Блоки из цемента и опилок цена: цена, размеры и основные характеристики
Строительные блоки в Рыбинске — производство, цены, характеристики
Уже более 30 лет строительные блоки возглавляют рейтинг самых прочных и надежных материалов. Их применяются для возведения коттеджей и многоквартирных домов. Тем более блоки востребованы при возведении фундамента – устойчивого, стабильного и способного выдержать практически любые нагрузки.
Наша компания представляет широкий сортамент стройматериала, который производится на фабрике в городе из различного сырья. С нашими блоками для строительства легко работать:
- малый вес;
- точные формы;
- поддаются распилу, что позволяет создавать материал нужного размера;
- правильная геометрия форм;
- высокие теплоизоляционные свойства;
- не требуют специальной обработки;
- долговечные.
Сфера применения
По сравнению с другими стройматериалами – кирпичом, ракушечником, натуральным и искусственным камнем, блоки можно назвать универсальными.
- возведения фундаментного слоя;
- цокольных этажей;
- наружной кладки;
- внутренних перегородок и т.д.
Главным связующим компонентом является бетон. Независимо от размерных параметров и компонентов, изделие всегда обладает высоким качеством, соответствующим стандартам ГОСТ 21520-89 «Блоки из ячеистых бетонов» и ГОСТ Р 57335-2016 «Блоки бетонные строительные». Все производство основано на соблюдении единых стандартов и нормативов.
Цена на строительные блоки в Рыбинске
На сегодняшний день мы производим строительные блоки таких видов:
- бетонные;
- керамические;
- газосиликатные;
- арболитовые;
- пенобетонные;
- полистиролбетонные;
- шлакобетонные;
-
утепленные керамзитобетонные.
Путем использования дополнительных компонентов в составе цемента за время работы мы существенно расширили ассортимент и сегодня готовы предложить стройматериал с особыми характеристиками по физическим параметрам, массе, габаритам и устойчивости перед агрессивной средой.
Наименование продукции |
Характеристика – размеры, плотность, прочность, масса, пустотность |
Цена, руб/шт. |
Керамзитобетонные поризованные |
390х188х190 |
30 |
Пескоцементные поризованные |
390х188х190 |
26 |
Керамзитобетонные для внутренних перегородок |
390х90х190 |
15 |
Пескоцементные для внутренних перегородок |
390х90х190 |
13 |
Керамзитобетонные без полостей |
390х188х190 |
43 |
|
390х188х190 |
38 |
Керамзитобетонные для внутренних перегородок без полостей |
390х90х190 |
23 |
Пескоцементные для внутренних перегородок полнотелая структура |
390х90х190 |
27 |
Бетонные строительные блоки
Для изготовления используется сложный бетонный раствор с добавлением песчанистого гравия по технологии вибропрессования. Для заказа доступны популярные размеры — 20х20х40, цена на них значительно ниже моделей 20х50х20 см.
Главные преимущества данного вида — долговечность кладки стен, экономный расход раствора и ускоренный монтаж. Что касается пустотелой серии, они лучше защищают от холода, не проводят шум, изделия легче по весу и имеют меньше цену за штуку. Облегченный вариант востребован для стен и других не несущих перегородок.
Пенобетонные строительные блоки
Изготавливаем из газосиликата, цемента, пастообразного алюминия и известнякового материала проходят автоклавный этап затвердевания в специальной герметичной камере. Данные особенности производства гарантируют высокую прочность стройматериала с ячеистой структурой и открытыми порами. Благодаря струнному способу разрезки, в результате изделие получает точные формы и размеры, которые варьируются в пределах 20-50х60х20-25 см.
Модификации для перегородок обладают меньшими размерами и ценами соответственно – 7,5-17,5 см. Пенобетонные изделия проходят особый производственный цикл. Вспененное сырье подготавливают в генераторе, после чего помещают в чащу миксера вместе с цементом. Бетонная смесь обволакивает капсулы воздуха, в результате чего поры выходят закрытыми. Далее раствор перемещают в формовку и оставляют для застывания при естественных условиях.
Шлакоблоки
Изготовляется данный вид продукции из опилок и цемента, помимо этого в состав входят доменные шлаки, дробленый кирпич, зола, частицы цементного изделия, перлит и щебень. Стройматериал имеет один нюанс, который заключается в ситообразной структуре, пропускающей влагу. Поэтому при его применении следует дополнительно соорудить защитный слой из водоотталкивающего стройматериала.
На бюджетный вид строительных блоков, размеры, цена не превышает стандартные параметры. Изделия производятся с габаритами 39х19х18,8 см, в случае с перегородочными вариациями, толщина сокращается до 9 см.
Керамзитобетон
На место шлаковой извести пришли вспененные глинистые гранулы, получившие плотную оболочку в процессе обжига.
Отлично подходит для строительства энергосберегающих жилых домов. в Рыбинске мы изготавливаем керамзитобетон в разном оформлении:
- с имитацией натурального гранита;
- известнякового материала;
- керамической облицовки или кирпича.
Стройматериал с полимерным наполнителем
За счет удачной комбинации композиционного бетонного раствора с вспененным полистиролом, строительный материал обрел легкость и степень теплопроводности ячеистого изделия, без ущерба в сторону прочности. Мы рекомендуем купить строительные блоки для возведения несущих стен, внутренних перегородок или утеплительного слоя.
Размеры стандартного материала равны 58,8х30х18,8-30 см, уменьшенные для тонких перегородок – 58,8х30х80-138 см.
Деревобетон (арболит)
Это – итог соединения опилок и цемента. Ячеистое изделие, включающее до 90% древесного материала, без примесей коры или листьев. Для него характерны низкая плотность при высокой прочности. В раствор добавляют сульфат алюминия, нейтрализующий повышенную степень сахара в древесном сырье, чтобы максимально увеличить адгезию.
Отходы лесопильных производств определенного калибра замачивают в жидкости с минерализатором, в раствор добавляют цементную смесь марки М400, после чего распределяют по подготовленным формам 50х30х20 см.
В итоге получается негорючий стройматериал с высокой степенью паропроницаемости и теплопроводности. Применяются для возведения жилых и общественных зданий, требуется дополнительная облицовка — блоки сильно поглощают влагу. Подвесной фасад или специальная экстерьерная штукатурка решит проблему.
ВИДЕО: Арболит – плюсы и минусы
youtube.com/embed/z2Ji9cvWjSs»>
Керамические изделия
Традиционный вид строительных блоков, особенности производства заключаются в таких этапах:
- Глинистую известь перемешивают с опилками.
- Помещают в формовку.
- Переносят в камеру для обжига.
При высокой температуре опилки сгорают и образуют поры по всему периметру.
Экологичный стройматериал имеет высокую стоимость, однако это полностью компенсируется низкой теплопроводностью, за счет чего происходит существенная экономия на энергопотреблении. Вес блока с размерами 38х24,8х23,8 см не превышает 17,5 кг, а большие габариты значительно ускоряют процесс кладки.
Весь ассортимент доступен для заказа в Рыбинске. Уточнить наличие товара на складе и стоимость можно у менеджеров интернет магазина или непосредственно на заводе.
ВИДЕО: Какие блоки подходят для строительства частного дома
youtube.com/embed/E0VNc8y0UPQ»>
Кирпич из опилок и цемента своими руками, пример малого бизнеса
Кирпич из опилок и цемента своими руками, идеи малого бизнеса и строительство собственных объектов.
Арболит получил широкое применение в 60 годах прошлого века, но в середине 90 был незаслуженно забыт. Причина снижения популярности кроется в том, что после развала союза перестали соблюдать ГОСТы при изготовлении изделий из опилок и цемента.
Низкое качество и кустарное производство привели к тому, что новые дома из арболита через некоторое время трескались, сыпались или поражались грибком.
Однако, в наши дни технология производства кирпичей из опилок и цемента опять набирает популярность. А всё потому, что производители в борьбе за клиентов, стали уделять большое внимание качеству.
Просто стало не выгодно выпускать изделия, не соответствующие стандартам, установленным ещё в советское время.
Если соблюдать все правила изготовления, то можно получить недорогой, прочный, долговечный, теплоизоляционный, строительный материал, именуемый арболитом.
Кирпич из опилок и цемента, технология
Технология изготовления арболитовых кирпичей предусматривает использование древесных опилок, или щепы. Сухая древесная стружка обрабатывается специальным раствором и заливается цементной смесью.
Доля древесины в готовом кирпиче, составляет примерно 80%, а цемента – 20%. А так как оба компонента стоят недорого, то происходит быстрая окупаемость вложений при открытии своего бизнеса.
Существуют три основных вида изделий из арболита:
- Теплоизоляционный для утепления строений;
- Конструктивно-теплоизоляционный — для возведения стен;
- Арбомонолит – это когда готовая, арболитовая смесь заливается непосредственно в опалубку, минуя стадию изготовления кирпича. При этом, вся конструкция жилого строения представляет собой единую, монолитную структуру.
Кирпичи из опилок и цемента отлично удерживают тепло, обладают высокой звукоизоляцией. Они пожаробезопасные. Но самое важное преимущество, перед другими строительными материалами – экологическая чистота и невысокая стоимость.
Многих привлекает простота изготовления, и они налаживают производство кирпичей из опилок и цемента своими руками.
Стоит заметить, что такое производство возможно осуществить в домашних условиях. Однако следует соблюдать некоторые правила, о которых мы расскажем далее, чтобы ваши изделия служили как можно дольше.
Кирпичи из опилок и цемента, в зависимости от предназначения, имеют различающуюся маркировку.
Пять марок изделий:
- M5;
- M10;
- M15;
- M25;
- M35.
В двух последних марках, номер 4 и 5, процентное содержание опилок минимальное, по сравнению с первыми номерами.
Поэтому, кирпичи данных марок намного прочнее и выдерживают повышенную нагрузку. Такие изделия применяют при строительстве несущих стен двухэтажных зданий.
Кирпич из опилок и цемента своими руками
Если вы решили изготовлять кирпичи из опилок и цемента своими руками, то, для начала следует узнать несколько важных правил от профессионалов. Эти правила помогут вам получить качественные изделия, с невысокой себестоимостью.
Правила изготовления арболитовых блоков:
- Желательно приобретать цемент только марки м500;
- Для строительства жилых помещений лучше всего использовать хвойные опилки или стружку, самое лучшее — сосна;
- Органический наполнитель, то есть опилки, стружка и так далее, должен быть абсолютно сухим. Нельзя применять опилки влажные, подопревшие, хранившиеся ненадлежащим образом. Это может привести к появлению плесени, грибка на готовых изделиях. А в результате брожения целлюлозы могут наблюдаться вздутие и разрыв блоков.
- Для устранения негативных явлений, описанных в пункте 3, следует применять химический нейтрализатор. Такой как сульфат алюминия или хлорид кальция. Это недорогие, достаточно эффективные ингибиторы. Также, в соответствии с ГОСТом, разрешается добавление жидкого стекла, сернокислого глинозёма, извести, силикат-глыбы.
- Для того, чтобы готовое изделие было более целостным и крепким, рекомендуется применять мелкую стружку или опилки.
Если у вас достаточно крупная щепа, то её следует предварительно раздробить на более мелкие фрагменты.
Как видим, правила достаточно простые, не затратные и легко выполнимые.
Изготовление кирпичей из опилок в промышленных масштабах
В том случае, когда вы хотите поставить производство кирпича из опилок и цемента на поток, открыть свой бизнес, то прежде всего следует составить бизнес-план.
В первую очередь рассчитайте затраты на закупку оборудования.
Для этого вам понадобятся:
- Бетономешалка;
- Дробилка для измельчения опилок и древесной стружки;
- Весы для взвешивания компонентов;
- Формовочные дозаторы;
- Вибростол;
- Сушильная камера;
- Склады для хранения сырья и готовых изделий;
- Специально оборудованная, крытая площадка или цех для производства кирпичей или утеплительных блоков.
Если вы не хотите, чтобы производство зависело от погодных условий, то лучше всего подумать о большом, просторном, отапливаемом помещении. В котором можно будет работать круглый год.
Второй, не менее важный аспект – заранее продумать куда вы станете сбывать готовую продукцию.
Рекомендуется ещё до начала производства следует найти перекупщиков, которые будут сбывать вашу продукцию населению.
Также, можно предложить свои изделия строительным фирмам, организациям и так далее.
Узнав рыночные закупочные цены, и приблизительно определив объём производства, вы сможете высчитать сроки, за которые окупятся ваши вложения.
Так как производство кирпичей из опилок и цемента не требует слишком больших вложений. То при наличии рынка сбыта, вы сможете выйти на чистую прибыль, примерно за три месяца.
Размеры изделий из опилок и цемента
Заводские размеры стандартных кирпичей из опилок и цемента равны соотношению:
- Высота – 20 или 25 сантиметров;
- Ширина – 20 или 30 сантиметров;
- Длина – 40 или 50 сантиметров.
Но, допускаются и другие соотношения, особенно, если вы строите для себя. При желании вы можете сделать блоки шире 30 сантиметров.
Или изготовить кирпичи выше, чем 20 сантиметров. Просто следует учитывать, что в этом случае блоки будут тяжелее, и нужно затрачивать больше сил на их транспортировку до объекта.
Размеры утеплительных панелей, также могут значительно варьироваться по своим размерам. Многие производители изготавливают панели по своим, проверенным временем размерам.
В среднем можно указать следующие размеры:
- Для утепления пола – 82 см х 62 см х 8 см;
- Для утепления стен – 82 см х 62 см х 10 см.
В составе утеплительных плит: 90% сосновой щепы и 10% цемента М500 + минерализаторы.
Производство
Высушенная древесина, лучше всего хвойных пород, пропускается через дробилку и далее поступает в барабан бетономешалки.
