Керамзитоблока состав: состав, виды, характеристики плюсы и минусы блоков из керамзитобетона
состав, виды, характеристики плюсы и минусы блоков из керамзитобетона
Керамзитоблок – это строительный камень, получаемый методом полусухого вибропрессования, имеющий форму прямоугольного параллелепипеда, производимый из керамзитобетона — смеси вяжущего вещества (цемента), наполнителя (песка, керамзита) и воды.
1. Состав керамзитоблока.
Представим состав керамзитобетонной смеси с удельным весом 1500 кг/м 3 в виде таблицы*.
Таблица 1: Состав керамзитобетонной смеси
Наименование материала | Масса, кг | % от массы |
---|---|---|
Цемент М400 | 430 | 26,7 |
Керамзит | 510 | 34 |
Песок | 420 | 28 |
Вода | 140 | 9,3 |
*Данные приведены для 1м3 керамзитобетонной смеси.
При снижении % содержания цемента и песка удельный вес керамзитобетонной смеси будет уменьшаться.
В составе легких смесей с удельным весом до 1000 кг/м 3 песок может отсутствовать, содержание цемента уменьшается, а керамзита — растёт.
1.1. Цемент (ГОСТ 10178-85).
Для производства блоков необходим цемент марки не ниже М-400.
1.2. Керамзит (ГОСТ 9757-90).
Керамзит – легкий пористый материал в виде гравия, получаемый в результате обжига легкоплавких глинистых пород. Чаще всего для производства керамзитоблоков используют фракции 5-10 мм.
1.3. Песок (ГОСТ 8736-93).
В качестве наполнителя используется песок крупной или средней фракций, который создаёт скелет блока.
1.4. Вода (ГОСТ 23732-79).
Предпочтительно применение воды без загрязняющих примесей.
2. Классификация.
Керамзитоблоки являются стеновыми бетонными камнями и должны соответствовать ГОСТ 6133-99. Они классифицируются по следующим параметрам:
2.1. По назначению.
- Теплоизоляционные (удельный вес 350-600 кг/м 3) — применяют для утепления зданий.
- Конструктивно-теплоизоляционные (удельный вес 600-1400 кг/м 3) — используют преимущественно для возведения однослойных стеновых панелей.
- Конструктивные (удельный вес 1400-1800 кг/м 3) — используются для несущих конструкций домов и инженерных сооружений (мосты, эстакады).
2.2. По применению.
- Стеновые блоки – для строительства стен (как наружных, так и внутренних).
- Перегородочные блоки – для возведения перегородок.
2.3. Размеры.
- ГОСТ 6133-99 предусматривает следующие размеры блоков для стен: 90х190х188мм, 190х190х188мм, 290х190х188мм, 390х190х188мм, 288х138х138мм, 288х288х138мм.
- Размеры перегородочных блоков — 190х90х188мм, 390х90х188мм, 590х90х188мм.
По согласованию с заказчиком размеры блоков могут меняться.
2.4. По форме.
- Полнотелые – сплошные блоки без пустот.
- Пустотелые – блоки как с глухими, так и со сквозными пустотами, формируемыми в процессе изготовления для придания блоку необходимых эксплуатационных характеристик.
3. Характеристики.
3.1. Прочность.
Значения прочности керамзитоблоков:
- теплоизоляционных — 5-25 кг/см2;
- конструктивно-теплоизоляционных – 35 — 100 кг/см2;
- конструктивных — 100 — 500 кг/см2.
3.2. Объёмный вес.
Объёмный вес керамзитоблоков:
- теплоизоляционных — 350-600 кг/м 3;
- конструктивно-теплоизоляционных – 600 — 1400 кг/м 3;
- конструктивных — 1400 — 1800 кг/м 3.
3.3. Теплопроводность.
Теплопроводность керамзитоблоков – 0,14-0,66 Вт/(м*К). Теплопроводность растёт с увеличением содержания цемента. По этому показателю теплоизоляционные блоки находятся на уровне дерева. Даже конструктивные предпочтительнее бетона и кирпича. Применение в строительстве пустотелых блоков уменьшает теплопроводность стен и делает дом теплее.
3.4. Морозостойкость.
Морозостойкость увеличивается с уменьшением пористости. Минимальные значения (15 — 50 циклов) — у теплоизоляционных керамзитоблоков. У конструктивно-теплоизоляционных — до 150 циклов, у конструктивных — до 500.
3.5. Усадка.
Усадка керамзитоблоков находится на уровне тяжелых бетонов — 0,3-0,5 мм/м.
3.6. Водопоглощение.
Водопоглощение керамзитоблоков – 5 — 10% по массе. Значение может быть снижено путём добавления в керамзитобетонную смесь комплексных добавок и пластификаторов.
3.7. Паропроницаемость.
Паропроницаемость керамзитоблоков — 0,3-0,9 мг/(м*ч*Па). Значение увеличивается с увеличением пористости и степени пустотелости. Для теплоизоляционных блоков значения максимальны, для конструктивных – минимальны.
3.8. Огнестойкость.
Предел огнестойкости керамзитоблоков – 180 минут при температуре 1050 С.
3.9. Стоимость.
Стоимость керамзитоблоков зависит от степени пустотелости, от прочности, определяющейся содержанием цемента, и находится в пределах 2200-3500 руб/м3.
3.10. Звукоизоляция.
Звукоизоляционные свойства керамзитоблоков улучшаются с увеличением пористости. Перегородка из теплоизоляционных блоков размерами 590х90х188 мм обеспечивает звукоизоляцию на уровне 45-50 Дб.
