Газобетон и газосиликат разница: Что лучше газобетон или газосиликат — сравнительная таблица
Газоблок и газосиликат: сравнение материалов — АлтайСтройМаш
Ячеистые бетоны занимают высокие позиции в рейтинге популярности и распространенности среди основных стройматериалов благодаря своим теплоизоляционным свойствам, легкости и сравнительной дешевизне. Газоблоки и газосиликат относятся к этой категории легких и «теплых» строительных конструкционных материалов. Но далеко не каждый строитель-каменщик ответит, в чем разница между газобетоном и газосиликатом. В этой статье мы объясним разницу между материалами и расскажем про плюсы и минусы газосиликатных и газобетонных блоков.
Чем отличается газобетон от газосиликата?
Главная отличительная особенность заключается в технологии производства.
- Газосиликатные блоки – это вспененный силикатный бетон. Его основные компоненты: известь (связующий компонент) и песок в соотношении 0,24:0,62. Процесс отвердевания происходит под действием автоклавов, на материал воздействуют высокая температура (180-200°С) и давление (8-14 атм.
). В Центральной России название «газосиликат» почти не используют, вместо него говорят «автоклавный газобетон», ведь чаще всего о нём идёт речь.
- Неавтоклавный газобетон – это ячеистый бетон из портландцемента (связующий компонент), песка и вспенивающего компонента (алюминиевая пудра или паста). Способ изготовления газоблоков предполагает отвердевание в обычных условиях или прогревание до температуры 40-60°С в простых прогревочных камерах.
Получается, газобетон от газосиликата отличается способом изготовления и сырьем, а значит и ценой.
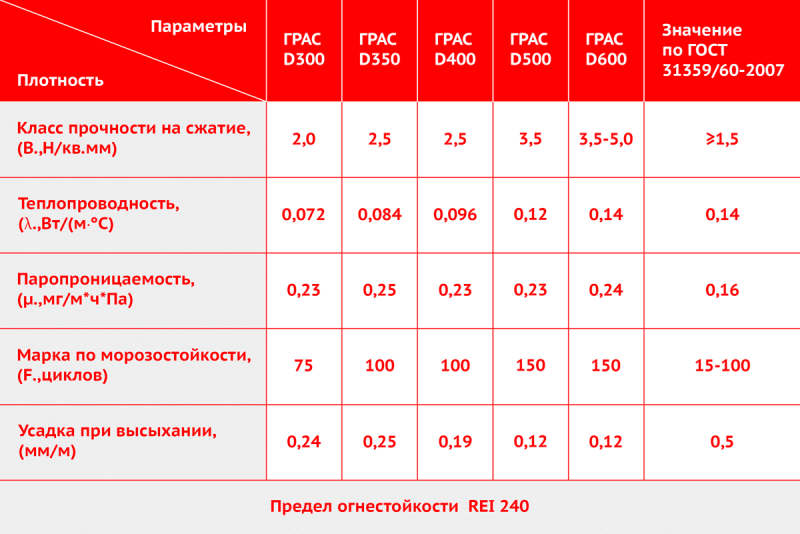
Газоблок и газосиликат: разница в технических параметрах
Чтобы выяснить, чем отличается газосиликат от газобетона, определимся с основными критериями оценки технических характеристик любых конструкционных стройматериалов:
- влаго- и паропроницаемость;
- морозостойкость;
- твердость и прочность;
- теплопроводность;
- пожаробезопасность и экологическая чистота;
- усадка стен.
Результаты сравнения газоблоков и газосиликата представим в таблице.
Характеристика |
Газосиликатные блоки |
Неавтоклавный газобетон |
Поглощение влаги |
25-30% |
16-25% |
Морозостойкость |
15-75 циклов |
|
Класс прочности |
B 1,5-15 |
B 0,5-12,5 |
Теплопроводность |
0,09-0,34 Вт·м°С | |
Усадка |
от 0,3 мм/м |
|
Огнеупорность |
не горит |
|
Экологичность |
нетоксичен |
Газосиликат или газобетон: что лучше?
Практически все технические характеристики в среднем одинаковы для газоблоков и газосиликатов. Исключение лишь в меньшей гидрофильности газобетонных блоков и их большей морозостойкости. Основное отличие газобетона в его стоимости за счет простоты изготовления и малых производственных издержек.
Под экономией подразумевается не разница в розничных ценах. Возможность сэкономить на общей строительной смете при самостоятельном изготовлении газоблоков из неавтоклавного газобетона – вот основное преимущество газобетона над газосиликатом. Такая экономия полностью исключена при выборе газосиликатных блоков.
Газобетон активно используется в индивидуальном и крупном строительстве. Высокую рентабельность и быструю окупаемость оборудования для производства газобетонных блоков неавтоклавным способом компании «АлтайСтройМаш» уже оценили как частные застройщики, так и представители среднего бизнеса России, Казахстана и Узбекистана.
что лучше выбрать, в чес разница и отличия
29 марта 2021
В последнее время выросла потребность в специализированных материалах, которые отличаются высокими техническими характеристиками.
Для того, чтобы избежать проблем с покупкой, предлагаем вам ознакомиться с этой статьёй. В ней мы сравним два материала, чтобы понять их различия и выбрать лучший вариант.
Начнём с составов и способов схватывания растворов.
Газобетон состоит из цемента, извести и песка. Это основа. Также в неё входит алюминиевая пудра.
Газобетонные блоки застывают либо в естественной среде, либо специальных автоклавах.
Газосиликат, в свою очередь, состоит из смеси песка (62%) и извести (24%).
Он всегда должен подвергаться термообработке паром при высокой температуре. Для него не характерен воздушный способ застывания.