Отдельно замешиваются вода, сульфат алюминия, цемент. Данным раствором заливаются сухие опилки и перемешиваются в течении пяти минут.
Важно!
По окончанию замеса смесь должна быть равномерно влажной, но не мокрой! То есть, не должно быть излишков воды в смеси.
Иначе, стекая при утрамбовке, она вымоет часть цемента из раствора.
После этого готовая смесь укладывается в формы, смазанные отработанным машинным маслом. Утрамбовывается при помощи вибрации и воздействия силы. Прессуется и поступает на просушку.
Сушится в течении 12 – 18 часов, в сушильной камере.
Чем меньше, в процентном содержании вы кладёте цемента, тем более изделие будет сохранять тепло. Однако, при этом уменьшается его прочность.
И наоборот, чем больше цемента, тем плотнее и прочнее изделие, но, при этом повышается теплопроводность.
Расход материала, пропорции
Подбор состава для изготовления арболита производится расчетно-экспериментальным методом. Многое зависит от влажности, качества исходного сырья и породы дерева.
Также, от того, изделие какой марки вы хотите получить на выходе. Для первоначального, пробного замеса, по ГОСТу рекомендуются применять пропорции, указанные в инструкции по изготовлению изделий из арболита – СН549-82.
В специальных таблицах которой изложены рекомендуемые пропорции всех компонентов, для первого замеса.
Находится данная инструкция по адресу: files.stroyinf.ru/Data1/2/2032/
Видео по теме изготовления кирпича из опилок, пример малого бизнеса.
Статьи по теме:
Блоки из опилок и цемента – характеристики арболитных блоков
Для того чтобы заниматься строительством, необходимо иметь определённое представление о стройматериалах, чтобы уметь всегда делать правильный выбор. В данной статье рассмотреть все материалы нам не получится, однако мы узнаем, основные качества и область применения арболита, в состав которого входят блоки из опилок и цемента.
1. Арболит обладает довольно высокой степенью тепло- и звукоизоляции благодаря своей пористости. Данный материал очень хорошо поддаётся обработке всеми отделочными материалами и не имеет существенных недостатков.
2. Помимо этого, арболит замечательно зарекомендовал себя в строительстве малоэтажных зданий, так как имеет небольшой вес, благодаря чему при возведении здания можно обойтись ленточным фундаментом, сэкономив тем самым довольно внушительную сумму денег.
3. Главным компонентом, из которого изготавливают блоки из опилок и цемента, является цемент марки 400, 500 и выше. Наполнителем выступают древесные опилки, мелкая щепка и стружка. При этом в состав блоков должно входить не более 5% от массы наполнителя остатков коры, хвои и листьев.
4. Помимо отходов деревообработки, для наполнения блоков используют также отходы льна и конопли, подвергшиеся обработке известковым раствором. Вся органика измельчается в дробилке до требуемых размеров. Толщина наполнителей должна составлять 5 мм, а длина – 25 мм.
5. Для нейтрализации сахара, содержащегося в органических отходах, используются химические добавки, такие как сернокислый алюминий и хлористый кальций. Для того чтобы блоки быстрее затвердевали, добавляют также жидкое стекло, однако при этом нельзя забывать, что общее количество добавок не должно превышать 4%.
6. Чтобы изготовить блоки из опилок и цемента следует сначала залить органические вещества водой, после чего смешать их с цементом. Оставшийся состав необходимо добавлять частями. Консистенция состава должна быть сыпучей, однако он должен при этом сохранять форму. Соотношение опилок, цемента и воды должно составлять примерно 3:3:4.
Блоки заливают в формы, состоящие из поддонов и боковых стенок. Размеры форм соответствуют требуемым размерам блоков.
Программа Перестройка об Арболите
Загрузка …Статьи по теме:
состав, пропорции, производство своими руками, отзывы и видео
Современный рынок загородного домостроения испытывает постоянную потребность в простых по своему изготовлению материалах с высокими технико-экономическими показателями.
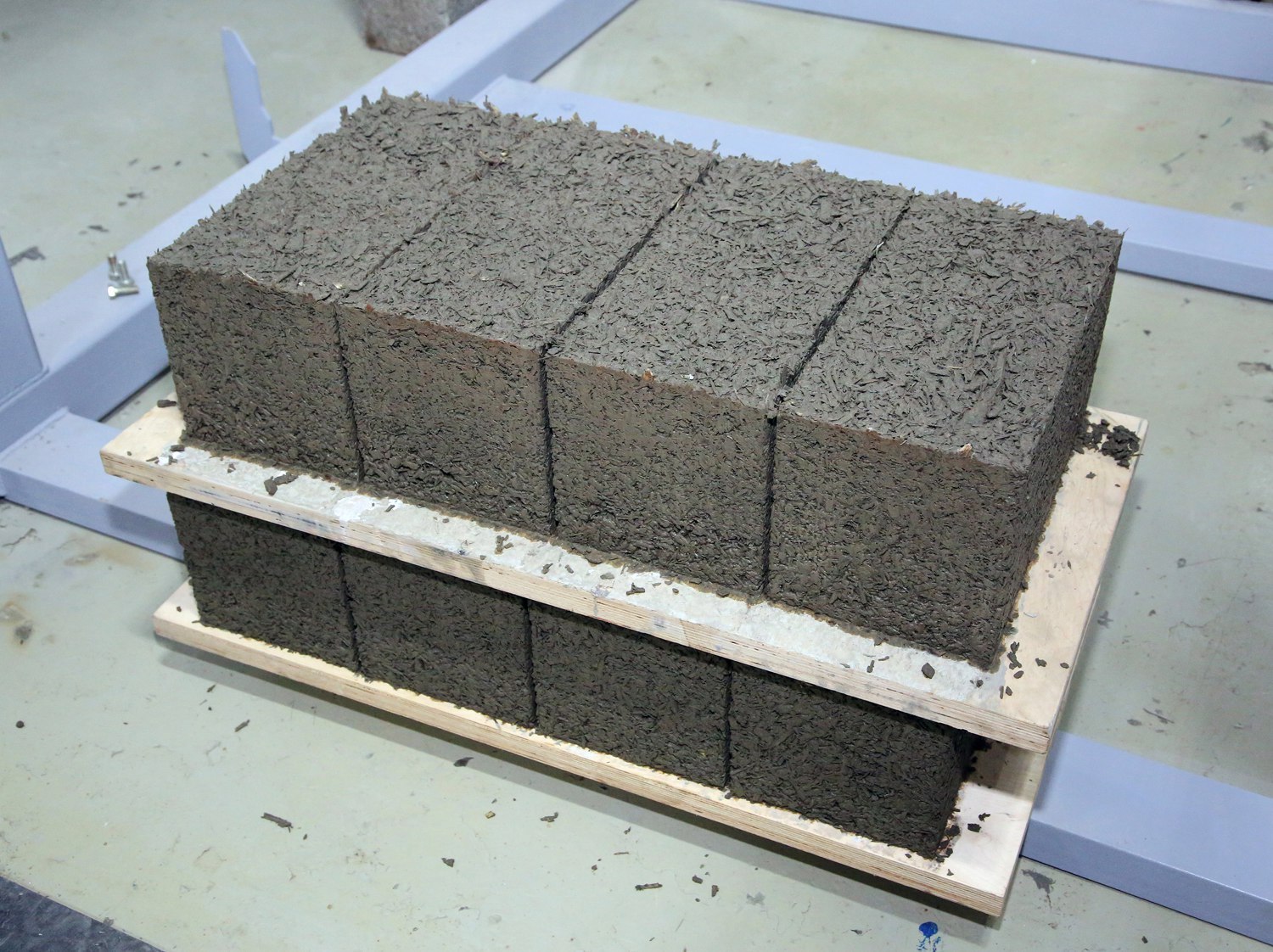
Блоки на основе стружки и цемента – область применения
Применяется материал в самых разных сферах, но в основном в возведении малоэтажных зданий. Чаще всего из опилкобетона строят дачи, гаражи, внутренние перегородки в частных домах, таун-хаусы, погреба, коттеджи, здания бытового использования.
Популярен опилкобетон и для проведения работ по утеплению подвальных помещений, капительных стен сооружений, создания изоляционного слоя. Могут пригодиться блоки при строительстве разного типа ограждений. Редко они используют там, где есть большие нагрузки – строительство фундамента, несущих стен, перекрытий и т. д.
Обычно используют по максимуму характеристики теплоизоляции и реализуют конструкционные решения внутри помещений, в создании ненагруженных конструкций и т.д.
Там, где отмечена повышенная влажность, плиты или блоки желательно выполнять с дополнительным слоем изоляции, так как они будут впитывать влагу. При должной защите и учете всех свойств опилкобетон из щепы способен долго сохранять геометрическую форму, а также механические и эксплуатационные свойства.
Достоинства
Опилкобетон как материал для строительства имеет ряд отличительных свойств и плюсов, которые способствуют его повсеместному использованию:
- доступность;
- возможность легко изготовить строительные блоки самостоятельно;
- низкая итоговая стоимость, наряду с относительной дешевизной ценой компонентов;
- возможность использования смеси для монолитного строительства;
- благодаря тому, что блоки получабтся большими и легкими, строительство с их помощью продвигается гораздо быстрее;
- натуральный продукт, не содержаший вредных для окружающей среды компонентов.
Эти признаки позволяют считать материал удобным и простым в использовании, включая и технологию, как сделать опилкобетон своими руками. Благодаря возможности не обращаться в строительные компании, опилкобетон распространен повсеместно.
Преимущества и недостатки
Прежде, чем начинать изготовление блоков из опилок и цемента своими руками, нужно хорошо изучить свойства материала, плюсы и минусы. С учетом специфичности его состава опилкобетон подходит далеко не для всех работ и условий эксплуатации, но при выполнении всех требований может стать действительно удачным выбором.
Основные достоинства опилкобетона:
- Высокий уровень теплоизолцяии – дома хранят прохладу летом, тепло зимой, словно термос.
- Экологичность и безопасность для людей – отсутствие токсинов и вредных выделений гарантирует в жилье положительный микроклимат и отсутствие аллергий.
- Прочность – неплохие структурные показатели, некоторые виды опилкобетона можно использовать для возведения несущих конструкций (но не выше 3 этажей).
- Стойкость к огню – за счет введения в состав синтетических добавок, делающих материал способным в течение 2 часов не гореть при температуре +1200 градусов.
- Прекрасная паропроницаемость – за счет пористой структуры опилкобетон пропускает воздух, не задерживает влагу.
- Стойкость к резким перепадам температур – не боится замораживания/оттаивания, не деформируется при внешних воздействиях.
- Доступная стоимость – немного дороже газобетона, но при самостоятельном изготовлении цена еще понижается.
- Хорошие показатели звукоизоляции – благодаря пористости материала он работает в обе стороны (снаружи/внутри).
- Простая работа – легкий монтаж за счет минимального веса и идеальных геометрических параметров, распил, сверление с сохранением целостности структуры и формы.
- Использование вторсырья – все виды цементно-стружечных блоков и плит создаются на базе щепы или стружки, которые представляют собой отходы деревообработки.
Купить опилки можно по небольшой цене.
- Длительный срок эксплуатации – при обеспечении оптимальных условий блоки из опилок и цемента служат десятилетия.
- Небольшой вес – что облегчает монтаж и снижает общее давление конструкции на основание.
Из недостатков материала стоит отметить такие, как: низкий уровень влагостойкости и необходимость в защите, ограниченный выбор сырья в плане пород древесины, большая длительность этапов производства (после того, как материал залит в формы, он должен затвердевать и сушиться минимум 3 месяца до начала работ).
Лучшие ответы
I’ll be back:
консистенцию не знаю, но ты в курсе что опил должен быть обезвожен и обработан спец. составом? а так почитай про бризолит, тоже самое…
Онлайн журнал Советы хозяевам:
Опилкобетон он же арболит, представляет собой смесь из опилок, песка воды и цемента. Правильная консистенция? Не совсем понятно, что имеется ввиду, если пропорции, то зависит от желаемой марки. В самом простом виде — три ведра опилок, ведро песка и ведро цемента. Если прочнее, два ведра опилок пол ведра песка и ведро цемента. Кроме того, если опилки свежие (до 2-х лет) обязательно добавляем около 5% от объема хлорида кальция, извести или жидкого стекла.
Если консистенция в смысле количества воды, то опять же от желаемой марки, но в общем порядка 0,8 от цемента. Дело в том, что для арболита, сколько воды не добавь, опилки впитают, все одно жидкого состава не получится. Поэтому воды много не нужно лить. Только прочность снизится. Из опыта, состав что-то вроде мокрых опилок получается, наваливаем в опалубки и хорошенько трамбуем. Слой не больше 20-25 см. Лучше всего форму из досок или листового металла сделать и готовить блоки, а из них уже строить. Но можно и послойно ставить опалубку из досок. Внизу такой опалубки делаем опорный брус. Набили, два-три дня подождали, переставили. Брус (20х20 максимум) если сделано аккуратно дает своеобразный шов, стена получается с рустами, довольно интересная. Что до промерзания, тут вопрос. 40 см арболита, это как бревно 25 -30 см по теплопроводности. Промерзнуть не промерзнет, но печку топить придется.
Но вообще-то арболит боится воды, так что снаружи лучше чем ни будь облицевать, а сразу можно и дополнительный слой утеплителя проложить. Ну и этажность не более двух этажей…
Блоки из опилкобетона: характеристика
Опилкобетон предполагает определенные свойства и требования по использованию в строительстве. Так, для предотвращения попадания влаги обычно цоколь дома делают из бетона или кирпича высотой минимум 50 сантиметров от отмостки. Также вылет карнизов за границу фасадных стен делают минимум 50 сантиметров с установкой системы отведения талой, ливневой воды.
Толщина швов между блоками составляет около 10-15 миллиметров, нередко блоки используют лишь для кладки утепляющего внутреннего слоя.