3.11. Максимальная этажность строения.
Конструктивные керамзитоблоки позволяют осуществлять высотное строительство. Возможно возведение 12-этажных домов
Таблица 2: Характеристики керамзитоблоков
Наименование показателя | Значение | Комментарий |
---|---|---|
Прочность, кг/см2 | 5-500 | Минимальные значения прочности — у легких теплоизоляционных блоков, максимальные — у самых тяжелых конструктивных |
Объемный вес, кг/м3 | 350 -1800 | При увеличении % содержания цемента в керамзитобетонной смеси увеличится объемный вес и прочность |
Теплопроводность, Вт/м*К | 0,14 – 0,66 | Показатель лучше, чем у кирпича и бетона; ухудшается с ростом % содержания цемента.![]() |
Морозостойкость, циклы | 15-500 | Минимальные значения — у легких теплоизоляционных блоков, максимальные — у самых тяжелых конструктивных |
Усадка, мм/м | 0,3 — 0,5 | Хороший показатель на уровне тяжелых бетонов |
Водопоглощение, % | 5-10 | Хороший показатель, который может быть улучшен применением комплексных добавок и пластификаторов |
Паропроницаемость, мг/(м*ч*Па) | 0,3-.0,9 | Высокое значение в сравнении с другими стройматериалами; увеличивается с ростом пористости и степени пустотелости блоков |
Огнестойкость, мин. при температуре 1050 С | 180 | Значение выше, чем у других легких бетонов |
Стоимость руб/м3 | 2200-3500 | Зависит от содержания цемента в смеси и степени пустотелости |
Звукоизоляция, Дб | 45-50 | Значение для перегородки из теплоизоляционных блоков размерами 590х90х188 мм; показатель растёт с увеличением содержания керамзита |
Максимальная этажность строения, этажей | 12 | Достигается при использовании конструктивных блоков |
4.

- Экологическая безопасность. Керамзитобетон производится из натуральных материалов (цемент, песок, глина), что обеспечивает его высокую экологичность. Материалу присвоен первый класс радиационной безопасности. Он полностью соответствует современным санитарно-гигиеническим требованиям по показателям звукоизоляции и паропроницаемости.
- Теплопроводность керамзитобетона и использование в строительстве пустотелых блоков делает дома из этого материала теплыми.
- Низкий удельный вес керамзитоблоков позволяет сэкономить на устройстве фундамента и транспортировке.
- азмеры и вес блоков снижают затраты рабочей силы и цементного раствора при возведении стен, ускоряют строительство.
- Низкая гидроскопичность и, как следствие, высокая морозоустойчивость повышают срок службы сооружений из керамзитоблоков, дают возможность экономии на защите стен.
- Применение блоков со сквозными пустотами позволяет сооружать внутри стен силовые каркасы, повышающие несущую способность конструкций.
- Низкие значения усадки обеспечивают экономию на косметических ремонтах.
5. Минусы строительства из керамзитоблоков.
- Керамзитобетон уступает в прочности тяжелым бетонам. Нежелательно использование керамзитоблоков при устройстве фундаментов.
- Неидеальная геометрия блоков.
- При многоэтажном строительстве необходимо использовать блоки с повышенным содержанием цемента. Следствием этого является необходимость устройства более мощного фундамента, ухудшение теплоизоляционных качеств сооружения и общее удорожание проекта.
6. Область применения.
В зависимости от назначения керамзитоблоки могут использоваться для утепления домов, строительства зданий (в том числе многоэтажных), возведения инженерных сооружений (мостов, эстакад).
7. Способы транспортировки.
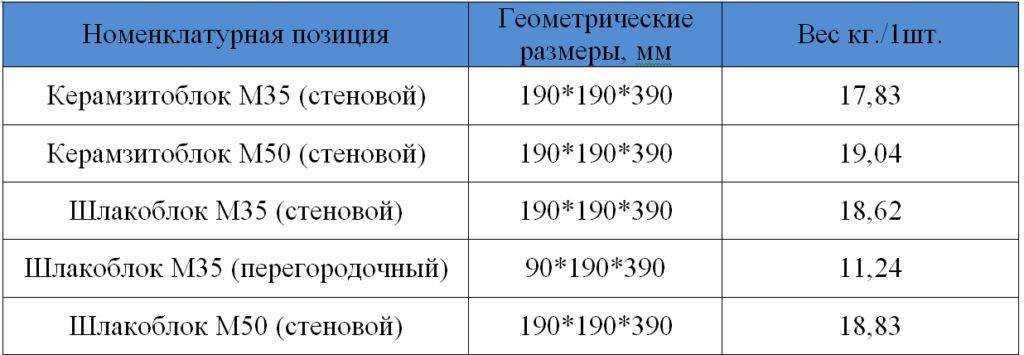
Перевозка керамзитоблоков осуществляется любым транспортом на поддонах. Высота пакета с поддоном не должна превышать 1,3 м. Камни с глухими отверстиями укладывают пустотами вниз. Сформированные транспортные пакеты складируются в один ярус. Не допускается проведение разгрузочно-погрузочных работ вручную.
Вопросы и ответы по теме
По материалу пока еще не задан ни один вопрос, у вас есть возможность сделать это первым
Что такое керамзитоблоки, их виды, фото, состав и марки, отличия от пеноблока, газоблока, шлакоблока и газобетона
Керамзитоблоки являются эффективным строительным материалом, получившим известность около полувека назад. При его производстве применяется смесь цемента, песка, керамзита и воды. Добавка керамзита в этот состав обеспечивает материалу легкость и теплоустойчивость, не приводя к значительному ухудшению прочностных качеств.
