Арболит технология производства в домашних условиях: Арболит своими руками — состав и пропорции для блоков
Арболит своими руками в домашних условиях: инструкция по изготовлению
Арболит представляет собой распространенный строительный материал, который применяется для сооружения жилых домов или других помещений. Из него строят и несущие стены, и перегородки. Все потому, что материал обладает прекрасными теплоизоляционными характеристиками. Стеновые арболитовые блоки часто применяются в промышленных проектах и частном строительстве. Однако обыватели порой не догадываются, что сделать арболит своими руками вполне реально.
Арболит представляет собой довольно распространенный материал.- Что такое арболит
- Достоинства и недостатки материала
- Технология производства в домашних условиях
- Состав и пропорции смеси
- Оборудование для изготовления
- Бункеры и формы
- Отработка технологии
- Применение арболитовых блоков
Что такое арболит
Перед тем как пытаться сделать арболит, нужно разобраться, что же это такое. Под этим термином понимают материал, который состоит всего из 2 основных компонентов. Основную часть вещества составляет наполнитель из древесной щепы и опилок. Эти элементы связаны вторым веществом — портландцементом.
В массу включают особые химические вещества, которые способствуют улучшению качественных характеристик древесины и повышают пластичность готового состава. Но их доля сравнительно невелика.
Достоинства и недостатки материала
Сделать арболитовые блоки своими руками в домашних условиях несложно. Для этого достаточно залить формы предварительно подготовленным составом.
Технология отличается простотой. Для этого достаточно ознакомиться с пропорциями. Процедуру можно провести самостоятельно, что поможет сэкономить средства на транспортировке строительных материалов.
Перед тем как начинать делать арболит, нужно ознакомиться с его преимуществами. Какие же плюсы имеет вещество? К ним относят следующее:
- Многофункциональность. Материал можно применять для разных видов строительных работ.
При этом ему удается придавать требуемую форму путем распила. - Экономичность. Продукция фактически получается из отходов. Потому производство арболитовых панелей имеет низкую себестоимость. К тому же материал отличается прекрасными теплоизоляционными свойствами. Это дает возможность экономить на отоплении.
- Жаропрочность. Арболит устойчив к огню, несмотря на высокое содержание древесины.
- Устойчивость к микроорганизмам. Это актуально лишь при правильной обработке.
- Высокий уровень звукоизоляции.
- Однородность и небольшой вес. Это очень актуально при строительстве дома на проблемном участке или в зоне с высокой сейсмической активностью.
- Прекрасная фиксация крепления и легкой арматуры. Дом из арболита легко может простоять много лет.
Перечень недостатков является сравнительно небольшим, однако его обязательно нужно учитывать при изготовлении арболитовых блоков своими руками. Итак, к основным минусам относят следующее:
- Высокий уровень поглощения влаги при нарушении технологии изготовления материала. Вещество требует хорошей гидроизоляции, иначе конструкция быстро разрушится.
- Предпочтительное применение в регионах с преобладающими заморозками.
При изготовлении арболита своими руками в домашних условиях обязательно соблюдать пропорции. Только в этом случае получится сформировать крепкие блоки с уникальными свойствами.
Технология производства в домашних условиях
Многих людей интересует про арболит — как сделать своими руками, состав, пропорции. Чтобы получить качественный материал, нужно учитывать цели его применения — частные или коммерческие. Для изготовления в личных целях можно не покупать дорогое оборудование.
Состав и пропорции смеси
Арболит представляет собой легкий бетон. Технология его приготовления считается практически стандартной. Однако есть и ряд нюансов.
Массу обязательно требуется прессовать. При этом для замеса применяется не обычная бетономешалка, а принудительная. В ней хорошо смешивается щепа с другими ингредиентами.
В состав материала входят такие ингредиенты:
- цемент — требуется использовать материал марок М400 или М500;
- вода;
- древесная щепа;
- химические примеси.
Важно, чтобы цемент был свежим и сухим. К тому же щепа должна обладать определенными размерами. Чем меньше пересортицы будет, тем более крепкими получатся блоки. К химическим компонентам относят хлорид кальция. Также в состав включают сернокислый алюминий и жидкое стекло.
