Прочность газобетон: Прочность газобетона, класс прочности газобетонных блоков
Прочность газобетона, класс прочности газобетонных блоков
Газобетон, относящийся к разряду ячеистых бетонов, считается одним из самых выгодных и экономичных строительных материалов. Он подходит для возведения внешних и несущих стен здания, закладки бетона, выстраивания перегородок, а армированные перемычки из газобетона востребованы во всех сферах строительства. Популярность этого типа материала обуславливается рядом преимуществ вроде долговечности, небольшого веса, легкости в монтаже, морозоустойчивости, огнеупорности и теплоизоляции. Газобетон не требует дополнительного ухода, а его стоимость располагает к приобретению вне зависимости от того, нужна покупка для частного или крупного строительства.
Одним из главных преимуществ материала является прочность газобетона, которая обуславливает его долговечность и износоустойчивость.
Прочность газобетона на сжатие
Ошибочное мнение о хрупкости изделий из газобетонного сырья возникает после ознакомления с его внешним видом и структурой.
Материал отлично сопротивляется процессу растяжения, а прочность газобетона на сжатие доказана большим числом экспериментов. Плотность материала на сжатие равна 35 кг/кв.м, что означает что он является идеальным вариантом для малоэтажного строительства.
Прочность газобетонных блоков обусловлена тем, что они имеют толстые стенки, по которым равномерно распределяется нагрузка в ходе строительства здания. Чтобы повысить долговечность здания, строители применяют горизонтальную кладку.
Для расчета методики создания качественного материала, который гарантирует строительство надежного здания, комфортного для проживания, существует определенная классификация, которой должны соответствовать производимые изделия. В ней учитывается и такой показатель как прочность. Класс прочности газобетона должен соответствовать требоаниям ГОСТ 10180, ГОСТ Р53231.
Показатели | Нормативные сопротивления ячеистого бетона сжатию Rbn, растяжению Rbtn и срезу Rshn; расчетные сопротивления для предельных состояний второй группы Rb,ser, Rbt,ser и Rsh,ser при классе бетона по прочности на сжатие | ||||||||||
Класс бетона по прочности на сжатие | В1 | В1,5 | В2,0 | В2,5 | В3,5 | В5 | В7,5 | В10 | В12,5 | В15 | В20 |
Сопротивлению осевому сжатию (призменная прочность) Rbnи Rb,ser | 0,95 9,69 | 1,40 14,3 | 1,90 19,4 | 2,4 24,5 | 3,3 33,7 | 4,60 46,9 | 6,9 70,4 | 9,0 91,8 | 10,5 107 | 11,5 117 | 16,8 168,3 |
Сопротивление бетонов растяжению Rbtn и Rbt, ser | 0,14 1,43 | 0,22 2,24 | 0,26 2,65 | 0,31 3,16 | 0,41 4,18 | 0,55 5,61 | 0,63 6,42 | 0,89 9,08 | 1,0 10,2 | 1,05 10,7 | 1,1 11,2 |
Сопротивление бетонов срезу Rshn, Rsh, ser |
0,2 2,06 | 0,32 3,26 | 0,38 3,82 | 0,46 4,56 | 0,6 6,03 | 0,81 8,08 | 0,93 9,26 | 1,31 13,09 | 1,47 14,7 | 1,54 15,44 | 1,6 16,2 |
Примечания 1.![]() 2. Величины нормативных сопротивлений ячеистых бетонов даны для состояния средней влажности ячеистого бетона 10% (по массе) |
От чего зависит прочность изделий?
Прочность газобетона для несущих стен зависит от нескольких факторов, в числе которых объемный вес, равномерность его структуры, а также от характеристик материалов, используемых в качестве сырья.
Прочность стен из газобетона может меняться в зависимости от высоты, а если блок обладает неравномерной структурой, следует ожидать разрушения периферийных слоев и ядра изделия. В случае с использованными в производстве материалами стоит говорить об их способности к поглощению влаги. Чем выше этот показатель, равно как и водоцементное отношение, тем ниже прочность изделия.
Выбирая материал для приобретения, помните, что различные марки газобетона обладают разными показателями прочности:
- D600 располагает повышенными показателями прочности и теплоизоляции.
Эта марка идеально подходит для кладки фасадов зданий.
- D500 выбирают при планировании возведения высотных домов и коттеджей.
- D400 показывает меньшую прочность, но актуален благодаря отличным теплоизоляционным качествам. Он подходит для строительства перегородок и улучшения теплоизоляции в доме.
Купить газобетонные блоки любого класса прочности можно на сайте компании УниверсалСнаб. Здесь вы найдете материалы высокого качества по выгодным ценам.
Газобетон: плотность vs прочность
Поскольку газобетон еще относительно новый продукт для отечественного рынка стройматериалов, часто возникает путаница в его свойствах. Сегодня мы покажем разницу между такими важными в строительстве качествами, как прочность и плотность автоклавного газобетона.
Плотность газобетона.
Плотность газобетонных блоков маркируется литерой D и имеет отношения к пористости материала. Напомним, что именно пористая структура делает газобетон наиболее предпочтительным, когда необходимо построить энергоэффективный дом без дополнительного утепления. Воздух, заполняющий застывшие в процессе изготовления пузырьки, является непревзойденным естественным теплоизолятором. Маркировка плотности газоблоков варьируется от D100 до D600. В гражданском строительстве применяют, в основном, газобетон плотностью от D100 до D500.
Чем выше количество пор в газобетоне, тем ниже его плотность, но и тем он теплее. Так, газоблоки с плотностью D300 позволяют построить значительно более теплый дом, чем D500. Поскольку тепло передается фрагментам блока по сплошной части, то у более пористого расстояние от комнат до улицы оказывается длиннее, и теплопередача затруднена. Более высокий показатель плотности говорит о том, что сплошных фрагментов больше, и расстояние от тепла к холоду короче.
Прочность газобетона.
Если говорить о прочности, то данный параметр обозначают литерой В, он характеризует устойчивость материала к несущим нагрузкам, а именно – прочность на сжатие. Выбирая для строительства газоблоки, необходимо учитывать, что далеко не все они способны выдерживать вес межэтажных перекрытий, верхних этажей. К тому же, в материале с более низкой прочностью трудно будет удержать крепёж навесных фасадов снаружи, радиаторов центрального отопления внутри и т.д.
Чем меньше прочность газобетонных блоков, тем менее высокие дома можно из них построить, тем меньше возможностей применения ЖБИ в качестве материала лестниц, балок, перекрытий. В таких случаях приходится применять пиломатериалы, которые куда менее долговечны.
Прочность маркируют от В1,5 до B3 с шагом 0,5.
Соотношение плотности и прочности.
Существует тесная взаимосвязь между плотностью и прочностью газоблоков. Количество пор в материале напрямую влияет на прочностные характеристики. Получается, что чем теплее дом из газобетона, тем более хрупкими окажутся его стены, можно ожидать появления трещин и крошки при попытке укрепить в них, например, дюбель и гвоздь. Стены из газобетона с более низкой плотностью (например, в промышленности и военной отрасли применяют газобетон D500, D600) будут и более устойчивыми на сжатие.
Можно ли добиться увеличения параметра «прочность» при сохранении низкой теплопроводности? Попытки разработки подобной технологии изготовления газобетона постоянно предпринимают производители. И на текущий момент уже есть определенный диапазон решений. В частности, значительно повышает прочность ячеистого бетона метод отвердения его в автоклавах. Вот почему сегодня трудно найти более дешёвый, лёгкий, тёплый и довольно прочный материал, чем автоклавный газобетон.
Расчеты газобетона на прочность | AEROC
Прочностные расчеты кладки из стеновых блоков должны выполняться в соответствии с действующими нормативными документами, в частности ДБН В.2.6-162:2010 «Каменные и армокаменные конструкции».
Газобетон AEROC предназначен для кладки как несущих, так и ненесущих стен и перегородок. Высокая точность размеров позволяет вести кладку на тонкослойных клеевых смесях со средней толщиной шва 2±1 мм.
Использование мелкозернистого клея не только повышает теплотехническую однородность кладки и увеличивает прочностные характеристики конструкций на 30% (в действующих нормах проектирования увеличение прочности при кладке на клею не отражено), но и ведет к общему снижению затрат на строительство.
Прочностные расчеты кладки из стеновых блоков должны выполняться в соответствии с действующими нормативными документами, в частности ДБН В.2.6-162:2010 «Каменные и армокаменные конструкции».
Расчетные характеристики бетона блоков
Марка по средней плотности, класс по прочности на сжатие | Расчетные сопротивления для предельных состояний I группы | Расчетные сопротивления для предельных состояний II группы | Начальный модуль упругости при сжатии eb, МПа | ||||
сжатия осевое rb, МПа | сопротивление растяжения rbt, МПа | сопротивление срезу rsh, МПа | сжатия осевое rb, МПа | сопротивление растяжения rbt, МПа | сопротивление среза rsh, МПа | ||
D500 C2,5 | 1,6 | 0,14 | 0,20 | 2,4 | 0,31 | 0,46 | 1400 |
D400 C2,5 | 1,6 | 0,14 | 0,20 | 2,4 | 0,31 | 0,46 | 1000 |
D300 C2,0 | 1,3 | 0,12 | 0,17 | 1,9 | 0,26 | 0,38 | 850 |
Кладка из блоков AEROC должна вестись на клею или строительном растворе марки не ниже М50.
Расчетные сопротивления кладки из блоков, МПа
Марка блоков по средней плотности | Прочность на сжатие R, мпа | Осевое растяжение, rt | Растяжение при перегибе, rtb | Срез по перевязанном пересечению, rsq | ||
по неперевязанному пересечению | по перевязанном пересечению | по неперевязанному пересечению | по перевязанном пересечению | |||
D500 C2,5 | 1,2 | 0,08 | 0,16 | 0,12 | 0,25 | 0,16 |
D400 C2,5 | 1,2 | |||||
D300 C2,0 | 0,8 |
Модуль упругости (начальный модуль деформаций) кладки из блоков Е0, МПа:
- Для блоков D400 і D500 В2,5; Е0 = 1867.
- Для блоков D300 В2,0; Е0 = 1350.
Расчетный модуль деформации кладки должен приниматься равным:
- При расчете конструкций по прочности для определения усилий в кладке Е = 0,5 · Е0;
- При определении кратковременных деформаций кладки от продольных и поперечных сил Е = 0,8/Е0.
Относительная деформация кладки из блоков с учетом ползучести ε = 3,5 · σ / Е0, де
σ — напряжение, при котором определяется ε.
Ненесущие конструкции
Основное количество газобетона, выпускаемого заводом «Аэрок», используется в многоэтажном домостроении при заполнении наружных ограждений каркасных зданий. В этом варианте газобетонные стены делаются с поэтажным опиранием на перекрытия. Несущей способности блоков классов по прочности С2,0 и С2,5 для восприятия вертикальных нагрузок оказывается более чем достаточно (при правильном устройстве деформационного шва между кладкой и вышележащим перекрытием).
Однако такие стены, особенно при большой этажности зданий, должны проверяться на устойчивость к горизонтальным нагрузкам (ветровой напор и отсос, кратковременные нагрузки от опирания на стены находящихся в помещении людей). В общем случае, газобетонные стены должны закрепляться к поперечным несущим стенам или колоннам в двух уровнях по высоте этажа.
Прочность газобетона
К основным преимуществам газобетона следует отнести: хорошую морозостойкость и небольшую теплопроводность, а также достаточную прочность на изгиб и сжатие. Важной характеристикой рассматриваемого материала считается небольшая усадка.
