Сколько кубов газобетона в одном поддоне: Сколько газоблоков в поддоне
Сколько газоблоков в поддоне
Цена газоблока при продаже указывается в метрах кубических. И для строительства используется эта же мера. Однако при всем своем удобстве и универсальности величина эта является абстрактной и, как правило, неподдающейся исчислению. Но вот пересчитать блоки поштучно вполне возможно, особенно если они аккуратно упакованы на поддоне.
Производителя все блоки для комфортного транспортирования размещают на паллетах (поддонах). Но в некоторых случаях возникает необходимость посчитать, сколько пеноблоков или газоблоков в поддоне. При продаже продукции всегда оговаривается, сколько пеноблоков расположено в поддоне. Производство пенобетона что осуществляется кустарным способом, поэтому рассчитать, сколько пеноблоков на поддоне несколько сложней.
На один поддон газобетона помещается один м2 газобетонных блоков, а в количество штук, размещаемых на поддоне, зависит от их размеров и физико-механических особенностей. При этом вес одного поддона может варьироваться от 750 до 1050 килограммов.
Размеры газобетонных блоков
По форме газоблоки разделяют на прямоугольные и U-образные. Прямоугольные газоблоки необходимы при выкладывании стен с ровной поверхностью. Размеры таких газоблоков весьма разнообразны. Их стандартные размеры могут быть: 100х250х625 мм, 150х250х625 мм, 200х250х625 мм, 240х250х625 мм, 300х250х625 мм и 400х250х625 мм.
Блоки U-образной формы применяются при укладке оконных и дверных проемов, а также для закрепления плит в перекрытиях. Размеры этих газоблоков имеют такие параметры: 200х250х600 мм, 400х250х600 мм и т.д.
Определить размеры газоблоков для расчета их количества на поддоне можно, зайдя на сайт производителя и найдя готовые таблицы с конкретными значениями.
Как самостоятельно рассчитать, сколько газобетонных блоков на поддоне?
Рассчитать сколько газоблоков на поддоне не так уж сложно. При возникновении такой необходимости следует выполнить несколько математических действий. В первую очередь нужно выяснить размеры одного блока и посчитать его объем в м3. Во вторых, необходимо один метр кубический разделить на объем одного блока, полученного ранее.
Пример. Посчитаем сколько газобетонных блоков с размерами 200х250х625 мм на поддоне. Для начала необходимо перевести размеры сторон одного блока в метры.
Объем одного блока будет равен: 0,2 *0,25 * 0,625 = 0,03125 м3.
Затем разделим 1 м3 на вычисленный ранее объем одного газоблока:
1/0,03125 = 32.
Таким образом, мы получили, что на одном поддоне будет расположено 32 штуки газоблоков размерами 200х250х625 мм.
Таблица. Сколько в поддоне газоблоков AEROC Classic.
Размер блока | Объем 1 блока | Количество м.куб. в 1 поддоне | Количество блоков в поддоне (шт) |
75×200×600 | 0,009 | 1,89 | 210 |
100×200×600 | 0,012 | 1,8/1,92 | 150/160 |
200×200×600 | 0,024 | 1,68/1,92 | 75/80 |
250×200×600 | 0,030 | 1,8 | 60 |
300×200×600 | 0,036 | 1,8 | 50 |
375×200×600 | 0,045 | 1,8 | 40 |
400×200×600 | 0,048 | 1,68/1,92 | 35/40 |
0,011 | 1,89 | 168 | |
100×250×600 | 0,015 | 1,92 | 128 |
200×250×600 | 0,03 | 1,92 | 64 |
240×250×600 | 0,036 | 1,728 | 48 |
300×250×600 | 0,045 | 1,8 | 40 |
365×250×600 | 0. | 1.752 | 32 |
375×250×600 | 0.056 | 1.8 | 32 |
400×250×600 | 0.06 | 1.92 | 32 |
Так же читайте нашу предыдущую статью: Технология кладки облицовочного кирпича
Сколько газоблоков в поддоне
Если вы запланировали постройку загородного дома из газобетонных блоков, то для вычисления потребности в строительных материалах должны владеть некоторыми данными. Сейчас рассматриваемые изделия продаются не поштучно, ведь стоимость обычно указывается за кубический метр или паллет (поддон), поэтому для вычисления необходимости материалов нужно знать, сколько таких блоков в кубе.
Сколько газоблоков размером 200×300×600 в поддоне
Методом простых расчётов можно вычислить, что на один куб объёма приходится 28 газобетонных изделий со стандартными размерами 200×300×600 миллиметров или 20×30×60 сантиметров. Для получения рассматриваемых показателей, достаточно разделить кубический метр на объём одного блока. Как известно, в кубе 1000000 см3 (получается методом умножения всех сторон 100×100×100), а в блоке 36000 см3 – 60×20×30, поэтому при делении 1000000/36000 получается 27,7 штук. Аналогичные расчёты можно проводить для материалов других размеров.
А теперь разберёмся с поддонами. Обычно на деревянной платформе помещается 0,9; 1,44 или 1,8 м
Количество нестандартных газобетонных блоков в поддоне
Далее разберёмся с газоблоком от производителя Стоунлайт, который грузят в поддоны нестандартного размера:
- для простеночных блоков с габаритными размерами 7,5×20×60 сантиметров при объёме поддона 1,62 – 180 штук;
- для каких же изделий с габаритными размерами 10×20×60 сантиметров с объёмом паллеты 2,16 м3 (считаем стандартным) – 180 штук;
- блоки для перегородок с размерами 12×20×60 (стандартный объём поддона) – 150 штук;
- для блоков 15×20×60 сантиметров (стандартный паллет) – 120 штук;
- блок для возведения несущих стен зданий с размерами 20×20×60 см (поддон с аналогичным объёмом) – 90 штук;
- изделия с габаритами 25×20×60 см (объём поддона 2,1 м3) – 70 штук;
- блоки 28×20×60 см (объём поддона 2,016 м3) – 60 штук;
- блок 30×20×60 см (паллет стандартного объёма) – 60 штук;
- блок 36×20×60 см – 50 штук;
- изделия из газобетона для несущих стен с габаритными размерами 37,5×20×60 см (объём поддона 1,8м3) – 40 штук;
- блок 40×20×60 см при объёме паллеты 1,92 м3 – 40 штук;
- блок для возведения несущих стен с габаритным размером 50×20×60 см при объёме поддона 2,4 м
Сколько газоблоков в 1 кубе: 200х300х600, 600х300х200, 250х300х600, 600х400х250
Газобетонные блоки являются самым распространенным типом стройматериала для возведения стен. Благодаря низкому весу изделий, нагрузка от несущей конструкции на фундамент будет незначительная. Для расчета требуемого количества строительных материалов следует знать, сколько газоблоков в 1 кубе и их габариты. Например, размеры ходового блока составляют 600х300х200 миллиметров. Такая особенность позволяет строить дома значительно быстрее, чем из кирпичного материала.
Если проект коттеджа или хозпостройки будет производиться самостоятельно, то необходимо просчитать нужное количество стройматериала. Когда при возведении стен и перегородок будут использовать газобетонные изделия, первым делом рекомендуется вычислить их объем в м3. В одном кубическом метре должно поместиться определенное количество вещества или материала. Поэтому перед тем как заказать блоки, нужно узнать, сколько газосиликатных блоков в 1 м3, и сколько газоблоков помещается в поддоне.
Газоблоки с размерами 200х300х600 мм используют для постройки несущих стен. Для постройки перегородок лучше применять панели ширина, которых составляет 10 см. Блоки производятся с различными размерами, что непосредственно влияет на показатели количества элементов в кубометре.
Сколько в 1м3 поместиться газоблоков
Чтобы лучше понять расчеты нужного количества стройматериалов будет рассмотрен такой пример:
- По проекту у дома будет 4 несущие стены, длина которых составляет 5 м, с высотой 3 м.
- В здании будет 4 оконных проема, с габаритами 1,2х1,5 м, и дверной проем 2х1 м.
- Сначала вычисляется объем стены из газоблоков: 5х4х3=60 м3. Окна и дверь на этом этапе не учитываются.
- Далее рассчитывается объем кладки, которая производится, не будет – оконные и дверные проемы 1,2х1,5х4+2=9,2м3.
- В итоге получается чистый объем, который составит 60-9,2 = 50,8 м3.
Теперь будет более понятно, зачем нужно рассчитывать нужное количество газоблоков в одном кубометре. Такая методика позволит посчитать, сколько кубов газоблока нужно на дом.
Далее для удобства расчетов переводят все данные в сантиметры — 1м3 будет равен 1000000 см3 (100х100х100). Объем одного блока будет равен 36000 см3. Для того чтобы рассчитать сколько в метре кубическом элементов, следует 1000000 разделить на 3600, в итоге получится 28 шт. Подсчет количества требуемого количества блоков для всей конструкции 28 шт. умножают на 50,8 в итоге получается 1422 шт.
Сколько газоблоков с размерами 20х30х60 в 1 кубометре?
Чтобы узнать, сколько газобетонных блоков в 1м3, следует знать габариты одного изделия. Распространенные размеры блоков:
- 250х300х600 мм;
- 600х400х250 мм;
- 600х300х300 мм;
- 625х200х250 мм.
При произведении расчетов следует числа в миллиметрах перевести в метры, для этого потребуется все числа разделить на 1000. Для примера были взяты параметры 20х20х60 см и 28,8х20х0,6 см.
- Умножают все стороны газоблока 0,2х0,2х0,6 в итоге получается объем одного блока, который равен 0,024. Далее 1 разделяют на 0,024 и получают количество единиц в одном кубометре – 41,66 шт.
- Во втором варианте расчетов все аналогично 0,288х0,2х0,6 объем одного изделия будет равен 0,03456. После 1 делят на 0,03456 и получают 28,93 строительных единиц в одном м3.
Сколько в 1 м3 газобетонных блоков в поддоне?
Отгружают строительные материалы в определенном количестве, товар упакован в поддоны. Поштучно газоблоки не продаются. Количество штук в поддоне газобетонных блоков, зависит от размеров одного изделия. По этой причине это число может составлять от 40 до 180 единиц. При составлении заказа рекомендуется уточнить у менеджера, он же может помочь посчитать требуемое количество.
Сколько весит куб газобетона, определяют по характеристикам плотности, которая обозначается буквой D, а цифры обозначают показатель плотности.
Какое количество газобетонных блоков в 1 м3 для простенков с параметрами 60х10х30 см? Из-за того что такие газобетонные панели имеют в два раза меньший объем чем стандартные блоки. Соответственно таких изделий в одном кубометре будет 56 строительных единиц.
