Прочность цемента: Как усилить прочность цемента — Официальный сайт производителя сухих строительных смесей в Москве
Как усилить прочность цемента — Официальный сайт производителя сухих строительных смесей в Москве
Один из определяющих факторов маркирования бетонных строительных материалов является прочность цемента. Также данный показатель определяет дальнейшие эксплуатационные показатели строения.
Что представляет собой показатель прочности цемента
Предельный показатель прочности цемента – это его марка. Его определяют опытным путем, проведя ряд испытаний. Исследователь создает небольшой участок цемента, после чего на него оказывается давление разной силы. Показатели заносятся в протокол испытаний. На основании этих данных цементу присваивается марка, определяющая максимальную прочность материала.
Существует три класса прочности цемента
- Сверхпрочный цемент выдерживает нагрузку от 50 МПа и выше.
- Прочный цемент справляется с давлением в 30-50 МПа.
- Цемент пониженной прочности может выдержать нагрузку не больше 30 Мпа.
Показатель прочности цемента играет большую роль, поскольку готовые бетонные конструкции будут подвергаться механическим, статическим и динамическим нагрузкам, перепадам температур, атмосферных осадков, неблагоприятным техногенным воздействиям.
Как повысить показатели прочности цемента и других технических характеристик?
Чтобы улучшить эксплуатационные и технические показатели цемента, производители бетона добавляют в состав смеси различные вспомогательные компоненты (пластификаторы), которые усиливают прочностные характеристики продукта и увеличивают продолжительность эксплуатации строений.
Увеличение прочностных показателей цемента требует дополнительных расходов и не всегда является целесообразным. В усилении нуждается материал, который будет эксплуатироваться в условиях повышенной влажности, сильных морозов, резких перепадов температур и давления.
Существует несколько типов химических реагентов, способных улучшить показатель прочности цемента. Как правило, это сырье синтетического происхождения, которое добавляют в жидкую смесь. Внедрять химические добавки после застывания бетона невозможно.
Виды повышающих прочность компонентов
- Ускорители набора прочности – добавка, способствующая быстрому схватыванию и застыванию бетона. Также она увеличивают марочную прочность готового бетона. В состав ускорителей входит хлористый кальций, благодаря его свойствам застывшая бетонная смесь не только становится крепче, но и в несколько раз быстрее набирает прочность. Следовательно, ускоряется весь процесс производства.
- Пластификаторы – компоненты, повышающие подвижность раствора и устойчивость бетона к динамическим нагрузкам. При этом прочность бетонных конструкций возрастает на 140%, повышается их водонепроницаемость и морозостойкость. Благодаря добавлению пластификаторов уменьшается расход цемента для замеса раствора на 25%.
- Противоморозные добавки (ПМД) – вещества, формирующие сопротивляемость бетона низким температурам.
Основными компонентами смеси являются гидрофобизаторы и нейтрализованная смола. Поэтому наряду с устойчивостью к низким температурам застывший бетон становится еще и водонепроницаемым. Благодаря химическому реагенту бетон не растрескивается во время морозов и позволяет выполнять бетонные работы в любое время года.
- Модификаторы – разнообразные добавки, придающие бетону дополнительные свойства: устойчивость к коррозии, снижение объемов усадки, предотвращение поражению плесенью, делают раствор более удобным для формования и укладки.
Благодаря разнообразным добавкам в сухую смесь уменьшается расход цемента и увеличивается качество бетона.
Пропитки и упрочнители
Повысить качество бетона после затвердевания помогут специальные пропитки и упрочняющие поверхностный слой составы. Жидкие пропитки и упрочнители содержат специальные компоненты, способные проникать в мельчайшие поры бетона. Чтобы эффект был максимальным, в составе раствора должны отсутствовать гидрофобизаторы.
При контакте с поверхностью бетона пропитка вступает в химическую реакцию, в результате которой образуется нерастворимое соединение. Данную пропитку можно наносить как на свежеизготовленные бетонные конструкции, так и на старую поверхность бетона. Как только упрочнитель наберет силу, бетон обретает устойчивость к более высоким нагрузкам, чем предполагает его марка.
Также для улучшения свойств цемента в раствор добавляют порошкообразный упрочнитель. Благодаря компонентам, входящим в состав упрочняющей смеси, окрепшая бетонная конструкция свободно выдерживает давление в районе 70 МПа. Это могут быть как статические, так и динамические нагрузки на сжатие\растяжение. Преимущества сухого упрочнителя перед растворами состоит в том, что сырье можно использовать для эксплуатации бетона в агрессивно среде. Применение упрочнителя увеличивает продолжительность эксплуатации монолита на 10-15 лет.
Современные технологии производства сухих смесей для изготовления раствора позволяют усилить прочность и другие технические характеристики цемента, готового раствора и сухого бетона, таким образом, современные монолитные и бетонные конструкции получили сроки эксплуатации на десятки лет дольше, чем у их предшественников.
Поделиться с друзьями
Предел прочности цемента — Справочник химика 21
Сцепление с арматурой является одним из условий работы железобетонных конструкций, так как если сцепления с арматурой не будет, то деформация каждого из материалов в железобетоне произойдет по отдельности и работа конструкции нарушится. Сцепление с арматурой определяется двумя факторами собственно сцеплением арматуры с цементом и сжатием стержней арматуры вследствие усадки бетона. Величина сцепления бетона с арматурой составляет примерно 0,15—0,20 от предела прочности цемента при сжатии, причем сцепление зависит от вида цемента, так, например, сцепление с арматурой для глиноземистого цемента значительно выше по сравнению с портландцементом.Машины и приборы для определения механических свойств материалов Приборы для испытания металлов и конструкций Универсальные и разрывные машины для испытания статической нагрузкой Приборы и машины для испытания материалов Машины разрывные предельной нагрузки 1—5 кгс для испытания металлических лент и проволоки Машины и приборы для испытания резины и резинотехнических изделий Машины испытательные для определения предела прочности цемента при изгибе Машины для механических испытаний материалов с приставками для низких и высоких температур (типа Инстрон )
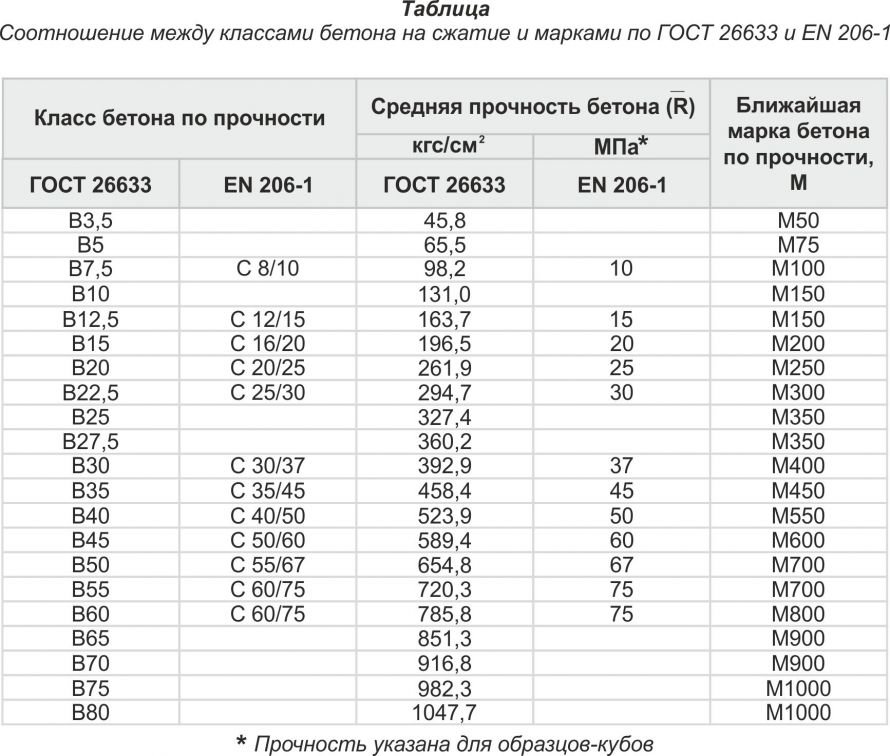
Маркой цемента называется предел прочности на сжатие образца цемента после затвердевания его в течение двадцати восьми суток, выражаемый в кг/см . Чем больше марка цемента, тем выше его качество. Существуют марки 400, 500 и 600.
Анализ табл. 261 показывает, что цементы с водоцементным отношением 0,5 имеют предел прочности на изгиб ниже установленного для горячих скважин. При снижении процента воды затворения прочность цементов повышается. [c.345]
Портландцемент и шлакопортландцемент ГОСТ 10178—76 применяют в качестве вяжущих для приготовления растворов при облицовке строительных конструкций кислотостойкими штучными материалами, в основном, для защиты от воздействия щелочных растворов. По механической прочности они разделяются на марки 300, 400, 500, 550, 600, означающие предел прочности при сжатии и изгибе образцов, испытанных через 28 суток с момента изготовления. Технические требования к цементам следующие тонкость помола — проход через сито 008 не менее 85 % сроки схватывания — начало не менее чем через 45 мин, конец не более чем через 10 ч предел прочности — в зависимости от марки при изгибе от 5,5 до 6,5 МПа, 17]
Вид цемента Предел прочности через 28 сут, МПа [кгс/см З, не менее [c.9]
В СССР цемент изготовляется путем размола доменного шлака, получаемого при плавке бокситовой железной руды, с добавкой извести и железного лома. Приобретает почти полную прочность через 15—24 ч после затворения. Сроки схватывания начало не ранее 45 мин, конец не позднее 12 ч. Предел прочности при изгибе образцов-балочек, испытанных через 28 сут твердения, может быть ниже прочности образцов, испытанных через 3 сут твердения, но не более чем на 10% (табл. 8).
