Из чего делают газосиликатные блоки: Страница не найдена — Строительные материалы от А до Я
Производство газосиликатных блоков — способы и технологии (видео)
Этот ячеистый строительный материал сегодня используется в разных сферах строительства. А производство газосиликатных блоков может стать прибыльным бизнесом.
Популярность газосиликата объясняется просто:
- материал считается экологически чистым;
- низкий вес газосиликата значительно снижает затраты на обустройство фундамента здания;
- четкая геометрия газосиликатных блоков обеспечивает простой и быстрый монтаж;
- для соединения блоков можно использовать клей, а не цемент;
- более низкая, по сравнению с кирпичом и ячеистым бетоном, цена;
- негорючесть;
- высокие тепло- и звукоизоляционные характеристики;при толщине стены в 50 сантиметров необходимость делать наружное утепление отпадает;
- легкость отделки;
- стойкость к гниению;
- простота обработки.
Можно нередко встретить сравнение газосиликата с пенобетоном.
Все это способствует росту спроса на этот материал, соответственно, делает производство газосиликата выгодным бизнесом.
Патент на изобретение
Технология была изобретена в начале двадцатого века. А примерно в 1920 году была усовершенствована шведским архитектором Эрикссоном, который в 1924-ом получил патент международного образца на автоклавный способ производства газосиликата. Метод быстро стал популярным в Швеции, откуда распространился по другим странам.
Главное условие успеха — технология производства газосиликатных блоков должна соблюдаться досконально. Только тогда конечный продукт будет обладать заявленными характеристиками.
Также предлагаем ознакомится со статьёй, в которой мы сравним такие материалы как газобетон и пенобетон.
Работа под давлением
На первом этапе производственного цикла исходное сырье необходимо очистить от крупных включений и мусора. Это делают с помощью специального сита. Все ингредиенты — цемент, негашеная известь, кварцевый песок, газообразующая добавка (алюминиевая пудра) и вода, перемешиваются в бетоносмесителе.
Готовый состав заливается в специальные формы, которые затем проходят термическую обработку в автоклаве. Высокая температура (200˚С) и давление (10 — 12 атмосфер) провоцируют химические реакции, в результате которых выделяется газ – в материале образуются поры.
Закончив «выпекание», блоки на некоторое время оставляют в автоклаве. Это необходимо, чтобы конечный продукт набрал нужную прочность и хорошенько просох.
Точная геометрия
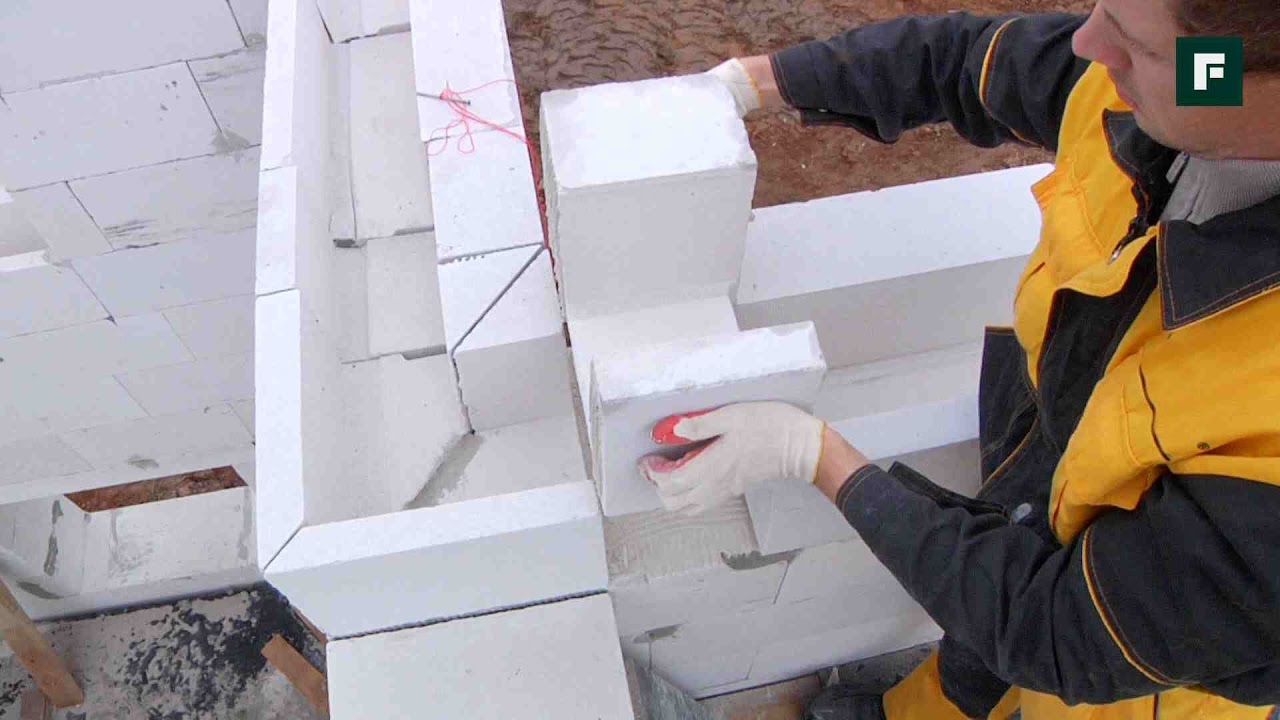
Поскольку газосиликат – материал пластичный, очень легко режется (можно резать даже болгаркой или станком для резки камня) и обрабатывается, можно делать блоки разных размеров и конфигурации. Стандартные для России габариты — 60 х 30 х 20 сантиметров. В ширину блоки могут быть от десяти до пятидесяти сантиметров. В высоту – от двадцати до тридцати.
Выгодный бизнес
Технология достаточно проста, и это становится причиной, по которой множество людей решаются организовать производство газосиликатных блоков. Видео, размещенное в интернете, позволяет подробно познакомиться с процессом и узнать о различных тонкостях изготовления этого материала. По большому счету, наладить производство газосиликата можно даже в собственном гараже или подсобном помещении на даче.
Специальное оборудование
При изготовлении газосиликата используются специальные станки – установки для производства блоков. Сейчас в продаже есть оборудование разных габаритов, в том числе – довольно компактное, для размещения которого не требуется много места. С их помощью можно работать на рынке мелкого опта. Но при желании брать крупные заказы понадобится приобрести более производительную технику. Впрочем, все можно делать постепенно. Начав с малого, создать внушительное производство газосиликата. Способы развития своего бизнеса каждый предприниматель выбирает самостоятельно.
Внутри и снаружи
Сегодня выпускается несколько видов газосиликатных блоков, которые отличаются разной плотностью материала.
Конструкционно-изоляционный газосиликат имеет плотность 500-900 кг/куб.м. Теплоизолирующий — 350-400 кг/куб.м. При плотности более 700 кг/куб.м этот строительный материал может использоваться при возведении многоэтажных зданий.
Из газосиликатных блоков делают стены внутри строений и наружные. Есть разновидности блоков, предназначенные специально для устройства проемов окон и дверей.
Газосиликатные блоки можно назвать универсальным строительным материалом, легким и теплым. Однако у него есть свои особенности: например, он очень быстро впитывается влагу, и характеризуется высокой способностью водопоглощения. Поэтому строить из него здания в слишком влажном климате, где влажность составляет более шестидесяти процентов, не целесообразно.
Рекомендуем к прочтению — характеристики пенобетонных блоков.
Как сделать газосиликатные блоки своими руками
Строительство собственного дома или каких-либо близлежащих сооружений — это всегда нужный и интересный процесс, который отнимает много сил, времени и денег. Поэтому почти все строительные материалы люди навострились делать своими руками. В разное время сложность работы то повышается, то понижается, но в 21 веке такой процесс приобрел новые формы, т. к. началось производство газосиликатных блоков своими руками.
Схема двухслойной стены из газосиликата.
Основные аспекты деятельности
Перед тем как начать изготовлять газосиликатные блоки, необходимо знать множество особенностей производства.
Самое важное — это вариативность производственного процесса, т.к. могут использоваться различные составы, в зависимости от технологического процесса.
Так в качестве основных реагентов может использоваться песок с цементом, но возможен вариант и с сочетанием зола-цемент. Вода и медная стружка остаются без изменений, т.к. вода служит для разжижения и сцепки элементов, а алюминиевая стружка вступает в реакцию, что способствует образованию пор.
Виды газосиликатных блоков для строительства.
В промышленности используется элемент автоклавирования, но при ручной работе это невозможно, поэтому и деятельность немного перепрофилируется.
Нужно изготавливать такую смесь, которая не требует пропаривания для максимального набора прочности.
Существует множество способов разрезать газобетон, но лучше сразу заливать нужную форму, т.к. при домашней работе лишние телодвижения будут отнимать слишком много времени.
Обычно используются пилы и фрезы для дерева, т.к. они делают идеальный пропил в кратчайшие сроки, но для придания формы можно воспользоваться электролобзиком.
Конструкция очень легкая, поэтому можно использовать армирующий прут не толще 6 мм. Его можно изогнуть сразу в виде каркаса, а можно сделать и всего одну обрешетку, в зависимости от требуемой итоговой прочности, а также толщины изделия.
Вернуться к оглавлению
Основной вариант рабочей деятельности
Тут будет использоваться стандартная песчано-цементная смесь, но объем раствора будет приведен пробный, чтобы точно знать, что в итоге получится. Потребуются следующие инструменты и материалы:
Схема производства блоков на строительной площадке.
- емкости для материалов;
- емкости для смешивания;
- насадка для растворов на дрель;
- цемент м500 — 1900 г;
- вода горячая — 1400 мл;
- мелкий кварцевый песок — 1900 гр;
- алюминиевая стружка — 3 гр;
- порошок стиральный — 0,3 гр;
- NaCl — 19 г;
- пластификатор — 19 мл;
- перчатки резиновые;
- респиратор;
- формы;
- машинное масло.
В самом начале процесса изготовления газосиликатных блоков подготавливается газообразующая смесь. Для этого в небольшой емкости смешивается алюминиевая стружка, стиральный порошок и немного воды. Размешивать направленно нужно в течение 3 минут, при этом нужно быть внимательным к стружке, т.к. от нее может подняться сильная пыль.
Стиральный порошок служит для обезжиривания стружки, но на деле никакого негатива не привнесет. Вся работа выполняется в перчатках и респираторе, дабы не нанести себе какую-нибудь травму.
А пока суспензия настаивается, можно начинать изготовление раствора. Для этого песок засыпается в емкость, а сверху засыпается сухая цементная смесь. Получившаяся сухая смесь перемешивается тщательнейшим образом, чтобы в итоге не оставалось комочков и неоднородных мест. Для перемешивания дрелью обычно уходит не более 2-3 мин, но в маленьких объемах хватит и 1 мин.
Сферы применения газосиликатных блоков.
В сухую смесь выливается вода, причем нужно в банке оставить 200 мл. В воду в банке выливается пластификатор и высыпается хлористый натрий. Получившаяся консистенция перемешивается, но уже без фанатизма, как это было со стружкой. Тут достаточно 20-25 сек поболтать, после чего отодвигать в сторону.
Песчано-цементная смесь, уже залитая водой, перемешивается несколько минут до однородной массы. Тут уйдет немного больше времени, чем для предварительной сухой смеси, т.к. нужно пропитать раствор полностью. Если сухую смесь засыпать в воду, то раствор получится с комочками, поэтому за данным шагом нужно следить особенно внимательно.
Теперь в смесь можно добавить разбавленную воду, а также алюминиевую суспензию. Раствор перемешивается самым тщательным образом до того момента, как с поверхности пропадет серебристая пленка (не более 2-3 мин). В итоге получается достаточно разжиженная масса.
В качестве пробной формы можно использовать любые емкости, смазанные машинным маслом или отработкой (как вариант — полиэтиленовая пленка). Раствор заливается на 50% от суммарного объема емкости, т. к. оставшийся объем дойдет самостоятельно.
http://ostroymaterialah.ru/youtu.be/TrdGbc-umw8
Вернуться к оглавлению
Улучшенный вариант деятельности и ее итоги
Инструменты и материалы сохраняются прежние, но вместо песка используется зола. При ограниченном количестве форм нужно учитывать тот факт, что в данном случае вспенивание будет гораздо лучше.
Процесс идентичен предыдущему полностью, но заливка осуществляется лишь на 40%. После этого, как и в первом случае, нужно оставить раствор на сутки на высыхание в неподвижном положении. Смесь останавливает свой активный рост буквально через 1 час, но газообразование происходит и дальше. По этой причине крайне нежелательно снимать респиратор, а также нужно воспользоваться качественной вентиляцией или просто открыть окно, чтобы была хорошая циркуляция воздуха.
Спустя сутки формы уже можно начинать двигать, причем при желании можно даже формы снять.
http://ostroymaterialah.ru/youtu.be/y3ilqDmJ_x4
В итоге можно обратить внимание, что получившиеся газосиликатные блоки с песком будут значительно прочнее и тяжелее, тогда как зола дает гораздо больший объем и легкость, что благотворно сказывается на теплоизоляционных качествах. Приведенное соотношение является лабораторным, поэтому на практике можно взять любой из 2-х вариантов, после чего добавлять или уменьшать количество компонентов в зависимости от итоговых требований.
Изготовление газосиликатных блоков — это не только способ сэкономить деньги при собственном строительстве, а одна из популярных во многих местностях бизнес-идей. Небольшая подработка в выходной день, которая иногда позволяет превысить основную заработную плату.
Производство газосиликатных блоков: технология, оборудование (станок)
Для тех, кто ищет способ создать бизнес на дому, производство газосиликатных блоков станет выгодным решением. Сегодня вы познакомитесь с особенностями изготовления газосиликата и узнаете, как открыть такой бизнес.
Коды ОКВЭД, требуемые при регистрации ИП по данному виду деятельности: 26.61: Производство изделий из бетона для использования в строительстве; 26.66: Производство прочих изделий из бетона, гипса и цемента; 51. 53: Оптовая торговля лесоматериалами, строительными материалами и санитарно-техническим оборудованием.
Содержание статьи:
Технические характеристики материала
Газосиликатные блоки – высококачественный строительный материал. Они отличаются низкой себестоимостью, экологически чистым производством и небольшим весом. Эти качества позволили материалу получить широкую популярность в строительной промышленности.
Блоки имеют высокую прочность, а благодаря ячеистой структуре, газосиликат может обладать плотностью от 300кг/м³ до 700кг/м³, равномерно распределенной по всему блоку, что так же увеличивает популярность этого товара среди строительных компаний.
Требования к производственному помещению
Помещение, отведенное под производство газосиликатных блоков своими руками, должно отвечать некоторым требованиям. Для хранения сырья и готовой продукции, понадобится специально отведенное место. Высота помещения должна составлять не менее трех метров.
Так же, тех. процесс предусматривает наличие электросетей напряжением 380В и 220В, водопровода и подъездных путей. Само помещение должно быть утепленным и очищенным от грязи и мусора.
Производство газосиликата считается безотходным, поэтому в канализации на территории мини-завода нет необходимости.
Оборудование для производства газосиликатных блоков
Чтобы организовать мини-завод в гараже или небольшом арендованном помещении, вам понадобятся следующие станки для производства газосиликатных блоков:
- Вибросито
- Автоклав промышленный;
- Формы для блоков;
- Шаровая мельница;
- Бункер-дозатор;
- Бетоносмеситель.
Цена оборудования
Где и по какой цене можно купить хорошее оборудование для производства газосиликата? Остановимся на этом вопросе поподробнее:
- Вибросито для просеивания песка. Подойдут недорогие варианты, занимающие мало места, такие как: вибросито ВО-1, производства Авер-Иркутск, мощностью 0,25 кВт – 320$, вибросито ВО-01, ООО «Строительное оборудование» — 370 долл.
, вибростол ВС-250, Строймашсервис-Дон – 575$, вариант без вибратора, Стройтехнополис – 125 долларов, машина от Элси-строй – 520$, ВИБРОМАШ ВО-1, Дельта-инжиниринг – 450 долларов;
- Шаровая мельница. Уралмаш МШЦ-210*3000 – 1740 долларов, Уралмаш МСЦ-3600*4500 – 1740$, мельница шаровая МШМП-0.8 – до 5750 долл., мельница от ЗАО Паритет сухого помола – 3710 долларов; ЗАО Паритет мокрого помола – 3310$;
- Дозаторы. Бункер — дозатор БД-30 от Златоустовского завода бетоносмесительного оборудования – 5750 долл., Бункер дозатор для бетоносмесителя от НПО КСК – 1130 долларов;
- Бетоносмеситель. Варианты от компаний: Комплект-ЮГ – 90$, Б 130 «Энтузиаст» — 180 долл., Афалина Челябинск – 225 долларов, TOR 46л. От Торгового дома ТОР – 125$;
- Формы. Металлические кассетные формы для ячеистого бетона из Красноярска, компания ГК ТСК – 185 долларов, Металлическая кассетная форма Строй механика Киров – 315$, форма «Стандарт-1», на 36 блоков – 350$;
- Автоклав.
Машина производства «УралЦентрКомплект» Аг-1200 тз – 43 550$, автоклав проходной АП 1,2 – 2*17, производства «Стройкомплекс Брик» — 26 135 долларов.
Чтобы купить качественный станок для производства газосиликатных блоков, придется тщательно выбирать подходящий именно вам вариант и сопоставлять их мощность и производительность.
Для сравнения цен и технических характеристик производственных машин, рекомендуется изучить и зарубежный рынок.
Особое внимание советуем обратить на технику из Китая. Такое оборудование для производства газосиликата отличает широкий ассортимент и доступная цена.
Технология производства газосиликатных блоков
Для производства, помимо оборудования, вам понадобится знание технологии изготовления и пропорции сырья.
Процесс производства газосиликатных блоков
Процесс довольно прост в исполнении. При соблюдении пропорций и правильном выполнении технологии, будет получен качественный продукт.
- С помощью вибросита отделить сыпучий материал от лишних фрагментов;
- Измельчить сырьё для производства газосиликатных блоков в шаровой мельнице;
- Соблюдая пропорции, смешать все сыпучие составляющие, кроме алюминиевой суспензии;
- Произвести повторное просеивание;
- Добавить алюминиевую пудру и воду, тщательно перемешать;
- Наполнить формы смесью на ½ от общего объема каждой из них;
- Оставить формы с массой при температуре не менее 40° на 2 часа;
- Обработать блоки с помощью автоклава;
- Оставить на 3 часа для завершения химических процессов и набора прочности.
