Газобетон состав: состав, виды, характеристики, плюсы и минусы
Состав газобетона на 1 м3, пропорции, изготовление в домашних условиях
Газобетонные блоки относятся к востребованным изделиям, успешно сочетающим теплоизоляционные и конструкционные свойства. При соблюдении пропорций и простых правил замеса они без проблем изготавливаются дома, при наличии подходящего оборудования и проведения автоклавной обработки выпуск продукции организовывается в промышленных масштабах. Итоговые характеристики зависят от качества сырья, тщательности его подготовки и последовательности соединений при замесе, правильный материал имеет однородную закрыто-ячеистую структуру.
Виды и состав газоблоков, соотношение
В зависимости от вида и соотношений используемого вяжущего выделяют следующие разновидности:
- Цементные, с долей ПЦ с маркой прочности от М300 и выше, достигающей 50 % от общей массы.
- Известковые, на основе негашеной помолотой кипелки (до 50 %), гипса, шлака, цемента или их смесей (до 15 %).
- Шлаковые, полученные путем вспенивания молотых отходов металлургии с другими видами вяжущего.
- Зольные, содержащие до 50 % продуктов уноса.
- Смешанные, получаемые путем соединения всех вышеперечисленных видов вяжущего, с долей ПЦ от 15 % и выше.
В качестве инертного заполнителя применяется кварцевый и другие виды песка и вторичные отходы металлургии и теплоэнергетики: зола уноса и гидроудаления, ферросплавные шлаки, продукты обогащения рудных материалов. Все они вводятся после тщательного размола, доля в общем составе варьируется от 20 до 40 %. Поризация обычного и автоклавного газобетона достигается за счет ввода алюминиевой пудры и хлорида кальция, для затворения смеси используется вода с минимальным содержанием солей. К улучшающим свойства добавкам относят упрочнители, полиамидные пластмассы и аналогичные вещества, снижающие усадку, их соотношение в общей массе очень низкое.
Ориентировочные пропорции сырья для газобетона без автоклавной обработки:
Наименование | Доля в общей массе, % | ||
Портландцемент | 15-50 | 51-71 | 35,3-49,4 |
Наполнитель | Кварцевый песок: 31-42 | Молотый микрокремнезем: 0,6-3,5 | Молотый известняк до удельной поверхности 300-700 м |
Алюминиевая пудра | 0,1-1 | 0,01-0,15 | 0,06-0,1 |
Известь | — | 0,04-0,7 | 2,6-2,65 |
Полуводный гипс | — | 0,1-0,4 | — |
Другие добавки | Каустическая сода: 0,05-0,45 | Хлористый кальций: 0,5-3 | Хлорид кальция: 0,18-0,25 |
Вода для затворения | Все остальное |
Приведенные пропорции также подходят для автоклавного производства газобетона, в перерасчете на вес на приготовление 1 м3 смеси с плотностью 600 кг/м3

Особые требования выдвигаются к порообразователю: для достижения равномерной ячеистой структуры материала применяется алюминиевая сухая пудра с долей активного металла в пределах 90-95 % или суспензии – до 93. Их ввод требует осторожности: при снижении доли менее 0,06 % блоки не достигают заданной пористости, при засыпке более 0,1 – выделяется избыток водорода, приводящий к образованию чересчур крупных ячеек, вырыванию из них газа и усадке изделий.
Существует четкая связь между качеством используемого наполнителя и прочностными характеристиками: чем тоньше будет его помол, тем лучше.
Лучшие результаты при изготовлении неавтоклавного газобетона наблюдаются при В/Ц=0,4, повышение этого показателя приводит к снижению прочности материала.
Технология получения газоблоков в домашних условиях
Для кладочных изделий помимо сырья и емкостей для замеса потребуются формы – заводские металлические или самоделки из фанеры и дерева. Их размеры зависят от назначения блоков: чем больше будет ячеек, тем быстрее пойдет процесс выпуска. Внутренние стороны форм выполняются из ламинированной фанеры или других влагостойких материалов, принимаются меры по исключения протеканию воды, с целью упрощения выемки стенки смазывают составами на основе воды и технического масла в соотношении 3:1, эту процедуру повторяют каждый раз перед заполнением.
Этап замеса считается самым сложным в домашнем производстве, без дозаторов и оборудования для подготовки компонентов пропорции подбираются только опытным путем. Любое изменение степени активности вяжущего, температурных условий или чистоты воды оказывает прямое влияние на процесс поризации и итоговое качество. Важную роль играет последовательность соединения ингредиентов: вяжущее, песок или другие сухие заполнители перемешиваются и затворяются водой порционно, вплоть до получения однородной консистенции (но не более 5 мин, в противном случае цемент начнет схватываться), далее в нее вводят хлористый кальций или каустическую соду (при наличии их в выбранном составе), и в последнюю очередь – алюминиевую пудру или суспензию. После засыпки порообразователя смесь перемешивается со всей возможной тщательностью не более, чем 1 минуту и заливается в предварительно подготовленные формы.
При изготовлении газобетонных блоков в домашних условиях раствором заполняется только половина ячейки. Реагирование ингредиентов начинается незамедлительно, объем массы нарастает в течение первых 5-10 минут, после чего она слегка усаживается. Полученную «горбушку» срезают струной, формы оставляют в теплом помещении на сутки.
Для получения автоклавных изделий они проходят обработку горячим паром под избыточным давление в специальных камерах, в домашних условиях этот этап пропускается. Это вместе с отсутствием возможности строгого контроля за составом и геометрической точностью форм объясняет уступку качества кустарных элементов заводским. С целью его улучшения принимается ряд мер:
- Площадка или помещение защищаются от сквозняков и холодной температуры. В идеале работы проводятся в теплое время года.
- Формы слегка прогревают перед смазыванием. После выемки изделий оценивается состояние стенок и проводится их тщательная чистка.
- Сухие компоненты перед затворением водой просеиваются сквозь сито и вводятся малыми порциями.
Состав газобетона: компоненты и технология производства
Газобетон является пористым материалом и относится к ячеистым бетонам, делится на автоклавный и неавтоклавный. Различия в плане состава между ними незначительны, но в процессе производства разница существенна.
Компоненты газобетона:
- Портландцемент высокой марки (35%).
- Песок очень мелкой фракции (35%).
- Измельченная известь (1%).
- Алюминиевая пудра (0.05%).
- Вода (28%).
Чем лучше измельчены все компоненты, тем прочнее получается газобетон.
Сама технология изготовления газобетона заключается в смешивании наполнителей (цемента и песка) с газообразующими добавками (известь и алюминиевая пудра). После их перемешивания, между алюминиевой пудрой и известью начинается химическая реакция с выделением газа – водорода. Именно этот газ и создает в газобетоне поры, которые обеспечивают хорошую теплоизоляцию и легкий вес.
Меняя количество газообразующих добавок, можно добиться различной плотности газобетона, то есть, чем больше газа в бетоне, тем он легче, соответственно, меньше его плотность и прочность. На рынке стройматериалов можно найти газобетон плотностью от D150 до D700.
Газобетон хорош тем, что поры в его составе распределены очень равномерно, что обеспечивает одинаковую прочность и теплопроводность по всей толщине блоков.
После процесса газообразования и первичного схватывания смеси, общий массив разрезается струной на отдельные блоки нужной толщины. Далее газоблоки набирают прочность.
Что такое автоклавирование газобетона
Если мы говорим про автоклавный газобетон, то он обязательно проходит процесс автоклавирования. Автоклавами называют большие емкости, в которых создается высокая температура (160-180 С) и давление насыщенного водяного пара.
Процесс автоклавирования длится около 12 часов, и его задача заключается в быстром наборе прочности газобетона. Обычный тяжелый бетон набирает 70% своей марочной прочности примерно через месяц, но если увеличить температуру до 180 градусов, то прочность наберется в 100 раз быстрее.
Это решает сразу несколько проблем: усадка блоков отсутствует, не требуется время для набора прочности газобетона. Далее газобетон упаковывают в защитную пленку и развозят заказчикам.
Свежий автоклавный газобетон является очень влажным, воды в нем около 30-40%. Из-за влаги, его плотность значительно выше заявленной. По этому, перед отделочными работами, выложенная газобетонная стена должна просохнуть хотя бы два сезона.
Автоклавный газобетон имеет более высокую прочность, в отличии от неавтоклавного.
В научной терминологии, автоклавный газобетон называют тоберморитом – искусственным пористым камнем. Так как камни являются минералами, то они абсолютно экологичны. Газобетон не выделяет никаких вредных веществ, и не является радиоактивным.
Отличия газобетона и пенобетона
В плане наполнителей эти ячеистые бетоны похожи, отличие в газообразующих добавках. Если в газобетоне пузыри образуются из-за выделяющихся пузырей газа, то в пенобетоне из-за пены, которую добавляют в смесь отдельно. Проблемой пенобетона может быть его неоднородность, то есть, в одном месте пузырей будет больше, а в другой – меньше.
Процесс изготовления пенобетона намного проще, из-за чего его производством занимаются в гаражных условиях. Доверие к качеству заводского автоклавного газобетона и его составу намного выше. Прочность и геометрия автоклавного газобетона лучше, чем у пенобетона.
Из чего состоит газобетон(видео)
Газобетон – экологически чистый материал
Экологичность – главный тренд 21 века. Переезжая из загрязнённого мегаполиса в частный дом за городом, люди хотят жить в максимально безопасной для здоровья среде. Поэтому так востребованы экологически чистые строительные материалы. Является ли газобетон таким материалом? Насколько он экологичен в сравнении с другими популярными стеновыми материалами?
Газобетон без каких-либо оговорок является экологически безопасным материалом. Если коротко, то его безопасность объясняется несколькими факторами:
- Газобетон – минеральный строительный материал.
Как и в любом другом минеральном веществе, в его сырьевой смеси нет ничего опасного для здоровья человека.
- Газобетон обладает нулевой эмиссией вредных веществ в окружающую среду в процессе эксплуатации.
- Газобетон – негорючий материал. При пожаре он не выделяет опасных для здоровья человека веществ.
