Цемент и опилки: изготовление вариантов для дома и бани своими руками, как называются виды под кирпич, отзывы
Опилки как утеплитель с цементом, известью, глиной и гипсом: пропорции, рецепты, рекомендации

Постоянный рост стоимости утеплительных материалов, а также высокая вероятность покупки некачественной или даже опасной продукции вынуждает искать другие способы и материалы, с помощью которых можно снижать теплопотери.
Один из наиболее эффективных материалов – это древесные опилки, полученные в результате распиливания древесины.
При правильном использовании они обладают меньшим коэффициентом теплопередачи, чем цельная или клееная древесина, а их покупка обходится в сотни раз дешевле.
Однако использование одних только опилок не позволяет достичь максимального эффекта, поэтому необходимы дополнительные компоненты, компенсирующие недостатки отходов распиливания древесины.
В этой статье мы расскажем о:
- несовершенстве утепления одними опилками, из-за которых необходимо использовать вяжущее вещество;
- различных вяжущих веществах, которые компенсируют недостатки отходов распиливания древесины;
- средстве, которое защитит утеплитель от бактерий и грызунов;
- способах применения опилок и остальных компонентов.
Почему опилки не применяют для утепления в чистом виде?
Несмотря на то, что чистые опилки хорошо снижают теплопотери любых строений, у них есть три серьезных недостатка:
- Они со временем слеживаются, из-за чего в утепляющем слое появляются пустоты, обладающие более высоким коэффициентом теплопередачи.
- Отходы распиливания древесины – это очень привлекательное место для различных грызунов, которые поселяются в них.
- Чистые опилки можно применять лишь для засыпки четко ограниченного пространства, поэтому их невозможно применить для утепления стен без пустот.
Нормальное уплотнение опилок невозможно без сильного увлажнения, которое резко снижает их теплоизоляционные свойства.
Поэтому при засыпке этого материала в предназначенные для них карманы, приходится мириться с вероятностью появления пустот, вызванных уплотнением опилок.
В местах таких пустот появляются мосты холода, что приводит к появлению холодных участков стен и увеличению расходов на отопление.
Еще один минус этого материала в том, что он привлекает грызунов.
Ведь по своей структуре отходы распиливания древесины очень похожи на почву, поэтому мыши и крысы роют в них норы и начинают усиленно размножаться.
После этого грызуны проделывают проходы в разные комнаты и начинают чувствовать себя в доме очень вольготно.
Третий недостаток связан с тем, что опилки не могут самостоятельно удерживать форму, поэтому их нельзя использовать снаружи или изнутри стены.
Три этих недостатка сильно ограничивают область применения этого материала.
Зато комбинация отходов распиливания древесины с различными типами вяжущих материалов не только снижает, а то и полностью устраняет описанные недостатки, но и позволяет успешно конкурировать с самыми современными утеплителями.
Наиболее популярные типы вяжущих веществ
Вот наиболее популярные вяжущие:
- гипс;
- цемент;
- глина;
- ПВА;
- навоз.
Гипс – наиболее популярный материал, преимуществом которого является малое время схватывания. Ведь гипсовый состав твердеет в течение десяти минут, а через 1–2 часа он полностью высыхает и обретает полную прочность.
Благодаря использованию этого вяжущего утеплитель получается легким и прочным, поэтому в нем не появляются провалы и вызванные ими мосты холода.
Однако такой состав нельзя использовать для наружного утепления без последующей отделки, ведь гипс — гидрофильный материал.
Поэтому дождь или роса будут разрушать утепляющий слой, лишая его прочности.
Тем не менее этим раствором можно утеплять стены изнутри, ведь там гипс не имеет прямого контакта с водой.
Цемент – менее удобный, но более прочный вяжущий элемент, ведь он застывает в течение суток, поэтому его сложней наносить на стены.
Однако смесь опилок и цемента вполне подходит для оштукатуривания наружных стен, ведь после застывания вяжущий компонент не боится стекающей воды. Его также можно наносить и методом передвижной опалубки.
Не менее эффективен цементно-опилочный состав и для заполнения подпольного и внутристенного состава, а также для потолочных перекрытий.
После застывания он превращается в рыхлый, но довольно прочный камень серого цвета, однако добавление колеров придает застывшей массе нужный оттенок.
Глина – один из самых дешевых вяжущих, единственный недостаток которого в том, что под действием высокой влажности или потоков воды засохшая глиняно-опилочная масса раскисает.
В отличие от цемента и гипса, в процессе высыхания (застывания) теряет массу из-за испаряющейся воды, ведь никаких химических реакций, в которых вода связывается с другими веществами, не происходит.
По прочности полностью высохший состав почти не уступает гипсовому или цементному утеплителю.
ПВА – этот клей наиболее эффективен там, где утеплитель будет подвержен частому или постоянному воздействию влажности и воды.
После застывания клей превращается в довольно жесткое и прочное вещество (поливинилацетат), нерастворимое в воде, поэтому и не боится высокой влажности.
Кроме того, винил пропускает водяной пар, поэтому во время летней жары частицы опилок теряют влажность и усыхают.
При этом подвижности и упругости вяжущего хватает для компенсации изменения размеров опилок, поэтому утеплитель не расслаивается и не теряет своей прочности.
Навоз – несмотря на то, что прочность засохшего навоза гораздо ниже прочности любого другого вяжущего, его использовали для утепления домов в течение многих столетий, а возможно и тысячелетий.
Причина этого в том, что смесь навоза с опилками, сеном или соломой после высыхания образует на поверхности стены пористую корку, обладающую превосходными теплоизолирующими свойствами.
Поэтому при одинаковой толщине слоя именно утеплитель на основе навоза будет обладать наименьшим уровнем теплопроводности.
Кроме того, после высыхания он перестает выделять неприятный запах, поэтому его можно оштукатурить глиняным или цементным раствором, а также оббить досками для защиты от дождя.
Применение различных вспомогательных компонентов
Вне зависимости от типа вяжущего вещества, общий принцип их применения одинаков – после высыхания/застывания вещество связывает опилки, образуя монолитный слой.
Однако для каждого вида работ используют собственную технологию, которая позволяет максимально использовать качества как свежей смеси, так и застывшего утеплителя.
Кроме того, для каждого из вяжущих есть собственная оптимальная пропорция компонентов, также время жизни готового состава, в течение которого его необходимо использовать.
Поэтому мы кратко расскажем о применении вяжущего для утепления различных частей дома, а потом покажем разницу в технологиях использования различных типов этого вещества.
Процесс утепления дома древесными опилками можно разделить на несколько этапов, то есть утепление:
- пола;
- стен;
- потолка;
- чердака.
Для утепления пола отходы распиливания древесины засыпают между лагами, чтобы они отделяли подбой или стяжку от досок чернового пола. Поэтому особой разницы между утеплением чистыми опилками и отходами с вяжущим нет.
Тем не менее, вяжущее вещество увеличивает срок службы такого утеплителя, ведь в нем прекращаются процессы распада и перегнивания, о которых вы можете прочитать в этой статье (Перегной из опилок).
Это особенно важно для комнат, где велика вероятность пролива воды или нередко появляется высокая влажность.
Такую технологию применяют как на деревянных, так и на бетонных полах.
Если же вы хотите узнать о ней более подробно, то рекомендуем прочитать эту статью (Утепление пола).
Поэтому в большинстве случаев при утеплении пола выбор вяжущего не играет особой роли, исключение составляют те деревянные полы, где по каким-то причинам сложно сделать подбой из достаточно прочного материала.
Поэтому там желательно использовать ПВА, ведь удельная масса готового состава будет меньше, чем с другим типом вяжущего вещества.
Утепление стен проводят тремя способами:
- засыпая или заливая утеплитель в пространство между досками или кирпичами;
- заполняя утепляющим материалом пространство между стеной и декоративным фасадом или фальшпанелью;
- обмазывая поверхность стены утепляющим составом.
В первом случае ни одно из описанных в статье вяжущих средств не имеет никаких серьезных преимуществ, ведь после приготовления смесь засыпают/заливают в пустоты и уплотняют, после чего она твердеет.
Разница лишь во времени жизни смеси, поэтому гипс применяют очень редко, ведь он застывает очень быстро.
Поэтому даже использование замедлителей твердения не позволяет использовать раствор в течение более чем получаса, что очень мало для заполнения даже небольшого участка стены.
Если же стену утепляют методом передвигающейся опалубки или постепенно заполняя отдельные куски, то гипсовый раствор можно использовать для заливки между стеной и декоративным фасадом или фальшпанелью.
В этом случае малое время жизни не будет существенным недостатком из-за небольших объемов.
Для утепления потолка используют ту же технологию, что и для утепления пола – готовую смесь засыпают в пространство между лагами.
Разница лишь в том, что утеплять потолок удобней через снятое покрытие пола следующего этажа.
Такую же технологию используют и для пола чердака, однако на чердаках с мансардой приходится утеплять еще и стены. Исключение составляют крыши, где утеплена кровля.
Также рекомендуем прочитать эти статьи Утепление каркасного дома, Потолка и Крыши, в них подробно рассказывают о различных методиках утепления опилками.
Вяжущие и их пропорции
Люди утепляют дома опилками сотни, а возможно и тысячи лет.
Это достаточное время для того, чтобы определить наиболее эффективные вяжущие вещества.
Кроме того, промышленность предлагает современные материалы, которых не было несколько веков назад.
Все это определило список наиболее эффективных и популярных типов вяжущих веществ, которые сделают утепление отходами распиливания древесины более качественным и долговечным.
Гипс
Смесь отходов распиливания древесины и извести насыпают в удобную для перемешивания емкость небольшими (1/5 от объема одной заливки) порциями и пересыпают гипсом.
Пропорции зависят от сорта вяжущего вещества – для гипса первого сорта составляют 10:1 (опилки/гипс), для второго сорта 5:1.
После заполнения емкости ее заливают водой из расчета 0,7 л воды на 1 кг гипса и энергично перемешивают. Время перемешивания 2–3 минуты, после чего готовую смесь нужно быстро залить в подготовленное для нее место.
Если смесь используют для обмазывания стен, то на 2 кг гипса наливают 1 л воды.
Однако такую смесь почти невозможно качественно перемешать вручную, поэтому ее делают только с помощью бетономешалки.
Если невозможно быстро использовать этот раствор, то в него нужно ввести замедлитель, в качестве которого можно использовать столярный (казеиновый) клей.
Также можно использовать смесь извести и мездрового клея. Для этого 1 кг клея замачивают на сутки в 5 л воды, затем добавляют 2 кг известкового теста и варят 5 часов. Замедлитель разбавляют водой в соотношении 1:50 и тщательно перемешивают.
Готовый замедлитель используют как обычную воду, он увеличивает время жизни раствора до получаса.
Если нет возможности или желания возиться с замедлителем, то можно использовать хвойные опилки с максимально сильным запахом. Пропитывающий их скипидар увеличивает время жизни готового утеплителя на 2–5 минут.
Цемент
Для работы с цементом используют другую технологию, ведь время жизни разведенного водой цемента (цементное молоко) превышает 3 часа.
Кроме того, использование присадок, увеличивающих подвижность раствора, позволяет снизить количество воды и повысить прочность застывшего утеплителя.
По механической прочности утеплитель с присадкой превосходит застывшие гипсовый и цементный утеплители на воде в 1,2–1,5 раза.
Кроме того, застывший цемент с пластификатором меньше боится воды.
Если же вместе с пластификатором добавить жидкое стекло, то после застывания материал вообще не будет подвержен воздействию воды.
Минус использования жидкого стекла в том, что такой утеплитель не будет пропускать водяной пар, поэтому его нельзя использовать в домах с неэффективной вентиляцией.
Это приведет к тому, что начнут сыреть стены, пол, потолок и мебель, затем появится гниль и плесень. Проживание в таком доме опасно для здоровья.
Поэтому перед утеплением стен цементно-опилочным раствором с жидким стеклом сначала установите рекуператоры для увеличения эффективности вентиляционной системы и наладьте воздухообмен в каждом из помещений.
Нежелательно использовать цемент марки ниже М400, особенно если он пролежал больше трех месяцев.
Ведь даже в течение первых трех месяцев потеря прочности при соблюдении условий хранения составляет 20–25%, а в течение года прочность портландцемента может упасть на 35–45%.
Максимальная прочность застывшего утеплителя будет лишь в том случае, если масса воды составляет ¼ от массы цемента.
Увеличение количества воды делает молоко и готовый состав более подвижным, но снижает его прочность в застывшем состоянии.
Такого количества воды недостаточно для получения цементного молока нужной вязкости, поэтому вместе с водой добавляют и пластификаторы.
В качестве таковых можно использовать как покупные, так и самодельные вещества.
Из покупных средств наиболее эффективны суперпластификаторы, которые производят различные компании.
Мы подготовили ссылки на сайты некоторых компаний, которые торгуют такой продукцией:
- Полипласт.
- Суперпласт.
- Форт.
Также в качестве пластификатора можно использовать любое жидкое мыло или шампунь. На мешок цемента необходимо 200–300 мл жидкого мыла или шампуня, поэтому эффект от его применения гораздо хуже того, что оказывает любое промышленно изготовленное средство.
Известь
Известь необходима для обеззараживания отходов распиливания древесины, а также для борьбы с грызунами.
Этот реагент подавляет размножение любых патогенных микроорганизмов, поэтому добавление извести надежно защищает утеплитель от гниения, гнили и других проблем.
Кроме того, после такой обработки утеплитель становится крайне некомфортным для любых грызунов, ведь известь – это сильная щелочь, наносящая животным тяжелые ожоги.
Чтобы приготовить пригодный для использования состав, свежие опилки любых пород и размеров смешивают в сухой гашеной известью в пропорции 1:10–1:15.
Еще один плюс от такой обработки заключается в том, что в опилках гибнут любые личинки, которые попали в них во время хранения.
Благодаря извести в утеплителе не заведутся никакие жуки и другие насекомые, которые могут из утеплителя пробраться в деревянные стены и повредить их.
Это особенно важно в тех случаях, когда для утепления домов используют отходы распиливания окоренной древесины, ведь личинки жучков-древоточцев очень маленькие и могут проскочить мимо зубьев пилы.
Для обработки опилок нельзя использовать свежую негашеную известь, потому что при контакте с водой она сильно нагреется и, вода превратится в концентрированный раствор щелочи.
После внесения извести, древесные отходы необходимо тщательно перемешать, чтобы равномерно распределить антисептик по всему утеплителю.
Только после этого можно вносить вяжущее любого типа.
Кроме того, известь можно использовать и в качестве вяжущего.
Однако в этой роли ее эффективность заметно ниже, чем любого другого вещества.
Тем не менее ее необходимо добавлять для обеззараживания и защиты от грызунов вне зависимости от выбора вяжущего вещества, ведь известь совместима с любыми типами вяжущего вещества.
Глина
Утеплители на основе глины применяют несколько тысячелетий, только вместо отходов распиливания древесины в них засыпали рубленые сено или солому.
Оптимальное соотношение глины и опилок от 1:2 до 1:10, причем чем меньше это соотношение, тем прочней получается утеплитель после застывания, а чем выше, тем меньше его уровень теплопроводности.
Это позволяет подбирать такие пропорции, которые лучше подходят к тем или иным задачам.
К примеру, для утепления пола или потолка лучше подходит пропорция 1:10.
Соотношение 1:5 подходит для наружного утепления полостей между стеной и фасадом, или для заполнения внутристенных пустот.
А вот для оштукатуривания стен как изнутри, так и снаружи необходимо использовать соотношение 1:2, ведь только оно обеспечивает достаточную прочность застывшего слоя.
Преимущество смеси опилок с глиной перед другими вяжущими веществами, в частности перед цементом, в том, что у нее не ограничено время жизни.
Ведь после того, как раствор станет слишком густым и потеряет пластичность, в него можно добавить немного воды и перемешать, после чего он обретет исходную консистенцию.
Для приготовления раствора можно использовать как покупную молотую красную или белую глину, так и накопанную в собственном огороде.
Однако в огороде глину необходимо брать с глубины 1,5 м и более. Ведь глина, расположенная выше, содержит в себе слишком много перегнивших растительных останков, поэтому опилки при контакте с ней также начнут перегнивать.
