Газосиликатные блоки чем резать: Блок D500 600 * 250 * 200, 1 сорт
Блок D500 600 * 250 * 200, 1 сорт
Особенности применения блоков из газосиликата ГРАС
Бетон хорош в строительстве и активно применяется по сей день, но кто сказал, что нельзя сделать лучше? Сейчас на рынке существует множество предложений, расширяющих существующие преимущества стандартного бетона и добавляющих к нему новые. Газосиликатные блоки, производством которых мы занимаемся — одно из них.
Что такое газосиликатные блоки?
Расширением списка полезных свойств бетона ученые озаботились еще в двадцатых годах прошлого века. Но технология производства газосиликатных блоков начала активно использоваться позже — когда столетие перешагнуло за половину. С тех пор новый материал для строительства набирает популярность и используется все большим и большим числом застройщиков.
Блоки состоят из:
- Цемента.
- Кварцевого песка.
- Извести.
- Алюминиевой пудры (именно этот ингредиент вызывает появление пор с воздухом в рабочей смеси).
Газосиликатные блоки принадлежат к категории так называемых ячеистых бетонов. Технология производства таких блоков достаточно трудоемка и высокотехнологична: для того, чтобы получить газосиликат, требуется множество ингредиентов. Среди них основной компонент — известь — и дополнительные элементы: кварцевый песок, вода, цемент и вспенивающий ингредиент, которым, как правило, служит алюминиевая пудра.
Взаимосвязь этих ингредиентов проходит под воздействием высоких температур и большого давления в специальных автоклавах. Именно поэтому газосиликатные блоки называют еще автоклавным бетоном, а процесс их производства — автоклавированием. В процессе термического воздействия в готовом материале возникают емкости с воздухом — поры, которые ощутимо влияют на преимущества нового стройматериала.
В чем преимущества газосиликатных блоков?
- Экологичность. Компания Грас добросовестно подходит к выбору материала для создания своего продукта. Все используемые компоненты – сырьевые, экологически чистые природные материалы, не имеющие вредных примесей.
Газосиликатные блоки Грас экологически безопасны для людей и окружающей среды на протяжении всего срока эксплуатации.
- Прочность. Структура газосиликатного блока имеет внутри сеть равномерно размещенных воздушных пор. Точно выверенная плотность этих пор обеспечивает прочность и надежность возводимой конструкции. Для соединения силикатных блоков между собой используется особый клей, который так же производит компания Грас.
- Практичная геометрия. Изготовление блоков — высокоточный научно-выверенный процесс. Каждый газосиликатный блок идентичен друг другу, что обеспечивает беспроблемную кладку. Выверенные размер и форма каждого блока облегчает проектирование и возведение любого здания с минимальными временными затратами.
- Легкость обработки. Газосиликатный материал неприхотлив в обработке практически любыми подручными инструментами: пилами, фрезами, сверлами и т.д. Готовому блоку можно придать любую необходимую форму, что позволяет создавать строения разнообразной архитектуры.
- Огнеупорность. Благодаря своему неорганическому составу, газосиликатные блоки являются негорючим материалом. В строениях, где газосиликатные блоки являются несущим материалом, или даже используются в качестве обшивки, пожаробезопасность увеличивается в разы.
- Термоустойчивость. Блоки обладают пористой структурой, что обеспечивает высокую теплоизоляцию, благодаря заключенному в ячейках воздуху. Высокие температуры так же не воздействуют на состав и прочность газосиликатного блока.
- Экономичность. Газосиликатные блоки в разы легче других строительных материалов, таких как кирпич, шлакоблок и т.д. При том, что легкость этого материала никак не сказывается на его прочности и надежности, застройщик экономит на транспортировке и самом строительстве, так как время кладки сокращается в 2 – 2,5 раза.
Активно использовать газосиликат в строительстве профессионалов подталкивает длинный список преимуществ такого материала. Известно, что газосиликатные блоки сочетают в себе характеристики камня и дерева. От дерева они получают легкость в обработке — газосиликатный блок легко разрезать на части, просверлить, отшлифовать. Вторым преимуществом этого материала, без сомнения, является его легкость, достигаемая за счет уже упомянутых выше воздушных пор. Газосиликатные блоки отличаются небольшой массой, а значит, перевозить и переносить их можно без особого труда, экономя не только на технике для обработки, но и на транспортных расходах.
Среди более важных преимуществ газосиликата можно выделить тот факт, что минеральная основа таких блоков не подвержена горению — то есть, постройки из такого материала отличает значительный уровень огнеупорности, а это значит, что опасность возгорания в домах из газосиликата, сокращается в разы. Пористая структура газосиликата также обеспечивает высокий уровень тепло- и шумоустойчивости, что делает этот материал незаменимым в жилищном строительстве. Благодаря заключенному в ячейках газосиликата воздуху такие блоки меньше проводят тепло, а это значит, что в домах, построенных из газосиликата, всегда будет поддерживаться оптимальная температура.
Производство газосиликатных блоков
Производство газосиликатных блоков по автоклавной технологии – это сложный технологичный процесс с применением специальных печей, в которых рабочая смесь поддается обработке высоким давлением и температурой. Такие печи и называют автоклавами – в них проходят процессы вспенивания раствора, под воздействием температуры около 200 градусов.
Производственный процесс заканчивается тем, что большие блоки на выходе из печей делят на малые, стандартные. Газосиликатные блоки применяются не только в строительстве несущих стен. Также они актуальны в строительстве перемычек, перегородок и т.д. Плотность таких блоков может достигать 700 кг/ м³ . Газоблоки с малой плотностью рекомендуют, когда требуется звукоизоляция и утепление наружных стен. Производство газосиликатных блоков обязательно включает в себя процесс автоклавирования, что придает материалу прочность.
Ну и, конечно же, нельзя упускать из виду главное достоинство газосиликата — его значительный запас прочности, который достигается за счет компонентов, подобранных в строгой пропорции, соблюдения всех правил обработки и автоклавирования, а также структуры внутренних пор стройматериала. Группа компаний «ГРАС» производит газосиликатные блоки любых размеров и предназначений — как стеновые, так и перегородочные. Обязательная сертификация продукции, тщательная проверка на соответствие необходимым нормам в лабораторных условиях и идеальная геометрия блоков, значительно облегчающая строительство — вот те правила, которым мы неукоснительно следуем в производстве газосиликата.
Газосиликатные блоки (справочная информация) — информация на сайте Кирпич.ру

Газобетон изготавливается из негорючего природного минерального сырья, не горит и не поддерживает горение. Он может в течение 3-7 часов выдерживать одностороннее воздействие огня.
Использование газобетона в строительстве позволяет снизить нагрузку на фундамент. Кладка методом тонких швов, по сравнению с традиционной кладкой, снижает расход кладочного раствора в шесть раз. Значительно снижается и трудоемкость строительных работ. 1 газосиликатный блок заменяет 15 – 20 кирпичей, следовательно, во время выкладки стены из газобетона рабочие должны будут произвести в 15 – 20 раз меньше операций, чем при кладке кирпичной стены такого же размера. Газосиликатнные блоки при большом размере имеют малый объемный вес. Для работы с ними не нужны специальные подъемные механизмы. Все это сокращает трудозатраты. При использовании газосиликатнных блоков скорость возведения здания увеличивается примерно в четыре раза, а стоимость строительства снижается.)
Воздух, заключенный в многочисленных порах, обеспечивает отличные теплосберегающие свойства газосиликата. Стены дома из газобетонных блоков соответствуют строительным нормам, предусмотренным для жилых и общественных зданий. Сухой газобетон имеет коэффициент теплопроводности 0,12-0,14 Вт/м•°С. Чем ниже объемный вес газобетона, тем выше его теплоизоляционные характеристики, однако с уменьшением плотности прочность газобетонных блоков уменьшается.
В настоящее время для возведения частных домов и коттеджей используется конструктивно-теплоизоляционный газобетон с объемным весом от 500 до 600 кг/м³, в котором прочность сочетается с достаточной легкостью и хорошими теплоизоляционными свойствами.
Гладкая поверхность и точные геометрические размеры газобетонных блоков позволяют применять технологию тонкошовной кладки. Свойства стен в домах, сложенных по этой технологии приближаются к свойствам монолитных стен. Зазор между блоками составляет всего 1 – 3 мм, что предотвращает образование «мостиков холода» и значительно уменьшает тепловые потери. Следствием низкой теплопроводности является меньшая тепловая инерция газосиликата. Дома, сложенные из газосиликатнных блоков, в отличие от кирпичных, прогреваются всего за несколько часов.)
Под морозостойкостью материала понимают его способность выдерживать полное замораживание и оттаивание в состоянии максимального насыщения водой. При проведении испытаний газосиликат погружают на 8 часов в воду, а затем на 8 часов помещают в морозильную камеру.
Такое действие считается одним циклом. Испытания повторяют до тех пор, пока газосиликат не начнет терять прочность и массу. Газосиликатные блоки пронизаны тысячами мелких пор, в которые при замерзании вытесняется лед и вода. Это обеспечивает сохранность газобетона при замерзании в течение 100 и более циклов. Для сравнения: нормы морозостойкости кирпича, пригодного для использования в Центральном регионе – строительный – 15-25 циклов, лицевой – 50 циклов. Пенобетон выдерживает до 35 циклов заморозки. )
Несмотря на небольшую объемную массу, составляющую для газобетона, обычно используемого в коттеджном строительстве, всего 500-600 кг/м³, материал обладает высокой прочностью на сжатие — 28-40 кгс/ м². Газобетон может применяться в малоэтажном строительстве для возведения безкаркасных строений высотой не более 14 метров, создания внутренних стен и перегородок. Срок службы газобетонных блоков примерно равен сроку службы традиционных кирпичей. Производители обычно дают гарантию на 80 лет, но уже сейчас понятно, что этот материал может служить дольше – стены зданий, построенных из газобетонных блоков более восьмидесяти лет назад, не обнаруживают никаких признаков разрушения или изменения основных характеристик материала.)
Данные блоки широко применяются в строительстве монолитных домов, зданий, сооружений в качестве стенового материала особенно широко газосиликатные блоки применяются в жилищном малоэтажном строительстве.
Газобетон легко обрабатывается обычным ручным и электрическим инструментом. Его можно сверлить, колоть и резать. Газобетонные блоки разрезают, используя обычную ручную или электрическую пилу. Штробы под арматуру и проводку прокладывают электродрелью со специальной насадкой. Отверстия под розетки и выключатели также высверливают дрелью. Округлые формы создают при помощи ленточной шлиф-машины. Газобетонные изделия могут использоваться в качестве отделочного и декоративного материала, из которого изготавливают колонны, подставки, тумбы, декоративные украшения, имитирующие лепнину.)
Газосиликатные блоки ГРАС
Особенности применения блоков из газосиликата ГРАС
Бетон необходим в сфере возведения жилья и иных строений, он постоянно используется по настоящее время, но откуда известно, что нет ничего лучше? На данный момент в строительной сфере существует огромный выбор предложений, наращивающих существующие плюсы стандартного бетона и обогащая его новыми. Газосиликатные блоки, продажу которых мы ведем — один из таких плюсов.
Итак, что же такое газосиликатные блоки?
На увеличение количества полезных свойств бетона умы обратили внимание еще в начале 20 века. Но лишь к середине 50х годов технология производства шагнула далеко вперед, газосиликатные блоки стали привлекать внимание в строительной сфере. Именно в то время технологический скачок обеспечил газобетонным блокам будущее, по сей день популярность которых только увеличивается.
Немного теории, состав используемый при производстве блока:
- Цемент.
- Кварцевый песок.
- Известь.
- Алюминиевая пудра (по секрету скажу, что как раз таки этот ингредиент является виновником появления тех самых воздушных пор).
Газосиликатные блоки относятся к категории условных ячеистых бетонов. Методика производства этих блоков весьма сложна и технологична: поэтому, для того чтобы изготовить газосиликат, необходимо использовать большое количество компонентов. Между тем главный ингредиент — известь — и второстепенные составляющие: кварцевый песок, вода, цемент и вспенивающий элемент, которым, по сути, является алюминиевая пудра.
Соединение всех элементов происходит под действием высоких температур и повышенного давления в особых автоклавах. Собственно в связи с этим газосиликатные блоки именуют еще автоклавным бетоном, а технология их изготовления — автоклавированием. В процедуре теплового влияния в итоговом материале появляются емкости с воздухом — поры, именно они сильно влияют на преимущества нового стройматериала.
В чем достоинства газосиликатных блоков?
-
Экологичность. Компания Грас ответственно подходит к подбору материала для изготовления своего продукта. Все используемые составляющие – сырьевые, экологически чистые природные материалы, не имеющих вредных добавок. Газосиликатные блоки Грас экологически безопасны для людей и окружающей среды на протяжении всего срока эксплуатации.
-
Прочность. Структура газосиликатного блока представляет собой по сути бетон с большим количеством равномерно размещенных воздушных пор. Точно сконцентрированная плотность этих пор гарантирует прочность и надежность возводимого строения.
Для кладки силикатных блоков, используется особый клей, он соединяет между собой отдельные блоки, при этом не образует так называемого «мостика холода», шов получается маленьким до 3 мм в толщину.
-
Практичная геометрия. Производство блоков — высокоточный научно-выверенный процесс. Каждый газосиликатный блок идентичен друг другу, что обеспечивает беспроблемную кладку. Выверенные размер и форма каждого блока облегчает проектирование и возведение любого здания с минимальными временными затратами.
-
Легкость обработки. Газосиликатный материал неприхотлив в обработке практически любыми подручными инструментами: пилами, фрезами, сверлами и т.д. Готовому блоку можно придать любую необходимую форму, что позволяет создавать строения разнообразной архитектуры.
-
Огнеупорность. Благодаря своему неорганическому составу, газосиликатные блоки являются негорючим материалом. В строениях, где газосиликатные блоки являются несущим материалом, или даже используются в качестве обшивки, пожаробезопасность увеличивается в разы.
-
Термоустойчивость. Благодаря воздушным порам из которых состоит материал газосиликатных блок, они имеют свойства высокой термоустойчивости. Одновременно с этим, материал является огнестойким, и предел разрушения блоков от огня очень велик и сравним с керамическим кирпичом.
-
Экономичность. Силикатные блоки по истине передовой материал, в сравнении с кирпичом, шлакоблоком, керамическими блоками и другими, этот материал обладает низким весом. Одновременно с этим вес материала ни как не сказывается на других свойствах материала, таких например как прочность, используя этот материал несомненна экономия на транспортировке, так как же как и на скорости выполнения работ, время кладки при использовании этого материала сокращается в 2 – 2,5 раза.
Есть ряд преимуществ этого материала, которые профессионалы не в коем случае не обойдут стороной. Чего стоит только тот факт, что данный материал сочетает в себе свойства таких материалов как камень и дерево. От дерева они получают легкость в обработке — газосиликатный блок легко разрезать на части, просверлить, отшлифовать. Вторым преимуществом этого материала, без сомнения, является его легкость, достигаемая за счет уже упомянутых выше воздушных пор. Газосиликатные блоки отличаются малым весом, это означает, что транспортировка и перемещение их возможна без особого труда, экономя не только на технике для обработки, но и на транспортных расходах.
