Как резать блоки газобетонные: Как и чем правильно пилить газобетонные блоки
Строим дом самостоятельно. Как и чем можно резать газобетон
Не секрет, что строительство частного дома своими руками в несколько раз дешевле, чем если предоставить эту работубригада из строительной компании.
Представим ситуацию, что вы уже решились строить самостоятельно, выбрали материал для стен (конечно, это газобетон), поняли, как укладывать блоки, но неожиданно во время работы один из блоков выходит за пределы кладки и его необходимо обрезать.
Вопрос о том, как обрезать газобетонный блок, чтобы он был ровным, часто возникает у начинающих строителей. Рассказываем подробно и даём рекомендации специалистов, как правильно обрезать блок, чтобы не нарушить технологию домостроения и не увеличить расходные материалы.
Газобетонные блоки — это те материалы, с которыми работать просто и удобно. Но пилить блоки нужно правильно, соблюдая технологию, которая основывается на особенностях производства. Газобетон относится к группе пенобетонов и их основная характеристика — присутствие в структуре большого количества воздушных пузырьков.
Важно!
Блок из газобетона хорошо поддается распилу, только тогда, когда он сухой. Затвердевшие перегородки между воздушными пузырьками разламываются и крошатся от инструмента. Из-за этого создается большое количество пыли в месте распила, но в процессе движения лезвие выталкивает ее на поверхность, и получается ровный и красивый срез. Но если блок будет влажным, мокрым, замерзшим, то лезвие инструмента будет крошить блок, образовывая влажную пыль. Эта вязкая масса будет прилипать к полотну и лезвию, инструмент будет застревать, и срез вряд ли получится ровным и точным.
А нарушать геометрию газоблоков не рекомендуется, ведь тогда возможно увеличение толщины кладочного шва, из-за которого ухудшаются эксплуатационные характеристики кладки и увеличивается расход клея.
Другой важный момент распила блоков — это выбор инструмента.
Рассмотрим возможные варианты.
Ножовка
Самый доступный и подходящий вариант, когда необходимо распилить немного газоблоков без сложной геометрии. Эксперты советуют выбирать ножовку из толстого металла, на зубьях которой есть победитовые напайки. Это положительно скажется на точности реза и сохранности инструмента. И резка не вызовет проблем даже у неопытных строителей.
Сабельная электропила
Если предстоит большой объём работы с газобетоном, вместо ножовки лучше выбрать ручную пилу, но работающую от электрической сети. Сабельная пила позволит выполнить рез быстро и точно. Также с помощью неё можно сделать закрытый рез, т. е. пилить деталь не полностью, а на некоторую глубину, и вырезать канавки нужного размера.
Для сабельной пилы существуют специальные лезвия по газобетону, и лучше для работы выбрать именно их.
Ленточная пила
С помощью ленточной пилы можно проводить косую и прямую резку, выполнять пропилы под углом, выпиливать из блоков детали разной формы. При этом линия реза получается точной и без сколов. Но поскольку ленточная пила больше напоминает целый станок, для начала ей необходимо научиться пользоваться.
Выравнивание
Также отдельно стоит упомянуть про инструменты, которые упрощают работу с газобетоном.
Во время кладки могут встречаться незначительные погрешности по высоте блоков —до 3 мм. В таких случаях возможно выравнивание поверхности с помощью рубанка и специальной тёрки.
Работа с обоими инструментами примерно одинакова. Движением от себя производят удаление слоя материала, постоянно контролируя плоскость. Рекомендуется выбирать приспособления с максимальной площадью рабочей части, чтобы на поверхности не образовывались лишние волны.
Штроборез
Штроборез необходим для создания штроб в газобетоне под армирование кладки и под коммуникации.
Помните, что инструменты для работы с газобетоном упрощают ход строительства, но главным всегда остается правильность технологии, поэтому при любых обрезных работах с газобетоном обращайте внимание на то, насколько ровной получается поверхность, проверяя каждый ряд уровнем.
