Асфальтобетонная отмостка технология: Технология устройства отмостки из асфальта. Как сделать отмостку из бетона вокруг дома? Цены на бетонную смесь
Правильная отмостка вокруг дома: расчет размеров, щебеночная отмостка. Отмостка вокруг дома из бетона (пошагово).. Устройство отмостки вокруг дома своими руками
Ограниченные защитные функции отмостки предполагают стандартный подход к ее устройству с соблюдением технологии, которую считают классической. Асфальтобетонная отмостка, отработавшая свой жизненный цикл на протяжении нескольких десятилетий, ушла в прошлое.
Сегодня для мощения отмостки благополучно используют твердое покрытием и мягкие материалы. Выбор за застройщиком. Единственно неизменным остается необходимость возведения отмостки.
Необходимость создания отмостки
Не подлежит сомнению, что устройство вокруг домовой отмостки представляет собой не только элемент благоустройства. Задачей отмостки является задержка воды и ее дренажное отведение в ливневую канализацию.
Если вы сомневаетесь, нужна ли отмостка вокруг дома, то практические доводы специалистов о водоотведении от фундамента и его утепления убедительны.
По этой причине устройство непрерывной отмостки для мелкозаглубленного фундамента считают обязательным. Водонепроницаемое покрытие должно сочетаться по общему стилю дизайна и материалами мощеных подъездов, тротуаров и дорожек. При устройстве необходимо учитывать параметры отмостки.
подбираем параметры отмостки
Параметрами правильной отмостки вокруг дома считают:
• ее ширину и наклон
• высоту цоколя
• тип облицовочного материала.
По существующим нормам и правилам, min. ширина отмостки вокруг дома составляет 0,8 м., max. зависит от застройщика. Существующая вероятность повреждения цокольной части увеличивается при дальности впитывания влаги.
Разумеется, наклон должен обеспечить свободное стекание воды в противоположном направлении от фундаментного пояса и цоколя. На ровной поверхности достаточно угла наклона 15 мм на 1м, что составляет 2% от ширины отмостки. Рекомендованный угол наклона обеспечивают вертикальная планировка при укладке покрытия и трамбовка грунта в траншее.
Между стеной дома и отмосткой устраивают технологический зазор (компенсационный шов 2 см) с последующим заполнением его песком.
В зависимости от вида отмостки – с твердым покрытием или «мягкой», для мощения используют плиточные материалы с шероховатой поверхностью.
Среди основных параметров отмостки не помешает замолвить словечко о рекомендованной гидроизоляция отмостки вокруг дома. Востребованными материалами для проведения горизонтальной отмостки считают геотекстиль рулонный и полимерные составы, плитный гидроизоляционный утеплитель.
Схемы устройства домовой отмостки
Схемы создания и устройства отмостки вокруг дома из тротуарной плитки и брусчатки классические. Укрупненно схема состоит из подстилающего и покрывного слоев, для которых применяют мелкофракционный щебень и песок с созданием подстилающего слоя до 20 см.
Покрывной слой набирают из крупного щебня, бетонных растворов и асфальтовую смесь используют редко.
Технологически различают такие отмостки:
• простую насыпную и насыпную с гидроизоляцией
• из готовых плит, брусчатки или плитки
• заливаемую бетонную.
Технологически устройство вокруг домовой отмостки идентично мощению плиточный тротуаров или дорожек.
насыпная щебеночная
Насыпная щебеночная отмостка это самый простой способ, рекомендованный при высоких грунтовых водах. Для устройства традиционно используют щебень фракции от 8 до 32 мм, укладываемый на грунт по периметру с трамбовкой и размещением геотекстиля. Последующую засыпку щебня слоем 10 см выполняют без песчаной подсыпки.
бетонная
Устройство бетонной отмостки вокруг дома пошагово
Разметка поля
Шаг 1. Размечаем поле под отмостку.
Шаг 2. Выемка грунта на глубину 25 см.
Организация и создание подстилающего слоя
Шаг 3. Насыпка песка толщиной слоя до 12 см.
Шаг 4. Утрамбовываем песчаные слои ручными трамбовками, особенно в местах образования пазух вблизи фундамента.
Шаг 6. Насыпка и распределение слоя щебеночного толщиной 6 см.
Размещение системы дренажа
Шаг 7. Установка дренажной систему по уклону.
Монтаж и возведение опалубки
Шаг 8. Возводим опалубку, учитывая непрерывность доставки свежеприготовленного бетонного раствора.
Гидроизоляция и утепление
Шаг 9. Производим горизонтальную гидроизоляцию, расстилая геотекстиль, вертикальную нанесением мастики или установки плит пеноплекса.
Армирование поверхности
Шаг 10.
Укладка прокладок для создания деформационных швов
Шаг 11. В углах и стенах размещаем прокладки в виде реек или виниловых лент.
Шаг 12. Поперек опалубки на расстоянии 2-3 м. устанавливаем рейки, пропитанные битумной мастикой для создания деформационного шва.
Заливка бетоном
Шаг 13. На месте подготавливаем бетонный раствор традиционным способом.
Шаг 14. Распределяем раствор в опалубочную часть по маякам (установленным деревянным рейкам).
Шаг 15. Производим уплотнение и железнение бетона. Железнение выполняем мокрым способом.
Шаг 16. Свежую бетонную поверхность накрываем смоченной водой грубой тканью.
После созревания бетонной заливки (7 дней) производим декоративную отделку.
Собственноручное устройство бетонной отмостки показано в видео.
В дополнение к собственноручному устройству отмостки вокруг дома, подскажем, что практичным решением покрытия является плитка тротуарная.
Ремонт отмостки бетонной и асфальтной: причины разрушения, методы ремонта
Отмостку вокруг дома обустраивают практически везде. Этот конструктивный элемент, при всей своей простоте и незначительности, выполняет крайне важные функции. Именно отмостка защищает фундамент дома от проникновения в него воды или атмосферных осадков.
Совершенно очевидно, что работая в таких условиях она сама подвергается различным нагрузкам и постепенно разрушается. Поврежденная же отмостка нуждается в немедленном ремонте.
Подготовка и армирование под будущую отмостку из бетона
В данной статье будут рассмотрены основные проблемы, которые могут являться причиной разрушения отмостки в процессе её эксплуатации, а также особенности ремонта данных конструкций в зависимости от использующихся для их изготовления материалов.
Устройство отмостки
Отмостка – это покрытие вокруг здания шириной в среднем от 80 до 150 см, защищающее фундамент от влаги и промерзания. Обустраивается она с определенным уклоном, чтобы обеспечить отвод дождевой воды от дома. По нормам строительства уклон должен составлять 5-10 см на каждый метр отмостки, при этом край, примыкающий к стене дома должен возвышаться, а противоположный – быть вровень с грунтом.
Обрешетку под заливку бетона при ремонте отмостки начинают делать от самого низкого места, то есть от точки слива воды.
Затем двигаются к противоположной стороне дома, постоянно отслеживая уровень уклона.
Материалы, используемые для обустройства защитной конструкции своими руками, это:
Защитный состав Элакор
Виды отмостки дома
Покрасить бетонную отмостку можно с помощью специальных защитных растворов. К ним относится Элакор. Данный препарат готовится на основе полиуретана, который и является действующим началом. Он применяется для предотвращения запыления и других бетонных конструкций, препятствия их разрушению. Наносится он тонким слоем. Отличительной особенностью является то, что Элакор проникает внутрь на несколько сантиметров, а на поверхности при этом образуется специальная защитная пленка. Последняя имеет в своем составе очень прочные кристаллы, которые обладают устойчивостью к влаге, воздействию химических веществ.
Проникший внутрь бетонной отмостки раствор повышает прочность конструкции и ее износоустойчивость. Наружный защитный слой максимально сцепляется с поверхностью и образует со всей конструкцией единый материал, вследствие этого он не отслаивается и не разрушается. Срок службы покрытия составляет до 15 лет, поверхность при этом менее подвержена механическим разрушением, она не становится скользкой.
youtube.com/embed/ENtq12la5_k?feature=oembed» frameborder=»0″ allow=»accelerometer; autoplay; encrypted-media; gyroscope; picture-in-picture» allowfullscreen=»»/>Почему возникают трещины в отмостке
Трещины в отмостке появляются со временем, при неравномерной осадке дома и при просадке
- Временной фактор. Если покрытие старое, то оно многократно подвергалось температурным влияниям (расширению и сжатию). В результате в отмостке образовались трещины, которые со временем склонны все более расширяться.
- Неравномерная осадка здания. Возникновение трещин в отмостке происходит из-за нарушения герметичности стыков между ней и цоколем.
Покрытие отсоединяется от дома, а в образовавшуюся щель проникает вода. Подобные трещины нуждаются в немедленном устранении.
- Просадка отмостки. Причиной этого явления служит оседание грунта или нарушение технологии укладки покрытия вокруг дома.
Возможные причины появления разрушений
Отмостка, обустроенная согласно всех технологических правил, способна прослужить, по меньшей мере, несколько десятков лет. Это касается как отмостки вокруг небольшого частного дома, так и отмостки вокруг многоквартирного здания.
Однако очень часто встречается ситуация, когда вполне естественное желание строителей сэкономить либо незнание всех особенностей технологии обустройства отмостки, приводит к тому, что данная конструкция выходит из строя гораздо раньше, чем того стоило ожидать.
Рассмотрим основные проблемы и ошибки в процессе строительства отмостки, которые являются типичной причиной нарушения её целостности, либо невыполнения этим водоотводящим элементом своих функциональных обязанностей.
Некачественная трамбовка подсыпанного выравнивающего слоя, либо его отсутствие
Правильная отмостка вокруг здания должна выполняться с двух слоев: первый – слой из песка и мелкофракционного щебня либо гравия, который будет выполнять функцию уплотнения, и выравнивания грунта, на котором располагается отмостка. Второй – это непосредственно бетон.
Пренебрегать слоем подсыпки категорически воспрещается – вы никогда не получите качественную отмостку, из одного асфальтобетона, который залит вокруг контура здания.
В таком случае, особенно это касается регионов с холодными зимами, при наступлении первых же холодов произойдет отрыв отмостки от цоколя здания, вследствие разности температур из-за замерзания воды, попавшей в микротрещины на бетоне.
Разрушенная бетонная отмостка
Дальше процесс только усиливается – в новые трещины попадает ещё большее количество воды, вследствие чего происходит дальнейшее разрушение отмостки вокруг дома, с гораздо ускорившимися темпами.
Если не выполнять постоянное «штопанье» такой горе-конструкции, то при прогрессе разрушений до определенного уровня, трещины доползут до фундамента, что грозит его просадками и образованием трещин в стенах дома, что само по себе уже является аварийной ситуацией.
Отсутствие демпферных швов
Наличие демпферных (температурных) швов в отмостке вокруг здания обязательно, так именно за счет этих элементов отмостка получает необходимую устойчивость к возникающему под внешним влиянием грунта напряжению.
В большинстве случаев в грунте постоянно происходят незаметные глазу, однако крайне пагубно сказывающиеся на строительных конструкциях пучения. Демпферные швы, которые располагаются на месте соединения цоколя и самой отмостки, позволяют уменьшить влияние деформации, которое грунт оказывает на бетон.
Такие швы чаще всего выполняются из специальной демпферной ленты, однако с тем же успехом можно использовать и подручные средства – рубероид, вспененный целлофан, либо монтажную пену.
Отсутствие армирования
Армирование конструкции крайне необходимо при обустройстве отмостки вокруг многоквартирного дома, расположенного на нестабильных грунтах. Пренебрежение армированием очень часто оправдывается тем, что требования СНИП не предусматривают обязательного армирования отмостки.
Однако практика показывает, что отмостка, которая является подвижной асфальтобетонной конструкций, без должного армирования разрушается гораздо быстрее, чем с ним.
Отмостка вокруг дома из тротуарной плитки
Более того, армирование придает ей большую устойчивость к сжатию и растяжению, к тому же армирования отмостка также сохраняет свою целостность, в случае серьезных деформаций – вследствие чего её гораздо проще отремонтировать.
Армирование отмостки выполняется обычной арматурной сеткой, с ячейками 100*100*4 мм, которая продается в любых строительных магазинах.
Арматурная сетка полностью заменяет полноценный арматурный каркас, который используется при армировании бетонных плит, при этом, стоит она гораздо дешевле, вследствие чего смета на строительство отмостки увеличивается крайне незначительно, в то время как прочность и надежность самой конструкции вырастает многократно.
Как поэтапно произвести ремонт своими руками
Шаг 1. Подготовка под заливку раствора.
Перед проведением основных работ следует очистить поверхность старого покрытия от пыли и грязи. Расширить трещины и удалить полностью разрушенные участки. Загрунтовать края трещин для улучшения сцепления. Чтобы заделать образовавшиеся промежутки для экономии цементного раствора можно использовать куски старой разрушенной отмостки. Для этого их раскладывают там перед заливкой.
Этап подготовки отмостки под заливку раствора
Шаг 2. Приготовление раствора.
Для этого применяются следующие ингредиенты: песок – 2,6 части, цемент М500 или М400 – 1 часть, щебень – 4,5 части, вода – 125 литров на 1 м. куб. готового раствора, а также другие добавки. Время пригодности готовой смеси около 2 часов.
Приготовление раствора для ремонта отмостки
Шаг 3. Укладка бетона.
Заливку бетона лучше начинать с самой верхней точки, периодически отслеживая соблюдение запланированного уклона. Ремонт крупных участков поврежденной отмостки следует производить с использованием армирующей сетки.
Третьим шагом выступает заливка бетона
После заливки бетон уплотняется и выравнивается.
После завершения работ поверхность накрывают влажной тканью и оставляют постепенно высыхать, время от времени орошая водой, для того, чтобы бетон не высыхал слишком быстро и не растрескался.
После полной просушки бетона опалубка снимается.
Как и чем заделать трещины толщиной около 1см между цоколем (фундаментом) и бетонной отмосткой?
У меня несколько вариантов.
1) Отмостка бетонная значит и щель заделывается бетоном.
Пропорции такие: цемент (марка 400-а) одна часть, песок две части, щебень пять частей.
Сантиметр для бетона мало (для герметика много), расширяем щель и углубляем, далее, очищаем от пыли, затем грунтуем (можно бетон-контактом, можно грунтовкой глубокого проникновения).
На последнем этапе заливаем бетон (грунтовка должна полностью высохнуть), выравниваем.
2) Не будем расширять щель, будем работать цементным раствором с добавлением эластичного плиточного клея.
Подготовка почти одинаковая, очищаем щель от грязи, пыли, грунтуем.
Далее готовим раствор, одна часть цемента. одна часть плиточного клея, три части песка (песок мелкий, сеянный).
Заливаем это раствор в щель и выравниваем заподлицо.
Плиточный клей влагостойкий, эластичный, у него высокая адгезия, есть клей для наружных работ, я бы порекомендовал Ceresit СМ 17.
www.remotvet.ru
Как устранить трещины в отмостке вокруг дома своими руками
Устранение глубоких трещин в бетоне
- В случае, когда трещины в отмостке небольшие, то после предварительной очистки, производится их заполнение жидким раствором цемента в соотношении 1:1 или 1:2 с добавлением разбавленного клея ПВА и затирка.
- Если размер щелей средний, то ремонт производится по-другому. Поверхность очищается, щели расширяются с применением перфоратора. Образовавшиеся каналы обрабатывают грунтовкой, дают ей просохнуть, после чего заливают бетоном.
- При отсоединении покрытия от цоколя вокруг здания образовавшиеся щели следует заполнить экструдированным пенополистиролом и заделать при помощи полиуретанового герметика. Сверху затереть цементным раствором. Ремонт в этом случае будет более затратным.
- Если причина появления трещин в отмостке вызвана просадкой старого покрытия, следует его полностью разрушить на этом отрезке, подсыпать и утрамбовать грунт. После чего восстановить все слои покрытия с последующей заливкой бетоном.
- Бывают случаи, когда разрушения покрытия слишком велики и ремонт уже невозможен. Единственное, что можно сделать – это произвести укладку новых конструкций поверх старого покрытия. В случае невозможности сделать отмостку поверх старой, следует демонтировать все ее слои и своими руками произвести укладку с самого начала, соблюдая технологию. Следует помнить, что через каждые полтора-два метра должны быть обустроены деформационные швы.
Ремонт легких повреждений в бетоне
Что лучше использовать
Выбор состава для ремонта бетонной поверхности зависит от того, как расположена дефектная поверхность: вертикально или горизонтально. Также на это влияют условия эксплуатации сооружения из бетона и время года, когда вы планируете сделать ремонт.
Замазать трещины на горизонтальной поверхности можно практически любыми растворами. Если проблема появилась на вертикальной стене, то в этом случае используйте густые и вязкие растворы. Альтернативой станет применение саморасширяющихся шнуров.
Нарушения технология укладки
- Отсутствие гидроизоляционного слоя. Этот важный элемент конструкции, отделяющий все остальные слои от грунта и предотвращающий проникновение влаги извне.
- Плохо утрамбованная неравномерная засыпка. Недостаточная толщина верхнего слоя.
- Проведение строительных работ при неблагоприятных климатических условиях. По технологии нельзя производить подобные работы в преддверии заморозков, в жару, перед наступлением дождей. Все эти факторы крайне негативно отразятся на качестве покрытия, нарушат процесс застывания и прорастания кристаллов цемента.
- Отсутствие температурных швов.
Многократное изменение температуры в течение года приводит к расширению, сжатию, морозному пучению грунта, что увеличивает вероятность разрушения бетонной конструкции. Чтобы этого не происходило, следует расположить в ней температурные швы, которые частично могут компенсировать эти явления. Обычно их располагают через 1,5-2 метра, чтобы распределить появляющиеся колебания, но можно меньше.
От качества бетонной конструкции, выполненной с соблюдением технологии, зависит прочность и долговечность фундамента, а также отсутствие незапланированных трат времени и денег на ремонт. Легче один раз сделать все своими руками в соответствии с установленными нормами, чем все время бороться с последствиями неверной укладки покрытия.
Применение эмалей
Плитка может быть хорошо защищена с помощью эмали. Хороший эффект дает смесь Полак. Она обладает хорошими адгезивными свойствами и ингибирует влияние вредных химически веществ на поверхность бетонной отмостки. По своему составу она напоминает эпоксидные краски. Преимуществами данного способа являются: устойчивость покрытия к ультрафиолетовому излучению, химическим веществам, влаге и атмосферостойкость. Кроме того, здесь имеет возможность цветового решения бетонной отмостки. Плитка становится более прочной и износостойкой. Эффект сохраняется десятки лет. Помимо эмалей, для обработки бетонной отмостки целесообразно применять различные смолы, к примеру, полиуретановые. Они очень эластичны, быстро полимеризуются, препятствуют возникновению коррозии, устойчивы к химическим раздражителям.