Прочность газобетона к сжимающим усилиям зависит от его марки и может колебаться от 12 до 140 кгс/см2, блоки с плотностью 500 кг/м3 выдерживают нагрузку в 2,5 МПа, газобетон марки Д 600 – 3,2 МПа. Значение на этот показатель оказывает объёмный вес, а также качество и количество вяжущего вещества. Также прочность будет зависеть от равномерности структуры изделия. Если пузырьки в материале расположены неравномерно и имеют разные диаметры, то разрушения газоблока может происходить в два этапа: сначала разрушаются периферийные слои, а затем ядро, имеющее большую прочность. В подобных случаях проблематично определить прочность испытуемого материала, но она будет гораздо меньшей, чем у материала с равномерной структурой.
Следует заметить, что улучшенные прочностные показатели имеет газобетон автоклавного твердения. Такие материалы изготовляют в больших объёмных формах, что будет способствовать более равномерному распределению пор. Большое влияние на рассматриваемый показатель оказывает расход цемента. При увеличении веса изделий улучшаются прочностные показатели и увеличивается теплопроводность. Так, вес теплоизоляционных материалов может колебаться от 300 до 500 кг/м3, а плотность конструкционных изделий, применяемых для кладки несущих стен, начинается с 600 кг/м3.
А теперь рассмотрим зависимость прочности газобетона от типа твердения материала. Газобетон неавтоклавного твердения застывает и приобретает основные характеристики в естественных условиях, причём максимальная его прочность достигается через три месяца от даты его изготовления, 35% через неделю и половина прочности примерно через месяц.
Газобетон автоклавного типа твердения имеет гораздо лучшие прочностные показатели, причём получить подобную характеристику можно со сравнительно небольшим расходом вяжущего вещества. Объяснить такое явление достаточно просто и это связано с тем, что порошкообразные кремнеземистые добавки вступают в реакцию с известью и компонентами цемента, в результате чего образуется новое вещество со свойствами вяжущего.
Что касается прочности газобетонного блока на изгиб, то она находится в пределах от 25% до 33% такого же показателя материала, но на сжатие.
Ответы на вопросы | gazobeton.org
ВОПРОСЫ О ПРОИЗВОДСТВЕ И ФИЗИКО-МЕХАНИЧЕСКИХ ХАРАКТЕРИСТИКАХ ПРОДУКЦИИ
В автоклаве происходит усадка? Некоторые производители режут после автоклавирования и этим достигают точности?
При автоклавной обработке газобетона в макропористой структуре материала практически не происходит объемных изменений. Все современные технологии производства автоклавного газобетона используют резательную технологию при полупластическом состоянии газобетона, до автоклавной обработки. Возможно, речь идет об отделении «доборных» элементов, когда из изделий стандартных типоразмеров вырезаются изделия особой формы, нарезаются дополнительные элементы или, в отдельных случаях, дополнительно шлифуются грани.
За счет чего достигается разница в классах В2, В2,5 и т.д.?
Класс по прочности зависит от плотности материала. Качество сырьевых материалов, рецептура и отлаженная технология также оказывают влияние.
За счет чего достигается прочность, если в газобетоне мало цемента?
В отличии от неавтоклавных ячеистых бетонов, где прочность материалу обеспечивает затвердевший поризованный цементно-песчаный раствор, в автоклавных ячеистых бетонах, прочность достигается при автоклавной обработке (при t до 195°С и давлении 12 атм.), при которой образуются новые минералы – различные гидросиликаты кальция, которые придают межпоровым перегородкам, а, следовательно, и самому материалу высокую прочность.
Зачем нужен гипс в технологии автоклавного газобетона?
В технологии автоклавного газобетона может использоваться (необязательно) небольшое количество гипсового камня в качестве добавки – регулятора газообразования и вспучивания газобетонного массива.
Зачем для внутренних ненесущих перегородок производятся боки двух плотностей, а не одна Д400?
С увеличением плотности повышается звукоизолирующая способность, прочность, однако менее плотные изделия обеспечивают меньшую массу перегородок.
Какова роль цемента при производстве автоклавного газобетона?
Современная технология автоклавного ячеистого бетона подразумевает применение смешанного вяжущего (цемент и известь негашеная), в различных пропорциях, подбираемых исходя из свойств местных сырьевых материалов. Цемент придает материалу первоначальную структурную прочность, необходимую для разопалубки и резки сырца на изделия. Химические соединения, входящие в состав цемента, такие как оксид кальция и алюминия участвуют в образовании новых минералов, низкоосновных гидросиликатов в процессе автоклавной обработки.
Какой песок используется в технологии?
В качестве кремнеземистого компонента используется песок речной и карьерный с минимальным содержанием глинистых примесей.
Правда ли, что в автоклаве не происходит объемных изменений в материале?
При автоклавной обработке в межпоровых перегородках материала проходит химическая реакция превращения компонентов в низкоосновные гидросиликаты кальция, но именно объемных превращений, отражающихся на макроструктуре и геометрических параметрах изделий – действительно не происходит.
Можно ли сразу после автоклава использовать газобетон для стройки?
Да, можно. Автоклавный газобетон после автоклавной обработки приобретает свои прочностные показатели, упаковывается и отправляется на склад готовой продукции. Соответственно, он может быть использован сразу, без дополнительного выдерживания.
Есть ли материалы, у которых показатель теплопроводность/прочность лучше?
Есть строительные материалы с более низкой теплопроводностью, есть с более высокой прочностью, но если говорить о конструкционно-теплоизоляционных стеновых материалах, то в этом отношении сочетание низкой теплопроводности с достаточно высокой прочностью при низкой цене, делают автоклавный газобетон в своем роде уникальным стеновым материалом.
Что придает газобетону белый цвет?
В процессе автоклавной обработки состав материала межпоровых перегородок определяется образовывающимися различными гидросиликатами кальция (минералами), которые и определяют цвет автоклавного газобетона.
Что могло бы убедить застройщика в том, что газобетон прочный?
Протоколы испытаний и сертификаты продукции. Документация на продукцию ООО «ЮДК» есть в разделе «Сертификаты».
Что мелется в шаровой мельнице?
В шаровой мельнице мелется песок с водой, в результате получается песчаный шлам, в котором песок (кремнеземистый компонент) в результате помола имеет удельную поверхность, необходимую для производства автоклавного газобетона низких плотностей.
Что такое В2, В2,5 и т.д.?
Так обозначается класс бетона по прочности на сжатие. В ДСТУ Б В.2.7-137:2008 «Блоки з ніздрюватого бетону стінові дрібні» приводится таблица соответствия класса бетона по прочности на сжатие, марки бетона по прочности на сжатие (М) и соответствующее им значение прочности бетона на сжатие в МПа (см. табл. 3 издания).
Чем принципиально отличается пено- от газобетона?
Принципиально: способом порообразования. В первом случае в бетонную смесь вводится пенообразователь, и ячеистая структура образовывается в результате перемешивания этой смеси, во втором случае – смесь вспучивается в форме в результате взаимодействия газообразователя с гидратами окиси кальция. Так же пенобетон производится преимущественно неавтоклавного твердения, тогда как газобетон преобладает автоклавный. Способ твердения оказывает влияние на физико-механические характеристики ячеистых бетонов.
ВОПРОСЫ О ПРИМЕНЕНИИ АВТОКЛАВНОГО ГАЗОБЕТОНА В СТРОИТЕЛЬСТВЕ
Всегда ли нужно устраивать армопоясы?
Для высотного каркасного строительства, когда стена из газобетона является самонесущей в рамках одного этажа, как правило, в этом не нуждается. Для малоэтажного коттеджного строительства количество и расположение армопоясов определяется проектно-конструкторским расчетом.
Как крепить внутренние перегородки к несущей стене?
Как и при традиционной кладке (перевязкой или встык с креплением гибкими анкерами). Зазор между перегородкой и перекрытием заполняется монтажной пеной.
Как понимать выражение, связанное с газобетоном, «не нуждается в отделке»?
Для защиты стены от атмосферных воздействий и как наиболее экономичный и эстетичный способ отделки для газобетона – является штукатурка. В общем случае, при защите стен кровлей от прямого увлажнения, дом может нормально эксплуатироваться без отделки.
Какая минимальная площадь опирания перемычек?
Ширина перемычек равна ширине стены, длина опирания не менее 150 мм с каждой стороны (см. «Руководство по проектированию и возведению зданий с использованием изделий торговой марки UDK GAZBETON»)
Какие шпаклевки надо использовать при наружной и внутренней отделке?
Для отделки газобетонных стен применяются паропроницаемые штукатурки снаружи, изнутри обычные шпаклевки для внутренних работ.
Какой максимальный пролет выдержит U-блок с арматурой 12 в 2 ряда?
U-образные (лотковые) блоки выполняют функцию несъемной опалубки при изготовлении армированной перемычке из обычного тяжелого бетона, а также повышает тепловую однородность ограждающей конструкции.
При проектировании перемычек из U-образных блоков следует исходить из общих правил проектирования железобетонных конструкций. Рекомендуемый диаметр продольных стержней 8-14 мм, класс бетона В15-В20. Отдельно изготовленными перемычками из U-образных блоков можно перекрывать пролеты до 2,5 м, а в случае изготовления сборно-монолитных перемычек (с установкой временных опор на отметке верха проема), максимальный пролет может достигать 4 м. Сечение арматуры, ее количество, тип арматурного каркаса, класс бетона назначают из расчета несущей способности перемычки и величины перекрываемого пролета.
Какой этажности можно строить здания из газобетона?
В высотном каркасном строительстве, где в качестве стенового материала применяются блоки из газобетона – сколько угодно, более того, низкая масса таких стен снижает нагрузку на каркас и фундамент здания. В малоэтажно строительстве, при существующих на рынке строительных материалах и изделиях есть практика строительства домов со стенами из автоклавного газобетона до 3-х этажей. В Европе, при использовании армированных плит перекрытия из автоклавного газобетона – до 5 этажей.
Какую можно применять наружную отделку, какую нет?
Отделочные покрытия для стен из автоклавного газобетона должны обладать высокой адгезией к минеральным поверхностям, а также обладать высоким коэффициентом паропроницаемости, не ниже чем у автоклавного газобетона.
Куда вкладывается минвата в армопояс?
Вкладыш из минеральной ваты вкладывается внутри U-блока, к наружной стенке.
Насколько отличается армопояс из U-блоков и пояс, сделанный путем штробления блоков?
Перемычки и армопояс выполненные из U-блоков позволяют получить необходимую несущую способность, при штроблении таких показателей достичь сложнее.
Проклеивать или не проклеивать стыки (паз-гребень)? А если заказчик настаивает?
Блоки с пазо-гребневой системой предназначены, прежде всего, для удобного и точного монтажа блоков при кладке. Их допускается монтировать без нанесения клеевого раствора на торцевые грани, и не означает, что это запрещено.
Можно ли на газобетонную стену навесить бойлер?
Современные анкерные крепежи позволяют выдерживать значительные нагрузки. Так, испытания, проведенные компанией Hilti показали, что к стенам из блоков UDK GAZBETON можно крепить любую навесную бытовую технику и мебель. Для правильного подбора анкерных крепежей рекомендуется пользоваться таблицами компаний-производителей.
Можно ли монтировать в газобетоне тяжелые двери?
Можно, как и в любые стены с использованием дополнительного металлического каркаса.
Можно ли строить из Д400 В2,0 несущие стены?
Хотя автоклавный газобетон с маркой по плотности D400 относится к классу теплоизоляционных материалов, современные технологии позволяют получать его с классом прочности В2,0, что уже позволяет отнести к конструкционно-теплоизоляционным материалам. Поэтому такой автоклавный газобетон можно использовать в различных несущих конструкциях, естественно после соответствующего конструкторского расчета.
Нужно ли армировать каждые 3 ряда кладки (ведь идет сильное удорожание)?
