Отзывы дома из керамзитобетонных блоков: Дом из керамзитобетонных блоков — плюсы и минусы, отзывы владельцев
Керамзитобетонные блоки — отзывы владельцев домов
Андрей, г. Новокуйбышевск
Собственный дом – это мечта, наверное, каждого жителя более-менее крупного города. Я – не исключение.
Поскольку в средствах был ограничен, хотелось построить двухэтажный дом из недорогого, но достаточно прочного материала с коэффициентом теплопроводности повыше, чем у обычного кирпича. Сразу скажу, что в итоге выбор пал на керамзитобетонные блоки, т.к. отзывы владельцев домов и тонны изученной информации позволили сделать заключение о его преимуществе над аналогичными материалами. Но обо всем по порядку.
Выбор встал между несколькими материалами:
Поскольку керамзит – это та же глина, пусть и обожженная, тем не менее, это решило мою дилемму в пользу керамзитобетонных блоков. По цене стройматериал выходил на 10% дороже газобетона, но, учитывая его прочность, я посчитал что это оправданные расходы. Также свой вклад в процесс выбора внес вот этот интересный ролик:
На участке почва сухая, песчаная, поэтому даже без геодезии было очевидно – нужен простой ленточный фундамент на глубину промерзания 90 см. Нанял бригаду и мне достаточно быстро залили бетонную ленту с армированием в 2 ряда и вывели цоколь на полметра. Особое внимание уделил армированию углов, так как по опыту знаю: многие работники ленятся делать правильный перехлест арматуры с усилением, из-за этого углы домов проседают, идет перекос стен.
После необходимого перерыва купил нужное количество керамзитобетонных блоков, кладочную теплую смесь с перлитом Основит Теплон и некоторые вспомогательные инструменты. Кладку выполнял сам совместно с 3 подсобными рабочими. Монтировать блоки легко, грани ровные, при необходимости быстро пилятся пилой с победитовым зубом.
Дом на этапе утепления пенопластом
Решил сделать дополнительное армирование стен, поэтому на шестом ряду проложили штробы и арматуру, под перекрытие – железобетонный пояс.
Сделал своеобразную страховку оконных и дверных проемов – усилил их кирпичом в 1 ряд.
После монтажа кровельной системы из профлиста с утеплением задумался о том, стоит ли сделать аналогичную теплоизоляцию стен или просто оштукатурить. Работы затянулись почти до зимы, поэтому, внимая отзывам компетентных специалистов, оставил все до следующей весны как есть.
За время простоя периодически приезжал, во время сильных ветров чувствовалось, что дом продувается. Значит, обязательно нужна фасадная отделка, включая цоколь. К тому же с удовольствием отметил для себя, что керамзитобетонные блоки слабо впитывают воду, то есть менее гигроскопичны, чем газобетон. Хотя по спецификации морозостойкость не превышает F50.
Когда потеплело, по совету знакомого архитектора решил утеплить обычным пенопластом. Экструдированный пенополистирол он категорически запретил использовать, так как велика вероятность появления грибка из-за разного уровня паропроницаемости. Клеили листы на клей для пенополистироловых плит.
Аппарат для нанесения клея
Чтобы избежать расхождения на стыках, выбрал шпунтованный пенопласт толщиной 10 см. На оконных проемах сделали рассечки, поверх утеплителя нанесли слой штукатурки с армирующей сеткой под покраску.
По итогам одного года проживания хотелось бы отметить, что отзывы о керамзитобетонных блоках соответствуют действительности только для некачественной продукции. Не могу назвать их хрупкими, непрочными, гигроскопичными. При толщине стены более 20 см их невозможно проломить кувалдой, но дополнительная теплоизоляция нужна в любом случае. Точно также как и для газобетона, пенобетона. В общем керамзитобетонные блоки – это отличная и недорогая альтернатива кирпичу.
Дмитрий, г. Москва
Побывав на строительной выставке Мосбилд, с удивлением обнаружил там нечто интересное – комбинированный стеновой керамзитобетонный блок с готовой внешней облицовкой под кирпич, песчаник, гранит и т. п. В аннотации к материалу особо отмечалось, что это теплоэффективный материал. Он значительно легче кирпича, что позволяет снизить расход на фундаментные работы. Были представлены две марки «Еврокам» и «Битэк». Самое приятное, что изготовители не просто выпускают продукцию, они ее запатентовали. Сотрудники ООО «БИТЭК» с гордостью демонстрировали патентное удостоверение.
Предложение последних сильно заинтересовало, так как сам планировал строительство дома, уже выбрал проект, дело оставалось за окончательным утверждением.
В Битэке привлекло то, что это блоки с пазогребневой системой соединения, изготавливаются методом вибролитья и выпускаются в 4 размерных модификациях:
- 400х190х400 мм;
- 400х190х600 мм;
- 200х190х400 мм;
- 600х190х600 мм.
То есть фактически это стандартные размеры, по которым проектируются дома из пенобетонных, газобетонных, газосиликатных блоков. При этом, по заявлению производителя, их продукция сочетается с любыми стройматериалами, монолитным железобетонным каркасом и другими конструктивами.
Блоки Битэк полнотелые, двухслойные, состоят из:
- мелкозернистого гранулированного керамзитобетона с плотной или поризованной структурой. Плотность наружной части соответствует D700;
- беспесчанного сырья с защитно-выравнивающим слоем. Плотностный показатель внутреннего слоя D450.