Найти подходящий инструмент для работы с газобетоном можно в нашем каталоге.
Производство газобетонных блоков: victorborisov — LiveJournal
Газобетон — современный энергоэффективный материал для индивидуального строительства. Он относится к ячеистым бетонам т.к. до 85% объема материала занимают пузырьки газа. Газобетон обладает превосходными теплоизоляционными характеристиками, имеет небольшую массу и легко поддается обработке. И самое главное — дом из газобетона можно построить самостоятельно, без посторонней помощи (один человек в день может выложить до 3 кубических метров газобетона).

Чтобы более подробно увидеть процесс производства газобетона я отправился на завод Ytong в Можайске, начавший свою работу в 2008 году. По объемам произодства газобетона, это самый крупный завод в России. Смотрим!
2. Для производства газобетона используется безопасное сырье: цемент (~20%), известь (~20%), кварцевый песок (~60%), алюминиевая паста (~1%) и вода. Все компоненты смешиваются в определённых пропорциях, которая определяется требуемой прочностью готовой продукции.
3. Основу газобетона составляет песок, который нужно предварительно обработать.
4. Для этого используются шаровые мельницы.
5. Внутри барабана находятся вот такие шары, которые измельчают песок до превращения в пыль. Это нужно для того, чтобы после формовки блоки было легче обрабатывать.
6. После этого исходное сырье поступает в накопительные бункера на хранение. Затем в газобетоносмесителе происходит смешивание песка, цемента и извести.
7. А непосредственно перед заливкой к уже смешанным компонентам добавляется вода и суспензия алюминиевой пасты. Готовая смесь заливается в специальную прямоугольную форму (стенки формы не имеют жесткого соединения с дном) примерно на 2/3.
8. Именно на этом этапе происходит самое интересное. Алюминиевая паста вступает в реакцию с известью, в результате получается водород. Он образует в сырьевой массе огромное количество пор размером от 0,5 до 2 мм, разномерно распределённых внутри. Поддоны со смесью медленно продвигаются в герметичном помещении с запредельной влажностью (это единственный кадр, который я успел сделать до того, как запотел объектив) до тех пор, пока смесь не увеличится в объеме до верхней кромки поддона.
9. Через некоторое время (2-3 часа) транспортёр переносит форму с застывшей смесью на следующий этап. Показательно, что подъемник только за счёт ваккуума удерживает поддон без дна.
10. Теперь застывшую форму разрезают на блоки равного размера. Сначала в поперечном, а затем продольном направлениях. На заводе одна линия, которая единовременно может производить блоки только одного размера. Для производства блоков другого типоразмера просто заменяют ножи. Большая площадь для складирования готовой продукции позволяет всегда иметь в наличии полный ассортимент продукции.
11. После этого внешняя проверхность блоков шлифуется и затем они прижимаются друг к другу.
12. Кран захватывает поддон с блоками и переносит их на следующий этап производства.
13. И сразу же укладывается новый поддон в основание для следующей партии блоков. Да, очень важный факт — производство на заводе полностью автоматизировано и практически не требует участия человека. Люди работают только на линии упаковки (она пока еще не настолько автоматизирована), складе и в испытательной лаборатории. Всего на заводе работает менее 80 человек (завод работает круглосуточно).
14. Теперь блоки нужно поместить в автоклав. Слева «сырые» блоки, справа уже «готовые». Здесь хочу упомянуть следующий момент, после автоклавирования блоки имеют влажность порядка 30%, которая постепенно (в течение года) упадёт до 5-10%.
15. Автоклавирование очень важный этап, улучшающий свойства газобетонных блоков.
16. Разрезанные блоки помещают в специальные автоклавные камеры, где они в течение 12 часов при повышенном давлении в 12 кг/кв. см. обрабатываются насыщенным паром при температуре 190°C. При этом температура в начале и конце цикла плавно поднимается и опускается в течение определённого времени.
