ΠΠ΅ΡΠ°ΠΌΠ·ΠΈΡΠΎΠ±Π΅ΡΠΎΠ½Π½ΡΠ΅ Π±Π»ΠΎΠΊΠΈ Π³Π°Π·ΠΎΡΠΈΠ»ΠΈΠΊΠ°ΡΠ½ΡΠ΅ Π±Π»ΠΎΠΊΠΈ: ΠΠ΅ΡΠ°ΠΌΠ·ΠΈΡΠΎΠ±Π΅ΡΠΎΠ½Π½ΡΠ΅ Π±Π»ΠΎΠΊΠΈ ΠΈΠ»ΠΈ Π³Π°Π·ΠΎΠ±Π΅ΡΠΎΠ½Π½ΡΠ΅ Π±Π»ΠΎΠΊΠΈ β ΡΡΠΎ Π»ΡΡΡΠ΅?
ΠΠ΅ΡΠ°ΠΌΠ·ΠΈΡΠΎΠ±Π΅ΡΠΎΠ½Π½ΡΠ΅ Π±Π»ΠΎΠΊΠΈ ΠΈΠ»ΠΈ Π³Π°Π·ΠΎΡΠΈΠ»ΠΈΠΊΠ°ΡΠ½ΡΠ΅ ΡΡΠΎ Π»ΡΡΡΠ΅
Π‘ΠΎΠ΄Π΅ΡΠΆΠ°Π½ΠΈΠ΅
- ΠΠ΅ΡΠ°ΠΌΠ·ΠΈΡΠΎΠ±Π΅ΡΠΎΠ½Π½ΡΠ΅ Π±Π»ΠΎΠΊΠΈ ΡΠ΅Ρ Π½ΠΈΡΠ΅ΡΠΊΠΈΠ΅ Ρ Π°ΡΠ°ΠΊΡΠ΅ΡΠΈΡΡΠΈΠΊΠΈ
- ΠΠΎΠΏΠΎΠ»Π½ΠΈΡΠ΅Π»ΡΠ½ΡΠ΅ ΡΠ²Π΅Π΄Π΅Π½ΡΡ
- Π₯Π°ΡΠ°ΠΊΡΠ΅ΡΠΈΡΡΠΈΠΊΠΈ Π³Π°Π·ΠΎΡΠΈΠ»ΠΈΠΊΠ°ΡΠ½ΡΡ Π±Π»ΠΎΠΊΠΎΠ²
- ΠΠΎΠΏΠΎΠ»Π½ΠΈΡΠ΅Π»ΡΠ½ΡΠ΅ ΡΠ²Π΅Π΄Π΅Π½ΡΡ
- ΠΠ΅ΡΠ°ΠΌΠ·ΠΈΡΠΎΠ±Π΅ΡΠΎΠ½Π½ΡΠ΅ Π±Π»ΠΎΠΊΠΈ
- ΠΠ°Π·ΠΎΡΠΈΠ»ΠΈΠΊΠ°ΡΠ½ΡΠ΅ Π±Π»ΠΎΠΊΠΈ
- ΠΠ°ΠΊΠ»ΡΡΠ΅Π½ΠΈΠ΅
ΠΠ±ΡΠΎΠ»ΡΡΠ½ΠΎ Π²ΡΠ΅ ΠΏΠΎΠ·Π½Π°Π΅ΡΡΡ Π² ΡΡΠ°Π²Π½Π΅Π½ΠΈΠΈ. ΠΠ΅Π»Π°Ρ Π²ΡΠ±ΠΎΡ Π² ΡΡ ΠΈΠ»ΠΈ ΠΈΠ½ΡΡ ΡΡΠΎΡΠΎΠ½Ρ, ΠΌΡ ΡΡΠΈΠΆΠ΄Ρ ΠΏΠΎΠ΄ΡΠΌΠ°Π΅ΠΌ ΠΈ ΡΡΠ°Π²Π½ΠΈΠΌ Π²ΡΠ΅ Π²ΠΎΠ·ΠΌΠΎΠΆΠ½ΡΠ΅ Π²Π°ΡΠΈΠ°Π½ΡΡ. Π ΡΡΡΠΎΠΈΡΠ΅Π»ΡΡΡΠ²Π΅ ΡΠΎΡΠ½ΠΎ ΡΠ°ΠΊ ΠΆΠ΅, Π²Π΅Π΄Ρ Π²ΡΠ±ΠΎΡ ΠΏΡΠΈΡ ΠΎΠ΄ΠΈΡΡΡ Π΄Π΅Π»Π°ΡΡ Π²ΡΠ΅Π³Π΄Π°. ΠΠ΅Π»ΠΎ Π² ΡΠΎΠΌ, ΡΡΠΎ ΡΡΠ½ΠΎΠΊ ΠΏΡΠ΅Π΄ΠΎΡΡΠ°Π²Π»ΡΠ΅Ρ Π½Π°ΠΌ Π±ΠΎΠ»ΡΡΠΎΠ΅ ΠΊΠΎΠ»ΠΈΡΠ΅ΡΡΠ²ΠΎ ΡΡΡΠΎΠΈΡΠ΅Π»ΡΠ½ΡΡ ΠΌΠ°ΡΠ΅ΡΠΈΠ°Π»ΠΎΠ², ΠΊΠΎΡΠΎΡΡΠ΅ ΠΈΠΌΠ΅ΡΡ ΡΠ²ΠΎΠΈ ΠΎΡΠΎΠ±Π΅Π½Π½ΠΎΡΡΠΈ ΠΈ Ρ Π°ΡΠ°ΠΊΡΠ΅ΡΠΈΡΡΠΈΠΊΠΈ. ΠΠ»Ρ ΡΡΡΠΎΠΈΡΠ΅Π»ΡΡΡΠ²Π° Π΄ΠΎΠΌΠΎΠ², Π³Π°ΡΠ°ΠΆΠ΅ΠΉ, Π±Π°Π½Ρ ΠΈΠ»ΠΈ Π΄ΡΡΠ³ΠΈΡ ΠΏΠΎΡΡΡΠΎΠ΅ΠΊ, ΠΌΠ½ΠΎΠ³ΠΈΠ΅ ΠΎΡΡΠ°Π½Π°Π²Π»ΠΈΠ²Π°ΡΡΡΡ Π½Π° Π»Π΅Π³ΠΊΠΈΡ Π±Π΅ΡΠΎΠ½Π°Ρ . ΠΠ΄Π½ΠΈ ΠΏΡΠ΅Π΄ΠΏΠΎΡΠΈΡΠ°ΡΡ ΠΊΠ΅ΡΠ°ΠΌΠ·ΠΈΡΠΎΠ±Π΅ΡΠΎΠ½Π½ΡΠ΅ Π±Π»ΠΎΠΊΠΈ, Π΄ΡΡΠ³ΠΈΠ΅ β Π³Π°Π·ΠΎΡΠΈΠ»ΠΈΠΊΠ°ΡΠ½ΡΠ΅ Π±Π»ΠΎΠΊΠΈ. Π Π΅ΡΠ»ΠΈ ΠΏΠΎΡΡΠ°Π²ΠΈΡΡ Π²ΠΎΠΏΡΠΎΡ ΡΠ΅Π±ΡΠΎΠΌ ΠΈ ΡΠ΅ΡΠΈΡΡ, ΠΊΠ΅ΡΠ°ΠΌΠ·ΠΈΡΠΎΠ±Π΅ΡΠΎΠ½Π½ΡΠ΅ Π±Π»ΠΎΠΊΠΈ ΠΈΠ»ΠΈ Π³Π°Π·ΠΎΡΠΈΠ»ΠΈΠΊΠ°ΡΠ½ΡΠ΅, ΡΡΠΎ Π»ΡΡΡΠ΅?
Π’Π°ΠΊ ΠΊΠ°ΠΊ Π²ΡΠ΅ ΠΌΠΎΠΆΠ½ΠΎ ΡΠ·Π½Π°ΡΡ Π² ΡΡΠ°Π²Π½Π΅Π½ΠΈΠΈ, ΠΌΡ ΡΠΎΠΏΠΎΡΡΠ°Π²ΠΈΠΌ ΡΡΠΈΡ
Π΄Π²Π° ΠΏΡΠ΅ΠΊΡΠ°ΡΠ½ΡΡ
ΠΌΠ°ΡΠ΅ΡΠΈΠ°Π»Π°, ΡΡΠΎΠ±Ρ ΡΠ·Π½Π°ΡΡ ΠΎΡΠ²Π΅Ρ Π½Π° ΡΡΠΎΡ Π²ΠΎΠΏΡΠΎΡ. ΠΡ ΡΠ°Π·Π±Π΅ΡΠ΅ΠΌ ΡΠ΅Ρ
Π½ΠΈΡΠ΅ΡΠΊΠΈΠ΅ Ρ
Π°ΡΠ°ΠΊΡΠ΅ΡΠΈΡΡΠΈΠΊΠΈ ΠΌΠ°ΡΠ΅ΡΠΈΠ°Π»ΠΎΠ², Π° ΡΠ°ΠΊΠΆΠ΅ ΠΎΡΡΠ°Π½ΠΎΠ²ΠΈΠΌΡΡ Π½Π° ΠΈΡ
ΠΏΠΎΠ»ΠΎΠΆΠΈΡΠ΅Π»ΡΠ½ΡΡ
ΠΈ ΠΎΡΡΠΈΡΠ°ΡΠ΅Π»ΡΠ½ΡΡ
ΡΡΠΎΡΠΎΠ½Π°Ρ
.
ΠΠ΅ΡΠ°ΠΌΠ·ΠΈΡΠΎΠ±Π΅ΡΠΎΠ½Π½ΡΠ΅ Π±Π»ΠΎΠΊΠΈ ΡΠ΅Ρ Π½ΠΈΡΠ΅ΡΠΊΠΈΠ΅ Ρ Π°ΡΠ°ΠΊΡΠ΅ΡΠΈΡΡΠΈΠΊΠΈ
ΠΡΠΈ Π±Π»ΠΎΠΊΠΈ ΡΠ΄Π΅Π»Π°Π½Ρ Π½Π° ΠΎΡΠ½ΠΎΠ²Π΅ ΠΈΠ·Π²Π΅ΡΡΠ½ΠΎΠ³ΠΎ Π²ΡΠ΅ΠΌ ΠΊΠ΅ΡΠ°ΠΌΠ·ΠΈΡΠ°, ΠΊΠΎΡΠΎΡΡΠΉ Π΄ΠΎΠ±Π°Π²Π»ΡΠ΅ΡΡΡ Π² Π±Π΅ΡΠΎΠ½Π½ΡΠΉ ΡΠ°ΡΡΠ²ΠΎΡ. Π ΡΠΎΡΡΠ°Π²Π΅ Π΅ΡΡΡ ΠΊΠ°ΠΊ ΠΊΠ΅ΡΠ°ΠΌΠ·ΠΈΡ ΠΊΡΡΠΏΠ½ΠΎΠΉ ΡΡΠ°ΠΊΡΠΈΠΈ, ΡΠ°ΠΊ ΠΈ ΠΊΠ΅ΡΠ°ΠΌΠ·ΠΈΡΠΎΠ²ΡΠΉ ΠΏΠ΅ΡΠΎΠΊ. Π Π·Π°Π²ΠΈΡΠΈΠΌΠΎΡΡΠΈ ΠΎΡ ΡΠΎΠ³ΠΎ, ΠΊΠ°ΠΊΠΎΠΉ ΡΠ°Π·ΠΌΠ΅Ρ ΠΈΠΌΠ΅Π΅Ρ Π½Π°ΠΏΠΎΠ»Π½ΠΈΡΠ΅Π»Ρ, Π·Π°Π²ΠΈΡΠΈΡ ΠΏΡΠΎΡΠ½ΠΎΡΡΡ Π±Π»ΠΎΠΊΠΎΠ² ΠΈ ΠΈΡ ΡΠ΅ΠΏΠ»ΠΎΠΈΠ·ΠΎΠ»ΡΡΠΈΠΎΠ½Π½ΡΠ΅ Ρ Π°ΡΠ°ΠΊΡΠ΅ΡΠΈΡΡΠΈΠΊΠΈ. ΠΡΠ΅ΠΌ ΠΈΠ·Π²Π΅ΡΡΠ½ΠΎ, ΡΡΠΎ ΠΊΠ΅ΡΠ°ΠΌΠ·ΠΈΡ ΠΈΡΠΏΠΎΠ»ΡΠ·ΡΠ΅ΡΡΡ Π² ΠΊΠ°ΡΠ΅ΡΡΠ²Π΅ ΡΡΠ΅ΠΏΠ»ΠΈΡΠ΅Π»Ρ. Π‘ΠΎΠΎΡΠ²Π΅ΡΡΡΠ²Π΅Π½Π½ΠΎ, Π² ΡΠ²ΠΎΠΉΡΡΠ²Π° ΠΊΠ΅ΡΠ°ΠΌΠ·ΠΈΡΠΎΠ±Π»ΠΎΠΊΠΎΠ² Π²Ρ ΠΎΠ΄ΠΈΡ Π²ΡΡΠΎΠΊΠΈΠΉ ΠΏΠΎΠΊΠ°Π·Π°ΡΠ΅Π»Ρ ΡΠ±Π΅ΡΠ΅ΠΆΠ΅Π½ΠΈΡ ΡΠ΅ΠΏΠ»Π°.
ΠΠ°ΡΠ½Π΅ΠΌ ΡΠΎ ΡΡΠ°Π½Π΄Π°ΡΡΠ½ΡΡ ΡΠ°Π·ΠΌΠ΅ΡΠΎΠ² ΠΊΠ΅ΡΠ°ΠΌΠ·ΠΈΡΠΎΠ²ΡΡ Π±Π»ΠΎΠΊΠΎΠ². ΠΠ° ΡΠ°ΠΌΠΎΠΌ Π΄Π΅Π»Π΅ ΡΠ°Π·ΠΌΠ΅ΡΡ ΠΌΠΎΠ³ΡΡ Π±ΡΡΡ ΡΠ°Π·Π½ΡΠΌΠΈ, Π² Π·Π°Π²ΠΈΡΠΈΠΌΠΎΡΡΠΈ ΠΎΡ ΠΏΠΎΡΡΠ΅Π±Π½ΠΎΡΡΠ΅ΠΉ ΠΈ ΡΠ΅Π»Π΅ΠΉ. ΠΠΎ ΡΡΠ°Π½Π΄Π°ΡΡΠΎΠΌ ΡΡΠΈΡΠ°ΡΡΡΡ ΡΠ°ΠΊΠΈΠ΅ Π²Π΅Π»ΠΈΡΠΈΠ½Ρ:
- 188Γ190Γ390 ΠΌΠΌ;
- 188Γ90Γ390 ΠΌΠΌ.
ΠΠ°ΠΊΡΠΈΠΌΠ°Π»ΡΠ½ΠΎ Π΄ΠΎΠΏΡΡΡΠΈΠΌΠΎΠ΅ ΠΎΡΠΊΠ»ΠΎΠ½Π΅Π½ΠΈΠ΅ ΠΎΡ ΡΡΠ°Π½Π΄Π°ΡΡΠ° β 10β12 ΠΌΠΌ. ΠΠ΅ΡΠ²ΡΠΉ Π²ΠΈΠ΄ Π±Π»ΠΎΠΊΠΎΠ² β ΠΈΠ·Π΄Π΅Π»ΠΈΡ Π΄Π»Ρ ΠΊΠ»Π°Π΄ΠΊΠΈ ΡΡΠ΅Π½, Π²ΡΠΎΡΠΎΠΉ β Π΄Π»Ρ ΠΏΠ΅ΡΠ΅Π³ΠΎΡΠΎΠ΄ΠΎΠΊ. ΠΡΠ»ΠΈ Π±ΡΠ°ΡΡ Π²ΠΎ Π²Π½ΠΈΠΌΠ°Π½ΠΈΠ΅ ΠΊΠ°ΡΠ΅ΡΡΠ²ΠΎ ΠΏΠΎΠ²Π΅ΡΡ
Π½ΠΎΡΡΠΈ Π±ΠΎΠΊΠΎΠ²ΠΎΠΉ Π³ΡΠ°Π½ΠΈ, ΡΠΎ ΠΊΠ΅ΡΠ°ΠΌΠ·ΠΈΡΠΎΠ±Π΅ΡΠΎΠ½ Π΄Π΅Π»ΠΈΡΡΡ Π½Π° ΡΡΠ΄ΠΎΠ²ΠΎΠΉ ΠΈ Π»ΠΈΡΠ΅Π²ΠΎΠΉ. Π ΡΠ΄ΠΎΠ²ΡΠ΅ Π±Π»ΠΎΠΊΠΈ ΠΈΡΠΏΠΎΠ»ΡΠ·ΡΡΡΡΡ Π΄Π»Ρ Π²ΠΎΠ·Π²Π΅Π΄Π΅Π½ΠΈΡ ΠΊΠΎΡΠΎΠ±ΠΊΠΈ, ΠΊΠΎΡΠΎΡΠ°Ρ Π±ΡΠ΄Π΅Ρ Π·Π°ΡΠΈΡΠ΅Π½Π° ΠΎΡΠ΄Π΅Π»ΠΊΠΎΠΉ. Π Π»ΠΈΡΠ΅Π²ΡΠ΅ ΠΈΡΠΏΠΎΠ»ΡΠ·ΡΡΡ Π΄Π»Ρ Π²ΠΎΠ·Π²Π΅Π΄Π΅Π½ΠΈΡ ΡΠΈΡΡΡΡ
ΡΡΠ΅Π½, Π±Π΅Π· Π΄ΠΎΠΏΠΎΠ»Π½ΠΈΡΠ΅Π»ΡΠ½ΠΎΠΉ ΠΎΡΠ΄Π΅Π»ΠΊΠΈ.
ΠΠ±ΡΠ°ΡΠΈΡΠ΅ Π²Π½ΠΈΠΌΠ°Π½ΠΈΠ΅! Π ΠΎΠ΄Π½ΠΎΠΌ ΠΊΠ΅ΡΠ°ΠΌΠ·ΠΈΡΠΎΠ±Π΅ΡΠΎΠ½Π½ΠΎΠΌ Π±Π»ΠΎΠΊΠ΅ ΠΏΠΎΠΌΠ΅ΡΡΠΈΡΡΡ ΠΎΡ 3 Π΄ΠΎ 7 ΠΏΡΠΎΡΡΡΡ ΠΊΠΈΡΠΏΠΈΡΠ΅ΠΉ.
ΠΡΠΎΠΌΠ΅ ΡΠΎΠ³ΠΎ, ΠΏΡΠΎΠ΄ΡΠΊΡΠΈΡ Π²ΡΠΏΡΡΠΊΠ°Π΅ΡΡΡ ΠΏΠΎΠ»Π½ΠΎΡΠ΅Π»Π°Ρ ΠΈ ΠΏΡΡΡΠΎΡΠ΅Π»Π°Ρ. ΠΠ»Π°Π³ΠΎΠ΄Π°ΡΡ ΠΏΡΡΡΠΎΡΠ°ΠΌ Π±Π»ΠΎΠΊ Π²Π΅ΡΠΈΡ Π΅ΡΠ΅ ΠΌΠ΅Π½ΡΡΠ΅, Π° Π΅Π³ΠΎ ΡΠ½Π΅ΡΠ³ΠΎΡΠ±Π΅ΡΠ΅ΠΆΠ΅Π½ΠΈΠ΅ Π½Π°ΠΌΠ½ΠΎΠ³ΠΎ Π²ΡΡΠ΅. Π Π²ΠΎΡ ΠΈΠ·Π΄Π΅Π»ΠΈΡ ΡΠΏΠ»ΠΎΡΠ½ΡΠ΅ Π±ΠΎΠ»Π΅Π΅ Π½Π°Π΄Π΅ΠΆΠ½ΡΠ΅ ΠΈ ΡΡΠΆΠ΅Π»ΡΠ΅. ΠΠΌΠΈ Π²ΠΎΠ·Π²ΠΎΠ΄ΡΡ ΠΊΠ°ΠΏΠΈΡΠ°Π»ΡΠ½ΡΠ΅ ΡΡΠ΅Π½Ρ, Π½Π° ΠΊΠΎΡΠΎΡΡΠ΅ ΠΎΠΊΠ°Π·ΡΠ²Π°Π΅ΡΡΡ Π±ΠΎΠ»ΡΡΠ°Ρ Π½Π°Π³ΡΡΠ·ΠΊΠ°.
ΠΠΎΠΏΠΎΠ»Π½ΠΈΡΠ΅Π»ΡΠ½ΡΠ΅ ΡΠ²Π΅Π΄Π΅Π½ΡΡ
- ΠΠ»ΠΎΡΠ½ΠΎΡΡΡ ΠΊΠ΅ΡΠ°ΠΌΠ·ΠΈΡΠΎΠ±Π΅ΡΠΎΠ½Π½ΡΡ
Π±Π»ΠΎΠΊΠΎΠ² Π·Π°Π²ΠΈΡΠΈΡ ΠΎΡ Π½Π°ΠΏΠΎΠ»Π½ΠΈΡΠ΅Π»Ρ ΠΈ Π΅Π³ΠΎ ΡΡΠ°ΠΊΡΠΈΠΈ. ΠΠΈΠ°ΠΏΠ°Π·ΠΎΠ½ Π΄ΠΎΠ²ΠΎΠ»ΡΠ½ΠΎ Π²Π΅Π»ΠΈΠΊ β 500β1800 ΠΊΠ³/ΠΌ3
. Π’Π°ΠΊΠΈΠ΅ ΠΏΠΎΠΊΠ°Π·Π°ΡΠ΅Π»ΠΈ Π²Π½ΡΡΠ°ΡΡ Π΄ΠΎΠ²Π΅ΡΠΈΡ. - ΠΡΠΎΡΠ½ΠΎΡΡΡ ΠΊΠ΅ΡΠ°ΠΌΠ·ΠΈΡΠΎΠ±Π΅ΡΠΎΠ½Π½ΡΡ Π±Π»ΠΎΠΊΠΎΠ² ΡΠΎΠΆΠ΅ Π²Π΅Π»ΠΈΠΊΠ° β 35β250 ΠΊΠ³/ΡΠΌ2, Π° ΡΡΠΎ ΠΏΠΎΠΊΠ°Π·Π°ΡΠ΅Π»Ρ ΠΎΡ Π3,5 Π΄ΠΎ Π20.
- ΠΠ΅Ρ β 5β35 ΠΊΠ³/ΡΡ.
- Π‘ΡΠΎΠΊ ΡΠ»ΡΠΆΠ±Ρ β Π±ΠΎΠ»Π΅Π΅ 60 Π»Π΅Ρ.
- ΠΠ½Π΅ΡΠ³ΠΎΡΠ±Π΅ΡΠ΅ΠΆΠ΅Π½ΠΈΠ΅ β ΠΎΡΠ΅Π½Ρ Π²Π°ΠΆΠ½ΡΠΉ ΠΏΠ°ΡΠ°ΠΌΠ΅ΡΡ. ΠΠ° ΡΡΠ΅Ρ Π½Π°Π»ΠΈΡΠΈΡ Π² ΡΠΎΡΡΠ°Π²Π΅ ΠΊΠ΅ΡΠ°ΠΌΠ·ΠΈΡΠ°, ΡΠ΅ΠΏΠ»ΠΎΠΏΡΠΎΠ²ΠΎΠ΄Π½ΠΎΡΡΡ ΠΌΠ°ΡΠ΅ΡΠΈΠ°Π»Π° Π½ΠΈΠ·ΠΊΠ°Ρ. Π§Π΅ΠΌ Π½ΠΈΠΆΠ΅ ΠΏΠ»ΠΎΡΠ½ΠΎΡΡΡ, ΡΠ΅ΠΌ Π»ΡΡΡΠ΅ ΡΠ½Π΅ΡΠ³ΠΎΡΠ±Π΅ΡΠ΅ΠΆΠ΅Π½ΠΈΠ΅. ΠΡΠΎ Π²ΠΈΠ΄Π½ΠΎ Π½Π° ΡΠ°Π±Π»ΠΈΡΠ΅ Π²Π½ΠΈΠ·Ρ.
- ΠΠΎΡΠΎΠ·ΠΎΡΡΡΠΎΠΉΡΠΈΠ²ΠΎΡΡΡ Π²Π»ΠΈΡΠ΅Ρ Π½Π° Π΄Π»ΠΈΡΠ΅Π»ΡΠ½ΠΎΡΡΡ ΡΡΠΎΠΊΠ° ΡΠ»ΡΠΆΠ±Ρ ΠΈΠ·Π΄Π΅Π»ΠΈΠΉ ΠΈ Π½Π΅ΡΡΡΡΡ ΡΠΏΠΎΡΠΎΠ±Π½ΠΎΡΡΡ ΡΡΠ΅Π½Ρ. ΠΠ΅ΡΠ°ΠΌΠ·ΠΈΡΠΎΠ±Π΅ΡΠΎΠ½Π½ΡΠ΅ Π±Π»ΠΎΠΊΠΈ ΠΈΠΌΠ΅ΡΡ Π½Π΅ΡΠΊΠΎΠ»ΡΠΊΠΎ ΠΏΠΎΠΊΠ°Π·Π°ΡΠ΅Π»Π΅ΠΉ ΡΡΡΠΎΠΉΡΠΈΠ²ΠΎΡΡΠΈ ΠΊ ΠΌΠΎΡΠΎΠ·Ρ. ΠΠ°ΡΠΊΠ° ΡΠΊΠ°Π·ΡΠ²Π°Π΅Ρ Π½Π° ΡΠΎΡΠ½ΠΎΠ΅ ΠΊΠΎΠ»ΠΈΡΠ΅ΡΡΠ²ΠΎ ΡΠΈΠΊΠ»Π° Π·Π°ΠΌΠΎΡΠΎΠ·ΠΊΠΈ ΠΈ ΡΠ°Π·ΠΌΠΎΡΠΎΠ·ΠΊΠΈ Π±Π»ΠΎΠΊΠ°. ΠΡΠΎ: F25, F35, F50, F75.
