Арболит технология производства в домашних условиях: Изготовление арболита своими руками: технология производства и самостоятельные работы
Изготовление арболита своими руками: технология производства и самостоятельные работы
Поэтапная технология изготовления арболита предвидит подготовку основания, определения компонентов и состава блочного материала. В данной статье рассмотрим особенности производства своими руками с применением необходимого оборудования, расчета массы и заливки.
Оглавление:
- Преимущества и недостатки арболита
- Технология производства арболита
- Подготовка основания для работы
- Компоненты и состав арболита
- Процесс и принципы изготовления
- Оборудование: применение на практике
- Блочные формы для арболита
- Процесс производства своими руками
- Советы экспертов при изготовлении блоков своими руками
Преимущества и недостатки арболита
Для многих строителей арболитные блоки являются ценным и качественным материалом для возведения домов.
1. Прочность материала составляет 600-650 кг/м3, что по компонентной структуре не уступает иному строительному материалу. Главной особенностью является пластичность, что формируется в результате использования древесины, которая качественно армирует блоки. Таким образом, арболит не трескается под тяжестью иных материалов, а может только слегка деформироваться сохраняя общую систему конструкции.
2. Стойкость к низким температурам, что очень важно в процессе возведения дома и его эксплуатации. Дело в том, что если здание нагреется и замерзнет несколько раз, то это не повлияет на качество материала. Фактически дом из арболита может простоять минимум 50 лет в любые погодные условия. Конструкции из пеноблоков не имеют подобных свойств, ведь при постоянном замораживании они быстро потеряют свою функциональность.
3. Арболит не поддается воздействию углекислого газа, так что не стоит беспокоиться о карбонизации блоков, ведь их структура не позволит превратиться материалу в мел.
4. Теплопроводность блоков свидетельствует о популярности материала. Сравнивая показатели, стоит отметить, что стена из арболита в 30 см равняется 1 метру толщины кирпичной кладке. Структура материала позволяет сохранять тепло внутри помещения даже в самые холодные зимы, что весьма экономично при строительстве.
5. Звукоизоляционные свойства свидетельствуют о высоком коэффициенте поглощения арболита, который составляет от 0,7 до 0,6. Для сравнения древесина имеет показатели 0,06 -0,1, а кирпич немного больше около 0,04-0,06.
6. Легкость материала, что позволяет сэкономить средства на заливку фундамента.
7. Арболит является экологически чистым и долговечным строительным материалом, что определяет компонентный состав блоков. После возведения дома он не образует плесень и грибок на стенах.
8. Материал является безопасным, так он не воспламенятся.
9. Арболитные блоки легко применять в строительных работах, поскольку без труда в них можно забить гвозди, просверлить отверстие, использовать шурупы и так далее. Внешняя структура материала позволяет покрывать его штукатуркой без использования специальных сеток и дополнительных утеплителей.
Мы рассмотрели преимущества арболитных блоков, но для полного воссоздания картины о данном строительном материале приведем некоторые недостатки:
1. Стеновая панель может не выделяться точными геометрическими параметрами, от чего для восстановления ровности стены используют вагонку, сайдинг или гипсокартон, а сверху все отделяют штукатуркой.
2. Блоки не являются дешевым строительным материалом, ведь изготовление щепы для арболита требует некоторых затрат. Делая расчеты по сравнению из газобетоном, данный строительный материал обойдется только на 10-15 процентов дороже, что не формирует полное преимущество.
Технология производства арболита
Изготовление арболита требует следованию технологиям производства с расчетом состава и объема для одного блока. Арболитные блоки представляют собой строительный материал простой по компонентному составу, в который входят древесина, вода, опилки, цемент и другие предметы.
Главной основой для производства считается древесная щепа. Составная часть арболитового блока определяет его прочность и устойчивость к повреждениям, что высчитывается высшим уровнем, чем у пено- или газоблоков. Производство в домашних условиях осуществить не сложно, однако необходимо придерживаться распределения массы предмета и следовать инструкции.
Подготовка основания для работы
Основной составляющей для изготовления щепы для арболита является соотношение пропорций стружки и опилок – 1:2 или 1:1. Все предметы хорошо высушивают, для чего их помещают на 3 – 4 месяца на свежий воздух, время от времени обрабатывая известью и переворачивая.
Примерно на 1 кубический метр средства потребуется около 200 литров извести 15-ти процентной. В них помещают все щепы на четыре дня и перемешивают их от 2 до 4 раз на день. Все работы проводятся с целью убрать сахар с древесины, который может спровоцировать гниение блоков. Щепу приобретают в готовом виде, однако, с помощью щепорезов можно сделать самостоятельно.
Компоненты и состав арболита
Компонентный состав арболита является самым важным этапом технологии производства и требует внимательного соотношения всех материалов. При изготовлении блоков важно следить за качеством и разновидностью приобретаемых материалов, которые определяют готовый строительный материал. После процесса изготовления в щепу добавляют следующие материалы, такие как:
- известь гашеную;
- жидкое стекло растворимое;
- портландцемент;
- хлористый калий;
- алюминий и сернокислый кальций.
Производство арболита в пропорциях представлено в таблице 1. Стоит учесть, что для всех компонентов масса рассчитана на четыре процента доли цемента. Данная компоновка помогает сохранить огнеупорность предмета и придает пластичности.
Таблица 1. Состав арболита по объему
Марка арболита | Цемент (М400) | Кол-во извести | Кол-во песка | Кол-во опилок | Получаемая плотность (кг/м3) |
5 | 1 | 1,5 | — | 15 | 300-400 |
10 | 1 | 1 | 1,5 | 12 | 600-700 |
15 | 1 | 0,5 | 2,5 | 9 | 900-1000 |
25 | 1 | — | 3 | 6 | 1200-1300 |
Процесс и принципы изготовления
Оптимальные параметры блоков для технологии производства арболита составляют 25х25х50 сантиметров. Установленные размеры удобны при кладке стен домов, а также в процессе промышленности. Заливка блока состоит из трех рядов смеси и арболита, после каждого этапа необходимо уплотнять раствор молотком, отделанным жестью.
Излишняя масса свертывается при содействии шпателя. Выдерживается блок при температуре 18 градусов тепла на раскрытом воздухе. По истечении суток арболит выстукивается из формы на ровную поверхность, где он скрепляется на протяжении 10 дней.
Оборудование: применение на практике
Для производства необходимо разное снабжение, например, станки для изготовления арболита, которые выбираются в соответствии с объемом продукции и количества сырья. Технология промышленного процесса должна отвечать требованиям и критериям СН 549-82 и ГОСТу 19222-84. В качестве основного материала для выработки выступают хвойные деревья. Раздробление древесины происходит с помощью рубильных машин, таких как РРМ-5, ДУ-2, а более скрупулезное дробление осуществляется на оборудовании ДМ-1.
Арболитовую смесь подготавливают со смесителями и растворителями различного цикличного воздействия на материал. Подвозят большие объемы обработанной смеси к формам с помощью приспособления в качестве бетонораздатчиков или кюбелей. Подъем или опускание машины должно осуществляться при параметрах 15о по верхнему подъему и 10о по нижнему, а скорость оборудования рассчитывается в 1 м/с. Разлив арболитовой смеси по формам делают на высоте до 1 метра.
Уплотнения раствора производят с содействием вибропреса или ручной трамбовки. Для производства небольшого количества блоков нужно применить мини-станок. Изготовление своими руками арболита не представляет особых трудностей, однако на промышленных объектах применяется специальное оборудование по смешиванию, изготовления блоков. На некоторых заводах присутствуют тепловые камеры с ИК-излучением или ТЭНом, что позволяет определить нужную температуру для высыхания блоков.
Блочные формы для арболита
Существуют разные блочные формы для обработки арболита, а примерные величины могут составлять: 20х20х50 см или 30х20х50 см. Выпускаются предметы и прочих размеров, особенно для постройки вентиляционных систем, покрытий и так далее. Формы можно приобрести в строительных магазинах или же подготовить все своими руками. Для этого, используют доски толщиной в 2 сантиметра, которые скрепляют до образования определенной конструкции. Внешне форма отделывается фанерой, или пленкой.
В зависимости от класса арболитовые блоки применяют в малоэтажном строительстве для возведения несущих стен, перегородок, а также для теплоизоляциии и звукоизоляции конструктивных элементов здания.
Процесс производства своими руками
Рассмотрев технологию изготовления состава арболита, можно приступать к выполнению работы самостоятельно. Для начала потребуются некоторые материалы и оборудование:
- специальный лоток для смеси;
- падающий и вибрирующий стол;
- стол с ударно-встряхивающим эффектом;
- разъемные формы и подставки;
- поддон из металла для форм.
Производить арболит своими руками очень сложно без использования необходимых инструментов, станков и оборудования. Как правило, на производстве потребуются некоторые приспособления:
1. Для получения качественного раствора необходимо применить бетономешалку. Разумеется, в процессе можно все сделать своими руками, однако придется, много времени потратить на получение раствора необходимой консистенции.
2. Для формирования структуры блоков важно приобрести формы соответствующих размеров. Как правило, арболит имеет прямоугольную форму, а в производстве используются пластиковые формы.
3. При помощи станка вы профессионально измельчите щепу.
4. Используя пресс можно получить хорошую плотность материала при трамбовке, при этом важно убрать воздух из консистенции. В качестве приспособлений применяется вибростол.
5. Обязательное наличие камеры для сушки арболита, что позволит его превратить в твердую однокомпонентную структуру.
6. В домашних условиях понадобится лопата для загрузки смеси в формы, а для скрепления блоков используют армирующую сетку.
При наличии выше перечисленных приспособлений можно производить в день около 350 – 450 м3 строительного раствора в месяц. Места для монтажа потребуется около 500 квадратных метров, а затрат на электроэнергию пойдет 15-45 кВт/ч. Для самостоятельного процесса органические средства заливаются водой, а также цементом до образования однородной смеси. Все пропорции и расчеты отображены в таблице 1, главное чтобы вышедшая смесь была сыпучей.
Перед заливкой раствора в формы, их обмазывают с внутренней стороны молочком известковым. После этого, средство скрупулезно и аккуратно укладывают и утрамбовывают специальными приспособлениями. Верхняя часть блока выравнивается с помощью шпателя или линейки и заливается раствором штукатурки на слой в 2 сантиметра.
После образованной формы арболита его потребуется тщательно уплотнить с помощью деревянной конструкции, оббитой железом. Прочными и надежными считаются блоки, которые выстоялись и схватились на протяжении десяти дней при температуре 15о. Чтобы арболит не пересох, рекомендуется периодически поливать его водой.
Технология изготовления арболита своими руками не представляет определенной сложности, а поэтому все работы провести легко при наличии необходимых инструментов и приспособлений. При соблюдении правил и критериев производства, правильного расчета компонентов строительный материал получится качественным и прочным для применения.
Советы экспертов при изготовлении блоков своими руками
Рекомендации специалистов по производству арболитных блоков основаны на практике их использования и применения. Чтобы достичь высокого качества продукции необходимо следовать некоторым факторам. В производстве рекомендуется применять не только большую щепу, но и использовать опилки, стружку из дерева. Обработка консистенции и выдавливание из него сахара позволяет избежать дальнейшего вспучивания строительного материала, что не приспускается при сооружении дома.
В процессе изготовления раствор следует тщательно перемешивать, чтобы все части оказались в цементе. Это важно для качественного и прочного скрепления древесины и иных материалов в блоке. В производстве не менее важным остается добавление следующих компонентов, таких как алюминий, гашеная известь и так далее. Весь состав образует дополнительные свойства арболита, например жидкое стекло не позволяет впитывать влагу блокам, а известь служит в качестве антисептика.
Хлористый калий способствует уничтожению микроорганизмов и других веществ, что не благотворно влияют на структуру. При добавлении всех компонентов стоит следить за таблицей пропорциональности, чтобы готовый раствор соответствовал требованиям производства арболитных блоков.
Изготовление арболита своими руками: технология производства и самостоятельные работы
Поэтапная технология изготовления арболита предвидит подготовку основания, определения компонентов и состава блочного материала. В данной статье рассмотрим особенности производства своими руками с применением необходимого оборудования, расчета массы и заливки.
Оглавление:
- Преимущества и недостатки арболита
- Технология производства арболита
- Подготовка основания для работы
- Компоненты и состав арболита
- Процесс и принципы изготовления
- Оборудование: применение на практике
- Блочные формы для арболита
- Процесс производства своими руками
- Советы экспертов при изготовлении блоков своими руками
Преимущества и недостатки арболита
Для многих строителей арболитные блоки являются ценным и качественным материалом для возведения домов. Главная особенность теплоизоляционных свойств позволяет из раствора производить напольные листы. Технология изготовления и принципы выдержки и сушки блоков предоставляют арболиту некоторые преимущества:
1. Прочность материала составляет 600-650 кг/м3, что по компонентной структуре не уступает иному строительному материалу. Главной особенностью является пластичность, что формируется в результате использования древесины, которая качественно армирует блоки. Таким образом, арболит не трескается под тяжестью иных материалов, а может только слегка деформироваться сохраняя общую систему конструкции.
2. Стойкость к низким температурам, что очень важно в процессе возведения дома и его эксплуатации. Дело в том, что если здание нагреется и замерзнет несколько раз, то это не повлияет на качество материала. Фактически дом из арболита может простоять минимум 50 лет в любые погодные условия. Конструкции из пеноблоков не имеют подобных свойств, ведь при постоянном замораживании они быстро потеряют свою функциональность.
3. Арболит не поддается воздействию углекислого газа, так что не стоит беспокоиться о карбонизации блоков, ведь их структура не позволит превратиться материалу в мел.
4. Теплопроводность блоков свидетельствует о популярности материала. Сравнивая показатели, стоит отметить, что стена из арболита в 30 см равняется 1 метру толщины кирпичной кладке. Структура материала позволяет сохранять тепло внутри помещения даже в самые холодные зимы, что весьма экономично при строительстве.
5. Звукоизоляционные свойства свидетельствуют о высоком коэффициенте поглощения арболита, который составляет от 0,7 до 0,6. Для сравнения древесина имеет показатели 0,06 -0,1, а кирпич немного больше около 0,04-0,06.
6. Легкость материала, что позволяет сэкономить средства на заливку фундамента.
7. Арболит является экологически чистым и долговечным строительным материалом, что определяет компонентный состав блоков. После возведения дома он не образует плесень и грибок на стенах.
8. Материал является безопасным, так он не воспламенятся.
9. Арболитные блоки легко применять в строительных работах, поскольку без труда в них можно забить гвозди, просверлить отверстие, использовать шурупы и так далее. Внешняя структура материала позволяет покрывать его штукатуркой без использования специальных сеток и дополнительных утеплителей.
Мы рассмотрели преимущества арболитных блоков, но для полного воссоздания картины о данном строительном материале приведем некоторые недостатки:
1. Стеновая панель может не выделяться точными геометрическими параметрами, от чего для восстановления ровности стены используют вагонку, сайдинг или гипсокартон, а сверху все отделяют штукатуркой.
2. Блоки не являются дешевым строительным материалом, ведь изготовление щепы для арболита требует некоторых затрат. Делая расчеты по сравнению из газобетоном, данный строительный материал обойдется только на 10-15 процентов дороже, что не формирует полное преимущество.
Технология производства арболита
Изготовление арболита требует следованию технологиям производства с расчетом состава и объема для одного блока. Арболитные блоки представляют собой строительный материал простой по компонентному составу, в который входят древесина, вода, опилки, цемент и другие предметы.
Главной основой для производства считается древесная щепа. Составная часть арболитового блока определяет его прочность и устойчивость к повреждениям, что высчитывается высшим уровнем, чем у пено- или газоблоков. Производство в домашних условиях осуществить не сложно, однако необходимо придерживаться распределения массы предмета и следовать инструкции.
Подготовка основания для работы
Основной составляющей для изготовления щепы для арболита является соотношение пропорций стружки и опилок – 1:2 или 1:1. Все предметы хорошо высушивают, для чего их помещают на 3 – 4 месяца на свежий воздух, время от времени обрабатывая известью и переворачивая.
Примерно на 1 кубический метр средства потребуется около 200 литров извести 15-ти процентной. В них помещают все щепы на четыре дня и перемешивают их от 2 до 4 раз на день. Все работы проводятся с целью убрать сахар с древесины, который может спровоцировать гниение блоков. Щепу приобретают в готовом виде, однако, с помощью щепорезов можно сделать самостоятельно.
Компоненты и состав арболита
Компонентный состав арболита является самым важным этапом технологии производства и требует внимательного соотношения всех материалов. При изготовлении блоков важно следить за качеством и разновидностью приобретаемых материалов, которые определяют готовый строительный материал. После процесса изготовления в щепу добавляют следующие материалы, такие как:
- известь гашеную;
- жидкое стекло растворимое;
- портландцемент;
- хлористый калий;
- алюминий и сернокислый кальций.
