Технология производства газобетонных блоков: Производство газобетонных блоков своими руками, оборудование, формы, технология и видео
Оборудование для производства газобетонных блоков: виды
Содержание
- 1 Виды и конструкция
- 1.1 Мобильные
- 1.2 Стационарные
- 1.3 Мини-установки
- 1.4 Конвейерные
- 2 Как правильно выбрать оборудование?
- 3 Технология производства
- 3.1 Подготовка форм
- 3.2 Приготовление смеси
- 3.3 Заливка
- 3.4 Сушка блоков
- 3.5 Упаковка и хранение
- 4 Вывод
На сегодняшний день применение газобетонных блоков пользуется большим спросом из-за своей легкости, экологичности и теплоизоляции. Технология производства газобетона несложная, но требует четкой последовательности выполнения действий. Материалы и оборудование доступны и легки в монтаже, а, значит, с их установкой справится не только начинающий строитель, но и дачник.
Виды и конструкция
Оборудование для производства газобетона условно делят на группы:
- мобильные установки;
- стационарные;
- мини-установки;
- конвейерные линии.
Применяют два вида изготовления газобетона – автоклавный и неавтоклавный. Применяя естественный способ твердения газобетонного материала, обеспечивается прочность конструкции и увеличивается несущая способность стен. Блоки, изготовленные автоклавным методом, имеют высокие теплоизоляционные характеристики.
Емкость газобетонных установок выполняется в виде прямоугольника или U-образная. Размеры изделий из газобетона исходят из форм, применяемых на этапе заливки. Преимущество заключается в возможности изготовления по индивидуальным размерам.
Вернуться к оглавлению
Мобильные
Перед тем как приступить к строительству поместья, заботятся о материалах и вспомогательных установках, которые необходимы для собственного изготовления неавтоклавного газобетона. Установка для изготовления газобетона включает в своем комплекте:
- компрессор;
- электродвигатель;
- набор для подключения агрегата;
- разливочный шланг;
- инструкцию с описанием технологии, с помощью которой производство газобетона не потребует больших усилий.
Применение установки для замеса бетонного раствора позволяет упростить процесс перемешивания и обеспечить высокое качество материалам. Использование компрессорной установки увеличит производительность на 25% и сэкономит расходные материалы. Установка имеет невысокую цену, но, несмотря на это обладает надежностью и простотой в использовании. Для приготовления газобетонных изделий с помощью агрегата, не нужны специальные навыки, можно просто изучить инструкцию или посмотреть обучающий урок на диске, который идет в комплекте. Мобильная установка не занимает много места, поэтому обустраивать специальное помещение для ее хранения не имеет надобности.
Вернуться к оглавлению
Стационарные
Стационарная установка.При наличии малой строительной компании пригодится стационарная линия изготовления неавтоклавного газобетона. Такие установки автономны и применения ручного труда не требуется. Хранить стационарные лини нужно в специально оборудованных помещениях. Перемещать установки на строительный объект нужно с использованием специально предназначенного оборудования. Стационарные линии включают в свою конструкцию дозаторы, которые автоматически измеряют нужное количество ингредиентов. Установка состоит из бойлера, в котором греется вода до нужной температуры, вибросита и ленточного конвейера для просеивания и передачи песка.
Стационарная линия размещается на площади в пятьсот квадратных метров, для работ требуется два обученных человека. Материал из оборудования выходит высшего качества, это позволяет закрывать глаза на недостаток установки – большие расходы на приобретение агрегата и занимаемая площадь.
Вернуться к оглавлению
Мини-установки
Стационарные линии только в уменьшенном виде представляют собой мини-установки. Изготовление блоков проходит по такой же технологии, как и в стационарных установках, только выход готового материала значительно меньше. Качество материалов также находится на высшем уровне и ничем не уступает блокам, изготовленным в стационарных линиях.
Установка состоит их неподвижных форм и перемещающегося смесителя. Мини-линии работают как от стационарной, так и от передвижной электростанции. Также при необходимости возможно перемещение агрегата по строительной площадке. Такая установка подойдет, когда занимаются малым производством продукции.
