Какие пропорции бетона: Правильное приготовление бетона в бетономешалке, как приготовить раствор бетонной смеси своими руками
как замешивать раствор? Рекомендации специалистов
Бетон является одним из главных материалов, применяемых при строительстве различных объектов, качество которого во многом зависит именно от человеческого фактора. Ведь состав бетонной смеси, высокое качество всех компонентов, а также соблюдение пропорций и технологии замешивания являются определительными факторами, влияющими на такие важные параметры для бетона, как прочность и долговечность. Как замесить бетон, пропорции подобрать, не ошибиться и сделать действительно качественный материал, характеристики которого, станут гарантом надёжности постройки? С этим вопросом, а также многими другими мы и будем разбираться далее.
По своей сути бетон — это каменный строительный материал искусственного происхождения, для получения которого необходимо рационально подобрать компоненты смеси, провести формировку, уплотнение, а также выждать период затвердевания. Для приготовления смеси понадобится три главных составляющих элемента, а именно вяжущее вещество (цемент), крупные и мелкие заполнители, а также вода.
В зависимости от целевого назначения существуют следующие виды:
- обычные бетонные смеси, использующиеся для работ в гражданских и промышленных строениях;
- специальные бетонные смеси, к которым относят дорожные, гидротехнические, теплоизоляционные и декоративные подвиды;
- бетонные смеси специального назначения, которые применяются в местах, где материалу необходимо обладать стойкостью перед химическими компонентами, ядерным излучением и т. д.
Основные компоненты состава бетона
Одним из главных составляющих бетонной смеси можно назвать песок. В принципе единственным, но в то же время важным ограничением по качеству песка является отсутствие глинистых компонентов. Так как даже незначительное их количество обязательно приведёт к уменьшению прочности материала.
В случае если природный песок без глины отсутствует на месте проведения работ, можно улучшить качество любого песка путём его промывки, выделения песка нужной фракции и смешивания с привозным песком высшего качества. После проведения всех процедур песок проверяют путём просеивания через сито. Также необходимо приготовить смесь, с использованием щебенки одной фракции, поскольку в обратном случае получится неоднородная консистенция.
Цемент и вода являются не менее важными связующими элементами, особенно это касается правильных пропорций, зависящих от марки цемента, фракции, а также влажности песка и щебня. Воду необходимо использовать чистую без каких-либо посторонних запахов и примесей, так как от её качества непосредственно зависят будущие характеристики бетона. В тёплое время года лучше всего использовать холодную воду, а в сезон морозов и холодов — нагретую до температуры 40 °C.
Существуют также специальные компоненты противоморозного действия. Бетон с незначительным количеством этих добавок укладывают при низких температурах. После того как раствор замёрз, он держится до прихода весны, следом начинается процесс гидратации цемента, то есть набирания должной прочности бетоном в результате контакта с водой.
Характеристика класса и марочной прочности бетона
Главным показателем, по которому можно судить о соответствии выбранного бетона проводимым работам является прочность на сжатие, что собственно и влияет на класс. Класс бетона — это свойство прочности, выраженное в числовом значении с гарантированной обеспеченностью 95%. То есть, производитель, наделяя изделие каким-либо классом, показывает, что в 95 случаях из 100 прочность достигает своего заявленного значения, и лишь в 5-ти случаях возможно невыполнения условий.
- Класс бетона обозначается латинской буквой «B» и цифрами с правой стороны, свидетельствующими о максимально выдерживаемом давлении, выраженном в мегапаскалях (МПа).
- Прочность также может задаваться марками (М) и цифрами от 50 до 1000, которые показывают предел прочности на сжатие, исчисляемый в кгс/см². Диапазон марок бетона колеблется от М50 до М1000, а наиболее ходовыми считаются материалы с маркой от М100 до М500. Разница между марками и классами заключается в том, что для марок берётся средний показатель прочности, а для классов, как уже упоминалось ранее, гарантированно обеспеченная прочность.