Дополнительные компоненты требуется вначале смешать с водой. Лишь после этого их нужно добавлять в щепу и перемешивать.
Воду можно применять любую питьевую. В ней не должно быть загрязнений. После равномерного намокания щепок в ведре можно добавлять в состав цемент. Нарушать последовательность изготовления арболитовых плит запрещено.
При изготовлении арболита требуется соблюдать рецепт. Стружечную массу нужно смешивать с портландцементом, соблюдая соотношение компонентов. Удельная масса цемента составляет 10-15 %. Количество пластификаторов не превышает нескольких единиц.
Итак, для самостоятельного изготовления арболита нужно сделать следуюдщее:
- Смешать 1 часть извести и 10 частей воды. Замочить в полученной смеси щепу минимум на 3 часа.
- Поместить щепки в бетономешалку и залить водой. Для этого нужно соединить 3 доли сырья и 4 объема воды. Включить перемешивание и добавить 1 % жидкого стекла от общей массы раствора.
- Добавить 4 массовых доли цемента М500 и перемешивать до однородности.
- Смазать борта форм отработанным маслом и наполнить сырьевым раствором. Немного уплотнить содержимое и оставить на сутки.
- Вытащить из формы и сушить в течение недели.
Оборудование для изготовления
Для изготовления монолитного арболита без каркаса своими руками требуется использовать специальное оборудование. Важным агрегатом для этой цели считается щепорез. Режущие детали нужно ставить под небольшим углом. При этом горловина для подачи щепы закрепляется вертикально.
Сделать самому щепорез можно из автомобильной рессоры. Также требуется использовать ось, металлические шпильки, подшипники. В интернете можно найти большое количество видео-уроков для изготовления конструкции.
Бункеры и формы
Промышленные формы обладают стандартными размерами. Они сопоставимы с габаритами блоков из пенобетона или полистиролбетона.
Арболит обычно делают размерами 20, 40 или 60 см. Делать заготовки самостоятельно достаточно сложно. Потому рекомендуется разрезать металлические листы болгаркой и заготовить специальную форму.
Арболит вполне реально сделать своими руками.Отработка технологии
Самым трудоемким этапом считается отработка технологии. На этой стадии нужно определить все нюансы функционирования оборудования. Вносить химические компоненты рекомендуется на разных этапах. Сначала следует добавлять хлористый натрий и сернокислый алюминий. Другие ингредиенты следует вносить в бункер перед замесом.
Применять жидкое стекло следует после готовности щепы. Затем раствор нужно залить в формы, утрамбовать и оставить, чтобы он затвердел. На схватывание вещества уходит 2-3 суток. Затем формы убирают, а блоки сушат.
Арболит часто применяют в строительстве.Применение арболитовых блоков
Сейчас арболитовые плиты устанавливают на перекрытия. Это обусловлено простотой их монтажа. Также блоки применяют для сооружения длинных прогонов в зданиях. Стандартные элементы используют для строительства домов и гаражей. Также может применяться обвязка пола с использованием арболита. При этом в состав нужно добавлять щебень.
Сделать арболит своими руками не очень сложно. Для этого нужно подготовить необходимое оборудование и четко придерживаться технологии. Немаловажное значение имеет правильный выбор материалов — желательно брать самые качественные.
» src=»https://www.youtube.com/embed/3bzOipggpFI?feature=oembed» allow=»accelerometer; autoplay; clipboard-write; encrypted-media; gyroscope; picture-in-picture» allowfullscreen=»»>технология, станок для блоков, оборудование
Содержание
- Состав
- Технология
- Процесс получения древоблоков
- Оборудование
- Производство своими руками
- Отзывы и рекомендации специалистов при самостоятельном производстве блоков
Производство арболита — особенная технология изготовления стройматериала, который по своим свойствам приближен к натуральной древесине. Деревобетон отличается низким уровнем теплопроводности и достаточно доступной стоимостью. Блоки из арболита обладают рядом положительных качеств, главное из которых – это пригодность к возведению стен любых зданий. Особенности производства были популярны еще во времена Советского Союза, потом схему изготовления заменили другие технологии. Популярность этих плит возвращается на современный строительный рынок.
