Пропорция для кладочного раствора: рецептуры, маркировка смесей и их свойства
как рассчитать состав и приготовить раствор
Автор Виктор Малков На чтение 13 мин Просмотров 3.9к. Опубликовано Обновлено
Кирпич уже много столетий остается одним из основных материалов для возведения жилых, промышленных, хозяйственных зданий. Долговечность конструкций в большой степени зависит от качества раствора для кладки кирпича. Современные технологии позволяют придать ему нужные свойства, обеспечить прочность и возможность вести строительство в любых климатических условиях.
Содержание
Компоненты кладочного раствора
Кладочная смесь состоит из трех основных ингредиентов. В качестве скрепляющих веществ используется известь, цемент или их смесь. Наполнитель — это мелкий (не более 2,5 мм) серый или белый песок. Оптимальная влажность — в пределах 10%. Еще один вид наполнителя — глина. Она должна пройти сложную механическую и химическую очистку, что не всегда возможно сделать в бытовых условиях.
Глину в качестве наполнителя не используют при кладке пустотелого кирпича. Мягкая смесь заполняет полости и снижает теплоизоляционные свойства строительного материала.
Сухая смесь разводится чистой водой без посторонних примесей. Лучший вариант — дистиллированная, при ее отсутствии подойдет отстоянная или отфильтрованная водопроводная вода. Для придания пластичности и устойчивости к морозам используют органические и неорганические добавки.
Основные характеристики
Согласно госту на изготовление раствора, раствор для кладки кирпича должен соответствовать определенным требованиям. Характеристики качественного материала:
- Прочность — главный показатель, от которого зависит срок службы постройки. Чем прочнее раствор, тем бо́льшие нагрузки сможет выдерживать конструкция.
- Устойчивость к низким температурам — чем она выше, тем большее количество циклов замораживания и размораживания выдерживает затвердевший раствор без потери прочности.
- Высокая адгезия, то есть сцепление раствора с поверхностью кирпича.
- Водонепроницаемость — свойство, предохраняющее кладку от разрушения под действием атмосферных осадков.
- Пластичность позволяет корректировать положение строительных блоков во время кладки.
- Способность удерживать воду не дает раствору расслаиваться.
- Подвижность смеси позволяет равномерно распределять ее по поверхности кирпича.
Значения показателей меняются в зависимости от требований к прочности возводимой конструкции и условий эксплуатации здания.
Типы кладочных растворов
Состав и пропорции кладочной смеси выбираются в соответствии с требованиями, предъявляемыми к прочности строения. Для наружных и внутренних стен, сухих и влажных помещений, наземной и подземной части зданий используют разные растворы.
Виды в зависимости от сферы применения
Специальный глино-шамотный состав с высокой огнеупорностью используют для строительства печей, резервуаров, дымоходов, каминов. Универсальная смесь разных марок подходит для любых строительных блоков, соединения бетонных плит, укладки фундаментов. Цветной раствор, кроме скрепления, выполняет декоративную функцию.
Цветная и белая смесь
С развитием частного строительства на рынке появились цветные кладочные смеси, позволяющие комбинировать оттенки швов с цветом кирпича. В готовые сухие смеси добавляется белый или темный цемент и полимерные пигменты, не влияющие на основные характеристики раствора. Цвет не смывается осадками и сохраняет насыщенность долгие годы. Кроме того, полимеры в составе кладочного раствора делают его более пластичным и снижают водопоглощение. Цветные растворы используют для облицовочных работ. Белый цвет раствора достигается повышенным количеством извести, добавлением окиси титана или цинка. Белую смесь часто используют в качестве контрастной для выделения структуры кирпичной кладки.
белая смесь для кирпичной кладкиПростые и сложные кладочные составы
Кладочные растворы, включающие одно вяжущее вещество, называются простыми. Сложная смесь состоит из нескольких скрепляющих компонентов и наполнителей. По типу вяжущего вещества кладочные смеси делят на четыре вида:
- Цементная — самая востребованная и подходящая для любого вида кладки. Она обладает высокой твердостью, но мало пластична. Для повышения показателя в раствор вносят специальные вещества — пластификаторы.
- Известковая — высокопластичная, с хорошими теплоизоляционными свойствами. Но затвердевший раствор плохо выдерживает большие нагрузки, поэтому используется только в строительстве частных домов. Минус известковой смеси — длительное затвердевание и выделение во время схватывания большого количества воды.
- Цементно-известковый раствор называют золотой серединой, он не имеет ограничений по использованию. Два вяжущих компонента обеспечивают оптимальные свойства — цемент придает прочность, известь делает массу пластичной.
- Смесь, содержащая глину, в частном строительстве используется редко из-за трудоемкости ее очистки. Глиняная масса обладает неоспоримыми достоинствами — она пластична и хорошо удерживает тепло в доме.