- ΠΠΎΠΆΠ°ΡΠΎΠ±Π΅Π·ΠΎΠΏΠ°ΡΠ½ΠΎΡΡΡ Ρ ΠΌΠ°ΡΠ΅ΡΠΈΠ°Π»Π° ΠΈΠ΄Π΅Π°Π»ΡΠ½Π°Ρ. ΠΠ½ ΠΏΠΎΠΏΡΠΎΡΡΡ Π½Π΅ Π³ΠΎΡΠΈΡ, ΠΏΠΎΡΡΠΎΠΌΡ ΠΈΠΌΠ΅Π΅Ρ ΠΊΠ»Π°ΡΡ ΠΏΠΎΠΆΠ°ΡΠΎΠ±Π΅Π·ΠΎΠΏΠ°ΡΠ½ΠΎΡΡΠΈ Π1. ΠΠ°ΠΆΠ΅ ΠΏΠΎΠ΄ Π²Π»ΠΈΡΠ½ΠΈΠ΅ΠΌ ΠΎΡΠΊΡΡΡΠΎΠ³ΠΎ ΠΎΠ³Π½Ρ, ΡΡΠ΅Π½Ρ Π½Π΅ Π±ΡΠ΄ΡΡ ΡΡΡΠΈΡΡΡΡ ΡΠ΅Π»ΡΡ 7 ΠΈΠ»ΠΈ 10 ΡΠ°ΡΠΎΠ².
- ΠΠ°ΡΠΎΠΏΡΠΎΠ½ΠΈΡΠ°Π΅ΠΌΠΎΡΡΡ Π²ΡΡΠΎΠΊΠ°Ρ, ΡΠ°ΠΊ ΠΊΠ°ΠΊ ΠΊΠ΅ΡΠ°ΠΌΠ·ΠΈΡ Β«Π΄ΡΡΠΈΡΒ». ΠΡΠΎ ΡΠΎΠ·Π΄Π°Π΅Ρ ΠΈΠ΄Π΅Π°Π»ΡΠ½ΡΠΉ ΠΌΠΈΠΊΡΠΎΠΊΠ»ΠΈΠΌΠ°Ρ Π² ΠΏΠΎΠΌΠ΅ΡΠ΅Π½ΠΈΠΈ.
Π₯Π°ΡΠ°ΠΊΡΠ΅ΡΠΈΡΡΠΈΠΊΠΈ Π³Π°Π·ΠΎΡΠΈΠ»ΠΈΠΊΠ°ΡΠ½ΡΡ Π±Π»ΠΎΠΊΠΎΠ²
ΠΠ°ΡΠ΅ΡΠΈΠ°Π» ΡΠΎΠΆΠ΅ ΠΈΠΌΠ΅Π΅Ρ ΠΏΠΎΡΠΈΡΡΡΡ ΡΡΡΡΠΊΡΡΡΡ.
ΠΠ°Π±Π°ΡΠΈΡΡ Π³Π°Π·ΠΎΡΠΈΠ»ΠΈΠΊΠ°ΡΠ½ΡΡ Π±Π»ΠΎΠΊΠΎΠ² ΠΌΠΎΠ³ΡΡ Π±ΡΡΡ ΡΠ°Π·Π½ΡΠΌΠΈ. ΠΡΠ΅ Π·Π°Π²ΠΈΡΠΈΡ ΠΎΡ Π·Π°Π²ΠΎΠ΄Π° ΠΈΠ·Π³ΠΎΡΠΎΠ²ΠΈΡΠ΅Π»Ρ. ΠΠ° ΠΏΡΠΈΠ»Π°Π²ΠΊΠ°Ρ Π²Ρ ΠΌΠΎΠΆΠ΅ΡΠ΅ Π²ΡΡΡΠ΅ΡΠΈΡΡ ΠΎΡΠ½ΠΎΠ²Π½ΡΠ΅ ΡΠ°Π·ΠΌΠ΅ΡΡ: 600Γ100Γ300 ΠΌΠΌ; 250Γ400Γ600 ΠΌΠΌ; 600Γ200Γ300 ΠΌΠΌ; 500Γ200Γ300 ΠΌΠΌ. Π Π²ΠΎΡ Π²Π΅Ρ Π·Π°Π²ΠΈΡΠΈΡ ΠΎΡ ΠΏΠΎΠΊΠ°Π·Π°ΡΠ΅Π»Π΅ΠΉ ΠΏΠ»ΠΎΡΠ½ΠΎΡΡΠΈ ΠΈ ΡΠ°Π·ΠΌΠ΅ΡΠΎΠ². ΠΠ½ Π½Π°Ρ ΠΎΠ΄ΠΈΡΡΡ Π² Π΄ΠΈΠ°ΠΏΠ°Π·ΠΎΠ½Π΅ ΠΎΡ 5 Π΄ΠΎ 40 ΠΊΠ³.
ΠΠ° ΡΡΠ΅Ρ ΡΠ²ΠΎΠ΅ΠΉ ΡΡΡΡΠΊΡΡΡΡ, Π±Π»ΠΎΠΊΠΈ Π΄ΠΎΠ²ΠΎΠ»ΡΠ½ΠΎ Π»Π΅Π³ΠΊΠΎ ΠΏΠΎΠ΄Π΄Π°ΡΡΡΡ ΠΎΠ±ΡΠ°Π±ΠΎΡΠΊΠ΅. Π Π½ΠΈΡ ΠΌΠΎΠΆΠ½ΠΎ Π΄Π΅Π»Π°ΡΡ ΡΡΡΠΎΠ±Ρ ΠΈ Π½Π°ΡΠ΅Π·Π°ΡΡ Π»ΡΠ±ΠΎΠΉ ΡΠΎΡΠΌΡ. ΠΡΠΎ ΡΡΡΠ΅ΠΊΡΠΈΠ²Π½ΡΠΉ ΠΌΠ°ΡΠ΅ΡΠΈΠ°Π», ΠΈΡΠΏΠΎΠ»ΡΠ·ΡΠ΅ΠΌΡΠΉ Π² ΡΡΡΠΎΠΈΡΠ΅Π»ΡΡΡΠ²Π΅.
ΠΠΎΠΏΠΎΠ»Π½ΠΈΡΠ΅Π»ΡΠ½ΡΠ΅ ΡΠ²Π΅Π΄Π΅Π½ΡΡ
- ΠΠ»ΠΎΡΠ½ΠΎΡΡΡ Π³Π°Π·ΠΎΡΠΈΠ»ΠΈΠΊΠ°ΡΠ½ΡΡ Π±Π»ΠΎΠΊΠΎΠ² β ΠΎΡ D400 Π΄ΠΎ D700, ΡΠΎ Π΅ΡΡΡ ΠΎΡ 350 Π΄ΠΎ 900 ΠΊΠ³/ΠΌ3.
- ΠΡΠΎΡΠ½ΠΎΡΡΡ Π³Π°Π·ΠΎΡΠΈΠ»ΠΈΠΊΠ°ΡΠ½ΡΡ
Π±Π»ΠΎΠΊΠΎΠ² β ΠΎΡ 10 Π΄ΠΎ 50 ΠΊΠ³/ΡΠΌ2 (Π0,75βΠ3,5 ΠΈ Π²ΡΡΠ΅).
- ΠΠ΅Ρ β 5β40 ΠΊΠ³/ΡΡ.
- Π‘ΡΠΎΠΊ ΡΠ»ΡΠΆΠ±Ρ β ΠΎΡ 50 Π»Π΅Ρ.
- ΠΠ½Π΅ΡΠ³ΠΎΡΠ±Π΅ΡΠ΅ΠΆΠ΅Π½ΠΈΠ΅ β 0,15-0,3 ΠΡ/ΠΌΠ‘.
- ΠΠΎΡΠΎΠ·ΠΎΡΡΡΠΎΠΉΡΠΈΠ²ΠΎΡΡΡ β F25βF75.
- ΠΠΎΠΆΠ°ΡΠΎΠ±Π΅Π·ΠΎΠΏΠ°ΡΠ½ΠΎΡΡΡ β Π½Π΅ Π³ΠΎΡΠΈΡ.
- ΠΠ°ΡΠΎΠΏΡΠΎΠ½ΠΈΡΠ°Π΅ΠΌΠΎΡΡΡ β 0,26β0,16 ΠΌΠ³/ΠΌ Ρ ΠΠ°.
Π’Π΅ΠΏΠ΅ΡΡ, ΠΊΠΎΠ³Π΄Π° Π²Ρ Π·Π½Π°Π΅ΡΠ΅ Ρ Π°ΡΠ°ΠΊΡΠ΅ΡΠΈΡΡΠΈΠΊΠΈ ΠΎΠ±ΠΎΠΈΡ ΠΌΠ°ΡΠ΅ΡΠΈΠ°Π»ΠΎΠ², ΠΌΠΎΠΆΠ½ΠΎ ΡΡΠ°Π²Π½ΠΈΡΡ ΠΈΡ ΠΈ Π²ΡΠ±ΡΠ°ΡΡ Π»ΡΡΡΠΈΠΉ. ΠΠ°Π²Π°ΠΉΡΠ΅ ΡΠ°ΡΡΠΌΠΎΡΡΠΈΠΌ ΠΏΠΎΠ»ΠΎΠΆΠΈΡΠ΅Π»ΡΠ½ΡΠ΅ ΠΈ ΠΎΡΡΠΈΡΠ°ΡΠ΅Π»ΡΠ½ΡΠ΅ ΡΡΠΎΡΠΎΠ½Ρ ΠΈΠ·Π΄Π΅Π»ΠΈΠΉ.
ΠΠ΅ΡΠ°ΠΌΠ·ΠΈΡΠΎΠ±Π΅ΡΠΎΠ½Π½ΡΠ΅ Π±Π»ΠΎΠΊΠΈ
ΠΡΠ΅ΠΈΠΌΡΡΠ΅ΡΡΠ²Π°:
- ΠΠΌΠ΅ΡΡ ΠΎΡΠ»ΠΈΡΠ½ΡΡ ΡΠ΅ΠΏΠ»ΠΎΠΏΡΠΎΠ²ΠΎΠ΄Π½ΠΎΡΡΡ. ΠΠΎΡΡΡΠΎΠΉΠΊΠΈ Π±ΡΠ΄ΡΡ ΡΠ΅ΠΏΠ»ΡΠΌΠΈ.
- ΠΠ±Π»Π°Π΄Π°ΡΡ ΡΠ²ΠΎΠΉΡΡΠ²Π°ΠΌΠΈ ΡΡΠΌΠΎΠΈΠ·ΠΎΠ»ΡΡΠΈΠΈ, Π½Π°ΠΌΠ½ΠΎΠ³ΠΎ Π»ΡΡΡΠ΅ Π³Π°Π·ΠΎΡΠΈΠ»ΠΈΠΊΠ°ΡΠ°.
- ΠΠΌΠ΅ΡΡ Π½ΠΈΠ·ΠΊΡΡ ΡΡΠΎΠΈΠΌΠΎΡΡΡ. Π Π²ΠΎΡ ΡΠΎΠΎΡΠ½ΠΎΡΠ΅Π½ΠΈΠ΅ ΡΠ΅Π½Π° β ΠΊΠ°ΡΠ΅ΡΡΠ²ΠΎ Π½Π° Π²ΡΡΡΠ΅ΠΌ ΡΡΠΎΠ²Π½Π΅.
- ΠΠ±Π»Π°Π΄Π°Π΅Ρ Π±ΠΎΠ»ΡΡΠ΅ΠΉ ΠΏΠ»ΠΎΡΠ½ΠΎΡΡΡΡ ΠΈ ΠΏΡΠΎΡΠ½ΠΎΡΡΡΡ, Π½Π΅ΠΆΠ΅Π»ΠΈ Π³Π°Π·ΠΎΡΠΈΠ»ΠΈΠΊΠ°Ρ.
- ΠΡΡΠΎΠΊΠΈΠΉ ΠΏΠΎΠΊΠ°Π·Π°ΡΠ΅Π»Ρ ΠΌΠΎΡΠΎΠ·ΠΎΡΡΡΠΎΠΉΡΠΈΠ²ΠΎΡΡΠΈ, Π±Π»Π°Π³ΠΎΠ΄Π°ΡΡ ΡΠ΅ΠΌΡ ΠΌΠ°ΡΠ΅ΡΠΈΠ°Π» ΡΠ»ΡΠΆΠΈΡ Π΄ΠΎΠ»ΡΡΠ΅.
- ΠΠ»Π°Π³ΠΎΡΡΡΠΎΠΉΡΠΈΠ², Π·Π° Π½ΠΈΠΌ Π½Π΅ Π½ΡΠΆΠ½ΠΎ ΡΡ
Π°ΠΆΠΈΠ²Π°ΡΡ.
ΠΠ°ΡΠ΅ΡΠΈΠ°Π» Π½Π΅ Π±ΠΎΠΈΡΡΡ ΠΏΠΎΠ³ΠΎΠ΄Π½ΡΡ ΡΡΠ»ΠΎΠ²ΠΈΠΉ. - ΠΠ±Π»Π°Π΄Π°Π΅Ρ Π½Π΅Π±ΠΎΠ»ΡΡΠΈΠΌ ΡΠ΄Π΅Π»ΡΠ½ΡΠΌ Π²Π΅ΡΠΎΠΌ.
- ΠΠΊΠΎΠ»ΠΎΠ³ΠΈΡΠ΅ΡΠΊΠΈ ΡΠΈΡΡΡΠΉ.
- ΠΠ° ΡΡΠ΅Ρ Ρ ΠΎΡΠΎΡΠ΅ΠΉ ΠΏΠ°ΡΠΎΠΏΡΠΎΠ½ΠΈΡΠ°Π΅ΠΌΠΎΡΡΠΈ, ΡΡΠ΅Π½Ρ Π±ΡΠ΄ΡΡ Π΄ΡΡΠ°ΡΡ.
- ΠΠΎΡΠ»Π΅ ΡΡΡΠΎΠΈΡΠ΅Π»ΡΡΡΠ²Π° Π½Π΅ Π΄Π°Π΅Ρ ΡΡΠ°Π΄ΠΊΠΈ.
ΠΠ΅Π΄ΠΎΡΡΠ°ΡΠΊΠΈ:
- Π’Π°ΠΊ ΠΊΠ°ΠΊ ΡΡΡΡΠΊΡΡΡΠ° ΠΌΠ°ΡΠ΅ΡΠΈΠ°Π»Π° ΠΏΠΎΡΠΈΡΡΠ°Ρ, ΡΠΎ ΡΠ°ΠΌΠΈ Π±Π»ΠΎΠΊΠΈ ΠΌΠΎΠΆΠ½ΠΎ Π½Π°Π·Π²Π°ΡΡ Ρ ΡΡΠΏΠΊΠΈΠΌΠΈ.
- ΠΡΠ»ΠΈ Π±ΡΠ°ΡΡ Π²ΠΎ Π²Π½ΠΈΠΌΠ°Π½ΠΈΠ΅ ΠΎΠ΄ΠΈΠ½Π°ΠΊΠΎΠ²ΡΠ΅ Ρ Π°ΡΠ°ΠΊΡΠ΅ΡΠΈΡΡΠΈΠΊΠΈ ΠΈΠ·Π΄Π΅Π»ΠΈΠΉ, ΡΠΎ ΡΠ΅ΠΏΠ»ΠΎΠΈΠ·ΠΎΠ»ΡΡΠΈΠΎΠ½Π½ΡΠ΅ ΡΠ²ΠΎΠΉΡΡΠ²Π° Ρ ΠΊΠ΅ΡΠ°ΠΌΠ·ΠΈΡΠΎΠ±Π΅ΡΠΎΠ½Π° Ρ ΡΠΆΠ΅.
- ΠΠ°ΡΠ΅ΡΠΈΠ°Π» Π½Π΅ ΠΎΠ±Π»Π°Π΄Π°Π΅Ρ ΡΠ΅ΡΠΊΠΈΠΌΠΈ ΠΈ ΠΈΠ΄Π΅Π°Π»ΡΠ½ΠΎ ΡΠΎΠ²Π½ΡΠΌΠΈ ΡΠΎΡΠΌΠ°ΠΌΠΈ.
Π ΠΎΡΡΠ°Π»ΡΠ½ΠΎΠΌ β ΡΡΠΎ ΠΏΡΠ΅ΠΊΡΠ°ΡΠ½ΡΠΉ ΡΡΡΠΎΠΈΡΠ΅Π»ΡΠ½ΡΠΉ ΠΌΠ°ΡΠ΅ΡΠΈΠ°Π», ΡΡΠΎ Π·Π°ΡΠ΅ΠΊΠΎΠΌΠ΅Π½Π΄ΠΎΠ²Π°Π» ΡΠ΅Π±Ρ ΡΠΎΠ»ΡΠΊΠΎ Ρ Π»ΡΡΡΠ΅ΠΉ ΡΡΠΎΡΠΎΠ½Ρ.
ΠΠ°Π·ΠΎΡΠΈΠ»ΠΈΠΊΠ°ΡΠ½ΡΠ΅ Π±Π»ΠΎΠΊΠΈ
ΠΠ°ΠΊ Π²ΡΠ΅Π³Π΄Π°, Π½Π°ΡΠ½Π΅ΠΌ Ρ ΠΏΡΠ΅ΠΈΠΌΡΡΠ΅ΡΡΠ² Π΄Π°Π½Π½ΠΎΠ³ΠΎ ΠΌΠ°ΡΠ΅ΡΠΈΠ°Π»Π°:
- ΠΠ΄Π΅Π°Π»ΡΠ½ΡΠ΅ ΡΠ°Π·ΠΌΠ΅ΡΡ, ΡΠΎΡΠ½ΠΎΡΡΡ ΠΈ Π½Π΅Π±ΠΎΠ»ΡΡΠΎΠΉ Π²Π΅Ρ. Π Π°Π±ΠΎΡΡ Π²ΡΠΏΠΎΠ»Π½ΡΡΡΡΡ Π±ΡΡΡΡΠΎ ΠΈ Π»Π΅Π³ΠΊΠΎ.
- ΠΡΡΡ Π²ΠΎΠ·ΠΌΠΎΠΆΠ½ΠΎΡΡΡ Π²ΡΠΏΠΎΠ»Π½ΡΡΡ ΠΊΠ»Π°Π΄ΠΊΡ Π½Π΅ Π½Π° ΡΠ°ΡΡΠ²ΠΎΡ, Π° Π½Π° ΡΠΏΠ΅ΡΠΈΠ°Π»ΡΠ½ΡΠΉ ΠΊΠ»Π΅ΠΉ.
- ΠΡΠ»ΠΈΡΠ½ΡΠ΅ ΠΏΠΎΠΊΠ°Π·Π°ΡΠ΅Π»ΠΈ ΡΠ±Π΅ΡΠ΅ΠΆΠ΅Π½ΠΈΡ ΡΠ΅ΠΏΠ»Π°.
- ΠΠ° ΡΡΠ΅Ρ ΡΠ°Π·ΠΌΠ΅ΡΠΎΠ², Π²Π΅ΡΠ°, Π³ΡΠ΅Π±Π½Π΅ΠΉ, Π·Π°Ρ
Π²Π°ΡΠΎΠ² ΠΈ ΠΏΠ°Π·ΠΎΠ², ΡΠ°Π±ΠΎΡΠ°ΡΡ Ρ ΠΌΠ°ΡΠ΅ΡΠΈΠ°Π»ΠΎΠΌ ΠΊΠΎΠΌΡΠΎΡΡΠ½ΠΎ.
ΠΠ³ΠΎ ΠΌΠΎΠΆΠ½ΠΎ ΡΠ΅Π·Π°ΡΡ, ΡΠ»ΠΈΡΠΎΠ²Π°ΡΡ, Π΄Π΅Π»Π°ΡΡ ΡΡΡΠΎΠ±Ρ ΠΈ ΡΡΠ°Π½ΡΠΏΠΎΡΡΠΈΡΠΎΠ²Π°ΡΡ Π±Π΅Π· ΠΎΡΠΎΠ±ΡΡ ΡΡΠΈΠ»ΠΈΠΉ.
- Π’Π°ΠΊ ΠΊΠ°ΠΊ ΡΡΡΡΠΊΡΡΡΠ° ΠΌΠ°ΡΠ΅ΡΠΈΠ°Π»Π° ΠΏΠΎΡΠΈΡΡΠ°Ρ, ΡΠΎ ΡΡΠ΅Π½Ρ Π±ΡΠ΄ΡΡ Β«Π΄ΡΡΠ°ΡΡΒ».
- ΠΠΊΠΎΠ»ΠΎΠ³ΠΈΡΠ΅ΡΠΊΠ°Ρ ΡΠΈΡΡΠΎΡΠ°. ΠΠΈΠΊΠ°ΠΊΠΈΡ ΡΠΎΠΊΡΠΈΠ½ΠΎΠ², ΡΠΏΠΎΡΠΎΠ±Π½ΡΡ Π½Π°Π²ΡΠ΅Π΄ΠΈΡΡ ΠΎΡΠ³Π°Π½ΠΈΠ·ΠΌΡ Π½Π΅Ρ.
ΠΠ±ΡΠ°ΡΠΈΡΠ΅ Π²Π½ΠΈΠΌΠ°Π½ΠΈΠ΅! ΠΠ° ΡΡΠ΅Ρ Π½Π΅Π±ΠΎΠ»ΡΡΠΎΠΉ ΠΏΠ»ΠΎΡΠ½ΠΎΡΡΠΈ ΠΈ Ρ ΠΎΡΠΎΡΠΈΡ ΡΠ²ΠΎΠΉΡΡΠ² ΡΠ΅ΠΏΠ»ΠΎΠΈΠ·ΠΎΠ»ΡΡΠΈΠΈ Π³Π°Π·ΠΎΡΠΈΠ»ΠΈΠΊΠ°ΡΠ°, Π²Π΅Ρ ΡΡΠ΅Π½ΠΎΠ²ΠΎΠΉ ΠΊΠΎΠ½ΡΡΡΡΠΊΡΠΈΠΈ ΠΌΠΎΠΆΠ½ΠΎ ΡΠΌΠ΅Π½ΡΡΠΈΡΡ. ΠΠ°ΠΏΡΠΈΠΌΠ΅Ρ, ΡΡΠ°Π²Π½ΠΈΠ²Π°Ρ Π³Π°Π·ΠΎΡΠΈΠ»ΠΈΠΊΠ°ΡΠ½ΡΡ ΡΡΠ΅Π½Ρ ΠΈ ΠΊΠΈΡΠΏΠΈΡΠ½ΡΡ, ΡΠΎ ΠΏΠ΅ΡΠ²Π°Ρ Π±ΡΠ΄Π΅Ρ Π² 3 ΡΠ°Π·Π° Π»Π΅Π³ΡΠ΅. Π ΠΏΠΎ ΡΡΠ°Π²Π½Π΅Π½ΠΈΡ Ρ ΠΊΠ΅ΡΠ°ΠΌΠ·ΠΈΡΠΎΠ±Π΅ΡΠΎΠ½ΠΎΠΌ β Π² 1,7 ΡΠ°Π·.
ΠΠ΅Π΄ΠΎΡΡΠ°ΡΠΊΠΈ Π³Π°Π·ΠΎΡΠΈΠ»ΠΈΠΊΠ°ΡΠ½ΡΡ Π±Π»ΠΎΠΊΠΎΠ²:
- ΠΠ°ΡΠ΅ΡΠΈΠ°Π» Ρ ΡΡΠΏΠΊΠΈΠΉ.
- ΠΡΠ΅Π½Ρ ΡΠΈΠ»ΡΠ½ΠΎ ΠΏΠΎΠ³Π»ΠΎΡΠ°Π΅Ρ Π²Π»Π°Π³Ρ, ΠΏΠΎΡΡΠΎΠΌΡ Π΅Π³ΠΎ Π½ΡΠΆΠ½ΠΎ Π·Π°ΡΠΈΡΠ°ΡΡ.
- ΠΠΌΠ΅Π΅Ρ Π½ΠΈΠ·ΠΊΡΡ ΠΏΡΠΎΡΠ½ΠΎΡΡΡ Π½Π° ΡΠΆΠ°ΡΠΈΠ΅.
- ΠΠΎΡΠΎΠ·ΠΎΡΡΡΠΎΠΉΡΠΈΠ²ΠΎΡΡΡ Π½ΠΈΠΆΠ΅.
- ΠΠΎΡΠ»Π΅ Π²ΠΎΠ·Π²Π΅Π΄Π΅Π½ΠΈΡ ΠΌΠ°ΡΠ΅ΡΠΈΠ°Π» Π΄Π°Π΅Ρ ΡΡΠ°Π΄ΠΊΡ.
- ΠΡΡΠΎΠΊΠ°Ρ ΡΡΠΎΠΈΠΌΠΎΡΡΡ.
ΠΡΠ»ΠΈ Π²ΠΈΠ·ΡΠ°Π»ΡΠ½ΠΎ Π²Π·Π³Π»ΡΠ½ΡΡΡ Π½Π° ΠΏΠΎΠΊΠ°Π·Π°ΡΠ΅Π»ΠΈ ΠΊΠ΅ΡΠ°ΠΌΠ·ΠΈΡΠΎΠ±Π΅ΡΠΎΠ½Π° ΠΈ Π³Π°Π·ΠΎΡΠΈΠ»ΠΈΠΊΠ°ΡΠ°, ΡΠΎ ΡΡΠ°Π·Ρ Π·Π°ΠΌΠ΅ΡΠ½ΡΠΌ ΡΡΠ°Π½ΠΎΠ²ΠΈΡΡΡ ΠΊΠΎΠ»ΠΈΡΠ΅ΡΡΠ²ΠΎ ΠΏΡΠ½ΠΊΡΠΎΠ² Π² ΠΏΠ΅ΡΠ²ΠΎΠΉ ΠΈ Π²ΡΠΎΡΠΎΠΉ Π³ΡΡΠΏΠΏΠ΅. ΠΠ΅ΡΠ°ΠΌΠ·ΠΈΡΠΎΠ±Π΅ΡΠΎΠ½ Π½Π° 10 ΠΏΠΎΠ»ΠΎΠΆΠΈΡΠ΅Π»ΡΠ½ΡΡ
ΡΡΠΎΡΠΎΠ½ ΠΈΠΌΠ΅Π΅Ρ ΡΠΎΠ»ΡΠΊΠΎ 3 Π½Π΅Π³Π°ΡΠΈΠ²Π½ΡΠ΅. Π Π΅ΡΠ»ΠΈ Π³ΠΎΠ²ΠΎΡΠΈΡΡ ΠΎΠ± Π³Π°Π·ΠΎΡΠΈΠ»ΠΈΠΊΠ°ΡΠ΅, ΡΠΎ Π½Π° 6 Π΄ΠΎΡΡΠΎΠΈΠ½ΡΡΠ² ΠΏΡΠΈΡ
ΠΎΠ΄ΠΈΡΡΡ ΡΠ΅Π»ΡΡ
6 ΠΌΠΈΠ½ΡΡΠΎΠ². Π¦ΠΈΡΡΡ Π³ΠΎΠ²ΠΎΡΡΡ ΡΠ°ΠΌΠΈ Π·Π° ΡΠ΅Π±Ρ. ΠΡΠ΅ ΠΆΠ΅, ΡΠ°Π·ΡΠΌΠ½ΠΎΠ΅ ΡΠ΅ΡΠ΅Π½ΠΈΠ΅ Π΄ΠΎΠ»ΠΆΠ½ΠΎ ΠΎΡΡΠ°ΡΡΡΡ Π·Π° Π²Π°ΠΌΠΈ.
