Цена за куб газобетона: Газобетонные блоки купить цена 3100 руб за куб
Цена за куб газобетона в Якутске: 623-товара: бесплатная доставка, скидка-7% [перейти]
Партнерская программаПомощь
Якутск
Каталог
Каталог Товаров
Одежда и обувь
Одежда и обувь
Стройматериалы
Стройматериалы
Здоровье и красота
Здоровье и красота
Текстиль и кожа
Текстиль и кожа
Продукты и напитки
Продукты и напитки
Детские товары
Детские товары
Электротехника
Электротехника
Дом и сад
Дом и сад
Промышленность
Промышленность
Сельское хозяйство
Сельское хозяйство
Торговля и склад
Торговля и склад
Все категории
ВходИзбранное
Газобетон СК блок прямой D600, 600*250*150 мм
ПОДРОБНЕЕ
Газобетон СК блок прямой с захватом D600, 600*250*200 мм
ПОДРОБНЕЕ
Газобетон СК блок прямой D600, 600*250*100 мм
ПОДРОБНЕЕ
Газобетон Bonolit D600, 600*125*250 мм, прямой блок
ПОДРОБНЕЕ
Газобетон Bonolit D500, 600*125*250 мм, прямой блок
ПОДРОБНЕЕ
Газобетон Bonolit D500, 600*150*250 мм, прямой блок
ПОДРОБНЕЕ
Газобетон СК блок прямой с захватом D600, 600*250*250 мм
ПОДРОБНЕЕ
Газобетон СК блок прямой с захватом D600, 600*250*300 мм
ПОДРОБНЕЕ
Газобетон Ytong A++ D300, 625*250*375 мм
ПОДРОБНЕЕ
Газобетон Ytong A++ D300, 625*250*500 мм
ПОДРОБНЕЕ
Газобетон Ytong A++ D300, 625*250*300 мм
ПОДРОБНЕЕ
Газобетон СК блок прямой D400, 600*250*200 мм
ПОДРОБНЕЕ
Газобетон СК блок прямой с захватом D600, 600*250*375 мм
ПОДРОБНЕЕ
Газобетон Bonolit D500, 600*100*250 мм, прямой блок
ПОДРОБНЕЕ
Газобетон Bonolit D500, 600*75*250 мм, прямой блок
ПОДРОБНЕЕ
Газобетон Bonolit D600, 600*300*200 мм, прямой блок
ПОДРОБНЕЕ
Газобетон Bonolit D600, 600*300*250 мм, прямой блок
ПОДРОБНЕЕ
Газобетон Bonolit D600, 600*250*250 мм, прямой блок
ПОДРОБНЕЕ
Газобетон Bonolit D600, 600*250*200 мм, прямой блок
ПОДРОБНЕЕ
Газобетон Bonolit D600, 600*200*200 мм, прямой блок
ПОДРОБНЕЕ
Куб газобетонаГазобетон Bonolit D600, 600*375*250 мм, прямой блок
ПОДРОБНЕЕ
Газобетон СК блок прямой с захватом D400, 600*250*300 мм Производитель: Газобетон СК, Марка
ПОДРОБНЕЕ
Газобетон ЛСР 375х250х625 мм D400 Тип: газосиликатный, Производитель: ЛСР, Марка плотности: D400
ПОДРОБНЕЕ
Газобетон Bonolit D600, 600*100*250 мм, прямой блок
ПОДРОБНЕЕ
Газобетон ЛСР D400 375х250х625мм Тип: газосиликатный, Производитель: ЛСР, Структура: полнотелый
ПОДРОБНЕЕ
Газобетон Ytong D400, 625*250*300 мм
ПОДРОБНЕЕ
Газобетон ЕвроАэроБетон D500, 625*250*250 мм, прямой блок Тип: газосиликатный, Длина: 500 мм,
ПОДРОБНЕЕ