Основным преимуществом газосиликата по сравнению с другими материала является тот факт, что минеральная основа этих блоков не подвержена горению — то есть, строения из этого материала являются в высоком уровне огнеупорными, что означает, что опасность возгорания в строениях из газосиликата, уменьшается в разы. Пористая структура газосиликата неизменно гарантирует отличный уровень тепло- и шумоустойчивости, что является незаменимым в жилищном строительстве при использовании этого материала. Вследствие того что в ячейках газосиликата находится воздух, такие блоки практически не проводят тепло, а это означает, что в строениях, построенных из газосиликата, в большей степени поддерживаться комфортная температура. Кроме того — газосиликатные блоки малой прочности специально спроектированы для того, чтобы использовать их в качестве термоизоляционного слоя!
Производство газосиликатных блоков
Изготовление газосиликатных блоков по автоклавной технологии – это трудоемкая технологичная процедура с использованием специализированных печей, в них рабочая смесь подвергается обработке повышенным давлением и температурой. Эти печи и называют автоклавами – в них происходят процедуры вспенивания смеси, под влиянием повышенной температуры около 200 градусов.
Производственный процесс завершается тем, что большие блоки на выходе из печей делят на малые, стандартные. Газосиликатные блоки используют не только в строительстве несущих стен. Кроме того они полезны в строительстве перемычек, перегородок и т.д. Плотность газосиликатного материала может достигать 600-700 кг/м3. Газоблоки же с низкой плотностью рекомендуют, когда необходима звукоизоляция и утепление наружных стен. Изготовление газосиликатных блоков обязательно включает в себя процедуру автоклавирования, что придает материалу прочность.
В завершение всего сказанного, нельзя не упомянуть основной факт и преимущество таких блоков — его повышенный запас прочности, который достигается за счет элементов, использованных в строгой пропорции, соблюдения всех правил обработки и автоклавирования, а также структуры внутренних пор газосиликатных блоков. Группа компаний «ГРАС» изготавливает газосиликатные блоки любых размеров и предназначений — как стеновые, так и перегородочные. Неотъемлемым является то, что вся продукция прошла соответствующую сертификацию, а так же всеобъемлющий контроль на соответствие необходимым нормам в лабораторных условиях, такие блоки имеют идеальную геометрию блоков, значительно облегчающая строительство — вот те правила, которым мы неукоснительно следуем в производстве газосиликата. Заказать стройматериалы в любом нужном количестве и по доступной цене можно как по телефону, так и на любой нашей розничной площадке.
Блоки газосиликатные
Газосиликат, сравнительно недавно появившийся на стройрынке, успел завоевать популярность. Стеновые газосиликатные изделия используют как профессиональные строители, так и частные лица, которые осуществляют строительство самостоятельно. Блоки газосиликатные относятся к группе легких ячеистых бетонов.
Пористая структура делает блоки газосиликатные цена, на которые является демократичной с учетом имеющихся физико-механических характеристик, достаточно конкурентноспособным материалом при сравнении с аналогичными стеновыми материалами. Стоимость зависит от разных факторов: сложность технологии, марка плотности изделий, физических характеристик (уровня теплопроводности, морозостойкости и других). Кроме того стоимость зависит от качества сырья, используемого производителем и оборудования, на котором блоки режут.
Газосиликат является ячеистым конструкционно-теплоизоляционным материалом, получаемым при твердении смеси кремнеземистого тонкодисперсного компонента, воды и газообразователя. Объемный вес блоков, используемых для стен, варьируется в пределах 350 -700 кг/м. куб., что дает возможность применить его для разных строительных задач.
Применение купить газосиликатные блоки
Принимая решение купить газосиликатные блоки, заказчик сможет применять их не только как основной стройматериал, но и как утеплитель для уже готового строения. Их можно использовать для заполнения ненужных проемов, а также для обустройства внутренних перегородок. Наличие ровных и гладких граней позволяет обойтись без трудоемкого выравнивания стен для последующей отделки, что значительно сэкономит строительный бюджет.
Производство газосиликатных блоков предполагает соблюдение определенной технологии – обязательного автоклавирования. Этот метод изготовления блоков позволяет добиться получения большей прочности и меньшей усадки материала. После автоклавной обработки получается прочный минерал с равномерным распределением воздушных ячеек и одинаково высокими качественными характеристиками в любой точке блока
Преимущества газосиликата
Газосиликат не содержит токсичных соединений, не нуждается в обработке химическими составами для повышения срока годности и является экологичным материалом. Дома из газосиликата имеют микроклимат сходный с микроклиматом деревянного дома. Стены из газосиликатных блоков аэропроницаемы, они могут «дышать», они не заражаются плесенью и гнилью. Благодаря пористой структуре внутри помещений сохраняется оптимальный уровень влажности.
Строительство стен из газосиликата и облицовочного кирпича
Строительство стен мы начали с гидроизоляции цоколя. Попросту говоря, нужно раскатать разрезанный на ширину цоколя кусок рубероида. Резать его, как оказалось, можно несколькими способами. Способ первый, это просто разрезать целый рулон пополам какой-нибудь ножовкой. А второй способ — это раскатать рубероид по цоколю в длину, отмерить раскатанным полотном нужную ширину цоколя, положить по всей длине рубероида капроновую нитку, согнуть лист рубероида по ширине цоколя так, чтобы нитка оказалась внутри сгиба, свободным концом нитки пропилить его по сгибу. Для этого просто нужно тянуть нитку она и будет его резать. Уфф… надеюсь понятно изъяснился!
Далее, нужно сделать так называемую «раскладку». Раскладка делается для того, чтобы не пилить в дальнейшем наш красивый облицовочный кирпич. Что мы для этого делаем? Без раствора выкладываем весь периметр дома с учетом швов, толщина которых 8-10 мм. Небольшой свес кирпича допускается, но не более 4 см.После этого, согласно проекту (если он имеется) отмечаем то место, где у нас будут дверь или двери. В моем случае мы просто убирали 4 кирпича у главного входа (получилось 104 см) и по 3 кирпича у выхода на веранду и входа в котельную (по 78 см).
Такие вещи как кирпичная кладка лучше доверить бригаде строителей, но чутко контролировать все процессы. И перед этим обязательно посмотреть несколько объектов, которые они сделали, и пообщаться с хозяевами этих объектов. А то кто знает, может они один объект на показ сделали, а остальные тяп-ляп.
Итак, кладем первый ряд облицовочного кирпича. От него и будем отталкиваться. Далее отмеряем 15 см внутрь дома (именно столько понадобилось мне для утеплителя и воздушной прослойки) и укладываем ряд газосиликатных блоков. Размер блоков 60х20х30 см. Укладываем на ту сторону, которая шириной 20 см. Тут нужно поговорить о том, на что укладывать. Многие рекомендуют укладывать на специальный клей. Это верно, потому что цементный шов, это попросту мостик холода (помним про расчет толщины стен). Я всецело за новые технологии, но трезво оценив кривизну блоков и трудозатраты на их доведение до идеальной ровности, махнул рукой и решил делать на цементном растворе. Так что, если заморачиваться на этой теме, то нужно не экономить на блоках и тщательно подходить к выбору их геометрии.Что делать с пустотой 15 см на дверных проемах? Мы отпиливали 35 сантиметров блока (20 толщина стены из блока+15 толщина зазора для воздушной прослойки и утеплителя), разворачивали его и ставили торцом. Таким образом, у нас весь периметр окон и дверей состоит из кирпича и блока.
Тут еще надо добавить, что лучше оставить «четверть» для установки окон и дверей. Чтобы потом, при установки окна изнутри дома, оно не вываливалось наружу, а аккуратненько упиралось в четверть и запенивалось. Тогда после установки окон снаружи не будет видно монтажной пены. А для этого, помним про тот торцевой блок? Так вот, нужно его положить таким образом, чтобы ширина окна (двери) из блоков была на 8-10 сантиметров шире ширины окна из кирпича. Не запутал надеюсь. Проще говоря, если ширина оконного проема в районе кладки из облицовочного кирпича 1,80 м, то ширина этого же проема там, где блоки лежат уже будет 1,88-1,90 м.
Когда первый ряд блоков выложен, время задуматься о том, как будет крепиться утеплитель к блокам. Для этого отрезаем кусок оцинкованной проволоки диаметром 3 мм длинной около 40 см от бухты, загибаем под 90 градусов конец сантимов в 7 и вбиваем этот конец в середину каждого блока. Загоняется такой утеплителедержатель в каждый блок со стороны цементного шва. Да! Именно вбиваем молотком или что там у нас под рукой? Он отлично войдет и никуда уже не денется.
Оставшийся ус после натягивания на него утеплителя перекидывается на цементный шов кирпичной кладки. Выкладываем еще ряд блоков. У нас уже получилась стена высотой 60 см, это как раз ширина утеплителя, который имеет размеры 100х60х10 см. Аккуратно накалываем утеплитель на торчащую из газосиликатной стены проволоку и фиксируем пластиковыми фиксаторами.
Выкладываем кирпич до уровня торчащей проволоки, загибаем ее на 90 градусов вправо или влево. У нас был полуторный кирпич высотой 88 мм, при такой раскладке 6 рядов кирпича приблизительно равно 2 рядам блоков и проблем с креплением проволоки не возникло.
Все вроде хорошо, но вот окна и двери кончились. И нужно как-то продолжить стену дома над оконным или дверным проёмом. Мы выбрали металлические уголки. Причем уголков у нас было 2 вида. 70х70 для блоков их по 2 штуки на окно и 100х100, на котором лежал облицовочный кирпич. Длину уголков берем равной ширине проёма плюс полметра, приблизительно (по 20-30 см с каждой стороны).
Когда достроили стены до нужной высоты , накрыли рубероидом и прижали кирпичами. Так дом остался зимовать.
То что началось весной: Далее >>
Проекты домов из газосиликатных блоков
Каталог
В нашем каталоге — проекты домов из газосиликата для строительства. Посмотрите все доступные варианты и выберите самый подходящий!
Недорогой проект дома из газосиликатных блоков до 200 кв.м. в классическом стиле. Нажмите на картинке и узнайте всё о проекте!
Ячеистый бетон в последнее время стал очень востребованным строительным материалом, и проекты домов из пенобетонных, газобетонных и газосиликатных блоков пользуются все большим спросом. И это неудивительно – этот материал легкий, недорогой, экологически безопасный, прекрасно сохраняет тепло, позволяет осуществить строительство в очень сжатые сроки. И это далеко не полный список преимуществ.
К группе ячеистых бетонов относятся газобетон и газосиликат. Часто их путают и считают, что это одно и то же. Однако они несколько отличаются друг от друга как по составу, так и по своим свойствам. Рассмотрим подробнее основные характеристики газосиликата, а также проекты домов из газосиликатных блоков как один из вариантов для строительства собственного жилья.
Особенности, преимущества и недостатки газосиликата
Готовый проект дома из газосиликата 150 кв.м. — большие окна, элегантный стиль. Нажмите на картинке для ознакомления!
В основе состава газосиликатных блоков – известь, которая повышает звукоизоляционные свойства и придает им белый цвет. Поэтому газосиликат особенно часто используется при возведении внутренних стен. Особенностью его является также то, что они скрепляются не цементным раствором, а специальным клеем для ячеистого бетона, отчего швы между блоками практически незаметны, и теплопроводность стен еще больше уменьшается.
Если сравнивать с другими материалами, то отличительным чертами газосиликата будут:
- Хорошая шумоизоляция.
- Однородная структура благодаря равномерному распределению пузырьков воздуха в блоке и, как следствие, более высокий показатель прочности.
- Точная геометрическая форма блоков от заслуживающих доверия производителей, что в дальнейшем облегчает отделку поверхностей.
- Невысокая стоимость газосиликатных блоков небольшой плотности (например, 300 кг/куб.м), которые подходят для возведения внутренних стен, — примерно вдвое дешевле, чем кирпич. Таким образом, реализовать проект коттеджа из газосиликата можно с заметной экономией в общей смете.
- Легко поддается обработке: блоки можно резать и штробить с относительно небольшими усилиями.
Отличная теплоизоляция. В том случае, если выбрана оптимальная толщина стен, то можно сэкономить на утеплении, ведь наружные стены сами по себе будут иметь хорошее термическое сопротивление.
Оригинальный готовый проект дома со стенами из газосиликатных блоков. Узнайте больше, нажав на изображении!
При всех этих замечательных свойствах газосиликат, тем не менее, имеет свои недостатки:
- Высокая гигроскопичность. При выборе проекта газосиликатного дома для строительства нужно иметь в виду, что отделка должна будет защищать стены от излишней влажности и, как следствие, от образования плесени, грибка и быстрого разрушения.
- Хрупкость, вследствие которой часть газосиликата может повредиться при транспортировке. Специалисты рекомендуют заказывать строительные материалы для реализации проекта с запасом.
- Относительно невысокая несущая способность. Так, например, проект двухэтажного дома из газосиликатных блоков реализовать еще можно, а вот более крупные здания — уже проблематично.
- Для того чтобы реализовать проект коттеджа из газосиликатных блоков потребуется надежный монолитный ленточный фундамент — сэкономить на этот моменте не получится.
- В течение года газосиликатные блоки могут давать усадку. Не рекомендуется использовать для отделки фасада штукатурку, т.к. она может уже в первые месяцы покрыться трещинами.
Наша компания предлагает готовые проекты домов и коттеджей из газосиликата на любой вкус. В каталоге Вы найдете до 500 различных решений – от практичных проектов одноэтажных домов из газосиликата до больших загородных особняков. Наши специалисты всегда готовы помочь Вам в выборе и ответить на все интересующие вопросы. Также мы оказываем услуги по составлению сметы-спецификации, адаптации и изменению проектов в случае необходимости.
Внимание! Вы можете получить проект дома из газосиликата бесплатно! Подробнее о нашем предложении можно узнать здесь.
как и чем можно распилить ручным способом, какая спецтехника может понадобиться, чтобы расколоть
Это относительно новый стройматериал, успевший завоевать популярность среди застройщиков.
