Технология производство газобетона: Технология производства автоклавного газобетона — этапы
Masa — Камнеформовочное оборудование, Автоклавный газобетон бетон, Силикатный пресс
Газобетон производится из следующих сырьевых материалов: кварцевый песок, известь, цемент, гипс (ангидрит), алюминиевая пудра/ паста и вода.
Песок перерабатывается в песчаный шлам в шаровой мельнице мокрого помола (01) и складируется в шламбассейнах. Далее песчаный шлам совместно с прочими сырьевыми компонентами подается в дозирующую и смесительную установку Masa (02). По окончании смесительного процесса смесь заливается в форму. Форма транспортируется в зону предварительного твердения, где свежеформованные газобетонные массивы после завершения процесса ферментации (03) достигают заданной резательной прочности. Только тогда осуществляется распалубка (04) – выемка газобетонного массива из формы. Пустые формы для заливки снова комплектуются, смазываются (05) и возвращаются в производственный цикл.
Газобетонный массив проходит через различные станции линии резки (06) и затем укладывается на запарочную решетку при помощи транспортной системы/ откидного стола (07).
Далее отвержденные газобетонные массивы подаются к столу для обратного кантования (10) и при известных условиях – к делителю (11). Вслед за этим газобетонные изделия транспортируются к устройству перестановки блоков (12) и позиционируются на деревянных поддонах. Далее может осуществляться упаковка (13) конечного продукта.
Использованные запарочные решетки и запарочные тележки возвращаются в производственный цикл через систему транспортировки запарочных решеток и обратной подачи запарочных тележек (10).
Газобетонная линия может быть дооснащена оборудованием для производства армированных изделий (14).
преимущества ячеистого бетона, технологии производства автоклавного газобетона
Искусственный камень
Это искусственный камень, автоклавный ячеистый бетон, прочный минерально-каменный искусственный материал, на поверхности которого находятся отверстия (поры) диаметром 1-3 мм. Газобетон путем термической обработки в автоклаве (сосуд с поддержанием высокой влажности и давления) смеси из тонко молотого песка, цемента, извести и воды. По тому, как расположены поры, какого они объема и насколько закрыты, определяется плотность и качество газобетонных блоков.
Природный материал
Основные компоненты автоклавного газобетона – известь и кварцевый песок. Поэтому можно смело утверждать, что он является экологически чистым строительным материалом. После определенного времени твердения смесь разрезается на блоки нужных размеров и отправляются в автоклавы, где под действием пара твердеют. Подобная технология дает блокам из газобетона большой набор положительных качеств, каких нет ни у одного другого строительного материала.
Оптимальный строительный материал
Сегодня все больше строительных организаций выбирают именно газоблок, за идеальное отношение массы и прочности и лёгкости в обработке. Он подходит для всех видов стен, как несущих, так и внутренних. Газобетонные блоки или другие элементы из этого материала используются во всех направлениях строительства.
Легкий строительный материал
Объемный вес материала может варьироваться в диапазоне от 300 до 1200 кг/м3. В настоящее время, с учетом комплексных требований к современным строительным материалам, в первую очередь к их теплопроводности, выпускаются ячеистые бетоны с минимальным объемным весом 400–600 кг/м3. Обычный, средний блок из ячеистого бетона (ГОСТ 21520-89), марки плотности Д500, размером 300х188х575 мм имеет массу до 20 кг и может заменить во внешней стене толщиной 640 мм 28 кирпичей, вес которых составляет 120 кг.
Быстрота и экономичность
Простота в монтаже достигается высокой размерной геометрической точностью блоков газобетон (+ — 1 мм) и возможность кладки на клей (специальная сухая смесь упакованная в мешках и приготовляемая путем добавления воды). За счет достаточно больших габаритов отдельных блоков и их небольшого веса, существенно возрастает скорость строительства. Газобетон легко обрабатывается любым режущим инструментом, пилится. В итоге — меньше трудозатраты, в 5–7 раз меньше расход сцепляющих веществ — клея или раствора. Все эти преимущества газобетонных блоков снижают общую себестоимость возводимых зданий.
Низкая теплопроводность
Коэффициент теплопроводности газобетона в сухом состоянии — 0,12 Вт/м °С, при влажности 12% — 0,145 Вт/м °С.При использовании в наружных стеновых конструкциях блоков удельным весом 400 кг/м2 и толщиной 300мм и 375мм по действующим нормам и СниП не требуется применения дополнительной теплоизоляции. В нашем регионе возможно устройство стен из газобетонных блоков (плотностью не более 500 кг/м3) толщиной 500 мм.
Энергосбережение
Экономия 20%-30% средств на отопление помещений благодаря высоким теплоизоляционным свойствам газобетонных блоков. Отсутствие мостиков холода (толщина кладочного шва до 3 мм и соответственно исключение промерзания). По теплопроводности блоки стандартной толщины (375 мм) эквивалентны 600-миллиметровой кирпичной кладке.