Производство арболита в пропорциях представлено в таблице 1. Стоит учесть, что для всех компонентов масса рассчитана на четыре процента доли цемента. Данная компоновка помогает сохранить огнеупорность предмета и придает пластичности.
Таблица 1. Состав арболита по объему
Марка арболита | Цемент (М400) | Кол-во извести | Кол-во песка | Кол-во опилок | Получаемая плотность (кг/м3) |
5 | 1 | 1,5 | — | 15 | 300-400 |
10 | 1 | 1 | 1,5 | 12 | 600-700 |
15 | 1 | 0,5 | 2,5 | 9 | 900-1000 |
25 | 1 | — | 3 | 6 | 1200-1300 |
Процесс и принципы изготовления
Оптимальные параметры блоков для технологии производства арболита составляют 25х25х50 сантиметров. Установленные размеры удобны при кладке стен домов, а также в процессе промышленности. Заливка блока состоит из трех рядов смеси и арболита, после каждого этапа необходимо уплотнять раствор молотком, отделанным жестью.
Излишняя масса свертывается при содействии шпателя. Выдерживается блок при температуре 18 градусов тепла на раскрытом воздухе. По истечении суток арболит выстукивается из формы на ровную поверхность, где он скрепляется на протяжении 10 дней.
Оборудование: применение на практике
Для производства необходимо разное снабжение, например, станки для изготовления арболита, которые выбираются в соответствии с объемом продукции и количества сырья. Технология промышленного процесса должна отвечать требованиям и критериям СН 549-82 и ГОСТу 19222-84. В качестве основного материала для выработки выступают хвойные деревья. Раздробление древесины происходит с помощью рубильных машин, таких как РРМ-5, ДУ-2, а более скрупулезное дробление осуществляется на оборудовании ДМ-1.
Арболитовую смесь подготавливают со смесителями и растворителями различного цикличного воздействия на материал. Подвозят большие объемы обработанной смеси к формам с помощью приспособления в качестве бетонораздатчиков или кюбелей. Подъем или опускание машины должно осуществляться при параметрах 15о по верхнему подъему и 10о по нижнему, а скорость оборудования рассчитывается в 1 м/с. Разлив арболитовой смеси по формам делают на высоте до 1 метра.
Уплотнения раствора производят с содействием вибропреса или ручной трамбовки. Для производства небольшого количества блоков нужно применить мини-станок. Изготовление своими руками арболита не представляет особых трудностей, однако на промышленных объектах применяется специальное оборудование по смешиванию, изготовления блоков. На некоторых заводах присутствуют тепловые камеры с ИК-излучением или ТЭНом, что позволяет определить нужную температуру для высыхания блоков.
Блочные формы для арболита
Существуют разные блочные формы для обработки арболита, а примерные величины могут составлять: 20х20х50 см или 30х20х50 см. Выпускаются предметы и прочих размеров, особенно для постройки вентиляционных систем, покрытий и так далее. Формы можно приобрести в строительных магазинах или же подготовить все своими руками. Для этого, используют доски толщиной в 2 сантиметра, которые скрепляют до образования определенной конструкции. Внешне форма отделывается фанерой, или пленкой.
В зависимости от класса арболитовые блоки применяют в малоэтажном строительстве для возведения несущих стен, перегородок, а также для теплоизоляциии и звукоизоляции конструктивных элементов здания.
Процесс производства своими руками
Рассмотрев технологию изготовления состава арболита, можно приступать к выполнению работы самостоятельно. Для начала потребуются некоторые материалы и оборудование:
- специальный лоток для смеси;
- падающий и вибрирующий стол;
- стол с ударно-встряхивающим эффектом;
- разъемные формы и подставки;
- поддон из металла для форм.
Производить арболит своими руками очень сложно без использования необходимых инструментов, станков и оборудования. Как правило, на производстве потребуются некоторые приспособления:
1. Для получения качественного раствора необходимо применить бетономешалку. Разумеется, в процессе можно все сделать своими руками, однако придется, много времени потратить на получение раствора необходимой консистенции.
2. Для формирования структуры блоков важно приобрести формы соответствующих размеров. Как правило, арболит имеет прямоугольную форму, а в производстве используются пластиковые формы.
3. При помощи станка вы профессионально измельчите щепу.
4. Используя пресс можно получить хорошую плотность материала при трамбовке, при этом важно убрать воздух из консистенции. В качестве приспособлений применяется вибростол.
5. Обязательное наличие камеры для сушки арболита, что позволит его превратить в твердую однокомпонентную структуру.
6. В домашних условиях понадобится лопата для загрузки смеси в формы, а для скрепления блоков используют армирующую сетку.
При наличии выше перечисленных приспособлений можно производить в день около 350 – 450 м3 строительного раствора в месяц. Места для монтажа потребуется около 500 квадратных метров, а затрат на электроэнергию пойдет 15-45 кВт/ч. Для самостоятельного процесса органические средства заливаются водой, а также цементом до образования однородной смеси. Все пропорции и расчеты отображены в таблице 1, главное чтобы вышедшая смесь была сыпучей.
Перед заливкой раствора в формы, их обмазывают с внутренней стороны молочком известковым. После этого, средство скрупулезно и аккуратно укладывают и утрамбовывают специальными приспособлениями. Верхняя часть блока выравнивается с помощью шпателя или линейки и заливается раствором штукатурки на слой в 2 сантиметра.
После образованной формы арболита его потребуется тщательно уплотнить с помощью деревянной конструкции, оббитой железом. Прочными и надежными считаются блоки, которые выстоялись и схватились на протяжении десяти дней при температуре 15о. Чтобы арболит не пересох, рекомендуется периодически поливать его водой.
Технология изготовления арболита своими руками не представляет определенной сложности, а поэтому все работы провести легко при наличии необходимых инструментов и приспособлений. При соблюдении правил и критериев производства, правильного расчета компонентов строительный материал получится качественным и прочным для применения.
Советы экспертов при изготовлении блоков своими руками
Рекомендации специалистов по производству арболитных блоков основаны на практике их использования и применения. Чтобы достичь высокого качества продукции необходимо следовать некоторым факторам. В производстве рекомендуется применять не только большую щепу, но и использовать опилки, стружку из дерева. Обработка консистенции и выдавливание из него сахара позволяет избежать дальнейшего вспучивания строительного материала, что не приспускается при сооружении дома.
В процессе изготовления раствор следует тщательно перемешивать, чтобы все части оказались в цементе. Это важно для качественного и прочного скрепления древесины и иных материалов в блоке. В производстве не менее важным остается добавление следующих компонентов, таких как алюминий, гашеная известь и так далее. Весь состав образует дополнительные свойства арболита, например жидкое стекло не позволяет впитывать влагу блокам, а известь служит в качестве антисептика.
Хлористый калий способствует уничтожению микроорганизмов и других веществ, что не благотворно влияют на структуру. При добавлении всех компонентов стоит следить за таблицей пропорциональности, чтобы готовый раствор соответствовал требованиям производства арболитных блоков.
Производство арболита своими руками: состав, пропорции, оборудование
Арболит (он же деревобетон) все чаще используется в малоэтажном строительстве. Во многом это связано с простотой производственной технологии и доступностью исходных компонентов. Именно о технологии, оборудовании и способах производства я расскажу в этой статье.
Производственное оборудование
Оборудование для производства арболита не отличается особой сложностью и габаритами. Его можно разместить на приусадебном или дачном участке, в любом боксе, цеху или просто на улице под навесом. Главное условие – наличие электроэнергии и удобство эксплуатации. Полный перечень заводского оборудования, необходимого для промышленного производства арбоблоков выглядит следующим образом:
- Шредер – измельчитель органических наполнителей (щепы, соломы и т.д.).
- Ёмкость для приготовления и розлива химических компонентов.
- Дозатор цемента.
- Дозатор органических наполнителей.
- Дозатор заполнителей для бетонного раствора.
- Бетоносмеситель для арболита принудительного типа действия.
- Подъёмно-поворотный бункер для приёма и дальнейшего розлива готового арболитового раствора.
- Система лебёдок для погрузочно-разгрузочных работ.
- Самозапечатываемые формы для отливки блоков.
- Вибропресс для арболита.
При кустарном производстве деревобетона, для собственных нужд, могут использоваться самодельные станки.
Состав арболита
Состав арболита регламентируется ГОСТ №19-222-84. Готовая к заливке арболитовая смесь состоит из следующих компонентов:
- Цементный раствор;
- Химические добавки;
- Органические наполнители.
Цемент
В качестве связующего компонента в производстве используется раствор на цементной основе. По ГОСТу, портландцемент для приготовления арболита должен иметь марку не ниже М-400.
Таблица . Технические характеристики цемента М-400
Добавлять песок в состав арболитного раствора не рекомендуется, так как это ухудшает показатели сцепки органических наполнителей с цементным вяжущим веществом. В результате блоки становятся менее прочными и склонными к расслоению и растрескиванию.
Химические добавки
Химические добавки предназначены для улучшения эксплуатационных характеристик арболита. В состав арболита входят следующие химические компоненты:
- Сернокислый алюминий, он же сульфат алюминия – неорганическая соль, хорошо растворимая в воде. При изготовлении арболита он используется в качестве гидроизолятора, увеличивающего стойкость материала к воздействию сырости.
Из-за высокой гигроскопичности, хранение сернокислого алюминия должно производиться в помещениях с низким уровнем влажности и в герметичной упаковке.
- Хлористый кальций – химический элемент, получаемый при промышленном производстве соды. Добавляется в арболитную смесь для связывания сахаров, содержащихся в органических заполнителях, что значительно повышает прочностные характеристики получаемого цементного раствора и позволяет повысить степень его сцепления с древесными компонентами.
- Жидкое стекло – водорастворённые силикаты натрия или калия.
При изготовлении смеси для деревобетона, жидкое стекло выполняет роль отвердителя, а также для придания цементному раствору кислотоупорных и гидроупорных свойств.
- Гашёная известь добавляется в раствор для нейтрализации содержащихся в органических добавках природных сахаров и улучшения связующих качеств цемента и древесины.
Органические заполнители
В качестве наполнителя при производстве арболита используются отходы деревообрабатывающего производства. Главное отличие арболита от других видов лёгких бетонов состоит в том, что в его состав входят достаточно крупные компоненты – древесная щепа, костра льна, конопляная солома и т.д. От процентного содержания органического наполнителя зависят основные показатели материала: плотность, гигроскопичность, коэффициент теплопроводности и т.д.
- Древесная щепа – наиболее часто используемый заполнитель. Согласно ГОСТу, её размер не должен превышать 4 х 1 х 0,5 см. В связи с этим, технические характеристики арболитовых конструкций отличаются от характеристик опилкобетона и фибролита (стружкобетона).
Древесная щепа – главная составляющая арболитового блока
Нужный размер органической фракции получают при помощи специального станка-щепореза (шредера). Содержание щепы в общем объёме арболита может быть разным, и составлять от 30% до 90%.
- Льняная костра добавляется в таком же виде, в каком она получается на льноперерабатывающем заводе после предварительной обработки сырья.
- Конопляную солому перед использованием следует перемолоть в шредере.
Согласно техническим нормативам, льняные и конопляные наполнители должны иметь следующие размеры:
- Длина – от 15 до 25 мм.
- Ширина – от 2 до 5 мм.
В разных регионах для производства арболитовых блоков и панелей могут применяться и другие органические заполнители: рисовая и гречневая солома, отходы обработки хлопчатника и т.п.
В таблице даны технические характеристики арболита, изготовленных с применением разных органических наполнителей:
Технология производства
Технология производства арболита имеет ряд отличительных особенностей, которые касаются подготовки сырья, рецепта приготовления, дозировки компонентов. Её соблюдение обязательно как при промышленном выпуске, так и при производстве арболита своими руками в домашних условиях.
Подготовка органических заполнителей
Для деревобетона может использоваться щепа древесины хвойных пород – ели, сосны, пихты, а также лиственных деревьев с твёрдой древесиной – дуба, ясеня, берёзы.
Не рекомендуется применять в производстве щепу лиственницы и бука из-за химического состава – их древесина содержит значительно больше сахаров, что приводит к значительному снижению качества блоков. В крайнем случае, при производстве раствора с лиственничной или буковой щепой, придётся, как минимум, вдвое увеличить количество химдобавок – извести или хлористого кальция.
Щепа березы и ясеня – лучший наполнитель для арболитового блока
Первым шагом древесные отходы измельчаются посредством щепореза до размеров, регламентируемых ГОСТ №19-222-84 – не более 40х10х50 мм. Фактически же оптимальными размерами древесной фракции для формовки блоков являются 25х5х3 мм, так как более крупные компоненты хуже связываются цементным раствором и более склонны к расслаиванию в процессе эксплуатации.
После измельчения щепа просушивается. На крупных производственных линиях для этих целей применяют специальные сушилки барабанного типа, в которые подаётся горячий воздух.
Если арболит производится в домашних условиях, щепу складируют для просушки под навесами на срок не менее месяца, при температуре воздуха +15С.
Непосредственно перед замешиванием щепа замачивается на 6-8 ч в растворе воды с химическими добавками. Вода для этого должна соответствовать ГОСТу №23-732-79, где регламентируется её химический состав, кислотность и т.д. На деле же, при кустарном производстве деревобетона применяется любая доступная вода – из водопровода, реки или колодца. Единственное необходимое условие – она должна быть чистой и иметь температуру не ниже +15…+20С. После замачивания древесный наполнитель должен иметь влажность не более 30%.
Костра льна и солома конопли, для удаления из неё излишков сахаров, выдерживается на открытом воздухе не менее 2 – 3 месяцев при плюсовой температуре, либо замачивается в известковом молоке на 3-4 дня. Известковый раствор приготавливается в следующих пропорциях на 1 куб. м органики.
Органический заполнитель | Гашёная известь | Вода | Дополнительные условия |
1 куб. м костры льна или конопли | 2 – 2,5 кг | 150 – 200 л в зависимости от влажности наполнителя | Смесь перемешивается каждые 2 дня |
Пропорции смеси
Пропорции замеса могут незначительно изменяться, в зависимости от класса прочности деревобетона. Для получения более высокой марки арболита увеличивают долю цемента в общем объёме раствора. Ниже представлены рекомендуемые пропорции замеса раствора для деревобетона различных марок на куб готового раствора:
Марка | Портландцемент М-400 | Органический наполнитель | Химдобавки | Вода |
М-5 | 200 – 220 кг | 280 – 320 кг | 12-14 кг | 350 – 400 л |
М-15 | 250 – 280 кг | 240 – 300 кг | 12 кг | 350 – 400 л |
М-25 | 300 – 330 кг | 240 – 300 кг | 12 кг | 350 – 400 л |
М-50 | 350 – 400 кг | 220 – 240 кг | 10-12 кг | 350 – 400 л |
Химические добавки могут добавляться как по отдельности, так и комплексно. К примеру, строительные нормативы СН №54982 допускают смешивание сернокислого алюминия с известью в пропорции 8 кг и 4 кг на куб раствора.
Очерёдность загрузки
При замесе раствора важно соблюдать не только пропорции, но и очерёдность загрузки компонентов. Для изготовления качественной арболитной смеси обычные бетоносмесители, используемые для замеса бетона, не подойдут – щепа в них не сможет хорошо перемешаться с цементным раствором. Бетономешалка для арболита должна быть принудительного типа, например отечественные модели серии СБ, РН, импортные ZZBO и т.д. В них перемешивание компонентов производится не вращением барабана, а расположенным внутри него шнеком или лопастью.
Таблица 3. Технические характеристики принудительных смесителей серии СБ:
- Первым шагом в барабан смесителя насыпается подготовленная щепа в нужной пропорции.
- Затем бетоносмеситель запускается и в него заливается вода с растворёнными в ней химическими добавками. Органический заполнитель размешивается с химраствором в течение 30-60 секунд, чтобы щепки хорошо пропитались.
- После этого добавляется цемент и продолжается размешивание смеси в течение 3-5 минут, до получения однородной массы.
Формирование блоков
Формовка арбоблоков происходит с помощью специальных матриц, в которые заливается готовый раствор. Они изготавливаются из нержавеющей стали разборной конструкции для более лёгкого извлечения блоков.
Также такие формы можно изготовить самому из дерева или фанеры, обив их изнутри линолеумом или жестью. Размеры ячеек матрицы могут быть различными, в зависимости от потребностей в блоках тех или иных габаритов.
