Газосиликатный блок вес: Блок газосиликатный 200х300х600 мм (d600) цена за штуку в Москве, вес, характеристики, купить в Москве, быстрая доставка.
Как рассчитать вес газосиликатного блока
Газосиликатные блоки – строительный материал, который изготавливается из бетона, относящегося к категории «ячеистых». То есть, вес газосиликатного блока несравнимо низок, если сравнивать с блоками из стандартного бетонного раствора. Но чтобы точно сказать, каков вес изделия, надо знать размеры блока и плотность используемого материала, соответственно газосиликата.
Вес зависит от размеров
Содержание
- 1 Стандартные размеры газосиликатных блоков
- 2 Плотность газосиликата
- 3 Примеры расчета веса
- 4 Другие технические характеристики
- 4.1 Преимущества и недостатки
- 5 Принципиальные моменты оштукатуривания блоков из газосиликата
Стандартные размеры газосиликатных блоков
Производители сегодня предлагают достаточно широкий модельный ряд газосиликатных блоков, потому что этот строительный материал используют и для возведения несущих стен, и для сооружения перегородок. В первом случае требуются блоки больших размеров с высокой несущей способностью, во втором камни с небольшими габаритами, потому что они практически не нагружаются.
Но необходимо отметить, что по длине все блоки являются одинаковыми. Здесь параметр равен – 600 или 625 мм. Этот стандартизированный подход к производству позволяет провести точный расчет требуемого материала по длине сооружаемой постройки. Что касается толщины (ширины) блока, то здесь также две позиции: 200 и 250 мм. Обычно первые применяют для возведения перегородок, вторые используют под несущие стены. Хотя разница незначительна, что дает возможность камни шириною 200 мм устанавливать под несущие стены одноэтажных строений.
А вот высота газосиликатных блоков – это достаточно широкая модельная линейка. Но здесь необходимо обозначить, что она не соответствует всем размерным габаритам, касающихся толщины изделия. Соотношение такое:
- при ширине камня в 200 мм, его высота может быть 150, 200, 250, 300 и 400 мм;
- при ширине в 250 мм, высота составляет 100, 150, 250, 300, 375, 400 и 500 мм.
Один из стандартных размеров
Плотность газосиликата
Чтобы определить, сколько весит газосиликатный блок, необходим объем изделия и плотность исходного материала. Объем подсчитать несложно, зная размеры камня, то есть перемножаются между собой высота, толщина и длина изделия. Касаемо плотности газосиликатного бетона.
Все зависит, из каких компонентов изготавливается сам раствор. В стандартную рецептуру входят: цемент, песок, газообразующий материал и вода. Цемент можно заменить известью, песок золой или другими схожими материалами. В качестве газообразующего вещества чаще всего используют алюминиевую пудру.
В процессе смешивания компонентов происходит химическая реакция, результатом которой становится выделения большого количества водорода. Он внутри образует поры, облегчая тем самым структуру газосиликатных блоков. При этом увеличиваются теплоизоляционные качестве изделия, но уменьшаются его несущие способности, соответственно и прочность.
Теперь о плотности. Обозначается она буквой «D» и цифровым значением, к примеру, D500. О чем говорит число. Это количество самого газосиликатного раствора в одном его кубе. То есть, в 1 м³ находится 500 кг бетона. Остальное место занимает поры, наполненные водородом. И чем выше плотность, тем тяжелее газосиликатные блоки.
- Обычно блочные изделия из газосиликата с плотностью D600-700 используют для строительства домов не выше пяти этажей. Эти камни относятся к категории несущих материалов.
- Блоки плотностью D500 можно применять в качестве несущих, если из них возводятся дома не выше двух этажей. Или в качестве перегородок в многоэтажных зданиях.
- Материал плотностью D400 – так называемый теплоизоляционный вариант. Относится к классу прочности на сжатие В2,5. Используют блоки только в перегородках или в качестве теплоизоляционных материалов.
- Плотность D350 – материал, который применяется в строительство только как утеплитель.
Толщина стены из газосиликата в зависимости от плотности
Необходимо добавить, что плотность блоков из газосиликата во многом зависит от того, по какой технологии они были изготовлены.
- Ручной, который используется при кустарном производстве. То есть, производится смешивание компонентов бетонного раствора, последний закладывается в формы, где остается до полного затвердевания. После чего блоки сушат несколько дней.
- Автоклавный. Здесь все те же позиции, только добавляется еще одна операция – обработка паром (+200С) под давлением. Ее и проводят в автоклаве – специальная емкость, куда закладываются формы с газосиликатным раствором, здесь же и происходит обработка паром. Внутри автоклава выдерживается повышенное давление (8-12 атм.), которое придает блокам повышенную прочность и плотность.
Примеры расчета веса
И несколько примеров, как рассчитать вес газосиликатных блоков.
Размер: 600х200х400 мм. Объем блока составляет с переводом в метры: 0,6х0,2х0,4=0,048 м³. При плотности – D500 этот камень будит весить: 0,048х500=24 кг. Если снизить плотность до D350, то вес будет таким: 0,048х350=16,8 кг.
Размер: 600х250х500 мм. Его объем будет составлять: 0,6х0,25х0,5=0,075 м³. При плотности D600, такой камень будет весить: 0,075х600=45 кг.
Видео:
Другие технические характеристики
Как и все блочные строительные материалы, газосиликатные блоки обладают несколькими техническими характеристиками, которые обязательно учитывают в строительстве зданий и сооружений. Вот они в таблице ниже.