Внешний декоративный слой изготавливается из обычного бетона, окрашивание не внешнее, а полноценное, то есть в процессе производства в состав смеси вводятся пигменты. Это очень удобно, так как даже царапины такому покрытию не страшны. При необходимости готовую стену можно перекрашивать. А можно заказать собственный декор.
Кладка проходит быстро, швы минимальные
Поскольку коэффициент теплопроводности – около 0.13 Вт/(м·°С), сам производитель для холодных регионов рекомендовал утепление минеральной ватой или другими паропроницаемыми теплоизоляционными материалами.
И наконец, то, что покорило меня – блоки можно укладывать на клей-пену монтажную либо теплый кладочный раствор слоем в несколько миллиметров.
Хотя отзывы на этот продукт пока отсутствуют, меня это не остановило. После выставки позвонил за консультацией и мне все подробно расписали, выслали на почту рекомендации по монтажу, вплоть до того как делать оконные проемы. Настоятельно рекомендовали использовать для перекрытий только заводские плиты. Так и поступил. Сделали расчет по чертежу и оформили заказ на требуемый объем блоков и полублоков.
На ленточный фундамент стандартной ширины блоки ложились отлично. Правда, сначала рабочих испугал неизвестный им материал, но приехавший вместе с партией инженер быстро разъяснил некоторые тонкости, далее дело пошло как по маслу.
Стена моего дома на этапе стройки
Стыкуются керамзитобетонные блоки легко, перемещать их несложно даже одному человеку. Вес одной штуки – около 15 кг, а заменяет он одновременно около 16 одинарных кирпичей. Под перекрытие сформировали армпояс. Далее дому потребовалась только кровля, отделка цоколя, внутренние ремонтные работы и коммуникации.
После окончания кровельных работ выяснился еще один положительный момент – несущие и перегородочные конструкции изнутри получились достаточно ровными, штукатурить которые – одно удовольствие.
После года эксплуатации, трещин, смещений и других дефектов не выявили, зимой было тепло (стоит газовый котел), нареканий практически нет.
Сергей, г. Ростов-на-Дону
Два года назад запланировал строительство одноэтажного дома из заводских двухпустотных керамзитобетонных блоков. Они мне достались по дешевке, поэтому особо не размышлял над тем, какой материал лучше, а который хуже (хотя отзывы все же посмотрел). Задача была в другом – найти оптимальное решение для одноэтажного дома постоянного проживания. Поэтому отыскал в сети теплотехнический калькулятор, ввел параметры и подобрал следующий стеновой «пирог»:
Облицовочная клинкерная керамика толщиной 5 см;- Пенополистирол слоем 5 см и пароизоляция;
- Теплоблок керамзитобетонный двухпустотный с заполнением пенобетоном М600;
- Штукатурка;
- Обои.
Ленту фундамента шириной 60 см заглубил на 1 метр (точка промерзания), цоколь выложил из стандартных ФБС, выровнял обычным керамическим кирпичом. Первый этаж возвел на удивление быстро. В качестве скрепляющего состава использовал самомесный теплый раствор на перлите. Для мансарды использовал уже полублок толщиной 20 см, на перекрытия пошли пустотные бетонные плиты, под ними – армпояс из бетона в 20 см.
Полнотелым кирпичом усилил дверные и оконные проемы, выложил в три ряда под мауэрлат. Под утеплитель ничего не использовал кроме клея для пенопласта, стыки запенивал. Поверх теплоизоляции наносился клеевой состав для керамики и монтировалась облицовка. Получилась своеобразная «колодезная кладка».
Изнутри дом оштукатурил, наклеил обои. Для проемов выбирал окна с так называемым «теплым» стеклопакетом. Микроклимат действительно оптимальный: летом прохладно, зимой тепло. По ощущениям в доме из керамзитобетонных блоков дышится также как и в старом кирпичном. Если бы меня попросили оставить отзыв – ничего плохого о керамзотобетоне я бы сказать не смог.
В заключении – еще одно видео с отзывом владельцев:
‘; blockSettingArray[0][«setting_type»] = 6; blockSettingArray[0][«elementPlace»] = 15; blockSettingArray[1] = []; blockSettingArray[1][«minSymbols»] = 0; blockSettingArray[1][«minHeaders»] = 0; blockSettingArray[1][«text»] = ‘
‘; blockSettingArray[1][«setting_type»] = 6; blockSettingArray[1][«elementPlace»] = 15; var jsInputerLaunch = 15;
Поделиться с друзьями:
Дом из керамзитобетона: Отзывы владельцев
Изначально керамзитобетонные блоки производились, как своеобразный утеплитель для кирпичной стены. Кладку из блоков организовывали с внешней стороны строения и ее предназначением было удерживать тепловое излучение внутри конструкции. По прочностным характеристикам керамзитобетон не подходим для организации ограждающих и несущих конструкций. Однако с развитием науки усовершенствовалось и производство данного вида строительного материала.
Содержание статьи:
- Характеристики керамзитобетонного строения
- Каков же на практике дом из керамзитобетона?