Если же цементно-стружечные блоки (плиты) используются для создания оконных/дверных перемычек, их обязательно армируют. Что касается остальных требований, то все они обусловлены особенностями материала.
Состав блоков
Основные компоненты опилкобетона:
- Песок – повышает прочность, но снижает свойства теплоизоляции (поэтому важно подобрать оптимальную пропорцию)
- Портландцемент – минимум марки М400
- Деревянная стружка (щепа) – усиливает звуко/теплоизоляцию, перед применением сушится
- Специальные добавки – для обеспечения огнестойкости, пропитки от грызунов и т.д.
Компоненты
В производстве опилкобетона могут использоваться отходы самых разных пород древесины: пихта, сосна, тополь, ель, бук, береза, ясень, граб, дуб, лиственница. Но лучшим выбором считается щепа хвойных деревьев, так как в ней повышена концентрация смолы, защищающей от гнили.
Для сосны характерно ускоренное твердение – блоки можно использовать в строительстве уже через 40 суток после заливки в формы. Дубовая щепа и лиственница продлевают срок набора прочности – они требуют отстаивания на протяжении минимум 100 суток.
С целью повышения прочности, стойкости к огню и понижения способности впитывать влагу древесные компоненты готовят специальным образом: вымачивают в известковом молоке, сушат (принудительно/естественно), замачивают в смешанном с водой жидком стекле (1 часть стекла и 7 частей воды). Для обеспечения однородности материала щепу пропускают сквозь сито с ячейками 10-20 миллиметров.
Пропорции
Соотношение материалов в составе напрямую влияет на плотность и другие характеристики. Опилкобетон бывает разных классов, которые определяют свойства и пропорции. Так, М5/10 классы используют для утепления и работ по реконструкции, М15/20 – для возведения внутренних/внешних стен.
Пропорции материалов для 1 м3 опилкобетона:
- 5 марка (плотность около 500 кг/м3) – по 50 кг цемента и песка, по 200 кг извести и опилок
- 10 марка (650 кг/м3) – 100 кг цемента, 200 кг песка, 150 кг извести и 200 кг опилок
- 15 марка (800 кг/м3) – 150 кг цемента, 350 кг песка, 100 кг извести и 200 кг опилок
- 20 марка (плотность 950 кг/м3) – 200 кг цемента, 500 кг песка, 50 кг извести, 200 кг опилок
Смешивание компонентов
Процесс смешивания такой: все материалы отмерить, смешать сухими песок и цемент, добавить известь и опилки, снова смешать тщательно, порционно вливать воду, добиваясь нужной консистенции раствора.
Сначала желательно сделать пробный замес, проверить смесь на эластичность: если комок рассыпается, нужно долить воды, если вода стекает – уменьшить объем. Правильно замешанный раствор твердеет в течение часа.
Размер опилок
Данный параметр мало влияет на прочность блоков, тут больше важна однородность материала, а не величина. Поэтому опилки выбирают такие, чтобы все компоненты были единого размера и дали возможность приготовить однородную смесь.
Подходит стружка с пилорамы – неважно, дисковой или ленточной. Но не стоит брать опилки с калибровочных или оцилиндровочных станков, так как они неоднородны по структуре.
Нюансы
Прежде чем заполнить деревянные формы опилкобетонной смесью, их устанавливают на ровные пластиковые или стальные поддоны, посыпанные тонким слоем опилок. Затем внутри ячеек устанавливают деревянные пробки, обернутые толем, которые необходимы для получения отверстия в блоках.
Когда смесь уложена в форму, ее трамбуют специальной трамбовкой. На протяжении последующих 3-5 дней материал приобретает от 30 до 40 процентов марочной прочности. По истечении этого срока форму для литья разбирают, а пробки извлекают из блоков. Готовые, но еще не высушенные изделия оставляют на этом же месте на 3-4 дня. За это время их прочность возрастает уже до 60-70 процентов.
Виды древесно-цементных материалов
Разнообразие древесно-цементных материалов не очень большое. Отличаются блоки по типу щепы и пропорциям материалов в составе, структуре, типу связующего. Самые популярные виды цементно-стружечных блоков: фибролит и арболит, цементно-стружечная плита, опилкобетон и ксилолит.
По прочности плиты бывают разных марок от М5 и классов от В0.35, плотности – показатель в диапазоне от 400 до 800 кг/м3.
Арболит
Производится из большого объема древесной щепы, песка, портландцемента, воды и химических добавок. Обычно в работу идут отходы деревообработки хвойных и лиственных пород, реже – солома-сечка, конопляная/льняная костра, измельченный стеблями хлопчатник и т. д.
Арболит бывает теплоизоляционным и строительным. В первом виде больше щепы, второй – более прочный. Где применяется: напольные плиты, кирпич под выгонку внутренних/наружных стен, покрытия и перекрытия, крупные стеновые панели.
Фибролит
Обычно поставляется в формате плит из цемента и стружки. Для производства используется щепа длиной 35 сантиметров и больше, шириной до 10 сантиметров, которая размалывается до состояния шерсти.
После помола сырье минерализируется хлористым калием, увлажняется водой, замешивается с бетоном, прессуется под давлением 0.4 МПа в плиты. Далее изделия проходят термообработку и сушатся. Фибролит также бывает изоляционно-конструкционным и теплоизоляционным.
Главные характеристики фибролита:
- Пожаробезопасность – отсутствие способности гореть открытым пламенем
- Шероховатая поверхность – обеспечивает хорошее сцепление с другими материалами
- Теплоизоляция – теплопроводность находится в районе 0.08-0.1 Вт/м2
- Влагопоглощение – 35-45%
- Легкость обработки – материал можно пилить, сверлить, забивать в него дюбеля и т.
д. без риска расколоть или деформировать
- Подверженность поражению плесенью и грибком при нахождении во влажности свыше 35%
Опилкобетон
Данный материал похож на арболит, но не так требователен к типу и параметрам щепы древесины. Состоит из цемента, песка, воды, опилок различной фракции, могут быть включены глина и известь. Пропорция песка тут может быть больше, чем в арболите, поэтому и прочность выше при идентичной плотности.
Опилкобетон обеспечивает больший вес несущей конструкции при одинаковом классе прочности. По теплоизоляционным характеристикам материал также уступает арболиту.
Основное преимущества опилкобетона – низкая стоимость при отсутствии особых условий по эксплуатации, что делает использование его в строительстве более выгодным.
Цементно-стружечные плиты
Материал создают из замешанной на цементе, воде и минеральных добавках древесно-стружечной смеси, которую потом дозируют, заливают в формы, прессуют и обрабатывают высокой температурой. Главные преимущества плит: негорючесть, стойкость к морозу, биологическая инертность.
Плиты нередко используют в сборных конструкциях, в реализации внутренних и фасадных работ. Плиты отличаются высоким уровнем влагостойкости, из недостатков можно выделить лишь достаточно большой вес и низкую эластичность. При изгибах плиты ломаются (при этой демонстрируют хорошую стойкость к продольным деформациям), поэтому применяются часто с целью усиления каркаса.
Ксилолит
Песочный материал, сделанный на базе магнезиального вяжущего и древесных отходов (мука и опилки). Также в состав вводят минеральные тонкодисперсные вещества: мраморную муку, тальк, щелочные пигменты и т.д. Производство осуществляется с применением температуры в +90 градусов и давления в районе 10 МПа, что делает материал особенно прочным после затвердевания. Обычно плиты данного типа используют при создании полов.
Характерные особенности ксилолита:
- Негорючесть
- Высокий уровень прочности на сжатие (5-50 МПа, зависит от вида материала)
- Стойкость к ударным нагрузкам, отсутствие риска смятия, сколов
- Отличные тепло/шумоизоляционные характеристики
- Стойкость ко влаге, морозу
Арболит
Часто опилкобетон путают с другим строительным материалом – арболитом, что совершенно неверно. Согласно ГОСТу, арболит определяется как бетон на цементном вяжущем, химических добавках и органических растворителях. Однако в классическом варианте арболитобетон предполагает использование древесной щепы. Именно она и определяет его уникальные свойства.
Ровно, как и опилкобетон, арболит является экологически благоприятным стеновым материалом, отличающимся высокими показателями огнестойкости и теплоизоляции. Тем не менее эти два материала, несмотря на схожесть структуры, имеют принципиальное отличие. Дело в том, что в производстве арболита вместо мелких древесных опилок, которые не могут обладать достаточными прочностными свойствами сами по себе, используют специальную древесную щепу, размер которой строго нормируется. Опилки, в отличие от щепы, не могут в достаточной мере армировать (усиливать) стеновой блок и давать ему «пластичность». Таким образом, арболитобетон прочнее опилкобетона с точки зрения прочности на изгиб и способности к временной деформации без полного разрушения. Справедливости ради стоит отметить, что опилкобетон по этому показателю превосходит остальные виды легких бетонов.
Для упрочнения блоков, заполнения пустот и уменьшения усадки в состав опилкобетона добавляют много песка, а для экономии вяжущего материала – также немало извести или глины. Использование большого количества песка негативно сказывается на огнестойкости рассматриваемого нами материала – при температуре +573 °С опилкобетон изменяется в объеме, что может привести к растрескиванию. Кроме того, из-за весомого содержания песка снижаются конструкционные характеристики блоков. Так, чтобы опилкобетон достиг прочности марки М25, его плотность должна составлять 950кг/м3. Из-за высокой плотности стоимость материала и его доставки повышается, а проведение строительных работ – усложняется.
У арболита аналогичной марки плотность составляет от 500 до 700 кг/м3. Учитывая, что с повышением удельного веса теплосберегающие свойства падают, теплопроводность опилкобетона и арболита отличается более чем в два раза в пользу последнего. Такая разница обусловлена невысоким количеством древесины в опилкобетоне по сравнению с арболитом: примерно 50 % против 80-90 % щепы. Это негативно сказывается на таком свойстве, как обеспечение пассивной вентиляции помещения. Здесь, опять же, стоит отметить, что по этому параметру опилкобетон значительно превосходит большую часть стеновых материалов. Он отлично подходит для строительства зданий малой этажности и уступает лишь своему «сопернику».
Таким образом, называть опилкобетон арболитом крайне некорректно, так как это совершенно разные материалы. Единственное сходство между ними – наличие древесного компонента в составе.
Изготовление блоков своими руками
Приступая к созданию блоков из опилок и цемента своими руками, необходимо хорошо изучить весь процесс и учесть нюансы.
Как создать блоки самостоятельно:
- Подготовить все инструменты для работы со смесью и устройства – бетономешалка, молотковая дробилка, рубильная машина, вибропрессовальная машина, вибростанок и т.
д.
- Подготовить сырье – купить в строительном магазине цемент М400 минимум, заказать чистый песок, известь (можно глину), найти на заводе много древесных опилок (желательно сухих, если регион влажный – нужно также запастись минерализаторами для обработки опилок, в качестве которых могут выступить жидкое стекло или известковое молоко).
- Тщательное измельчение древесины путем загрузки в рубильную машину, а потом в молотковую дробилку (для получения одинаковой фракции).
- Аккуратный просев щепы, чтобы отделить мусор, землю, кору и т.д.
- Пропитка щепы – вымачивание в смеси жидкого стекла с водой в пропорции 1:7. Для ускорения прохождения процесса минерализации и затвердевания материала можно добавить немного хлористого кальция.
- Обработка гашенной известью – дезинфекция от вредителей.
- Смешивание – для получения стандартной смеси берут 1 тонну портландцемента, 250 кг извести и 2.5 тонн песка. Объем щепы определяется отдельно, исходя из нужных характеристик и вида блоков.
Все смешивается в бетономешалке.
- Заливка смеси в формы, установка на вибропрессовальный аппарат.
- Сушка – натяжение пленки на емкость с формами, выдержка в помещении 12 суток при температуре +15 градусов и выше (в холоде гидратация будет проходить медленнее гораздо). Периодически материал можно проверять – если сухо, увлажнять водой.
Блоки из опилок и цемента – прекрасный выбор для выполнения множества работ в сфере ремонта и строительства малоэтажных зданий. При правильном выборе качественного материала и соблюдении технологии работы, создании оптимальных условий опилкобетон обеспечит надежность, прочность и долговечность конструкции.
Как приготовить раствор?
Глина с опилками хорошо работает как утеплитель для стен, только если материалы выбраны, подготовлены и нанесены правильно. Процесс утепления дома начинается с приготовления раствора и подбора материалов. Обе составляющие смеси можно получить бесплатно. Но стоит обратить внимание на их качество.
Глина
Материал доступен, стоит недорого, а в некоторых случаях его можно достать бесплатно. Следует обратить внимание на качество материала: не допускается наличие посторонних предметов в материале.
Можно использовать только что привезенную глину, но для получения идеальной консистенции смеси и долговечности утеплителя необходимо подготовить глину. Для этого ее заливают водой, перемешивают и оставляют на зиму. За это время материал переживает несколько циклов оттаивания и заморозки. Природная пучинистость вынуждает материал несколько раз расширяться и снова сужаться, глина становится однородной и пластичной.
Глина бывает «тощая» и «жирная», от показателя жирности зависит пластичность. При использовании «жирной» (пластичной) глины необходимо добавлять в состав утеплителя немного песка.
Глина для приготовления раствора
Глину перед началом работ необходимо подготовить: оставить на зиму в насыщенном водой состоянии.
Опилки
Опилки — это отход деревообрабатывающей промышленности. Их можно специально купить по невысокой цене на любом предприятии. Для утепления стен можно использовать разные опилки, обладающие своими полезными свойствами:
- Дуб почти не меняет свой размер и плотность под действием влаги, почти не гниет, стоек к воздействию бактерий.
- Хвойные опилки меньше чем остальные породы древесины подвержены образованию плесени из-за высокого содержания эфирных масел.