Трамбовка производится вручную, либо для этого используется вибростанок. В первом случае раствор заливается в формы слоями толщиной в 5 см, каждый из которых уплотняется металлической трамбовкой.
Во втором случае уплотнение раствора производится на вибростоле, которым обычно оборудуется промышленный станок для производства арболита.
Также при формовке для уплотнения раствора можно использовать ручной или механический пресс. Чтобы из уплотняемых блоков лучше выходил воздух, они периодически прокалывается металлическим стержнем.
Сушка
Сушка готовой продукции является завершающим этапом производственного процесса. В связи с особенностью конструкции, наилучшим вариантом является мягкий режим просушки.
Пропаривать арбоблоки по примеру железобетонных конструкций, не рекомендуется, так как материал теряет прочность из-за возрастающих внутренних напряжений. По этой же причине не следует пытаться ускорить высыхание блоков при помощи сушильных камер и других приспособлений.
Оптимальный режим просушки для арболита – температура 40-50 градусов, при влажности воздуха порядка 70-80%. В этом случае блоки набирают необходимую для распалубки прочность уже спустя 18-20 ч. что составляет около 1/3 от окончательной марочной. Дальнейшая выдержка материала производится при температуре 15-20 С в течение одной-двух недель – за это время деревобетон набирает окончательную прочность.
Арболитовые блоки своими руками. Как изготовить арболитовые блоки в домашних условиях
Арболитовые блоки – легкий строительный материал для стен малоэтажных зданий. Производится из древесной щепы, опилок, воды, химических реагентов и цемента.
Промышленные арбалитовые блоки имеют форму параллелепипедов правильной конфигурации. Изготовляются путем прессовки смеси щепы и раствора с помощью специального оборудования. Данный вид строительных материалов также известен под названием древобетон. Стройматериал данного типа легко изготавливается в домашних условиях при наличии необходимых ингредиентов, оборудования и выполнения технологических требований.
Сфера применения и классификация арболитовых кирпичей
Арболитовые изделия относятся к группе легких бетонов. Сфера их применения определяется характеристикой плотности данного стройматериала:
- Для теплоизоляцонной защиты помещений.
- Для стен, не испытывающих конструктивную нагрузку.
- Для возведения подсобных зданий, хозяйственных пристроек.
Арболит классифицируют по показателю плотности сухого материала:
- На теплоизоляционный – с показателем плотности менее 500 кг/м3.
- На конструкционный – с показателем плотности 500- 800 кг/м3.
По используемой для наполнения смесей основе, выделяют арболит из древесной щепы, соломы из риса, конопляного мочала, отработанного хлопчатника, льняного волокна.
Арболитовые блоки, технические характеристики
Технические показатели выполненных по ГОСТу арболитовых блоков и их зависимость от других факторов:
- Твердость – 0,35-3,5 MПa. Данная характеристика зависит от состава смеси, марки цемента, качества нейтрализации сахара. Является определяющей для создания блока заданной плотности и прочности.
- Плотность – среднее значение 400-850 кг/м3. Изготовление арболитовых блоков предполагает, что данная характеристика регулируется изменением пропорций цемента и органического наполнителя. Чем выше показатель средней плотности, тем прочнее изделие.
- Теплопроводность – 0,07-0,17 Вт/(моС). Чем больше доля связующих материалов, использованных при изготовлении смеси, тем выше этот показатель. Низкий показатель теплопроводности означает наличие у изделия свойств высокой теплоизоляции, и указывает на низкую прочность блоков.
- Морозоустойчивость – 25-50 циклов. Данная характеристика определяет предельно допустимое показание сезонной последовательной заморозки и оттаивания, которые выдерживает стройматериал, не подвергаясь полному разрушению. Обработка стен штукатуркой или другими защитными материалами увеличивает показатель.
- Усадка – 4-5 мм/м или 0,4-0,5%. Показатель находится в прямой зависимости от средней плотности материала – чем меньше плотность, тем выше усадка.
- Водопоглощение – 45-80%. В сравнении с популярным стройматериалом – пеноблоком, этот показатель выше, то есть, свойство водоотталкивания у арболита ниже в 3-4 раза. Арболитовые блоки нуждаются в дополнительных защитных мерах и обработке водоизолирующими препаратами.
- Паропроницаемость – 0,19 мг/(м ч Па). Высокое значение показателя, аналогичное паропроницаемости натуральной древесины.
- Звукопроницаемость – 126-2000 Гц. Высокое значение показателя, арболитовые блоки практически не нуждаются в принудительной звукоизоляции.
- Максимальная этажность здания из арболитовых блоков составляет 2-3 этажа при соответствующем весе перекрытий.
- Стоимость данного материала составляет около 90 EUR за 1 м3.
Арболитовые блоки, строительство: преимущества и недостатки
Арболитовые блоки являются уникальным материалом, оптимально сочетающим в себе большой спектр положительных, полезных характеристик при небольшом количестве недостатков. Преимущества этого строительного материала заключаются в следующем:
- Высокое сопротивление изгибающим нагрузкам, благодаря используемым при изготовлении наполнителям. Главное качество стройматериала – защита поверхностей от растрескивания при колебаниях и усадке.
- Высокие аэробные и анаэробные свойства. Материал не подвержен гниению, не создает условий для развития в объеме грибка и плесени.
- Процесс изготовления арболитовых блоков является экологически чистым. В составе не используются канцерогенные органические ингредиенты. Готовый кирпич в течение срока эксплуатации не выделяет вредные вещества, не пылит, не вызывает аллергические реакции.
- Пожаробезопасный материал, не поддерживает горение, имеет высокую сопротивляемость к воздействию высоких температур.
- Устойчив к механическим воздействиям, ударной силе, истиранию.
- Высокая вариативность. Арболитовые блоки, размеры и форма которых определяются исключительно фантазией, позволяют выполнить производство строительного кирпича по индивидуальным параметрам и заданным габаритам для эксклюзивного строения.
- Материал хорошо обрабатывается и надежно удерживает крепежные элементы.
- Блоки из арболита имеют низкий удельный вес. Возможность строить здания с легким фундаментом. Для декорирования внутренних и внешних поверхностей из арболита подходят любые виды отделочных материалов.
- Пластичность блока сохраняется даже после его полного высыхания. Амортизируя дополнительные нагрузки, блок сжимается до 10% без ущерба для своей внутренней структуры.
- Низкая теплопроводность материала позволяет экономить на обогреве здания.
Недостаток у арболитовых блоков имеется только один – высокий уровень поглощения воды. Единственный недостаток легко убирается при помощи нанесения специального защитного покрытия.
Оборудование для производства арболитовых блоков
Технология изготовления арболитовых блоков требует организации небольшого завода со специфическими приспособлениями. Производство арболитовых блоков, оборудование первостепенной важности:
- Уловитель для щепок.
- Емкость для смеси.
- Вибросито.
- Падающий стол.
- Стол ударно-встряхивающий.
- Вставки в форму.
- Разъемная форма.
- Металлический поддон формы.
- Установка виброформирования.
В домашних условиях арболит готовят из специфической смеси. Необходимый размер получают в специальных самодельных опоках. Форму изготавливают из обычных деревянных ящиков, оббитых изнутри линолеумом. Закладку арболита в форму производят послойно, в 2-3 захода, каждый слой тщательно утрамбовывают. Последний слой не разглаживают, а оставляют неровным, расстояние до края бортов выдерживают около 2 см, оно заполняется штукатурным раствором. Рекомендованное время выдерживания блока в форме — не менее 24 часов.
Для массового изготовления используют станок для арболитовых блоков. Производительность такого оборудования достигает 50 блоков в час, стоимость от 120 EUR.
Технология производства арболитовых блоков и необходимые материалы
Состав арболита содержит цемент М400/М500. Для придания изделиям высокой прочности возможно применение другой марки. Наполнителем для бетона служат мелкие древесные стружки, однородная щепа, опилки. Дефицит любого из перечисленных ингредиентов наполнения заменяется подручными материалами: хвоей, листвой, корой. Выдерживается обязательная процентная пропорция добавляемого заменителя, она не должна превышать 5 % от общей массы основного наполняющего материала.
Отслеживается фракционный размер наполнителей. Ограничение по толщине до 5 мм, по длине не более 25 мм. Органику предварительно пропускают через дробемолку, измельчают до установленного размера. Подготовленную смесь смешивают с цементным раствором.
В заводских условиях к органике и отходам органического происхождения обязательно добавляют нейтрализаторы органических сахаров. Мера необходимая для связывания и выведения сахара, пагубно влияющего на прочность готового арболита. Распространенный ингибитор – сульфат алюминия и хлорид кальция.
Производство арболита в домашних условиях исключает применение химических реактивов по причине их дефицита в свободной продаже. Без реакции расщепления сахаров приготовленная смесь начинает «бродить», газы вспучивают поверхность, образуя пустоты и дефекты в объеме.
Возможность исключить негативный процесс существует. Отходы из древесины просушиваются в проветриваемом помещении или на открытом пространстве 3,5-4 месяца. Под воздействие тепла и конвекции происходит естественное высушивание и испарение растворенных в воде веществ, включая сахарозы и их производные. В сухом дереве остаются только волокна с низким, допустимым содержанием целлюлозы.
Процесс замеса раствора:
- Древесная масса, органический наполнитель загружаются в дробилку, измельчаются до приемлемой консистенции.
- Для полной нейтрализации сахара, мелкую древесную массу перемешивают с сухим цементом и погружают в 5%-10% раствор извести. Выдерживают до 3-х часов.
- Откидывают массу на грохот. Дают стечь жидкости.
- К вязкой массе вливают по необходимости воду, перемешивают до однородности, чтобы получилась пастообразная густая кашица.
- Делают смесь с учетом пропорций основных материалов: на 4 части воды, 3 части цемента, 3 части наполнителя.
- Готовую смесь центрифугируют в бетономешалке до полного разбивания комков и сгустков.
- Проверяют массу на готовность. Качественная смесь рассыпчатая. При сжатии в руке сохраняет форму, не расплывается и не деформируется.
- Смесь загружается в формовки до застывания.
- Вынимаются готовые арболитовые блоки.
Строительство из доступного материала ведется по мере поступления самодельного заменителя кирпича. Правильно организованный и отлаженный процесс позволяет получать при ручном замесе до 100 штук в день.
Полезная информация о процессе изготовления арболитовых блоков
- Раствор из древесины и бетона перемешивают в бетономесителе, для качественного разбивания комков.
- Если готовая масса получилась вязкой, а не рассыпчатой, ее подсушивают естественным способом, добавляют четверть нормы цемента и четверть нормы наполнителя.
- Когда опилки и стружка выдерживаются на открытом воздухе, их необходимо время от времени перемешивать с помощью лопаты. Если сделать это невозможно, массу обрабатывают окисью кальция. На 1 м3 сырья в данном случае необходимо 200 л 1,5% раствора. Обработанную раствором стружку и опилки оставляют на 96 часов, перемешивая каждые 6-8 часов.
- Чтобы ускорить процесс затвердевания смеси, в нее добавляют сухой хлористый кальций.
Как изготовить самостоятельно арболитовые блоки, видео сюжет расскажет подробно и доходчиво.
Технология изготовления арболита. Арболит: технология производства, состав
Производство строительных материалов на сегодняшний день — довольно прибыльная отрасль. Обусловлено это высоким спросом на все, что связано с возведением зданий. Все застройщики стараются применять и проверенные материалы и внедрять новые технологии, которые будут менее затратными в себестоимости и более практичными в применении.
Несмотря на огромный ассортимент строительных блоков, огромной популярностью стал пользоваться и арболит. Технология производства его зависит от того, в каких условиях он изготавливается. Сам материал обладает отличными эксплуатационными свойствами и характеристиками.
Что такое арболит?
Это строительный материал, который выпускается в виде блоков. Они имеют определенные размеры и состав. Благодаря тому, что в его производстве используется натуральное сырье, он обладает отличными техническими характеристиками.
Способы производства арболитовых блоков
Технология изготовления арболита может быть применена:
- в заводском производстве;
- при домашнем изготовлении.
Сырье для производства арболита
Технология изготовления арболита характеризуется применением определенных материалов:
- бетон марки 400 или 500;
- химическая добавка;
- органический заполнитель.
Есть некоторые рекомендации по выбору сырья. Например, бетон нужно покупать тот, который изготавливается на основе вяжущего вещества. Также можно применять бетон более высокой прочности. В качестве химической добавки используют жидкое стекло, хлорид или нитрат кальция. Органические наполнители: древесная стружка, дробленые стебли хлопчатника, дробленая рисовая соломка и многое другое.
Арболит, технология производства которого отличается применением определенных средств, может иметь различный удельный вес. Например, блоки, имеющие плотность менее 500 кг/м3 относят к группе теплоизоляционного арболита. А те, которые имеют плотность более 500 кг/м3, принадлежат уже к группе конструкционных блоков.
Соответственно, первый вариант арболита наиболее часто используется для сооружения межкомнатных перегородок, а вот из второго выстраиваются несущие арболитовые конструкции.
Стадии изготовления материала
Технология изготовления арболита состоит из нескольких этапов:
- подготовка определенного количества органического заполнителя;
- работа по замачиванию древесной щепы в растворе хлорида кальция;
- дозирование определенных составляющих арболита;
- непосредственно изготовление блоков.
Подготовка органического заполнителя
Любое производство строительных материалов характеризуется предварительной подготовкой всего необходимого сырья. Древесина в брусках измельчается и формируется в определенные кучки. Их надо положить под навес и выдержать при оптимальной наружной температуре +15…+25 градусов около 1 месяца. После этого древесина измельчается в специальном оборудовании на щепку.
Только к такому действию нужно подходить ответственно. Щепа имеет свою определенную фракцию. Именно от нее зависит качество арболитовой смеси. Щепка размером в 10-20 мм характеризует фракционный состав в 70%, 5-10 мм уже относят к 30% фракции.
Замачивание древесины и приготовления раствора хлорида кальция
Полученную в ходе дробления щепку необходимо замочить в воде. Температура жидкости при этом должна быть не менее +20 градусов. Весь процесс замачивания длится до 6 часов. Все эти действия помогают увеличить прочность арболитовых блоков. Необходимо постоянно следить за наполняемостью древесины водой. Влажность полученного сырья должна быть не более 30%.
По истечении этого времени в бак с жидкостью выливается заранее приготовленный раствор хлорида кальция. В эту же емкость отправляется и пенообразователь.
Дозирование составляющих будущего строительного материала
Важный этап, которым обладает технология изготовления арболита, является правильное дозирование всех компонентов. Именно от этого зависит качество арболитовых блоков и его показатель прочности. Дозировка дробленой замоченной щепки должна учитывать влажность сырья. Все ингредиенты взвешиваются и дозируются согласно определенным установленным параметрам (ГОСТ). Можно использовать для этого процесса специальное оборудование. Нужно учитывать, что оно достаточно дорого, и в условиях некоммерческого производства покупать его нецелесообразно.
Процесс изготовления блоков
Необходимо подготовить специализированное оборудование для арболита. К нему на этапе смешивания ингредиентов относят бетономешалки и другие приспособления, которые могут качественно перемешивать смеси высокой плотности и доводить их до определенной консистенции.
Большую роль играет очередность закладки составляющих. Изначально засыпается подготовленная древесная щепка. Затем – цемент. После этого заливается вода и химические наполнители. Они могут меняться местами в производстве. Кому как будет удобно. Только подачу всех жидкостей стоит пропускать через специальный расходомер.
Далее происходит смешивание сырья. Мешать нужно до тех пор, пока смесь не станет однородной.
Необходимо заранее изготовить формы для блоков. Как правило, они деревянные, а размеры могут быть любыми. Внутри нее по всему периметру выкладывается линолеум. Он даст возможность после застывания смеси свободно вытащить блок из формы. Также его поверхность промазывается специальным средством.
Довольно часто в домашних условиях изготовления арболитовых блоков применяется вибростол. Он позволяет равномерно распределить смесь. После этого залитые составом формы выставляются под навес и находятся там до полного застывания. В некоторых случаях применяют определенные добавки, которые помогают сократить время отвердения цементного состава.
Строительство из арболита, который сделан в домашних условиях, может проводиться только по истечении определенного срока, обычно через 14-20 дней. За это время блоки полностью отвердеют, высохнут и будут готовы к кладке.
Особенности технологии производства арболитовых блоков, панелей и конструкций
Само название арболит раскрывает состав и технологию изготовления этого современного строительного материала. В переводе с греческого языка «арбо» означает дерево, «литое» — камень. Основой для изготовления блоков являются древесный заполнитель и цемент, обеспечивающие в сочетании с химической добавкой и водой особую прочность всей конструкции. Примерный расход компонентов на кубический метр арболита показан в таблице № 1.
