыхании:
- 500 кг/ м. куб. – теплоизоляционный;
- 500-850 кг/м. куб. – конструкционный.
Наполнитель
Состав наполнителя:
- древесная щепа;
- рисовые стебли и хлопчатник, остатки стеблей льна и конопли.
Назначение:
- материалы, обладающие малой плотностью, применяют для устройства теплоизоляционного слоя помещений и для создания перегородок между комнатами, а также в качестве стен, которые не являются несущими;
- при повышенной прочности материала, его используют при возведении стен, несущих нагрузку.
Технические характеристики
Прочностные характеристики арболита находятся в соответствии задачами, поставленными перед ним в соответствии с плотностью блока.
- Средняя плотность зависит от используемых компонентов в качестве наполнителя и связующего вещества. При росте плотности происходит увеличение прочности и, соответственно, повышается класс материала.
- Показатели теплопроводности увеличиваются с ростом количества связующего компонента в арболите. Повышение теплопроводности приводит к ухудшению прочностных свойств и потере конструкционных свойств.
- Морозоустойчивость находится на уровне 25-50 циклов.
- На степень усадки влияет плотность блока. Она возрастает при снижении этого показателя.
- Водопоглощение составляет 45-80%, что значительно превосходит этот показатель у других материалов.
- Паропроницаемость материала отличается высокими значениями, которые соответствуют аналогичному показателю древесины.
- Огнестойкость материала находится на высоком уровне. Арболит не способен поддерживать процесс горения и обладает возможностью длительное время выдерживать воздействие высокой температуры.
- Звукопроницаемость арболитных блоков находится на уровне, сопоставимом с натуральным деревом.
- Максимальное число этажей зданий, сооруженных из арболита, не превышает трех.
- Стоимость материала вполне доступна для массового потребителя.
Арболитовые блоки объединяют в себе свойства различных материалов
Рецепт и технология
Наполнитель
В качестве основы арболита (80-90% готового блока) используется щепа и опилки не мягких пород древесины. Возможно применение и других твердых частей растений (кора, солома, твердые стебли и т. п.). Все сырье предварительно обрабатывается: фракция строго регламентирована ГОСТом и не должна превышать 40 мм в длину, по ширине — до 5 мм.
В сырье допускаются примеси органического происхождения с той же фракцией. Объем включений — не более 5%.
Важное примечание. Песок, как наполнитель, в арболитовом блоке не используется. Его можно применять при производстве опилкобетона — это материал на той же основе, но из более мелкой фракции опилок.
В этом состоит отличие этих строительных материалов: арболит по ГОСТу производится без песка.
Вяжущее
В качестве вяжущего используют цемент и гипсовые вяжущие материалы:
- портландцемент марок М300, М400 и выше;
- портландцемент с добавками для повышения морозорстойкости;
- сульфатостойкий цемент, если используются сульфаты при приготовлении смеси;
- гипсоцементно-пуццолановые вяжущие. Это смеси на основе гипса и портландцемента с различными добавками, отличаются прогнозированным твердением.
Вяжущего используют порядка 250-300 кг на 1 м3 готовой продукции.
Отдельные добавки:
- хлорид кальция;
- сульфат алюминия;
- сульфат натрия;
- хлористый алюминий.
Добавки вводятся в цемент для лучшего связывания компонентов смеси: они нейтрализуют негативное действие сахаров в древесине, которые ослабляют химические реакции гидратации при застывании блоков. Объем химических добавок должен составлять 2…4% от количества цемента.
В качестве добавки также вводят жидкое стекло (силикаты) в объеме до 10 кг на 1 м3 блоков из арболита.
Вода
Вода как компонент должна быть очищенной, нехолодной (20…25 °С). Объем воды:
- на все процессы — до 400 л;
- на смешивание с цементом — до 250 л.
Армирующий каркас
ГОСТ допускает использование армирования арболита металлическими сетками, стержнями.
Техпроцесс
Оборудование для производства арболитовых блоков:
- щеподробилка;
- устройство для просеивания щепы;
- смеситель;
- формы для блоков.
Площадь для установки производительностью 1 м3 — порядка 10…20 м2, складские площади для малых объемов производства — сухое помещение минимум на 30…40 м3 полезного пространства.
В подготовленную щепу в работающем смесителе вливают воду. После добавляют негашеную известь. Смешивают порядка 10 минут для наибольшего выравнивания смеси по объему. Результат — органика темнеет, в конце процесса приобретает насыщенный коричневый оттенок. На 1 м3 щепы применяется порядка 100 л воды и 2,5-3 кг извести.
После вводят воду, вяжущее и добавки (если они ранее не введены в цемент). Вода должна быть теплой — как минимум 20…25 °С, чтобы к концу смешивания температура смеси составляла 15 °С — минимальная температура для нормального схватывания бетона. Но не стоит заливать смесь водой свыше 40 °С — гидратация цемента идет очень быстро, а вам надо успеть еще разлить смесь по формам. При массовом производстве также используют вибростолы (как и для других типов блоков) для быстрой усадки смеси в формы.
Выдержка арболита после застывания должна составлять 28 дней — полный срок схватывания бетона. За это же время блоки набирают и конструкционную прочность.
При производстве арболитовых блоков своими руками необходимо соблюдать основное правило: все компоненты смешать очень тщательно. Особенно при использовании ручного инструмента. Только качественное перемешивание сделает готовую продукцию гомогенной по составу и прочностным свойствам по всему объему.
Кладка арболита
Дома из арболитовых блоков строят практически также как и другие объекты, с одним небольшим отличием: кладку желательно сразу защищать от любого воздействия влаги. Это можно делать путем нанесения тонкого слоя штукатурного раствора. Другие особенности кладки:
- При кладке арболит рекомендуют выкладывать не более 3 рядов в сутки — для схватывания швов и равномерного распределения нагрузок.
- Армирующие пояса для 2-этажных зданий — облегченный.
- Толщина стен: гидроизолированных — 300 мм, негидроизолированных — не менее 500 мм.
- Блоки, при необходимости подгонки под размер, пилят.
- Раствор можно укладывать с помощью зубчатых шпателей, достаточный слой — до 10 мм.
За счет своего легкого веса, арболит быстро укладывается каменщиками в ряды. После высыхания кладки через 2…3 суток ее можно гидроизолировать.
Важно: арболит не любит влаги. Для кладки фундамент тщательно гидроизолируют: минимум — это должно быть три слоя битумной мастики.
Дом должен иметь правильную отмостку и систему ливневого водоотведения: вы должны отвести грунтовую влагу как можно дальше от фундамента. Кроме того необходимо продумать и выполнить внутреннюю систему вентиляции: арболитовый блок дышащий, но лишняя влага ему не нужна.
Узнать цену и условия выполнения заказа на строительство стен из арболитовых блоков можно по телефону 8-966-311-02-32
Вы планируете строить дом и не знаете кому можно доверить возведение стен дома? Наша команда превратит строительство дома в быстрый, приятный и недорогой процесс. В бригаде работают только профессионалы с солидным опытом работы. Мы контролируем каждый шаг строительства, скорость и качество работы наивысшие. За нашими плечами сотни работ в Подмосковье. Мы предлагаем целый ряд услуг по строительству.
Применение арболита в строительстве
Использовать арболит, даже конструкционный для сооружения домов высотой более 3 этажей нежелательно. В этом случае потребуется серьезное усиление конструкции стальной арматурой, а последняя, как известно, создает мостики холода. Для 2–3-этажного строения достаточно обычной армирующей сетки.
О том, чем облицевать стены из арболита, какой толщины должны они быть, как сделать их своими руками, читайте далее.
Стены
Арболит разных видов применяют при сооружении разных стен:
- несущие, то есть нагруженные – для них требуется конструкционный арболит, толщина такой стенки 50 см, хотя во многих облегченных постройках – гараж, дача, ограничиваются 30 см;
- самонесущие – также чаще всего обходятся толщиной в 30 см из блоков размером 30*20*50 см;
- перегородки – внутренние стены сооружают толщиной в 20 см из блоков 20*20*50 см.
Теплоизоляционный материал рекомендуется применять только для утепления. Его плотность слишком мала, чтобы служить опорой для чего бы то ни было. Впрочем, для перегородок применяют и этот материал.
Кладут блоки на цементно-песчаный или перлитовый раствор. Последний ближе по показателям теплоизоляции, а поэтому является лучшим выбором. Для кладки выбирают слегка недосушенный материал или обильно поливают его водой перед нанесением кладочного раствора: иначе влага из раствора окажется в блоках раньше, чем кладка успеет схватиться.
По ГОСТ деревобетон для возведения стен выпускают с готовым внешним отделочным слоем из декоративного бетона. Внутренний слой может наличествовать – штукатурка, может и отсутствовать. На деле редко встречаются блоки с любой готовой отделкой.
Арболит необходимо защищать от действия влаги, так как материал слишком хорошо ее впитывает. Чаще всего защитным слоем для стен из арболита выступает штукатурка, так как речь идет о конструкционном материале, у которого паропроницаемость ниже, чем у теплоизоляционного. Так что противоречий не возникает.
Внутренняя отделка стен из арболита никаких ограничений не имеет – от кафеля до обоев. Поскольку поверхность имеет высокую адгезию, то любая облицовка превосходно держится на стенах из арболита.
Следующий видеосюжет посвящен строительству стен из арболита:
Полы
Пол из арболита однозначного одобрения, судя по отзывам, не вызывает. Используется для этого монолитный арболит, который приходится либо делать самостоятельно, либо заказывать отдельно от блоков. Толщина слоя стяжки, как и слоя утепления достигает 10–15 см, что экономически не всегда оказывается выгодным.
Возможна укладка арболита на основание пола или для утепления на бетонную стяжку.
- В первом случае готовится цементно-песчаное основание и весьма тщательно: использование виброустановок обязательно. Затем укладывается арматура – ячейки 25*25 см, и заливается обычным бетоном. Проводится гидроизоляция – рубероидом или праймером, а затем заливается стяжка из арболита.
- На бетонное основание стяжка укладывается двухслойная: 7 см из арболита с большим содержанием щепы – теплоизоляционного, а последние 3 см – из более плотного деревобетона.
Такое устройство пола возможно только при высоких потолках. Про перекрытие из арболита читайте далее.
Перекрытие
Для перекрытий разработаны специальные комбинированные плиты, так как прочности арболита как такового явно недостаточно для изделия.
- Состоит плита из трех слоев: нижний из бетона марки М25 или М35 с арматурной сеткой, диаметром в 10–12 мм. Арматура предварительно напряжена, что заметно повышает надежность изделия. Средний слой состоит из теплоизоляционного арболита, а верхний – из бетона той же марки.
- Может быть и другой вариант, в котором из бетона состоит нижний слой и торцы плиты, перпендикулярные плоскости нижнего слоя. Такая плита дешевле и предупреждает неравномерное обжатие арболита во втором слое.
Выпускается плита длиной до 4,8 м. Однако для частного строительства судя по отзывам предпочтительнее плиты в 3,5 м.
О том, возможно ли сделать фундамент для дома из арболита своими руками, читайте ниже.
Более подробно о перекрытиях из опилкобетона расскажет это видео:
Строительство из арболита
Строительство из арболита только набирает обороты, этот строительный материал появился относительно недавно. Блоки из арболита позволяют подбирать практически любой участок под строительство. Даже при провале фундамента, на стене не появится трещина. Фундамент для дома может быть как ленточным, так и буронабивным. Стоимость строительства дома снижается, так как при использовании арболитовых блоков к фундаменту предъявляются минимальные требования. Цоколь необходимо делать не ниже 400-500 мм.
С помощью арболитовых блоков, можно строить не только одноэтажные дачные домики, но и двух- и трехэтажные дома. Толщина стен будет не больше 40 см. Кладка блоков из арболита напоминает сбор конструктора лего. Для строительства стен нужно сделать гидроизоляцию между стеной и фундаментом. При кладке обязательным условием надежности и стойкости стен является устранение мостиков холода.