При утеплении стен можно использовать смесь из нескольких видов опилок.
Перед началом работ опилки необходимо подготовить:
- Сначала опилки избавляют от примесей, просеивают и промывают.
- После этого опилки тщательно высушивают.
- Сухие опилки необходимо пропитать составами, защищающими дерево от гниения, плесени и возгорания.
Опилки для приготовления смеси
Можно использовать смешанные опилки для получения лучших свойств теплоизоляционного материала.
Приготовление раствора
Чтобы правильно приготовить смесь, необходим набор инструментов:
Сначала в одной из бочек замачивается глина. Ее оставляют на несколько часов и периодически помешивая, ждут, когда она станет однородной. После этого 1–2 ведра глины заливают в бетономешалку и постепенно добавляют туда опилки в пропорции 3:2 соответственно.
Для достижения лучших теплоизоляционных свойств в смесь добавляют техническую соль, но в этом случае пропорция глины и опилок меняется на 1:1.
После непродолжительного нахождения в бетономешалке смесь готова к использованию, ее переливают во вторую бочку или сразу приступают к монтажу.
Нанесение
Для нанесения утеплителя на стены можно применять опалубку, но этот метод очень трудоемкий, гораздо проще подготовить плиты из утеплителя:
- Чтобы изготовить плиты, необходимо заранее изготовить несколько форм для них. Их размер будет зависеть от параметров стены. Формы можно приготовить самостоятельно, собрав их из фанеры и брусков с помощью гвоздей и молотка. Толщина плит утеплителя будет зависеть от средней зимней температуры и наличия в составе смеси технической соли.
- Форму заливают приготовленным раствором небольшими порциями и периодически разравнивают. Желательно максимально сократить количество воздушных пузырьков и толще смеси.
- Монтаж плит осуществляется после затвердевания материала, можно использовать не до конца высушенные плиты, достаточно, чтобы они просто держали форму.
- Плиты устанавливаются вплотную друг у другу, закрепляются.
- Места стыков, сколы углов и зазоры замазывают остатками глиняной смеси.
Технология
Предварительно рекомендуется подготовить инструменты для изготовления блоков из опилкобетона своими руками. Рекомендуется запастись бетономешалкой, или техническим миксером. Также следует выделить пространство для просушивания готовых блоков и посыпать его опилками либо песком.
Далее следует придерживаться технологии изготовления:
- Заранее обработанные хлористым калием и высушенные опилки отсортировать, используя сито с ячейками 10х10 мм.
- Добавить все сухие составляющие (кроме опилок) в бетономешалку и размешать (либо воспольщоваться миксером).
- Добавить опилки и совершить несколько сухих прокручиваний.
- Добавить воду из расчета 15% на полностью сухие компоненты и 10%, если составляющие немного влажные.
- Размешивать до консистенции густой сметаны. При сжатии кома материала, на нём должны остаться отпечатки пальцев без выступающей воды.
- Разлить раствор в специальные формы и утрамбовать, чтобы воспрепятствовать появлению пустых, наполненных воздухом участков.
Форму также можно изготовить самостоятельно, сбив доски размером 20х20х40. Их внутренняя поверхность покрывается сталью или завешивается пластиком. Так, материал не будет прилипать и будет легко извлекаться, а жидкость из раствора не будет уходить в дерево.
Понять, готовы ли блоки можно ножом – проведя острой частью по поверхности, слудует изучить след. На застывшей массе останется неглубокая царапина. На полное высыхание уйдет до 90 дней.
Для равномерной просушки рекомендуется расположить блоки на ветру, обязательно укрывая их от дождя в непогоду.
Отзывы
На интернет-форумах по строительству можно встретить отзывы строителей и владельцев жилья из опилкобетона:
- Олег из г. Курска более 20 лет живет в доме из опилкобетона, однако утверждает, что конструкция «на ладан дышит», что вызвано высокой влаговпитываемостью блоков. Это сказывается и на состоянии комнат и стены. Они постоянно мокрые или влажные, на них заводятся насекомые. Олег жалеет, что при возведении не построил более высокий фундамент.
- Алексей из г. Ярославля самостоятельно построил баню из опилкобетонных блоков и за 5 лет эксплуатации не заметил существенных недостатков. В его случае, проблема влаги была решена нанесением гидроизоляционного слоя с обеих сторон стены.
- Михаил из г. Владивостока опилкобетонные блоки приобрел в магазине и своими руками построил из них сарай. Спустя 2 года от стены стали отваливаться куски.
- Анатолию из Воркуты самостоятельное изготовление блоков не удалось, однако дом из блоков, приготовленных строителями его удовлетворил.
Состав
Основным компонентом стройматериала является песок, а также цемент и стружка (щепа). Цемент влияет на прочность, обрабатываемость и некоторые другие эксплуатационные качества. Используемая для создания блоков марка цемента должна быть не ниже М400.
Повышенное содержание опилок усиливает шумопоглощающие и теплоизолирующие показатели арболитовых блоков. Перед использованием щепа должна тщательно просушиваться.
С ростом доли песка увеличивается прочность, но снижается теплоизоляция материала. Также при изготовлении применяются химические добавки, усиливающие различные качества.
Например, практически обязательно применяется компонент, повышающий огнестойкость материала. Кроме того, может использоваться вещество, отталкивающее грызунов и других вредителей.
Опилкобетон своими руками: пропорции, состав, видео
Опилкобетон – лёгкий бетон, в состав которого входит цемент, опилки, минерализаторы и песок. Материал экологически чистый, имеет низкий объёмный вес, высокую устойчивость к огню, низкую теплопроводность и высокую паропроницаемость. Используется для возведения монолитных зданий или для изготовления строительных блоков, в том числе применяется для возведения несущих конструкций, идеально подходит для малоэтажного строительства.
Опилкобетон может быть нескольких видов, в зависимости от плотности и, соответственно, прочности. Каждый из видов материала отвечает следующим маркам прочности: М5, М10, М15, М20. Первые две марки применяются исключительно в качестве утеплителя, возведение из них несущих конструкций нежелательно. В качестве несущих конструкций в малоэтажном строительстве применяют последние две марки. Если же проводится многоэтажное строительство из опилкобетона, то обязательно применение несущего каркаса.
Сфера применения опилкобетона
Материал имеет широчайший спектр применения, при этом он очень часто производится своими руками. С помощью данного материала можно возводить хозяйственные постройки, также часто практикуется строительство домов из опилкобетона, утеплительных стен для тех же домов, подвалов или даже бани из опилкобетона.
Материал сравнительно лёгкий и дешёвый, кроме этого, сэкономить можно и на основании для здания, используя ленточный фундамент. Если же проводить реконструкцию зданий или же утеплять их, то в усилении фундамента нет необходимости.
Фото: дом из опилкобетонных блоков
Подготовка сырья для изготовления опилкобетона своими руками
В предварительной подготовке нуждается только древесная часть состава. Для начала её нужно просеять через сито с размером ячейки не более одного квадратного сантиметра.
Опилки можно предварительно просушить, но это необязательно. В последующем просто будут внесены поправки с учётом влажности опилок. Если и сушить, то весь объём, а не частично!
Главнейшим этапом подготовки опилок является их минерализация. Проводится эта процедура для лучшего связывания цемента с древесной частью, придания ей стойкости к огню и биологическим факторам.
Проводится минерализация замачиванием опилок в растворе минерализатора. В качестве минерализатора допустимо использовать гашеную известь, жидкое стекло, кальция хлорид, сернокислый кальций.
Опилки для изготовления опилкобетонных блоков
Приготовление смеси для опилкобетона своими руками
Для приготовления смеси своими руками обычные бетономешалки практически не подходят, намного лучше использовать растворосмесители или же в крайнем случае ручное смешивание своими руками, что весьма затруднительно при больших объёмах.
Для приготовления каждой из марок материала используют свою пропорцию при одном и том же составе:
- М5 – для данной марки используют опилки, известь или глину, песок и цемент в соответствующей пропорции 4:4:1:1;
- М10 – опилки, известь или глину, песок и цемент смешивают в пропорции 4:3:4:2;
- М15 – смешивают опилки, известь или глину, песок и цемент в пропорции 4:2:7:3;
- М20 – используют следующую пропорцию опилок, извести или глины, песка и цемента 4:1:10:4.
Далее, медленно добавляют воду, например, из ведра или лейки, постепенно перемешивая смесь до получения рассыпчатой на вид консистенции, но сохраняющей форму после сжатия в кулаке, при этом не должно выделяться влаги.
Растворосмеситель
Рекомендуется использовать именно предложенные пропорции, так как они проверены опытом и являются оптимальными.
Совет прораба: всегда учитывайте тот факт, что чем выше плотность, тем хуже теплотехнические показатели, но тем выше несущая способность готового материала.
Литьё опилкобетона
При производстве опилкобетона своими руками по предложенному составу и пропорциям с последующим формированием его в готовое изделие пользуются заранее подготовленными формами для блоков нужного размера. Также можно пользоваться съёмными и несъёмными опалубками в случае монолитного строительства.
При производстве блоков своими руками объём уже замешанного состава помещают в формы, покрытые изнутри гидроизолятором. Для придания блокам большей прочности в раствор можно помещать продольную арматуру. Для облегчения изделия можно помещать вертикально расположенные пластиковые трубы на всю толщу формы.
Форма для изготовления опилкобетонных блоков
После заливки материал уплотняют вибротрамбовкой либо специально изготовленной ручной трамбовкой. Далее, блоки не вынимая из формы, оставляют на четыре дня накрытые целлофаном. После этого осторожно извлекают трубки из блоков, а сами блоки из форм и оставляют досушиваться на месяц. По прошествии этого времени из блоков можно строить, но стоит учитывать, что полная прочность достигается за три месяца, и с облицовкой спешить не нужно.
Совет прораба: при монолитном строительстве со съёмной опалубкой она устанавливается с использованием тех же принципов, что и для блочных форм. Армирование проводится через каждые 40 сантиметров. Несъёмная опалубка устанавливается совместно с арматурным каркасом, но стоит учитывать, что такая конструкция будет долго «сохнуть».
При чётком расчёте проекта опилкобетон, произведённый даже своими руками строго по предложенному составу и пропорциях, не уступает по качеству заводскому. А использование его как такового имеет по большей части отличные рекомендации не только от людей, строивших своими руками, но и такие же отзывы строителей профессионалов.
Видео
Блоки из стружки и цемента — великолепный материал во всех отношениях
Главная › Материалы › Подходит ли арболит из стружки и цемента для вашего строительства? Блоки из стружки и цемента (арболит, деревобетон) — экоматериал с крупнопористой структурой, легкой массой и прекрасными звуко- и теплоизоляционными способностями. Арболитовые блоки являют собой 15 — 26-киллограмовые параллелепипеды с параметрами 390х190х190 мм, 600х300х200 мм. В состав блоков входят вяжущее, заполнитель, химические добавки, вода. В качестве минерального вяжущего используется портландцемент (марка прочности 400, 500 и выше), заполнитель — продукт переработки древесины и льна, стебли конопли. Химические добавки призваны нейтрализовать сахара в цементно-стружковых блоках, с этой целью лучше всего справляются кальций хлорид и алюминий сернокислый в пропорции 1:1 (в количестве 4% от общей массы цемента).
Блоки из стружки и цемента широко применяются для строительства дачных домов и загородных коттеджей, а также бань и гаражей. Причин для популярности деревобетона более, чем достаточно:
- Высокие энергосберегающие характеристики;
- Высокие показатели огнестойкости;
- Создании здорового микроклимата: арболит регулирует воздухообмен и уровень влажность, защищает от поражения грибками и микроорганизмами, не подвержен гниению;
- Легкий вес блоков приводит к уменьшению массы здания;
- Механическая обработка арболита происходит без особых усилий;
- Стружковые блоки имеют хорошее сцепление с цементом из бетонной и штукатурной смеси, штукатурку можно наносить без сетки.
- Деревобетон очень прочен, не боится морозов, не вредит окружающей среде и человеку.
- По срокам возведения и капиталовложениям здания из арболита очень экономически выгодны.
Главная составляющая цементно-стружкового блока — это древесина.
Какой размер приемлем для изготовления арболитовых блоков, какие породы дерева лучше использовать? Лучше всего подходят игольчатые частицы длиной от 15 до 25 мм, толщиной от 2 до 5 мм. Более крупные частицы могут разрушить застывший деревобетон под воздействия влаги. Самые оптимальные породы для производства частиц: хвойные и твердолиственные (сосна, елка, пихта, бук, осина, тополь). Древесина может быть дробленная, либо в форме щепок, стружек, опилок; три последние можно смешивать в пропорции 1:1:1. Нельзя использовать сырую древесину, сырье требует выдержки на свежем пространстве или обработки специальной химией, чтобы устранить вредные для цемента сахара. Все преимущества описанного стройматериала сохранятся лишь при условии, если блоки из стружки и цемента будут приготовлены по правильной технологии.
Предыдущая запись Следующая запись
Изготовление опилкобетонных блоков своими руками
Опилкобетон является тем строительным материалом, который отличается пониженной плотностью.
Опилкобетон позволяет возводить крупные строения без строительства сложного фундамента, так как это очень легкий, но при этом прочный материал.
Изготовить опилкобетонные блоки своими руками не так сложно, как может показаться на первый взгляд, а популярность такой материал получил благодаря своим качествам:
- высокая степень экологической безопасности;
- пожароустойчивость;
- очень высокая прочность;
- высокие теплотехнические показатели;
- паропроницаемость;
- невысокая цена;
- устойчивость к морозам.
К тому же следует принять во внимание, что делать из опилок опилкобетонные блоки своими руками не трудно. Для этого понадобятся:
- бетономешалка или растворосмеситель.
- сито с ячейками 10 на 10 мм.