- Газобетон не подвержен поражению плесени. Биологическая стойкость – характеристика, которая не актуальна для минеральных материалов.
Теперь подробнее.
Сырьевая смесь: никаких вредных веществ
Современный газобетон, включая продукцию YTONG (Xella Россия), – это ячеистый бетон автоклавного твердения.
Сырьевая смесь газобетона YTONG
Все составляющие его сырьевой смеси – натуральные и экологически чистые: кварцевый песок, известь, цемент, вода, алюминиевая паста, обратный шлам и мука из отходов собственного производства. Последние два компонента – это переработанные фрагменты газобетона из предыдущих партий. Алюминиевая паста используется для образования пор, в процессе гидротации она превращается в гидроалюмосиликаты – химические соединения абсолютно нейтральные. Иными словами, не более опасные, чем алюминиевая кастрюля на кухне. Не говоря уж о том, что алюминиевая паста составляет всего 0,06% в сырьевой массе газобетона YTONG.
Известно, что цемент может «фонить», но вероятность появления радиоактивного цемента на рынке сильно преувеличена. В любом случае ведущие производители газобетона контролируют качество поступающего на заводы цемента, проверяя его в том числе на радиоактивность.
Что касается газобетона YTONG, то он гарантированно не «фонит»: есть независимые подтверждения этого от аккредитованных лабораторий. Согласно протоколу исследований, радиоактивность газобетона YTONG ниже, чем у других каменных материалов. Значение активности природных радионукледидов у него в несколько раз меньше требований нормативов и соответствует первому классу строительных материалов*. Разрешённая норма радиоактивности для материалов, применяемых в строительстве жилых и общественных зданий, – 370 Бк/кг. При этом продукция YTONG находится в пределах 20-44 Бк/кг.
Керамические (глиняные) кирпичи обладают репутацией экологически чистых материалов. Мало кто знает, что удельная эффективность природных радионуклидов у них в несколько раз выше, чем у газобетона. Из-за главного сырьевого компонента — глины. Впрочем, это не означает, что такие кирпичи опасны для здоровья. Их норма радиоактивности всё равно меньше нормативных требований. Что уж говорить про газобетон?
Добавим, что в отличие от обычного бетона в состав газобетона не входит гранитный щебень, который может иметь повышенную радиоактивность из-за концентрации в нём тория и урана.
Есть миф, что в порах газобетона содержится «ядовитый газ». Это не так. При производстве материала действительно образуется газообразный водород, который и создаёт пористую структуру газобетона. Но водород очень лёгкий и быстро улетучивается, замещаясь кислородом. Таким образом, в порах материала — только воздух.
В составе газобетона нет синтетических полимеров, химических добавок, токсичных и канцерогенных примесей. Поэтому у него нулевая эмиссия продуктов распада этих веществ в окружающую среду как при нагреве, так и при охлаждении. Также газобетон не вызывает аллергических реакций. Нет никакой опасности и в минеральном клее для тонкошовной кладки газобетонных блоков.
Эталонным материалом в плане экологии считается древесина. Самый популярный материал для деревянного малоэтажного строительства – клеёный брус. Однако не стоит забывать: такой брус состоит из тонких деревянных ламелей, продольно склеенных друг с другом тем или иным полимерным клеем. Составы для склеивания ламелей могут включать в себя в том числе меламиноформальдегидные смолы и другие токсичные компоненты. То есть способны выделять опасные летучие вещества в процессе эксплуатации дома. Чем дешевле клеёный брус, тем больше вероятность, что он изготовлен с использованием бюджетного, а значит, менее экологичного клея (формальдегидные смолы – дешёвый компонент, и потому их активно применяют для производства не только бруса, но и фанеры, ДСП и т. п.).
Верить на слово или потребовать сертификат?
Производители многих стройматериалов утверждают, что их продукция абсолютно экологически безопасна. Не стоит верить всем на слово. Запросите у компаний сертификаты, которыми они могут подтвердить свои слова (например, санитарно-гигиенический сертификат на клей в клеёном брусе). Причём, это должны быть документы, выданные авторитетными специализированными инстанциями, а не «ноунейм» лабораториями.
Так, у YTONG, помимо протокола радиоактивных испытаний, есть и другие сертификаты – как российские, так и международные, в том числе:
1. Сертификат соответствия стеновых блоков российским Единым санитарно-эпидемиологическим и гигиеническим требованиям.
2. Экологический сертификат соответствия EcoMaterial. Это независимый российский стандарт, оценивающий стройматериалы на основании законодательных актов РФ, ISO 14024, требований Всемирной организации здравоохранения, стандартов DGNB, BREEAM, LEED, рекомендаций международных организаций по «зеленому строительству». Согласно сертификату, продукция YTONG соответствует стандарту EcoMaterial 1.3. Это означает, что из неё можно строить жилые дома, детские дошкольные учреждения, лечебно-профилактические учреждения, санатории, дома инвалидов и престарелых, учебные учреждения, закрытые спортивные сооружения, служебные помещения, где постоянно находятся люди, и пр.
3. Заключения о применимости газобетонных блоков YTONG для возведения объектов по стандартам LEED и BREEAM. Это международные экологические стандарты для «зелёных» зданий. Стройматериал оценивается комплексно, в том числе с точки зрения энергоэффективности, долговечности, экологической безопасности для пользователей, экологичности завода по его изготовлению и пр.
Сертификация по стандартам EcoMaterial, LEED и BREEAM является добровольной. Компания Xella Россия (бренд YTONG) уверена в безопасности своей продукции для окружающей среды и потому не боится независимой экспертизы.
Пожарная безопасность
Во время пожара серьёзную угрозу для людей представляет выделение строительными материалами опасных для здоровья веществ под воздействием огня. Если материал не выделяет таких веществ, у людей есть достаточно времени на эвакуацию из здания. Поэтому перед покупкой стенового материала требуйте у продавцов результаты испытаний пожарной безопасности, причём не только стенового материала, а всей конструкции стены.
Обратите внимание: отвечая на вопрос о пожарной безопасности, многие производители показывают результаты испытаний на огнестойкость. Безусловно, огнестойкость очень важна: чем дольше конструкция сохраняет несущую способность под воздействием огня, тем больше шансов у людей спастись во время пожара. Но такие испытания не дают информацию о выделении при пожаре веществ, угрожающих здоровью человека. Такая информация есть в испытаниях, по результатам которых конструкцию относят к тому или иному классу пожарной опасности. Так что требуйте сертификат с указанием класса пожарной опасности.
Газобетон – негорючий материал. Несущая конструкция из газобетона YTONG на растворе для тонкошовной кладки по результатам независимых испытаний соответствует классу пожарной опасности К0(45)**. То есть является непожароопасной при времени теплового воздействия 45 минут. И может выступать в качестве противопожарной преграды. Такой класс присваивается только тем конструкциям, которые не поддерживают горение и не выделяют вредных веществ при прямом воздействии огня.
В средней полосе России стены из газобетонных блоков плотностью D400 и толщиной 375 мм, как правило, не нужно утеплять, они соответствуют современным требованиям по теплозащите. Однако если вы всё же хотите дополнительно утеплить их, не забывайте, что полимерная теплоизоляция (пенополистирол – обычный или экструдированный) относится к группам нормально или сильно горючих материалов. А значит, во время пожара они представляют опасность для здоровья человека. Что же касается утеплителей из минеральной ваты, то они являются негорючими.
Добавим, что огнестойкость стен из газобетона максимальная среди всех типов каменных или монолитных конструкций. Это объясняется тем, что у материала низкая теплопроводность, и фронт тепловой волны продвигается по кладке из газобетонных блоков медленно.
А как же плесень?
Плесень – это грибы, для появления и роста которых нужна питательная среда из органических веществ.
Неорганикой в чистом виде они не питаются. Поэтому грибам не интересна кладка, выполненная полностью из минеральных строительных материалов. Плесень может появляться, например, на отделочных материалах, примыкающих к стене. В частности, на обоях, грунтовке, картоне в составе гипсокартонных листов, органической краске, гипсовой штукатурке, деревянных брусках обрешётки и пр. Но сам по себе газобетон не подвержен поражению плесени, и ему просто не требуется биологическая стойкость.
Какой из всего этого вывод? Очень простой: газобетон не представляет никакой угрозы для здоровья человека.
Полную информацию о технологии возведения дома из газобетона можно получить на курсе по строительству из YTONG
* СанПиН 2.6.1.2523-09 «Нормы радиационной безопасности НРБ-99/2009», ГОСТ 30108-94 «Материалы и изделия строительные. Определение удельной эффективной активности естественных радионуклидов».
**В соответствии со СНиП 21-01-97 «Пожарная безопасность зданий и сооружений»
Состав и свойства ячеистого бетона
Ячеистый бетон (пенобетон, газобетон) относится к так называемым легким бетонам с большим содержанием ячеек воздуха. Размеры таких пузырьков бывают до 1 — 1,5 мм, количество воздушных пузырьков составляет около 85% объема бетона.
Производство ячеистого бетона происходит двумя способами:
структура газобетона |
- Механическим
- Химическим
Механический способ — это когда в уже приготовленный из воды песка и вяжущего вещества, в ячеистый бетон добавляют специальную пену. Такой материал называют пенобетон (пеноблоки).
Химический способ — это введение в вяжущее вещество газообразующих добавок, в результате реакции бетон вспучивается и приобретает пористость. Этот материал получил название газобетон.
Ячеистый бетон разделяют на:
- Теплоизоляционный, плотность 300 – 600 кг/м3 и прочность – 0,4 — 1,2 МПа;
- Конструктивный, плотность 600 – 1200 кг/м3 (чаще всего 800 кг/м3),и прочность – 2,5 — 15 МПа.
Изделия из автоклавного ячеистого бетона в настоящее время набирают популярность.