Схема армирования применяется по расчетам и решениям конструктора. Нет необходимости армирования каждых 3 рядов.
Нужно ли усиливать пол при утеплении старых домов газобетоном?
По всей видимости, речь идет об усилении фундамента. Нельзя однозначно ответить на этот вопрос, т.к. перед реконструкцией (тепловой санацией) здание должно быть обследовано и проведен расчет на запас несущей способности фундамента.
Нужен ли вент зазор между Слим-блоком и шлакоблоком при утеплении газобетоном?
При наружном утеплении между несущей стеной и слоем газобетонного утеплителя воздушный зазор не требуется.
Не вытянет ли газобетон влагу из раствора (1ряд кладки)?
Влаги в цементном растворе достаточно для его твердения.
Не прокорродируют ли гвозди, арматура и т.д. из-за сильной сульфидной реакции, которую вызывает гипс?
Любые анкерные крепежи, которые монтируются в газобетон, должны иметь антикоррозионное покрытие. Однако это не связано с гипсом.
Не покрывается ли газобетон пленкой, от которой со временем отслаивается штукатурка?
Эта проблема хорошо известна строителям, которые имеют практику работы с пенобетонными блоками, которые в большинстве случаев произведены по кассетной технологии. Антиадгезионная смазка, которая наносится на борта и перегородки форм остается и на гранях блоков.
Технология производства блоков из автоклавного газобетона – резательная, все грани, контактировавшие с бортоснасткой, обрезаются. Поэтому ни уплотненного слоя, ни антиадгезионной масляной пленки на гранях блоков нет.
Необходимо ли грунтование перед шпаклевкой?
Грунтование не обязательно, если стена сухая, перед шпаклеванием необходимо увлажнить поверхность (пользоваться рекомендациями производителей шпаклевок).
Необходимо ли штукатурить внутренние перегородки из газобетона?
Достаточно шпаклевания при ровной поверхности перегородки.
Есть ли ограничения по времени кладки по набору прочности клея или можно выложить сразу весь дом до кровли?
При кладке на клею таких ограничений нет.
Газобетон Стоунлайт, прочность газобетонных блоков
ЧТО ТАКОЕ КЛАСС ПРОЧНОСТИ ГАЗОБЕТОНА?
Очень многие путают плотность газобетона и его прочность. На самом деле это две абсолютно разных характеристики. Для производства газобетона завод сначала готовит специальную газобетонную смесь, похожую на кашицу, которая потом вспенивается и застывает, насыщаясь кислородом.
Логично предположить, что для приготовления некоторого объема жидкой смеси необходимо смешать некоторое количество килограмм составляющих, таких как песок, цемент, известь и т.д. Так вот плотность газобетона это по сути ответ на вопрос: сколько килограмм газобетонной смеси пошло на изготовление одного куба?
В зависимости от степени насыщения готового блока воздухом будут меняться физические размеры пузырьков воздуха. Если размеры пузырьков большие, то их в готовом изделии будет меньше, а если пузырьки маленькие, то в один куб готового газоблока их можно вместить больше.
Каждый воздушный пузырек имеет твердую оболочку. И такая характеристика, как класс прочности характеризует непосредственно прочность твердой оболочки воздушного пузырька.
Таким образом плотность и класс прочности это две абсолютно-разные величины, однако они очень тесно между собой связаны. Чтобы более понятно объяснить вам этот принципиальный вопрос мы написали специальную статью: Отличие газобетона плотностью Д400 от Д500, прочитав которую вы сразу все поймете.
Так как эта страница посвящена прочностным характеристикам газобетонных блоков определенного производителя, то мы предположим, что вы прочитали вышеуказанную статью и понимаете суть понятия «прочность».
ПРОЧНОСТЬ ГАЗОБЕТОНА СТОУНЛАЙТ
Газобетонные блоки СТОУНЛАЙТ характеризуются великолепными показателями по прочности на сжатие. Достигается это не только высоким качеством используемого для производства
сырья, но и очень высокой технологической дисциплиной на предприятии. Каждая партия блоков проходит самые тщательные испытания в специальной заводской лаборатории.
Блоки с плотностью Д400 и Д500 выполняются с классом прочности на сжатие минимум B2 т.е. 2,9 МПа (29кгс/см2). Основная же масса блоков выпускается с классом прочности В2,5. Следует отметить, что завод Стоунлайт является первым в Украине, который начал выпуск блоков плотности Д400 с классом прочности В2,5.
О чем это говорит?
Если вы возьмете блок размером 200х300х600мм, при этом 200мм будет его высотой, а площадь которая несет нагрузку будет ограничена размером 300 х 600 мм (30смХ60см), то нагрузку которую будет способен выдержать 1 такой блок можно рассчитать следующим образом: (30см х 60см)*29 кгс/см2= 52.200кг Много это или мало? Для сравнения блок с верхней площадью 40см х 60см несет нагрузку около 90 тонн при классе материала B2,5 (36кгс/см2)!
90 ТОНН — ЭТО ВЗЛЕТНАЯ МАССА САМОЛЕТА ТУ-154!
Если говорить о рассчетах конструкций — в любом случае, нагрузки и их рассчетные значения должен оценивать проектировщик руководствуясь значениями полученными при проведении испытаний профильными НИИ. Продукция марки СТОУНЛАЙТ тм сертифицирована, и мы с радостью предоставим Вам все необходимые данные для проведения проектных изысканий.
МОЖНО ЛИ НА ГАЗОБЛОК СТОУНЛАЙТ ЛОЖИТЬ ПЛИТЫ ПЕРЕКРЫТИЯ?
Да, плиты перекрытия на газобетон Стоунлайт ложить можно. Но делать это следует очень аккуратно.
Несмотря на то, что газобетон это невероятно прочный материал — суть его прочности заключается в распределении нагрузки. Возьмем пример обычного веника и человеческую руку. Уприте торец веника себе в ладонь сильно-сильно. Вы навряд ли почуствуете боль. А вот если вы выдерните из веника один пруток и упрете его себе в руку с силой? Вы можете получить сильную рану. Таким образом нагрузка бывает точечной (один прут) и распределенной (весь веник целиком).
Если предположить, что ваши строители уложат плиту идеально ровно — то блок поврежден не будет. Однако, на практике, кран не может поднять плиту таким образом, чтобы она была идеально параллельна газобетонной кладке. Обязательно какой то угол плиты будет опущен вниз, и в момент непосредственной укладки плиты этот злосчастный угол превратится в невероятную точечную нагрузку, которая имеет все шансы повредить вам стену.
Поэтому мы рекомендуем ложить плиты на твердый материал, который не боится точечных нагрузок. Таким материалом является либо кирпичная либо бетонная стяжка. Недостатком этих твердых оснований является их высокая теплопроводность, поэтому если толщину стяжки сделать равной толщине кладки она обязательно превратится в невероятный мостик холода.
Для исключения мостика холода, который может образоваться мы не советуем заливать бетон по всей толщине стены, а выполнить свою конструкцию по любому из ниже приведенных примеров на картинках:
Вариант А
Подготовка бетонной стяжки под плиту перекрытия. На рисунке виден метод утепления стяжки непосредственно газобетоном. Сама плита впоследствии также снаружи закрывается газобетонными блоками и конструкция находится как бы в теплоизоляционном дышащем коконе.
Вариант Б
Тут представлен вариант утепления конструкции плиты перекрытия (или монолитного перекрытия) газобетоном в комплексе с экструдированным пенополистиролом.
Вариант В
Тут представлена схема укладки плит на бетонную стяжку и схема утепления конструкции базальтовой минеральной ватой. Следует отметить, что мы рекомендуем использовать именно такую конструкцию. Для заливки бетонной стяжки были использованы специальные лотковые блоки Стоунлайт.
ПРОПЛАТИТЕ ГАЗОБЕТОН СТОУНЛАЙТ СЕГОДНЯ!
И МЫ ЗАФИКСИРУЕМ ВАМ ЦЕНУ НА ПОЛГОДА!
АКЦИОННАЯ ЦЕНА ОТ 565грн/куб до 10 ФЕВРАЛЯ 2014!
ЗВОНИТЕ 067-549-71-66
Газобетон Стоунлайт, цена на газоблок Стоунлайт, купить газоблок Стоунлайт в Киеве —
средняя оценка 4. 5 из
5
.
Всего
151 голос.
Что такое плотность газобетона и на что она влияет? – ЖБИ России
При выборе и покупке газобетонных блоков к нам часто обращаются с вопросами, касающимися плотности материала и её связи с прочностными и теплотехническими характеристиками. Чтобы разобраться и дать аргументированный ответ, предлагаем рассмотреть структуру блоков и вспомнить физику.
Что такое газобетон?
Автоклавный газобетон, по сути, синтезированный камень, полученный в результате химической реакции, возникающей при взаимодействии газообразующего агента и остальных компонентов. Вследствие активного газообразования исходный объем смеси увеличивается в несколько раз, а в её структуре образуются мелкодисперсные полости. После её схватывания и отвердения получаются газобетонные блоки полостями-порами, имеющими твердую оболочку и наполненными воздухом, имеющим низкий коэффициент теплопроводности.
Теплопроводность газобетона
Плотность материала показывает, какая масса вещества содержится в занимаемом им объеме, и зависит от макроструктуры — чем меньше пустотность (объем ячеек), тем ниже её значение. Теплопроводность измеряется в количестве теплоты, проходящей через образец газобетона в единицу времени.
Показатели плотности и теплопроводности прямо пропорциональны друг другу. Материал с мелкопористой структурой содержит множество ячеек с небольшим объемом и количеством воздуха, поэтому пропускает больше тепла. Соответственно, газобетон D500 c плотностью 500 кг/м3 имеет теплопроводность выше, чем D400 с параметрами 400 кг/м3.
Прочность газобетона
Как и в случае с теплопроводностью, значения плотности и прочности находятся в прямой зависимости друг от друга. Объяснение лежит в буквальном смысле на поверхности.
Из курса физики, прочность — способность сопротивляться разрушению под внешним воздействием, предел которой определяется отношением величины приложенной силы к площади поперечного сечения. Следовательно, показатели плотности при её вычислении не учитываются.
Почему же тогда прочность газобетона D500 выше, чем D400? Причина опять в макроструктуре — чем меньше пористость материала и объем ячеек, тем выше плотность, больше поверхность контакта, сила сцепления частиц и сопротивление ударному разрушению.
Смотрите информацию о продукции в каталоге газобетонных блоков.
