Производство блоков: что нужно и какой доход?
Производство керамзитобетонных блоков | Цена на керамзитобетонные блоки с отделкой
Данный вид стройматериала является достаточно новым, но он уже успел завоевать популярность. По сравнению с аналогичными изделиями он отличается невысокой ценой, чем так и привлекателен.
Производство строительных блоков осуществляется в несколько этапов:
- Приготовление керамзитбетона в бетономешалке. Для этого понадобятся — цемент, керамзит и вода.
- Заливка смеси в формы.
- Сушка изделий. Этот процесс длится до 10 дней после распалубки блока.
Оплата по наличному и безналичному расчету
Оплата
Компания «Инноблок», являясь ведущим российским производителем облицовочной плитки и декоративного камня, сотрудничает как с частными клиентами, так и с крупными компаниями. При этом, мы стремимся, чтобы сотрудничество с нами было максимально комфортным для всех, поэтому оплатить приобретенную у нас продукцию вы можете любым удобным для вас способом – мы принимаем как наличный, так и безналичный расчет.
Доставка транспортной компанией
Доставка
Если вы заинтересованы в приобретении облицовочной плитки и декоративного искусственного камня «Инноблок», но находитесь далеко за пределами столицы, не волнуйтесь – мы доставляем продукцию в любые регионы Российской Федерации. Для этого мы пользуемся услугами транспортных компаний и открыли официальные представительства со складами в каждом федеральном округе. Подробнее о сроках и способах доставки вы всегда можете узнать у наших менеджеров по телефону.
Цена на блоки с облицовкой
Коллекции
- Размер.
- Характеристики.
- Количество единиц в партии.
- Вид строительного материала.
Данный вид стройматериала широко используется при возведении наружных стен для малоэтажных зданий, а также обустройства вентиляционных систем и в качестве теплоизоляции.
Применение данного вида материала позволит существенно сократить бюджет, себестоимость и сроки строительства. При этом сооружениям будет обеспечена максимальная продолжительность эксплуатации.
Производство строительных блоков в Москве
В компании «Инноблок» производство керамзитных блоков осуществляется строго с соблюдением технологических процессов. Таким образом, приобретая у нас товары данного типа, вы получаете продукт с высокими эксплуатационными характеристиками.
Преимущества такого строительного материала обусловлено применением современных технологий и уникального сырья. К основным достоинствам можно отнести:
- Отличные прочностные показатели.
- Хорошие теплотехнические характеристики.
- Превосходные звукоизоляционные характеристики.
- Химическую и температурную устойчивость.
- Небольшую массу.
Стоимость строительных материалов у нас является наиболее демократичной среди прочих компаний. К тому же, мы предлагаем особые условия для дилеров и реселлеров. Более подробно ознакомиться с ними вы можете, связавшись с нашими менеджерами.
Для удобства клиентов на нашем сайте реализована возможность самостоятельного расчета необходимое количество материала. В специальной форме вам достаточно ввести параметры высоты дома и площади проемов. Затем система самостоятельно произведет расчет, и вы будете знать, сколько единиц продукции вам нужно для строительства объекта.
Производство строительных блоков нашей компанией дает возможность приобретать товары без торговой наценки, что позволяет сэкономить средства.
Сертификаты на продукцию
-
Сертификат
Достоинства стеновых керамзитобетонных блоков
Наши специалисты помогут вам купить блоки стеновые в необходимом количестве. Прямо на сайте вы сможете подать заявку на расчет.
Производство строительных блоков в Тольятти с доставкой
Строительные блоки обладают рядом преимуществ перед многими другими строительными материалами. Они обладают достаточно низкой себестоимостью; один блок по размеру может заменить 4-5 кирпичей, что существенно ускоряет и упрощает строительный процесс, кроме того они обладают достаточно высокой прочностью и высокой тепло и шумоизоляцией.
- Подготовка бетона для приготовления блоков;
- Непосредственное изготовление блоков;
- Просушка готовой продукции.
Рассмотрим каждый этап подробнее.