Газобетон Ytong 75х250х625 мм D500 Тип: газосиликатный, Производитель: Ytong, Структура: полнотелый
ПОДРОБНЕЕ
2 страница из 18
Цена за куб газобетона
Автоклавный газобетон на основе золы-уноса плотностью 350 кг/м3 как экологически чистый материал для энергетики
(I)
CrossMark
Доступно на сайте www. sciencedirect.com
ScienceDirect
Procedía Engineering 122 (2015) 39 — 46
Procedía Engineering
www.elsevier.com/locate/procedia
Операционные исследования в области устойчивого развития и гражданского строительства – встреча рабочей группы ЕВРО и 15-й немецко-литовско-польский коллоквиум (ORSDCE 2015)
Автоклавный газобетон на основе золы-уноса плотностью 350 кг/м как экологически чистый материал для энергосберегающих конструкций
Pawel Walczaka*, Pawel Szymanskib, Agnieszka Rozyckac
aH+H Polska Sp. о.о., ул. Купецка 6, 03-046 Варшава, Польша bПознаньский технологический университет, Факультет строительства и экологии, ул. Piotrowo 5, 60-965 Познань, Польша bФакультет материаловедения и керамики, AGH — Университет науки и технологии, al. Мицкевича 30, 30-059Краков, Польша
Abstract
В последние годы была проведена оценка коэффициента теплопередачи строительных материалов. С 1 января 2014 года значение U не может быть выше 0,25 [Вт/м2К], но с 2017 года это значение будет 0,23 и 0,20 с 2021 года.
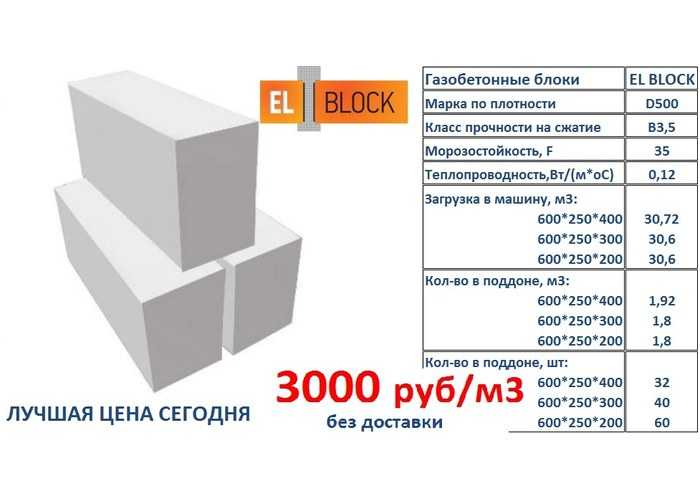
* Автор, ответственный за переписку. Тел.: +48 698 818 243 Адрес электронной почты: [email protected]
1877-7058 © 2015 Авторы. Опубликовано Elsevier Ltd. Это статья в открытом доступе по лицензии CC BY-NC-ND (http://creativecommons.Org/licenses/by-nc-nd/4.0/).
Рецензирование под ответственность организационного комитета Оперативных исследований в области устойчивого развития и гражданского строительства — встреча
рабочей группы ЕВРО и 15-й немецко-литовско-польский коллоквиум
doi:10.
© Авторы, 2015. Опубликовано ElsevierLtd. Это статья в открытом доступе под лицензией CC BY-NC-ND (http://creativecommons.org/licenses/by-nc-nd/4.0/).
Рецензирование под ответственность оргкомитета Оперативных исследований в области устойчивого развития и гражданского строительства — заседание рабочей группы ЕВРО и 15-й немецко-литовско-польский коллоквиум
Ключевые слова: Автоклавный газобетон, Гидротермические условия, Тоберморит, Технология процесса PGS, Кремнистая зола-унос. 9для наружных стен. С 2014 г. значение Uc не может быть ниже 0,25, с 2017 г. 0,23 и с 2021 г. 0,20 Вт/м2К, что указано в таблице 1.