Оборудование для производства арболита позволяет изготовить доступный и практичный строительный материал, который отвечает требованиям ГОСТ 54854-2011. Легкие бетоны на органических наполнителях растительного происхождения имеют множество достоинств:
- стойкость к биологическим воздействиям;
- материал обладает паропроницаемостью;
- хорошая звукоизоляция;
- блоки из арболита устойчивы к огню;
- простота монтажа и легкая обработка поверхности.
Состав
Компонентная составляющая арболита – это важный этап технологии производства, который нуждается во внимательном соотношении всех компонентов. При изготовлении древоблоков важно чтобы качество приобретаемых материалов было высоким. Любой бетон включает в себя вяжущие элементы, песок, наполнитель (может быть легким либо тяжелым).
Важно! При замесе щепы ее следует смочить таким образом, чтобы не выделялась лишняя влага, а сам слой игольчатой структуры был покрыт цементным составом.
При процессе трамбовки цемент послужит связующим звеном, наружные поры у блоков закроются, таким образом, изделие станет не продуваемым.
Размеры щепы влияют на количество цемента, который будет использоваться при приготовлении одного кубометра арболита. Когда щепа изготовлена из сухого дерева, получается мелкая фракция. Игольчатая структура для скрепления между собой требует большего количества цемента. Необходимый объем материалов для изготовления одного кубометра арболита:
- 8-10 кг химических препаратов;
- 250 кг цемента;
- примерно 200-250 кг щепы.
В щепу добавляют такие материалы:
- гашеную известь;
- раствор жидкого стекла;
- портландцемент;
- хлористый калий;
- алюминиевую и сернокислую кальциевую смесь.
Технология
Изготовление блоков из арболита организовывают как в домашних условиях, так и налаживают масштабное производство, как прибыльный бизнес. Для этого учитывают все аспекты и стадии изготовления, руководствуются нормативными документами.
Технологию производства арболита по ГОСТУ необходимо начать с подготовки нужных ингредиентов, из которых 85 % составляет деревянные компоненты. Применяется древесная щепа, опилки, стружка. Наиболее подходящие породы древесины: сосна, пихта, ель, тополь, осина, береза. Допускается присутствие коры, листьев и хвои – не больше 5 % от общего объема. Заготовки пропускаются через станок для щепы и измельчаются. Рекомендуемый размер частичек 5х25 мм. Разнофракционный состав будет обеспечивать нужную плотность арболита.
Производство плит из арболита крупных габаритов требует дополнительное армирование изделия. В форму, заполненную на половину, следует поместить арматурный каркас из арматуры и далее заполнить деревобетонным составом.
Технология подготовки древесного сырья в домашних условиях производится различными методами – сооружение щепореза своими руками либо заключение договора с лесопилкой о поставке отходов деревообработки.
В промышленном производстве в сырье добавляют химические реагенты – хлористый кальций, сернокислый алюминий, жидкое стекло. При домашнем изготовлении рекомендуется выдерживать щепу три месяца на улице при этом опилки следует периодически перемешивать. Чтобы ускорить процесс в насыпь добавляют окись кальция – на один кубометр идет 200 литров 1.5 % раствора.
В роли вяжущего элемента подойдет портландцемент 400 – 600 марки. Смесь состоит на 10-15 % из цемента и не более 1% пластификаторов и деминерализаторов. Перед смешиванием составляющих частей, древесный компонент заливают 10 % раствором извести, потребуется выдержать 3 часа. На промышленных предприятиях такая методика вымачивания в технической емкости занимает до 3 дней.
Все компоненты смешиваются в бетономешалке. В итоге получится однородная масса без комков. Состав воды-щепы-цемента равен 4:3:3. Смесь должна быть немного рассыпчатой по консистенции и при сжатии держать форму.
Процесс получения древоблоков
На стадии формовки используются лотки, которые придают изделиям стандартные размеры. Если требуется сделать блоки нестандартных габаритов, в формы вставляются пластины, которые увеличивают размер и массу изделия. Плита может быть треугольной или трапециевидной.
Для ускорения затвердевания в раствор добавляют сухую хлористо-кальциевую смесь. Заливание раствора делают слоями в три этапа в заранее обработанные формы известью. Далее смесь потребуется утрамбовать.