Для производства автоклавного ячеистого бетона (газобетона) используют портландцемент и известь-кипелку в соотношении 1:1, изделия твердеют в автоклаве под воздействием пара с давлением 0,8 – 1 МПа. Современный газобетон (или автоклавный ячеистый бетон) производится из песка, негашеной извести, цемента и алюминиевой пудры (гидратированный силикакт кальция (тоберморит) 50-60%; кварц 30-40%; сульфат кальция 1-3 %; карбонат кальция 1-2 %; гидратированный силикат алюминия 3-5 %). Известь, которую используют для приготовления такого автоклавного ячеистого бетона должна иметь высокую температуру гашения, около 85 °C и помол не ниже 3500 – 4000 см2/г, содержать не более 5% оксида магния, и не менее 70% оксида кальция.
Автоклавный изготавливается в промышленных условиях при помощи автоклавов, в которых поддерживается определенное давление и температура. При смешивании всех вышеперечисленных ингредиентов происходит выделение водорода в виде пузырьков газа диаметром около 1 мм, что вызывает необходимый рост объема сырой смеси и при застывании бетонной массы образуют в структуре материала огромное количество пор. Алюминиевого компонента используется очень небольшое количество. Во время застывания поры насыщаются воздухом.
микроструктура тоберморита |
Автоклавная обработка газобетона используется по нескольким причинам, так в автоклаве при температуре +180 °С и давлении до 14 бар в газобетоне образуется новый минерал – тоберморит, благодаря которому повышается прочность материала и, что особенно важно, в несколько раз уменьшается усадка.
За счет своих характеристик автоклавный бетон имеет гораздо больше способов применения. Ячеистый бетон автоклавного твердения имеет пониженную трещиностойкость и повышенную морозостойкость. Автоклавная обработка позволяет в более короткие сроки получать изделия с достаточно высокой прочностью.
В производстве ячеистых бетонов неавтоклавного твердения (пенобетон) используют цемент марки м-400 и выше. Одним из основных компонентов является мелкий кварцевый песок, с содержанием кремнезема не менее 90% , не более 0,5% слюды и 5% глины. Удельная поверхность песка для ячеистого бетона допускается 1200 – 2000 см2/г.
Строительство домов из газобетона под ключ можно заказать на нашем сайте в соответствующем разделе.
Автоклавный и неавтоклавный газобетон — что лучше?
Автоклавные блоки формируются при большой температуре и давлении, неавтоклавные — твердеют при атмосферном давлении или в условиях нагревания. Что лучше и почему?
Главные отличия АВТОКЛАВНОГО и неавтоклавного ГАЗОБЕТОНА:
- Качество. Автоклавные блоки изготавливаются только в заводских условиях. Производить автоклавный газобетон в подпольных условиях невозможно, а неавтоклавный — твердеет в естественной среде, поэтому изготовлять его можно в «кустарных» условиях;
- ГОСТ. Автоклавный газобетон производится согласно ГОСТу 2007 года — ГОСТ 31360-2007, такие блоки имеют сертификат качества. Клиенты могут быть уверены в качестве покупаемой продукции. Неавтоклавный газобетон изготавливается по ГОСТу 25485-89 и уже долгое время технология и качество не изменяется.
- Прочность. Ячеистые бетоны изготавливают разной плотности: от 400 до 800 кг/м3 классом. Наш самый ходовой блок является D500, при этом его плотность имеет класс по прочности на сжатие В2,5. Прочность неавтоклавного бетона может быть меньше В1,5, конструкция на таких блоках может не выдержать нагрузки;
- Крепление.
Автоклав значительно повышает прочность газобетона. В основание из автоклавного газобетона можно закрепить не только шкафы и полки, но и бойлеры, кондиционеры, вентиляционные фасады;
- Усадка не страшна. В сравнение с неавтоклавным газобетоном, автоклавные блоки полностью набирают свою прочность уже в процессе производства. Поэтому усадка им не страшна. Для автоклавного газобетона показатель усадки не превышает 0,5 мм/м, тогда как для неавтоклавных материалов он составляет от 1 до 3 мм/м. Неавтоклавные блоки дают большую усадку, она достигает до 0,23— 0,34 мм/м. Это может сильно повлиять на конструкцию здания;
- Экологичность. Мы не устанем говорить, что наш автоклавный газобетон полностью экологичный материал. Микроклимат в постройке из автоклавных блоков можно сравнивать с климатов деревянного дома. Газобетон изготавливается из материального сырья, поэтому он не поддается гниению. А его способность регулировать влажность, исключает вероятность появления плесени и грибков.
В составе неавтоклавного газобетона чаще всего добавляют смесь шлаков и золы. В результате химической реакции, полученный состав выделяет сферические поры;
- Геометрия. Точность геометрии блоков из автоклава регулируется современным ГОСТом. Геометрия неавтоклавный блоков разнородна. Блоки начинают крошиться и скалываться;
- Теплоизоляция. По сравнению с неавтоклавными блоками и кирпичом, автоклавный газобетон обладает на 30% лучшим показателем по теплоизоляции.
Давайте подведем итоги:
- Неавтоклавные блоки дешевле, чем бетон из автоклава;
- Газобетонные блоки автоклавного твердения отличаются физико-механическими свойствами
- Богатый выбор марок по прочности. Прочность автоклавных газоблоков выше в полтора-два раза неавтоклавных материалов;
- Производят автоклавные блоки только на современных заводах;
- Автоклавные блоки лишены такого недостатка, как усадка;
- Соответствие параметров ровности автоклавных блоков;
- Блоки из автоклава абсолютно экологичны.
Как мы видим, автоклавный газобетон превосходит неавтоклавный практически по всем показателям. На нашем заводе ПТЖБ изготавливаются газоблоки из автоклава. Только так мы можем быть уверенны в качестве своих изделий. Здания из таких блоков получаются более прочные, а постройка проходит легче и проще.
особенности газобетонных блоков, как выбрать газоблоки и пеноблоки
Одним из относительно новых строительных материалов является газобетонный блок, называющийся также пеноблоком или газоблоком. При использовании его в строительстве можно создать очень красивый дом, который благодаря свойствам материала будет хорошо сохранять температуру внутри помещений, экономя тем самым энергию. Благодаря клеящемуся составу, который применяется для соединения блоков, и их легкости обеспечивается более быстрая усадка зданий (вернее, такие здания практически не дают усадки).
Одной из лучших российских фирм, производящих пеноблоки, считается компания Bonolit. Это объясняется высоким качеством выпускаемой продукции и большими объемами производства. Bonolit не ухудшает состав газобетона в угоду количеству и использует только экологически чистые материалы. Основные виды выпускаемых этим производителем блоков имеют плотность от D300 до D600.
Пенобетон Bonolit используется для производства блоков несущих стен, внутренних перегородок и перемычек.
Состав и предназначение
Блоки фирмы Bonolit производятся из набора составляющих. Это смесь цемента, песка, различных газообразователей (к примеру, алюминиевой пыли) с добавками в виде известки, отходов от промышленного производства, шлака или золы. После смешивания цемента с вышеназванными материалами его смачивают водой, доводя до нужной консистенции, и заливают в форму, чтобы получить готовый блок.
Внутри формы идет химическое соединение газообразователей с цементом или известкой. Газы, а конкретно водород, выделяемый в ходе реакции, дает раствору пенистую структуру. Диаметр соединенных между собой пор составляет от одного миллиметра до трех. После того как смесь схватится, ее достают и делят на части необходимых размеров. Затем материал высушивают.
Общее название материала блоков, реализуемого фирмой Bonolit – ААС (Aerated Autoclaved Concrete – автоклавный аэрированный бетон, который называется также ячеистым бетоном или газобетоном). Он был придуман и создан в 1930-х годах в Швеции. За все время его существования технология улучшалась и развивалась, пока не заняла одну из главенствующих позиций среди материалов, используемых для строительства зданий.
Изготовление блоков для стен различного вида имеет некоторые различия. Это, безусловно, учитывается и на предприятиях Bonolit. Так как для внешних, опорных стен требуется большая прочность, пеноблоки затвердевают в специализированных автоклавах с использованием пара под давлением. Такой вид блоков стоит, конечно же, немного больше.
Для производства тех газоблоков, которые используются для монтажа внутренних перегородок, применяют отвердевание в электрических шкафах для горячей сушки или просто в условиях окружающей среды.
Преимущества
Газоблоки Bonolit широко используются в строительстве не только небольших коттеджей, домов, хозяйственных сооружений и торговых площадей, но и высотных зданий.
Это объясняется многочисленными преимуществами материала.
- Надежность газоблоков дает возможность осуществлять строительство без дополнительных работ и материалов по усилению несущей части и фундамента. Это позволяет экономить средства, время и ресурсы в процессе постройки, а значит — уменьшать итоговую стоимость здания.
- Благодаря прочности и долговечности материала любые здания, построенные из него, не поддаются старению и служат более 50 лет.
- Блоки обладают высокой безопасностью в пожарном плане. Это большой плюс для эксплуатации построек.
- Из-за легкости пеноблоков скорость возведения и монтажа здания ускоряется до четырех раз. Монтаж материала производят на клеящийся состав, что также увеличивает скорость сборки.
- Благодаря тому, что структура блоков содержит пенистые поры, они прекрасно сохраняют тепло и «дышат».
Это позволяет повышать тепловую энергетическую эффективность строений в разы.
- Пенистая структура, которую имеет газобетон, произведенный из экологически чистых материалов, является также прекрасным звуковым изолятором, не пропускающим внутрь постройки лишние звуковые вибрации.
- Материал устойчив к воздействию воды, а значит внутренние помещения будут меньше подвержены влиянию излишней влаги.
- Геометрически правильное строение блоков позволяет с легкостью создавать прямые стены и углы зданий.
- Для блоков Bonolit свойственна легкость их обработки любыми способами, будь то воздействие сверлом, пилой или иным методом.
Недостатки
Как и у любого строительного материала, у пеноблоков есть и недостатки.
- Проблема с использованием крепежа. Для такого материала бесполезно использовать гвозди, они будут просто выпадывать. Весь крепеж придется делать на саморезах.
- Трещины при неправильном монтаже фундамента. Если фундамент неправильно смонтирован, во время усадки он может вызвать появление трещин как на местах склеивания блоков друг с другом, так и на самих блоках.