Экологичность
Материал производится из песка, извести, цемента и алюминиевой пудры. Он не выделяет токсичных веществ и по своей экологичности уступает лишь дереву, но при этом не гниет и не стареет. Экологическая чистота — коэффициент экологичности: автоклавный газобетон — 2,0. Радиационный фон газобетона не превышает 9–11 мкр/ч. Дышащий материал — в доме, построенном из газобетона, микроклимат такой же, как и в деревянном.
Звукоизоляция
Благодаря ячеистой структуре газобетона, его звукоизоляционные свойства примерно в 10 раз выше, чем у аналогичной кирпичной кладки. При сооружении стены из газобетона толщиной 240 мм, такая стена полностью соответствует всем нормативным требованиям к звукоизоляции жилого дома, предъявляемым отечественными СНиП, предохраняет от воздействия сильных вредных шумов и совершенно не требует проведения каких-либо дополнительных звукоизоляционных мероприятий.
Пожаробезопасность
Данный материал может служить надежной защитой от распространения пожара. Газобетон соответствуют первой степени огнестойкости, что подтверждено соответствующими испытаниями. Газобетон, будучи неорганическим и негорючим материалом, выдерживает одностороннее воздействие огня в течение 3–7 ч. Это материал, способный защитить металлические конструкции от прямого воздействия огня. Сам материал при этом не разрушается.
Технология производства газобетона
В данной статье мы поговорим о технологии производства газобетона. Если вы собираетесь строить дом из газобетона, то необходимо понимать не только процесс постройки дома, но и иметь основные представления о газобетоне с возможными трудностями, которые могут возникнуть при строительстве дома.

Различия газобетона и газосиликата
В современном разговорном языке понятия газобетона и газосиликата перемешаны. Есть области в России, где распространен термин газосиликат. На северо-западе и центральной России чаще используется газобетон. По большинству описывается один и тот же материал – ячеистый бетон автоклавного твердения.
Смешение понятий возникло еще с 1960-1980 годов, когда производство автоклавных бетонов развивалось стремительно, параллельно существовали несколько способов производства. В частности были автоклавные бетоны на цементном, известковым и смешанном вяжущем.
В современной промышленности остались более долговечные на цементном и смешанном вяжущем, а чисто силикатные ячеистые бетоны вымерли как класс.
Поэтому сейчас, говоря «газосиликат», как правило, имеют в виду автоклавный газобетон.
Свойства газобетона определяется двумя технологическими переделами:
- Помол песка смалывается до тонины цемента (2000 – 3000 см²/г)
- Автоклавная обработка. Автоклав по сути большая скороварка, в которой поддерживается (нагнетается) давление 12 атм. при температуре 188°С и в течении 12 часов газобетонные массивы находятся в автоклаве
Кварцевый песок расходуется в синтезе гидросиликатов
SiO2 + h3O = h3SiO3
Синтезируется тоберморит – основной минерал, обеспечивающий прочность и долговечность газобетона. По сути силикатный кирпич, но только с ячеистой структурой.
Технология производства газобетона
Алюминиевая пудра, или любой другой металл, стоящий в электрохимическом ряду до водорода вводится в виде суспензии. Одновременно всё подается в бетономешалку известь, цемент, песчаный шлам (суспензия молотого песка) и просто вода. Компоненты проходят взвешивание, дозируются и затем отправляются на смешение в скоростную мешалку. Смешение происходит за 30 секунд в полном объеме, и за один массив выходит порядка 4,5 м³ газобетона. Заливается в формы разогретые до 40 °С, приблизительно половина от этого объема.
В результате реакции происходят газовыделения, когда алюминий вытесняет h3. Алюминий превращается в гидроксид, а затем участвует в гидросиликатах, где получаются алюминаты кальция и силикаты алюминия и т.д. Алюминий в окисленном состоянии, как в земной коре.
После заливания смесь отправляется в камеру созревания. Там происходит процесс парообразования. Образуется большое количество пор, массив возрастает до требуемого объема, набирая прочность, называемую транспортной. Затем массив при помощи тележки выезжает из камеры и отправляется на линию резки. Массив достаточно большой 4,5 метра по объему. Здесь происходит нарезка на блоки.
Далее из отдельных массивов формируются автоклавные поезда, которые поступают на автоклав. Здесь в течение 12 часов обрабатываются при высоком давлении в среде насыщенного водяного пара.
После автоклавной обработки блоки поступают на разделительную машину, т.к. в автоклаве могли слипнуться. На некоторых заводах разделение происходит до автоклавирования.
После разделения блоки упаковываются сверху в термоусадочную пленку или полиэтилен, это помогает сохранить влажность газобетона до начала строительства. Газобетон на заводах хранится на открытых площадках до 2-3 лет.
Далее со склада материал отправляется на строящийся объект.
IRJET-Запрошенная вами страница не найдена на нашем сайте Февраль 2022 г. Выполняется публикация…
Просмотр статей
IRJET Получено «Импакт-фактор научного журнала: 7,529» за 2020 год.
Подтвердить здесь Система контроля качества.
IRJET приглашает статьи из различных технических и научных дисциплин для тома 9, выпуск 2 (февраль 2022 г.) Документы
IRJET Получил «Импакт-фактор научного журнала: 7,529» за 2020 год.