Верхнюю поверхность блоков рекомендуется выровнять шпателем или правилом. После залить штукатурной смесью, примерно на 20 мм.
Когда образовалась у стройматериала форма, его уплотняют при помощи деревянного приспособления обитого металлической рамой. Наиболее прочным и надежным является стройматериал, который выстоял и затвердел на протяжении 10 суток при температуре +150 градусов Цельсия. Чтобы блоки не пересыхали, их периодически поливают водой.
Оборудование
Нужные агрегаты по изготовлению арболита продаются в сборе и включают в себя все циклы обработки и приготовления. Передовые технологии позволяют делать различные объемы стройматериала с разными размерами. Для сооружения станка своими руками, понадобятся такие агрегаты:
- щепорез, который также можно сконструировать своими руками;
- бетонорастворомешалка либо смесительный аппарат;
- пресс-формы;
- вибростанок.
Производить арболит можно самостоятельно организовав выпуск блоков, и при этом минимизировать затраты на нужную технику. Станок для дробления щепы также изготавливается своими руками при помощи использования подручных устройств. Для экономии средств вибросито заменяют на ручной метод просеивания.
Агрегат для изготовления рабочего раствора рекомендуется заменить автобетономешалкой. Ручной способ замешивания в методике недопустим, так как имеется риск образования в растворе комков и сгустков.
Формы требуемой величины делают из обычных деревянных ящиков. Дно и бока рекомендуется, заслать линолеумом либо пленкой из полиэтилена, это позволит составу не влипать в стенки.
Когда формы будут залиты по технологии, смесь уплотняют. Для этого понадобится молоток для простукивания стенок в емкости и дрель, которой делают вибропресс. Также используют самостоятельно сделанный вибростол. Этот аппарат уменьшит время изготовления и повысит производительность.
Если условия для сушки материала не подходят, рекомендуется воспользоваться сушильной камерой. Такой метод сушки увеличит затраты на производство и сделает прочность блоков выше.
Станок для блоков арболита своими руками чертеж
- Вибропресс с механизмом фиксации формы.
- Форма с функцией самозапечатывания.
- Подъемно-поворотный бункер с механической подвеской.
- Лебедка для управления бункером.
- Смеситель.
- Лебедка для подъема дозаторов с подвеской.
- Тележка с дозатором для щепы.
- Дозатор для цемента на тележке.
- Емкость для приготовления древесного консерванта.
- Платформа наклонная.
- Поддон.
- Рокла.
- Металлическая конструкция.
Производство своими руками
Технология самостоятельного изготовления арболита не сложная при наличии необходимого инструмента и устройств. Если соблюдать все правила и критерии изготовления, правильно рассчитать компоненты продукт будет иметь высокое качество и прочность.
Материалы и приспособления:
- Специальная емкость для компонентов.
- Вибрирующий стол.
- Поверхность с ударно встряхивающими функциями.
- Металлические поддоны.
- Для того чтобы получить качественный раствор необходима автобетономешалка. Если смешивать собственноручно, то для получения раствора нужной консистенции понадобится много времени и сил.
- Специальные пластиковые формы необходимых размеров. Арболитовые блоки имеют прямоугольную форму, стандартные размеры – 500х189х300 мм и 500х188х200 мм.
- Специальный станок профессионально измельчит щепу.
- При помощи пресса получается высокая плотность материала. При процессе трамбовки из материала по максимуму убирается воздух.
- Камера для сушки блоков из арболита превращает структуру в твердый однокомпонентный материал.
- Лопаты для того чтобы загрузить смесь в формы.
- Армирующая сетка применяется для скрепления древоблоков.
При наличии таких приспособлений в среднем производится за месяц от 400 до 500 кубометров строительной смеси. Рекомендуемая минимальная величина производственного помещения 500 м2. Расходы электроэнергии составят 15-45 кВт?ч. При подготовительных работах органические компоненты заливают жидким цементом до образования однородной массы. Соблюдая пропорции и расчеты, получившаяся смесь должна быть сыпучей.
Бункеры и формы имеют стандартный размер 20х40х60 см их можно сварить или сделать наборными из раскроенных листов металла. Рекомендуется блоки при изготовлении располагать вертикально, это упростит трамбовку при малой площади пресса.