Подготовка бетонной смеси для приготовления блоков
Выполняемая на этом этапе задача заключается в том, чтобы подготовить необходимый для дальнейшего производства раствор. Для этого применяется цемент марки от 450 до 550, а также различные мелкие и крупные заполнители. Мелкие заполнители представляют собой материалы с размером гранул не более 2,1 мм (чаще всего это песок). Диаметр элементов крупных наполнителей может превышать 6 мм и с увеличением этого диаметра возрастает прочность конечного изделия. В качестве заполнителей обычно используются шлаки, щебень, песок, древесная стружка и другие материалы. Нужно стараться избежать наличия в них большого количества пыли, льда и других посторонних элементов. Наличие в заполнителях посторонних элементов возможно, но оно должно быть минимальным (не более 1/10 части). В процессе производства бетона для строительных блоков применяется также универсальная пластифицирующая добавка (УПД) к бетону. Она ускоряет затвердевание бетона и делает его более пластичным. Для подготовки раствора нужно 1 часть цемента смешать с 3 частями мелкого и 3 частями крупного заполнителя, тщательно перемешать, после чего добавить воду, смешанную с раствором УПД.
Изготовление блоков
На этом этапе потребуется специальный станок для изготовления блоков. Процесс непосредственного изготовления блоков также состоит из нескольких стадий. Сначала в специальные формы станка вручную загружается подготовленный раствор бетона, затем на них устанавливаются специальные прижимы. После этого включается станок, который осуществляет прессовку блоков при помощи вибрации. Время вибрации отличается в зависимости от размера, формы блока и имеющихся пустот, но обычно не превышает нескольких секунд.
Просушка и хранение готовых блоков
Просушка блоков происходит за несколько часов. Если при изготовлении бетонной смеси не используется УПД, просушка будет происходить в течение 48 часов. Использование УПД сокращает время высыхания до 6-7 часов. Если имело место нарушение технологического процесса, то на этом этапе блоки могут начать разрушаться, так что нужно тщательно следить за качеством используемых материалов и соблюдать их пропорции. На складе блоки хранятся в специальных штабелях, на которых отображается дата и время их производства, при этом между ними оставляется небольшое пространство для того, чтобы блоки окончательно просохли. По истечении 5-6- дней блоки окончательно готовы к использованию.
Производство бетонных блоков | Masa Group
От сырья через смесь до готового камня проходит долгий путь. В этом процессе участвуют многие растительные компоненты. Только если компоненты системы согласованы, можно быть уверенным в бесперебойном процессе и экономичной работе завода по производству блоков.
- Интерактивная карта
- Посмотреть список
010203040506070809101112131415161718
Хотите узнать больше о процессе производства бетонных блоков Masa? С помощью интерактивной пошаговой системы узнайте, как производится бетонный блок из различного сырья.
- 1. Дозирующая установка для заполнителя и бетоносмесительная установка
- 2. Системы транспортировки бетона
- 3. Машина для производства бетонных блоков
- 4. Транспортировка мокрой стороны
- 5. Лифт
- 6. Пальцевая машина
- 7. Камера отверждения и вентиляция
- 8. Автомобиль промежуточного пальца
- 9. Опускатель
- 10. Обратный транспорт
- 11. Центрирующее устройство
- 12. Производственные поддоны — поперечная транспортировка и буфер
- 13. Кубирование
- 14. Кубический конвейер
- 15. Обработка поверхности
- 16.
- 17. Силовой агрегат
- 18. Система управления и предохранительные устройства
Дозатор заполнителей и бетоносмесительная установка
Качество с самого начала — вот наша философия. Применение комплексных и эффективных дозирующие системы гарантировать оптимальную и эффективную подачу сырья (например, песка, цемента, воды, добавок) к бетоносмесителям.
Использование проверенных бетоносмесителей Masa обеспечивает надежное и качественное перемешивание. Оба стационарные смесители серии «РН» так же хорошо как Смеситель Маса «S 350/500» демонстрируют очень желательные результаты с коротким временем смешивания и оптимальными затратами материала и энергии. Простота обслуживания и долговечность делают эту бетономешалка Masa выгодной долгосрочной инвестицией.
Еще одной важной частью производственного процесса является индивидуальное цветовое оформление брусчатки или других бетонных камней. Это может быть достигнуто как в простом, так и в сложном
многоцветные системы для основного и лицевого бетона.
