Блоки газосиликатные вес: Как рассчитать вес газосиликатного блока
Как рассчитать вес газосиликатного блока
Газосиликатные блоки – строительный материал, который изготавливается из бетона, относящегося к категории «ячеистых». То есть, вес газосиликатного блока несравнимо низок, если сравнивать с блоками из стандартного бетонного раствора. Но чтобы точно сказать, каков вес изделия, надо знать размеры блока и плотность используемого материала, соответственно газосиликата.

Вес зависит от размеров
Стандартные размеры газосиликатных блоков
Производители сегодня предлагают достаточно широкий модельный ряд газосиликатных блоков, потому что этот строительный материал используют и для возведения несущих стен, и для сооружения перегородок. В первом случае требуются блоки больших размеров с высокой несущей способностью, во втором камни с небольшими габаритами, потому что они практически не нагружаются.
Но необходимо отметить, что по длине все блоки являются одинаковыми. Здесь параметр равен – 600 или 625 мм. Этот стандартизированный подход к производству позволяет провести точный расчет требуемого материала по длине сооружаемой постройки. Что касается толщины (ширины) блока, то здесь также две позиции: 200 и 250 мм. Обычно первые применяют для возведения перегородок, вторые используют под несущие стены. Хотя разница незначительна, что дает возможность камни шириною 200 мм устанавливать под несущие стены одноэтажных строений.
А вот высота газосиликатных блоков – это достаточно широкая модельная линейка. Но здесь необходимо обозначить, что она не соответствует всем размерным габаритам, касающихся толщины изделия. Соотношение такое:
- при ширине камня в 200 мм, его высота может быть 150, 200, 250, 300 и 400 мм;
- при ширине в 250 мм, высота составляет 100, 150, 250, 300, 375, 400 и 500 мм.

Один из стандартных размеров
Плотность газосиликата
Чтобы определить, сколько весит газосиликатный блок, необходим объем изделия и плотность исходного материала. Объем подсчитать несложно, зная размеры камня, то есть перемножаются между собой высота, толщина и длина изделия. Касаемо плотности газосиликатного бетона.
Все зависит, из каких компонентов изготавливается сам раствор. В стандартную рецептуру входят: цемент, песок, газообразующий материал и вода. Цемент можно заменить известью, песок золой или другими схожими материалами. В качестве газообразующего вещества чаще всего используют алюминиевую пудру.
В процессе смешивания компонентов происходит химическая реакция, результатом которой становится выделения большого количества водорода. Он внутри образует поры, облегчая тем самым структуру газосиликатных блоков. При этом увеличиваются теплоизоляционные качестве изделия, но уменьшаются его несущие способности, соответственно и прочность.
Теперь о плотности. Обозначается она буквой «D» и цифровым значением, к примеру, D500. О чем говорит число. Это количество самого газосиликатного раствора в одном его кубе. То есть, в 1 м³ находится 500 кг бетона. Остальное место занимает поры, наполненные водородом. И чем выше плотность, тем тяжелее газосиликатные блоки.
- Обычно блочные изделия из газосиликата с плотностью D600-700 используют для строительства домов не выше пяти этажей. Эти камни относятся к категории несущих материалов.
- Блоки плотностью D500 можно применять в качестве несущих, если из них возводятся дома не выше двух этажей. Или в качестве перегородок в многоэтажных зданиях.
- Материал плотностью D400 – так называемый теплоизоляционный вариант. Относится к классу прочности на сжатие В2,5. Используют блоки только в перегородках или в качестве теплоизоляционных материалов.
- Плотность D350 – материал, который применяется в строительство только как утеплитель.

Толщина стены из газосиликата в зависимости от плотности
Необходимо добавить, что плотность блоков из газосиликата во многом зависит от того, по какой технологии они были изготовлены. Есть два варианта:
- Ручной, который используется при кустарном производстве. То есть, производится смешивание компонентов бетонного раствора, последний закладывается в формы, где остается до полного затвердевания. После чего блоки сушат несколько дней.
- Автоклавный. Здесь все те же позиции, только добавляется еще одна операция – обработка паром (+200С) под давлением. Ее и проводят в автоклаве – специальная емкость, куда закладываются формы с газосиликатным раствором, здесь же и происходит обработка паром. Внутри автоклава выдерживается повышенное давление (8-12 атм.), которое придает блокам повышенную прочность и плотность.
Примеры расчета веса
И несколько примеров, как рассчитать вес газосиликатных блоков.
Размер: 600х200х400 мм. Объем блока составляет с переводом в метры: 0,6х0,2х0,4=0,048 м³. При плотности – D500 этот камень будит весить: 0,048х500=24 кг. Если снизить плотность до D350, то вес будет таким: 0,048х350=16,8 кг.
Размер: 600х250х500 мм. Его объем будет составлять: 0,6х0,25х0,5=0,075 м³. При плотности D600, такой камень будет весить: 0,075х600=45 кг.
Видео:
Другие технические характеристики
Как и все блочные строительные материалы, газосиликатные блоки обладают несколькими техническими характеристиками, которые обязательно учитывают в строительстве зданий и сооружений. Вот они в таблице ниже.
Характеристика | Водопоглащение, % к общему весу | Морозоустойчивость, количество циклов | Паропроницаемость, мг/м² ч Па | Теплопроводность, Вт/м К | Прочность на сжатие, МПа | Звукоизоляция стены толщиною 30 см, дБ | Термостойкость, С |
Показатели | 20 | 15-100 | 0,14 | 0,1-0,28 | 1,5-10 | 30-47 | +400 |
Преимущества и недостатки
Из таблицы видно, то блоки данного типа обладают неплохой теплопроводностью, то есть, не самой высокой, если говорить о других блочных материалах. И это большой плюс в строительстве теплого дома. Небольшая плотность при неплохих прочностных характеристиках дает возможность сооружать под дома из газосиликатных блоков фундаменты небольших размеров, что влияет на снижении стоимость всего сооружения.
К плюсам добавим простоту монтажного процесса и легкость обработки. Такой материал легко режется, в нем несложно просверлить отверстия.
Касаемо отрицательных характеристик, то в первую очередь необходимо отметить, что материал данного типа является обладателем высокого влагопоглощения. Поэтому дома из силиката обязательно подвергают защитным мероприятием, связанным с нанесением защитных слоев на стены. Это может быть штукатурка, облицовка кирпичом, клинкером или другими схожими материалами, или установка вентилируемого фасада.
К минусам относится и низкая термостойкость, обозначенная максимальным показателем +400С. То есть, если по каким-то причинам температура выросла более данного значения, блоки просто начнут растрескиваться, разваливаться, снижая свою несущую способность, что приведет к разрушению здания.

Оштукатуривание стен из газосиликатных блоков
Принципиальные моменты оштукатуривания блоков из газосиликата
Есть некоторые требования, которые надо учесть, выполняя оштукатуривание.
- Материал выходит из производства с влажностью 30%. Это достаточно высокий показатель, который может повлиять на качественное состояние блоков, если их сразу начнут использовать в реализации проекта. Они растрескаются в течение года. Поэтому наносить штукатурку нужно через 1,5 года после окончания строительства коробки. Если такой возможности нет, то штукатурить начинают изнутри помещений, чтобы влага, находящаяся внутри блоков, могла постепенно испариться.
- Идеальный вариант – штукатурка изнутри, вентилируемый фасад снаружи. Это даст возможность оттока испарения от стен.
- Не стоит в качестве утеплителя снаружи использовать материалы гигроскопичные, даже если их закрыть гидроизоляционными мембранами. Состояние термоса для газосиликата губительно.
Удельный вес газосиликата, их параметры и разновидность
В процессе строительства зданий, на замену кирпича, стали применять более крупные и легкие газосиликатные и пеноблоки. В составе газосиликата много компонентов:
Для производства более прочных и устойчивых к нагрузкам блоков, в качестве сушки используют автоклав. Такой метод повышает качественные характеристики газосиликатных блоков в 5 раз, а соответственно и их стоимость. Кроме того, на показатель прочности влияет процентное соотношение цемента – если его увеличить блоки получаться более прочными. Недостатком такого материала станет большая плотность – пористость блока, что приведет к увеличению проводимости тепла.
Разновидности газосиликата и их характеристика
Газосиликатный строительный материал имеет свои преимущества в процессе эксплуатации:
Марка/плотность (кг/м3) | Размеры | Вес блока (кг) | Удельный вес 1 м3 (кг/м3) |
D400 | 600*100*250 | 7,2 | 480 |
D400 | 600*200*250 | 14,4 | 480 |
D400 | 600*300*250 | 21,6 | 480 |
D400 | 600*400*250 | 28,8 | 480 |
D500 | 600*100*250 | 8,7 | 580 |
D500 | 600*200*250 | 17,4 | 580 |
D500 | 600*300*250 | 26,1 | 580 |
D500 | 600*400*250 | 34,8 | 580 |
D600 | 600*100*250 | 10,8 | 720 |
D600 | 600*200*250 | 21,6 | 720 |
D600 | 600*300*250 | 32,4 | 720 |
D600 | 600*400*250 | 43,2 | 720 |
Так как формула для вычисления удельного веса выглядит следующим образом: Y = P/V, где P — вес материла, а V — объем, то очень легко можно вычислить вес 1 м3 газосиликата, для этого достаточно умножить вес на объем. То есть, например, вес куба газосиликата марки D500, размерами 600*400*250, при удельном весе в 580 кг/м3, будет весить 580 кг, так как 580 * 1 = 580.
Производители постоянно совершенствуют качественные характеристики газосиликатных блоков, так некоторым предприятиям, удалось добиться высокой устойчивости к морозу для плотных видов блоков. Но, чаще всего, газосиликаты могут выдержать 35 циклов размораживания. Кроме того, все виды блоков хорошо сохраняют тепло. При работе с газосиликатами, важно учитывать степень влажности.
Несмотря на все преимущества, строительные блоки такого вида имеют свои недостатки:
Основным классификационным критерием для газосиликатного материала выступает плотность. Приведем виды блоков и их качественные характеристики в таблице.
Вид блока | Объёмный вес газосиликата / плотность | Проводимость тепла | Количество циклов замораживания |
Конструкционный | От D 700 | 0,18 – 0,20 Вт/м | 50 — 100 |
Теплоизоляционный | D 400 | 0,08 – 0,10 Вт/м | 15 — 35 |
Конструкционно — теплоизоляционный | СD 500 – D 700 | 0,12 – 0,18 Вт/м | 35 |
Параметры газосиликата и их вес
Каждый застройщик самостоятельно подбирает необходимый размер строительного материала. Производители предлагают фиксированные размеры строительного материала. Вес газосиликата зависит от размера и плотности сырьевой смеси, которая использовалась в процессе производства. В таблице выше мы привели размеры и удельный вес газосиликата.
Вес газосиликатного блока 600х300х200
Многие считают, что газосиликатные блоки очень легкие, но это не совсем так. 1 куб такого материала весит действительно не так много, но один блок имеет довольно приличный вес в силу своих размеров.
Как рассчитать вес газосиликатного блока размером 600х300х200 мм?
На фото домов из газосиликатных блоков вы можете увидеть, что блоки имеют довольно крупный размер. Возникает вопрос, сколько же весит 1 такой блок и 1 м3 этого материала? Вес газосиликатных блоков зависит от его плотности и влажности окружающей среды.
На сегодняшний день на рынке есть три основных вида газосиликатных блоков, которые отличаются своей плотностью. Это марки D500, 600 и 700. Данные марки предназначены именно для стройки, а более низкие – для утепления.