- Выбор материала
- Тонкости строительного процесса
- Преимущества и недостатки org/ListItem»> Положительные стороны конструкции
- Отрицательные моменты
- Длительность эксплуатации
- Видео-обзор: Блоки из керамзитобетона
Характеристики керамзитобетонного строения
Сегодня керамзитобетон при относительно низком удельном весе (все зависит от степени пористости материала и качества связующего раствора) – до 1,5 раза меньше, чем у кирпичной кладки, обладает прочностью на сжатие 5-25 кг/см2. Это позволяет его использовать для возведения обычных домов малой этажности. Плюсом остается его низкая теплопроводность и высокие шумоизолирующие свойства.
К содержанию ↑
Каков же на практике дом из керамзитобетона?
Отзывы владельцев жилых построек только положительные.
- В первую очередь, существует миф о том, что керамзитобетонные блоки в первые годы своей эксплуатации выделяют в атмосферу помещения вредные газы и радон. Особо пытливые застройщики провели некоторые эксперименты и опровергают данный факт. Дома из керамзитобетонных блоков – экологически чистые. А их радиационный фон в несколько раз ниже, по сравнению со щебнем и кирпичом.
- Во-вторых, отзывы владельцев домов из керамзитобетона подтверждают сведения производителей данного материала о его низкой теплопроводности. В подобной конструкции летом прохладно, а зимой не холодно. Однако утверждения о том, что расходы на отопление уменьшаются в 3-4 раза, неверно. Да экономия присутствует, если провести правильное утепление.
Люди нарекают на присутствие конденсата на стенах и как следствие – развитие грибков и плесени. Это не следствие намокания керамзитобетонных блоков. Данный материал гигроскопичен. Решением проблемы является утепление здания из блоков. Это мероприятие защищает помещение от потери тепла, а конструкционный материал дома – от влаги.
Керамзитобетон – паропроницаем
Это доказано на практике. Атмосфера в доме из этого материала ничем не хуже, по сравнению с деревянными домами. Переизбытка влаги нет. Однако неправильная внутренняя отделка может нарушить данный баланс. Владельцы настаивают на паропроницаемых штукатурках и декоративных материалах.
Однако во время строительства есть множество нюансов, пренебрегая которыми можно прийти к плачевному конечному результату.
К содержанию ↑
Выбор материала
Что лучше выбрать для малоэтажного строительства? Рекомендуется использовать следующие марки материалов:
1). М25, М35, М50, М75, М100. М50 – для хозяйственных построек, однако она подойдет и для несущей стены, толщиной до 400 мм (см. Размеры керамзитобетонных блоков).
2). М75 – возводится несущая стена, толщиной в 200 мм.
3). Пустотелые блоки – идеальное решение для строительства загородного дома. Это облегченный вариант материала. Он имеет неровную поверхность, что отразится на стоимости дальнейшей его обработки.
4). Можно использовать полнотелый блок, но он весит много (более 1000 кг/куб.м) и требует к себе мощный фундамент.
К содержанию ↑
Тонкости строительного процесса
Относительно фундамента мнения большинства владельцев складываются в сторону монолитной конструкции с армирующим каркасом.
Если почва не устойчива и геодезические исследования подтверждают близкое пролегание грунтовых вод, то лучше использовать свайный вариант основания дома. Конечно, цена строительства в этом случае значительно возрастет (за счет сложности конструкции и привлечения спецтехники), но в результате получится прочный дом.
Цокольный этаж возводится, если перепад грунта большой, а его искусственное выравнивание не проводилось. Для этого используется специальный, цокольный кирпич, плюс армирующая сетка в несколько рядов. Результат на рисунке.
Перекрытие первого этажа обустраивается после того, как цоколь набрал прочность. Для этого берутся бетонные плиты с арматурой внутри.
Непосредственно укладка блоков:
Для несущих и ограждающих конструкций используется блок марки от М50. Для перегородок в доме – перегородочный материал. Блоки кладутся на цементный раствор. По рекомендациям владельцев домов каждый пятый ряд кладки армируется. Работы начинаются с выгонки углов, потом продвигаются вдоль стены.
После организации оконных проемов и первого этажа для укладки перекрытия для следующего этажа организовывается армапояс со съемной опалубкой.
После созревания цементного камня армапояса, укладываются плиты перекрытия. Относительно утепления стен дома и цокольного этажа большинство владельцев склоняются в сторону пенопласта на клею, вентилируемого зазора и облицовки дома декоративным кирпичом.
К содержанию ↑
Как и любое строение, так и дом из керамзитобетонных блоков имеет свои преимущества и недостатки.
Положительные стороны конструкции
К положительным характеристикам относятся низкая теплопроводность, большой объем при малом удельном весе. Это позволяет несколько сэкономить на закупке материала. Зная массу одного конструкционного элемента, легко рассчитать его прочность и теплопроводность. В соответствии с полученными данными можно определить оптимальную толщину и высоту фундамента.
К содержанию ↑
Отрицательные моменты
В ходе приобретения изделий рекомендуется взвесить несколько блоков из закупочной партии. На практике встречаются случай несоответствие параметром и веса материала нормам заявленной партии.
Для организации нормального температурного режима в доме из керамзитобетонных блоков необходима толщина стены до 1,2 м. Конечно, такого строить никто не будет. Поэтому все застройщики настаивают на дополнительном утеплении строения.
Пенопласт в данном случае не подходит, так как он горюч, а под дополнительным облицовочным слоем поверх утеплителя, его трудно будет загасить в случае пожара. Однако это теория. Многие люди все же прибегают к использованию именно этого утеплителя и остаются довольными.