Вернуться к оглавлению
Конвейерные
Конвейерные установки для производства газобетона.При больших объемах готовой продукции используют конвейерные установки, которые исключают применение ручного труда. Работа автоматизирована, что позволяет экономить на оплате труда работников. Установка конвейерного механизма требует больших площадей и обслуживающего персонала. Конструкция агрегата включает в себя перемещающуюся форму при неподвижном дозаторе и мешалки. За счет объемов выпуска готовой продукции и высокого качества материалов, обеспечивается соответствующая прибыль, которая в скором времени окупает дороговизну оборудования.
Вернуться к оглавлению
Как правильно выбрать оборудование?
Чтобы готовая продукция имела высокие характеристики качества, к ее выбору подходят с большой ответственностью. Важно найти поставщиков с проверенной репутацией и только потом приобретать у них сырье. Выбирая оборудование, учитывают транспортные расходы. Продукцию берут оптом, а, значит, для нее оснащают складские помещения. Изготавливая бетонный раствор, берут во внимание качество таких материалов: известь, алюминиевая паста, песок и цемент. При производстве бетона на строительном участке оснащают поступление воды. Если изделия включают в себя разные наполнители, то запас дополнительных компонентов обеспечивается заранее.
Совершая покупку, требуйте у поставщиков сертификаты к оборудованию. Коробка без повреждений и при необходимости с маркировкой. На каждое оборудование присутствует гарантийный срок, который указывается в гарантийном талоне.
Вернуться к оглавлению
Технология производства
Изготовление бетонных блоков хоть и несложный процесс, однако требует определенной последовательности в работе. При изготовлении с соблюдением требуемых условий выходит качественная продукция, готовая к применению. Технология по производству включает такие этапы:
- Приготовление раствора на основе песка, цемента, извести и воды.
- Подготовка форм, которые применяются в виде прямоугольника.
- Заливка.
- Сушка.
Вернуться к оглавлению
Подготовка форм
Кассетные формы для газобетона.После приготовления бетонного раствора приступают к заливке в специальные формы. Используя разборные емкости, вручную убирают борта прямоугольника, при сплошных формах процесс является автоматизированным. По составу емкости различают:
- металлические;
- пластиковые;
- деревянные.
В подогретые формы до 50 С заливают смесь на половину емкости, так как бетонный раствор поднимается как дрожжевое тесто. При надобности поверхность выравнивают, срезая неровности струной. Оставляют для выдержки на 10 часов. Заполняя емкости повторно новым раствором, их очищают и смазывают.
Вернуться к оглавлению
Приготовление смеси
Бетонный раствор готовят с засыпки ингредиентов и тщательного перемешивания. Для начала в воду всыпают цемент с известью и в течение 5 минут перемешивают, после чего вливают часть воды с алюминиевой стружкой. Важно тщательно перемешать компоненты смеси, чтобы исключить комочки. В результате консистенция напоминает густую сметану.
Вернуться к оглавлению
Заливка
После приготовления смеси заливают формы газобетонным раствором. Емкости очищают от остатков смеси и подогревают. Раствор вливают, используя шланг. После чего залитую форму выравнивают и застилают теплоизоляционным слоем.
Вернуться к оглавлению
Сушка блоков
Залитый раствор в формы подвергается сушке при 190 С. Продолжительность высыхания занимает 12 ч. в автоклаве. Сушка блоков из неавтоклавного газобетона достигает 48 часов.
Вернуться к оглавлению
Упаковка и хранение
Залитые бетонные изделия выдерживают 28 дней в сухом помещении, без сквозняков и перепадов температур. После изготовления блоков, их упаковывают и складируют на поддон. Упаковывают газобетонную продукцию термопленкой и транспортируют на склад. Нельзя грузить и транспортировать газобетонные изделия навалом, разгружать сбрасыванием.
Хранят продукцию в штабелях, устанавливая поддоны, друг на друга. При продолжительном хранении заготовок, защищаем помещения. Хранение газобетонных изделий в зимний период не отличается от другого времени года. Для избежания попадания влаги в результате осадков, газобетонные конструкции накрывают сверху брезентом. Бетону опасны таяния снега в весенний период.