Чем выше плотность блока, тем, соответственно, выше его вес. Так, самую большую массу имеют блоки с маркировкой D700 – около 29 кг, D600 имеют вес 25 кг, а D500 – около 21 кг.
Немаловажную роль имеет влажность воздуха. В сырую погоду вес блоков увеличивается, так как газосиликатные блоки сильно впитывают влагу. Это не является их сильной стороной, ведь они плохо её отдают.
Совет прораба: необходимо рассчитывать вес для фундамента с учетом того, что вес блоков увеличится при влажной погоде. Несоблюдение этого момента может привести к просадке фундамента в будущем.
В целом, на рынке строительных материалов идет расчет веса не на 1 шт., а на 1 м3, так как количество штук в кубе является постоянным, и так проще рассчитать вес будущей постройки. Блоков размером 200х300х600 в 1 м3 всегда 28, соответственно, его вес будет составлять 812 кг при сухой погоде.
Совет прораба: лучшим вариантом для разгрузки газосиликатных блоков будет сухая погода, таким образом, вы сможете снизить общий вес материалов до 100 кг на 1 м3.
Газосиликатные блоки, если брать отдельно 1 штуку, довольно приличного веса (особенно если имеют высокую плотность). Но их преимуществом является общий низкий вес постройки, так как 1 м3 такого материала весит в разы меньше, нежели тот же самый кирпич. Плюс, если учесть размер блоков, то они станут хорошей заменой классическим материалам в постройке дома.
виды, размеры и вес, недостатки и достоинства, область применения блоков
Главная / Статьи / Газосиликатные блоки
Блоки из газосиликата пользуются широким спросом в жилом и промышленном строительстве. Этот стройматериал по многим параметрам превосходит бетон, кирпич, натуральную древесину и др. Он изготавливается из экологически чистого сырья, отличается легкостью, огнеупорностью, простотой в эксплуатации и транспортировке. Применение этого легкого материала позволяет сократить расходы на обустройство тяжелого усиленного фундамента и тем самым удешевить строительство здания.
1. Что такое газосиликатные блоки
2. Как производятся газосиликатные блоки
3. Виды блоков
4. Типоразмеры и вес
5. Состав газосиликатных блоков
6. Характеристики материала
7. Преимущества и недостатки газосиликатных блоков
8. На сколько критичны недостатки
9. Где применяют газосиликатные блоки
Что такое газосиликатные блоки
Газосиликатный блок представляет собой легкий и прочный стеновой материал, который изготавливается из ячеистого бетона. Изделия имеют пористую внутреннюю структуру, что положительно сказывается на их тепло- и шумоизоляционных свойствах. Такой стройматериал может применяться в различных сферах строительной индустрии – для возведения дачных и загородных домов, автомобильных гаражей, хозяйственных сооружений, складских комплексов и др.
Как производятся газосиликатные блоки
Существуют две основные технологии производства газосиликатных строительных блоков.
- Неавтоклавная. При таком методе производства застывание рабочей смеси происходит в естественных условиях. Неавтоклавные газосиликатные блоки выделяются более низкой стоимостью, но имеют некоторые важные отличия от автоклавных. Во-первых, они менее прочны. Во-вторых, при их высыхании усадка происходит почти в 5 раз интенсивнее, чем в случае с автоклавными изделиями.
- Автоклавная. Для автоклавного производства газосиликата требуется больше энергетических и материальных ресурсов, из-за чего повышается конечная стоимость изделий. Изготовление осуществляется при определенном давлении (0,8–1,2 МПа) и температуре (до 200 градусов Цельсия). Готовые изделия получаются более прочными и устойчивыми к усадке.
Виды блоков
В зависимости от плотности, состава и функционального назначения блоки из газосиликата делятся на три основные категории.
- Конструкционные. Обладают высокими прочностными характеристиками. Плотность изделий составляет не менее 700 кг/м3. Применяются при строительстве высотных сооружений (до трех этажей). Способны выдерживать большие механические нагрузки. Теплопроводность составляет 0,18–0,2 Вт/(м·°С).
- Конструкционно-теплоизоляционные. Блоки с плотностью 500–700 кг/м3 используются при обустройстве несущих стен в малоэтажных зданиях. Отличаются сбалансированным соотношением прочностных и теплоизоляционных характеристик [(0,12–0,18 Вт/(м·°С)].
- Теплоизоляционные. Отличаются повышенными теплоизолирующими свойствами [(0,08–0,1 Вт/(м·°С)]. Из-за низкой плотности (менее 400 кг/м3) не подходят для создания несущих стен, поэтому применяются исключительно для утепления.
Типоразмеры и вес
Стеновые блоки из газосиликата имеют стандартные размеры 600 х 200 х 300 мм. Габаритные характеристики полублоков составляют 600 х 100 х 300 мм. В зависимости от компании-производителя типоразмеры изделий могут несколько различаться: 500 х 200 х 300, 588 х 300 х 288 мм и др.
Масса одного блока зависит от его плотности:
- конструкционные блоки весят 20–40 кг, полублоки – 10–16 кг;
- конструкционно-теплоизоляционные блоки и полублоки – 17–30 кг и 9–13 кг соответственно;
- теплоизоляционные блоки весят 14–21 кг, полублоки – 5–10 кг.
Состав газосиликатных блоков
Газосиликат – это экологически безопасный стройматериал, который изготавливается из нетоксичного сырья натурального происхождения. В состав блоков входит цемент, песок, известь и вода. В качестве пенообразователя применяется алюминиевая крошка, которая способствует увеличению коэффициента пустотности блоков. Также при производстве материала применяется поверхностно-активное вещество – сульфонол С.
Характеристики материала
Строительные блоки из газосиликата обладают следующими характеристиками.
- Теплоемкость. Изделия, изготовленные по автоклавной технологии, имеют коэффициент теплопроводности 1 кДж/(кг·°С).
- Теплопроводность. Конструкционно-теплоизоляционный газосиликат имеет среднюю теплопроводность около 0,14 Вт/(м·°С), тогда как для железобетона этот параметр достигает отметки 2,04.
- Звукопоглощение. Газосиликатные блоки значительно уменьшают амплитуду внешних шумов, индекс звукопоглощения для этого материала равен 0,2.
- Морозостойкость. Материал с плотностью 600 кг/м3 выдерживает до 35 циклов замораживания и оттаивания (что соответствует индексу F35). Изделиям с более высокой плотностью присвоен класс морозостойкости F50.
Преимущества и недостатки газосиликатных блоков
Основными достоинствами газосиликата являются следующие.
- Легкость. Блоки из газосиликата весят почти в 5 раз меньше, чем бетонные изделия тех же размеров. Это облегчает строительные работы и позволяет сократить расходы на транспортировку стройматериала.
- Эффективная тепло- и звукоизоляция. За счет наличия внутренних микропор достигаются высокие тепло- и шумоизоляционные характеристики газосиликата. Это позволяет создать комфортный микроклимат внутри помещений.
- Экологичность. В составе стройматериала не содержатся опасные токсины и канцерогены, которые могут причинить вред окружающей среде и человеческому здоровью.
- Огнеупорность. Газосиликат производится из негорючего сырья, поэтому не разрушается при интенсивном нагревании и не способствует распространению пламени при пожаре.
На сколько критичны недостатки
Как и любой другой стройматериал, газосиликат имеет некоторые недостатки.
- Низкий запас прочности. Материал с низкой плотностью (300–400 кг/м3) имеет сравнительно невысокие прочностные характеристики. Поэтому при строительстве необходимо в обязательном порядке выполнять работы по армированию стен.
- Гладкие поверхности. Лицевые части газосиликатных блоков имеют гладкую поверхность с низким коэффициентом шероховатости. Из-за этого ухудшается адгезия с отделочными материалами, что усложняет процесс отделки стен штукатуркой и другими покрытиями.
- Низкая влагостойкость. Из-за увеличенной пористости материал чувствителен к повышенной влажности. Вода и водяной пар проникают во внутренние микропоры и при замерзании увеличиваются в объеме, разрушая блоки изнутри. Поэтому стены из газосиликата нуждаются в дополнительной гидроизоляции.
Где применяют газосиликатные блоки
Газосиликатные блоки используются в жилом и промышленном строительстве. Этот материал применяется не только для постройки несущих элементов зданий, но и для повышения теплоизоляции, а также для защиты инженерных сетей (в частности, отопительных).
Область применения газосиликата определяется его характеристиками, в первую очередь плотностью.
- Изделия, плотность которых составляет 300–400 кг/м3, имеют низкий запас прочности, поэтому они используются преимущественно для утепления стен.
- Газосиликат с плотностью 400 кг/м3 пригоден для возведения одноэтажных домов, гаражей, служебных и хозяйственных пристроек. За счет более высокой прочности материал способен выдерживать значительные нагрузки.
- Блоки с плотностью 500 кг/м3 оптимальны в соотношении прочностных и теплоизоляционных свойств. Их часто используют для строительства коттеджей, дачных домов и других построек высотой до 3 этажей.
Наиболее прочными являются газосиликатные блоки с плотностью 700 кг/м3. Их применяют для возведения высотных объектов жилого и промышленного значения. Но из-за увеличенной плотности уменьшается коэффициент пористости материала и, следовательно, его теплоизоляционные свойства. Поэтому стены, построенные из таких блоков, требуют дополнительного утепления.
Процесс строительства и испытания блоков.
размеры, вес, преимущества и недостатки
Блоки газосиликат – это разновидность легкого ячеистого материала, который имеет достаточно обширную сферу применения в строительстве. Популярность пористые бетонные изделия такого типа заслужили благодаря высоким техническим качествам и многочисленным положительным характеристикам. Какие достоинства и недостатки имеют газосиликатные блоки, и в чем состоят особенности их использования при возведении домов?
Общие характеристики газосиликатного блока
Газосиликат считается улучшенным аналогом газобетона. Производственная технология его изготовления включает такие составные части:
- портландцемент высокого качества, который содержит более 50 процентов неорганического соединения силикат кальция;
- вода;
- алюминиевая пудра в качестве газообразовтеля;
- гашеная известь, обогащенная на 70 процентов оксидами магния и кальция;
- кварцевый мелкофракционный песок.
Из смеси таких компонентов получается высококачественный пористый материал с хорошими техническими характеристиками:
- Оптимальная теплопроводность. Такой показатель зависит от качества материала и его плотности. Марке газосиликатных блоков D700 отвечает теплопроводность 0,18 Вт/м°С. Этот показатель несколько выше многих значений других строительных материалов, включая железобетон.
- Морозостойкость. Газосиликатные блоки величиной плотности 600 кг/ м³ способны выдержать более 50 циклов замерзания и оттаивания. Некоторые новые марки имеют заявленный показатель морозостойкости до 100 циклов.
- Плотность материала. Такое значение колеблется в зависимости от типа газосиликата – от D400 до D700.
- Способность поглощать звуки. Шумоизоляционные свойства ячеистых блоков равняются коэффициенту 0,2 при звуковой частоте 1000 Гц.