Для наибольшей эффективности высохшего утеплителя, раствор нужно заливать участками любой длины, но небольшой (20–40 см) высоты, причем чем больше воды в растворе, тем меньше должна быть высота.
Это необходимо для того, чтобы залитый раствор мог нормально сохнуть, ведь чем больше высота залитого слоя, тем сложней воде испаряться из него.
Кроме того, чем жиже раствор, тем больше должен быть промежуток между заливками, поэтому оптимальная консистенция раствора соответствует густому бетону.
Такой раствор нужно уплотнять вибратором или палкой, ведь самостоятельно он очень плохо заполняет пустоты. Зато заливки можно делать 2–3 раза в день.
Можно налить меньше воды, но повысить подвижность готовой смеси с помощью извести пушенки, предварительно разведенной в подготовленной к заливке воде. На 50 л воды можно добавить 1–2 кг извести.
Однако работать с таким раствором нужно осторожно, используя резиновые перчатки и защитные очки.
Клей ПВА
Для создания раствора необходимо использовать Строительный и Универсальный клеи ПВА.
Канцелярский и Бытовой клеи обладают малой прочностью и хорошо подходят лишь для склеивания бумаги.
Кроме того, оба этих клея слишком жидкие, поэтому и смесь получится излишне текучей.
Для приготовления раствора используют сухие свежие опилки, которые смешивают с клеем в любой подходящей таре.
Время жизни такого раствора не менее полутора часов.
Универсальной пропорции не существует, однако оптимальное соотношение опилок и клея находится между 1:2 и 1:10.
Чем меньше клея в растворе, тем более легким и теплоизолирующим он получится.
Чем больше клея в растворе, тем более прочным и водостойким он будет.
Поэтому не стоит увеличивать соотношение более чем 1:10, ведь в этом случае опилки будут впитывать влагу и постепенно перегнивать.
Для увеличения прочности можно добавить цемент в соотношении 1:10 от массы клея. В этом случае сначала перемешивают свежие отходы распиливания древесины и цемент, затем добавляют клей и снова тщательно перемешивают.
Растворы на основе ПВА не стоит использовать для обмазывания стен, ведь они не обладают нужной пластичностью, поэтому лучше всего они подходят для заполнения различных пустот.
Если вы собираетесь заполнять пространство между стеной и фальшпанелью или фасадом, то учитывайте, что клей схватится с обеими поверхностями и соединит их, из-за чего достаточно сложно будет снять панель или фасад без повреждения.
Поэтому желательно застелить обе поверхности паропроницаемой пленкой или обмазать тонким слоем олифы.
Навоз как вяжущее средство
Экскременты животных после высыхания превращаются в довольно прочное и легкое вещество с низкой теплопроводностью.
Это свойство используют для утепления домов и подсобных строений.
Однако такой раствор подходит лишь для наружного утепления стен.
Свежие опилки смешивают со свежим навозом в соотношении от 1:1 до 4:1 и сразу же намазывают на стену слоем толщиной 1–5 см.
Если необходим более толстый утеплитель, то есть делают послойно, намазывая следующий слой после высыхания первого.
Однако не стоит делать слишком толстый слой, ведь снаружи его придется чем-то закрывать, иначе утеплитель размоет водой во время дождя.
Вывод
Применение вяжущих веществ увеличивает эффективность утепления опилками, ведь утепляющий материал становится более прочным и твердым, а также не проседает со временем.
Прочитав статью, вы узнали о:
- различных видах вяжущих веществ;
- особенностях готового утеплителя на их основе;
- методике приготовления и применения раствора из опилок и выбранного вяжущего.
Вконтакте
Одноклассники
Мой мир
Опилкобетон. Опилки и состав.Плюсы и минусы.В домашних условиях
Опилкобетон – это легкий бетон, состоящий из смеси воды, цемента, извести, глины, песка и опилок. Он применяется для производства строительных блоков и возведения монолитных зданий. По своему составу материал похож на арболит, но содержит более мелкий древесный наполнитель. Применение опилкобетона экологически целесообразно, поскольку он является полностью безопасным, отвечает санитарно-гигиеническим требованиям, кроме этого отличается повышенной теплоизоляцией и звукоизоляцией.
Где используется опилкобетон
Материал широко применяется в сфере строительства малоэтажных жилых и нежилых зданий. Чаще всего его используют при возведении загородных домов, гаражей, хозяйственных построек, фасады которых планируется штукатурить, закрывать сайдингом, вагонкой.
Несущие характеристики материала исключают возможность его использования для возведения многоэтажных зданий. Из опилкобетона можно строить короба высотой до 2-х этажей. Для его применения при кладке более высоких построек требуется проведение точных инженерных расчетов, а также заливка железобетонного армопояса по всему контуру.
Из опилкобетона нередко делается черновая стяжка пола. Для этого используется материал малых марок М5 и М10. Сверху стяжки могут укладываться лаги дощатого пола, ламинат, паркет и т.д. Стяжка совместима с системой водяного и электрического теплого пола.
Преимущества опилкобетона
Главным достоинством материала является применение при его производстве вторсырья. При этом опилки в бетоне не подвергаются горению и гниению, поэтому лишены своих основных недостатков. Их применение при производстве опилкобетона делает его дешевым и доступным.
Кроме пользы рационального применения отходов лесопилок, выбор для строительства опилкобетона имеет и другие положительные стороны:
- Высокие теплозащитные качества.
- Хорошая звукоизоляция.
- Малый вес построенных конструкций.
- Высокая устойчивость к растяжению.
- Огнеупорность несколько часов при температуре пламени 1200°С.
- Простой распил.
Это практически идеальный строительный материал соответствующий современным санитарно-гигиеническим нормам. Хотя в его составе и находятся волокна древесины, но в цементной среде они не могут выступить субстратом для разведения плесени, грибка, конечно при отсутствии чрезмерной влажности. Отдельного внимания заслуживают теплоизоляционные качества материала. Стена из опилкобетона толщиной всего 30 см сопоставима по теплозащитным свойствам с кирпичной кладкой шириной 1 м. Дома из опилкобетона теплые, их содержание на отопление и кондиционирование обходится дешевле.
В сравнении с классическим бетоном опилкобетон на порядок легче. Его применение в строительстве позволяет заливать более легкий фундамент, что существенно снижает общую смету строительства. Кроме этого, стены из опилкобетона способны переносить удары, воздействие на растяжение и изгиб. На них гораздо реже появляются трещины, чем на кладке из кирпича, шлакоблока, газоблока, пенобетона.
Стены из опилкобетона не горят. Хотя они содержат в себе древесину, но способны как минимум несколько часов переносить прямое воздействие пламени температурой 1200°С. При этом поверхность просто обугливается, выделяя небольшое количество дыма. При обугливании стена постепенно истончается, что происходит крайне медленно.
Положительным моментом является и удобство работы с опилкобетонными блоками, панелями. При необходимости они достаточно просто распиливаются ножовкой, бензопилой. Это очень важно для соблюдения шага укладки. В дальнейшем стена из такого материала отлично удерживает саморезы без дюбелей. На них можно без опаски навешивать кондиционер, кухонные шкафчики, полки.
Недостатки опилкобетона
Главным и единственным недостатком опилкобетона выступает уровень его влагопоглощения. В зависимости от плотности материала, впитываемость может составлять от 8 до 12%. Даже при добавлении в раствор опилкобетона специальных водоотталкивающих составов, уровень поглощения влаги может снизиться лишь на 2%. Именно поэтому здания из такого бетона должны иметь кровлю с широкими скатами, что исключает возможность намокания фасадов.
Сильное поглощение влаги также создает определенные трудности при строительстве. Кладка нуждается в качественном укрывании пленкой на время осадков. Также не рекомендуется проводить строительство хранимым под открытым небом материалом, не защищенным даже навесом. Он намного тяжелее, не имеет максимальной марочной прочности.
Требования к опилкам для производства опилкобетона
Для изготовления опилкобетона могут использоваться любые просеянные опилки, но от их качества зависят дальнейшие эксплуатационные характеристики раствора. Наиболее удачным решением считается применение опилок с фракцией частиц 1-5 мм из хвойных деревьев. Самым долговечным является опилкобетон на основе еловых опилок. Используемый наполнитель должен быть просеянным. Присутствие древесной пыли снижает связующие качества.
Состав и фракция опилок влияет на скорость отвердевания материала. Древесина содержит сахар, влияющий на рабочие характеристики цемента. От его концентрации зависит, как быстро изделие из опилкобетона станет достаточно прочным для применения. При использовании опилок из елки, поверхность затвердеет за 10 часов. При применении соснового вторсырья за 15 часов, а при добавлении опилок лиственных пород бетон застывает не менее чем за 4 суток.
Для снижения влияния опилок на цемент, их можно предварительно обработать. Для этого применяются специализированные химические составы или обычное выдерживание на открытом воздухе. Опилки хвойных пород могут окисляться на солнце за 3 месяца, после чего приобретают необходимые качества для производства твердого прочного опилкобетона. Ускорить данный процесс можно выдержав их в воде, а потом полностью высушив под естественными солнечными лучами.
Замачивание и сушка применяются только при кустарном домашнем производстве опилкобетона для собственных нужд. При его изготовлении в промышленных масштабах используется обработка жидким стеклом и хлористым кальцием. Добавление жидкого стекла способствует затвердению опилок, а включение хлористого кальция увеличивает их прочность. Промышленные производители могут также использовать хлористый алюминий, сернокислый натрий или аммиачную селитру. Такие решения делают производство более дорогим, поскольку химикаты используются в пропорции 1 к 40 частям опилок.
Опилкобетон в домашних условиях
Подавляющее большинство присутствующих в продаже блоков из опилкобеотона являются продуктом кустарного производства. Практически нет крупных предприятий производящих данный материал в полном соответствии с действующими требованиями ГОСТ. Продаваемый на рынке материал в своем большинстве совершенно не отвечает заявленным характеристикам и минимальным требованиям, необходимым для строительства.
Дешевизна производства опилкобетона делать его применение в строительстве выгодным, поэтому нередко его изготовляют в нужном количестве сами, непосредственно на стройплощадке. В таком случае опилкобетон заливается в опалубку поэтапно. Он размещается слоями. По мере высыхания опалубка постепенно поднимается вверх, в результате чего получаются несущие стены и перегородки здания. Это достаточно продолжительный и кропотливый процесс. Материал набирает окончательную марочную прочность только через 3 месяца, несмотря на то, что сам цемент достигает максимальных связующих качеств уже спустя 28 дней.
Прочность материала увеличивается по мере его высушивания. В связи с этим монолитное строительство из такого бетона должно проводиться только летом в самые жаркие и засушливые месяцы. Нельзя заливать массу большими слоями, поскольку нижний недосушенный слой склонен к деформации.
При изготовлении блоков из опилкобетона его оставляют в формах как минимум 1 сутки. Если их вытащить раньше, то блок может перекоситься, что приведет к нарушению геометрии.
Пропорции для приготовления опилкобетона
Опилкобетон производится различных марок прочности – М5-М25. Слабый бетон марок М5 и М10 применяется в качестве утеплителя. Его заливают вместо теплоизоляционного материала между кирпичной кладкой стен, применяют для утепления чердаков. Марки М15-М25 подходят для производства несущих стен, при условии отсутствия тяжелого бетонного межэтажного перекрытия.
Для приготовления 1 ведра опилкобетона марки М25 необходимо:
- Стружка – 2 кг.
- Цемент М500 – 3 кг.
- Песок – 6,7 кг.
- Вода.
Также возможно приготовление опилкобетона этой же марки с использованием глины и извести. В таком случае снижается концентрация цемента, что удешевляет производство.
Для замешивания ведра раствора обычно применяется соотношение компонентов:
- Цемент М400-М500 – 2 кг.
- Песок – 5 кг.
- Известь 0,5 кг.
- Глина – 1 кг.
- Опилки – 2 кг.
Очередность смешивания компонентов
Чтобы приготовить опилкобетон с оптимальной однородной консистенцией, важно проводить смешивание компонентов правильно. В первую очередь перемешиваются вяжущие составляющие и песок. После этого добавляются опилки, и только после этого вводится вода. Ее количество определяется визуально, поскольку данный показатель зависит от влажности древесины и песка. Раствор не должен быть жидким. Чем выше его густота, тем меньше дальнейшая усадка при высыхании.
Похожие темы:
пропорции объема ведрами, состав, приготовление
Дата: 21 августа 2017
Просмотров: 5172
Коментариев: 1
Специалистами строительной отрасли ведется постоянный поиск новых материалов. Одной из разновидностей легкого бетона, в котором используются опилки древесины, является опилкобетон. Он характеризуется повышенными теплозащитными характеристиками, огнестойкостью, соответствует санитарно-гигиеническим нормам. Смешивая бетон с опилками несложно приготовить своими руками готовые блоки для постройки коттеджей, домов, а также строений хозяйственного назначения. Важно соблюдать пропорции и технологию изготовления. Рассмотрим детально технологические нюансы, разберемся с различными вариантами рецептуры.
Готовые блоки используют для строительства малоэтажных зданий
Изготовление опилкобетона своими руками
Самостоятельное изготовление легкого бетонного композита осуществляется по следующему алгоритму:
- Выполняется подготовка необходимых материалов. Составляющие нет необходимости приобретать предварительно. Все компоненты можно заготовить непосредственно перед изготовлением, посетив магазины или склады стройматериалов, а также воспользовавшись отходами производства деревообрабатывающих предприятий.
- Смешиваются ингредиенты согласно пропорции. Перемешивание компонентов может осуществляться механическим способом с применением бетоносмесителя или ручным путем с использованием лопат. Автоматизация технологического процесса путем применения бетономешалки повышает производительность, улучшает интенсивность смешивания, положительно влияет на качество продукции.
- Производится формовка. Преимущественно используется групповой процесс формовки, когда предварительно перемешанный состав заливается в несколько десятков форм. Применяются единичные и групповые формы разборной конструкции, изготовленные из древесины толщиной 2 см и обитые металлом или пластиком. Применение полиэтиленовой пленки облегчает извлечение готовых изделий.
- Осуществляется сушка готовой продукции естественным путем. Снятие форм производится через 4–5 суток после заливки путем ослабления затяжки барашковых гаек, извлечения резьбовых шпилек и разборки формовочного ящика. Длится процесс естественной сушки в зависимости от пород древесины до трех месяцев, в течение которых значительно снижается концентрация влаги, и изделие приобретает эксплуатационную прочность.
Стандартный состав бетона с опилками: цементно-песочная смесь, деревянная стружка, известь (по необходимости)
Бетон с опилками – состав и соотношение компонентов
Опилкобетон производится на основе ингредиентов, полученных промышленным путем и составляющих природного происхождения:
- портландцемента марки М300;
- просеянного песка размером до 1,8 мм;
- извести;
- древесных опилок;
- воды.
Опилка следующих видов деревьев обеспечивает необходимое качество продукции:
- сосны;
- ели;
- березы;
- тополя;
- ясеня;
- дуба;
- лиственницы.
Период твердения блоков из различных видов древесины значительно отличается. По скорости набора прочности лидирует сосна, у которой процесс твердения завершается через полтора месяца после заливки. На последней позиции находится лиственница, блоки из которой можно использовать через 3,5 месяца после заливки.
Каждая марка арболита готовится по определенным пропорциям
Концентрация наполнителя и песка влияет на плотность материала. При уменьшении его концентрации удельный вес блоков снижается, что улучшает теплотехнические характеристики, однако уменьшает прочность. Увеличение объема вяжущих ингредиентов и песка повышает водонепроницаемость, а также устойчивость к воздействию отрицательных температур.
Рекомендуемое соотношение компонентов для приготовления состава средней плотности из 100 кг древесной стружки, составляет:
- цемент – 75 кг;
- известь – 50 кг;
- песок – 175 кг.
Пропорции и состав опилкобетона в ведрах
Для приготовления опилкобетона добавлять компоненты ведрами достаточно удобно.
Состав опилкобетона в ведрах регламентируется следующими пропорциями:
- Для марки опилкобетонных блоков М10 соотношение цемента, песка, тырсы и извести составляет 1:2,2:6,5:1,5.
- Опилкобетон, маркируемый М15, включает указанные выше ингредиенты в соотношении 1,2:3:7,8:0,8.