Вес
Заполнитель оказывает влияние на удельный вес изделий, за счет которого материал разделяют на несколько типов:
- Максимально легкие по структуре газоблоки содержат множество воздушных пор. Такой стройматериал применяют в качестве утеплителя. Вес газобетона 1 м3 составит меньше 500 кг.
- Легкие газоблоки представляют собой смесь с наполнителем — ракушечником или керамзитом. Вес поддона с газобетонными блоками составит от 500 до 1800 кг, показатели колеблются из-за показателей плотности материала. Песок является самым тяжелым из входящих в состав компонентов.
- Тяжелый тип газоблоков считают самым распространенным. В составляющую часть входят такие компоненты, как гравий и щебень.
Именно эти элементы оказывают влияние на вес изделий. Один кубометр весит 2 тонны и более. Например для того чтобы узнать сколько весит куб газобетона D500, достаточно взглянуть на цифру, которая обозначает 500 кг на 1м3.
- Особенно тяжелые блоки считаются самыми редкими. На бетонную массу оказывают влияние наполнитель крупного размера.
Показатель веса блоков зависит от плотности, которая указана на марке. Например, маркировка D600 означает, что плотность составляет 600 кг на 1 м3.
Когда известны показатели плотности, можно рассчитать массу одного или требуемого количества блоков. Для этого потребуется знать, сколько в кубе газобетона. Например, блок марки D500 с параметрами 20х30х60 мм имеет вес 18 кг.
Плотность
Для возведения несущих стеновых конструкций используют блоки, которые способны выдержать большие нагрузки. Рекомендуется использовать изделия с плотностью D400-500.
youtube.com/embed/1l3zGmFXu4M» src=»data:image/gif;base64,R0lGODlhAQABAAAAACH5BAEKAAEALAAAAAABAAEAAAICTAEAOw==»>?
Параметры
Чтобы выяснить количество кубов газобетона в одном поддоне, следует знать габариты изделий. Для стен применяют строительные элементы, толщина которых превышает 20 см. Такие размеры 200 или 250 мм являются самыми распространенными, их используют для постройки одноэтажных зданий. От параметров изделий зависит, сколько штук поместится в 1 кубе. При строительных работах монолитно-каркасной направленности частные строители и профессионалы используют газобетонные блоки с толщиной 250 мм. Если сравнивать такую стену с кирпичной кладкой, чтобы достичь аналогичных особенностей с газобетоном кирпичная стена должна составлять толщиной 1 метр.
Существует два типа газоблоков:
- Которые имеют прямоугольную форму.
- U-образные, такие элементы используют при создании перемычек.
Стандартные размеры изделий:
- длина – 60 либо 62, 5 см;
- высота – 20-25 см;
- ширина – 8,5-40 см.
Все вышеперечисленные габариты пользуются популярностью при постройке зданий, ширина может меняться в соответствии с поставленными задачами. Блоки легко поддаются обработке, при надобности размер изменяется.
U-образные изделия производят с такими параметрами:
- высота 25 см;
- длина 50-60 см;
- ширина 20-40 см.
Перед закупкой стройматериалов следует знать площадь помещения и размеры стен. Для того чтобы рассчитать сколько в 1 квадратном метре газоблоков, возьмем для примера показатели средней толщины стены 30 см.
Расчеты:
- Считают длину наружной стены для одноэтажной постройки с размерами 10х10 м, с высотой стен 3 метра.
- Общая длина стен – 10+10+10+10 получается 40 метров.
- После вычисляют показатели площади поверхности, для этого длина 40 метров умножается на высоту 3 метра, получается 120 м2.
- Из общих показателей площади вычитают дверные и оконные проемы. Например, 10 кв.м разделить на 120 кв.
м и отнять 10, получается 110 м2.
- Чтобы узнать, сколько газобетонных блоков в 1м2 кладки, следует рассчитать площадь одной строительной единицы – 0,2х0,6 получится 0,12 кв.м. На 1м2 получается 1:0,12 = 8,33 газобетонных блока.
- На все здание понадобится: 110 кв.м умножают на 8,33 шт. получается 916,3 единицы.
В этом примере не учли толщину швов с раствором. Аналогичным методом рассчитывают нужное количество газобетона на внутренние стены.
Сколько поддонов с газоблоком входит в манипулятор? В машину обычно входит от 10 до 12 поддонов с газоблоками.
Грамотный расчет нужного количества газобетонных блоков для постройки стен и перегородок, позволит минимизировать затраты на покупке стройматериалов, которые измеряют в кубических метрах или в единицах. Сколько газосиликатных блоков в пачке будет зависеть от таких параметров как высота, ширина и длина. В основном их количество газоблоков в поддоне колеблется от 32 до 60 штук.
Сколько газобетонных блоков в 1м3: в кубе, штук в упаковке, в поддоне размером 600х300х200
Вопрос о том, сколько газобетонных блоков в 1м3, актуален для всех, кто собирается использовать данный материал в осуществлении ремонтно-строительных работ. Газобетон с каждым годом приобретает все большую популярность, ввиду массы преимуществ являясь наиболее оптимальным выбором для возведения малоэтажных зданий.
Основные преимущества газобетона – это малый вес и идеальная геометрия, большой размер и возможность быстро построить дом своими руками за счет легкого и простого монтажа, высокий уровень теплосбережения и большое разнообразие блоков в ассортименте. Перед началом строительства очень важно рассчитать, сколько блоков входит в куб и какой объем материала нужен для выполнения всех работ.
Стандартный размер газобетонного блока составляет 60х30х20 сантиметров, но производители предлагают и множество других габаритов, поэтому до того, как выполнять расчеты, нужно определиться с размером блока. Далее считают, сколько нужно материала для строительства всех конструкций (внутренних перегородок и несущих стен) в кубометрах, вычисляют число блоков в 1 кубометре, считают нужное количество и с учетом информации о вместимости поддона получают искомую величину – точный объем строительного материала.
Читайте также: про строительство и ремонт.
Сколько в 1м3 газоблоков
Содержание статьи:
Чтобы вычислить, сколько газоблоков в одном кубе, необходимо знать точные размеры одной единицы. Данная информация указывается в числе первых в спецификациях и описаниях продукции, поэтому после выбора поставщика и оптимальных габаритов для блоков посчитать все не составит труда.
До начала выполнения вычислений все миллиметры/сантиметры переводят в единую систему измерения – в метры: для получения величин при указании производителем миллиметров нужно поделить на 1000, сантиметров – на 100. Так, стороны блока 600х300х200 миллиметров или 60х30х20 сантиметров будут равны 0.6х0.3х0.2 в метрах.
Теперь нужно узнать, какой объем равен одному газоблоку: умножить все стороны 0. 6х0.3х0.2, получается 0.036. Именно столько объема вмещает один блок стандартного размера. Теперь 1 кубический метр нужно поделить на 0.036 – и получается число блоков в 1 кубе: 1/0.036=27.7=28. Значит, в одном кубическом метре вмещается 28 блоков стандартного размера 60х30х20 сантиметров.
Чтобы понять, как это использовать на практике, можно рассмотреть пример расчета количества блоков в кубических метрах для одного дома.
Посчитать, сколько блоков нужно для строительства стены, используя именно габариты материала, сложно. Гораздо проще высчитать в кубических метрах нужный объем, а потом посчитать число блоков.
Пример расчета газоблоков для дома:
Исходные данные – коробка 4 на 6 метров, высота 3 метра. Будет установлено 3 окна величиной 1.5х1.5 метров и дверь 2х1 метр. Толщина стен составляет 30 сантиметров (0.3 метра).
Вычисление объема стен – (6+4+6+4)х3х0.3=18 кубических метров.
Учет окон и дверей – (1.5+1.5)х3х0.3=2.7 (окна), 2+1=3х0. 3=0.9 (дверь). Получается 2.7+0.9=3.6.
Объем материала – 18 – 3.6 = 14.4 кубических метров.
Выше было вычислено, что в одном кубическом метре помещается 28 газобетонных блоков стандартного размера – значит, для 14.4 кубометров нужно: 14.4х28=403 блока.
Сколько газоблоков 20х30х60 в 1 кубометре
Выше был представлен алгоритм вычислений и они достаточно просты, если вдуматься в суть и понять, что и для чего делается.
Как вычислить число газоблоков 20х30х60 сантиметров в кубометре:
- Для получения искомой величины сначала нужно выяснить, сколько кубометров вмещается в одном газоблоке. Для этого все стороны блока, переведенные в единую величину (метры) перемножаются: 0.6х0.3х0.2=0.036 газоблоков в одном кубическом метре.
Теперь можно узнать, сколько штук блоков входит в 1 кубометр: для этого число метров (1) делится на объем, занимаемый одним блоком (0.
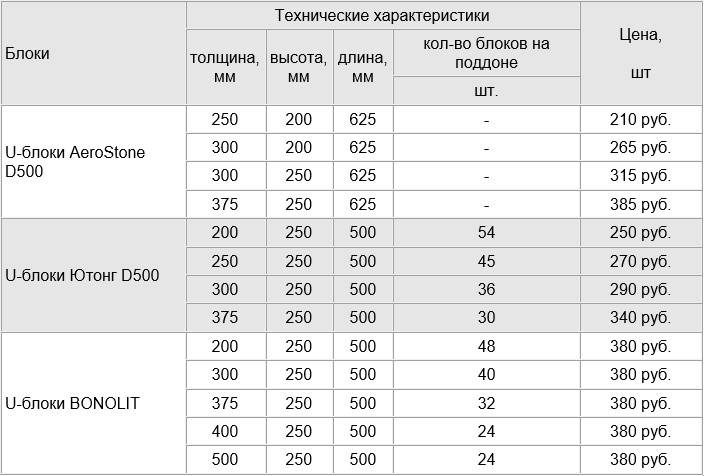
Если размеры газобетона другие, подставляются соответствующие значения. Чтобы вычисления были более наглядными, можно составить простые формулы.
Поиск объема, занимаемого блоком: высота х ширина х длина = объем одного блока.
Поиск числа блоков в 1 м3: 1 / объем одного блока = число газоблоков в кубическом метре.
Сколько в 1 м3 газобетонных блоков в поддоне
Чтобы высчитать, сколько блоков вмещается на поддоне, нужно точно знать размеры блоков и величину поддона. Как правило, в поддоне вмещают 40-180 блоков в зависимости от их размеров. Но и поддоны могут быть разными, поэтому обычно при заказе материала данный параметр узнают у менеджера. Зная, сколько штук газобетона вмещает поддон, указывают их число, а также могут понять, удастся ли доставить газобетон за одну ходку транспорта.
С другой же стороны, обычно кубические метры используют для вычисления числа газоблоков, нужных для работ. Этот же показатель указывают и при заказе материала, а покупателя особо не беспокоит число поддонов. Но при желании организовать доставку газоблоков на объект самостоятельно, бывает, что нужно и знать число штук на поддоне.