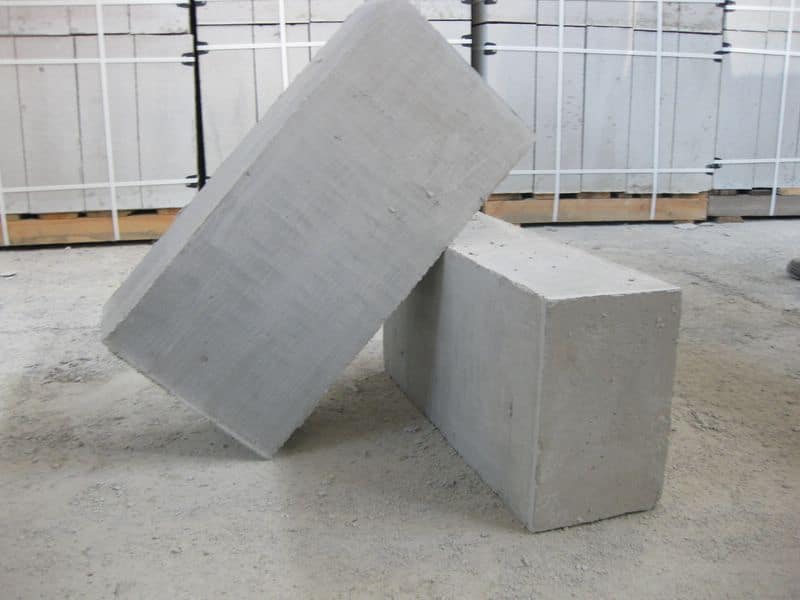
Многие технические параметры газосиликата в несколько раз превышают характерные показатели кирпича. Чтобы обеспечить оптимальную теплопроводность выкладывают стены толщиной 50 сантиметров. Для создания таких условий из кирпича требуется размер кладки в 2 метра.
Качество и свойства газосиликата зависят от соотношения используемых для его приготовления компонентов. Повысить прочность изделий можно, увеличив дозу цементной смеси, но при этом снизится пористость материала, что повлияет на другие технические его характеристики.
Виды
Газосиликатные блоки разделяют в зависимости от степени прочности на три основных вида:
- Конструкционные. Используются такой материал для сооружения зданий, не превышающих три этажа. Плотность блоков составляет D700.
- Конструкционно-теплоизоляционные. Газосиликат такого типа применяется для укладки несущих стен в зданиях не выше двух этажей, а также для строительства межкомнатных перегородок. Плотность его колеблется от D500 до D700.
- Теплоизоляционные. Успешно используется материал для снижения степени тепловой отдачи стен. Прочность его невысокая, а за счет высокой пористости плотность достигает всего D400.
Строительные блоки из газосиликата производят двумя способами:
- Автоклавным. Техника изготовления заключается в обработке материала под высоким давлением пара 9 бар и температурном режиме 175 градусов. Такое пропаривание блоков проводится в специальных промышленных автоклавах.
- Неавтоклавным. Подготовленная смесь газосиликата отвердевает естественным путем на протяжении более двух недель. При этом поддерживается необходимая температура воздуха.
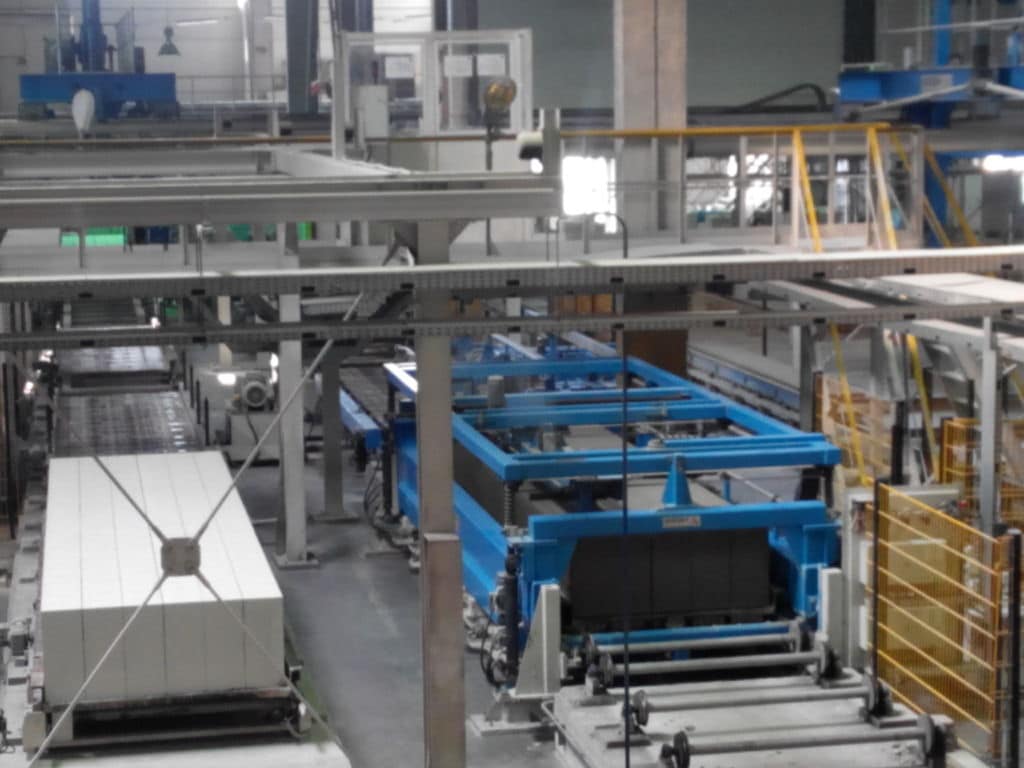
Газосиликат, изготовленный с помощью автоклавной обработки, обладает самыми высокими техническими характеристиками. Такие блоки имеют хорошие показатели прочности и усадки.
Типоразмер и вес
Размер блока газосиликата зависит от вида материала и его производителя. Наиболее распространенными являются такие габариты, которые выражены в миллиметрах:
- 600х100х300;
- 600х200х300;
- 500х200х300;
- 250х400х600;
- 250х250х600.
Газосиликат благодаря ячеистой структуре является достаточно легким материалом. Вес пористых изделий отличается согласно плотности материала и его типоразмера:
- D400 – от 10 до 21 кг;
- D500-D600 – от 9 до 30 кг;
- D700 – от 10 до 40 кг.
Небольшая масса блоков и возможность подбора необходимого их размера намного облегчает строительный процесс.
Сфера применения газосиликатных блоков
В строительстве газосиликат с успехом используют для таких целей:
- сооружение зданий;
- теплоизоляция различных построек;
- изоляция тепловых инженерно-строительных конструкций.
Количество ячеек на один метр кубический в выпускаемых газосиликатных блоках разное. Поэтому область применения материала напрямую зависит от плотности материала:
- 700 кг/ м³. Такие блоки наиболее эффективно используются при сооружении высотных домов. Строительство многоэтажек из газосиликата обходится намного дешевле, чем из железобетона или кирпича.
- 500 кг/ м³. Материал применяют для строительства невысоких зданий – до трех этажей.
- 400 кг/ м³. Такой газосиликат подходит для кладки одноэтажных помещений. Чаще всего его расходуют для недорогих хозяйственных построек. Кроме этого материал успешно применяется для теплоизоляции стен.
- 300 кг/ м³. Ячеистые блоки с низким показателем плотности предназначены для утепления несущих конструкций. Материал не способен выдерживать высокие механические нагрузки, поэтому не подходит для возведения стен.
Чем ниже плотность ячеистых блоков, тем выше их теплоизоляционные качества. В связи с этим сооружения из газосиликата с плотной структурой часто требуют дополнительного утепления. В качестве изоляционного материала используют плиты из пенополистирола.
Преимущества и недостатки
Возведение домов из газосиликатных блоков достаточно оправдано невысокой стоимостью материала и многочисленными его достоинствами:
- Блоки, предназначенные для сооружения домов, обладают высокой прочностью. Для материала средней плотности 500 кг/ м³ показатель механического сжатия 40 кг/ см3.
- Небольшой вес газосиликатных изделий позволяет избежать дополнительных затрат при доставке и установке блоков. Ячеистый материал в пять раз легче от обычного бетона.
- За счет хорошей теплоотдаче снижается расход теплоэнергии. Такое свойство позволяет значительно сэкономить на отоплении здания.
- Высокий показатель звукоизоляции. За счет наличия пор ячеистый материал защищает от проникновения шума в здание в десять раз лучше, чем кирпич.
- Хорошие экологические свойства. Блоки не содержат токсических веществ и совершенно безопасны в применении. По многим экологическим показателям газосиликат приравнивается к дереву.
- Высокая паропроницаемость изделий позволяет создать хорошие условия микроклимата в помещении.
- Негорючий материал препятствует распространению огня в случае пожара.
- Точные пропорции размеров блоков дают возможность выполнения ровной кладки стен.
- Доступная цена материала. При хороших технических показателях цена на газосиликатные блоки сравнительно невысокая.
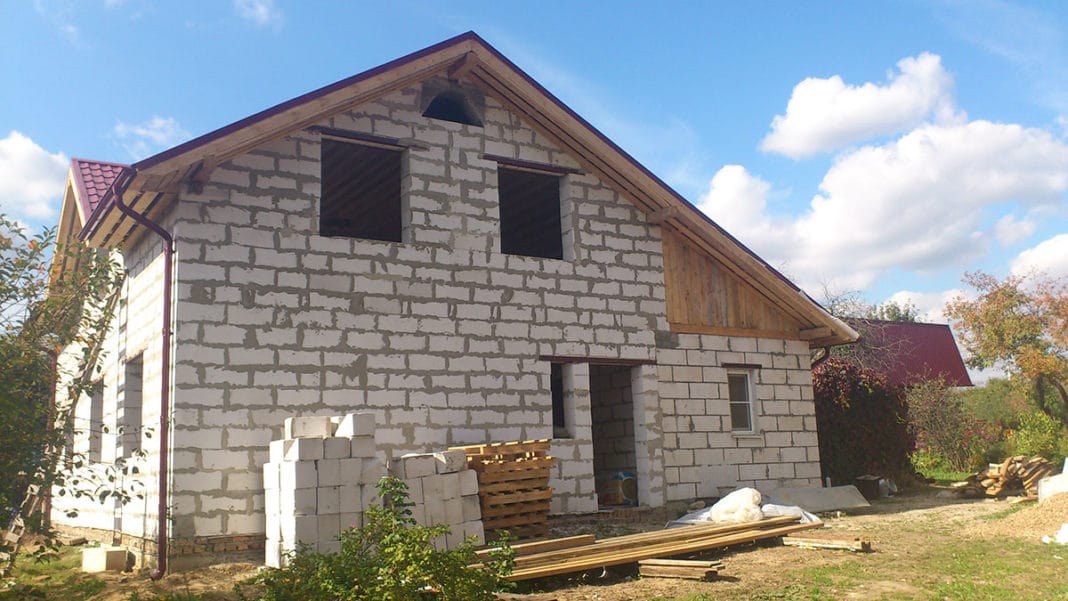
Наряду с немалым количеством преимуществ пористый материал имеет некоторые недостатки:
- Механическая прочность блоков несколько ниже от железобетона и кирпича. Поэтому при вбивании гвоздей в стену или вкручивании дюбелей поверхность легко крошится. Тяжелые детали блоки удерживают достаточно плохо.
- Способность влагопоглощения. Газосиликат хорошо и быстро впитывает воду, которая проникая в поры, снижает прочность материала и приводит к его разрушению. При строительстве зданий из различных типов пористого бетона применяется защита поверхностей от воздействия влаги. Штукатурку на стены рекомендуется наносить в два слоя.
- Морозостойкость блоков зависит от плотности изделий. Марки газосиликата ниже D 400 не способны выдерживать цикл в 50 лет.
- Материал склонен к усадке. Поэтому особенно у блоков марок ниже D700 первые трещины могут появляться через пару лет после сооружения здания.
При оформлении стен из газосиликата используется в основном гипсовая штукатурка. Она прекрасно скрывает все швы между блоками. Цементно-песчаные смеси не удерживаются на пористой поверхности, а при понижении температуры воздуха образуются небольшие трещины.