Смолы обладают способностью быстро и глубоко проникать в материал и повышать его устойчивость к неблагоприятным факторам окружающей среды. Покраска потребует наличие валика или кисти, лака, краски, эмали или другого раствора. Все вышеперечисленные средства смогут защитить вашу отмостку, а плитка будет служить долгие годы.
Как сделать отмостку вокруг гаража. Отмостка перед гаражом своими руками Фундамент заливка отмостки ворота гаража
Строительство гаража является тяжелым и очень длительным процессом, особенно если человек строит его самостоятельно. Стоит вопрос выбора кладки фундамента, применяемого материала. Когда фундамент будет залит, стены возведены, крыша сооружена, надо сделать важную часть — отмостку в гараж.
Главная функция фундамента — это опорная, благодаря этому строение стоит надежно, не клонится из-за подъема грунта весной.
Но все равно надо подумать об отводе воды в весенний период. Для такого случая и необходимо сделать отмостку.
Состав отмостки
По окончании облицовки цоколя или стен создается полоса, защищающая фундамент от грунтовых вод. Она состоит из подстилающего слоя, который представляет собой уплотненную ровную основу для укладки покрытия, в состав которой входит песок, мелкий щебень и гарцовка.
Подбор материалов зависит от выбранного покрытия. Защитную функцию отмостки осуществляет гидроизоляционный слой из глины. Подстилающий слой имеет толщину 20 см.
Покрывают отмостку перед гаражом слоем толщиной 5-10 см, который обладает водонепроницаемыми свойствами. Для его устройства можно использовать асфальт, бетон, тротуарные плиты, мелкий булыжник, смесь щебня или песка с глиной.
Отмостка: виды
Наиболее популярный вид отмостки — бетонный. Он делается по периметру гаража в виде водонепроницаемой полосы. Главное преимущество — это простота монтажа и недорогая стоимость строительства. Однако надо выполнить деформационные зазоры по предотвращению образования трещин.
Наиболее популярные виды защитных полос:
Кладка плитки поверх отмостки.
- перед въездом в гараж из асфальтобетона делается по простой технологии. Вначале в приготовленную траншею кладут основание из щебня 15 см и 5 см слоя асфальта. При выполнении работ вручную надо изучить особенности технологии и нюансы по работе с данным материалом, который выделяет вредные вещества;
- создание мягкой отмостки как декоративного элемента благоустройства. Данная полоса делается из 10 см глиняного слоя, который надо утрамбовывать и разравнивать.
Песка там быть не должно. Потом укладывается пленочная гидроизоляция, насыпается песок 5 см толщиной. Затем кладется геотекстиль, щебень (галька, керамзит, гравий) до 15 см и опять материал из пропиленовой нити (геотекстиль), который пропускает воду, но песку не даст заполнить пустоту в щебне. Завершающим этапом этой работы будет засыпание песка толщиной 5-6 см. Данная полоса имеет недостаток: по ней неудобно ходить, потому что утрамбовать плотно однородный материал — задача невыполнимая. Мягкая подмостка вполне подойдет, если строительство гаража происходит на земельном участке с малой интенсивностью эксплуатации;
- сделать отмостку можно из бетонной брусчатки разных цветов: черного, серого, коричневого и других. Это придаст гаражу привлекательный архитектурный облик. Многообразные формы материала: волна, прямоугольник, шестигранник, квадрат придадут полосе оригинальный внешний вид. Бетонная брусчатка имеет преимущества: высокая устойчивость к температурным перепадам, морозам, механическим нагрузкам, простой монтаж;
- устройство отмостки из каменной брусчатки.
Это выглядит красиво и стильно, особенно если она имеет желтый, серый, красный цвет или когда она черная базальтовая, мраморная с прожилками. Единственным недостатком является дороговизна. Монтаж такой полосы делается так: насыпается слой глины, кладется гидроизоляция, потом слой песка, покрытие и заполнение песком швов;
- монтаж защитной полосы из плитки признан самым универсальным вариантом. Это покрытие оригинальное и легко ремонтируемое.
Является задачей довольно сложной для выполнения. Причем имеется в виду не лишь общая трудоемкость процесса, но и необходимость технологического соответствия проводимых действий установленным нормам. Например, многими домашними мастерами (а иногда и профессионалами) часто уделяется поверхностное внимание сооружению отмостки вокруг постройки, что неправильно в корне. О том, как делается отмостка вокруг гаража своими руками и зачем это, вообще, делать, и пойдет речь в этой статье.
Общее описание
Прежде чем переходить к непосредственному описанию технологии сооружения отмостки, необходимо определиться с тем, что этот элемент собой представляет и для какой цели предназначен.
Отмостка – это элемент постройки, представляющий собой полосу материала вокруг периметра фундамента, основным назначением которой является защита этой части постройки от внешних воздействий.
Обратите внимание! От правильности изготовления отмостки зависит сохранность фундамента.
Немаловажно будет заметить, что отмостка может иметь как жесткую форму изготовления (бетонная заливка), так и нефиксированную (утрамбованный щебень). Однозначно сказать какой вариант является наиболее правильным нельзя, так как решать вопрос выбора необходимо исходя из конкретной ситуации. Однако стоит заметить, что какое бы технологическое решение ни было принято, необходимые для работ материалы должны быть качественными.
Изготовление бетонной отмостки
Как было сказано выше, одним из вариантов изготовления отмостки является выполнение бетонной заливки. Проводить этот процесс необходимо поэтапно:
- Сначала проводится подготовка к работам.
Здесь подразумевается очистка периметра гаража от возможных загрязнений, а также разметка. Дело в том, что ширина отмостки будет находиться в зависимости от ширины свесов крыши. Защита фундамента должна быть как минимум на 20 см шире, чем свесы. Для разметки участка грунта можно использовать металлические или деревянные колья, между которыми натягивается прочная нить.
- Далее следует очередь земляных работ. Внутри очерченного периметра снимается слой дерна и выкапывается траншея глубиной около 30 см. Дно траншеи стоит обработать гербицидными составами с целью предотвращения роста корней растений, что может впоследствии привести к растрескиванию отмостки. Основание также следует утрамбовать.
- Когда траншея буде готова, внутри нее нужно смонтировать опалубку. Для ее изготовления можно взять фанерные щиты. Высота этих частей может подбираться так, чтобы соответствовать высоте будущей отмостки, то есть, как минимум выступать над поверхностью земли на 5 см. Опалубка выполняется только по внешнему относительно гаража периметру траншеи.
- Далее внутрь траншеи насыпаются поочередно слой песка, толщиной около 10–15 см, а затем слой щебня средней фракции такой же толщины. Стоит добавить, что перед засыпкой щебня периметр внутри опалубки следует разделить деревянными досками соответствующей ширины. Назначение таких разделителей – не допустить возможность последующего растрескивания опалубки, а также обеспечить возможность посекционного выполнения работ. При установке этих элементов своими руками необходимо учитывать, что расстояние между ними может выбираться произвольно, но обычно составляет около 1 м.
- Поверх насыпанных слоев выполняется бетонная заливка. Для приготовления раствора необходимо смешать в пропорции 1/3 цемент и песок, которые разбавить водой до оптимальной консистенции. Верхний слой заливки разравнивается, подобно бетонной выравнивающей стяжке и оставляется до застывания.
В итоге работ получается жесткая отмостка, которая будет защищать фундамент. Кроме того, следует добавить, что, вследствие сезонных смещений грунта, отмостка может фундаменту повредить. Чтобы этого не происходило, между защитой и «телом» фундамента необходимо оставить небольшой зазор шириной около 1–2 см, для чего можно использовать, например, сложенный в несколько раз рубероид.
Нефиксированная отмостка
Ещё одним вариантом изготовления отмостки является так называемая нефиксированная отмостка. Для её изготовления потребуются следующие действия:
- Аналогично вышеописанному случаю выкапывается траншея.
- Дно траншеи покрывается слоем песка, толщиной около 15 см.
- Далее выполняется сама кладка с применением цементного раствора.
На этом основные моменты работ завершаются. С точки зрения монтажа этот вариант значительно проще, по сравнению с обозначенным выше способом, да и цена материала получается ниже.
Обратите внимание! Однако такая защита крайне чувствительна к механическим воздействиям. Поэтому в местах, которые планируются для проходов, требуется дополнительное усиление поверхности. Например, можно уложить тротуарную плитку.
Для этих целей поверх щебня насыпается слой песка, а затем с использованием цементного раствора укладывается плитка. Швы между отдельными элементами кладки затираются тем же раствором.
Как видно с изложенного выше материала, самостоятельное изготовление отмостки вокруг гаража вполне возможно, но при работах следует соблюдать все правила монтажа.
Видео
Благодаря видеоматериалу, вы сможете наглядно ознакомиться с технологией производства отмостки вокруг гаража:
Устройство отмостки описано в СНиП 2.02.01-83. В этом документе сказано, что водонепроницаемые полосы должны быть сделаны вокруг каждого здания. Зачем нужна отмостка? Ее нужно делать для защиты фундамента дома от влаги.
Горизонтальную защитную полосу стоит сделать шириной не менее 1-2 м, она должна проходить по периметру дома. При строительстве отмостки важно обращать внимание на ее прочность. Очень часто делают утепление защитной полосы. Кроме того, она должна не пропускать воду и плотно примыкать к стенам фундамента. Необходимо уделять пристальное внимание качеству строительства, чтобы вода не проникала в щель между отмосткой и цоколем.
Конструкция защитной полосы может быть 2 видов, строители используют для ее возведения разные материалы. Вы можете выбрать любую конструкцию, но следует помнить о том, что защита фундамента должна удовлетворять следующим функциональным требованиям:
- прочность;
- утепление;
- гидроизоляция.
Теперь вы знаете, для чего нужна отмостка.
Подробную информацию о размерах отмостки можно узнать, изучив СНиП. Обращайте внимание на вид грунта, поскольку каждый из них имеет свой тип просадочности. Все лессовые (глинистые) грунты можно отнести к просадочным. Если вы еще не знаете типа грунта на вашем участке, то для его определения обратитесь в специализированную лабораторию.
Изучив СНиП 2.02.01-83, вы увидите, что документ утверждает грунты 2 типов:
- Грунты I типа. К ним можно отнести те, просадка которых возможна при действии на них внешней нагрузки.
От собственного веса просадка очень мала, допустимо до 5 см.
- Грунты II типа. Это те грунты, величина просадки которых превышает 5 см. Возможна просадка не только от внешней нагрузки, но и под влиянием собственного веса земли.
В документе представлена информация о том, какой ширины стоит делать отмостку. Если на вашем участке грунт I типа, то заливайте бетонную ленту шириной 1,5 м. Если лабораторный анализ показал, что грунт относится ко II типу, то сделайте отмостку шириной не менее 2 м.
Если на участке грунты, которые можно отнести к нормально несущим, то ширина отмостки должна быть не менее 0,8 м. Толщина отмостки является важным параметром, но СНиП нормирует ее в меньшей степени.
Снимите растительный слой с почвы, произведите выемку грунта. Насыпьте на дно щебень, песок или глину. Толщина основания должна быть не менее 15 см. Положите слой гидроизоляции и теплоизоляции. Готовая отмостка из бетона должна возвышаться над нулевой отметкой хотя бы на 5 см.
Если вы хотите сделать пешеходную отмостку, то должны уделить особое внимание прочности бетонной площадки. Рекомендуется увеличить ее ширину — это позволит сделать бетонное покрытие более надежным и комфортным для пешеходов.
Обратите внимание на уклон защитной ленты из бетона. На 1 м покрытия уклон должен составлять не менее 1 см. Чаще всего эту величину увеличивают, заливая отмостку с уклоном 3 см. Помните о том, что не стоит делать слишком крутой скат, ведь это будет способствовать увеличению скорости стока воды. В этом случае отмостка начнет разрушаться с краю. 10 см на 1 м ширины считается максимально допустимым уклоном.
Схема отмостки с уклоном
Очень хорошо, если вы можете позволить себе выделить дополнительные средства на сооружение водоприемных желобов. Их устанавливают на внешней границе бетонной площадки. Установив желоба, вы отведете дождевые воды от дома. Выделите достаточно средств на устройство бетонной отмостки.
Сооружение отмостки своими руками
Существует несколько способов возведения отмостки. Проще всего залить горизонтальную бетонную ленту, схема строительства достаточно простая. Сначала сделайте разметку и выкопайте котлован, установите опалубку. Засыпьте глину или щебень, хорошо утрамбуйте основание. Соорудите гидроизоляцию и уложите слой утеплителя. После этого возьмите арматурную сетку и аккуратно поместите ее сверху утеплителя.
Теперь можно заливать бетон, используйте примерно 80% готового раствора. Разровняйте его и утрамбуйте, а когда основной слой затвердеет, сделайте разметку поперечного уклона. Используйте для этого специальные рейки, прибейте их к опалубке.
Вторую часть бетона делайте более густой, раствор нужно выкладывать по секциям. Разравнивайте его, ориентируясь на рейки.
Устройство бетонной отмостки может выполняться и другим способом. Он заключается в отсыпке выравнивающего слоя на первом этапе строительства защитной ленты из бетона. Насыпьте больше щебня или глины ближе к стенам цоколя, аккуратно распределите материал и хорошо его утрамбуйте.
Для контроля уклона используйте уровень, пригодится в работе и нивелир. Когда вы положите гидроизоляцию и поместите в котлован слой теплоизоляции, залейте опалубку. Контролируйте уклон, обрабатывайте поверхность правилом.
Обратите внимание на бетонный раствор. Лучше всего в этом вопросе ориентироваться на ГОСТ. Если вы живете в местности с суровым климатом, то купите автодорожный бетон. Используйте марку не ниже М200, тогда отмостка будет служить очень долго.
Есть еще одна технология возведения отмостки. Асфальтобетонная площадка имеет твердый верхний слой, который образуется при застывании минеральных наполнителей. Эта технология строительства наиболее выгодна, если рассматривать бюджет, ведь асфальтобетонная отмостка доступна многим.
Особенности возведения мягкой отмостки
Мягкой называют ту отмостку, которая не имеет твердого верхнего слоя. Магазины предлагают потребителям большой выбор современных материалов. Если вы не желаете тратить времени на устройство бетонной отмостки, то можете остановиться на мембранных материалах. Их можно монтировать в любом климате, погодные условия не оказывают влияния на процесс укладки. Срок службы мембраны более 60 лет.
Отмостка будет состоять из нескольких слоев, профилированная мембрана заменит гидроизоляционный материал. С ней очень легко работать, мембрана не разлагается в почве, она не трескается. Используя ее в строительстве отмостки, вы получите возможность реализовать самый смелый проект.
Выберите наиболее подходящее финишное покрытие для отмостки, учитывая тенденции ландшафтного дизайна. Это может быть растительный субстрат или гравий. Устройство отмостки из тротуарной плитки понравится многим владельцам загородных домов. Вы можете сделать ландшафтный проект индивидуальным, выложив отмостку из брусчатки.
Отмостка из бетона привычна многим, но чаще всего в новых домах используется другая технология. Мягкая отмостка позволит сэкономить, ведь строительство обойдется намного дешевле, если вы выберете эту технологию.
Для частного домостроения важно сделать ландшафтный дизайн уникальным. Мягкая отмостка даст вам эту возможность, например, вы можете использовать отмостку в качестве пешеходной дорожки. Можно сделать на ее месте озеленение или выбрать любой другой вариант.
Теперь вы знаете, для чего нужна отмостка и какие преимущества у этой технологии строительства.
Сроки службы любого строения напрямую зависят не только от качества самой постройки, но и от прочности фундамента. Именно на эту часть здания приходится основная нагрузка на протяжении всего периода эксплуатации.
Известно, что такие внешние факторы окружающей среды как вода и заморозки оказывают негативное воздействие на фундамент и приводят к его постепенному разрушению. Для того, чтобы минимизировать воздействие окружающей среды и максимально защитить фундамент гаража, создаётся специальная отмостка.
В этой статье мы расскажем, как сделать отмостку гаража и какие виды отмостки существуют.
Очень часто гаражи строят с подвальными помещениями, которые используют для хранения сезонной резины, запасных частей или продуктов питания. В этом случае создание отмостки является обязательным требованием при проектировании и постройке гаража.
К сведению. Даже если вы купили или построили гаражное помещение без отмостки, её можно сделать в любой момент самостоятельно и без привлечения сторонних специалистов.
Устройство и особенности отмостки для гаража
Отмостка – это специальный защитный пояс по всему периметру фундамента, защищающий его от воздействия морозов и влаги, однако, очень многие предпочитают экономить средства и время, пренебрегая этим. В качестве материала для отмостки обычно используется бетон, который заливается монолитным слоем, как показано на фото ниже, и не должен иметь никаких швов или трещин.
Если осуществляется с нуля, то создание защитного пояса необходимо стразу после возведения стен.
Обычно отмостка состоит из двух основных слоёв:
- Утепляющий слой , который укладывается по периметру фундамента и служит основой для финишного водонепроницаемого слоя.
- Финишный слой – это самый верхний слой защитного пояса, который обычно делается из бетона и составляет единое целое с фундаментной частью гаража. Для декорации отмостки можно использовать камни, кирпичи, тротуарную плитку и даже асфальтное покрытие.
К сведению. При создании такого защитного пояса для фундамента общая цена постройки гаража увеличивается незначительно, но полученный результат гарантирует целостность и нормальное функционирование фундамента долгие годы.
Основные виды отмостки
В зависимости от месторасположения гаража и интенсивности эксплуатации окружающей территории, необходимо выбрать нужный вид отмостки.
- Твердая отмостка у гаража изготавливается из бетона, который заливается по периметру гаража. Это самый быстрый и относительно не дорогой вид, который используется в том случае, если вокруг гаража практически никто не ходит и это пространство никак не используется. У такого варианта есть один существенный недостаток.
Она постоянно находится вод воздействием влаги, солнца и перепадов температуры, что приводит к растрескиванию бетона и каждые несколько лет её приходится ремонтировать.
- Мягкая отмостка для гаража потребует больших временных и финансовых затрат. В этом случае поверх бетонного слоя укладывают цементно-песчаную смесь и декорируют её тротуарной плиткой, камнями или кирпичами. Этот вид подходит в тех случаях, когда пространство у гаража используется для прохода людей, а также его необходимо гармонично вписать в общий дизайн ландшафта.
После того, как был выбран вид отмостки, можно приступать к процессу создания защитного пояса.
Создание отмостки твердого типа
Далее мы опишем пошаговый процесс создания защитного пояса, который может быть использован вами как инструкция для самостоятельной работы. Нам потребуется речной песок, щебёнка мелкой или средней фракции, цемент марки М-300 или выше.
Процесс создания выглядит следующим образом:
- Первым делом необходимо произвести выемку грунта по периметру гаража на глубину 40 см и с шириной от 60 до 100 см от стенки фундамента (см.
), после чего основание тщательно утрамбовывается. Рекомендуется обильно полить грунт раствором специального гербицида, который уничтожит корневую систему растений и предотвратит прорастание под отмосткой.