Подробнее о смесителе Masa
Бетоносмеситель Masa S 350/500
Бетоносмеситель Masa PH
Дозирование заполнителя
Передвижные загрузочные весы
Установка системы Premium Multi-color
Бетонотранспортные системы
В зависимости от компоновки системы бетоносмесители Masa располагаются непосредственно над машиной для производства бетонных блоков или вне завода. Транспортировка бетона от внешнего бетоносмесительного завода к блочному агрегату чаще всего осуществляется с помощью системы ковшового конвейера, хотя могут использоваться и другие системы. В соответствии с требованиями заказчика доступны различные варианты ковшового конвейера.
более
Двухковшовый конвейер
Машина для производства бетонных блоков
Сердцем каждого завода по производству бетонных блоков, несомненно, является машина для производства бетонных блоков. При правильном выборе вы можете выиграть на рынке в долгосрочной перспективе.
Более
Здесь все модели Masa впечатляют своей прочной конструкцией и использованием высококачественных материалов. Masa сочетает многолетний опыт с постоянным развитием — непревзойденная комбинация!
Предлагается специально для производства бетонных бордюров для «British Standard» с чисто гидравлической системой сжатия, Masa также предлагает бетонные бордюрные прессы .
Транспортировка мокрой стороны
Транспортировка мокрой стороны Masa обеспечивает бережную и без потери качества транспортировку свежеприготовленных продуктов от машины для изготовления блоков к элеватору. В то же время Masa не упускает из виду важность контроля качества.
В качестве проверенного стандартного решения Masa предлагает конвейер с шагающей балкой с сервоприводом, обеспечивающий транспортировку свежих продуктов с низким уровнем вибрации. Однако Masa также может поставлять альтернативные транспортные системы.
Перед фактическим путем транспортировки находится опускающееся коромысло, которое также можно использовать для удвоения производственных поддонов. В высокоскоростном S-пакете опускающееся коромысло сочетается с клиноременным конвейером. Он синхронизирован с подачей производственных поддонов станка для изготовления блоков.
Опционально можно установить дополнительные компоненты на мокрой стороне, например:
- щетка для очистки
- щетка для конструкции
- моечная установка
- Устройство наклона/отталкивания
- системы отделки и покрытия по запросу
- Системы контроля качества
Щетка для чистки
Элеватор
Транспортировка свежих продуктов в зону посола и последующее удаление и перемещение посоленных продуктов требуют интеллектуальной интеграции различных компонентов системы.
Элеватор Masa собирает производственные поддоны со свежими продуктами. Производственные поддоны циклически транспортируются вверх.
Как только подъемник достигает заданного предела, производственные поддоны поднимаются на тележке и транспортируются в одну из камер отверждения.
Палец-вагон
Палец-вагон состоит из гусеничной ходовой части (с поворотным устройством или без него, в зависимости от схемы установки) и верхней конструкции. После точного позиционирования пальцевой тележки перед камерой полимеризации происходит передача с низким уровнем вибрации в камеру полимеризации. Процесс закладки продуктов в сушильную камеру происходит в соответствии с указаниями пользователя.
После отверждения производственные поддоны снова поднимаются на тележку для пальцев и транспортируются либо сначала в тележку для промежуточных пальцев (опционально), либо непосредственно на опускатель.
Загрузка сушильных стеллажей полностью автоматической пальчиковой тележкой
Камера отверждения и вентиляция
Для отверждения продуктов Masa предлагает инновационную концепцию открытой планировки: Полная камера отверждения, а также лифт, пальчиковая тележка и опускатель будут установлены в согласованной климатической зоне. Система вентиляции Masa может оптимизировать процесс отверждения, создавая одинаковые климатические условия в камере отверждения.
Состоит из горизонтально расположенных вентиляторов циркуляции воздуха в отдельной вентиляционной шахте, вертикально расположенных вытяжных вентиляторов и диагонально расположенных датчиков влажности и температуры. С помощью датчиков контролируется циркулирующий воздух, соответственно регулируются вентиляторы циркуляционного и вытяжного воздуха.
Целями регулирования температуры и влажности в камере отверждения являются предотвращение различий в цвете однородных продуктов, обеспечение более быстрого отверждения и, в конечном счете, более эффективное использование цемента и красителя.