Подтвердить здесь
IRJET Получил сертификат регистрации ISO 9001:2008 для своей системы управления качеством.
IRJET приглашает статьи из различных технических и научных дисциплин для тома 9, выпуск 2 (февраль 2022 г.) Документы
IRJET Получил «Импакт-фактор научного журнала: 7,529» за 2020 год.
Подтвердить здесь
IRJET Получил сертификат регистрации ISO 9001:2008 для своей системы управления качеством.
IRJET приглашает статьи из различных технических и научных дисциплин для тома 9, выпуск 2 (февраль 2022 г.) Документы
IRJET Получил «Импакт-фактор научного журнала: 7,529» за 2020 год.
Подтвердить здесь
IRJET Получил сертификат регистрации ISO 9001:2008 для своей системы управления качеством.
IRJET приглашает статьи из различных технических и научных дисциплин для тома 9, выпуск 2 (февраль 2022 г.) Документы
IRJET Получил «Импакт-фактор научного журнала: 7,529» за 2020 год.
Подтвердить здесь
IRJET Получил сертификат регистрации ISO 9001:2008 для своей системы управления качеством.
IRJET приглашает статьи из различных технических и научных дисциплин для тома 9, выпуск 2 (февраль 2022 г.) Документы
IRJET Получил «Импакт-фактор научного журнала: 7,529» за 2020 год.
Подтвердить здесь
IRJET Получил сертификат регистрации ISO 9001:2008 для своей системы управления качеством.
IRJET приглашает статьи из различных технических и научных дисциплин для тома 9, выпуск 2 (февраль 2022 г.) Документы
IRJET Получил «Импакт-фактор научного журнала: 7,529» за 2020 год.
Подтвердить здесь
IRJET Получил сертификат регистрации ISO 9001:2008 для своей системы управления качеством.
IRJET приглашает статьи из различных технических и научных дисциплин для тома 9, выпуск 2 (февраль 2022 г.) Документы
IRJET Получил «Импакт-фактор научного журнала: 7,529» за 2020 год.
Подтвердить здесь
IRJET Получил сертификат регистрации ISO 9001:2008 для своей системы управления качеством.
Производство газобетона с использованием устройства вихревого слоя
Газобетон — разновидность легкого бетона, представляющая собой пористый искусственный материал, изготовленный из минеральных вяжущих (цемент, известь или гипс) и кремнеземистого заполнителя (кварцевый песок, зола-унос или кислые шлаки металлургической промышленности). Производство газобетона основано на процессах диспергирования, перемешивания, вспучивания смеси этих ингредиентов и ее твердения.
При производстве материала важно добиться высокой степени активации и равномерного распределения частиц газообразующей или пенообразующей добавки, а также гомогенизации и диспергирования составляющих массы.Для этих задач можно использовать устройство вихревого слоя (AVS) GlobeCore.
Преимущества газобетона
Основные характеристики пористого материала, повлиявшие на его популярность в строительной сфере:
- Высокие теплоизоляционные свойства
Поры в газобетоне могут занимать до 85% объема материала, что делает его чрезвычайно легким и обеспечивает высокие теплоизоляционные характеристики. Его отличает лучшая способность удерживать тепло по сравнению с обычными материалами, в том числе кирпичом.
Благодаря правильной геометрии и удобному фактору конфигурации строительство из бетонных блоков происходит быстрее и проще по сравнению с монолитным кирпичным строительством. Кроме того, при укладке блоков используется специальный клей, а не раствор. Это выгодно и просто. А швы толщиной всего до 3 мм не являются мостиками холода, в отличие от цементных прослоек между кирпичами.
Пористые блоки достаточно прочны как строительный материал. Поэтому поризованный бетон уже стал не просто вспомогательной альтернативой кирпичу, железобетону, но и существенно заменил их в ряде случаев.
Такие характеристики обеспечили высокую популярность пористого материала и широкий спектр его применения.
Область применения
В основном применение газобетона сосредоточено в области строительной теплоизоляции. Однако, кроме того, его используют для ограждения зданий и сооружений. В зависимости от этого материал классифицируют на теплоизоляционный, конструкционно-теплоизоляционный и конструкционный. Объемный вес разных видов варьируется от 300 до 1200 кг/м3.
В целом использование газобетона распространено в следующих областях:
- теплоизоляция железобетонных междуэтажных перекрытий, чердаков и стен;
- строительство перегородок, ограждающих конструкций;
- Возведение несущих стен, опор в малоэтажных домах, зданиях.
Газобетон применяется для строительства современных коттеджей, хозяйственных построек, промышленных объектов, других зданий и сооружений. Применяется при строительстве жилых комплексов, жилых кварталов, многоэтажных домов.
Учитывая такие перспективы, производство газобетона продолжает развиваться. Этот материал становится все более популярным на рынке как в сфере частного, малоэтажного строительства, так и при возведении крупных объектов строительными компаниями. Поэтому производство газобетона целесообразно наладить как на небольшом заводе строительных материалов, так и на крупном предприятии.
