Газобетон вес 1 м3: сколько весит газобетон 1 м3, газобетонный блок 600х300х200, газосиликатный поддон 600х400х250, удельный сибит
газобетон и газоблок по оптовой цене»
Використання при будівництві самих сучасних матеріалів дозволяє зводити якісні, міцні і надійні споруди з максимально тривалим терміном експлуатації. Час від часу на ринку будівельних матеріалів з’являються нові продукти, ще більш досконалі і висококласні. Наприклад, колись на зміну звичайному цеглі прийшли газобетонні блоки, які значно перевершують його в міцності і мають більш незначну вагу. Особливі властивості подібних блоків зробили їх неймовірно популярними серед будівельних компаній різної величини, адже блоки з газобетону дозволяють зводити будівлі відмінної якості висотою до 15 метрів.
При цьому вага газобетонного блоку є одним із самих головних його властивостей, унікальна технологія виробництва дозволяє значно скоротити вагу блоку в залежності від його щільності. На даний момент кожен бажаючий може дізнатися, скільки важить газобетонний блок використовуючи для прорахунку спеціальну формулу. Проте виробники і компанії, що займаються продажем даного будівельного матеріалу пропонують готовий прайс в якому можна знайти всю необхідну інформацію про вагу газобетонних блоків.
На ринку можна зустріти такі моделі газобетонних блоків як: D700, D600, D500. Вони вказують на щільність блоку, яка задається ще на етапі виробництва. В основному своїм незначною вагою блоки зобов’язані пористості, яка і визначається вищевказаної маркуванням. Так само на вагу газобетонного блоку впливає його розмір, який може значно відрізнятися, а дізнатися його можна вимірявши куб або заздалегідь вибравши продукцію потрібного розміру. Маркування D700 говорить про те, що куб з газобетону розміром в один метр буде важити 700 кг, тому знаючи кількість блоків в одному такому кубі можна з легкістю розрахувати вагу газобетонного блоку.
Знаючи, скільки важить газобетонний блок, можна приблизно розрахувати витрати на транспортування даного будівельного матеріалу. Це вкрай актуально для великих компаній, які займаються масштабним будівництвом і повинні ретельно розраховувати свій бюджет. Подібного роду інформація може бути корисна і звичайним покупцям, охочим придбати потрібну кількість матеріалу з газобетону. Знаючи загальний або хоча б приблизний вага партії газобетонних блоків можна розрахувати час і сили на її завантаження і розвантаження. Варто зауважити, що вага одного газобетонного блоку може знаходитися в межах від 10,8 до 38,7 кілограм.
Скільки важить 1 куб газоблоку d600, стінових блоків з ніздрюватого бетону, вага 1 м3 газоблоку d600, піноблоку. Кількість кілограм на 1 кубічний метр газоблоку Д600 (розміри 600 х 300 х 100, 600 х 300 х 200, 600 х 300 х 400), кількість тонн на 1 кубометрі ніздрюватих блоків, газобетонних піноблоку d 600, кг на 1 м3 газобетонних каменю. Об’ємна щільність газоблоку d600 питома вага газосилікатні блоки, піноблоку d600 (625х100х250, 625х150х250, 625х200х250, 625х240х250, 625х300х250, 625х400х250).
Що ми хочемо дізнатися сьогодні дізнатися?
Скільки важить 1 куб газоблоку d600, піноблоку, вага 1 м3 газоблоку d600, газосилікату?
Немає проблем, можна дізнатися кількість кілограм або кількість тонн відразу, маса ніздрюватих блоків (вага одного кубометра газосилікатні блоки Д600, вага одного куба газоблоку Д600, вага одного кубічного метра піноблоку Д 600, вага 1 м3 газосилікатні каменю) вказані в таблиці
1. Якщо комусь цікаво, можна пробігти очима невеликий текст нижче, прочитати деякі пояснення. Як вимірюється потрібну нам кількість речовини, матеріалу, рідини чи газу? За винятком тих випадків, коли можна звести розрахунок потрібної кількості до підрахунку товару, виробів, елементів в штуках (поштучні підрахунок), нам найпростіше визначити потрібну кількість Виходячи з обсягу і ваги (маси).
В побутовому відношенні самою звичною одиницею виміру обсягу для нас є 1 літр. Однак, кількість літрів, придатної для побутових розрахунків, не завжди застосовні спосіб визначення об’єму для господарської діяльності. Крім того, літри в нашій країні так і не стали загальноприйнятою «виробничої» та торгової одиницею виміру обсягу.
Один кубічний метр або скорочено варіанті ― один куб, виявився досить зручним і популярної для практичного використання одиницею об’єму. Практично всі речовини, рідини, матеріали і навіть гази ми звикли вимірювати в кубометрах. Це дійсно зручно. Адже їх вартість, ціни, розцінки, норми витрати, тарифи, договору на поставку майже завжди прив’язані до кубічних метрів (кубах), набагато рідше до літра.
