Газобетон или монолит: Газобетон монолитный: особенности
Газобетон монолитный: особенности
29 января 2014
9470
Оглавление: [скрыть]
- Составляющие для блоков
- Преимущества газобетона
- Недостатки материала
- Поэтапное строительство
- Необходимые материалы
- Последние штрихи
Монолитный газобетон — это вид бетона, который имеет в своей структуре ячейки. Этот строительный материал представляет собой искусственный камень с равномерно распределенными по всему объему ячейками диаметром 1-3 мм. Качество газобетона определяется равномерным распределением и одинаковым объемом ячеек, качеством закрытости пор.
Дом из газобетона теплый, прочный, легкий.
Составляющие для блоков
Наиболее применяемые компоненты для этого материала:
- кварцевый песок;
- цемент и специальные смеси, которые образовывают газ;
- не исключением в растворе могут быть такие компоненты как известь, гипс, шлаки, зола.
Газобразователем выступает алюминиевая пудра или паста, они вступая в химическую реакцию с водой, выделяют водород, который и создает поры.
В виде специализированных компонентов — газобразователей — используют алюминиевые пудры и пасты. Нужные компоненты тщательно перемешиваются с добавлением воды, после чего заливаются в формы. Газообразователь, вступая в реакцию с водой, выделяет водород, который создает поры. Таким образом раствор поднимается словно тесто на дрожжах. После первой реакции затвердения строительный материал разрезается и делиться на панели, плиты и блоки. После чего происходит производственный процесс, в котором почти готовое изделие (монолит) проходит закалку паром в автоклаве. Именно в этом процессе камень приобретает необходимую для материала жесткость. Существует процесс закалки камня путем электроподогрева. Такой способ тоже эффективно придает камню твердость.
В зависимости от способа обработки газобетона его делят на неавтоклавный материал газосиликатных блоков (что обрабатывался путем электроподогрева) и автоклавный (обработка материала проводилась путем закалки паром в устройстве автоклава).
Монолит газобетона отлично поддается обработке подручными инструментами: хорошо пилится, строгается, сверлится. В этот материал без труда можно вбить гвозди или скобы. С каждым годом газобетонная конструкция становиться тверже и прочнее. Компоненты, из которых состоит монолит газобетона, являются минералами. Они, как известно, не поддаются горению. Это немаловажный факт для тех строителей, которые заботятся о безопасности жильцов. По характеристикам экологической безопасности газобетон обладает низкой естественной радиоактивностью по сравнению с железобетоном или тяжелым бетоном. Это обусловлено меньшей плотностью строительного материала.
Монолит в виде газобетона прославился на весь мир. Его производство ведется более чем на 240 фабриках в 50-ти странах мира. Ежегодное изготовление газобетонных камней составляет 60 млн. м³.
Вернуться к оглавлению
Преимущества газобетона
Прочность стены из монолитного газобетона около 85%
Газобетон — материал, который используется для строительства коробки дома и обладает уникальными характеристиками. Прочность такого материала доходит до 85%, и он прекрасно сочетает в себе свойства камня и дерева.
В процессе производства получается сравнительно легкий материал, который обладает максимальной прочностью. Именно такой материал, как считают потребители и компании-производители, представляет собой выгодное сочетание легкости и прочности с оптимальными свойствами термоизоляции.
Объемная густота — это то, что отображается в соотношении газобетона к занятому объему. Это немаловажное качество газобетонных блоков, оно влияет на дальнейшие эксплуатационные, качественные характеристики. Величина объемной густоты влияет на прочность. Чем меньше густота объема, тем выше изоляционные свойства строительного газобетонного материала. Закрытые поры в процессе производства блоков содержат воздух, и именно он влияет на изоляцию и теплоту в доме. Но в этом есть и большой минус газобетона: чем ниже густота газобетонных блоков, тем ниже его звукоизоляция. Слышимость звуков в доме со двора будет легко уловима человеческому уху.
Благодаря прочности газобетон используют для строительства и возведения несущих стен домов, стен-наполнителей, самонесущих стен и перегородок.
Опалубку для монолитного газобетона можно построить своими руками без применения специальной техники.
Несмотря на объемный вид, монолит газобетона относительно легкий материал. Строительство из газобетона обходится без вмешательства строительной техники, то есть стены можно возводить без сторонней помощи, самостоятельно.
Монолитный газобетон легко поддается дополнительной обработке (если потребуется), легко пилится, без труда сверлится, штрабится, поддается обработке ручной ножовкой. Это качество особенно привлекательно для застройщиков.