Характеристика | Водопоглащение, % к общему весу | Морозоустойчивость, количество циклов | Паропроницаемость, мг/м² ч Па | Теплопроводность, Вт/м К | Прочность на сжатие, МПа | Звукоизоляция стены толщиною 30 см, дБ | Термостойкость, С |
Показатели | 20 | 15-100 | 0,14 | 0,1-0,28 | 1,5-10 | 30-47 | +400 |
Преимущества и недостатки
Из таблицы видно, то блоки данного типа обладают неплохой теплопроводностью, то есть, не самой высокой, если говорить о других блочных материалах. И это большой плюс в строительстве теплого дома. Небольшая плотность при неплохих прочностных характеристиках дает возможность сооружать под дома из газосиликатных блоков фундаменты небольших размеров, что влияет на снижении стоимость всего сооружения.
К плюсам добавим простоту монтажного процесса и легкость обработки. Такой материал легко режется, в нем несложно просверлить отверстия.
Касаемо отрицательных характеристик, то в первую очередь необходимо отметить, что материал данного типа является обладателем высокого влагопоглощения. Поэтому дома из силиката обязательно подвергают защитным мероприятием, связанным с нанесением защитных слоев на стены. Это может быть штукатурка, облицовка кирпичом, клинкером или другими схожими материалами, или установка вентилируемого фасада.
К минусам относится и низкая термостойкость, обозначенная максимальным показателем +400С. То есть, если по каким-то причинам температура выросла более данного значения, блоки просто начнут растрескиваться, разваливаться, снижая свою несущую способность, что приведет к разрушению здания.
Оштукатуривание стен из газосиликатных блоков
Принципиальные моменты оштукатуривания блоков из газосиликата
Есть некоторые требования, которые надо учесть, выполняя оштукатуривание.
- Материал выходит из производства с влажностью 30%. Это достаточно высокий показатель, который может повлиять на качественное состояние блоков, если их сразу начнут использовать в реализации проекта. Они растрескаются в течение года. Поэтому наносить штукатурку нужно через 1,5 года после окончания строительства коробки. Если такой возможности нет, то штукатурить начинают изнутри помещений, чтобы влага, находящаяся внутри блоков, могла постепенно испариться.
- Идеальный вариант – штукатурка изнутри, вентилируемый фасад снаружи. Это даст возможность оттока испарения от стен.
- Не стоит в качестве утеплителя снаружи использовать материалы гигроскопичные, даже если их закрыть гидроизоляционными мембранами. Состояние термоса для газосиликата губительно.
Сколько весят газобетонные блоки? — CemGid.

На сегодняшний день газосиликатный блок используется для строительства домов гораздо чаще, чем другие кладочные материалы. Он обладает высокой прочностью, при этом подходит для возведения одноэтажного дома или многоэтажного сооружения за счет малого веса и простоты в обработке.
Оглавление:
- Масса газобетона
- Пример расчета
- Стоимость
Вес блоков разных размеров
Основными факторами, влияющими на массу, являются габариты и плотность. Газосиликат относится к легким ячеистым бетонам, поэтому его плотность намного меньше, чем полнотелого кирпича или шлакоблока. Вес газосиликата варьируется от 500 до 1800 кг на 1 м3. Газообразователь в составе смеси обеспечивает ей пористость: чем интенсивнее его воздействие, тем больше получится воздушных пустот в готовой продукции.
Чтобы провести расчеты по необходимому количеству стройматериала и узнать, сколько весит один газоблок, нужно знать маркировку. Плотность обозначается буквой «D» и измеряется в кг/м3. Марки указаны в ГОСТе, если производитель точно следует технологии, то результаты расчетов будут наиболее достоверными.
В D300-D1200 цифра указывает на количество смеси, которая используется для производства и вспенивания для получения 1 м3 ячеистой структуры. К примеру, D500 будет весить 500 кг, а D800 – 800 кг. Чем выше показатель, тем меньше воздушных образований в теле газобетона. Таким образом, характеристики прочности, теплоизоляции и массы будут больше.
По назначению газосиликатные блоки делятся на:
- Теплоизоляционные – D300-D400. Содержание воздуха составляет около 75% от всего объема. Они наиболее легкие, но при этом достаточно хрупкие. Используются для возведения перегородок, стен небольших построек, а также теплоизоляционного контура. Обрабатывать ударными инструментами крайне нежелательно.
- Конструкционно-теплоизоляционные – D500-D900. Пористость равняется 55-70 %. Для строительства несущих и самонесущих стен одноэтажного дома, перегородок.
- Конструкционные – D1000-D1200. Количество пор – до 50 %. Наиболее прочные и надежные, поэтому подходят для несущих стен двух- или трехэтажного здания. При обработке способны выдержать сверление (о том, чем сделать отверстия в бетоне, читайте тут), штробление перфоратором, распил.
Практичным вариантом для жилого дома в 1 этаж будет марка D500-D600. Габариты также влияют на массу, поэтому блоки размером 600х300х200 мм будут весить больше, чем 300х100х100 при условии одинаковой плотности.
Типовой расчет массы газобетона
Определение веса проводится на примере блока 600х250х400 мм. Формула для вычисления имеет следующий вид: плотность (кг/м3) х объем (м3) = масса (кг).
- Определяется объем. Для этого размеры переводятся в метры и перемножаются между собой: 400х250х600 = 0,4х0,25х0,6 = 0,06 м.
- Далее смотрится плотность. В качестве примера используется марка D600. В этом случае 1 м3 будет весить 600 кг.
- Проводится расчет по формуле: 0,06х600=36 кг – столько будет весить один элемент.
Такой метод можно применять для любых размеров газоблоков разной плотности. Однако важно учитывать нагрузку, которая будет воздействовать на фундамент.