Популярность газосиликата с каждым годом возрастает. Ячеистые блоки обладают практически всеми качествам необходимыми для эффективного строительства малоэтажных зданий. Некоторые характеристики намного превышают достоинства других материалов. С помощью легких блоков из газосиликата можно построить надежное здание при небольших затратах за сравнительно короткий срок.
Вес газосиликатного блока
Газосиликатные блоки представляют собой искусственный камень, изготавливаемый из извести, цемента и песка с добавкой порошка алюминия (способствует образованию пор в рассматриваемом материале). Хорошая прочность и малый вес газосиликатных блоков делают его незаменимым материалом для быстрого возведения стен.
Плотность материала определяет его основные свойства и марку. Так марка блоков D500 и выше используется для кладки стен и перегородок, а марки ниже рассматриваемой являются теплоизоляционными материалами.
Вес газосиликатного блока будет зависеть от его номинального размера, плотности и применяемых материалов. Длина блока, зависимо от его формы (параллелепипед или параллелепипед с пазами) – 60 сантиметров или 62,5 сантиметров соответственно, высота таких блоков от 20 сантиметров до 30. Ширина газосиликатного блока зависит от толщины стены (10-20 сантиметров для перегородок и 30-40 для несущих стен). Плотность материала 350-750 килограммов на кубический метр.
Давайте рассмотрим сколько весит газосиликатный блок в зависимости от его размеров и плотности. Исходные размеры: длина – 60 сантиметров, высота – 25 сантиметров.
При ширине в 10 сантиметров и плотности 400 кг/м³ вес газосиликатного блока будет составлять 7,2 килограмма, при плотности 500 – 8,7 килограмма, при плотности 600 кг/м³ – 10,8 килограмма.
Если изменить ширину блока до 20 сантиметров, а плотность оставить той же, то при плотности 400 его вес увеличится вдвое и составит 14,4 килограмма, при плотности 500 – 17,4 килограмма, при плотности 600 – 21,6 килограмма.
Теперь рассмотрим изменение веса газосиликатного блока при его ширине 30 сантиметров. Плотность 400 кг/м³ – вес блока 21,6 килограмма; плотность 500 кг/м³ – вес блока 26,1 килограмма; плотность 600 кг/м³ – вес блока 32,4 килограмма.
Теперь рассмотрим последний вариант изменения веса блока при его ширине 40 сантиметров. Плотность 400 кг/м³ – вес блока 28,8 килограмма; плотность материала 500 кг/м³ – вес блока 34,8 килограмма; плотность 600 кг/м³ – вес блока 43,2 килограмма.
Машина для производства газосиликатных стеновых панелей
SINOPOWER! Завод газосиликатных блоков, Машина для производства фасадных бетонных блоков, Автоклав с реактором высокого давления!
Введение Кирпич / блок / панель из автоклавного ячеистого бетона (AAC)
Кирпич / блок / панель из автоклавного газобетона (AAC) — это легкий, многоклеточный новый строительный материал; К особенностям относятся более низкая плотность, теплоизоляция, возможность, огнестойкость и звукоизоляция. AAC изготавливается из кремниевого материала (кварцевый песок или переработанная летучая зола) и кальциевого материала (известь, цемент), смешивается с пенообразующей добавкой (алюминиевый порошок), замешивается, реакция между алюминием и бетоном вызывает появление микроскопических пузырьков водорода, расширяющихся. бетон примерно в пять раз больше первоначального объема.Он превращается в многоячеистый силикатный продукт в процессе формования, предварительного отверждения, резки, испарения и отверждения.
Внедрение линии по производству автоклавного газобетона (AAC)
1) Вес продукта соответствует 500 кг / м3, 600 кг / м3 700 кг / м3.
2) годовая мощность 100 000–400 000 м³.
3) заданная пропорция сырья: цемент 6,5%, известь-сырец 23%, зола или песок 68%, гипс 3%, порошок алюминиевой пасты 350 г / м3.
4) расход воды и материала 0,631
5) одна форма 3,024M3, 3,456M3, 4,23M3
6) Продолжительность цикла литья 5-6 минут, время цикла резки 5 минут.
7) температура литейного раствора 38-42 градуса
8) бесшумная остановка корпуса. Время составляет 1,5-2,5 часа, температура 50-90 градусов, после тихой остановки прочность корпуса составляет 0,15-0,18 МПа
9) Время цикла отверждения паром, вход и выход из автоклава около 0,5 часа, время цикла отверждения паром около 7.5 часов / 1,6 МПа, всего 8 часов
Газобетон производит технологический процесс:
1. Сырье хранится на складе материалов (или хранит горшок) после обработки запаса, такого как известь, цемент, гипс. , Песок (или зола-унос)
2. Алюминиевый порошок или алюминиевый лосьон обрабатывают резервный материал для использования
3. Сырье измеряется в соответствии с определенным соответствием с помощью меры электронного баланса, алюминиевого порошка, воды, помещенной в смеситель для алюминиевого порошка. Это суспензия для перемешивания жидкости после измерения
4.Дозируемая вода (холодная вода или горячая вода, кувшин, горячая вода) измеряется электронным водным балансом
5. Поместите в смесители и разлейте их в определенном порядке после того, как сырье, алюминиевый порошок суспендировали жидкость, вылейте и введите в пресс-форму после равномерного перемешивания (панель должна быть помещена в пресс-форму заранее сетевым срезом арматурного стержня)
6. Тихо, если она поднимается заранее, чтобы припарковаться через определенную температуру и время, транспортируется ли она к режущему станку для подвешивания на подъемном механизме После высадки на 90 ° после того, как основной корпус достигает определенной интенсивности, вырезается рисунок рисунка
a.Основание несёт на стороне и разрезает и фрезерует желоб по вертикали
сначала
b. Затем продолжайте вертикальный уровень, чтобы разрезать
c. Отрезать горизонтально окончательно
d. Разрежьте хорошее основание, поднимите в вагончик в котел, пройдите по одному ярду полок, разбейте его на группы, чтобы отпарить, перевезти, чтобы подвесить автомобиль, чтобы загрузить
7. Хорошо поднимите продукты, произведите после того, как котел сломает доску пальцами и большим пальцем. с помощью отламывания доски пальцами и машинкой для отпаривания
8.Сваливайте от подъемника готовой продукции или вилочного погрузчика до готовой продукции, складывайте контрфорс в соответствии со спецификацией для перевозки
9. Обработка паром и подъем вагона и бортового борта и попадание на следующий круг обращения и возвращение после этого, готовый продукт выгружается с опрокинутым подъемником ассоциация каркаса пресс-формы, которая выводит рисунки, восстанавливает возврат под 90 ° для повторной заливки смесителя после очистки
Основные машины из автоклавного газобетона (AAC) кирпич / блок
Оборудование будет разделено на две части: специализированное оборудование и универсальное оборудование.
В состав специализированного оборудования входят:
1. Режущее оборудование: подъемный кран, резак.
2. Дозировочное оборудование: электронные измерительные весы, машина для взбивания жидкого навоза,
Бак для хранения жидкого навоза, смеситель жидкого навоза.
3. Разливочное и автоклавное оборудование: смеситель для алюминиевого порошка. Смеситель для разливки, форма,
Боковая пластина, автоклав, тележка-носитель.
4. Транспортное оборудование: кран для полуфабрикатов, кран для готовой продукции.
Универсальная комплектация включает:
1.Оборудование сосудов под давлением: бойлер, автоклав.
2. Дробильное оборудование: шаровая мельница, дробилка.
3 Транспортное оборудование: кран, подъемная машина, питатель, ленточный конвейер, шламовый насос
, винтовой конвейер.
4. Оборудование для защиты требований: пылеуловитель
030303 Емкость Тип ПУНКТ
SP-AAC-5
SP-AAC-10
SP-AAC-15
SP-
SP-AAC-20 -AAC-30 Производительность, x103 м3 / год
50
100
150
200
200
4.2×1,2×0,6
4,2×1,2×0,6
4,2×1,5×0,6
4,8×1,2×0,6
6,0×1,2×0,6
Установочная мощность, кВт
600
800
900
1300
1400
34 6
6
6
6
Площадь цеха, м2
3000
3000
3000
5000 Площадь завода, м3
20000
20000
25000
30000
35000
Преимущества конструкции блока из автоклавного газобетона (AAC)
1.Звукоизоляция
Стена AAC имеет отличный класс передачи звука (STC), рейтинг 44. Результат: Практически звукоизолированные внутренние помещения
2. Теплоизоляция
Она имеет самый высокий тепловой рейтинг в отрасли… .R30! Таким образом обеспечивается хорошая теплоизоляция помещений, не пропускающая теплый воздух летом и холодный зимой. AAC снижает затраты на кондиционирование воздуха на 30%.
3.Устойчивость к землетрясениям
Силы землетрясения, действующие на конструкцию, пропорциональны весу здания, поэтому AAC демонстрирует отличную устойчивость к силам землетрясений.В регионах с высокой сейсмической активностью, таких как Япония, используется исключительно AAC. Было доказано, что он выдерживает ветровые нагрузки тропических штормов категории 5
4. Площадь пола
Использование более тонких блоков (6 дюймов вместо 9 дюймов внешних стен) из-за их превосходных водонепроницаемых и изоляционных свойств приводит к увеличению площадь от 3-5%.
5. Экономия затрат
Легкость AAC значительно снижает собственный вес здания, что приводит к снижению стоимости конструкции из стали (до 27%) и цемента (до 20%).Стены из AAC, в 8 раз превышающие размер глиняного кирпича, включают 1/3 швов, таким образом, общая экономия раствора составляет до 66%.
Его автоматический производственный процесс дает AAC исключительную точность размеров и гладкие поверхности, устраняет необходимость в трехслойной штукатурке стен и позволяет наносить окончательный слой 6 мм (шпатлевка / POP).
6. Огнестойкость
Лучшая в своем классе огнестойкость, 4 часа. Температура плавления AAC составляет более 1600 ºC, что более чем в два раза превышает типичную температуру 650 ºC при пожаре в здании.
7. Устойчивые к вредителям термиты ненавидят AAC
Изготовленный из неорганических минералов, он не способствует росту плесени.
8. Водяной барьер
Его структура не допускает капиллярного действия, что делает его непроницаемым для воды. Его водонепроницаемые свойства дополнительно улучшаются за счет добавления добавок на основе силикона.
Отношение прочности к весу выше, чем у бетона M150, и намного превышает требования индийских строительных норм.
Приглашаем Вас посетить наш завод.!
.Автоклавированные газированные бетонные бетонные производственная линия Аак / автоклав для завода
блока силиката газа Автоклавная линия по производству газобетона / автоклав для газосиликатных блоков
Введение Автоклавный газобетон (AAC) кирпич / блок
Кирпич / блок из автоклавного газобетона (AAC) — это легкий, многоклеточный новый строительный материал; К особенностям относятся более низкая плотность, теплоизоляция, возможность, огнестойкость и звукоизоляция.AAC изготавливается из кремниевого материала (кварцевый песок или переработанная летучая зола) и кальциевого материала (известь, цемент), смешивается с пенообразующей добавкой (алюминиевый порошок), замешивается, реакция между алюминием и бетоном вызывает появление микроскопических пузырьков водорода, расширяющихся. бетон примерно в пять раз больше первоначального объема. Он превращается в многоячеистый силикатный продукт в процессе формования, предварительного отверждения, резки, испарения и отверждения.
Внедрение линии по производству автоклавного газобетона (AAC)
1) Вес продукта соответствует контролю 500 кг / м3, 600 кг / м3, 700 кг / м3.
2) годовая мощность 100 000–400 000 м³.
3) установленная пропорция сырья: цемент 6,5%, известь-сырец 23%, зола или песок 68%, гипс 3%, порошок алюминиевой пасты 350 г / м3.