17. Каждый автоклав имеет длину более 30 метров. Использование автоклавирования позволяет повысить прочность газобетонных блоков и уменьшить его последующую усадку (менее 1 мм/м).
18. Каждая партия блоков после автоклавирования отправляется в лабораторию для проверки на соответствие заданным характеристикам. На этом станке нарезаются кубики правильной формы, которые затем отправятся на испытания.
19. А готовые блоки отправляются на линию упаковки. Здесь их складывают в 2 ряда. Позиционирование рядов блоков производят вручную.
20. Затем их переворачивают на бок под уже установленные деревянные паллеты. После чего блоки запечатываются в плёнку (чтобы защитить их от повреждений) и отправляются на склад.
21. Склад расположен под открытым небом, здесь всегда есть запас всей выпускаемой продукции. Ежедневно с завода отгружается покупателям более 2000 кубометров блоков.
22. Основная продукция завода это блоки толщиной от 50 до 500 мм с плотностью от 400 до 500 кг/куб.м.
И ещё несколько слов про различия газобетона и пенобетона. Понятно, что газобетон материал новый, но очень многие неосознанно их путают даже не понимая, что их характеристики существенно отличаются.
Во-первых, их различие кроется в названии. Для производства пенобетона используется пена, состоящая их вредных химических веществ (канифоль, клей, едкий натр и т.д.). А в производстве газобетона используется газ, образующийся в результате химической реакции извести и алюминиевой пасты, в результате получается просто водород. То есть газобетон является экологически чистым строительным материалом.
Во-вторых, пенобетон имеет очень низкие прочностные характеристики. А здесь, как известно, имеет место быть обратная зависимость. То есть, чем ниже плотность (и соответственно прочность), тем «теплее» материал. Но если газобетон плотностью D400 (400 кг/кв.м) можно использовать для несущих стен в домах до 3 этажей включительно и он будет обладать классом прочности В2,5 и морозстойкостью F100, то из пенобетона плотностью ниже D600 вообще нельзя делать несущие стены. Следовательно и теплопроводность пенобетона D600 будет значительно выше (то есть «холоднее»), чем газобетона D400.
В-третьих, технология производства пенобетона обычно не подразумевает использования автоклавов и нарезки блоков после застывания. Обычно его заливают сразу в готовые формы, а в результате блоки дают большую усадку (3-5 мм/м) после строительства. Не говоря уже о том, что сам процесс автоклавирования повышает прочность блоков в 3-4 раза.
Добавлено чуть позже:
Что уже сделано по строительству:
1. Начало
2. Подготовительный этап
3. Стеклопластиковая арматура
4. План дома
5. Земляные работы (часть 1)
6. Земляные работы (часть 2)
7. Фундамент (часть 1)
8. Фундамент (часть 2)
Aerotuff-блоки AAC, самые бетонные цементные блоки. ARL Infratech
AAC или автоклавный газобетон был разработан в Швеции в 1920-х годах с необходимостью сочетания качеств двух самых универсальных и наиболее используемых строительных материалов, дерева и Конкретный. Сформированный таким образом материал превзошел все ожидания, получил широкое признание и используется в качестве основного строительного материала в Европе, России, на Ближнем Востоке, в Японии, Китае, Австралии, Новой Зеландии и т.