Часто ручную обработку газобетонов применяют, когда строят дом в каком-нибудь архитектурном стиле, преобразовывая его в незабываемую историческую задумку.
Стены из газобетонных блоков возводятся очень быстро благодаря своему объему. К примеру, такая же кладка из кирпича занимает намного больше времени и действий.
Газобетон строит в первых рядах со стеновыми материалами, которые обладают наиболее низкой теплопроводностью. Таким образом, обеспечивается тепло помещений дома в холодную погоду. Но и в летние дни дом сохраняет прохладу, не пропуская жар сквозь стены.
Газобетон не поддается горению, то есть обладает стойкостью к огню и высокой температуре.
Основное оборудование для литья газобетона — это небольшой газобетонный смеситель, ёмкость которого 200-500 литров, его легко могут перемещать два рабочих- строителя.
Как оговаривалось выше, звукоизоляция материала зависит от густоты объема, от толщины стен и от технологии их возведения. Помимо газобетонных блоков, сегодня существует множество строительных материалов на рынке, которые обладают звукоизоляцией.
Газобетон имеет высокую стойкость при низких температурах воздуха. Холодные морозные дни не способны понизить температуру в доме. Структура строительного блока является устойчивой к воздействию мороза.
Газобетон обладает паропроницаемостью. Именно это его свойство способно обеспечить оптимальную сухость и влажность в доме.
Так как газобетон при производстве получается с закрытыми порами, то влажность его не превышает даже 8 %. Это преимущество учитывают, когда планируют построить дом.
Положительные эксплуатационные характеристики газобетонного блока доказаны годами. Его давно используют для строительства в разных странах. Дом из газобетона, если он возведен по надлежащим правилам и технологии, не подает даже малейших намеков на свой возраст. Таким образом, монолит газобетонных стен может прослужить не менее ста лет.
Вес одного блока из газобетона (если брать средние показатели изготовленного материала) составляет 25 кг. Такой же объем из кирпичей (28 шт.) завесит приблизительно 120 кг. Эти показатели значительно облегчают работу в процессе строительства.
По проведенным предварительно исследованиям было доказано, что монолитный газобетон обладает абсолютной устойчивостью к грибкам и плесени, он, наоборот, предотвращает их появление.
Вернуться к оглавлению
Недостатки материала
Помимо всех указанных преимуществ и плюсов строительных газобетонных блоков, недостатки в этом материале также имеются.
- Газобетон не стоит использовать для возведения помещений, в которых будет повышенная влажность. Газобетон способен абсорбировать большое количество влаги. Сам он при этом не повреждается, но отделка, которая находится на стенах, деформируется. Но этого можно избежать на начальных этапах строительства, выполнив комплекс мероприятий.
- Морозостойкость имеют виды материала с определенной плотностью, остальные пропускают холод.
- Отсутствие механической прочности. Традиционные крепежи портят блоки. Можно использовать специальный крепеж для ячеистых блоков.
- Дешевизна газобетонных блоков говорит о том, что материал низкого сорта.
Они способны долго прослужить.
- Строительство стен может быть недостаточным для удержания тепла в доме или прохлады в жаркие дни. Таким образом, идет перерасход энергии или газа на отопление или кондиционирование. С этой проблемой можно справиться, если при изначальном строительстве дома придерживаться норм и построить стены надлежащей толщины.
- Для дома с газобетонной кладкой стен в качестве основания используют монолит или ленточный фундамент. Таким образом исключаются проблемы усадочной деформации, которая может привести к появлению масштабных трещин в стенах.
- Известь, которая входит в раствор, используемый между блочными материалами, ускоряет процесс коррозии металлических вставок. Нужно использовать металлические вставки, которые более стойкие к коррозии, или иной раствор, без добавления извести.
Вернуться к оглавлению
Поэтапное строительство
Первый этап строительства — это возведение фундамента и опалубки.
На начальном этапе строительства возводится основа здания. Для этого вырывается котлован: можно самому это сделать, но с помощью строительной техники будет быстрее. Строя газобетонный дом, часто используют монолит или ленточный фундамент. Чтобы определиться, какой из них подойдет, необходимо выяснить состав грунта на строительной площадке, уровень грунтовых вод и глубину промерзания почвы на территории.
После того как заложен последний слой раствора в фундаменте, необходимо подождать определенное время до его полного застывания, не менее 30 дней. В это время можно заняться закупкой и доставкой строительного материала на площадку.
После затвердения фундамента его нужно обложить цоколем, после чего можно строить сам дом, то есть приступать к кладке стен. Помимо строительного материала и техники, нужно обзавестись и другими вспомогательными приборами и инструментами, которые будут верными помощниками.