Табл. 1. Средний расход компонентов в килограммах на 1 кубический метр арболита
Компоненты | Марка | ||||
5 | 10 | 15 | 25 | 35 | |
Портландцемент марки 400 | 260/290 | 280/310 | 300/330 | 330/360 | 360/390 |
Древесная дробленка (сухая) | 160/180 | 180/200 | 200/220 | 220/240 | 240/250 |
Сульфат алюминия | 6 | 6-7 | 7 | 8 | 8 |
Вода | 280/330 | 300/360 | 330/390 | 360/430 | 400/460 |
Расход составляющих каждой марки при использовании хвойной древесины размещен до косой линии, лиственной и смешанной – после. В качестве химической добавки могут быть использованы и другие компоненты: растворимое стекло, гашеная известь, хлористый кальций. Составляющие и схема производства могут варьироваться в зависимости от назначения и особенностей эксплуатации готового изделия.
Производство арболитовых блоков: станки, оборудование
Технологии изготовления арболита своими руками и промышленным методом не должны иметь особых различий в наличии и последовательности следующих технологических процессов для подготовки сырья:
- производство щепы – если производство щепы осуществляется на месте, то для этой операции необходимым оборудованием является щепорез, для изготовления арболита выбирают агрегат производительностью, сопоставимой объёмам производства готовой продукции. Для производства арболитовых блоков наилучше подходит древесина хвойных видов деревьев;
- просушка материала – для качественной просушки, древесный материл выдерживают на открытом воздухе в течение трёх месяцев.
Временами материал переворачивают для лучшей просушки нижних слоёв;
- придание древесине биологической стойкости – делают это для препятствия её гниению уже будучи в составе арболитовых блоков. Для этого удаляют из щепы сахар и минерализируют её при помощи обработки в растворе гашеной извести, хлористого кальция, сернокислых алюминия или кальция, жидкого стекла. Раствор может быть как однокомпонентным, так и комбинированным. Щепу выдерживают в растворе в течение четырёх суток, перемешивая по три раза на день. Объёмное соотношение в смеси должно составлять пять частей щепы и одна раствора.
Необходимое оборудование для производства арболитовых блоков
От предполагаемой производительности будет зависеть, какое оборудование необходимо применять и, соответственно, его цена. Стоит понимать, что чем более высока технологичность всего процесса, тем менее выраженными будут недостатки арболита.
В любом случае Вам понадобится:
- растворосмеситель, лучше принудительного действия;
- станок для вибрационной трамбовки либо ручной инструмент для трамбовки;
- формы для блоков с подставками к ним.
Перечисленный набор – это самый минимум, и он больше подходит для домашней мини-фабрики. Если же продукцию планируется выпускать в промышленных масштабах, то необходима целая производственная линия, где уже не обойтись без вибрационных столов, дорогостоящих смесительных, транспортировочных, сушильных и прочих установок и станков.
Совет прораба: при изготовлении арболитовых блоков своими руками можно прибегать ко всяческим хитростям для снижения цены оснащения. К примеру, можно собственноручно изготовить формы для заливки при помощи досок, которые сколачиваются вместе. Затем они оббиваются из внутренней стороны фанерой и покрываются слоем гидроизолирующего материала, будь то полиэтиленовая плёнка, линолеум или что-то другое, что не пропускает воду. Если вы решили провести собственноручное изготовление форм для арболитовых блоков, то стоит знать, что считаются стандартными их размеры — 20-30*20*50 сантиметров, но, конечно же, они могут иметь и другой размер, на Ваше усмотрение.
Также можно приспособить какой-либо вибрирующий инструмент для виброусадки смеси, помещённой в формы.
Фото: вибростанок
Форма для арболитового блока
Изготовление арболитовых блоков
Для начала необходимо приготовить смесь для производства арболитовых блоков, которая должна состоять из трёх частей древесной составляющей, четырёх частей воды и трёх – цемента. В имеющееся у Вас смесительное оборудование ингредиенты загружаются в очерёдности, соответствующей изложенной выше. В норме образовавшаяся смесь должна выглядеть рассыпчатой, но в то же время сохранять форму, приобретённую сжатием в руке.
Далее, полученный арболит помещают в форму для формирования блока. Излишки удаляют шпателем либо мастерком, форму накрывают крышкой и в течение пяти-десяти секунд подвергают вибротрамбовке. Лучше, когда операция проводится при помощи специального вибрационного станка, но можно обойтись ручной трамбовкой либо же модернизированным Вами виброинструментом.
Следующий этап производства – это сушка арболита. Для сушки с блока снимают форму, при этом он остаётся на подставке формы, на ней он и остаётся до полного затвердевания и высыхания. Также для повышения прочности изделий можно их заворачивать в плёнку на срок до десяти дней, для более медленной влагопотери.
Подводя итоги, можно сказать, что производство арболитовых блоков вполне возможно в домашних условиях, даже без использования дорогостоящих вибрационных станков и другого подобного оборудования, что значительно снижает цену на налаживание производства. С другой стороны, есть чёткая зависимость между ценой оборудования и качеством готовой продукции, снижение одного показателя неминуемо тянет за собой вниз второй, даже при соблюдении тончайших аспектов технологии.
Видео
Конопля: следующий прорыв в строительстве после дерева?
любезно предоставлено коноплей Заменитель древесины от HempWood Бетон, сталь и дерево сегодня составляют триумвират конструкционных строительных материалов. Большинство зданий содержат все три в той или иной степени и используют один из них в качестве преобладающей среды каркаса. Архитекторы и инженеры так часто отказываются от этих материалов, что рынок кажется непроницаемым для альтернатив. И тем не менее, четвертый вариант может появиться — и стать следующей прорывной технологией в строительстве после массивной древесины.
Популярность пеньки как строительного материала растет. Эта непсихоактивная форма растения каннабис годами использовалась для изготовления веревок, изоляции, биопластика и других промышленных материалов благодаря своей прочности и быстрому росту. До недавнего времени конопля оставалась второстепенным продуктом, наиболее известным из которых является Hempcrete, в строительной отрасли. Тем не менее, он становится все более жизнеспособным вариантом для более распространенных строительных элементов из-за изменений, связанных с его сходством с деревом и различиями с ним.
В настоящее время широко известно, что способность древесины поглощать углерод и связанный с ней благоприятный углеродный след по сравнению с бетоном и сталью способствовали расширению ее использования в строительстве зданий. Однако возрождение интереса к инженерным пиломатериалам вызвало новые опасения по поводу чрезмерной вырубки леса и вырубки лесов.
После того, как в 2018 году в Закон о фермерских хозяйствах США были внесены поправки, легализующие сельскохозяйственную коноплю, предприниматели и производители продукции обратили на это внимание. Как и древесина, конопля накапливает углерод.Тем не менее, быстрый рост конопли делает ее превосходным сырьем для улавливания углерода. Коноплю можно выращивать за 90–120 дней, что в 100 раз быстрее, чем дуб. Кроме того, растение улавливает в четыре раза больше углерода, чем лес такого же размера. Конопля поглощает более 20 метрических тонн [PDF] углерода на гектар, а ее способность собирать два раза в год эффективно удваивает это количество. По данным GoodEarth Resources, австралийской консалтинговой компании в области экоэнергетики, «научно доказано, что промышленная конопля поглощает больше CO 2 на гектар, чем любая лесная или коммерческая культура, и поэтому является идеальным поглотителем углерода.
Во многих строительных продуктах из конопли используются волокна растения несколько предсказуемым образом, например, для ткачества текстиля или армирования цементных материалов. Однако в настоящее время производители создают альтернативы древесине с «реверс-инжинирингом» в виде прессованных конопляных досок и блоков. В Мюррее, штат Кентукки, Fibonacci производит пиломатериалы, напольные покрытия, шкафы, рамы и мебель из растений конопли, собранных в радиусе 100 миль для своего продукта HempWood.Компания подвергает растительные волокна воздействию высоких температур, а затем прессует их в формах с помощью клея на основе сои или столярного клея. Цель Фибоначчи состояла в том, чтобы воссоздать стабильность, твердость и плотность дуба в пригодном для обработки материале, похожем на твердую древесину. По словам производителя, конопляное дерево можно резать, шлифовать и обрабатывать так же, как дуб, и оно почти в два раза прочнее. «Вся идея состоит в том, чтобы взять что-то слабое и быстро растущее и превратить его в замену чему-то сильному, но растущему медленно», — сказал основатель HempWood Грег Уилсон в интервью HempBuildMag .
Дарем, Северная Каролина Стартап Plantd преследует аналогичные цели. Соучредители Джош Дорфман и Хуаде Тан запустили компанию после поиска подходящей альтернативы деревьям из биомассы. Они признали, что значительная прочность конопли и углеродные характеристики делают ее оптимальным сырьем для жилых зданий. При финансовой поддержке гранта North Carolina Idea Seed производитель создает прототип OSB на основе конопли. Создавая свои собственные производственные процессы — более гибкие, а также более мобильные и экономически доступные, чем оборудование для лесопильных заводов, — Дорфман и Тан утверждают, что суррогатный материал также будет дешевле.По словам Дорфмана, строительство нового завода OSB может стоить 400 миллионов долларов, в то время как новый завод Plantd стоит 1 миллион долларов. «Наш подход устраняет необходимость в восьмиэтажном прессе весом в 4 миллиона фунтов, на который опирается вся отрасль», — говорит Дорфман. «Вместо этого мы строим микрофабрики, расположенные рядом или на рынках, где строится большинство домов». В отличие от деревьев, конопля является жизнеспособной культурой на большей части территории США, что позволяет локализовать сельское хозяйство и производство, чего не может достичь деревообрабатывающая промышленность.Кроме того, коноплю можно сушить на том же поле, с которого ее собирают, и не требуется энергоемкий промышленный процесс сушки сырой древесины.
Дорфман и Тан наблюдают за призом Илона Маска XPrize на 100 миллионов долларов за удаление углерода, четырехлетним соревнованием, целью которого является удаление 1 гигатонны атмосферного CO2 ежегодно. На первом этапе конкурса требуется демонстрация секвестрации 1000 тонн CO2 в год до 2025 года, что, по утверждению Дорфмана, может быть достигнуто с чуть менее чем 100 домами из конопляных OSB. «Наша цель — достичь гигатонных масштабов улавливания CO2, что требует производства материалов в масштабах деревообрабатывающей, сталелитейной и бетонной промышленности», — говорит он.
По иронии судьбы, преимущества современных пиломатериалов обеспечивают преимущество перед новообретенным конкурентом. Вновь обретенная популярность дерева обусловлена его выгодным углеродным следом, возобновляемым ростом и достижениями в обработке, но конопля имеет еще более высокие оценки в этих областях. Кроме того, возможность для фермеров участвовать в развивающейся распределенной экономике является плюсом.
Тем не менее, строительные материалы из конопли в ближайшем будущем могут оставаться ограниченными для более коротких пролетов и внутреннего применения. Например, пиломатериалы HempWood в настоящее время ограничены длиной 6 футов и используются внутри помещений. Обработка аналогична обработке клееного бруса, который был разработан для использования более мелких и разнообразных пород деревьев, а также в значительной степени не подходит для наружных работ.
Однако со временем конопля начнет конкурировать с бетоном, сталью и деревом, особенно в сфере жилищного строительства.Это преобразование только ускорилось из-за недавней нехватки пиломатериалов, что привело к росту цен. После запуска своих конструкционных панелей Plantd планирует представить элементы конструкционного каркаса, начиная с клееных стружечных пиломатериалов для применения в каркасных конструкциях. Компания также будет производить конопляные двутавровые балки из компонентов OSB и LSL. «На рынке жилья наша цель — в конечном итоге предложить строителям полный пакет каркасных конструкций», — говорит Дорфман. «Мы работаем над тем, чтобы представить все эти продукты на рынке как можно быстрее.Наша производственная технология позволяет нам производить все эти продукты на нескольких производственных линиях на одном заводе, впервые в отрасли».
Строительные материалы на основе конопли демонстрируют значительные потенциальные структурные, экономические и углеродные преимущества и могут представлять собой революционную технологию в строительстве. Остается еще много проблем, и такая трансформация потребует времени. Теоретически, если из конопли вместо бетона, стали или дерева будет построено достаточно новых зданий, строительная отрасль может резко перейти к нулевому выбросу углерода.«В этот момент, — говорит Дорфман, — строительная отрасль потенциально может улавливать даже больше углерода, чем выделяет».
Взгляды и выводы этого автора не обязательно совпадают с мнениями журнала ARCHITECT или Американского института архитекторов.
Бетонные дома
Бетонные дома: прочные, универсальные и долговечные
Бетонные дома предлагают функции, которые ценят покупатели и строители; прочная и надежная конструкция, обеспечивающая удобную защиту от обычных погодных условий и минимизирующая материальный ущерб, защищающая пассажиров от экстремальных погодных условий и стихийных бедствий.Однако одних только прочности и долговечности недостаточно: системы должны быть просты в проектировании и сборке, а также быть универсальными, чтобы соответствовать любому архитектурному стилю.
Экологические преимущества при строительстве
Материалы местного производства. Производственный процесс портландцемента, вяжущего элемента бетона, не привязан к определенному региону страны, а материалы, используемые в процессе, легко доступны по всей Северной Америке.
Использование переработанных компонентов. Бетонные стены могут включать переработанные дополнительные цементные материалы, такие как летучая зола и шлаковый цемент, двумя способами. Во-первых, портландцемент часто производится путем включения в производственный процесс переработанных промышленных побочных продуктов, таких как летучая зола, чтобы свести к минимуму зависимость от первичного сырья. Кроме того, в бетон могут быть включены летучая зола, шлаковый цемент, микрокремнезем и переработанные заполнители, тем самым отвлекая материалы от свалки и сокращая использование природных ресурсов.
В течение срока службы конструкции
Холод. Бетон светлого или натурального цвета уменьшает островки тепла, тем самым снижая температуру наружного воздуха, экономя энергию и уменьшая смог.
Устойчивость к стихийным бедствиям. Бетонные стены отличаются высокой долговечностью и прочностью. Они устойчивы к пожарам, ветру, ураганам, наводнениям, землетрясениям, дождям с ветром и влаге. Использование бетона может даже снизить ставки страхования от пожара.Узнайте больше об упругой конструкции.
Энергоэффективность. В домах, построенных из бетона, достигается экономия энергии за счет сочетания тепловой массы бетона с оптимальным количеством изоляции в сборных железобетонных стенах. По сравнению с деревом и сталью бетонные конструкции допускают минимальные колебания температуры. Следовательно, отопление, вентиляция и кондиционирование воздуха могут быть спроектированы с использованием оборудования меньшей мощности, что экономит деньги и ресурсы. Кроме того, стена действует как воздушный барьер, уменьшая инфильтрацию воздуха и экономя больше энергии.
Качество воздуха в помещении. Бетон имеет низкую эмиссию летучих органических соединений (ЛОС) и не ухудшает качество воздуха в помещении.
Пригоден для повторного использования. Бетонные конструкции в городских районах могут быть переработаны в материал насыпи и дорожного основания в конце их срока службы (от 5 до 20 процентов заполнителя в сборном железобетоне может быть переработанным бетоном).
Concrete Home Преимущества
Когда я дома, мне хочется тишины и покоя.Мой бетонный дом хранит молчание. Я не слышу соседских газонокосилок, и мои полы не скрипят. Вот почему я выбрал бетонные стены, полы и крышу своего нового дома.
Мало того, мой архитектор смог создать более длинные пролеты пола, используя бетон для большей открытости. Она смогла использовать множество различных отделочных материалов — лиственные породы, плитку и ковролин. Я сказал ей, что хочу что-то впечатляющее в прихожей, поэтому она использовала цвет и текстуру, отлитые в бетон, чтобы придать ему вид камня.
И я могу спать спокойно, зная, что мой бетонный дом обеспечивает дополнительную защиту от разрушительного действия матушки-природы — торнадо, ураганов, землетрясений, огня, гниения и вредителей. Масса бетона и воздухонепроницаемость также способствуют экономии энергии. В моем доме зимой теплее, а летом прохладнее. Я установил систему лучистого отопления в бетонный пол, что дает мне еще больше комфорта и экономии. Из года в год с низкими эксплуатационными расходами бетон был самым экономичным и беззаботным выбором.
Красоте бетона нет предела.
Современные бетонные дома обеспечивают непревзойденную гибкость дизайна
За последнее десятилетие растущей тенденцией в строительной отрасли стал спрос на прочные, энергоэффективные бетонные дома, построенные с использованием передовой системы предварительно собранных взаимосвязанных изолированных бетонных форм (ICF). Популярные за свою прочность и долговечность, ICF также часто выбирают домовладельцы из-за их высокой гибкости дизайна.