4) расход воды и материалов 0,631
5) одна форма 3,024 м3, 3,456 м3, 4,23 м3
6) Время цикла литья 5-6 минут, время цикла резки 5 минут.
7) температура литейного раствора 38-42 градуса
8) кузов тихая остановка.Время составляет 1,5-2,5 часа, температура 50-90 градусов, после тихой остановки прочность корпуса составляет 0,15-0,18 МПа
9) Время цикла отверждения паром, вход и выход из автоклава около 0,5 часа, время цикла отверждения паром около 7,5 часов / 1,6 МПа, всего 8 часов
Газобетон производит технологический процесс:
1. Сырье хранится на складе материалов (или хранит горшок) после обработки таких запасов, как известь, цемент, гипс, песок (или зола-унос)
2.Алюминиевый порошок или алюминиевый лосьон обрабатываются резервным материалом для использования
3. Сырье измеряется в соответствии с определенным соответствием с помощью меры электронного баланса, алюминиевый порошок, вода помещаются в смеситель для алюминиевого порошка, если это суспендировать жидкость для смешивания после измерение
4. Дозируемая вода (холодная вода или горячая вода из кувшина, горячая вода) измеряется электронным водным балансом
5. Поместите в смесители и разлейте их в определенном порядке после измерения исходных материалов, суспензии алюминиевого порошка, жидкости, залейте и войдите в форму после равномерного перемешивания (панель следует заранее положить в форму сетевым срезом арматурного стержня)
6.Тихо, если он поднимается заранее, чтобы припарковаться через определенную температуру и время, если он транспортируется к режущему станку, чтобы подвешивать его с отклонением на 90 ° после того, как основной корпус достигает определенной интенсивности, чертеж выкройки вырезается
a. Основание несёт на стороне и разрезает и фрезерует желоб по вертикали
сначала
b. Затем продолжите вертикальный уровень, чтобы разрезать
c. Отрежьте горизонтально окончательно
d. Вырезать хорошее основание кузова, поднять в котел автомобиль, пройти на один ярд, полки организовать в группы, чтобы отпарить, перевезти, чтобы подвесить, чтобы водить автомобиль, чтобы загрузить
7.Хорошо приподнять продукты, производить после котла, отламывая доску пальцами и большим пальцем, отламывая доску пальцами и большим пальцем машина для пара
8. Сваи от подъемника готовой продукции или вилочного погрузчика до поля готовой продукции, сложите контрфорс в соответствии со спецификацией для переноски.
9. Обработка паром и поднятие вагона и бортовой доски, попадание на следующую площадку обращения и возврат после того, как готовый продукт выгружается, при сброшенном соединении рамы пресс-формы подъемника, при котором рисунки выходят, восстанавливается возврат на 90 ° для заливки смесителя снова заливка после очистки
Основные машины из автоклавного газобетона (ААБ) кирпич / блок
Оборудование будет разделено на две части: специализированное оборудование и универсальное оборудование.
В состав специализированного оборудования входят:
1. Раскройное оборудование: подъемный кран, резак.
2. Дозирующее оборудование: электронные измерительные весы, машина для взбивания шламов,
Бак для жидкого навоза, смеситель навозной жижи.
3. Разливочное и автоклавное оборудование: смеситель для алюминиевого порошка. Разливочный смеситель, форма,
Боковая плита, автоклав, грузовой автомобиль.
4. Транспортное оборудование: кран для полуфабрикатов, кран для готовой продукции.
Универсальная комплектация включает:
1. Оборудование сосудов высокого давления: бойлер, автоклав.
2. Дробильное оборудование: шаровая мельница, дробилка.
3 Транспортное оборудование: кран, подъемная машина, питатель, ленточный конвейер,
Шламовый насос, шнековый конвейер.
4.Оборудование для защиты окружающей среды: пылеуловитель
Емкость Тип
ТОВАР
SP-AAC-5
SP-AAC-10
SP-AAC-15
SP-AAC-20
SP-AAC-30
Производительность, x103м3 / год
50
100
150
200
300
Размер жмыха, м3
4.2×1,2×0,6
4,2×1,2×0,6
4,2×1,5×0,6
4,8×1,2×0,6
6,0×1,2×0,6
Установочная мощность, кВт
600
800
900
1300
1400
Производственный цикл, пресс-форма / мин
5
6
6
6
6
Площадь цеха, м2
3000
3000
3500
4000
5000
Площадь завода, м3
20000
20000
25000
30000
35000
Преимущества конструкции из автоклавного ячеистого бетона (AAC) Блок
1.Звукоизоляция
Стена AAC имеет отличный класс передачи звука (STC), рейтинг 44. Результат: Практически звукоизолированные интерьеры
2. Теплоизоляция
Обладает самым высоким термическим рейтингом в отрасли… .R30! Таким образом обеспечивается хорошая теплоизоляция помещений, не пропускающая теплый воздух летом и холодный зимой. AAC снижает затраты на кондиционирование воздуха на 30%.
3. землетрясение
Силы землетрясения, воздействующие на конструкцию, пропорциональны весу здания, поэтому AAC демонстрирует отличную устойчивость к силам землетрясений.Районы с высокой сейсмической активностью, такие как & nb
. Aac Производственная линия Машина для производства паровых блоков Оборудование для производства блоков из пенобетона в автоклаве
SINOPOWER! Газосиликатные блоки, Линия по производству строительного кирпича, Машина для производства фасадных бетонных блоков, Автоклав с реактором высокого давления!
Введение Кирпич / блок / панель из автоклавного ячеистого бетона (AAC)
Кирпич / блок / панель из автоклавного газобетона (AAC) — это легкий, многоклеточный новый строительный материал; К особенностям относятся более низкая плотность, теплоизоляция, возможность, огнестойкость и звукоизоляция.AAC изготавливается из кремниевого материала (кварцевый песок или переработанная летучая зола) и кальциевого материала (известь, цемент), смешивается с пенообразующей добавкой (алюминиевый порошок), замешивается, реакция между алюминием и бетоном вызывает появление микроскопических пузырьков водорода, расширяющихся. бетон примерно в пять раз больше первоначального объема. Он превращается в многоячеистый силикатный продукт в процессе формования, предварительного отверждения, резки, испарения и отверждения.
Внедрение линии по производству автоклавного газобетона (AAC)
1) Вес продукта соответствует контролю 500 кг / м3, 600 кг / м3, 700 кг / м3.
2) годовая мощность 100 000–400 000 м³.
3) установленная пропорция сырья: цемент 6,5%, известь-сырец 23%, зола или песок 68%, гипс 3%, порошок алюминиевой пасты 350 г / м3.
4) расход воды и материалов 0,631
5) одна форма 3,024 м3, 3,456 м3, 4,23 м3
6) Время цикла литья 5-6 минут, время цикла резки 5 минут.
7) температура литейного раствора 38-42 градуса
8) кузов тихая остановка.Время составляет 1,5-2,5 часа, температура 50-90 градусов, после тихой остановки прочность корпуса составляет 0,15-0,18 МПа
9) Время цикла отверждения паром, вход и выход из автоклава около 0,5 часа, время цикла отверждения паром около 7,5 часов / 1,6 МПа, всего 8 часов
Газобетон производит технологический процесс:
1. Сырье хранится на складе материалов (или хранит горшок) после обработки таких запасов, как известь, цемент, гипс, песок (или летучая зола)
2.Алюминиевый порошок или алюминиевый лосьон обрабатывают резервный материал для использования
3. Сырье измеряется в соответствии с определенным соответствием с помощью меры электронного баланса, алюминиевый порошок, вода помещаются в смеситель для алюминиевого порошка, если это суспендировать жидкость для перемешивания после измерение
4. Дозируемая вода (холодная вода или кувшин горячей воды горячая вода) измеряется электронным водным балансом
5. Поместить в смесители и разлить между ними в определенном порядке после измерения сырьевых материалов, суспензии алюминиевого порошка, жидкости, залейте и войдите в форму после равномерного перемешивания (панель следует заранее положить в форму сетевым срезом арматурного стержня)
6.Тихо, если он поднимается заранее, чтобы припарковаться через определенную температуру и время, если он транспортируется к режущему станку, чтобы повесить его на расстроенном подъемнике, отклоненном на 90 ° после того, как основной корпус достигнет определенной интенсивности, чертеж выкройки вырезается
a. Основание несёт на стороне и разрезает и фрезерует желоб вертикально
, сначала
b. Затем продолжите вертикальный уровень, чтобы разрезать
c. Отрезать горизонтально окончательно
d. Вырезать хорошее основание кузова, поднять в котел автомобиль, пойти на один ярд, полки организовать в группы, чтобы отпарить, перевезти, чтобы подвесить, чтобы вести автомобиль, чтобы загрузить
7.Хорошо приподнять продукты, производить после котла, отламывая доску пальцами и большим пальцем, отламывая доску пальцами и большим пальцем машина для пара
8. Сваи от подъемника готовой продукции или вилочного погрузчика до поля готовой продукции, сложите контрфорс в соответствии со спецификацией для переноски.
9. Обработка паром и поднятие вагона и бортовой доски, попадание на следующую площадку обращения и возврат после того, как готовый продукт выгружается, при сброшенном соединении рамы пресс-формы подъемника, при котором рисунки выходят, восстанавливается возврат на 90 ° для заливки смесителя снова заливка после очистки
Основные машины из автоклавного газобетона (AAC) кирпич / блок
Оборудование будет разделено на две части: специализированное оборудование и универсальное оборудование.
В состав специализированного оборудования входят:
1. Раскройное оборудование: подъемный кран, резак.
2. Дозирующее оборудование: электронные измерительные весы, машина для взбивания шламов,
Бак для жидкого навоза, смеситель навозной жижи.
3. Разливочное и автоклавное оборудование: смеситель для алюминиевого порошка. Разливочный смеситель, форма,
Боковая плита, автоклав, грузовой автомобиль.
4. Транспортное оборудование: кран для полуфабрикатов, кран для готовой продукции.
Универсальная комплектация включает:
1. Оборудование сосудов высокого давления: бойлер, автоклав.
2. Дробильное оборудование: шаровая мельница, дробилка.
3 Транспортное оборудование: кран, подъемная машина, питатель, ленточный конвейер,
Шламовый насос, шнековый конвейер.
4.Оборудование для защиты окружающей среды: пылеуловитель
Емкость Тип
ТОВАР
SP-AAC-5
SP-AAC-10
SP-AAC-15
SP-AAC-20
SP-AAC-30
Производительность, x103м3 / год
50
100
150
200
300
Размер жмыха, м3
4.2×1,2×0,6
4,2×1,2×0,6
4,2×1,5×0,6
4,8×1,2×0,6
6,0×1,2×0,6
Установочная мощность, кВт
600
800
900
1300
1400
. дешевые строительные материалы для строительства силиката кальция блока
Почему выбирают нас?
1 .Специализация
Peakon входит в тройку самых быстрорастущих производителей в Китае и специализируется на 100% безасбестовых огнестойких плитах из силиката кальция и волокнистоцементных плитах в течение 8 лет.
2.Solution
Peakon предоставляет решения по противопожарной и теплоизоляции для более чем 5000 клиентов:
Архитекторы, специалисты по спецификациям, менеджеры объектов, агент, оптовый торговец, подрядчики, субподрядчики и даже конечные потребители в стране.