- полиэтиленовая пленка.
- шпатель.
Популярность материала
Состав блока опилкобетона.
Используются блоки из опилкобетона не только при возведении домов и коттеджей, но и во время утепления подвалов, при реконструкциях (не нужно усиливать фундамент, что является очень важны фактором, если дом строится своими руками). Надо отметить, что дом, при строительстве которого использовался такой материал, отличается легкостью: если площадь дома 250 кв. м, то весить он будет всего 50 т, так как опилкобетонные блоки отличаются легкостью. Этот фактор является очень важным, так как не нужно устанавливать сложный фундамент, что значительно сократит не только финансовые, но и временные расходы. Не следует упускать из внимания то, что такой материал обладает хорошей звукоизоляцией, сборка очень простая, срок эксплуатации долгий.
Что касается плотности блоков, то здесь все зависит от соотношения опилок и песка. Если песка ушло на много меньше на изготовление блоков, чем опилок, то будет меньше их плотность, теплотехнические характеристики при этом повышаются, но вот прочность уменьшается. Если добавить побольше песка и меньше опилок, то прочность значительно возрастает, водонипроницаемость и морозостойкость тоже возрастают.
Блоки из опилкобетона получаю все большее распространение не только, благодаря своим уникальным качествам, но и тем, что сделать их можно своими руками и компоненты, из которых они состоят, не нужно заготавливать заранее. Приобретение опилок не является трудным делом, их можно найти почти в любом магазине строительных материалов, но при этом нужно внимательно отнестись к выбору опилок, так как именно от них во многом зависит то, насколько вся дальнейшая работа будет качественной. Поэтому на приобретении опилок экономить не стоит, тем более, что стоят они не дорого. Все, что нужно для того, чтобы сделать блоки из опилкобетона, можно купить в большинстве строительных магазинов, так что начинать их заготовку можно буквально за день до того, как начнется строительство.
Изготовление блоков
Растворосмеситель значительно облегчит работу по изготовлению опилкобетонных блоков.
Для того чтобы сделать опилкобетон, желательно воспользоваться бетономешалкой или растворосмесителем, так как без этого оборудования процесс изготовления будет достаточно сложным и трудоемким. Начать следует с того, что хорошо просушенные опилки нужно просеять через сито (надо пользоваться таким ситом, где ячейки по размеру 10 на 10 мм), потом они смешиваются с цементом и песком. Теперь в готовую смесь из опилок , песка и цемента следует добавить заранее подготовленное тесто из глины или известняка и все как следует перемешать, налить воды, но не сразу, а постепенно, доливая ее из лейки. После того, как налили чуть-чуть воды, нужно все снова перемешать и снова добавить воды, все это делается своими руками, тогда можно быть уверенными в том, что все будет самого высокого качества.
Если полученную смесь сжать в кулаке и получится пластичный комок, на котором видны все вмятины от руки, то значит все сделано правильно и на высоком уровне. Не должны быть видны капельки воды, их наличие говорит о низком качестве. Если все в порядке, то можно лепить блоки из опилкобетона, однако следует помнить, что к этому процессу надо приступать не позднее, чем через 1,5-2 часа после того, как смесь была приготовлена, так как потом он будет твердеть. Когда смесь укладывается в форму, она должна хорошо утрамбовываться, чтобы там не было воздуха.
Опилкобетон можно сформировать в блоки любых размеров или даже панели – все зависит от проекта. Однако следует помнить – чем больше объем опилкобетона, тем больше времени уйдет на сушку.
Блоки из опилкобетона могут быть разных размеров, четких стандартов не существует. Размеры таких блоков могут зависеть от того, насколько толстые стены, проемы и простенки, какое расстояние от проемов до углов строения, нужно принимать во внимание и способ укладки. Чтобы строительные работы проходили с максимальным удобством, длина участков стены должны быть кратной блочным размерам.
Надо отметить, что в большинстве случаев толщина блоков из опилкобетона идентична толщине двух красных кирпичей, при этом нужно учитывать и уложенный между ними раствор, таким образом, получается в среднем 140 мм. Если блоки из опилкобетона делать большими, то нужно учитывать, что они сохнут достаточно долго, если есть необходимость в ускорении процесса, то рекомендуется сделать в них несколько отверстий. Благодаря этому блоки из опилкобетона будут сохнуть гораздо быстрее, а еще значительно улучшатся их теплозащитные свойства.
parent.postMessage%28%26%23039%3Bseraph-accel-lzl-v%3A1%26%23039%3B%2C%26%23039%3B%2A%26%23039%3B%29%3B%22%20style%3D%22position%3Aabsolute%3Bwidth%3A100%25%3Bheight%3A100%25%3Bbackground-image%3Aurl%28%27https%3A%2F%2Fi.ytimg.com%2Fvi%2FIHsniwvHKeU%2Fhqdefault.jpg%27%29%3Bbackground-position%3Acenter%3Bbackground-size%3Acover%3Bbackground-repeat%3Ano-repeat%3B%22%3E%3C%2Fa%3E%3Cspan%20style%3D%22position%3Aabsolute%3Bleft%3A50%25%3Btop%3A50%25%3Bwidth%3A68px%3Bheight%3A48px%3Bmargin-left%3A-34px%3Bmargin-top%3A-24px%3Bpointer-events%3Anone%3B%22%3E%3Csvg%20height%3D%22100%25%22%20version%3D%221.1%22%20viewBox%3D%220%200%2068%2048%22%20width%3D%22100%25%22%3E%3Cpath%20class%3D%22ytp-large-play-button-bg%22%20d%3D%22M66.52%2C7.74c-0.78-2.93-2.49-5.41-5.42-6.19C55.79%2C.13%2C34%2C0%2C34%2C0S12.21%2C.13%2C6.9%2C1.55%20C3.97%2C2.33%2C2.27%2C4.81%2C1.48%2C7.74C0.06%2C13.05%2C0%2C24%2C0%2C24s0.06%2C10.95%2C1.48%2C16.26c0.78%2C2.93%2C2.49%2C5.41%2C5.42%2C6.19%20C12.21%2C47.87%2C34%2C48%2C34%2C48s21. 79-0.13%2C27.1-1.55c2.93-0.78%2C4.64-3.26%2C5.42-6.19C67.94%2C34.95%2C68%2C24%2C68%2C24S67.94%2C13.05%2C66.52%2C7.74z%22%20fill%3D%22%23f00%22%3E%3C%2Fpath%3E%3Cpath%20d%3D%22M%2045%2C24%2027%2C14%2027%2C34%22%20fill%3D%22%23fff%22%3E%3C%2Fpath%3E%3C%2Fsvg%3E%3C%2Fspan%3E%3C%2Fbody%3E%3C%2Fhtml%3E» allowtransparency=»true»/>
Изготовление форм
Рекомендуется строить стену, не используя опалубку, а применяя заранее подготовленные блоки. Однако перед тем как приступить к строительству, блоки из опилкобетона нужно высушивать не менее 3-х месяцев, только после этого срока они приобретают свою марочную твердость. Форму с такого блока не следует снимать сразу, надо подождать 3-5 дней, для того чтобы процесс был ускорен, рекомендуется сделать сразу 10-20 форм. Если поступить таким образом, то работа не будет прерываться и не будет тратиться время на ожидание высыхания блоков. Что касается количества форм, то тут все зависит от того, сколько их нужно приготовить за один раз.
Для больших блоков нужно приготовить разборные двойные или одинарные формы, они представляют собой сделанные из досок ящики. Такие формы разъемные, поэтому они быстро собираются и разбираются. При их изготовлении нужно использовать доски, толщина которых равняется 20 мм, скрепляются такие конструкции при помощи стальных стержней, на них следует накрутить барашковую гайку.
Если нужно сделать блоки небольшого размера, то они приготавливаются в сотовых формах, которые собраны из 20-миллиметровых досок. Нужно учитывать, что когда блоки высыхают, то становятся меньше (результат усушки), поэтому форму нужно делать несколько больших размеров, чем блоки, которые должны получиться, разница должна составлять около 10%.
parent.postMessage%28%26%23039%3Bseraph-accel-lzl-v%3A2%26%23039%3B%2C%26%23039%3B%2A%26%23039%3B%29%3B%22%20style%3D%22position%3Aabsolute%3Bwidth%3A100%25%3Bheight%3A100%25%3Bbackground-image%3Aurl%28%27https%3A%2F%2Fi.ytimg.com%2Fvi%2FU1IY5emuMFU%2Fsddefault.jpg%27%29%3Bbackground-position%3Acenter%3Bbackground-size%3Acover%3Bbackground-repeat%3Ano-repeat%3B%22%3E%3C%2Fa%3E%3Cspan%20style%3D%22position%3Aabsolute%3Bleft%3A50%25%3Btop%3A50%25%3Bwidth%3A68px%3Bheight%3A48px%3Bmargin-left%3A-34px%3Bmargin-top%3A-24px%3Bpointer-events%3Anone%3B%22%3E%3Csvg%20height%3D%22100%25%22%20version%3D%221.1%22%20viewBox%3D%220%200%2068%2048%22%20width%3D%22100%25%22%3E%3Cpath%20class%3D%22ytp-large-play-button-bg%22%20d%3D%22M66.52%2C7.74c-0.78-2.93-2.49-5.41-5.42-6.19C55.79%2C.13%2C34%2C0%2C34%2C0S12.21%2C.13%2C6.9%2C1.55%20C3.97%2C2.33%2C2.27%2C4.81%2C1.48%2C7.74C0.06%2C13.05%2C0%2C24%2C0%2C24s0.06%2C10.95%2C1.48%2C16.26c0.78%2C2.93%2C2.49%2C5.41%2C5.42%2C6.19%20C12.21%2C47.87%2C34%2C48%2C34%2C48s21. 79-0.13%2C27.1-1.55c2.93-0.78%2C4.64-3.26%2C5.42-6.19C67.94%2C34.95%2C68%2C24%2C68%2C24S67.94%2C13.05%2C66.52%2C7.74z%22%20fill%3D%22%23f00%22%3E%3C%2Fpath%3E%3Cpath%20d%3D%22M%2045%2C24%2027%2C14%2027%2C34%22%20fill%3D%22%23fff%22%3E%3C%2Fpath%3E%3C%2Fsvg%3E%3C%2Fspan%3E%3C%2Fbody%3E%3C%2Fhtml%3E» allowtransparency=»true»/>
Полезные рекомендации
Для окончательной просушки блоки опилкобетона укладывают так, чтобы между слоями оставались зазоры для свободной вентиляции блоков.
Перед тем, как залить опилкобетоновую смесь в деревянные формы, их нужно установить на поддоны (они могут быть сделаны из бетона или пластика) и посыпать тонким слоем опилок. Потом смесь следует максимально плотно уложить в форму, для этого можно воспользоваться ручной трамбовкой. После того, как этот процесс завершен, формы с опилкобетоном следует оставить на 3 дня, за это время блоки станут прочными.
Когда установленное время истекло нужно аккуратно вынуть толь и пробки, формы разобрать, а блоки следует оставить еще на 3 дня для того, чтобы они стали еще более прочными. Потом материал надо отнести под навес для дальнейшего высушивания. Для того чтобы блоки из опилкобетона были наилучшего качества, надо соблюдать некоторые рекомендации:
- во время сушки лучше всего их раскладывать на сквозняке, тогда процесс сушки будет осуществляться равномерно;
- когда блоки укладываются для просушивания, между ними нужно оставлять зазоры;
- нужно учитывать, что может пойти дождь, поэтому, если не имеется навеса, то строительный материал надо накрыть полиэтиленовой пленкой.
После того, как блоки просушатся окончательно из них надо сделать столбы. Для этого на заранее обожженные кирпичи укладываются 2 блока, поперек них укладываются еще 2, потом поперек еще 2 и так далее по аналогичному принципу. Теперь строительный материал просохнет и затвердеет быстрее. Для того чтобы блоки из опилкобетона просохли на 100%, нужно не менее 3-х месяцев, по истечению этого срока материал отличается твердостью, прочностью, на нем нет никаких трещин.
1%22%20viewBox%3D%220%200%2068%2048%22%20width%3D%22100%25%22%3E%3Cpath%20class%3D%22ytp-large-play-button-bg%22%20d%3D%22M66.52%2C7.74c-0.78-2.93-2.49-5.41-5.42-6.19C55.79%2C.13%2C34%2C0%2C34%2C0S12.21%2C.13%2C6.9%2C1.55%20C3.97%2C2.33%2C2.27%2C4.81%2C1.48%2C7.74C0.06%2C13.05%2C0%2C24%2C0%2C24s0.06%2C10.95%2C1.48%2C16.26c0.78%2C2.93%2C2.49%2C5.41%2C5.42%2C6.19%20C12.21%2C47.87%2C34%2C48%2C34%2C48s21.79-0.13%2C27.1-1.55c2.93-0.78%2C4.64-3.26%2C5.42-6.19C67.94%2C34.95%2C68%2C24%2C68%2C24S67.94%2C13.05%2C66.52%2C7.74z%22%20fill%3D%22%23f00%22%3E%3C%2Fpath%3E%3Cpath%20d%3D%22M%2045%2C24%2027%2C14%2027%2C34%22%20fill%3D%22%23fff%22%3E%3C%2Fpath%3E%3C%2Fsvg%3E%3C%2Fspan%3E%3C%2Fbody%3E%3C%2Fhtml%3E» allowtransparency=»true»/>
Для того чтобы узнать насколько прочен приготовленный материал, следует провести такое испытание: блок нужно сбросить с высоты не менее 1 м, если он останется целым, то качество хорошее. И тогда можно будет через короткое время справлять новоселье в новом, прочном, уютном доме, который был построен без больших материальных затрат.