- Высокая гигроскопичность. Газобетон впитывает влагу из-за своей пенистой структуры. Он может ее впитать до трети своего объема, при этом не давая ей выходить. Если же материал будет пропитан влагой, то его теплоизоляционные свойства ухудшатся. По этой причине газобетонные блоки требуют наружной отделки, для чего можно использовать любые материалы (начиная от кирпича и заканчивая плиткой).
Выбор подходящего варианта
Одна из важнейших характеристик газоблоков Bonolit – плотность. Ее коэффициент указывает на то, насколько плотен газобетон в килограммах на м³. Больший индекс коэффициента указывает на большую твердость блока, более низкий коэффициент указывает на то, что он лучше сохраняет тепловую энергию.
Есть также такой параметр, как прочность на сжатие. Он обозначается латинской буквой B с числовым индексом, который указывает на давление, выдерживаемое блоком на каждый квадратный сантиметр.
К примеру, индекс B2,5 означает, что пеноблок выдержит давление до 25 кг/см2.
Плотность блоков Bonolit отражена в их названии после латинской буквы D.
Соответственно, и сами пеноблоки имеют разделение в зависимости от коэффициента.
- Блоки для навесных фасадов. Индекс плотности – D600. Они используются для монтажа внешних стен и фасадов, выдерживают повышенную нагрузку. Прочность на нагрузку у этих блоков — от B3,5 до B5.
- Конструкционные стеновые блоки. Индекс плотности – D500. Назначение – монтаж внешних стен и внутренних несущих перекрытий домов. Прочность на сжатие у данного вида блоков — от B2,5 до B3,5.
- Стеновые конструкционно-теплоизоляционные блоки. Индекс плотности – D400. Они используются для монтажа стен домов высотой менее трех этажей, а также в монтаже внутренних перегородок. Прочность на сжатие у данного вида блоков — от B2,0 до B2,5.
- Теплоизоляционные блоки. Они используются, как для монтажа внутренних, не несущих большую нагрузку перегородок, так и для теплоизоляции. Индекс плотности – D300. Прочность на сжатие у данного вида блоков — от B1,5 до B2,0.
Газобетонный блок для кладки стен имеет стандартную длину 600 мм, высоту 200 мм, ширину от 200 до 500 мм. Газоблок для монтажа перегородок имеет такую же длину и высоту, как и предыдущий вариант, но меньшую ширину — от 75 до 150 мм. Блок для перемычек отличается длиной 500 мм, высотой 200 мм, шириной от 250 до 400 мм.
Пеноблоки, имеющие U-образную форму, используются для создания монолитного пояса жесткости и внутренних скрытых конструкций. Пазогребневые модели имеют на боках впадины и выступы, благодаря чему при монтаже не возникает необходимости укладывать клеевой состав на вертикальные швы, газоблоки вставляются друг в друга.
Блоки вида «hh» позволяют за счет своей формы укладывать между плитами в перегородках теплоизоляционные слои.
Еще один параметр газоблока – сопротивляемость циклам заморозки и разморозки материала. Для указания того, сколько раз материал может быть полностью заморожен и разморожен без потери свойств, в марке газобетонного блока используют латинскую F с последующим числом, которое указывает на количество циклов разморозки и заморозки. Существуют варианты от F15 до F100. Все выпускаемые фирмой Bonolit блоки имеет индекс F100, то есть они без проблем выдерживают более сотни циклов полной заморозки/разморозки.
О том, как класть газобетон Bonolit, смотрите в следующем видео.
СИБИТ ЧТО ЭТО ТАКОЕ СВОЙСТВА ГАЗОБЕТОНА
Сибит один из популярных строительных материалов на сегодняшний день в Новосибирске. Сложно представить современный строительный рынок без такого известного материала как Газобетон. Сибит можно считать уникальным материалом в своем классе по всем техническим характеристикам. В этой статье рассмотрим Сибит подробно, узнаем что такое Сибит, историю возникновения, так же его необычные свойства.
Купить газобетон в Новосибирске от производителя +7 905 952 00 02
СИБИТ Что это такое?
СИБИТ это название торговой марки завода изготовителя ОАО «Главновосибирскстрой» расположенного в городе Новосибирск. Продукция СИБИТ это изделия из автоклавного газобетона — строительный материал. |
---|
Завод СИБИТ — построен и запущен в работу с 1994 года в городе Новосибирск, работающий по технологии и на оборудовании компании «ИТОНГ» (Германия). Завод оборудован своевременно новейшим автоматизированными линиями по выпуску востребованных строительных материалов такие как: блоки для несущих самонесущих стен, перегородочные блоки, панели перекрытия, несущие перемычки, теплоизоляционные плиты, насыпной утеплитель торговой марки СИБИТ.

Газобетон СИБИТ — продукция из ячеистого газобетона автоклавного твердения (термо-влажностная обработка), разновидность искусственно изготовленных, облегченных бетонных блоков с равно распределенными по всему объему воздушными камерами до 3 миллиметров. |
---|
Перейти в раздел > ЦЕНА НА СИБИТ РАЗМЕР СИБИТА ХАРАКТЕРИСТИКИ САМЫЙ ДЕШЕВЫЙ СИБИТ
Классификация СИБИТа
Применение — в жилищном, коммерческом, промышленном строительстве.
Назначение — конструкционные, конструкционно-теплоизоляционные, теплоизоляционные.
Вид вяжущего — цементные, известковые, шлаковые, гипсовые, специальные.
Вид заполнителей — плотные, пористые, специальные.
Структура — плотная, поризованная, ячеистая, крупнопористая.
Условия твердения — естественная, тепловлажностная при атмосферном давлении, тепловлажностная при давлении выше атмосферного (автоклавного твердения).

Автоклавный и не автоклавный в чем разница?
Автоклавирование (тепловлажностная обработка) — один из ключевых процессов технологии применяемый в производстве газобетона подразумевается так называемое «пропаривание» застывшего массива смеси при использовании высокого давления и высокой температуры, такой процесс позволяет получить материал с высоко эксплуатационными свойствами и характеристиками, какие невозможно получить в обычных условиях путем естественного твердения смеси. Тепловлажностная или автоклавная обработка газобетона СИБИТ используется в технологии не только для того, чтобы повысить скорость процесса твердения. Главный смысл заключается в том, что при автоклавной обработке СИБИТа в структуре газобетона происходят изменения кристаллической решетки, вследствие этого процесса образуется искусственно изготовленный минерал с уникальными свойствами похожими по своим характеристикам со структурой натурального камня — тоберморитом. Другими словами автоклавный газобетон — это искусственно созданный камень при соблюдении всех технологии и процессов в заводских условиях, а неавтоклавные бетоны — затвердевший цементно-песчаный раствор.
Преимущества автоклавной обработки:
1. Стабильность качества
2. Прочность
3. Однородность
4. Минимальная усадка при дальнейшей эксплуатации материалов
5. Экологичность
6. Точная геометрия
История возникновения газобетона
Из истории возникновения технологии газобетона -по одной из версий, первые опыты изготовления вспененного бетона были проведены в Чехии господином Гоффманом. Инженер получил реакцию вспенивания путем добавления в бетон различных химических веществ, при этом выделялось небольшое количество газа, который образовывал пористую структуру в бетоне, отсюда возникла приставка «газо». В 1889 году изобретатель получил патент на газобетон.
Первой кто начал выпуск газобетона в промышленных масштабах считается компания «Итонг» в 1929 году.
Газобетон в России — в России газобетон начал выпускаться с 1930 года. Начало масштабного производства газобетона началось с 1950 года, отечественные производители опережали европейских коллег в наработках этой области.
На сегодняшний день можно уверенно сказать о том, что изделия из газобетона имеют историю эксплуатации более 100 лет, строительный материал проверен не только временем, но и сложными климатическими испытаниями, как в Европе, так и в России. К примеру, в Санкт-Петербурге в городе с повышенной влажностью построенные жилые дома эксплуатируются с 1960 года, без видимых разрушений блоков. В городах с повышенной сейсмичностью Норильск, Ангарск эксплуатируются здания из неавтоклавного газобетона уже больше 40 лет. Так же больше 40 лет в городе Новосибирск где температурные отметки в зимний период могут достигать минус 35 градусов, эксплуатируют здание из газобетонных блоков. А с 1994 года в Новосибирске возводят дома из газобетона, изготовленного на заводе СИБИТ.
Свойства СИБИТа
Газобетон СИБИТ обладает высокой термоизоляцией в несколько раз превышающей кирпич. Стройматериал не горюч. Считается экологически чистым т.к. используются в основном природные материалы, не боится влаги. Изделия из газобетона морозостойкие и долговечные. Блоки из газобетона легко поддаются обработке, что делает работу с ним значительно легче в сложных конструкциях. Материал имеет относительно легкий вес, что в целом облегчает конструкцию. Точная геометрия изделий повышает скорость при работе и опять же хорошая геометрия поверхностей из газобетона позволяет экономить на отделочных работах (штукатурить стены уже не нужно, а только шпаклевать). Блоки монтируются на тонкий слой специального клея до 2,5 миллиметров, что не дает образовываться «мостику холода» как в классической кирпичной кладке. Конструкции не подвержены значительной усадке, что дает возможным производить внутренние работы сразу после их монтажа.
Все эти уникальные качества СИБИТа — делают его востребованным на строительном рынке материалом среди частных и коммерческих застройщиков.
Так в чем же уникальность газобетона СИБИТ?
Ключевым сырьем для изготовления газобетона по стандартам, принятым на заводе, представляют собой компоненты: песок, известь, цемент, вода. Все компоненты проходят тщательную подготовку, очищаются от возможных примесей, некоторые проходят помол. Все задействованные части компонентов в рецептуре строго соблюдаются в пропорциях. В качестве газообразователя используется алюминиевая пудра в примерном объеме 0,05% от единой массы замеса, которая в ходе реакции с известью, полностью исчезает при дальнейшей обработке в специальных камерах (автоклавах), процесс называется тепловлажностная обработка (ТВО). Все это дает высокое качество производства изделий в дальнейшем. В последствие на выходе производства получаются прочные изделия с пористой равномерной структурой. По составу напоминающий камень только не натурального происхождения, по своим характеристикам можно сравнить с редким минералом природного происхождения — тоберморит. Собственно такое подобие с естественным минералом делает газобетон СИБИТ — уникальным материалом, применяемым в строительстве.