Вернуться к оглавлению
Необходимые материалы
Материалы и инструменты для строительства стен из газобетона:
Для строительства стен дома вам понадобится:
1. Цемент.
2. Емкость для замешивания раствора.
3. Миксер для замешивания.
4. Мастерок.
5. Молоток.
6. Уровень.
7. Веревка.
8. Ручная ножовка
- Цемент или смесь для приготовления клея, который ложится на стыках между газобетонными блоками.
- Емкость для замешивания цементного раствора.
- Миксер для замешивания раствора, вручную будет очень долго.
- Мастерок для кладки цемента на стыки.
- Молоток. Он поможет подровнять блоки.
- Уровень. С его помощью определяют ровность стен.
- Веревка или леска. Также поможет подровнять газобетонные блоки и, соответственно, стену.
- Ручная ножовка подойдет для того, если нужно обработать или уменьшить газобетонный блок.
Этот список касается основных инструментов и материалов, в строительстве их применяют по своему усмотрению. Есть и дополнительные материалы. Например, для большей вязкости в цементном растворе используют небольшое количество золы.
Первые ряды кладки из газобетонных блоков важны для общей ровности стен. Для начала кладутся блоки по углам, от которых и начинается строительство стен. На каждый ряд натягивается веревка или леска. Каждый положенный блок выравнивается уровнем. Эти условия обязательны, иначе стены получатся кривыми. Дом в таком случае придется разбирать.
Вернуться к оглавлению
Последние штрихи
После возведения стен происходит их перекрытие для монтажа крыши. Этот процесс происходит довольно быстро, благодаря легкости самого материала. После окончания сбора конструкции крыши дом становится похожим на жилое здание.
На следующем этапе дом подвергается облицовке стен.
Как выбрать качественный газобетон — Монолит-Хаус
16.12.2019 Строительство домов из газобетона все больше завоевывает рынок загородного строительства.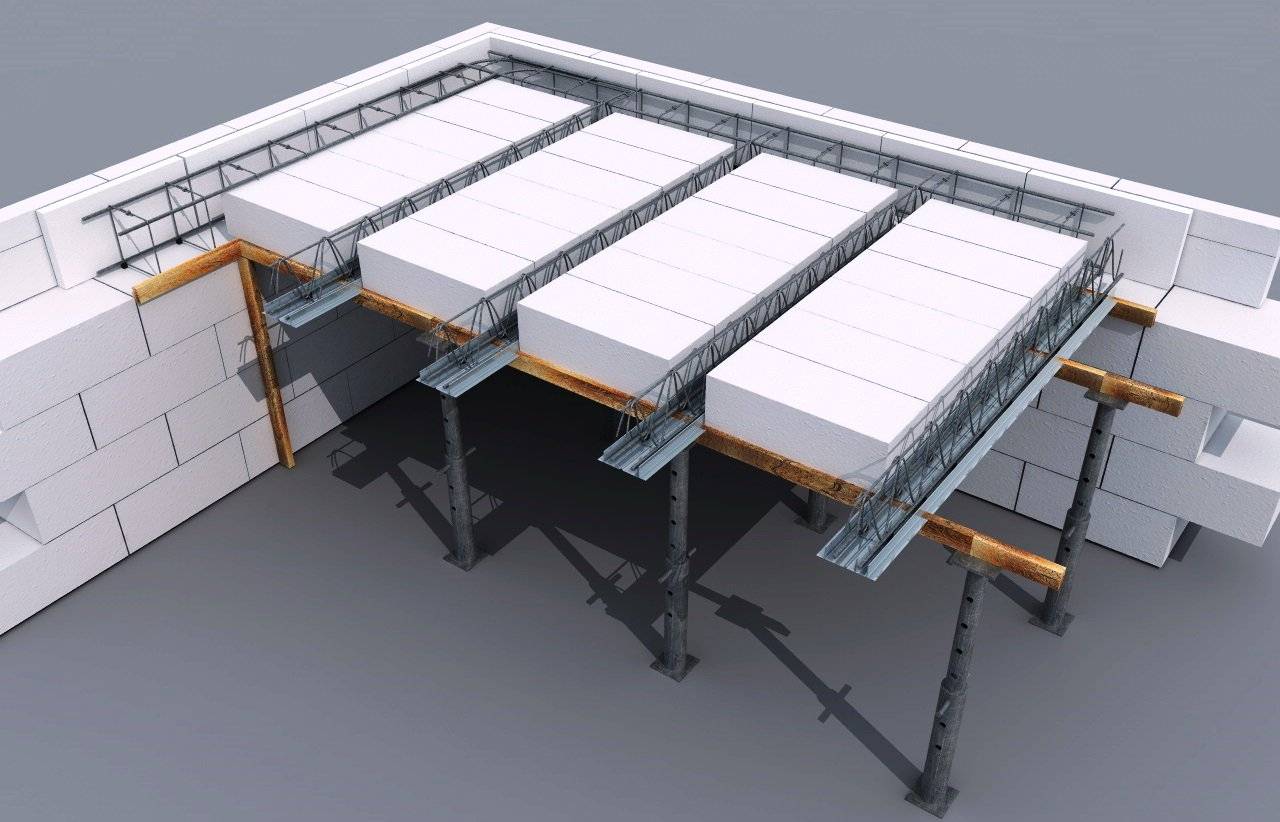
У газобетонных блоков есть несколько принципиальных различий, разобравшись в которых, можно сделать верный выбор. Итак, это:
1. Автоклавный или неавтоклавный газобетон
2. Толщина и ширина блоков
3. Плотность газобетона
4. Плоские блоки или с пазогребневой системой
5. Надежный производитель качественного газобетона
1. Автоклавный или неавтоклавный газобетон
Автоклавный газобетон производится на промышленном оборудовании в заводских условиях. Газобетонные блоки набирают высокую прочность в автоклавах (резервуарах) благодаря высокой температуре и давлению. Заводской газобетон имеет отличные геометрические формы и минимальные отклонения в размерах (не более 1 мм). Автоклавный газобетон имеет абсолютно однородную структуру по всему блоку.
Неавтоклавный газобетон изготавливают, соответственно, вне заводских условий и оборудования. Такой газобетон может иметь отклонения в геометрии блоков, неоднородную структуру и иметь некоторую усадку.