НЕ менш важливим для практичної діяльності виявляється знання Не тільки обсяг, але і ваги (маси) речовини, що займає цей обсяг: в даному випадку мова йде про те скільки важить 1 куб газосилікатні блоки (1 кубометр ніздрюватих блоків, газобетонних піноблоку d 600, 1 метр кубічний газобетонного каменю, 1 м3 піноблоки d600).
Знання маси і об’єму, дають нам досить повне уявлення про кількість піноблоку d600. Відвідувачі сайту, запитуючи скільки важить 1 куб газосилікату Д600, часто вказують конкретні одиниці маси, до яких їм хотілося б дізнатися відповідь на це питання. Як ми помітили, найчастіше хочуть дізнатися вага 1 куба газосилікатних каменю (1 кубометра ніздрюватих блоків, 1 кубічний метр газосилікатні блоки, 1 м3 газобетонних каменю) в кілограм (кг) або в тоннах (тн).
По суті, потрібні кг / м3 або тн / м3. Це тісно пов’язані одиниці визначають кількість газосилікатні каменю. В принципі можливий досить простий самостійний перерахунок ваги (маси) стінових бетонних піноблоків з тонн в кілограми і назад: з кілограмів до тонни.
Однак, як показала практика, для більшості відвідувачів сайту більш зручними варіантом було б відразу дізнатися скільки важить кілограм 1 куб (1 м3) газоблоку d600 (розміри 600 х 300 х 100, 600 х 300 х 200, 600 х 300 х 400), газобетонного піноблоку d 600 або скільки тонн важить 1 куб (1 м3) газоблоку d600 (625х100х250, 625х150х250, 625х200х250, 625х240х250, 625х300х250, 625х400х250), без перерахунку кілограм тонни або назад ― кількість тонн у кілограми на один метр кубічний (один кубометр, один куб, один м3).
Тому, у таблиці 1 ми вказали скільки важить 1 куб газосилікатні каменю Д 600 (1 кубометр ніздрюватих блоків, 1 метр кубічний газобетонного каменю) в кілограм (кг) і в тоннах (тн). Вибирайте той стовпчик таблиці, які вам потрібен самостійно. До речі, коли ми запитуємо скільки важить 1 куб (1 м3) піноблоку d600, ми маємо на увазі кількість кілограм газосилікатні каменю або кількість тонн стінових блоків з ніздрюватого бетону.
Однак, з фізичної точки зору нас цікавить щільність газобетонного піноблоку d 600 або питома вага стінових матеріалів для кладки стін будинку з ніздрюватого бетону. Маса одиниці об’єму або кількість речовини міститься в одиниці об’єму ― це об’ємна щільність або питома вага.
В даному випадку об’ємна щільність газобетонного каменю і питома вага газоблоку d600 ― стінових цеглин з ніздрюватого газобетону. Насипну щільність стінових блоків з ніздрюватого бетону і питома вага газобетонного каменю Д 600 у фізиці прийнято вимірювати не в кг / м3 або в тн / м3, а в грамах на кубічний сантиметр: гр / см3. Тому в таблиці 1 питома вага газосилікатні блоки і щільність газоблоку d600, стінових бетонних піноблоків (синоніми) вказані в грамах на кубічний сантиметр (г / см3).
Розміри і вага газосилікатних блоків.Газосилікатні блоки можуть мати різні розміри в залежності від заводу-виробника. Але найчастіше зустрічаються такі розміри: 600х200х300 мм, 600х100х300 мм, 500х200х300 мм, 250х400х600 мм, 250х250х600 мм і т. д.
Вага газосилікатного блоку
Вага блоків може відрізнятися в залежності від щільності. Для прикладу в таблиці нижче наведено вага блоків основних типорозмірів в залежності від щільності:
Щільність блоку | Розмір блоку, мм | Вага блоку, кг |
D700 | 600x200x300 | 20-40 |
D700 | 600x100x300 | 10-16 |
D500-D600 | 600x200x300 | 17-30 |
D500-D600 | 600x100x300 | 9-13 |
D400 | 600x200x300 | 14-21 |
D400 | 600x100x300 | 5-10 |
Плюси і мінуси газосилікатних блоків
До плюсів блоків з газосилікату можна віднести наступні якості:
- мала вага;
- достатня для малоповерхового будівництва міцність;
- хороші теплотехнічні характеристики;
- звукоізоляційні властивості;
- низька ціна;
- вогнестійкість.
Але є у них і свої недоліки, до яких можна віднести:
- необхідність навички зведення стін на спеціальних клеях;
- необхідність зовнішньої обробки для підвищення естетичності вигляду стін;
- висока паропроникність і гігроскопічність;
- необхідність міцного фундаменту для зведення стін.