Газобетон СИБИТ экологически чистый материал — в 2014 году завод вновь прошел комплексный аудит на проверку экологических стандартов в рамках проекта EcoMaterial и получил сертификат соответствия экологичности и безопасности материалов.
Некоторые вопросы/заблуждения о СИБИТе
1. СИБИТ насыщает влагу из-за присутствия извести.
Это неверные утверждения, чтобы ответить на этот вопрос, давайте вернемся к процессу изготовления газобетона СИБИТ. При смешении массы сырца для изготовления газобетона используются: цемент (ПЦ 500 Д0), песок (оксид кремния 85%), вода, известь, алюминиевая пудра 0,05% от единой массы. Последние два компонента взаимодействуя друг с другом в реакции, способствуют в формировании массы в формах. Полностью же реакция заканчивается в автоклавах под высоким давлением и термообработке в 190 градусов по Цельсию, по завершению образуется камень искусственного происхождения состоящего из 80% минерала гидросиликат-кальций и 20% песка — по своей структуре схожего на минерал тоберморит, что подтверждается официальными исследованиями в 2001 и 2007 году на базе НГАСУ был проведен спектральный анализ состава строения газобетона, он показал, что структура имеет сходство с минералом тоберморитом, а компоненты, которые присутствовали на начальной стадии производства: известь, алюминий и др. НЕ обнаружены. Другими словами в ходе реакции на начальном этапе двух компонентов: известь и алюминиевая пудра полностью исчезают при температурно-влажностной обработке в автоклавах и в завершенном изделии (новом образовавшемся минерале) их попросту нет.
2. СИБИТ из-за пористости структуры обладает высокой влагонасыщаемостью, что влияет на изменение состава и приводит к разрушению материала.
Да, действительно состав готовых изделий содержит до 75% пор, большую часть этой цифры приходится на макропоры, которые образуют пустоты округлой формы и перегородки между ними (образующиеся в результате реакции на начальном этапе) и микропоры (образующиеся в результате удаления излишней влаги). Поры можно разделить на две категории открытые и закрытые, первые в свою очередь породили легенду о наборе чрезмерной влаги в газобетон и разрушении структуры материала. Давайте разберемся в этом вопросе детально. Состав газобетона представляет собой структуру из влагонерастворимого минерала, значит, влага не имеет возможности послужить причиной к распаду кристаллической решетки, значит, не влияет на его характерные свойства. За счет открытых пор влага в действительности способна проникать вовнутрь материала, но не глубоко, однако за счет капилярнопористому строению материала позволяет ему довольно стремительно отдавать излишнюю влагу в окружающую среду. Собственно в связи с этим в первые несколько лет эксплуатировании сооружений из газобетона достигается равновесие влагосодержания материала. Иными словами ограждающие конструкции из газобетона «дышат». Они способны самостоятельно регулировать микроклимат, так например, стены из газобетона «возвращают» в помещение избыточно накопленную влагу при достаточно сухом воздухе в помещениях и наоборот, газобетон способен при избыточно влажном воздухе «забирать» влагу из помещения и отдавать «выводить» ее в окружающую среду посредствам своей пористой структуры. Материал регулирует и обеспечивает при этом благоприятные условия для жизни.
3. Замерзания воды внутри газобетона СИБИТ зимой приводит к микроразрывам структуры и его разрушению.
По части газобетона СИБИТ данные сомнения не оправданы. Микротрещины появляются вследствие механического влияния на материал, или в ходе процесса усадки сырья, за счет новейшего оборудования и стандартам взятых за основу на заводе, микротрещины попросту не могут возникнуть. Что касается разрыва материала при избыточной влажности при низких температурах эксплуатации, то резервные поры позволяют равномерно распределять влагу среди всей структуры, вследствие чего микротрещины образовываться не могут, разрушение изделий НЕ ПРОИСХОДИТ. В 2003 году газобетон завода ОАО «Главновосибирскстрой» прошел проверку по морозостойкости марки F250 и получил заключение лаборатории ОАО «Оргтехстрой».
В заключении можно сказать, что все эти вопросы вокруг газобетона СИБИТ всего лишь навсего домыслы и не имеют ни какого основания.
Объекты коммерческого назначения построенные из газобетона СИБИТ г.Новосибирск
Данные интегрированы с официального сайта «СИБИТ»
Наверх
Состав автоклавного газобетона (АГБ) и основных материалов.

Контекст 1
… сырье для основного материала газобетона, включая песок, зольную пыль, цемент, известь, гипс и воду, состав газобетона и основные материалы показаны в таблице 1. Алюминиевая паста и стабилизатор пены использовались для газобетона. …Контекст 2
… основной материал, прочность которого была выше, чем у AAC, что было близко к прочности обычного бетона, в то время как размер крупного заполнителя был небольшим, а дефекты между заполнителем и цементный камень был мелким, крупных дефектов поверхности раздела не было; как только появились трещины, энергия быстро высвободилась, и образец внезапно разрушился (как показано на рисунке 16d).Результаты испытания на осевую прочность на сжатие показаны в таблице 10. В таблице 10 коэффициент осевого сжатия между осевой прочностью и кубической прочностью газобетона превышает 0,9. …Контекст 3
… результаты испытаний на прочность на осевое сжатие показаны в Таблице 10.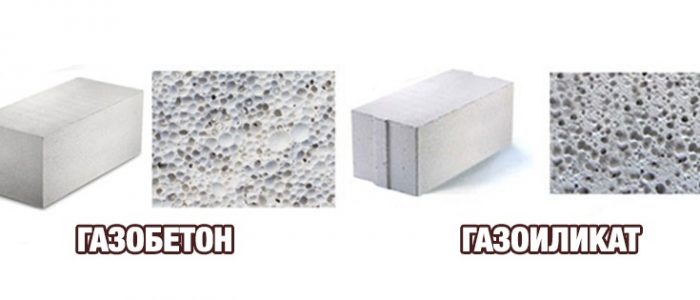
Контекст 4
… результаты испытаний модуля упругости газобетона и основного материала показаны в Таблице 11. — пиковая деформация на кривой напряжения-деформации. …Контекст 5
… Таблица 11, модуль упругости AAC и основного материала увеличивается с увеличением кажущейся плотности, а для AAC он меньше, чем у основного материала. Соотношение между модулем упругости газобетона и осевой прочностью на сжатие можно рассчитать по уравнению (12)….Контекст 6
… f — осевая прочность на сжатие (МПа), ε0 — средняя пиковая деформация (таблица 11), Em — средний модуль упругости (МПа), Esec — отношение осевой прочности на сжатие предел прочности до пиковой деформации, а γ — безразмерное число.
Контекст 7
… расчет прочности на растяжение при расщеплении показан в уравнении (15).Результаты испытаний представлены в Таблице 12. …Контекст 8
… была достигнута максимальная нагрузка, образец внезапно развалился на две части. Результаты испытаний на прочность на изгиб приведены в табл. 13. Из таблицы по формуле в п.п. [42,43], взаимосвязь между прочностью на изгиб и кубической прочностью на сжатие можно рассчитать по уравнению (17). …Влияние состава и отверждения на усадку газобетона при высыхании
Valore, R.C., «Ячеистые бетоны — физические свойства», , журнал Американского института бетона, . 25 (1954) 817–836.
Google Scholar
Зембика, Х. , «Влияние микропористой структуры на усадку ячеистого бетона», Cement and Concrete Research 7 (1977) 323–332.
Артикул Google Scholar
Невилл, А.М., Свойства бетона (Джон Вили и сыновья, Нью-Йорк, 1981).
Google Scholar
Хансен, В. и Алмудайхим, Дж. А., «Предельная усадка бетона при высыхании — влияние основных параметров», ACI Materials Journal 84 (1987) 217–223.
Google Scholar
Шуберт, П., «Усадочное поведение газобетона», в «Автоклавный газобетон, влажность и свойства», (Elsevier, 1983) 207–217.
Джорджиадес, А. и Ч. Фтикос, «Влияние микропористой структуры на усадку автоклавного ячеистого бетона», Исследование цемента и бетона 21 (1991) 655–662.
Артикул Google Scholar
Нильсен, А., «Усадка и ползучесть — параметры деформации автоклавного бетона», в «Автоклавный бетон, влажность и свойства» (Elsevier, 1983) 189–204.
Тада, С., «Структура пор и влажностные характеристики пористых неорганических строительных материалов», в «Достижения в автоклавном газобетоне» (А. А. Балкема, 1992) 53–64.
Хауст, Ю., Алоу, Ф. и Виттманн, Ф.Х., «Влияние содержания влаги на механические свойства автоклавного ячеистого бетона», в «Автоклавный ячеистый бетон, влажность и свойства» (Elsevier, 1983). ) 219–233.
Тада, С. и С. Накано., «Микроструктурный подход к свойствам влажного ячеистого бетона», в «Автоклавный газобетон, влажность и свойства» (Elsevier, 1983) 71–89.
Александерсон, Дж., «Взаимосвязь между структурой и механическими свойствами автоклавного ячеистого бетона», Исследование цемента и бетона 9 (1979) 507–514.
Артикул Google Scholar
Комитет ACI 516, «Отверждение паром под высоким давлением. Современная практика и свойства автоклавных продуктов», Журнал Американского института бетона 62 (1965) 868–907.
Google Scholar
Рекомендации RILEM. Автоклавный газобетон — свойства, испытания и проектирование (E and FN SPON, 1993).
Хоббс, Д. В. и Мирс, А. Р., «Влияние геометрии образца на изменение веса и усадку образцов воздушно-сухого раствора», Magazine of Concrete Research 23 (1971) 89–98.
Google Scholar
ASTM C 596, «Стандартный метод испытаний на усадку при высыхании раствора, содержащего портландцемент».(Американское общество испытаний и материалов, Филадельфия, 1989 г.).
Google Scholar
IS 6441 — Часть II, «Методы испытаний автоклавного ячеистого бетона — Определение усадки при высыхании» (Бюро индийских стандартов, Нью-Дели, 1972).