%PDF-1.3
%
66 0 объект
>
эндообъект
внешняя ссылка
66 1596
0000000016 00000 н
0000032271 00000 н
0000034115 00000 н
0000034330 00000 н
0000053395 00000 н
0000053445 00000 н
0000053495 00000 н
0000053545 00000 н
0000053595 00000 н
0000053645 00000 н
0000053695 00000 н
0000053745 00000 н
0000053795 00000 н
0000053845 00000 н
0000053895 00000 н
0000053945 00000 н
0000053995 00000 н
0000054045 00000 н
0000054095 00000 н
0000054145 00000 н
0000054195 00000 н
0000054245 00000 н
0000054295 00000 н
0000054345 00000 н
0000054395 00000 н
0000054445 00000 н
0000054495 00000 н
0000054545 00000 н
0000054595 00000 н
0000054645 00000 н
0000054695 00000 н
0000054745 00000 н
0000054795 00000 н
0000054845 00000 н
0000054895 00000 н
0000054946 00000 н
0000054997 00000 н
0000055048 00000 н
0000055099 00000 н
0000055150 00000 н
0000055201 00000 н
0000055252 00000 н
0000055303 00000 н
0000055354 00000 н
0000055405 00000 н
0000055456 00000 н
0000055507 00000 н
0000055558 00000 н
0000055609 00000 н
0000055660 00000 н
0000055711 00000 н
0000055762 00000 н
0000055813 00000 н
0000055864 00000 н
0000055915 00000 н
0000055966 00000 н
0000056017 00000 н
0000056068 00000 н
0000056119 00000 н
0000056170 00000 н
0000056221 00000 н
0000056272 00000 н
0000056323 00000 н
0000056374 00000 н
0000056425 00000 н
0000056476 00000 н
0000056527 00000 н
0000056578 00000 н
0000056629 00000 н
0000056680 00000 н
0000056731 00000 н
0000056782 00000 н
0000056833 00000 н
0000056884 00000 н
0000056935 00000 н
0000056986 00000 н
0000057037 00000 н
0000057088 00000 н
0000057139 00000 н
0000057190 00000 н
0000057241 00000 н
0000057292 00000 н
0000057343 00000 н
0000057394 00000 н
0000057445 00000 н
0000057496 00000 н
0000057547 00000 н
0000057598 00000 н
0000057649 00000 н
0000057700 00000 н
0000057751 00000 н
0000057802 00000 н
0000057853 00000 н
0000057904 00000 н
0000057955 00000 н
0000058006 00000 н
0000058057 00000 н
0000058108 00000 н
0000058159 00000 н
0000058210 00000 н
0000058261 00000 н
0000058312 00000 н
0000058363 00000 н
0000058414 00000 н
0000058465 00000 н
0000058516 00000 н
0000058567 00000 н
0000058618 00000 н
0000058669 00000 н
0000058720 00000 н
0000058771 00000 н
0000058822 00000 н
0000058873 00000 н
0000058924 00000 н
0000058975 00000 н
0000059026 00000 н
0000059077 00000 н
0000059128 00000 н
0000059179 00000 н
0000059230 00000 н
0000059281 00000 н
0000059332 00000 н
0000059383 00000 н
0000059434 00000 н
0000059485 00000 н
0000059536 00000 н
0000059587 00000 н
0000059638 00000 н
0000059689 00000 н
0000059740 00000 н
0000059791 00000 н
0000059842 00000 н
0000059893 00000 н
0000059944 00000 н
0000059995 00000 н
0000060046 00000 н
0000060097 00000 н
0000060148 00000 н
0000060199 00000 н
0000060250 00000 н
0000060301 00000 н
0000060352 00000 н
0000060403 00000 н
0000060454 00000 н
0000060505 00000 н
0000060556 00000 н
0000060607 00000 н
0000060658 00000 н
0000060709 00000 н
0000060760 00000 н
0000060811 00000 н
0000060862 00000 н
0000060913 00000 н
0000060964 00000 н
0000061015 00000 н
0000061066 00000 н
0000061117 00000 н
0000061168 00000 н
0000061219 00000 н
0000061270 00000 н
0000061321 00000 н
0000061372 00000 н
0000061423 00000 н
0000061474 00000 н
0000061525 00000 н
0000061576 00000 н
0000061627 00000 н
0000061678 00000 н
0000061729 00000 н
0000061780 00000 н
0000061831 00000 н
0000061882 00000 н
0000061933 00000 н
0000061984 00000 н
0000062035 00000 н
0000062086 00000 н
0000062137 00000 н
0000062188 00000 н
0000062239 00000 н
0000062290 00000 н
0000062341 00000 н
0000062392 00000 н
0000062443 00000 н
0000062494 00000 н
0000062545 00000 н
0000062596 00000 н
0000062647 00000 н
0000062698 00000 н
0000062749 00000 н
0000062800 00000 н
0000062851 00000 н
0000062902 00000 н
0000062953 00000 н
0000063004 00000 н
0000063055 00000 н
0000063106 00000 н
0000063157 00000 н
0000063208 00000 н
0000063259 00000 н
0000063310 00000 н
0000063361 00000 н
0000063412 00000 н
0000063463 00000 н
0000063514 00000 н
0000063565 00000 н
0000063616 00000 н
0000063667 00000 н
0000063718 00000 н
0000063769 00000 н
0000063820 00000 н
0000063871 00000 н
0000063922 00000 н
0000063973 00000 н
0000064024 00000 н
0000064075 00000 н
0000064126 00000 н
0000064177 00000 н
0000064228 00000 н
0000064279 00000 н
0000064330 00000 н
0000064381 00000 н
0000064432 00000 н
0000064483 00000 н
0000064534 00000 н
0000064585 00000 н
0000064636 00000 н
0000064687 00000 н
0000064738 00000 н
0000064789 00000 н
0000064840 00000 н
0000064891 00000 н
0000064942 00000 н
0000064993 00000 н
0000065044 00000 н
0000065095 00000 н
0000065146 00000 н
0000065197 00000 н
0000065248 00000 н
0000065299 00000 н
0000065350 00000 н
0000065401 00000 н
0000065452 00000 н
0000065503 00000 н
0000065554 00000 н
0000065605 00000 н
0000065656 00000 н
0000065707 00000 н
0000065758 00000 н
0000065809 00000 н
0000065860 00000 н
0000065911 00000 н
0000065962 00000 н
0000066013 00000 н
0000066064 00000 н
0000066115 00000 н
0000066166 00000 н
0000066217 00000 н
0000066268 00000 н
0000066319 00000 н
0000066370 00000 н
0000066421 00000 н
0000066472 00000 н
0000066523 00000 н
0000066574 00000 н
0000066625 00000 н
0000066676 00000 н
0000066727 00000 н
0000066778 00000 н
0000066829 00000 н
0000066880 00000 н
0000066931 00000 н
0000066982 00000 н
0000067033 00000 н
0000067084 00000 н
0000067135 00000 н
0000067186 00000 н
0000067237 00000 н
0000067288 00000 н
0000067339 00000 н
0000067390 00000 н
0000067441 00000 н
0000067492 00000 н
0000067543 00000 н
0000067594 00000 н
0000067645 00000 н
0000067696 00000 н
0000067747 00000 н
0000067798 00000 н
0000067849 00000 н
0000067900 00000 н
0000067951 00000 н
0000068002 00000 н
0000068053 00000 н
0000068104 00000 н
0000068155 00000 н
0000068206 00000 н
0000068257 00000 н
0000068308 00000 н
0000068359 00000 н
0000068410 00000 н
0000068461 00000 н
0000068512 00000 н
0000068563 00000 н
0000068614 00000 н
0000068665 00000 н
0000068716 00000 н
0000068767 00000 н
0000068818 00000 н
0000068869 00000 н
0000068920 00000 н
0000068971 00000 н
0000069022 00000 н
0000069073 00000 н
0000069124 00000 н
0000069175 00000 н
0000069226 00000 н
0000069277 00000 н
0000069328 00000 н
0000069379 00000 н
0000069430 00000 н
0000069481 00000 н
0000069532 00000 н
0000069583 00000 н
0000069634 00000 н
0000069685 00000 н
0000069736 00000 н
0000069787 00000 н
0000069838 00000 н
0000069889 00000 н
0000069940 00000 н
0000069991 00000 н
0000070042 00000 н
0000070093 00000 н
0000070144 00000 н
0000070195 00000 н
0000070246 00000 н
0000070297 00000 н
0000070348 00000 н
0000070399 00000 н
0000070450 00000 н
0000070501 00000 н
0000070552 00000 н
0000070603 00000 н
0000070654 00000 н
0000070705 00000 н
0000070756 00000 н
0000070807 00000 н
0000070858 00000 н
0000070909 00000 н
0000070960 00000 н
0000071011 00000 н
0000071062 00000 н
0000071113 00000 н
0000071164 00000 н
0000071215 00000 н
0000071266 00000 н
0000071317 00000 н
0000071368 00000 н
0000071391 00000 н
0000072478 00000 н
0000072500 00000 н
0000073465 00000 н
0000073487 00000 н
0000074485 00000 н
0000074508 00000 н
0000075609 00000 н
0000075632 00000 н
0000076847 00000 н
0000077077 00000 н
0000077301 00000 н
0000077863 00000 н
0000077904 00000 н
0000078480 00000 н
0000078502 00000 н
0000079511 00000 н
0000079534 00000 н
0000081420 00000 н
0000081443 00000 н
0000083978 00000 н
0000084218 00000 н
0000084500 00000 н
0000084867 00000 н
0000085104 00000 н
0000085385 00000 н
0000085625 00000 н
0000085928 00000 н
0000086165 00000 н
0000086405 00000 н
0000086642 00000 н
0000086934 00000 н
0000087232 00000 н
0000087472 00000 н
0000087764 00000 н
0000087986 00000 н
0000088272 00000 н
0000088640 00000 н
0000088871 00000 н
0000089186 00000 н
0000089393 00000 н
0000089684 00000 н
0000089894 00000 н
00000 00000 н
00000 00000 н
00000 00000 н
00000 00000 н
00002 00000 н
00002 00000 н
0000392106 00000 н
0000392355 00000 н
0000392536 00000 н
0000392785 00000 н
0000393034 00000 н
0000393283 00000 н
0000393532 00000 н
0000393782 00000 н
0000394032 00000 н
0000394282 00000 н
0000394533 00000 н
0000394784 00000 н
0000395030 00000 н
0000395221 00000 н
0000395466 00000 н
0000395657 00000 н
0000395900 00000 н
0000396091 00000 н
0000396272 00000 н
0000396512 00000 н
0000396703 00000 н
0000396887 00000 н
0000397123 00000 н
0000397314 00000 н
0000397495 00000 н
0000397679 00000 н
0000397912 00000 н
0000398103 00000 н
0000398284 00000 н
0000398465 00000 н
0000398696 00000 н
0000398887 00000 н
0000399078 00000 н
0000399306 00000 н
0000399497 00000 н
0000399722 00000 н
0000399903 00000 н
0000400126 00000 н
0000400317 00000 н
0000400508 00000 н
0000400729 00000 н
0000400947 00000 н
0000401138 00000 н
0000401353 00000 н
0000401544 00000 н
0000401754 00000 н
0000401945 00000 н
0000402215 00000 н
0000402406 00000 н
0000402669 00000 н
0000402860 00000 н
0000403041 00000 н
0000403293 00000 н
0000403484 00000 н
0000403665 00000 н
0000403846 00000 н
0000404085 00000 н
0000404276 00000 н
0000404509 00000 н
0000404700 00000 н
0000404933 00000 н
0000405124 00000 н
0000405355 00000 н
0000405546 00000 н
0000405774 00000 н
0000405965 00000 н
0000406195 00000 н
0000406386 00000 н
0000406615 00000 н
0000406806 00000 н
0000407033 00000 н
0000407224 00000 н
0000407449 00000 н
0000407640 00000 н
0000407865 00000 н
0000408056 00000 н
0000408283 00000 н
0000408474 00000 н
0000408701 00000 н
0000408892 00000 н
0000409115 00000 н
0000409306 00000 н
0000409529 00000 н
0000409720 00000 н
0000409940 00000 н
0000410131 00000 н
0000410351 00000 н
0000410542 00000 н
0000410762 00000 н
0000410953 00000 н
0000411173 00000 н
0000411367 00000 н
0000411582 00000 н
0000411773 00000 н
0000411990 00000 н
0000412184 00000 н
0000412400 00000 н
0000412594 00000 н
0000412811 00000 н
0000413002 00000 н
0000413219 00000 н
0000413413 00000 н
0000413624 00000 н
0000413818 00000 н
0000414030 00000 н
0000414224 00000 н
0000414435 00000 н
0000414629 00000 н
0000414840 00000 н
0000415034 00000 н
0000415245 00000 н
0000415439 00000 н
0000415650 00000 н
0000415844 00000 н
0000416052 00000 н
0000416244 00000 н
0000416452 00000 н
0000416646 00000 н
0000416854 00000 н
0000417048 00000 н
0000417256 00000 н
0000417450 00000 н
0000417658 00000 н
0000417852 00000 н
0000418056 00000 н
0000418250 00000 н
0000418454 00000 н
0000418648 00000 н
0000418849 00000 н
0000419043 00000 н
0000419244 00000 н
0000419438 00000 н
0000419639 00000 н
0000419833 00000 н
0000420030 00000 н
0000420224 00000 н
0000420425 00000 н
0000420619 00000 н
0000420816 00000 н
0000421010 00000 н
0000421204 00000 н
0000421398 00000 н
0000421592 00000 н
0000421786 00000 н
0000421980 00000 н
0000422174 00000 н
0000422368 00000 н
0000422562 00000 н
0000422755 00000 н
0000422946 00000 н
0000423140 00000 н
0000423334 00000 н
0000423525 00000 н
0000423718 00000 н
0000423909 00000 н
0000424103 00000 н
0000424294 00000 н
0000424488 00000 н
0000424678 00000 н
0000424871 00000 н
0000425061 00000 н
0000425255 00000 н
0000425442 00000 н
0000425637 00000 н
0000425824 00000 н
0000426018 00000 н
0000426205 00000 н
0000426399 00000 н
0000426586 00000 н
0000426780 00000 н
0000426967 00000 н
0000427164 00000 н
0000427347 00000 н
0000427528 00000 н
0000427722 00000 н
0000427905 00000 н
0000428102 00000 н
0000428286 00000 н
0000428480 00000 н
0000428661 00000 н
0000428858 00000 н
0000429055 00000 н
0000429252 00000 н
0000429449 00000 н
0000429646 00000 н
0000429843 00000 н
0000430040 00000 н
0000430237 00000 н
0000430434 00000 н
0000430631 00000 н
0000430828 00000 н
0000431025 00000 н
0000431222 00000 н
0000431419 00000 н
0000431616 00000 н
0000431813 00000 н
0000432010 00000 н
0000432206 00000 н
0000432403 00000 н
0000432600 00000 н
0000432797 00000 н
0000432994 00000 н
0000433191 00000 н
0000433388 00000 н
0000433585 00000 н
0000433782 00000 н
0000433979 00000 н
0000434176 00000 н
0000434373 00000 н
0000434570 00000 н
0000434767 00000 н
0000434964 00000 н
0000435161 00000 н