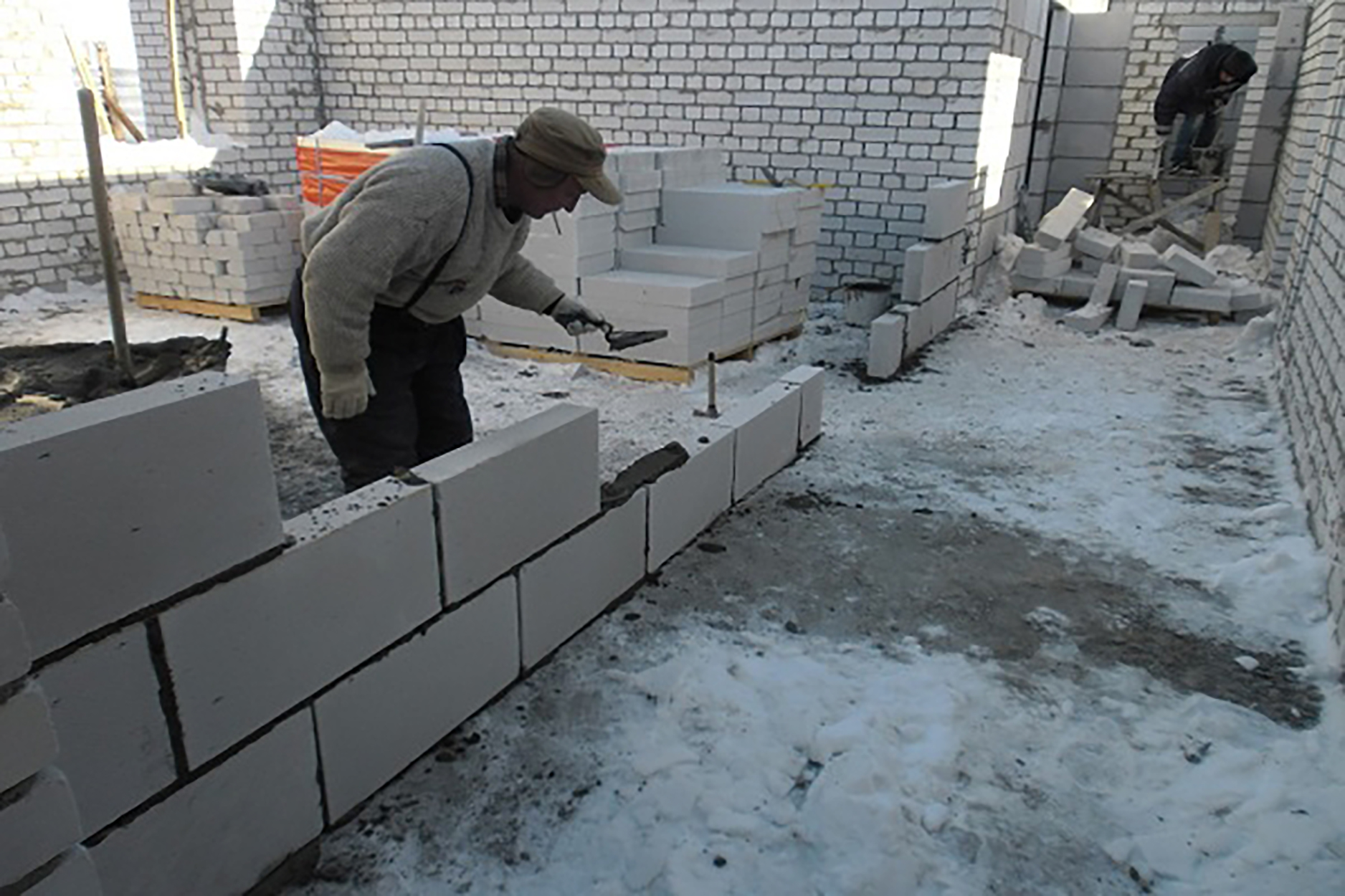
Блоки AAC были недавно представлены в Индии и за короткий промежуток времени стали предпочтительным строительным материалом среди строителей и архитекторов.
Газобетон – экологически чистый строительный материал, обладающий бесчисленными преимуществами, такими как высокое отношение прочности к весу, высокая тепло- и звукоизоляция, простота в обработке, низкий уровень выбросов углекислого газа во время применения и производства и т. д., и считается, что он произвел революцию в строительной отрасли Индии.
Быстрое и простое строительство
Большой и точный размер Большой размер и точная форма и размеры блоков AEROTUFF делают строительство из этих автоклавных бетонных блоков чрезвычайно быстрым и легким. Это также приводит к значительной экономии соединительного раствора и штукатурки и снижению стоимости проекта.