Ниже в таблице представлено число блоков разных размеров на поддонах:
Вес
Вес газоблока так же, как и размер, может быть очень разным и зависит не только от габаритов, но и от плотности. Чем плотность бетона выше, тем он весит больше.
Виды газобетона по весу и плотности:
Самые легкие – в них много пор, плотность минимальная, обычно материал используют как утеплитель, для кладки стен он не подходит из-за невысокой прочности. Масса таких блоков составляет 200-500 килограммов в кубическом метре.
Тяжелые газоблоки – наиболее распространенный вариант. Кубометр весит до 500-900 килограммов. Эти блоки идеальны для строительства стен малоэтажных зданий.
Сверх-тяжелые газоблоки – 900-1200 килограммов на кубический метр. Такие блоки используют в высотном строительстве, они считаются самыми прочными и плотными, но и тяжелыми тоже.
Чтобы не ошибиться при выборе материала, достаточно посмотреть на его марку – она соответствует плотности, количеству килограммов в кубическом метре. Так, марка газоблока D400 указывает, что плотность материала равна 400 кг/м3, D600 – 600 кг/м3 и т.д.
Плотность
Плотность материала, как было указано выше, напрямую связана с его весом и прочностью. Связь такая: чем более плотный газобетон, тем выше его прочность и больше вес, а также ниже теплосберегающие способности. Поэтому выбор у мастера всегда сложный: либо выбрать прочный и плотный, тяжелый материал (что затруднит монтаж и сделает дом менее теплым), либо строить из неплотного материала низкой прочности, который будет легким и обеспечит наилучшие теплоизоляционные и звукоизоляционные свойства.
Газобетонные блоки делятся на марки, которые обозначают не просто цифры, а плотность, количество килограммов материала на кубический метр. Блоки марки D200 имеют плотность 200 кг/м2 – то есть, их вес составляет 200 килограммов на кубический метр.
Плотность газобетона варьируется объемом газообразователя в составе материала. Блоки делают из смеси цемента, воды, песка и алюминиевой пудры. Объем пузырей в составе может варьироваться в пределах 20-90%. Воздушные пузыри в структуре напрямую влияют на плотность и прочность – чем их больше, тем менее плотный и прочный материал, но выше показатель теплосбережения.
Для строительства жилых объектов в 2-3 этажа чаще всего выбирают газобетон плотностью 400-500 килограммов на кубический метр. Это наиболее оптимальное соотношение характеристик.
Параметры
Размеры газоблоков могут быть самыми разными, как и форма, конструкция. Блоки для кладки стен обычно делают в форме большого параллелепипеда. Пример стандартного размера – 60 сантиметров в длину, 30 сантиметров в высоту и 20 в ширину. Также распространены несколько других типоразмеров, но существуют еще блоки для внутренних стен (они меньше), доборные элементы, изделия особой конструкции.
Существует два типа газоблоков
Для большинства задач на строительных объектах достаточно иметь газобетонные блоки двух типов – обычные прямоугольные и U-образные, которые актуальны для выполнения разных частей конструкции. Кроме того, по форме блоки могут быть и другими.
Какие бывают газоблоки по типу и форме:
- Блоки прямоугольной формы – используются для строительства внутренних перегородок, внешних несущих стен.
Балки из армированного газобетона – для создания потолков. Перекрытия монтируют из балок Т-образной формы размером 60х25х20 сантиметров, оконные/дверные проемы выполняют из U-образных блоков, которые позволяют существенно ускорить процесс монтажа и понизить трудозатраты.
Дугообразные газоблоки, перемычки – используются для облегчения процесса строительства (из них выполняют определенные части конструкции).
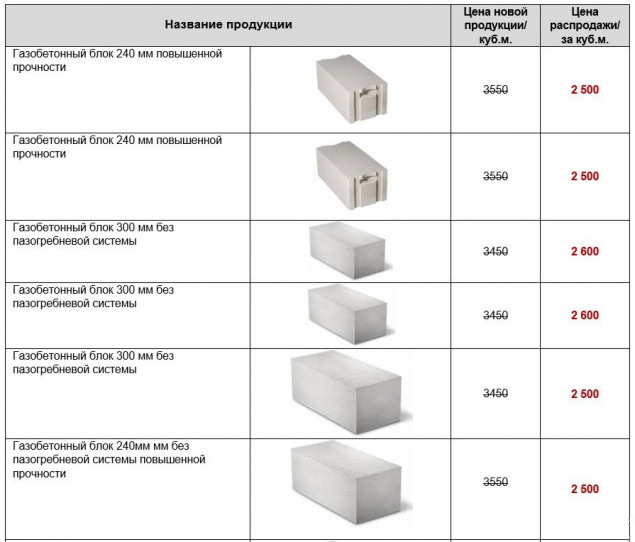
Выбирая блоки из газобетона, важно узнать технологию производства материала. Всего вариантов существует два и в целом они схожи, но отличаются в ключевых параметрах. Смесь готовят для заливки в форму по одному и тому же рецепту, но в случае автоклавного газобетона раствор заливают в одну большую форму и отправляют в автоклав, где на него воздействуют высокое давление и температура.
Неавтоклавный газобетон заливают в формы и потом сушат в естественных условиях. В таком случае материал получается менее прочным, на нем могут быть сколы и отслоения.
Для строительства лучше выбирать автоклавный газобетон, который может стоить дороже, но демонстрирует гораздо более высокие эксплуатационные характеристики.
Стандартные размеры изделий
Стандартные размеры блоков были указаны выше (600х300х200 миллиметров), также к их числу можно отнести другие типоразмеры.
Какие размеры используются обычно:
Длина – от 60 до 62.5 сантиметров.
Высота – от 20 до 25 сантиметров.
Ширина – от 8.5 до 40 сантиметров.
Ниже указаны возможные варианты:
U-образные изделия производят с такими параметрами
Изделия данной формы стандартные обычно имеют такие размеры: 25 сантиметров в высоту, 50-60 сантиметров в длину и 20-40 сантиметров в ширину. До закупки строительных материалов обязательно нужно все тщательно измерить и рассчитать, сколько и куда нужно газоблоков. Расчеты ведутся по той же схеме, что и в случае с обычными газоблоками.
Расчеты
Для выполнения расчетов и поиска нужного объема газобетона сначала нужно правильно посчитать конструкцию. Считают высоту и ширину стен, размеры всей постройки, внутренние перегородки. Потом длину стен перемножают на высоту и получают общую площадь в квадратных метрах. Далее определяются с толщиной стен и полученный показатель умножают на толщину в метрах (0.2, 0.3, 0.4, что равно 20, 30, 40 сантиметрам соответственно) и получают нужный объем газоблока в кубометрах.
После этого нужно отыскать, какой объем кубический приходится на блок – умножить все его стороны между собой и поделить на получившуюся цифру единицу. Потом достаточно число кубометров умножить на количество блоков в кубометре и получить искомую величину – количество штук газоблока.
Обычно в примерах не учитывают толщину шва, поэтому к получившемуся показателю можно не добавлять классические 7-10%. Швы могут быть тонкими при использовании специального клея или средней толщины, если кладка осуществляется на цементно-песчаный раствор.
Несмотря на то, что упаковка клея стоит больше, чем идентичный объем кладочной смеси, в итоге получается сэкономить как за счет толщины швов, так и на отоплении, так как клей не дает мостиков холода.
Знать, сколько газобетонных блоков в 1м3 желательно каждому, кто приступает к строительству. Даже если все эти объемы и цифры могут посчитать на производстве или в магазине, в корректности и правильности выполненных самостоятельно расчетов сомневаться не придется.
Источник
Блоки Бонолит количество штук в машине
Газосиликатные блоки D-600
Производитель: Завод «Bonolit »
размер блоков: 600x200x250
Наименование | |
Наименование: | Блоки |
Назначение: | перегородочные |
Состав: | газосиликат (газобитон) |
Пустотность: | ячеистый бетон |
Цвет: | белый |
Поверхность: | гладкая на клей |
Пазогребень: | нет |
Общая информация | |
Завод: | Bonolit |
Геометрические размеры | |
Размер, мм: | 600x200x250 |
Характеристики | |
Плотность кг/м3: | D-600 |
Класс прочности: | В-3,5 |
Теплопроводность (Вт/м*С): | 0,14 |
Прочность при сжатие (кгс/см²): | 1,5 |
Морозостойкость: | F 100 |
Паропроницаемость, мг/(м·ч·Па): | 0,16 |
Усадка при высыхании (мм/м): | 0,225 |
Предел огнестойкости: | REI 240 |
Вес 1 шт, кг: | |
Упаковка, доставка | |
Упаковка: | на поддонах/пленка/лента |
количество шт.![]() | 33,33 |
м3 на поддоне: | 1,8 |
м3 в машине: | 28,8 |
шт на поддоне: | 60 |
шт в машине: | 960 |
поддонов в машине: | 16 |
D 600 — самая высокая марка плотности блоков и перегородок Бонолит, которая обеспечивает повышенную прочность конструкций.Используется для изготовления перемычек и внутренних перегородок повышенной прочности. Блоки плотности D600 можно использовать в качестве самонесущих стен при строительстве домов до 5 этажей (до 20 метров). Данные блоки идеальны для крепления навесных фасадов, отлично выдерживают ветровые нагрузки (нагрузка на вырыв 4,08+/-0,13kN (1 kN=100кг).
Описание блоков
Компания «Строим Дом Вместе» предлагает Вам купить блоки по низкой цене.
Мы поможем Вам с выбором товара, оформлением заказа.
Мы организуем для Вас быструю доставку.
У нас прямые поставки от производителя.
Заказать товар или получить интересующую Вас информацию,
Вы можете по телефонам:
8 (926)917-50-62; 8 (985)265-15-91;
8 (905)557-12-15; 8 (925)839-83-75.
Другие размеры блоков завода БОНОЛИТ:
D-400
D-500
D-600
Номенклатура стеновых блоков Thermocube
Газобетон — это полностью искусственно созданный искусственный минерал, вобравший в себя все лучшие характеристики стеновых материалов: экологичность, прочность, легкость, негорючесть, теплота и простота обработки.