В чём плюс застывания в автоклавах?
- Состав схватывается намного быстрее.
- Такая обработка сделает его прочнее и обеспечит небольшую усадку в процессе эксплуатации.
- На выходе мы получаем хорошую теплоизоляцию.
В итоге мы получаем застывший раствор и можем различать его по цвету. Газобетон и газосиликат, которые застывали в автоклавах, имеют белый цвет. А вот если газобетон застывал сам, то он получится серым. Для некоторых людей цвет материала также важен при выборе, т.к. Белые дома смотрятся лучше. Поэтому, если для вас эстетическое восприятие стоит не на последнем месте, лучше не забывать про этот пункт.
С составами ознакомились, теперь разберём преимущества каждого материала.
У газобетона не так много пор, поэтому он не разрушается под воздействием воды. Из этого можно сделать вывод, что такие блоки более морозоустойчивы.
Из других плюсов газобетона:
- Он устойчив к огню. Возгорание происходит не сразу.
- Ему не страшны перепады температуры.
- Низкая стоимость материала. При постройке дома это будет выгодным вложением.
Из перечисленного выше видно, что у газобетона достаточно преимуществ, однако это не означает, что газосиликат во всём ему проигрывает.
Из-за этих самых пор газосиликатные блоки отличаются большей плотностью, т.к. пузырьки воздуха распределены по всей поверхности равномерно. Кроме того, за счёт пор получается неплохая звукоизоляция и теплоизоляция.
Вывод: если вы строите дом, то при возведении газосиликатных стен трещины будут появляться гораздо реже.
Именно поэтому из этого материала чаще строятся многоэтажные дома. Если выбор стоит между кирпичом и газосиликатом, то лучше обойтись вторым вариантов. Это будет дешевле и быстрее. А вот если выбор предстоит между газобетоном и газосиликатом, то тут решайте исходя из того, что для вас важнее – прочность, звукоизоляция или устойчивость к температурам и цена.
Что ещё можно сказать об этих материалах?
Кладка из газосиликата выходит легче, да и клея со штукатуркой нужно гораздо меньше. Так что оба материала различаются весом, что немаловажно.
Газобетон отличается повышенной теплопроводностью.
Силикат очень активно впитывает влагу. Это может стать причиной его разрушения. Если для вашего региона характерна повышенная влажность, то стоит забыть про этот вариант. Или задуматься о хорошей гидроизоляции, что выйдет дороже. Зато защитит материал от промерзания и плесени.
Мы не случайно упомянули выше способы затвердевания составов. Один и тот же блок из газобетона может быть различен по качеству. Об этом не стоит забывать. Если газобетон неавтоклавный, то его свойства уступают не только газосиликату, но и автоклавному газобетону. На этапе эксплуатации он будет отличаться низкой прочностью, да и теплоизоляционные качества будут намного ниже.
Неавтоклавный газобетон можно довольно часто встретить на рынке, т.к. производители хотят сэкономить и предоставляют некачественные составы. Поэтому будьте осторожны.
Автоклавный или неавтоклавный газобетон?
Вернемся к автоклавам. Что из себя представляет такая конструкция?
Это резервуар, в котором материал застывает при высоком давлении и температуре. Таким образом, он становится гораздо плотнее, чем был до этого.
Материал, который обрабатывается при помощи этого резервуара, имеет однородную структуру и белый цвет.
Неавтоклавный газобетон, в свою очередь, часто делается в домашних (гаражных) условиях. Из-за этого страдает геометрия поверхности, а структура выходит абсолютно неровной. Эти нюансы негативно сказываются на качестве газоблока. Единственный плюс неавтоклавного газобетона – его низкая стоимость. Но стоит ли это того? Даже если производитель добавляет фибру, это не является гарантией того, что со временем в стенах не появятся трещины.
Какой толщины должен быть материал?
Этот показатель очень важен при выборе, т.к. толщина стен влияет на то, будет ли в помещении холодно. Если газобетон или газосиликат выбрать потолще, то он однозначно лучше будет сохранять тепло. Более того, от толщины блоков будет зависеть несущая способность здания. А это тоже очень важный момент.
Если вы выберете достаточно плотный материал, то вам не нужно будет продумывать дополнительное отопление и тратить на это большое количество денег.
Ещё один момент. Если у нас есть такой блок, то его площадь будет больше, следовательно, нагрузка от других блоков, крыши и т.д. распределится более равномерно.
От себя советуем выбирать газобетон или газосиликат толщиной более 200 мм.
Какой высоты должны быть блоки?
У производителей встречаются самые разные виды материалов. Если у вас высокие блоки, то количество рядов заметно сократится, а расход клея будет не так велик.
Какую плотность выбрать?
Нашли блоки с плотностью D300 или D600? Они отлично подойдут для строительства небольших домов. Не больше двух этажей. Для D300 существует ограничение в один этаж.
Если уж вы занялись строительством многоэтажных зданий, то тут следует обратиться к таблицам в интернете, в которых есть наглядная информация о допустимой плотности материала.
Интересный факт. Чаще всего с трещинами сталкивается тот, кто предпочитает неавтоклавный газобетон с небольшой плотностью.
Вывод: применяйте такие блоки в качестве утепления, а для возведения стен используйте что-то более подходящее.
Многие люди используют блоки из газобетона именно для возведения ненесущих перегородок. При этом высота их обычно составляет 250 мм., а плотность доходит до D400.
Как работать с этими материалами?
Мы подготовили для вас несколько рекомендаций. Ознакомьтесь с ними.
- Для кладки используйте только специальные клеевые растворы.