Согласно нормам строения для утепления стен здания из керамзитобетонных блоком лучше применять минеральную или базальтовую вату в плитах. Необходима также дополнительная гидроизоляция, так как керамзитобетон – пористая структура.
К содержанию ↑
Длительность эксплуатации
Относительно прочности блоков также нареканий со стороны владельцев керамзитобетонных домов нет. Все гвозди на дюбелях держатся хорошо. Главное – правильно выбрать дюбель. Для мебели подойду на 10 мм. Для тяжелых конструкций – нужно воспользоваться саморезами. Керамзитобетон не растрескивается при перепаде температуры.
Видео-обзор: Блоки из керамзитобетона
Блоки из керамзитобетона. Особенности материала
Те, кто построил дом из этого стройматериала, отмечают, что микротрещины могут появиться в первые 3-5 года после его возведение, но такой тенденции подвержено только около 5% блоков.
Дома из блоков получаются прочными, удобными в эксплуатации, долговечными. Они имеют достойный вид. Большинство людей, воспользовавшись этим материалом, не пожалели о своем выборе.
Читайте также:
- Дом из керамзитобетонных блоков: Плюсы и Минусы
- Проекты домов из керамзитоблоков
- Дом из пеноблоков: отзывы владельцев
- Фундамент для дома из керамзитоблоков
Шлакоблок | Размеры, вес, стоимость, преимущества и недостатки
Содержание
В этой статье речь пойдет о шлакоблоке.
1.

Шлакоблоки можно определить как полые конструкции прямоугольной формы, обычно изготавливаемые из бетона и угольного шлака, которые используются для возведения стен на строительных площадках.
Зола используется в качестве заполнителя в шлакоблоке. Разница между бетонными блоками и шлаком заключается в том, что бетонные блоки готовятся с использованием цемента, заполнителя, песка, воды, но в шлаке вместо заполнителя используется зола.
2. Свойства шлакоблоков
а. Обычно изготавливается из бетона и шлака.
б. Он очень легкий по сравнению с последним из-за доли заполнителя
c. Он не очень силен, поэтому в нескольких местах им часто пренебрегают.
д. Они чаще гнутся, а коробление и ремонт в разы очень дороги, поэтому ими пренебрегают.
эл. Это самая старая мода, так как около 50% не производятся серийно.
ф. Он не имеет заметного количества прочности на растяжение.
3. Подготовка шлакоблоков
Обычный вес шлакоблока составляет около 26–33 фунтов (11,8–15,0 кг). Блоки из легкого бетона готовят путем удаления песка и гравия с керамзитом, сланцем или шифером. Керамзит, сланец и сланец изготавливаются путем дробления сырья и нагревания его примерно до 2000°F (109°С).3°С).
. доступная цена, соответствует спецификациям ASTM C-90.Общий размер, например 8 дюймов x 8 дюймов x 16 дюймов;
Блок бетонного настила
Это самый лучший и экономичный метод строительства настила. Этот тип блока сделан для клиентов DIY. Этот блок позволяет габаритную древесину. В этом блоке нет необходимости смешивать или насыпать огарки для общего размера, например, 7 «х 11» х 11 «.
Стандартный основной блок
Этот тип шлакоблока используется для возведения шлакоблоков для больших сооружений, таких как здания, школы и т. д. ;
Бетонный блок для настила Quikrete
Этот тип блока используется для поддержки настила и быстрого и прочного строительства. Общий размер, например, 10 дюймов x 10 дюймов x 10 дюймов; Фактические: 625 дюймов x 9,625 дюймов x 9,625 дюймов
5. Размеры шлакоблоков
. Их нормальные размеры на 3 ⁄ 8 дюймов (9,5 мм) меньше формальных размеров (чтобы обеспечить 3 ⁄ 8 (дюймовый раствор для швов между блоками в любой ориентации).
6. Стоимость шлакоблоков
Шлакоблоки больше не отличаются по стоимости в зависимости от типа. В то время как несколько замковых камней могут стоить 95 центов за штуку, обычная стоимость шлакоблока составляет от до 3 долларов за штуку.
7.
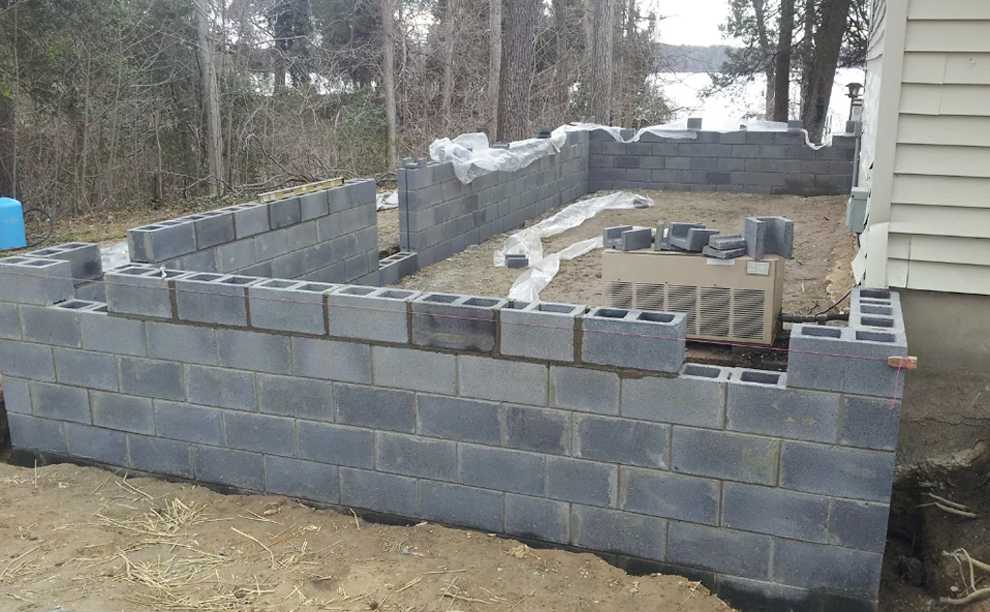
a. Перевязочные работы не требуются.