Стоимость газосиликата в Москве
Производитель | Марка | Размеры, мм | Цена за 1 м3, рубли |
Bonolit | D500 | 200x400x600 | 2800 |
D600 | 500x250x625 | 2750 | |
ЭКО | D600 | 350x250x600 | 2700 |
D600 | 150x250x600 | 2600 | |
E3CM | D400 | 100x250x625 | 2650 |
D500 | 50x250x625 | 2680 | |
D600 | 500x250x625 | 2700 |
промышленных продуктов на базе кремнезема от рисового корпуса пепла пепла
Спонсорное учреждение
Национальный институт продовольствия и сельского хозяйства
Статус проекта
Прекращенный
Источник финансирования
Accession Grant
Частота отчетности
Accession
.
0185982
Грант №
2001-35504-10044
Проект №
ARK01862
Предложение №
2000-01921
Multistate №
(N/A)
Программный код
(N/A)
Дата начала проекта
Dec 1,
Конец проекта
Nov 30, 2005
Год гранта
2001
Директор проекта
Проктор А.
Организация-получатель
УНИВЕРСИТЕТ АРКАНСАСА
(нет данных)
FAYETTEVILLE, AR 72703
Исполнительский отдел
ПИЩЕВАЯ НАУКА
Нетехническая сводка
Рисовая шелуха является основным отходом производства риса и представляет собой серьезную проблему утилизации. Этот проект исследует возможность производства керамических материалов из растворимого кремнезема, извлеченного из рисовой шелухи.
Компонент здоровья животных
(Н/Д)
Категории исследований
Базовый
(Н/Д)
Прикладной
3
3 10003 Developmental
(N/A)
Classification
511 1530 2000 40% 511 1530 2010 30% 511 1530 2020 30%
Область знаний
511 — Новые и улучшенные непищевые продукты и процессы;
Предмет исследования
1530 — Рис;
Область науки
2020 — Машиностроение; 2010 — Физика; 2000 — Химия;
Rice
Hulls
ASH
Силика
Промышленные продукты
Непроизводительные товары
Химия растений
Сельскохозяйственная инженерная инженерия
Силика
Scanning Electronning Mixernning Mixersning Mixersning Mixersning Electlonnning Electlonnning Electlonnning Electlonning Electlonnning Electlonnning Electlonnning Electlonnning Electlonnning.
0002 Механические свойства
рентгеновские дифракции
Инфракрасная спектроскопия
Анализ изображений
Осаждение
Прочность
Площадь поверхности
Размер карты
ТЕММЕРТИЯ
ОБЩЕСТВЕННЫЙ ПЛОНЕ
ЗАМЕТА / ОБЗОР . весовые блоки кремнезема из золы кремнезема от рисовой шелухи 2. Исследование физических свойств блоков кремнезема
Методы проекта
Кремний из рисовой шелухи растворяется путем щелочной экстракции для получения силикатного раствора. Затем силикагель будет осаждаться при снижении pH раствора. Прочность геля будет увеличиваться за счет старения и последующей сушки. Структурный анализ блоков будет выполнен с помощью рентгеновской дифракции и инфракрасной спектроскопии с преобразованием Фурье с нарушенным полным отражением. Атомно-силовая микроскопия и сканирующая электронная микроскопия будут использоваться для изучения микроструктуры ксерогеля. Средняя площадь поверхности и размер пор будут определяться адсорбцией газа по методу БЭТ.
Механические свойства и влияние температуры на механическую прочность будут определяться прямым прямым доступом к памяти. Изменения структуры в зависимости от температуры будут измеряться с помощью контролируемой температуры рентгеновской дифракции. Инфракрасное изображение позволит получить информацию о излучении излучения и полуколичественное определение свойств теплового потока.
Прогресс 01.12.00 — 30.11.05
Выходные данные
Зола промышленной рисовой шелухи является богатым источником аморфного кремнезема, полученного путем сжигания рисовой шелухи. Эту форму природного кремнезема легче использовать для производства адсорбентов и керамики на основе кремнезема, чем песок, который традиционно используется. Керамические ксерогели кремнезема были получены путем щелочной экстракции кремнезема из промышленной золы рисовой шелухи с последующим осаждением и сушкой. Ксерогели были получены из растворов щелочей, объемы которых были уменьшены для получения диоксида кремния в диапазоне концентраций 4-12%.
Образцы каждой концентрации доводили до pH 9., 10, 10,5 и 11 для осаждения силикагелей, которые затем сушили в течение 24 часов при 80°С. Рентгеноструктурные исследования показали, что все образцы представляли собой аморфный кремнезем, а анализ инфракрасной спектроскопии показал, что полимеризация кремнезема или удлинение цепи кремнезема, была выше при более высоком рН осаждения. Однако сшивание между полимерами было основным взаимодействием при более низком pH и усиливалось при использовании кремнезема.
концентрация. Стеклообразные твердые вещества были образованы путем осаждения при высоких значениях pH, тогда как пористые силикагели были получены при более высоких концентрациях кремнезема. Ксерогель, образованный из концентрированных растворов кремнезема, осажденных при рН 10, дает керамический блочный материал, обладающий наибольшей механической прочностью благодаря оптимальному сочетанию полимеризации кремнезема и сшивки. Кроме того, ксерогель керамического кремнезема высокой чистоты был получен путем удаления остаточных примесей ионов металлов путем интенсивной промывки осажденного кремнезема водой перед сушкой.
Было обнаружено, что промывка водой более эффективна, чем промывка кислотой.