Вернуться к оглавлению
Вывод
Выбирая оборудование для изготовления газобетонных изделий, исходят из своих строительных мощностей, денежных средств и планируемого объема выпуска готовой продукции. На цену влияет мощность агрегата и комплектация. Дорогой механизм для приготовления бетонного блока – конвейерная линия. Цена агрегата оправдывает себя только на крупных производственных цехах.
Газобетонный блок – проверенный строительный материал, который применяется не один десяток лет. Он актуален и по сей день за счет своих преимущественных характеристик и легкости производственного процесса.
методы производства и технологические нюансы
В решении целого комплекса строительных задач газобетон, универсальный и современный, станет надежным подспорьем при возведении зданий самых разнообразных размеров, конструкций и назначения – как одноэтажных загородных коттеджей, так и небоскребов, многоэтажных торговых и развлекательных комплексов на каркасной основе.
Среди множества преимуществ газобетона – экологичность, долговечность применения и огнестойкость, легкость в обработке, а также отличные теплоизоляционные свойства. Последняя характеристика весомее, если учитывать низкий удельный вес материала. При этом умеренная стоимость делает газобетонные блоки доступными для всех представителей среднего класса.
Даже человек без строительного образования благодаря несложной технологии применения этого материала с легкостью построит коттедж своей мечты, или любой другой малоэтажный дом.
Технология, которой пользуется любой производитель газобетона, достаточно проста. Газобетон входит в семейство ячеистых бетонов, которое также включает в себя пенобетоны и легкие аэрированные бетоны. Как видно из названия, основная черта отличия этих материалов – ячеистая структура. Малый объемный вес обеспечивается за счет пузырьков газа, которые могут занимать до 85% объема блока. Основными компонентами для изготовления газобетона являются известь, вода, кварцевый песок и, конечно же, цемент.

Далее по технологии в специальных емкостях происходит так называемое «вспучивание», где будущий газобетон подвергают вибрационным нагрузкам, что приводит к лучшему затвердению и ускорению химических реакций. Газобетон проходит и стадию предварительного твердения, которая сопровождается снятием неровной верхушки, а затем и разрезанием заготовки на ровные блоки. Затем куски газобетона обрабатывают в автоклаве, калибруют фрезерной машиной и отделывают фасадные поверхности.
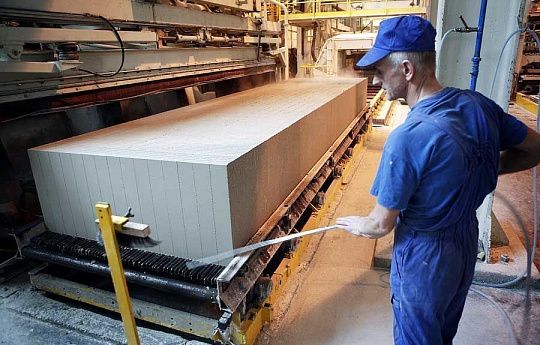
Применение компьютерного моделирования и прочих современных технологий делает газобетонные блоки однородными и одинаковыми по размеру, как в горизонтальном, так и в вертикальном направлении.
Автоклавная сушка газобетона
Автоклавирование направлено на улучшение технических свойств газобетонной смеси. Газобетонный блок, сформированный и разрезанный, помещают в камеры автоклавирования, где они на протяжении 12 часов подвергаются воздействию водяного пара температурой 190°С. При этом пар нагнетается до повышения уровня давления вплоть до 12 кг/см² и газобетонный блок надежно твердеет, становится более прочным, ограничивает усадку здания, к тому же, более однородным, а следовательно – может быть применен в строительстве в качестве как основного структурного материала, так и с целью звуко- и теплоизоляции. Низкий коэффициент теплопроводности (0,09-0,18 Вт/(м•°С) дает возможность применять газобетонные блоки автоклавного твердения в наших климатических условиях, и даже возводить однорядные стены с толщиной блока всего 375 – 400мм.