Раствор с большим содержанием вяжущего компонента называется жирным. Он обладает повышенной твердостью, но после усадки дает трещины. Тощая смесь с низким содержанием цемента или извести обладает малой прочностью и пластичностью. Оптимальный вариант — нормальная смесь, где пропорции сбалансированы с учетом планируемой нагрузки.
Марки кладочного раствора
Сухие смеси для кладки кирпича маркируются буквой «М» и числом, обозначающим прочность материала на сжатие в кг/см2 по ГОСТ Р 57337—2016.
Марка цементной смесиСмеси М25 и М50
Из всех марок раствор М25 для кирпичной кладки обладает наименьшей прочностью. Его используют для декоративной кладки, где нагрузка будет минимальной.
Марка М50 востребована благодаря сбалансированному соотношению цены и качества. При невысокой стоимости раствор обладает достаточной прочностью для возведения частных домов и хозяйственных построек.
Марка М75
Смесь М75 отличается высокой прочностью и водонепроницаемостью. Его применяют для строительства фундаментов и наземных частей зданий любого назначения. Благодаря невысокой стоимости компонентов марка М75 чаще других используется в частном строительстве.
Применение раствора М100
М100 редко используют в малоэтажном строительстве. Он предназначен для кладки тяжелых бетонных блоков, крупных кирпичей, заделки швов в конструкциях с высокой нагрузкой. Зимой в состав добавляются вещества, повышающие устойчивость к низким температурам. В качестве вяжущего вещества в марке М100 применяется высокопрочный портландцемент.
Смеси марок М125, М150, М200
Марку М125 используют для кладки наружных стен из каменных, бетонных, керамических блоков, гипсовой плитки. В составе используется песок мелкой фракции — от 0,5 до 1 мм.
Кладочный раствор М150, обладающий повышенной твердостью, применяют в промышленном строительстве. На частных домах смесью отделывают стены из бетона. Она хорошо выдерживает морозы, но работать с ней можно только при температуре не ниже +5°C.
Для жаростойкой водоотталкивающей смеси М200 требуется промытый кварцевый (горный) песок без следов органики. В качестве наполнителя дополнительно используются перемолотые ракушки или известняк.
Как правильно сделать раствор для кладки кирпича
Для получения качественного раствора важно правильно рассчитать количество материалов, соблюсти пропорции и технологию замеса. Перед началом кладки необходимо проверить подвижность готовой смеси.
Как определить подвижность растворной смеси?
Подвижность растворной смеси определяется по глубине погружения металлического стандартного конуса массой 300 г. Чем больше подвижность смеси, тем глубже погружается в нее стандартный конус. Подвижность повышается по мере увеличения содержания воды в смеси, повышения крупности песка и понижения его пустотности. Подвижность растворной смеси выбирают с учетом назначения раствора.
Таблица с рекомендуемой подвижностью строительных растворов
Назначение раствора | Глубина погружения конуса см.![]() |
Монтаж стен и расшивка швов в стенах из крупных панелей и блоков | 5 — 7 |
Кладка из обыкновенного кирпича, бетонных камней | 9 — 13 |
Кладка из пустотелого кирпича | 7 — 8 |
Кладка из бутовых камней обычная | 4 — 6 |
То-же вибрированная | 1 — 3 |
Заливка пустот в бутовой кладке | 13 — 14 |
Приготовление раствора для кладки кирпича, очень похоже с приготовлением пескобетона. Если вы уже приготовили кладочный раствор и хотите изучить приготовление пескобетона, то сделать это вы можете пройдя по следующей ссылке: Что такое пескобетон, его состав и применение.
Пропорции для приготовления раствора
Пропорции в простых цементных смесях рассчитываются исходя из цели использования. Соотношение ингредиентов для самостоятельного приготовления раствора:
Марка смеси | Марка цемента | Соотношение частей цемент:песок |
М25 | 300 | 1:9,5 |
М50 | 300 | 1:5,8 |
400 | 1:7,4 | |
М75 | 300 | 1:4,2 |
400 | 1:5,4 | |
500 | 1:6,7 | |
М100 | 300 | 1:3,4 |
400 | 1:4,3 | |
500 | 1:5,3 | |
М150 | 300 | 1:2,6 |
400 | 1:3,25 | |
500 | 1:3,9 |
Пропорции для замеса цементно-известковой смеси:
Марка цемента | Соотношение частей цемент:песок:известь |
М300 | 1:3,5:0,2 |
М400 | 1:1-0,3:2,5-4 |
М500 | 1:3:0,2 |
Сколько необходимо добавлять воды?
В простую цементную смесь вода добавляется из расчета 0,8 частей на 1 часть цемента.
Универсальный раствор
Кладочный раствор, подходящий для большинства строительных работ, состоит из цемента, песка, воды и пластифицирующих добавок. Чтобы удешевить стоимость в качестве последних используют бытовые моющие средства — шампунь, жидкость для мытья посуды, стиральный порошок. Их добавляют из расчета 1 чайная ложка на ведро цемента.