Следует отметить, что о прочности бетона сразу после укладки судить нельзя, так как она нарастает постепенно
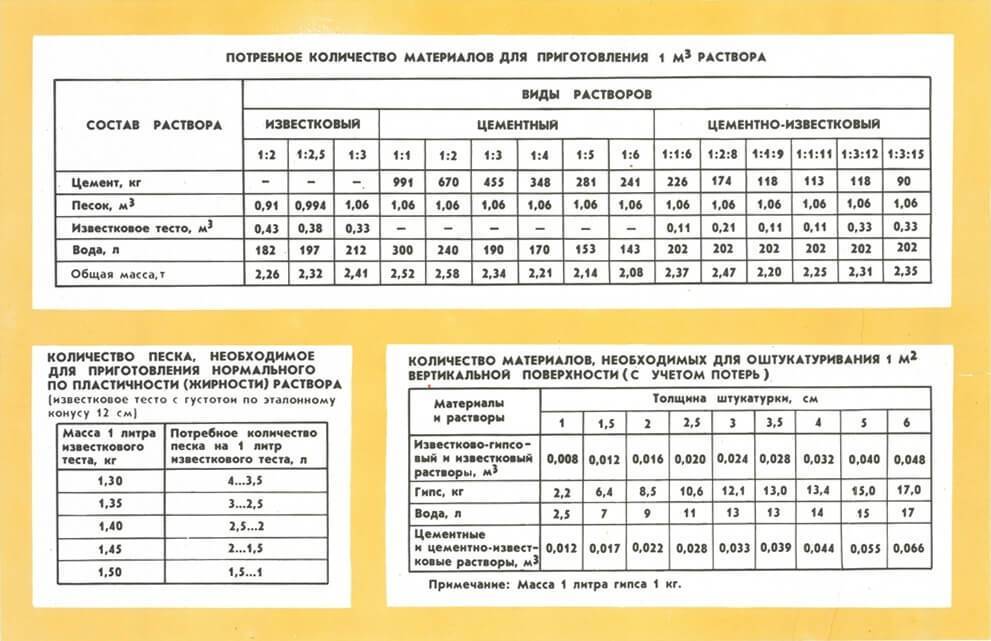
Выбор бетона той или иной марки, прежде всего зависит от информации, предоставленной в проекте сооружения. Если же такового не имеется, то довериться стоит рекомендациям строительной бригады или квалифицированному специалисту.
Особенности расчёта пропорций бетона
Приготовление бетона, пропорции компонентов и соблюдение технологии — вот залог получения качественного раствора. Но состав смеси, прежде всего, зависит от назначения материала и тех нагрузок, которым будет поддаваться будущая конструкция. Например, для приготовления бетона марки М 100 потребуется гораздо меньше цемента, чем на бетон, допустим, марки М 500. То есть, для замешивания каждой марки применяются свои индивидуальные пропорции бетона. В качестве примера рассмотрим средние пропорции (в кг) для наиболее часто используемых марок бетона:
- Для получения бетона марки М 200 из цемента марки М 400 следует придерживаться такой пропорции −
Если цемент был выбран марки М500, то пропорции будут иметь вид − 1: 3,5: 5,6;
- Для получения марки М 300 из цемента марки М 400 рекомендуется следовать такой пропорции — 1: 1,9: 3,7. Из цемента марки М 500 — 1: 2,4: 4,3;
- Для получения бетона марки М450 из цемента марки М 400, компоненты замешиваются в такой пропорции — 1: 1,1: 2,5. Из цемента марки М 500 — 1: 1,4: 2,9.
Количество воды носит индивидуальный характер, но в среднем
Последствия неправильного расчёта пропорций
Зачастую результаты неправильно замешанного раствора дают о себе знать довольно быстро в виде образовавшихся трещин на поверхности. При этом главная причина такого исхода заключается в неправильно подобранных пропорциях, поэтому прежде, чем приступать к замешиванию следует всё просчитать, и знать какое влияние оказывает каждый компонент на состояния бетона.
Следует уяснить, что вода влияет на густоту бетонного раствора. Слишком жидкий бетон имеет много воздуха, поэтому компоненты довольно неравномерно смешиваются, из-за чего материал просто стекает вниз, а создаваемая конструкция не обладает должной жесткостью. Затем поверхность лопается, щебень внутри раствора оседает на дно, а песок, наоборот, располагается сверху.
Безусловно, рассчитать теоретически пропорции можно, но вот при непосредственном замешивании, многие сталкиваются с одной проблемой, а именно — наличием дополнительной влаги в щебенке и песке. Климатические условия также вносят свои коррективы в виде повышенной влажности воздуха или дождя.