- Блоки с маркировкой М25 содержат портландцемент, просеянный песок, древесную стружку и известь в пропорции 1:2,8:6,4:0,8.
Важно не занижать количества вяжущего материала
На примере материала с маркировкой М10 рассмотрим пропорции ингредиентов при введении ведрами. Смесь включает:
- портландцемент – 1 ведро;
- песок – 2 ведра с горкой;
- опилки – 6 с половиной ведер;
- известь – полтора ведра.
Соблюдая указанные пропорции несложно своими руками подготовить раствор для изготовления блоков различных марок.
[testimonial_view id=”17″]
Опилкобетон – приготовление смеси
Технологический процесс приготовления смеси можно осуществлять следующим образом:
- подготовить цементный раствор путем разведения портландцемента водой с последующим добавлением просеянного песка, извести, древесной стружки;
- осуществить смешивание извести с тырсой, затем ввести портландцемент с песком, развести перемешанные ингредиенты водой.
Независимо от выбранного метода приготовления, необходимо обеспечить однородность смеси. Важным моментом технологии является предварительная сушка стружки, уменьшающая концентрацию влаги. Правильно приготовленная смесь начинает твердеть через пару часов. Именно поэтому важно готовить раствор в объеме, соответствующем количеству имеющихся форм. При укладке бетонной смеси следует тщательно уплотнить состав с целью недопущения образования воздушных пор.
Следует знать, что известь повышает взаимные адгезионные способности компонентов песко-цементного композита
Растворы для различных марок
В зависимости от концентрации ингредиентов опилкобетонные блоки делятся на следующие марки:
- М5. Характеризуется пониженной до 0,6 т/м3 плотностью, уменьшенным коэффициентом теплопроводности, равным 0,18. На один 50-килограммовый мешок цемента необходимо взять по 0,2 тонны опилок и извести, а также 20 кг присеянного песка;
- М10. Коэффициент теплопроводности составляет 0,21, а удельный вес возрастает до 0,8 т/м3. Для приготовления мешок портландцемента необходимо перемешать со 100 кг стружки и 100 кг песка, а также добавить 80 кг извести;
- М15. Плотность и коэффициент теплопроводности увеличиваются и составляют, соответственно, 0,8 т/м3 и 0,24. Для приготовления на 50 кг цемента вводится 70 кг тырсы, 30 кг извести и 115 кг песка;
- М20. Удельная плотность достигает величины 0,95 т/м3, а величина коэффициента теплопроводности увеличивается до 0,3. Опилкобетон готовится путем смешивания по 50 кг цемента и опилок с добавлением 130 килограмм песка и 15 кг извести.
С увеличением марки опилкобетона возрастает коэффициент теплопроводности, увеличивается плотность. Блоки высоких марок позволяют возводить увеличенные помещения, в которых из-за высокого коэффициента теплопроводности сложно поддерживать комфортный температурный режим. Введение специальных добавок, вымачивание древесного сырья в жидком стекле и известковом молоке позволяет использовать сырье с увеличенной влажностью и повышает огнестойкость блоков.
Марка М10 требует такие количества: полведра вяжущего сырья, ведро с горкой очищенного песка и немногим больше трех ведер со стружкой
Готовность перемешанных компонентов определяется путем сжатия подготовленной смеси ладонью. Пластичный и готовый к формовке материал сохраняет следы пальцев, что свидетельствует о готовности раствора к заливке.
Введение в раствор глины вместо извести
В состав материала допускается вводить вместо извести глину, что не сказывается на качестве изделий. Технология использования глины предусматривает следующие этапы:
- смешивание древесного сырья с портландцементом и песчаной массой;
- введение в смесь глиняного теста, тщательное перемешивание;
- добавление воды небольшими дозами;
- перемешивание состава до рабочей консистенции.
Предусмотренные рецептурой пропорции известкового и глиняного теста остаются неизменными.
Раствор на основе гипсового вяжущего вещества
Допускается в качестве вяжущего вещества использовать строительный гипс вместо портландцемента. Может возникнуть вопрос, как замедлить интенсивность твердение гипса при смешивании с водой? Проблема довольно просто решается введением в воду моющего средства, которое способствует замедленному твердению гипса.
Для обеспечения высокой скорости твердения в М5 добавляют гипс
Особенности применения строительного гипса:
- увеличение по сравнению с цементом скорости твердения блоков в 5 раз;
- незначительное увеличение затрат на изготовление опилкобетонной продукции.
Среди специалистов по строительству ведется полемика о возможности применения опилкобетонных блоков на основе гипса для возведения наружных стен зданий. Надежная защита опилкобетона от отрицательного влияния атмосферных факторов позволяет решить проблему поглощения материалом влаги.
Размер опилок
Несмотря на то что в ряде источников отмечается необходимость просеивания опилок на сите с квадратной ячейкой размером 1 см, размер используемой стружки не имеет принципиального значения.
Важно обратить внимание на следующие моменты:
- следует вводить древесное сырье, являющееся вяжущим веществом, в требуемом количестве;
- проблематично получить однородный состав при использовании опилок, крупность которых отличается в сотни раз;
- древесная стружка с калибровочных станков и оцилиндровочного оборудования не используется при изготовлении опилкобетона;
- целесообразно применять опилки с пилорамы, оснащенной ленточной пилой или дисковым рабочим органом.
Жирные растворы, содержащие вяжущее вещество в избыточном количестве, менее восприимчивы к крупности опилок по сравнению с тощими составами.
Итоги
Руководствуясь пропорциями, приведенными в материале статьи, несложно своими руками подготовить качественную смесь для изготовления опилкобетона необходимой марки. Самостоятельно изготовленные с соблюдением технологии опилкобетонные блоки отличаются прочностью, морозостойкостью, доступной ценой. Освоив технологию изготовления, можно оценить достоинства экологически чистого и простого в изготовлении материала.
На сайте: Автор и редактор статей на сайте pobetony.ru
Образование и опыт работы: Высшее техническое образование. Опыт работы на различных производствах и стройках – 12 лет, из них 8 лет – за рубежом.
Другие умения и навыки: Имеет 4-ю группу допуска по электробезопасности. Выполнение расчетов с использованием больших массивов данных.
Текущая занятость: Последние 4 года выступает в роли независимого консультанта в ряде строительных компаний.
Строительные блоки из опилок и цемента: характеристика и технология изготовления
Дата: 21 августа 2017
Просмотров: 4170
Коментариев: 0
При производстве изделий для строительства осуществляется смешивание цемента и щепы. Технология отличается доступностью, не требует применения специального оборудования. Самостоятельное производство блоков из опилок позволяет значительно снизить сметную стоимость строительства и своими руками подготовить материал, который отличается экологической чистотой. Повышенные эксплуатационные характеристики изделий из портландцемента и опилок позволяют осуществлять возведение жилых зданий, коттеджей, а также хозяйственных строений. Для правильного применения материала необходимо изучить характеристики, рецептуру, ознакомиться с достоинствами и недостатками, а также освоить технологию изготовления продукции из цемента и древесных отходов.
Блоки из опилкобетона – характеристика
Опилкоблоки представляют собой легкий строительный материал. Они являются разновидностью бетонных изделий, характеризующихся уменьшенным удельным весом. Благодаря уникальным свойствам, материал востребован в строительной отрасли.
Арболит представляет собой легкую разновидность бетона на основе опилок и высококачественного цемента
Отличается следующими характеристиками:
- теплотехническими свойствами. В зданиях, основой которых являются блоки из опилкобетона, легко поддерживать комфортный температурный режим;
- экологической безопасностью. Опилкоблоки производятся из сырья природного происхождения;
- повышенным запасом прочности. Блоки из опилкобетона обеспечивают устойчивость возводимых строений;
- пожарной безопасностью. Технология изготовления и используемые компоненты обеспечивают огнестойкость бетонного композита;
- повышенной проницаемостью паром. Структура массива способствует поддержанию благоприятной влажности помещения;
- стойкостью к колебаниям температуры. Блоки из стружки и цемента выдерживают многократные циклы замораживания с последующим оттаиванием;
- доступным уровнем цен. Применяя строительные блоки на основе цемента и щепы можно значительно снизить сметную стоимость строительства.
В зависимости от удельного веса опилкоблоки делятся на следующие виды:
- теплоизоляционные, характеризующееся плотностью 0,4–0,8 т/м3;
- конструкционные, удельная масса которых составляет 0,8–1,2 т/м3.
Высокие технические характеристики обеспечивают популярность изделий, изготовленных на основе цементного вяжущего и опилок.
Опилкобетон относится к категории легких материалов
Блоки из опилок и цемента – преимущества и недостатки
Опилкоблоки отличаются следующими достоинствами:
- повышенной степенью звукоизоляции. Опилкобетонный композит поглощает посторонние шумы, что позволяет чувствовать себя комфортно в помещении;
- безвредностью для окружающих. При эксплуатации изделий, произведенных на основе экологически чистого природного сырья, не выделяются вредные вещества;
- огнестойкостью. Блоки из опилок и цемента не воспламеняются при воздействии температуры до 1100 °C на протяжении двух с половиной часов;
- легкостью обработки. Материал быстро обрабатывается инструментом, сохраняет целостность при механическом воздействии;
- доступностью. Щепа является отходом производства деревообрабатывающих предприятий, отличается доступной ценой;
- простотой кладки. Строительные блоки, отличающиеся увеличенным объемом при небольшой массе, позволяют быстро возводить стены;
- длительным ресурсом эксплуатации. Качественно изготовленные и защищенные от впитывания влаги изделия отличаются долговечностью.
Блоки, сделанные из этих материалов, широко применяются при возведении домов, коттеджей, хозяйственных построек
Наряду с достоинствами, у материала также имеются слабые стороны:
- Продолжительный производственный цикл. Приобретение эксплуатационных характеристик происходит на протяжении трех месяцев с момента заливки в формы.
- Повышенное поглощение влаги. Опилкобетон нуждается в надежной влагозащите со всех сторон.
- Возможность использование щепы только из определенных видов древесины. Применяются опилки с пониженным содержанием сахаров, процесс распада которых влияет на прочность материала.
Оценив преимущества и проанализировав недостатки, многие застройщики отдают предпочтение изделиям на основе цемента и щепы.
Изготовление блоков из опилок и цемента своими руками
Производство блоков из опилок предусматривает следующие этапы:
- Заготовку сырья для изготовления опилкобетонных изделий. Наличие в строительных складах необходимых материалов позволяет приобрести все составляющие перед началом изготовления.
- Подготовку необходимого инструмента или оборудования для смешивания. Можно использовать бетономешалку для приготовления состава в увеличенных объемах или вручную осуществлять перемешивание в емкости с помощью лопат.
Несомненным преимуществом опилкобетона является то, что его можно сделать своими руками
- Смешивание компонентов в соответствии с рецептурой. Применение бетоносмесителей для автоматизации способствует повышению качества смешивания, производительности, улучшает качество опилкобетона.
- Заливку раствора в формы. Используются деревянные емкости разборного типа из досок толщиной 20 мм, облицованные пластиковыми листами или металлом.
- Сушку опилкобетона в естественных условиях. Приобретение эксплуатационной твердости и испарение влаги происходит на протяжении 90 дней после формовки опилкобетонных изделий.
Состав блоков
Опилкоблоки изготавливаются на основе следующих ингредиентов:
- портландцемента;
- песка;
- глины или гашеной извести;
- древесной щепы;
- воды.
Компоненты
Для производства используются отходы различных видов древесины:
- сосны;
- пихты;
- ели;
Для изготовления арболита требуется именно чистая щепа (частицы древесины), а не кора или листья
- тополя;
- ясеня;
- березы;
- бука;
- дуба;
- граба;
- лиственницы.
Оптимальный наполнитель – щепа, полученная при обработке хвойных деревьев. Повышенная концентрация смолы в хвойной щепе защищает материал от появления гнили.
Ускоренное твердение характерно для сосны. Изделия из сосновых опилок можно использовать через 40 суток после формовки. Продолжительный набор прочности происходит в опилкобетоне из дубовой щепы или лиственницы. Изделия из указанных видов древесины можно применять для возведения стен не ранее, чем через 100 суток после формования.
Подготовка древесного сырья позволяет увеличить прочностные характеристики опилкобетона, огнестойкость, снизить впитывание материалом влаги и включает следующие этапы:
- Вымачивание древесной фракции в известковом молоке.
- Сушку естественным или принудительным путем.
- Замачивание в жидком стекле, растворенном в воде в соотношении 1:7.
Приготовление рабочей смеси производится исходя из того, на какие цели будет использован строительный материал
Сепарирование щепы на сите с ячейками от 10 до 20 миллиметров позволяет обеспечить однородность наполнителя.
Пропорции
Пропорции применяемых компонентов определяются плотностью материала.
Например, для подготовки состава, обладающего повышенной плотностью, на тонну щепы потребуется:
- цемент – 1 т;
- известь – 0,25 т;
- песок – 2,5 т.
Соотношение компонентов корректируется опытным путем, зависимо от влажности.
Смешивание компонентов
Процесс перемешивания выполняйте в следующем порядке:
- Подготовьте необходимые материалы в требуемых количествах.
- Смешайте в сухом виде песок с портландцементом марки М300.
- Добавьте опилки и известь, равномерно перемешайте.
- Порционно добавляйте воду, перемешивая раствор до требуемой консистенции.
Важный нюанс изготовления блоков — смесь цемента и древесных опилок перед замешиванием должна быть сухой, то есть после выдержки щепу просушивают
Выполнение пробного замеса позволяет до начала работ откорректировать рецептуру. Эластичность подготовленного раствора при сжатии в ладони свидетельствует о его готовности. При рассыпании комка следует увеличить объем жидкости, а при отжимании воды – снизить. Правильно подготовленный раствор начинает твердеть через час после смешивания.
Размер опилок
Принимая решение по размеру органической фракции, помните:
- крупность опилок не является определяющим фактором при изготовлении опилкобетона;
- применение однородной древесной щепы способствует улучшению качества изделий.
Блоки из стружки и цемента – область применения
Сфера использования опилкобетона:
- возведение гаражей, хозяйственных построек, дач, жилых зданий;
- утепление капитальных стен домов и подвальных помещений;
- строительство различных видов ограждений;
- обустройство внутренних перегородок.
Подводим итоги
Самостоятельное изготовление блоков из опилок и цемента позволяет при небольших затратах возводить здания с комфортными условиями. Прочность, пожаробезопасность и экологическая чистота опилкобетона обеспечивает популярность недорогого строительного материала. Статья поможет разобраться с характеристиками материала, достоинствами и недостатками, особенностями технологии.
На сайте: Автор и редактор статей на сайте pobetony.ru
Образование и опыт работы: Высшее техническое образование. Опыт работы на различных производствах и стройках – 12 лет, из них 8 лет – за рубежом.
Другие умения и навыки: Имеет 4-ю группу допуска по электробезопасности. Выполнение расчетов с использованием больших массивов данных.
Текущая занятость: Последние 4 года выступает в роли независимого консультанта в ряде строительных компаний.
изготовление кирпича из щепы, стружек
Блоки из опилок и цемента – легкий и прочный современный строительный материал, входящий в группу бетонных изделий с пониженным удельным весом. Опилкобетон производится из щепы разных пород древесины и цементного раствора, выступающего в роли вяжущего. Материал обладает уникальными свойствами, что делает его популярным для использования в самых разных сферах строительства.
Виды опилкоблоков по удельному весу:Основные характеристики опилкобетона – высокие теплотехнические свойства, экологичность, повышенная прочность и стойкость к огню, хорошая паропроницаемость, сохранение свойств при резких перепадах температуры, высоком минусе и плюсе. Немаловажно и то, что стоимость блоков сравнительно невысокая и при желании их можно сделать своими руками.
- Теплоизоляционные – масса в пределах 0.4-0.8 т/м3
- Конструкционные – вес в диапазоне 0.8-1.2 т/м3
Прежде, чем применять блоки из стружки и цемента в тех или иных работах, необходимо тщательно изучить их технические характеристики и выполнить расчеты. При желании самостоятельно производить материал обязательно нужно ознакомиться с технологией и правилами выбора сырья.

