Как делают цемент: Как делают цемент – производство и технологический процесс
что входит в состав, сырье и пропорции при изготовлении
Цемент – это распространенный материал не только в строительстве, но и в декорировании. Из него создают строительные блоки и целые фундаменты, элементы интерьера или сада. Но чаще всего он используется в возведении сооружений. Рассмотрим подробнее этот материал, что это такое и из чего делают цемент.
Содержание
- Что такое цемент — описание и технические характеристики
- История появления и сфера использования
- Из чего сделан цемент, состав и пропорции сырья
- Марки цемента, какие бывают, применение
- Маркировка по виду добавок
- Что такое цементный клинкер
- Корректирующие добавки
- Производство цемента, основные этапы изготовления
Что такое цемент — описание и технические характеристики
Сухой цемент выглядит как мелкий порошок, который при перемешивании с жидкостью переходит в пластичную массу. В таком виде материал может принимать любые формы под воздействием человека. После продолжительного контакта с воздухом масса застывает до твердого, каменного состояния.
Смеси принято делить по следующим признакам:
- Назначению.
- Времени, за которое раствор схватывается.
- Виду основного материала (клинкера).
- Скорости затвердевания.
- Веществам, входящим в состав.
- Показателям прочности.
К основным техническим характеристикам материала относят:
- Морозоустойчивость. Сколько раз можно заморозить и дать оттаять материалу без потери прочности.
- Прочность. Проверяют путем механического давления на затвердевший образец. В зависимости от скорости разрушения цементу присваивается та или иная марка.
- Срок, за который схватывается материал. Важно при проведении работ в холодное время года.
История появления и сфера использования
Цемент пришел на смену вяжущим смесям, затвердевающим на воздухе, – гипсу и известняку. Эти материалы обладали низкой водостойкостью и быстро разрушались под воздействием внешних факторов. Прочность воздушных вяжущих веществ пытались повышать, добавляя к ним обожженную глину мелкого помола.
Точно известно, когда изобрели цемент, – в 1824 году. Тогда появился современный портландцемент, названный так из-за английского острова Портланд, состоящего из известняковых пород. После добавления в портландцемент мелких камней, песка и воды раствор можно было применять в качестве бетона. Он хорошо выдерживал нагрузки на сжатие, но плохо работал на растяжение. Через несколько десятилетий начали использовать металлическую арматуру для укрепления конструкций из цемента.
В зависимости от типа добавок и физических свойств цемент применяют в разных сферах:
- изготовление скульптур или частей фасадов,
- декоративное покрытие,
- создание конструкций, находящихся в постоянном контакте с водой, кислотами или под землей.
Некоторые марки раствора используют для проведения аварийных работ в условиях пониженных температур.
Из чего сделан цемент, состав и пропорции сырья
Требования, предъявляемые к физическим и химическим показателям цемента, влияют на состав.
Главные составляющие цемента:
- Клинкер (получают путем обжига известняка и глины. Под действием большой температуры происходит плавление и получается масса с большим содержанием кремнезема и диоксида кальция. От этих веществ зависят физические свойства материала).
- Гипс (от его количества зависит, как быстро затвердеет раствор).
- Добавки для придания тех или иных свойств.
Исходным сырьем при производстве цемента выступают различные горные породы. Это могут быть ископаемые карбонатного типа (мергель, мел, ракушечник, доломитовые породы) или осадочные породы (суглинок, лёсс, глинистый сланец).
Пропорции сырья для получения цемента:
- 60% – известь.
- 20% – кремниевый диоксид.
- 4% – алюминий.
- 2% – гипс.
К корректирующим добавкам относится: минерализаторы, железо, белитовый шлам, апатиты, глинозем и пр.
Самый распространенный состав цемента – портландцемент, имеет следующие пропорции: 25% кремниевого диоксида, 60% извести, 10% гипс и оксид железа, 5% глинозем.
Иногда говорят, что бетон – это то же, что цемент, но это неверное утверждение.
Марки цемента, какие бывают, применение
По ГОСТу упаковка смеси должна содержать информацию о нем: наименование, производителя, класс и марку. Марка обозначает предел прочности затвердевшего образца в килограммах на один квадратный сантиметр. Прочность зависит от того, из чего делали цемент.