Размеры стеновых блоков Thermocube®:
Длина/Высота/Ширина | Количество блоков на поддоне, шт. | Объём 1 блока в куб. м | Объём одного поддона, куб. м |
600/200/250 | 60 | 0,03 | 1,8 |
600/200/300 | 50 | 0,036 | 1,8 |
600/200/375 | 40 | 0,045 | 1,8 |
600/200/400 | 30 | 0,048 | 1,44 |
600/250/100 | 120 | 0,015 | 1,8 |
600/250/125 | 96 | 0,019 | 1,8 |
600/250/150 | 80 | 0,0225 | 1,8 |
600/250/250 | 48 | 0.![]() | 1,8 |
600/250/300 | 40 | 0.045 | 1,8 |
600/250/375 | 32 | 0.0562 | 1,8 |
600/250/400 | 24 | 0,06 | 1,44 |
600/250/500 | 24 | 0.075 | 1,8 |
В стеновых конструкциях из газобетонных блоков нет необходимости использовать дополнительные тепло- и звукоизоляционные материалы, что является эффективным как с экономической точки зрения, так и для надёжного, исключающего ошибки строительства.
Главный конкурент стеновых блоков в строительстве – традиционный кирпич. Но, стоит заметить, что строительство стен из кирпича, зачастую, требует сравнительно больших временных затрат. Благодаря большому, по-сравнению с кирпичом, размеру и незначительному весу блоков, кладка стен из газосиликатных блоков происходит в несколько раз быстрее.
Технология использования специального клеевого раствора для кладки стен из газосиликатных блоков требует тонкослойного нанесения. Что исключает появления «мостиков холода» (мест промерзания) в стене. Кроме этого блоки не требуют мощного фундамента под собой, так как отличаются низкой плотностью при высокой прочности. А также, благодаря огромному количеству маленьких пор в блоках изолируют в 7-10 раз лучше, чем обычный бетон или кирпич. Здания из стеновых блоков приятно прохладны летом и сокращают потери тепла зимой. Расходы по отоплению или охлаждению за счёт этого минимальны. Всё это положительным образом сказывается на стоимости Вашего строительства.
Стеновые блоки из ячеистого бетона автоклавного твердения (газосиликатные) применяют в строительстве и реконструкции стен и перегородок. А так как они являются неорганическим, абсолютно негорючим материалом, в связке с металлоконструкциями или как обшивка, и ко всему прочему, идеально подходят для строительства пожаростойких стен (брандмауэры), вентиляционных и лифтовых шахт.
Комплекс положительных свойств делает газосиликатные блоки технически и экономически предпочтительным строительным материалом, как в жилищном, так и в хозяйственном строительстве.
Преимущества газобетонных блоков Thermocube®:
- Точность размеров
- Легкая кладка и обработка
- Высокая прочность
- Высокие звуко- и теплоизоляционные свойства
- Экологичность
- Плотность блоков: D400, D500, D600
- Длина блоков: 600 мм
- Высота блоков: 200/ 250 мм
- Ширина блоков: 250, 300, 375, 400, 500 мм
Газобетон отличается от других строительных материалов ячеистой структурой. Данный эффект достигается с помощью добавления газообразователя во время производства газобетона. Такая структура материала позволяет блокам «дышать», пропускать воздух. Но при этом газобетонные блоки являются одним из самых лучших теплопроводимых материалов.
Костромской завод строительных материалов имеет все необходимые сертификаты на продукцию Thermocube®.
Газобетонные блоки Thermocube® производит «Костромской завод строительных материалов».
Сколько пеноблоков 200х300х600 в поддоне и кубе, правила расчета
Пеноблоки отгружаются поддонами, а продаются кубометрами. Соответственно, возникают вопросы, касательные, сколько ячеистого бетона в 1 м3 и транспортной таре. Пенобетон с параметрами 200х300х600 мм является наиболее востребованным в строительстве: за счет крупногабаритности кладка выполняется быстрее, а благодаря весу (в среднем 22 кг) конструкция не утяжеляется, и рабочий процесс проходит легче.
Оглавление:
- Сколько блоков в 1 м3?
- Стоимость
- Преимущества использования
Каково количество в кубе?
Сколько штук вмещает в себя 1 кубический метр, выяснить несложно. Достаточно выполнить ряд арифметических действий:
- вычислить объем элемента, перемножив его линейные размеры, то есть высоту, толщину, длину: 200х300х600=36000000 мм3;
- перевести получившееся значение в кубометры: поскольку в 1 мм3 0,000000001 м3, получается величина 0,036 м3;
- поделить 1 м3 на объем блока из пенобетона, определив количество в кубе: 1÷0,036≈27,8 шт.
В одном кубометре выходит 27 штук цельных элементов.
Сколько блоков 200х300х600 в поддоне?
Стандартные паллеты имеют размеры 1000х1200 мм. По общепринятым рекомендациям укладка материала должна выглядеть так: в длину идут 2 изделия, в ширину – 5, количество рядов – 5. Теперь следует перемножить эти значения: 2х5х5=50.
50 – столько штук пеноблоков располагает в себе паллета стандартного размера. Если умножить данное число на объем одного элемента, то получится узнать количество кубов в таре: 50∙0,036=1,8 м3.
Параметры европоддона несколько отличаются от «классики». Габариты здесь – 800х1200 мм, следовательно, укладывать предстоит чуть по-другому. Как в паллетах, рядов будет 5, в длину снова идут 2 изделия, но в ширину – лишь 4.
Умножив 2х4х5, итоговое число выходит равным 40. Это и будет ответ на вопрос, сколько штук блоков умещается в поддон европейского плана. Расчеты, касательные кубометров, аналогичны предыдущим: 40х0,036=1,44 м3.
Какова стоимость?
На расценки прежде всего влияют прочностные характеристики.
Плотность пенобетона (кг/м3) | Цена за шт, руб | Стоимость куба, рубли | Цена за поддон, рубли | |
Евро | Стандарт | |||
D400 | 68 | 1890 | 2720 | 3400 |
D500 | 81 | 2250 | 3240 | 4050 |
D600 | 93 | 2590 | 3720 | 4650 |
D700 | 105 | 2920 | 4200 | 5250 |
D800 | 122 | 3390 | 4880 | 6100 |
Стоимость 1 кубометра определялась путем умножения цены за штуку на 27,8 (количество в м3). За стандартную паллету и европоддон расчеты производились с аналогично. Только показатели, обозначающие количество ячеистых блоков в них, брались другие: 40 и 50 штук.
Почему пенобетон столь популярен?
Характеристики блоков обуславливают востребованность как в профессиональном строительстве, так и при использовании обывателями. Ккэффициент теплопроводности в несколько раз ниже, чем у кирпича. Чтобы достигнуть одинакового эффекта, толщина стен из пенобетона должна быть где-то 50 см, в то время как у кирпичной постройки – не менее 120 см.
С ячеистыми бетонами и работа движется быстрее, легче. Материал негорюч, морозостоек, имеет хорошую сопротивляемость к плесенеобразованию. За счет малого веса он не обременяет конструкцию повышенной нагрузкой, фундамент допускается возводить самого простого типа.
Облицовывать можно чем угодно, но наибольшее значение при выборе мастера отдают 2 критериям: надежности и дешевизне.
AAC в Дейтоне, Огайо — Продукция
«Стандарт на огнестойкие испытания строительных конструкций и материалов»
Характеристики крыши, полов и стен при воздействии огня важны для безопасности людей, находящихся в здании, их имущества и содержимого здания. Этот стандартный метод испытаний определяет допустимые и неограниченные характеристики для крыш и полов, а также несущие и ненесущие характеристики для стен при воздействии стандартного воздействия огня с наложенной нагрузкой, имитируя условия максимальной нагрузки.Стандарт предусматривает относительную меру способности сборки предотвращать распространение огня и сохранять свою структурную целостность. После того, как сборка подвергается стандартному воздействию огня, на нее воздействуют струей воды из стандартного пожарного шланга, предназначенной для стимуляции воздействия усилий при тушении пожара. Сборка должна успешно пройти обе части испытания, чтобы достичь определенного уровня огнестойкости.
Были испытаны две сборки панелей Aercon, UL K910 (сборка панели пола толщиной 8 дюймов) и UL P933 (сборка панели крыши толщиной 8 дюймов).Обе сборки достигли рейтинга ограниченной сборки 4 часа (с использованием панелей типа 1) и рейтинга неограниченной сборки 1 час (с использованием панелей типа 1) и 1,5 часа (с использованием панелей типа 2). Два протестированных типа панелей имели разную минимальную степень покрытия армирования; Тип 1 с минимальной крышкой 20 мм и Тип 2 с минимальной крышкой 45 мм. Сдерживание было обеспечено с помощью залитой на месте железобетонной кольцевой балки по периметру испытательной сборки. В соответствии с типами протестированных панелей, 10- и 12-дюймовые панели крыши и пола также имеют одинаковые рейтинги ограниченной сборки и неограниченной сборки.
Сборка блочной стены Aercon, UL U921, достигла 4-часового рейтинга несущей стены и 4-часового рейтинга несущей стенки при минимальной толщине 6 дюймов и классе прочности AC6 / 650. Основываясь на тепловых свойствах этого класса прочности, остальные классы прочности также имеют такие же номинальные характеристики несущей стенки и ненесущие стенки, равные 4 часам.
Правильное использование газобетона в автоклаве
16 октября 2008 г., 9:01 CDTПолучайте новости каменной промышленности на почту
Подпишитесь на Masonry Messenger , чтобы получать ресурсы по каменной кладке и информацию, необходимую для поддержания актуальности.
Нет, спасибо
Икспо Ричард Э. Клингнер
Примеры автоклавных элементов из газобетона. Изображение любезно предоставлено Ytong International.
Блоки автоклавного ячеистого бетона (AAC) чаще всего укладываются с использованием тонкослойного раствора и могут использоваться для кладки несущих стен. Положения по проектированию каменной кладки AAC приведены в Кодексе MSJC, а требования к строительству — в Спецификации Объединенного комитета по стандартам кладки (MSJC).В этой статье кратко рассматривается производство AAC; проиллюстрированы практические примеры возведения кладки из ААК; Обобщены проектные положения MSJC для кладки AAC; особое внимание уделяется практическому руководству по строительству каменной кладки из AAC. Автоклавный газобетон (AAC) — легкий, похожий на бетон материал с множеством небольших закрытых внутренних пустот. Спецификации материалов для AAC указаны в ASTM C1386. AAC обычно весит от одной шестой до одной трети веса обычного бетона и составляет от одной шестой до одной трети прочности. Подходит для несущих стен и стен с низким и средним этажом. Его теплопроводность составляет одну шестую или меньше, чем у обычного бетона, что делает его энергоэффективным. Его огнестойкость немного выше, чем у обычного бетона такой же толщины, что делает его полезным в приложениях, где важна огнестойкость. Из-за своих внутренних пустот AAC имеет низкую передачу звука, что делает его полезным с акустической точки зрения.