Бетонные блоки в эстакадах твердения
Промежуточная пальцевая тележка
Промежуточная пальцевая тележка Masa предшествует опускателю, служит промежуточным буфером и предотвращает время простоя пальцевой тележки. Это один из компонентов, используемых с одновременным использованием буфера производственных поддонов в поперечной транспортной зоне.
Опускатель
Опускатель Masa конструктивно идентичен подъемнику, но разбирает производственные поддоны вниз и передает их обратному транспорту.
Masa предлагает подъемно-опускные устройства, промежуточные и пальцевые тележки для различных схем установки. Грузоподъемность, количество этажей и высота этажа рассчитаны соответствующим образом. Весь процесс полностью автоматизирован.
Обратный транспорт
В области обратного транспорта Masa использует приводные системы с полностью электронным управлением.
Обратный транспорт реализован как конвейер с шагающими балками с сервоуправлением. Однако предлагаются и другие транспортные системы. Производственные поддоны с отвержденной продукцией транспортируются из нижнеукладчика в кубер или, как вариант, на переделку.
После снятия изделий с помощью кубообразующего устройства возвратный транспорт также транспортирует пустые производственные поддоны в буфер поперечного транспорта/производственного поддона.
Опционально на сухой стороне могут быть установлены дополнительные компоненты, например:
- устройство для соединения производственных поддонов
- центрирующее устройство и удвоитель блоков
- чистящие скребки или щетка для очистки в зависимости от типа производственного поддона
- упаковочные системы для отдельных слоев
Перевозка консервированных продуктов
Центрирующее устройство
Центрирующее устройство Masa является одним из многих компонентов для оптимального обращения с продуктом. Отвержденные продукты снимаются с производственного поддона и центрируются. Центрирование осуществляется четырехсторонним центрирующим зажимом как поперек направления транспорта, так и по ходу движения.
В зависимости от схемы установки требуется удвоение слоев продукта. Это можно реализовать с помощью удвоителя Masa. Дублер действует как центрирующее устройство, но снабжен подъемным устройством. Изделия рыхлят и центрируют, слои складывают вдвое. Опционально может быть предложено горизонтальное переворачивающее устройство для индивидуального поворота слоев продукта.
И центрирующий, и дублирующий привод управляются сервоприводом.
Производственные поддоны — поперечный транспорт и буфер
После удаления и нарезки готовой продукции куботером пустые производственные поддоны возвращаются в производственный цикл. Для двустороннего использования производственные поддоны переворачивают.
В зависимости от схемы установки транспортные поддоны транспортируются либо непрерывно в магазин производственных поддонов машины для производства бетонных блоков, либо после буферизации или складирования производственных поддонов.
Балансировка разного времени цикла на свежей и сухой стороне, а также возможность хранения только производственных поддонов играют решающую роль при выборе систем хранения производственных поддонов.
Masa предлагает различные буферные системы, которые, например, компенсируют (кратковременные) перерывы и гарантируют бесперебойный производственный процесс на машине для производства бетонных блоков.
более
Полностью автоматический буфер производственных поддонов
Кубирование
Высококачественный бетонный блок требует осторожного обращения. Для этого применения Masa предлагает полностью сервоуправляемые системы кубирования: С помощью «Cuboter» Masa предоставляет технологии и опыт для подготовки конечного продукта к отгрузке.
С помощью Куботера можно снять целый блок-укладчик с возвратного транспорта или с других позиций взлета и собрать его на последующем транспорте куба в каменный куб. Транспортные поддоны и упаковочные системы могут использоваться индивидуально.
более
Эффективно и подходит для материала: Masa Cuboter
Конвейер для кубов
После кубирования следует транспортировка кубов: Masa обычно использует прочный двойной цепной конвейер для транспортировки готовых каменных кубов к месту разгрузки или для подачи упаковочных систем, которые могут использоваться с транспортными поддонами или без них. При использовании специальных профилей (U-профилей) возможна автоматическая вертикальная обвязка без транспортных поддонов.
Конечно, возможны и другие индивидуальные решения, просто свяжитесь с нами!
Masa может интегрировать различные упаковочные системы в области транспортировки кубов, которые безопасно и надежно защищают готовую продукцию. Для последующей идентификации продукты могут быть идентифицированы с помощью системы маркировки .