% PDF-1.5 % 1 0 obj > endobj 2 0 obj > endobj 3 0 obj > endobj 4 0 obj > endobj 6 0 obj > / XObject> / ProcSet [/ PDF / Text / ImageB / ImageC] >>>> endobj 7 0 объект > endobj 8 0 объект [0 0 0 0 0 0 0 0 0 0 0 0 0 0 0 0 0 0 0 0 0 0 0 0 0 0 0 0 0 0 600 600 270 328 339 769 541 823 836 175 394 394 500 833 270 330 270 278541 541 541 541 541 541 541 541 541 299 299 833 833 833 383 986 760 657 720 766 584 553 769 806 354 354 715 571 903 796 803 803 701 546 695787 760 1030 713 659 579 394 278 394 1000 500 500 459 513 458519 457 306 451 560 274 269 546 267 815 560 516 519 513 374 382 325 560 484 700 492461383 500 500 500 833 600 541 600 230 541462 1000 500 500 500 1229 546 308 1037 600 579 600 600 230 230 462462 5
1000500 822 382 308 810 600 383 659 541 328 541 541 541 659 500 500 500 822 344 473 833 330 822 500 329 833 357 357 500 578 500 270 500 357 387 473848 848 849 383760 760 760 760 760 760 934 720 584584584 354 354 354 354 766 796 803 803 803 803 803 833 803 787 787 787 787 659 603 539 459 459 459 459 459 703 458 457 457 457 457 274 274 274 274 516 560 516 516 516 516 516 516 560 560 560 560 461 519 461] endobj 9 0 объект > endobj 10 0 obj > endobj 11 0 объект [0 0 0 0 0 0 0 0 0 0 0 0 0 0 0 0 0 0 0 0 0 0 0 0 0 0 0 0 0 0 600 600 270 368 339 769 541 778 810 175 382 382 500 833 271 329 271 278 541 541 541 541 541 541 541 541 541 282 282 833 833 833 412 986 713 678 701 752625 579725 793 348 431 743 602917774 799 623 799 660 532 671 819 694 995738 655 609 382 278 382 1000 500 500 491 405 491410292461493273248 456 255 765 521468 488 468 359 356 308 528 498 757 442470 391 500 500 500 833 600 541 600 271 541463 1000 500 500 500 1150 532 273 1044 600 609 600 600 271271463463 590 500 1000 500 822 356 273 719 600 391 655 541 368 541 541 541 541 500 500 500 822 400 428 833 329 822 500 329 833 357 357 500 578 500 271 500 357 361428 848 848 849 412 713 713 713 713 713 713 986 701625625625625348 348 348 348 762 774 799 799 799 799 799 833 799 819 819 819 819 655 637 484 491491491491491686 405410 410 410 410 273 273 273 27348 521 468 468 468 468 468 468 528 528 528 528 470 472 470] endobj 12 0 объект > endobj 13 0 объект > endobj 14 0 объект [0 0 0 0 0 0 0 0 0 0 0 0 0 0 0 0 0 0 0 0 0 0 0 0 0 0 0 0 0 0 1000 1000 342 402 587 867 711 1272 862 332 543 543 711 867 361 480 361 689 711 711 711 711 711 711 711 711 711 711 402 402 867 867 867 617 964 776 762 724 830 683 650 811 837 546 555 771 637 948 847 850 733 850 782710 682812 764 1128 764 737 6925453 689 543 867 711 711 668 699 588 699 664 422 699 712 342 403 671 342 1058 712 687 699 699 497 593 456 712 650 979 669 651 597 711 543 711 867 1000 711 1000 332 711 587 1049 711 711 711 1777 710 543 1135 1000 692 1000 1000 332 332 587 587 711 711 1000 711 964 593543 1068 1000 597 737 342 40 2711 711 711 711 543 711 711 964 598850 867 480 964 711 587 867 598 711 721 711 361 711 598 598 850 1182 1182 1182 617 776 776 776 776 776 1094 724 683 683 683 683546546546546830 847850 850850850 867850 812812812812 737 735 713 668 668 668 668 668 668 1018 588 664 664 664 342 342 342 342 67979 712 687 687 687 687 687 867 687 712 712 712 712 651 699 651] endobj 15 0 объект > endobj 16 0 объект > endobj 17 0 объект [0 0 0 0 0 0 0 0 0 0 0 0 0 0 0 0 0 0 0 0 0 0 0 0 0 0 0 0 0 0 750 750 278 278 355 556 556 889 667 191 333 333 389 584 278 333 278 278 556 556 556 556 556 556 556 556 556 556 278 278 58458458456 1015 667 667 722 722 667 611 778722 278 500 667556833 722778 667778722 667 611 722 667 944 667 667 611 278 278 278 469 556 333 500 556 556 278 556 556 222 222 500 222 833 556 556 556 556 333 500 278 556 500 722 500 500 500 334 260 334 584 750 556 750 222 556 333 1000 556 556 333 1000 667 333 1000 750 611 750 750 222222 233 333 350 556 1000 333 1000 500 333944750500 667 278 333 556 556 556 556 260 556 333 737 370 556 584 333 737 552 400 549 333 333 333 576 537 278 333 333 365 556834 834 834 611 667 667 667 667 667 667 1000 722 667 667 667 667 278 278 278 278 722 722 778 778 778 778 778 584 778 722 722 722 722 667 667 611 556 556 556 556 556 556 889 500 556 556 556 556 278 278 278 278 556 556 556 556 556 556 556 549 556 556 556 556 500 556 500] endobj 18 0 объект > endobj 19 0 объект > endobj 20 0 объект [0 0 0 0 0 0 0 0 0 0 0 0 0 0 0 0 0 0 0 0 0 0 0 0 0 0 0 0 0 0 1000 1000 342 402 587 867 711 1272 862 332 543 543 711 867 361 480 361 689 711 711 711 711 711 711 711 711 711 711 402 402 867 867 867 617 964 776 762 724 830 683 650 811 837 546 555 771 637 948 847 850 733 850 782710 682812 764 1128 764 737 6925453 689 543 867 711 711 668 699 588 699 664 422 699 712 342 403 671 342 1058 712 686 699 699 497 593 456 712 649 979 669 651 597 711 543 711 867 1000 711 1000 332 711 587 1049 711 711 711 1777 710 543 1135 1000 692 1000 1000 332 332 587 587 711 711 1000 711 964 593543 1068 1000 597 737 342 402711 711 711 711 543 711 711 964 598850 867 480 964 711 587 867 598 711 721 711 361 711 598 598 850 1182 1182 1182 617 776 776 776 776 776 1094 724 683 683 683 683 546 546 546 546 830 847 850 850 850850867850 812 812 812 812 737 735 713 668 668 668 668 668 668 1018 588 664 664 664 342 342 342 342 67979 712 686 686 686 686 686 867 686 712 712 712 712 651 699 651] endobj 21 0 объект > endobj 22 0 объект > endobj 23 0 объект [0 0 0 0 0 0 0 0 0 0 0 0 0 0 0 0 0 0 0 0 0 0 0 0 0 0 0 0 0 0 1000 1000 352 394 459 818 636 1076 727 269 454 454 636 818 364 454 364 454 636 636 636 636 636 636 636 636 636 454 454 818 818 818 545 1000 684 686 698 771 632 575775 75142145 693 557 843 748 787 603 787 695 684 616 732 684 989 685 615 685 454 454 454 818 636 636 60 521 623 596 352 623 633 274 344 592 274 973 633 607 623 623 427 521 394 633 592818 5925925635 454 635 818 1000 636 1000 269 636 459 818 636 636 636 1521 684 454 1070 1000 685 1000 1000 269 269 459 459 545 636 1000 636 977 521 454 981 1000 525 615 352 394 636 636 636 454 636 636 1000 545 645 818 454 1000 636 542 818 542 542 636 6426 364 636 542545 645 1000 1000 1000 545 684 684 684 684 684 684 984 698632 632 632 632 421421421421775 748 787787 787787818 787 732 732 732 615 605 620 601 601 601 601 601 955521596596596596 274 274 274 274 274 612 633 607 607 6018 607 607 607 633 633 633 633 592 623 592] endobj 24 0 объект > endobj 25 0 объект > endobj 26 0 объект [0 0 0 0 0 0 0 0 0 0 0 0 0 0 0 0 0 0 0 0 0 0 0 0 0 0 0 0 0 0 778 778 250 333 408 500 500 833 778 180 333 333 500 564 250 333250 278 500 500 500 500 500 500 500 500 500 500 278 278 564564 444 921 722 667 667 722 611 556 722 722 333 389 722 611 889 722 722 556 722 667 556611 722 722 944 722 722 611 333 278 333 469 500 333 444 500 444500 444 333 500 500 278 278 500 278 778 500 500 500 500 500 333 389 278 500 500 722 500 500 444 480 200 480 541 778 500 778 333 500 444 1000 500 500 333 1000 556 333 889 778 611 778 778 333 333 444 444 350500 1000 333980389333722778444722250 333500500500500200500 333760 276 500 564 333760 500 400 549 300 300 333 576 453250 333 300 310 500 750 750 750 444722 722 722 722 722 889 667 611 611 611 611 333 333 333 722 722 722 722 722 722 564 722 722 722 722 722 556 500 444 444 444 444 444 444 667 444 444 444 444 444 278 278 278 278 500 500 500 500 500 500 500 549 500 500 500 500 500 500 500 500] endobj 27 0 объект > endobj 28 0 объект > endobj 29 0 объект [0 0 0 0 0 0 0 0 0 0 0 0 0 0 0 0 0 0 0 0 0 0 0 0 0 0 0 0 0 0 1000 1000 352 394 459 818 636 1076 727 269 454 454 636 818 364 454 364 454 636 636 636 636 636 636 636 636 636 454 454 818 818 18 545 1000 683 686 698766 632 575 775 75142145 693 557 843 748 787 603 787 695 684 616 732 683 990 685 615 685 454 454 454 818 6236 601 521 623 596 352 622 633 274 344 587 274 973 633 607 623 623 427 521 394 633 591 818 59259 1525 635 454635 818 1000 636 1000 269 636 459 818 636 636 636 1519 684 454 1070 1000 685 1000 1000 269 269 459 459 545 636 1000 636 977 521 454 980 1000 525 615 352 394 636 636 636 454 636 636 1000 545 645 818 454 1000 636 542 818 542 542 636 6426 364 636 542545 645 1000 1000 1000 545 683 683 683 683 683 989 698632 632 632 632 421421421421766 748 787787 787 787 818 787 732 732 732 732 615 605 620 601 601 601 601 601 955 521 596 596 596 596 274 274 274 274 274 612 633 607 607 6018 607 607 607 633 633 633 633 591 623 591] endobj 30 0 объект > endobj 31 0 объект > endobj 32 0 объект > поток
Прочность газобетона на сжатие.

Контекст 1
… образцы были испытаны на физико-механические свойства, а именно на объемную плотность в высушенном состоянии, прочность на сжатие и теплопроводность. Эти свойства визуализированы на следующих рисунках. Сравнение насыпной плотности газобетона (рис.1) показывает уменьшение насыпной плотности в образцах, содержащих 13% зольную добавку FBC. Для газобетона эта тенденция явно положительна, поскольку насыпная плотность связана с теплоизоляционными свойствами материала.Через 2 года наблюдается небольшое увеличение насыпной плотности. Причину следует искать в микроструктуре газобетона и будет обсуждаться позже. Примесь золы FBC также оказала влияние на снижение прочности на сжатие (рис. 2). Это явление можно объяснить качеством золы от сжигания жидкого угля, особенно в отношении содержания SiO 2, а также его формы. Летучая зола из обычных порошковых слоев состоит на 80-95% из аморфных алюмосиликатов, тогда как зола FBC содержит в основном минеральные фазы. Таким образом, можно предположить, что SiO 2, содержащийся в золе FBC, будет менее реактивным, что было подтверждено с учетом механических свойств бетона. После 2 лет хранения у большинства образцов произошло небольшое снижение прочности на сжатие. Однако влияния зольной примеси FBC на прочность при сжатии после 2 лет хранения не наблюдалось. Зола FBC явно положительно влияет на теплопроводность согласно результатам, представленным на рис. 3. Как упоминалось выше, это связано в основном с более низкой насыпной плотностью газобетона, содержащего золу FBC.После 2 лет хранения коэффициент теплопроводности практически не изменился. После определения физико-механических свойств была проанализирована микроструктура образцов. На следующих рисунках представлены рентгеновские дифрактограммы газобетона после 2 лет хранения (рис. 4, 5) и СЭМ-изображения образцов (рис. 6, рис. 7). Рентгеновские дифрактограммы показывают, что образцы состоят в основном из тоберморита. Также присутствует некоторое содержание катоита (Ca 3 Al 2 (SiO 4) (OH) 8).