Для получения марки М25 смешивают 5 частей песка и 1 часть цемента. При строительстве цоколей и фундаментов нужна марка М50 с пропорциями 4:1 или М75 — 3:1.
Методика расчета количества материалов
Чтобы определить количество песка и цемента, необходимо высчитать кубатуру кладки. Порядок расчета:
- Умножьте периметр здания на высоту стен и толщину кладки.
- Из полученного числа вычтите площадь оконных и дверных проемов.
- Чтобы узнать общее количество состава в кубических метрах, умножьте объем стен на коэффициент 0,2 или 0,3.
- Количество цемента высчитывается путем деления общей кубатуры раствора на долю цемента согласно пропорции.
- Переведите объем в килограммы, умножив количество кубических метров на удельный вес 1300 кг/м3. Разделите общий вес цемента на 50, и вы получите необходимое количество мешков.
Рассчитать потребность в песке можно, исходя из его соотношения с цементом.
Кроме того, вы можете воспользоваться специальными калькуляторами на различных сайтах:
Расход готового раствора на 1 м
2Расход готового раствора на 1 кв. м зависит от вида и размера кирпича, толщины стены, ширины шва. Для сплошного кирпича потребуется меньше раствора, чем для пустотелого. Экономный вариант — кладка из строительных блоков большого размера.
Для 1 кубометра стандартного кирпича размером 250х120х62 потребуется 1/3 м3 смеси. В пересчете на квадратный метр это составит 75 литров готового раствора. За вычетом воды, которая составляет от 25 до 35% от объема, получается, что для кладки 1 м2 вам нужно около 33 кг цемента.
Для более точных расчетов предлагаем воспользоваться данной таблицей.
Подготовка к замешиванию
Перед началом работы подготовьте все необходимое. Вам понадобится:
- емкость для перемешивания — бетономешалка, таз или ведро в зависимости от нужного объема смеси;
- строительный миксер или дрель со специальной насадкой;
- весы для соблюдения пропорций ингредиентов;
- лопата;
- ведра для воды и наполнителя.
Технология замеса цементного раствора
Соблюдение правил замеса влияет в дальнейшем на прочностные характеристики кладки. Порядок действий:
- приготовьте ингредиенты в нужных количествах;
- проверьте качество цемента — он должен быть сухим и однородным;
- просейте песок, чтобы убрать мусор и крупные фракции;
- засыпьте сухие компоненты в емкость, где будет смешиваться раствор, и тщательно перемешайте;
- постепенно добавляйте воду до получения нужной консистенции.
Не стоит сразу замешивать большое количество раствора, так как через час или полтора он застынет и будет непригоден для работы.
Как сделать известковый раствор.
Известковая смесь готовится из песка, воды и известкового теста. Для кладочного раствора гашеная известь должна отстояться около 20 дней. Пропорции теста и песка — 1:2 или 1:5 в зависимости от жирности извести. Перемешайте ингредиенты до получения однородной массы, затем постепенно разбавляйте водой до консистенции густой сметаны.
Цементно-известковый раствор.
Цементно-известковый раствор замешивается следующим образом:
- Разведите гашеную известь до состояния молока и процедите через сито.
- Смешайте сухие ингредиенты в нужной пропорции.
- Постепенно вливайте известковое молоко в сухую смесь до получения нужной густоты.
Скорость схватывания цементно-известковой смеси — 1,5-2 часа.
Каким должен быть правильно приготовленный раствор.
Как определить готовность растворной смеси?
Готовность раствора к работе определяется простыми тестами. Наклоните емкость под углом 45°, готовая смесь вытекать не будет. Другой способ — сделать в растворе углубление. Если оно не заполняется и не меняет форму, можно приступать к кладке.
Как определить подвижность раствора.
От подвижности раствора зависит быстрота и удобство выполнения кладки. Существует способ определения параметра с помощью металлического конуса весом 300 г. Его опускают в готовую массу. Если она предназначена для полого кирпича, конус должен погружаться в раствор на не более чем на 7-8 см. Для цельного материала глубина погружения составит 9–13 см. В жаркую погоду это значение увеличивается до 12–14 см.
Правильно приготовить раствор для кладки своими руками поможет видеоурок:
Смотрите это видео на YouTube
Неукоснительное соблюдение пропорций и технологии приготовления кладочного раствора — гарантия прочности и длительной эксплуатации кирпичного строения.
Помогла ли данная статья приготовить раствор?
Пластификатор для кладочного раствора своими руками: видео
Содержание
- 1 Для чего нужен пластификатор?
- 2 Типы пластификаторов
- 2.
1 Ускорители
- 2.2 Морозостойкие
- 2.3 Суперприсадки
- 2.
- 3 Пластификатор для цементного раствора своими руками
- 4 Пластификатор для раствора: пропорции
Цементный кладочный раствор – старое, проверенное изобретение. Но современные технологии не стоят на месте. И производители стройматериалов неустанно трудятся над улучшением качеств составов для кладки. Сегодня в продаже имеется масса специальных добавок для растворов, или, как их еще называют, пластификаторов. Как их правильно выбирать и использовать, мы подробно рассмотрим в этой публикации.