Разновидности керамзитоблоков – от конструктивных особенностей к применению
Классификация материала выделяет готовые изделия по таким направлениям:
- конструкционные свойства – пустотелые и полнотелые;
- предназначение – стеновые, перегородочные и облицовочные.
Стеновой (конструкционный) керамзитоблок – применяется для кладки несущих стен. Материал имеет большую прочность и выдерживает давление до 5 МПа (марка М50).
В зависимости от особенностей применения стеновые керамзитоблоки могут быть полнотелыми и пустотелыми.
Полнотелые блоки используются для ответственных конструкций в двух- и трехэтажных домах. Пустотелые блоки оптимальны для одноэтажных зданий, обеспечивая максимальное сохранение тепла.
Применение керамзитоблоков в строительстве реализует две задачи – сэкономить на более дорогом кирпиче и получить тёплое здание. Эти задачи взаимосвязаны, поскольку пористый камень позволяет делать стены тоньше, снижая затраты на работу и расходные материалы.
Перегородочный (простеночный) керамзитоблок отличается от стенового меньшими размерами. Высота таких блоков обычно больше ширины, поскольку не требует выдерживать большие нагрузки и препятствовать температурному воздействию.
Облицовочный керамзитоблок – относится к разновидности конструкционных блоков и существенно ускоряет темп строительства, обеспечивая отделку стен с внешней стороны. Облицовочные блоки могут быть окрашенными или иметь декоративное покрытие.
Окрашенные и цветные блоки содержат в составе природные цветные глины или добавленные при производстве пигменты. Неорганическая природа последних отличается устойчивостью к воздействию окружающей среды, по сравнению с органическими красителями.
Декоративное наружное покрытие может имитировать камень, вагонку или разновидности штукатурки. Керамзитоблоки с облицовкой обычно массивны и заменяют 4-5 обычных блоков.
Их размеры составляют до 60?30?40 см (длина ? высота ? ширина), что позволяет делать кладку в один слой. Крупные размеры камня создают неудобства при переноске и укладке, но все равно позволяют выиграть в скорости работы.
Кладка из керамзитобетона – это отличная база для дальнейшей отделки. Она обладает хорошей теплоизоляцией, морозостойкостью и с легкостью поддается обработке.
В отдельный вид иногда выделяют
Характеристика керамзитоблоков и соответствие требованиям стандартов
Размеры камня и другие прочностные и эксплуатационные свойства нормируются требованиями ГОСТ 6133-99. Наиболее востребованные из стандартных блоков имеют габариты 390?190?188 мм, которые в коммерческих предложениях часто обозначены размерами 40?20?20 см.
Отличия связаны с допустимыми отклонениями (до 2-4 см) и прослойкой раствора, находящейся в кладке.
Прочность керамзитобетонных блоков характеризуется маркой – средним значением выдерживаемого давления (прочность на сжатие), выраженного в кгс/см2.
Класс морозоустойчивости блоков показывает количество циклов замерзания и оттаивания без существенной потери прочности и обозначается буквой F.
Для стен домов в центральной части РФ класс морозоустойчивости не должен быть хуже F25. Класс F15 подойдет для регионов страны с умеренным климатом. Морозы Сибири и сильные изменения погодных условий вынуждают использовать камни класса F50 и лучше.
Керамзитобетон выпускается специализированными предприятиями, способными правильно воспроизвести технологию производства. Фирмы-однодневки, не использующие автоматизированные системы смешения и дозировки компонентов, никогда не произведут качественный продукт.
Производство керамзитобетона основано на использовнии цемента, воды и керамзита. Керамзит получают путем обжига легкоплавкой глины.
Стоимость материала находится в пределах 2,5-4,5 тыс. р./м3. Самые легкие пустотелые блоки обойдутся в минимальную цену, соответствующую уровню газо- и пенобетона, обладая близкими к ним параметрами качества.
Характеристика керамзитоблоков, в сравнении с материалами-конкурентами
Среди существующих разновидностей строительных камней, являющихся альтернативой кирпичным и бетонным строениям, выделяются следующие:
- шлакоблок;
- пеноблок;
- газоблок.
Все строительные материалы отличаются индивидуальными свойствами. В зависимости от требований, которые предъявляются к зданию, его предназначения, а также погодных условий и бюджета стройки, можно выбрать наиболее подходящий вариант.
Свойства готовых изделий определяются содержанием керамзита и размером фракций. Все характеристики керамзитоблоков определяются ГОСТом и должны иметь соответствующий сертификат соответствия.
К примеру, главным отличием керамзитоблока от шлакоблока является использование керамзита в качестве добавки, а не шлака.
Сравнивая керамзитоблоки с другими камнями, стоит обращать внимание на комплекс их основных характеристик:
Свойства | Керамзитоблоки | Газосиликатные блоки | Пенобетонные блоки | Шлакоблок |
Плотность | От низкой до высокой | Низкая | Средняя | Средняя, высокая |
Теплопроводность | 0,10-0,30 Вт/(м2·?С) | 0,10-0,15 Вт/(м2·?С) | 0,14-0,30 Вт/(м2·?С) | 0,32-0,50 Вт/(м2·?С) |
Водопроницаемость | Керамзит в составе блоков может впитывать влагу, однако при соблюдении технологии производства эта проблема несущественна | Очень гигроскопичны | Гигроскопичны | Слабо гигроскопичен, однако быстро разрушается при воздействии воды |
Экологичность | Не обладает выраженными токсичными свойствами | Сами по себе не токсичны, однако после обводнения являются инкубатором грибков | Безопасен при современной технологии производства.![]() | Возможно выделение вредных веществ из шлака, а также не исключён повышенный естественный радиоактивный фон |
Прочность на сжатие | Средняя, не характеризуется большой долей брака в поставляемой продукции | Низкая | Низкая | Средняя, высокая |
Стоимость | От низкой до высокой – широкий ценовой диапазон | Низкая, однако может увеличиться во время эксплуатации | Низкая, на уровне газосиликатного материала | Низкая, средняя |
Возможность облицовки стен | Присутствует | Отсутствует.Требуют обязательной внутренней и внешней отделки | Присутствует | Присутствует |
Морозостойкость | Средняя, высокая | Высокая | Высокая | Высокая |
Разрушение при эксплуатации, деформация при усадке строения | Не характеризуются склонностью к разрушению, усадка минимальная | Высокое, склонны к значительной усадке | Склонны к ускоренному разрушению при повышенной влажности | Достаточно легко разрушаются (крошатся), однако не склонны к образованию трещин по всей толщине конструкции |
Отклонения в размерах блоков | Средние, компенсируются различным количеством раствора | Минимальные.![]() | Средние, компенсируются различным количеством раствора | Низкие, особенно для распространенных блоков кустарного производства. Компенсируются различным количеством раствора |
Керамзитоблоки обладают оптимальным комплексом свойств из альтернативных строительных материалов, отличаясь высокой стоимостью. Что лучше, решать потребителю, ориентируясь на предназначение будущей постройки.
Разумеется, нет смысла переплачивать за строительный материал, если его можно заменить более дешевым. Однако при желании сэкономить на кирпичной кладке и получить прочную, теплую и экологически безопасную постройку, керамзитобетонные блоки будут хорошим выбором.
В подтверждение этому можно посмотреть видео о том, чем керамзитоблоки лучше ячеистых бетонов:
размеры, плюсы и минусы, свойства, характеристики ГОСТ
Выбрать материал для строительства дома очень сложно. Дом должен быть теплым, надежным и прочным. А еще, очень желательно, чтобы материал для возведения стен был недорогим. Очень сложно «уместить» все параметры в один материал. Один из вариантов – блоки из керамзитобетона. Материал далеко не идеальный, но теплый, легкий, недорогой. Также размер керамзитобетонного блока может быть разным, что облегчает выбор оптимального размера.
Содержание статьи
- 1 Что такое керамзитобетонные блоки по ГОСТ
- 2 Плюсы и минусы дома из керамзитоблоков
- 2.1 Преимущества строительства из керамзитобетона
- 2.2 Недостатки
- 3 Размер керамзитобетонного блока по стандарту
- 3.1 Популярный размер керамзитобетонного блока для стен и перегородок
- 3.2 Нестандартные размеры
- 4 Типы керамзитобетонных блоков
- 4.1 Марки плотности и прочности на сжатие
- 5 Типовые решения для средней полосы
Какие керамзитобетонные блоки по ГОСТ
относят к керамзитобетонам 900 конкретный.
Дом из керамзитобетонных блоков строится быстро
Существует две технологии заводского изготовления изделий до нормальной прочности — в автоклаве и вибропрессование. В первом случае блоки отправляются в автоклав, где материал обрабатывается паром под давлением. Это делает керамзитобетонные блоки более прочными. Второй способ – вибрация с одновременным давлением. При вибрировании уходят все пустоты, раствор становится более однородным и текучим, обволакивая каждую из гранул керамзита. Результат – высокие прочностные показатели.
В кустарном производстве блоки просто оставляют «созревать». Теоретически для набора прочности бетону требуется не менее 28 дней. Но их можно продать раньше, чтобы они не занимали место. При этом прочность никто не гарантирует.
На поверхности блока угадываются округлые гранулы керамзита. В зависимости от марки они могут быть разных размеров, больше или меньше
Дело в том, что для нормального набора прочности цемента необходимо создание определенного тепловлажностного режима. Керамзитобетон в этом плане более капризен, чем обычный бетон. Из-за высокой впитывающей способности керамзита он может набрать слишком много воды. И жидкости будет недостаточно, чтобы бетонный камень набрал прочность, а не просто высох. Поэтому готовые блоки желательно поливать и накрывать пленкой хотя бы на несколько дней после изготовления. Не держите их на солнце и температура должна быть не ниже +20°С. В противном случае керамзитоблоки никогда не наберут необходимой прочности и будут крошиться даже при незначительных нагрузках и ударах.
Фабричные блоки стоят дороже. Но все равно. Если вы строите дом, а не хозблок или сарай, не стоит экономить и покупать блоки «гаражного» производства. Качество тут сомнительное.
Плюсы и минусы дома из керамзитоблоков
Керамзитблоки в разы больше кирпича… Даже вдвое. Размер легкого бетонного блока можно сравнить только с керамическими строительными блоками. А вот керамзитоблоки весят меньше, имеют лучшие характеристики теплопроводности. И, что немаловажно, намного дешевле. Прочность и морозостойкость сопоставимы с керамическим кирпичом.
Кладка кирпича похожа на работу с кирпичом, только быстрее
Преимущества строительства из керамзитобетона
К преимуществам домов из керамзитоблоков можно отнести следующие моменты:
Блоки могут иметь пазогребневую систему, что улучшает теплотехнические характеристики кирпичной кладки. Материал натуральный, дышащий, поэтому проблем с регулированием влажности в помещениях не возникнет.