Когда летучая зола используется в качестве силикатного компонента в ячеистом бетоне, в системе образуются CaO-Al 2 O 3 SiO 2 -H 2 O кальций-алюминат-силикат-гидраты, к которым также относится упомянутый выше катоит. Образование этого минерала во время гидротермальной реакции желательно, поскольку тоберморит также кристаллизуется из раствора растворенных ионов катоита на более поздних стадиях гидротермальной реакции. Формулы также показывают значительное содержание эттрингита, который вторично образовался в течение 2 лет хранения и является продуктом сульфатирования.Также присутствует кальцит, который указывает на карбонизацию газобетона. Присутствие этих минералов также может объяснить небольшое снижение прочности и увеличение насыпной плотности за 2 года. Сравнение рентгеновских дифактограмм образцов на основе высокотемпературной летучей золы и образцов, содержащих золу FBC, показывает, что использование золы FBC приводит к снижению интенсивности пика тоберморита. Сравнение химического состава золы (таблица 2) показывает существенное различие в содержании SiO 2, примерно на 5%.
10%. Важным фактором является также характер SiO 2 в золе, который аморфен в высокотемпературной золе и, следовательно, обладает высокой реакционной способностью. Можно предположить, что SiO 2, содержащийся в золе FBC, мало реакционноспособен и не вносит полного вклада в образование фаз CSH. Снимки, полученные с помощью SEM-микроскопа, показывают, что все образцы имеют микроструктуру хорошего качества, образованную в основном хорошо развитыми игольчатыми кристаллами тоберморита, которые хорошо сцеплены и образуют прочный каркас из пенобетона.Некоторые неиспользованные зерна летучей золы и, в небольшой степени, катоита наблюдались в бетоне без примеси золы FBC (рис. 6). Однако изометричные кристаллы катоита в основном присутствовали в бетоне с 13% зольной примеси FBC (рис. 7). На СЭМ-изображении этого газобетона также были обнаружены кристаллы кальцита, которые растут из места, покрытого тоберморитом. Следовательно, можно предположить наступление карбонизации бетона. Анализ микроструктуры зольного газобетона позволил сделать вывод о том, что в образцах могут наблюдаться признаки карбонизации и сульфатирования после 2 лет хранения в помещении с чередованием температурно-влажностного режима.
В частности, это проявилось в наличии в бетоне эттрингита и кальцита. Присутствие этих минералов в равной степени наблюдалось в обоих типах газобетона (сделанном с использованием высокотемпературной летучей золы и 13% -ной примеси золы FBC). Микроструктура этих двух газобетонов различалась в основном содержанием тоберморита. Было обнаружено, что добавление золы FBC отрицательно влияет на образование этого минерала. Результаты анализа микроструктуры были подтверждены при определении физико-механических свойств бетона.2 года хранения привели к небольшому увеличению насыпной плотности и снижению прочности на сжатие почти у всех образцов. Теплопроводность не изменилась. Примесь золы FBC положительно повлияла на насыпную плотность, то есть снизилась. Прочность на сжатие тоже, что, однако, отрицательно …
Все об автоклавном ячеистом бетоне (AAC)
Автоклавный газобетон (AAC) — это сборный железобетон, состоящий из природного сырья. Впервые он был разработан в Швеции в 1920-х годах, когда архитектор впервые объединил обычную бетонную смесь из цемента, извести, воды и песка с небольшим количеством алюминиевой пудры. Алюминиевая пудра служит расширителем, заставляя бетон подниматься, как тесто для хлеба. В результате получается бетон, который почти на 80 процентов состоит из воздуха. Бетон AAC обычно превращается в блоки или плиты и используется для строительства стен из цементного раствора, аналогично тому, как это используется для строительства стандартных бетонных блоков.
Как производится газобетон
Автоклавный газобетон начинается с того же процесса, который используется для смешивания всего бетона: портландцемент, заполнитель и вода смешиваются вместе, образуя суспензию.При введении алюминия в качестве расширительного агента пузырьки воздуха проникают по всему материалу, образуя легкий материал с низкой плотностью. Влажному бетону придают форму с помощью форм, затем после частичного высыхания разрезают на плиты и блоки. Затем блоки перемещаются в автоклав для полного отверждения под действием тепла и давления, что занимает всего от 8 до 12 часов.
Бетонные блоки AAC очень удобны в обработке и могут быть разрезаны и просверлены с помощью обычных деревообрабатывающих инструментов, таких как ленточные пилы и обычные дрели. Поскольку бетон легкий и относительно невысокий, его необходимо испытывать на прочность на сжатие, содержание влаги, объемную плотность и усадку.
Здание из бетона AAC
Бетон AAC можно использовать на стенах, полу, кровельных панелях, блоках и перемычках.
- Панели доступны толщиной от 8 дюймов до 12 дюймов и 24 дюймов в ширину и длиной до 20 футов.
- Блоки бывают длиной 24, 32 и 48 дюймов и толщиной от 4 до 16 дюймов; высота 8 дюймов.
Затвердевшие блоки или панели из газобетона в автоклаве соединяются с помощью раствора с тонким слоем, используя методы, идентичные тем, которые используются со стандартными бетонными блоками. Для дополнительной прочности стены могут быть усилены сталью или другими конструктивными элементами, проходящими вертикально через промежутки в блоках.
Бетон AAC можно использовать для стен, полов и крыш, а его легкий вес делает его более универсальным, чем стандартный бетон. Материал обеспечивает отличную звуко- и теплоизоляцию, а также прочность и огнестойкость. Однако, чтобы быть долговечным, AAC должен быть покрыт нанесенной отделкой, такой как модифицированная полимером штукатурка, натуральный или искусственный камень или сайдинг. Если они используются для подвалов, то внешняя поверхность стен из AAC должна быть покрыта толстым слоем водонепроницаемого материала или мембраны. Поверхности AAC, подверженные воздействию погодных условий или влаги почвы, будут разрушаться. Внутренние поверхности можно отделать гипсокартоном, штукатуркой, плиткой или краской или оставить незащищенными.
Свойства газобетона
По сути, AAC предлагает только умеренные значения изоляции — около R-10 для стены толщиной 8 дюймов и R-12.5 для стены толщиной 10 дюймов. AAC предлагает значение R около 1,25 на каждый дюйм толщины материала. Но AAC имеет высокую тепловую массу, что замедляет передачу тепловой энергии и может значительно снизить затраты на нагрев и охлаждение. А конструкции AAC можно сделать очень герметичными, чтобы уменьшить потери энергии из-за утечек воздуха. AAC также создает отличный звукоизоляционный барьер.
Свойства | Газобетон | Традиционный бетон |
Плотность (PCF) | 25–50 | 80–150 |
Прочность на сжатие (PSI) | 360–1090 | 1000–10000 |
Огнестойкость (часы) | ≤ 8 | ≤ 6 |
Теплопроводность (Btuin / ft2-hr-F) | 0.75–1,20 | 6,0–10 |
Преимущества и применение
Некоторые из преимуществ использования автоклавного газобетона включают:
- Превосходный материал для звукоизоляции и звукоизоляции
- Высокая огнестойкость и устойчивость к термитам
- Доступны в различных формах и размерах
- Высокая тепловая масса накапливает и выделяет энергию с течением времени
- Материал, пригодный для вторичной переработки
- Простота обращения и установка благодаря малому весу
- Легко прорезать пазы и отверстия для электрических и сантехнических линий
- Экономичная транспортировка и транспортировка по сравнению с заливным бетоном или бетонным блоком
Недостатки
Как и все строительные материалы, у AAC есть ряд недостатков:
- Продукция часто отличается нестандартным качеством и цветом.
- Необработанные внешние стены требуют внешней облицовки для защиты от погодных условий.
- При установке в среде с высокой влажностью внутренняя отделка требует низкой паропроницаемости, а внешняя — высокой.
- R-значения относительно низкие по сравнению с энергоэффективной изолированной стеновой конструкцией.
- Стоимость выше обычной бетонно-блочной и каркасной конструкции.
- Прочность AAC составляет от 1/6 до 1/3 прочности традиционного бетонного блока.
Цены на блоки AAC
Базовый блок AAC стандартного размера 8 x 8 x 24 дюйма по состоянию на июль 2018 года стоит от 2,20 до 2,50 долларов за квадратный фут, что немного больше, чем стандартный бетонный блок, который стоит около 2 долларов за квадратный фут. Однако затраты на рабочую силу для AAC могут быть ниже, поскольку его меньший вес упрощает транспортировку и установку. Стоимость будет варьироваться от региона к региону и зависит от местных ставок оплаты труда и требований строительных норм.
Оценка механических свойств блока из автоклавного ячеистого бетона (AAC) и его кладки
В. Сринивас, С. Сасмал, Экспериментальные и численные исследования поведения кирпичной кладки при предельной нагрузке. J. Inst. Англ. (Индия) Сер. A 97 (2), 93–104 (2016)
Статья Google ученый
S.H. Баша, Х. Кошик, Оценка нелинейных свойств материалов кирпичной кладки из зольной пыли при сжатии и сдвиге. J. Mater. Civ. Англ. (ASCE) 27 (8), 04014227 (2014)
Статья Google ученый
А. Радж, А.С. Борсайкия, Диксит США, Производство автоклавного газобетона (AAC): текущее состояние и будущие тенденции. in Advances in Simulation, Product Design and Development (Springer, Singapore, 2020), pp. 825–833
Д. Ферретти, Э. Мишелини, Г. Розати, Растрескивание в автоклавном ячеистом бетоне: экспериментальное исследование и моделирование XFEM. Джем. Concr. Res. 67 , 156–167 (2014)
Статья Google ученый
Н. Нараянан, К. Рамамурти, Микроструктурные исследования ячеистого бетона. Джем. Concr. Res. 30 (3), 457–464 (2000)
Артикул Google ученый
Дж. Александерсон, Связь между структурой и механическими свойствами автоклавного газобетона. Джем. Concr. Res. 9 (4), 507–514 (1979)
Артикул Google ученый
Л. Малышко, Е. Ковальска, П. Билко, Расщепление автоклавного пенобетона при растяжении: сравнение результатов различных образцов. Минусы. Сборка. Мат. 157 , 1190–1198 (2017)
Артикул Google ученый
Д. Ферретти, Э. Мишелини, Г. Розати, Механическое определение характеристик кладки из автоклавного газобетона, подвергнутой нагрузке в плоскости: экспериментальное исследование и КЭ моделирование. Минусы. Сборка.Мат. 98 , 353–365 (2015)
Статья Google ученый
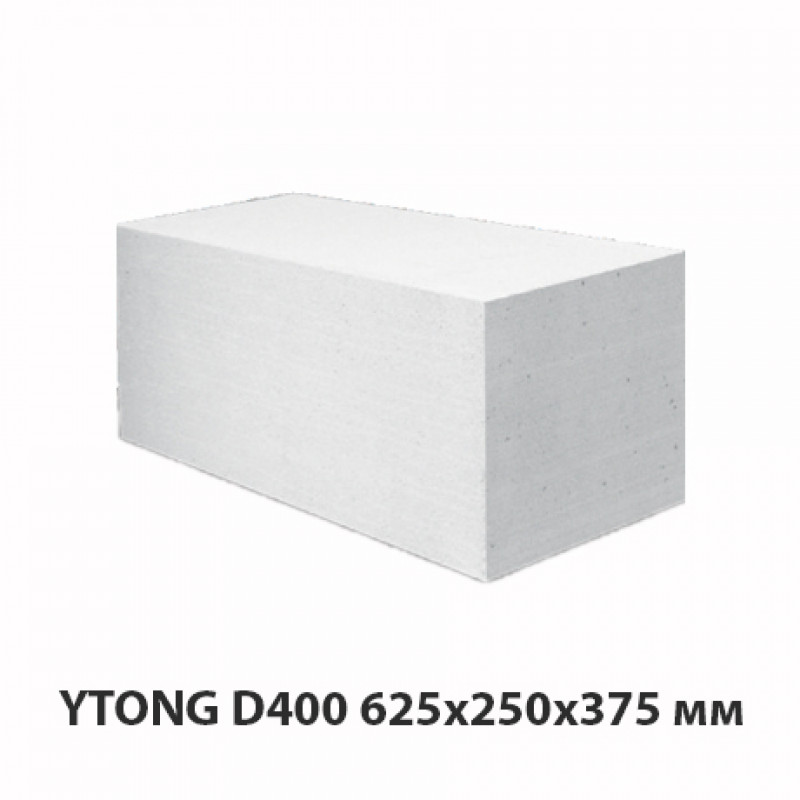
A. Bhosale, N.P. Заде, Р. Дэвис, П. Саркар, Экспериментальное исследование кладки из ячеистого бетона в автоклаве. J. Mater. Civ. Англ. (ASCE) 31 (7), 04019109 (2019)
Статья Google ученый
А. Радж, А.С. Борсайкия, США, Диксит, Прочность сцепления на сжатие и сдвиг блоков и кирпичной кладки с пазами из AAC.Mater. Struct. 52 (6), 116 (2019)
Статья Google ученый
https://brikolite.com/brikolite-user-guidelines/, получено 19 сентября 2019 г.