Для чего нужен пластификатор?
Основное назначение пластификаторов – совершенствовать технологические характеристики кладочных растворов. Однако не все так просто, у этих добавок довольно узконаправленный функционал. Иными словами, каждый вид пластификаторов нацелен на решение какой-то конкретной проблемы.
Соответственно делать выбор в каждой конкретной ситуации следует, в первую очередь исходя из основной функции, которую выполняет тот или иной пластификатор.
Итак, основные функции пластификаторов:
- Уменьшение усадки растворов.
- Снижение уровня содержания воды в составе.
- Продление «жизни» приготовленного кладочного раствора.
- Придание раствору эластичности и упрощение процесса кладки.
- Предотвращение образования трещин.
- Повышение уровня прочности смеси.
- Профилактика расслаивания растворов.
Типы пластификаторов
Исходя из своего назначения и функционала все добавки для растворов делятся на несколько типов.
Ускорители
Данные пластификаторы вводятся в цементный раствор для ускорения процесса отвердения. Параллельно они увеличивают прочность состава. Рекомендуются при проведении работ в холодные периоды, а также при сокращенном сроке строительства.
Такие добавки позволяют создать легкий бетон, так что при этом не страдает прочность и надежность состава.
Замедлители
Действие этих присадок – прямо противоположно описанному выше. Их используют, когда необходимо продлить период схватывания бетонной массы.
Кроме того, данные добавки:
- Защищают раствор от расслоения.
- Снижают степень усадки.
- Повышают прочностные характеристики.
- Позволяют уменьшить долю цемента в растворах.
Морозостойкие
Благодаря специальным компонентам такие добавки делают возможной работу при низких температурах – до -20С.
Некоторые присадки (типа карбоната кальция) позволяют бетонной смеси отлично затвердевать без потерь качества даже при морозе в -30С.
Суперприсадки
Их еще называют суперпластификаторами.
Такой пластификатор для цемента обладает массой положительных свойств:
- Увеличивает продолжительность периода схватывания растворов в 4 раза, что обеспечивает более комфортную работу мастера, без спешки.
- Дает возможность экономить цемент – до 50кг/м3.
- Улучшает показатели прочности на 25%.
Соотношение данных пластификаторов в растворе относительно доли цемента составляет 0,8-1,5%.
Пластификатор для цементного раствора своими руками
Современные добавки для цементных растворов можно приобрести в любом строймагазине. О том, как и применять, производители подробно описывают в инструкциях.
Цена таких пластификаторов довольно высока. Однако она является гарантией того, что все ингредиенты, входящие в их состав, действительно качественные.
Тем не менее пластификатор для раствора для кладки можно изготовить самостоятельно.
Итак, разберемся, какие вещества могут выполнять роль пластификаторов в кладочных растворах:
- Яичные желтки. Такая добавка довольна распространена в сельской местности. Включение в состав яичных желтков делает раствор более пластичным, а также повышает прочность смеси.
- Стиральный порошок – увеличивает показатели твердости. Вводится в раствор в разведенном с водой виде в соотношении 110-140гр на 1мешок с цементом.
- Жидкое мыло (шампунь) – ускоряют процесс затвердевания бетона в среднем на 2часа. Мыло или шампунь добавляют на начальной стадии приготовления раствора в соотношении 200гр на 50кг цемента.
- Порошки винилацетата и стиролакрила – вводятся для повышения уровня влагостойкости раствора, а также для повышения прочности и эластичности. Расход – до10-12% от количества цемента.
- Клей ПВА – служит улучшения влагостойких качеств растворов. На ведро цемента берут 250мл ПВА.
Пластификатор для раствора: пропорции
Приведем еще несколько рецептов пластификаторов собственного производства. Их можно использовать для улучшения качественных характеристик кладочных растворов. Пропорции будем приводить исходя из того, сколько пластификатора на ведро цемента потребуется.
- Фейри или другой гель для мыться посуды – придаст смеси пластичность. Нужно 2ст.л.
- Гашеная известь – улучшает показатели пластичности раствора, придает ему прочность, устойчивость к температурным перепадам, предотвращает растрескивание. Потребуется 2кг.
- Про свойства порошка для стирки мы уже писали. В перерасчете на ведро цемента нужно 2ст.л.
- Хозяйственное мыло – также направлено на повышение пластичности смесей.
Потребуется 2ст.л.
Данные добавки предварительно растворяют в воде, а уже затем вводят в состав растворов.
Поделиться с друзьями:
Твитнуть
Поделиться
Поделиться
Отправить
Класснуть
Adblock
detector
Кирпичная кладка | Испытание цемента
Соотношение растворной смеси означает разделение цемента и песка в растворе для обеспечения однородности характеристик и внешнего вида каменной кладки. Если разделение компонентов раствора идеальное, можно получить следующие преимущества:
а. постоянство прочности
b. постоянная работоспособность
c. стабильный цвет
d. постоянство пропорций и выходов
Как правило, разделение цемента и песка для строительного раствора выполняется с пропорцией по объему, в отличие от пропорции по весу.