Такая цементно-песчаная смесь обеспечивает быстрое схватывание поверхностей. Специальный клей затвердевает быстрее, следовательно, работа с блоками будет проходить быстрее.
- Не забывайте про отделочные материалы. Наружная отделка поверхности гарантирует хорошую защиту от осадков и промерзания.
- Если вы занимаетесь отделкой фасадов облицовочным кирпичом, то не забывайте про вентиляционный зазор.
- Паропроницательность отделочных материалов должна быть всегда больше, чем у изначальной поверхности. Иначе появится плесень.
- Для дополнительного утепления используйте минеральную вату.
- Любой крепеж к газосиликату выполняется за счёт крепежа с дюбелями.
Для газобетонных блоков используются болты.
- Для защиты стен используется армирование.
- Слой гидроизоляции лежит под конструкцией из газобетона или газосиликата.
Это основа, которую нужно знать для того, чтобы не получить неприятных сюрпризов.
Как выбрать материал в магазине?
Для начала необходимо обратить внимание на внешний вид материала, который вам нужен. Начните исследовать товар с самой упаковки. Она должна быть герметичной. Производители, которые любят сэкономить, часто допускают дефекты даже в этом.
Теперь переходим к осмотру газобетона или газосиликата. Материал должен быть равномерно окрашен. Никаких неровностей или разводов просто нельзя допускать. Пятна краски, масляные разводы – всего этого не должны быть на материале. Далее стоит обратить внимание на наличие сколов или трещин. Вы же не хотите переплачивать за некачественную продукцию?
Не стоит забывать и о самой структуре. По наличию мелких пузырьков можно понять, что перед вами именно газосиликат.
Важен ли производитель при выборе материала? Однозначно да. Разные компании производят различный по плотности, качеству и размеру газобетон или газосиликат. У одних производителей могут быть использованы современные технологии в обработке материалов, другие же могут экономить даже на способе застывания материала.
Вывод.
Не бывает материалов, которые имели бы только положительные аспекты. Всегда есть какое-то «но». Блоки из газобетона очевидно уступают блокам из газосиликата, но это не значит, что их лучше не использовать совсем. Напротив, каждый из этих материалов подходит под свои условия. Подходите грамотно к покупке материала, чтобы не столкнуться с нарушением технологии производства из-за недобросовестных производителей.
Теги:
- выбор стройматериала
Оцените материал:
Оставить комментарий / Всего комментариев: 0
Оставить комментарий
Отходы очистки дымовых газов от сжигания промышленных отходов в качестве частичной замены извести в автоклавном газобетоне
1. Мисевич Л. Рынок строительных материалов для возведения стен в Польше в 2020 г. Матер. Бутон. 2021; 4:8–9. (на польском языке) [Google Scholar]
2. Запоточна-Сытек Г., Балкович С. Автоклавный газобетон. ПВН; Варшава, Польша: 2013. (на польском языке) [Google Scholar]
3. Кунчариякун К., Асаваписит С., Сомбатсомпоп К. Свойства автоклавного ячеистого бетона с добавлением золы рисовой шелухи в качестве частичной замены мелкого заполнителя. Цем. Конкр. Комп. 2015;55:11–16. doi: 10.1016/j.cemconcomp.2014.07.021. [Перекрестная ссылка] [Академия Google]
4. Сун Ю., Ли Б., Ян Э., Лю Ю., Дин Ю. Технико-экономическое обоснование использования зольного остатка сжигания твердых бытовых отходов в качестве аэрирующего агента для производства автоклавного ячеистого бетона. Цем. Конкр. Комп. 2015;56:51–58. doi: 10.1016/j.cemconcomp.2014.11.006. [CrossRef] [Google Scholar]
5. Вонгкео В., Чайпанич А. Прочность на сжатие, микроструктура и термический анализ конструкционного легкого бетона автоклавного твердения и воздушной вулканизации, изготовленного из угольной золы и микрокремнезема. Матер. науч. англ. А. 2010;527:3676–3684. doi: 10.1016/j.msea.2010.01.089. [CrossRef] [Google Scholar]
6. Лагош А., Шимански П., Вальчак П. Влияние типа летучей золы на свойства автоклавного ячеистого бетона. Цем. Вапно Бетон. 2011;16:22–25. [Google Scholar]
7. Вальчак П., Шимански П., Ружицка А. Автоклавный газобетон на основе золы-уноса плотностью 350 кг/м 3 как экологически чистый материал для энергетики — Эффективные конструкции. проц. англ. 2015; 122:39–46. doi: 10.1016/j.proeng.2015.10.005. [Перекрестная ссылка] [Академия Google]
8. Лагош А., Шимански П., Вальчак П. Влияние свойств летучей золы на свойства автоклавного ячеистого бетона; Материалы 5-й Международной конференции по автоклавному газобетону «Обеспечение устойчивого будущего»; Быдгощ, Польша. 14–17 сентября 2011 г.; стр. 111–118. [Google Scholar]