На самом деле, гибкость дизайна МКФ начинает признаваться архитекторами, которые могут создавать уникальные контуры, углы, изгибы и арки по цене, конкурентоспособной по сравнению с традиционным деревянным каркасным строительством, что дает им неограниченную свободу, когда дело доходит до удовлетворения их потребностей. потребности клиентов в сочетании функциональности и красоты.
ЧТО ОБЕСПЕЧИВАЕТ УНИКАЛЬНУЮ ГИБКОСТЬ КОНСТРУКЦИИ ICFS?
«Сегодня практически любой план дома можно адаптировать под строительство МКФ. Системы ICF, состоящие из двух слоев изоляционного пенополистирола, окружающего монолитный бетон, могут быть отлиты во множество форм.Форма легко адаптируется: наклоны, кривые или другие варианты, которые вы создаете, могут быть включены в дизайн, что означает, что эстетическая привлекательность не должна жертвоваться ради достижения энергоэффективности», — объясняет Кевен Ректор Nudura, один из лидеров в этой инновационной технологии.
«Дом, построенный с использованием МКФ, может быть похож на дом, построенный из традиционных материалов, поскольку он может быть оформлен с использованием любой традиционной отделки, такой как дерево и виниловый сайдинг, натуральный камень и кирпич, или принять другой, более современный вид», — добавляет ректор. .
Использование ИКФ имеет много преимуществ: они энергосберегающие, гасят внешние шумы и огнестойкие до 4 часов. Кроме того, поскольку пенополистирол и бетон не содержат материалов, способствующих органическому росту, ICF устойчивы к росту плесени и грибка и, как следствие, к разрушению, которое часто происходит в деревянных каркасных конструкциях. Независимые тесты третьей стороны подтвердили, что изоляция из пенополистирола, используемая в конструкции ICF, не поддерживает рост плесени (влага и ICF: факты).
Кроме того, ICF позволяют создавать архитектурные решения в широком диапазоне стилей, а также могут учитывать углы, изгибы и большое разнообразие вариантов открывания — так же, как в деревянной или обычной конструкции CMU.
В жилых домах общая площадь конструкции обычно увеличивается, чтобы компенсировать более толстые стены, дверные косяки и подоконники. Таким образом, при проектировании внутренних помещений с помощью ICF архитекторы учитывают дизайн, учитывающий толщину стен при сохранении площади внутреннего пространства.Размер крыши также спроектирован так, чтобы быть немного больше, чтобы выдерживать большие размеры.
Кроме того, поскольку несущая способность стены ICF позволяет выдерживать системы перекрытий, которые охватывают большие расстояния, конструкции, построенные с использованием ICF, могут иметь большие помещения с чистым пролетом, свободные от стоек или других вертикальных опор. Поскольку ICF дает очень прочную и долговечную визуализацию, фундаменты, сделанные из ICF, могут, следовательно, поддерживать и более крупные конструкции.
ПРОЕКТИРОВАНИЕ С УЧЕТОМ ICFS
Хотя преобразовать детали деревянного каркаса в формат ICF несложно, проектирование с учетом ICF также имеет свои преимущества. Если архитектор допускает, чтобы заводские размеры продукта учитывались при проектировании, на рабочей площадке будет образовываться меньше отходов при резке блоков из пенополистирола, что означает меньшее воздействие на окружающую среду. Кроме того, при строительстве ICF обычно используется меньше материалов, что требуется другим методам строительства для достижения того же уровня производительности и защиты. А меньшее количество материалов снижает вероятность сбоев взаимодействия.
Для получения дополнительной информации о гибкости конструкции, долговечности и других преимуществах домов ICF посетите сайт www.nudura.com.
Устойчивое развитие | Бесплатный полнотекстовый | Оценка прочности альтернативного бетона домашнего производства с помощью экономического анализа
1. Введение
Зольная пыль экологически безопасна и дешевле цемента. Утилизация летучей золы и древесной золы также может стать еще одной проблемой в конце использования.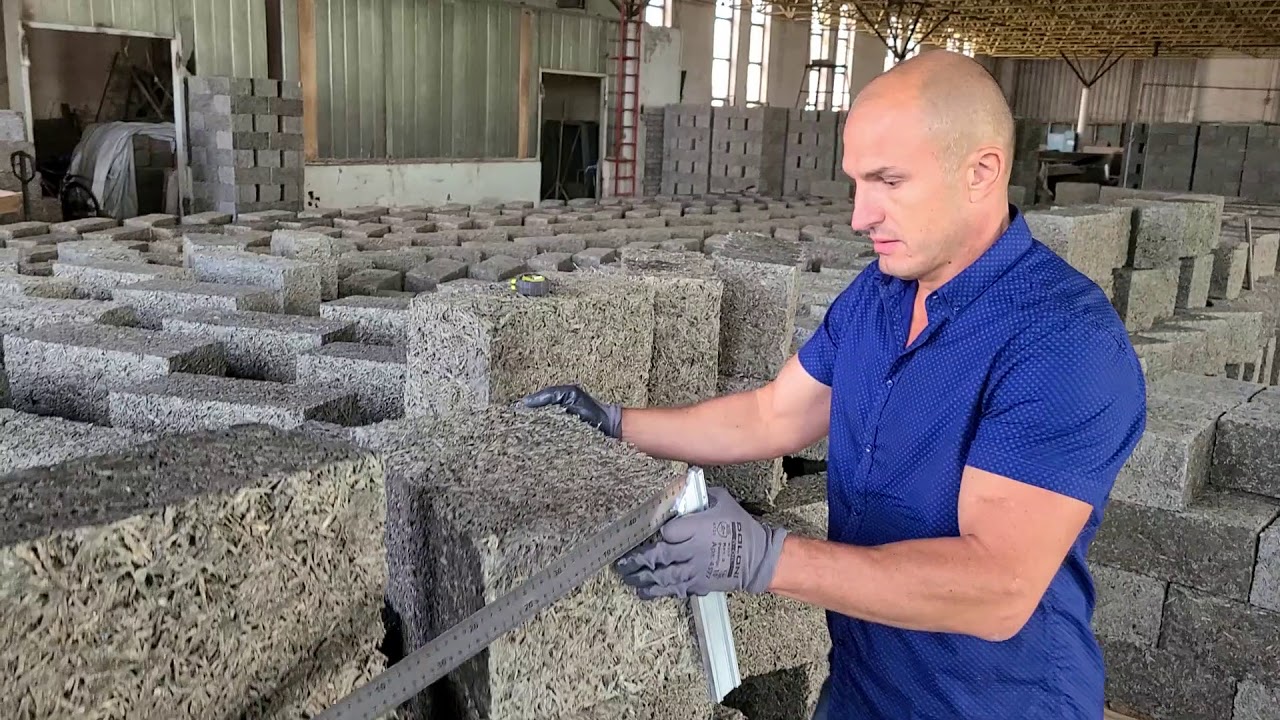

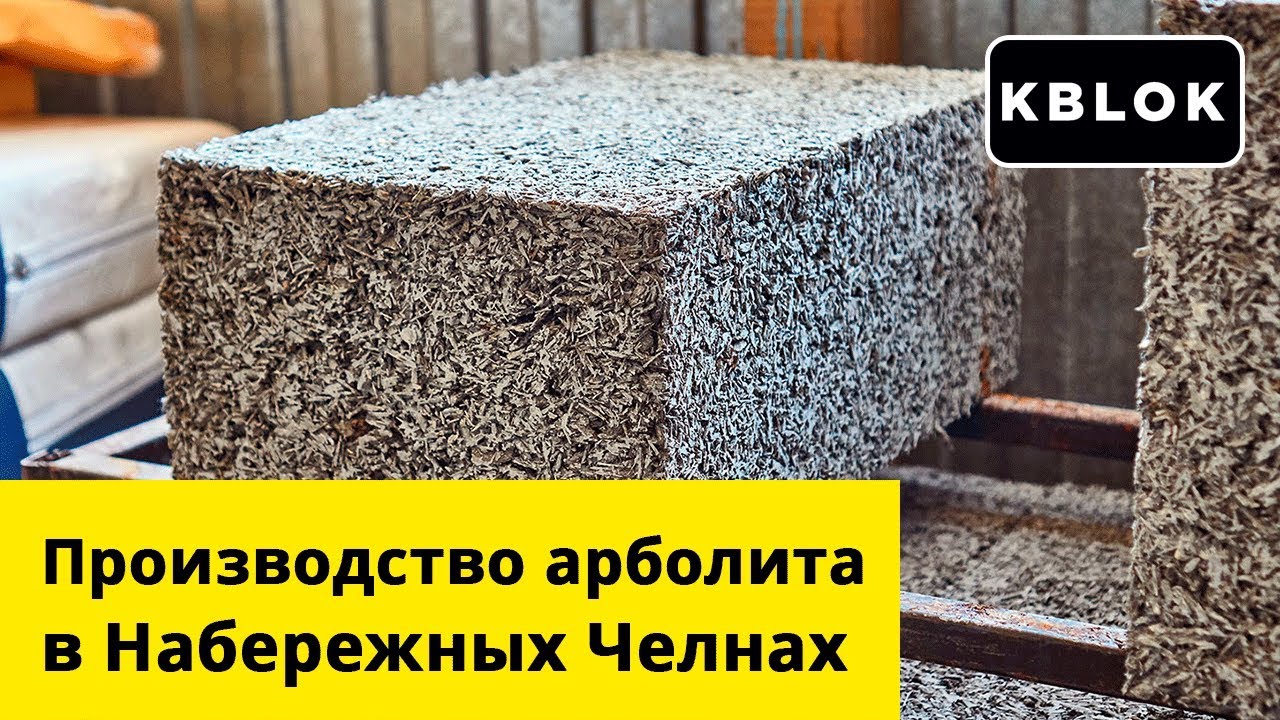
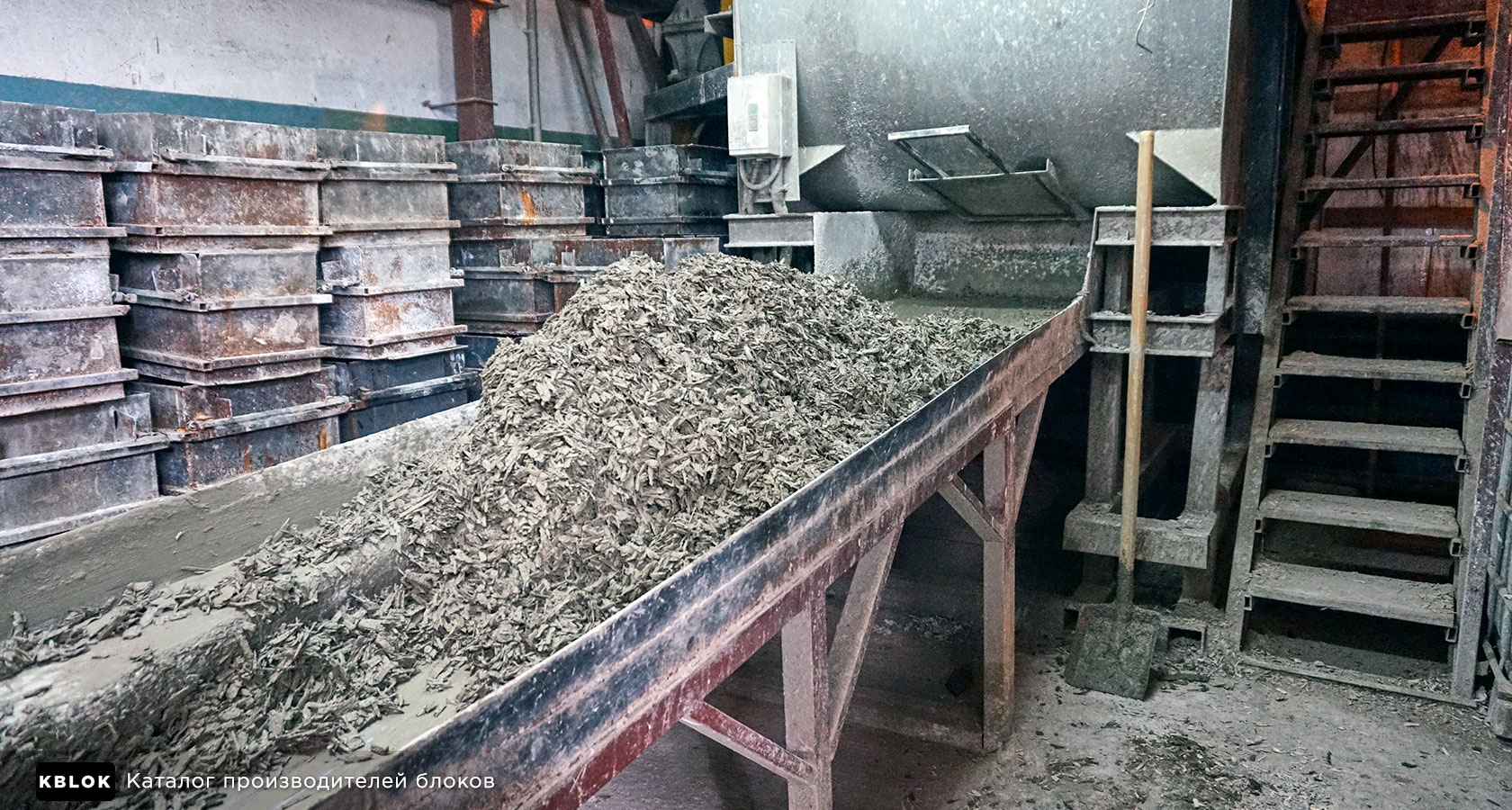
Целью исследования является внедрение бетона собственного производства для небольших проектов, таких как тротуары, задние дворы, или экономичное исправление существующего бетона. Привозить бетон с бетонного завода или из местных магазинов не всегда доступно, это не только дорого, но и требует времени. Наем местных подрядчиков для ремонта очень небольших участков вокруг домов не всегда эффективен. Материалы, используемые в этом исследовании, доступны на месте, особенно древесная зола. В большинстве районов Коннектикута в домах сжигают древесину, поэтому древесную золу можно использовать в качестве альтернативы цементу, что поможет сократить количество цемента в бетонах домашнего производства.
Исследование сосредоточено на методах анализа прочности на сжатие и проведения экономического анализа альтернативного бетона с устойчивыми материалами с использованием различных составов смесей. Составы бетонных смесей будут иметь различное процентное содержание летучей золы, древесной золы и переработанных заполнителей бетона. Другие примеси добавляться не будут. Исследуемый материал представляет собой обычную смесь, в которой портландцемент будет заменен золой-уносом класса С, древесная зола и обычные натуральные заполнители будут заменены заполнителями из переработанного бетона.Для достижения поставленных целей были смешаны четыре испытания бетонной смеси на основе летучей золы, содержащей 30%, 50%, 75% и 100% летучей золы. Было приготовлено четыре образца древесно-золобетонной смеси с содержанием древесной золы 18 %, 25 %, 33 % и 50 % и четыре состава смеси для бетона с заполнителями из вторичного бетона с содержанием 30 %, 50 %, 80 % и 100 % соответственно. Все три вида бетона были испытаны в течение 7 и 28 дней. Целевая прочность бетона составляла 2500 фунтов на квадратный дюйм как минимальная прочность.