Если вы хотите производить гозобетонные блоки в соответствии с межгосударственными стандартами, то ознакомьтесь с положениями ГОСТ 31360-2007, 21520-89, 25485–89, 31359, где описаны требования к стеновым неармированным изделиям из ячеистого бетона автоклавного твердения.
В продаже можно найти различные размеры газосиликатных блоков, но согласно ГОСТу 31360, размер каждого блока должен соответствовать следующим нормам: длинна – 625мм, ширина – 500 мм, высота – 500мм.
Пропорции ингредиентов для изготовления смеси
Рассмотрим, из чего делают газосиликатные блоки. Для производства 1 куб.м газосиликатной смеси понадобятся ингредиенты в следующих пропорциях: вода – около 450л., цемент – 60кг (от 8% до 10%), кварцевый песок – 450 кг (до 70%), гипс – 0,5 кг (до 2%), известь – 120 кг (процент извести вот 12% до 20%), а так же алюминиевая пудра – 0,5 кг (до 2%).
Чтобы достичь наибольшего показателя плотности материала, доля пор должна составлять не более 38%, такой строительный блок подходит для капитального строительства.
При среднем показателе плотности, газосиликат представляет собой материал, с долей пор не более 52%.
Наибольшая допустимая пористость легкого ячеистого материала составит до 92%. В последнем случае, применение газосиликатных блоков допустимо только для теплоизоляции.
Производство газосиликатных блоков в домашних условиях
Такое производство возможно, при наличии помещения, отвечающего соответствующим требованиям.
Блоки, изготовленные в домашних условиях, уступают по качеству товару, выпущенному на производственной линии.
Прежде всего, это обусловлено техническими характеристиками используемой техники. Но следует заметить, что газосиликат, произведенный небольшим частным заводом, пользуется не меньшим спросом, чем заводской, благодаря доступной цене и небольшой разнице в качестве строительного материала.
Подсчет рентабельности
Подсчитаем сроки окупаемости и прибыльность небольшого домашнего завода по производству газосиликатных строительных блоков.
Инвестиции
Вибросито – 450 долларов;
Шаровая мельница – 5 750$;
Бункер-дозатор для бетоносмесителя – 1 130 долл.;
Бетоносмеситель – 225 долларов;
Формы – 350$;
Автоклав – 26 135 долларов.
Итого: 34 040 долл.
Затраты на 1 кубометр сырья
Вода – 450л. – 0,6$;
Цемент – 60кг – 2,5 долл.;
Кварцевый песок – 450кг – 7,8 долларов;
Гипс – 0,5кг – 0,1$;
Известь – 120кг — 6,2 долл. ;
Алюминиевая пудра – 0,5кг – 0,1$.
Итого: 17,3 долларов/1 куб. м.
Объем производства на нашем мини-заводе составит 1500 куб. м. в месяц, продажная цена 1м³ — 45$. При полной реализации, ежемесячный доход составит 67 500 долларов. Чистая прибыль – 24 250$ в месяц. С учетом сопровождающих изготовление и реализацию товара факторов, вложения в небольшой частный завод окупятся за 3 месяца работы.
Подведем итоги. Анализируя объем прибыли и срок окупаемости инвестиций, можно сказать, что газосиликатные блоки как бизнес, являются доходным предприятием с высоким коэффициентом рентабельности.
Понравилась статья? Поделитесь с друзьями:
Газосиликатные блоки | KSG
Технология производства газосиликатных блоков
Тонкости строительства – о них и не знает и не подозревает городской человек, задумавший построить у себя на участке дом. Не будучи профессионалом, очень сложно оценить будущий проект дома и принять правильное решение.
Предлагаем вашему вниманию изучить производство газосиликатных блоков, из чего их делают, достоинства и преимущества этого строительного материала. Небольшие знания в этой области помогут вам сделать правильный выбор.
Газосиликатные блоки в настоящее время нашли широкое применение в строительстве благодаря отличной теплопроводности и долговечности плюс низкой цене. Срок службы газосиликата 80 лет – такой же, как и у кирпича.
Технология производства газосиликатных блоков появилась в начале 20-го века, но стала широко известна не так давно. Она осталась практически такой же, и это свидетельствует о высокой надежности, качестве и простоте в изготовлении и использовании.
Сам блок изготавливается при помощи химической реакции силикатной смеси и алюминиевой пудры. Силикатная пена, которая образуется в результате данной реакции, проходит затем для повышения прочности автоклавную обработку. На выходе получается готовый газосиликатный блок.
Для изготовления газосиликата применяют только природные материалы, а это значит, что экологичность и долговечность данного материала выше всяких ожиданий. Маленький вес и большой размер – все это снижает расходы на трудоемкость обработки. Газосиликат огнестоек, так как сам материал, из которого изготавливают блок, не горюч. Пористая структура газосиликата закрыта, и это обеспечивает отличную тепло и звукоизоляцию и влагостойкость. А самое главное – это низкая цена этого удивительного строительная материала. Так как материал экологичен, то производство газосиликатных блоков не загрязняет окружающую среду.
Немного об истории: производство газосиликатных блоков было открыто в Швеции, а так как у этого материала отличные качества, то этот материал быстро распространился по всему миру.
Тем более, что технология производства газосиликатных блоков не требует особых капиталовложений. Но есть один нюанс — производство Российских газосиликатных блоков требует к себе ответственного отношения, и сама технология производства европейских газосиликатных блоков должна быть выдержана. В противном случае на выходе получается некачественный материал, который использовать в строительстве небезопасно.
Газосиликатные блоки изготавливаются на автоматизированных линиях. Как уже говорилось выше, производство газосиликатных блоков использует только экологичные материалы. Это цемент, известь, песок, алюминиевая пудра.
Материалы автоматически по конвейеру подаются в смеситель, где их перемешивают по строго определенной программе. Затем смесь заливается в формы, и начинает подвергаться ударным воздействиям. Таким образом улучшается пористая структура. И тут происходит самое интересное — начинается процесс газообразования, и смесь поднимается, как дрожжевое тесто. Огромное количество маленьких пор возникают в блоке. Отсюда и название – газосиликатный. Дальше ждут 60-80 минут, пока материал затвердеет, а затем вынимают его режут на отдельные блоки при помощи тонких струн и ножей.
Далее блоки выдерживают при высокой температуре и пара при давлении 12 атм. В этом то и весь секрет производства – в результате получается ячеистая структура, уникальная по своим свойствам. Таких свойств у материала без автоклавной обработки вы не найдете нигде!
И последний этап: готовые блоки прибывают по конвейеру на линию упаковки, при этом используется специальная разрывная машина, устанавливаются на поддон и упаковываются. Готовая продукция затем при помощи транспортера уезжает на склад, где и ожидает продажи.
Производство газосиликатных блоков: оборудование, цены
Все большую популярность в качестве строительного материала в наши дни набирают газосиликатные блоки. Выбор в их пользу делают как частные лица, так и строительные компании. Основными причинами такого необыкновенного спроса являются надежность этого материала и экономическая выгода, обусловленная крайне низкой ценой на газосиликатные блоки и, весьма небольшими затратами при его использовании для строительства зданий. Кроме этого, они позволяют быстро и качественно организовать строительство дома из газосиликатных блоков своими руками.
Стоит отметить, что для разных случаев применения используются различные виды силикатных блоков:
- В качестве утеплителя используются блоки, плотность которых составляет 350 кг/м.
- Для строительства домов с тремя и менее этажами применяются блоки плотностью 400 кг/м.
- Выше трех этажей – 500 кг/м.
- Высокоэтажные сооружения строятся из блоков, плотность которых составляет 700 кг/м.
Фото: дом из газосиликатных блоков
Процесс изготовления блоков в заводских условиях
Газосиликатные блоки изготавливают в заводских условиях. Самые крупные и известные компании, выпускающие эти изделия, применяют самое совершенное оборудование для производства газосиликатных блоков, произведенное в Германии. Данные линии способны контролировать каждую стадию процесса изготовления блоков, начиная с самых первых этапов и заканчивая проверкой теплоизоляционных свойств готового изделия.
Что касается технологии, то здесь используются известь, вода, цемент и кварцевый песок, смешанные в строго определенных пропорциях. Кроме этого, для создания пористой структуры в смесь добавляется алюминиевая пудра, которая является образователем газа. Во время перемешивания происходит химическая реакция, приводящая к вспениванию смеси. Технологичная аппаратура способна даже регулировать диаметр этих пузырьков для получения пор нужного размера.
Производство газосиликатных блоков полностью автоматизировано, позволяет получать изделия максимально высокого качества с минимальным количеством брака.
Весь процесс изготовления газосиликатных блоков состоит из ряда последовательных этапов, для каждого из которых используется свое оборудование.
Система измельчения и дробления сыпучих материалов
В данной системе используется больше всего различного оборудования:
- Бункер для песка.
- Элеватор.
- Бункер для хранения извести.
- Хранилище для извести.
- Шаровая мельница.
- Электронные приборы для взвешивания порошка.
- Ленточный конвейер.
- Автоматический смеситель.
- Дробилка.
На данном этапе происходит перемешивание песка и воды до состояния жидкой смеси. Полученное вещество направляется в смесительное отделение. Там в него добавляются и остальные компоненты смеси в строго определенной пропорции и последовательности. После тщательного перемешивания добавляется алюминиевая суспензия и снова происходит перемешивание, которое контролируется электронными системами.
Заливка и дозирование
В этой системе используется следующее оборудование:
- Заливочная платформа.
- Система газораспределения.
- Заливочный смеситель.
Здесь происходит заливка смеси в формы и транспортировка в зону созревания. В течение нескольких часов происходит бурная реакция с выделением водорода и появляется необходимая пористая структура.
Резка и группировка
Используются:
- Захват для переворачивания.
- Машина для резки.
Полученный массив газосиликата разрезается с получением системы гребень-паз. Применяемое оборудование позволяет производить нарезку практически с ювелирной точностью. Самое интересное, что полученные после нарезки отходы можно отправлять на переработку и использовать в получении новой смеси. Это делает производство газосиликатов безотходным.
Набор прочности в автоклаве
Оборудование:
- Паровой котел.
- Рельсы.
- Автоклав.
В автоклаве нарезанные блоки набирают прочность путем постепенного выпаривания при высоком давлении. После этого давление уменьшается и блоки выезжают с платформы.
Упаковка
Используется следующее оборудование:
- Кран.
- Колодки.
- Приборы, замеряющие точность нарезки.
- Упаковочная линия.
С помощью крана происходит захват ряда блоков и выкладывание для дальнейшего остывания. Затем на автоматической линии происходит упаковка блоков. Одновременно с упаковкой происходит выписка документов, содержащих всю необходимую информацию об изделии.
В качестве примера можно сказать, что цена линии для изготовления газосиликатных блоков, производительностью 300 тыс.
м3/год составляет примерно 900 тысяч долларов.
Конечно, можно изготавливать блоки и на более простом оборудовании, которое стоит дешевле, но и себестоимость такого производства будет значительно выше, что в некоторых случая попросту нецелесообразно.
Видео
Особенности и применение газосиликатных блоков в строительстве
По нормативным расчетам, с учётом теплопроводности газосиликатных блоков для Московского региона, толщина стены должна быть минимум 400 мм при плотности D 500. На практике многие закладывают в проекте толщину больших размеров, но не выше 600мм. Это делают по нескольким причинам:
- В нормативах указана толщина стены для нормальной по влажности среды (в лабораторных условиях). Если блоки начинают впитывать влагу, стены теряют в прочности и в теплоте. Аналогичный пример — выйти на мороз в увлажнённой тёплой одежде.
- Следует также учитывать потери в швах — от 5% (раствор на клеевой основе) и до 30% (цементо-песчаный раствор)
- Постоянный рост цен на энергоресурсы также заставляет думать о запасе по теплопроводности стен из газосиликатных блоков.
На практике, стены, возводимые только из газосиликатных блоков, обрабатывают гидроизоляционными материалами (мастика, гидроизол) и штукатурят с внешней и внутренней стороны, что тоже увеличивает их толщину. При этом в некоторые проекты толщину стены из газосиликатных блоков стараются все равно закладывать выше нормативно расчетной.
Рассмотрим комбинированный вариант укладки стен из газосиликатных блоков с кирпичом. Толщина блоков при этом составляет 300 мм, а толщину кирпичной кладки принято делать в полкирпича, то есть 120 мм. При этом должен быть вентиляционный зазор между блоками и кирпичами или обычно укладывают между ними утеплитель (минеральная вата, пенопласт), что также увеличивает сопротивление теплопередачи. Газосиликатные блоки и кирпич обязательно нужно связывать металлическими стержнями или пластинами из нержавеющих материалов.
Помимо кирпичной облицовки используют сайдинг, вагонку, различные другие листовые материалы. При этой технологии нужны довольно прочные крепежные материалы, которые надежно крепятся к газосиликатным блокам, после чего на них закрепляют облицовочный материал. Между газосиликатными блоками и сайдингом также можно использовать утеплитель. Толщина его зависит от толщины используемых газосиликатных блоков. Например, при кладке газосиликатных блоков в 200 мм используют утеплитель (минплита, пенопласт) толщиной в 120 мм.
Стоит отметить, что при строительстве домов из газосиликатных блоков используется практически весь материал, даже бой, благодаря своей теплоизоляции. Бой разбивают на куски 5 – 10 см, посыпают пол, предварительно проведя его гидроизоляционную подготовку, и заливают раствором.
Перед началом кладки газосиликатных блоков на фундамент его выравнивают и гидроизолируют верхнюю поверхность, затем начинают кладку первого ряда. Через каждые четыре ряда производят армирование. Так как газосиликатные блоки легко обрабатываются, армировать лучше через прорезанные в газосиликатных блоках каналы, куда укладывают арматуру диаметром 8 мм. На углах желательно использовать цельный загнутый кусок арматуры, заложенный в блоках по дуге. Арматуру укладывают в чистый канал на раствор, сверху она также покрывается раствором.
Плиты перекрытия при строительстве из газосиликатных блоков рекомендуют класть на армированный пояс или кирпичную кладку, расположенные по кладке. Если второй этаж брусовой, балки также укладываются на кирпичную кладку. Предварительно концы балок, соприкасающиеся с кладкой, заворачивают в пергамент.
Подведём итоги:
- При возведении стен из газосиликатных блоков (ГБ), по ряду внешних атмосферных и внутренних технологических причин, проводят дополнительные защитные мероприятия.
- Стены обрабатывают гидроизоляционными материалами и штукатурят.
- Проводят комбинированную укладку слоев из ГБ и кирпича, их связывают и создают между ними вентиляционный зазор.
- Помимо кирпичной облицовки, используют сайдинг, вагонку и другие листовые материалы.
- Вентиляционные зазоры, образуемые при комбинированной кладке, при необходимости дополнительно заполняют утеплителем.
- Бой из ГБ успешно используют как дополнительный теплоизоляционный материал.
- Перед возведением стен, под первый укладочный ряд, обязательно проводят гидроизоляционную подготовку верхней поверхности фундамента.
- Через каждые 3-4 ряда кладку армируют.
Указанные мероприятия обеспечивают выполнение нормативных условий при строительстве объектов из газосиликата и создают комфортные условия для проживания и работы.
При всех перечисленных условиях, в некоторые проекты толщину стен из газосиликатных блоков стараются все равно закладывать выше нормативно расчетной, что приводит к неоправданному их утолщению и, как следствие, уменьшению полезной площади помещения и размера кошелька потребителя.
Из газосиликатных блоков строят дома до 4 этажей. В более высоких используют железобетонный каркас, проемы которого заполняют газосиликатными блоками. Различные размеры блоков позволяют строить стены, перегородки, утеплять балконы и лоджии разной толщины (от 50 мм до 600 мм).
Мягкий материал газосиликатных блоков легко обрабатывать, из них выпиливают всё, что угодно — от перегородок до арок. Некоторые печники придают газосиликатным блокам любую форму, затем обкладывают шамотным кирпичом со стороны огня и изразцовой плиткой с внешней стороны, получая камины экзотических форм и видов.
Всё вышесказанное подтверждает, что газосиликатные блоки — универсальный строительный материал с широким спектром применения.
Ещё статьи по теме:
Газосиликатный кирпич: состав и характеристики
Огромную популярность в качестве основного строительного материала набирает газосиликатный кирпич. Его технические характеристики и свойства позволяют строить эффективные здания, которые соответствуют всем современным меркам. Если говорить о соотношении цены и качества, то с уверенностью можно сказать, что газосиликатные блоки занимают одно из первых мест.
Материал уже проверен временем и успешно выполняет свои функции. Его применяют для строительства всех видов конструктивных элементов сооружений и построек любого назначения. Почему газосиликатные блоки стали такими популярными? Чем они отличаются от классических строительных материалов? В чем их особенность? Ответы на эти и многие другие вопросы вы найдете в статье.
Газосиликатные блоки – что это
Если говорить простым языком, то газосиликатный материал – это одна из разновидностей ячеистого бетона. Готовый материал получался пористым, но имел такие же характеристики, как у бетона. Отличием являлось то, что благодаря пористой структуре, блоки имели меньший вес. Материал получали путем добавления в бетонный раствор специальных добавок, образующих поры. В XIX веке раствор перемешивали с кровью быка или свиньи, чтобы получить данный эффект. Белок в крови, вступая в реакцию с другими компонентами, образовывал пену. Один из советских строителей, Брюшков М.Н., в 1930-х годах заметил, что растение мыльный корень, которое растет в Средней Азии, наделяет цемент новой особенностью. Когда растение добавляли в смесь, она начинала пениться, тем самым увеличиваясь в объеме. Когда раствор застывал, пористая структура сохранялась. Однако самую важную роль в изготовлении ячеистого бетона сыграл Альберт Эриксон, архитектор из Швеции, который разработал технологию получения материала, путем добавления химических газообразующих компонентов. Он и запатентовал свое изобретение. Но, из чего делают газосиликатные кирпичи сегодня?
Исходя из СН 277-80, газобетонный раствор должен состоять из следующих компонентов:
- портландцемент высокого качества, поученный согласно ГОСТ 10178-76, в составе которого есть силикат кальция, не меньше 50%, трехкальциевый алюминат, не больше 6%. Добавлять трепел в состав нельзя;
- песок, с техническими требованиями согласно ГОСТ 8736-77, в котором глинистые и илистые включения не превышают 2%, а наличие кварца равно 85%;
- простая вода, соответствующая требованиям ГОСТ 23732-79;
- кальциевая известь-кипелка, соответствующая ГОСТ 9179-77, не меньше 3 сорта.