Смеси с маркировкой М300 используют во время монтажа сооружений без больших нагрузок.
Цемент М400 подойдет для производства железобетонных изделий и малоэтажного строительства.
Марку М500 применяют для строительства многоэтажных объектов и производства ЖБИ повышенной прочности.
Самый прочный вид цемента – М600, используют для возведения мостов и строительства военных объектов.
Маркировка по виду добавок
Марки цемента указаны в ГОСТе 31108-2016. Это последовательность букв и цифр, которая зависит от использованных в ходе производства добавок и целевого назначения смеси.
Первым идет обозначение вида смеси:
- ЦЕМ I – обычный портландцемент, не имеющий добавок.
- ЦЕМ II – портландцемент с минеральными добавками (если добавок от 5 до 20%, то в маркировку добавляют букву А, если от 21 до 35% – В).
- ЦЕМ III – шлакопортландцемент, содержит размолотый шлак (имеет три подтипа в зависимости от его количества в смеси: А – от 6 до 20%, В – от 21 до 35%, С – от 36 до 60%).
- ЦЕМ IV – пуццолановый цемент с добавками вулканического происхождения.
- ЦЕМ V – композиционный цемент, может включать в себя несколько добавок.
После латинских букв А, В и С кириллицей указывается тип присадки:
- И – известняк.
- М, МК – микрокремнезем.
- З – зола-унос.
- Ш – шлак.
- П – пуццоланы.
- Г – глиеж.
- К – композиционный, содержащий несколько присадок.
Следом в маркировке указан класс прочности застывшего материала. Нормальным принято считать набор прочности за 28 дней, хотя проверка также проводится на второй и седьмой день. После этого на 28-й день образец испытывают на специальном станке. Цифры указывают, какое давление в МПа может выдержать материал.
Соответствие класса и марки представлено в таблице:
Класс | Марка |
22,5 | М300 |
32,5 | М400 |
42,5 | М500 |
52,5 | М600 |
После цифр могут идти буквы Б, Н или М. Они говорят о том, с какой скоростью затвердеет раствор: быстротвердеющий, нормальнотвердеющий или медленнотвердеющий. Этот показатель зависит от того, из чего была сделана цементная смесь.
Иногда на упаковке также встречается маркировка «СС». Она не относится к современному ГОСТу и говорит о том, что состав сульфатостойкий.
Нередко производители указывают на упаковке устаревший ГОСТ 10178-85. В нем маркировка материала отличается. Чтобы не запутаться, можно воспользоваться таблицей соответствия маркировок.
Клинкер – это материал, возникающий после первого этапа производства цемента. В специальной печи при температуре свыше 1000 градусов обжигают смесь известняка и глины. В результате получают гранулированный полуфабрикат.
Свойства готового клинкера определяются технологией нагрева, методом помола и охлаждения, составом сырья и добавлением присадок.
В клинкере обязательно присутствуют четыре элемента в определенных пропорциях: не менее 52% алита, 14-31% белита, 4-11% алюмината, 5-15% алюмоферрита.
Кроме изготовления цемента, клинкер используют для облицовки искусственных водоемов и печей, украшения фасадов зданий. Его применяют в качестве керамогранита для украшения интерьеров. Материал может выдержать высокую влажность, а также обладает хорошими теплоизоляционными свойствами.
Корректирующие добавки
Для доведения смесей до требуемых химических и физических показателей, при изготовлении цемента используют различные добавки, чтобы скорректировать его состав. Чаще всего их добавляют для получения оптимальной пропорции диоксида кремния и карбоната кальция в клинкере.
Недостаток диоксида кремния компенсируют добавлением в смесь песка или глины с высоким содержанием кремнезема. Для повышения количества диоксида железа добавляют колчеданные огарки.
Известковый компонент обычно не корректируют, так как его содержание в сырье является ключевым фактором использования именно такой извести для производства цемента.
В готовую смесь также добавляют корректирующие вещества, например, пластификаторы. Они повышают качество смеси, ее морозостойкость, улучшают физические свойства. Для этих целей используют апатиты, глинозем, кремнезем, плавиковый шпат.
