Изготовление цемента: Современные технологии производства цемента — Публикации на официальном сайте Holcim
Технология производства | Газметаллпроект
Главная»Продукция»Технология производства
Технология производства портландцемента
Портландцемент – это гидравлическое вяжущее вещество, твердеющее в воде и на воздухе и представляющее собой продукт тонкого измельчения клинкера, получаемого путем обжига до спекания искусственной сырьевой смеси.
Производство портландцемента включает в себя следующие основные этапы: добыча сырья; приготовление сырьевой смеси; обжиг сырьевой смеси и получение клинкера; совместный помол клинкера с гипсом, а в некоторых случаях также с различными добавками, способными придать портландцементу специальные свойства, причем первые три этапа являются наиболее энергоемкими и дорогостоящими, на них приходится около 70% себестоимости цемента.
При производстве портландцемента необходимо сочетание в сырьевой смеси карбонатного и глинистого компонентов, которые в разных пропорциях содержатся в мергеле – горной породе, их которой состоят склоны Маркхотского хребта.
Добыча мергеля осуществляется открытым способом в карьерах. Карьеры мергеля разрабатываются горизонтальными уступами высотой от 15до 20м. Основными процессами при добыче и переработке мергеля являются производство вскрышных работ, разрушение и добыча материала, погрузка экскаваторами и внутрикарьерное транспортирование карьерными самосвалами. Мергель из карьера поступает в дробильное отделение, где подвергается одно – либо двухстадийному дроблению в щековых, ударно – отражательных, молотковых дробилках. Дробленый мергель по системе транспортеров поступает на склад.
Существует два основных способа производства портландцемента – «мокрый» и «сухой».При «мокром» способе производства сырьевые материалы измельчают в помольных установках в присутствии воды, в результате чего получается текучая сметанообразная масса, называемая шламом, с влажностью 37 — 38%.
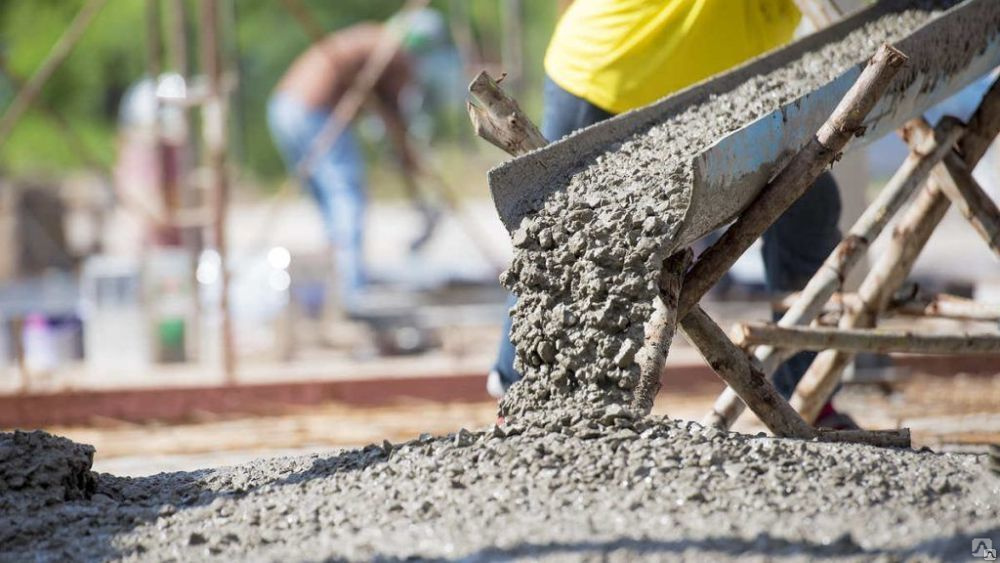
Типоразмеры вращающихся печей мокрого способа производства: Ø5х185м; Ø4х150м; Ø4х3,6х4х150м.
При «сухом» способе производства помол сырьевых материалов осуществляется с одновременной сушкой, в результате чего получается сырьевая мука с влажностью не более 1%, которая подается на обжиг в короткую вращающуюся печь с запечными теплообменными устройствами: циклонными теплообменниками и декарбонизатором.
Типоразмеры вращающихся печей «сухого» способа производства: Ø5,5х66м; Ø 5,2х65м. Во вращающейся печи «сухого» способа производства отсутствуют зоны сушки, остальные зоны и процессы, происходящие в них, аналогичны таковым печи «мокрого» способа. Процессы дегидратации и почти полностью — декарбонизации сырьевой смеси происходят в циклонных теплообменниках и декарбонизаторе, откуда сырьевая смесь поступает в короткую вращающуюся печь.
Существует также комбинированный способ производства портландцемента, который предполагает либо частичное обезвоживание шлама (до 16-18%) с применением вакуум – фильтров и концентраторов шлама, либо увлажнение сырьевой муки до влажности 10-14%, грануляцию сырьевой смеси и подачу ее на обжиг в короткую вращающуюся печь.
При выборе способа производства учитываются различные факторы: однородность химического состава сырьевых материалов, их физико – механические характеристики.
В настоящее время наиболее востребован «сухой» способ производства цемента, как более экономичный: удельный расход условного топлива на 1 тонну клинкера при «сухом» способе производства в два раза меньше, чем удельный расход условного топлива при «мокром» способе производства.
Экономия топлива является решающим аргументом в пользу «сухого» способа производства, так как одной из наибольших статей затрат при производстве портландцемента является расход условного топлива на обжиг клинкера.