Отзывы
Отзывы владельцев домов практически одинаковые и положительные, за исключением нескольких недовольных.
Артур, Смоленск: Отзыв мой положительный, потому что дачу поднял из монолитного арболита, сам вместе с семьей. Трудности были только при сооружении опалубки, много времени ушло. А вот с арболитом никаких проблем. Быстро сделали смесь в бетономешалке, быстро ее засыпали по месту. Дом получился теплым, прочным, нареканий никаких. Живем уже 5 лет.
Владимир, Омск: Прочитал года два назад в интернете, что строят из арболита дуплексы, дачи, многоэтажные коттеджи, много на этом строительстве экономя. Рисковать не стал, решил построить из этого материала гараж. Что могу сказать – стоит гараж полтора года, никаких проблем нет. Оштукатурил его с двух сторон и покрасил. Смотрится отлично.
Нюансы кладки арболитовых блоков
Используют два варианта работ. Первый, самый простой и популярный — монтажная пена. Второй — использование метода разрыва растворного шва по контуру арболитового блока. Для этого используют специальный планочки толщиной 12 мм. Цемент заливают между ними, выходит две полосы по бокам блока.
Для кладки идеальным будет не полностью сухой блок, а немного влажный. Блоки из арболита очень гигроскопичные, сухой блок при кладке вытягивает всю влагу из цементной смеси. Устройство перегородок не требует особый условий кладки.
Блоки из арболита можно подогнать по размеру и форме на месте строительства. Если заказывать на производстве подгонку размеров и формы, цена работы вырастет. Для того, чтобы придать желаемую форму достаточно камнерезной пилой разрезать облицовочную плитку, после этого блок можно подкорректировать бензопилой.
Утепление дома
Для утепления используется пенопласт, минеральная вата или целлюлозный утеплитель. Главное в доме из арболита утеплить пол, так как из него уходит больше половины тепла помещения. Для этого лучше использовать керамзит или минеральную вату, толщина которых не должна быть менее 15 см.
Потолок необходимо утеплять, если чердачное помещение не рассчитано для проживания, в ином случае теплоизоляция прокладывается на сваях крыши. Чтобы утеплить окна, щели заполняются герметиком, монтажной пеной или уплотнителем.
Арболит и влага
Из-за своей гигроскопичности, стены из арболитовых блоков необходимо защищать от сырости. Изнутри стены обшивают, снаружи облицовывают или штукатурят. Обязательно нужно прокладывать пароизоляционный материал между стеной из арболита и внутренней обшивкой. Между облицовкой снаружи и стеной надо оставлять свободное пространство. При использовании облицовочных арболитовых блоков, внешняя декоративная отделка будет не нужна. Стоимость строительства дома уменьшится.
Для строительства дома в Московской области арболитовые блоки — идеальный вариант, он экономный и надежный одновременно. Доверяйте строительство вашего дома только профессионалам. Результат вас приятно порадует.
Построить дом — одна из главных обязанностей мужчины (после этого посадить дерево и родить ребенка). Жить в собственном жилище мечтает каждый. Но, для этого придется приложить немало усилий, потратить определенную сумму денег и времени, особенно, если выполнять строительные работы самостоятельно. Другая проблема — выбор материала для строительства. На данный момент сырья для проведения работ настолько много, что можно сломать голову. Приходиться выбирать, анализируя плюсы и минусы материала, цели постройки здания, климат, располагаемые средства и т. д. Как показала практика, одним из лучших материалов для строительства жилого дома является арболит. Это практичный, легкий, долговечный, прочный и экологически чистый материал, который сделан на основе древесных опилок и портландцемента. Дома из арболитовых блоков отличаются своей энергоемкостью, ведь проводимость тепла арболита составляет 0,07-0,16, в зависимости от плотности. Жить в таком доме тепло и уютно.
В этой статье мы рассмотрим, как проходит строительство дома из арболитовых блоков, этапы выполнения работ своими руками и некоторые рекомендации по устройству фундамента и кладке стен. В статье присутствуют вспомогательные видео.
Создание фундамента
Арболит хорош еще и тем, что дом из него может быть установлен на любой вид фундамента, поскольку данный материал не дает трещин, если фундамент начнет вдруг проседать. Все дело в том, что стеновые блоки, выполненные из деревобетона, обладают большой степенью, так называемой, изгибной прочности. Такую прочность еще именуют «прочностью на излом». Это удивительное свойство арболита дает возможность использовать любой вид фундамента. В результате можно хорошо сэкономить на расходах, относящихся к сооружению фундамента. Если дом создается из деревобетона, то, как правило, для него выбирается фундамент, размещенный на буронабивных особых сваях. Неплохой альтернативой такому фундаменту является ленточная модификация.
В момент формирования фундамента необходимо помнить о минусах такого материала как деревобетон. Одним из таких минусов является плохая водоустойчивость. Поэтому при создании фундамента необходимо предусмотреть сооружение для него качественной гидроизоляции.
Гидроизоляция формируется следующими методами:
- Фундамент приподнимается над землей примерно на 1,5 метра;
- Создается подложка из кирпича, высота которой также равняется 1,5 метра.
Арболитные блоки необходимо размещать в известковом растворе, который перемешан с незначительным объемом цемента.
Мечтаете купить дом в Ялте? Узнайте цены на сайте dom-shop.org
Инструменты для выполнения работ
Вам не выполнить строительство дома без подходящих инструментов и материалов. Они должны быть подготовлены заранее и быть в исправном состоянии. Перечень следующий:
- лопата, камнерезная пила.
- уровень, рулетка, отвес;
- колья и длинная веревка;
- прутья арматуры Ø14 мм;
- емкость для раствора;
- мастерок, зубчатый шпатель или кельма для кладки блоков;
- резиновая киянка;
- леска, для выравнивания блоков.
Теперь можно приступать к строительству дома из арболитовых блоков.
Отделка дома
Отделка выполняет не только декоративную функцию, но и защитную, а именно, препятствует попаданию влаги внутрь стен. Отделка производится как внутри постройки, так и снаружи.
Важно! Арболитовые блоки имеют небольшую усадку, поэтому отделку можно выполнять сразу после завершения строительства.
Для отделки фасада подойдет вагонка, кирпич, сайдинг, штукатурка. При использовании вагонки или сайдинга необходимо обеспечить вентиляцию и гидроизоляцию.
Внутренняя отделка может выполняться из любого материала. Но если в помещении высокая влажность, то нужно позаботиться о качественной пароизоляции.
Приготовление раствора
Кладочный раствор должен обладать следующими параметрами: качество сцепления с поверхностью стены и достаточная прочность подготовленной консистенции. Ошибкой является добавление большого количества песка. Оптимальное сочетание цемента и песка показывает соотношение 1:3.
Чтобы на месте швов не было теплопотерь, необходимо добавить в раствор перлит. Это вещество сделает замес эластичным и позволит класть тонкие и ровные швы. Подмешивать добавку вместо песка нужно строго по инструкции.
Основные требования для хорошего раствора.
- Цемент смешивается с песком и перлитом в пропорциях 1:2:3. Важно не передержать последнюю добавку еще на стадии смешивания, иначе результатом станет «сворачивание» перлита в мелкие гранулы.
- Блоки должны быть хорошо увлажнены, чтобы более качественно проходил процесс адгезии с цементом.
- Смесь нужно делать погуще. При жидкой консистенции стройматериал будет давать постоянную «усадку». Это сделает невозможным дальнейшее выравнивание «по горизонту».
- Раствор наносят тонким слоем.
Увлажнив блоки, получается хорошая экономия на расходе раствора. Если замес выполнен правильно, то кладка будет с аккуратными швами.
Технология работы с разной густотой раствора
Если смесь получилась густая, то блоки укладываются плотно друг к другу «в прижим». Раствор должен хорошо заполнять промежутки. Выступившие на получившихся швах излишки нужно хорошо разровнять кельмой по плоскости ряда, растягивая смесь, в строну предыдущего блока.
Порядок действий:
- наносят слой раствора;
- устанавливают на него блок;
- выполняют силовой прижим к предыдущему;
- выравнивают блок относительно других и убирают выступивший раствор.
В случае жидкой смеси кладку делают «впритык». В этом случае швы заполняют не до конца. Прижимая рядом находящиеся элементы, получается естественное распределение раствора между соприкасаемыми стенками. Это позволяет добиться равномерных одинаковых швов. Остатки цемента нужно убрать с рабочего уровня кладки.
Независимо от вида смеси, с периодичностью в 2 ряда выполняют разделку швов. Процесс заключается в дополнительном нанесении и равномерном распределении цемента по швам. Эта процедура сделает более прочным скрепление блоков.
Будьте внимательны! Нужно постоянно контролировать правильность углов соединения стен и положение каждого ряда кладки. При этом, если раствор уже «схватился» с блоком, то перемещение делать запрещается.
Кладка первого ряда
Раскладка блоков и замер сторон дома
Перед кладкой первого ряда выполняют разметку мест примыкания перестенков к наружным стенам и дверных проемов. Для этого на поверхности цоколя делают соответствующую разметку из разложенных блоков. Выкладывая первый ряд без использования раствора. Это позволяет правильно определить длину стены и положение каждого элемента. Причём для перестенков материал кладется торцевыми частями.
Еще одним важным условием для работы будет температура воздуха. Показатель термометра не должен опускаться ниже отметки в +6° C.
Первыми закладываются углы дома. В случае если у нас дом 8*8 м берутся четыре угловых блока из арболита, которые впоследствии станут маяками для первого ряда. Первым устанавливают блок на раствор, начиная с наивысшего угла фундамента и от него выставляют остальные три. Совпадение горизонтального уровня контролируют водяным или лазерным уровнем. Для работы выбирают наиболее ровные блоки. После перепроверяем все углы, длину ширину наших стен, а также диагонали – они должны быть одинаковыми. Допускаются незначительные отклонения, но чем точнее будут выставлены наши крайние блоки и будет зависеть геометрическая точность всех стен.
По готовым углам дома натягивается строительный шнур. Это поможет избежать кривизны возводимой стены. Если нужно «подровнять» положение блока, то используют молоток с резиновой насадкой — киянку.
Выкладывая межугловые расстояния, приходится использовать доборные блоки. Арболит подрезают до нужных размеров ножовкой или болгаркой с диском для каменной резки. С трёх сторон его обмазывают раствором и укладывают в промежуток.
Готовый первый ряд обязательно проверяют уровнем!
Особенности монолитного строительства
Чтобы возвести монолитный дом, необходимо изучить технологию монтажа монолитных стен, а другие этапы строительства аналогичны процессу сооружения дома из блоков.
Технология возведения монолитных стен очень схожа с обычным бетонированием: также сооружается опалубка (высота – максимум 600 мм), производится армирование, заливается деревобетон слоем в 500 мм (не больше). После этого все утрамбовывается и сохнет в течение 3-4 дней. Затем опалубку поднимают вверх для того, чтобы залить следующий слой.
Дом из монолитного арболита в деталях – смотрите видео:
Кладка второго ряда
Установка и выравнивание блоков
Второй последующий ряд блоков также начинают с укладки угловых маяков. На этом этапе требуется соблюдение правила перевязки блоков — это когда вертикальные швы каждого рядя смещены половину относительно предыдущего. С каждым рядом перемещают натянутый строительный шнур. Этот способ перевязки рядов станет гарантией прочности стен. Такой же метод используется для образования стыков наружных и внутренних стен. Соответствие стыков наружных стен «прямому» углу можно проверять с помощью строительного деревянного угольника.