9. Ружицка Р., Пичор В. Влияние добавки отходов перлита на свойства автоклавного ячеистого бетона. Констр. Строить. Матер. 2016;120:65–71. doi: 10.1016/j.conbuildmat.2016.05.019. [CrossRef] [Google Scholar]
10. Li X., Liu Z., Lv Y., Cai L., Jiang D., Jian S. Использование зольного остатка при сжигании твердых бытовых отходов в автоклавном газобетоне. Констр. Строить. Матер. 2018;178:175–182. doi: 10.1016/j.conbuildmat.2018.05.147. [CrossRef] [Google Scholar]
11. Huang X., Ni W., Cui W., Wang Z., Zhu L. Приготовление автоклавного ячеистого бетона с использованием медных хвостов и доменного шлака. Констр. Строить. Матер. 2012; 27:1–5. doi: 10.1016/j.conbuildmat.2011.08.034. [Перекрестная ссылка] [Академия Google]
12. Ву Р., Дай С., Цзянь С., Хуан Дж., Тан Х., Ли Б. Утилизация твердых отходов большого объема кальциево-угольной пустой породы в автоклавном ячеистом бетоне: физико-механические свойства, продукты гидратации и экономические затраты. Дж. Чистый. Произв. 2021;278:1234416. doi: 10.1016/j.jclepro.2020.123416. [CrossRef] [Google Scholar]
13. Зафар М., Джавед У., Хушнуд Р., Наваз А., Зафар Т. Устойчивое включение гранитной пыли в качестве частичной замены песка в автоклавном газобетоне. Констр. Строить. Матер. 2020;250:118878. doi: 10.1016/j.conbuildmat.2020.118878. [Перекрестная ссылка] [Академия Google]
14. Эль-Дидамони Х., Амер А., Мохаммед М., Эль-Хаким М. Изготовление и свойства автоклавного ячеистого бетона, содержащего твердые отходы сельского хозяйства и промышленности. Дж. Билд. англ. 2019;22:528–538. doi: 10.1016/j.jobe.2019.01.023. [CrossRef] [Google Scholar]
15. Jiang J., Cai Q., Ma B., Hu Y., Quian B., Ma F., Shao Z., Xu Z., Wang L. Влияние ZSM- 5 дозировка отходов на свойства автоклавного газобетона. Констр. Строить. Матер. 2021;278:122114. doi: 10.1016/j.conbuildmat.2020.122114. [Перекрестная ссылка] [Академия Google]
16. Пэн Ю., Лю Ю., Чжан Б., Сюй Г. Приготовление автоклавного ячеистого бетона с использованием графитовых отходов в качестве альтернативного источника кремнезема. Констр. Строить. Матер. 2021;267:121792. doi: 10.1016/j. conbuildmat.2020.121792. [CrossRef] [Google Scholar]
17. Yuan B., Straub C., Segers S., Lu Q., Brouwers H.J.H. Шлак, активированный карбонатом натрия, как замена цемента в автоклавном ячеистом бетоне. Керам. Междунар. 2017;43:6039–6047. doi: 10.1016/j.ceramint.2017.01.144. [Перекрестная ссылка] [Академия Google]
18. Вонгкео В., Тонгсанитгарн П., Пимракса К., Чайпанич А. Прочность на сжатие, прочность на изгиб и теплопроводность автоклавного бетонного блока, изготовленного с использованием зольного остатка в качестве материалов для замены цемента. Матер. Дес. 2012; 35: 434–439. doi: 10.1016/j.matdes.2011.08.046. [CrossRef] [Google Scholar]
19. Хаузер А., Эггенбергер Ю., Мументалер Т. Зола-унос целлюлозной промышленности как вторичное сырье для автоклавного ячеистого бетона. Цем. Конкр. Рез. 1999; 29: 297–302. дои: 10.1016/S0008-8846(98)00207-5. [CrossRef] [Google Scholar]
20. Kurdowski W., Pawluk J. Известняковая мука как активная минеральная добавка для производства ячеистого автоклавного бетона. Цем. Вапно Бетон. 2019;24:154–160. doi: 10.32047/CWB.2019.24.2.7. [CrossRef] [Google Scholar]
21. Гуклюер К., Демир И. Использование метакаолина и доменных шлаков в производстве автоклавного ячеистого бетона. Преподобный Романа Матер. 2019;49:388–393. [Google Scholar]
22. Ван К.С., Чанг К.Ю., Линь С.М., Цай К.С., Сунь К.Дж. Влияние хлоридов на выбросы хлористого водорода при сжигании отходов. Хемосфера. 1999;38:1571–1582. doi: 10.1016/S0045-6535(98)00377-4. [PubMed] [CrossRef] [Google Scholar]
23. Ниссен В. Р. Применение в инженерии окружающей среды. КПР Пресс; Бока-Ратон, Флорида, США: 2010. Процессы сжигания и сжигания. [Google Scholar]
24. Чин Т., Ян Р., Лян Д.Т., Тай Дж.Х. Реакция гашеной извести с HCl в моделируемых условиях дымовых газов. Инд.Инж. хим. Рез. 2005;44:3742–3748. doi: 10.1021/ie040206z. [CrossRef] [Google Scholar]
25. Dal Pozzo A., Moricone R., Antonioni G., Tugnoli A., Cozzani V. Удаление хлороводорода из дымовых газов низкотемпературной реакцией с гидроксидом кальция. Энергетическое топливо. 2018; 32: 747–756. doi: 10.1021/acs.energyfuels.7b03292. [CrossRef] [Google Scholar]
26. Срода Б. Инновационные технологии в цементной промышленности. Цем. Вапно Бетон. 2021; 26: 444–451. doi: 10.32047/cwb.2021.26.5.7. [CrossRef] [Google Scholar]
27. Баран Т. Использование отходов и промышленных побочных продуктов и возможности сокращения выбросов CO 2 в цементной промышленности — промышленные испытания. Цем. Вапно Бетон. 2021; 26: 169–184. doi: 10.32047/cwb.2021.26.3.1. [CrossRef] [Google Scholar]