История AAC
AAC был впервые коммерчески произведен в Швеции в 1923 году.С тех пор его производство и использование распространились в более чем 40 странах на всех континентах, включая Северную Америку, Центральную и Южную Америку, Европу, Ближний Восток, Дальний Восток и Австралию. Этот обширный опыт позволил провести множество тематических исследований по использованию в различных климатических условиях и в соответствии с различными строительными нормами. В США современное использование AAC началось в 1990 году в жилых и коммерческих проектах в юго-восточных штатах. Производство простых и усиленных AAC началось в 1995 году на юго-востоке США и с тех пор распространилось на другие части страны.Общенациональная группа производителей газобетона была образована в 1998 году как Ассоциация автоклавных газобетонных изделий (AACPA, www.aacpa.org). Положения по проектированию и строительству каменной кладки AAC приведены в Кодексе и Спецификации MSJC. AACPA включает одного производителя в Монтеррее, Мексика, и многие технические материалы доступны на испанском языке. AAC одобрен для использования в категориях сейсмического проектирования A, B и C Дополнением 2007 г. к Международным строительным нормам и правилам, а также в других географических точках с одобрения местного строительного чиновника.
AAC можно использовать для изготовления неармированных блоков каменного типа, а также армированных на заводе панелей пола, кровельных панелей, стеновых панелей, перемычек, балок и других специальных форм. В этой статье рассматриваются в основном только каменные блоки.
Материалы, используемые в AAC
Материалы для AAC зависят от производителя и местоположения и указаны в ASTM C1386. Они включают некоторые или все из следующего: мелкодисперсный кварцевый песок; Летучая зола класса F; гидравлические цементы; кальцинированная известь; гипс; расширительные агенты, такие как мелкоизмельченный алюминиевый порошок или паста; и смешивание воды.Каменные блоки AAC не имеют внутреннего армирования, но могут быть усилены на строительной площадке с помощью деформированной арматуры, размещенной в вертикальных ячейках или горизонтальных связующих балках.Как производится AAC
Для производства AAC песок измельчается до необходимой степени измельчения в шаровой мельнице, если это необходимо, и хранится вместе с другим сырьем. Затем сырье дозируется по весу и доставляется в смеситель. В смеситель добавляют отмеренные количества воды и расширительного агента, и цементный раствор перемешивают. Стальные формы подготовлены для приема свежей AAC. Если должны производиться армированные панели AAC, стальные арматурные каркасы закрепляются внутри форм. После перемешивания кашицу разливают в формы. Расширяющий агент создает небольшие мелкодисперсные пустоты в свежей смеси, которые увеличивают объем примерно на 50 процентов в формах в течение трех часов.
Общие этапы производства автоклавного газобетона.
В течение нескольких часов после заливки начальная гидратация цементных смесей в AAC придает ему достаточную прочность, чтобы сохранять форму и выдерживать собственный вес.
После резки, газобетон транспортируется в большой автоклав, где завершается процесс отверждения. Автоклавирование необходимо для достижения желаемых структурных свойств и стабильности размеров. Процесс занимает от восьми до 12 часов при давлении около 174 фунтов на квадратный дюйм (12 бар) и температуре около 360ºF (180ºC), в зависимости от марки производимого материала. Во время автоклавирования устройства для обрезки проволоки остаются в исходном положении в блоке AAC. После автоклавирования их разделяют для упаковки.
Агрегаты AAC обычно помещаются на поддоны для транспортировки. Неармированные элементы обычно упаковываются в термоусадочную пленку, в то время как армированные элементы связываются только полосами с использованием угловых ограждений для минимизации потенциальных локальных повреждений, которые могут быть вызваны полосами.
Классы прочности AAC
AAC производится с различной плотностью и соответствующей прочностью на сжатие в соответствии с ASTM C1386. Плотность и соответствующие значения прочности описаны в терминах «классов прочности» (см. Таблицу 1).ТАБЛИЦА 1 — Классы прочности AAC | |||
Класс прочности | Установленная прочность на сжатие, фунт / дюйм2 (МПа) | Номинальная объемная плотность в сухом состоянии, фунт / фут3 (кг / м3) | Пределы плотности, фунт / фут3 (кг / м3) |
AAC 2,0 | 290 (2,0) | 25 (400) 31 (500) | 22 (350) — 28 (450) 28 (450) — 34 (550) |
AAC 4.![]() | 580 (4,0) | 31 (500) 37 (600) | 28 (450) — 34 (550) 34 (550) — 41 (650) |
AAC 6.0 | 870 (6.0 ) | 44 (700) 50 (800) 44 (700) 50 (800) | 41 (650) — 47 (750) 47 (750) — 53 (850) 41 (650) — 47 (750) 47 (750) — 53 (850) |
Типичные размеры блоков AAC каменного типа
Типичные размеры блоков AAC каменного типа (блоки каменного типа) показаны в таблице 2 ниже.ТАБЛИЦА 2 — Размеры каменной кладки AAC | |||
Тип блока AAC | Толщина, дюймы (мм) | Высота, дюймы (мм) | Длина, дюймы (мм) |
Стандартный блок | 2-15 (50-375) | 8 (200) | 24 (610) |
Jumbo Block | 4-15 (100-375) | 16–24 (400–610) | 24–40 (610–1050) |
Типичные области применения кладки AAC
Кладка AAC может использоваться в широком спектре структурных и неструктурных применений.
Конструктивное проектирование каменной кладки AAC Кладка
AAC спроектирована в соответствии с положениями Приложения A Кодекса MSJC (MSJC 2008), на который ссылаются коды моделей в США. Расчет кладки AAC аналогичен расчету прочности кладки из глины или бетона и основан на заданной прочности на сжатие.Соответствие указанной прочности на сжатие подтверждается испытанием на сжатие кубов AAC с использованием ASTM C1386, когда изготавливаются элементы каменного типа из AAC. Подробное практическое руководство по проектированию с использованием каменной кладки AAC представлено в 5-м издании Руководства для дизайнеров каменной кладки (MDG 2007).Комбинации изгиба и осевой нагрузки Кладка
AAC разработана для сочетания изгиба и осевой нагрузки с использованием тех же принципов, что и для расчета прочности глиняной или бетонной кладки.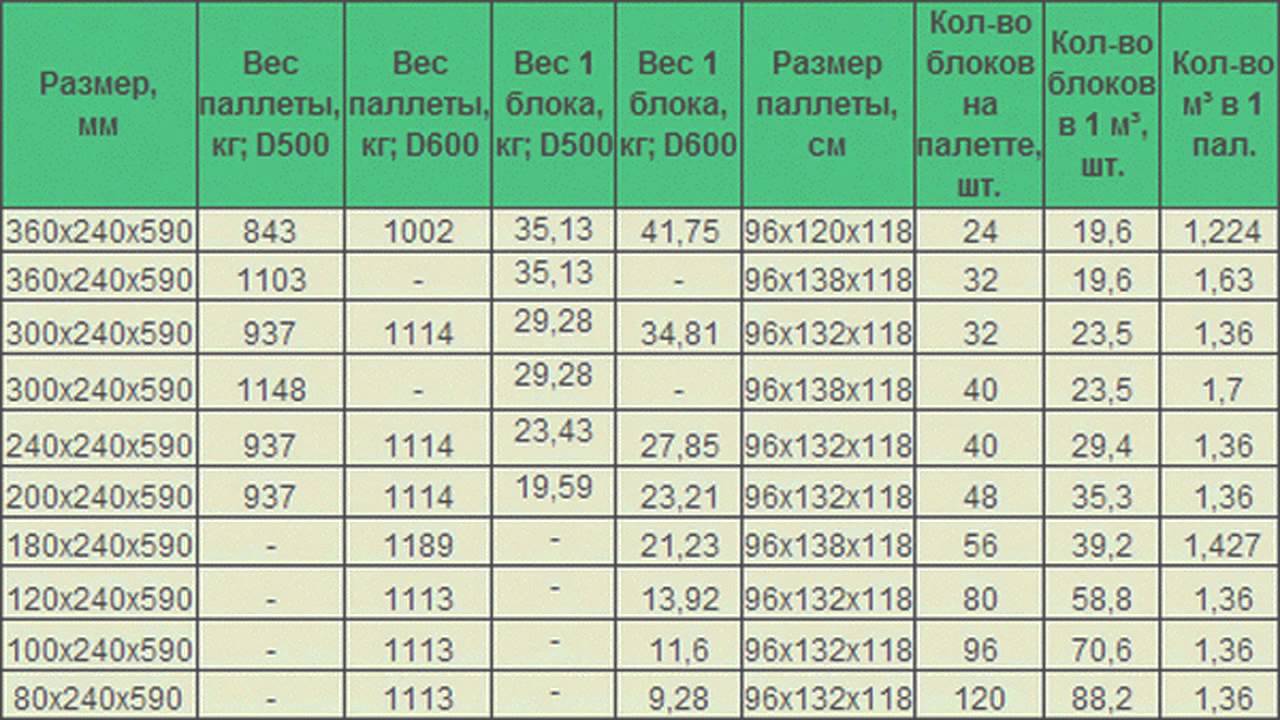
Выравнивающий слой и подкладки для первого ряда каменных блоков из AAC — первый ряд блоков из AAC укладывается на выравнивающий слой из раствора ASTM C270 типа M или S с использованием клиньев (при желании) для вертикального выравнивания и выравнивания блоков.
Соединение и развитие армирования
Армирование в кирпичной кладке AAC состоит из деформированной арматуры, помещенной в залитые вертикальные стержни или связующие балки и окруженных кладочным раствором.Требования к развитию и стыковке деформированной арматуры в растворе идентичны тем, которые используются для кладки из глины или бетона. Консервативно, материал AAC не учитывается при расчете покрытия на сопротивление раскалыванию.Сдвиг и опора
Как и в случае с глиняной или бетонной кладкой, сопротивление сдвигу кладки AAC вычисляется как сумма сопротивления сдвигу, обусловленного самим AAC, и сопротивления сдвигу, обусловленного арматурой, ориентированной параллельно направлению сдвига.
Укладка элементов каменной кладки AAC
На уровне диафрагмы стены кладки AAC соединяются с полом или крышей с помощью цементированной связующей балки, аналогично конструкции из глиняной или бетонной кладки. После укладки блоков кладки AAC плоскость стены можно выровнять с помощью шлифовальной доски, изготовленной для этой цели. Укладка блоков кладки AAC с использованием тонкослойного раствора и зубчатого шпателя — последующие слои укладываются с использованием модифицированного полимером тонкослойного раствора, наносимого специальным зубчатым шпателем.