недостатки
Дома из керамзитобетона имеют и серьезные недостатки. Их необходимо учитывать при выборе строительного материала.
Основной недостаток – высокая гигроскопичность. Глиняные гранулы могут поглощать много воды. Блоки, длительное время находящиеся на открытом воздухе, весят в несколько раз больше, чем те, которые остаются в сухих помещениях. Цемент от влаги становится только крепче. А вот сырые стены вряд ли вас порадуют. Поэтому важно сделать качественную гидроизоляцию фундамента, перекрыть все возможные источники «подсоса» влаги. Крышу лучше сделать с большими свесами и соорудить качественную водосточную систему.
Размер керамзитобетонного блока по стандарту
Дело в том, что отдельного стандарта на керамзитобетонные блоки не существует. Этот вид материала описывается группой стандартов, стандартизирующих легкие бетоны и изделия из них. Так размеры стеновых блоков из легкого бетона установлены ГОСТ 6133-99.
Типоразмер керамзитобетонного блока по ГОСТ 6133
Также указаны предельные отклонения. Они имеют длину ± 3 мм, высоту ± 4 мм, толщина стенок между перегородками может быть на 3 мм больше (тоньше быть не может).
Популярный размер керамзитобетонного блока для стен и перегородок
Чаще всего для кладки стен используются керамзитобетонные блоки размером 390*190*188 мм. Получается очень удобно, так как для средней полосы России оптимальная толщина стен 400 мм. То есть кладка ведется «в один блок». Перегородки обычно требуют меньшей толщины 90 мм. Длина и высота остаются прежними. То есть размер керамзитобетонного блока для перегородок 390 * 90 * 188 мм. Это не означает, что перегородки нельзя делать из более длинных или более коротких перегородочных пластин. Можно, но более короткие — больше швов, больше расход раствора, а более длинные — тяжелее, с ними труднее работать.
Перегородка из керамзитобетона: размеры по ГОСТ
Если вы хотите иметь наилучшие параметры звукоизоляции между помещениями, перегородки также можно сложить из стеновых блоков. Либо стандартная ширина 190 мм, либо те что тоньше 138 мм. Но затраты выше.
Нестандартные размеры
Стандарт содержит приписку, что по согласованию с заказчиком размер керамзитобетонного блока может быть любым. Так что можно найти продукцию любого формата.
Размер керамзитобетонного блока данного формата нельзя точно отнести к стандарту
Кроме того, существуют еще технические условия (ТУ), которые разрабатываются и регистрируются самими предприятиями. Если собираетесь закупать большую партию и маркировка не ГОСТ 6133-99, но ТУ, лучше ознакомиться с этим документом, чтобы не было сюрпризов.
Виды керамзитоблоков
Торцы блоков могут быть желобчатыми, плоскими или желобково-шпунтовыми. Для использования в углах один край может быть гладким. Кроме того, углы могут быть закругленными или прямыми. На опорных поверхностях (куда укладывается раствор) можно сформировать пазы для укладки арматуры. Эти пазы должны располагаться на расстоянии не менее 20 мм от угла.
Пример блоков пазогребневых стеновых керамзитобетонных и их цены
Блоки бывают с пустотами и без. Пустоты могут быть сквозными или нет, они располагаются равномерно, перпендикулярно рабочей поверхности. Максимально допустимый вес строительного блока из легкого бетона составляет 31 кг. Стандарт нормирует толщину стен, ограждающих пустоты:
- наружных стен — не менее 20 мм;
- перегородка над глухими пустотами — не менее 10 мм;
- между двумя пустотами — 20 мм.
Пустоты часто делают плоскими — в виде трещин. Количество «линий» с пустотами определяет теплопроводность материала. Чем больше пустот, тем теплее (и тише) будет стена. Воздух, как известно, плохо проводит тепло. В любом случае хуже бетона. Поэтому разбиение блока пустотами дает хороший результат.
Марки плотности и прочности на сжатие
По прочности и теплопроводности керамзитобетонные блоки делятся на две категории: конструкционно-конструктивно-теплоизоляционные. Каждая из групп может содержать изделия разной плотности. Плотность – это сухой вес одного кубического метра материала. Примерное значение после буквы Д. Например, Д600 — масса кубометра 600 кг, Д900 — 900 кг. И т.д.
В частном домостроении обычно применяют конструкционные и теплоизоляционные блоки. Для возведения наружных стен одноэтажных домов применяют керамзитобетонные блоки марки Д700 или Д800; для внутренних ненагруженных перегородок можно брать и более низкие марки.
Типовые решения для средней полосы
При строительстве дома правильнее всего заказать проект. Здесь вам все учтут, пропишут все узлы, материалы, в том числе размер керамзитобетонного блока, его параметры и количество. Осталось только купить все по списку. Но так делают немногие. Проект затратный, а денег мало. Поэтому сами пытаются «прикинуть» без расчета. Позиция тоже понятная, но не всегда приводит к экономии, т. к. «типовые решения» делаются с запасом прочности, а это растрата материала. Но, в целом, есть проверенные варианты составов пирога наружных стен из керамзитоблоков для России.
При выборе керамзитоблоков смотрим на два показателя: класс прочности на сжатие — для несущих стен он должен быть не ниже В3,0 (с запасом). Второй показатель – коэффициент теплопроводности. Чем она ниже, тем лучше.