ΠΠ°ΠΊΠ»ΡΡΠ΅Π½ΠΈΠ΅
ΠΠ»Π°Π³ΠΎΠ΄Π°ΡΡ ΡΡΠΎΠΉ ΡΡΠ°ΡΡΠ΅, Π²Ρ ΠΌΠΎΠ³Π»ΠΈ ΡΠ·Π½Π°ΡΡ ΠΏΠΎΠ΄ΡΠΎΠ±Π½ΠΎΠ΅ ΠΎΠΏΠΈΡΠ°Π½ΠΈΠ΅ ΡΠΎΠ³ΠΎ ΠΈ ΠΈΠ½ΠΎΠ³ΠΎ ΠΌΠ°ΡΠ΅ΡΠΈΠ°Π»Π°, ΠΈΡ ΡΠ΅Ρ Π½ΠΈΡΠ΅ΡΠΊΠΈΠ΅ Ρ Π°ΡΠ°ΠΊΡΠ΅ΡΠΈΡΡΠΈΠΊΠΈ ΠΈ ΠΎΡΡΠΈΡΠ°ΡΠ΅Π»ΡΠ½ΡΠ΅/ΠΏΠΎΠ»ΠΎΠΆΠΈΡΠ΅Π»ΡΠ½ΡΠ΅ ΡΡΠΎΡΠΎΠ½Ρ. ΠΠΎΠ½ΡΡΠ½ΠΎ, ΡΡΠΎ ΡΡΠ°Π·Ρ ΠΊΡΠΈΡΠΈΠΊΠΎΠ²Π°ΡΡ Π³Π°Π·ΠΎΡΠΈΠ»ΠΈΠΊΠ°Ρ Π½Π΅Π»ΡΠ·Ρ, ΡΠ°ΠΊ ΠΊΠ°ΠΊ Π² ΠΎΠΏΡΠ΅Π΄Π΅Π»Π΅Π½Π½ΡΡ ΠΎΠ±ΡΡΠΎΡΡΠ΅Π»ΡΡΡΠ²Π°Ρ ΠΏΠΎΠ΄ΠΎΠΉΠ΄Π΅Ρ ΠΈΠΌΠ΅Π½Π½ΠΎ ΠΎΠ½. ΠΡΠ΅ ΠΆΠ΅, Π΅ΡΠ»ΠΈ ΡΠ°ΡΡΡΠ΄ΠΈΡΠ΅Π»ΡΠ½ΠΎ ΡΠΊΠ°Π·Π°ΡΡ, ΠΊΠ°ΠΊΠΎΠΉ ΠΈΠ· ΠΌΠ°ΡΠ΅ΡΠΈΠ°Π»ΠΎΠ² Π»ΡΡΡΠ΅, ΡΠΎ Π²ΡΠ΅ ΡΡ ΠΎΠ΄ΡΡΡΡ Π²ΠΎ ΠΌΠ½Π΅Π½ΠΈΠΈ, ΡΡΠΎ ΠΊΠ΅ΡΠ°ΠΌΠ·ΠΈΡΠΎΠ±Π΅ΡΠΎΠ½ ΡΠ°Π³Π½ΡΠ» Π½Π°ΠΌΠ½ΠΎΠ³ΠΎ Π²ΠΏΠ΅ΡΠ΅Π΄. ΠΡΠ»ΠΈ Π²Π°ΠΌ Π½ΡΠΆΠ½ΠΎ ΠΏΠΎΡΡΡΠΎΠΈΡΡ ΡΠ΅ΠΏΠ»ΡΠΉ, Π΄ΠΎΠ»Π³ΠΎΠ²Π΅ΡΠ½ΡΠΉ, Π½Π°Π΄Π΅ΠΆΠ½ΡΠΉ ΠΈ ΡΠΈΡ ΠΈΠΉ Π΄ΠΎΠΌ, ΡΠΎ ΠΏΡΠ΅Π΄ΠΏΠΎΡΠΈΡΠ°ΠΉΡΠ΅ ΠΊΠ΅ΡΠ°ΠΌΠ·ΠΈΡΠΎΠ±Π΅ΡΠΎΠ½Π½ΡΠ΅ Π±Π»ΠΎΠΊΠΈ.
- Π‘ΠΎΡΡΠ°Π² ΠΈ ΠΏΡΠΎΠΏΠΎΡΡΠΈΠΈ ΡΠ°ΡΡΠ²ΠΎΡΠ° Π΄Π»Ρ ΠΊΠ»Π°Π΄ΠΊΠΈ ΠΊΠΈΡΠΏΠΈΡΠ°
- ΠΠ°ΠΊ ΡΠ΄Π΅Π»Π°ΡΡ ΡΠ²Π΅ΡΠ½ΠΎΠΉ ΡΠ°ΡΡΠ²ΠΎΡ Π΄Π»Ρ ΠΊΠΈΡΠΏΠΈΡΠ°
- Π Π°Π·ΠΌΠ΅Ρ ΠΈ Π²Π΅Ρ Π±Π΅Π»ΠΎΠ³ΠΎ ΡΠΈΠ»ΠΈΠΊΠ°ΡΠ½ΠΎΠ³ΠΎ ΠΊΠΈΡΠΏΠΈΡΠ°
- ΠΠΈΡΠΏΠΈΡ ΠΎΠ±Π»ΠΈΡΠΎΠ²ΠΎΡΠ½ΡΠΉ ΡΠΈΠ»ΠΈΠΊΠ°ΡΠ½ΡΠΉ
ΠΠ΅ΡΠ°ΠΌΠ·ΠΈΡΠΎΠ±Π΅ΡΠΎΠ½Π½ΡΠ΅ Π±Π»ΠΎΠΊΠΈ ΠΈΠ»ΠΈ Π³Π°Π·ΠΎΡΠΈΠ»ΠΈΠΊΠ°ΡΠ½ΡΠ΅: ΡΡΠΎ Π»ΡΡΡΠ΅
ΠΡΡΡΠΈΠ΅ ΡΡΡΠΎΠΈΡΠ΅Π»ΡΠ½ΡΠ΅ ΠΌΠ°ΡΠ΅ΡΠΈΠ°Π»Ρ: ΠΊΠ΅ΡΠ°ΠΌΠ·ΠΈΡΠΎΠ±Π΅ΡΠΎΠ½ ΠΈ Π³Π°Π·ΠΎΡΠΈΠ»ΠΈΠΊΠ°Ρ, ΡΠ°ΡΡΠΎ ΠΏΠΎΠΏΠ°Π΄Π°ΡΡ ΠΏΠΎΠ΄ ΡΡΠ°Π²Π½Π΅Π½ΠΈΠ΅, ΠΏΠΎΡΠΊΠΎΠ»ΡΠΊΡ ΠΎΠ½ΠΈ ΠΎΡΠ»ΠΈΡΠ°ΡΡΡΡ Ρ
ΠΎΡΠΎΡΠΈΠΌΠΈ ΠΏΡΠΎΡΠ½ΠΎΡΡΠ½ΡΠΌΠΈ Ρ
Π°ΡΠ°ΠΊΡΠ΅ΡΠΈΡΡΠΈΠΊΠ°ΠΌΠΈ, ΠΈΠΌΠ΅ΡΡ Π½Π΅ΠΌΠ°Π»ΠΎ ΠΏΡΠ΅ΠΈΠΌΡΡΠ΅ΡΡΠ², ΠΊΠΎΡΠΎΡΡΠ΅ ΠΏΡΠ΅ΠΎΠ±Π»Π°Π΄Π°ΡΡ Π½Π°Π΄ ΠΌΠΈΠ½ΡΡΠ°ΠΌΠΈ, ΠΈ ΠΌΠΎΠ³ΡΡ ΠΏΡΠΈΠΌΠ΅Π½ΡΡΡΡΡ Π΄Π»Ρ Π²ΠΎΠ·Π²Π΅Π΄Π΅Π½ΠΈΡ Π²ΡΠ΅Π²ΠΎΠ·ΠΌΠΎΠΆΠ½ΡΡ
ΠΏΠΎΡΡΡΠΎΠ΅ΠΊ β Π±Π°Π½Ρ, Π³Π°ΡΠ°ΠΆΠ΅ΠΉ, Π΄ΠΎΠΌΠΎΠ² ΠΈ ΠΏΡ. ΠΠ΄Π½Π°ΠΊΠΎ ΠΏΡΠΈ Π²ΡΠ±ΠΎΡΠ΅ Π½Π°ΠΈΠ±ΠΎΠ»Π΅Π΅ ΠΏΠΎΠ΄Ρ
ΠΎΠ΄ΡΡΠ΅Π³ΠΎ ΡΡΡΠΎΠΉΠΌΠ°ΡΠ΅ΡΠΈΠ°Π»Π° ΡΡΠΈΡΡΠ²Π°ΡΡΡΡ Π½Π΅ ΡΠΎΠ»ΡΠΊΠΎ Π΅Π³ΠΎ ΡΠ²ΠΎΠΉΡΡΠ²Π°, Π½ΠΎ ΠΈ ΠΎΡΠΎΠ±Π΅Π½Π½ΠΎΡΡΠΈ ΠΆΠ΅Π»Π°Π΅ΠΌΠΎΠΉ ΠΊΠΎΠ½ΡΡΡΡΠΊΡΠΈΠΈ, ΠΊΠ»ΠΈΠΌΠ°ΡΠΈΡΠ΅ΡΠΊΠΈΠ΅ ΡΡΠ»ΠΎΠ²ΠΈΡ ΠΈ ΡΠΈΠ½Π°Π½ΡΠΎΠ²ΠΎΠ΅ ΠΏΠΎΠ»ΠΎΠΆΠ΅Π½ΠΈΠ΅.
Π‘ΠΎΠ΄Π΅ΡΠΆΠ°Π½ΠΈΠ΅
- Π‘ΡΠ°Π²Π½Π΅Π½ΠΈΠ΅
- ΠΠΏΠΈΡΠ°Π½ΠΈΠ΅ ΠΈ ΡΠΎΡΡΠ°Π²
- ΠΠ»ΡΡΡ ΠΈ ΠΌΠΈΠ½ΡΡΡ
- ΠΠ°Π·ΠΎΡΠΈΠ»ΠΈΠΊΠ°Ρ
- ΠΠ΅ΡΠ°ΠΌΠ·ΠΈΡΠΎΠ±Π΅ΡΠΎΠ½
- Π§ΡΠΎ ΡΡΠΈΡΡΠ²Π°ΡΡ ΠΏΡΠΈ Π²ΡΠ±ΠΎΡΠ΅?
- ΠΠ°ΠΊΠΎΠΉ Π»ΡΡΡΠ΅?
Π‘ΡΠ°Π²Π½Π΅Π½ΠΈΠ΅
ΠΠΏΠΈΡΠ°Π½ΠΈΠ΅ ΠΈ ΡΠΎΡΡΠ°Π²
ΠΠ±Π° ΡΡΡΠΎΠΉΠΌΠ°ΡΠ΅ΡΠΈΠ°Π»Π° ΠΎΡΠ½ΠΎΡΡΡΡΡ ΠΊ ΡΡΠ΅ΠΈΡΡΡΠΌ Π±Π΅ΡΠΎΠ½Π°ΠΌ ΠΈ ΠΈΠΌΠ΅ΡΡ ΡΡ ΠΎΠΆΡΡ ΡΡΠ΅ΡΡ ΠΏΡΠΈΠΌΠ΅Π½Π΅Π½ΠΈΡ, Π½ΠΎ ΠΏΡΠΈ ΡΡΠΎΠΌ ΠΎΡΠ»ΠΈΡΠ°ΡΡΡΡ ΡΠΎΡΡΠ°Π²ΠΎΠΌ, ΡΠ΅Ρ Π½ΠΎΠ»ΠΎΠ³ΠΈΠ΅ΠΉ ΠΈΠ·Π³ΠΎΡΠΎΠ²Π»Π΅Π½ΠΈΡ ΠΈ ΡΠ²ΠΎΠΉΡΡΠ²Π°ΠΌΠΈ.
ΠΠ°Π·ΠΎΡΠΈΠ»ΠΈΠΊΠ°ΡΠ½ΡΠ΅ Π±Π»ΠΎΠΊΠΈ ΠΏΠΎΠ»ΡΡΠ°ΡΡ ΠΏΡΡΠ΅ΠΌ Π°Π²ΡΠΎΠΊΠ»Π°Π²Π½ΠΎΠ³ΠΎ ΡΠ²Π΅ΡΠ΄Π΅Π½ΠΈΡ. ΠΠ½ΠΈ Π²ΠΊΠ»ΡΡΠ°ΡΡ Π² ΡΠΎΡΡΠ°Π² ΠΈΠ·ΠΌΠ΅Π»ΡΡΠ΅Π½Π½ΡΠΉ ΠΏΠ΅ΡΠΎΠΊ ΠΈ ΠΈΠ·Π²Π΅ΡΡΡ, Π°Π»ΡΠΌΠΈΠ½ΠΈΠ΅Π²ΡΡ ΠΏΡΠ΄ΡΡ, Π²ΠΎΠ΄Ρ ΠΈ ΡΠ΅ΠΌΠ΅Π½Ρ. ΠΡΠΈ Π²Π·Π°ΠΈΠΌΠΎΠ΄Π΅ΠΉΡΡΠ²ΠΈΠΈ ΠΏΠΎΡΠΎΡΠΊΠ° Π°Π»ΡΠΌΠΈΠ½ΠΈΡ Ρ Π³Π°ΡΠ΅Π½ΠΎΠΉ ΠΈΠ·Π²Π΅ΡΡΡΡ Π·Π°ΠΏΡΡΠΊΠ°Π΅ΡΡΡ ΠΏΡΠΎΡΠ΅ΡΡ Π³Π°Π·ΠΎΠΎΠ±ΡΠ°Π·ΠΎΠ²Π°Π½ΠΈΡ, Π² ΡΠ΅Π·ΡΠ»ΡΡΠ°ΡΠ΅ ΡΠ΅Π³ΠΎ Π±Π»ΠΎΠΊΠΈ ΠΏΡΠΈΠ½ΠΈΠΌΠ°ΡΡ ΠΏΠΎΡΠΈΡΡΡΡ ΡΡΡΡΠΊΡΡΡΡ. ΠΠ΅ΡΠ°ΠΌΠ·ΠΈΡΠΎΠ±Π΅ΡΠΎΠ½ ΠΏΡΠΎΠΈΠ·Π²ΠΎΠ΄ΡΡ Π½Π° ΠΎΡΠ½ΠΎΠ²Π΅ Π²ΠΎΠ΄Ρ, ΠΏΠ΅ΡΠΊΠ°, ΠΊΠ΅ΡΠ°ΠΌΠ·ΠΈΡΠ° ΠΈ ΡΠ΅ΠΌΠ΅Π½ΡΠ°. ΠΠ½Π³ΡΠ΅Π΄ΠΈΠ΅Π½ΡΡ ΡΠΌΠ΅ΡΠΈΠ²Π°ΡΡ Π΄ΠΎ ΠΎΠ΄Π½ΠΎΡΠΎΠ΄Π½ΠΎΠΉ ΠΊΠΎΠ½ΡΠΈΡΡΠ΅Π½ΡΠΈΠΈ ΠΈ ΡΠ°Π·Π»ΠΈΠ²Π°ΡΡ ΠΏΠΎ ΡΠΎΡΠΌΠ°ΠΌ. Π§ΡΠΎΠ±Ρ ΠΈΠ·Π³ΠΎΡΠΎΠ²ΠΈΡΡ ΡΡΠΎΡ ΡΡΡΠΎΠΉΠΌΠ°ΡΠ΅ΡΠΈΠ°Π», Π½Π΅Ρ Π½Π΅ΠΎΠ±Ρ
ΠΎΠ΄ΠΈΠΌΠΎΡΡΠΈ ΠΏΡΠΈΠΌΠ΅Π½ΡΡΡ ΡΠΏΠ΅ΡΠΈΠ°Π»ΡΠ½ΠΎΠ΅ ΠΎΠ±ΠΎΡΡΠ΄ΠΎΠ²Π°Π½ΠΈΠ΅. ΠΡΠΈ ΠΆΠ΅Π»Π°Π½ΠΈΠΈ ΠΌΠΎΠΆΠ½ΠΎ ΡΠ΄Π΅Π»Π°ΡΡ ΠΊΠ΅ΡΠ°ΠΌΠ·ΠΈΡΠΎΠ±Π΅ΡΠΎΠ½Π½ΡΠ΅ Π±Π»ΠΎΠΊΠΈ ΡΠΎΠ±ΡΡΠ²Π΅Π½Π½ΠΎΡΡΡΠ½ΠΎ Π² Π΄ΠΎΠΌΠ°ΡΠ½ΠΈΡ
ΡΡΠ»ΠΎΠ²ΠΈΡΡ
.
ΠΠ»ΡΡΡ ΠΈ ΠΌΠΈΠ½ΡΡΡ
ΠΠ°Π·ΠΎΡΠΈΠ»ΠΈΠΊΠ°Ρ
ΠΠΎΠΏΡΠ»ΡΡΠ½ΡΠΉ Π² ΡΡΠ΅ΡΠ΅ ΡΡΡΠΎΠΈΡΠ΅Π»ΡΡΡΠ²Π° ΠΌΠ°ΡΠ΅ΡΠΈΠ°Π» ΠΎΠ±Π»Π°Π΄Π°Π΅Ρ ΡΠ°ΠΊΠΈΠΌΠΈ ΠΏΡΠ΅ΠΈΠΌΡΡΠ΅ΡΡΠ²Π°ΠΌΠΈ:
- Π²ΡΠ΄Π΅ΡΠΆΠΈΠ²Π°Π΅Ρ Π±ΠΎΠ»ΡΡΠΈΠ΅ Π½Π°Π³ΡΡΠ·ΠΊΠΈ;
- Π½Π΅ ΡΡΠ΅Π±ΡΠ΅Ρ Π΄ΠΎΠΏΠΎΠ»Π½ΠΈΡΠ΅Π»ΡΠ½ΠΎΠ³ΠΎ ΡΠΊΡΠ΅ΠΏΠ»Π΅Π½ΠΈΡ ΠΎΡΠ½ΠΎΠ²Π°Π½ΠΈΡ ΠΏΠΎΡΡΡΠΎΠΉΠΊΠΈ;
- Π²ΠΎΠ·Π²Π΅Π΄Π΅Π½Π½ΡΠ΅ Π³Π°Π·ΠΎΡΠΈΠ»ΠΈΠΊΠ°ΡΠ½ΡΠ΅ ΡΡΠ΅Π½Ρ ΠΎΡΠ»ΠΈΡΠ°ΡΡΡΡ ΠΈΠ΄Π΅Π°Π»ΡΠ½ΠΎΠΉ ΡΠΎΠ²Π½ΠΎΡΡΡΡ;
- ΡΠΊΠΎΠ»ΠΎΠ³ΠΈΡΠ΅ΡΠΊΠΈ ΡΠΈΡΡΡΠΉ;
- ΠΏΡΠΎΡΡ Π² ΡΠΊΠ»Π°Π΄ΠΊΠ΅ ΠΈ ΠΏΠΎΠ΄Π΄Π°Π΅ΡΡΡ ΡΠ»ΠΈΡΠΎΠ²ΠΊΠ΅, ΡΠ΅Π·ΠΊΠ΅;
- ΠΎΠ±Π»Π°Π΄Π°Π΅Ρ Π²ΡΡΠΎΠΊΠΎΠΉ ΡΠ΅ΠΏΠ»ΠΎΠΈΠ·ΠΎΠ»ΡΡΠΈΠ΅ΠΉ ΠΈ ΠΏΠ°ΡΠΎΠΏΡΠΎΡ ΠΎΠ΄ΠΈΠΌΠΎΡΡΡΡ;
- Π½Π΅ ΠΏΠΎΠ΄Π²Π»Π°ΡΡΠ΅Π½ Π²ΠΎΠ·Π΄Π΅ΠΉΡΡΠ²ΠΈΡ ΡΠ°ΠΊΡΠΎΡΠΎΠ² ΠΈΠ·Π²Π½Π΅.
ΠΠ΅ΡΠΌΠΎΡΡΡ Π½Π° Π½Π΅ΠΌΠ°Π»ΠΎΠ΅ ΠΌΠ½ΠΎΠΆΠ΅ΡΡΠ²ΠΎ ΠΏΠ»ΡΡΠΎΠ², Ρ Π°ΡΠ°ΠΊΡΠ΅ΡΠ½Ρ Π΄Π»Ρ Π³Π°Π·ΠΎΡΠΈΠ»ΠΈΠΊΠ°ΡΠ½ΡΡ Π±Π»ΠΎΠΊΠΎΠ² ΠΈ Π½Π΅Π΄ΠΎΡΡΠ°ΡΠΊΠΈ:
- ΡΠΏΠΎΡΠΎΠ±Π½ΠΎΡΡΡ Π±ΡΡΡΡΠΎ ΠΏΠΎΠ³Π»ΠΎΡΠ°ΡΡ Π²Π»Π°Π³Ρ;
- Π½Π΅Π²ΡΡΠΎΠΊΠ°Ρ ΠΏΡΠΎΡΠ½ΠΎΡΡΡ, ΡΠΈΡΠΊ Π²ΠΎΠ·Π½ΠΈΠΊΠ½ΠΎΠ²Π΅Π½ΠΈΡ ΡΡΠ΅ΡΠΈΠ½ ΠΈ ΠΏΡΠΎΡΠΈΡ Π΄Π΅ΡΠ΅ΠΊΡΠΎΠ²;
- Π½Π΅Π²ΠΎΠ·ΠΌΠΎΠΆΠ½ΠΎΡΡΡ ΠΏΡΠΈΠΌΠ΅Π½Π΅Π½ΠΈΡ Π΄Π»Ρ ΡΡΡΠΎΠΈΡΠ΅Π»ΡΡΡΠ²Π° Π½Π΅ΡΡΡΠΈΡ
ΡΡΠ΅Π½.
ΠΠ΅ΡΠ°ΠΌΠ·ΠΈΡΠΎΠ±Π΅ΡΠΎΠ½
Π£ ΠΊΠ΅ΡΠ°ΠΌΠ·ΠΈΡΠΎΠ±Π΅ΡΠΎΠ½Π½ΡΡ Π±Π»ΠΎΠΊΠΎΠ², ΠΊΠ°ΠΊ ΠΈ Ρ Π³Π°Π·ΠΎΡΠΈΠ»ΠΈΠΊΠ°ΡΠ½ΡΡ ΠΌΠ½ΠΎΠ³ΠΎ ΠΏΠΎΠ»ΠΎΠΆΠΈΡΠ΅Π»ΡΠ½ΡΡ ΠΌΠΎΠΌΠ΅Π½ΡΠΎΠ²:
- ΡΡΠΎΠΉΠΊΠΎΡΡΡ ΠΊ ΡΠ½ΠΈΠΆΠ΅Π½Π½ΠΎΠΉ ΡΠ΅ΠΌΠΏΠ΅ΡΠ°ΡΡΡΠ΅;
- ΠΌΠΈΠ½ΠΈΠΌΠ°Π»ΡΠ½ΡΠ΅ Π΄Π΅Π½Π΅ΠΆΠ½ΡΠ΅ Π·Π°ΡΡΠ°ΡΡ ΠΏΡΠΈ ΡΠΎΠ±ΡΡΠ²Π΅Π½Π½ΠΎΡΡΡΠ½ΠΎΠΌ ΠΈΠ·Π³ΠΎΡΠΎΠ²Π»Π΅Π½ΠΈΠΈ;
- Ρ ΠΎΡΠΎΡΠ°Ρ ΡΡΠΌΠΎΠΈΠ·ΠΎΠ»ΡΡΠΈΡ, ΠΎΠ³Π½Π΅ΡΠΏΠΎΡΠ½ΠΎΡΡΡ ΠΈ Π²Π»Π°Π³ΠΎΡΡΠΎΠΉΠΊΠΎΡΡΡ;
- ΡΠΎ Π²ΡΠ΅ΠΌΠ΅Π½Π΅ΠΌ Π½Π΅ ΡΠ΅ΡΡΠ΅Ρ ΠΏΡΠΎΡΠ½ΠΎΡΡΠ½ΡΡ Ρ Π°ΡΠ°ΠΊΡΠ΅ΡΠΈΡΡΠΈΠΊ, Π° Π»ΠΈΡΡ ΡΠ²Π΅Π»ΠΈΡΠΈΠ²Π°Π΅Ρ ΠΈΡ ;
- ΡΠΊΠΎΠ»ΠΎΠ³ΠΈΡΠ΅ΡΠΊΠ°Ρ Π±Π΅Π·ΠΎΠΏΠ°ΡΠ½ΠΎΡΡΡ.
