Композиционный цемент: НТБ МАЛИ :: Ошибка 404
СВОЙСТВА КОМПОЗИЦИОННЫХ ПОРТЛАНДЦЕМЕНТОВ CEM II/A, B-M
ЦЕМЕНТ
Гергичны З. проф., д. т. н., Силезский технологический университет, Гливице; Górażdże Cement S. A, Хорула, Польша
Alitinform №1 (33) 2014 г. 20-25 стр.
Аннотация
Минеральные добавки — это заслужившие доверие базовые компоненты обычных цементов, которые соответствуют стандарту EN197–1 [1] и присутствуют в составе цементов CEM II — CEM V. Известняк (LLL), доменный гранулированный шлак (S), кремнистая зола-унос (V), известковая зола-унос (W), а также природные и искусственные пуццоланы (P, Q) являются наиболее часто используемыми добавками к цементу.
Ключевые слова:
композиционный портландцемент; шлакопортландцемент; гранулированный доменный шлак; известняк; зола-унос; минеральные добавки
Продолжение читайте в журнале
Для этого вам нужно оформить один из вариантов подписки и можете читать все статьи без ограничений и в любом удобном для вас формате.
Оформить подписку
Цемент временный композиционный светоотверждаемый Tempolat-LC 5 гр., цена 89 грн
Назначение
Цемент временный композиционный светоотверждаемый Tempolat-LC предназначен к применению в терапевтической стоматологии для временного пломбирования и покрытия лекарственного препарата при лечении кариеса и не кариозных поражений зубных тканей. Использование Tempolat-LC позволяет обеспечить высокую стойкость временной пломбы в течение всего срока ее применения и сократить время проведения лечебной процедуры.
Состав и свойства
Цемент Tempolat-LC представляет собой композиционный материал, отвердевающий при воздействии света с длиной волны 400 ― 500 нм. Глубина отверждения цемента при засветке в течение 40 с галогеновой лампой мощностью 75 Вт составляет более 3 мм.
Паста цемента окрашена в универсальный светло-кремовый цвет (примерно В3 по шкале VitaTM Classic), имеет высокую пластичность и формуемость, не липнет к инструменту и хорошо фиксируется в пломбируемой полости.
Цемент приготовлен на основе олигоэфиракрилатного связующего с повышенной биосовместимостью. Содержание неорганического наполнителя в цементе составляет 77 масс.%. Цемент обладает хорошей водостойкостью и не подвержен дезинтеграции.
Способ применения
Полость препарируют, промывают и проводят запланированную лечебную процедуру (купирование воспалительного процесса, депульпирование, пломбирование корневого канала и т.п.). При этом не следует применять лечебные средства, содержащие резорцин, эвгенол, гваякол, пентахлофенол, метилсалицилат и препараты таннина. В случае применения водного или спиртового раствора лечебного препарата после внесения его в полость делают подсушку сжатым воздухом 15 с.

Рекомендации
Упомянутые в тексте дополнительные и вспомогательные средства (выделенные шрифтом) выпускаются Лабораторией «Стома-технология» и могут быть приобретены в дополнение к комплекту цемента Tempolat-LC.
Условия хранения и маркировка
Условия хранения
Tempolat-LC в упакованном виде должен храниться в закрытых прохладных помещениях, при температуре не выше +25˚С, защищенных от воздействия атмосферных осадков и прямых солнечных лучей. Для увеличения срока годности при длительном хранении рекомендуется использовать холодильник с температурой +5˚С.
Упаковка: шприц 5 г пасты
КОМПОЗИЦИОННЫЕ ВЯЖУЩИЕ ДЛЯ ОТДЕЛОЧНЫХ СОСТАВОВ
Белгородская область является одним из регионов-лидеров по строительству жилья, особенно частных домовладений. Этим обусловлен высокий спрос на отделочные материалы, в частности су-хие штукатурные и шпаклёвочные смеси, выпускаемые преимущественно на основе гипса. Однако местные производители подобных продуктов едва ли могут конкурировать с привозной продукцией за счёт более низкой цены. Причиной этого является отсутствие в Белгородской области, как во многих других регионах России, месторождений гипса и, как следствие, его достаточно высокая стоимость превышающая аналогичный показатель у портландцемента. Подобная ситуация делает актуальной разработку на основе цемента отделочных смесей, по потребительским качествам соответствующих гипсовым.

Елистраткин М.Ю.
Кандидат технических наук, ООО «Исследователь», Россия
Минакова А.В.
Джамиль А.Н.
Белгородский государственный технологический университет им. В.Г. Шухова, Россия
Куковицкий В.В.
Белгородский государственный технологический университет им. В.Г. Шухова, Россия
Эльян Исса Жамал Исса
Кандидат технических наук, доцент, Амман Арабский университет, Иордания
1. Семенов А.А. Российский рынок гипса: текущее состояние и перспективы развития // ALITinform: Цемент. Бетон. Сухие смеси. 2009. №1. С. 67 – 73.
3. Баженов Ю.М. Пути развития строительного материаловедения: новые бетоны // Технологии бетонов. 2012. №3-4 (68-69). С. 39 – 42.
4. Дребезгова М.Ю., Чернышева Н.В., Шаталова С.В. Композиционное гипсовое вяжущеес многокомпонентными минеральными добавками разного генезиса // Вестник Белгородского государственного технологического университета им. В.Г. Шухова. 2017. №10. С. 27 – 34.
5. Муртазаев С.А.Ю. Саламанова М. Ш., Сайдумов М.С., Аласханов, А.Х. Высокопрочные бетоны на основе многокомпонентных вяжущих и фракционированных заполнителей из отходов переработки горных пород // Экология и промышленность России. 2018. Т. 22. №6. С. 49 – 53.
6. Елистраткин М.Ю., Лесовик В.С., Когут Е.В., Куприна А.

7. Куприна А.А., Лесовик В.С., Елистраткин М.Ю., Гинзбург А.В. Композиционные вяжущие для эффективных строительных растворов. В сборнике: Эффективные строительные композиты Научно-практическая конференция к 85-летию заслуженного деятеля науки РФ, академика РААСН, доктора технических наук Баженова Юрия Михайловича. Белгородский государственный технологический университет им. В.Г. Шухова. 2015. С. 322 – 331.
8. Shi C., Jiménez A. F., Palomo A. New cements for the 21st century: the pursuit of an alternative to Portland cement //Cement and concrete research. 2011. Т. 41. №7. С. 750 – 763.
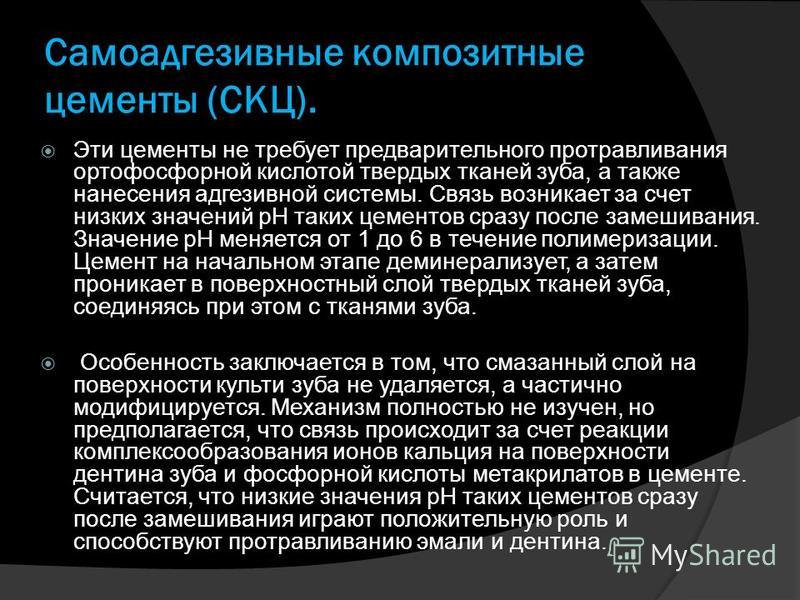
9. Елистраткин М.Ю., Минаков С.В. К вопросу выбора компонентов композиционных вяжущих. В сборнике: Современные строительные материалы, технологии и конструкции: Материалы Международной научно-практической конференции, посвященной 95-летию ФГБОУ ВПО «ГГНТУ им. акад. М.Д. Миллионщикова». Федеральное государственное бюджетное образовательное учреждение высшего профессионального образования «Грозненский государственный нефтяной технический университет имени академика М.Д. Миллионщикова» (ФГБОУ ВПО «ГГНТУ»), г. Грозный. 2015. С. 365 – 370.
10. Агеева М.С., Алфимова Н.И. Эффективные композиционные вяжущие на основе техногенного сырья: Монография. 2015.
11. Федюк Р.С. Свойства композиционных вяжущих на основе техногенных отходов Дальнего Востока // Вестник гражданских инженеров. 2016. №2. С. 132 – 136.
12. Batayneh M., Marie I., Asi I. Use of selected waste materials in concrete mixes // Waste management. 2007. Т. 27. №12. С. 1870 – 1876.
13. Neto A.
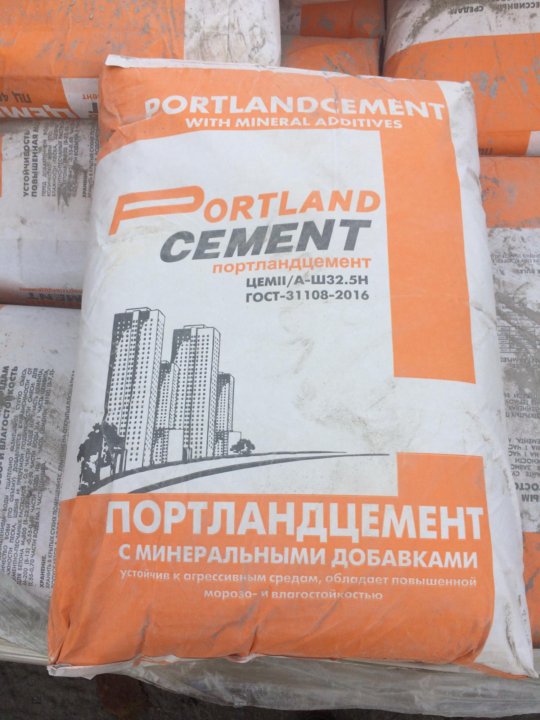
14. Толстой А.Д., Лесовик В.С., Милькина А.С. Особенности структуры бетонов нового поколения с применением техногенных материалов // Научный рецензируемый журнал «Вестник СибАДИ». 2018. №15 (4). С. 588 – 595.
15. Shui Z. et al. Rehydration reactivity of recycled mortar from concrete waste experienced to thermal treatment // Construction and Building materials. 2008. Т. 22. №8. С. 1723 – 1729.
16. Козлова В.К., Шкробко Е.В., Малова, Е.Ю., Афаньков А.Н., & Коньшин В.В. Состояние и перспективы развития производства многокомпонентных малоклинкерных вяжущих веществ // Ползуновский вестник. 2014. №1. С. 72 – 75.
17. Marinković S. et al. Comparative environmental assessment of natural and recycled aggregate concrete // Waste Management. 2010.
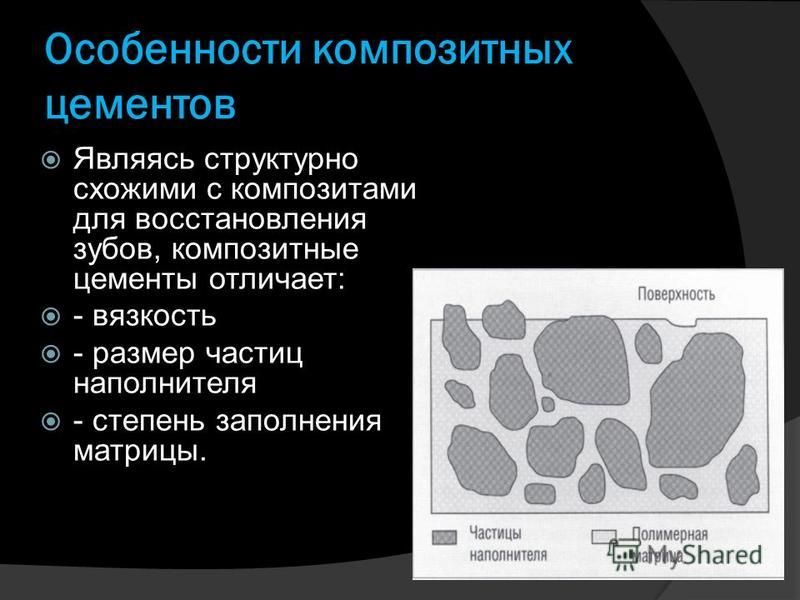
Елистраткин М.Ю., Минакова А.В., Джамиль А.Н., Куковицкий В.В., Эльян Исса Жамал Исса Композиционные вяжущие для отделочных составов // Строительные материалы и изделия. 2018. Том 1. №2. С. 37 – 44. https://doi.org/10.34031/2618-7183-2018-1-2-37-44
Проектирование предприятия по производству композиционного цемента
МИНИСТЕРСТВО ОБРАЗОВАНИЯ И НАУКИ РОССИЙСКОЙ ФЕДЕРАЦИИ
Федеральное государственное бюджетное образовательное учреждение высшего
образования
«ТЮМЕНСКИЙ ИНДУСТРИАЛЬНЫЙ УНИВЕРСИТЕТ»
Кафедра строительных материалов
[pic 1]
Курсовой проект по теме «Проектирование предприятия по производству композиционного цемента»
Тюмень
2016
Введение.огический каолин диатомит[pic 2]
В настоящее время цементная промышленность является одной из ведущих комплексно-механизированных отраслей тяжёлой индустрии. Гигантские темпы строительства в нашей стране обусловили резкий рост производства цемента. Расширяется ассортимент, выпускается целый ряд специальных цементов для различных областей строительства. Высокий технический уровень большинства предприятий цементной промышленности, механизации и автоматизации процессов производства, повышение качества цемента требуют от работников цементной промышленности для успешной работы глубоких и разносторонних знаний.