4. Результаты и обсуждение
4.1. Прочность на сжатие
Целевая прочность составляла 2500 фунтов на квадратный дюйм (17 МПа) в качестве минимальной прочности, которую можно использовать для небольших домашних проектов. Бетон 2500 фунтов на квадратный дюйм может быть полезен для проездов, пешеходных дорожек, тротуаров или ремонта трещин. Стандарт ACI 318 указывает минимальную указанную прочность на сжатие 2500 фунтов на квадратный дюйм для конструкционного бетона. Проще говоря, конструкционный бетон не может иметь прочность менее 2500 фунтов на квадратный дюйм.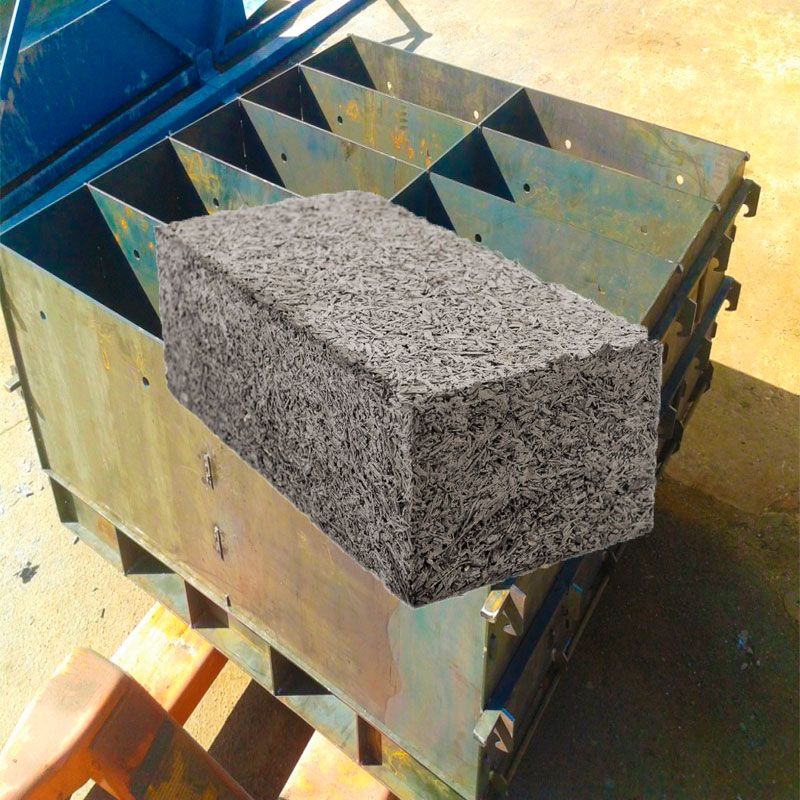
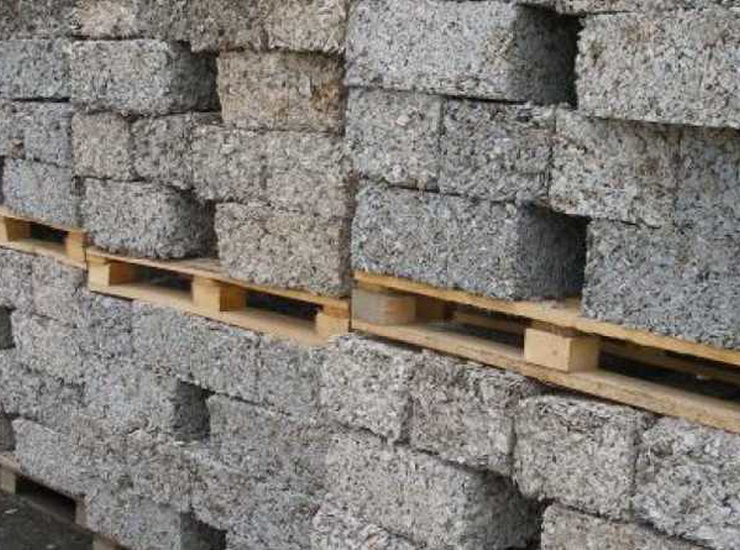
При 50% замене древесной золой прочность стала ниже половины 0% замены при 28-дневном испытании. Когда рассматривается целевая прочность, процент замены древесной золы должен составлять примерно 30% или меньше. Это очень похоже на зольный бетон. Прочность бетона становится бессмысленной при замене древесной золы свыше 33% при 28-дневном испытании.7-дневная прочность составляла примерно 75–77% от 28-дневной прочности бетона для 18% и 25%.
Бетон с переработанным заполнителем показывает гораздо меньшее снижение прочности по сравнению с двумя другими альтернативными бетонами. При замене 100% переработанного заполнителя 28-дневная прочность снизилась только на 10%, а 7-дневная прочность уменьшилась на 25%. Прочность бетона при 100% все еще составляла почти 3000 фунтов на квадратный дюйм в течение 28 дней.

4.2. Анализ затрат
Стоимость материалов является основной проблемой в строительной отрасли, а строительные материалы часто могут оказывать негативное воздействие на окружающую среду. Использование переработанного бетонного заполнителя в качестве альтернативы природному заполнителю — летучая зола и древесная зола в качестве альтернативы цементу в строительной отрасли — позволяет снизить стоимость материалов для производства бетонных изделий. В ходе исследования была проанализирована следующая информация.
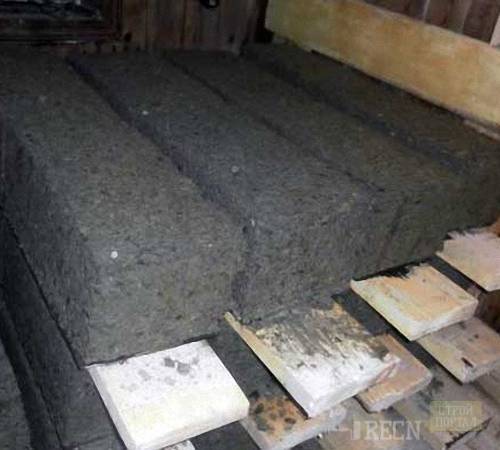
Существует много других важных факторов при анализе затрат, таких как транспорт, налоги, плата за доставку и стоимость рабочей силы. Однако существует высокая неопределенность, которую можно учитывать при анализе, поскольку эти факторы зависят от размера проекта, местоположения проекта, сезонных колебаний, колебаний рынка и так далее. Таким образом, анализ затрат для этого исследования сосредоточен на материалах.
Использование переработанных заполнителей для бетона могло бы заменить натуральные заполнители до 100%, но существенной экономии (5,6%) не было, однако, когда переработанный заполнитель считался бесплатным, тогда его стоимость снижалась на 19% по сравнению с обычным бетоном.

4.3. Региональный фактор
Бетонный материал для заполнителей варьируется в зависимости от местонахождения поставщиков. Ежегодник Геологической службы США (USGA) указывает среднюю стоимость и количество строительного песка и гравия, проданных или использованных производителями в США.С. по гос. Значение, показанное в отчете, как правило, отражает оптовиков для крупных потребителей и не подходит для непосредственного использования в этом исследовании, поскольку это исследование сосредоточено на бетоне домашнего производства для мелкого потребителя. Таким образом, региональный анализ затрат был проведен путем нормализации значения на основе предположения, что значение линейно коррелирует с ценами местных розничных продавцов на строительные материалы в Коннектикуте. Самый последний отчет USGA отражает данные за 2017 год, а на рисунке 3 показан усредненный коэффициент нормализации по сравнению с Коннектикутом.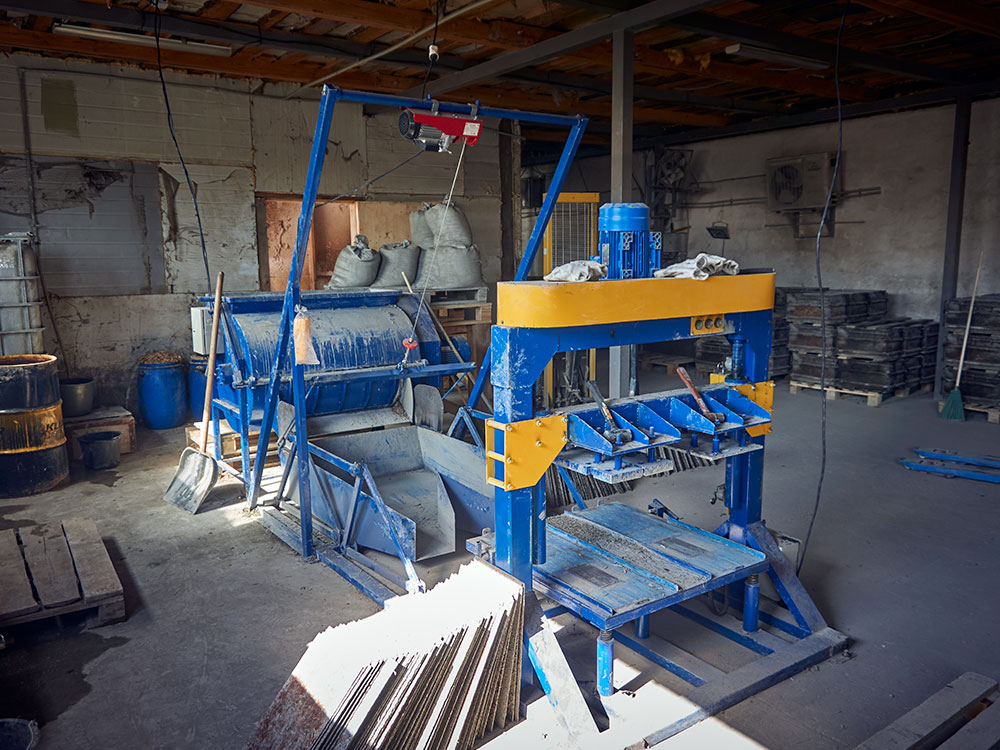

4.4. Факторы выбросов углерода (потенциал глобального потепления)
В строительной отрасли используется огромное количество бетона, что делает стоимость строительства такой высокой.Огромное количество строительных отходов от старых бетонных конструкций может быть повторно использовано в качестве альтернативного бетона в строительной отрасли. Это мотивировано не только защитой окружающей среды, но и сохранением природных совокупных ресурсов, складированием земель для захоронения отходов и увеличением стоимости обработки отходов перед захоронением. В Китае ежегодно образуется примерно 15,5 млн тонн строительных отходов [39]. Углекислый газ считается главной угрозой, вызывающей глобальное потепление.Было предпринято много возможных попыток уменьшить выбросы CO 2 путем замены широкого использования цемента другими альтернативными цементными материалами. Среди всех этих материалов летучая зола и древесная зола являются попыткой снизить содержание цемента в бетоне. Более того, использование золы в бетонной промышленности снижает дефицит засыпки и обращения с отходами.
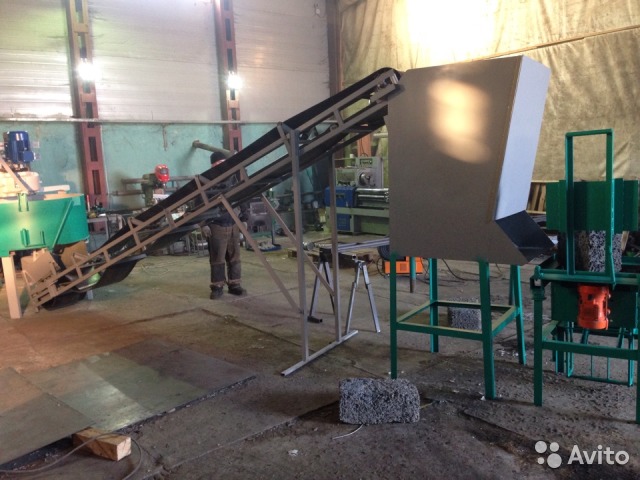

У переработанного заполнителя ПГП углерода в 25 раз меньше, чем у новых заполнителей, однако у заполнителей ПГП на 99,7% меньше, чем у цемента.Это показывает, что снижение содержания цемента в бетоне является наиболее важной мерой для обеспечения устойчивости и безвредности для окружающей среды в бетонной промышленности. Также очень интересно, что ПГП летучей золы почти в 17 раз выше, чем у древесной золы, однако бетон, произведенный с использованием 30% золы-уноса, имел более низкий общий ПГП, поскольку для получения аналогичной прочности требовалось меньше цемента с использованием золы-уноса. Кроме того, бетон с переработанным заполнителем снижает выбросы CO 2 всего на 1% по сравнению с обычным бетоном, а летучая зола снижает выбросы более чем на 28%.5%, а древесная зола экономит почти 24,5%.
Конкретные данные: тенденции в роскошных домах, другие в будущем?
10 августа 2018 г.
Ранее на этой неделе Wall Street Journal опубликовал в разделе «Особняк» статью, озаглавленную «Появление модных бетонных домов». Директор по маркетинговым исследованиям Home Innovation Эд Хадсон дал интервью и поделился своим опытом, основанным на данных и информации о тенденциях из нашего ежегодного исследования практики строителей.Ниже более подробно рассказывается о том, что он видит с точки зрения тенденций использования бетона в жилищном строительстве.
Бетонные дома не новы, и во многих местах по всему миру их нельзя назвать особенно «модными» или модными. Почти в каждом доме в Соединенных Штатах есть бетон, особенно на уровне земли и ниже, в то время как надземные части большинства жилых построек построены в основном с деревянным каркасом. Менее 10% новых домов в США построены с надземными бетонными стенами, и это не сильно изменилось за последние несколько десятилетий, хотя были небольшие приливы и отливы.
Большинство конструкций бетонных стен в Соединенных Штатах представляют собой бетонные блоки, и они в основном используются в Центральной и Южной Флориде, где много воды, ветра и термитов, которые в сочетании могут быть врагами деревянных конструкций. Менее 3% новых домов в Соединенных Штатах построены из монолитных или сборных железобетонных стен, включая такие варианты, как изоляционные бетонные опалубки, сборные стеновые системы и автоклавный газобетон.
За пределами Флориды бетон обычно встречается в элитных домах. Согласно данным нашего Ежегодного исследования практики строителей, вероятность того, что бетонные стены будут найдены в роскошном доме, примерно в три раза выше, чем в доме для начинающих.Возвращаясь к моему более раннему предположению, что бетон обычно не считается очень модным в большинстве случаев, вы можете задаться вопросом, почему он, кажется, так естественно обосновался в нише элитного строительства, для которой характерна высококачественная отделка и функции. На это есть несколько причин.
Сторонники бетонных домов заявляют, что они обеспечивают более тихий, более удобный, более прочный и более энергоэффективный дом. Некоторые даже осмеливаются утверждать, что эти преимущества связаны со стоимостью строительства, сравнимой со стенами из деревянной обшивки и пиломатериалов, хотя в большинстве случаев бетонные стены, по крайней мере, немного дороже в строительстве, чем стены из деревянного каркаса.Исследование Home Innovation, проведенное в начале 2000-х годов, показало, что домовладельцы могут ожидать платить на 3-5% больше за дом с бетонными стенами, при том же размере и характеристиках, по сравнению с домом, построенным с деревянным каркасом.
Источник: Годовой отчет о практике строителей Home Innovation, Structural Wall Systems
Источник: Ежегодные отчеты о практике строителей Home Innovation, Структурные стеновые системы
Дома из монолитного и сборного железобетона также с большей вероятностью будут возводиться мелкими строителями — строители, которые строят менее 10 домов в год, почти в четыре раза чаще строят дома с монолитными или сборными железобетонными стенами, чем те, кто строит более 50 домов в год. год.Это говорит о производственных последствиях строительства бетонных домов. Они по-прежнему являются прерогативой строителей, которые тратят гораздо больше времени (и затрат) на индивидуальный дом, чтобы удовлетворить конкретные индивидуальные потребности покупателя.
Источник: Годовой отчет о практике строителей Home Innovation, Structural Wall Systems
Так какое будущее у бетонных домов? Его использование на юго-востоке (Флорида) и рынке предметов роскоши, несомненно, будет продолжаться по тем же причинам, что и в прошлом.Кроме того, могут появиться растущие возможности, поскольку строительная промышленность реагирует на возросший интерес потребителей к долговечности и устойчивости. Это согласуется с продолжающимся перемещением населения с более густонаселенного северо-востока на юг и запад, где устойчивое к стихийным бедствиям строительство пользуется большим спросом. И, поскольку в прошлом рынок бетонных домов, по-видимому, стимулировался богатством — см. на диаграмме ниже, как бетонное строительство сильно упало после Великой рецессии — рост в США.S. доход и богатство, кажется, предвещают бетон. Однако в целом демографические показатели по-прежнему отдают предпочтение домам по более скромным ценам.
Источник: Ежегодные отчеты о практике строителей Home Innovation, Структурные стеновые системы
Существует также проблема производительности рабочих мест и текущей нехватки квалифицированной рабочей силы, которая является постоянной темой в этих статьях Trends. Для большинства существующих бетонных стеновых систем это, вероятно, компенсирует увеличение доли рынка.Но не сбрасывайте со счетов бетон. У него есть некоторые явные преимущества, которые могут существенно сократить время строительства и требуемые навыки, если они будут реализованы. Например, бетону можно придавать текстуру, цвет и форму, которые позволяют снизить трудозатраты, связанные с внешней и внутренней отделкой стен и пола. Системы панельных стен, используемые таким образом, сегодня становятся популярными во многих частях мира; при правильной системе он также мог бы стать популярным в этой стране.
Home Innovation будет рада помочь раскрыть историю и перспективы вашего строительного продукта или материала.Свяжитесь с нами, чтобы обсудить, как мы можем помочь вам сосредоточиться на ваших следующих рыночных возможностях.
Наверх
Преимущества замещения углерода древесными изделиями: критический обзор предположений | Углеродный баланс и управление
Допущение 1
«Изменения в темпах вырубки или производства приведут к соответствующему изменению в потреблении изделий из древесины, а также к противоположной реакции в использовании бетона, стали или ископаемого топлива.