Полученный одним из способов портландцементный клинкер после охлаждения поступает на склад клинкера и добавок.
Для получения портландцемента клинкер подвергается тонкому измельчению в мельничных агрегатах совместно с гипсом (применяется для регулирования сроков схватывания цементного теста), а также при производстве некоторых видов цемента — с различными добавками.
Готовый цемент по системе цементопроводов подается на хранение в специально оборудованные силосы, откуда отгружается потребителю в таре либо навалом в вагоны – цементовозы или автотранспорт.
Технология производства
Более 60% от производственных мощностей составляют линии производящие цемент по «сухому» способу, из которых новая линия ЦЗ «Верхнебаканский» и ЦЗ «Первомайский».
Производство цемента и состав цементного клинкера
Состав цементного клинкера который получается от производства цементного камня по новой технологии. Способы схем процесса производства цемента из клинкера.
В статье
Производство цемента из клинкера
Романцемент — получают путем обжига известняков, содержащих глинистых не менее 25% при температуре 1000-1200 градусов по Цельсию. Применение: производство бетонов низких марок, стеновые панели, блоки.
Портландцемент — после обжига известняков, мергелей и глинистых примесей получают цементный клинкер. Клинкер смешивают с добавками (ракушечник, доменный шлак).
Способы производства портландцемента
1. Мокрый — компоненты измельчают и смешивают в присутствии воды, полученную суспензию (шлам) обжигают.
2. Сухой — все тоже самое, только в сухом состоянии.
Минералогический состав цементного клинкера
Трехкальциевый силикат (алит) является активным минералом. Быстро твердеет и набирает прочность, сопровождается значительным тепловыделением.
Двухкальциевый силикат (белит) в начальный период твердеет медленно.
Трехкальциевый алюминат — низкая стойкость против серно-кислых соединений.
Четырехкальциевый алюмоферрит твердеет медленнее алита, но быстрее белита. Прочность ниже алита.
Применение портландцемента
Приготовление растворов невысоких марок для кладочных и штукатурных работ, бетонные изделия.
Виды портландцемента
Глиноземистый — быстро твердеет. Получают путем обжига известняков и бокситов (богаты глиноземом). Процесс твердения сопровождается большим тепловыделением.
Свойства: сульфатостойкий, водонепроницаемый, жаростойкий, в 3-4 раза дороже портландцемента.
Применение: срочные ремонтные работы, аварийные работы, бетонные работы в зимних условиях, производство жаростойких бетонов.
Водонепроницаемый расширяющийся портландцемент получают путем тщательного измельчения глиноземистого цемента, гипса и гидроалюминатов кальция. При взаимодействии двух последних происходит образование гидросульфатоалюминатов кальция. Твердение сопровождается увеличением объема.
Применение: создание гидроизоляционных покрытий, заделка стыков и трещин железобетонных конструкций.
Быстротвердеющий портландцемент характеризуется быстрым нарастанием прочности.
Конечно, скорость твердения не сравнить с гипсом. Но самая быстрая из всех видов цемента.
Применение: возведение монолитных сооружений, приготовление высокопрочных бетонов.
Шлакопортландцемент жаро-, водо- и сульфатостойкий. Процесс твердения медленный.
Применение: изготовление железобетонных конструкций для работы в горячих цехах, гидротехнические сооружения.
Пуццолановый портландцемент твердеет медленно, требует систематического увлажнения.
Свойства: водостойкий, сульфатостойкий, не морозостойкий.
Применение: бетонные и ж/б конструкции.
Пластифицированный позволяет снизить водопотребление бетонных смесей и расход цемента на 5-8%.
Применение: дорожные бетоны, аэродромное и гидротехническое строительство.
Гидрофобный по своим свойствам похож на пластифицированный. Применение тоже.
Белый и цветной портландцемент
Белый изготавливают из сырья в котором мало окрашивающих оксидов (чистый известняк). Цветной — в которых много (охра, железный сурик).
Применение: облицовочные плитки, фактурный слой стеновых панелей, искусственный мрамор.
Сульфатостойкий портландцемент изготавливают из клинкера с другими примесями не более 7%.
Производство цемента
Цемент — это один из самых востребованных строительных материалов на рынке. Однако, производство готового цемента является затратным как по капитальным вложениям, так и по использованию энергии. Заводы по его производству обычно расположены вблизи мест добычи основного сырьевого компонента, каковым является известняк. Сам цемент используется в строительстве, как в чистом виде, так и в качестве основы для изготовления незаменимых материалов (бетона и железобетона).
Производство цемента начинается с добычи клинкера. Затем клинкер измельчают и получают вещество в виде порошка, в которое добавляют гипсовый компонент и другое. Расходы на добычу клинкера — большая доля затрат в себестоимости цемента. В итоге такая статья затрат, как добыча сырья, составляет долю в себестоимости готового продукта равную 70%.
Метод, с помощью которого осуществляют добычу и разработку залежей известняка называется «сносом». Используя этот метод, часть горной породы «сносят», освобождая путь к известняку желто-зеленого цвета. Глубина залегания известняка обычно составляет 10 м, толщина пласта равна 70 см. До принятой глубины породу желто-зеленого цвета можно встретить еще примерно четыре раза. На следующем этапе добытый известняк с помощью ленты для транспортировки отправляется на измельчение. Здесь известняковая порода должна приобрести размер кусков не более 10 см в диаметре. Измельченный до таких размеров известняковый компонент транспортируется на сушку и повторное перемалывание, где к нему добавляются другие составляющие.