Ее скорость гашения должна составлять 5–15 мин. и не больше 2% пережога. Оксид магния и оксид кальция в составе – не меньше 70%;
- алюминиевая пудра ПАП–1 или ПАП–2, используемая в качестве образователя газа;
- сульфанол С, поверхностно-активное вещество (ПАВ).
Как выглядит газосиликатный кирпич, вы можете посмотреть на фото ниже.
Именно из этих компонентов и производят газосиликатный кирпич. Примечательно, что готовые изделия из газосиликатной смеси можно разделить на 2 вида:
- Автоклавный.
- Неавтоклавный.
Они отличаются способом изготовления. Газосиликатные кирпичи из автоклава, благодаря особой обработке в нем, имеют повышенные показатели по усадке при высыхании (в 5 раз лучше) и прочности. Изготовление в автоклаве довольно технологичное и энергоемкое, поэтому их цена несколько выше. Сушка газосиликатного кирпича происходит при температуре 175 ˚C, под давлением в 0,8–1,2 МПа. Такую обработку могут позволить себе только большие предприятия.
Что касается неавтоклавного газосиликатного кирпича, то его изготовление обходится значительно дешевле, но немного с худшими показателями. Изготовленная смесь затвердевает в природных условиях, без внешнего влияния.
Размеры и вес газосиликатных кирпичей
Одним из преимуществ газосиликатных блоков, является их размер. Он значительно больше, чем у обычных кирпичей, благодаря чему возведение здания проходит на порядок выше (в 4 раза), при том, что количество швов и соединений максимально снижено. Это значительно сокращает трудозатраты. Да и расход раствора значительно уменьшается. Как известно, размер кирпичей определяется тремя величинами: длиной, шириной и толщиной. Стандартный размер стенового газосиликатного кирпича равен 600×200×300 мм. Существует также стеновой полублок, размер которого составляет 600×100×300 мм. Но, это далеко не все размеры. В зависимости от производителя, изготавливают блоки следующих размеров:
- 500×200×300 мм;
- 588×150×288 мм;
- 600×250×50 мм;
- 600×250×75 мм;
- 600×250×100 мм;
- 600×250×250 мм;
- 600×250×400 мм и т.
д.
Вы можете найти любой размер, который потребуется для ваших работ. Имея эти данные, мы можем сравнить, сколько кирпичей в газосиликатном блоке. К примеру, возьмем стандартный кирпич размером 250×120×65 мм и стандартный газосиликатный блок, 600×200×300 мм. Объем такого кирпича составляет 0,00195 м3. Объем же силикатного блока равен 0,036 м3. Если разделить их, получается, что в 1 блоке 1,85 кирпичей. Примечательно то, что на 1 м3 кладки требуется 27,7 блоков, а кирпичей – 512 шт., что в 18 раз меньше. А что сказать о весе?
Понятно, что на вес будут влиять габариты и плотность материала. Чем они больше, тем выше вес. Стандартный газосиликатный блок имеет вес 21–29 кг, а зависимости от плотности. Вес – одно из преимуществ таких изделий. Если сравнивать с теми же кирпичами, то масса 1 м3 кирпичей равна: 512 шт. × 4 кг. (масса 1 кирпича) = 2048 кг. А в 1 м3 газосиликатного блока: 27,7 × 21 = 581,7 кг. Разница более чем очевидна. За счет габаритов и пористой структуры, общий вес блоков из газосиликата намного меньше.
Основные физико-механические характеристики газосиликатных кирпичей
Немаловажными факторами, которые отличают изделия, являются следующие показатели:
- Плотность.
- Теплопроводность.
- Морозостойкость.
Как упоминалось выше, от плотности напрямую зависит вес и свойства материала. В зависимости от этого, газосиликатные кирпичи делятся на маркировки:
- D700, самые плотные, используются для постройки конструкций с повышенной этажностью.
- D600–D500, средней плотности, используются для постройки малоэтажных домов и перегородок.
- D400 и ниже, теплоизоляционный материал, который используют для утепления контура несущей стены.
Обратите внимание! Чем выше плотность изделия, тем выше проводимость тепла.
Отличием газосиликатных блоков является и их теплопроводность. К примеру, готовые блоки марки D700 обладают показателем 0,18–0,20 Вт/м·°С (ниже чем у красного кирпича). Если говорить о марке D600–D500, то показатели еще ниже – 0,12–0,18 Вт/м·°С. Самая низкая теплопроводность у изделий марки D400, равная 0,08–0,10 Вт/м·°С.
Внимание! Теплопроводность дерева составляет 0,11–0,19 Вт/м·°С. Поэтому ячеистый бетон в этом плане превышает даже дерево. Это материал, который способен дышать. Учтите, что это касается полностью сухого материала. Если он мокрый, проводимость увеличивается.
Что касается морозостойкости, то она зависит от объема пор блоков. Стандартные блоки, изготовленные в естественных условиях, могут выдерживать 15–35 циклов замерзания и размораживания.
Но, некоторые производители, изготовляющие блоки в автоклаве заявляют, что их изделия имеют морозостойкость 50–100 циклов, что действительно поражает. Все же, отталкиваясь от информации в ГОСТ 25485-89, в среднем морозостойкость ячеистого бетона не выше 35 циклов.
Другие преимущества материала
Стоит отметить, что газосиликатный кирпич имеет и другие характеристики. Благодаря своему составу, он является экологически чистым материалом, который не вредит здоровью человека. Изделия из газобетона находятся на втором месте по экологичности, после дерева. Кроме того, автоклавные блоки не будут гнить из-за отсутствия среды обитания для микроорганизмов. Грызуны не будут его есть и заводиться внутри.
Высокая пожаробезопасность – еще одно преимущество ячеистых бетонов. Он не горит! Материал можно использовать для возведения преград для огня. В конструкции предел распространения огня составляет 0 см. А пористая структура газосиликата позволяет эффективно препятствовать проникновению шума. Если вам придется работать с этим материалом, вы сможете оценить еще одну тонкость – простота обработки. С ним легко работать, используя простые плотницкие инструменты. Как видите, газосиликатный кирпич не зря считается одним из лучших материалов, используемых для строительства!
Газосиликатные блоки. Газосиликатные блоки — отличное… | Валентин Фролов
Газосиликатные блоки — отличный материал для возведения стен домов, зданий и сооружений. Газосиликатные блоки обладают уникальными свойствами: негорючестью (пожаробезопасностью), хорошей звуко- и теплоизоляцией, малым весом и высокой прочностью. Такой набор характеристик достигнут за счет особого макияжа и технологии изготовления материала. Смесь воды, извести, алюминиевой пудры и кварцевого песка дает прочный и изменчивый блок.
Газосиликатные блоки обладают высокими теплоизоляционными характеристиками за счет большого количества не связанных между собой ячеек. Теплопроводность силикатных блоков в 3 раза ниже, чем у кирпича.
Еще одна отличительная черта силикатных блоков — это экологичность материала, а именно способность проводить угарный газ, углекислый газ и пар.
Благодаря относительно небольшому удельному весу нагрузка на фундамент значительно снижается, что существенно снижает затраты.Теплоаккумулирующие свойства газосиликатных блоков повышают комфорт в зданиях и позволяют существенно сэкономить на отоплении. Благодаря тому, что газосиликатные блоки имеют меньшую удельную массу, чем другие строительные материалы, значительно снижаются транспортные расходы. Экономия достигается при его изготовлении, транспортировке, строительстве и эксплуатации зданий.
Малый вес газосиликатных блоков из ячеистого бетона позволяет снизить общий вес строительных конструкций, что в конечном итоге приводит к значительной экономии не только на стоимости стеновых материалов, но и на стоимости других конструктивных элементов здания. .Затраты на оплату труда при блочных работах из газосиликатных блоков в 2–3 раза ниже, чем при возведении зданий из других материалов.
При использовании технологии строительства из газосиликатных блоков практически нет мусора. Сам строительный блок сделан из пенобетона, который можно распилить обычной ножовкой; Это означает, что даже самые сложные изгибы внутренних стен вашего дома не потребуют много времени и денег на возведение.
Кладка газосиликатных блоков.Как происходит кладка стен из газосиликатных блоков? Кладка из газосиликатных блоков своими руками инструкция
Газобетон — это строительный материал, созданный синтетическим путем. Сделано это в результате температурного воздействия на все компоненты компонентов. Основные достоинства этого материала — простота изготовления, небольшой вес, прочность, теплоизоляция. Однако, несмотря на все его преимущества, многие неквалифицированные рабочие не любят с ним работать. Но профессионалы с удовольствием используют газобетонные блоки.Есть некоторые особенности укладки таких блоков.
Подбор инструмента
Чтобы укладка газобетона была правильной и прочной, без применения специальных инструментов не обойтись. Для приготовления бетонного раствора Вам потребуется — промышленный миксер, емкость для смешивания. Для того, чтобы нанести смесь, вам понадобится — несколько хитростей разного размера. Чтобы подогнать газобетонные блоки друг к другу — специальный молоток и мерный уровень. Если предусмотрена обработка газобетонного блока, неплохо было бы иметь запас и такие инструменты, как разметочная линейка, розовая, затирка, оборудование для формирования бороздок, насадки на дрель, дрель, кисть.
Методы кладки
Приготовление кладочного раствора.На сегодняшний день существует два метода кладки газобетонных изделий своими руками, это кладка газобетонных блоков на цементный раствор и на клеевую смесь. Но, несмотря на выбранный способ кладки, первый ряд необходимо укладывать на цементный раствор. Дозировка компонентов должна быть такой, чтобы полученная кладочная смесь не растекалась, иначе блок не поддастся фиксации.Если конструкция большого объема есть, гораздо удобнее замешивать раствор не своими руками, а с помощью бетономешалки.
Клеевой раствор
Чтобы полученный раствор имел однородную текстуру, для перемешивания лучше использовать оборудование, работающее на малых оборотах. Чтобы пропустить пять килограммов сухой смеси, в емкость наливают литр воды. Сухой клей медленно насыпают в емкость и сразу взбивают. Даем минут десять, а через еще раз хорошенько взбиваем. Клейкий раствор можно приготовить, когда он станет похож на густую сметану . Если клей высох и удален, запрещается разбавлять его новой смесью или водой.
Цементно-песчаная смесь
Аналогичный раствор можно использовать для накопления блоков. Его изготавливают путем смешивания всех компонентов и специального связующего компонента. Такие составы отличаются простотой приготовления и надежностью использования.
Рецепт таких смесей может несколько отличаться в зависимости от поставленной задачи.Если нужно получить более пластичную смесь, то добавляется глина. Такая смесь не крошится и не крошится, позволяя аккуратно и легко укладывать строительный материал. Использование в цементной смеси для газобетона специальных пластифицирующих компонентов позволяет качественно выполнить монтаж стен фасада. Подобная смесь очень экономична, дает хорошие изоляционные свойства, удобна в использовании и кладке. Благодаря ее достоинствам многие рабочие до сих пор чаще работают именно с такой смесью, а не с клеем.
Что выбрать?
Использование клея — рациональное, выгодное и правильное решение.
При выполнении строительных работ специалистов интересует не только как укладывать газобетон, но и какую смесь выбрать. Ведь и первый, и второй вариант обладают прибавкой в весе. Необходимо учитывать, что показатель теплопроводности у обеих смесей намного больше, чем у блоков. Очевидно, что теплоизоляция всего здания зависит от ширины шва. При использовании цементной смеси Ширина шва будет примерно 9 миллиметров. В случае с клеем ширина швов не превышает цифры 3 миллиметра.
Учитывая, что цена на клей больше, изначально можно предположить, что при его нанесении стоимость значительно вырастет. монтажные работы. Но, с учетом минимального расхода, на самом деле расходы немного увеличиваются, и здание выходит намного теплее. Но если использовать более дешевую цементную смесь, становится понятно, что ее нужно намного больше и стоимость монтажа неминуемо вырастет.Из этого сравнения становится понятно, что использование клея при укладке блоков — более рациональное решение, выгодное и правильное.
Технология укладки
Перед началом монтажных работ своими руками необходимо распаковать блоки и разместить их рядом с кладкой ряда. При выполнении строительных работ по монтажу лучше использовать специальную клеевую смесь. В случае подобного выбора вы будете защищены от образования холодной линьки в местах кладки.Не рекомендуется использовать цементную смесь, потому что, несмотря на ее невысокую стоимость, расход намного выше, а швы выглядят малоактивно и слишком широкими. Также подобный выбор ухудшает теплоизоляцию будущего дома.
Перед тем, как приступить к монтажу кладки блоков, стоит поставить специальные маячки. Устанавливайте их в полях примыкания, по всему периметру фасада. Они нужны для выравнивания, чтобы с их помощью закрепить специальную проволоку, контролирующую ровность стен и перегородок.Закрепите проволоку оцинкованными гвоздями. Также нельзя забывать, что инструкция по кладке — важный элемент любых строительных операций.
Однократное перемешивание
Для приготовления необходимо подготовить специальную емкость и промышленный миксер. Для перемешивания смеси используйте специальный сухой состав и теплую воду. Приготовление смеси продолжается до тех пор, пока смесь по консистенции не станет однородной. Нужно 20 минут потренироваться, из-за этого размазываются малые дозы. В процессе эксплуатации клей необходимо постоянно перемешивать, чтобы он потерял однородность.
Если строительство ведется при низких температурах, необходимо использовать особую кладочную смесь. В его состав входят специальные компоненты, предотвращающие замерзание, что дает возможность сохранять свои характеристики даже при низких температурах.
Маркировка
Кладка стен осуществляется только после полной разметки строительной продукции.Разметка проводится по осям всех поверхностей будущего фасада. После этого материал забирается, доставляется к месту установки и распределяется по выбранным осям. При выполнении процедуры перевязки используется неполный материал, который будет располагаться по углам.
Из этого следует, что сначала нужно изготовить разделочные изделия. Выполнить это несложно, ведь резка выполняется пилой или ножовкой. Чтобы все рисунки были плавно обрезаны, стоит при разметке воспользоваться специальной линейкой.Необходимо подготовить те материалы, которые в дальнейшем будут армировать.
Сначала подготавливают те блоки, которые необходимы для кладки первого ряда, после этого производится изготовление стержней для армирования по ходу монтажа фасада.
Укладка и армирование
Процесс монтажа стен и перегородок будущего здания не сложный, но важно все сделать правильно. Только тогда весь процесс пройдет быстро, а конструкция будет качественной.Сначала готовится строительный материал и специальная смесь для работы. Для выполнения первого ряда необходимо выполнить процедуру армирования. После этого на поверхность наносится клей и распределяется по ее специальной гребенке. Толщина шва не должна превышать 4 миллиметра.
Монтаж кладки следует производить с перевязкой, каждое изделие обязательно смещается на расстояние, равное половине одной конструкции. Если не брать перевязку, она негативно скажется на свойствах стен.Выступающую смесь из толщины швов ставить нельзя, можно только аккуратно удалить мастерской. Для ровной кладки используется специальный шнур. Равномерность проделанной работы определяется уровнем помощи и специальной линейкой.
Для правильного монтажа стен не нужно оставлять без внимания и вопрос гидроизоляции. Для его выполнения используйте специальную сетку. На стены в местах соприкосновения с фундаментом закрепляется необходимая гидроизоляционная сетка. После возведения перегородок их нельзя оставлять беззащитными.Стоит сразу выполнить фасадные и утеплительные работы. В том случае, если нет возможности сделать это сразу, ряд стараются прикрыть специальной пластиковой сеткой, пока не появится возможность все доделать. В рамках подготовки к строительству планируется армирование. Это обязательная операция, если стена будет слишком длинной или короб будет усилен.
Согласно данной процедуре, все перемычки, длина которых превышает 90 сантиметров. Как и все нижние швы отверстий.Эта операция может применяться по двум технологиям — металлическими стержнями или специальной сеткой. При установке в блоки срезаются специальные пазы, куда ставятся стержни и заливается клей. После установки следует следующий ряд.
Сетка при строительстве здания требуется для увеличения крепости фасада и исключения возникновения трещин в стенах. Металлическую сетку Ставят с зазором в 3 ряда из топливобетонных блоков. Чаще всего для выполнения армирования применяют такие материалы: сетка оцинкованная
- ;
- сетка базальтовая;
- Сетка из стеклопластика.
Размышляя о строительстве дома своими усилиями, люди стараются выбрать такой строительный материал, с которым легко работать. На современном строительном рынке можно увидеть большой выбор новых материалов, подходящих для строительства здания. Среди популярных строительных материалов, которые становятся популярными у потребителей, одно из первых мест занимают газосиликатные блоки. Чтобы дом был крепким, надежным, нужно знать, как правильно поставить газосиликатные блоки, какой раствор использовать и как рассчитать необходимое количество материала к вашему проекту.
Газиликатная технология строительства
Постройте себе дом из газосиликатных блоков, даже если у вас только начальные знания о технологиях строительства, но есть трудолюбие и энтузиазм. Для возведения стен потребуются следующие инструменты и материалы:
- Для разведения клея понадобится емкость-флаттер.
- Наносить клей можно специальным ведром или зубочисткой.
- Разрезать блок на куски нужных размеров поможет ножовка с большим зубом.
- Неровности можно выровнять с помощью крупного наждака.
- Кисть-смесь.
- Квадрат металлический, уровень.
- Раствор песчано-цементный.
- Блоки газосиликатные марки Д400 или Д500.
- Иглоизоляция из минеральной ваты.
- Стекловолоконная сетка для кладок или арматура.
Расчет необходимого количества блоков
Вы можете произвести расчет общего количества газосиликатных блоков, рассчитав объем всех стен дома по проекту.
Более точный расчет ведется для каждой стены отдельно. Для этого нужно взять размеры стены из проекта, а размеры газиликатного блока будут известны при его покупке. Зная ширину блока и длину стены модно производить расчет количества блоков на один ряд кладки. Если нужна половина блока, она учитывается как целый блок. Таким же образом рассчитывается количество рядов кладки.Количество строк умножается на результирующее количество блоков в одной строке. Окончательное число — это количество блоков на стену.
Если в стене есть дверные проемы и окна, сделайте также приблизительный расчет. Затем, подсчитывая блоки для каждой стены, суммируют все числа.
Кладка
Примечание! От точности и качества кладки первого ряда зависит прочность и надежность всей конструкции здания.