- Затем на дно канавы укладывают слой речного песка с толщиной 10-15 см и так же тщательно утрамбовывают.
- Следующим слоем укладывается щебёнка толщиной 10 см и утрамбовывается максимально плотно. После чего устанавливается опалубка и укладывается арматура в виде сетки, как показано на рисунке ниже.
Важно. Как видно на фото, поперёк отмостки устанавливают деревянные доски, которые будут разделять заливаемое бетоном пространство на секции. Эти доски перед укладкой пропитывают антисептиками и желательно покрыть битумной мастикой. Они служат амортизаторами для бетона во время расширения или усадки при воздействии перепадов температур и предотвращают растрескивание.
- Последним шагом производится заливка бетона, но перед этим фундаментная часть строения очищается от мусора и грунтуется для лучшего сцепления с бетонной отмосткой.
После того, как отмостка своими руками гаража создана, её накрывают мешковиной на 3-5 дней. При этом мешковину нужно периодически смачивать для обеспечения равномерного застывания раствора.
После застывания можно дополнительно оштукатурить бетонное основание, только в штукатурный раствор добавить специальный полимерный пластификатор. Этот слой закроет установленные доски и полностью предотвратит растрескивание.
Потому что именно на него приходятся значительные нагрузки. Обильные дожди, таяния снегов, заморозки все это воздействует на фундамент, из-за чего появляются трещины, здание рушится и оседает. Для того чтобы предотвратить эти негативные последствия внешних факторов и сооружается отмостка.
Гараж такое же строение, как и любое другое здание. Гараж тоже имеет фундамент, основная функция которого есть опора.
Кроме того, как и в каждом здании в гараже есть подвальные и технические помещения. Существует вероятность их разрушений под воздействием факторов окружающей среды. Поэтому отмостка перед гаражом так же необходима, как и перед жилым домом.
Особенности и состав отмостки
Многие владельцы гаражей стараются сэкономить на этом элементе строительства. Отмостка вокруг гаража является защитой для его фундамента. Создание отмостки – это процесс создания беспрерывной полосы по всему периметру гаража. Материал для отмостки нужно выбирать качественный и подходящий по внешнему виду к остальным покрытиям, чтобы отмостка смотрелась гармонично.
Самый оптимальный вариант – это устройство бетонной отмостки. Она должна быть : без швов, стыков и щелей. Рекомендуется заарменировать отмостку и зажелезнить бетон.
Отмостка устанавливается по окончании процесса облицовки цоколя и стен. Отмостка вокруг гаража состоит из двух слоев:
- Подстилающий слой – плотное ровное основание для будущего покрытия.
- И само покрытие – водонепроницаемый слой. Материалом для покрытия может послужить булыжник, бетон, асфальт, тротуарные плиты. Если делается отмостка гаража своими руками, то выгоднее всего использовать бетон.
Правила устройства отмостки гаража
Создание защиты фундамента дома – это основа любого строения. Устройства отмостки гаража это не очень затратный процесс, который можно реализовать самостоятельно.
Итак, что такое отмостка гаража своими руками и как ее сделать? Рассмотрим этот процесс пошагово:
- Первым делом необходимо произвести выемку грунта по всему периметру гаража, глубина выемки должна быть 15-20 см. Днище канавы поливают специальным раствором – гербецидом, который уничтожает корни растений. Делается это для того, чтобы предотвратить дальнейшее возможное прорастание корней сорняков, деревьев, кустов.
- Второй этап – выполнение непосредственно самой отмостки. В приготовленную траншею укладывают и утрамбовывают слой песка, толщиной приблизительно 10 см (можно больше).
- Следующий слой – щебень. Ширина слоя щебня тоже должна составлять примерно 10 см.
- Поперек отмостки ставятся на ребра деревянные рейки и обмазываются битумом.
При этом отмостка перед гаражом, требует обязательного небольшого уклона, для того, чтобы обеспечить слив воды от гаража.
- Далее – укладка бетона. В этом процессе рейки служат своеобразными разделителями сплошного бетонного покрытия на участки. И они же предохраняют отмостку от трещин.
- Заключительный этап – железнение, то есть присыпание сухим цементом. Когда все этапы завершены, готовую отмостку покрывают влажной мешковиной и выдерживают от 2 до 7 дней, чтобы бетон лучше застыл и стал крепким. При этом мешковину нужно периодически смачивать.
Виды отмостки
Перед гаражом бывает двух видом: «мягкая» и «жесткая».
Как сделать жесткую отмостку?
Бетонирование – это самый простой и быстрый способ установки отмостки. Основное достоинство этого способа – экономия времени. Но есть и недостатки.
Постоянные перепады температуры отражаются на «жесткой» отмостке трещинами, в нее попадает вода и это не может не сказаться на качестве фундамента.
Поэтому отмостку такого вида придётся ремонтировать каждый сезон.
«Мягка» отмостка является более морозоустойчивой и не так подвержена влиянию внешних природных фактором, поэтому не требует постоянного ремонта.
Если гараж построен или строится, например, на загородном участке, где есть другие строения и жилые дома, то, конечно, нужно учесть это при заливке отмостки.
Она должна вписываться в общий ландшафт и гармонировать с другими строениями и покрытиями, чтобы территория выглядела благоустроенно и завершенно.
Как видим, при создании отмостки перед гаражом нужно учесть множество нюансов: выбор материала, время года, способ устройства отмостки и другое. Все это зависит от желания и бюджета владельца гаража.
Еще по этой теме на нашем сайте:
Обязательным и очень важным атрибутом каждого дома является отмостка. Обустройство отмостки вокруг дома – достаточно сложный процесс, поэтому необходимо знать его этапы и устройство самой...
Отмостка вокруг дома бывает мягкой и жесткой. В каждом отдельном случае, специалистом подбирается тот вид отмостки, который необходим для защиты фундамента и с учетом требований…
Главным элементом обустройства является отмостка вокруг колодца. Она не позволит талому снегу и поверхностным водам попасть в шахту, а также обеспечит удобный подход к сооружению….
Отмостка – это тротуарная полоса, которая примыкает к фундаменту здания по всему периметру. Зачем нужна отмостка? Она сохраняет фундамент и рядом расположенный грунт в сухости,…
Внедрение технологий дорожного покрытия | FHWA
Инновационные подходы к строительству и обслуживанию дорожных покрытий могут сэкономить деньги и повысить производительность. FHWA способствует их использованию по всей стране.
WisDOT
Департамент транспорта штата Висконсин строит экспериментальные участки шоссе 21 штата недалеко от Неседа, штат Висконсин, в рамках демонстрационного проекта по оценке характеристик асфальтовых покрытий с повышенной плотностью уплотнения. Здесь транспортное средство для перегрузки материалов помогает перемещать асфальтобетонную смесь от грузовика к асфальтоукладчику при постоянной температуре.
Сегодняшние пользователи автомагистралей ожидают качественного путешествия по безопасным и ухоженным дорогам с минимально возможными задержками. Федеральное управление автомобильных дорог играет ведущую роль в обеспечении развертывания и внедрения инновационных технологий, которые могут повысить безопасность и производительность транспортной системы, на дорогах страны.
Одним из направлений деятельности FHWA является программа ускоренного внедрения и развертывания технологий дорожного покрытия (AID-PT). Конгресс учредил программу в 2012 году в соответствии с Законом о движении вперед к прогрессу в 21 веке (MAP-21). Цель состоит в том, чтобы задокументировать, продемонстрировать и внедрить инновационные технологии дорожного покрытия, включая их применение, производительность и преимущества. В 2015 году Конгресс продолжил программу AID-PT в Законе об исправлении наземного транспорта Америки (FAST) с финансированием до 2020 финансового года.
Центральное место в программе AID-PT занимают различные мероприятия по передаче технологий и информационно-разъяснительной работе, которые доносят информацию, опыт и методы до транспортного сообщества посредством содержательных и рентабельных стратегий, начиная от обзоров объектов, демонстраций и вебинаров и заканчивая руководящими документами. Транспортные агентства внедрили ряд технологий в таких областях, как бетонные покрытия, долговечность асфальтового покрытия и устойчивость.
Текущие инициативы
В своем годовом отчете AID-PT за 2016–2017 годы FHWA освещает тематические исследования, в которых обсуждаются ожидаемые долгосрочные улучшения в плане экономии средств, сроков реализации проекта, устранения заторов, повышения безопасности и производительности дорожного покрытия благодаря программе.В частности, FHWA принимает участие в различных мероприятиях по улучшению материалов для дорожного покрытия и предоставляет рекомендации, помогающие дорожным службам более эффективно проектировать и строить как асфальтовые, так и бетонные покрытия.
Примеры текущих инициатив включают следующее:
- Поощрение внедрения методологии, описанной в Механическо-эмпирическом руководстве по проектированию дорожного покрытия , опубликованном Американской ассоциацией государственных служащих автомобильных дорог и транспорта.Четырнадцать дорожных ведомств внедрили порядок асфальтирования покрытий, еще 31 планируют внедрить. Что касается бетонных покрытий, то 13 агентств внедрили, и еще 32 планируют это сделать.
- Расширение использования и применения переработанного бетонного заполнителя в новых и реконструированных покрытиях и использование шинной резины в асфальтовых покрытиях. Эти методы не только позволяют сэкономить на затратах, но и поддерживают общее внимание к устойчивости и уменьшают воздействие дорожных покрытий на окружающую среду.
- Улучшение процессов строительства асфальтовых покрытий, в частности, использование более эффективных методов уплотнения, обеспечивающих более длительный срок службы покрытий при незначительных дополнительных затратах или вообще без них.
- Продвижение и продвижение подходов к разработке асфальтобетонных и бетонных смесей для дорожных покрытий, ориентированных на повышение производительности и долговечность.
При активной поддержке заинтересованных сторон программа AID-PT обеспечивает ряд преимуществ: от более коротких сроков реализации проектов и уменьшения заторов до экономии средств и снижения числа смертельных случаев на дорогах.
Усиление позиций
FHWA выделяет бетонные покрытия в своем отчете AID-PT из-за их растущей популярности как устойчивого и экономичного решения для обслуживания и сохранения дорожных покрытий. Использование бетонного покрытия для восстановления существующего дорожного покрытия дает такие преимущества, как продление срока службы, увеличение несущей способности конструкции, сокращение затрат на техническое обслуживание и снижение затрат в течение жизненного цикла.
Образец результатов программы AID-PT |
Программа AID-PT оказывает значительное влияние на правила дорожного движения:
|
Программа
FHWA по применению бетонных покрытий в полевых условиях, администрируемая Национальным центром технологии бетонных покрытий (CP Tech Center) в Университете штата Айова, отвечает на вопросы, часто возникающие в отношении этой технологии, в том числе когда и где использовать бетонные покрытия, а также соображения по проектированию и строительству.
«Целью программы является оказание технической помощи агентствам в общем процессе укладки бетона, от выбора проектов-кандидатов до проектирования и строительства самого проекта», — говорит Дейл Харрингтон, инженер-строитель Snyder and Associates, фирма, которая курирует программу CP Tech Center.
Другими словами, цель состоит в том, чтобы повысить осведомленность и знания среди государственных департаментов транспорта и местных агентств, подрядчиков и инженеров-консультантов о том, как успешно наносить бетонные покрытия.
Дейл Харрингтон, Технический центр CP
В рамках программы полевых работ по бетонному покрытию были организованы семинары, техническая поддержка и посещения объектов в этих местах по всей территории Соединенных Штатов.
Типы накладок
Бригады могут наносить как связанные, так и несвязанные бетонные верхние слои поверх существующих асфальтовых, композитных и бетонных покрытий. Если существующее дорожное покрытие находится в хорошем структурном состоянии, склеенные бетонные верхние слои могут устранить поверхностные повреждения или повысить прочность конструкции. Этот подход требует, чтобы бригады предпринимали определенные шаги для приклеивания нового верхнего слоя к существующему дорожному покрытию, чтобы оно вело себя как единая конструкция.
Если существующее дорожное покрытие изношено от умеренного до сильного, можно использовать несвязанные бетонные покрытия для восстановления несущей способности конструкции. Новый верхний слой отделяется от существующего покрытия, чтобы гарантировать, что повреждения нижележащего покрытия не повлияют на характеристики нового верхнего слоя.
Дейл Харрингтон, CP Tech Center
Пик использования бетонных перекрытий пришелся на 2009 г., и этот показатель продолжает расти гораздо более высокими темпами, чем в предыдущее десятилетие.
Просмотр результатов
Участники программы по применению бетонных накладок в полевых условиях получают знания о накладных решениях из первых рук, что позволяет их агентствам получать как технические, так и финансовые дивиденды.
«В рамках Программы технической помощи по бетонному покрытию был рассмотрен проект строительства 17-мильного [27-километрового] шоссе I–85 в Северной Каролине», — говорит Кларк Моррисон, инженер-конструктор дорожного покрытия из Департамента транспорта Северной Каролины (NCDOT).
Существующее дорожное покрытие представляло собой 50-летний бетонный шов с многочисленными асфальтовыми вставками. NCDOT выбрал несвязанный бетонный верхний слой. Группа технического центра CP посетила объект и провела семинар с инженерами NCDOT. По итогам семинара были выработаны две рекомендации: (1) оставить большую часть существующих асфальтовых заплат на месте и (2) использовать дренажную ткань вместо водопроницаемого асфальтового дренажного слоя, что привело к значительной экономии как затрат на строительство, так и времени.По оценкам Моррисона, экономия затрат только на капитальном ремонте составила не менее 3,25 миллиона долларов.
Виктор (Ли) Галливан, Gallivan Consulting Inc.
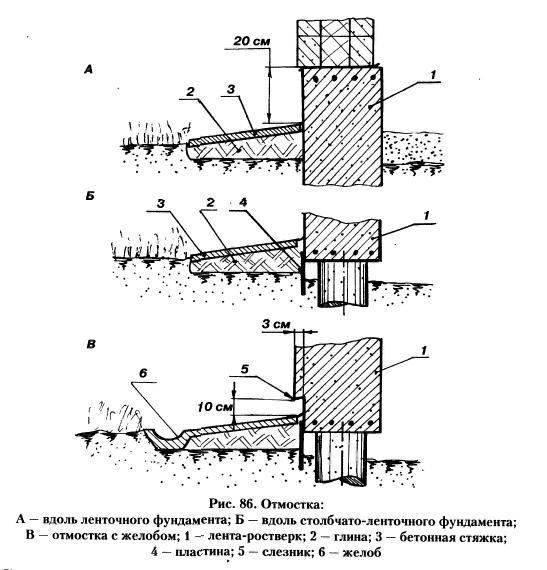
Департамент транспорта Пенсильвании использовал эти три катка с вибрационными стальными колесами, работающие в эшелонированном порядке, чтобы помочь достичь целей повышенной плотности на своих демонстрационных испытательных участках.
Использование бетонных покрытий растет и в других дорожных агентствах, по словам Харрингтона из CP Tech Center.«За последние несколько лет мы наблюдаем значительный рост использования бетонных покрытий, — говорит он. «С сентября 2013 г. по сентябрь 2016 г. 11 DOT различных штатов, которые прошли обучение по укладке бетонных покрытий, построили более 115 проектов укладки бетонных покрытий, что составляет более 750 миллионов долларов строительных затрат».
По мере того, как все больше агентств получают практические знания о бетонных покрытиях и опыт работы с этой технологией, официальные лица FHWA ожидают, что ее использование в качестве альтернативы для сохранения и восстановления дорожного покрытия будет расти.
Доступен ряд ресурсов, которые помогут дорожным службам оценить и применить бетонные покрытия. Руководства, технические описания, документация по конкретным случаям и обучение — это лишь некоторые из доступных ресурсов, которые охватывают все аспекты бетонных покрытий — от выбора до проектирования и строительства — и для целого ряда применений, включая автомагистрали, городские улицы и парковки. .
Для получения дополнительной информации посетите сайт www.cptechcenter.org/research/research-initiatives/overlays.
Повышенная плотность, повышенная износостойкость
В ежегодном отчете AID-PT FHWA также подчеркивается важность плотности асфальта на более чем 9,6 миллиона миль полос движения (15,4 миллиона километров), которые составляют сеть автомобильных дорог США — одно из крупнейших активов страны. Поддержание системы в рабочем состоянии обходится дорого. В своем отчете Конгрессу 2015 г. «Состояние автомобильных дорог, мостов и общественного транспорта страны: условия и эффективность » (FHWA-PL-17-001) FHWA оценивает среднегодовые инвестиции, необходимые в период с 2013 по 2032 г. для поддержания состояния и производительность системы автомобильных дорог страны в целом составляет 89 долларов.9 миллиардов.
Любые улучшения в работе конструкций дорожного покрытия помогли бы уменьшить величину требуемых ежегодных инвестиций. Одним из простых, прямолинейных и относительно недорогих способов улучшения характеристик асфальтовых покрытий является достижение более высоких уровней плотности во время строительства. Более высокие уровни плотности асфальта повышают износостойкость дорожного покрытия, продлевают срок его службы и отсрочивают будущие работы по восстановлению и реконструкции.
Источник: ФХВА.
Апелляция об объединении
За прошедшие годы инновации и усовершенствования в оборудовании, методах и технологиях повысили эксплуатационные характеристики дорожного покрытия и снизили затраты. Сегодня инженеры знают, что сочетание контролируемого уплотнения с более высокой плотностью дорожного покрытия на месте может оказать существенное влияние на характеристики асфальтового покрытия.
Исследования показали, что увеличение плотности и уменьшение содержания воздушных пор в асфальтовых покрытиях приводит к снижению водопроницаемости, повышению устойчивости к растрескиванию и колееобразованию под нагрузкой и, в конечном счете, к увеличению срока службы покрытия.Например, одно исследование, проведенное исследователями из Национального центра асфальтовых технологий в Обернском университете, показало, что увеличение уплотнения, приводящее к уменьшению содержания воздушных пустот на 1 %, может обеспечить увеличение усталостной долговечности на 8–44 %. От 7 до 66 процентов увеличения эффективности гона, как на основе лабораторных, так и полевых данных.
Сравнение предполагаемой стоимости жизненного цикла верхнего слоя асфальтобетонного покрытия, построенного с плотностью 92 процента от максимальной теоретической, с аналогичным верхним слоем, построенным с плотностью 93 процента, показывает потенциальную экономию, которая стала возможной за счет увеличения минимальной требуемой плотности на месте всего на 1 процент. Используя консервативное 10-процентное увеличение срока службы, в спонсируемом FHWA отчете Улучшенное уплотнение для повышения долговечности и продления срока службы дорожного покрытия: литературный обзор (отчет NCAT № 16-02) указывается экономия затрат в чистой приведенной стоимости 88 000 долларов на проект мощения стоимостью 1 миллион долларов.
MnDOT
Министерство транспорта Миннесоты использовало показанные здесь роликовые катки, оснащенные интеллектуальными приборами уплотнения, для контроля уплотнения тестовых участков.