Кладка стен из арболитовых блоков | Рекомендации, цена
Рекомендации по кладке стен из арболитовых блоков
Кладка стен из Арболитовых блоков существенно экономит время строительства и обустройство дома. Крупные блоки позволяют возводить стены буквально за считанные дни. Кладка стен из Арболитовых блоков – отличный способ сэкономить на строительстве и, возможно, даже выполнить его своими силами:достаточно соблюдать технологию кладки, технологию приготовления растворов из перлитовой кладочной смеси , не забывать об армировании (при необходимости) , и обустройстве армопояса. Соблюдение вышеуказанных правил позволяет сэкономить не только время работы, но и существенно уменьшить стоимость работ по строительству:
- За счет отсутствия применения некоторых материалов
- За счет отсутствия некоторых обязательных работ, выполняемых при строительстве из других строительных материалов. (ниже в тексте будем отмечать Вашу выгода «Внимание!!! Экономия!!!»)
- Заказав арболитовые блоки у производителя заблаговременно зимой (в декабре-январе) , получите наиболее выгодную цену , а также сможете начать строительство рано весной , так как в данный период стоимость строительных работ ниже.
Технология возведения стен из Арболитовых блоков предельно проста, хотя требует определенных знаний. Основные требования – ровная кладка по уровням, использование перлитовой кладочной смеси , армирование конструкции.
Арболитовые блоки дают минимальную усадку ( 0,001%), обладают отличной теплоизоляцией за счет пористой структуры и, соответственно, малым весом по сравнению с монолитными бетонными конструкциями. Небольшой вес Арболитовых блоков существенно снижает нагрузку на фундамент по сравнению с кирпичным или монолитным строительством. (Внимание !!! Экономия!!) Более подробно про фундамент читайте в Разделе: «Фундамент»
Технология кладки из арболитовых блоков
Общие моменты и рекомендации по кладке стен из Арболитового блоков:
- Заранее подготовьте все материалы, инструменты, площадку работ. Храните материалы под полиэтиленом, чтобы из блоков не испарялась остаточная отпускная влажность, предусмотренная заводом при отгрузке Арболитовых блоков. Подготовительные работы – важный этап строительства.
- Используйте только готовую, теплую кладочную смесь ( ткс-02) , ТАК КАК В ЕГО СОСТАВЕ НЕ ТОЛЬКО ЦЕМЕНТ И ПЕРЛИТОВЫЙ ПЕСОК, НО И ОЧЕНЬ ВАЖНЫЕ промышленные пластификаторы, И ТОЛЬКО СОЧЕТАНИЕ НУЖНЫХ КОМПОНЕНТОВ В ПРАВИЛЬНЫХ ПРОПОРЦИЯХ ПРИСУТСТВУЮЩИХ В ГОТОВОЙ ЗАВОДСКОЙ СМЕСИ это гарантия НУЖНЫХ физических свойств (часто строители предлагают использовать только перлитовый песок, что не допустимо).
Теплая смесь, всегда лучше, чем цементный раствор по своим физическим свойствам. Средняя толщина цементного шва – около 1 см. На теплой кладочной смеси 5-6 мм, при условии укладки шпателем – гребенка с гребнем 8 – 10 мм. Кроме малой толщины шва к преимуществам использования теплой смеси, относится хорошая теплоизоляция, повышенная прочность и хорошая работа на изгиб. Чем тоньше шов, тем лучше общая теплоизоляция постройки.
- Не смешивайте клеевой состав и цементную смесь. Нельзя выполнить часть работы на теплой смеси, часть на цементе. Учитывайте разные физические свойства материалов.
- Производить армирование каждые 4 ряда необходимо, если у вас не предусмотрен армопояс или заливка монолитной плиты перекрытия . Армирование производят армирующей сеткой с толщиной прутка 3 -4 мм, укладывая сетку на блок с отступом от краев не менее 5см.
- При укладывании Арболитовых блоков в стену, необходимо выравнивать блоки, как по горизонтальному, так и вертикальному уровню.
Отклонение от уровня необходимо проверять в каждом ряду. Именно поэтому использование лазера оптимально.
- Особое внимание хотим уделить устройству оконных и дверных проемов. Все проемы монтируются на металлический, предварительно загрунтованный , уголок. Проемы до 2,5м монтируются на уголок 50 х50мм, с заходом на стену 30 – 40 см. Укладка блоков на уголки производят на предварительно подготовленные прорези на кладочной стороне блока. Уголки в блоке располагаем, углом внутрь, чтобы избежать «мостиков холода» и проблем при нанесении штукатурки. Данный вид обустройства перемычек является наиболее эффективным, в части выполнения отделочных работ, отсутсвия дополнительных затрат на бетон и арматуру плюс выполнения тех же самых работ по обустройству этих перемычек, теплосбережения (нет мостов холода), сопротивления нагрузки и, что не маловажно, стоимости. (Внимание!! Экономия!!)
- Перед укладкой первого ряда Арболитовых блоков на плиту или ленту фундамента, необходимо наклеить гидроизолирующий материал (гидростеклоизол).
Это делается для предотвращения возможности подтягивания влаги из материала фундамента. Важно: Арболитовый блок укладывается на гидроизоляцию и дополнительное обустройство первыми рядами из кирпича или других материалов не требуется, чтобы не создавать дополнительное место промерзания и не вкладывать дополнительные средства на строительство. (Внимание !!! Экономия!!!)
- Все стены, включая внутренние перегородки, возводятся одновременно. Это важный момент. Блоки внутренних перегородок кладутся в перевязку с внешними стенами , чтобы придать дополнительную жесткость конструкции дома.
- После монтажа стен из арболитовых блоков, в зависимости от существующего проекта идет строительство монолитного перекрытия 1 -2 этажа. Первым шагом, перед установкой опалубки монолита, готовим место его опирания на стены дома. Последний ряд блоков, в несущих стенах, по периметру строения выкладываем специальными «L» образными блоками, которые предназначены для создания утепления торца плиты со стороны улицы.
Наличие этого утепления обязательно, для того чтобы предотвратить промерзания плиты и наличия холодного пола. Также эти блоки применяются при устройстве армирующего пояса.
- После заливки и выдержки времени для набора прочности бетона, монолитного перекрытия, производим кладку стен второго этажа. Все технологические и монтажные операции выполняются точно так же, как и при строительстве первого этажа.
- Завершающим венцом кладки второго этажа, будет ряд блоков «L» образной формы, для строительства армирующего пояса. Это конструкция из арматуры д8 – д10мм, залитая бетоном. Обычно она выполняется в выемку «L» блока по всем несущим стенам дома для укрепления внешнего периметра от воздействий раздвигающих нагрузок кровли здания.
- Следующим этапом строительства после кладки стен идет обустройство кровли . Об этом читайте в следующей нашей статье
Использование отходов древесного волокна, золы рисовой шелухи и отходов известнякового порошка в качестве материалов, заменяющих цемент для блоков из легкого бетона
https://doi.
Highlights
- •
Изучено влияние частичной замены портландцемента на WFW, RHA и LPW.
- •
Взаимодействия переменных параметров имели большое значение для свойств.
- •
Увеличение содержания RHA привело к снижению объемной плотности блоков.
Abstract
В данной работе представлено параметрическое экспериментальное исследование, в котором исследуется влияние частичной замены портландцемента отходами древесного волокна (WFW), золой рисовой шелухи (RHA) и отходами порошкообразного известняка (LPW) для производства легкие бетонные блоки как строительный материал. Изучены некоторые механические и физические свойства блочных материалов, имеющих различные уровни WFW, RHA и LPW. Прочность бетонных блоков на сжатие из-за эффекта наполнителя уменьшалась с увеличением замены цемента.Тем не менее, результаты показывают, что эффект замены 25 % масс. RHA и LPW портландцементом не приводит к внезапному хрупкому разрушению даже после разрушающих нагрузок, указывает на высокую способность поглощения энергии, резко снижает удельный вес. Как и ожидалось, увеличение содержания RHA вызвало снижение объемной плотности бетонных блоков. Статистический анализ показал, что взаимодействие вышеупомянутых переменных параметров было значимым как для механических, так и для физических свойств при доверительном уровне 5%.Оптимальный уровень замены WFW, LPW и RHA составлял 25% по весу; этот процент замены привел к хорошим физико-механическим свойствам. Переработка WSW, RHA и LPW в качестве перспективной добавки к сырью представляется перспективным решением не только экологической проблемы, но и проблемы экономичного проектирования зданий.
Ключевые слова
Бетонный блок
Отходы древесного волокна
Зола рисовой шелухи
Известняковый порошок
Прочность на сжатие
Все права защищены.
Рекомендуемые статьи
Ссылки на статьи
Инновационные формы деревянных и цементных блоков формируются в Онтарио
Углеродно-нейтральный цементный продукт звучит как оксюморон, но это реальность с системой Insulated Concrete Form (ICF) от Nexcem.
Как и стироловые формы ICF, система Nexcem Durisol Build предназначена для использования в качестве блочной строительной системы для формирования стен, в которые заливается бетон.
Разница в том, что продукция Nexcem изготавливается из переработанной девственной древесины, полученной на предприятиях по производству ферм и измельченной до мелких частиц.
Эти частицы размером от 0,2 мм до 2 мм затем обрабатываются для удаления сахаров, естественно присущих древесине, для предотвращения образования плесени и отпугивания насекомых, которых может привлечь пищевая ценность.
«Кроме того, нам необходимо обеспечить сцепление древесины с цементом и отвердителями», — говорит основатель Nexcem Випул В. Ачарья, который столкнулся с этой концепцией во время исследований в Университете Ватерлоо.
Nexcem — это запатентованный арболитовый материал, изготовленный из цемента и связанного древесного волокна, а секретным соусом является формула и добавки, которые связывают материалы вместе.
«Наш ICF обладает лучшими климатическими и звукоизоляционными свойствами, не гниет и обладает многими другими преимуществами», — говорит Ачарья, отмечая, что этот процесс также отводит древесные отходы со свалки, что помогает сделать конечный продукт практически углеродно-нейтральным, несмотря на использование цемента.
«Углерод поглощается продуктом и запирается», — говорит он.
Durisol использовался в основном в жилищном строительстве, но начинает набирать обороты в проектах ICI.
«Мы построили школы для Школьного совета округа Торонто, Школьного совета Пила, а также для округа Веллингтон», — говорит он.
Конкуренция жесткая в Европе, где концепция распространена и существует много производителей, но в Северной Америке есть много возможностей, и он работает даже в Австралии.
Другие продукты Nexcem включают листы толщиной два дюйма на 24 дюйма на 48 дюймов, панельные изделия для крупных проектов и специальные предварительно вырезанные или собранные блоки для кирпичных уступов, подшипниковые блоки, блоки небольшой высоты и блоки перемычки.
Концепция родилась в Швейцарии, говорит он, когда в послевоенные годы в Европе возникла необходимость быстрого и эффективного восстановления.
«Сначала они просто укладывали блоки друг на друга, но проблема, которую они обнаружили, заключалась в том, что со временем у вас возникала ползучесть нагрузки, и стена, особенно если она несла нагрузку дома, начинала сжиматься и сжиматься», — говорит он. «Вместо того, чтобы отказаться от него, они залили отверстия бетоном, и конструкция стала гораздо более устойчивой».
Nexcem взял на вооружение эту идею и создал второе поколение с улучшенным составом смеси.
«Как и в любом МКФ, вам нужно запускать арматуру горизонтально и вертикально», — говорит он.«Но преимущество в том, что вы можете прикрутить его прямо к нему. Вам не нужны обвязки или пароизоляция внутри. Вы можете просто прикрутить гипсокартон прямо к нему. воздушный зазор, то можно ставить сайдинг.»
Цементный продукт также гигроскопичен, что означает, что он притягивает и удерживает влагу, а затем высвобождает ее, когда влажность падает.
«Мы устанавливаем изоляцию на внешней стороне, чтобы сохранить баланс внутренней стороны», — сказал он.
Блоки имеют толщину шесть дюймов и 14 дюймов, а коэффициент изоляции варьируется от R28 до R8 в зависимости от конфигурации.
По словам Ачарьи, несмотря на некоторые дополнительные затраты на материалы, в других областях есть выгода.