Воздействие
Рис Двадцать процентов собранного риса состоит из рисовой шелухи. Экологические нормы ограничивают захоронение скорлупы на свалках, и, несмотря на ее использование в качестве куриного подстилки и в качестве корма для животных, не существует крупномасштабного использования, которое значительно уменьшит проблему отходов. Многие рисовые заводы используют шелуху в качестве источника топлива и производят аморфную силикатную золу, часть которой используется сталелитейной промышленностью в качестве огнеупорного материала. Тем не менее, по-прежнему необходимо найти крупные рынки сбыта для корпуса и золы, чтобы решить проблему удаления отходов, несмотря на сокращение объема отходов путем сжигания. Зола рисовой шелухи представляет собой малоценный материал, который можно легко превратить в полезные силикатные материалы. Рисовая и силикатная промышленность проявила интерес к новым продуктам на основе диоксида кремния, которые мы произвели, и мы стремимся к их коммерциализации.
Публикации
- Калапати, У., Проктор, А. и Шульц, Дж. 2000. Ксерогели кремнезема из золы рисовой шелухи: структура, плотность и механическая прочность в зависимости от гелеобразования, рН и концентрации кремнезема. Дж. Хим. Тех. и биотех. 75:464-468.
- Калапати, У., Проктор, А. и Шульц, Дж. 2000. Простой метод производства чистого кремнезема из золы рисовой шелухи. Технология биоресурсов 73:257-262.
- Калапати, У., Проктор, А. и Шульц, Дж. 2002. Усовершенствованный метод производства кремнезема из золы рисовой шелухи. Биорес. Тех. 85:285-289.
- Калапати, У., Проктор, А. и Шульц, Дж. 2003. Силикатный теплоизоляционный материал из кремнеземной золы рисовой шелухи. Инд.Инж. хим. Рез. 42:46-49.
- Kalapathy, U. and Proctor, A. 2000. Новый метод снижения содержания свободных жирных кислот в масле для фритюра с использованием силикатных пленок, полученных из золы рисовой шелухи. Варенье. Нефть хим. соц. 77:593-598.
Прогресс с 01.
01.04 по 30.12.04
Выходы
Однако остаточная зола имеет ограниченное применение. Тем не менее, зола рисовой шелухи является необычным материалом, поскольку она содержит более 60 процентов аморфного кремнезема, который гораздо более растворим, чем кристаллические геологические источники кремнезема. Процессы сжигания корпуса контролируются, чтобы свести к минимуму кристаллизацию кремнезема и максимально увеличить количество кремнезема, которое может быть извлечено щелочью. Ранее мы производили керамический изоляционный материал низкой плотности из кремнезема, экстрагированного щелочью, а совсем недавно исследовали влияние на горение для уменьшения остаточного углерода в золе. Нагревание золы при более низких температурах снижает содержание углерода с минимальной потерей аморфной структуры по сравнению с сжиганием при более высоких температурах. Снижение содержания углерода в золе перед экстракцией щелочью увеличит выход силикатов и уменьшит количество нерастворимых остатков.
Воздействия
Коммерческое предприятие по производству силиката натрия и углерода рисовой шелухи путем щелочной экстракции золы рисовой шелухи работает в Штутгарте, штат Арканзас, с 2004 года с использованием разработанной технологии, которая обеспечивает столь необходимое развитие сельских районов в южном Арканзасе. Возможности для промышленного производства керамических материалов будут развиваться по мере увеличения производства силиката натрия.
Публикации
- За этот период публикаций не было
Прогресс 01.01.03 — 31.12.03
Продукция
Зола рисовой шелухи может быть сырьем для рентабельного производства кремнезема и кремнезема. Кремнезем в основном находится в аморфном состоянии, что позволяет легко экстрагировать его водными растворителями. В противоположность этому коммерческие источники кремнезема являются высококристаллическими и требуют высокотемпературной плавки в печи для получения пригодного для использования продукта.
Силикатные блоки были изготовлены из силиката натрия, полученного из золы рисовой шелухи. Пористый легкий материал различной плотности получали кипячением силикатных растворов при различных скоростях нагрева. Плотность, прочность и теплопроводность увеличивались с увеличением скорости нагрева. Плотность материалов колебалась в пределах 0,33-0,42 грамма на кубический сантиметр при механической прочности, позволяющей силикату не разрушаться ниже усилия 145-19.6 ньютонов на квадратный сантиметр. Диапазон теплопроводности составлял 0,103-0,128 Вт на метр на килограмм. Изоляционные свойства будут
позволяют использовать материал для замены асбеста и органических полимеров. Ожидается, что работа по изучению влияния поверхностных свойств золы рисовой шелухи на ее химическую активность будет продолжена.
Воздействие
Недавние исследования показали, что из золы рисовой шелухи могут быть получены материалы с разнообразными свойствами для удовлетворения различных потребностей рынка.
В настоящее время в Арканзасе строится предприятие по производству коммерческого силиката натрия и углерода из рисовой шелухи из золы рисовой шелухи. Возможность коммерческого развития продуктов из рисовой шелухи с добавленной стоимостью будет увеличиваться, поскольку производство превышает текущий спрос.
Публикации
- Калапати, У., Проктор, А. и Шульц, Дж. 2003. Силикатный теплоизоляционный материал из кремнеземной золы рисовой шелухи. Инд.Инж. хим. Рез. 42:46-49.
Прогресс 01.01.02 по 31.12.02
Выходы
Сырье из рисовой шелухи и кремнезема может быть более 60% для производства рентабельных продуктов кремнезема и кремнезема. Кремнезем в основном находится в аморфном состоянии, что позволяет легко экстрагировать его водными растворителями. В противоположность этому коммерческие источники кремнезема являются высококристаллическими и требуют высокотемпературной плавки в печи для получения пригодного для использования продукта.