Подрядчики могут добиться более высокой плотности за счет повышенного уплотнения, но чрезмерное уплотнение может повредить дорожное покрытие. К счастью, недавние усовершенствования, такие как технологии теплой асфальтобетонной смеси (которые улучшают удобоукладываемость смеси), интеллектуальное уплотнение, высокотехнологичные асфальтоукладчики и процессы контроля качества, позволили достичь более высокой плотности на месте, избегая этого риска. И, в отличие от других методов достижения улучшенных характеристик дорожного покрытия, которые требуют более дорогих материалов или методов строительства, дополнительная плотность дорожного покрытия на месте не приводит к значительному увеличению стоимости для достижения существенного улучшения характеристик.
FHWA запускает демонстрационный проект
В 2016 году, признав важность плотности на месте для строительства экономичных и долговечных асфальтовых покрытий, FHWA инициировала демонстрационный проект под названием «Повышение долговечности за счет увеличения плотности покрытия на месте». Цель состояла в том, чтобы продемонстрировать, что плотность на месте, необходимая для улучшения характеристик асфальтового покрытия, может быть достигнута без значительного увеличения затрат на строительство.В процессе подачи заявок FHWA выбрало 10 штатов для строительства тестовых участков и участия в демонстрации.
На каждом демонстрационном участке бригады построили одну стандартную секцию в качестве контрольной и одну или две опытные секции повышенной плотности. Каждое государство также построило дополнительные испытательные участки с альтернативными подходами к повышению плотности дорожного покрытия. Эти альтернативы включали в себя ряд недавних технологических усовершенствований, таких как теплый асфальт, интеллектуальное уплотнение, измерители плотности прокатки и инфракрасное изображение.Другие испытанные альтернативы включали более традиционные изменения в практике, такие как дополнительные катки, транспортные средства для транспортировки материалов и улучшения в составе асфальтобетонных смесей, выборе материалов и планах обеспечения качества.
Судя по всему, демонстрационный проект удался. Ключевой вывод заключался в том, что бригады могли эффективно повысить плотность на месте: 8 из 10 штатов добились увеличения плотности по крайней мере на 1 процент в своих проектах.
Источник: FHWA/APTech.
Найденные методы достижения повышенной плотности подразделяются на пять основных категорий, которые могут служить контрольным списком для изучения дорожными службами:
- Улучшите спецификации, чтобы либо включить стимулы, либо увеличить существующие стимулы для подрядчиков для достижения более высокой плотности на месте.
- Скорректируйте состав смеси, чтобы получить немного более высокое содержание асфальта.
- Стремитесь к большей согласованности температуры смеси, скорости асфальтоукладчика и рисунка расположения катков.
- Следуйте передовым методам строительства.
- Используйте новые технологии, такие как теплый асфальт, инфракрасное изображение, измерители плотности прокатки и интеллектуальное уплотнение.
Семинары по передовому опыту
Ключом к успеху демонстрационных проектов стало партнерство, которое FHWA установило с промышленностью, а также с государственными дорожными агентствами и подрядчиками в государствах-участниках. Национальный центр технологии асфальтобетона и Асфальтовый институт организовали семинары, помощь в проектировании смесей и совещаниях перед началом строительства, мониторинг строительства и поддержку документации.Основная цель семинаров заключалась в том, чтобы представить передовой опыт уплотнения дорожного покрытия, не прибегая к использованию дополнительного уплотняющего оборудования или более дорогостоящих технологий уплотнения.
Отзывы государств-участников об однодневном семинаре были настолько положительными, что позднее семинар был проведен еще в 18 государствах. В общей сложности более 1400 участников из федеральных и государственных транспортных агентств и отраслевых организаций прошли обучение.
«Финансирование и семинар, предоставленные FHWA, сыграли важную роль в [Департаменте транспорта штата Висконсин (WisDOT)] приоритизации демонстрационного проекта повышенной плотности», — говорит Барри Пей, главный инженер по материалам в WisDOT, один из участников демонстрационного проекта FHWA. «Информация, полученная из этой демонстрации, позволила WisDOT обновить наши спецификации плотности для строительного сезона 2017 года, на год или два раньше, чем мы планировали изначально. Увеличение плотности на 1–1,5 процента приведет к увеличению срока службы дорожного покрытия на 10 или более процентов.Возврат от поощрения FHWA в размере 50 000 долларов и семинара будет отличным для Висконсина».
Для получения дополнительной информации о результатах демонстрационных проектов посетите сайт http://eng. auburn.edu/research/centers/ncat/files/technical-reports/rep17-05.pdf.
К устойчивым тротуарам
Еще одним важным моментом в годовом отчете AID-PT является Программа устойчивого дорожного покрытия FHWA. Эта программа поддерживает дорожные агентства, поскольку они работают для достижения экологических, социальных и экономических целей.Программа направлена на расширение знаний и практики проектирования, строительства и обслуживания более устойчивых дорожных покрытий посредством взаимодействия с заинтересованными сторонами, обучения и разработки руководств и инструментов.
Программа определяет устойчивое дорожное покрытие как покрытие, соответствующее местоположению и климату, по возможности с использованием местных материалов и отвечающее целям агентства по дизайну и характеристикам. С помощью технической рабочей группы Программа устойчивого дорожного покрытия FHWA претворяет знания в жизнь.Вот подробнее некоторые из основных мероприятий программы.
Привлечение заинтересованных сторон
В основе программы лежит Техническая рабочая группа по экологичным покрытиям. Рабочая группа, состоящая из 20 членов, представляющих федеральные, государственные и местные транспортные агентства, а также партнеров из отрасли и научных кругов, и более 300 «друзей», вносит общий технический вклад в программу и помогает повышать осведомленность специалистов по дорожному покрытию о проблемах устойчивого развития.
Группа собирается два раза в год для обмена информацией посредством технических презентаций, обзоров технической документации, а также дискуссий в группах и за круглым столом. На недавних встречах были затронуты такие темы, как оценка жизненного цикла дорожного покрытия и взаимодействие дорожного покрытия с транспортным средством.
По словам Лейфа Уотне, исполнительного вице-президента Американской ассоциации производителей бетонных покрытий и члена рабочей группы, «Программа экологически безопасных покрытий оказалась чрезвычайно плодотворной, объединив заинтересованные стороны и ведя содержательный диалог по всем вопросам, связанным с устойчивостью покрытий.
Определение игрового поля
Чтобы предоставить передовой опыт и практические рекомендации, FHWA выпустила множество справочных материалов и возможностей для обучения. Отличительным результатом программы является «На пути к устойчивым системам дорожного покрытия: справочный документ » (FHWA-HIF-15-002). В документе представлен обзор ключевых концепций и рекомендации о том, как сделать укладку более экологичной. Например, он побуждает агентства учитывать весь жизненный цикл, от добычи материалов и их транспортировки на площадку до этапов проектирования, строительства, использования и окончания срока службы дорожного покрытия.Он также советует агентствам признать, что не существует универсального подхода к устойчивости дорожного покрытия; найти компромисс между экономическими, экологическими и социальными факторами; и стремиться к повышению устойчивости от проекта к проекту в долгосрочной перспективе.
Программа «Устойчивые тротуары» также разработала основу для оценки воздействия систем дорожного покрытия на окружающую среду в течение всего жизненного цикла. Жизненный цикл дорожного покрытия Схема оценки (FHWA-HIF-16-014) является важным первым шагом в реализации и принятии принципов оценки жизненного цикла.Дорожные агентства и специалисты по дорожным покрытиям и материалам используют этот документ, чтобы помочь в разработке инструментов оценки жизненного цикла.
Например, Амлан Мукерджи, доктор философии, адъюнкт-профессор гражданской и экологической инженерии в Мичиганском технологическом университете, использовал этот документ для подготовки правила категории продукта и экологической декларации продукта для производства асфальтобетонного покрытия. «Система оценки жизненного цикла определяет все взаимосвязанные компоненты, имеющие отношение к проектированию, строительству и обслуживанию дорожных покрытий», — говорит Мукерджи.«При проведении оценки жизненного цикла асфальтобетонных смесей система использовалась для учета всех факторов, относящихся к асфальтовым покрытиям. Это гарантирует, что декларации об экологических продуктах асфальта могут быть легко интегрированы с другими компонентами оценки жизненного цикла дорожного покрытия и, в конечном счете, позволяют агентствам использовать их для целей проектирования дорожного покрытия и принятия решений по строительству».
Дорожная карта будущего
FHWA недавно разработало стратегическую «дорожную карту» Программы устойчивого дорожного покрытия (FHWA-HIF-17-029) , в которой указаны конкретные направления на 2015–2020 годы.Дорожная карта выделяет темы и результаты , которые могут оказать существенное влияние на , продвигая соображения устойчивого развития в сообществе дорожных покрытий. Содержание организовано по четырем широким целевым областям, каждая из которых включает процессы и действия, которые продвигают состояние практики к устойчивости. Для получения дополнительной информации посетите www.fhwa.dot.gov/pavement/sustainability/hif17029.pdf.
APTech
Двухслойное бетонное покрытие, как показано здесь, использует более высокий процент переработанного или маргинального заполнителя в более толстом нижнем слое, в то же время оставляя более прочный материал для более тонкого поверхностного слоя. Этот метод повышает устойчивость дорожного покрытия без ущерба для его эксплуатационных характеристик.
Применение знаний на практике
Внедрение более устойчивых методов дает множество преимуществ не только для окружающей среды, но и для финансовых результатов агентств. Например, при реконструкции платной дороги Мемориала Джейн Аддамс (I–90) платная дорога Иллинойса задокументировала повторное использование почти 1,2 миллиона тонн (1,1 миллиона метрических тонн) переработанных материалов, включая заполнитель, а также асфальт и бетонные покрытия из Сайт проекта.Точно так же Департамент транспорта Иллинойса задокументировал переработку более 2 миллионов тонн (1,8 миллиона метрических тонн) материалов в течение строительного сезона 2015 года. Переработка и повторное использование материалов снижает спрос на первичные материалы и связанные с этим транспортные и энергетические затраты.
Повторное использование материалов также дает значительные экологические преимущества и экономию средств на национальном уровне. Согласно опросу, проведенному FHWA и Национальной ассоциацией асфальтовых покрытий, в течение строительного сезона 2016 года более 76.9 миллионов тонн (69,7 миллиона метрических тонн) восстановленного асфальтового покрытия и почти 1,4 миллиона тонн (1,3 миллиона метрических тонн) переработанной битумной черепицы были использованы для новых покрытий в Соединенных Штатах, что сэкономило налогоплательщикам более 2,1 миллиарда долларов по сравнению с затратами. использование традиционных материалов для мощения. Кроме того, по оценкам Американской ассоциации строителей дорог и транспорта, использование летучей золы — побочного продукта угольных электростанций — в качестве замены цемента в бетонных смесях для дорожного покрытия позволило сэкономить 2 доллара.3 млрд за 5 лет.
Программа «Экологичные тротуары» будет продолжать оказывать поддержку дорожным агентствам, поскольку они учитывают принципы устойчивого развития в своей повседневной деятельности. В ближайшем будущем FHWA планирует подготовить дополнительные руководящие документы, создать простой калькулятор оценки жизненного цикла и разработать тематические исследования, посвященные передовым методам создания устойчивых дорожных покрытий.
Благодаря стратегическому партнерству с дорожными агентствами и другими организациями, занимающимися укладкой дорожного покрытия, FHWA использует федеральные инвестиции, чтобы максимизировать воздействие программы AID-PT и расширить преимущества для путешествующих.Полный отчет AID-PT доступен на www.fhwa.dot.gov/Pavement/pubs/hif17047.pdf.
Джина Альстром — руководитель группы материалов для дорожных покрытий в FHWA в Вашингтоне, округ Колумбия. Она отвечает за политику, стандарты, техническую и программную помощь, а также за внедрение инновационных технологий. Она получила B.S. в гражданском строительстве из Пенсильванского государственного университета и MS. в гражданском строительстве из Университета Мэриленда, Колледж-Парк.
Для получения дополнительной информации посетите www.fhwa.dot.gov/pavement или свяжитесь с Джиной Альстром по телефону 202–366–4612 или [email protected].
Инжиниринг — Национальная ассоциация асфальтобетонного покрытия
Асфальтовое покрытие — один из строительных блоков Америки
В Соединенных Штатах проложено более 2,7 миллиона миль дорог и автомагистралей с твердым покрытием, и 94 процента из них имеют асфальтовое покрытие. Многие из них представляют собой асфальтовые покрытия на всю глубину; другие представляют собой асфальтовые покрытия, используемые для восстановления характеристик изнашивающихся бетонных покрытий.
В стране насчитывается около 3500 асфальтовых заводов или, по крайней мере, по одному в каждом избирательном округе. Ежегодно эти заводы производят в общей сложности около 400 миллионов тонн материала для асфальтового покрытия на сумму более 30 миллиардов долларов. Промышленность поддерживает занятость более 400 000 американцев в секторах производства асфальта, щебня и дорожного строительства. Асфальтовый дорожный материал представляет собой тщательно спроектированный продукт, состоящий примерно на 95 процентов из камня, песка и гравия по весу и примерно на 5 процентов из асфальтового вяжущего, нефтепродукта.
Асфальтовые покрытия доставляют нас из дома на работу и в школу. Это дает нам доступ к медицинской помощи и экстренной помощи. Он переносит нас в места отправления культа, отдыха и покупок. С современными системами инвентаризации «точно в срок» шоссе — это склад, а производители и розничные продавцы полагаются на грузовики, чтобы доставлять товары к ним вовремя.
Пластик в асфальте
Активно выступая за ответственную переработку отходов, NAPA работает вместе с производителями асфальтовых покрытий, чтобы улучшить возможность повторного использования пластика в асфальтовых покрытиях.Выучить больше.
ПЛАСТИКИ В АСФАЛЬТЕ
Программа технологии асфальтобетонного покрытия аэропортов (AAPTP)
Обучение и образование
Обучение сотрудников показывает им, что вы цените их вклад и что ваша компания инвестирует в их будущее. Исследования показывают, что работники с вовлеченными менеджерами остаются в своей компании и работают более продуктивно. NAPA предлагает множество возможностей для обучения, чтобы расширить ваши знания об асфальтной промышленности.
ОБУЧЕНИЕ И ОБУЧЕНИЕ
РЕСУРСЫ
Нужен ли вам инструмент для завершения проектирования дорожного покрытия для проекта проектирования и строительства или вам просто нужно знать, когда ваши катки должны быть готовы к уплотнению свежеуложенного асфальтового покрытия, NAPA сотрудничает с экспертами в области технологий для разработки инструментов, которые могут помочь с критические задачи.
РЕСУРСЫ
Инженерные контакты
Дж. Ричард Уиллис, доктор философии.
Вице-президент по инженерии, исследованиям и технологиям
Бретт Уильямс
Директор по инженерно-технической поддержке
6 НОВЫЕ ТЕХНОЛОГИИ ПОКРЫТИЯ | Руководство по использованию существующего покрытия на месте и обеспечению долговечности
Ниже приведен неисправленный машиночитаемый текст этой главы, предназначенный для предоставления нашим собственным поисковым системам и внешним системам очень богатого, репрезентативного для глав текста каждой книги с возможностью поиска. Поскольку это НЕИСПРАВЛЕННЫЙ материал, рассмотрите следующий текст как полезный, но недостаточный заменитель для авторитетных страниц книги.
350
ВВЕДЕНИЕ
Существуют технологии бетона на портландцементе (PCC) и гибких дорожных покрытий, которые
пока не могут рассматриваться как варианты продления с длительным сроком службы, но могут стать таковыми в будущем.
будущее. Одна из рассмотренных технологий, сборное железобетонное покрытие, вероятно, является долговечным.
возможность продления в настоящее время. Ограничение состоит в том, что мало проектов находятся под трафиком
сделать такую оценку.Таким образом, термин «новые технологии дорожного покрытия» не
не обязательно означает, что концепция является новой. Некоторые из этих многообещающих технологий
были выбраны для краткого обзора и включают следующее:
• Жесткие тротуары
— Ультратонкие покрытия из сплошного армированного бетона (CRCP)
— Сборное железобетонное покрытие
• Гибкие или композитные покрытия
— Модифицированное смолой дорожное покрытие
Без сомнения, есть и другие технологии, которые можно было бы использовать; однако это
не является основной целью данного исследования. Эта короткая трактовка просто предполагает, что
существуют технологии, которые следует отслеживать по мере их дальнейшего развития и которые могут
быть или могут стать жизнеспособными компонентами для долгосрочного обновления дорожного покрытия.
ЖЕСТКИЕ ПОКРЫТИЯ
Ультратонкие накладки CRCP (UTCRCP)
Об этой инновационной обработке для восстановления дорожного покрытия впервые сообщили в 2004 г.
система накладок для стальных мостов. Эту технологию не следует путать с ультратонкой.
бетонные покрытия, армированные волокнами, которые получили более широкую оценку в Соединенных Штатах Америки.
6
ПОЯВЛЯЮЩЕЕСЯ ПОКРЫТИЕ
ТЕХНОЛОГИИ
351
НОВАЯ ТЕХНОЛОГИЯ ПОКРЫТИЯ
Государства (например, примеры, предоставленные Куо, Армагани и Шерлингом, 1999 г.).То
Подход UTCRCP был тщательно исследован в Южной Африке (Kannemeyer et
др., 2008). На рис. 6.1 показаны некоторые испытания симулятора большегрузного автомобиля (HVS), которые
был недавно завершен для испытательных участков UTCRCP недалеко от Йоханнесбурга. Южноафриканские экспериментальные секции в основном имели толщину 50 мм и располагались
на различных основаниях, от горячего асфальта (HMA) до природного гравия. Непрерывный
стальная сетка использовалась для армирования вместе с двумя типами стальной фибры (прямая и
зацепил).Непрерывная арматура в процентах от площади поперечного сечения
выше, чем для традиционного CRCP — около 1,0% в отличие от типичных значений 0,6%
для КРКП. Для недавних условий испытаний, в которых использовалась гранулированная основа, оценивается
что 50-мм UTCRCP имеет минимальный срок службы 25 миллионов эквивалентных нагрузок на одну ось.
(ESAL). Каннемейер и др. подсчитано, что этот тип наложения будет длиться от 14
и 55 лет, в зависимости от среднесуточного трафика грузовиков. (Каннемейер и др. предположили
что на каждый грузовик применялось 5 ESAL/грузовик.)
На трассе N12 в Йоханнесбурге уложена 50-мм накладка UTCRCP.
(дата завершения проекта ноябрь 2010 г.) вместе с 200-мм CRCP в медленном
переулки. UTCRCP был размещен на «быстрых» или внутренних дорожках для этих многополосных высокоскоростных линий.
способы. Базовой базой является HMA. Использовались два вида армирования.
проект: (1) проволока диаметром 5,6 мм с шагом 100 мм на 50 мм и (2)
проволока диаметром 4 мм с шагом 50 мм на 50 мм.