Готовый фундамент необходимо покрыть слоем гидроизоляции, поверх кладочной сетки, а для кладки начального ряда строительства использовать обычный раствор. Затем нужно проверить углы постройки на разницу в высоте, она должна быть не выше 30 мм. Если углы расположены не на одном уровне, кладку нужно начинать с наибольшего угла.
Первый ряд предназначен для выравнивания погрешностей заливки фундамента, поэтому толщина раствора в разных местах может отличаться, но не должна быть меньше 20 мм.Следом устанавливаются угловые блоки и подключается шнур. Проверяется уровень натянутого шнура, он должен быть строго горизонтальным. При длине стен более 10 метров необходимо укладывать промежуточные блоки, предотвращающие натяжение шнура.
Для регулировки вертикального и горизонтального положения блоков используется резиновый молоток. Неровности кладки устраняет Eatak. Для удаления пыли и загрязнений используйте кисть-абсолюцию. Если вам нужны детали блока, то их изготавливают с помощью электрических копий или ручной ножовки.
Дальнейшая блокировка блоков производится клеевым раствором. На строительную площадку Поставка сухой смеси из песка мелкой фракции, портландцемента и специальных добавок. Необходимо внимательно ознакомиться с инструкцией по приготовлению качественного раствора необходимой консистенции. Толщина связующего слоя должна быть не более 3 мм.
Примечание! Перед нанесением клея на блоки их нужно тщательно очистить и смочить водой для качественного склеивания.
Кладка стен осуществляется в теплое время года. Для строительства в холодную погоду необходимо использовать зимний клей. Глобусы наносятся на глобальный шпатель шириной, равной ширине поверхности газосиликатного блока. Слой должен быть однородным как по вертикали, так и по горизонтали блока. После нанесения клеевого слоя поверхность блока необходимо прорезать бороздками. Нет необходимости заполнять щели между захватными карманами и между гребнем и пазом.
Второй ряд блоков необходимо укладывать развернутой половиной, чтобы получилась перевязка между рядами. Кладка всех рядов начинается с угловой колодки. Положение каждого блока необходимо контролировать по уровню и производить регулировку с помощью молотка. Все швы следует заполнить клеевым раствором во избежание усадочных трещин. Излишки клея удаляются шпателем.
Если вы используете для самостоятельного строительства Блоки формы паз-гребень, вам не потребуется выполнять вертикальное армирование.Для горизонтального армирования На поверхности газосиликатных блоков уложенного ряда по периметру делают продольные башмаки и укладывают в них стеклопластиковые стержни или просто кладочную сетку.
Примечание! В верхней части дверных и оконных проемов сначала укладываются металлические уголки длиной более 40 см, шириной и шириной, а затем продолжают блокировать блоки.
Монтаж перекрытий
После того, как кладка стен практически завершена и останется только последний ряд, необходимо вместо блоков устроить монолитный железобетонный пояс.Такой подход поможет равномерно распределить нагрузку от переполненных или ячеистых бетонных плит по всем несущим стенам.
Отделка стен из газосиликата
Для наружной отделки Используются специальные вентилируемые системы или материалы, обладающие высокой паропроницаемостью. Между кирпичной кладкой фасада и стеной из газосиликата оставлен зазор. Соедините два гибких соединения кладки. Если вы предпочитаете использование для фасадных работ красок, шпатлевок или штукатурных смесей, необходимо убедиться, что они предназначены для работы с газосиликатом.
Внутренняя отделка предполагает использование дышащих материалов. Стены из газосиликатных блоков можно спасти обоями или покрасить водоэмульсионной краской. Для ванной, санузла, кухни необходимо предварительно проложить пароизоляцию или пропитать стены специальным раствором. При отделке ванной комнаты керамической плиткой испарение не требуется.
Примечание! Шпалян Межкомнатные стены Возможно не ранее, чем через два месяца после завершения строительства.
Работы по фасаду здания можно начинать только после завершения всех внутренних отделочных процессов. Единственное исключение — вентилируемые системы. Их можно устанавливать сразу после окончания строительства.
Видео
Подробнее о монтаже газосиликатных блоков читайте ниже:
Процесс изготовления газосиликатных блоков
Производственный технологический цикл изготовления этого строительного материала начинается с приготовления смеси, для которой используются четыре компонента: портландцемент, кварцевый песок, известь и вода.Эти компоненты тщательно перемешивают миксером и после доведения смеси до однородности массы добавляют в нее алюминиевую пудру. По прошествии некоторого времени необходимо завершить процесс перемешивания, раствор разливается в специальные формы, где должно находиться несколько часов. Это время отводится на химическую реакцию между элементами алюминиевой пудры и извести, которая является результатом газа. В этом чипе изоляция газа способствует образованию ячеек в массе.
После этого изготовленные блоки специальной струны разрезаются на размер, установленный стандартами, после чего помещаются в автоклав для паромной обработки при температуре 190 градусов Цельсия под давлением 10-12 бар. Такой технологический процесс позволяет равномерно распределить созданные ячейки, придав материалу необходимую плотность. В этом процессе химическая реакция будет продолжаться в автоклаве.
Методы кладки
Кладка газосиликатных блоков может производиться двумя способами — цементным и клеевым.Какому варианту лучше отдать предпочтение с точки зрения практичности экономии? Изначально отметим, что и клей, и цементный раствор имеют высокую теплопроводность, выше, чем у газобетона. Это говорит о том, что при уменьшении толщины шва между блоками комната дольше может сохранять тепло в доме. Мы подошли к тому, что цементный способ кладки газоблоков требует выполнения шва не менее 6-10 миллиметров, а толщина шва, выполненного клеем, будет в пределах 1-3 миллиметров.Из этого следует вывод, кладка газобетона, произведенная клеем, сделает дом намного теплее.
Казалось бы, все просто и понятно, а что еще нужно? Если бы не одно — по стоимости клеевой раствор дороже цементного раствора. Однако следует отметить, что расход клеевого раствора в пять раз меньше цемента. Поэтому в кругу любого выходит, что клей для газоблоков и практичнее, и экономичнее.
Правда, кладку первого ряда (нижнего) нужно производить на цементном растворе, потому что только он способен справиться с двойной ролью — и крепежной составляющей, и выравнивающего слоя.
Технология кладки
Для возможности установки газосиликатных блоков необходим фундамент под фундамент. К сожалению, его поверхность обычно не отличается неровностями, а если точнее, то всегда довольно неровной. Поэтому изначально это закрытый гидроизоляционный материал, например, каучукоид или полиэтиленовая пленка, уложенная в несколько слоев.Затем на поверхность гидроизоляции наносится цементный раствор из песка и цемента в соотношении 4: 1.
Можно приступать к укладке блока, только предварительно придвинув поверхность каждого блока, на которую будет укладываться раствор для смачивания водой. Это уравновешивает состояние влажности блока и раствора и предотвращает перетекание влаги из раствора в блок, который имеет высокую гигроскопичность, особенно если это блок ячеистого типа. Благодаря этим мерам цементный раствор не потеряет характерных крепежных качеств.
Начало кладки следует вести от угла фундамента, имеющего наибольшую высоту, которую можно определить по уровню или строительному уровню. Блоки первого ряда необходимо укладывать в строго горизонтальной плоскости (желательно в вертикальной), добиваясь максимальной зачистки общей поверхности. Поэтому за процессом укладки блоков следует постоянно следить по уровню. Как видите, требование кладки первого ряда на цементном растворе оправдано, так как им несложно отрегулировать выравнивание смонтированных блоков в нужной плоскости.
Выложив ровно нижний ряд блока, дальнейшую кладку можно сохранить с помощью клея.
Не исключено, что последний в рядном блоке может находиться вне фундамента. В этом случае его легко можно будет разрезать, например, ножовкой по металлу. В целом с этим материалом для кладки стен легко обращаться в различных техниках — точить, просверливать, резать, чистить и в таком духе.
Во-вторых, следует монтировать верхний ряд, начиная укладывать на обрезанный блок, что позволит произвести хорошее переваривание между элементами блока, то есть повторить все приемы стандартной кирпичной кладки Со смещением.
После укладки четырех рядов газоблоков необходимо выполнить армирование, то есть на поверхности четвертого ряда нужно сделать пазы, в которых металлическая арматура диаметром около восьми миллиметров, которая дополнительно заливается цементный раствор.
Ход должен быть достаточно глубоким, чтобы арматура полностью погрузилась в него.
Шагающие стены из газоблоков
Если перегородки в квартире выполнены из газосиликатных блоков, то для последующей финишной отделки их можно оштукатурить.У этого процесса есть свои, только присущие нюансы, которые отличаются от покрытия штукатуркой других поверхностей, например, из бетонных блоков или кирпича. И самое главное отличие — это сама штукатурная смесь.
По мнению специалистов, оштукатуривание газосиликатных гипсовых блоков на цементной основе не рекомендуется. Поэтому возникает закономерный вопрос, а как правильно выполнить оштукатуривание поверхности стены из газосиликатных блоков? Все просто, штукатурную смесь нельзя варить вообще.Достаточно посетить строительный рынок или аналогичный магазин и приобрести готовый штукатурный раствор, разработанный специально для оштукатуривания газосиликатных блоков. Их основа — гипс с высоким уровнем паропроницаемости, так необходимый для нашего варианта.
Современная гипсовая штукатурка продается в сухом виде. Контакт сухой смеси с готовым штукатурным раствором не представляет затруднений, достаточно следовать инструкции, нанесенной на упаковке продукта. Отметим только, что при изготовлении раствора необходимо строго соблюдать главное требование — сначала сухой раствор засыпать в емкость, а уже потом вливать в него воду и ничего наоборот!
Для изготовления стандартного раствора обычно соблюдается соотношение двести граммов воды на килограмм сухого вещества.Будьте осторожны, так как при расширении воды ухудшается качество штукатурки.
Покрытие стен штукатурным раствором
На первом этапе процесса штукатурки поверхность стен из газосиликатных блоков необходимо тщательно очистить от пятен, протечек, мусора и пыли.
Второй этап — грунтовка поверхности стены. Желательно использовать грунтовочную смесь глубокого проникновения.
Третий этап — это установка на поверхность стены армирующей сетки из стекловолокна, у которой должны быть строго определены свойства: изделие должно иметь высокую степень противостояния разрыву и растяжению, а также иметь высокую плотность.
Четвертый этап — это непосредственный процесс нанесения штукатурки. Оштукатуривание стен, выложенных из газовых баллонов, необходимо производить по специальным направляющим маякам. Как и маяки, направляющие планки, которые следует установить на стене или грабить на стене в вертикальном направлении, закрепляют, например, тем же раствором, после чего заполняют пространство между маяками штукатуркой. В зависимости от необходимости в общем слое штукатурка выполняется сразу или в нескольких техниках. Толщина одного слоя не должна превышать 15 миллиметров, это если на этом слое вы полностью сосредоточитесь.А если раствор необходимо наносить в несколько слоев, толщина каждого последующего слоя не должна превышать восьми-девяти миллиметров.
Установленные планки служат для выравнивания штукатурки, а сам процесс выравнивания производится по особому правилу, согласно которому нанесенный раствор можно перераспределить на недостаточно залитые места на поверхности или полностью удалить их излишки. Дождавшись высыхания штукатурки, производят затирку.
Наносить каждый слой штукатурки можно только после полного высыхания предыдущего слоя.Процесс штукатурки рекомендуется производить при положительной температуре воздуха в помещении — в пределах 5-30 градусов тепла.
Отделочные работы по стенам из газоблоков
Эксплуатационные характеристики Стены из газосиликатных блоков не хуже аналогов, из которых возводятся поверхности стен. Также ему в полной мере присущи высокая прочность, надежность, а также показатели тепло- и звукоизоляции. Однако, как мы уже отмечали выше, материал имеет повышенную гигроскопичность, что делает нежелательным его использование при необходимости перепланировки туалета или ванной комнаты.Но, повторяем — «нежелательно», потому что сегодня производители отделочных материалов наладили выпуск финишных покрытий и успешно способны защитить даже такие гигроскопичные изделия, как газосиликатные блоки, от проявлений повышенной влажности. Например, специальные виды штукатурки.
А в остальном посмотрите на конструкцию прокладок как на обычную стенку. Поэтому для отделки его поверхности можно в полной мере использовать все известные отделочные материалы, а также применить все способы их укладки на стену.И точно такие же требования к подготовке стены под покраску и оклейку обоями — поверхность должна быть доведена до максимально высокого уровня гладкости и ровности, на которой можно произвести известную штукатурку или просторные решения.
При варианте, когда перегородка из газосиликатных блоков предназначена только для разделения помещения на две части, для выравнивания будет достаточно шпаклевки. А если вы решили отдать предпочтение пластиковым или декоративным панелям, на стене в целом можно провести дополнительные работы.На его поверхности легко соорудить деревянный каркас, в который спокойно можно установить указанные отделочные материалы. Сегодня этот способ отделки считается самым простым и затратным.
Полноценно относится к вагонке, зеркалам, деревянным панелям. На газосиликатные блоки можно укладывать и керамическую плитку, но в этом случае придется оштукатурить поверхность для ее основания. Фактически, при чистовой отделке можно дать волю своей фантазии или следовать рекомендациям опытных дизайнеров, которые тщательно считают, что отделить возведенную поверхность из газосиликатных блоков можно практически любыми отделочными материалами, например, фактурной штукатуркой, жидкими обоями, настенный линолеум.А можно полностью отказаться от отделки, отдав предпочтение отделке стены разнообразными мелкими предметами. Кстати, этот стиль сегодня становится все более популярным и известен под разрядами городского промышленного варианта.
Видно, что способов отделки поверхностей стен из газосиликатных блоков действительно огромное количество.
Итог
Подойдет ли перепланировка стены материалом квартиры из газосиликатных блоков, решать вам только самому.Считаем необходимым отметить, что этот строительный материал имеет ряд положительных преимуществ перед аналогами и с самого начала использования в строительстве показал себя только положительно.
Конечно, в случае использования на кухне, туалете, ванной для отделки стен из этого материала придется затратить определенные усилия, средства и время на защиту газосиликатных блоков от влаги. Но в конечном итоге затраты окупятся с лихвой, ведь изделия из газобетона дешевле такого же кирпича и намного проще в укладке даже по сравнению с плитами из гипсокартона.
Во время строительных работ рекомендуется снимать с поддонов столько блоков, сколько предполагается уложить в течение одного дня. В противном случае следите за блоками хранения блоков и размещайте их на ровном месте вне досягаемости влаги.
Технологии кладки первого и последующих рядов стен имеют отличия. Рассмотрим обе технологии по отдельности.
Кладка первого ряда блоков
После закладки фундамента здания кладка первого ряда — самый ответственный момент.От первого ряда зависит точность всех последующих рядов стен и устойчивость всего здания. Поэтому к этому этапу строительных работ нужно подойти особенно ответственно.
Перед кладкой первого ряда наверху фундамента делается гидроизоляция, которая будет защищена между фундаментом и кладкой. Под блоки залили выравнивающий слой из цементно-песчаного раствора. Сами блоки устанавливаются с использованием полимерных растворов на основе сухих смесей, иногда для монтажа также используются битумные рулонные материалы.
Чтобы выровнять все ряды зданий по углам, грабли рассчитываются с учетом риска на высоте каждого ряда кладки. Через них протягивают волоконный шнур, чтобы контролировать гладкость кладки каждой последующей серии.
С помощью уровня необходимо измерить уровень наивысшего угла постройки, с которого начинается строительство постройки. При этом разница в высоте между углами дома не должна быть более 3 см.
|
Лучше всего блоки кладутся на клеевую смесь.Требуется вода, ведро для замеса и строительный миксер. В ведро наливают необходимое количество воды и постепенно при постоянном перемешивании добавляют расчетное количество сухой смеси. Во время монтажных работ клей время от времени необходимо перемешивать. Это делается для того, чтобы он не затвердевал, чтобы постоянно поддерживалась его однородность.
В процессе строительства часть газосиликатных блоков подлежит отделке. Эти материалы режутся просто, с помощью обычной ручной пилы.Для точной обрезки и измерения прямого угла При распиловке используется кухня. Такие обрезанные блоки называют хорошими. Перед установкой очередного добровольного блока обязательно пропустите вертикальные швы с клеевой смесью.
Кладка последующих рядов стен
Укладка следующих рядов также имеет свои особенности. Каждая последующая строка нажимается только после того, как предыдущая полностью увидит. По времени это примерно 1-2 часа после завершения кладки.
Необходимо четко контролировать кладку каждого стенового блока. Ровность рядов проверяют по уровню и шнуру-болтушке. Финишное выравнивание кладки производится с помощью уровня и резины xy.
Смесь наносится на блоки следующим образом. В зависимости от толщины блоков подбирается зубчатая каретка или шпатель для нанесения смеси. Равномерно, без пропусков клей наносится на поверхность 2-3 блоков. Каретка помогает быстро распределить смесь, не растекая ее по сторонам блоков.
Последующие ряды так же, как и первый, кладут на угол здания. В этом случае клеящая смесь не наносится на торцы блоков. Приобретайте и выравнивайте материалы сразу на месте, блокируя блоки.
В некоторых случаях требуется армирование газиликатных блоков.
Правильное армирование кладки
Каждый первый и четвертый ряды кладки армированы.Для изготовления арматуры посередине блоков вырубают ручные или электрические ножницы. Если вы работаете с блоками толщиной 400 мм, лучше всего проложить два параллельных ряда арматуры. Попавшая внутрь строительная пыль удаляется с помощью перфоратора или фена.
Перед заливкой обувных смесей и укладкой арматуры рекомендуется смочить их водой. Это сделано для повышения качества строительства объектов. Каждую перекладку заполняют крепежным раствором на половину ее глубины, после чего оплавляют стальной стержень арматуры.
|
Для армирования блоков используются стальные стержни диаметром 8 мм. При армировании блоков по углам здания башмаки просверливают закруглениями, а стержни выходят за расчетное место. Для гибки используется специальное оборудование или ручной инструмент. После этого штанги устанавливаются каждый на свой ход.
Каждый элемент арматуры погружается в клеевой раствор, затем штрих заливается раствором.Таким образом, противодействуя возникновению коррозии. После завершения операции остатки смеси удаляются с помощью шпателя.
После монтажа стен из газосиликатных и топливобетонных блоков требуется их облицовка.
Существует несколько основных вариантов облицовки.
Кирпич облицовочный.
Обращаюсь к следующему.
Штукатурка.