Соображения относительно пропорции растворной смеси: Если в песке присутствует влажность, то могут быть расхождения в измерении песка. Поэтому в этой ситуации следует уделить должное внимание. Если в песке присутствует влага, это приводит к набуханию песка.
Влажный песок будет содержать больше объема по сравнению с сухим песком, и измерение будет неполным. Из-за этого произойдет отклонение в количестве смеси, что значительно повлияет на прочность и характеристики сцепления раствора.
Если в растворной смеси присутствует чрезмерное количество песка, это приведет к получению грубой, а также невозможной смеси, что приведет к ухудшению сцепления.
Предлагается проверять измерение объема два раза в день, когда дозирование песка выполняется по объему в ящике, сформированном из фанеры или пиломатериала. Человек, ведущий процесс, сможет вести учет необходимых лопат песка для заполнения ящика. Таким образом, если объем песка изменяется, его можно легко отследить.
Удобоукладываемость раствора по отношению к бетону высокая, так как элементы кладки потребляют некоторое количество воды для уменьшения водоцементного отношения в растворной смеси, что влияет на прочность и сцепление.
Так, предлагается несколько раз погружать блоки кладки в воду до начала кладки. Организация избыточной воды выполнит это требование к абсорбции.
Растворная смесь не назначается с подвижностью и водоцементным отношением. Это наилучшее содержание влаги, определенное каменщиком. Если раствор слишком сухой, он не сможет идеально расширяться, что приведет к ухудшению сцепления и неполной гидратации цемента. Если раствор достаточно влажный, он быстро осядет, и его будет нелегко затирать.
Для получения дополнительной информации перейдите по следующей ссылке theconstructor.org
Журнал гражданского строительства и строительных технологий
РЕЗЮМЕ
В статье приведены результаты исследования стандартного кладочного раствора, содержащего песок и опилки в качестве заполнителей в пропорции смеси 1:3 и водоцементном отношении 0,55. Также оценивался модифицированный раствор с той же расчетной пропорцией смеси (1:3), но с другим водоцементным отношением и постоянной осадкой 74,3 мм для достижения более высокой удобоукладываемости. Были исследованы шесть различных процентов (5, 10, 15, 20, 30 и 50%) замены песка.
Ключевые слова: Опилки, раствор, бумажник, прочность кладки на сжатие, водопоглощение.
ВВЕДЕНИЕ
Спрос на новые строительные конструкции в развивающихся странах чрезвычайно высок из-за постоянно увеличивающегося роста населения. Этот спрос не может быть удовлетворен, так как стоимость строительства несостоятельна из-за постоянно растущей стоимости строительных материалов. Строительство в значительной степени зависит от традиционных материалов, таких как цемент, песок и камни для производства раствора и бетона.
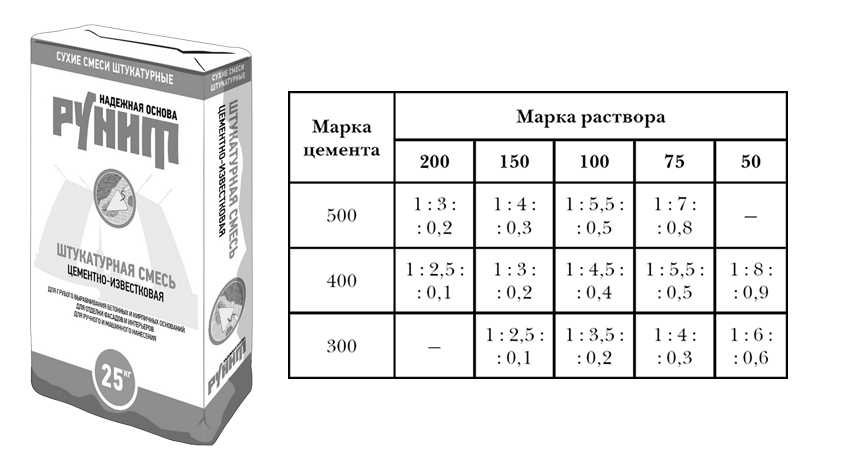
Опилки обычно утилизируются путем открытого сжигания с образованием вредного для здоровья дыма. Более экологически желательным способом его утилизации является использование его в цементных композитах. Огромные объемы опилок, образующихся в качестве отходов лесной промышленности, могут быть использованы в качестве частичной замены мелких заполнителей в производстве строительных растворов и бетона, чтобы уменьшить нагрузку на скудные доступные природные ресурсы. Композиты на основе опилок характеризуются низкими механическими характеристиками, малой долговечностью и плохой совместимостью (Lei et al., 2006). Попытки преодолеть эти недостатки были предприняты исследователями.