«Можно сказать, что ICF из пенополистирола стоит 4 доллара за квадратный фут, а мы — около 8 долларов», — говорит он. «Конечно, люди видят это и говорят, что это дорого. Но мы используем на 25 % меньше бетона, так что это сразу снижает затраты».
Durisol также допускает прямое крепление, потому что он более прочный.Он может быть проложен для прохождения инженерных сетей и приносит до 35 баллов LEED.
Влияние древесной золы в качестве частичного заменителя цемента при изготовлении древесно-цементных панелей
Материалы (Базель). 2019 сен; 12(17): 2766.
Viet-Anh Vu
1 Департамент древесины и лесоведения, Университет Лаваля, Квебек, QC G1V 0A6, Канада
Ален Клотье
1 , Laval University, Quebec, QC G1V 0A6, Canada
Benoit Bissonnette
2 Факультет гражданского строительства, Laval University, Quebec, QC G1V 0A6, Canada
Pierre Blanchet
1 , Университет Лаваля, Квебек, QC G1V 0A6, Канада
Жозе Дюшен
3 Факультет геологии и инженерной геологии, Университет Лаваля, Квебек, QC G1V 0A6, Канада
1 Департамент лесных и лесных наук Лаваля Университет, Квебек, QC G1V 0A6, Канада
2 Департамент гражданского строительства, Университет Лаваля, Квебек, QC G1V 0A6, Канада
3 Департамент геологии и геологии ological Engineering, Laval University, Quebec, QC G1V 0A6, Canada
Поступила в редакцию 9 августа 2019 г. ; Принято 23 августа 2019 г.
Abstract
Целью данного исследования было рассмотрение использования древесной золы из биомассы в качестве частичной замены цементного материала в древесно-цементно-стружечных плитах. Древесно-цементно-зольные плиты (WCAP) были изготовлены из 10%, 20%, 30%, 40% и 50% древесной золы в качестве частичной замены цемента древесными частицами и испытаны на прочность на изгиб, жесткость, водопоглощение, и термические свойства.Результаты испытаний показывают, что водопотребность увеличивается с увеличением зольности, а механические свойства несколько снижаются с увеличением зольности до 30% замены. С другой стороны, теплоемкость увеличивается с увеличением содержания древесной золы. WCAP может способствовать снижению скорости теплопотерь стен зданий, учитывая их относительно низкую теплопроводность по сравнению с гипсокартонными плитами. Было обнаружено, что замена цемента в количестве приблизительно 30% по массе дает оптимальные результаты.
Ключевые слова: биомасса, древесная зола, фиброцемент, прочность, раствор
1. Введение
Фиброцементные панели уже давно присутствуют на рынке. Первоначально в качестве армирующего материала использовался асбест, но из-за опасности для здоровья в 1980-х годах его заменили целлюлозой. В настоящее время эти панели используются в качестве наружного сайдинга, кровельной черепицы и черепицы для наружных работ. Древесно-цементно-стружечная плита имеет ряд преимуществ, так как она устойчива к термитам, не гниет, ударопрочна, обладает огнеупорными свойствами.Однако проведенные исследования совместимости древесины с цементом [1,2,3] показывают, что не все породы одинаково подходят для изготовления древесно-цементных плит. Породы хвойных пород на самом деле демонстрируют наибольший потенциал для этого типа применения. Результаты Tittelein et al. [4] показывают, что можно изготавливать древесно-цементные плиты низкой плотности (удельный вес около 0,7) с лучшими свойствами на изгиб, чем гипсокартонные плиты, и сопротивлением выдергиванию шурупа в 1,7 раза выше. Кроме того, эти панели можно резать ножом так же, как и гипсокартонные листы. Поэтому процесс установки панели по сути такой же. Благодаря высокой пористости теплопроводность древесно-цементных плит примерно в три раза ниже, чем у гипсокартона.
Забота об окружающей среде и экономическое давление являются одними из движущих сил современного промышленного развития. Поэтому во всем мире проводится несколько исследовательских проектов по использованию отходов для снижения угроз окружающей среде и оптимизации существующих методов удаления и переработки отходов, делая их более доступными [5].
Производство рядового портландцемента (ОПЦ) занимает третье место в мире среди производителей техногенного СО 2 после транспорта и энергетики. Выбросы CO 2 цементной промышленностью составляют 5–7 % от общемировых выбросов CO 2 в результате сжигания топлива и промышленной деятельности [6]. Использование добавок и заменителей OPC до сих пор было одним из наиболее успешных решений для снижения выбросов CO 2 , образующихся при производстве цемента.
Зола древесная (WA) образуется при сжигании древесины в бытовых дровяных печах или на промышленных электростанциях. В конце 80-х годов в провинции Квебек, Канада, целлюлозно-бумажной промышленностью ежегодно производилось около 45 000 тонн древесной золы [7]. В 2006 году производилось более 300 000 тонн древесной золы в год, две трети из которых поступали от целлюлозно-бумажных комбинатов, а остальная часть — от ТЭЦ, лесопильных заводов и других предприятий, связанных с деревообработкой. Химические характеристики WA различаются в зависимости от породы древесины, но в основном она содержит известь и кремнезем [8].Производство золы, вероятно, будет расширяться с ростом интереса к биоэнергетике.
В 2007 г. в Квебеке в качестве удобрений было использовано 150 000 тонн остаточной золы [9]. Большая часть остаточной золы (54%) использовалась в сельском хозяйстве. Остальное использовалось для восстановления растительности на деградированных участках, производства почвенных смесей, компостирования и других целей. Половина ежегодно производимого ресурса древесной золы по-прежнему вывозится на свалки [9]. При соблюдении благоприятных условий древесная зола может иметь некоторый пуццолановый потенциал, который можно использовать в системах на основе портландцемента.
В нескольких исследованиях изучалась пригодность древесной золы в качестве дополнительного вяжущего материала при производстве обычных и самоуплотняющихся бетонов. Субраманиам [10] сообщил об оптимальной дозировке древесной золы 15% при замене цемента (по массе) для производства бетона, имеющего достаточно высокую прочность на сжатие для литья блоков. Абдуллади [11] нашел оптимальную норму возмещения 20% и показал, что потребность в воде увеличивается с увеличением содержания древесной золы.Чоудхури и др. [12] охарактеризовали механическую прочность (на сжатие, растяжение и изгиб) бетона с древесной золой. Присутствие основного пуццоланового соединения (в соответствии с требованиями стандарта ASTM C618-15), содержание частиц малого размера и большая площадь поверхности частиц квалифицируют древесную золу, исследуемую в их исследовании, как пуццолановый материал.
Целью настоящего исследования была оценка физических, тепловых и механических свойств древесно-цементных плит, изготовленных с использованием древесной золы в качестве дополнительного вяжущего материала.
2. Материалы и методы
2.1. Материалы
В качестве основного вяжущего использовался обычный портландцемент CSA (Канадская ассоциация стандартов) типа 10 (GU, общего назначения).
Древесная зола, выбранная для исследования, поступала с теплоэлектроцентрали «La Cité Verte», жилого комплекса в Квебеке, Квебек, Канада.
Древесно-цементные смеси были приготовлены из высушенной на воздухе древесной щепы, полученной из белой ели ( Picea glauca (Moench), Восс, Норвегия), заготовленной в исследовательском лесу Петавава в Маттаве (Онтарио), Канада.Древесную щепу рафинировали в кольцевом рафинере Pallmann PSKM8-400 (Ludwig Pallmann K.G, Zweibrücken, Germany). Поступившие частицы просеивали, а частицы размером от 1 до 3 мм оставляли.
2.
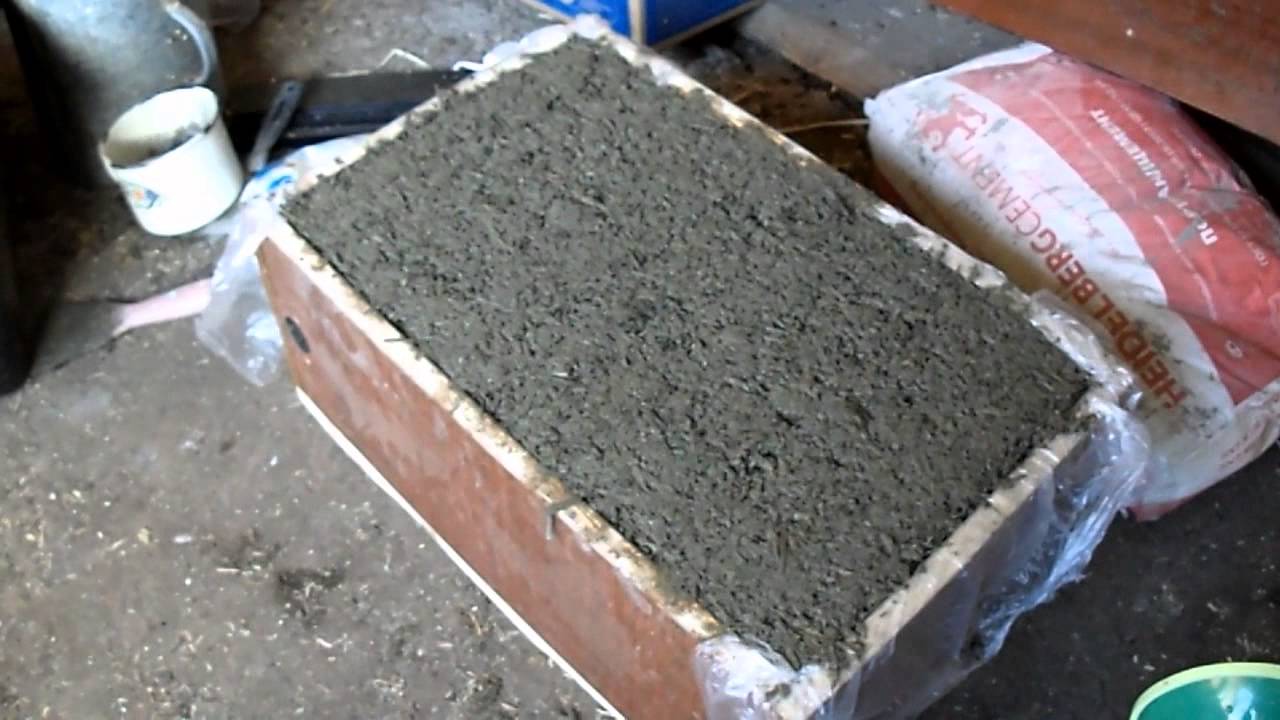
Все смеси древесно-цементных плит были приготовлены с соотношением древесины и вяжущего 0,35 по массе, где вяжущей фазой является сумма цемента и древесной золы. В общей сложности было исследовано шесть смесей, переменными по существу были доли цемента, замещенные древесной золой.Оценка смесей с различным процентным содержанием древесной золы была направлена на определение максимального количества древесной золы, которое можно было бы использовать без существенного влияния на свойства материала по сравнению со свойствами эталонной древесно-цементной смеси. Соответствующие смеси обозначены как P0, P1, P2, P3, P4 и P5 соответственно. Контрольная смесь (П0) была приготовлена только из цемента и древесных частиц, тогда как смеси П1, П2, П3, П4 и П5 были приготовлены с включением древесной золы в качестве частичной замены цемента в количестве 10%, 20%, 30%. %, 40% и 50% соответственно.
Было замечено, что последовательность смешивания оказывает решающее влияние на реологию материала, при этом небольшие изменения значительно изменяют поведение свежей смеси. Последовательность смешивания, сохраненная после предварительных испытаний, представлена на рис.
Таблица 1 9009
Шаг Шаг Смеситель скорость ротора (RPM) Совокупное время (ы) 1. Добавление цемента и дерева Ash 140 0 9 .Дополнение воды 140 60208 60 3.
Дополнение дерева частицы 140 120 4. Изменение скорости 285 180 5. Конец смешивания 0 270 Непосредственно после смешивания удобоукладываемость каждой смеси определяли с помощью теста на осадку в соответствии со стандартом ASTM C143/C143M-15a [13].