Безавтоклавные технологии сушки газобетонных блоков
Существует и безавтоклавные технологии сушки газобетонных блоков. Для них не требуется какого-то высокотехнологичного оборудования, однако газобетонные блоки изготовленные без участия автоклава характеризуются меньшей прочностью. Если автоклавный газобетон дает усадку 0,3-0,5 мм на метр высоты, то для газобетонных блоков неавтоклавного происхождения эти показатели приближаются к 3-5 мм/м. Выигрывает автоклавный газобетон и по прочности, превышая соответствующие показатели для неавтоклавного в 2-4 раза. Любой крупный производитель газобетона, такой как всемирно известные Ytong или Hebel, предпочитает изготавливать именно автоклавный газобетон.
В зависимости от целей использования той, или иной марки газобетон разделяется на три класса:
Теплоизоляционный обладает плотностью в сухом состоянии 300-500 кг/м³ и общей пористотью более 75%. Конструктивно-теплоизоляционный имеет соответствующие показатели на уровне 500-900 кг/м³, то есть, является более тяжелым, в то время как пористость его значительно снижена – от 55 до 75%. Наконец, самый плотный и наименее пористый, конструктивный газобетон имеет плотность на уровне 900-1200 кг/м³, а пористость от 40 до 55%.
На какие свойства газобетона имеет смысл обратить внимание:
В первую очередь, это его прочность и долгий срок службы. В коттеджном строительстве особой популярностью пользуется пенобетон с небольшой удельной массой 400-500 кг/м³ и высокой прочностью 28-40 кгс/ м². Поэтому газобетон легкоприменим в малоэтажном строительстве бескаркасных зданий высотой до 14 м, а также для создания перегородок.
При этом газобетон характеризуется довольно высоким сроком службы, приравнённым к сроку службы кирпича. И хотя производители предоставляют гарантию на 80 лет, уже сегодня становится ясно, что строения из газобетонных блоков могут служить намного дольше, ведь стены подобных зданий восьмидесятилетней давности не дают трещин и характеризуются высокой стойкостью материала.
Качественная теплоизоляция также является одним из достоинств газобетонных блоков, ведь заключенный в порах материала воздух великолепно ограничивают теплообмен. Например, сухой газобетон характеризуется довольно низким коэффициентом теплопроводности 0,12 Вт/м•°С.
Объёмный вес газобетона обратно пропорционален его плотности. Именно правильное сочетание этих параметров на уровне объемного веса газобетона до 400-600 кг/м³, обеспечит успешную постройку теплого и прочного дома. Этому будут способствовать также гладкая поверхность и точно контролируемые размеры и формы газобетонных блоков. При постройке из газобетона можно использовать технологию тонкошовной кладки, которая исключает образование «мостиков холода».
Еще одним преимуществом низкой теплопроводности является соответствующая низкая тепловая инертность этого материала. Таким образом, в отличие от кирпичных домов, дома из газобетона прогреваются намного быстрее.

Не последний вопрос при выборе материала для постройки – ценовая политика.
Более лёгкий, газобетон существенно снижает нагрузку на фундамент, а используемая при его укладке технология тонких швов способствует снижению затрат на кладочный раствор почти в шесть раз. Немаловажно снижение затрат времени и труда на сам процесс кладки, ведь один блок заменяет 15-20 кирпичей, что сокращает количество операций при укладке одного блока материала.
Несмотря на крупные габариты, газобетонный блок не требует дополнительной подъемной техники, так как обладает небольшим удельным весом. Суммируя все вышесказанное, применение газобетона для возведения зданий позволяет увеличить скорость возведения в четыре раза, пропорционально снижая и затраты на строительство.
Безопасность для жильцов
Надёжный производитель газобетонных блоков стремиться использовать только натуральные, экологически нейтральные компоненты. Вследствие этого хороший материал инертен и безопасен для здоровья людей и окружающей среды, так как не выделяет абсолютно никаких веществ. Газобетон относится к «дышашим» материалам и по своей пористости сходен с таким популярным натуральным строительным материалом, как дерево. Однако, в отличие от построек из дерева, постройки из газобетонных блоков характеризуются и легкостью монтажа, и долговечностью, не усыхают, держат форму, не реагируют на перепады температуры и воздействие повышенной влажности. При этом поры газобетона обеспечивают постоянный газообмен внутреннего пространства дома с окружающей средой – вредные газы и застоявшийся воздух покидают помещение, в то время как свежий, чистый воздух проникает в жилище. Замечено, что в домах из газобетона и дышится свободнее.