28. Форстер А.М., Валек Дж., Хьюз Дж.Дж., Пилчер Н. Известковые вяжущие для ремонта исторических зданий: рекомендации по CO 2 снижение. Дж. Чистый. Произв. 2020;252:119802. doi: 10.1016/j.jclepro.2019.119802. [CrossRef] [Google Scholar]
29. Методы испытаний цемента. Часть 6. Определение тонкости. Польский комитет по стандартизации; Варшава, Польша: 2019. [Google Scholar]
30. Порошковая металлургия. Определение водопокрывающей способности чешуйчатых порошков. Польский комитет по стандартизации; Варшава, Польша: 1977. [Google Scholar]
31. Руководство по классификации отходов в соответствии с категориями EWC-Stat. 2013. [(по состоянию на 21 марта 2022 г.)]. Доступно в Интернете: https://ec.europa.eu/eurostat/documents/342366/351806/Guidance-on-EWCStat-categories-2010.pdf/0e7cd3fc-c05c-47a7-818f-1c2421e55604
32. Холстед П.Е., Мур А.Е. Термическая диссоциация гидроксида кальция. Дж. Хим. соц. 1957; 769: 3873–3875. doi: 10.1039/jr9570003873. [CrossRef] [Google Scholar]
33. Бирсс Ф.В., Торвальдсон Т. Механизм гидратации оксида кальция. Канада. Дж. Хим. 1955; 33: 881–886. дои: 10.1139/v55-106. [CrossRef] [Google Scholar]
34. Методы испытаний каменных блоков — Часть 13: Определение плотности нетто и брутто в сухом состоянии каменных блоков (кроме природного камня) Польский комитет по стандартизации; Варшава, Польша: 2001. [Google Scholar]
35. Методы испытаний каменных блоков. Часть 1. Определение прочности на сжатие. Польский комитет по стандартизации; Варшава, Польша: 2015. [Google Scholar]
36. Руководство пользователя Модель анализатора теплопередачи ISOMET. [(по состоянию на 21 марта 2022 г.)]. Доступно в Интернете: https://www.appliedp.com/download/manual/isomet2114_ug_en.pdf
37. Chen Y., Ko M., Chang J., Lin C.-T. Переработка шлака сероочистки для производства автоклавного ячеистого бетона. Констр. Строить. Матер. 2018; 158:132–140. doi: 10.1016/j.conbuildmat.2017.09.195. [CrossRef] [Google Scholar]
38. Нараянан Н., Рамамурти К. Структура и свойства газобетона: Обзор. Цем. Конкр. Рез. 2000; 22: 321–329. doi: 10.1016/S0958-9465(00)00016-0. [CrossRef] [Google Scholar]
39. Shamas T., Schober G., Heinz G., Seifert S. Производство автоклавного ячеистого бетона с кремнеземным сырьем с более высокой растворимостью, чем кварц, часть I: Влияние кальцинированной диатомовой земли. Констр. Строить. Матер. 2021;272:122014. doi: 10. 1016/j.conbuildmat.2020.122014. [Перекрестная ссылка] [Академия Google]
40. Wan H., Hu Y., Liu G., Qu Y. Исследование структуры и свойств автоклавного ячеистого бетона, изготовленного из камнерезного раствора. Констр. Строить. Матер. 2018;184:20–26. doi: 10.1016/j.conbuildmat.2018.06.214. [CrossRef] [Google Scholar]
41. Цюй М.-Л., Тянь С.-К., Фань Л.-В., Ю З.-Т., Гэ Дж. Экспериментальное исследование и фрактальное моделирование на Эффективная теплопроводность новых композитов на основе автоклавного газобетона (АГБ) с кремнеземными аэрогелями (СА) Заявл. Терм. англ. 2020;179:115770. doi: 10.1016/j.applthermaleng.2020.115770. [CrossRef] [Google Scholar]
42. Jin H., Yao X., Fan L., Xu X., Yu Z. Экспериментальное определение и фрактальное моделирование эффективной теплопроводности автоклавного ячеистого бетона: влияние содержания влаги. Междунар. J. Тепломассообмен. 2016; 92: 589–602. doi: 10.1016/j.ijheatmasstransfer.2015.08.103. [CrossRef] [Google Scholar]
43. Chen G., Li F., Jing P., Geng J., Si Z. Влияние пористой структуры на теплопроводность и механические свойства автоклавного ячеистого бетона. Материалы. 2021;14:339. doi: 10.3390/ma14020339. [Бесплатная статья PMC] [PubMed] [CrossRef] [Google Scholar]
44. Straube B., Walther H. AAC с низкой теплопроводностью; Материалы 5-й Международной конференции по автоклавному газобетону «Обеспечение устойчивого будущего», которая состоится в Быдгоще в ознаменование 60-летия опыта AAC в Польше; Быдгощ, Польша. 14–17 сентября 2011 г. [Google Scholar]
45. Крефт О., Хаусманн Дж., Хубалкова Дж., Анезирис К.Г., Штраубе Б., Шох Т. Влияние распределения пор по размерам на теплопроводность легкого автоклавного ячеистого бетона. . Цем. Вапно Бетон. 2011;16:49–52. [Google Scholar]
46. Асади И., Шафиг П., Хассан З., Махьюддин Н. Теплопроводность бетона. Обзор. Дж. Билд. англ. 2018;20:81–93. doi: 10.1016/j.jobe.2018.07.002. [CrossRef] [Google Scholar]
47. Вакили К., Хуги Э., Карвонен Л. , Шневнил П., Виннефельд Ф. Термическое поведение автоклавного ячеистого бетона при воздействии огня. Цем. Конкр. Комп. 2015;62:52–58. doi: 10.1016/j.cemconcomp.2015.04.018. [CrossRef] [Google Scholar]