В основе использования коэффициентов замещения лежит основное предположение, а именно, что увеличение предложения первичной древесины приведет к увеличению общего потребления изделий из древесины [24, 31]. Экономическая теория говорит нам, что увеличение предложения первичной древесины приводит к тому, что функция предложения древесины пересекается с функцией спроса при более низкой цене, когда другие факторы, влияющие на спрос на изделия из древесины, остаются неизменными, что приводит к увеличению закупок. Однако степень, в которой более низкая цена приводит к более широкому использованию изделий из древесины в строительстве, является более тонкой, поскольку она зависит от эластичности спроса и предложения, где потребляется древесина, хранится она или сжигается.Например, бревна меньшего размера используются для производства другой смеси лесных товаров, если объемы лесозаготовок на фиксированном участке увеличиваются. Таким образом, по-прежнему сложно установить, вызывает ли увеличение объемов лесозаготовок изменения в потреблении лесоматериалов. На изменения в заготовках и производстве также влияет регулятивная и торговая политика, такая как Соглашение между США и Канадой о пиломатериалах хвойных пород [32]. Такая политика не обязательно сопровождается соответствующим увеличением или уменьшением потребления конкретных изделий из древесины.Некоторые исследования показывают, что если спрос на изделия из древесины возрастет, цена на эти изделия будет расти, что будет стимулировать увеличение предложения, урожая, глобального экспорта этих изделий [33].
Например, Джонстон и ван Кутен [34] обнаружили, что европейские субсидии на древесные гранулы, которые заменяют уголь при выработке электроэнергии, могут привести к существенным сбоям на мировых рынках лесных товаров. Это повысит цены на древесные гранулы, балансовую древесину и ориентированно-стружечные плиты и аналогичные продукты, одновременно снизив цены на пиломатериалы.Даже несмотря на то, что в некоторых исследованиях показана взаимосвязь между заготовкой и потреблением, многие результаты, основанные на моделях, сообщают об ожидаемом увеличении или уменьшении объемов заготовки, но многие из них не сообщают о соответствующем увеличении или уменьшении потребления изделий из древесины, как предполагается в расчетах замещения. Например, увеличение охраняемых лесных площадей или охрана лесных видов может привести к снижению внутренних норм вырубки, но может увеличить нормы вылова в других географических районах, если природоохранная политика приведет к повышению цен [35,36,37].Это называется утечкой [28].
В этом контексте есть много статей, в которых обсуждаются высокие уровни утечек, связанные с перемещением урожая в лесной промышленности [38,39,40]. Однако неясно, как повышенные темпы утечки повлияют на производство конкретных изделий из древесины и, следовательно, как утечка повлияет на потребление этих изделий из древесины. Документы, в которых обсуждаются возможные уровни утечек в бетонной и сталелитейной промышленности в ответ на увеличение доли рынка изделий из дерева в строительном секторе, трудно найти, что позволяет предположить, что эмпирически определенные уровни утечек в отношении цены и эластичности в некоторой степени отсутствуют.Это отсутствие усложняет определение того, как увеличение урожая может или не может быть напрямую связано с увеличением потребления изделий из древесины в строительном секторе.
Показатели лесозаготовок не влияют напрямую на потребление изделий из древесины, но, похоже, коэффициенты лесозаготовок меняются и влияют друг на друга в глобальном масштабе посредством изменения цен. Например, в то время как мировое использование древесины оставалось стабильным с 1990 года, потребление древесины сократилось в развитых странах и увеличилось в развивающихся странах, при этом глобальное производство круглого леса все больше приходится на незаконные лесозаготовки [29].Хотя большая часть этого урожая в развивающихся странах идет на топливную древесину, вполне вероятно, что любая целлюлоза или бумага, произведенная из древесины, заготовленной в развивающихся странах, может еще больше сократить заготовку древесины в Северной Америке [41], однако с неопределенным влиянием на потребление этих продуктов. . Помимо реальных примеров, в некоторых публикациях, основанных на моделях, оценивается связь между показателями лесозаготовок и потреблением изделий из древесины. Аптон и др. [42] включили в рамки моделирования предположение о том, что, когда в модели предполагается, что бетон является основным строительным материалом в строительном секторе США, избыточный лес, который больше не вырубается для строительных материалов, по-прежнему подвергается утечке примерно на 20%.
.Это предполагает, что спрос на лесные товары не полностью контролирует уровень лесозаготовок в лесах США из-за предположения, что леса не управляются идеально. Точно так же Эрикссон и соавт. [1] предполагают, что увеличение объемов деревянного строительства окажет лишь незначительное влияние на заготовку, достигаемое за счет баланса между увеличением заготовки пиловочника и снижением заготовки балансовой древесины.
В контексте Канады было бы полезно определить уровень утечки лесных ресурсов или вероятность утечки в секторе внутреннего лесного хозяйства.В исследовании Гана и Маккарла [43] изучались международные уровни утечек в результате принятия дополнительных мер по охране лесов, и был сделан вывод о том, что в Канаде низкий риск высоких утечек по сравнению с другими странами/регионами, считающимися важными в мировом производстве, потреблении и торговле лесом. лесная продукция. Следовательно, Канада была бы хорошим местом для создания большего количества охраняемых лесов, которые хранят углерод [43]. Это артефакт канадской системы землевладения и политики. Подавляющее большинство лесов Канады находятся в государственной собственности и недоступны для хозяйственной эксплуатации, в то время как правительства провинций регулируют нормы вырубки.Учитывая, что большинство лесов находятся за пределами экстенсивной границы (недоступны для лесохозяйственных операций), внутренние усилия по увеличению количества долгоживущих изделий из древесины в Канаде должны быть связаны с политикой, направленной на увеличение использования лесозаготовок на интенсивной границе. Это, однако, также приведет к увеличению инвестиций в лесоводство и выбросам CO 2 , связанным с такими инвестициями. Поскольку изделия из древесины, как правило, имеют более низкие выбросы CO 2 , связанные с ними, мы не собираемся рекомендовать меры по сокращению утечек из изделий из древесины.
Хотя есть некоторые свидетельства того, что увеличение урожая приведет к увеличению потребления изделий из древесины, имеется ограниченное количество доступных исследований, которые эмпирически показывают эту взаимосвязь с учетом исторических данных. В заключение, может быть важно показать эту линейную зависимость в будущих исследованиях, посвященных нормам сбора урожая и их последствиям для потребления, что позволит политике, направленной на использование этой зависимости, для достижения положительного результата с точки зрения сокращения выбросов.
Предположение 2
«Деревянные строительные изделия заменяют бетон и сталь.
Изделия из дерева, вероятно, являются лучшим вариантом, чем сталь или бетон в строительном секторе, с точки зрения смягчения последствий изменения климата и сокращения выбросов [40]. Хотя многие изделия из дерева в настоящее время используются в строительном секторе, неясно, насколько все возможные изделия или древесные конструкции могут быть напрямую заменены нынешним типичным строительным дизайном. В значительной степени взаимозаменяемость учитывается в исследованиях, лежащих в основе коэффициентов смещения, которые сравнивают функционально эквивалентные здания или строительные элементы [44, 45]. Факторы, влияющие на заменяемость, включают технические свойства изделий из дерева по сравнению с бетоном и сталью, цену этих новых изделий из дерева по сравнению с традиционными строительными материалами, принятие новых строительных материалов и строительных норм, регулирование новых изделий из дерева и обучение заинтересованных сторон, связанных с отраслью. . Кроме того, в конце срока службы деревянные строительные изделия, как правило, необходимо использовать для создания биоэнергии, которая вытесняет источники энергии из ископаемого топлива, что обеспечивает дополнительный стимул к их преимуществу вытеснения [45].Исследование Nässin et al. [46] даже предположили, что деревянные здания принесут пользу только в том случае, если биоэнергия, произведенная из продуктов с истекшим сроком службы, будет генерироваться с помощью технологий улавливания и хранения углерода.
Деревянное каркасное здание, состоящее в основном из балочных балок [47], считалось прямой заменой нынешним железобетонным зданиям в итальянских регионах, а перекрестно-клееная древесина все чаще используется в строительном секторе для все более и более высоких зданий [48] . Однако Хурмекоски и соавт. [49] предполагают, что большинство типов зданий и чертежей придется изменить, чтобы доля изделий из дерева в строительном секторе увеличилась. Таким образом, большинство строительных норм и правил необходимо будет изменить, чтобы обеспечить добавление на строительный рынок большего количества изделий из дерева [29]. Если бы это было так, потребовалось бы дальнейшее изучение того, как изменения политики или плана могут повлиять на вместимость жилья в сообществе. Обновленная версия Национального строительного кодекса Канады (NBC) в 2015 году разрешила строительство деревянных каркасных конструкций высотой до шести этажей, и Министерство природных ресурсов Канады сообщает, что это привело к завершению строительства более 500 зданий средней этажности. или на стадии проектирования и разработки.Предполагается, что коэффициенты замещения обеспечивают функциональные эквиваленты существующих продуктов конечного использования; поэтому функциональная эквивалентность деревянного здания по сравнению с бетонным зданием, возможно, потребует дальнейшего изучения в будущих исследованиях.
Цена также может быть препятствием для замены дерева бетоном и сталью. Изделия из конструкционной древесины, такие как изоляционные плиты из древесного волокна, клееный брус, клееный брус и клееный брус, могут обладать техническими характеристиками, соответствующими строительным материалам, производство которых в большей степени зависит от ископаемого топлива.Однако в настоящее время они экономически не способны предоставлять что-то большее, чем нишевые продукты в более крупной строительной отрасли [50]. Гвардигли и др. [47] предполагает, что древесина не сможет проникнуть в строительный сектор, пока технология не станет экономически конкурентоспособной с существующими строительными материалами. Некоторые возможные решения, позволяющие деревянным строительным материалам стать экономически конкурентоспособными, включают налог на выбросы углерода на продукты, субсидии или политику закупок, например, поддержку первого использования.В целом, политические инструменты, которые позволяют интернализовать внешние затраты на выбросы углерода, обеспечат структурные изменения, которые могут увеличить использование изделий из древесины [51].
Необходимо учитывать и другие характеристики рынка. Например, внедрение новых технологий обработки древесины зависит от распространения производственных технологий в строительной отрасли, не склонной к риску [49]. Что касается высотных деревянных зданий, производство стали и бетона является отраслью промышленности со 150-летней историей [52]. Трудно определить, насытят ли строительную отрасль новые и появляющиеся технологии изделий из древесины.Из-за нынешней устойчивости строительной системы, отсутствия знаний в отрасли о применении изделий из дерева, отсутствия финансирования, недостаточных стимулов для замены старых технологий и высоких затрат увеличение доли изделий из дерева в отрасли маловероятно. и затрудненное [23, 50].
С точки зрения рыночного спроса может быть важно определить, существует ли негативное отношение к использованию более долговечных изделий из дерева в зданиях. Обзор поддержки стратегий по снижению выбросов углекислого газа в лесах показал, что лица, прямо или косвенно нанятые B. Лесной сектор C. с меньшей вероятностью поддержал какую-либо из предложенных стратегий смягчения последствий [53]. Однако вполне вероятно, что увеличение производства долговечных изделий из древесины за счет более эффективного управления лесным хозяйством могло бы принести непосредственную пользу Британской Колумбии. лесной сектор [53]. Таким образом, для увеличения поддержки лесным сектором деревянного строительства зданий может быть важно способствовать распространению информации о положительных экономических последствиях, которые такое более эффективное управление лесами может иметь для возможностей трудоустройства в этом секторе.
Что касается канадской общественности, то здесь недостаточно исследований, непосредственно анализирующих общее восприятие конструктивных изделий из древесины; однако в некоторых работах изучалось отношение общественности к долговечным изделиям из древесины в других географических районах. Большинство респондентов опроса на Тихоокеанском северо-западе США заявили, что высокие деревянные здания имеют больший риск пожара, требуют большего обслуживания и не так долговечны, как сталь или бетон [54]. Данные опросов в строительном секторе Великобритании показывают, что конечные пользователи, не имеющие информации о изделиях из древесины, предвзято относятся к использованию древесины в качестве строительного материала, поскольку считают, что она имеет более низкую огнестойкость и присущие ей проблемы с безопасностью [55].Если эти данные применить к строительному сектору Канады, может оказаться важным повысить осведомленность общественности о безопасности и преимуществах изделий из дерева, или может отсутствовать общественное одобрение строительства деревянных зданий.
Архитекторы также будут играть важную роль в расширении строительства зданий из инженерных деревянных изделий. В Швеции опрос, направленный архитекторам, выявил несколько распространенных причин, по которым они не выбирают изделия из инженерной древесины для строительства зданий, в том числе отсутствие ответственности за выбор материалов, отсутствие достаточных знаний о материалах и неуверенность в качестве материалов. Внешний вид или долговечность с течением времени [56].Тем не менее, они также обнаружили, что причины, по которым архитекторы выбирают изделия из инженерной древесины, включают в себя предполагаемое низкое воздействие на окружающую среду и эстетику [56]. Чтобы повысить одобрение архитекторов и использование изделий из дерева в своих проектах, может быть важно сосредоточиться в основном на этих факторах при выборе и увеличить объем доступной информации о факторах, которых следует избегать.
Примером использования долговечных изделий из древесины в Канаде стало строительство здания Brock Commons на территории кампуса Университета Британской Колумбии в Ванкувере.Brock Commons представляет собой 18-этажную жилую гибридную структуру, построенную из комбинации бетона, стали, поперечно-клееного бруса (CLT), клееного бруса (GLT) и пиломатериалов из параллельных прядей (PSL) [57]. Тешнизи и др. [57] показывает, что Brock Commons работает лучше, чем обычная железобетонная конструкция, по ряду категорий воздействия на окружающую среду, включая потенциал глобального потепления и потенциал истощения ископаемого топлива. Однако исследование также показывает, что общая стоимость владения, связанная со структурами, выше примерно на 7% за квадратный метр [23].Ограничением исследования Брока Холла было отсутствие доступных данных, касающихся определенной конкретной информации об окружающей среде, что предполагает, что потребуется больше данных, чтобы лица, принимающие решения, могли полагаться на эти или аналогичные результаты при планировании будущих проектов. Однако они также отмечают, что получение большей части этих данных может занять много времени и что их сбор может оказаться нецелесообразным на этапе проектирования будущих зданий. Даже с учетом этих ограничений, если стоимость высотных деревянных зданий останется выше, чем у обычных зданий, цена может стать препятствием для расширения использования CLT, GLT и/или PSL в будущем.
Возможности по производству изделий из дерева также могут стать препятствием для замещения. В Канаде массивные деревянные здания обычно строятся из изделий из древесины CLT из-за их высокого качества и характеристик устойчивости [58]. Например, CLT был одним из основных изделий из дерева, используемых при строительстве здания Brock Commons в Университете Британской Колумбии [59]. Хотя ожидается, что спрос на канадские пиломатериалы хвойных пород и конструкционные панели возрастет в связи с растущими рынками жилья в Северной Америке, существует вероятность того, что на производство в Канаде могут негативно повлиять нашествия вредителей и лесные пожары в Западной Канаде [60].Учитывая это потенциальное снижение канадских мощностей по производству CLT, при увеличении потребления конструктивных изделий из древесины в соответствии с политикой необходимо учитывать источники доступных CLT, поскольку это может сделать Канаду более зависимой от конструктивных изделий из древесины из других стран.
В заключение, важно понять проблемы, связанные с внедрением использования древесины в современной строительной отрасли, прежде чем использовать значения коэффициента смещения для информирования политики. Авторы существующих исследований могут понять, что коэффициент смещения основан на контрфактическом анализе увеличения количества древесины в строительстве. Тем не менее, допущения, лежащие в основе этого гипотетического сценария, должны быть поняты лицами, ответственными за разработку политики, которые намереваются увеличить объемы производства изделий из древесины с целью увеличения объема недопущенных выбросов.
Предположение 3
«То же самое сочетание продуктов может быть произведено за счет увеличения урожайности на данной площади».
В некоторых исследованиях по смягчению последствий изменения климата предполагается, что лесозаготовки или использование лесов увеличатся для производства дополнительных долговечных изделий из древесины [61, 62].Однако лишь немногие опубликованные работы содержат данные о том, изменится ли впоследствии вид вырубаемого леса или насколько однородны лесные ресурсы. Важно понимать, какая доля лесозаготовок приходится на недолговечные или долгоживущие изделия из древесины. Например, в Германии около 47% годовой заготовки древесины идет на производство недолговечной продукции со средним сроком службы менее 25 лет, в то время как только 22% годовой заготовки древесины используется в качестве строительной древесины со средним сроком службы около 50 лет. 63].Для Британской Колумбии доля долгоживущих изделий из древесины составляла около 1/3 с периодом полураспада от 30 до 90 лет [64, 65]. Эта информация актуальна, так как не все типы леса могут быть использованы для создания долгоживущих продуктов; необходимо учитывать виды деревьев, диаметр древесины, качество накопления углерода и требования к прореживанию, прежде чем можно будет предположить, что конкретный древостой подходит для строительного сектора [63]. Например, заготовка пиловочника и балансовой древесины не может быть заменена напрямую, поскольку увеличение производства пиловочника имеет тенденцию к увеличению производства балансовой древесины, а увеличение производства балансовой древесины имеет тенденцию к снижению производства пиловочника [35, 66].Чтобы сделать больше лесов пригодными для производства долговечных изделий из древесины, необходимо увеличить время оборота [39], увеличить базальную площадь [16] и оценить общее качество производимой древесины [1].