Строительные заполнители, произведенные из глиняного кирпича, содержащего гипс
1 Исходная ситуация
Глиняные кирпичи для кладки являются строительными материалами с давними традициями. Дальнейшее развитие свойств их продукции является предметом широкого круга усилий. Чтобы подтвердить устойчивость этих строительных материалов, в настоящее время основное внимание уделяется их вторичной переработке как новому аспекту. Особенно это относится к легким глиняным кирпичам с наполнителем из теплоизоляционных материалов, которые используются для наружных стен. В качестве внутренней штукатурки часто используются строительные материалы на основе гипса из-за их строительно-физических свойств. С точки зрения утилизации минеральные теплоизоляционные материалы являются примесями, а гипс нежелателен как с точки зрения применения, так и с точки зрения водохозяйственной деятельности. В более ранних исследованиях было доказано, что теплоизоляционные материалы можно отделить от кирпича грубого помола с помощью разделения воздуха [1]. Для размеров частиц <8 мм это невозможно. Для гипсовых штукатурок не существует подходящего процесса механического разделения. Их удаление до демонтажа возможно, но это очень трудоемкий и дорогостоящий процесс.
Одним из подходов, позволяющих перерабатывать гипссодержащие отходы глиняного кирпича, является их использование в качестве сырья для производства легкого заполнителя со свойствами продукта, соответствующими свойствам стандартизированных легких заполнителей, таких как керамзит. Подход основан на собственных исследованиях авторов по утилизации кирпичсодержащих строительных отходов [2], [3], [4], [5]. В соответствии с этим кладочный щебень с содержанием кирпича не менее 50% масс. можно перерабатывать в термическом процессе до легкого заполнителя. Исходный материал измельчают, измельчают, добавляют вспенивающий агент и гранулируют на гранулирующем диске. При последующей термической обработке сырые грануляты стабилизируются и одновременно вспучиваются при температуре от 1 150 до 1 250 °С. Требование к расширителю состоит в том, чтобы в интервале температур образования фазы расплава он разлагался с выделением газообразного компонента.
Далее сообщается об исследованиях, в которых вначале в качестве исходного материала для производства легкого заполнителя использовалась модельная стена, состоящая из вертикально перфорированных глиняных кирпичей с гипсовой штукатуркой. Во-вторых, применялись глиняные кирпичи с наполнителем из теплоизоляционных материалов с добавлением гипса в качестве вторичного сырья.
2 Современные знания
Современные знания о генезисе легких заполнителей основаны главным образом на гранулятах, изготовленных из глин. Процесс расширения может иметь место только при наличии достаточного количества фазы расплава с соответствующей вязкостью в температурном диапазоне, в котором выделяется расширительный газ. Приблизительная оценка потенциала исходного материала в отношении фазообразования плавления возможна на основе содержания оксидов SiO 2 , Al 2 O 3 , Fe 2 O 3 , CaO, MgO, K 2 O и Na 2 O. Вязкость расплава зависит от соотношения содержания флюса к содержанию свободного кварца. За образование расширительного газа ответственны различные химические реакции. В качестве основного источника расширения газа определены окислительно-восстановительные реакции оксидов железа с органическим углеродом, когда они протекают в интервале температур пиропластического состояния.
Для проверки пригодности глинистого сырья и отходов для производства легких заполнителей обычно используется тройная диаграмма, опубликованная Райли в 1953 г. и дополненная Уайтом в 1960 г. [6], [7]. Диаграмма Райли основана на измерениях вздутия, т. е. расширения 39 глин со Среднего Запада США. Легкие грануляты, изготовленные из них, имеют плотность от 290 до 990 кг/м³. Чтобы лучше представить конкретную роль оксидов железа в процессе расширения, эта диаграмма была далее развита Куньи до четвертичной диаграммы в 1990 [8].
Идея разделения гипса с помощью этого процесса основана на фундаментальных исследованиях термического разложения сульфата кальция. Из исследований, проведенных в начале прошлого века, которые и сегодня остаются нашим текущим уровнем знаний, известно, что термическая диссоциация ангидрита происходит только выше 1 200°С [6]. В присутствии других оксидов разложение смещается в сторону более низких температур:
Диссоциация ангидрита в присутствии кремниевой кислоты
CASO 4 + SIO 2 Casio 3 + SO 2 + 0,5 O 2
Начало разложения при 1000 ° C, конец 1 250 ° C
Присутствие оксида железа
CASO 4 + FE 2 O 3 CAO*FE 2 O 3 + SO 2 + 0,5 O 2 400092 , конец при 1 250 °C
При соблюдении этих температур не предотвращается снижение содержания сульфатов и увеличение объема, вызванное процессом расширения, и их можно использовать для разделения гипса с одновременным получением вспученных гранулятов.
3 Характеристика исходных материалов
Следующие исходные материалы поставлялись производителями гипса и глиняного кирпича и плитки:
Модель стены, построенная из вертикально перфорированных глиняных кирпичей и оштукатуренная гипсовой штукатуркой (»Рис. 1)
Один поддон из глиняных кирпичей, заполненных минеральной ватой, и один поддон из глиняных кирпичей, заполненных перлитом (»Рис. 2), к которым были добавлены измельченные гипсовые формы.
Глиняные кирпичи, заполненные минеральной ватой, состояли из 80,0 % по массе глиняного кирпича и 20,0 % по массе минеральной ваты. Кирпичи, наполненные перлитом, состояли из 88,2% масс. кирпича и 11,8% масс. перлита. В поставляемый глиняный кирпич с наполнителем добавляли различные гипсовые компоненты в количестве 5,0 и 15,0% масс. в виде измельченных гипсовых форм и гипсовых штукатурок.