Производство пенобетона — традиционные технологии
Существует несколько способов производства газобетона.В зависимости от этого формы твердеют автоклавным или неавтоклавным способом, а получение пористости смеси основано на газообразовании, пенообразовании или аэрации. В результате получаем газобетон соответствующих марок:
- газобетон;
- пенобетон;
- газированный продукт.
Таким образом, технологии в основном отличаются способом получения пористости материала и способом его упрочнения. Например, газобетон готовят путем смешивания всех ингредиентов в сухом и влажном виде с помощью миксеров и мельниц, после чего сырье помещают в формы, где происходит дальнейшее порообразование.А пенобетон производится путем приготовления смеси с помощью миксеров с одновременным ее вздутием, после чего уже вспененный продукт отправляется в формы.
Обсудим эффективность включения АВС в процесс производства газобетона на примере популярной технологии с использованием газогенерирующего агента. Для начала разберем проблемы, которые поможет решить новое оборудование от GlobeCore .
Недостатки классической технологии производства газобетона
Популярная технология производства газобетона предполагает использование газообразующего реагента, с помощью которого происходит вспучивание смеси.Как правило, в качестве такого ингредиента используется алюминиевая пудра. При реакции с водным раствором гидроксида кальция выделяется порообразующий кислород.
Чем равномернее расположены поры в бетоне и чем меньше их размер, тем выше эксплуатационные характеристики конечного материала. Для этого важно максимально равномерно распределить газообразователи по всему объему смеси, добиваясь высокой степени ее дисперсности.Кроме того, на качество влияет количество активного СаО в приготовленной массе.
Для достижения высокой пористости материала исходные ингредиенты (песок, известь) можно обработать и дополнительно измельчить. В этом случае может применяться раздельный мокрый помол песка или комбинированный сухой помол ингредиентов.
Дополнительная обработка газообразователя заключается в частичном удалении парафиновой пленки с поверхности частиц. Это делается путем смешивания с водой и поверхностно-активными веществами.Однако традиционные смесители отличаются низкой эффективностью удаления парафиновой пленки.
Кроме того, при приготовлении газообразователя частицы алюминиевой пудры местами образуют комки. В дальнейшем эти скопления частиц вызывают избыточное, неравномерное выделение кислорода при химической реакции — образуются большие поры и пустоты. В результате бетонное изделие отличается низкой прочностью в этом месте и может треснуть.
А при недостаточном газовыделении в смесь добавляют до 25% извести.Кроме того, известь способствует достижению необходимой прочности бетона до окончания газогенерирующих процессов, что необходимо для получения пористой структуры.
Таким образом, к основным проблемам традиционной технологии производства газобетона можно отнести:
- образование пустот, трещин в материале;
- недостаточный выход газа для порообразования;
- низкая однородность смеси.
Использование устройства вихревого слоя GlobeCore помогает решить проблемы, связанные с агрегацией частиц, недостаточной активностью и неравномерным распределением газообразующего агента по объему массы.
Производство газобетона с помощью устройства вихревого слоя
Приготовление газообразователя с помощью устройства вихревого слоя заключается в обработке алюминиевой суспензии в электромагнитном поле с применением ферромагнитных частиц . Кроме того, в этих условиях осуществляется приготовление и активация известково-песчаных, цементно-песчаных смесей.
Смесь обрабатывается в немагнитной рабочей камере, в пространстве которой с высокой интенсивностью перемещаются ферромагнитные иглы за счет воздействия электромагнитного поля, создаваемого индуктором, — создается вихревой слой.Эти иглы превращаются в миниатюрные миксеры и дробилки. В результате такой обработки мы получаем однородную массу с высокой степенью дисперсности и активации обрабатываемых веществ и смесей. Перемешивание, активация и измельчение происходят под воздействием электромагнитного поля, акустических колебаний, высокого локального давления и электролиза.
Эффективность приготовления суспензии из алюминиевой пудры с помощью устройства вихревого слоя исследована и описана Д.Д. Логвиненко. В табл. 1 представлены изменения физико-механических свойств газосиликата, полученного на основе газогенерирующего агента, обработанного и необработанного в АВС.
Таблица 1
Эксперимент № | Условия приготовления суспензии | Производительность установки АВС-100, л/ч | Механические свойства газосиликата | |||||
После обработки подвески в АВС | После обработки суспензии в обычном смесителе | |||||||
Объемный вес, γ, г/см3 | Предел прочности на скалывание, σс*10-5, Па | Коэффициент прочности | Объемный вес, γ, г/см3 | Предел прочности на скалывание, σс*10-5, Па | Коэффициент прочности | |||
1 | Алюминиевая пудра — 100% по отношению к расчетному количеству | 120 | 385 | 18.![]() | 2,56 | 396 | 15,2 | 2,03 |
377 | 10,3 | 1,47 | 419 | 79,5 | 0,92 | |||
414 | 11,8 | 1,41 | 438 | 10,8 | 1,14 | |||
2 | Алюминиевая пудра — 90% по отношению к расчетному количеству | 950 | 386 | 14,5 | 1.85 | 437 | 14,1 | 1,51 |
427 | 15,2 | 1,70 | – | – | – | |||
375 | 12,3 | 1,80 | – | – | – |
Производство газобетона с использованием газообразователя, обработанного в АВС, позволило получить материал с прочностью на 10–30 % выше, чем у традиционно изготовленного образца.Коэффициент качества газобетона увеличился на 20–60 % по сравнению с исходными данными.