Google Scholar
Фултон, Ф. С., «Координированный подход к испытанию бетона и строительных растворов на усадку», Magazine of Concrete Research 13 (1961) 133–140.
Google Scholar
ASTM C 618, «Стандартные технические условия на летучую золу и необработанный или прокаленный природный пуццолан для использования в качестве минеральной добавки в бетон на портландцементе» (Американское общество испытаний и материалов, Филадельфия, 1989 г.).
Google Scholar
Нараянан, Н., «Влияние состава на микроструктуру и свойства газобетона», М.S. Диссертация (IIT Madras, июнь 1999 г.).
Лохнер, Р. Х. и Матар, Дж. Э., Проектирование для обеспечения качества (Чепмен и Холл, 1990).
Кьелльсен, К. О. и Атласси, Э. Х., «Структура пор в цементно-кремнеземных дымовых системах — наличие пустотелых пор», Cement and Concrete Research 29 (1999) 133–142.
Артикул Google Scholar
Пористость и механическая прочность автоклавного глиняного ячеистого бетона
В данной статье исследуются пористость и механическая прочность автоклавного глиняного ячеистого бетона (АССС) со вяжущим, изготовленным из 75 % масс. каолинитовой глины и 25 % масс. портландцемента.В качестве пенообразователя использовали алюминиевый порошок в количестве от 0,2 % до 0,8% по массе, получая образцы с различной пористостью. Результаты показывают, что образцы с более высоким содержанием алюминия демонстрируют слияние пор, что может объяснить более низкую пористость этих образцов. Пористость, полученная при использованном в исследовании содержании алюминия, была высокой (около 80%), что объясняет низкую механическую прочность исследованных ячеистых бетонов (максимум 0,62 МПа). Тем не менее, сравнивая результаты, полученные в этом исследовании, с результатами для низкотемпературного глинистого газобетона с аналогичными составами, можно отметить, что автоклавирование эффективно для повышения механической прочности материала.
1. Введение
Ячеистый бетон представляет собой затвердевший портландцементный раствор, который был аэрирован перед схватыванием для получения однородной пустотной или ячеистой структуры, содержащей 50–80 об. % или более пузырьков воздуха, пустот и капиллярной пористости [1]. ]. Тепло- и звукоизоляция и огнестойкость — вот некоторые из свойств, которые делают ячеистый бетон очень интересным материалом для применения в строительстве [2–4].
Существует множество возможных способов производства ячеистого бетона.Различные составы вместе с различными методами отверждения могут использоваться для получения различных конечных свойств, таких как плотность, механическая прочность, тепловая и акустическая проводимость [1].
Конечные свойства ячеистого бетона во многом зависят от его пористости, которую можно изменять, изменяя тип и содержание пенообразователя. Очень пористый материал обладает превосходными тепло- и звукоизоляционными свойствами из-за большого количества вовлеченного воздуха. Однако эти свойства достигаются в ущерб механической прочности, которая снижается с увеличением объема пор.Поэтому характеристика пористости и ее влияние на механическую прочность ячеистого бетона является очень важным фактором, подлежащим анализу при производстве такого материала.
Некоторые исследования [5] показывают, что при той же пористости и составе механическая прочность ячеистого бетона может быть повышена путем изменения способа твердения. Автоклавный газобетон (AAC), то есть отвержденный под давлением пара при температурах между и обычно имеет более высокую прочность на сжатие, чем бетоны из неавтоклавного газобетона (NAAC), отвержденные влажным способом при комнатной температуре.Кроме того, при автоклавировании материал достигает своей окончательной микроструктуры, тогда как НААК претерпевает со временем микроструктурные изменения и, как следствие, медленные и постепенные изменения своей механической прочности [5].
Композиция ячеистого бетона на каолинитовой глинистой основе была исследована Goual et al. [6–8]. В своих исследованиях глиняный ячеистый бетон (CCC), как он был обозначен, отверждался во влажном состоянии при относительной влажности 90%. Поскольку реакции между каолинитом и портландцементом при комнатной температуре протекают очень медленно, этому материалу могут потребоваться месяцы, прежде чем будет достигнута его окончательная механическая прочность.Инновация, предложенная в этой статье, связана с использованием автоклава для улучшения свойств материала этого вида ячеистого бетона.
Это исследование направлено, в частности, на изучение пористости и механической прочности автоклавного глиняного ячеистого бетона (ACCC) и сравнение результатов с результатами, представленными CCC с аналогичными составами, о которых сообщается в литературе.
2. Экспериментальный
2.1. Материалы
Используемая глина состояла из 98,3% каолинита (Caulina Minérios, Бразилия), а цемент представлял собой стандартный портландцемент с высокой начальной прочностью (CP V-ARI-RS, Votorantim, Бразилия). Алюминиевый порошок представлял собой Stanlux Flake CL 4010 (Aldoro, Бразилия) со средним размером частиц 16 мкм. Для повышения удобоукладываемости глиняно-цементного теста использовали суперпластификатор на основе поликарбоксилата (Glenium 51, BASF, Германия) (32 мас.% сухих веществ).
2.2. Композиции
Автоклавный глинисто-ячеистый бетон (АССС) получали путем аэрации водной пасты каолинитовой глины и портландцемента с использованием алюминиевой пудры в качестве пенообразователя. Порошок алюминия реагирует с раствором щелочи, который выделяется во время реакции гидратации, с образованием пузырьков газообразного водорода [7].В конце процесса вспенивания водород уходит в атмосферу и замещается воздухом, который удерживается в виде пузырьков в пасте, превращаясь в сферические поры после полного схватывания цемента, образуя ячеистую структуру [6].
Были проанализированы четыре композиции, отличающиеся количеством используемого алюминиевого порошка. Количества, рассчитанные в процентах по массе сухих глиняно-цементных материалов, были следующими: 75% по массе глины, 25% по массе цемента, 65% по массе воды и суперпластификатор на основе поликарбоксилата (0. 8 масс.%, массовый процент твердых веществ по отношению к сухим материалам), к которым добавляли от 0,2 масс.% до 0,8 масс.% алюминиевого порошка с шагом 0,2%. Образцы в этом исследовании были обозначены как A2 для 0,2, A4 для 0,4, A6 для 0,6 и A8 для 0,8 вес.% алюминия.
2.3. Подготовка образцов
В этом эксперименте глину и цемент смешивали в сухом виде в планетарном смесителе на низкой скорости в течение 2 минут. Затем постепенно добавляли воду, продолжая перемешивание на низкой скорости еще 2 минуты.Делали короткую 1,5-минутную остановку перемешивания для того, чтобы соскоблить материал, прилипший к стенкам емкости для смешивания. Затем смесь гомогенизировали при низкой скорости в течение 1 минуты, а затем в течение 2 минут при высокой скорости. Добавляли суперпластификатор, в то время как смеситель оставался остановленным в течение 30 секунд. После добавления этой добавки пасту перемешивали на низкой скорости в течение 1 минуты и затем останавливали еще на 30 секунд для добавления порошка алюминия, который перемешивали и гомогенизировали в пасту в течение 1 минуты на низкой скорости.
По восемь образцов каждой смеси отливали в цилиндрические (50 100 мм 3 ) металлические формы, предварительно смазанные маслом для облегчения извлечения из формы. Через шестнадцать часов после формования лишние расширенные участки отрезали. Через 48 часов образцы извлекали из форм и выдерживали во влажном помещении при 25 и 90% относительной влажности в течение 2 дней, после чего автоклавировали при 12 атм в течение 10 часов. Перед началом экспериментов образцы высушивали в сушильном шкафу при температуре 70°С до достижения постоянного веса.
Микроструктуру и фазы АССС сравнивали с микроструктурой и фазами низкотемпературного глинистого ячеистого бетона, отвержденного при температуре окружающей среды во влажной комнате при температуре 25°С и относительной влажности 90% в течение 21 дня.
2.4. Плотность, пористость и механическая прочность
Относительная плотность ячеистого бетона соответствует отношению между кажущейся плотностью (геометрически измеренной) ячеистого материала и плотностью твердого вещества, составляющего матрицу этого ячеистого материала [9]. ]:
Пористость определяется выражением [9]
Для измерения образцов АССС из центра 2 образцов каждого состава были вырезаны диски диаметром примерно 50 15 мм 3 .Затем были измерены их масса и относительные размеры для расчета объема, при этом кажущаяся плотность определялась по (3) где определяется по геометрической формуле расчета цилиндрического объема.
Для измерения использовали гелиевый пикнометр (Multipycnometer, QuantaChrome, США). Для этого анализа были измельчены репрезентативные образцы каждого состава. Для измерения использовали приблизительно 4 г порошка каждого состава. Всего было проведено 10 измерений для каждого образца порошка, при этом окончательное значение было получено как среднее арифметическое.
Для определения механической прочности образцов пять цилиндрических образцов (50 100 мм 3 ) каждого состава были испытаны на универсальной машине для механических испытаний (DL 20000, Emic, Бразилия) в соответствии с бразильским стандартом [10]. Базовые поверхности образцов были покрыты гипсом для получения плоских и параллельных поверхностей. Используемая скорость нагрузки составляла 1 мм/мин.
2.5. Микроструктура и фазовый анализ
Продукты в этой работе были охарактеризованы с помощью рентгеновской дифрактометрии (XRD, Phillips, model Xpert, Нидерланды) и сканирующей электронной микроскопии (SEM, Phillips, Нидерланды).
3. Результаты и обсуждение
3.1. Плотность и пористость
На рис. 1 показаны кажущаяся плотность и пористость проанализированных образцов ACCC в зависимости от процентного содержания порошка алюминия. Как можно заметить, плотность не менялась, как ожидалось, для различных количеств Al. Как правило, плотность ячеистого бетона уменьшается по мере увеличения процентного содержания пенообразователя из-за большего количества образующихся пор. Однако в данном случае такое поведение как раз и наблюдалось для образцов с 0.2 и 0,4 мас.% Al. Для образцов с большим количеством порошка Al плотность увеличилась. Такое же аномальное поведение было отмечено для пористости образцов АССС. Пористость увеличилась между образцами А2 и А4, но впоследствии уменьшилась для образцов А6 и А8, достигнув более высокого значения на образце А4 (83,2%).