Электрические и сантехнические установки в AAC
Электрические и сантехнические установки в кирпичной кладке AAC размещаются в проложенных пазах. При установке желобов необходимо соблюдать осторожность, чтобы обеспечить сохранение структурной целостности элементов AAC. Не сокращайте арматурную сталь и не уменьшайте конструкционную толщину элементов AAC, за исключением случаев, когда это разрешено проектировщиком.В вертикально перекрывающихся элементах AAC горизонтальная прокладка разрешается только в областях с низкими напряжениями изгиба и сжатия. В элементах AAC, охватывающих горизонтально, следует минимизировать вертикальную маршрутизацию. Когда это возможно, может быть полезно предусмотреть специальные выемки для большого количества трубопровода или водопровода.Внешняя отделка для AAC
Незащищенная внешняя поверхность AAC ухудшается при воздействии циклов замораживания и оттаивания в насыщенном состоянии. Чтобы предотвратить такое ухудшение состояния при замораживании-оттаивании, а также для улучшения внешнего вида и устойчивости к истиранию AAC, следует использовать внешние отделочные покрытия.
Доступно множество различных типов внешней отделки. Модифицированные полимером штукатурки, краски или отделочные системы являются наиболее распространенной внешней отделкой для AAC. Они увеличивают сопротивление проникновению воды AAC, позволяя пропускать водяной пар. Тяжелые краски на акриловой основе, содержащие заполнители, также используются для повышения стойкости к истиранию. Как правило, нет необходимости выравнивать поверхность, а горизонтальные и вертикальные швы могут быть скошены как архитектурный элемент или могут быть заполнены.
Кладочный шпон можно использовать поверх каменной кладки AAC во многом так же, как он используется для других материалов. Шпон крепится к стене из кладки AAC с помощью специальных стяжек. Пространство между AAC и кладкой можно оставить открытым (образуя дренажную стену) или заполнить раствором.
Когда панели AAC используются в контакте с влажной или насыщенной почвой (например, в стенах подвала), поверхность, контактирующая с почвой, должна быть покрыта водонепроницаемым материалом или мембраной. Внутренняя поверхность должна быть либо без покрытия, либо иметь паропроницаемую внутреннюю отделку.
Изображение любезно предоставлено Aercon Florida.
Внутренняя отделка для каменной кладки AAC
Внутренняя отделка используется для повышения эстетики и долговечности AAC. Они должны быть совместимы с лежащим в основе AAC с точки зрения теплового расширения и модуля упругости, а также должны быть паропроницаемыми.Доступно множество различных видов внутренней отделки. Внутренние стеновые панели AAC могут иметь тонкий слой штукатурки на минеральной основе для достижения гладкой поверхности.Легкая внутренняя штукатурка на основе гипса может обеспечить более толстое покрытие для выравнивания и выпрямления стен, а также для создания основы для декоративных красок для внутренних помещений или отделки стен. Внутренние штукатурки содержат связующие вещества, повышающие их адгезию и гибкость, и обычно наносятся путем распыления или затирки.
Гипсокартон при нанесении на внутреннюю поверхность наружных стен из AAC следует крепить с помощью полос, обработанных под давлением. При нанесении на внутренние стены влагостойкий гипсокартон можно наносить непосредственно на поверхность AAC.
Для коммерческих применений, требующих высокой прочности и низких эксплуатационных расходов, часто используются покрытия на акриловой основе. Некоторые содержат заполнители для повышения стойкости к истиранию.
Когда керамическая настенная плитка должна быть уложена поверх AAC, подготовка поверхности обычно требуется только тогда, когда поверхность AAC требует выравнивания. В таких случаях перед укладкой керамической плитки на поверхность AAC наносится покрытие на основе портландцемента или гипса. Затем керамическую плитку следует приклеить к обшитой паркетом стене с помощью тонкого раствора на цементной основе или органического клея.Во влажных помещениях, таких как душевые, следует использовать только паржевое покрытие на основе портландцемента, а керамическую плитку следует укладывать только на цементный тонко застывший раствор.
Типовые детали конструкции для элементов AAC
Широкий спектр деталей конструкции для каменной кладки AAC доступен на веб-сайтах отдельных производителей, доступных через веб-сайт AACPA.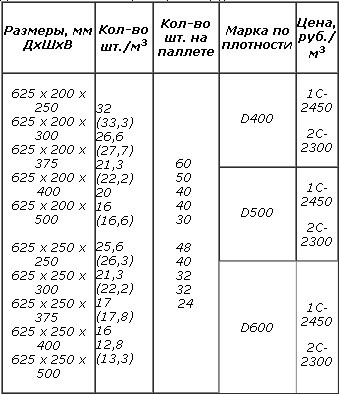
Об авторе
Ричард Клингнер, Ph.D. — профессор Л. П. Гилвина гражданского строительства в Техасском университете в Остине, где он специализируется на поведении и проектировании каменной кладки, особенно на сейсмические нагрузки.Он также является автором «Структурного дизайна кладки» и бывшим председателем Объединенного комитета по стандартам кладки (MSJC).
Статьи по теме
Файлы Фешино: Арки
Присоединяйтесь к MCAA сейчас всего за 799 долларов
Реставрация кладки: замена кирпича, камня и материалов
Другие заголовки о масонстве
Блок из автоклавного газобетона Falcon
АВТОКЛАВИРОВАННЫЙ ПЕРИОДНЫЙ БЕТОН СТАНДАРТНЫЙ (60x20xТолщина)
ТОЛЩИНА (см) | ||||||
---|---|---|---|---|---|---|
ВЕС на поддон (1 x 1,2 x 1,5 м) | ||||||
кг / м 2 | кг / блок | кг / поддон | Unit | M 2 | M 3 | |
7,5 | 45 | 5,4 | 1 080 | 200 | 24 | 1,8 |
10 | 60 | 7,2 | 1 080 | 150 | 18 | 1,8 |
12,5 | 75 | 8,78 | 1 080 | 120 | 14,4 | 1,8 |
15 | 90 | 10,53 | 1 080 | 100 | 12 | 1,8 |
17,5 | 105 | 12,6 | 1,134 | 90 | 10,8 | 1,89 |
20 | 120 | 14,4 | 1,152 | 80 | 9,6 | 1,92 |
JUMBO АВТОКЛАВНЫЙ ПЕРИОДНЫЙ БЕТОН (ТОЛЩИНА 60X40X)
ТОЛЩИНА (см) | ||||||
---|---|---|---|---|---|---|
ВЕС на поддон (1 x 1,2 x 1,5 м) | ||||||
кг / м2 | кг / шт.![]() | кг / поддон | шт. | M 2 | M 3 | |
7,5 | 45 | 10,8 | 1 080 | 100 | 24 | 1,8 |
10 | 60 | 14,4 | 1 080 | 75 | 18 | 1,8 |
12,5 | 75 | 18,0 | 1 080 | 60 | 14,4 | 1,8 |
15 | 90 | 21,6 | 1 080 | 50 | 12 | 1,8 |
17,5 | 105 | 25,2 | 1,134 | 45 | 10,8 | 1,89 |
20 | 120 | 28,8 | 1,152 | 40 | 9,6 | 1,92 |
Пример использования FISSAC 2 | FISSAC
Место нахождения: Измир, Турция.
Общее описание: Целью практического примера 2 является производство блоков из автоклавного ячеистого бетона (AAC) в промышленных масштабах со стандартными размерами для возведения стены (360 единиц).
Стеновые блоки из автоклавного газобетона (AAC) стандартных размеров (длина: 60 см, ширина: 25 см, толщина: 15 см) были произведены в классе G2 / 350 с использованием керамических отходов, шлака электродуговой печи (EAF) и ковша. печной шлак (LF) в качестве вторичного сырья, поставляемый региональными поставщиками (anakkale Seramik и Ekinciler Demir & elik, входящие в консорциум) для обеспечения возможности тиражирования.
AAC производится в шесть этапов:
1) Подготовка сырья.
Поставка SRM, используемого в стеновых блоках AAC, была произведена за счет отходов местных поставщиков. Количество отходов, необходимых для промышленного производства, составило 275,1 кг отходов керамической плитки, 27,6 кг шлака ДСП и 192,6 кг шлака LF. Керамические отходы уже были измельчены поставщиком, шлаки из ДСП и НЖ измельчались в шаровой мельнице для получения частиц размером 90 мкм.
2) Смешивание.
План промышленного производства был подготовлен таким образом, что были отформованы три формы из суспензии AAC, содержащей каждый из трех типов SRM. Одна форма стандартной AAC была отформована в начале формования суспензии AAC, содержащей первый SRM. В конце формования суспензии AAC, содержащей последний SRM, и между каждыми тремя формами AAC, содержащими каждую из SRM. В общей сложности четыре формы стандартной суспензии AAC были отформованы с суспензией AAC, содержащей каждый из SRM.Таким образом, 275,1 кг отходов керамической плитки для стен, 27,6 кг шлака EAF и 192,6 кг шлака LF потребовались для трех форм для суспензии AAC, и в целом девять форм для AAC были отлиты в промышленном производстве. Чтобы приготовить форму для суспензии AAC, сначала в смесительный резервуар были добавлены кварцит, известняк и SRM, в который было добавлено соответствующее количество воды и все перемешано для получения песчаной суспензии на минеральной основе. Требуемое количество SRM подавалось в смесительный резервуар вручную, в то время как другая сырая мука подавалась в смесительный резервуар через единицу дозирования одновременно, поскольку не было дополнительной единицы дозировки для SRM.
Рециркулируемую суспензию ААС, полученную смешиванием воды и рециркулированных частиц ААС в отдельном резервуаре, добавляли в резервуар для смешивания и смешивали с суспензией песка в резервуаре для смешивания. Наконец, цемент, известь и пенообразователь были загружены в смесительный резервуар соответственно, и вся сырая мука была смешана с получением конечной суспензии ААС, которая должна быть отформована в металлические формы, используемые для промышленного производства продукта ААС.
3) Предварительное отверждение.
В процессе предварительного отверждения суспензия ААС, приготовленная в смесительном резервуаре, подвергалась определенным условиям, таким как температура 55 ° C и относительная влажность 80%. Предварительное отверждение суспензии ААС в металлических формах продолжалось до тех пор, пока суспензия ААС не была переведена в форму сырого кека, также называемого полупродуктом ААС. Суспензию алюминия, используемую в качестве пенообразователя, готовили путем смешивания порошка алюминия и воды в отдельном сосуде. Алюминиевый порошок прореагировал с известью (гидроксид кальция), что привело к образованию газообразного водорода, который пузырился из суспензии AAC, что привело к увеличению в 4 раза первоначального объема суспензии AAC.Во время процесса предварительного отверждения суспензия ААС была переведена в форму сырого кека, которую можно извлечь из формы и перемещать подъемным краном. Вынутый из формы зеленый пирог подавали в секцию резки для придания ему необходимого размера.
4) Раскрой.