Более того, усовершенствованная технология производства газобетона стала более рентабельной. Расход газообразователя снижен на 10%, а извести меньше на 2%. При этом конечный продукт не стал тяжелее; наоборот, его объемный вес уменьшился. Прочность блоков увеличилась.
Не исключено, что физико-механические свойства газобетона улучшились за счет обработки известково-песчаной и цементно-песчаной смесей в АВС.Это связано с активацией частиц SiO2, вызванной образованием активных центров на поверхности песчинок.
Преимущества устройства вихревого слоя в производстве пенобетона
Производство газобетона с применением АВС предполагает оптимизацию технологических процессов в линии с повышением качества продукции за счет более эффективной переработки сырья и смесей. Это достигается за счет следующих преимуществ АВС:
Вихрево-пластовое устройство подходит как для активации и приготовления суспензии из газогенерирующего агента, так и для перемешивания, диспергирования и активации остальных ингредиентов цементно-песчаной или известково-песчаной смеси. Оборудование подходит для мокрого помола, смешивания ингредиентов, активации, измельчения песка и комбинированного сухого смешивания ингредиентов газобетона.
- Повышение качества продукции
В результате приготовления ингредиентов и добавок в АВС мы получаем газобетон с лучшими физико-механическими характеристиками.
Помимо того, что оборудование более экономично по сравнению с обычными агрегатами по энергозатратам, оно позволяет снизить расход ингредиентов на вспучивание массы и сократить время обработки смесей.
Устройство вихревого слоя может быть интегрировано в существующую линию производства газобетона. Кроме того, для установки не требуется сооружение каких-либо тумб и дополнительных конструкций, а устройство достаточно компактно.
Производство газобетона с помощью устройства вихревого слоя позволяет получить более качественный строительный материал и оптимизировать технологические процессы, что сказывается на снижении себестоимости продукции и увеличении ее объемов.
Газобетон из местного сырья | Маталка
Нараянан Н. и К. Рамамурти. «Структура и свойства газобетона: обзор». Цементно-бетонные композиты 22, вып. 5 (2000): 321-329.
Нараянан Н. и К. Рамамурти. «Микроструктурные исследования газобетона». Исследования цемента и бетона 30, вып. 3 (2000): 457-464.
Мицуда, Такеши, Каори Сасаки и Хидэки Исида.«Фазовая эволюция в процессе автоклавирования газобетона». Журнал Американского керамического общества 75, вып. 7 (1992): 1858-1863.
Гоуаль М.С., А. Бали и М. Кенеудек. «Эффективная теплопроводность глинистого газобетона в сухом состоянии: экспериментальные результаты и моделирование». Журнал физики D: Прикладная физика 32, вып. 23 (1999): 3041.
Маталка, Фарис, Парвиз Сорушян, Сакиб Уль Абидин и Амирпаша Пейванди. «Использование золы сжигания недревесной биомассы при разработке щелочеактивированного бетона.»Строительство и строительные материалы 121 (2016): 491-500.
Маталка, Фарис, Парвиз Сорушян, Ранкотге Ранджит Вирасири и Амирпаша Пейванди. «Разработка местных вяжущих в качестве строительных материалов». Труды Института инженеров-строителей-Строительные материалы (2017): 1-10.
Маталка, Фарис, Парвиз Сорушян, Анаги Балчандра и Амирпаша Пейванди. «Характеристика активированного щелочью геополимерного бетона на основе золы из недревесной биомассы.Журнал материалов в гражданском строительстве (2016): 04016270.
Маталка, Фарис, Ливэй Сюй, Венда Ву и Парвиз Сорушян. «Механохимический синтез однокомпонентного щелочного алюмосиликатного гидравлического цемента». Материалы и конструкции 50, вып. 1 (2017): 97.
Даксон, Питер и Джон Л. Провис. «Разработка прекурсоров для геополимерных цементов». Журнал Американского керамического общества 91, вып. 12 (2008): 3864-3869.
Рамамурти, К., Э.К. Кунханандан Намбиар и Г.Инду Шива Ранджани. «Классификация исследований свойств пенобетона». Цементно-бетонные композиты 31, вып. 6 (2009): 388-396.
Abdullah, M.M.A.B., et al., Легкий геополимерный бетон на основе летучей золы с использованием пенообразователя. Международный журнал молекулярных наук, 2012. 13(6): с. 7186-7198.
Сингх, М. и М. Гарг, Исследование прочного гипсового вяжущего для строительных материалов. Строительство и строительные материалы, 1992. 6(1): с. 52-56.
Маталка, Ф.и др., Разработка и характеристика вяжущего на основе гипса. Европейский журнал достижений в области техники и технологий, 2017. 4(3): с. 153-157.