Через гігроскопічність матеріалу, його не бажано використовувати в приміщеннях з підвищеною вологістю без спеціальної обробки, не пропускає вологу до стін з газосилікату.
Вартість блоків з газосиликона
Судячи з прайс-листами, поданими в інтернеті на сайтах заводів виробників, вартість одного блоку розміром 600х100х300 мм становить приблизно $1,8-1,9 за штуку, а блок розміром 600х200х300 обійдеться вам приблизно в $3 за 1 шт.
Ціни вказані на момент написання публікації та можуть відрізнятися від поточних цін на ринку, тому при необхідності уточнюйте актуальну вартість у виробників.
Види блоків по щільності
В залежності від щільності всі газосилікатні блоки прийнято ділити на конструкційні, конструкційно-теплоізоляційні і теплоізоляційні.
До конструкційних блоків відносять блоки з щільністю не нижче D700. Такий матеріал можна використовувати для будівництва несучих стін в будинках-до 3 поверхів.
Конструкційно-теплоізоляційні блоки мають щільність від D500 до D700. Такі блоки добре підійдуть для влаштування міжкімнатних перегородок, а також стін будівель висотою не більше 2 поверхів.
Теплоізоляційні газосилікатні блоки мають високу пористість і саму низьку міцність. Володіючи щільністю D400, такі блоки знайшли своє застосування в якості матеріалу підвищує теплотехнічні характеристики стін, виконаних з найменш енергоефективних матеріалів.
Теплопровідність газосилікатних блоків
За своїми показниками теплопровідності блоки з газосилікату мають досить високі характеристики. Значення теплопровідності в залежності від щільності наведені в таблиці нижче:
Марка газосилікатного блоку | D400 і нижче | D500-D700 | D700 і вище |
Теплопровідність, Вт/м°С | 0,08-0,10 | 0,12-0,18 | 0,18-0,20 |
Морозостійкість газосилікатних блоків
Морозостійкість блоків залежить від обсягу пір і, як правило, витримують від 15 до 35 циклів заморожування-розморожування.
Але, деякі сучасні підприємства, які вже освоїли випуск газосилікатних блоків з заявленої морозостійкістю від 50 до 75 і навіть до 100 циклів.
Однак, в середньому, у відповідності з ГОСТ 25485-89 слід орієнтуватися на показник морозостійкості блоків щільністю D500 рівний 35 циклів.
Виробництво газосилікатних блоків
До складу суміші для виробництва газосилікату входять:
- високоякісний портландцемент, що містить не менше 50% силікату кальцію;
- пісок з вмістом кварцу не менше 85% і включенням мулистих і глинистих частинок не більше 2%;
- вапно-кипелка зі швидкістю гасіння 5-15 хв і вмістом оксиду кальцію та оксиду магнію не менше 70%;
- газоутворювач з алюмінієвої пудри;
- сульфанол С;
- вода.
Блоки з газосилікату можуть виготовлятися як з використанням автоклава, так і без нього. При цьому, автоклавний спосіб дозволяє отримати блоки з більш високими характеристиками міцності і усадки при висиханні.
Блоки, що виготовляються без використання сушіння в автоклаві, мають в п’ять разів більшу усадку, ніж блоки, просушені в автоклаві, а також гірші показники міцності. Але при цьому коштують дешевше.
Автоклавний спосіб виготовлення застосовується на великих підприємствах, так як цей спосіб досить технологічний і вимагає великої кількості енергії. Пропарюють блоки з газосилікату при температурі до 200 градусів при тиску до 1,2 МПа.
Змінюючи процентне співвідношення інгредієнтів, що входять до складу суміші для приготування газосилікату, можна змінювати характеристики одержуваного матеріалу. Так, збільшуючи вміст цементу, можна підвищити міцність виробу, але при цьому зменшиться кількість часу, що в кінцевому підсумку вплине на його теплотехнічні характеристики, збільшивши значення теплопровідності.
Нові технології створюють гідну конкуренцію природним будівельним матеріалам. При цьому створені людиною склади несуть в собі властивості, за Які нам полюбилися натуральні вироби. Є потреби описувати всі достоїнства дому з натурального дерева, але є потреба описати матеріал для зведення будинку, що володіє структурою, притаманною дереву. Такими властивостями технологи наделилы матеріали, що відносяться до блоків з ніздрюватого бетону.
Спробуємо розібратися, чим відрізняється піноблок від газосилікатні блоки. Як вже зазначалося в них спільне походження: бетонний розчин нафаршировалы порожнечами, що значно збільшило їх теплоізоляцію та зменшили вагу. А от далі вже йде відміну піноблоку від газосилікатні блоки. По перше відрізняється технологія появи бульбашок в обох структурах.