В таком случае действовать нужно будет в зависимости от сложившейся ситуации, так как все точные пропорции и формулы полностью актуальны лишь в помещениях с неизменным уровнем влажности. Конечно, совет приготавливать раствор в помещении не всегда применим. Бетонная смесь по окончании замешивания должна быть средней сметанообразной густоты, но никак не жидкой. Если работать с жидким бетоном, то по окончании периода высыхания он обязательно треснет.
Своими силами приготавливать бетонный раствор не очень сложно, так как главный секрет создания прочного и долговечного материала заключается именно в соблюдении пропорций и следованию одной простой истины, а именно чем более жидкий раствор, тем менее прочный получится бетон.
Пропорции бетона в ведрах
На производстве, необходимое количество компонентов для приготовления бетона рассчитывается автоматически, и на строительную площадку доставляется смесь готовая к заливке. Но что делать, если у вас самым серьезным инструментом является миксер, а из теоретических знаний только таблицы для приготовления большого количества смеси? Будем рассчитывать компоненты в ведрах.
Говоря о заливке фундамента, можно смело заявлять, что монолитный ленточный вариант, считается самым простым и в то же время прочным для основы любого дома. Здесь можно обойтись без использования сложной техники и самостоятельно приготовить бетон для заливки такой основы. Главное выдерживать пропорции и помнить, что любое нарушение приведет к снижению прочности бетона и соответственно надежности всей конструкции.
Разбираемся в количестве компонентов
Индивидуальное строительство ведется по уже давно переделенным схемам и пропорции бетона здесь «избиты» годами. Оптимальным вариантом считается соотношение 1:3:5 – цемент, песок и щебень соответственно. Вода добавляется согласно консистенции, и ее количество определяется при замешивании и здесь в учет берутся особенности строительства.
Если армирование опалубки произведено по усиленной схеме, то для лучшего проникновения и обволакивания всех элементов понадобится больше жидкости, чтобы сделать бетон более текучим. Если нет, можно замесить вязкий раствор, он быстрее застынет и будет надежнее без дополнительного армирования.
Отойдя от привычной всем схемы заливки фундамента, необходимо сказать и о бетоне для работ по заливке садовых дорожек. В этих целях используется цемент марки М 100, и в этом случае пропорции меняются: 1: 11.
Расчет компонентов в ведрах
Песчано-гравийная смесь, используемая при изготовлении бетона на предприятиях, уже имеет выдержанную пропорцию. И поскольку заполнители, используемые в приготовлении, классифицируются одинаковой насыпной плотностью, в ведрах расчет бетона на 1 м3 определяется следующим образом:
- цемент 25 ведер;
- песок 40-43 ведра;
- наполнители (щебень или гравий) 90;
- вода 18 ведер.
Если считать количество цемента, то показатель в 25 ведер – это примерно 7 мешков. При работе с небольшим миксером для приготовления бетона, то такое количество компонентов не поместится за один подход. В этом случае в ведрах показатели будут следующие: цемент – 1, песок – 2, заполнители – 4, вода – половина ведра. Исходя из размеров бетономешалки, количество можно прибавлять.
Количество бетона по площади
В индивидуальном строительстве обычно нет точных чертежей. А объем, и вес материала рассчитывается «на глазок». Поэтому количество и прочность бетона подбирается составлением примерной формулы. Вначале рассчитывается заливаемая площадь. Как это сделать? Здесь все просто, необходимо иметь калькулятор и рулетку. Измеряется длина фундаментной ленты и ширина рва и высота. Возьмем за основу приблизительные цифры: 10 метров, 1 и 0,5 соответственно. Умножаем все показатели, и получается, что на заливку такой площади потребуется 5 м3 бетона.
Исходя из вышеприведенных показателей расчета на 1 м3, для заливки такой площади потребуется: 105 ведер цемента, 200 песка, 450 гравия или щебня и примерно 80 воды.
Пропорции в ведрах не могут быть точными, поэтому при расчете количества компонентов, к полученной сумме необходимо прибавить процентов 15 на непредвиденные расходы.
Основы бетона — ConcreteState
КАК ПРОИЗВОДИТСЯ ЦЕМЕНТ
Портландцемент является основным компонентом бетона. Бетон формируется из портландцемента, образующего пасту с водой, которая связывается с песком и камнем для затвердевания. Цемент
производится из тщательно контролируемой химической комбинации кальция, кремния, алюминия, железа и других ингредиентов.