Пробы извести, предназначенные для иснытания па гидравлическую известь, подвергались помолу в лабораторной шаровой мельнице. Определение предела прочности при сжатии образцов производилось на кубиках размером 7,0 X 7,0 X 7,0 см, приготовленных из раствора с нормальным песком 1 3 но ГОСТ 310-41 Цементы. Методы физических и механических испытаний .

А. ПРЕДЕЛ ПРОЧНОСТИ ПРИ ИЗГИБЕ и ПРИ СЖАТИИ ЦЕМЕНТОВ [c.255]
Среднюю величину предела прочности при сжатии испытуемого цемента рассчитывают как среднее арифметическое четырех наибольших значений из шести испытанных образцов. Форма записи приведена ниже. [c.263]
Ход работы. Для определения величины предела прочности при сжатии из испытуемого цемента готовят цементное тесто [c.263]
Сульфат натрия и сульфат кальция при взаимодействии с гидроалюминатом кальция образуют гидросульфоалюминат состава ЗСаО-А120з-ЗСа804-31Н20. Гидросульфоалюминаты кальция занимают объем, более чем в два раза превосходящий объем исходных алюминатов. Вследствие этого возникают внутренние напряжения, превышающие предел прочности цемента при растяжении. Сульфат магния вступает в реакцию с гидроксидом, гидросиликатом и гидроалюминатом кальция. Один из продуктов этой реакции — М (ОН)2 —очень мало растворим, и поэтому реакция идет до конца. Часто такой вид агрессии наиболее опасен. [c.369]
Имеющийся опыт показывает, например, что увеличение тонкости помола цементного клинкера с доведением его удельной поверхности с 2500-—3000 до 4000—5000 слг /г (при определении удельной поверхности по методу Товарова) позволяет повысить предел прочности цемента с 300—400 до 600—800 /сг/сл . Благодаря этому значительно сокращается расход цемента в растворах и бетонах. С другой стороны, повышение удельной поверхности позволяет получить быстротв.ердеющие цементы и тем самым обеспечивает значительное упрощение и ускорение технологического процесса производства. [c.211]
Примечание. За ЮО б принят предел прочности цемента, не содержащего Р2О5, через 28 суток после изготовления образца. [c.13]
Пример 2.9. Подобрать машину для измельчения известняка высокой плотности с начальным размером частицы бншах = 6Х Х10″ м, пределом прочности при сжатии сТсж = 200-10 Па, модулем упругости = 5. 10 Па и насыпной плотностью р = = 1800 кг/м . Материал подается на измельчение с производительностью С = 30 т/ч и далее используется для производства цемента мокрым способом. Конечный размер частиц должен быть меньше 0,15-10- м. [c.56]
Пределы прочности при сжатии кислотоупорного цемента через 4 суток после изготовления 13,0—14,0 Мн1м , через 28 суток 16,0—17,0 Мн/м . Предел прочности при растяжении равен 10% от предела прочности при сжатии. Химическая стойкость кислотоупорного бетона такая же, как и кислотоупорных цементов. [c.459]
Скорость нарастания пластической прочности в период упрочнения структуры цементного теста увеличивается. Предел прочности на одноосное сжатие образцов цементного камня, полученных из виброактивированного теста, оказался значительно более высоким, чем для образцов, приготовленных без активирования. Это обусловлено увеличением равномерности распределения воды между зернами цемента при низком В/Ц, приводящее к повышению пластичности и снижению прочности коагуляционной структуры, дополнительным механическим диспергированием зерен цемента и ускорению процессов гидратации за счет усиления процессов адсорбционного и химического диспергирования и постоянного отвода продуктов гидратации с поверхности вибрирующих зерен и обнажения свежих поверхностей для дальнейшей гидратации [435]. [c.187]
Согласно ГОСТу 10178—62 портландцемент делится на семь марок (200, 250, 300, 400, 500, 600, 700), которые обозначают предел прочности (в кГ1см ) при сжатии образцов, изготовленных из смеси цемента с нормальным вольскнлг песком (в весоом соотношении 1 3) и испытанных через 28 дней после затво-рення водой. Наиболее распространенными являются марки от 300 до 600. [c.339]
ГОСТ 1581—63 предусматривает также испытание тампонажных цементов на временное сопротивление изгибу. Испытанию подвергаются балочки размером 40 X 40 X 160 мм, изготовленные из цемента (без добавок) с водоцемент-ныы отношением 0,5, после твердения в течение двух суток в воде. Цементы, предназначенные для тампонирования холодных скважин, должны иметь предел прочности при изгибе не менее 27 кГ/см в случае затворения пресной водой и 32 кГ1см при затворении морской водой. Для горячих скважин яременное сопротивление изгибу должно быть не менее 62 кГ)см нри затворе- 1ии как пресной, так и морской водой температура затворения 75 3°С. [c.343]
По стандарту портланд-цемент делится на марки от 300 до 900. Эти марки соответствуют пределу прочности при сжатии (в кг1см ) образцов, полученных при затворении с водой смеси цемента с песком через 28 дней. Начало схватывания при 24— 25%-ном содержании воды наступает не ранее чем через 45 мин, конец — не позже чем через 12 ч от начала затворения. [c.244]
Марки цемента соответствуют пределу прочности при сжатии половинок образцов-балочек, изготовленных в соответствии с ГОСТ 310—60 (табл. 7). Начало схватывания для всех цементов должно наступать не ранее чем через 45 мин, а конец схватывания— не позднее чем через 12 ч после начала затворения. Портландцемент используют для приготовления обычных и жаростойких бетонов и растворов. Его не следует применять для кладки фундаментов и конструкций, соприкасающихся с кислыми, мягкими, минерализованными сточными водами. В клинкерном портландцементе содержание SiOj не должно превышать 3%.

Марки жаростойких бетонов, определяемые величиной предела прочности при сжатии образцов-кубиков размером ЮОХ X100X100 мм, выдержанных в течение 3 суток для бетонов, изготовленных на глиноземистом цементе и жидком стекле, и 7 суток для бетонов, изготовленных на портландцементе и пе-риклазоБом цементе, а затем высушенных при температуре 100—110° в течение 32 час. , находятся в пределах 100—300 в зависимости от расчетных данных. [c.33]
В современной практике использования вяжущих веществ большое значение отводится использованию быстротвердеющих и особо быстротвердеющнх цементов, т. е. цементов БТЦ и ОБТЦ. Характерная особенность этих цементов заключается в том, что после затворения водой прочность их нарастает значительно быстрее, чем у обычных цементов. Поэтому ГОСТ П78—62 предусматривает нормативную величину предела прочности при сжатии стандартных образцов не 28-суточного, как для обычных цементов, а 3-суточного возраста. При этом прочность таких об разцов должна составлять для быстротвердеющего портландце мента не менее 200 кГ/ см 200-98066 н/м ) и для быстротверде ющего шлакопортландцемента не менее 150 кГ/см (или 150-98066 н/ж2). [c.254]
Соответственно с марочностью цементов для каждого из них нормируется и величина предела прочности при изгибе, которая должна составлять для цементов марок 200, 250, 300, 400, 450 и 500 соответственно 35, 40, 50, 60, 65 и 70 кГ/ см чтобы выразить приведенные величины в н/м , необходимо числовые значения их умножить на переводной коэффициент 98066,5. [c.254]
Для определения предела прочности при изгибе и предела прочности при сжатии цемента необходимо установить водо-це-ментное отнощение раствора и приготовить раствор требуемой гост консистенции из цементного раствора отформовать образцы в виде балочек стандартных размеров выдержать изготовленные образцб по предусмотренным ГОСТ 310—60 условиям и срокам подвергнуть образцы испытанию на определение величины предела прочности при изгибе полученные в результате предыдущего испытания половинки балочек n nbiTatb на сжатие. [c.255]
Влиянию пониженных температур —попеременному замораживанию и оттаиванию — подвергаются практически все открытые сооружения, служащие в условиях атмосферного воздействия. Особенно опасная ситуация возникает, когда воздействуют одновременно низкая температура и растворы солей, например при работе бетона в морских сооружениях. Суть действия пониженной температуры в бетоне заключается, в возникновении деформации расширения замерзающей воды в опасных порах, которая может привести к оазрушению. Возникают но меньшей мере два источника разрушающих сил первый — увеличение объема воды при замерзании — 9%), что ведет к возникновению большого гидравлического давления иа стенки пор и капилляров, второй — осмотическое давление, возникающее благодаря локальному увеличению концентрации раствора из-за отделения замерзающей воды от раствора. По мнению некоторых исследователей, величина осмотического давления может достигать 1—2 МПа. Многократные теплосмены постепенно расшатывают структуру цементного камня и бетона, снижают его прочность и в момент, когда давление расширения превышает предел прочности при растяжений, бетон разрушается. Как показано Б. Г. Скрамтаевым, В,- М. Москвиным7 В. В. Стольниковым и С. Д. Мироновым, основную роль в разрушении при действии низких температур играют как общая пористость, так и характер капиллярно-пористой структуры материала — в искусственном камне имеются поры, наиболее опасные и ответственные за развитие разрушения материала. Практически не опасны, например, — очень мелкие поры геля, поскольку вода в них замерзает толы о при температуре ниже 193 К.