2. Толщина и ширина блоков
Толщина газобетонных блоков влияет на теплопроводность и на общую несущую способность. Если сравнить газобетон одинаковой плотности, то чем блок толще, тем он лучше сохраняет тепло. Соответственно, чем плотность газоблока ниже, тем лучше он сохраняет тепло.
Для строительства загородных домов в Санкт-Петербурге и Ленинградской области мы, как правило, используем автоклавный газобетон марки D400 толщиной 400мм.
Для уменьшения затрат на отопление дома в будущем, лучше сделать более толстые стены, к тому же, в кладке все равно будут небольшие мостики холода, которые уменьшат реальную теплоэффективность стен.
Также, увеличенная толщина блока имеет большую площадь, и чем эта площадь больше, тем лучше распределяется нагрузка от вышестоящих блоков, армопоясов, перекрытий, крыши и т. д. Этот показатель имеет особое значение при строительстве домов выше одного этажа.
Высотой блоки могут быть по 200 мм и по 250 мм. Чем блок выше, тем меньшее количество рядов понадобится, вместе с этим уменьшится расход клея на швы.
3. Плотность газобетона
Для строительства 1-3 этажных загородных домов обычно используют газоблоки плотностью от D300 до D600. Число в данном случае и означает плотность (кг/м3). Мы рекомендуем использовать газобетон плотностью не менее D400. Газобетон меньшей плотности возможно использовать для небольших хозяйственных или временных построек. Но не стоит забывать, что блоки с меньшей плотностью обладают и меньшей прочностью. Из-за этого в кладке со временем могут появиться трещины.
4. Плоские блоки или с пазогребневой системой
Как понятно из заголовка, газобетонный блок может быть плоским или с пазами. В блоках с пазами есть специальные карманы, за которые их удобно брать и переносить.
На газоблоки с пазом уходит меньше клея, а это значит, что кладка происходит быстрее, а расход клея уменьшается. Но пазы становятся неудобными в процессе создания доборных блоков, так как иногда приходится спиливать или счесывать паз теркой.
Есть и плоские блоки без паза, но с карманом для захвата.
Выбор этого параметра уже лежит на производителе работ. На технических характеристиках блока и конструкции в целом, это никак не отражается.
5. Надежный производитель качественного газобетона
Мы в своей работе используем только автоклавный газобетон местных производителей, надежно зарекомендовавших себя на рынке строительных материалов. Это Aerok и Н+Н, чьи производства расположены в Ленобласти, а это значит отсутствие дополнительной наценки на транспортировку. За их качество мы всегда уверены!
Монолит-Хаус. Качественное и надежное загородное строительство в Санкт-Петербурге и Ленинградской области с 2007.