более
Обработка поверхности
Из-за повышенного спроса на отдельные изделия из бетона производители уделяют все больше внимания вариантам отделки поверхности. Особые цветовые акценты, а также дизайн оптики и поверхностей становятся все более важными.
Masa поставляет компоненты для популярных методов отделки, таких как
мойка или
расщепление .
Старение или дробеструйная обработка или другое оборудование для обработки поверхности могут быть включены в процесс или использоваться индивидуально.
Бетонные блоки с шероховатой поверхностью под натуральный камень
3-позиционная система мойки
Модернизация
Из-за различных размеров досок и слоев камня на производственных предприятиях иногда необходимо увеличивать или уменьшать количество слоев блоков в направлении процесса. Поэтому Masa предлагает несколько способов подготовки бетонных блоков в соответствии с требованиями заказчика, подходящих для транспортировки.
Например, переключатель Masa (по конструкции аналогичен Маса Куботер ) — это один из методов, а столы расталкивания и разделения — другой пример. Специальные версии доступны по запросу. Мы будем рады проконсультировать вас.
Модернизация и кубирование
Powertainer
В Masa Powertainer есть все: с самого начала шкафы управления предварительно установлены в нужном месте. Это защищенное и чистое место предлагает оптимальные условия для этих компонентов. Кроме того, возможен простой климат-контроль. Система управления кабелями в Powertainer обеспечивает соответствие кабелей требованиям ЭМС и снижает количество отказов. По возможным неисправностям неисправности в Powertainer могут быть обнаружены гораздо легче.
Для клиента очевидно еще одно преимущество: Masa также предлагает испытанную концепцию закрытой электрической операционной!
Masa идет еще дальше, разрабатывая «контейнерную концепцию…»
более
Инновационный и изысканный: Masa Powertainer
Шкафы управления внутри «Powertainer».
Система управления и предохранительные устройства
Производственные системы Masa характеризуются высокой степенью автоматизации, что обеспечивает, соответственно, высокую эксплуатационную эффективность. В дополнение к надежной конструкции компонентов ключевым фактором успеха в использовании системы Masa является ориентированная на клиента концепция управления.
Программное обеспечение для управления заводом Masa (Masa FAST Factory Automation Service Tools) представляет собой модульное программное обеспечение для единообразной работы и визуализации компонентов. Ключевой особенностью является то, что установка управляется с помощью единого программного обеспечения, что обеспечивает интегрированную единую концепцию данных для всей работы установки.
Встроенная система помощи оператору основана на известных операционных системах. Свободно программируемая визуализация и масштабируемое программное обеспечение могут быть адаптированы компанией Masa к индивидуальным требованиям заказчика. Программное обеспечение расширяется в соответствии с требованиями заказчика. Узнать больше!
Индивидуальные и практически ориентированные на растения концепции безопасности разработаны многопрофильной командой опытных сотрудников Masa. Подробнее…
- Узнайте больше о базовой настройке завода по производству бетонных блоков Masa.
Из бункеров для заполнителей различное сырье транспортируется на дозировочно-смесительную установку (01), где различные заполнители перерабатываются в основной или облицовочный бетон.
Бетон подается, в зависимости от схемы завода, с помощью транспортной системы (02) к машине для производства бетонных блоков (03). Здесь бетон заливается в каменную форму и уплотняется вибрацией. Изделия могут быть изготовлены с лицевой смесью и без нее.
Все еще свежие бетонные изделия затем поступают на производственных поддонах через мокрый боковой транспорт (04) к элеватору (05) и, при желании, с привлечением систем контроля качества.
Производственные поддоны перемещаются в пальчиковую тележку (06), которая затем направляется в систему стеллажей для отверждения (07). После отверждения производственные поддоны с камнями проходят через пальчиковую тележку и промежуточную пальчиковую тележку (08) в опускатель (09).
Опускатель циклически перемещает производственные поддоны на обратный транспорт (10).
Дополнительное центрирующее устройство (11) разрыхляет и центрирует отвержденные камни на производственных поддонах.
В кубометре (13) камни собираются в кубики и подготавливаются к дальнейшему удалению.
С помощью кубического транспортера (14) пакеты с камнями достигают конечной точки разгрузки (например, с помощью вилочного погрузчика).