Корректирующие добавки применяют для снижения стоимости готовых смесей. К ним можно отнести отходы других отраслей промышленности – колошниковую пыль (отделяется в доменных печах), газовые отходы ТЭС, шлаковые отходы цветной и черной металлургии.
Производство цемента, основные этапы изготовления
Сухой способ производства п/ц.В первую очередь добывают сырье (глина и известняк), доставляют его до места переработки, измельчают и смесь обжигают под воздействием высоких температур.
С целью сокращения затрат на транспортировку, заводы по изготовлению цемента чаще строят недалеко от места добычи сырья.
Существует три способа изготовления цемента:
- Сухой.
- Мокрый.
- Комбинированный.
Сухой способ используется в основном зарубежными странами, тогда как в России производят цемент в основном по мокрому. Сырьем для мокрого выступает мягкая глина и сухой твердый известняк. В начале производства материалы тщательно измельчают (сначала дроблением, а затем помолом). Известняк дробят до частиц размером 8-10 мм.
Измельченная глина попадает в мельницу, где к ней добавляют известняк. Компоненты перемешивают и размалывают. В результате получают шлам влажностью 40%, который погружают в вертикальный бассейн. На этом этапе происходит корректировка состава с помощью добавок и оценка качества шлама. Одобренная смесь перекладывается в горизонтальные накопители, где она ожидает обжига.
В печи для обжига под действием высоких температур шлам расплавляется в клинкер. После охлаждения, его отправляют в дробилки, а затем в мельницы. Туда же досыпают гипс и добавки. Готовый цемент проходит оценку качества, упаковывается и поступает в продажу, или отправляется навалом.
В сухом методе все исходные компоненты – мергель, мел, известняк, глину, уголь – пропускают сквозь сушильный барабан и загружают в мельницу. Измельченные и перемешанные составляющие проходят оценку, и происходит корректировка состава смеси.
В комбинированном способе сырье подготавливается также, как в мокром. Затем шлам в специальном фильтре обезвоживается до влажности 12-15%. После смесь обжигают в печи, и дальше процесс повторяет мокрый способ.
Теперь известно, как производят этот материал, что входит в его состав. Останется только вычислить, сколько же потребуется цемента по формуле или через специальные онлайн калькуляторы, и можно приступать к необходимым работам.
Как делают цемент. — Как это сделано, как это работает, как это устроено — LiveJournal
Цементная промышленность является одной из важнейших отраслей материального производства.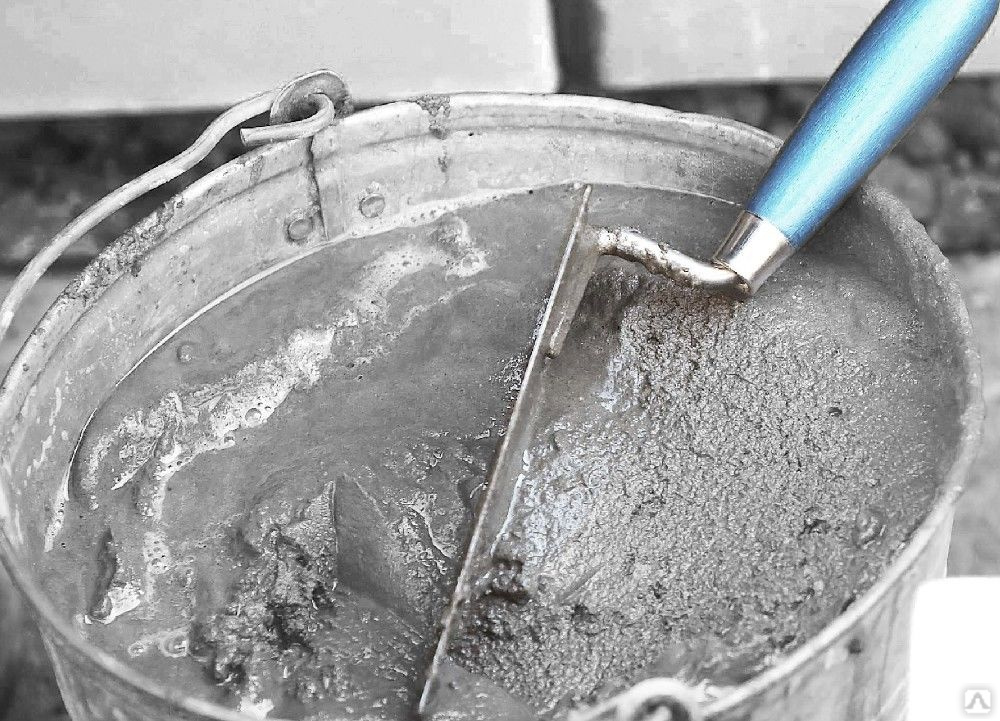
Я провёл съемку на заводе Lafarge («Уралцемент») расположенном в поселке Первомайский, Челябинской области. Завод производит цемент по мокрому способу с 1957 года и по объемам производства находится в десятке крупнейших цементных заводов России. Для производства цемента используют глину и известняк. В качестве топлива выступает природный газ.