3.Надежность:
Через сертификаты ISO14001, ISO9001, OHSAS 18001, SGS и CE. Тест CE обычно считается более обременительным, чем другие режимы тестирования, это тестирование на устойчивость к огню, ударам, шуму, влаге, морозной влажности, формальдегиду …
Дешевые строительные материалы Блок силиката кальция
Картон из силиката кальция — это композитный материал, состоящий из кварцевого песка, цемента и волокон целлюлозы.В этом продукте используется импортная чистая бумага из Канады, без макулатуры. Плиты из силиката кальция производятся в виде листов и используются для внутренних и внешних подвесок, перегородок и полов. Нормальный размер составляет 1220 × 2440 мм, толщина от 3 до 25 мм, а плотность составляет 0,95–1,30 г / см3. Есть низкая плотность, средняя плотность и высокая плотность.
Характеристики продукта:
1. Структурно сильный
2.Огнестойкость (класс A)
3. Отличная теплоизоляция
4.100% без асбеста
5. Отличные звукоизоляционные свойства
6. Влагостойкость
7. Легкий вес
8. Устойчивость к грибкам и термитам
9. Устойчивость к паразитам
10 .Удобный для пользователя и простой в установке
11.Безопасный и экологичный
12.Экономичный
Параметры плиты из силиката кальция толщиной 50 мм:
Технические характеристики 2440 * 1220/2400 * 1200 мм Толщина : 3-30мм Ширина 1200-1220мм Длина 2440мм Цвет как изображения или индивидуальный Плотность 0.95 ~ 1,3 г / см3 Содержание воды ≤10 Огнестойкость Негорючесть Класс A Теплопроводность <0,3 Вт / мк Прочность на изгиб Класс 4 (> 10 МПа) Радиоактивность GB8624-2006 Класс A Асбест 100% без асбеста Сертификация ISO / CE / SGS
Области применения
Области применения плит силиката кальция:
Широко используется в сталелитейной промышленности, цементной промышленности, без черной металлургии и углеродной промышленности, стекольной промышленности, керамической промышленности, электростанциях, электрическом нагревательном оборудовании.Облицовка стальной конструкции, огнестойкая перегородка, сердцевина противопожарной двери, компоненты противопожарной двери, двери лифта, камины и печи и т. Д.
Толщина Вес Профиль кромки Применение 6 мм 24 кг квадратная кромка / коническая кромка внутренняя облицовка 8 мм 32 кг квадратная кромка / коническая кромка внутренний / внешний потолок 9 мм 36 кг скошенная кромка / скошенная кромка внутренняя перегородка / внешняя облицовка стен / влажная зона и основа из плитки / напольное покрытие 10 мм 40 кг квадратная кромка / коническая кромка внутренняя перегородка / внешняя облицовка стены / для влажных помещений и подложки из плитки / на напольное покрытие 12mm 48kg 90 074 квадратная кромка / коническая кромка внешняя облицовка стен / влажная зона и основа из плитки / напольное покрытие 15 мм 60 кг квадратная кромка / скошенная кромка внутренние перегородки с особыми требованиями / приподнятый пол 18 мм 72 кг квадратная кромка внутренние перегородки с особыми требованиями / приподнятый пол 20 мм 80 кг квадратная кромка внутренние перегородки с особыми требованиями / приподнятый пол
Наш проектный кейс:
Упаковка и отгрузка
Упаковка: деревянный поддон + полиэтиленовое покрытие + угловой протектор + прочная лента
0 2 900 Доска силиката кальция Пикон РАЗМЕР 9007 5 КОЛИЧЕСТВО ВЕС ОБЪЕМ 1220 * 2440 * 6 мм 900PCS 21600KGS 25CBM 1220 *
0 * 9mm 25 куб.см 1220 * 2440 * 12 мм 450 шт. 21600 кгс 25 куб. М. Информация о компании
О нас:
Peakon — это частная китайская компания, основанная в 2011 году в городе Дунсин, Китай.Генеральный директор приобрел немецкое передовое оборудование и технологии и быстро признал Peakon инновационным материалом для пассивной противопожарной защиты в сфере отопления, вентиляции, кондиционирования воздуха и строительства и представил, как этот уникальный продукт может решить многие проблемы противопожарной защиты в других отраслях промышленности Китая. Основным продуктом являются 100% безасбестовые противопожарные плиты, волокнисто-цементные плиты низкой и средней плотности, плиты из силиката кальция, другие высокотехнологичные энергосберегающие плиты для защиты окружающей среды.
Peakon с тех пор превратилась в всемирно признанного поставщика пассивных систем противопожарной защиты, сертифицированного по стандартам ISO 9001, ISO 14001, CE и SGS, с проверенными и внесенными в список проектами для решения большинства проблем противопожарной защиты. Компания Peakon разработала множество решений для противопожарной защиты и теперь имеет китайские патенты на широкий спектр систем для использования в противопожарной промышленности.
Компания Peakon разработала множество уникальных систем пассивной противопожарной защиты для некоторых из самых ценных активов в мире. Благодаря нашей приверженности исследованиям и разработкам и постоянному совершенствованию, Peakon завоевала доверие наших клиентов в плане защиты людей и собственности по всему миру.Доска Peakon широко экспортируется в США, Юго-Восточную Азию, ОАЭ, Ближний Восток и Африку.
FAQ
Q1.Каков ваш MOQ, можем ли мы заказать смешивание разных размеров?
A: Конечно, обычно минимальный объем заказа каждого размера составляет 1 × 20-футовый контейнер, но для вашего качества тестирования мы можем принять небольшой заказ / выборку для разных размеров
Q2. Какой порт вы можете поддерживать?
A: Порт Фанчэн или любой другой порт Китая, который вам нужен. Если указан порт назначения, для справки можно указать CFR и CIF.
3 кв. Каковы сроки доставки вашей продукции?
A: Обычно отправка товара морским или воздушным транспортом занимает около 10-15 дней после получения аванса.
.
03 Емкость Тип ПУНКТ
SP-AAC-5
SP-AAC-10
SP-AAC-15
SP-
SP-AAC-20 -AAC-30 Производительность, x103 м3 / год
50
100
150
200
200
4.2×1,2×0,6
4,2×1,2×0,6
4,2×1,5×0,6
4,8×1,2×0,6
6,0×1,2×0,6
Установочная мощность, кВт
600
800
900
1300
1400
34 6
6
6
6
Площадь цеха, м2
3000
3000
3000
5000 Площадь завода, м3
20000
20000
25000
30000
35000
Преимущества конструкции блока из автоклавного газобетона (AAC)
1.Звукоизоляция
Стена AAC имеет отличный класс передачи звука (STC), рейтинг 44. Результат: Практически звукоизолированные внутренние помещения
2. Теплоизоляция
Она имеет самый высокий тепловой рейтинг в отрасли… .R30! Таким образом обеспечивается хорошая теплоизоляция помещений, не пропускающая теплый воздух летом и холодный зимой. AAC снижает затраты на кондиционирование воздуха на 30%.
3.Устойчивость к землетрясениям
Силы землетрясения, действующие на конструкцию, пропорциональны весу здания, поэтому AAC демонстрирует отличную устойчивость к силам землетрясений.В регионах с высокой сейсмической активностью, таких как Япония, используется исключительно AAC. Было доказано, что он выдерживает ветровые нагрузки тропических штормов категории 5
4. Площадь пола
Использование более тонких блоков (6 дюймов вместо 9 дюймов внешних стен) из-за их превосходных водонепроницаемых и изоляционных свойств приводит к увеличению площадь от 3-5%.
5. Экономия затрат
Легкость AAC значительно снижает собственный вес здания, что приводит к снижению стоимости конструкции из стали (до 27%) и цемента (до 20%).Стены из AAC, в 8 раз превышающие размер глиняного кирпича, включают 1/3 швов, таким образом, общая экономия раствора составляет до 66%.
Его автоматический производственный процесс дает AAC исключительную точность размеров и гладкие поверхности, устраняет необходимость в трехслойной штукатурке стен и позволяет наносить окончательный слой 6 мм (шпатлевка / POP).
6. Огнестойкость
Лучшая в своем классе огнестойкость, 4 часа. Температура плавления AAC составляет более 1600 ºC, что более чем в два раза превышает типичную температуру 650 ºC при пожаре в здании.
7. Устойчивые к вредителям термиты ненавидят AAC
Изготовленный из неорганических минералов, он не способствует росту плесени.
8. Водяной барьер
Его структура не допускает капиллярного действия, что делает его непроницаемым для воды. Его водонепроницаемые свойства дополнительно улучшаются за счет добавления добавок на основе силикона.
Отношение прочности к весу выше, чем у бетона M150, и намного превышает требования индийских строительных норм.
Приглашаем Вас посетить наш завод.!
.Автоклавированные газированные бетонные бетонные производственная линия Аак / автоклав для завода
блока силиката газа Автоклавная линия по производству газобетона / автоклав для газосиликатных блоков
Введение Автоклавный газобетон (AAC) кирпич / блок
Кирпич / блок из автоклавного газобетона (AAC) — это легкий, многоклеточный новый строительный материал; К особенностям относятся более низкая плотность, теплоизоляция, возможность, огнестойкость и звукоизоляция.AAC изготавливается из кремниевого материала (кварцевый песок или переработанная летучая зола) и кальциевого материала (известь, цемент), смешивается с пенообразующей добавкой (алюминиевый порошок), замешивается, реакция между алюминием и бетоном вызывает появление микроскопических пузырьков водорода, расширяющихся. бетон примерно в пять раз больше первоначального объема. Он превращается в многоячеистый силикатный продукт в процессе формования, предварительного отверждения, резки, испарения и отверждения.
Внедрение линии по производству автоклавного газобетона (AAC)
1) Вес продукта соответствует контролю 500 кг / м3, 600 кг / м3, 700 кг / м3.
2) годовая мощность 100 000–400 000 м³.
3) установленная пропорция сырья: цемент 6,5%, известь-сырец 23%, зола или песок 68%, гипс 3%, порошок алюминиевой пасты 350 г / м3.
4) расход воды и материалов 0,631
5) одна форма 3,024 м3, 3,456 м3, 4,23 м3
6) Время цикла литья 5-6 минут, время цикла резки 5 минут.
7) температура литейного раствора 38-42 градуса
8) кузов тихая остановка.Время составляет 1,5-2,5 часа, температура 50-90 градусов, после тихой остановки прочность корпуса составляет 0,15-0,18 МПа
9) Время цикла отверждения паром, вход и выход из автоклава около 0,5 часа, время цикла отверждения паром около 7,5 часов / 1,6 МПа, всего 8 часов
Газобетон производит технологический процесс:
1. Сырье хранится на складе материалов (или хранит горшок) после обработки таких запасов, как известь, цемент, гипс, песок (или зола-унос)
2.Алюминиевый порошок или алюминиевый лосьон обрабатываются резервным материалом для использования
3. Сырье измеряется в соответствии с определенным соответствием с помощью меры электронного баланса, алюминиевый порошок, вода помещаются в смеситель для алюминиевого порошка, если это суспендировать жидкость для смешивания после измерение
4. Дозируемая вода (холодная вода или горячая вода из кувшина, горячая вода) измеряется электронным водным балансом
5. Поместите в смесители и разлейте их в определенном порядке после измерения исходных материалов, суспензии алюминиевого порошка, жидкости, залейте и войдите в форму после равномерного перемешивания (панель следует заранее положить в форму сетевым срезом арматурного стержня)
6.Тихо, если он поднимается заранее, чтобы припарковаться через определенную температуру и время, если он транспортируется к режущему станку, чтобы подвешивать его с отклонением на 90 ° после того, как основной корпус достигает определенной интенсивности, чертеж выкройки вырезается
a. Основание несёт на стороне и разрезает и фрезерует желоб по вертикали
сначала
b. Затем продолжите вертикальный уровень, чтобы разрезать
c. Отрежьте горизонтально окончательно
d. Вырезать хорошее основание кузова, поднять в котел автомобиль, пройти на один ярд, полки организовать в группы, чтобы отпарить, перевезти, чтобы подвесить, чтобы водить автомобиль, чтобы загрузить
7.Хорошо приподнять продукты, производить после котла, отламывая доску пальцами и большим пальцем, отламывая доску пальцами и большим пальцем машина для пара
8. Сваи от подъемника готовой продукции или вилочного погрузчика до поля готовой продукции, сложите контрфорс в соответствии со спецификацией для переноски.