б. Он очень легкий по весу.
в. Требуется не так много навыков.
д. Он конструктивно прочнее кирпича.
эл. Возможны более тонкие стены, что обеспечивает большую площадь ковра.
ф. Он большой по размеру, а значит нет. суставов меньше.
г. Лучшая изоляция от тепла, звука и сырости.
ч. Он не нуждается в штукатурке.
я. Требуется меньше раствора, что экономит деньги.
8. Недостатки шлакоблока
1. Вероятность просачивания.
2. Материалы могут не подходить для разных мест.
9. Часто задаваемые вопросы
1. Сколько весит шлакоблок?
Вес шлакоблока составляет около 26–33 фунтов (11,8–15,0 кг).
2. Сколько стоят шлакоблоки?
Обычная стоимость шлакоблока составляет от 1 до 3 долларов за штуку.
3. Какой высоты шлакоблок?
Шлакоблоки имеют высоту 16 дюймов (410 мм).
4. Насколько велик шлакоблок?
Шлакоблоки имеют длину 16 дюймов (410 мм) и ширину 8 дюймов (200 мм). Они легкие и обладают прочностью, долговечностью, огнестойкостью, отличными звукоизоляционными качествами, энергосбережением и доступной ценой
Последние новости
Механические свойства и морозостойкость бетона на легком заполнителе с использованием искусственного глинистого заполнителя
Ключевые слова: легкий заполнитель; легкий бетон; предел прочности при изгибе; циклы замораживания-оттаивания
1 Введение
В последние периоды дальнейшее рассмотрение было сосредоточено на улучшении легкого бетона (LWC), поскольку он снижает стоимость строительства, облегчает строительство и является более устойчивым строительным материалом [1]. LWC имеет различные конструкционные применения, такие как предварительно напряженные и сборные элементы LWC, опоры мостов, настилы и балки, особенно когда оно превышает 17 МПа и используется в качестве элементов конструкции, не подвергающихся высокой нагрузке [2]. LWC может быть создан с использованием легкого заполнителя (LWA). Бетон с легким заполнителем (LWAC) используется в строительстве зданий в качестве облегченных блоков и позволяет снизить собственную нагрузку на фундаменты и элементы конструкций [3]. Глины при термической обработке расширяются в объеме до пяти-шести раз в результате газовыделения, в результате чего образуется пористый заполнитель клинкеровидной структуры с прочным спекшимся слоем на внешней поверхности [4]. По сравнению с различными промышленными сырьевыми ингредиентами, большие технические характеристики и различные преимущества могут быть получены при использовании заполнителей из керамзита, которые обеспечивают самую высокую прочность на сжатие среди LWA [5].
Искусственная легкая глина изучалась во многих видах исследований в качестве LWA, и ее преимущества заключались в снижении общего веса здания, снижении затрат, повышении долговечности и повышении огнестойкости [6,7]. Алдакше и др. [8] изучали производство LWC с использованием пемзового заполнителя в качестве эталонной смеси и 1, 3, 5 и 9% замены (реп) пемзового заполнителя отходами бора (ВА). Результаты показали увеличение прочности на сжатие и прочности на разрыв LWC при использовании BA для всех уровней замещения. Кроме того, экологический эффект был достигнут за счет использования в качестве заполнителя промышленных отходов «Борные отходы». Balamuralikrishnan и Saravanan [9] исследовали влияние частичной замены Alccofine (AF), «который представляет собой чрезвычайно тонкий материал, полученный из отходов стекла», на прочность на сжатие кубиков цементного раствора. Результаты показали, что 10% AF по объему цемента был лучшим уровнем замены и давал самую высокую прочность на сжатие около 53 MPa.
В некоторых исследованиях [10] в качестве крупнозернистого ЛБС в бетоне для получения ЛБК использовали отходы термокамня. В LWAC, по сравнению с растворной матрицей, LWA как компонент может обладать более низкими свойствами, поэтому характеристики LWA являются важными факторами, влияющими на конечные свойства бетона. Таким образом, это исследование направлено на оценку свойств LWAC с использованием иранского искусственного глиняного заполнителя с использованием суперпластификатора, а также изучение влияния циклов замораживания-оттаивания (FTC) на LWC, изготовленных с использованием этого искусственного глиняного заполнителя, поскольку, согласно Mehta и Monteiro [11], несколько факторов в LWA влияют на свойства бетона, такие как тип заполнителя, плотность, содержание воды, условия окружающей среды и т. д. Одной из существенных причин износа бетона является воздействие нескольких циклов замораживания и оттаивания, что влияет на срок службы конструкций. .