Блоки на основе стружки и цемента – область применения
Применяется материал в самых разных сферах, но в основном в возведении малоэтажных зданий. Чаще всего из опилкобетона строят дачи, гаражи, внутренние перегородки в частных домах, таун-хаусы, погреба, коттеджи, здания бытового использования.
Популярен опилкобетон и для проведения работ по утеплению подвальных помещений, капительных стен сооружений, создания изоляционного слоя. Могут пригодиться блоки при строительстве разного типа ограждений. Редко они используют там, где есть большие нагрузки – строительство фундамента, несущих стен, перекрытий и т.д.
Обычно используют по максимуму характеристики теплоизоляции и реализуют конструкционные решения внутри помещений, в создании ненагруженных конструкций и т.д.
Там, где отмечена повышенная влажность, плиты или блоки желательно выполнять с дополнительным слоем изоляции, так как они будут впитывать влагу. При должной защите и учете всех свойств опилкобетон из щепы способен долго сохранять геометрическую форму, а также механические и эксплуатационные свойства.

Преимущества и недостатки
Прежде, чем начинать изготовление блоков из опилок и цемента своими руками, нужно хорошо изучить свойства материала, плюсы и минусы. С учетом специфичности его состава опилкобетон подходит далеко не для всех работ и условий эксплуатации, но при выполнении всех требований может стать действительно удачным выбором.
Основные достоинства опилкобетона:- Высокий уровень теплоизолцяии – дома хранят прохладу летом, тепло зимой, словно термос.
- Экологичность и безопасность для людей – отсутствие токсинов и вредных выделений гарантирует в жилье положительный микроклимат и отсутствие аллергий.
- Прочность – неплохие структурные показатели, некоторые виды опилкобетона можно использовать для возведения несущих конструкций (но не выше 3 этажей).

- Стойкость к огню – за счет введения в состав синтетических добавок, делающих материал способным в течение 2 часов не гореть при температуре +1200 градусов.
- Прекрасная паропроницаемость – за счет пористой структуры опилкобетон пропускает воздух, не задерживает влагу.
- Стойкость к резким перепадам температур – не боится замораживания/оттаивания, не деформируется при внешних воздействиях.
- Доступная стоимость – немного дороже газобетона, но при самостоятельном изготовлении цена еще понижается.
- Хорошие показатели звукоизоляции – благодаря пористости материала он работает в обе стороны (снаружи/внутри).
- Простая работа – легкий монтаж за счет минимального веса и идеальных геометрических параметров, распил, сверление с сохранением целостности структуры и формы.

- Использование вторсырья – все виды цементно-стружечных блоков и плит создаются на базе щепы или стружки, которые представляют собой отходы деревообработки. Купить опилки можно по небольшой цене.
- Длительный срок эксплуатации – при обеспечении оптимальных условий блоки из опилок и цемента служат десятилетия.
- Небольшой вес – что облегчает монтаж и снижает общее давление конструкции на основание.
Из недостатков материала стоит отметить такие, как: низкий уровень влагостойкости и необходимость в защите, ограниченный выбор сырья в плане пород древесины, большая длительность этапов производства (после того, как материал залит в формы, он должен затвердевать и сушиться минимум 3 месяца до начала работ).
Блоки из опилкобетона: характеристика
Опилкобетон предполагает определенные свойства и требования по использованию в строительстве. Так, для предотвращения попадания влаги обычно цоколь дома делают из бетона или кирпича высотой минимум 50 сантиметров от отмостки. Также вылет карнизов за границу фасадных стен делают минимум 50 сантиметров с установкой системы отведения талой, ливневой воды.
Толщина швов между блоками составляет около 10-15 миллиметров, нередко блоки используют лишь для кладки утепляющего внутреннего слоя.
Если же цементно-стружечные блоки (плиты) используются для создания оконных/дверных перемычек, их обязательно армируют. Что касается остальных требований, то все они обусловлены особенностями материала.

Состав блоков
Основные компоненты опилкобетона:
- Песок – повышает прочность, но снижает свойства теплоизоляции (поэтому важно подобрать оптимальную пропорцию)
- Портландцемент – минимум марки М400
- Деревянная стружка (щепа) – усиливает звуко/теплоизоляцию, перед применением сушится
- Специальные добавки – для обеспечения огнестойкости, пропитки от грызунов и т.д.
Компоненты
В производстве опилкобетона могут использоваться отходы самых разных пород древесины: пихта, сосна, тополь, ель, бук, береза, ясень, граб, дуб, лиственница. Но лучшим выбором считается щепа хвойных деревьев, так как в ней повышена концентрация смолы, защищающей от гнили.

Для сосны характерно ускоренное твердение – блоки можно использовать в строительстве уже через 40 суток после заливки в формы. Дубовая щепа и лиственница продлевают срок набора прочности – они требуют отстаивания на протяжении минимум 100 суток.
С целью повышения прочности, стойкости к огню и понижения способности впитывать влагу древесные компоненты готовят специальным образом: вымачивают в известковом молоке, сушат (принудительно/естественно), замачивают в смешанном с водой жидком стекле (1 часть стекла и 7 частей воды). Для обеспечения однородности материала щепу пропускают сквозь сито с ячейками 10-20 миллиметров.

Пропорции
Соотношение материалов в составе напрямую влияет на плотность и другие характеристики. Опилкобетон бывает разных классов, которые определяют свойства и пропорции. Так, М5/10 классы используют для утепления и работ по реконструкции, М15/20 – для возведения внутренних/внешних стен.
Пропорции материалов для 1 м3 опилкобетона:- 5 марка (плотность около 500 кг/м3) – по 50 кг цемента и песка, по 200 кг извести и опилок
- 10 марка (650 кг/м3) – 100 кг цемента, 200 кг песка, 150 кг извести и 200 кг опилок
- 15 марка (800 кг/м3) – 150 кг цемента, 350 кг песка, 100 кг извести и 200 кг опилок
- 20 марка (плотность 950 кг/м3) – 200 кг цемента, 500 кг песка, 50 кг извести, 200 кг опилок

Смешивание компонентов
Процесс смешивания такой: все материалы отмерить, смешать сухими песок и цемент, добавить известь и опилки, снова смешать тщательно, порционно вливать воду, добиваясь нужной консистенции раствора.
Сначала желательно сделать пробный замес, проверить смесь на эластичность: если комок рассыпается, нужно долить воды, если вода стекает – уменьшить объем. Правильно замешанный раствор твердеет в течение часа.
Размер опилок
Данный параметр мало влияет на прочность блоков, тут больше важна однородность материала, а не величина. Поэтому опилки выбирают такие, чтобы все компоненты были единого размера и дали возможность приготовить однородную смесь.
Подходит стружка с пилорамы – неважно, дисковой или ленточной. Но не стоит брать опилки с калибровочных или оцилиндровочных станков, так как они неоднородны по структуре.

Виды древесно-цементных материалов
Разнообразие древесно-цементных материалов не очень большое. Отличаются блоки по типу щепы и пропорциям материалов в составе, структуре, типу связующего. Самые популярные виды цементно-стружечных блоков: фибролит и арболит, цементно-стружечная плита, опилкобетон и ксилолит.
По прочности плиты бывают разных марок от М5 и классов от В0.35, плотности – показатель в диапазоне от 400 до 800 кг/м3.
Арболит
Производится из большого объема древесной щепы, песка, портландцемента, воды и химических добавок. Обычно в работу идут отходы деревообработки хвойных и лиственных пород, реже – солома-сечка, конопляная/льняная костра, измельченный стеблями хлопчатник и т.д.
Арболит бывает теплоизоляционным и строительным. В первом виде больше щепы, второй – более прочный. Где применяется: напольные плиты, кирпич под выгонку внутренних/наружных стен, покрытия и перекрытия, крупные стеновые панели.
Фибролит
Обычно поставляется в формате плит из цемента и стружки. Для производства используется щепа длиной 35 сантиметров и больше, шириной до 10 сантиметров, которая размалывается до состояния шерсти.
После помола сырье минерализируется хлористым калием, увлажняется водой, замешивается с бетоном, прессуется под давлением 0.4 МПа в плиты. Далее изделия проходят термообработку и сушатся. Фибролит также бывает изоляционно-конструкционным и теплоизоляционным.
Главные характеристики фибролита:- Пожаробезопасность – отсутствие способности гореть открытым пламенем
- Шероховатая поверхность – обеспечивает хорошее сцепление с другими материалами
- Теплоизоляция – теплопроводность находится в районе 0.08-0.1 Вт/м2
- Влагопоглощение – 35-45%
- Легкость обработки – материал можно пилить, сверлить, забивать в него дюбеля и т.д. без риска расколоть или деформировать
- Подверженность поражению плесенью и грибком при нахождении во влажности свыше 35%

Опилкобетон
Данный материал похож на арболит, но не так требователен к типу и параметрам щепы древесины. Состоит из цемента, песка, воды, опилок различной фракции, могут быть включены глина и известь. Пропорция песка тут может быть больше, чем в арболите, поэтому и прочность выше при идентичной плотности.
Опилкобетон обеспечивает больший вес несущей конструкции при одинаковом классе прочности. По теплоизоляционным характеристикам материал также уступает арболиту.
Основное преимущества опилкобетона – низкая стоимость при отсутствии особых условий по эксплуатации, что делает использование его в строительстве более выгодным.
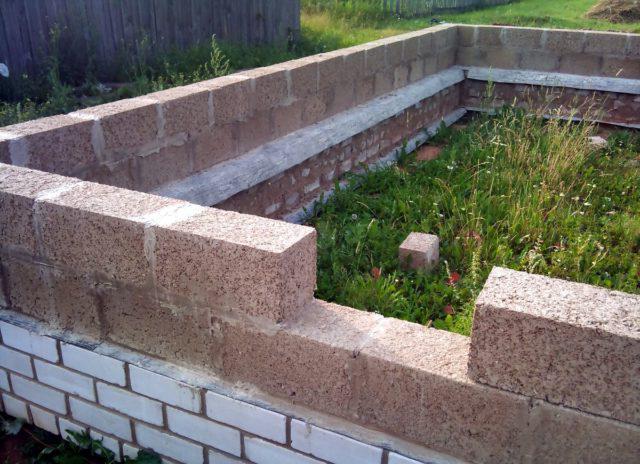
Цементно-стружечные плиты
Материал создают из замешанной на цементе, воде и минеральных добавках древесно-стружечной смеси, которую потом дозируют, заливают в формы, прессуют и обрабатывают высокой температурой. Главные преимущества плит: негорючесть, стойкость к морозу, биологическая инертность.
Плиты нередко используют в сборных конструкциях, в реализации внутренних и фасадных работ. Плиты отличаются высоким уровнем влагостойкости, из недостатков можно выделить лишь достаточно большой вес и низкую эластичность. При изгибах плиты ломаются (при этой демонстрируют хорошую стойкость к продольным деформациям), поэтому применяются часто с целью усиления каркаса.

Ксилолит
Песочный материал, сделанный на базе магнезиального вяжущего и древесных отходов (мука и опилки). Также в состав вводят минеральные тонкодисперсные вещества: мраморную муку, тальк, щелочные пигменты и т.д. Производство осуществляется с применением температуры в +90 градусов и давления в районе 10 МПа, что делает материал особенно прочным после затвердевания. Обычно плиты данного типа используют при создании полов.
Характерные особенности ксилолита:- Негорючесть
- Высокий уровень прочности на сжатие (5-50 МПа, зависит от вида материала)
- Стойкость к ударным нагрузкам, отсутствие риска смятия, сколов
- Отличные тепло/шумоизоляционные характеристики
- Стойкость ко влаге, морозу

Изготовление блоков своими руками
Приступая к созданию блоков из опилок и цемента своими руками, необходимо хорошо изучить весь процесс и учесть нюансы.
Как создать блоки самостоятельно:- Подготовить все инструменты для работы со смесью и устройства – бетономешалка, молотковая дробилка, рубильная машина, вибропрессовальная машина, вибростанок и т.д.
- Подготовить сырье – купить в строительном магазине цемент М400 минимум, заказать чистый песок, известь (можно глину), найти на заводе много древесных опилок (желательно сухих, если регион влажный – нужно также запастись минерализаторами для обработки опилок, в качестве которых могут выступить жидкое стекло или известковое молоко).
- Тщательное измельчение древесины путем загрузки в рубильную машину, а потом в молотковую дробилку (для получения одинаковой фракции).

- Аккуратный просев щепы, чтобы отделить мусор, землю, кору и т.д.
- Пропитка щепы – вымачивание в смеси жидкого стекла с водой в пропорции 1:7. Для ускорения прохождения процесса минерализации и затвердевания материала можно добавить немного хлористого кальция.
- Обработка гашенной известью – дезинфекция от вредителей.
- Смешивание – для получения стандартной смеси берут 1 тонну портландцемента, 250 кг извести и 2.5 тонн песка. Объем щепы определяется отдельно, исходя из нужных характеристик и вида блоков. Все смешивается в бетономешалке.
- Заливка смеси в формы, установка на вибропрессовальный аппарат.
- Сушка – натяжение пленки на емкость с формами, выдержка в помещении 12 суток при температуре +15 градусов и выше (в холоде гидратация будет проходить медленнее гораздо). Периодически материал можно проверять – если сухо, увлажнять водой.
Блоки из опилок и цемента – прекрасный выбор для выполнения множества работ в сфере ремонта и строительства малоэтажных зданий. При правильном выборе качественного материала и соблюдении технологии работы, создании оптимальных условий опилкобетон обеспечит надежность, прочность и долговечность конструкции.
Опилкобетон своими руками — пропорции строительства дома и бани блоками из опилок и цемента, плюсы и минусы
Современный рынок загородного домостроения испытывает постоянную потребность в простых по своему изготовлению материалах с высокими технико-экономическими показателями. Наступает эпоха ренессанса таких технологий, как арболит и опилкобетон. Несмотря на всю свою схожесть свойства двух лёгких бетонов, ровно как и состав, имеют существенные различия. Опилкобетон своими руками изготовить проще, стоимость его ниже, но он менее технологичен, нежели арболит. Впрочем, его характеристик достаточно для строительства жилых домов, а также вспомогательных и хозяйственных построек.