Ранее мы синтезировали гели и ксерогели простой щелочной экстракцией кремнезема в виде силиката натрия с последующим осаждением добавлением кислоты при рН 7. Однако мы обнаружили, что продукты содержали значительные минеральные загрязнения. Мы обнаружили, что можем значительно снизить загрязнение осажденного кремнезема минералами, добавляя экстрагированный силикат натрия к кислоте, а не добавляя кислоту к силикатам. Таким образом, мы осаждали диоксид кремния при рН 7, повышая рН, а не снижая его. Материал более высокой чистоты лучше подходит для пищевых продуктов и
непищевые адсорбционные применения, в которых контакт минералов с пищевыми продуктами был бы нежелательным. Дополнительная работа по разработке блоков силиката натрия из золы рисовой шелухи показала, что увеличение скорости сушки раствора силиката натрия дает более прочный и плотный материал, тогда как более низкая скорость нагревания дает материал с низкой плотностью, обладающий превосходными изоляционными свойствами.
Воздействие
Недавние исследования показали, что из золы рисовой шелухи можно производить материалы с разнообразными свойствами для удовлетворения различных потребностей рынка.
Силикагель был первым продуктом, который мы разработали из золы рисовой шелухи, и предприятие по производству коммерческого силиката натрия из рисовой шелухи скоро будет построено в Арканзасе рисовой компанией.
Публикации
- Калапати, У., Проктор, А. и Шульц, Дж. 2002. Усовершенствованный метод производства кремнезема из золы рисовой шелухи. Биорес. Тех. 85:285-289.
Прогресс 01.01.01 по 31.12.01
Выходы
Рисовая шелуха может быть экономически выгодным сырьем для производства кремнезема и золы, содержащей более 60% кремнезема продукты. Метод, ранее разработанный в нашей лаборатории для производства ксерогеля кремнезема, включал растворение кремнезема золы рисовой шелухи в растворе щелочи с образованием раствора силиката натрия и последующее формирование аквагеля кремнезема путем добавления соляной кислоты для снижения pH до 7 с последующей промывкой и сушкой аквагеля для образования ксерогеля.
. Ксерогель кремнезема, полученный с использованием этого метода, содержал более 4% натрия в качестве загрязнителя. Недавняя работа в нашей лаборатории привела к усовершенствованной методике производства ксерогеля кремнезема с содержанием натрия <0,5%. Усовершенствованный способ включал получение аквагеля кремнезема путем добавления раствора силиката к растворам соляной, лимонной или щавелевой кислоты с рН 1,5 до достижения рН 4,0. Затем аквагель промывают и сушат, получая ксерогель диоксида кремния. Кремнезем, полученный при кислом рН 4,0 с использованием щавелевой или лимонной кислоты, имел более низкое содержание натрия, чем кремнезем.
получают при щелочном pH 7,0 с использованием любой из трех кислот, а кремнезем получают при pH 4,0 с использованием соляной кислоты. Эта новая процедура устранила обширную промывку высушенного геля, которая требовалась в предыдущем методе для производства чистого силикагеля. Кроме того, раствор силиката натрия, полученный из золы рисовой шелухи путем взаимодействия кремнезема с 1M NaOH, использовался для производства высокопористых теплоизоляционных блоков низкой плотности с использованием простого метода выпаривания.
Скорость нагрева для получения силикатных блоков оказала значительное влияние на плотность блока, механическую прочность и теплопроводность. Плотность, пиковое усилие разрыва и теплопроводность силикатных блоков, полученных при более высокой скорости нагрева, составляли 0,33 гсм-3, 150 Нсм-2 и 0,103 Вт-м-1К-1 соответственно.
Воздействие
Зола рисовой шелухи является малоценным побочным продуктом рисовой промышленности, и существует коммерческая потребность в использовании этого материала для производства продуктов с добавленной стоимостью, чтобы избежать затрат на утилизацию. Содержание аморфного кремнезема может быть легко извлечено и использовано для производства ряда продуктов на основе кремнезема. Разработка материалов, описанных в этой работе, дает возможность недорого производить дорогостоящие продукты. Современное коммерческое производство кремнезема связано с использованием значительного количества энергии. Методы, использующие золу рисовой шелухи, просты и требуют очень мало энергии по сравнению с обычными методами, использующими традиционные источники кремнезема.
В частности, высокопористые силикатные блоки, произведенные из золы рисовой шелухи, могут быть использованы в качестве экологически безопасного теплоизоляционного материала.
Публикации
- Калапати, У. и Проктор, А. и Шульц, Дж. 2001. Легкий теплоизоляционный материал из кремнезема рисовой шелухи: производство и свойства. В обзоре J. Chem. Технологии и биотехнологии. В обзоре.
- Калапати, У., Проктор, А. и Шульц, Дж. 2001. Усовершенствованный метод производства кремнезема из золы рисовой шелухи. Биорес. Технол. В обзоре.
Легкая сэндвич-панель из вспененного полистирола-Легкая стеновая плита
Цементная сэндвич-панель DQ Eps
из легкого энергосберегающего стенового материала, содержащего армированный силикат кальция
доска в качестве лицевой панели, с цементом, полистиролом, летучей золой в качестве основного материала и формированием одним
одноразовое соединение.
Его рождение знаменует собой замену стенового материала — на
заменить традиционный блок, его новая архитектурная концепция и отличное
производительность может удовлетворить современные требования к окружающей среде здания.
Область применения
1) Широко используется в различных типах старых и
новая ненесущая внутренняя или наружная перегородка
2) Применимо к пожару в промышленном здании
стены, а также внутренние и наружные ненесущие стены
3) Применить к стальной конструкции здания
внутренние и внешние стены
4) Применяется для преобразования старых
здания, которые по требованиям к несущей способности стены здания
5) Применимо к
Случай, который имеет более высокие требования к огнестойкости, звукоизоляции и влагостойкости.
Строительный чертеж
Особенности продукта
1、Энергия
Экономичный, экологически чистый
Композитная сэндвич-панель DQ использует защиту окружающей среды
материал с морозостойкостью и теплосохранением.