Поскольку морозостойкость искусственного камня зависит от характера и величины общей пористости, то е снижением можно добиться существенного повышения морозостойкости. Общую пористость можно уменьшить снижением В/Ц, использованием цемента с пониженной водопотребностью, а также введением разных типов добавок — пластифицирующих, гидрофобизирующих, воздухововлекающих. [c.369]
Прочность цементного камня. Механическая прочность цеменг-ного камня является важнейшей характеристикой и оценивается пределом прочности при сжатии, изгибе и растяжении. Существующие ГОСТ 10178—76 и 310—76 регламентируют испытание цементов и определение их свойств. По активности портландцементы делят на четыре марки — 400, 500, 550 и 600. [c.376]
таблица на сжатие по классам в МПа, от чего зависит
Прочность – это техническая характеристика, по которой определяется способность выдерживать механические или химические воздействия. Для каждого этапа строительства требуются материалы с разными свойствами. Для заливки фундамента здания и возведения стен применяется бетон разных классов. Если использовать материал с низким прочностным показателем для строительства конструкций, которые будут подвергаться значительным нагрузкам, то это может привести к растрескиванию и разрушению всего объекта.
Оглавление:
- От чего зависит значение прочности?
- Способы проверки качества бетона
- График набора прочности
- Маркировка растворов
Как только в сухую смесь добавляется вода, в ней начинается химический процесс. Скорость его протекания может увеличиваться или уменьшаться из-за многих факторов, например, температуры или влажности.
Что влияет на прочность?
На показатель оказывают влияние следующие факторы:
- количество цемента;
- качество смешивания всех компонентов бетонного раствора;
- температура;
- активность цемента;
- влажность;
- пропорции цемента и воды;
- качество всех компонентов;
- плотность.
Также он зависит количества времени, которое прошло с момента заливки, и использовалось ли повторное вибрирование раствора. Наибольшее влияние оказывает активность цемента: чем она выше, тем больше получится прочность.
От количества цемента в смеси также зависит прочность. При повышенном содержании он позволяет увеличить ее. Если же использовать недостаточное количество цемента, то свойства конструкции заметно снижаются. Увеличивается этот показатель лишь до достижения определенного объема цемента. Если засыпать больше нормы, то бетон может стать слишком ползучим и дать сильную усадку.
В растворе не должно быть слишком много воды, так как это приводит к появлению в нем большого количества пор. От качества и свойств всех компонентов напрямую зависит прочность. Если для замешивания использовались мелкозернистые или глинистые наполнители, то она снизится. Поэтому рекомендуется подбирать компоненты с крупными фракциями, так как они значительно лучше скрепляются с цементом.
От однородности замешанной смеси и применения виброуплотнения зависит плотность бетона, а от нее – прочность. Чем он плотнее, тем лучше скрепились между собой частицы всех компонентов.
Способы определения прочности
По прочности на сжатие узнаются эксплуатационные характеристики сооружения и возможные на него нагрузки. Вычисляется этот показатель в лабораториях на специальном оборудовании. Используются контрольные образцы, сделанные из того же раствора, что и отстроенное сооружение.
Также вычисляют ее на территории строящегося объекта, узнать можно разрушаемым или неразрушаемым способами. В первом случае либо разрушается сделанная заранее контрольная проба в виде куба со сторонами 15 см, либо с помощью бура из конструкции берется образец в виде цилиндра. Бетон устанавливается в испытательный пресс, где на него оказывается постоянное и непрерывное давление. Его увеличивают до тех пор, пока проба не начнет разрушаться. Показатель, полученный во время критической нагрузки, применяется для определения прочности. Этот метод разрушения пробы является самым точным.
Для проверки бетона неразрушаемым способом используется специальное оборудование. В зависимости от типа приборов он делится на следующие:
- ультразвуковой;
- ударный;
- частичное разрушение.
При частичном разрушении на бетон оказывают механическое воздействие, из-за чего он частично повреждается. Провести проверку прочности в МПа этим методом можно несколькими способами:
- отрывом;
- скалыванием с отрывом;
- скалыванием.
В первом случае к бетону на клей крепится диск из металла, после чего его отрывают. То усилие, которое потребовалось для его отрыва, и используется для вычисления.
Метод скалывания – разрушение скользящим воздействием со стороны ребра всего сооружения. В момент разрушения регистрируется значение приложенного давления на конструкцию.
Второй способ – скалывание с отрывом – показывает наилучшую точность по сравнению с отрывом или скалыванием. Принцип действия: в бетоне закрепляются анкера, которые впоследствии отрываются от него.
Определение прочности бетона ударным методом возможно следующими путями:
- ударный импульс;
- отскок;
- пластическая деформация.
В первом случае фиксируется количество энергии, создаваемой в момент удара по плоскости. Во втором способе определяется величина отскока ударника. При вычислении методом пластической деформации используются приборы, на конце которых расположены штампы в виде шаров или дисков. Ими ударяют о бетон. По глубине вмятины вычисляются свойства поверхности.
Метод с помощью ультразвуковых волн не является точным, так как результат получается с большими погрешностями.
Набор прочности
Чем больше прошло времени после заливки раствора, тем выше стали его свойства. При оптимальных условиях бетон набирает прочность на 100 % на 28-ой день. На 7-ой день этот показатель составляет от 60 до 80 %, на 3-ий – 30 %.
Рассчитать приблизительное значение можно по формуле: Rb(n) = марочная прочность*(lg(n)/lg(28)), где:
- n – количество дней;
- Rb(n) – прочность на день n;
- число n не должно быть меньше трех.
Оптимальной температурой является +15-20°C. Если она значительно ниже, то для ускорения процесса затвердения необходимо использовать специальные добавки или дополнительный обогрев оборудованием. Нагревать выше +90°C нельзя.
Поверхность должна быть всегда влажной: если она высохнет, то перестает набираться прочность. Также нельзя допускать замерзания. После полива или нагрева бетон снова начнет повышать свои прочностные характеристики на сжатие.
График, показывающий, сколько времени требуется для достижения максимального значения при определенных условиях:
Марка по прочности на сжатие
Класс бетона показывает, какую максимальную нагрузку в МПа он выдерживает. Обозначается буквой В и цифрами, например, В 30 означает, что куб со сторонами 15 см в 95% случаев способен выдержать давление 25 МПа. Также прочностные свойства на сжатие разделяют по маркам – М и цифрами после нее (М100, М200 и так далее). Эта величина измеряется в кг/см2. Диапазон значений марки по прочности – от 50 до 800. Чаще всего в строительстве применяются растворы от 100 и до 500.
Таблица на сжатие по классам в МПа:
Класс (число после буквы – это прочность в МПа) | Марка | Средняя прочность, кг/см2 |
В 5 | М75 | 65 |
В 10 | М150 | 131 |
В 15 | М200 | 196 |
В 20 | М250 | 262 |
В 30 | М450 | 393 |
В 40 | М550 | 524 |
В 50 | М600 | 655 |
М50, М75, М100 подходят для строительства наименее нагружаемых конструкций. М150 обладает более высокими прочностными характеристиками на сжатие, поэтому может применяться для заливки бетонных стяжек пола и сооружения пешеходных дорог. М200 используется практически во всех типах строительных работ – фундаменты, площадки и так далее. М250 – то же самое, что и предыдущая марка, но еще выбирается для межэтажных перекрытий в зданиях с малым числом этажей.
М300 – для заливки монолитных оснований, изготовления плит перекрытий, лестниц и несущих стен. М350 – опорные балки, фундамент и плиты перекрытий для многоэтажных зданий. М400 – создание ЖБИ и зданий с повышенными нагрузками, М450 – плотины и метро. Марка меняется в зависимости от количества содержащегося в нем цемента: чем больше его, тем она выше.
Чтобы перевести марку в класс, используется следующая формула: В = М*0,787/10.
Перед сдачей в эксплуатацию любого здания или другого сооружения из бетона оно обязательно должно быть проверено на прочность.
Что влияет на прочность бетона, полезные советы
Основной состав бетона состоит из трех компонентов цемент, как главный связующий элемент, вода и наполнитель (песок). Также в бетон иногда добавляются различные химические добавки для увеличения его прочности и морозостойкости.
Однако, даже без каких-либо добавок имеющийся трехкомпонентный состав должен на высшем уровне обеспечивать надлежащую прочность и морозостойкость строительного материала. Несмотря на то, что для изготовления смеси бетона используются по сути дела компоненты природного происхождения и сам технологический процесс замешивания смеси не требует особых новаторских технологий за исключением соблюдения необходимых пропорций, требуется пристальное внимание к составу компонентов бетонной смеси. Примером подбора некачественных исходных материалов может послужить снижение качества материала и разрушение будущей бетонной конструкции в целом.
Для достижения максимальной прочности бетона следует руководствоваться одним правилом: правильный подбор песчаного заполнителя. Прежде всего это означает, что следует подбирать песок мелкозернистой структуры, поскольку чем меньше образуется зазоров между зернами песка, тем лучше происходит их склеивание цементной смесью и соответственно увеличивается крепость бетона.
Как правило, песок одной массы в общем объеме на 4/10 содержит пустоты, в то же время сборный песок из различных масс намного плотнее. В целях получения максимальной прочности бетонной смеси перед замешиванием, песок делят на крупный мелкий по размерам песчаных зерен. Затем смешивают в определенных пропорциях песок, тем самым получают песчаный наполнитель. В таком наполнителе песчаные зерна будут плотнее прилегать к друг другу соответственно будет более прочное их склеивание цементной массой. Таким образом изготовленная сухая смесь бетона будет иметь максимальную прочность при минимальных затратах цемента.
В основной своей массе бетонная смесь замешивается из заполнителя произвольных песчаных масс, добыча которых производится в карьерах, а также путем дробления камней. В таком случае получить надежно прочный бетон вряд ли получится. Для достижения минимально необходимой прочности потребуется большое количество цемента.
Не мало важную роль играет вода, для бетонной смеси она должна быть максимально чистой от всех примесей. Содержащиеся в обычной воде жиры, кислоты, сульфаты могут оказать негативное воздействие на структуру и прочность бетона. В идеале следует использовать очищенную воду, предназначенную для питья.
Если так или иначе приходится использовать грунтовые или речные воды, то следует помнить, что они насыщенны различными органическими веществами и перед началом процесса замешивания следует установить какие именно органические вещества входят в состав воды. Если используются промышленные воды, то в их составе как правило присутствуют остаточные количества гипса и серной кислоты. Так или иначе все вышеуказанные типы вод с содержанием примесей могут спровоцировать ослабление прочности бетона и его разрушение.
Огромное влияние на прочность бетона имеет используемый в замесе цемент. При выборе цемента действует все то же правило, чем меньше помол, тем крепче связующие элементы. Именно поэтому целесообразно использовать цемент с наименьшим зерном помола.
Наиболее часто используемый в промышленном строительстве вид цемента – сульфатостойкий. Он менее всего подвержен воздействиям внешних агрессивных сред. Сфера применения такого вида цемента весьма различна от простых промышленных сооружений до мостовых конструкций.
Для иных случаев строительства используют обычный цемент, он подразделяется на марки по классификациям – М100, М200, М300, М400, М500. При возрастании порядкового номера увеличивается вяжущая способность цемента.
Прочность цементного камня — Энциклопедия по машиностроению XXL
Цементный камень, являющийся минеральным клеем, скрепляющим зерна заполнителя, должен обладать достаточной собственной прочностью и адгезией, т.е. хорошо сцепляться (срастаться) с зернами заполнителя. Эти свойства цементного камня зависят от качества и количества новообразований при гидратации, объема и характера пор. Прочность цементного камня и скорость его твердения зависят от минералогического состава клинкера, тонкости помола цемента, содержания воды, влажности, температуры среды и продолжительности хранения. Проницаемость цементного камня определяется его пористостью и наличием трещин.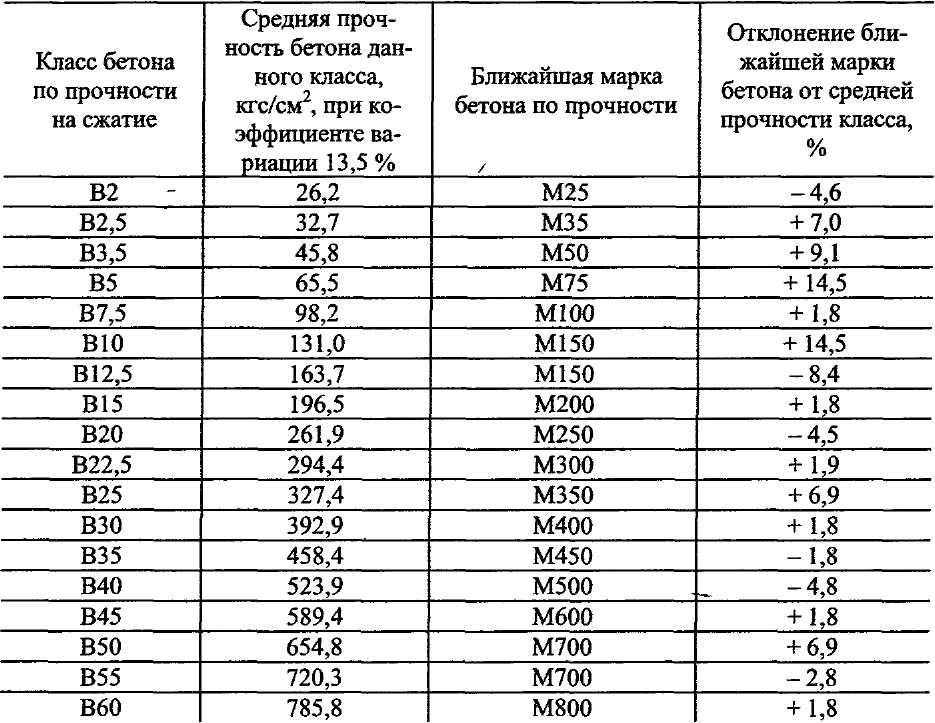
Механические свойства асбестоцемента зависят от содержания асбестового волокна и его качества (длины и диаметра волокон), активности цемента, плотности асбестобетона, условий твердения и др. При плотности 1600… 1800 кг/м асбестоцемент имеет пределы прочности выше пределов прочности цементного камня при растяжении в 3—5 раз — [c.334]
Рис. 15. Влияние вида тонкомолотого заполнителя на прочность цементного камня при нагревании |
Рис. 16. Изменение прочности цементного камня при нагревании в зависимости от количества кремнефтористого натрия (в процентах от веса жидкого стекла) |

При воздействии температуры выше 700 (до 900°) в результате частичного образования жидкой фазы происходят усадка и снижение прочности цементного камня. [c.31]
При измельчении цемента повышается степень дисперсности и увеличивается реакционная поверхность. С ростом удельной поверхности цемента возрастает и прочность цементного камня на его основе. Эта закономерность сохраняется у цемента с удельной поверхностью до 7—10 тыс. сж /г. Дальнейшее измельчение иногда приводит к уменьшению прочности. Однако на заводах и в лабораториях цемент измельчается до удельной поверхности 2,5—5 тыс. см 1г, поэтому можно считать, что с ростом удельной поверхности возрастает и прочность цементного камня. [c.109]
Предел прочности цементного камня, кГ/см , армированного различными видами стеклянного волокна [c.174]
Коррозия второго вида происходит вследствие обменных реакций между составными частями цементного камня и химическими веществами, содержащимися в воде.
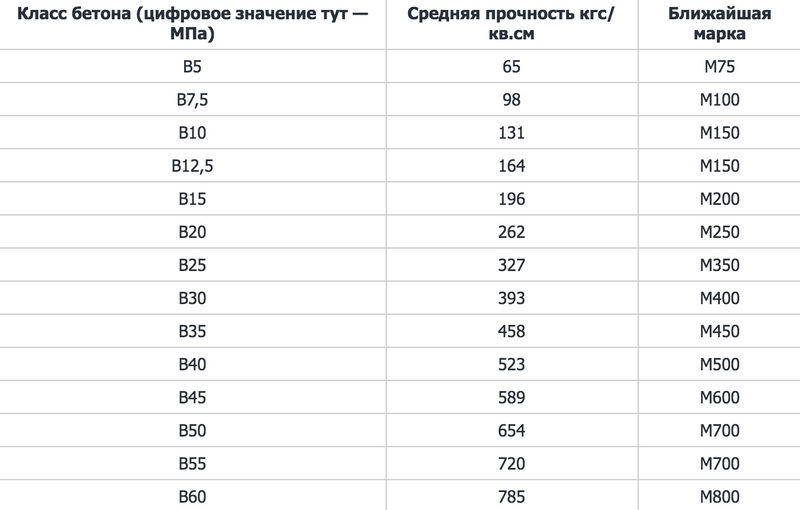
Асбестоцемент является цементным камнем, армирован-ным тонкими короткими волокнами асбеста. Высокая прочность волокон асбеста повышает предел прочности цементного камня при растяжении, изгибе и ударных нагрузках. [c.50]
Наличие начальных напряжений вызывает возникновение в цементном камне микротрещин, снижающих прочность (главным образом при растяжении). [c.364]
Плотность является главным классификационным признаком бетонов, так как с ней связаны его основные свойства — прочность, морозостойкость, водонепроницаемость, теплопроводность и др. Плотность бетона зависит главным образом от плотности цементного камня, вида заполнителей и его структуры.