Второй проект UTCRCP был построен на шоссе N1 к северо-востоку от Паарла.
(недалеко от Кейптауна), Южная Африка (рис. 6.2). В настоящее время этот проект обслуживает 12 000
автомобилей в день с 20% грузовых автомобилей (Ebels and Burger, 2010) и служит подъемным
переулок. Расчетная нагрузка составляет 40 миллионов автомобилей E80 за 25-летний период, а длина пробега 50 мм.
толщина. В смеси используются полипропиленовые волокна, стальная сетка диаметром 5,6 мм.
с шагом 50 мм на 100 мм, максимальный номинальный размер заполнителя 6,7 мм,
и различные примеси. В результате получается смесь с прочностью на сжатие около
15000 фунтов на квадратный дюйм и минимальная прочность на изгиб 1500 фунтов на квадратный дюйм.Потенциал для долгосрочной работы
Следует отслеживать опыт Южной Африки с UTCRCP, поскольку он
тщательно оценены с помощью экспериментов HVS и теперь используются на реальных автомагистралях.
Сборные панели и сборные предварительно напряженные бетонные покрытия (PPCP)
Практические примеры PPCP
За последнее время в Соединенных Штатах было построено несколько сборных железобетонных тротуаров.
10 лет; три хорошо задокументированных проекта включают места в Техасе (завершены в
2001 г.), Калифорния (завершено в 2004 г.; Мерритт, Маккалоу и Бернс, 2005 г.) и
Миннесота (завершен в 2005 г .; Бернхэм, 2007 г.).Впоследствии проекты были
завершено в Миссури (2005 г.) и Айове (2006 г.; Федеральное управление автомобильных дорог,
2009). Целью этих проектов была оценка жизнеспособности сборного железобетона.
тротуары для быстрого строительства и ремонта. Эти проекты относительно
короткая. Самая длинная из них — проект фасадной дороги Texas I-35 на высоте 2300 футов. Caltrans
Проект I-10 составлял 248 футов, проект Миссури — 1010 футов, а проект Айовы — 4300 футов2.
352
РУКОВОДСТВО ПО ИСПОЛЬЗОВАНИЮ СУЩЕСТВУЮЩЕГО ПОКРЫТИЯ НА МЕСТЕ И ДОСТИЖЕНИЮ ДОЛГОВЕЧНОСТИ
(а) (б)
(компакт диск)
(д) (е)
Рисунок 6. 1. Тестирование тонкого CRCP на симуляторе большегрузного автомобиля в Южной Африке. (а) Тестирование тонкого CRCP
недалеко от Гейдельберга, Южная Африка. (b) HVS-испытания CRCP толщиной 50 мм. (c) Тестирование включает существенный инструментарий.
для измерений на месте. (d) Тестирование HVS обычно продолжается до тех пор, пока не будет достигнуто состояние отказа. д) Ранее
испытанный участок, иллюстрирующий армирование. (f) Крупный план армирования.
Фотографии: Джо Махони.
353
НОВАЯ ТЕХНОЛОГИЯ ПОКРЫТИЯ
Рисунок 6.2. UTCRCP на шоссе N1 недалеко от Кейптауна, Южная Африка.
Фотографии: Винанд Стейн.
Более ранние проекты, построенные в Южной Дакоте, Японии и Техасе, были задокументированы Мерриттом.
и другие. (2000). Самый ранний техасский проект был построен в 1985 году как монолитный монолитный дом толщиной 6 дюймов.
предварительно напряженное дорожное покрытие.
Меррит и др. (2000) отметили, что для расчета толщины разумный нижний предел для
Толщина сборных панелей должна быть не менее 50–60 % от толщины обычных панелей. крит тротуар. Анализ, сравнивающий сборное железобетонное покрытие с более
традиционный CRCP предполагает, что 14-дюймовый.-толстый CRCP будет эквивалентен 8-дюймовой толщине
сборные железобетонные панели. Также было отмечено, что 6-в. Построенный в Техасе монолитный предварительно
нагруженное покрытие не показало никаких повреждений после 15 лет эксплуатации.
Концепция техасского проекта 2001 г. формулировалась следующим образом: «разработать
концепция сборного железобетонного покрытия, отвечающая требованиям, предъявляемым к
строении и что это возможно с точки зрения проектирования, строительства,
экономичность и долговечность. Предлагаемая концепция должна иметь расчетный срок службы 30 или
больше лет, чтобы сделать его сравнимым с обычными монолитными покрытиями в настоящее время
строятся» (Merritt et al., 2000). Этот проект, как отмечалось ранее, составлял 2300 футов.
в длину с панелями 10 футов на 20 футов или 10 футов на 36 футов, все толщиной 8 дюймов (Федеральное шоссе
Администрация, 2009).
Секций с постнатяжением было 7 на 250 футов, 1 на 225 футов и 1.
на высоте 325 футов. Скорость монтажа панелей составила 25 панелей за 6 часов. На рис. 6.3 представлен
вид с воздуха на проект, а на рис. 6.4 показаны фотографии, сделанные в декабре 2010 г.
чтобы проиллюстрировать производительность на сегодняшний день. На момент фото тротуару было 9 лет.
были сняты графики, и в то время они не демонстрировали никаких проблем, кроме нескольких плотно закрытых
продольные трещины.Следует отметить, что на этой дороге ограничено интенсивное движение.
В проекте Caltrans 2004 года использовались 8-футовые сборные панели, в результате чего в общей сложности было
31 панель для достижения длины 248 футов. Толщина панелей составляла 10 дюймов.
требуется, чтобы соответствовать существующему дорожному покрытию. Каждая панель весила 21,5 тонны, что ограничивало
доставка одной панели за цикл грузовика к месту работы. Компенсаторы были разработаны
354
РУКОВОДСТВО ПО ИСПОЛЬЗОВАНИЮ СУЩЕСТВУЮЩЕГО ПОКРЫТИЯ НА МЕСТЕ И ДОСТИЖЕНИЮ ДОЛГОВЕЧНОСТИ
для отверстия ‰¤1 дюйм. Скорость монтажа панелей составила 15 панелей за 3 часа. Это было
по оценкам, расчетный срок службы будет варьироваться от 30 до 57 лет. Общая стоимость на месте
этого проекта стоила 224 доллара за ярд2.
Проект Миссури 2005 года был построен на I-57 недалеко от Сикестона. Продолжительность проекта составила
1010 футов (две полосы движения плюс обочины), в которых использовались панели размером 10 на 38 футов в диапазоне от 5,75
до 11,0 дюймов толщиной (более тонкие участки связаны с плечами). посттен-
было 4 секции по 250 футов. Скорость установки панелей составила 12 панелей за 6 часов.Сборные панели были размещены на проницаемом асфальтовом основании толщиной 4 дюйма.
Сборные панели
Сборные панели использовались для замены короткой секции железобетонных покрытий с соединениями.
(JRCP) в Миннесоте. Проект был построен на магистральном шоссе (TH) 62 во время
Июнь 2005 г. в районе Миннеаполис-Сент. Международный аэропорт Пола (Бернем,
2007). Первоначальное дорожное покрытие имело толщину 8 дюймов по стандарту JRCP.
Совместный ремонт произведен в 1986 г.,
но около 20 лет спустя тротуар нуждался в дополнительной реабилитации.В
В 2005 г. на ТД-62 был произведен бетонный восстановительный ремонт, а также добавлены
Рисунок 6.3. Участок PPCP: передняя дорога Texas I-35.
355
НОВАЯ ТЕХНОЛОГИЯ ПОКРЫТИЯ
сборный испытательный участок (рис. 6.5). Сборный испытательный участок имел длину 216 футов на 12 футов.
широкий, для чего потребовалось 18 панелей (система сборного железобетона Fort Miller Co.). Каждая панель была
12 футов в длину, 12 футов в ширину и 9,25 дюйма в толщину. Сборные панели не были привязаны к
соседняя полоса JRCP, и они не были предварительно натянуты; скорее они были прибиты к
поперечные суставы.Испытательный участок был отшлифован примерно через 5 месяцев после строительства с
результаты международного индекса шероховатости (IRI) приведены в таблице 6.1. Передача нагрузки
измерения эффективности для поперечных соединений составляли от 90% до 95% в течение одного года. после строительства.
ТАБЛИЦА 6.1. ОБЗОР РЕЗУЛЬТАТОВ IRI ДЛЯ СБОРНЫХ ПАНЕЛЕЙ, МИННЕСОТА TH-62
Среднее время и активность IRI для обеих колесных дорожек (дюймы/миля)
ТН-62 до постройки 150
Новые сборные панели (осень 2005 г.) 140
После шлифовки панелей (осень 2005 г.) 76
Шесть месяцев после измельчения (апрель 2006 г.) 50
Источник: После Бернема, 2007 г.Рисунок 6.4. Участок PPCP, передняя дорога Texas I-35, декабрь 2010 г.
Фотографии: Джо Махони.
Типичный продольный
трескаться. Продольная трещина
(крупный план).
356
РУКОВОДСТВО ПО ИСПОЛЬЗОВАНИЮ СУЩЕСТВУЮЩЕГО ПОКРЫТИЯ НА МЕСТЕ И ДОСТИЖЕНИЮ ДОЛГОВЕЧНОСТИ
Потенциал для долгосрочной работы
Сборные железобетонные покрытия демонстрируют значительные перспективы. Отслеживание производительности
существующие тротуары необходимы. Стоимость и сроки строительства, вероятно, снизятся по мере увеличения
строятся проекты.
ГИБКИЕ ИЛИ КОМПОЗИТНЫЕ ПОКРЫТИЯ
Покрытие, модифицированное смолой (RMP)
RMP был описан Алрихом и Андертоном (1991) как «полужесткий, полужесткий». поверхностный курс.Это слой HMA открытого типа с содержанием воздушных пустот от 25% до 30%.
которые заполняются цементным раствором, модифицированным смолой. Как отмечают Альрих и
Anderton, «RMP — прочный и долговечный облицовочный материал, который сочетает в себе гибкость
характеристики асфальтобетонного материала с топливной, абразивной и износостойкостью.
бетона на портландцементе». Первоначальная концепция RMP была разработана в
Европа в 1960-е годы.
Основной процесс RMP выглядит следующим образом (согласно Ahlrich and Anderton, 1991):
1.Поместите слой HMA с открытой градацией. Этот слой определяет толщину РМП.
2. Залейте цементный раствор (портландцемент, мелкий заполнитель, воду и добавку смолы).
тив) на HMA, шваброй по поверхности и вибрацией в пустоты с
малый вибрационный каток.
3. Отверждайте затирочный материал стандартным распыляемым отвердителем с белым пигментом.
Сборные панели
JRCP переулок
Рисунок 6.5. Секция сборного железобетона, Миннесота, TH-62.
Источник: Бернхэм, 2007 г.
357
НОВАЯ ТЕХНОЛОГИЯ ПОКРЫТИЯ
Альрих и Андертон (1991) сообщили об ускоренных испытаниях дорожного покрытия с использованием
устройство FHWA ALF в Turner Fairbank.В торговле использовались сдвоенные шины, загруженные до
19 000 фунтов при давлении в шинах 140 фунтов на квадратный дюйм. После 80 000 проходов поверхность RMP
хорошо зарекомендовал себя без ухудшения.
Во время испытаний Инженерного корпуса армии США стоимость RMP колебалась
между традиционной HMA и PCC.
Более поздние исследования RMP включают 5-летнюю оценку производительности Bat-
тей и Уиттингтон (2007) в штате Миссисипи (см. построение RMP, рис. 6.6).
Три системы были оценены для использования на сигнальных перекрестках на US-72 в Коринфе,
Миссисипи:
1.слой износа RMP толщиной 2 дюйма,
2. Ультратонкий белый топпинг толщиной 3 дюйма и
3. Наложение ХМА на связующее ПГ 82-22.
Сравнение этих трех вариантов проводилось через 5 лет службы.
Порядок сравнения показал, что в целом лучшим вариантом был PG 82-22 HMA. оверлей, за которым следует ультратонкая белая глазурь, и в последнюю очередь RMP. Однако оценка-
Исследование также показало, что RMP не проявлял колейности, но был самым дорогим.
Ультратонкий белый топинг начал трескаться через 2 года службы и в конечном итоге был
сняты со службы.RMP также проходит оценку в Южной Африке. Фотографии, показанные на рис. 6.7, были
снято в 2009 г. на РМП, который 2 года эксплуатировался на станции взвешивания грузовых автомобилей.
(при этом во всех транспортных потоках участвуют грузовики, движущиеся с малой скоростью). По состоянию на 2009 год ни рутинга, ни
произошло значительное растрескивание.
Рисунок 6.6. Строительство РМП. Нанесение раствора на НМА открытого типа.
Источник: Бэтти и Уиттингтон, 2007 г.
358
РУКОВОДСТВО ПО ИСПОЛЬЗОВАНИЮ СУЩЕСТВУЮЩЕГО ПОКРЫТИЯ НА МЕСТЕ И ДОСТИЖЕНИЮ ДОЛГОВЕЧНОСТИ
Потенциал для долгосрочной работы
RMP кажется системой, подходящей только для курсов ношения (в основном из-за
стоимость и сложности строительства). Производительность кажется довольно хорошей, особенно
относительно устойчивости к колееобразованию, но превзойдет ли RMP традиционные плотные
оценка HMA пока неясна. Надеюсь, те, кто построил этот тип тротуара
будут продолжать следить за производительностью и сообщать о своих выводах.
СРАВНЕНИЕ СТОИМОСТИ
Сравнение затрат на новые технологии представляет собой проблему на нескольких уровнях, поскольку
их использование в экспериментальных проектах, ограниченное производство, обменные курсы и т. д.
Кроме того, затраты на материалы и строительство тротуаров довольно изменчивы, а
неуловимая, актуальная национальная статистика.Таким образом, фон, основанный на полученных затратах
от Департамента транспорта штата Вашингтон (WSDOT) для асфальта
бетон и бетонные материалы для мощения показаны ниже (стоимость на сентябрь
2010 г.; WSDOT, 2010), а также имеющиеся данные по другим проектам (см. Таблицу 6.2).
В Таблице 6.3 приведены расчетные сроки службы и затраты на типичные методы консервации.
менты, разработанные в рамках исследования ШРП 2 R26, которые обеспечивают дополнительную стоимость
перспективы.
РЕЗЮМЕ
Три новые технологии, проиллюстрированные в этом документе, являются лишь примером
перспективные разработки дорожного покрытия.Соответствуют ли проиллюстрированные концепции в конечном счете
широкое распространение долгосрочных вариантов обновления пока неясно. В национальном масштабе система
необходимы тематические отчеты по этим типам технологий (наряду с другими, которые еще предстоит
выявлено).
(а) (б)
Рисунок 6.7. Покрытие, модифицированное смолой. (a) Модифицированное смолой дорожное покрытие на станции взвешивания грузовиков на трассе N3 рядом с
Йоханнесбург, ЮАР. (b) Крупный план цемента, модифицированного смолой, который был помещен на HMA с открытой маркировкой.
Фотографии: Джо Махони.
359
НОВАЯ ТЕХНОЛОГИЯ ПОКРЫТИЯ
ТАБЛИЦА 6.2. ОЦЕНКА СТОИМОСТИ ТРАДИЦИОННЫХ И НОВЫХ ТЕХНОЛОГИЙ
Традиционные системы мощения Типичная базовая стоимость на тонну База на ярд2
Асфальтобетон (HMA) толщиной 12 дюймов 64 долл. США за тонну 64 долл. США за тонну 42 долл. США за ярд2
Бетон на портландцементе толщиной 12 дюймов $130/ярд3 $64/тонна $43/ярд2
Накладка HMA толщиной 2 дюйма 64 долл. США за тонну 64 долл. США за тонну 7 долл. США за ярд2
Чип-уплотнение — $2/ярд2
Стоимость проекта Прочая информация Основа на ярд2
UTCRCP (шоссе N1, Южная Африка, завершено в июне
2010). Секция содержала ˆ 16 000 м2 дорожного покрытия UTCRCP.
590 рандов/м2 ~85$/м2 ~70$/ярд2
TH-62 Миннесота: сборные панели 12 футов х 12 футов х 9.25 дюймов
(завершен в июне 2005 г.). Стоимость/ярд2 не включает управление движением,
шлифовка и полоскание. Стоимость/ярд2 включает удаление
из ранее существовавших 8-дюймовых. JRCP. Содержит 288 ярдов2 сборного железобетона
панели.
— Тестовый участок был небольшим,
≈ 288 ярдов2
$575/ярд2
Сборный испытательный участок Caltrans с предварительным натяжением, построенный
в 2004 году.
— Тестовый раздел был
≈ 1000 ярдов2
$224/ярд2
Примечание: за ярд2 на основе равной толщины HMA и PCC. Учитывались только материальные затраты. Предполагается
плотность составляет 145 фунтов/фут3 для HMA и 150 фунтов/фут3 для PCC.
ТАБЛИЦА 6.3. ОЖИДАЕМАЯ ЭФФЕКТИВНОСТЬ И ЗАТРАТЫ, СВЯЗАННЫЕ С ВЫБОРОМ
ПРОЦЕДУРЫ ДЛЯ СОХРАНЕНИЯ ПОКРЫТИЯ
Тип покрытия
Ожидаемое лечение
Производительность (лет) Ориентировочная стоимость единицы
Существующее покрытие HMA с покрытием
Заполнение трещины 2–4 0,10–1,20 долл. США/фут
Герметизация трещин 3–8 0,75–1,50 долл. США/фут
Шламовое уплотнение 3–5 0,75–1,00 долл. США/ярд2
Стружкодробление, одинарный ряд 3–7 1,50–4,00 долл. США/ярд2
Тонкое покрытие HMA (плотное градуированное; толщина 0,875–1,5 дюйма) 5–12 3,00–6,00 долл. США/ярд2
Профильное фрезерование 2–5 0,35–0,75 долл. США/ярд2
Ультратонкий белый топпинг (2–4 дюйма.толстый) нет данных $15,00–$25,00/ярд2
Существующее покрытие PCC
Повторная герметизация швов 2–8 $1,00–2,50 $/фут
Заделка трещин 4–7 0,75–2,00 долл. США/фут
Алмазная шлифовка 8–15 $1,75–5,50 $/ярд2
Заделка бетона неполной глубины 5–15 75–150 долл. США/ярд2
(на основе исправленной области)
Заделка бетона на всю глубину 5–15 от 75 до 150 долл. США/ярд2
(на основе исправленной области)
Модернизация дюбеля 10–15 от 25,00 до 35,00 долл.
/бар
Тонкая накладка HMA (толщина 0,875–1,5 дюйма) 6–10 от 3,00 до 6,00 долл./ярд2
Источник: По Пешкину и др., 2010.