Перед процессом резки поверхности зеленого коржа, за исключением нижней поверхности, были удалены из формы и зачищены стальной проволокой. Производственные отходы, полученные в процессе сглаживания, были доставлены в резервуар для вторичного использования AAC, чтобы повторно использовать их в промышленном производстве AAC.Объем зеленого жмыха уменьшился с 6 м 3 до 5,4 м 3 после процесса разглаживания. Зеленый пирог, содержащий каждый из SRM, удаленных из формы, был разрезан перпендикулярно и горизонтально соответственно путем перемещения нескольких стальных проволок режущего блока, чтобы получить блоки AAC размером 60 см X 25 см X 15 см, необходимые для демонстрационной площадки. .
5) Отверждение в автоклаве.
Автоклав — это большое оборудование с паровым обогревом и давлением, в котором автоклавные изделия из ячеистого бетона отверждаются при высокой температуре и высоком давлении после процесса резки.Отверждение в автоклаве — один из наиболее важных процессов производства ААС с точки зрения механических свойств конечного продукта. зеленые лепешки переносили в автоклавы и выдерживали при давлении пара 12 бар в течение 5 часов при температуре приблизительно 190 ° C. Связи в структуре тоберморита, которые образуются в процессе предварительного отверждения, укрепляются под действием высокой температуры и высокого давления, что обеспечивает повышение механической прочности продукта AAC.
Каждая форма составляет 5,4 м 3 и всего 16,2 м 3 Керамические отходы AAC, 16,2 м 3 Шлак EAF, использованный AAC, 16,2 м 3 LF шлак, используемый AAC, и 21,6 м 3 стандартных AAC продукты вулканизируются в автоклаве при давлении 12 бар в течение 5 часов с общим временем 9 часов для полного процесса от начала до конца.
6) Упаковка.
Продукты AAC, которые вышли из автоклава, были перенесены в упаковочную единицу.Блоки AAC, содержащие каждый из SRM, были помещены на деревянные поддоны для упаковки цветной пластиковой пленкой, на которую была наклеена этикетка, напечатанная для проекта.
7) Установка на месте.
Во время монтажа на месте были построены и сняты две внешние стены (360 единиц стеновых блоков AAC для 54 м стены 2 ) в реальном здании, расположенном в Кемальпаша / Измир. Для установки на месте всего 6 поддонов (2 поддона для каждого SRM, и каждый поддон содержит 60 единиц AAC) продуктов AAC, переданных на демонстрационную площадку.
Автоматическая линия для производства неавтоклавного бетона
Производство стеновых блоков из неавтоклавного газобетона с использованием прогрессивной виброударной технологии.
Впервые в мире производства газобетонных изделий на ОПК представлена технологическая схема производства, объединяющая лучшие отечественные (российские) разработки по формированию газобетонной смеси вибрацией и не имеющей аналогов среди зарубежных технологий для ленты. резка необработанного массива ножом на платформе нового поколения с быстропрограммируемыми настройками для получения строительных блоков практически любого заданного размера.
За счет использования вибрационной технологии данная технологическая схема производства обеспечивает: снижение расхода цемента до 150-200 кг / 1м3 готовой продукции (с использованием золы ТЭС и доменного шлака), снижение результирующей влажности бетона и шорткера срок доводки массивного изделия до его раскроя на блоки заданных размеров, что значительно снижает потребность в металлообрабатывающей технике Кроме того, внедрение вибрационной технологии и автоматизированного управления процессом дозирования бетонной смеси позволяет производить газированный продукт насыпью плотностью 350-700 кг / м3 для обеспечения высоких физико-технических характеристик готовой продукции отечественных и международных стандартов.В этих строительных блоках может быть достигнута резка комплекса РИФ-1 с последующей резкой массива на блоки заданных размеров с точностью + / -1 — 1,5 мм, что позволяет использовать кладочный клей при строительстве не более Толщина шва 3 мм. При этом номенклатура типов и размеров блоков увеличится с 27 до 340, что соответствует разнообразным требованиям заказчиков. Рациональное использование отечественного высоконадежного автоматизированного импортного оборудования позволяет существенно снизить трудоемкость производственных операций и сэкономить электроэнергию.
Краткая характеристика оборудования для производства автоклавного бетона
Максимальная производительность — до 200 м3 готовой продукции / сутки.
Изделия отделочные — стеновые и перегородочные блоки средней плотности Д500-Д700 с пределом прочности на сжатие В1,5-В3,5 (ГОСТ 21520-89).
Габариты блока в стандартной комплектации 198х295х598.
Возможна установка других размеров.
Объем массива — 1 м3.
Время заполнения одного массива — около 7 минут.
Время выпуска для массива — 3-4 часа.
Время выпуска нарезанного массива перед упаковкой — 12-16 часов.
Установленная мощность оборудования — 120кВт.
Расход воды — 60 т / сутки.
Обслуживающий персонал — 6 человек (без складской площадки).
Условия размещения — помещение магазинного типа при отсутствии атмосферных осадков и температуре не ниже + 50С.
Площадь цеха не менее 2500м2.
Высота в зоне заливки 7,5м.
Высота остальной части помещения не менее 3,5м.
Формовка, резка, транспортировка
Готовая смесь через нижнюю горловину смесителя загружается в металлическую форму. Форма массива состоит из двух частей: поддона и подвижного бордюра. Перед заливкой бетонной смесью подвижный бордюр собирают, смазывают специальным маслом или прокладывают промасленной бумагой и устанавливают на поддон. После виброударной обработки форма, заполненная бетонной смесью, транспортируется на зачистку.Его продолжительность зависит от многих факторов (структура бетона, марка цемента, тип заполняющего материала и т. Д.) И варьируется от 3 до 5 часов. Для обеспечения высокой прочности материала обязательно соблюдение температурного режима. В зависимости от используемых материалов перед резкой массива необходимо обеспечить температуру 40-500С на объекте (3-4 часа). При достижении необходимой прочности подвижный бордюр разбирается и поддон с массивом на нем перемещается к месту распила. Подвижный бордюр очищается, смазывается, устанавливается на свободный поддон и перемещается на место наполнения смесителя.
Массив приобрел пластичную прочность, улавливается специальным позиционирующим транспортером и перемещается на резку. Сначала на ленточнопильном станке вырезают верх массива (до 5 мм) и его низ. Затем на раскройном станке РИФ-1 производится поперечная и продольная резка на блоки. После этого разрезанный на блоки массив перемещают в автоклав. После автоклава вырезанный массив перемещается на разборку. Блоки укладываются на транспортные поддоны, обвязываются лентой и перемещаются на склад вилочными погрузчиками.Освободившийся поддон очищается, покрывается пластиковой или масляной бумагой и перемещается обратно на место наполнения.
Электромонтаж и установка электрооборудования
К моменту монтажа электрооборудования все части установки должны быть правильно установлены, кабели должны быть чистыми и готовыми. Все кабельные распределительные шкафы должны быть на своих местах. Монтаж электрооборудования возможен только при положительной температуре в цехе (выше + 50С).На время проведения работ с электрооборудованием Заказчик должен предоставить электрика, который будет обслуживать оборудование в будущем, а также косвенных работников.
Монтажные и пусконаладочные работы
Результатом ПНР считается «сухой» пробный пуск, ввод в эксплуатацию и обучение персонала Заказчика, изготовление опытной партии изделий насыпной плотностью 600 кг / м3. Получена плотность 500кг / м3. после определенного периода эксплуатации после достижения операторами соответствующих профессиональных навыков и оптимизации соотношения компонентов смеси Заказчиком на месте.Аналогично плотности 400 кг / м3, если качество используемого сырья позволяет. Перед вводом в эксплуатацию Заказчик обязан предоставить сырье, необходимое на производственной площадке. Перед прибытием монтажной и пусковой бригады важно убедиться, что все промышленные площадки готовы и соответствуют заданным габаритам. Необходимо предоставить воду и токопровод. Необходимо, чтобы все подъемные механизмы были в наличии. Все операции по подготовке площадки и установке вспомогательного оборудования следует прекратить.Процесс установки и запуска не включает в себя подготовку площадки, сборку и установку железных дорог или любые строительные работы. Детали, предоставленные Заказчиком, также не входят в установку. Персонал, который будет работать на оборудовании, должен находиться на месте в течение всего периода монтажных и пусконаладочных работ. Заказчик должен предоставить электриков, слесарей и косвенный персонал. Заказчик обеспечивает специалистов компании ОПК жильем, транспортировкой на / с объекта на весь период монтажных работ.Срок монтажных и пусконаладочных работ составляет один месяц.
Монтажные и пусконаладочные работы оговариваются отдельно в зависимости от назначения объекта и их стоимость составляет от 10 до 20% от общей стоимости оборудования.
< автоклавный газобетон
Airtec Большие бетонные стеновые блоки | Блоки из легкого газобетона
Стеновые блоки Airtec Large предназначены для обеспечения значительно улучшенной теплоизоляции и герметичности внутренних и внешних стен за счет уменьшения доли строительных швов в стене.Этот эффект даже больше, когда используется в сочетании с конструкцией с тонкими швами толщиной 2 мм, где доля раствора может быть уменьшена примерно на 87% по сравнению с обычными стенами с использованием швов из раствора 10 мм.
Их также можно использовать в качестве напольных покрытий, для получения дополнительной информации см. Большие блоки из пенобетона.
Эти бетонные стеновые блоки могут вдвое сократить количество блоков, необходимых для строительства стены, по сравнению с традиционными стеновыми блоками высотой 215 мм.Однако, несмотря на то, что они вдвое превышают высоту обычного блока 215 мм, их очень небольшой вес соответствует рекомендациям по ручному обращению и сводит к минимуму количество требуемых повторяющихся подъемов.
Вся продукция Airtec имеет сертификаты качества ISO 9001 и ISO 14001, а также имеет наивысший рейтинг BES 6001 Responsible Sourcing «Отлично».
Как и все другие блоки Airtec, эти легкие большие бетонные блоки предлагают самую лучшую категорию допусков по размерам «Тонкослойный раствор B» (TLMB), но идеально подходят для строительства швов из обычного 10-миллиметрового раствора.
Наши пеноблоки для стен доступны с отделкой «Стандартная» текстура, обеспечивающая гладкую, гладкую ячеистую текстуру, которая является подходящим фоном для нанесения штукатурок и штукатурок.
Как и весь пенобетон в Великобритании, поверхности строительных блоков могут содержать произвольное количество более крупных естественных пузырьков воздуха / ячеек на поверхности блока из-за неизбежных последствий производственного процесса. Эти большие ячейки совершенно нормальны, не являются дефектом и никоим образом не снижают производительность.Хотя блоки можно красить, мы не можем гарантировать, что поверхности не будут содержать некоторые из этих более крупных ячеек, и поэтому мы не рекомендуем использовать Airtec для окраски или облицовки.