Низкая теплопроводность имеет и еще одно, на этот раз действительно приятное следствие. Стены из газобетона всегда на ощупь теплые, а также выводят лишнюю влагу, препятствуя гниению и появлению плесени на стенах.
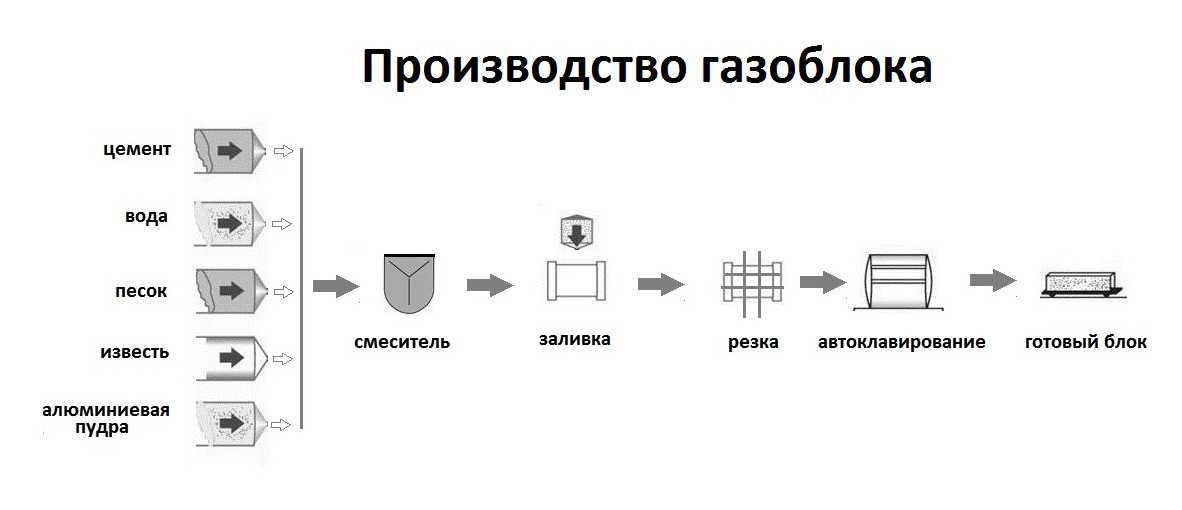
Еще один бонус при применении газобетона – его огнестойкость. Он способен выдерживать воздействие огня на протяжении 3-7 часов, при этом не горя и не поддерживая горение, защищая в свою очередь от огня и металлические внутренние конструкции.
Газобетонные блоки обладают также и завидной морозостойкостью, что немаловажно для нашего региона. Испытания, заключавшиеся в восьмичасовом насыщении газобетонного блока водой, а затем в восьмичасовом же заключении в морозильной камере, показали, что он способен при полном водном насыщении всех пор выдерживать полный цикл заморозки и оттаивания. Прежде чем разрушиться, блок выдержал 100 полных циклов без потери прочности. Морозостойкость кирпича, кстати, намного ниже – всего 15-25 циклов, а пенобетона – 50.
Разнообразные размеры (ширина может колебаться от 50 до 500 мм) и особенности конструкции газобетонных блоков разных марок говорят о высокой технологичности этого материала.

Удобен газобетон и в обработке, легко поддаваясь воздействию как ручного, так и электрического инструмента, сверлению, раскалыванию и нарезанию обычной, или электроприводной пилой. Электродрель со спецнасадкой решит вопрос прокладывания штрома под арматуру и проводку, как и создание отверстий под розетки и выключатели. Скруглить блок можно пользуясь шлиф-машиной, потому блоки из газобетона используются и в качестве отделочного материала с хорошими декоративными возможностями: для изготовления колонн, подставок и тумб, а также украшений, имитирующих лепнину.
Перед многими желающими построить свой дом встает выбор между газобетоном и газосиликатом. В чем же разница? Действительно, эти материалы схожи по технологиям изготовления, однако имеется одно существенное отличие, а именно – состав наполнителя.