Несмотря на эти преимущества, опилкобетон демонстрирует неравномерное время схватывания и плохую адаптацию к изменению размеров в качестве основных недостатков (Adeagbo, 1999).
ЭКСПЕРИМЕНТАЛЬНАЯ ПРОГРАММА
Материалы
В исследовании использовали обычный портландцемент с прочностью на сжатие через 28 дней 42,5 Н/мм 2 . В качестве мелкого заполнителя использовали речной песок с максимальным размером заполнителя 2 мм и удельным весом 2,53. Опилки, полученные от лесопильной компании, также использовались в качестве частичной замены мелких заполнителей. Для эксперимента был приготовлен стандартный кирпичный раствор с расчетным соотношением смеси 1:3 (цемент:песок) и водоцементным отношением 0,55. Мелкий заполнитель был частично заменен опилками. Рассматриваемые проценты замены составляли 5, 10, 15, 20, 30 и 50. Также были изготовлены карманы приблизительно квадратной формы с использованием приготовленного раствора в качестве материала для швов.
Детали образцов
При каждой процентной замене 2 призмы (испытать на 28 день твердения), 9 кубиков (испытать на 7 9 0, и 28 день отверждения) и 3 кошелька (для испытаний 28 день отверждения). Общее количество образцов для испытаний состояло из 28 призм (40 мм x 40 мм x 160 мм) для испытания на прочность при растяжении при изгибе, 126 кубов (100 мм) для испытания на прочность при сжатии и 42 кошельков приблизительных размеров 1,2 м x 1,5 м, которые были изготовлены для испытания прочности каменной кладки на сжатие. . Пятьдесят процентов всех испытательных образцов были отлиты из каждого раствора.
Подготовка образцов
Для приготовления стандартного раствора использовали стандартное расчетное соотношение смеси 1:3 (цемент: песок) с водоцементным отношением 0,55. Для каждого процента замены был получен более твердый (сухой) раствор с быстрой потерей осадки. В связи с этим для исследования был приготовлен модифицированный строительный раствор с такой же удобоукладываемостью (подвижностью), что и контрольный строительный раствор. Основная цель состояла в том, чтобы найти разумный баланс между удобоукладываемостью, прочностью, долговечностью и стоимостью раствора. Модифицированный строительный раствор имел постоянную осадку 74,3 мм (такую же, как у контрольного образца), что делало его пригодным для обработки, легко перемешиваемым и укладываемым. Материалы загружали по весу в чашу для смешивания и тщательно перемешивали всухую перед добавлением воды. При каждом процентном замещении описанные выше процедуры повторялись. Для отливки кубов и призм соответственно использовались металлические и деревянные формы. Бумажники были изготовлены из блоков размером 450 мм х 225 мм х 100 мм (длина х ширина х высота) и прочностью на сжатие 15 Н/мм 9 .0034 2 с использованием строительного раствора толщиной 10 мм.
Процедуры испытаний
Испытания на распределение частиц по размерам проводились как на опилках, так и на песке в соответствии с BS EN 1015-1. Осадку и объемную плотность свежего строительного раствора определяли в соответствии с BS EN 1015-3 и BS EN 1015-6 соответственно. Кроме того, объемная плотность (BS EN 1015-10), прочность на сжатие, прочность на растяжение при изгибе (BS EN 1015-11), водопоглощение (BS EN 1015-18) затвердевшего раствора и прочность каменной кладки на сжатие (BS EN5628-1) были изучены. Прочность растворов на растяжение при изгибе определяли, просто поддерживая образцы для испытаний на жесткой стальной раме в Лаборатории гражданского строительства KNUST, Кумаси. Монотонные нагрузки прикладывались через стальную траверсу к образцу со скоростью 0,10 кН/с. Типичная конфигурация загрузки также показана на рисунке 1.9.0003
Прочность каменной кладки на сжатие была получена из предела прочности кирпичной кладки или блочной панели, испытанной на разрушение в соответствии с BS EN5628-1. Определена прочность на сжатие блоков каменной кладки. Три идентичные панели (приблизительно 1,2 м в высоту и 1,5 м в длину) были изготовлены для каждого процента замены. Приблизительно квадратные панели были выбраны, чтобы избежать проблемы изгиба под нагрузкой. Кроме того, конструкция стального каркаса не могла вместить панели большего размера, чем было выбрано. Панели загружались равномерно по всей площади верхней и нижней граней с помощью траверсы. Монотонную нагрузку прикладывали со скоростью 0,20 кН/с до разрыва панели. Схематический эскиз установки показан на рисунке 2, а типичная конфигурация загрузки показана на рисунке 3. Это было сделано для обоих наборов минометов.
РЕЗУЛЬТАТЫ И ОБСУЖДЕНИЕ
Классификация заполнителя
Опилки в виде мелкого заполнителя имели размер от 0,15 до 2 мм. С другой стороны, песок имел частицы размером от 0,075 до 2,0 мм. С точки зрения гранулометрического состава и песок, и опилки имели схожие свойства. Процент агрегатов, оставшихся на каждом сите, был одинаковым. Например, самый высокий процент удержания составил 22,4 и 21,61% для песка и опилок соответственно на сите 0,3 мм. Таким образом, в отношении состава заполнителя не ожидалось, что добавление опилок сильно повлияет на свойства строительного раствора.