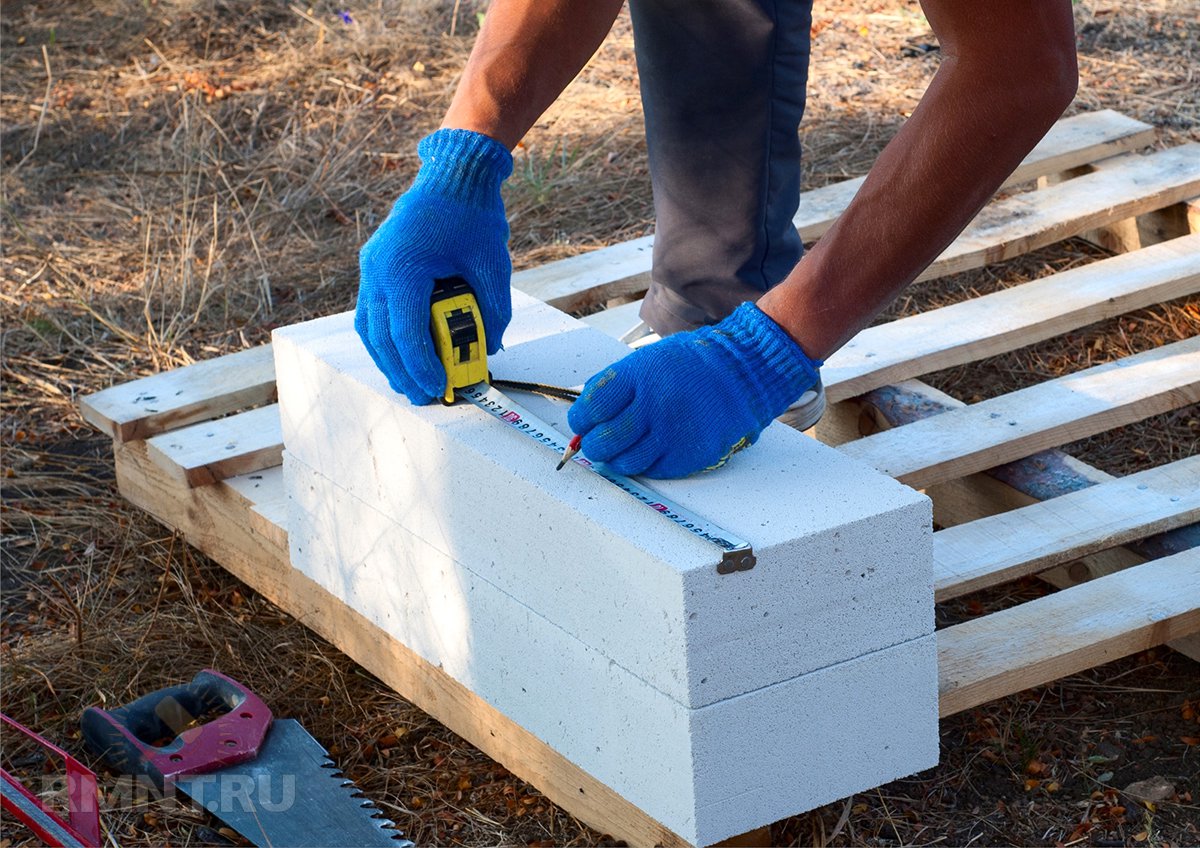
Чем разрезать ячеистый бетон
При расчете пеноблоков для дома можно попытаться подобрать их по размеру так, чтобы уложить изделия без резки. Но данный способ весьма трудоемкий, и скорее всего это вряд ли удастся.
Еще одним вариантом может быть варьирование толщины вертикальных швов. Но это тоже не так просто сделать. Большая ширина зазоров между блоками способна серьезно ухудшить теплотехнические характеристики кладки.
Кроме того, без использования нестандартных по размеру элементов невозможно обойтись при выполнении дверных и оконных проемов или каких-то сложных архитектурных форм здания.
Изделия из ячеистого бетона легко обрабатываются своими руками
При устройстве проемов не обойтись без резаных элементов
Для создания сложных архитектурных форм требуется распил деталей
Этот материал очень легко обрабатывается: его можно распилить под любым углом, придать разнообразную форму. Поэтому проще будет разобраться, как и чем резать пеноблоки.
Для такой работы можно использовать ручные или механические инструменты:
- Ножовку по дереву;
- Ручную пилу для распиливания ячеистых материалов;
- Болгарку (УШМ) с алмазными дисками;
- Канатное оборудование;
- Электропилу сабельного типа;
- Ленточную пилу для блоков.
Обычная ручная пила по дереву
Чем распилить пеноблок? Проще всего – специальной ручной пилой!
Резка бетонных блоков УШМ
Сухая резка блоков струнами
Сабельная пила “BOSCH”
Линия для распила блоков с ленточными пилами
Совет: не стоит применять цепные электропилы.
Они дают большую ширину пропила, неровный срез и быстро изнашиваются.
Для резки бетона также используют лазерное оборудование.
Ручной инструмент
Чем можно резать пеноблок?
Проще всего и дешевле будет использование ручного инструмента. Но оно подойдет только для небольших объемов работы.
Вручную достаточно легко распилить элементы для подгонки дверных и оконных проемов, устройства углов стен. Распил пеноблоков ручным инструментом отличается маневренностью операций, простотой выполнения.
Для большей точности работы с ручными инструментами потребуются также:
- Обычная линейка;
- Карандаш или маркер;
- Уголок из металла или рейка.
Резка блоков ручным инструментом
Чем отрезать пеноблок вручную?
Для этого подойдут следующие инструменты:
- Ножовка по дереву поможет, если распила требуют несколько блоков. При больших объемах работы инструмент надо будет часто точить, что довольно трудоемко.
Кроме того, работать таким приспособлением тяжело.
- Специальная ручная пила для резки пористых материалов отличается от обычной ножовки большей толщиной металла — за счет этого она меньше гнется. Также пила имеет специальное напыление или напайку из твердого сплава на крупных зубьях. Инструменты производятся с одной или двумя ручками. Полотно выполняется различной длины.
Ножовка по дереву мало подходит для работы с пористыми материалами
Чем можно резать пеноблоки – специальной ножовкой для ячеистых материалов
Ножовка по пенобетону
Более эффективным вариантом будет использование механизированного инструмента.
Электрический инструмент
Электроинструмент обладает гораздо большей производительностью, чем ручной. Если объем производимых работ довольно большой, то эффективнее будет использование механизированной резки.
- Сабельная электропила хорошо подойдет для не очень больших по объему работ. Принцип ее действия схож с обычной электроножовкой.
Работает она от электросети.
- Ленточная пила представляет собой ленту, на одной из сторон которой закреплены стальные зубья. Она производит распил намного быстрее и точнее, чем ручные приспособления.
- Болгарка с алмазными дисками – угловая шлифовальная машина (УШМ), при резке пеноблоков создает большое количество пыли и шума. Это приводит к необходимости постоянной чистки инструмента, чтобы он не перегревался. Кроме того, при работе с ней потребуются средства индивидуальной защиты.
На заметку: Но применение болгарки возможно при выпиливании ниш, увеличении оконных и дверных проемов в готовых стенах. Для этих целей используют диски диаметром 30 см. Сбор пыли лучше осуществлять промышленным пылесосом.
- Канатное или струнное оборудование для резки легких бетонов также требует возможности подключения к электросети. Для его работы необходима проточная вода. Струны для резки пеноблоков представляют собой металлические тросы с включением алмазных элементов – перлин.
Распиливание блоков сабельной электропилой
Ленточная пила для станков
Диски для резки бетона УШМ
Алмазная резка канатом
Цена на такое оборудование достаточно высокая. Поэтому его применение должно быть экономически оправдано.
Лазерное оборудование
Еще недавно такой инструмент можно было использовать только в промышленных условиях. Новые технологии позволили создать достаточно мобильное оборудование.
Резка бетона лазером
Доставка и подключение аппаратуры занимает немного времени.
Преимуществ у такого способа обработки пенобетона достаточно много:
- Разрез получается очень точным и ровным.
- Поверхность пеноблоков не требует дополнительного шлифования.
- Нагреванию повергается небольшая область элемента.
- Конструкция стены не подвергается деформациям.
- Можно выполнять большие объемы работ.
- Несложно сделать вырезы сложной формы.
- Возможность настройки режимов распила.
Цен на лазерную резку довольно значительна
При работе с лазерным инструментом отсутствует шум. Но такое оборудование имеет высокую стоимость. По этой причине оно распространено не сильно.
Когда может потребоваться резка или распил?
Бетонные блоки выпускаются в стандартных размерах и рынок строительных материалов редко сосредотачивает внимание на продаже чего-то не стандартного.
В процессе строительства мастер понимает, что требуется отыскать такой блок, который мог бы закончить кладку в определенном месте, при этом стандартный материал здесь не подойдет. В такой ситуации приходится прибегнуть к распилу блочного бетонного материала.
Если бетоноблоки нестандартного размера необходимы в большом количестве, то лучше отлить их самостоятельно с применением самодельных форм. Также можно заказать нестандартные блоки у завода-изготовителя, но это обойдется дороже.
Зачастую строителю может понадобится половина или четвертина от целого бетоноблока. Тогда необходимо сделать распил.
Подобные ситуации часто случаются при заливке ленточного фундамента, когда все блоки должны быть одного размера, а при завершении его обустройства не хватает нескольких элементов. Эта же ситуация может возникнуть при возведении здания по установленному проекту, когда толщина стен уже четко прописана и отступать от величин нельзя.
Часто при кладке углов не получается правильно вписать бетоноблок и остаются щели между камнями. Многие строители заполняют их осколками материала, что тоже не до конца верно. В этом случае рекомендуется обратить внимание на инструменты и способы, которыми можно быстро и легко распилить бетонный блочный материал.
Как резать ячеистые блоки
Если работать приходится ручным инструментом, то вопрос – как резать пеноблоки, решается достаточно просто:
- Пеноблок укладывают на ровную горизонтальную поверхность.
- Размечают места распила.
- Блок устанавливают на опоры – можно использовать другие блоки.
- Придерживая элемент рукой, плавными движениями отпиливают необходимую часть.
Резка пеноблока струной:
- Канат накидывают на блок.
- Трос фиксируют в специальной машине.
- Оборудование приводит струну в действие – происходит распиливание элемента.
Пила для пеноблоков
Механизированный распил блоков
Струна для резки пеноблока приводится в действие специальным агрегатом
Технологически это довольно сложный способ распиливания.
Пила ленточная
Это многорезцовый инструмент, который представляет собой круговую ленточку из стали с зубчиками по одной стороне. Такая лента используется в специальном станке лентопилочного типа. Такой станок позволяет распиливать газобетон намного быстрее по сравнению с ручной пилой, но стоимость его велика. Полотно изготавливают из металла твердого сплава, высота рабочей поверхности станка регулируется. Натяжка режущего полотна происходит автоматически, что увеличивает точность распила.
Режущее полотно направляется сверхточными роликами. Можно долго работать без остановок, так как отходы быстро удаляются через просвет в станке. Режущее полотно можно легко и быстро заменить при необходимости. Станок легко транспортируется с помощью колес. А для большей устойчивости станка при работе применяют упоры.
Инструкция по кладке стены из газосиликатных блоков. Пошаговая инструкция по самостоятельной укладке газоблоков Укладка газосиликатных блоков
Несмотря на кажущуюся простоту работы с газобетоном, кладка стен из этого материала должна выдерживаться в соответствии с особыми требованиями , часть из которых регламентируется СНиП.
В первую очередь это касается используемого для этого раствора, не рекомендуется использовать обычный цемент , а исключительно клей заводского изготовления или изготовленный по специальному рецепту прямо на объекте.
Согласно требованиям ГОСТ допускается строительство зданий с несущими стенами из газобетона, высотой до 20 м, но исключительно из автоклавного материала
, характеризующегося более высокими прочностными характеристиками, в отличие от гидроизоляционных.
Но в основном строительство из газобетона редко возводят выше трех этажей За последнее десятилетие этот материал стал настоящим хитом у частных застройщиков, которые, к тому же, зачастую работают самостоятельно.
Типы кладки из газобетона
Из газобетона можно строить как несущие стены, так и внутренние перегородки … Несущая кладка может быть как однорядной, так и многорядной, а внутренние стены, за редким исключением, всегда выполняются в один ряд.
Чаще всего однорядная кладка как несущих, так и внутренних стен выполняется методом порядковой цепной перевязки … При выполнении перевязки необходимо придерживаться следующих правил:
- смещенные блоки следующего ряда должны быть не менее 2/5 высоты самого блока при условии, что их высота находится в пределах 250 мм;
- если блоки имеют высоту более 250 мм , то смещение должно быть не менее 1/5 этого значения.
Для двух- или многорядной кладки используют прием с вертикальной перевязкой , величина которой составляет 1/5 ширины (толщины) стены.
Но может быть применен и способ перевязки кладки стежковыми рядами , например, по такой схеме: два ложковых ряда обвязываются одним стыком, или три ложковых — одним стыком.
А если планируется перевязка кладки, в которой блоков разной ширины , то для определения глубины перевязки следует учитывать толщину самой кладки — она должна составлять 1/5 от этого значения.
Двойная кладка может и не иметь вертикальной перевязки … Но этот вариант, как правило, подразумевает устройство внутренней теплоизоляции между рядами.
Соединительные крепежные элементы такой кладки арматура выступает, которая изготавливается из металлических стержней, с антикоррозийной обработкой, чаще всего это горячеоцинкованная обеспечивающая надежный защитный слой не менее 0,2 мм.
Можно использовать и нержавеющую сталь , но это приводит к удорожанию конструкции или стеклопластика, которые обладают достаточными прочностными свойствами для эксплуатации в условиях постоянных сжимающе-растяжимых нагрузок материала.
Армирование кладки
При строительстве домов из газобетона необходимо обеспечить устойчивость фундамента , по возможности исключить возникновение усадочных процессов, способствующих растрескиванию блоков. Но полностью нельзя исключить усадку , особенно если строительство ведется на подвижных грунтах или уровень грунтовых вод расположен достаточно близко к поверхности. Поэтому возникает необходимость армирования кладки, а под межэтажными перекрытиями устраиваются монолитные железобетонные пояса .
Первый ряд кладки
Перед укладкой первого ряда газоблоков необходимо выполнить следующие операции:
- устроить надежную горизонтальную гидроизоляцию , являющуюся разделительным элементом между фундаментом и стеной;
- в качестве гидроизоляционного средства, может применяться в качестве листовых материалов — рубероид или другие битумные изделия, а также различные мастики, растворы;
- проверить уровнями все углы здания, с учетом того, что максимально допустимая разница высот между ними должна быть не более толщины шва, то есть 2-3 мм, в противном случае необходимо выровнять уровни механическим способом – срезав верхний слой фундамента;
- первый блок следует установить по самому высокому углу , и подогнать по нему уровни остальных с помощью цементного раствора, который специалисты рекомендуют использовать для кладки первого ряда;
- затем натяните шнуры ориентировки с каждой стороны здания и вдоль них уложите весь ряд, а затем, продвигая их вверх, уложите все последующие ряды, соблюдая правила перевязки.
Сборка коробки дома
- после укладки следующего ряда проверяют его горизонтальный и вертикальный уровень;
- для контроля вертикального уровня по углам кладки устанавливаются специальные отвесы;
- перед тем, как приступить к укладке следующего ряда , поверхность предыдущего выравнивают по горизонтали, тщательно очищают от остатков клея и попавшей на нее строительной пыли; при этом следует учитывать, что клей нельзя растирать, а необходимо дождаться его схватывания и удалить разрезанием.
Инструменты и материалы, которые обязательно понадобятся при кладке стен из газобетонных блоков
Должно быть позаботится о емкости , в которой будет готовиться клеевой раствор для кладки. Наиболее удобны небольшие пластиковые емкости, так как из-за довольно быстрого схватывания раствор нужно готовить достаточно часто , но небольшими порциями.
Вам также потребуется приобрести:
- дрель с насадкой-миксером , для перемешивания раствора;
- зубчатый шпатель для выравнивания клея по поверхности блока;
- шпатель для раствора или с мастерком;
- резиновый молоток «киянка» для регулировки положения блока;
- терка и/или рубанок для выравнивания горизонтальной поверхности блоков;
- ножовка для резки блоков;
- уровень ;
- шнур для маркировки и индикации маяков;
- чеканная фреза;
- с небольшой метлой или щеткой для очистки поверхности блока от пыли;
- ведро или другая емкость для чистой воды, которая потребуется для смачивания газобетона, если температура воздуха превышает 25°С или для удаления пыли с поверхности.