Наиболее предпочтительные для покупателя в нашем регионе компании, проверенные и на мировом рынке. Например, всемирно известная компания Ytong стала первым в мире производителем газобетонных блоков автоклавного типа, сразу после изобретения технологии автоклавных ячеистых бетонов в 1924 году. Еще один известный производитель газобетона, торговая марка Hebel, названная так в честь изобретателя, который предложил новейшую технологию производства высокоточных геометрически блоков.

Сегодня обе компании находятся в собственности транснациональная компания Xella – крупный промышленный производитель стройматериалов. Следствием фактического слияния этих двух компаний стало изготовление газобетонов обеих марок по одной технологии и с использованием одного и того же оборудования, которое является представителем традиций качества обеих корпораций. Xella это прекрасное качество и геометрия газобетона по умеренной цене.
Возврат к списку
Каков процесс производства блоков AAC? Путеводитель Brikolite – Brikolite
Автоклавные газобетонные блоки становятся все более популярными на индийском рынке. Фактически, Индия считается вторым по величине производителем блоков в мире после Китая. По мере того, как все больше и больше мелких игроков открывают заводы по производству газобетонных блоков в Индии, реальный вопрос заключается в том, как производятся эти блоки?
Мы предоставляем вам подробное руководство по изготовлению блоков Brikolite AAC и процессу их массового производства.
Что такое блоки AAC?
По сравнению с традиционным кирпичом из красной глины газобетонные блоки легкие, но прочные по своей природе. Они обладают высокой изоляцией и изготовлены из перерабатываемых материалов на основе цемента, включая летучую золу, гипс, известь, воду и алюминиевую пудру, которая широко используется в качестве пенообразователя, что делает эти кирпичи портативными.
Газобетонные блоки считаются экологически чистыми из-за их экологически нейтральной продукции. Более того, поскольку их легче использовать, чем кирпичи из красной глины, спрос на них на индийском рынке растет.
Как изготавливаются блоки AAC?
Процесс производства газобетонных блоков понятен неспециалистам, и за ним легко следовать. Его можно изготовить в любом месте и в любом месте без значительных инвестиций, потому что эти блоки легко доступны на рынке.
Процесс производства газобетонных блоков следующий:
- Подготовка сырья: Летучая зола составляет основу газобетонных блоков.
Поскольку он легко доступен в виде промышленных отходов, он используется в смеси для производства газобетонных блоков. На первом этапе все сырьевые материалы, в том числе пригодные для повторного использования, такие как гипс, алюминиевая пудра и цемент, помещаются в дозатор.
- Дозирование и смешивание Ингредиенты: Летучая зола затем превращается в суспензию и добавляется в смесительный барабан. Остальное сырье добавляется в барабан с помощью винтовых конвейеров. Для обеспечения правильных пропорций, добавляемых на этапе смешивания, устанавливаются автоматические системы подачи. После того, как ингредиенты тщательно перемешаны, они готовы к заливке в формы.
- Формование, подъем и предварительное отверждение: Каждый газобетонный блок изготавливается в форме. Эти формы должным образом смазаны маслом, чтобы избежать липкого материала на поверхности. Суспензию добавляют в формы, где алюминий вступает в реакцию с известью и водой, расширяя смесь суспензии.
Это процесс подъема, который делает блок легким. Затем следует процесс резки проволоки, чтобы каждый блок AAC был одинаковой высоты и ширины. После этого процесса блоки AAC предварительно отверждаются, что занимает от 1 до 3 часов в зависимости от погодных условий.
- Автоклавирование: Последний этап производственного процесса называется автоклавированием. Здесь блоки AAC нагреваются в автоклавной камере для повышения прочности и стабильности. Это осуществляется в течение 8-12 часов, нагревая блоки до 180 градусов. После этого газобетонные блоки транспортируются на гранулах на завод, где проводятся испытания качества для выпуска блоков на рынок.