Камарини, Г. и Дж.А. De Milito, смеси полугидрата гипса и цемента для повышения долговечности штукатурки. Строительство и строительные материалы, 2011. 25(11): с. 4121-4125.
Элсен, Дж., Микроскопия исторических растворов — обзор. Исследования цемента и бетона, 2006. 36(8): с. 1416-1424 гг.
Маталка Ф. и др., Разработка сэндвич-композитов для строительства зданий с использованием местных материалов. Строительство и строительные материалы, 2017. 147(С): с. 380-387.
Хамад, Али Дж. «Материалы, производство, свойства и применение легкого ячеистого бетона: обзор». Международный журнал материаловедения и инженерии 2, вып. 2 (2014): 152-157.
Современное российское оборудование и завод по производству автоклавного газобетона
Мировое производство ячеистого бетона перешло на производство высокоточной резки автоклавного газобетона.Специалисты ТМЗ спроектировали и построили конкурентоспособное и уникальное в инженерной разработке раскройно-формовочное оборудование. Это оборудование может быть использовано для производства автоклавного газобетона (АГБ) на заводах из силикатного кирпича, прошедших реконструкцию, или может заменить устаревшие раскройные станки на предприятиях по производству АФК. Существующая инфраструктура может быть эффективно использована, в том числе: теплоэнергетические системы, мельницы, смесители, дозаторы, автоклавы, приемники, хранилища и т. д.В ситуации, когда в результате растущих объемов строительства мы видим большой спрос на оборудование для строительной отрасли, это представляется наиболее разумным путем развития производства автоклавного газобетона в России.
Первым проектом стала реконструкция завода по производству силикатного кирпича ЗАО «ВКСМ» в г. Воронеже, Россия. Второй связан с переходом от устаревшего режущего оборудования к технологии производства автоклавного газобетона. Недавно был введен в эксплуатацию третий раскройно-формовочный комплекс на ОАО «Оршастройматериалы», Республика Беларусь.
Используемое в настоящее время на заводах раскройно-формовочное оборудование для производства газобетонных блоков (Универсал-60) в силу своих конструктивных особенностей не позволяет по геометрической точности соответствовать современным требованиям. Комплекс, разработанный ТМЗ, может заменить эти устаревшие раскройные станки.
Производственный процесс (рис. 1):
После заливки суспензии в формы (1) и отверждения неспеченные лепешки перемещаются в положение манипулятора сборки/разборки формы (4).Форма (1) приварена к точной геометрической форме; состоит из каркаса корпуса и съемного бокового ограждения, выполняющего функции закалочного лотка (2). Манипулятор (4) поднимает форму (1) с зажимами, перемещает ее к мосту режущего комплекса. Затем он поворачивает форму на 90° и ставит ее на режущую тележку (6). Специальные устройства открывают форму, а лоток с тортом остается на тележке для резки. Манипулятор перемещает корпус формы по обратному конвейеру (14), где собирает форму и устанавливается на рельсы для перемещения в положение заливки суспензии.
Лоток с блоком на отрезной тележке проходит через станок боковой резки (7), где формируется длина блока и при необходимости дорабатывается «паз» и «язычок». После этого блок проходит через машину горизонтальной резки (8) и машину вертикальной резки (9), где при необходимости в блоках делаются углубления для захвата руками. Затем блок помещается на транспортную тележку (11), подается в вакуумную систему (10) для снятия фланца и, наконец, перемещается в рабочую зону блока транспортировки.
Блок переноса (12) перемещает лоток с блоком на тележку автоклава (13). Автоклавная тележка с блоком перемещается в автоклав с передаточным мостом (15), где блок подвергается гидротермической обработке. После обработки тележка автоклава и блок перемещаются в рабочую зону узла передачи (16), где лоток повторно штабелируется, а блоки разделяются (17). Затем реклаймер укладывает блоки на деревянные поддоны, и блоки транспортируются на склад с помощью конвейерной системы на вынос.
1 — пресс-форма; 2 — лоток; 3 — узел переноса формы; 4 — манипулятор сборки/разборки форм; 5 — автоматический комплекс для резки газобетона; 6 — режущая тележка; 7 — бокорезная машина; 8 — горизонтально-отрезной станок; 9 — вертикально-отрезной станок; 10 — вакуумное устройство; 11 — транспортная тележка; 12 — укладчик лотков на тележке автоклава; 13 — автоклавные тележки; 14 — система обратного конвейера поддона твердения; 15 — мост передачи тележек; 16 — укладчик лотков на тележке автоклава; 17 — блок-сепаратор; 18 — конвейер возврата закалочных лотков.
Благодаря малой длине режущих струн, точности перемещения лотка и гибкости в регулировке скорости резки данное оборудование позволяет изготавливать блоки точной геометрической формы. Боковые поверхности могут быть плоскими или могут быть выполнены с канавкой и шпунтом, что позволяет скреплять блоки без использования клея или вертикальных соединений. Точные размеры по высоте (± 1 мм) позволяют толщине клея, на который помещаются блоки, составлять 2 мм. Установка блоков точного размера с пазом и шпунтом не только ускоряет процесс строительства, но и снижает его стоимость.Кроме того, использование клея обеспечивает лучшие изоляционные свойства. Режущий комплекс позволяет выполнять карманное шлифование, предназначенное для удобства перемещения и установки блоков.