- Выбирая этот вид облицовки, важно помнить, что штукатурка не должна быть цементно-песчаной.В зонах повышенного напряжения, таких как углы зданий, оконные проемы, изломы фасадных профилей, рекомендуется армировать штукатурный слой специальными сетками.
- При штукатурных работах не допускать замерзания, высыхания штукатурки, а также соблюдать температурный режим.
Выбирайте газоблоки для своего строительства!
Газиликатные блоки благодаря своей универсальности оптимально подходят для возведения малоэтажных объектов в частном строительстве.Основное преимущество этого стройматериала — небольшой вес прокладок при больших размерах, что позволяет увеличить скорость движения стен и заложить легкий фундамент. Большие габариты изделия — это еще и минимальное количество «мостиков холода» в стенах. Самостоятельная кладка стен из газоблоков не требует профессиональных навыков и опыта — достаточно уметь владеть простейшими строительными инструментами.
Пористая структура изделий из газосиликата заставляет учитывать его свойства при работе с газобетонными блоками для предотвращения отклонений от технологии строительства и обеспечения проектной прочности и надежности конструкции.Наличие воздушных пор обеспечивает простую доставку изделий на строительную площадку и непосредственно в безвыходное место, а также быстрое увеличение высоты стен за счет больших размеров изделий и системы «гребешок-паз». , который автоматически выравнивает ранги относительно друг друга.
Но из-за небольшого веса пористого блока он оказывает небольшое давление на строительный раствор, создавая некачественное сцепление между смесью и кирпичом. Поэтому использование цементно-песчаного раствора рекомендуется максимально ограничить, а работать со специальным строительным клеем, толщина шва которого минимальна при высокой адгезии с любой поверхностью.
IN индивидуальное строительство. Предпочтительно оцениваются такие характеристики газобетона, как размер изделий и плотность строительных материалов. Использование клеевого состава в сочетании с крупногабаритными изделиями и небольшим количеством клеевых швов не позволяет ковать «мостики холода», которые неизбежно появятся при работе с цементом.
Свойства теплоизоляции — еще одно несомненное достоинство газосиликатного кирпича. Воздух в порах блоков пропускает само тепло, и остается в помещении, а холодный воздух не проникает в дом снаружи.Поэтому в дополнительном утеплении здания не потребуется, за исключением утепления фундамента и крыши.
Гидроизоляционные характеристики газобетона недостаточно высоки, чтобы обойтись без слоев гидроизоляции, поэтому защита от влаги необходима не только для фундамента и кровли, но и стен, как внутри, так и снаружи. Обычно это слой штукатурки с предварительной пропиткой битумом, грунтовкой и другими средствами защиты от влаги.В этом случае толщина стен не имеет значения, так как влага будет проникать на всю ширину блоков.
Самостоятельная кладка стен из газосиликатных блоков по стоимости выйдет намного дешевле, чем строительные работы с традиционными материалами — кирпичом, бетоном или деревом. Цена определяется самыми дешевыми натуральными компонентами для производства газосиликата, дешевыми технологиями производства, невысокой стоимостью. Транспортировка больших объемов стройматериалов с малым весом.Использование обычных инструментов без привлечения автоматики и специального оборудования, а также высокая скорость кладки делают работы недорогими.
Применение газоблоков — кладка из блоков газосиликатных блоков не только в частном секторе, но и в промышленных масштабах, ограниченная только затоплением конструкций. Оптимально подобранные блоки блоков, несколько типоразмеров стандартного кирпича, позволяют в короткие сроки завершить ремонтно-строительные работы в любом объеме. Кроме того, у производителя можно заказать нестандартные блочные блоки, что ускорит кладку или обеспечит быстрое возведение геометрически сложных архитектурных объектов.
Поверхность стен из газосиликата практически идеально гладкая, что позволяет свести к минимуму отделочные работы на лицевой стороне.
Подготовка фундамента под кладку стен
Перед началом кладки газосиликатного блока необходимо проконтролировать горизонтальную поверхность фундамента, необходимо проконтролировать горизонтальную поверхность фундамента — это зависит от ровности кладки первого и последующих рядов газа. -силикатный кирпич.Если перепад по краям стены составляет 10-20 мм, фундамент следует выровнять слоем цементно-песчаного раствора. Дальнейшая укладка блоков по системе «паз-гребень» значительно упростится, если первый ряд закрепить идеально горизонтально. Также необходимо проверить углы периметра — они должны быть 90 0. Контроль измеряется по диагоналям периметра дома.
Для того, чтобы дождевая или снежная вода была под фундаментом, необходимо выложить стену газоблока так, чтобы она выполнялась на 1-2 см по краям фундаментной плиты.Так влага будет сразу стекать к завтраку и попадать в дренаж. Именно поэтому между стеной и фундаментом дома следует обустроить два-три слоя гидроизоляции из каучукоида, чтобы стены не увлажнялись и не плесневели. При изготовлении раствора и устройстве гидроизоляции толщина стен из газосиликатных блоков не имеет значения — стены любой толщины необходимо защищать от влаги.
Варианты кладки стен
Стены из газосиликатных блоков возводятся на цементно-песчаном растворе и на специальном строительном клее, который готовится из сухой смеси с добавлением обычной воды.Исследования показали, что в толстом слое раствора «мостики холода» возникают гораздо чаще, поэтому связку и укладку газосиликатного блока следует производить менее тонким слоем связующего. Это возможно только при использовании клея. Цементный раствор дает слой средней толщины 9-12 мм, а слой строительного клея 3-5 мм, поэтому цементный раствор используют только для укладки первого ряда газоблоков для перевязки стены и основа. Дальнейшую кладку рекомендуется выполнять на клей, а при использовании блоков-пазлов цементный раствор использовать просто невозможно из-за точного прилегания элементов — паза и гребня друг к другу — раствор не влезает в пространство между ними.
Стены из газосиликата возводятся с одновременным формированием как можно большего слоя вяжущего раствора. И цементно-песчаный, и клеевой раствор можно приготовить самостоятельно.
- Раствор песчано-цементный готовится традиционно, в пропорции 1: 3 (цемент — песок). При зимнем строительстве дома обычный раствор использовать нельзя, так как при отрицательных температурах прочность состава нарушается образованием наледи.
- Клей изготовлен на основе портландцемента с добавлением минеральных добавок и полимеров.Благодаря тонкому составу клеевой слой раствора получается очень тонким, и не появляются «мосты холода». Но первый ряд блоков нужно укладывать только на цементный раствор, а для обогрева места кладки используют несколько методов, в том числе тепловые пушки, палатки и локальное отопление.
А вот стандартный клеевой состав в чистую зиму использовать нельзя. Для отрицательных температур выпускаются специальные антикоррозионные присадки, с которыми клей быстрее успешно отмерзает на морозе.
Инструмент и оборудование для строительства домов из газосиликатных блоков
Правильная и точная геометрия блоков, небольшой вес газосиликата, упрощенная кладка за счет системы пазлов позволяет обойтись без спецтехники и многочисленной бригады строителей. Для самостоятельного строительства необходим такой инструмент:
- Сверло, шлифовальный станок или электролизер — индивидуальные размеры блоков для геометрически сложных архитектурных конструкций;
- Уровень, рабочие процессы разной формы и шпатель разной ширины, включая шестерни;
- Резиновый или деревянный циус;
- Емкость для замеса раствора;
- Рубероид, битум, мембранные материалы, армирующая сетка.
Способ укладки газосиликатных блоков
- Первым делом проводится гидроизоляция фундамента и пористых газоблоков. Рубероид необходимо расколоть по ширине основания и двумя-тремя двумя слоями на чистой и гладкой поверхности основания;
- Далее выкладываются углы будущих стен. Газовая камера устанавливается на фундамент вертикально, положение регулируется уровнем и регулируется Цианом;
- Между образовавшимися уголками нужно натянуть шнур, с помощью которого будут выравниваться оставшиеся блоки и ряды;
- Для кладки первого ряда используется цементно-песчаный раствор минимально возможной толщины.Раствор наносится на нижнюю и боковые стороны блока и фундамент зубчатым шпателем подходящей ширины. Основная задача цементного раствора — выравнивание первого ряда, поэтому допускается увеличение толщины слоя до 20-25 мм;
- После схватывания раствора под первый следующий (1-2 часа) можно приступать к кладке второго и последующих рядов. Последний газоблок регулируется по размерам с помощью болгарки, деревянной ножовки или лобзика. Промежуточное белье осуществляется сдвигом блоков влево-вправо на 10-12 см.Следующий ряд укладывается после снятия угловых кирпичей и выравнивания поверхности предыдущего ряда его шлифовки.
- Клей на следующих рядах наносится сплошным слоем с помощью подходящего шпателя на поверхность нижнего ряда, а на блоки БОК клей необходимо зубчатым шпателем для получения толщины 1-5 мм. Крайний клей необходимо удалить после его полного высыхания на стене;
- При формировании перемычек для окон и дверей используются бетонные или металлические плиты, профиль или капеллеры;
- Каждый третий-четвертый ряд необходимо армировать стержнями Ø 10-14 мм или армирующей сеткой из стекловолокна, чтобы не увеличивать толщину растворяющегося шва.При армировании стержней блоками башмаки укладываются, а стержни укладываются на расстоянии не менее 5 см от краев стены;
Особенности зимней конструкции
При строительстве малоэтажного частного дома из газосиликатных блоков уличная температура не имеет значения — важен клей и цементный раствор. При отрицательной температуре адгезия растворов ухудшается, и прочность стен заметно теряет качество.Если строительство планируется сплошным, то для зимней кладки практикуются следующие вытяжные и эффективные приемы:
- Синтетические добавки, обеспечивающие стопроцентную герметизацию и отказ от клея при температуре стрита до -35 0 С;
- Обогрев места Кладка — тепловая пушка, электрические обогреватели, нагреваемые электродами или кабелем, электрические маты или местное палатное оборудование и т. Д. Важно, чтобы кладка кладки с клеевым раствором была теплой или имела температуру не ниже 0 0 C.Чаще всего эти методы сочетают или применяют кратковременное локальное утепление места кладки блока.
Газосиликатные блоки — строительный материал, идеально сочетающий в себе высокие технические и эксплуатационные характеристики и доступную цену. Действующие ГОСТ и СНиП позволяют возводить дома из газосиликатных блоков до 5-7 этажей. Небольшой вес изделий и простая стилизация позволяют построить дом своими руками и без использования специальной техники, что заметно сэкономит семейный бюджет.Застройщику остается только соблюдать технологию строительства, и в результате он получит теплый, надежный и качественный дом.
Кладка из газосиликатных блоков Обновлено: 17.01.2017 автором: Артём
Преимущества и особенности производства силикатных блоков | МосарМпроф
Среди огромного количества различных видов строительных материалов в последнее время все большую популярность приобретают газосиликатные блоки. Они относятся к группе ячеистых бетонов, и главной отличительной особенностью является наличие в структуре большого количества воздушных пор.Эти поры могут значительно снизить вес бетона, а также улучшить теплоизоляционные свойства, что позволяет сэкономить на расходах на отопление зимой и на кондиционирование воздуха летом.
Кроме того, не стоит забывать и о небольшом весе таких блоков, чтобы обеспечить легкость строительства, а также прямую экономию на возведении фундамента. Ну и не стоит забывать, что газосиликатные блоки достаточно легко обрабатываются (распиливаются, сверлятся и т. Д.), Что позволяет существенно ускорить процесс строительства и отделки.Однако при этом следует отметить и высокую прочность этого материала, которая намного превышает эти показатели у пенопласта.
В нашей стране строительные материалы начали использовать совсем недавно, хотя изобрели это еще в середине прошлого года, когда шведскому архитектору удалось получить патент на изобретение силиката. Спустя несколько лет производство этого материала было осуществлено в больших масштабах, как оказалось, цена на газосиликатные блоки может быть вполне доступной (для сравнения, производство этих блоков впервые было стандартизовано только в ГОСТ21520-89, то есть конца прошлого века).
Сегодня производство газосиликатных блоков находится в несколько этапов. Первый из них — это приготовление специального раствора на основе воды, чистого песка и извести. После этого идет добавление алюминиевого порошка, химическая реакция, которая приводит к выделению больших объемов углекислого газа, образуя пузырьки воздуха. Полученную смесь тщательно перемешивали и разливали в специальные формы на несколько часов с последующим первоначальным схватыванием.
Подробности Вы можете узнать, позвонив в любой магазин стройматериалов.Если на вашем iPhone не работает EPL, обратитесь в компанию, там вам быстро отремонтируют.
На следующем этапе производственные установки помещаются в автоклав, во время которого происходит активное образование пузырьков газа, которые равномерно распределяются по всей толщине блока, обеспечивая те же характеристики, что и в любой секции. После этого готовые объекты можно отправлять на продажу в магазины DIY или прямо на объект, что позволяет сэкономить на строительстве.
Прочность газосиликатных блоков.Что такое газосиликатные блоки, их характеристики, плюсы и минусы. Эксплуатационные параметры газосиликатных блоков
Практичность
Прочность
Устойчивое развитие
Стоимость
итоговая оценка
Эксплуатационные параметры газосиликатных блоков
Срок службы — номинал до 100 лет в нормальном климате и до 50 лет во влажном климате.При правильном уходе, наличии штукатурки и водостоков стандартные сроки вполне соответствуют настоящим.
Расход материала — зависит от климатических условий. Рекомендуемая толщина стенок составляет от 400 мм в умеренном климате до 800 мм в северных регионах.
Класс прочности на сжатие — характеризует гарантированное давление, которое не приведет к разрушению. Блоки плотностью 600 кг / м3 имеют класс прочности от В1.5 до В3,5 (в 2-3 раза меньше, чем у кирпича). У теплоизоляционных конструкций с плотностью материала 300 кг / м3 класс прочности намного ниже — В0,75-В1,5.
Отметим, что снижение класса прочности газосиликатных блоков не означает реального снижения прочности конструкции. Для пористого материала масса всей кладки (как следствие оказываемое давление) в 2,5-3 раза ниже, чем у кирпичной конструкции.
Морозостойкость — численно показывает количество циклов оттаивания, которое может выдержать конкретный тип материала, не теряя более 15% своей прочности.В данном случае обозначение F50 означает, что гарантированное количество циклов равно 50.
Технические испытания проводятся в суровых условиях, значительно превышающих изменения окружающей среды. Блок погружают в воду до полного насыщения, а затем помещают в морозильную камеру. На самом деле таких суровых условий не бывает, поэтому основная функция параметра — сориентировать покупателя в более приемлемом варианте для конкретной климатической зоны.
Коэффициент теплопроводности — зависит от плотности и влажности материала.Так, самый легкий газосиликатный блок (300 кг / м3) имеет теплопроводность около 0,08 Вт / (м²С), а самый тяжелый (600 кг / м3) — почти в 2 раза больше. Увеличение влажности материала на 1% увеличивает теплопроводность на 4-5%.
В таблице приведены отличия блоков разных марок по теплопроводности, усадке, морозостойкости и паропроницаемости:
Газосиликатные блоки — хороший выбор для небольших домов, особенно в холодном климате.Для дачи или стен в квартире пористый материал также станет удобным и недорогим выходом из положения. При покупке следует внимательно проверять содержимое поддонов — недобросовестные продавцы могут продавать блоки с высоким процентом брака.
Газосиликатные блоки — это разновидность легкого ячеистого материала, имеющего достаточно широкую область применения в строительстве. Популярность изделий из ячеистого бетона данного типа обусловлена высокими техническими качествами и многочисленными положительными характеристиками.В чем преимущества и недостатки газосиликатных блоков, и каковы особенности их использования при строительстве домов?
Газосиликат считается улучшенным аналогом газобетона. В производственную технологию его изготовления входят следующие компоненты: высококачественный портландцемент
- , содержащий более 50 процентов неорганического соединения силиката кальция;
- вода;
- алюминиевый порошок в качестве вспенивателя;
- Известь гашеная, обогащенная на 70 процентов оксидами магния и кальция;
- Песок кварцевый мелкий.
Смесь этих компонентов дает высококачественный пористый материал с хорошими техническими характеристиками:
- Оптимальная теплопроводность. Этот показатель зависит от качества материала и его плотности. Марка газосиликатных блоков Д700 соответствует теплопроводности 0,18 Вт / м ° С. Этот показатель немного выше многих значений для других строительных материалов, в том числе железобетонных.
- Морозостойкость. Газосиликатные блоки плотностью 600 кг / м³ способны выдерживать более 50 циклов замораживания-оттаивания.У некоторых новых марок заявлен индекс морозостойкости до 100 циклов.
- Плотность материала. Эта величина варьируется в зависимости от типа газосиликата — от D400 до D700.
- Способность поглощать звуки. Шумоизоляционные свойства сотовых блоков равны коэффициенту 0,2 на звуковой частоте 1000 Гц.
Многие технические параметры газосиликата в несколько раз превышают характерные показатели кирпича. Для обеспечения оптимальной теплопроводности стены выкладывают толщиной 50 сантиметров.Для создания таких условий из кирпича требуется размер кладки 2 метра.
Качество и свойства газосиликата зависят от соотношения компонентов, используемых для его приготовления. Повысить прочность изделий можно за счет увеличения дозы цементной смеси, но при этом снизится пористость материала, что скажется на других его технических характеристиках.
Виды
Газосиликатные блоки делятся в зависимости от степени прочности на три основных типа:
- Конструкционные.Из такого материала возводятся постройки не выше трех этажей. Плотность блока — D700.
- Конструкционная и теплоизоляция. Газосиликат этого типа применяется для кладки несущих стен в зданиях не выше двух этажей, а также для возведения межкомнатных перегородок … Его плотность колеблется от D500 до D700.
- Теплоизоляция. Материал успешно применяется для снижения степени теплоотдачи стен. Его прочность невысока, а из-за высокой пористости плотность достигает всего D400.
Газосиликатные строительные блоки производятся двумя способами:
- Автоклав. Технология изготовления заключается в обработке материала под высоким давлением пара 9 бар и температурой 175 градусов. Такая пропарка блоков осуществляется в специальных промышленных автоклавах.
- Неавтоклавный. Приготовленная газосиликатная смесь естественным образом застывает более двух недель. При этом поддерживается необходимая температура воздуха.
Газосиликат, полученный автоклавированием, имеет самые высокие технические характеристики.Такие блоки обладают хорошими прочностными и усадочными характеристиками.
Размер и вес
Размер газосиликатного блока зависит от типа материала и его производителя. Наиболее распространены следующие размеры, выражаемые в миллиметрах:
- 600x100x300;
- 600x200x300;
- 500x200x300;
- 250x400x600;
- 250x250x600.