Таблица 1. Значение Uc(max) в следующем году в Польше для наружных стен
Температура внутри Значение Uc(max)
с 2014 с 2017 с 2021
Внутренняя температура Ti > 16oC 0,25 0,23 0,20
Внутренняя температура 8oC < Ti< 16oC 0,45 0,45 0,45
Внутренняя температура Ti < 16oC 0,90 0,90 0,90
Автоклавный пенобетон – это материал, который очень хорошо соответствует текущим и будущим коэффициентам теплопередачи. Низкая теплопроводность обусловлена огромным количеством мелких пор, которые заполнены воздухом. Количество пор увеличивается с уменьшением плотности автоклавного газобетона (АГБ). Как известно, газобетон на основе золы-уноса обладает лучшей теплоизоляцией, чем газобетон на основе песка с той же плотностью, и именно поэтому авторы предпринимают исследования для получения автоклавного бетона на основе золы-уноса плотностью 350 кг/м3.
Автоклавный газобетон является привлекательным на мировом рынке, а на польском рынке его доля на рынке стеновых элементов превышает 40% [1,2]. Газобетон – это материал, начало которого относится к концу XIX – началу XX века. Алюминиевый порошок впервые был использован в 1914 году [3], а процесс автоклавирования — в 1923 году [4], в последнее время он используется для пенообразования. Первые заводы в Польше начали производство в 1951 году. В это время было создано несколько польских технологических процессов, таких как: UNIPOL (универсальная технология производства газобетона), SW (медленнотвердеющий бетон на силикатной основе), PGS (пористый силикатный бетон).
AAC производится с использованием цемента, негашеной извести, гипса и кремнистых материалов, таких как песок или летучая зола, а в качестве пенообразователя используется алюминиевая пудра. По прошествии нескольких часов реакции мягкую и удобоукладываемую массу режут на линии реза [9] и отверждают в гидротермальных условиях в течение 5-10 часов при температуре 180-190°С с использованием насыщенного пара под давлением 10-12 бар. Готовые изделия в соответствии с PN-EN 771-4:2012 имеют среднюю прочность на сжатие от 1,5 до 8,0 Н/мм2 и плотность не выше 1000 кг/м3.
Благодаря использованию гидротермических условий газобетон позволяет улучшить свои свойства за столь короткое время, так как с повышением температуры и продолжительности процесса автоклавирования растворимость кремнеземистого материала повышается [10], что обусловливает использование заполнителя в качестве вяжущего. Наиболее частым продуктом гидратации в газобетоне являются: C-S-H* [11-18], тоберморит [19-37], который был предметом многих исследований, или гидрогранаты [38-43], которые присутствуют в газобетонном камне, если зола-уноса появляется в исходном состоянии.
Технологический процесс PGS является очень специфическим процессом производства ячеистого бетона автоклавного твердения, поскольку цемент не используется. В качестве вяжущего используются только: негашеная известь, гипс и часть кремнистой золы-уноса. Как известно, польский
*AAC — Автоклавный газобетон *C-S-H — Гидраты силиката кальция
Энергетическая политика строится на угле, а производство AAC на основе летучей золы является идеальным направлением для утилизации этих отходов. В конечном итоге расположение рядом с электростанцией может привести к низким затратам на транспортировку сырья и производство пара, который также можно использовать от электростанции. На рисунке 1 представлена схема технологического процесса PGS [44].
Рис. 1. Технологический процесс PGS
2. Материалы и методы испытаний
2.1. Материалы
Материалами, выбранными для эксперимента, являются техническая негашеная известь и гипс, которые очень часто используются в производстве автоклавного ячеистого бетона в технологии PGS. Использованная кремнистая зола-унос была получена на электростанции Скавина. В связи с применением технологического процесса PGS применялась негашеная известь с T60 26 минут в соответствии с EN 197-1:2012. Химический состав всех сырьевых материалов: негашеной извести, гипса и золы-уноса был составлен в соответствии с 196-2:2006, и все результаты приведены в таблице 2.