Обычные материалы, используемые для производства цемента, включают известняк, ракушки и мел или мергель в сочетании со сланцами, глиной, сланцем, доменным шлаком, кварцевым песком и железной рудой. Эти ингредиенты при нагревании при высоких температурах образуют похожее на камень вещество, которое растирается в мелкий порошок, который мы обычно называем цементом.
Каменщик Джозеф Аспдин из Лидса, Англия, впервые изготовил портландцемент в начале 19 века, сжигая порошкообразный известняк и глину в своей кухонной плите. С помощью этого грубого метода он заложил основу для промышленности, которая ежегодно перерабатывает буквально горы известняка, глины, цементной породы и других материалов в порошок настолько мелкий, что он проходит через сито, способное удерживать воду.
Лаборатории цементных заводов проверяют каждый этап производства портландцемента с помощью частых химических и физических испытаний. Лаборатории также анализируют и тестируют готовый продукт, чтобы убедиться, что он соответствует всем отраслевым спецификациям.
Наиболее распространенным способом производства портландцемента является сухой способ. Первым шагом является добыча основного сырья, в основном известняка, глины и других материалов. После добычи порода дробится. Это включает в себя несколько этапов. Первое дробление уменьшает камень до максимального размера около шести дюймов. Затем порода поступает на вторичные дробилки или молотковые мельницы для измельчения примерно до трех дюймов или меньше. Щебень смешивают с другими ингредиентами, такими как железная руда или летучая зола, измельчают, смешивают и подают в цементную печь.
Цементная печь нагревает все ингредиенты примерно до 2700 градусов по Фаренгейту в огромных цилиндрических стальных вращающихся печах, облицованных специальным огнеупорным кирпичом. Печи часто достигают 12 футов в диаметре — достаточно больших, чтобы вместить автомобиль, и во многих случаях длиннее, чем высота 40-этажного здания. Большие печи установлены с небольшим наклоном оси от горизонтали.
Мелкоизмельченное сырье или суспензия подается в верхнюю часть. В нижней части находится ревущий взрыв пламени, создаваемый точно контролируемым сжиганием порошкообразного угля, нефти, альтернативных видов топлива или газа при принудительной тяге.
Когда материал проходит через печь, некоторые элементы удаляются в виде газов. Остальные элементы объединяются, образуя новое вещество, называемое клинкером. Клинкер выходит из печи в виде серых шариков размером с мрамор.
Клинкер выгружается раскаленным докрасна из нижнего конца печи и обычно доводится до рабочей температуры в различных типах охладителей. Нагретый воздух из охладителей возвращается в печи, что позволяет экономить топливо и повышает эффективность горения.
После охлаждения клинкера цементные заводы измельчают его и смешивают с небольшим количеством гипса и известняка. Цемент настолько мелкий, что в одном фунте цемента содержится 150 миллиардов зерен. Цемент теперь готов к транспортировке на заводы по производству товарного бетона для использования в различных строительных проектах.
Хотя сухой процесс является наиболее современным и популярным способом производства цемента, в некоторых печах в Соединенных Штатах используется мокрый процесс. Эти два процесса по существу похожи, за исключением мокрого процесса, когда сырье измельчается с водой 9.0006 р перед подачей в печь.
КАК ИЗГОТОВЛЕН БЕТОНВ своей простейшей форме бетон представляет собой смесь пасты и заполнителей или горных пород. Паста, состоящая из портландцемента и воды, покрывает поверхность мелких (мелких) и крупных (крупных) заполнителей. Благодаря химической реакции, называемой гидратацией, паста затвердевает и набирает силу, образуя каменную массу, известную как бетон.
В этом процессе лежит ключ к замечательным свойствам бетона: он пластичен и податлив при свежем смешивании, прочен и долговечен при затвердевании. Эти качества объясняют, почему из одного материала, бетона, можно строить небоскребы, мосты, тротуары и супермагистрали, дома и плотины.
Пропорционирование
Ключом к получению прочного и долговечного бетона является тщательное дозирование и смешивание ингредиентов. Смесь, в которой недостаточно пасты, чтобы заполнить все пустоты между заполнителями, будет трудно укладывать, и она будет давать шероховатую поверхность и пористый бетон. Смесь с избытком цементного теста легко укладывается и дает гладкую поверхность; однако полученный бетон нерентабелен и может легко треснуть.
Химический состав портландцемента оживает в присутствии воды. Цемент и вода образуют пасту, которая покрывает каждую частицу камня и песка — заполнители. Благодаря химической реакции, называемой гидратацией, цементное тесто затвердевает и набирает прочность.
Качество пасты определяет характер бетона. Прочность пасты, в свою очередь, зависит от соотношения воды и цемента. Водоцементное отношение – это отношение массы воды затворения к массе цемента. Высококачественный бетон производится за счет максимально возможного снижения водоцементного отношения без ущерба для удобоукладываемости свежего бетона, что позволяет правильно его укладывать, уплотнять и затвердевать.
Правильно подобранная смесь обладает желаемой удобоукладываемостью для свежего бетона и требуемой долговечностью и прочностью для затвердевшего бетона. Как правило, смесь содержит от 10 до 15 процентов цемента, от 60 до 75 процентов заполнителя и от 15 до 20 процентов воды. Вовлеченный воздух во многих бетонных смесях также может занимать еще от 5 до 8 процентов.
Прочие ингредиенты
Практически любая природная вода, пригодная для питья и не имеющая ярко выраженного вкуса или запаха, может использоваться в качестве воды для затворения бетона. Чрезмерное количество примесей в воде для затворения может не только повлиять на время схватывания и прочность бетона, но также вызвать высолы, образование пятен, коррозию арматуры, нестабильность объема и снижение долговечности. Спецификации бетонной смеси обычно устанавливают ограничения на содержание хлоридов, сульфатов, щелочей и твердых веществ в воде затворения, если только нельзя провести испытания для определения влияния примеси на конечный бетон.
Хотя большая часть питьевой воды подходит для замешивания бетона, заполнители выбирают тщательно. Заполнители составляют от 60 до 75 процентов от общего объема бетона. Тип и размер используемого заполнителя зависит от толщины и назначения конечного бетонного изделия.
Относительно тонкие секции зданий требуют использования мелкого крупного заполнителя, хотя в больших плотинах используются заполнители диаметром до шести дюймов. Для эффективного использования пасты желательна непрерывная градация размеров частиц. Кроме того, заполнители должны быть чистыми и не содержать каких-либо веществ, которые могут повлиять на качество бетона.
Начало гидратации
Вскоре после соединения заполнителей, воды и цемента смесь начинает твердеть. Все портландцементы представляют собой гидравлические цементы, которые схватываются и затвердевают в результате химической реакции с водой, называемой гидратацией. В ходе этой реакции на поверхности каждой частицы цемента образуется узел. Узел растет и расширяется, пока не соединится с узлами из других частиц цемента или не прилипнет к соседним агрегатам.
После того, как бетон будет тщательно перемешан и пригоден для обработки, его следует поместить в формы до того, как смесь станет слишком густой.
Во время укладки бетон уплотняется, чтобы уплотнить его внутри форм и устранить потенциальные дефекты, такие как соты и воздушные карманы.
Для плит бетон выдерживают до тех пор, пока не исчезнет пленка влаги на поверхности, затем с помощью деревянной или металлической терки сглаживают бетон. Затирка дает относительно ровную, но слегка шероховатую текстуру, которая обладает хорошей устойчивостью к скольжению и часто используется в качестве окончательной отделки для наружных плит. Если требуется гладкая, твердая, плотная поверхность, после затирки следует стальная затирка.
Отверждение начинается после того, как открытые поверхности бетона затвердеют в достаточной степени, чтобы противостоять повреждениям. Отверждение обеспечивает постоянную гидратацию цемента, благодаря чему бетон продолжает набирать прочность. Бетонные поверхности затвердевают, обрызгивая водяным туманом или используя влагоудерживающие ткани, такие как мешковина или хлопчатобумажные маты. Другие методы отверждения предотвращают испарение воды, герметизируя поверхность пластиком или специальными спреями, называемыми отвердителями.
Специальные технологии используются для отверждения бетона в экстремально холодную или жаркую погоду для защиты бетона. Чем дольше бетон будет оставаться влажным, тем прочнее и долговечнее он станет. Скорость твердения зависит от состава и крупности цемента, пропорций смеси, влажности и температурных условий. Бетон продолжает становиться прочнее с возрастом. Большая часть гидратации и увеличения прочности происходит в течение первого месяца жизненного цикла бетона, но гидратация продолжается более медленными темпами f