Для приготовления исходных смесей поставляемые материалы измельчались в щековой дробилке. Затем добавляли карбид кремния SiC, используемый в качестве расширителя. Смеси измельчали в шаровой мельнице и при этом гомогенизировали. После измельчения в случае модельной стенки 98 об.% исходного материала приходится на частицы размером < 63 мкм. В случае глиняных кирпичей содержание < 63 мкм составляло 90 об.% для глиняных кирпичей, наполненных минеральной ватой, и 85 об.% для глиняных кирпичей, наполненных перлитом.
Химический состав исходных материалов (»Таблица 1) различается содержанием Al 2 O 3 и CaO. Содержание Al 2 O 3 несколько выше в глиняных кирпичах, наполненных перлитом, содержание СаО несколько ниже. Количество добавленного гипса отражается на увеличении содержания SO 3 .
Первую оценку пригодности исходных материалов для производства расширенных гранулятов дает тройная диаграмма для SiO 2 – флюс FA – Al 2 O 3 . Используемые здесь материалы лежат полностью внутри или немного снаружи областей, типичных для керамзита (»Рис. 3). При добавлении гипса содержание СаО незначительно увеличивается. Состав немного смещается в сторону «уголка флюса».
Для возможности использования термического процесса производства облегченного гранулята для десульфатации обезвоженный до ангидрита гипс должен разлагаться в диапазоне температур, не превышающем интервал расширения, вызванный выделением расширительного газа. Это было подтверждено с помощью анализа дифференциального сканирования и микроскопии на предметном столике в горячем состоянии. При микроскопическом анализе на горячем этапе цилиндрический образец нагревают в трубчатой печи, и изменение площади его тени определяется в зависимости от температуры с помощью камеры и наносится на график с помощью программного обеспечения устройства. Температуры, при которых возникают характерные формы, полученные при исследовании шлака [9].] выводятся, как и все данные измерения изменения площади в зависимости от температуры образца. Результаты дифференциального сканирующего анализа и микроскопии в горячем состоянии показаны в качестве примера для модельной стены, построенной из вертикально перфорированных глиняных кирпичей на »рис. 4 и »рис. 5. Согласно им, разложение CaSO 4 , происходит из гипсовой штукатурки, происходит в интервале температур от 975 до 1 100 °С (»рис. 4). При сферической температуре 1 186 °C цилиндрические зеленые грануляты принимают форму шариков (»рис. 5 вверху). Увеличение площади достигает первого максимума при 1 147 °C. Он завершается при 1 226 °C (рис. 5 внизу). Соответственно, вышеуказанное условие выполняется.
4 Производство расширенных гранулятов на пилотной установке IAB
4.1 Этапы процесса и используемые агрегаты
На первом этапе процесса высушенные и грубо измельченные исходные материалы измельчались партиями по 200 кг каждая в шаровой мельнице с объем камеры 500 литров (»рис 6). Затем зеленые гранулы были приготовлены на грануляционном поддоне диаметром 1,0 м (»Рис. 7). После повторной сушки эти гранулы обжигали во вращающейся печи, обогреваемой природным газом (»Рис 8). Вращающаяся печь имеет внутренний диаметр 0,60 м и облицована слоем огнеупорного раствора толщиной 0,15 м. По конструктивным условиям его длина ограничена 6 м. Наклон можно изменять с шагом 0,5°/1°/2°/3° и скорость вращения от 0,3 до 3,0 об/мин. Печь может эксплуатироваться в диапазоне температур от 500 до 1 500 °С. Он оснащен многочисленными приборами для измерения температуры, давления и состава выхлопных газов. Дымовые газы очищаются на рукавном фильтре с добавлением гашеной извести.
Из опыта приготовления легких заполнителей в описанной вращающейся печи и параллельных измерений температуры и времени пребывания было установлено, что время пребывания в зоне обжига слишком мало, чтобы полностью использовать потенциал объемного расширения ( »Рис 9). Более того, для этого был необходим второй, а иногда и третий цикл обжига. В случае гранулятов из глиняных кирпичей с наполнителем из-за повреждения фурмы горелки и связанного с этим изменения температурного профиля эта процедура не дала желаемого эффекта увеличения объема гранулята или снижения плотности. Для определения фактического потенциала расширения в муфельной печи была проведена дополнительная термическая обработка.
4.2 Свойства легких заполнителей, произведенных во вращающейся печи
На экспериментальной установке из модельной стены и двух смесей кирпично-изоляционного материала с различными добавками гипса 0, 5 и 15% масс., около 200 кг вспененного материала В каждом случае готовили гранулят на партию (»Рис. 10).
Содержание сульфатов в гранулах модели стенки, обожженной во вращающейся печи, уменьшается по сравнению с содержанием сульфатов в сырых гранулах (»Таблица 2). Уже после одного обжига во вращающейся печи были достигнуты значения ниже 0,7% масс., которые еще больше снижаются при втором обжиге. Тип кирпичной закладки не имел никакого значения. Для легких и переработанных заполнителей, предназначенных для использования в производстве легкого бетона, напр. для кладочного кирпича содержание кислоторастворимого сульфата не должно превышать значения 0,8 % масс. [10], [11]. Это предельное значение надежно соблюдается. Концентрации вымываемого сульфата легких заполнителей, приготовленных из модельной стенки, определенные на элюате «ЛАГА» [12] с водо-твердым отношением 10:1, были ниже 50 мг/л (» табл. 3). Соответственно, использование материала в несвязанных слоях дорожного строительства, что является еще одним применением легких гранулятов, также возможно без каких-либо ограничений.