ΠΠΌΠ΅ΡΡΡΡ Ρ ΠΊΠ΅ΡΠ°ΠΌΠ·ΠΈΡΠΎΠ±Π΅ΡΠΎΠ½Π° ΠΈ Π½Π΅Π΄ΠΎΡΡΠ°ΡΠΊΠΈ, Π² ΡΠΈΡΠ»Π΅ ΠΊΠΎΡΠΎΡΡΡ
ΠΏΠΎΠ²ΡΡΠ΅Π½Π½Π°Ρ Ρ
ΡΡΠΏΠΊΠΎΡΡΡ ΠΈ Π½Π΅ΡΠΏΠΎΡΠΎΠ±Π½ΠΎΡΡΡ Π²ΡΠ΄Π΅ΡΠΆΠΈΠ²Π°ΡΡ Π±ΠΎΠ»ΡΡΠΈΠ΅ Π½Π°Π³ΡΡΠ·ΠΊΠΈ, ΠΏΠΎΡΡΠΎΠΌΡ ΡΡΠΎΡ ΡΡΡΠΎΠΈΡΠ΅Π»ΡΠ½ΡΠΉ ΠΌΠ°ΡΠ΅ΡΠΈΠ°Π» Π½Π΅ ΠΏΠΎΠ΄Ρ
ΠΎΠ΄ΠΈΡ Π΄Π»Ρ ΡΠΎΠΎΡΡΠΆΠ΅Π½ΠΈΡ Π½Π΅ΡΡΡΠΈΡ
ΡΡΠ΅Π½. Π ΡΠΎΠΌΡ ΠΆΠ΅ ΠΊΠ΅ΡΠ°ΠΌΠ·ΠΈΡΠΎΠ±Π΅ΡΠΎΠ½Π½ΡΠ΅ Π±Π»ΠΎΠΊΠΈ ΡΡΠ΅Π±ΡΡΡ Π΄ΠΎΠΏΠΎΠ»Π½ΠΈΡΠ΅Π»ΡΠ½ΠΎΠ³ΠΎ Π²ΡΡΠ°Π²Π½ΠΈΠ²Π°Π½ΠΈΡ ΠΈ Π΄Π»Ρ ΠΈΡ
ΡΠ°ΡΠΏΠΈΠ»ΠΎΠ²ΠΊΠΈ Π½Π΅ ΠΎΠ±ΠΎΠΉΡΠΈΡΡ Π±Π΅Π· ΡΠΏΠ΅ΡΠΈΠ°Π»ΡΠ½ΡΡ
ΠΈΠ½ΡΡΡΡΠΌΠ΅Π½ΡΠΎΠ². Π‘ΡΠΎΠΈΡ ΠΎΠ±ΡΠ°ΡΠΈΡΡ Π²Π½ΠΈΠΌΠ°Π½ΠΈΠ΅, ΡΡΠΎ Ρ ΠΊΠ΅ΡΠ°ΠΌΠ·ΠΈΡΠΎΠ±Π΅ΡΠΎΠ½Π° Π΄ΠΎΠ²ΠΎΠ»ΡΠ½ΠΎ Π²ΡΡΠΎΠΊΠΈΠ΅ ΡΠ΅ΠΏΠ»ΠΎΠΈΠ·ΠΎΠ»ΡΡΠΈΠΎΠ½Π½ΡΠ΅ ΡΠ²ΠΎΠΉΡΡΠ²Π°, ΠΎΠ΄Π½Π°ΠΊΠΎ ΠΈΡ
Π½Π΅ ΡΡΠ°Π²Π½ΠΈΡΡ Ρ ΡΠ΅ΠΏΠ»ΠΎΠΏΡΠΎΠ²ΠΎΠ΄Π½ΠΎΡΡΡΡ, ΠΊΠΎΡΠΎΡΠΎΠΉ ΠΎΠ±Π»Π°Π΄Π°Π΅Ρ ΡΠΎΡ ΠΆΠ΅ Π°ΡΠ±ΠΎΠ»ΠΈΡ (Π°ΡΠ±ΠΎΠ»ΠΈΡΠΎΠ²ΡΠ΅ Π±Π»ΠΎΠΊΠΈ ΠΏΠΎ ΡΡΠΎΠΌΡ ΠΊΡΠΈΡΠ΅ΡΠΈΡ Π·Π°Π½ΠΈΠΌΠ°ΡΡ Π»ΠΈΠ΄ΠΈΡΡΡΡΠΈΠ΅ ΠΏΠΎΠ·ΠΈΡΠΈΠΈ, ΠΈΡ
ΡΠ΅ΠΏΠ»ΠΎΠΏΡΠΎΠ²ΠΎΠ΄Π½ΠΎΡΡΡ ΡΠΎΡΡΠ°Π²Π»ΡΠ΅Ρ 0,08β0,17 ΠΡ/ΠΌ Π). ΠΠΎΡΡΠΎΠΌΡ ΠΊΠΎΠ½ΡΡΡΡΠΊΡΠΈΠΈ ΠΈΠ· ΠΊΠ΅ΡΠ°ΠΌΠ·ΠΈΡΠ° Π½ΡΠΆΠ΄Π°ΡΡΡΡ Π² ΡΡΠ΅ΠΏΠ»Π΅Π½ΠΈΠΈ, ΡΡΠΎ ΡΡΡΠ΅ΡΡΠ²Π΅Π½Π½ΠΎ ΡΠ²Π΅Π»ΠΈΡΠΈΠ²Π°Π΅Ρ Π·Π°ΡΡΠ°ΡΡ.
Π§ΡΠΎ ΡΡΠΈΡΡΠ²Π°ΡΡ ΠΏΡΠΈ Π²ΡΠ±ΠΎΡΠ΅?
ΠΡΠ±ΠΈΡΠ°Ρ ΠΌΠ΅ΠΆΠ΄Ρ Π³Π°Π·ΠΎΡΠΈΠ»ΠΈΠΊΠ°ΡΠ½ΡΠΌΠΈ ΠΈ ΠΊΠ΅ΡΠ°ΠΌΠ·ΠΈΡΠΎΠ±Π΅ΡΠΎΠ½Π½ΡΠΌΠΈ Π±Π»ΠΎΠΊΠ°ΠΌΠΈ, Π½ΡΠΆΠ½ΠΎ ΡΡΠΈΡΡΠ²Π°ΡΡ, ΡΡΠΎ ΠΏΠ΅ΡΠ²ΡΠ΅ ΠΈΠ· Π½ΠΈΡ ΠΎΡΠ»ΠΈΡΠ°ΡΡΡΡ ΠΏΠΎΠ²ΡΡΠ΅Π½Π½ΠΎΠΉ ΡΡΠΏΡΡΠ΅ΡΡΡΡ, ΠΏΠΎΡΡΠΎΠΌΡ Π·Π°ΡΠΈΠΊΡΠΈΡΠΎΠ²Π°ΡΡ Π½Π° ΡΠ°ΠΊΠΈΡ ΡΡΠ΅Π½ΠΊΠ°Ρ ΡΡΠΆΠ΅Π»ΡΠΉ ΠΏΡΠ΅Π΄ΠΌΠ΅Ρ Π±ΡΠ΄Π΅Ρ ΡΠ»ΠΎΠΆΠ½ΠΎ. ΠΡΠ»ΠΈ ΡΡΠ°Π²Π½ΠΈΠ²Π°ΡΡ ΡΡΡΠΎΠΈΡΠ΅Π»ΡΠ½ΡΠ΅ ΠΌΠ°ΡΠ΅ΡΠΈΠ°Π»Ρ ΠΏΠΎ ΡΠΏΠΎΡΠΎΠ±Π½ΠΎΡΡΠΈ ΡΠΎΡ ΡΠ°Π½ΡΡΡ ΡΠ΅ΠΏΠ»ΠΎ, ΡΠΎ Π² ΡΡΠΎΠΌ ΡΠ»ΡΡΠ°Π΅ ΠΎΠ½ΠΈ Π½Π΅ ΠΊΠΎΠ½ΠΊΡΡΠ΅Π½ΡΡ, ΠΏΠΎΡΠΊΠΎΠ»ΡΠΊΡ ΠΈ ΠΊΠ΅ΡΠ°ΠΌΠ·ΠΈΡΠΎΠ±Π΅ΡΠΎΠ½, ΠΈ Π³Π°Π·ΠΎΡΠΈΠ»ΠΈΠΊΠ°Ρ ΡΡΠ΅Π±ΡΠ΅Ρ ΡΡΠ΅ΠΏΠ»Π΅Π½ΠΈΡ. ΠΠ°ΠΆΠ½ΠΎ ΡΡΠΈΡΡΠ²Π°ΡΡ ΠΈ ΡΠΎΡ ΡΠ°ΠΊΡ, ΡΡΠΎ ΠΏΡΠΈ Π²ΠΎΠ·Π²Π΅Π΄Π΅Π½ΠΈΠΈ ΡΠΎΠΎΡΡΠΆΠ΅Π½ΠΈΡ ΠΈΠ· Π±Π΅ΡΠΎΠ½Π° Π½Π° ΠΎΡΠ½ΠΎΠ²Π΅ ΠΈΠ·Π²Π΅ΡΡΠΈ, Π½Π΅ΠΎΠ±Ρ ΠΎΠ΄ΠΈΠΌΠΎ ΠΌΠΎΠ½ΡΠΈΡΠΎΠ²Π°ΡΡ ΠΏΠΎΠ²Π΅ΡΡ ΡΡΠ΅Π½ Π°ΡΠΌΠΎΠΏΠΎΡΡ. ΠΠ΅ΡΠ°ΠΌΠ·ΠΈΡΠΎΠ±Π΅ΡΠΎΠ½Π½ΡΠ΅ ΡΡΠ΅Π½Ρ Π² Π±ΠΎΠ»ΡΡΠΈΠ½ΡΡΠ²Π΅ ΡΠ»ΡΡΠ°Π΅Π² ΠΎΠ±Ρ ΠΎΠ΄ΡΡΡΡ Π±Π΅Π· Π½Π΅Π³ΠΎ.
ΠΡΠ»ΠΈ ΠΏΡΠΈ ΡΡΡΠΎΠΈΡΠ΅Π»ΡΡΡΠ²Π΅ ΠΈΡΠΏΠΎΠ»ΡΠ·ΡΠ΅ΡΡΡ Π³Π°Π·ΠΎΡΠΈΠ»ΠΈΠΊΠ°Ρ, ΡΠΎ ΠΎΠ½ ΡΡΠ΅Π±ΡΠ΅Ρ Π°ΡΠΌΠΈΡΠΎΠ²ΠΊΠΈ, ΡΡΠΎ ΠΏΠΎΠ²Π»Π΅ΡΠ΅Ρ Π·Π° ΡΠΎΠ±ΠΎΠΉ Π΄ΠΎΠΏΠΎΠ»Π½ΠΈΡΠ΅Π»ΡΠ½ΡΠ΅ ΡΠ°ΡΡ ΠΎΠ΄Ρ.ΠΡΠΈ Π²ΡΠ±ΠΎΡΠ΅ Π»ΡΡΡΠ΅Π³ΠΎ ΡΡΡΠΎΠΈΡΠ΅Π»ΡΠ½ΠΎΠ³ΠΎ ΠΌΠ°ΡΠ΅ΡΠΈΠ°Π»Π° Π±Π΅ΡΡΡ Π²ΠΎ Π²Π½ΠΈΠΌΠ°Π½ΠΈΠ΅ ΠΈ ΡΠΎΡ ΠΌΠΎΠΌΠ΅Π½Ρ, ΡΡΠΎ Π³Π°Π·ΠΎΡΠΈΠ»ΠΈΠΊΠ°ΡΠ½ΡΠ΅ ΠΊΠΎΠ½ΡΡΡΡΠΊΡΠΈΠΈ ΠΏΠΎ ΡΡΠ°Π²Π½Π΅Π½ΠΈΡ Ρ ΠΊΠ΅ΡΠ°ΠΌΠ·ΠΈΡΠΎΠ±Π΅ΡΠΎΠ½Π½ΡΠΌΠΈ ΡΠΎΠΎΡΡΠΆΠ΅Π½ΠΈΡΠΌΠΈ Π²ΡΡ
ΠΎΠ΄ΡΡ Π·Π½Π°ΡΠΈΡΠ΅Π»ΡΠ½ΠΎ Π΄ΠΎΡΠΎΠΆΠ΅. ΠΡΠΎ ΠΎΠ±ΡΡΠ»ΠΎΠ²Π»Π΅Π½ΠΎ ΡΠ΅ΠΌ, ΡΡΠΎ ΠΏΡΠΈ ΠΈΡ
Π²ΠΎΠ·Π²Π΅Π΄Π΅Π½ΠΈΠΈ Π΄ΠΎΠΏΠΎΠ»Π½ΠΈΡΠ΅Π»ΡΠ½ΠΎ ΡΡ
ΠΎΠ΄ΡΡ ΡΠ°ΡΡ
ΠΎΠ΄Ρ Π½Π° Π°ΡΠΌΠΈΡΠΎΠ²Π°Π½ΠΈΠ΅, ΡΡΠ΅ΠΏΠ»Π΅Π½ΠΈΠ΅ ΠΈ Π΄ΠΎΡΡΠΈΠΆΠ΅Π½ΠΈΠ΅ ΠΎΠΏΡΠΈΠΌΠ°Π»ΡΠ½ΠΎΠΉ ΡΠΎΠ»ΡΠΈΠ½Ρ Π½Π΅ΡΡΡΠ΅ΠΉ ΡΡΠ΅Π½Ρ, ΠΊΠΎΡΠΎΡΠ°Ρ Π·Π°ΡΠ°ΡΡΡΡ Π²ΡΡ
ΠΎΠ΄ΠΈΡ Π±ΠΎΠ»ΡΡΠ΅ ΠΊΠ΅ΡΠ°ΠΌΠ·ΠΈΡΠΎΠ±Π΅ΡΠΎΠ½Π½ΠΎΠΉ. Π ΡΠΎΠΌΡ ΠΆΠ΅ Π΄Π»Ρ ΡΡΡΠΎΠΈΡΠ΅Π»ΡΡΡΠ²Π° ΠΏΡΠΎΡΠ½ΠΎΠ³ΠΎ Π·Π΄Π°Π½ΠΈΡ ΠΏΡΠΈΠΎΠ±ΡΠ΅ΡΠ°ΡΡ Π³Π°Π·ΠΎΡΠΈΠ»ΠΈΠΊΠ°Ρ Π½ΡΠΆΠ½ΠΎ ΡΠΎΠ»ΡΠΊΠΎ ΠΊΠ°ΡΠ΅ΡΡΠ²Π΅Π½Π½ΡΡ
ΠΈ Π΄ΠΎΡΠΎΠ³ΠΎΡΡΠΎΡΡΠΈΡ
ΠΌΠ°ΡΠΎΠΊ.
ΠΠ°ΠΊΠΎΠΉ Π»ΡΡΡΠ΅?
ΠΠΎΠ΄ΡΠΎΠ±Π½ΠΎ ΠΈΠ·ΡΡΠΈΠ² Ρ
Π°ΡΠ°ΠΊΡΠ΅ΡΠΈΡΡΠΈΠΊΠΈ Π³Π°Π·ΠΎΡΠΈΠ»ΠΈΠΊΠ°ΡΠ½ΡΡ
ΠΈ ΠΊΠ΅ΡΠ°ΠΌΠ·ΠΈΡΠΎΠ±Π΅ΡΠΎΠ½Π½ΡΡ
Π±Π»ΠΎΠΊΠΎΠ², ΠΈΡ
ΠΏΠ»ΡΡΡ, ΠΌΠΈΠ½ΡΡΡ, ΡΠ΅Π½ΠΎΠ²ΡΡ ΠΏΠΎΠ»ΠΈΡΠΈΠΊΡ, ΠΊΠ°ΠΆΠ΄ΡΠΉ ΡΡΡΠΎΠΈΡΠ΅Π»Ρ ΡΠΌΠΎΠΆΠ΅Ρ Π²ΡΠ±ΡΠ°ΡΡ Π΄Π»Ρ ΡΠ΅Π±Ρ Π½Π°ΠΈΠ±ΠΎΠ»Π΅Π΅ ΠΏΠΎΠ΄Ρ
ΠΎΠ΄ΡΡΠΈΠΉ ΡΡΡΠΎΠ΅Π²ΠΎΠΉ ΠΌΠ°ΡΠ΅ΡΠΈΠ°Π». ΠΠ΄Π½Π°ΠΊΠΎ ΠΎΠΏΡΡΠ½ΡΠ΅ Π±ΡΠΈΠ³Π°Π΄ΠΈΡΡ ΡΠ΅ΠΊΠΎΠΌΠ΅Π½Π΄ΡΡΡ ΡΡΠΈΡΡΠ²Π°ΡΡ ΠΈ ΠΌΠ½Π΅Π½ΠΈΡ Π΄ΡΡΠ³ΠΈΡ
ΡΠΏΠ΅ΡΠΈΠ°Π»ΠΈΡΡΠΎΠ², Π° ΡΠ°ΠΊΠΆΠ΅ ΠΏΡΠΈ Π²ΡΠ±ΠΎΡΠ΅ ΠΌΠ°ΡΠ΅ΡΠΈΠ°Π»Π° Π±ΡΠ°ΡΡ Π²ΠΎ Π²Π½ΠΈΠΌΠ°Π½ΠΈΠ΅ ΠΏΡΠ΅Π΄Π½Π°Π·Π½Π°ΡΠ΅Π½ΠΈΠ΅ ΠΏΠΎΡΡΡΠΎΠΉΠΊΠΈ, Π²ΠΎΠ·ΠΌΠΎΠΆΠ½ΠΎΡΡΡ Π½Π°ΠΉΠΌΠ° ΡΠΏΠ΅ΡΠΈΠ°Π»ΠΈΠ·ΠΈΡΠΎΠ²Π°Π½Π½ΠΎΠΉ ΡΠ΅Ρ
Π½ΠΈΠΊΠΈ ΠΈ ΡΠΈΠ½Π°Π½ΡΠΎΠ²ΡΠΉ Π°ΡΠΏΠ΅ΠΊΡ. Π’Π°ΠΊ, Π΅ΡΠ»ΠΈ Π²ΡΠ΅ΠΌΠ΅Π½ΠΈ Π½Π° ΡΡΡΠΎΠΈΡΠ΅Π»ΡΡΡΠ²ΠΎ ΠΌΠ°Π»ΠΎ, ΡΠΎ Π»ΡΡΡΠ΅ Π²ΠΎΡΠΏΠΎΠ»ΡΠ·ΠΎΠ²Π°ΡΡΡΡ Π±ΠΎΠ»ΡΡΠΈΠΌΠΈ, Π½ΠΎ Π»Π΅Π³ΠΊΠΈΠΌΠΈ Π³Π°Π·ΠΎΡΠΈΠ»ΠΈΠΊΠ°ΡΠ½ΡΠΌΠΈ Π±Π»ΠΎΠΊΠ°ΠΌΠΈ. Π ΡΠΎΠΌΡ ΠΆΠ΅ ΠΈΠΌ ΡΠ»Π΅Π΄ΡΠ΅Ρ ΠΎΡΠ΄Π°ΡΡ ΠΏΡΠ΅Π΄ΠΏΠΎΡΡΠ΅Π½ΠΈΠ΅ ΠΈ Π΅ΡΠ»ΠΈ ΡΠΎΠΎΡΡΠΆΠ°Π΅ΠΌΠΎΠ΅ Π·Π΄Π°Π½ΠΈΠ΅ Π΄ΠΎΠ»ΠΆΠ½ΠΎ ΠΏΡΠΎΡΠΈΠ²ΠΎΡΡΠΎΡΡΡ ΠΌΠΈΠ½ΡΡΠΎΠ²ΡΠΌ ΡΠ΅ΠΌΠΏΠ΅ΡΠ°ΡΡΡΠ°ΠΌ, ΠΏΠΎΡΠΊΠΎΠ»ΡΠΊΡ ΠΊΠ΅ΡΠ°ΠΌΠ·ΠΈΡ Π±ΠΎΠ»Π΅Π΅ Π²ΠΎΡΠΏΡΠΈΠΈΠΌΡΠΈΠ² ΠΊ Π³ΡΠ°Π΄ΡΡΠ°ΠΌ Π²ΠΎΠ·Π΄ΡΡ
Π° Π½ΠΈΠΆΠ΅ 0 ΠΈ Π½ΡΠΆΠ΄Π°Π΅ΡΡΡ Π² Π·Π°ΡΠΈΡΠ½ΠΎΠΉ ΠΎΡΠ΄Π΅Π»ΠΊΠ΅. ΠΡΡΡΠΈΠΉ Π²Π°ΡΠΈΠ°Π½Ρ β ΠΈΡΠΏΠΎΠ»ΡΠ·ΠΎΠ²Π°ΡΡ Π΄Π²Π° ΡΡΡΠΎΠΉΠΌΠ°ΡΠ΅ΡΠΈΠ°Π»Π° Π²ΠΌΠ΅ΡΡΠ΅, ΡΡΠΎ ΡΠ»ΡΡΡΠΈΡ ΡΡΡΠΎΠΉΡΠΈΠ²ΠΎΡΡΡ ΠΏΠΎΡΡΡΠΎΠΉΠΊΠΈ, ΡΠ²Π΅Π»ΠΈΡΠΈΡ Π΅Π΅ Π΄ΠΎΠ»Π³ΠΎΠ²Π΅ΡΠ½ΠΎΡΡΡ ΠΈ ΡΡΠΊΠΎΠ½ΠΎΠΌΠΈΡ Π±ΡΠ΄ΠΆΠ΅Ρ.
ΠΠ·Π΄Π΅Π»ΠΈΡ ΠΈΠ· ΠΊΠ΅ΡΠ°ΠΌΠ·ΠΈΡΠ° | ΠΠ΅ΡΠΎΠ½
ΠΠ΅ΡΠ°ΠΌΠ·ΠΈΡ Π»Π΅Π³ΠΊΠΈΠΉ Π±Π΅ΡΠΎΠ½, Π² ΠΊΠΎΡΠΎΡΠΎΠΌ Π½Π°ΠΏΠΎΠ»Π½ΠΈΡΠ΅Π»Π΅ΠΌ ΡΠ²Π»ΡΠ΅ΡΡΡ ΠΊΠ΅ΡΠ°ΠΌΠ·ΠΈΡ — ΡΡΠ΅ΠΈΡΡΡΠΉ ΠΌΠ°ΡΠ΅ΡΠΈΠ°Π» Π² Π²ΠΈΠ΄Π΅ Π³ΡΠ°Π½ΡΠ». Π‘ΡΡΡΠ΅ΠΌ Π΄Π»Ρ ΠΏΡΠΎΠΈΠ·Π²ΠΎΠ΄ΡΡΠ²Π° ΠΊΠ΅ΡΠ°ΠΌΠ·ΠΈΡΠ° ΡΠ»ΡΠΆΠ°Ρ ΡΡΠ³Π»ΠΈΠ½ΠΊΠΈ ΠΈ Π³Π»ΠΈΠ½Ρ β ΡΠΊΠΎΠ»ΠΎΠ³ΠΈΡΠ΅ΡΠΊΠΈ ΡΠΈΡΡΡΠ΅ ΠΌΠ°ΡΠ΅ΡΠΈΠ°Π»Ρ. ΠΠΎ ΡΠ΅ΠΏΠ»ΠΎ- ΠΈ Π·Π²ΡΠΊΠΎΠΈΠ·ΠΎΠ»ΡΡΠΈΠΎΠ½Π½ΡΠΌ ΡΠ²ΠΎΠΉΡΡΠ²Π°ΠΌ, Π²Π»Π°Π³ΠΎ- ΠΈ Ρ ΠΈΠΌΠΈΡΠ΅ΡΠΊΠΎΠΉ ΡΡΠΎΠΉΠΊΠΎΡΡΠΈ ΠΎΠ½ Π½Π΅ ΡΠΎΠ»ΡΠΊΠΎ Π½Π΅ ΡΡΡΡΠΏΠ°Π΅Ρ ΠΎΠ±ΡΡΠ½ΡΠΌ ΠΈ Π΄ΡΡΠ³ΠΈΠΌ Π»Π΅Π³ΠΊΠΈΠΌ Π±Π΅ΡΠΎΠ½Π°ΠΌ, Π½ΠΎ ΠΈ ΠΏΡΠ΅Π²ΠΎΡΡ ΠΎΠ΄ΠΈΡ ΠΈΡ . ΠΠ»ΠΎΠΊΠΈ ΠΈΠ· ΠΊΠ΅ΡΠ°ΠΌΠ·ΠΈΡΠ° Π½Π°Π·ΡΠ²Π°ΡΡ Β«Π±ΠΈΠΎΠ±Π»ΠΎΠΊΠ°ΠΌΠΈΒ», Π² ΠΊΠ°ΡΠ΅ΡΡΠ²Π΅ ΠΈΡΡ ΠΎΠ΄Π½ΠΎΠ³ΠΎ ΡΡΡΡΡ ΠΈΡΠΏΠΎΠ»ΡΠ·ΡΡΡΡΡ ΡΠΎΠ»ΡΠΊΠΎ ΡΠΊΠΎΠ»ΠΎΠ³ΠΈΡΠ΅ΡΠΊΠΈ ΡΠΈΡΡΡΠ΅ Π½Π°ΡΡΡΠ°Π»ΡΠ½ΡΠ΅ ΠΊΠΎΠΌΠΏΠΎΠ½Π΅Π½ΡΡ. ΠΠ° ΠΎΡΠ½ΠΎΠ²Π΅ ΡΡΠΎΠ³ΠΎ ΠΏΠΎΠ»ΡΡΠΈΠ» Π·Π°ΡΠ»ΡΠΆΠ΅Π½Π½ΠΎΠ΅ ΡΠ°ΡΠΏΡΠΎΡΡΡΠ°Π½Π΅Π½ΠΈΠ΅ ΠΊΠ΅ΡΠ°ΠΌΠ·ΠΈΡ, ΠΏΡΠΎΠΈΠ·Π²ΠΎΠ΄ΡΡΠ²ΠΎ ΠΈ ΠΈΡΠΏΠΎΠ»ΡΠ·ΠΎΠ²Π°Π½ΠΈΠ΅ ΠΊΠΎΡΠΎΡΠΎΠ³ΠΎ Π±ΡΡΡΡΠΎ ΡΠ°ΡΡΠ΅Ρ.