Отзывы и рекомендации специалистов при самостоятельном производстве блоков
Эксперты и частные строители, практикующие изготовление арболитовых блоков оставляют отзывы, в которых советуют следовать правилам, помогающим достичь высокого качества продукции.
- В технологии производства рекомендуется применять не только щепу больших размеров, но и применять опилки и деревянную стружку.
- Консистенцию древесины обрабатывают таким образом, чтобы из нее удалился сахар.
Методика позволит предотвратить дальнейшее вспучивание готового материала, что категорически недопустимо в постройке домов.
- В процессе изготовления раствор нужно тщательно перемешать и проследить, чтобы все части были в цементном растворе. Этот момент важен для качественного и прочного скрепления древесных и прочих материалов в блоках.
- При изготовлении важно добавлять алюминий, гашеную известь и прочие компоненты. Например, добавленное в состав жидкое стекло не будет позволять впитывать влагу готовому стройматериалу, а гашеная известь обладает антисептическими свойствами.
- Хлористый калий не позволит образоваться в структуре микроорганизмам и прочим веществам, влияющим неблагоприятно на материал.
- При смешивании компонентов рекомендуется следить за пропорциональностью, чтобы приготовленная смесь соответствовала требованиям производства блоков из арболита.
Первый в своем роде дом, напечатанный на 3D-принтере из смеси бетона и дерева печатная структура в США.
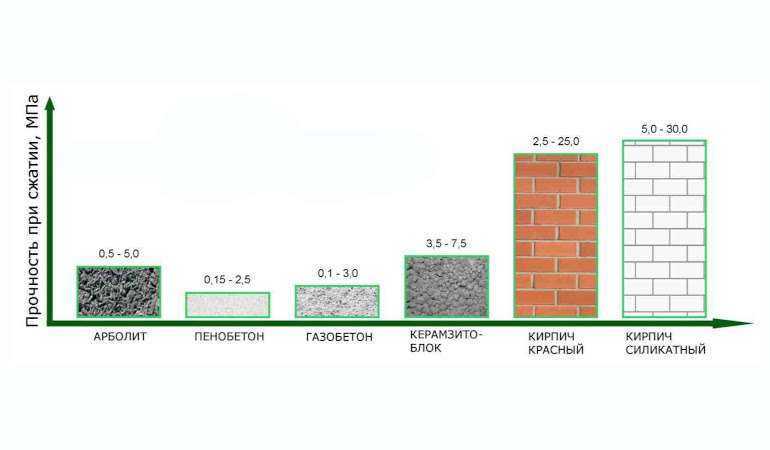
В дополнение к этому достижению, дизайнеры Лесли Лок и Саса Живкович, доценты кафедры архитектуры Колледжа архитектуры, искусства и планирования (AAP) и соруководители проектного бюро HANNAH, говорят о двухэтажном односемейном home демонстрирует инновационные процессы строительства, которые можно масштабировать до многоквартирных и многофункциональных застроек, помогая решить проблему нехватки жилья.
Авторы и права: Лесли Лок и Саша Живкович/Предоставлено
Строительный 3D-принтер COBOD BOD2 строит структурные элементы дома в Хьюстоне, который станет первой многоэтажной структурой, напечатанной на 3D-принтере в Соединенных Штатах.
Их первая в своем роде гибридная конструкция соединяет структурные элементы, состоящие из бетона, напечатанного на 3D-принтере, с традиционным деревянным каркасом, характерным для большинства жилых домов США. Комбинация показывает, как каждый материал можно использовать там, где он работает лучше всего, с минимальными отходами, для создания зданий, которые будут эффективными, устойчивыми к все более интенсивным погодным явлениям и потенциально более доступными.
«Наш гибридный подход к строительству создает строительную систему, которая структурно эффективна, легко воспроизводима и чувствительна к материалам», — сказал Лок. «Проект также подчеркивает захватывающий дизайнерский потенциал массово настраиваемых архитектурных компонентов для удовлетворения потребностей домовладельцев и упрощения интеграции строительных систем».
Живкович добавил: «Эти усилия по проектированию направлены на повышение воздействия, применимости, устойчивости и экономической эффективности 3D-печати для будущих жилых и многоквартирных зданий в США».
