Технология автоклавного производства газобетона: Технология производства газобетона YTONG
Линия газобетона — Оборудование из Китая
Газобетонный завод из КитаяОборудование из Китая для производства автоклавного газобетона характеризуется высокой степенью автоматизации, рациональным размещением. Линия газобетона надежна и проста в эксплуатации.
Наш завод является лидером в области производства оборудования для изготовления автоклавного газобетона. Технические специалисты всегда готовы оказать всем клиентам профессиональную помощь и поддержку. Благодаря комплексной системе поставок сырьевого материала (закупка, анализ качества, хранение и транспортировка) вместе с передовым производственным оборудованием, позволяют нам производить станки высокого качества и доставлять ее заказчику. Перед отправкой заказчику, газобетонное оборудование проходит строжайший анализ качества. Каждый станок сопровождается технической документацией.
Автоклавный газобетон – материал, изготавливаемый путем термической обработки в автоклаве. Сырьевые ингредиенты: цемент, кварцевый песок и специализированные газообразователи, известь. В состав смеси добавляют гипс, золу и шлаки металлургических производств. В качестве специализированных газообразователей используются алюминиевые пасты и суспензии. В ходе химической реакции смесь вспенивается, и внутри образуются поры разной величины, заполненные воздухом.
Благодаря многолетнему опыту работы в сфере изготовления линий производства бетонных изделий, наша компания предлагает Вам широкий выбор промышленных линий производства с ежегодной производительностью от 150-350 тыс. м3.
Приобретая наши производственные линии, наша компания также предлагает Вам различные виды вспомогательного оборудования, а также резательные комплексы. Например, если Вы решили приобрести линию производства газобетонных блоков размерами 240 мм, мы рекомендуем Вам приобрести также станок резки с формой размерами 4.8×1.2м. В отличие от формы размерами 5×1.2м, данная форма позволит отделять большее количество излишек бетонного массива для последующей переработки и использования.
Параметры газобетонных линий
Параметры | Ед. | 200,000 м³ | 300,000 м³ | 350,000 м³ |
Производ-ть | м³ | 200,000 | 300,000 | 350,000 |
Форма | м | 4.8×1.2×0.6 | 6.0×1.2×0.6 | 6.0×1.5×0.6 |
Сырье |
|
|
|
|
Песок | т/г | 84,000 | 147000 | |
Известь | т/г | 20,400 | 30600 | 35700 |
Гипс | т/г | 3,600 | 5400 | 6300 |
Цемент | т/г | 12,000 | 18000 | 21000 |
Мощность | кВт | ≈1,200 | ≈1600 | ≈1650 |
Электро- энергия в год | 10,000 kWh | ≈271. | ≈362.3 | ≈373.62 |
Вода в год | т | ≈108,000 | ≈162000 | ≈178500 |
Газ в год | т | ≈36,000 | ≈54000 | ≈52500 |
Площадь завода | га | ≈3.5 | ≈45 | ≈50 |
Площадь | м2 | ≈7,000 | ≈9200 | ≈10000 |
Складская площадь | м2 | ≈8,000 | ≈10000 | ≈12000 |
1. Подготовка сырьевых материалов
После дробления известь и гипс хранятся в вертикальном силосе. Затем гранулы извести и гипса направляются в шаровую мельницу по ленточному транспортеру. Песок размалывается во влажной шаровой мельнице до консистенции шлама и перекачивается в шламобассейн.
2. Дозирование, смешивание и заливка бетонной смеси
В определенных пропорциях происходит добавление песчаного шлама, цемента в смеситель. Путем подачи пара происходит нагрев сырьевого материала до температуры 40-45 градусов и смешивание. После завершения цикла смешивания 3 ~ 4 минуты, открывается загрузочный клапан алюминиевой пасты и добавляется в смеситель. Происходит дальнейшее перемешивание около 40 секунд. Полученную смесь заливают в формы. Весь цикл составляет 6 ~ 8 минут. Формы перевозятся в зону вспенивания и отверждения (созревания) при температуре 40-45 градусов. Время отверждения составляет 90-150 минут. После чего формы перевозят в зону резки.
3. Резка бетонного массива
От зоны созревания форма передвигается под кантовочный манипулятор, который поднимает ее, разворачивает на 90° и устанавливает на резательные платформы. На тележке резательной линии борт (платформа) с массивом двигается через секции линии резки. Вначале устройство предварительной обрезки срезает излишки, образовавшиеся в верхней части массива во время созревания. Затем блоки обрезаются по длине и ширине будущего продукта. При необходимости вырезается контур (паз и гребень). Потом горизонтальный режущий автомат разрезает блоки по толщине. Автоматический станок вертикальной резки осуществляет точную обрезку блоков по высоте и длине. Проволочные струны обрабатывают массив сверху донизу. Все срезанные остатки и обрезки массива сбрасываются в шламканал и отправляются обратно в шламбассейн для последующего использования.