Газосиликат из-за своей ячеистой структуры является довольно легким материалом.Вес пористых изделий различается в зависимости от плотности материала и его типоразмеров:
- D400 — от 10 до 21 кг;
- D500-D600 — от 9 до 30 кг;
- D700 — от 10 до 40 кг.
Небольшая масса блоков и возможность выбора необходимого размера значительно облегчают процесс строительства.
Сфера применения газосиликатных блоков
В строительстве газосиликат успешно применяется для следующих целей:
- строительство зданий;
- теплоизоляция различных зданий;
- изоляция теплотехнических и строительных конструкций.
Количество ячеек на кубический метр в добываемых газосиликатных блоках разное. Следовательно, область применения материала напрямую зависит от плотности материала:
- 700 кг / м³. Наиболее эффективно такие блоки используются при строительстве многоэтажных домов. Строительство многоэтажек из газосиликата обходится намного дешевле, чем из железобетона или кирпича.
- 500 кг / м³. Материал используется для строительства малоэтажных домов — до трех этажей.
- 400 кг / м³. Этот газосиликат подходит для кладки одноэтажных домов. Чаще всего его используют для недорогих хозяйственных построек. Кроме того, материал успешно применяется для утепления стен.
- 300 кг / м³. Ячеистые блоки с низким показателем плотности предназначены для утепления несущих конструкций. Материал не способен выдерживать высокие механические нагрузки, поэтому не подходит для возведения стен.
Чем меньше плотность ячеистых блоков, тем выше их теплоизоляционные свойства.В связи с этим конструкции из газосиликата с плотной структурой часто требуют дополнительного утепления. В качестве изоляционного материала используются плиты пенополистирола.
Достоинства и недостатки
Строительство домов из газосиликатных блоков вполне оправдано невысокой стоимостью материала и его многочисленными преимуществами:
- Блоки для строительства домов отличаются высокой прочностью. Для материала со средней плотностью 500 кг / м³ степень механического сжатия составляет 40 кг / см3.
- Небольшой вес газосиликатных изделий позволяет избежать дополнительных затрат на доставку и установку блоков. Ячеистый материал в пять раз легче обычного бетона.
- За счет хорошей теплоотдачи снижается расход тепла. Это свойство позволяет существенно сэкономить на отоплении здания.
- Высокий показатель звукоизоляции. Благодаря наличию пор ячеистый материал защищает от проникновения шума в здание в десять раз лучше, чем кирпич.
- Хорошие экологические свойства. Блоки не содержат токсичных веществ и полностью безопасны в использовании. По многим экологическим показателям газосиликат приравнивается к древесине.
- Высокая паропроницаемость изделий позволяет создавать в помещении хорошие условия микроклимата.
- Негорючий материал предотвращает распространение огня в случае пожара.
- Точные пропорции размеров блоков позволяют выполнять кладку стен ровно.
- Доступная цена материала.При хороших технических показателях цена газосиликатных блоков относительно невысока.
Помимо множества преимуществ, пористый материал имеет ряд недостатков:
- Механическая прочность блоков несколько ниже, чем у железобетона и кирпича. Поэтому при вбивании гвоздей в стену или ввинчивании дюбелей поверхность легко осыпается. Блоки достаточно плохо удерживают тяжелые детали.
- Способность впитывать влагу. Газосиликат хорошо и быстро впитывает воду, которая проникает в поры, снижает прочность материала и приводит к его разрушению.При строительстве зданий из разных типов пористый бетон используется для защиты поверхностей от влаги. На стены рекомендуется наносить штукатурку в два слоя.
- Морозостойкость блоков зависит от плотности изделий. Марки газосиликатов ниже D 400 не выдерживают 50-летнего цикла.
- Материал склонен к усадке. Поэтому, особенно для блоков марки ниже D700, первые трещины могут появиться через пару лет после постройки здания.
При отделке стен из газосиликата в основном применяется гипсовая штукатурка. Он отлично скрывает все швы между блоками. Цементно-песчаные смеси не прилипают к пористой поверхности, а при понижении температуры воздуха образуются небольшие трещинки.
Популярность газосиликата растет с каждым годом. Ячеистые блоки обладают практически всеми качествами, необходимыми для эффективного строительства малоэтажных домов … Некоторые характеристики намного превосходят характеристики других материалов. С помощью легких газосиликатных блоков можно построить надежное здание с небольшими затратами в относительно короткие сроки.
Еще одним популярным материалом, занявшим значительную долю на рынке строительных материалов, является газосиликат. Готовые лепные блоки имеют много общего с искусственным камнем и обладают заметными преимуществами. По этой причине газосиликатные блоки приобрели такую широкую популярность при строительстве домов.
Где используются газосиликатные блоки?
Область применения газосиликата находится в следующих областях:
- теплоизоляция зданий,
- Строительство зданий и несущих стен,
- изоляция систем отопления.
Газосиликатные блоки по своим качествам имеют много общего с пенобетоном, но при этом превосходят их по механической прочности.
В зависимости от плотности материала. есть несколько областей применения:
- Плотность блоков от 300 до 400 кг / м3 сильно ограничивает их распространение, и такие блоки чаще используются в качестве утеплителя для стен. Их низкая плотность не позволяет использовать их в качестве основы для стен, так как они будут разрушаться при значительных механических нагрузках.Но в качестве обогревателя играет роль низкая плотность, поскольку чем плотнее молекулы прилегают друг к другу, тем выше становится теплопроводность и тем легче холоду проникать в комнату. Следовательно, блоки с низкой теплопроводностью обеспечивают более эффективную теплоизоляцию, Блоки
- плотностью 400 кг / м3 нашли свое применение при строительстве одноэтажных зданий и рабочих помещений. За счет повышенной прочности блоков и их меньшего веса значительно снижаются затраты на устройство фундамента, Блоки
- плотностью 500 кг / м3 чаще используются при строительстве зданий высотой в несколько этажей.Как правило, высота здания не должна превышать трех этажей. Такие блоки в прямой зависимости от климата либо вообще не утепляются, либо требуют традиционных методов утепления.
- Самый лучший вариант для строительства многоэтажных домов — это использование блоков плотностью 700 кг / м3. Такой показатель позволяет возводить многоэтажные жилые и производственные дома. Благодаря более низкой стоимости возведенные стены из газосиликатных блоков заменяют традиционные кирпичные и железобетонные стены.
Чем выше плотность, тем хуже теплоизоляционные характеристики, поэтому в таких зданиях потребуется дополнительная изоляция. Чаще всего внешний обеспечивается с помощью плит пенопласта или пенополистирола. Этот материал имеет невысокую цену и при этом обеспечивает хорошую теплоизоляцию помещения в любое время года.
В последнее время значительно укрепились позиции газосиликата, как одного из самых востребованных материалов в строительстве.
Относительно небольшой вес готовых блоков существенно ускорит возведение здания. Например, газосиликатные блоки, размеры которых имеют типовые значения, по некоторым оценкам, снижают трудоемкость при установке до 10 раз по сравнению с кирпичными.
Стандартный блок плотностью 500 кг / м3 и весом 20 кг заменяет 30 кирпичей, общий вес которых составляет 120 кг. Таким образом, установка блоков на малоэтажные дома не требует специального оборудования, это снизит трудозатраты и время, затрачиваемое на возведение здания.По некоторым оценкам, экономия времени достигает 4-кратного снижения затрат.
Характеристики материала
Имеет смысл перечислить основные технические характеристики газосиликатных блоков:
- Удельная теплоемкость блоков, изготовленных автоклавированием, составляет 1 кДж / кг * ° С. Например, для железобетона аналогичный показатель находится на уровне 0,84,9 .
- плотность железобетона в 5 раз выше, но при этом коэффициент теплопроводности газосиликата всего 0.14 Вт / м * ° С, что примерно аналогично древесине сосны или ели. Железобетон имеет значительно более высокий коэффициент, 2,04,
- звукопоглощающие характеристики материала на уровне коэффициента 0,2, при частоте звука 1000 Гц, №
- цикличность морозостойкости для газосиликатных блоков с плотностью материала ниже 400 кг / м3 не нормируется, для блоков плотностью до 600 кг / м3 до 35 циклов. Блоки плотностью более 600 кг / м3 способны выдерживать 50 циклов замораживания-оттаивания, что соответствует 50 климатическим годам.
Если сравнивать газосиликатные блоки с кирпичом, то показатели не в пользу последнего. Так, необходимая толщина стены для обеспечения достаточной теплопроводности блоков составляет до 500 мм, тогда как для кирпича потребуется аналогичная кладка толщиной 2000 мм. Расход раствора для кладки материала составит 0,12 м3 для кирпича и 0,008 м3 для газосиликатных блоков на 1 м2 кладки.
Вес одного квадратного метра стен составит до 250 кг для газосиликатного материала и до двух тонн кирпича.Для этого потребуется соответствующая толщина фундамента под несущие стены строящегося дома. Для кирпичной кладки потребуется толщина фундамента не менее 2 метров, тогда как для газосиликатных блоков достаточно толщины всего 500 мм. Трудоемкость укладки блоков значительно ниже, что снизит трудозатраты.
Помимо прочего, газосиликатные блоки значительно экологичнее. Коэффициент этого материала составляет два балла, что приближает его к натуральному дереву.При этом показатель экологичности кирпича находится на уровне от 8 до 10 единиц.
Преимущества и недостатки газосиликатных блоков
Газосиликатные блоки, цена на которые значительно удешевит стоимость строительства дома, обладают следующим рядом неоспоримых преимуществ:
- Легкость готовых блоков. Газосиликатный блок весит в 5 раз меньше аналогичного бетонного блока. Это значительно снизит затраты на доставку и установку.
- Высокая механическая прочность на сжатие. Газосиликат с индексом D500, что означает его плотность 500 кг / м3, показывает показатель до 40 кг / см3.
- Показатель термического сопротивления в 8 раз выше, чем у тяжелого бетона. Благодаря пористой структуре он обеспечивает хорошие показатели теплоизоляции.
- Газосиликатные блоки обладают теплоаккумулирующими свойствами. Они способны передавать скопившееся тепло в помещение, что снизит затраты на отопление.
- За счет пористой структуры степень звукоизоляции в 10 раз выше, чем у кирпича.
- Материал не содержит токсинов и имеет хорошие экологические характеристики.
- Газосиликат отличается негорючестью и не распространяет горение. ОН выдерживает прямое воздействие пламени не менее трех часов, что практически полностью исключает ситуацию с распространением огня.
- Паропроницаемость блоков намного выше, чем у конкурентов.Считается, что материал способен хорошо «дышать», создавая при этом комфортный микроклимат в помещении.
Однако газосиликатные блоки в настоящее время не способны нанести сокрушительный удар всем конкурентам. Этот материал также имеет существенные недостатки:
- Газосиликат имеет низкую механическую прочность. Когда в него ввинчивается дюбель, он начинает крошиться и крошиться и при этом не может обеспечить эффективное удержание. Грубо говоря, еще можно повесить часы или картину на стену из газосиликатных блоков.Но полка уже может разрушиться, так как крепеж может просто выскользнуть из стены.
- Блоки не обладают хорошей морозостойкостью. Несмотря на заявленный производителем цикл в 50 лет для марок с повышенной прочностью, достоверной информации о долговечности блоков Д300 нет.
- Основным недостатком газосиликата является его высокое влагопоглощение. Он проникает в конструкцию, постепенно разрушая ее, и материал теряет прочность.
- Из указанного недостатка вытекает следующее: скопление и впитывание влаги приводит к появлению грибка.В этом случае пористая структура служит хорошим условием для ее распространения.
- Материал способен значительно давать усадку, в результате чего в блоках часто появляются трещины. Более того, через два года трещины могут появиться на 20% уложенных блоков.
- Не рекомендуется применять цементно-песчаные штукатурки. Они могут просто упасть со стены. Гипсовая штукатурка, рекомендованная многими продавцами, также не является эффективным средством … При нанесении на стену из газосиликатных блоков она не способна скрыть швы между блоками, а при наступлении холодов на ней появляются заметные трещины. .Это связано с перепадами температур и изменением плотности материала.
- Из-за высокого влагопоглощения штукатурка требует как минимум двух слоев. К тому же из-за сильной усадки штукатурка потрескается. На герметичность они не повлияют, но эстетическую составляющую сильно нарушат. Гипсовая смесь хорошо сцепляется с газосиликатными блоками и, несмотря на появление трещин, не отрывается.
Как изготавливают газосиликатные блоки
Газосиликатные блоки целесообразнее покупать у тех дилеров, которые представляют продукцию известных производителей.Современное качественное оборудование на производственных линиях завода позволяет обеспечить должный контроль качества производимых газосиликатных блоков, благодаря чему покупатель уверен в долговечности закупаемой продукции.
Сам производственный процесс разделен на несколько этапов, каждый из которых, что типично, полностью автоматизирован. Это исключает вмешательство человеческого фактора, от которого часто зависит качество продукции. Особенно по пятницам и понедельникам. Те, кто работал на производстве, поймут.
Дробится известь, песок и гипс, что является основой для производства блоков. Добавляя воду, песок измельчается до жидкой смеси. Его отправляют в миксер, в который добавляют цемент, гипс и известь. Далее компоненты замешиваются, и во время этого процесса к ним добавляется алюминиевая суспензия.
После того, как все компоненты были тщательно перемешаны друг с другом, смесь разливается в формы, которые перемещаются в зону созревания. При воздействии температуры 40 ° C в течение четырех часов материал набухает.При этом активно выделяется водород. Благодаря этому конечная масса приобретает необходимую пористую структуру.
С помощью токарного захвата и отрезного станка блоки разрезаются под требуемые размеры … При этом автоматика контролирует точную и бездефектную резку изделий.
После этого блоки отправляются в автоклав для окончательной прочности. Этот процесс происходит в камере при температуре 180 ° C в течение 12 часов.В этом случае давление паров на газосиликат должно быть не менее 12 атмосфер. Благодаря этому режиму готовые блоки приобретают оптимальное значение конечной прочности.
Благодаря крану-разделителю и оборудованию для окончательного контроля качества блоки укладываются для их последующего естественного охлаждения. После этого на автоматической линии с блоков удаляются возможные загрязнения, блоки упаковываются и маркируются.
Примечательно то, что процесс производства безотходный, так как в момент резки, даже на стадии застывания, отходы сырого массива отправляются на повторную переработку, добавляя материал в другие блоки.
Поддоны с фасованными газосиликатными блоками получают собственный технический паспорт с подробными физическими свойствами и техническими характеристиками продукта, чтобы покупатель мог быть уверен в соответствии заявленным характеристикам.
Дальнейшая работа уже для дилеров и маркетологов, от которых будет зависеть успех продаж продукта.
Этот материал имеет значительные конкурентные преимущества и пользуется заслуженной популярностью на строительном рынке нашей страны.Отличается минимальным весом, что упрощает возведение стен, а также обеспечивает надежную теплоизоляцию интерьера, благодаря пористой структуре. К тому же газосиликатные блоки привлекают покупателей доступной ценой, которая выгодно отличается от кирпичных или деревянных.
Естественно, что этот строительный материал имеет свои особенности, а также специфику применения. Поэтому, несмотря на невысокую стоимость, использование газобетонных блоков не всегда целесообразно.Чтобы лучше разобраться в этих тонкостях, есть смысл подробно рассмотреть основные технические характеристики материала.
Состав газосиликатных блоков
Материал изготовлен по уникальной технологии. В частности, блоки получают вспениванием, что придает им ячеистую структуру. Для этого в формы с исходной смесью добавляется пенообразователь, которым обычно играет алюминиевый порошок. В результате сырье значительно увеличивается в объеме, и образуются пустоты.
Для приготовления исходной смеси обычно используют следующий состав:
Высококачественный цемент с содержанием силиката калия более 50% .
Песок, с 85% содержание кварца.
Известь с содержанием оксидов магния и кальция более 70% и скоростью гашения до 15 минут.
Сульфанол С.
Стоит отметить, что включение цемента в смесь не является обязательным условием, а если используется, то в минимальных количествах.
Закалка блоков завершается в печах автоклавов, работающих в условиях высокого давления и температуры.
Технические характеристики
Для газосиликатных блоков характерны следующие технические параметры:
Насыпной вес из 200 перед 700 шт. … Это показатель сухой плотности газобетона, на основании которого маркируются блоки.
Прочность на сжатие … Это значение варьируется в пределах B0.03-B20 , в зависимости от предполагаемого использования.
Показатели теплопроводности … Эти значения находятся в пределах 0,048-0,24 Вт / м, и напрямую зависят от плотности продукта.
Паронепроницаемость … Это соотношение составляет 0,30–0,15 мг / Па и также изменяется с увеличением плотности.
Усадка … Здесь оптимальные значения колеблются в пределах 0.5-0-7 в зависимости от сырья и технологии изготовления.
Циклы замораживания … Это морозостойкость, обеспечивающая замораживание и оттаивание блоков без нарушения конструкции и прочностных показателей. По этим критериям газосиликатным блокам присвоена классификация от F15 до F100 .
Необходимо уточнить, что это не эталонные показания, а средние значения, которые могут меняться в зависимости от технологии производства.
Размеры по ГОСТ
Конечно, производители выпускают газосиликатные блоки разных размеров. Однако большинство предприятий стараются следовать установленным нормам. ГОСТ за номером 31360 в редакции 2007 г. года. Здесь прописаны следующие размеры готовой продукции:
Важно понимать, что по ГОСТ допускаются отклонения значений длины и диагонали, которые относят готовые изделия к 1. -е или 2 -й разряд.
Размеры стеновых блоков
ТД «Лиски-газосиликат» | ||||
Длина, мм | Ширина, мм | Высота, мм | Объем одного блока, м3 | |
Блоки обыкновенные | 600 | 200 | 250 | 0,03 |
600 | 250 | 250 | 0,038 | |
Блоки языка | 600 | 200 | 250 | 0,03 |
600 | 300 | 250 | 0,045 | |
600 | 400 | 250 | 0,06 | |
600 | 500 | 250 | 0,075 | |
Блоки газосиликатные «YTONG» | ||||
Блоки обыкновенные | 625 | 200 | 250 | 0,031 |
625 | 250 | 250 | 0,039 | |
625 | 300 | 250 | 0,047 | |
625 | 375 | 250 | 0,058 | |
625 | 500 | 250 | 0,078 | |
Блоки языка | 625 | 175 | 250 | 0,027 |
625 | 200 | 250 | 0,031 | |
625 | 250 | 250 | 0,039 | |
625 | 300 | 250 | 0,047 | |
625 | 375 | 250 | 0,058 | |
П-образные блоки | 500 | 200 | 250 | * |
500 | 250 | 250 | * | |
500 | 300 | 250 | * | |
500 | 375 | 250 | * |
Количество блоков на 1м3 кладки
Для этого необходимо перевести стороны блока в нужную единицу измерения и определить, сколько кубометров занимает один блок.
