Пеносиликатные блоки характеристики: Газосиликатный блок: технические характеристики различных видов
Технические характеристики газосиликатных блоков ‘Забудова’
- Главная /
- Статьи /
- Технические характеристики газосиликатных блоков ‘Забудова’
Строительство из газосиликатных блоков в нашей стране уже обычное явление. И, несмотря на то, что кирпич был и остается самым надежным и популярным строительным материалом, газоблоки тоже имеют хорошие характеристики. Рассмотрим, например, более подробно технические характеристики газосиликатных блоков «Забудова».
Завод строительных конструкций «Забудова» производит достаточно обширный ряд строиетльных материалов, в том числе и газосиликатные блоки.
В соответствии с официальной документацией завода, ячеистые блоки имеют следующие технические характеристики.
Длина L, мм |
Ширина B, мм |
Высота H, мм |
Объемная плотность, кг/м3 |
Класс бетона по прочности на сжатие |
Морозостойкость |
625 (599) 625 (599) 625 (599) 625 (599) 625 (599) 625 (599) 625 (599) 625 (599) 625 (599) 625 (599) 625 (599) 625 (599) 625 (599) 625 (599) |
50 75 100 125 150 175 200 250 300 350 375 400 450 500 |
250 |
350 400 450 500 |
В 1,0 В 1,0 (В 1,5) В 1,5 |
F 25 F 25 F 35 (25) F 35 (25) |
Рассмотрим также характеристики ячеистого бетона по теплопроводности и паропроницаемости.
Класс бетона по прочности на сжатие |
Характеристики материала в сухом состоянии |
Марка по морозостойкости, не менее |
||
Плотность γ, кг/м3 |
Удельная теплоемкость С, кДж/(кг oС) |
Коэф. теплопроводности λ0, Вт/(мoС) |
||
В 1,0 |
350 |
0,84 |
0,09 |
F 25 |
В 1,0 (В 1,5) |
400 |
0,84 |
0,10 |
F 25 |
В 1,5 |
450 |
0,84 |
0,11 |
F 35 (25) |
В 1,5 (В2,5/В2,0) |
500 |
0,84 |
0,12 |
F 35 (25) |
В 2,5 (В 3,5) |
600 |
0,84 |
0,14 |
F 35 (25) |
В 3,5 |
700 |
0,84 |
0,18 |
F 50 (35) |
Газосиликатные блоки «Забудова» производятся в соответствии с технологией немецкой фирмы «Hebel», в соответствии с которой, ячеистый бетон может быть различного объема, веса или прочности.
Ячеистый бетон обладает рядом преимуществ, рассмотрим некоторые из них:
1. Небольшой вес – несмотря на то, что некоторые блоки имеют достаточно большую прочность, у них все равно намного меньший вес по сравнению с кирпичом того же объема. В связи с чем, с блоками намного проще обращаться и перемещать, а также не нужно строить мощный фундамент, способный выдерживать значительный вес – что, в свою очередь, приводит к меньшим тратам на постройку.
2. Теплоизоляция – по сравнению с тем же кирпичом, ячеистый бетон обладает высокими теплоизоляционными свойствами.
3. Безопасность – газосиликатные блоки негорючи. При этом, были проведены исследования в Германии, Швеции и Финляндии, которые показали, что прочность газосиликатных блоков, при увеличении температуры до +400С, увеличивается на 85%.

5. Шумоизоляция – в соответствии с проведенными испытаниями виброаккустической лабораторией института БелНИИС блоки соответствуют всем нормативным требованиям.
При анализе технических характеристик данного материала, можно сказать что он соответствует современным требованиям — большие размеры блоков позволяют быстрее возводить стены любой конструкции, он экологичен, имеет небольшой вес, по сравнению с традиционным кирпичом, недорого стоит, долговечен.
Дата публикации: 27.03.2018
Газосиликатные блоки D500 для постройки дома до 3-х этажей
Один из современных материалов в строительстве — Газосиликатный блок, его характеристики удовлетворяют всем необходимым требованиям. Газосиликатный блок – это строительный материал, в виде бетона с равномерно распределенными порами, диаметром от 0,5 до 3 мм. В процессе изготовления бетонной смеси в нее добавляют известь, кварцевый песок и алюминиевую пудру как газообразователь.
Благодаря свойствам газобетона его применяют в качестве конструкционного и теплоизолирующего материала. В качестве конструкционного материала его используют при изготовлении строительных блоков для коммерческого, жилищного и промышленного строительства. Прочность Газосиликатный блока полностью удовлетворяет строительству малоэтажных зданий, при этом у него низкий коэффициент теплопередачи, что позволяет получить экологически чистое и энергосберегающее сооружение. Вес одного строительного блока, для возведения наружных стен, составляет 17 кг., а при том же объеме требуется 8 кирпичей весом в 36 кг. Тем самым при выборе газобетона появляется возможность существенно сэкономить на возведении фундамента.
Основные показатели и характеристики Газосиликатных блоков:
— Пониженная плотность при повышенной прочности.
— Теплоизоляция. Наличие пор в газобетоне позволяет сберегать тепло в 5 раз эффективнее, чем обычный бетон или кирпич. Блоки из газобетона позволяют возводить здание с толщиной стен в один ряд без дополнительной теплоизоляции.
— Экологичность. За счет своих свойств газобетон поддерживает определенную влажность внутри помещения. Здания из газобетона поддерживают летом – прохладу, зимой тепло. Строительные блоки из газобетона не выделяют вредных веществ и применяются во всех климатических зонах.
— Сейсмостойкость. Небольшой удельный вес газобетона в сочетании с повышенной прочностью снижают нагрузки на почву. При строительстве сооружений в сейсмоопасных зонах применяют армированные элементы.
На ряду всех своих достоинств газобетон имеет и недостатки:
— Впитывание влаги. При строительстве во влажных районах, для защиты стен, рекомендуется делать фасадную отделку.
— Низкая прочность при изгибе. При неправильно подсчитанной толщине стен, фундаменте, армировании могут возникать трещины.
Исходя из вышесказанного, можно сделать вывод: применение газобетона сокращает трудозатраты, энергозатраты и экономит средства покупателей, а качество Газосиликатного блока ничем не уступает своим аналогам.
Инструмент для газосиликатных (газобетонных) блоков
технические характеристики, размеры и цена за штуку
Газоблоки относятся к искусственному камню с ячеистой структурой. В состав смеси входят цемент, песок и специальные газообразователи в виде алюминиевой пасты или пудры. Некоторые производители в раствор добавляют шлак, золу, гипс или известь.
Оглавление:
- Область использования
- Преимущества и недостатки
- Виды и характеристики
- Габариты
- Правила монтажа
- Расценки
Сфера применения
Они очень распространены для возведения частных домов и сооружений. За счет правильных геометрических форм и крупных размеров строительство осуществляется в короткие сроки без ущерба качеству. Не требуют устройства мощного фундамента и более экономичны по сравнению с кирпичной или шлакоблочной кладкой.
Газосиликатные блоки можно использовать для стен и перегородок промышленных, административных, агропромышленных, хозяйственных и жилых зданий высотой до 4-5 этажей. Средств на изделия затрачиваются гораздо меньше, чем на другие камни, при этом они обладают высокой надежностью и долговечностью. Очень часто применяются для проведения перепланировки помещений, а за счет больших габаритов их укладка не занимает много времени.
Свойства
Материал особенно практичен в частном строительстве, так как обладает массой полезных преимуществ, необходимых для обеспечения уюта в доме:
- Малый вес и простота в обработке позволяет возводить стены и сооружения любой конфигурации.
- Теплоизоляция защитит здание от потерь тепла из-за отсутствия мостиков холода и ячеистой структуры.
- Звукоизоляция обеспечит защиту от посторонних шумов, особенно при строительстве в густонаселенных районах или около проезжей части.
- Паропроницаемость поддерживает хороший микроклимат.
- Пожаробезопасность позволяет защитить дом от распространения огня, при этом они не воспламеняются и не выделяют токсичных веществ при воздействии высоких температур. Способны удерживать пламя на протяжении 7-8 часов без потери прочности.
- Надежность – выдерживают большие нагрузки, однако важно подбирать соответствующий тип для возведения несущих и ненесущих стен.
Газоблоки также имеют некоторые недостатки:
- Они обладают высокой прочностью на сжатие, но очень низкой на изгиб.
- За счет пористости быстро впитывают воду.
Чтобы обезопасить дом от появления трещин и частичного разрушения в процессе эксплуатации, рекомендуется приобретать только сертифицированный товар высокого качества. Также обязательно проводить армирование между рядами и устраивать бетонный армопояс для укладки любого типа перекрытий над каждым этажом. Это относится и к деревянным, так как стропильная система тоже оказывать существенную нагрузку на стены.
Виды и технические характеристики
Блоки из газосиликата изготавливаются автоклавными и неавтоклавными. Последние делаются из смеси, которая застывает в естественных условиях. Они относятся к наиболее дешевому варианту, однако это сказывается на технических параметрах. Они менее прочные и обладают в несколько раз большей усадкой при высыхании.
Автоклавные практически не подвержены усадке и имеют высокие эксплуатационные качества. Такое производство более технологичное и энергоемкое, поэтому его могут позволить только крупные предприниматели. Пропарка осуществляется в автоклавах под давлением до 1,2 МПа и температурой до 200°C. За счет этого изделия приобретают большую прочность и устойчивость к внешним воздействиям.
Изменяя процентное соотношение компонентов при замешивании раствора, можно получить несколько разные технические показатели. К примеру, используя больше цемента, повышается морозостойкость за счет избавления от «опасных пор», но снижаются теплоизоляционные свойства.
Газосиликатные блоки различаются по физико-механическим параметрам, и основным считается их плотность:
- Теплоизоляционные марки D300-D400 Этот тип используется для обеспечения теплоизоляционного контура стен, возведенных из более надежного материала (кирпич, шлакоблок). Плотность составляет всего 300-400 кг/м3.
- Конструкционно-теплоизоляционные D500-D800. Для перегородок или стен одноэтажного дома. Однако некоторые производители экономят на изготовлении, поэтому D500 часто является теплоизоляционной маркой. D600-D700 относятся к наиболее практичным для строительства жилого здания.
- Конструкционные – D900-D1200. Наиболее прочные с плотностью до 1200 кг/м3, пригодны для многоэтажных сооружений.
По теплопроводности газосиликатные изделия разделяются на теплоизоляционные – 0,09-0,11 Вт/м·°С (сравнимы с древесиной), конструкционно-теплоизоляционные – 0,12-0,18 Вт/м·°С и конструкционные – 0,19-0,20 Вт/м·°С (лучше чем у глиняного кирпича).
По ячеистой структуре:
- Резервные – поры составляют до 50 % от всего объема.
- Безопасные – 50-60 %.
- Опасные – 60-75 %.
Последние обладают наименьшей прочностью, поэтому любое серьезное усилие способно частично или полностью их разрушить. Это связано с большим диаметром воздушных пор, их запрещено использовать для несущих элементов зданий и подвергать высоким нагрузкам. Безопасные имеют меньше пор, тем самым обеспечивают большее сопротивление усилиям на сжатие. Они пригодны для возведения самонесущих стен дома или основных для бани, бассейна или хозпостройки.
Резервный блок так называется за счет наличия воздушных пустот, предназначенных для влаги, которая может проникнуть в материал. Она скапливается в порах и равномерно распределяется, не нарушая целостную структуру. Также это необходимо при высоких морозах, чтобы вода при расширении не разрушила изделие.
Морозостойкость описывает количество циклов, которое элемент способен выдержать. По классу различаются маркой F15, F25, F35. Производители часто заявляют, что их продукция обладает маркировкой F50-100, однако это редко является действительностью.
Размеры газосиликатных блоков
Изделия из газобетона по назначению делятся на три типа:
- Стеновые. Стандартные размеры – 200х300х600 мм (глубина, ширина и длина).
- Перегородочные или полублоки – 100х300х600.
- Специальные – выпускаются на заказ с нестандартными параметрами. К ним относятся пазогребневые, арочные, U-образные, дугообразные и другие конфигурации. Они предназначены для более легкого изготовления различных конструкций.
В некоторых случаях типовые варианты непрактичны или нет возможности их использования. Поэтому заказываются индивидуальные габариты, размеры таких блоков могут составлять 150х288х588, 250х400х600, 100х576х588, 75х300х625 мм и другие.
Правила укладки газобетона
Монтируются на различные типы растворов, от чего зависит точность размеров:
- На клей.
В этом случае отклонения – всего 1,5 мм, так как слой клеевого раствора не превышает 3 мм. Прямолинейность граней и скол углов может варьироваться в пределах 2-3 мм и не более.
- Для блоков 2-го сорта. Менее качественные, могут иметь отклонения до 3 мм по размерам и прямолинейности ребер. Но углы не должны быть сбиты более чем на 2 мм.
- Для кладки на ЦПС. Габаритные отклонения составляют 3-4 мм, так же как и по прямоугольности граней. Сколы в глубину – менее 10 мм.
Стоимость газоблоков в Московской области
Производитель | Марка | Размеры, мм | Цена за штуку, рубли |
Bonolit | D500 | 50x250x625 | 35 |
75x250x625 | 45 | ||
100x250x625 | 57 | ||
200x300x625 | 125 | ||
Ytong | D400 | 400x250x625 | 342 |
D500 | 250x250x625 | 180 | |
150x250x625 | 110 | ||
200x250x625 | 165 |
youtube.com/embed/3d5foWKOjnU» frameborder=»0″ allowfullscreen=»allowfullscreen»/>
Газосиликатные блоки – основные свойства и характеристики. Технические характеристики газосиликатных блоков Блоки газобетонные прочность
В современных строительных технологиях большое значение придается выбору материала для возведения того или иного типа зданий. Одним из наиболее популярных строительных материалов сегодня считают газосиликатные блоки, которые отличаются рядом преимуществ и используются достаточно часто.
Их широкое применение обусловлено оптимальным балансом цены и качества – по большому счету никакой другой строительный материал не выдерживает эту пропорцию столь же выгодно.
Если разобраться, то вряд ли газобетон относится к современным стройматериалам – его разработали еще в конце 19 века. В начале прошлого столетия группа ученых даже запатентовала открытие нового чудо-материала, однако его свойства были далеки от тех, которыми отличается сегодняшний газосиликат.