The Takeaway
По сравнению с обычными кирпичами блоки AAC демонстрируют максимальную долговечность и эффективность и, следовательно, являются идеальным выбором для строителей в Индии. Если вы ищете идеальный строительный материал для своего проекта, вам следует выбрать блоки Brikolite AAC для их успешного завершения.
Завод по производству газобетонных блоков, Производитель машин для производства газобетонных блоков
Перейти к содержимому
Lontto Завод по производству газобетонных блоковЗавод по производству газобетонных блоков LONTTO также называется станком для производства газобетонных блоков, некоторые также называют его станком для производства газобетонных блоков. Наш завод по производству газобетонных блоков представляет собой линию по производству газобетонных блоков. Полное название завода по производству газобетонных блоков LONTTO — завод по производству автоклавных газобетонных блоков.
Наш завод газобетонных блоков производит автоклавные газобетонные блоки различных размеров. Размеры имеют следующие размеры: длина 600 мм, высота 200/250/300 мм и ширина 60/120/180/240 мм или 75/100/125/150 мм. Производительность завода по производству газобетонных блоков LONTTO составляет 50000 м³-300000 м³ в год.
Сырье для производственной линии газобетона бывает двух типов: кремнистые материалы (песок, летучая зола и т. д.), кальциевые материалы (известковый цемент и т. д.). Процесс производства газобетонных блоков LONTTO прост и требует заливки ингредиентов, расширения газа, резки и последующего отверждения готовых газобетонных блоков. Это новые легкие теплоизоляционные строительные материалы. Завод по производству газобетонных блоков LONTTO — это экологически чистая технология, позволяющая экономить земельные ресурсы.
Система резки газобетонных блоков является ключевой частью завода по производству газобетонных блоков. В соответствии с методом резки его можно разделить на два способа: один тип — переворот с земли, а другой — переворот с воздуха. Наш завод по производству газобетонных блоков использует немецкую технологию, а затем объединяет потребности рынка в используемых газобетонных блоках для разработки самого современного оборудования для резки. Завод по производству газобетонных блоков LONTTO является ведущим международным рычагом. Основная машина завода газобетонных блоков использует прямоугольную квадратную трубу в качестве каркаса, что гарантирует стабильную работу.
Завод по производству газобетонных блоков: Полное руководство
Заливочный смеситель завода по производству газобетонных блоков — еще одна часть. Смеситель для заливки использует принцип смешивания с приводом, скорость смешивания высокая и равномерная. Реверсивный разбрасыватель является одной из основных частей системы резки завода по производству газобетонных блоков. Лучше всего, когда вам нужен разворот на 90 градусов. Другие части завода по производству газобетонных блоков включают в себя паромную тележку, пресс-форму для газобетона, пропарочную тележку, шаровую мельницу, котел и автоклав.
В соответствии с вашим местным сайтом вы можете выбрать различное сырье. Основными материалами являются аэрированный блок из песка или аэрированный блок из летучей золы. В качестве основного сырья вы можете выбрать песок или летучую золу. Вся конструкция линии по производству газобетонных блоков предотвращает загрязнение пылью. Все операции автоматизированы с помощью системы управления ПЛК, что обеспечивает длительный срок службы.
Машины для газобетонных блоков являются экологически чистыми строительными материалами с низкой теплопроводностью, которая составляет всего 0,09-0,17 Вт/м.кв. Блок AAC имеет очень хорошие характеристики теплоизоляции. Плотность может составлять 300 кг/м3, что делает его легким, тем самым снижая вес здания и улучшая сейсмостойкость.
Компания LONTTO, производитель газобетонных блоков с верхним рычагом, была основана в 1990 году. У нас более 30 лет опыта в производстве и экспорте газобетонных блоков. Более 300 производственных линий AAC были поставлены заказчикам как на внутреннем, так и на внешнем рынке. Наша компания прошла ISO9001 и CE в 2000 году. На нашем заводе по производству газобетонных блоков работает более 1100 сотрудников.
Также мы предлагаем техническую поддержку 247 и бесплатное обновление программного обеспечения.
Наш завод поставляет идеальное решение для всех заводов по производству газобетонных блоков, позволяющее повысить конкурентоспособность за счет эффективного управления эксплуатацией и техническим обслуживанием.