Плюсы опилкобетона
Монолит и блоки из опилкобетона обладают следующими достоинствами:

- простота изготовления, любой человек даже без строительного образования способен самостоятельно смешать ингредиенты в нужных пропорциях и получить этот материал;
- слагаемые имеют приемлемую цену, цемент, песок, известь и опилки легко приобрести на рынке, отходы деревообрабатывающих предприятий иногда удаётся получить бесплатно;
- короткие сроки возведения дома при наличии готовых блоков, ровные и красивые стены из опилкобетона легко монтировать;
- материал имеет хорошие тепло и звукоизоляционные свойства благодаря древесному наполнителю;
- отсутствие вредных примесей, дом из опилкобетона отвечает всем современным экологическим требованиям;
- стены из этого материала не гниют и обеспечивают хорошую огнезащиту.
Минусы опилкобетона
Наряду с многочисленными достоинствами, этот строительный материал наделён присущими ему недостатками:

- высокая гигроскопичность, опилки впитывают влагу и уваливаются в объёме, разрушая целостность строительного камня;
- долговечность конструкции находится в сильной зависимости от качественной отделки стен, т. к. материал поглощает влагу извне, и это, в свою очередь, снижает его морозостойкость.
Строительство из опилкобетона
Область применения
Данная технология возведения зданий находит применение при строительстве подсобных построек, гаражей и малоэтажных жилых домов. Обязательным требованием для стен из опилкобетона является последующая отделка, несущая не только декоративные, но и защитные свойства.
По своей плотности и прочностным характеристикам камень можно разделить на две категории: теплоизоляционный и конструктивный. Для создания несущих стен дома рекомендуется использовать марку опилкобетона М25 и выше, допускается применение менее прочных составов в одноэтажных строениях жилого и нежилого характера.
Проектирование
Строительству дома должен предшествовать этап проектирования. В этот период принимаются все ключевые технические решения, определяются материальные затраты на строительство.
Проектирование зданий из опилкобетона происходит по тем же правилам, что и для других конструкций на основе блоков из лёгких бетонов. Однако, для этого материала нет действующего ГОСТа, а его точную прочность нужно определять на основании лабораторных испытаний.
Фундамент и цоколь здания
Бетоны с содержанием опилок и стружки категорически нельзя использовать в фундаменте дома. Подобная экономия приведёт к тому, что все дальнейшие вложения будут сделаны впустую, поскольку жилище будет опасно для своих обитателей, и его эксплуатация станет невозможной.
Выбор типа фундамента должен осуществляться с учётом несущей способности грунтов, залегающих под будущим строением, уровня грунтовых вод, пучинистости, наличия пустот и т. д.
Стены
Существует выбор между двумя доступными вариантами стен дома из опилкобетона. Здесь возможно использование заранее приготовленных или купленных блоков для кладки или же создание монолитной конструкции. Для принятия оптимального решения стоит разобрать преимущества и недостатки каждого из этих способов.
Кладка из блоков
Данный подход обеспечит простоту выполнения и сжатые сроки завершения работ. Второе особенно важно, так как материал очень долго набирает прочность, а строительство нужно успеть закончить до наступления холодов. По удобству работы с материалом его можно сравнить с арболитом. Опикобетон имеет больший удельный вес и хуже режется, но он явно превосходит по этим характеристикам классические бетонные блоки, являясь этаким крупным кирпичом из опилок. В вопросах перевязки швов и армирования такая кладка идентична газобетонной.


Монолитные стены

Перед началом монолитных работ в пространстве будущей стены устанавливаются деревянные рамы примерно через каждые 1,5 м. Их используют для закрепления опалубки, и впоследствии эти каркасы будут играть роль противоусадочных швов. Строительную смесь заливают слоями по 150 мм высотой и трамбуют. Для этой цели хорошо подойдёт инструмент, сделанный из бруса, с небольшим заострением внизу. Продольную арматуру, в виде сетки рабицы или узкой доски, размещают через каждые 400 мм.
Монолитная технология является оптимальной, если все компоненты, из которых производится опилкобетон постоянно доступны, в наличии ёмкость для приготовления смеси, микшер.
Окончание стены. Монолитный пояс или деревянный брус
Под опорами кровли и перекрытий в доме из опилкобетона всегда присутствует какая-нибудь разгружающая конструкция. Чаще это обвязочный брус, поскольку предпочтительным типом перекрытия будет деревянное, потому что оно легче бетонного. Использование же металлических балок нежелательно из-за наличия извести в составе опилкобетона. Торцы деревянных балок перекрытия следует оборачивать гидроизоляцией.
Кровля
Наилучшей кровлей будет та, что выглядит красиво, защищает от дождя и снега, обеспечивает теплоизоляцию и вдобавок прочная и лёгкая. Таким образом, одним из оптимальных выборов, будет скатная кровля, покрытая, для примера, битумной черепицей.
Свесы у крыши отступают примерно на полметра от края внешних стен жилища. Дождевая вода отводится при помощи сточных труб и желобов в дренаж или ливнёвку.
Требования к отделке стен

Приятной особенностью материала будет тот факт, что отверстия для крепежа в нём сверлятся хорошо, а прочности хватает для надёжной фиксации мебели и бытового оборудования.
Изготовление опилкобетона
Как уже не раз отмечалось в статье, материал несложен в производстве. Большинство инструментов, которые понадобятся для изготовления блоков из стружки и цемента, стоят недорого, а некоторые, и вообще, можно сделать самостоятельно. Но для начала, стоит рассказать о растворе.
Состав опилкобетона
Для изготовления строительной смеси нужны: цемент, песок, известь и органический заполнитель в виде опилок. Получение 1 м3 готового материала пропорции опилкобетона будут следующим, в зависимости от требуемой марки:
- Теплоизоляционный материал с маркой прочности М5: 50 кг цемента марки М400, 50 кг песка, 200 кг гашёной извести, 200 кг опилок. Готовый продукт будет иметь плотность около 500 кг/м3;
- Марка М10, пригодного для ограждающих так и для несущих стен подсобных построек: 100 кг цемента марки М400, 200 кг песка, 150 кг гашёной извести, 200 кг опилок. Готовый продукт будет иметь плотность около 650 кг/м3;
- для более прочного М15, применяемого как М10, но также пригодного для возведения одноэтажных жилых домов: 150 кг цемента марки М400, 350 кг песка, 100 кг гашёной извести, 200 кг опилок. Готовый продукт будет иметь плотность около 800 кг/м3;
- Конструкционный опилкобетон с маркой по прочности М25, подходящего для возведения несущих стен жилых построек высотой до трёх этажей: 200кг цемента марки М400, 500 кг песка, 50 кг гашёной извести, 200 кг опилок. Готовый продукт будет иметь плотность около 950 кг/м3.
- Для ускорения затвердевания опилкобетона в смесь подмешивают нитрат кальция, жидкое стекло или сульфат амония. Другого эффекта на блоки из опилок эти присадки не имеют.
Требования к опилкам