История портландцемента начинается 21 октября 1824 года, когда английский каменщик Джозеф Аспдин получил патент на вещество, которое назвал «портландцемент», поскольку его цвет напоминал серый цвет скал, находившихся вокруг города Портланд.
Портландцемент — гидравлическое вяжущее вещество, получаемое путем совместного тонкого измельчения портландцементного клинкера, гипса и специальных добавок. Свойства портландцемента зависят от состава клинкера и степени его измельчения. Важнейшее свойство портландцемента — способность твердеть при взаимодействии с водой. Оно характеризуется маркой портландцемента, определяемой по прочности на сжатие и изгиб стандартных образцов цементно-песчаного раствора после 28 суток твердения во влажных условиях.
2. Производство цемента складывается из двух основных технологических процессов: получение клинкера (наиболее трудоемкий и энергозатратный этап) и его помол с соответствующими добавками.
3. Для изготовления цемента сначала добывают известняк и глину из карьера.
4.
5.
6. Пройдя предварительную обработку, исходные материалы поступают в мельницу мокрого самоизмельчения «Гидрофол», где перерабатываются в шлам. Затем шлам домалывается в сырьевых мельницах и усредняется в шламбассейнах.
7. На заводе находится специальная лаборатория, в которой производят постоянный контроль качества и дозировку сырьевых материалов и добавок. И в том числе проводят тестирование конечного продукта на прочность.
8.
9.
10.
11. Затем тонкомолотый сырьевой шлам вводится во вращающуюся печь (длиной около 200 м и диаметром 4 м) и обжигается при температуре 1450 градусов Цельсия.
12. При обжиге частички сырья сплавляются между собой, образуя клинкер.
13. Печь для обжига представляет собой вращающийся металлический цилиндр, который наклонен к горизонтальной плоскости под углом 3-4 градуса, чтобы обеспечить возможность движения материала вдоль печи.
14. Полученный клинкер охлаждается в холодильниках, дробится и подается транспортерами в бункеры цементных мельниц для помола.
15. Электрофильтры на вращающихся печах позволяют сократить выбросы пыли в атмосферу в 10-30 раз.
16.
17.
18. Остывший клинкер подается в мельницу.
19.
20. Это самый шумный участок производства. Находится в цеху без наушников просто невозможно.
21. Цемент получают путем совместного тонкого измельчения портландцементного клинкера, минеральных добавок (10-15%) и гипса (3-7%), который служит для регулирования сроков схватывания. Размер зерен цемента лежит в пределах от 1 до 100 мкм.
22.
23.
24. Процедура LOTOTO (LockOut / TagOut / TryOut). Комплекс действий для повышения безопасности на производстве.
25. Различные минеральные добавки служат для придания бетонам, растворам и др. изделиям на основе цемента специальных свойств (скорость затвердевания, устойчивость в природных водах, морозостойкость).
26.
27.
28. Полученный портландцемент транспортируется из мельниц в силосы для хранения.
29. Из силосов цемент отгружают железнодорожными вагонами и автомобильным транспортом в следующем виде: навалом, специальными контейнерами МКР весом до 1 тонны, бумажными мешками весом 50 кг.