12 сентября представители СМИ были приглашены наблюдать за ходом печати дома с тремя спальнями, тремя ванными комнатами, гаражом на две машины и 40-футовым дымоходом, что делает дом одним из самых высоких печатных домов. структур на сегодняшний день.
Дом строится в сотрудничестве с компанией PERI 3D Construction, которая выполнила шесть 3D-печатных конструкций в США и Европе; Хьюстонский инженерно-строительный подрядчик CIVE; и другие партнеры строительной отрасли. Команда проекта продолжает искать отраслевых партнеров и спонсоров.
Для Лока, который возглавляет Лабораторию инноваций в сельском и городском строительстве в AAP, и Живковича, который возглавляет Лабораторию роботизированного строительства, проект является последним результатом многолетних исследований потенциала 3D-печати для обеспечения «массовой настройки» без увеличения расходы. Ранее они экспериментировали с гибридным дизайном, используя бетон, напечатанный на 3D-принтере, и переработанную древесину для проекта Ashen Cabin в северной части штата Нью-Йорк. Установка Lok HoloWall на Arts Quad исследовала настройку с использованием неоднородных строительных материалов и инструментов цифрового моделирования. Предыдущее исследование Живковича связано с разработкой новых методов печати бетона и механически изготовленных деревянных компонентов.
Хьюстонский проект площадью 4000 квадратных футов продвигает эту работу в более крупном масштабе, который потребует еще одного американского «первого» — переноса большого портала, поддерживающего принтер, размером примерно 60 футов в длину, 30 футов в ширину и 30 футов в высоту. , чтобы завершить структуру.
Авторы и права: Лесли Лок и Саша Живкович/Предоставлено
Визуализация двухэтажного дома в Хьюстоне, спроектированного Лесли Локом и Сашей Живковичем, который отличается первым в своем роде гибридным дизайном с использованием бетона, напечатанного на 3D-принтере, и деревянного каркаса.
В различных системах — от изоляции напыляемой пеной до системы отопления, вентиляции и кондиционирования воздуха, более распространенной в коммерческих зданиях — проектировщики говорят, что дом объединяет процессы проектирования и строительства, хорошо подходящие для многоквартирных застроек, которые потребуются для увеличения жилой площади. в быстрорастущих городах, таких как Хьюстон.
Разработчики заявили, что их подход также может ускорить сроки строительства и снизить затраты, поскольку бетонные принтеры могут обслуживать всего три-четыре человека. Это также сводит к минимуму отходы, поскольку материал можно смешивать по требованию и печатать только для структурно важных секций, а также можно более эффективно интегрировать деревянный каркас в модульную конструкцию.
«Помимо технологии печати, важными аспектами реализации такого проекта являются интеграция печати со строительным дизайном и строительными материалами, а также оптимизация процесса строительства», — сказал Живкович. «Мы используем этот проект, чтобы продемонстрировать, что 3D-печать не только готова к выходу на рынок, но и способна создавать хорошо спроектированную и высокопроизводительную архитектуру».
Для дома в Хьюстоне печатные материалы получают из местных источников и используют цемент с уменьшенным углеродным следом, смесь, которая может включать летучую золу, шлак и другие промышленные побочные продукты. Дизайнеры сотрудничают с коллегами из Инженерного колледжа в исследованиях, касающихся экологически чистых строительных материалов, в том числе потенциала бетона для хранения метана, мощного парникового газа. Деревянный каркас, тем временем, является возобновляемым ресурсом, но часто является продуктом лесных монокультур и может перевозиться на большие расстояния.
Лок и Живкович сказали, что в доме в Хьюстоне оптимизируется использование обоих материалов, в то же время лучше используется потенциал их дизайна, чем во многих конструкциях, ограниченных только одним из них.
«Нет ни одного проекта, — сказал Лок, — в котором учитывалось бы многоквартирное жилье с использованием этих двух систем вместе».