Якщо у випадку з пінобетоном до складу суміші додають спеціальні речовини (вапно і алюмінієвий пил), які при перемішування починають реагувати між собою з виділенням водню, то у другому випадку до складу вноситься речовина ― піноутворювач. Обидва варіанти застигають до того, як газ або бульбашки повітря покинуть структуру. Піноблоки і газосиликатні блоки відміну мають у структурі самих бульбашок. У першому варіанті вони, як і при будь-якої хімічної реакції, Намагаються покинуть межі реакційний суміші, спрямовуючись угору.
У другому ― піноутворювач тримає повітря в замкнутій системі до тих пір, поки вистачає у нього сил, після чого бульбашки починають лопатися, ущільнює структуру. За рахунок характеру бульбашок газосилікатні блоки і піноблоки відміну мають в плані гігроскопічності. Волозі важче потрапити в замкнуті осередки пінобетону, а порожнечі газобетону утворюють вертикальні доріжки, по Яких намагався вирватися газ, і за них простіше волозі потрапити всередину.
За розміром і кількістю пустот, обох видів блоків, їх поділяють на:
• Конструкційні (невелика кількість дрібних пір),
• теплоізоляційні (багато великих пор),
• конструкційно-теплоізоляційні (проміжний між двома різновидів).
За популярністю використання різновидів, відмінність газосилікатні блоки і піноблоки не мають. В обох типах широко використовується в будівництві як раз проміжний варіант, який об’єднав в собі здатність утримувати несучу конструкцію і добре зберігати тепло. Відмінність піноблоки і газосиликатні блоки не мають і в плані маркування виробів. На маркуванні обов’язково Повинні знаходиться відомості про водопоглинання, морозостійкості, міцності і щільності.
Чим відрізняються піноблоки від газосилікатних блоків в плані технології виробництва? Для виробництва газобетону склад, виготовлений згідно з рецептурою, заливають у велику ємність, де проходить процес газоутворення. Далі форму відправляють у величезний автоклав, де відбувається пропарювання суміші під тиском. Затверділий матеріал піддають сегментації за визначеними розмірами допомогою натягнутої струни. При разрезаниы блоків від струни залишається специфічна Шорсткість поверхні ― відмінність газосилікатні блоки від піноблоку.
При виготовленні пінобетону, змішаний в бетономішалку склад, заливають у форму з отворами. За технологією термін перебування суміші в формі становить 28 днів. Газосилікат або піноблок можна відрізнити по ідеально гладкої поверхні останнього. Гладкі боку блоку не дають можливості легкого проникнення вологи ззовні.
Чем отличается пеноблок от газосиликатные блоки в плане прочности? Если сравнивать два блока одинаковой прочности, то выяснится, что газоблок окажется несколько легче, что говорит о его большей пористости, при аналогичной способности выдерживать нагрузку. Пенобетон, как и все производные цемента, имеют период усадки. В период разгара строительных работ вы рискуете купит «свеженькие» блока, не прошедшие усадку, что незамедлительно скажется на качестве сооружения.
Каждый материал, пеноблок или газосиликат, имеют свои особенности. В любом случае, потребитель НЕ окажется в проигрыше, Выбрав один из них. Поскольку получив НЕ дорогой материал, сможет сэкономить на вторых конструкционных деталях. Так для несущих конструкций, будь то газосиликатные блоки или пеноблоки, можно делать облегченный фундамент, использовать меньше арматуры в перекрытиях и т. Д.
Можно до бесконечности описывать, чем отличаются газосиликатные блоки от пеноблоков. Все зависит от конкретной ситуации и от ожидаемого результата.
Статьи pp-budpostach.com.ua Все о бане
Статті по пїноблоку,пінобетону,пінобетонним блокам
Статті pp-budpostach.com.ua Статті по бетону
Статті Все про парканах
Статті pp-budpostach.com.ua Все про дахах ( види, матеріал, як краще вибрати)
Статті Все про Фундаменті
Статті по газобетону ( газоблокам ), газобетонних блоків, блоків газосиликатнных
Новини, статті, чутки, факти, різне і по чу-чуть
Статті по цеглині ( рядовому, особового,облицювальної,клинкерному, шамотною, силікатній,)
Газобетонные блоки НЛМК Липецк Hebel 600x250x250 на поддоне в плёнке. Продукция завода
- Главная
- Каталог продукции
- Блоки стеновые
- Газосиликатные блоки
4500.00 руб M3
Добавить в корзину
Газобетонный блок стеновой НЛМК Липецк Hebel, размер 600x250x250, на деревянном поддоне в упаковке из стрейч-пленки синего цвета ГОСТ 31359-2007, ГОСТ-31360-2007 Марка по плотности (кг/м3) D-500, класс по прочности на сжатие B 2,5 и D-600, класс по прочности на сжатие B 3,5 морозостойкостью 100 циклов F-100. Теплопроводность, 0,12 Вт/(м·°С). Паропроницаемость, 0,20 мг/(м·ч·Па). Количество на поддоне 1,35 м3 (36 штук), объем блока 0,0375 м3, вес 1-го блока: – 25,3-30,4 кг. Вес поддона 950 кг., размер поддона: длина – 1200 мм; ширина – 800 мм; высота пакета – 1600 мм.