4. Автоклавная обработка газобетонных блоков
Вагонетки вталкивается в автоклав. После закрытия крышки в автоклаве создается вакуум и нпри температуре 190оС, давлении пара 1.2 мРа происходит процесс твердения газосиликата. Эти параметры сохраняются несколько часов. В конце автоклавного цикла давление снижается до атмосферного. Цикл автоклавирования составляет 11-12 ч. После завершения процеса крышка автоклава открывается. Автоклавные вагонетки вытягиваются передаточной платформой и толкаются на отдельный путь для разгрузки. Конденсат, образованный при разнице температуры дренажируется, охлаждается и направляется на повторное использование.
Автоклавированные блоки перемещаются на делитель и по очереди разделяются. Формы отвозятся в зону очистки и последующей заливки. Отходы собираются вместе и затем перемешиваются со свежей шламовой массой в определенных пропорциях. Полученная смесь используется в дальнейшем.
Преимущества газобетонного оборудования из Китая 1. Весь процесс производства газобетонных блоков, начиная с подготовки сырьевого материала и заканчивая упаковкой, проходит слаженно и без задержек. Формы для выдерживания смеси-сырца, транспортные и автоклавные тележки двигаются по индивидуальным накопительным путям, что позволяет им без преград осуществлять транспортировку материала и возвращаться к рабочей зоне для последующего цикла.
2. Распалубочная машина, укладчик для бетонных заготовок, делитель и разгрузочный манипулятор работают на базе гидравлики и портального крана, которые способны разворачивать бетонные блоки в различных направлениях. Применение данной технологии упрощает процесс производства, устраняет необходимость использования тяжеловесных промышленных кранов, упрощает процесс проектирования заводского помещения и снижает затраты на его постройку.
3. Запатентованный кантующий манипулятор оснащен специальными скребками, которые удаляют излишки массива со всех шести сторон.
4. Транспортные тележки оборудованы цепным приводом, а также механизмом позволяющим ей автоматически двигаться в заданном направлении, позволяя полностью автоматизировать процесс транспортировки материала.
5. Сортировочная установка осуществляет сортировку и транспортировку массива к делителю, который, в свою очередь, выполняет разделение одного слоя массива вдоль намеченных швов.
6. Разгрузочный манипулятор выполняет погрузку блоков на деревянные паллеты, расположенные на упаковочной линии. После того как этап упаковки завершен, блоки погружаются на автопогрузчик и транспортируются на склад готовой продукции. Применение данного вида оборудования позволило перейти на автоматизированную транспортировку готовой продукции и снизить нагрузку операторов.
7. Система центрального управления линией производства может быть разделена на несколько источников управления, каждый из которых будет самостоятельно выполнять свою функцию и позволит операторам вести визуальный контроль над производством. Такая система позволит улучшить эффективность производства, качество продукции, снизит нагрузку операторов и коэффициент субъективных ошибок.
Мы будем рады проконсультировать Вас и ответить на все Ваши вопросы. Мы предложим Вам линию, полностью соответствующую Вашим потребностям и пожеланиям.
- Оборудование производства газобетонных блоков
Автоклавный газобетон: технология производства и характеристики
За последние 15 лет автоклавный газобетон (АГБ) завоевал сразу 2 рынка: в качестве стенового материала и теплоизоляционного материала. К 2017 году, доля АГБ на рынке стеновых стройматериалов превысила 50%, и с каждым годом этот процент растет. Причина успеха заключается в том, что технологии производства газобетонных блоков позволяют увеличить энергоэффективность строительства. В этой статье мы расскажем, как производят газобетон, и где он успешно применяется.
Технология производства автоклавного газобетонаЧто же такое, автоклавный газобетон? Это экологичный пенобетонный строительный материал, который на 85% состоит из ячеек, наполненных воздухом.
Он устойчив к влаге, огню и морозу. Легкий вес газоблоков снижает нагрузку на фундамент почти в 5 раз, а скорость строительства из газобетона увеличивается в 10 раз. Продукты АГБ включают блоки для стен, перегородочные панели, облицовочные панели, перемычки и т.д.
В Украине высококачественный автоклавный газобетон производится в соответствии с европейской нормой EN 771 (часть 4. Блоки стеновые из ячеистого газобетона автоклавного твердения) и ДСТУ Б В.2.7-137:2008 (Блоки из ячеистого бетона стеновые мелкие). Согласно этим стандартам, производство газобетонных блоков происходит в несколько этапов:
1. Сырье.От качества сырья зависят дальнейшие характеристики газобетонных блоков. Поэтому кварцевый песок, цемент М400, известь и алюминиевая паста, доставляемые на производство, проходят ряд проверок в лабораториях завода.
2.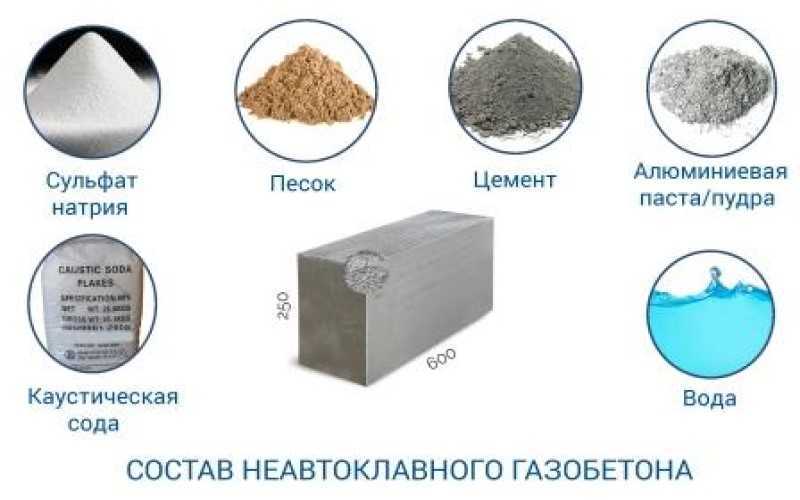
Все компоненты подаются в смеситель и перемешиваются с водой по заданной программе. Этот процесс происходит в автоматическом режиме, а от пропорций смеси зависят виды газобетона. Необходимые характеристики газобетона закладываются уже на этом этапе.
3. ГазообразованиеЧтобы готовые блоки имели ячеистую структуру, смесь должна пройти через этап газообразования. Для этого ее заливают формы, где она в течении 3-6 часов поднимается, как дрожжевое тесто. В результате этого процесса, в структуре бетона образуется большое количества пор с газом. Излишки вспученной смеси срезают, и газобетон еще в течении 60-80 минут твердеет, набирая необходимую прочность для резки.
4. НарезкаФормы блоков должны отвечать современным стандартам строительства. Для этого высокотехнологичное оборудование задает нужные размеры, а специальные ножи струны разрезают массу на блоки, и формируют пазы и гребни.
5.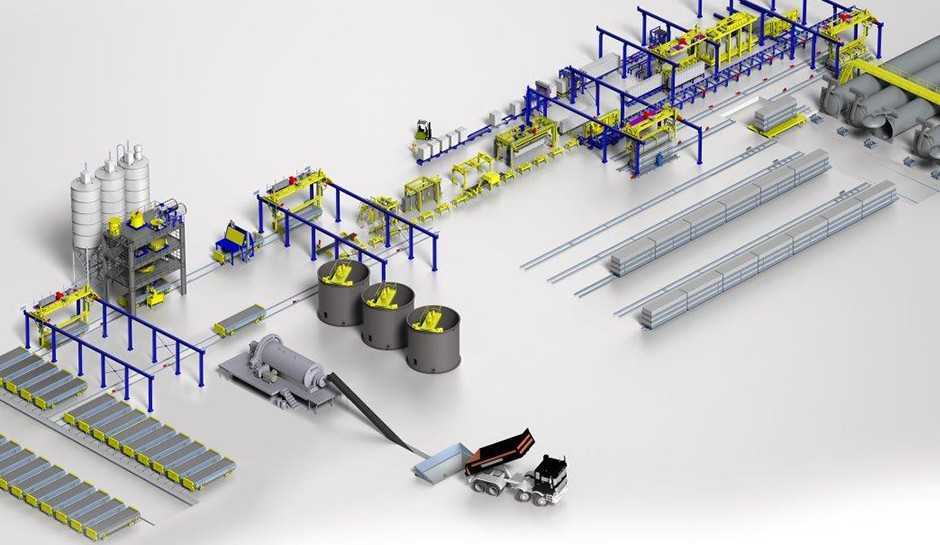
Это завершающий этап производства. Нарезанные блоки отправляются в автоклав, где обрабатываются паром при давлении в 12 атмосфер и с температурой 180 °C. Обработка газобетона в автоклаве позволяет сократить срок набора прочности и получить кристаллическую структуру. Благодаря автоклавированию газоблоки не дают усадку. Технология обработки в автоклаве учитывает вид и массивность блоков. Чтобы не допустить образование трещин в изделиях, температура и давление периодически повышаются и опускаются. Этот процесс занимает от 2 до 6 часов.
6. Контроль качестваОн осуществляется на всех этапах производства. А более тщательное исследование происходит последнего этапа производства. В отделе технического контроля и лаборатория проверяют образцы готового материала на соответствия с классом прочности и маркой. Готовая продукция сертифицируется.
7. УпаковкаПосле сертификации продукция отправляется на линию упаковки. Блоки устанавливаются на поддоны и упаковываются таким образом, чтобы газобетонные блоки сохранили целостность и свои характеристики. Упаковки отправляются на склад готовой продукции.
Вся необходимая информация о стройматериале доступна на упаковках и в сопроводительных документах. Современные технологии производства ячеистого бетона помогают снизить себестоимость продукции, энергозатраты и объем изделий для строительства объекта. Это позволяет газобетону быть доступнее других строительных материалов.
Характеристики автоклавных газоблоковБлагодаря воздуху, заключенному в порах, газобетонные блоки обладают прекрасными теплоизоляционными свойствами. Это позволяет уравнять температурные изменения. Летом газоблоки аккумулируют прохладу, а зимой тепло, что позволяет значительно экономить на отоплении. Теплопроводность газобетона в зависимости от марки прочности варьируется от 0,08 до 0,12 Вт/(м*°C).
Не менее важной характеристикой газоблоков является паропроницаемость. Так как газоблоки на 85% состоят из воздуха, материал считается «дышащим». Благодаря этому пар, проходя сквозь стену из автоклавного газобетона не успевает скапливаться в ее толще. Коэффициент паропроницаемости газоблоков равен 0.18–0.2 мгч*Па*м.
Морозостойкость газобетона F35-F100, в зависимости от плотности блоков. То есть, в течении 35-100 циклов замораживания-оттаивания блоки не подвергаются разрушению от перепадов температур. Звукоизоляция газоблоков зависит от их плотности, и толщины стен. Марки D400 и D500 обладают высокими показателями звукоизоляционных свойств. Стена из газобетона в 10 см защищает от влияния звуков в 35-37 дБ, что позволяет не делать дополнительную звукоизоляцию.
Огнестойкость газобетона соответствует нормативам ДСТУ Б В.1.1-4-98 «Строительные конструкции. Методы определения огнестойкости. Общие требования» и ДСТУ Б В.1.1-15:2007 «Защита от пожара. Перегородки. Методы определения огнестойкости» (EN 1364-1:1999, NEQ). Так как автоклавный газобетон является негорючим материалом, он выдерживает воздействие огня в течении 3-7 часов.
Низкая плотность газобетона по сравнению с другими стройматериалами, дает ему преимущество. Вес блоков легче, их также легко резать и пилить, что определенно влияет на скорость строительства. Плотность блоков варьируется от 300 до 1200 кг/м3, и это влияет на область применения этого стройматериала.
Применение автоклавного газобетонаГазобетонные блоки последнее время чаще используются для частного строительства. Точные геометрические параметры блоков, позволяют рассчитать необходимое количество стройматериала, и закупить газобетон оптом. А знание характеристик разного вида газоблоков, поможет определить область их применения.
Газобетон с плотностью в 300-400 кг/м3 (D300 и D400) обладает самыми лучшими показателями теплоизоляции и звукоизоляции, что делает их прекрасным теплоизоляционным материалом.
Но не стоит пренебрегать ими при возведении межкомнатных перегородок. Высокий коэффициент звукопоглощения этим марок газобетона, позволит сэкономить на шумоизоляции.
Прочность газоблоков марки D500 и D600 позволяет использовать их для несущих и самонесущих конструкций. 3-х этажный дом из автоклавного газобетона марки D500 прослужит вам не один десяток лет.
Строительство из автоклавного газобетона поможет снизить затраты на раствор в 8-10 раз. Прочность постройки, и ее долговечность напрямую зависят от качества стройматериала. Прежде чем купить газобетон, убедитесь в наличии сертификатов качества. Только завод-изготовитель или официальный дилер смогут предоставить все необходимые документы, и гарантировать качество стройматериала.
Легкой вам стройки!
Использование малоклинкерных вяжущих в производстве автоклавного газобетона по технологии резки Василий Сердюк, Дмитрий Рудченко, Наталья Дюжилова :: ССРН
Восточно-Европейский журнал предпринимательских технологий, 6 (1 (108)), 63–71 , 2020. doi: https://doi.org/10.15587/1729-4061.2020.217308
9 страниц Опубликовано: 2 марта 2021 г.
Смотреть все статьи Василия Сердюка
Винницкий национальный технический университет
ООО «Аэрок»
ООО «Аэрок»
Дата написания: 11.12.2020
Реферат
Возможности оптимизации технологии резки для производства автоклавного ячеистого бетона и применения -исследованы клинкерные вяжущие в ней. С учетом ценового фактора, энергоэкологических тенденций развития промышленности строительных стеновых и теплоизоляционных материалов автоклавный газобетон имеет значительные перспективы развития производства.
С переходом на производство автоклавного газобетона меньшей плотности, с одной стороны, снижается общая материалоемкость производства, а с другой — увеличиваются удельные затраты вяжущего (цемента) на единицу массы газобетона . Исследования были направлены на реализацию ряда технологических решений. Они предполагают снижение энергоемкости производства за счет минимизации клинкерной составляющей в сырьевой смеси и интенсификацию производственного процесса с целью повышения коэффициента структурного качества материала, а также возможность серийного производства низкосортных материалов. -плотный газобетон. Снижение клинкерной составляющей путем замены ее активными минеральными добавками, доменным гранулированным шлаком в условиях технологии резания возможно при условии решения задачи ускорения набора пластической прочности газобетонного сырья на стадии формирования его макроструктуры. решается.
Установлено, что осуществление форсированного синтеза эттрингита на стадии формирования газобетонной смеси с высоким В/Т-соотношением позволяет сократить время предавтоклавной выдержки сырьевого массива. Это позволяет использовать минеральные добавки и повышает прочность конечного продукта. Замена 10–15 % цемента добавкой ГБФС в составе газобетонной смеси при дополнительном содержании гипсового камня 5–10 % в составе песчаного шлама обеспечивает интенсивное повышение пластической прочности бетона. сырья перед разделкой на изделия и высокой прочностью конечного продукта.
Ключевые слова: газобетон; минеральные добавки; гранулированный доменный шлак; малоклинкерное вяжущее; эттрингит
Рекомендуемое цитирование: Рекомендуемая ссылка
Сердюк, Василий и Рудченко, Дмитрий и Дюжилова, Наталья, Использование малоклинкерных вяжущих в производстве автоклавного газобетона по технологии резки (11 декабря 2020 г.). Восточно-Европейский журнал корпоративных технологий, 6 (1 (108)), 63–71, 2020. doi: https://doi.org/10.15587/1729-4061.2020.217308, доступно в SSRN: https://ssrn.com/abstract=3757606
ASC Process Systems — ASC Process Systems
Автоклавный ячеистый бетон (AAC), также известный как автоклавный ячеистый бетон (ACC), представляет собой материал на основе бетона с высокой теплоизоляцией, используемый как для внутреннего, так и для внешнего строительства. AAC обладает отличными теплоизоляционными качествами, а также легко монтируется. Еще одним преимуществом является то, что его можно фрезеровать, шлифовать и резать по размеру на месте с помощью стандартных инструментов из углеродистой стали.
Автоклавы используются для твердения газобетона с использованием острого пара. Эти автоклавы обычно очень длинные, чтобы приспособиться к методам загрузки железнодорожных вагонов и большим частичным загрузкам. ASC — один из немногих отечественных производителей автоклавов для твердения пенобетона в США.
Безопасность благодаря конструкции
Компания ASC гордится разработкой чрезвычайно безопасных (AAC) автоклавов для обработки. Мы используем нашу проверенную на практике быстро открывающуюся дверцу и проектируем значительные допуски на коррозию и коэффициент безопасности для всех наших сосудов под давлением автоклавов AAC, чтобы обеспечить многолетнюю безопасную эксплуатацию. ASC производит автоклавные системы для производства пенобетона в соответствии с ASME, PED и другими нормами для сосудов под давлением в соответствии с местным законодательством.
Конфигурации дверей
Автоклавы AAC могут изготавливаться с вертикальными, боковыми или поворотными дверями. Конструкции ASC проверены на практике и будут адаптированы к требованиям вашего предприятия и производственного процесса.
Распределение тепла
Наши автоклавы AAC, используемые для обработки ячеистого бетона, были разработаны для обеспечения превосходной передачи тепла бетонной загрузке и обеспечения равномерной температуры по всей длине автоклава. Внутренние трубопроводы и парораспределительные коллекторы спроектированы таким образом, чтобы точно соответствовать вашим требованиям к нагрузке и времени цикла.
Системы загрузки
ASC может поставить автоклав AAC с полностью интегрированной рельсовой системой, системой загрузки, тележками и автоматизированными мостами для карьеров. Сообщите нам, каковы ваши конкретные требования, и мы разработаем систему, соответствующую вашим потребностям.
Нажмите здесь, чтобы распечатать макет.
Изготовление в полевых условиях автоклава ASC размером 28 футов x 120 футов
Если автоклавы становятся слишком большими для перевозки на грузовике, автоклав должен полностью собираться в полевых условиях. ASC является одним из самых опытных производителей автоклавов в мире, каждый год реализуя несколько параллельных полевых проектов.
Когда имеет смысл производить полевое производство?
Если внутренний диаметр автоклава превышает 12 футов (3,6 м), транспортировка автоклава по стране может стать очень дорогой. ASC обычно проводит анализ затрат и выгод, чтобы определить, какой метод изготовления обеспечит наилучшую ценность для клиента. Из-за погодных и других факторов производство в полевых условиях по своей природе менее эффективно, чем производство в цеху, поэтому все факторы необходимо взвешивать вместе.
Сколько времени занимает сборка в полевых условиях?
Время изготовления на месте может составлять от 50 недель до оборота и до 90 недель. Время зависит от размера и сложности автоклава, а также от текущего времени изготовления стали, головок и поковок.
Несколько секций, сваренных вместе в цилиндрический сосуд
Изготовление в полевых условиях с установленным тентом над сосудом
Поковки стопорных колец устанавливаются для сборки.
Фланец кожуха и стопорное кольцо устанавливаются на сосуд.
Головка и фланец головки устанавливаются на сосуд.
Производственный участок готовится к токарной обработке валков
Процесс изготовления на месте
Для проектов изготовления на месте ASC тесно сотрудничает с заказчиком, чтобы определить, где будут построены сосуд и автоклав. Если заказчик может вовремя подготовить фундамент автоклавной ямы, ASC предпочитает строить автоклав в яме. Однако это не всегда возможно либо из-за неготовности здания и фундамента, либо из-за ограничений и осложнений, связанных с одновременными производственными требованиями заказчика. В этом случае ASC попросит заказчика предоставить поблизости бетонную площадку, которую можно использовать для строительных работ.
Как только проект начнется, ASC немедленно закупит крышки сосудов, стальной лист и поковки дверей, которые будут использоваться для сосуда под давлением. Листовая сталь будет поставляться непосредственно с завода, и ожидается, что время выполнения заказа составит 10-14 недель. Как только сталь будет готова к доставке, она будет отправлена ближайшему поставщику для прокатки. После прокатки, которая может занять 2-3 недели, прокатные секции обечайки будут доставлены на место изготовления. Головки будут поступать от конкретного поставщика головок, и на это потребуется от 14 до 20 недель в зависимости от размера. Кованые детали стопорного кольца (фланец обечайки, стопорное кольцо и фланец головки) потребуют 10-12 недель для ковки, а затем еще 8-12 недель для механической обработки. Как только прокатные стальные секции прибудут на площадку, полевой персонал ASC доставит каждую отдельную секцию из грузовика и поместит их на предварительно установленные поворотные ролики. Поворотные валки представляют собой мощные машины, которые используются для вращения секций сосуда, так что для сварки кольцевых швов сосуда можно использовать автоматические аппараты поддуговой сварки.
На этом этапе полевой персонал может насчитывать 3-4 рабочих, и их задача будет ограничиваться сваркой секций вместе с помощью электродуговой сварки (корневой проход) и поддуговой сварки (защитные проходы). К сожалению, одновременно может выполняться только один кольцевой или продольный шов, поэтому объем работ несколько ограничен. Этот процесс сварки кольцевых и длинных швов может занять несколько месяцев в зависимости от размера сосуда высокого давления.
В отличие от заводского производства, работа в полевых условиях связана с дополнительными расходами, в том числе с необходимостью укрытия на случай непогоды и холода. В некоторых случаях ASC накрывает автоклав во время критических производственных процессов.
В какой-то момент в процессе шовной сварки на место должны прибыть передняя и задняя головки. Крупные головки могут поставляться в одной секции или могут быть разделены для транспортировки. Когда задняя головка прибудет на место, она будет разгружена и немедленно размещена на конце секции корпуса в сборе. Когда обработанные детали стопорного кольца прибудут на место, полевой персонал начнет сборку и сварку дверного узла. Это включает в себя установку и приварку угловых клиньев к проушинам, крепление гидравлических цилиндров и приварку передней головки к кованому фланцу головки.
После заклинивания узла фланец обечайки и поковки стопорного кольца удаляются из узла и помещаются на сосуд высокого давления. Поковка фланца обечайки будет приварена к главному цилиндру.
Когда основной прямостенный цилиндр будет полностью сварен, полевой супервайзер приступит к разметке и бурению проходок судна. Этот процесс займет 2-3 дня. После того, как компоновка будет завершена, полевая группа начнет процесс размещения и сварки патрубков, фланцев и других отверстий в сосуде. Этот процесс может длиться 2-4 недели в зависимости от сложности и количества проходок. После того, как все отверстия будут полностью заварены, автоклав можно снять с поворотных валков и установить на стальные седла. Седла предназначены для удержания сосуда высокого давления и распределения его нагрузки на большую площадь. Седла либо изготавливаются заранее и доставляются из магазина ASC, либо изготавливаются в полевых условиях. Большой кран используется для подъема сосуда высокого давления с вращающихся валков на предварительно установленные седла. Также в это время передняя крышка и фланец головки будут установлены на место в передней части автоклава и временно зафиксированы на месте. В это время полевой персонал начнет крепление узла петли и/или дверного механизма. Эта сборка обычно изготавливается заранее в мастерской ASC или, в некоторых случаях, в полевых условиях.
Наконец, когда сосуд готов и все предварительные осмотры сосуда, рентгеновский контроль и термообработка завершены, сосуд высокого давления заполняется водой и проводится гидроиспытание. Гидроиспытание используется для безопасного повышения давления в автоклаве до 130 % от максимального проектного давления для проверки и проверки конструкции автоклава. Гидравлические испытания проводятся под наблюдением уполномоченного инспектора сосудов высокого давления, и, если все идет хорошо, инспектор подписывает отчет с данными ASME U1A, указывающий на завершение сборки сосуда высокого давления.
Как только изготовление сосуда будет завершено, ASC направит на площадку дополнительный персонал и начнет работу, необходимую для превращения сосуда высокого давления в автоклав. Это будет включать 15-25 полевых сотрудников, которые изготовят и установят изоляцию, футеровку, пол, узел вентилятора и все другие элементы автоклава. Для очень больших судов в это же время будет изготовлен узел дверного портала. После начала работ по сборке автоклава ASC обсудит с заказчиком монтаж и перемещение сосуда под давлением от места изготовления до его конечного местоположения в карьере. Общее время сборки автоклава после гидроиспытания корпуса высокого давления обычно составляет 4-6 месяцев.
Нажмите здесь, чтобы распечатать макет.
Гексафторид урана (UF6) представляет собой радиоактивный и высокотоксичный материал, который используется в процессе обогащения производителями ядерного топлива. Ядерные автоклавы используются на протяжении всего жизненного цикла обработки топлива для переноса и отбора проб UF6 из резервуаров для хранения. Из-за опасного характера UF6 эти ядерные автоклавы рассчитаны на высокую надежность и несколько уровней коэффициента безопасности. В случае крупного сейсмического события эти автоклавы должны уцелеть, не высвобождая никакого радиоактивного содержимого.
Сертификация ASME NQA-1
Компания ASC построила ядерные автоклавы для отбора проб и передачи ядерных продуктов для крупнейших мировых производителей ядерного топлива. При проектировании и производстве этих ядерных автоклавов требуется соблюдение и сертификация ядерных стандартов ASME NQA-1. ASC может выполнить всю программу проектирования и сборки или взять на себя часть сборки, используя проекты, предоставленные заказчиком.
Автоклавы для отбора проб
Автоклавы для отбора проб используются для медленного нагрева и плавления обогащенного UF6 (гексафторида урана), который хранится в цилиндрах 30B и 48F/Y. После полного расплавления цилиндра автоклав и цилиндр наклоняют вперед, чтобы небольшое количество продукта можно было перелить в небольшие бутыли для проб. Эти автоклавы очень сложны, в них используется несколько систем безопасности и блокировок. Автоклав служит нескольким целям: нагрев, отбор проб, повторное затвердевание и локализация.
ASC — единственная компания в США, которая в настоящее время сертифицирована и способна поставлять автоклавы для отбора проб для ядерной топливной промышленности.