Следующая стадия заключается в обработке клинкера. В первую очередь, клинкер дробят. Одновременно проходит процесс подсушки минеральных компонентов и дробление гипсового камня. Затем все компоненты смешивают и еще раз подвергают перемалыванию.
Поскольку сырье имеет порой разные технические и физические характеристики, то в промышленности существует три метода производства готового продукта. Так, при производстве цемента применяется три способа изготовления готовой смеси: мокрый, сухой и комбинированный.
Цементная смесь, произведенная мокрым способом, сделана на основе карбоната (мела), силикатов (глины) и добавок, содержащих железо. К последним относятся конвертерный шлам, огарки пирита и железистый продукт. При этом глина должна содержать влагу не более 20%, а мел не более 29%. Все компоненты смеси проходят измельчение в воде, в итоге получается суспензия, влажность которой составляет 30-50%. Суспензия, а вернее шлам, поступает в специальные печи, где проходит обжиг. Печь для обжига имеет весьма внушительные размеры: ее высота составляет 7 м, а длина — 200 м. В процессе обжига из шлама происходит выделение углекислот. На выходе из печи после обжига получается клинкер, который имеет вид шариков. Эти шарики измельчают и получают готовую цементную смесь.
При сухом способе производства происходит сушка всех сырьевых составляющих цемента, и только затем перемалывание. Таким образом, смесь имеет вид порошка.
При комбинированном способе осуществляется частичное использование двух предыдущих. Таким образом, комбинированный способ производства подразделяется на два вида. При первом из них смесь сырьевых компонентов готовят по мокрому способу, и только затем влажность смеси снижают с помощью специальных фильтров, она не должна превышать 16-18%. Потом эту массу отправляют на обжиг. При втором виде для получения смеси используется способ сухого получения первоначальной смеси, а затем в нее добавляют воду.
Дата публикации статьи: 6 ноября 2014 в 11:32
Последнее обновление: 19 января 2021 в 15:50
Закладка фундамента для производства цемента с нулевым выбросом углерода
Являясь ключевым компонентом бетона, цемент является неотъемлемой частью нашей повседневной жизни. На самом деле, это второй по потреблению продукт в мире после питьевой воды, и он используется почти во всем, что мы строим — от домов и городских пейзажей до дамб и дамб. В то же время он также вносит основной вклад в глобальные выбросы CO 2 .
Как ученые, так и правительства призывают к ужесточению целевых показателей выбросов парниковых газов (ПГ) по мере того, как последствия изменения климата становятся все более очевидными. В последнее время цель сместилась с удержания повышения температуры ниже 2,0 градусов по Цельсию на 1,5 градуса по Цельсию, при этом более 77 1 1. Елена Косолапова, «77 стран, более 100 городов взяли на себя обязательство добиться нулевых выбросов углерода к 2050 году на климатическом саммите», Международный институт устойчивого развития, 14 сентября 2019 г., sdg.iisd.org. страны взяли на себя обязательство добиться нулевого уровня выбросов к 2050 году. Дополнительным давлением на отрасль является пандемия COVID-19, которая сильно ударила по отрасли, подорвав спрос из-за неопределенности в отношении того, насколько глубоким будет спад и сколько времени займет восстановление.
Хотя неясно, как будут развиваться дебаты о климате, достижение таких целей к 2050 году будет особенно сложной задачей для цементной промышленности, поскольку большая часть ее выбросов CO 2 является результатом неизбежного химического процесса, известного как кальцинирование. В отличие от других отраслей, которые могут продвинуться дальше, разработка новых технологий обезуглероживания цемента может быть не масштабируемой в течение многих лет. Тем не менее наше исследование показывает, что в принципе к 2050 году отрасль может сократить свои выбросы на уровне 2017 года более чем на три четверти9.0005
Учитывая его эксплуатационные характеристики и широкую доступность известняка, цемент (и, следовательно, бетон), вероятно, останется предпочтительным строительным материалом во всем мире. Однако на местном уровне его доля может уступить место более устойчивым альтернативным материалам, таким как кросс-клееная древесина (CLT). Другие изменения, в том числе более активное информационное моделирование зданий (BIM) и модульное строительство, могут еще больше снизить потребление цемента, фактически сократив спрос, несмотря на общий рост строительной активности. Таким образом, экономический рост и декарбонизация представляют собой серьезные взаимосвязанные задачи. Как это ни парадоксально, возможно, COVID-19может ускорить реакцию отрасли на эти фундаментальные структурные тенденции. По мере того, как игроки решают проблемы неопределенного спроса, у них появляется возможность пересмотреть стратегии: определить наилучший путь к обезуглероживанию, оценить цифровые и технологические достижения, в которые можно инвестировать, и переосмыслить свои продукты, портфели, партнерства и методологии строительства — области, которые мы рассмотрим позже. . Дальновидные игроки могут получить возможность совершить прорыв и стать лидерами отрасли.
Мы стремимся предоставить людям с ограниченными возможностями равный доступ к нашему веб-сайту. Если вам нужна информация об этом контенте, мы будем рады работать с вами. Пожалуйста, напишите нам по адресу: [email protected]
Изменение климата и цементная промышленность: базовый уровень
Только на цементную промышленность приходится около четверти всех отраслевых выбросов CO 2 , и она также производит наибольшее количество выбросов CO 2 на доллар дохода (Иллюстрация 1). Около двух третей этих общих выбросов являются результатом прокаливания, химической реакции, которая происходит, когда сырье, такое как известняк, подвергается воздействию высоких температур.