Анализ поверхности изломов образцов АССС показал, что смеси А6 и А8 имеют поры неоднородной формы, которые больше, чем наблюдаемые для смесей А2 и А4, что свидетельствует о слиянии пор смесей с более высоким содержанием Al.Это может объяснить неожиданные результаты для плотности и пористости. На рисунках 2(а) и 2(б) показана поверхность излома образцов А2 и А8 соответственно.
При слиянии пор они приобретают больший объем и стремятся вырваться из материала [1] из-за более сильных сил, действующих на них со стороны жидкости (выталкивающая сила, оказываемая вяжущей массой на пузырьки газа). Таким образом, часть газа, образующегося во время реакции между Al и гидроксидами, не эффективна для образования пор, что приводит к более низкой пористости образцов A6 и A8.
Фактором, который может объяснить слияние пор в этих образцах, является высокая реакционная способность порошка алюминия, использованного в этом исследовании. Как показано на Рисунке 1, содержания Al 0,2 вес.% уже достаточно для получения пористости 81,8%. При добавлении более высоких концентраций Al количество образовавшихся пузырьков водорода могло быть настолько большим, что для них было более устойчивым слияние, чем оставаться изолированными. Коалесценция обеспечивает минимизацию общей площади поверхности пор, что приводит к более стабильной конфигурации системы [11].
Возможными решениями этой проблемы могут быть минимизация количества суперпластификатора, используемого для повышения вязкости вяжущего теста, чтобы предотвратить выход пузырьков водорода, и оптимизация количества используемого алюминиевого порошка (Stanlux Flake CL4010), так как меньшего количества этого порошка достаточно для получения высокой пористости.
3.2. Механическая прочность
Механическая прочность образцов ACCC соответствовала результатам по плотности и пористости, то есть более высокая пористость приводила к более низкой механической прочности, что можно наблюдать на рисунке 3.
Различные значения механической прочности на сжатие, представленные образцами, проанализированными в этом исследовании, являются следствием их клеточной морфологии. В образцах А2 и А4 из-за большего количества и равномерного распределения пор межпоровые перемычки тоньше, что придает материалу меньшую прочность. Однако в образцах А6 и А8, хотя поры больше из-за коалесценции, распорки толще, что привело к более высокой прочности на сжатие. Даже в этом случае полученные значения были очень низкими, достигая максимума 0.62 МПа для состава А8 (пористость 78,23%).
Согласно Гибсону и Эшби [9], механическая прочность ячеистого материала является потенциальной функцией его относительной плотности, следующей уравнению: где – механическая прочность абсолютно плотного материала, – геометрическая константа пропорциональности, его пористость и эмпирический показатель.
С помощью этого уравнения на основе данных, представленных в литературе [6], были оценены значения механической прочности, которые имели бы образцы CCC, если бы они имели такую же пористость, что и образцы ACCC, проанализированные в этом исследовании. Сравнение показано на рисунке 4.
Можно заметить, что значения механической прочности, оцененные для образцов CCC, значительно меньше, чем значения, измеренные для ACCC с той же относительной плотностью. Это позволяет сделать вывод об эффективности автоклавирования при упрочнении ячеистого бетона на глинистой основе, так как при одинаковом значении пористости прочность на сжатие АССС существенно выше, чем у ССС, твердеющего при комнатной температуре.
Поскольку более высокая прочность на сжатие, проанализированная в этом исследовании, равнялась 0.62 МПа для образца с 0,8% масс. Al, становится ясно, что необходимо уменьшить количество используемого порошка Al, чтобы получить образцы с более низкой пористостью и, следовательно, более высокой механической прочностью для соответствия техническим требованиям. Однако, если цель состоит в том, чтобы использовать материал с такой же пористостью, как и проанализированные здесь, следует исследовать некоторые изменения в составе.
3.3. Микроструктура и фазовый анализ
Кристаллические фазы АССС сравнивали с фазами глинистого ячеистого бетона, отвержденного при относительной влажности 90 % в течение 21 дня (рис. 5).В обоих случаях можно наблюдать пики каолинита и галлуазита из непрореагировавшей глины. Относительная интенсивность пика кальцита снижается при автоклавировании CCC, что приводит к образованию тоберморита. Типичные игольчатые структуры тоберморита [12, 13] более заметны в образце ACCC (рис. 6(b)) по сравнению с отвержденным CCC. при низкой температуре (рис. 6(а)).
4. Выводы
Данное исследование было направлено на изучение влияния автоклавной выдержки на механическую прочность ячеистого бетона на глинистой основе.Проанализированы пористость и механическая прочность образцов разного состава, отличающихся только содержанием Al, и результаты сопоставлены с литературными данными для глинистого ячеистого бетона, отвержденного при комнатной температуре (CCC).
По результатам можно сделать следующий вывод. (i) Образцы с содержанием алюминиевого порошка от 0,6 до 0,8% производили столько водорода, что поры больше не оставались дискретными, то есть поры сливались до такой степени, что избыток водорода может сбежать из матрицы.Это означает, что, вероятно, оптимальный уровень добавления алюминия находится в диапазоне от 0,4 до 0,6% для получения максимальной пористости. (ii) Механическая прочность образцов ACCC варьировалась в зависимости от их пористости, то есть она увеличивалась по мере уменьшения пористости. . Однако полученные значения были очень низкими, достигая максимума 0,62 МПа для образца с более низкой пористостью (78,23%). (iii) Путем экстраполяции данных, представленных в литературе [6] для образцов CCC, было обнаружено, что, при одинаковой пористости и составе автоклавный глинисто-ячеистый бетон (АССС) демонстрирует значительно более высокую механическую прочность, чем ССС, что показывает, что автоклавирование эффективно укрепляет этот вид материала. (iv) Следует использовать меньшее количество порошка Al, чтобы уменьшить пористость и повысить механическую прочность. Другой возможностью может быть изменение твердофазного состава исследуемого здесь АССС.
Благодарности
Авторы выражают благодарность г-ну Zanon и г-ну Nogara из Celucon (Criciúma, SC, Бразилия) за предоставление алюминиевого порошка, используемого в этом исследовании, а также за разрешение использовать их автоклав для нашей экспериментальной работы.
Обзор — Университет штата Аризона
TY — JOUR
T1 — Структура и свойства газобетона
T2 — Обзор
AU — Нараянан, Н.
AU — Ramamurthy, K.
PY — 2000/10
Y1 — 2000/10
N2 — Ячеистый бетон относительно однороден по сравнению с обычным бетоном, так как он не содержит фазу крупного заполнителя, но имеет большие различия в его свойствах. Свойства газобетона зависят от его микроструктуры (пустотно-паста) и состава, на которые влияют тип используемого вяжущего, способы порообразования и твердения. Хотя газобетон изначально рассматривался как хороший изоляционный материал, интерес к его структурным характеристикам возобновился ввиду его легкого веса, экономии материала и возможности крупномасштабного использования отходов, таких как пылевидная топливная зола.Целью данной статьи является классификация исследований свойств газобетона с точки зрения физических (микроструктура, плотность), химических, механических (прочность на сжатие и растяжение, модуль упругости, усадка при высыхании) и функциональных (теплоизоляция, перенос влаги). , долговечность, огнестойкость и звукоизоляция).
AB — Газобетон относительно однороден по сравнению с обычным бетоном, так как не содержит фазы крупного заполнителя, но при этом демонстрирует большие различия в своих свойствах.Свойства газобетона зависят от его микроструктуры (пустотно-паста) и состава, на которые влияют тип используемого вяжущего, способы порообразования и твердения. Хотя газобетон изначально рассматривался как хороший изоляционный материал, интерес к его структурным характеристикам возобновился ввиду его легкого веса, экономии материала и возможности крупномасштабного использования отходов, таких как пылевидная топливная зола. Целью данной статьи является классификация исследований свойств газобетона с точки зрения физических (микроструктура, плотность), химических, механических (прочность на сжатие и растяжение, модуль упругости, усадка при высыхании) и функциональных (теплоизоляция, перенос влаги). , долговечность, огнестойкость и звукоизоляция).
UR — http://www.scopus.com/inward/record.url?scp=0034300785&partnerID=8YFLogxK
UR — http://www.scopus.com/inward/citedby.url?scp=0034300785&partnerID=8YFLogxK
U2 — 10.1016 / S0958-9465 (00) 00016-0
DO — 10.1016 / S0958-9465 (00) 00016-0
м3 — Статья
An — Scopus: 0034300785
VL — 22
SP — 321
EP — 329
EP — 329
Jo — цементные и бетонные композиты
JF — цементные и бетонные композиты
SN — 0958-9465
— 5
— 5
ER —
Формирование тоберорита на разных материалах Состав газированного Бетон
[1]
К. Куатбаев К., Физико-химические свойства процессов твердения и долговечности гидротермально обработанных алюмосиликатных и силикатных материалов, Алматы: Кандидатская диссертация, (1982).
[2] Н.Ю. Мостафа, С.А.С. Эль-Хемали, Э.И. Аль-Вакил, С.А. Эль-Кораши, Активность микрокремнезема и деалюминированного каолина при разных температурах, Cement and Concrete Res. 31 (2001) 905-911.
DOI: 10.1016/s0008-8846(01)00489-6
[3]
Н. Ю. Мостафа, А.А. Shaltout, H. Omar, S.A. Abo-El-Enein, Гидротермальный синтез и характеристика алюминий- и сульфатзамещенных тоберморитов размером 1,1 нм, J. Alloys and Comp. 467 (2009) 332-337.
DOI: 10.1016/j.jallcom.2007.11.130
[4] С.А. Риос, К.Д. Уильямс и М.А. Фуллен, Гидротермальный синтез гидрограната и тоберморита при 175 °C из каолинита и метакаолинита в системе CaO-Al2O3-SiO2-h3O: сравнительное исследование, Appl. Глина наук. 43 (2009) 228-237.