[c.300]
Мелкозернистый бетон отличается большим содержанием цементного камня, поэтому его усадка и ползучесть несколько выше. Свойства мелкозернистого бетона определяются теми же факторами, что и обычного. Однако качество песка оказывает более заметное (на 25…30%) влияние на прочность. Мелкозернистый бетон обладает повышенной прочностью на изгиб, хорошей водонепроницаемостью и морозостойкостью. [c.306]
Цементно-полимерные бетоны характеризуются наличием двух активных составляющих минерального вяжущего и органического веществ. Вяжущее вещество с водой образует цементный камень, склеивающий частицы заполнителя в монолит. Полимер по мере удаления воды из бетона образует на поверхности пор, капилляров, зерен цемента и заполнителя тонкую пленку, которая обладает хорошей адгезией и способствует повышению сцепления между заполнителем и цементным камнем, улучшает монолитность бетона и работу минерального скелета под нагрузкой. В результате цементно-полимерный бетон приобретает особые свойства повышенную по сравнению с обычным бетоном прочность на растяжение и изгиб, более высокую морозостойкость, хорошие адгезионные свойства, высокую износостойкость, непроницаемость. В то же время для этого бетона отмечается несколько повышенная деформируемость, а также снижение показателей прочности при водном хранении.
[c.316]
Асбестоцемент отличает высокая предельная растяжимость — 8…16 10″, превышающая растяжимость цементного камня в 6—10 раз. Теплопроводность при плотности 1900 кг/м и естественной влажности составляет 0,35 Вт/(м К). Предельная температура применения асбестоцементных изделий на портландцементе 250°С, но значительное снижение прочности наступает после нагрева до 400…500°С. Однако при использовании вяжущего вещества с кремнеземистыми добавками можно получить изделия, выдерживающие температуру 1000°С. [c.335]
Ремонт шелушения цементобетонных покрытий. Как отмечалось ранее, причина шелушения цементобетонных покрытий заключается в недостаточной прочности поверхностного слоя цементобетона, а также в возникновении в нем при климатических воздействиях напряжений сжатия и растяжения, вследствие чего происходит нарушение связности между цементным камнем и заполнителем, расслоение поверхности и выкрашивание из бетона мелких частиц. К основным факторам, способствующим шелушению, относятся
[c.472]
Кроме того, в цементные смеси перед бетонированием целесообразно вводить специальные добавки. Последние должны также обладать полифункциональными свойствами и обеспечивать ускорение твердения цемента управляемое, согласованное е увеличением прочности расширение цементного камня регулирование схватывания и пластифицирующий эффект высокую анодную поляризуемость стали, стабильную в присутствии хлоридов эффективность катодного процесса, достаточную для поддержания коррозионного потенциала в области пассивации. - [c.119]
Помимо трех основных видов коррозии, охватывающих подавляющее большинство процессов, которые приводят к разрушению бетона, исследованы также некоторые специфические виды коррозионного воздействия, из которых следует выделить процессы адсорбционного понижения прочности капиллярно-пористых материалов. Эти процессы развиваются при действии на бетон поверхностноактивных веществ, которые, адсорбируясь на цементном камне, существенно уменьшают его поверхностную энергию, что способствует развитию микротрещин в бетоне и понижению его прочности. Учитывать адсорбционное понижение прочности следует прежде всего в тех случаях, когда поверхностно-активные вещества воздействуют на бетон, находящийся в напряженном состоянии.
[c.121]
Замедление твердения пуццоланового портландцемента вызывается тем, что добавка разбавляет цементный раствор, уменьшая количество чистого портландцемента. Но как только значительное количество активного кремнезема добавки вступит во взаимодействие с выделяющимся гидратом окиси кальция, твердение материала намного ускоряется, и его прочность по сравнению с прочностью затвердевшего портландцемента возрастает. Более высокая конечная прочность пуццоланового портландцемента объясняется тем, что эти добавки связывают гидрат окиси кальция в гидросиликат кальция, и в таком цементном камне его содержится больше, чем в обычном портландцементе. [c.187]
При температуре 100° происходит значительное уплотнение структуры и повышение прочности различных составов цементного камня с шамотным заполнителем (рис. 16 и 17).
[c.22]
Однако, анализируя результаты наших испытаний (см. рис. 17), а также результаты испытаний К. А. Полякова — можно отметить, что характер изменения прочности образцов цементного камня при нагревании не зависит от модуля жидкого стекла. [c.23]
В интервале 500—600° происходит некоторое разрыхление структуры у большинства составов цементного камня. Одновременно снижается прочность (см. рис. 15, 17), что вызвано модификационным превращением -кварца, образовавшегося в результате кристаллизации геля. Наибольшее снижение прочности наблюдается у образцов с кварцевым и андезитовым заполнителями вследствие большого содержания кристаллического кварца непосредственно в заполнителе. В этом случае снижение прочности продолжается вплоть до 700° и составляет приблизительно 70% от прочности высушенных образцов (см. рис. 15). [c.24]
При нагревании до 800—900° у большинства составов цементного камня наблюдается снижение прочности, тем большее, чем больше вводится в цемент кремнефтористого натрия, силиката натрия, чем ниже модуль жидкого стекла и огнеупорность заполнителя.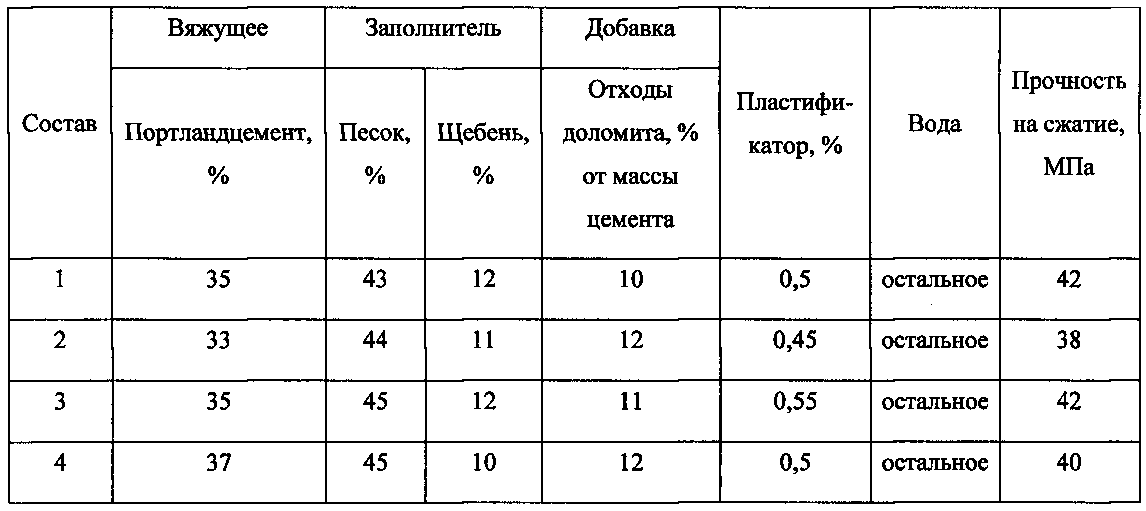
На рис. 18 приведены кривые изменения прочности образцов, цементного камня с высокоогнеупорными заполнителями хромо- [c.25]
На рис. 19 приведены кривые изменения прочности образцов цементного камня с хромомагнезитом при нагревании в зависимости от добавки кремнефтористого натрия. [c.26]
Рис. 19. Изменение прочности образцов цементного камня с хромомагнезитовым заполнителем при нагревании в зависимости от количества кремнефтористого натрия (в процентах от веса жидкого стекла) |
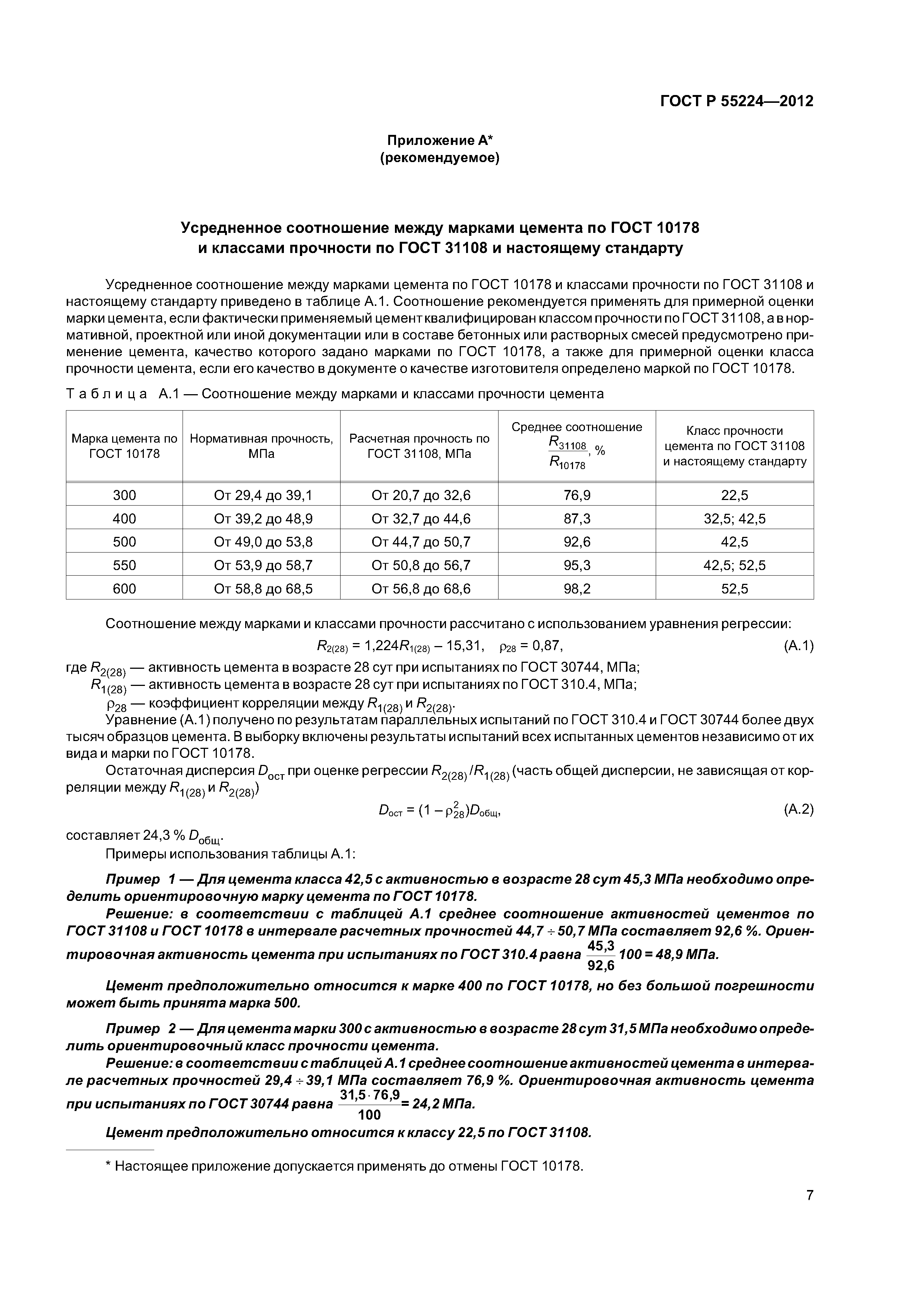
Бетоны, полученные на глиноземистом цементе, обладают водо-, воздухо- и морозостойкостью. Они устойчивы в пресных и сульфатных водах и в меньшей степени, чем портландцемент,-разрушаются растворами кислот и щелочей. При нагревании с 25 до 100° С прочность цементного камня уменьшается, поэтому такой цемент нельзя применять для изготовления обогреваемых конструкций. [c.317]
Песок. Желательно брать песок с остроугольными зернами — он лучше сцепляется с цементным камнем и придает бетону большую прочность. Промывка песка от глины сложна и дорога, поэтолгу обычно предпочитают речной песок. [c.455]