Кривая классификации песка и опилок представлена на рисунке 4. и другие физические характеристики, а также примеси (Mehta and Monteiro, 2006).
Сравнительно, шероховатые, угловатые и удлиненные частицы требуют большего количества цементного теста для получения удобоукладываемых кладочных смесей. Осадка контрольного миномета составила 74,3 мм. Он последовательно снижался до 71,8, 63,65, 52,65, 48,9.5, 47,3 и 45,05 мм при увеличении процента содержания опилок до 5, 10, 15, 20, 30 и 50% соответственно. Это наблюдение было также сделано Shen et al. (2016), когда они изучали влияние различных свойств речного песка и промышленного песка на свойства бетона. Они обнаружили, что большое количество мелких частиц, угловатая форма частиц и относительно более высокое содержание пустот в произведенном песке привели к получению бетона с более высоким водопотреблением при той же осадке. Также Касрави и др. (2009 г.) признали, что бетон с более чем 50% заменой песка стальным шлаком оказывает негативное влияние на удобоукладываемость бетона и, следовательно, требует большего количества воды для достижения желаемой удобоукладываемости. Низкая удобоукладываемость растворов может быть связана с более высоким сродством опилок к воде. Древесная природа опилок, в отличие от кристаллического песка, заставляет их поглощать воду, тем самым уменьшая свободную воду, доступную для гидратации.
Прочность на сжатие
Общее снижение прочности на сжатие для обоих наборов по мере увеличения процентного содержания опилок. Аналогичные наблюдения были сделаны Алнуайми (2012 г.) и Рашадом (2016 г.), поскольку мелкий заполнитель бетона частично заменяется другими материалами. Тем не менее модифицированные строительные растворы всегда обладали относительно более высокой прочностью на сжатие при каждой замене. Например, при 5% замене прочность на сжатие на 28 сут для модифицированного и стандартного растворов составила 7,45 и 6,9.9 Н/мм 2 соответственно. Эти значения неуклонно снижались до 2,76 и 2,33 Н/мм 2 соответственно при 50% замене (таблицы 1 и 2). Внезапное снижение прочности на сжатие (с 7,31 Н/мм 2 при 0 % до 1,13 Н/мм 2 при 50 %) в стандартном строительном растворе можно объяснить неспособностью надлежащим образом уплотнить строительный раствор из-за плохой удобоукладываемости. Прочность находится в твердой части материала; следовательно, наличие пустот препятствует набору прочности. В многофазных материалах, таких как строительный раствор, пористость каждого компонента материала может быть источником снижения прочности. Обычные (природные) заполнители, как правило, плотные и прочные из-за своей кристаллической природы, в то время как опилки древесные и мягкие. На рис. 5 показан график 28 -й -й день прочности на сжатие для каждого процента замены.
Также установлено, что прочность и проницаемость гидратированных цементных масс связаны между собой через капиллярную пористость, на которую влияет водоцементное отношение и степень гидратации. По мере протекания процесса гидратации капиллярные поры сужаются, что приводит к снижению коэффициента абсорбции. Таблицы 1 и 2 показывают, что по мере увеличения содержания опилок коэффициент поглощения также увеличивается, а прочность на сжатие снижается. Бетон с высоким коэффициентом водопоглощения обладает меньшей прочностью (Basar and Deveci, 2012).
Сухая плотность
Наблюдалось общее снижение насыпной сухой плотности, которое становилось более значительным при более высоком содержании опилок (табл. 1 и 2). Однако модифицированный раствор имел относительно более высокие (от 5 до 20%) значения плотности в сухом состоянии для всех уровней замены. Сингх и Сиддик (2014) сделали аналогичное наблюдение и предсказали, что потеря прочности бетона на сжатие будет линейно зависеть от потери массы при изучении свойств бетона, включающего золу угольного остатка в качестве частичной или полной замены песка.
Прочность на растяжение при изгибе
Прочность растворов на растяжение при изгибе снижается с увеличением содержания опилок (табл. 1 и 2). В целом, произошло значительное улучшение прочности на изгиб (2,56 Н/мм 2 при 0% и 0,85 Н/мм 2 при 50%) модифицированных растворов по сравнению со стандартным раствором (2,54 Н/мм). 2 при 0 % и 0,52 Н/мм 2 при 50 %). Геометрия материала также влияет на прочность раствора на растяжение. Образец опилок имел заполнитель удлиненной формы, который, как полагают, оказывает положительное влияние на прочность на изгиб призмы строительного раствора. На рис. 6 представлены 28 -й -й день прочности на изгиб обоих растворов.