Таблица 2. Химический состав сырья
Содержание, % Негашеная известь Гипс Зола-унос
SiO2 2,4 3,6 49,0
SO3 0,4 39,8 0,7
Fe2O3 1,1 0,4 6,8
А№3 0,0 0,0 24,4
СаО 89,8 31,4 4,2
MgO 3,0 1,7 3,2
Na2O 0,2 0,2 1,7
K2O 0,0 0,2 3,4
TiO2 0,0 0,1 1,1 9000 3
LOI 3.1 22.6 5.5
Удельная поверхность, см2/г 2900 3700 4300
Образцы, приготовленные для исследования были изготовлены в технологическом масштабе на обычном производственном предприятии. Негашеную известь, гипс и некоторые части летучей золы измельчали вместе в качестве связующего. Далее вяжущее смешивали с остальной сухой золой-уносом, часть
зеленых отходов, воды и алюминиевой пудры. Все образцы имели одинаковый сырьевой состав с постоянным соотношением CaO/SiO2 0,437 и соотношением CaO/(SiO2+Al2O3) 0,339. После смешивания все образцы были отлиты в стальные формы объемом 4,25 м3. Первоначально образцы затвердели при атмосферном давлении и температуре 65°С в течение примерно 180 минут, после чего были вырезаны на линии реза и автоклавированы при 182°С в гидротермальных условиях с давлением пара 11,5 бар в течение 8 часов.
2.2. Методы испытаний
Все образцы были подготовлены, и все испытания проводились в соответствии с PN-EN 771-4:2012. После автоклавирования из блоков вырезали 100 мм куб., как показано на рис. 2.
прямого выращивания
Рис. 2. Система вырезки кубических образцов из блока газобетона
Из одного блока вырезают 6 кубических образцов: 2 с 1/3 высоты от вершины блока, 2 из середины блоков, и 2 куб. от 1/3 высоты от низа блоков. Три куба (по одному каждого уровня) используются для определения плотности и три для определения прочности на сжатие. После резки образцы сушили при 105°С ± 5°С до постоянной массы до исследуемой плотности в сухом состоянии. Следующий кубический срез из тех же блоков сушили при 50°С до влажности 6% и после охлаждения проводили испытание на прочность на сжатие кубических образцов размером 100 мм при температуре 20°С на гидравлическом прессе 9.0003
PW 10.
Химический состав образцов определяли с помощью рентгеноструктурного анализа с использованием Philips PW 1130 и микроструктуры с помощью сканирующего электронного микроскопа Nova Nano SEM 200 с анализатором EDS EDAX.
Измерения теплопроводности проводились в соответствии с PN-EN ISO 6946:1999 с использованием FOX 314. Испытывались образцы, изготовленные в ходе данного исследования, и другие образцы на основе песка и зольной пыли различной плотности.
3. Результаты испытаний и обсуждение
Средняя плотность образцов в сухом состоянии и прочность на сжатие приведены в таблице 3.
Таблица 3. Результаты плотности и прочности при сжатии в сухом состоянии
Образцы ААС 1 ААС 2 ААС 3
Средняя плотность в сухом состоянии, кг/м3 365 ± 5 360 ± 5 340 ± 5
Средняя прочность на сжатие 1,6 ± 0,1 2,3 ± 0. 1 1,6 ± 0,1
В соответствии с PN-EN 771-4:2012 элементы несущих стен должны иметь прочность на сжатие не ниже 1,5 Н/мм2, а все изготовленные исследуемые образцы имеют более высокую прочность на сжатие. Различия в плотности не превышают 15 кг/м3 в соответствии с расчетной плотностью.
Все собранные значения теплопроводности — X для образцов, изготовленных в данном исследовании и для различной плотности как: автоклавного газобетона на основе песка, так и кремнистой золы-уноса приведены на рисунке 3.