В Канаде проекты по моделированию углерода в лесах оценивают ряд различных индивидуальных стратегий смягчения последствий изменения климата. Во многих исследованиях изучалось как более эффективное использование урожая, так и более долговечные изделия из древесины в качестве стратегий управления лесами для смягчения последствий изменения климата [61, 62, 67].Стратегия более высокого уровня использования увеличивает товарное использование и заготовку отходов, эффективно увеличивая процент стволовой древесины, переходящей в изделия из дерева, без изменения общей площади заготовки. Это допущение основано на некоторых утверждениях, обсуждавшихся выше, в том смысле, что та же площадь леса может обеспечить увеличение объема заготовки, по крайней мере того же качества, что и исходная заготовленная древесина. Стратегия долгосрочных изделий из древесины увеличивает долю заготовленной древесины, направляемой на такие продукты, как панели, а не на целлюлозу и бумагу.Точно так же это основано на предположении, что древесина, используемая для производства целлюлозы и бумаги, точно так же пригодна для изготовления изделий из цельной древесины.
Кроме того, как стратегии более широкого использования, так и стратегии производства более долговечных изделий из древесины могут быть объединены вместе для создания аддитивных взаимодействий, поскольку для производства более долговечных изделий становятся доступными более высокие урожаи. Более широкое использование и более долговечные изделия из древесины часто оказываются одним из лучших путей сокращения выбросов в лесном хозяйстве в рамках этих исследований, поэтому было бы полезно определить, как Канада может реализовать политику для поддержки этих действий.
В этом контексте может быть важно понять, как можно использовать деревья более низкого качества или меньшего размера для создания изделий из инженерной древесины, особенно таких изделий, как CLT. Одно исследование показало, что, хотя распиловка бревен меньшего диаметра обычно дает меньший выход по объему, чем бревна большего диаметра, метод распиловки в реальном времени и трапециевидной кромки для производства CLT-панелей увеличивает выход продукции почти на 20% по сравнению с обычным методом распиловки. 68]. Другое исследование, проведенное Эспинозой и Бюльманном [69], предполагает, что малоиспользуемые, малоценные и подверженные нарушениям лиственные породы могут быть отличными вариантами для производства CLT.Однако существуют технические и политические барьеры для этих вариантов производства CLT из деревьев меньшего диаметра или более низкого качества. Важно, чтобы лесная промышленность могла обеспечить необходимое техническое руководство для массового производства этой продукции, и должен быть внутренний толчок, чтобы начать уделять приоритетное внимание заготовке малоиспользуемых лиственных пород по сравнению с хвойными породами, даже при существующей разнице в ценах [68]. ]. Существует возможность создания гибридных CLT, но для этого все еще требуется техническое руководство со стороны промышленности.
Для поддержки этих действий могут потребоваться государственные субсидии или программы, которые позволяют и поощряют управляющих лесным хозяйством и представителей отрасли заниматься альтернативным производством изделий из древесины, что поможет ослабить экономическое давление, которое может стать препятствием для производства конструктивных изделий из древесины. Широкомасштабный налог на выбросы углерода может увеличить стоимость остатков урожая для продуктов, особенно если бизнес, как обычно, заключается в сжигании этих остатков, как это принято в Британской Колумбии. Исследования и разработки, направленные на расширение использования изделий из древесины, будут более полезными, если будет изучен ряд продуктов, включая существующие и разрабатываемые типы продуктов.Как стандарты использования, так и права владения вторичным оптоволокном могут помочь расширить доступ к неиспользованным лесным остаткам для лицензиатов и заинтересованных сторон. Может стать все более важным требование к компаниям и лицензиатам доказать, что они пытались продать любые оставшиеся послеуборочные остатки, прежде чем давать разрешение на сжигание. В конечном счете, изменение уровня лесозаготовок, вероятно, должно быть достигнуто за счет твердой юридической приверженности устойчивому управлению лесами, тем самым сохраняя существующий углерод, хранящийся в лесах [70].
В заключение необходимо учитывать однородность лесных ресурсов, включенных в коэффициент замещения. Если лицо, определяющее политику, желает реализовать выгоду от замещения, предложенную в исследовательской работе, ему необходимо обеспечить, чтобы рассматриваемый лесной ресурс можно было легко использовать для создания предполагаемого продукта. Если это допущение не принимать во внимание, в лесных ресурсах может отсутствовать способность создавать продукт, в результате чего расчетный коэффициент замещения будет неверным.Например, более высокий спрос на CLT может привести к сокращению пиломатериалов из домов на одну семью, что приведет к небольшому или отсутствию выгоды от перемещения, если только CLT не будет сделан из волокна, используемого для товаров с более коротким сроком службы.
Предположение 4
«Нет никакой реакции рынка на увеличение использования древесины».
Здесь нам необходимо провести различие между двумя разными точками зрения: первая — это типичный атрибутивный анализ жизненного цикла (LCA), когда экономический агент (потребитель) должен выбирать между двумя разными продуктами. Как только выбор сделан, другой продукт не потребляется и не создается, и, следовательно, эти выбросы не происходят [71]. Второй аспект — это атмосфера. Если политика введена в действие или продукт потребляется, происходят ли выбросы от альтернативной политики или продукта? Например, предположим, что изменение политики означает, что больше многоквартирных домов строится из дерева, а не из бетона и стали. С точки зрения застройщика замена произошла, но с точки зрения атмосферы следует, что если спрос на многоквартирные дома из бетона и стали снизится, последующее падение цен на сталь и бетон, таким образом, вызовет увеличить использование таких материалов в других местах, что приводит к межотраслевой утечке [34].Нам не удалось найти исследования межотраслевых утечек в строительной отрасли. Однако экономисты обнаружили доказательства утечки углерода в более общем плане, когда только часть юрисдикций вводит политику смягчения последствий изменения климата; выбросы просто перемещаются в другие юрисдикции.
Хуже того, чистый эффект потенциально может привести к зеленому парадоксу, когда общие выбросы увеличиваются [72, 73], хотя в реальном мире это редко имеет место. Хармон [23] обнаружил, что потенциальные выгоды от замещения сильно зависели от скорости межотраслевых утечек.
Потенциально межсекторальные утечки можно было бы учитывать в процессах учета, если предположить, что выбросы будут предотвращены до конца рассматриваемого периода, или если будет сделано предположение о том, что выбросы будут предотвращены благодаря развитию альтернативных технологий [74]. Общая методологическая проблема, связанная с непостоянством, заключается в том, что хранение в течение 100 и более лет считается постоянным [75]. Единственный способ гарантировать предотвращение выбросов — это либо создать новую технологию, которая превосходит продукты с более высоким содержанием CO 2 , либо сегодня производить выбросы, которые скапливаются в постоянном стоке, оба из которых кажутся маловероятными [75]. Тем не менее, необходимо рассмотреть больше вопросов несколько более внимательно.
С точки зрения Канады может оказаться необходимым изучить варианты политики для борьбы с межсекторальной утечкой. Как уже отмечалось, было бы также важно определить продолжительность пребывания в Канаде. Обычный методологический срок для принятия составляет около 100 лет [75]. Однако более подходящий и полезный подход, предложенный Ciricacy-Wantrup [76], заключается в взвешивании физических потоков углерода в зависимости от того, когда они происходят.Это делает выбор подходящей схемы взвешивания (по сути, ставки дисконтирования будущих потоков углерода) политическим выбором, который определяется безотлагательностью, связанной с необходимостью решения проблемы изменения климата [28, 77]. Предположим, что проект по посадке деревьев удалит 1000 т CO 2 из атмосферы через 101 год. Для 100-летней временной шкалы углерод, удаленный в 101 году, не имеет значения. Таким образом, эта политика неявно предполагает, что углерод дисконтируется по годовой ставке около 15%; этот показатель сделал бы удаление в 101 году или позже фактически равным нулю сегодня. Серьезная климатическая чрезвычайная ситуация предполагает, что CO 2 , удаленный из атмосферы через 20 лет, не имеет значения, поскольку общество больше не существует в том виде, в каком мы его знаем, тогда удаление 1000 т CO 2 в 21 году должно дисконтироваться по годовой ставке. более 90%, чтобы сделать его неактуальным сегодня. Ставка, выбранная для взвешивания будущего углерода, является политическим инструментом, который зависит от срочности, с которой необходимо смягчить последствия изменения климата [34]. Рассмотрение этих вариантов дисконтирования, имеющих отношение к политике, может помочь ограничить межотраслевую утечку, которая может снизить возможность полной реализации предлагаемых преимуществ замещения.
Если выбран 100-летний график, может быть важно исследовать вероятность того, что деревянные строительные изделия будут использоваться для производства электроэнергии, скажем, с соответствующими выбросами, выпущенными после того, как этот 100-летний график будет достигнут. Это также требует понимания будущей энергоемкости и возможных технологических разработок в области улавливания углерода, поскольку повторная передача углерода может вызывать меньше беспокойства, если интенсивность выбросов строительной продукции в целом будет снижена.Технологии улавливания углерода быстро развиваются, чтобы предоставить нефтегазовым предприятиям возможность оставаться прибыльными в условиях все более жестких целей по сокращению выбросов. Однако стоимость неправильного использования технологий улавливания углерода или переоценка их текущей способности улавливания может иметь длительные негативные последствия с точки зрения смягчения последствий изменения климата [78]. Мы не смогли найти примеров улавливания углерода, связанных с производством строительных элементов.
Другие подходы к сокращению межотраслевых утечек включают налог на выбросы углерода в масштабах всей экономики и принятие юрисдикциями обязательств по глобальным действиям по сокращению выбросов CO 2 e. Мы ожидаем, что рынки отреагируют так, что, если спрос на строительные материалы из бетона и стали снизится, их цена упадет. Налог на выбросы углекислого газа на такие продукты снизит привлекательность и, как мы надеемся, уменьшит количество межотраслевых утечек. Однако эти действия лучше всего работают при глобальном распределении по международным рынкам. Отсюда рекомендация о приверженности на международном уровне целям смягчения последствий изменения климата.
Фальшполы — APA — The Engineered Wood Association
Система фальшпола представляет собой сборку балок и ферм, лаг пола и настила пола из фанеры или ориентированно-стружечной плиты (OSB), все они должных размеров, соединены вместе и размещены на фундаменте.Система фальшпола предназначена для поднятия жилого пространства над землей, изолируя его от влаги и вредителей. Американские дома были построены на системах фальшполов с колониальных времен, и эстетические и практические причины для строительства фальшпола актуальны и сегодня.
Многие термины часто используются для описания систем фальшполов в разных регионах страны. Примеры включают фальшпол из дерева, некондиционный пол, фундамент из пирса и балки и конструкцию подполья.Независимо от точного термина или используемого метода строительства, система фальшпола имеет множество преимуществ.
См. примеры использования фальшполов.
Типы фундаментных систем фальшполов
Прочный фундамент – самая важная часть нового дома. Фальшпол может поддерживаться различными типами фундамента (некоторые из них представлены ниже). Всегда проверяйте местные строительные нормы и правила для конкретных требований к фундаменту. Независимо от используемой системы фундамента фундамент и фундаменты должны иметь достаточный размер и прочность, чтобы выдерживать расчетные нагрузки.После того, как фундамент установлен, система балок и ферм, лаг пола и обшивки пола из фанеры или ориентированно-стружечной плиты (OSB) устанавливается для завершения фальшпола.
Пирс-балочный фундамент
У строителя есть несколько вариантов построения опор при возведении столбчато-балочного фундамента. Опоры могут опираться на точечные или сплошные фундаменты. Размещение и расстояние между опорами и опорами определяется расположением несущих стен и пролетами балок перекрытия.
Фундамент стволовой стены
Сплошная фундаментная стена по периметру дома. Он часто строится из армированной кладки или монолитного бетона и поддерживается непрерывным железобетонным фундаментом.
Фундамент стены из деревянного ствола
Сплошной фундамент из деревянных каркасных стен, обшитых конструкционной фанерой или плитами ОСП поверх сплошного фундамента. Стены из деревянного ствола снижают затраты на бетон, упрощают выравнивание и легко возводятся на месте.
Фундаменты из деревянных свай и столбов
Обработанные деревянные сваи и деревянные опоры сводят к минимуму или полностью исключают использование бетона. Они популярны в прибрежных районах для достижения необходимой высоты, но также могут быть экономически выгодными для поднятия полов всего на несколько футов. Сваи часто используют в грунтах с низкой несущей способностью.
10 причин для строительства фальшполов
Строители, которые предлагают вариант фальшпола с каркасом из прочной, возобновляемой древесины, создают ценность не только для своих клиентов, но и для себя.Конструктивные преимущества системы фальшпола включают:
1. Затраты на строительство меньше, чем у плиты на засыпке
Система фальшпола из деревянного пола может быть конкурентоспособной по стоимости альтернативой системе бетонных плит, особенно когда необходимо внести грязь для поднятия конструкции.
2. Ускоряет планирование торгов
Конструкция фальшпола помогает планировать торговлю. Например, бетонные и каменные работы не должны ждать установки и осмотра сантехники, как это обычно бывает с плитным фундаментом.
3. Ускоряет строительство
Формование и отверждение бетона требует много времени. Перетаскивание засыпной земли и ее правильное уплотнение добавляет больше времени. Плохая погода и проверки могут привести к длительным задержкам бетона. Возведение столбчато-балочного или свайного фундамента, как утверждают строители, происходит быстрее, независимо от погодных условий.
4. Обеспечивает более ровный фундамент на любом типе грунта
Системы фальшполов могут быть построены на любом типе почвы и очень хорошо работают на проблемных почвах, таких как экспансивная глина, которая может расколоть обычные бетонные плиты.В то время как любой фундамент может осесть, использование опор с системой фальшпола упрощает выравнивание или ремонт. Ремонт или выравнивание треснувшей, поврежденной бетонной плиты может быть очень дорогим.
5. Решает поймы и наклонные участки
Подъем плиты с насыпным грунтом для соответствия требованиям высоты поймы может быть дорогим, трудоемким и трудным для надлежащего уплотнения. Система фальшпола представляет собой практичное и доступное решение для соблюдения правил и защиты дома от паводковых вод.Для участков с уклоном фальшпол на опорах более экономичен и практичен, чем строительство плитного фундамента по принципу «вырежи и засыпь». Меньше возмущается почва, снижается эрозия, а опоры устраняют необходимость в усиленных подпорных стенках.
6. Упрощает ремонт и реконструкцию
Монтаж, техническое обслуживание и модификация инженерных коммуникаций, таких как водопровод, канализация и электричество, просты и экономичны по сравнению с плитными системами. Прокладка и перекладка проводки для электричества, телефона, телевидения и домашних развлечений выполняется быстрее.Ремонт или перенос сантехники относительно просты и менее затратны.
7. Идентифицирует строителя как зеленого и прогрессивного
Деревянный фальшпол — правильный выбор для окружающей среды. Древесина является возобновляемым ресурсом, для производства которого требуется гораздо меньше энергии, чем для производства бетона или стали. Последние достижения в области изделий из дерева и строительных технологий помогают создавать более прочные и эффективные дома.
8. Продает дома быстрее и с большей прибылью
Эстетика дома с фальшполом производит впечатление на покупателей жилья.«Люди это замечают, — говорит строитель Джон Купер из Cooper Homes. «Если они не будут платить больше за (эстетику) — что, я думаю, они делают — дом будет продаваться быстрее, чем дом на плите».
9. Соответствует меняющимся потребительским предпочтениям
Все больше и больше покупателей жилья стремятся к традиционному стилю и шарму, но не хотят жертвовать современными удобствами. Фальшполы «дают владельцам домов удобства настоящего, сохраняя при этом стиль прошлого», — говорит строитель Деннис Коллиер из Collier Construction.В районах, подверженных наводнениям, «людям нравятся (фальшполы) просто для душевного спокойствия», — говорит строитель Питер Рассел из Bay Homes.
10. Сокращает количество обратных вызовов и ответственность
Прочные, долговечные деревянные дома служат нескольким поколениям.