48. Muthu Kumar E., Ramamurthy K. Влияние дисперсности и дозировки алюминиевой пудры на свойства газобетона влажного отверждения. Констр. Строить. Матер. 2015;95: 486–496. doi: 10.1016/j.conbuildmat.2015.07.122. [CrossRef] [Google Scholar]
49. Ружицка А., Котвица Л., Малолепши Ю. Синтез однофазного гиролита в системе CaO-кварц-Na 2 O-H 2 O. Матер. лат. 2014; 120:166–169. doi: 10.1016/j.matlet.2014.01.003. [CrossRef] [Google Scholar]
50. Guo X., Meng F., Shi H. Микроструктура и характеристика гидротермального синтеза Al-замещенного тоберморита. Констр. Строить. Матер. 2017; 133: 253–260. doi: 10.1016/j.conbuildmat.2016.12.059. [CrossRef] [Google Scholar]
51. Nocun-Wczelik W. Влияние Na и Al на фазовый состав и морфологию автоклавированных гидратов силиката кальция. Цем. Конкр. Рез. 1999; 29: 1759–1767. doi: 10.1016/S0008-8846(99)00166-0. [CrossRef] [Google Scholar]
52. Ружицка А., Котвица Л. Влияние щелочи на синтез однофазного гиролита в системе CaO-кварц-H 2 O. Constr. Строить. Матер. 2020;239:117799. doi: 10.1016/j.conbuildmat.2019.117799. [Перекрестная ссылка] [Академия Google]
53. Капелюшна Э., Котвица Л., Ружицка А., Голек Л. Включение Al в гели C-A-S-H с различным соотношением Ca/Si и Al/Si: микроструктурные и структурные характеристики с анализом ДТА/ТГ, XRD, FTIR и TEM. Констр. Строить. Матер. 2017; 155: 643–653. doi: 10.1016/j.conbuildmat.2017.08.091. [CrossRef] [Google Scholar]
54. Маэда Х., Исида Э., Касуда Т. Гидротермальное получение тоберморита, включающего фосфаты. Матер. лат. 2012; 68: 382–384. doi: 10.1016/j.matlet.2011.11.017. [Перекрестная ссылка] [Академия Google]
55. Скавиньска А., Овсяк З., Баран Т., Херник К. Влияние добавок галлуазита на образование тоберморита в смеси СаО и кварца в гидротермальных условиях. Цем. Вапно Бетон. 2017;22:426–434. [Google Scholar]
56. Дрочитка Р., Черный В. Влияние добавки золы-уноса сжигания в кипящем слое на гидротермальный синтез тоберморита в смеси с кварцевым песком, высокотемпературной золой-уносом и известью. Констр. Строить. Матер. 2020;230:117033. doi: 10.1016/j.conbuildmat.2019.117033. [CrossRef] [Google Scholar]
57. Майдинасаб А., Юань К. Синтез алюминий-замещенного тоберморита 11 Å с использованием отходов стеклобоя: исследование микроструктуры. Матер. хим. физ. 2020;250:123069. doi: 10.1016/j.matchemphys.2020.123069. [CrossRef] [Google Scholar]
58. Gou X., Song M. Микронаноструктуры тоберморита, полученные гидротермальным синтезом из летучей золы и летучей золы при сжигании твердых бытовых отходов. Констр. Строить. Матер. 2018;191:431–439. doi: 10.1016/j.conbuildmat.2018.10.03rf0. [Перекрестная ссылка] [Академия Google]
59. Цуцуми Т., Нишимото С., Камешима Ю., Мияке М. Гидротермальное получение тоберморита из доменного шлака для сорбции Cs + и Sr 2+ . Дж. Азар. Матер. 2014; 226:174–181. doi: 10.1016/j.jhazmat.2013.12.024. [PubMed] [CrossRef] [Google Scholar]
60. Gou X., Zhang T., Song M. Гидротермальные синтезированные и наномодифицированные стеновые материалы из твердых отходов. Констр. Строить. Матер. 2019;217:242–250. doi: 10.1016/j.conbuildmat.2019.05.069. [Перекрестная ссылка] [Академия Google]
61. Коулман Н.Дж., Брассингтон Д.С. Синтез Al-замещенного 11 Å тоберморита из остатков переработки газетной бумаги: технико-экономическое обоснование. Матер. Рез. Бык. 2003; 38: 485–497. doi: 10.1016/S0025-5408(02)01056-5. [CrossRef] [Google Scholar]
62. Цао П., Ли Г., Лу Дж., Рао М., Цзян Х., Пэн З., Цзян Т. Армированный щелочью гидротермальный синтез реечных тоберморитовых волокон с использованием смеси угольная летучая зола и известь. Констр. Строить. Матер. 2020;238:117655. doi: 10.1016/j.conbuildmat.2019.117655. [CrossRef] [Google Scholar]
63. Ding J., Tang Z., Ma S., Wang Y., Sheng S., Zang Y., Shen S. , Xie Z. Новый процесс синтеза тоберморитового волокна. из высокоглиноземистой золы. Цем. Конкр. Комп. 2016; 65:11–18. doi: 10.1016/j.cemconcomp.2015.10.017. [CrossRef] [Google Scholar]
64. Смалакис Г. Гидротермальный синтез тоберморита размером 1,13 нм из отходов порошка распиловки гранита. Керам. Силик. 2020; 64: 239–248. doi: 10.13168/cs.2020.0013. [Перекрестная ссылка] [Академия Google]
Исследование автоклавного ячеистого кирпича с использованием геополимера – IJERT
Исследование автоклавного ячеистого кирпича с использованием геополимера
S. N. Kannan1 , D. Karthick Raja1, A. Sangaiyya1,P. Satheesh Kumar1,
1UG Студентка факультета гражданского строительства,
Инженерно-технологический колледж Надар Сарасвати, Тени.