В современном виде газосиликатный материал получили в конце 20 века – это бетон с ячеистой структурой, твердение которого происходит в автоклаве. Этот метод нашли еще в 30-х годах, и с тех пор он особых изменений не претерпел. Совершенствование характеристик происходило за счет внесения уточнений в технологию его получения.
Газобетон является одной из основ для производства газосиликатных блоков
Принцип изготовления
В качестве исходных ингредиентов для получения газобетона используются следующие вещества:
- песок;
- цемент;
- известь;
- гипс;
- вода.
Чтобы получить ячеистую структуру, в состав добавляют порцию алюминиевого порошка, который служит для образования пузырьков. После смешивания массу выдерживают нужное время, дожидаясь вспучивания, после чего разрезают на части и ставят в автоклав. Там масса отвердевает в паровой среде – эта технология является энергосберегающей и высокоэкологичной. При изготовлении газобетона не происходит выделения вредных веществ, которые могут нанести ощутимый вред окружающей среде или здоровью человека.
Свойства
Характеристики, которыми отличаются газосиликатные блоки, позволяют рассматривать их как стройматериал, который хорошо подходит для возведения зданий. Эксперты утверждают, что газобетон соединил в себе наилучшие качества камня и древесины – стены из него прочны и хорошо защищают от холода.
Пористая структура блоков гарантирует высокие показатели пожаробезопасности
Ячеистая структура объясняет маленький коэффициент теплопроводности – он гораздо ниже, чем у кирпича. Поэтому здания из газосиликатного материала не столь требовательны в плане утепления – в некоторых климатических поясах оно вообще не требуется.
Ниже мы приводим основные свойства газосиликата, благодаря которым он стал столь востребованным в строительной сфере:
- маленькая масса при внушительных размерах – это свойство позволяет ощутимо снизить расходы на монтаж.
Кроме того, для погрузки, перевозки и возведения стен не требуется кран – достаточно обыкновенной лебедки. Скорость строительства по этой причине также гораздо выше, чем при работе с кирпичом;
- хорошая обрабатываемость – газосиликатный блок можно без проблем пилить, сверлить, фрезеровать, используя при этом обычный инструмент;
- высокая экологичность – специалисты говорят, что этот показатель у газобетона сравним с деревом. Материал не выделяет никаких вредных веществ и не загрязняет окружающую среду, при этом, в отличие от дерева, он не гниет и не подвержен старению;
- технологичность – газосиликатные блоки сделаны таким образом, чтобы с ними было удобно работать. Кроме маленькой массы, они отличаются удобной формой и технологическими выемками, захватами, пазами и т.п. Благодаря этому скорость работы с ними возрастает в 4 раза по сравнению с возведением зданий из кирпича;
- низкая теплопроводность газосиликатных блоков – она обусловлена тем, что газобетон на 80 процентов состоит из воздуха.
В зданиях, которые построены из этого материала, снижаются расходы на отопление, к тому же можно на одну треть слабее их утеплять;
В доме из газосиликата в любое время года будет поддерживаться устойчивый микроклимат
- морозостойкость – в структуре есть специальные пустоты, куда вытесняется влага при замерзании. Если выдержаны все технические требования к изготовлению, морозостойкость газобетона превышает две сотни циклов;
- звукоизоляция – очень немаловажный параметр, поскольку сегодня уровень шума на улицах достаточно высок, а дома хочется отдохнуть в тишине. По причине пористой структуры газосиликат хорошо задерживает звук, выгодно отличаясь в этом плане от кирпича;
- пожаробезопасность – минеральные вещества, которые используются для изготовления газосиликата, не поддерживают горения. Газосиликатные блоки способны выдерживать воздействие огня на протяжении 3-7 часов, поэтому его используют для возведения дымоходов, шахт лифтов, огнестойких стен и т.
п;
- высокая прочность – газосиликат выдерживает очень высокие сжимающие нагрузки, поэтому подходит для постройки зданий с несущими стенами высотой до трех этажей или каркасно-монолитных зданий без всяких ограничений;
- негигроскопичность – газобетон не впитывает воду, которая попав на него быстро высыхает, не оставляя никаких следов после себя. Это объясняется тем, что пористая структура не задерживает в себе влагу.
Результаты Голосовать
Где вы предпочли бы жить: в частном доме, или квартире?
Назад
Где вы предпочли бы жить: в частном доме, или квартире?
Назад
Основным недостатком газосиликата является недостаточная прочность на изгиб, однако специфика его использования такова, что практически исключает возможность изгибающих нагрузок, поэтому этот недостаток не играет большой роли.
Чем меньше в теле искусственного камня воздуха, тем выше его прочность и плотность
Марки газоблоков
Плотность газосиликатных блоков является основным критерием, который рассматривается при маркировке.
В зависимости от ее величины стройматериал обладает разными наборами характеристик, что обуславливает сферу его применения.
Ниже мы рассмотрим различные марки газосиликата и то, как их используют в строительстве:
- D300 – наиболее подходящий стройматериал для возведения монолитных зданий. Плотность газосиликатных блоков этой марки составляет 300 кг/м 3 – она хорошо подходит для постройки стен малоэтажных домов в один слой или для двуслойных монолитных домов с высокой степенью теплоизоляции;
- D400 – его используют для постройки двухэтажных зданий и коттеджей, а также для теплоизоляции наружных несущих стен высотных зданий;
- D500 – это разновидность с наилучшей комбинацией утепляющих и конструкционных характеристик. По плотности она идентична бревну или деревянному брусу и применяется для возведения перегородок и внутренних стен зданий, проемов окон и дверей, а также оболочки армированных перемычек, стропил и ребер жесткости;
- D 600 – это газосиликатный блок с самой высокой плотностью, которая составляет 600 кг/м 3 , он используется там, где необходимо ставить прочные стены, подверженные высоким нагрузкам.
Ниже приводится таблица, иллюстрирующая другие параметры, которыми отличаются газосиликатные блоки разных марок.
В зависимости от плотности все газосиликатные блоки принято делить на конструкционные, конструкционно-теплоизоляционные и теплоизоляционные
Точность размеров
Газосиликаты могут иметь некоторые отклонения в своих габаритах. В зависимости от их величины различают три категории точности этого материала:
- Первая категория – она предназначена, чтобы класть блок насухо или на клей. В ней разрешается погрешность размеров по высоте, длине и толщине до полутора миллиметра, прямоугольности и углов – до двух миллиметров, ребер – до пяти миллиметров.
- Вторая категория применяется, чтобы класть газосиликатные блоки на клей. В ней погрешность по основным габаритам допускается до двух миллиметров, прямоугольность – до 3 миллиметров, углы – до 2 миллиметров и ребра – до 5 миллиметров.
- Третья категория газоблоков кладется на раствор, в ней погрешность по основным габаритам не более 3 миллиметров, по прямоугольности – менее 3 мм, углы – до 4 миллиметров, ребра – до 10 миллиметров.
Выбор газосиликата
При покупке газосиликатных блоков обычно оценивают три критерия, которые влияют на решение:
- функциональные характеристики – плотность, морозостойкость, коэффициент теплопроводности и т.п.;
- размеры одного блока;
- объем одного блока;
- стоимость.
Массовое применение газосиликатных блоков в строительстве свидетельствует о их огромной популярности. В плане соотношения цены и качества при замечательных характеристиках газобетонных блоков ничего наиболее оптимального, чем газосиликат пока что не придумали. Газобетон представляет собой ячеистый бетон автоклавного твердения – проверенный временем стройматериал, применяемый практически во всех видах конструктивных элементов сооружений и зданий самого разного назначения. Но откуда взялась технология производства ячеистого бетона, и когда он стал использоваться в своём современном виде? Разработки, направленные на получение нового многофункционального стройматериала велись ещё с конца ХIХ-го века. К началу ХХ-го несколько зарубежных ученых-экспериментаторов успели получить патент на изобретение так называемого «чудо-бетона», ведь в то время мир крайне нуждался в больших количествах искусственно производимого камня для строительства. Экспериментируя с составными элементами, методом проб и нередких ошибок был получен прототип современного газобетонного раствора. Однако свойства и характеристики газосиликатных блоков такими, как мы их знаем сейчас, в то время, конечно, не были. Современные газоблоки появились лишь в 90-тые годы. Это всем известные пенобетонные, полистеролбетонные и газобетонные блоки. Касательно последних — они бывают 2-ух видов: неавтоклавного и соответственно автоклавного способа затвердения. Неавтоклавные газобетоны неоднородны и довольно часто содержат в себе вредные воздухопоры, дающие большую усадку в ходе процесса эксплуатации. Газобетон, полученный в результате применения автоклавного метода, гораздо экологичнее и прочнее неавтоклавного (примерно в два раза).
Метод по изготовлению ячеистого бетона предложен был в тридцатых годах и с тех пор, в принципе, мало изменился, хотя свойства газосиликатных блоков непрестанно улучшались и сфера его применения расширялась. Для его изготовления применяются песок, цемент, известь, гипсовый камень и обычная вода. В смесь из указанных материалов в незначительном количестве добавляется и алюминиевый порошок, который способствует образованию в смеси мелких воздушных ячеек, которые и делают материал пористым. Сразу после вспучивания, непродолжительной выдержки и разрезания массива на изделия необходимых размеров ячеистобетонную массу помещают в автоклав, где в паровой среде происходит ее твердение. Данная энергосберегающая технология не оставляет никаких отходов, которые загрязняли бы воздух, почву и воду. Газосиликатные блоки автоклавного твердения представляют собой материал, обладающий уникальными свойствами. Ведь в нем соединились наилучшие качества 2-ух древнейших строительных материалов: древесины и камня.
В последние годы в связи с заметным повышением требований к теплоизоляционным качествам ограждающих конструкций в жилых и общественных зданиях одной из немногочисленных разновидностей бетонов, из коих возможно возведение по-настоящему теплоэффективных конструкций оптимальной толщины стали именно ячеистые бетоны. Характеристики и свойства газосиликатных блоков дают этому стройматериалу ряд весьма важных преимуществ:
Газосиликатные блоки лёгкий вес.
Вот, пожалуй, главное и неоспоримое преимущество газосиликата перед кирпичом. Вес газосиликатного блока находится в диапазоне 488 – 500-сот килограмм/м3, в зависимости от размера газобетонных блоков.
Обычный блок (по ГОСТу 21520-89) имеет марку плотности Д500 и размер 250 на 625 толщиной 400 мм и массу около 30,5 килограм и по теплопроводности может заменить стену толщиной в 64 см из двадцати восьми кирпичей, чей вес составляет сто двадцать килограмм. Большие размеры газосиликатных блоков при незначительном весе значительно сокращают затраты на монтаж и заметно уменьшают время строительства. Для осуществления подъема газобетона не нужен кран: с этим справятся несколько человек, либо можно воспользоваться обыкновенной лебедкой, следовательно, легкий вес такого ячеистого бетона позволяет снизить не только транспортно-монтажные работы, но и затраты на обустройство фундаментов. Газобетонные блоки гораздо легче, нежели пенобетон, поддаются обработке. Их можно пилить, сверлить строгать и фрезеровать при помощи обычного инструмента.
Блоки газосиликатные экологичность.
Поскольку газобетон автоклавного твердения получается из песка, цемента, извести и алюминиевой пудры, им не выделяется токсичных веществ, в результате по своей экологичности он приближен к дереву, однако при этом не склонен к гниению и старению. Газобетонные изделия совершенно безопасны для человека, в доме, выстроенном из него, дышится столь же легко, как и в возведённом из дерева.
Быстрота и экономичность при работе с газосиликатными блоками.
Благодаря такой характеристике газосиликатных блоков как их внушительные габариты (600 на (50-500) на 250 мм) при малом весе процесс строительства протекает быстро и легко. Скорость строительства при этом возрастает действительно существенно (раза в 4) и, соответственно, уменьшаются трудозатраты. В торцах некоторых видов газосиликатного блока сформированы специальные пазы и гребни, а также захватные карманы, предназначенные для рук. Совершенно не нужно 1-1,5 см раствора в кладке, вполне достаточно клеевого слоя в 3-5 миллиметров, наносимого зубчатой кельмой, дабы надежно укрепить блок. Блоки из газобетона обладают почти идеальной конфигурацией (поскольку допустимое отклонение их граней не превышает одного миллиметра), что и дает возможность использования технологии тонкошовной кладки, заметно снижает затраты на выполнение работ. Стоимость газосиликатных блоков бывает невысока по сравнению с тем же кирпичом, но клей для выполнения тонких швов примерно в два раза дороже цены песчано-цементного раствора, зато расход материала при производстве кладки газобетонного блока снижается примерно в шесть раз. В конечном итоге получаемая тонкошовная кладка даёт возможность втрое снизить затраты на кладочный раствор, кроме того, ввиду минимальной толщины соединительного клея уменьшаются мостики холода в стенах и дом получается теплее.
Газосиликатные блоки низкая теплопроводность.
Её обеспечивают пузырьки воздуха, которые занимают около 80-ти процентов материала. Действительно, именно благодаря им среди положительных качеств газобетонных блоков есть высокая теплоизоляционная способность, за счёт которой снижаются затраты на отопление процентов на 20-30 и можно отказаться от применения дополнительных теплоизолирующих материалов. Стены, которые выполнены из газосиликатных блоков, полностью отвечают новым СНиПовским требованиям, что предъявляются к теплопроводности стен общественных и жилых зданий. В сухом состоянии коэффициент теплопроводности у газобетона равен 0,12 Вт/м °С, при 12%-ной влажности — 0,145 Вт/м °С. В средней полосе России возможно возведение стен из газосиликатных блоков (плотностью не больше 500 килограмм/м3), чья толщина составляет 40 см.
Энергосбережение благодаря газосиликатным блокам.