Экспонат 1
Мы стремимся предоставить людям с ограниченными возможностями равный доступ к нашему веб-сайту. Если вам нужна информация об этом контенте, мы будем рады работать с вами. Пожалуйста, напишите нам по адресу: [email protected]
Цемент действует как связующее вещество между заполнителями (мелкими и крупными породами) при формировании бетона. Хотя цемент составляет лишь небольшой процент смеси (примерно 12 процентов по объему), почти исключительно он отвечает за образование CO 9 .0003 2 выбросов. В процессе производства цемента сырье нагревается до высоких температур в печи в ходе энергоемкого процесса, известного как пирообработка (Иллюстрация 2). В результате получается клинкер, небольшие комки каменистого остатка, которые измельчаются в порошок и объединяются с другими ингредиентами для производства цемента.
Экспонат 2
Мы стремимся предоставить людям с ограниченными возможностями равный доступ к нашему веб-сайту. Если вам нужна информация об этом контенте, мы будем рады работать с вами. Пожалуйста, напишите нам по адресу: McKinsey_Website_Accessibility@mckinsey. com
Давление на обезуглероживание цементной промышленности быстро возрастает не только со стороны общества, но и со стороны инвесторов и правительств. Фактически, в настоящее время правительства все чаще запрашивают оценку воздействия на окружающую среду, прежде чем принимать решение о выделении финансирования. Поскольку общественное внимание к выбросам CO 2 усиливается, сохраняется риск того, что производители цемента могут быть «пристыжены», как это было с нефтегазовыми или горнодобывающими компаниями в прошлом.
Потенциальные пути декарбонизации
У компаний есть несколько вариантов обезуглероживания цемента. Наш анализ оптимистично показывает, что выбросы CO 2 могут быть сокращены на 75 процентов к 2050 году (Иллюстрация 3). Однако лишь небольшая часть (около 20 процентов) будет получено за счет операционных достижений, а оставшаяся часть должна быть получена за счет технологических инноваций и новых горизонтов роста.
Экспонат 3
Мы стремимся предоставить людям с ограниченными возможностями равный доступ к нашему веб-сайту. Если вам нужна информация об этом контенте, мы будем рады работать с вами. Пожалуйста, напишите нам по адресу: [email protected]
Эксплуатационные достижения, такие как меры по повышению энергоэффективности, уже в значительной степени реализованы, а потенциал сокращения выбросов за счет альтернативных видов топлива и замены клинкера ограничен уменьшением доступности исходных материалов. Таким образом, более инновационные подходы, такие как новые технологии и альтернативные строительные материалы, будут необходимы для достижения целей по сокращению выбросов углерода к 2050 году. При этом наиболее многообещающие рычаги с точки зрения потенциала сокращения выбросов все еще находятся в разработке и только пилотные или внедренные в небольшом масштабе (см. врезку «Глубокое погружение в рычаги декарбонизации»).
Поскольку разработка таких технологий, как улавливание, использование и хранение углерода (CCUS) и отвержденный углеродом бетон, может занять до десяти лет, инвестиции должны быть сделаны как можно скорее. Наша кривая затрат на снижение выбросов (Рисунок 4) оценивает затраты на несколько крупномасштабных инвестиций, направленных на сокращение выбросов CO 2 на одну тонну (на основе предполагаемых будущих затрат, цен на CO 2 и объемов снижения выбросов). Отрицательные затраты на сокращение выбросов, например, для заменителей клинкера, означают выгоду для производителя, а не снижение затрат.
Экспонат 4
Мы стремимся предоставить людям с ограниченными возможностями равный доступ к нашему веб-сайту. Если вам нужна информация об этом контенте, мы будем рады работать с вами. Пожалуйста, напишите нам по адресу: [email protected]
Затраты на снижение загрязнения указаны в диапазоне, поскольку точная цена товаров зависит от региональной и будущей доступности. Например, по мере того, как металлургический и энергетический секторы активизируют свои усилия по декарбонизации, доступность заменителей клинкера, таких как пылевидная топливная зола (зольная пыль) и гранулированный шлак, будет уменьшаться. То же самое относится и к биомассе, спрос на которую, вероятно, будет расти со стороны других отраслей.
В связи с тем, что затраты на снижение выбросов, связанные с некоторыми рычагами, превышают цены CO 2 , производители цемента сталкиваются с дилеммой: общественность и финансовые инвесторы оказывают давление, требуя, чтобы они быстро снижались, хотя для этого нет экономического обоснования. Мало того, что экономика кажется далекой от звездной, но необходимые инвестиции должны быть направлены на меры по снижению затрат для производителей цемента, чтобы сохранить свою долю стоимости в более широкой строительной отрасли.
Комбинезон будущего CO 9Ожидается, что выбросы 0003 2 в 2050 году будут соответствовать мировому спросу, немного увеличившись до 2,9 ГтCO 2 (Иллюстрация 5). Региональные различия сохранятся, и потенциал
их сокращение будет варьироваться в зависимости от региона из-за подходов к регулированию в конкретных странах, различных потребностей в потреблении и различных уровней, на которых местные отрасли реализуют меры по обезуглероживанию.