2 Экспериментальная программа
На рис. 1 показаны детали экспериментальной программы.
Рисунок 1
Блок-схема методологии исследования.
1) Используемые материалы: во всех смесях использовался обычный портландцемент тип-I (завод «Кар» в г. Наджаф) в качестве крупного заполнителя с использованием заполнителей максимальным размером 10 мм с фракцией, указанной в таблице 1, и фракцией мелкого заполнителя. показано в Таблице 2 и соответствовало индийским стандартам IS-383 [12]. Искусственный керамзитовый заполнитель (легкий) также использовался в процентах от крупного заполнителя (замена), некоторые свойства этого LWA приведены в таблице 3. Гиперпластичный PC200 (ранее известный как Flocrete PC200) соответствует ASTM C49.4 [14], а в качестве высокоэффективной суперпластифицирующей добавки использовались типы А и G, свойства которых приведены в табл. 4.
Таблица 1
Классификация и некоторые свойства крупного заполнителя
Таблица 2
Класс мелкого заполнителя
Таблица 3
Некоторые свойства LWA (керамзит)
Таблица 4
Некоторые свойства использованного в исследовании суперпластификатора ПЦ-200
2) Пропорции смеси: использовалась эталонная смесь 1:1:1,2 (цемент:песок:гравий) с соотношением воды и цемента 0,42. Смеси с заменой крупного заполнителя различным содержанием иранского глинистого заполнителя 3, 5, 10, 15, 20, 25, 30, 40 и 50 % усовершенствованы высокоэффективным суперпластификатором бетона типа ПК-200, желто- оранжевый цвет. На рис. 2 представлен искусственный керамзитовый заполнитель, а также суперпластификатор ПК-200. В этом исследовании было использовано 1,5 л суперпластификатора на каждые 100 кг цемента, а соотношение вода/цемент было снижено до 0,28 для сохранения удобоукладываемости.
Рисунок 2
Искусственный керамзит и суперпластификатор ПК-200.
3) Образцы и испытания: кубические формы с размерами 10 см × 10 см × 10 см использовались для испытаний на прочность при сжатии, а небольшие балки размером 10 см × 10 см × 40 см использовались для испытаний на прочность на изгиб, как показано на рисунке 3. Три использовались образцы для каждого испытания и для каждой смеси, а затем определялось среднее значение. Кроме того, кубические образцы были взвешены перед проведением испытаний на прочность на сжатие, чтобы определить плотность бетона для всех смесей. Испытание на прочность при сжатии проводили путем нагружения образцов после 28 дней отверждения и воздействия одноосной нагрузки до разрушения.
Рисунок 3
Некоторые образцы бетона кубической формы с заменой на 3% после заливки и бетонная балка с заменой на 10% при открытии формы.
Испытание на прочность при изгибе было проведено в соответствии со стандартом ASTM C78-02 [15] с использованием испытания на нагрузку в третьей точке согласно уравнению (1). На рис. 4 показан LWAC при различных испытаниях.
(1) MR=p×lb×d2,
, где MR — модуль разрыва (МПа). p — максимальная прилагаемая нагрузка (Н). l — расстояние между опорами балки (мм). b и d – ширина и глубина балки (мм).
Рисунок 4
Некоторые образцы проходят испытания на сжатие, изгиб и раскалывание.
С использованием цилиндров размером 100 мм × 200 мм было проведено испытание на прочность на растяжение и испытание методом раскалывания, как показано на рисунке 4 и в соответствии с уравнением (2).
(2) Ft=2PπDL,
, где F t – предел прочности при растяжении при раскалывании (МПа). P — максимальная прилагаемая нагрузка (Н). D и L диаметр и длина цилиндра (мм).
По мнению многих исследователей, для оценки устойчивости бетона к замораживанию-оттаиванию использовалось несколько стандартов и методов, таких как ASTM C666 [16], европейский стандарт CEN/TR 15177 [17] и китайская спецификация GB/T 50082-2009.[18]. В настоящем исследовании тест проводился в соответствии с CEN/TS-12390-0 [19]. Испытание на замораживание-оттаивание проводили с использованием образцов кубической формы, испытываемых в морозильной камере в течение 12 часов при температуре -18°C и 12 часов при температуре +20°C в течение 1 месяца и 2 месяцев. На рис. 5 показаны образцы во время FTC.
Рисунок 5
Образцы, проходящие испытания на FTC.
3 Результаты и обсуждения
В табл. 5 приведены механические свойства эталонных смесей и смесей с заменой на ЛВС различных пропорций из нормального крупного заполнителя, а также плотности для каждой смеси. Формирование LWC начинается с замены 20% LWA, и эта смесь имеет плотность менее 2000 кг/м 3 . Плотность бетона уменьшилась при замене обычного заполнителя на LWA, а также все механические свойства уменьшились при увеличении замены LWA. Это можно объяснить двумя причинами: во-первых, низкой плотностью LWA, который является пористым, а во-вторых, низкой прочностью LWA по сравнению с обычным заполнителем. Прочность на сжатие эталонной смеси оказалась равной 35,4 МПа, которая затем снизилась до 9,54 МПа при 50% замене. Из Таблицы 5 видно, что смеси с заменой 30% дали прочность на сжатие менее 17 МПа, что является низким значением для конструкционного LWC согласно его определению.