Перед приготовлением смеси опилки стоит подержать на улице, свалив навалом под открытым небом. Возможный дождь пойдёт только на пользу, ибо поможет смыть с деревянного сырья ненужные сахара. Кстати, получить ингредиент можно абсолютно бесплатно, договорившись забрать отходы на мебельном или другом деревообрабатывающем предприятии.
Другие варианты приготовления раствора
Гашёную известь в составе смеси можно заменить на глину, пропорции компонентов при этом не изменяются.
Ещё одна возможная замена – вяжущее вещество. В качестве альтернативы цементу выступает гипс. Чтобы приготовленный раствор не схватывался слишком быстро, в воду добавляют моющее средство. Опилкобетон, полученный таким образом, имеет скорость твердения в 4 – 5 раз выше и выходит несколько дороже по цене. При этом также повышается чувствительность материала к воде, и снижаются его прочностные характеристики.
В каком порядке смешивать ингредиенты?
Сначала разводят цемент в воде, затем в него подмешивают нужное количество опилок, песка и извести.
Находящиеся в ёмкости для приготовления раствора опилки смешиваются с известью, далее к ним добавляется цемент и песок, полученная смесь затворяется необходимым количеством воды.
Обе последовательности применяются на равных. Чтобы определить раствор, готовый к укладке в опалубку рукой берётся и сжимается небольшое его количество. Качественно выполненный материал сохраняет вмятины от пальцев руки, не растекается и не рассыпается, т. е. является однородной пластичной массой.
Самостоятельное изготовление опилкобетонных блоков
Полученный раствор укладывают в формы. Их можно сколотить из досок или купить готовые. Оптимально подойдёт оборудование для отливки шлакоблоков. В зависимости от наличного инструмента применяется метод ручной или механической трамбовки состава в форме. Для удаления пустот часто используются уплотняющие штыри. Снятие форм производится через 4–5 суток, после этого начинается процесс сушки, который занимает 2 – 3 месяца. Создавать их нужно заранее, чтобы опилкобетонные блоки успели высохнуть к началу монтажа стен.
В итоге опилкобетон оказывается достаточно интересным материалом, когда речь идёт о загородном малоэтажном строительстве. Здесь он имеет широкую область применения. Может быть как утеплителем, так и конструкционным материалов. Материал лёгок в использовании, понятен и экономичен.
Отличные полы из стружко- и опилкобетона арболита своими руками
Ответы знатоков
Александр Знайка:
Опилкобетон получают следующим образом. Сначала на деревянный щит насыпают необходимое количество песка, добавляют смесь цемента и извести и все тщательно перемешивают, пока смесь не станет однородной. Затем добавляют соответствующее количество опилок и снова перемешивают. Продолжая перемешивание, массу равномерно увлажняют.
2. На 1 м опилкобетона берется 250…350 п воды. Нижняя граница
относится к более тяжелым бетонам (М 25), а верхняя к пегким (М 5).
Количество воды удобно определить экспериментальным путем. Оно
должно быть таким, чтобы при сжатии свежеприготовленная смесь
сохраняла форму: но не выделяла воду.
3. Опилкобетон марки 5 можно использовать только как теплоизоляцнонныл материал; 10 — для наружных стен одноэтажных зданий с мансардой, несущих внутренних капитальных стен, выравнивающего слоя
нал фундаментами, под мауэрлатом И цр. ; 25 для наружных стен двух
этажных зданий, несущих внутренних капитальных стен, а также для
неотапливаемых опилок поливают раствором цемента и извести и тщательно перемешивают до получения однородной густой массы.
Приготовление опилкобетона вручную — очень трудоемкий процесс, поэтому по возможности надо использовать бетоно или растворосмесители.
Опилкобетон можно пилить, обрабатывать топором и долотом, а также можно вбивать в него гвозди.
Свежие опилки из древесины хвойных пород можно использовать без предварительной обработки, а старые, долго пролежавшие, и те, которые во время эксплуатации могут быть подвергнуты действию влаги, следует обработать 10%-м раствором хлорида кальция или известковым молоком, высушить и еще раз обработать раствором жидкого стекла (1:7) или битумной эмульсией.
Я полагаю, что хлорид натрия может используют иногда также как хлорид кальция.
Вообще-то, как я вижу, использование хлорида натрия (поваренной соли) нетипично. Обычно используют известь Приготовление сырья для изготовления арболитовой смеси Наполнителем будут служить отходы деревообработки и лесозаготовок – щепа, стружка, опилки и т. п
Обратите внимание, что частицы древесины должны быть мелкими (менее чем 40х10х5 мм) , так как при контакте с влагой дерево набухает, что может стать причиной разрушения арболитового блока. Древесные отходы перед применением необходимо подготовить соответствующим образом – либо выдержать на воздухе 3-4 месяца, либо обработать раствором извести
Известковый раствор готовят в следующих пропорциях: 2,5 кг извести и 150-200 литров воды на каждый кубический метр наполнителя. После обработки древесные отходы выдерживают трое суток, каждый день перемешивая.
Химические добавки используются самые различные. Многие добавляют гашёную известь (от 2 до 4% от количества портландцемента) .
Кроме того, отличными добавками являются: хлористый кальций, хлористый алюминий, сернокислый алюминий. Их также нужно использовать в размере 2-4%. Например, 1% хлористого кальция и 1% сернокислого алюминия. Добавлять можно и жидкое стекло (8-10 кг на 1 куб. метр арболита) , и некоторые минеральные удобрения. или вот этата же ссылка: (нажать на Proceed to this site.)
Николай:
вот интересная статья про арболитовые блоки
nesmetnoe /stroitelstvo/stroim-dom/71-arbolitovye-bloki
минусы расчет производство фото
SUPERPUPER MAN ВАСИЧКИН:
На каком языке ты щас это высрал ?
Трояко Дышащий:
Теплопроводность материалов очень низкая…
Chelovek:
Из-за большой пористости, рыхлости.
Достоинства и недостатки
Арболит обладает огромным количеством плюсов по сравнению с другими строительными материалами.
- Экологичность сырья. Изготавливается в основном из натуральных компонентов.
- Высокая огнестойкость. Несмотря на то, что арболит главным образом состоит из древесных отходов, он не горюч.
- Хорошая паропроницаемость. Это свойство позволяет зданиям дышать и сохранять свой микроклимат.
- Небольшой вес древоблоков. Этот фактор заметно упрощает строительство.
- Лёгкая обработка режущими инструментами. Блоку можно легко придать любую нужную форму.
- Простота в обращении. При укладке блоки из арболита не требуют профессиональных навыков.
- Устойчивость к плесени, грибкам и вредителям. Материал обладает IV классом биостойкости.
- Высокая теплопроводность. По этой причине арболит часто используется при постройке частных домов.
- Устойчивость к усадке. Стены и перегородки в этом случае не пойдут трещинами.
- Высокое звукопоглощение. Благодаря этому материал может использоваться и для строительства промышленных зданий.
- Устойчивость к сейсмической активности.
К минусам относятся следующие факторы.
- Если не предпринять меры для защиты от влаги, арболит быстро начинает разлагаться, теряя свои свойства.
- Блоки не обладают идеально ровной поверхностью из-за характерных особенностей состава.
- Арболитовым стенам требуется дополнительная отделка.
- Материал обладает низким уровнем сцепления со штукатурными смесями.
- Из-за огромного количества кустарных производств на рынке часто встречается некачественный товар.
- Небогатый ассортимент изделий.
- Отсутствие масштабного производства сказывается на высокой цене материала и сложностях с доставкой.
Состав блоков
Для изготовления арболита древесные отходы, как правило, берут хвойных пород – они меньше подвержены биологическому разрушению. Как вяжущее – применяют цемент (иногда для удешевления его часть заменяют глиной и известью). Рецептур существует достаточно много, но как правило, берут количество цемента с водой равное по весу с весом сухого заполнителя.
Для увеличения прочности стружкобетона в него добавляют песок, но следует учитывать тот факт, что с увеличением количества песка растёт вес арболита и уменьшаются его теплоизоляционные свойства.
Ещё в состав стружкобетона (да и остальных материалов с отходами древесины) входят обязательно специальные соли, которые делают древесные отходы не горючими, и они практически не поражаются грибками и бактериями.
Нюансы
Прежде чем заполнить деревянные формы опилкобетонной смесью, их устанавливают на ровные пластиковые или стальные поддоны, посыпанные тонким слоем опилок. Затем внутри ячеек устанавливают деревянные пробки, обернутые толем, которые необходимы для получения отверстия в блоках.
Когда смесь уложена в форму, ее трамбуют специальной трамбовкой. На протяжении последующих 3-5 дней материал приобретает от 30 до 40 процентов марочной прочности. По истечении этого срока форму для литья разбирают, а пробки извлекают из блоков. Готовые, но еще не высушенные изделия оставляют на этом же месте на 3-4 дня. За это время их прочность возрастает уже до 60-70 процентов.
Арболит
Часто опилкобетон путают с другим строительным материалом – арболитом, что совершенно неверно. Согласно ГОСТу, арболит определяется как бетон на цементном вяжущем, химических добавках и органических растворителях. Однако в классическом варианте арболитобетон предполагает использование древесной щепы. Именно она и определяет его уникальные свойства.
Ровно, как и опилкобетон, арболит является экологически благоприятным стеновым материалом, отличающимся высокими показателями огнестойкости и теплоизоляции. Тем не менее эти два материала, несмотря на схожесть структуры, имеют принципиальное отличие. Дело в том, что в производстве арболита вместо мелких древесных опилок, которые не могут обладать достаточными прочностными свойствами сами по себе, используют специальную древесную щепу, размер которой строго нормируется. Опилки, в отличие от щепы, не могут в достаточной мере армировать (усиливать) стеновой блок и давать ему «пластичность». Таким образом, арболитобетон прочнее опилкобетона с точки зрения прочности на изгиб и способности к временной деформации без полного разрушения. Справедливости ради стоит отметить, что опилкобетон по этому показателю превосходит остальные виды легких бетонов.
Для упрочнения блоков, заполнения пустот и уменьшения усадки в состав опилкобетона добавляют много песка, а для экономии вяжущего материала – также немало извести или глины. Использование большого количества песка негативно сказывается на огнестойкости рассматриваемого нами материала – при температуре +573 °С опилкобетон изменяется в объеме, что может привести к растрескиванию. Кроме того, из-за весомого содержания песка снижаются конструкционные характеристики блоков. Так, чтобы опилкобетон достиг прочности марки М25, его плотность должна составлять 950кг/м3. Из-за высокой плотности стоимость материала и его доставки повышается, а проведение строительных работ – усложняется.
У арболита аналогичной марки плотность составляет от 500 до 700 кг/м3. Учитывая, что с повышением удельного веса теплосберегающие свойства падают, теплопроводность опилкобетона и арболита отличается более чем в два раза в пользу последнего. Такая разница обусловлена невысоким количеством древесины в опилкобетоне по сравнению с арболитом: примерно 50 % против 80-90 % щепы. Это негативно сказывается на таком свойстве, как обеспечение пассивной вентиляции помещения. Здесь, опять же, стоит отметить, что по этому параметру опилкобетон значительно превосходит большую часть стеновых материалов. Он отлично подходит для строительства зданий малой этажности и уступает лишь своему «сопернику».
Таким образом, называть опилкобетон арболитом крайне некорректно, так как это совершенно разные материалы. Единственное сходство между ними – наличие древесного компонента в составе.
Технология производства
Сегодня применяют несколько способов изготовления стеновых блоков для наружных и внутренних стен. Чаще всего они производятся методом прямого прессования или с помощью вибролитья (вибропрессования).
Первый способ представляет собой сравнительно молодую и довольно бюджетную технологию. Она предусматривает суточную выдержку арболита в формах. Но полученная при этом масса не отличается однородностью, что грозит внутренними напряжениями в готовом изделии.
Однако основной процесс изготовления в обоих методах одинаков.
Он состоит из трех важных этапов.
- Сортировка и размельчение органики.
- Смешивание щепок с химическими компонентами, цементом и водой. Операция занимает 10 минут.
- Формовка и высушивание готового раствора.
Виды блоков с древесными наполнителями
Ещё стружкобетоны или арболиты можно разделить по таким видам:
- теплоизоляционный. Плотностью до 450 кг/м3;
- теплоизоляционно-конструкционный. Плотностью 450-650 кг/м3;
- конструкционный. Плотностью 600-800 кг/м3.
Арболит и опилкобетон применяют в виде стеновых панелей, в виде монолитной заливки и в виде блоков различных типоразмеров. Особенности монолитной заливки в том, что стена из арболита схватывается относительно неравномерно и возможны коробления. А блоки стараются не делать более 20 сантиметров в толщину, так как они будут долго сохнуть, да и класть тяжёлые блоки более трудоёмко.
Ещё одна из отличительных особенностей стружкобетона это то, что стены, построенные из него, не потеют и не текут. Так как он с одной стороны сохраняет многие полезные свойства дерева, а с другой стороны – по сравнению с другими строительными материалами (кирпич, пенобетон), имеет более высокую паропроницаемость.
Можно даже говорить о частичной вытеснительной вентиляции через стены из арболита, опилкобетона. Это уникальный вид вентиляции, когда воздух просачивается через структуру самого материала, он нагревается, проходя через многочисленные волокна и вытесняет уже нагретый «отработанный» воздух в доме.
Благодаря этому в домах из стружкобетона отсутствуют «застойные зоны», существенно уменьшаются (или вовсе отпадают за ненадобностью) затраты на обустройство вентиляции. А вследствие – уменьшаются также теплопотери дома.
Можно подвести итоги:
- Арболит (и все блоки с древесными наполнителями) – материал для тех, кто заботится о своей семье, и в то же время хочет уменьшить затраты не строительстве дома. Ведь арболит легче кирпича в 4 раза, значит нужен не такой крепкий фундамент (более дешёвый).
- Стена из стружкобетона в 35 см толщиной соответствует кирпичной кладке 1 метр по теплоизолирующим свойствам.
- Уменьшаются затраты на систему вентиляции.
- Стружкобетон или арболит не подвержен повреждения грызунами, насекомыми, грибками, бактериями и огнём, по сравнению с обычным деревянным домом.
- Из-за пористой поверхности, на арболите прекрасно удерживаются штукатурка и шпаклёвка.
- Арболит легко поддаётся обработке, его можно легко рубить, пилить, вбивать гвозди и вкручивать шурупы.
На пучинистых и других нестабильных грунтах стружкобетон (арболит, опилкобетон) практически незаменим. Ведь он обладает хорошей упругой деформацией. И при малейших шевелениях фундамента (через морозы или шевелении грунта) другие кладочные материалы потрескаются.
А стружкобетон может немного помяться, ведь стружка и щепа, входящие в его состав, выполняют роль армирующих волокон с одной стороны и с другой стороны могут вминаться.
Из относительных недостатков и особенностей следует отметить то, что стены из стружкобетон рекомендуют снаружи штукатурить или обкладывать кирпичом, или по-другому защитить от прямого воздействия осадков. Также делая дом из стружкобетона, надо следить за тем, чтобы материал был качественным, ведь некоторые умельцы могут продавать откровенно некачественный материал, дискредитируя такой отличный материал.
Лучшие ответы
I’ll be back:
консистенцию не знаю, но ты в курсе что опил должен быть обезвожен и обработан спец. составом? а так почитай про бризолит, тоже самое…
Онлайн журнал Советы хозяевам:
Опилкобетон он же арболит, представляет собой смесь из опилок, песка воды и цемента. Правильная консистенция? Не совсем понятно, что имеется ввиду, если пропорции, то зависит от желаемой марки. В самом простом виде — три ведра опилок, ведро песка и ведро цемента. Если прочнее, два ведра опилок пол ведра песка и ведро цемента. Кроме того, если опилки свежие (до 2-х лет) обязательно добавляем около 5% от объема хлорида кальция, извести или жидкого стекла.
Если консистенция в смысле количества воды, то опять же от желаемой марки, но в общем порядка 0,8 от цемента. Дело в том, что для арболита, сколько воды не добавь, опилки впитают, все одно жидкого состава не получится. Поэтому воды много не нужно лить. Только прочность снизится. Из опыта, состав что-то вроде мокрых опилок получается, наваливаем в опалубки и хорошенько трамбуем. Слой не больше 20-25 см. Лучше всего форму из досок или листового металла сделать и готовить блоки, а из них уже строить. Но можно и послойно ставить опалубку из досок. Внизу такой опалубки делаем опорный брус. Набили, два-три дня подождали, переставили. Брус (20х20 максимум) если сделано аккуратно дает своеобразный шов, стена получается с рустами, довольно интересная. Что до промерзания, тут вопрос. 40 см арболита, это как бревно 25 -30 см по теплопроводности. Промерзнуть не промерзнет, но печку топить придется.
Но вообще-то арболит боится воды, так что снаружи лучше чем ни будь облицевать, а сразу можно и дополнительный слой утеплителя проложить. Ну и этажность не более двух этажей…
Смешивание
Одной из наиболее трудоемких стадий в производстве опилкобетона (своими руками изготовить блоки может даже начинающий строитель) является перемешивание, поэтому рекомендуется использовать бетономешалку или хотя бы растворосмеситель. Это позволит сделать процедуру смешивания не только более комфортной, но и более качественной. Прежде чем засыпать высушенные опилки в бетономешалку, их нужно просеять через сито со стороной ячейки 1 см. Затем можно смешать опилки с цементом. Лишь после этого в смесь добавляют глиняное или известковое тесто, заготовленное заранее. Все компоненты нужно тщательно перемешать и развести водой. Воду нужно добавлять малыми порциями. После каждого долива необходимо перемешивать смесь опилкобетона. Пропорции компонентов устанавливаются индивидуально, в зависимости от назначения конечного изделия. Чем больше нагрузки будет приходиться на блоки, тем выше их марка.
Если замес опилкобетона произведен надлежащим образом, то при сжатии в кулаке смесь будет образовать пластичный комок, на котором при отсутствии капель воды будут просматриваться вмятины от пальцев. Это считается основным показателям правильно приготовленной смеси.