- Внутренний и наружный лист пустотелых стен до 3 этажей.
- Внутренние перегородки.
- Заполнение перекрытия блочно-балочного типа.
- BRE Green Guide Стены класса A +.
- Внешний или внутренний лист стенок полости.
- Нагрузочные и ненагружаемые стены.
- Сторона или разделительные стены в части E.
- Прочные детали Стены для вечеринок.
- Фланговые стены к партийным стенам.
- Конструкция с тонкими стыками.
- Огнестойкие стены.
Лучший строительный материал, который нельзя купить
Это ссылка на статью Майкла Чусида, написанную более 20 лет назад.С тех пор несколько производителей AAC попытались вести бизнес в США, но большинство из них потерпели неудачу. Хотя это по-прежнему выдающийся строительный материал, я подозреваю, что появление на рынке новых строительных систем снижает вероятность того, что AAC станет основным продуктом в США. Но я бы хотел, чтобы меня доказали, что он неправ. Автоклавный ячеистый бетон (ACC) [теперь известный как автоклавный газобетон (AAC)] — это сборный пенобетон, который можно использовать для строительных блоков и панелей. ACC не производится и не доступен в США или Канаде, но является основным строительным материалом во всем мире.Поскольку североамериканские архитекторы и строители все больше конкурируют на мировом рынке, отечественная строительная отрасль должна учитывать такие строительные материалы, как ACC, для удовлетворения строительных потребностей этой страны.
Действительно, повышенное внимание в США уже сосредоточено на ACC: ведется планирование для заводов ACC во Флориде и Нью-Джерси. Несколько других предпринимателей и иностранных компаний активно изучают производство или импорт ACC в США. Крупная компания по производству материалов была близка к обязательству построить несколько производственных мощностей ACC в США.С. пока не изменил свои планы прошлой осенью. Университет Западной Вирджинии, который сформировал Исследовательский центр АКК, выступающий в качестве центра обмена информацией, в ноябре прошлого года привлек более 50 заинтересованных сторон на национальную конференцию по АКК. И несколько демонстрационных проектов были недавно построены в США. Еще одним основанием для ACC здесь стала оценка материала Советом американских строительных чиновников и HUD. Ожидаются утверждения других строительных норм.
Производство и свойства
Для производства ACC суспензия портландцемента, извести, кварцевого песка или летучей золы и воды смешивается с небольшим количеством порошкообразного алюминия и разливается в формы.Алюминий вступает в химическую реакцию, выделяя миллионы крошечных пузырьков водорода, которые расширяют бетон до пятикратного его первоначального объема. В течение нескольких часов бетонная пена затвердевает настолько, что ее можно удалить из формы. Затем его нарезают на блоки или плиты необходимого размера и отверждают паром в автоклаве. Поскольку он полностью гидратирован, ACC более стабилен по размерам, чем обычный бетон. Фактически, ACC превращается в горную породу, образуя микроскопические кристаллы минерала тоборморит, форму гидрата силиката кальция.
Что делает ACC привлекательным строительным материалом, так это его уникальная комбинация или свойства. 11 легкий, термически эффективный, огнестойкий, прочный и устойчивый к нагрузкам. ACC обычно производится с плотностью всего 35 фунтов на кубический фут, что меньше, чем у древесины. Его бесчисленные маленькие ячейки приводят к теплопроводности около 0,8 Btu / ft2 (hr) F / в толщине, что значительно ниже, чем у обычного бетона или кирпичной кладки; в мягком климате стены или настил ACC могут не потребовать дополнительной изоляции.ACC также негорючий; Перегородки толщиной всего три дюйма могут обеспечить потрясающую трехчасовую огнестойкость.
ACC относительно недороги в производстве и монтаже, а затраты на установку, по оценкам, ниже, чем у большинства сопоставимых строительных систем. Небольшой вес ACC не только снижает статические нагрузки на конструкцию, но и может повысить производительность, поскольку блоки или панели большего размера можно поднимать и размещать без тяжелого оборудования.

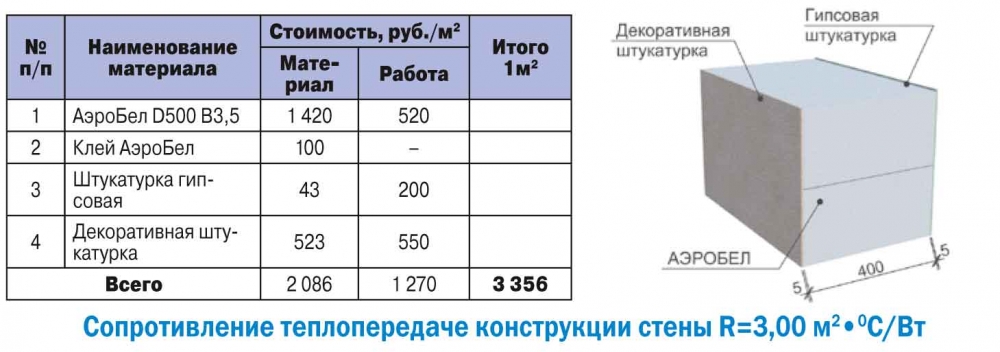
ACC изобилует конструктивными возможностями
Хотя материал может подвергаться воздействию погодных условий, он легко принимает различные виды отделки, включая краску, штукатурку, синтетическую штукатурку, керамическую плитку и тонкую кирпичную или каменную облицовку. Из-за того, что его можно легко разрезать, из материала также можно вылепить барельеф, орнамент, графику и другие архитектурные украшения.Лепку можно сделать либо на заводе. Японские фирмы, например, производят панели ACC с широким спектром геометрических рисунков поверхности. И легкость, с которой могут быть выполнены индивидуальные проекты, несомненно, улучшится, поскольку система CAD проектировщиков напрямую связана с производственной системой с числовым программным управлением, управляемой компьютером.
ACC имеет ту же способность, что и пенопласт, используемый в системах внешней изоляции и отделки (EIFS). Однако с ACC возможны более сложные формы, потому что его не нужно оборачивать тканевой сеткой. ACC также похож на EIFS в том, что оба они легкие, изолирующие и экономичные. Но ACC не представляет пожарной опасности пенопласта, имеет меньше отдельных компонентов для сборки и более долговечен. ACC — это «система структурной изоляции и отделки».
Рынок материалов
ACC производился еще в 1920-х годах, но после Второй мировой войны его использование быстро увеличилось. Сначала он поступил в продажу в Швеции и Германии, затем распространился по остальной Европе, а затем по всему миру.Сегодня более 200 заводов по крайней мере в 35 странах производят более восьми миллиардов кубических футов в год. Единственный завод в Северной Америке находится в Мехико, хотя завод работал в Монреале в 1970-х годах и произвел несколько сотен зданий. Здания, построенные из материалов заводов в Мехико и Монреале, хорошо себя зарекомендовали и доказали эффективность работы ACC в различных климатических условиях Северной Америки. В последнее время в нашей стране было построено несколько проектов АСС с использованием импортных материалов.

Но если ACC — такой выдающийся строительный материал, почему он еще не широко используется в Соединенных Штатах? Этот вопрос задавали уже столько десятилетий, что он породил атмосферу скептицизма, который может быть самым большим препятствием для ACC, которое здесь необходимо преодолеть.Ответ проливает свет на маркетинговые и экономические факторы, которые формируют палитру материалов, доступных современным архитекторам. Завод ACC, укомплектованный автоклавами и автоматическим оборудованием для разрезания буханки сырого бетона на блоки и панели, стоит около 10 000 000 долларов. Поскольку ACC является громоздким для транспортировки, у каждого завода есть только ограниченная рыночная площадь, с которой можно окупить первоначальные инвестиции. В этой стране ACC сталкивается не только с неизвестным рыночным спросом, но и с прочно укоренившейся конкуренцией со стороны бетонной кладки, металлических строительных панелей и кровельных настилов, сборного железобетона, EIFS, перегородок из гипсокартона и других материалов.Миссионерская работа, необходимая для того, чтобы добиться признания в отношении совершенно другого строительного материала, может занять годы. Эти факторы превышают риски, на которые большинство инвесторов готовы пойти.
Однако грядущие изменения в обществе и строительстве, похоже, благоприятствуют уникальным характеристикам ACC. Например, строительная отрасль сталкивается с растущей нехваткой квалифицированной рабочей силы, которая может отдать предпочтение сборным и простым в установке панелям ACC, а не кирпичной кладке, изготовленной на месте. На протяжении большей части истории нашей молодой страны дерево использовалось для разделения зданий с открытым пространством.Однако по мере развития нашей страны повышенная долговечность и огнестойкость ACC может стать более востребованной. И растущее желание соревноваться во всем мире, а также взаимное обогащение между американскими дизайнерами, практикующими за границей, и иностранными разработчиками, работающими в США, несомненно, продолжат стимулировать интерес к ACC.
Еще одна причина, по которой ACC привлекает все больше внимания, заключается в том, что это экологически чистый материал. АСС инертен и нетоксичен. Он производится из экологически чистого, недорогого и легкодоступного сырья.Фактически, используя летучую золу, отходы угольных электрогенераторов, ACC даже решает проблему удаления твердых отходов, с которой сталкиваются электроэнергетические компании. Производство требует относительно небольшого количества энергии и не выделяет загрязняющих веществ; лом можно даже измельчить и снова добавить в смесь. Поскольку он не горит, ACC не выделяет токсичных частиц сгорания и не способствует загрязнению воздуха в помещении. Напротив, ACC позволяет парам и концентрациям других газов диффундировать через свою ячеистую структуру и был одобрен европейскими природоохранными агентствами, включая Федеральную ассоциацию здоровых строительных материалов и Международный институт здорового строительства. Забота об окружающей среде, связанная с пенопластом и волокнистыми изоляционными материалами, — еще одна причина рассматривать ACC как альтернативу используемым в настоящее время материалам.
Как и в случае с любой незнакомой строительной техникой, проектировщикам и строителям придется научиться определять и устанавливать ACC. И хотя ACC — это проверенная строительная система, ее, возможно, придется модифицировать, чтобы приспособить ее к местным строительным практикам. Например, окна и проходы в стенах должны быть тщательно детализированы, чтобы избежать попадания воды в ячеистый бетон.Но другие зарубежные строительные технологии, такие как однослойная кровля и EIFS, были успешно интегрированы в отечественную строительную практику: ACC со временем найдет себе место и здесь. Архитекторам, работающим с зарубежными проектами, следует воспользоваться возможностью получить опыт работы с ACC. Это строительный материал т.к. что вы услышите больше и должно стать долгожданным дополнением к архитектурной палитре.