Х.Р. Кумават, Экспериментальное исследование механических свойств кладки из глиняного кирпича путем частичной замены мелкого заполнителя отходами глиняного кирпича. J. Inst. Англ. (Индия) Ser A 97 (3), 199–204 (2016)
Статья Google ученый
М. Кешава, С.Р. Рагхунатх, Экспериментальные исследования каменных стен с осевой и внецентренной нагрузкой. J. Inst. Англ. (Индия) Ser A 98 (4), 449–459 (2017)
Статья Google ученый
G. Sarangapani, B.V.V. Редди, К. Джагдиш, Кирпичная кладка и прочность на сжатие. J. Mater. Civ. Англ. (ASCE) 17 (2), 229–237 (2005)
Статья Google ученый
A.J. Фрэнсис, К.Б. Хорман, Л. Jerrems, Влияние толщины шва и других факторов на прочность кирпичной кладки при сжатии. in Proceedings of 2 nd International Brick Masonry Conference , ed. Автор: HWH West, Британская керамическая ассоциация, Сток-он-Трент, стр. 31–37 (1971)
Индийский стандартный свод правил [IS: 6441-1972, подтвержден в 2001 г.] для испытаний изделий из ячеистого бетона в автоклаве (пятая редакция) , Нью-Дели, Индия
H.B. Кошик, Д.К. Рай, С.К. Джайн, Напряженно-деформированные характеристики кладки из глиняного кирпича при одноосном сжатии. J. Mater. Civ. Англ. (ASCE) 19 (9), 728–739 (2007)
Статья Google ученый
S.B. Сингх, П. Мунджал, характеристики прочности связи и напряжения-деформации при сжатии кирпичной кладки. J. Build. Англ. 9 , 10–16 (2017)
Статья Google ученый
Индийский стандартный свод правил [IS: 3495-1976, подтвержден в 2002 г.] для испытания строительных кирпичей из обожженной глины (третья редакция), Нью-Дели, Индия
Американские стандартные методы испытаний для отбора проб и испытаний кирпича и структурной глиняной плитки , ASTM C67-00, 4-е изд., Американское общество испытаний и материалов (ASTM), Филадельфия, Соединенные Штаты, (2001)
Американский стандартный метод испытания прочности на разрыв кирпичных блоков при разделении, ASTM C 1006-07 , Американское общество испытаний и материалов (ASTM) Вест Коншохокен, США, (2007)
Индийский стандартный свод правил [IS 2250-1981, подтвержден в 2002 г.] для подготовки и использования строительных растворов (первая редакция), Нью-Дели, Индия
Индийский стандартный свод правил [IS 1905-1987, подтвержден в 2002 году ] для структурного использования неармированной кирпичной кладки (Третья редакция), Нью-Дели, Индия
Американский стандартный метод испытания прочности сцепления раствора с каменными элементами, ASTM C 952-91, Соединенные Штаты, (1991)
С. Малликарджуна, Экспериментальное определение параметров для критерия разрушения, основанного на микромоделировании, для стены сдвига из блочной кладки AAC, М.тех. диссертация, Индийский технологический институт, Гувахати, Индия, 2017 г.
В. Алеччи, М. Фагоне, Т. Ротунно, М. Де Стефано, Прочность на сдвиг кирпичных стен, собранных с использованием различных типов раствора. Минусы. Сборка. Мат. 40 , 1038–1045 (2013)
Артикул Google ученый
A.A. Коста, А. Пенна, Г. Магенес, А. Галаско, октябрь. Оценка сейсмостойкости каменных зданий из автоклавного ячеистого бетона (AAC).in Proceedings of the 14th World Conference on Earthquake Engineering , (Пекин, Китай), 05-04 (2008)
Пористость и механическая прочность автоклавного глинистого ячеистого бетона
В этой статье исследуются пористость и механическая прочность автоклавный глинистый ячеистый бетон (ACCC) со связующим, изготовленным из 75 мас.% каолинитовой глины и 25 мас. % портландцемента. В качестве вспенивателя использовали алюминиевый порошок от 0,2 до 0,8 мас.%, Получая образцы с разной пористостью.Результаты показывают, что образцы с более высоким содержанием алюминия продемонстрировали слияние пор, что может объяснить более низкую пористость этих образцов. Пористость, полученная с использованием использованного в исследовании содержания алюминия, была высокой (около 80%), что объясняет низкую механическую прочность исследованных ячеистых бетонов (максимум 0,62 МПа). Тем не менее, сравнивая результаты, полученные в этом исследовании, с результатами для низкотемпературного глинистого газобетона с аналогичными составами, можно заметить, что автоклавирование эффективно для увеличения механической прочности материала.
1. Введение
Ячеистый бетон — это затвердевший раствор портландцемента, который перед схватыванием был аэрирован для получения однородной пустотной или ячеистой структуры, содержащей 50–80 об.% Или более пузырьков воздуха, пустот и капиллярной пористости [1 ]. Тепловая и акустическая изоляция и огнестойкость — вот некоторые из свойств, которые делают ячеистый бетон очень интересным материалом для применения в строительстве [2–4].
Есть много возможных способов производства ячеистого бетона.Различные композиции вместе с различными методами отверждения могут использоваться для получения различных конечных свойств, таких как плотность, механическая прочность, термическая и акустическая проводимость [1].
Конечные свойства ячеистого бетона во многом зависят от его пористости, которую можно изменить, изменив тип и состав пенообразователя. Очень пористый материал будет иметь отличные тепло- и звукоизоляционные свойства из-за большого количества увлеченного воздуха. Однако эти свойства достигаются в ущерб механической прочности, которая уменьшается с увеличением объема пор.Таким образом, определение пористости и ее влияние на механическую прочность ячеистого бетона является очень важным фактором, который необходимо анализировать при производстве этого вида материала.
Некоторые исследования [5] показывают, что при той же пористости и составе, механическая прочность ячеистого бетона может быть увеличена путем изменения метода твердения. Автоклавный газобетон (AAC), то есть отверждаемый под давлением пара при температурах между и обычно имеет более высокую прочность на сжатие, чем бетон неавтоклавного пенобетона (NAAC) влажного отверждения при комнатной температуре.Кроме того, во время автоклавирования материал достигает своей окончательной микроструктуры, в то время как NAAC претерпевает микроструктурные изменения со временем и, как следствие, медленные и постепенные изменения своей механической прочности [5].
Состав ячеистого бетона на каолинитовой глинистой основе был исследован Goual et al. [6–8]. В их исследованиях Clayey Cellular Concrete (CCC), как его называли, отверждался во влажной среде при относительной влажности 90%. Поскольку реакции между каолинитом и портландцементом очень медленные при комнатной температуре, этому материалу могут потребоваться месяцы, прежде чем будет достигнута его окончательная механическая прочность. Нововведение, предложенное в этой статье, связано с использованием автоклава для улучшения свойств материала ячеистого бетона этого типа.
Это исследование направлено, в частности, на изучение пористости и механической прочности автоклавного глинистого ячеистого бетона (ACCC) и сравнение результатов с результатами, представленными CCC с аналогичными составами, о которых сообщается в литературе.
2. Экспериментальная
2.1. Материалы
Используемая глина состояла на 98,3% из каолинита (Caulina Minérios, Бразилия), а цемент представлял собой стандартный портландцемент с высокой начальной прочностью (CP V-ARI-RS, Votorantim, Бразилия).Алюминиевый порошок представлял собой Stanlux Flake CL 4010 (Aldoro, Бразилия) со средним размером частиц 16 мкм. Для повышения удобоукладываемости глиняно-цементного теста был использован суперпластификатор на основе поликарбоксилата (Glenium 51, BASF, Германия) (32 мас.% Твердых веществ).
2.2. Композиции
Автоклавный глинистый ячеистый бетон (ACCC) был получен путем аэрации водной пасты каолинитовой глины и портландцемента с использованием алюминиевого порошка в качестве пенообразователя. Алюминиевый порошок реагирует с раствором каустика, который выделяется во время реакции гидратации, с образованием пузырьков газообразного водорода [7].В конце процесса вспенивания водород улетучивается в атмосферу и замещается воздухом, который удерживается в виде пузырьков в пасте, превращаясь в сферические поры после полного схватывания цемента, создавая ячеистую структуру [6].
Были проанализированы четыре состава, различающиеся количеством используемого алюминиевого порошка. Количества, рассчитанные в виде массовых процентов сухих глино-цементных материалов, были следующими: 75 мас.% Глины, 25 мас.% Цемента, 65 мас.% Воды и суперпластификатор на основе поликарбоксилата (0.8 мас.%, Массовый процент твердых веществ по отношению к сухим материалам), к которому добавляли от 0,2 до 0,8 мас.% Алюминиевого порошка с шагом 0,2%. Образцы в этом исследовании были обозначены как A2 для 0,2, A4 для 0,4, A6 для 0,6 и A8 для 0,8 мас.% Алюминия.
2.3. Подготовка образцов
В этом эксперименте глина и цемент были смешаны в сухом состоянии в смесителе с планетарной осью на низкой скорости в течение 2 минут. Затем постепенно добавляли воду, продолжая перемешивание на низкой скорости еще 2 минуты.Сделали короткую остановку на 1,5 минуты при перемешивании, чтобы соскрести материал, прилипший к стенкам емкости для смешивания. Затем смесь гомогенизировали на низкой скорости в течение 1 минуты, а затем в течение 2 минут на высокой скорости. Суперпластификатор добавляли при остановленном миксере в течение 30 секунд. После добавления этой добавки пасту перемешивали на низкой скорости в течение 1 минуты и затем останавливали еще на 30 секунд для добавления алюминиевого порошка, который смешивали и гомогенизировали в пасту в течение 1 минуты на низкой скорости.
Восемь образцов каждой смеси были отлиты в цилиндрические (50 100 мм 3 ) металлические формы, предварительно смазанные маслом для облегчения извлечения из формы. Через шестнадцать часов после формования лишние расширенные части были отрезаны. Через 48 часов образцы вынимали из форм и выдерживали во влажном помещении при 25 и 90% относительной влажности в течение 2 дней, а затем автоклавировали при 12 атм в течение 10 часов. Перед началом экспериментов образцы сушили в сушильном шкафу при температуре 70 ° С до достижения постоянного веса.
Микроструктуру и фазы ACCC сравнивали с микроструктурой и фазами низкотемпературного глинистого ячеистого бетона, отвержденного при температуре окружающей среды во влажном помещении при относительной влажности 25 и 90% в течение 21 дня.