Аннотация- В этом исследовании сравнивается поведение геополимерного кирпича и геополимерного пенобетона. Геополимер содержит гидроксид натрия и силикат натрия,
A. Зола-уноса
II МАТЕРИАЛЫ
которая вступает в реакцию с водой и выделяет тепло в процессе теплоты гидратации. Геополимерный кирпич укладывается в соотношении 1:3 (т.е. 1 кг золы-уноса и 3 кг М песка) и 200 грамм геополимера смешать с 500 мл воды. Кладка геополимерного газобетона производится в соотношении 1:3 (имеется в виду 1 кг золы-уноса и 3 кг песка М) и 200 г геополимера смешивают с 500 мл воды. Дополнительно 20 г порошка алюминия смешивают с 25 мл воды. Кирпичи проходят испытания на сжатие (7, 14, 28 дней), испытание на водопоглощение. Результат испытания на сжатие геополимерного кирпича (7, 14, 28 дней) 8,7 МПа, 190,53 МПа, 24,56 МПа. и испытание для геополимерного газобетона (7, 14, 28 дней) 8,4 МПа, 18,92 МПа, 23,53 МПа. Испытание на водопоглощение геополимерного кирпича 2.45. и испытание для геополимера Газобетонный автоклавный кирпич 1,98
Ключевые слова: Зола-унос, Силикат натрия, Гидроксид натрия и алюминиевая пудра.
Летучая зола, промышленный побочный продукт тепловых электростанций
(ТЭС), с текущим годовым производством около 108 миллионов тонн и доказанной пригодностью для различных применений в качестве добавки в цемент/бетон/строительный раствор, известково-пуццолановая смесь ( кирпичи/блоки) и т. д. — идеальный материал, привлекающий всеобщее внимание. На долю цементной и бетонной промышленности приходится 50% утилизации летучей золы, общее использование которой в настоящее время составляет 30 тонн (28%). Другими областями применения являются засыпка низин (17%), дороги и насыпи (15%), возведение дамб (4%), производство кирпича (2%) и т. д. Стоимость жизненного цикла строительных материалов/конструкций на основе летучей золы составляет гораздо ниже, принимая во внимание экологические преимущества и аспекты долговечности.
ВВЕДЕНИЕ
Спрос на бетон как строительный материал растет, как и производство цемента. Производство цемента увеличивается примерно на 3% в год. При производстве одной тонны цемента в атмосферу выделяется около одной тонны CO2. Среди парниковых газов CO2 способствует примерно 65% глобального потепления. Кроме того, сообщается, что долговечность обычного бетона на портландцементе находится в стадии изучения, поскольку многие бетонные конструкции, особенно те, которые построены в агрессивных средах, начинают разрушаться через 20–30 лет, даже если они были рассчитаны на более чем 50 лет службы. жизнь. Хотя использование портландцемента в обозримом будущем неизбежно, предпринимаются многочисленные усилия по сокращению использования портландцемента в бетоне. С другой стороны, обильная доступность летучей золы во всем мире создает возможность использования этого побочного продукта сжигания угля в качестве заменителя OPC для производства бетона. При использовании в качестве частичной замены OPC в присутствии воды и при температуре окружающей среды летучая зола реагирует с гидроксидом кальция в процессе гидратации OPC с образованием геля гидрата силиката кальция (C-S-H). Разработка и применение бетона с большим объемом летучей золы, который позволил заменить OPC до 60% по массе, является значительным достижением. Давидовиц предположил, что связующие могут быть получены полимерной реакцией щелочных жидкостей с кремнием и алюминием в исходных материалах геологического происхождения или побочных материалах, таких как летучая зола и зола рисовой шелухи. Он назвал эти связующие геополимерами.
III) СВОЙСТВА МАТЕРИАЛОВ
ХИМИЧЕСКИЙ АНАЛИЗ ЗОЛЫ ЛЕЧА
Таблица 1 Элементы, присутствующие в материалах
ХИМИЧЕСКИЙ КОМПОНЕНТ
ПРОЦЕНТ%
Сио2
59,32
Al2o3
19,72
Сио2/Ал2О3
3,01
SiO2+Al2O3
79.04
Цао
6,90
Fe2o3
7,22
Мго
2,23
С03
0,36
Na2O
1,11
К2О
1,27
Тио2
1,00
Мно2
0,18
P2o5
0,1
ООО
0,23
Элементы, присутствующие в материалах
B.
НАТРИЯ ГИДРОКСИД
Гидроксид натрия, также известный как щелочь или каустическая сода, имеет молекулярную формулу NaOH и представляет собой высокоедкое металлическое основание. Это белое твердое вещество, доступное в виде пеллет, лаков, гранул и в виде 50% насыщенного раствора. Гидроксид натрия растворим в воде, этаноле и метаноле. Эта щелочь расплывается и легко поглощает влагу и углекислый газ на воздухе. Гидроксид натрия используется во многих отраслях промышленности, в основном в качестве сильной химической основы в производстве целлюлозы и бумаги, текстиля, питьевой воды, моющих средств из мыльного песка и в качестве очистителя канализации. Мировое производство в 2004 году составило примерно 60 миллионов тонн, а спрос составил 51 миллион тонн. Хотя расплавленный гидроксид натрия обладает свойствами, аналогичными свойствам других форм, его высокая температура сравнительно ограничивает его применение.
NaOH молекулярная масса
Молярная масса NaOH = 39,99711 г/моль.