Плотность гранулятов, приготовленных из стенки модели без добавления SiC, составляет от 2,1 до 2,2 г/см³. При добавлении SiC достигается значительное снижение плотности до 0,73 г/см³ (»Таблица 4).
Плотность легких заполнителей из кирпича с наполнителем уменьшилась по сравнению с плотностью сырого гранулята, однако не достигла ожидаемых значений по вышеуказанным причинам. (»Таблица 5).
Чтобы проверить, какой потенциал расширения все еще присутствует после обжига во вращающейся печи, в дополнение к испытаниям на опытной установке была проведена термическая обработка в муфельной печи (»Рис. 11). Независимо от предварительной обработки гранулятов, подаваемых в муфельную печь – необработанных сырых гранулятов, гранулятов из вращающейся печи после одного обжига, гранулятов из вращающейся печи после двух обжигов, плотность была значительно ниже 1 г/см³. Кирпичи с наполнителем из минеральной ваты имеют меньшую плотность, чем кирпичи с наполнителем из перлита. Это согласуется с данными, полученными с помощью микроскопии на горячем предметном столике.
Из вторичного сырья, которое в будущем будет поступать из «глиняных кирпичей, наполненных минеральной ватой» или «глиняных кирпичей, наполненных перлитом», можно производить легкие каменные заполнители с плотностью от низкой до очень низкой.
5. Резюме
Гипсосодержащие отходы кладки или глиняные кирпичи, заполненные изоляционными материалами и покрытые гипсовой штукатуркой, в настоящее время вряд ли могут быть утилизированы и поэтому должны быть захоронены. Альтернативой является использование этих материалов в качестве сырья для производства легких заполнителей в термическом процессе. Из кирпичей, наполненных минеральной ватой и перлитом, к которым было добавлено 5 или 15 % масс. гипса, такие легкие заполнители можно было производить на пилотной установке IAB Weimar gGmbH. Содержание сульфата в этих заполнителях после обжига было даже при добавлении гипса в количестве 15% по массе ниже содержания растворимого в кислоте сульфата в размере 0,8% по массе, которое должно обеспечиваться легкими или переработанными заполнителями. Менее 50 мг/л, отмываемый SO 3 2- практически перестал существовать. Плотность соответствовала плотности коммерческих легких заполнителей. Благодаря этому и знаниям, имеющимся в IAB, следующий шаг – монтаж и эксплуатация завода промышленного масштаба – становится достижимым.
Благодарность
Исследования проводились в рамках программы «FuE-Förderung gemeinnütziger externer Industrieforschungseinrichtungen – Innovationskompetenz» (Поддержка НИОКР некоммерческих внешних промышленных организаций – Экспертиза инноваций), инициированной Федеральным министерством экономики Германии и Энергия в рамках спонсорства проекта EuroNorm Gesellschaft für Qualitätssicherung und Innovationsmanagement mbH.
Проект осуществлялся при финансовой поддержке специалистов отрасли и сотрудников глиняно-кирпичной и гипсовой промышленности. Авторы хотели бы выразить благодарность за большой интерес, а также за критические и конструктивные обсуждения во время проектных встреч.
Литература / Литература
[1] Мюллер, А. и др.: Entwicklungen zum Recycling von Ziegeln und Ziegelmauerwerk (Teil 1). Ziegelindustrie International 2020, Heft 2, S. 12-19.
[2] Рейнхольд, М.; Мюллер, А.: Легкий заполнитель, полученный из мелких фракций строительных и сносных отходов. Конференция: Дизайн для деконструкции и повторного использования материалов. Карлсруэ, Германия. CIB Publication 272, Paper 3, 2002.
[3] Mueller, A.; Соколова, С., Н.; Верещагин В. И. Характеристики легких заполнителей из первичного и вторичного сырья. Строительство и строительные материалы. 22 (2008), стр. 703-712.
[4] Мюллер, А.; Шнелл, А .; Рубнер, К.: Aufbaukörnungen aus Mauerwerkbruch. Chemie Ingenieurtechnik 2012, Vol. 84, №. 10, с. 1780-1792.
[5] Мюллер, А.; Шнелл, А .; Рюбнер, К.: Производство легких заполнителей из переработанного каменного щебня. Строительство и строительные материалы. 98 (2015), стр. 376-387.
[6] Swift, W.M. et al.: Разложение сульфата кальция: обзор литературы. Аргоннская национальная лаборатория, Аргонн, Иллинойс, 1976.
[7] Riley, C.M.: Связь химических свойств со вздутием глины , Варенье. Керам. соц. 34 (1951) 121–128.
[8] Уайт, Вашингтон: Легкий заполнитель из сланцев Иллинойса, Геологическая служба штата Иллинойс, Урбана, 1960, Circular 290.
[9] Prüfung fester Brennstoffe – Bestimmung des Asche-Schmelzverhaltens. DIN 51730:2007-09
[10] Бетон – Festlegung, Eigenschaften, Herstellung und Konformität; Немецкий Фассунг EN 206:2013+A2. 2021.
[11] Beton nach DIN EN 206-1 и DIN 1045-2 mit rezyklierten Gesteinskörnungen nach DIN EN 12620. Ausgabe Сентябрь 2010. DAfStb Richtlinie, Ausgabe Сентябрь 2010.
[12] Anenunger ungerford LAGA2-0 Mitte die stoffliche Verwertung von Mineralischen Abfällen – Technische Regeln.