Газобетонные блоки автоклавного твердения Hebel ПАО «НЛМК» производят в Липецке на оборудовании «Hebel International GmbH&Co» (Германия). Строительные изделия из газобетона выпускают по технологии немецкой фирмы «Хебель». В производственной линейке представлен огромный ассортимент изделий из ячеистого бетона. Завод выпускает стеновые блоки различных марок по плотности D-200, D-300, D-400, D-500 и D600, и классами прочности B 0,35; В 0,75; В 1,0; В 1,5; В 2,0; В 2,5; В 3,5; В 5,0. Длиной 600 мм. и шириной 200 мм., 250 мм., 300 мм., 350мм., 375 мм., 400мм., и 500 мм. Газобетон — разновидность ячеистого бетона, получаемая из смеси вяжущего, песка, воды и газообразователя. В качестве вяжущего используется смесь портландцемента и извести-кипелки.
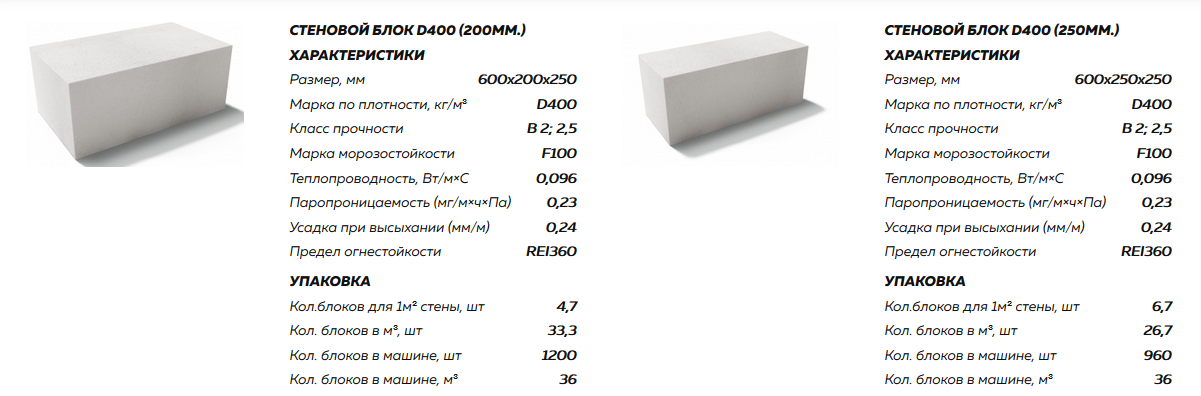
АВТОМАТИЗИРОВАННАЯ ЛИНИЯ ПО ПРОИЗВОДСТВУ ГЕБЕТОННЫХ БЛОКОВ С ПЕСКОМ ЗАПОЛНИТЕЛЕМ, производительностью 50 м3/смена
Технические характеристики линии
Емкость | 50 м 3 /смена (100 м 3 /день) |
Потребляемая мощность | 54 кВт/ч (без нагрева воды) |
Использование воды | ~11 тонн/смена |
Использование цемента | ~14 тонн/смена |
Использование песка | ~10,5 тонн/смена |
Производство | блоки стеновые мелкие по ГОСТ 21520-89 |
Требуемая площадь производственного помещения | 500-1000 м |
Высота потолка в зоне смешения | не менее 6 м* |
Высота потолка в производственной зоне | не менее 3 м* |
Температура окружающей среды | не ниже +15 o С |
Требуемый персонал | 6 рабочих, 1 начальник производства/прораб |
ПРЕИМУЩЕСТВА
Автоматизация управления процессами
На производственных линиях используются электронные системы для контроля загрузки и дозирования сырья в зоне смешивания.
Точность дозирования
Сырье подается на весы с тензодатчиками и весовым контроллером, позволяющим точно дозировать.
Большая емкость
Высокая производительность обеспечивается автоматизированной системой загрузки и дозирования сырья, а также высокой скоростью заполнения смесителя водой и сырьем. Мощный раскройный станок обеспечивает высокую скорость резки монолита на блоки заданного размера.