2.3. Подготовка образцов для испытаний
После смешивания в растворомешалке (HOBART A-120, Hobart Canada Inc, Дон Миллс, Онтарио, Канада) каждую смесь древесины, цемента, золы и воды заливали в деревянную форму размером 450 × 330 × 15 мм.
плесень.После заливки смеси форму закрывали крышкой, удерживаемой С-образными зажимами. Эта установка позволяла заливать материал толщиной до 15 мм. Влажную смесь залили в форму, поверхность выровняли деревянной стяжкой и окончательно закрепили крышку. От давления крышки толщина панели уменьшилась до 14 мм. Затвердевшие панели вынимали из формы в возрасте 3 дней и затем хранили в камере кондиционирования при температуре 23 °C и относительной влажности 60%.Различные образцы для испытаний вырезали из панелей (по 3 панели на смесь) в день испытаний.
2.4. Методы испытаний
Панели были отверждены и протестированы для определения их механических характеристик через 3, 7 и 28 дней отверждения в соответствии со стандартом ASTM D 1037-12 [14]. Модуль упругости при изгибе (MOR) и модуль упругости (MOE) определяли в одном и том же возрасте с помощью универсальных испытательных рам MTS QTest-5 (корпорация MTS systems, Иден-Прери, Миннесота, США) с использованием модульной системы управления Elite.
Сопротивление выкручиванию винта, водопоглощение и набухание по толщине также были испытаны в соответствии со стандартом ASTM D 1037-12 [14]. Тепловые свойства древесно-цементных плит измеряли с помощью измерителя теплового потока FOX 314 (TA tools-LaserComp Inc, Уэйкфилд, Массачусетс, США) в соответствии со стандартом ASTM C518 [15]. Плата помещалась между двумя пластинами при регулируемой температуре и с каждой стороны к ней приклеивался флюсометр, чтобы можно было измерять температуру и тепловой поток на поверхности платы, которая может подвергаться температурным колебаниям.По этим четырем параметрам (двум температурам и двум тепловым потокам) можно рассчитать теплоемкость и теплопроводность. Растворимость WA оценивали по потере массы 15 г WA, помещенных в 100 мл дистиллированной воды и перемешиваемых в течение часа при 23 °C. Остаток затем фильтруют под вакуумом и промывают дистиллированной водой. Остаток WA помещают в печь на ночь, затем измеряют потерю массы. Растворимая доля соответствует средней потере массы образцов деревьев.
Наконец, твердые образцы исследовали под сканирующим электронным микроскопом JEOL JSM-840A (JEOL USA Inc, Пибоди, Массачусетс, США) (SEM), оснащенным системой энергодисперсионного рентгеновского анализа (EDS). Для наблюдений с помощью СЭМ образцы крепились целыми на двухстороннюю клейкую ленту и покрывались тонким сплавом Au-Pd. Условия эксплуатации были установлены на уровне 15 кВ.
3. Результаты
3.1. Характеристика материала
3.1.1. Древесные частицы
Распределение частиц древесины по размерам оценивали с использованием сит пяти размеров: 1.19, 1,4, 1,7, 2,38, 2,8 и 3 мм. По результатам, приведенным в , 100 % частиц были размером менее 3 мм, а наибольшую массовую долю (57 %) составляют частицы диаметром 1,7 мм.
Гранулометрический состав древесных частиц.
3.1.2. Древесная зола
Анализ размера и формы частиц
Анализ формы с помощью сканирующей электронной микроскопии показал, что частицы золы имеют неправильную форму и сферическую форму (b).
Древесная зола подходит для использования в качестве наполнителя/частичной замены цемента в бетоне с высокими эксплуатационными характеристиками благодаря усиленному эффекту «шариковой опоры», создаваемому сферической формой WA.Эффект «подшипника» древесной золы создает смазывающий эффект, когда бетон находится в пластическом состоянии. Согласно результатам, представленным на рис. , значения D10, D50 и D90 WA составили 2,5, 18,5 и 114,1 мкм соответственно. Древесная зола содержит количество ультрадисперсных частиц 18 % (диаметр частиц ϕ < 5 мкм).
Сканирующая электронная микроскопия древесной золы (WA) при малом увеличении ( a ) и при большом увеличении ( b ).
Анализ размера частиц WA.
Химический состав
Результаты химического анализа исследуемой древесной золы приведены в .Установлено суммарное содержание в оксиде железа (Fe 2 O 3 = 1,22 %), оксиде алюминия (Al 2 O 3 = 2,25 %) и диоксиде кремния (SiO 2 = 7,80 %).
составляет 11,27 %, что значительно меньше минимального количества, необходимого для отнесения материала к пуццолану, установленного на уровне 70 % [16].