Автоклавы для переноса
Автоклавы для переноса аналогичны автоклавам для отбора проб, однако их цель состоит в нагревании UF6 до тех пор, пока он не достигнет своего парообразного состояния. В этот момент UF6 переводится из цилиндров 30B/48F/48Y во вторичный процесс.
ASC снова является единственной компанией в США, которая в настоящее время сертифицирована и способна поставлять автоклавы для переноса ядер.
Нажмите здесь, чтобы распечатать макет.
Автоклав Econoclave® GLS компании ASC является самым передовым автоклавом для ламинирования стекла. Система автоклавов для ламинирования стекла Econoclave® GLS работает и легко интегрируется со всеми системами линий ламинирования стекла, представленными на рынке, и способна отверждать все типы промежуточных слоев PVB, включая специальные полимеры, такие как SentryGlas®
Superior laminating
Автоклавы ASC GLS разработаны с непревзойденная температура и однородность потока для обеспечения равномерного нагрева и охлаждения вашей стеклянной загрузки. В каждом автоклаве используется наша запатентованная система потока H-Slot™ для создания равномерного фронта потока от передней части автоклава к задней.
Сокращение времени цикла
В стандартную комплектацию Econoclave® GLS входит усовершенствованная система циркуляции воздуха, которая обеспечивает в среднем на 50 % больше потока для ламинированной загрузки, чем автоклавы конкурентов. Благодаря увеличенной скорости воздуха, проходящего через рабочую зону автоклава, ваша загрузка по ламинированию стекла сократит время цикла почти на 50 % по сравнению с обычными автоклавами для ламинирования стекла. Это означает большую производительность и меньшую стоимость загрузки.
Экономия затрат на электроэнергию = «зеленое решение»
Эксплуатационные расходы на воздушный компрессор и обогрев автоклава могут существенно снизить прибыль, полученную от ламинаторов стекла. Мы учли это при разработке Econoclave® GLS. Уникальная конструкция Econoclave® означает, что при том же объеме производства размер сосуда высокого давления нашего автоклава будет на 20 % меньше, чем у конкурирующих автоклавов для ламинирования стекла. Это уменьшение общего размера автоклава пропорционально снижает затраты на компрессор и отопление, что может сэкономить до 100 000 долларов в год в условиях высокой производительности.
Повторное использование благодаря инновациям
Компания ASC также может предоставить нашу запатентованную систему CRS (Compression Reduction System), которая предназначена для повторного использования и переработки сжатого воздуха в автоклаве, обеспечивая экономию сжатия на 30 % и десятки тысяч долларов в год в операционные затраты.
Конфигурации внутреннего потока
Компания ASC может поставить систему Econoclave® GLS, точно отвечающую вашим требованиям к конфигурации производства. Мы можем спроектировать блок с продольным потоком воздуха, используя боковые воздуховоды, верхние воздуховоды или напольные воздуховоды. Мы также можем предоставить автоклав с вертикальным потоком воздуха (снизу вверх или сверху вниз) для удовлетворения требований производителя ветрового стекла.
Рабочие тележки
Инженерный персонал компании ASC может разработать тележки для автоклавов в точном соответствии с вашими требованиями. Наш магазин способен изготовить тележку любого размера.
Нажмите здесь, чтобы распечатать макет.
Автоклавы для вулканизации используются в резиновой промышленности для преобразования натурального каучука в отвержденный и сшитый вулканизированный каучук. Вулканизирующие автоклавы также можно использовать для отверждения пластмасс. В вулканизационных автоклавах используется острый внутренний пар, смесь острого пара и горячего воздуха или только горячий воздух. Вулканизирующие автоклавы используются для отверждения шин, шлангов и многих других продуктов, которые не поддаются стандартному процессу компрессионного формования на основе прессования.
В зависимости от типа резины процесс вулканизации может происходить при температуре от комнатной (например, силиконы) до 350 °F (170 °C) или выше (например, шины).
Любого размера и любой мощности
Независимо от того, ищете ли вы вулканизатор для мелких деталей или автоклав для земляных работ диаметром 17 футов (5,2 м), ASC может спроектировать и построить в соответствии с вашими потребностями. Наше производственное предприятие способно изготавливать автоклавы с внутренним диаметром 17 футов (5,2 м) и длиной до 150 футов (45,7 м).
Если вы ищете вулканизатор еще большего размера, ASC может собрать его прямо на вашем объекте.
Любая конфигурация
Вулканизационные автоклавы ASC могут быть рассчитаны на горизонтальную или вертикальную ориентацию.