30.
31.
32.
33.
Оригинал взят у victorborisov в Как делают цемент
Tags: Челябинская область, завод, производство, цемент
Основы производства цемента
специальный артикул
Основы производства цемента
Цемент является основным компонентом бетона. Бетон образуется, когда портландцемент образует пасту с водой, которая связывается с песком и камнем для затвердевания.
Цемент изготавливается из тщательно контролируемой химической комбинации кальция, кремния, алюминия, железа и других ингредиентов.
Обычные материалы, используемые для производства цемента, включают известняк, ракушки и мел или мергель в сочетании со сланцами, глиной, сланцем, доменным шлаком, кварцевым песком и железной рудой.
Эти ингредиенты при нагревании при высоких температурах образуют похожее на камень вещество, которое растирается в мелкий порошок, который мы обычно называем цементом.
Портландцемент, наиболее часто используемый цементный продукт, был впервые разработан в начале 19 века. Наиболее распространенным способом производства портландцемента является сухой способ.
Первым шагом является добыча основного сырья, в основном известняка, глины и других материалов. После добычи порода дробится. Это включает в себя несколько этапов. Первое дробление уменьшает размер породы до максимального размера около 6 дюймов. Затем порода поступает на вторичные дробилки или молотковые мельницы для измельчения примерно до 3 дюймов или меньше.
Щебень смешивают с другими ингредиентами, такими как железная руда или летучая зола, измельчают, смешивают и подают в цементную печь.
Цементная печь нагревает все ингредиенты примерно до 2700 градусов по Фаренгейту в огромных цилиндрических стальных вращающихся печах, облицованных специальным огнеупорным кирпичом. Печи часто достигают 12 футов в диаметре — достаточно больших, чтобы вместить автомобиль, и во многих случаях длиннее, чем высота 40-этажного здания. Большие печи установлены с небольшим наклоном оси от горизонтали.
Мелкоизмельченное сырье или суспензия подается в верхнюю часть. В нижней части находится ревущий взрыв пламени, создаваемый точно контролируемым сжиганием порошкообразного угля, нефти, альтернативных видов топлива или газа при принудительной тяге.
Когда материал проходит через печь, некоторые элементы удаляются в виде газов. Остальные элементы объединяются, образуя новое вещество, называемое клинкером. Клинкер выходит из печи в виде серых шариков размером с мрамор.
Клинкер выгружается раскаленным из нижнего конца печи и обычно доводится до рабочей температуры в различных типах охладителей. Нагретый воздух из охладителей возвращается в печи, что позволяет экономить топливо и повышает эффективность горения.
После охлаждения клинкера цементные заводы измельчают его и смешивают с небольшим количеством гипса и известняка. Цемент настолько мелкий, что 1 фунт цемента содержит 150 миллиардов зерен. Цемент теперь готов к транспортировке на предприятия по производству товарного бетона для использования в различных строительных проектах.
Хотя сухой процесс является наиболее современным и популярным способом производства цемента, в некоторых печах в Соединенных Штатах используется мокрый процесс. Эти два процесса в основном похожи, за исключением мокрого процесса, сырье измельчается с водой перед подачей в печь
Адаптировано из «Как производится цемент» Portland Cement Association.
Лучшее восстановление
Тематическая статья
Строительство более качественных и устойчивых зданий и инфраструктуры в наших сообществах в соответствии с более высокими стандартами, чем того требуют действующие строительные нормы и правила, имеет решающее значение для будущего благополучия миллионов людей во всем мире.
Углеродно-нейтральный бетон
Характеристика Артикул
Бетон. Это самый распространенный в мире строительный материал. По оценкам, на цементный и бетонный секторы приходится примерно от 5 до 7% глобальных выбросов углерода.
Промышленность по производству портландцемента: Национальные стандарты выбросов опасных загрязнителей воздуха (NESHAP)
На этой странице:
- Сводка правил
- История правил
- Дополнительные ресурсы
- Соответствие
Сводка правил
Портландцементявляется основным ингредиентом бетона, который используется во всем мире в качестве основного строительного блока для строительства инфраструктуры, а также для коммерческих и жилых зданий.