360
РУКОВОДСТВО ПО ИСПОЛЬЗОВАНИЮ СУЩЕСТВУЮЩЕГО ПОКРЫТИЯ НА МЕСТЕ И ДОСТИЖЕНИЮ ДОЛГОВЕЧНОСТИ
ИСПОЛЬЗОВАННАЯ ЛИТЕРАТУРА
Альрих, Р.и Г. Андертон. «Строительство и оценка дорожного покрытия, модифицированного смолой»,
Заключительный отчет, технический отчет GL-91-13, Инженерный корпус армии США, Виксбург, штат Миссисипи,
1991.
Бэтти Р. и Э. Уиттингтон. «Отчет о строительстве, испытаниях и производительности
Демонстрационный проект дорожного покрытия, модифицированного смолой, отчет FHWA/MS-DOT-RD-07-137,
Департамент транспорта штата Миссисипи, Джексон, 2007 г.
Бернхэм, Т. «Сборные бетонные панели для дорожного покрытия на магистральном шоссе 62 в Миннесоте — первый
Отчет об эффективности за год, MN/RD 2007-19, Министерство транспорта Миннесоты,
св.Пол, 2007 год.
Эбельс Л.-Дж. и Р. Бургер. Испытание новой технологии бетонного покрытия на N1
Автострада. Журнал гражданского строительства, Vol. 18, № 7, август 2010 г., с. 50.
Федеральное управление автомобильных дорог (FHWA). «Сборное предварительно напряженное бетонное покрытие для
Реконструкция и восстановление существующих покрытий, технология бетонных покрытий
Программа Федерального управления автомобильных дорог, 2009 г.
Каннемейер Л., Б. Перри, П. Штраус и Л. дю Плесси. «Сверхтонкий CRCP: Моделирование,
Тестирование в рамках ускоренных испытаний дорожного покрытия и подача заявки на автомобильные дороги.†Представлено на
9-я Международная конференция по бетонным покрытиям, Сан-Франциско, 17–21 августа 2008 г.
Куо С., Дж. Армагани и Д. Шерлинг. «Ускоренные испытания дорожного покрытия
Ультратонкое армированное волокном бетонное покрытие, заполнитель из переработанного бетона и заделка
Материалы», Proc., Первая международная конференция по ускоренным испытаниям дорожного покрытия, Рино,
Нев., 1999.
Меррит Д., Б. Маккалоу, Н. Бернс и А. Шиндлер. «Возможность использования сборного железобетона
Бетонные панели для ускорения строительства дорожного покрытия», отчет об исследовании 1517-1,
Центр транспортных исследований Техасского университета в Остине, 2000 г.
Меррит Д., Б. Маккалоу и Н. Бернс. Проектирование-конструкция сборного, предварительно напряженного
Бетонное покрытие межштатной автомагистрали 10, Эль-Монте, Калифорния. Журнал PCI, Vol. 50, № 2,
Март-апрель 2005 г.
Пешкин Д., К. Смит, А. Уолтерс, Дж. Крстуловид, Дж. Моултроп и К. Альварадо.
«Руководство по сохранению дорог с интенсивным движением», Проект окончательного руководства.
линии, проект R26, SHRP 2, Совет по транспортным исследованиям национальных академий,
Вашингтон, округ Колумбия, 2010 г.
Департамент транспорта штата Вашингтон (WSDOT).«Тенденции в Highway Mate-
риальные расходы», Департамент транспорта штата Вашингтон, Олимпия, 21 октября 2010 г.
http://www.wsdot.wa.gov/biz/construction/CostIndex/pdf/constructioncosts.pdf.
Проектирование и технология дорожного покрытия, Управление и технология дорожного покрытия и дренажа, Инженерное дело
Чтобы помочь в экономичном и эффективном проектировании и строительстве дорожных покрытий, NJDOT представляет следующие руководства, презентации, веб-ссылки и примеры:
- Консервация дорожного покрытия
Подразделение NJDOT по управлению и технологиям дорожного покрытия и дренажа продвигает использование методов консервации дорожного покрытия на дорогах штата для повышения безопасности, повышения долговечности, улучшения качества обслуживания клиентов и минимизации затрат.Восстановление покрытия необходимо для поврежденных дорог, но сохранение покрытия может продлить срок службы покрытия для государственных автомагистралей в хорошем и удовлетворительном состоянии. Для получения дополнительной информации посмотрите видео или прочитайте описание на ссылки ниже:
- Обработка поверхности с высоким коэффициентом трения
- Руководство по проектированию дорожного покрытия
- Рекомендуемые входные параметры проектирования для метода проектирования AASHTO 1993 г.
- Darwin ME Руководство по анализу и проектированию дорожного покрытия для NJDOT
- Блок-схема выбора смеси
- Инструмент для проектирования гибких покрытий
- Примеры проектирования дорожного покрытия
- Часто задаваемые вопросы (FAQ)
- Полезные ссылки NJDOT для тротуаров
- Полезные звенья для асфальтового покрытия
- Полезные звенья для бетонного покрытия
- Другие полезные звенья для тротуаров
Примеры конструкции
Композитное покрытие дорожного покрытия (pdf 28k)Гибкое покрытие (pdf 16k)
Гибкое покрытие дорожного покрытия (pdf 23k)
Презентации дорожного покрытия
Презентации и/или обучение предоставлены для справочных целей и могут быть не применимы в полной мере к конкретным проектам.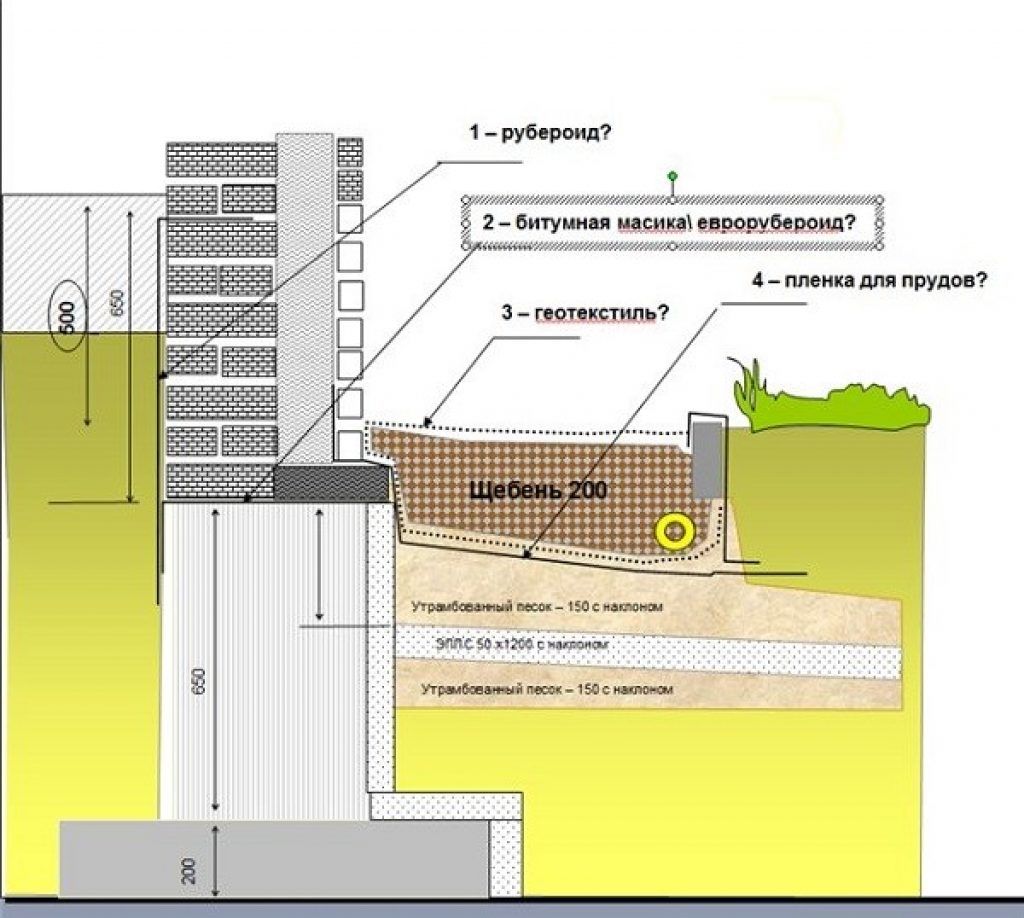
Текущий
В архиве
Загрузите следующие презентации:
Демонстрация программного обеспечения (swf 373k)Программное обеспечение: NJ Companion Manual to AASHTO 1993 Design Guide (swf 1.3м)
Влияние технологии укладки, материалов покрытия и конструкций на усталостные свойства двухслойных покрытий
Технология укладки двухслойного покрытия, являющаяся новой технологией строительства асфальтобетонных покрытий, в течение нескольких лет привлекала все большее внимание исследователей. Однако лишь немногие исследования были сосредоточены на влиянии толщины слоя асфальтобетонного покрытия и сочетаний типов смесей на усталостные свойства двухслойного покрытия. Поэтому в данной работе изучались усталостные свойства двухслойных и традиционно асфальтобетонных покрытий.Влияние двух технологий укладки, трех комбинаций смесей и двух комбинаций толщины слоя асфальта на усталостные свойства асфальтовых покрытий было изучено с помощью испытаний балки на изгиб, а уравнение усталости различных асфальтовых покрытий было установлено с использованием двухпараметрического распределения Вейбулла. Впоследствии усталостная долговечность различных дорожных одежд сравнивалась и анализировалась при одной и той же циклической нагрузке. Результаты показывают, что прочность на изгиб и усталостная долговечность двухслойного покрытия увеличились по меньшей мере на 10% и 54% соответственно по сравнению с аналогичными показателями конструкции дорожного покрытия с традиционным покрытием.Качество соответствия уравнения, полученного с использованием распределения Вейбулла, превысило 0,90.
Для традиционной технологии укладки, по сравнению с комбинацией структуры дорожного покрытия из 4 см поверхностного слоя AC-13/6 см нижнего слоя AC-20, усталостная долговечность 3 см поверхностного слоя AC-13/7 см AC- 20 нижний слой может быть увеличен не менее чем на 8%, в то время как усталостная долговечность других конструкций дорожной одежды значительно снижается. Результаты также показывают, что усталостная долговечность двухслойной дорожной одежды с 3-сантиметровым верхним слоем AC-13 и 7-сантиметровым нижним слоем AC-20 может быть увеличена не менее чем на 114 % по сравнению с традиционным покрытием. структура (4 см поверхностный слой АС-13/6 см нижний слой АС-20).Кроме того, можно повысить усталостную долговечность других конструкций дорожного покрытия. Для эффективного увеличения усталостной долговечности асфальтового покрытия рекомендуется двухслойная конструкция покрытия с сочетанием 3-сантиметрового верхнего слоя AC-13 и 7-сантиметрового нижнего слоя AC-20.
1. Введение
Конструкции и типы материалов дорожного покрытия существенно влияют на усталостную долговечность асфальтового покрытия [1–4]. Поверхностный слой (4 см АС-13), средний слой (6 см АС-20) и нижний слой (8–12 см АС-25, АТБ-25 или АТБ-30) составляют основное асфальтобетонное покрытие. структура высококлассных автомобильных дорог Китая [5, 6].Кроме того, комбинация 5-сантиметрового поверхностного слоя AC-13 и 6-7-сантиметрового нижнего слоя AC-20 в основном используется в качестве типичной конструкции Национальной системы магистральных автомобильных дорог Китая [5, 6]. Большинство асфальтовых покрытий было уложено с использованием традиционной технологии укладки, то есть послойной укладки и послойного уплотнения из-за нехватки строительной техники. В полевых условиях между структурными слоями асфальта обычно разбрызгивают липкое масло для покрытия, чтобы улучшить силу сцепления между слоями асфальтобетона [7, 8].Однако, несмотря на то, что липкое масло для покрытия может в некоторой степени улучшить адгезию между двумя конструкционными слоями, верхний слой горячей асфальтовой смеси для дорожного покрытия не может быть встроен в нижний слой, который был охлажден и уплотнен.
Следовательно, эффект выдавливания заполнителей между двумя структурными слоями плохой, а их связующее действие слабое. Плохие границы раздела «заполнитель-вяжущее» и «заполнитель-заполнитель» приводят к плохой механической прочности, влагочувствительности и плохим характеристикам асфальтобетона при высоких и низких температурах [9-11].Это серьезно влияет на надежность конструкции дорожной одежды и долговечность асфальтобетонного покрытия [12], тем самым увеличивая стоимость строительства и обслуживания дорожного покрытия. Кроме того, при традиционном укладке трудно избежать многих недостатков, таких как быстрое рассеивание тепла, длительные сроки строительства и низкая эффективность работы строительной техники.
Технология двухслойной укладки асфальтобетонных покрытий, являющаяся новой строительной технологией, одновременно завершает укладку и укатку двух конструктивных слоев [13, 14].Основное преимущество этой технологии укладки состоит в том, что одновременная укладка и укатка двухслойной асфальтобетонной конструкции позволяет эффективно избежать контакта «холодной и горячей комбинации» между двумя структурными слоями, созданными при традиционном укладке, и гарантирует, что два слоя асфальта бетон одновременно укладывают и уплотняют с условием «горячего и горячего» контакта. Таким образом, асфальт в смесях верхнего и нижнего слоев может полностью соприкасаться друг с другом, а заполнители в смесях верхнего и нижнего слоев могут экструдироваться вместе во время строительства, что приводит к хорошей адгезии и экструзии между слои смеси [15, 16].Кроме того, при двухслойной укладке не применяется межслойная обработка, что не только экономит использование липкого масла и сокращает период строительства, но и принципиально решает проблему разрыва между слоями традиционно уложенного покрытия, тем самым обеспечивая хороший эффект сцепления между слоев [15, 16]. Существенны и другие преимущества, такие как снижение температурных потерь асфальтобетонной смеси при строительстве и отсутствие ограничения по принципу 2,5–3,0-кратного соотношения толщины конструкции дорожной одежды к номинальному максимальному размеру частиц заполнителя в асфальтобетонной смеси. [15–17].В настоящее время Швеция, Нидерланды и Германия освоили передовую технологию двухслойного мощения. В Германии высококачественное дорожное покрытие с двухслойной конструкцией дорожного покрытия достигло ~4 млн м 2 , и дорожное покрытие используется хорошо.
Процесс двухслойной укладки также одобрен строительными нормами европейских стран, таких как Германия [18].
В последнее время, в связи с разработкой и применением оборудования для укладки двойного слоя, исследователи дорожного строительства провели ряд исследований асфальтобетонных смесей с технологией укладки двойного слоя.Гросманн и др. считают, что двухслойная технология укладки способствует улучшению эффекта межслойного сцепления слоев асфальта [19]. Мюллер обнаружил, что двухслойная технология укладки полностью использует теплоемкость, хранящуюся в асфальтовой смеси нижнего слоя, тем самым позволяя асфальтовой смеси верхнего слоя легко достигать хорошего состояния уплотнения [20]. Морган и др. исследовали возможность применения технологии двухслойного покрытия для двухслойного асфальтобетонного покрытия с большими зазорами. Результаты показали, что было возможно и более экономично применять эту технологию мощения при строительстве асфальтового покрытия с большими зазорами. Более того, эта технология не только повысила скорость строительства и уменьшила потери температуры, но и обеспечила лучшую плотность асфальтобетонной смеси [21]. Фюлеки считал, что двухслойное асфальтовое покрытие выгодно для улучшения эффекта сцепления заполнителя между слоями, тем самым помогая противостоять относительному смещению между слоями, вызванному напряжением сдвига, создаваемым транспортной нагрузкой [22]. Куэннан сообщил, что технология укладки асфальта с двумя подъемами не только помогает нам повысить долговечность асфальтового покрытия, но также повышает его способность противостоять транспортной нагрузке и повреждению покрытия [23].Ван сравнил свойства межслойного сдвига керна, пробуренного из традиционного и двухслойного дорожного покрытия, используя испытание на косой сдвиг. Результаты показали, что характеристики сдвига керна, пробуренного из двухслойного асфальтового покрытия, значительно увеличились по сравнению с традиционным покрытием, а данные испытаний были более стабильными.
Кроме того, лабораторные испытания на колейность также показали, что сопротивление деформации двухслойных образцов с твердым покрытием было явно лучше [24].Карабахи и др. обнаружили, что по сравнению с обычными асфальтовыми покрытиями двухслойные асфальтовые покрытия показали лучшую устойчивость к колееобразованию и прочность на сдвиг [25]. Используя полевые испытания и лабораторные анализы, Ли продемонстрировал, что двухслойное покрытие может замедлить процесс снижения температуры и улучшить эффект уплотнения асфальтовых покрытий [26]. Лю и др. обнаружили, что по сравнению с покрытиями, построенными с использованием традиционной технологии строительства, прочность на сдвиг двухслойных асфальтовых покрытий была улучшена, а эффективное время уплотнения увеличено [27].Ван и др. создала модель прогнозирования потери температуры смеси методом конечных элементов, основанную на теории теплопроводности, для изучения эффективного времени прокатки и температуры прокатки асфальтобетонной смеси с технологией двухслойного покрытия.
Кроме того, был построен тестовый участок для проверки модели. Результаты показали, что асфальтобетонная смесь с двухслойным покрытием требует более длительного эффективного времени укатывания [28]. Ян и др. проанализировали закон распределения напряжений между слоями двухслойного покрытия с использованием метода конечных элементов и изучили усталостные характеристики двухслойного покрытия с помощью лабораторных испытаний.Результаты показали, что двухслойная технология укладки способствует снижению межслойного горизонтального напряжения и повышает усталостную прочность асфальтобетонного покрытия [29]. Цзян и др. изучали влияние технологии мощения, материалов покрытия и конструкций на сопротивление колееобразованию двухслойных покрытий с помощью лабораторных испытаний. Результаты показали, что комбинация 3-сантиметрового поверхностного слоя AC-16 и 7-сантиметрового нижнего слоя AC-20 может улучшить устойчивость асфальтовых покрытий к колееобразованию при высоких температурах [30].
Вышеупомянутые исследования, несомненно, способствовали пониманию технологии двухслойного мощения и развитию таких технологий. Тем не менее, связанные исследования, которые были ограничены существующими конструкциями дорожных покрытий и комбинациями типов смесей, в первую очередь изучали влияние этой технологии укладки на сцепление между слоями асфальта, закон дисперсии температуры во время строительства, характеристики сдвига, дорожные характеристики и т. д. Более того, исследования сведения о влиянии толщины слоя асфальтобетонного покрытия и сочетаний типов смесей на усталостные свойства двухслойного покрытия немногочисленны.