Состав
Как можно понять из названия, определяющим элементом этого материала являются древесные опилки. Кроме того, в состав опилкобетона входят песок, цемент, а также глина или известь. Благодаря благоприятным санитарно-гигиеническим показателям материал оптимален для возведения стен жилых помещений.
Плотность строительного материала зависит от соотношения опилок и песка. Чем больше в опилкобетоне песка и вяжущих материалов, тем больше его плотность. В таком случае материал обладает высокими прочностными, но низкими теплотехническими характеристиками. С увеличением количества опилок прочность понижается. Вместе с ней снижается морозостойкость материала и его водонепроницаемость, что, в свою очередь, негативно сказывается на коррозионной стойкости стальной арматуры. Арматура используется при укладке стен. Из вышесказанного можно сделать вывод, что прежде чем начать возводить дом из опилкобетона, необходимо изучить особенности влияния состава материала на его свойства
Выбирая тот или иной состав, стоит принимать во внимание толщину стен, этажность здания и назначение стен (внутренняя, наружная или же несущая)
Плюсы и минусы опилкобетона
Опилкобетон все чаще выбирается для создания дачных домиков. Его использование может приносить определенные плюсы, поскольку в материале можно выделить следующие положительные качества:
- нагрузка на фундамент заметно снижается;
- наблюдается повышенная теплоизоляция;
- стоимость строительства более низкая;
- стены устойчивы к морозам и не воспламеняются;
- имеется защита от воздействия микроорганизмов;
- дом имеет прекрасную звукоизоляцию;
- можно облицевать стены разным материалом.
Однако, как и у других строительных материалов, опилкобетон имеет некоторые недостатки, которые также нужно учитывать при строительстве:
- несущая способность является низкой;
- блоки способны впитывать влагу;
- обязательно требуется облицовывать стены;
- материал дает усадку.
Сравнение с другими материалами
Для возведения жилого здания или хозяйственной постройки очень важно правильно выбрать строительные компоненты. Но следует знать, что не бывает хороших или плохих материалов, есть только подходящие и не очень
Керамзитобетон. Так же как и арболит, это экологически чистый материал и относится к классу легкого бетона. В его состав входят керамзит (обожженная глина или глинистый сланец), цемент, песок и вода. Однако керамзитоблоки обладают показателем теплопроводности (0,5 – 0,7 Вт/м·К), то есть немного хуже, чем у арболита. Поэтому для дома, с точки зрения сохранения тепла, лучше выбрать древоблоки. Несмотря на более высокую прочность, керамзитобетон может не выдержать превышение давления. Это объясняется полым пространством внутри изделия.
- Опилкобетон. По составу этот материал очень похож на арболит. В обоих случаях используются древесные отходы. Так же как и арболит считается экологичным строительным материалом, обладает высокими теплозащитными качествами и устойчив к растяжению, сгибу и удару.
- Газобетон. Ячеистая композиция состоит из песка, цемента, воды и газообразователя, благодаря которому и появляется характерная пористость. В отличие от арболита, у газоблока наблюдается чёткая геометрия изделия. Материал характеризуется высокой гидроустойчивостью и хрупкостью. Если сравнить этот материал и арболит, то по многим характеристикам газобетон выигрывает.
- Полистиролбетон. Это разновидность лёгкого бетона, состоящего из портландцемента, гранул вспененного полистирола и воздухововлекающих добавок. Отличается он высокой конструкционной прочностью. Даёт усадку, но значительно меньшую, чем газоблоки и пеноблоки. Так же как и арболит, обладает хорошими теплоизоляционными свойствами. Полистиролбетонные блоки не нуждаются в дополнительном утеплении.
- Соломенные блоки. Они представляют собой строительный материал, состоящий из экологически чистого сырья – прессованной соломы. Соломенные блоки обладают лучшим, чем у арболита показателем теплопроводности (0,05 – 0,065). Но имеют и такие недостатки, как высокая влагопоглащаемость и низкая огнестойкость.
- Брус. Это высокоэкологичный дышащий материал, изготовленный из клеёных досок или брёвен. Отличается замечательным показателем теплопроводности и высокой прочностью. Является достойным конкурентом арболита.
- Газосиликат. Этот ячеистый материал получают из раствора мелкого песка, извести, газообразующих добавок и воды. По структуре схож с газобетоном, но есть разница в составе, а следовательно, и в свойствах. Характеризуется хорошей теплопроводностью, высокой хрупкостью и повышенным влагопоглощением.
- Фибролит. Это аналог арболита с очень похожим составом. В обоих случаях в качестве составляющих выступают древесные отходы. Но если в первом варианте идёт стружка, то в фибролите используется древесное волокно, изготавливаемое в виде тонких и узких лент. Так же как и арболит, обладает хорошей теплопроводностью (0,08 – 0,1 Вт/м·К) и нуждается в дополнительной защите от влаги.
- Сибит. Состоит из бетона, гипса, алюминиевой пудры с добавлением ПАВ и воды. Считается экологически чистым материалам, так как в результате реакций образуется искусственный камень. Обладает чрезвычайно высокой морозостойкостью (до 250 циклов замораживания и оттаивания), но низкой прочностью на излом. Для малоэтажного дома обычно не применяется.
- Саман. Это самый древний строительный материал, состоящий из экологичного сырья – глинистого грунта и соломы. Саман обладает отличным коэффициентом теплопроводности (0,1 – 0,4). Однако имеет важный недостаток – повышенную влагопроницаемость.
О плюсах и минусах арболита, в видео ниже.
Окончательная сушка
Последней стадией изготовления опилкобетона является сушка. Для окончательной сушки блоки необходимо перенести под навес или накрыть полиэтиленом. Желательно, чтобы они находились на сквозняке. Укладывая блоки, необходимо оставлять между ними зазоры для вентиляции. Как правило, укладку производят в виде столбов. Для начала на два обожженных кирпича кладут пару стеновых блоков, затем поперек них еще пару и так далее. Спустя месяц блоки затвердеют, высохнут и достигнут 90 % прочности. Чтобы они получились максимально прочными, рекомендуется подождать еще три месяца, прежде чем начать строительство. Пренебрегать этим правилом или нет – решать вам, все зависит от типа здания, для которого заготавливается материал. К примеру, для возведения бани из опилкобетона вовсе не обязательно ждать, пока изделия высохнут на 100 %. Полностью готовые блоки должны быть твердыми, прочными и не иметь трещин. При падении с метровой высоты они не должны разбиваться.
Преимущества возведения дома из опилкобетона
Для каждого застройщика важно, чтобы жилье обошлось как можно дешевле, также важна быстрота возведения и получение теплого и комфортного дома. Именно под такие характеристики и попадает опилкобетон
Для осуществления строительства зданий можно обозначить некоторые преимущества материала:
- В составе имеются компоненты, которые являются общедоступными, поэтому их легко можно купить, что весьма удобно, если нет склада для хранения большого запаса элементов.
- Составляющие имеют низкую стоимость, поэтому и цена готовой конструкции будет не слишком высокой. Точную стоимость назвать непросто, так как в каждом регионе цена на составляющие различна. С точностью лишь можно утверждать, что сумма окажется намного ниже, чем, если применять иные легкие бетоны.
- Возвести дом можно очень быстро. Даже если строительство будет идти с нуля, уже за сезон удастся выполнить задуманное.
- Имеется возможность возведения, как монолитных зданий, так и из блоков, заготовленных заранее. Каждый из данных способов отличается удобством, однако большую популярность завоевывает заливная технология, поскольку дом возводится намного быстрее и возни с блоками не возникает.
- При возведении дома любым из способов нет материалов, обладающих большим весом, поэтому справиться сможет даже один человек. Помощники будут необходимы только при создании перекрытий и сооружении кровли.
При возведении дома из опилкобетона можно выделить и минусы, которые, впрочем, можно рассматривать как особенности материала:
Необходимо г8рамотно подбирать состав для возведения конструкции, поскольку он может получиться различной плотности, следовательно, это отразится на несущей способности и проводимости тепла.
Важно основательно изучить технологию выбранного варианта строительства, поскольку из-за недостаточного количества опыта, стены могут получиться кривыми, едва выдерживающими даже собственную тяжесть. Подобные погрешности сделают облицовку стен весьма затруднительной.
Необходимо следовать технологии по внесению веществ минерализирующегося типа, иначе из-за высокого водопоглощения срок службы здания заметно снизится, да и эксплуатировать его станет не очень комфортно.. https://www.youtube.com/embed/KCC1XoEtFq4
Если подвести итог, то опилкобетон является лучшим, что можно выбрать для возведения собственного дома, особенно если это делать своими силами. Преимуществ у данного материала имеется предостаточно, а если правильно осуществить подход, то и минусов не останется. Тем более что многие недостатки легко устраняются. Фасад дома можно оштукатурить или использовать вагонку для облицовки, допустимо и применение иных материалов. Таким образом, жилище приобретает красивый внешний вид. Если сделать надежную влагоизоляцию стен, то такой дом будет служить довольно долго. Опилкобетон – прекрасный вариант для сооружения небольших малоэтажных зданий, особенно, когда стоит вопрос об экономии средств.
Зола опилок в качестве порошкового материала для самоуплотняющегося бетона, содержащего нафталинсульфонат
Испытания проводятся для определения текучести портландцементной пасты Ashaka и ее совместимости с золой опилок в качестве порошкового материала для смесей самоуплотняющегося цемента (SCC) . Результаты исследования показали, что насыщение достигается при соотношении в / ц 0,4 и 0,42, при дозировках суперпластификаторов нафталинсульфоната 3,5% и 2% соответственно. Оптимальный уровень замены для смеси SCC составлял 10 мас.% цемента по АСД и 2% от дозировки суперпластификатора. Достигнутое время распространения и истечения составило 26 см и 8 секунд и находится в пределах указанного диапазона от 24 см до 26 см и от 7 до 11 секунд, соответственно. Статистический вывод показал, что смесь, w / c, и взаимодействие между смесью и соотношением w / c являются значительными.
1. Введение
Суперпластификаторы часто добавляют на стадии смешивания бетона в небольших количествах, связанных с массой цемента, для увеличения текучести свежего бетона, увеличения прочности и продления срока службы затвердевшего бетона.Исследования показали, что совместимость цемента и суперпластификаторов зависит от таких факторов, как содержание фазы C 3 A и C 4 AF в клинкере ПК, общее количество щелочи, крупность цемента, а также тип и количество сульфата кальция [ 1].
Сообщалось о проблемах совместимости суперпластификаторов и цемента, которые могут характеризоваться текучестью цементного теста и его потерей со временем [2, 3]. Добавление суперпластификатора снижает предел текучести пасты почти до нуля, но пластичность существенно не снижается [4].Суперпластификатор нафталинсульфонат часто используется для улучшения реологии свежего бетона [5]. Termkhajornkit и Nawa [4] сообщили в своей работе, что поверхностный потенциал летучей золы отличается от обычного портландцемента (OPC) как по знаку, так и по величине, и, таким образом, это является причиной флокуляции летучей золы и цементного теста. Когда суперпластификатор нафталинсульфонат был введен в зольную цементную пасту, признаки были такими же и поэтому хорошо диспергировались из-за более высокого потенциального барьера.Адсорбция суперпластификаторов нафталинсульфоната на поверхность частиц цемента изменяет дзета-потенциал поверхности частиц на отрицательный и, таким образом, увеличивает его абсолютное значение [6, 7].
Текучесть опилочно-золоцементного теста не сообщается. В этом исследовании было сочтено необходимым определить, во-первых, реологические свойства цементного раствора с использованием суперпластификатора нафталинсульфонат и, во-вторых, влияние SDA и его совместимость на свойства текучести.Зола древесных опилок (ЗДД) была получена при сжигании древесных отходов мукомольной промышленности, и зола содержит в основном силикаты (67%). Методы получения, сжигания и характеристики SDA были полностью обсуждены в предыдущей статье, где он использовался с бетоном [8]. SDA обладает пуццолановыми свойствами и поэтому является многообещающим дополнительным материалом для производства бетона.
2. Эксперимент
Рисунок 1 представляет собой блок-схему, используемую при разработке смеси для самоуплотняющегося бетона; Использовался портландцемент «Ашака» стандарта BS 12 [9].Использовали АСД, полученный из термически активированных древесных отходов при температурах от 400 до 600 ° С [8]. Физико-химические свойства портландцемента Ashaka и SDA приведены в таблице 1. Мелкодисперсный заполнитель представляет собой речной песок с удельным весом 2,57, влажностью 14,4% и насыпной плотностью 1472 кг / м. 3 и зона 2 в классификационной таблице согласно BS 882 [10]. Суперпластификатор представлял собой промышленный суперпластификатор нафталинсульфоната, производимый W.R. Grace and Co., США, названный Daracem 19. Он имеет удельный вес 1,18 и pH 9,5, а сухой экстракт по массе составляет 40%.
|
2.1. Тест на совместимость (тест на текучесть)
В таблице 2 показаны пропорции смеси для теста на совместимость (тест на текучесть). Соотношение воды и связующего в пасте составляло от 0,3 до 0,42. Дозировка суперпластификатора варьировалась от 0 до 4 мас.% Цемента. Чтобы оценить совместимость портландцемента с суперпластификатором нафталинсульфонат, для измерения расхода использовался стандартный усеченный конус (рис. 2). Он имеет верхний внутренний диаметр 70 мм, нижний внутренний диаметр 100 мм и высоту 60 мм.Конус помещался на стеклянную пластину размером 750 мм × 750 мм и заполнялся навеской раствора. Верхнюю поверхность раствора обработали шпателем и конус подняли вертикально. Диаметр распространения раствора после подъема конуса измеряли в двух перпендикулярных направлениях (и) с помощью линейки и записывали среднее значение. Результаты представлены в Таблице 3.
|
|
2.2. Тест на содержание порошка
Тест на содержание порошка проводился сразу после достижения насыщения в результате испытания на совместимость (текучесть).Это было сделано с помощью тестов потока и V-воронки (рисунок 3). Пропорции смеси для испытания показаны в Таблице 4. Оптимальная дозировка 2% суперпластификатора нафталинсульфоната и содержание цемента 479 кг / м. 3 были использованы при водном соотношении 0,42. Это были значения в точке насыщения из теста совместимости (текучести). Коэффициенты замещения SDA в тесте на содержание порошка варьировались от 0 до 20 мас.% Цемента. Всего было использовано 5 смесей (от PC-01N до PC-05N). PC-01N представлял собой контрольную смесь, содержащую NS без SDA (порошкового материала), в то время как PC-05N содержал SDA 20 мас.% цемента в качестве замены. Буква P обозначает порошковый материал. Для каждого уровня замены проводилось два теста, и фиксировалось среднее значение. Результаты представлены в Таблице 5.
|
|
3. Результаты и обсуждение
SDA представляет собой скрытый гидравлический материал и содержит примерно 67% силикатов.Ему требуется больше воды для консистенции, и при добавлении в цемент он запускает пуццолановую реакцию с избытком Ca (OH) 2 , образующимся во время гидратации цемента. Таким образом, SDA замедляет гидратацию пасты и увеличивает время схватывания [9]. Было установлено, что несгоревший углерод (<5%) влияет на адсорбцию суперпластификаторов [4]; поэтому потери при прокаливании SDA не превышали 4,6%, и, таким образом, влияние несгоревшего углерода в этой работе не учитывалось.
Результаты испытаний на текучесть показаны на рисунках 4 (a) –4 (c).Отношения между реологией строительного раствора при различных дозировках суперпластификатора довольно параллельны. Совместимость (текучесть) при водном соотношении 0,3 (рис. 4 (а)) увеличивалась с увеличением дозировки NS без какой-либо точки насыщения. Однако при соотношении 0,4 в / ц (рис. 4 (б)) текучесть также увеличивалась, но насыщение достигалось при дозировке примерно 3,5%. При соотношении в / ц 0,42 (рис. 4 (с)) текучесть строительного раствора не увеличилась значительно при дозировке 2%.Диаметр потока при этой дозировке составляет 28 см. Это точка насыщения, а 2% — пороговая дозировка. Можно сказать, что эти значения удовлетворяют требованиям правил для материалов SCC [11].
Период технологичности определяется взаимодействием порошковых материалов и добавки [12]. На рисунке 5 показан график уровней замещения в зависимости от потока и времени для смесей SDA (от PC-01N до PC-05N). Расход уменьшался по мере увеличения процента замены. Время достижения такого потока также увеличилось.Объяснение такому поведению можно получить из работ Termkhajornkit и Nawa [4] по летучей золе. В таблице 6 показаны значения дзета-потенциалов и потока в системе, сообщенные Термхаджорнкитом и Навой [4]. Видно, что, когда система не содержала суперпластификатора, дзета-потенциал OPC имел заряд, противоположный заряду летучей золы. Это стимулировало флокуляцию. Это означает, что полная потенциальная энергия частицы цемента и частицы летучей золы стала ниже, чем энергия между частицами OPC.Обратное было при нанесении суперпластификатора. Заряды были такими же, и, следовательно, происходило отталкивание и улучшение потока. SDA можно классифицировать как летучую золу класса C, и, таким образом, можно привести те же причины для поведения смесей SDA без и с нафталинсульфонатом. В коде [11] указано, что смесь, прошедшая испытание на SCC, должна иметь диаметр разбрасывания от 24 см до 26 см, а также время истечения от 7 до 11 секунд. Из таблицы результатов теста на содержание порошка смесью, которая удовлетворяла обоим условиям, была смесь PC-03N, которая содержала 10% замену цемента суперпластификатором нафталинсульфоната.
| ||||||||||||||||||||||||||||||||||||||||
Тип летучей золы . |
4. Статистический анализ
4.1. Тест на совместимость (тест текучести)