300 350 400 450 500 550 600 650 700 сухой плотность, кг/м3
♦ Газобетон на основе песка ■ Газобетон на основе золы-уноса
Рис. 3. Результаты значения теплопроводности
Теплопроводность уменьшается с уменьшением сухой плотности газобетона. Как видно, автоклавный газобетон на основе золы-уноса имеет более низкое значение Х, чем автоклавный газобетон на основе песка при той же плотности в сухом состоянии. Образцы, проведенные в исследовании, имели плотность в сухом состоянии 345 кг/м3 и значение Х 0,074 Вт/мК. Газобетон на основе песка должен иметь плотность примерно на 15 кг/м3 ниже, чтобы иметь такое же значение теплопроводности. Это означает, что использование газобетонных блоков на основе летучей золы может привести к утончению наружных стен с тем же значением коэффициента теплопередачи, или к лучшей теплопроводности, или к уменьшению толщины изоляции. Различия в теплопроводности автоклавного газобетона на основе песка и золы-уноса обусловлены фазовым составом исходных материалов: песка и золы-уноса. Как известно, песок имеет кристаллическую структуру, а кремнистая зола-уноса в основном имеет вид стекла, содержание которого составляет от 30 до 80 % [45-47]. Это привело к тому, что фазовый состав также отличается от того, что наблюдалось с помощью СЭМ и показано на рис.
4.9.0003
8 HV WD 18,00 кВ 6,3 мм mag 10 000 X det LVD Spot 4,0 HFW 29,8 мкм
3H5 I WD mag det Spot HFW 1 — -20 pm-
15 00 kV 4 7 мм 5000X LVD 40 59,7 мкм|
Рис.4. СЭМ образцов: ААС на основе золы-уноса (слева) и ААС на основе песка (справа)
Зола-унос содержит много стекла, поэтому можно наблюдать дифференциальный фазовый состав: тоберморитоподобное волокно, гель C-S-H или гидрогранаты, что вызвано высоким содержанием Al2O3 в летучей золе. В образце песка AAC наблюдается только тоберморитоподобная пластинка. Такой фазовый состав подтвержден рентгенофазовым анализом.
Теплопроводность газобетона улучшается при уменьшении его плотности. Автоклавный газобетон является одним из лучших строительных материалов с очень хорошими свойствами теплопроводности. На рисунке 5 приведены сравнения различных видов популярных строительных материалов в Польше.
Бетон Силикатный AAC 600 Керамический AAC 400 AAC 350 AAC 350
(на основе (на основе золы-уноса) песка)
Рис. 5. Толщина наружной стены со значением U 0,25 из различного материала
Толщина стен на рисунке 5 была рассчитана с использованием заявленного значения Х на сайтах различных производителей для достижения значения U, равного 0,25 Вт/м2К. стена из керамики должна быть на 44 см толще, чем стена из газобетона на основе золы-унос плотностью 350.
Лучшая теплопроводность – это не только преимущество газобетона с меньшей плотностью. Меньшая плотность означает меньше отходов в будущем, более экологичный продукт и большую пропускную способность. На рисунке 6 показано сравнение транспортной способности различных материалов (включая влажность материала).
■ строительный материал
Рис. 6. Транспортная способность различных строительных материалов
В качестве эталонного транспорта использовался газобетон плотностью 600. Перевозка традиционного бетона или силиката привела к снижению пропускной способности и более высокому загрязнению окружающей среды грузовиками. При использовании газобетона плотностью 300 можно транспортировать в два раза больше материала, чем при использовании газобетона плотностью 600.
5. Выводы
По результатам исследования можно сделать следующие выводы:
• возможно производство автоклавного газобетона на основе золы-уноса плотностью 350 кг/м3,
• автоклавный газобетон на основе золы-уноса имеет лучшую теплоизоляцию, чем автоклавный газобетон на основе песка той же плотности,
• продукт гидратации в летучей золе ААС менее кристалличен, чем в ААС на основе песка,
• использование газобетона с более низкой плотностью увеличивает пропускную способность и снижает загрязнение окружающей среды,
• использование газосиликатного асфальтобетона с более низкой плотностью приводит к уменьшению толщины наружных стен или уменьшению толщины изоляции .