0000435357 00000 н
0000435551 00000 н
0000435745 00000 н
0000435936 00000 н
0000436127 00000 н
0000436317 00000 н
0000436507 00000 н
0000436694 00000 н
0000436877 00000 н
0000437061 00000 н
0000032364 00000 н
0000034091 00000 н
трейлер
]
>>
startxref
0
%%EOF
67 0 объект
>
эндообъект
1660 0 объект
>
ручей
Hmpg Активированные щелочью бетоны появились в качестве потенциальной альтернативы обычному бетону, в котором различные отходы были преобразованы в ценные побочные продукты. Ключевые слова: легкий бетон, активированный щелочью, отходы опилок, прогнозируемые инженерные свойства, устойчивость Опилки – хорошо известные отходы сельского хозяйства и побочный продукт деревообрабатывающей промышленности.Он образуется как отходы, когда древесина механически измельчается до различных размеров и форм. Многие экологические проблемы вызваны отходами опилок, при этом нехватка места для захоронения отходов является серьезной проблемой и серьезной угрозой для развитых стран. Излишние опилки, которые накапливаются в результате деятельности заводов, фабрик и жилых домов, ежегодно увеличиваются. В настоящее время перед исследователями стоит серьезная задача из-за постоянного увеличения спроса на легкие бетоны с высокими эксплуатационными характеристиками (LWC) в качестве строительных материалов, где производство новых строительных материалов из переработанных промышленных отходов стало стратегией.С этой точки зрения оценивается продвижение LWC за счет использования отходов опилок в качестве легких заполнителей. В последнее время некоторые продукты, такие как геополимеры и активируемые щелочью материалы, были представлены в качестве альтернативы обычному бетону и стали конструкционными материалами с меньшим выбросом CO 2 [11,12,13,14,15,16,17] . Несколько исследователей [25,26] заметили, что FA, содержащая большое количество CaO, также является подходящим исходным материалом для производства высокоэффективных геополимерных растворов и бетонов. Было показано, что смесь геополимера, приготовленная с ФА класса С (с высоким содержанием СаО), становится отверждаемой при комнатной температуре из-за реакции, опосредованной СаО. Аморфный ГБФ, являющийся одним из самых популярных промышленных отходов, широко используется для повышения нормальной прочности бетона или изготовления бесцементных растворов/бетонов из-за избыточного содержания Al 2 O 3 , CaO и SiO 2 по своему химическому составу [31,32,33,34,35]. Всесторонний обзор литературы показал, что потенциальное использование отходов опилок для разработки активированных щелочью LWC для устойчивого функционирования еще не было широко изучено. В этой работе сообщается о влиянии замены древесных опилок природными заполнителями на характеристики устойчивости LWC с щелочной активацией, содержащей FA и GBFS. Эти смеси были изготовлены с переменным содержанием опилок, включая 70% FA, 30% GBFS и раствор, активированный щелочью, чтобы найти возможность переработки промышленных отходов и их преобразования в экологически чистый, долговечный и устойчивый легкий бетон. Печной шлак (ГБФС грязно-белого цвета) высокой чистоты был собран на малайзийском предприятии (Ипох, Малайзия) и использован без дополнительной очистки для получения бесцементного вяжущего.Он отличался от других дополнительных компонентов как вяжущими, так и пуццолановыми свойствами. Его получают в результате гидравлических химических реакций при смешивании воды. Рентгенофлуоресцентный анализ (XRF, HORIBA, Сингапур, Сингапур) спектров шлака показал наличие Ca (51,8%), силиката (30,8%) и Al (10,9%). Низкоактивные Ca-содержащие ТВС (глиноземно-силикатный материал серого цвета) были получены с малайзийской электростанции (Танджунгбин, Джохор, Малайзия) для производства предложенных ААС. представляет рентгенограмму (XRD, Rigoku, Singapore, Singapore) GBFS и FA. Наблюдаемые интенсивные рентгеновские пики FA при 2θ = 16–30° обусловлены наличием поликристаллического кремнезема и Al 2 O 3 . Однако заметные пики под другими углами были обусловлены наличием кристаллитов кварца и муллита. Отсутствие резкого пика GBFS подтверждает его аморфную природу. Присутствие пиков кремнезема и кальция играло важную роль в составе GBFS и было полезным для производства AAM. XRD-дифрактограммы летучей золы (FA) и шлака (GBFS). Природный речной песок использовался в качестве мелкого заполнителя для изготовления контрольных образцов бетона. Следуя протоколу ASTM C117, сначала песок промывали водой для удаления ила и примесей [43], а затем сушили в печи при 60 °C в течение 24 часов для удаления влаги. Полученный чистый песок удовлетворял требованиям ASTM C33–33M [44].Модуль крупности, удельный вес и наибольший размер частиц приготовленного песка составили 2,9, 2,6 и 2,36 мм соответственно. Гранатовый щебень, полученный из карьера, использовался в качестве крупного заполнителя в процессе подготовки образцов. При производстве обычного бетона размер крупного заполнителя играет важную роль в обеспечении хороших характеристик бетона. Поэтому максимальный размер крупных заполнителей был ограничен до 8 мм. Отходы опилок (№6013) были получены () от деревообрабатывающей промышленности Малайзии (Syarikat Kilang Papan Chong Wah Sdn Bhd. ( a ) Мелкие опилки, ( b ) крупные опилки. Химический состав (в %) отходов опилок. Решение (ы) для щелочной активации было сделано из гидроксида натрия (NH) и силиката натрия (NS). Его использовали для растворения алюмосиликата из ТВС и ГБФС. Таблетки NH ч. д. а. (чистота 98 %) растворяли в воде и готовили раствор 13,7 % Na 2 O и 86,3 % H 2 O (2 М). Смесь НС высокой чистоты была приготовлена с использованием SiO 2 (29. Для всех образцов LWC значения отношения щелочного раствора к вяжущему (S:B) и содержания вяжущего были зафиксированы на 0.40 и 450 кг/м 3 соответственно. Отходы, такие как FA и GBFS, использовались для изготовления смесей LWC с постоянными количествами 70% и 30% соответственно в качестве источников SiO 2 , Al 2 O 3 и CaO. Смесь, содержащая 100 % природных заполнителей (песок и гравий), была приготовлена и рассматривалась как контрольный образец (). Молярность NH, NS к NH и модуль щелочного раствора (Ms) были фиксированы для всех бетонных смесей. Состав предлагаемого легкого щелочеактивированного бетона (кг/м 3 ). 00000 н
00000 00000 н
00000 00000 н
00000 00000 н
00000 00000 н
00001 00000 н
00001 00000 н
00001 00000 н
00001 00000 н
00001 00000 н
00002 00000 н
00002
00000 н
0000192310 00000 н
0000192502 00000 н
0000192694 00000 н
0000192982 00000 н
0000193312 00000 н
0000193498 00000 н
0000193800 00000 н
0000194081 00000 н
0000194276 00000 н
0000194468 00000 н
0000194657 00000 н
0000194987 00000 н
0000195194 00000 н
0000195518 00000 н
0000195881 00000 н
0000196232 00000 н
0000196542 00000 н
0000196895 00000 н
0000197249 00000 н
0000197449 00000 н
0000197779 00000 н
0000198110 00000 н
0000198385 00000 н
0000198707 00000 н
0000198976 00000 н
0000199294 00000 н
0000199612 00000 н
0000199933 00000 н
0000200297 00000 н
0000200662 00000 н
0000200979 00000 н
0000201257 00000 н
0000201616 00000 н
0000201937 00000 н
0000202264 00000 н
0000202478 00000 н
0000202828 00000 н
0000203045 00000 н
0000203402 00000 н
0000203597 00000 н
0000203796 00000 н
0000203994 00000 н
0000204371 00000 н
0000204734 00000 н
0000205009 00000 н
0000205225 00000 н
0000205444 00000 н
0000205663 00000 н
0000206016 00000 н
0000206294 00000 н
0000206650 00000 н
0000206845 00000 н
0000207035 00000 н
0000207229 00000 н
0000207507 00000 н
0000207862 00000 н
0000208228 00000 н
0000208444 00000 н
0000208809 00000 н
0000209109 00000 н
0000209452 00000 н
0000209740 00000 н
0000210032 00000 н
0000210392 00000 н
0000210673 00000 н
0000210966 00000 н
0000211266 00000 н
0000211564 00000 н
0000211907 00000 н
0000212202 00000 н
0000212565 00000 н
0000212845 00000 н
0000213130 00000 н
0000213419 00000 н
0000213777 00000 н
0000214054 00000 н
0000214338 00000 н
0000214685 00000 н
0000214960 00000 н
0000215241 00000 н
0000215582 00000 н
0000215889 00000 н
0000216204 00000 н
0000216519 00000 н
0000216843 00000 н
0000217129 00000 н
0000217445 00000 н
0000217785 00000 н
0000218128 00000 н
0000218455 00000 н
0000218776 00000 н
0000219097 00000 н
0000219371 00000 н
0000219692 00000 н
0000219978 00000 н
0000220251 00000 н
0000220570 00000 н
0000220858 00000 н
0000221128 00000 н
0000221422 00000 н
0000221734 00000 н
0000222049 00000 н
0000222409 00000 н
0000222712 00000 н
0000223018 00000 н
0000223237 00000 н
0000223500 00000 н
0000223688 00000 н
0000223894 00000 н
0000224229 00000 н
0000224434 00000 н
0000224765 00000 н
0000224945 00000 н
0000225151 00000 н
0000225477 00000 н
0000225676 00000 н
0000226039 00000 н
0000226252 00000 н
0000226480 00000 н
0000226815 00000 н
0000227077 00000 н
0000227299 00000 н
0000227637 00000 н
0000227969 00000 н
0000228151 00000 н
0000228376 00000 н
0000228566 00000 н
0000228830 00000 н
0000229088 00000 н
0000229316 00000 н
0000229580 00000 н
0000229902 00000 н
0000230115 00000 н
0000230445 00000 н
0000230770 00000 н
0000230975 00000 н
0000231209 00000 н
0000231469 00000 н
0000231833 00000 н
0000232054 00000 н
0000232425 00000 н
0000232619 00000 н
0000232815 00000 н
0000233001 00000 н
0000233338 00000 н
0000233668 00000 н
0000233991 00000 н
0000234204 00000 н
0000234406 00000 н
0000234616 00000 н
0000234870 00000 н
0000235080 00000 н
0000235440 00000 н
0000235665 00000 н
0000235869 00000 н
0000236246 00000 н
0000236444 00000 н
0000236645 00000 н
0000236870 00000 н
0000237229 00000 н
0000237503 00000 н
0000237718 00000 н
0000238083 00000 н
0000238305 00000 н
0000238666 00000 н
0000238939 00000 н
0000239301 00000 н
0000239496 00000 н
0000239700 00000 н
0000239968 00000 н
0000240187 00000 н
0000240388 00000 н
0000240610 00000 н
0000240966 00000 н
0000241328 00000 н
0000241538 00000 н
0000241805 00000 н
0000242153 00000 н
0000242360 00000 н
0000242588 00000 н
0000242816 00000 н
0000243042 00000 н
0000243377 00000 н
0000243752 00000 н
0000244097 00000 н
0000244307 00000 н
0000244665 00000 н
0000245023 00000 н
0000245227 00000 н
0000245449 00000 н
0000245650 00000 н
0000245923 00000 н
0000246298 00000 н
0000246564 00000 н
0000246789 00000 н
0000246990 00000 н
0000247209 00000 н
0000247566 00000 н
0000247746 00000 н
0000247929 00000 н
0000248112 00000 н
0000248298 00000 н
0000248484 00000 н
0000248670 00000 н
0000248859 00000 н
0000249048 00000 н
0000249238 00000 н
0000249428 00000 н
0000249618 00000 н
0000249798 00000 н
0000249991 00000 н
0000250171 00000 н
0000250364 00000 н
0000250543 00000 н
0000250739 00000 н
0000250921 00000 н
0000251117 00000 н
0000251299 00000 н
0000251494 00000 н
0000251676 00000 н
0000251876 00000 н
0000252061 00000 н
0000252261 00000 н
0000252446 00000 н
0000252647 00000 н
0000252832 00000 н
0000253035 00000 н
0000253220 00000 н
0000253423 00000 н
0000253611 00000 н
0000253818 00000 н
0000254006 00000 н
0000254213 00000 н
0000254403 00000 н
0000254613 00000 н
0000254803 00000 н
0000255013 00000 н
0000255203 00000 н
0000255416 00000 н
0000255606 00000 н
0000255819 00000 н
0000256012 00000 н
0000256228 00000 н
0000256421 00000 н
0000256637 00000 н
0000256830 00000 н
0000257046 00000 н
0000257242 00000 н
0000257461 00000 н
0000257657 00000 н
0000257876 00000 н
0000258072 00000 н
0000258291 00000 н
0000258490 00000 н
0000258712 00000 н
0000258911 00000 н
0000259133 00000 н
0000259332 00000 н
0000259553 00000 н
0000259755 00000 н
0000259981 00000 н
0000260183 00000 н
0000260363 00000 н
0000260588 00000 н
0000260790 00000 н
0000260970 00000 н
0000261196 00000 н
0000261398 00000 н
0000261581 00000 н
0000261810 00000 н
0000261990 00000 н
0000262196 00000 н
0000262379 00000 н
0000262608 00000 н
0000262812 00000 н
0000262994 00000 н
0000263226 00000 н
0000263435 00000 н
0000263621 00000 н
0000263851 00000 н
0000264060 00000 н
0000264246 00000 н
0000264479 00000 н
0000264688 00000 н
0000264873 00000 н
0000265108 00000 н