У него хорошее тепло
функция теплоизоляции и сохранения тепла. Он может автоматически регулировать воздух
содержание влаги с сезонным изменением климата, соответствует тенденции развития
современных экологических жилых домов.
2、Водонепроницаемый,огнестойкий
Композитные сэндвич-панели DQ имеют предел огнестойкости 4 часа.
против высокой температуры 1000 ℃ и стандарта негорючести достичь национального
уровень А, и материал не выделяет токсичных газов, полностью смешивает
международные экологические стандарты.
Композитные сэндвич-панели DQ могут быть выполнены в виде емкости для наполнения водой
без штукатурки, без малейших протечек.
3、 Звук
изоляция и абсорбция
Сэндвич-панели DQ обладают хорошей звукоизоляцией и
звукопоглощающими свойствами, плита DQ толщиной 90 мм имеет объем звукоизоляции
45 дБ, традиционный блок имеет уровень звукоизоляции 20 дБ.
4、Свет
вес, экономия места, экономия затрат
Легкая перегородка DQ является прочным ядром новой стены.
материалы, легкие материалы, значительно снижающие несущую способность
строительство. Его толщина между
60 мм-180 мм, по сравнению с традиционной толщиной блока значительно экономит
строительное пространство. Например: традиционный блок для увеличения среднего
толщина 240 мм +40 мм, при использовании 9Легкая стеновая плита DQ толщиной 0 мм
внутренняя стена может удовлетворить все потребности и соответствовать национальным стандартам тестирования.
5、 Простая конструкция и
более короткое время
Конструкция сэндвич-панели DQ Ион для сборки
конструкция, весь процесс сборки или строительства прост, эффективен,
нестроительные отходы, не касаясь золы, сокращают продолжительность.
511 — Новые и улучшенные непищевые продукты и процессы;
1530 — Рис;
2020 — Машиностроение; 2010 — Физика; 2000 — Химия;
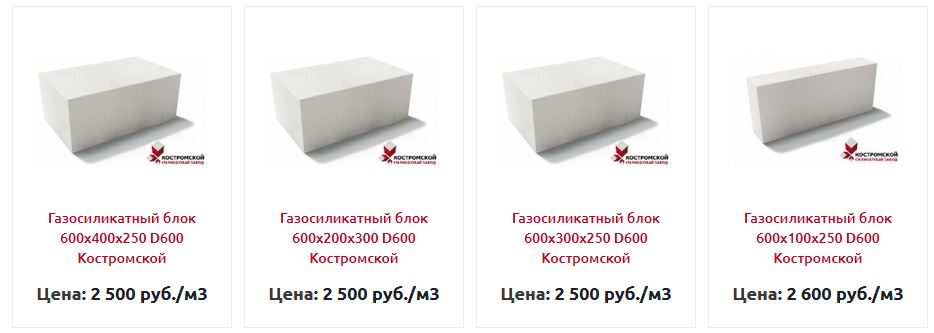
Кремний из рисовой шелухи растворяется путем щелочной экстракции для получения силикатного раствора. Затем силикагель будет осаждаться при снижении pH раствора. Прочность геля будет увеличиваться за счет старения и последующей сушки. Структурный анализ блоков будет выполнен с помощью рентгеновской дифракции и инфракрасной спектроскопии с преобразованием Фурье с нарушенным полным отражением. Атомно-силовая микроскопия и сканирующая электронная микроскопия будут использоваться для изучения микроструктуры ксерогеля. Средняя площадь поверхности и размер пор будут определяться адсорбцией газа по методу БЭТ.

Прогресс 01.12.00 — 30.11.05
Выходные данные
Зола промышленной рисовой шелухи является богатым источником аморфного кремнезема, полученного путем сжигания рисовой шелухи. Эту форму природного кремнезема легче использовать для производства адсорбентов и керамики на основе кремнезема, чем песок, который традиционно используется. Керамические ксерогели кремнезема были получены путем щелочной экстракции кремнезема из промышленной золы рисовой шелухи с последующим осаждением и сушкой. Ксерогели были получены из растворов щелочей, объемы которых были уменьшены для получения диоксида кремния в диапазоне концентраций 4-12%. Образцы каждой концентрации доводили до pH 9., 10, 10,5 и 11 для осаждения силикагелей, которые затем сушили в течение 24 часов при 80°С. Рентгеноструктурные исследования показали, что все образцы представляли собой аморфный кремнезем, а анализ инфракрасной спектроскопии показал, что полимеризация кремнезема или удлинение цепи кремнезема, была выше при более высоком рН осаждения. Однако сшивание между полимерами было основным взаимодействием при более низком pH и усиливалось при использовании кремнезема.
концентрация. Стеклообразные твердые вещества были образованы путем осаждения при высоких значениях pH, тогда как пористые силикагели были получены при более высоких концентрациях кремнезема. Ксерогель, образованный из концентрированных растворов кремнезема, осажденных при рН 10, дает керамический блочный материал, обладающий наибольшей механической прочностью благодаря оптимальному сочетанию полимеризации кремнезема и сшивки. Кроме того, ксерогель керамического кремнезема высокой чистоты был получен путем удаления остаточных примесей ионов металлов путем интенсивной промывки осажденного кремнезема водой перед сушкой.
Было обнаружено, что промывка водой более эффективна, чем промывка кислотой.