Возврат к списку
АВТОМАТИЗИРОВАННАЯ ЛИНИЯ ПО ПРОИЗВОДСТВУ ПЯТОБЕТОННЫХ БЛОКОВ С ПЕСКОМ ЗАПОЛНИТЕЛЕМ, производительностью 100 м3/смена
Технические характеристики линии
Емкость | 100 м 3 /смена (200 м 3 /день) |
Потребляемая мощность | 98 кВт/ч (без нагрева воды) |
Использование воды | ~22 тонны/смена |
Использование цемента | ~28 тонн/смена |
Использование песка | ~21 тонна/смена |
Производство | блоки стеновые мелкие по ГОСТ 21520-89 |
Требуемая площадь производственного помещения | 1000-1500 м 2 |
Высота потолка в зоне смешения | не менее 6 м* |
Высота потолка в производственной зоне | не менее 3 м* |
Температура окружающей среды | не ниже +15 o С |
Требуемый персонал | 9 рабочих, 1 начальник производства/прораб |
ПРЕИМУЩЕСТВА
Автоматизация управления процессами
На производственных линиях используются электронные системы для контроля загрузки и дозирования сырья в зоне смешивания. В системах управления предусмотрены функции регистрации и контроля сырья. Зона смешивания контролируется одним оператором. В зоне раскроя имеется раскройный станок, которым также управляет один оператор. Процесс демонтажа формы и укладки блоков автоматизирован.
Точность дозирования
Сырье подается на весы с тензодатчиками и весовым контроллером, позволяющим точно дозировать.
Большая емкость
Высокая производительность обеспечивается автоматизированной системой загрузки и дозирования сырья, а также высокой скоростью заполнения смесителя водой и сырьем. Мощный раскройный станок обеспечивает высокую скорость резки монолита на блоки заданного размера.
Высокое качество
Система автоматизации технологических процессов обеспечивает высокое качество продукции и гарантирует точность дозирования, а также стабильный и однородный состав, что позволяет нам предоставлять качественную и конкурентоспособную продукцию.
СЫРЬЕ ДЛЯ ПРОИЗВОДСТВА ЯБЕТОНА
- Вяжущее.
Портландцемент ПЦ-500 Д0, ПЦ-400 Д20 ГОСТ30515 и ГОСТ 10178 применяется в качестве вяжущего для газобетонных изделий.
- Компонент кремния. Песок применяемый соответствует ГОСТ 8736 и содержит не менее 90 % SiO2 или не менее 75 % кремнезема, не более 0,5 % слюды, не более 3 % щебня и глины.
- Вода для затворения. Вода соответствует требованиям ГОСТ 23732.
- Разделительная смазка для форм. Смазки для пресс-форм SDF или другие антиадгезивы используются для обеспечения эффективного удаления пресс-форм.
- Укрепляющие агенты. Полипропиленовые волокна диаметром 12 мм используются в качестве армирующего агента.
- Модифицирующие агенты . ГОСТ 24211
- Газообразующие вещества. Алюминиевая пудра или пыль на ее основе применяются в качестве газообразователя.
ОБЗОР ПРОЦЕССА
1. Производство газобетонной смеси
Заполнение миксера водой
Для дозирования воды используется электронный счетчик воды. Оператор участка смешивания набирает необходимое количество воды и запускает цикл загрузки смесителя.
Загрузка сырья в смеситель
Весовой контроллер используется для загрузки сырья (цемента, песка) в весы и реагентов в весы химических добавок. Цемент и добавки транспортируются винтовыми конвейерами, а песок загружается ленточным конвейером. Цемент и песок теперь выгружаются из весов в смеситель. Раствор перемешивают в течение 2–3 минут до достижения однородности. Когда раствор готов, добавки выгружают в смеситель и снова перемешивают газобетонную смесь в течение 1–2 минут.
Оператор контролирует все процессы на участке смешивания в режиме реального времени. Оператор может использовать панель управления для исправления или изменения рецепта, времени смешивания и других параметров процесса.
Оборудование поддерживает как ручной, так и автоматический режимы.
2. Монолитный молдинг
По готовности газобетонная смесь выгружается в форму 0,85 м 3 через вентиль смесителя. Форма заполняется за один раз. Состоит из основания и съемных сменных боковин. Перед заполнением форму смазывают и транспортируют в зону смешивания для заполнения.
3. Отверждение газобетонных монолитов
Заполненная форма транспортируется по рельсам в зону твердения (в камеру термообработки), где монолит достигает отрывной прочности. Заказчику рекомендуется предусмотреть герметичные туннельные камеры с полной теплоизоляцией по всем поверхностям. Температура в камере должна быть +30…+40 оС. Достижение отрывной прочности может занять от 3 до 5 часов и зависит от плотности, активности газобетона, типа кремнезема, температуры и т.д.