Из материалов, кроме самих газобетонных блоков нужно приготовить клей , компоненты для приготовления цементного раствора для первого ряда, приобрести арматуру в достаточном количестве. Также следует позаботиться о гидроизоляционных материалах фундамента . Необходимо заранее обеспечить доступ к источнику с чистой водой для приготовления клеевого состава и подготовить материалы для изготовления строительных лесов или позаботиться об их аренде.
Некоторые нюансы и правила работы с газобетонными блоками
Работа с газобетонными блоками предполагает соблюдение определенных правил , которые в итоге значительно облегчают работу с данным материалом. В первую очередь вам нужно:
Видео
Расчет стоимости кладки
Итак, сколько стоит кладка газобетонных блоков? Конечно, строить из крупногабаритных блоков намного быстрее, а отсутствие необходимости использования специализированной техники позволяет снизить затраты.
Перед началом строительства дома должен быть выполнен полный и подробный расчет всех затрат , львиную долю которых составляет стоимость стройматериалов. Также потребуются средства на приобретение клея, арматуры, инструментов и т. д. Но перед этим следует позаботиться об устройстве надежного фундамента и его гидроизоляции.
Далее пополняется расходная часть: транспортировка блоков, их погрузка/разгрузка … Для проведения самой кладки коробки в домашних условиях можно привлечь профессиональных специалистов или, при наличии хотя бы минимального строительного опыта и необходимых инструментов, рискнуть и сделать это своими руками. В первом случае необходимо учесть трудозатраты , которые рассчитываются исходя из кубатуры строительства, средняя стоимость 1м³ кладки составляет от 1200 до 2500 руб.
Иногда возможна оптимизация затрат, в случае если закупка блоков осуществляется в фирме предоставляющей бесплатную транспортировку на строительную площадку, а иногда и разгрузку. В некоторых случаях можно договориться с самими рабочими за небольшую доплату о включении в перечень их работ разгрузки газоблоков.
Можно здорово сэкономить, если строить своими руками, но в этом случае нужно быть полностью уверенным в своих силах, иначе призрачная выгода выльется во вполне ощутимые дополнительные затраты.
После того, как будет составлена полная смета на строительство коробки из газобетона, следует предусмотреть от 15 до 25% этой суммы на непредвиденные расходы.И тогда можно смело приступать к строительству.
Задумываясь о строительстве дома своими силами, люди стараются выбрать строительный материал, с которым легко работать. На современном строительном рынке можно увидеть большой выбор новых материалов, пригодных для возведения здания. Газосиликатные блоки занимают одно из первых мест среди строительных материалов, пользующихся популярностью у потребителей. Чтобы сделать дом крепким, надежным, нужно знать, как правильно класть газосиликатные блоки, какой раствор использовать и как рассчитать необходимое количество материала для вашего проекта.
Газосиликатная технология строительства
Построить собственный дом из газосиликатных блоков можно даже имея лишь базовые знания строительных технологий, но есть трудолюбие и энтузиазм. Для возведения стен вам потребуются следующие инструменты и материалы:
- Для разбавления клея нужна емкость, мутовка перфоратора. №
- Клей можно наносить специальным ведром или зубчатым шпателем.
- Ножовка с крупным зубом поможет распилить блок на части нужного размера.
- Неровности можно сгладить крупнозернистым наждаком.
- Щетка-метла.
- Металлический угольник, уровень.
- Песчано-цементный раствор.
- Блоки газосиликатные марки Д400 или Д500.
- Пароизоляция из минеральной ваты.
- Кладочная стеклосетка или арматура.
Расчет необходимого количества блоков
Рассчитать общее количество газосиликатных блоков можно, рассчитав объемы всех стен дома по проекту.
Более точный расчет проводится для каждой стены отдельно. Для этого нужно взять размеры стены из проекта, а размеры газосиликатного блока станут известны при его покупке. Зная ширину блока и длину стены, модно рассчитать количество блоков на ряд кладки. Если требуется половина блока, он считается целым блоком. Таким же образом рассчитывают количество рядов кладки. Количество рядов умножается на полученное количество блоков в одном ряду.Последнее число — это количество блоков на стене.
При наличии в стене дверных и оконных проемов также производится примерный расчет. Затем, посчитав блоки для каждой стены, сложите все цифры.
Кирпичная кладка
Внимание! От аккуратности и качества кладки первого ряда зависит прочность и надежность всей конструкции здания.
Готовый фундамент необходимо покрыть гидроизоляционным слоем, сверху кладочной сеткой, а для кладки стартового ряда конструкции использовать обычный раствор. Затем нужно проверить углы постройки на разницу по высоте, она не должна быть выше 30 мм. Если углы находятся не на одном уровне, кладку нужно начинать с самого высокого угла.
Первый ряд предназначен для выравнивания погрешностей заливки фундамента, поэтому толщина раствора в разных местах может отличаться, но не должна быть менее 20 мм. Далее устанавливаются угловые блоки и соединяются между собой шнуром. проверяется уровень натянутого шнура; она должна быть строго горизонтальной.Если длина стен более 10 метров, необходимо уложить промежуточные блоки, чтобы предотвратить провисание шнура.
Воспользуйтесь резиновым молотком, чтобы исправить вертикальное и горизонтальное положение блоков. Неровности кладки удаляются наждаком. Щетка-метла используется для удаления пыли и грязи. Если вам нужна часть блока, то распилите ее электропилой или ручной ножовкой.
Далее кладка блоков выполняется с использованием клеевого раствора.На строительную площадку доставляется сухая смесь из мелкого песка, портландцемента и специальных добавок. Необходимо внимательно прочитать инструкцию по приготовлению качественного раствора необходимой консистенции. Толщина клеевого слоя должна быть не более 3 мм.
Внимание! Перед нанесением клея на блоки их необходимо тщательно очистить и смочить водой для обеспечения хорошей адгезии.
Возведение стен в теплое время года.Для строительства в холода необходимо использовать зимний клей. Клей наносят на блоки зубчатым шпателем на ширину, равную ширине поверхности газосиликатного блока. Слой должен быть равномерным как с вертикальной, так и с горизонтальной стороны блока. После нанесения клеевого слоя поверхность блока должна быть рифленой. Нет необходимости заполнять раствором зазоры между карманами захвата и между гребнем и канавкой.
Второй ряд блоков необходимо укладывать с половинным смещением для получения перевязки между рядами.Все ряды укладываются угловым блоком. Положение каждого блока нужно контролировать уровнем и подправлять молотком. Все стыки должны быть заполнены клеем, чтобы избежать усадочных трещин. Излишки клея удаляются кельмой.
Если вы используете для самостоятельного строительства пазогребневые блоки, вам не нужно будет выполнять вертикальное армирование. Для горизонтального армирования на поверхности газосиликатных блоков уложенного ряда по периметру делают продольные пазы и укладывают в них стержни из стекловолокна или просто кладочную сетку.
Внимание! В верхней части дверных и оконных проемов сначала укладывают металлические уголки длиной, превышающей ширину проема не менее чем на 40 см, а затем продолжают кладку блоков.
Устройство полов
После того, как кладка стен почти завершена и осталось сделать только последний ряд, необходимо вместо блоков устроить монолитный железобетонный пояс. Такой подход поможет равномерно распределить нагрузку от многопустотных или ячеистых бетонных плит на все несущие стены.
Отделка стен из газосиликата
Для наружной отделки применяют специальные вентилируемые системы или материалы с высокой паропроницаемостью. Между кладкой фасадного кирпича и газосиликатной стеной оставляют зазор. Соедините две кладки гибкими стяжками. Если вы предпочитаете использовать для фасадных работ краски, шпаклевки или штукатурные смеси, нужно убедиться, что они предназначены для работы с газосиликатом.
Интерьер выполнен из дышащих материалов.Стены из газосиликатных блоков можно оклеить обоями или покрасить водоэмульсионной краской. Для санузла, санузла, кухни необходимо предварительно уложить пароизоляцию или пропитать стены специальным раствором. Когда для отделки ванной используется керамическая плитка, пароизоляция не нужна.
Внимание! Внутренние стены можно шпаклевать не ранее, чем через два месяца после окончания строительства.
Работы на фасаде здания можно начинать только после завершения всех процессов внутренней отделки.Единственным исключением являются вентилируемые системы. Их можно устанавливать сразу после окончания строительства.
Видео
Подробнее об установке газосиликатных блоков вы можете узнать ниже:
Газосиликатные блоки благодаря своей универсальности оптимальны для возведения малоэтажных домов в частном строительстве. Основным преимуществом этого строительного материала является малый вес газоблоков при больших габаритах, что позволяет увеличить скорость возведения стен и укладки облегченного фундамента.Большие габариты изделий также означают минимальное количество «мостиков холода» в стенах. Самостоятельная кладка стен из газоблоков не требует профессиональных навыков и опыта – достаточно уметь владеть простейшими строительными инструментами.
Пористая структура газосиликатных изделий обуславливает необходимость учета ее свойств при работе с газобетонными блоками с целью недопущения отклонений от технологии строительства и обеспечения расчетной долговечности и надежности конструкции.Наличие воздушных пор обеспечивает несложную доставку изделий на строительную площадку и непосредственно к месту кладки, а также быстрое увеличение высоты стен за счет больших габаритов изделий и «пазогребневой» конструкции. система, которая автоматически выравнивает строки относительно друг друга.
Но из-за небольшого веса поризованного блока он оказывает малое давление на раствор, создавая некачественное сцепление смеси с кирпичом. Поэтому рекомендуется максимально ограничить применение цементно-песчаного раствора, а работать специальным строительным клеем, толщина шва которого минимальна при высокой адгезии к любой поверхности.
В индивидуальном строительстве в основном ценятся такие характеристики газобетона, как размер изделий и плотность строительного материала. Использование клеевого состава в сочетании с большими размерами изделий и малым количеством клеевых швов не допускает образования «мостиков холода», которые неизбежно появятся при работе с цементом.
Теплоизоляционные свойства – еще одно несомненное достоинство газосиликатного кирпича.Воздух в порах блоков плохо пропускает через себя тепло, и оно остается внутри помещений, а холодный воздух не проникает в дом снаружи. Поэтому никакого дополнительного утепления зданию не нужно, за исключением утепления фундамента и кровли.
Гидроизоляционные характеристики газобетона недостаточно высоки, чтобы обойтись без гидроизоляционных слоев, поэтому защита от влаги необходима не только для фундамента и кровли, но и для стен, как внутри, так и снаружи. Обычно это слой штукатурки с предварительной пропиткой битумом, грунтовкой и другими влагозащитными средствами. При этом толщина стены не имеет значения, так как влага будет проникать во всю ширину блоков.
Самостоятельная кладка стен из газосиликатных блоков будет значительно дешевле по стоимости, чем строительные работы из традиционных материалов — кирпича, бетона или дерева. Цена определяется дешевизной природных компонентов для производства газосиликата, дешевизной технологий производства, низкой себестоимостью транспортировки больших объемов строительных материалов с малым весом.Использование обычных инструментов без привлечения автоматики и специального оборудования, а также высокая скорость кладки делает работу недорогой.
Применение газоблоков – это кладка газосиликатных блоков не только в частном секторе, но и в промышленных масштабах, ограниченных только этажностью зданий. Оптимально подобранные размеры блоков, кратные стандартным размерам кирпича, позволяют выполнить ремонтно-строительные работы в любом объеме в короткие сроки. Кроме того, у производителя можно заказать блоки нестандартных размеров, что ускорит кладку или обеспечит быстрое возведение геометрически сложных архитектурных объектов.
Поверхность стен из газосиликата получается практически идеально ровной, поэтому экономия от минимизации отделочных работ очевидна.
Подготовка фундамента перед кладкой стен
Перед началом кладки газосиликатного блока необходимо проконтролировать горизонтальность поверхности фундамента водяным уровнем – от этого зависит ровность кладки первого и последующих рядов газосиликатного кирпича.Если перепад по краям стены составляет 10-20 мм, фундамент следует выровнять слоем цементно-песчаного раствора. Дальнейшая укладка блоков системой «паз-гребень» будет намного проще, если первый ряд будет уложен идеально ровно по горизонтали. Также нужно проверить углы периметра – они должны быть 90 0 . Контроль осуществляется путем измерения диагоналей периметра дома.
Для предотвращения затекания дождевой или снеговой воды под фундамент необходимо выкладывать газоблочную стену так, чтобы она выступала на 1-2 см по краям фундаментной плиты. Так влага будет стекать сразу на отмостку и попадать в дренаж. Именно поэтому между стеной и основанием дома необходимо обустроить два-три слоя рубероида, чтобы стены не промокали и не плесневели. При принятии решения и обустройстве гидроизоляции толщина стен из газосиликатных блоков не имеет значения – стены любой толщины должны быть защищены от влаги.
Варианты кладки стен
Стены из газосиликатных блоков возводятся на цементно-песчаный раствор, и на специальный строительный клей, который готовят из сухой смеси с добавлением обычной воды.Исследования показали, что в толстом слое раствора гораздо чаще возникают «мостики холода», поэтому склеивание и укладку газосиликатного блока следует производить как можно более тонким слоем вяжущего. Это возможно только при использовании клея. Раствор на цементе дает слой толщиной в среднем 9-12 мм, а слой строительного клея — 3-5 мм, поэтому цементный раствор используют только для кладки первого ряда газоблоков для соединения стены и фундамента . Дальнейшую кладку рекомендуется вести на клей, а если используются пазогребневые блоки, то использовать цементный раствор просто невозможно из-за точного прилегания элементов — паз и конек друг к другу — миномет не влезет в пространство между ними.
Газосиликатные стены возводят с одновременным формированием максимально тонкого слоя вяжущего раствора. И цементно-песчаный, и клеевой раствор можно приготовить самостоятельно.
- Раствор песчано-цементный готовят традиционно, в пропорциях 1:3 (цемент — песок). При строительстве дома зимой использовать обычный раствор нельзя, так как при отрицательных температурах прочность состава нарушается за счет образования льда.
- Клей готовят на основе портландцемента, в который добавляют минеральные добавки и полимеры.Благодаря мелкодисперсному составу клея слой раствора получается очень тонким, и в нем не возникают «мостики холода». Но первый ряд блоков нужно класть только на цементный раствор, а зимой для обогрева места кладки применяют несколько способов, в том числе тепловые пушки, палатки и локальный обогрев.
Но даже стандартный клеевой состав в чистом виде нельзя использовать зимой. Для отрицательных температур выпускаются специальные антифризные добавки, с которыми клей успешно затвердевает на морозе быстрее.
Инструменты и оборудование для строительства дома из газосиликатных блоков
Правильная и точная геометрия блоков, малый вес газосиликата, упрощенная кладка за счет пазогребневой системы позволяют обойтись без спецтехники и большой бригады строителей. Для самостоятельного строительства вам понадобится такой инструмент:
- Дрель, болгарка или лобзик — подгоняйте размеры некоторых блоков под геометрически сложные архитектурные конструкции;
- Уровень, мастерки разной формы и кельмы разной ширины, в том числе зубчатые;
- Резиновый или деревянный молоток;
- Емкость для смешивания раствора;
- Кровельный материал, битум, мембранные материалы, армирующая сетка.