На сегодняшний день энергосбережение стало одним из важнейших показателей. Бывает, что пренебрежение данным параметром приводит к невозможности эксплуатации добротного дома из кирпича: владелец попросту не мог позволить себе финансово отапливать настолько большое помещение. При использовании газобетонного блока с весом 500 килограмм/м3, толщиной 40 см достигаются показатели по энергосберегающему параметру в пределах нормы. Использование газобетонных блоков плотностью более, чем 500 килограмм/м3 приводит к заметному ухудшению параметров (теплотехнические свойства понижаются на пятьдесят процентов при использовании блоков, имеющих плотность в 600-700 килограмм/м3). Газосиликатные блоки плотностью меньше, чем 400 килограмм/м3 можно применять в строительстве лишь в качестве утеплителя , ввиду их низких характеристик прочности.
Блоки газосиликатные морозостойкость.
Качества газобетонных блоков в плане морозостойкости позволяют им стать рекордсменами среди материалов, которые используются в малоэтажном строительстве. Отличная морозостойкость объясняется присутствием резервных пустот, в которые при замерзании вытесняется вода, при этом сам газосиликатный блок не разрушается. Если технология строительства из газобетона соблюдается неукоснительно, морозостойкость стройматериала превышает двести циклов.
Звукоизоляционные качества газобетонных блоков.
За счёт его ячеистой мелкопористой структуры, звукоизоляционные качества газосиликата во много раз выше, нежели у кирпичной кладки. При существовании воздушного зазора меж слоями газобетонных блоков, либо при выполнении отделки стеновой поверхности более плотными стройматериалами, обеспечивается звуковая изоляция примерно в 50 дБ.
Блоки автоклавного твердения пожаробезопасность.
Ячеистые газобетонные блоки не боятся огня. Дымоходы из газосиликатных блоков прокладывают сквозь любые деревянные конструкции без проведения разделки, поскольку тепло они проводят плохо. А поскольку для получения газобетона применяется лишь минеральное сырье природного происхождения, газобетонные блоки принадлежат к группе не поддерживающих горение материалов и способны выдерживать одностороннее огненное воздействие на протяжении 3–7-ми часов. При использовании газобетонных блоков в связке с металлоконструкциями, либо в качестве обшивки они идеально подходят для возведения пожаростойких стен, лифтовых и вентиляционных шахт.
Блоки газобетонные прочность.
При низком объемном весе газосиликатного блока — 500 килограмм/м3 — он имеет довольно высокий показатель прочности на сжатие — в районе 28–40 кгс/см3 благодаря автоклавной обработке (для сравнения тот же пенобетон — всего 15 кгс/ см3). На практике прочность блока бывает таковой, что он может смело использоваться при постройке домов с несущими стенами до 3-ех этажей, либо без ограничения этажности — в каркасно-монолитных строительстве.
Газосиликатные блоки легкость и рациональность обработки.
Блоки из газобетона достаточно легко поддаются любой механической обработке: без проблем их можно пилить, сверлить, строгать, фрезеровать, применяя при этом стандартные инструменты, что используются для обработки древесины. Каналы под трубы и кабели можно прокладывать с помощью обычного ручного инструмента, а можно для ускорения процесса применять и электроинструмент. Ручная пила позволит легко придать газосиликату любую конфигурацию, что полностью решает вопросы с доборными блоками, а также внешней архитектурной выразительности сооружений. Каналы и отверстия для обустройства электропроводки, розеток, трубопроводов и т.д. можно прорезать, используя электродрель.
Блоки газосиликатные размеры.
Процесс по изготовлению блоков автоклавного твердения гарантирует высокоточные размеры — обычно 250 на 625 миллиметров при различной толщине в 50 – 500 миллиметров (+- миллиметр). Отклонения, как видите, настолько минимальны, что только что выложенная стена являет собой поверхность, которая абсолютно готова для нанесения шпаклевки, являющейся основой под обои или покраску.
Негигроскопичность газобетонного блока.
Хотя автоклавный газобетонный блок является высокопористым материалом (его пористость способна доходить до 90-та процентов), материал не является гигроскопичным. Попав, например, под дождь, газобетон, в отличие от той же древесины довольно быстро высыхает и совершенно не коробится. По сравнению же с кирпичом газобетон совершенно не «всасывает» воду, так как капилляры его прерываются особыми сферическими порам.
Газобетонные блоки применение.
Самые легкие по весу газосиликатные блоки, имеющие плотность в 350 килограмм/м³ используются в качестве утеплителя . Газобетонные блоки плотностью четыреста кг/м³ идёт на постройку несущих стен и перегородок в малоэтажном домостроении. Имеющие высокие прочностные свойства газосиликатные блоки — 500 килограмм/м³ — применимы для строительства как нежилых, так и жилых объектов, достигающих более 3-ех этажей в высоту. И, наконец, те газосиликатные блоки, чья плотность равняется 700-та кг/м³ идеально подходят для возведения многоэтажных домов при армировании междурядьев, а также используются для создания легких перекрытий. Не требующие особого ухода газосиликатные блоки строители называют неприхотливыми и вечными. Блок автоклавного твердения отлично подходит для тех, кто стремится уменьшить себестоимость строительства. Стоимость газобетонных блоков невелика, к тому же на постройку дома из газосиликата нужно меньше отделочных и строительных материалов, нежели кирпичного. Да и работать с газосиликатными блоками достаточно просто, что снижает трудозатраты и ускоряет процесс возведения зданий — постройка из газосиликатных блоков ведётся в среднем раза в четыре быстрее, нежели при работе с кирпичом.
Блоки газосиликатные доставка и хранение.
Блоки газосиликата упаковываются производителем в довольно-таки прочную термоусадочную герметичную пленку, которая надежно предохраняет материал от влажностного воздействия. Потому нет необходимости заботиться о надлежащей защите газобетона от негативных атмосферных воздействий. Главной задачей покупателя, который самостоятельно перевозит газобетонные блоки становится защита их от разного рода механических повреждений. При транспортировке в кузове паллеты с установленными блоками должны жестко закрепляться мягкими стропами, которые призваны предотвращать поддоны с блоками от перемещений и трений. При выгрузке стройматериала также используются мягкие стропы. Если газобетонные блоки будут освобождены от защитной плёнки и станут храниться на открытой площадке, подвергаясь осадкам – учтите, что от повышенной влажности характеристики газобетонных блоков ухудшаются, потому этот материал следует держать под навесом или даже на закрытом складе.
Кладка из газобетонных блоков.
Работы по постройке зданий из газобетонных блоков могут производиться при температуре вплоть до – 50 градусов; при использовании специального морозостойкого клея. Поскольку газобетон – довольно легкий материал, он не вызывает выдавливания клея. В отличие от кирпичных стен, выполняемые из газобетона выкладывать можно без пауз. Согласно строительным нормативам для выкладывания наружных стен применяются газосиликатные блоки, имеющие толщину 375 — 400 миллиметров, для межкомнатных – не менее 250. Для того чтобы предотвратить проникновение влаги из подвала, кладку газосиликатных блоков следует вести на гидроизолирующий слой (к примеру, рубероид) — размеры его должны быть немного больше, чем ширина газобетонных блоков в кладке. 1-вый слой из газосиликатных блоков с целью выравнивания кладется на раствор, дабы компенсировать имеющиеся неровности фундамента. Начинают кладку газосиликатного блока с наивысшего по своим размерам зданиевого угла. Блоки при помощи уровня и молотка из резины выравниваются, шлифуются — с помощью терки, после чего кладка тщательно очищается от пыли. Укладке самого первого ряда газосиликатных блоков надо уделить особенное внимание, ведь от её ровности зависит удобство всей дальнейшей работы и конечное качество выполнения постройки. Контролировать укладку газосиликатных блоков можно при помощи уровня и шнура. Следующий ряд кладки газосиликатных блоков начинается с любого из углов. С тем чтобы обеспечить максимальную ровность рядов, не забывайте использовать уровень, а при большой длине стены – ещё и маячные промежуточные блоки. Производится укладка рядов с обязательной перевязкой газосиликатных блоков – то есть смещением каждого последующего ряда относительно предыдущих. Минимальной величиной смещения становится 10 сантиметров. Клей, который выступает из швов, не затирают, а удаляют с помощью мастерка. Блоки из газосиликата со сложной конфигурацией и доборные изготавливаются ножовкой для блоков.
Внутренние перегородки из газосиликатных блоков.
Независимо от того, какую из современных конструкций перегородок вы решите применить в собственном доме (к примеру, перегородки из металлопрофилей и гипсокортонных листов), вам все равно нужно будет делать какую-либо сэндвич-систему с применением утеплителя, дабы добиться оптимального уровня шумоизоляции. А, как известно, любая из сэндвич-систем по трудоемкости гораздо выше и дороже, нежели кладка из газосиликатных блоков. Проблему с перегородками легко решает газобетонный блок. Для возведения внутренних перегородок берутся газобетонные блоки, имеющие толщину в 75 и 100 миллиметров и плотность в 500. Стена в результате получается довольно-таки прочной, тепло- и шумоизолированной, но вместе с тем легкой.
Армирование при кладке из газосиликатных блоков.
При обустройстве стен в малоэтажных жилых домах из газобетонных блоков применяется арматура, которая назначается по спецрасчету, в соответствии с определённым проектом. Как правило, армирование производится через два — четыре ряда кладки; дополнительно арматура устанавливается и в углах зданий.
Газобетонные блоки, таким образом, представляет собой поистине экономичный и эффективный стройматериал, чьи свойства позволяют в кратчайшие сроки сооружать постройки различного назначения. Выпускаются газосиликатные блоки в двух видах: стеновые и перегородочные. И те, и другие сертифицированы согласно ГОСТ. Изготавливается этот высокоэкологичный материал по передовым технологиям с использованием самого современного оборудования, что обеспечивает газосиликатному блоку высочайшее качество и постоянство важных технических характеристик. Если вы заинтересованы в его покупке, обращайтесь в компанию Атрибут-С , ведь мы знаем о газобетоне всё и предлагаем своим покупателям только качественные газосиликатные блоки, изготовленные по всем технологическим нормам и имеющие безупречные характеристики прочности, теплоизоляции, долговечности и др. Атрибут-С обеспечит вас любыми объёмами газобетонных блоков и, что немаловажно, помимо продажи мы предлагаем вам ещё и быструю доставку газосиликатных блоков с бережной разгрузкой. Вы по достоинству оцените наш безупречный сервис и цены на газосиликатные блоки, которые заметно ниже, чем у многих подобных организаций в Московском регионе. Заказать газосиликатные блоки с доставкой легко, вам всего лишь нужно связаться с нами по телефону 8-499-340-35-47, или же отправить заявку на адрес
Этот e-mail адрес защищен от спам-ботов, для его просмотра у Вас должен быть включен Javascript
.
Можете не сомневаться, вам обязательно ответят и обговорят все условия оплаты и доставки газосиликатных блоков. А если у вас появились вопросы – пишите и получите все интересующие вас ответы.
Дополнительная информация о газобетонных блоках:
Блоки из газосиликата пользуются широким спросом в жилом и промышленном строительстве. Этот стройматериал по многим параметрам превосходит бетон, кирпич, натуральную древесину и др. Он изготавливается из экологически чистого сырья, отличается легкостью, огнеупорностью, простотой в эксплуатации и транспортировке. Применение этого легкого материала позволяет сократить расходы на обустройство тяжелого усиленного фундамента и тем самым удешевить строительство здания.
Что такое газосиликатные блоки
Газосиликатный блок представляет собой легкий и прочный стеновой материал, который изготавливается из ячеистого бетона. Изделия имеют пористую внутреннюю структуру, что положительно сказывается на их тепло- и шумоизоляционных свойствах. Такой стройматериал может применяться в различных сферах строительной индустрии — для возведения дачных и загородных домов, автомобильных гаражей, хозяйственных сооружений, складских комплексов и др.
Как производятся газосиликатные блоки
Существуют две основные технологии производства газосиликатных строительных блоков.
- Неавтоклавная . При таком методе производства застывание рабочей смеси происходит в естественных условиях. Неавтоклавные газосиликатные блоки выделяются более низкой стоимостью, но имеют некоторые важные отличия от автоклавных. Во-первых, они менее прочны. Во-вторых, при их высыхании усадка происходит почти в 5 раз интенсивнее, чем в случае с автоклавными изделиями.
- Автоклавная . Для автоклавного производства газосиликата требуется больше энергетических и материальных ресурсов, из-за чего повышается конечная стоимость изделий. Изготовление осуществляется при определенном давлении (0,8-1,2 МПа) и температуре (до 200 градусов Цельсия).
Готовые изделия получаются более прочными и устойчивыми к усадке.
Виды блоков
В зависимости от плотности, состава и функционального назначения блоки из газосиликата делятся на три основные категории.
- Конструкционные . Обладают высокими прочностными характеристиками. Плотность изделий составляет не менее 700 кг/м 3 . Применяются при строительстве высотных сооружений (до трех этажей). Способны выдерживать большие механические нагрузки. Теплопроводность составляет 0,18-0,2 Вт/(м·°С).
- Конструкционно-теплоизоляционные . Блоки с плотностью 500-700 кг/м 3 используются при обустройстве несущих стен в малоэтажных зданиях. Отличаются сбалансированным соотношением прочностных и теплоизоляционных характеристик [(0,12-0,18 Вт/(м·°С)].
- Теплоизоляционные . Отличаются повышенными теплоизолирующими свойствами [(0,08-0,1 Вт/(м·°С)]. Из-за низкой плотности (менее 400 кг/м 3) не подходят для создания несущих стен, поэтому применяются исключительно для утепления.
Типоразмеры и вес
Стеновые блоки из газосиликата имеют стандартные размеры 600 х 200 х 300 мм. Габаритные характеристики полублоков составляют 600 х 100 х 300 мм. В зависимости от компании-производителя типоразмеры изделий могут несколько различаться: 500 х 200 х 300, 588 х 300 х 288 мм и др.
Масса одного блока зависит от его плотности:
- конструкционные блоки весят 20-40 кг, полублоки — 10-16 кг;
- конструкционно-теплоизоляционные блоки и полублоки — 17-30 кг и 9-13 кг соответственно;
- теплоизоляционные блоки весят 14-21 кг, полублоки — 5-10 кг.
Состав газосиликатных блоков
Газосиликат — это экологически безопасный стройматериал, который изготавливается из нетоксичного сырья натурального происхождения. В состав блоков входит цемент, песок, известь и вода. В качестве пенообразователя применяется алюминиевая крошка, которая способствует увеличению коэффициента пустотности блоков. Также при производстве материала применяется поверхностно-активное вещество — сульфонол С.