Экспонат 5
Мы стремимся предоставить людям с ограниченными возможностями равный доступ к нашему веб-сайту. Если вам нужна информация об этом контенте, мы будем рады работать с вами. Пожалуйста, напишите нам по адресу: [email protected]
Например, Китай выиграет от снижения спроса (примерно на 45 процентов), и следует ожидать, что в ближайшие десятилетия он применит как операционные достижения, так и технологические инновации для декарбонизации. Юго-Восточная Азия и Индия приступили к разработке политики, направленной на содействие усилиям по декарбонизации. В 2012 году правительство Индии внедрило рыночный механизм повышения энергоэффективности, в котором более Участвуют 85 цементных заводов. Однако урбанизация и экономическое развитие в этих регионах, а также связанный с этим рост спроса могут свести на нет эти усилия.
Хотите узнать больше о нашей химической практике?
Контроль со стороны инвесторов и давление регулирующих органов с целью сокращения выбросов углерода на рынках Европы и Северной Америки, вероятно, усилится. Амбициозный «Зеленый курс» Европейского союза и его исчерпывающий пакет мер, включая введение механизма корректировки углеродных границ для цемента, могут сократить выбросы углерода во всем регионе. В Северной Америке усилия по декарбонизации продвигаются через инициативы штата и страны, такие как инициатива Канады 2019 г.реализация программы Carbon Pricing Backstop.
Следующая норма: переосмысление цементной промышленности
Декарбонизация цементной промышленности требует решения двух стратегических задач. Во-первых, компаниям необходимо будет определить наилучшие пути к декарбонизации за счет операционных достижений и технологических инноваций, а также новых горизонтов роста. Во-вторых, им нужно будет разработать портфель для нового горизонта роста, который использует возможности по всей цепочке создания стоимости «устойчивого строительства».
Операционные достижения
Опираясь на десятилетия усилий по повышению эффективности, традиционные рычаги сокращения выбросов могут сократить выбросы примерно на одну пятую к 2050 году. Промышленность может добиться этого сокращения за счет использования большего количества заменителей клинкера, снижения энергоемкости за счет более эффективного использования заводов и повышения эффективности оборудования. Утилизация отработанного тепла (побочного продукта машин или процессов, использующих энергию) также может обеспечить безуглеродное электричество.
Еще одним рычагом повышения эффективности является расширенная аналитика. Один европейский производитель цемента добился 6-процентной экономии топлива, создав самообучающиеся модели теплового профиля печи и оптимизировав форму и интенсивность пламени печи. Будущие цементные заводы смогут обойти конкурентов, объединив цифровые технологии и более экологичные операции. Наконец, использование альтернативных видов топлива, таких как отходы и биомасса, для замены ископаемого топлива, что является многолетней тенденцией в отрасли, может сократить выбросы почти на 10 процентов к 2050 году. 2 2. Технологическая дорожная карта: переход на низкоуглеродные технологии в цементной промышленности , Международное энергетическое агентство, апрель 2018 г., webstore.iea.org.
Ничто из этого не будет легким. Поставки биомассы варьируются в зависимости от региона, и за них борются другие отрасли. Заменители клинкера тоже ограничены. Природные пуццоланы (например, вулканическая порода и пепел) еще не оценивались в масштабе. А побочные продукты промышленности, которые служат альтернативой клинкеру, такие как летучая зола от угольных электростанций и шлак от сталеплавильных доменных печей, могут оказаться в дефиците, поскольку энергетическая и сталелитейная промышленность обезуглероживают и производят меньше отходов.
Технологические инновации
Инновации будут иметь решающее значение для достижения устойчивого потенциала цементной промышленности, и уже появляются многообещающие возможности. Например, один стартап использует меньшую долю известняка в своем цементе, что приводит к меньшему количеству технологических выбросов и выбросов топлива; процесс этой компании также фиксирует дополнительный CO 2 , который добавляется до отверждения бетона. Добавление CO 2 делает бетон более прочным и снижает количество необходимого цемента. Бетон, отвержденный углеродом, также может использовать CO 9.0003 2 захвачен во время производства цемента. Сегодняшние методы могут улавливать до 5 процентов CO 2 , образующегося в процессе производства, но новые технологии могут улавливать от 25 до 30 процентов. Такие продукты, как углеродсодержащий бетон, позиционируемые по-другому, могут принести «зеленую премию», потенциально давая компаниям преимущество среди покупателей, заботящихся об окружающей среде, и большую ценовую власть.
На горизонте технологии CCUS. Хотя зачастую они являются дорогостоящими и, возможно, (на данный момент) более подходящими для производства более ценных продуктов, таких как сталь, а не цемент, к 2050 году они могут сократить выбросы более чем вдвое. В настоящее время проводится ряд пилотных проектов по улавливанию углерода после сжигания, проводимых крупными производителями цемента. Другие компании тестируют кислородное сжигание, многообещающую, но дорогую технологию, которая приводит к высоким концентрациям CO 9 .0003 2 в дымовых газах, что, в свою очередь, обеспечивает почти полное улавливание углерода.
В конечном счете, для извлечения выгоды из технологий и инноваций потребуются дополнительные инвестиции, а также изменение мышления для компаний, которые слишком привыкли к существующему положению дел. Многие производители цемента не привыкли полагаться на партнерские отношения или работать в экосистемах, которые являются второй натурой в других отраслях. При сроках внедрения инноваций от пяти до десяти лет эти компании вскоре могут оказаться в ситуации, когда им предстоит играть в догонялки.