Избыточная вода остается в бетоне в виде водяных пор или испаряется, оставляя воздушные поры. В обоих случаях цементный камень в бетоне ослабляется, поперечное сечение тела камня, противостоящее нагрузке, уменьшается, а вокруг пор концентрируются местные напряжения. Поэтому прочность бетона будет тем меньше, чем больше пористость цементного камня, т. е чем больше было взято воды по отношению к весу цемента в свежеизготовленной бетонной смеси и чем меньше воды связалось химически в процессе твердения бетона.
[c.1020]
Для дорожного бетона применяют портландцемент высоких марок, качественные высокопрочные заполнители — щебень крупностью до 40 мм и чистый песок, что улучшает сцепление цементного камня с заполнителем и обеспечивает необходимую прочность на изгиб. Долговечность бетона достигается ограничением водоцементного соотношения, которое должно быть не более 0,5 для сурового, 0,53 для умеренного и 0,55 для мягкого ютимата. [c.306]
Влияние нагревания на свойства цементного камня изучалось по результатам термографических и микроскопических исследований, на основании испытаний прочности образцов при сжатии в нагретом и охлажденном состоянии и деформации образцов под нагрузкой при высоких температурах, а также по потерям воды при нагревании и изменению линейных размеров рбразцов.
[c.17]
Лрочность образцов цементного камня при высушивании повышается, причем это увеличение прочности наибольшее у составов с шамотным заполнителем. Шамот интенсивно поглощает влагу из жидкого стекла, увлекая вместе с ней в поры гидросиликат натрия, не связанный с кремнефтористым натрием, и гель кремневой кислоты, что вызывает уплотнение и упрочнение образцов. На рис. 15 приведены кривые изменения прочности образцов цементного камня на жидком стекле при нагревании в зависимости от вида заполнителя. [c.22]
Образцы цементного камня с заполнителем в виде технического глинозема после изготовления и хранения на воздухе в течение 7 суток, а также после высушивания имели сравнительно невысокую прочность (25—44 кг/см по сравнению с 150—-170 кг1см-для других заполнителей), что вызывается образованием нефелина и альбита при затворении цементной смеси жидким стеклом. [c.22]
Во время высушивания образцов цементного камня с шамотным заполнителем без кремнефтористого натрия наблюдается резкое увеличение прочности.

Как увеличить прочность и качество цементного раствора в несколько раз. | Дачный СтройРемонт
В наше время это можно сделать дешево и легко. Если вас интересует как, сейчас расскажу…
Замешиваем бетон доступными методамиЗамешиваем бетон доступными методами
На полках строительных магазинов в настоящее время можно найти множество добавок, которые в разы улучшают качество раствора, а так же уже готовые смеси и всевозможные виды клея. Но расценки на все это разнообразие, мягко говоря, неприличные.
Но есть одна добавка, которая добавлялась в раствор еще во времена СССР. Подойдет этот ингридиент практически для любых типов смеси.
В Советское время достать и купить готовый цементный и клеевой раствор было почти нереальной и не выполнимой задачей. Поэтому народ придумал свой способ изготовления такого раствора. Этот способ включал в себя добавление клея ПВА в цементный раствор. Такой цементный раствор использовали для всех видов работ: для штукатурки, укладки плитки, бетонировании полов и прочих работ.
При добавлении клея, раствор становился более эластичным, крепким и цепким, что повышало в несколько раз качество работ.
Фото с сайта https://kakkley.ruФото с сайта https://kakkley.ru
К сожалению, есть одно «НО». Не каждый клей подойдет для данного метода. Для получения положительного эффекта нужен клей ПВА — МБ. В его составе находиться полимер под названием поливинилацетат. Он очень устойчив к низким и высоким температурам, пластичен и имеет высокую адгезию ко всем видам поверхности.
Но тогда назревает следующий вопрос: сколько или в каком соотношении нужно добавлять клей в раствор. Все зависит от того, для каких целей вы замешиваете раствор.
- если нужен раствор для кладки керамической плитки (особенно для кладки на стены), то берется 1 часть цемента, 5 частей песка. И в эту сухую смесь добавляется клей ПВА-МБ в соотношении 20 % от количества цемента. При необходимости добавляется немного воды;
Добавление клея в цементный раствор
- для увеличения прочности бетонной смеси и повышения её пластичности добавляют 5 — 10 % клея от количества цемента;
- для бетонирования пола замешивают 50 килограмм цемента, 100 килограмм песка, 150 килограмм щебня. Добавляют 10 кг клея (20 % от массы цемента). Воды уменьшают на количество добавленного клея;
- для ремонта осыпающихся бетонных стен применяют состав в соотношениях: 1 часть цемента, 3 части песка и 0,5 части клея.
Такой раствор очень крепко сцепляется со старым покрытием;
- для оштукатуривания поверхностей раствор замешивают в пропорциях: 1 часть цемента, 4 — 5 частей песка. И на 10 кг данного раствора добавляют 60 — 80 мл клея ПВА-МБ.
Получился качественный и эластичный раствор
В конце 90-х я с отцом выкладывал в ванной плитку размером 10 на 10 см. И в раствор мы лили именно клей ПВА. 2 года назад решил сменить плитку на более красивую и большую, но при демонтаже старой я долго ругал тех, кто ложил старую плитку.
С огромным трудом я все таки демонтировал её. Поэтому я на практике убедился в эффективности добавления клея ПВА-МБ в цементный раствор.
Дорогие
читатели! Буду чрезмерно рад вашему лайку и подписке на канал!Цемент с повышенным содержанием минеральных добавок
Опубликовано 20 апреля 2020, среда
С целью снижения содержания клинкерной части в цементах, широкого использования минеральных компонентов – отходов промышленности, снижения выбросов углекислого газа при производстве клинкера во многих передовых странах мира получили широкое распространение цементы с высоким содержанием (от 30 до 80%) активных минеральных добавок. Использование активных минеральных добавок при производстве цемента обусловлено не только необходимостью экономии дорогостоящего клинкера, но и необходимостью придания бетонам определенных строительно-технических свойств (повышенная водонепроницаемость, морозостойкость, трещиностойкость, стойкость к коррозии). Данное положительное влияние на свойства бетона обусловлено наличием пуццоланической активности у минеральных компонентов (шлак, кислая зола-уноса, пуццолана, микрокремнезем), т.е. способностью взаимодействовать с гидроксидом кальция, который образуется в значительном количестве (15-20%) при гидратации основных клинкерных минералов, с образованием низкоосновных гидросиликатов кальция гелевидной структуры, которые уплотняют и упрочняют структуру цементного камня. Наиболее широко в мировой практике для производства цементов применяются золы-уноса и шлаки. Пуццоланы имеют высокую водопотребность, поэтому их использование ограничено. Микрокремнезем по причине высокой удельной поверхности имеет низкую технологичность (зависает в силосах, налипает на транспортирующие и дозирующие устройства), поэтому при производстве цемента не используется.