Высокое качество
Система автоматизации технологических процессов обеспечивает высокое качество продукции и гарантирует точность дозирования, а также стабильный и однородный состав, что позволяет нам предоставлять качественную и конкурентоспособную продукцию.
СЫРЬЕ ДЛЯ ПРОИЗВОДСТВА ЯБЕТОНА
- Вяжущее.
Портландцемент ПЦ-500 Д0, ПЦ-400 Д20 ГОСТ30515 и ГОСТ 10178 применяется в качестве вяжущего для газобетонных изделий.
- Компонент кремния. Песок применяемый соответствует ГОСТ 8736 и содержит не менее 90 % SiO2 или не менее 75 % кремнезема, не более 0,5 % слюды, не более 3 % щебня и глины.
- Вода для затворения. Вода соответствует требованиям ГОСТ 23732.
- Разделительная смазка для форм. Смазки для пресс-форм SDF или другие антиадгезивы используются для обеспечения эффективного удаления пресс-форм.
- Укрепляющие агенты. Полипропиленовые волокна диаметром 12 мм используются в качестве армирующего агента.
- Модифицирующие агенты . ГОСТ 24211
- Газообразующие вещества.
ОБЗОР ПРОЦЕССА
1. Производство газобетонной смеси
Заполнение миксера водой
Для дозирования воды используется электронный счетчик воды. Оператор участка смешивания набирает необходимое количество воды и запускает цикл загрузки смесителя.
Загрузка сырья в смеситель
Весовой контроллер используется для загрузки сырья (цемента, песка) в весы и реагентов в весы химических добавок. Цемент и добавки транспортируются винтовыми конвейерами, а песок загружается ленточным конвейером. Цемент и песок теперь выгружаются из весов в смеситель. Раствор перемешивают в течение 2–3 минут до достижения однородности. Когда раствор готов, добавки выгружают в смеситель и снова перемешивают газобетонную смесь в течение 1–2 минут.
Оператор контролирует все процессы на участке смешивания в режиме реального времени. Оператор может использовать панель управления для исправления или изменения рецепта, времени смешивания и других параметров процесса.
Оборудование поддерживает как ручной, так и автоматический режимы.
2. Монолитный молдинг
По готовности газобетонная смесь выгружается в форму 0,85 м 3 через вентиль смесителя. Форма заполняется за один раз. Состоит из основания и съемных сменных боковин. Перед заполнением форму смазывают и транспортируют в зону смешивания для заполнения.
3. Отверждение газобетонных монолитов
Заполненная форма транспортируется по рельсам в зону твердения (в камеру термообработки), где монолит достигает отрывной прочности. Заказчику рекомендуется предусмотреть герметичные туннельные камеры с полной теплоизоляцией по всем поверхностям. Температура в камере должна быть +30…+40 оС. Достижение отрывной прочности может занять от 3 до 5 часов и зависит от плотности, активности газобетона, типа кремнезема, температуры и т.д.
4. Демонтаж форм и резка массивов
После набора массивом необходимой прочности форму, содержащую массив, передают к демонтажной машине по рельсовым путям, основание формы закрепляют на рельсовом пути. Затем четыре стенки формы снимаются и поднимаются с помощью захвата. После демонтажа формы основу формы и массив переносят на участок резки. Затем свободные стены крепятся к свободному основанию, которое находится на соседней железной дороге. Закрытая форма направляется в секцию заливки. Массив разрезается на блоки заданных размеров на режущем агрегате АРК-004. На раскройном участке расположены два отдельных последовательных модуля для вертикальной и горизонтальной резки массива.
Основание пресс-формы фиксируется захватом на вертикальном модуле, в то время как оператор запускает вертикальный модуль. Двигаясь по направляющим, модуль рассекает массив в вертикальной плоскости и подрезает его с обоих концов. После вертикальной резки основание формы с массивом переносится в зону горизонтального модуля, фиксируется захватом, после чего разрезается в горизонтальной плоскости на блоки заданных размеров, а также нижний слой и верхушка срезана. Пока работает горизонтальный модуль, в зону вертикального модуля подается следующий массив. Таким образом, происходит резка двух массивов одновременно, что обеспечивает высокую производительность линии.
5. Укладка блоков на поддоны, упаковка и хранение
Форма-основа с вырезанным массивом передается на узел укладки блоков. Основание пресс-формы фиксируется на рельсе. Затем половину распила массива с помощью захвата укладывают на поддон. Для того, чтобы укомплектовать поддон, восемь блоков укладываются вручную. Затем укладывается вторая половина массива, а также восемь блоков вручную (в зависимости от их габаритов). Поддон с блоками обтянут стрейч-пленкой.