9. Обработка паром и поднятие вагона и бортовой доски, попадание на следующую площадку обращения и возврат после того, как готовый продукт выгружается, при сброшенном соединении рамы пресс-формы подъемника, при котором рисунки выходят, восстанавливается возврат на 90 ° для заливки смесителя снова заливка после очистки
Основные машины из автоклавного газобетона (ААБ) кирпич / блок
Оборудование будет разделено на две части: специализированное оборудование и универсальное оборудование.
В состав специализированного оборудования входят:
1. Раскройное оборудование: подъемный кран, резак.
2. Дозирующее оборудование: электронные измерительные весы, машина для взбивания шламов,
Бак для жидкого навоза, смеситель навозной жижи.
3. Разливочное и автоклавное оборудование: смеситель для алюминиевого порошка. Разливочный смеситель, форма,
Боковая плита, автоклав, грузовой автомобиль.
4. Транспортное оборудование: кран для полуфабрикатов, кран для готовой продукции.
Универсальная комплектация включает:
1. Оборудование сосудов высокого давления: бойлер, автоклав.
2. Дробильное оборудование: шаровая мельница, дробилка.
3 Транспортное оборудование: кран, подъемная машина, питатель, ленточный конвейер,
Шламовый насос, шнековый конвейер.
4.Оборудование для защиты окружающей среды: пылеуловитель
Емкость Тип
ТОВАР
SP-AAC-5
SP-AAC-10
SP-AAC-15
SP-AAC-20
SP-AAC-30
Производительность, x103м3 / год
50
100
150
200
300
Размер жмыха, м3
4.2×1,2×0,6
4,2×1,2×0,6
4,2×1,5×0,6
4,8×1,2×0,6
6,0×1,2×0,6
Установочная мощность, кВт
600
800
900
1300
1400
Производственный цикл, пресс-форма / мин
5
6
6
6
6
Площадь цеха, м2
3000
3000
3500
4000
5000
Площадь завода, м3
20000
20000
25000
30000
35000
Преимущества конструкции из автоклавного ячеистого бетона (AAC) Блок
1.Звукоизоляция
Стена AAC имеет отличный класс передачи звука (STC), рейтинг 44. Результат: Практически звукоизолированные интерьеры
2. Теплоизоляция
Обладает самым высоким термическим рейтингом в отрасли… .R30! Таким образом обеспечивается хорошая теплоизоляция помещений, не пропускающая теплый воздух летом и холодный зимой. AAC снижает затраты на кондиционирование воздуха на 30%.
3. землетрясение
Силы землетрясения, воздействующие на конструкцию, пропорциональны весу здания, поэтому AAC демонстрирует отличную устойчивость к силам землетрясений.Районы с высокой сейсмической активностью, такие как & nb
. Aac Производственная линия Машина для производства паровых блоков Оборудование для производства блоков из пенобетона в автоклаве
SINOPOWER! Газосиликатные блоки, Линия по производству строительного кирпича, Машина для производства фасадных бетонных блоков, Автоклав с реактором высокого давления!
Введение Кирпич / блок / панель из автоклавного ячеистого бетона (AAC)
Кирпич / блок / панель из автоклавного газобетона (AAC) — это легкий, многоклеточный новый строительный материал; К особенностям относятся более низкая плотность, теплоизоляция, возможность, огнестойкость и звукоизоляция.AAC изготавливается из кремниевого материала (кварцевый песок или переработанная летучая зола) и кальциевого материала (известь, цемент), смешивается с пенообразующей добавкой (алюминиевый порошок), замешивается, реакция между алюминием и бетоном вызывает появление микроскопических пузырьков водорода, расширяющихся. бетон примерно в пять раз больше первоначального объема. Он превращается в многоячеистый силикатный продукт в процессе формования, предварительного отверждения, резки, испарения и отверждения.
Внедрение линии по производству автоклавного газобетона (AAC)
1) Вес продукта соответствует контролю 500 кг / м3, 600 кг / м3, 700 кг / м3.
2) годовая мощность 100 000–400 000 м³.
3) установленная пропорция сырья: цемент 6,5%, известь-сырец 23%, зола или песок 68%, гипс 3%, порошок алюминиевой пасты 350 г / м3.
4) расход воды и материалов 0,631
5) одна форма 3,024 м3, 3,456 м3, 4,23 м3
6) Время цикла литья 5-6 минут, время цикла резки 5 минут.
7) температура литейного раствора 38-42 градуса
8) кузов тихая остановка.Время составляет 1,5-2,5 часа, температура 50-90 градусов, после тихой остановки прочность корпуса составляет 0,15-0,18 МПа
9) Время цикла отверждения паром, вход и выход из автоклава около 0,5 часа, время цикла отверждения паром около 7,5 часов / 1,6 МПа, всего 8 часов
Газобетон производит технологический процесс:
1. Сырье хранится на складе материалов (или хранит горшок) после обработки таких запасов, как известь, цемент, гипс, песок (или летучая зола)
2.Алюминиевый порошок или алюминиевый лосьон обрабатывают резервный материал для использования
3. Сырье измеряется в соответствии с определенным соответствием с помощью меры электронного баланса, алюминиевый порошок, вода помещаются в смеситель для алюминиевого порошка, если это суспендировать жидкость для перемешивания после измерение
4. Дозируемая вода (холодная вода или кувшин горячей воды горячая вода) измеряется электронным водным балансом
5. Поместить в смесители и разлить между ними в определенном порядке после измерения сырьевых материалов, суспензии алюминиевого порошка, жидкости, залейте и войдите в форму после равномерного перемешивания (панель следует заранее положить в форму сетевым срезом арматурного стержня)
6.Тихо, если он поднимается заранее, чтобы припарковаться через определенную температуру и время, если он транспортируется к режущему станку, чтобы повесить его на расстроенном подъемнике, отклоненном на 90 ° после того, как основной корпус достигнет определенной интенсивности, чертеж выкройки вырезается
a. Основание несёт на стороне и разрезает и фрезерует желоб вертикально
, сначала
b. Затем продолжите вертикальный уровень, чтобы разрезать
c. Отрезать горизонтально окончательно
d. Вырезать хорошее основание кузова, поднять в котел автомобиль, пойти на один ярд, полки организовать в группы, чтобы отпарить, перевезти, чтобы подвесить, чтобы вести автомобиль, чтобы загрузить
7.Хорошо приподнять продукты, производить после котла, отламывая доску пальцами и большим пальцем, отламывая доску пальцами и большим пальцем машина для пара
8. Сваи от подъемника готовой продукции или вилочного погрузчика до поля готовой продукции, сложите контрфорс в соответствии со спецификацией для переноски.
9. Обработка паром и поднятие вагона и бортовой доски, попадание на следующую площадку обращения и возврат после того, как готовый продукт выгружается, при сброшенном соединении рамы пресс-формы подъемника, при котором рисунки выходят, восстанавливается возврат на 90 ° для заливки смесителя снова заливка после очистки
Основные машины из автоклавного газобетона (AAC) кирпич / блок
Оборудование будет разделено на две части: специализированное оборудование и универсальное оборудование.
В состав специализированного оборудования входят:
1. Раскройное оборудование: подъемный кран, резак.
2. Дозирующее оборудование: электронные измерительные весы, машина для взбивания шламов,
Бак для жидкого навоза, смеситель навозной жижи.
3. Разливочное и автоклавное оборудование: смеситель для алюминиевого порошка. Разливочный смеситель, форма,
Боковая плита, автоклав, грузовой автомобиль.
4. Транспортное оборудование: кран для полуфабрикатов, кран для готовой продукции.
Универсальная комплектация включает:
1. Оборудование сосудов высокого давления: бойлер, автоклав.
2. Дробильное оборудование: шаровая мельница, дробилка.
3 Транспортное оборудование: кран, подъемная машина, питатель, ленточный конвейер,
Шламовый насос, шнековый конвейер.
4.Оборудование для защиты окружающей среды: пылеуловитель
Емкость Тип
ТОВАР
SP-AAC-5
SP-AAC-10
SP-AAC-15
SP-AAC-20
SP-AAC-30
Производительность, x103м3 / год
50
100
150
200
300
Размер жмыха, м3
4.2×1,2×0,6
4,2×1,2×0,6
4,2×1,5×0,6
4,8×1,2×0,6
6,0×1,2×0,6
Установочная мощность, кВт
600
800
900
1300
1400
. дешевые строительные материалы для строительства силиката кальция блока
Почему выбирают нас?
1 .Специализация
Peakon входит в тройку самых быстрорастущих производителей в Китае и специализируется на 100% безасбестовых огнестойких плитах из силиката кальция и волокнистоцементных плитах в течение 8 лет.
2.Solution
Peakon предоставляет решения по противопожарной и теплоизоляции для более чем 5000 клиентов:
Архитекторы, специалисты по спецификациям, менеджеры объектов, агент, оптовый торговец, подрядчики, субподрядчики и даже конечные потребители в стране.
3.Надежность:
Через сертификаты ISO14001, ISO9001, OHSAS 18001, SGS и CE. Тест CE обычно считается более обременительным, чем другие режимы тестирования, это тестирование на устойчивость к огню, ударам, шуму, влаге, морозной влажности, формальдегиду …
Дешевые строительные материалы Блок силиката кальция
Картон из силиката кальция — это композитный материал, состоящий из кварцевого песка, цемента и волокон целлюлозы.В этом продукте используется импортная чистая бумага из Канады, без макулатуры. Плиты из силиката кальция производятся в виде листов и используются для внутренних и внешних подвесок, перегородок и полов. Нормальный размер составляет 1220 × 2440 мм, толщина от 3 до 25 мм, а плотность составляет 0,95–1,30 г / см3. Есть низкая плотность, средняя плотность и высокая плотность.
Характеристики продукта:
1. Структурно сильный
2.Огнестойкость (класс A)
3. Отличная теплоизоляция
4.100% без асбеста
5. Отличные звукоизоляционные свойства
6. Влагостойкость
7. Легкий вес
8. Устойчивость к грибкам и термитам
9. Устойчивость к паразитам
10 .Удобный для пользователя и простой в установке
11.Безопасный и экологичный
12.Экономичный
Параметры плиты из силиката кальция толщиной 50 мм:
Технические характеристики 2440 * 1220/2400 * 1200 мм Толщина : 3-30мм Ширина 1200-1220мм Длина 2440мм Цвет как изображения или индивидуальный Плотность 0.95 ~ 1,3 г / см3 Содержание воды ≤10 Огнестойкость Негорючесть Класс A Теплопроводность <0,3 Вт / мк Прочность на изгиб Класс 4 (> 10 МПа) Радиоактивность GB8624-2006 Класс A Асбест 100% без асбеста Сертификация ISO / CE / SGS
Области применения
Области применения плит силиката кальция:
Широко используется в сталелитейной промышленности, цементной промышленности, без черной металлургии и углеродной промышленности, стекольной промышленности, керамической промышленности, электростанциях, электрическом нагревательном оборудовании.Облицовка стальной конструкции, огнестойкая перегородка, сердцевина противопожарной двери, компоненты противопожарной двери, двери лифта, камины и печи и т. Д.