Как класть газосиликатные блоки
- Первый этап — гидроизоляция фундамента и поризованных газоблоков.
Рубероид необходимо нарезать по ширине фундамента и уложить в два-три слоя на чистую и ровную поверхность основания;
- Далее выкладываются углы будущих стен. Газоблок устанавливается вертикально на фундамент, положение контролируется уровнем и корректируется киянкой;
- Между образовавшимися уголками нужно натянуть шнур, по которому будут выравниваться остальные блоки и ряды;
- Для кладки первого ряда используйте цементно-песчаный раствор минимально возможной толщины.Раствор наносится на дно и боковые стороны блока и фундамента зубчатым шпателем подходящей ширины. Основная задача цементного раствора – выровнять первый ряд, поэтому допускается поднять толщину слоя до 20-25 мм;
- После схватывания раствора под первым рядом (1-2 часа) можно приступать к кладке второго и последующих рядов. Последний газоблок подгоняют по размеру с помощью болгарки, ножовки по дереву или электролобзика. Междурядная связка осуществляется путем смещения блоков влево-вправо на 10-12 см.
Следующий ряд кладут после удаления угловых кирпичей и выравнивания поверхности предыдущего ряда путем его шлифовки.
- Клей следующих рядов наносится сплошным слоем подходящей кельмой на поверхность нижнего ряда и на боковые стороны блоков; клей следует разровнять зубчатым шпателем до получения толщины 1–5 мм. Выдавленный клей необходимо удалить после его полного высыхания на стене;
- При формировании перемычек окон и дверей применяют бетонные или металлические плиты, профили или швеллеры;
- Каждый третий-четвертый ряд необходимо армировать стержнями Ø 10-14 мм или армирующей сеткой из стекловолокна, чтобы не увеличивать толщину растворного шва.При армировании стержнями в блоках закладывают пазы, а в них укладывают стержни на расстоянии не менее 5 см от краев стены;
Особенности зимней конструкции
При строительстве малоэтажного частного дома из газосиликатных блоков уличная температура особого значения не имеет — важна клея и цементного раствора. При отрицательных температурах ухудшается адгезия растворов, а прочность стен заметно теряет в качестве.Если строительство планируется беспрерывным, то для зимней кладки газоблоков практикуются следующие проверенные и эффективные приемы:
- Синтетические добавки, обеспечивающие стопроцентную адгезию и твердение клея при температуре наружного воздуха до -35 0 С;
- Обогрев места кладки — тепловые пушки, электронагреватели, обогрев электродами или кабелями, электроматы или местное палаточное оборудование и др. Важно, чтобы место кладки с клеевым раствором было теплым или имело температуру не ниже 0 0 С.Чаще всего эти способы комбинируют или используют кратковременный локальный прогрев места укладки блока.
Газосиликатные блоки – строительный материал, прекрасно сочетающий в себе высокие технические и эксплуатационные характеристики и доступную цену. Действующие ГОСТ и СНиП позволяют строить дома из газосиликатных блоков высотой до 5-7 этажей. Небольшой вес изделий и простой монтаж позволяет построить дом своими руками и без использования специальной техники, что существенно сэкономит семейный бюджет. Строителю остается только соблюдать технологию строительства, и в результате он получит теплый, надежный и качественный дом.
Кладка из газосиликатных блоков обновлено: 17 января 2017 г. автором: Artyom
Газобетон представляет собой синтетически созданный строительный материал. Производится в результате температурного воздействия на все составляющие компоненты. Основными преимуществами этого материала являются простота производства, малый вес, прочность, теплоизоляция.Однако, несмотря на все его достоинства, многие чернорабочие не любят с ним работать. Но профессионалы с удовольствием используют газобетонные блоки. Есть некоторые особенности укладки таких блоков.
Выбор инструмента
Чтобы кладка газобетона была правильной и прочной, без использования специальных инструментов не обойтись. Для приготовления бетонного раствора вам понадобится промышленный миксер, емкость для смешивания. Для того чтобы нанести смесь, вам потребуются — несколько мастерков разного размера. Для подгонки газобетонных блоков – специальный молоток и мерный уровень. Если предусматривается обработка газобетонного блока, то неплохо было бы запастись такими инструментами, как разметочная линейка, напильник, затирка, приспособления для формирования пазов, насадки для дрели, дрель, щетка.
Методы кладки
Приготовление раствора для кладки.На сегодняшний день существует два способа укладки газобетонных изделий своими руками, это укладка газобетонных блоков на цементный раствор и на клеевую смесь.Но, несмотря на выбранный способ укладки, первый ряд нужно укладывать на цементный раствор. Дозировка компонентов должна быть такой, чтобы полученная кладочная смесь не растекалась, иначе блок не поддается фиксации. Если конструкция большого объема, то гораздо удобнее замешивать раствор не своими руками, а с помощью бетономешалки.
Клеевой раствор
Чтобы полученный раствор имел однородную консистенцию, для смешивания лучше использовать оборудование, работающее на малых оборотах. Для замешивания клея из пяти килограммов сухой смеси в сосуд набирается литр воды. Сухой клей медленно насыпают в сосуд и тут же взбивают. Дайте настояться десять минут, а затем снова тщательно взбейте. Раствор клея можно считать готовым, когда он станет похож по консистенции на густую сметану . Если клей засох и затвердел, запрещается разбавлять его новой смесью или водой.
Цементно-песчаная смесь
Аналогичный раствор можно использовать для блокировки.Изготавливается путем смешивания всех ингредиентов и специального связующего. Такие составы отличаются простотой приготовления и надежностью использования.
Состав таких смесей может незначительно отличаться в зависимости от поставленной задачи. Если необходимо получить более пластичную смесь, то в состав добавляют глину. Такая смесь не крошится и не крошится в процессе эксплуатации, позволяя аккуратно и легко укладывать строительный материал. Использование в составе цементной смеси для газобетона специальных пластифицирующих компонентов позволяет качественно выполнить монтаж фасадных стен. Такая смесь очень экономична, дает хорошие теплоизоляционные свойства, удобна в применении и кладке. Благодаря ее достоинствам многие рабочие до сих пор работают с этой смесью чаще, чем с клеем.
Что выбрать?
Использование клея – рациональное, выгодное и правильное решение.
При выполнении строительных работ специалистов интересует не только, как класть газобетон, но и какую смесь выбрать. Ведь и первый, и второй вариант имеют массу преимуществ.Следует отметить, что теплопроводность обеих смесей намного выше, чем у блоков. Отсюда очевидно, что от ширины шва зависит теплоизоляция всего здания. Если использовать цементную смесь, ширина шва составит примерно 9 миллиметров. В случае клея ширина швов не превышает 3 миллиметров.
Учитывая, что цена на клей выше, можно предположить изначально, что при его использовании значительно возрастет и стоимость монтажных работ.Но, с учетом его минимального расхода, в реальности затраты увеличиваются совсем немного, а здание выходит намного теплее. Но если использовать более дешевую цементную смесь, то становится понятно, что нужно гораздо больше и стоимость монтажа неизбежно возрастет. Из этого сравнения становится понятно, что использование клея при кладке на блоки – решение более рациональное, выгодное и правильное.
Технология кладки
Перед началом монтажных работ своими руками необходимо распаковать блоки и разместить их рядом с кладкой ряда.При выполнении строительных работ по установке лучше использовать специальную клеевую смесь. В случае такого выбора вы будете защищены от образования холодных ветров на участках кладки. Цементную смесь использовать не рекомендуется, так как, несмотря на ее дешевизну, расход значительно выше, а швы выглядят неаккуратно и слишком широко. Также такой выбор ухудшает теплоизоляцию будущего дома.
Перед началом кладки монтажа блоков стоит установить специальные маяки.Их устанавливают в местах примыкания, по всему периметру фасада. Они нужны для выравнивания, чтобы с их помощью закрепить специальную проволоку, контролирующую ровность стен и перегородок. Закрепите проволоку оцинкованными гвоздями. Также нельзя забывать, что инструкция по укладке является важным элементом любой строительной операции.
Замешивание смеси
Для приготовления необходимо подготовить специальную емкость и промышленный миксер. Для замеса смеси используйте специальный сухой состав и теплую воду.Взбивание продолжают до тех пор, пока смесь не станет однородной по консистенции. Отрабатывать нужно 20 минут, из-за этого смешиваются малые дозы. В процессе использования клей необходимо постоянно вымешивать, чтобы он терял однородность.
Если строительство происходит при низких температурах, то необходимо использовать специальный вид кладочной смеси. В его состав входят специальные компоненты, препятствующие замерзанию, что дает ему возможность сохранять свои характеристики даже при низких температурах.
Разметка
Кладка стен производится только после полной разметки строительных изделий. Разметку проводят по осям всех поверхностей будущего фасада. После этого материал берется, доставляется к месту установки и распределяется по выбранным осям. При выполнении процедуры перевязки используется неполный материал, который будет располагаться по углам.
Из этого следует, что сначала нужно нарезать продукты.Сделать это несложно, ведь резка производится пилой или ножовкой. Чтобы все конструкции были точно вырезаны, при разметке стоит пользоваться специальной линейкой. Необходимо заранее подготовить те материалы, которые в дальнейшем будут армироваться.
Сначала подготавливаются те блоки, которые необходимы для кладки первого ряда, после чего делаются пазы прутьев для армирования при монтаже фасада.
Кладка и армирование
Процесс монтажа стен и перегородок будущего здания не сложный, но важно все сделать правильно.Только тогда весь процесс пройдет быстро, а конструкция будет качественной. Сначала готовится строительный материал и специальная смесь для работы. Для выполнения первого ряда необходимо выполнить процедуру армирования. После этого на поверхность наносится клей и распределяется специальной расческой. Толщина шва не должна превышать 4 миллиметров.
Монтаж кладки производить с перевязкой, каждое изделие должно быть смещено на расстояние, равное половине одной конструкции.Если перевязку не выполнить, это негативно скажется на свойствах стен. Выступающую из толщины швов смесь нельзя растирать, ее можно только аккуратно удалить кельмой. Для ровности кладки используется специальный шнур. Ровность проделанной работы определяют с помощью строительного уровня и специальной линейки.
При правильном монтаже стен своими руками нельзя обойти стороной вопрос гидроизоляции. Для его выполнения используется специальная сетка.Обязательно закрепите гидроизоляционную сетку на стенах в зоне соприкосновения с фундаментом. После возведения перегородок их нельзя оставлять без защиты. Стоит сразу выполнить фасадные и утеплительные работы. В случае, когда нет возможности сделать это сразу, ряд стараются накрыть специальной полиэтиленовой сеткой до тех пор, пока не появится возможность все закончить. Армирование планируется еще при подготовке к строительству. Это обязательная операция, если стена слишком длинная или коробка будет находиться под повышенным давлением.
Этой процедуре подлежат все прыгуны, длина которых более 90 сантиметров. А также все нижние швы пройм. Эта операция может быть применена по двум технологиям – с помощью металлических стержней или с помощью специальной сетки. При монтаже в блоках вырезаются специальные пазы, куда укладываются стержни и заливается клей. Далее следует укладка следующего ряда.
Сетка при строительстве здания необходима для повышения прочности фасада и исключения возникновения трещин в стенах.Металлическая сетка укладывается с интервалом в 3 ряда газобетонных блоков. Чаще всего для выполнения армирования используются такие материалы:
- сетка оцинкованная;
- сетка базальтовая;
- сетка из стекловолокна.
Во время строительных работ рекомендуется снимать с поддонов столько блоков, сколько предполагается штабелировать за один день. В остальное время соблюдайте правила хранения блоков и размещайте их на ровной площадке, недоступной для влаги.
Технологии кладки первого и последующих рядов стен разные. Рассмотрим обе технологии по отдельности.
Укладка первого ряда блоков
После установки фундамента здания укладка первого ряда – самый ответственный момент. От первого ряда зависит точность всех последующих рядов стены и устойчивость всего здания. Поэтому к этому этапу строительных работ нужно подходить особенно ответственно.
Перед укладкой первого ряда выполняется гидроизоляция по верхнему уровню фундамента, который будет выполнять роль защиты между фундаментом и кладкой. Под блоки заливается выравнивающий слой цементно-песчаного раствора. Сами блоки монтируются с использованием полимерных растворов на основе сухих смесей, иногда для монтажа используются и битумные рулонные материалы.
Для выравнивания всех рядов здания по углам по высоте каждого ряда кладки укладывают рейки с рисками. Через них протягивают причальный шнур для контроля ровности кладки каждого последующего ряда.
С помощью уровня необходимо измерить уровень самого высокого угла здания, с которого начинается строительство здания. При этом разница по высоте между углами дома не должна быть более 3 см.
|
Блоки лучше всего укладывать на клеевую смесь.Для его изготовления вам понадобится вода, ведро для замеса и строительный миксер. В ведро наливают необходимое количество воды и при постоянном помешивании постепенно добавляют миксером расчетное количество сухой смеси. Во время монтажных работ клей необходимо время от времени перемешивать. Это делается для того, чтобы он не затвердел, чтобы постоянно сохранялась его однородность.
В процессе строительства часть газосиликатных блоков приходится резать. Эти материалы режут просто с помощью обычной ручной пилы.Для точной резки и измерения прямого угла при резке используется угольник. Такие усеченные блоки называются дополнительными блоками. Перед установкой очередного дополнительного блока обязательно промазывайте вертикальные швы клеевой смесью.
Кладка последующих рядов стены
Кладка следующих рядов также имеет свои особенности. Каждый последующий ряд укладывается только после полного схватывания предыдущего. По времени это примерно 1-2 часа после завершения кладки.
Необходимо четко контролировать кладку каждого блока стены. Ровность рядов проверяют по уровню и причальному шнуру. Финишное выравнивание кладки производится с помощью уровня и резиновой киянки.
Смесь наносится на блоки следующим образом. В зависимости от толщины блоков для нанесения смеси выбирают зубчатую каретку или шпатель. Равномерно, без зазоров клей наносится на поверхность 2-3 блоков. Каретка помогает лучше распределить смесь, не стекая по бокам блоков.
Последующие ряды, как и первый, располагаются от угла здания. При этом клеевая смесь не наносится на торцы блоков. Материалы укладываются и выравниваются сразу по месту, блоки перевязываются.
В некоторых случаях газосиликатные блоки нуждаются в армировании.
Правильное армирование кладки
Каждый первый и четвертый ряд кладки армирован.Для изготовления армирования в середине блоков ручным или электрическим штроборезом вырезаются пазы. Если вы работаете с блоками толщиной от 400 мм, лучше всего укладывать два параллельных ряда арматуры. Строительная пыль, попавшая внутрь, удаляется веником или феном.
Перед заполнением пазов клеевой смесью и укладкой арматуры рекомендуется смочить их водой. Это делается для повышения качества строительства конструкции.Каждая канавка заполняется крепежным раствором на половину ее глубины, после чего в нее вставляется стальной арматурный стержень.
|
Для армирования блоков используются стальные стержни диаметром 8 мм. При армировании блоков по углам здания пазы сверлят с закруглениями, а стержни загибают в расчетном месте. Для гибки используется специальное оборудование или ручной инструмент. После этого штанги устанавливаются каждая в свой штроб.