6. Блок тепловлажностной обработки
В зависимости от климатической зоны и вида изготавливаемого материала блоки, укладываемые на поддоны, могут набирать сортную прочность на складе готовой продукции или при термовлажностной обработке. Термовлажностная обработка блоков необходима для ускорения набора прочности блоков. Тепловлажностная обработка заключается в том, что блоки выдерживают в камере от 8 до 12 часов при температуре от +40 до 60оС. Режим тепловлажностной обработки также зависит от плотности материала, активности цемента и определяется заказчиком для каждого конкретного вида выпускаемой продукции.
7. Переработка отходов резки
Режущие модули вырезают монолит с обоих концов, сверху и снизу. Инновационным решением является использование измельчителя отходов DG-1 для переработки отходов резки. Он позволяет измельчать отходы газобетона до частиц размером до 0–30 мм. Измельченный материал можно использовать в качестве насыпного утеплителя крыш, чердаков, пола и т. д. Измельчитель делает производство бетона практически безотходным.
СПЕЦИФИКАЦИЯ ЛИНИИ
Н | Имя | Количество |
Участок хранения, подготовки и отгрузки сырья | ||
1 | Шнековый конвейер для цемента (L = 6 м*, мотор-редуктор (Италия), N = 4 кВт) | 1 |
2 | Вибросито ВГ-1 (N = 3кВт, от 1 т/час**) | 1 |
3 | Ленточный конвейер для песка (L = 7 м*, N = 3 кВт) | 1 |
Зона смешивания | ||
1 | Электронная система управления (со встроенным счетчиком воды + подкачивающий насос) | 1 |
2 | Весы для цемента (тензодатчики, пневматический клапан) | 1 |
3 | Весы для песка (тензодатчики, пневматический клапан) | 1 |
4 | Весы химических примесей ДХД-1 (N = 0,5 кВт) | 1 |
5 | Газобетономешалка ГБ-0,85 (N = 11 кВт, V = 0,85 м 3 ) | 1 |
6 | Компрессор C200LB40 (500 л/мин, 8–10 атм.![]() | 1 |
Область резки монолита | ||
1 | Автоматизированный раскройный комплекс АРК-004 (N=19,5 кВт) | 1 |
2 | Форма ФМ-0,91 м 3 для газобетонных монолитов (V = 0,91 м 3 ). | 55 |
3 | Трансферная тележка | 4 |
4 | Комплекс для демонтажа пресс-форм (N = 2,0 кВт) | 1 |
5 | Комплекс для укладки блоков на поддоны (N=2,5 кВт) | 1 |
Зона измельчения отходов резки | ||
1 | Измельчитель ДГ-1 (N = 4,5 кВт) | 1 |
РАСХОД МАТЕРИАЛА* НА 1 м
3 ИЗ ПЕНОБЕТОН НЕАВТОКЛАВНЫЙ Д-600Материал | Количество |
Цемент (ПЦ500 Д0), кг | 280 |
Песок, кг | 210 |
Вода, л | 220 |
Газообразующий агент, кг | 0,5-1,5 |
Волокно, кг | 0,6 |
Химические добавки, кг | ** |
* Рецептуры корректируются с учетом свойств сырья, выбранного заказчиком.
** Тип и количество добавок определяются на этапе проектирования бетона.
ОБЩИЕ
Для снижения затрат заказчика линия поставляется без силоса для цемента, бункера для песка и перил для транспортировки формы. Заказчику предоставляются чертежи для самостоятельного изготовления этих узлов.
Кроме того, заказчик несет ответственность за подогрев воды до +35…+40°С и устройство пропарочных камер. Работа линии в 2 смены требует дополнительных фундаментов опалубки.
Гарантийный срок на поставляемое оборудование составляет 12 месяцев. Комплектация каждой единицы оборудования указана в договоре, паспорте оборудования и Акте сдачи-приемки.
Специалисты «Сибирских строительных технологий» (СКТ) проектируют размещение оборудования на производственном объекте заказчика. Оборудование устанавливается по макету силами и за счет заказчика. Заказчику предоставляется схема расположения оборудования (чертежи) для соответствующих помещений и подробная иллюстрированная инструкция по установке.
После того, как заказчик завершит монтаж и подключение оборудования, СКТ выполняет следующие работы:
• ввод оборудования в эксплуатацию;
• проектирование газобетона;
• оптимизация технологии производства;
• обучение персонала заказчика.
Заказчик несет ответственность за соблюдение всех правил техники безопасности, требований по охране труда и окружающей среды, а также других локальных нормативных актов.
Заказчик берет на себя все расходы по транспортировке и размещению персонала SCT на период проведения работ. Оптимизация технологии включает в себя оптимизацию состава бетона на основе предоставленного заказчиком сырья. SCT предоставляет услуги поддержки.
После ввода оборудования в эксплуатацию заказчику предоставляется техническая документация, включающая:
• технические регламенты на производства;
• технологическая схема;
• должностные инструкции;
• инструкции по технике безопасности;
• ГОСТы.