2.4. Плотность, пористость и механическая прочность
Относительная плотность ячеистого бетона соответствует соотношению между кажущейся плотностью (геометрически измеренной) ячеистого материала и плотностью твердого вещества, составляющего матрицу этого ячеистого материала [9 ]: Пористость определяется по [9]
Для измерения образцов ACCC диски размером приблизительно 50 15 мм 3 были вырезаны из центра 2 образцов каждой композиции.Затем были измерены их масса и относительные размеры для расчета объема, т.е. кажущаяся плотность, определенная по (3). где определяется геометрической формулой для расчета цилиндрического объема.
Для измерения использовался гелиевый пикнометр (Multipycnometer, QuantaChrome, США). Для этого анализа измельчали репрезентативные образцы каждого состава. Для измерения использовали примерно 4 г порошка каждой композиции. Для каждого образца порошка было выполнено в общей сложности 10 измерений, что являлось окончательным значением, полученным как среднее арифметическое.
Для определения механической прочности образцов пять цилиндрических образцов (50 100 мм 3 ) каждого состава были испытаны на универсальной машине для механических испытаний (DL 20000, Emic, Brazil) в соответствии с бразильским стандартом. [10]. Базовые поверхности образцов были покрыты штукатуркой Paris для получения плоских и параллельных поверхностей. Используемая скорость нагрузки составляла 1 мм / мин.
2,5. Микроструктура и фазовый анализ
Продукты в этой работе были охарактеризованы с помощью рентгеновской дифрактометрии (XRD, Phillips, модель Xpert, Нидерланды) и сканирующей электронной микроскопии (SEM, Phillips, Нидерланды).
3. Результаты и обсуждение
3.1. Плотность и пористость
На рис. 1 показаны кажущаяся плотность и пористость проанализированных образцов ACCC в зависимости от процентного содержания порошка Al. Как можно видеть, плотность не изменилась, как и ожидалось для разных количеств Al. Как правило, плотность ячеистого бетона уменьшается по мере увеличения процентного содержания пенообразователя из-за большего количества образующихся пор. Однако в данном случае такое поведение как раз наблюдалось для образцов с 0.2 и 0,4 мас.% Al. Для образцов с большим количеством порошка Al плотность увеличивалась. Такое же аномальное поведение было отмечено для пористости образцов ACCC. Пористость увеличилась между образцами А2 и А4, но впоследствии она уменьшилась для образцов А6 и А8, достигнув более высокого значения в образце А4 (83,2%).
Анализ поверхностей излома образцов ACCC показал, что смеси A6 и A8 имели поры неоднородной формы, которые были больше, чем наблюдаемые для смесей A2 и A4, что свидетельствует о слиянии пор смесей с более высоким содержанием Al. Это могло объяснить неожиданные результаты по плотности и пористости. На рисунках 2 (а) и 2 (б) показаны поверхности излома образцов А2 и А8 соответственно.
Когда поры соединяются вместе, они приобретают больший объем и имеют тенденцию выходить из материала [1] из-за более сильных сил, оказываемых на них жидкостью (плавучесть, оказываемая цементной пастой на пузырьки газа). Таким образом, часть газа, образующегося во время реакции между Al и гидроксидами, не эффективна для образования пор, что приводит к более низкой пористости образцов A6 и A8.
Фактором, который может объяснить слияние пор этих образцов, является высокая реакционная способность порошка алюминия, использованного в данном исследовании. Как показано на Рисунке 1, 0,2 мас.% Al уже было достаточно для получения пористости 81,8%. Когда было добавлено более высокое содержание Al, количество образовавшихся пузырьков водорода могло быть настолько большим, что для них было более стабильным слияние, чем оставаться изолированными. Коалесценция обеспечивает минимизацию общей площади поверхности пор, что приводит к более стабильной конфигурации системы [11].
Возможные решения этой проблемы заключаются в минимизации количества суперпластификатора, используемого для увеличения вязкости цементирующей пасты, чтобы задержать выход пузырьков водорода, и в оптимизации количества используемой энергии Al (Stanlux Flake CL4010), поскольку меньшего количества этого порошка достаточно для получения высокой пористости.
3.2. Механическая прочность
Механическая прочность образцов ACCC соответствовала результатам по плотности и пористости, то есть более высокая пористость приводила к более низкой механической прочности, что можно увидеть на рисунке 3.
Различные значения механической прочности на сжатие, представленные образцами, проанализированными в этом исследовании, являются следствием их ячеистой морфологии. В образцах A2 и A4 из-за большего количества и однородного распределения пор межпоровые стойки тоньше, что придает материалу меньшую прочность. Однако в образцах A6 и A8, хотя поры больше из-за слияния, стойки толще, что привело к более высокой прочности на сжатие. Даже в этом случае полученные значения были очень низкими, достигая максимального значения 0.62 МПа для состава А8 (пористость 78,23%).
Согласно Гибсону и Эшби [9], механическая прочность ячеистого материала является потенциальной функцией его относительной плотности в соответствии с уравнением: где — механическая прочность полностью плотного материала, — геометрическая константа пропорциональности, его пористость и эмпирический показатель степени.
С помощью этого уравнения значения механической прочности, которые образцы CCC представили бы, если бы они имели такую же пористость, как образцы ACCC, проанализированные в этом исследовании, были оценены на основе данных, представленных в литературе [6].Сравнение показано на рисунке 4.
Можно заметить, что значения механической прочности, оцененные для образцов CCC, значительно меньше, чем значения, измеренные для ACCC с такими же относительными плотностями. Это позволяет сделать вывод, что автоклавирование эффективно для упрочнения ячеистого бетона на глинистой основе, поскольку при равной пористости прочность на сжатие ACCC существенно выше, чем у CCC, который отверждается при комнатной температуре.
Поскольку более высокая прочность на сжатие, проанализированная в этом исследовании, была равна 0.62 МПа для образца с 0,8 мас.% Al, становится ясно, что необходимо уменьшить количество используемого порошка Al, чтобы получить образцы с более низкой пористостью и, следовательно, более высокой механической прочностью, чтобы соответствовать техническим условиям. Однако, если целью является использование материала с пористостью, аналогичной анализируемым здесь, необходимо изучить некоторые изменения в составе.
3.3. Микроструктура и фазовый анализ
Кристаллические фазы ACCC сравнивали с таковыми из глинистого ячеистого бетона, выдержанного при 90% относительной влажности в течение 21 дня (рис. 5).В обоих случаях могут наблюдаться пики каолинита и галлуазита из непрореагировавшей глины. Относительная интенсивность пика кальцита уменьшается при автоклавировании CCC, что приводит к образованию тоберморита. Типичные игольчатые структуры тоберморита [12, 13] более заметны в образце ACCC (рис. 6 (b)) по сравнению с образцом, отвержденным CCC. при низкой температуре (Рисунок 6 (а)).
4. Выводы
Это исследование было направлено на изучение влияния выдержки в автоклаве на механическую прочность ячеистого бетона на глинистой основе.Были проанализированы пористость и механическая прочность образцов разного состава, различающихся только содержанием Al, и результаты сопоставлены с литературными данными для глинистого ячеистого бетона, отвержденного при комнатной температуре (CCC).
По результатам можно сделать следующий вывод: (i) Образцы с содержанием алюминиевого порошка от 0,6 до 0,8% производили столько водорода, что поры больше не оставались дискретными, то есть поры слились до такой степени, что избыток водорода мог вырваться из матрицы. Это означает, что, вероятно, будет оптимальный уровень добавления алюминия в диапазоне от 0,4 до 0,6% для получения максимальной пористости. (Ii) Механическая прочность образцов ACCC варьировалась в зависимости от их пористости, то есть она увеличивалась по мере уменьшения пористости. . Однако полученные значения были очень низкими, достигая максимума 0,62 МПа для образца с более низкой пористостью (78,23%). (Iii) Путем экстраполяции данных, представленных в литературе [6] для образцов CCC, было обнаружено, что, при той же пористости и составе автоклавный глинистый ячеистый бетон (ACCC) имеет значительно более высокую механическую прочность, чем CCC, что показывает, что автоклавирование эффективно для упрочнения этого типа материала.(iv) Следует использовать меньшие количества порошка Al, чтобы уменьшить пористость и повысить механическую прочность. Другой возможностью было бы изменение твердофазного состава исследуемого ACCC.
Благодарности
Авторы благодарны г-ну Занону и г-ну Ногара из Селукона (Крисиума, Южная Каролина, Бразилия) за предоставленный алюминиевый порошок, используемый в этом исследовании, а также за разрешение использовать их автоклав для нашей экспериментальной работы.
ФАКТОРЫ, ВЛИЯЮЩИЕ НА ПЛОТНОСТЬ И ПРОЧНОСТЬ ПЕРИОДИЧЕСКОГО БЕТОНА
Газобетон является относительно однородным материалом по сравнению с обычным бетоном, поскольку он лишен фазы крупного заполнителя, но при этом демонстрирует значительные различия в своих свойствах.Большинство исследований в прошлом ограничивалось автоклавированными продуктами. В данной статье представлены результаты систематического исследования, проведенного с целью определения влияния соотношения известково-цементный раствор, летучей золы как частичной / полной замены песка, размера частиц песка и дозировки аэрирующего агента на плотность и прочность на сжатие. газобетон влажного твердения и автоклавного твердения. Это исследование устанавливает, что с точки зрения снижения плотности летучая зола может играть ключевую роль в ячеистом бетоне без особого ущерба для прочности.Наблюдается, что повышенное соотношение известково-цементное покрытие отрицательно сказывается на прочности, тогда как уменьшение размера частиц песка ниже определенного уровня не оправдано в случае неавтоклавного пенобетона. (А)
- Наличие:
- Корпоративных авторов:
Томас Телфорд Лимитед
Лондон, объединенное Королевство - Авторов:
- Рамамурти, К
- НАРАЯНАН, N
- Дата публикации: 2000-6
Язык
Информация для СМИ
Предмет / указатель терминов
Информация для подачи
- Регистрационный номер: 00795011
- Тип записи: Публикация
- Агентство-источник: Транспортная исследовательская лаборатория
- Файлы: ITRD
- Дата создания: 7 июля 2000 г.
, 00:00
ASTM International — Международные стандарты
Стандарты для автоклавного ячеистого бетона способствуют экологичности
Автоклавный газобетон был впервые представлен в Швеции в конце 1920-х годов.Это легкий материал без крупного заполнителя, полученный путем смешивания цемента, извести, песка или летучей золы, алюминиевого порошка и воды. Из алюминиевого порошка образуется газообразный водород при смешивании с цементным тестом, который, в свою очередь, образует пузырьки воздуха в бетонной матрице, что приводит к пористой структуре AAC.
С точки зрения устойчивости, AAC является образцовым строительным материалом, поскольку он производится из натуральных материалов, которые легко доступны. Из-за своего легкого веса AAC имеет явное преимущество в энергии транспортировки по сравнению с более плотными материалами, такими как бетон или кладка.Отходы AAC во время строительства минимальны, поскольку детали можно разрезать до точных размеров с помощью стандартных деревянных режущих инструментов. AAC — это очень прочный материал, который после утилизации может быть легко переработан. Поскольку он изготовлен из инертных материалов, AAC не оказывает отрицательного воздействия на качество воздуха в помещении. Наиболее важным является экономия энергии за счет замечательных термических свойств материала. На рисунке 1 показано строительство в США с использованием AAC.