Таблица 5
Механические свойства эталонных образцов и образцов LWAC

В таблице 6 представлены те же смеси, но улучшенные высокоэффективным суперпластификатором ПК-200. Все смеси показывают более высокие значения прочности на сжатие, растяжение и изгиб. 30% замещающие смеси при добавлении этой добавки дают 19,8 МПа и могут быть использованы в качестве конструкционных LWC.
Таблица 6
Механические свойства эталонных образцов и образцов LWAC, модифицированных ПК-суперпластификатором
Смесь | Прочность на сжатие (МПа) | Прочность на растяжение (МПа) | Прочность на изгиб (МПа) | Плотность (кг/м 3 ) |
---|---|---|---|---|
1:1:1,2 | 43,87 | 4,33 | 5,61 | 2 528 |
3% репс | 39,96 | 4.![]() | 5,23 | 2 408 |
5% повтор | 37,81 | 3,86 | 4,76 | 2 306 |
10% репс | 32,80 | 3,23 | 4,22 | 2 237 |
15% репс | 29,45 | 2,94 | 3,85 | 2 157 |
20% репс | 25.30 | 2,32 | 3,48 | 2 009 |
25% повтор | 21,92 | 1,88 | 3,30 | 1 942 |
30% репс | 19,81 | 1,71 | 2,81 | 1 887 |
40% репс | 16,35 | 1,45 | 2,60 | 1 793 |
50% репс | 13,28 | 1,37 | 2,53 | 1 704 |
с заменой 40 и 50 % не давали структурных ЛВК даже при добавлении суперпластификатора. Их прочность на сжатие все еще была ниже 17 МПа, что может быть связано с более высоким уровнем замены крупного заполнителя для этих смесей. На рисунках 6–8 показана взаимосвязь между заменой обычного заполнителя на LWA и прочностью на сжатие, растяжение и изгиб соответственно. Рисунки 9–11 показано сравнение между обычными смесями и модифицированными смесями (с суперпластификатором ПЦ-200) по прочности на сжатие, растяжение и изгиб.
Рисунок 6
Соотношение между % замены нормального заполнителя с LWA и прочностью на сжатие без PC-суперпластификатора.
Рисунок 7
Соотношение между % замены нормального заполнителя с LWA и пределом прочности при растяжении без PC-суперпластификатора.
Рисунок 8
Соотношение между % замены нормального заполнителя с LWA и прочностью на изгиб без PC-суперпластификатора.
Рисунок 9
Соотношение между % замены обычного заполнителя на LWA и прочностью на сжатие для обычных смесей (нижняя кривая) и модифицированных смесей (верхняя кривая).
Рисунок 10
Соотношение между % замены обычного заполнителя на LWA и пределом прочности при растяжении для обычных смесей (нижняя кривая) и модифицированных смесей (верхняя кривая).
Рисунок 11
Соотношение между % замены обычного заполнителя на LWA и прочностью на изгиб для обычных смесей (нижняя кривая) и модифицированных смесей (верхняя кривая).
В таблице 7 показано влияние FTC на прочность смесей при сжатии. Снижение прочности эталонных смесей после 2-х месячной выдержки было очень высоким (около 32%). Это может быть связано с тем, что микротрещины начали расти внутри бетона во время FTC из-за морозного расширения. С другой стороны, снижение прочности уменьшается в смесях LWC, как показано в таблице 7, и это может быть связано с уменьшением количества безвредных пор из-за высокой дозы суперпластификатора, поэтому давление из-за замерзания может быть значительно снижено. Кроме того, эту характеристику можно интерпретировать следующим образом: гидравлическое давление, возникающее в результате инея, может быть сброшено, поскольку наличие пустот в LWA может играть очень важную роль в качестве «расширительных камер», которые будут рассеивать давление; поэтому легкие смеси демонстрируют более высокую стойкость к циклам замораживания и оттаивания в этом исследовании, и это также наблюдали Bogas [20], Polat et al. [21] и Thienel et al. [22].
Таблица 7
Прочность на сжатие после FTC
Смесь | Прочность на сжатие до FTC (МПа) | Прочность на сжатие через 1 месяц FTC (МПа) | Прочность на сжатие через 2 месяца FTC (МПа) | Снижение прочности через 2 месяца (%) |
---|---|---|---|---|
1:1:1,2 | 43,87 | 35,31 | 29,70 | 32,2 |
3% репс | 39,96 | 36,65 | 35,12 | 12,1 |
5% повтор | 37,81 | 35,20 | 33,58 | 11,2 |
10% репс | 32,80 | 31,91 | 30,78 | 6,2 |
15% репс | 29,45 | 28,54 | 28.![]() | 4,6 |
20% респ | 25.30 | 24,65 | 23,91 | 5,5 |
25% репс | 21,92 | 21.50 | 20,78 | 5,2 |
30% репс | 19,81 | 19.17 | 18,86 | 4,7 |
40% репс | 16,35 | 16.10 | 15,91 | 2,7 |
50% репс | 13,28 | 13.04 | 12,89 | 2,9 |
4 Заключение
LWAC была достигнута за счет использования иранской искусственной глины в качестве крупного заполнителя в этом исследовании.
Легкие конструкции с прочностью на сжатие более 17 МПа были достигнуты в 3–25% замен, более 25% замен давали прочность на сжатие менее 17 МПа.