4. Демонтаж форм и резка массивов
После набора массивом необходимой прочности форму, содержащую массив, передают к демонтажной машине по рельсовым путям, основание формы закрепляют на рельсовом пути. Затем четыре стенки формы снимаются и поднимаются с помощью захвата. После демонтажа формы основу формы и массив переносят на участок резки. Затем свободные стены крепятся к свободному основанию, которое находится на соседней железной дороге. Закрытая форма направляется в секцию заливки. Массив разрезается на блоки заданных размеров на режущем агрегате АРК-004. На раскройном участке расположены два отдельных последовательных модуля для вертикальной и горизонтальной резки массива.
Основание пресс-формы фиксируется захватом на вертикальном модуле, в то время как оператор запускает вертикальный модуль. Двигаясь по направляющим, модуль рассекает массив в вертикальной плоскости и подрезает его с обоих концов. После вертикальной резки основание формы с массивом переносится в зону горизонтального модуля, фиксируется захватом, после чего разрезается в горизонтальной плоскости на блоки заданных размеров, а также нижний слой и верхушка срезана. Пока работает горизонтальный модуль, в зону вертикального модуля подается очередной массив. Таким образом, происходит резка двух массивов одновременно, что обеспечивает высокую производительность линии.
5. Укладка блоков на поддоны, упаковка и хранение
Форма-основа с вырезанным массивом передается на узел укладки блоков. Основание пресс-формы фиксируется на рельсе. Затем половину распила массива с помощью захвата укладывают на поддон. Для того, чтобы укомплектовать поддон, восемь блоков укладываются вручную. Затем укладывается вторая половина массива, а также восемь блоков вручную (в зависимости от их габаритов). Поддон с блоками обтянут стрейч-пленкой.
6. Блок тепловлажностной обработки
В зависимости от климатической зоны и вида изготавливаемого материала блоки, укладываемые на поддоны, могут набирать сортную прочность на складе готовой продукции или при термовлажностной обработке. Термовлажностная обработка блоков необходима для ускорения набора прочности блоков. Тепловлажностная обработка заключается в том, что блоки выдерживают в камере от 8 до 12 часов при температуре от +40 до 60оС. Режим тепловлажностной обработки также зависит от плотности материала, активности цемента и определяется заказчиком для каждого конкретного вида выпускаемой продукции.
7. Переработка отходов резки
Режущие модули вырезают монолит с обоих концов, сверху и снизу. Инновационным решением является использование измельчителя отходов DG-1 для переработки отходов резки. Он позволяет измельчать отходы газобетона до частиц размером до 0–30 мм. Измельченный материал можно использовать в качестве насыпного утеплителя крыш, чердаков, пола и т. д. Измельчитель делает производство бетона практически безотходным.
СПЕЦИФИКАЦИЯ ЛИНИИ
Н | Имя | Количество |
Участок хранения, подготовки и отгрузки сырья | ||
1 | Шнековый конвейер для цемента (L = 6 м*, мотор-редуктор (Италия), N = 4 кВт) | 2 |
2 | Ленточный конвейер для песка (L = 7 м*, N = 3 кВт) | 2 |
Зона смешивания | ||
1 | Электронная система управления (со встроенным счетчиком воды + подкачивающий насос) | 2 |
2 | Весы для цемента (тензодатчики, пневматический клапан) | 2 |
3 | Весы для песка (тензодатчики, пневматический клапан) | 2 |
4 | Весы химических примесей ДХД-1 (N = 0,5 кВт) | 2 |
5 | Газобетономешалка ГБ-0,85 (N = 11 кВт, V = 0,85 м 3 ) | 2 |
6 | Компрессор C200LB40 (500 л/мин, 8–10 атм.![]() | 1 |
Область резки монолита | ||
1 | Автоматизированный раскройный комплекс АРК-004 (N=19,5 кВт) | 2 |
2 | Форма ФМ-0,91 м 3 для газобетонных монолитов (V = 0,91 м 3 ). | 110 |
3 | Вращающееся основание для пресс-формы ФМ-0,91 | 60 |
4 | Трансферная тележка | 6 |
5 | Комплекс для демонтажа пресс-форм (N = 2,0 кВт) | 1 |
6 | Комплекс для укладки блоков на поддоны (N=2,5 кВт) | 1 |
Зона измельчения отходов резки | ||
1 | Измельчитель ДГ-1 (N = 4,5 кВт) | 1 |
РАСХОД МАТЕРИАЛА* НА 1 м
3 ИЗ ПЕНОБЕТОН НЕАВТОКЛАВНЫЙ Д-600Материал | Количество |
Цемент (ПЦ500 Д0), кг | 280 |
Песок, кг | 210 |
Вода, л | 220 |
Газообразующий агент, кг | 0,5-1,5 |
Волокна, кг | 0,6 |
Химические добавки, кг | ** |
* Рецептуры корректируются с учетом свойств сырья, выбранного заказчиком.