Новые горизонты роста
Устойчивое развитие в конечном итоге может стать катализатором, который подтолкнет отрасль к поиску роста за счет новых бизнес-моделей, партнерских отношений и подходов к строительству. Бетон на основе цемента останется предпочтительным строительным материалом во всем мире, но цепочки создания стоимости «устойчивого строительства», вероятно, появятся на региональном и местном уровнях, что потребует переориентации многих корпоративных портфелей.
В Соединенном Королевстве, например, переработанный материал из отходов строительства и сноса все чаще используется для замены заполнителей в бетоне. Производители цемента не спешили использовать эту возможность, уступив бизнес по переработке отходов местным строительным компаниям. Между тем, на других рынках традиционный цемент может конкурировать с улучшенным вариантом — энергетически модифицированным цементом (ЭМС), который выделяет меньше углерода и требует меньше энергии для производства. EMC уже использовался (в сочетании с традиционным цементом) для различных проектов в Техасе.
Помимо цемента и бетона существуют и другие возможности. Альтернативные строительные материалы и другие подходы, вероятно, будут играть важную роль в обезуглероживании цементной промышленности, хотя остается большая неопределенность в отношении того, насколько они сократят выбросы. Например, CLT уже используется на ряде рынков и поддерживается репутацией экологически чистого материала. Если примерно 10 процентов цемента будет заменено CLT, выбросы углерода будут сокращаться на 750 миллионов тонн в год (около 2 процентов глобальных выбросов). 3 3.
Для этого потребуется устойчивая вырубка примерно одной десятой части существующих бореальных лесов (расположенных в Северном полушарии). Преимущество CLT заключается в значительной секвестрации углерода: на каждую тонну предотвращенных выбросов углерода приходится две дополнительные тонны углерода.
Дополнительные новые пулы стоимости включают сборные и модульные дома, которые включают производство за пределами площадки, и BIM. Большая прозрачность означает меньше отходов и, вероятно, уменьшение необходимого количества цемента или бетона. Действительно, цифровые технологии одновременно поддерживают усилия цементной промышленности по обезуглероживанию и способствуют решению проблем ее роста.
Начало работы
Компании, которые надеются возглавить усилия по декарбонизации отрасли, должны определить наилучший путь вперед, использовать правильные технологические достижения и переосмыслить свои продукты, портфели и партнерские отношения. Тем не менее, принятие решений об инвестициях в текущие активы останется сложной задачей. Возможные решения включают построение кривой снижения выбросов, определение различных сценариев и создание дорожной карты, позволяющей принимать решения на основе результатов различных сценариев.
Двойная систематическая оценка вариантов декарбонизации может обеспечить прозрачность существующих рычагов и ускорить развертывание при одновременном внедрении инноваций в сотрудничестве с другими отраслями или секторами. Это включает в себя оценку конкретных предприятий и создание тепловых карт и кривых снижения выбросов, а также оценку партнерства местных экосистем со стартапами, другими участниками производственно-сбытовой цепочки или государственными учреждениями.
Климатическая математика: какой путь займет 1,5 градуса
Чтобы понять изменения в пулах стоимости, производители цемента должны разработать видение будущего целевого портфеля и последствий бизнес-модели, чтобы отразить ценность решений для устойчивого строительства. Промышленность останется местным бизнесом; следовательно, остается необходимость строить этот перспективный микрорынок за микрорынком. Оттуда результаты должны быть подняты, а сквозные возможности, такие как устойчивый бетон, должны быть приоритетными.
Успех такой стратегии, однако, зависит от способности лидеров добиться изменения мышления в масштабах всей организации, которое способствует переосмыслению текущего способа работы. Поэтому руководителям следует рассмотреть наилучшие способы поощрения всей организации на пути к декарбонизации.
Производители цемента приближаются к моменту истины. Такие проблемы, как обезуглероживание, постоянное нарушение цепочки создания стоимости и конкуренция со всей лоскутной игрой игроков строительной экосистемы, становятся все более значительными. При правильном подходе обезуглероживание и переосмысление могут идти рука об руку: точно так же, как автопроизводители все чаще рассматривают свою роль в обеспечении мобильности, а не просто в производстве автомобилей, цементные компании также могут заниматься предоставлением строительных решений. По мере того как климатические нагрузки усиливаются, а продажи традиционного цемента и бетона сталкиваются с угрозами, сочетание нового мышления, инноваций и новых бизнес-моделей будет иметь решающее значение для обеспечения прибыльного и более экологичного будущего.
Производители цемента разрабатывают план по сокращению выбросов CO2
Одна из крупнейших мировых отраслей промышленности и ведущий производитель выбросов парниковых газов, возможно, наконец-то предпринимает шаги для борьбы с изменением климата.
Недавно Всемирная ассоциация производителей цемента провела свой первый глобальный форум по изменению климата, на котором лидеры отрасли и ученые обсудили стратегии по сокращению углеродного следа отрасли. Это поможет в разработке плана действий по борьбе с изменением климата, который WCA намерена опубликовать в сентябре и который направлен на определение путей производства цемента с низким содержанием углерода.
«Форум по глобальному изменению климата ясно показал важность стимулирования инноваций, если мы хотим иметь хоть какую-то надежду на достижение парижских целей в области климата», — заявил Бернар Матье, директор программы WCA по изменению климата.
В то время как отрасли всех видов изучают способы сокращения своего углеродного следа, цементная промышленность — как бы непривлекательно это ни звучало — является одной из наиболее значимых для участия в обсуждении.