Усталостная долговечность является ключевым эксплуатационным параметром асфальтобетонных покрытий [31, 32]. Усталостные трещины асфальтового покрытия из-за недостаточной усталостной долговечности постепенно перерастут в трещины по всей конструкции дорожного покрытия. Кроме того, это снизит водостойкость, комфортность и безопасность асфальтового покрытия; сократить срок службы дорожного покрытия; увеличить периодичность ремонта дорожного покрытия и сроки капитального и среднего ремонта; и увеличить стоимость жизненного цикла дороги [33–35]. В настоящее время нет общепринятых стандартизированных лабораторных испытаний на усталостное растрескивание для составления рутинных смесей или целей скрининга горячей асфальтобетонной смеси на трещиностойкость [36]. Во всем мире обычно используются методы испытаний, в основном, метод непрямого растяжения, метод изгиба трапециевидной консольной балки и метод изгиба балки. Непрямой метод растяжения является наиболее распространенным при испытании асфальтобетонных смесей на раннюю усталость. Однако из-за некоторых недостатков режима испытаний от него постепенно отказываются исследователи усталости асфальтобетонных смесей.Испытания на изгиб трапециевидной консольной балки и испытания на усталость при изгибе балки являются наиболее популярными методами испытаний на усталость небольших образцов. Первый в основном используется в Европе, а второй послужил основой для многочисленных экспериментальных исследований и применений в США, Южной Африке и Австралии. Образец для испытания балки на изгиб прост в изготовлении, а операция испытания проста по сравнению с испытанием на усталость при изгибе трапециевидной консольной балки.
Кроме того, испытание на усталость при изгибе балки обладает отличной чувствительностью с точки зрения проверки влияющих факторов и надежности [37].Таким образом, в этом исследовании испытание на усталость при изгибе балки используется для изучения влияния толщины конструкционного слоя асфальта и комбинаций типов смеси на усталостные свойства двухслойного дорожного покрытия. Влияние двух комбинаций толщины (поверхностный слой 3 см/нижний слой 7 см и поверхностный слой 4 см/нижний слой 6 см) и трех комбинаций типа смеси (поверхностный слой АС-13/нижний слой АС-20, Поверхностный слой АС-16/нижний слой АС-20 и поверхностный слой АС-16/нижний слой АС-25) на усталостные свойства двухслойного дорожного покрытия изучались посредством лабораторных испытаний.Впоследствии, исходя из оптимальных усталостных характеристик при двухслойной технологии укладки, рекомендуется сочетание типа смеси и толщины слоя дорожной одежды.
2. Материалы и методы
2.1. Материалы
2.1.1. Асфальт
В этом исследовании в асфальтовой смеси использовался сингапурский дорожный нефтяной битум Esso A-70, который был получен из города Шанлуо, провинция Шэньси, Китай. Кроме того, стирол-бутадиен-стирол-(СБС-) (I-C) модифицированный асфальт, собранный в городе Карамай, Синьцзян-Уйгурский автономный район, Китай, использовался в качестве связующего материала между двумя слоями асфальта.Технические характеристики асфальта, использованного в данном исследовании, приведены в таблице 1. )
2.1.2. Заполнитель
Крупный заполнитель асфальтовой смеси поверхностного слоя, использованный в этом исследовании, представлял собой амфиболит, полученный из города Шанлуо, провинция Шэньси, Китай, а крупным заполнителем асфальтовой смеси нижнего слоя был известняк из города Луонань, провинция Шэньси, Китай.Мелким заполнителем асфальтобетонной смеси поверхностного и нижнего слоев был известняк из города Луонань, провинция Шэньси, Китай. Минеральный порошок, использованный в этом исследовании, представлял собой порошок известняковой руды из округа Луонань, провинция Шэньси, Китай. Все заполнители, использованные в данном исследовании, удовлетворяли техническим условиям устройства автомобильных асфальтобетонных покрытий (JTG F40-2004) [17], а их технические показатели не учитывались.
2.2. Исследовательские программы
2.2.1. План испытаний
Для изучения влияния различных типов смесей на усталостные свойства асфальтовых покрытий были выбраны четыре типа асфальтовых смесей: АС-13, АС-16, АС-20 и АС-25.Асфальтовая смесь АС-13 или АС-16 использовалась в поверхностном слое, тогда как асфальтобетонная смесь АС-20 или АС-25 использовалась в нижнем слое. В таблице 2 приведены градации асфальтобетонных смесей, использованных в данном исследовании. Кроме того, в табл. 3 приведены расчетные данные асфальтобетонных смесей, в которых VV, VFA, VMA, MS и FL определены как объем воздушных пустот, объем пустот, заполненных асфальтом, пустот в минеральном заполнителе, устойчивость по Маршаллу и текучести асфальтобетонной смеси соответственно. Примечательно, что все типы асфальтобетонных смесей, использованных в данном исследовании, были рассчитаны по стандартной методике Маршалла.
|
|
Для изучения последствий различных комбинаций структуры асфальтирования на усталостных свойствах асфальтовых покрытий. Общая толщина асфальта была установлен на 100 мм, и были выбраны два типа комбинаций конструкции дорожной одежды с различной толщиной поверхностного и нижнего слоев: поверхностный слой 3 см/нижний слой 7 см и поверхностный слой 4 см/нижний слой 6 см.
Для изучения влияния различных технологий укладки на усталостные свойства асфальтобетонных покрытий было проведено сравнение двух технологий укладки: традиционной и двухслойной.
2.2.2. Методы подготовки образцов
Процесс подготовки образцов смеси по традиционной технологии укладки для испытаний на усталость в лаборатории был разделен на четыре основных этапа: (1) Формование обрезной плиты нижнего слоя: обрезная плита размером 300 мм × 300 мм ×60 /70 мм (длина × ширина × высота) была произведена катком с оптимальным содержанием асфальта.Вальцеуплотняющая машина останавливается, когда плотность вырезанных образцов плиты и стандартных цилиндрических образцов становится одинаковой. Затем образцы нарезанных досок выдерживали при комнатной температуре не менее 24 часов (рис. 1(а)). мм (длина × ширина × высота) пресс-форма для обрезной доски. Затем на поверхность обрезной доски равномерно распылили модифицированный СБС асфальт в количестве 0,45 кг/м 2 с отверждением в течение не менее 2 часов (рис. 1(б)).(3) Формование обрезной плиты поверхностного слоя: определенный вес асфальтобетонной смеси для поверхностного слоя помещается в форму обрезной плиты и уплотняется катком до тех пор, пока высота плиты не станет 100 мм (рис. 1(c)). (4) Изготовить образец балки: подготовленную доску (300 мм × 300 мм × 100 мм) разрезали на образцы балки размером 250 мм × 100 мм ×100 мм (длина ×ширина ×высота (рис. 1(d))
Процесс подготовки образцов смеси, изготовленной по технологии двухслойного укладки, для испытаний на усталость в лаборатории был разделен на три основных этапа: (1) Распределение смесей нижнего слоя: определенная масса асфальтобетонной смеси нижнего слоя. была помещена в форму для обрезной плиты (300 мм × 300 мм × 100 мм) и затем помещена в печь при 165°C после первоначального прессования с помощью молотка (рис. 2(a)) (2) Распределите смеси поверхностного слоя и уплотнение: определенная масса асфальтобетонной смеси поверхностного слоя помещается в форму для обрезной доски и компостируется. прокатным прессом до достижения высоты 100 мм (рис. 2(b) и 2(c)) (3) Изготовление образца балки: подготовленная обрезная плита (300 мм × 300 мм × 100 мм) разрезается на балку образцы размером 250 мм × 100 мм × 100 мм (длина × ширина × высота), как показано на рисунке 2(d)
2.2.3. Метод испытания на усталость
Испытания на усталость, используемые для оценки усталостных свойств асфальтобетонных смесей в лаборатории, в основном включали испытание на усталость при изгибе балки, непрямое растяжение и испытание на усталость при полукруглом изгибе [38, 39]. По сравнению с испытанием на усталость при непрямом растяжении и полукруглом изгибе процесс подготовки образца для испытания на усталость изгибающей балки более сложен, а разброс данных эксперимента более значителен. Более того, испытание на изгиб могло бы лучше имитировать стрессовые условия реальных конструкций дорожного покрытия, а результаты эксперимента можно было бы непосредственно использовать для проектирования конструкций асфальтобетонного покрытия.Однако, поскольку общая толщина конструкции асфальтобетонного покрытия составляла 100 мм, было трудно провести испытание на усталость с использованием испытания на усталость при непрямом растяжении или полукруглом изгибе. Кроме того, испытание на покрытие можно использовать для оценки устойчивости к растрескиванию асфальтовых покрытий, но устройства для испытания на покрытие в Китае мало [33–36]. Поэтому для изучения усталостных свойств асфальтобетонных покрытий было принято испытание на усталость при изгибе балки. На рис. 3 показана модель испытания на усталость, использованная в этом исследовании.
Как правило, для испытаний на усталость существуют два основных режима контроля: контролируемая деформация и контролируемая нагрузка. Для испытания на усталость с контролируемой деформацией усталостная долговечность материалов определяется как количество циклов нагрузки, соответствующее 50%-ному снижению жесткости; в то время как для испытания на контролируемое напряжение усталостная долговечность материалов определяется как число циклов нагружения, соответствующее разрушению образцов [40, 41]. Из-за неоднородности балки модуль балки нельзя было рассчитать на основе испытаний на усталость.Таким образом, в этом исследовании было использовано испытание на контролируемое напряжение, а усталостная долговечность балки была получена в соответствии с количеством циклов нагрузки, соответствующих разрушению образцов.
Испытание балки на усталость при изгибе было разделено на два основных этапа: (1) Испытание балки на изгиб. Прочность на изгиб образца балки (250 мм × 100 мм × 100 мм), полученного с использованием двухслойной и традиционной технологий укладки, измерялась с использованием система испытаний материалов (MTS). Температура испытания составляла 15°С, а скорость нагружения составляла 50 мм/мин.(2)Испытание на усталость при изгибе Испытание на усталость проводилось на MTS при 15°C. Была использована синусоидальная нагрузка. Диаграмма сигнала нагрузки, используемая в этом исследовании, показана на рисунке 4. Для поддержания контакта между индентором MTS и образцами во время испытания на усталость индентор прикладывал только вертикальное давление (без напряжения). Частота нагрузки синусоиды составляла 10 Гц. Значение циркуляционной характеристики ( R ) (определяемое как отношение максимального напряжения к минимальному напряжению) равнялось 0.1, и были выбраны пять уровней стресса: 0,3, 0,4, 0,5, 0,6 и 0,7. Примечательно, что критерии разрушения, принятые для испытаний на усталость, соответствуют разрушению образцов.
3. Результаты и обсуждение
3.1. Испытание балки на изгиб
Прочность на изгиб является основным параметром, используемым для определения уравнения усталости при изгибе. Испытание на изгиб балки повторяли шесть раз; в дальнейшем метод Граббса применялся для проверки и получения среднего значения результатов испытаний [42, 43].Реплики балки мотыги использовались для каждого материала в соответствии с условиями испытаний. Результаты испытаний на изгиб асфальтобетонных покрытий с различными технологиями укладки, типами смесей и структурной толщиной покрытия приведены в таблице 4, где P d и P t представляют собой прочность на изгиб образца бруса, изготовленного по двухслойной и традиционной технологиям мощения соответственно. Кроме того, P d / P t представляет собой отношение прочности на изгиб образца балки, полученной двумя технологиями укладки.
Как показано в Таблице 4, сопротивление изгибу образцов с двухслойным покрытием с теми же типами смеси и толщиной конструкции покрытия увеличилось не менее чем на 10 % по сравнению с сопротивлением образцов с традиционным покрытием. Межслойный контакт образцов традиционного мощения демонстрирует «холодное и горячее сочетание». В этом случае эффект межслойного склеивания обеспечивается, прежде всего, липким маслом; таким образом, достижение хорошего эффекта экструзии заполнителя между слоями асфальта затруднено. Напротив, межслойный контакт двухслойных образцов с твердым покрытием демонстрирует «горячее и горячее сочетание». В этом случае эффекты экструзии между слоями асфальта значительны, сливая асфальтовые смеси поверхностного и нижнего слоев в одно целое и способствуя формированию структурного скелета.Это основные причины лучшей устойчивости к изгибу двухслойных образцов с твердым покрытием. 3.2. Испытание на усталость при изгибеНа рис. 5 показан процесс испытания на усталость двухслойных балок с твердым покрытием. На основе данных, представленных в таблице 4, были рассчитаны максимальное и минимальное напряжения нагрузки. Затем была проверена усталостная долговечность образцов. В табл. 5 приведены результаты испытаний на усталость при изгибе образцов, изготовленных с использованием различных технологий укладки, типов смесей и толщины конструкции дорожной одежды.Обратите внимание, что реплики культиватора были использованы для каждого материала в соответствии с условиями испытаний.
Таблица 5 показывает, что коэффициент вариации () результатов испытаний на усталость составляет около 10%, что указывает на стабильность и надежность результатов испытаний. Кроме того, таблица 5 также показывает, что усталостная долговечность образцов двухслойного мощеного или традиционно мощеного бруса снижается по мере увеличения уровня напряжения. Кроме того, следует отметить, что результаты испытаний образцов на усталость неодинаковы даже при одинаковых уровнях напряжения.В этом случае трудно проанализировать данные об усталости и точно оценить, какая комбинация конструкции дорожного покрытия или технология укладки лучше. Недавно некоторые дорожные исследователи успешно применили распределение Вейбулла к анализу усталостной долговечности и обнаружили, что такое распределение особенно полезно для анализа надежности усталостной долговечности [44, 45]. Поэтому распределение Вейбулла использовалось для анализа данных испытаний на усталость двухслойных образцов балки в этом исследовании. Эквивалентная усталостная долговечность и вероятность отказа ( P ) соответствуют следующему уравнению [38, 39, 46]: Уравнение (1) может быть преобразовано в следующее уравнение после использования логарифмического преобразования: где 0 — параметр формы, u — параметр масштаба. Подставляя результаты испытаний на усталость, представленные в таблице 5, в модель распределения Вейбулла (уравнение (2)), ее коэффициенты, такие как м 0 , ln u и приведены в таблице 6.
|
от Таблицы 6 наблюдается, что значения R 2 модели распределения WIBULL больше 0.90. Эти наблюдения показывают, что результаты испытаний на усталость, рассмотренные с помощью модели распределения Вейбулла, являются надежными.
3.3. Уравнение усталости
В таблице 7 показана эквивалентная усталостная долговечность () образцов двухслойной балки при различных уровнях напряжения ( S ) и вероятности разрушения ( P ) после подстановки коэффициентов (приведенных в таблице 6) в уравнение Вейбулла модель распределения (уравнение (2)).
Связь между усталостной долговечностью и уровнем напряжения представлена следующим образом [38, 39, 46]: где N — усталостная долговечность образцов, S — уровень напряжения, использованный при испытании на усталость, а a и b — коэффициенты уравнения усталости.
Значение a представляет точку пересечения на продольной оси координатной оси уравнения усталости, отражающую усталостные характеристики образцов; чем больше значение a , тем лучше усталостные характеристики образцов. Значение b представляет собой абсолютное значение наклона уравнения усталости, отражающее чувствительность усталостных характеристик образцов к изменению уровня напряжения; чем меньше значение b , тем ниже чувствительность усталостных характеристик образцов к изменению уровня напряжения [39, 46].
Из уравнения (3) и комбинаций с использованием значений в таблице 7 уравнения усталости двухслойных образцов балки были установлены с использованием регрессионного анализа. В таблице 8 приведены коэффициенты регрессии a , b и R 2 уравнения (3).
|
Таблица 8 показывает, что коэффициенты корреляции R 2 уравнений усталостных уравнений образцов, выпускаемых с различными структурными комбинациями и технологиями мощения, не менее 0 .97. Эти результаты показывают, что существует хорошая двойная логарифмическая линейная зависимость между уровнем напряжения и усталостной долговечностью.
3.4. Анализ факторов влияния усталостных свойств
3.4.1. Анализ усталостной долговечности
Различные исследования показывают, что уровень растягивающего напряжения, создаваемого транспортной нагрузкой на асфальтовом покрытии, обычно составляет менее 0,45 [47]. Поэтому в данном исследовании усталостная долговечность образцов анализировалась при уровне напряжения 0.45. Однако отношение приложенной нагрузки к прочности материала на разрушение определяется как уровень напряжения. Таким образом, сравнение усталостной долговечности при одном и том же уровне напряжения не может точно выявить усталостные свойства различных материалов.
Таблица 4 показывает, что при уровне напряжения 0,45 нагрузка ( F ) традиционно уложенной комбинации 4-сантиметрового верхнего слоя AC-13/6-сантиметрового нижнего слоя AC-20 составляет 4,15 кН ( F = 0,45 × 9,23 кН = 4,15 кН). Поэтому оценка усталостной долговечности образцов с разными технологиями укладки, типами смесей и толщиной конструкции дорожной одежды при одинаковой нагрузке 4.15 кН более разумно. В таблице 9 приведены результаты усталостной долговечности образцов при одинаковой нагрузке.
|
3.4.2. Эффекты технологии укладки
Отношение ( N d / N t ) усталостной долговечности образцов с одинаковыми типами смеси и толщиной структуры, полученными двухслойным и традиционным 6.
Из рисунка 6 видно, что при нагрузке F = 4,15 кН усталостная долговечность образцов, изготовленных по технологии двухслойного мощения, увеличивается не менее чем на 54 % по сравнению с полученными по традиционной технологии мощения.Это связано с тем, что для технологии двухслойного укладки асфальтобетонная смесь верхнего и нижнего слоев представляет собой «горячую и горячую комбинацию» во время уплотнения. В этом случае заполнитель между поверхностным и нижним слоями асфальтовой смеси может образовывать замковое соединение, чтобы избежать разрывов между слоями асфальта. Таким образом, повышается целостность этой конструкции дорожного покрытия, снижается концентрация напряжений, создаваемых колесной нагрузкой, и улучшаются усталостные свойства асфальтового покрытия.
3.4.3. Влияние типов смесей и толщин конструкций
На рис. 7 показано соотношение ( N t / N c ) усталостной долговечности образцов с различной структурой покрытия по сравнению с комбинацией конструкции дорожного покрытия из 4-сантиметрового верхнего слоя АС-13 и 6-сантиметрового нижнего слоя АС-20, изготовленного по той же технологии укладки.
На рис. 7 показано, что по сравнению со стандартной конструкцией дорожного покрытия с традиционным покрытием (поверхностный слой AC-13 4 см/нижний слой AC-20 6 см) усталостная долговечность комбинации конструкции дорожного покрытия с традиционным покрытием 3 см Поверхностный слой AC-13/нижний слой AC-20 толщиной 7 см можно увеличить как минимум на 8%, в то время как усталостная долговечность других конструкций дорожного покрытия с традиционным покрытием значительно снижается.
Кроме того, отношение усталостной долговечности образцов с различными комбинациями конструкций дорожной одежды, изготовленных по технологии двухслойного покрытия Комбинация 4-сантиметрового поверхностного слоя AC-13 и 6-сантиметрового нижнего слоя AC-20, изготовленного по традиционной технологии мощения, показана на рис. 8.