Каждый элемент арматуры погружается в раствор клея, затем раствором заполняется штроба. Таким образом предотвращается коррозия. После завершения работ остатки смеси удаляются кельмой.
После устройства стен из газосиликатных и газобетонных блоков требуется их облицовка.
Существует несколько основных вариантов облицовки.
Кирпич облицовочный.
Лицом к лицу.
Штукатурная отделка.
- При выборе данного вида облицовки важно помнить, что штукатурка не должна быть цементно-песчаной. В местах повышенных нагрузок, таких как углы зданий, оконные проемы, изломы фасадного профиля, рекомендуется армировать штукатурный слой специальными сетками.
- При проведении штукатурных работ необходимо не допускать замерзания, пересыхания штукатурки, а также соблюдать температурный режим.
Выбирайте газоблоки для своего строительства!
Преобразование распространенных минералов силиката магния для увеличения секвестрации CO2
В результате этого процесса из 100 г оливина было получено в общей сложности 35 г Mg(OH) 2 с добавлением 1 г Mg(OH) 2 на стадии осаждения кремнезема. Приблизительно 5 г оксида железа было осаждено при добавлении 0,32 г NaOH, что составляет <1% от общего извлеченного Mg(OH) 2 .Всего на стадии осаждения также было извлечено 35 г аморфного кремнезема. СЭМ-изображение и график ТГА, представленные на рис. 2a, b, показывают, что материал, извлеченный после электролиза, в основном состоял из Mg(OH) 2 . Результаты XRD, представленные на рис. 2c, показывают, что восстановленный кремнезем был преимущественно аморфным SiO 2 с некоторым остаточным непрореагировавшим оливином, и подтверждают, что материал, извлеченный после электролиза, представлял собой преимущественно Mg(OH) 2 . Состав необработанного оливинового песка, извлеченного Mg(OH) 2 и извлеченного кремнезема из оливина, определенный с помощью рентгенофлуоресцентного анализа (XRF), представлен в таблице 1 и согласуется с другим анализом характеристик материала.
a СЭМ-изображение извлеченного Mg(OH) 2 в результате электролиза раствора для вываривания оливина, b ТГА извлеченного Mg(OH) 2 из оливина, c XRD извлеченного Mg(OH) 2 и восстановленного кремнезема (B: брусит, L: лизардит, F: форстерит).
Таблица 1 Элементный состав необработанного оливинового песка и восстановленного Mg(OH) 2 и кремнезема из оливина, определенный рентгенофлуоресцентным анализом. В дополнение к первично извлеченному Mg(OH) 2 также могут быть использованы вторичные материалы из гидроксида железа и кремнезема. Например, гидроксид железа можно использовать в качестве сырья высокой чистоты для производства железа или в качестве абсорбента, а аморфный кремнезем можно использовать в качестве частичной замены портландцемента при производстве бетона, который вносит значительный промышленный вклад в мировой CO 2 выбросы 20 . Наш подход обеспечивает почти полностью закрытую систему для производства Mg(OH) 2 с добавлением только оливина в качестве источника Mg и небольшого количества NaOH.
CO
2 и энергетические последствия извлечения гидроксида Mg В целом, преобразование оливина в Mg(OH) 2 не приводит к прямым выбросам CO 2 , а HCl, использованный для пищеварения, полностью извлекался. Крупномасштабное и промышленное использование сильных кислот, таких как HCl, имеет серьезные последствия при попадании в окружающую среду. Тем не менее, это проблема только в том случае, если происходит потеря сдерживания процесса. Крупномасштабное обращение с HCl без потери герметичности хорошо зарекомендовало себя в химической промышленности благодаря его использованию в товарных материалах, таких как производство ПВХ и травление стали.Что наиболее важно, так это то, что ни HCl, ни хлор не покидают процесс, описанный в нашей работе, так как они повторно используются внутри процесса.
Общая энергия, необходимая, включая разработку карьеров и измельчение, для производства Mg(OH) 2 из оливина, по расчетам, составляет 6,28 ГДж тонн −1 (см. рис. 1 и Дополнительные методы для определения энергии и расчетов). Дальнейшее усовершенствование процесса может обеспечить более широкое использование восстановленного Mg(OH) 2 для регулирования pH, снижение общей требуемой энергии и уменьшение количества NaOH.Mg(OH) 2 может быть дополнительно переработан в MgO, но для секвестрации CO 2 ; однако известно, что Mg(OH) 2 является более быстрым реагентом, чем MgO 10 .
На каждую тонну CO 2 , секвестрированного в виде карбоната Mg, включая нескехонит и гидромагнезит, требуется 1,3 тонны Mg(OH) 2 , что приводит к потреблению энергии 8,17 ГДж тонн −1 CO 2 (рис. 1, см. Дополнительные методы расчетов).Использование метода, изложенного в этой статье, приведет к чистому отрицательному выбросу CO 2 , даже если для получения необходимой энергии использовался уголь, хотя и с эффективностью связывания ~ 25%. Общие выгоды от секвестрации углерода существенно улучшились бы, если бы использовались источники энергии с низким содержанием углерода или даже смешанное электроснабжение. Например, в Калифорнии, где примерно 50% электроэнергии производится из неископаемых видов топлива, ~ 500 кг CO 2 будет выбрасываться на каждые 1000 кг CO 2 , захваченного и превращенного в карбонат Mg.
Чтобы подтвердить способность извлеченного Mg(OH) 2 связывать CO 2 , водную суспензию Mg(OH) 2 с помощью концентрированного CO 2 довели до давления 4 бара. За 48-часовой период >50% Mg(OH) 2 превратилось в гидратированный карбонат Mg, что свидетельствует о возможном превращении CO 2 в твердое вещество. Реакционная способность извлеченного Mg(OH) 2 также была подтверждена быстрым увеличением pH до ~10,5 при добавлении его к деионизированной воде.Как отмечалось ранее, существует ряд других методов секвестрации CO 2 с помощью Mg(OH) 2 с использованием водного раствора 12,21 или методов прямой реакции твердого тела с газом 10 . Предлагаемый нами процесс потенциально может обеспечить существенный источник энергоэффективного низкоуглеродистого Mg(OH) 2 для использования в различных методах секвестрации углерода, которые в настоящее время разрабатываются другими исследователями.
Ресурсы оливина и возможности их реализации
Ультраосновные породы, обогащенные оливином, составляют ~1% земного ландшафта, значительную долю океанической коры и >50% верхней мантии 22 . Богатые оливином месторождения (рис. 3) в основном присутствуют в пределах населенных пунктов циркум-тихоокеанского и средиземноморского регионов 23,24 . Оливин присутствует во многих горных породах, таких как базальт и другие ультрамафиты. Мы хотели бы отметить, что хотя оливин оценивался и использовался в этом исследовании, его метаморфический эквивалент серпентин (Mg 3 Si 2 O 5 (OH) 4 ) с его высокой реакционной способностью в HCl и мировых месторождениях , может расширить масштабы и последствия этого исследования.Наши предварительные исследования показали, что Mg также можно извлекать из базальта; однако мы в первую очередь сосредоточим наше обсуждение на двух обогащенных и доступных месторождениях оливина: офиолитовом Семаиле (Оман) и ультрабазитовом комплексе Ред-Хиллз (Новая Зеландия), которые консервативно содержат 1,4 × 10 5 и 871 миллиард тонн оливина, соответственно ( см. Дополнительные методы для источников и оценочных расчетов).
Показано общее распространение ультраосновных пород (включая перидотиты и серпентиниты) по всему миру. Распределение ультраосновных пород основано на данных о местоположении Oze et al. 24 и по сравнению с Реалом и Вишалом 23 . Обратите внимание, что месторождений ультраосновных горных пород больше, чем показано, и что квадраты не представляют конкретные места. Показаны миллиарды тонн оливина в год, необходимые для секвестрации всего антропогенного CO 2 и сокращения глобального атмосферного CO 2 , а также для пожизненного запаса оливина из Красных холмов (Новая Зеландия) и Семаилского офиолита (Оман). и на основе расчетов, представленных в дополнительных методах.
Использование Mg(OH) 2 для удаления и связывания антропогенного CO 2 по оценкам на 2020 год (40 миллиардов тонн) в карбонате Mg потребуется ~105 миллиардов тонн оливина. Снижение глобального уровня CO 2 в атмосфере еще на 10 миллиардов тонн потребует дополнительных 26 миллиардов тонн оливина. Сумма оливина, необходимая для всего этого, составит 131 миллиард тонн; 0,1 % Оманского офиолита или 16 % Ред-Хиллз, Новая Зеландия (рис. 3). Чтобы изолировать весь антропогенный CO 2 , эти два месторождения просуществовали бы примерно от десяти лет (Красные холмы) до 1000 лет (Семаил), если предположить, что отложения содержат не менее 60% оливина.Степень серпентинизации каждого месторождения и обилие других минералов, таких как орто- и клинопироксен, будут влиять на общую эффективность извлечения. Меньшие по размеру месторождения офиолитов Семаила или Красных Холмов по всему миру могут значительно способствовать глобальному сокращению антропогенного выброса CO 2 .
Последствия
Концепция использования ультраосновных пород и их метаморфических эквивалентов в качестве источников Mg для секвестрации CO 2 рассматривалась в течение как минимум двух десятилетий. Однако одно ограничение в отношении предыдущего и текущего подходов связано с расстоянием между источником газа CO 2 и ультраосновным участком. В настоящее время концентрированный CO 2 транспортируется по трубопроводу на ультраосновные участки для прямой закачки в недра. Несмотря на то, что ультраосновные участки есть по всему миру, многие из них не находятся достаточно близко к районам промышленности с высоким содержанием CO 2 . Наш подход позволяет более эффективно транспортировать объемный Mg(OH) 2 в места/отрасли, где его можно использовать на месте для контроля выбросов из точечных источников.Например, транспортировка достаточного количества Mg(OH) 2 для секвестрации 1 тонны CO 2 от места производства до точечного источника, такого как цементный завод на расстоянии 1000 км по железной дороге, приведет к получению 37 кг CO 2 выбросы 25 .
Кроме того, небольшие модификации этого подхода путем дальнейшего преобразования Mg(OH) 2 в MgO могут позволить производить строительные материалы, такие как кирпичные блоки Mg 26 , а не просто закапывать CO 2 . Существует значительный интерес к потенциальному использованию MgO в качестве альтернативы традиционному портландцементу 13 ; однако существует ряд проблем, которые необходимо решить, в том числе низкий pH порового раствора, что затрудняет его использование в конструкциях, армированных сталью, и высокая потребность в воде, что затрудняет обращение. Одной из основных экологических проблем, связанных с цементами на основе Mg, является то, что подавляющее большинство MgO производится из MgCO 3 , что приводит к выделению CO 2 в той же пропорции, что и портландцемент.Альтернатива извлечения MgO из морской воды, как отмечалось ранее, также имеет значительное воплощение CO 2 из-за использования CaO, полученного из карбонатов, в процессе извлечения. Если MgO будет использоваться в качестве строительного материала, тогда потребуется подход к извлечению минералов с низким содержанием углерода. Масштаб и возможности смягчения последствий изменения климата с использованием Mg-содержащих минералов из ультраосновных и основных пород огромны, но наши эксперименты и другие исследования подтверждают, что это возможно.
Расширение масштабов и повышение эффективности процессов, описанных и проверенных здесь, потребует значительных усилий по развитию и индустриализации.Мы ожидаем, что технические проблемы, связанные с производством Mg(OH) 2 для использования в секвестрации CO 2 , как показано на рис. 1, сравнимы с другими хорошо известными промышленными процессами. Одна из самых больших проблем, однако, заключается в том, как использовать миллиарды тонн произведенного карбоната для компенсации антропогенных выбросов CO 2 , и это требует дополнительной осмотрительности. Более реалистичный и эффективный подход к решению проблемы глобального потепления заключается в сокращении выбросов CO 2 .До тех пор мы продемонстрировали процесс, который осуществим и является глобальным, в котором могут участвовать многие страны и отрасли. В целом, извлечение гидроксида магния из пород, богатых оливином (и потенциально богатых серпентином), обеспечивает основу для прямого пути к снижению глобального антропогенного выброса CO 2 и связанного с ним воздействия изменения климата.