Использованные производственные поддоны возвращаются обратно в машину для изготовления бетонных блоков через поперечную транспортировку и/или буферную систему производственных поддонов (12) .
Для производства продуктов с особыми свойствами поверхности Masa предлагает различное оборудование для обработки поверхности (15) как для свежей, так и для сухой стороны.
Для системы электроснабжения завода Masa предпочитает установку силовых панелей в Powertainer (17).
Устройства управления и безопасности установки Masa (18) обеспечивают оптимальную и безопасную работу технологического процесса, что обеспечивает высокую эксплуатационную готовность завода по производству блоков.
Текущие брошюры
Почему завод-изготовитель Masa?
- современные и сложные технологии
- полностью автоматические машины для производства бетонных изделий
- Многолетний опыт компетентных специалистов
- Сервисные центры по всему миру
- Энергичный консалтинг от планирования до установки
- Надежное снабжение запасными частями и обслуживание клиентов
Заинтересовали ли мы вас? Свяжитесь с нами и отправьте запрос.
- Отдел продаж Andernach
- Тел.: +49 2632 9292-0
- Факс: +49 2632 9292-11
- Электронная почта: [email protected]
- Процесс производства песчано-бетонных блоков
- 1. Комплектование
- 2. Смешивание материалов
- 3. Формование песчано-бетонных блоков
- 4. Уплотнение
- 5. Укладка песчано-бетонных блоков 6
900 900 06
- Испытания песчано-бетонной составляющей
- Испытание мелких заполнителей
- Испытание песчано-бетонных блоков
- 1.
Испытание на прочность при сжатии
- 2. Объемная плотность
- 3. Водопоглощение
- 4. Проверка размеров
- 1.
Производство и испытание песчано-бетонных блоков
🕑 Время чтения: 1 минута
Песчано-бетонные блоки и кирпичи представляют собой каменные блоки, изготовленные из смеси цемента, песка и воды, и играют решающую роль в строительстве зданий. Пескобетонные блоки в основном используются для несущих и ненесущих стен и фундаментов. Производственный процесс и необходимые испытания, проводимые как на сырье, так и на песчано-бетонных блоках, обсуждаются в следующих разделах.
В комплекте: 9 шт.0003
Процесс изготовления керамоблоков выглядит следующим образом:
1. ДозированиеОтмеривание материалов для производства песчано-бетонных блоков называется дозированием. Существует два метода дозирования, включая весовой и объемный.
Рис. 1: Весовой дозатор, используемый для измерения количества каждого материала
2. Смешивание материалов Смешивание материалов осуществляется после дозирования. Это могло быть сделано как вручную, так и механически. Первый метод используется для производства большого количества песчано-бетонных блоков. Однако последний рекомендуется, когда требуется небольшое количество блоков. Цемент и песок необходимо тщательно перемешать, а затем в смесь добавить воду. Этот процесс должен быть выполнен правильно, иначе качество блока будет скомпрометировано.
Наконец, следует избегать добавления чрезмерного количества воды, так как это приводит к усадке и деформации блоков при сушке.
После смешивания формы заполняются материалами. Для производства песчано-бетонных блоков доступны различные машины и формы. Например, электрическая вибрационная машина, ручной пресс и местная стальная/деревянная ручная форма. Качество блоков, производимых каждой формовочной машиной, различно из-за различий в степени уплотнения. Электрическая вибрационная машина производит блоки высокого качества и прочности по сравнению с другими методами формования.
Рис. 2: Ручное формование песчано-бетонных блоков
Рис. 3: Машинное формование песчано-бетонных блоков
4.
После заполнения форм материал уплотняется для устранения пустот внутри смешанных материалов. Процесс уплотнения не только улучшает качество песчано-бетонных блоков, но и повышает их долговечность. Затем уплотненные блоки выталкивают из форм на плоскую поверхность.
Рис. 4: Извлечение блока из формы
5. Отверждение песчано-бетонных блоковОн включает смачивание блоков водой, чтобы обеспечить надлежащую гидратацию и затвердевание и, в конечном итоге, достичь полной прочности. Обработку можно производить с помощью лейки, резинового шланга или ведра, либо разбрызгивая воду на блоки и накрывая их брезентом или влажными мешками.