Было также сделано наблюдение, что хотя факторы, ведущие к уменьшению пористости строительного раствора, приводят к общему улучшению прочности строительного раствора как на сжатие, так и на изгиб, результат показывает, что величина снижения прочность на изгиб при растяжении осталась относительно выше, как показано в таблицах 1 и 2
Долговечность
Образцы образцов для испытаний на прочность при сжатии подвергали циклам влажных и сухих условий в течение 5 месяцев, а затем испытывали их прочность на сжатие для оценки долговечности строительного раствора. Как и ожидалось, прочность большинства продуктов на основе цемента увеличивается с возрастом. Было увеличение (около 4,7%) прочности на сжатие для 5 и 10% замен модифицированного раствора. Это может быть связано с образованием большего количества продуктов гидратации, которые предположительно заполнили немногочисленные пустоты в затвердевшем растворе. Однако другие образцы (15, 20, 30 и 50% замен) показали снижение прочности на сжатие (таблицы 1 и 2). Циклы расширения и сжатия опилок могли вызвать нестабильность размеров, которая, как считается, ослабила межфазную связь опилки-цемент. Снижение прочности на сжатие снова может быть связано с более высоким водопоглощением при более высоком проценте замещения. Это свидетельствует о наличии пустот в застывшем растворе. Пористая природа опилок фактически сделала затвердевший раствор также пористым и слабым при более высоких процентах замены. А поскольку пустоты препятствуют набору прочности, прочность на сжатие, как и ожидалось, снизилась. Аналогичные наблюдения были сделаны Shafigh et al.
(2014).
Прочность на сжатие каменной кладки
Как правило, для каждого типа раствора прочность на сжатие кладочной кладки снижается с увеличением содержания опилок. Без опилок как стандартные, так и модифицированные растворы имели прочность кладки на сжатие 6,41 Н/мм 2 . Это уменьшилось до 1,30 и 1,42 Н/мм 2 при 50% замене соответственно, как показано на рис. 7. В основном произошло увеличение прочности кладки на сжатие для модифицированного раствора по сравнению со стандартными растворами для всех замен. За исключением 30- и 50-процентных опилок, кладочные карманы которых разрушились вдоль шва, остальные процентные замены модифицированного раствора характеризовались трещинами разрушения вдоль кладочных блоков. С увеличением консистенции прочность сцепления на границе раздела блок-раствор предположительно улучшилась, что привело к увеличению прочности кладки на сжатие.
Сравнительное исследование прочности кладки на сжатие образца и ожидаемой прочности кладки на сжатие BS 5628 показывает, что 8 и 13% замен опилок для стандартного и модифицированного растворов соответственно дали прочность кладки на сжатие 5,3 Н. /мм 2 , который может быть классифицирован как миномет типа II с тем же кодом.
ЗАКЛЮЧЕНИЕ
Строительный раствор, приготовленный из опилок в виде частичных мелких заполнителей, был исследован. Стандартный раствор с соотношением смеси 1:3 и водоцементным отношением 0,55, принятый в исследовании, привел к неудовлетворительной удобоукладываемости. В связи с этим был также приготовлен модифицированный раствор повышенной удобоукладываемости с постоянной осадкой 74,3 мм. Прочность на сжатие и прочность на изгиб строительного раствора и прочность на сжатие каменной кладки кошельков оценивали по испытательным образцам. Результаты показали, что опилки обладают характеристиками хорошо отсортированного заполнителя. Плотность в сухом состоянии, прочность на сжатие и прочность на растяжение при изгибе снижались с увеличением содержания опилок. Более пористый раствор был получен с повышенным содержанием опилок. Однако модифицированный раствор был немного непроницаем по сравнению со стандартным раствором. Следовательно, с точки зрения долговечности модифицированный раствор можно считать более прочным. При более высоком процентном содержании опилок дробление кубиков не было внезапным по сравнению с контролем для обоих типов раствора. Разрушение кладочных кошельков для модифицированного раствора характеризовалось растрескиванием вдоль блоков кладки, в то время как для стандартного раствора наблюдалось разрушение вдоль шва кирпич-раствор. Это можно наблюдать на Рисунке 8. Лучшее сцепление в случае модифицированного раствора можно объяснить улучшенной удобоукладываемостью, что привело к лучшей адгезии между кирпичами и раствором. В микромасштабе лучшая адгезия также может быть связана с проникновением волокон опилок в поверхность блоков. Плотность обоих растворов значительно уменьшалась с каждым процентом замены. Низкой плотности раствора можно добиться за счет частичной замены мелких фракций опилками. Тщательное изучение приведенных выше результатов и обсуждений показывает, что существует возможность замены мелких заполнителей опилками при приготовлении кладочного раствора.
При процентном замещении 8 и 13% стандартные и модифицированные строительные растворы, соответственно, давали строительные растворы со свойствами, которые достаточно хорошо сравнимы с теоретическими значениями BS 5628:19.92 Код.
КОНФЛИКТ ИНТЕРЕСОВ
Авторы не заявили о конфликте интересов.
ССЫЛКИ