Вес газобетонных блоков AEROTUFF составляет приблизительно 1/3 веса глиняных кирпичей и 1/4 веса обычных бетонных блоков.
Небольшой вес этих блоков приводит к уменьшению статической нагрузки на конструкцию здания и обеспечивает экономию в стоимости конструкции.
Блоки AEROTUFF AAC отличаются гибкостью и простотой работы на стройплощадке. Автоклавные бетонные блоки Aerotuff AAC можно РЕЗАТЬ, СВЕРЛИТЬ, ПРИБИВАТЬ ГВОЗДЯМИ, ГАЗАТЬ по желанию пользователя с помощью простых ручных инструментов и, следовательно, обеспечивают простоту использования.
Поскольку блок AAC очень прост в обращении, манипулировать и использовать обычные инструменты для резки дерева, такие как дрель, ленточные пилы и т. д., можно легко использовать для резки и выравнивания AAC. Кроме того, блоки AAC имеют большие размеры и меньше соединений. В конечном итоге это приводит к ускорению строительных работ
Энергоэффективность и комфортная жизнь
Высокая теплоизоляция Уникальная ячеистая структура блоков AEROTUFF AAC с захваченными пузырьками воздуха обеспечивает им самую низкую теплопроводность среди всех строительных материалов. В связи с растущими затратами на энергию и повышенными требованиями к энергоэффективности многие строители вкладывают средства в специальные методы изоляции, такие как полые стены, наружная облицовка из полиуретана, специальные краски и т. д. Высокая теплоизоляция блоков AEROTUFF AAC делает использование таких дорогостоящих методов совершенно ненужным. . В конечном итоге это приводит к снижению нагрузки на кондиционирование воздуха и, как следствие, к повышению энергоэффективности.
Блоки AEROTUFF AAC обладают очень хорошими акустическими свойствами и значительно снижают шум, проникающий в здание или помещение. Обладая классом звукопропускания до 45, эти блоки демонстрируют лучшую устойчивость к звукопередаче по сравнению с бетонными блоками или глиняными кирпичами эквивалентной толщины. Пористая структура блоков AAC обеспечивает улучшенное звукопоглощение. Класс звукопередачи (STC) AAC блокирует до 45 дБ. Таким образом, блоки AAC были наиболее идеальным материалом для строительства стен в аудиториях, отелях, больницах, студиях и т. д.
AEROTUFF AAC – это нетоксичный продукт, который не загрязняет воздух, землю или воду. В процессе производства отходы резки перерабатываются вместе с сырьем и снова используются. При строительстве практически не образуется отходов. Энергия, потребляемая в производственном процессе, составляет лишь часть по сравнению с производством других материалов. Газобетон производится из натурального сырья. Готовый продукт в три раза превышает объем используемого сырья, что делает его чрезвычайно ресурсосберегающим и экологически безопасным.
Блоки AAC являются признанным зеленым строительным материалом и могут помочь строителям получить дополнительные баллы рейтинга экологичности в соответствии с Системой оценки экологичности зданий LEEDS/GRIHA для сертификации экологичности зданий.
Safe Living
Fire Resistnat «Когда безопасность является проблемой AEROTUFF принимает тепло»
Блоки AEROTUFF AAC обладают лучшей в своем классе огнестойкостью с пределом огнестойкости 4-6 часов. в зависимости от толщины блоков.
Блоки изготовлены из неорганического материала, поэтому они не воспламеняются и не выделяют токсичных газов, а также соответствуют классу «0» по распространению пламени
Несоединяющаяся ячеистая структура блоков AEROTUFF AAC предотвращает проникновение воды через блоки и обеспечивает прочный водный барьер. Эта структура крошечных пузырьков усиливается в процессе автоклавирования и, следовательно, обеспечивает длительное сопротивление просачиванию воды через стены AAC.