Смеси могут быть улучшены за счет использования ПК-суперпластификатора и достижения конструкционного облегчения до 30% замены.
Более высокая прочность FTC была достигнута за счет использования искусственной легкой глины в качестве крупного заполнителя по сравнению с обычным заполнителем, где снижение прочности на сжатие после 2 месяцев использования FTC колебалось от 3 до 12%.
Конфликт интересов: Авторы заявляют об отсутствии конфликта интересов.
Заявление о доступности данных: Большинство наборов данных, созданных и/или проанализированных в этом исследовании, включены в представленную рукопись.
Другие наборы данных доступны по разумному запросу от соответствующего автора с прилагаемой информацией.
Ссылки
[1] JiaHao L, Chin Lian F, Hejazi F, Azline N. Изучение свойств и прочности бетона без фракций. Sustain Civ Constr Eng Conf. 2019; 357:1–13. 10.1088/1755-1315/357/1/012009.Поиск в Google Scholar
[2] Патил П., Сонар И., Шинде С. Бетон без фракций. Int J Concr Technol. 2017;3(2):1–13. https://www.academia.edu/349
/No_Fine_Concrete.Search in Google Scholar[3] Tekin R, Kotan T, Osmanson A, Brostow W, Gencel O, Gonzalo M. Свойства легких бетонных блоков с отходами цеолитового туфа . Mater Sci J. 2020; 26 (4): 463–70. 10.5755/j01.ms.26.4.22777.Search in Google Scholar
[4] Озгувен А., Гундуз Л. Исследование эффективных параметров производства керамзитобетона. Cem Concr Compos. 2012;34:781–7. 10.1016/j.cemconcomp.2012.02.007.Поиск в Google Scholar
[5] Рашад AM. Легкий керамзит как строительный материал – обзор. Constr Build Mater. 2018;170:757–75. 10.1016/j.conbuildmat.2018.03.009. Поиск в Google Scholar
[6] Банавайр А. Прочность легкого заполнителя в бетоне – обзор. Серия конференций IOP – Науки о Земле и окружающей среде; 2017. с. 1–5.10.1088/1755-1315/357/1/012017Поиск в Google Scholar
[7] Субанди Р., Кусума С., Аснан М. Легкий конструкционный искусственный заполнитель. Энн Чим Наука Матер. 2019;43(4):213-6. 10.18280/acsm.430403.Поиск в Google Scholar
[8] Алдакше А., Чаглар Х., Чаглар А., Аван Ч. Исследование использования в качестве заполнителя в производстве легкого бетона отходов бора. Civ Eng J. 2020;6(7):1328–35. 10.28991/cej-2020-03091551.Search in Google Scholar
[9] Balamuralikrishnan R, Saravanan J. Влияние добавления алкофина на прочность на сжатие кубиков цементного раствора. Emerg Sci J. 2021;5(2):155–70. 10.28991/esj-2021-01265.Поиск в Google Scholar
[10] Тумадхир М. Влияние использования вторичного легкого заполнителя на свойства бетона. Дж. Вавилонский унив. 2015; 3:1–10, https://www.iasj.net/iasj/download/5b482158ed80164b. Поиск в Google Scholar
[11] Мехта П., Монтейро П. Бетон: микроструктура, свойства и материалы. Третье изд. США: Макгроу Хилл; 2006. Поиск в Google Scholar
[12] IS-383. Спецификации индийских стандартов для крупных и мелких заполнителей из природных источников для бетона, Second Revis. Нью-Дели: Бюро индийских стандартов; ПОДТВЕРЖДЕНО В 2002 г. с. 20.Поиск в Google Scholar
[13] ASTM C131. Стандартный метод испытаний на устойчивость мелкозернистого крупного заполнителя к разрушению при истирании и ударе в машине Лос-Анджелес. Американское общество испытаний и материалов; 2006. 10.1520/C0131_C0131M-14. Поиск в Google Scholar
[14] ASTM C 494-05. Стандартная спецификация химических добавок для бетона. Американское общество испытаний и материалов; 2005. Поиск в Google Scholar
[15] ASTM C666/C666M-03 Стандартный метод испытаний на устойчивость бетона к быстрому замораживанию и оттаиванию. Американское общество испытаний и материалов; 2008. с. 6.Поиск в Google Scholar
[16] ASTM C666/C666M-03. StTest метод устойчивости к быстрому замораживанию Оттаивание; 2008. с. 6.Поиск в Google Scholar
[17] CEN/TR 15177. Испытание бетона на морозостойкость. Повреждение внутренней структуры. европейский стандарт; 2006. с. 34.Поиск в Google Scholar
[18] GT/B 50082-2009. Стандарт на методы испытаний долговечности и долговечности рядового бетона. Министерство жилищного строительства и городского и сельского развития Китая; 2009.Поиск в Google Scholar
[19] Vandewalle L, Beeidens A. Методы сравнительного исследования устойчивости бетона к циклам замораживания-оттаивания, описанные в CEN/TS-12390-9, ISO DIS-4846-2. Документ конференции; Август 2009 г. Поиск в Google Scholar
[20] Bogas JA. Характеристика конструкционных бетонов с легкими заполнителями из керамзита. Кандидатская диссертация в области гражданского строительства. Португалия: Высший технический институт (IST), Лиссабонский университет; 2011.