AAC широко используется в Европе, но только недавно были построены крупные производственные предприятия в Соединенных Штатах.Медленное поступление AAC на рынок США может быть в первую очередь связано с маркетинговыми условиями, отсутствием технической информации и ограниченным пониманием преимуществ AAC в проектировании и строительстве. Первый крупный производственный завод был построен в США только в 1996 году. Два крупных европейских конгломерата возглавили внедрение AAC в США. Немецкая группа Hebel через Hebel USA и Ytong Inc., дочерняя компания немецкой компании Ytong Holding, начали производство AAC в США в 1996 и 1997 годах соответственно. Изначально дома строились из импортных блоков AAC и армированных панелей из Европы. Строительная система, состоящая из панелей пола и крыши с внешними блочными стенами, продавалась в США и успешно использовалась для жилищного строительства на курортах и жилых домов во Флориде.
Сегодня AAC получает быстрое признание в качестве нового строительного продукта в США в результате растущего значения, уделяемого экономии энергии (как экономии энергии за счет теплоизоляции, так и количества энергии, необходимого для массового производства товар).Растущая стоимость пиломатериалов и растущая озабоченность по поводу окружающей среды также сыграли свою роль в повышении интереса к AAC. Наличие технической информации и стандартов ASTM для AAC послужит инструментом для дальнейшего продвижения и расширения использования материала.
РАЗРАБОТКА СТАНДАРТОВ ASTM ДЛЯ AAC
Исследования AAC в США начались в конце 1980-х годов на импортированных блоках и панелях из AAC. Однако после того, как в конце 1990-х были созданы производственные предприятия, стало очевидно, что дополнительные исследования U. Требовался AAC производства S. Исследования, спонсируемые производителями AAC, были сосредоточены на свойствах материала AAC и структурном поведении элементов AAC, армированных сталью. Исследования, которые обычно проводились Алабамским университетом в Бирмингеме и Техасским университетом в Остине, легли в основу стандартов ASTM для AAC. На рисунке 2 показаны испытания AAC в лаборатории UAB.
Процесс разработки стандартов ASTM для AAC начался в 1992 году благодаря усилиям Подкомитета C27 ASTM.20 по архитектурным и конструкционным изделиям, часть комитета ASTM C27 по сборным железобетонным изделиям. Поскольку работа над стандартами AAC выросла до уровня, выходящего за рамки компетенции подкомитета, было решено организовать отдельный подкомитет ASTM, который специально сосредоточился бы на AAC. В 1999 году был сформирован Подкомитет C27.60 по сборному автоклавному ячеистому бетону, и примерно в то же время подкомитет C15.10 по автоклавному газобетону был создан как часть Комитета C15 по промышленным каменным блокам для решения вопросов, которые конкретно относятся к строительству. кирпичной кладки.С того времени члены обоих подкомитетов работали вместе над созданием стандартов ASTM, которые принесут наибольшую пользу отрасли AAC.
Благодаря усилиям комитетов C27 и C15 ASTM, за последние 10 лет ASTM разработало и опубликовало четыре стандарта AAC. Этими стандартами являются:
• ASTM C 1386, Спецификации для сборных конструкций из пенобетона в автоклаве
• ASTM C 1452, Спецификации армированных элементов из пенобетона в автоклаве
• ASTM C 1555, Практика для автоклавной кладки из пенобетона
• ASTM C 1591, Метод испытаний для определения модуля упругости AAC
ОСНОВНЫЕ НАПРАВЛЕНИЯ ТЕКУЩИХ СТАНДАРТОВ AAC
ASTM C 1386
Стандарт C 1386 охватывает блочные блоки AAC, используемые при строительстве прочных ненесущих и несущих стен.Стандарт обеспечивает процедуры испытаний для определения прочности на сжатие, содержания влаги и объемной плотности AAC. Также представлены подробные сведения об испытании на усадку при сушке. Физические требования к AAC, включая прочность на сжатие, номинальную насыпную плотность в сухом состоянии и среднюю усадку при высыхании для каждого из трех классов прочности AAC, указаны в стандарте (Таблица 1). Также предписаны допуски на размеры для стандартных блоков AAC.
Испытание на сжатие предусматривает использование кубических образцов размером 4 дюйма.Длина кромки (10 мм), испытанная в условиях воздушной сушки при содержании влаги от 5 до 15 процентов по массе. Испытанию подлежат минимум три образца, и по возможности один образец берут из верхней трети блока, один из середины и один из нижней трети, определяемых в направлении подъема массы во время изготовления. Направление подъема отмечено на всех экземплярах.
Содержание влаги в ААС определяют путем сушки образцов в вентилируемой печи при температуре от 100 до 110 ° C до тех пор, пока два последовательных определения массы с 2-часовыми интервалами не покажут приращение потерь не более 0.2 процента от последней ранее определенной массы образца. Точные размеры измеряются штангенциркулем и определяется объем образцов. Насыпную плотность в сухом состоянии каждого образца определяют путем деления сухой массы на его объем.
Для определения усадки при высыхании образцы упаковывают в пластик и хранят не менее 24 часов при температуре от 18 до 22 ° C для равномерного распределения влаги. Затем их хранят на решетке, чтобы обеспечить достаточное движение воздуха при температуре 20 ± 2 ° C и относительной влажности 45 процентов.Массу и длину образца определяют регулярно, пока содержание влаги не упадет ниже 4 процентов. Затем определяется содержание влаги в этих образцах, и средние значения относительного изменения длины и содержания влаги для каждого показания отображаются графически и соединяются кривой.
ASTM C 1452
ASTM C 1452 охватывает несущие и ненесущие армированные сталью автоклавные газобетонные элементы полов, крыш, стен и лестниц, используемые в качестве компонентов для строительных конструкций.Для проволочной арматуры стандарт определяет минимальный предел текучести 70 тысяч фунтов на квадратный дюйм (485 МПа) и минимальный предел прочности на растяжение 80 тысяч фунтов на квадратный дюйм (550 МПа). Требуется минимальное бетонное покрытие стальной арматуры 0,375 дюйма (10 мм).
Испытание защиты от коррозии стальной арматуры в AAC выполняется путем погружения армированных образцов AAC в водный раствор хлорида натрия, 3% NaCl по массе, на двухчасовые периоды с интервалом в три дня.Это повторяется всего 10 циклов испытаний. После завершения образцы оставляют для высыхания на воздухе в течение четырех часов, и AAC вокруг стальной арматуры удаляют как с эталонных, так и с испытуемых образцов. Площадь покрытия стали ржавчиной определяется визуальным осмотром и выражается в процентах от общей площади образца.
Стандарт также предусматривает процедуру определения прочности на сдвиг в точке сварки сборных стальных проволочных сепараторов. Образец отбирают произвольно из сварного арматурного каркаса перед нанесением антикоррозионного состава.В качестве образца для испытаний выбирают проволоку с наибольшим диаметром. Образец, работающий на сдвиг, зажимается в испытательном приспособлении таким образом, чтобы стержень растяжения располагался по центру и предотвращалось вращение стержня крепления. Скорость нагружения не превышает 112 фунтов силы / с (0,5 кН / с). Типичное устройство для захвата испытуемого образца показано в стандарте.
В рамках этого стандарта описана полномасштабная процедура испытаний для определения бокового прогиба и несущей способности армированных панелей пола и крыши из AAC при изгибе.Используется симметричная четырехточечная схема нагружения (рисунок 3). Длина подшипника (Sb) регулируется таким образом, чтобы минимальная длина подшипника была эквивалентна наименьшей длине подшипника, поставляемой производителем, или не менее 1,6 дюйма (40 мм). Двухточечные нагрузки передаются на поверхность элемента AAC стальными профилями, имеющими достаточную опорную площадь для создания равномерного давления в подшипнике, не превышающего 50 процентов прочности на сжатие материала AAC. Регистрируется предельная нагрузка и проводятся наблюдения за режимом разрушения образца.
Стандарт ASTM C 1591
Стандарт C 1591 — это самый последний стандарт испытаний ASTM на AAC, который появился в печати в 2005 году. Он охватывает определение модуля упругости AAC при сжатии, полученного из данных испытаний на растяжение. Образцы для испытаний представляют собой призмы, имеющие размеры 100 мм x 100 мм x 200 мм. Образцы подготавливаются таким образом, чтобы нагрузка прикладывалась к поверхности размером 100 мм x 100 мм и перпендикулярно направлению подъема во время изготовления (Рисунок 4).
Электрические тензодатчики или механический компрессометр для определения деформации образца во время нагружения прикрепляют к двум противоположным продольным поверхностям образца вблизи средней части. Применяется базовая нагрузка, равная 0,33 предела ожидаемой прочности на сжатие, f ’ aac , для материала, и сохраняется в течение 90 секунд. Соответствующие деформации, e b1 и e b2 , измеряются в течение последних 30 секунд приложенной нагрузки.Если e b1 и eb2 отклоняются более чем на 20 процентов, приложенная нагрузка считается эксцентрической. Затем образец следует выгрузить, выровнять, повторно загрузить до 0,33 f ’ aac и измерить соответствующие деформации. Когда показания деформации при 0,33 f ’ aac находятся в пределах 20 процентов, постепенно уменьшайте нагрузку до достижения значения 0,05f’ aac (это должно занять приблизительно 30 секунд). Эта нагрузка сохраняется в течение 90 секунд, а соответствующие деформации, e a1 и e a2 , измеряются в течение последних 30 секунд приложенной нагрузки.Если разница в показаниях двух манометров (e b1 — e a1 , e b2 — e a2 ), соответствующая приложенным нагрузкам 0,33 f ‘ aac и 0,05 f’ aac отклоняется более чем на 20 процентов приложенная нагрузка считается эксцентричной. Затем образец следует выгрузить, выровнять и повторить испытание. Если разница в показаниях двух манометров (e b1 — e a1 , e b2 — e a2 ), соответствующая приложенным нагрузкам 0.33 f’aac и 0,05 f’aac отклоняются друг от друга в пределах 20 процентов, цикл загрузки повторяется.
Нагрузка принята 0,33 f ’ aac ; прочитать eb1 и eb2 и вычислить средний eb; уменьшить нагрузку до 0,05 f’aac; прочтите e a1 и e a2 и вычислите среднее значение e a . Эти значения будут использоваться для расчета модуля упругости E aac . После завершения этого второго цикла нагружения компрессометр должен быть удален, а образец нагружен до отказа.Полный цикл загрузки показан на рисунке 5.
Модуль упругости E c определяется по
, где fa = напряжение, зарегистрированное при 0,05f aac ; f b = напряжение, зарегистрированное при 0,33 f aac ; e a = средняя деформация, рассчитанная при 0,05f aac , и e b = средняя деформация, рассчитанная при 0,33f aac .
ASTM C 1555
Стандарт C 1555 был разработан специально для материалов, испытаний и качества изготовления кладки из блоков AAC.Дана прямая ссылка на ASTM C 1386 для спецификации материалов и испытаний. В примечании к стандарту рекомендуется использовать испытание модуля упругости для AAC после его разработки Подкомитетом C27.60 (в настоящее время ASTM C 1591). Требования к качеству изготовления, изложенные в Спецификации ACI / ASCE для каменных конструкций, приняты и дополнены дополнительными требованиями, специфичными для каменной кладки из AAC. Подробно описан тест на проницаемость для жидкости для обработки наружных поверхностей, которые используются для защиты кладки AAC от погодных условий.
Были предложены дополнительные стандарты ASTM для AAC, которые в настоящее время разрабатываются. Примеры таких стандартов — методы испытаний на прочность на изгиб, сдвиг и стойкость к замерзанию. Эти испытания необходимы, поскольку современные методы испытаний для обычного бетона или кирпичной кладки могут быть неприменимы непосредственно к AAC.
AAC — это относительно новый строительный материал в США, и поэтому техническая информация необходима для предоставления рекомендаций по использованию, а также испытанию материала.