УСЛОВИЯ ПОСТАВКИ
Стоимость указана для EXW-Новосибирск (Россия) и не включает стоимость растаможки и пересылки. Срок изготовления оборудования: от 30 рабочих дней с момента поступления предоплаты.
УСЛОВИЯ ОПЛАТЫ
Оплата 1—70% от стоимости контракта в течение 5 дней с момента подписания контракта.
Оплата 2—30% от стоимости контракта в течение 5 дней с момента получения подтверждения о готовности оборудования к отгрузке.
Экспериментально-аналитическое поведение однонаправленных фибробетонных плит, армированных сеткой из стекловолокна и без нее, при испытании на четырехточечный изгиб
Чтобы прочитать этот контент, выберите один из следующих вариантов:
Айя Катауна (Кафедра гражданского строительства, Иорданский университет, Амман, Иордания) (Прикладной университет Аль-Балка, Амман, Иордания)
Рабаб Аллузи (Кафедра гражданского строительства, Иорданский университет, Амман, Иордания)
Самих Какиш (Кафедра гражданского строительства, Иорданский университет, Амман, Иордания)
Международный журнал строительной патологии и адаптации
«> ISSN : 2398-4708
Дата публикации статьи: 31 августа 2022 г.
Загрузки
Аннотация
Цель
Основная цель данного исследования состоит в том, чтобы изготовить односторонние плиты из LWFC с низкой плотностью и достаточной прочностью на сжатие, пригодные для конструкционных целей, а затем изучить их поведение при изгибе при различных типах армирования и толщине плиты, а также влияние добавление армирующих полипропиленовых волокон на механические свойства железобетонных плит. Образцы испытывали с четырехточечным нагружением. Были получены результаты, касающиеся несущей способности, прогиба и характера разрушения, а также картины трещин для каждого образца. Кроме того, проводится аналитическое исследование влияния полипропиленового волокна и GFG на поведение пенобетонных плит при изгибе с целью изучения значительной роли полипропиленового волокна в распределении напряжений в армированном пенобетоне и прогнозирования способности к изгибному моменту.
Проект/методология/подход
Материалами, использованными в данном исследовании, являются цемент, мелкий заполнитель (песок), вода, полипропиленовые волокна, пенообразователь, химические добавки, если необходимо, стальная арматура и сетка из стекловолокна. Комбинация этих составляющих материалов будет использоваться для производства пенобетона в этом исследовании. Затем в этом исследовании будет представлена экспериментальная программа односторонних пенобетонных плит, включая плиты, армированные сетками GFR, и плиты со стальной арматурой. Плиты будут испытаны в лаборатории в условиях статической нагрузки, чтобы исследовать их предельные возможности. Поведение при изгибе представляет интерес для плит, армированных арматурными сетками GFR, по сравнению с плитами со стальными арматурными стержнями. Рассматриваются три группы. (1) Группа I: две плиты из пенобетона с полипропиленовым волокном с минимальным необходимым армированием. (2) Группа II: две плиты из пенобетона с полипропиленовым волокном и сеткой из стекловолокна. (3) Группа III: две плиты из пенобетона с полипропиленовым волокном с минимально необходимым армированием и сетками из стекловолокна.
Выводы
Результаты экспериментов подтвердили эффективность и действенность этой новой системы при производстве бетона с низкой плотностью ниже 1900 кг/м. 3 имели соответствующую прочность не менее 17 МПа. Кроме того, присутствие полипропиленовых волокон заметно улучшило значения прочности на изгиб для всех исследованных плит. Было установлено, что образцы, армированные стальной армирующей сеткой, обладали более высокой несущей способностью по сравнению с образцами, армированными только GFG. Образцы, армированные GFG, показали самую низкую способность к изгибу из-за отделения GFG от бетонной подложки. Кроме того, было проведено аналитическое исследование для прогнозирования прочности на изгиб всех испытанных образцов. Аналитические результаты согласуются с экспериментальными результатами. Таким образом, LWFC сегодня можно использовать в качестве заменителя легкого бетона для производства конструкционного бетона в строительной отрасли.
Ограничения/выводы исследований
Пенобетон – широкая область для обсуждения. Для достижения целей проекта исследование сосредоточено на пенобетоне со следующими ограничениями: (1) поскольку целью этого исследования является производство пенобетона, подходящего для конструкционных целей, было решено производить смеси в диапазоне плотности 1300–1900 кг/м 3 . (2) Рассматриваются свободно опертые плиты. (3) Это исследование также рассматривает с использованием СКФ и без него.
Оригинальность/ценность
Основными задачами данного исследования являлись изготовление конструкционных пенобетонных плит и исследование их реакции на изгиб для жилых помещений.