Цемент является наиболее широко используемым из существующих искусственных материалов. Он образует бетон при смешивании с водой и используется при строительстве всего, от зданий и мостов до дорог и тротуаров и всех видов другой инфраструктуры.
Но хотя цемент в значительной степени сформировал современную застроенную среду, он также является крупным источником углекислого газа в атмосферу. По оценкам Международного энергетического агентства, на его долю приходится около 7 процентов всех глобальных выбросов углерода. Это делает его вторым по величине промышленным источником выбросов в мире, уступая только черной металлургии.
Это проблема, которой общественность часто не уделяет должного внимания. Но беспокойство среди ученых растет. По мере роста населения планеты, по некоторым оценкам, к 2050 году производство цемента может увеличиться на целых 23 процента. А некоторые эксперты предполагают, что, если промышленность существенно не сократит свои выбросы, это может поставить под угрозу глобальные климатические цели Парижского соглашения.
В апрельском отчете IEA и инициативы по устойчивому развитию цемента, возглавляемой отраслью, отмечается, что отрасль в ее нынешнем виде не соответствует траекториям, которые позволили бы миру достичь целевого показателя температуры в 2 градуса Цельсия. Достижение этой цели, говорится в отчете, «предполагает значительно большие усилия по сокращению выбросов от производителей цемента».
Гонка за решениями
Портландцемент — наиболее широко используемый тип цемента во всем мире и продукт, указанный во многих современных строительных нормах и правилах — был запатентован почти 200 лет назад и стал важным компонентом застройки. По словам Гаурав Сант, профессора гражданской и экологической инженерии Калифорнийского университета в Лос-Анджелесе, с тех пор мало что изменилось в производственном процессе.
«Были улучшения в эффективности процессов, но в целом разница невелика», — сказал он E&E News.
Это большая проблема для климата, потому что в процессе выделяется большое количество углекислого газа. Огромный углеродный след отрасли частично связан с ее высокими потребностями в топливе, которые в основном удовлетворяются за счет ископаемого топлива. Но более половины его выбросов — а по некоторым оценкам, возможно, даже две трети — на самом деле связаны с самим процессом химического производства, который выделяет большое количество углекислого газа в качестве побочного продукта.
Портландцемент производится в основном из известняка, породы, состоящей в основном из химического соединения, называемого карбонатом кальция. По словам эксперта по гражданскому и экологическому строительству Клэр Уайт из Принстонского университета, для производства липкого вяжущего цемента известняк необходимо нагревать до высоких температур — около 1500 °C.
Интенсивный процесс нагрева сам по себе, отметила она, требует огромного количества топлива. Но это также вызывает химическое разложение известняка, оставляя после себя соединение, называемое оксидом кальция, которое используется в конечном продукте цемента, выделяя углекислый газ в атмосферу.
Особая формула, используемая для цемента, и тот факт, что она так долго оставалась неизменной, делают отрасль необычайно сложной, когда речь идет о борьбе с изменением климата. В комментарии, опубликованном в прошлом месяце в журнале Science , оцениваются различные услуги и процессы, которые трудно декарбонизировать. Он отметил, что для решения проблемы с цементом нет единого решения — для этого потребуются различные подходы, включая серьезные изменения как в используемых материалах, так и в самом производственном процессе.
В последние годы эта проблема привлекла внимание крупных международных организаций, некоторые из которых в настоящее время консультируют промышленность по вопросам сокращения выбросов углерода. В апрельском отчете МЭА содержится дорожная карта низкоуглеродных технологий, направленная на сокращение выбросов цементной промышленности на 24 процента к 2050 году. сам цементный продукт.
Исследовательские группы по всему миру уже занимаются многими из этих проблем. Некоторые группы работают над химическими формулами, которые уменьшат количество «клинкера» — вещества, которое требует нагревания известняка, — которое входит в состав цемента.
Уайт, инженер из Принстона, возглавляет университетскую группу устойчивого цемента, которая работает над тем, чтобы полностью исключить потребность в клинкере. Она отметила, что можно производить похожие на цемент продукты, используя вместо этого другие вещества, в том числе переработанные побочные продукты из других отраслей, такие как сталелитейный шлак, летучая зола с угольных установок или определенные типы глин. Обработка этих веществ специальными химическими соединениями, известными как щелочи, «может сделать порошки реактивными, — сказал Уайт, — и мы можем сформировать аналогичные строительные блоки на молекулярном уровне по сравнению с тем, что содержится в портландцементном бетоне».
Тем не менее, есть некоторые споры о том, сколько именно углерода связано с активируемыми щелочью цементами, добавила она, что иногда может затруднить сравнение с портландцементом. Это частично зависит от того, какой именно источник щелочи и в каком количестве используется в процессе, и как далеко должны быть доставлены материалы. По некоторым оценкам, эта практика может снизить выбросы на 40-80 процентов по сравнению с портландцементом, сказал Уайт.
Другие исследователи используют другую тактику. Сант, инженер Калифорнийского университета в Лос-Анджелесе, участвует в исследовательской группе, разрабатывающей продукт, который они назвали «CO2NCRETE». Процесс основан на «переработке углерода» — использовании выбросов CO2, уловленных в результате промышленной деятельности, для производства похожего на цемент и потенциально углеродно-нейтрального строительного материала. По словам Сэнта, процесс CO2NCRETE уникален, потому что он может использовать захваченные выбросы углерода как есть, без необходимости дополнительной обработки.