** Тип и количество добавок определяются на этапе проектирования бетона.
ОБЩИЕ
Для снижения затрат заказчика линия поставляется без силоса для цемента, бункера для песка и перил для транспортировки формы. Заказчику предоставляются чертежи для самостоятельного изготовления этих узлов.
Кроме того, заказчик несет ответственность за подогрев воды до +35…+40°С и устройство пропарочных камер. Работа линии в 2 смены требует дополнительных фундаментов опалубки.
Гарантийный срок на поставляемое оборудование составляет 12 месяцев. Комплектация каждой единицы оборудования указана в договоре, паспорте оборудования и Акте сдачи-приемки.
Специалисты «Сибирских строительных технологий» (СКТ) проектируют размещение оборудования на производственном объекте заказчика. Оборудование устанавливается по макету силами и за счет заказчика. Заказчику предоставляется схема расположения оборудования (чертежи) для соответствующих помещений и подробная иллюстрированная инструкция по установке.
После того, как заказчик завершит монтаж и подключение оборудования, СКТ выполняет следующие работы:
• ввод оборудования в эксплуатацию;• проектирование газобетона;
• оптимизация технологии производства;
• обучение персонала заказчика.
Заказчик несет ответственность за соблюдение всех правил техники безопасности, требований по охране труда и окружающей среды, а также других локальных нормативных актов.
Заказчик берет на себя все расходы по транспортировке и размещению персонала SCT на период проведения работ. Оптимизация технологии включает в себя оптимизацию состава бетона на основе предоставленного заказчиком сырья. SCT предоставляет услуги поддержки.
После ввода оборудования в эксплуатацию заказчику предоставляется техническая документация, включающая:
• технические регламенты на производства;• технологическая схема;
• должностные инструкции;
• инструкции по технике безопасности;
• ГОСТы.

УСЛОВИЯ ПОСТАВКИ
Стоимость указана для EXW-Новосибирск (Россия) и не включает стоимость растаможки и пересылки. Срок изготовления оборудования: от 30 рабочих дней с момента поступления предоплаты.УСЛОВИЯ ОПЛАТЫ
Оплата 1—70% от стоимости контракта в течение 5 дней с момента подписания контракта.
Оплата 2—30% от стоимости контракта в течение 5 дней с момента получения подтверждения о готовности оборудования к отгрузке.
Анализ характеристик шпонки на сдвиг в плите из автоклавного ячеистого бетона (AAC), подвергаемой циклическим нагрузкам
Серия: Достижения инженерных исследований
Авторы
Fachmi Fadli 1 , Лутфи Мухаммад Маулудин 2 , * , Хери Касьянто 21 Магистр инженерной инфраструктуры (MTRI), Politeknik Negeri Bandung 90 084
2 Инженерно-строительный отдел, Политехник Негери Бандунг
* Автор корреспонденции. Электронная почта: [email protected]
Автор, ответственный за корреспонденцию
Лутфи Мухаммад МаулудинДоступно в Интернете 23 ноября 2021 г.
- DOI
- 10.2991/aer.k.211106.040Как пользоваться DOI?
- Ключевые слова
- Срезной ключ; плита; ААС; Диафрагма
- Abstract
В настоящее время легкие плиты из автоклавного ячеистого бетона (AAC) применяются в качестве альтернативного метода по сравнению с обычными плитами. Утверждается, что это нововведение сделает монтаж плиты в зданиях более быстрым и практичным. Применение газобетонных плит для инфраструктуры пешеходных мостов является довольно новым и очень сложным, поскольку при применении газобетонных плит существуют стыки между ними и требуется более пристальное внимание. В методе плиты газобетона в системе соединений используется только заливка раствором между плитами, который, как предполагается, имеет относительно небольшую способность к сдвигу. В соответствии с требованиями индонезийского стандарта (SNI 2847-2013) плиты в конструктивной системе должны вести себя как единое целое (монолитная система), поэтому система плит из газобетона должна быть способна передавать боковые нагрузки, равномерно воздействующие на вертикальные элементы конструктивной системы.