Таблица 2
Физико-химические свойства древесной золы.
Свойства Значение Химический состав (%) Условные параметры SiO 2 7.80 Органический материал (мг / кг) <10 OL 2 O 3 3 2 9 PH 13 Fe 2 O 3 1.
22 MgO 7,47 Физические свойства CaO 46,70 Плотность (кг/м 3 ) 2970 Na 2 O 9086 Удельная поверхность (м 2 /кг) 261 K 2 O 9,61 TiO 2 0,11 MnO 4,51 P 2 O 5 2,34 Cr 2 O 3 <0.
01 В 2 О 5 <0,01 ZrO 2 <0,02 ZnO 0,04 Потери при прокаливании 14,20
Зарегистрированные потери при прокаливании при 950°С составили 14,2%, что превышает максимальное требование для пуццоланов в 12% [16].
Это означает, что зола содержит значительное количество несгоревшего углерода, что снижает ее пуццолановую активность. Было обнаружено, что содержание щелочи (%Na 2 O + 0,658 × %K 2 O) составляет 7,18%, что превышает максимальное содержание щелочи в 1,5%, необходимое для пуццолана. Удельный вес древесной золы оказался равным 2,97, что намного меньше плотности портландцемента (3,15). WA содержит более 99% (по весу) неорганического материала и дает пористый раствор с высоким pH.
Тест на растворимость
показывает процент древесной золы, растворенной в воде во время теста на растворимость. Растворимость WA оценивается в 7%, включая известь и гидроксиды щелочных металлов, которые хорошо растворяются в воде в лабораторных условиях. Этот растворимый компонент играет важную роль в реакции гидратации.
Таблица 3
Испытание на растворимость древесной золы в воде.
14.
10 0.90 0.90 6.30 9 15.00 1.20 80209 3 3 14.30 0.30 Среднее 6,90
3.
2. Изменение плотности

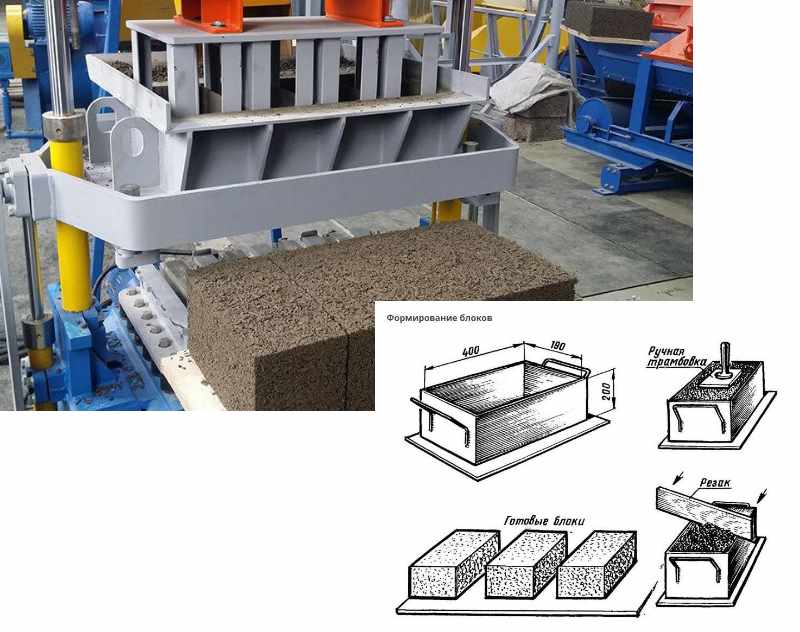
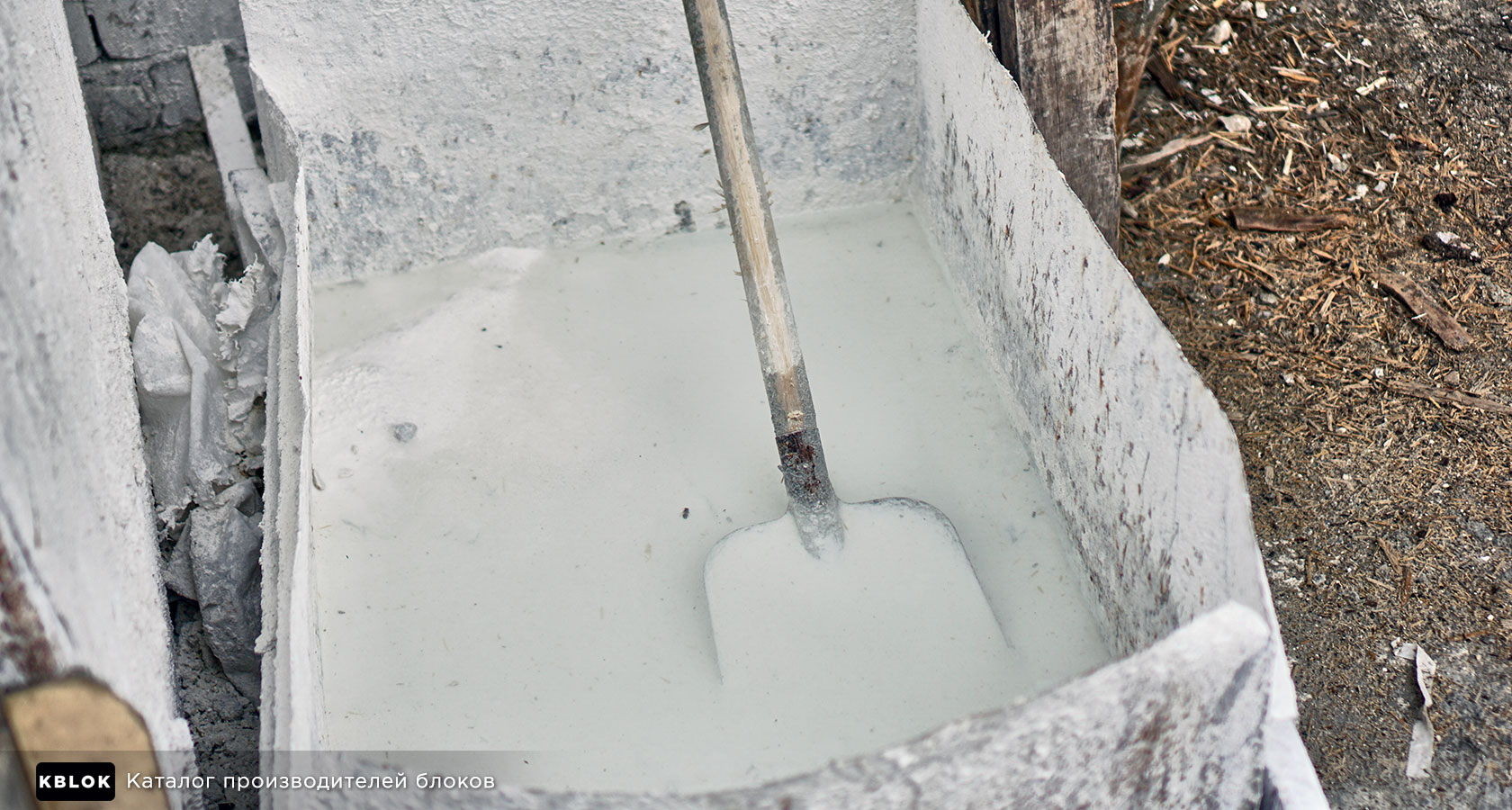

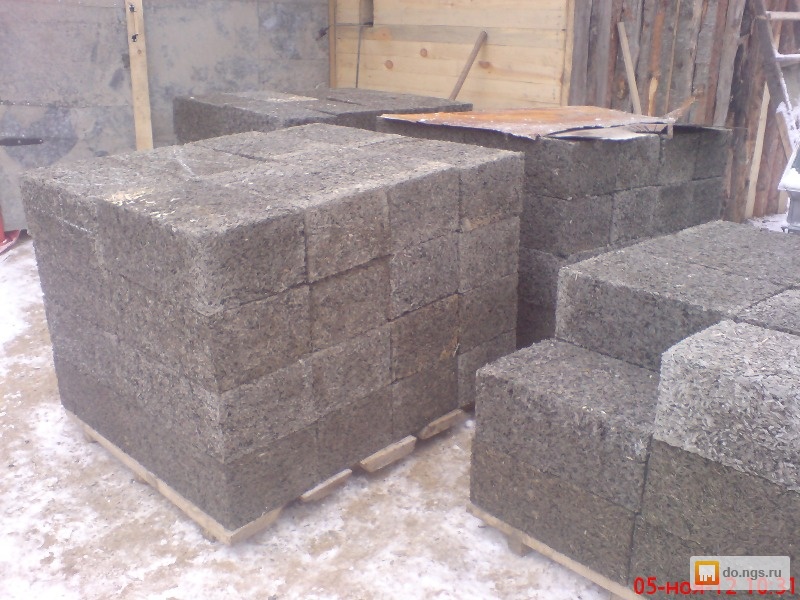


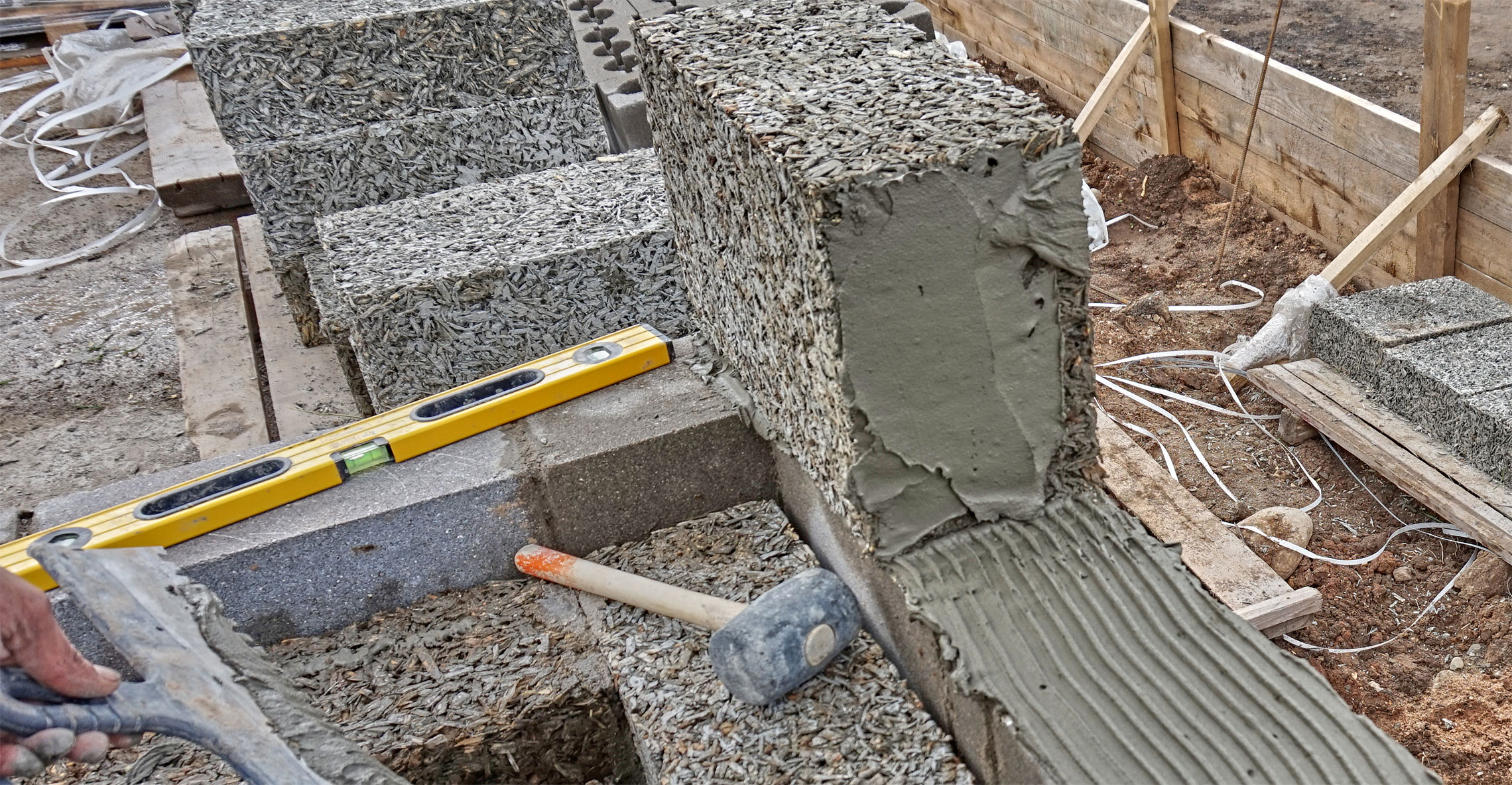
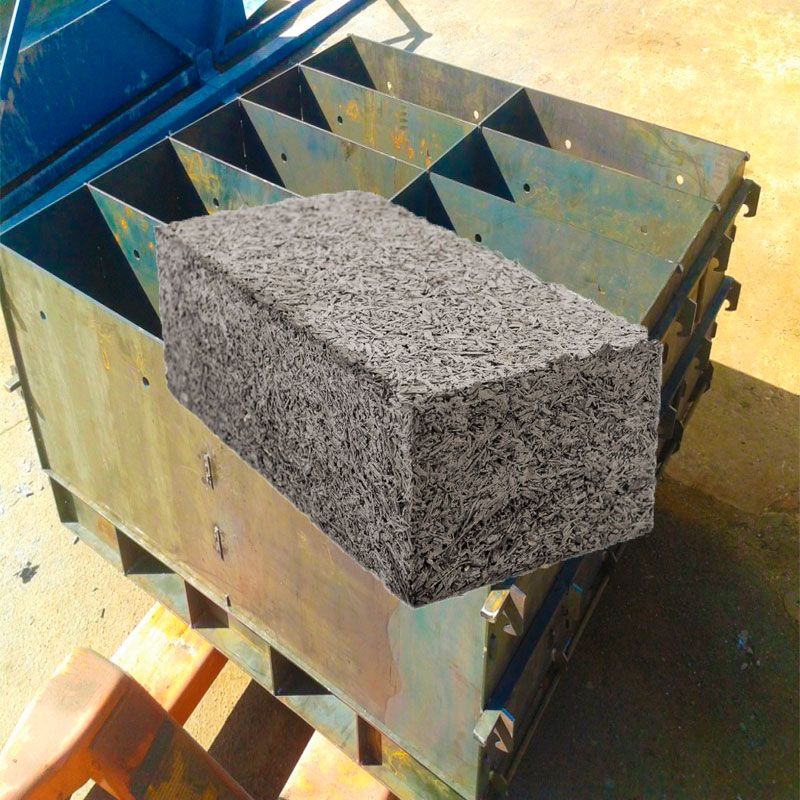
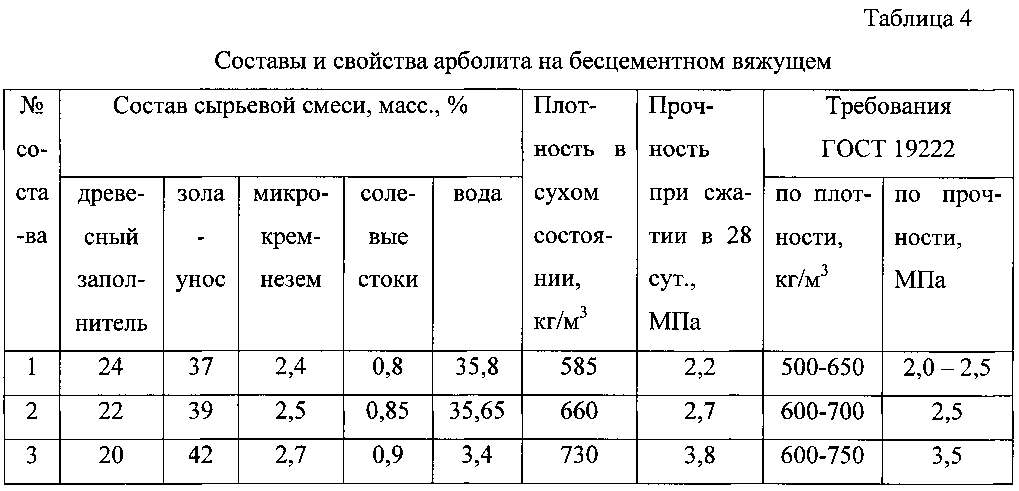
Вес всех панелей регистрировали в начале и в конце периода отверждения (3 дня в форме) для определения изменений удельного веса панелей.За этот период он уменьшился примерно на 5% из-за того, что используемая форма не была абсолютно водонепроницаемой. Часть воды, вероятно, впитала сама форма, так как она была сделана из фанеры.
Масса панели вышла на плато примерно через 6 дней после извлечения из формы, что означает, что к тому времени большая часть свободной воды в цементном тесте испарилась в камере кондиционирования при температуре 23 °C и относительной влажности 60%.
3.3. Работоспособность
показывает результаты, полученные для теста на согласованность.Результаты показывают, что потребность в воде увеличивается с увеличением содержания древесной золы. Древесная зола, введенная в цемент, увеличила содержание углерода, тем самым увеличив количество воды, необходимое для достижения удовлетворительной удобоукладываемости.
Таблица 4
Результаты испытаний на совместимость.
Массовое соотношение | P0 | P1 | P2 | P3 | P3 | P4 | P5 | P5 | ||||||||||||||||||||||||||||||||||||||||||||||||||||||||||||||||||||||||||||||||||||||||||||||||||||||||||||||||||||||||||
---|---|---|---|---|---|---|---|---|---|---|---|---|---|---|---|---|---|---|---|---|---|---|---|---|---|---|---|---|---|---|---|---|---|---|---|---|---|---|---|---|---|---|---|---|---|---|---|---|---|---|---|---|---|---|---|---|---|---|---|---|---|---|---|---|---|---|---|---|---|---|---|---|---|---|---|---|---|---|---|---|---|---|---|---|---|---|---|---|---|---|---|---|---|---|---|---|---|---|---|---|---|---|---|---|---|---|---|---|---|---|---|---|---|---|---|---|---|---|---|---|---|---|---|---|---|---|---|---|---|---|
Древесовая зола / цемент | 0.00 | 0,10 | 0,20 | 0,30 | 0,40 | 0,50 | ||||||||||||||||||||||||||||||||||||||||||||||||||||||||||||||||||||||||||||||||||||||||||||||||||||||||||||||||||||||||||||
Wood / Binder | 0,35 | 0,35 | 0,35 | 0,35 | 0,35 | 0,35 | ||||||||||||||||||||||||||||||||||||||||||||||||||||||||||||||||||||||||||||||||||||||||||||||||||||||||||||||||||||||||||||
Вода / Binder | 3.![]() Как описано выше, панели испытывали на изгиб через 3, 7 и 28 дней после изготовления.Каждое испытание проводилось на трех образцах, среднее значение представлено в . Таблица 5Средние результаты испытаний на изгиб древесно-цементно-зольных плит (WCAP). Средние значения с одним и тем же верхним индексом существенно не различаются для p = 0,05; стандартное отклонение указано в скобках.