Рис. 5: Затвердевание песчано-бетонных блоков
6. ШтабелированиеЭто расположение блоков один на другом, готовое к продаже или использованию.
Рис. 6: Сложенные блоки
Песок, используемый для производства пескобетонных блоков, должен быть чистым и не содержать вредных примесей. Поэтому необходимо провести испытания образцов, чтобы убедиться в пригодности песка перед его утилизацией.
1. Ситовой анализСитовой анализ может быть выполнен на основе Стандартного метода испытаний для ситового анализа мелких и крупных заполнителей (ASTM C136 / C136M-14) или любых других применимых стандартов. Это свидетельствует о пригодности песка для пескобетонных блоков. Например, если количество мелкодисперсных материалов велико, то весьма вероятно, что прочность блока будет нарушена.
2. Тест на содержание ила и глины Это испытание может быть проведено на основе стандартного метода испытаний для определения гранулометрического состава (градация) мелкозернистых почв с использованием седиментационного (гидрометрического) анализа (ASTM D7928-17) и IS: 2386 (Часть II) 1963.
Тест на органическое содержание может быть выполнен на основе стандартных методов определения влажности, золы и органического вещества торфа и других органических почв (ASTM D29).74 – 14)
Испытание песчано-бетонных блоков 1. Испытание на прочность при сжатииЭто испытание используется для оценки прочности на сжатие песчано-бетонных блоков. Прочность на сжатие — это способность блоков выдерживать нагрузку, приложенную в осевом направлении на кромку или поверхность основания блока. Для оценки прочности блоков на сжатие используется машина для испытаний на сжатие. Испытание проводят на блоках в возрасте 28 дней и тестируют три образца. Нагрузка воздействует на блок до тех пор, пока он не сломается; в этот момент будет зафиксирована максимальная сжимающая нагрузка.
2.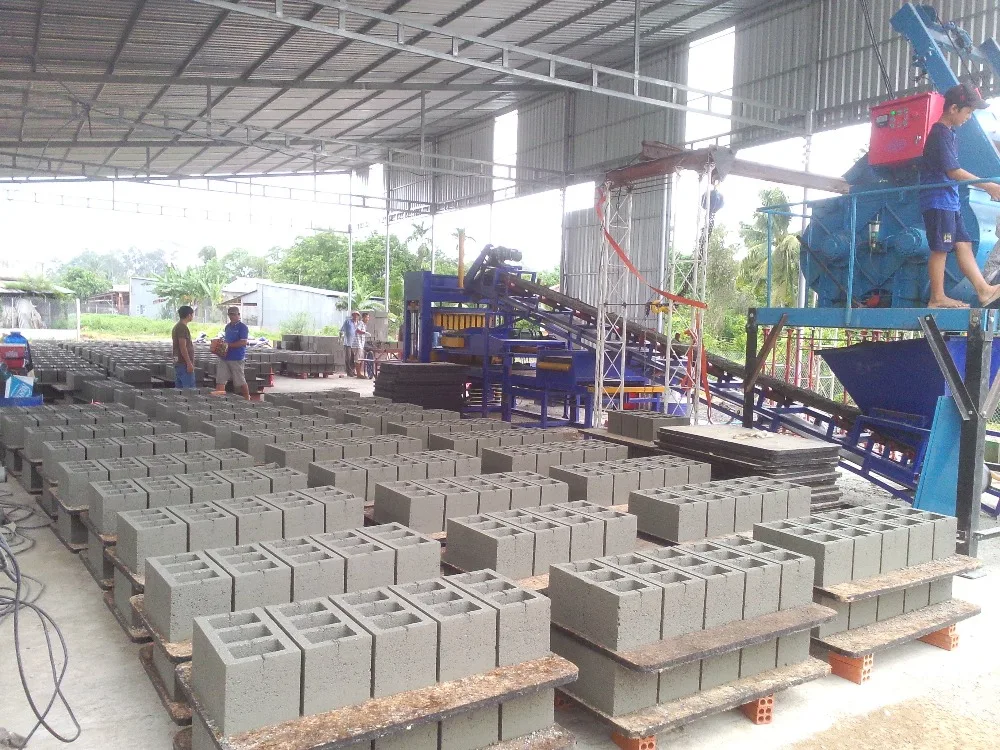