Классификация цементов и их характеристики прописаны в ГОСТ 31108-2003 «Цементы общестроительные. Технические условия».
Целью курсового проекта является приобретение навыков в правильном подборе компонентов при расчёте сырьевой шихты, при составлении материального баланса цехов и завода по производству цемента, а также при выборе основного технологического оборудования цементного завода.
Номенклатура выпускаемой продукции[pic 3]
1.1. Номенклатура.
На данном предприятии будет выпускаться композиционный цемент марки М500
Цемент производится в соответствии с ГОСТ 31108-2003 «Цементы общестроительные».
1.2 По содержанию портландцементного клинкера и добавок цементы типов ЦЕМ II — ЦЕМ V подразделяют на подтипы А и В.
1.3 По прочности на сжатие в возрасте 28 сут. цементы подразделяют на классы: 22,5; 32,5; 42,5; 52,5.
1.4 По прочности на сжатие в возрасте 2 (7) сут. (скорости твердения) каждый класс цементов, кроме класса 22,5, подразделяют на два подкласса: Н (нормальнотвердеющий) и Б (быстротвердеющий)
2. Характеристика сырьевых компонентов[pic 4]
Известняк.
Средняя плотность известняков достигает 2400-2700 кг/м3. влажность 2-6%. Известняк содержит до 90% и более углекислого кальция и большие количества кварцевого песка, глинистых минералов и др. химический состав известняка характеризуется значительным содержанием оксида кальция, до 50% и более, и [pic 5] ,до 40% и более. Также известняк содержит небольшие количества кремнезема, глинозема и др. Содержание МgО более 3-3,5% и серного ангидрита более 1-1,3 % недопустимо.
При разработке технологической схемы производства цемента, прежде всего учитывают химический состав, физические свойства и влажность карбоновых пород.
Глина.
Глины -тонкодисперсные осадочные горные породы, легко дают суспензии при смешивании с водой. Глины различаются по минеральному и гранулометрическому составам. Часто содержат значительное количество включений в виде песка и гравия, что вызывает необходимость предварительного обогащения глин.
По минеральному составу глины характеризуются преимущественным содержанием водных алюмосиликатов и кварцевого песка.
Легкоплавкие глины состоят в основном из кремнезема (70-80%), глинозема (3-10%), оксида железа (3-6%) и небольшого количества карбонатов кальция и магния. Иногда содержание оксида кальция может достигать 10-25%, а оксидов магния 3-5%. Также в глинах могут присутствовать соединения, содержащие [pic 6]включения веществ с этими оксидами, а также MgО нежелательны и их количество должно сводиться к минимуму.
Влажность глин 15-25%. Средняя плотность комовой глины 1800-2000 кг/м. [1][pic 7]
COMPOSITE WEIGHTED GROUTING MORTARS OVCHINNIKOV V. Показана эффективность применения в качестве утяжеляющей добавки в портландцементных смесях типа ЦТТС баритового минерала. Приведены физико-механические свойства сформированного на их основе камня, при температуре 120 оС и давлении 40 Мпа окружающей среды. Предложен термостойкий состав на основе цементошлаковой композиции, представлены физико-механические свойства раствора и сформированного на их основе камня. The article shows the effectiveness of the use of barite mineral as a weighting additive in Portland cement mixtures of the CTTC type. The physicomechanical properties of the stone formed on their basis are presented at a temperature of 120 ° C and a pressure of 40 MPa of the environment. Если вас интересует полный текст статьи, Вы можете заказать ее в издательстве. 1. Данюшевский В.С., Алиев Р.М., Толстых И.Ф. Справочное руководство по тампонажным материалам. М.: Недра, 1987. 372 с. 1. Danyushevskiy V.S., Aliyev R.M., Tolstykh I.F. Spravochnoye rukovodstvo po tamponazhnym materialam [Reference guide for cementing materials]. Moscow, Nedra Publ., 1987, 372 p. (In Russian). Комментарии посетителей сайта | Авторизация Овчинников В. д.т.н., профессор, заведующий кафедрой «Бурение нефтяных и газовых скважин» Тюменский государственный нефтегазовый университет Мелехов А.В. аспирант Тюменский индустриальный университет Овчинников П.В. д.т.н., профессор Российский государственный геологоразведочный университет Рожкова О.В. аспирант кафедры «Бурение нефтяных и газовых скважин» Тюменский государственный нефтегазовый университет (ТюмГНГУ) Ключевые слова: тампонажный раствор, барит, плотность, физико-механические свойства, цемент, пласт, давление, буровой раствор Keywords: cement slurry, barite, density, physical and mechanical properties, cement, layer, pressure, drilling mud Просмотров статьи: 1972 |
Subject area | English | Russian |
Makarov.![]() | bismaleimide resin matrix for composites | бис-малеимидное связующее для композиций |
nano | boron-reinforced resin composite | боропластик |
nano | carbon-fiber/epoxide resin composite | КМ на основе матриц из эпоксидной смолы, армированной волокнами углерода |
nano | carbon-fiber/epoxide resin composite | графитопластик |
nano | carbon-fiber/epoxide resin composite | графитоэпоксидный КМ |
tech. | composite resin | композитный пластик (MichaelBurov) |
dentist. | composite resin | гелекомпозит (MichaelBurov) |
dentist. | composite resin | светокомпозит (MichaelBurov) |
dentist.![]() | composite resin | фотополимер (MichaelBurov) |
dentist. | composite resin | фотокомпозит (MichaelBurov) |
dentist. | composite resin | гелиокомпозит (MichaelBurov) |
tech. | composite resin | композиционный пластик (MichaelBurov) |
tech. | composite resin | композит (MichaelBurov) |
dentist. | composite resin | гелеокомпозит (MichaelBurov) |
dentist. | composite resin | композиционная смола (igisheva) |
dentist. | composite resin | пломба-гелиокомпозит (MichaelBurov) |
dentist.![]() | composite resin | пластиковая пломба (MichaelBurov) |
dentist. | composite resin | композитная смола (igisheva) |
dentist. | composite resin | композитная пластмасса (igisheva) |
med. | composite resin | композиционная пластмасса (зубопротезная) |
dentist. | composite resin cement | адгезивный композитный цемент (MichaelBurov) |
dentist. | composite resin cement | композит (MichaelBurov) |
dentist. | composite resin cement | полимерцемент (MichaelBurov) |
dentist. | composite resin cement | композитный цемент (MichaelBurov) |
med.![]() | composite restoration resin | композиционная пломбировочная смола |
dentist. | dental composite resin | пластиковая пломба (MichaelBurov) |
dentist. | dental composite resin | гелекомпозит (MichaelBurov) |
dentist. | dental composite resin | гелеокомпозит (MichaelBurov) |
dentist. | dental composite resin | светокомпозит (MichaelBurov) |
dentist. | dental composite resin | композиционная пластмасса (MichaelBurov) |
dentist. | dental composite resin | пломба-гелиокомпозит (MichaelBurov) |
dentist. | dental composite resin | фотополимер (MichaelBurov) |
dentist.![]() | dental composite resin | фотокомпозит (MichaelBurov) |
dentist. | dental composite resin | гелиокомпозит (MichaelBurov) |
dentist. | dual-cure composite resin cement | адгезивный композитный цемент двойного отверждения (MichaelBurov) |
dentist. | dual cure composite resin cement | композитный цемент двойного отверждения (MichaelBurov) |
dentist. | dual-cure composite resin cement | композит двойного отверждения (MichaelBurov) |
dentist. | dual cure composite resin cement | композит двойного отверждения (MichaelBurov) |
dentist. | dual cure composite resin cement | адгезивный композитный цемент двойного отверждения (MichaelBurov) |
dentist.![]() | dual-cure composite resin cement | композитный цемент двойного отверждения (MichaelBurov) |
dentist. | dual-polymerizing fluoride-containing composite resin | фторсодержащий композит двойного отверждения (olga don) |
polym. | glass fiber-reinforced phenolic resin composite | фенолоформальдегидный стекловолокнит |
polym. | glass fiber-reinforced phenolic resin composite | феностекловолокнит |
polym. | glass fiber-reinforced phenolic resin composite | стекловолокнит на основе фенолоформальдегидной смолы |
fire. | glass-resin composite | стеклопласт (resin-glass composite) |
tech. | graphite fiber-reinforced epoxy resin matrix composite | композит на основе усиленной графитовыми нитями эпоксидной смолы |
nano | graphite-polyimide resin composite | полиимидный графитопластик |
nano | graphite-polyimide resin composite | углепластик на полиимидном связующем |
nano | graphite resin composite | графитопластик |
med.![]() | light-cured composite resin | композиционная пластмасса, полимеризованная светом |
nano | polyimide resin-based composite | полиимидный углепластик |
nano | resin-bonded composite | КМ со связующим на основе смолы |
dentist. | resin composite | полимерный композит (А. Гордеев) |
chem. | resin composite | композит на смоляной матрице (Svetlana17) |
chem. | resin composite | смоляная матрица, образующая композит (Svetlana17) |
tech. | resin composite | композит со смоляной матрицей (bonly) |
fire. | resin-fabric composite | текстолит |
fire.![]() | resin-glass composite | стеклопласт (resin-glass composite) |
tech. | resin matrix composite | композиционный материал со смоляной матрицей |
tech. | resin-matrix composite | композиционный материал со смоляной матрицей |
polym. | Seeman Composite Resin Infusion Moulding Process | Метод Зеемана литьевого формования композитных смол (2GW) |
tech. | Seemann Composites Resin Infusion Molding Process | формование композитов методом Зеемана инфузии смолы (bonly) |
tech. | Seemann Composites Resin Infusion Molding Process | SCRIMP-метод (bonly) |
dentist. | self-adhesive composite resin cement | обычный адгезивный композитный цемент (MichaelBurov) |
dentist.![]() | self-adhesive composite resin cement | самоклеющийся композит (MichaelBurov) |
dentist. | self-adhesive composite resin cement | самоклеющийся композитный цемент (MichaelBurov) |
dentist. | self-adhesive composite resin cement | самоклеящийся композитный цемент (MichaelBurov) |
dentist. | self-adhesive composite resin cement | обычный самоклеящийся композитный цемент (MichaelBurov) |
dentist. | self-adhesive composite resin cement | самоклеящийся композит (MichaelBurov) |
fire. | thermally stable resin composite | термически устойчивый композиционный пластик (материал на основе смолы) |
Фамилия, имя, отчество, учёная степень, звание, должность. Полное и сокращённое наименование организации, адрес организации. | Ермилова Е.Ю. – ведущий специалист по проектированию ВК
E-mail:
Этот e-mail адрес защищен от спам-ботов, для его просмотра у Вас должен быть включен Javascript
ООО «Инженерный Центр Высотные Специальные Технологии»
Адрес организации: 420088, Россия, г. Казань, ул. Журналистов, д. 54
Камалова З.А. – кандидат технических наук, доцент
E-mail:
Этот e-mail адрес защищен от спам-ботов, для его просмотра у Вас должен быть включен Javascript
Рахимов Р.З. – доктор технических наук, профессор
E-mail:
Этот e-mail адрес защищен от спам-ботов, для его просмотра у Вас должен быть включен Javascript
Щелконогова Я.В. – студент
E-mail:
Этот e-mail адрес защищен от спам-ботов, для его просмотра у Вас должен быть включен Javascript
Казанский государственный архитектурно-строительный университет
Адрес организации: 420043, Россия, г.![]() |
Название статьи. | Определение состава продуктов гидратации композиционного цементного камня с комплексной добавкой термоактивированной полиминеральной глины и известняка |
Аннотация. | Постановка задачи. Цель работы – определение состава продуктов гидратации в возрасте 28 суток композиционного цементного камня с комплексной добавкой на основе термоактивированной полиминеральной глины и карбонатной породы с содержанием кальцита 99 %.