Устойчивость к вредителям Минеральный состав и твердая структура блоков AEROTUFF AAC делают их устойчивыми ко всем видам вредителей, плесени, насекомых и т. д. Блок из автоклавного газобетона (AAC) состоит из неорганического материала по своему составу, который помогает предотвратить и избежать термитов, повреждений или потерь от вредителей и грызунов и т. д. аналогичные или улучшенные свойства. Благодаря этому строители получают дополнительную площадь ковра в своих зданиях с той же площадью застройки.
Шаг к
Устойчивый рост Устойчивое будущее возможно только при признании средств устойчивого развития
Когда речь идет о снижении воздействия на окружающую среду, блоки AEROTUFF AAC намного опережают своих конкурентов.
Топ
АВТОМАТИЗИРОВАННАЯ ЛИНИЯ ПО ПРОИЗВОДСТВУ ПЕТРОБЕТОННЫХ БЛОКОВ С ЗОЛЬНЫМ ЗАПОЛНИТЕЛЕМ. Производительность 50 м3/смена
Характеристики линии
Емкость | 50 м 3 /смена (100 м 3 /день) |
Потребляемая мощность | 54 кВт/ч (без нагрева воды) |
Использование воды | ~13 тонн/смена |
Использование цемента | ~12,5 тн/смена |
Утилизация летучей золы | ~10,5 тонн/смена |
Производство | блоки стеновые мелкие по ГОСТ 21520-89 |
Требуемая площадь производственного помещения | 500-1000 м 2 |
Высота потолка в зоне смешения | не менее 6 м* |
Высота потолка в производственной зоне | не менее 3 м* |
Температура окружающей среды | не ниже +15 o С |
Требуемый персонал | 6 рабочих, 1 начальник производства/прораб |
ПРЕИМУЩЕСТВА
Автоматизация управления процессами
На производственных линиях используются электронные системы для контроля загрузки и дозирования сырья в зоне смешивания.
Точность дозирования
Сырье подается на весы с тензодатчиками и весовым контроллером, позволяющим точно дозировать.
Большая емкость
Высокая производительность обеспечивается автоматизированной системой загрузки и дозирования сырья, а также высокой скоростью заполнения смесителя водой и сырьем. Мощный раскройный станок обеспечивает высокую скорость резки монолита на блоки заданного размера.
Высокое качество
Система автоматизации технологических процессов обеспечивает высокое качество продукции и гарантирует точность дозирования, а также стабильный и однородный состав, что позволяет нам предоставлять качественную и конкурентоспособную продукцию.
СЫРЬЕ ДЛЯ ПРОИЗВОДСТВА ЯБЕТОНА
- Вяжущее.
Портландцемент ПЦ-500 Д0, ПЦ-400 Д20 ГОСТ30515 и ГОСТ 10178 применяется в качестве вяжущего для газобетонных изделий.
- Кремнеземный компонент. Зола-унос применяется для ТЭЦ с содержанием SiO2 не менее 45%, CaO не более 10%, R2O не более 3%, SO3 не более 3%.
- Вода для затворения. Вода соответствует требованиям ГОСТ 23732.
- Разделительная смазка для форм. Смазки для форм SDF или другие антиадгезивы используются для обеспечения эффективного удаления форм.
- Укрепляющие агенты. Полипропиленовые волокна диаметром 12 мм используются в качестве армирующего агента.
- Модифицирующие агенты . ГОСТ 24211
- Газообразующие вещества. Алюминиевая пудра или пыль на ее основе применяются в качестве газообразователя.
ОБЗОР ПРОЦЕССА
1. Производство газобетонных смесей
Заполнение миксера водой
Для дозирования воды используется электронный счетчик воды. Оператор участка смешивания набирает необходимое количество воды и запускает цикл загрузки смесителя.
Загрузка сырья в смеситель
Весовой контроллер используется для загрузки сырья (цемента, золы-уноса) в весы и реагентов в весы химических добавок. Цемент, зола-уноса и добавки транспортируются винтовыми конвейерами. Цемент и летучая зола теперь выгружаются из весов в смеситель. Раствор перемешивают в течение 2–3 минут до достижения однородности. Когда раствор готов, добавки выгружают в смеситель и снова перемешивают газобетонную смесь в течение 1–2 минут.