Воздушные токсические вещества, также называемые опасными загрязнителями воздуха (ОЗВ), представляют собой те загрязнители, которые, как известно или подозреваются, вызывают рак или другие серьезные последствия для здоровья. Производство портландцемента представляет собой энергоемкий процесс, при котором цемент производится путем измельчения и нагревания смеси сырьевых материалов, таких как известняк, глина, песок и железная руда, во вращающейся печи. Печь представляет собой большую печь, работающую на угле, нефти, газе, коксе и/или различных отходах. Продукт (называемый клинкером) из печи охлаждают, измельчают, а затем смешивают с небольшим количеством гипса для получения портландцемента.
Основным источником выбросов токсичных веществ в атмосферу на заводе по производству портландцемента является печь. Выбросы возникают в результате сжигания топлива и нагрева исходных материалов. Ядовитые вещества в воздух также выделяются на этапах измельчения, охлаждения и обработки материалов в производственном процессе. Загрязняющими веществами, регулируемыми в соответствии с этим правилом, являются твердые частицы, органические HAP, металлы посредством контроля твердых частиц, ртуть, кислые газы и диоксин/фуран.
История правил
25.07.2018 — Окончательный обзор рисков и технологий, правило
21.09.2017 — Предлагаемое правило проверки рисков и технологий
11.08.2017 — Последнее правило уважительной причины
11.08.2017 — Предлагаемое правило (возобновление периода комментариев)
19.06.2017 — Прямое итоговое правило
19.06.2017 — Параллельное предлагаемое правило
25.07.2016 — Прямое итоговое правило
25.07.2016 — Параллельное предлагаемое правило
11.09.2015 – Окончательное правило; корректирующие поправки
27.07.2015 – Окончательные изменения
19.11.2014 – Предлагаемое правило
12.02.2013 – Окончательное правило
18.07.2012 – Предлагаемые правила о пересмотре
17.05.2011 — Отказ в частичном удовлетворении и частичное удовлетворение ходатайств о пересмотре
18.01.2011 – Прямое итоговое правило; поправки
09.09.2010 – Окончательное правило
09. 06.2009 — Уведомление о проведении общественных слушаний и продлении периода общественного обсуждения
06.05.2009 – Предлагаемое правило
20.12.2006 – Окончательное правило
09.01.2006 – Предлагаемое правило
02.12.2005 — Предлагаемое правило; поправки
06.12.2002 – Окончательное правило; поправки
05.07.2002 – Окончательное правило; разъяснения и исправления
02.07.2002 – Частичный отзыв прямого окончательного правила
05.04.2002 – Предлагаемое правило и прямое окончательное правило
04.10.2001 – Предлагаемое мировое соглашение для общественного обсуждения
14.06.1999 – Окончательное правило
24.03.1998 — Предлагаемое правило
Дополнительные ресурсы
Информационный бюллетень: Окончательный обзор рисков и технологий (13.07.2018)
Информационный бюллетень: Прямое окончательное и параллельное предложение (19.06.2017)
Краткий обзор воздействия портландцемента на окружающую среду и затрат на 2010 г. NESHAP
Анализ регулирующего воздействия Апрель 2009 г.
Анализ регулирующего воздействия: Поправки к Национальным стандартам выбросов опасных загрязнителей воздуха (NESHAP) и Стандартам эффективности новых источников (NSPS) для отрасли по производству портландцемента Заключительный отчет
2010 Ответ на комментарии
Окончательные правила для заводов по производству портландцемента. Информационные бюллетени (действия от 1999 — 2015)
Чтобы найти дополнительные подтверждающие документы для правил до 2011 года, просмотрите документы в папке с досье.
Чтобы найти дополнительные подтверждающие документы для правил после 2011 года, просмотрите документы в папке с досье.
Инструмент навигации по нормативным требованиям: инструменты Reg Nav помогают владельцам и операторам объектов в определенных отраслях определять требования конкретных нормативных актов. Инструменты Reg Nav являются интерактивными онлайн и используют введенную информацию для оценки потенциальных нормативных требований.