Таким образом, налаживание производства автоклавного ячеистого бетона может осуществляться путем замены устаревшего оборудования на существующих мощностях, либо путем модернизации заводов силикатного кирпича с использованием части оригинального оборудования: мельниц, смесительных машин, транспортных единиц, дозаторов, автоклавов и т.п. ., что менее затратно и не требует столько времени.Стоимость режущего и формовочного оборудования составляет 30—35% от себестоимости технологических линий.
Оборудование для газобетонных блоков включает в себя:
· формы со съемными закалочными лотками
· манипулятор для сборки и разборки формы
· автоматический комплекс для резки газобетона
· гусеница для перемещения тележки
· Режущая тележка
· транспортная тележка
· Бокорез
· Станок горизонтально-раскроечный
· Станок вертикально-отрезной
· вакуумное устройство
· Укладчик лотков и промышленные тележки для автоклавов
· тележки для автоклавов
· Устройство для разборки газобетонных изделий
· конвейер для возврата закалочных лотков
· конвейер для готовой продукции
Все части режущего и формовочного оборудования ТМЗ управляются автоматически.Есть режим регулировки для регулировки механизмов. На панелях управления установлены мониторы, отображающие всю диагностическую информацию, связанную с текущим состоянием комплекса.
Все оборудование, предназначенное для производства газобетонных блоков, сначала собирается и испытывается на территории ТМЗ. Затем его разбирают на крупные компоненты. Специалисты ТМП контролируют процесс сборки. Оборудование для производства газобетонных блоков известно своей надежностью в работе и простотой обслуживания.Гарантийный срок – один год. Оборудование для автоклавных газобетонных блоков очень надежное и простое в обслуживании.
Обзор использования отходов для производства автоклавного ячеистого бетона†
Обзор использования отходов производства автоклавного ячеистого бетона †
- Рахман Р.А. 1 , Фазлизан А. 1,* , Асим Н. 1 , А.Тонгта 2
2 Кафедра физики, Факультет естественных наук, Университет Наресуан, Пхитсанулок, 65000, Таиланд
* Автор, ответственный за переписку: А.
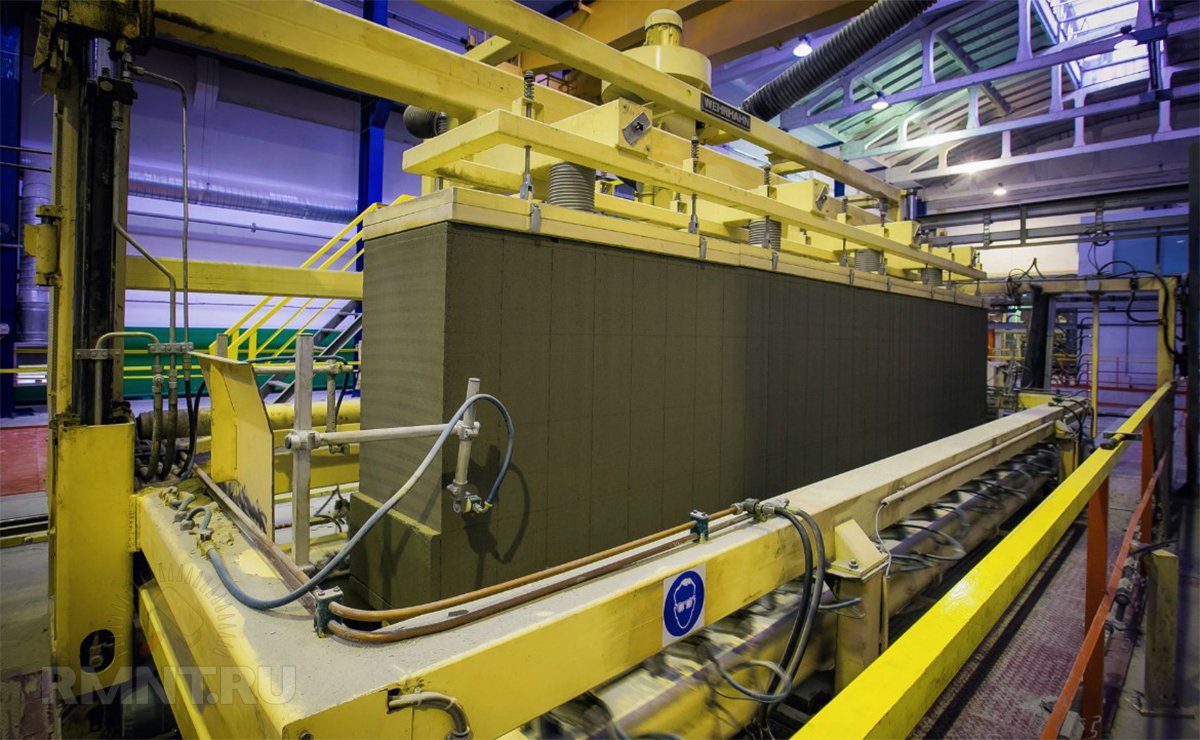
(Эта статья относится к этому специальному выпуску: Возобновляемые материалы для устойчивого развития)
Поступила в редакцию 01 августа 2020 г.; Принято 13 октября 2020 г.; Выпуск опубликован 30 ноября 2020 г.