Оператор контролирует все процессы на участке смешивания в режиме реального времени. Оператор может использовать панель управления для исправления или изменения рецепта, времени смешивания и других параметров процесса.
Оборудование поддерживает как ручной, так и автоматический режимы.
2. Монолитный молдинг
По готовности газобетонная смесь выгружается в форму 0,85 м 3 через вентиль смесителя. Форма заполняется за один раз. Состоит из основания и съемных сменных боковин. Перед заполнением форму смазывают и транспортируют в зону смешивания для заполнения.
3. Отверждение газобетонных монолитов
Заполненная форма транспортируется по рельсам в зону твердения (в камеру термообработки), где монолит достигает отрывной прочности. Заказчику рекомендуется предусмотреть герметичные туннельные камеры с полной теплоизоляцией по всем поверхностям. Температура в камере должна быть +30…+40 о С. Достижение отрывной прочности может занять от 3 до 5 часов и зависит от плотности, активности газобетона, типа кремнезема, температуры и т.д.
4. Демонтаж форм и резка массивов
После набора массивом необходимой прочности форму, содержащую массив, передают к демонтажной машине по рельсовым путям, основание формы закрепляют на рельсовом пути. Затем четыре стенки формы снимаются и поднимаются с помощью захвата. После демонтажа формы основу формы и массив переносят на участок резки. Затем свободные стены крепятся к свободному основанию, которое находится на соседней железной дороге. Закрытая форма направляется в секцию заливки. Массив разрезается на блоки заданных размеров на режущем агрегате АРК-004. На раскройном участке расположены два отдельных последовательных модуля для вертикальной и горизонтальной резки массива.
Основание пресс-формы фиксируется захватом на вертикальном модуле, в то время как оператор запускает вертикальный модуль. Двигаясь по направляющим, модуль рассекает массив в вертикальной плоскости и подрезает его с обоих концов. После вертикальной резки основание формы с массивом переносится в зону горизонтального модуля, фиксируется захватом, после чего разрезается в горизонтальной плоскости на блоки заданных размеров, а также нижний слой и верхушка срезана. Пока работает горизонтальный модуль, в зону вертикального модуля подается очередной массив. Таким образом, происходит резка двух массивов одновременно, что обеспечивает высокую производительность линии.
5. Укладка блоков на поддоны, упаковка и хранение
Форма-основа с вырезанным массивом передается на узел укладки блоков. Основание пресс-формы фиксируется на рельсе. Затем половину распила массива с помощью захвата укладывают на поддон. Для того, чтобы укомплектовать поддон, восемь блоков укладываются вручную. Затем укладывается вторая половина массива, а также восемь блоков вручную (в зависимости от их габаритов). Поддон с блоками обтянут стрейч-пленкой.
6. Блок тепловлажностной обработки
В зависимости от климатической зоны и вида изготавливаемого материала блоки, укладываемые на поддоны, могут набирать сортную прочность на складе готовой продукции или при термовлажностной обработке. Термовлажностная обработка блоков необходима для ускорения набора прочности блоков. Тепловлагообработка заключается в том, что блоки выдерживают в камере от 8 до 12 часов при температуре от +40 до 60оС. Режим тепловлажностной обработки также зависит от плотности материала, активности цемента и определяется заказчиком для каждого конкретного вида выпускаемой продукции.
7. Переработка отходов резки
Режущие модули вырезают монолит с обоих концов, сверху и снизу. Инновационным решением является использование измельчителя отходов DG-1 для переработки отходов резки. Он позволяет измельчать отходы газобетона до частиц размером до 0–30 мм. Измельченный материал можно использовать в качестве насыпного утеплителя крыш, чердаков, пола и т. д. Измельчитель делает производство бетона практически безотходным.