Воздействие
Рис Двадцать процентов собранного риса состоит из рисовой шелухи. Экологические нормы ограничивают захоронение скорлупы на свалках, и, несмотря на ее использование в качестве куриного подстилки и в качестве корма для животных, не существует крупномасштабного использования, которое значительно уменьшит проблему отходов. Многие рисовые заводы используют шелуху в качестве источника топлива и производят аморфную силикатную золу, часть которой используется сталелитейной промышленностью в качестве огнеупорного материала. Тем не менее, по-прежнему необходимо найти крупные рынки сбыта для корпуса и золы, чтобы решить проблему удаления отходов, несмотря на сокращение объема отходов путем сжигания. Зола рисовой шелухи представляет собой малоценный материал, который можно легко превратить в полезные силикатные материалы. Рисовая и силикатная промышленность проявила интерес к новым продуктам на основе диоксида кремния, которые мы произвели, и мы стремимся к их коммерциализации.
Публикации
- Калапати, У., Проктор, А. и Шульц, Дж. 2000. Ксерогели кремнезема из золы рисовой шелухи: структура, плотность и механическая прочность в зависимости от гелеобразования, рН и концентрации кремнезема. Дж. Хим. Тех. и биотех. 75:464-468.
- Калапати, У., Проктор, А. и Шульц, Дж. 2000. Простой метод производства чистого кремнезема из золы рисовой шелухи. Технология биоресурсов 73:257-262.
- Калапати, У., Проктор, А. и Шульц, Дж. 2002. Усовершенствованный метод производства кремнезема из золы рисовой шелухи. Биорес. Тех. 85:285-289.
- Калапати, У., Проктор, А. и Шульц, Дж. 2003. Силикатный теплоизоляционный материал из кремнеземной золы рисовой шелухи. Инд.Инж. хим. Рез. 42:46-49.
- Kalapathy, U. and Proctor, A. 2000. Новый метод снижения содержания свободных жирных кислот в масле для фритюра с использованием силикатных пленок, полученных из золы рисовой шелухи. Варенье. Нефть хим. соц. 77:593-598.
Прогресс с 01. 01.04 по 30.12.04
Выходы
Однако остаточная зола имеет ограниченное применение. Тем не менее, зола рисовой шелухи является необычным материалом, поскольку она содержит более 60 процентов аморфного кремнезема, который гораздо более растворим, чем кристаллические геологические источники кремнезема. Процессы сжигания корпуса контролируются, чтобы свести к минимуму кристаллизацию кремнезема и максимально увеличить количество кремнезема, которое может быть извлечено щелочью. Ранее мы производили керамический изоляционный материал низкой плотности из кремнезема, экстрагированного щелочью, а совсем недавно исследовали влияние на горение для уменьшения остаточного углерода в золе. Нагревание золы при более низких температурах снижает содержание углерода с минимальной потерей аморфной структуры по сравнению с сжиганием при более высоких температурах. Снижение содержания углерода в золе перед экстракцией щелочью увеличит выход силикатов и уменьшит количество нерастворимых остатков.
Воздействия
Коммерческое предприятие по производству силиката натрия и углерода рисовой шелухи путем щелочной экстракции золы рисовой шелухи работает в Штутгарте, штат Арканзас, с 2004 года с использованием разработанной технологии, которая обеспечивает столь необходимое развитие сельских районов в южном Арканзасе. Возможности для промышленного производства керамических материалов будут развиваться по мере увеличения производства силиката натрия.
Публикации
- За этот период публикаций не было
Прогресс 01.01.03 — 31.12.03
Продукция
Зола рисовой шелухи может быть сырьем для рентабельного производства кремнезема и кремнезема. Кремнезем в основном находится в аморфном состоянии, что позволяет легко экстрагировать его водными растворителями. В противоположность этому коммерческие источники кремнезема являются высококристаллическими и требуют высокотемпературной плавки в печи для получения пригодного для использования продукта. Силикатные блоки были изготовлены из силиката натрия, полученного из золы рисовой шелухи. Пористый легкий материал различной плотности получали кипячением силикатных растворов при различных скоростях нагрева. Плотность, прочность и теплопроводность увеличивались с увеличением скорости нагрева. Плотность материалов колебалась в пределах 0,33-0,42 грамма на кубический сантиметр при механической прочности, позволяющей силикату не разрушаться ниже усилия 145-19.6 ньютонов на квадратный сантиметр. Диапазон теплопроводности составлял 0,103-0,128 Вт на метр на килограмм. Изоляционные свойства будут
позволяют использовать материал для замены асбеста и органических полимеров. Ожидается, что работа по изучению влияния поверхностных свойств золы рисовой шелухи на ее химическую активность будет продолжена.
Воздействие
Недавние исследования показали, что из золы рисовой шелухи могут быть получены материалы с разнообразными свойствами для удовлетворения различных потребностей рынка. В настоящее время в Арканзасе строится предприятие по производству коммерческого силиката натрия и углерода из рисовой шелухи из золы рисовой шелухи. Возможность коммерческого развития продуктов из рисовой шелухи с добавленной стоимостью будет увеличиваться, поскольку производство превышает текущий спрос.
Публикации
- Калапати, У., Проктор, А. и Шульц, Дж. 2003. Силикатный теплоизоляционный материал из кремнеземной золы рисовой шелухи. Инд.Инж. хим. Рез. 42:46-49.
Прогресс 01.01.02 по 31.12.02
Выходы
Сырье из рисовой шелухи и кремнезема может быть более 60% для производства рентабельных продуктов кремнезема и кремнезема. Кремнезем в основном находится в аморфном состоянии, что позволяет легко экстрагировать его водными растворителями. В противоположность этому коммерческие источники кремнезема являются высококристаллическими и требуют высокотемпературной плавки в печи для получения пригодного для использования продукта. Ранее мы синтезировали гели и ксерогели простой щелочной экстракцией кремнезема в виде силиката натрия с последующим осаждением добавлением кислоты при рН 7. Однако мы обнаружили, что продукты содержали значительные минеральные загрязнения. Мы обнаружили, что можем значительно снизить загрязнение осажденного кремнезема минералами, добавляя экстрагированный силикат натрия к кислоте, а не добавляя кислоту к силикатам. Таким образом, мы осаждали диоксид кремния при рН 7, повышая рН, а не снижая его. Материал более высокой чистоты лучше подходит для пищевых продуктов и
непищевые адсорбционные применения, в которых контакт минералов с пищевыми продуктами был бы нежелательным. Дополнительная работа по разработке блоков силиката натрия из золы рисовой шелухи показала, что увеличение скорости сушки раствора силиката натрия дает более прочный и плотный материал, тогда как более низкая скорость нагревания дает материал с низкой плотностью, обладающий превосходными изоляционными свойствами.