Это соединение также известно как гидроксид натрия. Перевести граммы NaOH в моли или моли NaOH в тограммы
Расчет молекулярной массы: 22,98977 + 15,9994 + 1,00794
Рис. 2 Гидроксид натрия
1.4 СИЛИКАТ НАТРИЯ
Силикат натрия — это общее название соединения метасиликата натрия, Na2SiO3, также известного как жидкое стекло или жидкое стекло. Он доступен в водном растворе и в твердой форме и используется в цементах, пассивной противопожарной защите, огнеупорах, текстильной и деревообрабатывающей промышленности, а также в автомобилях. Карбонат натрия и диоксид кремния реагируют при расплавлении с образованием силиката натрия и диоксида углерода: [1]
Na2CO3 + SiO2 Na2SiO3 + CO2
2
2
2 [1]
2 [1]
Безводный силикат натрия содержит цепной полимерный анион, состоящий из тетраэдра {SiO4} с общим углом, а не дискретный ион SiO3. Помимо безводной формы существуют гидраты с формулой Na2SiO3·nh3O (где n = 5, 6, 8, 9), которые содержат дискретный, приблизительно тетраэдрический анион SiO2(OH)2 с водой гидратации.
Например, коммерчески доступный пентагидрат силиката натрия Na2SiO3·5h3O имеет формулу Na2SiO2(OH)2·4h3O, а нонагидрат Na2SiO3·9h3O формулируется как Na2SiO2(OH)2·8h3O.[2]
СВОЙСТВА
Силикат натрия представляет собой белый порошок, который легко растворяется в воде, образуя щелочной раствор. Это одно из ряда родственных соединений, которые включают ортосиликат натрия, Na4SiO4, пиросиликат натрия, Na6Si2O7 и другие. Все стекловидные, бесцветные и растворимы в воде.
ПРОЧНОСТЬ НА СЖАТИЕ
Испытание на сжатие используется для определения твердости образца кирпича. Прочность образца кирпича зависит от летучей золы, цемента, мелкого заполнителя, стекловолокна, водоцементного соотношения, температуры отверждения, возраста и размера образца. Образцу необходимо дать достаточно времени для затвердевания, а затем выдержать в течение 21 дня. Через 21 день он должен быть загружен в тестирование
Тип образца | Средняя прочность на сжатие, Н/мм2 | ||
7 дней | 14 дней | 28 дней | |
0% Геополимер | 9. | 17,7 | 24 |
0,02% Геополимер AABrick | 9,2 | 17,9 | 24,2 |
0,04% Геополимер AABrick | 9,2 | 18 | 24,4 |
0,06% Геополимер AABrick | 9,3 | 18,2 | 24,7 |
0,08% Геополимер AABrick | 8 | 16,7 | 22 |
машина и испытана на максимальную нагрузку.
Испытание проводилось в соответствии со стандартом IS 3495 (части 1-4): 1992. Для определения прочности кирпича на сжатие использовались кирпичи стандартного размера 230 мм x 100 мм x 70 мм. Образцы укладывали на опорную поверхность УТМ с усилием 2000 кН без эксцентриситета и равномерной скоростью
до разрушения кирпича применялась нагрузка 140 кг/см в минуту. Отмечали максимальную нагрузку и рассчитывали прочность на сжатие.
Рис. 6. Испытание кирпича на сжатие
Таблица 2. Прочность кирпича на сжатие
Прочность на сжатие (fck) кирпича составляет Нагрузка на сжатие, Н
A – Площадь образца кирпича, мм2 Таблица 1.3 Прочность на сжатие
Прочность на сжатие кирпича
ИСПЫТАНИЕ НА ВОДОПОГЛОЩЕНИЕ
Это испытание проводилось в соответствии со стандартом IS 3495 (части с 1 по 4): 1992. Сухой вес кирпичей определяют с помощью весов. Количество образцов для испытания выбирают в соответствии с IS 5454:1976. Полностью высушенный образец погружают в чистую воду при температуре 27±2°С на 24 часа. Удалите образец, сотрите все следы воды влажной тканью и взвесьте образец. Завершите взвешивание через 3 минуты после извлечения образца из воды (М2). Водопоглощение, % по массе, после 24-часового погружения в холодную воду определяется по следующей формуле:
Таблица 1.4 Испытание на водопоглощение
4. 2.1 Испытание на водопоглощение ВЫВОДЫ
С помощью метода изотермической калориметрии удалось идентифицировать процесс геополимеризации системы щелочь-метакаолин при различных температурах отверждения. Отмечено существование оптимальной температуры отверждения 60 °С для получения наилучшего процесса геополимеризации. Этот факт был подтвержден анализом выщелачивания
, проведенным для этих неорганических геополимеров. В результате этого геополимер, полученный при этой температуре, показал наилучшие физико-механические свойства. Полученная информация способствует лучшему пониманию процесса геополимеризации и открывает возможность разработки синтеза этого типа геополимеров для конкретных приложений.
Тип образца | Водопоглощение в % | ||
Дней | 14 дней | 21 день | |
0% Геополимер AABrick | . | 8,15 | 7,93 |
0,02% Геополимер AABrick | 8,6 | 8.05 | 7,65 |
0,04% Геополимер AABrick | 8.2 | 7,75 | 7.11 |
0,06% Геополимер AABrick | 7,57 | 7.03 | 6,65 |
0,08% Геополимер AABrick | 6,89 | 6,52 | 5,79 |
ССЫЛКИ
А.М.И. Абдул Алим, P.D. Arumairaj Оптимальная смесь для геополимерного бетона Indian Journal of Science and Technology Vol. 5 № 3 (март 2012 г.) ISSN: 0974-6846.
Benjamin C. McLellan1a, Ross P. Williamsb, Janine Laya, Arie van Riessen Затраты и выбросы углерода для геополимерных паст по сравнению с обычным портландцементом.