Результаты. С использованием рентгенофазового анализа и дифференциально-сканирующей калориметрии определен состав продуктов гидратации композиционного цементного камня в возрасте 28 суток твердения с комплексной добавкой термоактивированной глины и известняка. С помощью результатов РФА и ДСК показано, что использование 20 % комплексной добавки термоактивированной полиминеральной глины и известняка в композиционном портландцементе позволяет существенно снизить содержание образовавшегося портландита, увеличить количество новообразований в виде низкоосновных гидросиликатов и гидрокарбосиликатов кальция, находящихся в аморфной фазе, что приводит к увеличению прочностных характеристик.![]() |
Ключевые слова. | композиционный цемент, цементный камень, комплексная добавка, известняк, термоактивированная глина, РФА, ДСК. |
First name, Middle name, Last name, Scientific degree, Scientific rank, Current position. Full and brief name of the organization, The organization address. | Ermilova E.Yu. – leading specialist in designing WS
E-mail:
Этот e-mail адрес защищен от спам-ботов, для его просмотра у Вас должен быть включен Javascript
OOO «Engineering Center of High-Rise Special Technology»
The organization address: 420088, Russia, Kazan, Journalists st., 54
Kamalova Z.![]() |
Title of the article | Hydration products composition of blended cement stone with a complex additive calcined polymineral clay and limestone |
Abstract. | Problem statement. The aim of this – the determination of the composition of hydration products at 28 days blended cement stone with a complex additive based on calcined polymineral clay and carbonate rock with calcite content of 99 %.![]() |
Keywords.![]() | blended cement, cement stone, complex additive, limestone, calcined clays, XRD, DSC. |
Для цитирования: | Ермилова Е.Ю., Камалова З.А., Рахимов Р.З., Щелконогова Я.В. Определение состава продуктов гидратации композиционного цементного камня с комплексной добавкой термоактивированной полиминеральной глины и известняка // Известия КГАСУ. 2017. №4(42) С.289-295. |
For citations: | Ermilova E.Yu., Kamalova Z.A., Rakhimov R.Z., Shchelkonogova Ya.V. Hydration products composition of blended cement stone with a complex additive calcined polymineral clay and limestone // Izvestiya KGASU. 2017. №4(42) P.289-295. |
Composite Cement – обзор
2.5.1 Минеральные добавки
Как уже указывалось в разделе 2.2, матрицы TRC должны иметь значительно улучшенный баланс энергии и выделения CO 2 . Очевидным вариантом является замена части портландцементного клинкера латентно-гидравлическими и пуццолановыми материалами. Это можно сделать путем производства композиционных цементов, содержащих эти материалы, или путем смешивания этих материалов в качестве минеральных добавок с бетоном во время производства. Как правило, в отличие от железобетона, снижение значения pH матрицы из-за пуццолановых реакций не вызывает беспокойства, как раз наоборот: низкая щелочность матрицы в большинстве случаев очень благоприятна с точки зрения долговечности неметаллической арматуры. .Следовательно, для матриц TRC можно использовать гораздо более высокое содержание пуццолана по сравнению с бетоном, используемым для производства железобетонных элементов. Ограничивающим фактором здесь является по большей части долговечность самой матрицы, особенно в отношении ее морозостойкости. В следующих параграфах кратко рассматриваются и оцениваются различные пуццолановые материалы с точки зрения их фактической или возможной роли в матрицах для TRC.
Microsilica (SF) представляет собой искусственный высокореактивный пуццолан, имеющий очень маленькие сферические частицы со средним размером около 100 нм (Taylor, 1997). При использовании в системах на основе цемента увеличивает плотность упаковки (эффект микронаполнителя) матрицы. Кроме того, он вступает в реакцию с гидроксидом кальция, одним из основных продуктов гидратации цемента, что приводит к дальнейшему уплотнению матрицы и повышению прочности, причем в раннем возрасте, а также к значительному увеличению долговечности, особенно по отношению к химическому воздействию. Последняя особенность может быть прослежена прежде всего к стабильности продуктов пуццолановой реакции по сравнению со стабильностью гидроксида кальция.Кроме того, более плотная микроструктура матриц, модифицированных SF, способствует сцеплению между матрицей и текстильным армированием. Очень большая удельная поверхность SF, примерно 15–35 м 2 /г, оказывает существенное влияние на водопотребность и, как следствие, на удобоукладываемость матриц; однако при низком проценте добавления SF водопотребность вяжущей системы цемент-SF снижается из-за эффекта микронаполнителя SF.
При добавках, превышающих примерно 5% по массе по отношению к цементу, эта тенденция меняется на противоположную; более высокие значения предела текучести и пластической вязкости измеряются с увеличением содержания SF.
Зола-унос представляет собой остаток от сжигания угля на электростанциях и имеет средний размер частиц в диапазоне обычного портландцемента, то есть 10–30 мкм; однако, в отличие от цемента, зольная пыль имеет преимущественно сферические частицы. Из-за низкой водопотребности золы-уноса замена части цемента золой-уносом улучшает удобоукладываемость бетонных смесей. При более медленной реакции по сравнению с SF, использование летучей золы в долгосрочной перспективе приводит к более плотной микроструктуре, что приводит к улучшению механических характеристик и повышению устойчивости к химическому воздействию; однако развитие прочности в раннем возрасте замедлено по сравнению с бетоном без летучей золы (Mobasher, 2011).Как уже указывалось выше, пуццолановые реакции снижают щелочность порового раствора в матрицах ТРК и тем самым повышают долговечность стеклоармированной или базальтовой арматуры.
Замена части портландцементного клинкера на гранулированный доменный шлак (ГБФС) приводит к улучшению механических свойств бетона и его стойкости к химическим веществам, а также к снижению щелочности порового раствора . Латентно-гидравлическая природа GBFS задерживает развитие ранней прочности и снижает теплоту гидратации.В долгосрочной перспективе бетон, изготовленный с использованием ГБФС, имеет более высокую прочность и более высокую химическую стойкость, чем бетон, изготовленный из портландцемента в качестве единственного вяжущего; однако морозостойкость снижается с увеличением содержания ГБФС. Подобно летучей золе и SF, доступность GBFS напрямую зависит от масштабов промышленной деятельности, в результате которой эти материалы образуются в качестве побочных продуктов. В настоящее время во многих развитых промышленных странах почти все такие побочные продукты уже используются в производстве бетона.Поскольку соответствующие отрасли промышленности в этих странах не развиваются, в ближайшем будущем нельзя ожидать увеличения использования их собственных побочных продуктов.
Метакаолин представляет собой высокореактивный пуццолан; это приводит к более высокой прочности на сжатие и изгиб, а также к лучшей связи между матрицей и текстильным армированием. Подобно SF, его добавление приводит к более плотной структуре материала, увеличению долговечности и снижению проницаемости бетона. Кроме того, использование метакаолина снижает усадку (Siddique, 2009).
Каменные порошки — прежде всего известняковый порошок — часто используются в качестве инертных минеральных добавок для снижения содержания энергоемких реакционноспособных вяжущих. Это способствует стабильности свежеприготовленных бетонных смесей, но также может привести при правильном выборе кривой гранулометрического состава к более высокой плотности укладки. Так как известняковый порошок инертен, замена части цемента этим составляющим приводит к снижению показателей прочности и долговечности; однако за счет увеличения плотности упаковки это уменьшение можно частично компенсировать.
Хигучи и др. (2014) предлагают использовать двухкальциевый силикат γ-фазы и летучую золу в качестве частичной замены цемента в сочетании с обработкой CO 2 , выбрасываемой электростанцией. По данным авторов, количество CO 2 , выделившееся при приготовлении бетона, было ниже нуля. Они показали осуществимость подхода на бетонных цилиндрах и предложили использовать эту технологию для производства неармированных бетонных элементов, таких как блоки берегоукрепления, поскольку бетон, полученный таким образом, имеет значение pH ниже 8 и, таким образом, не обеспечивает никакой химической защиты стальной арматуры. .Однако применение этого нового подхода к TRC было бы даже более выгодным по двум причинам: (1) элементы TRC обычно тонкостенные, поэтому процесс карбонизации может быть достигнут во всем элементе за относительно короткое время; (2) неметаллический текстиль не требует щелочной среды; как объяснялось выше, щелочная среда часто может даже привести к порче волокна и полимеров, используемых для его пропитки. Матрицы со значениями рН, приближающимися к нейтральному, открыли бы возможность для использования чувствительного к щелочи недорогого текстиля из Е-стекла или натуральных волокон, получаемых из сизаля, джута или кокосовых растений.Использование натуральных волокон стало бы еще одним шагом на пути к высокоустойчивым, «зеленым» TRC, при условии, что будут решены некоторые проблемы долговечности таких волокон.
Цементный композит – обзор
Прочность на сжатие . Прочность на сжатие цементных композитов, включая ферроцемент, волокнистый RC и TRC, в основном определяется прочностью цементной матрицы. Таким образом, любые достижения в матрице могут быть перенесены на композит, например, использование матриц с высокими или сверхвысокими характеристиками, прочность которых превышает 150–200 МПа, и где ожидается значительное повышение долговечности.
Прочность на изгиб . Согласно нескольким исследованиям ферроцементных и тонких цементных композитных плит, армированных либо обычными стальными проволочными сетками, либо высокоэффективными сетками из FRP (или текстилем или тканями из углерода, кевлара, Spectra), предел MOR составляет около 50 МПа или эквивалентная прочность на упругий изгиб наблюдалось (Naaman and Al-Shannag, 1994; Naaman and Guerrero, 1996; Naaman and Chandrangsu, 2000; Naaman, 2000, 2003b, 2005; Naaman et al. , 2005). С FRP или текстильным армированием этот предел был достигнут, когда в матрице использовались микроволокна для улучшения как вертикального, так и межслойного сопротивления сдвигу. Аналитические исследования показывают, что оптимальные значения должны достигать 60–70 МПа в многослойных изгибаемых элементах (Parra-Montesinos and Naaman, 2001). В предыдущих исследованиях с использованием низкокачественных полимерных сеток (или текстиля или тканей), таких как полипропилен и нейлон, был получен предел MOR 25 МПа, даже когда объемная доля армирования была настолько высокой, насколько это практически возможно (Naaman, 2000).Более того, в низкосортных полимерных тканях и цементных матрицах нормальной массы наблюдались большая ширина трещин и большие остаточные (неустранимые) деформации ползучести (Naaman, 2000). Это представляет собой существенный недостаток.
Потенциальное сопротивление изгибу . Используя матрицу UHPC и арматуру из гибридной стали, состоящую из непрерывных прядей и прерывистых волокон примерно в 10% от общего объема арматуры, Вилле и Нааман сообщили о значении MOR, близком к 230 МПа (Вилле и Нааман, 2012). Такое значение останется целью TRC, хотя для многих приложений достаточно гораздо более низких значений.
Прочность на растяжение . Сопротивление растяжению большинства цементных композитов с непрерывным армированием можно рассчитать напрямую, используя следующее простое соотношение (Naaman, 2000): σtu-composite=ηo×Vr×σru, где рассматриваемого направления, V r – общая объемная доля арматуры, а σ ru – предельное сопротивление арматуры растяжению.Предполагается, что матрица треснула и не оказывает никакого сопротивления. Обратите внимание, однако, что высокое сопротивление растяжению не всегда означает хорошие характеристики, поскольку деформации и ширина трещин могут быть слишком большими для данного применения.
Стоимость . Стоимость матрицы в типичных тонких армированных цементных композитах очень мала (5%) по сравнению со стоимостью армирования и рабочей силы, которые в большинстве развивающихся стран того же порядка (Naaman, 2000, 2005). Таким образом, снижение затрат должно быть направлено не только на материальные затраты, но и на затраты труда. Использование 3D-текстиля окажет значительное влияние на снижение трудозатрат.
Облегченные матрицы . Как указано в простом механическом правиле, изложенном в разделе 18.3, текстиль или ткани, изготовленные из полимерных волокон низкого качества, могут быть совместимы с легкими цементными матрицами. Облегченность подразумевает здесь плотность в диапазоне от 0,5 до 1. Автору неизвестны какие-либо систематические исследования с участием таких матриц.Можно просто предсказать, что их MOR будет менее 25 МПа (как это наблюдается с полимерными сетками и цементными матрицами нормальной массы).
Самонапрягающиеся композиты . До сих пор в этой области сделано очень мало. В (Крстулович-Опара и Нааман, 2000; Нааман, 2000) сообщалось об уровнях предварительного напряжения, близких к 7 МПа, для тонких образцов цемента.
Использование армированного композитного полимерного цемента в качестве компенсации за уменьшение длины штифта
Постановка проблемы: Считается, что цементы с высокой удерживающей способностью позволяют использовать более короткие штифты.
Цель: В этом исследовании изучалось использование армированного композитного полимерного цемента в качестве компенсации уменьшенной длины дюбеля.
Материал и методы: Были оценены показатели ретенции штифтов из нержавеющей стали (параллельные ParaPost и конусовидные Dentatus длиной 5, 8 и 10 мм), с фиксацией композитной смолой Flexi-Flow, армированной титаном, и цементами на основе фосфата цинка. Однокорневые удаленные зубы человека с коронками (n = 120), удаленные по цементно-эмалевой границе, были случайным образом разделены на 4 группы по 30 образцов в каждой. Штифты разной длины фиксировались либо Flexi-Flow, либо фосфатом цинка. Каждый образец помещали в специализированное приспособление и на разрывную машину со скоростью траверсы 2 мм/мин до разрушения. Влияние различных штифтов и цементов на силу, необходимую для смещения штифтов, оценивали с помощью множественного дисперсионного анализа (ANOVA).Однофакторный ANOVA с контрастом Шеффе был применен для определения влияния различной длины штифтов на ретенционную несостоятельность штифтов, зафиксированных двумя агентами.
Результаты: Композитный цемент на основе композитной смолы, армированный Flexi-Flow, значительно увеличил удержание штифтов ParaPost и Dentatus (P<0,001) по сравнению с фосфатом цинка. Однофакторный дисперсионный анализ не выявил статистически значимой разницы (P>.05) между средней ретенцией обоих дюбелей, затянутых Flexi-Flow, для всей используемой длины штифта (5 мм = 8 мм = 10 мм). Средние значения ретенции в группах с фосфатом цинка показали статистически значимую разницу (P<0,001) для штифтов разной длины (10 > 8 > 5 мм). Штифты ParaPost с параллельными сторонами продемонстрировали более высокую среднюю ретенцию, чем конические штифты Dentatus (P<0,001).
Вывод: В этом исследовании армированный композитный композитный цемент Flexi-Flow компенсировал уменьшение длины более коротких штифтов ParaPost с параллельными сторонами и конических штифтов Dentatus.
Новый инъекционный композитный цемент полугидрата сульфата магния/кальция для регенерации костей
Цель. Здесь сообщалось о новом инъекционном композите полугидрата сульфата магния/кальция (Mg/CSH) с улучшенными свойствами. Методы. Были оценены состав, время схватывания, инъецируемость, прочность на сжатие и биоактивность в имитированной жидкости организма (SBF) композита Mg/CSH. Кроме того, были исследованы клеточные реакции стромальных клеток костного мозга собак (cBMSCs) и способность к формированию кости после имплантации Mg/CSH в дефекты большеберцовой кости собак. результатов. Mg/CSH обладает увеличенным временем схватывания и заметно улучшенными инъекционными свойствами и механическими свойствами. Образцы Mg/CSH продемонстрировали лучшую способность к разложению, чем CSH в SBF после 21 дня замачивания. Более того, степень прикрепления клеток, пролиферация и способность к остеогенной дифференцировке на образцах Mg/CSH были выше, чем на CSH, без значительной цитотоксичности и с повышенным индексом пролиферации, активностью ALP и уровнями экспрессии интегрина β 1 и Coll I в cBMSCs.Mg/CSH повышал эффективность образования новой кости в области дефекта большеберцовой кости, включая значительно повышенную минеральную плотность кости, долю площади кости и уровень экспрессии Coll I.
Выводы. Результаты показали, что этот новый костный каркас для инъекций имеет многообещающие перспективы для восстановления кости и имеет большой потенциал в инженерии костной ткани.
1. Введение
Дефекты кости обычно возникают в результате травмы и несращения, а аутологичный костный трансплантат широко известен как золотой стандарт в восстановлении дефектов кости [1].Только в США ежегодно проводится около 1,6 млн операций костной пластики для лечения костных дефектов [2]. Однако клиническое использование аутологичного костного трансплантата сопровождается ограничениями по размеру и значительной болезненностью донорского участка, например, кровотечением, гематомой, инфекцией и хронической болью. В настоящее время для реконструкции костных дефектов используются различные биоматериалы, такие как костные цементы на основе акрилата, фосфата кальция или апатита, а также пористые композиты [3].
Полугидрат сульфата кальция (CaSO 4 ·1/2H 2 O; CSH) уже давно используется в клинике в качестве материала для регенерации кости, поскольку характеризуется низкой температурой отверждения (около 30°C), быстрое схватывание, отличная биосовместимость, не вызывающая воспалительной реакции, и стимуляция заживления костей [4–8]. Тем не менее, производимый в настоящее время цемент CSH все еще имеет некоторые ограничения, которые значительно ограничивают его клиническое применение. Затвердевшая паста CSH имеет плохие механические свойства, что не позволяет обеспечить постоянную долговременную механическую поддержку места дефекта [9, 10]. Низкая биоактивность CSH-цемента препятствует образованию им химической связи с костной тканью на раннем этапе терапии [8, 11]. Более того, быстрая резорбция CSH-цемента может негативно сказаться на регенерации кости [12, 13].
Среди различных биоразлагаемых материалов магний (Mg) и его сплавы использовались в качестве металлических материалов для медицинских имплантатов из-за их уникальной биосовместимости, нетоксичности, плотности и модуля упругости, подобных тем, что имеют человеческие кости, и стимулирующего воздействия на образование новой кости. [14–18].Однако в физиологических условиях они быстро подвергаются коррозии и вследствие этого теряют механические свойства [19]. Чтобы снизить степень биодеградации сплавов Mg, были изучены такие подходы, как термическая обработка щелочью [18], фторидное конверсионное покрытие [20] и плазменная иммерсионная ионная имплантация [21]. Однако следует учитывать биосовместимость при использовании материала трансплантата в организме человека. Принимая во внимание преимущества и недостатки сплавов CSH и Mg, предполагается, что добавление Mg в CSH может привести к получению композитного цемента с улучшенными свойствами, а композитный каркас Mg/CSH можно использовать для восстановления костных дефектов.
В настоящем исследовании композитный цемент был приготовлен путем добавления Mg в CSH; в то же время оценивали время схватывания, инъецируемость, механические свойства, биоактивность in vitro и биосовместимость со стромальными клетками костного мозга собак (cBMSCs). Кроме того, была исследована способность in vivo к формированию кости путем имплантации каркаса Mg/CSH в модель дефекта большеберцовой кости собаки. Ожидалось, что новый композиционный цемент Mg/CSH потенциально может быть использован для клинического восстановления костных дефектов.
2. Материалы и методы
2.1. Подготовка и характеристика образцов
Порошки Mg в основном были приготовлены путем нанесения фтористого покрытия и обработки микродуговым оксидированием (обработано Институтом исследования металлов Китайской академии наук, Шэньян, Китай). Порошок Mg/CSH готовили путем добавления порошков Mg (массовое соотношение: 0%, 10% и 20%) в порошок CSH (приобретенный у Allgens Co., Ltd., Китай). Затем добавляли деионизированную воду с соотношением жидкости и порошка, равным 0.6 мл/г для увлажнения этих порошков. Смеси перемешивали в течение 60 с до образования однородной пасты, переносили в тефлоновые формы (10 мм × 20 мм) и затем выдерживали при 37°С в течение 24 ч; наконец, были получены отвержденный композит 10% Mg/CSH, композит 20% Mg/CSH и чистые цементы CSH. Фазовые составы этих образцов охарактеризованы методом рентгеновской дифракции (XRD; D8 Advance, Bruker (Beijing) Technology Co. , Ltd., Китай) на монохроматизированном медном излучении ( = 1,5405 Å, 120 мА, 40 кВ) в режим непрерывного сканирования.Диапазон 2 θ составлял от 10° до 90° при скорости сканирования 8°/мин.
2.2. Время схватывания, инъецируемость и прочность на сжатие
Время схватывания композитных паст CSH и Mg/CSH измеряли с помощью иглы Вика (LeiYun Experimental Apparatus Manufacturing Co., Ltd., Шанхай, Китай) в соответствии со стандартом ISO9597-1989E. Начальное время схватывания определяли как время, необходимое для того, чтобы легкая игла (228,6 г, 5,067 мм) погрузилась в пасту, не оставляя видимого отпечатка на поверхности пасты, а окончательное время схватывания определялось как необходимое время. для толстой иглы (306 г, 1.140 мм), чтобы на поверхности пасты больше не оставалось видимого отпечатка. Для каждой группы проводили пять повторов и рассчитывали среднее значение.
Инъекционную способность CSH и композитных паст проверяли путем выдавливания определенного количества пасты через 10-мл шприц с открывающейся насадкой (диаметр: 2,8 мм) в соответствии с методом, описанным ранее [22]. Эти пасты набивались в шприц, и шприц осторожно нажимался со скоростью 15 мм/мин до тех пор, пока либо пасты не были полностью выдавлены, либо не было достигнуто максимальное усилие 100 Н.Затем измеряли массу экструдированных паст и рассчитывали инъецируемость по следующей формуле: Инъецируемость (%) = (масса экструдированной пасты/масса всей пасты, изначально содержащейся в шприце) × 100%.
Кроме того, была измерена прочность на сжатие отвержденных образцов композита CSH и Mg/CSH (диаметр 10 мм × высота 20 мм) при скорости нагружения 0,5 мм/мин на универсальной испытательной машине (ZWICK Co. Ltd., Германия). ) способом, аналогичным описанному в ASTM D695-91.Измерения проводились пять раз для каждой группы.
2.3.
In Vitro Испытание на погружение в искусственную жидкость организма (SBF) В соответствии с методом, описанным Kokubo [23], был приготовлен SBF, в котором оценивали деградацию и биологическую активность композитных цементов CSH и Mg/CSH. SBF состоял из 142,0 мм Na + , 5,0 мм к + , 1,5 мм мг 2+ , 2,5 мм Ca 2+ , 148,8 мм C1 — , 4,2 мм HC и 1,0 мМ HP и был забуферен при рН 7. 25 с 45 мМ соляной кислоты (HCl) и 50 мМ трисгидроксиметиламиноэтана ((CH 2 OH) 3 (CNH 2 )). После схватывания в течение 24 ч отвержденные образцы композитов CSH и Mg/CSH погружали в SBF с отношением площади поверхности к объему 0,1 см 2 /см 3 при 37°C на 21 день. Температуру SBF поддерживали с помощью встряхивающей водяной бани, а SBF полностью обновляли каждый день. Для каждой группы из SBF извлекали по пять образцов после инкубации в течение 2, 4, 7, 10, 14 и 21 сут соответственно.В каждый момент времени образцы осторожно промывали деионизированной водой, сушили в печи при 37°C в течение 24 часов, а затем взвешивали. Для измерения деградации in vitro рассчитывали процент потери веса по следующей формуле: Коэффициент деградации = × 100%, где и представляют собой сухую массу разложившегося образца и исходного образца соответственно.
Кроме того, для оценки биоактивности образцов in vitro сканирующая электронная микроскопия (СЭМ) с энергодисперсионным рентгеновским детектором (EDX; Tescan Ltd. , Шанхай, Китай). Кроме того, значения рН SBF измеряли во время теста с использованием pH-метра электролитного типа.
2.4. Культура клеток и индукция остеогенеза
После внутривенной анестезии 5% пентобарбиталом натрия (0,5 мл/кг) 5 мл костного мозга собирали из подвздошных гребней взрослой собаки породы бигль, переносили в 10 мл предварительно гепаринизированную центрифужную пробирку и центрифугировали в удалить жир и гепарин. Мононуклеарные cBMSC выделяли методом центрифугирования в градиенте перколла (1,073 мкг/мл, Sigma, США) [24] и культивировали в полной среде, содержащей модифицированную по Дульбекко среду Игла с низким содержанием глюкозы (L-DMEM; Gibco, США) с 10% фетальной бычьей сывороткой. (FBS; Hyclone, США) и 100 ЕД/мл стрептомицина при плотности 5 × 10 4 /см 2 .Клетки инкубировали при 37°C во влажной атмосфере, содержащей 5% CO 2 . Культуральную среду обновляли через 48–72 ч, а затем каждые 2–3 дня. При достижении 80–90% слияния клеток клетки открепляли 0,25% трипсином, содержащим 0,01% ЭДТА (Invitrogen, США), а затем пересевали.
Для клеточной остеогенной дифференцировки cBMSC четвертого поколения культивировали в среде, содержащей DMEM с высоким содержанием глюкозы (H-DMEM, Life Technologies, Inc., США) с 10% FBS, 100 нМ дексаметазона (Sigma-Aldrich Co.Ltd., США), 10 мМ β-глицерофосфата натрия (Sigma, США) и 200 мкМ М аскорбиновой кислоты (Sigma-Aldrich Co. Ltd., США). Среду заменяли каждые 2 дня. Весь уход за животными и процедуры проводились в соответствии с Руководством по уходу за животными Комитета по этике животных Общего госпиталя Народно-освободительной армии Китая.
2.5.
In Vitro Биосовместимость2.5.1. Анализ цитотоксичности
Анализ цитотоксичности проводили путем культивирования cBMSC в экстрактах составных образцов CSH и Mg/CSH и с использованием 3-(4,5-диметилтиазол-2-ил)-2,5-дифенилтетразолия бромида (МТТ). (Сигма-Олдрич Ко.Ltd., США) количественный анализ пролиферации. Согласно ISO 10993-1: Биологическая оценка медицинских изделий, часть 1: Оценка и тестирование в рамках процесса управления рисками, экстракты с концентрацией 0,2 г/мл готовили путем замачивания цемента в среде для культивирования клеток в течение 1 дня при 37°C, 5% CO 2 (экстракт по 10 мл на каждый цемент). КСКМ третьего поколения после остеогенной дифференцировки открепляли 0,25% трипсином, а затем клеточную суспензию переносили в 96-луночные планшеты (объем: 200 мк л/лунку, плотность: 5 × 10 4 /мл).На каждую цементную группу было заложено по шесть скважин. После инкубации при 37°C во влажной атмосфере 5% CO 2 в течение 24 ч кСКМ культивировали в присутствии 100 мкл л экстрактов, после чего среду обновляли каждые 2 дня. Через 2, 4, 6 и 8 дней в каждую лунку добавляли по 20 мкл мкл МТТ (5 г/л) и инкубировали кСКМ в течение следующих 4 часов. Затем осторожно удаляли супернатант из каждой лунки и добавляли 150 мкл л диметилсульфоксида.После встряхивания в течение 10 мин значения оптической плотности (ОП) при 490 нм оценивали с помощью устройства для считывания микропланшетов.
2.5.2. Пролиферация cBMSCs и тест клеточного цикла на основе проточной цитометрии
Пролиферацию cBMSCs, посеянных на чистый CSH и композитный цемент Mg/CSH, оценивали с использованием теста клеточного цикла на основе проточной цитометрии. Через 24, 48 и 72 ч инкубации кСКМ собирали трипсинизацией и центрифугированием при 1000 об/мин и дважды промывали PBS. Затем кСКМ ресуспендировали в PBS, фиксировали в 70%-ном этаноле при 4°С в течение ночи.Наконец, образцы центрифугировали и окрашивали 0,5 мл гипотонического раствора, содержащего 50 мкг мкг/мл PI, 0,2% Triton X-100 и 100 мкг мкг/мл РНКазы А в течение 30 мин в темноте при 4°C. Количество клеток на разных фазах клеточного цикла анализировали с помощью проточного цитометра с полосой возбуждения 488 нм. Индекс пролиферации клеток рассчитывали следующим образом: Индекс пролиферации = (S + G2M)/(G0G1 + S + G2M) × 100%.
2.5.3. Остеогенная дифференцировка и биосинтез щелочной фосфатазы (ЩФ)
Для остеогенной дифференцировки измеряли биосинтез ЩФ в cBMSCs, культивируемых на чистом CSH и композитных цементах Mg/CSH.Через 7, 14, 21 и 28 дней инкубации культуральную среду удаляли, а кСКМ дважды промывали PBS. Приблизительно 1 мл буфера для лизиса клеток, содержащего 0,2% Triton X-100, добавляли для лизиса cBMSC при комнатной температуре и получали лизат клеток. После центрифугирования ровно 100 мкл л супернатанта переносили в 96-луночные планшеты и добавляли 100 мкл л раствора субстрата п-нитрофенилфосфата (pNPP, 1 мг/мл). После инкубации в течение 30 мин при 37 °C реакцию гасили добавлением 50 90 137 мкл 90 138 л NaOH и количественно определяли поглощение при 405 нм с помощью планшет-ридера.Каждое испытание проводилось пять раз.
2.5.4. Клеточная морфология и прикрепление cBMSCs
Клеточная морфология и прикрепление cBMSCs были исследованы на основе прямой визуализации в SEM. Сначала к образцам прикрепляли клетки на 3, 7 и 14 дней при 37°С в атмосфере 100% влажности и 5% СО 2 . Затем клеточно-цементные конструкции дважды промывали PBS и фиксировали 2,5% раствором глутарового альдегида в течение 2 ч при 4°C. Затем фиксированные конструкции трижды промывали PBS и обезвоживали в этаноле определенной концентрации (об./об.: 50, 60, 70, 80, 90 и 100%).После сушки CO 2 в течение ночи в эксикаторе образцы напыляли золотом перед наблюдением с помощью СЭМ.
2.5.5. Экспрессия генов, связанных с остеогенезом и прикреплением
Относительную экспрессию генов, связанных с остеогенезом и прикреплением, в cBMSCs исследовали с помощью RT-PCR в реальном времени (Thermo, США). После культивирования на отвержденных конструкциях в течение 8, 24 и 48 ч кСКМ гомогенизировали в реагенте Тризол. Тотальную РНК экстрагировали и обратно транскрибировали в кДНК в соответствии с инструкциями производителя.Последовательности праймеров для коллагена I типа (Coll I), интегрина β 1 и β -актина показаны в таблице 1. ПЦР в реальном времени SYBR Green проводили для измерения экспрессии генов в соответствии с его руководство. Относительную экспрессию каждого целевого гена оценивали по методу [25].
|
2.

Всего 24 здоровых взрослых самца породы бигль весом 16 ± 1 кг были случайным образом разделены на 4 группы (по 6 собак для каждого типа имплантата). Собак анестезировали 3% пентобарбиталом (общая анестезия) и 1% лидокаином (анестезия операционной области) и помещали в положение лежа на спине. В стерильных условиях выполняли продольный разрез кожи длиной 3 см в переднемедиальной части левой большеберцовой кости. Кожу и подкожную клетчатку осторожно рассекают до надкостницы, обнажая кость.Затем хирургическим путем был создан один туннель большеберцовой кости (диаметром 3 мм и длиной 15 мм). Дефекты заполняли конструкцией 20% Mg/CSH, 10% Mg/CSH или чистым CSH, а костные дефекты контрольной группы оставляли незаполненными. Все раны обычно зашивали и всем животным вводили пенициллин (25 000 ЕД/кг) в течение 3 дней. После операции клыки содержались свободно в клетках и получали обычный режим питания и воды.
Животных умерщвляли через 4 и 12 недель после операции, образцы большеберцовой кости собирали и фиксировали в 4% параформальдегиде. Локальную минеральную плотность костной ткани (МПКТ) измеряли с помощью системы двухэнергетической рентгеновской абсорбциометрии (ДРА), а долю площади новой кости (ФАК) определяли количественно через 1 день, 4 и 8 недель после имплантации по следующей формуле: = AB/AT, где AB — площадь новообразованной кости, а AT — общая площадь материала. Для гистологического анализа через 4, 8 и 12 недель после операции декальцинированные и некальцинированные образцы кости заливали соответственно в парафин и твердый пластик. Срезы тканей окрашивали гематоксилином и эозином (H&E) и трихромом Массона соответственно, а затем исследовали под световым микроскопом (Olympus BX51, Япония).Кроме того, образцы ткани (5 мм × 5 мм × 5 мм) вокруг материалов для имплантации были удалены и немедленно погружены в раствор RNAlater. Затем тотальную тканевую РНК экстрагировали и обратно транскрибировали в кДНК, а уровни транскрипции собачьего остеопонтина, связанного с остеогенезом, костного морфогенетического белка-2 (BMP-2) и Coll I измеряли с помощью RT-PCR.
2.7. Статистический анализ
Экспериментальные данные были выражены как среднее ± стандартное отклонение. Для сравнительного анализа были применены односторонний и двусторонний ANOVA с апостериорными тестами Тьюки.Различия считали статистически значимыми при .
3. Результаты
3.1. Характеристика Mg/CSH
После отверждения в течение 24 часов фазовый состав затвердевшего композита Mg/CSH был охарактеризован с помощью XRD. Конструкция CSH содержала дифракционные пики CaSO 4 · 2H 2 O (рис. 1(b)), а смесь CaSO 4 · 2H 2 O и Mg можно было увидеть на рентгенограммах Композиты Mg/CSH с 10% и 20% Mg (рис. 1(c) и 1(d)).Наличие CaSO 4 ·2H 2 O можно объяснить реакцией CaSO 4 ·1/2H 2 O и H 2 O.
3.2. Время схватывания, инъецируемость и прочность на сжатие Mg/CSH
Начальное и конечное время схватывания 10% и 20% композитов Mg/CSH были значительно выше, чем у чистого CSH, и время схватывания увеличивалось с увеличением весового соотношения Mg. Наибольшее время схватывания () наблюдалось в композите 20% Mg/CSH с начальным и конечным временем схватывания 8 ± 0.72 мин и 14,5 ± 0,8 мин соответственно (рис. 2(а)). Инъецируемость композитных паст Mg/CSH была значительно улучшена по сравнению с пастой CSH (1). Более того, инъецируемость композитных паст Mg/CSH резко увеличивалась с увеличением содержания Mg, а композитная паста 20% Mg/CSH демонстрировала самую высокую инъекционную способность (69 ± 2%, ) (рис. 2(b)). После отверждения в течение 24 часов прочность на сжатие затвердевших конструкций также значительно возросла () с увеличением содержания Mg и достигла максимального значения 18.6 ± 2,7 МПа в композите 20% Mg/CSH, в то время как нет существенной разницы () между композитами 10% Mg/CSH и 20% Mg/CSH (рис. 2(c)).
3.3.
In Vitro Биоактивность, разложение и изменение значения pH в SBF СЭМ-микрофотографии поверхности показали влияние SBF на микроструктуру материалов (рис. 3). После замачивания в течение 2 и 4 дней в образцах CSH наблюдались крупные ребристые кристаллы (рис. 3(а) и 3(d)). При длительном погружении на поверхности образовывался слой осадка (рис. 3(ж), 3(к), 3(м) и 3(р)).Для образцов композита Mg/CSH шарообразные частицы Mg и кристаллы CaSO 4 проявлялись после 2 и 4 дней погружения (рис. 3(b)–3(c) и 3(e)–3(f)) . Впоследствии образовалось много отложений, которые далее скапливались, образуя слой на поверхности образца, в то время как частицы Mg не демонстрировали очевидных изменений (рис. 3(e)-3(f), 3(h)-3(i), 3(k). )-3(l), 3(n)-3(o) и 3(q)-3(r)). Не было очевидной разницы между поверхностями композитов 10% и 20% Mg/CSH после погружения. EDX показал, что поверхности чистого Mg содержали ионы Mg, C и O (рис. 4 (a)), а цемент CSH содержал некоторое количество O, S и Ca (рис. 4 (b)).Составные образцы 10% и 20% Mg/CSH состояли в основном из Mg, C, O, S и Ca (рис. 4(c) и 4(d)) после выдержки в течение 21 дня.
Степень деградации образцов характеризовалась степенью потери массы после выдержки в SBF в течение различных периодов времени. Видно, что существенных различий () в степени деградации среди всех образцов от 2 до 14 дней не было, в то время как степень деградации композита 20% Mg/CSH была значительно выше (), чем у других конструкций после 21 дня выдержки. замачивание (рис. 5(а)).При погружении в SBF образцы приводили к кислой среде, вызывая снижение значений pH SBF. Однако заметной разницы между тремя типами конструкций в выбранные моменты времени не наблюдалось (рис. 5(b)).
3.4. Жизнеспособность, пролиферация, дифференциация, прикрепление и морфология cBMSC после инкубации с биоматериалами
Изменения жизнеспособности cBMSC, культивируемых в различных экстрактах, оценивали с помощью анализа МТТ. Было замечено, что значения OD во всех экстрактах увеличивались со временем, что указывает на то, что три конструкции не вызывали значительной цитотоксичности в отношении клеток в различные периоды времени.Однако жизнеспособность cBMSCs в экстрактах как 10%, так и 20% Mg/CSH составных образцов была значительно выше (), чем жизнеспособность cBMSCs в экстрактах чистого CSH после инкубации в течение 8 дней (рис. 6(a)).
Значимой разницы () между индексами пролиферации cBMSC, культивируемых на разных материалах в течение 24 и 48 часов, не наблюдалось. Однако композиты Mg/CSH (10% и 20%) могут значительно () увеличить пролиферацию клеток по сравнению с CSH через 72 часа культивирования (рис. 6(b)).
Клеточная дифференцировка оценивалась путем тестирования активности ЩФ в cBMSC, культивируемых на образцах конструкции в течение 7, 14, 21 и 24 дней. Активность ALP клеток, выращенных на всех трех материалах, повышалась со временем, в то время как не было существенной разницы () между активностью ALP cBMSCs в трех группах в определенный момент времени (рис. 6(c)).
Клетки прочно прикрепились и имели нормальный морфологический вид на поверхности конструкций 10% Mg/CSH и CSH через 3 дня культивирования (рис. 7(a) и 7(d)).Клетки разрастались и хорошо распределялись через 7 дней культивирования (рис. 7(b) и 7(e)), в конечном итоге образуя сливной слой с плотным прилеганием к поверхности материала через 14 дней (рис. 7(c) и 7(f)) .
Относительные значения экспрессии гена интегрина β 1 были резко повышены () в cBMSC, культивируемых на композитах Mg/CSH (10% и 20%), по сравнению с конструкцией CSH, в то время как не наблюдалось существенной разницы () между 10% и 20% Mg/CSH через 8, 24 и 48 ч (рис. 8(а)).Выражения Coll I показали аналогичные тенденции (рис. 8 (б)).
3.5.
In Vivo Анализ DXA Для количественной оценки кальцификации восстановленной большеберцовой кости у всех животных измеряли BMD на DXA через 4 и 12 недель после операции. Трансплантаты Mg/CSH показали более высокие значения BMD, чем CSH и контрольные группы, как через 4, так и через 12 недель. Тем не менее, не было заметной разницы () между трансплантатами с 10% и 20% Mg/CSH (рис. 9(а)). Между тем, BAF применяли для оценки новообразованной кости после операции в течение 1 дня, 4 и 8 недель.BAF композитного трансплантата Mg/CSH были значительно выше, чем у CSH как через 4, так и через 8 недель (рис. 9(b)).
3.6.
In Vivo Гистологический анализЧерез 4 недели после имплантации новые хондроциты появились во многих областях композитного имплантата 10% Mg/CSH, а в центре области костного дефекта можно было увидеть некоторые воспалительные клетки (рис. 10(a)) . Клеточная дифференцировка появилась через 8 недель (рис. 10(b)) и большее количество клеток собралось в пучки на границе между материалами имплантата и принимающей костью через 8 недель (рис. 10(c)).Окрашивание по Массону показало, что новая костная ткань не наблюдалась на границе раздела имплантата CSH через 4 (рис. 10(d)) и 8 (рис. 10(e)) недель, в то время как новые трабекулы можно было увидеть в имплантированном композите 10% Mg/CSH. срез в 8 недель (рис. 10(g)).
При гистологическом исследовании недекальцинированной кости можно предпочтительно продемонстрировать клеточные компоненты кости, костный метаболизм и формирование. Новые хондроциты все еще были видны в областях имплантатов с 10% Mg/CSH через 4–16 недель (рис. 11(a)–11(c)) в соответствии с результатами окрашивания декальцинированного материала.Более того, границы между нормальной окружающей тканью и составными образцами постепенно стирались из-за биодеградации, а остаточные материалы были окружены участками новообразованной костной ткани в течение 4–12 недель (рис. 11(г)–11(е)).
3.7. Анализ экспрессии генов
Относительные уровни экспрессии остеопонтина в тканях вокруг трех материалов трансплантата не показали значительных различий () после имплантации в течение 4 и 12 недель, что было сходно с экспрессией BMP-2.Тем не менее, уровни экспрессии Coll I в обеих составных группах Mg/CSH были значительно выше (), чем уровни экспрессии конструкции CSH через 4 и 12 недель (рис. 12(a) и 12(b)).
4. Обсуждение
Поскольку кость необходима для минерального резерва, передвижения, опоры и защиты внутренних органов, дефект кости приводит к инвалидности и представляет собой медицинскую и социально-экономическую проблему. Тканевая инженерия играет решающую роль в регенерации кости [3]. Идеальный материал для костной пластики должен обладать не только механической стабильностью и отличной биоактивностью, но также обладать остеокондуктивностью и остеоиндуктивностью [26–28].В настоящем исследовании композитный цемент Mg/CSH продемонстрировал более продолжительное время схватывания с улучшенной инъекционной способностью и повышенной механической прочностью благодаря добавлению Mg по сравнению с одним только CSH. Кроме того, композитные конструкции Mg/CSH также демонстрировали значительно улучшенную способность к деградации и стимулирующее действие на пролиферацию и остеогенную дифференцировку cBMSC in vitro . Гистологическая оценка и анализ DXA и экспрессии генов показали, что Mg/CSH может повышать эффективность формирования новой кости по сравнению с CSH.Это означало, что этот новый костный каркас для инъекций (композит Mg/CSH) будет иметь большой потенциал для восстановления кости в тканевой инженерии.
Применимость биоматериала для костного цемента во многом зависит от его характеристик самозатвердевания, включая инъекционную способность и время затвердевания [29]. Кроме того, при клиническом применении цемент необходимо экструдировать и наносить до начала его первоначального схватывания во время операции [30]. По сравнению с чистой пастой CSH, у которой было короткое начальное и конечное время схватывания, композитные пасты Mg/CSH показали относительно длительное время схватывания.Увеличенное время схватывания улучшило инъецируемость цемента и могло дать очевидные преимущества для хирургов, так как у них было больше времени для работы до того, как паста начнет схватываться. Механические свойства затвердевшего цемента — еще один важный показатель клинического применения костных материалов [29]. Тем не менее, предыдущие исследования показали, что чистый цемент CSH не соответствует этому показателю из-за его плохой и почти постоянной механической прочности [9, 31]. Напротив, прочность на сжатие композитных конструкций Mg/CSH увеличивалась вместе с увеличением содержания Mg (по сравнению с чистым CSH), и это обеспечивало бы гораздо лучшую механическую поддержку места дефекта в процессе регенерации кости.
Биоактивность определяется как способность биоматериалов образовывать адгезионную, прямую и прочную связь с костной тканью [32]. По имеющимся данным, цемент CSH всегда лишен способности образовывать химическую связь с костной тканью на ранней стадии имплантации из-за его низкой биоактивности [8, 11–13]. Однако в настоящем исследовании анализы SEM и EDX показали, что отложение апатита не наблюдалось на поверхности всех чистых CSH и композитов Mg/CSH в течение 21 дня после замачивания в SBF.Было указано, что добавление Mg может не способствовать склонности CSH к образованию костеподобного апатита в SBF. Однако необходимы дальнейшие исследования для улучшения биологической активности композитных конструкций Mg/CSH. При этом биоматериал должен быть деградируемым и постепенно замещаться новообразованной костной тканью [33]. Надлежащая разлагаемость биоматериала в физиологической среде является одной из важнейших характеристик [28]. В нашем настоящем исследовании композитные цементы Mg/CSH продемонстрировали значительно более высокую способность к разложению, чем чистый CSH, а 20% Mg/CSH имели лучшую способность к разложению после 21 дня погружения, что позволяет предположить, что степень разложения композитного цемента можно регулировать добавлением мг.
Общепризнано, что in vitro клеточные ответы на биоматериалы, включая прикрепление клеток, пролиферацию и дифференцировку, также являются основными компонентами способности биоматериалов к восстановлению кости [34]. Остеогенный потенциал СККМ был продемонстрирован как in vitro , так и in vivo [35-37]. Поэтому СККМ часто используются для оценки биосовместимости синтетических материалов для костной инженерии. В настоящем исследовании композитные пасты Mg/CSH не вызывали значительной цитотоксичности и способствовали пролиферации cBMSC по сравнению с чистым цементом CSH.Среди всех молекул коллагена костного волокна Coll I является наиболее важным типом коллагеновых волокон и считается необходимым геном для формирования и ремоделирования кости, который также может обеспечить армирование цемента волокнами [28]. Кроме того, интегрин играет важную роль в процессе клеточной адгезии и растяжения и является важным белком, связывающим остеобласты и костные заменители, который также является необходимым специфическим геном клеточной адгезии и остеогенеза [38]. В настоящем исследовании повышенная экспрессия Coll I и интегрина β 1 в cBMSC, культивируемых на композитных конструкциях Mg/CSH, продемонстрировала выдающуюся способность клеточной адгезии и остеогенеза при добавлении Mg по сравнению с чистым CSH.Таким образом, результаты исследования in vitro показали, что этот композит обладает благоприятной биосовместимостью за счет улучшения прикрепления клеток и стимуляции пролиферации и дифференцировки клеток.
В отличие от аутотрансплантатов, запасы которых ограничены и существует значительный потенциальный риск повреждения нервов, инфицирования, передачи заболевания и иммунного ответа [28, 39], заменители костного цемента являются многообещающими подходами к регенерации кости [3]. Сообщается, что CSH и Mg широко используются в клинике в качестве каркаса для регенерации кости, хотя сохраняется ряд недостатков.В исследовании in vivo МПК трансплантата Mg/CSH была значительно выше, чем у чистого CSH через 4 и 12 недель после имплантации. Кроме того, повышенный BAF указывал на то, что в группах композита Mg/CSH формировалось больше новой кости по сравнению с CSH через 4 и 8 недель после трансплантации. Гистологическая оценка также показала, что в области дефекта появляются новые хондроциты, трабекулы и зрелый оссеин, границы между нормальной окружающей тканью и композитом постепенно становятся нечеткими из-за биодеградации, а остаточные материалы окружены участками новообразованной костной ткани в процессе биодеградации. 8 недель после имплантации композитного цемента.Напротив, через 8 недель на поверхности имплантата CSH не наблюдалось новой костной ткани, а границы между нормальной окружающей тканью и CSH были четкими. Это может быть связано с добавлением Mg, который может ускорить рост новой костной ткани, как сообщалось ранее [40, 41]. Таким образом, эти результаты in vivo показали, что композиты Mg/CSH демонстрируют не только более быструю биоразлагаемость, но и более эффективный остеогенез и остеоинтеграцию в области дефекта кости, чем чистый цемент CSH.
5. Выводы
Новый инъекционный композит Mg/CSH был разработан путем включения Mg, покрытого фтором, в CSH в этом исследовании. Композиты Mg/CSH показали увеличенное время схватывания с улучшенной инъекционной способностью. Механическая прочность и биоразлагаемость композита Mg/CSH были улучшены. Композит Mg/CSH может способствовать прикреплению, пролиферации и дифференцировке собачьих cBMSC и демонстрирует превосходную биосовместимость без цитотоксичности. Кроме того, композитный имплантат Mg/CSH также продемонстрировал эффективный остеогенез и остеоинтеграцию.В заключение, этот новый вид биоматериала для инъекций с улучшенными свойствами позволит разработать более многообещающий заменитель тканевого трансплантата для регенерации кости.
Конфликт интересов
Авторы заявляют об отсутствии конфликта интересов в отношении публикации данной статьи.
Благодарности
Это исследование было поддержано Государственным фондом естественных наук Китая (грант № 81200819), специальным финансовым грантом (грант № 2013T60943) и общим финансовым грантом второго класса (грант №2012M512121) из Китайского фонда докторских наук.
Композитный сайдинг и фиброцемент – Sherwood Lumber
Что лучше: композитный сайдинг или фиброцемент?
Выбор лучшего материала для сайдинга сегодня очень запутан, потому что на рынке доступно так много типов. Разные компании предлагают сайдинг из разных материалов и разного качества. Поэтому вам нужно быть очень осторожным и осторожным, когда вы покупаете сайдинговый материал для своего дома.Как ответственный домовладелец, вы должны учитывать дизайн своего дома, а также его фон.
Это поможет вам в выборе правильного цвета и дизайна сайдинга, который вы хотите приобрести. Говоря о сайдинговых материалах, мы собираемся сравнить композитный сайдинг и фиброцементный и решить, какой из них выбрать. Мы собираемся посмотреть на их установку, долговечность, внешний вид и производительность.
Монтаж сайдинга Процесс установки композитного сайдинга по сравнению с фиброцементным сайдингом сильно отличается. В случае с композитным сайдингом мы имеем дело с досками, и эти плиты очень просты в монтаже. Это просто вопрос прибивания их один за другим. Вы можете прибить их горизонтально или вертикально в зависимости от ваших предпочтений.
Для фиброцемента вам предстоит много работы в процессе укладки. Кроме того, изделие очень тяжелое, и вам потребуется время, прежде чем вы закончите монтаж сайдинга. Таким образом, стоимость рабочей силы выше.
Долговечность
Композитный сайдинг и фиброцемент не так легко повреждаются влагой.Однако через некоторое время использования фиброцемент может стать восприимчивым к повреждениям из-за длительного воздействия влаги. Со временем вы заметите, что ваш сайдинг начинает трескаться, и это ухудшает его изоляционные свойства. Это происходит из-за свойства расширения и сжатия фиброцемента.
Для композитного сайдинга вам не нужно беспокоиться о трещинах, потому что вы их не встретите. Эти сайдинги очень прочны и могут прослужить более 30 лет без необходимости замены или ремонта. На них не действует ни влага, ни насекомые, ни даже суровые погодные условия. Если вы правильно ухаживаете за сайдингом, он будет гарантировать долгую службу.
Внешний вид сайдинга
Бесшовный внешний вид композитного сайдинга несравним с любым типом сайдинга. С композитным сайдингом легко работать, и вы можете покрасить его в любой цвет. С другой стороны, фиброцемент жесткий и с ним очень трудно работать. Вот почему вы найдете много домов с одинаковым цветом и дизайном сайдинга из фиброцемента.Так что, в зависимости от вашего вкуса, вы должны выбрать то, что вы предпочитаете.
Что выбрать, композитный сайдинг или фиброцемент?В общем, каждый домовладелец должен знать особенности того типа сайдинга, который ему нужен. Чтобы получить лучший и качественный сайдинг, вам следует провести надлежащее исследование и просмотреть несколько статей. Это расскажет вам о лучшем материале для сайдинга и марке сайдинга.
Из нашего сравнения композитного сайдинга и фиброцемента преимущества композита перевешивают преимущества фиброцемента. Если вы хотите приобрести композитный сайдинг, пиломатериалы Sherwood будут лучшим местом для приобретения высококачественного композитного сайдинга Everlast.
Композиционные материалы на основе цемента | СпрингерЛинк
Действия
‘) var buybox = document.querySelector(«[data-id=id_»+ метка времени +»]»).parentNode ;[].slice.call(buybox.querySelectorAll(«.вариант-покупки»)).forEach(initCollapsibles) функция initCollapsibles(подписка, индекс) { var toggle = подписка.querySelector(«.цена-варианта-покупки») подписка.classList.remove(«расширенный») var form = подписка.querySelector(«.форма-варианта-покупки») var priceInfo = подписка.querySelector(«.Информация о цене») var PurchaseOption = переключатель.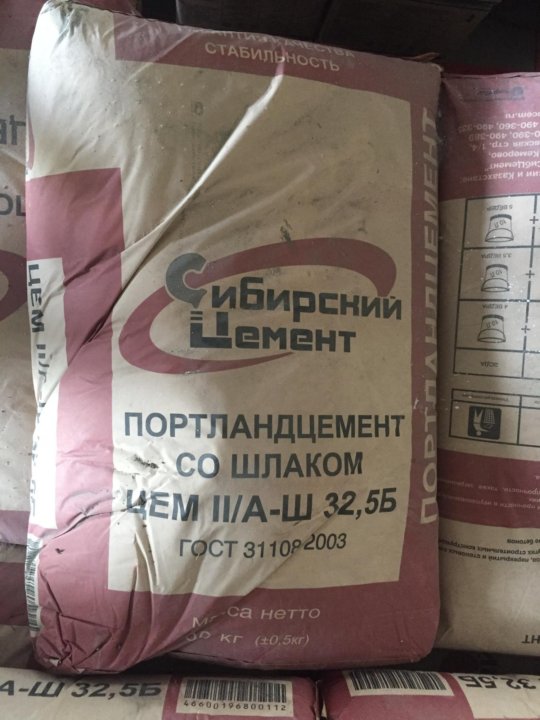


Характеристика композита, образованного цементом и пшеничной соломой, обработанной гидроксидом натрия :: BioResources
Сильва, Дж.В. Ф., Бьянки, Н. А., Оливейра, К. А. Б., Караски, Дж.
Abstract
Композиты на основе цемента с лигноцеллюлозными остатками (например, пшеничной соломой, рисовой шелухой и жмыхом) в качестве наполнителей имеют меньшую плотность и стоимость. К этому сырью применялась предварительная обработка для улучшения его совместимости с цементом.Эта работа была направлена на изучение композитов, изготовленных из частиц цемента и пшеничной соломы, которые были химически обработаны (2% раствор NaOH) при двух различных температурах (30 °C и 60 °C). Определены значения насыпной плотности (209 кг·м-3) и удельной плотности (679 кг·м-3) для соломы пшеницы при влажности 12%. Выход соломы составил 71,9%, а распределение частиц по размерам показало большие концентрации частиц пшеничной соломы размером от 5 до 10 меш. Композиты, изготовленные из частиц соломы пшеницы, по сравнению с контрольной обработкой показали вдвое меньшую плотность, т. е.е., от 1800 до 900 кг·м-3. Кроме того, кривая напряжения х деформации показала более высокую деформацию перед разрушением. Предварительная обработка NaOH не влияла на механические свойства композитов из пшеничной соломы.
Скачать PDF
Полный текст статьи
Характеристика композита, образованного цементом и пшеничной соломой, обработанной гидроксидом натрия
Жоао В. Ф. Силва, a, * Наталия А. Бьянки, a Каролина А. Б. Оливейра, a Хосе К. Караски, b Александр Дж.Д. де Соуза, b Хулио К. Молина, b , и Кристиан И. де Кампос, b
Композиты на основе цемента с остатками лигноцеллюлозы (, например, пшеничная солома, рисовая шелуха и багасса) в качестве наполнителей имеют меньшую плотность и стоимость. К этому сырью применялась предварительная обработка для улучшения его совместимости с цементом. Эта работа была направлена на изучение композитов, изготовленных из частиц цемента и пшеничной соломы, которые были химически обработаны (2% раствор NaOH) при двух различных температурах (30 °C и 60 °C). Определены значения насыпной плотности (209 кг·м -3 ) и удельной плотности (679 кг·м -3 ) для соломы пшеницы при влажности 12%. Выход соломы составил 71,9%, а распределение частиц по размерам показало большие концентрации частиц пшеничной соломы размером от 5 до 10 меш. Композиты, изготовленные из частиц соломы пшеницы, по сравнению с контрольной обработкой показали вдвое меньшую плотность, т.е. , от 1800 до 900 кг·м -3 . Кроме того, кривая напряжения х деформации показала более высокую деформацию перед разрушением.Предварительная обработка NaOH не влияла на механические свойства композитов из пшеничной соломы.
Ключевые слова: Биомасса; Портландцемент; Сельскохозяйственные отходы; NaOH; Предварительная обработка частиц
Контактная информация: a: Факультет машиностроения, UNESP – Государственный университет Сан-Паулу, Avenida Ariberto Pereira da Cunha, 333, Guaratinguetá/SP, Бразилия; b: UNESP – Государственный университет Сан-Паулу, Кампус Итапева, Rua Geraldo Alckmin, 519, Itapeva/SP, Бразилия;
* Автор, ответственный за переписку: jvf. [email protected]
ВВЕДЕНИЕ
Использование сельскохозяйственных отходов в производстве цементно-стружечных плит является альтернативой традиционным строительным материалам. Эти композиты обладают устойчивостью к биологической порче и заражению насекомыми, а также огнестойкими свойствами и не содержат формальдегида (Qiao et al. 2016; Davies and Davies 2017). С другой стороны, эти материалы имеют ограниченные механические характеристики и чувствительны к влаге (Calegari and Oliveira 2016).
Кобрерос и др. (2014) и Naik and Kiran (2018) утверждают, что солома зерновых может заменить и улучшить качество традиционных материалов, таких как изделия из дерева и асбестоцемент, тем самым повысив их устойчивость, но в применении этих остатков достигнут незначительный прогресс. Исследования композита из частиц цемента и пшеничной соломы проводятся редко, хотя эти плиты потенциально могут заменить существующие древесные плиты в производстве мебели, а также для внутренней и наружной отделки (Qiao et al. 2016).
По данным Эльбашири и соавт. (2017), широко исследовалась возможность замены обычных строительных материалов композитами, армированными натуральными волокнами. Солома является удобным армирующим материалом в хрупкой цементной матрице, особенно в развивающихся странах, таких как Китай, где этот материал широко доступен (Khorami and Ganjian 2011; Chen et al. 2018). Необходимы дополнительные исследования, связанные с применением местных остатков лигноцеллюлозы, чтобы увеличить их использование в Бразилии, хотя документы были сосредоточены на производстве облегченных земляных блоков (Калегари и Оливейра, 2016).В этой статье используется другой подход, поскольку для производства цементно-соломенных композитов использовалась местная пшеничная солома.
Солома широко используется в строительстве, в кровельных решениях, в качестве волокнистой арматуры в самане, в облегченных земляных блоках и в сплошных земляных стенах, обладая такими преимуществами, как хорошая теплоизоляция, энергосбережение, сейсмостойкость, огнестойкость и шумоизоляция (Cobreros). и др. 2014; Елбаширы и др. 2017). С экономической точки зрения утилизация сельскохозяйственных отходов увеличивает стоимость соломы, что приносит пользу местным фермерам (Qiao et al. 2016).
Для улучшения свойств композита к лигноцеллюлозным отходам может быть применена химическая или механическая предварительная обработка. Предварительная обработка и химические добавки влияют на плотность и прочность на сжатие композитных материалов, а также на другие свойства, такие как прочность на изгиб и внутреннее сцепление (Davies and Davies 2017). Наиболее распространенными методами предварительной обработки натуральных волокон являются приготовление на пару, паровой взрыв, физическое облучение, жидкая горячая вода и химическая обработка (Elbashiry et al. 2017).
Основной целью предварительной обработки соломы является улучшение совместимости ее поверхности с цементной матрицей, что происходит за счет растворения низкомолекулярных примесей и придания поверхности шероховатости (Cai et al. 2017; Yu et al. 2017).
Щелочная предварительная обработка также вызывает некоторые изменения в пшеничной соломе, такие как увеличение площади поверхности, изменение структуры лигнина и набухание целлюлозы (Elbashiry et al. 2017).После предварительной обработки восковой слой соломенного волокна разрушается, и поверхность соломенного волокна становится шероховатой с большим количеством отверстий неправильной формы, что увеличивает шероховатость волокон и увеличивает трение между цементным тестом и соломенным волокном (Cai и др. ). 2017). В большинстве исследований представлена предварительная обработка волокон соломы вместо частиц соломы (Basta et al. . 2011; Khorami and Ganjian 2011; Qiao et al. 2016; Elbashiry et al. 2017; Naik and Kiran 2018).
Чтобы определить эффект предварительной обработки частиц соломы в композитном цементе, в этой работе были охарактеризованы композиты на основе частиц цемента и соломы пшеницы, которые были химически обработаны (раствор 2% NaOH) при двух разных температурах (30 °C и 60 °C).
ЭКСПЕРИМЕНТАЛЬНЫЙ
Пшеничная солома была предоставлена фермерами из региона Итапева в штате Сан-Паулу, Бразилия. Портландцемент, применяемый в производстве цементно-цементного композита из пшеничной соломы, относится к типу CPII – E32.Солома пшеницы была охарактеризована физически для определения ее объемной массы, удельной плотности, содержания влаги и выхода соломы, как описано в следующих подразделах.
Определение объемной и удельной плотности
Плотность биомассы определяли, как описано Lam et al . (2007). Длина каждого элемента пшеничной соломы измерялась линейкой (точность 0,1 мм), диаметр и толщина стенки измерялись штангенциркулем (точность 0,01 мм), а масса измерялась прецизионной шкалой (0,01 мм).точность 01 г).
Определялись два вида плотности: насыпная плотность и удельная плотность. Насыпная плотность рассматривала пшеничную солому как заполненный цилиндр (уравнение 1), а удельная плотность использовала толщину стенки и рассматривала пшеничную солому как полый цилиндр (уравнение 2).
В f = [(π* D ²* L )/4] * 10 -9 (1)
, где V f — объем заполненного баллона (м³), D — средний диаметр соломинки (мм), а L — длина соломинки (мм).Объем полого цилиндра (м³) определяется по формуле
В ч = [( D * t – t ²)*π* L ] * 10 -9 (07) (2)
, где t — средняя толщина стенки (мм).
Всего было использовано 69 образцов пшеничной соломы для определения насыпной и удельной плотности. Уравнение 3 в целом описывает, как определялась плотность. Плотность соломы (кг·м -3 ) определяется выражением,
D s = ( м / В ) * 10 -3 (3)
, где m – масса (г), а V – объем (м³).
Определение содержания влаги
Для определения влажности пшеничной соломы использовали 7 проб массой не менее 4,0 г. Массу образца измеряли на лабораторных весах с точностью до 0,0001 г, а затем сушили в лабораторной печи при 103 (± 2) °C до достижения постоянной массы (отклонение менее 0,2% между двумя последовательными измерениями). Содержание влаги определяли по уравнению. 4, согласно стандарту ABNT NBR 7190 (1997),
M = [( миль – мд )/( мд )] * 100 (4)
, где M — влажность (%), mi — исходная масса образца (г), а md — масса высушенного образца (г).
Определение выхода соломы
Выход соломы определяли по 6 образцам массой не менее 5,0 г, взятым с 6-13 растений. Соотношение между массой соломы и массой зерна учитывалось при получении выхода соломы (уравнение 5), который измерялся на лабораторных весах с точностью 0,01 г,
.Y = ( мс / мг ) *100 (5)
, где Y — урожай соломы (%), ms — масса соломы (г), а mg — масса зерна (г).
Производство цементных композитов из пшеничной соломы
Солому измельчали до частиц с помощью молотковой мельницы, а пропорциональный состав частиц определяли с помощью электромагнитного сита с несколькими отверстиями в соответствии с рекомендациями Qiao et al . (2016). Частицы высушивали в лабораторном сушильном шкафу при 103 ± 2 °С в течение 24 ч, достигая 3% влажности перед изготовлением композитов.
Были протестированы две предварительные обработки частиц с использованием 2% раствора NaOH в течение 2 часов.Обработку проводили на водяной бане (30 °С и 60 °С), где частицы замачивали в весовом соотношении 1:0,25 (, т.е. , раствор реагента: частицы пшеницы). После обработки частицы неоднократно промывали дистиллированной чистой водой, как описано Morsy (2011) и Elbashiry et al . (2017).
Было проведено четыре обработки: «T1» был контрольным, произведенным только с цементом и водой; «T2» — композит, изготовленный из необработанных частиц пшеничной соломы; «T3» представлял собой композит, полученный из частиц пшеничной соломы, обработанных при 30 °C; а «T4» представлял собой композит, полученный из частиц пшеничной соломы, обработанных при 60 °C. В производстве композита использовали портландцемент от Cauê InterCement ® , тип CP II E32.
Соотношение частиц соломы/цемента, используемое при производстве композитов, составляло 0,15, как указано Cai et al . (2017) как оптимальное количество пшеницы в цементных композитах. Используемое водоцементное отношение составляло 0,80, в отличие от Cai и др. . (2017), для которых оптимальным значением было 0,60 для пшеничных волокон из-за более высокого водопоглощения, наблюдаемого на частицах.
Композитные образцы цемента из пшеничной соломы были изготовлены и испытаны в соответствии со стандартом ABNT NBR 7215 (1996). Были определены следующие свойства и параметры: плотность обработки, жесткость при сжатии и прочность на сжатие через 28 дней.
Подробное описание методов характеризации приведено в следующих подразделах. Обработку производили путем смешивания частиц пшеничной соломы, цемента и воды до получения однородной смеси, а затем каждый образец формовали в короткой трубке из ПВХ цилиндрической формы (диаметром 50 мм и высотой 100 мм). Материал уплотнялся внутри трубы деревянным уплотнителем.
Определение жесткости при сжатии
Жесткость при сжатии определяли для линейного растяжения кривой напряжения по сравнению с кривой деформации , полученной для испытуемых образцов. Эти испытания также основывались на стандарте ABNT NBR 7215 (1996) и проводились на универсальной испытательной машине (EMIC, INSTRON, Itapeva, SP, Бразилия) мощностью 300 кН. Расчет жесткости на сжатие показан на формуле.8,
CS = (4 * h / π * d 2 ) * [( p 50 — p 10 ) / ( di 50 — di 10 )] (8)
где Cs жесткость при сжатии (МПа), h начальная высота образца (мм), d начальный диаметр образца (мм), ( P 50 – P 10 ) — увеличение нагрузки от 10% до 50% от P 50 – P 10 ) применяется (мм).
Статистический анализ
Было проведенотеста Тьюки (со значимостью 5%), чтобы определить, показали ли лечение значительные различия. Средние доверительные интервалы (при 5% значимости) определяли по результатам испытаний сырья. Все статистические анализы проводились с использованием программного обеспечения R версии 3.5.1 (R Core Team 2018).
РЕЗУЛЬТАТЫ И ОБСУЖДЕНИЕ
В таблице 1 показаны результаты, полученные после испытаний, проведенных с пшеничной соломой.Также представлены статистические параметры и количество рассматриваемых выборок в каждом случае.
Пшеничная солома, используемая для производства цементного композита из пшеничной соломы, имела плотность выше обычной, что объяснялось содержанием влаги в частицах. Чжан и др. . (2012) определили более низкие значения содержания влаги в пределах от 5% до 8%.
Лам и др. . (2007) определили более низкую насыпную плотность (в диапазоне от 93 до 106 кг·м -3 ) и удельную плотность (в диапазоне от 395 до 557 кг·м -3 ) пшеничной соломы по сравнению с результатами, показанными в таблице 1. Чжан и др. . (2012) проверили объемную плотность соломы пшеницы из разных регионов со значениями в диапазоне от 97,5 до 177,2 кг·м -3 .
Таблица 1. Физические свойства пшеничной соломы
Ли и Гроув (2005) изучили шесть сортов пшеничной соломы и обнаружили, что урожайность колеблется от 68% до 83%. Эти значения находятся внутри среднего доверительного интервала, показанного в таблице 1.
Распределение частиц по размерам показано графически на рис.1. Большая часть измельченной соломы имела размер от 5 до 10 меш, что считается крупными частицами. По словам Чжана и др. . (2012), от 6 до 43% частиц были крупнее 20 меш.
Рис. 1. Распределение частиц по размеру отверстий трех сит (5 меш, 10 меш и 32 меш)
В таблице 2 показаны результаты физических и механических испытаний, проведенных для композитов на основе цемента из пшеничной соломы. Значения стандартного отклонения были помещены в круглые скобки, а дисперсионный анализ показан буквами в каждой строке.
Плотность обработки T1 была в два раза выше, чем у композитов из пшеничной соломы, что указывает на значительное снижение плотности материала при добавлении частиц соломы и замене цемента. Полученные значения уступали значениям, полученным Qiao et al. (2016 г.), которые были близки к 1000 кг·м -3 .
Плотность композита не снижалась при повышении температуры предварительной обработки (, например, , обработка T4 была произведена с частицами, обработанными при самой высокой температуре, и по-прежнему демонстрировала средние значения плотности по сравнению с другими обработками).
Прочность на сжатие и жесткость композита из частиц соломы пшеницы были ниже, чем в контрольной обработке. Ожидалось снижение прочности на сжатие из-за более низкой плотности композита. Согласно Chen et al. (2018), увеличение доли соломы в композите снижает его прочность. По этой причине для использования ее в ненесущих конструкциях следует добавлять не более 5% соломы.
Таблица 2. Физические и механические свойства композитов пшеничной соломы
Частицы пшеничной соломы в процессе смешивания с цементом поглощали воду, образуя агломераты частиц внутри композита.Cai и др. (2017) описано, что волокна соломы также легко впитывают воду, что приводит к агломерации волокон соломы, что снижает механические свойства композитного материала.
Morsy (2011) изготовил композит из рисовой соломы и цемента (массовое соотношение 0,075:1), обработанный 1,0% NaOH при комнатной температуре в течение 24 часов в растворе для замачивания 10:1. Эти композиты были изготовлены с частицами размером 10 и 20 меш и достигли прочности на сжатие, близкой к значениям в таблице 1, варьирующимся от 0.от 42 МПа до 6,63 МПа.
Соотношение напряжения сжатия и деформации цементных композитов из пшеничной соломы показано на рисунке 2. Обратите внимание, что обработки T2, T3 и T4 представлены одной и той же пунктирной линией из-за одинакового механического поведения.
Рис. 2. Поведение при сжатии композита из частиц соломы пшеницы (ось сжимающих напряжений выходит за пределы шкалы)
В отличие от Morsy (2011), который сообщил, что химическая обработка улучшила механические характеристики композита, не было улучшения характеристик прочности на сжатие после химической обработки с NaOH при обеих температурах 30 °C и 60 °C по сравнению с необработанный материал.Таким образом, более длительная обработка агропромышленных остатков большим количеством замачивающего раствора давала лучшие результаты, улучшая взаимодействие композиционной матрицы и наполнителя.
Следует отметить, что кривая контрольной обработки (T1) показала хрупкое поведение, в отличие от средней кривой, представленной для композитов из соломенного цемента (T2, T3 и T4), которая показывает большую пластическую деформацию. Та же тенденция наблюдалась и в случае древесно-цементных композитных материалов, что является преимуществом для некоторых конкретных применений из-за более высокого рассеивания энергии (Frybort et al. 2008).
Между обработанной и необработанной соломой существенных различий не наблюдалось. Баста и др. (2011) подтвердили улучшение прочности на сжатие и увеличение плотности в композитах с волокнами рисовой соломы, предварительно обработанными льняным маслом. Хотя Cai и др. . (2017) утверждают, что высокие значения прочности на сжатие соломенно-цементных композитов не могут быть достигнуты, поскольку солома разлагается на сахара в щелочной среде, результаты, представленные в таблице 2, свидетельствуют о том, что щелочная обработка не повлияла на частицы.
ВЫВОДЫ
- Предварительная обработка пшеничной соломы NaOH не повлияла на прочность и жесткость композитов. Композиты, полученные с частицами соломы, показали вдвое меньшую плотность, чем контрольная обработка без соломы.
- Пшеничная солома имела более высокую насыпную и удельную плотность, а также более высокое содержание влаги, чем значения, указанные ранее.
Распределение частиц по размерам показало концентрацию крупных частиц от 5 до 10 меш. Величина выхода соломы была аналогична результатам, опубликованным ранее.
ССЫЛКИ
АБНТ НБР 7190 (1997). «Проектирование деревянных конструкций», Associação Brasileira de Normas Técnicas, Рио-де-Жанейро, RJ.
АБНТ НБР 7215 (1996). «Портландцемент – определение прочности на сжатие», Associação Brasileira de Normas Técnicas, Рио-де-Жанейро, RJ.
Баста, А. Х., Сефаин, М. З., и Эль-Равайни, И. (2011). «Роль некоторых обработок в повышении экологичности использования лигноцеллюлозных отходов при производстве цементно-волокнистых кирпичей», BioResources 6(9), 1359-1375.
Цай, Дж., Ли, Дж., Ян, С. и Сунь, Ю. (2017). «Исследование совместимости пшеничной соломы и портландцемента», в: Proceedings of the Asia-Pacific Engineering and Technology Conference 2017 , Куала-Лумпур, Малайзия, стр. 1080-1087.
Калегари, Э. П., и Оливейра, Б.Ф. де (2016). «Композиты из возобновляемых источников как альтернатива для разработки продуктов», Sustentabilidade em Debate 7(1), 140-155. DOI: 10.18472/SustDeb.v7n1.2016.17623
Чен, Дж., Эльбашири, Е.М.А., Тао, Ю., Рен, Ю., Го, З., и Лю, С. (2018). «Прогресс исследований строительных материалов на основе цемента из пшеничной и рисовой соломы в Китае», Magazine of Concrete Research 70(2), 84-95. DOI: 10.1680/jmacr.17.00064
Кобрерос, К., Эспиноса, Д., Идальго, Ф., Мансано-Рамирес, А., и Рейес, Дж. Л. (2014). «Анализ производства соломы зерновых, доступность материалов и карта провинции для производства устойчивых сборных панелей», BioResources 9(1), 786-800.
Дэвис, И. О. Э., и Дэвис, О. О. А. (2017). «Цементно-стружечные плиты из агроотходов: обзор», MAYFEB Journal of Environmental Science 2, 10–26.
Эльбашири, Е.М.А., Чен, Дж., Туо, В., Рен, Ю. и Го, З. (2017). «Обзор методов предварительной обработки строительных материалов из пшеничной соломы», Journal of Reinforced Plastics & Composites 37(1), 35-48. DOI: 10.1177/0731684417730442
Фрайборт С., Мауриц Р., Тайшингер А. и Мюллер У.(2008). «Композиты на цементной основе — механический обзор», BioResources 3(2), 602-626.
Хорами, М., и Ганджян, Э. (2011). «Сравнение поведения при изгибе фиброцементных композитов, армированных жмыхом: пшеница и эвкалипт», Construction and Building Materials 25(9), 3661-3667. DOI: 10.1016/j.conbuildmat.2011.03.052
Лам, П.С., Сохансандж, С., Би, X., Мани, С., Лим, С.Дж., Вомак, А.Р., Хок, М., Пэн, Дж., ДжаяШанкар, Т., Наими, Л.Дж., и Наяран, С.(2007). «Физические характеристики влажной и сухой соломы пшеницы и проса – объемная и удельная плотность», в: Ежегодное международное совещание ASABE 2007 , Миннеаполис, США, стр. 1-22.
Ли, К., и Гроув, Дж. (2005). Урожайность соломы шести сортов мелкозерновых , Департамент растениеводства и почвоведения, Университет Кентукки, Лексингтон, США. (https://wheatscience.ca.uky.edu/sites/wheatscience. ca.uky.edu/files/rr04-05pg3.pdf)
Морси, Миннесота (2011). Свойства вяжущего композита из рисовой соломы , Ph.D. Диссертация, Дармштадтский технологический университет, Александрия, Египет.
Найк, Д. Л., и Киран, Р. (2018). «Наивный байесовский классификатор, многомерная линейная регрессия и экспериментальное тестирование для классификации и характеристики пшеничной соломы на основе механических свойств», Industrial Crops & Products 112, 434-448. DOI: 10.1016/j.indcrop.2017.12.034
Цяо, Дж., Ван, А., и Ли, X. (2016). «Приготовление и применение композитной плиты из пшеничной соломы с неорганическим клеем», BioResources 11(1), 819-826.DOI: 10.15376/biores.11.1.819-826
Основная группаR (2018 г.). «R: язык и среда для статистических вычислений», R Foundation for Statistical Computing , Вена, Австрия, (https://www.R-project.org/).
Ю Т., Рен Ю., Го З. и Чен Х. (2017). «Ход исследований строительных материалов на основе цемента из хлопковой и кукурузной соломы в Китае», Advances in Cement Research, 30(3), 93-102.