Воздействие
Недавние исследования показали, что из золы рисовой шелухи можно производить материалы с разнообразными свойствами для удовлетворения различных потребностей рынка. Силикагель был первым продуктом, который мы разработали из золы рисовой шелухи, и предприятие по производству коммерческого силиката натрия из рисовой шелухи скоро будет построено в Арканзасе рисовой компанией.
Публикации
- Калапати, У., Проктор, А. и Шульц, Дж. 2002. Усовершенствованный метод производства кремнезема из золы рисовой шелухи. Биорес. Тех. 85:285-289.
Прогресс 01.01.01 по 31.12.01
Выходы
Рисовая шелуха может быть экономически выгодным сырьем для производства кремнезема и золы, содержащей более 60% кремнезема продукты. Метод, ранее разработанный в нашей лаборатории для производства ксерогеля кремнезема, включал растворение кремнезема золы рисовой шелухи в растворе щелочи с образованием раствора силиката натрия и последующее формирование аквагеля кремнезема путем добавления соляной кислоты для снижения pH до 7 с последующей промывкой и сушкой аквагеля для образования ксерогеля. . Ксерогель кремнезема, полученный с использованием этого метода, содержал более 4% натрия в качестве загрязнителя. Недавняя работа в нашей лаборатории привела к усовершенствованной методике производства ксерогеля кремнезема с содержанием натрия <0,5%. Усовершенствованный способ включал получение аквагеля кремнезема путем добавления раствора силиката к растворам соляной, лимонной или щавелевой кислоты с рН 1,5 до достижения рН 4,0. Затем аквагель промывают и сушат, получая ксерогель диоксида кремния. Кремнезем, полученный при кислом рН 4,0 с использованием щавелевой или лимонной кислоты, имел более низкое содержание натрия, чем кремнезем.
получают при щелочном pH 7,0 с использованием любой из трех кислот, а кремнезем получают при pH 4,0 с использованием соляной кислоты. Эта новая процедура устранила обширную промывку высушенного геля, которая требовалась в предыдущем методе для производства чистого силикагеля. Кроме того, раствор силиката натрия, полученный из золы рисовой шелухи путем взаимодействия кремнезема с 1M NaOH, использовался для производства высокопористых теплоизоляционных блоков низкой плотности с использованием простого метода выпаривания.
Скорость нагрева для получения силикатных блоков оказала значительное влияние на плотность блока, механическую прочность и теплопроводность. Плотность, пиковое усилие разрыва и теплопроводность силикатных блоков, полученных при более высокой скорости нагрева, составляли 0,33 гсм-3, 150 Нсм-2 и 0,103 Вт-м-1К-1 соответственно.
Воздействие
Зола рисовой шелухи является малоценным побочным продуктом рисовой промышленности, и существует коммерческая потребность в использовании этого материала для производства продуктов с добавленной стоимостью, чтобы избежать затрат на утилизацию. Содержание аморфного кремнезема может быть легко извлечено и использовано для производства ряда продуктов на основе кремнезема. Разработка материалов, описанных в этой работе, дает возможность недорого производить дорогостоящие продукты. Современное коммерческое производство кремнезема связано с использованием значительного количества энергии. Методы, использующие золу рисовой шелухи, просты и требуют очень мало энергии по сравнению с обычными методами, использующими традиционные источники кремнезема. В частности, высокопористые силикатные блоки, произведенные из золы рисовой шелухи, могут быть использованы в качестве экологически безопасного теплоизоляционного материала.
Публикации
- Калапати, У. и Проктор, А. и Шульц, Дж. 2001. Легкий теплоизоляционный материал из кремнезема рисовой шелухи: производство и свойства. В обзоре J. Chem. Технологии и биотехнологии. В обзоре.
- Калапати, У., Проктор, А. и Шульц, Дж. 2001. Усовершенствованный метод производства кремнезема из золы рисовой шелухи. Биорес. Технол. В обзоре.



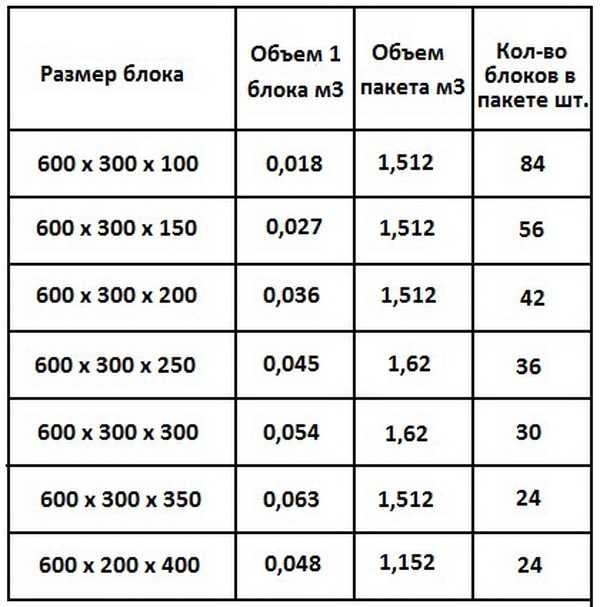