ΠΠ·Π΄Π΅Π»ΠΈΡ ΠΈΠ· ΠΊΠ΅ΡΠ°ΠΌΠ·ΠΈΡΠ°, ΠΈΡΠΏΠΎΠ»ΡΠ·ΡΠ΅ΠΌΡΠ΅ Π² ΠΊΠ°ΡΠ΅ΡΡΠ²Π΅ Π½Π΅ΡΡΡΠΈΡ
ΠΊΠΎΠ½ΡΡΡΡΠΊΡΠΈΠΉ Π² ΠΆΠΈΠ»ΠΈΡΠ½ΠΎΠΌ, Π³ΡΠ°ΠΆΠ΄Π°Π½ΡΠΊΠΎΠΌ ΠΈ ΠΏΡΠΎΠΌΡΡΠ»Π΅Π½Π½ΠΎΠΌ ΡΡΡΠΎΠΈΡΠ΅Π»ΡΡΡΠ²Π΅. ΠΠ±ΡΠ΅ΠΌΠ½ΡΠΉ Π²Π΅Ρ ΠΊΠ΅ΡΠ°ΠΌΠ·ΠΈΡΠ° Π²ΡΡΠΎΠΊΠΈΡ
ΠΌΠ°ΡΠΎΠΊ ΠΏΡΠΈΠΌΠ΅ΡΠ½ΠΎ Π² 2,5 ΡΠ°Π·Π° ΠΌΠ΅Π½ΡΡΠ΅ ΡΡΠΆΠ΅Π»ΠΎΠ³ΠΎ Π±Π΅ΡΠΎΠ½Π°. Π’Π°ΠΊΠΈΠΌ ΠΎΠ±ΡΠ°Π·ΠΎΠΌ, ΠΏΡΠΈΠΌΠ΅Π½Π΅Π½ΠΈΠ΅ ΠΊΠ΅ΡΠ°ΠΌΠ·ΠΈΡΠ° ΠΏΠΎΠ·Π²ΠΎΠ»ΡΠ΅Ρ Π·Π½Π°ΡΠΈΡΠ΅Π»ΡΠ½ΠΎ ΡΠ½ΠΈΠ·ΠΈΡΡ Π²Π΅Ρ Π·Π΄Π°Π½ΠΈΠΉ ΠΈ ΡΠΎΠΎΡΡΠΆΠ΅Π½ΠΈΠΉ, Π΄ΠΎΡΡΠΈΠ³Π½ΡΡ ΡΡΠ΄ ΠΏΠΎΠ»ΠΎΠΆΠΈΡΠ΅Π»ΡΠ½ΡΡ
ΡΠ΅Ρ
Π½ΠΈΠΊΠΎ-ΡΠΊΠΎΠ½ΠΎΠΌΠΈΡΠ΅ΡΠΊΠΈΡ
ΠΏΠΎΠΊΠ°Π·Π°ΡΠ΅Π»Π΅ΠΉ. Π ΠΊΠ»ΠΈΠΌΠ°ΡΠΈΡΠ΅ΡΠΊΠΈΡ
ΡΡΠ»ΠΎΠ²ΠΈΡΡ
ΠΏΡΠΈΠΌΠ΅Π½Π΅Π½ΠΈΠ΅ ΠΎΠ΄Π½ΠΎΡΠ»ΠΎΠΉΠ½ΡΡ
Π½Π°ΡΡΠΆΠ½ΡΡ
ΡΡΠ΅Π½ ΠΈΠ· ΠΊΠ΅ΡΠ°ΠΌΠ·ΠΈΡΠΎΠ±Π΅ΡΠΎΠ½Π° ΠΏΠΎΠ·Π²ΠΎΠ»ΡΠ΅Ρ ΡΡΡΠ΅ΠΊΡΠΈΠ²Π½ΠΎ ΠΈΡΠΏΠΎΠ»ΡΠ·ΠΎΠ²Π°ΡΡ Π΅Π³ΠΎ ΡΠ΅ΠΏΠ»ΠΎΡΠΈΠ·ΠΈΡΠ΅ΡΠΊΠΈΠ΅ ΡΠ²ΠΎΠΉΡΡΠ²Π°.
ΠΠ°ΡΠ΅ΡΠΈΠ°Π» Π½Π΅ Π³ΠΎΡΠΈΡ, Π½Π΅ Π³Π½ΠΈΠ΅Ρ, Π² ΠΎΡΠ»ΠΈΡΠΈΠ΅ ΠΎΡ Π΄Π΅ΡΠ΅Π²Π° ΠΈ Π½Π΅ ΡΠΆΠ°Π²Π΅Π΅Ρ ΠΏΠΎ ΡΡΠ°Π²Π½Π΅Π½ΠΈΡ Ρ ΠΌΠ΅ΡΠ°Π»Π»ΠΎΠΌ, Π½ΠΎ ΠΎΠ±Π»Π°Π΄Π°Π΅Ρ ΡΠ²ΠΎΠΉΡΡΠ²Π°ΠΌΠΈ ΠΊΠ°ΠΊ Π΄Π΅ΡΠ΅Π²Π°, ΡΠ°ΠΊ ΠΈ ΠΊΠ°ΠΌΠ½Ρ. ΠΠ΅ΡΠ°ΠΌΠ·ΠΈΡ ΠΈΠΌΠ΅Π΅Ρ ΠΏΡΠ΅ΠΈΠΌΡΡΠ΅ΡΡΠ²Π° ΠΈ ΠΏΠ΅ΡΠ΅Π΄ Π»ΠΈΡΠ΅Π²ΡΠΌ ΠΊΠΈΡΠΏΠΈΡΠΎΠΌ. ΠΠΎ-ΠΏΠ΅ΡΠ²ΡΡ
, ΡΠ΄Π΅Π»ΡΠ½ΡΠΉ Π²Π΅Ρ ΠΈΡ
Π±Π»ΠΎΠΊΠΎΠ² Π² 2 ΡΠ°Π·Π° Π½ΠΈΠΆΠ΅, ΡΠ΅ΠΌ Ρ ΠΊΠΈΡΠΏΠΈΡΠ½ΠΎΠΉ ΠΊΠ»Π°Π΄ΠΊΠΈ. ΠΠΎ-Π²ΡΠΎΡΡΡ
, ΡΡΠ°Π½Π΄Π°ΡΡΠ½ΡΠΉ ΠΊΠ΅ΡΠ°ΠΌΠ·ΠΈΡΠΎΠ±Π΅ΡΠΎΠ½Π½ΡΠΉ Π±Π»ΠΎΠΊ 7 Π·Π°ΠΌΠ΅Π½ΡΠ΅Ρ ΠΊΠΈΡΠΏΠΈΡ. Π ΡΠ΅Π·ΡΠ»ΡΡΠ°ΡΠ΅ ΡΠΌΠ΅Π»ΡΠΉ ΠΊΠ°ΠΌΠ΅Π½ΡΠΈΠΊ Π·Π°ΠΊΠ»Π°Π΄ΡΠ²Π°Π΅Ρ ΠΎΡΡΡΡΠΏ ΠΎΡ Π΅Π΄ΠΈΠ½ΠΈΡΡ ΠΎΠ±ΡΠ΅ΠΌΠ° ΡΡΠ΅Π½Ρ Π² ΡΡΠΈ ΡΠ°Π·Π° Π±ΠΎΠ»ΡΡΠΈΠΉ, ΡΠ΅ΠΌ ΠΊΠΈΡΠΏΠΈΡΠ½ΠΎΠΉ ΠΊΠ»Π°Π΄ΠΊΠΈ. Π ΡΡΠΎ ΠΏΡΠΈ ΡΠΎΠΌ, ΡΡΠΎ ΠΏΠΎ ΡΠ²ΠΎΠΈΠΌ ΡΠΊΠΎΠ»ΠΎΠ³ΠΈΡΠ΅ΡΠΊΠΈΠΌ ΡΠ²ΠΎΠΉΡΡΠ²Π°ΠΌ ΠΊΠ΅ΡΠ°ΠΌΠΎΠ³ΡΠ°Π½ΠΈΡ Π½Π΅ ΡΡΡΡΠΏΠ°Π΅Ρ ΠΊΠΈΡΠΏΠΈΡΡ. ΠΡΠ°ΠΊΡΠΈΠΊΠ° ΠΏΠΎΠΊΠ°Π·ΡΠ²Π°Π΅Ρ, ΡΡΠΎ ΠΈΡΠΏΠΎΠ»ΡΠ·ΠΎΠ²Π°Π½ΠΈΠ΅ Π»Π΅Π³ΠΊΠΎΠ±Π΅ΡΠΎΠ½Π½ΡΡ
Π±Π»ΠΎΠΊΠΎΠ² Π²ΠΌΠ΅ΡΡΠΎ ΠΊΠΈΡΠΏΠΈΡΠ° Π² ΠΌΠ°Π»ΠΎΡΡΠ°ΠΆΠ½ΠΎΠΌ ΡΡΡΠΎΠΈΡΠ΅Π»ΡΡΡΠ²Π΅ ΡΠ½ΠΈΠΆΠ°Π΅Ρ ΡΡΠΎΠΈΠΌΠΎΡΡΡ ΡΠ°Π±ΠΎΡ Π½Π° 30-40% (!!!).
ΠΠ΅ΡΠ°ΠΌΠ·ΠΈΡΠΎΠ²ΡΠ΅ Π±Π»ΠΎΠΊΠΈ Π²ΡΡΠΎΠΊΠΎΠ³ΠΎ ΠΊΠ°ΡΠ΅ΡΡΠ²Π°, ΠΈΠ·Π³ΠΎΡΠ°Π²Π»ΠΈΠ²Π°Π΅ΠΌΡΠ΅ Π½Π° ΠΎΡΠ½ΠΎΠ²Π΅ ΠΊΠ΅ΡΠ°ΠΌΠ·ΠΈΡΠΎΠ±Π΅ΡΠΎΠ½Π½ΠΎΠ³ΠΎ Π³ΡΠ°Π²ΠΈΡ ΠΌΠ΅Π»ΠΎΡΠΈ — 5-10 ΠΌΠΌ. ΠΠ»ΠΎΠΊΠΈ ΠΈΠ·Π³ΠΎΡΠ°Π²Π»ΠΈΠ²Π°ΡΡΡΡ Π½Π° ΡΠΎΠ²ΡΠ΅ΠΌΠ΅Π½Π½ΡΡ Π²ΠΈΠ±ΡΠΎΠΏΡΠ΅ΡΡΠ°Ρ Ρ ΠΏΠΎΡΠ»Π΅Π΄ΡΡΡΠ΅ΠΉ ΡΠ΅ΡΠΌΠΈΡΠ΅ΡΠΊΠΎΠΉ ΠΎΠ±ΡΠ°Π±ΠΎΡΠΊΠΎΠΉ. ΠΡΠΎ ΠΎΠ±Π΅ΡΠΏΠ΅ΡΠΈΠ²Π°Π΅Ρ Π²ΡΡΠΎΠΊΡΡ ΠΏΡΠΎΡΠ½ΠΎΡΡΡ ΠΈ Ρ ΠΎΡΠΎΡΡΡ ΡΠ΅ΠΏΠ»ΠΎΠΈΠ·ΠΎΠ»ΡΡΠΈΡ. Π£ ΡΠ°ΡΡΠ½ΡΡ Π·Π°ΡΡΡΠΎΠΉΡΠΈΠΊΠΎΠ² Π±Π»ΠΎΠΊΠΈ ΠΏΠΎΠ»ΡΠ·ΡΡΡΡΡ ΠΏΠΎΠ²ΡΡΠ΅Π½Π½ΡΠΌ ΡΠΏΡΠΎΡΠΎΠΌ ΠΈΠ·-Π·Π° ΠΎΠΏΡΠΈΠΌΠ°Π»ΡΠ½ΠΎΠ³ΠΎ ΡΠΎΠΎΡΠ½ΠΎΡΠ΅Π½ΠΈΡ ΡΠ΅Π½Π°/ΠΊΠ°ΡΠ΅ΡΡΠ²ΠΎ.
ΠΠ»Π°Π³ΠΎΠ΄Π°ΡΡ Ρ
ΠΎΡΠΎΡΠΈΠΌ ΠΏΡΠΎΡΠ½ΠΎΡΡΠ½ΡΠΌ Ρ
Π°ΡΠ°ΠΊΡΠ΅ΡΠΈΡΡΠΈΠΊΠ°ΠΌ Π»Π΅Π³ΠΊΠΎΠ±Π΅ΡΠΎΠ½Π½ΡΠ΅ Π±Π»ΠΎΠΊΠΈ ΠΏΡΠΈΠΌΠ΅Π½ΡΡΡΡΡ Π² ΠΌΠ½ΠΎΠ³ΠΎΡΡΠ°ΠΆΠ½ΠΎΠΌ Π΄ΠΎΠΌΠΎΡΡΡΠΎΠ΅Π½ΠΈΠΈ, Π° ΡΠ°ΠΊΠΆΠ΅ ΠΏΡΠΈ Π²ΠΎΠ·Π²Π΅Π΄Π΅Π½ΠΈΠΈ ΠΆΠΈΠ»ΡΡ
Π΄ΠΎΠΌΠΎΠ², ΡΠ°ΡΡΠ½ΡΡ
Π΄ΠΎΠΌΠΎΠ², Ρ
ΠΎΠ·ΡΠΉΡΡΠ²Π΅Π½Π½ΡΡ
ΠΏΠΎΡΡΡΠΎΠ΅ΠΊ ΠΈ Π³Π°ΡΠ°ΠΆΠ΅ΠΉ. ΠΠΏΡΡ ΠΈΡΠΏΠΎΠ»ΡΠ·ΠΎΠ²Π°Π½ΠΈΡ Π°Π³ΡΠ΅Π³Π°ΡΠΎΠ² ΠΏΠΎΠΊΠ°Π·Π°Π», ΡΡΠΎ Π΄Π»Ρ ΡΡΡΠΎΠΈΡΠ΅Π»ΡΡΡΠ²Π° ΠΌΠ°Π»ΠΎΡΡΠ°ΠΆΠ½ΡΡ
Π΄ΠΎΠΌΠΎΠ² Π½Π΅ ΡΡΠ΅Π±ΡΡΡΡΡ Π΄ΠΎΠΏΠΎΠ»Π½ΠΈΡΠ΅Π»ΡΠ½ΡΠ΅ ΡΠΏΠ΅ΡΠΈΠ°Π»ΡΠ½ΡΠ΅ ΠΊΠΎΠ½ΡΡΡΡΠΊΡΠΈΠ²Π½ΡΠ΅ ΡΠ΅ΡΠ΅Π½ΠΈΡ. ΠΠ»Π°Π³ΠΎΠ΄Π°ΡΡ ΠΈΠΌΠ΅Π½Π½ΠΎ ΡΠ²ΠΎΠ΅ΠΉ ΡΠ°Π·ΠΌΠ΅ΡΠ½ΠΎΡΡΠΈ ΠΊΠ΅ΡΠ°ΠΌΠ·ΠΈΡΠΎΠ±Π»ΠΎΠΊΠΈ ΠΏΡΠ΅ΠΊΡΠ°ΡΠ½ΠΎ ΡΠΎΡΠ΅ΡΠ°ΡΡΡΡ ΡΠΎ Π²ΡΠ΅ΠΌΠΈ Π²ΠΈΠ΄Π°ΠΌΠΈ ΠΌΠ΅Π»ΠΊΠΎΠ³Π°Π±Π°ΡΠΈΡΠ½ΡΡ
ΡΡΡΠΎΠΈΡΠ΅Π»ΡΠ½ΡΡ
ΠΌΠ°ΡΠ΅ΡΠΈΠ°Π»ΠΎΠ², ΠΠΠ, ΡΡΠ°Π»ΡΡ, Π΄Π²Π΅ΡΠ½ΡΠΌΠΈ ΠΈ ΠΎΠΊΠΎΠ½Π½ΡΠΌΠΈ ΠΏΡΠΎΠ΅ΠΌΠ°ΠΌΠΈ. ΠΠ»ΠΎΠΊΠΈ ΠΈΠ· Π»Π΅Π³ΠΊΠΎΠ³ΠΎ Π·Π°ΠΏΠΎΠ»Π½ΠΈΡΠ΅Π»Ρ Β«Π΄ΡΡΠ°ΡΒ», ΡΠ΅Π³ΡΠ»ΠΈΡΡΡ Π²Π»Π°ΠΆΠ½ΠΎΡΡΡ Π² ΠΏΠΎΠΌΠ΅ΡΠ΅Π½ΠΈΠΈ. ΠΠΎΠ½ΡΡΡΡΠΊΡΠΈΠΈ ΠΈΠ· ΠΊΠ΅ΡΠ°ΠΌΠ·ΠΈΡΠ° ΠΏΡΠ°ΠΊΡΠΈΡΠ΅ΡΠΊΠΈ Π²Π΅ΡΠ½ΡΠ΅ ΠΈ Π½Π΅ ΡΡΠ΅Π±ΡΡΡ ΡΡ
ΠΎΠ΄Π°. ΠΠ΅ΡΠ°ΠΌΠ·ΠΈΡ Π·Π° ΡΡΠ΅Ρ ΠΎΡΠΎΠ±Π΅Π½Π½ΠΎΡΡΠ΅ΠΉ ΡΠ²ΠΎΠ΅ΠΉ ΡΡΡΡΠΊΡΡΡΡ ΠΎΠ±Π΅ΡΠΏΠ΅ΡΠΈΠ²Π°Π΅Ρ Π·Π½Π°ΡΠΈΡΠ΅Π»ΡΠ½ΠΎΠ΅ ΡΠ»ΡΡΡΠ΅Π½ΠΈΠ΅ Π·Π²ΡΠΊΠΎΠΈΠ·ΠΎΠ»ΡΡΠΈΠΎΠ½Π½ΡΡ
ΡΠ²ΠΎΠΉΡΡΠ² Π²ΠΎΠ·Π²ΠΎΠ΄ΠΈΠΌΡΡ
ΠΊΠΎΠ½ΡΡΡΡΠΊΡΠΈΠΉ ΠΏΠΎ ΡΡΠ°Π²Π½Π΅Π½ΠΈΡ Ρ ΠΎΠ±ΡΡΠ½ΡΠΌ Π±Π΅ΡΠΎΠ½ΠΎΠΌ ΠΈ ΠΊΠΈΡΠΏΠΈΡΠΎΠΌ.
Π ΠΌΠΎΠ½ΠΎΠ»ΠΈΡΠ½ΠΎΠΌ Π±Π΅ΡΠΎΠ½Π½ΠΎΠΌ Π΄ΠΎΠΌΠΎΡΡΡΠΎΠ΅Π½ΠΈΠΈ ΠΊΠ΅ΡΠ°ΠΌΠ·ΠΈΡΠΎΠ±Π»ΠΎΠΊΠΈ ΠΏΡΠΈΠΌΠ΅Π½ΡΡΡ ΠΏΡΠΈ Π²ΠΎΠ·Π²Π΅Π΄Π΅Π½ΠΈΠΈ ΠΌΠ΅ΠΆΠΊΠ²Π°ΡΡΠΈΡΠ½ΡΡ , ΠΌΠ΅ΠΆΠΊΠ²Π°ΡΡΠΈΡΠ½ΡΡ ΠΏΠ΅ΡΠ΅Π³ΠΎΡΠΎΠ΄ΠΎΠΊ. ΠΡΠΈ ΡΠ°Π²Π½ΡΡ ΡΠΈΠ·ΠΈΠΊΠΎ-ΠΌΠ΅Ρ Π°Π½ΠΈΡΠ΅ΡΠΊΠΈΡ ΡΠ²ΠΎΠΉΡΡΠ²Π°Ρ ΠΏΠ΅Π½ΠΎΠ±Π΅ΡΠΎΠ½ ΠΈ Π³Π°Π·ΠΎΡΠΈΠ»ΠΈΠΊΠ°ΡΠ½ΡΠ΅ Π±Π»ΠΎΠΊΠΈ Ρ Π»Π΅Π³ΠΊΠΈΠΌ Π·Π°ΠΏΠΎΠ»Π½ΠΈΡΠ΅Π»Π΅ΠΌ ΠΎΠ±Π»Π°Π΄Π°ΡΡ Π»ΡΡΡΠΈΠΌΠΈ ΠΏΠΎΠΊΠ°Π·Π°ΡΠ΅Π»ΡΠΌΠΈ ΠΏΠ°ΡΠΎΠΏΡΠΎΠ²ΠΎΠ΄Π½ΠΎΡΡΠΈ ΠΈ Π·Π°Π±ΠΈΠ²Π°Π΅ΠΌΠΎΡΡΠΈ.
ΠΠ΅ΡΠΎΠ½Π½ΡΠΉ Π±Π»ΠΎΠΊ
ΠΠ΅ΡΠ΅ΠΉΡΠΈ ΠΊ ΠΎΡΠ½ΠΎΠ²Π½ΠΎΠΌΡ ΡΠΎΠ΄Π΅ΡΠΆΠ°Π½ΠΈΡ
Π ΠΎΠ±ΠΈΠ½ ΠΡ
ΠΠ΅Π½Π΅Π΄ΠΆΠ΅Ρ ΠΏΠΎ ΠΏΡΠΎΠ΄Π°ΠΆΠ°ΠΌ Π² Linyi Osino Machinery Co.
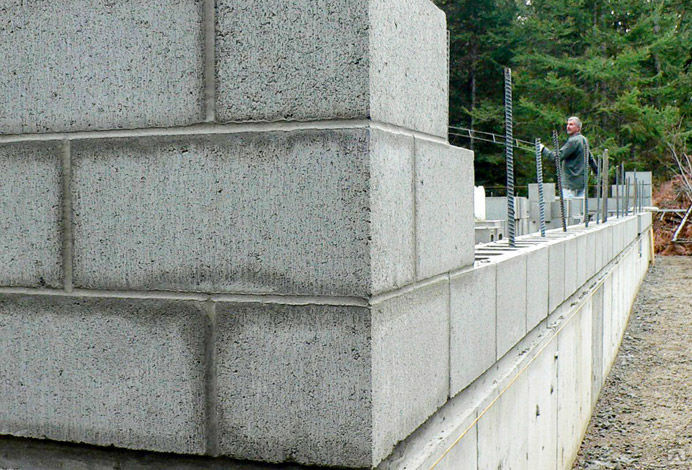
ΠΠΏΡΠ±Π»ΠΈΠΊΠΎΠ²Π°Π½ΠΎ 4 ΠΎΠΊΡΡΠ±ΡΡ 2016 Π³.
+ ΠΠΎΠ΄ΠΏΠΈΡΠ°ΡΡΡΡ
Π Π°Π±ΠΎΡΠ΅Π΅ Π²ΠΈΠ΄Π΅ΠΎ Π΄Π»Ρ Π°Π²ΡΠΎΠΌΠ°ΡΠΈΡΠ΅ΡΠΊΠΎΠΉ ΠΌΠ°ΡΠΈΠ½Ρ Ρ Π³ΠΈΠ΄ΡΠ°Π²Π»ΠΈΡΠ΅ΡΠΊΠΈΠΌ Π±Π»ΠΎΠΊΠΎΠΌ QT10-15 https://youtu.be/2BrqMDDuoz0?list=PLaeAUciJLZDxiQdyTgNJXneW_CC-fiwV1
Π€ΠΎΠ½
ΠΠ΅ΡΠΎΠ½Π½ΡΠΉ Π±Π»ΠΎΠΊ Π² ΠΎΡΠ½ΠΎΠ²Π½ΠΎΠΌ ΠΈΡΠΏΠΎΠ»ΡΠ·ΡΠ΅ΡΡΡ Π² ΠΊΠ°ΡΠ΅ΡΡΠ²Π΅ ΡΡΡΠΎΠΈΡΠ΅Π»ΡΠ½ΠΎΠ³ΠΎ ΠΌΠ°ΡΠ΅ΡΠΈΠ°Π»Π° ΠΏΡΠΈ Π²ΠΎΠ·Π²Π΅Π΄Π΅Π½ΠΈΠΈ ΡΡΠ΅Π½. ΠΠ½ΠΎΠ³Π΄Π° Π΅Π³ΠΎ Π½Π°Π·ΡΠ²Π°ΡΡ Π±Π»ΠΎΠΊΠΎΠΌ Π±Π΅ΡΠΎΠ½Π½ΠΎΠΉ ΠΊΠ»Π°Π΄ΠΊΠΈ (ΠΠΠ£). ΠΠ΅ΡΠΎΠ½Π½ΡΠΉ Π±Π»ΠΎΠΊ ΡΠ²Π»ΡΠ΅ΡΡΡ ΠΎΠ΄Π½ΠΈΠΌ ΠΈΠ· Π½Π΅ΡΠΊΠΎΠ»ΡΠΊΠΈΡ ΡΠ±ΠΎΡΠ½ΡΡ ΠΆΠ΅Π»Π΅Π·ΠΎΠ±Π΅ΡΠΎΠ½Π½ΡΡ ΠΈΠ·Π΄Π΅Π»ΠΈΠΉ, ΠΈΡΠΏΠΎΠ»ΡΠ·ΡΠ΅ΠΌΡΡ Π² ΡΡΡΠΎΠΈΡΠ΅Π»ΡΡΡΠ²Π΅. Π’Π΅ΡΠΌΠΈΠ½ ΡΠ±ΠΎΡΠ½ΡΠΉ ΠΎΡΠ½ΠΎΡΠΈΡΡΡ ΠΊ ΡΠΎΠΌΡ ΡΠ°ΠΊΡΡ, ΡΡΠΎ Π±Π»ΠΎΠΊΠΈ ΡΠΎΡΠΌΠΈΡΡΡΡΡΡ ΠΈ Π·Π°ΡΠ²Π΅ΡΠ΄Π΅Π²Π°ΡΡ Π΄ΠΎ ΡΠΎΠ³ΠΎ, ΠΊΠ°ΠΊ ΠΎΠ½ΠΈ Π±ΡΠ΄ΡΡ Π΄ΠΎΡΡΠ°Π²Π»Π΅Π½Ρ Π½Π° ΡΡΡΠΎΠΈΡΠ΅Π»ΡΠ½ΡΡ ΠΏΠ»ΠΎΡΠ°Π΄ΠΊΡ. ΠΠΎΠ»ΡΡΠΈΠ½ΡΡΠ²ΠΎ Π±Π΅ΡΠΎΠ½Π½ΡΡ Π±Π»ΠΎΠΊΠΎΠ² ΠΈΠΌΠ΅ΡΡ ΠΎΠ΄Π½Ρ ΠΈΠ»ΠΈ Π½Π΅ΡΠΊΠΎΠ»ΡΠΊΠΎ ΠΏΠΎΠ»ΡΡ ΠΏΠΎΠ»ΠΎΡΡΠ΅ΠΉ, Π° ΠΈΡ ΡΡΠΎΡΠΎΠ½Ρ ΠΌΠΎΠ³ΡΡ Π±ΡΡΡ ΠΎΡΠ»ΠΈΡΡ Π³Π»Π°Π΄ΠΊΠΈΠΌΠΈ ΠΈΠ»ΠΈ Ρ ΡΠΈΡΡΠ½ΠΊΠΎΠΌ. ΠΡΠΈ ΠΈΡΠΏΠΎΠ»ΡΠ·ΠΎΠ²Π°Π½ΠΈΠΈ Π±Π΅ΡΠΎΠ½Π½ΡΠ΅ Π±Π»ΠΎΠΊΠΈ ΡΠΊΠ»Π°Π΄ΡΠ²Π°ΡΡΡΡ ΠΏΠΎ ΠΎΠ΄Π½ΠΎΠΌΡ ΠΈ ΡΠΊΡΠ΅ΠΏΠ»ΡΡΡΡΡ ΡΠ²Π΅ΠΆΠΈΠΌ Π±Π΅ΡΠΎΠ½Π½ΡΠΌ ΡΠ°ΡΡΠ²ΠΎΡΠΎΠΌ, ΡΡΠΎΠ±Ρ ΡΡΠΎΡΠΌΠΈΡΠΎΠ²Π°ΡΡ ΡΡΠ΅Π½Ρ ΠΆΠ΅Π»Π°Π΅ΠΌΠΎΠΉ Π΄Π»ΠΈΠ½Ρ ΠΈ Π²ΡΡΠΎΡΡ.