Стенограмма: Химия в ее стихии: кремний(Промо) Вы слушаете Химию в ее стихии, представленную вам Chemistry World , журналом Королевского химического общества. (Конец рекламного ролика) Мира Сентилингам На этой неделе мы отправляемся в мир научной фантастики, чтобы исследовать жизнь в открытом космосе. Вот Андреа Селла. Андреа Селла Когда мне было около 12 лет, мы с друзьями прошли этап чтения научной фантастики. Там были фантастические миры Айзека Азимова, Ларри Нивена и Роберта Хайнлайна, предполагающие невозможные приключения на загадочных планетах — успехи космической программы «Аполлон» в то время только помогли нам отложить наше недоверие. Я вспомнил об этих чтениях пару недель назад, когда пошел на выставку работ пары моих друзей.Названный «Каменная дыра», он состоял из потрясающих панорамных фотографий, сделанных в очень высоком разрешении внутри морских пещер в Корнуолле. Пока мы бродили по галерее, мне пришла в голову одна мысль. «Можно ли представить мир без кремния?» Неудивительно, что на каждой фотографии преобладали породы на основе кремния, и это было убедительным напоминанием о том, что кремний является вторым наиболее распространенным элементом в земной коре, уступая первое место кислороду, элементу, с которым он неизменно связан. Силикатные породы, в которых кремний тетраэдрически окружен четырьмя атомами кислорода, существуют в поразительном разнообразии, причем различия определяются тем, как строительные блоки тетраэдров соединяются друг с другом, и какие другие элементы присутствуют для полноты картины. Когда тетраэдры соединяются один с другим, получается безумный клубок цепей, похожий на огромную кастрюлю со спагетти — такие структуры можно увидеть в обычном стекле. Самым чистым из этих цепочечных материалов является двуокись кремния (диоксид кремния), довольно часто встречающийся в природе в виде бесцветного минерального кварца или горного хрусталя.В хорошем кристаллическом кварце цепочки расположены красивыми спиралями, и все они могут закручиваться влево. Или вправо. Когда это происходит, образующиеся кристаллы являются точным зеркальным отражением друг друга. Но не накладные — как левая и правая обувь. Для химика эти кристаллы хиральны, свойство, которое когда-то считалось исключительным свойством элемента углерода, а хиральность, в свою очередь, представлялась фундаментальной чертой самой жизни. Наиболее грандиозно то, что можно создавать пористые трехмерные структуры, немного похожие на молекулярные соты, особенно в присутствии других тетраэдрических линкеров на основе алюминия. Эти эффектные материалы называются цеолитами или молекулярными ситами. Тщательно подбирая синтетические условия, можно создать материал, в котором поры и полости имеют четко определенные размеры — теперь у вас есть материал, который можно использовать как ловушки для лобстеров, чтобы ловить молекулы или ионы соответствующего размера. А что же сам элемент? Освободить его от кислорода тяжело, он висит, как суровая смерть, и требует жестоких условий.Хамфри Дэви, химик и шоумен из Корнуолла, первым начал подозревать, что кремнезем должен быть соединением, а не элементом. Он применил электрический ток к расплавленным щелочам и солям и, к своему удивлению и восторгу, выделил несколько чрезвычайно реакционноспособных металлов, включая калий. Свойства кремния — ни рыба, ни мясо. Темно-серого цвета и с очень блестящим стеклянным блеском, он выглядит как металл, но на самом деле является довольно плохим проводником электричества, и во многом именно в этом заключается секрет его окончательного успеха. Проблема в том, что электроны застревают, как кусочки на чертежной доске, где нет свободных мест.Что делает кремний и другие полупроводники особенными, так это то, что один из электронов можно переместить на пустую доску — зону проводимости, — где они могут свободно двигаться. Но есть и другой способ заставить кремний проводить электричество: он кажется извращенным, но путем преднамеренного введения таких примесей, как бор или фосфор, можно слегка изменить электрические свойства кремния.Такие приемы лежат в основе функционирования кремниевых чипов, позволяющих слушать этот подкаст. Менее чем за 50 лет кремний превратился из интригующей диковинки в один из основных элементов нашей жизни. Но остается вопрос: не ограничивается ли значение кремния исключительно минеральным миром? Перспективы не кажутся радужными — силикатные волокна, подобные волокнам синего асбеста, как раз такого размера, чтобы проникать глубоко внутрь легких, где они прокалывают и разрезают внутреннюю оболочку легких. Следовательно, можно ли где-то в космосе найти инопланетян на основе кремния? Моя догадка, вероятно, была бы нет.Уж точно не как стихия. Он слишком реактивен, и его всегда можно обнаружить связанным с кислородом. Но даже в связи с кислородом это кажется маловероятным, или, по крайней мере, не в тех мягких условиях, которые мы наблюдаем на Земле. Но опять же, нет ничего лучше неожиданности, чтобы заставить задуматься. Как выразился генетик Дж. Б. С. Холдейн, «Вселенная не более странная, чем мы думаем. Она более странная, чем мы можем предположить». Мира Сентилингам Так что маловероятно, что в космосе могут скрываться какие-то кремниевые сюрпризы.Это была вечно обнадеживающая Андреа Селла из Университетского колледжа Лондона с химией кремния, формирующей жизнь. На следующей неделе мы услышим о рентгении, элементе, который нам нужен, чтобы получить правильное решение. Саймон Коттон Идея заключалась в том, чтобы заставить ионы никеля проникнуть в ядро висмута, чтобы два ядра слились вместе, образуя более крупный атом. Энергию столкновения нужно было тщательно контролировать, потому что, если бы ионы никеля двигались недостаточно быстро, они не смогли бы преодолеть отталкивание между двумя положительными ядрами и просто отлетели бы от висмута при контакте.Однако, если бы у ионов никеля было слишком много энергии, образовавшееся «составное ядро» имело бы столько избыточной энергии, что оно могло бы просто распасться и развалиться. Хитрость была, как каша Златовласка, чтобы было «в самый раз», чтобы произошло слияние ядер, как раз. (Акция) (Конец акции) |
Патент США на газобетон, армированный волокном, и способы его изготовления (Патент № 6,773,500, выдан 10 августа 2004 г.)
ПЕРЕКРЕСТНАЯ ССЫЛКА НА РОДСТВЕННОЕ ПРИЛОЖЕНИЕНастоящим заявлено преимущество предыдущей предварительной заявки США № 60/208,247, поданной 31 мая 2000 г.
ОБЛАСТЬ ИЗОБРЕТЕНИЯИзобретение относится к способу создания дешевого армированного фиброй газобетона и составам для таких бетонов.
ПРЕДПОСЫЛКИ ИЗОБРЕТЕНИЯ Предшествующий уровень техники, как правило, сосредоточен на производстве либо автоклавного ячеистого бетона (AAC), либо его разновидностей для производства легкого бетона с хорошей прочностью для использования в качестве строительных блоков или панелей. В качестве альтернативы был выявлен предшествующий уровень техники, в котором можно производить ячеистый бетон, армированный волокнами, с использованием либо алюминия, либо пены. Процессы AAC основаны на дорогостоящем автоклавном оборудовании для отверждения смеси цемента, песка, извести и других материалов, которые были аэрированы в результате реакции порошкообразного алюминия и цемента / извести с высоким pH.Были предложены различные другие процессы с системами, основанными на использовании аэрирующих и других агентов и литейных форм для получения желаемой формы материала или разрезания неотвержденного материала проволокой. Большинство этих процессов основано на высоком процентном содержании цемента в смеси для достижения желаемой прочности продукта.
Система, описанная в настоящем документе, производит газобетон, армированный волокном, различных точных форм за счет применения уникального процесса.Композиции включают использование высокого процента дешевой угольной летучей золы, цемента, выбранных волокнистых материалов, других реагентов и выбранных активирующих реагентов для производства ячеистого бетона, армированного волокнами. В процессе эти материалы объединяются и тщательно смешиваются с водой в высокоскоростном дисперсионном смесителе. Затем смесь помещают в форму и отверждают в течение 12-24 часов при естественно повышенных температурах, возникающих в результате химических реакций, протекающих в монолитной массе. После дополнительного отверждения в течение 1-2 дней материал распиливается на блоки или панели точной формы.Затем распиленные материалы отправляются на строительную площадку для сборки с использованием стандартных технологий соединения газобетона.
Настоящее изобретение будет объяснено дополнительно в сочетании с прилагаемыми чертежами и последующим подробным описанием.
КРАТКОЕ ОПИСАНИЕ ЧЕРТЕЖАРИС. 1 представляет собой схематический чертеж технологического процесса, иллюстрирующий этапы изготовления блоков из пенобетона, армированного волокнами, в соответствии с изобретением;
РИС.2 представляет собой схематический чертеж процесса, показывающий этапы процесса, следующие за этапами, изображенными на фиг. 1; и
РИС. 3 представляет собой кривую время/температура, показывающую идеальные условия отверждения суспензии.
ПОДРОБНОЕ ОПИСАНИЕ ПРЕДПОЧТИТЕЛЬНОГО ВЫПОЛНЕНИЯСмесь из ячеистого бетона, армированного фиброй, изготавливается из следующих материалов:
Образцовый Предпочтительный Летающий пепел 20-70% 45-70% Портландцемент 10-50% 25-50% Армирующие волокна .001-2.00 .005-.020 Активирующий агент .0001-2.00 .001-.020Вышеуказанные добавляют до 100 мас.% неводных компонентов смеси. Воду добавляют в количестве примерно 20-60 мас.% в расчете на общую массу неводных компонентов.
При желании к смеси могут быть добавлены дополнительные реагенты для улучшения различных качеств продукта, включая известь, гипс, гипс, силикат натрия, а также промышленные ускорители и полимеры. Каждый из этих дополнительных компонентов реагента может быть добавлен в количестве приблизительно 2 следовых количеств. 0 мас.%, предпочтительно около 0,25-4% от общей части неводного компонента смеси. Добавление этих материалов может сократить время отверждения и повысить прочность изделия.
Активирующий реагент состоит из мелкозернистого металлического алюминия (95%-325 меш) в форме пасты для покрытия алюминия, чтобы предотвратить окисление алюминия и сохранить его реакционную способность. Предпочтительная алюминиевая паста доступна от Silberline, Mfg. Co., Тамаква, Пенсильвания, под названием «Flexcrete Aerating Agent». Этот продукт включает мелкие частицы алюминия (325 меш) в пастообразной смеси с уайт-спиритом и диэтиленгликолем.Мы обнаружили, что полезно добавлять в пасту небольшое количество воды примерно 1-6%, предпочтительно 2-4%.
В качестве компонента активатора можно использовать множество различных поверхностно-активных веществ или пенообразователей. В качестве одного из компонентов активатора может быть использован этиленгликоль. Кроме того, поверхностно-активное вещество или пенообразователь могут содержать в качестве компонента либо «Geofoam Liquid», либо «Meacel 3532», которые доступны от Engelhard. Первый содержит гексиленгликоль, гептагидрат сульфата железа и 2-бутоксиэтанол в качестве компонента на листе паспорта безопасности.Последний включает в качестве компонента 2-бутоксиэтанол.
Другие поверхностно-активные вещества, такие как альфа-олефиновые сульфонаты, винзольные смолы (экстракты соснового дерева), лаурилсульфаты натрия и продукты конденсации этиленоксида и алкилфенолов, также могут быть упомянуты в качестве примеров компонентов активирующего агента.
Как правило, поверхностно-активные вещества используются, когда используется компонент летучей золы с высоким LOI. Большое количество углерода замедляет реакцию между алюминием и цементом и делает продукт нестабильным на начальной стадии отверждения, что может привести к разрушению продукта.В настоящее время предпочтительно использовать неионогенное поверхностно-активное вещество, такое как простой эфир полиэтиленгликоля нонилфенола, доступный от PB&S Chemical, Хендерсон, Кентукки. Соответственно, композиции в соответствии с изобретением могут включать множество различных типов летучей золы.
Дополнительные реагенты могут быть добавлены к активирующему реагенту, включая реагенты оксида и гидроксида магния, такие как кальцинированный магнезит и брусит. Активирующий реагент добавляется в различных количествах и количествах для получения строительных продуктов и материалов различной плотности.Например, если требуется материал типа перемычки, требующий несколько большей прочности, плотность армированного фиброй газобетона можно увеличить до 40-50 фунтов. за кубический фут или больше. Общеизвестно, что чем выше плотность газобетона, тем больше его прочность на сжатие. И наоборот, если желательны легкие блоки и стеновые панели, активирующий реагент можно варьировать для получения материала массой 30-40 фунтов. на кубический фут диапазона. Что касается компонента летучей золы, можно использовать как золу «С», так и «F» и их смеси, хотя в настоящее время предпочтительно использовать золу-унос класса «F».
Наиболее предпочтительно в цементный раствор также добавляют небольшое количество ускорителя схватывания. В настоящее время предпочтительный ускоритель продается под торговой маркой Anti-Hydro компанией Anti-Hydro Inc., Farmington, N.J. 08822. Считается, что этот продукт содержит CaCl2.
Кроме того, в суспензию можно добавить небольшое количество агента, регулирующего термическую усадку, такого как один или несколько различных коммерчески доступных акриловых полимеров, для контроля термической усадки во время начального отверждения массы.В настоящее время для этой цели мы предпочитаем использовать «Duraweld», поставляемый W. R. Grace. Это дисперсия поливинилацетатного полимера и сополимера винилацетата и дибутилмалеата в воде.
Процесс смешивания и контроль времени На начальном этапе летучая зола угля, цемент, волокно и вода помещаются в накопительный резервуар, оборудованный перегородками, расположенными по бокам резервуара. Материалы смешиваются с использованием высокоскоростного дисперсионного смесителя с соответствующей мощностью и соотношением диаметра лопасти/резервуара. При желании в смесь добавляют также дополнительные реагенты, такие как известь, гипс и силикат натрия. Материалу дают тщательно перемешаться в течение 2-5 минут.
Добавляют волокнистые материалы и перемешивание продолжают еще 2-5 минут для полного диспергирования волокон. Активирующие реагенты добавляют в смеситель для дисперсии и дают возможность тщательно перемешаться с другими материалами в течение дополнительных 1-4 минут.
После этапа смешивания активированная смесь помещается в форму для подъема аэрации и отверждения.Перенос из смесительного бака в форму должен происходить в течение примерно 5-6 минут.
Размещение формы и отверждение Хорошо перемешанные материалы помещают в большую форму размерами не менее 2 футов × 2 фута × 8 футов со сплошными боковыми и нижними панелями и открытым верхом. Дно формы состоит из съемной пластины, которая прилегает к бокам формы на стадии отверждения, но может быть удалена вместе с монолитной вяжущей массой при открытии формы. Можно использовать формы больших или особенно длинных размеров.Армирующая проволока или стержневые системы могут быть помещены или «подвешены» в форму перед добавлением активированных панелей различной толщины. Это позволяет производить армированные панели для крыш, перемычек или стеновых конструкций на этапе резки и калибровки.
Форма для отверждения массы может быть глубже, шире и длиннее, чем конкретная конструкция формы, указанная выше. Фактически длина может составлять около 20 футов, ширина может составлять около 4 футов, а высота 3 фута. В качестве альтернативы можно использовать формы колонн с диаметром до 3 футов и высотой до 8 футов.
Объединение активирующих реагентов с цементом с высоким pH и другими материалами, такими как известь, в процессе смешивания приводит к химической реакции с образованием газообразного водорода. Этот газ является результатом реакции мелкодисперсного, хорошо диспергированного металлического алюминия и реагентов оксида магния, если он присутствует. Образующийся газообразный водород приводит к образованию мелких пузырьков, которые заставляют смесь расширяться и «подниматься», чтобы полностью заполнить форму. Это приводит к легкой, «ячеистой» структуре материала.
Считается, что реакция in situ протекает следующим образом:
CaO+2Al+3h3O→CaAl2 O4+6h3↑
Отверждение расширенного смесевого материала происходит по мере того, как портландцемент, летучая зола и другие реагенты объединяются с образованием стабильных силикатных соединений кальция, магния и алюминия.Эти химические реакции выделяют тепло. Из-за большой массы материала, который отверждается в процессе, это тепло не рассеивается полностью и вызывает повышение температуры смеси в форме до 150-180°F. Когда форма изолирована, как с изолированной крышкой и боковыми стенками эта повышенная температура поддерживается в течение 16-24 часов и значительно улучшает отверждение и прочность продукта. После отверждения в форме в течение 16-36 часов форму открывают и материал удаляют с помощью вилочного погрузчика или мостового крана, поднимая пол формы вместе с отвержденной цементной массой. Монолиту дают высохнуть при температуре окружающей среды в течение дополнительных 12-36 часов, прежде чем перейти к процессу резки.
После этапа отверждения. Монолит из ячеистого бетона, армированного волокнами, разрезается на соответствующие формы строительных материалов. Начальный шаг включает в себя использование ленточной пилы типа «лесопилка» в качестве абразивной проволоки или вращающейся или циркулярной «циркулярной пилы» для резки материалов на панели размером 2 фута × 8 футов и любой толщины от 1 ″-8. ″ или толще.Резка материала стандартным оборудованием вызывает приемлемый износ пильного диска из-за высокого содержания летучей золы в вяжущей композиции изобретения. Хорошо известно, что летучая зола состоит из очень маленьких зольных «шариков», не имеющих острых краев, притупляющих лезвие пилы. Однако в газобетоне и многих других типах ячеистого бетона используется молотый кварцевый песок, и попытка разрезать такой материал быстро затупит пильное полотно.
Если армирующая проволока была добавлена в форму до процесса отверждения, распиловка продолжается таким образом, чтобы получилась панель с армирующей проволокой, встроенной в центр панели.Если в состав панелей не входит армирующая проволока, можно выполнить дополнительную резку с помощью циркулярной или ленточной пилы, чтобы получить блоки практически любого размера и размера. Из-за своего легкого веса 30-50 кг. на кубический фут, производимые блоки могут быть относительно больше, чем обычные цементные блоки, и при этом с ними легко обращаться на строительной площадке. При распиловке материалов получаются строительные изделия точного размера, которые можно быстро собрать на строительной площадке.
Далее изобретение будет описано в сочетании со следующими примерами, которые не следует рассматривать как ограничения изобретения.