Это исследование начинается с экспериментальных испытаний физико-механических свойств плит из газобетона с точки зрения прочности на сжатие, модуля упругости, удельного веса, содержания влаги и прочности на растяжение стальной арматуры. Эти данные используются в качестве параметров для численного моделирования плиты из газобетона, а также в качестве параметров для применения плиты из газобетона к конструкции пешеходного моста. Результаты численного анализа с помощью ANSYS 2019Программное обеспечение R3 получило прочность соединения между плитой AAC для целевого сдвига 1% 86,37 кН, целевого значения сдвига 2,5 % 237,07 кН, целевого значения сдвига 5 % 406,63 кН и целевого значения сдвига 7,5 % 399,93 кН, где прочность связи между AAC плита уменьшилась при целевом искажении сдвига 7,5% или контроль смещения 45 мм. Результаты моделирования с использованием программного обеспечения SAP2000 v14 с использованием газобетонной плиты на конструкции пешеходного моста позволяют снизить вес конструкции на 49,002% по сравнению с использованием обычной плиты.
- Copyright
- © 2021 Авторы. Опубликовано Atlantis Press International B.V.
- Открытый доступ
- Это статья с открытым доступом под лицензией CC BY-NC.
Загрузить статью (PDF)
- Название тома
- Материалы 2-го Международного семинара по науке и прикладным технологиям (ISSAT 2021) Серия
- Достижения инженерных исследований
- Дата публикации
- 23 ноября 2021 г.
- ISBN
- 10.2991/aer.k.211106.040
- ISSN
- 2352-5401
- DOI
- 10.2991 /aer.k.211106.040Как использовать DOI?
- Copyright
- © 2021 Авторы. Опубликовано Atlantis Press International B.V.
- Открытый доступ
- Это статья с открытым доступом под лицензией CC BY-NC.
Цитировать эту статью AU — Фахми Фадли AU — Лутфи Мухаммад Маулудин AU — Хери Касьянто ПГ — 2021 ДА — 23.11.2021 TI — Анализ характеристик шпонки на сдвиг в плите из автоклавного ячеистого бетона (AAC), подвергаемой циклическим нагрузкам BT — Материалы 2-го Международного семинара по науке и прикладным технологиям (ISSAT 2021) ПБ — Атлантис Пресс СП — 251 ЭП-258 СН — 2352-5401 УР — https://doi.
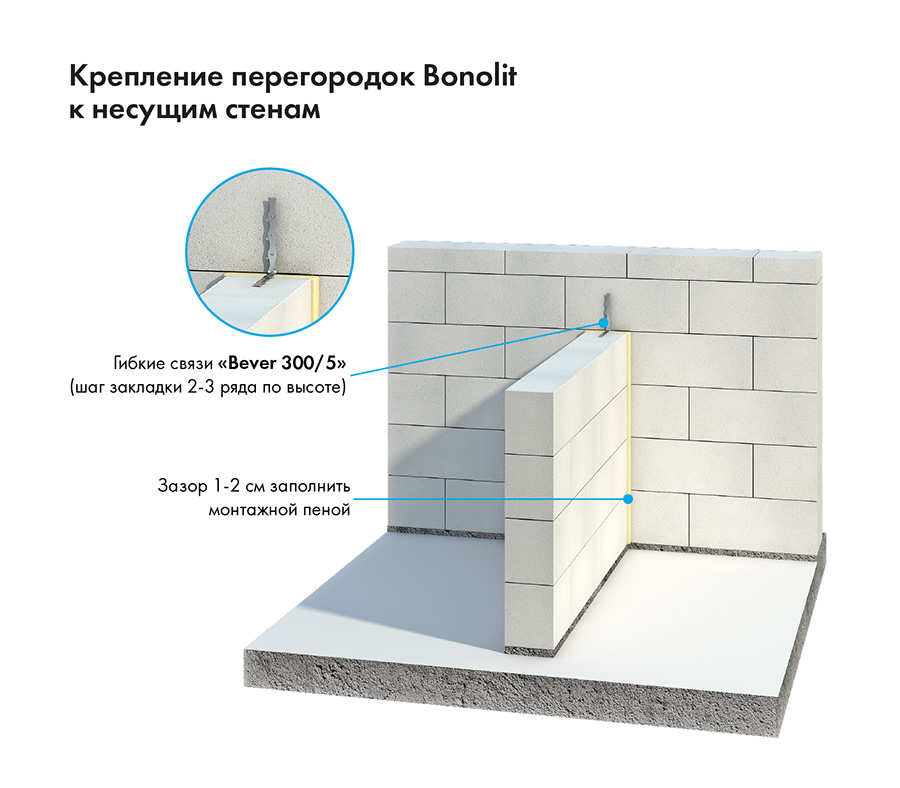