ΠΠ΅ΡΠΎΠ½Π½ΡΠΉ ΡΠ°ΡΡΠ²ΠΎΡ ΠΈΡΠΏΠΎΠ»ΡΠ·ΠΎΠ²Π°Π»ΡΡ ΡΠΈΠΌΠ»ΡΠ½Π°ΠΌΠΈ Π΅ΡΠ΅ Π² 200Β Π³. Π΄ΠΎ Π½.Ρ. ΡΠ²ΡΠ·ΡΠ²Π°ΡΡ ΡΠ°ΡΠΎΠ½Π½ΡΠ΅ ΠΊΠ°ΠΌΠ½ΠΈ Π²ΠΌΠ΅ΡΡΠ΅ ΠΏΡΠΈ ΡΡΡΠΎΠΈΡΠ΅Π»ΡΡΡΠ²Π΅ Π·Π΄Π°Π½ΠΈΠΉ. ΠΠΎ Π²ΡΠ΅ΠΌΡ ΠΏΡΠ°Π²Π»Π΅Π½ΠΈΡ ΡΠΈΠΌΡΠΊΠΎΠ³ΠΎ ΠΈΠΌΠΏΠ΅ΡΠ°ΡΠΎΡΠ° ΠΠ°Π»ΠΈΠ³ΡΠ»Ρ, Π² 37β41Β Π³ΠΎΠ΄Π°Ρ
Β Π½.Β Ρ.Β , Π½Π΅Π±ΠΎΠ»ΡΡΠΈΠ΅ Π±Π»ΠΎΠΊΠΈ ΡΠ±ΠΎΡΠ½ΠΎΠ³ΠΎ ΠΆΠ΅Π»Π΅Π·ΠΎΠ±Π΅ΡΠΎΠ½Π° ΠΈΡΠΏΠΎΠ»ΡΠ·ΠΎΠ²Π°Π»ΠΈΡΡ Π² ΠΊΠ°ΡΠ΅ΡΡΠ²Π΅ ΡΡΡΠΎΠΈΡΠ΅Π»ΡΠ½ΠΎΠ³ΠΎ ΠΌΠ°ΡΠ΅ΡΠΈΠ°Π»Π° Π² ΡΠ°ΠΉΠΎΠ½Π΅ ΡΠΎΠ²ΡΠ΅ΠΌΠ΅Π½Π½ΠΎΠ³ΠΎ ΠΠ΅Π°ΠΏΠΎΠ»Ρ, ΠΡΠ°Π»ΠΈΡ. ΠΠΎΠ»ΡΡΠ°Ρ ΡΠ°ΡΡΡ Π±Π΅ΡΠΎΠ½Π½ΡΡ
ΡΠ΅Ρ
Π½ΠΎΠ»ΠΎΠ³ΠΈΠΉ, ΡΠ°Π·ΡΠ°Π±ΠΎΡΠ°Π½Π½ΡΡ
ΡΠΈΠΌΠ»ΡΠ½Π°ΠΌΠΈ, Π±ΡΠ»Π° ΡΡΠ΅ΡΡΠ½Π° ΠΏΠΎΡΠ»Π΅ ΠΏΠ°Π΄Π΅Π½ΠΈΡ Π ΠΈΠΌΡΠΊΠΎΠΉ ΠΈΠΌΠΏΠ΅ΡΠΈΠΈ Π² ΠΏΡΡΠΎΠΌ Π²Π΅ΠΊΠ΅. Π’ΠΎΠ»ΡΠΊΠΎ Π² 1824 Π³ΠΎΠ΄Ρ Π°Π½Π³Π»ΠΈΠΉΡΠΊΠΈΠΉ ΠΊΠ°ΠΌΠ΅Π½ΡΠΈΠΊ ΠΠΆΠΎΠ·Π΅Ρ ΠΡΠΏΠ΄ΠΈΠ½ ΡΠ°Π·ΡΠ°Π±ΠΎΡΠ°Π» ΠΏΠΎΡΡΠ»Π°Π½Π΄ΡΠ΅ΠΌΠ΅Π½Ρ, ΠΊΠΎΡΠΎΡΡΠΉ ΡΡΠ°Π» ΠΎΠ΄Π½ΠΈΠΌ ΠΈΠ· ΠΊΠ»ΡΡΠ΅Π²ΡΡ
ΠΊΠΎΠΌΠΏΠΎΠ½Π΅Π½ΡΠΎΠ² ΡΠΎΠ²ΡΠ΅ΠΌΠ΅Π½Π½ΠΎΠ³ΠΎ Π±Π΅ΡΠΎΠ½Π°.
ΠΠ΅ΡΠ²ΡΠΉ ΠΏΡΡΡΠΎΡΠ΅Π»ΡΠΉ Π±Π΅ΡΠΎΠ½Π½ΡΠΉ Π±Π»ΠΎΠΊ Π±ΡΠ» ΡΠΏΡΠΎΠ΅ΠΊΡΠΈΡΠΎΠ²Π°Π½ Π₯Π°ΡΠΌΠΎΠ½ΠΎΠΌ Π‘. ΠΠ°Π»ΠΌΠ΅ΡΠΎΠΌ Π² 1890 Π³ΠΎΠ΄Ρ Π² Π‘Π¨Π. ΠΠΎΡΠ»Π΅ 10 Π»Π΅Ρ ΡΠΊΡΠΏΠ΅ΡΠΈΠΌΠ΅Π½ΡΠΎΠ² ΠΠ°Π»ΠΌΠ΅Ρ Π·Π°ΠΏΠ°ΡΠ΅Π½ΡΠΎΠ²Π°Π» ΠΊΠΎΠ½ΡΡΡΡΠΊΡΠΈΡ Π² 1900 Π³ΠΎΠ΄Ρ. ΠΠ»ΠΎΠΊΠΈ ΠΠ°Π»ΠΌΠ΅ΡΠ° Π±ΡΠ»ΠΈ ΡΠ°Π·ΠΌΠ΅ΡΠΎΠΌ 8 Π΄ΡΠΉΠΌΠΎΠ² (20,3 ΡΠΌ) Π½Π° 10 Π΄ΡΠΉΠΌΠΎΠ² (25,4 ΡΠΌ) Π½Π° 30 Π΄ΡΠΉΠΌΠΎΠ² (76,2 ΡΠΌ), ΠΈ ΠΎΠ½ΠΈ Π±ΡΠ»ΠΈ Π½Π°ΡΡΠΎΠ»ΡΠΊΠΎ ΡΡΠΆΠ΅Π»ΡΠΌΠΈ, ΡΡΠΎ ΠΈΡ ΠΏΡΠΈΡ ΠΎΠ΄ΠΈΠ»ΠΎΡΡ ΠΏΠΎΠ΄Π½ΠΈΠΌΠ°ΡΡ Π½Π° ΠΌΠ΅ΡΡΠΎ Ρ ΠΏΠΎΠΌΠΎΡΡΡ Π½Π΅Π±ΠΎΠ»ΡΡΠΎΠΉ ΠΊΡΠ°Π½. Π 1905 Π³ΠΎΠ΄Ρ ΠΎΠΊΠΎΠ»ΠΎ 1500 ΠΊΠΎΠΌΠΏΠ°Π½ΠΈΠΉ ΠΏΡΠΎΠΈΠ·Π²ΠΎΠ΄ΠΈΠ»ΠΈ Π±Π΅ΡΠΎΠ½Π½ΡΠ΅ Π±Π»ΠΎΠΊΠΈ Π² Π‘ΠΎΠ΅Π΄ΠΈΠ½Π΅Π½Π½ΡΡ Π¨ΡΠ°ΡΠ°Ρ .
ΠΡΠΈ ΠΏΠ΅ΡΠ²ΡΠ΅ Π±Π»ΠΎΠΊΠΈ ΠΎΠ±ΡΡΠ½ΠΎ ΠΎΡΠ»ΠΈΠ²Π°Π»ΠΈΡΡ Π²ΡΡΡΠ½ΡΡ, ΠΈ ΡΡΠ΅Π΄Π½ΡΡ ΠΏΡΠΎΠΈΠ·Π²ΠΎΠ΄ΠΈΡΠ΅Π»ΡΠ½ΠΎΡΡΡ ΡΠΎΡΡΠ°Π²Π»ΡΠ»Π° ΠΎΠΊΠΎΠ»ΠΎ 10 Π±Π»ΠΎΠΊΠΎΠ² Π½Π° ΡΠ΅Π»ΠΎΠ²Π΅ΠΊΠ° Π² ΡΠ°Ρ. Π‘Π΅Π³ΠΎΠ΄Π½Ρ ΠΏΡΠΎΠΈΠ·Π²ΠΎΠ΄ΡΡΠ²ΠΎ Π±Π΅ΡΠΎΠ½Π½ΡΡ
Π±Π»ΠΎΠΊΠΎΠ² ΠΏΡΠ΅Π΄ΡΡΠ°Π²Π»ΡΠ΅Ρ ΡΠΎΠ±ΠΎΠΉ Π²ΡΡΠΎΠΊΠΎΠ°Π²ΡΠΎΠΌΠ°ΡΠΈΠ·ΠΈΡΠΎΠ²Π°Π½Π½ΡΠΉ ΠΏΡΠΎΡΠ΅ΡΡ, ΠΊΠΎΡΠΎΡΡΠΉ ΠΌΠΎΠΆΠ΅Ρ ΠΏΡΠΎΠΈΠ·Π²ΠΎΠ΄ΠΈΡΡ Π΄ΠΎ 2000 Π±Π»ΠΎΠΊΠΎΠ² Π² ΡΠ°Ρ.
Π‘ΡΡΡΠ΅
ΠΠ΅ΡΠΎΠ½, ΠΎΠ±ΡΡΠ½ΠΎ ΠΈΡΠΏΠΎΠ»ΡΠ·ΡΠ΅ΠΌΡΠΉ Π΄Π»Ρ ΠΈΠ·Π³ΠΎΡΠΎΠ²Π»Π΅Π½ΠΈΡ Π±Π΅ΡΠΎΠ½Π½ΡΡ Π±Π»ΠΎΠΊΠΎΠ², ΠΏΡΠ΅Π΄ΡΡΠ°Π²Π»ΡΠ΅Ρ ΡΠΎΠ±ΠΎΠΉ ΡΠΌΠ΅ΡΡ ΠΏΠΎΡΠΎΡΠΊΠΎΠΎΠ±ΡΠ°Π·Π½ΠΎΠ³ΠΎ ΠΏΠΎΡΡΠ»Π°Π½Π΄ΡΠ΅ΠΌΠ΅Π½ΡΠ°, Π²ΠΎΠ΄Ρ, ΠΏΠ΅ΡΠΊΠ° ΠΈ Π³ΡΠ°Π²ΠΈΡ. Π ΡΠ΅Π·ΡΠ»ΡΡΠ°ΡΠ΅ ΠΏΠΎΠ»ΡΡΠ°Π΅ΡΡΡ ΡΠ²Π΅ΡΠ»ΠΎ-ΡΠ΅ΡΡΠΉ Π±Π»ΠΎΠΊ Ρ ΡΠΎΠ½ΠΊΠΎΠΉ ΡΠ΅ΠΊΡΡΡΡΠΎΠΉ ΠΏΠΎΠ²Π΅ΡΡ Π½ΠΎΡΡΠΈ ΠΈ Π²ΡΡΠΎΠΊΠΎΠΉ ΠΏΡΠΎΡΠ½ΠΎΡΡΡΡ Π½Π° ΡΠΆΠ°ΡΠΈΠ΅. Π’ΠΈΠΏΠΈΡΠ½ΡΠΉ Π±Π΅ΡΠΎΠ½Π½ΡΠΉ Π±Π»ΠΎΠΊ Π²Π΅ΡΠΈΡ 38β43 ΡΡΠ½ΡΠ° (17,2β19,5 ΠΊΠ³). ΠΠ°ΠΊ ΠΏΡΠ°Π²ΠΈΠ»ΠΎ, Π±Π΅ΡΠΎΠ½Π½Π°Ρ ΡΠΌΠ΅ΡΡ, ΠΈΡΠΏΠΎΠ»ΡΠ·ΡΠ΅ΠΌΠ°Ρ Π΄Π»Ρ Π±Π»ΠΎΠΊΠΎΠ², ΠΈΠΌΠ΅Π΅Ρ Π±ΠΎΠ»Π΅Π΅ Π²ΡΡΠΎΠΊΠΈΠΉ ΠΏΡΠΎΡΠ΅Π½Ρ ΠΏΠ΅ΡΠΊΠ° ΠΈ ΠΌΠ΅Π½ΡΡΠΈΠΉ ΠΏΡΠΎΡΠ΅Π½Ρ Π³ΡΠ°Π²ΠΈΡ ΠΈ Π²ΠΎΠ΄Ρ, ΡΠ΅ΠΌ Π±Π΅ΡΠΎΠ½Π½ΡΠ΅ ΡΠΌΠ΅ΡΠΈ, ΠΈΡΠΏΠΎΠ»ΡΠ·ΡΠ΅ΠΌΡΠ΅ Π΄Π»Ρ ΠΎΠ±ΡΠ΅ΡΡΡΠΎΠΈΡΠ΅Π»ΡΠ½ΡΡ ΡΠ΅Π»Π΅ΠΉ. Π ΡΠ΅Π·ΡΠ»ΡΡΠ°ΡΠ΅ ΠΏΠΎΠ»ΡΡΠ°Π΅ΡΡΡ ΠΎΡΠ΅Π½Ρ ΡΡΡ Π°Ρ, Π³ΡΡΡΠ°Ρ ΡΠΌΠ΅ΡΡ, ΠΊΠΎΡΠΎΡΠ°Ρ Π΄Π΅ΡΠΆΠΈΡ ΡΠΎΡΠΌΡ ΠΏΡΠΈ ΠΈΠ·Π²Π»Π΅ΡΠ΅Π½ΠΈΠΈ ΠΈΠ· ΡΠΎΡΠΌΡ Π΄Π»Ρ Π±Π»ΠΎΠΊΠΎΠ².
ΠΡΠ»ΠΈ Π²ΠΌΠ΅ΡΡΠΎ ΠΏΠ΅ΡΠΊΠ° ΠΈ Π³ΡΠ°Π²ΠΈΡ ΠΈΡΠΏΠΎΠ»ΡΠ·ΡΠ΅ΡΡΡ Π³ΡΠ°Π½ΡΠ»ΠΈΡΠΎΠ²Π°Π½Π½ΡΠΉ ΡΠ³ΠΎΠ»Ρ ΠΈΠ»ΠΈ Π²ΡΠ»ΠΊΠ°Π½ΠΈΡΠ΅ΡΠΊΠΈΠΉ ΠΏΠ΅ΠΏΠ΅Π», ΠΏΠΎΠ»ΡΡΠ΅Π½Π½ΡΠΉ Π±Π»ΠΎΠΊ ΠΎΠ±ΡΡΠ½ΠΎ Π½Π°Π·ΡΠ²Π°ΡΡ ΡΠ»Π°ΠΊΠΎΠ±Π»ΠΎΠΊΠΎΠΌ. Π ΡΠ΅Π·ΡΠ»ΡΡΠ°ΡΠ΅ ΠΏΠΎΠ»ΡΡΠ°Π΅ΡΡΡ ΡΠ΅ΠΌΠ½ΠΎ-ΡΠ΅ΡΡΠΉ Π±Π»ΠΎΠΊ Ρ ΡΠ΅ΠΊΡΡΡΡΠΎΠΉ ΠΏΠΎΠ²Π΅ΡΡ
Π½ΠΎΡΡΠΈ ΠΎΡ ΡΡΠ΅Π΄Π½Π΅ΠΉ Π΄ΠΎ Π³ΡΡΠ±ΠΎΠΉ, Ρ
ΠΎΡΠΎΡΠ΅ΠΉ ΠΏΡΠΎΡΠ½ΠΎΡΡΡΡ, Ρ
ΠΎΡΠΎΡΠΈΠΌΠΈ Π·Π²ΡΠΊΠΎΠΈΠ·ΠΎΠ»ΡΡΠΈΠΎΠ½Π½ΡΠΌΠΈ ΡΠ²ΠΎΠΉΡΡΠ²Π°ΠΌΠΈ ΠΈ Π±ΠΎΠ»Π΅Π΅ Π²ΡΡΠΎΠΊΠΈΠΌΠΈ ΡΠ΅ΠΏΠ»ΠΎΠΈΠ·ΠΎΠ»ΡΡΠΈΠΎΠ½Π½ΡΠΌΠΈ ΡΠ²ΠΎΠΉΡΡΠ²Π°ΠΌΠΈ, ΡΠ΅ΠΌ Ρ Π±Π΅ΡΠΎΠ½Π½ΠΎΠ³ΠΎ Π±Π»ΠΎΠΊΠ°. Π’ΠΈΠΏΠΈΡΠ½ΡΠΉ ΡΠ»Π°ΠΊΠΎΠ±Π»ΠΎΠΊ Π²Π΅ΡΠΈΡ 26β33 ΡΡΠ½ΡΠ° (11,8β15,0 ΠΊΠ³).
ΠΠ΅Π³ΠΊΠΈΠ΅ Π±Π΅ΡΠΎΠ½Π½ΡΠ΅ Π±Π»ΠΎΠΊΠΈ ΠΈΠ·Π³ΠΎΡΠ°Π²Π»ΠΈΠ²Π°ΡΡΡΡ ΠΏΡΡΠ΅ΠΌ Π·Π°ΠΌΠ΅Π½Ρ ΠΏΠ΅ΡΠΊΠ° ΠΈ Π³ΡΠ°Π²ΠΈΡ ΠΊΠ΅ΡΠ°ΠΌΠ·ΠΈΡΠΎΠΌ, ΡΠ»Π°Π½ΡΠ΅ΠΌ ΠΈΠ»ΠΈ ΡΠ»Π°Π½ΡΠ΅ΠΌ. ΠΠ΅ΡΠ°ΠΌΠ·ΠΈΡ, ΡΠ»Π°Π½Π΅Ρ ΠΈ ΡΠ»Π°Π½Π΅Ρ ΠΏΡΠΎΠΈΠ·Π²ΠΎΠ΄ΡΡΡΡ ΠΏΡΡΠ΅ΠΌ ΠΈΠ·ΠΌΠ΅Π»ΡΡΠ΅Π½ΠΈΡ ΡΡΡΡΡ ΠΈ Π½Π°Π³ΡΠ΅Π²Π°Π½ΠΈΡ Π΅Π³ΠΎ ΠΏΡΠΈΠΌΠ΅ΡΠ½ΠΎ Π΄ΠΎ 2000Β°F (109Β°Π‘).3Β°Π‘). ΠΡΠΈ ΡΡΠΎΠΉ ΡΠ΅ΠΌΠΏΠ΅ΡΠ°ΡΡΡΠ΅ ΠΌΠ°ΡΠ΅ΡΠΈΠ°Π» ΡΠ°Π·Π΄ΡΠ²Π°Π΅ΡΡΡ ΠΈΠ»ΠΈ Π²Π·Π΄ΡΠ²Π°Π΅ΡΡΡ ΠΈΠ·-Π·Π° Π±ΡΡΡΡΠΎΠ³ΠΎ ΠΎΠ±ΡΠ°Π·ΠΎΠ²Π°Π½ΠΈΡ Π³Π°Π·ΠΎΠ², Π²ΡΠ·Π²Π°Π½Π½ΠΎΠ³ΠΎ ΡΠ³ΠΎΡΠ°Π½ΠΈΠ΅ΠΌ Π½Π΅Π±ΠΎΠ»ΡΡΠΈΡ ΠΊΠΎΠ»ΠΈΡΠ΅ΡΡΠ² ΠΎΡΠ³Π°Π½ΠΈΡΠ΅ΡΠΊΠΎΠ³ΠΎ ΠΌΠ°ΡΠ΅ΡΠΈΠ°Π»Π°, ΠΏΠΎΠΏΠ°Π²ΡΠ΅Π³ΠΎ Π²Π½ΡΡΡΡ. Π’ΠΈΠΏΠΈΡΠ½ΡΠΉ ΠΎΠ±Π»Π΅Π³ΡΠ΅Π½Π½ΡΠΉ Π±Π»ΠΎΠΊ Π²Π΅ΡΠΈΡ 22-28 ΡΡΠ½ΡΠΎΠ² (10,0-12,7 ΠΊΠ³) ΠΈ ΠΈΡΠΏΠΎΠ»ΡΠ·ΡΠ΅ΡΡΡ Π΄Π»Ρ Π²ΠΎΠ·Π²Π΅Π΄Π΅Π½ΠΈΡ Π½Π΅Π½Π΅ΡΡΡΠΈΡ ΡΡΠ΅Π½ ΠΈ ΠΏΠ΅ΡΠ΅Π³ΠΎΡΠΎΠ΄ΠΎΠΊ. Π Π°ΡΡΠΈΡΠ΅Π½Π½ΡΠΉ Π΄ΠΎΠΌΠ΅Π½Π½ΡΠΉ ΡΠ»Π°ΠΊ, Π° ΡΠ°ΠΊΠΆΠ΅ ΠΏΡΠΈΡΠΎΠ΄Π½ΡΠ΅ Π²ΡΠ»ΠΊΠ°Π½ΠΈΡΠ΅ΡΠΊΠΈΠ΅ ΠΌΠ°ΡΠ΅ΡΠΈΠ°Π»Ρ, ΡΠ°ΠΊΠΈΠ΅ ΠΊΠ°ΠΊ ΠΏΠ΅ΠΌΠ·Π° ΠΈ ΡΠ»Π°ΠΊ, ΡΠ°ΠΊΠΆΠ΅ ΠΈΡΠΏΠΎΠ»ΡΠ·ΡΡΡΡΡ Π΄Π»Ρ ΠΈΠ·Π³ΠΎΡΠΎΠ²Π»Π΅Π½ΠΈΡ Π»Π΅Π³ΠΊΠΈΡ Π±Π»ΠΎΠΊΠΎΠ².
Π Π΄ΠΎΠΏΠΎΠ»Π½Π΅Π½ΠΈΠ΅ ΠΊ ΠΎΡΠ½ΠΎΠ²Π½ΡΠΌ ΠΊΠΎΠΌΠΏΠΎΠ½Π΅Π½ΡΠ°ΠΌ Π±Π΅ΡΠΎΠ½Π½Π°Ρ ΡΠΌΠ΅ΡΡ, ΠΈΡΠΏΠΎΠ»ΡΠ·ΡΠ΅ΠΌΠ°Ρ Π΄Π»Ρ ΠΈΠ·Π³ΠΎΡΠΎΠ²Π»Π΅Π½ΠΈΡ Π±Π»ΠΎΠΊΠΎΠ², ΠΌΠΎΠΆΠ΅Ρ ΡΠ°ΠΊΠΆΠ΅ ΡΠΎΠ΄Π΅ΡΠΆΠ°ΡΡ ΡΠ°Π·Π»ΠΈΡΠ½ΡΠ΅ Ρ
ΠΈΠΌΠΈΡΠ΅ΡΠΊΠΈΠ΅ Π²Π΅ΡΠ΅ΡΡΠ²Π°, Π½Π°Π·ΡΠ²Π°Π΅ΠΌΡΠ΅ Π΄ΠΎΠ±Π°Π²ΠΊΠ°ΠΌΠΈ, Π΄Π»Ρ ΠΈΠ·ΠΌΠ΅Π½Π΅Π½ΠΈΡ Π²ΡΠ΅ΠΌΠ΅Π½ΠΈ ΠΎΡΠ²Π΅ΡΠΆΠ΄Π΅Π½ΠΈΡ, ΠΏΠΎΠ²ΡΡΠ΅Π½ΠΈΡ ΠΏΡΠΎΡΠ½ΠΎΡΡΠΈ Π½Π° ΡΠΆΠ°ΡΠΈΠ΅ ΠΈΠ»ΠΈ ΡΠ»ΡΡΡΠ΅Π½ΠΈΡ ΡΠ΄ΠΎΠ±ΠΎΡΠΊΠ»Π°Π΄ΡΠ²Π°Π΅ΠΌΠΎΡΡΠΈ. Π ΡΠΌΠ΅ΡΡ ΠΌΠΎΠ³ΡΡ Π±ΡΡΡ Π΄ΠΎΠ±Π°Π²Π»Π΅Π½Ρ ΠΏΠΈΠ³ΠΌΠ΅Π½ΡΡ, ΡΡΠΎΠ±Ρ ΠΏΡΠΈΠ΄Π°ΡΡ Π±Π»ΠΎΠΊΠ°ΠΌ ΠΎΠ΄Π½ΠΎΡΠΎΠ΄Π½ΡΠΉ ΡΠ²Π΅Ρ, ΠΈΠ»ΠΈ ΠΏΠΎΠ²Π΅ΡΡ
Π½ΠΎΡΡΡ Π±Π»ΠΎΠΊΠΎΠ² ΠΌΠΎΠΆΠ΅Ρ Π±ΡΡΡ ΠΏΠΎΠΊΡΡΡΠ° Π·Π°ΠΏΠ΅ΠΊΠ°Π΅ΠΌΠΎΠΉ Π³Π»Π°Π·ΡΡΡΡ Π΄Π»Ρ ΠΏΡΠΈΠ΄Π°Π½ΠΈΡ Π΄Π΅ΠΊΠΎΡΠ°ΡΠΈΠ²Π½ΠΎΠ³ΠΎ ΡΡΡΠ΅ΠΊΡΠ° ΠΈΠ»ΠΈ Π΄Π»Ρ Π·Π°ΡΠΈΡΡ ΠΎΡ Ρ
ΠΈΠΌΠΈΡΠ΅ΡΠΊΠΎΠ³ΠΎ Π²ΠΎΠ·Π΄Π΅ΠΉΡΡΠ²ΠΈΡ. ΠΠ»Π°Π·ΡΡΠΈ ΠΎΠ±ΡΡΠ½ΠΎ ΠΈΠ·Π³ΠΎΡΠ°Π²Π»ΠΈΠ²Π°ΡΡΡΡ ΠΈΠ· ΡΠ΅ΡΠΌΠΎΡΠ΅Π°ΠΊΡΠΈΠ²Π½ΠΎΠ³ΠΎ ΡΠΌΠΎΠ»ΡΠ½ΠΎΠ³ΠΎ ΡΠ²ΡΠ·ΡΡΡΠ΅Π³ΠΎ, ΠΊΠ²Π°ΡΡΠ΅Π²ΠΎΠ³ΠΎ ΠΏΠ΅ΡΠΊΠ° ΠΈ ΡΠ²Π΅ΡΠ½ΡΡ
ΠΏΠΈΠ³ΠΌΠ΅Π½ΡΠΎΠ².
ΠΡΠΎΠΈΠ·Π²ΠΎΠ΄ΡΡΠ²ΠΎ
ΠΡΠΎΡΠ΅ΡΡ ΠΡΠΎΠΈΠ·Π²ΠΎΠ΄ΡΡΠ²ΠΎ Π±Π΅ΡΠΎΠ½Π½ΡΡ Π±Π»ΠΎΠΊΠΎΠ² ΡΠΎΡΡΠΎΠΈΡ ΠΈΠ· ΡΠ΅ΡΡΡΠ΅Ρ ΠΎΡΠ½ΠΎΠ²Π½ΡΡ ΠΏΡΠΎΡΠ΅ΡΡΠΎΠ²: ΡΠΌΠ΅ΡΠΈΠ²Π°Π½ΠΈΠ΅, ΡΠΎΡΠΌΠΎΠ²Π°Π½ΠΈΠ΅, ΠΎΡΠ²Π΅ΡΠΆΠ΄Π΅Π½ΠΈΠ΅ ΠΈ ΡΠΎΡΠΌΠΈΡΠΎΠ²Π°Π½ΠΈΠ΅ ΠΊΡΠ±ΠΎΠ². ΠΠ΅ΠΊΠΎΡΠΎΡΡΠ΅ ΠΏΡΠΎΠΈΠ·Π²ΠΎΠ΄ΡΡΠ²Π΅Π½Π½ΡΠ΅ ΠΏΡΠ΅Π΄ΠΏΡΠΈΡΡΠΈΡ ΠΏΡΠΎΠΈΠ·Π²ΠΎΠ΄ΡΡ ΡΠΎΠ»ΡΠΊΠΎ Π±Π΅ΡΠΎΠ½Π½ΡΠ΅ Π±Π»ΠΎΠΊΠΈ, Π² ΡΠΎ Π²ΡΠ΅ΠΌΡ ΠΊΠ°ΠΊ Π΄ΡΡΠ³ΠΈΠ΅ ΠΌΠΎΠ³ΡΡ ΠΏΡΠΎΠΈΠ·Π²ΠΎΠ΄ΠΈΡΡ ΡΠΈΡΠΎΠΊΠΈΠΉ ΡΠΏΠ΅ΠΊΡΡ ΡΠ±ΠΎΡΠ½ΡΡ ΠΆΠ΅Π»Π΅Π·ΠΎΠ±Π΅ΡΠΎΠ½Π½ΡΡ ΠΈΠ·Π΄Π΅Π»ΠΈΠΉ, Π²ΠΊΠ»ΡΡΠ°Ρ Π±Π»ΠΎΠΊΠΈ, ΠΏΠ»ΠΎΡΠΊΡΡ Π±ΡΡΡΡΠ°ΡΠΊΡ ΠΈ Π΄Π΅ΠΊΠΎΡΠ°ΡΠΈΠ²Π½ΡΠ΅ ΡΠ»Π΅ΠΌΠ΅Π½ΡΡ Π»Π°Π½Π΄ΡΠ°ΡΡΠ½ΠΎΠ³ΠΎ Π΄ΠΈΠ·Π°ΠΉΠ½Π°, ΡΠ°ΠΊΠΈΠ΅ ΠΊΠ°ΠΊ ΠΎΠΊΠ°Π½ΡΠΎΠ²ΠΊΠ° Π³Π°Π·ΠΎΠ½ΠΎΠ². ΠΠ΅ΠΊΠΎΡΠΎΡΡΠ΅ Π·Π°Π²ΠΎΠ΄Ρ ΡΠΏΠΎΡΠΎΠ±Π½Ρ ΠΏΡΠΎΠΈΠ·Π²ΠΎΠ΄ΠΈΡΡ 2000 ΠΈ Π±ΠΎΠ»Π΅Π΅ Π±Π»ΠΎΠΊΠΎΠ² Π² ΡΠ°Ρ.
Π‘Π»Π΅Π΄ΡΡΡΠΈΠ΅ ΡΡΠ°ΠΏΡ ΠΎΠ±ΡΡΠ½ΠΎ ΠΈΡΠΏΠΎΠ»ΡΠ·ΡΡΡΡΡ Π΄Π»Ρ ΠΈΠ·Π³ΠΎΡΠΎΠ²Π»Π΅Π½ΠΈΡ Π±Π΅ΡΠΎΠ½Π½ΡΡ Π±Π»ΠΎΠΊΠΎΠ².
Π‘ΠΌΠ΅ΡΠΈΠ²Π°Π½ΠΈΠ΅- 1 ΠΠ΅ΡΠΎΠΊ ΠΈ Π³ΡΠ°Π²ΠΈΠΉ Ρ ΡΠ°Π½ΡΡΡΡ ΡΠ½Π°ΡΡΠΆΠΈ Π² ΡΡΠ°Π±Π΅Π»ΡΡ ΠΈ ΡΡΠ°Π½ΡΠΏΠΎΡΡΠΈΡΡΡΡΡΡ Π² Π±ΡΠ½ΠΊΠ΅ΡΡ Π½Π° Π·Π°Π²ΠΎΠ΄Π΅ Ρ ΠΏΠΎΠΌΠΎΡΡΡ Π»Π΅Π½ΡΠΎΡΠ½ΠΎΠ³ΠΎ ΠΊΠΎΠ½Π²Π΅ΠΉΠ΅ΡΠ° ΠΏΠΎ ΠΌΠ΅ΡΠ΅ Π½Π΅ΠΎΠ±Ρ ΠΎΠ΄ΠΈΠΌΠΎΡΡΠΈ. ΠΠΎΡΡΠ»Π°Π½Π΄ΡΠ΅ΠΌΠ΅Π½Ρ Ρ ΡΠ°Π½ΠΈΡΡΡ ΡΠ½Π°ΡΡΠΆΠΈ Π² Π±ΠΎΠ»ΡΡΠΈΡ Π²Π΅ΡΡΠΈΠΊΠ°Π»ΡΠ½ΡΡ ΡΠΈΠ»ΠΎΡΠ°Ρ , ΡΡΠΎΠ±Ρ Π·Π°ΡΠΈΡΠΈΡΡ Π΅Π³ΠΎ ΠΎΡ Π²Π»Π°Π³ΠΈ.
- 2 ΠΠΎΠ³Π΄Π° Π½Π°ΡΠΈΠ½Π°Π΅ΡΡΡ ΠΏΡΠΎΠΈΠ·Π²ΠΎΠ΄ΡΡΠ²Π΅Π½Π½ΡΠΉ ΡΠΈΠΊΠ», Π½Π΅ΠΎΠ±Ρ
ΠΎΠ΄ΠΈΠΌΠΎΠ΅ ΠΊΠΎΠ»ΠΈΡΠ΅ΡΡΠ²ΠΎ ΠΏΠ΅ΡΠΊΠ°, Π³ΡΠ°Π²ΠΈΡ ΠΈ ΡΠ΅ΠΌΠ΅Π½ΡΠ° ΠΏΠΎΠ΄Π°Π΅ΡΡΡ ΡΠ°ΠΌΠΎΡΠ΅ΠΊΠΎΠΌ ΠΈΠ»ΠΈ ΠΌΠ΅Ρ
Π°Π½ΠΈΡΠ΅ΡΠΊΠΈΠΌΠΈ ΡΡΠ΅Π΄ΡΡΠ²Π°ΠΌΠΈ Π² Π²Π΅ΡΠΎΠ²ΠΎΠΉ Π΄ΠΎΠ·Π°ΡΠΎΡ, ΠΊΠΎΡΠΎΡΡΠΉ ΠΎΡΠΌΠ΅ΡΡΠ΅Ρ Π½Π°Π΄Π»Π΅ΠΆΠ°ΡΠ΅Π΅ ΠΊΠΎΠ»ΠΈΡΠ΅ΡΡΠ²ΠΎ ΠΊΠ°ΠΆΠ΄ΠΎΠ³ΠΎ ΠΌΠ°ΡΠ΅ΡΠΈΠ°Π»Π°.
- 3 ΠΠ°ΡΠ΅ΠΌ ΡΡΡ ΠΈΠ΅ ΠΌΠ°ΡΠ΅ΡΠΈΠ°Π»Ρ ΠΏΠΎΡΡΡΠΏΠ°ΡΡ Π² ΡΡΠ°ΡΠΈΠΎΠ½Π°ΡΠ½ΡΠΉ ΡΠΌΠ΅ΡΠΈΡΠ΅Π»Ρ, Π³Π΄Π΅ ΠΎΠ½ΠΈ ΠΏΠ΅ΡΠ΅ΠΌΠ΅ΡΠΈΠ²Π°ΡΡΡΡ Π² ΡΠ΅ΡΠ΅Π½ΠΈΠ΅ Π½Π΅ΡΠΊΠΎΠ»ΡΠΊΠΈΡ ΠΌΠΈΠ½ΡΡ. ΠΠ±ΡΡΠ½ΠΎ ΠΈΡΠΏΠΎΠ»ΡΠ·ΡΡΡΡΡ Π΄Π²Π° ΡΠΈΠΏΠ° ΡΠΌΠ΅ΡΠΈΡΠ΅Π»Π΅ΠΉ. ΠΠ΄ΠΈΠ½ ΡΠΈΠΏ, Π½Π°Π·ΡΠ²Π°Π΅ΠΌΡΠΉ ΠΏΠ»Π°Π½Π΅ΡΠ°ΡΠ½ΡΠΌ ΠΈΠ»ΠΈ ΡΠ°ΡΠ΅Π»ΡΡΠ°ΡΡΠΌ ΠΌΠΈΠΊΡΠ΅ΡΠΎΠΌ, Π½Π°ΠΏΠΎΠΌΠΈΠ½Π°Π΅Ρ Π½Π΅Π³Π»ΡΠ±ΠΎΠΊΡΡ ΡΠΊΠΎΠ²ΠΎΡΠΎΠ΄Ρ Ρ ΠΊΡΡΡΠΊΠΎΠΉ. Π‘ΠΌΠ΅ΡΠΈΡΠ΅Π»ΡΠ½ΡΠ΅ Π»ΠΎΠΏΠ°ΡΡΠΈ ΠΏΡΠΈΠΊΡΠ΅ΠΏΠ»Π΅Π½Ρ ΠΊ Π²Π΅ΡΡΠΈΠΊΠ°Π»ΡΠ½ΠΎΠΌΡ Π²ΡΠ°ΡΠ°ΡΡΠ΅ΠΌΡΡΡ Π²Π°Π»Ρ Π²Π½ΡΡΡΠΈ ΡΠΌΠ΅ΡΠΈΡΠ΅Π»Ρ. ΠΡΡΠ³ΠΎΠΉ ΡΠΈΠΏ Π½Π°Π·ΡΠ²Π°Π΅ΡΡΡ Π³ΠΎΡΠΈΠ·ΠΎΠ½ΡΠ°Π»ΡΠ½ΡΠΌ Π±Π°ΡΠ°Π±Π°Π½Π½ΡΠΌ ΡΠΌΠ΅ΡΠΈΡΠ΅Π»Π΅ΠΌ. ΠΠ½ Π½Π°ΠΏΠΎΠΌΠΈΠ½Π°Π΅Ρ Π±Π°Π½ΠΊΡ ΠΈΠ·-ΠΏΠΎΠ΄ ΠΊΠΎΡΠ΅, ΠΏΠ΅ΡΠ΅Π²Π΅ΡΠ½ΡΡΡΡ Π½Π° Π±ΠΎΠΊ, ΠΈ ΠΈΠΌΠ΅Π΅Ρ ΡΠΌΠ΅ΡΠΈΡΠ΅Π»ΡΠ½ΡΠ΅ Π»ΠΎΠΏΠ°ΡΡΠΈ, ΠΏΡΠΈΠΊΡΠ΅ΠΏΠ»Π΅Π½Π½ΡΠ΅ ΠΊ Π³ΠΎΡΠΈΠ·ΠΎΠ½ΡΠ°Π»ΡΠ½ΠΎΠΌΡ Π²ΡΠ°ΡΠ°ΡΡΠ΅ΠΌΡΡΡ Π²Π°Π»Ρ Π²Π½ΡΡΡΠΈ ΠΌΠΈΠΊΡΠ΅ΡΠ°.
- 4 ΠΠΎΡΠ»Π΅ ΡΠΌΠ΅ΡΠΈΠ²Π°Π½ΠΈΡ ΡΡΡ ΠΈΡ ΠΌΠ°ΡΠ΅ΡΠΈΠ°Π»ΠΎΠ² Π² ΡΠΌΠ΅ΡΠΈΡΠ΅Π»Ρ Π΄ΠΎΠ±Π°Π²Π»ΡΠ΅ΡΡΡ Π½Π΅Π±ΠΎΠ»ΡΡΠΎΠ΅ ΠΊΠΎΠ»ΠΈΡΠ΅ΡΡΠ²ΠΎ Π²ΠΎΠ΄Ρ. ΠΡΠ»ΠΈ Π·Π°Π²ΠΎΠ΄ ΡΠ°ΡΠΏΠΎΠ»ΠΎΠΆΠ΅Π½ Π² ΠΊΠ»ΠΈΠΌΠ°ΡΠ΅, ΠΏΠΎΠ΄Π²Π΅ΡΠΆΠ΅Π½Π½ΠΎΠΌ ΡΠΊΡΡΡΠ΅ΠΌΠ°Π»ΡΠ½ΡΠΌ ΡΠ΅ΠΌΠΏΠ΅ΡΠ°ΡΡΡΠ°ΠΌ, Π²ΠΎΠ΄Π° ΠΌΠΎΠΆΠ΅Ρ ΡΠ½Π°ΡΠ°Π»Π° ΠΏΡΠΎΠΉΡΠΈ ΡΠ΅ΡΠ΅Π· Π½Π°Π³ΡΠ΅Π²Π°ΡΠ΅Π»Ρ ΠΈΠ»ΠΈ ΠΎΡ Π»Π°Π΄ΠΈΡΠ΅Π»Ρ, ΡΡΠΎΠ±Ρ ΡΠ΅Π³ΡΠ»ΠΈΡΠΎΠ²Π°ΡΡ Π΅Π΅ ΡΠ΅ΠΌΠΏΠ΅ΡΠ°ΡΡΡΡ. Π ΡΡΠΎ Π²ΡΠ΅ΠΌΡ ΡΠ°ΠΊΠΆΠ΅ ΠΌΠΎΠ³ΡΡ Π±ΡΡΡ Π΄ΠΎΠ±Π°Π²Π»Π΅Π½Ρ Ρ ΠΈΠΌΠΈΡΠ΅ΡΠΊΠΈΠ΅ Π΄ΠΎΠ±Π°Π²ΠΊΠΈ ΠΈ ΠΊΡΠ°ΡΡΡΠΈΠ΅ ΠΏΠΈΠ³ΠΌΠ΅Π½ΡΡ. ΠΠ°ΡΠ΅ΠΌ Π±Π΅ΡΠΎΠ½ ΠΏΠ΅ΡΠ΅ΠΌΠ΅ΡΠΈΠ²Π°ΡΡ Π² ΡΠ΅ΡΠ΅Π½ΠΈΠ΅ ΡΠ΅ΡΡΠΈ-Π²ΠΎΡΡΠΌΠΈ ΠΌΠΈΠ½ΡΡ.
- 5 ΠΠΎΡΠ»Π΅ ΡΡΠ°ΡΠ΅Π»ΡΠ½ΠΎΠ³ΠΎ ΠΏΠ΅ΡΠ΅ΠΌΠ΅ΡΠΈΠ²Π°Π½ΠΈΡ Π±Π΅ΡΠΎΠ½Π½Π°Ρ ΠΏΠ°ΡΡΠΈΡ Π²ΡΠ³ΡΡΠΆΠ°Π΅ΡΡΡ Π² Π½Π°ΠΊΠ»ΠΎΠ½Π½ΡΠΉ
- ΠΊΠΎΠ²ΡΠΎΠ²ΡΠΌ ΠΊΠΎΠ½Π²Π΅ΠΉΠ΅ΡΠΎΠΌ ΠΈ ΡΡΠ°Π½ΡΠΏΠΎΡΡΠΈΡΡΠ΅ΡΡΡ Π² ΠΏΡΠΈΠΏΠΎΠ΄Π½ΡΡΡΠΉ Π±ΡΠ½ΠΊΠ΅Ρ.
Π¦ΠΈΠΊΠ» ΡΠΌΠ΅ΡΠΈΠ²Π°Π½ΠΈΡ Π½Π°ΡΠΈΠ½Π°Π΅ΡΡΡ ΡΠ½ΠΎΠ²Π° Π΄Π»Ρ ΡΠ»Π΅Π΄ΡΡΡΠ΅ΠΉ Π·Π°Π³ΡΡΠ·ΠΊΠΈ.
- 6 ΠΠ· Π±ΡΠ½ΠΊΠ΅ΡΠ° Π±Π΅ΡΠΎΠ½ ΠΏΠΎΠ΄Π°Π΅ΡΡΡ Π² Π΄ΡΡΠ³ΠΎΠΉ Π±ΡΠ½ΠΊΠ΅Ρ Π½Π° Π²Π΅ΡΡ Π½Π΅ΠΉ ΡΠ°ΡΡΠΈ ΠΌΠ°ΡΠΈΠ½Ρ Π΄Π»Ρ ΠΏΡΠΎΠΈΠ·Π²ΠΎΠ΄ΡΡΠ²Π° Π±Π»ΠΎΠΊΠΎΠ² Ρ ΠΈΠ·ΠΌΠ΅ΡΠ΅Π½Π½ΡΠΌ ΡΠ°ΡΡ ΠΎΠ΄ΠΎΠΌ. Π Π±Π»ΠΎΠΊ-ΠΌΠ°ΡΠΈΠ½Π΅ Π±Π΅ΡΠΎΠ½ ΠΏΠΎΠ΄Π°Π΅ΡΡΡ Π²Π½ΠΈΠ· Π² ΡΠΎΡΠΌΡ. Π€ΠΎΡΠΌΡ ΡΠΎΡΡΠΎΡΡ ΠΈΠ· Π²Π½Π΅ΡΠ½Π΅ΠΉ ΠΊΠΎΡΠΎΠ±ΠΊΠΈ ΡΠΎΡΠΌΡ, ΡΠΎΠ΄Π΅ΡΠΆΠ°ΡΠ΅ΠΉ Π½Π΅ΡΠΊΠΎΠ»ΡΠΊΠΎ Π²ΠΊΠ»Π°Π΄ΡΡΠ΅ΠΉ ΡΠΎΡΠΌΡ. ΠΠΊΠ»Π°Π΄ΡΡΠΈ ΠΎΠΏΡΠ΅Π΄Π΅Π»ΡΡΡ Π²Π½Π΅ΡΠ½ΡΡ ΡΠΎΡΠΌΡ Π±Π»ΠΎΠΊΠ° ΠΈ Π²Π½ΡΡΡΠ΅Π½Π½ΡΡ ΡΠΎΡΠΌΡ ΠΏΠΎΠ»ΠΎΡΡΠ΅ΠΉ Π±Π»ΠΎΠΊΠ°. ΠΠ΄Π½ΠΎΠ²ΡΠ΅ΠΌΠ΅Π½Π½ΠΎ ΠΌΠΎΠΆΠ½ΠΎ ΡΠΎΡΠΌΠΎΠ²Π°ΡΡ Π΄ΠΎ 15 Π±Π»ΠΎΠΊΠΎΠ².
- 7 ΠΠΎΠ³Π΄Π° ΡΠΎΡΠΌΡ Π·Π°ΠΏΠΎΠ»Π½Π΅Π½Ρ, Π±Π΅ΡΠΎΠ½ ΡΠΏΠ»ΠΎΡΠ½ΡΠ΅ΡΡΡ ΠΏΠΎΠ΄ Π΄Π΅ΠΉΡΡΠ²ΠΈΠ΅ΠΌ Π²Π΅ΡΠ° Π²Π΅ΡΡ Π½Π΅ΠΉ Π³ΠΎΠ»ΠΎΠ²ΠΊΠΈ ΡΠΎΡΠΌΡ, ΠΎΠΏΡΡΠΊΠ°ΡΡΠ΅ΠΉΡΡ Π½Π° ΠΏΠΎΠ»ΠΎΡΡΠΈ ΡΠΎΡΠΌΡ. ΠΡΠΎ ΡΠΏΠ»ΠΎΡΠ½Π΅Π½ΠΈΠ΅ ΠΌΠΎΠΆΠ΅Ρ Π±ΡΡΡ Π΄ΠΎΠΏΠΎΠ»Π½Π΅Π½ΠΎ Π²ΠΎΠ·Π΄ΡΡΠ½ΡΠΌΠΈ ΠΈΠ»ΠΈ Π³ΠΈΠ΄ΡΠ°Π²Π»ΠΈΡΠ΅ΡΠΊΠΈΠΌΠΈ ΡΠΈΠ»ΠΈΠ½Π΄ΡΠ°ΠΌΠΈ Π΄Π°Π²Π»Π΅Π½ΠΈΡ, Π²ΠΎΠ·Π΄Π΅ΠΉΡΡΠ²ΡΡΡΠΈΠΌΠΈ Π½Π° Π³ΠΎΠ»ΠΎΠ²ΠΊΡ ΠΏΡΠ΅ΡΡ-ΡΠΎΡΠΌΡ. ΠΠΎΠ»ΡΡΠΈΠ½ΡΡΠ²ΠΎ Π±Π»ΠΎΡΠ½ΡΡ ΠΌΠ°ΡΠΈΠ½ ΡΠ°ΠΊΠΆΠ΅ ΠΈΡΠΏΠΎΠ»ΡΠ·ΡΡΡ ΠΊΠΎΡΠΎΡΠΊΠΈΠ΅ ΠΈΠΌΠΏΡΠ»ΡΡΡ ΠΌΠ΅Ρ Π°Π½ΠΈΡΠ΅ΡΠΊΠΎΠΉ Π²ΠΈΠ±ΡΠ°ΡΠΈΠΈ Π΄Π»Ρ Π΄Π°Π»ΡΠ½Π΅ΠΉΡΠ΅Π³ΠΎ ΡΠΏΠ»ΠΎΡΠ½Π΅Π½ΠΈΡ.
- 8 Π£ΠΏΠ»ΠΎΡΠ½Π΅Π½Π½ΡΠ΅ Π±Π»ΠΎΠΊΠΈ Π²ΡΡΠ°Π»ΠΊΠΈΠ²Π°ΡΡΡΡ ΠΈΠ· ΡΠΎΡΠΌ Π½Π° ΠΏΠ»ΠΎΡΠΊΠΈΠΉ ΡΡΠ°Π»ΡΠ½ΠΎΠΉ ΠΏΠΎΠ΄Π΄ΠΎΠ½. ΠΠΎΠ΄Π΄ΠΎΠ½ ΠΈ Π±Π»ΠΎΠΊΠΈ Π²ΡΡΠ°Π»ΠΊΠΈΠ²Π°ΡΡΡΡ ΠΈΠ· ΠΌΠ°ΡΠΈΠ½Ρ Π½Π° ΡΠ΅ΠΏΠ½ΠΎΠΉ ΠΊΠΎΠ½Π²Π΅ΠΉΠ΅Ρ. Π Π½Π΅ΠΊΠΎΡΠΎΡΡΡ
ΠΎΠΏΠ΅ΡΠ°ΡΠΈΡΡ
Π±Π»ΠΎΠΊΠΈ Π·Π°ΡΠ΅ΠΌ ΠΏΡΠΎΡ
ΠΎΠ΄ΡΡ ΠΏΠΎΠ΄ Π²ΡΠ°ΡΠ°ΡΡΠ΅ΠΉΡΡ ΡΠ΅ΡΠΊΠΎΠΉ, ΠΊΠΎΡΠΎΡΠ°Ρ ΡΠ΄Π°Π»ΡΠ΅Ρ ΡΡΡ
Π»ΡΠΉ ΠΌΠ°ΡΠ΅ΡΠΈΠ°Π» Ρ Π²Π΅ΡΡ
Π½Π΅ΠΉ ΡΠ°ΡΡΠΈ Π±Π»ΠΎΠΊΠΎΠ².
- 9 ΠΠΎΠ΄Π΄ΠΎΠ½Ρ Ρ Π±Π»ΠΎΠΊΠ°ΠΌΠΈ ΡΡΠ°Π½ΡΠΏΠΎΡΡΠΈΡΡΡΡΡΡ ΠΊ Π°Π²ΡΠΎΠΌΠ°ΡΠΈΠ·ΠΈΡΠΎΠ²Π°Π½Π½ΠΎΠΌΡ ΡΠΊΠ»Π°Π΄ΡΠΈΠΊΡ ΠΈΠ»ΠΈ ΠΏΠΎΠ³ΡΡΠ·ΡΠΈΠΊΡ, ΠΊΠΎΡΠΎΡΡΠΉ ΡΠ°Π·ΠΌΠ΅ΡΠ°Π΅Ρ ΠΈΡ Π½Π° ΡΡΠ΅Π»Π»Π°ΠΆΠ΅ Π΄Π»Ρ Π²ΡΠ΄Π΅ΡΠΆΠΈΠ²Π°Π½ΠΈΡ. ΠΠ°ΠΆΠ΄Π°Ρ ΡΡΠΎΠΉΠΊΠ° Π²ΠΌΠ΅ΡΠ°Π΅Ρ Π½Π΅ΡΠΊΠΎΠ»ΡΠΊΠΎ ΡΠΎΡΠ΅Π½ Π±Π»ΠΎΠΊΠΎΠ². ΠΠΎΠ³Π΄Π° ΡΡΠ΅Π»Π»Π°ΠΆ Π·Π°ΠΏΠΎΠ»Π½ΡΠ΅ΡΡΡ, Π΅Π³ΠΎ Π·Π°ΠΊΠ°ΡΡΠ²Π°ΡΡ Π½Π° ΡΠ΅Π»ΡΡΡ ΠΈ ΠΏΠ΅ΡΠ΅ΠΌΠ΅ΡΠ°ΡΡ Π² ΡΡΡΠΈΠ»ΡΠ½ΡΡ ΠΏΠ΅ΡΡ.
- 10 ΠΠ΅ΡΡ ΠΏΡΠ΅Π΄ΡΡΠ°Π²Π»ΡΠ΅Ρ ΡΠΎΠ±ΠΎΠΉ Π·Π°ΠΊΡΡΡΠΎΠ΅ ΠΏΠΎΠΌΠ΅ΡΠ΅Π½ΠΈΠ΅, ΡΠΏΠΎΡΠΎΠ±Π½ΠΎΠ΅ ΠΎΠ΄Π½ΠΎΠ²ΡΠ΅ΠΌΠ΅Π½Π½ΠΎ Π²ΠΌΠ΅ΡΡΠΈΡΡ Π½Π΅ΡΠΊΠΎΠ»ΡΠΊΠΎ ΡΡΠ΅Π»Π»Π°ΠΆΠ΅ΠΉ Ρ Π±Π»ΠΎΠΊΠ°ΠΌΠΈ. Π‘ΡΡΠ΅ΡΡΠ²ΡΠ΅Ρ Π΄Π²Π° ΠΎΡΠ½ΠΎΠ²Π½ΡΡ
ΡΠΈΠΏΠ° ΡΡΡΠΈΠ»ΡΠ½ΡΡ
ΠΏΠ΅ΡΠ΅ΠΉ. ΠΠ°ΠΈΠ±ΠΎΠ»Π΅Π΅ ΡΠ°ΡΠΏΡΠΎΡΡΡΠ°Π½Π΅Π½Π½ΡΠΌ ΡΠΈΠΏΠΎΠΌ ΡΠ²Π»ΡΠ΅ΡΡΡ ΠΏΠ°ΡΠΎΠ²Π°Ρ ΠΏΠ΅ΡΡ Π½ΠΈΠ·ΠΊΠΎΠ³ΠΎ Π΄Π°Π²Π»Π΅Π½ΠΈΡ. Π ΡΡΠΎΠΌ ΡΠ»ΡΡΠ°Π΅ Π±Π»ΠΎΠΊΠΈ Π²ΡΠ΄Π΅ΡΠΆΠΈΠ²Π°ΡΡ Π² ΠΏΠ΅ΡΠΈ ΠΎΡ ΠΎΠ΄Π½ΠΎΠ³ΠΎ Π΄ΠΎ ΡΡΠ΅Ρ
ΡΠ°ΡΠΎΠ² ΠΏΡΠΈ ΠΊΠΎΠΌΠ½Π°ΡΠ½ΠΎΠΉ ΡΠ΅ΠΌΠΏΠ΅ΡΠ°ΡΡΡΠ΅, ΡΡΠΎΠ±Ρ ΠΎΠ½ΠΈ Π½Π΅ΠΌΠ½ΠΎΠ³ΠΎ Π·Π°ΡΠ²Π΅ΡΠ΄Π΅Π»ΠΈ. ΠΠ°ΡΠ΅ΠΌ ΠΏΠΎΡΡΠ΅ΠΏΠ΅Π½Π½ΠΎ Π²Π²ΠΎΠ΄ΡΡ ΠΏΠ°Ρ Π΄Π»Ρ ΠΏΠΎΠ²ΡΡΠ΅Π½ΠΈΡ ΡΠ΅ΠΌΠΏΠ΅ΡΠ°ΡΡΡΡ Ρ ΡΠ΅Π³ΡΠ»ΠΈΡΡΠ΅ΠΌΠΎΠΉ ΡΠΊΠΎΡΠΎΡΡΡΡ Π½Π΅ Π±ΠΎΠ»Π΅Π΅ 60Β°F Π² ΡΠ°Ρ (16Β°C Π² ΡΠ°Ρ). ΠΠ»ΠΎΠΊΠΈ ΡΡΠ°Π½Π΄Π°ΡΡΠ½ΠΎΠ³ΠΎ Π²Π΅ΡΠ° ΠΎΠ±ΡΡΠ½ΠΎ ΠΎΡΠ²Π΅ΡΠΆΠ΄Π°ΡΡΡΡ ΠΏΡΠΈ ΡΠ΅ΠΌΠΏΠ΅ΡΠ°ΡΡΡΠ΅ 150-165Β°F (66-74Β°C), Π° Π»Π΅Π³ΠΊΠΈΠ΅ Π±Π»ΠΎΠΊΠΈ ΠΎΡΠ²Π΅ΡΠΆΠ΄Π°ΡΡΡΡ ΠΏΡΠΈ 170-185Β°F (77-85Β°C). ΠΠΎ Π΄ΠΎΡΡΠΈΠΆΠ΅Π½ΠΈΠΈ ΡΠ΅ΠΌΠΏΠ΅ΡΠ°ΡΡΡΡ ΠΎΡΠ²Π΅ΡΠΆΠ΄Π΅Π½ΠΈΡ ΠΏΠΎΠ΄Π°ΡΡ ΠΏΠ°ΡΠ° ΠΎΡΠΊΠ»ΡΡΠ°ΡΡ, Π° Π±Π»ΠΎΠΊΠΈ ΠΎΡΡΠ°Π²Π»ΡΡΡ Π½Π° 12-18 ΡΠ°ΡΠΎΠ² ΠΏΡΠΎΠΏΠΈΡΡΠ²Π°ΡΡΡΡ Π³ΠΎΡΡΡΠΈΠΌ Π²Π»Π°ΠΆΠ½ΡΠΌ Π²ΠΎΠ·Π΄ΡΡ
ΠΎΠΌ.
ΠΠΎΡΠ»Π΅ Π·Π°ΠΌΠ°ΡΠΈΠ²Π°Π½ΠΈΡ Π±Π»ΠΎΠΊΠΈ ΡΡΡΠ°Ρ, Π²ΡΠΏΡΡΠΊΠ°Ρ Π²Π»Π°ΠΆΠ½ΡΠΉ Π²ΠΎΠ·Π΄ΡΡ ΠΈ ΠΏΠΎΠ²ΡΡΠ°Ρ ΡΠ΅ΠΌΠΏΠ΅ΡΠ°ΡΡΡΡ Π² ΠΏΠ΅ΡΠΈ. ΠΠ΅ΡΡ ΡΠΈΠΊΠ» ΠΎΡΠ²Π΅ΡΠΆΠ΄Π΅Π½ΠΈΡ Π·Π°Π½ΠΈΠΌΠ°Π΅Ρ ΠΎΠΊΠΎΠ»ΠΎ 24 ΡΠ°ΡΠΎΠ².
- ΠΡΡΠ³ΠΈΠΌ ΡΠΈΠΏΠΎΠΌ ΠΏΠ΅ΡΠΈ ΡΠ²Π»ΡΠ΅ΡΡΡ ΠΏΠ°ΡΠΎΠ²Π°Ρ ΠΏΠ΅ΡΡ Π²ΡΡΠΎΠΊΠΎΠ³ΠΎ Π΄Π°Π²Π»Π΅Π½ΠΈΡ, ΠΊΠΎΡΠΎΡΡΡ ΠΈΠ½ΠΎΠ³Π΄Π° Π½Π°Π·ΡΠ²Π°ΡΡΒ Π°Π²ΡΠΎΠΊΠ»Π°Π²ΠΎΠΌ. Π ΡΡΠΎΠΌ ΡΠΈΠΏΠ΅ ΡΠ΅ΠΌΠΏΠ΅ΡΠ°ΡΡΡΠ° ΠΏΠΎΠ²ΡΡΠ°Π΅ΡΡΡ Π΄ΠΎ 300-375Β°F (149-191Β°C), Π° Π΄Π°Π²Π»Π΅Π½ΠΈΠ΅ ΠΏΠΎΠ²ΡΡΠ°Π΅ΡΡΡ Π΄ΠΎ 80-185 ΡΡΠ½ΡΠΎΠ² Π½Π° ΠΊΠ². Π΄ΡΠΉΠΌ (5,5-12,8 Π±Π°Ρ). ΠΠ»ΠΎΠΊΠΈ Π²ΡΠ΄Π΅ΡΠΆΠΈΠ²Π°ΡΡ ΠΎΡ ΠΏΡΡΠΈ Π΄ΠΎ Π΄Π΅ΡΡΡΠΈ ΡΠ°ΡΠΎΠ². ΠΠ°ΡΠ΅ΠΌ Π΄Π°Π²Π»Π΅Π½ΠΈΠ΅ Π±ΡΡΡΡΠΎ ΡΠ±ΡΠ°ΡΡΠ²Π°Π΅ΡΡΡ, ΡΡΠΎ Π·Π°ΡΡΠ°Π²Π»ΡΠ΅Ρ Π±Π»ΠΎΠΊΠΈ Π±ΡΡΡΡΠΎ Π²ΡΡΠ²ΠΎΠ±ΠΎΠΆΠ΄Π°ΡΡ Π·Π°Ρ Π²Π°ΡΠ΅Π½Π½ΡΡ Π²Π»Π°Π³Ρ. ΠΡΠΎΡΠ΅ΡΡ ΠΎΡΠ²Π΅ΡΠΆΠ΄Π΅Π½ΠΈΡ Π² Π°Π²ΡΠΎΠΊΠ»Π°Π²Π΅ ΡΡΠ΅Π±ΡΠ΅Ρ Π±ΠΎΠ»ΡΡΠ΅ ΡΠ½Π΅ΡΠ³ΠΈΠΈ ΠΈ Π±ΠΎΠ»Π΅Π΅ Π΄ΠΎΡΠΎΠ³ΠΎΠΉ ΠΏΠ΅ΡΠΈ, Π½ΠΎ ΠΏΠΎΠ·Π²ΠΎΠ»ΡΠ΅Ρ ΠΏΡΠΎΠΈΠ·Π²ΠΎΠ΄ΠΈΡΡ Π±Π»ΠΎΠΊΠΈ Π·Π° ΠΌΠ΅Π½ΡΡΠ΅Π΅ Π²ΡΠ΅ΠΌΡ.
- 11 Π‘ΡΠ΅Π»Π»Π°ΠΆΠΈ Ρ ΠΎΡΠ²Π΅ΡΠΆΠ΄Π΅Π½Π½ΡΠΌΠΈ Π±Π»ΠΎΠΊΠ°ΠΌΠΈ Π²ΡΠΊΠ°ΡΡΠ²Π°ΡΡΡΡ ΠΈΠ· ΠΏΠ΅ΡΠΈ, ΠΏΠΎΠ΄Π΄ΠΎΠ½Ρ Ρ Π±Π»ΠΎΠΊΠ°ΠΌΠΈ ΡΠ°ΡΠΊΠ»Π°Π΄ΡΠ²Π°ΡΡΡΡ ΠΈ ΡΠΊΠ»Π°Π΄ΡΠ²Π°ΡΡΡΡ Π½Π° ΡΠ΅ΠΏΠ½ΠΎΠΉ ΠΊΠΎΠ½Π²Π΅ΠΉΠ΅Ρ. ΠΠ»ΠΎΠΊΠΈ ΡΡΠ°Π»ΠΊΠΈΠ²Π°ΡΡΡΡ ΡΠΎ ΡΡΠ°Π»ΡΠ½ΡΡ ΠΏΠΎΠ΄Π΄ΠΎΠ½ΠΎΠ², Π° ΠΏΡΡΡΡΠ΅ ΠΏΠΎΠ΄Π΄ΠΎΠ½Ρ Π²ΠΎΠ·Π²ΡΠ°ΡΠ°ΡΡΡΡ Π² Π±Π»ΠΎΠΊ-ΠΌΠ°ΡΠΈΠ½Ρ Π΄Π»Ρ ΠΏΠΎΠ»ΡΡΠ΅Π½ΠΈΡ Π½ΠΎΠ²ΠΎΠ³ΠΎ Π½Π°Π±ΠΎΡΠ° ΡΠΎΡΠΌΠΎΠ²Π°Π½Π½ΡΡ Π±Π»ΠΎΠΊΠΎΠ².
- 12 ΠΡΠ»ΠΈ Π±Π»ΠΎΠΊΠΈ Π΄ΠΎΠ»ΠΆΠ½Ρ Π±ΡΡΡ ΠΈΠ·Π³ΠΎΡΠΎΠ²Π»Π΅Π½Ρ Π² Π²ΠΈΠ΄Π΅ Π±Π»ΠΎΠΊΠΎΠ² Ρ ΡΠ°Π·ΡΠ΅ΠΌΠ½ΠΎΠΉ ΠΏΠΎΠ²Π΅ΡΡ
Π½ΠΎΡΡΡΡ, ΠΎΠ½ΠΈ ΡΠ½Π°ΡΠ°Π»Π° ΡΠΎΡΠΌΡΡΡΡΡ Π² Π²ΠΈΠ΄Π΅ Π΄Π²ΡΡ
Π±Π»ΠΎΠΊΠΎΠ², ΡΠΎΠ΅Π΄ΠΈΠ½Π΅Π½Π½ΡΡ
Π²ΠΌΠ΅ΡΡΠ΅.
ΠΠ°ΠΊ ΡΠΎΠ»ΡΠΊΠΎ ΡΡΠΈ Π΄Π²ΠΎΠΉΠ½ΡΠ΅ Π±Π»ΠΎΠΊΠΈ Π·Π°ΡΠ²Π΅ΡΠ΄Π΅Π²Π°ΡΡ, ΠΎΠ½ΠΈ ΠΏΡΠΎΡ ΠΎΠ΄ΡΡ ΡΠ΅ΡΠ΅Π· ΡΠ°Π·Π΄Π΅Π»ΠΈΡΠ΅Π»Ρ, ΠΊΠΎΡΠΎΡΡΠΉ ΡΠ΄Π°ΡΡΠ΅Ρ ΠΏΠΎ Π½ΠΈΠΌ ΡΡΠΆΠ΅Π»ΡΠΌ Π»Π΅Π·Π²ΠΈΠ΅ΠΌ Π²Π΄ΠΎΠ»Ρ ΡΡΠ°ΡΡΠΊΠ° ΠΌΠ΅ΠΆΠ΄Ρ Π΄Π²ΡΠΌΡ ΠΏΠΎΠ»ΠΎΠ²ΠΈΠ½ΠΊΠ°ΠΌΠΈ. ΠΡΠΎ ΠΏΡΠΈΠ²ΠΎΠ΄ΠΈΡ ΠΊ ΡΠΎΠΌΡ, ΡΡΠΎ Π΄Π²ΠΎΠΉΠ½ΠΎΠΉ Π±Π»ΠΎΠΊ Π»ΠΎΠΌΠ°Π΅ΡΡΡ ΠΈ ΠΎΠ±ΡΠ°Π·ΡΠ΅Ρ Π³ΡΡΠ±ΡΡ ΠΊΠ°ΠΌΠ΅Π½Π½ΡΡ ΡΠ΅ΠΊΡΡΡΡΡ Π½Π° ΠΎΠ΄Π½ΠΎΠΉ ΡΡΠΎΡΠΎΠ½Π΅ ΠΊΠ°ΠΆΠ΄ΠΎΠΉ ΡΠ°ΡΡΠΈ.
- 13 ΠΠ»ΠΎΠΊΠΈ ΠΏΡΠΎΡ ΠΎΠ΄ΡΡ ΡΠ΅ΡΠ΅Π· ΠΊΡΠ±Π΅Ρ, ΠΊΠΎΡΠΎΡΡΠΉ Π²ΡΡΠ°Π²Π½ΠΈΠ²Π°Π΅Ρ ΠΊΠ°ΠΆΠ΄ΡΠΉ Π±Π»ΠΎΠΊ, Π° Π·Π°ΡΠ΅ΠΌ ΡΠΊΠ»Π°Π΄ΡΠ²Π°Π΅Ρ ΠΈΡ Π² ΠΊΡΠ±: ΡΡΠΈ Π±Π»ΠΎΠΊΠ° Π² ΡΠΈΡΠΈΠ½Ρ, ΡΠ΅ΡΡΡ Π±Π»ΠΎΠΊΠΎΠ² Π² Π³Π»ΡΠ±ΠΈΠ½Ρ ΠΈ ΡΡΠΈ ΠΈΠ»ΠΈ ΡΠ΅ΡΡΡΠ΅ Π±Π»ΠΎΠΊΠ° Π² Π²ΡΡΠΎΡΡ. ΠΡΠΈ ΠΊΡΠ±Ρ Π²ΡΠ½ΠΎΡΡΡΡΡ Π½Π° ΡΠ»ΠΈΡΡ Π²ΠΈΠ»ΠΎΡΠ½ΡΠΌ ΠΏΠΎΠ³ΡΡΠ·ΡΠΈΠΊΠΎΠΌ ΠΈ ΠΏΠΎΠΌΠ΅ΡΠ°ΡΡΡΡ Π½Π° Ρ ΡΠ°Π½Π΅Π½ΠΈΠ΅.
ΠΠΎΠ½ΡΡΠΎΠ»Ρ ΠΊΠ°ΡΠ΅ΡΡΠ²Π°ΠΡΠΎΠΈΠ·Π²ΠΎΠ΄ΡΡΠ²ΠΎ Π±Π΅ΡΠΎΠ½Π½ΡΡ
Π±Π»ΠΎΠΊΠΎΠ² ΡΡΠ΅Π±ΡΠ΅Ρ ΠΏΠΎΡΡΠΎΡΠ½Π½ΠΎΠ³ΠΎ ΠΊΠΎΠ½ΡΡΠΎΠ»Ρ Π΄Π»Ρ ΠΏΠΎΠ»ΡΡΠ΅Π½ΠΈΡ Π±Π»ΠΎΠΊΠΎΠ² Ρ ΡΡΠ΅Π±ΡΠ΅ΠΌΡΠΌΠΈ ΡΠ²ΠΎΠΉΡΡΠ²Π°ΠΌΠΈ. ΠΠ΅ΡΠ΅Π΄ ΠΏΠΎΠΌΠ΅ΡΠ΅Π½ΠΈΠ΅ΠΌ Π² ΡΠΌΠ΅ΡΠΈΡΠ΅Π»Ρ ΡΡΡΡΠ΅ Π²Π·Π²Π΅ΡΠΈΠ²Π°Π΅ΡΡΡ ΡΠ»Π΅ΠΊΡΡΠΎΠ½Π½ΡΠΌ ΡΠΏΠΎΡΠΎΠ±ΠΎΠΌ. Π‘ΠΎΠ΄Π΅ΡΠΆΠ°Π½ΠΈΠ΅ Π·Π°Ρ
Π²Π°ΡΠ΅Π½Π½ΠΎΠΉ Π²ΠΎΠ΄Ρ Π² ΠΏΠ΅ΡΠΊΠ΅ ΠΈ Π³ΡΠ°Π²ΠΈΠΈ ΠΌΠΎΠΆΠ½ΠΎ ΠΈΠ·ΠΌΠ΅ΡΠΈΡΡ Ρ ΠΏΠΎΠΌΠΎΡΡΡ ΡΠ»ΡΡΡΠ°Π·Π²ΡΠΊΠΎΠ²ΡΡ
Π΄Π°ΡΡΠΈΠΊΠΎΠ², Π° ΠΊΠΎΠ»ΠΈΡΠ΅ΡΡΠ²ΠΎ Π²ΠΎΠ΄Ρ, Π΄ΠΎΠ±Π°Π²Π»ΡΠ΅ΠΌΠΎΠΉ Π² ΡΠΌΠ΅ΡΡ, Π°Π²ΡΠΎΠΌΠ°ΡΠΈΡΠ΅ΡΠΊΠΈ ΡΠ΅Π³ΡΠ»ΠΈΡΡΠ΅ΡΡΡ Π΄Π»Ρ ΠΊΠΎΠΌΠΏΠ΅Π½ΡΠ°ΡΠΈΠΈ. Π ΡΠ°ΠΉΠΎΠ½Π°Ρ
Ρ ΡΠ΅Π·ΠΊΠΈΠΌΠΈ ΠΏΠ΅ΡΠ΅ΠΏΠ°Π΄Π°ΠΌΠΈ ΡΠ΅ΠΌΠΏΠ΅ΡΠ°ΡΡΡ Π²ΠΎΠ΄Π° ΠΏΠ΅ΡΠ΅Π΄ ΠΈΡΠΏΠΎΠ»ΡΠ·ΠΎΠ²Π°Π½ΠΈΠ΅ΠΌ ΠΌΠΎΠΆΠ΅Ρ ΠΏΡΠΎΡ
ΠΎΠ΄ΠΈΡΡ ΡΠ΅ΡΠ΅Π· ΠΎΡ
Π»Π°Π΄ΠΈΡΠ΅Π»Ρ ΠΈΠ»ΠΈ Π½Π°Π³ΡΠ΅Π²Π°ΡΠ΅Π»Ρ.
ΠΠΎΠ³Π΄Π° Π±Π»ΠΎΠΊΠΈ Π²ΡΡ ΠΎΠ΄ΡΡ ΠΈΠ· ΡΡΠ°Π½ΠΊΠ°, ΠΈΡ Π²ΡΡΠΎΡΡ ΠΌΠΎΠΆΠ½ΠΎ ΠΏΡΠΎΠ²Π΅ΡΠΈΡΡ Ρ ΠΏΠΎΠΌΠΎΡΡΡ Π΄Π°ΡΡΠΈΠΊΠΎΠ² Π»Π°Π·Π΅ΡΠ½ΠΎΠ³ΠΎ Π»ΡΡΠ°. Π ΠΏΠ΅ΡΠΈ Π΄Π»Ρ ΠΎΡΠ²Π΅ΡΠΆΠ΄Π΅Π½ΠΈΡ ΡΠ΅ΠΌΠΏΠ΅ΡΠ°ΡΡΡΠ°, Π΄Π°Π²Π»Π΅Π½ΠΈΠ΅ ΠΈ Π²ΡΠ΅ΠΌΡ ΡΠΈΠΊΠ»Π° ΠΊΠΎΠ½ΡΡΠΎΠ»ΠΈΡΡΡΡΡΡ ΠΈ Π·Π°ΠΏΠΈΡΡΠ²Π°ΡΡΡΡ Π°Π²ΡΠΎΠΌΠ°ΡΠΈΡΠ΅ΡΠΊΠΈ, ΡΡΠΎΠ±Ρ ΠΎΠ±Π΅ΡΠΏΠ΅ΡΠΈΡΡ ΠΏΡΠ°Π²ΠΈΠ»ΡΠ½ΠΎΠ΅ ΠΎΡΠ²Π΅ΡΠΆΠ΄Π΅Π½ΠΈΠ΅ Π±Π»ΠΎΠΊΠΎΠ² Π΄Π»Ρ Π΄ΠΎΡΡΠΈΠΆΠ΅Π½ΠΈΡ ΡΡΠ΅Π±ΡΠ΅ΠΌΠΎΠΉ ΠΏΡΠΎΡΠ½ΠΎΡΡΠΈ
ΠΠ²ΡΠΎΠΌΠ°ΡΠΈΡΠ΅ΡΠΊΠ°Ρ ΠΌΠ°ΡΠΈΠ½Π° GiantLin QT4-25 Π΄Π»Ρ Π±Π»ΠΎΠΊΠΎΠ² ΠΈ ΡΠ΅ΠΌΠ΅Π½ΡΠ°
2 Π½ΠΎΡΠ±ΡΡ 2018 Π³.
ΠΠ²ΡΠΎΠΌΠ°ΡΠΈΡΠ΅ΡΠΊΠ°Ρ ΠΌΠ°ΡΠΈΠ½Π° Π΄Π»Ρ ΠΏΡΠΎΠΈΠ·Π²ΠΎΠ΄ΡΡΠ²Π° Π±Π΅ΡΠΎΠ½Π½ΡΡ Π±Π»ΠΎΠΊΠΎΠ²
27 ΠΌΠ°Ρ 2017 Π³.
ΠΠ°ΠΊ ΡΠ΄Π΅Π»Π°ΡΡ Π±Π΅ΡΠΎΠ½Π½ΡΠ΅ Π±Π»ΠΎΠΊΠΈ Ρ ΠΏΠΎΠΌΠΎΡΡΡ Henry Machinery
1 Π°ΠΏΡ.
2017 Π³.
Π‘ΡΠ°Π½ΠΎΠΊ Π΄Π»Ρ ΠΏΡΠΎΠΈΠ·Π²ΠΎΠ΄ΡΡΠ²Π° Π±Π΅ΡΠΎΠ½Π½ΡΡ Π±Π»ΠΎΠΊΠΎΠ² β 10 Π³Π»Π°Π²Π½ΡΡ ΠΏΡΠΈΡΠΈΠ½ ΠΏΡΠΈΠΎΠ±ΡΠ΅ΡΡΠΈ Henry Block Machine
31 ΠΌΠ°ΡΡΠ° 2017 Π³.
QMY4-45 ΠΠ°ΡΠΈΠ½Π° Π΄Π»Ρ ΠΈΠ·Π³ΠΎΡΠΎΠ²Π»Π΅Π½ΠΈΡ Π±Π»ΠΎΠΊΠΎΠ² Π΄Π»Ρ ΡΠΊΠ»Π°Π΄ΠΊΠΈ ΡΠΈΡ
3 Π½ΠΎΡΠ±ΡΡ 2016 Π³.
ΠΠ»ΠΈΠ΅Π½ΡΡ ΠΈΠ· Π‘ΡΠ΄Π°Π½Π° Π·Π°ΠΊΠ°Π·ΡΠ²Π°ΡΡ ΡΡΠ°Π½ΠΎΠΊ Π΄Π»Ρ ΠΈΠ·Π³ΠΎΡΠΎΠ²Π»Π΅Π½ΠΈΡ Π±Π»ΠΎΠΊΠΎΠ² ΠΠ΅Π½ΡΠΈ QTJ4-25
2 Π½ΠΎΡΠ±ΡΡ 2016 Π³.