ПРИМЕР 1Состав
Смесь разработана таким образом, что кубический фут готового продукта будет весить 28 фунтов. Следующие материалы составляют 28 фунтов:
а) Вода добавляется из расчета 40% от веса сухих ингредиентов. За 28 фунтов. на кубический фут готового продукта добавляется вода из расчета 11,2 фунта. за кубический фут. Вода соединяется с ингредиентами в различных цементирующих реакциях и становится частью матрицы отвержденного твердого продукта.
b) 60% (фактически 59,3% или 16,6 фунтов) веса составляет летучая зола угля.
c) 40% (фактически 39,57% или 11,08 фунтов) веса приходится на портландцемент типа I или типа II.
d) Очень небольшой процент веса продукта на самом деле состоит из полипропиленового волокнистого материала 130 граммов на кубический фут (0,29 фунта) и 20 граммов на кубический фут (0,04 фунта). Эти материалы объединяют в соответствии со следующими этапами процесса.
Процесс смешивания
1.Воду с температурой 40°С помещают в резервуар для хранения/смеси, оборудованный перегородками типа «волнобой».
2. Высокоскоростной смеситель для диспергирования со скоростью вращения лопастей 2000 об/мин опускается в смесительный бак.
3. Летучая зола добавляется в смесительный бак и перемешивается в течение трех минут.
4. Цемент добавляется в смесительный бак и перемешивается в течение трех минут.
5. Этапы 3 и 4 могут быть объединены в один трехминутный этап смешивания.
6. На этом этапе можно добавить дополнительные реагенты, включая известь, гипс и силикат натрия, и перемешать в течение трех минут.
7. Добавляют волокнистые материалы и перемешивают в течение трех минут.
8. Добавляется активатор и перемешивается в течение двух минут.
9. Смешанная суспензия переносится в форму для отверждения через нижний выпускной клапан в смесительном баке.
ПРИМЕР 2Состав
Состав смеси рассчитан таким образом, что кубический фут готового продукта будет весить 28 фунтов. Следующие материалы составляют 28 фунтов:
а) Вода добавляется из расчета 40% от веса сухих ингредиентов.За 28 фунтов. на кубический фут готового продукта добавляется вода из расчета 11,2 фунта. за кубический фут. Вода соединяется с ингредиентами в различных цементирующих реакциях и становится частью матрицы отвержденного твердого продукта.
b) ˜70% (фактически 63,7% или 17,84 фунта) веса приходится на летучую угольную золу.
c) ~30% (фактически 27,3% или 7,64 фунта) веса приходится на портландцемент типа I или типа II.
d) 2 % извести (0,56 фунта), 4 % гипса (0,1,16 фунта) и силиката натрия 1 % (0,56 фунта).28 фунтов).
e) Очень небольшой процент веса продукта на самом деле состоит из полипропиленового волокнистого материала 140 г/куб. фут (0,31 фунта), 140 г/куб. фут волокон стекловолокна (0,31) и активатора из расчета 20 г/куб. фут (0,04 фунта). Эти материалы объединяют в соответствии со следующими этапами процесса.
Состав смесиварьируется в зависимости от типа и качества золы. Следующие предпочтительные составы смесей основаны на летучей золе класса F с электростанции навахо, расположенной в Пейдже, штат Аризона.
ПРИМЕР 3Портландцемент типа I и II (умеренная щелочность) — 40 %
Летучая зола (тип F ASTM 618) — 60 %
Соотношение воды и цемента — 45%
Duraweld C — 850 мл/год
Антигидро — 850 мл/цикл
Алюминиевая паста (Siberline) — 1,18 фунта/год
Щелочестойкие стеклянные волокна — 0,5%
ПАВ — 0
Состав смеси в % веса каждого компонента. В настоящее время это предпочтительная смесь. *Портландцемент должен соответствовать стандарту ASTM C-150.
Процесс смешивания
1. Вода при температуре 40°С помещается в резервуар для хранения/смеси, оборудованный перегородками типа «волнобой».
2. Высокоскоростной смеситель для диспергирования со скоростью вращения лопастей 2000 об/мин опускается в смесительный бак.
3. Летучая зола добавляется в смесительный бак и перемешивается в течение трех минут.
4. Цемент добавляется в смесительный бак и перемешивается в течение трех минут.
5. Этапы 3 и 4 можно объединить в один трехминутный этап смешивания.
6.В этот момент добавляют дополнительные реагенты, т. е. известь, гипс, силикат натрия, Duraweld™ и Antibydro™, и перемешивают в течение трех минут.
7. Добавляют волокнистые материалы и перемешивают в течение трех минут.
8. Добавляется активатор и перемешивается в течение двух минут.
9. Смешанная суспензия переносится в форму для отверждения через нижний выпускной клапан в смесительном баке.
Обращаясь теперь к чертежам, показана схематическая технологическая диаграмма с выделением этапов процесса, используемых для изготовления строительных конструкций из ячеистого бетона, армированного волокнами, в соответствии с изобретением.Портландцемент или другой гидравлический вяжущий материал хранится в бункере 2, а летучая зола хранится в бункере 4. Каждый из этих компонентов подается через соответствующие дозирующие клапаны 6, 8 в чан 10. В чан также добавляется вода, и температура добавленная вода тщательно контролируется. Температуру суспензии регулируют на уровне примерно 112-118°F. Это регулирует реакцию алюминия и подъем продукта. Он играет ключевую роль в получении конечных температур, которые составляют около 165-180°F.после девяти часов отверждения. Эти температуры получаются из комбинации температуры исходной смеси и теплоты гидратации цемента и теплоты раствора хлорида кальция. Идеальная температурная кривая показана на фиг. 3.
Акриловый полимер используется в качестве буфера для поддержания постоянной температуры и контроля термической усадки. Предусмотрена высокоскоростная рассеивающая лопасть 12, работающая со скоростью около 1500-2500 об/мин. Эта лопасть снабжена дефлекторами по ее периферии, а внутри чана могут быть снабжены деформационными дефлекторами по внутреннему диаметру.
Растворы активатора затем добавляют в чан следующим образом. Сначала в смеситель добавляют ускоритель схватывания и регулятор термической усадки, продолжая перемешивание в течение примерно трех минут. Затем добавляют активатор из алюминиевой пасты и полученный вяжущий раствор перемешивают в течение примерно 2,5 минут. Затем в чан высыпают волокна из стекловолокна и/или полипропилена.
Затем жидкая суспензия выливается в пятигранную металлическую форму, обозначенную на чертеже ссылочной позицией 20.Форма имеет открытый верх, и жидкая суспензия заливается в форму так, чтобы она заполнила примерно около 50% объема формы. Используют вибратор или другое подобное средство и помещают его в жидкую суспензию для перемешивания пузырьков воздуха, которые могут образоваться в суспензии. Это приводит к более однородной ячеистой структуре и помогает увеличить прочность готового продукта.
Суспензия поднимется примерно через 20-24 минуты, а затем ей дают застыть в форме в течение примерно 1.0-1,5 часа. Затем на опалубку 20 помещают бетонное покрытие или подобное покрытие, чтобы предотвратить утечку влаги и замедлить потерю тепла в окружающую среду. Термопары могут быть включены в затвердевающую суспензию для измерения температуры, поскольку суспензия отверждается при температуре и давлении окружающей среды в течение примерно 16-24 часов. Затем стороны 22, 24, 26 и 28 формы удаляются, оставляя блок 40 из ячеистого бетона, армированного волокнами, на нижней части формы. Сам блок может быть размером 4’×20’×2’, или на некоторых экспериментальных установках мы изготавливали эти блоки в форме 2’×2’×8’.
Затем блок 40 можно подавать на распиловочную станцию, которая может включать, например, 16-дюймовую мостовую пилу, которая будет перемещать блок 40 в продольном направлении для вырезания панелей или ломтиков из блока. Каждая панель 50 затем подается на другую распиловочную станцию, которая, как показано, включает циркулярную пилу 52, которая будет резать панель 50 поперек ее продольного направления, чтобы получить блоки 60. Затем в каждом из цементных блоков 60 можно просверлить соответствующие отверстия. с тем, чтобы обеспечить размещение в нем арматурных стержней и т.п. во время возведения соответствующей строительной конструкции.Затем набор блоков помещают на поддон, как показано на чертежах позицией 70, и поддон обертывают термоусадочной пленкой 80 или другим паронепроницаемым средством, чтобы поддерживать влажность в блоках, чтобы придать блокам повышенную прочность на сжатие. Мы обнаружили, что блоки на поддонах должны быть завернуты в термоусадочную пленку примерно на три дня, чтобы они не потеряли лишнюю влагу и чтобы проблемы усадки при высыхании были сведены к минимуму.
Мы предполагаем, что на полномасштабном заводе блок 40 будет распиливаться многоголовочной пилой с двойной оправкой, а затем блок 50 будет распиливаться многоголовочной пилой.
После этого блоки готовы к использованию на строительной площадке. Блок можно распилить вручную, а шурупы, гвозди, болты и т.п. можно легко вставить и закрепить в поверхностях.
Типичные физические свойства изделий из ячеистого бетона, армированного фиброй, приведены в таблице 1.
ТАБЛИЦА 1 ФИЗИЧЕСКИЕ СВОЙСТВА Тип I Тип II Прочность на сжатие (f′m), psi 350 475 Прочность на изгиб, фунтов на квадратный дюйм 60 80 Плотность в сухом состоянии, фунт/фут 32 +/− 1.5 фунтов 39 +/- 1,5 фунта.Сравнительные исследования с обычным продуктом автоклавного отверждения показаны в таблице 2.
ТАБЛИЦА 2 СРАВНЕНИЕ С НОМИНАЛЬНЫМИ АВТОКЛАВИРОВАННЫМИ АЭРИРОВАННЫМИ КОНКРЕТНЫЙ Тип I Тип II Номинальный AAC Изобретение Изобретение Автоклавированный Аэрированный Прочность на сжатие 350 фунтов на квадратный дюйм 475 фунтов на квадратный дюйм 320-420 фунтов на квадратный дюйм Предел прочности при изгибе 60-100 фунтов на квадратный дюйм 80-200 фунтов на квадратный дюйм 80-100 фунтов на квадратный дюйм Единица измерения 32 фунта/фут3 39 фунтов.
В следующей Таблице 3 перечислены продукты, которые могут быть изготовлены с использованием композиции по изобретению и описанных выше способов. Этот список предназначен для целей иллюстрации и не должен рассматриваться как ограничение изобретения.
ТАБЛИЦА 3 СПИСОК ПРОДУКТОВ Пункт Номинальные размеры Нет. Пункт Длина Высота Толщина 1 Кирпичные блоки — нагрузка 24 дюйма 8 дюймов 8, 10, 12, Несущий дюймы 2 Кирпичные блоки — не- 24 дюйма 8 дюймов 6, 8, 10, 12 Подшипник нагрузки дюймы 3 U-блок 24 дюйма 8 дюймов 4, 6, 8, 10, 12, дюймы 4 Перемычки 6.5 футов, 8, 10, 12 4, 6, 8, 10, 12, максимум дюймы дюймы 5 Настенная панель 20 футов, 24 дюйма 4, 6, 8, 10, 12, максимум дюймы 6 Панель пола 20 футов, 24 дюйма 4, 6, 8, 10, 12, максимум дюймы 7 Панель крыши 20 футов, 24 дюйма 4, 6, 8, 10, 12, максимум дюймы Предполагаемое в настоящее время оборудование и параметры процесса смешивания следующие.
Процесс смешивания — в настоящее время предпочтительный
1. В смесительный чан добавляется вода. Температура воды варьируется в зависимости от температуры летучей золы и цемента. Таким образом мы контролируем тепловой баланс материалов и получаем идеальную кривую отверждения (см. приложение).
2. Микшер включен.
3. Цемент и летучая зола добавляются через 10 секунд и перемешиваются в течение трех минут.
4. Через одну минуту трехминутного цикла в цементный раствор добавляют добавки Duraweld C и Antihydro.
5. Смеситель-активатор включается одновременно со смесителем периодического действия и добавляются ингредиенты: вода, алюминиевая паста и возможное поверхностно-активное вещество для высокоуглеродистой летучей золы.
6. Затем в конце трехминутного цикла к партии добавляют суспензию активатора и перемешивают в течение двух с половиной минут.
7. В течение последних 30 секунд последовательности смешивания добавляются щелочестойкие стеклянные волокна. Если желательна высокая прочность на изгиб, то вместо стекловолокна добавляются полипропиленовые волокна и добавляются одновременно с алюминием.
8. Микшер выключен.
9. Клапан открывается, материал выливается в форму 20 футов × 4 фута × 2 фута, и клапан закрывается
Состав смесиможет сильно различаться в зависимости от типа и качества летучей золы и, следовательно, от каждого отдельного завода, производящего материал.В некоторых случаях может потребоваться добавление дополнительных добавок к бетону или минералов, таких как известь, чтобы получить физические характеристики, соответствующие нашим рейтингам одобрения кода. Некоторые химические вещества и минералы, которые могут быть добавлены в смесь, и не должны ограничиваться этими добавками, включают известь, гипс, брусит, оксид магния, силикат натрия, алюминат кальция, промышленные понизители воды, ускорители, полимеры, отвердители, и усилители силы. Предполагаемые в настоящее время оптимальные составы попадают в диапазоны, указанные ниже.
Диапазон Портландцемент типа I и II (умеренный 30%-60% щелочь) Летучая зола (тип F ASTM 618) 30%-80% Соотношение воды и цемента 40%-50% Дюравальд С 0,2%-1,5% Анти-Гидро 0,2%-2,0% Алюминиевая паста 0.1%-0,22% ПАВ 0,02%-0,05% Волокна 0,05%-2,00% Лайм 2%-4% Гипс 2%-4% Брусит 0,1%-0,5% Оксид магния 0,1%-0,5% Силикат натрия 0,25%-2,0% алюминат кальция 0,1%-1,25% Промышленные редукторы воды Зависит от конкретного продукта Отраслевые акселераторы Зависит от конкретного продукта Промышленные полимеры Зависит от конкретного продукта Промышленные отвердители Зависит от конкретного продукта Промышленные усилители прочности Зависит от конкретного продукта *Все проценты основаны на сухой массе цемента и летучей золы.Очевидно, что настоящее изобретение обладает явными преимуществами, представляющими значительный коммерческий интерес. Например, изложенные здесь композиции и способы изобретения обеспечивают следующие преимущества:
1. Легкий, неавтоклавный газобетон на основе цемента/зольной пыли, обладающий такими же физическими свойствами, как и другие производимые газобетонные изделия.
2. Производственный процесс, при котором производится такое же количество и качество продукции, что и на заводе по производству газобетонных блоков, при этом требуется лишь {доля (1/7)} первоначальных капиталовложений.Стандартная установка AAC может стоить от 35 до 40 миллионов долларов, в то время как установка, использующая настоящее изобретение, будет стоить всего от 4,5 до 5 миллионов долларов первоначальных капиталовложений.
3. Возможность производства продукта с любым типом и качеством летучей золы. Это делается аналогично нашему процессу фиксации углерода. Добавляется тот же тип поверхностно-активного вещества, за исключением того, что это может быть сделано на заводе в процессе смешивания.