Характеристики материала
Строительные блоки из газосиликата обладают следующими характеристиками.
- Теплоемкость . Изделия, изготовленные по автоклавной технологии, имеют коэффициент теплопроводности 1 кДж/(кг·°С).
- Теплопроводность . Конструкционно-теплоизоляционный газосиликат имеет среднюю теплопроводность около 0,14 Вт/(м·°С), тогда как для железобетона этот параметр достигает отметки 2,04.
- Звукопоглощение . Газосиликатные блоки значительно уменьшают амплитуду внешних шумов, индекс звукопоглощения для этого материала равен 0,2.
- Морозостойкость . Материал с плотностью 600 кг/м 3 выдерживает до 35 циклов замораживания и оттаивания (что соответствует индексу F35). Изделиям с более высокой плотностью присвоен класс морозостойкости F50.
Преимущества и недостатки газосиликатных блоков
Основными достоинствами газосиликата являются следующие.
- Легкость . Блоки из газосиликата весят почти в 5 раз меньше, чем бетонные изделия тех же размеров.
Это облегчает строительные работы и позволяет сократить расходы на транспортировку стройматериала.
- Эффективная тепло- и звукоизоляция . За счет наличия внутренних микропор достигаются высокие тепло- и шумоизоляционные характеристики газосиликата. Это позволяет создать комфортный микроклимат внутри помещений.
- Экологичность . В составе стройматериала не содержатся опасные токсины и канцерогены, которые могут причинить вред окружающей среде и человеческому здоровью.
- Огнеупорность . Газосиликат производится из негорючего сырья, поэтому не разрушается при интенсивном нагревании и не способствует распространению пламени при пожаре.
На сколько критичны недостатки
Как и любой другой стройматериал, газосиликат имеет некоторые недостатки.
- Низкий запас прочности . Материал с низкой плотностью (300-400 кг/м 3) имеет сравнительно невысокие прочностные характеристики. Поэтому при строительстве необходимо в обязательном порядке выполнять работы по армированию стен.
- Гладкие поверхности . Лицевые части газосиликатных блоков имеют гладкую поверхность с низким коэффициентом шероховатости. Из-за этого ухудшается адгезия с отделочными материалами, что усложняет процесс отделки стен штукатуркой и другими покрытиями.
- Низкая влагостойкость . Из-за увеличенной пористости материал чувствителен к повышенной влажности. Вода и водяной пар проникают во внутренние микропоры и при замерзании увеличиваются в объеме, разрушая блоки изнутри. Поэтому стены из газосиликата нуждаются в дополнительной гидроизоляции.
Где применяют газосиликатные блоки
Газосиликатные блоки используются в жилом и промышленном строительстве. Этот материал применяется не только для постройки несущих элементов зданий, но и для повышения теплоизоляции, а также для защиты инженерных сетей (в частности, отопительных).
Область применения газосиликата определяется его характеристиками, в первую очередь плотностью.
- Изделия, плотность которых составляет 300-400 кг/м 3 , имеют низкий запас прочности, поэтому они используются преимущественно для утепления стен.
- Газосиликат с плотностью 400 кг/м 3 пригоден для возведения одноэтажных домов, гаражей, служебных и хозяйственных пристроек. За счет более высокой прочности материал способен выдерживать значительные нагрузки.
- Блоки с плотностью 500 кг/м 3 оптимальны в соотношении прочностных и теплоизоляционных свойств. Их часто используют для строительства коттеджей, дачных домов и других построек высотой до 3 этажей.
Наиболее прочными являются газосиликатные блоки с плотностью 700 кг/м 3 . Их применяют для возведения высотных объектов жилого и промышленного значения. Но из-за увеличенной плотности уменьшается коэффициент пористости материала и, следовательно, его теплоизоляционные свойства. Поэтому стены, построенные из таких блоков, требуют дополнительного утепления.
Процесс строительства и испытания блоков.
В строительной сфере применяются изделия из газосиликата. Процесс производства блоков осуществляется при высоком давлении, а также в естественных условиях. Благодаря пористой структуре они хорошо удерживают тепло. Популярен газосиликатный блок D500, характеристики которого обеспечивают возможность использования данного материала при возведении домов. В результате применения блоков увеличенных размеров сокращается цикл постройки здания. Рассмотрим основные технические характеристики, которые нужно учитывать при выборе материала.
Что представляют собой блоки газосиликатные
Блочные изделия из газосиликата – современный строительный материал, изготовленный из следующего сырья:
- портландцемента, являющегося вяжущим ингредиентом;
- кварцевого песка, вводимого в состав в качестве заполнителя;
- извести, участвующей в реакции газообразования;
- порошкообразного алюминия, добавляемого для вспенивания массы.
При смешивании компонентов рабочая смесь увеличивается в объеме в результате активно протекающей химической реакции.
Газосиликатные блоки широко применяются в сфере строительства
Формовочные емкости, заполненные силикатной смесью, застывают в различных условиях:
- естественным образом при температуре окружающей среды.
Процесс отвердевания длится 15-30 суток. Полученная продукция отличается уменьшенной стоимостью, однако имеет недостаточно высокую прочность;
- в автоклавах, где изделия подвергаются нагреву при повышенном давлении. Пропаривание позволяет повысить прочностные характеристики и удельный вес газосиликатной продукции.
Изменяются показатели плотности и прочности в зависимости от способа изготовления. Указанные характеристики материалов определяют область использования.
Блоки делятся на следующие типы:
- изделия конструкционного назначения. Они обозначаются маркировкой D700 и востребованы для строительства капитальных стен, высота которых составляет не более трех этажей;
- теплоизоляционно-конструкционную продукцию. Марка D500 соответствует данным блокам. Они применяются для сооружения внутренних перегородок и строительства несущих стен небольших зданий;
- теплоизоляционные изделия. Для них характерна повышенная пористость и уменьшенная до D400 плотность.
Это позволяет использовать газосиликатный материал для надежной теплоизоляции стен.
Цифровой индекс в маркировке блоков соответствует массе одного кубического метра газосиликата, указанной в килограммах. С возрастанием плотности материала снижаются его теплоизоляционные свойства. Изделия марки D700 постепенно вытесняют традиционный кирпич, а продукция с плотностью D400 не уступает по теплоизоляционным свойствам современным утеплителям.
Газосиликатные блоки превосходят по механической прочности пенобетон
Блоки газосиликатные – плюсы и минусы материала
Изделия из газосиликата обладают комплексом серьезных достоинств. Главные плюсы газосиликатных блоков:
- уменьшенная масса при увеличенных объемах. Плотность газосиликатного материала в 3 раза меньше по сравнению с кирпичом и примерно в 5 раз ниже, если сравнивать с бетоном;
- увеличенный запас прочности, позволяющий воспринимать сжимающие нагрузки. Показатель прочности для газосиликатного блока с маркировкой D500 составляет 0,04 т/см³;
- повышенные теплоизоляционные свойства.
Материал успешно конкурирует с отожженным кирпичом, теплопроводность которого трехкратно превышает аналогичный показатель газосиликата;
- правильная форма блоков. Благодаря уменьшенным допускам на габаритные размеры и четкой геометрии, кладка блоков осуществляется на тонкий слой клеевого раствора;
- увеличенные габариты. Использование для возведения стен зданий крупногабаритных силикатных блоков с небольшим весом позволяет сократить продолжительность строительства;
- хорошая обрабатываемость. При необходимости несложно придать газосиликатному блоку заданную форму или нарезать блочный материал на отдельные заготовки;
- приемлемая цена. Используя блочный газосиликат для возведения коттеджа, частного дома или дачи, несложно существенно снизить сметную стоимость строительных мероприятий;
- пожаробезопасность. Блоки не воспламеняются при нагреве и воздействии открытого огня. Они относятся к слабогорючим строительным материалам, входящим в группу горючести Г1;
- высокие звукоизоляционные свойства.
Они обеспечиваются за счет пористой структуры. По способности поглощать внешние шумы блоки десятикратно превосходят керамический кирпич;
- экологичность. При изготовлении газосиликатной смеси не используются токсичные ингредиенты и в процессе эксплуатации не выделяются вредные для здоровья компоненты;
- паропроницаемость. Через находящиеся внутри газосиликатного массива воздушные ячейки происходит воздухообмен, создающий благоприятный микроклимат внутри строения;
- морозостойкость. Газосиликатные блоки сохраняют структуру массива и эксплуатационные характеристики, выдерживая более двухсот циклов продолжительного замораживания с последующим оттаиванием;
- теплоаккумулирующие свойства. Газосиликатные блоки – энергосберегающий материал, который способен накапливать тепловую энергию и постепенно отдавать ее для повышения температуры помещения.
Область применения зависит от плотности материала
Несмотря на множество достоинств, газосиликатные блоки имеют слабые стороны. Главные недостатки материала:
- повышенная гигроскопичность. Пористые газосиликатные блоки через незащищенную поверхность постепенно поглощают влагу, что разрушает структуру и снижает прочность;
- необходимость использования специального крепежа для фиксации навесной мебели и оборудования. Стандартные крепежные элементы не обеспечивают надежной фиксации из-за ячеистой структуры блоков;
- недостаточно высокая механическая прочность. Блочный материал крошится под нагрузкой, поэтому требует аккуратного обращения при транспортировке и кладке;
- образование плесени и развитие грибковых колоний внутри и на поверхности блоков. Из-за повышенного влагопоглощения создаются благоприятные условия для роста микроорганизмов;
- увеличенная величина усадки. В реальных условиях эксплуатации под воздействием нагрузок блоки постепенно усаживаются, что вызывает через некоторое время образование трещин;
- пониженная адгезия с песчано-цементными штукатурками.
Необходимо использовать специальные отделочные составы для оштукатуривания газосиликата.
Несмотря на имеющиеся недостатки, газосиликатные блоки активно используются для сооружения капитальных стен в области малоэтажного строительства, а также для возведения теплоизолированных стен многоэтажных строений и для теплоизоляции различных конструкций. Профессиональные строители и частные застройщики отдают предпочтение газосиликатным блокам благодаря весомым преимуществам материала.
Газосиликатный блок D500 – характеристики стройматериала
Конструкционно-теплоизоляционный блок марки D500 используется для различных целей:
- сооружения коробок малоэтажных строений;
- обустройства межкомнатных перегородок;
- усиления дверных и оконных проемов.
Газосиликатные блоки обеспечивают хорошую теплоизоляцию помещения
Приняв решение приобрести блочный силикат с маркировкой D500, следует детально ознакомиться с эксплуатационными свойствами популярного строительного материала.
Остановимся на главных характеристиках.
Прочностные свойства
Класс прочности материала на сжатие изменяется в зависимости от метода изготовления блоков:
- газосиликат марки D500, полученный автоклавный методом, характеризуется показателем прочности B2,5-B3;
- класс прочности на сжатие для аналогичных блоков, произведенных по неавтоклавной технологии, составляет B1,5.
Прочность блоков D500 достигает 4 МПа, что является недостаточно высоким показателем. Для предотвращения растрескивания газосиликатного материала выполняется усиление кладки сеткой или арматурой. Относительно невысокий запас прочности позволяет использовать блочный стройматериал в сфере малоэтажного строительства. При возведении многоэтажных зданий газосиликатные блоки применяются совместно с кирпичом для теплоизоляции возводимых стен.
Удельный вес
Плотность газосиликатных блоков – важный эксплуатационный показатель, характеризующий пористость блочного массива. Плотность обозначается маркировкой в виде латинской буквы D и цифрового индекса. Цифра в маркировке характеризует массу одного кубометра газосиликата. Так, один кубический метр газосиликата с маркировкой D500 весит 500 кг. Зная маркировку изделий по плотности, размеры блоков и их количество, несложно рассчитать нагрузку на фундаментную основу.
Газосиликатные блоки — экологичный материал
Теплопроводные характеристики
Теплопроводность газосиликатных блоков – это способность передавать тепловую энергию. Значение показателя характеризует коэффициент теплопроводности газосиликатных блоков.
Величина коэффициента изменяется в зависимости от концентрации влаги в материале:
- коэффициент теплопроводности сухого газосиликатного материала марки D500 составляет 0,12 Вт/м⁰С;
- при увеличении влажности до 5% теплопроводность блоков D500 увеличивается до 0,47 Вт/м⁰С.
В строениях, построенных из газосиликатных блоков, благодаря пониженной теплопроводности материала, круглогодично поддерживается благоприятный микроклимат.
Морозоустойчивость
Способность газосиликатных блоков воспринимать температурные перепады, связанные с глубоким замораживанием и оттаиванием, характеризует маркировка. Показатель морозоустойчивости для изделий D500 составляет F50. По сравнению с другими видами композитного бетона это достаточно неплохой показатель. На морозостойкость влияет концентрация влаги в блоках. С уменьшением влажности материала морозоустойчивость блоков возрастает.
Срок эксплуатации
Газосиликат отличается продолжительным периодом использования. Структура газосиликатного массива сохраняет целостность на протяжении более полувека. Изготовители блоков гарантируют срок службы изделий в течение 60-80 лет при условии защиты блоков от впитывания влаги. Оштукатуривание материала позволяет продлить срок службы.
Пожарная безопасность
Газосиликатные блоки – пожаробезопасный стройматериал с огнестойкостью до 400 ⁰С. Испытания подтверждают, что покрытая штукатуркой газосиликатная стена способна выдержать воздействие открытого огня на протяжении трех-четырех часов. Блоки подходят для сооружения пожароустойчивых стен, перегородок и дымоходов.
Заключение
Блочный газосиликат – проверенный материал для строительства малоэтажных зданий. Характеристики блоков позволяют обеспечивать устойчивость возводимых строений и поддерживать внутри зданий комфортный микроклимат.
Рекомендуем также
характеристики. Размеры, отзывы и цены
Блоки газосиликатные, технические характеристики которых будут представлены в статье, сегодня достаточно распространены. Это обусловлено тем, что данный ячеистый бетон обладает незначительным весом и отличным качеством.
Состав газосиликата
При производстве упомянутых изделий используется портландцемент высокого качества, среди ингредиентов которого должен содержаться силикат кальция в объеме, равном ½ от общего веса. Помимо прочего, к смеси добавляется песок, в котором есть кварц (85% или больше). Тогда как ила и глины в этой составляющей не должно оказаться больше 2%. Добавляется в процессе производства и известь-кипелка, скорость гашения которой равна примерно 5-15 минутам, а вот оксида кальция и магния в ней должно быть примерно 70% или больше. Изделия имеют в составе и газообразователь, который выполняется из алюминиевой пудры. Есть в блоках и жидкость, а также сульфанол С.
Блоки газосиликатные, цена которых будет представлена ниже, могут быть изготовлены с использованием автоклава или без него. Первый способ производства позволяет сформировать блоки, прочность которых гораздо выше, их усадка получается тоже не столь внушительной, что ценится потребителями.
Изделия, которые производятся с использованием автоклава, но не проходят этап сушки, обладают в 5 раз более внушительной усадкой по сравнению с блоками, которые сушатся в автоклаве, кроме того, у них и не столь внушительная прочность, однако и стоят они меньше.
Автоклавный метод производства используется, как правило, на больших предприятиях, это обусловлено тем, что данный способ технологичен и предполагает трату большого количества энергии. Блоки в процессе производства проходят стадию пропаривания при 200 0С, тогда как давление достигает показателя в 1,2 МПа. Производители меняют соотношение ингредиентов, которые входят в состав смеси, что позволяет изменять характеристики материала. Например, с увеличением объема цемента будет повышена прочность блока, однако пористость будет уменьшена, что в результате повлияет на теплотехнические качества, а теплопроводность в значительной степени будет увеличена.
Технические характеристики
Блоки газосиликатные, технические характеристики которых предпочтительнее рассмотреть перед приобретением, делятся на типы по плотности. В зависимости от этого показателя, блоки могут быть конструкционными, теплоизоляционными и конструкционно-теплоизоляционными. Конструкционные изделия – это те, что обладают плотностью, обозначаемой маркой D700, но не меньше. Эти изделия применяются при возведении несущих стен в постройках, высота которых не превышает 3 этажей. Конструкционно-теплоизоляционные изделия обладают плотностью в пределах D500-D700. Данный материал превосходно подходит для возведения межкомнатных перегородок и стен построек, высота которых не превышает 2 этажей.
Теплоизоляционные блоки газосиликатные, технические характеристики которых важно знать перед тем, как применять их при возведении стен, обладают достаточно внушительной пористостью, это указывает на то, что прочность их является самой низкой. Их плотностью равна пределу D400, их используют в роли материала, который способен повысить теплотехнические качества стен, возведенных из не столь энергоэффективных материалов.
Качества теплопроводности
По показателям теплопроводности газосиликат обладает довольно внушительными характеристиками. Теплопроводность находится в прямой зависимости от плотности. Так, газоликат марки D400 или ниже обладает теплопроводностью, равной 0,08-0,10 Вт/м°С. Что касается блоков марки D500-D700, упомянутый показатель у них колеблется в пределах от 0,12 до 0,18 Вт/м°С. Блоки марки D700 и выше имеют теплопроводность в пределах 0,18-0,20 Вт/м°С.
Морозостойкость
Блоки газосиликатные, технические характеристики которых непременно стоит узнать перед совершением покупки, обладают и определенными качествами морозостойкости, которые зависят от количества пор. Таким образом, разные блоки на основе газосиликата способны выдержать примерно 15-35 циклов замораживания и оттаивания. Однако техническое развитие не стоит на месте, и некоторые предприятия научились производить блоки, которые способны претерпевать подобные циклы до 50, 75 и даже 100 раз, что очень привлекательно, как и вес газосиликатного блока. Но если вы приобретаете изделия, которые были произведены по ГОСТ 25485-89, то при строительстве дома необходимо ориентироваться на показатель морозостойкости марки D500, равный 35 циклам.
Габариты и масса блоков
Перед тем как начинать возводить стены из газосиликатных блоков, необходимо узнать, какие размеры могут иметь изделия. Как правило, к продаже представлены блоки, размеры которых равны: 600х200х300, 600х100х300, 500х200х300, 250х400х600, а также 250х250х600 мм, но и это далеко не полный перечень.
Масса блока зависит от плотности. Так, если блок имеет марку D700, а его габариты находятся в пределах 600x200x300 мм, то вес блока будет варьироваться в пределах от 20 до 40 кг. А вот марка блока D700 с габаритами в пределах 600x100x300 мм обладает весом, эквивалентным 10-16 кг. Блоки с плотностью от D500 до D600 и размерами 600x200x300 мм имеют вес от 17 до 30 кг. Для плотности газосиликата D500-D600 и его размера в блоке 600x100x300 мм вес будет равен 9-13 кг. При плотности в D400 и габаритах, равных 600x200x300 мм, масса будет равна 14-21 кг. Марка газосиликата D400, заключенная в размеры 600x100x300 мм, будет весить примерно 5-10 кг.
Положительные стороны газосиликатного блока
Когда вам известна толщина газосиликатного блока, можно узнать и о его остальных характеристиках, в том числе о положительных и отрицательных сторонах. Среди плюсов можно выделить незначительный вес, а также прочность, которая является достаточной для малоэтажного строительства. Кроме того, подобные изделия обладают отличными качествами теплосбережения. Через такие стены плохо проходит шум, а стоимость изделий при всем при этом остается доступной. Блоки не горят. Производить строительство с помощью газосиликатных блоков можно на основе специальных клеев, которые позволяют получить шов минимальной толщины.
Отрицательные качества
Рассматривая минусы газосиликатных блоков, можно выделить необходимость проведения наружной отделки, что повышает эстетичность стен. Блоки не столь привлекательны становятся тогда, когда потребитель узнает об их качествах гигроскопичности. А перед началом строительства требуется возводить прочный фундамент.
Цена блоков
Блоки газосиликатные, цена которых может меняться в зависимости от размеров, допустимо укладывать самостоятельно. Их вес не предполагает использования специальной техники. Таким образом, если блок имеет размер в пределах 600х100х300 мм, то его стоимость за единицу будет равна $1,8-1,9.
Газосиликатные блоки первой категории
Газосиликатные блоки укладываются на клеевой раствор, толщина которого должна быть 2-3 мм. Теплозащитные качества газосиликатных блоков очень высокие, благодаря этому квадратный метр кладки из такого материала стоит дешево. А еще нет необходимости производить отделочные работы, поэтому, если финансы имеют большое значение, то лучше использовать газосиликатные блоки. Если речь идет о строительстве, где применяется тонко шовная кладка, то лучше использовать газосиликатные блоки. К примеру: для того чтобы добиться одинаковой теплопроводности, стена из керамзитобетона должна в два раза превышать толщину стены из газосиликатных блоков.
Газосиликатные блоки обладают следующими преимуществами:
— теплопроводность ниже, поэтому можно существенно сэкономить на толщине стен;
— теплопроводность стен снижается, если делать кладку на тонком слое клея;
— кладка не вызывает трудностей потому, что обработка легкая;
— можно не делать штукатурку, если проводится внутренняя отделка;
— блоки стыкуются между собой прочно, они могут быть самых разных размеров.
Надо отметить, что при его применении на строительство стены уходит времени в 3 раза меньше, чем если использовать кирпич. И это качество ценит все больше людей.
При этом на силикатные блоки излишне грешат, за использование извести и алюминиевой пудры. Однако стоит знать, что известь в газосиликате находится в связанном состоянии, в виде силикатов кальция, которые безвредны для человека. По поводу алюминия та же ситуация. После вступления в химическую реакцию алюминий превращается в водород, который также безвреден для здоровья.
Низкая теплопроводность, прочность, экологичность, высокое звукопоглощение, а также приемлемая цена делают газосиликатные блоки безусловным лидером на рынке стеновых кладочных материалов.
По некоторым характеристикам, таким как теплопроводность, плотность, ячеистый бетон схож с древесиной, однако дает гораздо больше возможностей для строительства. Так, используя газосиликатные блоки, можно сделать толщину стен значительно большую, чем, например, при использовании древесины, кирпича и других стеновых материалов! Кроме того, сам процесс кладки требует намного меньше трудовых и временных ресурсов. Ведь при размерах, в десятки раз превышающих размеры кирпича, газосиликатный блок могут без проблем поднять и перенести один или два человека.
Одним из наиболее важных преимуществ газосиликатных блоков является их техническая и экологическая безопасность. Благодаря низкой теплопроводности, ячеистый бетон способен в течение длительного времени выдержать контакт даже с открытым огнем. В то же время стены, выполненные из газосиликатных блоков, способны сохранить тепло в доме даже в лютые морозы. Данное свойство достигается не только благодаря химическим и физическим характеристикам газосиликатных блоков. Практически идеальная геометрия, а также использование специальных клеевых составов позволяют свести толщину швов между блоками к минимуму. Отсутствие радиоактивных веществ, канцерогенов, тяжелых металлов и других вредных веществ позволяет использовать ячеистый бетон в строительстве жилых домов без опасений за здоровье. Использование специальных материалов внутренней и внешней отделки помогают сохранить данные характеристики стен, выполненных из газосиликатных блоков, на протяжении длительного времени. Прочность блоков из ячеистого бетона позволяет с легкостью нести нагрузку плит перекрытий, а также позволяет возводить двух, трехэтажные здания.
Этот строительный материал становятся с каждым годом более востребованным, чем кирпич, что совершенно неудивительно: стоит он дешевле, кладка осуществляется легче, все работы происходят быстрее. Следует по возможности приобретать материал у проверенных фирм, так как это является гарантией того, что товар предлагается высокого качества.
Всю необходимую информацию сможете получить, обратившись к нашим специалистам! Будем рады Вам помочь в этом выборе.
С уважением, руководство компании ООО «Компас-Инвест»!
5 различий между блоками из пенополистирола и блоками из пенополистирола
В сфере строительства из пеноблоков, независимо от того, используется ли он для изоляции, дорог, ландшафтного дизайна или коммерческих зданий, термин «пенополистирол» часто используется и неправильно используется, когда речь идет о блоках из пенополистирола (EPS). Пенополистирол на самом деле является торговой маркой Dow Chemical Company, которая технически относится к экструдированному пенополистиролу с закрытыми порами (вспомните пенопластовые кофейные чашки, контейнеры для еды на вынос и упаковочный материал).Однако этот экструдированный пенополистирол часто ошибочно используют, когда говорят о пенополистироле, который во многом похож, но отличается. Если вы обратитесь к пенополистиролу, когда на самом деле ищете материал для строительных проектов, известный как пенополистирольные блоки, вы определенно не получите то, за что платите.
Как эксперты в области строительства из пенополистирола, мы здесь, чтобы установить рекорд по сравнению экструдированного и пенополистирола, чтобы вы как потребитель могли быть лучше информированы о типе материалов, в которые вы инвестируете для своего следующего проекта.Вот 5 различий между блоками из пенополистирола и блоками из пенополистирола.
Экструдированный и пенополистирол Основное различие между пенополистиролом и блоками из пенополистирола заключается в том, что пенополистирол изготавливается из экструдированного полистирола (XPS), а блоки из пенополистирола изготавливаются из пенополистирола. Итак, в чем реальная разница между экструдированным и расширенным? Оба являются пенополистироловыми изделиями, изготовленными из полистирольных смол, но изготавливаются в виде листов и блоков совершенно по-разному.Для пенополистирольных блоков вспенивающий агент, который используется для формирования конечного продукта, быстро покидает шарики полистирола, что создает тысячи крошечных ячеек, заполненных воздухом. Вспенивающий агент, используемый для изготовления продуктов из XPS или пенополистирола, остается в гранулах в течение длительного времени, тем самым предотвращая и уменьшая поток воздуха через материал. Это дает пене XPS более низкий рейтинг влагопоглощения по сравнению с EPS. Чтобы добавить, XPS производится с использованием процесса непрерывной экструзии, который создает форму с закрытыми порами, в то время как EPS производится с помощью процесса расширения, который формирует сферические шарики и использует тепло и давление для сплавления продукта из пенопласта.
Существует много различий в физических свойствах блоков из пенополистирола и пенополистирола. У одного цвет другой. Вы часто будете видеть оригинальные листы пенополистирола синего цвета, в то время как пенополистирольные блоки имеют белый цвет, если только они не окрашены по индивидуальному заказу. Пенополистирол легкий, но имеет высокую плотность, что делает его более прочным и долговечным, чем пенополистирол. Многие рассматривают пенополистирол в качестве наполнителя благодаря его прочности на сжатие и способности выдерживать большие нагрузки в течение длительных периодов времени.Его рейтинг проницаемости выше, чем у пенополистирола, что делает его более оптимальным для защиты от воды и плесени.
Возможность вторичной переработки является еще одним важным фактором, отличающим пенополистирол от пенополистирола. В то время как пенополистирол не подлежит вторичной переработке, пенополистирол чрезвычайно пригоден для вторичной переработки. Он считается очень зеленым, что хорошо сочетается с постоянно растущей тенденцией к зеленому строительству. Пенополистирол состоит из органических элементов, что означает, что он не содержит токсичных химических веществ, таких как хлорфторуглероды (ХФУ) или гидрохлорфторуглероды (ГХФУ).И последнее, но не менее важное: пенообразователи, используемые для производства пенополистирола, экспоненциально менее вредны для окружающей среды, чем те, которые используются для производства пенополистирола.
Когда речь идет об использовании блоков и листов пенополистирола или пенополистирола, пенополистирол является более идеальным вариантом для строительных проектов, требующих долговечности и устойчивости к суровым внешним условиям. Его применение включает в себя стабилизацию грунта, насыпи дорог, обшивку, укладку под землю, изоляцию, изоляцию конических крыш, бассейны и ландшафтный дизайн.
Производительность Пеноблоки EPS имеют тенденцию превосходить пеноблоки XPS. Материалы также немного различаются по значению R, которое является мерой сопротивления тепловому потоку, также известной как эффективность теплоизоляции. EPS имеет тенденцию превосходить XPS с точки зрения долгосрочного R-значения, что означает, что это лучший изоляционный продукт. Потенциал высыхания геопены EPS в суровых условиях позволяет ей сохранять термостойкость с течением времени. Кроме того, цена пенополистирола EPS, как правило, ниже по себестоимости, что дает более высокую ценность при оценке его долговечности и эффективности в качестве наполнителя.
В следующий раз, когда вы услышите, что пенополистирол используется для обозначения геопены EPS, вы поймете конкретные различия между ними. Различия в конечном итоге связаны с тем, как они производятся: пенополистирол формируется в процессе экструзии, а пенополистирол формируется путем расширения. Уникальная форма придает пенополистиролу и пенополистиролу различные свойства. Хотя листы и блоки из пенополистирола и пенополистирола часто используются взаимозаменяемо в качестве строительного наполнителя и изоляционного материала, использование пенополистирола в определенных ситуациях имеет ряд больших преимуществ. Для тех, кто ищет недорогой изоляционный материал, более устойчивый к повреждениям от влаги и более устойчивый к более суровым внешним факторам, таким как погода и сжатие, блоки из геопены EPS являются лучшим вариантом.
Geofoam International здесь, чтобы помочь вам со всеми вашими потребностями в строительстве блоков из пенополистирола. От обучения вас точным различиям и преимуществам EPS geofoam по сравнению с другими типами строительных материалов до предоставления вам нестандартных пеноблоков и услуг для удовлетворения ваших потребностей, обращайтесь в Geofoam International.
Газобетон или пеноблок? Характеристики материалов
Прежде чем строить собственный дом, вы можете в случае необходимости решить вопрос о том, какой именно строительный материал вы будете использовать. В этой статье мы попытаемся решить, какой из двух материалов лучше: газобетон или обычный пеноблок. Их характеристики схожи, поэтому выбор может быть затруднен.
Поры в нем появляются не из-за того, что его накачали воздухом (как думают дилетанты), а из-за добавления в него специальных реагентов, выделяющих различные газы. Благодаря высокой пористости и малой массе материал отличается прекрасными теплоизоляционными свойствами и способностью поглощать шум. Вот почему пеноблок, характеристика которого это подтверждает, является отличным строительным материалом.
А теперь займемся газобетоном.Его структура во многом схожа со своим предшественником. Отличие в том, что он изготавливается по совершенно другой технологии. В частности, алюминиевая пудра ответственна за образование воздушных пор, которые вступают в реакцию с другими компонентами материала. Готовая смесь для блоков заливается в специальные формы, в которых с помощью струн нарезается газобетон.
После резки лотки загоняются в автоклавы, где под высоким давлением из них забирается практически вся влага.
В результате газобетон по массе не отличается от пеноблока, а по другим характеристикам у них схожие. Однако его прочностные показатели несколько лучше. Однако гигроскопичность газобетона намного выше. При прочих равных в важной среде он напоминает губку: с такой скоростью впитывается вода.Конечно, для готового здания это не очень хороший показатель. Поэтому пеноблок, характеристики которого в этом отношении гораздо лучше, можно использовать даже для строительства бань.
В итоге можно сказать, что у этих материалов очень много общего. Из них можно успешно строить дома самого разного назначения и характеристик. По своей теплопроводности они сравнимы с натуральным деревом, а тот же кирпич во много раз превосходит. Но, как мы уже говорили, пеноблоки (характеристики, которые могут быть самыми разными по размеру) гораздо меньше впитывают влагу, что позволяет снизить затраты на отделку готового дома.
Если вы решили строить свой дом из газобетона, то даже после доставки с завода материал необходимо как следует высушить, чтобы удалить лишнюю влагу. Специалисты утверждают, что газоблоки лучше всего держать на открытой местности не менее года. При строительстве необходимо позаботиться о качественной гидроизоляции и пароизоляции, иначе впоследствии могут возникнуть проблемы. Таким образом, в большинстве случаев целесообразнее использовать простой пеноблок. Его характеристики несколько лучше.
Пенополистирол (пена EPS): использование, структура и свойства
Что такое пенополистирол (EPS)?
Что такое пенополистирол (EPS)?
E расширенный P oly S tyrene (EPS) – белый пенопласт, изготовленный из твердых шариков полистирола. Он в основном используется для упаковки, изоляции и т. д. Это жесткий вспененный материал с закрытыми порами, изготовленный из:- Стирол, образующий ячеистую структуру
- Пентан – используется в качестве пенообразователя
И стирол, и пентан являются углеводородными соединениями и получаются из побочных продуктов нефти и природного газа.
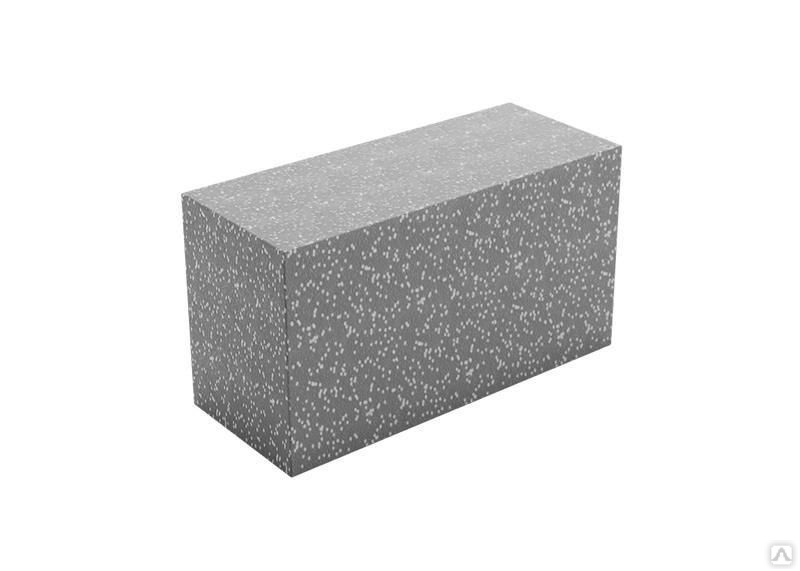
EPS очень легкий, с очень низкой теплопроводностью, низким влагопоглощением и превосходными амортизирующими свойствами. Одним из серьезных ограничений пенополистирола является достаточно низкая максимальная рабочая температура ~80°С. Его физические свойства не меняются в диапазоне рабочих температур (т.е. до 167°F/75°C) при длительном температурном воздействии.
Его химическая стойкость почти эквивалентна материалу, на котором он изготовлен – полистиролу.
EPS на 98% состоит из воздуха и подлежит вторичной переработке.
Как производится пенополистирол?
Как производится пенополистирол?
Превращение вспенивающегося полистирола в пенополистирол осуществляется в три этапа: Предварительное вспенивание, Созревание/стабилизация и Формование Полистирол производится из стирола, получаемого в результате нефтепереработки. Для изготовления пенополистирола шарики полистирола пропитывают пенообразователем пентаном . Пенополистирольный гранулят предварительно вспенивают при температуре выше 90°С.
Эта температура вызывает испарение пенообразователя и, следовательно, раздувание термопластичного основного материала в 20-50 раз по сравнению с его первоначальным размером.
После этого гранулы хранятся в течение 6-12 часов, позволяя им достичь равновесия. Затем шарики передаются в форму для изготовления форм, подходящих для конкретного применения.
Производство листов/форм из пенополистирола
На заключительном этапе стабилизированные шарики формуются либо в виде больших блоков (процесс блочного формования), либо в нестандартных формах (процесс формованного формования).
Материал может быть модифицирован путем добавления добавок, таких как антипирен, для дальнейшего повышения огнестойкости пенополистирола.
Свойства и основные преимущества пенополистирола
Свойства и основные преимущества пенополистирола EPS — это легкий материал с хорошими изоляционными характеристиками, обладающий такими преимуществами, как:- Тепловые свойства (изоляция) — EPS имеет очень низкую теплопроводность благодаря своей закрытоячеистой структуре, состоящей на 98% из воздуха.
Этот воздух, захваченный в ячейках, является очень плохим проводником тепла и, следовательно, придает пене превосходные теплоизоляционные свойства. Теплопроводность пенополистирола плотностью 20 кг/м 3 составляет 0,035 – 0,037 Вт/(м·К) при 10 °С.
ASTM C578 Стандартные технические условия для теплоизоляции из жесткого ячеистого полистирола касаются физических свойств и эксплуатационных характеристик пенополистирола применительно к теплоизоляции в строительстве.
- Механическая прочность — Гибкое производство делает пенополистирол универсальным по прочности, которую можно регулировать в соответствии с конкретным применением. EPS с высокой прочностью на сжатие используется для тяжелых несущих конструкций, тогда как для образования пустот можно использовать EPS с более низкой прочностью на сжатие.
Как правило, прочностные характеристики увеличиваются с увеличением плотности, однако на амортизирующие характеристики упаковки из пенополистирола влияет геометрия формованной детали и, в меньшей степени, размер шариков и условия обработки, а также плотность.
- Размерная стабильность — EPS обеспечивает исключительную размерную стабильность, оставаясь практически неизменным в широком диапазоне факторов окружающей среды. Можно ожидать, что максимальное изменение размеров пенополистирола составит менее 2%, что соответствует стандарту ASTM Test Method D2126.
Плотность (фунтов на кубический фут) | Напряжение при сжатии 10 % (psi) | Прочность на изгиб (psi) | Прочность на растяжение (psi) | Прочность на сдвиг (psi) |
1.0 | 13 | 29 | 31 | 31 |
1,5 | 24 | 43 | 51 | 53 |
2,0 | 30 | 58 | 62 | 70 |
2,5 | 42 | 75 | 74 | 92 |
3,0 | 64 | 88 | 88 | 118 |
3.![]() | 67 | 105 | 98 | 140 |
4,0 | 80 | 125 | 108 | 175 |
Типичные свойства формованной упаковки из пенополистирола (температура испытания 70°F)
(Источник: EPS Industry Alliance)
- Электрические свойства — Диэлектрическая прочность пенополистирола составляет примерно 2 кВ/мм. Его диэлектрическая проницаемость, измеренная в диапазоне частот 100-400 МГц и при брутто-плотностях от 20-40 кг/м 3 , находится в пределах 1.02-1.04. Формованный пенополистирол можно обрабатывать антистатическими агентами, чтобы соответствовать спецификациям упаковки для электронной промышленности и военной техники.
- Водопоглощение — EPS не гигроскопичен. Даже при погружении в воду он поглощает лишь небольшое количество воды. Поскольку стенки ячеек водонепроницаемы, вода может проникнуть в пену только через крошечные каналы между слитыми шариками.
Посмотреть все марки пенополистирола с низким водопоглощением »
- Химическая стойкость – Вода и водные растворы солей и щелочей не действуют на пенополистирол.Однако EPS легко подвергается воздействию органических растворителей. Ознакомьтесь с марками пенополистирола с хорошей химической стойкостью »
- Устойчивость к атмосферным воздействиям и старению – EPS устойчив к старению. Однако воздействие прямых солнечных лучей (ультрафиолетового излучения) приводит к пожелтению поверхности, что сопровождается легким охрупчиванием верхнего слоя. Пожелтение не имеет значения для механической прочности изоляции из-за малой глубины проникновения.
- Огнестойкость – EPS легко воспламеняется.Модификация антипиренами значительно снижает воспламеняемость пены и распространение пламени.
Экструдированный полистирол против пенополистирола
Экструдированный полистирол против пенополистирола
XPS часто путают с EPS.
Пенополистирол (EPS) | Экструдированный полистирол (XPS) |
|
|
Также читайте: Экструзия пенопласта — основы и введение
Источник: Owens Corning
EPS — безопасность, экологичность и возможность вторичной переработки
EPS — безопасность, экологичность и возможность вторичной переработки
EPS Insulation состоит из органических элементов – углерода, водорода и кислорода – и не содержит хлорфторуглеродов (CFC) или гидрохлорфторуглеродов (HCFC).EPS пригоден для вторичной переработки на многих этапах своего жизненного цикла.
Пенополистирол на 100% пригоден для вторичной переработки и имеет идентификационный код пластиковой смолы 6.
Однако сбор пенополистирола может быть серьезной проблемой, поскольку продукт очень легкий. Переработчики полистирола создали систему сбора, при которой пенополистирол доставляется на короткие расстояния на предприятие, где материал подвергается дальнейшей обработке:
- Грануляция — пенополистирол добавляется в гранулятор, который измельчает материал на более мелкие кусочки.
- Смешивание – материал подается в блендер для тщательного смешивания с аналогичными гранулами.
- Экструзия – материал подается в экструдер, где расплавляется. Можно добавить цвет, а затем экструдированный материал превращается в новый продукт с добавленной стоимостью.
Материалы EPS можно перерабатывать и формовать для производства новых упаковочных продуктов или товаров длительного пользования
Несколько стран установили официальные программы по переработке пенополистирола по всему миру.
Преимущества устойчивости , связанные с EPS:
- Производство EPS не включает использование разрушающих озоновый слой CFC и HCFC
- При его производстве не образуются остаточные твердые отходы
- Способствует экономии энергии, так как является эффективным теплоизоляционным материалом, помогающим сократить выбросы CO 2
- EPS пригоден для вторичной переработки на многих этапах своего жизненного цикла
- EPS инертен и нетоксичен. Не выщелачивает никаких веществ в грунтовые воды
Посмотрите интересное видео о переработке пенополистирола!
Источник: Moore Recycling Associates
Найдите подходящий пенополистирол марки
Ознакомьтесь с широким ассортиментом марок пенополистирола, доступных сегодня на рынке, проанализируйте технические характеристики каждого продукта, получите техническую помощь или запросите образцы.
Прогресс 01.06.14 – 31.07.15 Результаты Воздействия Публикации
| Прогресс 01.06.14 по 31.05.15 Результаты Воздействия Публикации
|
Различия пенопластов: EPS, XPS и EPU
В настоящее время для создания изолированных бетонных форм используется по меньшей мере пять различных типов пенопластов.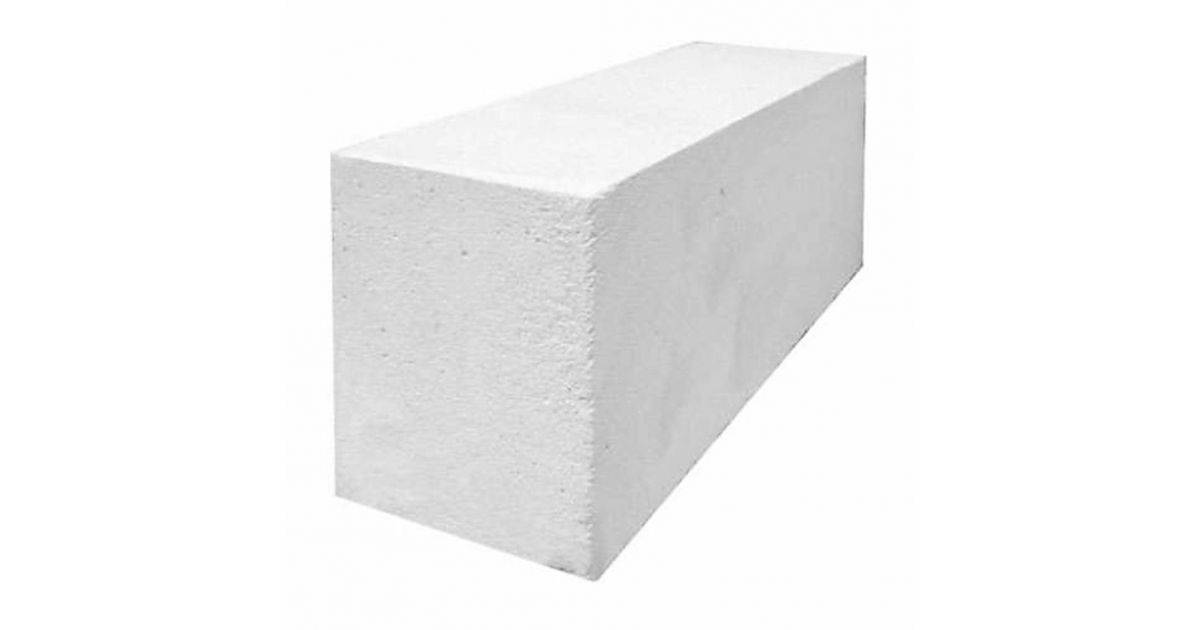



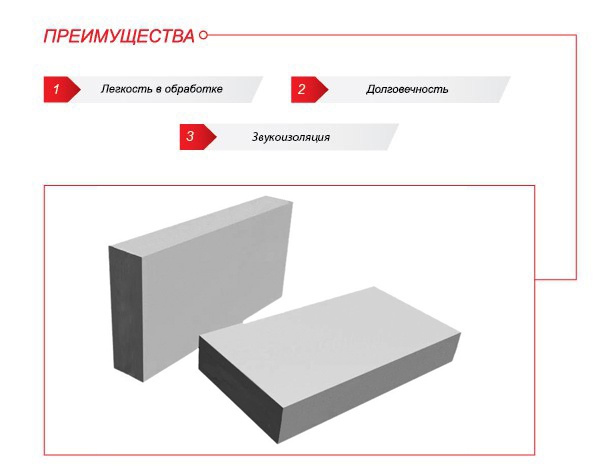
Новые ICF выкатываются из формовочной машины.
Затем формовщик впрыскивает пар высокой температуры и высокого давления, который еще больше расширяет шарики и полностью заполняет форму. Конечным результатом являются пеноблоки или панели.
Эта iForm от Reward является типичным примером стандартного блока ICF, сделанного из EPS.
Физические свойства пенополистирола варьируются в зависимости от типа используемого шарика, и его можно формовать с различной плотностью для удовлетворения конкретных требований ICF. Увеличение плотности пены также обеспечивает более высокое значение R на дюйм и повышенную прочность, но это дорого и требует больше материала.Вот почему, несмотря на то, что значения R могут варьироваться от 3,8 до 4,3 на дюйм толщины, почти все EPS, используемые в ICF, находятся в нижней части шкалы. Более 95% всех проданных ICF используют формованный пенополистирол.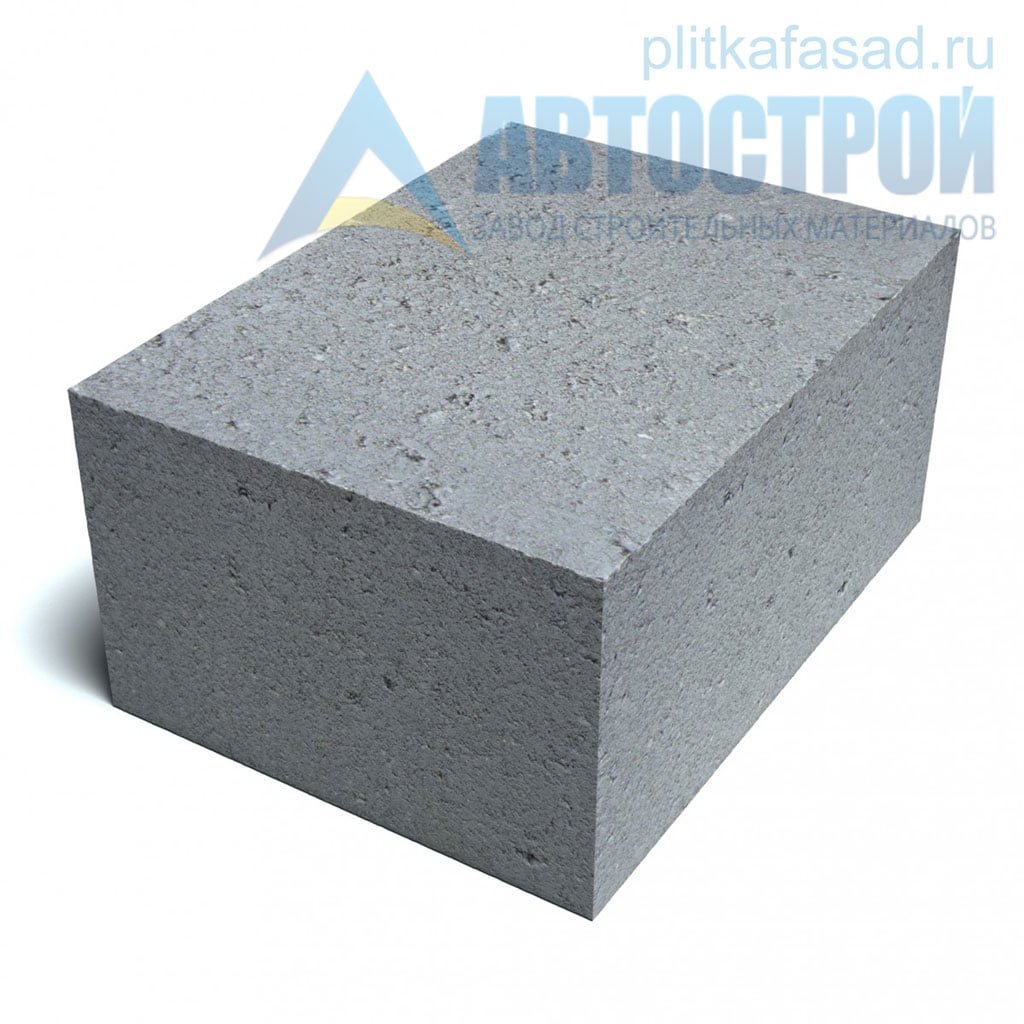

Эта формовочная матрица используется для формирования панелей XPS. Вспенивающаяся жидкость вытесняется через прямоугольное отверстие справа от машины.
XPS дороже, чем EPS — в некоторых случаях на 50% дороже — и поэтому встречается не так часто. Тем не менее, он более чем в два раза прочнее и обеспечивает примерно на 25% большую изоляцию при той же толщине (около R-5 на дюйм). Он также гораздо более постоянен по плотности и имеет более высокую прочность на сжатие, чем пенополистирол.Nudura, TF System, Lite-Form и ArmoPanel предлагают панели XPS в качестве опции. Неопор Новейшей пеной, используемой для ICF, является Neopor, тип пенополистирола, в котором используются запатентованные черные шарики от BASF. В настоящее время единственным ICF на рынке, изготовленным из Neopor, является серия Logix Platinum. В отличие от обычного пенополистирола, Неопор содержит порошкообразный графит, придающий пене неповторимый серый цвет. В отличие от красителей, о которых говорилось ранее, графит значительно влияет на характеристики пены.
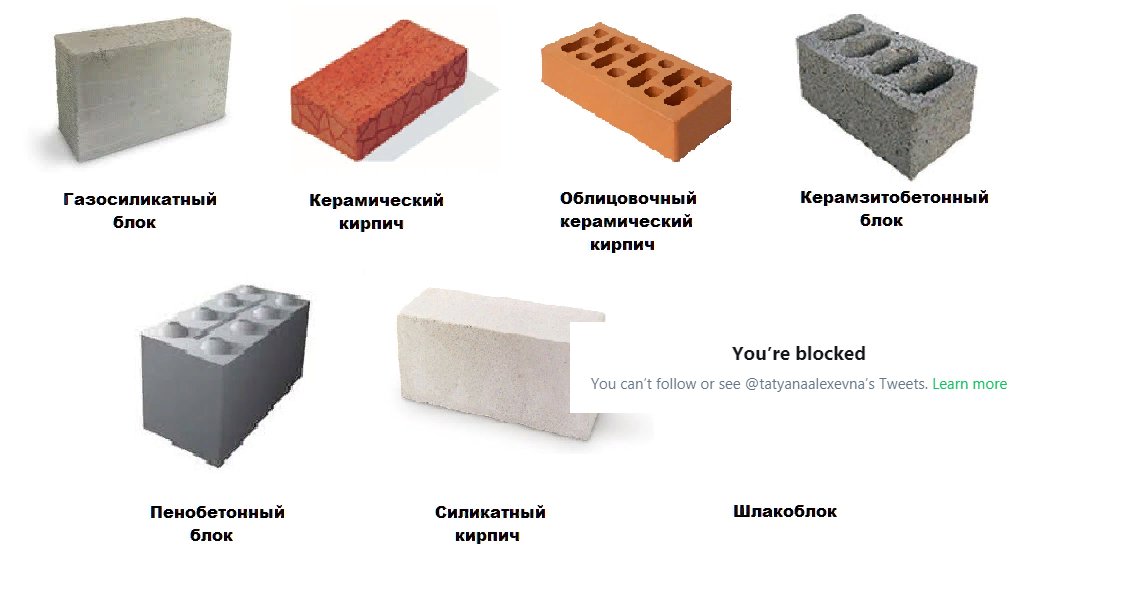

Толщина стен из пеноблоков для Урала. Стандартный размер пеноблока и расчет суммы на строительство дома
В современном мире Строительство дома или другой недвижимости – это дорогостоящий процесс, который доступен не каждому.Сегодня, чтобы значительно сократить расходы на него, применяют пеноблоки. Этот строительный материал становится все более популярным и востребованным благодаря ряду своих преимуществ.
Преимущества и особенности строительного материала
Пеноблоки имеют ряд преимуществ:
- Низкая цена по сравнению с другими строительными материалами, которые используются в строительстве. Это делает его экономичным.
- Может использоваться для строительства жилых домов, сельскохозяйственных объектов и других типов зданий.Есть только один нюанс, который следует учитывать – ограничение по высоте.
Она должна быть не более 12 метров.
- Обладает хорошими теплоизоляционными и звукоизоляционными свойствами. Зимой он обеспечит тепло в доме, а летом прохладу.
- Высокое качество.
- Стойки на любые погодные условия: дождь, снег, мороз или палящее солнце. Не дышит, не трескается и не впитывает влагу. Поэтому исключены случаи горения и гниения.
- Долгий срок службы.
Размеры пеноблока существенно отличаются от кирпича. Их гораздо больше. Благодаря этому можно сэкономить время и трудозатраты на возведение здания. Пористая структура дает возможность легко выполнять в доме любую работу, например, просверлить отверстие. Это также позволяет создать комфортный микроклимат в доме. Он приравнивается к тому, что создается в деревянных постройках.
Этапы производства
Изготовить данный строительный материал по такой схеме:
- Смешать воду и отработанную пену в соединительном центре на соответствующем оборудовании.
- Затем все помещают в бетоносмесительную машину и добавляют цемент, песок, которые растворяются в воде.
- Далее делаем пену. В течение пяти минут все перемешивается до получения однородной консистенции.
- Полученную смесь разлили по формам.
- Оставить для застывания.
- Снять с форм и оставить на сутки для закрепления пеноблочной конструкции.
Что такое пенобетонные блоки?
Пеноблоки имеют ряд особенностей и отличий, которые следует учитывать при их выборе.Итак, главные из них — класс и сила. Они напрямую зависят от плотности. Его показатель находится в разных пределах, и подобрать можно для каждого здания. Имеет значение и размер пеноблока.
Существует несколько видов пеноблоков, различающихся по плотности в зависимости от их назначения:
- для кладки внутренних стен;
- для наружных и несущих стен;
- для теплоизоляции.
То, что размер пеноблока в несколько раз превышает стандартный кирпич, делает его использование еще более выгодным.Таким образом, не только сокращается время, необходимое на строительную площадку, но и значительно улучшается внешний вид стен: минимум швов, стыков. Для склеивания потребуется меньше раствора.
Размеры пеноблока
Размеры пеноблоков производители предлагают выбирать исходя из того, какое здание строится, или предпочтений владельца. Это делается предварительный расчет. При этом учитывают нагрузку и характеристики строительного материала. Это позволит сделать правильный выбор.
Основными факторами, влияющими на него, являются ширина, длина и толщина. Последнее наиболее важно при создании теплоизоляционных свойств.
Совсем недавно размер пеноблока (стандартный) равнялся 200 х 200 х 400 мм. Таким образом, он был максимально приближен к обычному силикатному кирпичу. Но со временем производители предлагали разные пеноблоки. Стандарт впоследствии принял свою позицию. Теперь они ведут к прибыли и сбережениям. Тем не менее, бывают случаи, когда традиционные размеры становятся необходимыми.
Какой размер использовать для строительства жилого дома?
Сегодня стали более популярны и востребованы такие пеноблоки для строительства дома, как 600 х 300 х 200 мм. А масса одного 25 кг. Такие показатели придают ему качественные теплоизоляционные свойства, которые очень важны при строительстве домов.
Размеры пеноблоков для строительства дома рассчитываются заранее. Это позволяет четко определить необходимое количество и оптимизировать расход используемого материала.
Сколько стоят?
Со пеноблоки. Габариты и цена это две взаимообусловленные составляющие: чем толще и больше — тем дороже.
Сегодня производителям предлагается большой ассортимент Товара, что делает его доступным для всех слоев населения. Таким образом, вы можете выбрать стоимость, которая подходит для вас. Стоит учитывать только тип стен и виды пеноблоков, размеры которых потребуются. Для наружных стен самый выгодный и удобный – 600 х 300 х 200 мм.При необходимости снижения шумоизоляции значения длины увеличивают на 100 мм.
Размеры пеноблоков для перегородок усредненные, и необходимо проверять их для своих целей. Особую роль в их использовании сыграл профессионализм специалистов, которые будут выполнять работы. Так как они определяют толщину слоя крепежного материала.
Для типоразмеров устанавливается фиксированная цена:
- Для стен преимущественно она равна 2200 руб./куб.м. Отсюда получается, за одну вещь нужно будет заплатить около 80 рублей.
- Для перегородок — чуть дороже, 2300 руб. за 1 куб.м. м.
Как рассчитать необходимое количество
При определении и расчете количества стоит учесть главный момент: увеличение расчета стоимости на поправку, так как в некоторых случаях требуется подгонять и подгонять размер строительного материала. Это все обусловлено особенностями конструкции.Также будет процент поврежденного пеноблока. Этот показатель составит в среднем до 5%. Поэтому рекомендуется приобретать количество пеноблока с запасом. Примерно более 10%.
Для этого выполняются такие расчеты:
- Определяем сколько блоков потребуется в один ряд. Для этого периметр дома делится на длину блока.
- Затем вычисляет, сколько строк будет в блоке.
Высота планируемого здания разбивается на высоту или ширину блоков.
- Первое и второе значения умножаются друг на друга.
Виды пеноблоков, размеры которых известны заранее, позволяют произвести их расчет. Всего несколько простых действий – и получите точную цифру, определяющую количество необходимого стройматериала и какой в данном случае лучше использовать.
Как доставить пеноблоки?
Пеноблоки перевозить на автомобиле нельзя. Поэтому используется спец, на который их грузят, упаковывают на поддонах.Эти устройства можно продолжать использовать и вернуть деньги в торговую точку. В противном случае им придется заплатить определенную сумму.
Использование пеноблока наиболее выгодно и целесообразно. Он идеально подходит по своим качествам и цене для любой конструкции. Купить их несложно, так как в каждом городе есть большое количество компаний, которые занимаются этим вопросом.
Пенобетон получил широкое применение в строительстве, так как имеет ряд преимуществ всех основных строительных материалов, и в то же время лишен их недостатков, и при этом дешевле.
Общие сведения о пеноблоке
Основными компонентами для пенобетона являются: песок, цемент, пенообразователь и вода. Также допускается использование отвердителей, пластификаторов, волокон, что позволяет повысить прочность блока и другие его характеристики.
Пеноблоки марки
Чаще всего в строительстве используются строительные блоки — Д600 и Д800. Следует отметить, что D800 является конструкционной маркой и имеет низкую теплопроводность.D600 обладает хорошими теплоизоляционными структурными характеристиками.
Прочность D600 позволяет строить двухэтажные дома из бетонных перекрытий. Правда, между бетоном и перекрытием необходимо сделать армированный пояс для равномерного распределения нагрузки на блоки.
Совет: Использование этого материала также позволит сэкономить 30 процентов на отоплении.
В результате D600 является самой оптимальной маркой в строительстве. Поскольку размер стандартного пеноблока больше, чем, например, кирпича, то экономия в строительстве очевидна. Один блок способен заменить несколько силикатных кирпичей.
Пеноблоки марок ниже D600 не предназначены для кладки несущих стен, так как имеют меньшую плотность. Но, большое содержание пузырьков воздуха обеспечивает им хорошие теплоизоляционные свойства.
Применение пенобетона
В отличие от газобетона, этот материал имеет пористую структуру закрытого типа. За счет этого он превосходит по мощности планету своими теплозащитными и морозостойкими свойствами.Пенобетон можно использовать на стыках тепло-холод и в условиях повышенной влажности.
Расчет количества пеноблоков
Для расчета берутся следующие исходные данные:
- Толщина стен и перегородок;
- Высота и периметр и кладка;
- Количество и площадь отверстий.
Кроме того, есть еще один момент, который необходимо учитывать – это процент расщепления материала при транспортировке.Этот показатель зависит от ряда факторов, вплоть до состояния машины и дорог, но производители обычно имеют средние цифры.
И так, для расчета количества материала есть такая инструкция:
- В первую очередь нужно разбить все стены на группы по их толщине. Например, в первую группу войдут наружные стены, во вторую — внутренние несущие (если толщина отличается от наружных стен), а в третью — внутренние перегородки.
- Затем необходимо рассчитать общую длину стен в каждой из групп.
- Затем для каждой группы рассчитывается общая площадь дверей и окон.
- На четвертом этапе следует рассчитать объем кладки по каждой группе. Для этого умножьте высоту, длину и .
- Из полученного объема следует вычесть объем проемов в каждой группе.
- На последнем этапе необходимо разделить объем кладки каждой группы на объем соответствующего блока.
Разбиение на группы нужно делать по той причине, что размеры пеноблока Д600, который чаще всего используется для кладки, отличаются от блоков для перегородок. Обычно наружные стены выделяют из блоков 200х300х600 мм в два слоя по толщине, с кладкой по краю.
Внутренние несущие стены, возводимые обычно из блоков того же размера, но пластмассовых, т.е. высотой 200 мм. Для перегородок используется материал размером 100х300х600 мм. Соответственно объем стенового блока равен 0.036 м куб., а секционированный — 0,018 м куб.
К полученному материалу необходимо добавить запас в размере 3-5%. Кроме того, необходимо добавить процент сплита при доставке, если он неизвестен, то нужно взять примерную цифру 2-3 процента от суммы.
Совет!
Для уменьшения количества испорченных блоков при выгрузке необходимо производить ее вручную.
Не сбрасывайте приобретенный материал с помощью самосвала, так как более 30 процентов будут сломаны.
Пример расчета
В качестве примера возьмем проект одноэтажного дома 8х10 м с размерами внутренних перегородок и внутренней несущей стены. Дом включает в себя: холл, спальню, кухню, ванную комнату, туалет и прихожую.
Толщина наружной стены равна 40 см, внутренней несущей — 30 см, ширина перегородки — 10 см.
- Первая группа имеет периметр стен — 34,4 м, высоту стен — 3 м, площадь проемов, в которых шесть окон и одна наружная дверь — 12.9 квадратных метров. Соответственно объем кладки равен 36,12 куб.м.
- Внутренняя несущая стена Вторая группа имеет длину 7,2 м, два дверных проема общей площадью 3,2 кв.м. Объем кладки 5,52 кв.
- Третья группа содержит стены длиной 18 м, три дверных проема. Объем кладки 5,16 метра куб.
Размеры пеноблоков для строительства дома принимаются стандартные — 200х300х600 мм, а для возведения перегородок — 100х300х600 мм.Что касается первой и второй группы, то использовался один и тот же материал, объемы можно суммировать, в результате чего получилось 41,64 метра кубической кладки.
Исходя из объема одной единицы, потребуется 1157 и 286 септум-блоков. Если к этому количеству материала добавить 6 процентов на бой при транспортировке и отделке, то для постройки такого дома потребуется 1227 стеновых блоков и 304 перегородки.
Внимание!
Материал перегородки несколько дороже стены.
Это связано с большими затратами на их производство.
Обсуждение размеров
При выборе пенобетонных блоков стоит учитывать тот факт, что их размеры могут не соответствовать заявленным производителем. Иногда расхождение ширины, высоты и длины может составлять несколько миллиметров.
Чем больше разброс, тем больше клея уйдет при укладке. В некоторых случаях нельзя выполнять кладку на клей. При большой разнице в размерах производить кладку можно только на цемент. Чем толще шов, тем больше холода будет проникать в помещение, так как раствор обладает плохими теплоизоляционными свойствами.
Кроме того, при покупке материала проверьте его на прочность. Его можно сделать своими руками — попробуйте растереть между пальцами небольшой кусочек бруска в порошок. Если такое случается, значит, материал некачественный.
Выход
Пенобетон вполне оправдан в строительстве. Это один из немногих строительных материалов, размер которого можно заказать индивидуально. В этом случае все расходы, связанные с приобретением материала, можно просчитать заранее.
Видео в этой статье дополнит информацию по этой теме.
Пеноблоки — строительный материал, внешне напоминающий пористый искусственный алмаз. Производят их из цемента, песка и воды с добавлением специального пенообразователя. Производство этого материала регламентировано ГОСТ 21520-89 и ГОСТ 25485-89. Однако в наши дни эти нормы не являются обязательными и не все производители их придерживаются.
По способу изготовления пеноблоки можно разделить на:
- Кассета.Раствор заливается в формы-ячейки необходимых размеров, в которых материал твердеет около 10 часов;
- Прошлая автоматическая платформа. Это модернизированный вариант кассетного производства — формы располагаются в специальном станке. В формы заливается раствор и через 14 часов выходит готовый пеноблок на поддон;
- Нарезано из массива.
Смесь компонентов заливается в большую форму, объем которой может достигать 3 м 3 , где происходит застывание материала в течение 15 часов, после чего пенобетонная плита разрезается на блоки нужных размеров.
Независимо от способа производства пенобетонные блоки обладают высокими теплоизоляционными свойствами, незначительным весом и необходимой прочностью.
По сфере применения пеноблоки делятся на теплоизоляционные (используются в качестве теплоизоляционного слоя), конструкционные (наиболее популярны в строительстве, используются как стеновой материал) и конструкционно-теплоизоляционные (используются достаточно редко для возведения перегородок и несущие стены).
Качественные блоки из пенобетона обладают правильной геометрией, что позволяет значительно экономить кладочный раствор.В роли последнего выступает специальный клеевой состав. Его использование позволяет не только сохранить теплосберегающие свойства строительного материала, но и минимизировать расстояние между блоками.
Какие бывают размеры пеноблоков
В зависимости от области применения материал подразделяется на:
- Стена . Размеры пенобетонных блоков 200х400х600 мм (толщина-высота-длина).При этом вес одной единицы (в зависимости от прочности) может варьироваться от 11,7 кг (Д300) до 47,5 кг (Д1200).
- Перегородка пенобетон. Размер блоков 100х300х600 мм, вес материала материала прочности Д 300 5,8 кг, по мере увеличения прочности вес увеличивается и для марки Д1200 составляет 23,8 кг
Толщина пеноблоков — в пределах 500-400 мм.В стандартном исполнении размеры стройматериалов могут быть — 200х300х500 мм, 200х300х600 мм, 300х400х600 мм, 200х400х600 мм и т.д.
Используя в производстве технологию резки, можно получать пеноблоки разных размеров, однако согласно требованиям ГОСТ 21520-89 длина одного блока не должна превышать 600 мм. 1 Такой элемент конструкции из пенобетона размерами 200х300х600мм, в кладке может заменить в кладке 17 рядовых или 15 силикатных кирпичей.
При покупке пенобетонных блоков главным в их размерах должна быть геометрическая точность и отсутствие разброса.Проверить их можно с помощью уровня и мерной рулетки. Покупайте стройматериалы у продавцов, которые гарантируют соответствие размеров пенобетона. Это позволит в будущем сэкономить на утеплении дома.
Расчет количества пеноблоков для строительства дома
- Перед тем, как приступить к расчету, следует уточнить – результаты подсчета напрямую зависят от толщины стен дома, например выбранного пенобетона, а также количества внутриквартирных перегородок.Попробуем произвести примерный подсчет количества блоков при условии, что размеры каждого из них 200х400х600 мм, а длина здания 7 м, высота стен 3 м, ширина дома 6 м.
- Периметр ограничения рассчитывается следующим образом: 7 + 7 + 6 + 6 = 26 м.
- Полученное значение нужно разделить на пеноблок 0,6 м, в результате чего получаем 43,3 (количество штук в ряду по периметру дома).
- Затем подсчитайте количество строк. Делим высоту (3м) на 0,2 м (высота блока) = 15.
- Умножаем 15 (количество рядов) на 43,3 (количество блоков в одном ряду) и получаем 649,5
Подведем итоги — на постройку коробки дома нам понадобится 650 блоков пенобетона. Дополнительно делаем расчет количества материала для возведения внутренних перегородок, после чего прибавляем к 650, а также определяем площадь окон и дверей и полученное число приводим к этому количеству.
С точки зрения экономичности при использовании пенобетонных блоков Вы сможете сэкономить инструменты практически в два раза по сравнению со строительством дома из кирпича или дерева.
Главная » Стены » Толщина стен из пеноблоков для Урала. Стандартный размер пеноблока и расчет суммы на строительство дома
Используем пеноблоки в строительстве. Отзывы и характеристики материала
Пеноблок, относящийся к классу ячеистых бетонов, является отличным материалом для строительства качественного и недорогого дома. Учтите, что пенобетон по многим своим свойствам во много раз превосходит традиционно используемый в строительстве кирпич. Скорость возведения дома из такого материала просто поражает. Во многом это связано с тем, что размер даже самого маленького блока во много раз превышает размер стандартного кирпича. Словом, пеноблоки (отзывы говорят сами за себя) — отличный материал для строительства.
Вы сможете значительно сэкономить, если будете самостоятельно привозить строительный материал от производителя на свою строительную площадку.Очень важно убедиться, что пластиковая упаковка защищает агрегаты от влажного воздуха в идеальном состоянии. Даже когда строительство из пеноблоков уже ведется, хранить материал следует исключительно под навесами.
Преимущество ленточного фундамента еще и в том, что в таких постройках можно организовать цокольный этаж. Тот же цоколь из того же пеноблока. В результате можно не только значительно ускорить ход строительства, но и избавиться от необходимости дополнительного утепления цоколя.Конечно, перед началом возведения следует тщательно проверить уровень фундамента, так как найденные огрехи в дальнейшем исправить будет намного сложнее.