ЛИНИИ ХАРАКТЕРИСТИКИ
Н | Имя | Количество |
Участок хранения, подготовки и отгрузки сырья | ||
1 | Шнековый конвейер для цемента (L = 6 м*, мотор-редуктор (Италия), N = 4 кВт) | 1 |
2 | Винтовой транспортер золы-уноса (L = 6 м*, мотор-редуктор (Италия), N = 4 кВт) | 1 |
Зона смешивания | ||
1 | Электронная система управления (со встроенным счетчиком воды + подкачивающий насос) | 1 |
2 | Весовой дозатор (тензодатчики, пневмоклапан, макс.![]() | 1 |
3 | Весы химических примесей ДХД-1 (N = 0,5 кВт) | 1 |
4 | Газобетономешалка ГБ-0,85 (N = 11 кВт, V = 0,85 м3 3 ) | 1 |
5 | Компрессор C200LB40 (500 л/мин, 8–10 атм.) | 1 |
Область резки монолита | ||
1 | Автоматизированный раскройный комплекс АРК-004 (N – 19,5 кВт) | 1 |
2 | Форма ФМ-0,91 м 3 для газобетонных монолитов (V = 0,91 м 3 ). | 55 |
3 | Трансферная тележка | 4 |
4 | Комплекс для демонтажа пресс-форм (N = 2,0 кВт) | 1 |
5 | Комплекс для укладки блоков на поддоны (N=2,5 кВт) | 1 |
Зона измельчения отходов резки | ||
1 | Измельчитель ДГ-1 (N = 4,5 кВт) | 1 |
РАСХОД МАТЕРИАЛА* НА 1 м
3 НЕАВТОКЛАВИРОВАННОГО ПЕНОБЕТОН Д-600Материал | Количество |
Цемент (ПЦ500 Д0), кг | 250 |
Зола-унос, кг | 210 |
Вода, л | 250 |
Газообразующий агент, кг | 0,5-1,5 |
Волокно, кг | 0,6 |
Химические добавки, кг | ** |
* Рецептуры корректируются с учетом свойств сырья, выбранного заказчиком.
** Тип и количество добавок определяются на этапе проектирования бетона.
ОБЩИЙ
Для снижения затрат заказчика линия поставляется без силоса для цемента, бункера для песка и перил для транспортировки формы. Заказчику предоставляются чертежи для самостоятельного изготовления этих узлов.
Кроме того, заказчик несет ответственность за подогрев воды до +35…+40°С и устройство пропарочных камер. Работа линии в 2 смены требует дополнительных фундаментов опалубки.
Гарантийный срок на поставляемое оборудование составляет 12 месяцев. Комплектация каждой единицы оборудования указана в договоре, паспорте оборудования и Акте сдачи-приемки.
Специалисты «Сибирских строительных технологий» (СКТ) проектируют размещение оборудования на производственном объекте заказчика. Оборудование устанавливается по макету силами и за счет заказчика. Заказчику предоставляется схема расположения оборудования (чертежи) для соответствующих помещений и подробная иллюстрированная инструкция по установке.
После того, как заказчик завершит монтаж и подключение оборудования, СКТ выполняет следующие работы:
• ввод оборудования в эксплуатацию;
• проектирование газобетона;
• оптимизация технологии производства;
• обучение персонала заказчика.
Заказчик несет ответственность за соблюдение всех правил техники безопасности, требований по охране труда и окружающей среды, а также других локальных нормативных актов.
Заказчик берет на себя все расходы по транспортировке и размещению персонала SCT на период проведения работ. Оптимизация технологии включает в себя оптимизацию состава бетона на основе предоставленного заказчиком сырья. SCT предоставляет услуги поддержки.
После ввода оборудования в эксплуатацию заказчику предоставляется техническая документация, включающая:
• технические регламенты на производства;
• технологическая схема;
• должностные инструкции;
• инструкции по технике безопасности;
• ГОСТ.