и показать поведение на изгиб WCAP при разном времени отверждения. Это показывает, что значения прочности на изгиб и жесткости образцов панелей увеличиваются со временем отверждения. Они мало изменились через 7 дней отверждения, что обычно наблюдается для материалов на основе портландцемента. Результаты статистического анализа показали, что существует достоверная разница между образцами по показателям прочности на изгиб и жесткости на всех стадиях твердения (3 дня твердения: p < 0.001, 7 дней отверждения: p < 0,001, 28 дней отверждения: p < 0,05). Прочность на изгиб и жесткость P4 и P5 были значительно ниже, чем у других панелей на всех стадиях отверждения. Оптимальная прочность на изгиб, наблюдаемая в этих испытаниях, была получена при замене 30% древесной золы (P3) после 28 дней влажного отверждения. Изменение модуля прочности при изгибе WCAP в зависимости от продолжительности отверждения во влажном состоянии. 3.5. Сопротивление отвинчиваниюпоказывает сопротивление отвинчиванию WCAP в зависимости от содержания WA.Это показывает, что сопротивление извлечению винта уменьшается по мере увеличения скорости замены WA. Результаты статистического анализа показывают, что сопротивление вытягиванию шурупа незначительно изменяется до коэффициента замещения 30% древесной золы. Однако выше этого значения он быстро уменьшается. Влияние степени замещения древесной золы на сопротивление вытягиванию шнека WCAP (средние значения с одним и тем же верхним индексом существенно не отличаются для p = 0,05; стандартное отклонение указано в скобках). 3.6. Водопоглощение Результаты испытаний на водопоглощение показаны на . Величина водопоглощения увеличивается с увеличением процента замены WA и времени погружения в воду. показывает, что набухание WCAP по толщине в воде невелико (<2%). Согласно результатам, водопоглощение всех плит с древесной золой выше, чем у контрольного образца через 28 дней выдержки. Водопоглощение и набухание по толщине WCAP зарегистрированы в зависимости от содержания WA. Таблица 6Среднее водопоглощение и набухание WCAP в зависимости от содержания WA.
Thermal Properties показывает результаты испытаний теплоемкости и теплопроводности WCAP. Таблица 7Средние тепловые свойства и плотность WCAP в зависимости от содержания WA.
|

Согласно результатам, показанным на , между двумя образцами нет четких различий в микроструктуре. Оба они обладают низкой пористостью и размером пор менее 10 мкм. Появление сферических частиц, имеющих форму WA, можно наблюдать на b, как показано белыми стрелками.
Сканирующая электронная микроскопия контрольного цемента ( a ) и цемента + 30% WA ( b ).
4. Обсуждение
Хотя исследуемая древесная зола не относится к пуццолану, ее можно использовать для замены цемента в значительных количествах без существенного влияния на физико-механические свойства древесно-цементных плит.В предыдущих исследованиях сообщалось о максимальных долях древесной золы порядка 15–20 % [10,11]. По сравнению с контрольным образцом (P0), WCAP, приготовленный с использованием 30% древесной золы вместо цемента (P3), показал умеренное снижение механических свойств на 10% для MOR на изгиб и на 21% для сопротивления выдергиванию винта. Значение pH увеличивается с гидратацией цемента. Высокощелочной раствор способствует реакционной способности кремнезема, присутствующего в WA, что усиливает пуццолановую активность на начальной стадии.Повышенный уровень pH способствует образованию водного кремнезема. Это соединение реагирует с ионами Ca 2+ с образованием нерастворимых соединений, которые являются вторичными цементирующими продуктами [10]. Кроме того, WA может выступать в качестве наполнителя в смесях.
Установлено, что плотность образцов уменьшается по мере увеличения скорости замещения WA из-за несколько меньшей плотности золы и, что наиболее важно, повышенного количества воды ( и ). В результате большего объема капиллярных пор механические и физические свойства, в том числе плотность, ухудшаются.Действительно, водопоглощение значительно увеличилось при замене 30% WA. Это можно объяснить меньшим количеством частиц цемента при увеличении содержания древесной золы. Поэтому реакция гидратации была снижена, а вода быстро испарялась в пористой среде с высокой пористостью из-за присутствия древесных волокон.
Часть золы около 7% растворяется в воде и способствует процессу гидратации. Большая площадь поверхности, связанная с частицами золы, также может быть фактором, поскольку она в некоторой степени действует как центры зародышеобразования для гидратации цемента.Действительно, на основании СЭМ-исследования не было обнаружено существенной разницы в микроструктуре смеси чистого цемента и смеси, содержащей 30% WA взамен, обе демонстрируют плотную и однородную микроструктуру.
Увеличение теплоемкости WCAP после замены цемента древесной золой показало, что он может снизить теплопотери стен зданий благодаря улучшенной изоляции, которую он обеспечивает. Действительно, WCAP имеет низкую теплопроводность, примерно в три раза ниже, чем у гипсокартона (0,0.32 Вт/м·К) [4]. Эта низкая теплопроводность в основном связана с более высокой пористостью WCAP по сравнению с пористостью гипса, поскольку теплопроводность пустых пустот очень низкая (около 0,025 Вт/м·К).
5. Выводы
В данном проекте изучались физические, термические и механические свойства древесно-цементных плит с добавлением древесной золы. Было обнаружено, что древесная зола обладает прекрасным потенциалом для частичной замены портландцемента. На основании результатов, полученных в этом исследовании, оптимальная степень замещения составляет около 30% по весу.На этом уровне замены инженерные свойства WPCA были умеренно снижены (MOR на изгиб на 12 %, MOE на изгиб на 20 %, сопротивление вытягиванию шурупа на 21 %) по сравнению с чистым контрольным образцом из древесного цемента. При замене на 30 % механические и физические свойства начинают снижаться со значительно большей скоростью (MOR на изгиб на 43 %, MOE на изгиб на 41 % и сопротивление извлечению винта на 60 % при частоте замены 40 %). Применение древесной золы повышает теплоемкость ВКУП на 11 % по сравнению с чистым древесно-цементным контрольным образцом.
Описанная здесь работа является весьма перспективной с точки зрения производства экологически чистых древесно-цементных панелей с улучшенными характеристиками по сравнению со стандартными гипсокартонными плитами. Будущая работа должна включать измерение огнестойкости и акустических свойств этого материала. Состав и технологические этапы также могут быть усовершенствованы. В частности, следует изучить использование бумажного поверхностного слоя для улучшения механических свойств панели.
Благодарности
Авторы также благодарны промышленным партнерам Промышленной кафедры NSERC по экологически ответственному деревянному строительству (CIRCERB) и страховой компании SSQ за предоставление древесной золы из «La Cité Verte».
Вклад авторов
Концептуализация, В.-А.В., А.С., Б.Б. и П.Б.; Курирование данных, В.-А.В.; Формальный анализ, В.-А.В.; Приобретение финансирования, PB; Следствие, В.-А.В., А.С., Б.Б., П.Б. и Джей Ди; Методика, В.-А.В., А.С., Б.Б., П.Б. и Джей Ди; Администрация проекта, AC и PB; Надзор, AC и BB; Валидация, A.C., B.B., P.B. и Джей Ди; Написание — первоначальный вариант, В.-А.В.; Написание — обзор и редактирование, A.C., BB, P.B. и JD
Финансирование
Эта работа является частью исследовательской программы Совета по естественным наукам и инженерным исследованиям Канады (NSERC) кафедры промышленных исследований экостроительства из дерева (CIRCERB) в рамках программ IRC (IRCPJ 461745-12) и CRD (RDCPJ 445200-12).
Конфликт интересов
Авторы заявляют об отсутствии конфликта интересов.
Литература
1. Соват Н., Селл Р., Мугель Э., Зулалян А. Изучение гидратации обычного портландцемента древесиной методом изотермической калориметрии. Хольцфоршунг. 1999; 53: 104–108. doi: 10.1515/HF.1999.016. [Перекрестная ссылка] [Академия Google]2. Ша В., О’Нил Э., Го З. Исследование обычного портландцемента методом дифференциальной сканирующей калориметрии. Цем. Конкр. Рез. 1999; 29: 1487–1489. doi: 10.1016/S0008-8846(99)00128-3.[Перекрестная ссылка] [Академия Google]3. Морис Д., Клотье А., Бернар Р. Совместимость древесины и цемента некоторых лесов Восточной Канады с помощью изотермической калориметрии. За. Произв. Дж. 2004; 10:49. [Google Академия]4. Тителейн П., Клотье А., Биссоннетт Б. Проектирование древесно-цементно-стружечной плиты низкой плотности для внутренней отделки стен. Цем. Конкр. Композиции 2012; 34: 218–222. doi: 10.1016/j.cemconcomp.2011.09.020. [Перекрестная ссылка] [Академия Google]5.
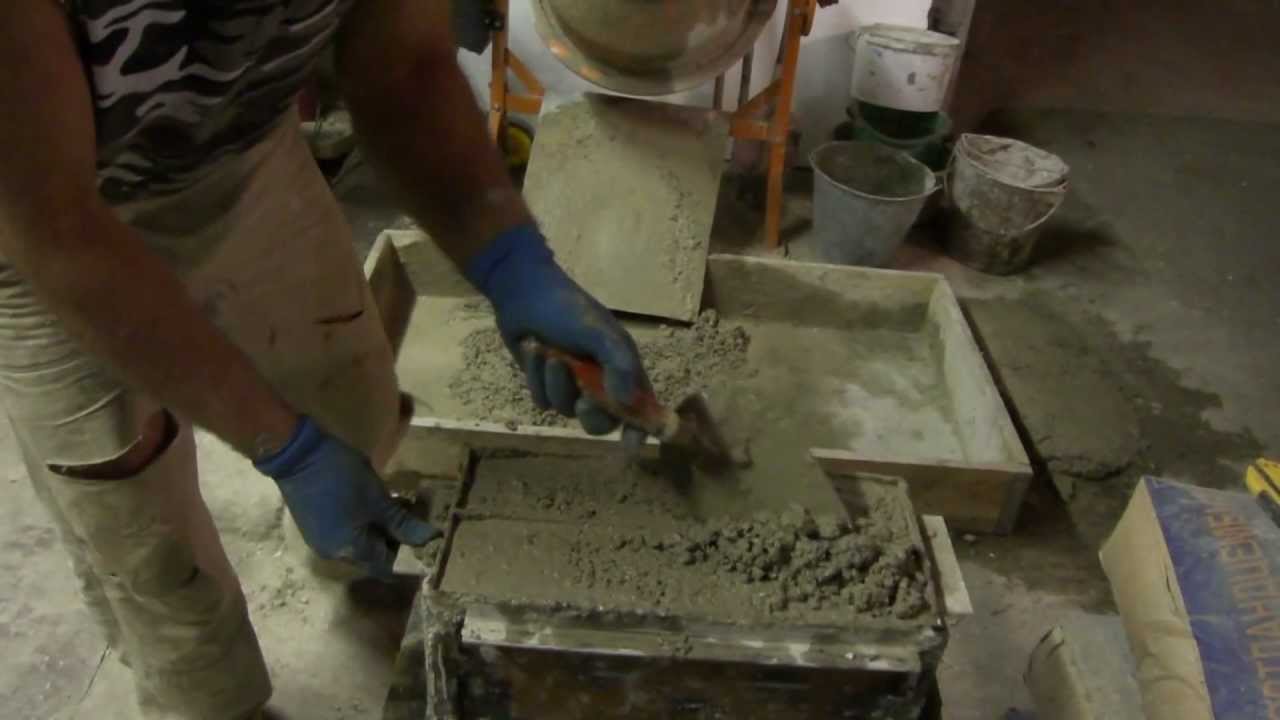

Древесные отходы делают переработанный бетон прочнее, чем когда-либо
Производство цемента, используемого в бетоне, является огромным источником выбросов CO2, поэтому чем больше мы можем переработать существующий бетон, тем лучше. Вот тут-то и появляется новое исследование, которое указывает на то, что выброшенный бетон становится еще прочнее, чем был раньше, когда в него добавляют древесные отходы.