Другие эксперты отмечают, что бетон естественным образом поглощает углекислый газ. Это медленный процесс, но в течение десятилетий он сможет поглотить значительное количество выбросов, которые он выбрасывает в атмосферу, в первую очередь за счет нагревания известняка.
В статье 2016 года в Nature Geoscience предполагается, что бетон в мире поглощает около 43 процентов этих первоначальных выбросов. Сант отметил, что могут быть некоторые способы ускорить или усилить этот процесс поглощения — это область, на которой сосредоточена его собственная исследовательская группа.
Стивен Дэвис, специалист по системам Земли из Калифорнийского университета в Ирвине, один из авторов статьи Nature Geoscience , а также комментария Science , опубликованного на прошлой неделе, отметил, что поглощающий потенциал бетона подразумевает, что могут быть способы сделать производство цемента углеродно-отрицательным.
Если бы, например, все предприятия по производству цемента были оснащены технологиями улавливания и хранения углерода, то можно было бы предотвратить попадание значительного количества выбросов, производимых на месте, в атмосферу. Позже произведенный бетон будет поглощать еще больше углекислого газа, что в конечном итоге может привести к «чистому поглощению из атмосферы», сказал он E&E News.
В то время как различные исследовательские группы используют разные подходы, технологическая дорожная карта МЭА предполагает, что для достаточно быстрого сокращения выбросов, необходимого для достижения глобальных климатических целей, потребуются различные стратегии, работающие вместе. По словам Уайта, это, вероятно, самый успешный подход.
«Могут быть лидеры с точки зрения того, что может помочь или что мы можем использовать в ближайшем будущем, но это не значит, что мы не должны искать более инновационные материалы в будущем», — сказала она. «Это не просто одна технология, на которую нам нужно обратить внимание, чтобы решить проблемы устойчивости, связанные с бетонной промышленностью».
Несмотря на растущий интерес к исследованиям и разработкам, существуют препятствия для внедрения решений. Одним из них является отсутствие политических стимулов для убеждения производителей цемента инвестировать в новые технологии.
«Что касается крупных производителей, то мне не ясно, является ли это очень большим приоритетом», — сказал Дэвис. «У меня нет ощущения, что они считают, что это рынок для потенциальных прорывов».
Ограничение выбросов или системы ценообразования на выбросы углерода являются одними из наиболее часто обсуждаемых решений. Тем не менее, даже там, где такие рамки существуют, могут возникнуть проблемы.
В прошлом Система торговли выбросами Европейского Союза подвергалась критике за предоставление бесплатных квот на выбросы углерода крупным загрязнителям, включая производителей цемента. В недавнем отчете CDP, британской организации, которая выступает за прозрачность воздействия корпораций на окружающую среду, отмечается, что «углеродное регулирование для сектора остается щадящим, а сектор в Европе продолжает извлекать выгоду из избыточных бесплатных квот». В отчете предполагается, что цены на углерод, возможно, должны вырасти в три-шесть раз, чтобы стимулировать внедрение улавливания углерода и других инновационных технологий.
Есть и другие проблемы. Цементная промышленность — очень консервативный сектор, отметил Сант, и не без оснований. Строительство жизненно важной инфраструктуры, такой как здания и мосты, сопряжено с большим беспокойством по поводу безопасности и большим беспокойством по поводу внедрения новых, менее проверенных материалов.
«Поскольку мы используем этот материал так долго, с ним связано большое доверие пользователей», — сказал Сант. Возможно, это сделало отрасль более устойчивой к инновациям, чем другие.
Правительственные регулирующие органы могут быть столь же консервативны, когда речь идет о строительных нормах. По словам Уайта, в США, Европе и многих других развитых странах эти нормы обычно основаны на химическом составе портландцемента. Использование другого продукта для строительного проекта, скорее всего, потребует одобрения соответствующего регулирующего органа, что не всегда легко получить.
«В этой области ведется активная работа, чтобы попытаться предоставить информацию, необходимую организациям, занимающимся кодами, о том, как они могут дополнить коды, чтобы обеспечить больше инноваций в строительных материалах», — сказала она. Это означает, что необходимы новые идеи о том, как сократить выбросы в отрасли, демонстрируя при этом, что эти новые продукты безопасны.
В то время как исследовательский интерес растет, прогресс в частном секторе на данный момент проявляется, но может быть медленным.
В недавнем отчете CDP оценивается готовность 13 крупнейших в мире публичных цементных компаний к переходу на низкоуглеродные технологии. Это говорит о том, что выбросы компаний снижаются в среднем примерно на 1 процент в год. Но в нем отмечается, что этого едва ли достаточно, чтобы идти в ногу с траекториями, соответствующими климатической цели 2C. В отчете также отмечается, что доля инвестиций в исследования и разработки в объеме продаж невелика по сравнению с другими отраслями.
Тем не менее, недавний форум по изменению климата, организованный Всемирной цементной ассоциацией, может свидетельствовать о том, что отрасль начинает настаивать на дополнительных действиях. И разнообразие различных подходов, которые изучают эксперты, может помочь облегчить этот путь.
«Вы не хотите пытаться навязывать изменения в одночасье — вы хотите иметь возможность инсценировать изменения», — сказал Сант. «Вы хотите иметь возможность оценивать пути с низким и высоким риском, чтобы вы действительно создали портфель решений, а не только тот, который подходит для конкретных вещей».