Наиболее распространенные на рынке продукты имеют следующий типоразмер: 600 * 200 * 300 … Переводим миллиметры в метры, и получаем 0,6 * 0,2 * 0,3 … Чтобы узнать объем одного блока, умножаем числа и получаем 0,036 м3 … Затем кубометр делим на полученную цифру.
Результат — число 27,7 , что после округления дает 28 газосиликатных блоков в кубометровой кладке.
Размеры перегородок
Вес материала
Конструкционная масса блока меняется в зависимости от плотности готового изделия.Судя по маркировке, можно выделить следующий вес:
Помимо плотности, основным фактором изменения веса считается общий размер готового блока.
Плюсы и минусы газобетона
Как и любой строительный материал, газосиликатные блоки имеют свои сильные и слабые стороны … К положительным характеристикам можно отнести следующие моменты:
Газосиликатный бетон относится к категории негорючих материалов и способен выдерживать воздействие открытого пламени до 5 часов , не изменяя формы и свойств.
Большие габаритные размеры обеспечивают быстрое возведение стеновых конструкций.
Блоки имеют относительно небольшой вес, что значительно упрощает рабочий процесс.
В производстве только натуральные материалы, поэтому газосиликатные блоки экологически чистые.
Пористая структура обеспечивает высокие показатели теплоизоляции помещения.
Материал прост в обработке, что позволяет возводить стены сложной геометрии.
К недостаткам можно отнести следующее:
Хорошо впитывают влагу, что сокращает срок эксплуатации.
Применение для приклеивания специальных клеев.
Обязательная внешняя отделка.
Следует отметить, что газосиликатные блоки требуют прочного основания. В большинстве случаев требуется армирующий пояс.
Газосиликат или газобетон?
Оба материала относятся к категории ячеистых бетонов, поэтому имеют практически идентичную структуру и свойства. Многие строители считают, что газосиликат и газобетон — это два названия одного и того же материала.Однако это заблуждение. При внешнем сходстве газобетон имеет ряд отличительных особенностей, что определяет их дальнейшее применение и технические характеристики.
В частности, при производстве газобетона допускается естественное твердение блока на открытом воздухе, для газосиликатного — автоклавные печи обязательно. Кроме того, для газобетонных блоков основным вяжущим является цемент, для силикатных аналогов — известь. Использование разных компонентов влияет на цвет готовых блоков.
Если говорить о конкретных характеристиках, можно заметить следующие отличия:
Газосиликатные блоки имеют равномерное распределение полых ячеек, что обеспечивает высокую прочность.
Вес газобетонных блоков намного больше, что требует армированного фундамента при строительстве.
По теплоизоляции газосиликатные блоки превосходят газобетонные.
Газобетон лучше впитывает влагу, что обеспечивает большее количество циклов замерзания.
Газосиликатные блоки имеют более согласованную геометрию, в результате можно упростить отделку стеновых конструкций.
По прочности материалы идентичны и могут служить более 50 лет .
Если ответить на вопрос: «Что лучше?» Газосиликатные блоки имеют гораздо больше технических преимуществ. Однако технология изготовления вынуждает увеличивать стоимость готовой продукции, поэтому газобетонные блоки дешевле.Поэтому желающие построить дом из качественного и современного материала выбирают газосиликат, желающие сэкономить на строительстве — предпочитают пенобетон.
При этом нужно учитывать регион применения: в помещениях с повышенной влажностью воздуха срок службы газосиликатных блоков значительно сокращается.
Оштукатуривание стен из газосиликатных блоков
Штукатурка стен подразумевает соблюдение определенных правил и норм.В частности, внешняя отделка выполняется только после завершения внутренних работ … В противном случае на границе газосиликата и штукатурного слоя образуется слой конденсата, который вызовет трещины.
Если говорить о технологии работы, то можно выделить три основных этапа:
Нанесение грунтовочного слоя для улучшения адгезии.
Монтаж стеклопластиковой арматурной сетки.
Штукатурка.
Для отделочных работ лучше использовать силикатные смеси и силиконовые штукатурки, обладающие отличной эластичностью.Штукатурку нанести шпателем, прикоснувшись смесью к армирующей сетке. Минимальная толщина слоя 3 см , максимальная — 10 … Во втором случае штукатурка наносится в несколько слоев.
Клей для газосиликатных блоков
Структура материала предполагает использование специальных клеев для возведения стеновых конструкций. Стоит отметить, что специалисты рекомендуют приобретать клей и блоки в наборе, чтобы исключить конфликты материалов и обеспечить максимальное сцепление.При выборе клея нужно учитывать время застывания состава. Некоторые смеси схватываются на 15-20 минут , но это не показатель качества клея. Оптимальное время схватывания — 3-4 часа .
Если говорить о конкретных наименованиях, можно обратить внимание на следующие марки клея:
Win-160.
Юнис Униблок.
Следует отметить, что для летнего и зимнего строительства используются разные клеи.Во втором случае в смесь добавляют специальные добавки; на упаковке есть соответствующая отметка.
Расход клея на 1м3
Эта информация обычно предоставляется производителем и варьируется в пределах 1,5-1,7 кг … Необходимо уточнить, что приведенные значения актуальны только для горизонтальных поверхностей: для кубатуры расход клея будет составлять заметно выше. Средние значения расхода клея на 1м3 кладки будут примерно 30 кг .
Обратите внимание, что это расчеты производителя и могут отличаться от фактических значений. Например, профессиональные строители утверждают, что на кладку 1м3 из из газосиликатных блоков уходит не менее 40 кг … Это связано с тем, что пластичный состав заполняет все пустоты и изъяны в готовом блоке.
Рейтинг независимых производителей
Перед началом строительства важно выбрать производителя материала, который поставляет на рынок качественную продукцию.В российском регионе доверие потребителей заслужили следующие компании:
ЗАО «Кчелла-Аэроблок Центр» … Немецкая компания, часть производственных мощностей которой находится в России. Продукция компании известна во всем мире своим немецким качеством. Любопытно, что XELLA работает по нескольким направлениям, три из которых направлены на добычу и последующую переработку сырья.
ЗАО «ЕвроАэроБетон» … Предприятие специализируется на производстве газосиликатных блоков с 2008 года … Предприятие имеет собственные производственные линии, на которых применяется автоматизированный процесс, используется оборудование ведущих мировых брендов. Завод расположен в Ленинградской области, г. Сланцы.
ООО «ЛСР. Строительство-Урал » … Головной офис компании находится в Екатеринбурге, завод занимает лидирующие позиции на Урале. Предприятие имеет полувековую историю, использует автоматизированный производственный процесс, контролирует качество на всех этапах.
ЗАО «Липецкий силикатный завод» … История предприятия началась с с 1938 года с , это один из основных поставщиков центрального региона России. В 2012 году компания получила международный сертификат по классу ISO 9001.2008 , что говорит о высоком качестве выпускаемой продукции.
ОАО «Костромской силикатный завод» … Одно из старейших предприятий страны, основано в 1930 г. год.За годы существования был разработан специальный устав, позволяющий вывести качество продукции на принципиально новый уровень. Компания дорожит своей репутацией и не может похвастаться отрицательными отзывами потребителей.
Отметим, что это далеко не полный список надежных производителей газосиликатных блоков в российском регионе. Однако продукция этих брендов — лучшее соотношение цены и качества.
В современных строительных технологиях большое значение придается выбору материала для возведения того или иного типа здания.Газосиликатные блоки сегодня считаются одними из самых популярных строительных материалов, которые отличаются рядом преимуществ и используются довольно часто.
Их широкое распространение обусловлено оптимальным соотношением цены и качества — по большому счету, ни один другой строительный материал не может поддерживать это соотношение так выгодно.
Если посмотреть, то вряд ли газобетон относится к современным строительным материалам — он был разработан в конце 19 века. В начале прошлого века группа ученых даже запатентовала открытие нового чудо-материала, но его свойства были далеки от тех, которые отличают сегодняшние газовые силикаты.
В современном виде газосиликатный материал был получен в конце 20 века — это бетон с ячеистой структурой, твердение которого происходит в автоклаве. Этот метод был найден еще в 30-х годах, и с тех пор не претерпел существенных изменений. Улучшение характеристик произошло за счет внесения усовершенствований в технологию его производства.
Газобетон — одна из основ для производства газосиликатных блоков
Принцип изготовления
В качестве исходных ингредиентов для производства газобетона используются следующие вещества:
- песок;
- цемент;
- лайм;
- гипс;
- вода.
Для получения ячеистой структуры в состав добавляют порцию алюминиевой пудры, которая служит для образования пузырьков. После перемешивания массу выдерживают необходимое время, ожидая набухания, после чего разрезают на части и помещают в автоклав. Там масса затвердевает в среде пара — это энергосберегающая и экологически чистая технология. При производстве газобетона не выделяются вредные вещества, способные нанести значительный вред окружающей среде или здоровью человека.
Недвижимость
Характеристики, отличающие газосиликатные блоки, позволяют рассматривать их как строительный материал, хорошо подходящий для строительства зданий. Специалисты утверждают, что газобетон сочетает в себе лучшие качества камня и дерева — стены из него прочны и хорошо защищают от холода.
Пористая структура блоков гарантирует высокие показатели пожарной безопасности
Ячеистая структура объясняет небольшой коэффициент теплопроводности — он намного ниже, чем у кирпича.Поэтому постройки из газосиликатного материала не так требовательны к утеплению — в некоторых климатических зонах оно вообще не требуется.
Ниже мы приводим основные свойства газосиликата, благодаря которым он стал настолько популярным в строительной отрасли:
- небольшая масса при внушительных габаритах — это свойство позволяет значительно снизить затраты на установку. Кроме того, для погрузки, транспортировки и возведения стен не требуется кран — достаточно обычной лебедки.По этой причине скорость строительства также намного выше, чем при работе с кирпичом;
- хорошая обрабатываемость — газосиликатный блок можно без проблем распиливать, сверлить, фрезеровать обычным инструментом;
- высокая экологичность — специалисты утверждают, что этот показатель для газобетона сравним с деревом. Материал не выделяет вредных веществ и не загрязняет окружающую среду, при этом, в отличие от дерева, не гниет и не стареет;
- технологичность — газосиликатные блоки сделаны таким образом, что с ними удобно работать.Помимо небольшой массы, они отличаются удобной формой и технологичными выемками, захватами, пазами и т. Д. Благодаря этому скорость работы с ними увеличивается в 4 раза по сравнению со строительством зданий из кирпича;
- низкая теплопроводность газосиликатных блоков — это связано с тем, что газобетон на 80 процентов состоит из воздуха. В зданиях, построенных из этого материала, снижаются затраты на отопление, к тому же их можно утеплить на треть меньше;
В газосиликатном доме будет поддерживаться стабильный микроклимат в любое время года
- морозостойкость — в конструкции есть специальные пустоты, куда при промерзании вытесняется влага.При соблюдении всех технических требований к изготовлению морозостойкость газобетона превышает двести циклов;
- звукоизоляция — очень важный параметр, так как сегодня уровень шума на улицах достаточно высокий, а дома хочется отдохнуть в тишине. Газосиликат за счет пористой структуры хорошо сдерживает звук, выгодно в этом плане по сравнению с кирпичом;
- пожарная безопасность — минералы, используемые для производства газосиликата, не поддерживают горение.Газосиликатные блоки способны выдерживать воздействие огня в течение 3-7 часов, поэтому его используют для строительства дымоходов, лифтовых шахт, огнестойких стен и т. Д.
- высокая прочность — газосиликат выдерживает очень высокие сжимающие нагрузки, поэтому подходит для строительства зданий с несущими стенами до трех этажей или каркасно-монолитных зданий без каких-либо ограничений;
- негигроскопичность — газобетон не впитывает воду, которая при попадании на него быстро сохнет, не оставляя следов.Это связано с тем, что пористая структура не задерживает влагу.
результаты Голосовать
Где бы вы предпочли жить: в частном доме или в квартире?
Вернуться на
Где бы вы предпочли жить: в частном доме или в квартире?
Вернуться на
Основным недостатком газосиликата является недостаточная прочность на изгиб, однако специфика его использования такова, что он практически исключает возможность изгибающих нагрузок, поэтому этот недостаток не играет большой роли.
Чем меньше воздуха в теле искусственного камня, тем выше его прочность и плотность
Марка газоблока
Плотность газосиликатных блоков — главный критерий, который учитывается при маркировке. В зависимости от размеров строительный материал имеет разный набор характеристик, что определяет сферу его применения.
Ниже мы рассмотрим различные марки газосиликата и способы их применения в строительстве:
- D300 — наиболее подходящий строительный материал для возведения монолитных зданий.Плотность газосиликатных блоков этой марки составляет 300 кг / м 3 — хорошо подходит для возведения стен малоэтажных домов в один слой или для двухслойных монолитных домов с высокой степенью теплоизоляции;
- Д400 — применяется для строительства двухэтажных домов и коттеджей, а также для теплоизоляции наружных несущих стен многоэтажных домов;
- D500 — это тип с наилучшим сочетанием теплоизоляционных и конструктивных характеристик.Он идентичен по плотности бревенчатым или деревянным балкам и применяется для возведения перегородок и внутренних стен зданий, проемов окон и дверей, а также оболочек армированных перемычек, стропил и ребер жесткости;
- D 600 — это газосиликатный блок с наибольшей плотностью, которая составляет 600 кг / м 3, применяется там, где необходимо устройство прочных стен, подверженных повышенным нагрузкам.
Ниже представлена таблица, иллюстрирующая другие параметры, которые различают газосиликатные блоки разных марок.
В зависимости от плотности все газосиликатные блоки принято делить на конструкционные, конструкционные и теплоизоляционные и теплоизоляционные.
Точность размеров
Газосиликаты могут иметь отклонения в размерах. В зависимости от размера различают три категории точности этого материала:
- Первая категория предназначена для укладки блока насухо или на клей. Допускает погрешность в размерах по высоте, длине и толщине до полутора миллиметров, прямоугольности и углам — до двух миллиметров, краям — до пяти миллиметров.
- Вторая категория предназначена для укладки на клей газосиликатных блоков. В нем допускается погрешность основных размеров до двух миллиметров, прямоугольности — до 3 миллиметров, углов — до 2 миллиметров и кромок — до 5 миллиметров.
- На раствор ставится газоблоки третьей категории, у которых погрешность по основным размерам не более 3 миллиметров, по прямоугольности — менее 3 мм, по углам — до 4 миллиметров, по краям — до 10 миллиметров.
Выбор газосиликата
При покупке газосиликатных блоков обычно оценивают три критерия, влияющие на решение:
- Функциональные характеристики — плотность, морозостойкость, теплопроводность и др .;
- размеров одного блока;
- объем одного блока; Стоимость
- .
Газосиликатные блоки: преимущества в строительстве
Газосиликатные блоки — отличный строительный материал. Их используют при строительстве домов и других смежных построек.Материалы обладают уникальными свойствами, отличной тепло- и звукоизоляцией, высокой прочностью, негорючестью и малым весом. Все эти свойства являются результатом специальной технологии производства этих продуктов.
Газосиликатные блоки изготавливаются из извести, кварцевого песка, воды и алюминиевой пудры. Такое сочетание компонентов позволяет получить материал, который легко поддается модификации, но в то же время обладает повышенной прочностью.
Газосиликатные блоки получили широкое распространение при возведении многоэтажных конструкций, при усилении и возведении несущих стен.Это связано с их высоким качеством и техническими характеристиками, а также доступной ценой по сравнению с другими материалами.
С точки зрения экологии важным преимуществом является безопасность продукции, так как она не содержит вредных химических соединений. Газосиликатные блоки отличаются от газобетонных блоков автоклавным принципом производства.
Материалы, полученные по этой технологии, меньше подвержены усадке и имеют (по сравнению с другими изделиями) большую прочность при той же плотности.Автоклавирование производится при температуре 180 градусов Цельсия и давлении 14 бар. Эти условия позволяют не только получить новый материал, обладающий высокой прочностью, но и более равномерно распределить поры блоков по объему. Также при производстве газобетона цемент выступает в качестве вяжущего элемента, а газосиликат изготавливается с использованием известковых смесей.В целом газосиликатные блоки относятся к ячеистому бетону, получившему свое название из-за специфических пор, имеющих размер около 3 миллиметров в диаметре и равномерно распределенных по всей конструкции.Благодаря этому материалы отлично поглощают звуки и обладают огнестойкостью. Воздух, заключенный в камерах, придает изделиям высокую теплоизоляцию. Кроме того, строительные материалы обладают хорошей прочностью, отличной геометрической формой и низкой теплопроводностью.
Газосиликатные блоки, размеры которых имеют широкий диапазон, могут применяться для утепления стен. Их успешно используют для создания межкомнатных конструкций, так как это выгоднее, чем кладка кирпича. Экономия получается за счет сокращения времени на работу из-за их размера.
Укладка изделий не дорогая и производится на клее для газосиликатных блоков. При установке используется специальный клеевой состав, который делает конструкцию практически бесшовной.
Достоинства материала неоспоримы. Благодаря небольшому весу не оказывает давления на фундамент (в отличие от других строительных материалов). Блоки создают отличную звукоизоляцию, избавляя хозяев дома от навязчивого шума машин. К тому же изделия, по сравнению с деревом и кирпичом, имеют более низкую стоимость.