В России нет зол-уноса требуемого качества для производства цемента, поэтому единственный материал, пригодный для производства цемента с повышенным содержанием минеральных добавок класса прочности не ниже 42.5 – это доменный гранулированный шлак.
Пластифицированный цемент низкой водопотребности
Данная технология производства цемента была разработана в СССР для обеспечения нужд военно-промышленного комплекса. Технология предполагает совместный помол компонентов цемента в присутствии органического модификатора с целью механохимической активации клинкера и минеральных добавок. Преимущества данной технологии производства цемента следующие:
- Снижение клинкерной части до 30% за счет замещения ее минеральными добавками до 70%
- Повышение прочности цементов до класса 82,5 (до 100 МПа) за счет увеличения степени гидратации клинкера и снижения водопотребности
- Повышение гарантированного срока хранения цемента до 12 месяцев
- Снижение удельных затрат топлива и выбросов СО2 и Nox на каждую тонну цемента в 2-3 раза
- Улучшение технологических параметров работы цементных мельниц, перекачиваемости цементов
- Повышение качества и долговечности бетонов
На заводе Щурово было проведено несколько промышленных тестов по производству цемента низкой водопотребности. В качестве минерального компонента использовался шлак Северсталь и кварцевый песок в количестве около 40%. В качестве органического модификатора использовалась химическая добавка на основе эфиров поликарбоксилатов, которая показала более высокую эффективность по сравнению с нафталин сульфонатами. Характеристики цемента (по ПНСТ 19-2014 — расплыв конуса 130 мм) представлены в таблице ниже.
№ |
Прочность при сжатии | Сроки схватывания | Н.Г.Ц.Т. | Блэйн | Шлак | Песок | Химическая добавка ЭПК | |||
2 суток | 7 суток | 28 суток | начало | конец | ||||||
MПa | MПa | MПa | мин | мин | % | см2/г | % | % | ||
1 |
45.![]() |
55.7 | 62.6 | 247 | 377 | 22.0 | 4656 | - | 40 | 0.6 |
2 |
58.0 | 72.5 | 86.0 | 246 | 380 | 22.2 | 4729 | 37 | - | 0.6 |
Из таблицы видно, что прочностные характеристики цемента со шлаком значительно выше во все сроки твердения, поскольку песок является инертным компонентом. Также необходимо отметить низкую водопотребность цемента (22%) по причине использования химической добавки. Водопотребность обычных цементов в пределе 27-28%. С использованием данных цементов были изготовлены стандартные составы бетона (расход цемента 330 кг/м3), характеристики которых представлены в таблице ниже.
№ | Плотность [кг/м3] | В/Ц |
ОК [см] |
ОКt [см] |
t [мин] |
R ТВО [МПа] |
R 3 сут [МПа] |
R 7сут [МПа] |
R 28/56 сут [МПа] |
Без химических добавок |
|||||||||
№1 песок | 2380 |
0.![]() |
21 | 12 | 120 | 21.8 | 22.2 | 26.3 | 30.6/30.8 |
№2 шлак | 2390 | 0.49 | 20 | 11 | 105 | 31.9 | 26.0 | 36.1 | 47.0/52.3 |
Зика Пласт Е-4 0.5% |
|||||||||
№1 песок | 2480 | 0.42 | 23 | 10 | 180 | 36.5 |
39.![]() |
46.2 | 53.6/57.8 |
№2 шлак | 2500 | 0.46 | 21 | 10 | 110 | 44.1 | 38.1 | 46.1 | 62.7/68.4 |
Зика Пласт Е-4 1.0% |
|||||||||
ЦЕМ II/А-К(Ш-И) 42.5Н ЩУР | 2400 | 0.56 | 21 | 13 | 130 | 26.3 | 25.9 | 33.5 | 41.4 |
ЦЕМ I 42.5Н ЩУР | 2430 |
0.![]() |
22 | 13 | 190 | 32.0 | 30.8 | 40.2 | 48.8 |
По результатам испытаний можно сделать следующие выводы:
-
• Возможность производства на цементе со шлаком бетонов класса прочности В35 без химических добавок и В50 с химическими добавками • Возможность производства на цементе с песком бетонов класса прочности В22.5 без химических добавок и В40 с химическими добавками • Остановка кинетики набора прочности после 28 суток на цементе с песком без химических добавок • Недостаточная сохраняемость подвижности бетонов на цементах низкой водопотребности
Кроме того, была зафиксирована потеря пластифицирующего эффекта цемента с химической добавкой на основе эфиров поликарбоксилатов в процессе хранения. При этом, себестоимость цемента низкой водопотребности значительно выше по сравнению с обычными цементами по причине использования химической добавки. Таким образом, широкое применение цемента низкой водопотребности невозможно по вышеуказанным причинам. Альтернативная возможность для производства цемента с повышенным содержанием минеральных компонентов – цемент ЦЕМ II/В-Ш 42.5Н с количеством шлака 30%.
Цемент ЦЕМ II/В-Ш 42.5Н с количеством шлака 30%
С целью изучения возможности производства данного типа цемента на заводах Щурово и Ферзиково были проведены сравнительные тесты с целью определения возможности производства продукта оптимального качества. Сырьевые компоненты на данных заводах отличаются. Активность клинкера Ферзиково выше Щурово по причине наличия в сырьевой базе Щурово высокого содержания оксида магния. Кроме того, шлак Тулачермет, который использует завод Ферзиково, имеет преимущества по активности и размалываемости перед шлаком Северсталь, который использует завод Щурово. Характеристики цемента ЦЕМ II/В-Ш 42.5Н (по ГОСТ 30744) представлены в таблице ниже.
№ |
Прочность при сжатии | Сроки схватывания |
Н.![]() |
Блэйн | Шлак | |||
2 суток | 7 суток | 28 суток | начало | конец | ||||
MПa | MПa | MПa | мин | мин | % | см2/г | % | |
1 ЩУР |
20.8 | 27.5 | 46.9 | 171 | 245 |
28.![]() |
4922 | 33 |
2 ФЕР |
24.1 | 35.7 | 48.3 | 205 | 265 | 27.0 | 3932 | 32 |
Из таблицы видно, что начальная прочность цемента, производства Щурово значительно уступает цементу Ферзиково, в то время, как разница в марочной прочности незначительна. Удельная поверхность цемента, при которой были достигнуты требуемые показатели прочности, завода Ферзиково значительно меньше завода Щурово по причине более высокой активности клинкера и шлака завода Ферзиково. С использованием данных цементов были изготовлены стандартные составы бетона (расход цемента 330 кг/м3) без использования химических добавок (вариант тарированного применения), характеристики которых представлены в таблице ниже.
Плотность [кг/м3] |
В/Ц |
ОК [см] |
ОКt [см] |
t [мин] |
R ТВО [МПа] |
R 3 сут [МПа] |
R 7сут [МПа] |
R 28 сут [МПа] |
|
Без химических добавок |
|||||||||
1 ЩУР | 2360 | 0.68 | 21 | 14 | 135 | 18.9 | 16.0 |
20.![]() |
31.9 |
2 ФЕР | 2370 | 0.68 | 20 | 15 | 130 | 21.8 | 17.4 | 21.1 | 31.1 |
ЦЕМ II/А-К(Ш-И) 42.5Н ЩУР | 2350 | 0.72 | 20 | 14 | 120 | 13.4 | 13.2 | 18.5 | 25.5 |
ЦЕМ II/А-И 42.5Б ФЕР | 2410 | 0.71 | 21 | 14 | 105 |
17.![]() |
17.4 | 20.2 | 27.4 |
Из таблицы видно, что характеристики цементов ЦЕМ II/В-Ш по всем параметрам сопоставимы с рядовыми цементами ЦЕМ II/А заводов Ферзиково и Щурово, а прочность в марочном возрасте даже превосходит. Результаты тестирования стандартных составов бетона (расход цемента 330 кг/м3) с использованием химических добавок (вариант навального применения) представлены в таблице ниже.
Плотность [кг/м3] |
В/Ц |
ОК [см] |
ОКt [см] |
t [мин] |
R ТВО [МПа] |
R 3 сут [МПа] |
R 7сут [МПа] |
R 28 сут [МПа] |
|
Зика Пласт Е-4 1. |
|||||||||
1 ЩУР | 2430 | 0.54 | 21 | 15 | 230 | 31.9 | 27.6 | 35.8 | 48.4 |
2 ФЕР | 2420 | 0.53 | 20 | 15 | 170 | 32.2 | 30.5 | 37.2 | 46.0 |
ЦЕМ II/А-К(Ш-И) 42.5Н ЩУР | 2400 | 0.56 | 21 | 13 | 130 |
26.![]() |
25.9 | 33.5 | 41.4 |
ЦЕМ II/А-К(Ш-И) 42.5Н ФЕР | 2410 | 0.55 | 21 | 13 | 150 | 28.9 | 30.9 | 37.9 | 45.6 |
Из таблицы видно, что характеристики цементов ЦЕМ II/В-Ш по всем параметрам сопоставимы с рядовыми цементами ЦЕМ II/А заводов Ферзиково и Щурово, а прочность в марочном возрасте даже превосходит.