Литература
[1] Л. Мисевич, Материалы будущего, 4 (2011), с. 2
[2] Л. Мисевич, Materialy Budowlane, 4 (2012), p. 2
[3] Бо. Г. Хеллерс, Бо. Р. Шмидт, V Международная конференция по автоклавному газобетону, Быдгощ, 2011, с. 63
[4] A. Paprocki, «Betony komorkowe», Wydawnictwo Arkady, Warszawa, 1966
[5] H. Jatymowicz, J. Siejko, G. Zapotoczna-Sytek, «Technologia autoklawizowanego betonu komorkowego», Wy заря Аркадий, Варшава, 19tnastolecie Stowarzyszenia Producentow Betonu» http://stow-bet.com.pl/new/sources/15lecieSPB.pdf
[7] Г. Запоточна-Сытек, М. Собон, V Международная конференция автоклавного газобетона, Быдгощ, 2011 , p. , стр. 23
[10] Х. Гундлах, «DampfgeharteteBaustoffe», Bauverlag GmbH, 365, Wiesbaden, 1973
[11] В. Курдовски, Цемент Вапно Бетон, 4 (2008), с. 216
[12] Даймонд В. Гидравлические цементные пасты: их структура и свойства, Тр. конф. в Университете Шеффилда, апрель (1976 г.), с. 2
[13] H.M. Jennings, B.S. Далглиш, П.Л. Пратт, Дж. Ам. Керам. Соц., Том. 64 (1981), с. 567
[14] H.M. Jennings, Cement and Concrete Research, Vol. 30 (2000), с. 101
[15] П.Д. Tenis, HM Jennings, Cement and Concrete Research, Vol. 30 (2000), с. 855
[16] А. Нонат, Исследования цемента и бетона, Том. 34 (2004), с. 1521
[17] А. Нонат, К. Курто, Д. Дамидо, Цемент ВапноБетон, (2001), с. 184
[18] M. Gawlicki, «Aktywnosc гидравлическая модификация ß-Ca2[SiÖ4]», Polskie Towarzystwo Ceramiczne, Krakow, 2008
[19] C.F. Чан, Т. Мицуда, Исследование цемента и бетона, Vol. 8 (1978), с. 135
[20] M. Sakiyama, T. Mitsuda, Cement and Concrete Research, Vol. 7 (1977), с. 681
[21] С.А.С. Эль-Хемали, Т. Мицуда, Х.Ф.В. Тейлор, Исследование цемента и бетона, Vol. 7 (1977), с. 429
[22] Дж. Кикума, М. Цунашима, Т. Исикава, С. Мацуно, А. Огава, К. Мацуи, М. Сато, Журнал химии твердого тела, Vol. 184 (2011), с. 2066
[23] Дж. Кикума, М. Цунашима, Ю. Исикава, С. Мацумо, А. Огава, К. Мацуи, V Международная конференция автоклавного газобетона, Быдгощ, 2011, с. 71
[24] Н. Ису, Х. Исида, Т. Мицуда, Исследование цемента и бетона, Том. 25 (1995), с. 243
[25] T. Mitsuda, H.F.W. Taylor, Mineral Mag., Vol. 42 (1978), с. 229
[26] К. Мацуи, Дж. Кикума, М. Цунашима, Т. Исикава, С. Мацуно, А. Огава, М. Сато, Исследования цемента и бетона, Том. 41 (2011), с. 510
[27] К. Мацуи и др. др., V Международная конференция по автоклавному газобетону, Быдгощ, 2011, с. 147
[28] G.L. Kalousek, J. Am. Цер. Соц., Том. 40 (1957), с. 74
[29] С. Даймонд, Дж. Л. Уайт, В. Л. Долч, Ам. Мин. 51 (1966), с. 388
[30] S. Shaw, S.M. Clark, C.M.B. Хендерсон, Химическая геология, том. 167 (2000), с. 129
[31] Н.Ю. Мостафа, А.А. Шалтоут, Х. Омар, С.А. Або-Эль-Энейн, Журнал сплавов и соединений, Vol. 467 (2009), с. 332
[32] P. Faucon, JM Delaye, J. Virlet, JF Jacquinot, F. Adenot, Cement and Concrete Research. Том. 27 (1997), с. 1581
[33] W. Nocun-Wczelik, Cement and Concrete Research, Vol. 27 (1997), с. 83
[34] W.