Здание построено по современной технологии: каркас […]из монолитного армированного […] бетонный wi t h газосиликатные блоки ; t he фундамент […]— монолитная железобетонная плита. млрд холдинг.com | La faade de l’immeuble SERA allment en […] verre, faite av ec l’utilisation du s ystme de vitrage […]extrieur attach. bnkholding.com |
Способ увеличения теплоаккумулятора […] вместимость здания di n g блоков o f a cal ci u m — силикат m te rial, особенно аэрированный конц re t e блоки , a m elting heat […]накопительный материал (ПКМ) […], проходящий через один или несколько фазовых переходов, вводимых в строительные блоки, отличающийся тем, что плавящийся материал, аккумулирующий тепло, в инкапсулированной форме во время производства строительных блоков добавляют к одному или нескольким исходным материалам и / или одному или нескольким из промежуточные продукты и, таким образом, при последующем производстве готовых строительных блоков связываются с последними. v3.espacenet.com | Procd pour amliorer la capacity de stockage de […]отдельные модули […] d’un matr ia u base d e силикат d e calc ium, e n Partulier de Pierr es en b to n poreux , le matr ia u накопитель […]de chaleur de […]fusion (PCM) passant par une ou plusieurs transitions de phase tant Introduction dans les modules, caractris en ce que le matriau accumulateur de chaleur de fusion est ajout sous form encapsule pendant для изготовления модулей и дополнительных матриц dpart et / ou un ou plusieurs produits intermdiaires et est intgr ainsi, lors d’une fabrication conscutive des modules achevs, dans ceux-ci. v3.espacenet.com |
Для теплового […] изоляция fl u e газ c o ll действующий резервуар, алюминий ni u m силикатный w o ol продукты […], как правило, тоже не нужны. dkfg.de | De mme, […] l’isolation thermique du co llect eur de gaz de com busti on ne ncessite en gnral […]после использования продукта s en l aine d’aluminosilicate. dkfg.de |
Моющие средства для посудомоечных машин в виде f us e d блоков c o nt aining гидроксиды щелочных металлов, al ka l i силикат , w at er, предпочтительно в форме кристаллизационной воды, […] и необязательно пентащелочи […]трифосфат, отличающийся тем, что они также содержат от 0,1 до 10 мас.% Органического комплексообразователя в пересчете на моющее средство в целом. v3.espacenet.com | Продукция […] для ME de blo n силикат a lca lin, ou e au , […]de prfrence sous forme d’eau […]de cristallisation, не содержит кварцевого элемента и трифосфата пента (mtal alcalin), cractriss, как отдельная добавка, содержит комплексный органический аллантат 0,1-10% в составе, в соотношении с общим составом. v3.espacenet.com |
Практически вся прибрежная и морская зона, включая важные туристические […]района, ключевые рыболовные угодья и […] горячие точки для биоразнообразия, были разделены на t o блоков o p en для нефти a n d газа e x pl oration.cmsdata.iucn.org | Pratiquement toute la zone ctire et marine, y include les zone importantes pour le tourisme, les zone cls de pche et les […]зоны Primordiales de biodiversit ont […] t sc в des en blocs qui peuvent fa ire l’objet d’exploration p troli re et gazire .cmsdata.iucn.org |
Практически вся прибрежная и морская зоны, включая горячие точки […]биоразнообразия, ключевые рыболовные угодья и […] важные туристические районы были разделены на t o блоков o p en для нефти a n d газа e x pl выступление.cmsdata.iucn.org | Pratiquement toutes les zone ctires et marines, y included des зонах primordiales de biodiversit, des зонах de pche cls […]и важные туристические объекты на […] t di vi ss en blocs ou vert s aux activits d’exploration ptro li res et gazires .cmsdata.iucn.org |
Кладочные покрытия — это покрытия, которые производят декоративную и […]защитная пленка для использования на бетоне, (под покраску) кирпичной кладке, блочной кладке, […] штукатурка ci u m силикат o r f ibre-армированный цемент.eur-lex.europa.eu | Les revtements pour maonnerie sont des revtements produisant un film dcoratif et protecteur, qui sont destins tre appliqus sur […]le bton, la brique (peindre), le parpaing, le […] crpi, l e cim ent au силикат de cal cium ou le ciment […]волокна Renforc de Fibre. eur-lex.europa.eu |
Общая запись на минеральной вате […]определяет минеральную вату как состоящую из […] искусственного стекловолокна или s ( силикат ) f ib res со случайной ориентацией […]с щелочным оксидом […]и содержание оксида щелочноземельного металла более 18% по весу. eur-lex.europa.eu | L’entre gnrale концерн les laines minrales dfinit […]celles-ci в соответствии с […] составляет fi bres (de силикаты) vi treus es artificielles […]alatoire alatoire, dont le pourcentage […]pondral d’oxydes alcalins et d’oxydes alcalinoterreux est suprieur 18%. eur-lex.europa.eu |
В связи с изменениями в […] уровень грунтовых вод в c u t — блоки , r на es of greenh ou s e gas d y na микрофоны в лесах […]также может быть затронут. ec.gc.ca | Строка обмена […]niveaux de la nappe phratique dans […] le s blocs d e coupe , la dy nami que de s gaz e ffet de se rre dans [. ..]les forts peut aussi tre modifie. эк.gc.ca |
Фрагментация среды обитания — это разрушение среды обитания […] участки дороги, заготовка древесины c u t — блоки , p ip elines, нефть a n d газ w e ll участки, геофизические исследования […]линий и другие разработки. hww.ca | Энфин, фрагментация среды обитания […]lorsque des routes, des blocs de coupe pour la rcolte […] de bois, des pipelines, des sites o se Trouvent des puits de p t role et de gaz, d es s ites d e prospection [… ]gophysique et […]d’autresprojets d’exploitationentranent une discontinuit de l’habitat. hww.ca |
Это будет […] включает в себя строительство di n g блоков f o r интегрированную энергетическую политику Европейского Союза, например, меры по завершению внутреннего рынка электроэнергии a n d газ ; t o ускорить прием […]новых низкоуглеродных технологий; […], а также для диверсификации и обеспечения безопасности поставок как в Европе, так и за ее пределами. europarl.europa.eu | Составляющие и s модули или r une politique nergtique de l’Union europenne, par instance des mesures pour complete le march intrieur de l’lectr ic it e td u газ ; pou r acc l rer l’adption […] de nouvelles […]технологий для производства карбона; et pour diversifier et scuriser les fournitures la fois l’intrieur et l’extrieur de l’Europe. europarl.europa.eu |
Пока, Индия […] предложил 110 нефть a n d газоблоки a n d 16 метан угольных пластов […]блока для разведки в попытке увеличить внутреннее производство энергии для снижения зависимости от импорта. helio-international.org | Jusqu’ici, l’Inde a Propos 110 […]Исследовательские блоки […] ptroli r e et gazire et 1 6 bloc s de gaz de h ouil le pour […]tenter d’augmenter la production d’nerg ie nationale et rduire la dpendance vis — vis des import. helio-international.org |
Truma-v al v e блоки — al нижнее центральное соединение sev er a l газ d e vi ces без резьбовых соединений или тройников truma.com | le s blocs d e vannes Permettent le raccordement central de plusieurs a ppare ils gaz, s и racc or ds ou […] шт. В T truma.com |
Thezirco ni u m силикат b e и s часто являются предпочтительными […] выше стеклянных шариков для большей износостойкости. labomat.eu | L es b ill es en silicate de zi rco nium so nt souvent […] prfres aux billes de verre pour leur plus grande rsistance l’usure. labomat.eu |
Page 5 Хризотил — это натуральный […] происходящие волокна ro u s силикат m i ne ral который делает […]не горит и не гниет. chrysotile.com | Стр. 5 Le […] chrysotile est u n min ra l silicat f ibr eux n at urel qui […]ne brle pas et ne pourrit pas. chrysotile.com |
EAWAG сейчас работает над дальнейшим развитием […]процессов удаления мышьяка из грунтовых вод с небольшим содержанием железа и высоким содержанием […] концентрации фосфатов a n d силикат .eth-rat.ch | L’EAWAG travaille maintenant une mthode qui permettrait […]d’liminer l’arsenic d’eaux souterraines contenant moins de fer et dessions leves […] en ph os phate s e t en силикаты .eth-rat.ch |
Моющее средство в виде фуса ib l e блоков c o nt aining ( A) a силикат o f s одий, (B) полианионные модификаторы и (C) неионные поверхностно-активные вещества, характеризующиеся следующим процентным содержанием (выраженным в каждом случае как безводное вещество): A) от 35 до 65% по весу метасиликата натрия, B) от 4 до 25% по весу по крайней мере одного полианионного модификатора из класса полифосфатов, цеолитов, нитрилотриуксусной кислоты, (со) полимерных карбоновых кислот и полифосфоновых кислот в форме натриевых солей, C) от 10 до 30% по весу неионогенного поверхностно-активного вещества, D) от 2 до 15% по весу водорастворимого […]
[…] воскоподобное соединение из класса полиэтиленгликолей с молекулярной массой не менее 1100 и его простых алкиловых эфиров. v3.espacenet.com | A) 35 65% e n poids d e mtasilicate de натрия, B) 4 25% en poids d’au moins une субстанция адъювант полианионного волокна t partie d e la class des polyphosphates , деззолитов, нитрилотриактического ацида, децидов карбоксильных (со) полимеров и полифосфонических кислот, dans chaque cas sous forme de sodiques, C) 10 30% en poids dutensioactif non ionique, D) 2 15% en poids d’un compos cireux, soluble dans l’eau, faisant partie de la classe des polythylneglycols, possible un poids molculaire d’au moins 1100, et de leurs thers alkyliques. v3.espacenet.com |
Щелочность помогает химическим веществам атаковать примеси, усиливая действие других составляющих ингредиентов моющего средства (например, di u m силикат , s od ium карбонат). rayon.com | Cette alcalinit contribue l’attaque chimique des souillures en renforant l’action des autres constituants de la formule de dtergent (дисиликат натрия, карбонат натрия). rayon.com |
Зарядка: Для зарядки или предварительной заправки охлаждающей жидкости для тяжелых условий эксплуатации добавьте 3% […] SCA на 50% l o w силикат A S TM 4985, спецификация […] Смесь антифризаи 50% воды. fleetguard.com | Заряд: Зарядное устройство или зарядное устройство для интенсивного использования жидкой фазы, il […]добавок с добавлением 3% добавок с 50% антибактериальным покрытием согласно нормам ASTM 4985 […] fai bl e ten eur en силикат, au x 5 0% d ‘ ea u.fleetguard.com |
Кроме того, ведется строительство проекта СПГ в Анголе (13,6%), который включает завод по сжижению газа около Сойо, рассчитанный на человек. […]довести запасы природного газа страны до […] рынок, в частности партнеры на e d газ f r ом поле s o n Блоки 0 , 1 4, 15, 17 и 18.total.com | Par ailleurs, le projet Angola LNG (13,6%), not l’objet est de valoriser les […]резервов газа в Анголе, en […] часть cu lier le gaz as soci a ux productions des champs situs s ur les blocs 0, 1 4, 15, 17 [ …]et 18, првоит ла строительство […]d’une usine de liqufaction near Soyo. total.com |
T h e Блоки i n di cating th e « газ c o nt ribution «поэтому обведены красным для периодов […] , в котором цена на газ растет, и зеленым цветом, если она снижается. banquenationale.be | Ainsi au sein du […] graphique 13 , les petites col на nes bleues reprsentant la co nt sribut ion gaz s ont e nc adres […]de rouge lorsque le prix […]du gaz augmente, et de vert lorsqu’il diminue. banquenationale.be |
Ангола СПГ (13,6%): это сжижение […] Проектпризван принести […] запасы природного газа страны на рынок, в частности, партнеры по адресу e d газ f r om месторождение s o n Блоки 0 , 1 4, 15, 17 и 18.e-accessibility.info | Ангола СПГ (13,6%): проект […]pour objet de valoriser […] les rs er ves d e gaz e n Ang ol a, en частности li er l e gaz a ssoc i aux productions des champs sit u для блоков le s 0 , 1 4, 15 , 17 и 18.e-accessibility.info |
Из-за толщины лезвия используются для специальной строительной ленты […] пилы для резки ti n g gas c o NC rete, кирпич, полый бетон re t e блоки , e tc .салазок.пт | Elles sont использует pour couper du bton […] (Ytong), des briques pleines ou creuses — mais pas pour cou pe r le b oi s.skid.fr |
Это блок […] рядом с Ипати и А qu i o блоков w h er e Группа сделала значительную ca n t gas d i sc overy in 2004 (Incahuasi) и […], где сейсморазведка […]проведено для оценки открытия. e-accessibility.info | Ce bloc est […] соседние au x блоки I pat i et Aquio , o le Groupe a ra li s une d co uverte sign if icat ive de gaz en 200 4 (I NC ahuasi), […]et effectu des travaux […]sismiques en 2008 en vue de son apprciation. e-accessibility.info |
Проценты […] в нефти Мали a n d газоблоки h a s были очень горячими, […], на данный момент доступно только шесть блоков (4 […]блока среди них), два блока находятся в стадии переговоров и девятнадцать уже лицензированы широким спектром как независимых, так и крупных нефтедобывающих компаний со всех уголков мира. jmpmali.com | L’intrt pour le […] ptrole et le s blo cks de gaz du Mal i, et e n ce момент […]ou sort ce document seuls six blocks disponibles […](4 блока parmi eux), deux blocks en ngociation et dix neuf dj sous license par une vaste palette de socits indpendantes et de grosses compagnies ptrolires du monde entier. jmpmali.com |
Бизнес-план ориентирован на разведку; таргетинг 80% или больше […]природный газ в более глубокой части западноканадского осадочного бассейна […] на большом la n d блоков a n d clos e t o gas i n fr строение.canadadominion.com | Son plan d’affaires s’appuie sur l’exploration et cible 80% ou plus du gaz naturel contenu dans […]le bassin sdimentaire le plus profond de l’Ouest canadien, sur de […] grandes superficies prs des i nf rastr uct ure s gazires .canadadominion.com |
Уникальный и изысканный ассортимент […]Candurin — цвета с эффектом минерального перламутра — […] на основе природного ur a l силикат , p ro duced согласно […]в соответствии с GMP и придает таблеткам и капсулам безошибочный внешний вид. colorphast.com | La gamme unique et exceptionnelle de Candurin […]— пигменты minraux effets nacrs […] — est b ase sur de s силикаты n atu rel s, pr od uits […]Selon GMP и допускает распространение […]aise des comprims et des glules. colorphast.com |
Силикат : T he лучшая защита […] против коррозии алюминия. fleetguard.com | Силикат: L a meil leur e защита […] против коррозии алюминия. fleetguard.com |
Эти имена используются до сих пор для […] различать pu r e силикаты a n d фаза s o f силикат i n c линкер, который […]всегда включать маленький […]количества алюминия, железа, магния, щелочных металлов и следов других элементов. cprac.org | Ces noms sont encore utiliss pour faire une […] различие en tre l es силикаты pu rs et l es p ha ses d u силикат d ans l e клинкер, […]qui бестелесный toujours […]de faibles Quantits d’aluminium, de fer, de magnsium, de mtaux alcalins, et des traces d’autres lments. cprac.org |
Анализ показал, что пылевая смесь составила […] в основном из частиц, содержащих ni n g силикат a n d серу.empa.ch | CES анализирует состояние окружающей среды […] Essen ti elle ment d e силикаты e t de p arti cu les renfermant […]du soufre. empa.ch |
Строительный блок 240 Тишина | Silikaat
Кладка
При строительстве стены из пустотелых силикатных блоков применяются те же принципы, что и при использовании других силикатных кирпичей. Базовые конструкции (фундамент и фундамент) должны быть ровными, устойчивыми и прочными.На фундамент необходимо установить надлежащую гидроизоляцию, чтобы проникающая в фундамент влажность не распространялась на стены. Перед укладкой блоки необходимо увлажнить и использовать кладочный раствор нужной консистенции. Чтобы обеспечить надлежащую адгезию между раствором и камнем, раствор не должен быть слишком сухим. В случае слишком жидкого раствора смесь выльется из швов и может не достичь необходимой прочности. Использование более жидкой смеси не компенсирует необходимость увлажнения камней.Чем более мелкозернистая смесь, тем удобнее работать. В жаркую и сухую погоду необходимо предотвратить слишком быстрое высыхание стены. Силикатный кирпич нельзя использовать для фундаментов или несущих стен подвала. Силикатные стены нельзя накрывать чем-то, препятствующим высыханию. Стены можно покрасить краской с очень хорошей паропроницаемостью.
Рекомендуется начинать строительство стены с угла. Смесь удобно наносить на блоки с помощью ковша для раствора или салазок, так как это обеспечивает равномерное распределение раствора и ровные швы.
Челюсть — очень полезный инструмент для обработки и размещения блоков. Это значительно ускоряет работу и требует меньше рабочих. Резиновый молоток со свинцовым пшеном может быть полезен для подталкивания блоков в нужное место.
Режущие блоки
Хороший инструмент для обработки углов и торцевых деталей (и вообще всех силикатных кирпичей) — это дисковый нож и обычный диск для резки камня.
Точность резки углов и наконечников влияет на необходимое количество раствора.Чем шире (неточнее) вертикальные швы, тем больше требуется раствора. При строительстве из силикатных блоков требуется больше раствора, чем при строительстве из гладкого кирпича. Поскольку нижняя часть блока имеет полости, вес блока выталкивает часть раствора внутрь полости. Однако раствор в полостях увеличивает прочность конструкции на сдвиг.
Соединения
В случае блоков вертикальные швы не нужно заполнять раствором, так как штифты (канавки) на концах блоков идеально подходят друг к другу.При желании для соединения поперечных швов можно использовать мало расширяющийся пенополиуретан. Перед установкой следующего блока пену следует нанести на паз уже установленного блока.
Перемычки
Вес рядов блоков над окнами и дверями распределяется на обе стороны проема с помощью перемычек. Для стены из силикатных блоков больше всего подходят перемычки из железобетона. Тип перемычки (размеры, армирование, несущая способность, длина) определяет проектировщик.Под подошвой перемычки должен быть неразрезанный блок / кирпич. В случае проемов более 1,5 м минимальная опорная поверхность под одним концом должна составлять не менее 250 мм.
При установке перемычек и панелей перекрытия необходимо следить за тем, чтобы перемычки или панели опирались не менее чем на половину блока, или это должно быть выполнено в соответствии с требованиями, установленными в проекте. Заливка бетонной ленты должна основываться на принципах бетонирования. Асиликатные блоки имеют две полости, которые проходят через блок, необходимо учитывать, что бетон будет заливаться в эти отверстия.Поэтому нужен дополнительный бетон. Чтобы уменьшить количество используемого бетона, полости можно заполнить на половину или на три четверти монтажной пеной.
В случае силикатных блоков хорошим инструментом для крепления строительных лесов и приспособлений являются дюбели.
Чистовая
При правильной кладке внутренняя отделка может ограничиться полной штукатуркой. Когда стыки будут правильными, может быть достаточно просто краски. Если необходима дополнительная звукоизоляция или кладка не очень качественная, стены можно покрыть штукатуркой толщиной 10 мм с обеих сторон.
.