Бетон производится путем смешивания заполнителя, такого как гравий, с водой и цементом. Как только смесь затвердевает, цемент затвердевает и связывается с заполнителем, образуя твердый блок материала.
Под руководством зам. Профессор Юя Сакаи, ученые из Токийского университета, измельчили куски такого бетона в порошок, затем добавили воду вместе с лигнином, полученным из древесных отходов. Лигнин представляет собой сильно сшитый органический полимер и является ключевым компонентом опорной ткани в васкуляризированных (водопроводящих) растениях — именно он придает древесине жесткость.
Затем смесь одновременно нагревали и помещали под высокое давление. Было обнаружено, что путем точной настройки таких переменных, как соотношение бетона и лигнина, содержание воды, температура, а также количество и продолжительность давления, лигнин превращается в высокоэффективный клей, связывающий куски бетонного порошка вместе.
Последующие испытания показали, что переработанный бетон обладает большей прочностью на изгиб, чем исходный бетон, из которого он был изготовлен. В качестве дополнительного бонуса, из-за содержания в нем лигнина материал, вероятно, должен биоразлагаться после выброса.
Более того, ученые считают, что вместо него можно использовать лигнин, полученный из других растительных источников (например, сельскохозяйственных отходов). Возможно, в конечном итоге станет возможным создание нового «чистого» бетона, в котором вместо цемента используется лигнин.
«Эти результаты могут способствовать переходу к более экологичной и экономичной строительной отрасли, которая не только сокращает запасы отходов бетона и дерева, но и помогает решить проблему изменения климата», — говорит Сакаи.
Интересно отметить, что исследование, проведенное в 2018 году в Национальном университете Сингапура, показало, что добавление древесных отходов в цемент и раствор делает их более прочными и водонепроницаемыми.
Источник: Токийский университет
Откуда берутся шлакоблоки? Капитальная кладка
Что такое шлакоблок?
Что вы знаете о шлакоблоках? Если вы сразу же думаете о тех блоках, которые вы использовали для изготовления дешевых полок в колледже, вам нужно обновить свое мышление. Шлакоблоки возрождаются в планировках садов повсюду и показывают нам, насколько универсальными и привлекательными могут быть эти прочные блоки.
Из чего сделаны шлакоблоки?
Когда вы сжигаете уголь или дрова, остается остаток, который мы называем пеплом или пеплом.Чтобы сделать шлакоблоки, вы смешиваете эти шлаки с цементом. В результате получается легкий, полый и прочный блок.
Краткая история шлакоблоков
Шлакоблоки имеют долгую славную историю в американской строительной промышленности. В конце восемнадцатого века угольные заводы доминировали в промышленном ландшафте США. Весь этот уголь произвел огромное количество золы, которую люди превратили в шлакоблоки.
В 1900 году Хармон С. Палмер изобрел первую машину, которая могла производить большое количество шлакоблоков.Это в сочетании с растущей промышленностью портландцемента сделало шлакоблоки одним из основных строительных материалов в стране.
Современные шлакоблоки
Сегодня вы не увидите, чтобы многие дома в США были построены из шлакоблоков или бетона. Бетон и шлакоблоки популярны в таких местах, как Флорида, потому что они могут противостоять ураганам. Они также являются распространенными строительными материалами в Европе, Латинской Америке и Карибском бассейне.
Шлакоблоки и бетонные блоки — это одно и то же?
Хотя люди часто смешивают шлакоблоки, бетонные блоки, строительные блоки и каменные бетонные блоки вместе, на самом деле между шлакоблоками и бетонными блоками есть разница.
Шлакоблоки изготавливаются из золы и золы, а бетонные блоки изготавливаются из стали и цемента. В результате шлакоблоки получаются пустотелыми и легкими. Бетонный блок тяжелый и прочный.
Различные варианты использования для разных блоков
Эти различия означают, что два материала используются в строительстве по-разному. В общем, вы бы использовали бетонные блоки для строительства несущих стен, фундаментов, подпорных стен и других конструкций, требующих чрезвычайной прочности.
Шлакоблоки лучше подходят для декоративных стен, ступеней, уличных каминов и небольших строительных объектов. Установка шлакоблоков быстрее и проще, чем установка бетонных блоков, которые могут быть тяжелыми и трудными в работе.
Как лучше всего использовать шлакоблоки или бетонные блоки?
Бетон и шлакоблоки имеют много преимуществ перед другими строительными материалами:
- Они выдерживают любую суровую погоду.
- Они никогда не гниют и не ржавеют.
- Вы не получите урона от термитов.
- Они невероятно прочные.
- Они водонепроницаемы и пожаробезопасны.
- Они защищают от большинства вредителей.
Шлакоблоки отлично подходят для всех наружных установок, включая стены, внутренние дворики, уличные камины, навесы для горшков, курятники, пешеходные дорожки и многое другое.
Если вы думаете об использовании камня для проекта, рассмотрите возможность использования шлакоблоков.Во многих случаях это доступная альтернатива.
Профессиональная установка для достижения наилучших результатов
Шлакоблоки и бетонные блоки могут быть тяжелыми и трудными в обращении. Их также сложно правильно растушевать. Если вам нужна конструкция из шлакоблока, обратитесь в профессиональную каменную компанию для безопасной и квалифицированной установки. Capital Masonry — отмеченная наградами каменная компания третьего поколения, специализирующаяся на укладке всех видов камня и бетона.
или раствор, какой из них лучше
Клей для кладки по сравнению с раствором, если вы находитесь на этой странице, вы, вероятно, хотите узнать разницу или решить, какой из них подходит для вашего дома или проекта.В этой статье мы постараемся выделить основные различия и объяснить, в чем заключается каждое из них, чтобы вы могли принять наиболее обоснованное решение.
В большинстве проектов по кладке для скрепления кирпичей, блоков и камней используется раствор. Тем не менее, есть много коммерчески доступных клеевых продуктов, которые предлагают альтернативу. Есть много названий, таких как клей для кирпича, клей для кладки или клей для кладки, но, по сути, все они одинаковы. Они используют клей, чтобы скрепить куски кирпича или камня.
Строительный раствор и клей для кладки частично совпадают, но, как правило, они используются в разных ситуациях. В некоторых проектах предпочтение отдается раствору, в то время как другие лучше работают с клеем. Есть и косметические отличия. Некоторые люди предпочитают внешний вид клея, а другим нравится традиционный вид раствора. Вот некоторые из основных различий между ними, чтобы вы могли решить, что лучше всего подходит для вашего проекта кладки.
Клей для каменной кладкипротив раствора — что вы будете использовать, зависит от сборки
Клейочень хорошо работает в условиях отсутствия провисания.Когда существует небольшая опасность провисания несущего кирпича или камня, тогда клей или клей — хороший минималистский, восточный вариант применения. Он отлично работает на тонких кирпичных или каменных стенах, например, на внешней кирпичной кладке. Многие каменщики также используют клинкерный клей для декоративных шапочек на каменных стенах.
Растворлучше всего подходит для более толстой и тяжелой кладки. Когда вам нужно что-то прочное и должно выдерживать значительный вес, лучше всего подойдет строительный раствор. Он держится на месте и служит дольше, поэтому его предпочитают для высоких стен и тяжелых каменных построек.
Понимание некоторых недостатков строительного клея
Строительный клей прост в использовании и хорош во многих случаях. Тем не менее, каждый владелец недвижимости и начинающий каменщик должен понимать его ограничения. Использование растворного клея в проекте, который лучше подходит для раствора, может вызвать проблемы в будущем. Зная, когда использовать любой из них, вы получите красивый и долговечный проект каменной кладки.Выравнивание — у клея не так много места для маневра, если вам нужно, чтобы поверхности были очень ровными.На вертикальной стене проще выравнивать с помощью растворного клея, но такие проекты, как укладка плитки, лучше работают с раствором, который имеет большую эластичность, поэтому в конечном итоге все становится ровным. Более тонкие клеи оставляют меньше места для ошибок, когда нужно выровнять вещи.
Шанс «отдачи» – клей более склонен уступать под давлением. Это важно, когда вы работаете над проектом, который находится под постоянным давлением, например, пол или несущая стена. Его никогда не следует использовать в структурном проекте.
Нанесение на древесину. Когда химически обработанную древесину необходимо нанести на поверхность каменной кладки, это проблема для растворного клея. Древесина не будет хорошо держаться и, вероятно, отвалится быстрее, чем если бы использовался раствор.
Знай свой вариант использования
Мы знаем, что люди ненавидят, когда они задают вопрос, а в ответ говорят: «Ну, это зависит от обстоятельств». Тем не менее, это, безусловно, относится к раствору и клею. Есть определенные ситуации, в которых клей предпочтительнее раствора. Обычно это косметические проекты, которые можно сделать быстро.Такие вещи, как замена одного кирпича или прикрепление шпона к каменной стене, идеальны. Кроме того, клей можно использовать на каменных дорожках, на которых мало людей.
Вы можете купить растворный клей, он быстро придет к вам и прост в использовании. Это особенно хорошо для небольшого ремонта каменной кладки, который домашние мастера хотят попробовать, не нанимая профессионального каменщика за помощью.
Тем не менее, при использовании растворного клея обязательно ознакомьтесь с техническими характеристиками продукта. Не наносите клей на что-либо тяжелое или большее, чем рекомендовано производителем.В итоге вы получите поврежденные кирпичи и камни. Если вы используете клей на тяжелых камнях, падение также может привести к повреждению имущества в этом районе. С клеем лучше оставаться косметическим и простым.
Раствор по-прежнему отлично подходит для крупных проектов
Несмотря на то, что клей проще в использовании и очистке, строительный раствор имеет более широкие возможности и области применения для кладочных работ. Крепление структурных стен или столбов следует каждый раз выполнять с помощью раствора. Точно так же, если стена более трех футов, вам следует серьезно подумать об использовании только раствора для работы с кирпичом или камнем.
Растворвыдержит испытание временем и более эффективно выдержит вес кирпича и камня. С годами вы увидите меньше провисаний, и вам не придется беспокоиться о том, что камни или кирпичи будут трястись.
Принимая во внимание рентабельность
Большинство владельцев недвижимости должны учитывать стоимость. Многие сторонники растворного клея быстро указывают на тот факт, что клей не требует смешивания, быстрее очищается и стоит меньше, чем раствор. Хотя это правда, владельцы недвижимости также должны убедиться, что они используют правильный продукт, чтобы избежать затрат на ремонт в будущем.Использование неправильного клея, будь то раствор или клей, повлияет на кладку в будущем.
Убедитесь, что вы изучили стоимость раствора по сравнению с клеем, но более важно использовать правильный продукт, который удержит камень или кирпичную кладку на месте.
Внешний вид клея для раствора по сравнению с раствором
Также имеет значение то, как строительный раствор или растворный клей выглядит на кирпичной стене или каменной дорожке. Иногда выбор между клеем и раствором сводится к личным дизайнерским предпочтениям.Миномет толще и более выражен. Клей очень тонкий; таким образом, он привлекает больше внимания к кирпичам или камням. Это более тонко.
Если вы хотите, чтобы кирпичная или каменная стена выглядела традиционно или контрастировала с оттенками или цветами, раствор предоставит вам больше возможностей. Если вам нравится минимальное количество швов и вы хотите, чтобы основное внимание уделялось облицовке из камня или кирпича, то этот клей для вас.
Оба варианта имеют большое значение для того, чтобы ваша собственность выглядела великолепно, а камни и кирпичи оставались на месте.Если вы сомневаетесь, обратитесь к профессиональному каменщику или поговорите с производителями продукции, чтобы получить рекомендации о том, что лучше всего подходит для вашего конкретного проекта.