На рис. Поверхностный слой AC-13/нижний слой AC-20 толщиной 6 см, изготовленный по традиционной технологии мощения, увеличивает усталостную долговечность всех двухслойных конструкций дорожного покрытия.Усталостная долговечность двухслойной конструкции дорожной одежды, состоящей из 3-сантиметрового верхнего слоя АС-13 и 7-сантиметрового нижнего слоя АС-20, может быть увеличена не менее чем на 114 %.
На рис. 8 также показано, что при одинаковой толщине конструкции и технологии двухслойного покрытия усталостная долговечность конструкции дорожной одежды, состоящей из поверхностного слоя АС-13 и нижнего слоя АС-20, выше, чем у АС-16. Комбинации поверхностного слоя/нижнего слоя AC-20 и поверхностного слоя AC-16/нижнего слоя AC-25.При одинаковых условиях испытаний усталостная долговечность асфальтобетонной смеси снижается с увеличением VV асфальтобетонной смеси; чем больше VV, тем меньше усталостная долговечность асфальтобетонной смеси [48–50]. Поверхностный слой комбинации поверхностный слой АС-13/нижний слой АС-20 представляет собой асфальтовую смесь АС-13, тогда как нижний слой такой же, как и в комбинации поверхностный слой АС-16/нижний слой АС-20. . Таким образом, относительно меньшая VV (табл. 3) асфальтобетонной смеси АС-13 по сравнению с асфальтобетонной смесью АС-16 может эффективно препятствовать расширению трещин, улучшая тем самым усталостные свойства смесей [48, 49].Кроме того, VV асфальтобетонных смесей поверхностного слоя и нижнего слоя комбинации поверхностный слой AC-13/нижний слой AC-20 меньше, чем VV комбинации конструкции дорожного покрытия из поверхностного слоя AC-16/нижнего слоя AC-25, тем самым уменьшая концентрацию напряжений в асфальтовом покрытии и развитие трещин, а также указывая на лучшие усталостные свойства [48, 49].
Кроме того, как показано на рис. 8, для комбинации типа смеси поверхностный слой AC-13/нижний слой AC-20 усталостная долговечность комбинации толщин поверхностного слоя 3 см/нижнего слоя 7 см больше. чем комбинация толщины 4-сантиметрового поверхностного слоя и 6-сантиметрового нижнего слоя.Значения толщины асфальтобетонной смеси нижнего слоя влияют на способность дорожной одежды к противоусталостному растрескиванию [51, 52]. Когда типы смесей одинаковы, увеличение толщины нижнего слоя может эффективно улучшить усталостные характеристики двухслойного дорожного покрытия [52]. Это основная причина, по которой комбинация конструкции дорожного покрытия из 3-сантиметрового поверхностного слоя и 7-сантиметрового нижнего слоя демонстрирует лучшую усталостную прочность, чем комбинация конструкции из 4-сантиметрового поверхностного слоя и 6-сантиметрового нижнего слоя.
4. Выводы
В этом исследовании изучалось влияние технологий укладки, материалов покрытия и конструкций на усталостные свойства двухслойного асфальтобетонного покрытия. На основании полученных результатов можно сделать следующие выводы: (1) Образцы асфальтобетонных смесей, изготовленные по технологии двухслойного укладки с теми же типами смесей и толщиной конструкции дорожного покрытия, демонстрируют более высокую прочность на изгиб и усталостную долговечность, чем образцы, изготовленные по традиционной технологии укладки.(2) Испытание на усталость при изгибе балки показывает высокую практичность, воспроизводимость и согласованность данных. Усталостная долговечность образцов из двухбалочной смеси подчиняется распределению Вейбулла, а уравнения усталости при различных технологиях укладки, комбинациях типов смесей и толщине конструкции покрытия эффективно отражают усталостную долговечность комбинированных образцов. (3) Усталостная долговечность комбинированных образцов. Комбинация 3-сантиметрового поверхностного слоя/7-сантиметрового нижнего слоя конструкции дорожного покрытия лучше, чем комбинация конструкции дорожной одежды из 4-сантиметрового поверхностного слоя/6-сантиметрового нижнего слоя, когда сочетания типов смеси идентичны.(4) Двухслойное дорожное покрытие с комбинацией 3-сантиметрового верхнего слоя AC-13 и 7-сантиметрового нижнего слоя AC-20 применимо в полевых и промышленных условиях и будет эффективно улучшать усталостные свойства асфальтовых покрытий.
По сравнению с типичной конструкцией дорожного покрытия с традиционным покрытием (поверхностный слой AC-13 4 см/нижний слой AC-20 6 см), верхний слой AC-13 толщиной 3 см/нижний слой AC-20 толщиной 3 см с двойным Технология многослойной укладки не только экономит битумное вяжущее (содержание асфальта, используемого в АС-13, выше, чем в АС-20) и липкое масло, но также повышает долговечность асфальтового покрытия.Таким образом, затраты на строительство и обслуживание асфальтобетонных покрытий заведомо ниже. Наконец, настоящее исследование было сосредоточено в первую очередь на влиянии технологий укладки, материалов покрытия и конструкций на усталостные свойства двухслойных асфальтобетонных покрытий. Соответственно, в нашем будущем исследовании будет изучено их влияние на низкотемпературные характеристики асфальтовых покрытий против растрескивания.
Доступность данных
Данные, использованные для поддержки результатов этого исследования, включены в статью.
Конфликт интересов
Авторы заявляют об отсутствии конфликта интересов.
Благодарности
Это исследование было поддержано Научным проектом Коммуникации провинции Чжэцзян (Грант № 2015J23), Научным проектом Коммуникации провинции Хэнань (Грант № 2020J-2-2) и Научным исследованием Центральных колледжей Китая для Университет Чанъань (грант № 300102218212).
Некоторые старые технологии бетонных дорожных покрытий возвращаются и дают асфальту преимущество в цене
Технологии бетонных покрытий, используемых на дорогах и автомагистралях нашей страны, существуют уже некоторое время, но новые разработки в области оборудования и добавок открыли рынок для некоторых из них, сделав их последними тенденциями в бетонном покрытии.Эти тенденции включают бетонные покрытия, бетон, уплотненный роликами, и рекультивацию на всю глубину.
Бетонные покрытия
В связи с тем, что новое строительство ведется мало из-за отсутствия законопроекта о долгосрочном финансировании автомагистралей, сохранение дорожного покрытия стало приоритетом для большинства агентств и муниципалитетов. Это область, где бетонные покрытия показывают большие перспективы.
«Бетонные покрытия существуют уже некоторое время, но особенно за последние семь-восемь лет мы наблюдаем огромный рост использования этой технологии», — говорит Билл Дэвенпорт, вице-президент по коммуникациям в American Concrete. Ассоциация тротуаров (ACPA).«Спад в экономике сыграл свою роль в этом. Агентства должны делать больше с меньшими затратами. У них нет денег, чтобы сделать все, что они хотели бы сделать, или все, что им нужно сделать, поэтому в дело вступает бетонное покрытие».
Существует несколько типов бетонных покрытий, которые можно разделить на две категории: связанные и несвязанные. В рамках этих категорий верхние слои укладываются на поврежденные асфальтовые, бетонные или композитные покрытия. Одним из наиболее распространенных применений является склеивание бетона поверх асфальта.В этих случаях, как правило, верхние 2-5 дюймов слоя износа асфальта срезаются и заменяются бетоном. Тонкое бетонное покрытие быстро разрушается по сравнению с полной заменой дороги, что позволяет открыть дорогу для движения намного быстрее.
«Как отрасль, мы пытаемся информировать агентства и подрядчиков о преимуществах бетонных покрытий, а также информировать их о потенциальных применениях», — говорит Давенпорт. ACPA работает через своих штатных инженеров, дочерние ассоциации и Национальный центр технологии бетонных покрытий, чтобы предоставить информацию и техническую помощь, но Давенпорт говорит, что еще многое предстоит сделать.Один пример: вопросы, поднятые во время недавнего веб-семинара ACPA по наложению бетона. «Они подчеркнули, что нам все еще нужно получить информацию о том, как воспользоваться преимуществами технологии наложения бетона, где можно использовать наложения и как правильно их построить», — говорит он.
Бесструнная технология может играть большую роль в бетонных покрытиях, облегчая их изготовление. Асфальтоукладчик может использовать компьютеризированные электронные системы управления и лазерную технологию для контроля толщины и гладкости уложенного слоя и внесения корректировок по ходу движения.«Бесструнная технология завоевывает популярность у многих подрядчиков, поскольку она делает рабочую площадку более безопасной и помогает улучшить окончательные результаты гладкости при правильном применении», — говорит Дэвенпорт. «По мере продвижения вперед производство будет увеличиваться, а автомобилисты будут меньше неудобств». Бетон с катковым уплотнением
Несмотря на то, что это не новая технология, роликовый уплотненный бетон (RCC) все еще является новым для многих людей. Он начинался как специальный продукт, размещаемый специализированными подрядчиками, но растет интерес к его использованию в различных приложениях, включая поворотные полосы, улицы и дороги с низкой интенсивностью движения, парковки, а также ограниченное применение на автомагистралях, например, на обочинах.
Дополнительную информацию об этих технологиях можно найти в Интернете и в печати.Национальный центр технологии бетонных покрытий опубликовал «Руководство по бетонным покрытиям: устойчивые решения для восстановления и восстановления существующих покрытий» (3-е издание), которое доступно на сайте cptechcenter.org.
Публикация PCA «Руководство по бетонным покрытиям, уплотненным катком» представляет собой руководящую спецификацию по строительству открытых железобетонных конструкций для дорог и других применений. Он предоставляет владельцам / агентствам, подрядчикам и консультантам руководство по спецификациям, направленное на установление и поддержание неизменно высокого стандарта качества изготовления.Его можно найти на сайте www.cement.org.
Другой публикацией, предлагаемой PCA, является «Руководство по рекультивации на полную глубину» (FDR) с использованием цемента, которое можно получить на сайтеmembers.cement.org.
PCA также предлагает Руководство по интегрированным решениям для дорожного покрытия на основе цемента. В этом руководстве представлено краткое описание 10 конкретных применений инженерных дорожных покрытий. Он доступен на member.cement.org.
Коллекция веб-приложений и приложений для настольных компьютеров доступна на веб-сайте ACPA. Приложения созданы для помощи в проектировании, строительстве и анализе бетонных покрытий.Эти приложения можно найти на сайте apps.acpa.org.
ACPA предлагает две веб-программы обучения, спонсируемые Федеральным управлением автомобильных дорог. Один касается безопасности в зонах бетонных строительных работ, а другой касается бесструнного мощения. В этом году будут представлены еще два модуля по передовым методам устройства гладких бетонных покрытий и передовым методам управления запасами. Курсы предлагаются бесплатно на сайте acpa.org.
Веб-сайт Wikipave находится в процессе разработки ACPA.Онлайн-ресурс будет предлагать информацию обо всем, что связано с технологией бетонных покрытий, включая продукты и технологии, а также фотографии, диаграммы, графики и т. д. После того, как сайт будет запущен, любой, у кого есть подключение к Интернету, сможет получить доступ к информации.
«Бетон, уплотненный катками, представляет собой интересный материал для мощения, — говорит Уэйн Адаска, директор отдела дорожного покрытия Ассоциации портландцемента (PCA). «Он хорошо конкурирует с асфальтобетонным покрытием по стоимости и скорости строительства.Бетон с нулевой посадкой, в котором не используются формы или арматура, укладывается асфальтоукладчиками, а затем уплотняется до высокой плотности с помощью вибрационных катков».
Ключом к скорости строительства RCC является то, что он уложен слоями гораздо более толстыми, чем асфальт. Там, где асфальт укладывается в несколько слоев от 3/4 до 2 дюймов, ЖБК укладывается в один более толстый слой до 9 дюймов. В течение последних пяти лет RCC была принята многими подрядчиками по укладке дорожного покрытия, которые вступают в нее из-за потенциала этой технологии для замены асфальта, стоимость которого резко возросла.
Одна из проблем, с которыми столкнулась компания RCC, заключается в том, что поверхность больше похожа на асфальт, чем на бетон. Он имеет открытую текстуру, поэтому те, кто ожидает внешний вид обычного бетона, могут быть разочарованы. «Внешний вид RCC становится намного лучше, — говорит Адаска. «Заполнитель верхнего размера был уменьшен с 3/4 дюйма до 1/2 дюйма, что привело к более плотной текстуре поверхности; тем не менее, он еще не на том этапе, когда он выглядит как обычный бетон».
Для улучшения внешнего вида поверхности имеется многообещающая добавка.Добавка распыляется на поверхность уплотненного железобетона, а затем затирается, в результате чего получается более гладкая и плотная поверхность. Прошлым летом смесь использовалась в проекте в районе Чикаго. До сих пор, по словам Адаски, результаты были выдающимися, но важно посмотреть, как они выдержат зиму. Адаска считает, что примеси в целом будут играть большую роль в RCC в будущем.
В течение нескольких лет ACPA возглавляет работу по улучшению качества изготовления и качества RCC.В начале 2011 года ассоциация сформировала целевую группу, состоящую из экспертов, которые давали рекомендации по продвижению RCC, как в техническом плане, так и в плане развития рынка.
Восстановление на всю глубину
В связи с заботой государственных учреждений о сохранении и реабилитации в наши дни возобновился интерес к рекультивации на полную глубину (FDR). Хотя FDR не относится к семейству бетонных дорожных покрытий, он является одним из самых устойчивых продуктов для дорожного покрытия на рынке, поскольку сохраняет все на месте.Эта 30-летняя технология произвела революцию на современном рынке благодаря более крупному и мощному оборудованию. Регенераторы или смесители для измельчения были ключевым компонентом в оживлении рынка за счет ускорения строительства и повышения экономичности FDR.
FDR раньше отнимал много времени. Утилизаторам приходилось делать несколько проходов, чтобы разбить старую дорогу, и требовалось специальное оборудование, такое как рыхлители и дробилки, чтобы сделать материал пригодным для использования. Сегодня регенераторы могут измельчать асфальт и гранулированное основание всего за один проход на глубину до 18 дюймов.Затем распределяют цемент, а материал повторно перемешивают, при необходимости добавляют воду, уплотняют и отверждают. В результате получается прочная долговечная основа, которая строится быстрее и экономичнее, и является гораздо более устойчивой, чем удаление и замена существующей дороги. Основание подходит для бетонных или асфальтовых покрытий.
Поддержание дорожного движения
Важнейшим направлением индустрии бетонных покрытий является обеспечение движения в зонах строительных работ. «Агентства находятся под огромным давлением, чтобы начать и завершить проекты быстро, поэтому все чаще от подрядчиков требуется поддерживать движение транспорта вокруг рабочих зон и максимально избегать сбоев и задержек участников дорожного движения», — говорит Давенпорт.«Это область, в которой национальная ассоциация вместе с местными отделениями, государственными ассоциациями дорожного покрытия и подрядчиками будет работать вместе с агентствами, чтобы найти дополнительные решения».
Демонстрация объединенного фонда продвижения новых технологий дорожного покрытия
С 2013 года в рамках Программы ускоренного внедрения и развертывания технологий дорожного покрытия (AIDPT) в партнерстве с Государственными департаментами транспорта (DOT), академическими и промышленными кругами были определены достижения в области асфальтобетонного покрытия и реализованы эффективные стратегии для быстрого развертывания новых технологий. и перспективные технологии.Этот проект с объединенными фондами продолжит достижение целей программы AIDPT, выступая в качестве механизма для развертывания и демонстрации технологий и ресурсов дорожного покрытия. Недавние демонстрационные инициативы под руководством Федерального управления автомобильных дорог (FHWA) включают увеличение плотности асфальта на месте и улучшение технических характеристик бетонных смесей. Для дальнейшего развития демонстрационных инициатив Программы FHWA определит до трех тем для рассмотрения в рамках этого проекта с объединенным финансированием, которые соответствуют программным областям FHWA «Дорожное покрытие и материалы».Темы для рассмотрения включают следующее: (1) Программа разработки сбалансированной смеси (BMD) для асфальта и специальной смеси (PEM) для бетона; (2) Реализация стратегических программ сохранения дорожного покрытия; и (3) Интеграция устойчивости и отказоустойчивости в процесс принятия решений, технические рамки, усилия по обучению и взаимодействие с заинтересованными сторонами. Этот объединенный фонд направлен на поддержку и демонстрацию внедрения инновационных технологий, продуктов и процессов дорожного покрытия департаментами транспорта штата за счет использования федеральных инвестиций в партнерстве с департаментом транспорта штата.
Язык
Проект
- Статус: Запрограммировано
- Финансирование: $600000
- Номера контрактов:
ТПФ-5(478)
- Спонсорские организации:
Департамент транспорта Аризоны
206 Южная 17-я авеню
Феникс, Аризона Соединенные Штаты 85007Департамент транспорта Колорадо
4201 Восточный Арканзас-авеню
Денвер, Колорадо Соединенные Штаты 80222Департамент транспорта Джорджии
600 West Peachtree Rd
Атланта, Джорджия Соединенные Штаты 30308Департамент транспорта Айдахо
С.O. Box 7129
3311 W. State Street
Boise, ID Соединенные Штаты 83707-1129Департамент транспорта штата Иллинойс
2300 S. Dirksen Parkway
Спрингфилд, Иллинойс Соединенные Штаты 62764Департамент транспорта Айовы
800 Lincoln Way
Эймс, IA Соединенные Штаты 50010Департамент транспорта Миссисипи
С.O. Box 1850
Джексон, Миссисипи Соединенные Штаты 39215-1850Департамент транспорта штата Миссури
1617 бульвар Миссури.
Почтовый индекс Box 270
Джефферсон-Сити, Миссури Соединенные Штаты 65102Департамент транспорта Северной Дакоты
608 East Boulevard Avenue
Бисмарк, Северная Дакота Соединенные Штаты 58505-0700Департамент транспорта Пенсильвании
Keystone Building
400 North Street
Harrisburg, PA Соединенные Штаты 17120Департамент транспорта Техаса
125 Э.11-я улица
Остин, Техас Соединенные Штаты 78701-2483Департамент транспорта Висконсина
PO Box 7910
4802 Sheboygan Avenue, Room 104
Madison, WI Соединенные Штаты 53707-7910Оклахома Транспорт
200 NE 21st Street
Оклахома-Сити, Оклахома Соединенные Штаты 73105Департамент транспорта Гавайев
2530 Likelike Highway
Гонолулу, Гавайи Соединенные Штаты 96817 - Руководители проектов:
Снид, Шэрон
202-366-1553ШАРОН[email protected] - Дата начала: 20210422
- Ожидаемая дата завершения: 0
- Фактическая дата завершения: 0
Тема/указатель Термины
Информация о подаче
- Регистрационный номер: 01769713
- Тип записи: Исследовательский проект
- Источник агентства: Федеральное управление автомобильных дорог
- Номера контрактов: TPF-5(478)
- Файлы: RIP, USDOT, STATEDOT
- Дата создания: 19 апр 2021 15:20