Толщина Вес Профиль кромки Применение 6 мм 24 кг квадратная кромка / коническая кромка внутренняя облицовка 8 мм 32 кг квадратная кромка / коническая кромка внутренний / внешний потолок 9 мм 36 кг скошенная кромка / скошенная кромка внутренняя перегородка / внешняя облицовка стен / влажная зона и основа из плитки / напольное покрытие 10 мм 40 кг квадратная кромка / коническая кромка внутренняя перегородка / внешняя облицовка стены / для влажных помещений и подложки из плитки / на напольное покрытие 12mm 48kg 90 074 квадратная кромка / коническая кромка внешняя облицовка стен / влажная зона и основа из плитки / напольное покрытие 15 мм 60 кг квадратная кромка / скошенная кромка внутренние перегородки с особыми требованиями / приподнятый пол 18 мм 72 кг квадратная кромка внутренние перегородки с особыми требованиями / приподнятый пол 20 мм 80 кг квадратная кромка внутренние перегородки с особыми требованиями / приподнятый пол
Наш проектный кейс:
Упаковка и отгрузка
Упаковка: деревянный поддон + полиэтиленовое покрытие + угловой протектор + прочная лента
0 2 900 Доска силиката кальция Пикон РАЗМЕР 9007 5 КОЛИЧЕСТВО ВЕС ОБЪЕМ 1220 * 2440 * 6 мм 900PCS 21600KGS 25CBM 1220 *
0 * 9mm 25 куб.см 1220 * 2440 * 12 мм 450 шт. 21600 кгс 25 куб. М. Информация о компании
О нас:
Peakon — это частная китайская компания, основанная в 2011 году в городе Дунсин, Китай.Генеральный директор приобрел немецкое передовое оборудование и технологии и быстро признал Peakon инновационным материалом для пассивной противопожарной защиты в сфере отопления, вентиляции, кондиционирования воздуха и строительства и представил, как этот уникальный продукт может решить многие проблемы противопожарной защиты в других отраслях промышленности Китая. Основным продуктом являются 100% безасбестовые противопожарные плиты, волокнисто-цементные плиты низкой и средней плотности, плиты из силиката кальция, другие высокотехнологичные энергосберегающие плиты для защиты окружающей среды.
Peakon с тех пор превратилась в всемирно признанного поставщика пассивных систем противопожарной защиты, сертифицированного по стандартам ISO 9001, ISO 14001, CE и SGS, с проверенными и внесенными в список проектами для решения большинства проблем противопожарной защиты. Компания Peakon разработала множество решений для противопожарной защиты и теперь имеет китайские патенты на широкий спектр систем для использования в противопожарной промышленности.
Компания Peakon разработала множество уникальных систем пассивной противопожарной защиты для некоторых из самых ценных активов в мире. Благодаря нашей приверженности исследованиям и разработкам и постоянному совершенствованию, Peakon завоевала доверие наших клиентов в плане защиты людей и собственности по всему миру.Доска Peakon широко экспортируется в США, Юго-Восточную Азию, ОАЭ, Ближний Восток и Африку.
FAQ
Q1.Каков ваш MOQ, можем ли мы заказать смешивание разных размеров?
A: Конечно, обычно минимальный объем заказа каждого размера составляет 1 × 20-футовый контейнер, но для вашего качества тестирования мы можем принять небольшой заказ / выборку для разных размеров
Q2. Какой порт вы можете поддерживать?
A: Порт Фанчэн или любой другой порт Китая, который вам нужен. Если указан порт назначения, для справки можно указать CFR и CIF.
3 кв. Каковы сроки доставки вашей продукции?
A: Обычно отправка товара морским или воздушным транспортом занимает около 10-15 дней после получения аванса.
.
ПУНКТ
SP-AAC-5
SP-AAC-10
SP-AAC-15
SP-
SP-AAC-20 -AAC-30Производительность, x103 м3 / год
50
100
150
200
200
4.2×1,2×0,6
4,2×1,2×0,6
4,2×1,5×0,6
4,8×1,2×0,6
6,0×1,2×0,6
Установочная мощность, кВт
600
800
900
1300
1400
6
6
6
6
Площадь цеха, м2
3000
3000
3000
Площадь завода, м3
20000
20000
25000
30000
35000
1. Сырье хранится на складе материалов (или хранит горшок) после обработки таких запасов, как известь, цемент, гипс, песок (или зола-унос)
2.Алюминиевый порошок или алюминиевый лосьон обрабатываются резервным материалом для использования
3. Сырье измеряется в соответствии с определенным соответствием с помощью меры электронного баланса, алюминиевый порошок, вода помещаются в смеситель для алюминиевого порошка, если это суспендировать жидкость для смешивания после измерение
4. Дозируемая вода (холодная вода или горячая вода из кувшина, горячая вода) измеряется электронным водным балансом
5. Поместите в смесители и разлейте их в определенном порядке после измерения исходных материалов, суспензии алюминиевого порошка, жидкости, залейте и войдите в форму после равномерного перемешивания (панель следует заранее положить в форму сетевым срезом арматурного стержня)
6.Тихо, если он поднимается заранее, чтобы припарковаться через определенную температуру и время, если он транспортируется к режущему станку, чтобы подвешивать его с отклонением на 90 ° после того, как основной корпус достигает определенной интенсивности, чертеж выкройки вырезается
a. Основание несёт на стороне и разрезает и фрезерует желоб по вертикали
сначала
b. Затем продолжите вертикальный уровень, чтобы разрезать
c. Отрежьте горизонтально окончательно
d. Вырезать хорошее основание кузова, поднять в котел автомобиль, пройти на один ярд, полки организовать в группы, чтобы отпарить, перевезти, чтобы подвесить, чтобы водить автомобиль, чтобы загрузить
7.Хорошо приподнять продукты, производить после котла, отламывая доску пальцами и большим пальцем, отламывая доску пальцами и большим пальцем машина для пара
9. Обработка паром и поднятие вагона и бортовой доски, попадание на следующую площадку обращения и возврат после того, как готовый продукт выгружается, при сброшенном соединении рамы пресс-формы подъемника, при котором рисунки выходят, восстанавливается возврат на 90 ° для заливки смесителя снова заливка после очистки
ТОВАР
SP-AAC-5
SP-AAC-10
SP-AAC-15
SP-AAC-20
SP-AAC-30
Производительность, x103м3 / год
50
100
150
200
300
Размер жмыха, м3
4.2×1,2×0,6
4,2×1,2×0,6
4,2×1,5×0,6
4,8×1,2×0,6
6,0×1,2×0,6
Установочная мощность, кВт
600
800
900
1300
1400
Производственный цикл, пресс-форма / мин
5
6
6
6
6
Площадь цеха, м2
3000
3000
3500
4000
5000
Площадь завода, м3
20000
20000
25000
30000
35000
1. Сырье хранится на складе материалов (или хранит горшок) после обработки таких запасов, как известь, цемент, гипс, песок (или летучая зола)
2.Алюминиевый порошок или алюминиевый лосьон обрабатывают резервный материал для использования
3. Сырье измеряется в соответствии с определенным соответствием с помощью меры электронного баланса, алюминиевый порошок, вода помещаются в смеситель для алюминиевого порошка, если это суспендировать жидкость для перемешивания после измерение
4. Дозируемая вода (холодная вода или кувшин горячей воды горячая вода) измеряется электронным водным балансом
5. Поместить в смесители и разлить между ними в определенном порядке после измерения сырьевых материалов, суспензии алюминиевого порошка, жидкости, залейте и войдите в форму после равномерного перемешивания (панель следует заранее положить в форму сетевым срезом арматурного стержня)
6.Тихо, если он поднимается заранее, чтобы припарковаться через определенную температуру и время, если он транспортируется к режущему станку, чтобы повесить его на расстроенном подъемнике, отклоненном на 90 ° после того, как основной корпус достигнет определенной интенсивности, чертеж выкройки вырезается
a. Основание несёт на стороне и разрезает и фрезерует желоб вертикально
, сначала
b. Затем продолжите вертикальный уровень, чтобы разрезать
c. Отрезать горизонтально окончательно
d. Вырезать хорошее основание кузова, поднять в котел автомобиль, пойти на один ярд, полки организовать в группы, чтобы отпарить, перевезти, чтобы подвесить, чтобы вести автомобиль, чтобы загрузить
7.Хорошо приподнять продукты, производить после котла, отламывая доску пальцами и большим пальцем, отламывая доску пальцами и большим пальцем машина для пара
9. Обработка паром и поднятие вагона и бортовой доски, попадание на следующую площадку обращения и возврат после того, как готовый продукт выгружается, при сброшенном соединении рамы пресс-формы подъемника, при котором рисунки выходят, восстанавливается возврат на 90 ° для заливки смесителя снова заливка после очистки
ТОВАР
SP-AAC-5
SP-AAC-10
SP-AAC-15
SP-AAC-20
SP-AAC-30
Производительность, x103м3 / год
50
100
150
200
300
Размер жмыха, м3
4.2×1,2×0,6
4,2×1,2×0,6
4,2×1,5×0,6
4,8×1,2×0,6
6,0×1,2×0,6
Установочная мощность, кВт
600
800
900
1300
1400
2.Огнестойкость (класс A)
3. Отличная теплоизоляция
4.100% без асбеста
5. Отличные звукоизоляционные свойства
6. Влагостойкость
7. Легкий вес
8. Устойчивость к грибкам и термитам
9. Устойчивость к паразитам
10 .Удобный для пользователя и простой в установке
11.Безопасный и экологичный
12.Экономичный
0 * 9mm
Информация о компании
О нас:
Peakon — это частная китайская компания, основанная в 2011 году в городе Дунсин, Китай.Генеральный директор приобрел немецкое передовое оборудование и технологии и быстро признал Peakon инновационным материалом для пассивной противопожарной защиты в сфере отопления, вентиляции, кондиционирования воздуха и строительства и представил, как этот уникальный продукт может решить многие проблемы противопожарной защиты в других отраслях промышленности Китая. Основным продуктом являются 100% безасбестовые противопожарные плиты, волокнисто-цементные плиты низкой и средней плотности, плиты из силиката кальция, другие высокотехнологичные энергосберегающие плиты для защиты окружающей среды.
Peakon с тех пор превратилась в всемирно признанного поставщика пассивных систем противопожарной защиты, сертифицированного по стандартам ISO 9001, ISO 14001, CE и SGS, с проверенными и внесенными в список проектами для решения большинства проблем противопожарной защиты. Компания Peakon разработала множество решений для противопожарной защиты и теперь имеет китайские патенты на широкий спектр систем для использования в противопожарной промышленности.
Компания Peakon разработала множество уникальных систем пассивной противопожарной защиты для некоторых из самых ценных активов в мире. Благодаря нашей приверженности исследованиям и разработкам и постоянному совершенствованию, Peakon завоевала доверие наших клиентов в плане защиты людей и собственности по всему миру.Доска Peakon широко экспортируется в США, Юго-Восточную Азию, ОАЭ, Ближний Восток и Африку.
FAQ
Q1.Каков ваш MOQ, можем ли мы заказать смешивание разных размеров?
A: Конечно, обычно минимальный объем заказа каждого размера составляет 1 × 20-футовый контейнер, но для вашего качества тестирования мы можем принять небольшой заказ / выборку для разных размеров
Q2. Какой порт вы можете поддерживать?
A: Порт Фанчэн или любой другой порт Китая, который вам нужен. Если указан порт назначения, для справки можно указать CFR и CIF.
3 кв. Каковы сроки доставки вашей продукции?
A: Обычно отправка товара морским или воздушным транспортом занимает около 10-15 дней после получения аванса.