В таблице 7 перечислены коэффициенты независимых переменных с их соответствующим стандартным отклонением (SD), значением скорости и вероятности, а значение указывает на значимость переменной в модели, соответствующей вероятность.Если значение меньше или равно 5% (≤ 0,05), переменная принимается как значимая на уровне 5%. Анализ Таблицы 7 показывает, что только независимые переменные водоцементного отношения (в / ц) и дозировка нафталинсульфоната представляют значения ниже 5%; следовательно, оставшаяся переменная (репликация) не является статистически значимой. Стандартное отклонение () составляет 1,25, коэффициент корреляции% и adj = 92,8%. Уравнение регрессии выглядит следующим образом: расход = 8,11 + 3,38 w / c + 1.13 дозировок.
| ||||||||||||||||||||||||||||||||||
S = 1,260; R -кв = 93,0%; R -кв (прил.) = 92,8%. |
В таблице 8 представлен анализ дисперсии, степени свободы (DF), суммы квадратов (SS), средних квадратов (MD), () и вероятности (). Статистически подтверждается наличие регрессии на уровне значимости 5%. Степени свободы регрессии и остаточной ошибки равны 3 и 128 соответственно.На рисунке 6 представлен график остатков в зависимости от скорректированных значений. Этот график показывает, что дисперсия постоянна; то есть точки равномерно разбросаны около нуля.
|
испытание нормы 9000 Остатки, показанные на Фигуре 7, показывают, что остатки и, следовательно, ответ подчиняются нормальному распределению.
4.2. Тест Power Content
Статистический анализ двух тестов (распространение и время V-воронки), проведенный для теста Power Content, показывает, что сочетание и константа в регрессионном анализе значимы для распространения, а для V- Важна только воронка.Они показаны в таблицах 9, 10, 11 и 12. Они могут быть представлены, соответственно, как spread = mix и time = mix with =% и%, соответственно. Графики нормальности и невязки показаны на рисунках.
| |||||||||||||||||||||||||||||||||||
S = 0,6856; R -Sq = 94,0%; R -Sq (прил.) = 93,3%. |
|
| |||||||||||||||||||||||||||||||||||
S = 1,740; R -Sq = 90,6%; R -Sq (прил.) = 87,9%. |
|
5. Выводы
На основании результатов В ходе настоящего исследования можно сделать следующие выводы: (i) Оптимальная дозировка суперпластификатора 2% и содержание цемента 417 кг / м 3 с соотношением в / ц 0,42 достигли насыщения и соответствуют техническим требованиям.(ii) Суббота
.Оценка физико-механических свойств потолочных плит, склеенных из кукурузных початков и опилок
[1] С. П. Раут, Р. В. Ралегаонкар и С. Мандавган, Разработка экологически безопасных строительных материалов с использованием твердых промышленных и сельскохозяйственных отходов: обзор кирпичей, создающих отходы, Строительные и строительные материалы, стр.4037-4042, (2011).
DOI: 10.1016 / j.conbuildmat.2011.04.038
[2] С.Одейеми, М. Акинпелу, О. Атоэби и Р. Яхая, Определение несущей способности глиняных кирпичей, армированных соломой, Int. J. Sustain. Констр. Англ. Technol., Т. 8. С. 2180–3242, (2017).
[3] О.Д. Атоеби, С. О. Одейеми, С. А. Белло и К. О. Огбейфун, Оценка прочности на разрыв легкого пенобетона, армированного стальным волокном из отходов шин, Международный журнал гражданского строительства и технологий, вып. 9, вып. 9, стр.1129-1137, (2018).
[4] Дж.Пинто, Дж. Виейра, Х. Перейра, К. Хасинто, П. Вилела и А. Пайва, Легкий бетон из кукурузных початков для неструктурных применений, Строительные и строительные материалы, стр. 346-351, (2012).
DOI: 10.1016 / j.conbuildmat.2012.02.043
[5] ИКС.-у. Чжоу, Ф. Чжэн, Х.-г. Ли и Ч.-л. Лу, экологически чистый теплоизоляционный материал из волокон стеблей хлопка, Энергия и строительство, т. 42, стр 1070-1074, (2010).
DOI: 10.1016 / j.enbuild.2010.01.020
[6] Н.Чусилп, К. Джатурапитакку и К. Краттикомол, Использование золы из жома в качестве пуццоланового материала в бетоне, Строительный материал, стр.3352-3358, (2009).
DOI: 10.1016 / j.conbuildmat.2009.06.030
[7] К.Гунасекаран, Р. Аннадурай и П. С. Кумар, Характеристики пластической усадки и прогиба бетонной плиты из скорлупы кокосового ореха, Строительный материал, стр.203-207, (2013).
DOI: 10.1016 / j.conbuildmat.2013.02.019
[8] П.Лертсуттхивонг, С. Хунтон, К. Сиралертмукул, К. Ноомун и С. Чандркрачанг, Новые изоляционные древесно-стружечные плиты, полученные из смеси твердых отходов производства папиросной бумаги и кукурузной кожуры, Технология биоресурсов, стр. 4841-4845, (2008).
DOI: 10.1016 / j.biortech.2007.09.051
[9] О.Атоеби, О. Садик, Экспериментальные данные по прочности на изгиб железобетонных элементов с частицами стеклянных отходов в качестве частичной замены мелкозернистого заполнителя, Краткие данные, т. 18. С. 846–859, (2018).
DOI: 10.1016 / j.dib.2018.03.104
[10] О.Д. Атоеби, Т. Ф. Аволуси и И. Э. Дэвис, Оценка с помощью искусственной нейронной сети цементно-стружечных плит, изготовленных из опилок красного железа (Lophira alata) и остатков скорлупы ядер пальм, Примеры строительных материалов, том. 19, стр. 2340-2343, (2018).
DOI: 10.1016 / j.cscm.2018.e00185
[11] О.М. Садик, О. Д. Атоеби, Определение прочности на изгиб железобетонных элементов с частичной заменой стеклянных отходов мелкозернистым заполнителем ,,, NSE Tech. Пер. Журнал Нигерийского общества инженеров, вып. 49. С. 74–81, (2015).
[12] В.М. Мангеш, В. Р. Рахул и А. М. Сачин, Применение агроотходов в качестве экологически чистых строительных материалов: обзор, Строительные и строительные материалы, т. 38, стр. 872-878, (2013).
DOI: 10.1016 / j.conbuildmat.2012.09.011
[13] О.Атоеби, С. Одейеми и Дж. Орама, Экспериментальные данные по пределу прочности при раскалывании латеритного бетона, армированного бамбуком, с использованием стеблей различных размеров ,,, Краткие данные, т. 20. С. 1960-1964, (2018).
DOI: 10.1016 / j.dib.2018.09.064
[14] Н.Сун-Чинг и Л. Кав-Сай, Теплопроводность газобетонных панелей из легкого газобетона, Энергия и строительство, стр.2452–2456, (2010).
DOI: 10.1016 / j.enbuild.2010.08.026
[15] С.Хассе, М. Грене, А. Бонтемпс, Р. Дендивель и Х. Салле, Реализация, испытание и моделирование сотовых стеновых панелей, содержащих материал с фазовым переходом, Энергия и здания, стр. 232-238, (2011).
DOI: 10.1016 / j.enbuild.2010.09.017
[16] Н.Quaranta, M. Caligaris, H. López, M. Unsen, N. Lalla, M. Franzoy, M. Carrasco, J.Cotroni и M. Avenda., Добавление полимерных отходов в качестве порообразователей в легкие керамические кирпичи. по экологии и окружающей среде, стр. 447-458, (2010).
DOI: 10.2495 / arc100381
[17] Д.Адесанья и А. Рахим, Исследование характеристик удобоукладываемости и прочности на сжатие цементного бетона с добавлением золы кукурузного кочана, Строительные и строительные материалы, стр. 311-317, (2009).
DOI: 10.1016 / j.conbuildmat.2007.12.004
[18] Д.Адесанья и А. Рахим, Разработка цемента с добавлением золы кукурузного початка, Строительные и строительные материалы, стр. 347-352, (2009).
DOI: 10.1016 / j.conbuildmat.2007.11.013
[19] Д.Адесанья, Влияние теплопроводности и химического воздействия на цемент с добавлением золы кукурузного кочана, Профессиональный строитель, стр. 3-10, (2001).
[20] Дж.Коутиньо, Комбинированные преимущества CPF и золы из рисовой шелухи в улучшении долговечности бетонных конструкций. ,, Цемент и бетонные композиты, стр. 51-59, (2003).
DOI: 10.1016 / s0958-9465 (01) 00055-5
[21] М.Нехди, Дж. Дукетт и А. Эль-Даматти, Характеристики золы из рисовой шелухи, полученной с использованием новой технологии в качестве минеральной добавки в бетон, Исследование цемента и бетона, стр.1203-1210, (2003).
DOI: 10.1016 / s0008-8846 (03) 00038-3
[22] Д.Буй, Дж. Ху и П. Стровен, Влияние размера частиц на прочность портландцементного бетона с добавлением зольной и рисовой шелухи, смешанного с зазором., Цемент и бетонные композиты, стр. 357-366, (2005).
DOI: 10.1016 / j.cemconcomp.2004.05.002
[23] U.Томас и Дж. Мл., Исследование использования потолочной плиты Pleko для применения в теплоизоляционных и звукоизолирующих материалах, Международный журнал передовых наук и технологий, стр. 23-32, (2014).
DOI: 10.14257 / ijast.2014.66.03
[24] П.Анабела, С. Перейра, А. Са, Д. Круз, Х. Варум и Дж. Пинто, «Вклад в определение характеристик теплоизоляции древесностружечных плит кукурузного початка». «Энергия и строительство», стр. 274-279, (2012).
DOI: 10.1016 / j.enbuild.2011.11.019
[25] П.Сорушян и М. Хассан, Оценка цементно-стружечных плит по сравнению с альтернативными материалами сайдинга на цементной основе, Строительные и строительные материалы, стр.77-82, (2012).
DOI: 10.1016 / j.conbuildmat.2012.02.011
[26] С.Караде Р. Цементно-стальные композиты из лигноцеллюлозных отходов // Строительные и строительные материалы. 24, вып. 8, стр.1323-1330, (2010).
DOI: 10.1016 / j.conbuildmat.2010.02.003
[27] А.Ашори, Т. Табарса и С. Сепахванд, Цементно-композитные плиты из тополиных нитей // Строительные и строительные материалы, вып. 26, стр.131-134, (2012).
DOI: 10.1016 / j.conbuildmat.2011.06.001
[28] ФАО, ФАОСТАТ, 7 октября 2016 г.[В сети]. Доступно: http://faostat3.fao.org/search/ World% 20maize% 20producers / E.
[29] BS EN 317: 1993, ДСП и ДВП.Определение набухания по толщине после погружения в воду, Британский институт стандартов, Лондон (1993).
[30] BS EN 310: 1993, Панели на древесной основе.Определение модуля упругости при изгибе и прочности на изгиб, Британский институт стандартов, Лондон, (1993).
DOI: 10.3403 / 00299457u
[31] А.A208-1-1999, Американский национальный институт стандартов. Американский национальный стандарт — ДСП, Гейтерсбург: Ассоциация композитных панелей, (1999).
[32] А.Олоруннисола и О. Адефисан, Пробное производство и испытания цементно-стружечных плит из отходов мебели из ротанга, Wood Fiber Science, vol. 34, нет. 1. С. 116–124, (2002).
[33] Olorunnisola, Прочностные и водопоглощающие характеристики цементно-стружечных плит, полученных из кокосовой шелухи.,, Журнал исследований и практики гражданского строительства, вып. 3, вып. 1, с.41–49, (2006).
DOI: 10.4314 / jcerp.v3i1.29150
.цемент из опилок — определение — английский
Примеры предложений с «цементными опилками», память переводов
патент-wipo Легкий, водостойкий строительный продукт и метод, который включает формирование смеси из сухой смеси, включающей опилки, цемент, набухающую в воде коллоидную глину и диатомит, вода и сжатый воздух. Патенты-WIPO Композиция строительного блока по настоящему изобретению включает в сухом весе: опилки (20-70%), цемент (20-50%), гипс или известь (5-20%). Спрингер Эксперименты с цементом -гнездники из опилок показали явное предпочтение глубоких ящиков глубиной 19 см (измеряется от входного отверстия) ящикам глубиной 14 или 9 см.EurLex-268.09 * ПАНЕЛИ, ПЛИТКИ, ПЛИТКИ, БЛОКИ И АНАЛОГИЧНЫЕ ИЗДЕЛИЯ ИЗ РАСТИТЕЛЬНОГО ВОЛОКНА, ДРЕВЕСНОГО ВОЛОКНА, СОЛОМЫ, ДРЕВЕСНЫХ СТРЕЛКОВ ИЛИ ДЕРЕВЯННЫХ ОТХОДОВ (ВКЛЮЧАЯ ОПИЛКИ), АГЛОМЕРИРОВАННЫХ С ЦЕМЕНТОМ, ПЛАСТМАССОВЫМ УЗОРОМ * С ДРУГИМИ МИНЕРАМИ -268.09 * ПАНЕЛИ, ПЛИТКИ, ПЛИТКИ, БЛОКИ И АНАЛОГИЧНЫЕ ИЗДЕЛИЯ ИЗ РАСТИТЕЛЬНОГО ВОЛОКНА, ДРЕВЕСНОГО ВОЛОКНА, СОЛОМЫ, ДРЕВЕСНОЙ СТРЕЛКИ ИЛИ ДЕРЕВЯННЫХ ОТХОДОВ (ВКЛЮЧАЯ ОПИЛКИ), АГЛОМЕРИРОВАННЫХ ЦЕМЕНТОМ, ГЛАДКОЙ ИЛИ С ДРУГИМИ МИНЕРАЛЬНЫМИ ВЕЩЕСТВАМИ смесь, подходящая для изготовления строительного элемента, содержащая в пересчете на сухой вес от 20 до 50% опилок, от 30 до 50% цемента и от 5 до 20% извести (оксид кальция).Патенты-wipo Сухая смесь, подходящая для изготовления строительного элемента, содержащая по сухому весу от 10 до 50% опилок, от 20 до 50% цемента и от 5 до 40% гипса (сульфат кальция). Giga-fren Примеры отраслей промышленности, которые могут быть в этом отношении наиболее заметными являются целлюлозно-бумажные комбинаты, сталелитейные заводы, карьеры, муниципальные или другие мусоросжигательные заводы, цементные заводы, лесопилки (горелки для измельчения и опилок) и нефтеперерабатывающие заводы. EURLex-2 Панели, плиты, плитки, блоки и аналогичные изделия из растительного волокна, соломы или из стружки, щепок, частиц, опилок или других отходов древесины, агломерированных с цементом, гипсом или другими минеральными связующимиОтображение страницы 1.Найдено 61 предложения с фразой опилки цемента.Найдено за 6 мс.Накопители переводов создаются человеком, но выравниваются с помощью компьютера, что может вызвать ошибки. Найдено за 0 мс.Накопители переводов создаются человеком, но выравниваются с помощью компьютера, что может вызвать ошибки. Они поступают из многих источников и не проверяются. Имейте в виду.
.Роторная сушилка для золотых опилок для цементного порошка, Роторная сушилка для высококачественных опилок, Роторная сушилка для руды
Cement Power Роторная сушилка для опилок золотой руды,
Роторная сушилка для высококачественных опилок
Внедрение сушилки для металлической руды, роторной сушилки для опилок золотой руды
Наша компания произвела новую роторную сушилку с использованием роторной сушилки подъемная пластина, которая имеет направляющую, средний ток, подъем и многие другие функции, делают материал в сушилке полностью однородным радиальным поперечным сечением, ожидается, что он станет тонким, однородным, полным, полным контактом с горячим воздухом, чтобы полностью использовать тепловой энергии.Наша роторная сушилка с разумными рабочими параметрами, потреблением угля и электроэнергии ниже на 10-15%, чем средняя сушилка, увеличение производства на 10-15%, она широко используется на предприятиях по переработке цемента и минералов.
Применение роторной сушилки для металлической руды, роторной сушилки для опилок золотой руды
Роторная сушилка может широко использоваться для сушки материалов с влажностью или зернистостью в отраслях обогащения минералов, строительных материалов, металлургии и химической промышленности, таких как металлообработка и неметаллический минерал, глина в цементной промышленности и уголь в угольной шахте и т. д.Его отличительные черты — широкий объем поставки и простота эксплуатации.
Характеристики роторной сушилки для металлической руды, ротационной сушилки для опилок золотой руды
1. Ролик роторной сушильной машины изготовлен из легкой листовой нержавеющей стали, которая имеет отличную термостойкость, гладкую внутреннюю стенку, может уменьшить материалы » износ.
2. Эффективный радиатор со свинцовым воздуховодом в разумных пределах, чтобы горячий воздух мог напрямую контактировать с материалами, что значительно повышает эффективность сушки и экономит энергию.
3. Используя компьютерное управление, мы можем установить различную температуру роторной сушки и время сушки роторного барабана в соответствии с требованиями сушки.
4. Вход для материала большого диаметра облегчает вход и выход материалов и значительно повышает эффективность сушки.
Принцип работы сушилки металлической руды, роторной сушилки опилок золотой руды
Роторная сушилка состоит из цилиндра, подъемной плиты, трансмиссии, опорных устройств и прочего. Благодаря разумной компоновке и альтернативному изменению угла, равномерно распределенному в цилиндре, подъемная пластина разбрасывает влажный материал внутри вращающегося цилиндра.Поток горячего воздуха превращает воду в пар, выходящий в воздух, и получается целевой сухой материал.
Область применения: Роторная сушилка широко применяется в горнодобывающей, металлургической, строительной, химической и других отраслях промышленности, в основном для сжигания минерального порошка, шлака, глины, известняка, лигнита и других материалов.
Метод работы Роторная сушилка для руды / минералов, роторная сушилка
Рабочее место ротационной сушильной машины для руды / минералов, роторная сушилка
Основные параметры
Параметры ротационной сушилки для руды / минералов, ротационной сушилки
Модель (м) | Объем корпуса | Производительность | Градиент | Максимальная температура входящего воздуха | Главный двигатель | Масса |
Φ1,2 × 8,0 | 9,0 | 1,9 — 2,4 | 3-5 | 700-800 | 7.5 | 9 |
Φ1.2 × 10 | 11,3 | 2,4 — 3,0 | 3 — 5 | 700-800 | 7,5 | 11 |
Φ1,5 × 12 | 21,2 | 4,5 — 5,7 | 3 — 5 | 700-800 | 15 | 18 .5 |
Φ1,5 × 14 | 24,7 | 5,3 — 6,6 | 3 — 5 | 700-800 | 15 | 19,7 |
Φ1,5 × 15 | 26,5 | 5,7 — 7,1 | 3 — 5 | 700-800 | 15 | 20,5 |
Φ1.8 × 12 | 30,5 | 6,5 — 8,1 | 3 — 5 | 700-800 | 18,5 | 21,5 |
Φ1,8 × 14 | 35,6 | 7,6 — 9,5 | 3 — 5 | 700-800 | 18,5 | 23 |
Φ2.2 × 12 | 45,6 | 9,7 — 12,2 | 3-5 | 700-800 | 22 | 33,5 |
Φ2.2 × 14 | 53,2 | 11,4 — 14,2 | 3 — 5 | 700-800 | 22 | 36 |
Φ2.2 × 16 | 60,8 | 13,0 — 16,2 | 3-5 | 700-800 | 22 | 38 |
Φ2,4 × 14 | 63,3 | 13,5 — 16,9 | 3-5 | 700-800 | 37 | 45 |
Φ2,4 × 18 | 81.4 | 17,4 — 21,7 | 3 — 5 | 700-800 | 37 | 49 |
Φ2,4 × 20 | 90,4 | 19,3 — 24,1 | 3 — 5 | 700-800 | 45 | 54 |
Φ2,4 × 22 | 99,5 | 21 .2 — 26,5 | 3 — 5 | 700-800 | 45 | 58 |
Φ2,6 × 24 | 127,4 | 27,4 — 34,0 | 3 — 5 | 700-800 | 55 | 73 |
Φ3,0 × 20 | 141,3 | 30.1 — 37,7 | 3 — 5 | 700-800 | 75 | 85 |
Φ3,0 × 25 | 176,6 | 37,7 — 47,1 | 3 — 5 | 700-800 | 75 | 95 |
Φ3.2 × 25 | 201 | 42.9 — 53.6 | 3 — 5 | 700-800 | 90 | 110 |
Φ3,6 × 28 | 285 | 60,8 — 76,0 | 3 — 5 | 700-800 | 160 | 135 |
Упаковка и доставка
Наши услуги
Наша миссия — обеспечить наших клиентов своевременное, быстрое и качественное обслуживание.
√ Быстрый ответ
На предложенный вами вопрос или на отзывы мы обязательно ответим в ближайшее время.
√ Предоставление дизайна решения:
По результатам общения с вами мы оперативно предоставим вам дизайнерское решение.
√ Инспекция Наш завод и машины:
Если у вас есть интересы, приглашаем вас посетить наш завод и осмотреть машину.
√ Выполнение заказа:
Предоставьте чертеж компоновки оборудования, чертеж фундамента и подробные инструкции по эксплуатации оборудования. Своевременно сообщать вам график производства и сопутствующие фотографии.
√ Быстрая доставка:
Мы можем организовать быструю и безопасную доставку в срок.
√ Послепродажное обслуживание:
Если вам нужно, мы отправим инженера на объект для руководства установкой, отладкой и обучением операторов.Если вам нужны специалисты по установке и эксплуатации, предлагаются
Информация о компании
Zhengzhou HengXing Heavy Equipment Co., Ltd
Это акционерное общество, объединяющее научные исследования, производство, маркетинг и экспорт с основными нацелена на крупную и среднюю серию тяжелого оборудования для горнодобывающей промышленности, отбора руды, стеновых материалов, формованного угля, металлургии и т. д. Компания расположена в Национальной зоне развития высоких технологий Чжэнчжоу.
Наша компания установила компьютерную информацию внутри компании, компьютерное управление производством, CAD и CAPP для производственных исследований и проектирования процессов. Наша компания также оснащена мощными машинами и оборудованием для обработки, ковки, сварки заклепок, термической обработки науглероживания. В то же время наша компания имеет долгосрочные отношения сотрудничества с научно-исследовательскими институтами дома и за рубежом, представила базу с передовыми технологиями, процессами и обнаружением для разработки новых продуктов и продвижения технологий.
.