DOI: 10. 1016/j.clay.2008.09.014
[5] Д.Тунега и А. Зауи, Понимание связующих и механических характеристик вяжущего минерала тоберморита из первых принципов, J. Comput. хим. 32 (2011) 306-314.
DOI: 10.1002/jcc.21622
[6]
Р.Вектарис, Б. Лескаускас и К. Саснаускас, Влияние добавок гипса на процесс образования низкоосновных гидратов силиката кальция, Труды: Рез. Строить. Матер. Вильнюс, (1987).
СТРУКТУРА И СВОЙСТВА ЯБЕТОНА: ОБЗОР
Газобетон относительно однороден по сравнению с обычным бетоном, так как не содержит крупнозернистой фазы заполнителя, однако его свойства сильно различаются.Свойства газобетона зависят от его микроструктуры (пустотно-паста) и состава, на которые влияют тип используемого вяжущего, способы порообразования и твердения. Хотя газобетон изначально рассматривался как хороший изоляционный материал, интерес к его структурным характеристикам возобновился ввиду его легкого веса, экономии материала и возможности крупномасштабного использования отходов, таких как пылевидная топливная зола. Целью данной статьи является классификация исследований свойств газобетона с точки зрения физических (микроструктура, плотность), химических, механических (прочность на сжатие и растяжение, модуль упругости, усадка при высыхании) и функциональных (теплоизоляция, перенос влаги). , долговечность, огнестойкость и звукоизоляция).(А)
- Наличие:
- Корпоративные Авторы:
Эльзевир
Бульвар, Лэнгфорд Лейн
Кидлингтон, Оксфорд объединенное Королевство OX5 1 ГБ - Авторов:
- НАРАЯНАН, N
- Рамамурти, K
- Дата публикации: 2000
Язык
Информация о СМИ
Тема/Указатель Термины
Информация о подаче
- Регистрационный номер: 00799821
- Тип записи: Публикация
- Агентство-источник: Транспортная исследовательская лаборатория
- Файлы: ITRD
- Дата создания: 6 октября 2000 г.
, 00:00
Рахул Малхотра — Химия материалов 2013
БЛЕСТЯЩИЙ! ИМЕННО ТО, ЧТО Я ПОСЛЕ
ПРИМЕЧАНИЕ. НАВЕДЕНИЕ МЫШИ НАД ИЗОБРАЖЕНИЕМ ПОКАЗЫВАЕТ ЕГО ССЫЛКУ
Автоклавный газобетон — это легкий строительный материал, который используется для многих целей в строительной отрасли.Материал считается более экологичным, чем другие строительные материалы. AAC предлагает отличные свойства, которыми должны обладать многие строительные материалы, и поэтому он становится все более популярным в строительстве. Автоклавный газобетон теперь широко известен как бетон Hebel, поскольку компания, производящая бетон, известна как Hebel.
Происхождение
Автоклавный газобетон имеет более чем 90-летнюю историю. Этот материал был изобретен в 1920-х годах шведским архитектором Йоханом Акселем Эрикссоном.В то время был большой дефицит древесины и срочно требовались новые строительные материалы. Йохан Эрикссон использовал простое сырье, которое было доступно для производства этого типа легкого газобетона. Йохан также поместил бетон в автоклав, чтобы ускорить производственный процесс, и именно так материал получил свое название. AAC был официально запатентован в 1924 году под названием; пористый бетон.
Развитие в истории
С момента своего изобретения конструкция и конструкция газобетона были усовершенствованы.В 1929 году материал был впервые произведен в Швеции. Бетон тогда назывался Ytong, и его популярность быстро росла благодаря полезным свойствам. В 1945 году Йозеф Хебель усовершенствовал процесс производства газобетона. Он разработал метод включения стальной арматуры в производство этого бетона. Он запатентовал этот метод и открыл собственную компанию под названием Hebel, которая также производила газобетон автоклавного твердения. В 1975 году Ytong перестала использовать в своих бетонных изделиях вид сланца, считающийся небезопасным для людей.Это привело к тому, что автоклавный газобетон стал еще безопаснее для здоровья людей. До конца 20-го века Hebel и Ytong были основными поставщиками AAC, но с тех пор объединились в одну компанию. В настоящее время Hebel Concrete продается почти в 30 странах мира. Его производственный процесс сегодня такой же, как и при его изобретении, за исключением нескольких улучшений. Теперь из Hebel можно сделать множество различных продуктов, таких как блоки, стеновые панели и панели крыши, чтобы использовать его для различных целей в здании.
Производство Автоклавный газобетон
изготавливается из трех основных материалов; песок, известь и портландцемент. Стальная арматура также добавляется в процессе производства стеновых и кровельных панелей, чтобы сделать их еще прочнее. При производстве также используются алюминиевый порошок, разрыхлитель и вода.
Настройка и формирование
Во-первых, все сырье смешивают в смесь густой жидкости и заливают в формы, готовые к формованию различных изделий.Пока смесь находится в форме, алюминиевый порошок вызывает образование в смеси множества отверстий для водородного воздуха. Эти отверстия снижают плотность материала и заставляют его удваиваться по сравнению с первоначальным размером, поэтому все изделия из газобетона такие легкие. Затем материал оставляют затвердевать на целых 4 часа, и если требуется стальная арматура, ее добавляют в формы. Как только он становится твердым, материал разрезается проволокой на нужную форму с помощью множества автоматических машин.
Отверждение
Водород заменяется воздухом, а бетон отправляется в автоклав для отверждения.В автоклаве пар с температурой 180 градусов подается под высоким давлением на бетон, поэтому может произойти вторая химическая реакция, которая сделает материал более прочным и жестким. Этот процесс занимает около 8-14 часов, что намного быстрее, чем при традиционном методе отверждения. Весь производственный процесс обычно выполняется автоматическими машинами и не вызывает выброса каких-либо загрязняющих или токсичных веществ в атмосферу.
Химические уравнения
Существуют две основные химические реакции, которые используются при производстве газобетона:
Во-первых, реакция алюминиевой пудры и серной кислоты в бетоне приводит к образованию в смеси миллионов пузырьков водорода, уравнение этой реакции:
- Алюминий + серная кислота —> сульфат алюминия + водород
- 2Al (т) + 3H 2 SO 4 (водн.
) -> Al 2 (SO 4 ) 3 (водн.) + 3H 2 (г).
Другой реакцией является реакция алюмосиликата кальция с известью с образованием цемента, состоящего из силиката кальция и алюмината кальция:
- Алюмосиликат кальция + известняк —> силикат кальция + алюминат кальция + углекислый газ
- CAAL 2 SI 2 O 8 O 8 + 6CACO + 6CACO 3 -> 2CA 2 SIO 4 + Ca 3 (ALO 3 ) 2 + 6CO 2
Эта реакция дает портландцемент; компонент ААС.
Процесс изготовления показан на видео ниже:
Воздействие на окружающую среду Автоклавный газобетон
оказывает как положительное, так и отрицательное воздействие на окружающую среду. Однако, по сравнению с традиционным бетоном, он намного лучше для окружающей среды.
Положительный
БетонHebel был протестирован организацией Good Environmental Choice Australia (GECA) на предмет того, насколько он безвреден для окружающей среды, и оказалось, что он на 60 % более безвреден для окружающей среды, чем другие строительные материалы, в таких аспектах, как эффекты глобального потепления, канцерогены, образующиеся отходы и используемая энергия. в производстве.В целом газобетон имеет на 73% меньше воплощенной энергии и на 61% меньше выбросов парниковых газов, чем другие строительные материалы.
Производство
В процессе производства газобетон использует только четверть сырья, которое используется в традиционных строительных изделиях, и, следовательно, имеет гораздо меньший углеродный след. Они даже используют сырье, которое имеется в изобилии и может быть легко получено рядом с заводом-изготовителем, поэтому воздействие транспорта на окружающую среду сводится к минимуму. Кроме того, все отходы бетона и других материалов, которые производятся во время производства, используются повторно, поэтому не образуются постоянные отходы.Производственный процесс также экономит электроэнергию, так как отверждение паром в автоклаве происходит при низких температурах и не требует повторного нагрева. В процессе не выделяются токсичные газы, а вода также экономится за счет многократного сбора и повторного использования на бетоне. В целом для газобетона требуется около 0,4 кг сырья на м3 (см. график).
Использовать
Тепловые свойства газобетона во время его использования снижают затраты на отопление и охлаждение в зданиях и, следовательно, их углеродный след.Точность процесса раскроя на производстве снижает количество отходов от раскроя изделий при сборке. Если вы строите из газобетона, вам не нужно использовать изоляцию в стенах и крышах, что снижает воздействие здания на окружающую среду.
Утилизация и переработка
Производители газобетонных блоков осуществляют программы сортировки и утилизации отходов газобетонных материалов, которые могут быть переработаны перед отправкой на свалку, что снижает их воздействие на окружающую среду. Кроме того, материал не содержит токсичных веществ, поэтому не представляет опасности даже на свалке.
Отрицательный
Хотя автоклавный газобетон кажется действительно экологически чистым материалом, он имеет свои негативные последствия. Все автоматические машины, используемые при производстве газобетона, используют и сжигают ископаемое топливо и производят большое количество выбросов углерода. Выбросы углерода от транспорта присутствуют и оставляют углеродный след. Известь, содержащаяся в бетоне, также содержит большое количество углекислого газа и поэтому менее экологична.Он содержит около 1000 кг CO2 на тонну.
Химический состав
Автоклавный газобетон состоит из следующих материалов:
- Песок, содержащий более 85% кремнезема (SiO 3 ) и глины (силикаты алюминия-AlSi)
- Алюминиевый порошок/паста (Al)
- Известь, которая содержит 75% оксида кальция (CaO), а также другие соединения.
- Диоксид кремния (SiO 2 )
- Гипс; дегидрат или фосфогипс, содержащий триоксид серы (SO 3 )
и;
- Портландцемент, состоящий из силиката кальция-Ca 2 SiO 4 и алюмината кальция-Ca 3 (AlO 3 ) 2
Химическая структура силиката кальция:
Макроскопические свойства
Макроскопические свойства автоклавного газобетона приведены в таблице ниже: