Как добывают цемент: Как производят цемент?
Как производят цемент?
Дата публикации: 06.07.2019
224
Цемент может использоваться как самостоятельный продукт, так и входить в состав растворов. Обычно цемент представляет собой сухую порошковую смесь. Вступая в реакцию с водой, смесь становится пластичной, а спустя определенный промежуток времени затвердевает. Характеристики цемента варьируются в зависимости от состава.
Цемент, как конечный продукт представляет собой приготовленный и измельченный клинкер. Клинкером называют гранулы, полученные в рамках промежуточного производства. Классически в состав клинкера входит смесь известняка и глины в пропорции 3/1.
Добывают ли цемент?Сам цемент нельзя добыть, так как по определению он является измельченным клинкером. Однако в природе нашелся материал, идентичный по своему составу клинкеру. Его называют мергелем. В силу ограниченности запасов, несовершенства технологии добычи и малого числа известных месторождений, использование мергеля в промышленности невозможно. Маленький объем неспособен удовлетворить потребности крупного производства.
Добыча необходимых для производства цемента определенной марки минералов производится открытым способом. В число добываемых элементов входят карбонаты (доломит, ракушечник, мел, прочий известняк) и глины (лесс, суглинки и сланцы).
Как производят цемент?Ограниченность природного клинкера вынудила большую часть производителей использовать его искусственный вариант. Глина и известняк смешиваются в пропорции 1/3 в большой емкости посредством специальных барабанов. Масса поступает в обжиговую печь и подвергается термическому воздействию на протяжении 4-х часов. Температура при этом достигает 1500°С. Время и температура обжига могут изменяться в зависимости от требований к конечной смеси. Состав в печи спекается в небольшие гранулы и после остывания они отправляются на помол. Помол осуществляется в барабанах. В полученный на этапе помола порошок вмешиваются необходимые добавки, определяющие марку и состав цемента.
Готовый цементный материал отправляется на хранение или переводится на участок расфасовки.
Вопреки общей технологии производства, кажущейся простой, существует три актуальных способа приготовления цемента:
- Сухой
Эффективный, наименее энерго- и ресурсозатратный вариант. Сырье дробится до мелких фракций. Ингредиенты смешиваются в определенных пропорциях и измельчаются до состояния муки.
- Мокрый
В этом случае в состав включается известняк, глина и вода. Полученная вязкая масса называется шламом, который поступает в печь и подвергается обжигу. Следующим этапом становится измельчение полученных гранул, их перемешивание с размолотыми добавками. Последний шаг – сортировка.
- Комбинированный
Совмещает в себе сильные стороны двух предыдущих вариантов. Сначала замешивается шлам, затем искусственно обезвоживается и поступает в обжиговую печь. Далее полученные гранулы смешиваются с наполнителями, измельчаются и сортируются.
Вас интересуют оптовые поставки цемента? Компания ПартнерГрупп
готова оказать комплексные услуги, будучи крупным игроком рынка строительных материалов. Мы сотрудничаем непосредственно с производителями, гарантируя своим клиентам привлекательные цены. Арсенал насчитывает несколько больших складов. На их территории цемент хранится согласно актуальным технологиям, сохраняя свои практические свойства.
Мы предоставляем «свежую» продукцию, если хотите купить оптом — обращайтесь в ПартнерГрупп
!
Из чего делают цемент, его виды и состав
Все о компонентах и способах производства цемента
Состав и характеристика компонентов
Разновидности вяжущего
Три способа изготовления
- Сухой
- Мокрый
- Комбинированный
Материал используется очень широко. Его применяют как самостоятельный продукт и вводят в растворы. Все это благодаря свойству сухой смеси — она может становиться пластичной при добавлении воды и через некоторое время отвердевать, превращаясь в подобие камня.
В его составе всегда пять основных ингредиентов. Разберем их на примере портландцемента, одной из самых востребованных разновидностей:
- окись кальция — не меньше 61%;
- кремния диоксид — не менее 20%;
- глинозем около 4%;
- окись железа — не меньше 2%;
- окись магния — не менее 1 %.
Instagram zgbi_kamenskii
В смесь вводятся добавки, улучшающие определенные характеристики материала. В качестве сырья могут использоваться разные породы. Производство обычно размещают в непосредственной близости от месторождений.
Необходимые минералы добывают открытым способом, это:
- Карбонатные породы: доломит, мергель, ракушечник, мел и другие известняки.
- Глинистые породы: лесс, суглинки, сланцы.
В качестве добавок используются апатиты, плавиковый шпат, кремнезем, глинозем и т. д.
В продажу поступает множество разновидностей цемента. Они отличаются друг от друга по целому ряду характеристик:
- Прочность. Важнейший показатель, который указывается на маркировке. Она выполняется в виде буквы М и цифры. Последняя и обозначает прочность. Ее определяют в результате проведения технических испытаний.
- Фракция. Определяется помолом смеси. Чем он тоньше, тем более качественной считается продукция. Идеальным считается состав из крупных и мелких частиц, поскольку только тонкий помол требует слишком большого количества воды при замесе.
- Скорость отвердевания. Варьируется путем введения в смесь гипса. В зависимости от назначения продукта может существенно различаться.
- Морозоустойчивость. Определяется реакцией на цикл замораживание и размораживание. Материал характеризуется количеством таких циклов, которые он выдерживает без изменения своих свойств.
Instagram metallgroupvitebsk
Потребность в воде при замесе раствора зависит от плотности материала, поэтому количество воды для замеса разных марок разнится. Избыток жидкости уменьшает прочность цемента.
В зависимости от области применения выделяется несколько типов цементных смесей.
Портландцемент
Отвердевает на воздухе и в воде. Минеральные добавки отсутствуют. Широко используется для возведения разноплановых монолитных конструкций.
Сульфатостойкий
Его особенность — повышенная устойчивость к химическим агрессивным средам. Характеризуется невысоким коэффициентом насыщения. Это позволяет применять сульфатостойкий цемент для строительства гидротехнических, подземных сооружений и т.п.
Пуццолановый
Может считаться разновидностью сульфатостойкого, но с добавлением активных минералов. Медленно отвердевает, имеет высокую водостойкость. Используется для гидротехнического строительства.
Глиноземистый
Повышено содержание окиси кальция и глинозема. Это позволяет смеси быстро отвердевать. Применяется для изготовления быстро твердеющих жаростойких и строительных растворов, которые находят применение при ремонтных работах, скоростном строительстве, зимнем бетонировании и т. д.
Кислотоупорный
В состав входит кварцевый песок и кремнефтористый натрий. Замешивается не водой, а жидким стеклом. Используется для получения кислотостойких покрытий. Не выдерживает постоянного воздействия воды.
Пластифицированный
Изготавливается со специальными добавками, придающими морозостойкость и повышенную подвижность приготовленным на этом цементе растворам. Они приобретают большую прочность, лучше сопротивляются коррозионным воздействиям и отличаются повышенной водонепроницаемостью.
Шлакоцемент
В его рецепт включается шлак, процент содержания которого может варьироваться от 20% до 80% от массы продукта. Это удешевляет материал, замедляет скорость его отвердевания и увеличивает жаростойкость. Применяется для возведения наземных, подводных и подземных объектов.
Instagram tsement_82
Как показывает практика, самым востребованным вариантом является портландцемент. Именно его имеют в виду, когда речь идет о цементе.
Технология изготовления заключается в получении и последующем измельчении клинкера. Так называются гранулы, которые являются промежуточным продуктом производства. Их состав всегда неизменен. Это известняк и глина, смешанные в пропорции 3:1. В природе существует минерал, полностью идентичный по составу клинкеру. Он называется мергель. Однако его запасы ограничены и не могут обеспечить потребность производства.
Поэтому на заводах используется искусственный аналог мергеля. Для его получения необходимые ингредиенты тщательно смешиваются в больших емкостях специальными барабанами. Подготовленная таким образом масса подается в печи, где обжигается около четырех часов. Температура процесса составляет порядка 1500оС. В таких условиях порошок начинает спекаться в небольшие гранулы. После остывания клинкерные зерна направляются на помол. Их измельчают в больших барабанах с шаровыми ситами грохотами. На этом этапе важно размолоть гранулы и получить порошкообразный продукт определенных размеров.
Instagram tsement_82
Готовые цементные материалы поступают на хранение или на участок расфасовки, где распределяются в тару различной вместимости либо загружаются в специальные автомобили-цементовозы.
Несмотря на общую технологию, для производства состава в зависимости от свойств сырья могут использоваться три способа.
Сухой способ
Этот метод позволяет значительно сократить время и затраты на изготовление цементной смеси. Он предполагает несколько этапов:
- Сырье дробится до получения зерен мелкой фракции.
- Подготовленные гранулы сушатся до достижения нужной влажности. Это делается, чтобы облегчить последующие операции.
- Ингредиенты смешивают в определенных пропорциях. После чего измельчают, получая муку.
- Порошок подается во вращающуюся печь, где обжигается, но не спекается в гранулы.
После остывания готовый продукт направляется на склад или на участок фасовки.
Сухой способ считается наименее энергозатратным, а потому очень выгоден для производителей. К сожалению, он применим не для всех категорий сырья.
Мокрый способ
В некоторых случаях необходимо увлажнение подготовленного к производству материала. В таких случаях используется мокрый способ. Для приготовления клинкера, который состоит из известняка и глины, замешивается смесь из основных компонентов с добавлением воды. В результате получается вязкая масса, которую называют шламом.
Ее закладывают в печь, где происходит обжиг. В этом процессе из шлама формируются гранулы, которые после остывания отправляются на измельчение.
Instagram tabys.cement

Комбинированный способ
Применяется для снижения стоимости готовой продукции. Представляет собой своеобразный симбиоз сухой и мокрой технологии. Изначально замешивается шлам, который впоследствии обезвоживается. Таким образом делают клинкер. Он поступает в печь, работающую по «сухой» технологии. Далее при необходимости проводится смешивание с наполнителями, и продукт готов. Более подробно процесс показан на видео.
Качество цемента во многом зависит от сырья, из которого он произведен, и точности соблюдения всех технологических этапов. Учитывая, что характеристики изготовленных из него строительных материалов определяются качеством смеси, стоит обратить на нее самое пристальное внимание.
Материал подготовила
Инна Ясиновская
Сократите выбросы углерода и токсичных веществ, сделайте цемент чистым и экологичным
Блог экспертов
Если бы цементная промышленность была страной, она занимала бы четвертое место в мире по выбросам парниковых газов.
Саша Сташвик (квасцы)
Директор, программа промышленной политики, климата и чистой энергии
Рис. 1. Слева показан процесс производства бетона, а справа показаны выбросы парниковых газов из бетона, из которых 90 % приходится на цемент и 10 % — на заполнители и другие материалы, а также на разработку карьеров, транспортировку и подготовку сырья.
Кредит:
Источник: Carbon 180
Декарбонизация цементных заводов является важной частью достижения наших целей в области климата. Цемент является ключевым компонентом бетона, который является наиболее широко используемым искусственным материалом на планете, и практически не имеет жизнеспособных альтернатив. Цемент невероятно грязен в производстве: хотя он составляет всего 10-15% массы бетона в типичной смеси, на его долю приходится до 90% выбросов парниковых газов (ПГ) (рис. 1).
Если бы цементная промышленность была страной, она занимала бы четвертое место в мире по объему выбросов парниковых газов, уступая только Китаю, США и Индии, на долю которых приходится примерно 7-8% мирового выброса CO 2 загрязнение (рис. 2). Если мы не предпримем шаги по обезуглероживанию цемента, это число, вероятно, увеличится, поскольку спрос на бетон продолжает расти.
Рисунок 2: Доля мировых выбросов CO2, связанных с производством цемента (данные за 2017 г.).
Авторы и права: Источник: McKinsey
При производстве цемента также выделяется много опасных загрязнителей воздуха, которые наносят вред здоровью. Цементная промышленность является третьим по величине источником промышленных загрязнений воздуха, таких как двуокись серы, оксиды азота (NOx) и окись углерода.
Проще говоря, очистка цементной промышленности имеет решающее значение для достижения наших целей в области климата и здоровья. Но, в отличие от двигателя внутреннего сгорания, у цемента нет доступной замены, которая могла бы масштабироваться достаточно быстро, чтобы соответствовать требованиям чрезвычайной климатической ситуации. Таким образом, хотя сокращение портландцемента и замена его существующими и появляющимися альтернативами может и должно быть приоритетом, наша зависимость от этого материала не только сохранится, но и, вероятно, возрастет в ближайшие десятилетия — сроки, наиболее важные для борьбы с изменением климата, — по мере урбанизации и обновления инфраструктуры. нарастить. Поэтому крайне важно, чтобы мы поддерживали инновации, которые помогают производителям цемента адаптироваться к чистому будущему.
Хорошей новостью является то, что импульс растет в штатах и на федеральном уровне, поскольку законодатели ищут разумные подходы к ограничению выбросов от производства цемента и используют покупательную способность правительства для расширения рынков более чистых альтернатив. Обязательства отрасли по углеродной нейтральности и дорожные карты также распространяются. Хотя некоторые из стратегий обезуглероживания, которые используют некоторые производители цемента, весьма проблематичны с точки зрения окружающей среды и/или здоровья, это говорит о том, что отрасль знает, что должна сформулировать план по борьбе с выбросами.
По мере того, как эти усилия продвигаются вперед, важнейший принцип, за который выступает NRDC, заключается в том, что сокращение выбросов углерода от цемента не должно происходить за счет местного загрязнения.
Почему при производстве цемента так много углерода: горение и технологические выбросы.
На два аспекта процесса производства портландцемента приходится огромная доля его углеродного следа. Цемент в основном производится путем сжигания ископаемого топлива, такого как уголь и нефтяной кокс, в цементных печах, похожих на большие печи, для нагревания известняка (сырья) до очень высоких температур (~2640°F/1500·9).0045 или С). Тепло вызывает химическую реакцию, которая превращает известняк в клинкер, который затем измельчается вместе с гипсом для образования цемента. Выбросы от сжигания топлива составляют примерно 40 % выбросов CO 2 в течение жизненного цикла цемента (часто называемых воплощенными выбросами) (рис. 3). Остальные ~60% являются результатом неизбежной химической реакции (прокаливания), происходящей при нагревании известняка, в результате которой из карбоната кальция в известняке выделяется CO 2 .
Рис. 3. Источники выбросов CO2 в цементной промышленности Калифорнии в 2015 г.
Авторы и права: Источник: Global Efficiency Intelligence
Опасные загрязнители, включая критерий загрязнителей воздуха и ртуть, также выбрасываются как в выбросы, связанные с топливом, так и в выбросы, связанные с технологическими процессами. Эти загрязнители связаны с преждевременной смертью, неврологическими проблемами, астмой и другими респираторными заболеваниями.
Некоторые альтернативные виды топлива, продвигаемые промышленностью, обходятся местному населению неприемлемо дорого.
Среди рычагов, часто упоминаемых для декарбонизации цементной промышленности, переход на твердые отходы топлива для замены ископаемого топлива в цементных печах. К сожалению, эти альтернативы, часто называемые цементной промышленностью «низкоуглеродными», включают пластик и твердые отходы, такие как шины (иногда называемые «топливом, полученным из шин»), которые выделяют очень опасные токсичные загрязнения.
Независимо от того, что сжигается, при сжигании отходов образуются и/или выделяются вредные химические вещества и загрязнители, в том числе загрязнители воздуха, такие как вызывающий рак бензол, ПФА, диоксины и твердые частицы, а также тяжелые металлы, такие как свинец и ртуть, которые вызывают неврологические заболевания, как обсуждают здесь наши коллеги. Эти химические вещества и загрязняющие вещества попадают в воздух, воду и продукты питания вблизи мусоросжигательных заводов и попадают в организм людей, когда они вдыхают, пьют и едят загрязняющие вещества.
Сообщества десятилетиями боролись с токсичным загрязнением от цементных заводов, и NRDC утверждает, что снижение выбросов углерода может и должно быть достигнуто без увеличения токсического загрязнения. По этим причинам NRDC выступает против использования в качестве топлива для декарбонизации цементных печей топлива, которое выделяет токсичные загрязнения, включая пластик и другие отходы.
Ключевым решением для обезуглероживания цемента является сжигание меньшего количества
чего-либо .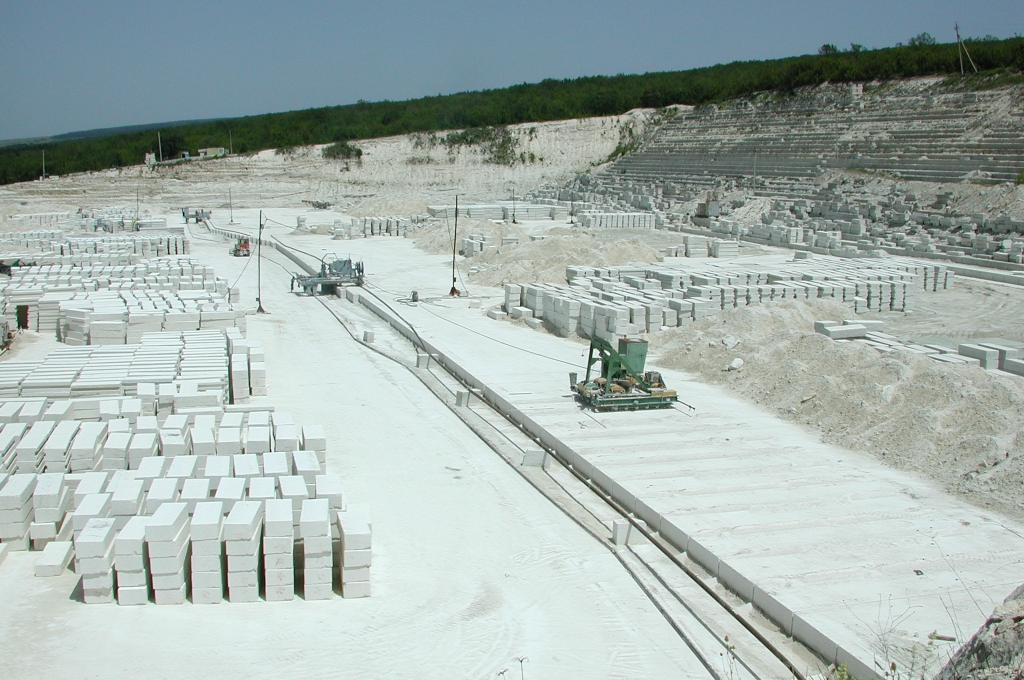
В дополнение к отказу от перехода на другие токсичные виды топлива, статус-кво сжигания газа и угля также токсичен. Вот почему NRDC выступает за:
- Использование меньшего количества цемента — например, за счет снижения чрезмерной спецификации цемента в бетонных смесях и поощрения использования дополнительных вяжущих материалов, таких как пуццоланы из молотого стекла, для частичной замены цемента в бетонных смесях;
- Сделать печи для обжига цемента более эффективными, чтобы они потребляли меньше топлива; и
- В конечном итоге переход на действительно более чистые виды топлива, например, электрификация из возобновляемых источников, если и где это возможно, а также зеленый водород.
Кроме того, NRDC поддерживает политику, направленную на то, чтобы цементные заводы могли получить доступ к набору передовых технологий для сведения к нулю своих выбросов, включая варианты улавливания, утилизации и хранения углерода, как мы обсуждаем здесь. Улавливание углерода в цементе — это не способ продлить сжигание грязного ископаемого топлива, которое можно заменить, а способ уменьшить большую часть технологических выбросов, которые невозможно уменьшить иным образом для материала, на который мы полагаемся.
Сжигание отходов не является хорошим способом уменьшить загрязнение климата цементом или справиться с потоками пластиковых отходов.
Реальные решения по обращению с пластиковыми отходами должны быть направлены на сокращение отходов в их источнике, производство меньшего количества пластика и использование эффективных и проверенных методов механической и органической переработки, а не стимулирование сжигания этих материалов.
NRDC поддерживает четыре направления деятельности по сокращению загрязнения пластиком:
- Устранение проблемных и ненужных пластиков, таких как одноразовые пластики;
- Инновации и масштабирование моделей повторного использования и заправки;
- Создание нетоксичных материалов для замены пластика, полученного из ископаемого топлива; и
- Распространите проверенные решения по механической переработке или компостированию.
Типовая политика обезуглероживания цемента и бетона должна снизить токсичное загрязнение парниковыми газами
и . Поскольку правительства штатов и федеральные правительства являются такими крупными покупателями бетона, политика государственных закупок является мощным способом создания спроса на низкоуглеродистый бетон и, в более широком смысле, стимулирования использования цемента с меньшим и меньшим содержанием углерода. Законодательные собрания многих штатов приняли или активно обсуждают законы о закупках низкоуглеродистого бетона для строительных проектов, финансируемых государством, включая Калифорнию, Нью-Йорк, Нью-Джерси, Колорадо и Вирджинию. Ключевым принципом в этой работе должен быть запрет на включение цемента, произведенного с использованием грязного топлива, в государственные спецификации низкоуглеродистого бетона, другими словами, на получение «зеленого» кредита за изменения, которые могут снизить выбросы парниковых газов, но увеличить местное загрязнение воздуха.
Но политика закупок со стороны спроса — не единственный рычаг, доступный для политиков, стремящихся решить проблему воздействия цементной промышленности на климат и здоровье населения. NRDC будет продолжать выступать за пакет политик, который включает стимулы для сокращения выбросов углерода в готовых бетонных смесях; стандарты для прямой декарбонизации цементной промышленности в соответствии с государственными и национальными целями в области климата; и обязывает предотвращать увеличение вредного загрязнения.
Например, в 2021 году в Калифорнии был принят новый закон, который не только направлен на достижение нулевых выбросов парниковых газов, связанных с цементом, используемым в Калифорнии не позднее 2045 года, но также требует улучшения качества воздуха и поддержки экономического развития и развития рабочей силы для поселения возле цементных заводов. Другие штаты-лидеры в области климата, такие как Нью-Йорк, должны последовать этому примеру в этом году, демонстрируя беспроигрышную выгоду для климата и общественного здравоохранения.
Смежные вопросы
Промышленное производствоТоксиныСправедливость и справедливость
Пропустить элементы карусели
Будущее чистой энергии: важно, как мы туда доберемся
Блог экспертаСеверная Каролина, СШААнна Рид, Кэти Пелч
Чистое и устойчивое энергетическое будущее необходимо для решения проблемы изменения климата, но то, как мы этого достигнем, имеет значение. В разгар глобальных усилий по очистке и прекращению использования пер- и полифторалкильных веществ (PFAS) Chemours удваивает…
Недавние химические катастрофы побуждают ужесточить федеральные правила безопасности
Блог экспертаСША, Нью-Джерси, Луизиана, Северная КаролинаСахана Рао
Конгресс и Агентство по охране окружающей среды: Защитите людей от загрязнения токсичными пластиками
Экспертный блогСоединенные ШтатыДэниел Розенберг
NRDC и 200 других организаций недавно направили письмо в Конгресс, призывая всех сенаторов и представителей не выступать соавторами законопроекта, поддерживаемого лоббистами химической промышленности, который отменит защиту Закона о чистом воздухе и будет способствовать повсеместному сжиганию пластика.
Озеленение производства цемента
Цементная промышленность является одним из крупнейших в мире источников выбросов углекислого газа.© Michael Milner/Moment/Getty
Цементная промышленность ежегодно производит около 3,5 миллиардов тонн общего портландцемента, наиболее распространенной формы, при этом выбросы в этом секторе составляют около 7% от общих глобальных антропогенных выбросов ПГ. Если бы цементная промышленность была страной, она была бы третьим по величине источником выбросов углекислого газа в мире с годовым объемом производства до 2,8 млрд тонн.
Теперь группа под руководством Ан Джи Вана, директора флагманского центра минерализации углерода Корейского института геолого-геофизических исследований и минеральных ресурсов (KIGAM), разработала метод производства зеленого цемента, который частично заменяет известняк, основной компонент цемента. и сырье для выбросов углекислого газа с побочными промышленными продуктами. Кроме того, команда смогла производить этот цемент при температуре примерно на 200°C ниже отраслевого стандарта.
Проезжая мимо Портленда
Для производства портландцемента известняк смешивают с сырьем, таким как кремнистый камень и глина, и нагревают примерно до 1450 °C. В ходе этого процесса образуется промежуточный продукт, называемый «клинкер», и около 44 весовых процентов известняка выделяется в виде углекислого газа.
Новая технология производства сырого цемента, однако, синтезирует клинкер из сульфоалюмината кальция (CSA) путем смешивания части известняка с сырьем, таким как угольная зола и побочный глинозем, образующийся на тепловых электростанциях.
Тепловая энергия, необходимая для производства 1 кг сырого цементного клинкера, составляет около 570 килокалорий, что меньше, чем общая тепловая энергия портландцемента, составляющая около 720 килокалорий. «Это снижает потребление энергии на 20 % и выбросы углекислого газа на 2 %, — объясняет Ан.
«Кроме того, наш сырой цемент в два раза лучше портландцемента для высокопрочных бетонов (исходя из трехдневной прочности, прочность на сжатие портландцемента составила 12,5 МПа, тогда как сырой цемент — 25 МПа) и расширяемость (портландцемент — 25 МПа). содержание цемента составляло 0,01%, тогда как содержание сырого цемента составляло 0,03%), поэтому его можно применять в таких областях строительства, как здания и мосты. А благодаря своим улучшенным водоотталкивающим характеристикам зеленый цемент в будущем можно будет использовать в качестве наполнителя для заброшенных шахт, месторождений отработанных газов и месторождений отработанного масла», — добавляет она.
Совершенствование международных стандартов
В октябре 2021 года представители правительства Южной Кореи и лидеры почти 200 стран встретились на 26-м заседании Конференции сторон (COP26) РКИК ООН в Глазго, Великобритания. COP26 была предназначена для ускорения действий по достижению Парижского соглашения 2015 года, которое направлено на ограничение роста средней глобальной температуры ниже 2 ° C к 2050 году по сравнению с доиндустриальным уровнем. На встрече Южная Корея обязалась сократить выбросы парниковых газов не менее чем на 40 % к 2030 г. по сравнению с уровнем 2018 г. и обязалась достичь углеродной нейтральности к 2050 г.
Ан Чжи Ван, Корейский институт геолого-геофизических исследований и минеральных ресурсов (КИГАМ).© KIGAM
Технология зеленого цемента KIGAM не только снижает выбросы парниковых газов, но и отвечает одной из целей механизма устойчивого развития COP26 — сократить использование известняка, минерального природного ресурса, и преодолеть отклонения и вредность промышленных побочных продуктов. «Около 88,7% внутренних запасов полезных ископаемых составляют неметаллические руды, из которых почти 72% приходится на известняк, и большая часть этих полезных ископаемых используется в цементной промышленности», — объясняет Ан. В дополнение к технологии зеленого цемента Ан разработал новую методологию Механизма чистого развития (CDM) для использования в цементной промышленности, которая имеет много ограничений на углеродные кредиты.
«Новая методология CDM является международным стандартом для оценки выбросов парниковых газов, которые сокращаются за счет конкретных видов деятельности, и необходимо сертифицировать эффективность сокращения выбросов парниковых газов нашей технологии производства зеленого цемента», — объясняет она.
Самым сложным аспектом регистрации технологии по методологии CDM была оценка количества двуокиси углерода, уменьшенного за счет технологии производства цемента, вспоминает Ан. По ее оценкам, цемент, разработанный с использованием этой технологии, выделяет на 0,281 тонны углекислого газа (tCO2) меньше выбросов на тонну произведенного цемента, чем при производстве обычного портландцемента.
«Возьмите, к примеру, данные за 2019 год — если бы сырой цемент составлял 5% (2 912 710 тонн) от общего объема производства цемента в 2019 году, можно было бы сократить около 820 000 т CO2 от общего количества парниковых газов».
Методология CDM была одобрена и объявлена в октябре 2020 года Рамочной конвенцией Организации Объединенных Наций об изменении климата (РКИК ООН).