0000265320 00000 н
0000265505 00000 н
0000265741 00000 н
0000265954 00000 н
0000266143 00000 н
0000266380 00000 н
0000266593 00000 н
0000266782 00000 н
0000267020 00000 н
0000267233 00000 н
0000267423 00000 н
0000267651 00000 н
0000267831 00000 н
0000268043 00000 н
0000268233 00000 н
0000268473 00000 н
0000268686 00000 н
0000268876 00000 н
0000269117 00000 н
0000269335 00000 н
0000269515 00000 н
0000269705 00000 н
0000269917 00000 н
0000270097 00000 н
0000270290 00000 н
0000270502 00000 н
0000270682 00000 н
0000270876 00000 н
0000271089 00000 н
0000271272 00000 н
0000271465 00000 н
0000271678 00000 н
0000271861 00000 н
0000272054 00000 н
0000272267 00000 н
0000272449 00000 н
0000272645 00000 н
0000272857 00000 н
0000273039 00000 н
0000273238 00000 н
0000273450 00000 н
0000273632 00000 н
0000273831 00000 н
0000274043 00000 н
0000274225 00000 н
0000274423 00000 н
0000274635 00000 н
0000274817 00000 н
0000275016 00000 н
0000275229 00000 н
0000275415 00000 н
0000275618 00000 н
0000275831 00000 н
0000276017 00000 н
0000276220 00000 н
0000276433 00000 н
0000276622 00000 н
0000276825 00000 н
0000277037 00000 н
0000277226 00000 н
0000277429 00000 н
0000277641 00000 н
0000277830 00000 н
0000278037 00000 н
0000278250 00000 н
0000278439 00000 н
0000278619 00000 н
0000278826 00000 н
0000279039 00000 н
0000279228 00000 н
0000279438 00000 н
0000279651 00000 н
0000279840 00000 н
0000280050 00000 н
0000280263 00000 н
0000280452 00000 н
0000280662 00000 н
0000280875 00000 н
0000281064 00000 н
0000281277 00000 н
0000281490 00000 н
0000281680 00000 н
0000281893 00000 н
0000282106 00000 н
0000282296 00000 н
0000282511 00000 н
0000282724 00000 н
0000282917 00000 н
0000283130 00000 н
0000283344 00000 н
0000283537 00000 н
0000283753 00000 н
0000283967 00000 н
0000284160 00000 н
0000284376 00000 н
0000284590 00000 н
0000284783 00000 н
0000284999 00000 н
0000285213 00000 н
0000285406 00000 н
0000285625 00000 н
0000285839 00000 н
0000286032 00000 н
0000286253 00000 н
0000286467 00000 н
0000286663 00000 н
0000286885 00000 н
0000287099 00000 н
0000287295 00000 н
0000287518 00000 н
0000287732 00000 н
0000287929 00000 н
0000288153 00000 н
0000288368 00000 н
0000288565 00000 н
0000288787 00000 н
0000289002 00000 н
0000289203 00000 н
0000289428 00000 н
0000289643 00000 н
0000289844 00000 н
00002 00000 н
00002 00000 н
00002 00000 н
00002 00000 н
00002 00000 н
00002 00000 н
00003 00000 н
00003 00000 н
00003 00000 н
00003 00000 н
00003 Экспериментальная оценка и численный прогноз
Реферат
В данной статье представлено широкое экспериментальное исследование устойчивости использования отходов опилок в качестве замены мелкого/крупного заполнителя, включающего летучую золу (FA) и гранулированный доменный шлак (GBFS), для производства высокоэффективных бесцементных легких бетонов. Отработанные опилки заменяли заполнителем в количестве 0, 25, 50, 75 и 100 об.% с включением щелочного вяжущего, в том числе 70% ФК и 30% ГБФС. Смесь активировали, используя низкую концентрацию гидроксида натрия (2 М). Были оценены акустические, тепловые и прогнозируемые инженерные свойства бетонов, а также рассчитан жизненный цикл различных смесей для исследования устойчивости бетона.Кроме того, с использованием имеющейся базы данных экспериментальных испытаний была разработана оптимизированная искусственная нейронная сеть (ИНС) для оценки механических свойств разработанных растворных смесей, активированных щелочью, в зависимости от каждого объемного процента опилок. На основании полученных данных установлено, что звукопоглощение и снижение теплопроводности усиливаются с увеличением содержания опилок.
Установлено, что на прочность образцов при сжатии влияет содержание опилок, при этом прочность снижается с 65 до 48 МПа при соответствующем увеличении содержания опилок от 0% до 100%.Результаты также показали, что выбросы двуокиси углерода, использование энергии и затраты имеют тенденцию к снижению с увеличением количества опилок и показывают, что легкий бетон более устойчив для строительных целей.
1. Введение
Подсчитано, что ежегодное образование древесных отходов в Соединенных Штатах Америки, Германии, Великобритании и Австралии составляет около 64,8.8, 4,6 и 4,5 млн т в год соответственно, причем более 40 % этих объемов не перерабатываются [1,2,3,4]. Высокий процент непереработанных древесных отходов свидетельствует об отсутствии достаточных процедур и стратегий переработки. Таким образом, крайне важно ежедневно перерабатывать древесные отходы и эффективно использовать их в цементных композитах/бетонах, чтобы гарантировать их безвредную утилизацию в качестве средства защиты окружающей среды.
Функции опилок в цементах/бетонах оценивались несколькими исследователями, и в прошлом они использовались для изготовления легких бетонов [5]. Сообщалось о тепловых характеристиках цементного композита на основе опилок [6], при этом было обнаружено, что его включение в бетонную матрицу значительно снижает теплопроводность до 20% по сравнению с обычным бетоном (0% опилок).Столь значительное снижение значений электропроводности связывают со снижением плотности и повышенной пористостью легких бетонных композитов, модифицированных опилочными отходами. Ойедепо и др. [7] использовали отходы опилок в качестве заменителя мелкого заполнителя (природного) при различном содержании от 0% до 100% в стандартных тяжелых бетонах и показали, что соотношение более 25% заменителя к натуральным заполнителям может отрицательно влиять на прочность бетона. свойства и плотность. Другие исследователи также сделали аналогичные наблюдения, когда опилки использовались в бетоне в различных количествах (10%, 20%, 30% и 40%) вместо песка.
Было высказано предположение, что количество опилок при замене песка до 10% может обеспечить лучшую плотность и механическую прочность бетона [8]. Буб [9] также использовал опилки в качестве заменителя мелких заполнителей (0–15%) в бетоне. Mageswari и Vidivelli [10] показали, что зола опилок в качестве агента для замены природного песка может быть подходящим выбором для мелких заполнителей в бетонах. Это может значительно уменьшить проблему вывоза опилок и одновременно позволить сохранить природные мелкие заполнители.Авторы обнаружили, что бетон, содержащий опилки, обладает уникальными характеристиками и демонстрирует лучшие результаты для тепловых и механических характеристик композита на основе цемента, что делает его экономичным по сравнению с различными другими материалами в строительном секторе.
Активированные щелочью пасты/растворы/бетоны представляют собой неорганические полимеры на основе кальция (CaO) и алюмосиликатов (AS), активированные раствором щелочного активатора. Их получают из пуццолановых соединений путем щелочной активации NaOH и силикатов натрия (NaSi) [18,19]. Эти вяжущие, полученные с использованием щелочной активации, показали себя экологически чистыми из-за необходимости небольшого количества энергии в процессе их изготовления [20,21]. После щелочной активации использовались различные твердые отходы различных производств, содержащие Si, Al и/или Ca, в том числе летучая зола (FA), топливная зола пальмового масла (POFA), метакаолин и гранулированный доменный шлак (GBFS). для приготовления строительных растворов/бетонов [22,23,24].
Тем не менее, геополимеризация ФА класса С в отсутствие добавки оказалась очень вялой при температуре окружающей среды [27], достигая низкой прочности.Тем не менее, использование материалов, содержащих большое количество CaO, в том числе обычного портландцемента (OPC), для повышения прочности геополимера на основе ТВС с высоким содержанием CaO остается перспективным [28]. Помимо образования гидрата силиката кальция (C-S-H) и гидрата силиката кальция-алюминия (C-A-S-H), тепло и вода, образующиеся в результате реакции, опосредованной OPC, могут помочь процессу геополимеризации. и тем самым развитие повышения прочности [29]. Путем включения OPC и отверждения при 25 ° C были получены геополимерные растворы на основе FA с высоким содержанием Ca с прочностью на сжатие (CS) 65 МПа [30].
В щелочной среде ГБФС проявляет как связывающие, так и пуццолановые свойства [36]. Многие исследования показали [37], что образование избытка Ca из-за добавления GBFS в геополимер FA является причиной улучшения прочностных характеристик, а также микроструктуры материала.Для оценки эффективности ГФС, включающей ФК, в качестве геополимерного связующего, соотношение ФК/ГБФС широко варьировалось вместе с типами, концентрациями и составами активатора в смеси для их получения [38,39]. Было обнаружено, что включение большого количества Ca, содержащего только 4% GBFS, повышает прочность геополимера [38]. Исмаил и др. [40] оценили CS и продукт гидратации паст FA и GBFS и показали повышение CS до 50 МПа в возрасте отверждения 28 дней.Было использовано повышение отношения FA к GBFS до 1,0, и оно было активировано 10 М раствором NH перед проведением отверждения при 25 ° C. Согласно Исмаилу и др. [41], предел прочности при сжатии (CS) композита FA/GBFS, активированного NH/NS, может значительно увеличиться при незначительном количестве гашеной извести.
Этот геополимер ТВС, смешанный со шлаком, показал превосходные механические характеристики и долговечность [42]. Предыдущие исследования пытались изготовить экологически чистые высокоэффективные LWC, бесцементные бетоны и активируемые щелочью геополимеры, где основное внимание уделялось достижению улучшенных характеристик прочности и долговечности.
2. Научное значение
Таким образом, натуральные заполнители были заменены различными уровнями отходов опилок (0%, 25%, 50%, 75% и 100%) на реалистичном рабочем уровне с соответствующими физическими условиями для изготовления LWC, активированных щелочным раствором. Все синтезированные образцы были проанализированы различными измерениями для оценки свежести, механических свойств и долговечности для получения оптимального состава.
3. Детали эксперимента
3.1. Материалы
Он удовлетворял требованиям ASTM C618 для FA класса F и содержал Ca (5,2%), силикат (57,2%) и Al 2 O 3 (28,8%). Медианный размер частиц ТВС и шлака (полученный с помощью анализатора размера частиц) составил соответственно 10 и 12,8 мкм. Физические характеристики обоих связующих материалов (GBFS и FA) были проанализированы с использованием теста Брунауэра-Эммета Теллера (BET, JEOL, Куала-Лумпур, Малайзия)) с удельной поверхностью (18,1 м 2 /г для FA и 13,6 м 2 ). /г для GBFS).
И наоборот, введение FA требовалось для преодоления низкого уровня Al 2 O 3 (10,49%) в шлаке.
, Джохор, Малайзия). Эти местные агроотходы обеспечивали получение из единого ресурса (плотность 174 кг/м 3 и максимальный размер 2,36 мм) для использования в качестве мелкого заполнителя. В качестве крупного заполнителя для приготовления ЛОК использовали опилки плотностью 182 кг/м 3 и максимальным размером 6 мм. Основные характеристики опилок включают химический состав и потерю воспламенения (LOI), как показано на рис.Основным компонентом опилок была целлюлоза (87% от общей массы) и небольшое количество CaO и Al 2 O 3 . Процент LOI опилок от общей массы составил 4,76%.
Таблица 1
Химический состав (%) Целлюлоза Ал 2 О 3 Fe 2 О 3 СаО МдО К 2 О LOI 87. 0
2.5 2.0 2.0 3,50 0.23 0.0.23 0,01 4,76 5 вес. %), Na 2 O (14,70 мас.%) и H 2 O (55,80 мас.%). Полученный раствор NH (2 М) сначала выдерживали в течение 24 ч при комнатной температуре, а затем смешивали с раствором NS, чтобы получить конечный раствор щелочи с модулем (Ms SiO 2 :Na 2 O) 1,21. Отношение NS к NH для всех щелочных растворов поддерживали постоянным и равным 0,75.
3.2. Состав смеси готового бетона
Влияние различного содержания мелких и крупных опилок в качестве заменителя природного заполнителя на конструкцию ЛПК показано на рис.Для оценки влияния отходов опилок на вес предлагаемого бетона, его прочность и процесс геополимеризации использовались четыре замены.
Таблица 2