3D-печатный дом Корнельского университета из смеси бетона и дерева
Дом Вокруг света 3D-печатный дом Корнельского университета из смеси бетона и дерева
3D-печатный дом Корнельского университета Исследователи Корнельского университета строят 3D-печатные дома, используя смеси бетона и дерева, чтобы сократить отходы и затраты. Их первая в своем роде гибридная конструкция соединяет структурные элементы, состоящие из бетона, напечатанного на 3D-принтере, с обычным деревянным каркасом, характерным для большинства жилых домов США. Комбинация показывает, как каждый материал можно использовать там, где он работает лучше всего, с минимальными отходами, для создания зданий, которые будут эффективными, устойчивыми к все более интенсивным погодным явлениям и потенциально более доступными.
Дом строится в сотрудничестве с компанией PERI 3D Construction, которая выполнила шесть 3D-печатных конструкций в США и Европе; Хьюстонский инженерно-строительный подрядчик CIVE; и другие партнеры строительной отрасли.
Дизайнеры Лесли Лок и Саса Живкович, доценты кафедры архитектуры Колледжа архитектуры, искусства и планирования (AAP) и соруководители проектного бюро HANNAH, говорят, что двухэтажный дом для одной семьи демонстрирует инновационные процессы строительства это может быть расширено до многоквартирных и многофункциональных застроек, что поможет решить проблему нехватки жилья.
«Наш гибридный подход к строительству создает строительную систему, которая структурно эффективна, легко воспроизводима и чувствительна к материалам», — сказал Лок. «Проект также подчеркивает захватывающий дизайнерский потенциал массово настраиваемых архитектурных компонентов для удовлетворения потребностей домовладельцев и упрощения интеграции строительных систем».
3D-печатный дом строится в партнерстве с PERI 3D Construction, которая завершила шесть 3D-печатных конструкций в США.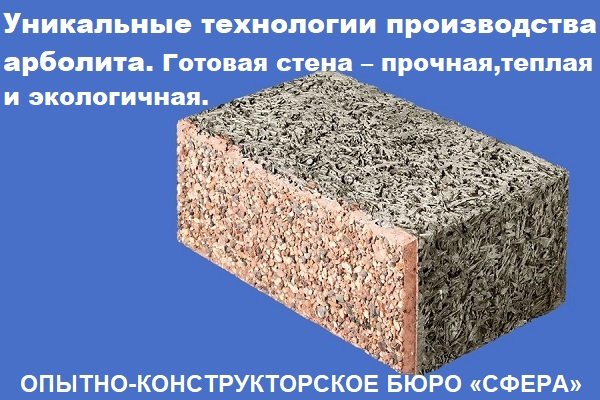
Хьюстонский проект площадью 4000 квадратных футов продвигает эту работу в более крупном масштабе, который потребует еще одного американского «первого» — перемещение большого портала, поддерживающего принтер, размером примерно 60 футов в длину, 30 футов в ширину и 30 футов в высоту, чтобы завершить конструкцию.
Особенности здания;
- Три спальни, три ванные комнаты
- Гараж на две машины
- 40-футовый дымоход
- Процессы проектирования и строительства хорошо подходят для многоквартирных домов
, экологичность и рентабельность 3D-печати для будущих жилых и многоквартирных домов в США». добавил Живкович.
Разработчики заявили, что их подход также может ускорить сроки строительства и снизить затраты, поскольку бетонные принтеры могут обслуживать всего три-четыре человека. Это также сводит к минимуму отходы, поскольку материал можно смешивать по требованию и печатать только для структурно важных секций, а также можно более эффективно интегрировать деревянный каркас в модульную конструкцию.
«Помимо технологии печати, важными аспектами реализации такого проекта являются интеграция печати со строительным дизайном и строительными материалами, а также оптимизация процесса строительства», — сказал Живкович. «Мы используем этот проект, чтобы продемонстрировать, что 3D-печать не только готова к выходу на рынок, но и способна создавать хорошо спроектированную и высокопроизводительную архитектуру».
Помимо технологии печати важными аспектами реализации такого проекта являются интеграция печати со строительным дизайном и строительными материалами, а также оптимизация процесса строительства», — сказал Живкович. «Мы используем этот проект, чтобы продемонстрировать, что 3D-печать не только готова к выходу на рынок, но и способна создавать хорошо спроектированную и высокопроизводительную архитектуру».
Для дома в Хьюстоне печатные материалы получают из местных источников и используют цемент с уменьшенным углеродным следом, смесь, которая может включать летучую золу, шлак и другие промышленные побочные продукты.