По результатам испытаний можно сделать следующие выводы:
- Результаты промышленных тестов показали возможность выпуска цемента ЦЕМ II/В-Ш 42.5Н с повышенным до 32% содержанием минеральной добавки шлака сопоставимого по качеству с текущими продуктами ЦЕМ II/А-К(Ш-И) 42.
5Н заводов Ферзиково и Щурово
- По причине низкой активности шлака производства Северсталь и высоких затрат на помол выпуск цемента ЦЕМ II/В-Ш 42.5Н на заводе Щурово экономически нецелесообразен
- По причине высокой активности шлака производства Тулачермет экономически целесообразно выпускать цемент ЦЕМ II/В-Ш 42.5Н на заводе Ферзиково
Понравилась статья?
Поделиться в соцсетях:
Оценка прочности и долговечности портландцементных растворов, приготовленных из богатой водородом воды
Мы исследовали влияние воды, богатой водородом (HRW), на прочность и долговечность портландцементных растворов. Мы провели сравнительную оценку характеристик растворов на основе HRW (HWM) по сравнению с цементными растворами, изготовленными из контрольной воды (CWM). Результаты показывают, что использование HRW значительно улучшает прочность растворов на сжатие, изгиб и растяжение при раскалывании как в раннем, так и в более позднем возрасте отверждения. Долговечность оценивали по капиллярному поглощению, скорости ультразвукового импульса (UPV), динамическому модулю упругости (DEM) и удельному электрическому сопротивлению (ER). Мы приписываем в целом улучшенные механические свойства и долговечность HWM образованию большего количества гидратов цемента с меньшим количеством пустот в среде, богатой водородом. Основываясь на анализе рентгеновской дифракции (XRD), инфракрасной спектроскопии с преобразованием Фурье (FTIR) и сканирующей электронной микроскопии (SEM), мы пришли к выводу, что использование HRW в портландцементных растворах дает более компактную, плотную и прочную микроструктуру с меньшим пустоты из-за более высокой степени гидратации.
1. Введение
Бетон на основе портландцемента является наиболее широко используемым строительным материалом. Это побудило исследователей изобретать новые технологии производства цемента и исследовать использование различных материалов и добавок. Бетонные конструкции подвергаются воздействию агрессивных сред, что влияет на их долгосрочную работоспособность и долговечность [1]. Долговечность бетона определяется как его способность сохранять структурную целостность, защитные свойства и эстетические характеристики в течение длительного периода времени.Исследователи всегда работают над созданием более прочного и долговечного бетона. Кроме того, стремление к более короткому времени схватывания и высокой начальной прочности побудило исследователей модифицировать портландцемент с использованием инновационных химических и минеральных добавок для удовлетворения этих требований. Необходимость производить более устойчивый бетон привела исследователей к разработке сложных смесей, в которых используются вторичные минеральные добавки и широкий спектр химических добавок для улучшения характеристик бетона [2].
Наиболее важное соображение, которое следует учитывать при использовании различных продуктов в бетоне, — это их возможное влияние на устойчивость конечной конструкции.Как правило, цемент частично заменяют минеральными добавками (золой-уносом, шлаком, золой рисовой шелухи, микрокремнеземом и т. д.) для повышения долговечности бетонных материалов за счет получения плотных и компактных микроструктур [3–6]. Кроме того, минеральные добавки улучшают поверхность раздела между цементным тестом и заполнителями за счет увеличения плотности цементного теста, что способствует улучшению механических характеристик. Хотя минеральные добавки являются дешевыми материалами, что приводит к снижению проницаемости, низкой теплоте гидратации и повышению химической стойкости получаемых бетонных материалов, они часто связаны с некоторыми недостатками, такими как снижение прочности в раннем возрасте и более длительное время отверждения. 7].В дополнение к минеральным добавкам инженеры также используют различные химические добавки в бетон для улучшения его характеристик. Обычно ускорители схватывания (как хлоридные, так и нехлоридные) используются для сокращения времени схватывания и повышения ранней прочности бетонных материалов. Однако недостатком ускорителей схватывания на основе хлоридов является депассивация стальной арматуры.
Латекс и стеарат кальция снижают проницаемость, повышают водонепроницаемость бетонных материалов и повышают их долговечность.Некоторые гидрофобные материалы (гидрофобизаторы) также имеют тенденцию повышать сопротивление впитыванию и тем самым долговечность бетона [8]. Понизители содержания воды и суперпластификаторы, такие как лигносульфонат и поликарбоксилат, также имеют тенденцию улучшать механические характеристики и долговечность бетона за счет снижения водоцементного отношения, не влияя на текучесть [9]. Использование эпоксидных смол [10], пенополистирола [11] и субабсорбирующих полимеров [12] также привело к повышению прочности и долговечности цементных растворов.Некоторые самоотверждающиеся химические вещества также повышают долговечность бетона за счет снижения водотранспортных свойств за счет более высокой степени гидратации [13].
Обзор литературы показывает, что минеральные и химические добавки определяют прочностные и долговечные свойства бетона. С химической точки зрения важно ускорить скорость гидратации силиката трикальция (C 3 S), который отвечает за производство гидрата силиката кальция (CSH) — основного продукта гидратации, обеспечивающего повышенную прочность и долговечность. Однако иногда эта повышенная реакция гидратации отрицательно сказывается на прочности и долговечности. На основании обширного литературного исследования установлено, что влияние богатой водородом воды (ГВП) на долговечность цементной системы еще предстоит изучить должным образом. Поэтому мы исследовали влияние использования обогащенной водородом воды в качестве химической добавки на прочность и долговечность цементных растворов. Мы сравнили наши результаты с результатами для растворов, изготовленных из обычной (контрольной) воды.В нашей предыдущей работе мы продемонстрировали, что HRW ускоряет механизм гидратации цемента, заставляя простые цементные пасты схватываться с большей скоростью [14]. HRW представляет собой тип воды с высоким содержанием молекулярных водородных соединений (H 2 ). HRW обладает уникальным потенциалом подавления ряда заболеваний человека [15, 16]. В данном исследовании HRW производилась с использованием химической смеси, содержащей глицерин, гидрид магния и гидрид кремния.
Во время производства HRW система производит гидроксид магния, а также гидроксид кремния, что, в свою очередь, увеличивает pH системы.Это указывает на увеличение концентрации OH — (гидроксила) в системе HRW. Результаты, полученные в ходе этого исследования, позволяют предположить, что HRW оказывает положительное влияние на прочностные и долговечные свойства портландцементных растворов. По мнению Главинда [17], цели устойчивого бетона должны достигаться за счет использования изначально экологически полезных свойств бетона, например, высокой прочности и хорошей долговечности. Для гражданской инфраструктуры ключевыми вопросами устойчивости являются прочность и долговечность, поскольку, если долговечность хуже, срок службы конструкции будет сокращен, а воздействие на окружающую среду конечного бетона может быть неблагоприятным.Кроме того, основным аспектом устойчивости химических добавок является рабочая среда; примесь (химическая или минеральная) не должна представлять опасности для рабочих и здоровья конструкции.
Установленная склонность HRW к ускорению благоприятствует его использованию вместо хлорида кальция, что связано с серьезными проблемами долговечности армированного и предварительно напряженного бетона. HRW, с другой стороны, считается устойчивым развитием в области химических добавок, которые не только сокращают время схватывания, но также улучшают прочность и долговечность цементных растворов.
2. Экспериментальный
2.1. Материалы
Портландцемент, соответствующий стандарту ASTM C150, с удельным весом 3,09, предоставленный Sayeong Inc., Корея, использовался в качестве основного связующего материала в этом исследовании. Его химический состав приведен в Таблице 1. Использовался речной песок со средним размером частиц 2,34 мм и удельным весом 2,72, соответствующий требованиям классификации ASTM C33. HRW была произведена с использованием химической смеси, предоставленной H 2 Vision Inc., Корея (http://www.h3vision.co.kr). Это химическое вещество производит водород в обычной воде. Химический состав смеси состоял из 95 % глицерина, 4 % MgH 2 и 1 % SiH 4 .
|
2.2. Пропорции смесей и изготовление строительных растворов
Всего было приготовлено 5 пропорций смесей из обычной воды и HRW. Водоцементное отношение и пескоцементное отношение поддерживались постоянными для каждого состава смеси и составляли 0,485 и 2,75 соответственно. CWM были произведены с использованием обычной воды, а HWM — с использованием HRW.Концентрации HRW составляли 0,2, 0,3, 0,4 и 0,5 млн. Концентрацию водорода в воде контролировали с помощью игольчатого датчика водорода, предоставленного Японией. Растворы были промаркированы следующим образом: нормальная вода (контроль) — CWM0, а растворы, приготовленные из 0,2, 0,3, 0,4 и 0,5 ppm концентрированных HRW, — HWM0,2, HWM0,3, HWM0,4 и HWM0,5, соответственно. Сводное изложение состава для минометных смесей в таблице 2.