Аннотация
Автоклавный газобетон (АГБ) стал более привлекательным благодаря
его отличные и экологически чистые свойства в строительстве.ААС
относительно легкий, обладает более низкой теплопроводностью, более высокой термостойкостью, меньшей усадкой и прочной конструкцией, чем обычный бетон. ААС — это
сочетание кварцевого песка, цемента, гипса, извести, воды и расширительного агента.
Чтобы улучшить его физико-механические свойства и снизить себестоимость производства,
были сделаны огромные инновации, в которых отходы использовались в качестве частичной замены материалов AAC. Эта статья предназначена для представления литературы
по утилизации отходов как средства частичной замены газобетона
материалы для улучшения его физико-механических свойств и тепловых характеристик.Физические свойства, такие как микроструктура и механические свойства
такие как плотность, прочность на сжатие, водопоглощение представлены для классификации
исследование, которое было сделано в таких новшествах. Кроме того, было представлено обсуждение инноваций для улучшения его тепловых характеристик.
Согласно обзору, увеличение применения газобетона приводит к образованию большого количества отходов на строительных площадках и переработке порошка бетонных отходов в стеновой бетон; в частности, газобетон не часто применялся в строительстве.
Ключевые слова
Автоклавный газобетон; микроструктура; отходы; прочность на сжатие
Процитировать эту статью
Рахман, Р. А., Фазлизан, А., Асим, Н., Тонгта, А. (2021). Обзор использования отходов производства автоклавного ячеистого бетона † . Журнал возобновляемых материалов, 9(1) , 61–72.
Что такое автоклавный газобетон?
Газобетон – это строительный материал, набирающий популярность, особенно для зданий, требующих сертификации LEED.
Этот тип сборного железобетона, состоящий из природного сырья, является строительным стандартом с середины 1920-х годов.
Предлагая его в качестве строительного материала, вы можете увеличить свой доход, если у вас есть подходящее оборудование для его эффективного производства.
Давайте подробнее рассмотрим, как изготавливается автоклавный газобетон, и преимущества его использования.
Производство автоклавного газобетона
Этот материал, изобретенный шведским архитектором Йоханом Эрикссоном, стал побочным продуктом продолжающейся индустриализации, которая происходила в мире с начала до середины 1900-х годов.
Первоначально он был изготовлен с использованием процесса, включающего квасцовый сланец; однако позже было обнаружено, что радиоактивный газ был побочным продуктом материала.
Начиная с 1975 года в качестве заменителя использовались более безопасные вяжущие (песок, известь, алюминиевая пудра).
Материал требует производства промышленного оборудования.
В автоклавных системахдля отверждения газобетона после его формования используется процесс под давлением пара.
Кварцевый песок в смеси вступает в реакцию с гидроксидом кальция из-за огромного давления.
В результате этой реакции образуется гидрат силиката кальция, вещество, придающее пенобетону его уникальные свойства.
Преимущества автоклавного газобетона
Материал имеет несколько уникальных характеристик, которые дают ему преимущество перед традиционным бетоном, в том числе:
- Огнестойкость.
- Уменьшенный вес.
- Эффективность нагрева и охлаждения.
- Долговечный.
- Экологичность и возможны кредиты LEED.
- Изоляция (которая со временем экономит деньги ваших клиентов).
Автоклавный газобетон более хрупок, поэтому рабочие должны обращаться с ним с особой осторожностью.
Автоклавные растворы для газобетона по индивидуальному заказу
Ваши потребности и спецификации — это план, который мы используем для проектирования и создания вашей системы автоклавов.
Индивидуальная автоклавная система для газобетона имеет несколько преимуществ, в том числе:
- Произведено в США. Многие автоклавы, используемые для производства автоклавного ячеистого бетона в США, были произведены в европейских странах. Производство вашей системы автоклавов здесь, в США.S. значительно сокращает время производства и транспортные расходы, связанные с доставкой автоклава на предприятие.
- Повышенная производительность. Производство автоклавной системы, отвечающее вашим уникальным потребностям, сводит к минимуму необходимость последующей адаптации или настройки типовой системы в соответствии с вашими спецификациями, что может увеличить ваши общие расходы.
- Специализированный ремонт. Нет никого, кто бы лучше подходил для обслуживания и/или ремонта вашего автоклава, чем те, кто построил его с нуля.
Вы можете получить все необходимое для автоклавной системы для газобетона в нашем универсальном магазине — от проектирования самой системы до трубопроводов, автоматизации и обработки материалов — для перемещения вашего газобетона на протяжении всего производственного процесса.
Мы производим каждый компонент вашего автоклава. Это также означает, что вы в надежных руках для любого ремонта, который потребуется вашей системе в будущем.
Ваша система автоклавного газобетона нуждается в обновлении?
Автор: Джеффри Липпинкотт